plans FROM TO results
Elizabeth Creswell unveils ADCO Constructions’ digital transformation journey with Revizto software.

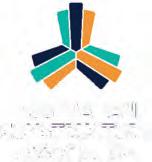



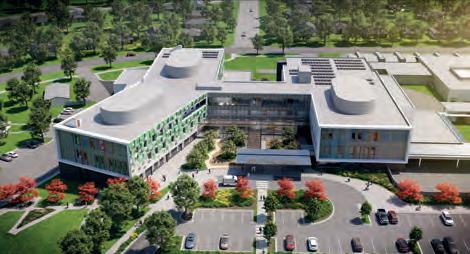
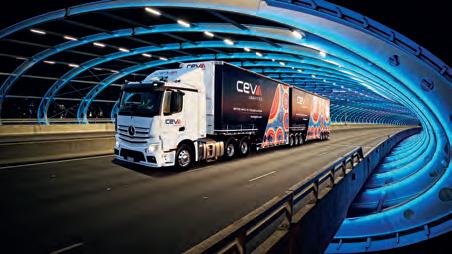
Elizabeth Creswell unveils ADCO Constructions’ digital transformation journey with Revizto software.
19 Locked and loaded
Nord-Lock shines a light on its partnership with Hobson Engineering, bolstering bolt security throughout Australia’s construction sector.
ADCO Constructions reveals how Revizto software is enhancing project outcomes across its national portfolio.
PROFILES
44 Candace Garraway: Behind the blueprint
Discover how Candace Garraway’s passion for drawing sparked her successful career in architecture.
46 Kayla Shadbolt: Hire horizons
Kayla Shadbolt, general manager at Swan Hill Hire, reflects on her career journey from apprentice to leader in the hire and rental sector.
OPINION
56 Reinforcing a safety culture
Dr Gretchen Gagel outlines key steps to strengthen the culture of safety within the construction industry.
ASSOCIATIONS
48 ‘Better’ just to hold it?
The National Association of Women in Construction unveils its latest campaign, advocating for the availability of safe and accessible toilets on construction sites.
50 The marvels of glass-reinforced concrete
The National Precast Concrete Association Australia highlights the potential of glass-reinforced concrete in modern structures, spotlighting The Ribbon project.
52 One year into industry pledge
Delve into the Australian Constructors Association’s critical initiatives to transform the industry landscape.
54 Trade ties
Empowered Women in Trades’ Melinda Davis underscores the value of jobs and career exhibitions in creating connections and fostering careers in trades.
23 Light-weight steel supports inspired façade
Find out why light gauge steel structural framing made from TRUECORE steel was the material of choice for an eye-catching façade structure in Prahran, Victoria.
26 World-class construction
Gain exclusive insights into McConnell Dowell’s execution of Tasmania’s largest-ever transport infrastructure project. 30
In motion: More choices, more solutions
Motion shares how it is living up to its promise to provide industrial businesses with ‘more choices and more solutions’. 34
Getting the balance right
Blackwoods offers personalised guidance for selecting the right personal protective equipment.
Building sustainable supply chains
Explore how MEGATRANS 2024 will pave the way towards a resilient and sustainable future for the construction industry’s supply chain.
41 A revolution in bulk handling
Dive into this year’s Australian Bulk Handling Expo, offering a vital platform for professionals connected to the bulk solids handling and construction sectors.
As the Australian construction industry strides into the digital age, our focus this month is on the companies and technology providers driving its evolution.
Embracing a wave of digitalisation, the Australian construction sector has witnessed a surge in the adoption of technologies such as building information modelling (BIM), data analytics and artificial intelligence. This paradigm shift, though manifesting at varying paces across sectors, heralds a promising future for the industry, where digital innovation becomes the cornerstone for enhanced productivity and sustainability.
As digitalisation continues to permeate the construction sector, stakeholders are recognising the significant benefits that technology‑driven solutions can offer, particularly major contractors. In this edition, we delve into the innovation journey of one of Australia’s leading construction firms, exploring how the development of a digital engineering strategy paved the way for the adoption of BIM collaboration software, streamlining efficiencies and elevating project outcomes.
In the pursuit of great project outcomes, one contractor stands out for their achievements on a multi‑residential development in Victoria, leveraging light gauge steel framing made from a premium structural steel for the façade’s structure. We explore how the project team achieved precision, efficiency and durability through the utilisation of this lightweight yet strong material. Durability is increasingly prioritised across Australia’s built environment, highlighted by a partnership between a renowned global supplier of engineering and bolting technologies and its Australian distributor. Together, they’re supplying nuts and washers known for their exceptional durability
and quality to the Australian market. Inside Construction unveils how these washers are poised to play a pivotal role in ensuring the success of the 2032 Olympic and Paralympic Games.
This edition also spotlights two upcoming events that provide vital platforms for sharing new industry solutions: the Australian Bulk Handling Expo and MEGATRANS, both returning this September. The Australian Bulk Handling Expo promises to offer a crucial platform for professionals in the bulk solids handling and construction sectors, while MEGATRANS aims to unite companies providing advanced technologies and services that contribute to a sustainable supply chain.
This issue, we also dive into the career journeys of Kayla Shadbolt, general manager at Swan Hill Hire, and Candace Garraway, project architect at EJE Architecture. Both of these remarkable women have an inspiring story, making significant strides in their respective fields.
We hope you enjoy our June 2024 edition of Inside Construction.
Chief Executive Officer John Murphy
Chief Operating Officer Christine Clancy
Group Managing Editor Andrew Hobbs andrew.hobbs@primecreative.com.au
Editor Ashley Grogan ashley.grogan@primecreative.com.au
Sales Director Brad Buchanan bradley.buchanan@primecreative.com.au
Art Director/Design Daz Woolley, Caterina Zappia
Head of Design Blake Storey blake.storey@primecreative.com.au
Design Production Manager Michelle Weston michelle.weston@primecreative.com.au
Business Development Manager Nhung Nguyen nhung.nguyen@primecreative.com.au p: +61 0412 845 608
Client Success Manager Glenn Delaney glenn.delaney@primecreative.com.au
Cover image credit ADCO Constructions
Head Office
Prime Creative Pty Ltd 379 Docklands Drive, Docklands, Victoria 3008 Australia p: +61 3 9690 8766 f: +61 3 9682 0044 enquiries@primecreative.com.au www.insideconstruction.com.au
Subscriptions
+61 3 9690 8766 subscriptions@primecreative.com.au
Inside Construction is available by subscription from the publisher. The rights of refusal are reserved by the publisher
Articles
All articles submitted for publication become the property of the publisher. The Editor reserves the right to adjust any article to conform with the magazine format.
Copyright
Inside Construction is owned by Prime Creative Media and published by John Murphy. All material in Inside Construction is copyright and no part may be reproduced or copied in any form or by any means (graphic, electronic or mechanical including information and retrieval systems) without written permission of the publisher. The Editor welcomes contributions but reserves the right to accept or reject any material. While every effort has been made to ensure the accuracy of information, Prime Creative Media will not accept responsibility for errors or omissions or for any consequences arising from reliance on information published. The opinions expressed in Inside Construction are not necessarily the opinions of, or endorsed by the publisher unless otherwise stated.
With a strong pipeline of construction projects on the horizon, this month we take a look at some of the key developments shaping Australia’s built environment.
Contractor: McConnell Dowell
Current value: Over $152 million
Details: On behalf of Unitywater, McConnell Dowell is currently delivering vital water and wastewater infrastructure in Queensland’s booming Sunshine Coast to support the new Aura and Harmony communities. For the Aura development, which anticipates a population of 50,000 residents by 2050, McConnell Dowell is installing over 12km of 900mm diameter wastewater pipeline, a pump station and a 12ML water reservoir linked to Ewen Maddock Dam via 12km of 800mm pipeline. For the Harmony development, which anticipates a population of 21,000 people by 2036, McConnell Dowell is delivering 2.2km of 500mm pipeline and a 12ML reservoir.
Status: The project team has been onsite for nearly 12 months, achieving 36.8 per cent completion (as of 25 March 2024). The Aura Pump Station is well advanced, with most materials sourced locally. Despite the heavy rainfall, exceeding 1.3m since November 2023, ground conditions are expected to improve in the coming months, allowing the construction team to progress swiftly towards completion. The foundation for the Harmony Reservoir has been poured, and walls will soon be lifted into pride of place. The Harmony Pipeline is nearing completion, transitioning to final testing and commissioning over the coming months. The foundation for the Aura Reservoir is set, with pipeline construction set to begin shortly.
Initiatives: In a partnership with The Compass Institute, a National Disability Insurance Scheme supplier and not-for-profit social enterprise, McConnell Dowell has built a project veggie garden and chicken coop entirely from donations made by subcontractors and team members. The team has not only provided a positive space for Compass Trainees to learn and contribute to the program but has also created opportunities for trainees to gain real-life work experience in meaningful positions. So far, the Compass Trainees have accumulated over 211 hours of training and project work hours and have just rolled out a vehicle maintenance program.
Contractor: Lendlease
Current value: $1.1 billion
Details: The Frankston Hospital redevelopment is being delivered by the Victorian Health Building Authority in partnership with Peninsula Health and the Exemplar Health consortium. The Exemplar Health consortium comprises Capella Capital as sponsor and investor, Aware Super as investor, Lendlease as builder and Honeywell and Compass Group Australia as facilities and maintenance managers. The redevelopment will deliver a new tower with 12 levels of clinical services and main entrance, 130 more beds, new spaces for mental health and oncology services and 15 new operating theatres. Additionally, it will deliver expanded women’s and children’s services including new maternity, obstetrics and paediatric wards, a women’s clinic and a special care nursery. An expansion of the emergency department will include a new mental health, alcohol and other drugs hub and a dedicated paediatric zone.
Status: The redevelopment is on track, with main works now past the halfway point and the project is expected to be completed in 2025.
Initiatives: The redevelopment will be a model of environmental sustainability and include an all-electric energy solution for the new tower, resulting in carbon-neutral power use from day one. Innovative energy-saving technology to preserve water, resources and energy will be incorporated. The mechanical system will deliver 100 per cent fresh air throughout the new tower building. In addition, electric vehicle charging stations and circadian rhythm lighting will feature as part of the redevelopment.
Contractor: BESIX Watpac
Details: The Gold Coast University Hospital’s Secure Mental Health Rehabilitation Unit (SMHRU) will be the first facility of its kind on the Gold Coast. Its 40 beds will be divided between two self-contained units on each level. The facility will be connected to the hospital by a semi-enclosed linkway, which will also connect the new unit to existing mental health facilities.
BESIX Watpac began early site works in February 2023 and completed the standard and special prototype bedrooms that serve as the blueprint for the 40-bed facility. The team recently celebrated a significant milestone with the project topping out. The final roof sheet was installed in March, marking a shift in construction as the team now focuses on fitting out the facility’s interior.
Initiatives: The project has been a collaborative effort involving input from clinicians, stakeholders and individuals with lived experience. It is being carefully constructed by BESIX Watpac to ensure the facility meets the specific needs of its future users.
Contractor: Built
Current value: $84 million
Details: The Translational Research Institute (TRI) Australia is constructing Australia’s first scale-up biomedical manufacturing facility for maturing, high-potential, med-tech and biotech start-ups. Built has been engaged to deliver both the early and main works. The main works involve the construction of a four-storey facility to house Good Manufacturing Practices (GMP) compliant cleanrooms, Physical Containment Level 2 laboratories, and co-working and innovation spaces. The facility will be adjacent to the newly formed University of Queensland Dutton Park Campus. With the new building adding 6,484 square metres of gross floor area to TRI’s existing 38,390 square metres, the combined facilities will create the largest end-to-end translational research hub of its kind in Australia.
Status: Main works are underway, with construction set for completion in late 2025 for an early 2026 opening.
Initiatives: To accommodate increased services and provide structural support for the new facility, the early works required extensive civil construction. The site has seen approximately 28,000 hours of early construction works by more than 1,300 people. During the excavation process, Built safely managed the removal and disposal of more than 8,500 cubic metres of contaminated waste and an additional 2,000 cubic metres of clean waste – equivalent to roughly three Olympic-sized swimming pools – before continuing with the main works. Furthermore, Built leveraged its digital approach, using virtual reality to lock in major design elements with end users, optimising project delivery and providing certainty before the main works commenced.
Suburban Connect (CPB Contractors, Acciona Construction
uburban Rail Loop (SRL) will deliver a 90km orbital rail line through Melbourne’s middle suburbs, linking every major train service from the Frankston Line to the Werribee Line via Melbourne Airport. The $3.6 billion SRL East Tunnels South contract – 16km of tunnels between Cheltenham and Glen Waverley, 55 cross passages, two portal structures, and two station box excavations – was awarded in December 2023 to Suburban Connect, a global consortium of companies CPB Contractors, Ghella and Acciona Construction. onstruction works have started with site establishment, borehole and site investigation works and procurement underway. Major works are
uburban Connect will now use four tunnel boring machines instead of the six initially proposed. This will reduce the impact and extent of tunnelling operations on the local community and deliver a more efficient tunnelling program. A ‘ground freezing’ technique will also be used to build safety passages between the twin tunnels, allowing passages to be constructed below ground instead of from the surface – significantly reducing disruption to residents and local road traffic. SRL will not only transform Melbourne’s public transport network, but it will also bring thousands more homes, jobs and services, with proposed planning changes to help deliver 70,000 more homes and 230,000 more jobs to the areas around the six new SRL East stations.
Contractor: Laing O’Rourke
Current value: $500,000
Details: The Suburban Rail Loop Initial Works and Early Works Managing Contractor contract was awarded to Laing O’Rourke in March 2022. The scope of works comprises utility relocations and preparatory works across seven locations, including six future station sites in Cheltenham, Clayton, Monash, Glen Waverley, Burwood and Box Hill, as well as a Stabling Facility in Heatherton. These works will pave the way for future packages of works, including tunnelling and stations.
Status: Works are underway across all seven locations. The tram
Contractor: Mirvac
Details: Mirvac will deliver a mixed-used precinct including a new-era workplace at 7 Spencer Street, LIV Aston’s 474 build-to-rent apartments (set to launch in mid-2024), and quality retail, all in Melbourne’s emerging new Northbank precinct on the Yarra River. Northbank will create a vibrant hub that brings great businesses and workforces together, where retailers will thrive and residents will have the opportunity to live in a new mixed-use quarter closely connected to transport and other amenities.
Status: Due for completion in late 2025, 7 Spencer Street is in the early stages of construction. Mirvac and capital partner Daibiru are set to deliver 21 levels and approximately 46,000 square metres of state-of-the-art office space, featuring extensive outdoor terraces.
Initiatives: The building will be fully electrified and aims to meet ambitious sustainability targets, including 5 Star Green Star ratings. Fronting the Yarra River and waterfront parkland, the 7 Spencer Street development will also target a 4.5 Star NABERS Water rating, a 5.5 Star NABERS Energy rating and a Gold WELL Core and Shell rating. Primely located on the corner of Flinders Street, in close proximity to Southern Cross Station and the tram line interchange, the combined project is delivering over 550 new construction jobs.
Through a strategic adoption of Revizto software, ADCO Constructions is enhancing project outcomes across its national portfolio, delivering added value to clients and optimising internal operations.
“When faced with complex construction methodologies or sequences, Revizto proves to be an invaluable tool.”
With an illustrious portfolio boasting nearly 4,000 completed buildings, ADCO Constructions (ADCO) is recognised for its adaptability, dedication to continuous improvement and unwavering commitment to delivering excellence. Building on this legacy and embracing innovation, the company has implemented Revizto across its operations to enhance project outcomes.
Revizto, a building information modelling (BIM) collaboration software, utilises gaming technology and cloud solutions to provide a unified platform for 3D and 2D workflows, connecting contributors across platforms, model types and teams. It enables seamless communication among all project stakeholders, facilitating real-time coordination, automated clash detection and issue tracking throughout a project’s lifecycle.
ADCO began implementing Revizto several years ago on projects valued between $20 million and $60 million. The positive outcomes of this initial phase paved the way for its integration into larger projects, such as the Griffith Base Hospital Redevelopment – a $250 million endeavour situated in the Murrumbidgee region of New South Wales. Subsequently, as part of its digital engineering strategy emerging from the ADCO Leaders Program, the company secured an unlimited agreement with Revizto, enabling the technology’s implementation across all ADCO projects.
Elizabeth Creswell, state design manager for New South Wales at ADCO, reflects on the company’s digital engineering journey. She recalls that two years ago, ADCO set an ambitious goal of leading the industry in the digital engineering space, resulting in the Revizto rollout.
“As part of our digital engineering strategy developed in 2022, we evaluated the various software packages and digital engineering platforms that we were using, ultimately recognising Revizto as the optimal solution with the capacity to fulfill all our requirements,” says Creswell. “While digital engineering and modelling have long been integral to our projects, we were aware that a nationally standardised approach would improve consistency and efficiency.”
“Introducing Revizto has transformed this landscape, enabling us to uniformly train and
upskill our teams on a cutting-edge platform.
“Having this unified, robust tool in place empowers our staff, consultants and subcontractors to utilise a standardised platform, enhancing collaboration and coordination at all levels of our projects.”
Creswell highlights several reasons why Revizto stood out as the premier technology partner for ADCO, with the simplicity and ease of use of the technology being a major factor. Revizto empowers every member of the ADCO team, from site managers with varying levels of digital proficiency to BIM experts, by providing a user-friendly interface that allows them to seamlessly harness its capabilities.
“Establishing a standardised enterprise agreement with Revizto has also enabled us to extend platform access to all our consultants and trade partners,” she says.
“From the beginning of a project, they are trained to use Revizto across their respective scopes of work.
“We provide them with software licenses and training and consequently, with each
project engagement, they acquire additional skills and knowledge – it’s not only upskilling our people but also the broader market.”
Furthermore, the versatility of Revizto across various devices enhances its utility. Revizto effortlessly accommodates the needs of ADCO’s site, project and design managers, whether they are in the office on a desktop computer or onsite with a tablet, underscoring its adaptability and accessibility.
Creswell notes, “The compatibility of Revizto also proved to be exceptional, facilitating the integration of models created in different platforms with relative ease.”
She also highlights its advanced functionality, which extends beyond basic usage. Revizto offers ADCO the opportunity to continually enhance its workflows over time with features such as advanced collaboration tools, clash detection capabilities and the potential for future integration with 4D, 5D and 6D applications.
Douglas Zuzic, ADCO’s chief information officer, echoes Creswell’s sentiments, also emphasising the effective implementation
and rollout process.
“Signing the unlimited agreement has resulted in approximately 20 projects now using Revizto, marking a significant increase in traction,” says Zuzic. “Our proficiency in using Revizto applications has also improved.”
“The effectiveness of the rollout process was not solely attributed to the software but also to the accompanying guidelines, policies and procedures.
“As previously mentioned, the ability to use Revizto on tablets onsite, with 700 tablets across our fleet nationally, adds substantial value.”
Zuzic says that over the past decade, ADCO has progressively shifted from 2D CAD drawings to 3D modelling; the transition to digital engineering and high-quality models was inevitable. While some project teams within the company had already embraced this shift both in design and onsite, consolidating these practices nationally has helped take operations to the next level.
“Given the evolving landscape of our industry, it’s now uncommon to encounter
Artist’s impression:
The Griffith Base Hospital Redevelopment is scheduled for completion in 2025.
a contractor on larger projects who isn’t utilising BIM models,” says Zuzic. “The key differentiator lies in how these technologies are rolled out and leveraged, aspects we are continuously refining.”
Guiding the initial implementation process was Ben Yee, design and BIM manager at ADCO. During this phase, ADCO began using Revizto on the Griffith Base Hospital Redevelopment, which is scheduled for completion in 2025. ADCO is the appointed principal contractor for the new purpose-built three-storey Clinical Services Building at the Griffith Base Hospital, which, once complete, will house all major health services under one roof.
“Revizto has proven instrumental in the successful delivery of this critical health infrastructure project,” says Yee. “With Revizto accessible on tablets, along with having access to all stamps or clashes, we can promptly identify and address any issues onsite.”
“One notable instance of the platform’s capabilities occurred during the construction phase, where Revizto’s clash detection feature detected a potential clash between a metal stud and a mechanical duct.
“By catching this discrepancy early, our project team avoided potentially costly and time-consuming rework.
“We have resolved thousands of such clashes using the model over the course of the Griffith Base Hospital Redevelopment.”
Reflecting on the evolution of ADCO’s
digital capabilities, Yee adds, “It’s remarkable how far we’ve come, from our trade partners and clients lacking access to models to now having access, to being able to swiftly and accurately validate the placement of structural and services elements.”
Creswell adds that ADCO can integrate various add-ons into Revizto for its clients.
For the Griffith Base Hospital Redevelopment, the project team utilised virtual reality, enabling the client to explore the hospital spaces before they were built – an invaluable asset for stakeholders who may struggle with traditional drawings. This also offered significant advantages to the furniture, fixtures and equipment process, which is often challenging to manage with drawings. Another valuable aspect of the rollout, explains Creswell, was ADCO’s introspection into its practices. The company established baseline standards for digital engineering on every project, regardless of client requirements. While some clients demand sophisticated digital engineering, others may not have explicit needs in this regard.
“However, by setting our own standards, we ensure a consistent approach across all projects, maintaining a baseline process that guarantees efficiency and quality,” says Creswell.
With considerable success using the platform thus far, ADCO plans to further leverage Revizto to enhance its construction processes and outcomes. Given the software’s
user-f riendly interface, including features like clash detection, Revizto is poised to bolster ADCO’s internal capabilities.
“We are committed to continually enhancing the skillset of our teams and the broader market, both in terms of current Revizto functionality and its ongoing evolution with each new version,” says Creswell.
“Our focus will increasingly be on leveraging BIM for 4D visualisation, program alignment and refining our construction methodologies.
“When faced with complex construction methodologies or sequences, Revizto proves to be an invaluable tool.
“Therefore, we anticipate utilising our models more extensively in program development, integrating them with construction plans.
“Already, we have begun using our models for carbon measurement, aligning with the emerging mandates in New South Wales and across the country.”
From a strategic technology adoption perspective, Zuzic explains ADCO’s approach as twofold – identifying the technology’s
Revizto, he adds, exemplifies software that fulfills both these value propositions. Revizto has overall enhanced ADCO’s operations, improving efficiency, bolstering internal digital engineering capabilities and minimising reliance on external consultants. Revizto facilitates deeper client engagement, providing them with detailed insights into sequencing and methodologies that were previously unavailable.
For ADCO, Revizto is more than just a software addition – it delivers tangible benefits. Drawing reviews have improved, potential issues are spotted early, safety meetings are streamlined, and costly errors have been reduced.
Reflecting on the widespread success of Revizto’s adoption, Yee underscores its role in fostering collaborative work across all disciplines and levels. Its user-friendly interface ensures seamless integration and cooperation among teams, granting site and delivery teams direct access to BIM. This, in turn, has fostered accountability regarding
“With Revizto accessible on tablets, along with having access to all stamps or clashes, we can promptly identify and address any issues onsite.”
Hobson Engineering takes pride in its role as a trusted distributor of Nord-Lock nuts and washers, ensuring bolt security even in challenging construction environments.
Since 1982, Nord-Lock, a renowned global supplier of engineering and bolting technologies, has been safeguarding the integrity of mechanical systems in the construction industry. With a steadfast commitment to maintaining a world-class team globally, the company has forged a robust partnership with Hobson Engineering. Together, they supply Nord-Lock nuts and washers to the Australian market.
Jeff Jared, who has served as the general manager for Oceania at Nord-Lock Australia for six years, is tasked with bolstering Nord-Lock’s regional presence and providing support to local partners. He speaks highly of the collaboration with Hobson Engineering, stating, “Hobson Engineering’s extensive network connectivity, high attention to detail and commitment to showcasing premier products in its catalogue make it an ideal distributor of Nord-Lock products.”
“Hobson Engineering’s detail-oriented structure enables the efficient distribution of premier products like ours to the masses.”
At the forefront of Nord-Lock’s product line are its revolutionary washers. Meticulously designed with cutting-edge wedge-locking technology, they prevent bolt loosening even under the most rigorous conditions of vibration and dynamic loads.
In the construction industry particularly, this technology plays a pivotal role in ensuring the reliability of machinery and the construction of enduring structures characterised by exceptional durability and quality. Secure bolts are crucial for maintaining structural integrity, ensuring safety, preventing failures, complying with regulations, upholding construction quality standards, and extending the lifespan of buildings, infrastructure and equipment.
Jared often reflects on the many instances where he has encountered individuals whose $500,000 machines have been brought to a halt by the failure of a single bolt.
“Our product is engineered to prevent such occurrences,” he says. “Once a Nord-Lock washer is installed, the bolt is not going to come loose on its own.”
“The only plausible scenario for bolt loosening is human intervention – beyond that, our washers provide unyielding security against vibration or dynamic loads.”
Unlike traditional flat washers, Nord-Lock washers comprise two parts with serrated edges that grip the mating material. Its internal cam system boasts an angle exceeding the bolt thread pitch, requiring any force attempting to loosen the bolt to overcome cam resistance from the cams.
Furthermore, these washers undergo rigorous testing, enduring a minimum of 1,000 hours in the Neutral Salt Spray Test – an established method for verifying corrosion resistance according to ISO 9227 – ensuring optimal performance over time in harsh environments.
received full
“Hobson Engineering’s
detail-oriented structure enables the efficient distribution of premier products like ours to the masses.”
What truly distinguishes this product, however, is Nord-Lock’s lifetime warranty on the initial installation. Once the bolted joint is secured by a Nord-Lock washer, the company guarantees its integrity for the lifespan of that joint, until it is uninstalled. “For instance, if the joint is installed today and remains uninstalled for 10 years, we assure that the joint will remain secure throughout that period,” explains Jared. In addition to its durability and lifetime guarantee, Nord-Lock washers have recently received full endorsement with the CE marking certification. “Our entire range of washers is CE marking certified,” says Jared.
“However, the CE marking certification signifies much more than just suitability for construction.”
“It guarantees our manufacturing process, the quality of our product, and no other wedge-locking washer carries such a certification from a regulatory body like CE markings. Stringent checks and balances are ingrained in our manufacturing processes, ensuring the precision and reliability of every unit we produce.
“We leave no room for error, carefully reviewing each step from production to installation, so we can confidently uphold our
mechanical tensioners, Boltight hydraulic tensioners and Expander System pivot pins.
Jared underscores the indispensable role of the Expander System in construction projects, offering a direct alternative to pivot pins in various earthmoving machinery, such as diggers, excavators and cranes. Traditional pivot pins often suffer from lug wear due to clearance between the bore and the pins, which necessitates line boring repairs. In contrast, the Expander System is engineered to eradicate lug wear entirely.
“As soon as our pins are integrated into a pivot joint, the lug will remain intact for the lifespan of the machine,” explains Jared. “We’ve seen numerous success stories of our pins being utilised in earthmoving equipment across Western Australia, South Australia, Victoria, New South Wales and Queensland.”
Nord-Lock Superbolt mechanical tensioners, Boltight hydraulic tensioners, Expander System pivot pins and wedge-locking technology washers.
promise of durability and performance.”
The quality of Nord-Lock washers is further evidenced by their selection for key infrastructure and construction projects across Victoria, Western Australia and Queensland. Notably, with the 2032 Olympic and Paralympic Games on the horizon, Brisbane is undergoing extensive upgrades to its public transport system and sports venues. One company, awarded 12 contracts for infrastructure projects associated with the games, has exclusively specified Nord-Lock washers for all 12 ventures.
Beyond their acclaimed washers, Nord-Lock offers three additional product lines: Superbolt
For larger bolts crucial in the construction industry, Nord-Lock’s tensioners take centre stage. Jared points out that in most bolted applications, when tightening with a torque wrench, suppliers claim to achieve torque accuracy within 3 to 5 per cent, but this doesn’t necessarily align with preload specifications. Accurate preload is imperative in construction, as any deviation poses significant risks to joints assembled for critical projects.
“Accurate preload is crucial for construction projects, and our Superbolt tensioners ensure this accuracy,” he says.
As a trusted distributor of Nord-Lock products, Hobson Engineering continues to reinforce the foundation of construction projects across Australia with exceptional bolt security. Together, Nord-Lock’s innovative technologies and lifetime warranty, combined with Hobson Engineering’s dedication to delivering premier products and comprehensive expertise, raise the bar for structural reliability and durability in the industry.
“Once a Nord-Lock washer is installed, the bolt is not going to come loose on its own.”
Lightweight yet strong, light gauge steel structural framing made from TRUECORE® steel was the material of choice for this striking façade structure.
Situated in Prahran overlooking the Grattan Gardens, this multi-residential development boasts a skilfully raked façade, offering more than just architectural harmony with its surroundings.
By utilising light gauge steel (LGS) framing made from TRUECORE steel for the façade’s structure, the project team delivered the Viridi Apartments with great success.
Engineered precision
Peter Blythe, director of Dynamic Steel Frame, emphasises the meticulous fabrication of the façade frame made from TRUECORE steel. The frame was fabricated to fine tolerances to structurally support and accommodate the roof tiles, and a specialised flashing system that channels waterflows around the windows and down the façade.
Efficient construction
Alex Salom, contracts administrator at Cobild, highlights that the fully-engineered façade solution was prototyped and tested prior to prefabrication. The thorough detailing
Detailing completed during the design phase resulted in the smooth installation of the façade.
carried out during the design phase, along with the exact tolerances achievable with prefabrication, resulted in the smooth installation of the façade system onsite.
Lightweight yet strong
Blythe and Salom both emphasise the pivotal role of contractor collaboration in ensuring the structural integrity of the façade frame, essential for supporting the significant weights of roof tiles and the protruding windows on the building.
Project highlights
Situated amongst heritage cottages and cafés and across from Grattan Gardens, this striking multi-residential development blends artfully into its surroundings. The sloping façade, tiled in hues of green, gently pulls away from the street, allowing it to sensitively harmonise with the park around it. The windows that punctuate the façade’s design capture views of the surrounding environment and allow light to fill the internal spaces.
Viridi Apartments, Prahran
Fabricator
Dynamic Steel Frame
Façade engineer
Inhabit
Builder
Cobild
Architect
Plus Architecture
Developer
Little Projects
Façade installer
Bolt Blue Constructions
Principal steel product
13,000 lineal metres
LGS framing made from TRUECORE® steel
Photographer
Tom Roe Photography
Address
Grattan Street, Prahran, Victoria
The appointed builder, Cobild, not only delivered on the design intent of this façade but enhanced it with the clever selection of cladding material and the structure required to support it. The façade design originally called for the use of hot-rolled structural steel with a glass-fibre reinforced concrete skinned cladding (GRC). With the desire to improve the façade’s enduring visual appeal and serviceability, Cobild recommended that the façade structure was changed to that of a structurally engineered LGS frame, designed to support roof tiles as well as the distinctively large windows.
Varying in colour from deep forest greens to lighter turquoise, the skilful blending of the high gloss imported tiles delivers an intensity of colour that heightens the visual interest of the façade’s finish. However, the modularity and weight of the imported terracotta tiles, at 70kg per square metre, also added to the design complexity and demand on the façade structure underneath.
these flashings. Leaving nothing to chance, a prototype of the window details was designed, manufactured and tested prior to full-scale fabrication of the façade structure.
Post-tensioned concrete slabs were used at each level of the build, providing rigidity to the structure. Using over 800 brackets and 1,600 bolts, the LGS façade structure was then securely connected to these slabs using a method that allowed for slab deflections. The final façade structure was also designed so that the battens could be appropriately installed at defined intervals to support the roof tiles.
Salom says: “Significant effort was required at the design stage to ensure the prefabricated LGS frames were consistent with the architect’s vision, performed structurally and could be efficiently installed during construction.”
“We underestimated the design’s complexity at the start of the project, so it was pleasing to have such a successful outcome during construction.”
Lightweight yet strong, LGS structural framing made from TRUECORE steel was the material of choice for the façade structure. Utilising almost 13,000 lineal metres of TRUECORE steel, Bolt Blue Constructions and Dynamic Steel Frame collaborated with the façade engineers to deliver a façade frame with the structural adequacy to support the substantial weight of the roof tiles and the protruding windows (some up to 300kgs).
With the window reveals protruding above the face of the tiled façade, a specialised flashing system was required to ensure waterflows were channelled around the windows and down the façade. The LGS façade made from TRUECORE steel was fabricated to fine tolerances to both structurally support and appropriately accommodate
Given the uniqueness and complexity of the design, Dynamic Steel Frame spent many hours finalising the details of the fully-engineered LGS façade structure prior to its manufacture. This commitment, coupled with the exact tolerances achievable with LGS fabrication, resulted in the efficient installation of the façade structure onsite.
“Once familiar with the approach, the lightness and accuracy of LGS frames made for efficient installation,” explains Salom.
“Using installers that specialise in LGS framing installation was also beneficial.”
“We underestimated the design’s complexity at the start of the project, so it was pleasing to have such a successful outcome during construction,” adds Blythe. Blythe highlights the Viridi Apartments as a prime example of what structural framing made from TRUECORE steel can achieve with the right expertise.
“Once familiar with the approach, the lightness and accuracy of LGS frames made for efficient installation.”
Window details were designed and tested prior to full-scale fabrication.
Harnessing its global engineering prowess, McConnell Dowell is delivering Tasmania’s most ambitious transport infrastructure project to date.
Constructing large-scale, world-class infrastructure demands exceptional skill, meticulous planning and technical proficiency – challenges that McConnell Dowell boldly embraces. This constant focus is proving pivotal in the successful execution of Tasmania’s largest-ever transport infrastructure project, including the construction of one of Australia’s longest road bridges over water.
Jointly funded by the Australian and Tasmanian governments as part of the Hobart City Deal, the $786 million New Bridgewater Bridge project aims to bolster Tasmania’s national highway, enhance connectivity among local communities and bridge the gap between the Brooker Highway and Midland Highway. Central to the project is the construction of a 1.2-kilometre-long bridge over the River Derwent, set to replace the existing lift-span bridge constructed in the 1940s and the convict-built causeway from the mid-1830s. Designed as a dual two-lane thoroughfare, the new bridge will significantly slash travel times for 22,000 daily commuters while facilitating smoother freight movement around the state.
The project also involves the delivery of free-flowing interchanges at Granton and Bridgewater, with noise walls and seamless connections for cyclists and pedestrians.
According to Peter Fraser, project director for the New Bridgewater Bridge project at McConnell Dowell, its sheer scale and technical complexity distinguish it from previous projects in the state, elevating it to a world-class standard.
“We were awarded the contract by the Tasmanian Department of State Growth with an innovative design and construction methodology, together with our commitment to fostering local industry participation,” says Fraser. “We are fully dedicated to fulfilling that commitment.”
“With a project of this scale and location, maintaining a strong social license is essential for our successful and timely project completion.
“This aligns naturally with the values and objectives of McConnell Dowell and the continued support of both the community
and the state government who remain deeply invested in the project’s success.”
Fraser notes that community feedback thus far has been overwhelmingly positive, despite some inevitable traffic disruptions. McConnell Dowell remains steadfast in its efforts to minimise such disruptions, and despite occasional inconveniences, community conversations reflect an enthusiasm and interest for the project’s progress.
“Our focus remains on delivering the New Bridgewater Bridge project with efficiency and transparency and minimising community impact,” says Fraser.
“We’re on track with both schedule and budget, and our community engagement efforts are yielding promising results.”
Global expertise
The technical complexity of the New Bridgewater Bridge project is considerable, positioning it as a world-class endeavour.
This distinction is particularly noteworthy for Tasmania, where such large-scale projects are rarely undertaken, necessitating collaboration with both international and local stakeholders.
“Our primary aim has been to secure the right blend of local and international talent
for the team – this was our challenge, but one we’ve tackled head-on with great success,” says Fraser. “We have a good balance of impressive talent and experience from engaging local industries while supplementing with national and international expertise.”
To this end, McConnell Dowell has forged partnerships with international firms such as Tony Gee and Partners from Hong Kong, renowned for its bridge design expertise, and Jacobs, a leading engineering services company overseeing civil engineering and construction undertakings on the project.
“With a project of this scale and location, maintaining a strong social license is essential for our successful and timely project completion.”
The project team has enlisted the expertise of Tonkin and Taylor for geotechnical engineering activities. GHD and pitt&sherry, both with local Tasmanian offices, are providing independent verification and proof engineering services respectively.
“Our focus remains on delivering the New Bridgewater Bridge project with efficiency and transparency and minimising community impact.”
The meticulous planning and integration of construction, engineering and design are vital aspects of this project. The structure itself is 1.2 kilometres, comprising 21 spans of box girder construction. Complexity is compounded by the need for 46 extremely deep monopiles installed in environmentally sensitive marine areas, posing challenges for both construction and ecological preservation. Installing the piles, some reaching depths of up to 90 metres, requires specialised capabilities and technologies not widely available.
Fraser emphasises the importance of reliable access for bridge construction whilst minimising environmental impact. “We’ve invested significantly in providing minimally invasive access for people, material and
equipment whilst supporting a demanding construction schedule – relying on traditional floating plant was not the solution,” he says.
“Our approach has been to install a bespoke temporary bridge across the river channel with purpose-built barges, manufactured in Indonesia, sitting on the shallow mud to form a continuous fixed link.
“This approach ensures crucial construction access and minimises our impact upon important local flora and fauna in the environmentally sensitive mudflats and seagrass beds.
“Each relationship we have – Tasmanian, national and international – with individuals and organisations is critical to the successful delivery of this project.”
A pivotal partnership exemplifying this synergy is with international bridge specialists VSL, which is McConnell Dowell’s main construction partner for the New Bridgewater Bridge project.
Together, they’ve established a purpose-built precast concrete production facility producing
over 1,000 segments for the bridge’s box girders and commissioned bespoke erection equipment. A fully integrated team of VSL and McConnell Dowell personnel is managing both production and segment erection. Fraser emphasises, “Having VSL involved from the project’s inception working through fundamental methodologies was crucial; their absence would have rendered the task immensely challenging, if not insurmountable.”
McConnell Dowell has also maintained close collaboration with Tasmanian environmental authorities to ensure full alignment with project operations and environmental management.
“I believe we’ve truly pioneered a new approach in our collaboration with government agencies,” says Fraser. “We see them as partners, integral members of our team.”
In conjunction with these agencies, McConnell Dowell is proactively ensuring the protection of all environmental aspects during construction. This pragmatic problem-solving approach, which includes sophisticated modelling and monitoring, coupled with close collaboration with government agencies, establishes a precedent for future projects.
Within Tasmania, McConnell Dowell has collaborated with various local contractors, including Batchelor, BridgePro and Hazell Bros.
Hazell Bros, for instance, is designing and reliably supplying complex concrete mixes tailored to the project’s demanding specifications, leveraging its regional proficiency and direct access to local quarries. BridgePro has worked closely with McConnell Dowell since the development of its tender to develop innovative solutions, including those for temporary bridge installation and the erection of the 42 in-situ concrete piers.
Local participation is reflected in the average $12 million per month the project is spending with local industry, with over 350 of the project’s suppliers based in Tasmania. Ed McPhillips, construction manager for the New Bridgewater Bridge project at McConnell Dowell, emphasises that the
benefits extend beyond the local supply chain. In addition to supporting local businesses, McConnell Dowell is actively contributing to the region’s economy through a robust training and employment initiative.
“Currently, around 350 individuals are engaged on the project, with a significant portion recruited from the local workforce,” says McPhillips.
“For instance, within the precast yard, there are approximately 120 local employees. “What’s particularly advantageous about such a manufacturing facility is its ability to accommodate workers with varying skill levels.
“We’ve successfully integrated individuals new to the industry with seasoned professionals, resulting in many of them now excelling in their roles and well-equipped with the necessary skills to tackle future construction projects in Tasmania.”
A landmark achievement
Building upon the expertise and achievements being rolled out for the New Bridgewater Bridge project, McConnell Dowell is focussed on developing value-for-money solutions for upcoming large-scale projects in Tasmania, where it can enhance and support local capability with an established delivery team and expertise.
According to McPhillips, the projects to be developed in Tasmania present significant technical challenges and opportunities for collaboration, particularly in hydro and water infrastructure.
“Fortunately, we’ve assembled a strong team for this project, providing extensive upskilling and training, and we aim to transition them to these upcoming projects in the state,” he says. “Major infrastructure projects often share similar hurdles, and our experienced teams, alongside our local and international partners, are well-equipped to tackle them.”
The New Bridgewater Bridge project showcases McConnell Dowell’s prowess in executing large-scale construction endeavours, leveraging its world-class engineering expertise and experience, while also fostering local talent and capabilities. As the company continues to expand its presence in Tasmania, the local economy is poised to reap the rewards.
With an unparalleled selection of products, expertise and branches nationwide, Motion Australia is living out its promise to provide industrial businesses with ‘more choices and more solutions’.
Employing over 1,600 people across more than 200 branch locations and 12 distribution centres in the Asia Pacific, Motion Australia (Motion) supplies everything needed for construction machinery repair; from transmissions, electric motors, gearboxes and bearings to industrial hoses, seals and Fluid Power Solutions, to name just a few.
Having grown from a father-son partnership begun in 1955, Motion has been the industrial division of the General Parts Company since 2019, which also owns automotive companies Repco and the National Automotive Parts Association (NAPA).
“Anything that is moving in any way, shape or form, we’ve got components and services that build into that,” says Stephen Forbes, executive general manager of Fluid Power Solutions at Motion.
Jeff Mrak, marketing manager for lead generation and market research at Motion, discusses the company’s pivotal role in the construction industry. “Motion delivers industry leading solutions, tailored to keep you moving,” says Mrak.
“This is a major contribution that we perform for hundreds of customers within the
Motion’s strategy includes collaborating with global original equipment manufacturers (OEMs) to maximise productivity for Australian construction and infrastructure projects. Mrak adds, “We offer further localised solutions for key repairers, contractors and hire companies in both the construction and civil earthmoving segments, ranging from large global operations to local small business owners needing partnering support in delivering larger projects.”
Motion is currently transitioning to become the parent company of multiple heritage brands. Having these heritage brands allows Motion to access a variety of different parts, offering customers a wider range of solutions. Forbes says that by moving towards rebranding its collection of heritage brands, customers will better recognise the overarching name – Motion.
“Motion as a brand is fairly new to Australia; it has been very long standing in the US and Canada but less so in Australia,” he says.
Some examples of Motion’s heritage brands include driveshaft manufacturer
“Anything that is moving in any way, shape or form, we’ve got components and services that build into that.”
business Seal Innovations, and hydraulic and industrial hose business Powell.
“Each business within the Motion family comes with its own specialty,” says Ryan Kendrigan, executive general manager of Engineering and Services at Motion. “What’s advantageous is that with all of these businesses and their specialties consolidated, our customers have an incomparable breadth of offer.”
Cram, another heritage brand within Motion Australia, specifically caters to the construction market. It provides hydraulic services for both fixed and mobile plant and offers sales and servicing of final drives and other track-related equipment critical for construction projects.
A key focus of this transition for the future is providing customers with the expertise for niche products that they may have difficulty finding elsewhere. The company recognises that everyone has different priorities and works in different environments. Additionally, customers have varying needs regarding what they aim to achieve using a machine.
This is where Motion provides unmatched expertise for its customers.
“We have a team of approximately 70 dedicated engineers that can actually go out and work with a customer on their site,” says Forbes. “There are experts in many different business lines.”
“If you need a particular gasket for a slurry pump, we have guys that are experts in gasketing. We have absolute experts on a global scale from a driveshaft perspective; the same goes with hoses.
“These are just some of the examples of our business lines that we have experts in.”
Motion can also design products to meet specific needs and provide customers with value-added solutions. “This could be as simple as someone needs a hose, so we make a hose assembly for them,” says Forbes.
Kendrigan gives the example of a customer needing a custom-built acid tank but facing a key constraint: the available space in their facility was very limited. Motion came up with a solution where the tank was half-built in its workshop, then lowered into place through the facility roof, before building the top part of the tank in-situ.
“Each business within the Motion family comes with its own specialty.”
“Once upon a time this would have required six or seven different companies to make that happen,” says Kendrigan. “Instead, we created the process, and saw the solution executed from concept to delivery – ensuring it was working effectively afterwards.”
Adding to this, Mrak highlights the real-world impact of Motion’s expertise on other significant projects.
“Motion delivers industry leading solutions, tailored to keep you moving.”
“We are engaged on a multitude of major projects which are underway in our region,” says Mrak.
“We are currently working on some of the largest generational power infrastructure project requirements nationally.
“Additionally, we continue to work closely with customers in delivering mining infrastructure projects with solid activity in Western Australia and Queensland.”
Having such a broad range of expertise means that the Motion Engineering and Services team can come up with a process for a wide range of challenging situations.
“It’s being able to offer that turnkey solution,” says Kendrigan “We can design a concept, manufacture a concept, install it, and maintain it. It’s a full-service offering.”
To make it even easier for Motion’s experts to find the best solutions to a problem, it operates a fleet of mobile service vans for customers experiencing an equipment breakdown.
“These vans can go out and service equipment on the customers’ site,” says Forbes. “For example, if you’re in a breakdown situation, you can call and a service van will come out and repair a hose for you.”
If a customer is having a machine refurbished and knows it won’t be used for a period of time, the service vans can also come out on a scheduled basis.
“Alternatively, we can set up a workshop on site and train people to actually make their own pieces of equipment such as hoses,” says Forbes.
AGRICULTURE FARMING EDUCATION WASTE
MANAGEMENT RESOURCE MANAGEMENT
CONSERVATION MANUFACTURING RESOURCES
ENERGY HEALTH & SAFETY INFRASTRUCTURE
ENGINEERING MINING CONSTRUCTION
QUARRYING AGRICULTURE FARMING EDUCATION
WASTE MANAGEMENT RESOURCE MANAGEMENT
CONSERVATION MANUFACTURING RESOURCES
ENERGY HEALTH & SAFETY INFRASTRUCTURE
ENGINEERING MINING CONSTRUCTION
QUARRYING AGRICULTURE FARMING EDUCATION
WASTE MANAGEMENT RESOURCE MANAGEMENT
CONSERVATION MANUFACTURING RESOURCES
ENERGY HEALTH & SAFETY INFRASTRUCTURE
ENGINEERING MINING CONSTRUCTION
QUARRYING AGRICULTURE FARMING EDUCATION
WASTE MANAGEMENT RESOURCE MANAGEMENT
SEARCH FOR TOP INDUSTRY TALENT THROUGH OUR JOBS BOARD.
CONNECT WITH ALIGNED CANDIDATES.
BOOST YOUR CHANCES OF FINDING SKILLED APPLICANTS.
SCAN TO CREATE AN ACCOUNT TODAY AND DISCOVER YOUR PERFECT MATCH!
Committed to the safety and wellbeing of construction workers, Blackwoods offers personalised guidance for selecting the right personal protective equipment tailored to individual job roles and working conditions.
Safe Work Australia emphasises the necessity for businesses to adhere to work health and safety standards regarding PPE, requiring the selection of PPE that fits properly, is comfortable, and is compatible with other protective gear.
Recognised across the construction industry, personal protective equipment (PPE) serves as the final line of defence against workplace hazards, especially pertinent within the demanding conditions of construction projects and Australia’s diverse climate. The critical importance of selecting the appropriate PPE for both task and environment cannot be overstated. That’s why Blackwoods’ exclusive brand, Workhorse, has introduced its new Stretch Range of workwear.
Excessive heat can lead to a worker’s core temperature reaching dangerous levels, potentially resulting in organ failure or even death. Given the demanding, labour-intensive nature of construction work, compounded by Australia’s hot climate, construction workers face a heightened susceptibility to heat stress. Utilising breathable fabrics like cotton can serve as a valuable measure to alleviate this risk.
While in Europe, PPE apparel often utilises man-made fabrics for their ability to maintain fluorescent high-visibility properties, Australia’s harsh climate presents unique challenges. In such conditions, man-made fabrics can be uncomfortable and exacerbate heat for workers.
Safe Work Australia emphasises the necessity for businesses to adhere to work health and safety (WHS) standards regarding PPE, requiring the selection of PPE that fits properly, is comfortable, and is compatible with other protective gear.
In light of this, Blackwoods highlights the advantages of high-visibility apparel chiefly made from cotton or natural fibres, despite the potential for faster fading over time. The benefits of enhanced worker comfort and the resultant boost in productivity outweigh the cost of more frequent replacements.
In fact, Australia is the only country in the world that has specifications for high-v isibility cotton workwear.
Maintaining the balance between comfort and safety becomes even more crucial when considering the threat of heat stress.
In Australia, balancing safety and comfort is imperative to ensure workers are adequately protected and comfortable. Experience has shown that workers are more inclined to use PPE correctly if it does not impede their movement or cause overheating.
The new Stretch Range of workwear from Blackwoods’ exclusive brand, Workhorse, takes all these factors into consideration. This range, made from 98 per cent natural cotton and two per cent elastane, is specifically designed with the Australian climate in mind. It features underarm and upper back cooling vents and a sun collar extension to maximise worker comfort.
Additionally, the ergonomic fit and elasticated waistband address the practical needs of construction workers, supporting a full range of motion essential for tasks involving bending, lifting and sustained physical activity.
Blackwoods’ commitment to supplying innovative PPE ensures that its products are not only compliant with safety standards but also enhance the overall work experience, contributing to higher compliance rates and a safer, more productive construction workforce in Australia.
MEGATRANS 2024 promises to unveil the latest breakthroughs in logistics, offering a path towards a resilient and sustainable future for the construction industry’s supply chain.
Event MEGATRANS 2024
Date
18-19 September 2024
Venue
Melbourne Convention and Exhibition Centre
Registrations
Registrations for MEGATRANS are free.
To attend, visit www.megatrans.com.au
This September, industry leaders from across the supply chain will converge in Melbourne for MEGATRANS 2024, to deliberate on the future of the logistics landscape.
As Australia’s largest integrated conference and exhibition dedicated to the logistics industry, MEGATRANS brings together companies offering advanced technologies and services, categorised by their contributions to the sustainable supply chain.
Since the peak of the COVID-19 pandemic, the construction sector has grappled with supply chain disruptions and material shortages, which have been exacerbated by global economic strains. Against this backdrop, the timing of MEGATRANS 2024 couldn’t be more opportune.
The pivotal role of transport visibility providers and consultants in streamlining the logistical flow of construction materials has been indispensable for maintaining the industry’s momentum during these trying times. The construction industry relies on the logistics sector to successfully coordinate materials and equipment, ensuring that projects are completed on time and on budget. Without effective logistics, construction projects can face delays, increased costs and disruptions in workflow.
Among the forward-thinking exhibitors at MEGATRANS 2024 is CEVA Logistics (CEVA), a company committed to championing
sustainable supply chains. Guy Meredith, CEVA’s managing director in Australia and New Zealand, highlights the company’s role in advancing sustainability initiatives that contribute to the broader economic landscape.
“As a global leader in third-party logistics, CEVA is committed to more sustainable logistics solutions, helping pave the way for low-carbon solutions and encouraging the shift toward more sustainable supply chains,” says Meredith. “We are conscious of our responsibility to shape the supply chain of the future in a responsible, ethical and sustainable way in line with Australia’s best interests for the people and natural environment.”
CEVA Logistics in Australia offers a full spectrum of logistics services, supporting infrastructure projects and engineering procurement and construction projects to ensure smooth and efficient operations from start to finish.
Meredith underscores the inherent risks, substantial investments and complexity associated with construction logistics.
“We are able to combine construction logistics with risk analysis and solution design to achieve high standards of operational excellence, ensuring customers’ quality, health, safety, security and environment (QHSSE) and compliance requirements are met,” he says. “For example, CEVA manages the logistics required by an original
equipment manufacturer to supply materials for the construction of a large grid-scale battery at the Eraring Power Station.
“We’re proud to support this important energy transition project in New South Wales, Australia.”
Sustainability initiatives implemented by the logistics industry play a crucial role in helping construction customers reduce their Scope 3 emissions. As a freight forwarder, CEVA has relatively few assets and works with multiple suppliers to transport its customers’ goods by sea, air, road and rail. As contract logistics experts, the company operates warehouses, most of which are leased. CEVA is responsible for decarbonising its own assets, as well as encouraging its suppliers and subcontractors to invest in the technologies of tomorrow.
“In terms of materials storage for construction customers, CEVA has nearly 40 warehouses across Australia,” says Meredith.
“All our new sites are rated 5-star Greenstar ratings, installed with LED lights, solar power systems, rainwater harvest systems and charging stations for electric vehicles.
“Our operations are closely monitoring and tracking our recycling performance, working
towards the goal of net-zero waste to landfill. For the delivery logistics of heavy machinery and building materials, CEVA’s sustainable procurement charter and low-carbon solutions help reduce harmful emissions.
“For ground, ocean and air transport, CEVA offers carbon visibility and carbon optimisation options, and in some cases, alternative energy and carbon offset solutions.”
Additionally, CEVA is investing in innovative design solutions aimed at optimising operational performance for its ground fleet. These solutions include intelligent routing, quantity forecasting, optimising truck space and reducing the number of deliveries. Moreover, information providing carbon visibility is available to customers through CEVA’s digital platform, myCEVA.
CEVA is a prime example of the sustainable excellence that will take centre stage at this year’s event. Showcasing cutting-edge technology, initiatives and services, MEGATRANS 2024, to be held on 18 and 19 September at the Melbourne Convention and Exhibition Centre, is poised to pave the way for a sustainable supply chain for Australia’s construction industry and beyond.
“As a global leader in third-party logistics, CEVA is committed to more sustainable logistics solutions, helping pave the way for low carbon solutions and encouraging the shift toward more sustainable supply chains.”
The countdown has begun for the eagerly anticipated return of the Australian Bulk Handling Expo in 2024.
This year, the Australian Bulk Handling Expo (BULK2024) promises to be more vibrant than ever, offering a vital platform for professionals connected to the bulk solids handling and construction sectors. Attendees will witness the industry’s evolution firsthand as BULK2024 sets the stage for a ground-breaking showcase of innovative technological solutions.
Australia’s economy thrives on the back of the bulk solids handling industry, which plays a pivotal role in facilitating the movement of crucial commodities. Recognising its significance in maintaining global security and economic stability, the Australian Bulk Handling Expo (BULK2024) is poised to make its return this September.
With a mission to present forward-thinking solutions – and with a major focus on technology and automation – BULK2024 aims to fortify the industry’s resilience and ensure a sustainable future. From advancements in conveyor systems to pioneering developments in crane technology, attendees can expect to be immersed in a world of innovation and progress.
The symbiotic relationship between the bulk handling and construction industries underscores the critical importance of events like BULK2024.
The bulk handling industry forms a crucial support for the construction sector by ensuring the efficient, cost-effective and timely movement of materials and equipment essential for building structures and infrastructure.
Advancements in bulk handling technology can lead to cost savings for construction companies, by optimising material and equipment handling processes, reducing labour requirements and minimising waste, therefore lowering overall project costs. Further, advancements in bulk handling technologies, such as conveyor systems, automated material handling equipment and innovative storage solutions, improve the efficiency of material movement on construction sites.
Grydale is one of this year’s exhibitors eager to spotlight its inventive solutions for the bulk handling and construction sectors, demonstrating how its dust control solutions can not only help mitigate health, safety and environmental risks but also provide operational efficiencies and valuable by-products.
Lisa Andrews, business development manager at Grydale, expresses satisfaction with the company’s participation in the 2022 Australian Bulk Handling Expo, highlighting
Event
Australian Bulk Handling Expo 2024
Date
18-19 September 2024
Venue
Melbourne Convention and Exhibition Centre
Registrations
Available via the Australian Bulk Handling Expo website
the positive impression of both the quantity and calibre of delegates in attendance.
“Following the success of last year’s expo, we are eager to participate in and support BULK2024,” says Andrews. “We aim to showcase the latest advancements in dust control technology and share recent case studies in mining, quarrying and bulk material handling applications.”
With the increase in dust control regulations in construction and bulk handling, Grydale is committed to providing both industries with effective solutions to achieve compliance.
Andrews emphasises that prioritising health, safety and environmental risk mitigation remains paramount for both the bulk handling and construction markets. Technological advancements are enabling the advanced monitoring, control and mitigation of these risks.
“Environmental, social and governance standards require companies to ensure they are working towards sustainable and energy efficient solutions,” says Andrews.
“As a manufacturer, we are committed to innovation, research and development to ensure our dust control and ventilation solutions can also support these key agendas and enable companies to report on the positive measures they are undertaking.”
“We encourage BULK2024 attendees from both the construction and bulk handling industries to speak with our experienced teams.
“We aim to showcase the latest advancements in dust control technology and share recent case studies in mining, quarrying and bulk material handling applications.”
“As a company, Grydale is committed to innovation and continuing to invest in research and development to provide transformational technology, empowering the construction industry to protect the health and safety of workers and the environment, while remaining operationally competitive,” says Andrews.
“Our in-house engineering teams are working with clients to provide the right temporary and permanent dust control solutions, while our aftermarket service teams are supporting the ongoing efficiency of our solutions.”
“Drop by our stand to learn how Grydale can deliver tailored dust control solutions, effectively mitigating risks while optimising operational efficiencies for your company.”
As professionals from across sectors converge to explore the latest advancements and exchange ideas, BULK2024 promises to be a transformative event – one that sets the stage for a brighter, more resilient future for bulk handling and construction alike.
Registrations for BULK are free. To attend, visit www.bulkhandlingexpo.com.au
•
•
•
Candace Garraway’s love for drawing ignited almost as soon as she could grasp a pencil. Today, as a project architect at EJE Architecture, she channels that passion into bringing buildings and spaces to life.
For Candace Garraway, the desire to pursue architecture has been a lifelong calling.
From her earliest memories, she found herself captivated by the art of drawing buildings, often sketching out the structures of friends’ and relatives’ homes without yet understanding the concept of architecture.
Encountering someone with such unwavering certainty in their chosen path from childhood is rare. But for Garraway, architecture isn’t just a career – it’s a natural and perfect fit.
“I’ve always had a love for hand drawing, and I’m fascinated by the stories that buildings tell, reflecting the lives of those using them,” says Garraway. “After finishing high school, I tried to gain work experience at architecture firms in Dubbo, my hometown, but encountered difficulties as they were looking for candidates with prior experience and were hesitant to take on a recently graduated high school student.”
“So, I enrolled at the University of Newcastle, where I completed a Bachelor of Design (Architecture) degree.”
Following her undergraduate studies and a gap year spent travelling the world, Garraway furthered her education, earning a Master of Architecture degree. Alongside her academic pursuits, she worked with a not‑for profit organisation closely aligned with the architectural field, overseeing impactful projects such as the renovation of a women’s shelter. Then, with two degrees in hand, Garraway joined EJE Architecture – marking her first professional role at an architecture firm.
“Since joining EJE Architecture in 2018, it’s been a fantastic experience,” says Garraway.
motel project in regional New South Wales. The client sought to expand and diversify their business by acquiring land adjacent to its existing RSL and constructing a motel.
As part of her role, Garraway drew up designs for the motel, navigating through the challenges presented by the narrow site, along with acoustic and heritage concerns, and gained council approval for the development. After receiving approval, her team’s collaboration with consultants – in fields such as electrical, mechanical, structural and energy efficiency – ensured precise planning for construction.
“Subsequently, we initiated the tender process, engaging with multiple builders before final selection,” she says. “Throughout construction, our role involved diligent contract administration, including onsite verification of completed works against builder claims.”
“It was a really informative and rewarding project as it allowed my hands on involvement from conception to execution.”
“I’ve always had a love for hand drawing, and I’m fascinated by the stories that buildings tell, reflecting the lives of those using them.”
“I feel very fortunate that my team allows me to work on projects from start to finish.”
“Unlike some roles in architecture where you might only contribute to initial concepts, here I have the privilege of witnessing the entire process unfold.
“Seeing a design transform from a drawing to a tangible structure, utilised by people, is incredibly gratifying.”
In the years that followed, Garraway immersed herself in her work, primarily overseeing renovation projects. However, she’s also had the opportunity to engage in ground up construction projects, such as a
With a wealth of experience and a portfolio of diverse projects under her belt, Garraway obtained registration as an architect in 2022. Despite holding a master’s degree in the field, graduates can’t legally use the title ‘architect’ due to its protected status. Similar to lawyers having to pass the bar exam in the US, Garraway was required to compile a comprehensive logbook showcasing a minimum of 3,300 hours of varied architectural work, demonstrating proficiency across all design stages from inception to construction services. Following the logbook submission, she undertook a written exam and then an examination by interview. Only after successfully completing all three stages of the Architectural Practice Examination and obtaining registration with the NSW Architects Registration Board could she officially call herself a registered architect.
“It is a process,” says Garraway. “Also, once you are registered, you have to keep up your continuing professional development hours every year and report this to the board.”
“This ensures architects remain current with industry advancements and best practices and uphold a standard of competence and professionalism in all client interactions.”
Garraway emphasises that this stringent
process serves to protect consumers. For instance, if a client presents a $2 million budget for a project and she proposes a design costing $5 million, there could be repercussions. Registration ensures architects are accountable, safeguarding the interests of those who engage their services.
As a registered architect, Garraway continues to demonstrate excellence in her field. Presently, she is immersed in a project involving the expansion of a gym at a club in the Central Coast region of NSW. In NSW, clubs, functioning as not for profits, often oversee additional amenities like childcare centres, motels or gyms, in addition to their primary club premises. Consequently, Garraway frequently finds herself engaged in enhancing these ancillary facilities alongside the clubs themselves.
Regarding her current projects, Garraway elaborates, “I’m also involved in the renovation of an RSL in the mid north coast of NSW, and we’re delving into the development of clubhouses at manufactured home estates.”
“These estates typically cater to individuals aged 55 and above, offering communal amenities such as kitchens, games rooms and swimming pools.
“There’s a psychology phenomenon called the ‘third place’, defined as a place other than your home or workplace that you feel comfortable being in.
“These projects epitomise this concept, as they generally involve a place you can go, that isn’t your home or work, where you feel at ease.”
Garraway is particularly passionate about people centric architecture, creating spaces where life’s moments can unfold. She aspires to continue her work on projects that offer this vital ‘third place’ experience to people. In addition to her academic accomplishments and her contributions within EJE Architecture, Garraway is an active member of the Property Council of Australia’s Hunter Future Directions Committee. This committee, for aspiring leaders under 35 in the property industry, facilitates networking events and professional growth opportunities, a role Garraway finds highly fulfilling. Reflecting on her involvement, she says, “I perceive
the architecture industry as somewhat insular. Through the committee’s events, I have the opportunity to establish deeper professional connections with consultants on a personal level, extending beyond our routine work interactions.”
Garraway emphasises the significance of embracing diverse viewpoints within the industry, a principle she upholds through her participation in the committee.
“I strongly advocate for gaining insights from various perspectives – by comprehending each other’s viewpoints, we can pursue our collective objectives with enhanced effectiveness and collaboration.”
So, what lies ahead for Garraway? She aspires to continue championing people‑centric architecture, particularly in regional areas. Additionally, she has set her sights on assuming a leadership role within EJE Architecture and one day managing her own team. Given her lifelong dedication to the field of architecture, there’s little doubt that Garraway will realise these aspirations.
“Seeing a design transform from a drawing to a tangible structure, utilised by people, is incredibly gratifying.”
Instilled with a resolute “never say no” ethos, Kayla Shadbolt has been instrumental in driving success at Swan Hill Hire, while also leaving a lasting impact on the hire and rental sector at large.
“The opportunities in the hire industry are boundless, much like construction.”
When Kayla Shadbolt started in the hire and rental sector in 2019, she brought with her no prior industry experience. Beginning her career journey at the age of 16, she initially embarked on a full-time career as an apprentice mechanic at a local workshop in Swan Hill, Victoria. Finding success in this field, she transitioned to a local dealership, completed her apprenticeship and climbed the ranks.
However, after eight years in the automotive industry, Shadbolt found she and the industry were evolving in different directions. Feeling a misalignment between dealership culture and her values as she entered her mid-twenties, she sought a new horizon and embraced the then unfamiliar territory of the hire and rental industry –joining Swan Hill Hire.
“When I started in the hire and rental industry in early 2019, I did so with little to no prior insight into its inner workings,” says Shadbolt. “Initially, like many, I simplistically viewed it as a matter of renting out equipment and having it returned.”
“While not entirely wrong, this perspective barely scratches the surface of the industry’s multifaceted nature.
“What I didn’t realise at the time was the sheer size of the hire sector and that it was the beginning of my newfound passion for what we do.”
Despite her mechanical background, Shadbolt’s steadfast commitment to exceptional customer service and “never say no” mentality enabled her to quickly thrive at Swan Hill Hire. Starting as a hire consultant/controller – a customer-facing role integral to all aspects of customer service – she found herself initially overwhelmed by the over 1,000 pieces of equipment she “knew nothing about” and was “trying to sell” to customers. Yet, within just four years, Shadbolt progressed from this entry-level position to operations manager and now serves as the general manager of the company.
In her current capacity, Shadbolt’s responsibilities span the breadth of Swan Hill Hire’s operations, due to the company’s size and regional location. She is deeply involved in every aspect of the business, ensuring its continued success and growth.
“With a team of 15 spread across four departments – front of house, maintenance, workshop and accounts – I work closely with managers and staff, ensuring workflow is at peak performance,” says Shadbolt.
“My responsibilities extend to coordinating major projects with clients and our team, identifying training and development opportunities, overseeing staff performance and productivity, and implementing processes and procedures.
“I’m also responsible for managing fleet requirements including asset procurement and sales, budget planning, recruitment and conducting strategic sessions with colleagues to continually enhance our business operations.”
Shadbolt’s rapid rise from an entry-level role to general manager within just four years is an impressive feat in itself. Yet, her contributions far surpass this achievement. By spearheading initiatives and guiding the Swan Hill Hire team, she played a pivotal role in their recognition as finalists for the National Hire Company of the Year at the
Hire Industry Excellence Awards in 2021. Further, under her leadership, the company clinched the award for the second time in 2023 (the first win dating back to 2017, predating her tenure).
Since joining Swan Hill Hire, Shadbolt has implemented significant positive changes, including transitioning the company from manual to digital operations. “Initially, our operations relied on pen and paper, a rather antiquated approach with bookings noted in a physical calendar,” she says. “Recognising the need for modernisation, I championed the adoption of technology-based solutions.”
“Now, we operate fully digitally, driving growth and expanding our service area significantly.”
servicing of all equipment, ensuring compliance with both WorkSafe Victoria and industry safety standards.
She also believes that the collaboration between the hire and the construction industries is vital in the progress of construction and the economy as a whole.
This year, she earned a place on the committee of the Hire and Rental Industry Association. Additionally, she remains dedicated to promoting diversity at Swan Hill Hire, reflected in the current team composition of 15 individuals, with 40 per cent female representation.
“When I first joined, there were only three women on the team,” says Shadbolt. “Now, we have female colleagues in every department, contributing just as much as their male counterparts.”
Throughout her impactful journey in the hire and rental sector, Shadbolt has come to appreciate its profound impact on the construction industry, surpassing conventional perceptions and assumptions.
“The presence of the hire sector in the construction industry is far more substantial than a lot of people realise,” she says. “We share an economy, and as a result we are creating a more sustainable environment.”
“When you drive past a building site with 20 to over 200 pieces of elevation equipment, the equipment is often on hire, not owned by contractors.
“When you choose to hire, it’s not just about obtaining equipment; it’s about accessing professionals with specialised expertise and building relationships where you’re at the forefront.”
Shadbolt highlights the significant advantage the hire industry offers by alleviating the financial burden associated with purchasing, maintaining and storing assets. For example, Swan Hill Hire assumes
“We have some fantastic industry initiatives that align with the sustainability push and goals of environmentally friendly construction sites,” says Shadbolt. “Renewable energy options are becoming more readily available, with manufacturers building electric, hydrogen and hybrid models of equipment that were previously only available in diesel.”
“Safety is also a huge priority, ensuring the wellbeing of machine operators, site workers and the general public through continuous development of training, licensing and technology.”
Shadbolt envisions abundant growth and advancement opportunities in both sectors, given their versatility and diverse career paths. “The opportunities in the hire industry are boundless, much like construction,” she says. “Whether you’re just starting your working career or looking for a change, I’d highly recommend exploring these fields that may be unfamiliar to you.”
She emphasises the transferability of skills, encouraging individuals to embrace opportunities even when job descriptions request specific industry experience.
“My advice? Do it scared, get comfortable with discomfort, and perhaps you can drive a positive impact,” says Shadbolt.
Rising from an apprentice to a leader in the hire and rental industry, Shadbolt credits her success to the support and opportunities provided by her employer, colleagues and various programs. Her journey exemplifies the power of embracing the unknown and seizing opportunities.
“The presence of the hire sector in the construction industry is far more substantial than a lot of people realise.”
The National Association of Women in Construction has launched a new campaign in an effort to ensure safe and accessible toilets are available on all construction sites in Australia.
“The National Association of Women in Construction has just launched its latest campaign: ‘Better’ just to hold it?”
Brittany* works in the Northern Territory in a trade. While she now works in Darwin, during her four-year apprenticeship, she was required to travel throughout the Territory to remote sites to gain the different skills and experience needed for her job. A common experience for Brittany was that the only women’s toilet would be in the administration building, far away from where she was working. When she tried to use the ‘unisex’ toilets onsite, closer to her work area, the men would tell her she couldn’t use those and that she needed to go to the administration building. One day, while learning a new part of the job and covered in dirt and grime, she was told to wash off and go to the administration building toilet, still not allowed to use the unisex toilet. Brittany also worked on a remote worksite where the women’s toilets didn’t have a sanitary bin, a significant issue if you have your period in the middle of nowhere. For Brittany, the answer to the question of what needs to be done is pretty simple – the bare minimum is equality for everyone and having the same access to facilities that men do.
The National Association of Women in Construction (NAWIC) has just launched its latest campaign: ‘Better’ just to hold it? For too long, both women and men have been required to travel to, share or use unsafe toilets, or have had no access to toilets at all.
In Australia, every state and territory mandate that employers must provide ‘appropriate’ facilities. But what does this mean?
While the government hasn’t designated what constitutes an appropriate toilet – they have stated that toilets should be:
- Fitted with a hinged seat and lid;
- P rovided with adequate lighting and ventilation;
- Clearly signposted;
- Fitted with a hinged door capable of locking from each side of the cubicle;
- Positioned to ensure privacy for users;
- Separate from any other room by an airlock, a sound-proof wall and a separate entrance that is clearly marked; and
- Supplied with an adequate supply of toilet paper, handwashing facilities, rubbish bins, and for female workers – hygienic disposal of sanitary items.
If you are in a mobile workplace, it is the responsibility of your employer to locate and
provide access to a toilet, allowing additional time for travel in addition to your regular breaks. For remote workers, employers need to provide portable toilets, in a secure place with safe access. Do your toilets meet these standards? Not being able to access safe toilets at work is a workplace safety risk. It’s your right to have accessible and safe toilets at your workplace – we need to take action to enforce minimum standards.
You can find out more about our #dobinadunny campaign on our website.
NAWIC is a not-for-profit organisation led by a team of employees and volunteers who all strive to champion and empower women to reach their full potential. Our mission is to drive changes that will aid in the increased recruitment, retention and further vocational development of women in the construction industry. You can join the conversation on our socials @nawicau, and keep up with our advocacy, events and opportunities at www.nawic.com.au
“It’s your right to have accessible and safe toilets at your workplace – we need to take action to enforce minimum standards.”
The National Association of Women in Construction
The National Precast Concrete Association Australia highlights the potential of glass‑reinforced concrete in modern structures, spotlighting The Ribbon in Sydney’s Darling Harbour.
The Ribbon, W Hotel
Location
Darling Harbour, Sydney, New South Wales
Architect
Hassell
Engineer
WSP
Builder
Probuild/Multiplex
Master Precaster
Asurco Roofing and Cladding
In the realm of contemporary architecture, innovation is the cornerstone of progress.
Structures no longer solely serve utilitarian purposes; they are canvases for artistic expression, statements of engineering prowess and embodiments of sustainable practices. Amid this architectural renaissance, one material stands out for its transformative potential: glass-reinforced concrete (GRC).
The marriage of glass fibres and concrete ushers in a new era of possibilities, redefining the boundaries of construction. Among the myriad of awe-inspiring examples, The Ribbon in Sydney’s Darling Harbour emerges as a beacon of GRC’s spectacular results, showcasing its unparalleled benefits in shaping the skylines of tomorrow.
At the heart of Sydney’s bustling waterfront, The Ribbon, a part of the W Hotel complex, captivates onlookers with its sinuous form and ethereal façade. Rising from the vibrant surroundings like a modernist sculpture, its seamless curves and undulating surfaces command attention. Yet, beyond its aesthetic allure lies a testament to the versatility and durability of GRC.
National Precast Concrete Association Australia (National Precast) Master Precaster member Asurco Roofing and Cladding engineered, manufactured and installed the feature curved wall panels for the project. The panels were strengthened with steel frames to withstand the area’s wind loads.
According to National Precast’s CEO Sarah Bachmann, GRC offers architects a palette of possibilities previously unimaginable with traditional building materials.
“GRC has afforded the architect the flexibility to design intricate shapes and daring designs, which is difficult to achieve in other materials and transcends the limitations of conventional construction methods,” says Bachmann. “Sinuous forms elevate guest arrival experiences by creating a unique and welcoming environment amid a myriad of road infrastructure.”
“We are fortunate to have a company which is able to carry out such intricate work, right here in Australia.”
Hassell’s principal Glenn Scott agrees. “The Ribbon’s sinewy silhouette is a testament to this freedom, as GRC has enabled base building architect Hassell to design fluid
forms that reflect the concept of The Ribbon, which is play on the ribbon-like quality of the surrounding expressways,” says Scott. “The GRC references the ‘concrete infrastructure environment’ but represents it by harnessing the material’s incredible adaptability.”
GRC’s lightweight nature offers a myriad of practical benefits as well, revolutionising the construction process. Unlike its traditional counterparts, GRC significantly reduces the weight of structures without compromising strength or durability. This not only streamlines assembly but also minimises the structural load, resulting in cost savings and environmental efficiencies. The Ribbon’s intricate façade, adorned with GRC panels, exemplifies this lightweight advantage, allowing for swift installation and ensuring structural integrity without excess weight. In an era defined by environmental consciousness, sustainability takes centre stage in architectural discourse. Here, GRC emerges as a champion of eco-f riendly
design, embodying the principles of sustainability without sacrificing performance. Composed of recyclable materials and requiring less energy-intensive production processes, GRC minimises the carbon footprint of construction projects. Being fully manufactured by Asurco Roofing and Cladding in Australia, the carbon impact is significantly reduced, as it is not shipped in from overseas.
Furthermore, its longevity and resistance to weathering ensure lasting durability, reducing the need for frequent maintenance and preserving resources in the long run. As The Ribbon stands resilient against the passage of time, it serves as a testament to GRC’s sustainable legacy, inspiring a new generation of eco-conscious architects.
Beyond its aesthetic and practical advantages, GRC holds the power to redefine perceptions of space and light. Its translucent properties allow for the diffusion of natural light. With its GRC façade acting as a canvas
for light, dynamic patterns and shadows are cast that animate the surrounding spaces. This interplay of light and material transcends the physical boundaries of architecture, imbuing the structure with a sense of ethereal beauty and serenity.
As The Ribbon in Darling Harbour showcases the transformative potential of GRC, it beckons us to reimagine the possibilities of architecture. In its sinuous curves and luminous façade, we find a synthesis of form, function and sustainability – a vision of the future cast in concrete and glass. As architects continue to push the boundaries of innovation, GRC remains an indispensable tool in their arsenal, shaping the skylines of tomorrow with its boundless potential. In embracing this versatile material, we embark on a journey towards a more sustainable, resilient and aesthetically captivating built environment – a testament to the enduring legacy of GRC in the annals of architectural history.
“The GRC references the ‘concrete infrastructure environment’ but represents it by harnessing the material’s incredible adaptability.”
As the momentum of the construction sector clashes against the challenge of labour shortages, the Australian Constructors Association is pioneering critical initiatives to transform the industry landscape – and progress is already in motion.
Australia’s construction industry is facing a daunting challenge – the industry is short of 229,000 workers to build the new homes, hospitals and schools needed, the transport infrastructure to keep Australia moving, the defence infrastructure to keep our country safe and the energy infrastructure required to reach net-zero emissions commitments. Delivering the pipeline of work ahead of the construction industry seems like an impossible task.
The dramatic shift from a surplus of workers to a shortage is a wake-up call. It has highlighted deeper issues that can’t be solved with simply supply and demand economics. It has exposed a cultural flaw that is perpetuating long work hours, high stress levels and alarming rates of mental illness and suicide. It is a realisation that resonates with me deeply, having witnessed firsthand the toll it takes on workers across construction sites.
The good news is that just about everybody recognises the need for change.
We are at a pivotal moment in the industry’s evolution and for the first time ‘harden up’ no longer holds sway.
For the contractors’ part, members of the Australian Constructors Association representing the nation’s major contractors, made a ground-breaking pledge in 2023 to transform the culture of the industry within a five-year time frame. As we mark the one-year milestone of this pledge, I am encouraged by the progress we have made.
The first significant step towards this transformation is the commitment made by contractors to achieve the Workplace Gender Equality Agency (WGEA) Employer of Choice citation by 2028. This isn’t just about addressing gender disparities in pay; it’s about creating an inclusive environment where opportunities are available to all, irrespective of gender. Laing O’Rourke, John Holland and Clough have already achieved this milestone, setting a powerful precedent for the industry. As one of the most male-dominated industries in Australia, imagine the impact on the industry as more major contractors attain the citation.
Workers everywhere, both men and women, are demanding more than just work – they want a life. We hear this daily on sites but a recent study by the Construction Industry to the industry is another important part of
wellbeing. Pilot projects implementing The clouds are indeed clearing. change requires a construction sector that serves the best interests
Empowered Women in Trades’ Melinda Davis highlights the value of jobs and career exhibitions in creating connections and fostering careers in trades.
“We have just launched a new initiative to allow businesses that wish to support us and the programs we run to bring more women into skilled trades.”
in Trades.
May seems to be the month of jobs and career exhibitions around the country. The team at Empowered Women in Trades (EWIT) has already attended seven events. Jobs and career exhibitions are unique; they bring many industry connections into one place at one time with the primary purpose of connection, learning new information and building your knowledge. However, if you don’t nail the purpose of being there, they can also come at a big cost in time, money and value.
I want to introduce you to the Trades & Tech Fit Expo run in Melbourne by the team at Head Start and funded by the Victorian Department of Education, where the Melbourne Convention and Exhibition Centre comes to life over two days in May. Unlike other events, the unique attribute of this event is that it is only for female and non-binary secondary school students across the state who come to explore the world of trades and learn about career opportunities and pathways. In its third year, this event continues to grow in
momentum with the exhibition in 2024 attracting registrations from 128 schools (up from 119 in 2023), 103 exhibitors (up from 85 in 2023) and attendance of over 3,000 female and non-binary students across the two days. The excitement from the students is always palpable as they enter through the doors.
“I wasn’t sure I wanted to attend, I didn’t think I would be interested in technology or trades but having come here today and tried so many different things, especially the AR/VR activities, I am reconsidering my options,” said one female Year 9 student.
We are often asked how organisations can get involved in these kinds of events and programs, and we do need industry support to achieve the kinds of success that are needed to make permanent change.
We have just launched a new initiative to allow businesses that wish to support us and the programs we run to bring more women into skilled trades. Called Alliance Membership, it provides an opportunity for all organisations, large and small, to directly support EWIT programs. Alliance Members promote their support of a diverse skilled workforce through the activities we provide the industry, and their support enables us to focus on the many programs we offer, including attracting more school-aged kids
to consider skilled trades. If you would like to find out more about Alliance membership, visit the EWIT website (ewitrades.com).
In the recently announced Federal budget, $55.6 million dollars has been allocated to the Building Women’s Careers initiative. These projects aim to support women in pursuing high-paying careers in key male-dominated industries and sectors, particularly construction, clean energy, technology and digital, and manufacturing. A crucial aspect of the plan should be to draw inspiration from the successes in Victoria and focus on building a pipeline of emerging female talent from schools wanting to be part of the skills solution.
Creating a safe and inclusive space for female and non-binary students from different cultures and demographic backgrounds to explore traditionally male-dominated industries with some of the biggest skills shortages around the country is imperative as we work to future-proof building and construction and connect more women to construction. The EWIT team is looking forward to delivering more school-based programs in partnership with Freestyle by North Melbourne Football Club to continue being part of the solution as we move towards the vision of having 30 per cent of trades roles filled by women by 2030.
“Jobs and career exhibitions are unique; they bring many industry connections into one place at one time with the primary purpose of connection, learning new information and building your knowledge.”
Dr Gretchen Gagel outlines key steps to strengthen the culture of safety within the construction industry.
“Thinking about the ways in which you, as a leader, create and support a culture of safety at your workplace is critical.”
Last year, I was vacationing in the US with a group of women I went to engineering school with back in the 1980s. We set off for a day of snorkelling, two groups of four in two cars, to meet our boat. The location was a bit difficult to find because of construction taking place along the road leading past the entrance. After my group parked our car, we realised that the other car was lost. My dear friend of 40 years walked out to the entrance to see if she could flag down the other car when it arrived –right into an area where two heavy pieces of equipment were operating. No one stopped. I yelled for her to remove herself from this dangerous situation, but she waved me off. She eventually walked back to our car. What should have happened? Should I have run to her to drag her away, risking my own safety? Should one of the operators have stopped their piece of equipment, stepped down, and removed her from the area? How could this situation have been avoided in the first place? These are all excellent questions. These are the scenarios we grapple with every day on our construction sites. One moment of lost concentration, one “it will be fine just this one time”, one vacationing person mindlessly walking into danger, and injury or even death can occur in an instant.
I’ve put a great deal of thought into both physical and mental safety in our industry over the last four decades. As chair of the Board of Brinkman Construction (US), my worst nightmare is envisioning visiting a family who has lost someone because we did not do all we could to instil a culture of safety. Now that I have joined the Risk Committee of the Board of GHD Engineering, my contemplation of risk and safety has broadened to a global, even more complex perspective.
Here are the key steps I believe we as construction industry leaders need to take to continue to reinforce a culture of safety within our industry:
• Zero tolerance for safety infractions: When I chaired the Judging Panel of the Australian Construction Achievement Award (ACAA) in 2023, I was travelling to inspect a construction project site in Sydney. I had been informed that the project was complete, so I left my steel-toed boots and other personal
protective equipment (PPE) in Melbourne. However, upon arrival, it was decided that we would visit a portion of the project that wasn’t complete – oh no, no steel-toed boots. We quickly and rightly made the decision not to visit that portion of the project. People are watching us as leaders, every minute, to see what we do. Just recently, during my quarterly project visit for Brinkman Construction, a member of the project team pointed out to me that I was wearing an older, less visible version of our reflective safety vest. Good for them. We’ve instituted new hard hats with
chin straps, and I pointed out to one of our board members that their strap was undone. These seem like little things, but each small infraction sends a signal that we don’t take our safety policies seriously. Empowering everyone on a jobsite to point out these safety infractions is important.
• Leverage artificial intelligence to improve safety: During my editorial last month on global construction industry trends, I told the story of TDIndustries and how this organisation dramatically reduced
its total recordable incident rate by leveraging artificial intelligence (AI) to analyse 90,000 pre-job planning/safety meetings, and then training their foremen and superintendents on the words and phrases that increased crew participation in safety discussions.
John Holland’s use of AI-based personalised adaptive learning for safety training with partner Area9 Lyceum was recently an Inside Construction cover story. Construction project teams are utilising jobsite pictures and AI to analyse risk, safety hazards and unsafe behaviours. These are but three of the dozens
“I have a vision of a construction industry where everyone returns home in the same condition as when they came to work.”
of examples I’m hearing of how cutting-edge contractors are leveraging AI for safety, and I’m excited to see how we continue to leverage AI in our industry for safety and many other aspects of our project performance.
• Utilising additional technologies for safety: The hardest presentations for me to hear at construction conferences are those recounting accidents that let to avoidable deaths on jobsites. One story that has stuck in my mind is of a crane operator taking a break, climbing back into his cab, and failing to notice the person leaning against the counterweight. This unfortunate accident prompted the company to implement an equipment/personnel interaction system, notifying all equipment operators if anyone is within a certain distance of their equipment. This system would have been helpful in the situation I shared at the beginning of this article, and during a recent project visit where I saw people walking dangerously close to operating equipment. According to the US Bureau of Labor Statistics, in 2022, 1,069 construction employees died (9.6 fatalities per 100,000 workers). Falls, slips and trips remained the leading cause with 410 deaths, and “contact with an object or equipment” was fourth with 149 deaths. The fatality rate in the Australian construction industry is much lower, with 27 deaths reported in 2023, equating to a rate of 2.2 deaths per 100,000 workers. Additionally, across all industries in Australia, “being hit by moving objects” was the second leading cause of death, accounting for 26 fatalities (13 per cent of total deaths). These are people that will never see a child grow up, never again experience a beautiful dinner with a loved one. We can do better, and technology can help. It is worth the investment.
• Being mindfully present is critical: I heard a fabulous presentation years ago of a pharmaceutical company that hired a sports psychology company to work with each of its global construction sites. The sports psychology company trained the crew leaders to have daily pre-job meetings with their crew to determine if everyone on the crew was “mentally present” and prepared to work. These jobsite leaders created the psychological
safety for someone to be able to raise their hand and say, “I had a huge fight with my spouse last night and was up half the night”, or “I had a few too many at a party last night”; and in turn, “I’m not prepared to be mentally present at work today”. These people were asked to take the day off with pay. Of course, repeat instances of this were addressed, but how powerful is this for someone to be able to say, “I’m not quite right today” and not be penalised for that. These are the people who are distracted, exhausted, unaware, and who end up injured or killed on our sites.
• Reinforce that safety moments have impact: Years ago I was visiting our team during a preconstruction Lean pull-planning session, and given that there was snow on the ground, the pre-meeting safety moment was about how to “walk like a penguin” to avoid falling. When we all left the meeting that evening for dinner, guess what? We were all walking like penguins. And laughing, and safer. Taking safety moments seriously, remembering that they bring our minds back to best-practices, is important. I’m reminded of the email signature of my friend Margaret Reese Walker, retired vice president of Engineering and Technology Centers for Dow – “Take safety everywhere you go”. It’s a reminder each time I see it.
I have a vision of a construction industry where everyone returns home in the same condition as when they came to work. I’m certain that each of you share this vision. We’ve made huge strides over the past decades and more can be done. Thinking about the ways in which you, as a leader, create and support a culture of safety at your workplace is critical.
Dr Gretchen Gagel is chair of Brinkman Construction (US) and a member of the Global Risk Committee for GHD Engineering, the National Academy of Construction (US), the Construction Industry Culture Taskforce (AUS), and the Associated General Contractor (AGC) of America National Diversity and Inclusion Committee. Gretchen is passionate about leading change in the construction industry and developing its future leaders. You can hear more from Gretchen on her Spotify podcast, “Greatness”.
When this distinctive circular designed school required completion for the start of the academic year, light gauge steel framing made from TRUECORE® steel delivered.
Prefabricated and then assembled on site, impressively large roof truss and frame modules were craned to height, then safely and e ciently installed into their elevated positions.
The end result is a state-of-the-art learning space designed in the round and produced on time. Visit truecore.com.au to learn more.