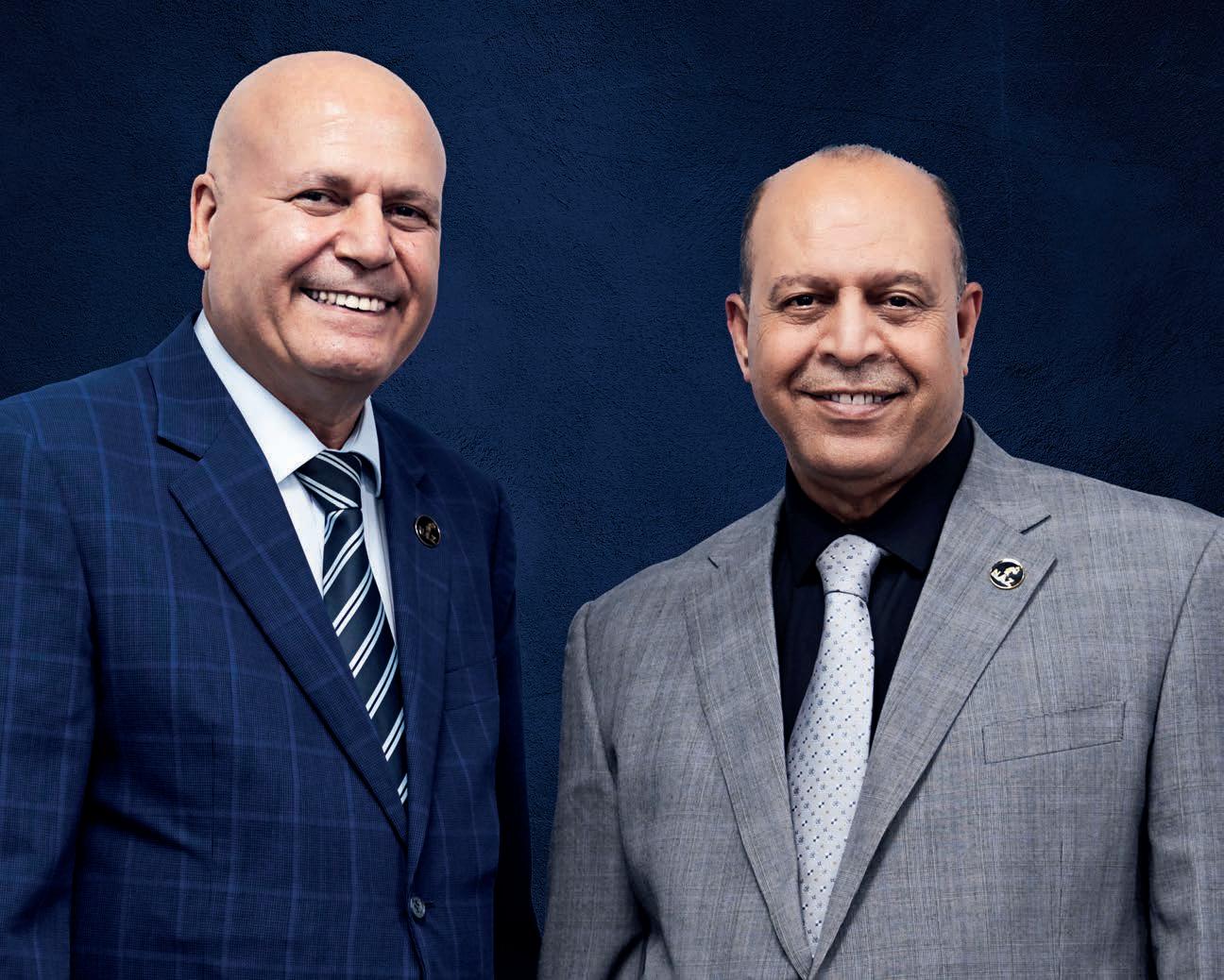
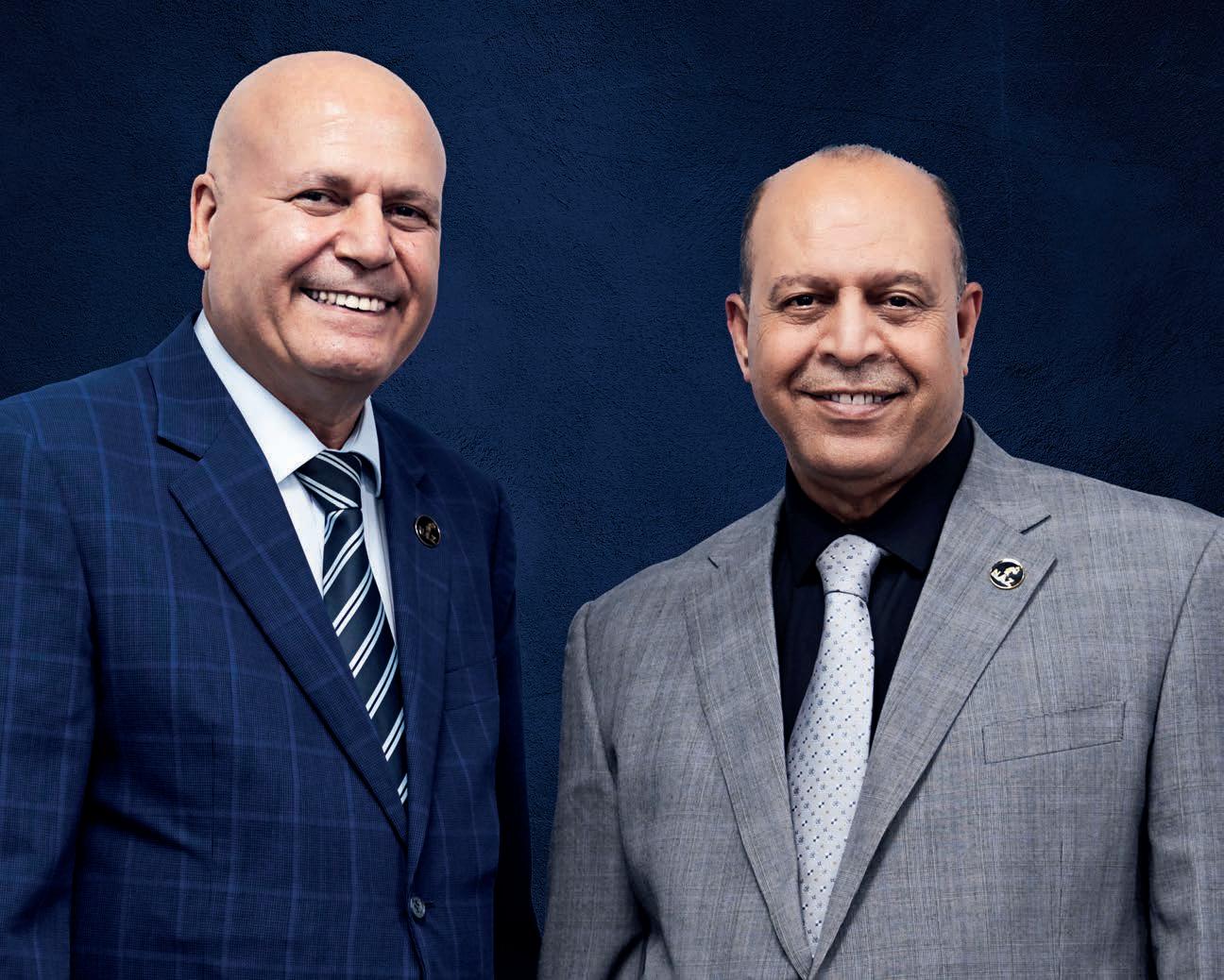
CHALLENGE US!
INDIVIDUAL RUNNING GEAR SOLUTIONS FOR SPECIAL TRANSPORT TASKS.
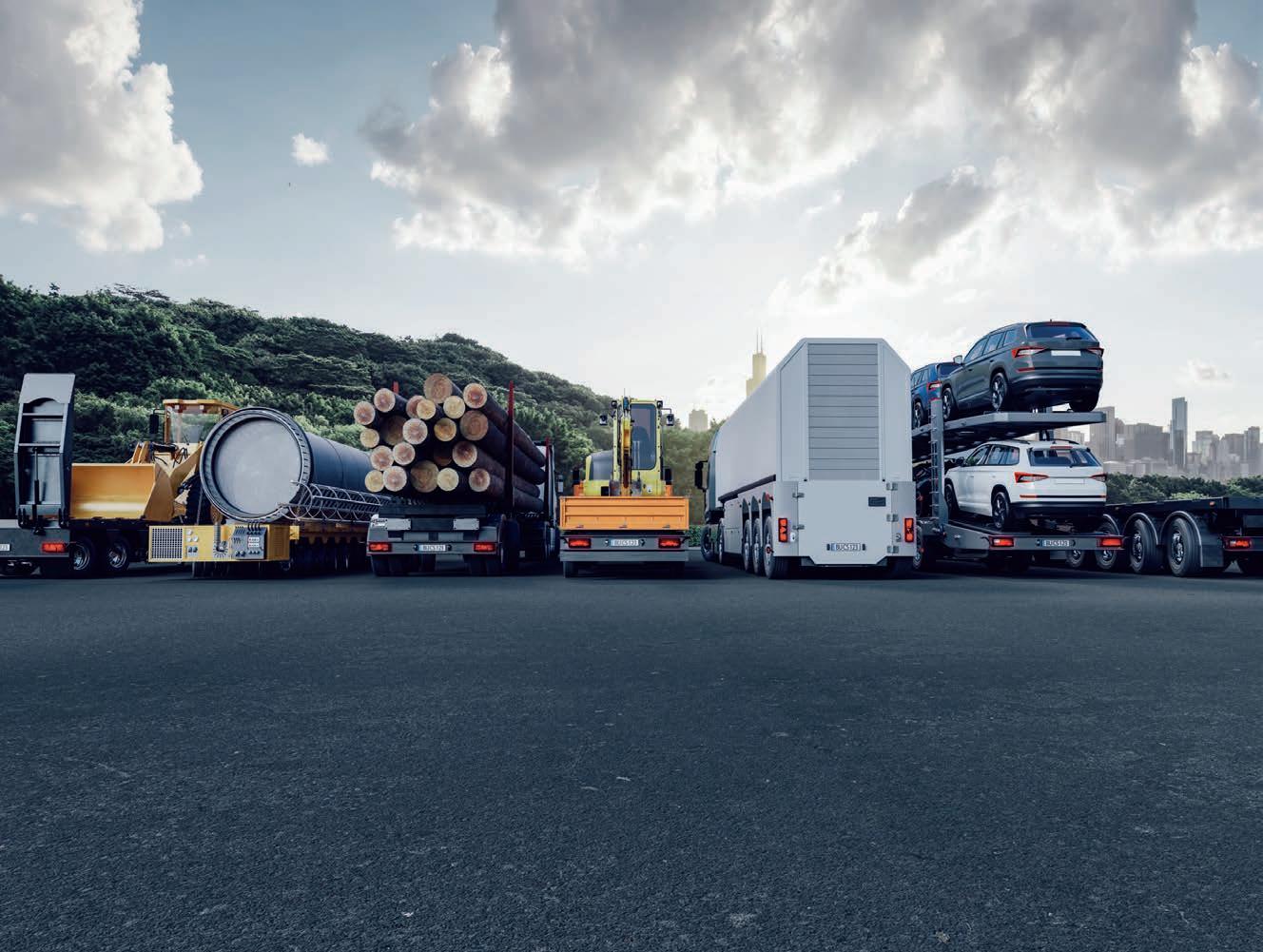
With our running gears and special axle solutions, there is nothing that can’t be transported. Your requirements motivate us to create new things. They inspire us to use our entire engineering expertise and decades of experience to develop innovative and reliable solutions together with you – customised for the type of vehicle and intended use.
The swing axle masters any heavy transport - even on critical ground and difficult terrain. It is part of our individual solutions that are uniquely powerful and resilient. Challenge us!
MORE INFORMATION: SPEZIALACHSEN.BPW.DE/EN/
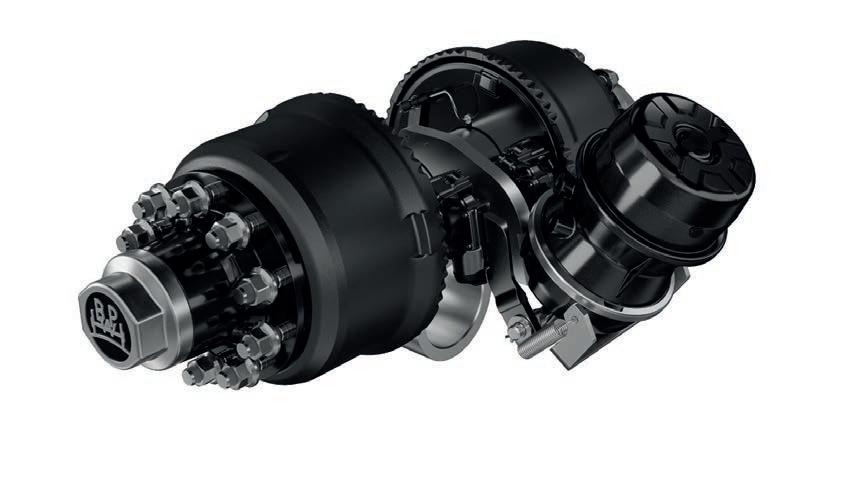
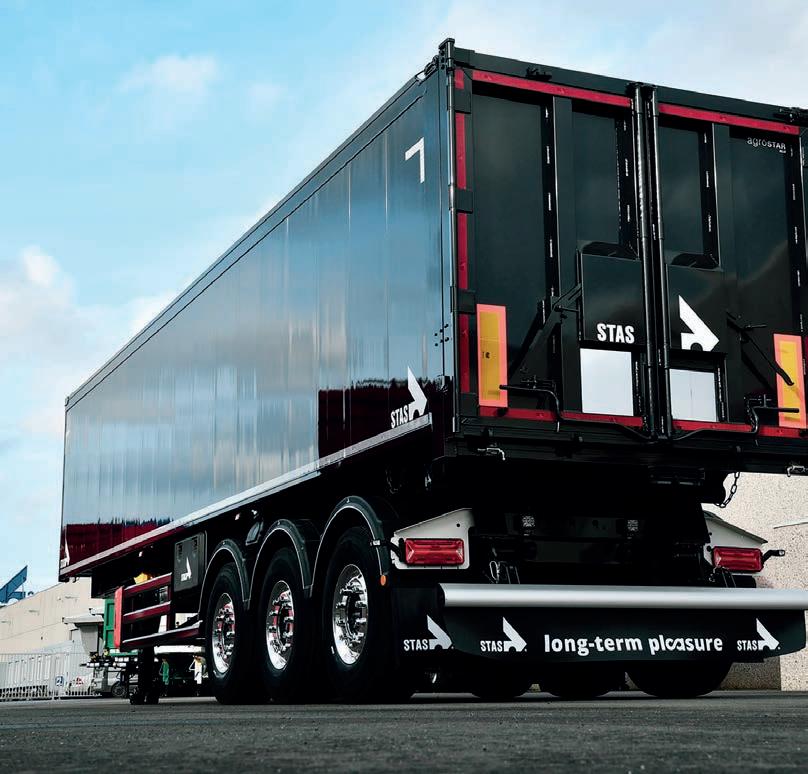
A VISION OF SUCCESS
It was an African proverb that helped NAZ Industries CEO, Adel Mir, understand both the passion and direction when he arrived in his new home of Dubai 30 years ago. That same proverb’s message has helped him reach new heights in trailer manufacturing, but it has been the strength of teamwork and a unique friendship that has made the ultimate difference.
“IF YOU HAVE GOOD PEOPLE ON YOUR TEAM, IT DOESN’T MATTER HOW DIFFICULT BUSINESS IS OR WHAT CHALLENGES YOU FACE. YOU WILL SUCCEED.”
NAZ Industries CEO, Adel Mir.
24 MARKET REPORT
A look at the state of Europe’s economic powerhouse, Germany.
36 INDUSTRY VOICE
Conversations at an executive level with Kögel and TIP.
44 WORLD VIEW
Recent trends with industrial logistics assets coupled with some bold moves by international logistics and road transport companies could disrupt the market quite significantly.
48
What you need to know about the World Green Summit.
52 SPECIAL REPORT
Cybersecurity persists as a hot industry topic.
28 TPMS
Wielton Group unveils its latest developments in Tyre Pressure Monitoring Systems.
30 TANKERS & SILOS
Whether it’s dangerous goods, foodstuff or waste, Kässbohrer has a road tanker or silo for the freight task.
32 BUILT TO TASK
Trailer deliveries and robotic automation.
40 MOBILITY
See how SAF-Holland and BPW are contributing to advances in heavy vehicle mobility.
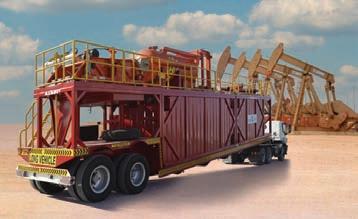
52
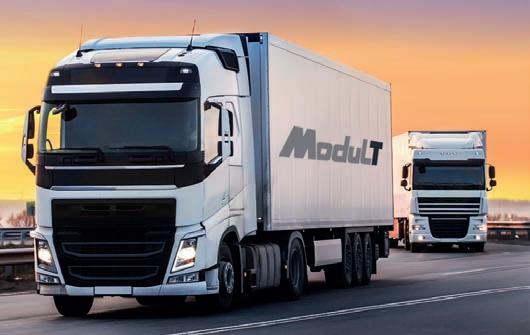
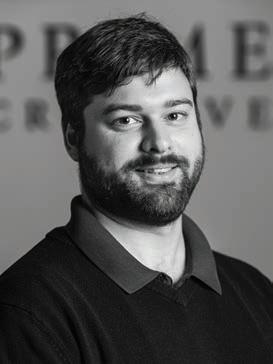
HERE COME THE DRUMS
LATE LAST YEAR I ATTENDED
the launch and grand unveiling of a chemical steel tanker – a fusion of innovation and craftmanship – at Essendon Airport, Melbourne. The new product marked a significant milestone for a specialist in the design and manufacture of bulk liquid storage and transport systems.
This innovation followed five years of growth and design maturity – a resounding success in the supply of aluminium tankers across Australia under a model of offering reliable, high quality alternatives at low price points for road transport operators. In essence, this is what we celebrate, at Global Trailer – growing and maintaining the relationships between fleets, manufacturers and suppliers that enable industry to improve safety outcomes and achieve greater productivity.
There is so much to look forward to in 2024 with the rollout of Tyre Pressure Monitoring Systems (TPMS), research dedicated to bolstering the cold chain as well as the other critical components and trailer technologies keeping freight around the world on the move.
This edition we unpack the economics of Europe with a focus on Germany. As an aside, when looking at government funding priorities, a national employer association
in Australia pointed to decarbonisation, diversification and digitalisation as key priorities. These are the areas, Ai Group said, that require long-term investment especially when industry is working through challenges such as inflation and in some instances uncertainty. It asserted that such a focus can help businesses better manage the tension between short-term challenges and long-term investment needs. For example, promoting investment, reforming regulatory barriers and supporting skills for energy transition opportunities should assist with the gradual decarbonisation of industry. Similarly, trade promotion efforts and commitment to skilled migration should lead to further diversification, while automation, AI, data stewardship and cybersecurity investments will reinforce digitalisation. This is where transport and logistics will truly see positive change.
We also speak with executive leadership at Kögel and TIP, review recent trends with industrial logistics assets and more broadly the acquisitions and mergers of road transport companies, discuss sustainability, marvel at robotic automation and more.
CEO
John Murphy john.murphy@primecreative.com.au
COO
Christine Clancy christine.clancy@primecreative.com.au
INTERNATIONAL SALES
Ashley Blachford ashley.blachford@primecreative.com.au
MANAGING EDITOR
Luke Applebee luke.applebee@primecreative.com.au
JOURNALISTS
Louise Surette louise.surette@primecreative.com.au
Peter White peter.white@primecreative.com.au
DESIGN PRODUCTION COORDINATOR
Michelle Weston michelle.weston@primecreative.com.au
ART DIRECTOR
Blake Storey
DESIGN
Kerry Pert, Louis Romero
CLIENT SUCCESS MANAGER
Salma Kennedy salma.kennedy@primecreative.com.au
COVER
Image: NAZ Industries
HEAD OFFICE
Prime Creative Pty Ltd
379 Docklands Drive Docklands VIC 3008 Australia
+61 3 9690 8766 enquiries@primecreative.com.au www.globaltrailermag.com
SUBSCRIPTIONS
+61 3 9690 8766 subscriptions@primecreative.com.au Global Trailer is available by subscription from the publisher. The rights of refusal are reserved by the publisher.
ARTICLES
All articles submitted for publication become the property of the publisher. The Editor reserves the right to adjust any article to conform with the magazine format.
COPYRIGHT
Global Trailer is owned by Prime Creative Media and published by John Murphy. All material in Global Trailer is copyright and no part may be reproduced or copied in any form or by any means (graphic, electronic or mechanical including information and retrieval systems) without written permission of the publisher. The Editor welcomes contributions but reserves the right to accept or reject any material. While every effort has been made to ensure the accuracy of information, Prime Creative Media will not accept responsibility for errors or omissions or for any consequences arising from reliance on information published. The opinions expressed in Global Trailer are not necessarily the opinions of, or endorsed by the publisher unless otherwise stated.

Follow us on twitter @Globaltrailer
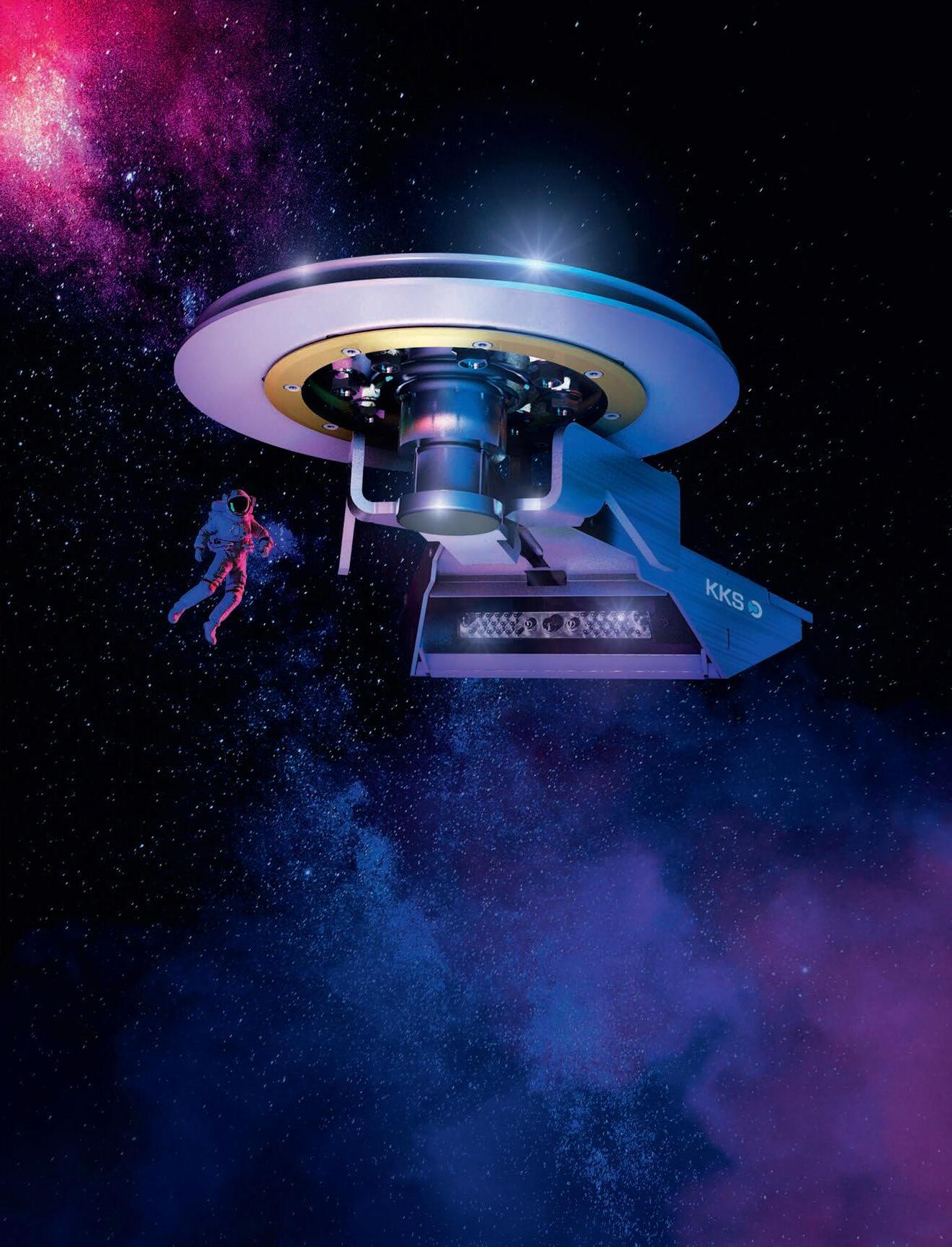
NEW:
OUT OF THIS WORLD
JOST KKS – push-button trailer coupling
#futurenow – Thanks to our revolutionary coupling system you can now change semitrailer quickly and safely out of the cab. Your start in the future of logistics. Ready to beam up?
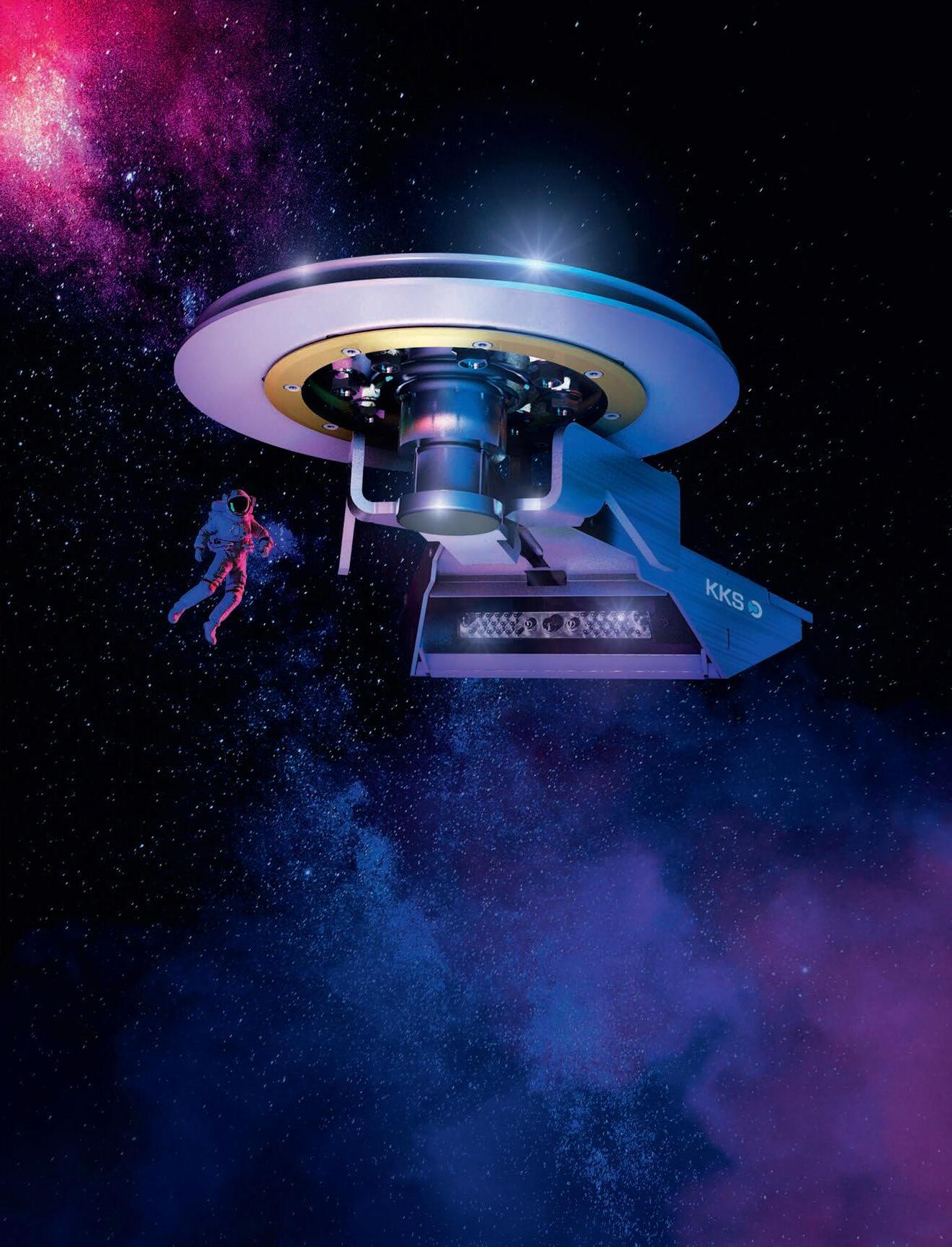
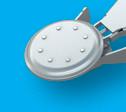
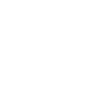
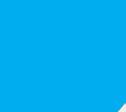

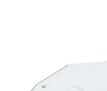
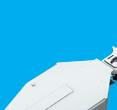
KKS-U CONNECTOR RETROFITTABLE TO EXISTING TRAILERS
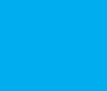

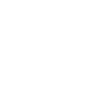
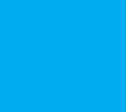

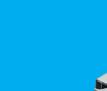
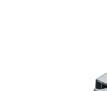
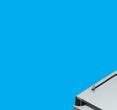
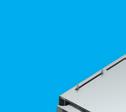
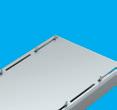

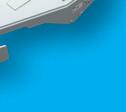
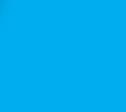

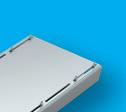

NEWS INTERNATIONAL
NORTH AMERICA
US
American AIT Worldwide Logistics has secured the purchase of Mach II Shipping Ltd, a UK-based freight forwarder specialising in worldwide distribution of pharmaceuticals and related products.
According to AIT, the acquired company has earned a reputation for high-quality shipping solutions in the life sciences industry, including transportation programs for clinical trials, active pharmaceutical ingredients, pharmaceutical machinery and finished products.
“In addition to temperature-controlled air freight, Mach II provides outstanding dedicated road service for high-value life sciences moves throughout Europe,” said AIT Executive Vice President, Life Sciences, Chris Amberg. “Additionally, their valueadded services include in-house customs clearance and a temperaturecontrolled warehouse near London Heathrow Airport.”
CANADA
Canada Post Corporation has announced it will sell its third-party logistics business SCI Group Inc. as it looks to ‘transforming’ to better serve its customers.
Montréal-based Metro Supply Chain has agreed to purchase SCI which specialises in warehouse fulfilment, supply-chain solutions and transportation management.
It operates independently with more than 75 locations totalling almost 400,000 square metres and employs approximately 3,000 team members.
The potential sale process began in 2023 after a detailed review and assessment of Canada Post’s long-term strategic plan.
Canada Post is now in the process of finalising the transaction with Metro Supply Chain, which is subject to regulatory approval.
Canada Post is a Crown corporation that functions as the primary postal operator in Canada.
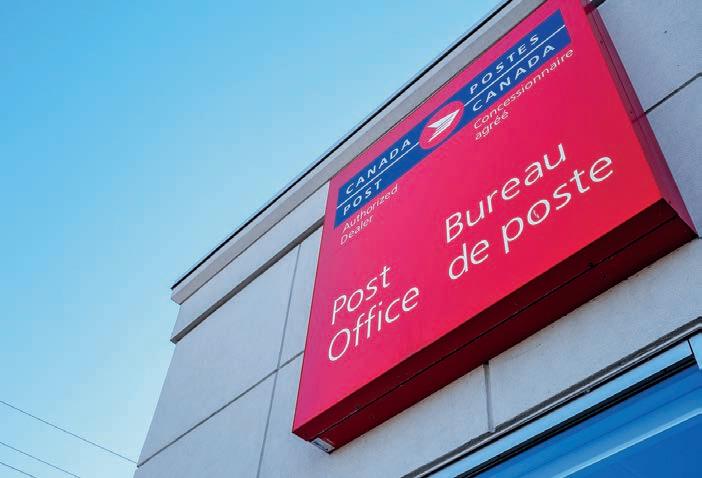
US
DHL Express has announced the appointment of a new regional CEO for the Americas, with the incumbent moving to a new role as CEO for DHL Express Europe.
Andrew Williams, the current CEO for DHL Express Canada, will take on the role as the new regional CEO.
Current Americas CEO Mike Parra will begin a new role as the CEO for DHL Express Europe. Both will report to John Pearson, Global CEO for DHL Express, and will be members of the DHL Express Global Management Board.
“These appointments recognise the strong leadership and commitment to service excellence and to our customers’ success of both Mike Parra and Andrew Williams,” said Pearson. Williams, who grew revenue by nearly four times and doubled the Canadian team in size, will now be responsible for the management of the DHL Express business in more than 55 countries and territories.
US
Trucking company, XPO Inc, was the top bidder at a sale of bankrupt Yellow’s assets, winning the right to 28 service centres at a price tag of $870 million. The 100-year-old transport firm, which serviced the less-than truckload market, filed for bankruptcy protection in August blaming ongoing strike action by the International Brotherhood of Teamsters union for its financial woes. Yellow’s 17.5 million annual shipments made it the third largest in the U.S., but it had an outstanding debt of about $1.5 billion as of March, despite receiving a $700 million loan from the federal government in 2020.
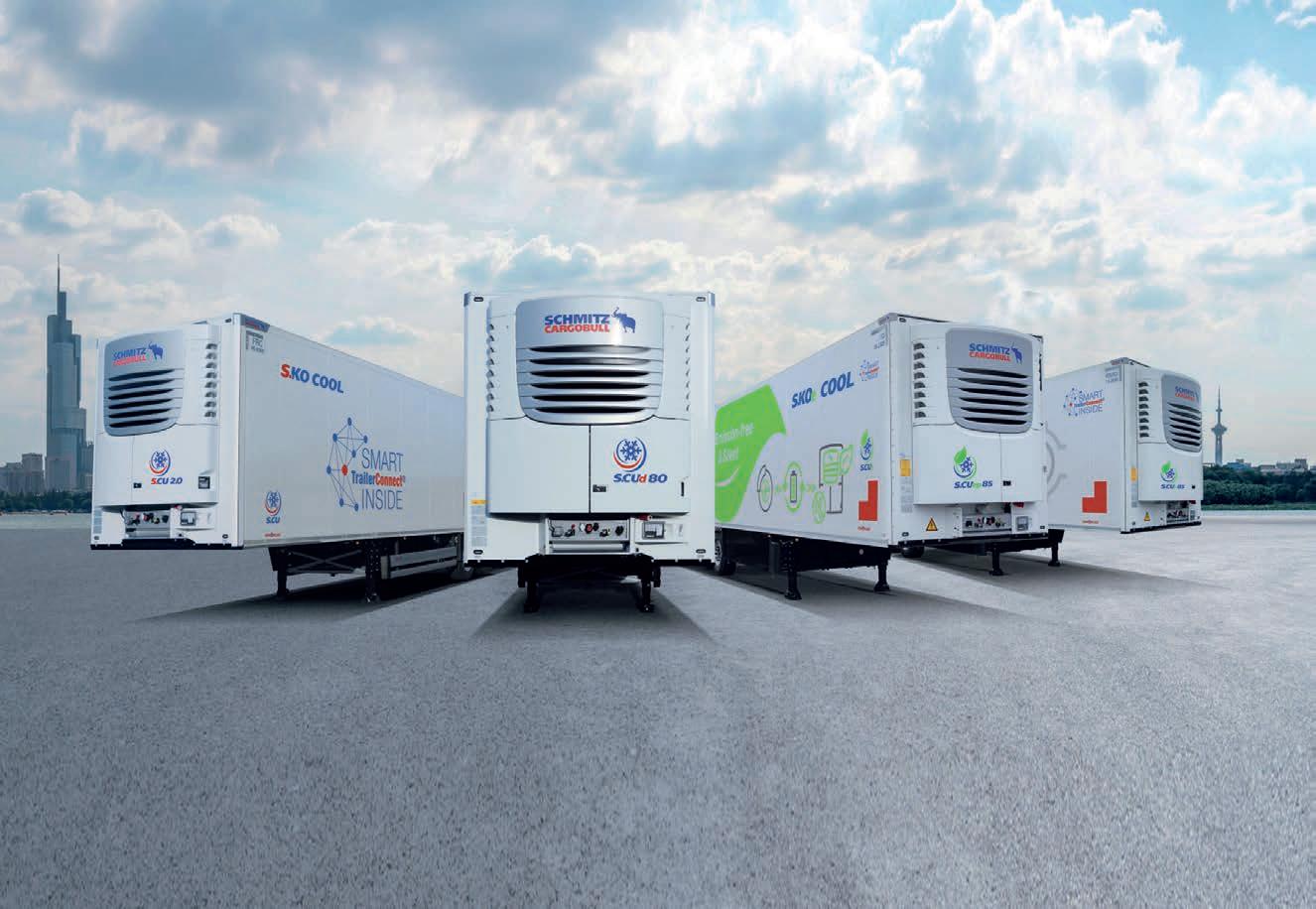
NORTH AMERICA
According to a report by Reuters, XPO expects the deal, which is subject to court approval, to add to core profit in 2024 and adjusted profit per share from continuing operations from 2025.
CANADA
Transport and logistics company, Kuehne + Nagel, is expanding its customs brokerage services in North America following its latest acquisition announcement.
Kuehne + Nagel is acquiring Farrow, an operation with 830 employees, 41 locations across Canada and the US and headquartered in Windsor, Ontario.
The acquisition is reported to complement cross-border capabilities at the US borders with Canada and Mexico.
Completion of the transaction is expected during the first quarter of 2024. The acquisition is subject to approval from regulatory authorities and customary closing conditions. Upon close, Farrow will become a fully owned subsidiary of Kuehne + Nagel.
US
Commercial vehicle parts manufacturer, STEMCO, has struck a deal with Great Dane to make its Auto-Torq axle
Canada Cartage buys GTI Image: Canada Cartage.

fastener standard on all Great Dane trailers.
Introduced to the market earlier this year, the Auto-Torq eliminates the need
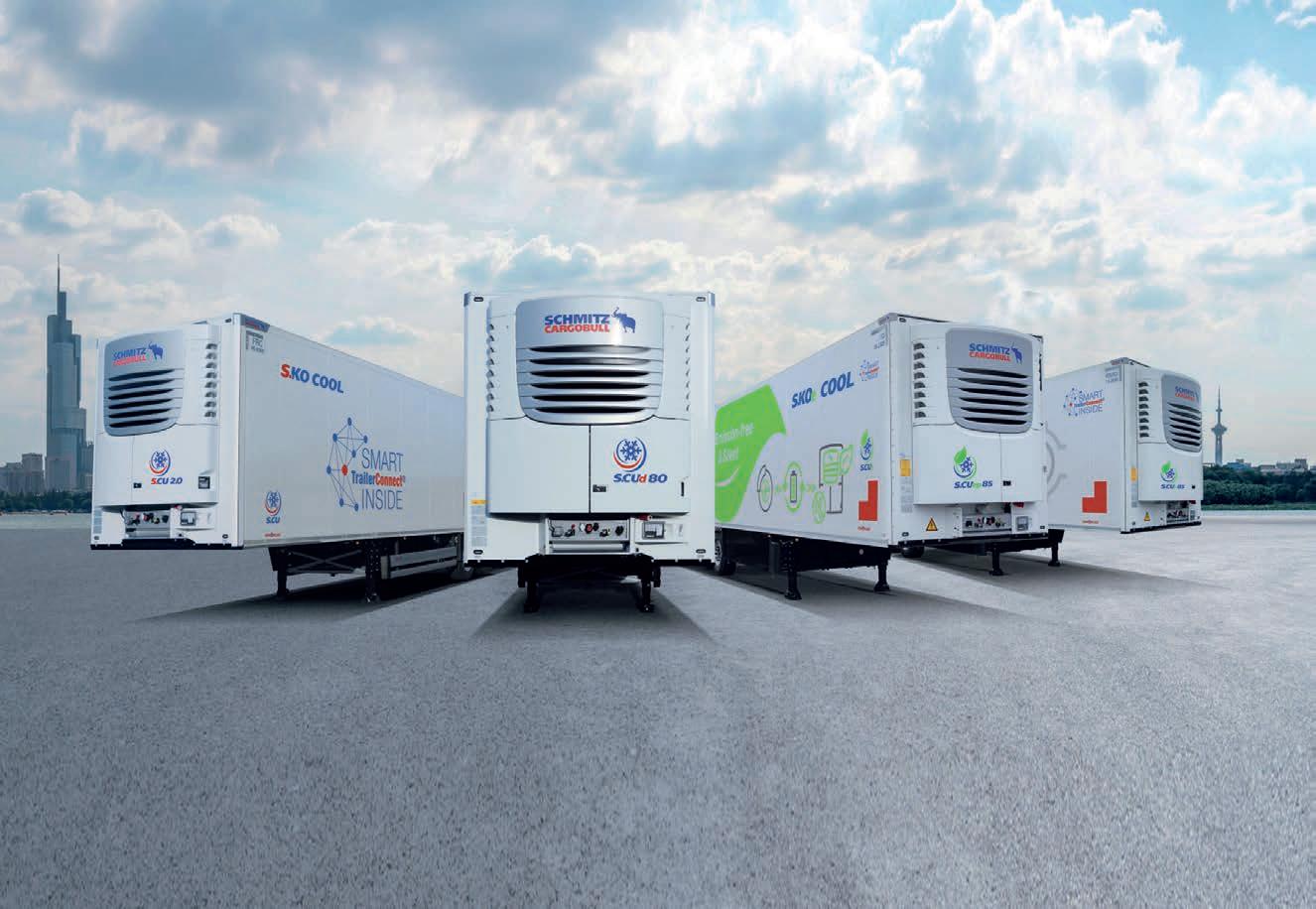
Perfectly
NEWS INTERNATIONAL
NORTH AMERICA & SOUTH AMERICA
for complex processes and specialty tools. It securely applies the optimum clamp load on the bearings to minimise wear and maximise service life.
“This works with any industry hub manufacturer, simplifies installation, and extends bearing life by ensuring that the optimum clamp load is applied,” said VP of Product and Sales Engineering for Great Dane, Barry Personett.
The American trailer builder said it foresees the all-in-one solution streamlining wheel end installation and underscores the company’s desire to meet its customers evolving needs.
CANADA
Transport and logistics provider, Canada Cartage Corporation, will acquire The GTI Group (GTI), increasing its scale in services such as freight management, freight brokerage and specialised freight hauling.
Headquartered in Montreal, Quebec, GTI provides customers in Canada and the United States with a range of supply chain service offerings, allowing Canada Cartage to enter the US market for the first time in its 110-year history. GTI has offices in Houston, Texas, Des Moines, Iowa, and Franklin, Tennessee. With the acquisition, Canada Cartage is expected to generate over C$1 billion of annual revenue on a combined basis.
CANADA
Polaris Transportation Group, a North American provider of cross border transportation and logistics, announced the company’s new President.
Richard Kunow has been the company’s CEO since 2020 and will now, as President, oversee Polaris
Transportation Group and Polaris Commercial Warehousing companies. Dave Cox will hold the position of Polaris CEO. In this role, Cox will be at the forefront of leading growth and visionary initiatives, sustainability efforts, workplace culture, communityfocused programs and technological advancements, the company said in a statement.
US
December’s US preliminary net trailer orders increased nominally from November to December, but at 24,300 units, orders were lower compared to last December by 58 per cent.
“While orders were down materially from year-ago levels, preliminary net orders, at 17,200 seasonally adjusted, were about 10 per cent higher sequentially,” said Director CV Market Research & Publications at ACT Research, Jennifer McNealy, adding that December’s preliminary net orders aligned with less-thanstellar expectations, particularly amid a backdrop of weak profitability for truckers and anecdotal commentary from trailer manufacturers who have shared that orders are coming but at a slower pace than they have the last few years.
CHILE
Chile has become the first country in the Latin America region to become part of the Rhenus perishable vertical, providing temperature-sensitive transportation.
Rhenus Fresh is a tailored logistics solution created specifically for the transportation of perishable goods globally.
This development represents a significant milestone for the company in Latin America, expanding the organisation’s expertise in perishable cargo while leveraging the country’s growing demand for the exports of fresh products.
Chile is strategically positioned to serve domestic and international markets, ranking among the world’s largest fruit exporters.
Rhenus Chile’s significant trade in fresh perishables with Asia highlights the growing demand for cherries, peaches, blueberries, and other fruits shipped to China.
Rhenus Fresh has said it will soon expand to other Latin American countries.
BRAZIL
CEVA Logistics has announced a strategic appointment to support growth in the Latin America (LATAM) region.
The transport and logistics company has appointed Milton Pimenta to the role of Managing Director LATAM. With his decades-long knowledge and experience in the logistics sector, Pimenta is tasked with leading the LATAM region into the next phase of the company’s strategic growth plan for LATAM.
“We have a deep-rooted culture of operational excellence at CEVA, and I am committed to building upon that culture by delivering innovative logistics solutions and exceptional service to our valued customers,” said Pimenta.
Pimenta’s journey at CEVA began in 2001. Since then, he has showcased his leadership in a variety of roles,
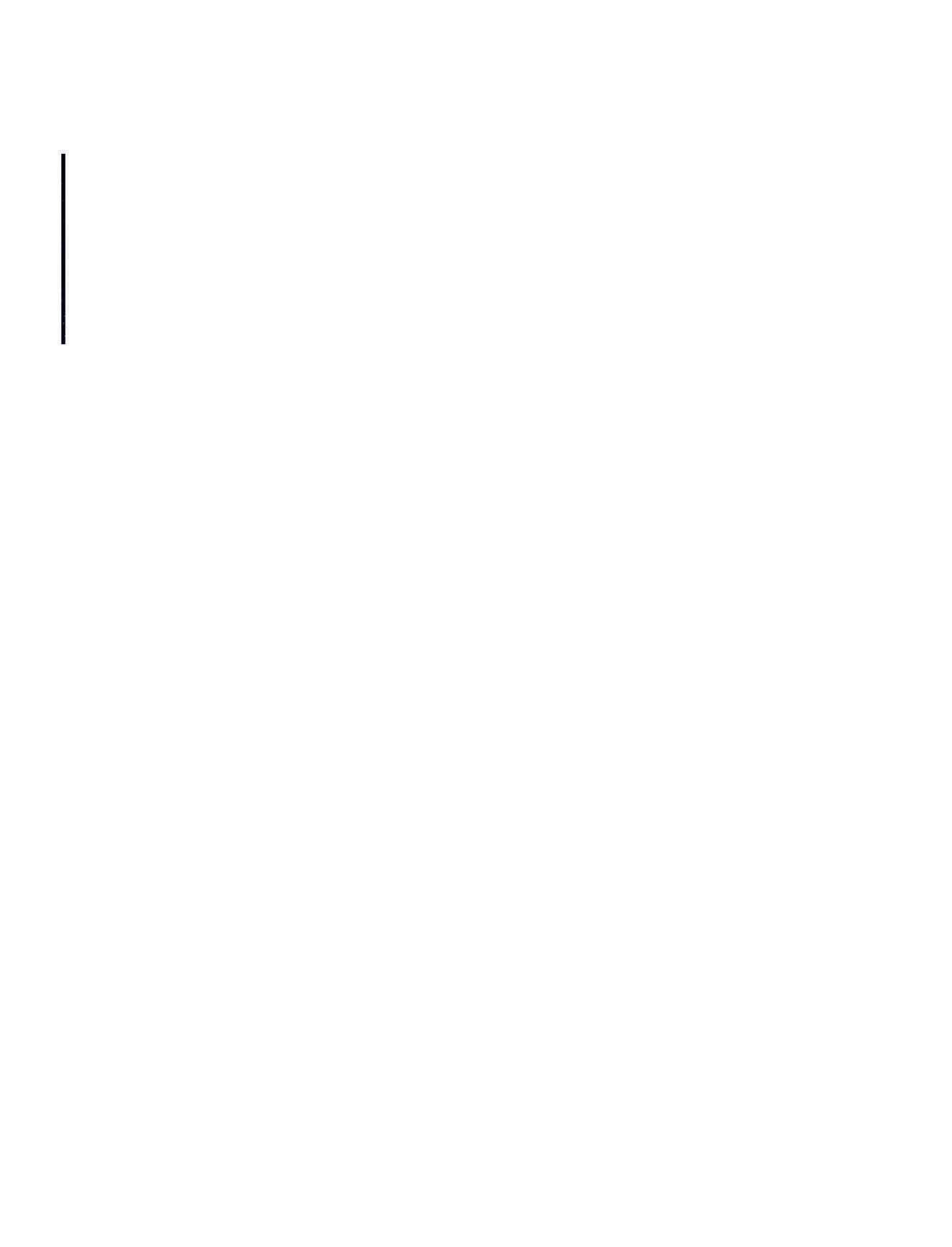
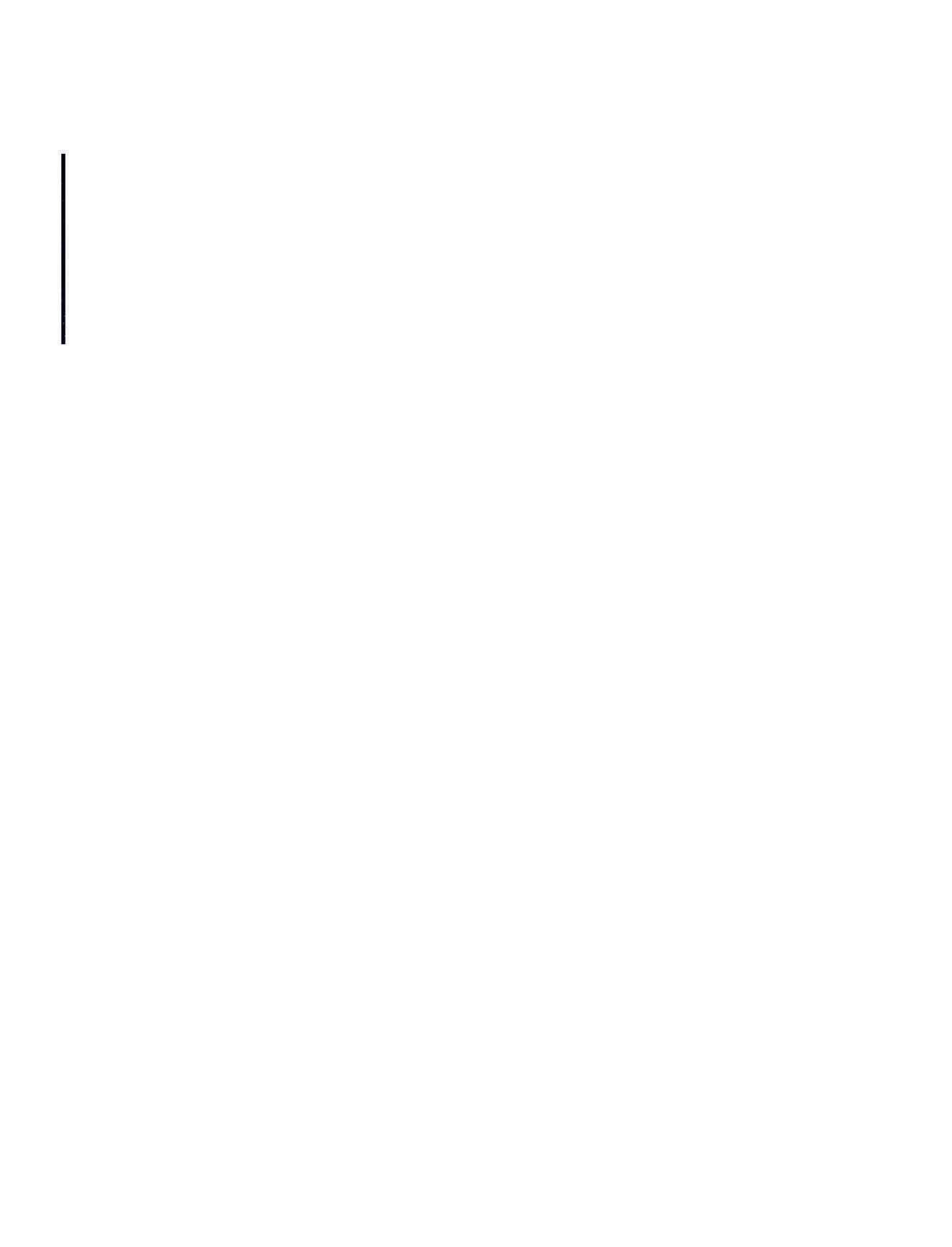
NEWS INTERNATIONAL
ASIA
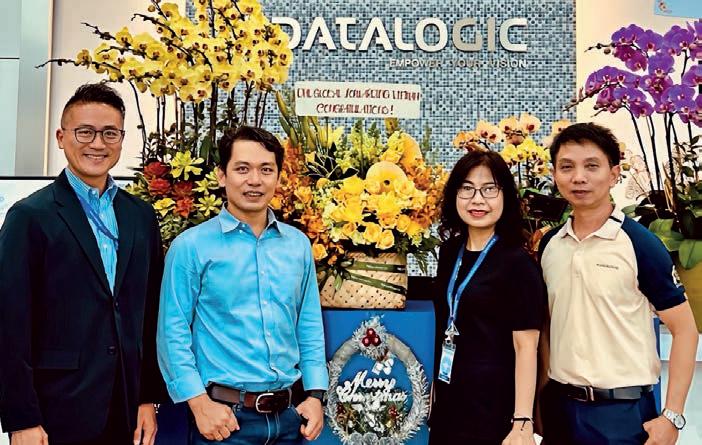
including business development and operations.
He served as Senior Vice President of Contract Logistics and Ground Transportation between 2015 and 2018.
INDIA
Equipment specialist, JOST, has established its second production plant in India which is located near Chennai. This facility is reported to be set up to produce front loaders and associated implements and backhoes for the agriculture brand Quicke at Greenbase Industrial and Logistics Park belonging to the Hiranandani group.
The first facility in Jamshedpur, which produces fifth wheels, axles, suspensions and other products, opened in 2008.
With a construction period of less than 12 months, the established plant is strategically located close to the port and in the heart of the most industrialised Oragadam area of Chennai.
Modern manufacturing technologies
and assembly lines for production have been installed on the 16,866m² premises. The neighbourhood of the plant includes leading multinational commercial vehicle, passenger car manufacturers and global R&D centres.
VIETNAM
DHL Global Forwarding Vietnam has formed a partnership with Datalogic to reduce CO₂ emissions.
A global technology company that specialises in data capture and factory automation markets, Datalogic will become the first customer in Vietnam to adopt DHL’s GoGreen Plus Solution which offers shipments that substitute heavy fuel oils with eco-friendly alternatives.
GoGreen Plus reduces carbon emissions in Full-Container Load and Less-Than-Container Load shipments with a combination of insetting and offsetting methods using eco-friendly fuel alternatives such as biofuels or sustainable marine fuel and carbon credits. This collaboration is expected
to reduce 40,000 kilograms of CO₂ emissions.
MALAYSIA
Owner-managed logistics company
Röhlig Logistics has further expanded its global footprint with the opening of a new sales office in Penang, Malaysia. “The state of Penang has been a focal point of foreign direct investment, particularly from the high-tech manufacturing industry,” said General Manager for Röhlig Malaysia, Dickson Ooi.
A busy international airport and a feeder seaport connecting Penang to the region’s main ports provide the necessary infrastructure to support growing supply chain demands, the company said.
Röhlig has appointed Samantha Saw as Branch Manager for the new office.
TAIWAN
Dimerco Express Group has appointed Jeffrey Shih as CEO in charge of the third-party logistics company’s three business divisions – air freight, ocean freight and contract logistics.
Shih has 35 years of logistics industry experience include leadership roles in both corporate logistics and 3PL operations, primarily with Dimerco, having run its operations in Southeast Asia and, most recently, North America.
“My focus, first and foremost, will be taking care of the customer and providing the high level of logistics management service they expect,” said Shih. “Looking ahead, Dimerco will continue its global expansion efforts, particularly in the US market.” Meanwhile, Dimerco will continue to innovate through digitalisation.
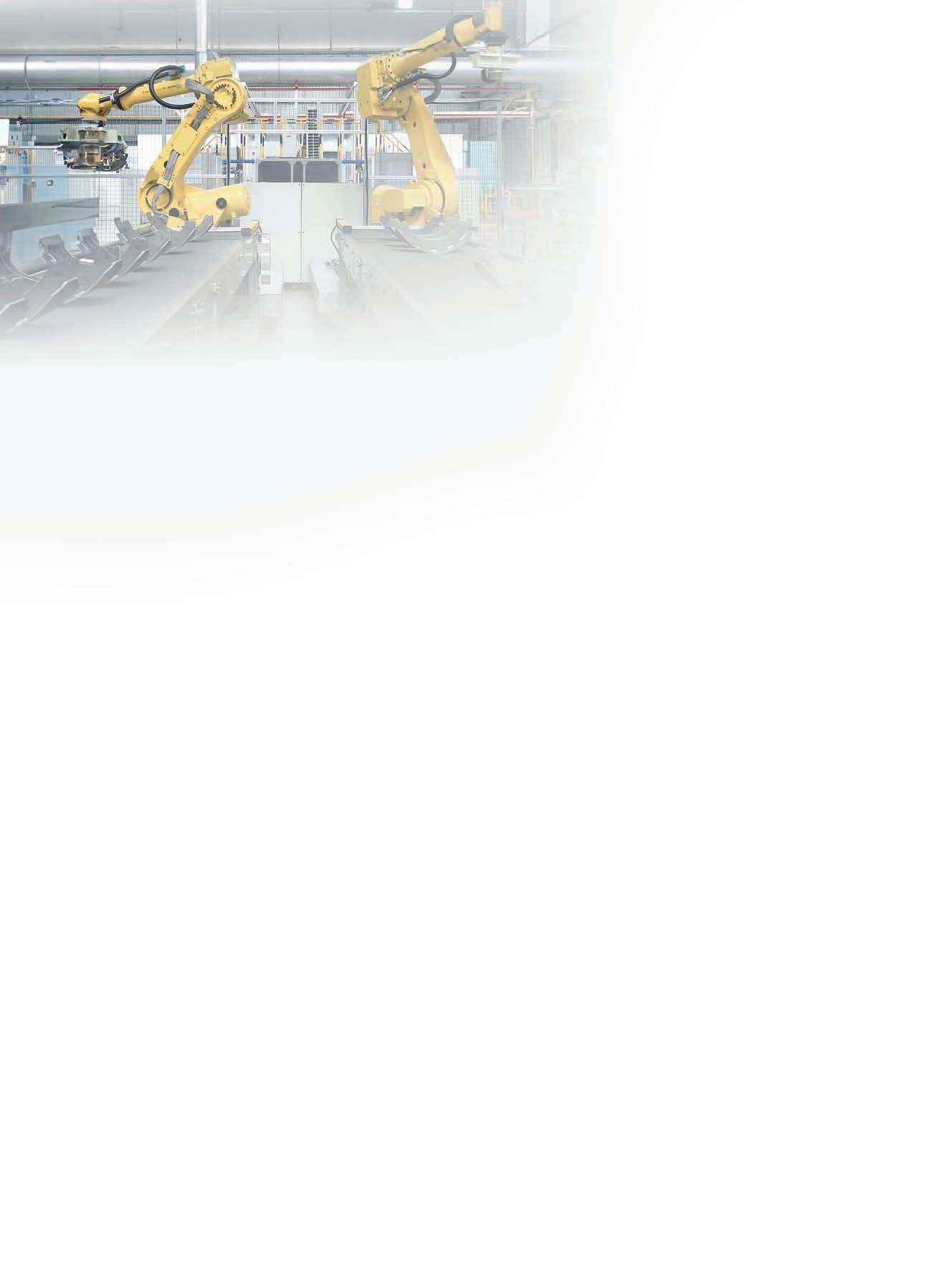
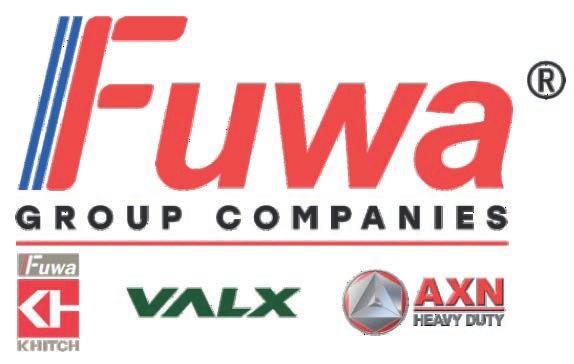
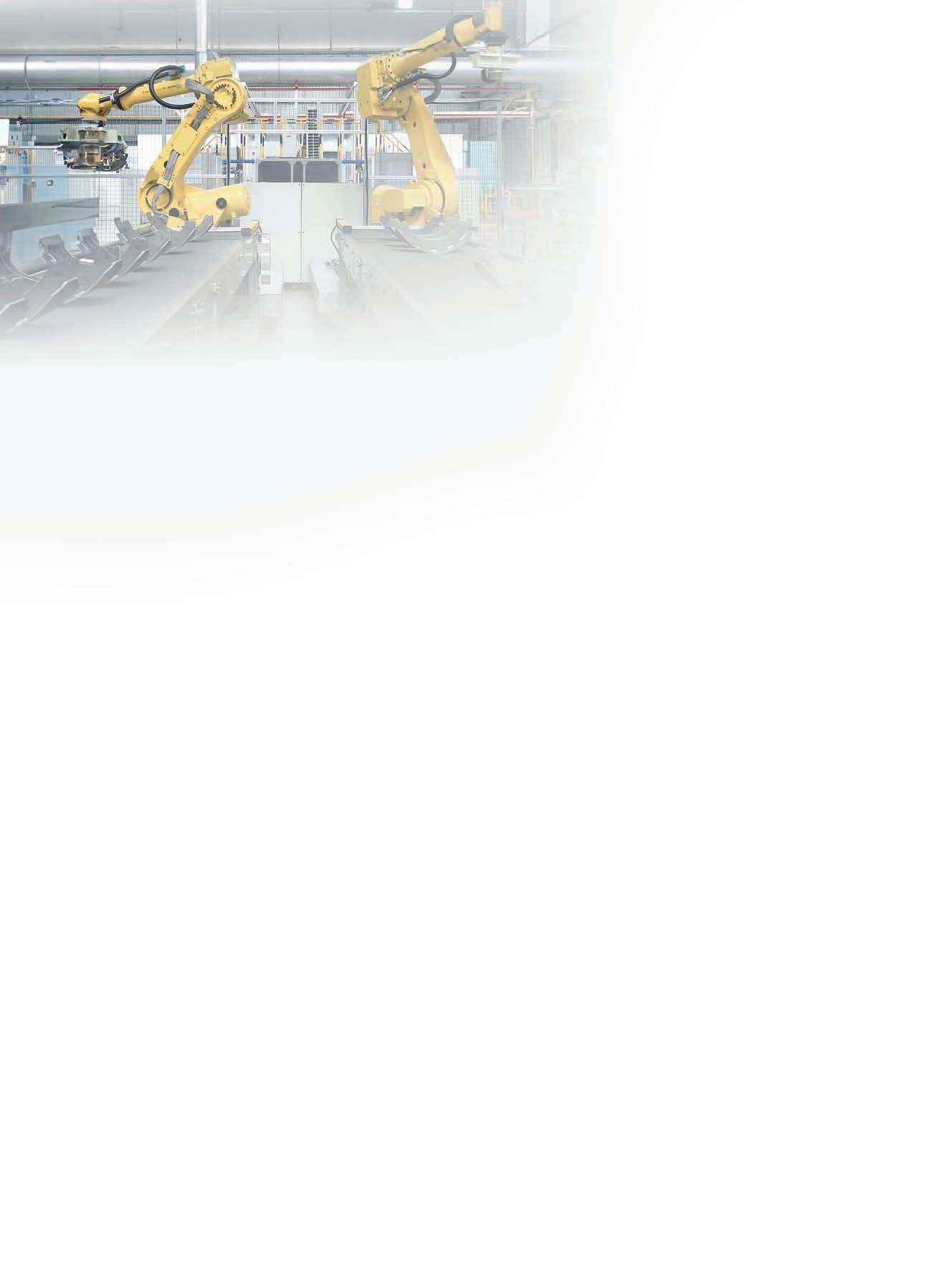
A state of the art, upgraded and fully integrated global manufacturing centre of trailer systems and On/Off highway systems. Expertly designed and engineered with worldwide accessibility, offering you private label and OEM manufacturing solutions.
Drawing upon decades of expertise spanning Asia, Australia, US, and in Europe, Fuwa stands as a global manufacturing powerhouse, unrivalled as the foremost network of specialists in truck and trailer components across the globe.
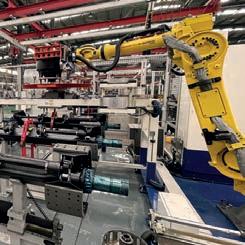
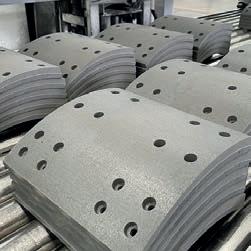
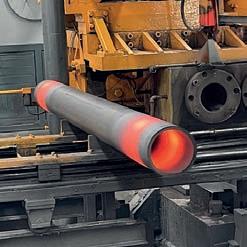

P:
P:
P:
NEWS INTERNATIONAL
ASIA & EUROPE
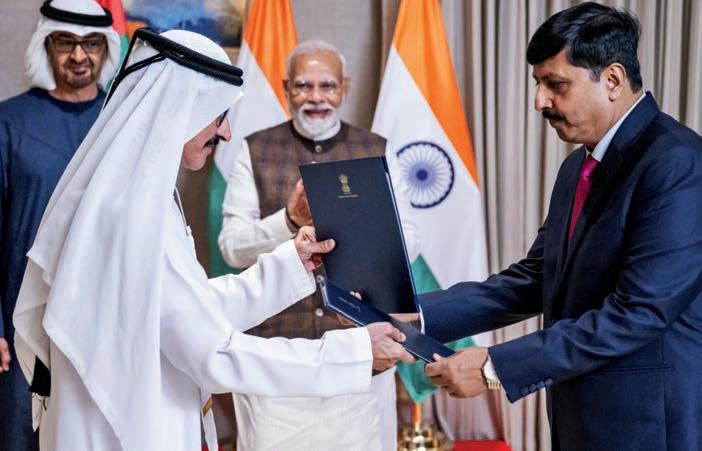
INDIA
DP World will strengthen its commitment to supporting Gujarat, an Indian state known as an important centre for ocean trade.
The global logistics company has signed Memorandums of Understanding (MoUs) worth 250 billion INR ($3 billion USD) with the Government of Gujarat, covering the development of new ports, terminals and economic zones, highlighting Gujarat’s potential as the growth engine of the country.
“We are honoured to continue our partnership in the state by committing to strengthening its logistics and maritime infrastructure to further enable trade,” said Chairman and CEO, DP World, Sultan Ahmed bin Sulayem, adding that the company has been operating in India for almost 20 years and in that time, has invested almost $2.5 billion USD.
JAPAN
In a move that will create one of the biggest steel companies outside of
China, Japanese steel giant Nippon Steel Corporation (NSC) has announced plans to buy US Steel.
The deal is said to be worth almost $15 billion (US) at $55 (US) per share in an all-cash transaction, representing a 40 per cent premium.
In a media release, NSC said the purchase would allow it to diversify its global footprint by securing integrated steel manufacturing capabilities in the United States, adding to exisiting operational bases.
“NSC has long admired US Steel with deep respect for its advanced technologies, rich history and talented workforce, and we believe we can jointly take on the challenge of raising our aspirations to even greater heights,” said NSC President, Eiji Hashimoto.
US Steel, which employees more than 22,000 people globally, including 14,00 in the United States, has been on the hunt for a buyer since August when it rejected a smaller, unsolicited bid from US rival.
UK
Geolocation technology specialist, TomTom, has released its annual Traffic Index report which provides data and information on the traffic trends of 387 cities in 55 countries in 2023.
Topping the list as the slowest city to drive through, with an average speed of 14 km an hour in rush hour, was London’s city centre where the travel time for 10km is 37 minutes and 20 seconds on average.
Following close behind the UK capital city were Dublin, Ireland; Toronto, Canada; Milan, Italy and Lima; Peru. The TomTom Traffic Index is based on data from more than 600 million in-car navigation systems and smartphones. For each city (both the city centre and the wider metropolitan area), TomTom calculates the average travel time per kilometre.
SWITZERLAND
A recently released report from the World Road Transport Organisation (IRU) shows that truck driver shortages increased globally in 2023 and it is forecasting that things will get worse in the coming years.
IRU found that last year, there were more than three million unfilled truck driver jobs, or seven per cent of total positions, in the 36 countries that were studied. The only two exceptions were Europe and the United States, where shortages eased slightly last year due to softer transport demand.
According to the IRU research, the shortage will get worse, predicting that without action
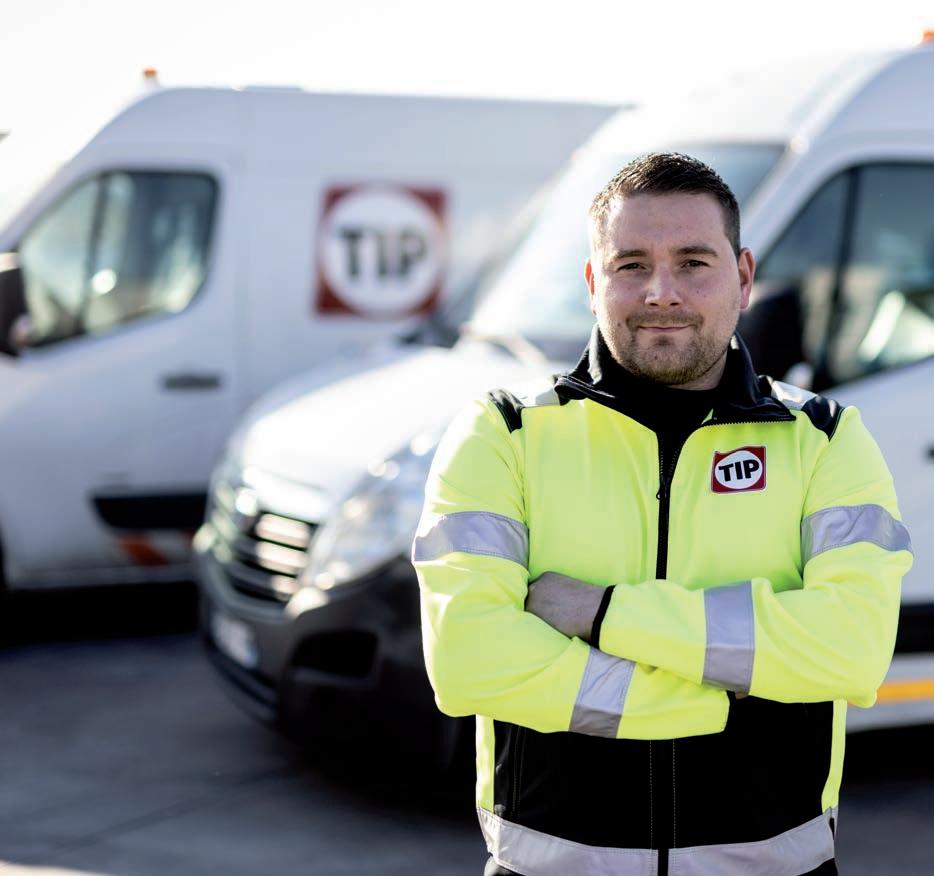
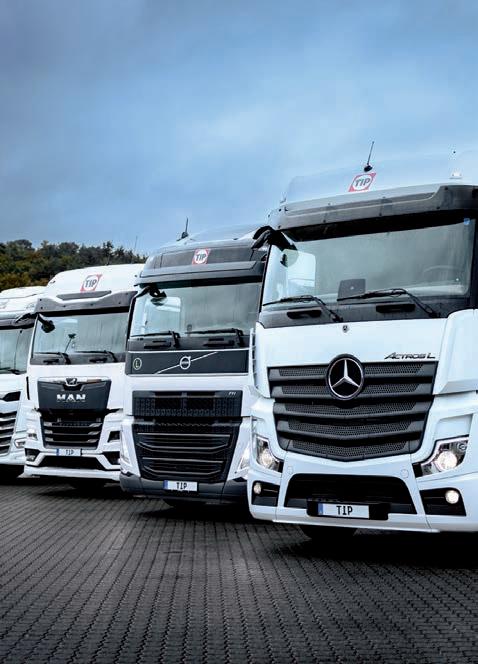
EUROPE
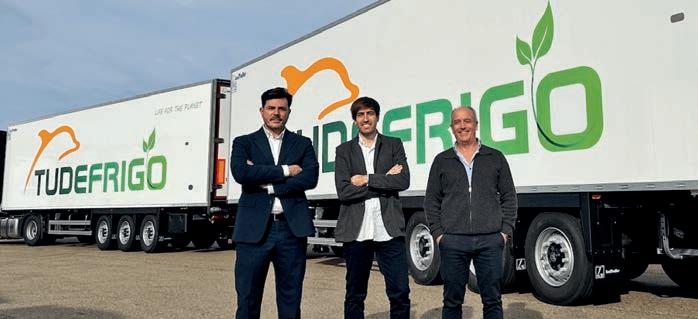
to attract and retain drivers, more than seven million driver positions could be unfilled by 2028, including 4.9 million in China
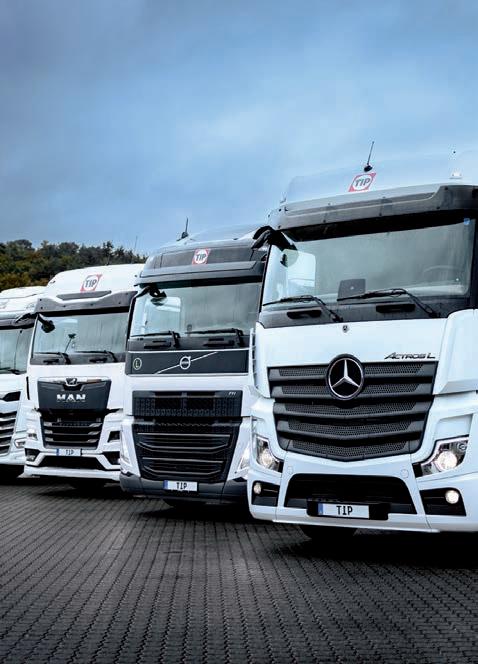
and 745,000 in Europe.
IRU is reported to uphold the interests of heavy vehicle operators to ensure economic growth and prosperity.
FRANCE
Scan Global Logistics (SGL) continues to expand its European presence, opening a new office in Marseille.
Marking its fourth establishment in France since its initial opening in Lille in 2021, the new office provides direct access to France’s second-largest commercial port area, and trade routes to Asia and the USA. It is, however, the port’s direct connectivity to Africa and the Middle East which presents significant business prospects.
Expanding SGL’s service offerings in the South of France introduces expertise to the company’s network and enhances
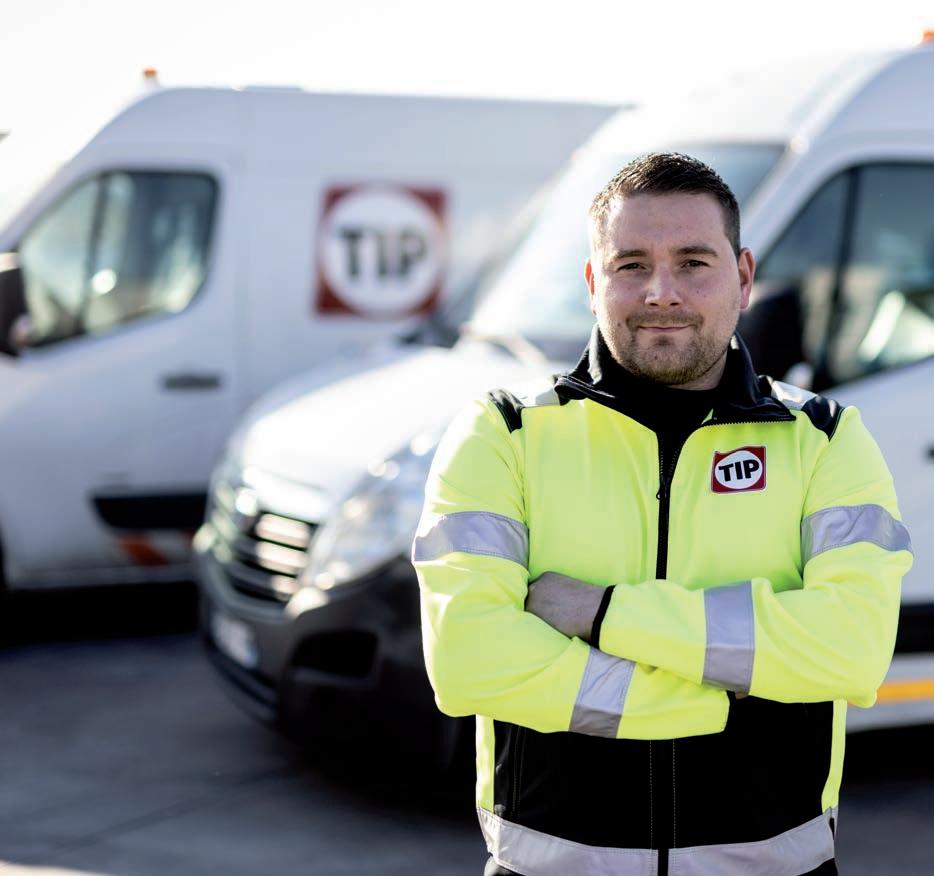
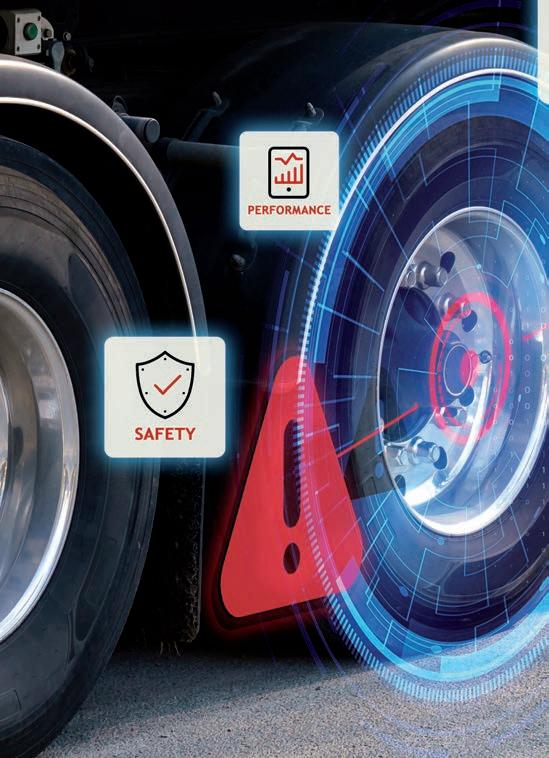

NEWS INTERNATIONAL
EUROPE
the commercial and operational closeness to the company’s customers in the Mediterranean region, especially within ocean shipments and airfreight from Marseille and Nice airports.
GERMANY
To support integration in the electrified transportation space, Thermo King is partnering with BPW Group and idem telematics.
By partnering with experts in their fields, Thermo King creates a unique value proposition for its customers by offering a holistic view of the refrigerated trailer operations. Customers using idem telematics platform cargofleet 3, will also have access to all Thermo King refrigeration units’ and AxlePower smart energy generating system’s performance data. The AxlePower combines BPW’s ePower axle with Thermo King trailer refrigeration unit (TRU) and power management technology. The system delivers the electric power needed to run the cooling unit by converting energy recovered by the trailer’s axle during braking and driving downhill.
SPAIN
Spanish refrigerated transport company, Tudefrigo, has received two Evolution duotrailer sets as well as 27 Evolution trailers, all from Lecitrailer. A fast-growing family business, Tudefrigo is based in the north of the country and was interested in the sustainable transportation element and reduction in fuel consumption the duotrailers provide.
The two duotrailer sets are made up of refrigerated semi-trailers connected to each other through a Lecitrailer single-
axle dolly and equipped with the most innovative refrigeration equipment on the market. One set is equipped with the Thermo King Advancer A-400 and the other duotrailer, with the Carrier Vector HE 17 equipment.
SWEDEN
Dachser has acquired Frigoscandia as the global logistics company looks to further bolster its geographic coverage in Europe and the Nordics.
A full-service provider in temperaturecontrolled and frozen food logistics in the Nordic region, Frigoscandia is headquartered in Helsingborg, Sweden. “Our focus remains on growing organically and sustainably. In addition, this year we’ve strengthened our presence in key markets such as Benelux, Oceania, South Africa, Italy, and now the Nordics through targeted acquisitions,” said the CEO of Dachser, Burkhard Eling.
Frigoscandia has a workforce of 1,300 employees with 12 warehouses in Sweden and three in Norway. Upon completion of the transaction, Frigoscandia will be fully integrated into the Dachser Food Logistics Network.
UK
TIP has partnered with axle and suspension system provider, BPW, to formally train and re-train hundreds of its UK trailer technicians. The joint initiative is aimed at updating and further improving TIP technicians’ skill levels to drive compliance and improve safety and reliability.
Upon successful completion of the course, technicians receive a ‘BPW Approved Maintenance Technician’
certificate, valid for three years. In addition to training TIP’s workshop technicians, training is also offered to its nationwide network of service providers to ensure comprehensive skills coverage. Courses will be held on an ongoing basis, and it is expected that more than 300 technicians will be trained annually, making TIP the largest employer of BPW trained technicians in the country.
GERMANY
Four battery-electric refrigerated truck trailers from Krone have been put to the test in the DACHSER network as part of the German logistic company’s Climate Protection strategy.
The eTrailers will be used in Erlensee, Hamburg and Langenau as DACHSER aims to gain experience, with the still evolving technology, in everyday logistics.
With a fully charged battery, the trailer can be cooled for around five to six hours, even without an additional external power supply or the generator axis. The battery is charged within three to four hours directly at the loading gates. This is also where the pre-cooling takes place.
In addition to the battery, the generator axis supplies energy for cooling using kinetic energy from driving. If the truck is traveling at more than 20 km/h, the generator axis supplies enough power to operate the cooling system completely independent of the battery and also to charge the battery.
UK
The board of Kinaxia has chosen a new group CEO who is set to spearhead the UK-based logistics company’s
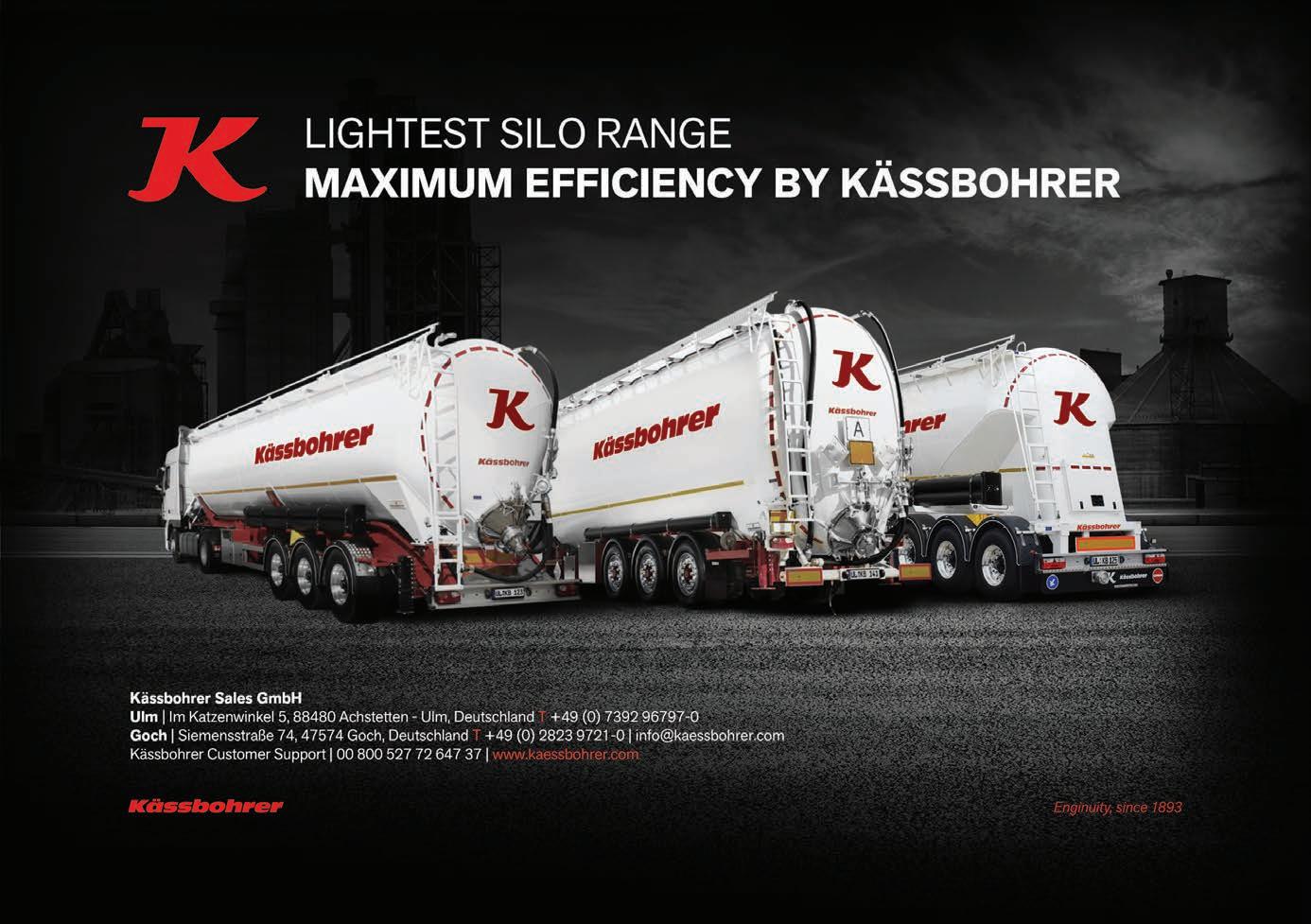
EUROPE
next phase of development.
Michael Conroy was the former chief executive of Palletforce where he led that company through a significant period of expansion, taking the express freight distribution network’s turnover from £20m to £200m during a 13year tenure.
Conroy’s remit at Kinaxia will focus on unlocking further growth potential through scale and technology while simplifying and harmonising company processes, inspiring
sustainable initiatives and continuing to deliver customer excellence.
NETHERLANDS
Netherlands-based trailer builder, Broshuis, has received an order for 557 Medium Equipment Trailers (METs) for the US Department of Defence.
The order is for 2+4 PL2 pendulum axle dolly low loader combinations for transporting military equipment that will be delivered between 2026 and 2031. The contract
million. Broshuis will again execute this contract in collaboration with its US partner Oshkosh Defense. The order includes the delivery of 2+4-axle PL2 pendulum axle dolly low loader combinations.
ITALY
Mirko Marraccini has been appointed to take over the position of Schmitz Cargobull’s Country Manager Italy, succeeding Vincenzo Zaghi, who retired at the end of 2023.
“We would like to thank Vincenzo Zaghi for his outstanding work and
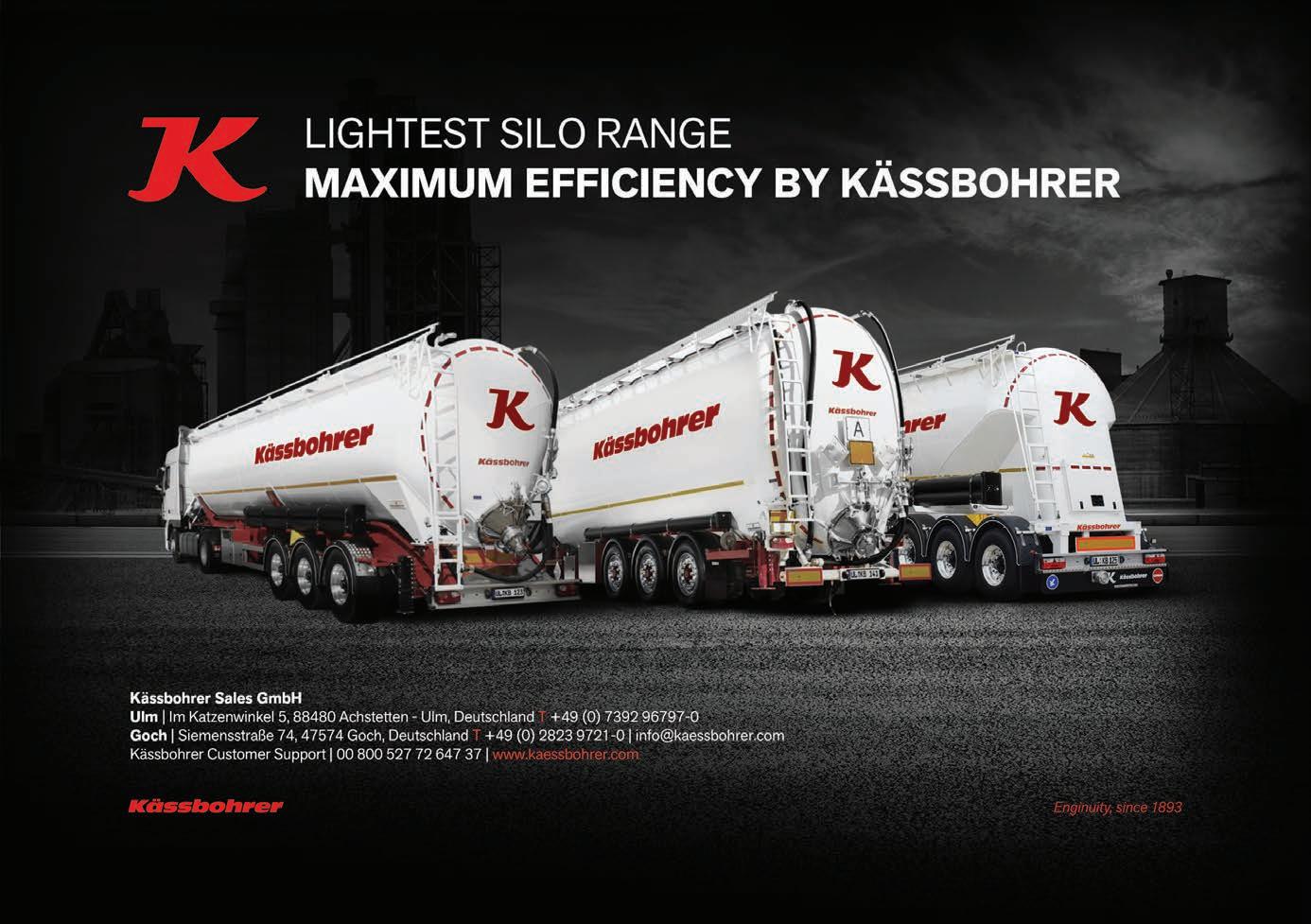
NEWS INTERNATIONAL
EUROPE
years,” said Chief Sales Officer, Boris Billich. “With his technical expertise and market knowledge, he has made a significant contribution to the development and success of Schmitz Cargobull in Italy. Marraccini has been working as Regional Sales Manager in Italy since 2004 and has in-depth specialist and company knowledge. In his new position, he reports directly to Schmitz Cargobull’s Chief Sales Officer Boris Billich.
GERMANY
Rhenus Road Freight is updating the structural process behind its European groupage freight network, with the goal of cutting transit times and boosting reliability.
The system is called Groupage Network 2.0 and Rhenus has now strengthened the first routes in various European countries – and particularly in Germany – during a pilot phase. The solution will be rolled out in the new year to include all cross-border services in Europe.
The new structure is designed to enable transit times of no more than 96 hours (premium service) for almost 90 per cent of all the consignments within the groupage freight network. The newly defined processes also create greater transparency within the network, the company said.
The company has set itself the goal of transporting a much larger proportion of consignments in a significantly shorter time, with countries working on the new structure for more than two years in order to gradually establish the processes.
POLAND
Cold chain logistics company, Lineage,
has opened its new Central Eastern European Headquarters in Warsaw, Poland.
The new office reinforces Lineage’s presence in the region after the company’s 2020 acquisition and rebranding of Pago, a warehousing, distribution and transport logistics provider in Poland.
The opening also solidifies Lineage’s focus on streamlining Europe’s food supply chain, the company said, presenting customers with a comprehensive solution for transporting products across Europe, significantly improving operational efficiencies.
FRANCE
The European Clean Transport Network (ECTN) Alliance has launched a low-carbon, long-distance test using alternative energies through “relay stations” along one of France’s major
highway networks.
The alliance, made up of CEVA Logistics, utilities company ENGIE and SANEF, a motorway operator, will run the tests over a distance of more than 900 kilometres between Avignon and Lille, with the goal of finding practical solutions to facilitate the decarbonisation of long-distance road freight transport.
The concept relies on a network of terminals for low-carbon truck refuelling and trailer exchange.
The Alliance’s draws inspiration from the traditional “relay” concept by establishing stations equipped with electric chargers and bioCNG refuelling pumps. At these relay stations, trailers are disconnected and reconnected to a new tractor unit and driver for the next segment of transport.
Starting initially with four bioGNC trucks operated by F.D.E. Transports,
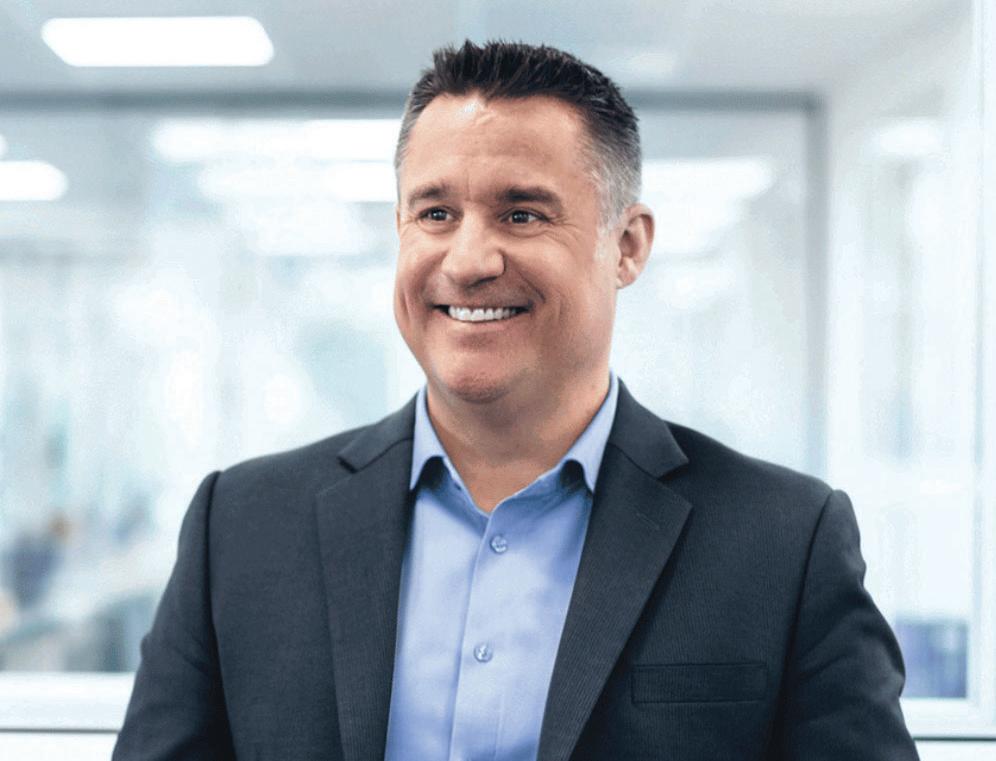
SAF-Holland SE CEO, Alexander Geis. Image:
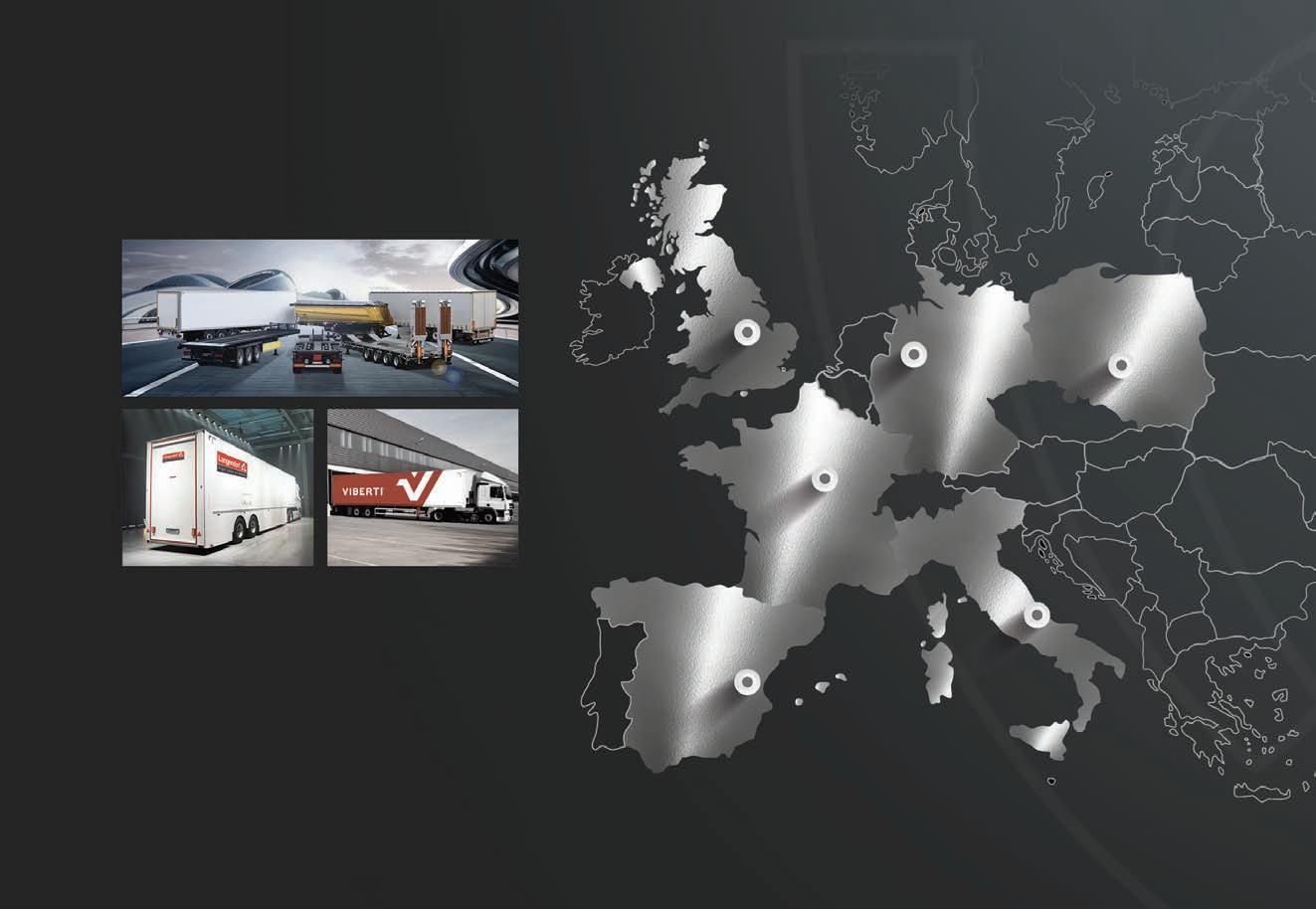
EUROPE
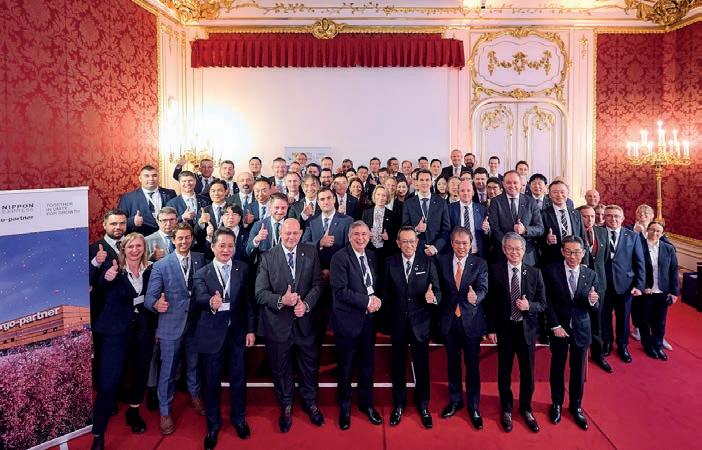
the pilot will gradually expand to include 16 trucks, including 12 electric vehicles and will welcome new transport partners and shippers.
GERMANY
Equipment specialist, SAF-Holland, has taken over a distribution partner.
SAF-Holland has acquired IMS Group B.V., Barneveld, Netherlands, from its former exclusive distribution partner, Pon Group.
IMS Group distributes the group’s own quality brands SAF and Holland in the original equipment sector and the aftermarket in Benelux. It also offers
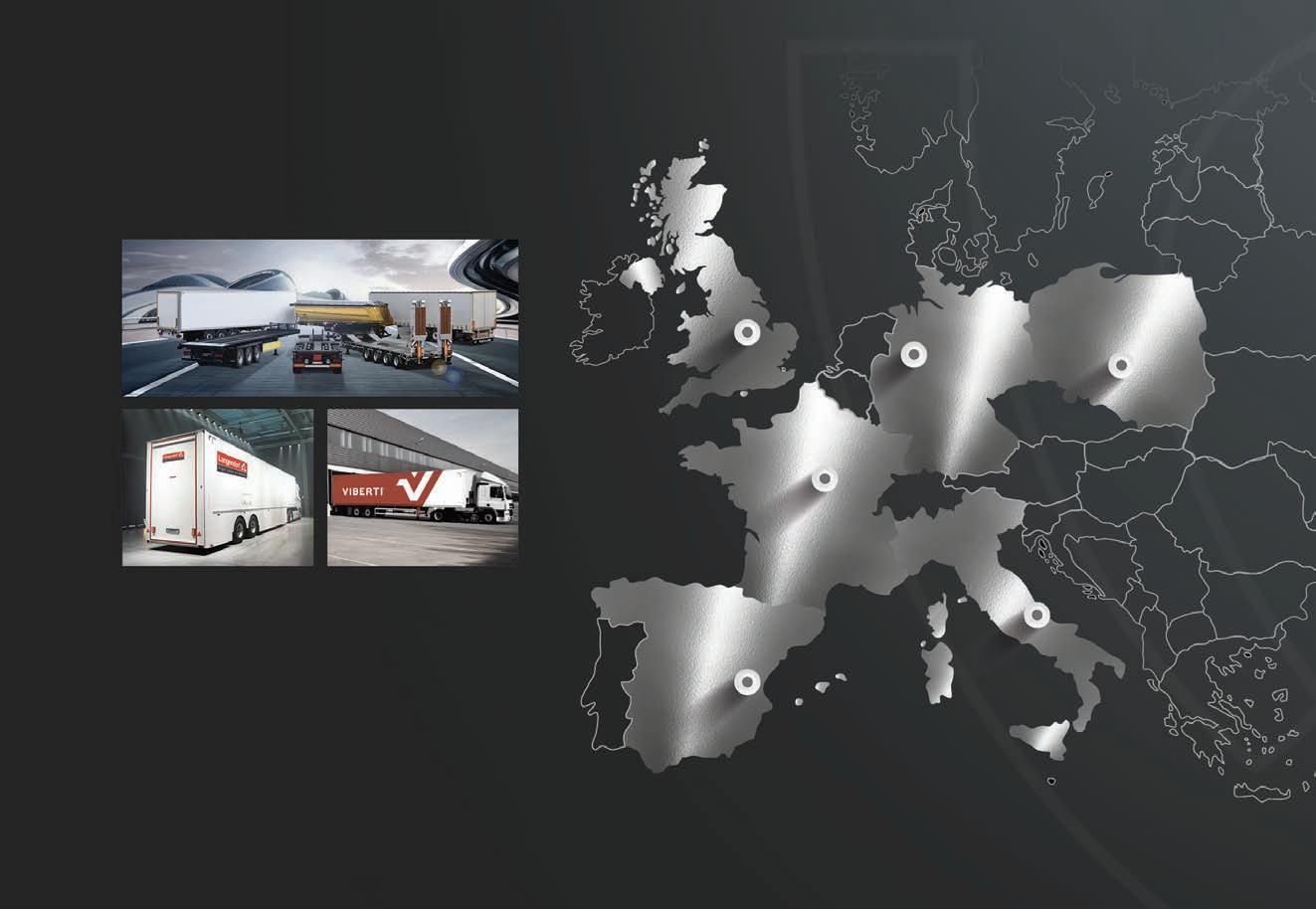
NEWS INTERNATIONAL
EUROPE & MIDDLE EAST
mechanical and hydraulic systems.
NETHERLANDS
Dachser’s Dutch subsidiary for food logistics, Müller Fresh Food Logistics, has become a partner in the European Food Network (EFN).
The move helps strengthens the Europe-wide food distribution network, which is made up of leading logistics companies who provide groupage transport, especially for temperaturecontrolled foods.
For its part, Müller Fresh Food Logistics gains direct access to a high-performance network of reliable partners in 34 European countries. The European Food Network can transport and deliver shipments of chilled and non-chilled food quickly, reliably, and with high quality across the continent. Dachser acquired Müller at the beginning of 2023 and has pursued a path of collaboration and integration. Since then, the companies have been able to combine their expertise in the field of food logistics and synchronise their processes and IT infrastructure.
AUSTRIA
The Hofburg, Vienna’s imperial palace, played host to the formal celebration marking the completion of Nippon Express Holdings’ acquisition of Austrian logistics company, cargopartner.
The ceremony provided a platform for key figures from both cargo-partner and NX Group to discuss the strategic vision and collaborative initiatives that can be expected.
In accordance with the share transfer agreement with cargo-partner Group Holding AG, NX Group acquired
all shares of several cargo-partner subsidiaries based mainly in Central and Eastern Europe that provide logistics services worldwide. The subsidiarisation of cargo-partner will complement the NX Group’s logistics infrastructure in Central and Eastern Europe, expected to see significant future growth as a production base within the European region, and will enable the NX Group to further expand its global network and enhance the services it provides in the European region.
REPUBLIC OF IRELAND
Hellmann Worldwide Logistics has established a new national company in the Republic of Ireland and opened its first Irish branch at Dublin Airport.
This new arm of the business, under the leadership of Hellmann General Director, Niamh Savage, will focus on the pharmaceutical, healthcare and electronics logistics segments.
“The opening of our new national company in the Republic of Ireland is another important milestone in our growth strategy towards a comprehensive European network,” said Hellmann Regional CEO West Europe, Jens Tarnowski.
GERMANY
Schmitz Cargobull’s Supervisory Board has unanimously extended the mandate of Dr. Günter Schweitzer as Chief Operations Officer for a further five years.
Dr. Schweitzer has been a member of the Executive Board since September 1, 2021, responsible for the areas of purchasing, logistics, supply chain and
the production site network.
In his position as Chief Operations Officer, Dr. Schweitzer is also responsible for the sustainability strategy at Schmitz Cargobull. The company assumes ecological and social responsibility along the entire value chain and is pursuing the goal of making both the production processes in the network and the product portfolio sustainable.
DUBAI
Speaking at the World Green Economy Summit in Dubai, the IRU (International Road Transport Union) has presented a roadmap to decarbonise commercial road transport without undermining vital mobility and logistics services. Leading political, industry and academic figures are all gathered, invited by Sheikh Mohammed bin Rashid Al Maktoum, to the annual event to discuss advancing the global green economy and sustainability agenda to achieve the UN Sustainable Development Goals.
In the Summit’s principal session on green transportation, the IRU stressed the essential role of road transport and reinforced its vision and mission on sustainable transport, and the broader industry’s responsibility in driving its own decarbonisation.
UGANDA
In a country that has one of Africa’s worst road traffic incident rates, Transaid is pleased to see its driver training project surpass its initial goal. The international development organisation has concluded phase
AFRICA & OCEANIA
two of its Professional Driver Training project in Uganda, with 890 predominantly HGV drivers being trained over a two-year period –exceeding the project’s original training goal of 15 per cent.
Delivered in partnership with local non-governmental organisation Safe Way Right Way, the project set out to improve the standards of driver training in a country which claims an estimated 12,000 lives a year in traffic accidents. Key to the project was the aim of encouraging more women into the sector, which Transaid believes will benefit transport companies, contribute to improved safety and generate new career opportunities for women. Future recommendations for professional driver training in Uganda include an increased emphasis on fuelefficient driving techniques, to improve sustainability, and the recruitment of female trainers to encourage continued involvement of female drivers.
NEW ZEALAND
Cold chain logistics company, Lineage, has opened a new next-generation cold-storage facility in Tauranga, New Zealand.
Lineage Regional Vice President for New Zealand, Guy Moniz, said the access to the Port of Tauranga was one of the many advantages of building the world-class facility.
“With our new facility less than 20km from one of the country’s largest ports, we are well-positioned to continue delivering excellence in supply chain solutions and serve our customers in the region,” he said.
In line with Lineage’s commitment to sustainability, energy efficiency
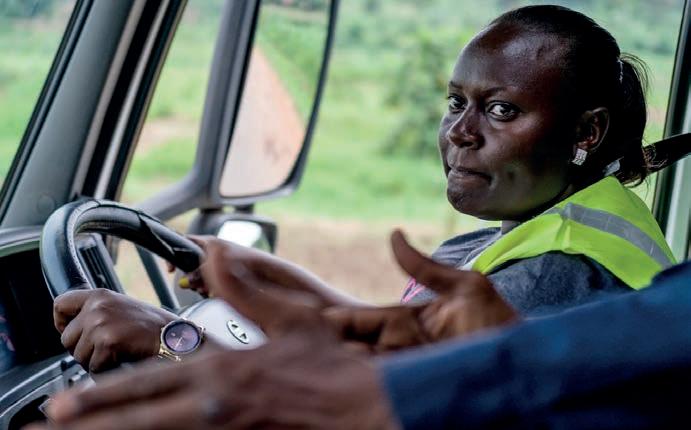
was a central consideration in the construction of the project. The warehouse is equipped with a rainwater harvesting system for refrigeration condensing, rapid doors on all chambers to minimise temperature fluctuations, and features an 890kW solar array for power generation. Lineage in New Zealand now has 25 facilities across the country, stretching from Auckland to Dunedin.
AUSTRALIA
Austria’s Gebrüder Weiss is expanding its network in Australia with the opening of a new Air and Sea office in Brisbane.
This is now the third location operated by the international logistics company in Australia, following on from Sydney and Melbourne, and will be tailored to customers from the engineering, agriculture and medical equipment sectors.
“Opening a location in Brisbane represents another key step in our efforts to increase our presence in Australia,” said
Managing Director Australia and New Zealand, Andrew Antonopoulos. “The services include air & sea transports, customs clearance and a customised logistics mix for project orders.”
Brisbane’s container port, with a record throughput of 1.56 million standard containers last year, is the most important international transhipment hub in the city, while the nation’s most significant import partners are China, the United States as well as other Asian countries such as South Korea and Japan. Gebrüder Weiss has plans to open additional locations in the north and west of Australia to provide blanket coverage for the whole continent. It also has a foothold in New Zealand with locations in Auckland and Christchurch. Gebrüder Weiss recently organised the transportation of an innovative solar car from Switzerland to Australia.
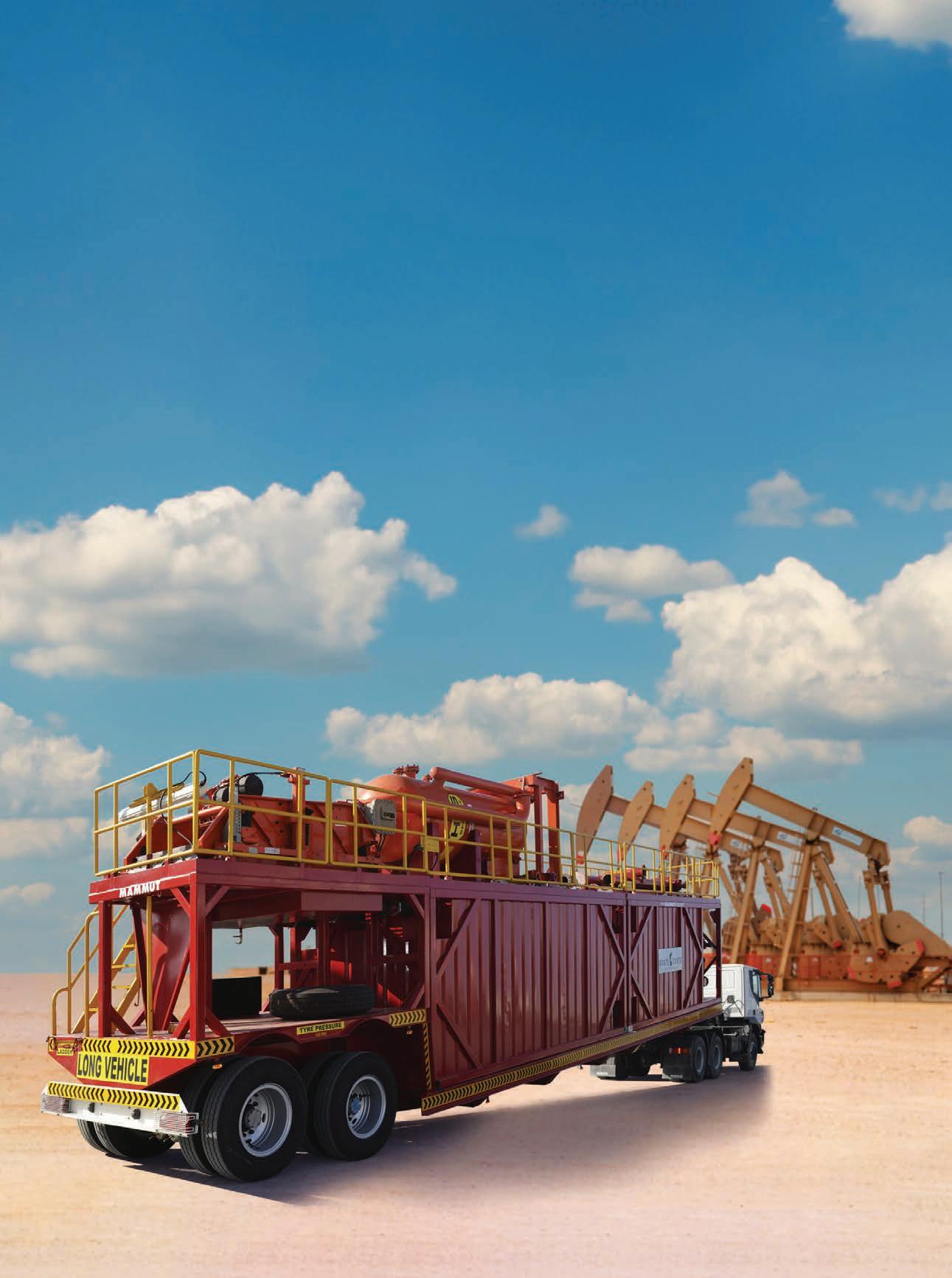
A VISION OF SUCCESS
IT WAS AN AFRICAN PROVERB THAT HELPED NAZ INDUSTRIES CEO, ADEL MIR, UNDERSTAND BOTH THE PASSION AND DIRECTION OF HIS NEW HOME IN DUBAI. THAT SAME PROVERB’S MESSAGE HAS HELPED HIM REACH NEW HEIGHTS IN TRAILER MANUFACTURING, BUT IT HAS BEEN THE STRENGTH OF TEAMWORK WHICH HAS MADE THE ULTIMATE DIFFERENCE.
In his book MyVision:ChallengesintheRacefor Excellence, His Highness Sheikh Mohammed bin Rashid Al Maktoum, the ruler of Dubai, uses the analogy of the speed both a gazelle and a lion are required to survive – one needs it to stay alive and the other to stay fed.
For Adel Mir, who arrived in the United Arab Emirates 30 years ago, the book and analogy helped him understand the dedication his new country had to its growth and global image. It also planted a seed, helping him forge his own path.
A Ukrainian Citizen with a degree in commerce, Mir arrived in Dubai in search of new opportunities. He moved there at a time of a huge economic growth and development; a surge fostered by the UAE leaders as they looked to modernise the country and put it on the global economic map. Throughout his subsequent career in Dubai, Mir took on leadership roles working with international companies including Shell Exploration and Harsco.
While this was happening, NAZ Industries, formerly known as MAMMUT Industries, was a small facility that had been established in 1996. It was a time when new and used trailers in the UAE were being imported from other countries at high price tags, as there was very little domestic manufacturing.
When Mir joined NAZ in 2021, the company was dealing with aftereffects of the Covid pandemic. It was also working through a name and partnership change, making it 100 per cent UAE owned.
He tells Global Trailer that he had three fundamental goals when he, as Operation GM, and his colleague Hussein Al Sharu as Commercial GM took the leadership of the company and jointly prepared the path for growth. The three fundamental goals in their minds were: boosting sales and business, motivating the team and controlling the cost.
Mir considered himself lucky to have the support and friendship of Al Sharu, working in partnership as Commercial GM.
“Hussein and I were a great match in leadership for NAZ,” Mir said. “Hussein had sales and technical knowledge, while I had costing and financial knowledge. Having both leaders involved in all decision making, was the best model of leadership to build the company’s success and future.”
At the beginning of 2023 Mir was promoted to the position of CEO and Al Sharu to the position of CCO, although Mir adds that the pair still run the business with the same management style and enjoy “running the show together”.
Al Sharu has a master’s degree in economics and joined NAZ in 1999.
“We started jointly looking after all the challenges ahead and within a few months we were able to refine the procedures, motivate the team and make some outstanding results for the company,” said Mir.
Leading by example, the pair are most proud of creating a spirit of teamwork and empowering their employees. Their strategy worked. The company had a growth rate of 80 per cent during the 2021 to 2022 financial years and 100 per cent from 2022 to 2023 and going forward, ‘teamwork’ is still the motto.
Engineering excellence
While Mir and Al Sharu know they have among the best quality products in the Middle East, their beliefs are backed by the fact that their trailers’ resale value within that same market is so high. In fact, NAZ’s Mammut brand trailers has become the number one in the market.
NAZ produces more than 45 different products in categories that include body mounted, semi-trailers, oil & gas equipment and process vessels. Its standard products, which are tippers, flatbeds, low-beds and reefers are produced in batches and sold in UAE and neighbouring countries.
The chassis are built from high quality steel with high grades. The components including axles, hydraulic systems, lighting, brakes, landing legs and rims are mainly imported from Europe, primarily Germany and Italy
Products are currently sold throughout the Middle East as well as a number of African nations including Nigeria, Ethiopia, Sudan and Senegal. The team is also working on a project that will see it supply special trailers to North America.
NAZ’s growth rate at more than 70 per cent over the last few years has meant planning for expansion.
“We are not behind the market, the market is behind us,” said Mir. “The number of orders we are receiving are much more than our production capacity. We run the business on budget and projection basis, and we look at the figures every month carefully. We have a vision and we are ambitious to exceed our goals.”

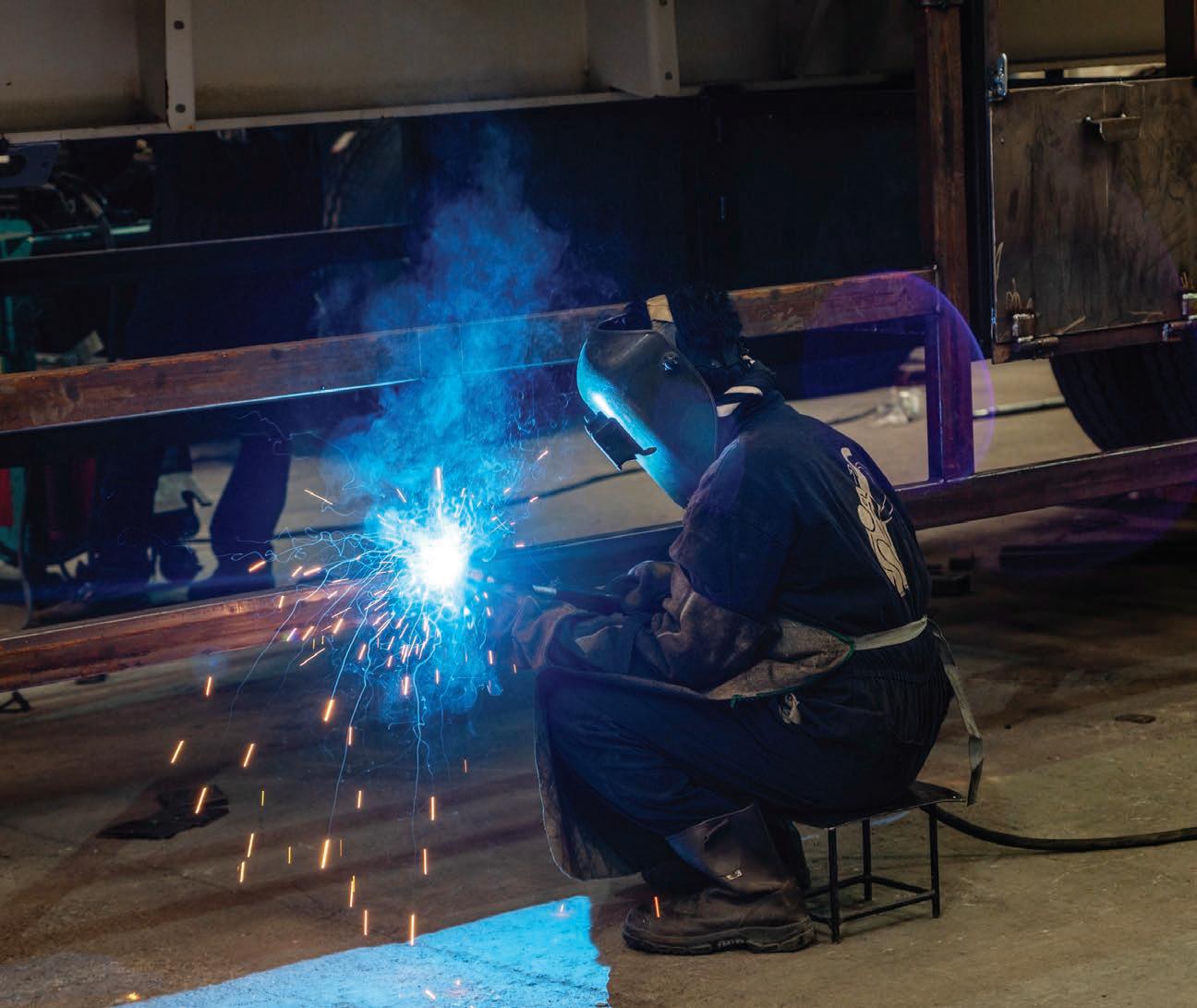
The only major challenge the company has experienced post-Covid has been procuring the necessary materials, as well as the logistics challenges caused by the disruption in the supply chain. This has been somewhat of a learning experience, however, with planning becoming a priority, implementing long term procurement of components two years out.
Location, location, location
While certainly a vision, hard work and expertise have been the secret to NAZ’s success, there is no question there was an aligning of the stars. In a country that found itself in dire need of tools to help give it the global presence it required, the transport industry became a shining star and NAZ’s offerings a hot commodity.
Mir has seen the changes firsthand watching Dubai go from what was essentially a small town to a global business hub, followed soon after by nearby Qatar. With that growth also came higher standards which the industry and NAZ had to stay doggedly on top of.
“25 years ago, no country in the region was following road regulations and any tonnage of cargo was allowed to be loaded,” said Mir. “Now they have implemented specific road regulations, requiring truck and trailers manufacturers to use their best in design and engineering in order to reduce the truck and trailers weight.”
That same regional surge in industry and infrastructure growth has also made the UAE an
easy place to do business, with Dubai arguably the central economic hub for the Middle East and Africa.
“Safety, high living and business standards, availability of the resources, advanced banking, great logistics and ports facilities and many other benefits make UAE a unique country in the region for establishing business,” he said – adding that he predicts the Kingdom of Saudi Arabi will see similar developments in the near future. “There aren’t many countries within 5000 kilometres of United Arab Emirates that have close to the same facilities and standards for business.”
The fast pace of development in the Middle East and the various regions’ many different stages and requirements means NAZ has had to become extremely customer focused. As Mir explains, the company provides solutions for logistics,
FAST FACT
Today, NAZ Industries is found in Dubai Investment Park 2, a well-known commercial and industrial area in the city. Its headquarters is home to a more than 30,000-square-metre manufacturing facility, working two daily shifts and producing 3200 units per year. There are 338 staff members with that number set to increase to 580 before by the end of 2024.
Thanks to demand, the company is now building an even larger factory in the nearby Free Zone which will have the capacity to produce 4,500 units per year. It is due to be complete before the end of the year. In addition to its own facilities, a local manufacturer is currently under a long-term contract for the supply of beams and chassis for its standard trailers.
According to the company, its production processes follow 16 independent technical and commercial standards.
Last year the company was named the county’s best truck and trailer manufacturer.
construction and other industries and the current market is different from one country to another. For instance, Qatar and the UAE don’t have major construction projects, however, since they have created new cities and developments, they do require waste management equipment. The situation changes again in the countries that are announcing major construction projects.

The employee equation
The biggest challenge Mir had when he began at NAZ was creating a team spirit among its employees and ensuring there was adequate motivation among them. Today his team is the company’s biggest strength and what he is most proud of.
“We’ve created an environment in the company where all employees think about the success of the business,” he said. “From day one we told them that if the company succeeds with its budgets and milestones, then they will ultimately benefit from that.” Open communication with staff is a must, Mir said, insisting on meetings every three months, with employees in both the office and the factory, to discuss their results, challenges and goals as well as adequately rewarding staff with bonuses and incentives.
“If they work hard to make the impossible possible, then they deserve to benefit from that,” he said. “We treat everyone as if they are all part of the same family.”
That family is looking forward to the future which, by all estimates, looks bright. In 2020’s financial year, the company produced and sold 380 units, while in 2023 it saw more than 3000 units produced. The goal now is to increase production to 12,000 units per year.
“If you asked me what the three main elements are to having a successful business I would always say ‘people, people and people’,” said Mir. “If you have good people on your team, it doesn’t matter how difficult business is or what challenges you face. You will succeed.”
www.nazindustries.ae

DEUTSCHLAND RESILIENT
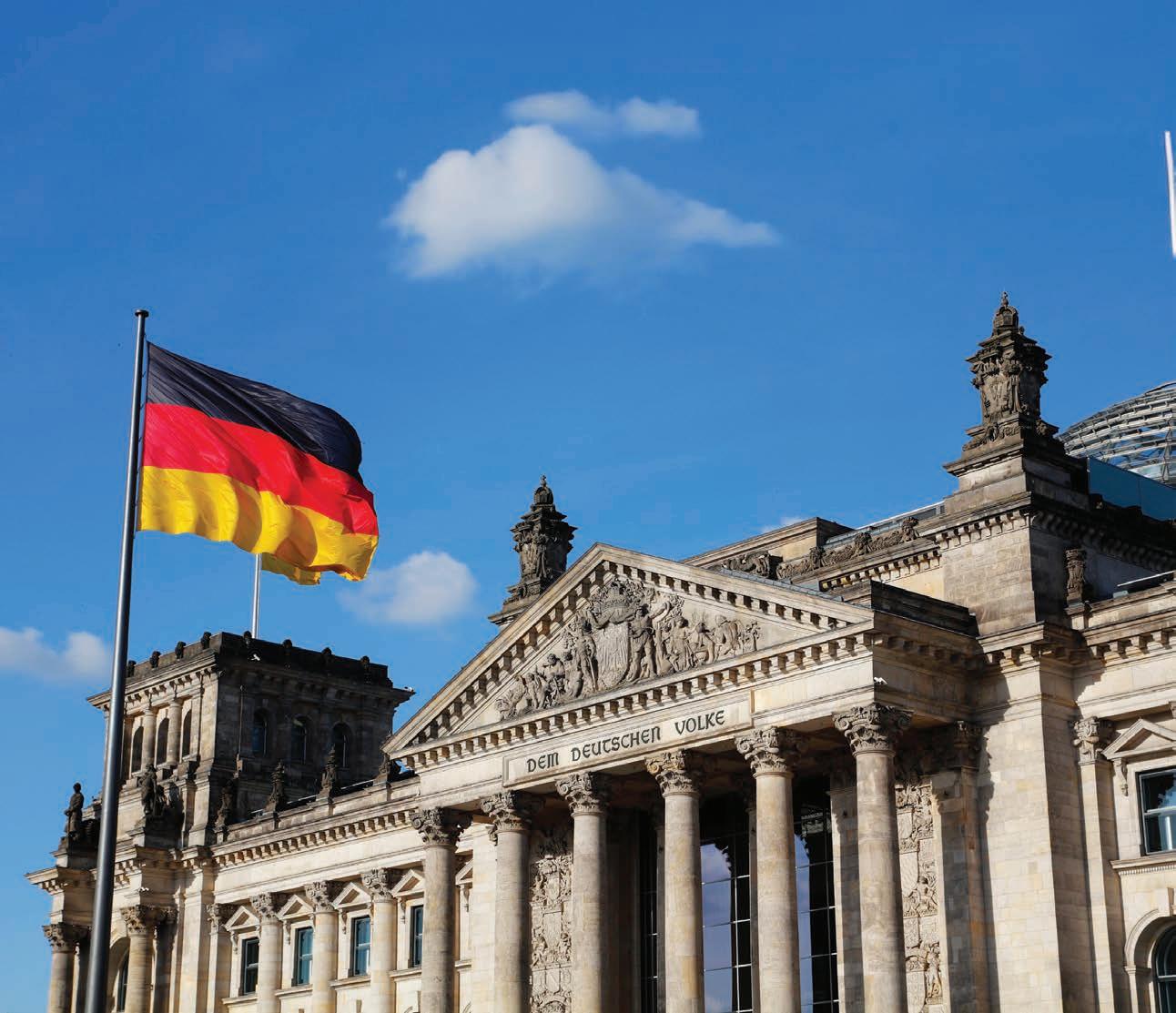
AS EUROPE’S ECONOMIC POWERHOUSE, GERMANY IS POISED TO MEET SEVERAL CHALLENGES HEAD-ON TO ENSURE INDUSTRY CONTINUES TO PREVAIL.
Germany has been Europe’s engine for decades, helping the region pull through whatever economic crisis it found itself in. But that resilience appears on the wane.
The most recent figures on German Gross Domestic Product (GDP) show that its output was 0.3 per cent lower in 2023 than the year before. Comparatively, the International Monetary Fund’s research shows that the US economy grew 2.1 per cent last year with China growing 5 per cent. The European Union as a whole recorded 0.7 per cent, negatively impacted by Germany, which is the region’s largest contributor.
The results of the IMD World Competitiveness Ranking demonstrates that Germany has been losing ground among top economies. Ranked 15th overall in 2022, it dropped seven positions in 2023, deteriorating across all the dimensions considered in the ranking: economic performance, business efficiency, government efficiency and infrastructure. According to the International Monetary Fund’s (IMF) latest report, it’s set to be the
only major world economy to shrink this year.
What’s the problem?
The reasons behind Germany’s struggles are varied according to economists. Challenges that have been pinpointed include everything from a surge in energy costs and the demise of combustionengine cars, to rising interest rates. Some blame infighting among Chancellor Olaf Scholz’s coalition party, suggesting that it has become a major pollical distraction.
“Years of underinvestment has left Germany lagging,” said chief European economist for
Bloomberg Economics, Jamie Rush. “Berlin will need to spend more and make it easier for infrastructure projects to get off the ground.”
It is mostly likely a range of issues that have come together in a perfect storm.
The country was hit hard by a rise in energy costs, compounded by the fact that it was relying on cheap Russian energy until the invasion of Ukraine in 2022.
Like many countries, sizeable inflationary pressures have disrupted German companies’ production processes. Then there are rising interest rates that have made it harder for German businesses to secure financing, as well as increasing their operating costs and weakening domestic and foreign demand.
Some say a newfound ‘self-sufficiency’ in China, which is seeing the country increasingly investing domestically, has reduced its dependence on foreign technology and the import of foreign products and services. A problem for German
companies that have heavily relied on the Chinese market over the past two decades.
What does this mean?
Unfortunately, economists see German growth lagging behind the rest of the region for years to come.
The Organisation for Economic Co-operation and Development predicts Germany could suffer in the coming year due to weakening trade and higher interest rates worldwide.
The rate of unemployment is expected to be impacted as well and is already showing strong signs with 2.6 million people unemployed in 2023 up from 191,000 in 2022.
More than 1 million Germans will reach retirement age — about 320,000 more than those becoming adults. By the end of the decade, the German employment agency says the shortfall will rise to as much as 500,000 — roughly equivalent to the city of Nuremberg, adding to the strains on the economy.
According to Bloomberg, Germany finds itself it a position where it is behind when it comes to sustainable energy needs, and is too dependent on old-school methods, adding that the country needs to quickly learn to pivot to faster-growing sectors as soon as possible.
In that same report, it is suggested the most pressing issue for Germany is getting its energy transition on track, suggesting that having affordable power is a key to industrial competitiveness and manufacturers will go elsewhere if it isn’t rectified.
The government has responded with a cap on power prices for some of the industries that use a lot of energy, but at a high cost to taxpayers, it’s considered a temporary solution.
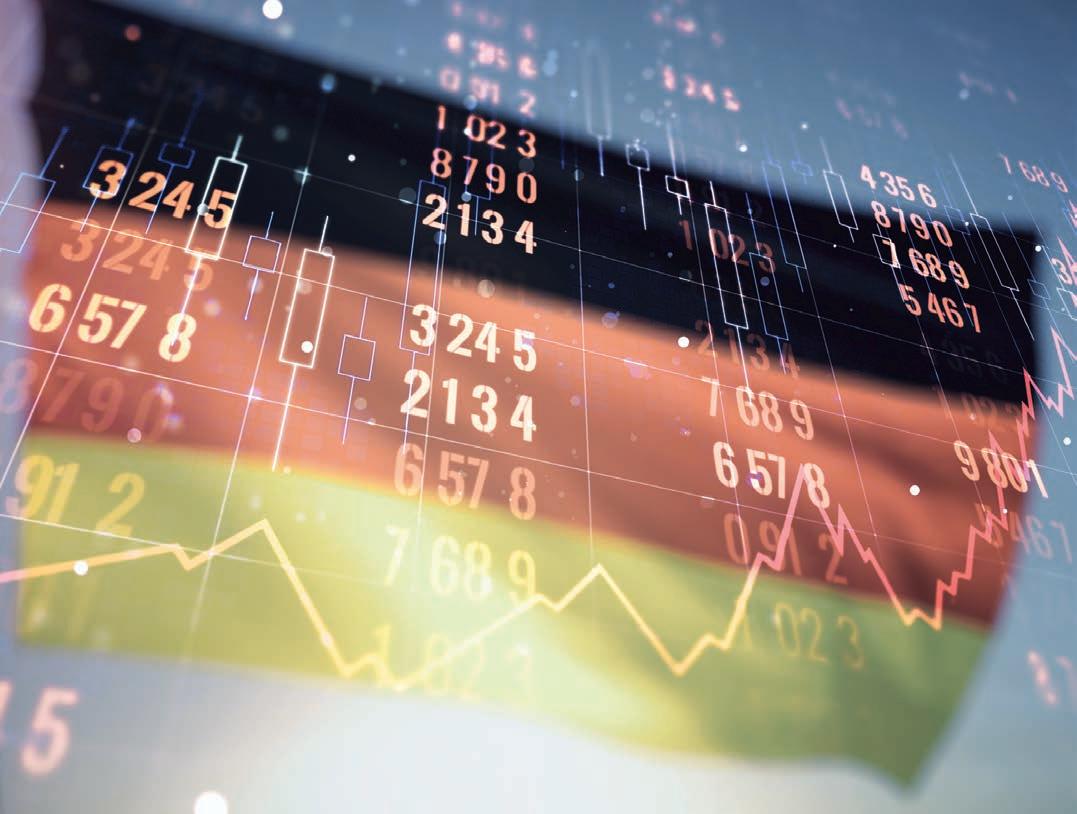
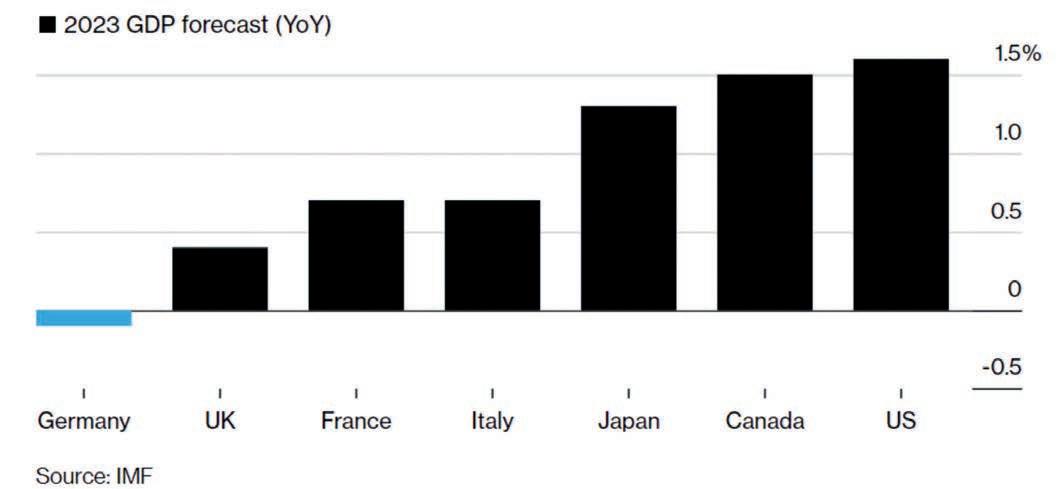
For the government, who has always been averse to debt, this situation has made the development of the 2024 budget difficult.
A court ruling threw the government’s finances into disarray, leaving a €17 billion (around $18.6 billion) gap to fill in the 2024 budget. A final outcome isn’t expected until later in the year but is expected to contain a mix of expenditure cuts, increased tax revenue and a partial deviation from the debt brake rule with a return to debt compliance in 2025.
What is being done?
Germany is taking its energy issues seriously. Last year it shut the last of its nuclear reactors and is on track to phase out coal by 2030. As a replacement is has installed 10 gigawatts of wind and solar capacity, but still requires more.
The Scholz’s administration is aiming for 625 million solar panels and 19,000 wind turbines by 2030 and is looking to accelerate the rollout.
Realistically, a major issue is the fact that the country has a small coastline and limited sunshine and so it is looking to places such as Australia and Canada to investigate importing hydrogen and the technology that could support it.
Energy experts say Germany must speed up the construction of high-voltage grids linking wind farms off the coasts in the north to factories and cities further south and make sure there is enough storage in the event of disruptions.
“Germany needs cross-party agreement on the speed of expansion of renewable energy infrastructure,” Claudia Kemfert, professor of energy economics at the DIW research institute in Berlin told Bloomberg. “After the next national election in 2025, other political constellations could stall the energy transition again. That would not be good for Germany as a place of business.”
On a positive note, innovative ideas, and the funding required to back them, is still a big German priority with the country’s spending on research and development being the fourth highest in the world after the United States, China and Japan. The World Patent Office reports that a third of the patents filed in Europe come from Germany.
According to the OECD, small manufacturing companies are still thriving, but the number of start-ups is declining, a problem if Germany wants to stay innovative and competitive. To deal with the issue, experts say the country needs to shed its long-held
cultural aversion to risk and boost venture-capital investment – $11.7 billion in 2022 compared to $234.5 billion in the US.
The country also, many say, needs to take a hard look at its once-lauded automobile sector which is at risk of becoming redundant if companies don’t start to look past the combustion-engine era. So far, its electric cars have arguably struggled compared to other markets.
Another suggestion is unwinding the country’s reliance on overseas markets for orders and raw materials, although companies are finding that easier said than done.
Germany also needs to improve its digital technology, ranking 51st in the world for fixed-line internet speeds. The government has acknowledged a delayed roll-out for installing fibre-optic cables and mobile communications infrastructure and is looking to overhaul the planning process.
While all of these concerns and potential solutions may simply seem like a Germany problem, the rest of Europe should be watching carefully say experts.
Dana Allin, a professor at the School for Advanced International Studies told Bloomberg. “The health of the German economy is crucial for the broader European economy, and the bloc’s harmony and solidarity.”
www.globaltrailermag.com


WIELTON GROUP’S OWN
TELEMATICS SOLUTION
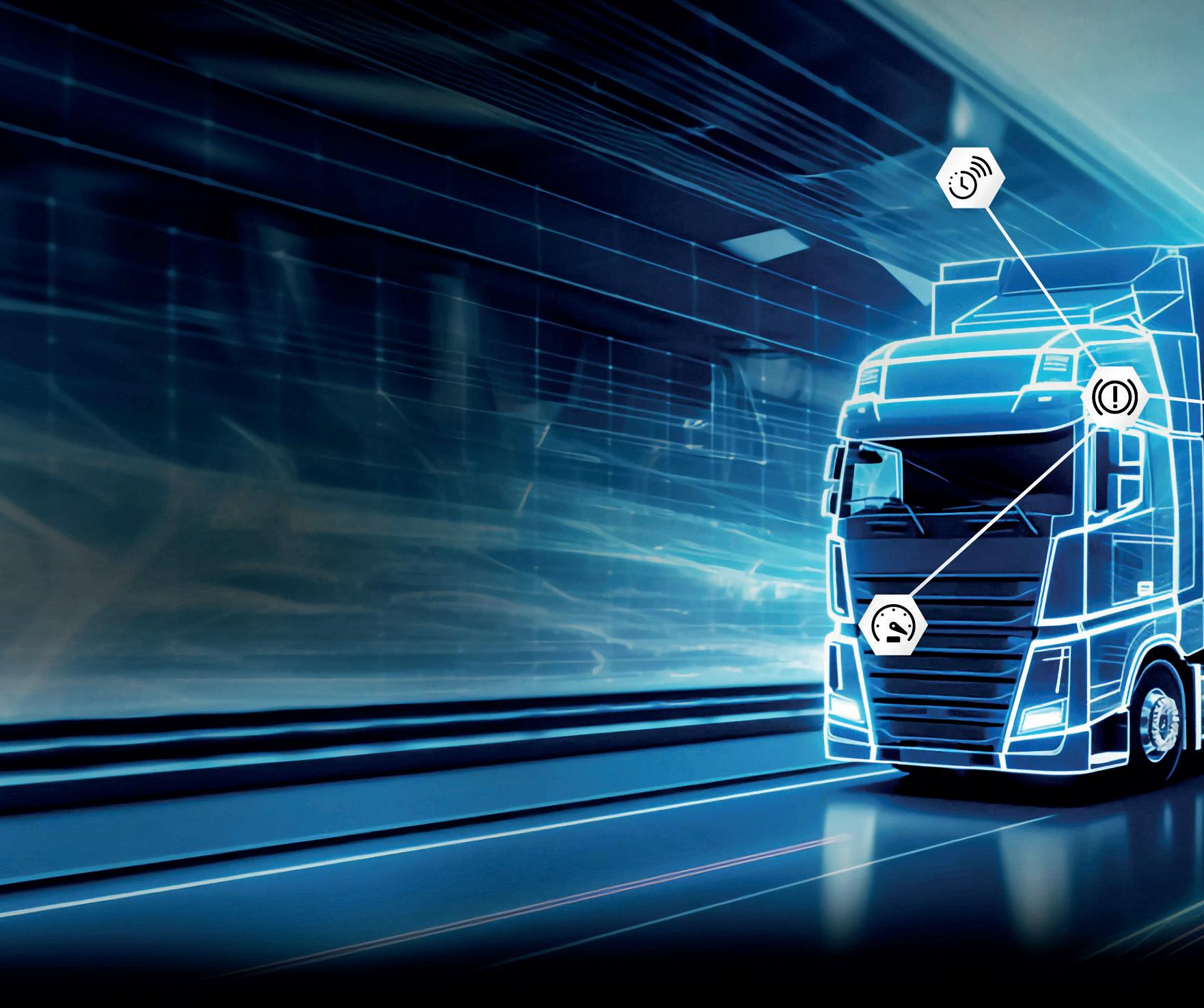
TYRE PRESSURE MONITORING SYSTEMS HAVE EMERGED AS AN EFFECTIVE TOOL FOR ENHANCING ROAD SAFETY AND IN MANY JURISDICTIONS ARE NOW MANDATED. ABERG CONNECT, PART OF THE WIELTON GROUP, IS RESPONSIBLE FOR THE DEVELOPMENT AND IMPLEMENTATION OF TELEMATICS SOLUTIONS IN VEHICLES.
The Wielton Group is one of the three largest manufacturers of semi-trailers, trailers and car bodies in Europe andis reported to be the 10th largest manufacturer of its type in the industry worldwide.
To meet customers’ needs in the field of transport digitalisation, Wielton Group founded Aberg Connect which aims to provide the best telematics solutions available on the market. The company develops telematics solutions and Tyre Pressure Monitoring Systems (TPMS) for the products of all Wielton Group brands and strengthens its position as the specialist for IT solutions dedicated to the transport industry. Brand products will be available in the European markets where Wielton Group companies are currently present. This extensive reach ensures that Aberg’s innovative technologies will be accessible to a vast network of fleet managers and drivers, empowering them to optimise their operations and enhance the
performance of their vehicles.
“At Wielton Group we are committed to providing innovative solutions that help our customers improve fleet efficiency and transport safety,” said Wielton Group CEO, Paweł Szataniak.”Introducing our own telematic and TPMS solution was a natural next step in our strategy to digitise our product portfolio. This technology will provide our customers with actionable insights on their fleet’s performance, enabling them to make informed decisions that can lower transport costs, while reducing its negative

impact on the environment.”
New TPMS regulations
UN ECE R141 is a regulation that sets out uniform provisions for the approval of vehicles about TPMS. The regulation states that the driver of the vehicle needs to be alerted in case the tire becomes underinflated. The warning signal must be displayed to the driver within not more than 10 minutes from the occurrence of the event related to pressure loss. This regulation will affect newly registered semitrailers starting from the beginning of July 2024.
Safety and transport efficiency
Aberg Connect telematics solutions enable real-time monitoring of the status of semi-trailers, making it
easier to operate and maintain the proper condition of transport assets. They make it possible to track the location of vehicles, their speed, and many other parameters, including axle load and other signals indicating the condition of the vehicle. Analysis of the information obtained in this form contributes to improving transport efficiency, reducing fleet operating costs, and above all, increasing the safety of both drivers and transported loads.
Trailer TPMS can help improve safety by reducing the number of accidents caused by underinflated tires. Underinflation can lead to loss of control of driving a vehicle, increased stopping distances, increased tire wear, and in extreme cases even dangerous blow-outs. Keeping the tire pressure at optimal values will also help improve fuel efficiency which directly translates to savings. Properly inflated tires have less rolling resistance and will therefore lead to lower CO2 emissions.
Telematics solutions from Aberg Connect
Aberg Connect has combined both telematic and TPMS functionality into one system. On top of the basic functionality required by R141, we are providing our customers with access to the state-of-the-art telematic portal – ATP, which stands for Aberg Telematics Portal. It is a web-based platform that provides fleet managers with real-time data and insights into the performance of their semi-trailers. The portal can be used to monitor a variety of parameters, including. GPS position, EBS data, and the aforementioned TPMS. ATP is a step towards digitalisation of fleet management. Many relevant parameters can be tracked during everyday use, allowing fleet managers to plan and optimise fleet maintenance as well as help with everyday transport operations.
“Digitisation has revolutionised the way our customers manage their transport operations as well as their fleets,” said Aberg Connect Vice President of the Board, Michał Skorupowski. “By seamlessly integrating telematics with our TPMS technology, we have created a comprehensive platform that provides our customers with a wealth of information to optimise their operations, enhance safety, and save money. Our ATP portal is the cornerstone of this digital transformation, providing real-time insights into trailer performance, driving behaviour, and potential maintenance issues. This data-driven approach has enabled us to significantly improve our customers’ fleet efficiency, safety and overall profitability.”
Business optimisation
ATP portal offers an advanced feature that allows users to create personalised and easily configurable alerts based on their specific needs and preferences. This capability is particularly beneficial for fleet managers who want to stay informed about critical events and take proactive measures to prevent potential issues. Each customer can in no time prevent disruptions to their operations by identifying potential maintenance issues before they escalate into major problems. When the issue is detected, a prompt notification (by SMS or E-mail) is sent to the responsible person allowing them to take preventive measures and solve problems before they escalate.
Aberg Connect understands customers’ existing IT landscape. It provides them with open API to allow integration with other systems. This secures undisturbed information flow that supports their everyday business.
The company is also active in the fast-growing discipline of AI. Team of experts is working on future solutions in the field fleet managers optimise the performance and longevity of their semi-trailers, reducing maintenance costs and improving overall fleet efficiency.
The complete selection of Wielton Group products and solutions, including the Aberg Connect brand, will be available to see at the international commercial vehicle trade fair IAA Transportation. The event will take place from September 17-22 in Hannover.
https://wieltongroup.com/en/ https://www.abergtelematics.com/
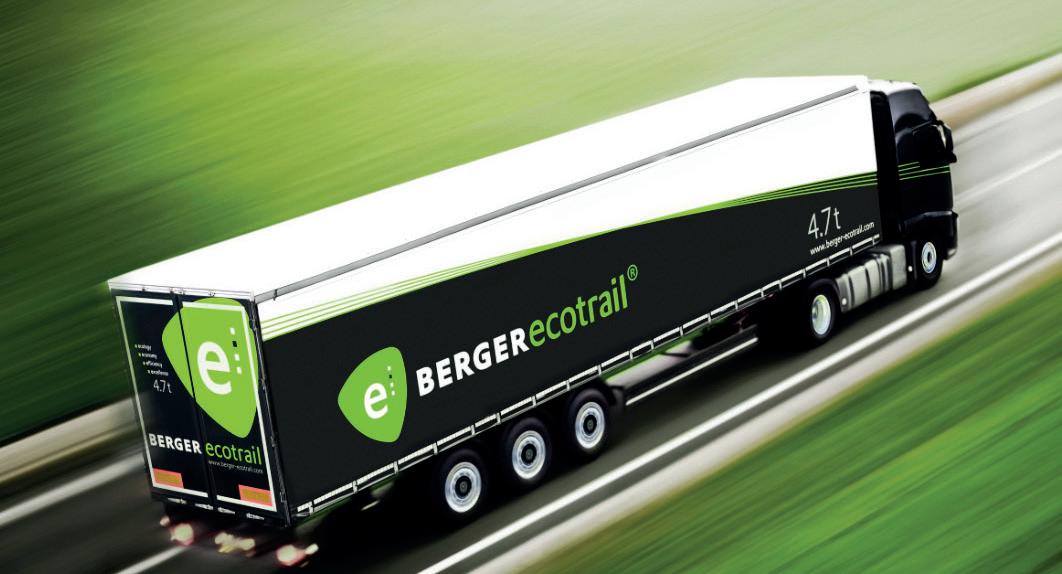
LIGHTFUTURE
AS A SPECIALIST FOR PREMIUM LIGHT CONSTRUCTION VEHICLES, BERGER FAHRZEUGTECHNIK IS ALREADY ACTIVE THROUGHOUT EUROPE IN A FOCUSED SEGMENT. NOW, HAVING ENTERED A PARTNERSHIP WITH SCHMITZ CARGOBULL, THE BERGERECOTRAIL BRAND WILL BE EVEN MORE WIDELY KNOWN AND MARKETED IN THE FUTURE.
Schmitz Cargobull’s 49 per cent investment in Berger Fahrzeugtechnik has been approved, giving the trailer builder a more extensive product portfolio.
The two firms have launched their relationship with the marketing of the lightweight BERGERecotrail trailer which is now available to purchase via the Schmitz Cargobull Europe-wide sales network.
“We are delighted that we will now be able to offer our customers an even more extensive product portfolio as a result of our collaboration with Berger,” said Schmitz Cargobull Chief Sales Officer, Boris Billich. “Transport firms will benefit from a greater range of vehicles and an extensive package of services for both product lines. Customers can now purchase the specialist lightweight BERGERecotrail vehicles through their Schmitz Cargobull contact partners. This is hugely advantageous for our customers.”
Berger Fahrzeugtechnik specialises in premium lightweight vehicles with extensive expertise in lightweight construction. Its BERGERecotrail semi-trailers are in high demand among customers who are looking for high payload.
“Our lightweight BERGERecotrail semi-trailers are in particularly high demand among customers looking for high payloads. However, two of the main reasons why lightweight trailers are becoming increasingly relevant for transport firms is their ability to optimise payload and increase sustainability,” said Managing Director Sales at Berger Fahrzeugtechnik,
Roland Schneider. “Customers can now use Schmitz Cargobull’s Europe-wide sales and service network, which offers huge added value.”
With its BERGERecotrail vehicles, Berger Fahrzeugtechnik is a renowned specialist in premium lightweight vehicles with extensive expertise in lightweight construction. Now that the two companies have consolidated their strengths, BERGERecotrail lightweight trailers from the Radfeld factory in Tyrol are now also available through Schmitz Cargobull’s sales channels.
Customers will also be able to access comprehensive European spare parts supply through the Schmitz Cargobull Service Partner network. The next step will see Schmitz Cargobull’s entire service portfolio being extended to cover Berger lightweight vehicles.
www.cargobull.com
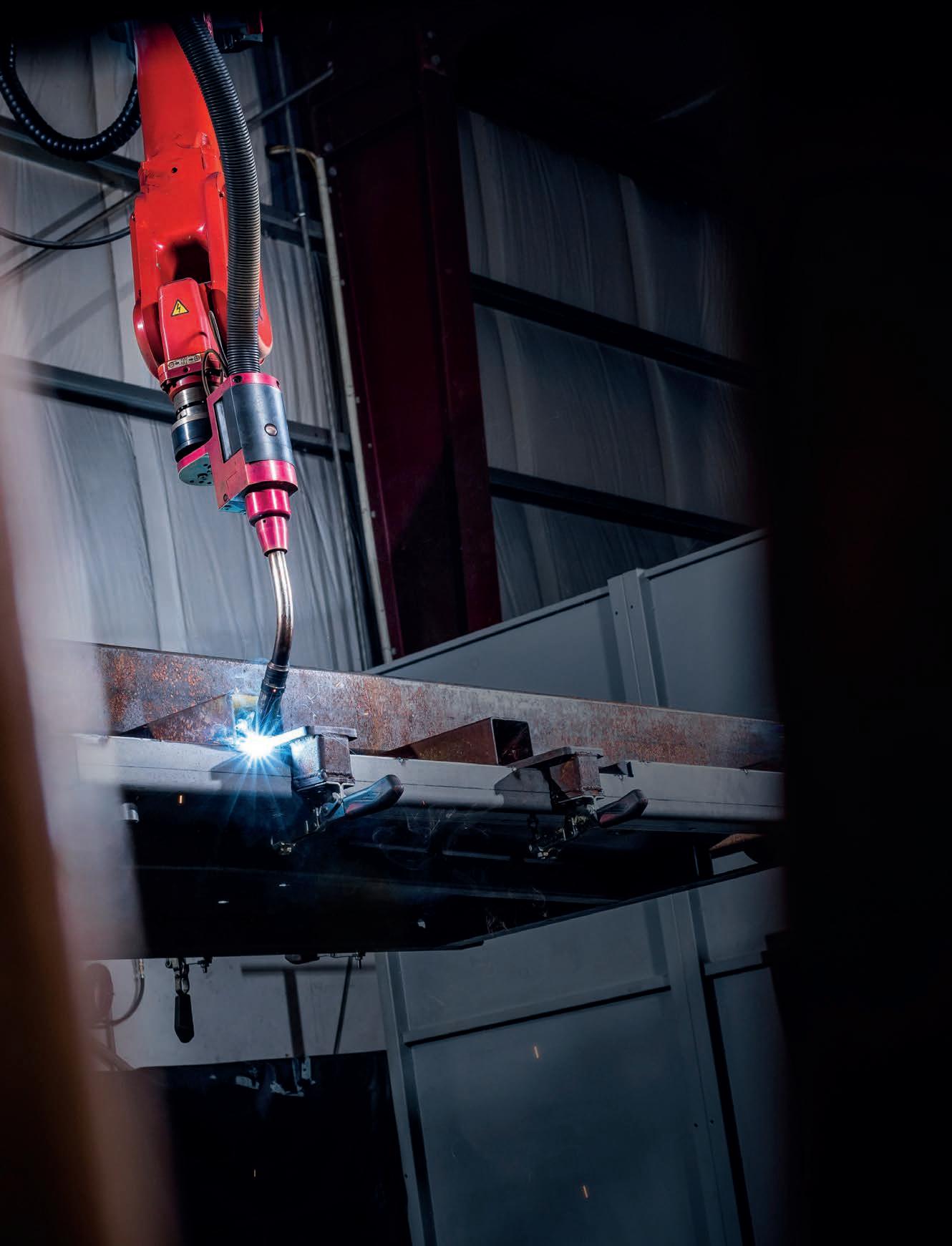
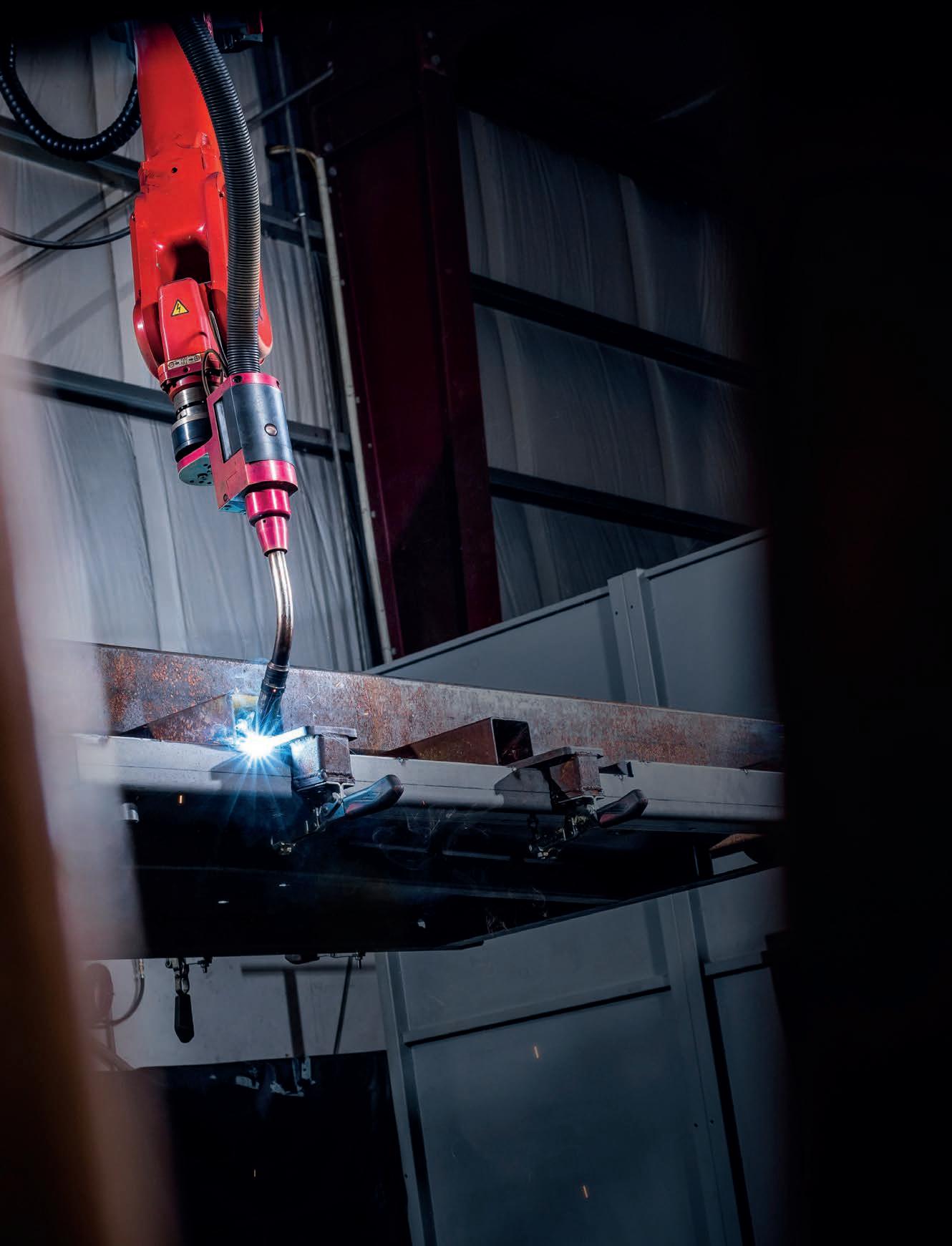
From welding robots to quality wire: all under one roof
Are you interested in switching to robotic welding, and would you prefer to have one point of contact rather than several? With more than 45 years of experience in robotic welding, Valk Welding offers tailor-made total solutions, including welding wire, consumables, software, training and support. This way, you are never alone before, during and after your changeover.
Valk Welding for large and small
We can help you with production automation from large series to single pieces and from small to large products. Our systems are suitable for various types of steel, stainless steel, aluminium and plastic.
The strong connection
ENHANCED SAFETY
WHEN YOUR CLIENTS ARE AS VAST AND UNIQUE AS KÄSSBOHRER’S, YOU NEED TO HAVE AN ARSENAL OF TRANSPORT OPTIONS. WHETHER IT’S DANGEROUS GOODS, FOODSTUFF OR WASTE, IT HAS A TANKER AND SILO VEHICLE SOLUTION FOR JUST ABOUT EVERYTHING.
Fuel oil, bitumen and even manure. These are just a few of a long list of typical but sometimes dangerous products that need to be transported at any given time, and they often have specific requirements.
That’s why Kässbohrer provides tanker and silo vehicles in ten product groups with more than 100 different vehicles, all having a design focused squarely on being light and safe.
The SafeTanker range includes 26 different vehicles offered in either stainless steel or aluminium, which is optimal for the high hygiene requirements of the food sector, safe and secure transportation of hazardous chemicals For the most efficient and flexible transport operation, Kässbohrer offers various compartment, insulation, heating and pump options that might be needed. In its Lightest Silo range, Kässbohrer offers tipping K.SSK silos from 40 to 90 m3 including the lightest ADR tipping silo vehicles that are suitable for transporting powder, or granular materials. Meanwhile its 31to 54 m3 K.SSL non-tipping silos are suitable for the transportation and discharge of low-density materials.
Among its other products are:
Bitumen Tanker K.STS – award-winning, this tanker meets all the needs of hot petrochemical goods and comes with remote control and enhanced safety options. It provides maximum payload with a tare weight starting from 6,050 kg and can be equipped with various heating options, such as steam, water and electrical heating.
Fuel Tanker K.STB – a standout within liquid dangerous goods transportation, it
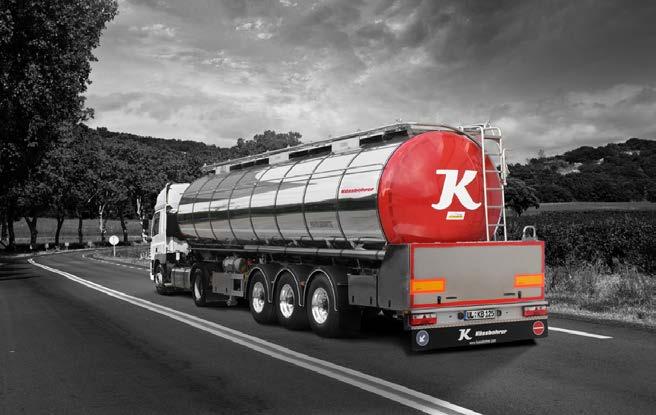
has features for advanced safety, including overfill protection and Sealed Parcel Delivery, which monitors load capacity for any changes during operations. It also has anti-theft options. Its low tare weight starts from 4,750 kg and is available with one to 6 compartment options, mechanical and electronic dipstick systems, pump, counter, hose reel and collector.
Chemical Substance Tanker K.STC PR – This tanker is available in 30 m3 with 6,450 kg tare weight to 37.5 m3 with 6,980 kg tare weight. It has a stainless-steel body and offers a number of filling and cleaning manholes which conform to EN 140 25 standards. With a walkthrough baffle option, it enables an easy cleaning operation with the possibility of walking between baffles by entering the tank from a single filling manhole.
Food Tankers K.STL and K.STL P – Serving all foodstuff transport needs, from oils and beverages to delicate goods such as chocolate, these are ATP certified and pressurised with various volume and compartment options. Easy to clean, it also has a tare weight starting from 5.550 kg, enabling increased load capacity and is more environmentally friendly.
Waste Tanker K.STN – developed for natural waste, it minimises the health risks and hazards during the transportation of manure to power plants and renewable energy centres. It is equiped with various pump and filling hoppper options and pneumatic leveling control as well as overpressure and vacuum valves. With an empty weight of 5,450 kg and steering axle equipment if offers maximum mobility. www.kaessbohrer.com
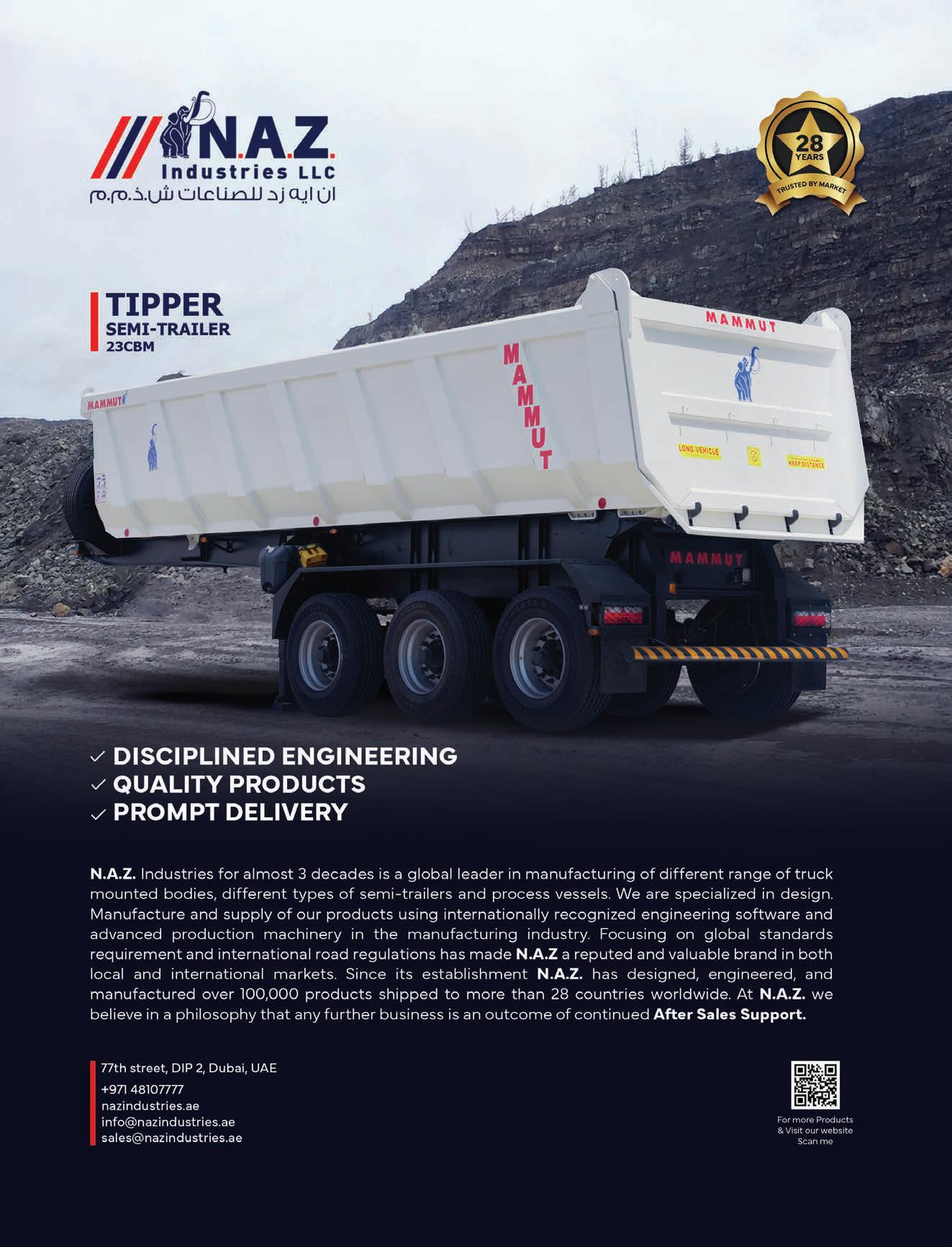
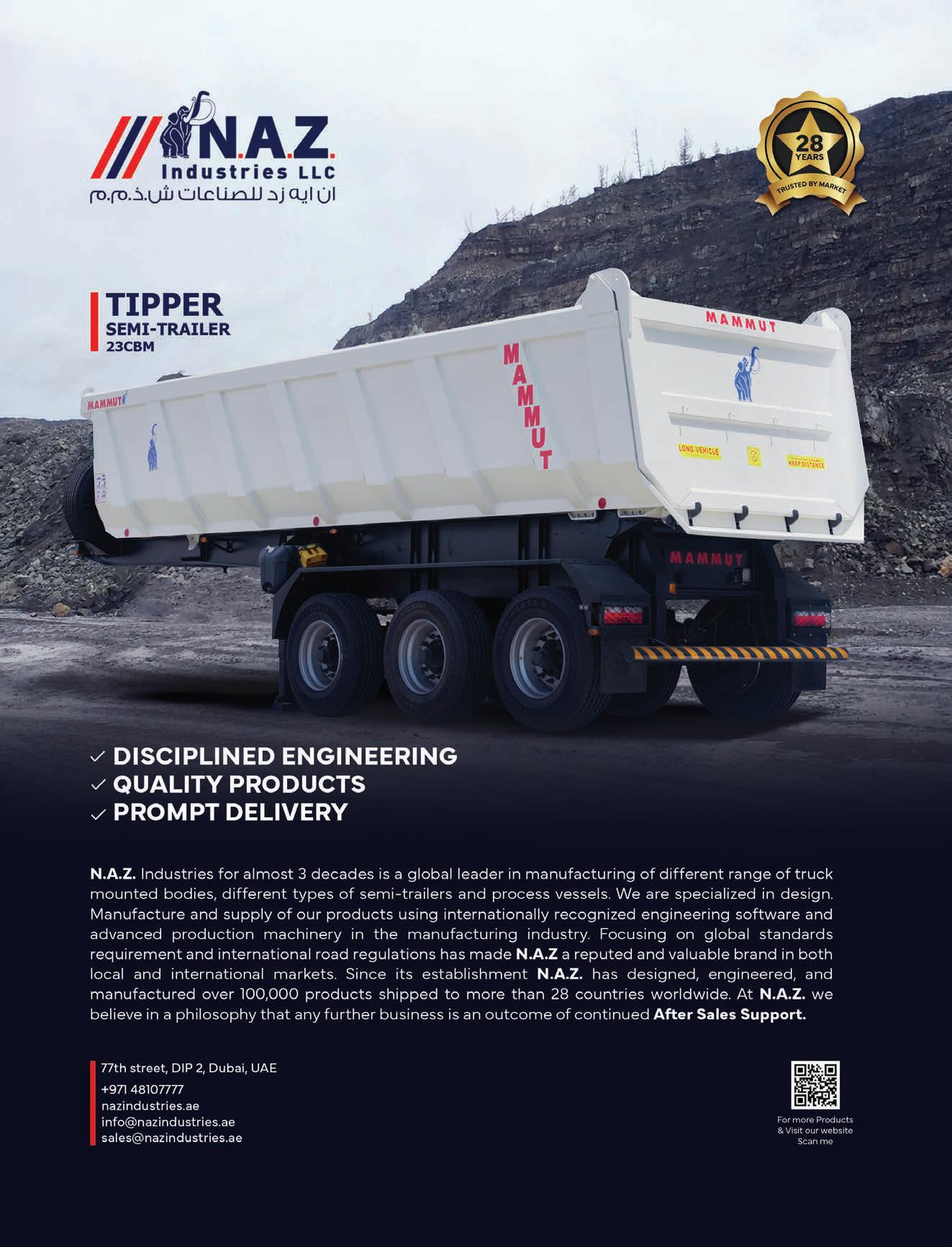
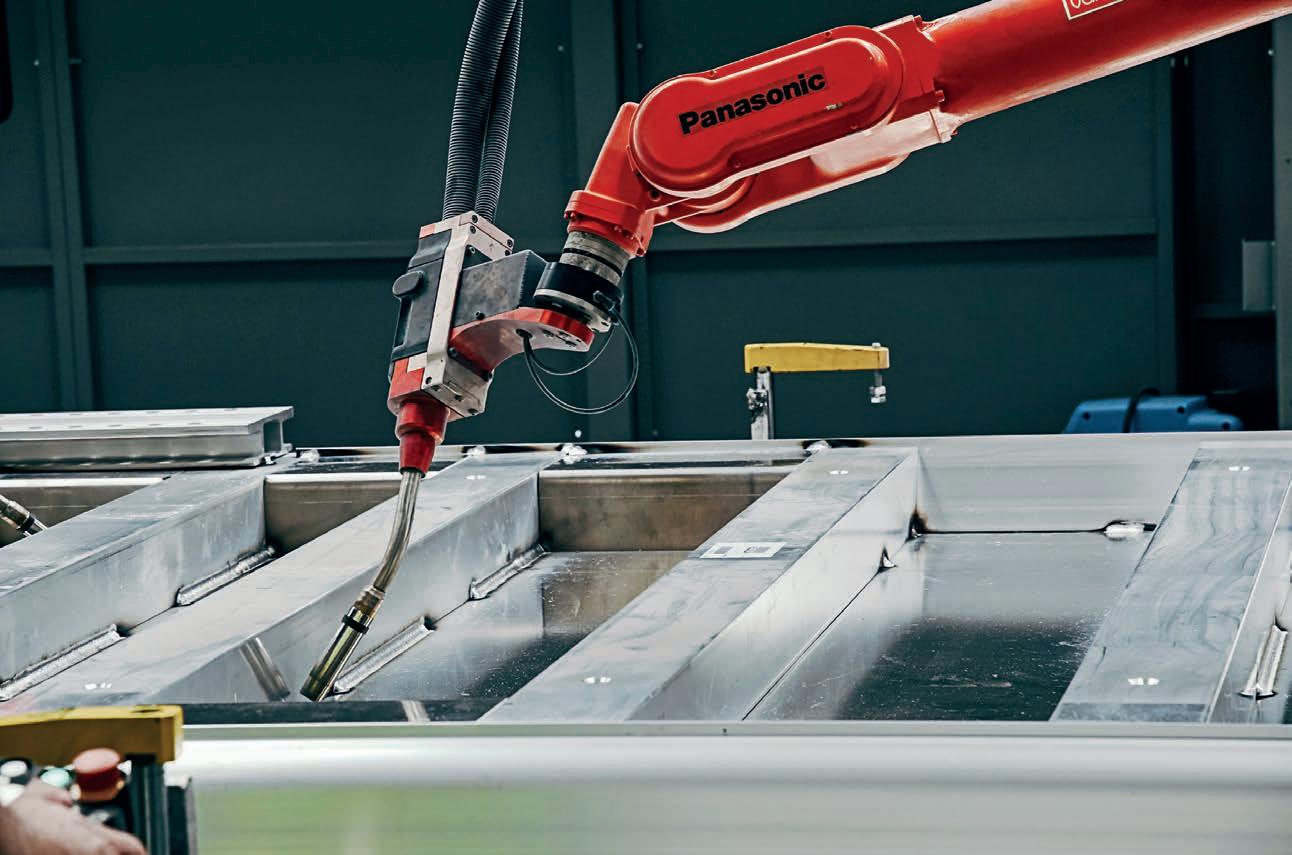
WELDING WONDER
IT WAS A SHORTAGE OF WELDERS IN THE LATE NINETIES THAT PROMPTED STAS BELGIUM TO LOOK TO WELDING AUTOMATION. MORE THAN 18 YEARS LATER AND ITS COLLABORATION WITH VALK WELDING IS STILL GOING STRONG, WITH THE TRAILER MANUFACTURER FULLY EMBRACING TECHNOLOGY.
It was 2007 when Valk Welding delivered the first welding robots to the STAS factory in Doornik, Belgium.
Today that successful partnership continues, recently marked with the delivery of a large welding robot installation for the main STAS plant in Waregem, where its aluminium tipper trucks are produced.
In the last 18 years STAS has undoubtedly undergone a significant evolution in technology, even receiving ‘Factory of the Future’ award for both of its sites.
What STAS has learned is that automation doesn’t negate the need for people – quite the opposite.
“Within the factory of the future, a human-centred organisation is paramount, and this is largely reflected in the way we have automated production, especially the welding department,” said Senior Automation Engineer, Patrick Hugelier.
Aluminium tippers
With its aluminium self-dischargers and tippers, STAS focuses on the transportation of bulk goods. Transporters using self-dischargers and tippers place great importance on stability, reliability and low vehicle weight.
Welding aluminium panels requires special attention because of specific challenges, such as the low melting point and the high risk of contamination of the weld pool. In previous installations in Doornik, STAS used many short robot programs per production order. This lowered the entry threshold for the welders who were operating the installation. The combination of STAS’s control software and Valk Welding’s robot expertise has proven that a stable process can be achieved.
Six welding robots
The most recent project at STAS consists of two production lines with a total of six welding robots. These installations are used for producing aluminium floor panels and sidewalls for tippers
and can significantly reduce production lead times.
“High user-friendliness of the installations has always been the starting point,” Hugelier said. “The machine must adapt to the people, not the other way around. This has mainly been solved through software. Within this setup, our welders are now process and quality controllers, providing higher added value to the entire organisation.”
Custom software
Key to making the technology work and remain sucessful at STAS was the establishment of an internal automation department which works hand in hand with Valk Welding’s software engineers.
“Thanks to the combination of our own machine control and Valk Welding’s ROSE server, we can control, monitor, and adjust production within the new installation,” Hugelier said. “We have also created our own link to our Enterprise Resource Planning (ERP) package. It is safe to say that an important part of the success of ‘human-friendly’ automation lies with the software.”
SQUADRON
Having this newfound knowledge has meant sharing information via SQUADRON, a network of business process experts. Through SQUADRON, STAS offers its experience to assist other SME manufacturing companies with endto-end digital transitioning. Besides welding automation, SQUADRON also takes care of linking IT-related matters, such as ERP integration and MS Power Apps, to operational matters such as project management, the development of userfriendly software and the visualisation of production data.
Single-piece production
SQUADRON has developed an ERP package with a vehicle configurator for STAS, allowing dealers to configure all available variants there. When the configuration is converted into an order, this data automatically drives and generates material procurement, production planning, and welding programs. In this way, STAS can achieve single-piece production, similar to the automotive industry.
Challenges
The next step for STAS is further integration to reduce even more ancillary activities .
“The goal is to add value only to the end product and to eliminate all waste,” Hugelier said. “We are also still at the beginning when it comes to processing data. If we can add AI intelligence to the data, we should be able to initiate preventive actions online to avoid downtime. Realising this will be an exciting challenge in the future.” valkwelding.com
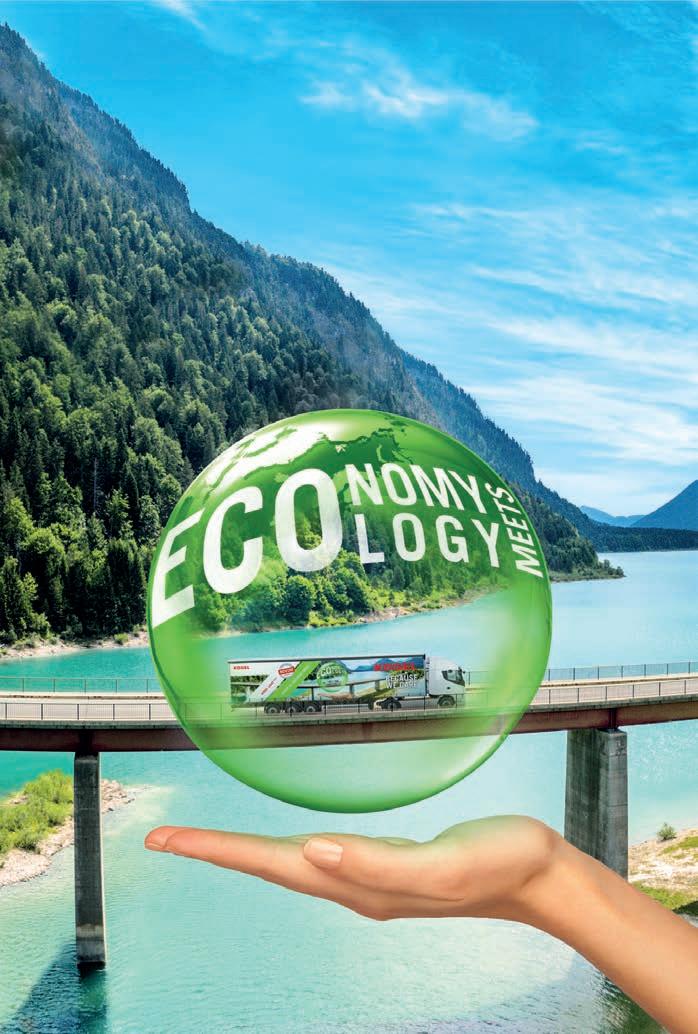
GREEN DRIVING
Following the release of TIP Group’s Sustainability Report 2022, Deputy CEO, Arjen Kraaij, spoke to Global Trailer about the company’s dedication to sustainability and the innovative products paving the way for achieving their ambitious goals.
Q: Balancing the environmental impact and economic significance of transportation is a complex challenge. How is your senior leadership team actively committed to driving positive change and mitigating the industry’s contribution to climate change?
A: There’s no two ways about it, the transportation industry significantly contributes to CO2 emissions. At the same time, it’s a fundamental part of the economy, both globally and especially in Europe. As a senior leadership team, we’re convinced that climate change is imminent, and we need to stay within certain limits to prevent severe consequences and leave the planet in a decent state for future generations. We believe that as a leader in leasing, rental, and maintenance of these assets, we need to step up and take charge. This belief is more than just a conviction; it’s a deep-seated commitment within our senior leadership team. We feel a strong obligation to act and drive change in our industry for the betterment of us all.
Q: You’ve emphasised your commitment to steering the industry toward greater sustainability. Can you outline the concrete steps TIP Group has taken to integrate responsible practices into your operations and decision-making processes?
A: We began this journey right at our own doorstep. We established a dedicated ESG function and have an ESG Committee that includes both the CEO and members of the Executive Management Team to oversee our strategy. We’ve ramped up our internal controls and introduced new guidelines and policies. This isn’t just about compliance or checking boxes; it’s about weaving responsible conduct and ESG considerations into the very fabric of our decision-making process.
I’m proud to say that we have taken significant steps towards our goals, which have been recognised by external independent organisations. Sustainalytics recognised us as the leader in the transport industry with a ‘negligible’ ESG Risk Rating, while our EcoVadis score improved to 56 from 62 in 2023, placing us among the top 2 per cent of companies worldwide. Our goal is, of course, to continue improve. The insights from EcoVadis give us a clear roadmap for this journey.
These ratings aren’t just accolades; they’re proof to our clients that we’re not just talking
the talk – we’ve got our act together and are fully equipped to help them make their own impact.
Q: How does TIP Group address these challenges for customers, and in which ways does the company support them in reaching their sustainability goals?
A: For our customers, the primary motivation to switch to zero- and low-emission technologies is clear: to combat the direct effects of climate change. But let’s face it, there are also several practical hurdles, like the still-developing charging infrastructure, the steep upfront cost of electric trucks, uncertainties about their residual value and maintenance costs, not to mention the price of electricity. At TIP Group, we’re not just aware of these challenges – we’re actively working to overcome them in close cooperation with our clients and partners.
There’s a huge opportunity right now that extends beyond just truck engines; it also involves reefer trailers equipped with fossil fuel engines for cooling. The main challenge is that these
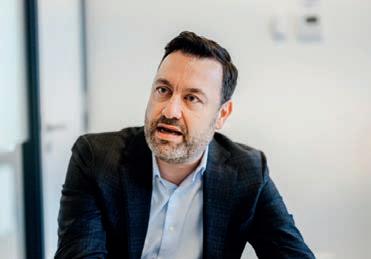
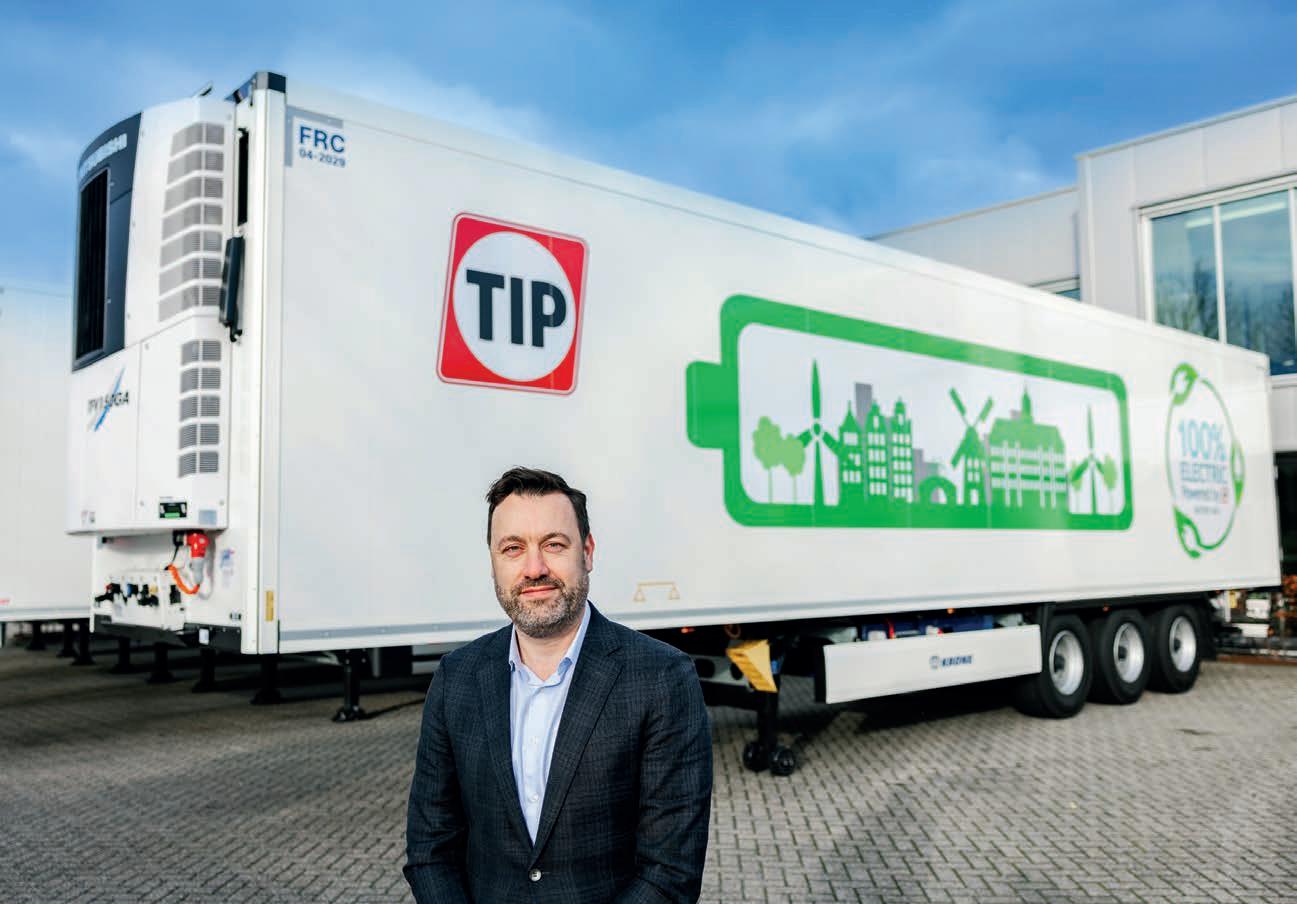
diesel-powered cooling units aren’t meeting the low emission regulations required for new trucks. That’s where e-reefer technology steps in as a gamechanger. Fuel (diesel) powered cooling units can efficiently be replaced with electric engines, and that solution is available right now. This switch is an effective way to slash emissions across the industry in the short term, and it’s an option we’re making available to all our clients. We’re not new to this tech; we’ve got ample experience and know firsthand it’s a win-win solution from every angle.
Q: Beyond the electrification of the leasing and rental fleet are there any other developments or initiatives in TIP Group’s strategy?
A: “Data is another tool we can harness to not only cut down emissions but also boost efficiency. Within the next five years, we anticipate that at least 80 per cent of our assets will be digitally connected, with all that data being aggregated on our TIP Insights platform. The key here is enabling our clients to harness the insights from this data to optimise their fleet operations more effectively. Minimising maintenance and implementing proactive maintenance can drastically reduce
unnecessary travel for servicing. This, in turn, leads to a significant reduction in emissions.
A beautiful example from the field is BrakePlus, our Electronic Braking Performance Monitoring System. It offers a smart solution for monitoring the braking system performance of your trailers and its analysis is accepted by the UK’s Driver and Vehicle Standards Agency. BrakePlus replaces the need to conduct physical roller brake tests throughout the year and is exactly the type of innovation we want our technology to unlock.
Q: What specific actions is the company taking in the next few years to turn these commitments into tangible results?
A: “Right now, there are countless ESG topics we’ve yet to touch on. We’re working on narrowing the gender pay gap, pioneering Green Financing to secure more eco-friendly funding, transforming our workshops to be greener and more sustainable, and aim to refurbish over 5,300 trailers by 2025, among other initiatives. For those eager to dive deeper, I highly recommend our 2022 Sustainability Report, which you can find on the TIP Group website.
As I mentioned earlier, our goal at TIP Group is to lead the change in introducing zero-emission vehicles in our sector. By 2030, we aim for 40-50 per cent of our fleet to be compriseed of green, net-zero emission vehicles. This won’t just be limited to electric options; we’re exploring a diverse array of solutions. Achieving this would represent a tremendous triumph in our sustainability efforts. More importantly, it would signal that we’ve successfully crafted an appealing business case, encouraging truck owners and fleet operators to adopt these zero- or low-emission technologies.”
www.tip-group.com
https://www.tip-group.com/en/about/sustainability
LEADERSHIP PROVEN
WITH A CLEAR MANDATE, KÖGEL’S NEW CHIEF FINANCIAL OFFICER IS DETERMINED TO PUT THE TRAILER BUILDER’S LONG TERM FUTURE ON SOLID GROUND.
It isn’t just Kögel’s products and services that has newly appointed CFO, Christian Spengler, excited about his new role, it is also the company’s broad-reaching potential for growth.
“I am very much looking forward to working with Christian Renners and the entire Kögel team to help harness the potential within this extremely broad area of responsibility,” Spengler said about his appointment. “This interesting variety of challenges and combination of tradition and innovation are what I need to drive me.”
Spengler, who is a qualified banker and a graduate of business economics, has had a long-standing career as a financial expert and controller, as well as experience in various commercial leadership positions.
Along with his appointment, Spengler will also become a member of the Kögel Trailer executive board. In a dual leadership role with the Chief Executive Officer, Christian Renners, he will manage the traditional Burtenbach-based company as of the beginning of 2024.
Spengler joined Kögel in 2016 as an authorised signatory and head of controlling and he went on to become head of the commercial department, for which he will now share responsibility initially.
In the long term, however, the plan is to relieve the commercial department by reinforcing the Controlling and Financial Accounting Departments. Spengler is also the managing director of the Italian subsidiary Kögel Italia S.R.L. In addition, he will shortly be appointed as the second managing director of the sandwich panel production department at Kögel PurFerro GmbH & Co. KG in Duingen, Germany.
Spengler said he is determined to optimise processes for greater efficiency and to put
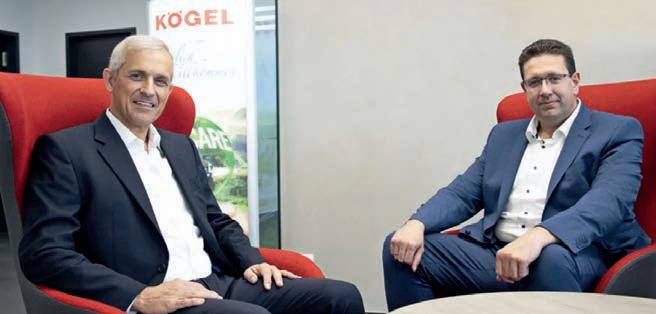
Kögel’s long-term future on solid ground.
As well as implementing a sustainable finance strategy, as CFO, he will also work to advance digitalisation in the company, improving the networking of the individual company divisions and departments. This is expected to strengthen internal cooperation between the individual Kögel divisions and the new leadership structure, as well as administrative communication with customers.
He also believes that efficiency must pay off and a focus on sustainability is especially important during the current consolidation of the trailer industry and persistent recession, adding that all future measures will follow the company’s guiding principle: “Economy meets ecology – because we care.”
For Spengler, the advancement of customer benefits in terms of ecological footprint, which have been achieved through lightweight construction and weight optimisation, are an essential prerequisite for securing the future of one of Europe’s leading trailer manufacturers.
Meanwhile, CEO, Christian Renners, is confident in the choice for the position, adding that the two leaders complement each other.
“The joint leadership of Kögel provides the best conditions for securing Kögel’s future with continuity and reliability throughout the current transformation of the industry, both internally and externally, and to position ourselves even more successfully in the international trailer market.”
www.kogel.com
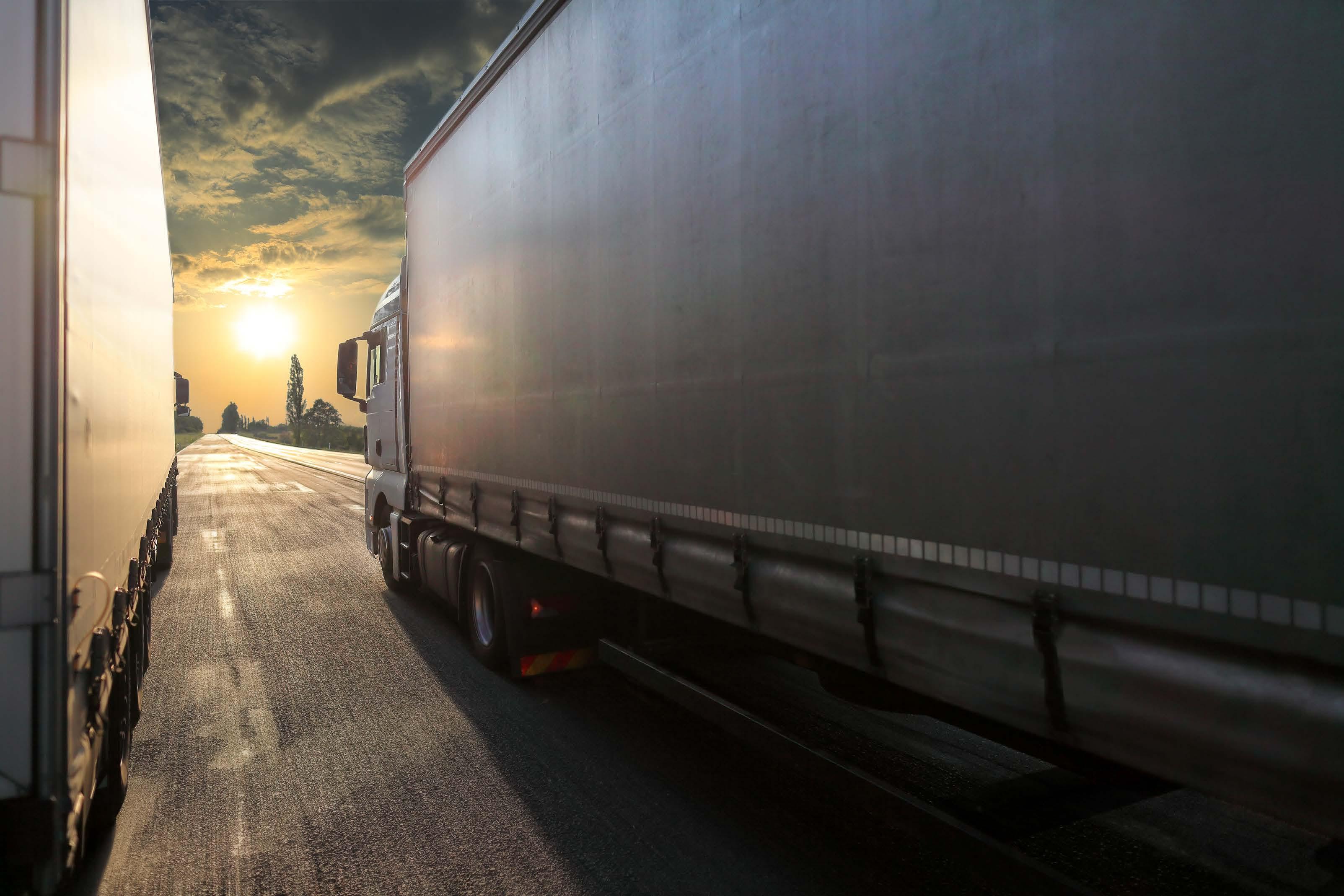
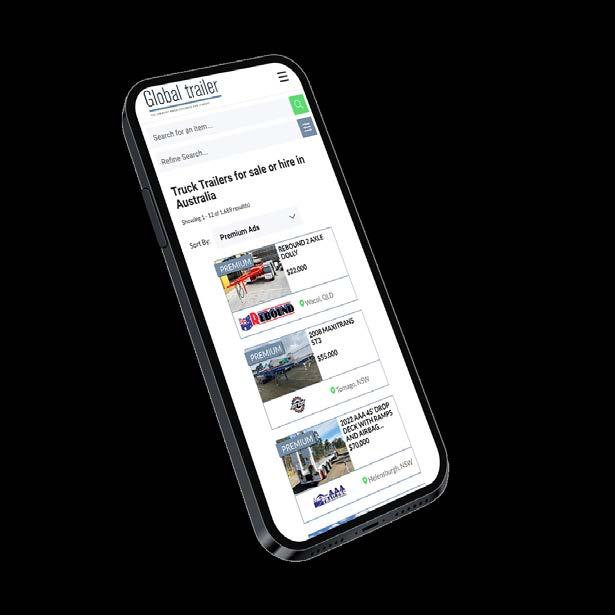
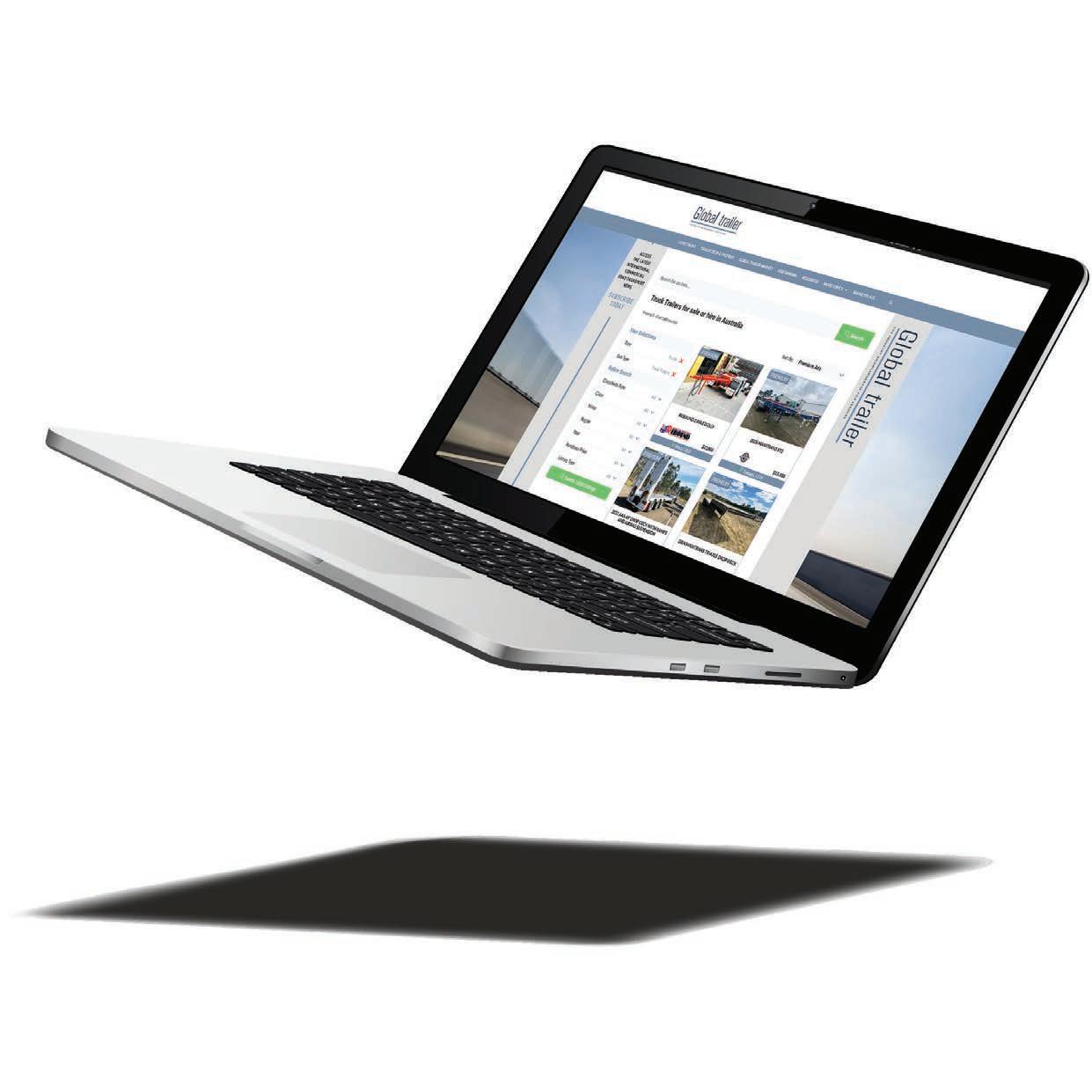
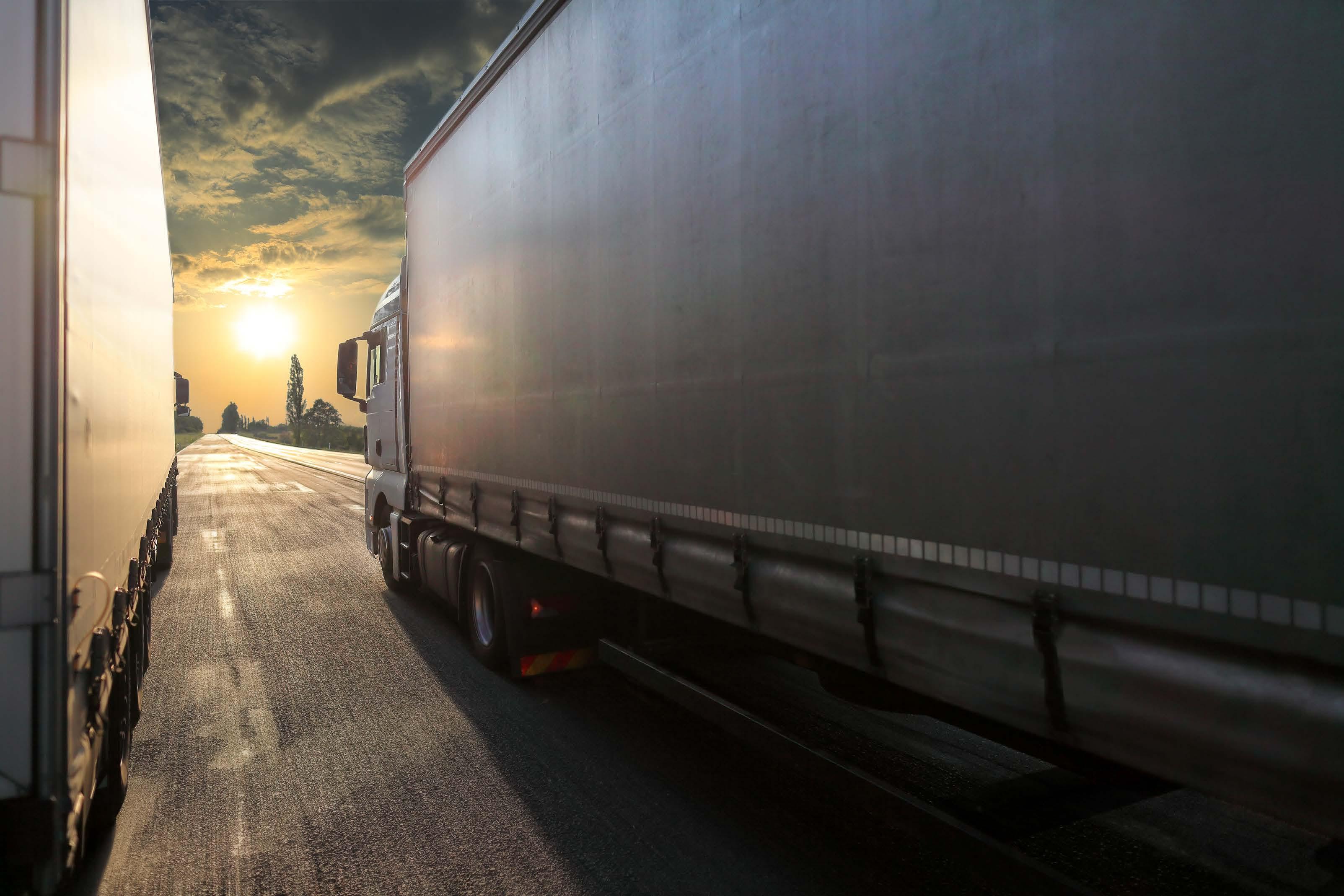

SPEED BRAKE
THEY WERE POPULAR IN THEIR OWN RIGHT BUT SINCE SAF-HOLLAND’S OFFICIAL ACQUISITION OF HALDEX LAST YEAR, ITS BRAKE PRODUCTS HAVE BEEN GIVEN A NEW BOOST AND THE MODULT TRAILER DISC BRAKE CONTINUES TO BE ITS RISING STAR.
SAF-Holland was one of Haldex’s biggest global customers and the two companies had a close working relationship for almost 15 years, often integrating their products. Inevitably, for SAF-Holland, the acquisition of the Swedish brake and air suspension manufacturing company became a fundamental step in terms of business growth and product development.
The plan was to create a new global champion for chassis-related commercial vehicle components.
SAF-Holland CEO, Alexander Geis, at the time, called the deal an ‘industry-changing partnership’.
He explained that the acquisition would mean the company could offer a majority of key components from a single source, and Haldex would benefit from an enhanced onestop shop solution throughout the entire product life cycle – from initial consultation and configuration to delivery and maintenance.
“Together, we would have the unique ability to offer integrated mechatronic systems and smart solutions for suspensions, axle systems and electronic braking system modules,” he said.
Since the official acquisition announcement, the company has been working to integrate the new Haldex brand into the SAF-Holland Group, combining axle and suspension systems, telematics and EBS control into one intelligent unit.
One of its first combined forays into the public domain was at last year’s SOLUTRANS trade fair in Lyon, France where it showcased its amplified offering.

Haldex had expertise that spanned more than a century, which made them a trusted partner for major manufacturers of heavy trucks, trailers, and buses worldwide. Today Haldex offerings can be grouped into two product areas – foundation brakes, which are wheel-end products for brake actuation and lining wear adjustment such as disc brakes, brake adjusters and actuators, as well as air controls, which includes products that improve the safety and driving dynamics of the braking system, such as compressed air dryers, valves, ABS and EBS.
Among its foundation brakes, the Haldex ModulT trailer disc brake, which entered European markets more than ten years ago, has proven to be one of the most reliable in the field, with few support issues reported over the years. According to Haldex, there are many design features that ensure its longevity:
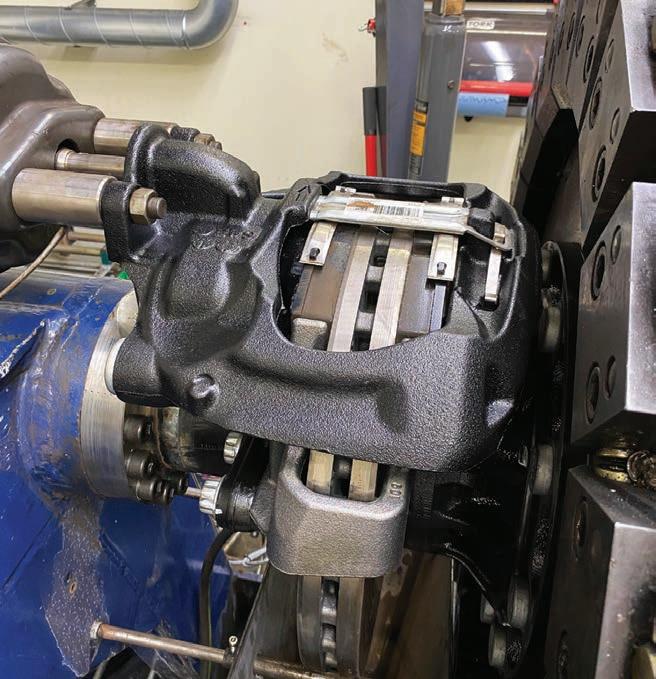
• The disc brake design, although open enough to allow for cooling and drainage, a folded bellows mechanism protects moving parts from the impact of stone chippings, salt and surface water kicked up from the road.
• Haldex is the only brake OEM to fit stainless steel pins in the brake for the caliper to slide on during operation. The steel provides a second layer of defence (in addition to protective metal caps) against the risk of binding due to rust. To simplify maintenance, composite trailing-edge bushings prevent the need for manual lubrication.
• The cast body of the caliper has been designed specifically for strength and integrity, at an absolute minimum of weight. One particularly important issue is the taper, the transition between thick and thin areas, since the ratio of surface area to volume determines cooldown time. Haldex ensures that no taper is too extreme, since cooling times could differ so greatly that they could lead to structural imperfections.
• Haldex brake calipers are produced in an extremely automated process. That means that the manufacturing system repeats from one brake to the next in batches running into thousands. Any variations in an individual part will be detected automatically by in-process measurements at each production station and supplemented by random production sampling regimes.
• While Haldex reduces the weight of the brake by featuring a single, rather than a double, tappet mechanism between the brake chamber and the disc thrust plate, this can risk uneven wear and more frequent pad changes. To prevent this, ModulT brakes incorporate a wide mechanism to provide even force distribution.
• There can sometimes be the risk of hysteresis – the loss of braking force due to frictional losses – which Haldex minimises by fitting back-to-back double roller bearings.
• To improve the ease of routine servicing, ModulT brakes require no tooling for the regular task of changing the pads. The pad retainers are removed by sliding them out from the caliper after compressing a spring clip. Despite the ease, all aftermarket pad kits contain a detailed instruction kit.
Meanwhile, Haldex plans to continue expanding its portfolio of commercial vehicle products. Next year, it will begin series production of 17-inch and 19-inch brake calipers for a medium-duty truck with new designs for both the cast parts and the pads.
ww.haldex.com
THINKING FORWARD
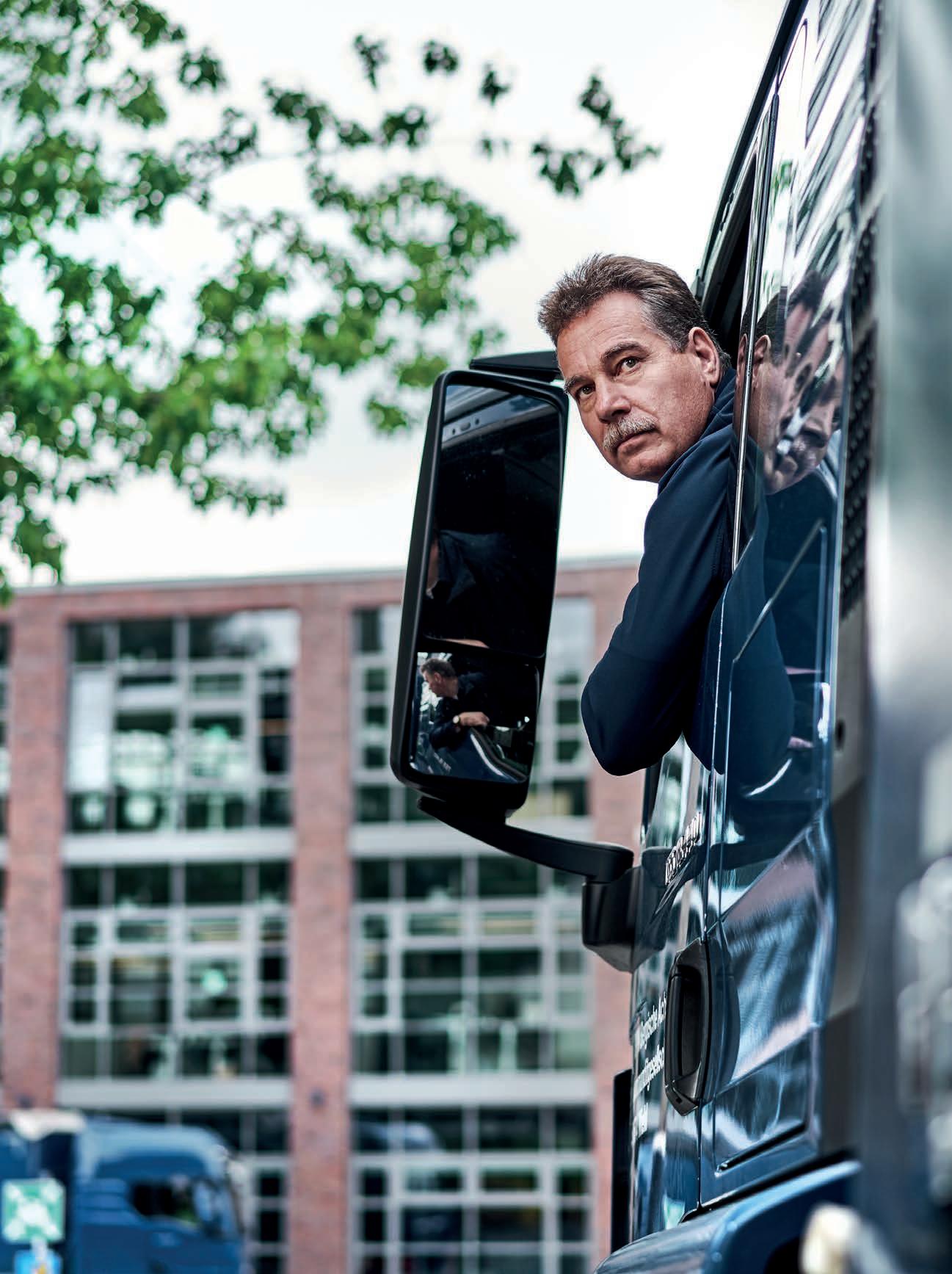
TURNING A TRUCK IS A CHALLENGE FOR THE DRIVER, BUT ALSO FOR THE TRAILER MANUFACTURER. WITH ITS ‘ACTIVE REVERSE CONTROL’ ELECTRO-HYDRAULIC AUXILIARY STEERING SYSTEM, BPW HAS TURNED TRAILERS INTO MANOEUVRING MARVELS AND RADICALLY SIMPLIFIED INSTALLATION. EQUIPMENT MANUFACTURER IS UPPING THE ANTE WITH WHEELS THAT CAN ALSO BE STEERED WHILE DRIVING FORWARDS.
Charming old towns, narrow loading ramps, overcrowded car parks, busy construction sites, old-fashioned petrol stations and quaint little dairy farms have all one thing in common – they are all a nightmare for any truck driver.
Turning or threading a trailer in the tightest of spaces makes even the most experienced truckers work up a sweat. One hapless move and there’s a risk of damage that jeopardises both time and business plans.
The vehicle industry has therefore long grappled with the development of all kinds of auxiliary steering systems. However, most of them proved to be too complicated to operate, too complex to install and ultimately too expensive for trailers in most price categories and application scenarios.
But now, BPW is offering Active Reverse Control (ARC), a solution that immediately impressed experts and drivers alike.
It is based on the proven BPW self-steering axles and an innovative gyroscope sensor technology controlling the steering angle electro-hydraulically. ARC facilitates and speeds up previously hair-raising turning manoeuvres, reduces the risk of accidents and also enables drivers to fulfil the demanding transport tasks more quickly.
But it is also the plug & play system design for the vehicle manufacturer that has helped the ARC achieve industry-wide recognition.
How it works
The steering cylinder and sensors are mounted directly on the axle. This means the steering system is completely free of the clunky, conventional steel rods.
There is also no need for an extra sensor on the king pin. ARC’s control unit and the hydraulic tank can be mounted anywhere under the trailer.
Power can be supplied either via the towing vehicle or independently via a battery. This unprecedented flexibility and compact design enable vehicle manufacturers to equip a wide range of trailers with ARC – including low loaders, where the installation space is a matter of millimetres.
The system covers a range of drum and disc brakes.
A streamlined installation is an economical one which allows manufacturers to target broader trailer market segments with ARC. BPW delivers the axles with pre-assembled parts ex works, ensuring a seamless integration process. The software is also pre-installed.
As another industry first, BPW has developed a smartphone app that enables effortless initial commissioning and remote diagnostics. Notably, no additional adaptations to the vehicle frame are required, eliminating unnecessary complexity. A sample test report in accordance with ECE R79 and EMC certificates in accordance with ECE R10 are included for compliance and safety.
Enhanced agility
When reversing, sensors and electrical and hydraulic systems ensure that the wheels are steered at the optimum angle. The driver can also manually select the steering angle when reversing by remote control. This gives the driver even greater manoeuvrability. Now, for the first time, the operator can remotely steer the wheels when manoeuvring forward at speeds up to 10 km/h with the same steering angle as reversing.
Previously, during forward manoeuvring, the wheels followed the natural movement of the self-steering axle. However, this required the vehicle to travel a few metres.
Now the wheels can also be manually steered forwards. With radio control, the driver can drive the trailer both forwards and backwards in confined spaces, reducing the number of manoeuvres required.
This saves time, effort and wear on the wheels.
The BPW engineers took up suggestions from drivers who had gained experience with the ARC. Drivers and vehicle engineers were correspondingly enthusiastic during the first drives that BPW offered the manufacturers with a test vehicle.
The additional function does not make the ARC any more complicated – forward driving is activated by the EBS system.
To implement the new feature, BPW makes clever use of the EBS’ ISS (Integrated Speed Switch) interface. The ARC will be connected to the EBS with an additional cable set. BPW supplies the appropriate cable set for the vehicle ex works. This means that the ARC remains a plug & play system, with which BPW is once again proving itself to be a forward thinker within the industry.
www.bpw.de
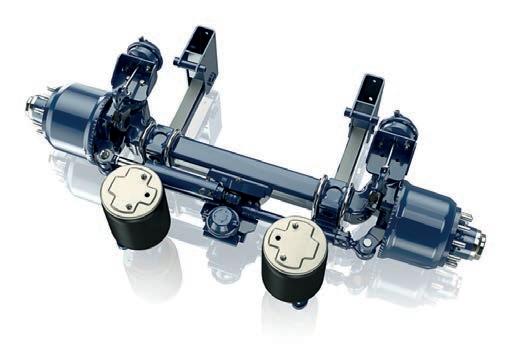
Image: BPW.
DEAL OR
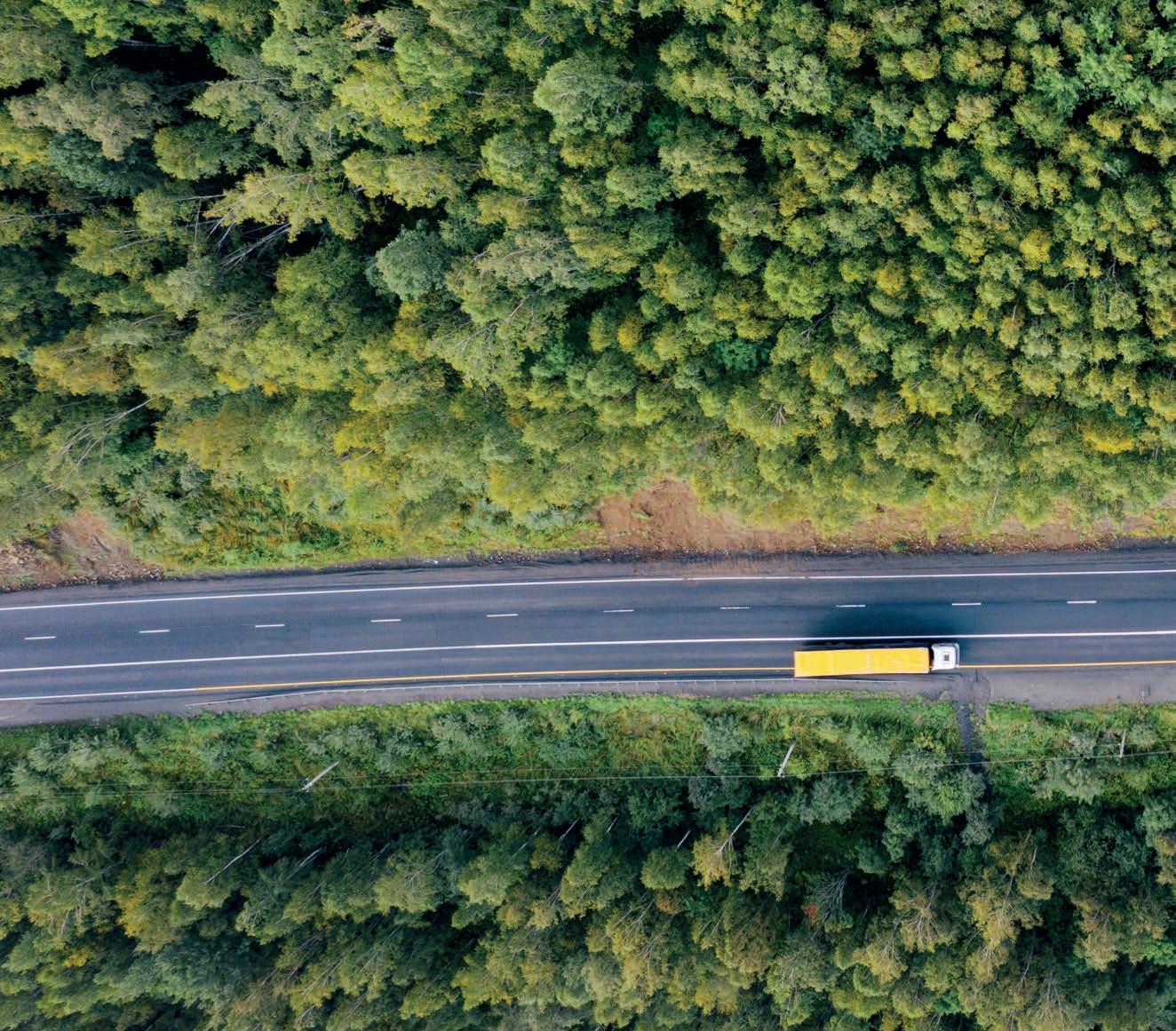
RECENT TRENDS WITH INDUSTRIAL LOGISTICS ASSETS COUPLED WITH SOME BOLD MOVES BY INTERNATIONAL LOGISTICS AND ROAD TRANSPORT COMPANIES COULD DISRUPT THE MARKET QUITE SIGNIFICANTLY.
Arise in e-commerce sales, consumer demand for faster delivery times, geopolitical reshoring of manufacturing and post-pandemic inventory rebuilding are contributing factors for growing demand in the logistics space according to David Roberts, Head of Real Estate Strategy at Macquarie. Despite growing demand and rent rises, higher interest rates and capital market volatility are triggering refinancing and redemption pressure among asset owners who are selling down highly liquid logistics assets. With the rise in building costs which have impaired construction activity, there could be a supply issue for industrial assets in the future.
Logistics, according to Roberts, is a simple business at its core – efficiently distributing goods to households, retailers and businesses.
“But the apparent simplicity hides a fast-growing, sophisticated and complex network of operations feeding an ever-more-demanding consumer,” he said.
“Traditional mail-order timeframes have evolved into today’s fast-paced system of next-day, same-day, and even within-the-hour delivery. But alongside the rapid growth of e-commerce, businesses are also investing in reshoring global supply chains and building inventories to protect against future shortages –further fuelling demand for warehousing space.”
NO DEAL
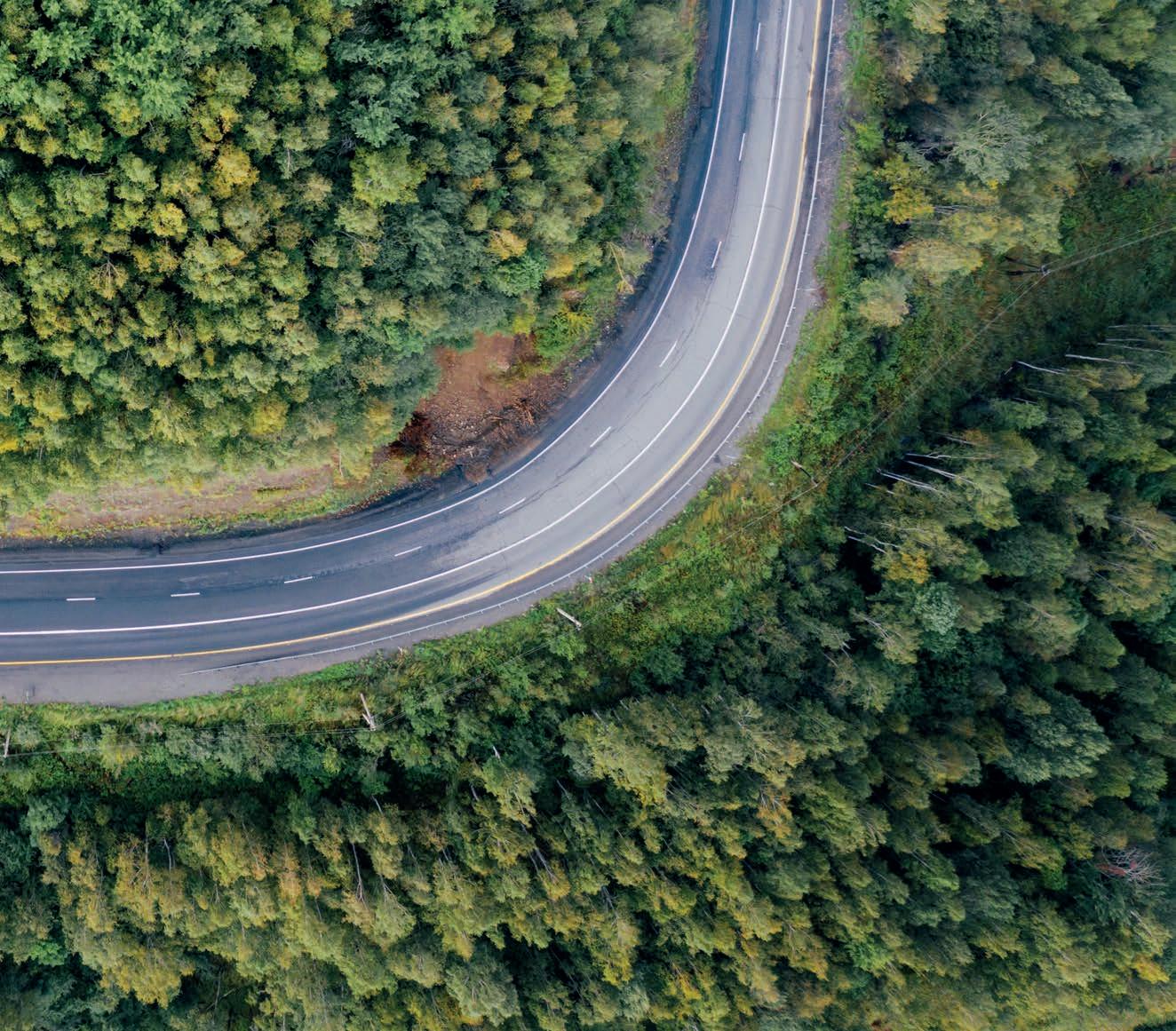
In contrast to other key developed markets, Roberts said accommodative lending conditions and positive leverage continue to support logistics pricing in Japan.
“Attractive cash-on-cash yields and strong demand fundamentals are supporting demand for logistics exposure from domestic and foreign real estate investors. Furthermore, monetary policy is likely to remain accommodative as Japan grapples with demographic headwinds and underlying soft demand conditions as its population ages.
“Should rates tighten over the next 12-24 months, for example to support a cyclical recovery in the currency, any tightening is likely to be quickly reversed when the global monetary easing cycle begins and
underlying demand conditions weaken.”
Demand for logistics space, according to JLL, is now at cyclical highs reflecting the ongoing shift to online spending, consolidation of existing operations and drive for efficiency with occupiers shifting to newer modern facilities underpinning development strategies.
Firms, Roberts explained, are also increasingly considering automation of their facilities to address labour shortages which is boosting demand for modern logistics facilities that can accommodate such shifts.
He said rents are expected to continue to rise, reflecting a combination of higher land prices and construction costs which is putting upward pressure on prices for newly completed properties. Rising construction costs are also likely to impact development pipelines for weaker projects in non-core locations.
Looking at industrial rental growth change between June 2020 to June 2023 (data via PMA, CoStar, JLL, as at September 2023), London has seen the most change at nearly 60 per cent. Inland Empire falls in at close to 50 per cent while Los Angeles and Sydney sit near the
40-per-cent mark. Other cities reported include New York (30 per cent), Munich (29 per cent), Singapore (25 per ent), Paris (18 per cent) and Hong Kong and Greater Tokyo under 10 per cent.
Fleet moves down under
In September 2023, Liquefied Petroleum Gas (LPG) marketer, Elgas, agreed to acquire Rivet Energy, which it claims is Australia’s largest LPG fleet operator.
Rivet Energy, a provider of gas and liquid fuel transportation and distribution services, currently services 100 per cent of Elgas’ bulk haulage requirements across Australia.
As part of the acquisition, Elgas will purchase all of Rivet Energy’s assets including its transport fleet of trailers, tankers and prime movers.
It will also retain Rivet Energy’s depots and workforce.
Elgas and BOC Managing Director, Binod Patwari, said the acquisition would secure Elgas’ LPG supply chain nationally and provide strong security of supply to thousands of customers across Australia.
“We are delighted to welcome Rivet Energy to the Elgas business and are confident this acquisition will safely deliver greater efficiencies and productivity across our transport fleet with access to industry-leading transport maintenance facilities and expertise,” he said.
“Rivet Energy has a highly experienced management team and drivers who share our strong
commitment to safety and have an excellent track record hauling dangerous goods.
“We look forward to working closely together to strengthen Elgas’ national LPG supply chain and deliver strong security of supply to Elgas customers.”
Rivet Energy General Manager, Mark Anderson, said he was delighted to expand the longstanding, productive partnership between Rivet Energy and Elgas.
“We are thrilled to be securing the future of the Rivet Energy business, including the ongoing employment of our experienced staff and drivers who can now be part of Australia’s largest supplier of LPG,” he said.
“Our transport industry experience and specialist workshops in key metropolitan locations throughout Australia will be a valuable addition to the Elgas transport fleet and delivery services for customers.”
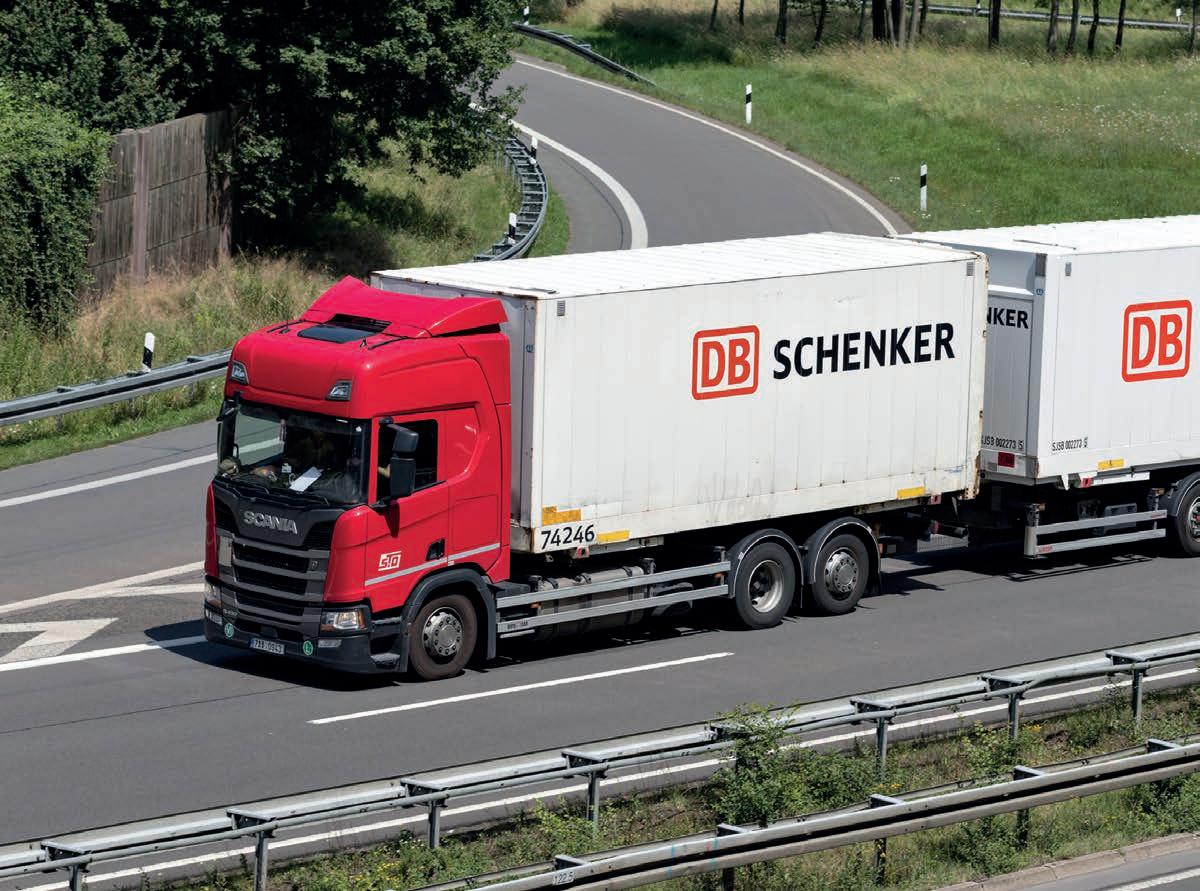
Meanwhile, Austria’s Gebrüder Weiss is expanding its network in Australia with the opening of a new Air and Sea office in Brisbane.
This is now the third location operated by the international logistics company in Australia, following on from Sydney and Melbourne, and will be tailored to customers from the engineering, agriculture and medical equipment sectors.
“Opening a location in Brisbane represents another key step in our efforts to increase our presence in Australia,” said Managing Director Australia and New Zealand, Andrew Antonopoulos. “The services include air & sea transports, customs clearance and a customised logistics mix for project orders.”
Brisbane’s container port, with a record throughput of 1.56 million standard containers last year, is the most important international transhipment hub in the city, while the nations’s most significant import
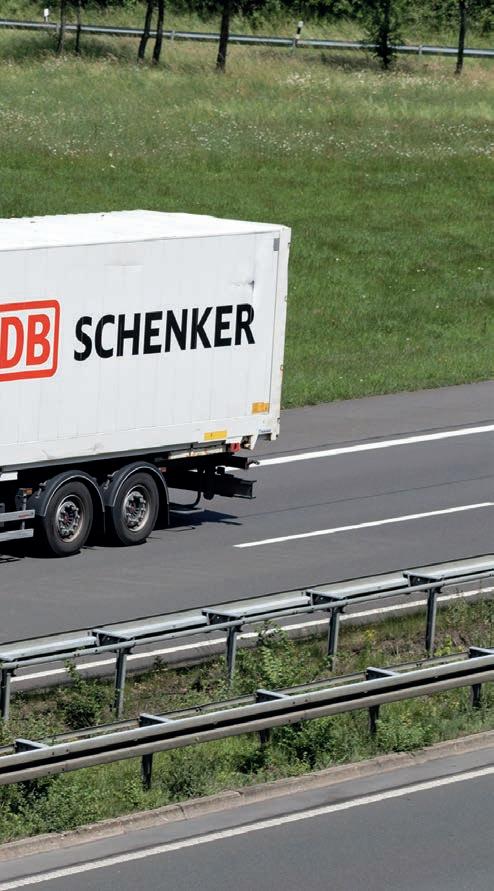
partners are China, the United States as well as other Asian countries such as South Korea and Japan.
“We offer efficient end-to-end logistics solutions for connections with the rapidly growing amount of intra-Asian traffic,” said Regional Manager East Asia/Oceania, Michael Zankel.
Most recently, Gebrüder Weiss organised the transport of an innovative solar car from Switzerland to Australia and back for the ETH Zurich’s aCentauri Solar Racing Team who covered a distance of 3,000 km across the Australian outback using only solar power.
Gebrüder Weiss has plans to open additional locations in the north and west of Australia to provide blanket coverage for the whole continent. It also has a foothold in New Zealand with locations in Auckland and Christchurch.
North American sales
Trucking company, XPO Inc, was the top bidder at a sale of bankrupt Yellow’s assets, winning the right to 28 service centres at a price tag of $870 million USD.
The 100-year-old transport firm, which serviced the less-than truckload market, filed for bankruptcy protection in August blaming ongoing strike action by the International Brotherhood of Teamsters union for its financial woes.
Yellow’s 17.5 million annual shipments made it the third-largest in the US, but it had an outstanding debt of about $1.5 billion as of March, despite receiving a $700 million loan from the federal government in 2020. The company had been in an ongoing battle with the Teamsters union, which represents 22,000 drivers and dock workers, over unpaid pension and health insurance contributions.
According to a report by Reuters, XPO expects the deal, which is subject to court approval, to add to core profit in 2024 and adjusted profit per share from continuing operations from 2025.
XPO’s successful bid was part of a court-supervised auction that saw nearly two dozen companies, including Estes Express Lines and Knight-Swift Transportation Holdings, win rights to purchase Yellow’s assets for $1.88 billion, as per a court filing on Monday.
European game changer
The DB Group is looking to minimise debt by potentially selling its logistics business.
A sale will only be settled, according to DB Group, if it has apparent economic advantages for Deutsche Bahn in all respects.
“A sale would significantly accelerate Deutsche Bahn’s focus on its core business and the implementation of the Strong Rail strategy,” DB Group said in a statement.
“Deutsche Bahn has already completed or contractually agreed the sale of several of its business units in foreign markets and would be taking another big step by letting go of DB Schenker. Our goal is to serve the climate, people and the economy by substantially increasing the cargo and passenger volumes handled by eco-friendly rail services.”
While DB Schenker has contributed positively to DB Group’s economic growth over the years, the DB subsidiary will need additional capital and flexibility for its own growth.
In December 2022, the Supervisory Board of Deutsche Bahn AG assigned DB’s Management Board the task of examining the case and preparing for a potential sale of its entire shares in DB Schenker. The final decision on a sale of DB Schenker will be based on a separate resolution adopted by the Supervisory Board of Deutsche Bahn AG at the end of the sale process. The process is also subject to general capital market developments.
Compared to its competitors, DB Schenker has a strong position in all the relevant industry sectors – land, air and ocean freight – and in comprehensive and specialised logistics solutions. With some 76,600 employees at over 1,850 locations in more than 130 countries, the company is one of the world’s leading logistics providers.
www.globaltrailermag.com
EARTH MISSION
THE WORLD’S LARGEST CLIMATE MEETING WAS HELD IN DUBAI AT THE END OF LAST YEAR WITH THE GOAL OF DEVELOPING A NEW PLAN TO ADDRESS THE MOUNTING CRISIS OF HUMAN DRIVEN CLIMATE CHANGE. SO, WHAT EXACTLY WAS THE OUTCOME, AND WHAT DOES IT MEAN FOR THE TRANSPORTATION INDUSTRY?
Many observers were calling the COP28 event – the United Nations Climate Conference – the most important meeting in 28 years of international climate negotiations. Others proclaimed it didn’t go far enough, falling short of delivering the decisive action that science says is required.
As the biggest gathering of its kind, the global event attracted 85,000 participants, including more than 150 heads of state and government, as well as representatives from industry, business, Indigenous groups, youth sectors and philanthropy.
It was, even more importantly, the first chance to conduct what was dubbed a ‘Global Stocktake’ of the world’s efforts to address climate change since the creation of the Paris Agreement – a legally binding international treaty on climate change adopted by 196 parties at the UN Climate Change Conference in 2015.
In fact, the Global Stocktake was arguably the most scrutinised text at COP28 and influenced both the direction and agenda of the event, thanks in part by the concern that progress since the Paris Agreement was too slow across all areas of climate action, whether it was supporting vulnerable nations or reducing greenhouse gas emissions.
The beginning of the end
Most reports from COP28, and subsequent summaries of the outcome, suggest there was a clear and unified desire to transition away from fossil fuels. But there was consistent concern that the steps put forward, as to how to address the transition, were too incremental, especially considering the urgency at that moment – the gathering taking place during what scientist had found to be the globe’s hottest year on record.
By all accounts, participants by the end of the conference weren’t so bold as to declare the complete end of fossil fuels, but agreed that significant progress had been made.
“Whilst we didn’t turn the page on the fossil fuel era in Dubai, this outcome is the beginning of the end,” said UN Climate Change Executive Secretary, Simon Stiell in his closing speech. “Now all governments and businesses need to turn these pledges into real-economy outcomes, without delay.”
The language may still be relatively watereddown in the summit’s final document, but the support was there, with more than 140 countries publicly stating that they were in support of a fossil-fuel phase out. There were even calls from the Pope stating that it was ‘essential that there be a breakthrough that is not a partial change of course’ and demanding the total elimination of fossil fuels.
Among the reported improvements in the final text was the addition of the projection of peak global emissions between 2020-2025. Also made explicit now are the details around emission reductions, consistent with the goals of limiting warming to 1.5°C above preindustrial levels, as well as reaching net zero emissions by 2050.
The final text more strongly ‘called on’ nations to take a variety of actions to reduce emissions. It also stated the intention of ‘accelerating and substantially reducing non-CO2 emissions globally, including in particular methane emissions by 2030’.
Fossil fuels and transport
The global transport industry had an important role to play at COP28, having the distinction of the highest reliance on fossil fuels of any sector. According to the United Nations Economic Commission for Europe (UNECE) in 2021 itit accounted for approximately 77 per cent of global
NET ZERO EXPLAINED
Net zero means cutting greenhouse gas emissions to as close to zero as possible, with any remaining emissions re-absorbed from the atmosphere, by oceans and forests for example.
Science shows that if we are to avert the worst impacts of climate change, global temperature increase needs to be limited to 1.5°C above pre-industrial levels.
Currently, the Earth is already about 1.1°C warmer than it was in the late 1800s, and emissions continue to rise. To keep global warming to no more than 1.5°C – as called for in the Paris Agreement – emissions need to be reduced by 45 per cent by 2030 and reach net zero by 2050.
A growing coalition of countries, cities, businesses and other institutions are pledging to get to net-zero emissions. More than 140 countries, including the biggest polluters – China, the United States, India and the European Union – have set a net-zero target, covering 88 per cent of global emissions.
The problem is that commitments made by governments to date still fall short of what is required. Hitting global targets will require a dramatic reduction in the levels of carbon released into the atmosphere — through such initiatives as green transport, regulated agriculture and clean energy.
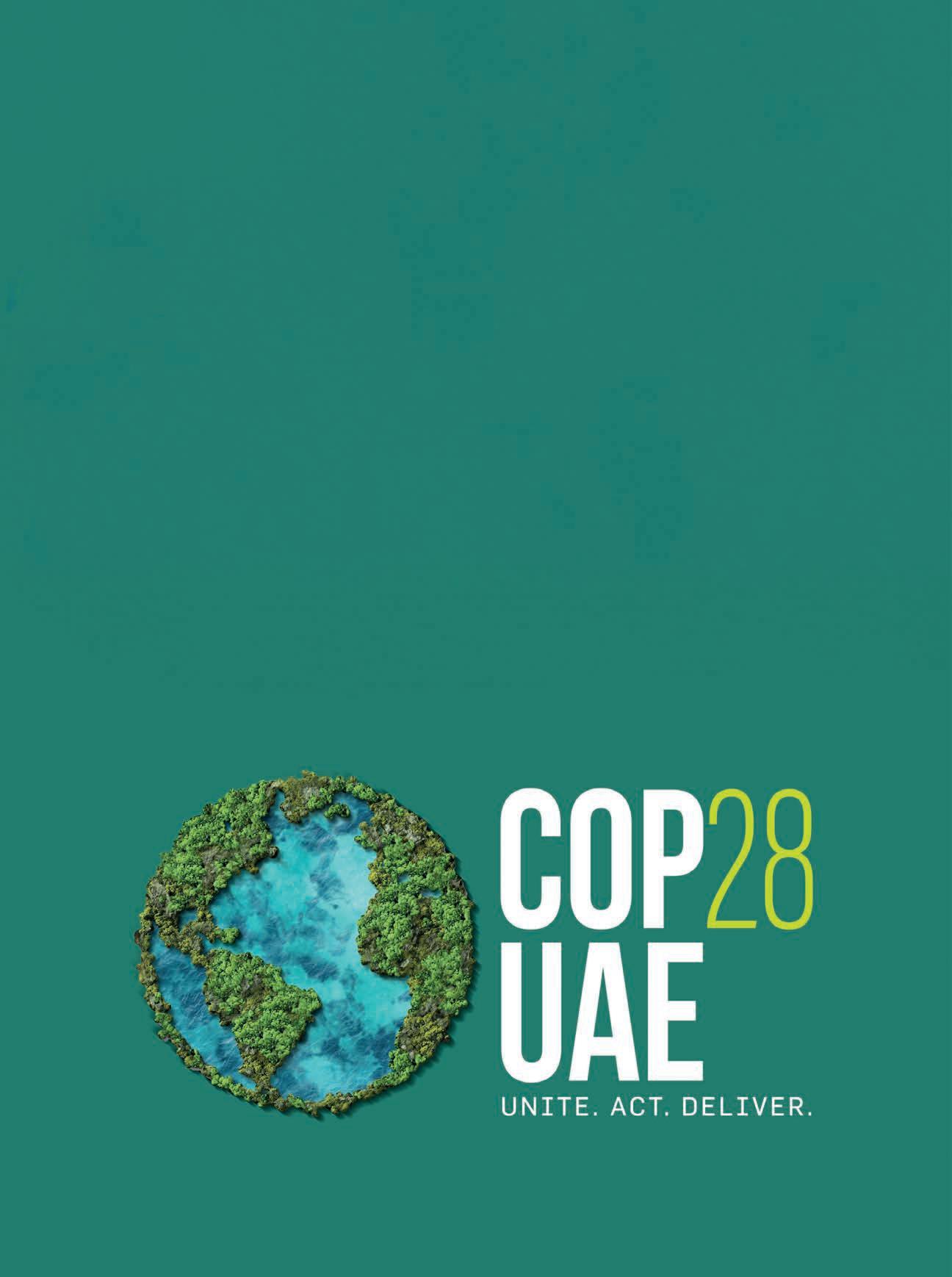
transport related greenhouse gas (GHG) emissions.
Shelia Watson, the Deputy Director of the FIA Foundation, a global charity specialising in sustainable transport, was in attendance and highlighted the importance of transport being part of the conversation and the solution.
“Transport is a vital and often overlooked part of the climate action agenda,” she said. “During COP28 we were pleased to join a range of partners from across all elements of transport in calling for urgent action to move away from fossil fuel reliance, for investment in active mobility and for a just transition. It is clear that we must change how we move now, and that change must happen in a rapid, effective, and inclusive way.”
The goal
The 2015 Paris Agreement established a mandate that the world must limit global temperature rises to well below 2°C compared to pre-industrial levels, and preferably to no further than 1.5°C.
This requires what is called the Net Zero Emissions (NZE) by 2050 Scenario, meaning cutting greenhouse gas emissions to as close to zero as possible, with any remaining emissions re-absorbed from the atmosphere by oceans and forests.
In order to reach NZE by the 2050 deadline, UNECE has calculated that CO2 emissions from the transport sector must fall by more than three per cent per year to 2030. At the moment, today’s combustion engine dominated transport sector continues to rely on oil products for nearly 91 per cent of its energy.
Sustainable, low carbon mobility is therefore a high policy priority for practically all governments and central to delivering on the Paris Agreement. This is not an easy task however, especially considering the sector’s heavy dependance on fossil fuels, surpassing every other industry. The onus is now on the transport industry to make the necessary changes and reach global targets.
“As the world faces a projected increase of 79 per cent in transport passenger demand and 100 per cent in freight demand by 2050, the road-based transport sector bears a unique
and urgent responsibility in helping countries meet their climate change mitigation goals and decarbonise,” said UNECE Executive Secretary, Tatiana Molcean.
The UNECE believes that the decarbonisation of transport should go hand in hand with the integrated planning of transition in the energy sector. This means any investments in the grid need to support the electrification of transport and the integration of renewable electricity. The organisation believes that the combination of high transport accessibility requirements and drastic reductions in emissions will only be achieved through a mix of policies and measures. These, it says, need to include fiscal incentives, strong regulations, investment in infrastructure and a push toward fewer emitting modals.
While there are still question marks as to how ending fossil fuels will ultimately be achieved, there were some tangible results from the summit. Among the major COP28 transport outcomes were:
• The creation of a transportation coalition that includes more than 60 members from various companies, governments and NGOs. The group has issued a call to action to “double the share of energy efficient and fossil-free forms of land transport by 2030.”
• The release of figures from the International Council on Clean Transportation that highlighted the progress of manufacturers towards electric vehicle goals. The group found that if manufacturers meet their current goals, electric vehicle sales would be about 32 per cent by 2030.
• Ten companies joining the Cargo Owners for Zero Emission Vessels, bringing the total to more than 35 freight buyers working towards zero-emission ocean transport.
• Twelve more countries joining the Net Zero Government Initiative, increasing the total to 30 that have committed to put their national government operations on a path to reach net zero emissions by 2050. With transportation being a significant source of
emissions, it is hoped that this commitment will steer government investments towards zero emission transportation options.
• An official response from transportation to the COP28 Global Stocktake –used to monitor its implementation and evaluate the collective progress made in achieving agreed goals –which will hopefully lead to more specific and formalised transportation sector targets.
• A number of new countries, including Australia and Norway, joining action groups committed to ending overseas public financing of fossil fuel projects.
Continued sector progress
For its part, the transportation industry knows what is on the horizon and there are a number of key companies, especially within the trailer building industry, working diligently to be ahead of the sustainability curve. They made their presence known at COP28 participating in round table events and demonstrating what they have done so far to tackle emissions.
For example, SSAB, which produces steel that

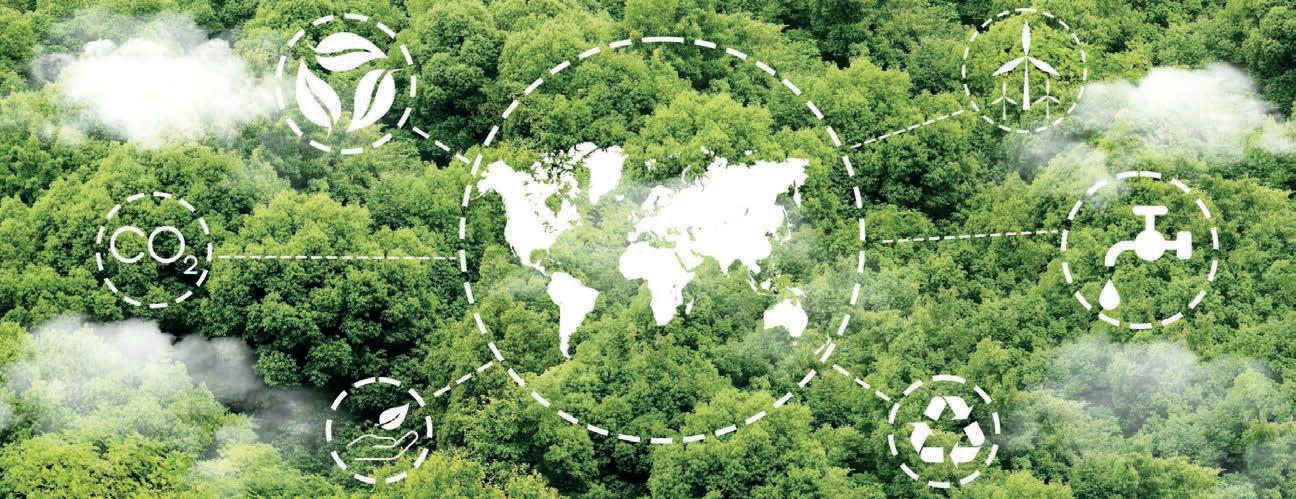
is used by manufacturers, joined COP28 as part of the Swedish delegation. The company which is already a leader in the steel industry’s green transition asked that policymakers prioritise research and development and faster permission
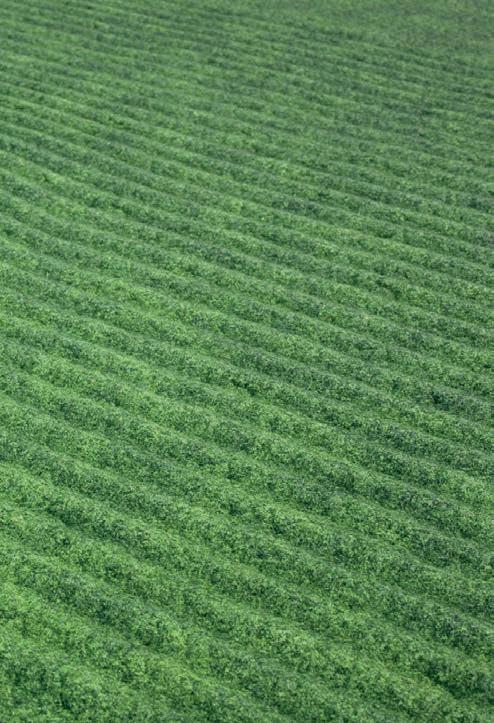
for green industrial projects.
“Our research and innovation and production of fossil-free steel can change an entire industry and its value chain,” said SSAB Chief Technology Officer, Martin Pei. “Now policymakers nationally and globally need to create the right conditions to support the steel industry’s green transition.”
Trane Technologies, whose brand ThermoKing is a leader in global refrigerated transport, was represented at the conference, underscoring the need for the adoption of accelerated climate policy and transparent emissions reporting.
The company, which was a signatory of the COP28 open letter, called for an increase in public-private collaboration and action to reduce emissions across global value chains.
“Accelerating decarbonisation requires not only innovation, but also advocating for policies that remove barriers and support adoption at scale,” said Trane’s Vice President of Sustainability, Scott Tew. “Companies around the world, across all sectors, must be held accountable for meeting commitments and driving urgent action now as we collectively work toward a more sustainable future.”
Trane Technologies is advancing its 2030 sustainability commitments, including the Gigaton Challenge, a pledge to reduce customer greenhouse gas emissions by one billion metric tons as well as its goal to be net-zero by 2050.
The sustainable future
Experts still insist reaching net zero within the transport industry by 2050 is still within the realm of possibility, but time is of the essence. According to CDP Worldwide, a notfor-profit that helps companies assess their global environmental impact, the sector is not well-prepared for the change that is coming.
A 2021 CDP assessment found more than a third of companies had not set any targets to reduce emissions, and 41 per cent were members of trade associations that hold positions on legislation that could hinder progress towards a low-carbon economy.
Approaching quickly is the next COP climate meeting which will take place in November 2024 in Azerbaijan. Participants and organisers are no doubt hopeful that by then the planet will be that little bit closer to saving itself.
www.globaltrailermag.com
CYBER ATTACK
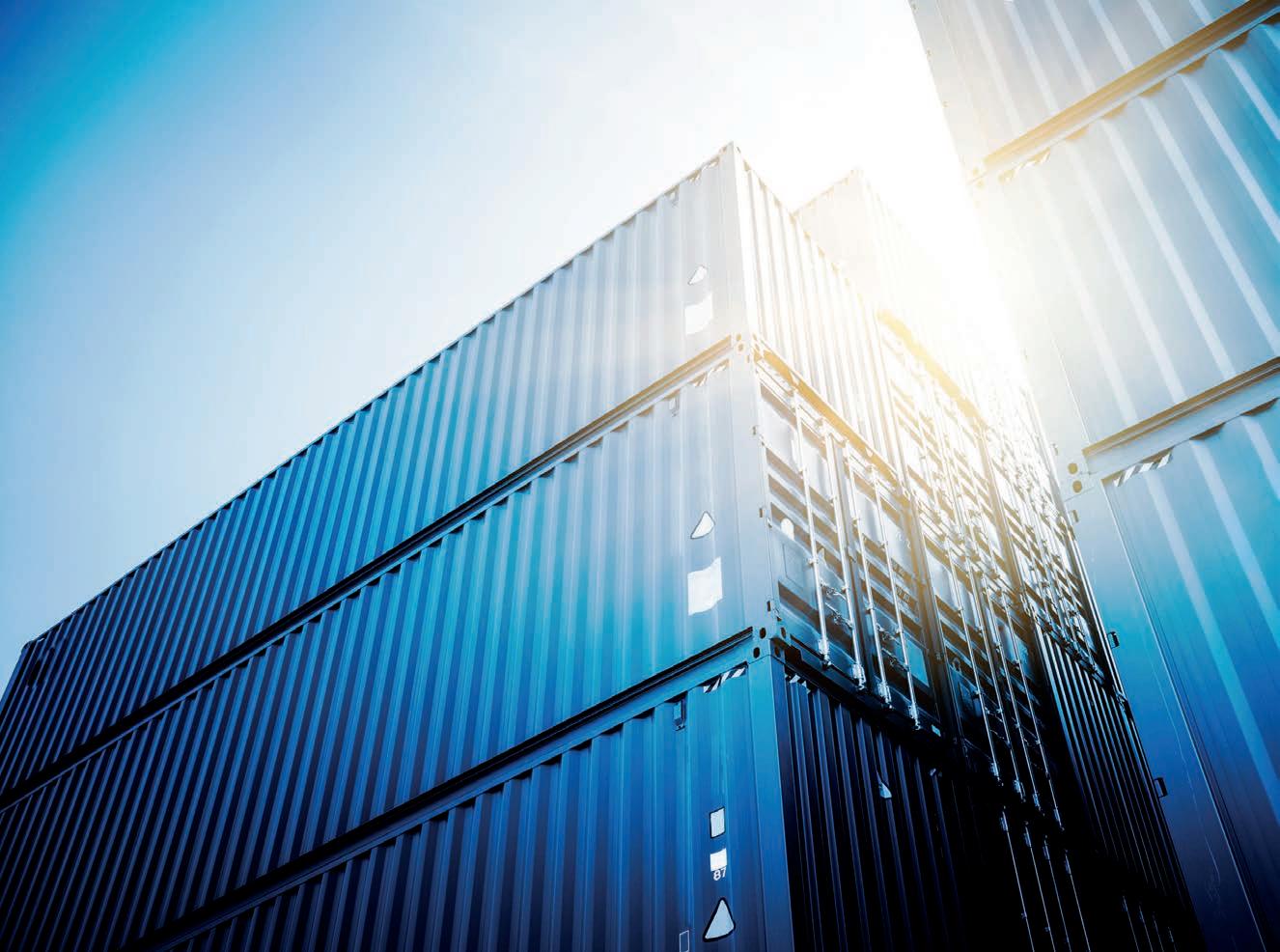
THE TRANSPORT AND LOGISTICS INDUSTRY IN AUSTRALIA WAS DISRUPTED LAST YEAR BY MALICIOUS CYBER SECURITY ACTIVITY. HERE’S WHAT HAPPENED.
Port operator, DP World Australia (DPWA), reported an IT vulnerability in 2023 which exposed sensitive information – specifically customer, employee, stakeholder and supplier details – to users with unauthorised access.
On 10 November 2023, DPWA announced the suspension of its internet connection until the threat was resolved. As a result, 40 per cent of Australia’s maritime freight and port operations functioned inadequately during that time, causing disruptions to the key systems which support Australian port operations.
DP World’s operating systems were disconnected for three days before the recovery of their system and operations across all Australian ports on 13 November.
The investigation into the cyber attack continued along with ongoing remediation work. It also emphasised the interdependency of the industrial sectors and the critical and multifaceted levels of a security breach.
National Road Transport Association (NatRoad) CEO, Warren Clark, said the impacts of the cyber attack will snowball.
Maritime Union of Australia (MUA), which includes DP World employees, has requested the Minister for Home Affairs, Claire O’Neil, to launch an investigation into the local port managers’ state of knowledge on the cyber attack.
According to MUA, DP World Australia container terminals generated a record $830 million AUD in revenue in 2022, and their Australian profits increased 140 per cent. DP World does not pay corporate tax in Australia.
DPWA parent company DP World (Dubai Ports) is owned and controlled by the Dubai Government. The vulnerabilities of DP World’s IT systems were reportedly well documented. DP World’s software Citrix was not applied during the attack.
“This cyber attack was not a terrible accident but an appalling failure and the managers responsible should be held accountable,” said MUA Assistant National Secretary, Adrian Evans.
“Patches were available but not applied, so the company must be held responsible for this
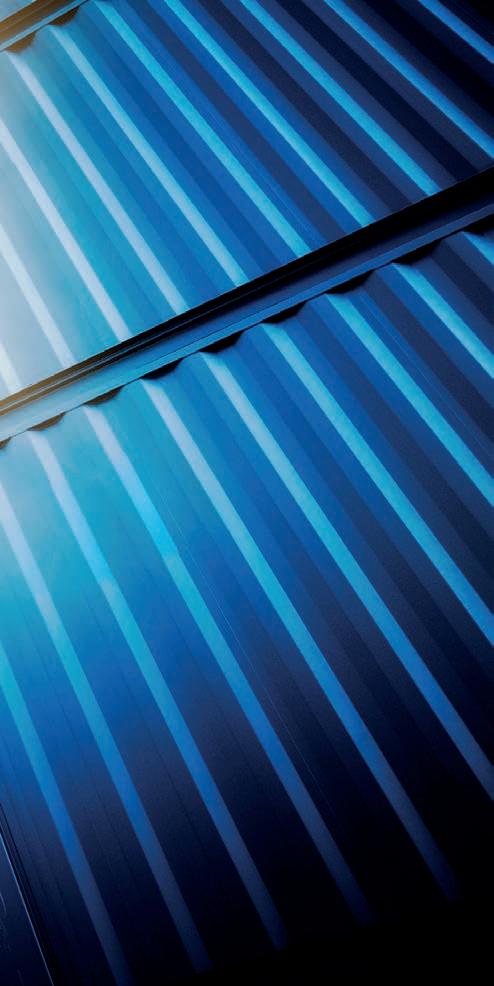
FAST FACT
Reefer World, according to DP World, is the largest refrigerated container cleaning and repair service facility of its kind in Sydney, Australia, and is expected to enhance the quality of freshness of perishable cargo delivered to destinations around the world. DP world doubled its empty refrigerated container capacity in March 2023 following the opening of Reefer World. It now has capability to pre-trip and wash more than 100 refrigerated containers daily.
catastrophic failure and the massive sovereign risk in Australia’s supply chains it has exposed us to.”
Lead of the UNSW Institute for Cybersecurity, Dr Sushmita Ruj, has 15 years of experience in cybersecurity, leading programs with companies such as Samsung and Cisco. Dr Ruj acknowledged the multiple data breaches this year which have
resulted in millions of dollars of losses for the Australian economy.
“Cyber attacks can completely paralyse the freight system depending on the extent and type of attack,” said Dr Ruj.
“Botnets can cause malicious activities like changing routing information which might cause loss and delay of goods. Data breaches can reveal information about the movement of sensitive items, reveal addresses and credit card numbers and composition of items which can harm organisations … credential information can be sold on the dark web.”
Dr Ruj said the use of state-of-the-art software is essential in combating online threats as it can regularly update, patch and encrypt.
“Security should be inbuilt in all systems and not taken as an afterthought,” she said.
“The cyber risks should be clearly communicated to all stakeholders and the board so that the freight companies invest money and time to ensure security.”
The Australian Cyber Security Centre has guidelines for Australian Businesses on cybersecurity matters. Government and private stakeholders worked closely with DP World to resolve the issue and minimise the consequences of the security breach.
National Cybersecurity Coordinator Darren Goldie said he had co-chaired the meeting with the National Emergency Management Agency and his office had been involved in the cyber attack within hours of the alarm being raised.
“The Australian Signals Directorate’s Australian Cyber Security Centre (ACSC) is engaged with DP World Australia and is providing technical advice and assistance,” he said.
DP World Australia, Optus, Medibank and Energy Australia have all experienced major data breaches in 2023.
Minister for Infrastructure, Catherine King, praised DP World for their response, “they did the right thing, they notified government very quickly, they shut their system down to stop the attack very quickly”.
The Australian economy relies heavily on the successful operation and effectiveness of the transport and logistics industries. With an increase in cyber threats leading up to the holiday season, tighter cyber security is essential for logistics companies, suppliers and manufacturers.
Head of International Freight & Logistics at the Freight & Trade Alliance (FTA), Tom Jensen, shed light on the long-lasting impacts of a security breach,
“While DP World were quick to engage government in the cyber incident, the flow-on effects are extraordinary with most ports expected to take at least a week to catch up … as long as two-to-three weeks,” said Jensen.
“This in conjunction with the ongoing protected industrial action causes significant disruption to imports/exports with schedules thrown into disarray. The impacts have also led to shipping lines omitting certain ports to minimise delays and ensure schedule integrity further down the chain which also adds to the pain.”
The FTA and Cyber Citadel are offering a penetration test of systems service to FTA and Australian Peak Shipper Association (APSA) members. The FTA also encourage businesses to review Cyber Citadel’s Cyber Security in the Logistics Sector review.
The DP World cyber attack has called for an immediate and proactive conversation surrounding cyber security.
The National Office of Cyber Security is holding free online information sessions for small to medium businesses that work in supply chains that support critical infrastructure, including vendors to critical infrastructure owners and operators. The National Office of Cyber Security is aware of the significance that cyber attacks have on Australia’s supply chain, and the interdependent sectors that rely upon smooth operations to perform effectively.
www.globaltrailermag.com
TRUCKING ALONG
Touted as North America’s largest commercial truck event, Work Truck Week will be held at the Indiana Convention Center in Indianapolis from 5-8 March.
The Work Truck Association (NTEA) is calling it more than a trade show as it will offer commercial vehicle industry professionals with “unmatched opportunities to explore the latest trucks, equipment and trends.”
The main exhibition hall will showcase commercial products from more than 500 different companies, while a New Exhibitor pavilion will become a dedicated space for presenting first-time exhibitors.
“This year, we’re emphasizing the many ways Work Truck Week increasingly gives you more,” said NTEA President and CEO, Steve Carey. “More equipment, more connections and more answers.”
The four-day event will also include series of educational seminars involving industry experts. Sessions include topics such as upfitting on EVs, principals of fleet management and workforce development.
“Work Truck Week education and training sessions bring in experts from across the global commercial vehicle industry,” said NTEA Senior Director of Content, Jennifer Mitchell.
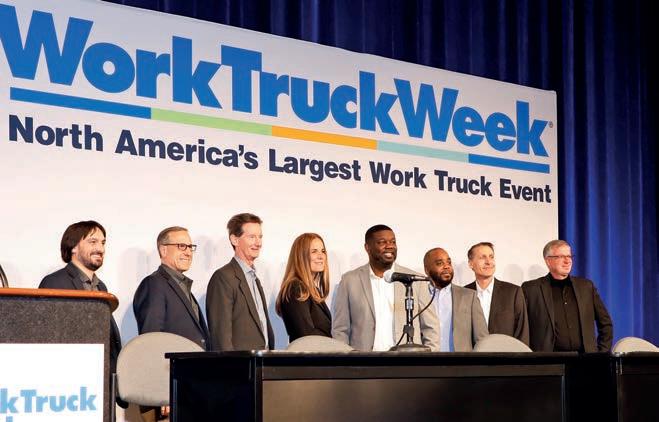
“Sessions address challenges attendees are facing right now, like grappling with recruiting and training employees, specifying and upfitting alternative fuel vehicles and maximizing productivity.”
Work Truck Week will also host Green Truck Summit, a full-day advanced vehicle and fuel technology conference which will provide information and resources in support of the commercial vehicle industry’s drive toward greater sustainability and efficiency.
Meanwhile, later in the month, the Mid-America Trucking Show (MATS) will take place at the Kentucky Expo Center in Louisville, Kentucky.
The event, slated for 21-23 March, is expecting more than 850 exhibitors and 55,000 attendees, with organisers putting a big emphasis on interactive exhibits allowing industry professionals to experience new equipment and technology. There will also be a host of educational seminars discussing the latest industry topics, emerging technologies and solutions.
“MATS is the one event on the industry calendar that brings the entire industry together face-to-face to see the latest innovations and collaborate to define the future of trucking,” said MATS President, Toby Young. “It is the best opportunity for more than tens of thousands of trucking professionals to experience hands-on demonstrations and find solutions to improve their businesses.”
www.worktruckweek.com
www.truckingshow.com
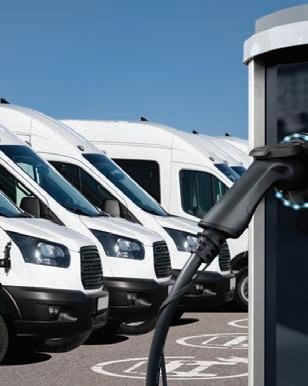
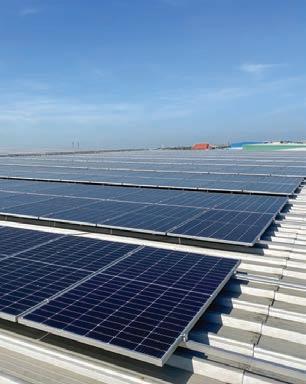
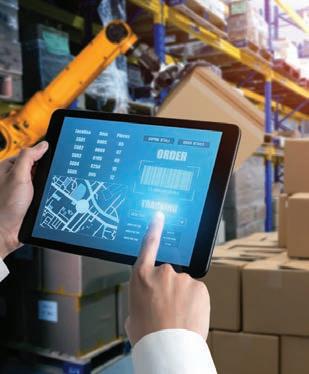
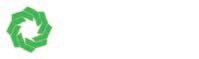
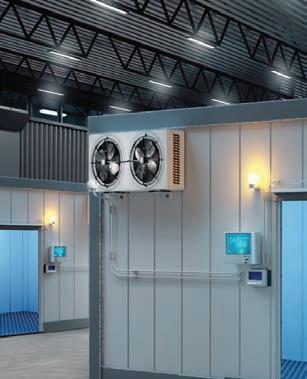
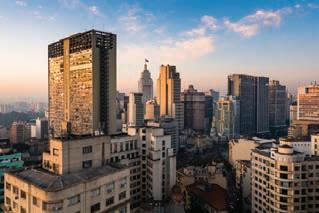
INTERMODAL SOUTH AMERICA 2024
5-7 MARCH
São Paulo, Brazil
With a focus on logistics, foreign trade and sustainable technologies, participants will meet to discuss innovation and the state of the supply chain in the Americas.
www.intermodal.com.br
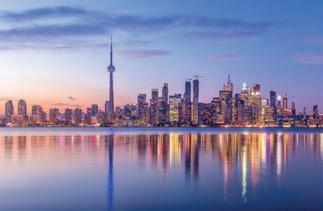
Toronto, Canada
Canada’s largest trucking industry event, it will showcase the latest trucks, equipment and innovations with a focus on emerging technologies, industry trends and best practices.
www.truckworld.ca
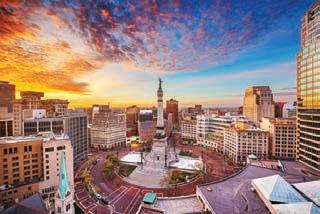
WORK TRUCK WEEK 2024
5-8 MARCH
Indiana, US
For more than 20 years, this event has gathered the people who design, build, use and maintain commercial vehicles and equipment around the world.
www.worktruckweek.com
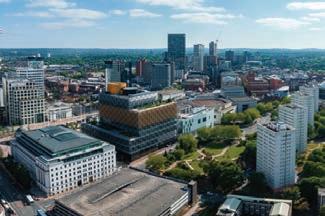
Birmingham, UK
The Commercial Vehicle Show is reported to be the largest road freight transport, distribution and logistics event in the UK.
www.cvshow.com
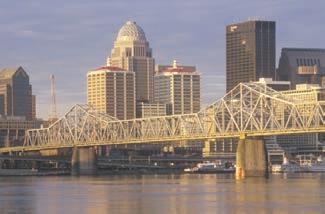
MID-AMERICA TRUCKING SHOW 2024
21-23 MARCH
Louisville, Kentucky, US
Three days of exhibits, education, networking and entertainment, it is a platform for industry professionals to experience new equipment and technology.
www.truckingshow.com
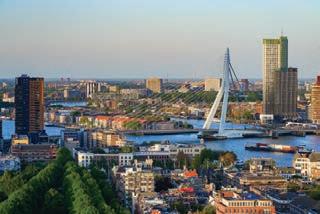
BREAKBULK EUROPE 2024
21-23 MAY
Rotterdam, Netherlands
Leading cargo and breakbulk industry experts and specialised service providers will gather to discuss current trends and developments.
www.europe.breakbulk.com
KEEP A LOOK OUT
Intermodal Asia
22-24 May
Shanghai, China
www.intermodal-asia.com
Elmia Lastbil 2024
21-24 August
Jönköping, Sweden
www.elmia.se/en/lastbil
IAA Transportation 2024
17-22 September
Hanover, Germany
www.iaa-transportation.com
MEGATRANS 2024
18-19 September
Melbourne, Australia
www.megatrans.com.au
Innotrans 2024
24-27 September
Berlin, Germany
www.innotrans.de
Bauma 2025
7-13 April
Munich, Germany
www.bauma.de/en
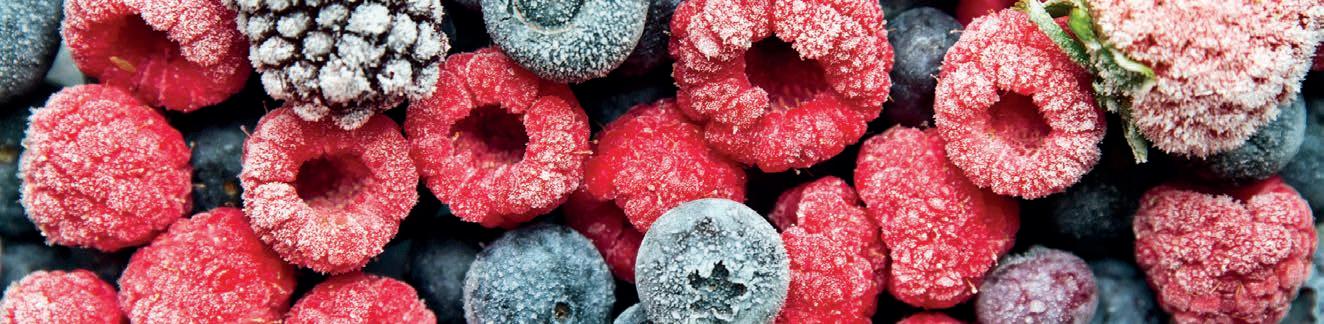
SEPARATION THREE DEGREES OF
BACKED BY EXPERT RESEARCH, DP WORLD IS ASKING THE REGRIGERATED TRANSPORT INDUSTRY TO RAISE ITS STANDARD TEMPERATURE FOR THE SAKE OF THE PLANET. THEY SAY THIS COLD CHAIN CHANGE IS SIMPLE, WON’T COMPROMISE FOOD SAFETY AND WILL SLASH CARBON EMISSIONS.
Three degrees doesn’t sound like much but according to recently released university researchers, it’s the equivalent of the emissions of 3.8 million cars per year.
Results from academics at the International Institute of Refrigeration, the University of Birmingham and London South Bank University have found that raising the standard temperature of transported frozen food by three degrees could save 17.7 million metric tonnes of carbon dioxide per year and bring energy savings of between five and 12 per cent.
Global logistics company, DP World, supported the research and have used the results to spearhead an industry-wide coalition to explore the feasibility of raising the standard frozen food temperature to 15°C.
Most frozen food is transported and stored at -18°C, a standard that was set 93-years-ago and has not changed since. Annually, hundreds of millions of tonnes of food is transported around the world and while freezing food extends its shelf life, it comes with a significant environmental cost – two to three per cent more energy is required for every degree below zero that food is stored.
“Frozen food standards have not been updated in almost a century and are long overdue for revision,” said Group Chief Sustainability Officer at DP World, Maha AlQattan. “A small temperature increase could have huge benefits but, however committed each individual organisation is, the industry can only change what’s possible by working together.”
DP World’s coalition has already caught the attention of leading industry organisations including Daikin, AP Moller-Maersk, the Global Cold Chain Alliance, Kuehne + Nagel and Lineage.
The demand for frozen food is increasing as appetites evolve in developing countries and price-conscious consumers seek nutritious but affordable food, yet experts estimate that 12 per cent of food produced annually is wasted due to a lack of refrigerated and frozen logistics. This adds to the overall statistic that 1.3 billion tonnes of edible food is thrown away every year – a third of global food production for human consumption.
Some regions are worse off than others. In Pakistan in 2022, for example, half of exportable mangoes were lost due to an extreme heatwave. Meanwhile, according to the United Nations Food and Agriculture Organisation, two billion people suffer from food insecurity.
“Cold chains are critical infrastructure, vital for a well-functioning society and economy,” said Director for the Centre for Sustainable Cooling, Toby Peters.
“They underpin our access to safe and nutritious food and health as well as our ability to spur economic growth.”
Climate change-driven events such as droughts and floods can reduce crop yields and harm livestock productivity but freezing food can protect food sources and their nutritional value for months amid such crises.
“Cutting cold chain emissions and transforming how food is safely stored and moved today helps ensure we can keep sustainably feeding communities as populations and global temperatures rise, protecting nutritious food sources for years to come,” said Peters.
“DP World’s coalition can be a key tool for overcoming today’s food challenges too, providing a stable inventory of quality food for the 820 million starving people worldwide and security for another two billion who are struggling with food scarcity.
www.globaltrailermag.com
FAST FACT
The global frozen food market was worth $284.2 billion in 2023 and is expected to grow to $363.7 billion by 2028 representing a compound annual growth rate of 5.1 per cent. There is evidence that the preference for frozen food is also increasing in developing economies with 27 per cent of households globally expected to own a freezer in 2027, up from 24 per cent in 2022.
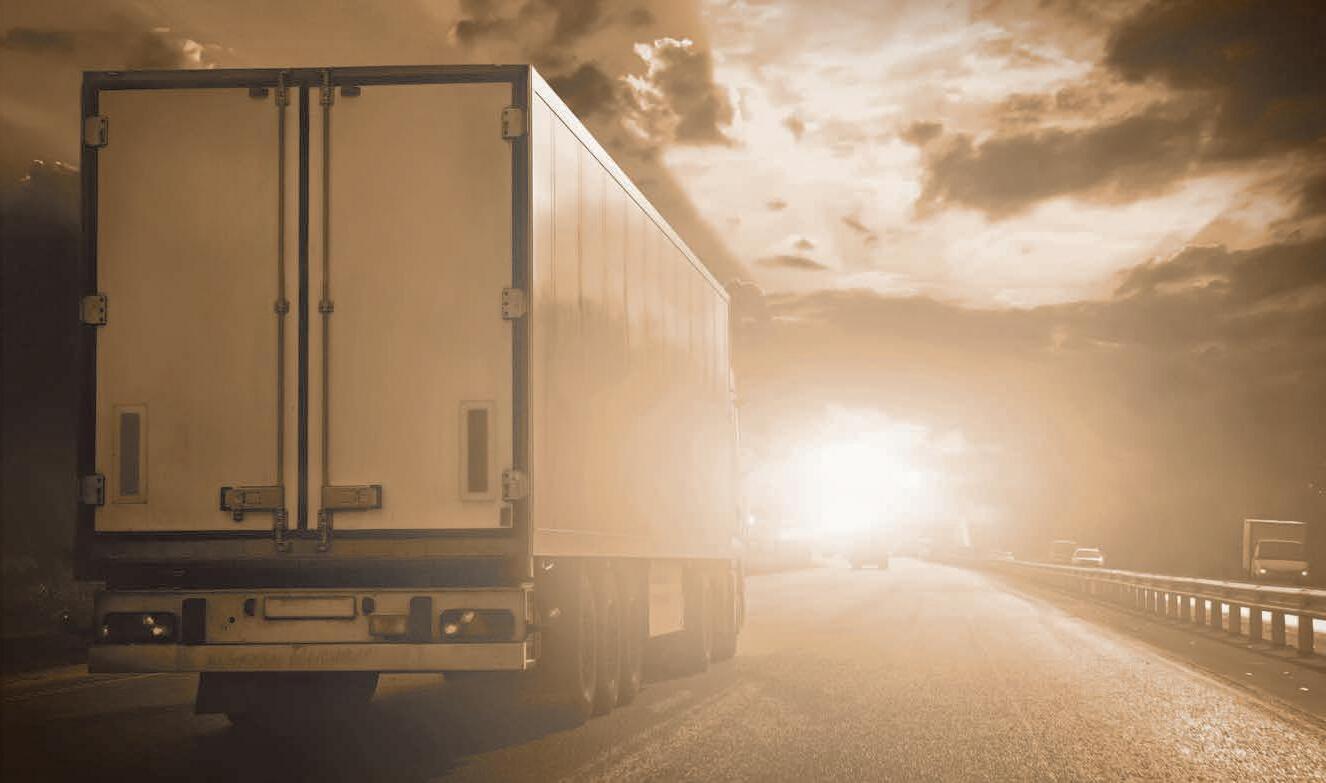

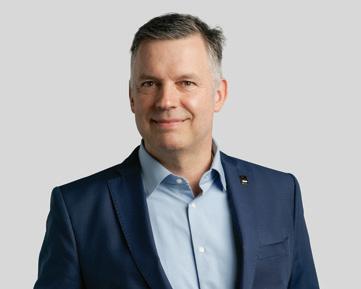


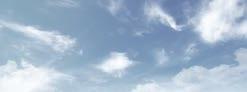






Into E-Mobility with SAF-HOLLAND

Heavy transportation traffic becomes electric, green and quiet with the recuperation axle SAF TRAKr
Every great E-Mobility concept begins with a first step: the new e-axle system from SAF-HOLLAND – the innovative technology for the electric transformation. safholland. com