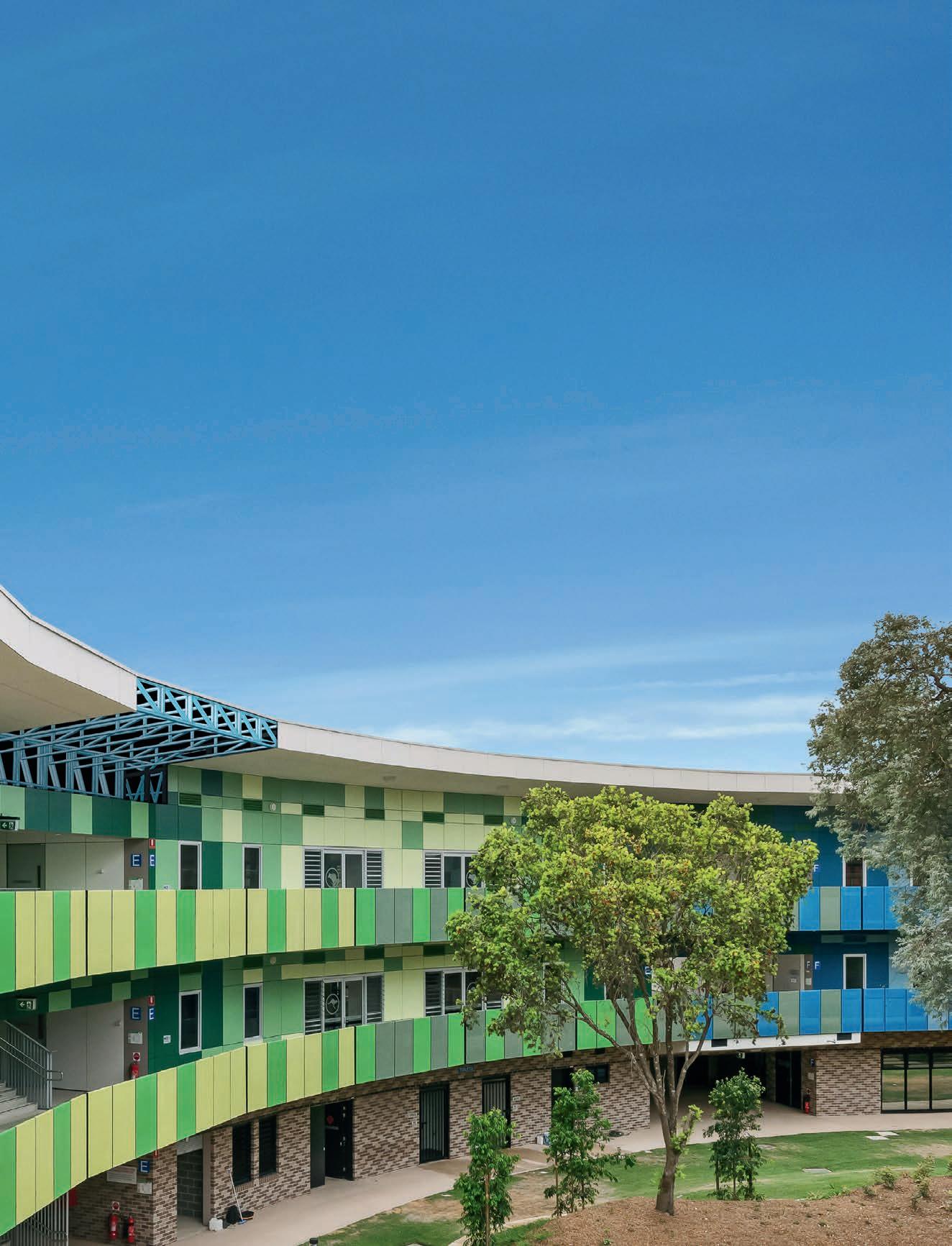
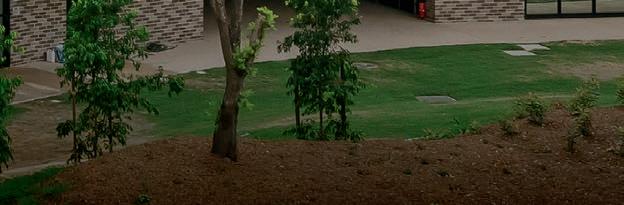

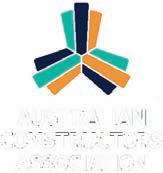
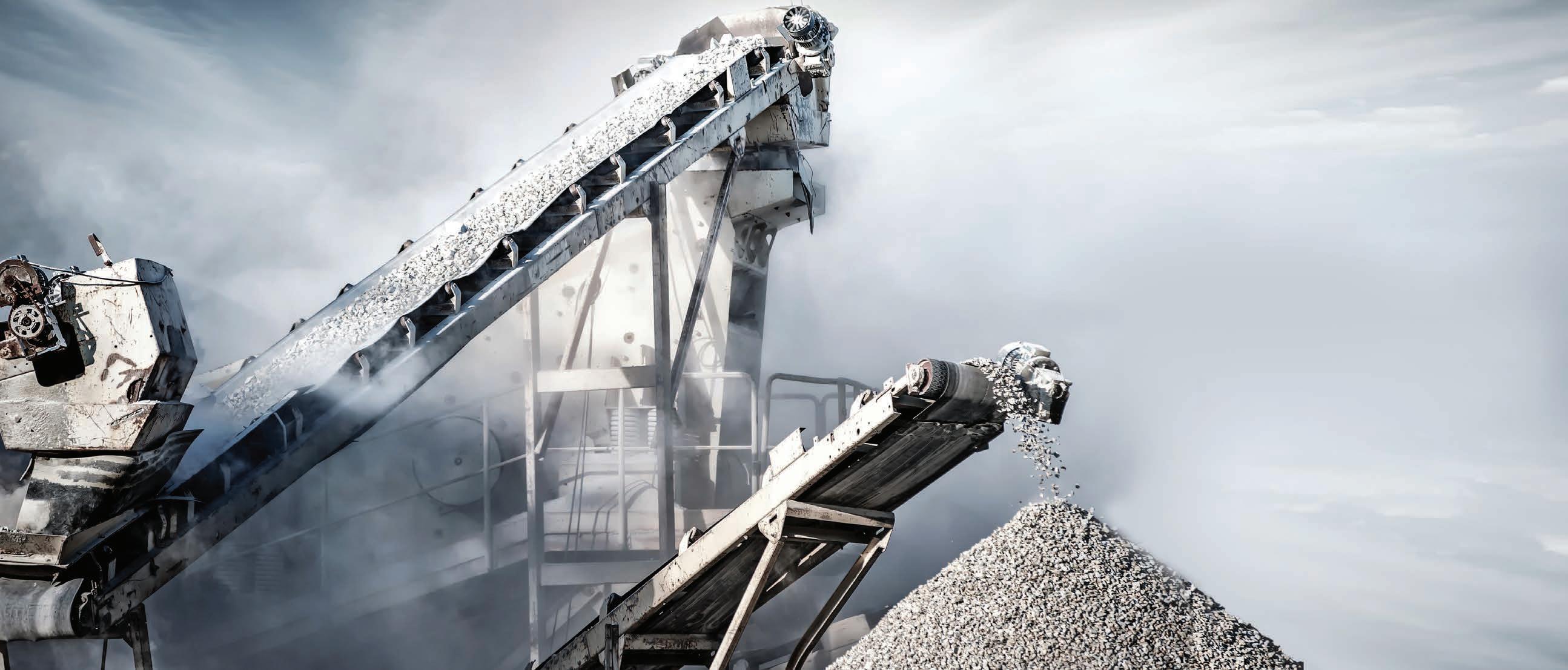
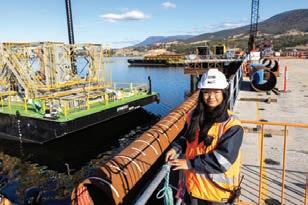

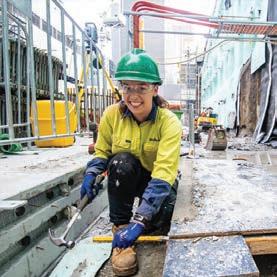

4 Editor’s Note
6 Project Picks
COVER STORY
14 Safety meets style
SilkSurface presents its 100 per cent silica-free alternative to engineered stone.
PROFILES
36 Kelsey Godwin-Smith: advancing to new heights
Find out how Kelsey Godwin-Smith, an experienced architectural designer in the built environment, shifted gears and joined the construction industry.
38 Allyssa Hudson: a rising talent
Allyssa Hudson, carpenter at Lendlease, underscores the value of embracing unconventional paths and seizing opportunities in the construction industry.
OPINION
56 Project managing life
Dr Gretchen Gagel offers a unique project management perspective or fiction
Australian Constructors Association’s Jon Davies urges a collaborative effort to steer the future of major project delivery in Australia toward better outcomes.
48 Pioneering efforts in skilled trades diversity
Empowered Women in Trades shares how it is tirelessly working to boost the presence of women in skilled trades.
50 Navigating skills shortages
The Formwork Industry Association’s Michael Sugg puts forth a series of solutions to the enduring safety challenges within the formwork sector.
52 Luxury precast landmark
The National Precast Concrete Association Australia highlights precast benefits in the Mondrian Gold Coast project.
54 Laying the foundation for equality
The National Association of Women in Construction explains how it has adopted a proactive strategy to redefine opportunities for women in construction.
EVENTS
40 Construction re-imagined
The Future of Construction Summit is back in 2024; find out what this year’s event has to offer.
42 Get ready for Sydney Build 2024
Dive into Australia’s premier construction and design show.
44 BULK is back
Discover the cutting-edge solutions taking centre stage at this year’s Australian Bulk Handling Expo.
12 Safety triumphs
Uncover the implications of the national ban on engineered stone for the construction industry.
28 Opportunity knocks for new grads
Explore how McConnell Dowell’s Graduate Program is effectively cultivating a vibrant pipeline of new, eager talent.
32 Lightweight construction delivers new-school thinking
BlueScope reveals how frames made from TRUECORE steel are proving to be a game-c hanger for the Redland Bay State School project.
19 Elevating excellence
Dr Darius Danesh emphasises the critical need for certified project managers in the construction industry.
22 Adapt and thrive
Procore spotlights the innovative solutions shared by prominent construction and property leaders at its recent roundtable.
Turning the page on 2023, the construction industry is primed for a year of substantial growth and success, laying the groundwork for pioneering strides in sustainability and productivity.
In the spirit of progress, it is imperative for the construction industry to introspectively examine the challenges and triumphs of the preceding 12 months, harnessing valuable learnings to shape a future characterised by innovation, efficacy and resilience.
The challenges from 2023 –escalating costs, cash flow difficulties, supply chain disruptions, slow technology adoption, narrow project margins, low productivity, delays, unsustainable practices and a shortage of skilled labour, among others – persist into 2024. While these issues continue to evolve, they are not novel. So, how can we proactively address and surmount these enduring problems this year?
The abundance of solutions ready to effectively address and overcome these hurdles presents a positive outlook. Numerous construction businesses are already championing these solutions in their own operations, serving as inspirational models for the rest of the industry to emulate.
Take, for instance, the skilled labour shortage, which has prompted contractors to adopt innovative solutions supported by investments in training and employment programs. In this issue, we highlight an industry heavyweight creating pathways for the next generation of construction professionals through its comprehensive graduate program. Additionally, we spotlight organisations advocating for flexible working arrangements, gender parity, increased education and awareness, as well as inclusivity and diversity in the industry. Technology companies are also coming to the table, delivering solutions that empower construction businesses to succeed by harnessing the power of data. As part of this month’s Project Management feature,
Inside Construction sat down with one of the world’s leading construction management software providers. We explore solutions presented at its recent roundtable, How NSW Property Leaders Navigate 2023 with Vision and Resilience, delving into current and emerging opportunities for construction businesses to take project delivery to the next level.
Adding to the feature, we are excited to share the insights of Dr Darius Danesh, chief executive officer at the Australian Institute of Project Management. Dr Danesh underscores the critical need for construction businesses to invest in qualified project managers, emphasising the role this plays in safeguarding project success and company reputation.
This year is the year for change. As we step into 2024, Inside Construction remains committed to sharing the narratives of companies, leaders, and organisations who are blazing a trail towards a future where the construction industry thrives and leaves a lasting impact. With our first edition of 2024, we invite you to join us in embracing the winds of change and the promising transformations that lie ahead.
Chief Executive Officer
John Murphy
Chief Operating Officer
Christine Clancy
Group Managing Editor
Andrew Hobbs andrew.hobbs@primecreative.com.au
Editor
Ashley Grogan ashley.grogan@primecreative.com.au
Sales Director
Brad Buchanan bradley.buchanan@primecreative.com.au
Art Director/Design
Daz Woolley, Caterina Zappia
Head of Design
Blake Storey blake.storey@primecreative.com.au
Design Production Manager
Michelle Weston michelle.weston@primecreative.com.au
Business Development Manager
Nhung Nguyen nhung.nguyen@primecreative.com.au
p: +61 0412 845 608
Client Success Manager
Glenn Delaney glenn.delaney@primecreative.com.au
Cover image credit
SilkSurface
Head Office
Prime Creative Pty Ltd
379 Docklands Drive, Docklands, Victoria 3008 Australia p: +61 3 9690 8766 f: +61 3 9682 0044 enquiries@primecreative.com.au www.insideconstruction.com.au
Subscriptions +61 3 9690 8766 subscriptions@primecreative.com.au
Inside Construction is available by subscription from the publisher. The rights of refusal are reserved by the publisher
Articles
All articles submitted for publication become the property of the publisher. The Editor reserves the right to adjust any article to conform with the magazine format.
Copyright
Inside Construction is owned by Prime Creative Media and published by John Murphy. All material in Inside Construction is copyright and no part may be reproduced or copied in any form or by any means (graphic, electronic or mechanical including information and retrieval systems) without written permission of the publisher. The Editor welcomes contributions but reserves the right to accept or reject any material. While every effort has been made to ensure the accuracy of information, Prime Creative Media will not accept responsibility for errors or omissions or for any consequences arising from reliance on information published. The opinions expressed in Inside Construction are not necessarily the opinions of, or endorsed by the publisher unless otherwise stated.
This month’s Project Picks spotlights exemplary construction and infrastructure projects, showcasing the industry’s unwavering commitment to navigating a path that harmonises environmental sustainability with tangible benefits for local communities.
The Gold Coast will soon be home to a new six-star luxury development aptly named COAST, located at 43 Garfield Terrace. The 37-level project by Sydney-based developer Sammut Group, in partnership with Alceon Group, comprises a collection of 53 opulent residences that are set to redefine luxury living on the East Coast.
Construction has been underway for over a year, with two major milestones recently achieved. The excavation, reaching a depth of 12 metres and removing over 20,000 cubic metres of sand for an underground carpark, made way for the major raft pours. Over the course of two days, these pours contained over an Olympic swimming pool’s worth of concrete and 400 tonnes of recycled reinforcement to strengthen foundations. In early 2024, the establishment of the basement car park will continue, accompanied by the construction of the podium level. This level will boast unobstructed ocean views and a range of luxury amenities.
COAST is using an innovative rechargeable battery in lieu of diesel generators to power the site, thereby reducing the carbon footprint during construction and saving approximately 500 tonnes of CO2 emissions associated with diesel use.
Contractor: Laing O’Rourke
Current value: $955 million
Details: Since contract award in 2018, Laing O’Rourke has delivered a new underground pedestrian concourse connecting Chalmers Street through to Eddy Avenue, an upgrade to the Northern concourse with transformed pedestrian thoroughfares and a new landmark roof canopy, significant accessibility upgrades as a result of the installation of 14 new lifts and 42 new escalators, and new underground Sydney Metro platforms at Australia’s busiest railway station. Status: Construction is practically complete, with testing and commissioning activities underway prior to metro services commencing in 2024. During construction, Laing O’Rourke undertook over 90 community initiatives, volunteered 1,100 hours in the community, collaborated with 17 of its supply-chain partners on local initiatives, raised over $130,000 via fundraising campaigns, and made substantial in-kind donations to two local charity partners.
Initiatives: The project attained a 6 Star Green Star Design Review rating from the Green Building Council of Australia, signifying world leadership in sustainable building design. Throughout this process, several outcomes were recognised, including a 90 per cent reduction in potable water consumption, the implementation of a Climate Adaptation Plan, and a 123 per cent total cumulative saving across 13 Life Cycle Environmental indicators (such as climate change and ozone layer depletion) associated with material selection and operational energy efficiency, compared to a reference project.
Sydney’s Central Station Metro North-South concourse.
(Image: Justin Sanson, Rusty Goat Photography)
With up to six barges being in operation, the piling and headstock activities are making significant progress at the La Perouse project site.
(Image: Damien Ford Photography)
McConnell Dowell
$78 million
On behalf of the New South Wales Government, McConnell Dowell is delivering the Kamay Ferry Wharves Project in Botany Bay. Replacing the previous ferry wharves at La Perouse and Kurnell that were destroyed during a storm in 1974, the project is part of the Kamay Botany Bay National Park, Kurnell Master Plan. The wharves will provide a valuable recreational resource for the community and allow future ferry access between both sides of the national park. The project recognises the rich culture and ongoing importance of the area to Aboriginal people. The La Perouse wharf extends around 184 metres in length and Kurnell around 224 metres and can accommodate commercial and recreational vessels of up to 20 metres in length and ferries of up to 40 metres.
All piles for both ferry wharves, at Kurnell and La Perouse, are due to be in place by the end of February this year as well as the completion of the pre-cast headstock installation. Up to six barges have been in operation during the piling and headstock activities, making an impressive visual sight and showcasing McConnell Dowell’s marine construction capability. Construction activities are being undertaken with great care, given the unique environmental and cultural heritage elements of the job. Project completion is expected by late 2024.
The McConnell Dowell team has formed a partnership with the innovative Australian technology company, SiteHive. SiteHive has supplied smart devices that specialise in monitoring noise, dust and vibration levels, ensuring that the project minimises its impact on the environment and nearby communities. This includes safeguarding items such as the Captain Cook Landing Place monument in Kurnell, a testament to the project’s commitment to preserving local heritage.
Contractor: BESIX Watpac
Current value: $90 million
Details: The six-story Eastwood Private Hospital development includes a six-theatre perioperative floor, a 51-bed ward, a multi-level car park, a café and retail area, as well as medical imaging and pathology services. BESIX Watpac will complete fitout works for all lobby and corridor areas and levels three and four, containing the perioperative floor, including all associated plant, equipment, support services, courtyards and external landscaping. The project is projected to reach a peak workforce of 140 and is targeting a 4 Star Green Star rating. It’s the first hospital project the BESIX Watpac team has undertaken in the state of South Australia. The Australian-grown and globally backed construction company is primed to deliver the project with extensive expertise, a collaborative approach and knowledge of the technical and services requirements of health and sciences infrastructure. The hospital is due to open in 2025 and is predicted to ease pressure on the state’s stressed health system.
Status: The project commenced construction with a Welcome to Country and Smoking Ceremony performed by local Traditional Owners from Kuma Kaaru to bless the site late last year. In-ground works are nearing completion and the structural cores have now commenced.
In-ground works are nearing completion at BESIX Watpac’s Eastwood Private Hospital project.
(Image: BESIX Watpac)
CPB Contractors-Ghella joint venture
Sydney Metro – Western Sydney Airport is the new metro railway line that will service Greater Western Sydney, connecting the new Western Sydney International (Nancy-Bird Walton) Airport with the new city of Bradfield (Aerotropolis) and St Marys and the existing Sydney Trains suburban T1 Western Line. The CPB Contractors-Ghella joint venture (CPBG) is delivering twin 9.8-kilometre tunnels and excavating five new metro stations and two services facilities.
Significant milestones in 2023 included excavation works completed on five station boxes and two services shafts. Four tunnel boring machines (TBMs) were assembled in early 2023. The two TBMs building the 5.5-kilometre southern tunnels launched from Airport Business Park and have had four breakthroughs on the Airport Terminal site while en route to Aerotropolis. Two TBMs are almost halfway in excavating the 4.3-kilometre northern tunnels linking the Orchard Hills and St Marys metro station sites. Innovative environmental outcomes have contributed to the greater sustainability goal to offset 100 per cent of CO2 emissions. A major initiative was to reuse two TBMs which had already built Sydney Metro City and Southwest tunnels. Installing 99-kilowatt solar array panels on two site office roofs reduced the project’s carbon footprint by 430 tonnes of emissions – equal to driving between Sydney and Perth 370 times.
Contractor: John Holland on behalf of Melbourne Water
Current value: $200 million
Details: John Holland is partnering with Melbourne Water to upgrade the Hobsons Bay Main Sewer to ensure the continued reliability of Melbourne’s sewage network. John Holland is delivering the new 670-metre sewer stretching from Westgate Park, Port Melbourne, to Scienceworks in Spotswood, under the Yarra River. The current sewer, originally built in the 1960’s, is responsible for the transfer of 30 per cent of Melbourne’s wastewater. When completed in 2024, the new pipeline will double the current capacity to cater for Melbourne’s future growth and demand.
Status: In November 2023, a huge milestone was reached at the Hobsons Bay Main Upgrade as tunnel boring machine ‘Lucey’ arrived at Port Melbourne following a 670-metre journey under the Yarra River from Spotswood. During tunnelling, Lucey operated at depths of between 24.5 metres and 27 metres below the surface of the Yarra, alongside the original sewer main.
Initiatives: The project has achieved gender parity, with an equal number of men and women working in the engineering team. The team is working towards making Hobsons Bay John Holland’s first net-zero project, incorporating solar power, sustainable concrete and recycled materials.
WOMEN IN INDUSTRY NOMINATIONS ARE NOW OPEN. Now is your chance to nominate an industry leader who you believe is advocating for positive change and deserves to be recognised.
PROUDLY PRESENTED BY
The Women in Industry Awards recognise outstanding women leaders from across Australia’s industrials sector.
In a crucial move to safeguard lives and prioritise the health and safety of construction workers nationwide, the use of engineered stone has been banned in Australia. But what makes this measure so crucial?
“The vast majority of silicosis cases identified in recent years are in engineered stone workers.”
In response to growing health concerns, Commonwealth, State and Territory work health and safety (WHS) ministers convened in December last year to establish a unified national response to a recommended ban on engineered stone.
The recommendation itself originated from Safe Work Australia’s Decision Regulation Impact Statement (Decision RIS): Prohibition on the use of engineered stone. According to Safe Work Australia, the Decision RIS incorporated insights from a thorough evaluation by independent experts, an economic impact analysis conducted independently, and input from stakeholders following the release of a consultation paper in March 2023. Various submissions were received during the consultation process, encompassing perspectives from workers, persons conducting a business or undertaking (PCBUs), representatives of employers and workers, WHS professionals, medical experts, academics, government agencies and industry and peak bodies.
The ministers not only endorsed the conclusions of the statement but also supported the suggestions outlined in the recommendation. This consensus resulted in the implementation of a nationwide ban on the use, distribution and production of all engineered stone, in accordance with the model WHS laws. Most jurisdictions are set to enforce this ban starting from 1 July 2024.
Until the ban on engineered stone comes into force in coming months, Safe Work Australia has advised workers and businesses they can continue operations involving engineered stone under controlled conditions. As per the model WHS Regulations, those engaged in cutting, grinding, trimming, sanding, abrasive polishing or drilling engineered stone using power tools or other mechanical equipment must utilise either a water suppression (wet cutting) system, an on‑tool dust extraction system or a local exhaust ventilation system. All workers handling engineered stone must also be provided with respiratory protective equipment and adhere to its consistent usage.
In 2021, WorkSafe Victoria processed 73 claims from workers who had developed silica related diseases due to workplace exposure, with five individuals tragically
losing their lives. Reports indicate that more than 300 Australians contract silicosis annually. While cases of silicosis have been identified across various industries, engineered stone workers are at highest risk. Silicosis, an occupational lung disease triggered by inhaling minute silica dust or respirable crystalline silica (RCS) particles, poses severe health risks, including inflammation, lung cancer, kidney disease and autoimmune conditions.
The crystalline silica content can differ among various rock products. Engineered stone presents the highest risk, containing up to 97 per cent crystalline silica, as reported by Safe Work Australia.
Safe Work Australia CEO Marie Boland highlighted that workplace exposure to RCS has resulted in an alarming surge in the incidence of silicosis and other related diseases, signalling an unacceptable risk to workers’ health.
“Expert analysis shows that silica dust from engineered stone poses unique hazards and there is no evidence that low silica engineered stone is safe to work with,” said Boland. “The vast majority of silicosis cases identified in recent years are in engineered stone workers.”
“The cost to industry, while real and relevant,
cannot outweigh the significant costs to workers, their families and the broader Australian community that result from exposure to respirable crystalline silica from engineered stone.
“Continued work with engineered stone poses an unacceptable risk to workers, which is why we recommended a prohibition on the use of all engineered stone.”
The first case of silicosis linked to engineered stone in Australia was reported in 2015.
The affected individual, a 52 year old man, had been exposed to silica through the cutting and polishing of engineered stone kitchen and bathroom countertops – as reported in an article titled LATE-BREAKING
ABSTRACT: Complicated silicosis in an Australian worker from cutting engineered stone countertops: An embarrassing first for Australia, authored by Anthony Frankel, Lucinda Blake and Deborah Yates, and featured in the European Respiratory Journal in September 2015. Although regulations overseeing silica exposure control have been in place in Australia for decades, a notable lack of awareness regarding the associated hazards endured until only recently.
Since this initial reported case, the incidence of silicosis among engineered stone workers
in Australia has significantly increased. While cases of silicosis have been identified across various industries and professions, engineered stone workers are at highest risk.
“This prohibition will make Australian workplaces safer and healthier,” said Boland. “Now that a prohibition has been agreed by WHS ministers, Safe Work Australia will progress amendments to the model WHS Regulations and develop guidance to support PCBUs and workers understand and prepare for the change.”
The ban on the use, distribution and production of engineered stone in Australia represents a significant step in protecting the lives of the nation’s workers. However, it is crucial for governments, industry players and unions to remain vigilant and proactive in identifying and addressing potential hazards to workers’ health from other sources.
The long a nticipated ban on engineered stone serves as a catalyst for researchers and manufacturers to seize the moment and develop safer alternatives. Innovations resulting from these regulatory changes will play a crucial role in shaping the future landscape of workplace safety.
“Continued work with engineered stone poses an unacceptable risk to workers, which is why we recommended a prohibition on the use of all engineered stone.”
SilkSurface is a 100 per cent silica‑free alternative to engineered stone.
(Images: SilkSurface)
“SilkSurface exemplifies the industry’s proactive approach to regulatory changes, and we’re excited to deliver a safer product to the market.”
As Australia prepares for the imminent ban on engineered stone, SilkSurface benchtops stand out as a safe, durable and attractive solution for the building sector.
In response to growing concerns about the health hazards associated with engineered stone, SilkSurface has been proactively exploring alternative materials for stone benchtops. Prioritising safety, the company now offers a diverse range of benchtops that not only look appealing and are cost‑effective but are also manufactured in a manner that ensures the wellbeing of construction workers.
The allure of engineered stone has found a fervent following among Australians, who are drawn to its distinctive look and feel. Yet, beneath the surface lies a perilous reality for construction workers. Activities involving
engineered stone products, including cutting, grinding and sanding, produce respirable dust containing crystalline silica, commonly referred to as silica dust. Prolonged inhalation of silica dust poses a grave risk to workers’ health, leading to severe respiratory diseases and, in some instances, proving fatal.
Ben Scott, founder and managing director of SilkSurface, highlights that SilkSurface initiated the exploration of safer stone benchtop alternatives as the industry began questioning the dangers of engineered stone.
“For some time, we have been developing a product to provide customers with an alternative to engineered stone, prior to
the government’s discussion around its future,” says Scott. “The recently announced ban on engineered stone has presented the construction industry with an opportunity to deliver improved and safer options for both customers and workers, and that’s exactly what we’ve achieved.”
“SilkSurface exemplifies the industry’s proactive approach to regulatory changes, and we’re excited to deliver a safer product to the market.”
SilkSurface not only mimics the look and feel of natural stone but surpasses it in durability and ease of maintenance. Through meticulous manufacturing techniques, SilkSurface achieves the desired aesthetic and robustness sought by the building industry and end users, utilising safe materials in the process.
Comprising a blend of bauxite (aluminium hydroxide) and a polyester binder, each SilkSurface sheet undergoes formation under 400 tonnes of pressure before being diamond polished, resulting in its resilient and durable surface. These benchtops are distinguished by their outstanding durability, boasting high the same ease as timber,” he explains. “This
what customers want: a quality product that looks good, is affordable and can be manufactured with safety for workers in mind.”
affordable and can be manufactured with safety for workers in mind.”
“Testing affirms that SilkSurface is a safe and reliable choice for customers embarking on apartment, office or residential building projects.”
Further solidifying SilkSurface as a safe alternative to engineered stone, the product recently underwent comprehensive independent testing conducted by stone product experts. In January of this year, researchers from the University of Adelaide’s School of Public Health verified that SilkSurface stands as a genuine, 100 per cent silica f ree alternative to engineered stone. Leveraging their previous experience in testing stone products, the University of Adelaide had the expertise to thoroughly evaluate and authenticate the SilkSurface product.
for customers embarking on apartment, office or residential building projects,” says Scott. “This assurance extends to the safety of both construction workers and end users, instilling confidence in cabinet makers, stone masons, builders, architects, interior designers and homeowners when choosing our product.”
SilkSurface aims to provide a safe and user‑friendly product for all benchtops used in buildings nationwide, offering an extensive range of colours to suit diverse customer needs. Championing safety and quality, SilkSurface is well positioned to become the construction industry’s go to product, particularly with the upcoming enforcement of the engineered stone ban in July.
Infinity Deluxe Standard
Colours:
Colours:
Colours:
Albastera Bianco Pearl Arctic White
Bronzite Calcutta Snow Blanca Granite
Ice Nuovo Carrara Star Dust
Luminice Cobblonite White Crystal Boulder
Lustra Silk Lapis Salt
Opalora Moonstone
Riverina Organica
Silk Whisper
Stratiss Nuovo
Terramoss
Terranite
Topaz
AGRICULTURE FARMING EDUCATION WASTE MANAGEMENT RESOURCE MANAGEMENT
CONSERVATION MANUFACTURING RESOURCES
ENERGY HEALTH & SAFETY INFRASTRUCTURE ENGINEERING MINING CONSTRUCTION
QUARRYING AGRICULTURE FARMING EDUCATION
WASTE MANAGEMENT RESOURCE MANAGEMENT CONSERVATION MANUFACTURING RESOURCES
ENERGY HEALTH & SAFETY INFRASTRUCTURE ENGINEERING MINING CONSTRUCTION
QUARRYING AGRICULTURE FARMING EDUCATION
WASTE MANAGEMENT RESOURCE MANAGEMENT
CONSERVATION MANUFACTURING RESOURCES
ENERGY HEALTH & SAFETY INFRASTRUCTURE ENGINEERING MINING CONSTRUCTION
QUARRYING AGRICULTURE FARMING EDUCATION
WASTE MANAGEMENT RESOURCE MANAGEMENT
SEARCH FOR TOP INDUSTRY TALENT THROUGH OUR JOBS BOARD.
CONNECT WITH ALIGNED CANDIDATES.
BOOST YOUR CHANCES OF FINDING SKILLED APPLICANTS.
SCAN TO CREATE AN ACCOUNT TODAY AND DISCOVER YOUR PERFECT MATCH!
Delving into this month’s theme, industry expert Dr Darius Danesh emphasises the critical need for certified project managers in the construction industry to effectively address ongoing productivity and cost challenges.
In the dynamic world of construction, the significance of qualified and certified project managers cannot be overstated. The role of project management in the construction sector is indispensable, ensuring effective cost control, timely project completion, efficient risk mitigation and overall success through streamlined processes and clear communication with stakeholders.
This comprehensive approach involves effective budgeting, resource allocation and continuous expenditure monitoring, facilitated by skilled project management throughout the construction process, resulting in efficient cost control. Project management guarantees timely project completion, minimising delays, fostering success and ensuring client satisfaction.
Project managers also play a pivotal role in maintaining and enhancing construction quality standards, overseeing processes, inspections and quality control measures to ensure final deliverables meet or exceed expectations.
Effective communication is paramount in projects with multiple stakeholders, and project managers facilitate communication between owners, contractors, subcontractors and regulatory authorities, ensuring alignment with project goals.
(Image: Halfpoint/stock.adobe.com)
Strategic optimisation of resources, including labour, materials, equipment and finances enhances cost‑effectiveness under the guidance of project managers, aiming to allocate resources efficiently and prevent unnecessary waste.
Critical to project success is the clear definition and effective management of the scope of work. In scope management, project managers play a central role, ensuring clarity and preventing deviations from the project’s initial objectives, ultimately contributing to the seamless execution of construction projects.
Elevating project managers’ skills and competency standards is paramount in navigating the dynamic challenges of construction projects. This enhancement ensures adaptability, informed decision making, client satisfaction, innovation integration, effective team leadership and regulatory compliance, and cultivates a culture of continuous improvement.
Empowered with improved skills, project managers swiftly adapt to unexpected challenges, ensuring project continuity and success. Their thorough understanding of construction processes, industry trends and risk factors enables informed decision‑making, reducing the likelihood of costly errors. Competent project managers not only deliver projects that meet or exceed client expectations but also foster positive relationships, potentially leading to repeat business and referrals.
Continuous improvement in skills allows project managers to stay current with
the latest construction technologies and innovations, resulting in increased efficiency and productivity on projects. Possessing strong leadership qualities, skilled project managers foster collaboration, motivation and a positive team culture, contributing to higher morale and increased productivity among construction teams.
In a field subject to numerous regulations, improved competency ensures project managers are well versed in compliance requirements, reducing legal risks and potential setbacks. Emphasising skill enhancement and maintaining high competency standards promotes a culture of continuous improvement, encouraging project managers to seek new ways of optimising processes and achieving better outcomes, ultimately contributing to the overall growth and success of construction projects.
The construction industry faces challenges, from budget constraints and tight timelines to evolving technologies and shifting regulations.
In the absence of qualified project managers that possess the essential skills to navigate the multifaceted challenges inherent in project management, these challenges can escalate into serious issues, leading to project delays, cost overruns and compromised quality. Moreover, when projects involve community
infrastructure or services, the consequences of mismanagement can reverberate throughout the community, affecting residents, businesses and public resources. The stakes are high not only for project outcomes and the reputation of companies but also for the safety of the broader community. This underscores the critical importance of ensuring that project managers possess the requisite qualifications, skills and competency standards to navigate the complexities of project management effectively. In parallel to chartered engineers who undergo certification and competency assessments, the construction industry requires qualified project managers to navigate its complexities successfully. While a registered professional engineer concentrates on the technical intricacies of a particular domain, the responsibilities of a project manager encompass the orchestration and management of the entire project life cycle. Therefore, the impact of unqualified project managers on a project, company or community can be significantly more profound compared to the role of a registered professional engineer focused on a specific aspect, such as structural design.
Establishing a national benchmark for project management competency standards will not only ensure the credibility of project managers but will also contribute to a culture of continuous improvement within the industry. Recognising and enforcing these standards is essential to maintaining the integrity of the construction process.
It is imperative to promote the engagement of certified project managers, particularly in complex construction projects. Recognising this need, the Australian Institute of Project Management (AIPM), as a leading project management body in Australia, continuously spearheads efforts to enhance project management skills and advocates for the implementation of regulations and competency assessments. Through a focus on skill enhancement, advocating for industry regulations and offering certifications such as the Registered Project Manager (RegPM), the AIPM contributes to the overall success and integrity of projects across the nation.
We are committed to fortifying our alliance with the dynamic and vital construction sector. Our dedication extends beyond the
traditional realms, with tailored training programs and certifications meticulously designed to cater to the distinctive needs of construction professionals. By actively engaging in collaborative efforts with industry associations and key stakeholders, we ensure that the AIPM remains at the forefront of project management excellence within the construction landscape.
We aim to provide invaluable insights to address the unique challenges faced by those involved in construction projects and support to the professionals who shape the built environment through offering thought leadership resources and publications, facilitation of industry review working groups and active participation in construction events. It is time for all industries to invest in qualified project managers to safeguard the success of their projects and the reputation of their organisations. By prioritising skill improvements, certifications and competency assessments, we can collectively contribute to a thriving and sustainable construction sector.
“Effective project management serves as the pivotal element for achieving success in the construction industry. The AIPM’s commitment to nurturing excellence and integrity in project management underscores its recognition of the critical role it plays in navigating the complexities of our industry. Our steadfast collaboration with the construction sector is more than a partnership; it is a shared journey. Together, we tirelessly elevate project management standards, empower professionals and sow the seeds of sustained growth and success in construction projects nationwide. We are not just building structures; we are forging a foundation for excellence and innovation that resonates across communities, inspiring a future of unparalleled achievement and transformative impact.”
Dr Darius Danesh, chief executive officer at the Australian Institute of Project Management.
“Elevating project managers’ skills and competency standards is paramount in navigating the dynamic challenges of construction projects.”
Late last year, Procore held a roundtable discussion spotlighting the strategic prowess and resilience displayed by construction and property leaders in New South Wales throughout 2023. This yielded a plethora of innovative solutions poised to help propel construction projects to success.
In a constantly evolving landscape of technological breakthroughs, unique challenges and economic fluctuations, proficient project management is a critical linchpin for construction businesses vying to sustain a competitive edge. Procore, standing at the forefront of effective solutions as one of the leading construction management software providers globally, is dedicated to empowering contractors to achieve project success and raise their operations to new heights.
With a robust pipeline of projects on the horizon in New South Wales, Procore recently convened a roundtable discussion that brought together some of the state’s prominent construction and property leaders. The aim was to explore current and emerging opportunities for construction businesses to take their operations and project delivery to the next level.
In collaboration with The Property Council of Australia, the roundtable underscored how these leaders navigated 2023 with vision
and resilience, imparting valuable insights that contractors can leverage for their own projects and businesses.
The attendees included:
• John Carter, joint chief executive officer at Aspen Group;
• D uncan Challen, general manager - business development at Celestino;
• Saumya Menon, director health safety & environment at Landcom;
• Hide Seguchi, chief executive officer, apartment & mixed-use developments at Sekisui House Australia;
• David Hopper, joint managing director at Kaipara Property Group;
• Adrian McLay, director at Turner & Townsend;
• Peter Brown, senior director, sales at Procore;
• Matthew Hoskin, enterprise account executive at Procore;
• Jeremie Henry, industry partnerships manager at Procore;
• K atie Stevenson, NSW executive director at The Property Council of Australia; and
• Catherine Maude, NSW/ACT commercial director at The Property Council of Australia. Held in Sydney on 5 September 2023, the roundtable facilitated discussions centred around the potential of data in optimising construction workflows, exploring the benefits of integrating technology to improve construction speed, safety and cost efficiency, and understanding how leaders in the NSW construction and property sector are tackling longstanding challenges.
According to Katie Stevenson, executive director of The Property Council of Australia’s NSW chapter, driving technology innovation and cultivating a global community of ground breakers is imperative across the property and construction landscape.
“Controlling costs, mitigating risks and identifying opportunities for efficiencies in construction has never been more critical than it is today given the economic challenges that we’re all facing in our businesses,” Stevenson told attendees.
Stevenson’s insights resonated strongly at the roundtable, with attendees unanimously echoing her views. They collectively affirmed the value of embracing technology, not merely as a survival tactic, but as the key to thriving in an industry on the cusp of substantial transformation. This shared perspective underscores the industry’s recognition that data and innovation are vital for navigating the challenges and opportunities that lie ahead.
Participants agreed that data plays a crucial role in informing strategic decisions, enhancing project efficiency and leading to timely completion, cost-effectiveness and improved quality of construction projects.
It was acknowledged that harnessing data analytics in the construction industry holds the potential to mitigate risks, elevate project performance and enhance overall operational efficiency. Beyond these primary advantages, incorporating data-driven approaches brings forth several additional benefits. It enables precise project cost estimations, facilitates better resource allocation, promotes proactive issue identification, streamlines communication among project
stakeholders and ultimately contributes to the development of more sustainable and resilient structures. Embracing data in construction not only optimises decision-making but also paves the way for innovation, allowing for the exploration of advanced technologies and methodologies for continued industry advancement.
While data analytics plays a crucial role in decision-making, it is essential to align advanced technologies with well-defined strategies and performance metrics to effectively measure return on investment, as highlighted by the roundtable attendees.
The industry’s future success hinges significantly on the integration of artificial intelligence (AI) and data analytics. Insights from the McKinsey Global Institute’s 2017 report, Reinventing construction: A route to higher productivity, suggest that leveraging data could potentially boost onsite productivity by as much as 50 per cent.
According to Jeremie Henry, Procore’s APAC industry alliances leader, there is still a need for further advancement in data strategy, as indicated by insights from Procore’s benchmark report, How We Build Now 2023. Shockingly, the report reveals that only 11 per cent of companies in NSW have a formalised data strategy in place. This glaring statistic prompts crucial questions about the industry’s preparedness to leverage the full potential of data. The roundtable discussion firmly reinforced not only the vital importance of data-driven decision-making but also the transformative capacity of data to reshape processes and outcomes in the construction sector.
The consensus among the roundtable participants was clear: the adoption of a data-d riven approach is not just a necessity; it’s an imperative step for construction businesses to consistently achieve positive project results and remain competitive in a rapidly evolving industry.
The construction industry is experiencing a surge in technology adoption, with construction management platforms and payment technologies taking the lead. “Look beneath the headlines – cost escalations, cash flow worries, high interest rates and supply
“To me, it’s all about embracing technological transformation and exploring the boundless possibilities.”
wave of optimism sweeping through the construction industry. Procore’s report indicates that businesses within the sector are gearing up to embrace the power of construction intelligence and management platforms, along with advanced payment technologies, over the next 12 months. Their goal? To improve efficiency and generate cost savings.
“We’re working towards advancing our technological infrastructure as part of an ongoing improvement journey.”
This proactive approach involves tapping into the advanced capabilities and intelligence embedded in construction management platforms to elevate daily productivity among teams and streamline both internal and external operations.
According to the Procore report, businesses in NSW are increasingly investing in technology that improves sustainability, productivity and efficiency. National statistics underscore this momentum, with 47 per cent anticipating an increase in spending on construction technologies in the next 12 months.
“NSW businesses are slightly more confident than other states,” Henry said, explaining this can largely be attributed to their financial stability and a well-managed supply chain.
“Concurrently, investments in infrastructure and a robust economy have significantly bolstered businesses operating in risk-prone sectors.”
Duncan Challen, general manager of business development at Celestino, emphasised the need for the construction industry to continue to invest further in technology, implement effective data strategies and actively develop the talent pipeline by directly contributing to
essential for businesses to maintain their competitiveness, relevance and sustainability in the modern era.
“For our organisation, a key priority is driving purposeful transformation, particularly considering the abundant opportunities presented by the current era of extensive technological disruption and advancements,” said Challen. “To me, it’s all about embracing technological transformation and exploring the boundless possibilities.”
However, despite the evident benefits, the resistance to technology adoption often stems from a cultural reluctance to change. Criticism is frequently directed at the technology itself rather than addressing the need to alter work and lifestyle paradigms.
This sentiment, expressed during the roundtable discussion and reflected in the Procore report, points to the significant challenge posed by the intersection of established practices and the integration of innovative technology.
Overcoming this resistance requires more than simply adopting new tools; it demands a concerted effort to cultivate a cultural shift towards a technology-enabled, forward-t hinking construction landscape. This transformative shift is indispensable for unlocking unparalleled potential, enhancing productivity and ensuring sustainable growth, said John Carter, Aspen Group’s joint CEO and director. Navigating cultural transformation can pose challenges, especially for Aspen
Group’s comparatively compact business which faces considerable complexity.
“We’re a relatively small business, but we have reasonable complexity because we essentially buy properties that need fixing, so we can see lots of gaps in technology,” said Carter.
“And we are a small team and a small head office; therefore, technology needs to be simple to run because we don’t have our own IT department.
“We’re working towards advancing our technological infrastructure as part of an ongoing improvement journey.”
As technology evolves and younger generations enter the workforce, organisations must undergo a cultural shift to embrace new ways of working, ensuring that technology not only complements but also enhances existing practices.
During the roundtable, Saumya Menon, director of health, safety and environment at Landcom, emphasised that the true potential of technology lies in revolutionising how people work, enhancing their efficiency and productivity.
As the industry undergoes this transformative shift, there is a growing acknowledgment of the need to engage with stakeholders responsible for project delivery. However, challenges like infrastructure and compliance costs pose significant obstacles, particularly in Western Sydney, where escalating costs continue to impact development prospects, as highlighted by Challen.
In Western Sydney, despite abundant potential and promise, seizing these opportunities proves financially demanding. Utilising analytics and data to showcase to the government that there are cost-effective alternatives for policy implementation is crucial, explained Challen. It might also necessitate a re-evaluation of their planning controls.
“From our standpoint, it’s about harnessing smart technologies that can generate valuable data to enhance productivity and experiences,” Challen said. “Moving forward, it’s about more than just utilising data and employing sophisticated tools and infrastructure.”
as revealed by attendees. According to BCI Central’s 2023 construction outlook, Analysing Australia’s Construction Pipeline, 90 per cent of surveyed builders consider labour shortages a prominent challenge for their businesses.
“There’s a significant reset happening, especially in capital markets and property valuations.”
An effective strategy involves striking a balance between harnessing the innate tech-savviness of the younger generation and embracing the established practices deeply rooted in the construction industry. This endeavour is crucial, serving not only to draw in fresh talent but also to seamlessly integrate state-of-the-art technologies and digital fluency into the construction landscape.
According to Adrian McLay, director of Turner & Townsend, “being future-ready and getting better at understanding risk and calculating risk” is important. He said that a key part of the company’s global purpose is to help transform the industry towards innovation.
“The biggest challenge for us is implementing that in the industry: bringing new ideas, and mobilising and engaging with those who are responsible for the delivery of these major projects to adopt those new ideas and make change,” said McLay.
McLay emphasised that the real catalyst for change lies in leveraging data rather than relying solely on elaborate tools and flashy innovations. He asked, “How can we maximise efficiency by harnessing the potential of data?”
Attendees conveyed optimism regarding the future of the construction and property industry, recognising opportunities for
robust data strategies and prioritise education to ensure competitiveness and sustainability in today’s dynamic landscape. The emphasis was on adaptability, collaboration and innovation as key drivers for navigating the rapid changes within the industry.
Despite facing challenges, the construction sector continues to demonstrate resilience and ingenuity. It appears well-positioned to overcome obstacles through collaborative efforts and proactive approaches.
Henry’s perspective on crisis-driven innovation in construction was echoed, emphasising the importance of seizing opportunities during challenging times. “Make the most of a crisis,” he said.
David Hopper, joint managing director of Kaipara Property Group, highlighted the market’s current challenges as a chance for a significant reset. “The current market is challenging, but we see this as an opportunity,” said Hopper. “There’s a significant reset happening, especially in capital markets and property valuations.”
“I believe that for those astute groups able to identify value and secure advantageous deals, there’s a strong opportunity to position themselves well for the upcoming wave.”
The invaluable insights and experiences exchanged during Procore’s roundtable prove essential for construction businesses and leaders committed to achieving success in their projects and operations. Thriving amidst advancements in technology, processes and culture requires adaptation and evolution, qualities that set the path for enduring success.
In the midst of the ongoing global shortage of skilled workers in the construction sector, McConnell Dowell is successfully cultivating a pipeline of new and eager talent through its Graduate Program.
Recognised for its instrumental role in propelling recent graduates into thriving careers in construction, McConnell Dowell’s Graduate Program provides invaluable hands-on learning opportunities for the next generation of industry professionals.
Allowing participants to learn the ropes and gain practical insights into the execution of major construction projects, the two-year program not only addresses the industry’s talent gaps but also ensures a steady influx of capable individuals ready to contribute to the growth of Australia’s built environment.
Michael Caswell, general manager of human resources (HR) for McConnell Dowell’s Australian business unit, emphasises the significance of forward-thinking programs and initiatives like these in forging a brighter future for the sector. Drawing on his extensive experience in human resources, he highlights the importance of the Graduate Program for emerging professionals and for McConnell Dowell and the industry at large.
“McConnell Dowell’s Graduate Program offers a unique opportunity for new university graduates or individuals who have recently completed equivalent qualifications in relevant fields as they embark on their professional journey,” says Caswell. “This multifaceted program allows participants to delve into areas such as engineering, operations, finance, commercial or health, safety, environment and quality (HSEQ).”
“Graduate programs are helping develop the future leaders of the construction industry.”
“It’s an exceptional opportunity for new graduates eager to experience the construction industry first-hand, allowing them to gain valuable experience and knowledge and make informed decisions about their future professional paths.
“We aim to support the beginning of their careers by providing exposure to the various facets of our business through onsite experiences, mentorship, continuous learning and development opportunities, and rotations spanning diverse projects within our portfolio.”
McConnell Dowell’s Graduate Program isn’t just about theoretical learning – it’s a chance for participants to contribute to a Tier 1 construction company and gain genuine insights into the industry. The dynamic program undergoes regular reviews to ensure it not only provides a robust introduction
for young professionals but also offers an authentic glimpse into the realities of working on construction projects. For example, engineering graduates work alongside design engineering teams, delivery teams and project management, gaining practical experience in site operations and project delivery. This immersive experience exposes them to the complexities of analysing project requirements, contributing to temporary works designs, collaborating with consultancies, suppliers and subcontractors, and crafting construction solutions. This exposure extends to critical aspects of McConnell Dowell’s pre-contract and business development processes, including activities like tendering and estimating. If a graduate expresses a specific interest in a particular area, McConnell Dowell is also committed to facilitating their involvement in that domain. For some entering the McConnell Dowell team through this program, it represents not only their first full-time job but also their initial foray into the responsibilities inherent in project work. Caswell explains that working in project delivery demands an intense pace often underestimated by those who haven’t directly experienced it. Through the Graduate Program, McConnell Dowell provides a valuable support system, guiding
individuals through their initial exposure to the fast-paced world of construction and assisting them in adapting to its demands. This program is not just about filling a talent gap; it’s about nurturing the future leaders of the construction sector.
“We are continually striving to enhance our learning offerings year after year,” says Caswell. “Our commitment extends to delivering a curated schedule that not only enriches knowledge but also fosters connections among graduates, allowing them to bond with peers who share similar experience levels.”
“Additionally, we offer graduates the opportunity to rotate through a variety of projects, covering a diverse range of sectors and disciplines such as marine, road, commercial and rail construction.”
From an organisational standpoint, McConnell Dowell seizes the opportunity to bring new, enthusiastic individuals into its ranks, acquainting them with the company’s operations and steering them on a path aligned with its core values and purpose. This approach ensures a seamless integration of fresh talent, fostering a collaborative and purpose-driven team environment.
“Further, expediting the entry of young talent not only into our organisation but also
into the industry as a whole is crucial,” says Caswell. ”This accelerates their access to opportunities for personal and professional development, equipping them with a holistic understanding of their growth potential within the construction sector.”
“It’s not solely about attracting and recruiting new talent; it’s equally crucial to retain them, ensuring a steadfast pipeline of construction professionals both now and in the future.
“To achieve this, we establish a clear pathway for graduates, allowing them to envision their future beyond the program.”
Upon completing the two-year program, graduates transition into full-time positions as members of McConnell Dowell’s standard workforce, reflecting the company’s commitment to providing a long-term career path for program participants.
The company has achieved significant success in attracting, recruiting and retaining new talent through its Graduate Program, exemplified by the notable journey of Hannah Yap. Starting as a graduate environmental and sustainability advisor in 2020, she successfully completed the program in 2022.
Throughout her tenure in the program, Yap contributed to the environmental and sustainability advisory team on the Inland Rail Tottenham to Albury Tranche 1 project.
“We are continually striving to enhance our learning offerings year after year.”
“Our commitment extends to delivering a curated schedule that not only enriches knowledge but also fosters connections among graduates, allowing them to bond with peers who share similar experience levels.”
Additionally, she undertook rotations to other projects, where she worked alongside the onsite environmental advisory team for the Cranbourne Line Upgrade and the Aviation Road, Laverton level crossing removal project. Upon successfully completing the program, McConnell Dowell extended an offer to Yap for a position as an environmental advisor on the New Bridgewater Bridge Project in Tasmania. Determined to make the most of the opportunity, she has been thriving in this role for over 12 months, earning praise from
Caswell as a valuable addition to the team.
Underscoring her achievements, Yap clinched a victory at the National Association of Women in Construction’s (NAWIC) TAS Awards for Excellence 2023, recognised for her significant contribution to the New Bridgewater Bridge Project. Reflecting on the award, Yap said: “It was an incredible night celebrating so many powerful women at the NAWIC TAS Awards for Excellence 2023; I am tremendously humbled to have won in the ‘Contribution to a Project’ category.”
“I want to take this moment to pay my appreciation forward to all the women in the construction industry that have paved the way forward, to all the women that have showed up boots on the ground every single day, and to all the women that have redefined what a career in construction can be.
“As I look ahead, I find myself excited to advocate for working cultures that empower every woman to rewrite their own success and leadership.”
Another exemplar of success within the program is Mario Russo, the newly appointed managing director of McConnell Dowell’s Australian business unit, succeeding Jim Frith. Russo joined McConnell Dowell in 2005 after graduating with a Bachelor of Civil Engineering from the University of
Dowell, Russo has demonstrated a consistent progression in his leadership capabilities within project and new business management. With a dedicated focus on cultivating strong customer relationships, ensuring the timely and budget-conscious delivery of high-quality projects and aligning with the company’s Vision 2025 and Horizon 2030 strategic plans, Russo has been pivotal in solidifying McConnell Dowell’s standing as a Tier 1 contractor in South Australia. Additionally, Russo and his team have effectively steered McConnell Dowell’s re-entry into the Western Australian market while fostering collaboration between the company’s infrastructure and vertical building businesses in South Australia.
These two graduates stand as shining examples of the success achievable through McConnell Dowell’s Graduate Program, fully embracing the opportunities and building prosperous and fulfilling careers within the company. “While not every graduate is expected to step in and become the next managing director, we aim to attract talented individuals who can follow a trajectory towards more senior roles and exert a lasting influence on the company’s direction,” says Caswell.
Beyond being a valuable opportunity for emerging construction professionals, the program strategically positions McConnell Dowell for success in a competitive market. By identifying key areas for cultivating future leaders within the company, and considering the existing skill shortage, McConnell Dowell actively seeks applicants capable of contributing tangible value to these targeted areas. In essence, the company looks for candidates who have successfully completed
tertiary education in a field aligned with its resource planning needs.
“The program was launched five years ago, and in the intervening period, our business has experienced substantial growth, presenting us with evolving challenges each year,” says Caswell. “Consequently, we have continuously sought to align our program with the specific skills required to navigate these challenges.”
The program is open to new applicants every year, with 16 graduates starting this year from the last intake. McConnell Dowell will be opening the program to new recruits again this year, looking for a new intake to start with the company in 2025.
Frames made from TRUECORE® steel are proving to be a game‑changer for the Redland Bay State School project, offering both structural strength and the ability for ADCO Constructions to control costs.
In the heart of Queensland, the Redland Bay State School project stands as a testament to the advantages derived from employing light gauge steel (LGS) framing made from TRUECORE® steel. Nestled along Serpentine Creek Road, the new educational facility opened its doors in early 2024, catering to students from Prep to Year Six. The school is strategically positioned to serve the fast‑growing community emanating from the new Shoreline development.
By utilising LGS made from TRUECORE steel for the walls, trusses and bracing, the project has achieved a host of benefits.
Collaboration from the start
Working closely with builder ADCO Constructions (ADCO) and Inertia Engineering from the initial stages of the
project, Hytek Framing designed, fabricated and installed LGS walls, trusses and bracing for the new school. Setting early expectations on design parameters and documentation helped ADCO keep project risks (e.g. increasing costs, delays) to a minimum.
Minimising risks in today’s economy
Redland Bay State School comprises nine buildings, eight on slabs and one on a floating slab. After the completion of the slabs, builder ADCO confidently handed over the erection of the wall frames and trusses to Hytek Framing, utilising its own experienced installation teams. Andrew Park, senior project manager at ADCO, highlighted the efficiency of using LGS framing made from TRUECORE steel for the building designs on this project. In comparison to structural steel, this choice not
only saved a full week of build time, but also streamlined trade coordination, reducing the likelihood of cost overruns and delays.
TRUECORE steel provides confidence
Using LGS framing made from TRUECORE steel instils confidence in both subcontractors and engineers. On the Redland Bay project, test certificates for the steel could be provided almost immediately. This assurance gave the engineers confidence that locally sourced TRUECORE steel met their specifications, eliminating the need for further testing.
Lightweight and preferred by trades
LGS framing made from TRUECORE steel was pre punched with service holes making it easy for following trades to speed up during
the installation phase. Lightweight steel frames at the Redland Bay site were easily carried by two apprentices, making light work for the installation team.
Project highlights
The Redland Bay State School was deemed essential to help educate school children, who would be primarily living within the new Shoreline Development, and will help provide enrolment relief to surrounding schools within this new catchment area.
The new school is part of the Queensland Government’s ambitious plan to invest $2.1 billion in education infrastructure in 2023 24 alone. The infrastructure plan is set to build, improve, expand and maintain schools right across the state, creating 3,700 jobs.
Project
Redland Bay State School, Queensland
Fabricator
Lee Jones, general manager at Hytek Framing
Builder
Andrew Park, senior project manager at ADCO
Constructions
Architect
Conrad Gargett Architectus
Principal Steel Product
140,000 lineal metres of LGS made from TRUECORE® steel
Photographer
Aaron Ng, Primal Agency
Address
350-372 Serpentine Creek Road, Redland Bay
Stage One of the new Redland Bay State School included an administration building, prep and junior general learning areas, a student support and staff building, an information and resource centre, a multi‑purpose hall, a canteen, an oval, a multi purpose court, and general and student amenities as well as car parking.
for the project and cover off expectations regarding shared documentation.”
“Previously we’ve used LGS framing made from TRUECORE steel on other jobs and had no issues or concerns with Hytek Framing’s recommendation to use TRUECORE steel again.
“Steel allows us to mitigate risk against termite issues and frame movement over time – we never see any bowing or warping in the light gauge steel walls.”
Hytek Framing provides commercial builders with an onsite install capability, using their own in house carpentry team or experienced, long term subcontractors.
“Steel allows us to mitigate risk against termite issues and frame movement over time – we never see any bowing or warping in the light gauge steel walls.”
ADCO was tasked with managing all aspects of the state school project. “A key learning from this project is to ensure everyone’s on the same page right from the start,” says Park. “It makes a lot of sense to coordinate an upfront review with the principal engineer and steel fabricator to confirm the design parameters
“In the commercial space in Queensland, a supply only a rrangement wouldn’t work for most Tier 1 builders,” says Lee Jones, general manager at Hytek Framing. “They need to reduce their risk in terms of escalating costs and ensure on t ime delivery.”
“I’ve been a carpenter for 35 years and spent the last 15 years working with steel framing; I’ve learnt it comes down to being up front and delivering what you say you’re going to deliver – TRUECORE steel helps us do that.”
Light weight frames made from TRUECORE steel have an impressive strength-to-weight ratio, allowing for wide spans and flexible designs to suit multi-purpose spaces.
Light gauge steel framing made from TRUECORE steel has been used in a variety of school projects and may offer several advantages over other construction methods.
Precision engineered – Made to exact tolerances, light gauge steel frames are often pre-modelled and prefabricated offsite. Being prefabricated offsite means there is less need for adjustment once onsite, which may assist in reducing installation timeframes and in turn deliver labour savings.
High strength-to-weight ratio supports longer-spans – Light gauge steel framing made from TRUECORE steel boasts an impressive strength-to-weight ratio, potentially reducing the need for hot-rolled structural steel sections in a project.
Strong foundations – Light gauge steel framing made from TRUECORE steel is straight and true and won’t warp, twist or shrink, providing a solid foundation for buildings that are designed to last generations.
Designed to support onsite safety –Framing made from TRUECORE steel is lightweight and can be designed
to support safe onsite handling while minimising the exposure of workers who are working at heights.
Supports healthy learning environments
– Framing made from TRUECORE steel won’t burn or support the spread of flame, is 100 per cent termite proof, and will not rot or harbour mould. Importantly, TRUECORE steel has been independently tested and is classed as low volatile organic compound (VOC) emitting. It also does not require ongoing chemical treatments for termites, supporting healthier learning environments for students.
Design durability and versatility – Light gauge steel lends itself to structures that are designed for long life, built resilient and flexible to accommodate multiple future reuse options without reinvestment in structural alteration.
Green Star: Best practice – The combination of the product-specific Environmental Product Declarations (EPDs) for TRUECORE steel, and ResponsibleSteel™ certification for Port Kembla Steelworks where the steel in TRUECORE steel is manufactured, equates to a Responsible Product Value of 15 in the Green Building Council of Australia’s Responsible Products Score Checker. This is considered “Best Practice” under the Responsible Products Framework and may contribute to a building’s Green Star rating.
“Previously we’ve used LGS framing made from TRUECORE steel on other jobs and had no issues or concerns with Hytek Framing’s recommendation to use TRUECORE steel again.”
In 2022, Kelsey Godwin-Smith, an experienced architectural designer in the built environment, shifted gears and joined the construction industry, signalling a fresh and exciting chapter in her career.
Kelsey Godwin-Smith has charted a distinctive course into the construction industry, diverging from the typical career paths often observed in the sector. As a passionate design professional, her journey began in the world of architecture, with tenures at various architectural firms, including her most recent role at Billard Leece Partnership (BLP).
While traditional architectural positions often entail minimal onsite involvement, the landscape shifted amid the COVID-19 pandemic, leading to her increased presence on construction sites. It was during this period that Godwin-Smith seized the opportunity to step up as a site design lead, as part of BLP, for the $632 million Campbelltown Hospital Stage 2 Redevelopment, which was delivered by Health Infrastructure in partnership with South Western Sydney Local Health District and builder CPB Contractors. Reflecting on the project, she emphasises how it afforded her increased exposure to the construction facets of the built environment.
more extensive technical expertise,” she says. “The initial experience was intimidating, but I soon discovered that my distinctive background allowed me to offer a fresh perspective and unique skills.”
“ADCO was also very supportive in my journey and offered a range of training and development programs that assisted me in adapting to the transition and advancing my career.
“I bring a different voice to the room, and by sharing that voice my confidence within my role continues to grow – this, I believe, is a key factor in my success in this field.”
Starting as a design manager at ADCO, Godwin-Smith quickly progressed to the position of senior design manager within six months of joining the company. This swift advancement aligns with ADCO’s strong focus on providing development opportunities for women in construction and supporting career pathways in management.
“The dynamic nature of my work ensures that each day presents new challenges and opportunities.”
“As someone constantly seeking new challenges, working onsite of the Campbelltown Hospital Redevelopment affirmed that the construction industry offers the level of challenge I thrive on,” says Godwin-Smith. “Collaborating with the CPB Contractors team not only exposed me to the intricacies of a site environment but also reinforced my enthusiasm for working with a large and supportive team.”
These experiences ultimately influenced her decision to join ADCO Constructions (ADCO) in 2022. Transitioning from architecture to construction design was a significant change, yet Godwin-Smith found her skillset, especially in project management, translated seamlessly into this new field.
In her previous role as an associate/project lead at BLP, Godwin-Smith was tasked with managing people, collaborating with consultants and ensuring organisational efficiency. Consequently, many of these skills were transferable to her new position in the construction industry.
“Coming from an architecture background, entering the construction sector felt like being thrown in the deep end, especially given that many in the field have studied construction management, possessing
In her current capacity, she orchestrates the involvement of consultants, supervises design and construct (D&C) trades and ensures the delivery of outcomes that align with budget and program, all while meeting specific site and client requirements.
Her scope of responsibility spans the entire design process, necessitating the efficient and accurate development of each design to guarantee site readiness within tight time frames.
“On any given day, I could have 50 people coming to me seeking direction and advice on how to move forward with the design,” says Godwin-Smith. “The dynamic nature of my work ensures that each day presents new challenges and opportunities.”
Currently, Godwin-Smith is leading the design efforts for a $250 million hospital redevelopment for the NSW Government.
As the appointed building contractor, ADCO is delivering the project, which includes the development of crucial facilities such as an emergency department, maternity and paediatric services, operating theatres, surgical and medical inpatient units, medical imaging and ambulatory and outpatient services.
In addition to her role in the hospital redevelopment, Godwin-Smith is managing the design for a major school relocation project in New South Wales, where initial works have begun onsite. ADCO is the main works
contractor for the project, which involves the delivery of modern flexible learning spaces for up to 1,500 students; a new library, canteen and administration spaces; a multi-purpose sports and performance hall; a new outdoor sports field and courts; and landscaped recreation and outdoor learning spaces.
In her initial venture into the construction industry, Godwin-Smith primarily focused on education projects. However, she says her true passion lies within the health sector.
“With the state intensifying its investment in health infrastructure, there’s a wealth of opportunities in this field,” she says.
“I particularly enjoy the intricacies of these projects and find satisfaction in their complexity.”
Godwin-Smith says she finds the most fulfillment in her work when engaging in meaningful projects, particularly those within the health domain.
“Creating solutions that directly contribute to the wellbeing and advancement of the community is a gratifying experience,”she says. “Also, collaborating with a diverse team of consultants adds another layer of enjoyment to my work – the industry is teeming with talented individuals, making each day both challenging and rewarding.”
This commitment and dedication to the projects she undertakes earned Godwin-Smith the Young Achiever Award at the ADCO annual staff conference in July of last year. Another source of pride for her is achieving the position of associate at the young age of 25.
“In the field of architecture, reaching a leadership role often requires considerable time and dedication, making this achievement one I’m very proud of, and one I encourage more women to consider,” says Godwin-Smith. “The construction industry is a great place to work and has so many different career opportunities.”
Drawing on her wealth of experience and accomplishments, Kelsey has recently assumed a leadership role in the NSW Women of ADCO program. She views this as a significant opportunity to inspire and support younger women within the company, further reinforcing her commitment to fostering growth and diversity in the construction industry.
Despite being in the early stages of her construction industry career, Godwin-Smith has already made significant strides, serving as a testament to the diverse pathways that can lead to success in this sector.
“Creating solutions that directly contribute to the wellbeing and advancement of the community is a gratifying experience.”
Allyssa Hudson exemplifies the myriad opportunities inherent in the construction industry, having already contributed to several high-profile major projects across diverse sectors since starting her carpentry apprenticeship in 2020.
“I enjoy contributing to community-focused projects, like the Prince of Wales Hospital, as it brings me a sense of purpose to be part of delivering something that not only benefits but is also actively utilised by the community.”
As a qualified carpenter at Lendlease, Allyssa Hudson has helped deliver some of Sydney’s most iconic buildings and infrastructure, despite construction not being her initial career trajectory.
During her schooling, Hudson received constant encouragement from educators to prioritise academic studies and pursue a university degree post her higher school certificate (HSC). Interestingly, a career in construction or a skilled trade was never presented as a viable option. In fact, Hudson recalls joking with friends about the unconventional notion of ‘dropping out’ and becoming a tradesperson.
“My high school placed a strong emphasis on the HSC and university path, with minimal exposure to or discussion about the construction industry,” says Hudson. “I vividly remember joking with a friend about the idea of leaving school to become ‘tradies’ – an option that our teachers never suggested to us.”
“After school I enrolled in university and started a double degree – a Bachelor of International Studies and a Bachelor of Arts –and only lasted around six weeks.”
Eager to contribute meaningfully to society, but having realised university wasn’t right for her, Hudson entered the workforce as a traffic controller in January 2018 with the support of her mother, who at the time was an accountant at a labour hire company.
Although this role was more her speed, Hudson continued searching for a field that resonated with her interest in hands-on work. She stuck with traffic control for two years, during which she had the opportunity to work around major projects led by Tier 1 contractors, including Lendlease.
“I spent most of my time researching and engaging with countless individuals involved in the projects I was controlling traffic for, delving into their varied roles and responsibilities,” says Hudson. “Frequently subcontracted to Lendlease, I had the opportunity to interact with one of their apprentices who shared insights into his job and expressed genuine satisfaction in his role.”
Inspired by this interaction, Hudson decided to pursue a career in the construction industry, with Lendlease standing out as an excellent employer to begin her journey. In late 2019, she sought a carpentry apprenticeship through
My Gateway, an organisation that employs apprentices and trainees and hosts them to businesses within their chosen industry. Hudson not only successfully secured a position but also spent three fulfilling years as an apprentice hosted by Lendlease.
During her apprenticeship, Hudson played a role in the delivery of numerous significant projects in Sydney, New South Wales. As a component of Lendlease’s comprehensive professional development offerings, the company actively facilitates opportunities for apprentices to acquire valuable experience, collaborate with senior leadership and cultivate essential skills on a diverse range of major projects spanning multiple sectors. This initiative encompasses the entire spectrum of project types that the company undertakes.
“During my apprenticeship I got to see and work on five different project sites, all of them unique,” says Hudson.
“These included the Prince of Wales Hospital in Randwick, Salesforce commercial office tower, HMAS Watson Royal Australian Navy base, North Sydney Metro Station and One Sydney Harbour residential apartments.
“I enjoy contributing to community-focused projects, like the Prince of Wales Hospital, as it brings me a sense of purpose to be part of delivering something that not only benefits but is also actively utilised by the community.”
Lendlease also arranges onsite placements for apprentices to gain hands-on experience across mixed trades. As part of this program, Hudson worked alongside tradespeople within Lendlease’s subcontractor network, spending two weeks with the electricians, one week with the sprinkler fitters, three months with the formworkers and six weeks with the gyprockers. This allowed her to acquire a comprehensive understanding of each trade, progressively gaining new skills and knowledge throughout the process.
“In a relatively short period, I gained exposure to a wide spectrum of fields, spanning heath, commercial, Defence, infrastructure and residential sectors, while also delving into various trades and roles within the industry,” says Hudson.
This multifaceted journey reached a pinnacle in the third year of Hudson’s apprenticeship when she was honoured with the Transport for NSW Tradesperson Scholarship at the National Association of Women in Construction’s (NAWIC) 2022 New South Wales Awards for Excellence.
“As I approached the conclusion of my apprenticeship, winning this scholarship felt like a gratifying and meaningful way to cap off all the knowledge and new skills I had acquired throughout the course,” says Hudson. “This scholarship has not only provided a sense of accomplishment but has also paved the way for numerous opportunities.”
“Now, I am an active member of the NAWIC community, connecting with other women thriving in trades and the broader construction industry.”
Upon completing her carpentry apprenticeship in January 2023, Lendlease extended an offer to Hudson for a full-time carpentry role, an opportunity she keenly accepted. Hudson is currently part of Lendlease’s defects crew, responsible for
Beyond inspections, Hudson also takes on additional carpentry responsibilities, including the installation of handrails, emergency signage and edge protection.
“You need to be adaptable, as you could be working in any of the different crews within the business,” she says.
“Remaining open to learning from all colleagues and seizing opportunities for growth is equally important.”
Having accumulated a wealth of experience, Hudson consistently underscores the value of embracing unconventional paths and seizing opportunities in a field that may not always be presented as an obvious choice.
Her guidance for aspiring individuals venturing into the construction industry is straightforward: take the initiative, get a start, and once in, learn as much as possible.
“In a relatively short period, I gained exposure to a wide spectrum of fields, spanning heath, commercial, Defence, infrastructure and residential sectors, while also delving into various trades and roles within the industry.”
For the fourth successful year, the construction industry’s premier national event is back, focused on creating a more progressive, productive and sustainable sector.
Date
14 – 15 May 2024
Venue
Royal International Convention Centre, Brisbane
Registrations
Available via the FCON website
The Future of Construction Summit (FCON) has set the benchmark in Australia as the annual industry event where critical issues related to policy, reform, productivity, project pipelines, sustainability, innovation and technology are discussed, and important relationships are forged.
Launched in 2021, FCON has previously been held in Sydney and Melbourne. In 2024, it relocates to Brisbane, acknowledging the “once-in-a-generation” infrastructure boom taking place in Queensland, where billions of dollars are being invested to deliver the 2032 Olympic Games and support an ever-g rowing population.
Recent data by Arcadis highlights that South-East Queensland will continue to see a significant rise in the volume of major project spend over the next five years. This construction boom will be predominantly led by government investment, and the strongest and most active sectors will comprise:
• Civil/road infrastructure ($9 billion between 2024 and 2032);
• Rail infrastructure ($8.6 billion between 2024 and 2032);
• 2032 Games investment ($7 billion);
• Health (Capital Expansion Program –$5.5 billion); and
• Education, housing and other critical infrastructure.
On 14 and 15 May 2024, the industry’s foremost thought leaders from across the nation will assemble at the Royal International Convention Centre in Brisbane to discuss the big priorities for the coming 12 months and why and how the construction industry needs to evolve.
The program has been developed in true collaboration with leading figures representing contractors, infrastructure and asset owners, financiers, industry think-tanks, technology leaders, material suppliers and sustainability experts. It’s a program that is fit for the times – reflecting the big challenges, opportunities and ideas reshaping the sector.
The first day of the event will commence with a Government Address by Leah Kelly, deputy director-general from Queensland’s Department of State Development, Infrastructure, Local Government and Planning. This will be followed by an update on one of Queensland’s most transformational projects – the Cross River Rail. Spanning a remarkable 17 construction sites and employing thousands of workers, the Cross River Rail project comprises 10.2 kilometres of track, 5.9 kilometres of tunnelling, several new stations, and the redevelopment of three others between Brisbane and the Gold Coast.
During the morning of Day One, the Australian Construction Industry Forum (ACIF) will deliver the ACIF Forecast Briefing, which will highlight the projects being funded across Australia and what this means for project owners, constructors, government and the entire industry.
There will also be a construction leaders panel discussion examining the macro trends driving change and opportunity across the construction sector, featuring Camilla Drover, deputy secretary, infrastructure and place at Transport for NSW; Jason Spears, managing director at CPB Contractors; Louise Adams, group chief operating officer at Aurecon;
departments will share updates on the progress of projects being undertaken, the labour required to deliver them, and the impact on both the construction industry and Queensland.
Achieving a more diverse and inclusive workforce has been the goal of construction companies for some time. Leading figures with responsibility for people and culture, along with key industry associations, will discuss how the sector can foster cultural change, encouraging more women, Gen Z and Indigenous Australians into construction.
Sustainability will also be a big topic on the first day, with Fulton Hogan’s case study on dealing with the Scope 3 data challenge and a comprehensive panel discussion on net zero and more sustainable construction practices. The panel will include representatives from Bouygues Construction Australia, Lendlease, Aurecon, John Holland Group, the Infrastructure Sustainability Council and the Australian Sustainable Built Environment Council.
Moving towards the second day, the morning program will focus on collaboration and productivity, with an opening international presentation on how innovation and technology play a fundamental role in developing unique solutions for complex construction projects.
The second day will also examine coopetition and how contractors can both partner and compete for the greater good. Considering the complex nature of infrastructure projects and ways to solve the productivity crisis, c-level executives from CIMIC Group, Richard Crookes, Hansen Yuncken, ADCO Constructions and Helix Legal will discuss how to foster greater industry collaboration and break down
investment and the secrets to securing a return on investment across multiple projects and stakeholders. Specialists from McConnell Dowell, John Holland, Mirvac and RSGx will present a panel discussion and Dean James, digital design manager at Richard Crookes, will share a case study on exploring the role digital design is having on the automation of construction processes.
To wrap up two days of insights from industry leaders, the focus will be on digital innovation. Another stellar panel will cover how to create a future-ready, agile business that can fully leverage the benefits of digital technology through organisational change management. The afternoon will also showcase McMahon Services’ case study on custom building a ConTech application and the now famous ConTech SharkTank, featuring four leading start-ups, delivering solutions to meet the ever-evolving challenges of the construction sector.
This year’s FCON is proudly supported by the ACIF, the Australasian Procurement and Construction Council (APCC), the Queensland Major Contractors Association (QMCA), the Infrastructure Association of Queensland (IAQ), the National Association of Women in Construction (NAWIC), Australian Owned Contractors (AOC), the Society of Construction Lawyers Australia (SoCLA) and MATES in Construction.
For more information and how to register for FCON 2024, visit: futureofconstructionsummit.com
In 2024, FCON relocates to Brisbane, acknowledging the “once-ina-generation” infrastructure boom taking place in Queensland.
Australia’s premier construction and design show is returning to Sydney this May; a golden opportunity to connect with industry leaders and stay informed about cutting‑edge innovations.
Sydney Build has long been a cornerstone event in the construction and design industry, serving as a magnet for over 20,000 leading contractors, architects, civil engineers, developers, councils, housebuilders and construction professionals. This year, the anticipation is palpable as Sydney Build gears up to deliver an even more expansive and enriching experience.
Scheduled for 1 and 2 May 2024 at the ICC Sydney, Sydney Build will be co-located with Digital Construction Australia and Australia HVACR Expo, promising a unique and comprehensive development opportunity over the two days.
AI and Robotics Stage; Architecture and Design Stage; Digital Construction Stage; Sustainability Stage; Diversity, Inclusion and Reconciliation Stage; and more.
Key speakers from the government, contractors and architecture firms include:
• Meagan McCool, director at SafeWork NSW;
• Burak Turgutoglu, director design and project at Fairfield City Council;
• Neil Logan, co-CEO at BVN;
• Alberto Sanchez, head of planning at Lendlease;
• Rajitha Herath, technical director at AECOM;
• Harman Singh, smart cities and places lead at GHD Digital; and
• Janitha Senavirathna, project management professional at CPB Contractors.
With over 500 exhibitors showcasing the latest services, products and innovations transforming the construction industry, Sydney Build will also provide continuing professional development (CPD) training workshops. Covering digital construction, architecture and design, and heat, energy, air and water, these workshops will provide CPD points for attending professionals. All conference sessions are informally and formally CPD accredited.
New in 2024
Future Tech, AI And Robotics Stage
the forefront of technological innovation at the Future Tech, AI and Robotics Stage. Stay informed about the latest breakthroughs in artificial intelligence (AI) and robotics, gaining valuable insights into their profound impact on diverse industries and society. Engage in interactive discussions and demonstrations that aim to inspire individuals to embrace and harness the transformative power of these emerging technologies.
HVACR Workshops – Delve into crucial topics such as climate control, clean and renewable energy, net-zero initiatives, sustainability and the circular economy.
International Business Stage – Connect with the visionaries driving the world’s largest construction projects at the International Business Stage. Engage with developers, architects, contractors and investors as they share insights and best practices for successfully delivering sustainable and world-leading projects.
Building Solutions and Materials Workshop
– Embark on a journey of exploration in the Building Solutions and Materials Workshop, where innovative solutions and materials in construction and architecture take centre stage. Participants will learn about the latest advancements in building materials, sustainable design practices and construction techniques through hands-on activities and expert guidance. This workshop aims to inspire creative thinking and problemsolving skills to address industry challenges, promoting the use of new technologies for more sustainable and efficient buildings.
Ambassador and Referral Program –Join the mission to better the future of the construction industry. Become a Sustainability in Construction and Mental
Additionally, Sydney Build’s Meet the Buyer event will offer a valuable opportunity for suppliers and partners to acquaint themselves with procurement teams from top contractors, gaining insights into upcoming projects and tenders.
For enthusiasts of building planning and design, Sydney Build’s Architect’s Hub will showcase an array of project displays and 3D models of upcoming projects from renowned architects.
Meanwhile, those eager to explore the latest project and tender opportunities can leverage the Government Hub, offering a platform to meet with government agencies spanning the sector.
A range of exclusive networking events co-hosted with leading industry bodies will be held over the two days – a great way for attendees to expand their connections – as well as inclusive Ambassador Programs supporting Women in Construction, Diversity in Construction, Sustainability in Construction and Mental Health in Construction.
Furthermore, the largest networking parties for Women and Diversity in Construction will celebrate success and unite individuals passionate about driving change and equality across the industry.
Throughout the two days, DJs, musicians, live performances, celebrity guests and competitions will also keep attendees entertained.
The event will be open from 9am to 5pm on both days. Registrations for Sydney Build 2024 are free. To attend, visit www.sydneybuildexpo.com
A range of exclusive networking events co-hosted with leading industry bodies will be held over the two days.
“In line with market feedback, this year’s show will focus on industry trends such as the future of automation.”
The Australian Bulk Handling Expo is set to make its return in 2024, offering a dynamic platform for professionals in the bulk solids handling and construction industries to delve into and exchange innovative technological solutions.
The bulk solids handling industry, a linchpin of Australia’s economy encompassing many crucial commodities, plays a pivotal role in global security. Dedicated to presenting solutions for safeguarding the future of this vital sector, the Australian Bulk Handling Expo (BULK2024) is back this September.
At the heart of BULK2024 will be cutting‑edge technologies, taking centre stage to demonstrate their effectiveness in optimising efficiency and streamlining operations into the coming decade. Serving as Australia’s only dedicated exhibition for the bulk solids handling industry, BULK2024 is slated to take place from
10am to 5pm, from 18 to 19 September 2024, at the Melbourne Convention and Exhibition Centre. Bringing together esteemed companies and leaders from across the industry and supporting sectors, the event will provide a forum for professionals to connect, explore emerging technologies, leverage them to their advantage, and collaborate on further strategies to enhance operational efficiencies. In the construction sector, the bulk handling industry is instrumental in transporting substantial quantities of essential raw materials like aggregates, sand, gravel and cement to construction sites. These materials form the backbone of various
“It will address key challenges currently faced by the industry, including skills shortages and an ageing workforce.”
bridges, buildings and infrastructure.
Moreover, the construction industry heavily relies on specialised equipment such as conveyor systems, cranes and loaders for handling bulk materials. The continuous advancement of this equipment by the bulk handling industry contributes significantly to the overall progress of construction processes.
The seamless coordination between the bulk handling and construction industries is fundamental for the smooth execution of building and infrastructure projects, making BULK2024 an invaluable event for construction leaders and businesses seeking new ways to bolster their operations.
Lauren Chartres, BULK2024 show director, emphasises the event’s commitment to equipping the industry with essential tools for success. “In line with market feedback, this year’s show will focus on industry trends such as the future of automation,” says Chartres.
“It will address key challenges currently faced by the industry, including skills shortages and an ageing workforce.”
The event is designed to empower those in heavy industry to move their products to where they are needed most, both on a national and global scale. It will feature an expansive trade show, spotlighting the latest industry solutions, and will host a two day informative conference discussing strategies for businesses to stay at the leading edge in a constantly changing world.
transformations driven by technological advancements and the surge in automation, BULK2024 will pave the way for visionary businesses. It will accelerate the progress of not only the bulk handling industry but also the sectors it supports, propelling them toward success.
Registrations for BULK2024 are free. To attend, visit www.bulkhandlingexpo.com.au
To steer the future of major project delivery in Australia towards timely and cost-effective outcomes, the Australian Constructors Association’s Jon Davies urges a collaborative effort from the government, industry and unions.
Hot on the heels of another on-time ribbon cutting for the extension of the City and Southwest line to Western Sydney Airport, the latest section of Sydney Metro West, between Bankstown and Liverpool, has just been completed on time and on budget. The Liverpool section cost 30 per cent less per kilometre than the preceding sections of Sydney Metro West, between Bankstown and the CBD, and was constructed in a fraction of the time.
This is obviously a fictitious story, but let’s just imagine it isn’t for a moment.
Following the recommendations of the Independent Review of the Metro project conducted by Mike Mrdak AO and Amanda Yeates in 2023, the project has been funded through the development of mixed-use station precincts along the route, which have created over 25,000 new homes and breathed life into several previously underutilised and run-down areas of the city.
Project director Fatima Hussain credited the successful project outcome to a positive team culture created by developing a diverse and fully integrated project team drawn from all invested stakeholders.
“All signatories to the contract, from Sydney Metro to the contractor, designer, suppliers and unions had ‘skin in the game’ and were aligned to achieving this great outcome,” said Hussain. “By coming together at concept design stage, we were able to identify significant cost savings in project alignment without the need to revisit expensive and lengthy environmental approval processes.”
“Station designs were standardised to allow components to be manufactured locally using concrete and steel, with over 70 per cent less embodied carbon than in earlier stages of the Metro project, and these components were delivered to site as required, reducing the footprint of the site and impact on the local community through a reduction in noisy operations.
“The unions were fantastic and worked with us to set up targeted training programs and develop flexible work rosters that all helped optimise site productivity.
“Whilst the project operated 24 hours a day, seven days a week, nobody worked more than five days in a row or more than 40 hours a week, myself included.”
Following the run of successful major project outcomes, local educational institutes have reported a significant increase in enquiries for construction-related courses and apprenticeships. Infrastructure NSW has been contacted by delivery agencies across Australia and overseas wanting to know how these results can be replicated
Imagine if this was the future of major project delivery in Australia.
The fact is, many of the elements of this story are readily achievable or already happening right now, just not in a joined up or coordinated way.
Lean construction, a project delivery process that uses tools and techniques from the manufacturing industry to reduce waste in construction, has been demonstrated to reduce overall cost and time on projects by up to 30 per cent. Using a modular design and doing away with fancy architectural embellishments, the Madrid subway extension, comprising 131 kilometres of track and 76 stations, was completed in just eight years. Sydney Metro is currently made up of 113 kilometres of
track and 46 stations and is scheduled to take over twice as long to complete.
Formed in May 2015, the Victorian Level Crossing Removal Authority was tasked with removing 50 level crossings across Melbourne. Using a panel of contractors and a collaborative delivery model, the authority delivered the vast majority of crossing removals either on time and on budget or, in many cases, ahead of time and under budget.
So successful has the model been that the scheme has been continually expanded and has now removed 74 level crossings with plans to remove another 36 by 2030.
School Infrastructure NSW has embarked on a program to deliver new schools using modern methods of construction, such as using prefabricated components manufactured offsite by local industries. Estimates are that this will result in time savings of 30 per cent and a greatly reduced carbon footprint. Chemical polymer replacements for cement have been developed that reduce the embodied carbon of concrete by over 80 per cent and further reductions
are possible through the use of green steel produced using electric arc furnaces.
In a notoriously male dominated industry where women make up only 13 per cent of the workforce, the Queensland Government recently completed a 20-apartment, five-storey social housing complex project with 31 per cent overall female participation, including 22 per cent of women in frontline trades such as plumbing and electrical.
Workers on vertical construction projects are increasingly working a five-day week. Trials are being undertaken as part of a proposed nationwide construction ‘culture standard’ to embed flexible working arrangements into all government funded projects, including major roads and railway developments.
The future is already here. We are calling on the Federal Government to lead the way by bringing together all levels of government, industry and unions to join the dots and regularly achieve on-time and on-budget outcomes through the development of a National Construction Strategy. #Imaginewhen
“Trials are being undertaken as part of a proposed nationwide construction ‘culture standard’ to embed flexible working arrangements into all government funded projects, including major roads and railway developments.”
Empowered Women in Trades is passionately committed to a transformative mission, tirelessly working to boost the presence of women in skilled trades.
Empowered Women in Trades (EWIT) is on a mission that’s nothing short of transformational. In a country facing critical skill shortages and a housing crisis, EWIT stands at the forefront of change, championing a cause that is central to Australia’s future success. With a vision as bold as necessary, EWIT is committed to leading the charge to increase female representation in skilled trades from a meagre 3 per cent to an ambitious 30 per cent by 2030.
Australia’s skill shortage and housing crisis are complex problems that require innovative solutions. As the demand for skilled labour continues to outstrip supply, the consequences ripple across various sectors, particularly in construction and infrastructure development. Simultaneously, the housing crisis exacerbates affordability and availability issues, putting immense pressure on both individuals and the economy.
It’s against this backdrop that EWIT’s mission takes centre stage. By advocating for increased female representation in skilled trades, EWIT aims not only to bridge the gender gap but also to contribute significantly to the resolution of these pressing national concerns. Through empowerment, education and recognition, EWIT is supporting organisations and industry leaders to foster a dynamic and diverse workforce that can address skill shortages and provide a strong foundation for tackling the housing crisis.
Tackling the skill shortage head-on
Australia’s skill shortage is not a new problem, but its implications have far‑reaching consequences. Infrastructure and construction projects, often the lifeblood of the nation’s progress, depend on a skilled workforce to thrive. EWIT recognises that empowering women in trades is a powerful remedy for this crisis. Through meticulously designed programs aimed at recruiting women into skilled trades and comprehensive consulting services that foster workplace cultures promoting psychological wellbeing and safety, EWIT is actively addressing this skill shortage.
The housing crisis in Australia is a multifaceted challenge, characterised by soaring property prices, dwindling affordability and a severe shortage of available housing. This crisis doesn’t just affect our wallets; it touches the very essence of our society. However, where there are challenges, there are also opportunities.
A key solution to the housing crisis lies in expanding the skilled workforce. By doing this, we can accelerate construction projects, increase the housing supply and potentially alleviate affordability issues. One crucial aspect of addressing the housing crisis and
“As we march forward in our mission, EWIT invites you to join us at The Trust
in Melbourne on 23 February 2024 for a momentous event – the EWIT Gala.”
We believe that professions within the construction industry should be presented as viable career options to all students, regardless of their gender. However, we recognise the need for a particular focus on opening the doors of opportunity within our industry to female and non binary students. This is why we take immense pride in our Kicking Goals in Trades program, a partnership between EWIT and the North Melbourne FC’s Freestyle Program. This program opens the doors of opportunity for female students, allowing them to explore skilled trades as a potential career path. By introducing them to these industries, we inspire the next generation of skilled tradespeople and bridge the gap in the construction workforce.
The upcoming gala – shining a spotlight As we march forward in our mission, EWIT invites you to join us at The Trust in Melbourne on 23 February 2024 for a momentous event – the EWIT Gala and Awards. This gathering is more than just a celebration; it’s a spotlight on the achievements of individuals and organisations dedicated to achieving 30 per cent female representation within skilled trades by 2030. At the gala, we will present awards that honour the incredible women,
men and organisations that are driving change within the industry. It’s a night to celebrate their exceptional contributions and to inspire others to join the cause.
By attending the gala, you are not only supporting these phenomenal individuals but also contributing to a brighter future for the construction industry and Australia. Join us, be a part of the solution, and together, let’s empower women in trades and
“Australia’s skill shortage and housing crisis are complex problems that require innovative solutions.”
In response to the enduring safety challenges within the formwork sector, executive leader Michael Sugg puts forth a series of solutions.
Association.
As the Australian construction industry grapples with a shortage of skilled workers, the formwork sector faces unique challenges in maintaining safety standards alongside the demand for specialised skills. Formwork construction demands precision, expertise and an unwavering commitment to safety. In this article, we delve into the safety implications of skills shortages in the Australian formwork industry and propose comprehensive solutions that prioritise training, collaboration and safety.
1. Specialised safety knowledge: Formwork construction is classed as ‘high-risk’ and requires a specific set of skills. It involves unique safety considerations, including securing formwork structures, managing loads and ensuring the stability of temporary works, as well as managing specific formwork work health and safety (WHS) hazards. The shortage of skilled workers in the formwork industry can lead to gaps in safety knowledge, increasing the risk of accidents and injuries, with costs to all involved.
2. Inadequate safety training: A shortage of skilled workers often means a shortage of workers adequately trained in safety protocols. In the formwork sector, a high-risk working environment where precision is paramount, insufficient safety training can result in increased incidents, compromising both workers’ wellbeing and project timelines.
3. Ageing workforce and safety risks: Like the broader construction industry, the formwork sector grapples with an ageing workforce. Many skilled formwork professionals are nearing retirement, leaving a void that is difficult to fill with adequately trained and experienced workers. Ensuring a pipeline of well-t rained, safety-conscious workers becomes crucial to maintaining a safe
“Formwork construction demands precision, expertise and an unwavering commitment to safety.”
risk management, controlling formwork hazards, proper installation procedures and awareness of the Formwork Code of Practice. Collaboration with safety experts and regulatory bodies can ensure the creation of effective and up-to-date safety training modules that can be delivered onsite.
2. Safety-centric apprenticeships: Apprenticeship programs should not only focus on technical skills but also prioritise safety education. Mentorship during apprenticeships should emphasise the importance of adhering to safety protocols, instilling a culture of safety from the early stages of a formworker’s career. Digital micro-credential safety training courses should be available to apprentices at all times.
3. Continuous safety education: The formwork industry should embrace ongoing safety education to keep workers abreast of evolving safety standards and emerging technologies. Regular onsite workshops, micro-credential courses, seminars and safety drills can enhance the safety consciousness of the workforce.
4.Collaborative safety initiatives: Formwork companies, industry associations, industry players, educational institutions, government
bodies and safety regulators should collaborate to establish and enforce safety standards. A collective effort can lead to the development of industry-specific safety guidelines, ensuring a consistent approach to safety across projects.
The skills shortages in the Australian formwork industry require a targeted and collaborative approach that places safety at the forefront. By investing in comprehensive, formwork-specific safety training, safety-centric apprenticeships, continuous education, collaborative safety initiatives and the integration of technological solutions, the formwork sector can effectively address skills shortages. This, in turn, will ensure the wellbeing of our workforce and contribute to the success of construction projects, fostering the continued growth of Australia’s built environment.
Addressing these challenges head-on, the Formwork Industry Association’s (FIA) proposed new education and skills pathway, and particularly the Safe Formworker Program, emerges as a beacon of hope. It offers tailored solutions to bridge the skills gap and fortify safety practices within the formwork industry.
“A skills and education pathway is essential for our industry, including formworkspecific safety training programs and certified qualifications.”
Queensland’s fast‑growing Burleigh Heads has welcomed two iconic 24 and 25 storey precast concrete towers that set a new benchmark for hospitality and residential living.
Project
Mondrian Gold Coast
Location
Burleigh Heads, Queensland
Architect
Elenberg Fraser
Engineer
ADG Engineers
Head contractor
Hutchinson Builders
Precast installer
HD Rigging
Master Precaster
Euro Precast
A joint initiative between global hospitality group Accor and Vitale Property Group, Mondrian Gold Coast epitomises a fusion of luxury accommodation and lifestyle amenities in one of Australia’s most scenic coastal areas. It features 83 exquisite residential apartments and a five-star hotel boasting 208 guestrooms. The buildings are united by a three-storey podium that acts as the building’s common space and activity hub, housing a porte-cochère, hotel lobby, cafés and restaurants. Additionally, there are three levels of basement car parking.
Australia (National Precast) Master Precaster, Euro Precast, manufactured over 750 precast elements for the project including walls, columns, arches, spandrels and balustrades. According to Euro Precast’s Queensland general manager Jeff Stratford, his team worked tirelessly with Hutchinson Builders, ADG Engineers and architects Elenberg Fraser to deliver high-quality elements to meet the project’s demanding schedule.
Complex geometric elements
“This is one of the most comprehensive projects we have been involved in, with complex geometries across the majority
vertical connections to maximise the off-form oadbearing walls, both single and double
What sets this project apart is its porte-cochère – a covered entrance that is both functional and visually stunning. Designed as a hub of activity that also provides shelter from the sun and rain, it is a unique and eye-catching focal point for visitors and locals alike. Features such as outdoor seating, public art installations and a range of retail and dining options offer a place where people can come together, relax and enjoy the vibrant energy of the Burleigh Heads community.
Precast elements supplied for this part of the project included columns, arches and arch segments and spandrels.
Digitised QA delivers new transparency
According to Stratford, quality requirements were unprecedented for the Mondrian Gold Coast project, and tight quality control during both manufacture and installation was essential to the project’s success.
Utilising National Precast Industry Partner CONQA’s new digitised quality control software, Euro Precast was able to ensure transparency during manufacture by conducting virtual inspections of every element. This involved reviewing moulds, concrete strength, reinforcement, tolerances and class of finish.
Onsite, careful attention was given to transportation, temporary bracing, placement, caulking and grouting.
Partnering with National Precast members
“We also partnered with many other National Precast members for the project, including PSA, HD Rigging, Construc, PROGRESS GROUP, Reid Construction Systems, Milwaukee Tools and Actech,” says Stratford.
The Mondrian Hotel and Residential complex represents a harmonious blend of luxury living, unparalleled views and a vibrant community spirit. It has become a landmark, attracting tourists, investors and locals alike, setting new benchmarks for sophisticated coastal living and appealing to discerning residents and travellers seeking a refined lifestyle experience amidst the
“This is one of the most comprehensive projects we have been involved in, with complex geometries across the majority of the elements that form the hotel tower, the residential tower and particularly the porte-cochère.”
To tackle the persistent challenge of the construction industry’s ‘leaky pipeline’, the National Association of Women in Construction has adopted a proactive strategy to redefine opportunities for women in construction.
“At NAWIC, our vision is to achieve 25 per cent female participation in the construction industry by 2025.”
In the fast-paced world of the construction industry, there is a widely acknowledged challenge commonly referred to as the ‘leaky pipeline’. Recognising the urgency of this issue, the National Association of Women in Construction (NAWIC) has embraced a proactive stance to confront and overcome this obstacle.
This article invites you to explore NAWIC’s approach in addressing the leaky pipeline of women in construction. We will delve into the complexities of the strategy that not only aims to fix the leaks but also seeks to create an environment where women, and everyone, can thrive throughout their careers in construction. We need support from the industry to ensure we are creating a future characterised by inclusivity, diversity and empowerment within the construction sector.
• High school: Develop and implement initiatives to increase awareness of career opportunities in construction.
• Apprenticeships and university study: Establish safe learning environments and advocate for diversity in educational materials.
• P romote the creation of safe workplaces for women.
• Address childcare accessibility and workplace flexibility.
• Ensure fair and equitable remuneration.
• P rovide equal opportunities for advancement.
• Implement the 12 recommendations
(Image: Martinan/stock.adobe.com)
outlined in the Breaking down the barriers for apprentices report, 2022, by the Queensland Training Ombudsman.
• Establish a National Gender Equality Strategy.
3. Family and work balance
• Develop quotas and initiatives to increase the number of female teachers in TAFE and university environments.
• Implement the Cultural Standards outlined by the Construction Industry Culture Taskforce (CICT).
• Introduce workplace mentoring and buddy systems.
• Ensure the provision of onsite amenities catering to the needs of female employees.
• P ursue the Employer of Choice for Gender Equality (EOCGE) citation from the Workplace Gender Equality Agency (WGEA).
4. Remuneration and career growth
• Ensure affordable and flexible childcare options are available for all parents.
• Customise childcare solutions to align with onsite work hours.
• Introduce portable parental and long service leave policies.
• Encourage job share, part-time and work-f rom-home options.
• E liminate the pay gap for women in equivalent positions.
5. Inclusivity and recognition
• Establish and implement career pathway and upskilling strategies for women.
• Introduce ‘Male Allies’ education programs.
• Conduct organisation-wide diversity and inclusion (D&I) training.
• Establish a menopause policy.
• Introduce executive and board quotas.
• Celebrate and promote the success stories of women in construction, fostering the ethos “You can be what you can see”.
At NAWIC, our vision is to achieve 25 per cent female participation in the construction industry by 2025. Currently, we are sitting at 12 per cent. While this goal may pose challenges, we are committed to continuing the conversation, breaking down barriers and transforming the construction culture to create a safe and equitable place for women.
Stay connected with NAWIC through our social media platforms, The Leaky Pipeline podcast and membership. Learn more about our initiatives and the impactful work we do at www.nawic.com.au
“We need support from the industry to ensure we are creating a future characterised by inclusivity, diversity and empowerment within the construction sector.”
Dr Gretchen Gagel offers a unique project management perspective on life, advocating for the application of strategic plans to personal life, mirroring the organisational approach commonly employed on construction projects.
“We are incredible project managers when it comes to construction projects. Should we be applying some of these principles to our lives as well?”
Those of you who regularly read my Inside Construction editorials know that I try to align my thoughts with the theme of the edition. Hearing that the theme for this edition is effective project management, my mind immediately conjured up all of the elements of effective construction project management. These include putting in place a physical and mental safety plan that ensures every project team member goes home in the same condition they arrived; aligning the team on the goals and measurable objectives of the project; making sure the project schedule is achievable and that we are meeting project milestones; developing a game plan for ensuring that the quality of the construction meets the specifications and the expectations of the client.
Then I thought, wait a minute, all of these construction project management practices apply to our lives as well. My work on the Steering Committee of the Construction Industry Culture Taskforce (CICT) here in Australia and the Associated General Contractors (AGC) of America’s Diversity and Inclusion Committee has underscored many of the challenges I’ve witnessed in the construction industry during my 40-year career – high suicide rates, people that are stressed out and not taking care of themselves, and people not attracted to our industry. We are incredible project managers when it comes to construction projects. Should we be applying some of these principles to our lives as well? I would argue yes and here’s why.
We would never start a construction project today without a solid physical and mental safety plan in place. So why do some of us do that in our personal lives?
A dozen years ago I was CEO/president of a company, working long hours, raising two teenagers, volunteering for everything under the sun, and divorcing. During this time, I was not taking care of myself, physically or mentally. I went down hard. I developed severe heart arrhythmias, including premature ventricular contractions (PVCs) and premature atrial contractions (PACs). Essentially, all four chambers of my heart were beating out of rhythm. I learned that there are cardiologists who function like plumbers,
addressing blockages, and others who act like electricians, dealing with electrical signals in our hearts. Who knew? I spent a month in bed until they found a beta blocker that controlled the problem without me passing out every time I stood up. I’m thankful I didn’t just drop dead of a heart attack.
After five years of focusing on my physical and mental health (yoga, the gym, running, more ‘me’ time), I was able to stop taking the beta blocker. Now, I only slightly experience these arrhythmias when the adrenaline of something like speaking in front of hundreds of people triggers them, or when I neglect my wellbeing routine by not getting enough sleep or not exercising. It’s like having a little stress meter in my body, and I listen to it.
We shouldn’t wait for a situation like this to ensure that we have a good physical and mental safety plan in place for ourselves. As I often say, you must put on your own oxygen mask first. You are no good to anyone – your work team or your family – if you aren’t physically and mentally safe.
When considering a construction project schedule, we divide it into activities by trade and develop critical path schedules outlining the necessary steps in the project, their sequence and the estimated hours/days
required to complete each task. We prioritise activities to meet this schedule and the ultimate deadline for the project, with the hope of completing the construction project on time.
I argue that we need to apply that same schedule discipline to our lives. We vote for our priorities with our time. Not only should we take the time to align ourselves with the goals and measurable objectives of a construction project, but we should also take the time to align on our personal goals and measurable objectives – our life priorities.
Back when this heart problem began, I started doing what I call the “pie of life” exercise. Every so often, I draw a large circle in my journal and write ‘168’ at the top. The significance of this number? It’s the number of hours in a week, and it’s the same for all of us. We all think we can blow up this ‘pie of life’ like a balloon, creating more hours, but we can’t. It’s the same for all of us.
The first time I drew the ‘pie of life’, I carved out the slice of ‘sleep’ first, but I wasn’t truly making it my top priority. I realised that, to regain my health, I needed to prioritise both sleep and exercise. Here’s a vulnerable moment. I said my family was my next most important priority, but was I voting for that with my time? Probably not, and more needed to change in my life.
We all experience weeks when the world seems to collapse, and we find ourselves spending more time at work. However, if we allow work to consistently interfere with our life priorities in the long term, we won’t find true happiness. It might even lead us to let down our project teammates or eventually leave the industry.
I encourage you to have a long-term outlook on the project plan of your life. Think about how all of our effective construction project management elements – safety, budget, schedule, quality – apply to your life to ensure that you are living life to the fullest and in line with your priorities.
Dr Gretchen Gagel is chair of Brinkman Construction (US), a member of the National Academy of Construction (US), a member of the Construction Industry Culture Taskforce (AUS), and a member of the Associated General Contractors (AGC) of American Diversity and Inclusion Taskforce. As president/managing director of Greatness Consulting, she continues to advise organisations within the construction industry on optimising capital program delivery and developing great leaders. You can hear more from Gretchen on her Spotify podcast, “Greatness”.
“We would never start a construction project today without a solid physical and mental safety plan in place. So why do some of us do that in our personal lives?”
The
When this distinctive circular designed school required completion for the start of the academic year, light gauge steel framing made from TRUECORE® steel delivered.
Prefabricated and then assembled on site, impressively large roof truss and frame modules were craned to height, then safely and e ciently installed into their elevated positions.
The end result is a state-of-the-art learning space designed in the round and produced on time. Visit truecore.com.au to learn more.