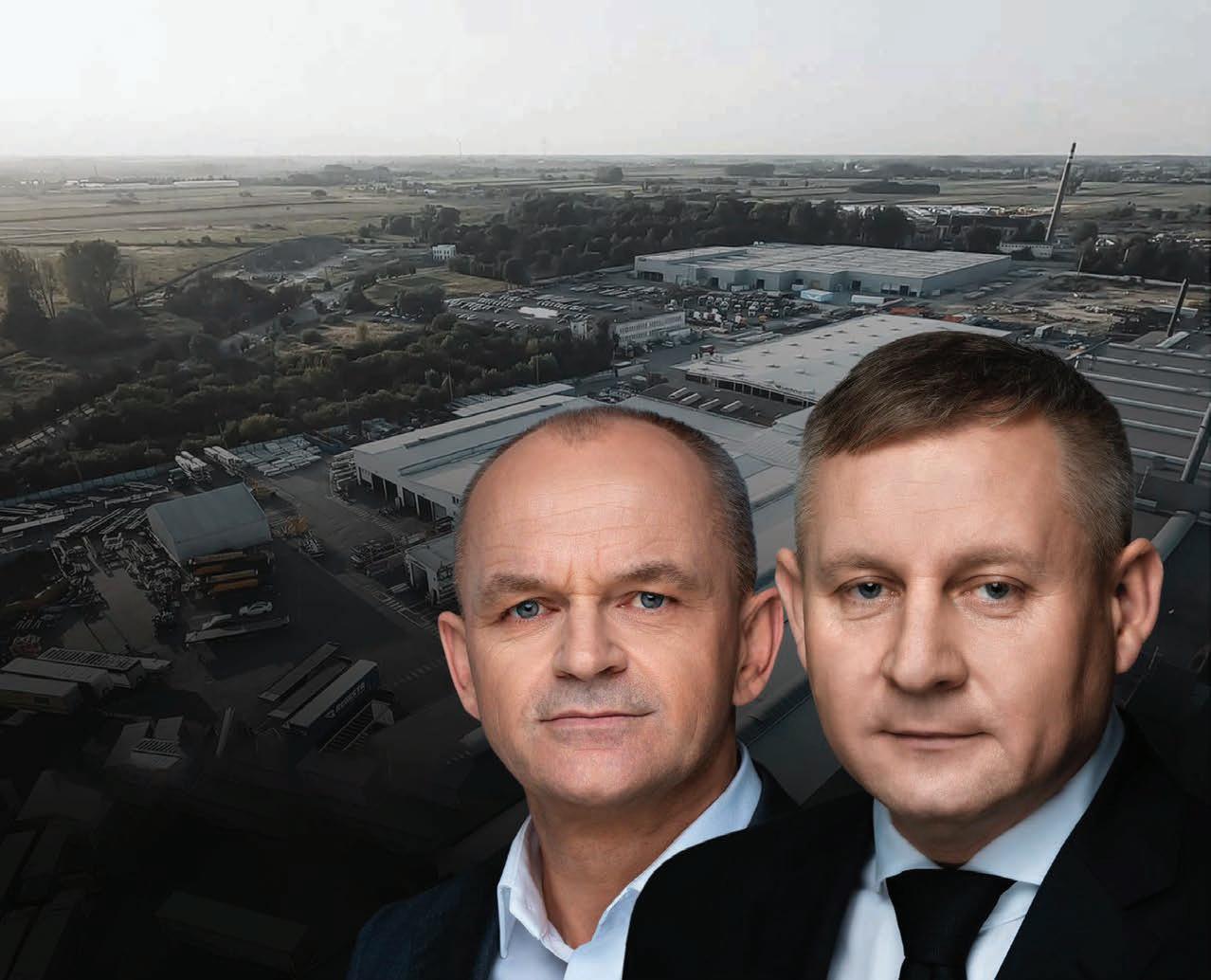
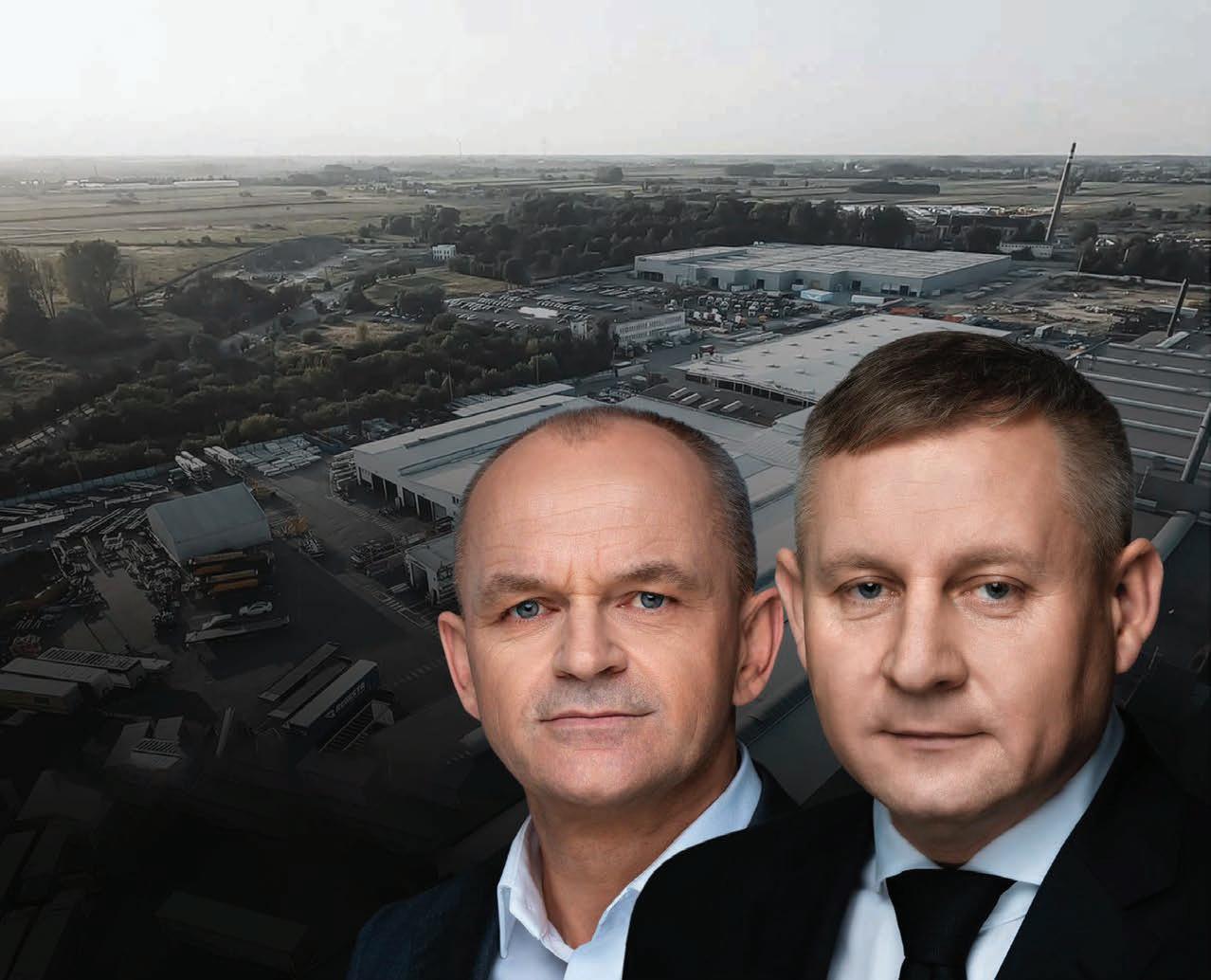
CHALLENGE US!
With our running gears and special axle solutions, there is nothing that can’t be transported. Your requirements motivate us to create new things. They inspire us to use our entire engineering expertise and decades of experience to develop innovative and reliable solutions together with you – customised for the type of vehicle and intended use.
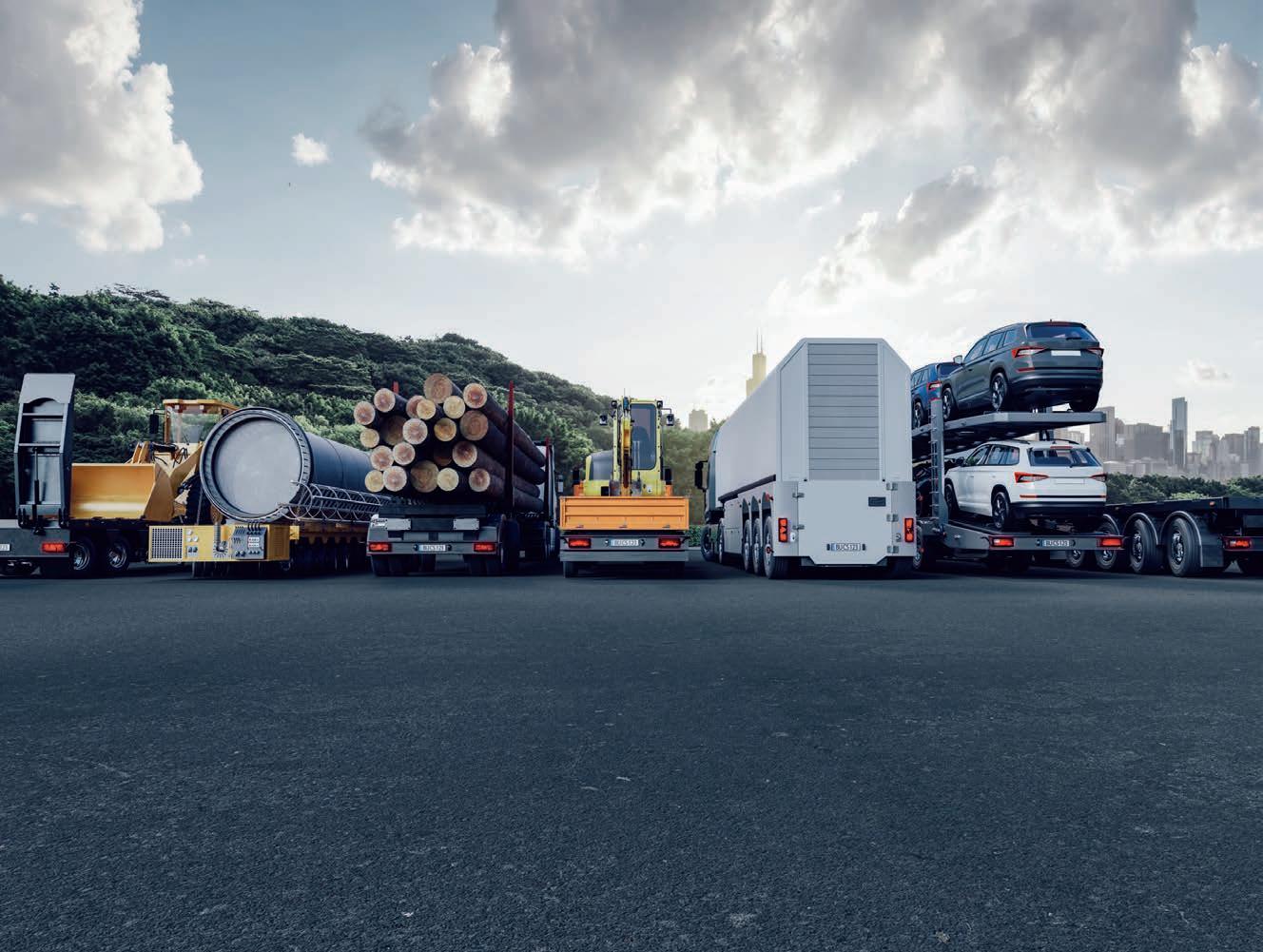
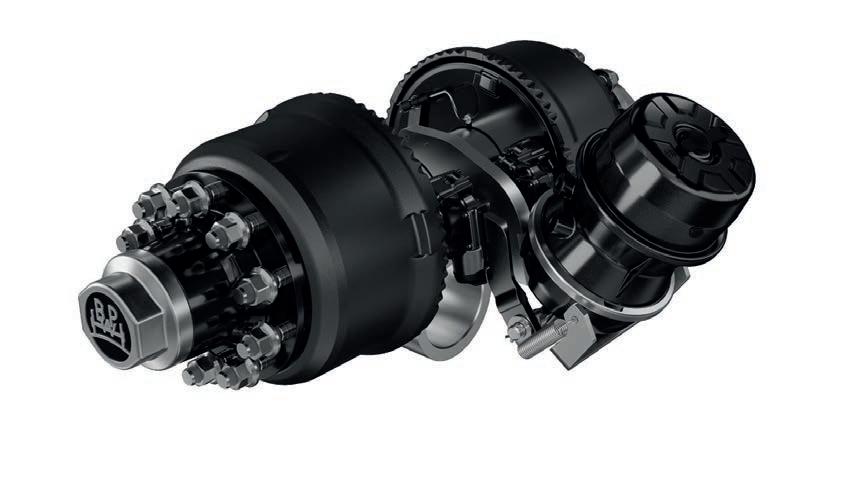
The swing axle masters any heavy transport - even on critical ground and difficult terrain. It is part of our individual solutions that are uniquely powerful and resilient. Challenge us!
INDIVIDUAL RUNNING GEAR SOLUTIONS FOR SPECIAL TRANSPORT TASKS. MORE
Carbon emission reduction is a priority for TIP.
52 BRAKING TECHNOLOGY
See the latest developments from several system suppliers.
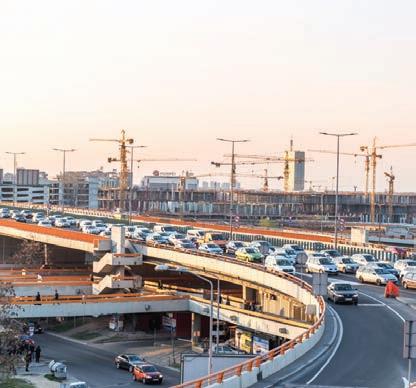
62 BUILT TO TASK
The uptake of robotic welding is on the rise.
THE INTEGRATED POWER OF WIELTON GROUP
Wielton Group has expanded its brand portfolio in recent years and entered new markets. Global Trailer takes a trip down memory lane to learn more about the business’ rich history.
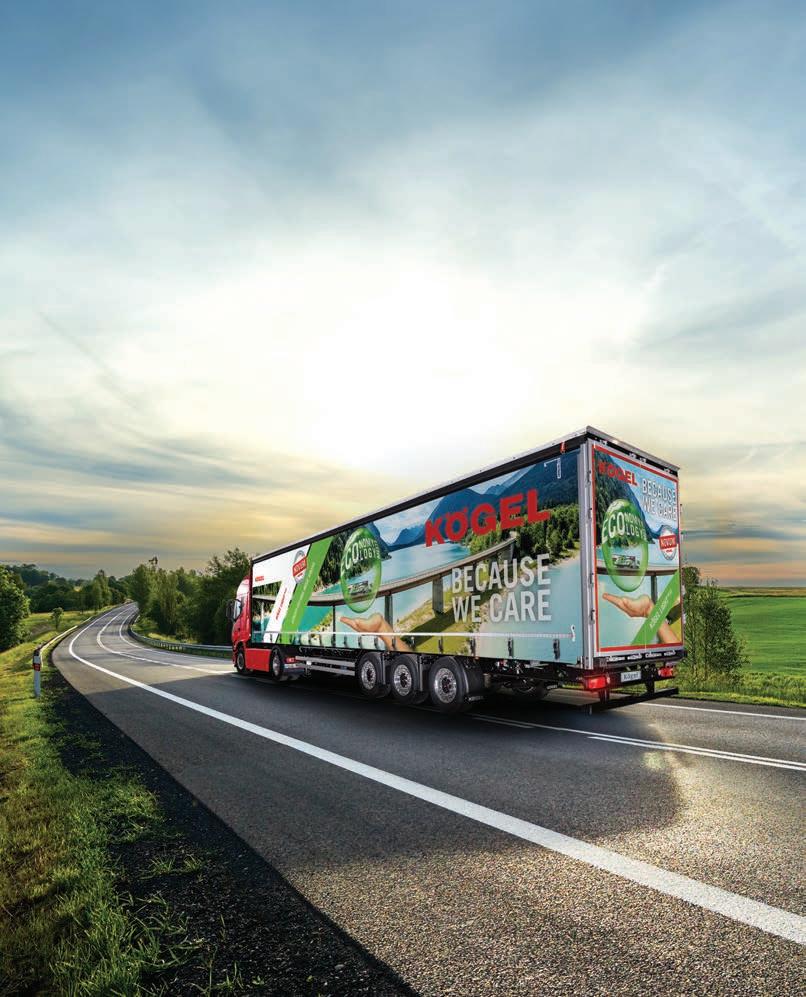
“TODAY WIELTON IS A COMPLETELY DIFFERENT ORGANISATION THAN IT WAS 27 YEARS AGO. WE ARE NOW AN INTERNATIONAL GROUP, THAT IS ONE OF THE LEADING SEMI-TRAILER MANUFACTURERS IN EUROPE AND EMPLOY ALMOST 3,600 PEOPLE.”

SHOW ME WHAT YOU’VE GOT
NEVER UNDERESTIMATE THE power of a face-to-face conversation. As an international publication based in Melbourne, Australia, we often conduct interviews and other meetings with industry partners remotely whether it be over the phone or online via Microsoft Teams. This was especially true in recent years while we adapted our work/life routines amid pandemic. In 2023 many offices are now working to a hybrid model, with staff operating one or more days from home. This flexibility has generally been received well for the benefits it can bring from maximising productivity to improving general health and wellbeing. But in those moments, chatting away in front of a computer screen, while we can see and hear each other – unless the internet drops out – there is potential for complication. When you’re not physically present you can be easily distracted, idly working on other things in the background. Not being able to read body language can
also be problematic, something we generally take for granted face-to-face, and can guide us as to whether we need to press further or pivot to another talking point. This all goes to show how important direct communication is. Even more so, how integral trade fairs and industry events are. The industries we detail in these pages thrive on meet and greets, the exchange of ideas and demonstration through action. It is our mission here at Global Trailer to continue to document, and where possible participate, in the events that shape and transform this incredible industry. Modern trailer design, the latest componentry and safety technologies – among other adjacent developments – are contributing to the growth of organisations and individuals in the short-term but are also raising the bar for the next generation.
CEO
John Murphy john.murphy@primecreative.com.au
COO
Christine Clancy christine.clancy@primecreative.com.au
INTERNATIONAL SALES
Ashley Blachford ashley.blachford@primecreative.com.au
MANAGING EDITOR
Luke Applebee luke.applebee@primecreative.com.au
JOURNALIST
Peter White peter.white@primecreative.com.au
DESIGN PRODUCTION COORDINATOR

Michelle Weston michelle.weston@primecreative.com.au
ART DIRECTOR
Blake Storey DESIGN
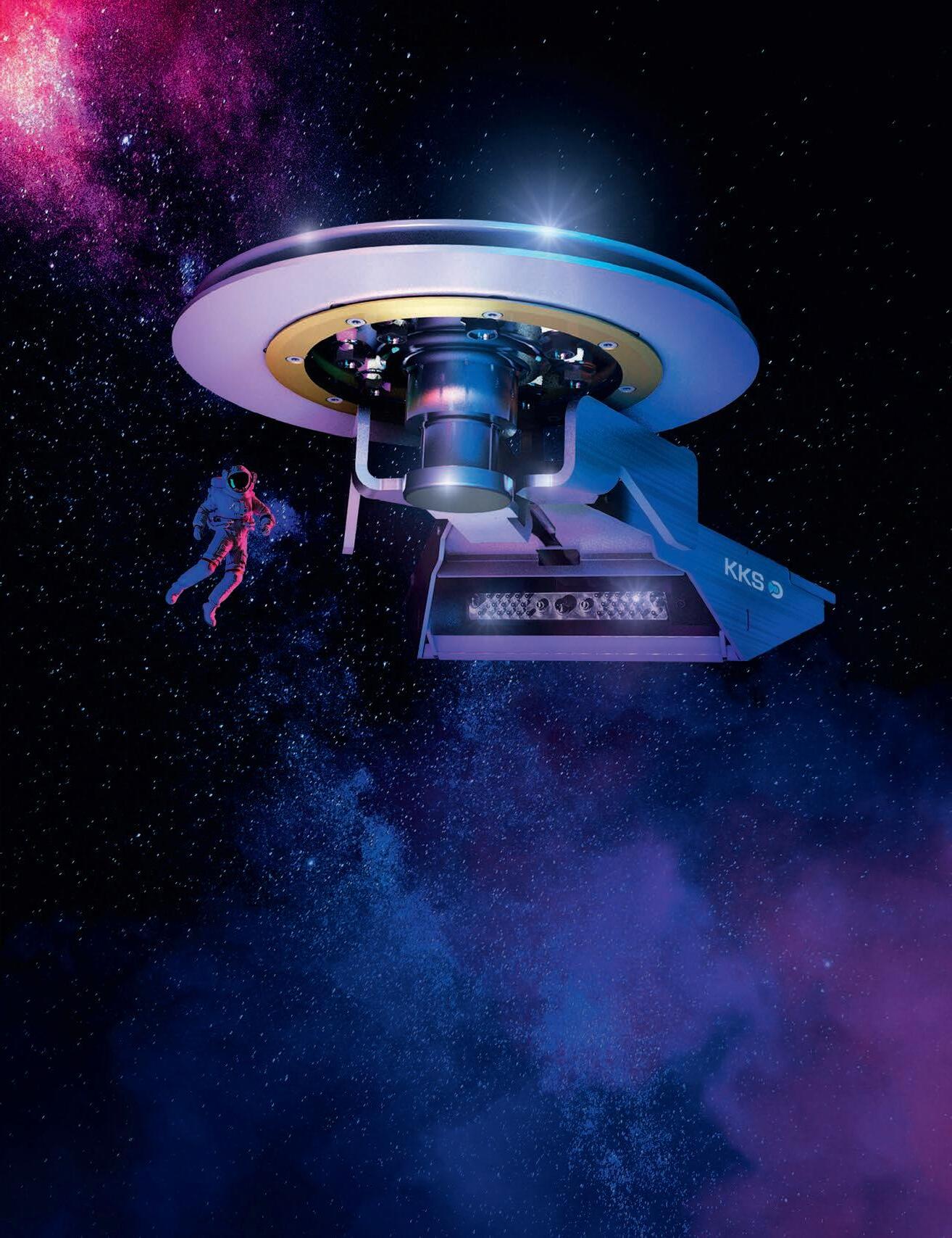
Kerry Pert, Louis Romero
CLIENT SUCCESS MANAGER
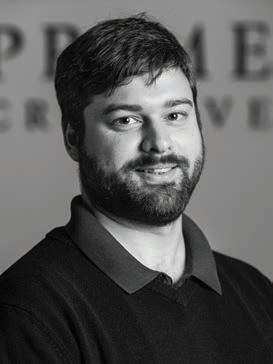
Salma Kennedy salma.kennedy@primecreative.com.au
HEAD OFFICE
Prime Creative Pty Ltd
379 Docklands Drive Docklands VIC 3008 Australia p: +61 3 9690 8766 f: +61 3 9682 0044 enquiries@primecreative.com.au www.globaltrailermag.com
SUBSCRIPTIONS
+61 3 9690 8766 subscriptions@primecreative.com.au Global Trailer is available by subscription from the publisher. The rights of refusal are reserved by the publisher.
ARTICLES
All articles submitted for publication become the property of the publisher. The Editor reserves the right to adjust any article to conform with the magazine format.
COPYRIGHT
Global Trailer is owned by Prime Creative Media and published by John Murphy. All material in Global Trailer is copyright and no part may be reproduced or copied in any form or by any means (graphic, electronic or mechanical including information and retrieval systems) without written permission of the publisher. The Editor welcomes contributions but reserves the right to accept or reject any material. While every effort has been made to ensure the accuracy of information, Prime Creative Media will not accept responsibility for errors or omissions or for any consequences arising from reliance on information published.
The opinions expressed in Global Trailer are not necessarily the opinions of, or endorsed by the publisher unless otherwise stated. Follow us on twitter @Globaltrailer
OUT OF THIS WORLD
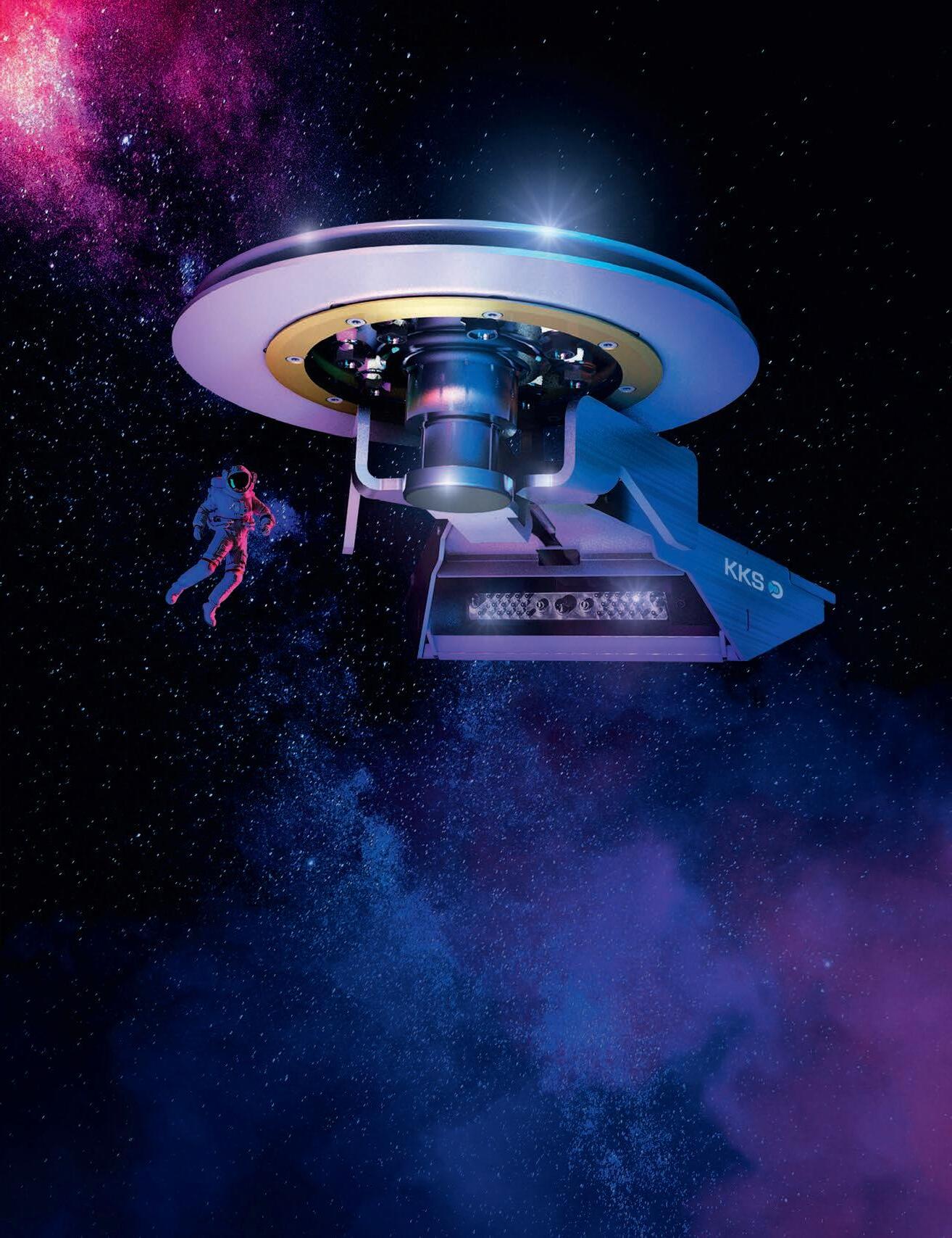
JOST KKS – push-button trailer coupling
#futurenow – Thanks to our revolutionary coupling system you can now change semitrailer quickly and safely out of the cab. Your start in the future of logistics. Ready to beam up?
NEWS INTERNATIONAL
AFRICA & ASIA AFRICA
To support expansion and stronger service in Africa, Kuehne + Nagel has unveiled its latest plan, Roadmap 2026.
Alexandre Muratore was recently appointed Managing Director of the newly established West Africa Cluster comprising Senegal, Nigeria, Ghana, Ivory Coast, Guinea, Burkina Faso, Gambia, Sierra Leone, Liberia, Togo, Benin, Mauritania and Guinea Bissau. He will be operating out of Abidjan, Ivory Coast. Together with the local teams, Muratore will develop new business opportunities and grow Kuehne + Nagel’s presence in West Africa, supporting the company’s strategy to expand its footprint on the continent.
This step also reflects the company’s newly announced Roadmap 2026. Within the framework of its cornerstone ‘Market Potential’, Kuehne + Nagel focuses on expanding its geographic footprint in growth regions. Muratore’s career with Kuehne + Nagel began in 2014 as District Branch Manager and National Sea Logistics Manager in Angola. In his most recent role, he was the Managing Director of Kuehne + Nagel Qatar.
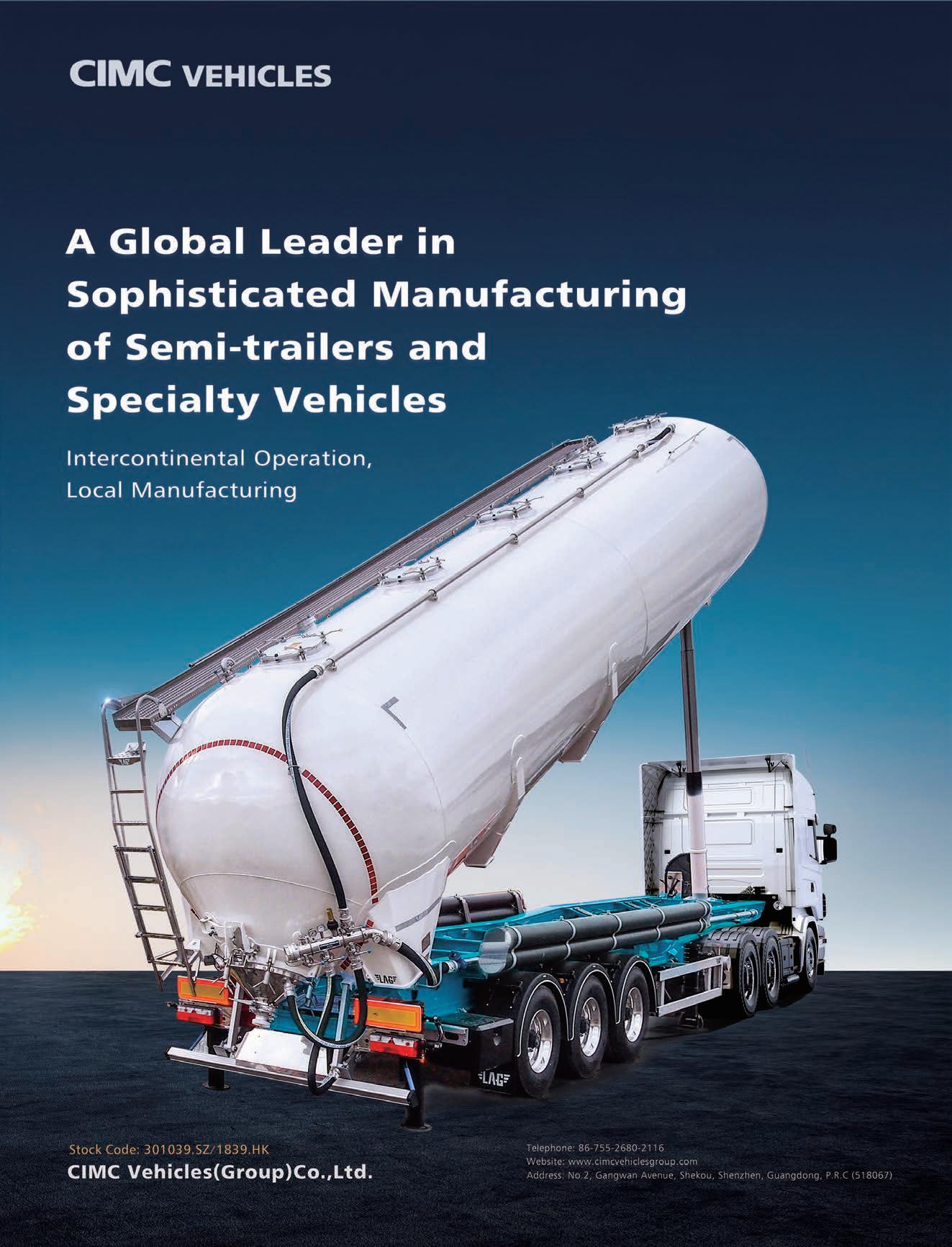
“I look forward to relocating to Africa and leading the West African team as Managing Director,” said Muratore. “Our primary goal is to expand our presence in this key market by strengthening and developing local partnerships with our suppliers and customers.”
Bradley Francis, until now Regional Business Development Manager, Healthcare, Middle East and Africa, replaces Muratore as Managing
Director of Kuehne + Nagel Qatar. Francis first joined the company in 2007 and held the National Air Logistics Manager position in South Africa and the United Arab Emirates. “I am delighted to join this team that has a firm focus on customer needs and service excellence,” said Francis. “I look forward to building on the many successes that have been realised by Alexandre and his team and believe that our West Africa Cluster will benefit tremendously from his experience and commitment.”
Lee I’Ons, President of Kuehne+Nagel Middle East and Africa, said: “Kuehne+Nagel is strengthening its leadership team to support the company’s continued growth and success in the Middle East and Africa region.
“Alexandre Muratore’s appointment as Managing Director of the West Africa Cluster will drive new business opportunities, leveraging his extensive knowledge of the region. For Qatar, logistics is regarded as a critical component of its 2030 vision, which aims to create a diverse and sustainable economy.
“Bradley Francis, as the new Managing Director of Qatar will continue to build on the strong base Alexandre has created, taking advantage of its strategic location and proximity to major Asian and European markets, supported by a solid infrastructure and a business-friendly environment.”
CHINA
According to a recent report by Container xChange, global container rates are experiencing a significant decline, with contract rates moving
closer to spot rates. This trend is reportedly evident in regions such as China and Southeast Asia where shipping demand remains weak due to global inflation and restricted demand – thus leading to a significant drop in freight prices.
“The long-term outlook for the shipping industry remains uncertain, as the low consumer demand in North Europe and the slow market pickup in China suggest that the shipping industry will continue to struggle,” the report stated.
“Container prices in major ports across Asia, such as Ningbo, Shanghai, and Singapore, have fallen sharply in the past year, indicating that the current situation may persist in the foreseeable future.”
After comparing the prices of a 20ft container in the top three ports of Asia – Ningbo, Shanghai, and Singapore – to their prices in January 2022, Container xChange observed a significant decline in all three ports.
The average price in Ningbo decreased from €2,326.25 to €1,219.79 (approx. $2,460 to $1,290 USD), while in Shanghai it fell from €2,240.82 to €1,200.70 (approx. $2,370 to $1,270 USD), and in Singapore it went down from €2,278.62 to €1,172.40 (approx $2,410 to $1,240 USD).
In Southeast Asia, container prices saw a 32 per cent year-on-year (YOY) drop from €3,590.80 in January 2022 to €2,448.50 in January 2023 (approx. $3,798 to $2,590 USD).
Asia-US West Coast rates in January 2023 were 11 per cent lower than in January 2020, and Asia US-East Coast rates were 84 per cent lower than in January 2022.
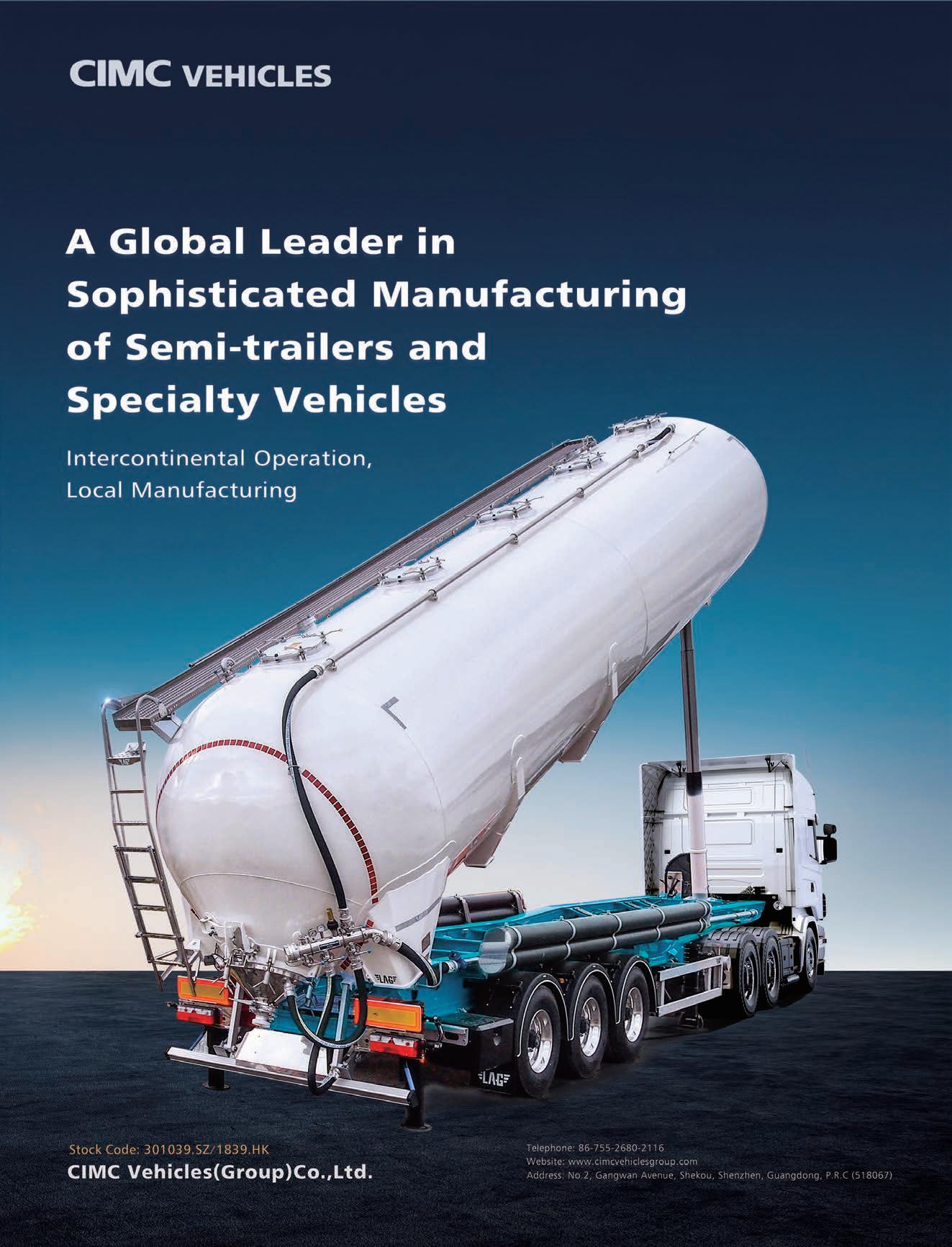
FOR SUCCESS.
NEWS INTERNATIONAL
ASIA & EUROPE
Container xChange CEO & Co-Founder, Christian Roeloffs, said container trends are a crucial barometer of economic progress and global trade, and the current market outlook appears bleak.
“Container prices and leasing rates are plummeting, with the global shipping industry witnessing a freefall in container rates,” he said.
“The blank sailings have not been able to control the sliding prices, and the mid-term outlook for the industry indicates a slowdown in container trade on Asia to EU and Asia to America trade lane.
“However, contract rates are closer to spot rates, indicating the lack of demand for long-term commitments, which can be attributed to market uncertainty.”
Global Trailer Ad-FINAL.indd 1
According to Roeloffs, Intra-Asia trade is showing some resilience, with comparatively better demand for containers.
“Nonetheless, the mid-term outlook does not project demand to rise to the heightened levels witnessed in 2020 and 2021, except for a possible inventory replenishment cycle that may bring about some demand for containers,” he said.

“The falling rates and increased availability of containers in certain regions of the world are indicative of weak demand and slower economic growth.”
Container xChange predicts that export growth and outbound container volumes will remain low in the first quarter of 2023.
SOUTH KOREA
Transport and logistics company, Toll
Group, has announced a €6.4 million investment into its Baeksa, South Korea, warehouse facility to support growing customer demand.
The investment includes state-of-theart advanced automation technology – one of the first of its kind in South Korea – to support the growth in ecommerce, retail and omnichannel fulfilment for retail customers.
The advanced automation technology will include a tote-to-person operation using a carton-transfer unit and a modular conveyor belt system to deliver high inventory picking, which will reportedly increase productivity and operational efficiency by 70 per cent.
The 23,000 square-metre expanded facility has the capacity to store 300,000 inventory items and is tripling Toll’s warehouse footprint in South Korea.
Toll Group Korea Country Manager, Park Seungtaek, said the investment is part of Toll’s broader strategy to grow its Asia business.
“The investment reflects Toll’s commitment to grow this important market and service our customers across retail, chemicals, medical, pharmaceutical and cosmetics industries,” he said.
“We are seeing exponential growth and strong demand from our customers for advanced warehouse management solutions.
“Our automation technology enables us to provide customers with improved productivity, as well as real-time tracking and traceability.
“The picking stations will dispatch items more quickly, enabling our customers to deliver their ecommerce
orders faster, more economically and sustainably.”
Combining decades of experience gathered in Asia, Australia, Europe and the US, global manufacturing powerhouse Fuwa has forged the strongest network of truck trailer component specialists in the world. Merging local expertise with world-leading manufacturing prowess and an irrevocable commitment to innovation, our entire range of axles, suspension systems, landing legs, couplings, king pins, fifth wheels and ball races have been designed for one goal only -- to guarantee your success. Join the Group. Join the Revolution.
The Icheon facility is strategically located in the Gyeonggi Province, in close proximity to Seoul and the Metropolitan area.
The Icheon warehouse complements Toll Group’s existing logistics in Seoul and Incheon, and freight forwarding facilities in Pyeongtaek and the Busan Port.
Toll now has 160 facilities in 13 markets across Asia and is making a significant investment in the region, with €414.8 million of investments planned over the next four years.
FRANCE
Transports Devoluy has been acquired by Geodis Group. This acquisition is reported to consolidate Geodis’s foothold in one of the few parts of France where the group does not have a direct presence in the groupage business.
This new asset strengthens its 12/24and 24/48-hour distribution capacity in the Hautes-Alpes.
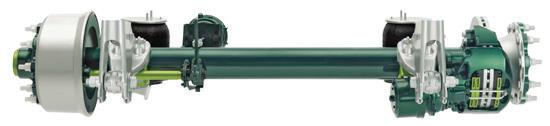
Founded in 1932, Transports Devoluy is a family-owned company specialising in distribution and express services to and from the Hautes-Alpes. It employs around 40 people and runs a fleet of about sixty vehicles. A long-standing partner of Geodis, Transports Devoluy delivers more than 1,200 parcels per day throughout the department, from Gap to Briançon, including distribution to winter sports resorts during the winter.
“Transports DEVOLUY is recognised for its quality of service and its expertise in delivering to mountain regions,” said Geodis CEO France,
GROUPED FOR .
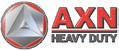
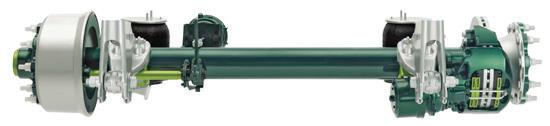


NEWS INTERNATIONAL
EUROPE
Stéphane Cassagne.
“Our long-standing partnership will be the basis for a successful integration as part of Geodis.
“I am very glad to welcome the 46 employees of Transports Devoluy to our French network of 110 Distribution & Express agencies.”
Yann Pacalet, Chairman of Transports Devoluy, said: “After several decades of partnership, it feels quite natural for Transports Devoluy to become part of the Geodis group. For the company, for our employees and for our customers, this merger will create new openings.” Distribution & Express is the Geodis line of business specialising in last-mile deliveries.
Geodis provides 24- and 48-hour groupage deliveries and express service in France. It makes 6,000 daily rounds and delivers approx. million packages per annum.
GERMANY
Equipment specialist, SAF-Holland SE, recently published preliminary financial figures for FY2022.
As a result of the continued solid production figures for trucks and especially trailers in the core markets of North America and Europe and the above-market sales performance of SAF-Holland products, Group sales in the fourth quarter of 2022 increased by 21.0 per cent to €389.5 million (previous year: €321.8 million). Adjusted for exchange rate and acquisition effects, organic growth was strong at 13.0 per cent.
For full-year 2022, SAF-Holland was able to expand Group sales by 25.6 per cent (organic: 17.9 per cent) to a new record level of €1,565.1 million
(previous year: €1,246.6 million). This resulted in Group sales exceeding the forecast, which had already been raised several times during the year, with the latest sales forecast around the upper end of the range of €1.4 billion to €1.5 billion. Strong growth in the Americas (+47.0 per cent) and APAC (+44.5 per cent) regions was the main contributor to the Group’s performance. As the regional market leader in the increasingly important Indian transport market, the company benefitted from the ongoing government expansion program for transport infrastructure, as well as from the more demanding regulatory requirements for braking systems for trucks and trailers.
In the EMEA region, the Group achieved sales growth of 11.0 per cent, despite the particularly challenging macroeconomic and supply chain situations in the 2022 financial year. The Original Equipment (OE) business benefitted from both market share gains and catch-up effects in customer demand following the restrained investment of fleet operators and carriers during the Covid-19 pandemic and supply chain issues.
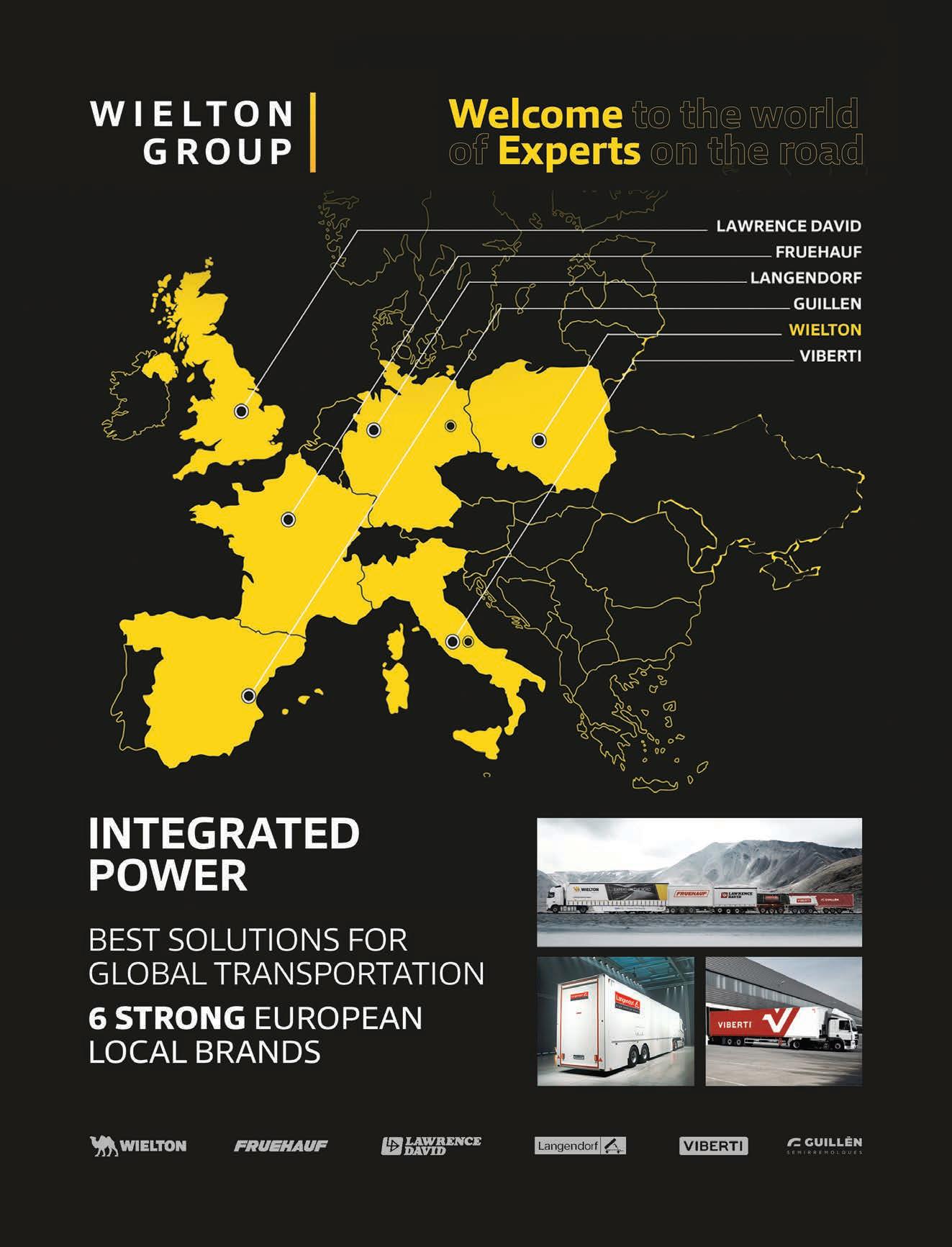
OE business with the truck and trailer manufacturers grew 27.6 per cent in 2022. The Group generated €1,144.0 million (previous year: €896.8 million) in sales in this customer segment. In the cyclically resilient spare parts business, sales also rose sharply, supported by the growing population of SAF-Holland axle and suspension systems in the market.
At €421.1 million (previous year: €349.8 million), the Aftermarket business contributed 20.4 per cent
more to Group sales than in the previous year. The integration of the Swedish braking systems specialist Haldex AB, which generates around half of its business in the aftermarket, will significantly increase the share of this business in the sales of the combined Company.
“Despite a thoroughly challenging environment, we were able to significantly exceed the targets we set ourselves for 2022,” said SAF-Holland CEO, Alexander Geis.
“With our product offering, we benefitted to an extraordinary extent from the solid demand from truck and trailer manufacturers and gained market share.
“Internally, we have further optimised our processes, reduced costs and positioned ourselves technologically for the future through our acquisition of Haldex. We expect the transaction to close in the coming weeks.”
Adjusted EBIT margin rises to 8.0 per cent.
The company passed on the sharp rise in steel, freight and energy costs either through price adjustments or by offsetting them through standardisation and better efficiency in production-related areas, supplemented by cost savings in administrative functions.
As a result, adjusted EBIT increased 33.8 per cent, outpacing Group sales growth in percentage terms, and amounted to €124.6 million (previous year: €93.1 million). The adjusted EBIT margin, also supported by a favourable product mix, reached 8.0 per cent, compared to 7.5 per cent in the previous year, placing it at the upper end of the target range of 7.0 per cent
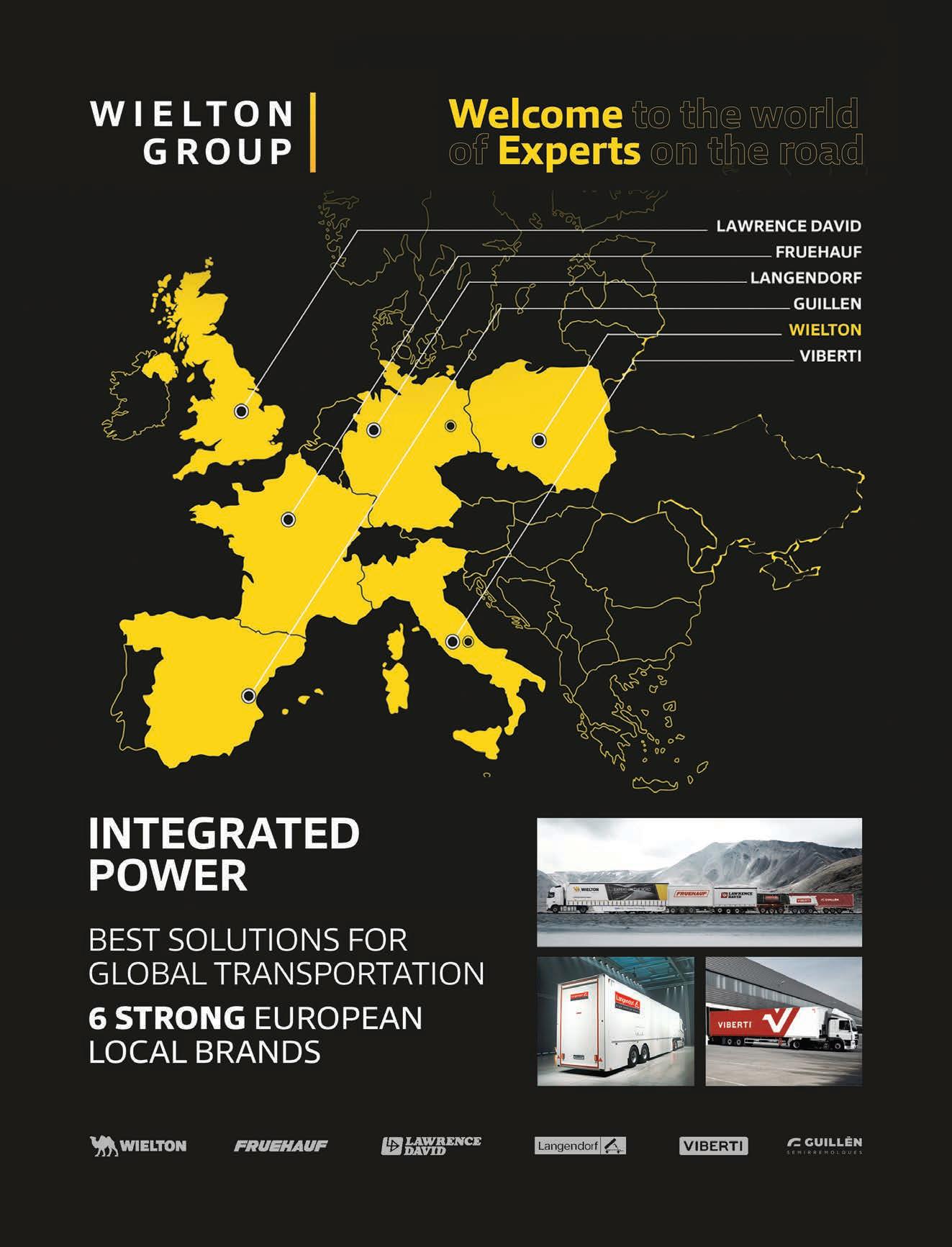
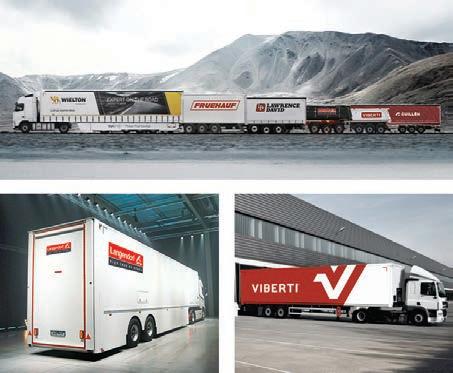
NEWS INTERNATIONAL
EUROPE
to 8.0 per cent, reflecting the most recent upward revision in July 2022. Among the segments, the development in the APAC region stood out in particular, driven by the strong sales performance in India and Australia and successful cost reductions in the China business, which does not yet contribute to profits. The adjusted EBIT margin in the APAC region improved overall to 10.1 per cent (previous year: 1.7 per cent). Result before income tax rises more rapidly than sales.
The finance result reflects the increase in interest rates and the higher finance expenses resulting from the financing of the Haldex shares acquisition and amounted to €–13.0 million, compared to €–9.5 million in the previous financial year. The result before income tax increased by 41.2 per cent to €88.5 million (previous year: €62.7 million). SAF-Holland will publish the full audited consolidated figures for the 2022 financial year and its forecast for the 2023 financial year on 30 March 2023.
GERMANY
Deutsche Post DHL Group has helped around 19,650 refugees integrate into its business since 2015.
The company is reported to rank second among the 50 best-performing global companies for hiring refugees. Ranked number eight, the logistics group is also among the top 10 when it comes to refugee integration. This is according to a report published in February 2023 by Refugee Integration Insights (RII), a dedicated provider of private sector refugee data. “We are proud to have been able
to provide prospects for so many refugees and facilitate their entry into the labor market,” said Thomas Ogilvie, Board Member for Human Resources and Labor Director at Deutsche Post DHL Group.
“Integration is a responsibility we live out as a global company, and a means of realising our goal of connecting people and improving their lives.”
On the subject of labor migration, Ogilvie added: “People looking for a new home in our country enrich the workforce. They are important for our country’s future and the functioning of our economy, not to mention demographics. That’s why, at the ‘Alliance of Opportunities’, for example, we are working with other companies to remove any remaining obstacles blocking fast access to the German labor market for immigrants.”
At Post & Parcel Germany, 435 Ukrainians have been hired since the outbreak of the war. Around 300 refugees have started a traineeship with the Bonn-based logistics company, the majority of whom as courier, express and postal services specialists (234), professional drivers (38) and mechatronics engineers (17). The aim of DPDHL Group’s commitment to helping refugees is to integrate them into the German labor market, to reduce existing barriers to placement and enable them to lead self-determined lives through employment subject to compulsory insurance.
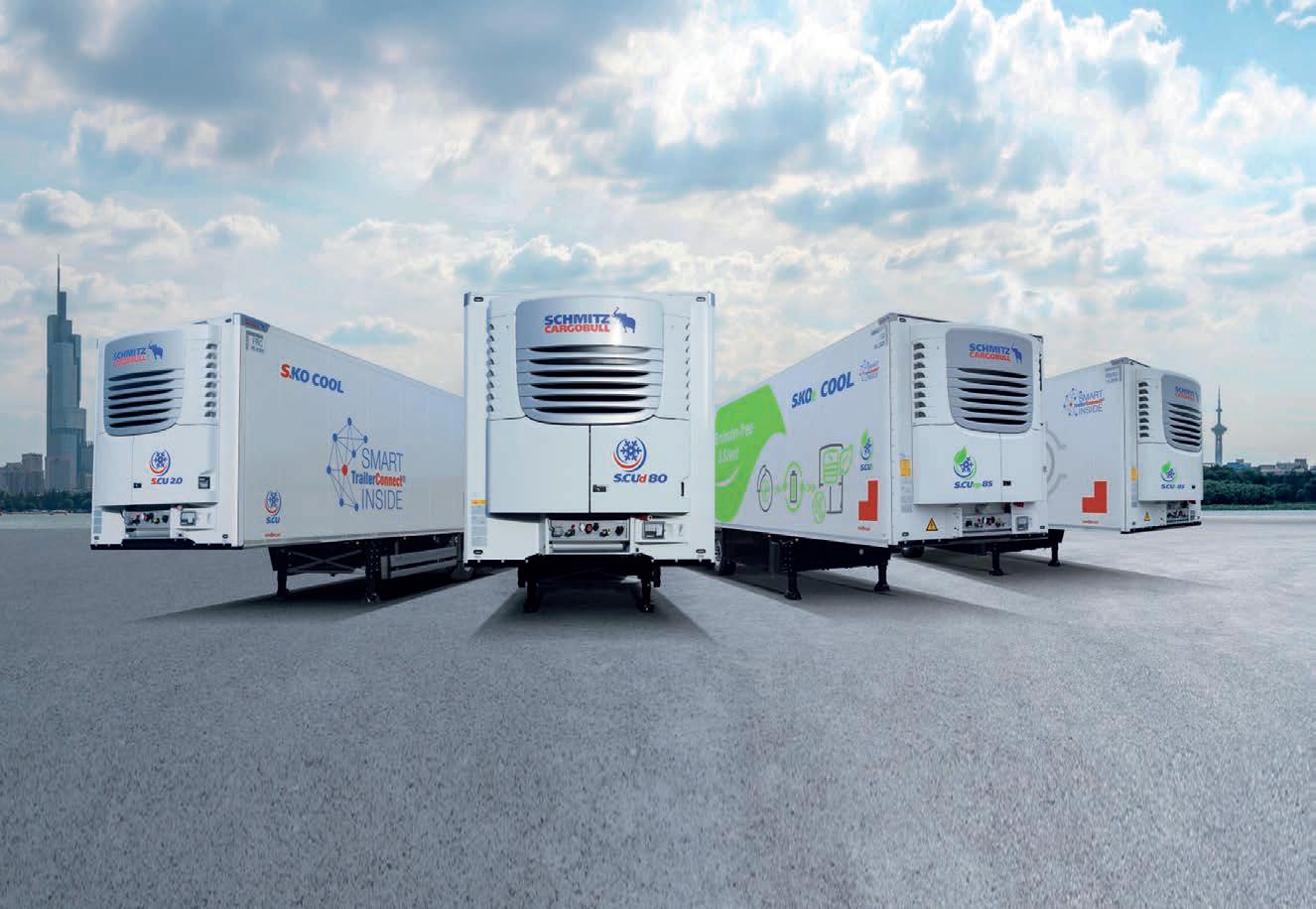
Thanks to a variety of measures, including application training, mentoring programs, internships, and language courses, DPDHL Group not only prepares refugees for the world of
work but also offers them employment prospects – within or outside the company.
The deployment of refugees from countries such as Syria, Eritrea, Somalia, Iran, Iraq, and Ukraine takes place within the framework of employment, traineeships and internships. The focus is on projects and programs that promote language acquisition.
Using a specially developed in-house language learning app, for example, DPDHL Group also helps them learn German.
In 2022, the Group received the e-Learning AWARD 2022 for its integrative social approach. The initiative is supported by volunteer employees who get involved as mentors, trainers, coaches or reading and language mentors in large numbers throughout Germany.
GERMANY
European distributor for automatic tyre inflation systems, Celerity DRS, has appointed Andre Gerken as General Manager, effective 1 March 2023.
Gerken, who has worked as Regional Sales Manager for the company for over five years, brings a wealth of knowledge and experience to the position, helping to drive the company into its next stage of growth.
“We have a strong team from across various countries and I look forward to growing and developing strong relations as the automatic tyre inflation industry faces new opportunities with the new R141 Regulation,” said Gerken.
“Andre has been an integral part of our
EUROPE
organisation,” said Celerity DRS CEO, Brian Hall.
“He has shown passionate leadership skills from the outset and we know his valuable expertise will help move the company forwards.”
Celerity DRS has been P.S.I.’s exclusive partner since 2017, growing the business to a good position for the upcoming R141 regulation which requires all trailers built in Europe after July 2024 to be equipped with either an Automatic Tyre Inflation System (ATIS) or Tyre Pressure Monitoring System (TPMS).
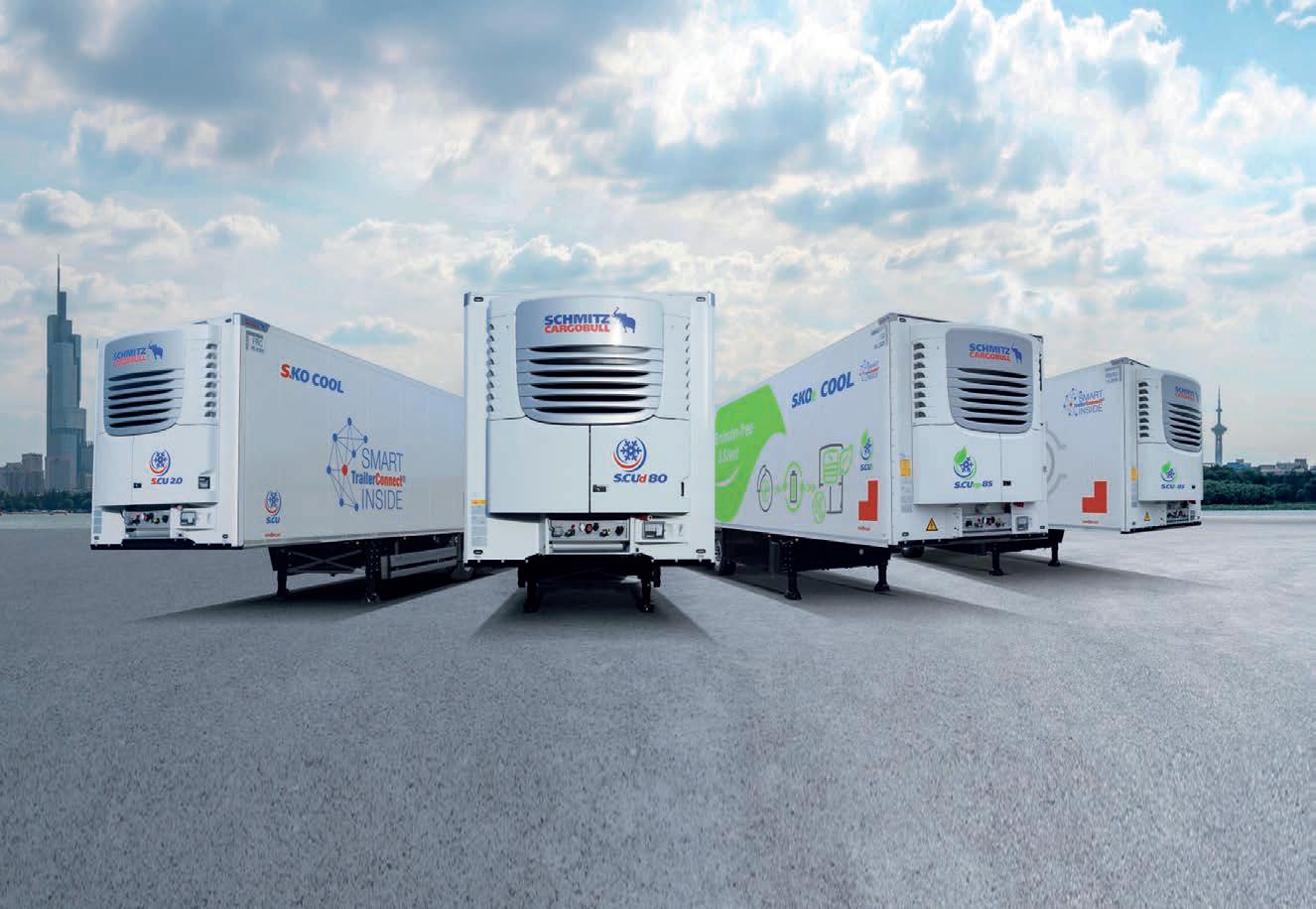
Celerity DRS GmbH is based in
Recklinghausen, Germany, centrally located to cover the entire European region and is part of the Bremsen Technik Group.
UK
Two Schmitz Cargobull curtainsiders have improved the efficiency of MDF Transport’s operations. The Great Yarmouth-based business uses the S.CS Coil and S.CS Mega trailers, sourced as part of a fleet renewal program, to transport normal and abnormal loads for customers across Europe.
“For our general and European
Perfectly effective
transport, the semi-trailers give us much better flexibility to put what would normally be a specialist trailer load inside a curtainsider,” said MDF Transport Managing Director, Mark Farrow.
“The S.CS Coil is great for heavy and wide loading with the extra-long side curtain.
“Around 15 per cent of our work is in Europe. We might go to Italy, Spain or parts of Scandinavia with a load of drill pipe inside the S.CS oil because it’s easier to reload with a curtainsider than a flat trailer.
“As a tall curtainsider, the S.CS Mega
Transport temperatured goods more cost-effectively with the S.KO COOL reefer. The innovative insulation system FERROPLAST® together with the efficient S.CU cooling unit and the smart TrailerConnect® telematics system ensure optimized and reliable transportation. Also available fully electric as S.KOe COOL. More Information: www.cargobull.com
NEWS INTERNATIONAL
offers excellent load capacity for some of our general haulage work. It’s fantastic because it offers so much flexibility with its 3m-plus internal height. You can also raise the roof and put loads through the side.”
Equipped with Schmitz Cargobull’s galvanised Modulos chassis, both curtainsiders are specified with its Varios height-adjustable bodies and come with heavy lashing packages and stanchions inside to aid load securing. The curtainsiders join a 50-strong mixed fleet of trailers at MDF Transport.
The order builds on MDF Transport’s 20-year relationship with Schmitz Cargobull, with the company now operating around 12 trailers supplied by the German manufacturer.
“Schmitz Cargobull engineering design is really innovative and at MDF Transport we like to keep up with the latest technology when we refresh our fleet,” said Farrow.
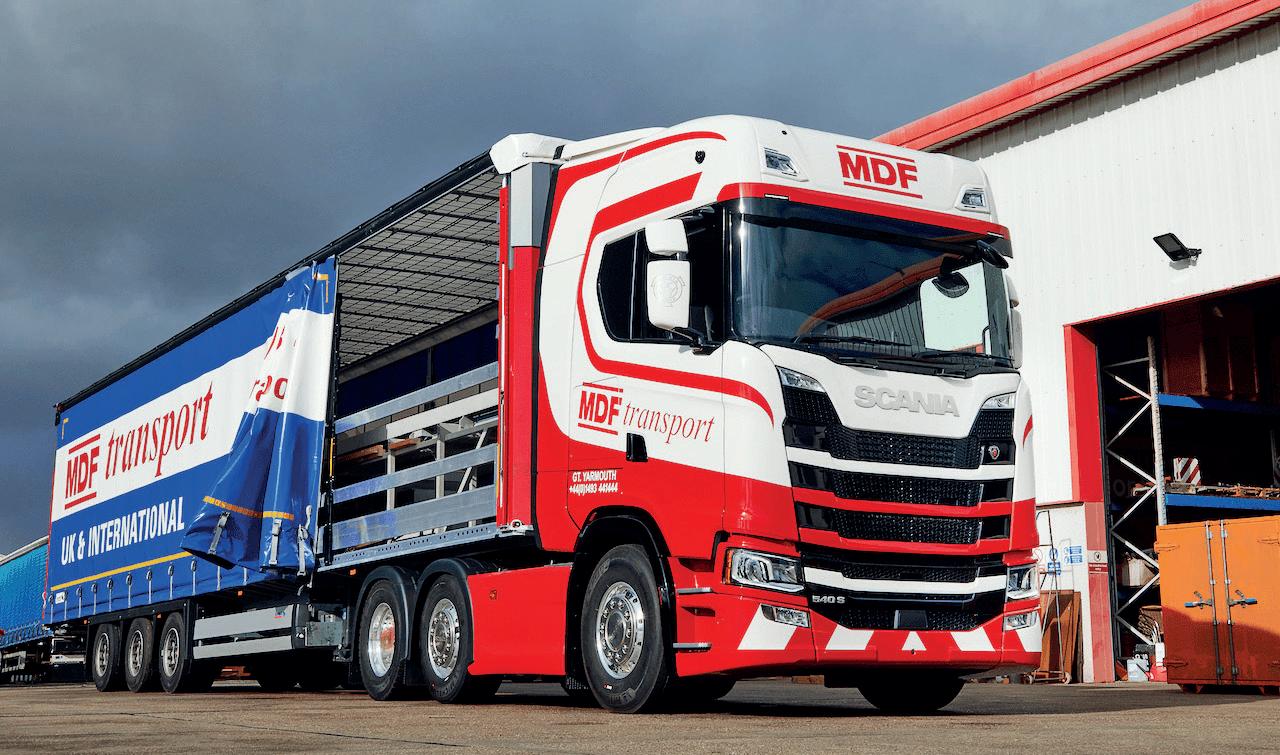
“Another major benefit is the longevity of the trailers and semi-trailers with their galvanised chassis.
“When you buy a Schmitz Cargobull trailer, you know they are robust and built to last a long time. That’s a huge benefit when we are moving heavy and abnormal loads long distances across the UK and continental Europe.”
POLAND
Freight carrier, Francepol, has ordered 50 standard Curtain Masters and 50 Curtain Master Mega curtainsiders from Wielton.
The first part of the order is expected to be delivered this month. The remainder will be delivered in May this year.
The vehicles are characterised by low curb weight, quick-release tarpaulin, and the ability to open the roof in two directions.
The improved structure of the tarpaulin or modern elements of the roof crown seal the loading space, protect goods against moisture. The safety of the goods, according to the OEM, assured due to he floor profile and the load securing strip.
“The construction of the semi-trailers is based on modern hybrid welding technology, which guarantees durable and precise welds,” said Wielton.
“The weight of the Curtain Master
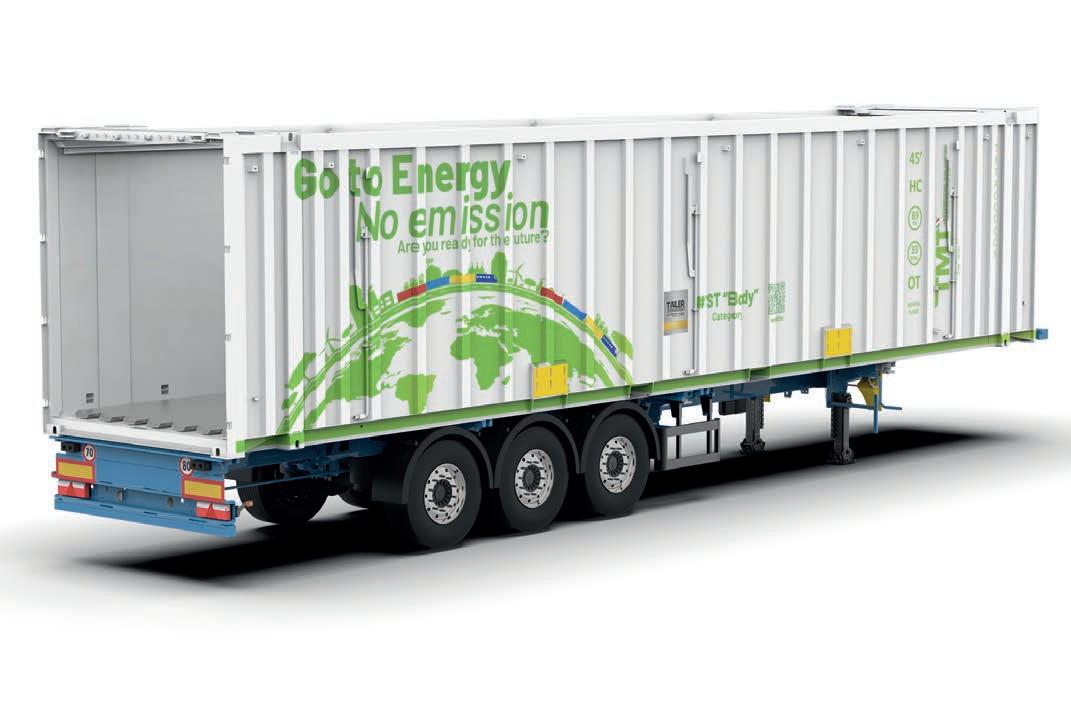
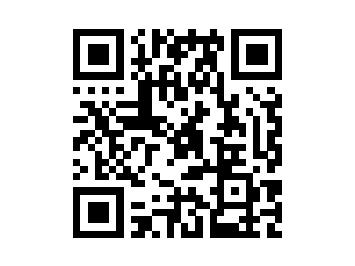
NEWS INTERNATIONAL
EUROPE
trailer has been reduced, and as an additional option, it is possible to install a roll stop and the VL vertical load securing system. The loading area of the Curtain Master Mega semitrailer allows the transport of goods up to 3m high, thanks to the lowering of the frame and suspension level. Used in particular in the automotive industry and where a large loading capacity is required. Standard equipment includes SAF 19.5′ axles.” Przemysław Skrivanek, Fleet Sales Director of Wielton SA, said: “We are glad that such an experienced company as Francepol Sp. z o. o. again decided to enlarge its fleet with our vehicles. Curtain Master semitrailers, like all Wielton products, are equipped with components from leading manufacturers. The fact that contractors come back for our products confirms their highest quality and reliability. We take care of every detail for the sake of customer satisfaction and safety. We are constantly working on increasing our production capacity in order to carry out orders even more effectively. A total of 100 curtain semi-trailers manufactured for Francepol will leave our production plants in May and will go on tour.”
PTH Francepol Sp. z o. o. specialises in truck transport and forwarding within the European Union and in countries in the Schengen area. The company’s drivers usually transport groupage and full truck loads. Currently, the company consists of a specialised staff of 600 people. It is an experienced carrier with 30 years of experience. Annually, it carries out about 80,000 orders with a fleet of nearly 500
different trucks.
“As a company with an established position on the market, we need proven, durable and reliable vehicles,” said Francepol General Director, Artur Nowacki.
“We want our business partners to additionally have an extensive range of maintenance services and technical support. We have been finding all this for several years at the Wieluń manufacturer.
“We are constantly developing our offer to meet individual customer expectations. Thanks to the new, universal Curtain Master semi-trailers from Wielton SA, we will be able to adapt to the needs of service recipients to an even greater extent, as well as transport more loads in one transport. We could entrust such a large order only to a proven manufacturer.” This is another order carried out by Wielton SA for this contractor. During nine years of cooperation, the manufacturer from Wieluń produced 318 products for Francepol, including 58 curtain semi-trailers and 130 spatial sets (130 truck trailers and 130 truck bodies).
POLAND
Raben Group now has more than 11,000 people across 15 countries. This, according to CEO Ewald Raben, is satisfying growth due to increasing reach and improving services. “It was possible thanks to our customers, business partners, suppliers and our team of People with Drive – they all contributed to this success.
“At the same time, just across our border, we are witnessing a situation
that should not be happening in free Europe, and yet it has become a reality. “Ukraine is part of our business, and we are trying to support our employees by getting involved in various aid initiatives.
“In these difficult times, as a company we care not only about the people, but also about the environment. That is why last year we implemented various sustainability projects with future generations in mind, often engaging our customers. We believe that together we can do more.”
In February 2022, the acquisition of 100 per cent of the shares of Austrian company Bexity from its previous owner, Mutares Holding, was finalised. As a result, Raben has depots already in 15 markets and has added more than 500 employees and 16 locations to its European family. Raben and Bexity have been partners for more than 10 years, and the two companies also share a ‘green’ approach to logistics – many of the Austrian company’s terminals offer direct rail connections.
A new depot has already appeared in the new market: in Inzersdorf in south Vienna, the operator has 17,000 square metres of warehouse capacity and 900 square metres of office space, more than 90 loading ramps, four rail ramps and a 200-metre railway siding. As a result, it is able to meet the requirements of a wide range of industries while ensuring sustainable transport.
Less than 150km further to the east, but already on the other side of the border, another facility was erected. In Győr, Hungary, in March 2022, a warehouse was opened with 3,000
EUROPE
square metres of capacity (expandable) and several types of ramps adapted to a variety of vehicles. A month later, construction of the cross-dock warehouse in Dunaharaszti on the outskirts of Budapest began. Nearly 40 ramps, including multi-functional ones, and an expansion of capacity by approximately 75 per cent compared to the existing space allows for greater flexibility and better service for growing order volumes.
In terms of the number of investments, the real record-holder is the country where Raben’s history began. In the Netherlands, a warehouse in Etten-Leur (25,000 square metres, 38,574 pallet places) and a new depot in Hazerswoude-Dorp (1,250 square metres of cross-dock area) were commissioned last year, and in addition, construction of a new warehouse facility was started (capacity of 13,000 square metres). This is a huge source of pride for the entire Group – the first zero-emission warehouse on 15 markets, which will be completed in March 2023.
The Estonian company, on the other hand, has held the IFS Logistics 2.3 service provider certification for the transport of temperature-controlled food products since the middle of last year. Thanks to this, Raben Eesti OÜ has gained the opportunity to expand not only its existing services, but also its customers‘ portfolio.
It is also worth mentioning the solutions introduced in the company to at least partially offset the difficulties associated with the shortage of workers in the TFL industry. Raben Group has been consistently investing in Robotic Process Automation
(RPA) – by 2022 robots carried out over 140 processes in the company. This solution relieves employees of monotonous, repetitive tasks and allows them to use their potential for more developmental projects. In parallel with the development of infrastructure, Raben Group continued its extensive project to expand and reorganise its connections on the Old Continent. This endeavour was launched in 2018 in Germany and entered a key phase in 2021 with the inclusion of nine countries of Central and Eastern Europe and the Baltic coast.
Reacting to the economic situation and the needs of customers, but also taking into account its acquisitions and investments, the operator integrates the distribution networks of the acquired companies into its own system and additionally launches new lines. By the end of 2022, Raben already had more than 600 international connections within Europe, including nearly 180 so-called groupage linehauls running between Bulgaria, Romania, Hungary, Slovakia, Czechia, Poland, Lithuania, Latvia and Estonia.
In the last 12 months alone, the Group launched more than 40 new routes in this extremely important European region for the Group. This result was made possible also by opening the smallest branches in each country to direct international volume exchange.
POLAND
Global logistics provider, Kuehne + Nagel, closed the 2022 financial year with an exceptionally strong result. Group net turnover increased by 20
per cent to €39.5 billion, EBIT by 28 per cent to €3.8 billion and net profit by 30 per cent to €2.8 billion. The conversion rate, which describes the ratio of EBIT to gross profit of the group, was 33.9 per cent.
According to Kuehne + Nagel, all business units contributed significantly to the company’s success. However, due to the overall economic slowdown, the result in the fourth quarter of 2022 was weaker compared to the rest of the year.
“From today’s perspective, the macroeconomic environment will remain challenging in 2023 due to geopolitical developments and inflation,” Kuehne + Nagel said in a statement.
“However, we expect the positive growth and earnings trend that has continued for many years to continue this year, albeit excluding the exceptional business volumes and results in financial years 2021 and 2022, which were the result of a corona-related special economic situation.”
Net turnover in the Road Logistics business unit amounted to €4.0 billion and EBIT to €146.2 million. In the Contract Logistics sector, net turnover amounted to €4.9 billion and €187.3 million.
“The 2022 financial year was exceptional for Kuehne + Nagel in many respects – a year of great financial success, but also with challenges for us and our customers,” said Stefan Paul, CEO of Kuehne + Nagel International AG.
“Thanks to our dedicated employees, we were able to provide our customers around the world with high-quality
NEWS INTERNATIONAL
EUROPE & NORTH AMERICA & SOUTH AMERICA
logistics services.
“Now is the right time to launch our new strategic Roadmap 2026 and ensure Kuehne + Nagel’s sustainable future success with a dedicated focus on quality, customer satisfaction and employee motivation.”
MEXICO
Equipment specialist, SAF-Holland, is building a new site in Piedras Negras, Coahuila.
The approx. 14,647-square-metre facility, located on 9.25 acres of land, is projected to be completed by August 2023 and is expected to focus on fifth wheel manufacturing for the US and Mexico.
Joining the SAF-Holland executive management team for the groundbreaking ceremony was the Mayor of Piedras Negras, leaders of the local economic development council, and representatives of the AMISTAD company, a full service Industrial Real Estate, construction services company
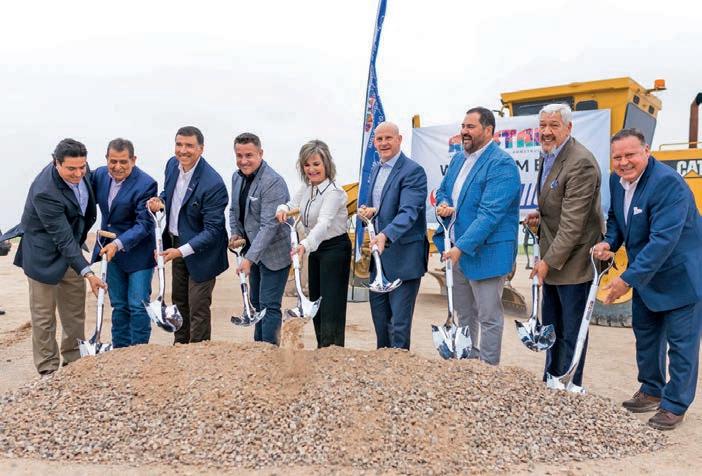
in Mexico and Texas.
SAF-Holland production capabilities will include state-of-the-art robotic welding equipment to manufacture its wide range of fifth wheel model offerings including stationary, sliding and top plate assemblies.
“This investment allows us to better meet customer demand, delivering our fifth wheels more quickly to tractor manufacturers, dealers and customers,” said SAF-Holland President – Americas, Kent Jones. “The additional manufacturing space not only enables us to serve our customers better but provides for future growth.”
US
Food Shippers of America (FSA) and FTR, a transportation intelligence company, have announced a new partnership to help optimise supply chains, improve efficiency and reduce costs.
FTR under this new arrangement
will advance the sharing of relevant transportation industry information among FSA members.
“We are thrilled to partner with FTR and bring their deep expertise and data-driven information to our members,” said FSA Executive Director, Paul Newbourne.
“As an organisation that represents the interests of the food shipping industry, we are constantly looking for ways to help our members improve their operations and improve their supply chains.
“This partnership with FTR is a natural fit, as both organisations share a commitment to innovation and excellence.”
The partnership will include FSA member access to FTR’s transportation intelligence tools and resources as well as regular updates on market trends and regulatory changes that impact the industry. FSA members will also have the opportunity to participate in webinars and other educational events that provide insights into best practices and emerging trends in transportation.
“Partnering with Food Shippers of America is an exciting opportunity for FTR to expand our reach and provide valuable insights to a critical sector of the transportation industry,” said FTR CEO, Jonathan Starks. “We look forward to working with FSA members to help them optimise their operations and navigate the complex landscape of transportation.”
BRAZIL
In its 74 years of operation, Brazilbased OEM, Randon Companies, has achieved a new record for consolidated
SOUTH AMERICA & OCEANIA
net revenue.
Randon reported a net revenue of €11.2 billion BRL (approx. €1.9 billion) in its 2022 financial results. This represents a 23 per cent increase compared to the same period in 2021. As for consolidated EBITDA, it surpassed 2022 projections with a total of 1.5 billion BRL (approx. €265.4 million) with an EBITDA margin of 13.5 per cent.
Revenue from the foreign market, which includes exports from Brazilian units and sales from subsidiaries located abroad, reached 436 million BRL (approx. €77.1 million) in the year, a 40 per cent increase when compared to 2021 and 18 per cent above the top guidance forecast for that indicator.
Key factors for the indicators achieved include: a diversified business model, with access to markets in new countries, portfolio expansion, company acquisitions, winning new customers and offering innovative and more sustainable products, combined with positive scenarios in markets such as replacement auto parts. Global expansion and sustainability is on the horizon for Randon.
Last year saw the OEM enter the US trailer market following the acquisition of Hercules in November as well as unprecedented export of semi-trailers made in Brazil to the US.
More recently, in February, the Fras-le subsidiary announced the acquisition of the UK auto parts manufacturer, Juratek, an operation made possible with part of the follow-on funds carried out in April 2022.
Actions to achieve the objectives outlined in the Randon Companies’ ESG Ambition were accelerated. By
2030, the company expects to invest more than 100 million BRL to generate renewable energy, which will supply industrial units around the world. Frasle’s operation in China already has its first photovoltaic plant, and the next delivery, from a series of projects, will be a plant with around 2,300 solar panels, which is under construction at the Centro Tecnológico Randon (CTR), in Brazil.
“We are strengthened and confident about the future, which is very promising due to the various opportunities we envision, such as increased exposure to the North American and European market, synergy gains with new acquisitions, and with the launch of innovative and disruptive solutions for transport.” said Randon Companies CEO, Sérgio L. Carvalho.
“These projects, in addition to increasing our market share and consolidating us in a leadership position, allow us to bring benefits to our customers and society, also contributing to the global sustainability agenda, and which reflect our purpose of connecting people and wealth, generating prosperity.”
AUSTRALIA
Flex Contract Logistics acquired Doug Hayes Transport (DHT) in April.
The acquisition is part of Flex Contract Logistics’ five-year strategy to become a leading player within the transport and logistics industry.
With warehouses in Melbourne, Sydney and Brisbane, the DHT acquisition will allow Flex Contract Logistics to transport less-than-full
truck loads with one-pallet to 36-pallet options.
Flex Contract Logistics Managing Director, Lachlan Boyd, said the acquisition will give the company a strategic advantage in its growth plan. “It provides us with an expanded footprint along the eastern seaboard, much needed additional equipment and the ability to now provide customers a full service offering for interstate requirements,” he said. “There are existing customers in both the DHT and Flex businesses who can now access a wider range of services. “This is just one of the synergies we expect to extract from the acquisition and we are confident this will fast track our growth over the next 12-18 months.”
DHT Director, Doug Hayes, has agreed to stay on board and support the integration of the two businesses. According to Boyd, this will play a major role in the growth of the business.
“Having Doug stay around is beneficial to the entire Flex business, and we will ensure that everyone gets the opportunity to spend time with him and learn as much as possible,” he said. “Through continued investment in our people, technology and safety, Flex will continue to grow with our customer base and continue to go the extra mile to ensure our customers are well looked after.”
AUSTRALIA
Freight specialist, DHL Global Forwarding, has opened a new site in Brisbane to meet a surge in demand for perishable goods.
The facility is reported to be a $17
NEWS INTERNATIONAL
OCEANIA
million investment over a period of 10 years.
Queensland’s total agricultural and food exports hit $10.72 billion in 2022, a steep 25.5 per cent increase from the previous year. To cater to this growing demand, the newly launched 4,880-square-metre facility houses the largest international cold chain services in Brisbane at 1,700 square metres, offering complete cold chain services for goods such as high-quality meat, fresh produce and seafood. It is at Brisbane airport with airside access, the first and only freight forwarder to have such access, and is close to the Port of Brisbane.
“We built the new Brisbane facility to meet the fast-growing demand for perishables,” said DHL Global Forwarding Australia Managing Director, George Lawson.
“The agricultural and fisheries sector is a key foundation of Queensland’s economy, and it has remained robust despite the disruptions caused by the pandemic.
“Queensland’s total agricultural and food export has seen a 16 per cent increase from the average of the past five years and is set to continue rising in the foreseeable future.
“Expanding our facilities will help cater to this rising demand and help our customers transport these time and temperature-sensitive perishable goods quickly and efficiently.
“The new facility will also support general cargo growth in Queensland.”
Lachlan Elliott, Station Manager –Queensland, DHL Global Forwarding Australia, said: “Queensland’s agricultural produce is renowned for being high quality, safe and
nutritious, which makes it very popular among global consumers. In fact, Queensland exports more than half of its agricultural output. The right supply chain solutions are critical to ensuring that these perishables can reach consumers in pristine condition. Our new facility in Brisbane will do exactly that, especially in our environmentally sustainable offerings, to help customers achieve a greener supply chain.”
AUSTRALIA
Transport and logistics company, Toll Group, has welcomed three appointments to its global leadership team.
The new appointments include Toll President Government & Defence, Perry Singh, Toll President Resources & Industrials, Chris Carbone, and Toll President Retail & Consumer, Nick Vrckovski.
“Toll has significant investment planned in Australia, including expanding warehouse facilities and
upgrading fleet, as we work closely with our customers to support their growth in these important industries,” said Toll.
AUSTRALIA
All seven members of BPW Transpec’s welding team have successfully passed the transport equipment manufacturer’s welding standards test. BPW Transpec Product Manager, Steve Civelle, said the nature of the equipment that BPW Transpec manufactures, as well as its high durability and reliability standards, means specific welding knowledge is required.
“Because we manufacture trailer axles and suspensions, if the welding isn’t done correctly, cracks could appear in the product,” he said. The company decided last year to unify their welders by coming up with an in-house standardised test and qualification. The test included a hands-on demonstration and safety quiz.
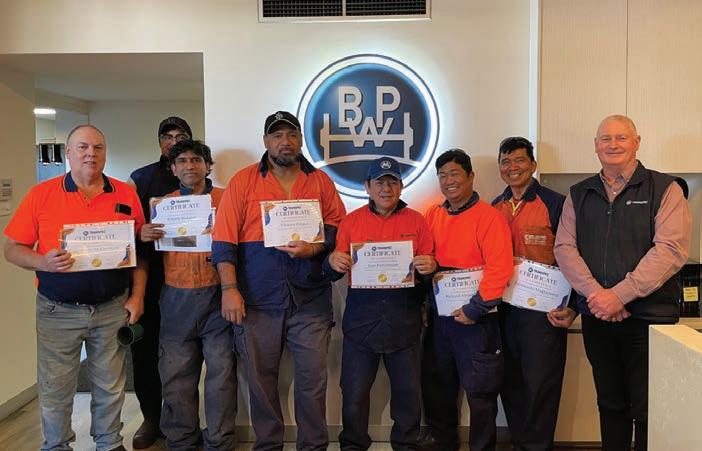
The welders were assessed by an external provider.
To recognise their achievement, the welders were presented with certificates.
“They were really pleased,” said Civelle. “They all passed and it’s been acknowledged that they’ve achieved a high standard and we appreciate their work.”
AUSTRALIA
The National Heavy Vehicle Regulator (NHVR) has released the Heavy Vehicle Industry Safety Survey 2022 report.

NHVR CEO, Sal Petroccitto during a recent speech at the VTA State Conference 2023, offered attendees a sneak preview as to what the longanticipated report might contain. The Heavy Vehicle Industry Safety Survey measures how the industry manages its safety responsibilities and seeks feedback from industry employees, drivers, managers and operators. According to the latest report,
approximately one in three – or 35 per cent – of respondents use the NHVR’s Safety Management Systems (SMS) guidance materials. Of these respondents, 97 to 99 per cent said they are useful.
65 per cent of industry respondents said they have a basic SMS in their business – a two per cent increase from the previous report in 2020. Meanwhile, organisations with Performance-Based Standards (PBS) vehicles had higher rates of SMS implementation compared to those who do not (70 per cent versus 64 per cent).
NHVR Chief Regulatory, Policy and Standards Officer, David Hourigan, said the safety survey is a vital tool for the NHVR as it seeks to implement initiatives that achieve better heavy vehicle safety outcomes.
“This is the third iteration of the survey and to have almost 6,000 industry participants is very encouraging as it demonstrates the importance industry has for improving
safety,” he said.
“The results indicate that since 2020 there have been incremental improvements to safety across the industry, which in turn informs our forward-thinking work program.”
According to the report, overall scores across all items were stronger since 2020, with the biggest increase in the Safety Assurance, Promotion and training and General Business items. Hourigan said the results demonstrate the ongoing commitment from industry to keep pursuing improved safety outcomes.
“I want to thank everyone who responded to our survey as your feedback will help us shape and deliver key safety initiatives with our industry partners in 2023 and 2024,” he said. “One area the NHVR has worked tirelessly to deliver on since 2020 is greater awareness and uptake of SMS and we’re encouraged to see an increase in implementation by businesses of this important safety tool.”
THE INTEGRATED POWER OF
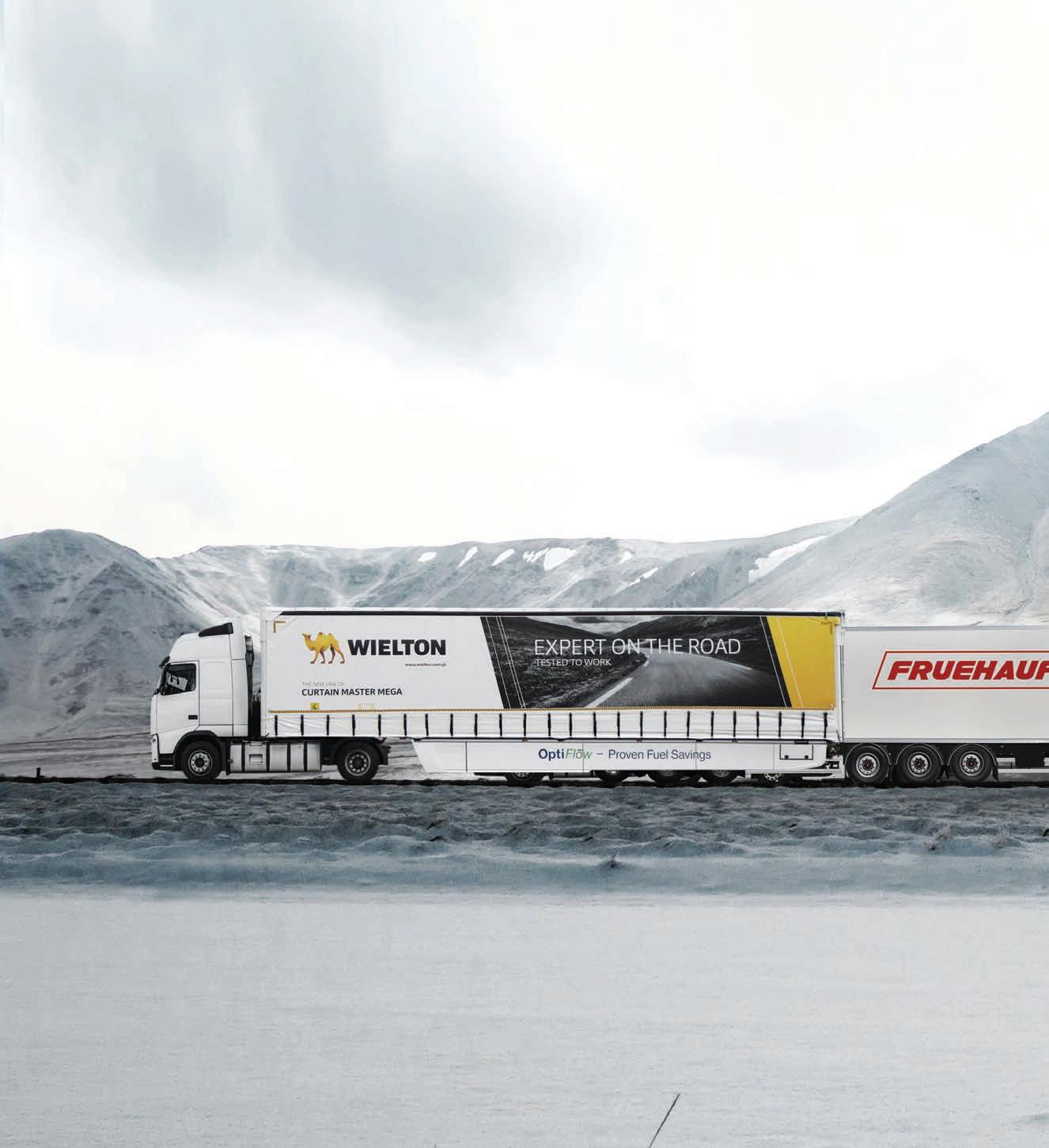
WIELTON GROUP
THE WIELTON GROUP IS CURRENTLY THE THIRD LARGEST SEMI-TRAILER, TRAILER AND TRUCK BODY MANUFACTURER IN EUROPE AND 10TH IN THE WORLD. THE COMPANY, WHICH IS BUILDING ITS GLOBAL POSITION ON A MULTI-BRAND BASIS, HAS STEADILY EXPANDED ITS BRAND PORTFOLIO IN RECENT YEARS, ENTERING NEW MARKETS AND ADDING MORE NEW PRODUCTS TO ITS OFFER. ALTHOUGH IT HAS BEEN IN EXISTENCE FOR 27 YEARS, COLLECTIVELY, ALL OF ITS COMPANIES ARE ALMOST 550 YEARS OLD. WHAT IS THEIR HISTORY?
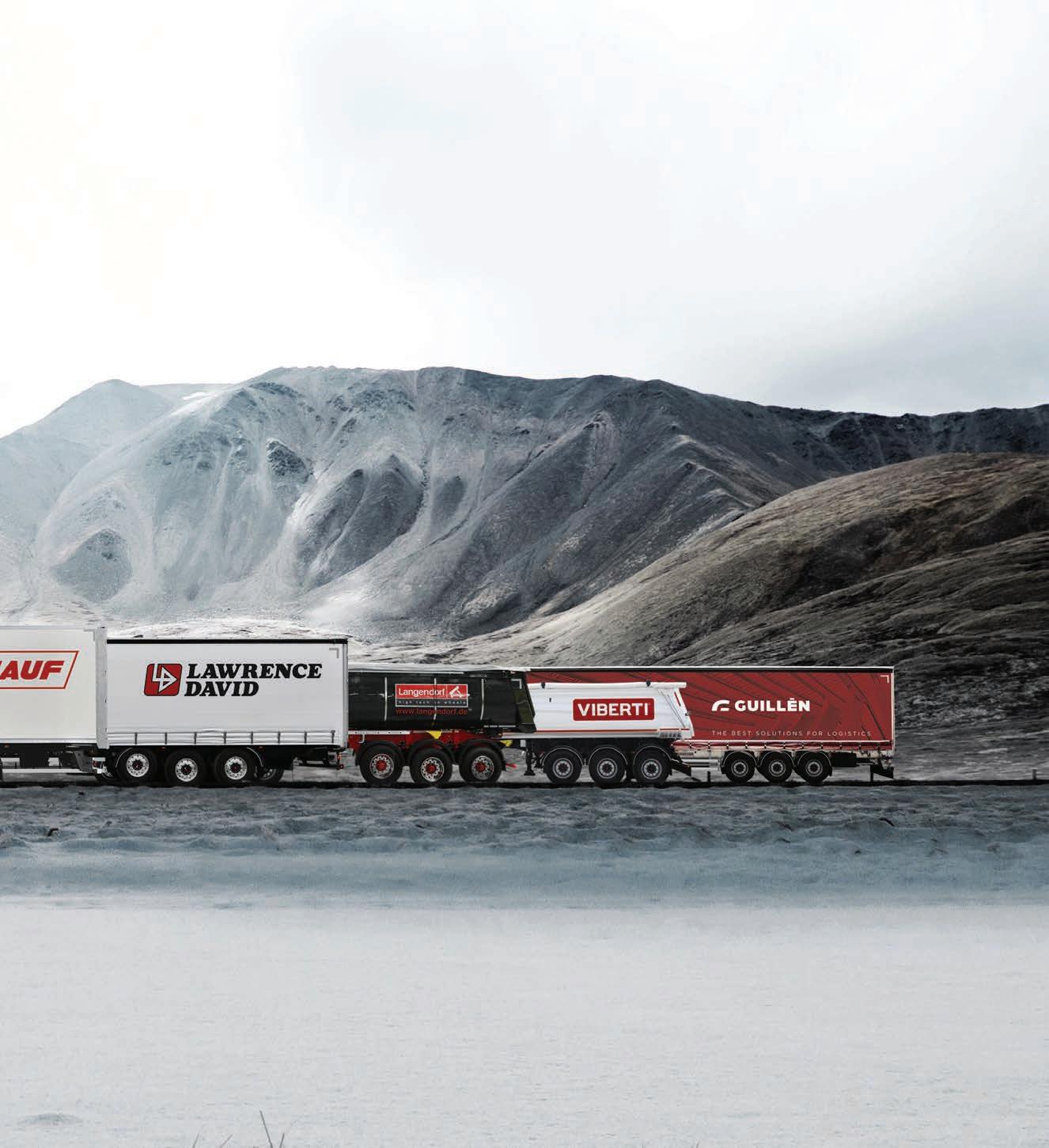
The last eight years have been a period of extremely dynamic growth for the Wielton Group. A successively implemented strategy based on geographical diversification and the potential of acquired brands has ensured that the Group has maintained its strong position among the world’s top ten producers. Developing such a strong position has been possible thanks to the renowned brands that have joined and strengthened the Group. A turning point in history came in 2015
when the Group acquired the leading Italian brands Viberti and Cardi, as well as the French company Fruehauf. Thus, it began to build an international structure.
In May 2017, the Group acquired the German company Langendorf, thereby expanding its product range with, among other things, specialised vehicles for the transport of glass and precast concrete. The acquisition of Lawrence David in September 2018 allowed the Group to enrich its offer with further unique vehicles, such as home delivery bodies and pillarless curtainsider semi-trailers. In turn, the acquisition of Guillén made it possible to expand the Group’s operations into another important market – Spain. The Wielton Group’s brands have been present in local markets for several decades to more than a century. During this time, they have developed a strong portfolio consisting of specialised vehicles and products tailored to the needs of customers and the relevant
market. In total, the Wielton Group brands are almost 550 years old and all have a very interesting history of origin.
“We decided that a multi-brand strategy, based on locally recognisable brands, would allow us to operate successfully in many countries and expand our business into new markets,” said Wielton Group Chairman, Paweł Szataniak.
“Thanks to the consistently implemented strategy, the Group is today present in almost all of Europe. For us, the acquired companies are first and foremost business partners. As we look for common synergies, it is crucial for us to ensure their autonomy and dynamic development. To this end, we are jointly implementing new investments and expanding the product portfolio of the brands. The strong position of the individual companies is for us a guarantee of success and further development for the entire Wielton Group.”
Wielton – 27 years of Polish innovation
Wielton has travelled a bumpy road to becoming Europe’s leading semi-trailer and trailer manufacturer. The company was founded in 1996 in Wieluń, a small Polish town. The first owners were Ryszard Prozner and Krzysztof Tylkowski, who started in an automotive workshop before moving on to modernising semi-trailers years later. This knowledge and experience allowed them to start their semi-trailer production.
In 2002, sales of semi-trailers and trailers of the Wielton brand began. The focus was on successively expanding the factory and storage space. The production plant was equipped with modern technologies such as lasers and industrial robots. In 2004 the joint stock company Wielton S.A. was established. However, over the years, when the company started to manufacture more products and catch the wind in its sails, the owners felt capital constraints and the further development of the company became questionable. At this point, help came from Paweł and Mariusz Szataniak, who had in the past also been involved in the reconstruction and improvement of semi-trailers. Thus, in 2006, Wielton S.A. gained new owners, and the following year the company debuted on the Stock Exchange. An important stage in the company’s development was the modernisation of the facilities for assembling tipper bodies. The year 2009 saw the establishment of the Wielton AGRO brand, which focuses on the production of agricultural trailers. Over the
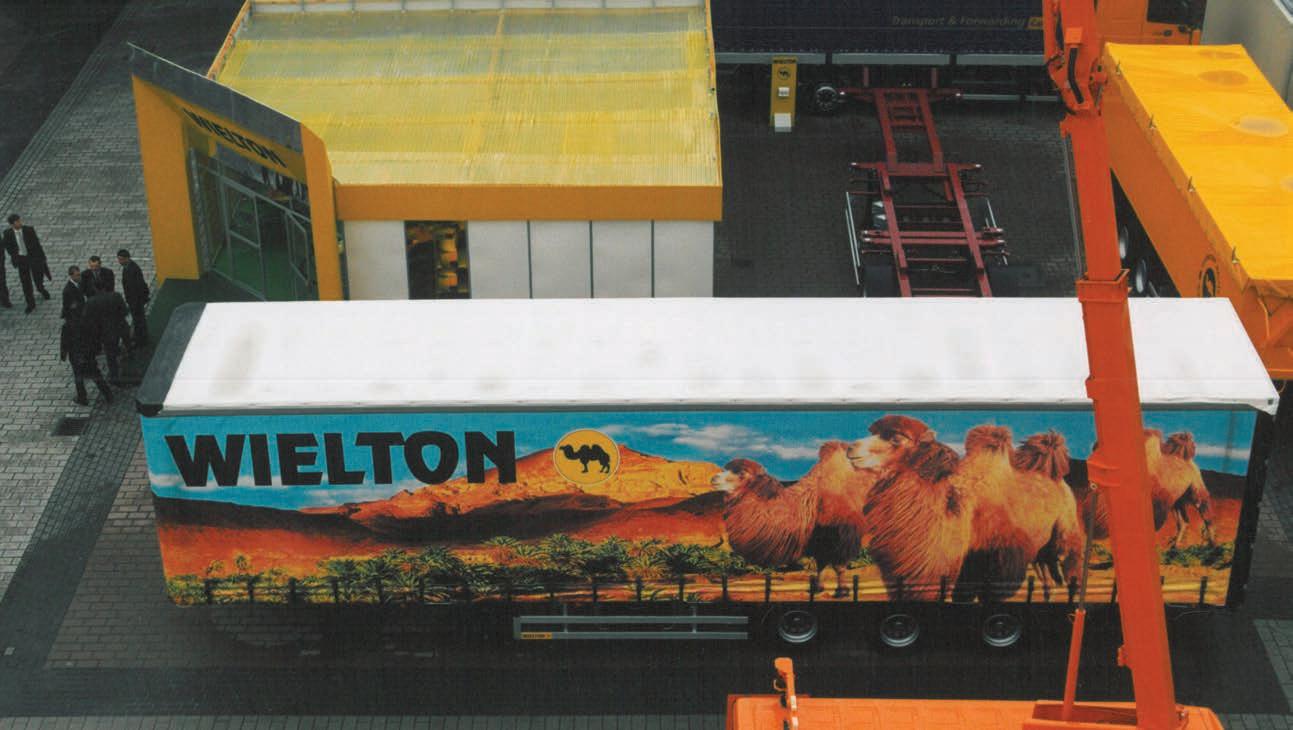
following years, the Wieluń-based producer grew in strength and developed rapidly. In 2016, the opening of Wielton’s Research and Development Centre took place, which has the only full-vehicle semi-trailer testing station in Poland and the third in Europe.
Over time, Wielton became a Group with five production centres: in Poland, France, the UK, Germany and Spain, as well as an assembly plant in Italy. The Group continues to grow and strengthen its position in the European and global markets by establishing further production, sales, and technology companies. It currently employs around 3,600 people.
French Fruehauf – the story of an idea
In 1914, August Fruehauf, together with Otto Neumann, his long-time colleague and friend, created a vehicle that changed the face of world
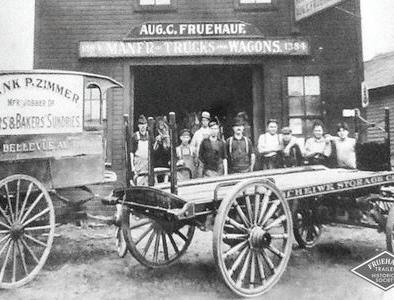
transportation. They converted, at the request of a customer, his recently purchased Model T Ford so that he could transport a sailboat with it. The vehicle could easily carry more weight and was also more manoeuvrable. It proved to be a hit with most local US companies, who saw this solution as an opportunity to really save time and money.
In 1916, August already had single and doubleaxle trailers and semi-trailers on offer. Orders started coming in at such an intensity that August founded in 1918 his first company, the Fruehauf Trailer Company. Two years later, the company’s turnover had reached one million dollars, and 10 years later it was one of the largest international companies: it had nine production sites and 88 branches worldwide. The company’s innovative approach to transport allowed it to quickly launch its first vans, revolutionary suspension and pneumatic lift, but also the first refrigerators, cisterns, tippers and sea containers.

Fruehauf vehicles did not appear in Europe until 1944 with the Allied landing in Normandy. The American military used these vehicles until the end of the war as an effective way of resupplying soldiers at the front. The semi-trailers left on the old continent were purchased by Raoul Massardy, who took charge of their further sale. As interest grew and correspondingly increased customs duties, the first assembly plant for vehicles imported from the US was built in 1946 in cooperation with the American Fruehauf Trailer Company. In 1958, an ultra-modern production facility was built in Auxerre, which in 1975 employed 2,000 people and produced 700 vehicles and 800 containers per month. For more than eight years now, Fruehauf has been part of the Wielton Group and has continued its growth with a focus on innovative products and production automation.
The 50-year history of British Lawrence David
Lawrence David was founded in 1973 by Lawrence Marshall in a rented barrack in the Peterborough area. It quickly gained a reputation for quality and prospective design and construction thinking. In 1978, the company bought back an eight-acre manufacturing facility with 12 stations. This tripled the company’s production capacity. Its head office was moved to St Peters House in 1982, and a year later a paint facility was built and additional production stations were put into operation.
In 1985, the Roscope production facility was established. Another 10 production stations were built in Morley Way, which allowed for the optimal use of this location. Five years later, the business expanded into repairs and Advance Body Repairs was founded to repair trailers of all brands. In 2000, Lawrence Marshall retired, handing over control of the day-to-day operations of the company to his son, Laurence. In 2003, the company purchased land adjacent to Morley Way, which was converted into the new company headquarters. Three loading platform assembly stations were also created.
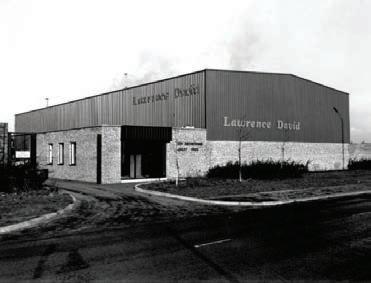
The Roscope plant was moved to a new location in Kettering in 2005, which resulted in a double increase in production capacity, and in 2009 the company began to repair and service of loading platforms. In the following years, plants were purchased, which doubled the company’s existing production capacity and the product range expanded to include vans and commercial vehicles. In 2018, Lawrence David Ltd became part of the Wielton Group and the following year introduced the Wielton chassis to the British transport market. The company is currently in the process of robotising and automating production and digitalising the business. This year, the company is celebrating Lawrence David’s 50th anniversary.
Over 130 years of German Langendorf development
Langendorf is a family company with over 130 years of experience, including over 70 years in the production of trailers. The company’s history began in 1898 when Heinz Langendorf founded a blacksmith’s workshop to start producing carriage wagons and vehicles for agriculture three years later. In 1950, Langendorf built a factory hall in which he began producing agricultural trailers with pneumatic tyres two years later. The first produced vehicles were intended for the agricultural sector, and in the 1960s the production of specialized low-loader vehicles for the construction industry began. The company’s dynamic development was reflected in the introduction of further types of
vehicles for the transport of prefabricated elements and glass.

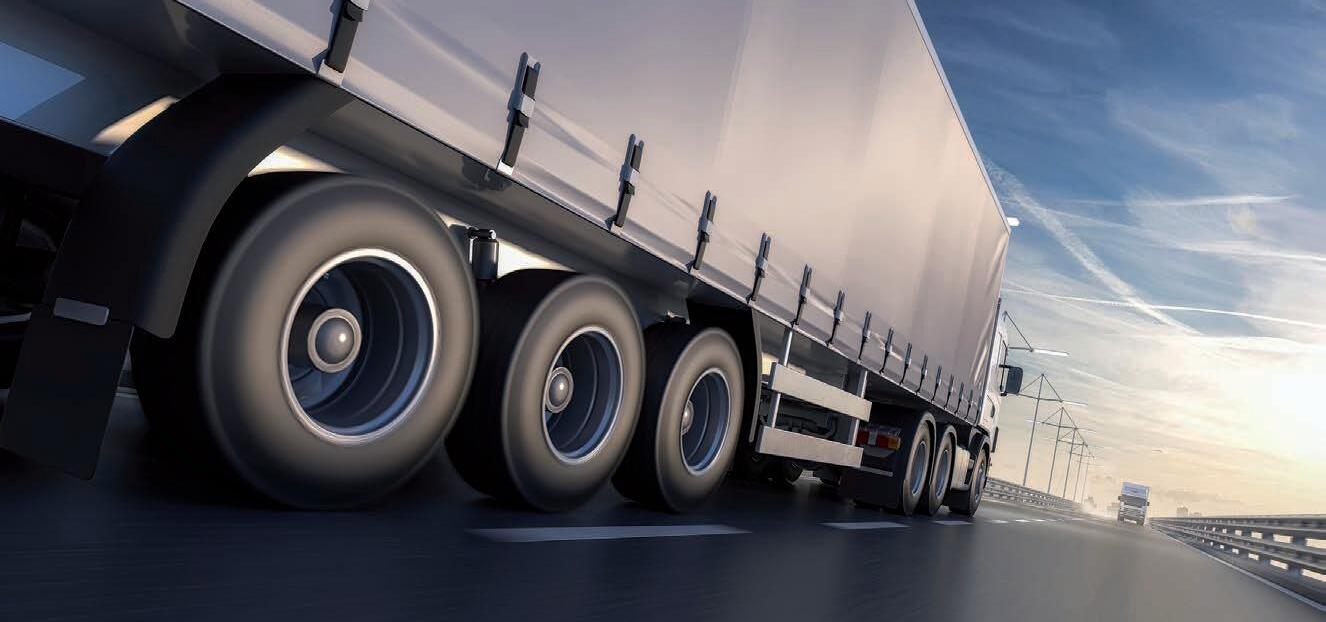
The beginning of the 1970s started with the assembly of tippers with an aluminium box, in later years the assembly of trailers with a gutter box structure was launched. Langendorf has a modern production plant in Waltrop with an area of 60,000m2 and a network of 45 partner sites in Germany and abroad. In 2017, Langendorf joined the Wielton Group and in October 2020, Langendorf Poland was established. The company in Poland strengthens the Langendorf company and supports the competence center for niche low-volume vehicles in Waltrop, to which it reports directly.
Over 100 years of Italian Viberti tradition
In 1922 Candido Viberti began producing his first car models in a small workshop located on the outskirts of Turin. After a few years, Viberti decided to take the next step, founding his own company Candido Viberti in 1928. He also purchased an old plant that was dedicated to the production of tanks, buses, trailers, semi-trailers, special bodies, trolleybuses and trucks.
In 1932, Viberti linked its brand to trailers, which have been the company’s hallmark over the years. From that moment on, the plant experienced a period of unprecedented prosperity and continuous development. An important event in Viberti’s history was the acquisition of a company specialising in the manufacture of tanks. In 1937, the Italian manufacturer began serial production of trucks for the distribution of aviation fuel.
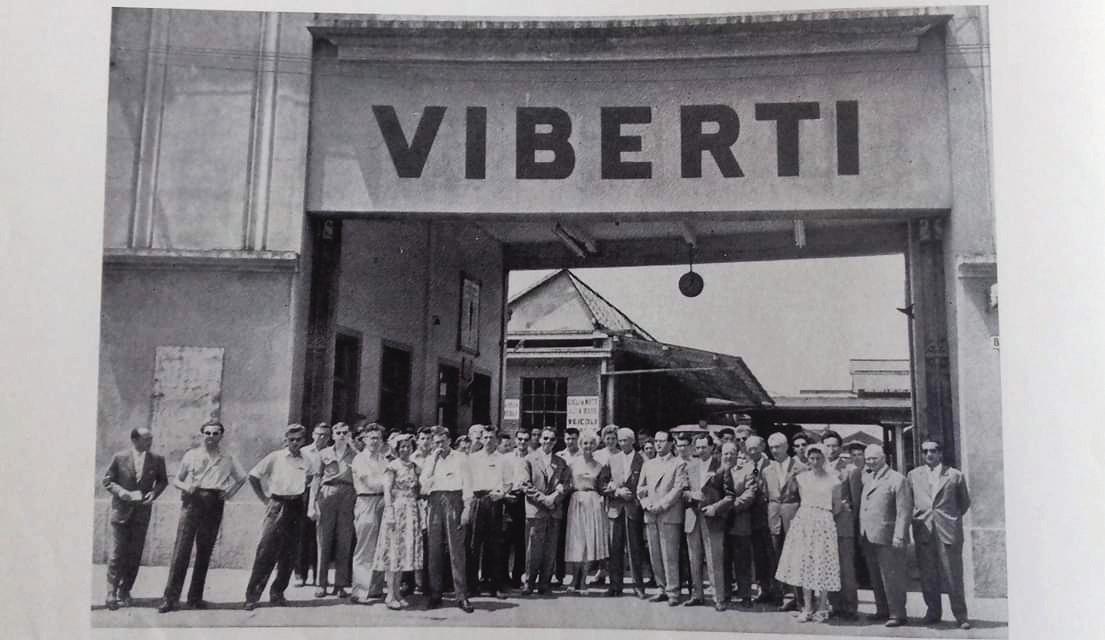
In 1940, Italy became involved in hostilities and Viberti was entrusted with the production of trailers with special containers for the transport of liquids and fuels for the army, navy and aviation. The outbreak of war, however, was not only a period of increased orders. The company was affected by the bombing, with heavy losses. However, consistency in action and the inclusion of new products, such as the three-axle articulated vehicle, contributed to the revival of the company’s business. In addition, a series of acquisitions made between 1952 and 1960 allowed Viberti to achieve a significant share of the national market and offer customers differentiated products. The
headquarters were also changed to a new location. An important historical event was the acquisition of the Viberti brand, in 2010, by Compagnia Italiana Rimorchi, which owns the Merker and Cardi brands. In 2015, the company became part of the Wielton Group, changing its name first to Italiana Rimorchi S.r.l. and then to the current Viberti Rimorchi S.r.l.
Development of Spanish Guillén over 130 years
The Guillén company was founded almost 130 years ago as a small workshop in Valencia. Its founder began manufacturing animal-drawn carts in 1895. The company grew very quickly, focusing on high quality, innovation, and closeness to its customers. It concentrated on diversifying its offer, specialising in bodywork assembly and offering a range of products and services related to goods transport. Specialized, artisanal, and personalised production was carried out until 2005, after which a more serialized production process began.
Over time, ‘Carrocerías L.I. Guillén’ produced bodywork for rigid trucks, semi-trailers, and even
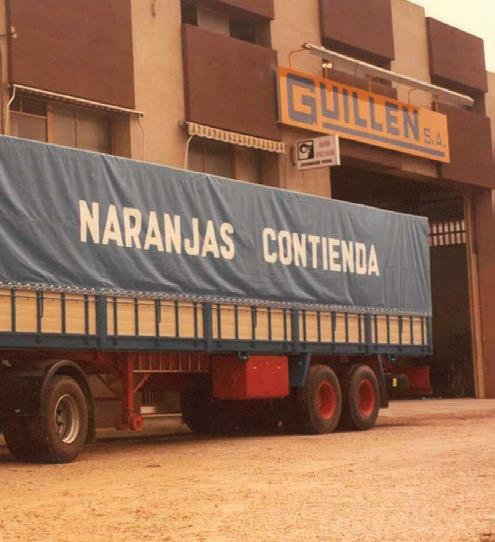
railway-road mobile containers. In the 1980s, the Valencian company embarked on a new project in collaboration with architect Fernando M. García Ordoñez. It used shipping containers as the basis for building prefabricated houses that could be transported by land, sea, or air and assembled anywhere in the world.
In 2005, Guillén underwent a significant change that influenced the future of the company. It introduced a curtain model representing a new dimension of quality. This was the result of a research and development process that lasted several years and led to an innovative and highly competitive product. The company also decided to change its production process from an individualized production system to a chain-based process. This change allowed the company to increase its operational efficiency and cost-effectiveness. Guillén has become a significant player in the semi-trailer market and has considerably improved its position in the industry. One of the key factors in Guillén’s success has been its team, which has always maintained a close relationship with its customers, listening to their needs and offering personalized solutions. Today, together with the Wielton Group, the company continues to consolidate its position among Spain’s leading semi-trailer manufacturers. Attention to quality, innovation, and customer service has been the key to Guillén’s success and continuous growth for almost 130 years.
“Today Wielton is a completely different organisation than it was 27 years ago,” said Wielton Group CEO, Mariusz Golec.
“We are now an international Group, that is one of the leading semi-trailer manufacturers in Europe and employ almost 3,600 people. We are characterised by state-of-the-art R&D and robotised production, resulting in competitive products that customers trust. If we do not lose our ambition, in a dozen years we can become the leader in Europe and occupy leading positions worldwide, and the Wielton Group will be one of the most recognisable players in the industry. We will soon tell you about our plans for the coming years.”
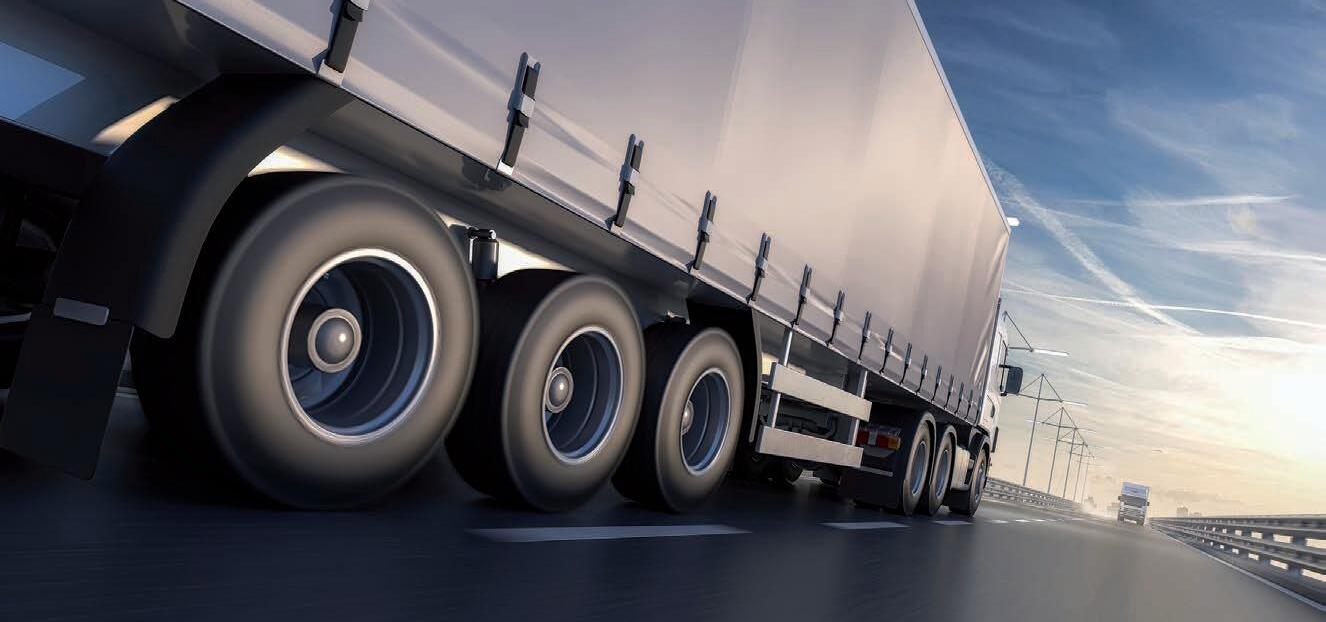
New chapter in the history
In 2022, the Wielton Group began another chapter in its history – it started implementing a new strategy with a five-year outlook. The Group has embraced interesting directions for further development, based on continued expansion, modern products and innovative technologies. Publication of the strategy is scheduled for the second quarter of this year.
www.wielton.com.pl
CROSSROADS AT THE
AN
Serbia is an upper-middle-income country located in Southeast Europe with a population of approximately seven million people. The country’s economy is a mix of services, industry, and agriculture. The services sector is the largest contributor to the country’s Gross Domestic Product (GDP), followed by industry and agriculture. Serbia’s major industries include automotive, metal processing and food processing. The country has a relatively skilled workforce, and labour costs are lower compared to other European countries. The government of Serbia has implemented several economic reforms in recent years to attract foreign investment, promote entrepreneurship, and reduce the country’s debt. Despite these efforts, Serbia’s economy faces several challenges, including high unemployment, corruption, an inefficient regulatory framework and a significant informal economy.
The Covid-19 pandemic has also had a negative impact on the country’s economy, particularly in the tourism sector. However, the government remains committed to promoting economic growth and development, and the country’s strategic location and relatively low labour costs make it an attractive destination for foreign investment.
The transport and logistics industry is an essential component of any country’s economy, and Serbia is no exception. Located in the heart of the Balkan Peninsula, Serbia has a strategic location that makes it an ideal hub for transportation and logistics activities in the region.
Freight connections and infrastructure
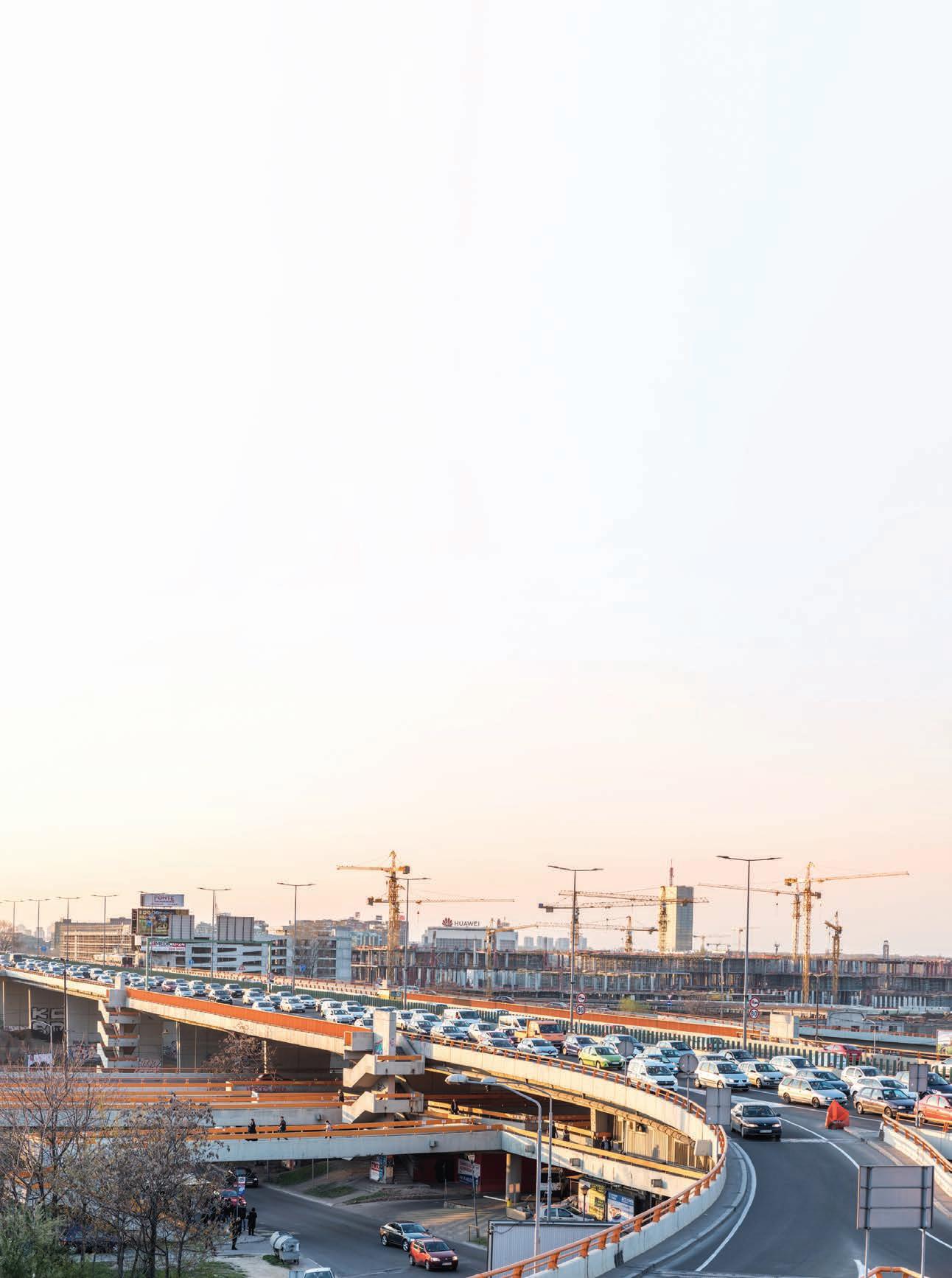
Serbia has a relatively developed infrastructure for transportation and logistics activities. The country has a network of highways, railways, and airports that connect it to the rest of Europe and beyond. The road network in Serbia covers more than 40,000km, and the major highways include the E70, E75, and E80. The railway network covers over 3,800km and is an essential component of Serbia’s transportation infrastructure, particularly for the transportation of goods. Serbia has five international airports, with the Belgrade Nikola Tesla Airport being the largest and most important in the country.
Key players in transport
The transport and logistics industry in Serbia is dominated by several key players. The leading
FAST FACT
Transfera in recent years has been growing its operation in Serbia. The transport and logistics company built new facilities in the Novi Banovci industrial zone near Belgrade. Last year it completed the construction of its first set of logistics centres. The first site covers an area of 30,000 square metres of which 3,000 square metres is zoned for office space and intended for administration activities. The remainder of the space comprises storage, recreation facilities and eateries. The entire 53,000 square metres of terminal space will be fully operated by a Yard Management system (YMS) and Dock Management System (DMS).
transport companies in Serbia include Posta Srbije, Serbian Railways, and Air Serbia. Posta Srbije is the country’s postal service provider, which also offers logistics services. Serbian Railways is the stateowned railway company that provides rail transportation services for passengers and goods. Air Serbia is the national airline of Serbia, which operates both domestic and international flights. In addition to these key players, there are also several private logistics companies operating in Serbia, including DHL, FedEx, and UPS.
Challenges to overcome
Despite the relatively developed infrastructure and the presence of key players, the transport and logistics industry in Serbia faces several challenges. One of the most significant challenges is the outdated and inefficient regulatory framework that governs the industry. The regulatory framework for transport and logistics in Serbia is complex and it can be challenging for companies to navigate the system. Another challenge is the poor condition of some of the infrastructure, particularly the road network. The road network in Serbia is in need of significant investment to bring it up to modern standards. Finally, corruption and bureaucracy are also significant challenges for the transport and logistics industry in Serbia, which can make it difficult for companies to do business.
Opportunities for change
The transport and logistics industry in Serbia offers several opportunities for companies operating in the sector. One of the most significant opportunities is the country’s strategic location in the heart of the Balkans. Serbia is well-positioned to serve as a hub for transportation and logistics activities in the region. Additionally, the country has a relatively low labour cost compared to other European countries, which can make it an attractive location for companies looking to establish operations in the region. Finally, the government of Serbia has expressed a commitment to improving the infrastructure and regulatory framework for transport and logistics, which could create significant opportunities for companies operating in the sector.
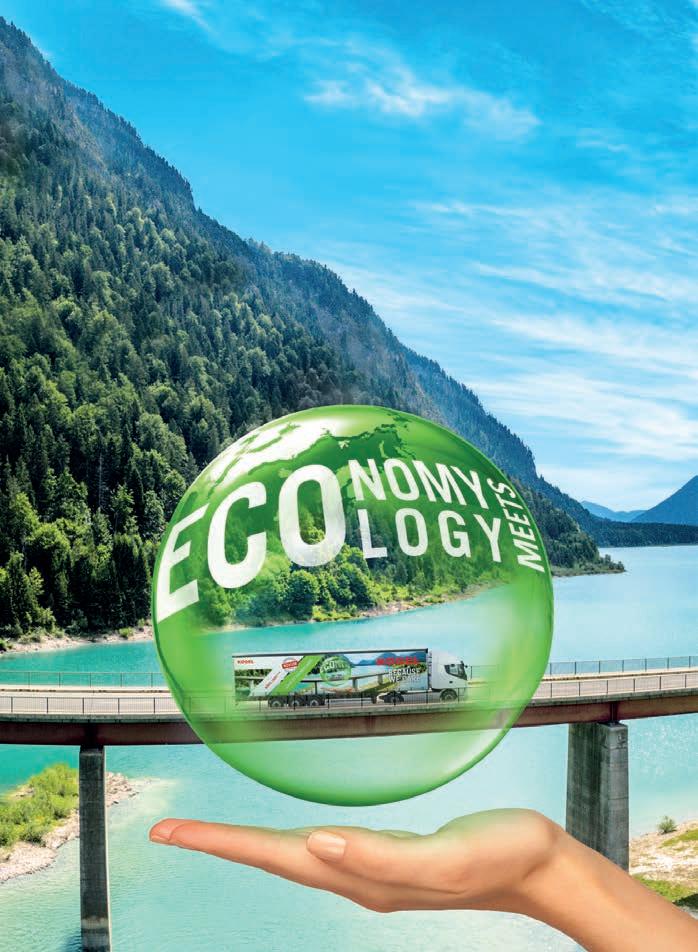
www.globaltrailermag.com
ü maximum payload*
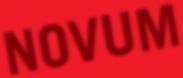
ü proven fuel savings*
ü tested stability


LIGHT IS THE NEW LARGE. BECAUSE WE CARE!
CALL OF HEAVY DUTY
EQUIPMENT SPECIALIST, JOST, SUPPLIES INDUSTRY WITH A RANGE OF COMPONENTS SPECIFIED FOR HEAVY HAULAGE APPLICATIONS.
Low Loaders & Heavy Haulage
Special transport poses particular challenges for a freight forwarder. Whenever very heavy and large parts such as turbine blades, bridge elements, machinery or prefabricated modules have to be transported under difficult road conditions, only special vehicles with excellent equipment are capable of mastering this task. JOST, ROCKINGER and TRIDEC offer the right components in well-known market leader quality making all kind of special transports possible.
JOST offers a comprehensive range of components for high and maximum load conditions such as the heavy-duty fifth wheel coupling JSK50 made of cast steel which is for highest loads with imposed load up to 50 tonnes. The JSK52 is a super heavy-duty fifth wheel coupling with imposed load up to 74 tonnes, especially suitable for mining. Both fifth wheels can handle difficult transport challenges easily with the robust JOST King pins with a diameter of 3 1/2”.
Another solution for special transport is the heavy-duty landing gear Modul CH. The advantages: maximum resistance to bending thanks to outer reinforcement and reinforced inner tube, heavy-duty bearing for better shock resistance and increased static test load (66 tonnes). The Modul CH has a full-length back plate for high mounting variability and is also available with two side operation and special crank.
JOST is one of Europe’s foremost manufacturers of steering, suspension and axle
systems for truck and trailer applications – also regarding special transport. The modular systems provide a great variety of solutions and adaptation of JOST leadings axles to the individual use case. Load-supporting axles for all 6x2 and 8x4 vehicles can be handed-over customer-specific and are also available with an arched axle tube as a leading axle with especially short wheel base. The ball bearing turntable is the first product which started the success story of JOST in 1952. Naturally, JOST has further developed the product for heavy transport. The double-row ball bearing turntable is extremely robust, strong and durable. The extra large support balls transmit the axial loads over a wide area directly onto the vertical bar of the ring parts. Horizontal forces in pull or push direction, as well as the moment load resulting from braking and centrifugal forces, are supported by the interplay of the two ball rows.

The e-coating ensures an outstanding corrosion protection.
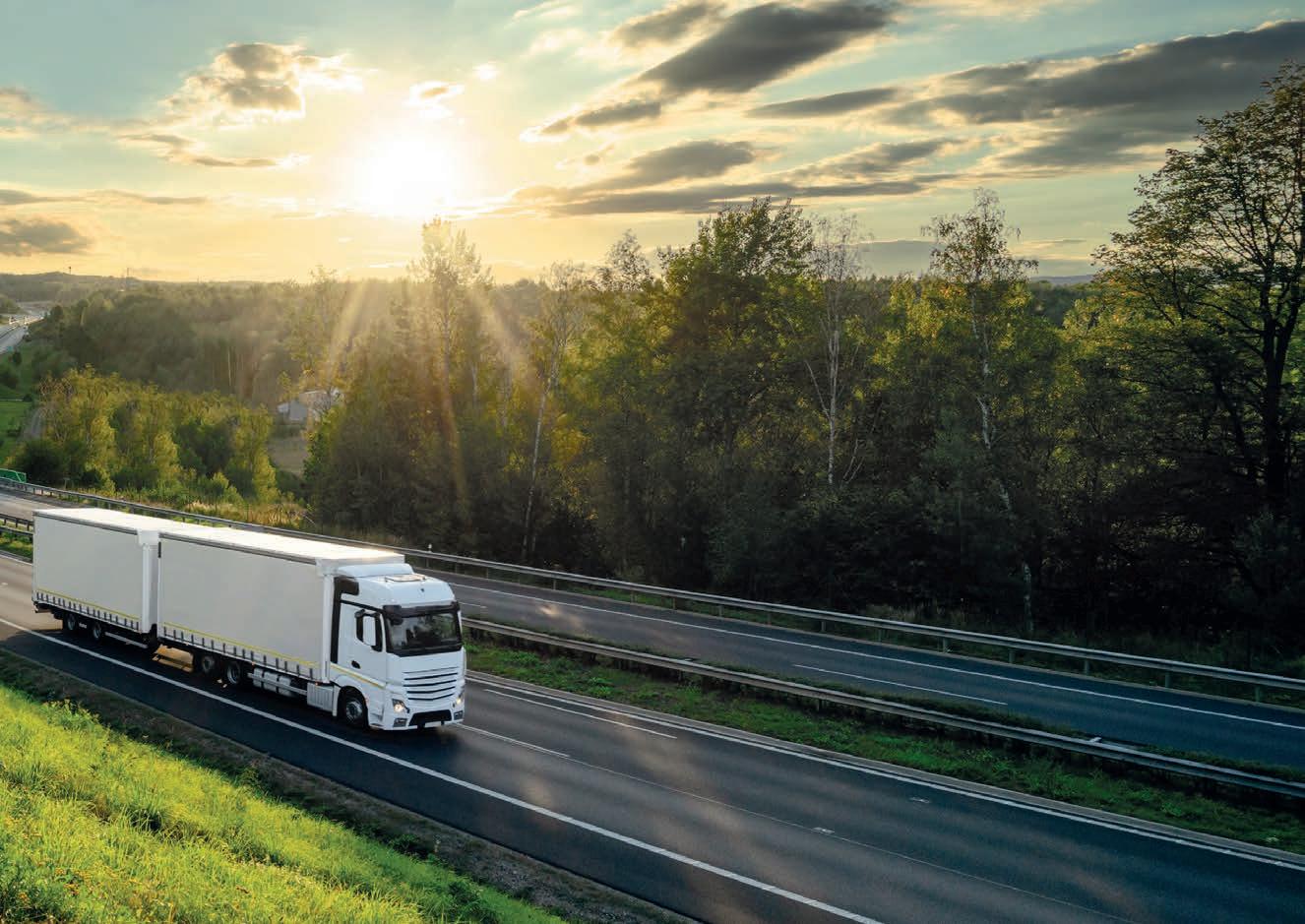
ROCKINGER
Nothing is too heavy with the RO*56 E, the heavy-duty towing hitch for regular special transport applications up to 500 tonnes. It is suitable for all types of special transport trailers. The hinged hitch head allows towing eye swivel angles ranging between -58° and +35°, also on poor-terrain. For the highest demands in the special transport ROCKINGER offers the RO*58: the world’s only automatic towing hitch with a trailer load of 1,000 tonnes. With 300 kg net weight the RO*58 is robust and user-friendly at the same time. It and can be easily operated via the hand lever. The automatic towing hitch is approved for use in road traffic. As counter pieces for the RO*56 E and RO*58 ROCKINGER additionally offers matching heavy-duty towing eyes.
TRIDEC
Products from TRIDEC are the safe choice for any special project. Mechanical, hydraulic or electronic steering systems as well as wheel and axle suspensions are needed when building special vehicles for special transport applications. TRIDEC develops and manufactures the ideal solution for every transport challenge – regardless of the axle or vehicle manufacturer.
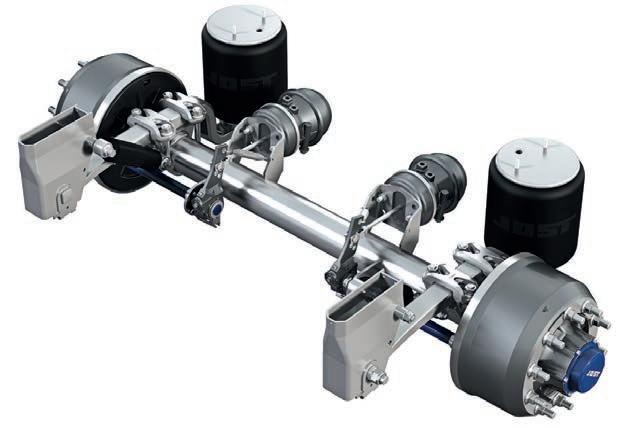
TRIDEC’s hydraulic steering systems are primarily installed in special transport vehicles and vehicles of exceptional length or width. Due to the significant dimensions of these vehicles, installing a steering system is often necessary to satisfy legal requirements. Hydraulic steering is exceptionally well suited for extendable trailers, as there is no mechanical linkage between the fifth wheel and the axle. Optional manual steering by wireless remote control further contributes to the vehicle’s manoeuvrability.
One of TRIDEC’s innovations is the TRIDEC Tritronic Trailer Management System which supplements the hydraulic TRIDEC steering and suspension systems. Tritronics offers unique functionality, ease of operation and safety in special transport applications. The high-performance remote control for operating various trailer functions includes manual steering, automatic tracking, automatic ride height control, ramp control, gooseneck control, hydraulic landing gear, warning lights and much more. Another solution especially for low loaders is the new TRIDEC swivel axle
suspension TP-O Low, opening up a new market for independent trailer manufacturers. With suspension travel of 600 mm, the TP-O Low offers the lowest ride height with 12 tonnes per axle line, combined with a greater steering angle than any other suspension solution.
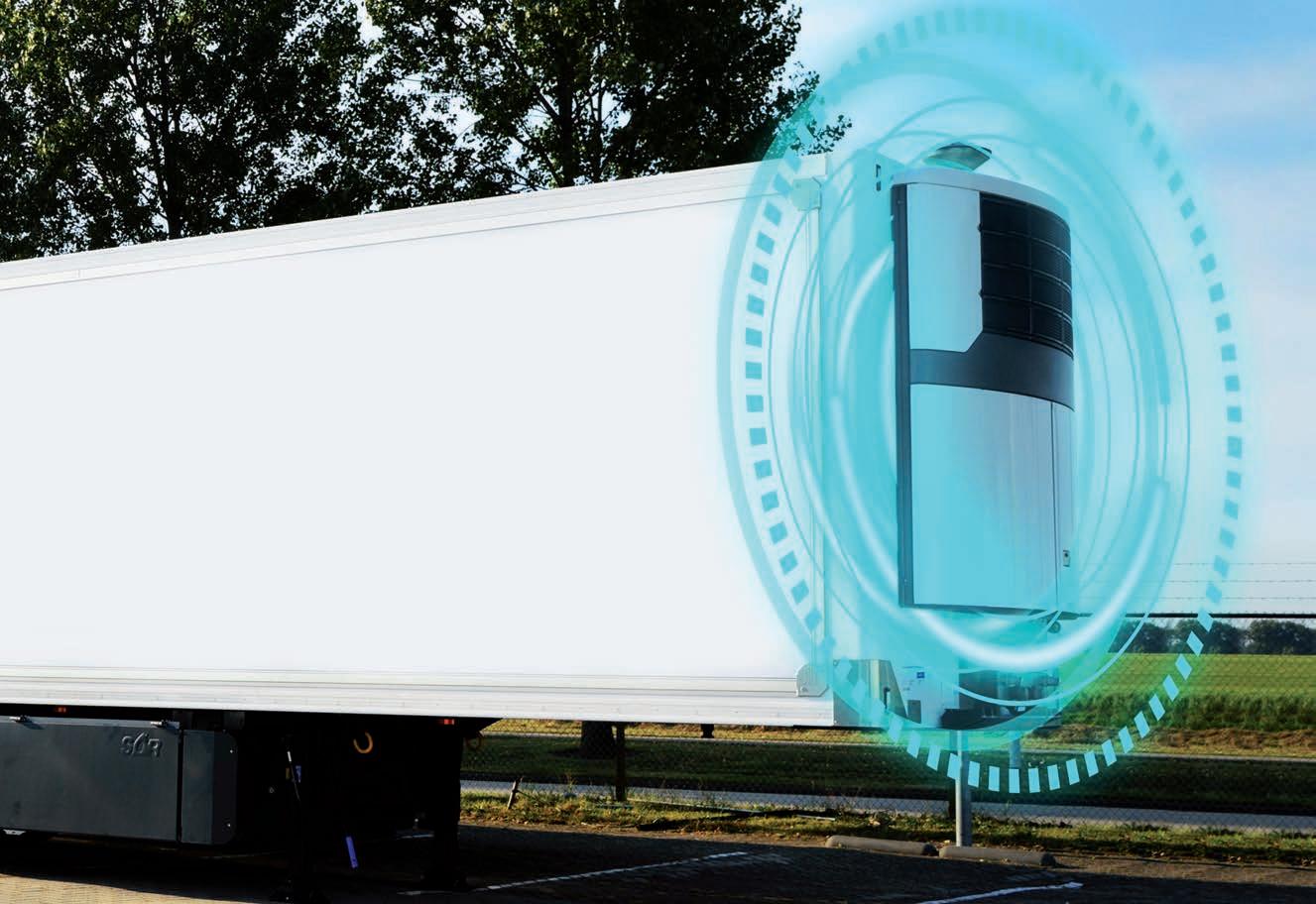
JOST Brake Pads
Brake pads are an important element of any disc brake system and can have a huge impact on road safety. They are exposed to the most adverse weather and road conditions. The innovative JOST brake pads grant for safe braking of heavy weight commercial vehicles due to a high friction coefficient stability. They are suitable for all truck and trailer applications, notably for challenging transport missions on demanding topographical mountain terrain. With the JOST friction material the brake system is brought to its optimal brake performance and lowest braking distance.
JOST DCA-L7 Disc Brake
The DCA-L7 disc brake for 22.5” applications is designed for maximum payload thanks to a weight-saving construction. Up to 24 kg weight reduction per three-axle unit allows a higher loading capacity and significantly increases the
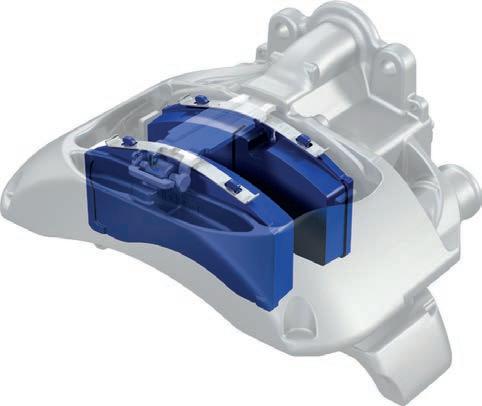

operation’s profitability and efficiency. An increased maximum braking torque permits a wide range of applications while improving safety at the same time. The DCA-L7 is particularly durable and robust thanks to the high-quality corrosion protection. The disc brake is available for all axles of the DCA series with 22.5” wheel diameter.
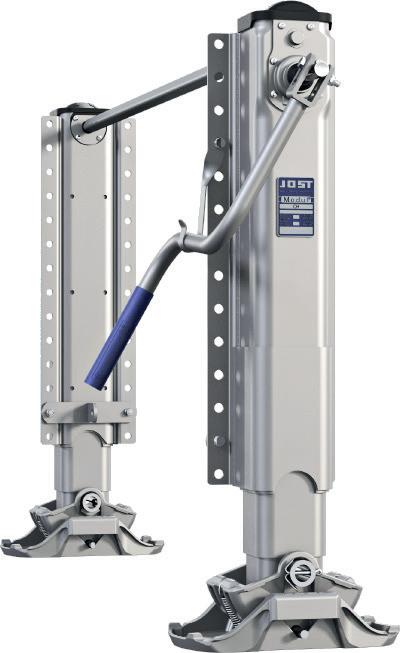
JOST DMA: new drum modular axle
In order to provide the right solutions to meet the needs of customers all over the world, JOST is adding the DMA series drum modular axle to its axle portfolio. The drum modular axles in the DMA series ensure maximum flexibility for every transport application. The drum modular axle combines a robust tubular axle with a modular leaf spring system known from the DLS series, which can be adapted to match the customer’s individual specifications.
The DMA’s most striking feature is the external brake drum design, which allows the brake linings to be replaced without having to disassembled the wheel hub – making it extremely easy to service and maintain. In addition, the proven brake design requires minimal repair effort and offers maximum benefit to customers.
To ensure optimum brake performance at all times and enable ideal wear behaviour, great emphasis has been placed on the interplay between the brake drum and lining during development. This is supported by gradual interaction with an automatic, selfregulating slack adjuster, which controls the brake pressure depending on the wear conditions.

www.jost-world.com
ZERO EMISSION REFRIGERATED TRAILER
With the e-reefer, we pave the way to achieving net zero carbon emissions in temperature-controlled transport
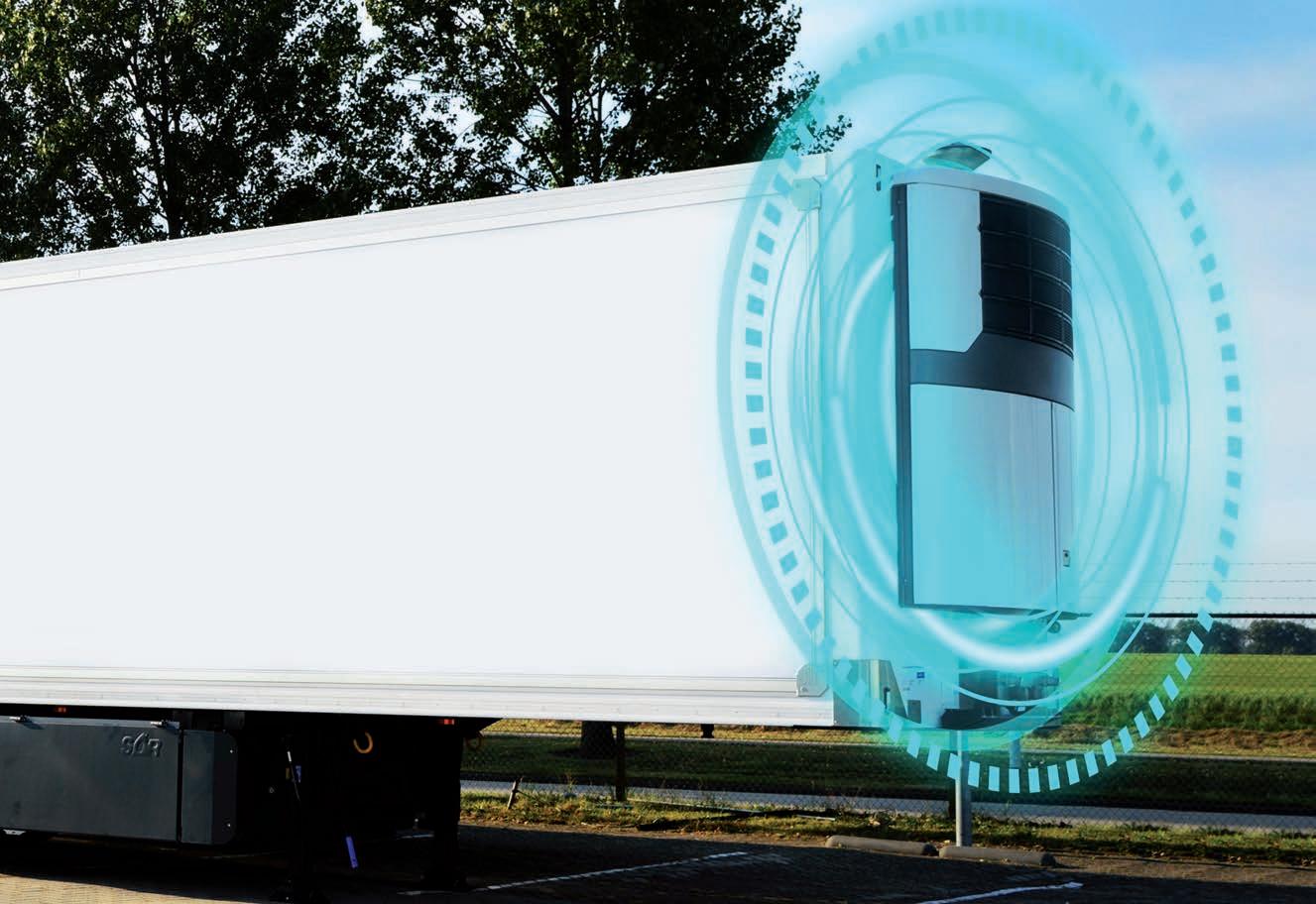
THE FUTURE IS NOW
The ‘TPMS’ regulation UN ECE R141 came into effect on 6 July 2022 with the aim to improve road safety. In addition to Tyre Pressure Monitoring Systems (TPMS), the regulation also includes TPRS (Tyre Pressure Refill Systems) and CTIS (Central Tyre Inflation Systems).
For end users, transport companies and fleets, the new regulation will come into effect on 7 July 2024 on every new trailer, meaning every new trailer needs to have some form of ‘TPMS’ installed during registration of the vehicle.
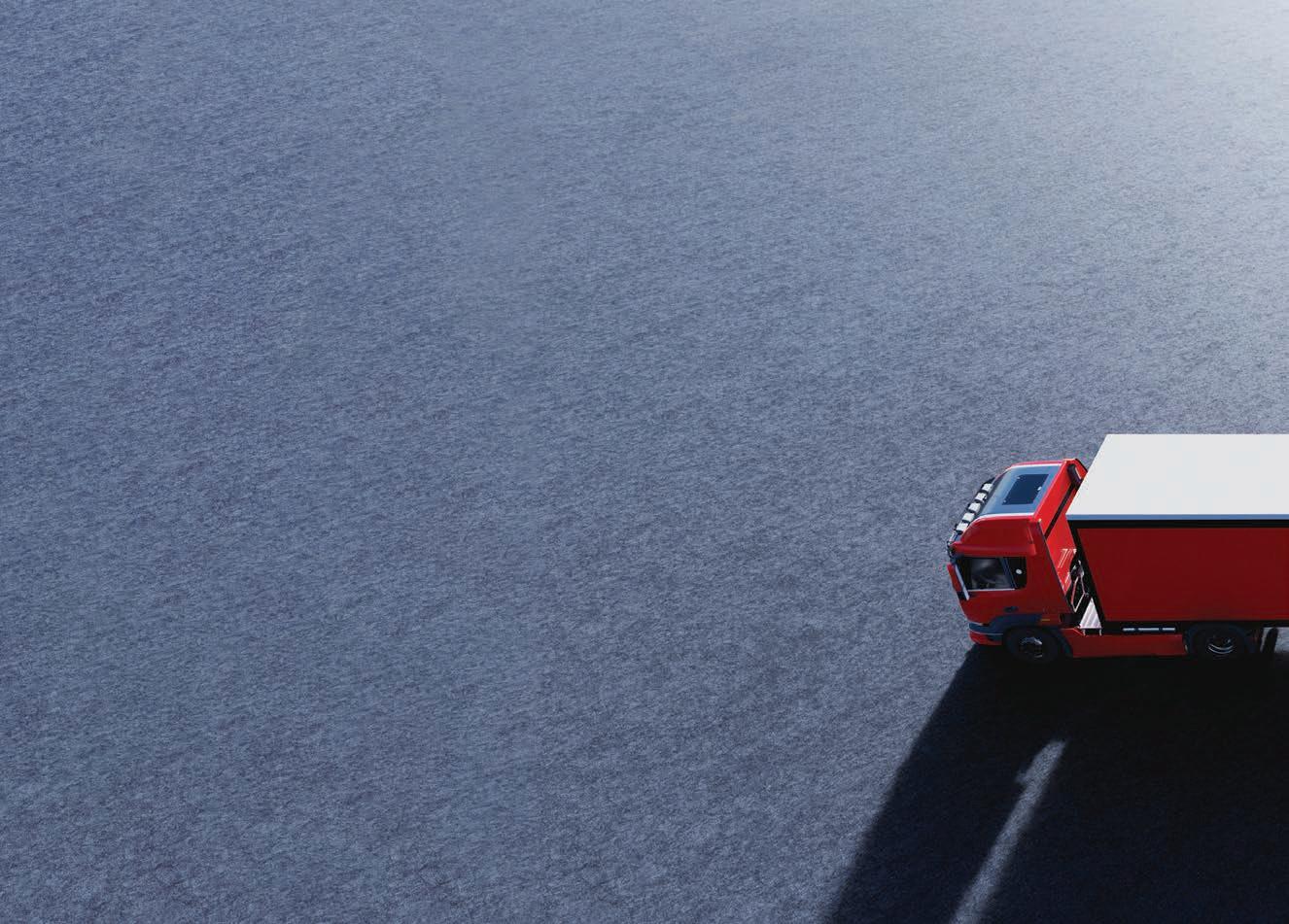
Celerity DRS General Manager, Andre Gerken, said this hasn’t been clearly communicated to the market.
“Not everyone in the industry has knowledge of the legislation and the resulting measures,” he said. “Our aim is to provide more information about the different solutions that are available.”
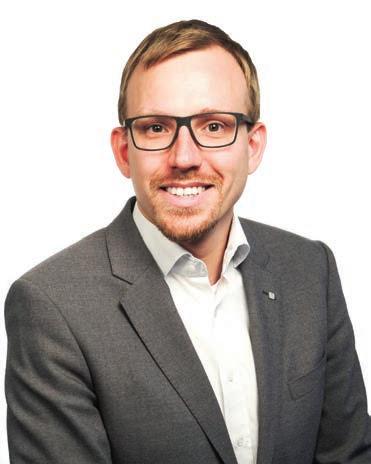
TPMS typically performs a function to evaluate inflation pressure of the tyre or the variation of inflation pressure over time and to transmit corresponding information to the heavy vehicle driver/user during operation.
In terms of functionality and performance, there are two types of TPMS, direct and indirect.
A direct TPMS is using an additional pressure sensor, installed inside the wheel or on
CELERITY DRS DETAILS WHAT FLEETS AND MANUFACTURERS NEED TO KNOW ABOUT THE ‘TPMS’ EUROPEAN REGULATION UN ECE R141.Celerity DRS General Manager, Andre Gerken.
the tyre valve, and an indirect TPMS is using the existing EBS/ABS sensors to determine the status of the tyre pressure. Currently, according to Gerken, there are no indirect TPMS options for commercial vehicle trailers available.
One of the key advantages of a TPMS is being informed immediately about a pressure change in the tyre. This allows the driver to adjust the optimum tyre pressure to reduce tyre wear and fuel consumption. “But a TPMS still requires a human intervention to ensure the right tyre pressure,” said Gerken.
The battery life of a TPMS sensor depends on the data transmission interval and the data size. The information provided by the TPMS manufacturer on the lifetime of sensors varies from up to three to 10 years. “The majority of available sensors cannot be recharged so far and need to be replaced, if the battery is empty,” he said. “Depending on the fleet size, this could be hundreds of sensors per year, which is not positive from an ecological point of view.”
For an optimal working TPMS, the radio performance of the individual sensors is important, particularly for special vehicles such as B tank trailers or in-loaders.
In these vehicles, the high amount of metal parts can disturb the communication, which could lead to connection failures.” Connectivity is also an important consideration.
“Certain TPMS allow an integration in existing telematic devices,” said Gerken. On one hand this helps to inform the Backoffice about the tyre status and it allows to register tyre issues and records when a tyre is below an accepted pressure.
On the other hand the driver can be held more responsible, if a damage occurs despite an in-built TPMS, because he was informed about a pressure loss in advance.
While the up-front investment into these systems is what has kept many fleets from adopting, fleets will find that the added costs result in an overall operating savings that provides a highly desirable return on investment.
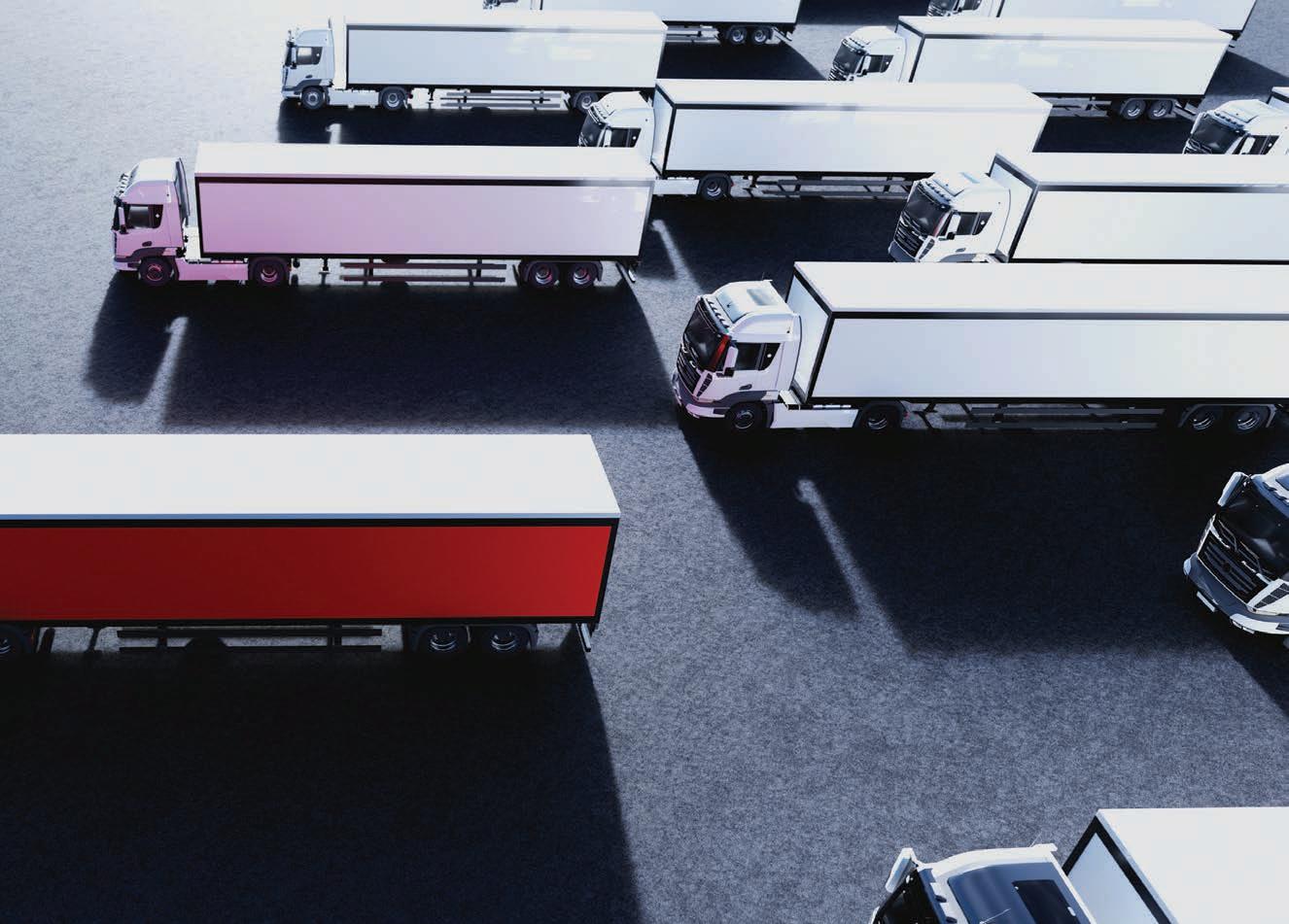
Here, the TPRS scores with low follow-up costs and the advantage that human intervention is reduced to a minimum. With a TPMS, if the driver does not respond to a warning, it can still cause a problem as the tire is not being re-inflated.”
“Due to the R141, fleets need to have a system installed, therefore I expect that they will choose the system which will bring them the most benefit,” said Gerken. “Maybe at the beginning the cheapest option will be chosen, but at the end the benefits are important.
TPRS presents an opportunity for fleets to invest in better road safety measures compared to TPMS.
“There are already several fleets that are convinced of the benefits of TPRS,” said Gerken. “We even have customers using both systems, combining the benefits of TPRS and TPMS.
For this reason, in addition to a standard TPRS-R141 solution, we are also working a stand-alone TPMS solution.”
Ultimately, whether it’s TPRS or TPMS, it is better than having no system installed.
“Active tyre pressure monitoring informs the driver and, if necessary, the fleet manager of a loss of pressure at the tyre,” said Gerken. “With this information, countermeasures can be initiated immediately i.e. to avoid a complete loss of the tyre and related failures. Without a system, it is almost impossible for a driver to detect a loss of tyre pressure while driving. This is also the reason why we regularly see vehicles with blow-outs parked on the side of the road. The early information can also reduce downtime. It is easier, faster and safer to repair/replace a tyre in a workshop than at a rest area or even at a hard shoulder. Every prevented blowout also helps to ensure that other road users are not hindered or even injured by tyre parts.”
So, what do manufacturers and fleets need to do right now to prepare for this regulation?
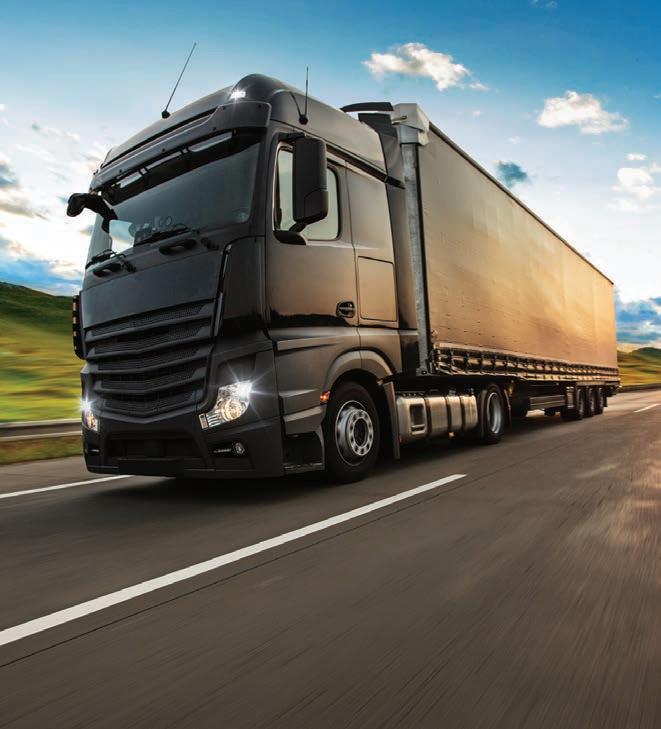
“Vehicle manufacturers should check to what extent TPRS and TPMS are already being used and how the production is prepared for it,” said Gerken. “Depending on the system, there are various installation and initial operation steps that have to take into account in the production process.
“In addition, it must be checked whether current orders are already affected by the R141. If the delivery of the vehicle falls after the date when the R141 goes into force, a system needs to be installed.
“I would recommend fleets that have not yet dealt with the topic of tyre control systems, to start with it. It makes sense to identify the right system in advance so that you don’t encounter any bad surprises afterwards.
“For manufacturers and fleets it’s important that all involved employees (production, sales, drivers, workshop managers) are trained upfront on how to use the system in order
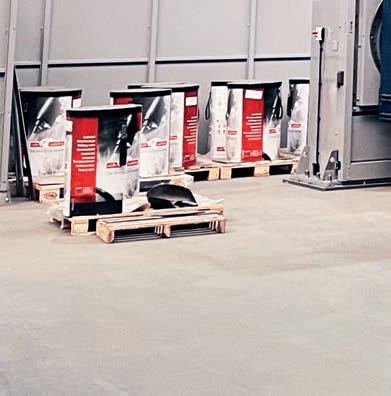
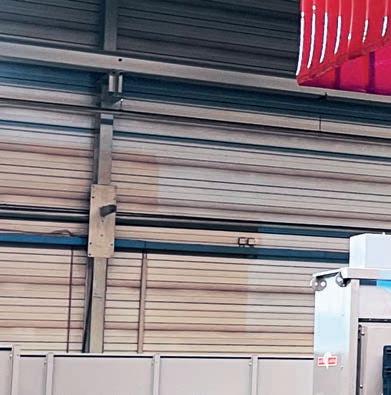
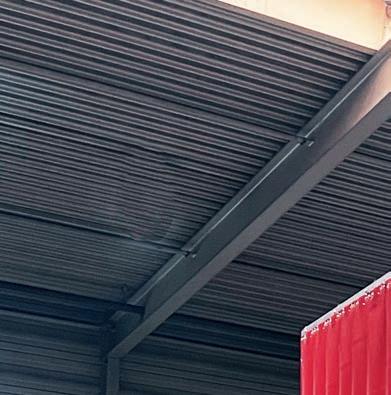
FAST FACTS
What is a TPMS?
A TPMS or Tyre Pressure Monitoring System is a system fitted on a vehicle, able to perform a function to evaluate the inflation pressure of the tyre or the variation of this inflation pressure over time and to transmit corresponding information to the user while the vehicle is in operation.
What is a TPRS?
A TPRS or Tyre Pressure Refill System is a system fitted on a vehicle, which can refill underinflated tyres fitted to an axle of the vehicle with air pressure from a vehicle mounted reservoir (infrastructure) while the vehicle is running but not limited to.
What to do when a leaking tyre is detected with TPMS?
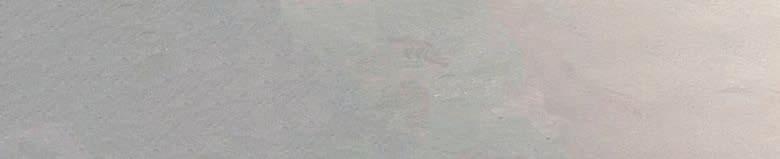
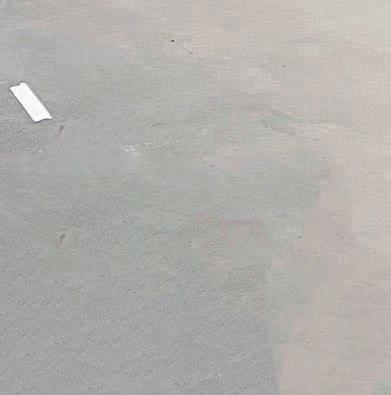
Find a suitable place to stop, check and refill the tyre. If required, reset the TPMS and see how the tyre responds. If the response is positive, the driver could continue their journey, keeping close attention to the refilled tyre. If the tyre is emptying too quickly (20 per cent less or lower versus the required tyre pressure), stop immediately and take the appropriate action (replacing the tyre or receiving help). Continuing the journey without taking the necessary action would be strongly advised against.
Why should I invest in a TPRS as opposed to a TPMS?
A TPRS will help you to maintain the correct tyre pressure whilst the vehicle is stationary or in transit. In case of a pressure loss in a tyre the system will automatically start refilling the tyre to the pre-set level and informs the driver accordingly. The human intervention is reduced to a minimum. Instead, a TPMS will only inform you about the pressure loss in a tyre. Without human intervention the vehicle will continue its journey with a wrong tyre pressure. The benefits of an TPRS against TPMS are higher uptime, longer tyre life and lower fuel consumption.
to ensure a smooth process.”
In terms of regulation compliance, there are some challenges ahead.
“The advantage for the vehicle manufacturer is that system providers can have their system pre tested from test authorities. The test reports ensure that the system meets the requirements of R141 and will ease the homologation process.”
www.celeritydrs.com
Valk Welding Group
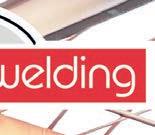
Tel. +31 78 69 170 11
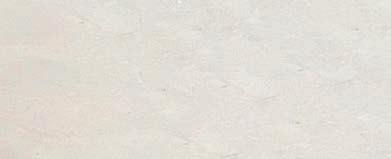
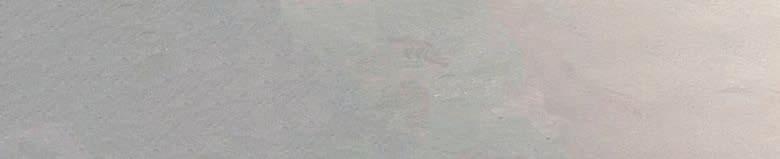

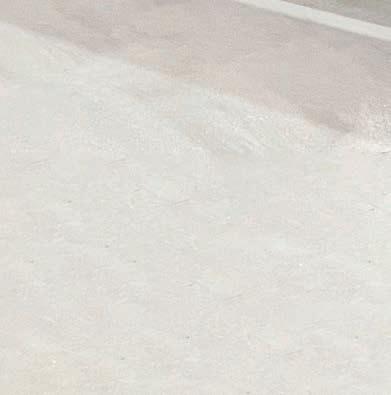
info@valkwelding.com
www.valkwelding.com
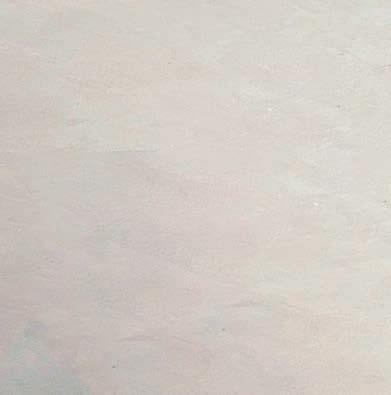
Automate your welding production with Valk Welding
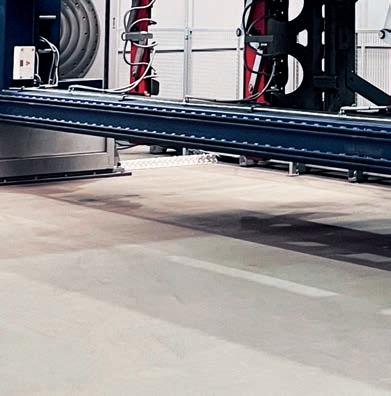
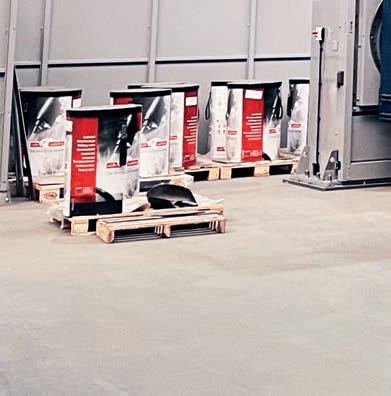
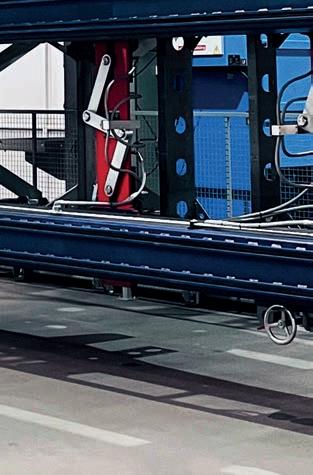
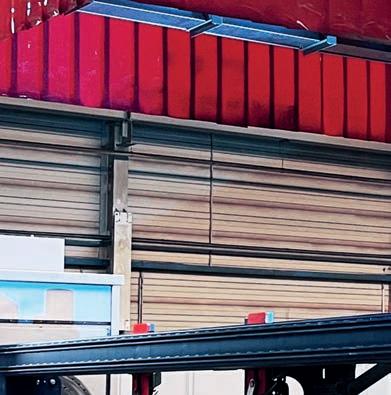
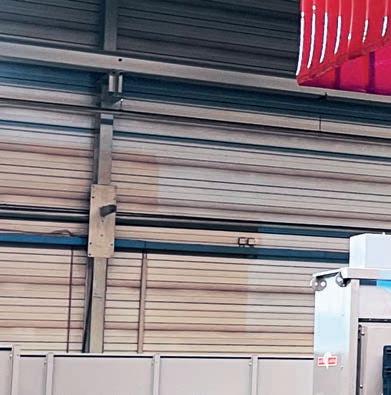
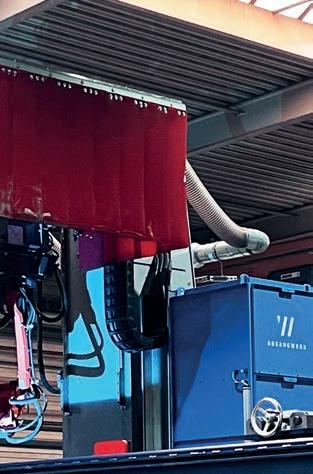

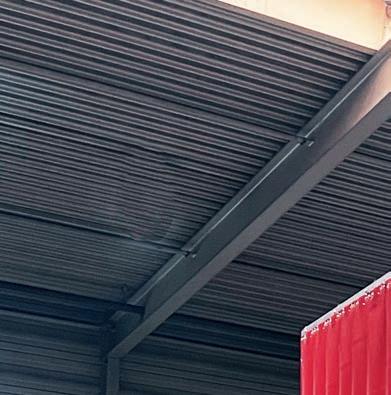
Valk Welding offers the automa�on solu�on that ensures your welding work is of the highest quality every day and your produc�vity is guaranteed all year round. The flexible welding robot systems of Valk Welding are designed for welding small parts to large construc�ons made of different materials, think of steel, thin-walled stainless steel and aluminum. Due to far-reaching technological developments, the welding robot systems are suitable for both large series and single piece produc�on. Thanks to the systems of Valk Welding, this is also within your reach. We supply a total package including so�ware, wear parts, welding wires, training and start-up support. One clear point of contact that will take care of everything for you: Valk Welding.
Please contact us or take a look at the various possibili�es on our website (www.valkwelding.com).

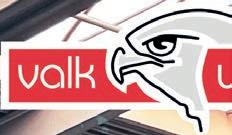
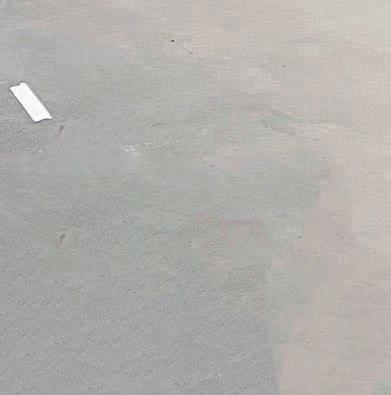

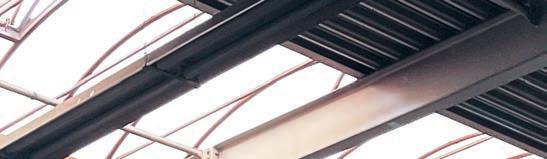
The strong connection
Watch our videos
STANDING THE TEST OF TIME
TMT TANKS & TRAILERS SPECIALISES IN INNOVATIVE PRODUCT DESIGN FOR A RANGE OF CLIENTS AND APPLICATIONS. IN RECENT TIMES, THE ITALIAN OEM HAS DEVELOPED AN ELECTRIC AXLE MOVING FLOOR SEMI-TRAILER, CONTAINER MOVING FLOOR AND IS WORKING ON A STEEL SEMI-TRAILER.
From a 75,000-square-metre facility in the centre of Italy, TMT Tanks & Trailers has capacity to build about 300 trailers per annum and is rapidly growing. The business has also bolstered its aftersales support with a network of workshops and sales personnel who are poised to serve quickly and efficiently.
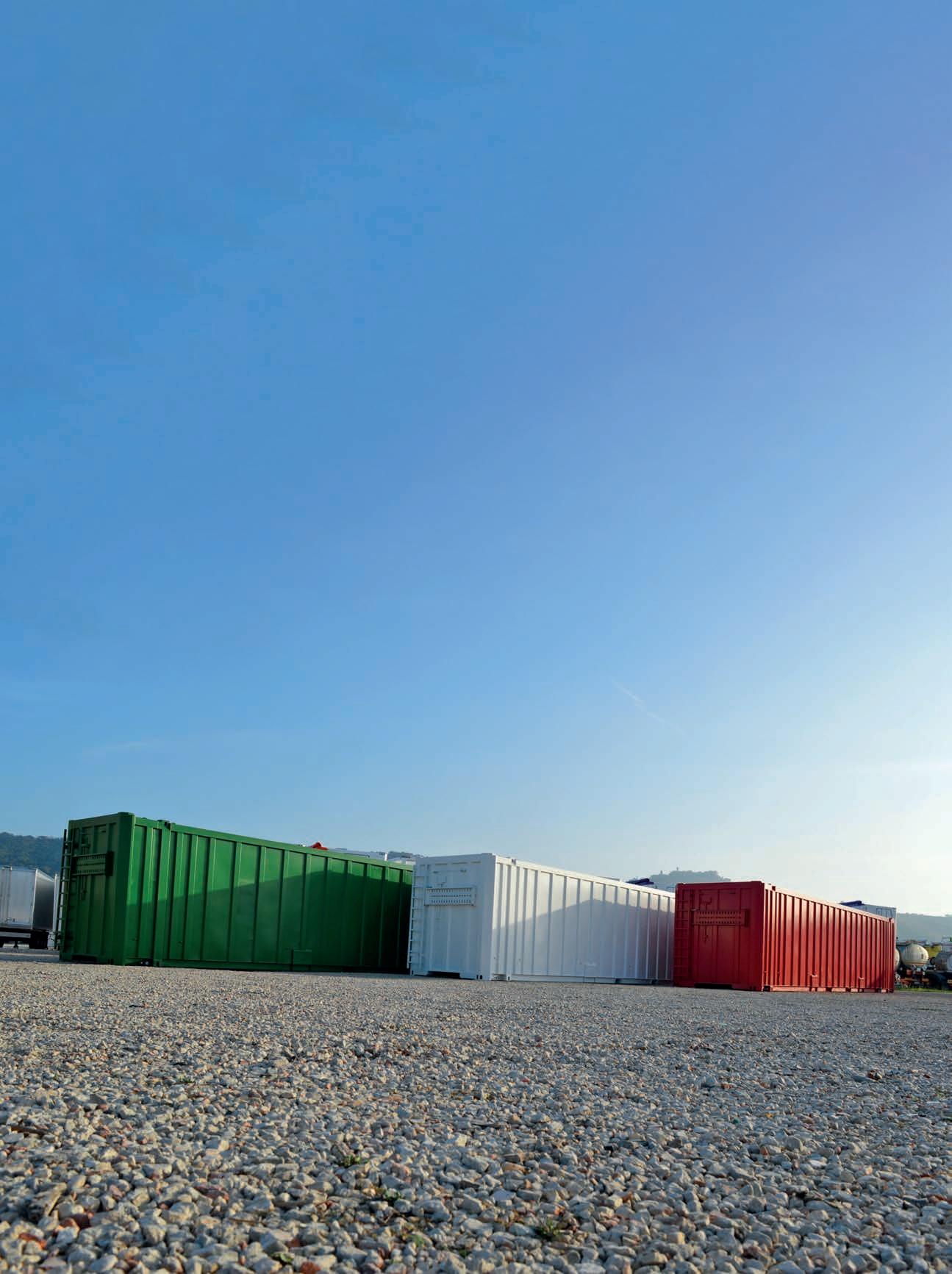
TMT predominantly services large European companies and is focused on increasing production and attracting new customers abroad with its innovative road transport equipment technologies.
“The Italian market is an established market and we now want to grow in the same way in Europe,” said Alfredo Spinozzi, CEO at TMT International. “The most complex step will be to become a major player outside Europe as well. We already sell in Australia and have developed an optimal kit to distribute our semi-trailers worldwide.”
TMT is particularly ineterested in expanding in the US and United Arab Emirates with the aim of increasing the value of ‘Made in Italy’ around the world.
At this year’s Transport Logistic event in Munich, Germany, TMT Tanks & Trailers showcased its ongoing development of intermodal solutions.
The OEM is proud to be the first Italian
company to win a Trailer Innovation award in the ‘body’ category.
The high cube and open top pallet Container Moving Floor trailer is a unique design and one of of TMT’s flagship products.
TMT has also produced an e-axle moving floor trailer.
“The aim of the product is to charge and discharge the moving-floor trailer via a battery connected to the axle,” said Spinozzi. “The axle will charge both when braking and in motion and is designed to give maximum utility to the driver. We are currently testing our prototype which you can see at the trade fairs we are attending. We are currently working on the battery part to lighten the weight and to have maximum performance for
loading and unloading goods. The main idea was to create an autonomous semi-trailer that could also perform while uncoupled from the truck.”
Product portfolio
TMT CONCHIGLIA is a multifunctional and efficient Moving Floor semi-trailer. Its selfsupporting frame is made of Strenx 700 steel, which guarantees robustness but at the same time lightness. It is a flexible vehicle suitable for almost all general cargo transports, from parcels to bulk materials with its load capacity of 92m3 and an internal usable length of 13,400mm. This model can be equipped with 6,300mm side doors, both left and right. From these openings, it is possible to load all types of panels, boxes, profiles and palletised material as well as bulk material in maximum certified safety.
TMT SCRIGNO features full-opening doors and sliding column with a clear advantage: high flexibility for the most diverse return loads,
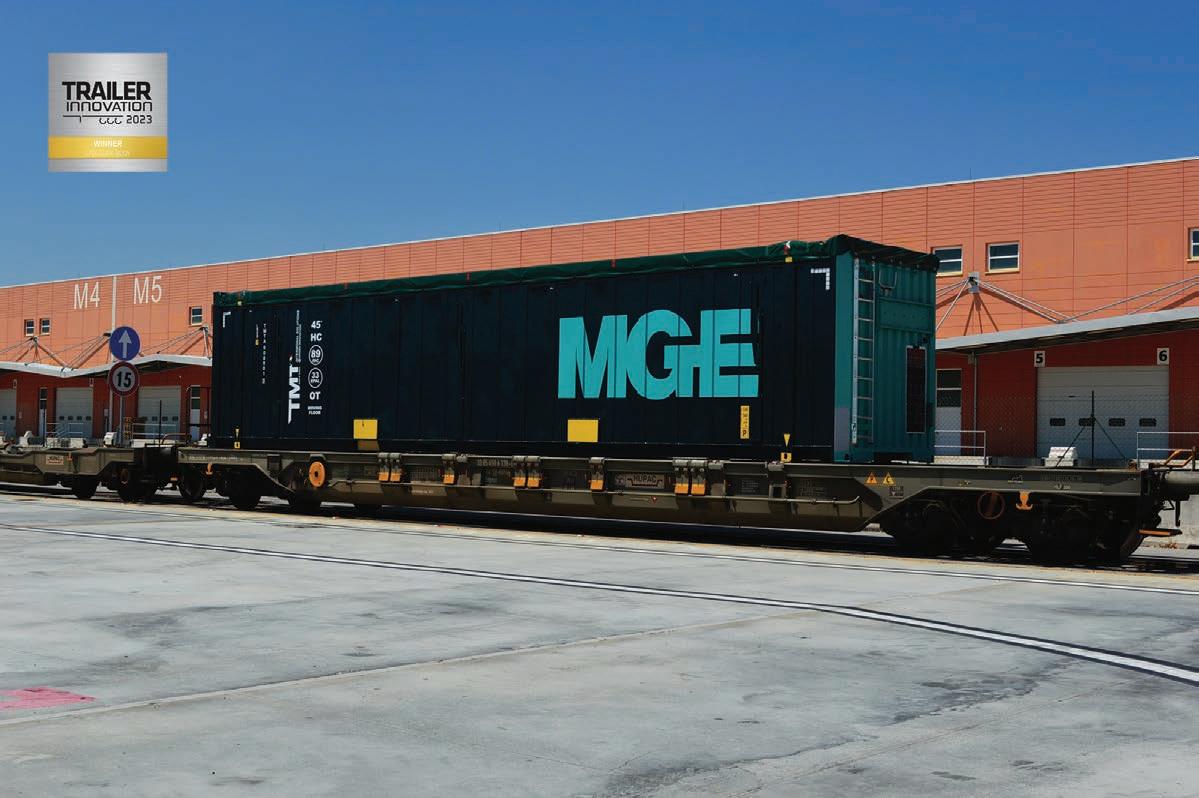
reduces the empty running rate and increases profitability. With a side loading width of the box semitrailer of 12,300mm and a continuous loading height from 2,540mm, long items can be stored without any problems. When opened individually, the folding doors allow partial unloading. Load securing is also optimised thanks to the DIN EN 12642 approval (code XL). As a result, almost all

general cargo transports are covered safely and efficiently.

TMT LEAKPROOF retains all liquid waste hermetically, being totally watertight. Thanks to pre-delivery tests, we can guarantee that 20,000 litres of water are perfectly sealed.
The 45’ High Cube TMT CONTAINER MF features an opening roof and automatic unloading moving floor technology. 45’ steel container; moving floor for road - sea - rail transport. Tare weight, thanks to the use of ultra-high strength steels, up to 7,100kg. The containers, guaranteed against corrosion for five years and able to work from -40° to + 80°, have been tested according to the stringent US standards for road - sea - rail transport.
The EcoFuturo scientific committee awarded TMT International, among more than 1,000 companies, for the technological innovation of its moving-floor container at the 2019 Ecomondo annual trade fair in Rimini. TMT Container Moving Floor also won Trailer Innovation Award 2023 “Body” Category.
TMT INTERMODAL MF is a specific semi-trailer designed for road-sea-rail travel. This is why it meets the standards of the transport white paper for journeys over 300km.
TMT believes in the values of environmental sustainability also with the products that are manufactured every year in the factory. Intermodal is an environmentally
FAST FACT
For TMT Tanks & Trailers, aftersales and support is a strategic asset. The OEM said: “From the very beginning we have always reasoned in such a way that the customer has a complete and quick service because we want to ensure that the customer gets the most out of our vehicles.”
sustainable form of transport that needs to be further developed for the future.
White certificates for energy efficiency can be applied for using these vehicles. White certificates are negotiable securities certifying the achievement of savings in energy end-use through energy efficiency measures and projects. One certificate is equivalent to saving one tonne of oil equivalent (TOE).
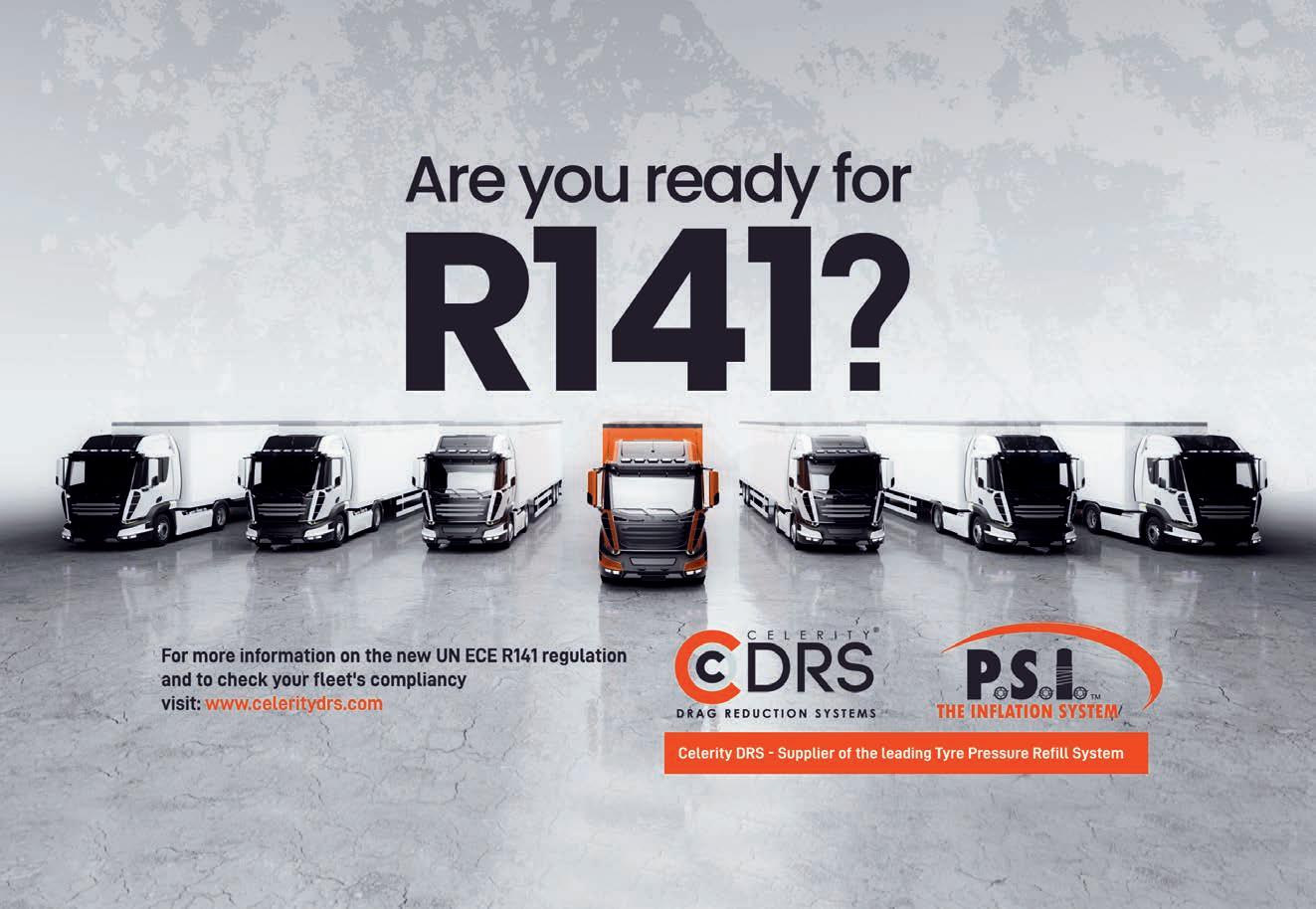
TMT CONTAINER CHASSIS is a special customised chassis, equipped with a wooden or skeleton floor, with corner blocks for transporting containers.
The container carrier has various approvals: ADR, AT, FL, OX, EXII, EXIII. The tare weight is 6,040kg, with a length of 12,160mm and a
“IN EUROPE, WE ARE TACKLING CLIMATE CHANGE WITH MAJOR REFORMS. OUR PRODUCTS ARE WHAT REFLECT THIS IDEA.”
Alfredo Spinozzi, TMT International CEO
FAST FACT
TMT Tank & Trailers was founded in 2014 and has been innovating ever since. In 2019, the manufacturer produced its first moving floor container trailers and has been critically acclaimed for technological innovation. Last year saw the Italian OEM develop a prototype trailer with a generator axle.
width of 2550mm.
TMT TANK is designed, built and equipped vehicles for the transport of: fuels for civil, military and aviation use; water for civil and military use; common waste; exhausted oils.
TMT is committed to helping fleets overcome industry-related challenges.
“We live in an ever-changing world in search of sustainability,” said Del Sordo. “In Europe, we are tackling climate change with major reforms. Our products are what reflect this idea. They are intermodal, for rail, sea and road. They are
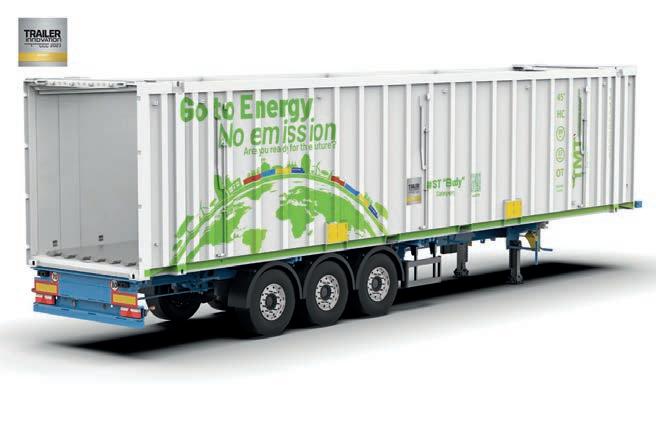
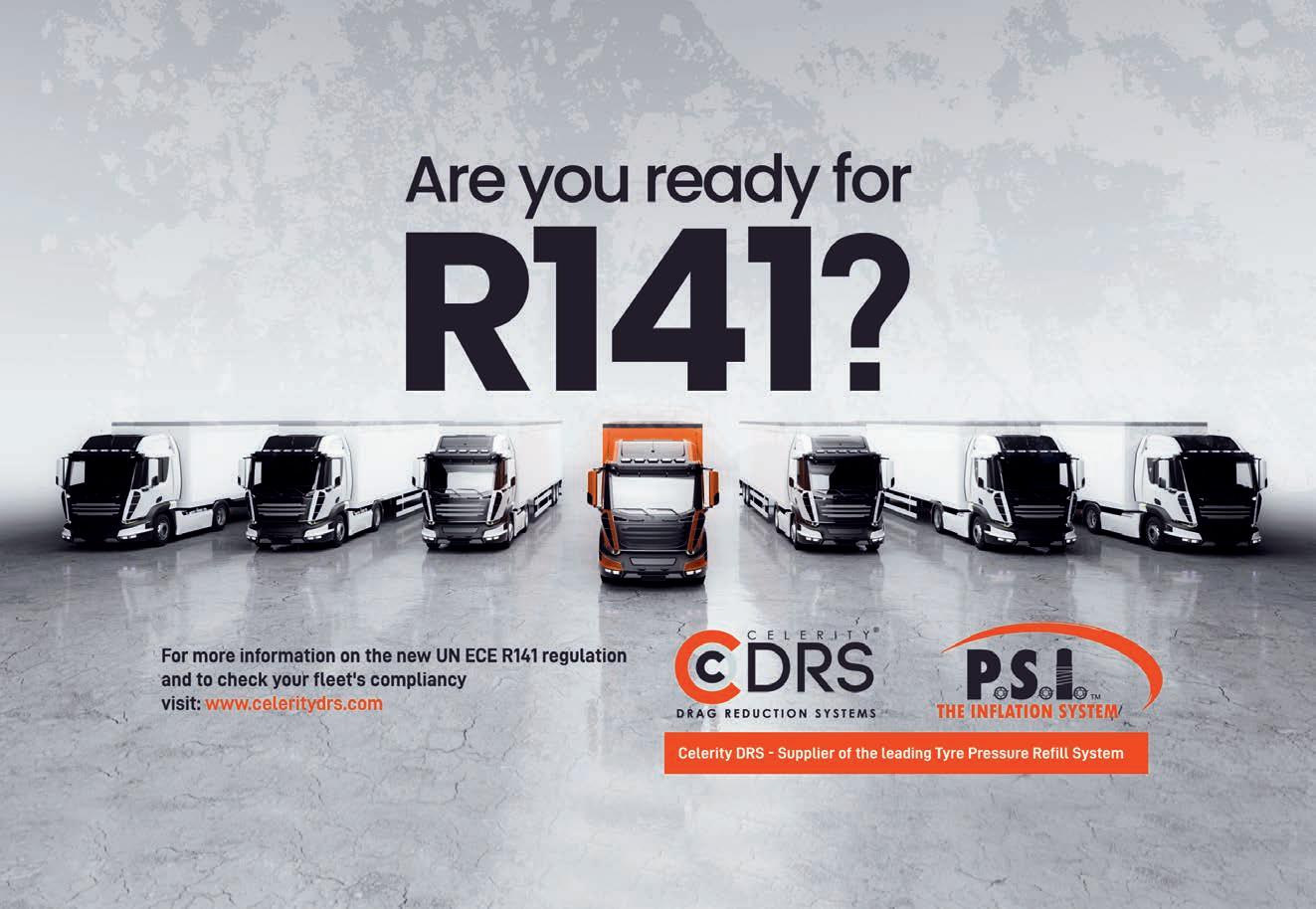
zero impact on the environment despite the technology. They support the practices of transport companies that use green practices. These for us are the challenges that the industries will face in the coming years, so we want to be there for them.”
www.tmtinternational.it
WATERRESISTANT
TRAILER BODIES WITH CGS
THE EFFICIENT AND RELIABLE TRANSPORTATION OF TEMPERATURE-SENSITIVE GOODS REQUIRES QUALITY TRAILER DESIGN WHICH IS A SPECIALITY OF COLDSTORES GROUP OF SAUDI ARABIA.
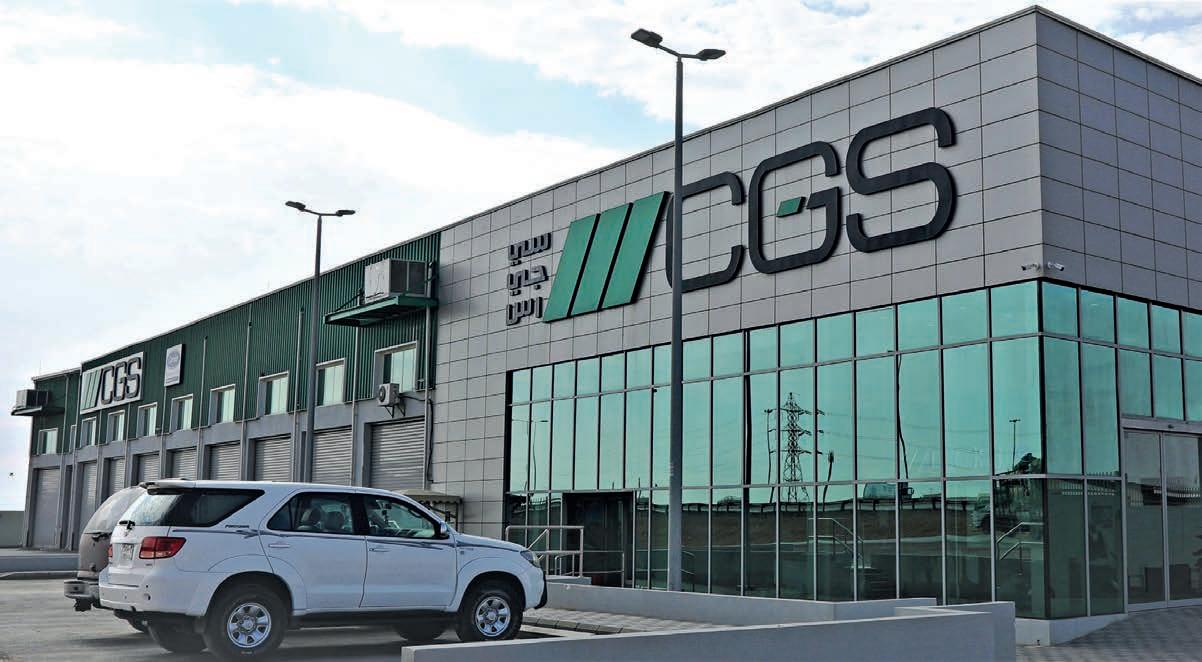
Refrigerated bodies are used in a wide range of industries. These bodies are designed to maintain a constant temperature which is critical for preserving the freshness and safety of food and pharmaceutical products. Vapour tightness of such bodies is essential to keep operating costs to a minimum. Water penetrating the body will result in higher service frequency for cooling units, increase the risk of cooling unit breakdowns (with a chance to spoil the loaded goods), reduced payload due to “heavy” water replacing “light” foam and increase the operational life time of the body. To achieve vapour tightness, bodies are constructed using a variety of carefully selected materials and components.
One of the critical components of a waterproof refrigerated box, according to Coldstores Group of Saudi Arabia (CGS), is its assembly by gluing. This process involves bonding the different parts of the box together using an adhesive. The glue creates a watertight seal that prevents water from entering the box and damaging the contents. The glue used for this purpose is specially formulated to withstand extreme temperatures and humidity levels, ensuring that it maintains its strength and integrity over time. Glue plays also a key part in
structural integrity of a body.
Waterproof rivets are another important component of a waterproof refrigerated box. These small metal fasteners are designed to secure the different parts of the box together. They are usually made from stainless steel and are specially designed to resist water penetration when the body is washed out. Waterproof rivets ensure that the insulation material remains in an optimal condition and can withstand harsh conditions, such as exposure to saltwater or extreme temperatures.
Metal skins are another important component of a waterproof refrigerated box. They are used to provide strength and durability to the box, making it capable of withstanding harsh conditions. The metal skins used for this purpose are typically coated with a layer of paint and protective material to prevent rust and corrosion. Metal skins are especially important for refrigerated boxes that are used in outdoor environments, as they provide protection against weathering and other external factors. They are also more impact resistant than other skin materials.
Rubber seals for door leaves are also an essential component of a waterproof refrigerated box. These seals are designed to create a watertight seal around the door of the box, ensuring that water cannot enter the interior. The rubber used for these seals is specially formulated to withstand extreme temperatures and humidity levels, ensuring that it remains flexible and does not crack or break over time.
A thermal barrier around the doors is typically achieved by using a combination of insulation material and wood. Without a thermal barrier, condensation can cause damage to the loaded goods. The barrier is installed between the steel skins of the box and the interior liner and is typically glued or sealed in place to prevent any air or moisture from entering the cavity. When installed, a GRP strip creates an additional barrier that helps to prevent condensation. The strip acts as an additional layer of insulation around the doors, reducing the amount of heat that can penetrate the body structure.
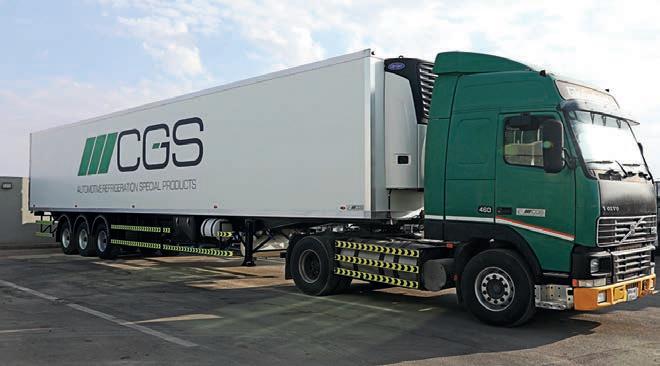
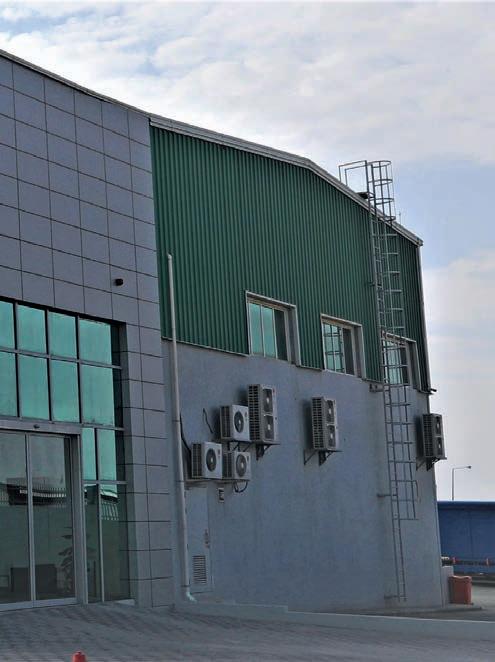
Finally, the GRP floor is another component of a waterproof refrigerated box. GRP stands for Glass Reinforced Plastic, and it is a type of composite material. It is not as strong as other floor types but cost effective for floor applications A GRP floor is designed to withstand loading by forklifts and resists water penetration, ensuring water cannot reduce the life expectancy of the floor structure (wood can rot away) and that the floor remains in good condition.
In conclusion, a waterproof refrigerated box is a crucial piece of equipment for many industries. Its components, including its assembly by gluing, water-proof rivets, steel skins, rubber seals for door leaves, and GRP floor, are all carefully designed to provide strength, durability and protection against water penetration and therefore reduce total cost of ownership. When purchasing a waterproof refrigerated box, it is essential that all of these
components are of the highest quality to ensure that the box is capable of withstanding harsh conditions and keeping its contents safe and fresh.
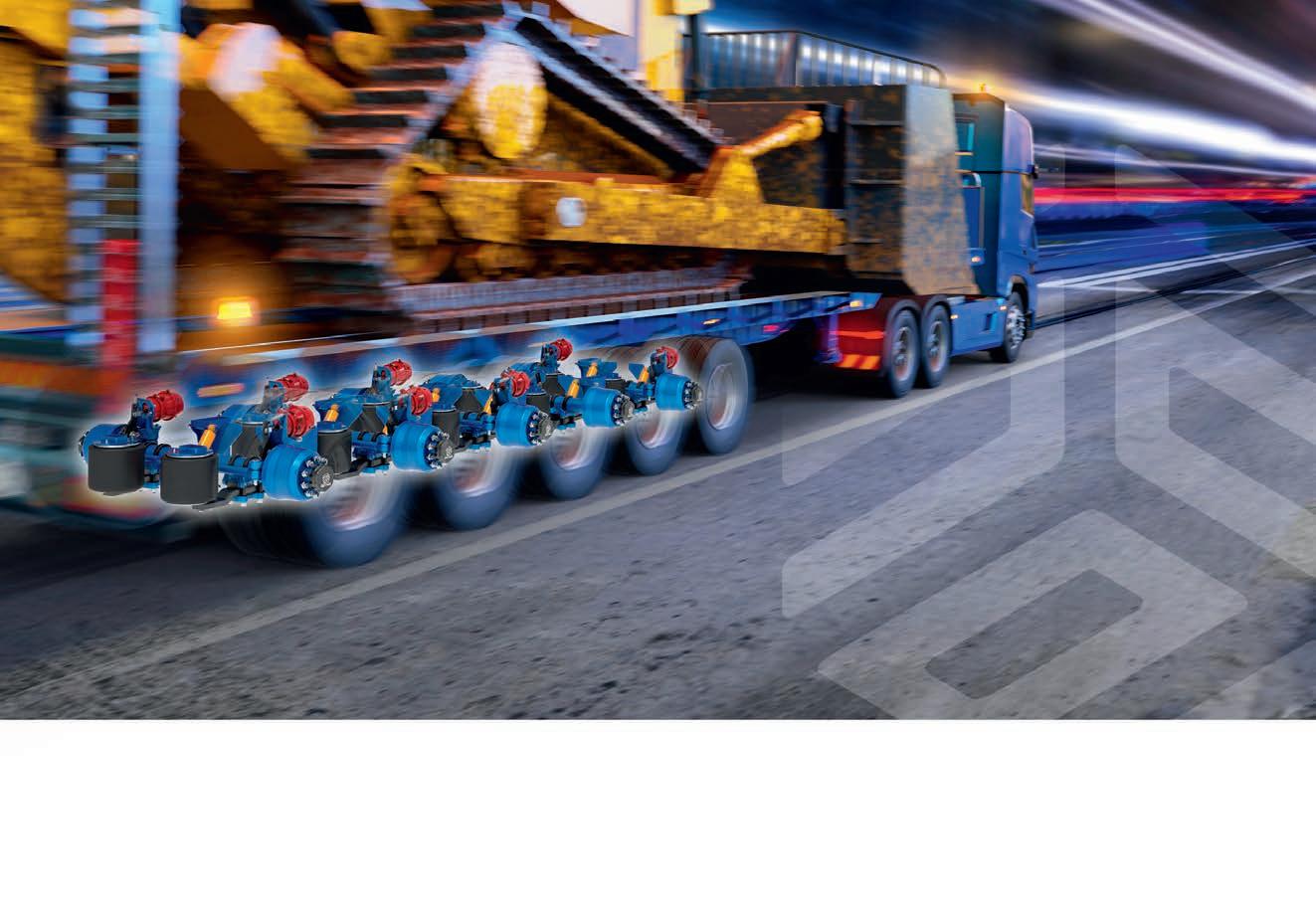
CGS is using state-of-the art design and production technologies and processes to enhance the quality and performance of its products. Material characteristics and physical laws guide CGS in the appropriate material selection for its products to optimise total cost over life time. To reduce production timeframes and deliver quality products, CGS relies on modern fabrication processes like robot welding.
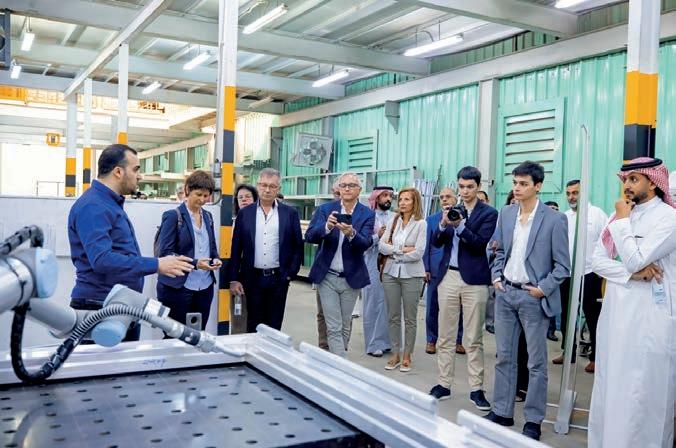
1. Speed and efficiency. Robot welding is much faster than manual welding since robots can perform welding tasks continuously without the need for breaks or fatigue. This can significantly increase production speed, which can be especially beneficial for companies that need to produce large volumes of welded products quickly. The speed of robot welding can also help businesses to meet tight deadlines and respond quickly to changes in demand.
2. Precision and consistency. Robots can be programmed to perform welding tasks with a high degree of accuracy and consistency. This is because they can precisely control the speed, angle, and position of the welding tool, resulting in consistent and high-quality welds. In contrast, manual welding can be prone to inconsistencies, which can lead to defects, rework and a decrease in product quality.
3. Safety. Robot welding can improve safety in the workplace by reducing the need for manual welding, which can be a hazardous job. Robots can perform welding tasks in hazardous environments, such as high heat, toxic fumes, and confined spaces, without putting human workers at risk. This can help to reduce workplace accidents and injuries.
4. Cost savings. Although the initial cost of implementing robot welding can be high, it can result in significant cost savings in the long run. Robot welding can reduce labour costs by decreasing the number of workers needed to perform welding tasks. It can also improve product quality and reduce the need for rework, which can result in cost savings related to material waste and labour hours.
5. Flexibility. Robots can be programmed to perform different welding tasks and switch between them quickly, making them highly flexible in a production process. This can be especially beneficial for companies that need to produce a variety of products or adapt to changes in demand. Additionally, robots can be easily reprogrammed to perform different tasks as production needs change, providing even more flexibility.
CGS also uses 3D scanners for reverse engineering and software to build complex geometries while boosting production time. A 3D scanner typically captures the shape and surface geometry of an object by projecting light or lasers onto it and recording the reflections. The resulting data is a point cloud or a mesh of triangles, which can then be converted into a 3D model using specialised software. By using a 3D scanner to capture the geometry of a physical object, it is possible to create a digital model of the object that can be used for reverse engineering purposes. The digital model can be modified and refined to create a new product or to improve an existing one. This can be particularly useful in industries such as automotive, aerospace, and consumer goods, where reverse engineering can be used to create replacement parts, improve product performance, or reduce manufacturing costs.
The OEM is also using the latest Finite Element Analysis (FEA) software for design validation of its products according to internal standards.
1. Cost-effective. FEA can be much more costeffective than physical testing. It is much faster to run simulations using FEA than to build

prototypes and test them in the real world. This can save companies a lot of money and time in the design process.
2. Accuracy. FEA can provide accurate predictions of how a design will behave under various loading conditions. By analysing the behaviour of individual elements within the design, FEA can provide a detailed picture of how the entire system will perform.
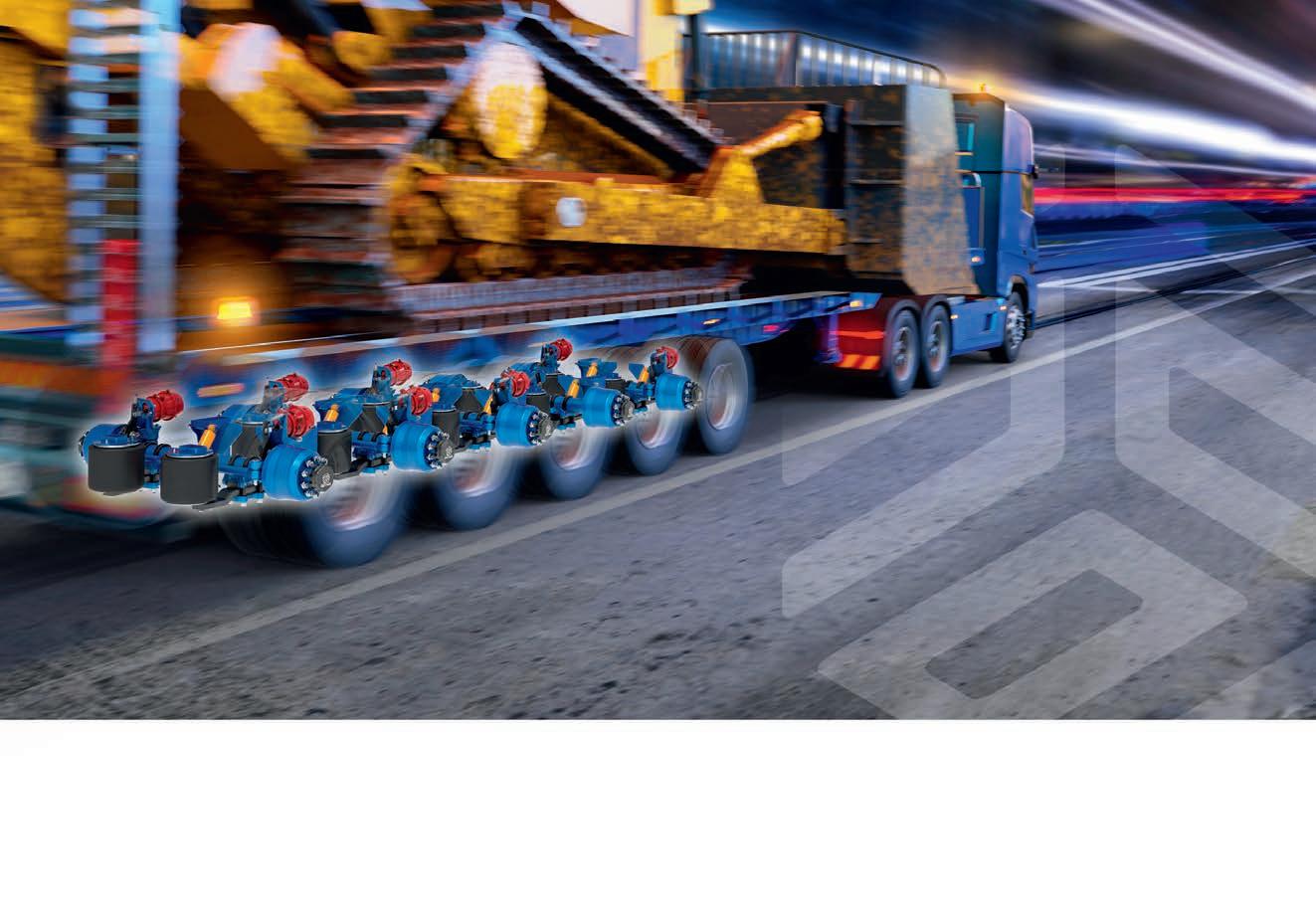
3. Optimisation. FEA can help engineers optimise their designs. By running simulations with different parameters, engineers can identify the optimal design for a given set of requirements.
4. Flexibility. FEA allows engineers to test a wide range of scenarios and loading conditions. This makes it possible to identify potential failure points in the design and make changes before the design is built.
5. Risk reduction. FEA can help reduce the risk of design failure. By analysing the design in detail, engineers can identify potential weaknesses and make changes to strengthen the design.
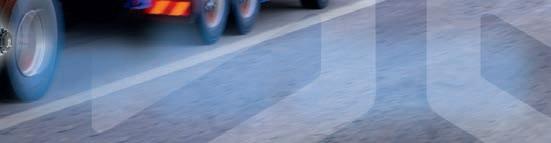
CGS has developed customised structural testing
jigs to validate different design aspects before commencing production. Customised testing jigs are crucial for structural testing of products because they enable precise, repeatable and consistent testing of a product’s structural integrity. These jigs are designed specifically to simulate the forces that the product may encounter during its expected use so that the theoretical calculations can be verified in a real life environment.
Here are some of the key reasons why customised testing jigs are so important for structural testing of products:
1. Consistency. Customised testing jigs ensure consistent testing conditions, which is critical for producing reliable test results. By holding the product in place in a consistent manner, the testing jig eliminates variability in the testing process that could affect the results.
2. Accuracy. Customised testing jigs enable precise testing of a product’s structural integrity by simulating the forces that the product may encounter during its expected use. This enables manufacturers to identify any weak points in the product’s design and make necessary improvements.
3. Efficiency. Customised testing jigs can be designed to allow for high throughput testing, enabling manufacturers to quickly and efficiently test large quantities of products. This can be particularly important for manufacturers that produce products in high volumes.
4. Safety: Customised testing jigs can help ensure that products are safe for consumers to use by identifying any potential structural issues before the products are released to the market.
5. Cost-effectiveness: Customised testing jigs can help manufacturers save money by reducing the need for expensive prototype testing or product recalls due to structural issues.
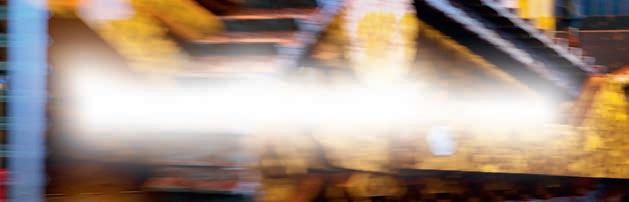
www.cgs.com.sa
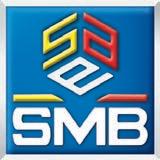
COMBINED TRANSPORT THE PERKS OF
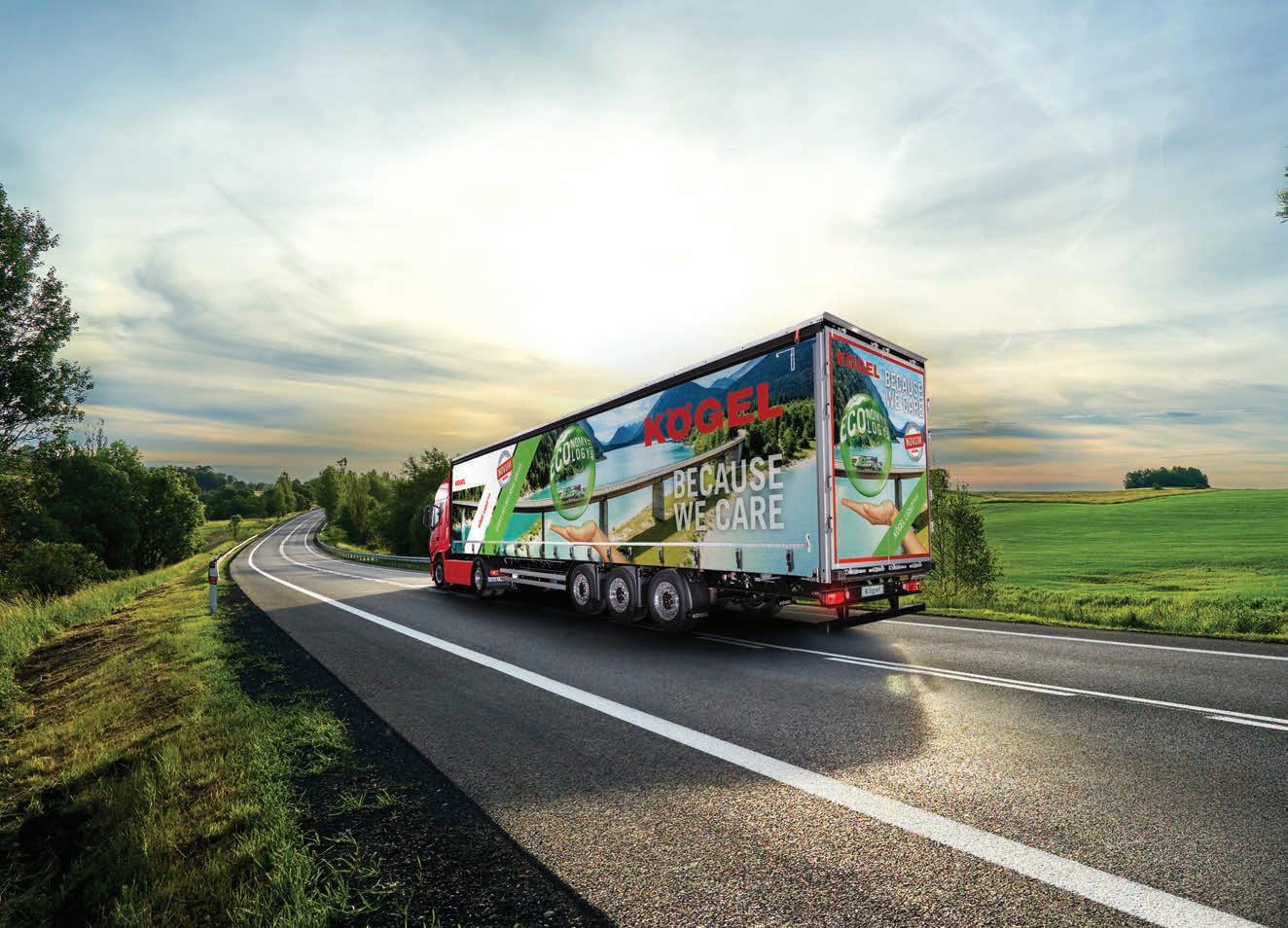
AN INTERMODAL INNOVATION AT KÖGEL HERALDS THE BEGINNING OF A NEW ERA FOR THE AMBITIOUS TRAILER BUILDER.
With a train loading at the combined transport terminal in Munich-Riem, Kögel has successfully demonstrated that the extended semi-trailer (long truck type 1) can also be transferred to all common pocket wagons in the latest generation with a length of 15 metres.
The latest generation of the Kögel EuroTrailer Cargo Rail (long truck type 1) that can be loaded on trains, with a total train length of 17.88 metres, can also be loaded onto all standard pocket wagons in accordance with the relevant regulations. This applies to variants with body heights of 3,950mm (rail code P395) and 4,000mm (P400) or clear interior heights of 2,710mm and 2,760mm as well as folding underride protection. Kögel proved this during a test loading at the combined transport terminal in Munich-Riem. There, under the supervision of representatives of Deutsche Bahn, the EuroTrailer Cargo Rail was
transferred to a type T3000 wagon with a support frame height of 980mm. This means that the EuroTrailer Cargo Rail can be used in conjunction with all modern pocket wagons (c, e, f, h, i).
The latest generation of the Kögel EuroTrailer is 1.38 metres longer than a standard semitrailer and is therefore eight centimetres longer than the previous generation. The addition became possible with the validity of the 9th Amendment Ordinance to the Ordinance on Exceptions to Road Traffic Regulations for Oversized Vehicles and Vehicle Combinations. Codification ensures that the trailer will fit within the envelope of each wagon and is identified with compatibility codes on the code number plate affixed to the body sidewall. As a result, the EuroTrailer not only optimises CO2 emissions on the road by around 10 per cent compared to a conventional articulated lorry, but can also be used in environmentally friendly combined road-rail transport without any problems. Due to its high level of practicality, the extended semi-trailer is suitable for around half of all transports, in contrast to the 25.25-metrelong trucks of types 2 and 3, making it an extremely effective and immediately available tool in the fight against climate change. Kögel therefore advocates unlimited approval of the Type 1 long truck, as has already been decided for Types 2 and 3, and appeals to Federal Transport Minister Volker Wissing (FDP) to take the necessary steps.
In addition to this latest innovation, Kögel CEO, Christian Renners, shares more details in an exclusive interview with Global Trailer
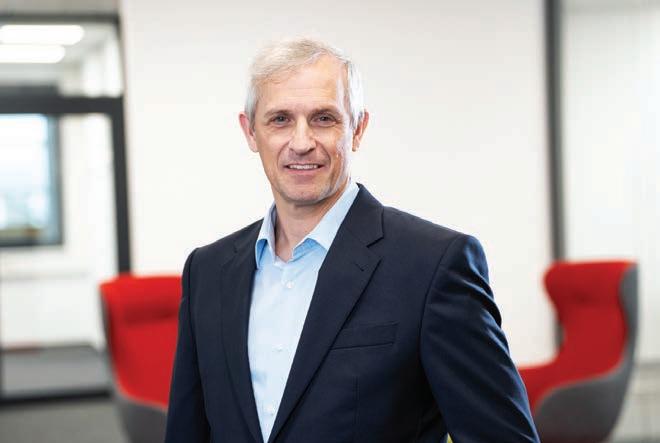
Q: What has business been like over the past 12 months? Are there any highlights or milestone achievements you would like to mention?
A: The last 12 months have been marked by extreme market volatility and the crises we are currently facing in Europe but also worldwide. Of course, we are still under the impact and shock of the Ukraine crisis. It is important to know that Kögel is traditionally strong in the Eastern European markets. With the loss of the Russian market, we had to focus on other markets. So far, we have been successful in this. This has enabled us to concentrate our sales activities primarily on Central and Southern Europe. Italy, in particular, is a market that we have built up very successfully. But we have also repositioned ourselves in the Baltic States and in the Alpine countries with our own organisation and strong partners.
Q: Any updates to facility capabilities, new investments, technologies?
A: We invest sustainably in the future of our company. And that’s what our shareholder Ulrich Humbaur is strongly emphasising by the way. In addition to building new facilities, we renovate
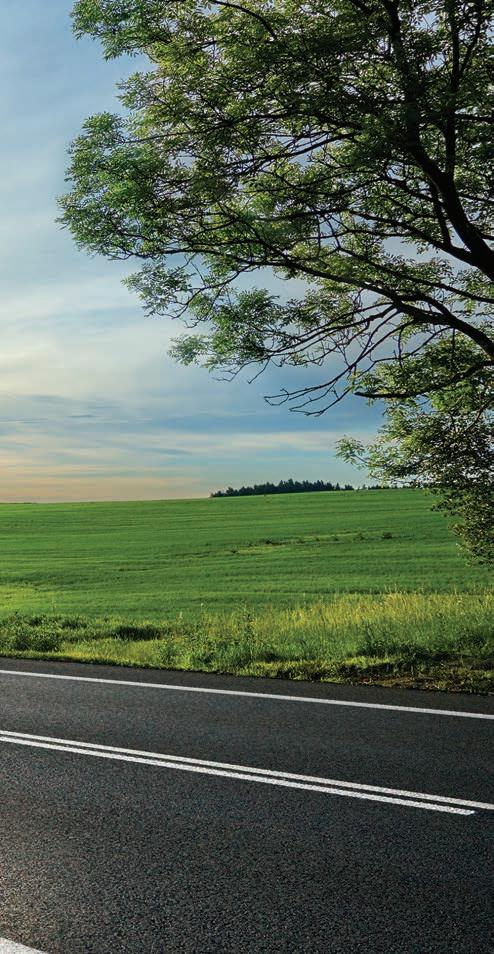
old buildings. For example, we have recently invested in a completely new workshop hall on our premises in Burtenbach, Bavaria. In addition, there is a new training workshop, a photovoltaic system on the roof of the production facility and other investments in the future of Kögel that I do not want to reveal at this time. We have also invested heavily in our chassis production in Chocen, Czech Republic. Personnel was hired there, processes were streamlined and equipment was renewed. From this perspective, one can say: Kögel is optimally equipped for the future.
Q: How large is your aftersales network currently?
A: We currently have a Europe-wide service network of around 1,000 partners – 500 of which are located in Germany. In addition, there are also cooperation agreements with Mercedes TruckWorks, MAN Complete and Scania Deutschland. Depending on the degree of specialisation of our service partners, all trailer-related services are offered from inspections to brake repairs. The services offered by the individual service partners can be found on our website via service partner search.
Q: What was the feedback like for the ‘All Round’ concept at last year’s IAA Transportation? Are you seeing further uptake of telematics, full-service contracts and trading of used trailers?
A: The points you mentioned are exactly the business areas in which we want to grow in near future. The digitalisation and networking of our trailers will also have a significant influence on the business of our customers throughout Europe. That is why it is extremely important to define service as cost transparency and plannability. Intelligent trailer telematics, an analysis of life cycle costs and needs-based repair and maintenance contracts over the entire life of the product are indispensable.
Q: How is Kögel tracking with its quest to deliver sustainable transport solutions to give freight carriers that competitive edge and minimise their carbon footprint?
A: All sectors will change in the next five to 10 years in the direction of increased sustainability and economic efficiency; the energy crisis is already forcing us to do so. The transport industry must and will also become more sustainable. For us at Kögel, this means changing framework conditions, market requirements and customer needs. We respond to market challenges with
innovation. It is in our DNA. Our company motto is ‘Economy meets Ecology – Because we care’. This means directly addressing and supporting customers as well as focusing on later benefits already during planning and development. We focus on weight reduction, TCO, digitalisation and electromobility. The expansion of multimodality is a Kögel speciality –hardly anyone can hold a candle to our experience and expertise. We serve the compatibility with transport requirements in road and rail transport with the first lightweight semi-trailer for combined transport.
Q: For 2023, what is your strategic focus?
A: We need to sharpen the Kögel profile even more. Intermodality, lightweight construction and efficient transport solutions are our core values and will play an important role in the logistics of tomorrow. Every customer in Europe and beyond should know what Kögel stands for.
Q: Is there a specific emerging trend that you are following closely?
A: In the field of energy-consuming temperaturecontrolled transport, we are working on solutions for CO2-free power supply. In this way, we make a significant contribution to reducing the ecological footprint of our customers. Kögel unveiled a CO2free eCool refrigerated trailer last year at the IAA. During fully electric operation, the refrigeration unit requires no conventional fuel and does not emit any pollutants or CO2. Depending on the use of the trailer, the overall consumption of the semi-trailer combination can be reduced by two to three litres of diesel per 100 kilometres. This also means lower operating costs. Further benefits of the system include lower noise emissions and wear. As a result, the Kögel eCool is also suitable for night-time deliveries in inner cities and opens up additional business models and greater freedom in vehicle scheduling. In addition, the significantly quieter all-electric system ensures greater comfort and does not disturb the sleep of truck drivers at the rest area.
Q: We’re seeing an increase in demand for intermodal equipment and collaboration across all modes of transport in the supply chain. Do you have any comments to share about this trend?
A: The intermodality of freight transport is crucial for the continued existence of European transport. Transport routes are congested and long intracontinental road freight transports do not fit

the goal of low-emission logistics. That is why I am all the more pleased to be working in a company that has a long tradition in the field of intermodal transport. We are already noticing that the demand is growing here. This is a very positive development that I personally welcome.
Q: Did Kögel encounter any new technical or compliance challenges with the design and build of this new trailer?
A: Our light is the new strong: The Kögel Lightplus Rail was presented as our Highlight at the IAA Transportation last year. It is the first lightweight trailer for combined transport. Despite the added payload of almost a ton, customers need not compromise on either functionality or handling. The Kögel Lightplus Rail offers a weight advantage of up to a ton compared with comparable standard versions, and thus combines the economic and ecological benefits of lightweight trailers using environmentally friendly rail transport.
Q: How complicated was the task to design a trailer for precise intermodal use? Any recent feedback from the trials?
A: It seems like squaring the circle to combine stability and lightweight. Kögel developers fundamentally revised the frame of the Kögel Cargo Rail and based the design on lightweight trailers from the Lightplus series. They succeeded in reducing the tare weight of
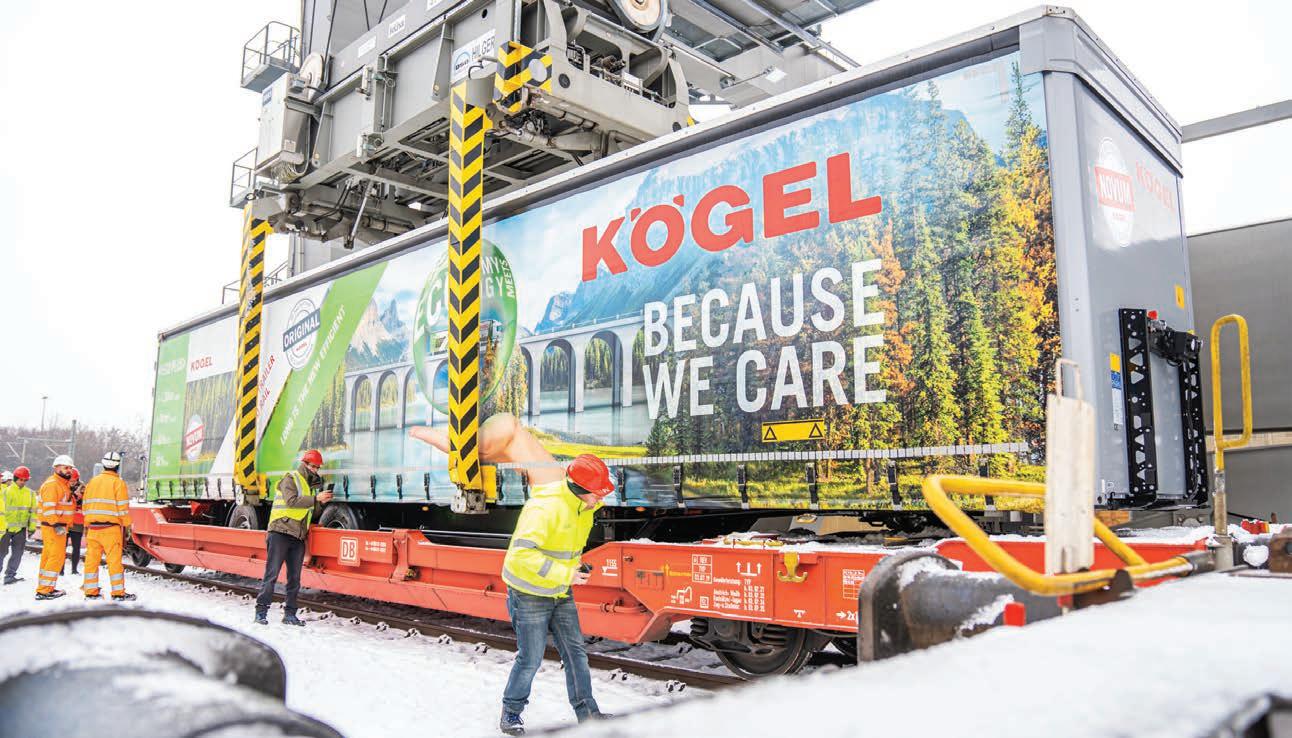
the trailer significantly while retaining the same high load-bearing capacity by using high-strength steels, in particular, which provided the opportunity to reduce material thicknesses specifically.
Q: What is the sales potential of the Kögel Cargo Rail Euro Trailer?
A: The latest generation of the Kögel Euro Trailer measures 1.38 metres longer than a standard semi-trailer, eight centimetres more than the previous generation. The addition was made possible by the implementation of the 9th amendment to the Regulations on Exemptions from Road Traffic Law Provisions in Germany governing Overlength Vehicles and Vehicle Combinations. The codification ensures that the trailer fits into the swept envelope of the wagon and is identified with compatibility codes on the code number sign applied to the side wall of the body. This means that the Euro Trailer is proven not only to optimise CO2 emissions on the road by approximately ten percent compared with a conventional semi-trailer combination but can also be used without any problems in environmentally friendly combined road and rail transport. Thanks to its highly practical design, the extended semi-trailer is ideal for roughly half of all transport operations, in contrast to the 25.25-metre type 2 and 3 longer trucks.
Q: Are there other trailer designs or products we should mention?
A: Lots of them! For example, we can’t forget our container chassis, or our tipper trailer for construction. These are important segments that will continue to play a bigger role in the European markets in the future.
Q: Trade shows have proven to be as popular. Would you like to discuss any upcoming exhibitions and trailer displays?
A: We will talk to our customers in many of our core markets – in direct dialogue. Where we are present in associations or at trade fairs, we are in contact. The IAA Transportation in Hanover remains the most important trade fair for us, but the smaller trade fairs have also gained in quality. For example, Nufam in Karlsruhe and Solutrans in Lyon are important industry meetings for us at Kögel.
www.koegel.com
DECARBONISING THE COLD CHAIN WITH e TRU s
AS THE WORLD GRAPPLES WITH THE CHALLENGES OF CLIMATE CHANGE, THE TRANSPORTATION SECTOR HAS EMERGED AS A KEY BATTLEGROUND IN THE FIGHT AGAINST CARBON EMISSIONS.
Among the most important sectors within transportation is the cold chain – the network of refrigerated transportation and storage systems that keep temperature-sensitive goods such as food and medicine safe and fresh. Decarbonising the cold chain is thus a critical priority for sustainability efforts worldwide.
One promising solution in this area is the emergence of electric Trailer Refrigeration Units (eTRUs) that can operate with zero emissions. These units represent a major breakthrough in sustainable transportation, offering the potential to reduce the carbon footprint of the cold chain dramatically.
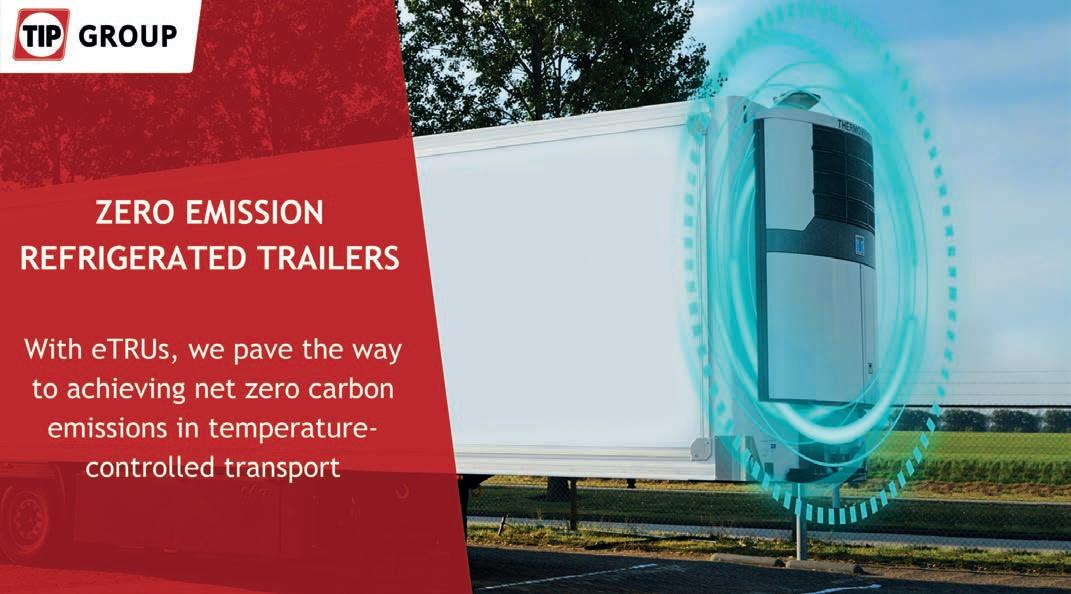
TIP has been at the forefront of researching and developing eTRUs, and is proud to
offer a range of sustainable solutions that can help companies decarbonize their operations.
eTRUs vs. Traditional TRUs
Traditional Trailer Refrigeration Units (TRUs) are powered by diesel engines and emit greenhouse gases and other pollutants. In contrast, eTRUs are powered by electric motors, meaning that they emit no harmful pollutants, making them a more sustainable option for companies looking to
reduce their carbon footprint. Moreover, eTRUs are designed to be highly efficient, with advanced insulation and temperature control technologies that ensure goods are transported at optimal temperatures with minimal energy usage. This not only reduces emissions but also saves money on fuel costs, making eTRUs a smart investment for companies looking to cut costs while going green.
Innovative Technologies
TIP recognise the urgency of decarbonising the cold chain and are committed to developing sustainable solutions. That is why we it is investigating three different technologies for eTRUs: charging the battery through a plug, charging with an energy axle, and charging with solar panels.
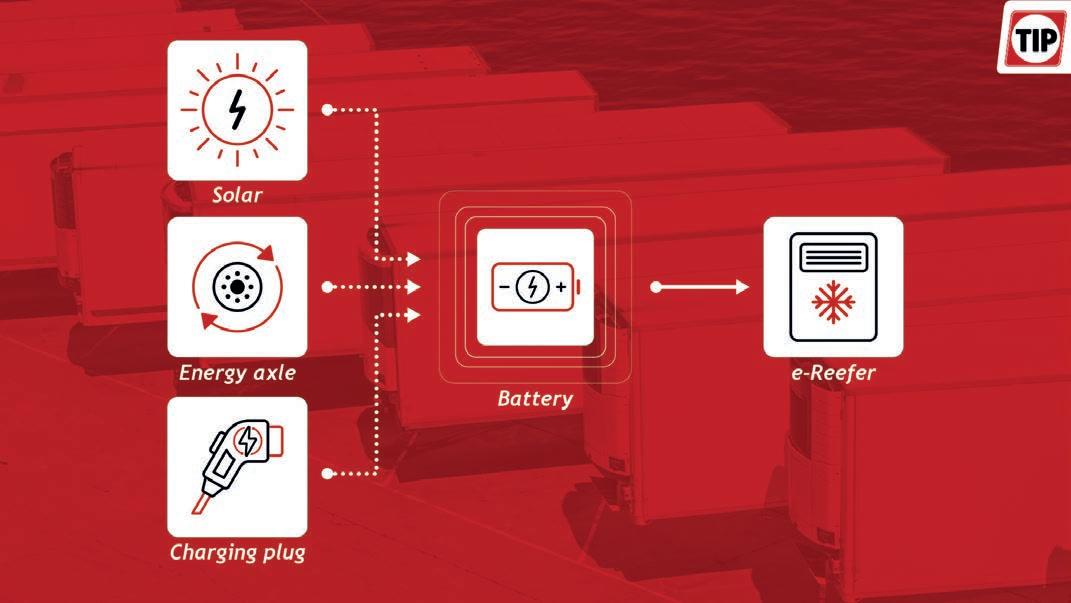
Charging the battery through a plug is the most straightforward solution. It involves connecting the eTRU to a power source, such as a charging station or a standard electrical outlet, to recharge the battery. This method is convenient and widely available, making it an attractive option for many businesses.
Charging with an energy axle is another promising technology that we are exploring. In this method, the eTRU’s axle is equipped with an energy recovery system that converts the kinetic energy generated during braking into electric power to recharge the battery. This technology has the
potential to significantly reduce energy consumption and increase the range of the eTRU. Finally, charging with solar panels is a renewable energy solution that TIP is investigating. By installing solar panels on the roof of the eTRU, the system can generate electricity from the sun to power the refrigeration unit. This method has the added benefit of reducing reliance on electrical grids and increasing the eTRU’s autonomy.
Let’s innovate now!
It has become clear for the logistics sector that the temperature controlled distribution network needs to innovate towards trustworthy zero-emission solutions. Relying on outdated diesel engines is no longer viable. Current battery-based solutions show promising results, but there is definitely still much to gain in the on-board generation of power to become more independent and secure energy-efficiency.
“TIP has seen its customers increasingly look to adopt cleaner and more efficient trailer solutions,” said TIP Group Vice President Global Sales and Marketing, Rogier Laan.
“We support innovative solutions that drive the industry to be more sustainable so replacing diesel-powered TRU with electric TRU is progress we believe in. That is why we invest in it, test it and get the proof of concept. We do not make things, but we do make things happen.”
As industry leaders, TIP take the responsibility driving the industry towards sustainability to improve the health of our planet. It is an exciting proposition to electrify the cold chain for many parties, from shipper to carrier and equipment provider, lowering costs while making improvements that improve living quality and fight climate change on a large scale. With such innovations, we enable our customers to achieve their sustainability, efficiency and safety targets faster and at bigger scale.
For more information on TIP’s innovation, read the eTRU white paper or reach out to your nearest TIP contact.
www.tip-group.com
FOURTH GENERATION EBS: HALDEX
REMOTE CONTROL AND REMOTE DATA ACCESS ARE TWO KEY BENEFITS OF HALDEX’S EB+ 4.0 PLATFORM WHICH COMMENCED SERIAL PRODUCTION IN 2022.
The EB+ 4.0 system applies or releases the brakes by responding to electrical signals received from the brake pedal, which responds by using solenoids to modulate air pressure in a closed compressed air system connected to axlemounted brake actuators.
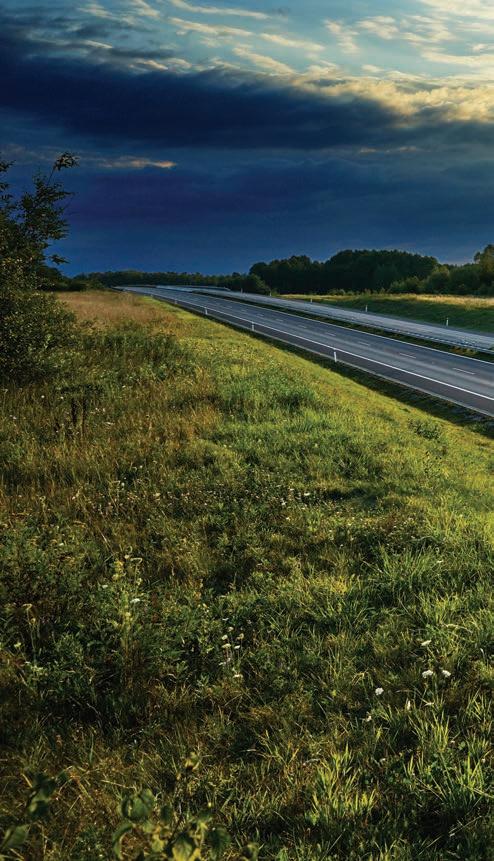
That design is maintained for service brakes. But unit’s new modular design provides additional features, as well as facilitating hardware and software customisation.
Thanks to a new optional valve bank, extends electronic control for the first time to the parking (spring) brake side of the double-diaphragm brake actuator. Previously, connecting the red Suzie coil between truck and trailer would automatically release the parking brake if the red knob of the park and shunt valve is not activated. Now, the system provides additional control of that process, via the EBS ECU (electronic control unit) and an extra solenoid valve. The EB+ 4.0 supports a 12V and 24V voltage supply of the vehicle, thereby making it suitable for customers in all global markets.
First, this so-called ‘Mobiliser’ feature connects the parking brake release command to other onboard microprocessor- controlled systems for additional security checks – such as the closure of the rear door lock, or the detachment of a charging cable, in the case of an electric fridge assembly. To prevent theft or misuse of the trailer, it could compare the VIN of the tractor it has been hitched to, to a white list of approved tractors, before releasing the brake.
Or, with this system, the tractor might remain locked in place until it is able to reach, via a telecommunications box connected to the data cloud, a remote telematics system. This might compare its transmitted location to the expected position based on its planned itinerary, to make sure it has not been taken outside of its authorised area. Alternatively, the ‘go’ signal might come direct from head office. (Semi-trailers with parking brakes fitted with conditional control do not require continuous power, but they do require an electrical connection from the tractor and to be able to receive a data signal.)
These are just a few examples and by no means exhaustive; such functions must be programmed into the system via a new application programming interface (API). Haldex
is quite flexible when it comes to implementing such modifications. On behalf of the customer, the company can develop customised functionalities or incorporate customer functions into regular software updates, and by the same token, a customer-specific release plan can also be agreed. What makes all of this possible is strict separation between application software and braking software. Previously, any change to braking system software could affect the vehicle’s type approval and might face regulatory review. Not so
with EB+ 4.0, as Haldex has further separated safety-related brake control features from customer-specific software.
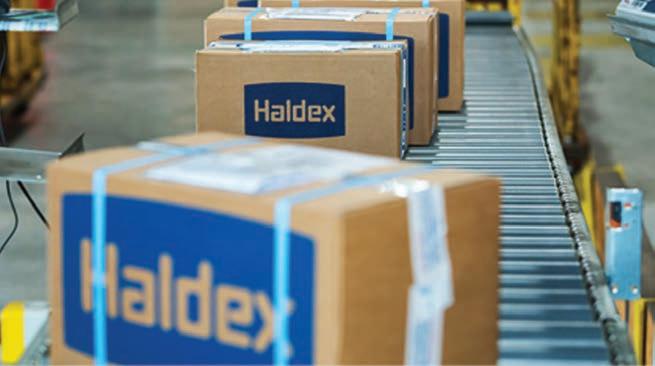
That means that it is potentially easier to make changes and maintain the overall safety of the system with EB+ 4.0. Beyond the mobiliser feature, the new connectivity aspect provides real-time, remote access to operational data. One immediate benefit is compliance: trailers fitted with EB+ 4.0
comply with the new European regulation R141 for on- board TPMS. This regulation requires EBS to transit the tyre pressure and temperature information to the tractor unit. And access to real-time information from the EBS system can lead to further potential logistics and engineering benefits, once that data is provided available for connection to external fleet management software for further processing and analysis. TPMS can give information about pressure and temperature, and so might indicate tyre wear and pressure if the temperature increases. EBS knows the load profiles, and deceleration levels and ABS events and stability systems, so may give an indication to the system about brake pads and wheel bearings.
Alexander Kraus, Senior Commercial Product Manager, said: “In the truck and trailer

world, software features and telematics is all about the cargo, so fleets would like to know everything about the goods they are carrying. However, from a preventive maintenance perspective, information from the system and its capability becomes quite important. It is also useful in autonomous driving. The current system’s capability is substantial for AI to know what the system is capable of, to plan the next braking event. Access to the status of the system is crucial capability for AI for the control unit to understand its next manoeuvre.”
EB+ 4.0 also offers two other system enhancements that improve the safety of trailers in operation, without involving customisable software or optional features.
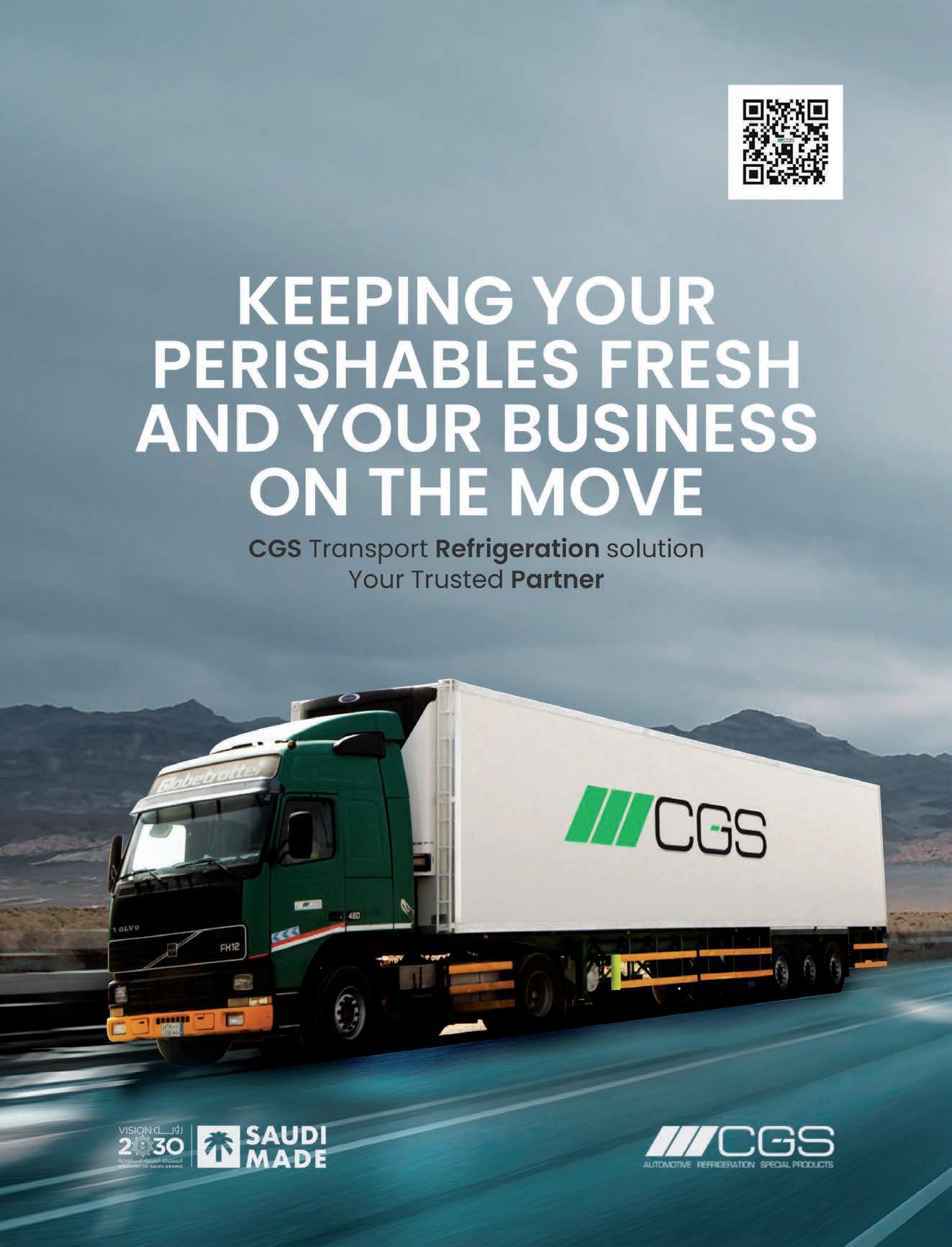
First, the existing Safe Parking system, which provides extra safety when coupling and uncoupling, has been improved. Safe Parking + will not release the parking brake until the system detects a safe condition: that the air brake system is fully pressurised, and the driver has depressed the service brakes or the service brake is applied by the trailer control valve of the truck. That means that the air coils have been connected (and in the correct order), and that the driver is back in the cab.
This increases the protection of roll-away incidents compared to the previous Safe Parking system, which would only release the semi-trailer brake when the driver pressed a lever mounted to the side of the vehicle. In addition, it prevents the possibility of rollaway if the combination were parked on a grade and the driver forgot to apply the tractor parking brake, or if it were on a grade and the driver attached the coils in the wrong order. Second, another safety system added is emergency brake override, though it is not in fact new; it was a feature on Haldex EB+ Gen1 and has been reintroduced. It comes as Standard with most EBS variants, and blocks emergency application of the parking brake when the vehicle is moving (by reading input from the wheel speed sensors). This is perfectly legal. ECE R13 safety regulations stipulate that if the energy supply between truck and trailer is lost, the trailer must apply emergency braking. This could be via the parking brake, as has been the case with previous versions. While this will bring the truck and trailer to an almost immediate halt, during that process the trailer wheels will lock, destroying the trailer tyres and threatening those vehicles travelling near the vehicle. But the safety regulation also allows emergency actuation via the trailer service brakes. That offers several advantages, the least of which is that braking can be controlled by ABS protection. A greater advantage is that this option facilitates the use of the emergency
FAST FACT
EB+ 4.0 brings parking brake control into electronic management; a new modular and customisable approach to functions which provide new digital services opportunities; 35 per cent weight saving and 30 per cent reduction in embedded CO2; and additional safety features as standard.
brake override system. If the emergency brake override detects that the energy supply has been disconnected or lost, but if there is sufficient air pressure in the system to operate the service brakes, it will do two things: trigger a red warning light in the cab, and override immediate actuation of the brakes. During this time, the driver will be able to use the existing air pressure to operate the service brakes as normal to stop in a controlled manner at the nearest possible opportunity. Such manoeuvres depend on an intact electrical connection between tractor and trailer. Once the truck reaches a lower brake pressure threshold, the emergency braking system applies the spring brake, as the regulations require.
New hardware in EBS+4.0 includes redesigned solenoids that are smaller, more robust but lighter than before. In addition, the system is also lighter, as it is now constructed from engineering-grade polymer. A switch from metal to engineering plastic for construction of the new valve control unit, plus redesigned solenoids, achieves a weight savings of 35 per cent to 3.9kg, and total embedded CO2 of 30 per cent (to 43.3kg per unit).
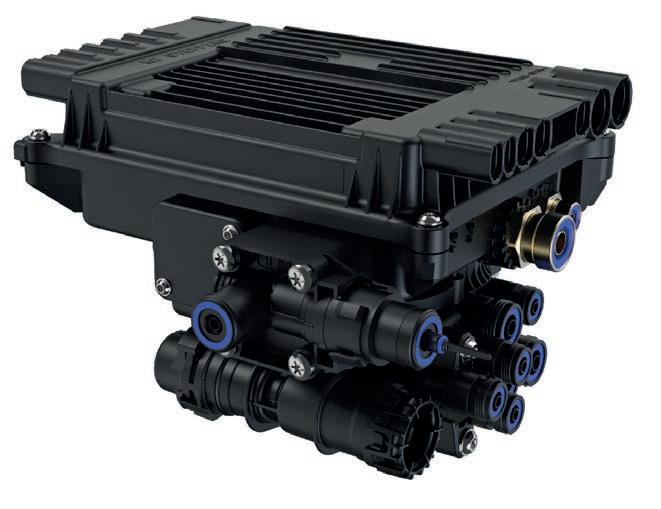
Four different versions are available: a basic EBS with two modulators and two wheel-speed sensors with no emergency brake override; a basic EBS with emergency brake override; a premium EBS with two additional electrical interfaces, which can be extended to eight sensors and four modulators; and an additional modulator, which is used to map larger systems. As Standard, EBS+ 4.0 comes in a 2S/2M configuration suitable for fitment to three-axle semi-trailers.
Haldex has signed a long-term agreement with several trailer manufacturers for the supply of EB+ 4.0 for trailers. The system has been in development for seven years.
www.safholland.com
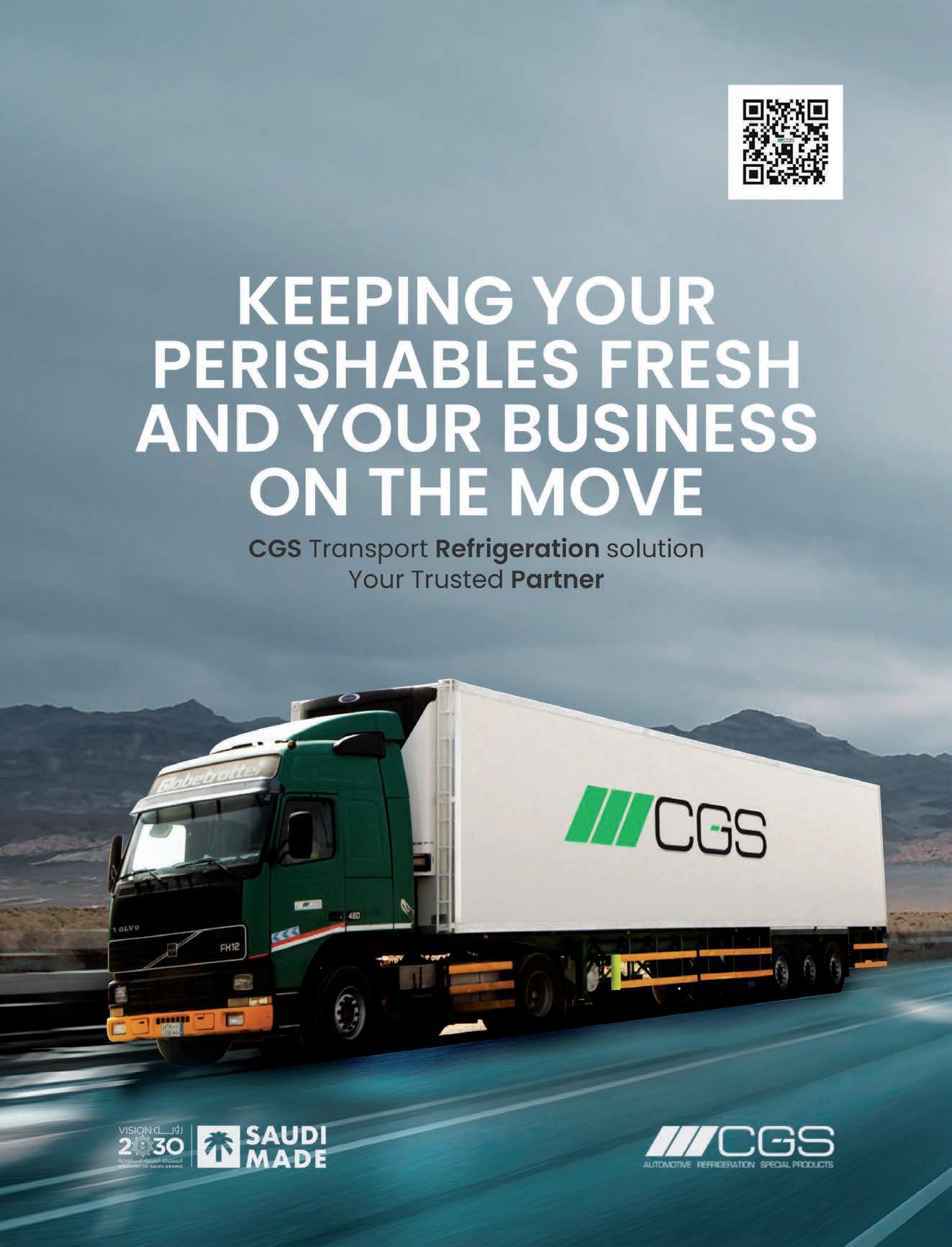
INTELLIGENT PRODUCTION
DEVELOPMENT.
In 2019, Fuwa invested about 0.3 billion euros to establish an intelligent and state-ofthe-art production line for trailer axles, including the use of robotic arms, automatic equipment, and advanced facilities, and laid a solid foundation for the top value of quality-oriented development.
This innovative step of digital transformation marks a significant breakthrough in both product quality and production efficiency. Following the ambitious target of high-quality development, Fuwa continues its leading role in and explores the field of intelligent manufacturing in further ways.
After three years of effort and preparation, the intelligent manufacturing workshop for brake pads was officially launched in October of 2022, with an overall investment of 14 million euros and the annual production capacity of more than 12 million pieces. Currently, it is the largest production workshop of trailer brake pads in China.
The intelligent production line is a computer-operated system that links up different processes. It’s equipped with a main computer that offers real-time monitoring and execution of tasks, as instructed by the center control of the entire operation.
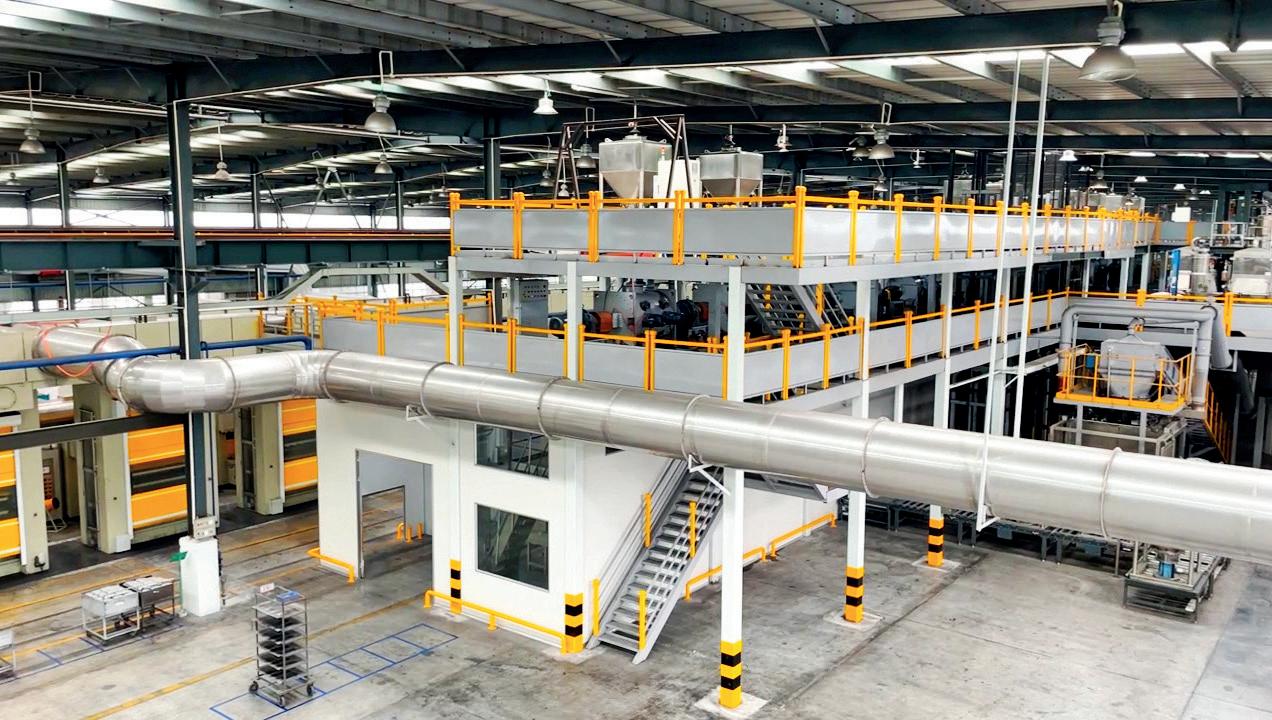
The intelligent production line links different processing through a sophisticated and interconnected computer system. With network-based supervision and real-time
operation, each production line is equipped with at least one screen, and each procedure is implemented by computer instructions, to make sure the precise and trackable process, ranging from transporting, storing, measuring, and mixing, to packaging. The whole process only takes about five minutes.
As an integrated part of the high-tech research and development system, Fuwa’s friction materials laboratory, covering an area of over 800 m2, is specially established and owns more than 60 kinds of testing equipment, including three 1:1 brake dynamometer stations.
The environmental advantages of FUWA brake lining
The Fuwa-manufactured brake pad applies its
specially patented ingredients and processing method, which makes it a premier and ecofriendly product. It does not include asbestos, harmful metals, or any hazardous substances. The unparalleled friction properties allow for efficient braking while remaining silent and withstanding wear longer than competitor products. This FUWA product achieves a remarkable price quality in terms of the lifecycles of brake pad and brake drum.
With its friction performance and stable, efficient braking ability, this brake pad is quiet, has excellent wear resistance and no corrosion of the brake drum, resulting in an extended useful life.
VALX teases new product
The Valx 17.5” drum brake axle will soon enter the market.
Customer satisfaction is always what Valx values and appreciates. In response to diversified market needs, VALX always responds quickly to potential business opportunities and makes customised plans for axle product improvement. Therefore, the project of the 17.5” drum brake axle was initially designed and launched in 2021. After having strict limit testing for exceptional performance, this type of Valx axle will become the new addition to the family of drum brake
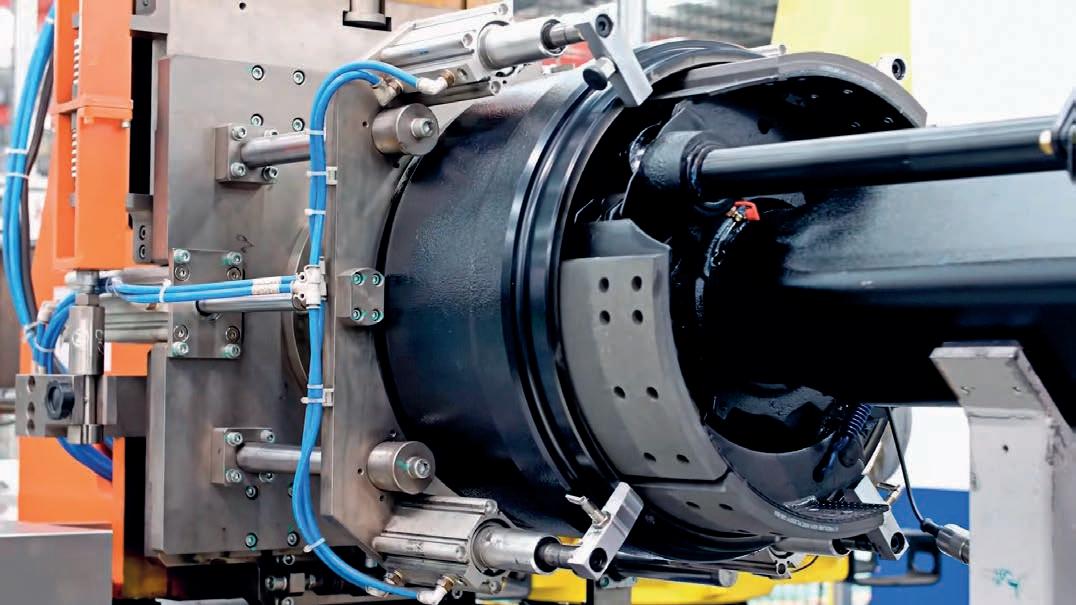
axles within the upcoming few months. In the IAA 2022, Valx showcased this new dimensioned axle for the first time, and it attracted numerous visitors, customers and business partners to preview its first impression to the world.
The 17.5” drum brake axle has a smaller wheel size, with brake dimensions of 300*200mm and an axle load of 11 tonnes, which provides a greater range of use for different trailers. With regards to the axle beam, it is applied with the premium e-coating and powder coating process, which enables the remarkably corrosion-resistant and durable hub and brake drum. This axle is ideal for those who are looking for a smaller wheel size option with the same braking power as a larger axle.
www.valx.eu/en
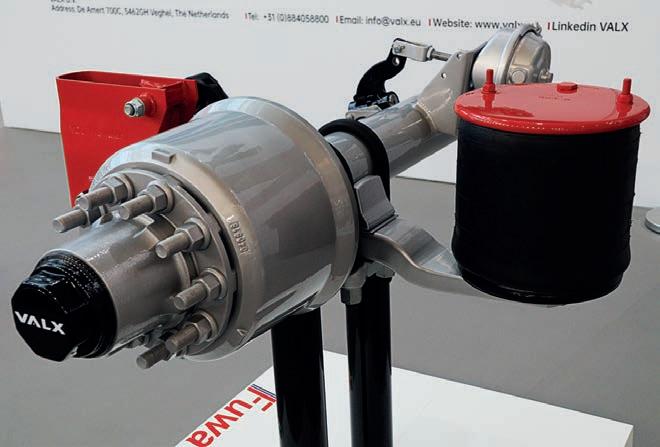
BPW takes easy service and repair for braking technology to the next level with its patented ECO principle – fast disassembly and assembly according to the Formula 1 method via a central axle nut, while the variants score points with the time-saving exchange of discs, drums and linings.
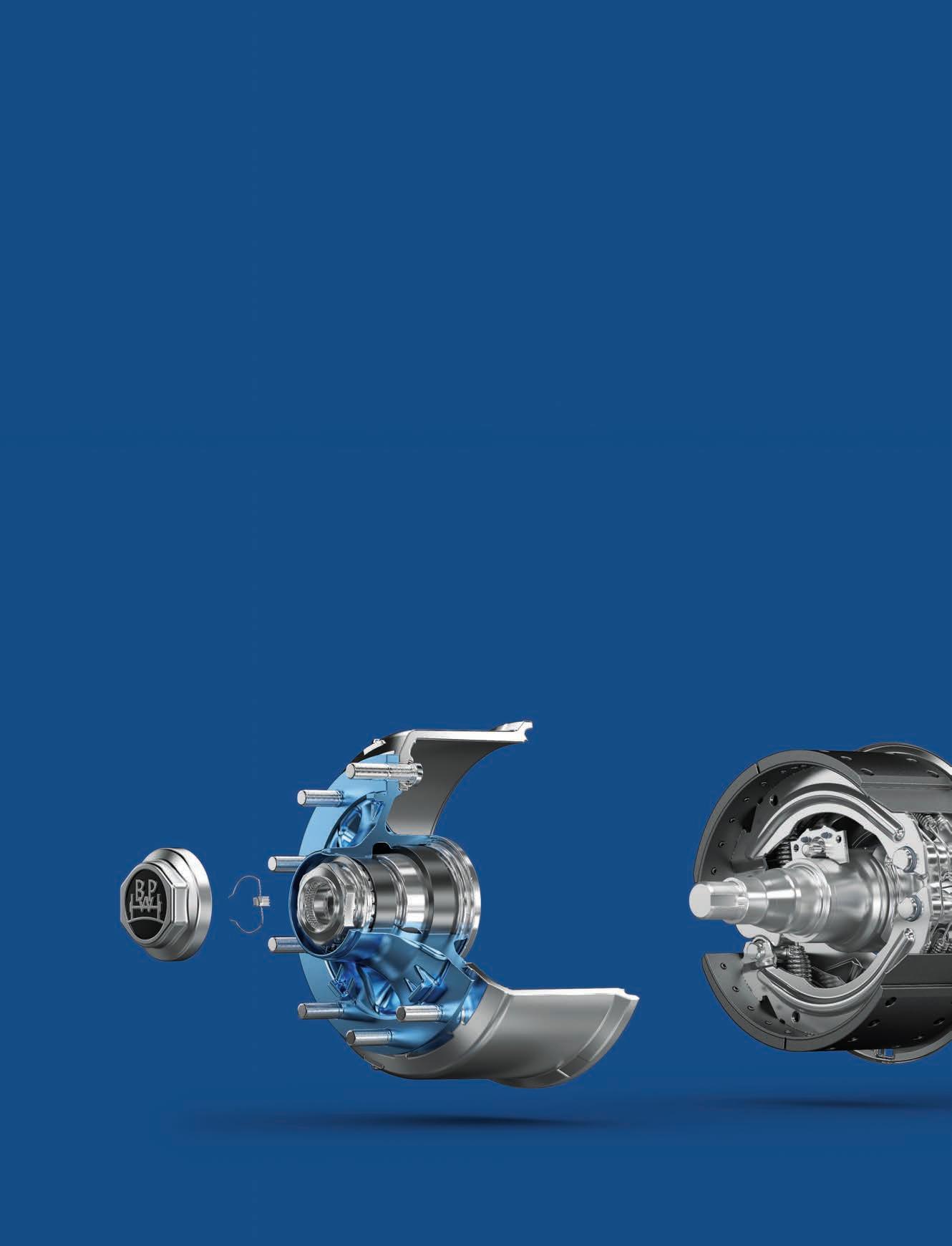
TO LAST ENGINEERED
BPW DETAILS WHAT YOU NEED TO KNOW ABOUT CHOOSING THE BEST BRAKES FOR YOUR TRAILER.
DDisc brakes, according to BPW Product Manager, Thorsten Grahl, are generally considered to be the superior choice over drum brakes in the commercial vehicle industry. In fact, about 80 per cent of the European market specify disc brakes. However, there are still regional variations. The UK, for instance, is considered ‘drum brake country’, while eastern and southern Europe is increasingly turning to trailers with disc brakes. Are drum brakes then simply an English quirk? Not at all. There are still good reasons to consider drum brakes when procuring a trailer. With the drive transformation towards more environmentally stable mobility and the introduction of the Euro 7 emission standard, the drum could become even more important due to its technical features.
System expertise enable a good foundation for making a decision
As a system provider, BPW has been manufacturing trailer axles for numerous applications for 125 years and supplies trailer manufacturers with individual components, all the way down to complete running gear systems. Thanks to BPW’s comprehensive product portfolio, it has extensive system expertise for everything to do with trailers, providing both brake discs and brake drum technology.
“We continuously develop both versions and put them to the acid test,” said Grahl. “They are subjected to numerous tests and driving trials on the test bench and the road. We aim to draw on our experience to provide the best possible choice of suitable brakes for individual needs.”
The self-contained design protects drum brakes in off-road use
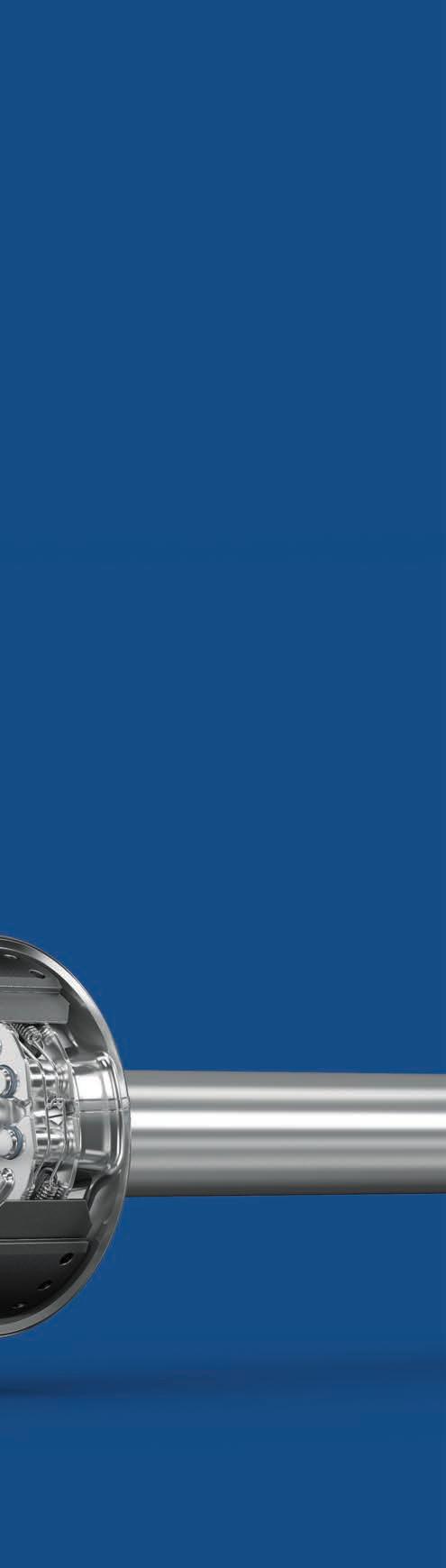
Drum brakes show their strengths wherever a robust system is an advantage. The fact that the brake is concealed in a closed drum protects it against mud, dust and other dirt. So, it makes sense to equip vehicles with drum brakes which are predominantly driven off-road, such as tippers, trailers and low load trailers.
Drum brakes are more resilient in seasonal use
This applies particularly if the trailer is only used at certain times and left standing off-season. The brake linings of disc brakes are at risk of vitrifying if they are not used enough or there is a lot of down time; plus brake discs can corrode over time, as then are constantly exposed to the wind and weather. This is not only the case for construction vehicles, but also with trailers which are used in the agricultural and forestry transport environment. Or for semi-trailers which are used in multi-mode traffic and travel long distances on rails or water and only short routes on their own axles.
Drum brakes are forgiving of errors and moderate maintenance
A drum brake is basically a robust component. It often proves itself resilient even with only moderate maintenance. Plus, if a semi-trailer is used with alternating tractor units or those which also have a drum brake, this proves itself to be the better variant. Disc brakes, on the other hand, require good tractor/trailer synchronisation to prevent the trailer from over-braking with a drawbar trailer. This would lead to uneven wear on the brake linings and, as a result, the friction combination would not achieve its theoretical maximum lifespan.
Disc brakes are the first choice for on-road use
On the other hand, tarmac roads are the natural environment for trailers with disc
brakes. Following its establishment for on-road use in trucks, today, the technology is also standard in trailers. If the coordination with the tractor unit is good, then truck drivers often report better braking performance. The reason for this is also the disc brake design principle, which is less susceptible to over-heating when the braking effect is very heavily utilised. There is no ‘fading’ here, which is sometimes the case with drum brakes. In combination with the other advantages, international long-distance and inner-city traffic is generally the domain of disc brakes.
Disc brakes enable a clear payload benefit
Disc brakes have a weight advantage. At BPW, the ECO Disc (TS2 4309, offset 120) in a three-axle suspension has a weight advantage of 30 kilograms compared to the drum brake. With the ECO Disc TS2 3709 with offset 0, there is even up to 90 kilograms more useable load. This makes disc brakes perfect for transport in which every kilogram of usable load counts, such as for tank silos, as well as coil, paper and beverage transport.
A question of the price and operating costs
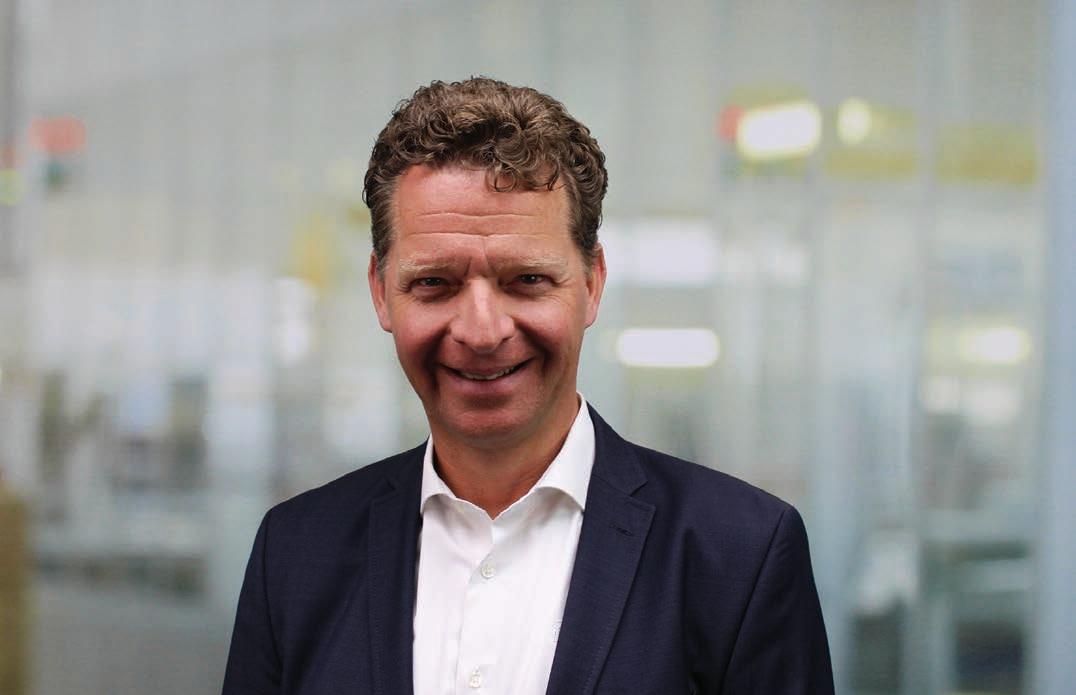
The decision for or against disc brakes depends on the price. This is also the factor which is most difficult to evaluate, as it depends on many fleet-specific conditions. Disc brakes and drum brakes are not necessarily worlds apart in terms of price. But whether that is actually the case in reality depends largely on the price policy of the respective vehicle manufacturer. The same applies for the price of wear and spare parts. The individual price policy of the OE manufacturer or provider of the independent aftermarket also plays a role here. Fleets with their own service operation benefit from a high level of transparency here, while others are dependent on information from the garage.
The maintenance required for disc brakes is generally lower
The maintenance required for disc brakes is often lower, as the relevant wear parts are easily accessible thanks to the open construction and therefore replacing them takes less time, at least in theory.
“At BPW, we have taken easy service and repair for braking technology to the next level: thanks to our patented ECO principle, i.e. fast disassembly and assembly according to the formula 1 method via a central axle nut, the variants score points with the time-saving exchange of discs, drums and linings,” said Grahl. “With the ECO Disc in a three-axle, this can even save up to three hours and therefore reduces garage costs compared to standard competitors solutions. However, there is a systematic disadvantage in maintenance effort with drum brakes due to the regular lubrication of bearings in brake camshafts and automatic slack adjusters.”
Drum brakes require regular maintenance, but on the other hand, the wear parts, such as the brake linings and drum, last longer than brake pads and brake discs. The decision for or against
a brake system is highly individual in this point in particular and depends on several factors, such as the idle times of the wear parts, spare part prices, the holding period of the vehicle and whether you have your own garage, for example, or if you rely on third party garages.
Higher demand for disc brakes create higher residual values
Ultimately, disc brakes are favoured in terms of the trailer’s residual value. After working as a trailer with this type of equipment, the demand in the aftermarket is higher. That’s why better prices can generally be achieved for the used trailer. However, with increasing performance, these positions become relative.
Lower particle emission with drum brakes
During servicing, the encapsulated construction of drum brakes is usually more of a disadvantage. But this may soon turn into an advantage. With the introduction of the emissions standard Euro VII from July 2027, the legislator will initially also regulate particle emissions – among other things through abrasion on brake linings. Wear
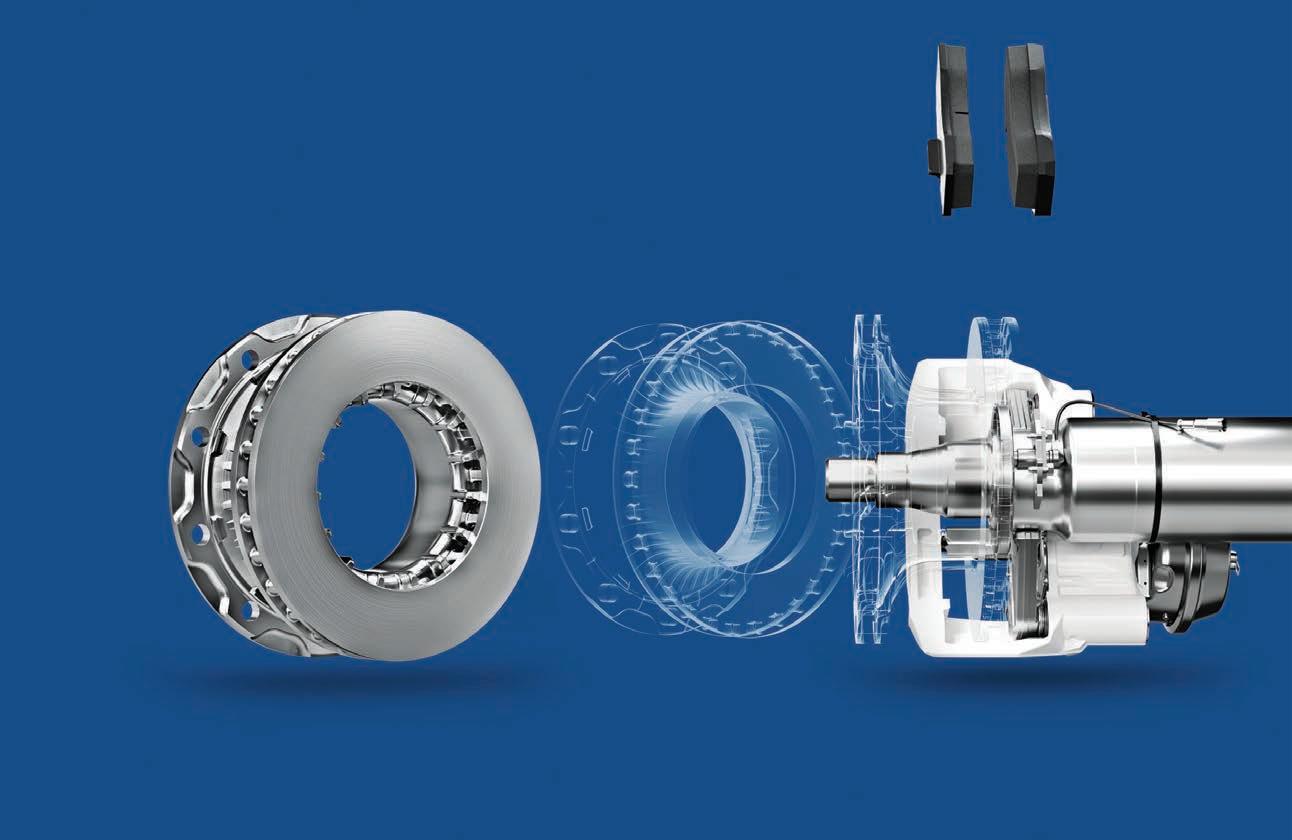
is lower with drum brakes today, this also means fewer particle emissions are created and it is anticipated that it will be much easier to capture the unwanted dust particles, so they never make it into the air in the first place. There will also be suitable solutions for disc brakes, although that may require more effort.
The advantages of drum brakes for e-mobility
Car manufacturers are already equipping their e-vehicles with a drum brake on the rear axle. The axle is braked by the kinetic energy recovery through recuperation, i.e. through an electric brake resistance and the kinetic energy can be restored as electric energy in the drive battery. The brake on the rear axles of e-vehicles has much less to do than in a standard vehicle. In e-trucks, the same effect could result as in vehicles used in seasonal or combined traffic: in the worst case, the disc threatens to corrode and the result could be uneven braking which will be seen as a fault be technical services during regular checks.
Always be on the safe side with BPW braking systems
The selection of suitable brakes depends on many factors. Both technologies have their benefits, but they predominantly reveal their advantages if they are attuned to the specific usages of the trailers. Still, one thing is certain: fleet operators who rely on BPW brake systems will have a economically efficient solution with optimised operating costs. BPWs system expertise gained over 125 years of experience ensures that all brakes are technically developed to a high standard and can safely perform their service - regardless of whether a drum or brake is used.
www.bpw.de
DISTINCTION WITH STATE-OF-THE-ART
ROBOTIC
WIELDING
SEVERAL LEADING TRAILER BUILDERS CHOOSE TO DEPLOY STATE-OF-THE-ART WELDING ROBOT SYSTEMS FROM THE DUTCH WELDING ROBOT INTEGRATOR, VALK WELDING.
Deployment of welding robots and automation in general offers a solution to compensate both the shortage of skilled workers and the high labour costs in Europe. Compared to manual welders, welding robots have the advantage of offering a higher and more consistent weld quality. This factor is often of decisive importance in the transition to robotic welding, as greater demands are placed on the strength and quality of the welded chassis frames. Requirements that are hardly achievable without welding robot technology.
Weld robot technology
Valk Welding supplies complete robotic systems with all the components necessary to enable the automation of high quality welding, utilising Panasonic’s welding robots, which have been specifically developed for the automation of arc welding processes. Given the strong increase in high mix/low volume production, the speed and ease of deployment of welding robots is also a decisive factor to partner with Valk Welding.
In addition to this, Valk Welding has invested heavily over the past 40 years in developing tools in the robotic welding sector, this includes:
• water cooled robotic torches with pneumatic cut off;
• seam search and tracking systems;
• offline programming (DTPS) and automated offline programming (ARP);
• friction free wire feeding systems; and
• custom frame and track solutions including manipulators.
Each of these developments are what contribute to the continuous high-quality welding process, high duty cycle and strong increase in output that Valk Welding can supply.
Offline programming
Programming complete assemblies such as chassis frames is virtually impossible without software
tools. Valk Welding, with more than 1,500 licences of the desktop simulation and programming software DTPS, plays a trendsetting role in this.
For well-known trailer manufacturers, including Wielton, Faymonville, Kögel, Van Hool, Stas, Fruehauf, BMI, Knapen, System Trailers and many more, this software has enabled the deployment of welding robots within the high mix/low volume environment.
In fact, according to Daniel Kemp, Manufacturing Manager at Van Hool, offline programming is one of the most important items in the automation process.
“We are among the early adopters in the field of offline programming,” he said. “Together with Valk Welding, we have witnessed the evolution in this field over the past 25 years up to automation of the programming process. The most recent step is Automatic Robot Programming with AI (in partnership with Oqton). By taking automation technology to the next level, in partnership with Valk Welding, we are able to produce high-quality custom products in a wide variety.”
Welding processes
To meet the high strength and quality requirements,
the use of the right welding process is crucial. For Faymonville, which specialises in building trailers for heavy transport, higher weld quality is of primary importance. To that end, the company uses the digitised welding processes that are standard in the Panasonic WGH robots.
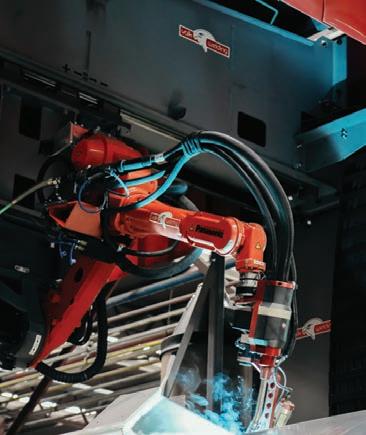
“Of these, we use the ‘deep penetratio’ welding process,” said Faymonville. “This guarantees a very deep penetration that also allows the welding seam preparation to be adjusted so that welding costs can also be reduced. For the heavy construction we apply multilayer welding. Programming in the classic way would take an enormous amount of time. Panasonic offers ‘Thick Plate Software Solutions’ especially for this purpose. With this software, we program a new product every day. Thanks to the total package of hardware and software from Valk Welding, we have been able to make a considerable improvement in the efficiency of welding small batches. We know how to keep the production in the various branches within Europe competitive and we have been able to further strengthen our position in Europe.”
High mix/low volume
Within the European trailer construction industry, competition is fierce. The German manufacturer System Trailers, as an independent producer of semi-trailers and trailers, has acquired a distinctive position in this.
“Partly due to the use of welding robot systems from Valk Welding,” said System Trailers Director, Ralf Saatkamp. “In order to offer our customers a consistently high quality and favourable purchase price, we have completely geared our organisation, production and automation to high mix/low volume production. Due to the large number of different trailers, the changeover time of the welding robot is a crucial factor. We were looking for a partner who could flexibly set up the entire programming for this. With the offline programming system DTPS, the welding robot can immediately start working with the
programs, almost without corrections. Partly due to the logistics automation, we reduced the lead time of the longitudinal supports for the chassis by 30 per cent. It is important to build a partnership with the customer in order to get to know the customer’s wishes better. On that same philosophy, we work together with Valk Welding.”
Distinctive in welding seam tracking technology
Also, for the Polish manufacturer of trailers and semi-trailers, Wielton, the integration of Valk Welding welding robot systems has been decisive for the company’s substantial growth over the past two decades. In terms of production numbers, Wielton is now among the largest European trailer builders. One of the problems the company ran into was weld seam detection on aluminium parts in particular. Their desire was to solve that with a vision system instead of conventional search finding systems.
“While existing vision systems couldn’t do that because of the reflections on aluminium, Valk Welding could with their Arc-Eye laser sensor,” said Wielton Robot Programming Manager, Mariusz Skupinski. “With this, we were able to correct deviations in welds in real time in the welding program, so that the seam is followed exactly by the welding robot. Also, thanks to the use of their welding robot technology, we were able to double the capacity of our W5 line within the same floor space.”
Halving production time
LAG Trailers, Europe’s largest producer of aluminium tank trailers, deploys Valk Welding welding robots for the production of bulk trailers and bulk containers. The reason was to relieve the fabricators of the monotonous welding work, by using robots. Through standardisation and design of line production, the company has been able to greatly reduce production time in ten years. For example, LAG Trailers today makes a tilt-bulk truck in 250 hours where it used to take 800 hours. “Deploying welding robots does mean that when there is downtime, the entire line comes to a halt,” said LAG Trailers CEO, Rob Ramaekers. “That’s why we asked several robot integrators, with a high reliability requirement at the top of the list. With their knowledge and experience in the field of welding robot technology, Valk Welding was able to fill in the complete picture, both hardware and software-wise. In addition, their methodology of offline programming makes it possible that line production does not have to be interrupted for programming.”
Specialist in the field
It is clear that a successful transition to welding robotisation in trailer construction requires highquality welding robot technology in which all aspects such as welding processes, programming, weld seam tracking, wire feeding and manipulation are optimally coordinated. Valk Welding distinguishes itself as a specialist in this field, with a high level of knowledge and an organisation that, with its scale, is one of the few to successfully realise such large automation projects.
www.valkwelding.com
”IT IS IMPORTANT TO BUILD A PARTNERSHIP WITH THE CUSTOMER IN ORDER TO GET TO KNOW THE CUSTOMER’S WISHES BETTER. ON THAT SAME BASIS, WE WORK TOGETHER WITH VALK WELDING.”
Ralf Saatkamp, System Trailers
MEETING IN MUNICH
DISRUPTED SUPPLY CHAINS, INNOVATION IN MOBILITY, CLIMATE CHANGE AND THE EVER-PRESENT THEME OF SUSTAINABILITY ARE EXPECTED TO BE THE KEY TALKING POINTS AT THIS YEAR’S TRANSPORT LOGISTIC EVENT.
Transport Logistic, the international trade fair for logistics, mobility, IT and supply chain management will be held 9-12 May at the Trade Fair Center in Munich, Germany.
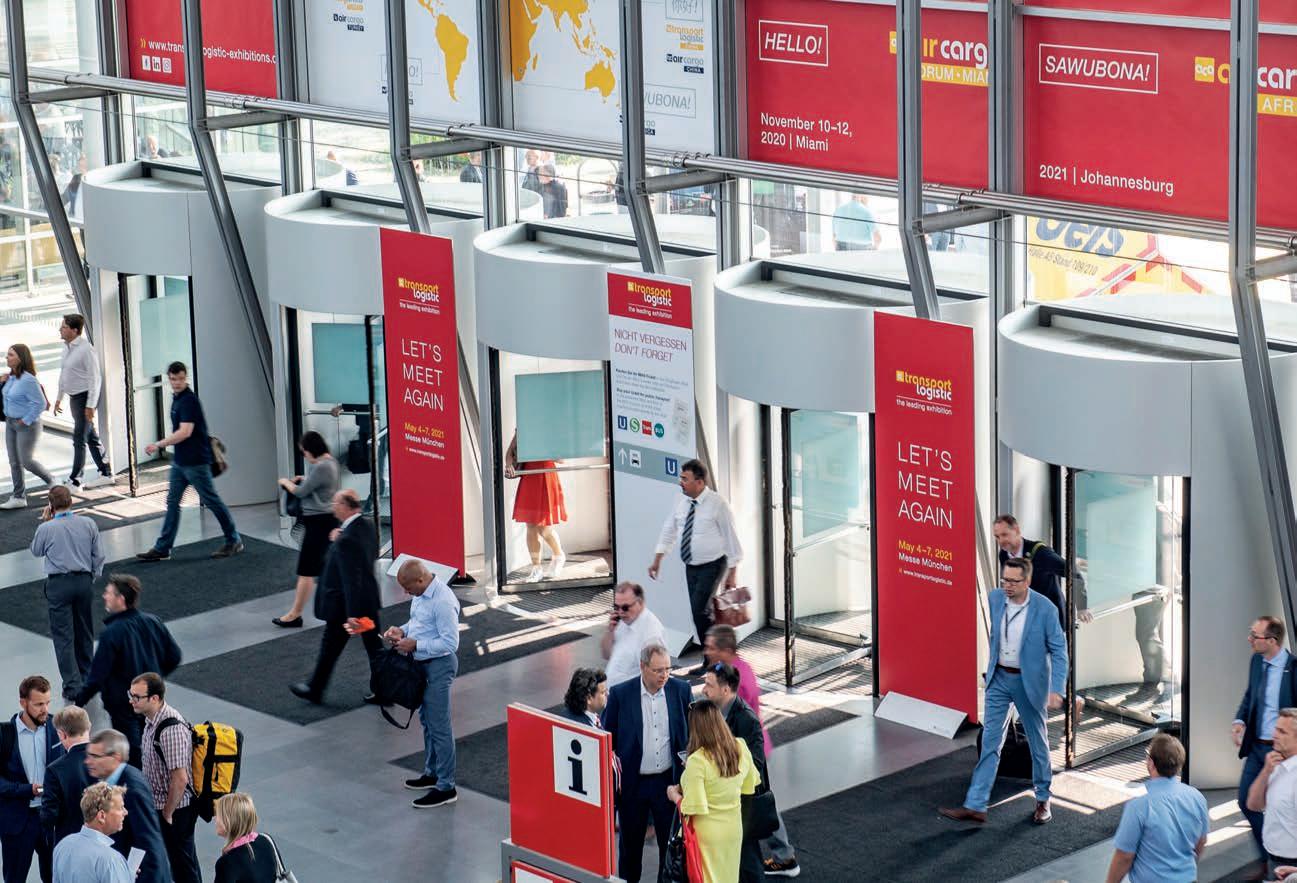
Prof. Dr. Dirk Engelhardt, Spokesman of the Board of the Federal Association of Road Haulage, Logistics and Disposal (BGL) eV said: “Logistics currently has to overcome many major challenges. Resources are scarcer than ever. This means that everyone involved in the supply chain must work together to find justifiable, practicable and reliable solutions. To this end, transport logistic brings everyone – from the shipper to the recipient and from the logistics service provider to the technology provider – together in Munich. This underlines the importance of logistics and sends a clear signal on the way to a sustainable future.”
With 58 sessions, the transport logistic conference program lists around 20 per cent more lectures and panel discussions than in 2019. The topics show the challenges the industry has to face. The topic of sustainability runs like a red thread through the entire program.
The German Transport Forum (DVF) gets to the heart of the matter under the title
‘Balancing the world economy, meeting climate targets: How does logistics deliver?’ and discusses with top politicians and representatives of the logistics industry how the energy transition with new drives, alternative fuels and new production chains can succeed.
Whether infrastructure, supply chains, digitisation or skilled workers – many topics of the conference program contribute directly or indirectly to a more sustainable treatment of the environment and people with expert knowledge. The lectures range from the meta-level of geopolitical developments to everyday business practice. The four forums located in the
halls deal with innovative technologies and resourcesaving concepts. The program includes topics such as the decarbonisation of modes of transport, nationwide e-mobility in logistics, efficient supply chains in combined transport and on the last mile in city centres or uniform standards for real estate and data.
“Logistics drives sustainability,” said Deutsches Verkehrsforum Managing Director, Dr Florian Eck.
“It bundles flows of goods, invests in new technologies and collects its treasure trove of data along the entire supply chain, across all modes of transport.
“Transport Logistic makes visible what is happening in the industry. With a view to our climate goals and the necessary energy transition, the crossmodal and international trade fair is more important than ever as a showcase and innovation hub.”
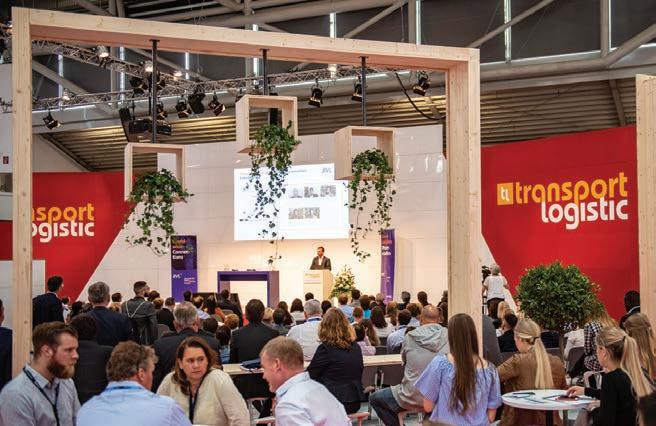
For the first time since 1978, there is no trade fair catalogue for Transport Logistic.
In order to reduce paper consumption in general, only one visitor guide will be published. In the hall aisles, the trade fair also dispenses with 25,000 square meters of carpeting.
The exhibition team also pays attention to the use of sustainable materials in the construction of all forums and special areas. From assembly to dismantling, consistent collection and recycling of all recyclable materials used should reduce the waste rate. Exhibitors can also use a GoGreen CO₂ audit
by Messe München to determine and compensate for their ecological footprint.
The stand builder meplan is also offering a CO₂-neutral system stand made from sustainable materials for the first time.
For a climate-friendly journey, 110 charging stations on the exhibition grounds support electromobility.
In addition, Messe München already switched completely to regeneratively generated electricity in 2020.
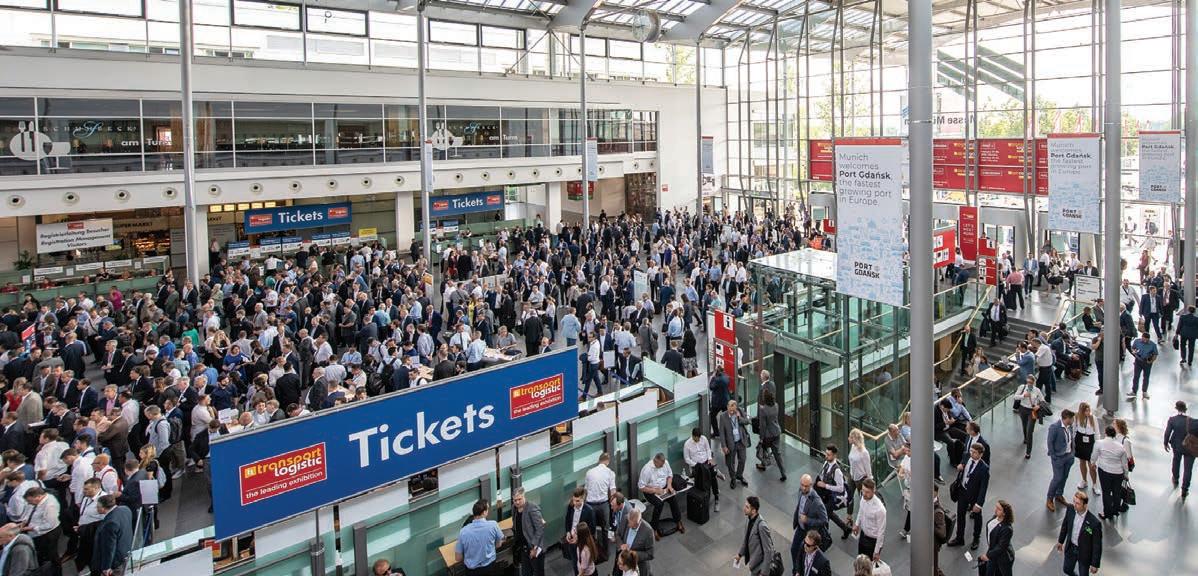
The complete conversion now saves around 6,400 tonnes of carbon dioxide per year in normal operation.
And visitors can also do something: as an alternative to the normal admission ticket, the so-called GoGreen ticket offsets the average ecological footprint with five euros for climate protection projects.
www.transportlogistic.de
SETTING NEW RECORDS IN DUBAI
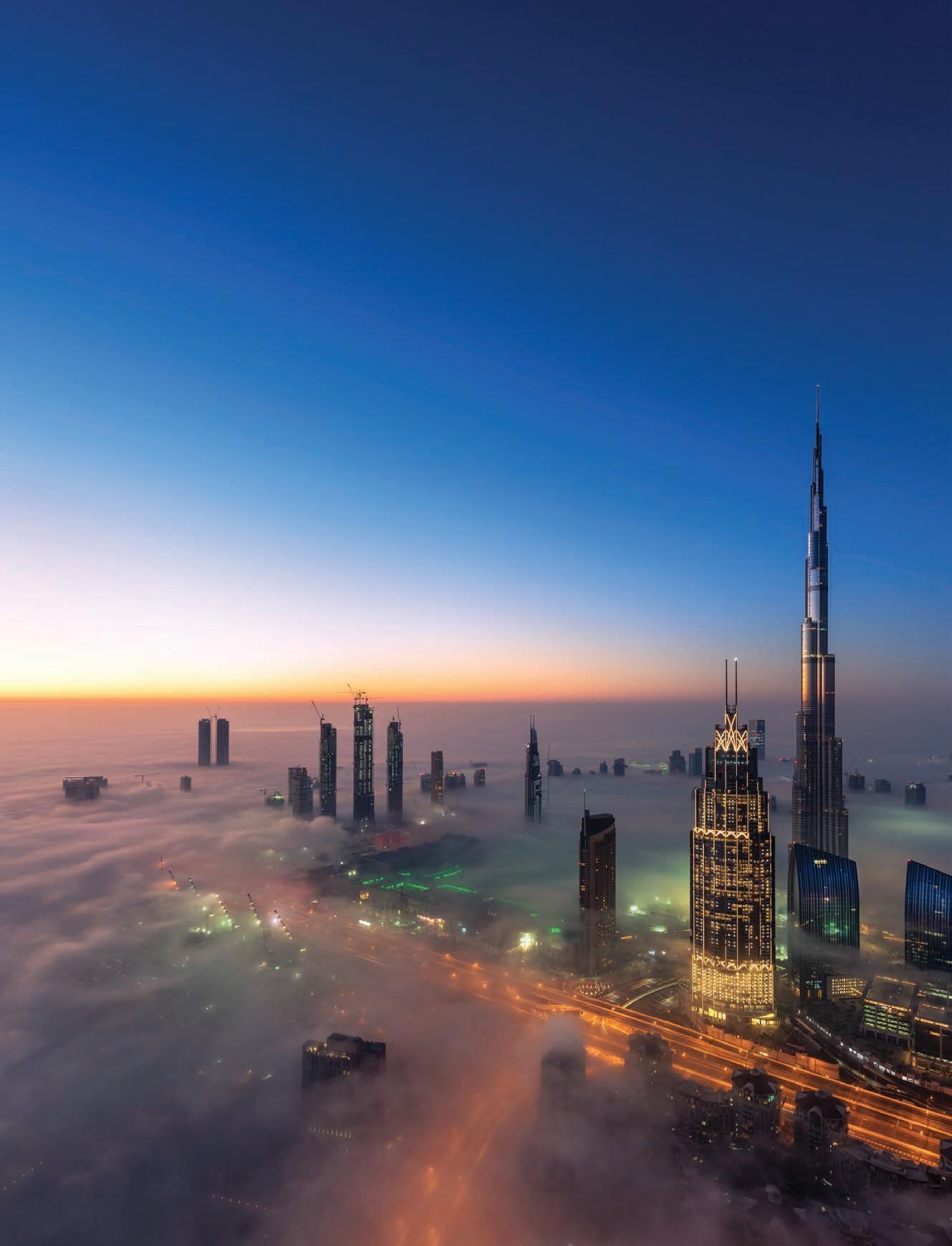
BREAKBULK MIDDLE EAST 2023 HAS BEEN DEEMED A STUNNING SUCCESS BY THE EVENT ORGANISERS.
This year saw 6,496 people attend Breakbulk Middle East 2023, a two-day event at the Dubai World Trade Centre.
“We are thrilled with the turnout and the engagement we saw from attendees this year,” said Ben Blamire, event director at Breakbulk Middle East. “The fact that we exceeded our own expectations in terms of footfall validates that there is a real appetite for knowledge-sharing and networking in the region’s breakbulk and project cargo sector, and BBME is playing a massive role in catering to it.”
Sponsored by Dubai-based port operator, DP World, Breakbulk Middle East 2023 also welcomed a record number of exhibitors from across the supply chain, including shippers, carriers, equipment manufacturers, forwarders, tech companies, port and terminal operators and heavy-lift specialists. Amid surging demand for exhibition space in the run-up to the event, the floor plan was expanded an unprecedented four times. With a 94 per cent rebook rate for 2024, a third hall will be added to accommodate current exhibitors who have requested a larger stand, and to make room for new companies looking to leverage the Breakbulk Middle East platform for new business opportunities.
“Networking is the backbone of the shipping sector,” said John Pittalis, Marketing and Communications Director at AAL and a member of the Breakbulk Europe Advisory Board.
“As companies grow, we become more disparate and we move into different regions, so it’s important that we can engage as close as possible with our audiences. Breakbulk offers AAL the opportunity to do that.”
Filiz Bozat, Chief Risk Officer at heavy transport specialist, Oznakliyat,” said: “Dubai is a central hub where there are so many opportunities to make connections. The response we have got is wonderful and we have met some great people and businesses.”
The exhibition hall’s main stage once again played host to a series of thought-provoking and engaging panel sessions, with expert speakers tackling hot topics such as sustainability, artificial intelligence and the exciting buildout of Saudi giga-projects.
Breakbulk’s inaugural Golf Day took place at the Dubai Hills Golf Club on the Sunday prior to the exhibition, while for the first time ever, a networking reception for event attendees was held on the evening of Day one at the 25Hours Hotel adjacent to the World Trade Centre.
On Day two, Breakbulk Media & Marketing Director, Leslie Meredith, hosted the popular Women in Breakbulk Breakfast, this year sponsored by Bureau Veritas, while the long-running Education Day designed to inform and inspire the next generation of logistics professionals welcomed more than 50 students and graduates to the all-day session.
“As always, Breakbulk Middle East is very well organized. It is the ideal platform to meet industry leaders and to network. The dialogues are inspiring and we are so happy to be a part of this event,” said Shikha Mishra, Marketing Executive at Bureau Veritas, and a speaker at the Women in Breakbulk Breakfast.
“Breakbulk Middle East has been one of the best events we have attended,” said Anfal Zahir Al Affani, Market Lead at Oman’s Ministry of Transportation, Communication and IT. Breakbulk Middle East 2024 will return to the Dubai World Trade Centre on 12-13 February.
www.middleeast.breakbulk.com
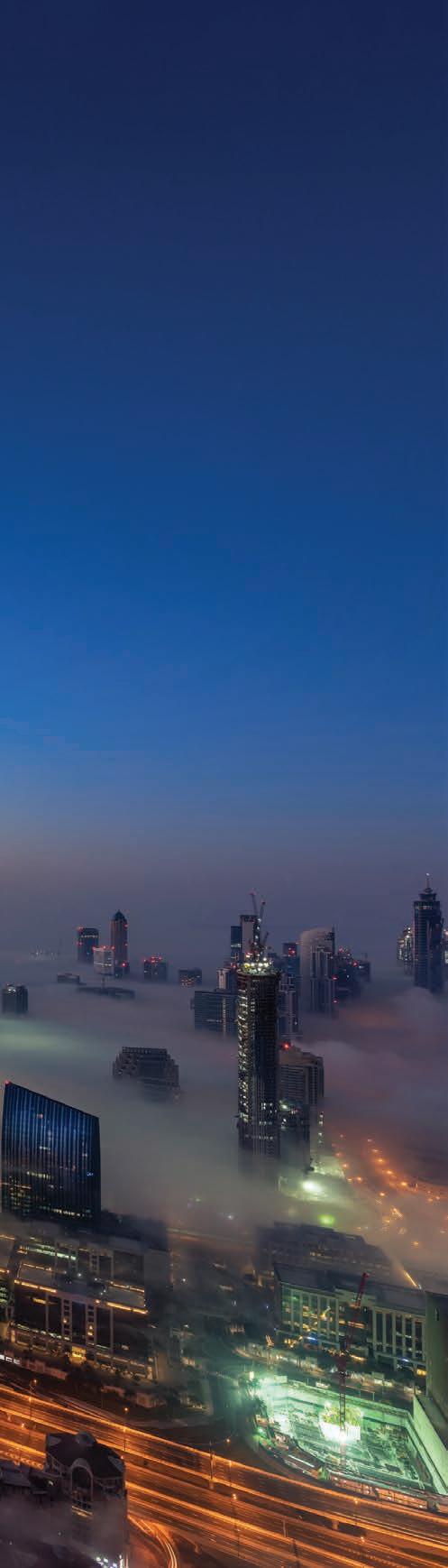
TRANSPORT LOGISTIC 9-12 MAY
Munich, Germany
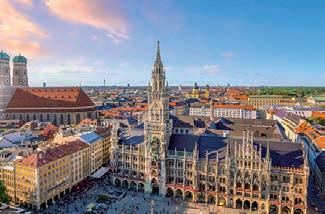
A trade fair for logistics, mobility, IT and supply chain management.
www.transportlogistic.de
TRANSPORT & LOGISTICS 24-26 APRIL
Jakarta, Indonesia
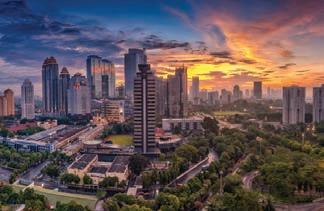
Scandinavia’s leading transport fair is the place for transport industry professionals to network and demonstrate innovation.
https://logistics-indonesia.net/
INTERMAC
10-13 MAY
Bangna, Thailand
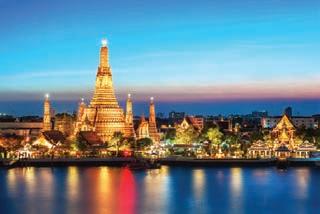
The 39th Intermach event presents the integration of advanced technology solutions including Industry 4.0, robotics and machinery in manufacturing processes.
www.intermachshow.com
EXPOCAM 2023 25-27 MAY
Montreal, Canada
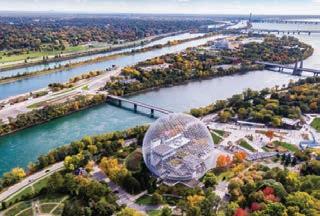
The meeting place for Canada’s trucking industry including new products, ideas and solutions for trucks, equipment and technology.
www.expocam.ca
BRISBANE TRUCK WEEK 18-21 MAY
Brisbane, Australia

Australia’s biggest trucking event which includes a showcase of truck and trailer technology and so much more.
www.brisbanetruckshow.com.au
TRUCK EXPO 2023 8-10 JUNE
Plovdiv, Bulgaria
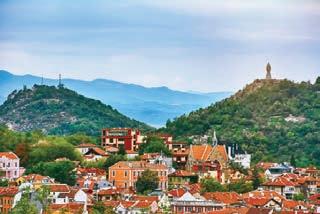
Truck Expo is reported to be the largest exhibition in Bulgaria for heavy and light cargo trucks, buses and specialised vehicles.
https://www.fair.bg/
KEEP A LOOK OUT
LogiMat China
14-16 June
Shanghai, China
www.logimat.cn
Coldchain Philippines 2023
12-14 July
Manila, Philippines
www.coldchainphilippines.com
Supply Chain & Logistics Arabia
19-20 July
Dubai, UAE
www.sclarabia.com
CeMAT Australia
25-27 July
Sydney, Australia
www.cemat.com.au
Elmia Lastbil
21-24 August
Sweden
www.elmia.se/en/lastbil
NUFAM 2023
21-24 September
Karlsruhe, Germany
www.nufam.de
Solutrans 2023
21-25 November
www.solutrans.eu
Bauma 2025
7-13 April
Munich, Germany
www.bauma.de/en
BREAK THE ICE
The global refrigerated road transport market will reportedly grow to $95.15 billion in 2027 at a compound annual growth rate of of 8.6 per cent.
This follows a release of The Business Research Company’s ‘Refrigerated Goods Trucking Global Market Report 2023’ which is touted to be a comprehensive source of information that covers every facet of the refrigerated goods trucking market.

“Increasing demand for perishable foods such as ready-to-eat food items, milk and dairy products, and fruits and vegetables is predicted to contribute to the growth of the refrigerated goods trucking market,” Business Research Company said in a statement.
North America, according to the report, is expected to hold the largest refrigerated goods trucking market share.
Some of the major trailer manufacturers competing in this space include Schmitz Cargobull, Great Dane, CIMC, Kögel and Hyundai Translead.
Major companies operating in this market are said to be continuously investing in introducing new technologies such as cloud computing, IoT solutions, solar-powered systems and communication technologies such as machine learning, GPS, and 5G for greater accountability, visibility and performance in refrigerated storage and transport.

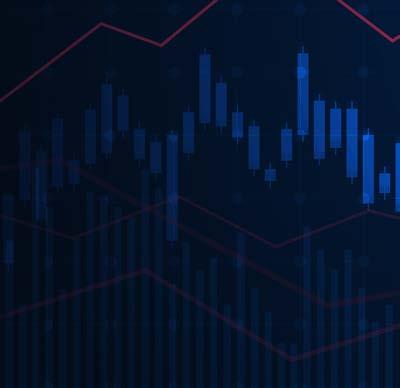
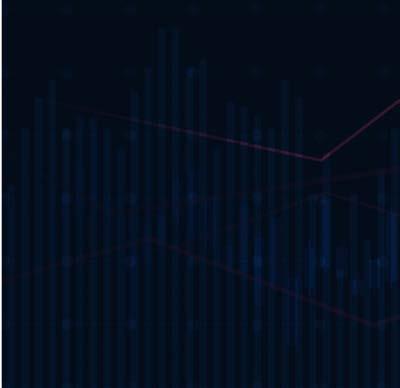
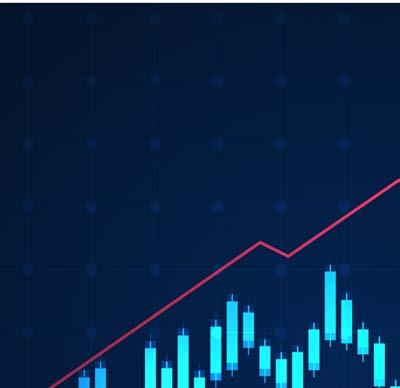

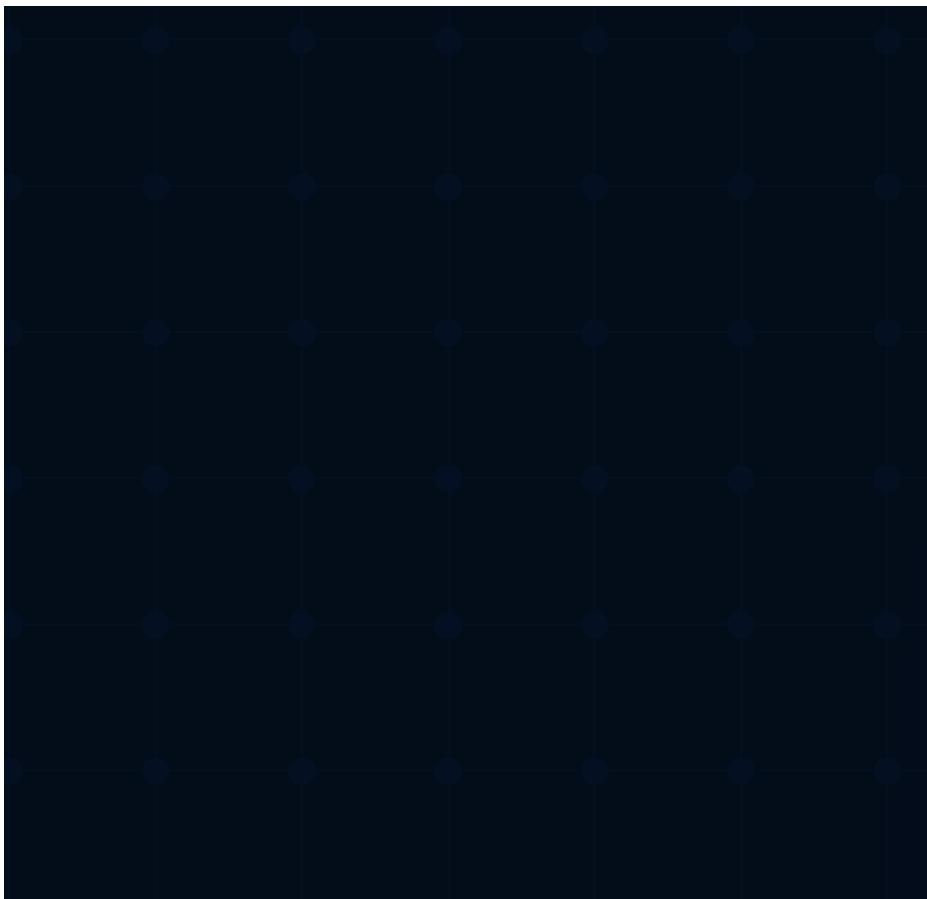
The Business Research Company has estimated that investments in this field are likely to reach $40 billion by the end of 2020.
The role cold chain carriers play in the storage and transportation of perishable goods is essential for keeping supermarkets stocked. Earlier this year, in Australia, it came to light that ‘unsustainable contacts’ were a root cause for the collapse of the nation’s largest freight carrier in this niche. The Transport Workers Union (TWU) had listed ‘uncommercial customer arrangements as a result of intense market competition’ as
a key reason for Scott’s Refrigerated Logistics being placed into voluntary administration. Other contributing factors are reported to include costs associated with fleet renewal, the operational impact of Covid-19 on the nation’s supply chain, floods and derailments. As a result, the TWU has been calling for supply chain parties to sign on to principles for a safer, fairer and more sustainable transport industry.
Almost 200 Australian companies in the sector became insolvent during the 2021-22 financial year.
At the time of the liquidation, it was understood that Scott’s Refrigerated Logistics had 24 warehouses in its portfolio across Australia that required clearing with food expected to go to waste as there was not enough storage capacity to relocate stock.
Government and industry, worldwide, must consider reform in the interests of maintaining continuity of food supply. www.globaltrailermag.com
Readyforbeing electrified?
EveryhugeE-Mobility-Conceptstartswith asmalldetail:ThenewE-Axle-Systemby SAF-HOLLAND–yourfirstprogressivestepinto therightdirection. Getreadyforthemostsustainablewayrunningyourbusiness andstarttodevelopyourfleettowardsmoreefficiency,safetyand responsibilityforthefuture.
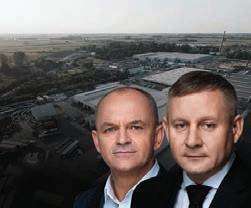

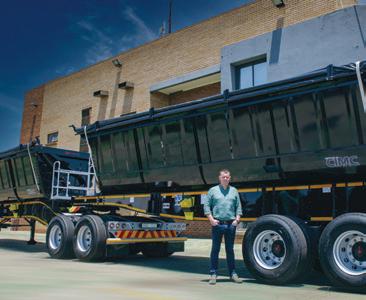





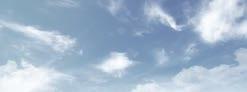
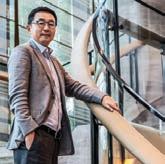
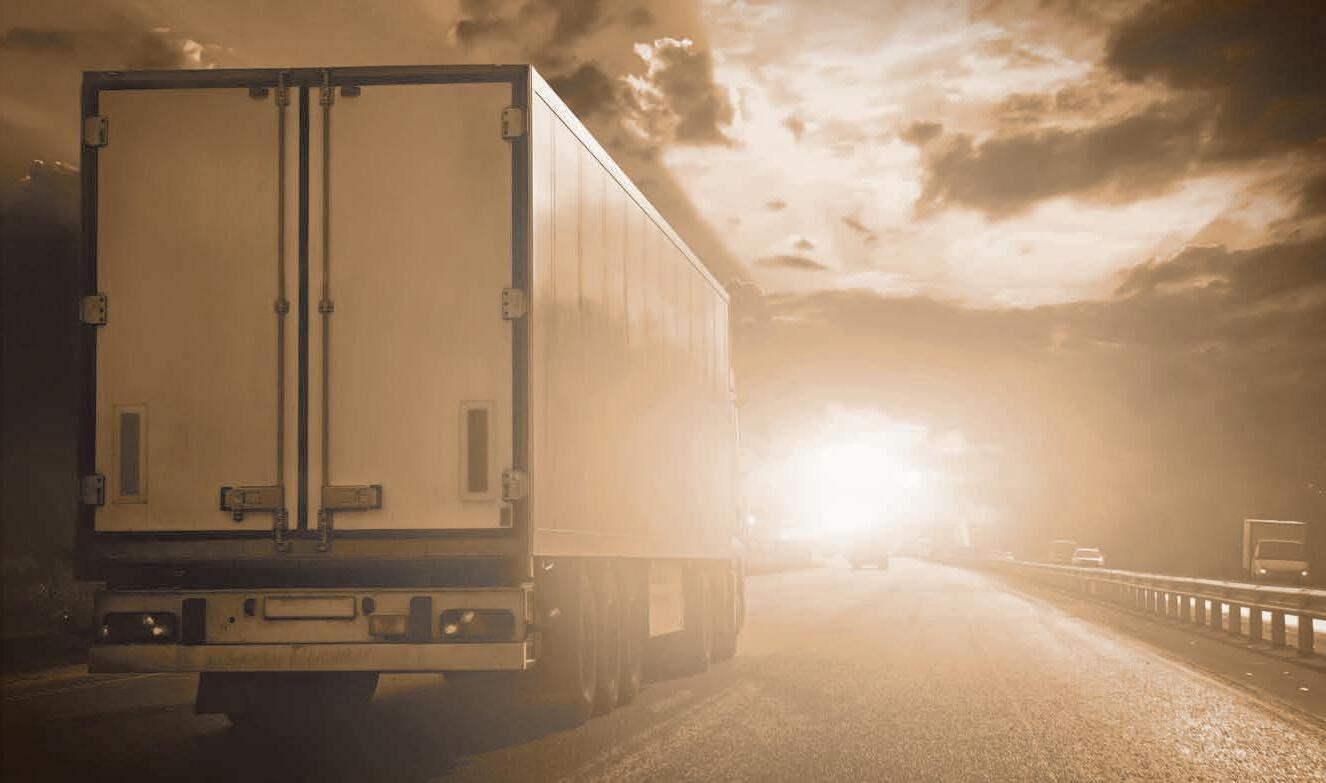
Into E-Mobility with SAF-HOLLAND
Heavy transportation traffic becomes electric, green and quiet with the recuperation axle SAF TRAKr
Every great E-Mobility concept begins with a first step: the new e-axle system from SAF-HOLLAND – the innovative technology for the electric transformation.

safholland. com
