ISSUE 01 AUGUST/SEPTEMBER 2022 Exploring Creative Construction with McConnell Dowell’s Executive General Manager – Engineering, Dr James Glastonbury EnergyShift Helping with the Focus ShowcaseConTechonsafelyatWorkingheights MediaOfficialPartner
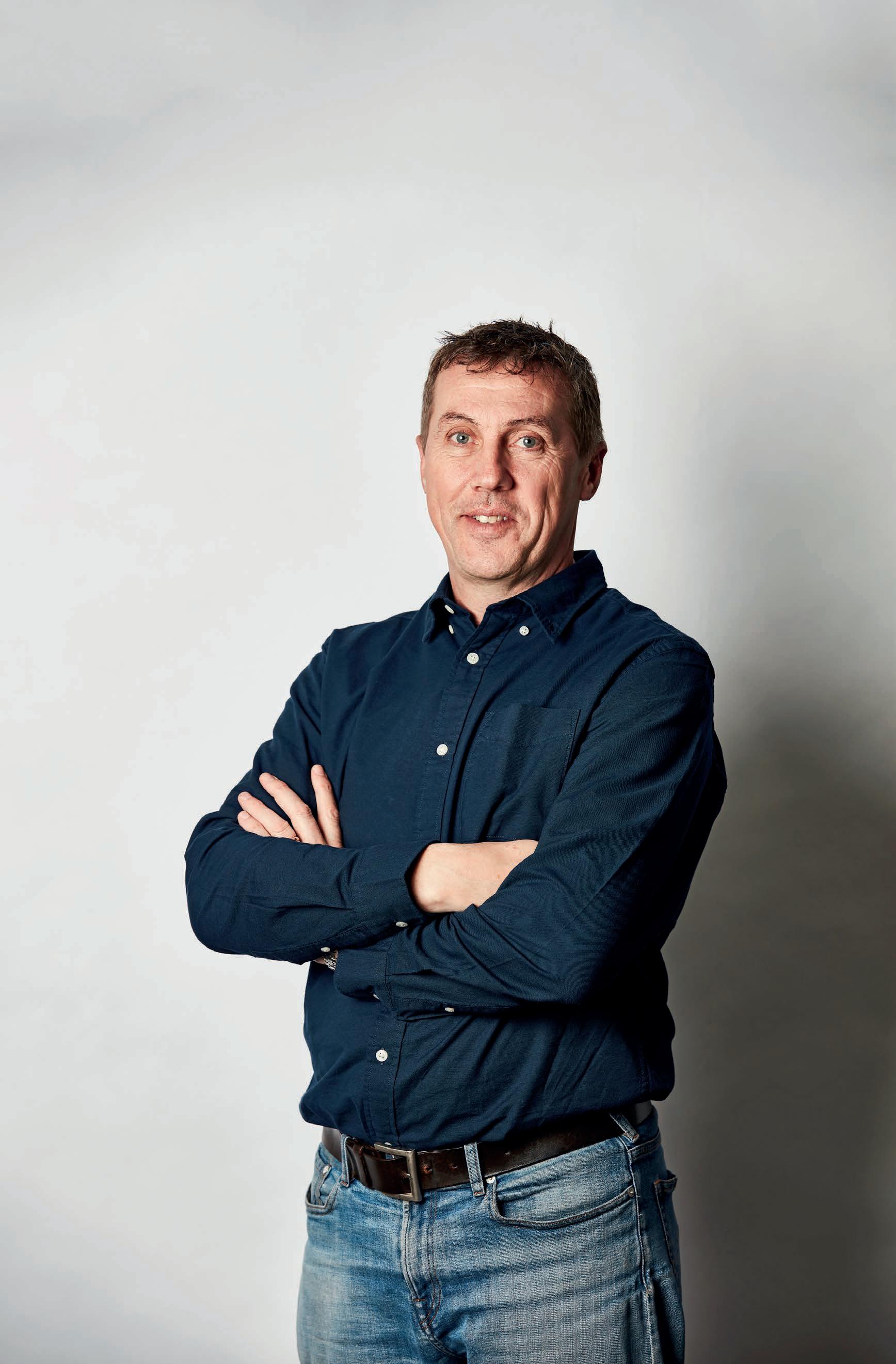
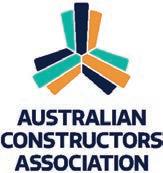
Request a demo. coins-global.com We do it all. Manage your construction business with one software system.
www.insideconstruction.com.au INSIDE CONSTRUCTION 3 4 Editor’s Note 6 Executive Summary COVER STORY 16 Helping with the energy shift McConnell Dowell playing their role in addressing the construction energy shift EVENTS 20 25 years of ACA award Celebrating 25 years of the Australian Construction Achievement Award 46 Future of Construction Summit 2022 Key takeouts from this year’s Future of Construction Summit 62 CONEXPO-CON/AGG ’23 North America’s largest construction trade show returns in 2023 ASSOCIATIONS 56 Formwork Industry Association Construction site safety & competence 58 Australian Constructors Association Escalating construction crisis solutions 60 National Precast Association Stamping out secondary lifters PROFILE 50 Rachael Keiley Plumber to project manager 52 Sarah Marshall Champion for people, safety and sustainability OPINION 56 Dr Gretchen Gagel Looking at industry trends CONTECH SHOWCASE 22 Trimble Viewpoint: scrap the construction silos Scrapping silos and embracing connected construction workflows 26 InEight: a maturing view on construction digitalisation Changing how the construction industry thinks about, and approaches, its most essential processes COINS SOFTWARE 29 COINS transforms the construction industry Construction Industry Solutions sets a benchmark for positive industry change through innovative software CONQA TECHNOLOGY 32 Mark of quality Changing attitudes towards quality assurance (QA) with easy-to-use, conveniently accessible digital tools WORKING AT HEIGHTS SAFELY 39 Importance of height safety systems Latest news and information about working at heights safely 40 Innovation in a matured industry – not likely? Paramount Safety become a part of PIP Global highlighting their mission for developing and offering high quality safety products 42 The importance of training when working at height Vertical Horizonz recognises the importance of height safety training in the lifting and construction industry INVENTORY SOLUTIONS 44 Blackwoods introduce on-site industrial vending machines Blackwoods partners with City of Canada Bay introducing on-site vending machines to solve inventory challenges REGULAR FOCUS 32 44 50 60 ISSUE 01 AUGUST/SEPTEMBER 2022
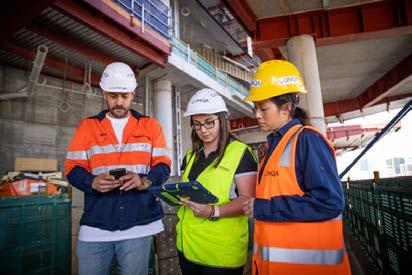
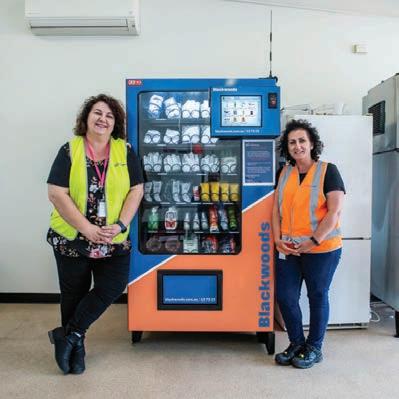


From the editorial team
In this issue we bring together organisations that are driving collaborative construction through new technologies, approaches to complex projects and construction operations.The Inside Construction team is also proud to be partnering with the Australian Constructors Association, National Precast Concrete Association Australia and Formwork Industry Association.Wehopeyou enjoy our August 2022
4 INSIDE CONSTRUCTION Chief Executive Officer John Murphy Chief Operating Officer Christine Clancy Group Managing Editor Sarah sarah.baker@primecreative.com.auBaker Editor Ashley ashley.grogan@primecreative.com.auGrogan Sales Director Brad bradley.buchanan@primecreative.com.auBuchanan Art Director/Design Daz Woolley Art Director Blake blake.storey@primecreative.com.auStorey Design Production Manager Michelle michelle.weston@primecreative.com.auWeston Business Development Manager Adele adele.haywood@primecreative.com.auHaywoodp:+610403500544 Client Success Manager Glenn glenn.delaney@primecreative.com.auDelaney Head Office Prime Creative Pty Ltd 11-15 Buckhurst Street South Melbourne VIC 3205 Australia p: +61 3 9690 8766 f: +61 3 9682 enquiries@primecreative.com.au0044www.insideconstruction.com.au Subscriptions +61 3 9690 subscriptions@primecreative.com.au8766 Inside Construction is available by subscription from the publisher. The rights of refusal are reserved by the publisher Articles All articles submitted for publication become the property of the publisher. The Editor reserves the right to adjust any article to conform with the magazine format. Copyright Inside Construction is owned by Prime Creative Media and published by John Murphy. All material in Inside Construction is copyright and no part may be reproduced or copied in any form or by any means (graphic, electronic or mechanical including information and retrieval systems) without written permission of the publisher. The Editor welcomes contributions but reserves the right to accept or reject any material. While every effort has been made to ensure the accuracy of information, Prime Creative Media will not accept responsibility for errors or omissions or for any consequences arising from reliance on information published. The opinions expressed in Inside Construction are not necessarily the opinions of, or endorsed by the publisher unless otherwise stated. innovative solutions such as cloud management software, improved working policies for construction workers and constructive technology disruption.InAustralia, the construction industry records more insolvencies each year than any other sector. This highlights the need for positive industry change. At an incremental and major level, construction professionals need to be embracing innovation and collaboration to avoid becoming another insolvency statistic. We’re seeing the gradual improvement of collaborative workforce structures and more and more construction companies are adopting this approach.
According to a recent Australian Bureau of Statistics (ABS) report, Innovation in Australian Business, in the two-year period ended 30 June 2021 only 38% of construction companies were known to be ‘innovation-active’.Australianconstruction companies are now addressing the importance of innovation in the industry, with the adoption and successful implementation of new technologies, softwares, processes and ways of working.Collaborative and connected construction has stood out as the key approach to the current industry climate. Collaboration provides a platform for innovative and creative thinking, leading to a better connected workforce and improved project outcomes. The importance of collaborative construction is everincreasing as our industry continues to tackle skilled labour shortages, rising material costs, the Covid pandemic and the tide of natural disasters that have devastated our nation in recent years. The demand for innovative construction contractors has risen sharply in the past two years, yet the construction sector faces ongoing difficulties in filling skilled labour positions and managing inflationary pressures. A collaborative or connected approach to these challenges opens the floor to
On behalf of the team, we’re excited to share our first print edition of Inside Construction. Along with our established digital platforms, the launch of our Inside Construction print publication furthers our capacity to provide a leading source of construction news and insights showcasing the very best that the construction industry has to offer.
Welcome to Inside Construction WELCOME
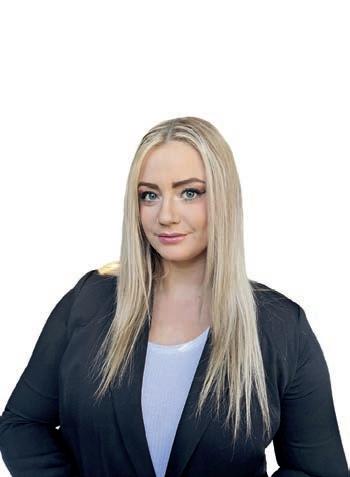

One: › Integrated Software Suite › Trusted Set of Data › Easy Way to Access Technology › Partner for the Future ViewpointOne brings together the industry’s best finance and HR applications with fully integrated project management and mobile field tools to connect all the parts of your business. VIEWPOINT.com/ViewpointOneANZ ©2021 Viewpoint, Inc. All Rights Reserved.

In the InEight Global Capital Projects Outlook (GCPO) report for 2021, APAC was the most technologically forwardthinking global region surveyed. Yet this is an achievement the region has been curiously unable to replicate according to this year’s 2022 report. Brad Barth, Chief Product Officer at InEight, weighs in on these developments and the impacts disconnected digital adoption is having on APAC communications, efficiency and project performance. Looking into the future, InEight are calling for the construction industry regain its momentum and adopt more integrated approaches to digital transformation based on holistic thinking and higher-order needs.
InEight see a clear demand for more accessible and actionable insights among construction employees. InEight provides field-tested project management software for the owners, contractors, engineers and architects who are building the world around us.
This year marked a 25-year history of the Australian Construction Achievement Award (ACAA) Presented by The Australian Constructors Association and Engineers Australia who have been proudly partnered since 1997, the 2022 event brought together over 450 people excited to celebrate the industry’s achievements.Thepresentation event, held in Sydney on 4 May, saw the Sydney Metro City & Southwest Tunnel and Station Excavation (TSE) Works by John Holland, CPB Contractors and Ghella Joint Venture announced as the winner of the 2022 ACAA. Pages 14-15. Technology holds the keys to unlocking productivity in the construction sector – improving efficiencies, reducing costs, increasing speed of delivery and delivering better outcomes. Construction companies are increasingly looking for innovate ways to plan, design, and build. This month we caught up with industry leaders in the ConTech space to explore the technology solutions shaping the future of construction. Trimble Viewpoint believe truly connected construction is possible through technology. As construction and technology both become more advanced, Trimble Viewpoint are moving the industry towards scrapping the traditional siloed approach to managing construction projects.
NEWS Executive summaryTalkingCreativeConstructionwithDrJamesGlastonbury
ConTech Showcase. Pages 23-27.
6 INSIDE CONSTRUCTION August/September 2022
This issue at a glance
Andrew Tucker, APAC senior product manager for Trimble Viewpoint shares their global product strategy, Trimble Construction One, and delves into the necessity of a connected construction environment in today’s rapidly changing industry. A 2020 survey highlighted that nearly a quarter of all construction companies are using six or more separate applications to manage their daily operations. On top of this Trimble Viewpoint’s recent research found that some 48% of project managers said their project management software had only basic or no data and workflow connections among the other software systems in their company.
Trimble Viewpoint One means everyone in the business is working on the same set of data resulting in a connected construction environment that fosters teamwork, collaboration and innovation.
This month we caught up with Dr James Glastonbury, Executive General Manager – Engineering at McConnell Dowell to discuss ‘creative construction’. McConnell Dowell have been successfully delivering complex infrastructure for over 60 years and were recently contracted to take on the Kidston Pumped Storage Hydro Project in Far North Queensland. Creative Construction is at the core of how McConnell Dowell operate and the journey of development of the Kidston scheme, the first of its kind natural battery storage facility, is a powerful example of that approach to the market.
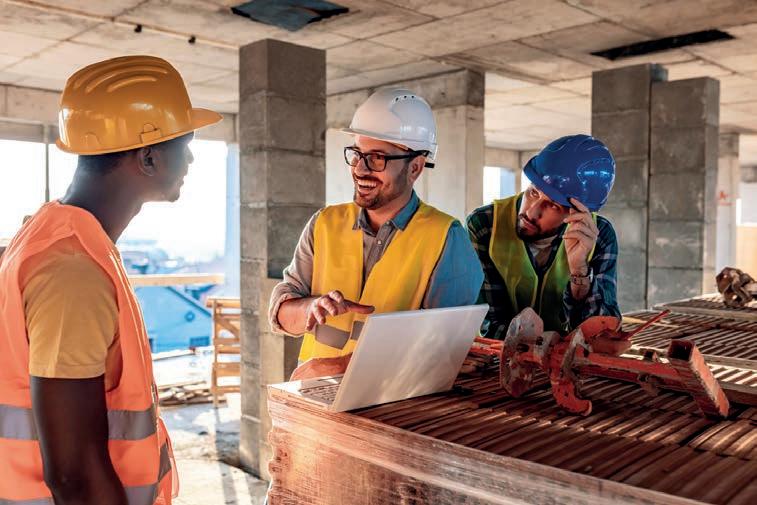
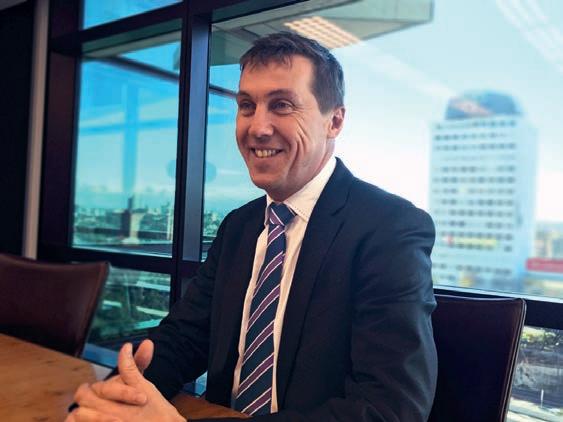
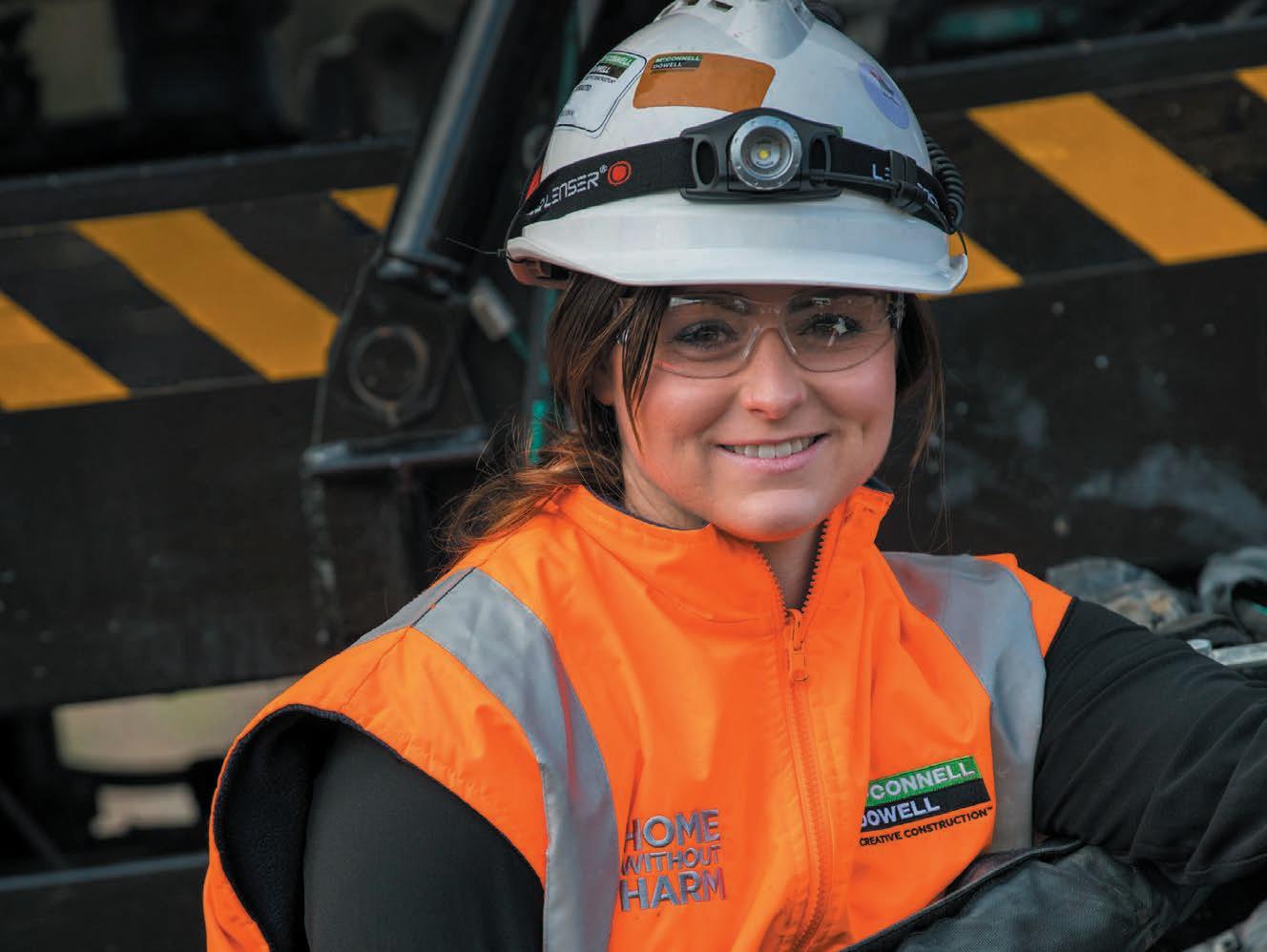
McConnell Dowell is an engineering-led, specialist contractor, successfully delivering complex infrastructure with our customers and the community. We’re always looking for great people, visit us at: mcconnelldowell.com
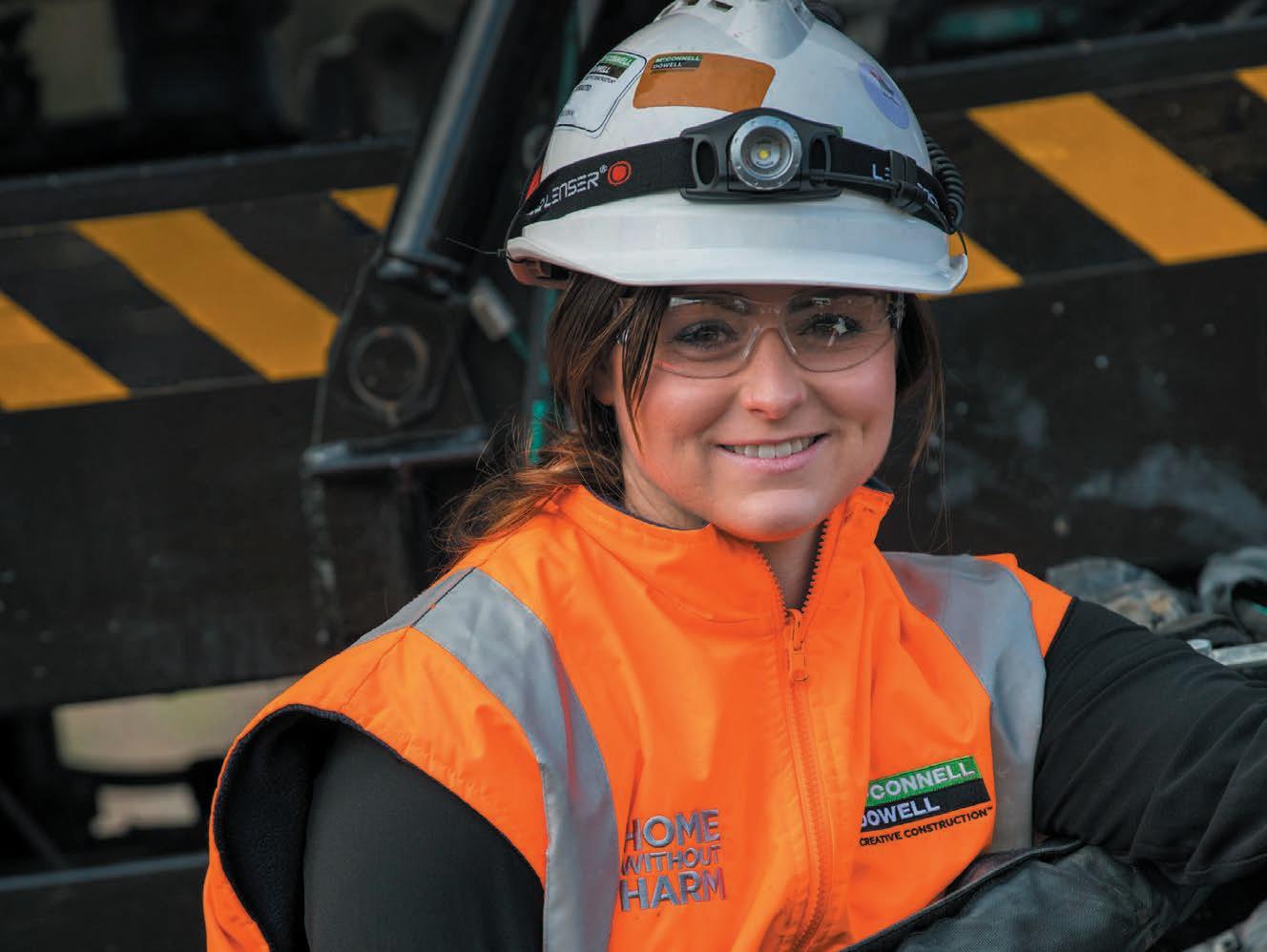
The takeaway from this year’s Future of Construction Summit (FCON22) - be bold, be brave, and do it together as an industry. Partnering with FuturePlace, the national representative body for major contractors, the Australian Constructors Association brought key issues to the forefront of discussions at the newest national conference for the construction sector, FCON. Held in Sydney from 4 - 5 May, the event featured a stellar line up of speakers from government, industry and the supply chain.
Exploring the key fromtakeoutsFCON22
The on-site vending machines provide the council with the much needed access to inventory 24/7 for essential safety and PPE items, increasing productivity and reducing the time staff need to spend off-site. The vending machines have given the council a distribution point for site approved PPE, Covid related items such as hand sanitiser, antibacterial wipes and disposable respirators. Further to that the vending machines are an innovative technology that provide automated reporting and management Pages 44-45.
Daniel QAofCo-FounderO’Donoghue,andCEOCONQAintroducessoftware
Once completed, the project’s entirely new approach to large-scale energy storage will generate enough electricity to power 143,000 homes for 8 hours. McConnell Dowell have identified a huge opportunity in the world of construction data and the adoption of technology to back their creative construction approach. As part of the Western Program Alliance, McConnell Dowell are doing their part in the Victorian State Government’s level crossing removal program which is set to remove 85 level crossings by 2025. Their teams are working with a landscape of relevant technologies such as robotic vision to improve people and plant separation issues. Pages 16-20. Construction Industry Solutions (COINS) is setting a benchmark for positive industry change in construction driving collaborative working through innovative software. Their complete product suite, COINS Construction Cloud, provides construction businesses the ability to access their data in an integrated system where it’s all in one platform with one source of truth. Jim Farrer, Managing Director addresses the benefits of adopting software to coordinate and manage large workforces and increase productivity, profitability and certainty. Their recent work with Georgiou Group saw COINS introduce a single integrated platform to streamline project management in the business, consolidating the multitude of specialist systems Georgiou Group had accumulated over time. COINS software captures all company data in near real time so that people have a live picture of what’s happening in the business. At the most fundamental level, it enables the processing of all transactions and the capture of all data associated with those transactions. At an incremental level, businesses have complete visibility of their day-to-day operations. Pages 29-31.
subcontractors have on their phone, making it easy for them to complete their Inspection Test Checklist (ITC’s) and Inspection Test Plans (ITP’s) as theyRecentgo. reports have looked into trends in the construction industry, showing Australian construction companies spend on average one in every eight hours, or 12 per cent of their time, on rework. Daniel O’Donoghue, CoFounder and CEO of CONQA, explains how CONQA can improve standards and generate significant cost savings for the construction industry. One of CONQA’s clients that has seen significant benefits from implementing the platform on site is a concrete subcontractor based in Queensland. Initially the workforce had limited experience with digital construction technology and the company wasn’t certain that there would be uptake of the QA CONQA’ssystem.solution, to engage the team with the QA process to document their work, now saves the concrete subcontractor hundreds of thousands of dollars each year. Pages 32-37.
8 INSIDE CONSTRUCTION August/September 2022 have introduced on-site industrial vending machines across Canada Bay Council store departments. Canada Bay Council became the first council in the Sydney Metropolitan area to adopt the vending machine solution.
NEWS Executive summary
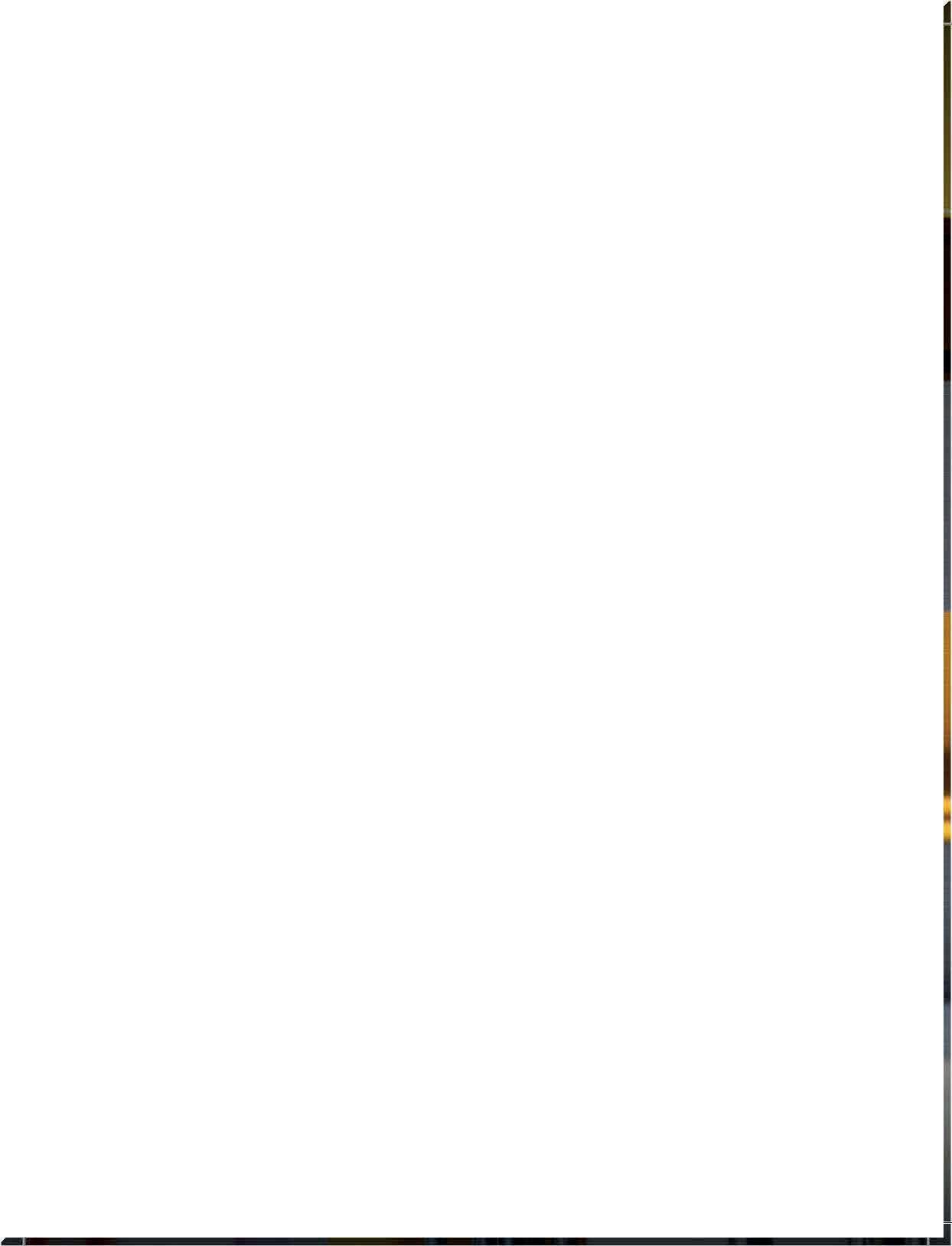
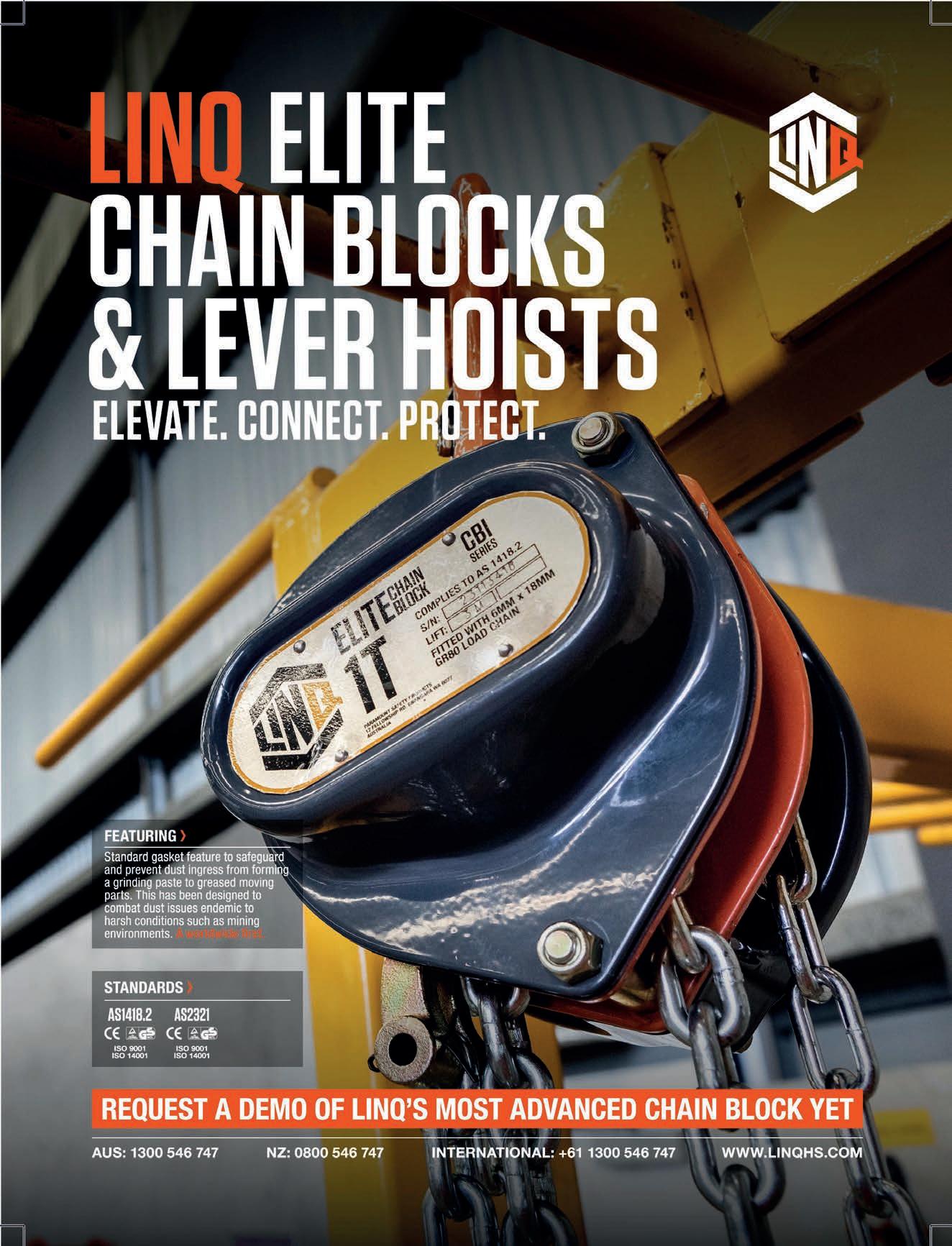
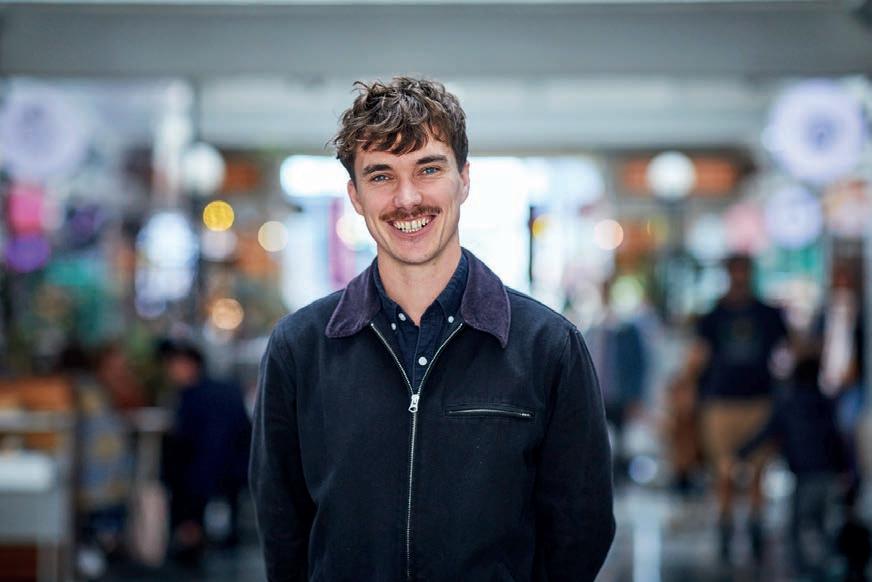
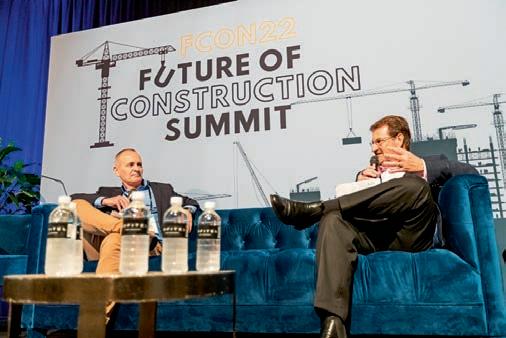
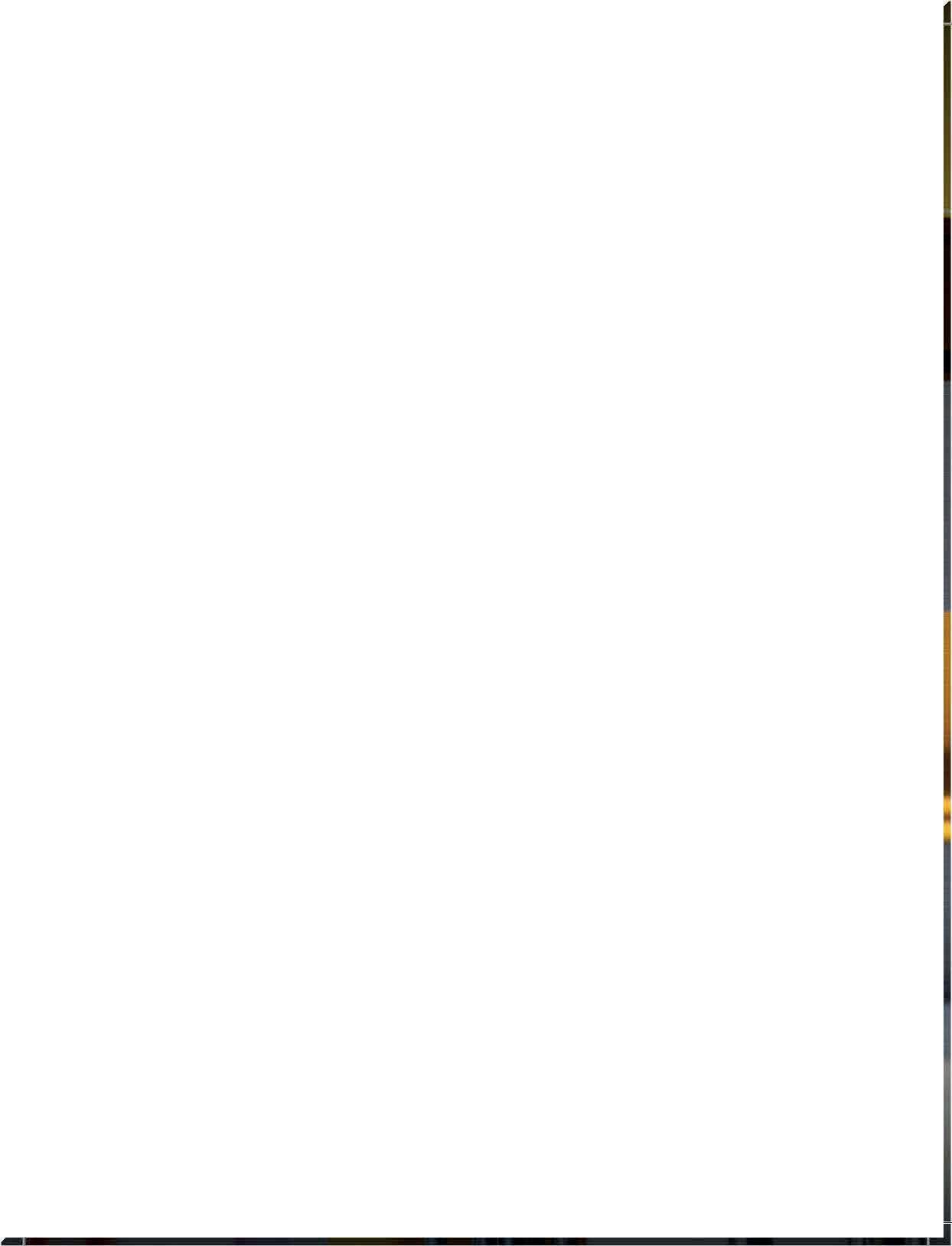
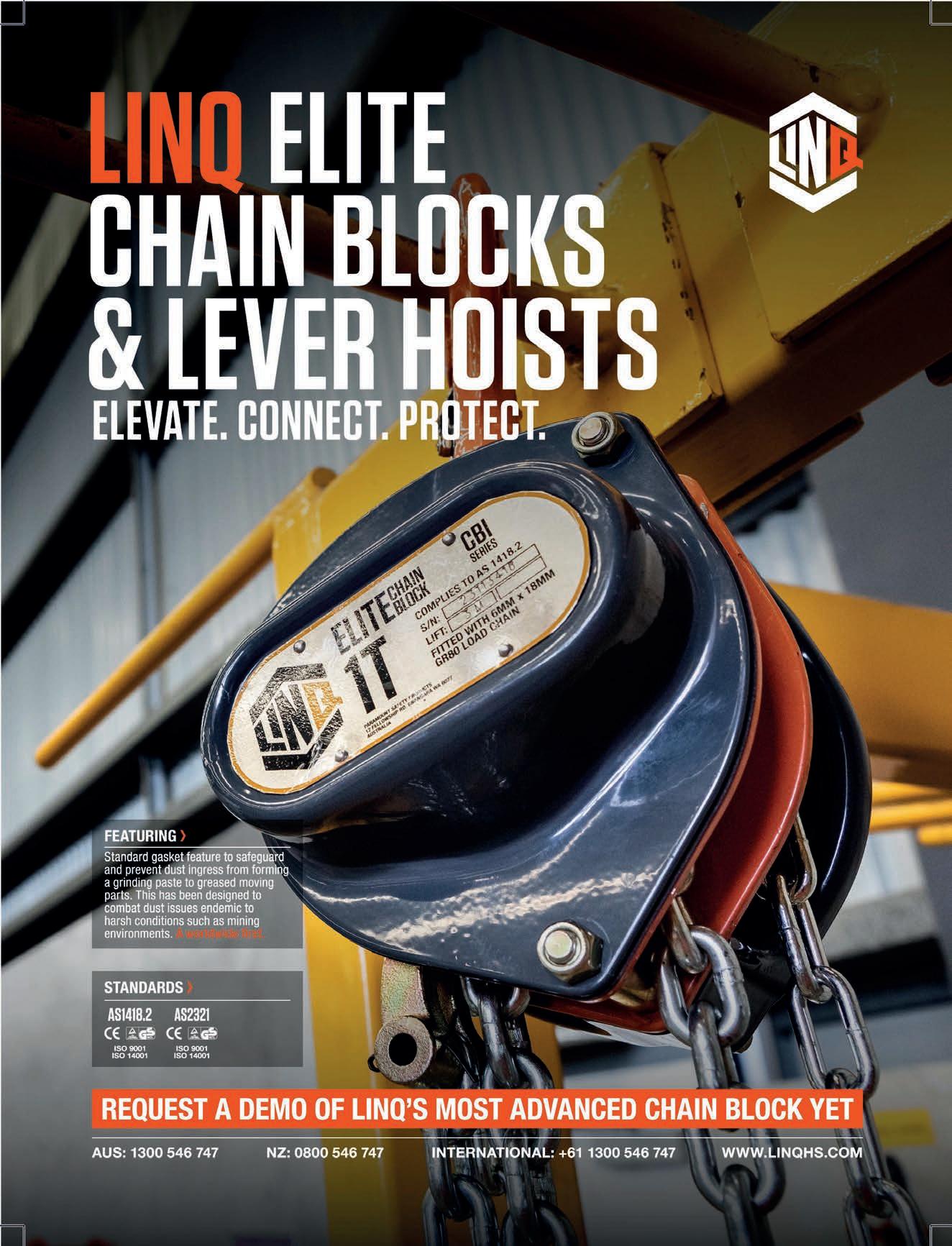

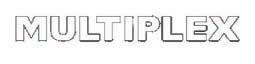
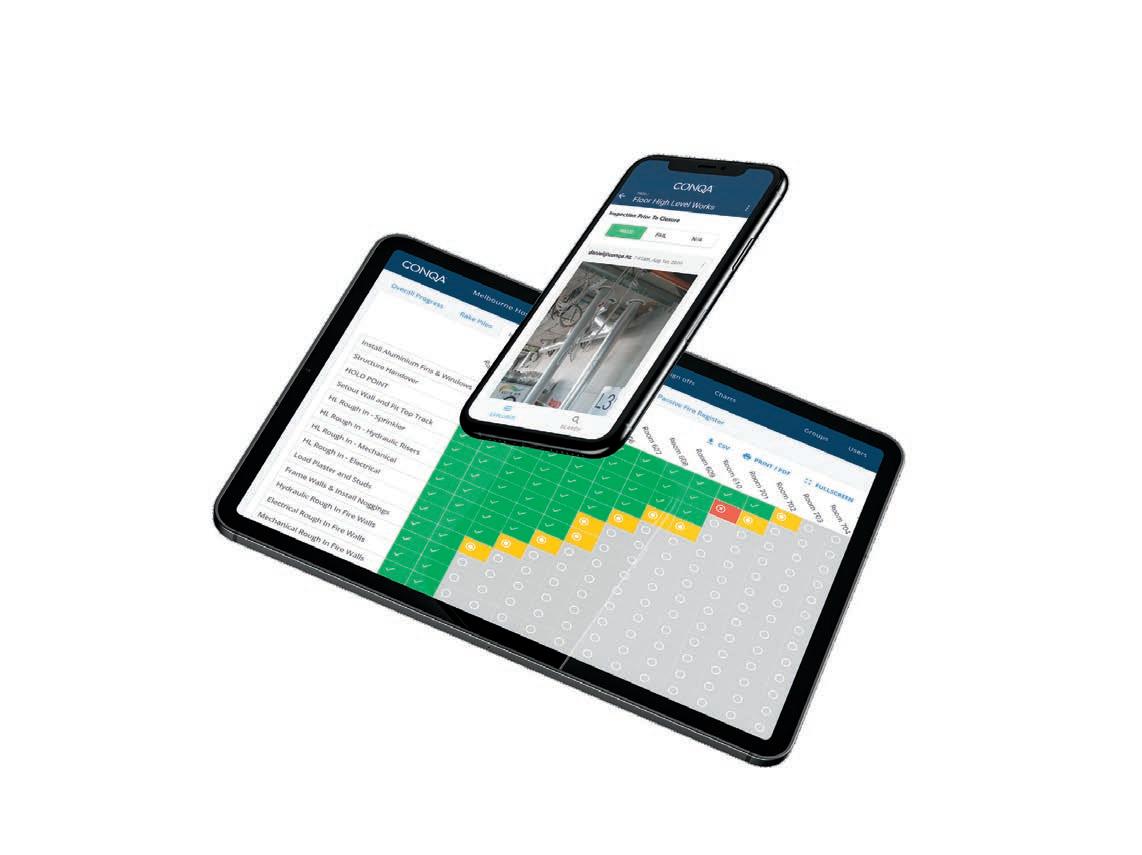
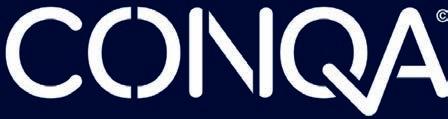

NEWS Executive
Paramount Safety began in Perth in the early 1990s, laundering cotton safety gloves for reuse, but quickly recognised the opportunity to grow its own line of personal protective equipment. The passion for safety underpinned every decision made by Paramount to expand, leading to the development of the Linq range of lifting and rigging equipment.
Stephen Sugden has been developing lifting, rigging, and height safety products since the 90s right across the globe. Since joining the team at Paramount’s Linq and PIP Global’s network, he continues to use his extensive experience to develop products in reaction to industry specific needs.TheLinq chain block and lever hoists are products that have been designed by Sugden and the team at Paramount. Vertical Horizonz recognises the importance of height safety in the lifting and construction industry.
www.insideconstruction.com.au INSIDE CONSTRUCTION 11
The team at Inside Construction magazine has been working with the Working at Heights Association (WAHA) and a number of WAHA members to bring you news and information about working at heights safely. It is a critical topic for the construction sector and all too often we read about injuries and worse as a result of safe working at heights practices not being adhered to.
In 2021, Safe Work Australia acknowledged that working at heights is the leading cause of serious injury and death, with the construction industry leading the way. In the Australian vocational education and training sector, Vertical Horizonz deliver nationally-recognised training to the residential and civil construction, energy, and transport industries. International research supports training as the recognised strategy to improve safe work performance. As a construction worker you are more likely to suffer a fall from height when you do not attend a safety training course. As members of the Working at Height Association, VHA is part of a national body dedicated to developing a pathway to better safety standards. Working at heights safely. Pages 39-43.
Sarah Marshall, General Manager - People, Safety and Sustainability at Fulton Hogan, has spent her professional career spearheading positive cultural change in the construction sector. Bringing more than 25 years of construction knowledge and experience to the industry, Marshall has worked in multiple corporate executive positions and held senior positions on many large/mega projects around Australia.
The FCON22 agenda reflected three key pillars: positive industry culture; equitable and aligned commercial frameworks; and sufficient capability, capacity and skills. The technology leaders panel reported that the construction and technology worlds are colliding. They spoke on the amount of data in existence and how to effectively use it. Beyond the three pillars and technology, FCON also highlighted the importance of environmental sustainability which recently emerged as a key focus area for the Australian Constructors Association. Discussions from FCON22 promised to bring about transformative change at an accelerated pace. Planning is underway for FCON23 to be held in Melbourne from 3 - 4 May 2023. Pages 46-49. People. Pages 50-55. Rachael Keiley ’s career in construction spans almost 20 years across plumbing and building, both on and off the tools. Now in a project management position for boutique developer, Coulson Operations, the plumber by trade is heading up an exciting, new project soon to be revealed to the public.
WAHA is a professional membership organisation and a centre for the working at heights, safety, engineering, and design communities to come together and advocate for best practice in the discipline.
Dr. Gretchen Gagel looks back upon 25 years of project excellence and forward to the challenges construction faces as an industry. summary
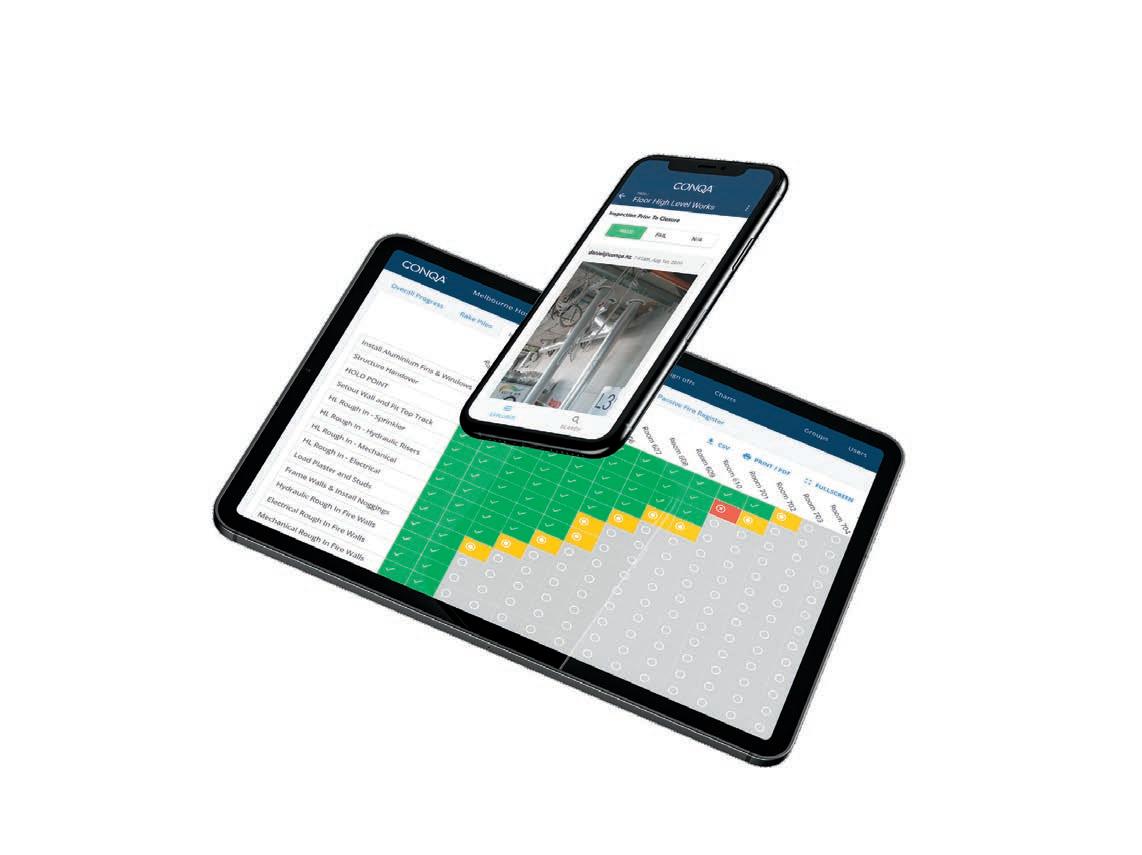
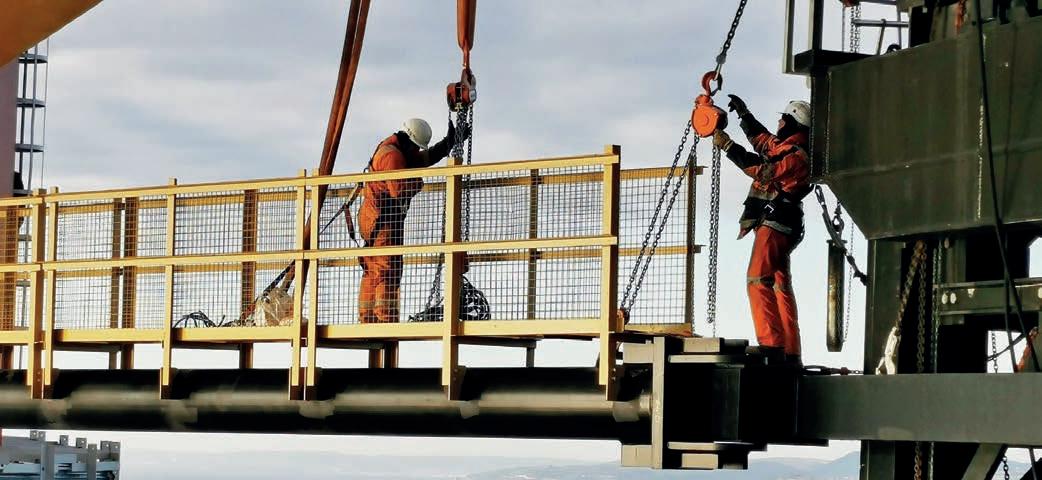
National Precast Concrete Association Australia CEO Sarah Bachmann has seen members manufacturing to fulfil orders booked well into the future. Meanwhile, as the peak body for the precast industry, National Precast addresses a number of industry matters with government and Standards
TheAustralia.requirement for secondary – or backup – lifters, has made its way into the State’s Code of Practice and Bachmann, along with National Precast, are requesting change.
Jon Davies, CEO Australian Constructors Association shares his views into construction cost inflation. Covid caused significant delay and disruption to many projects and led to a massive increase in the number of projects as governments sought to stimulate the economy. The increase in work caused huge demand for workers, with Infrastructure Australia forecasting a 105,000 worker shortfall in the next 12 months. Davies and the Australian Constructors Association are taking action.
Building new relationships in the construction community and discovering new equipment, services and people in the industry is what the show is all about. The show will also host over 150 Education Sessions providing attendees the opportunity to obtain cutting edge information for today’s fast paced construction environment.
CONEXPO-CON/AGG
North America’s largest construction trade show, CONEXPO-CON/AGG returns on March 14-18, 2023. The heavy equipment expo comes to Las Vegas, Nevada only once every 3 years and brings together the construction community from all over the world. Over 130,000 industry professionals and guests attend each year.
NEWS Executive summary
Earlier this year Gretchen interviewed forty-four construction industry leaders in Europe, Australia, Asia, and the United States to explore current trends, issues and solutions. Technology adoption, asset sustainability, supply chain and estimating, power, labour shortage and mental wellbeing were among the key themes that arose. Dr. Gagel dives deeper into these industry challenges. Associations. Pages 56-61. In addition to addressing the current formwork qualification issues and access to government funding for apprenticeship programs, the Formwork Industry Association (FIA) over the past four years has sought to address the safety issue of workers on site. Industry feedback requested the FIA create industry wide and recognised minimum levels of safety to get workers safely on site. As such an initial pathway for workers to receive micro credential learning on formwork specific WHS issues was proposed so that workers can return home safely at the end of theTheday.Safe Formworker Pilot Program was released in early July and will have 300 workers complete the program by the end of October 2022.
12 INSIDE CONSTRUCTION August/September 2022

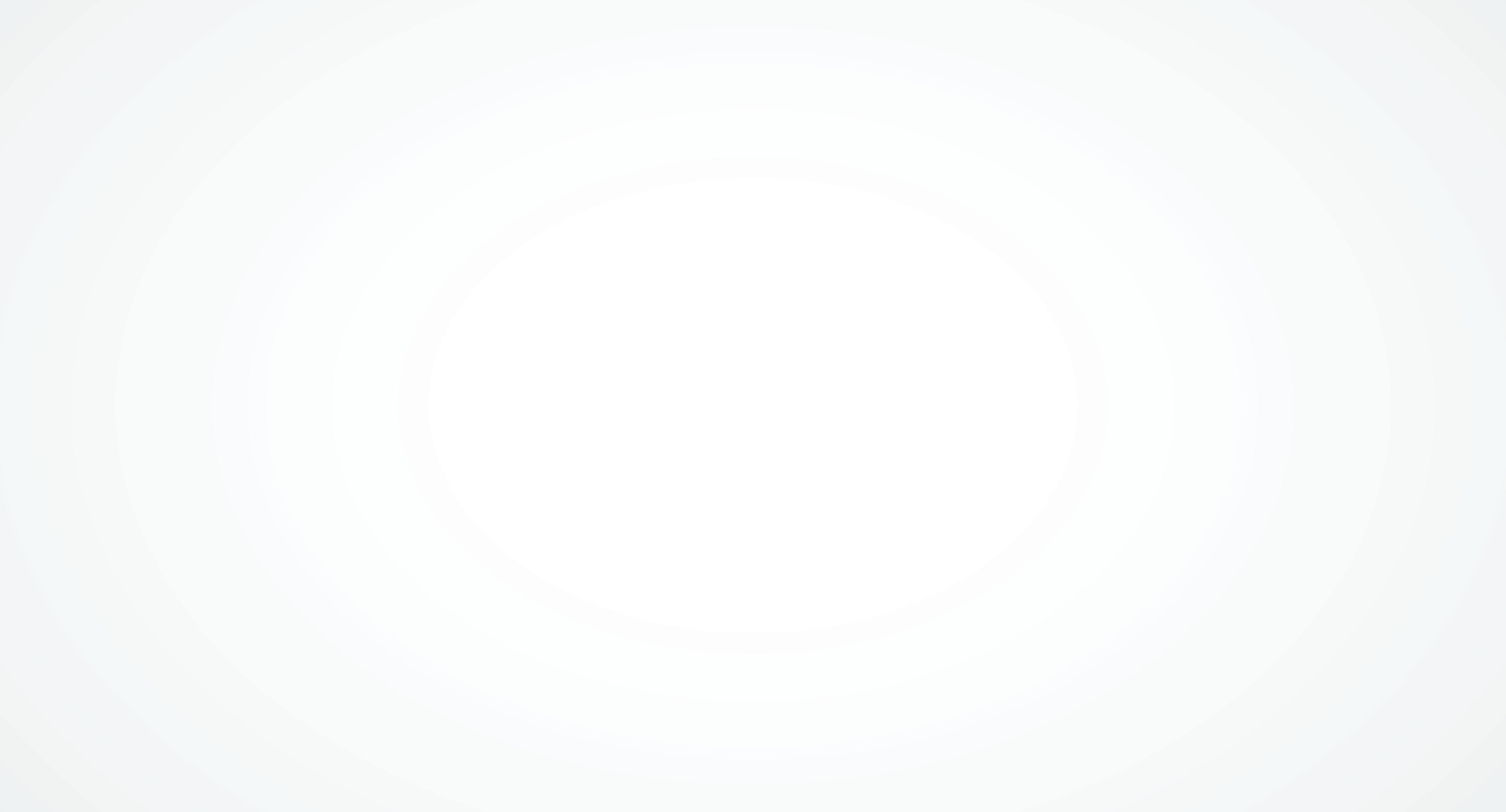
TRANSFORMING THE WAY THE WORLD BUILDS Software for Capital Projects The Evolution of PROBLEMSSOLVING Learn more at InEight.com/Solving-Problems
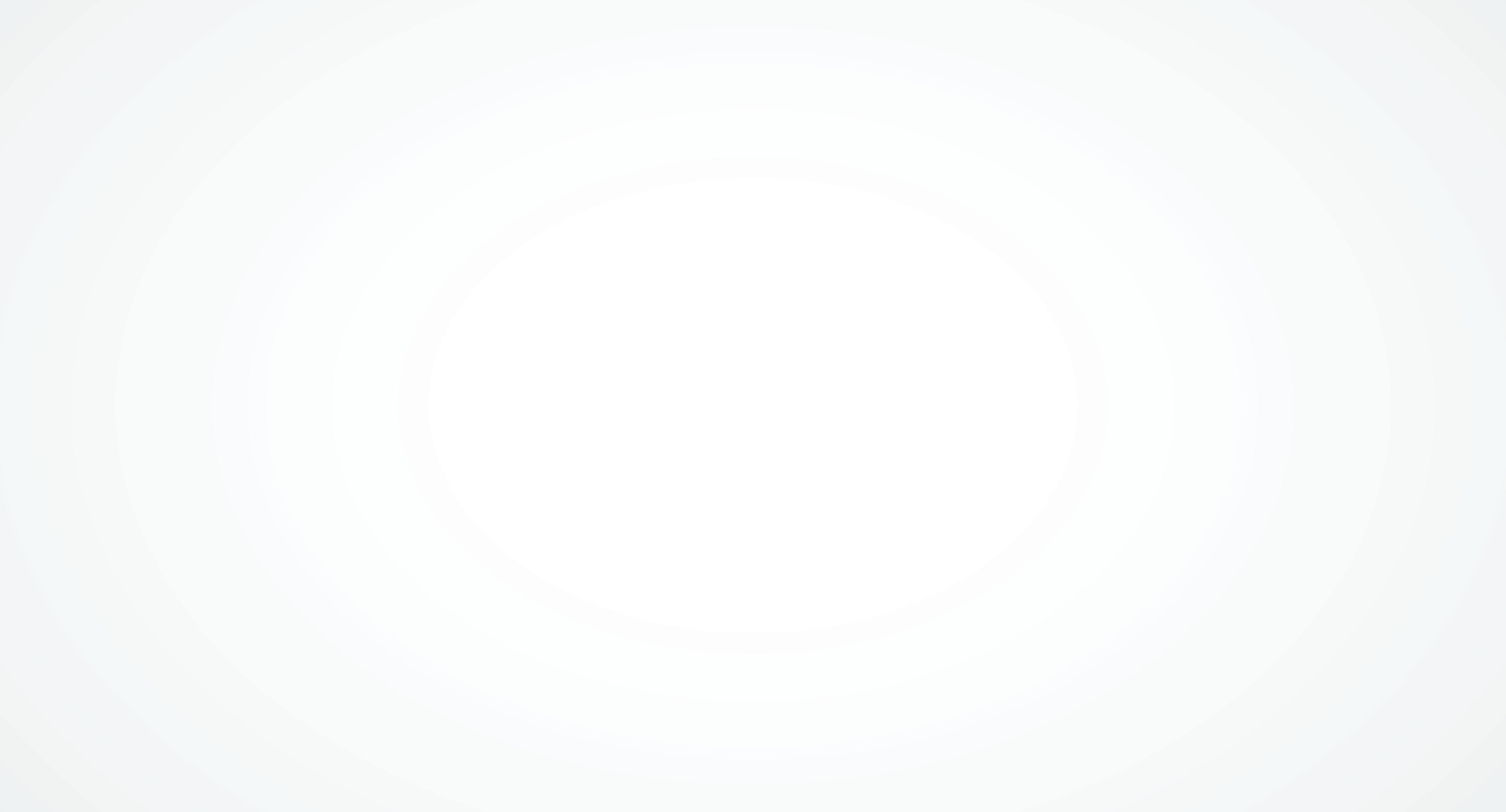
14 INSIDE CONSTRUCTION August/September 2022
Celebrating 25 years of construction excellence
EVENTS Australian Construction Achievement Award ACAA winners2022
The EngineersAssociationConstructorsAustralianandAustralia have proudly partnered since 1997 in presenting one of the country’s leading awards – the Australian (ACAA).AchievementConstructionAward
This year marked a 25-year history of the ACAA. The presentation event, held in Sydney on 4 May, was particularly special with over 450 people energised to celebrate the industry’s achievements. Iconic brands Adbri, Caterpillar, Cbus, InEight and InfraBuild headlined as the ACAA partners – all of whom were deemed part of the industry’s success stories.Witha focus on showcasing expertise in delivering complex and innovative solutions, the ACAA also highlighted the social and economic benefits of infrastructure projects. Projects selected as finalists were all delivered efficiently and in a way that nurtured worker wellbeing, improved the skills of the workforce and promoted environmentally responsible outcomes. Collectively, these features contribute to a more sustainable construction industry and are what makes the ACAA projects the best of the best. Considered to be one of the most intensive award processes, this year’s finalists each underwent a two-stage assessment process by a panel of independent expert judges. Finalists were chosen from initial entries, followed by a detailed judging process by an independent judging panel. Taking the win against an impressive line-up of finalists, the Sydney Metro City & Southwest Tunnel and Station Excavation (TSE) Works by John Holland, CPB Contractors and Ghella Joint Venture was announced the winner of the 2022 LabelledACAA.an‘underground masterpiece’, the project was delivered in the heart of the busy Sydney CBD and included a whopping 15.5-kilometre twin rail tunnel, dive structures and six complex underground stations between Chatswood and Sydenham, including the first rail tunnels under Sydney Harbour.Theproject, which achieved the highest ever ISC Infrastructure Sustainability rating, saw a team of 11,000 people work in challenging geotechnical conditions alongside heritage and live transport infrastructure.
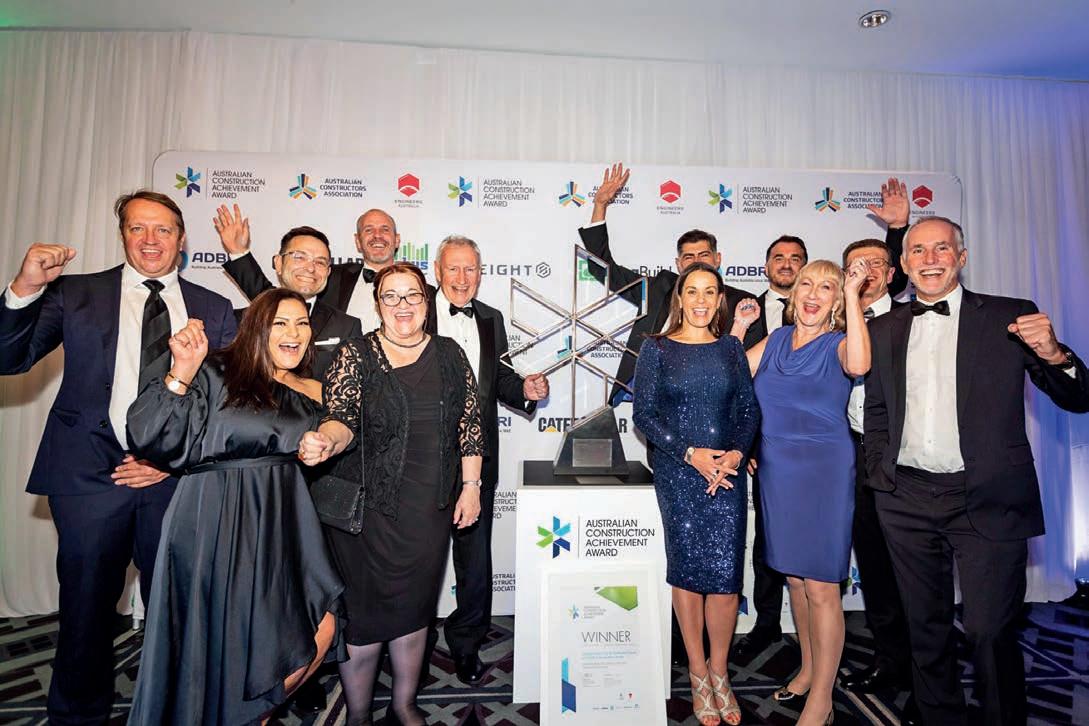
Inside Construction looks forward to attending the 2023 ACAA presentation event in Melbourne on 3 May.
BOOK TRAININGYOURTODAY WORK AT HEIGHT BASIC - 1 day RIIWHS204E Work Safely at Height CPCCM2010B Work Safely at Heights WORK AT ADVANCEDHEIGHT-2days RIIWHS204E Work Safely at Height PUASAR022 Participate in rescue operations WORK IN A CONFINED SPACE BASIC OPERATOR - 1 day RIIWHS202E Enter and Work in a confined spaces MSMPER205 Enter confined spaces MSMPER200 Work in accordance with an issued permit View complete training offerings https://verticalhorizonz.com.au/ RTO Provider Number: 31160 WHAT ABOUT US We believe training leads to safe performances. Our subject matter experts have been delivering real training that saves lives, for over 2 Wedecades.provide structured training solutions to industry; underpinning our training and assessment with nationally recognised qualifications, ensuring the approved Australia quality standards are met. 1800 143 113 or 07 3633 verticalhorizonz.com.auadmin@verticalhorizonz.com.au0153
• T he Regency Road to Pym Street Projec t, South Australia by R2P Alliance - Department for Infrastructure and Transport, McConnell Dowell, Arup and Mott MacDonald
“I’m not a construction engineer by background, but I am constantly in awe of what the construction industry is capable of,” she said. “I can’t help but marvel at the buildings and infrastructure we see nowadays, and I never stop admiring construction projects I walk or drive past, whether it’s the building of a light rail system or the magical task of building a skyscraper in an impossibly small footprint.”
Other FinalistsACAA
“The Award is about more than individual projects, it’s about a more sustainable construction industry, and this is what makes the Australian Construction Achievement Award the preeminent annual award.”
The works were further complicated by the numerous existing infrastructure assets under the Harbour, mining under heritage buildings and the design and construction of massive bespoke formwork for an underground station that won international awards.Onthe award night, Australian Constructors Association President, Duncan Gibb said, “Whether connecting communities, keeping them safe and sheltered or rebuilding after devastation, the construction industry matters in everyone’s lives.”
• Additional Works Package 1 - Cheltenham and Mentone Level Crossing Removal Project, Victoria by Southern Program Alliance: Acciona, Coleman Rail, WSP, Metro Trains Melbourne (MTM) and the Level Crossing Removal Project (LXRP).
• Mordialloc Freeway, Victoria by McConnell Dowell, Decmil Group and Major Road Projects Victoria
• Quay Quarter Tower, Circular Quay, New South Wales by Multiplex Constructions Pty Ltd
• Woolgoolga to Ballina Pacific Highway Upgrade, New South Wales by Pacific Complete – Laing O’Rourke and WSP
The ACAA has been bringing together the best construction projects delivered by the top construction companies in Australia for 25 years.
Chief Engineer, Engineers Australia, Jane MacMaster said the ACAA presentation event is a night for celebration.
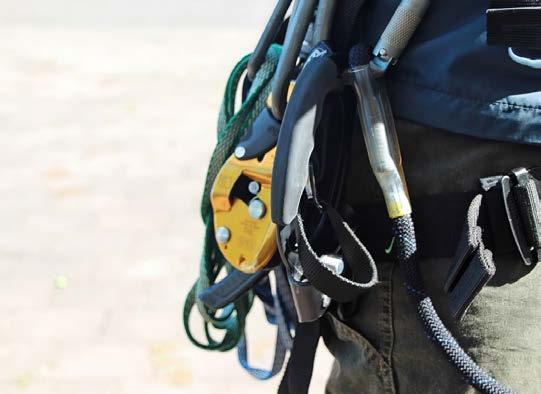
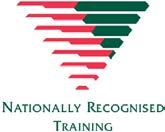
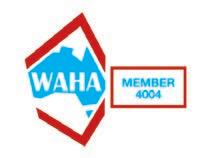
16Helping with the energy shift
The Kidston Pumped Storage Hydro Project in Far North Queensland involves the world first conversion of a disused gold mine into a pumped storage hydroelectric power McConnell Dowell have been successfully delivering complex infrastructure for over 60 years backed by their innovative and creative approach to construction, an approach that marked them as the right partner to take on the first of its kind natural battery storage facility alongside John Holland. Creative Construction is a term McConnell Dowell pride themselves on and the journey to explore and test options with our clients and partners, a willingness to challenge whether there is a better way – all leading to better project outcomes,” says Glastonbury.“Construction is no doubt a very competitive industry and we are seeing lots of evidence across the globe that the sector is finding it tough. It is also a sector of huge interest in terms of investment, particularly in construction technology. This opens the door to new solutions, but it requires constant exploration and testing to find new and better ways.“The very real challenge for me is supporting our project teams to keep the day job running, which is complex, demanding and relentless in its own right, and then also to ask them to consider something new on top of that. Work underway next to the water storage component of the HydroPumpedKidstonStorageProject
COVER STORY Creative construction
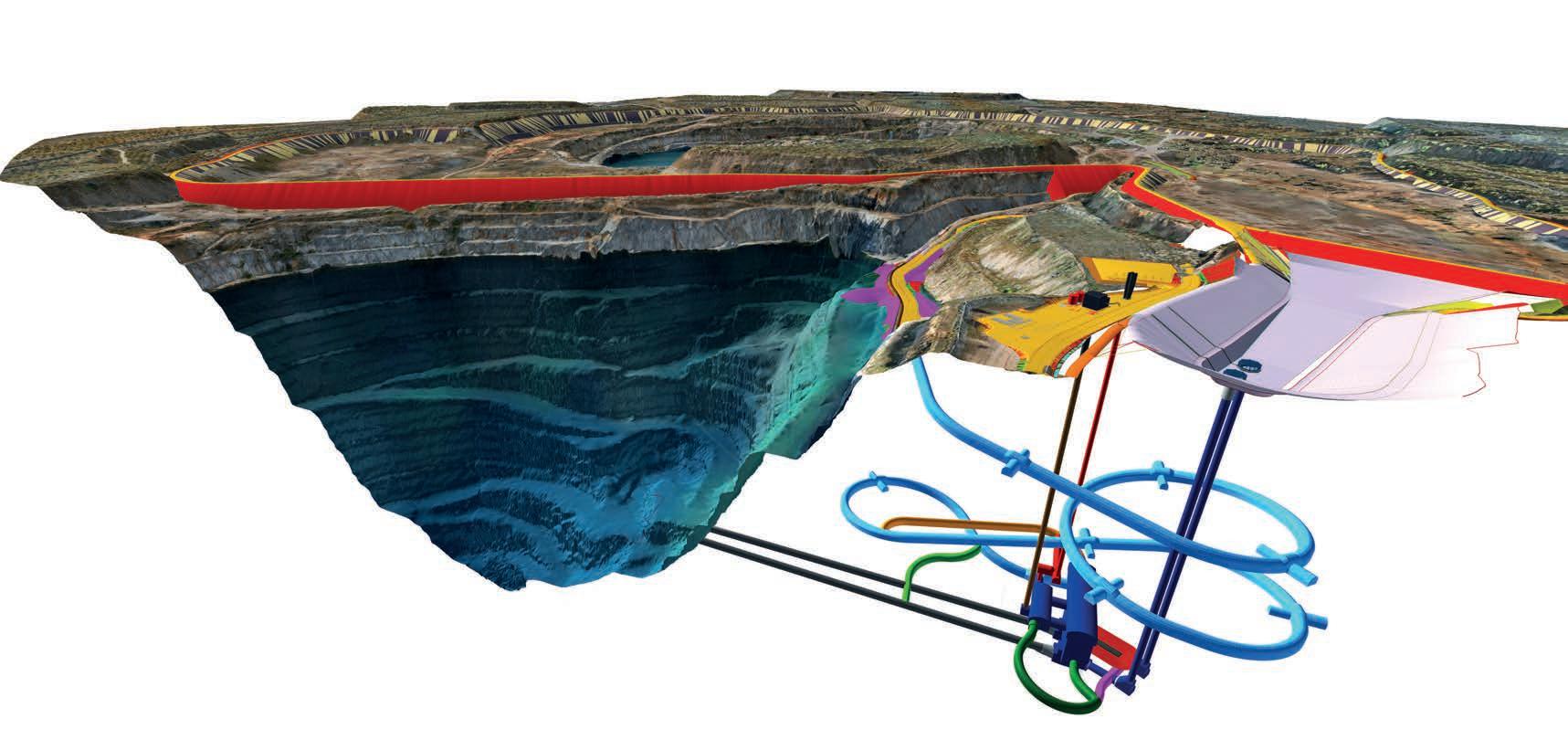
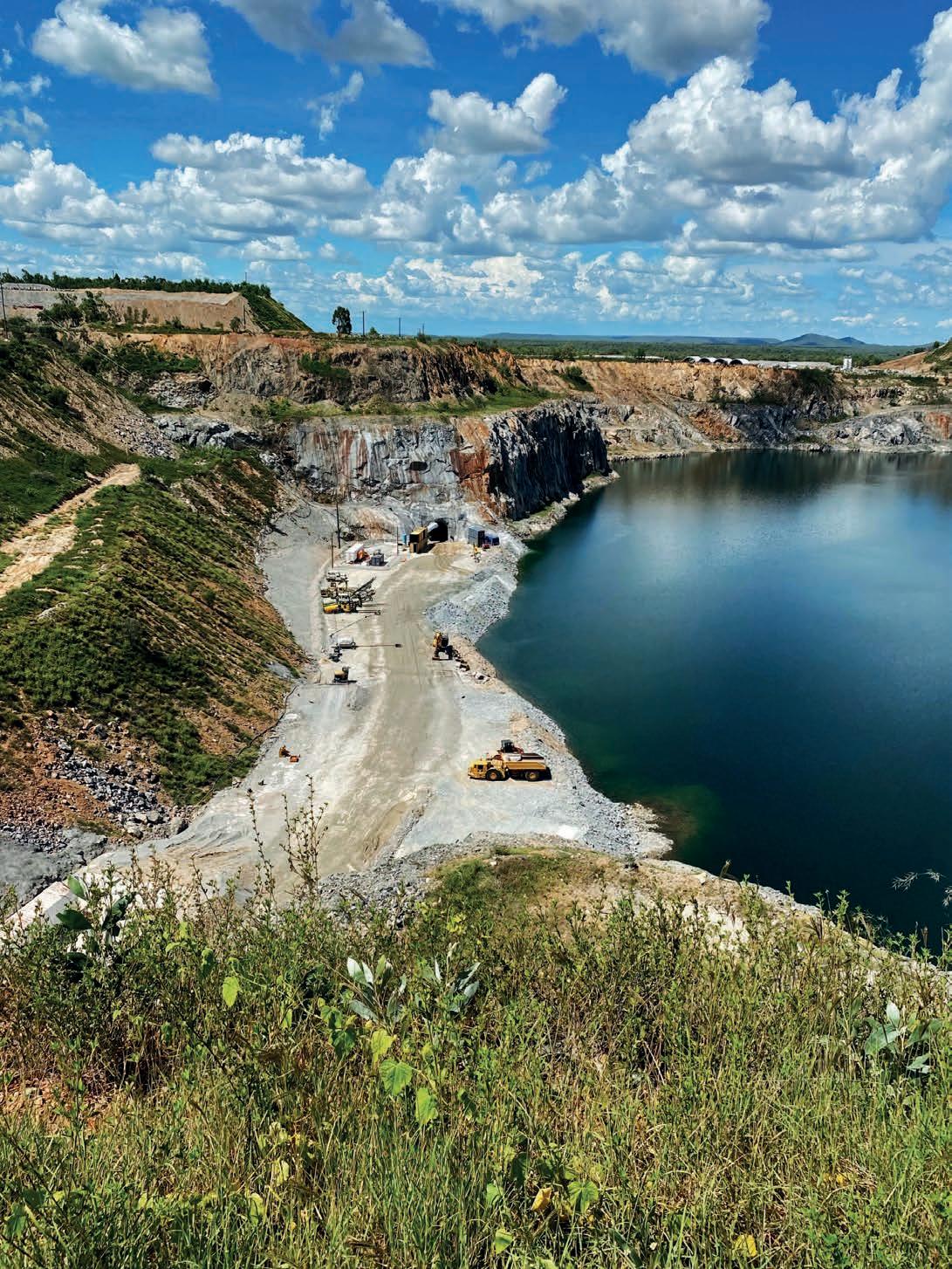
www.insideconstruction.com.au INSIDE CONSTRUCTION 17
It’s akin to trying to change a car tyre while the car is still moving. “I’m constantly impressed with the innovative and creative mindset our teams take and have seen examples across the business of an intelligent technology or method from other industries brought to bear on a construction project, with better results flowing from that. We need to continue to explore not just within but beyond our sector.”
As part of the Western Program Alliance, McConnell Dowell is doing their part in the Victorian State Government’s level crossing removal program which is set to remove 85 level crossings by 2025. Their teams are working with a landscape of relevant technologies such as robotic vision to improve people and plant separation issues. They are also working with a major telco organisation to create a “connected sites” network providing project data and insights. Originally a Geotechnical Engineer by training, James has worked in consulting, research and delivery roles across transport, tunnelling, mining and oil and gas industries. “About a decade ago, I moved across from professional services into construction, into a role that was very focussed on the “positive disruption” of the construction sector. That sparked my interest to explore how to shift an industry, how to challenge entrenched and traditional practices constructively and positively, and how to create the working environment where individuals and teams can think differently,” says Glastonbury. “It is not simply the application of technology that will change our industry. There is no shortage of beneficial technology that can address many of the issues we have in our sector. We have to also look at the culture, the environment and diversity of thinking we create in our teams to help embed this positive change.”Glastonbury says McConnell Dowell teams right across their business continue to explore and identify new ways of working in order to remain competitive, but also because it’s the right thing to do in terms of safety and sustainability.“Thelastdecade or more for me has been about the positive disruption of the construction industry. If we look at the industry scorecard, there is still a lot of work to do to address waste, rework, safety issues, productivity and environmental impact and that’s just to name a few key areas for improvement, so we need to be urgently progressing with the positive disruptors and opportunities for change,” says Glastonbury.
According to the 2021 report from the Clean Energy Finance Corporation, Australian buildings and infrastructure: Opportunities for cutting embodied carbon, up to 10 per cent of national greenhouse gas emissions come from embodied carbon and 28 per cent of emissions come from the building and Extensive digital engineering has been used in the development of the Kidston solution to resolve design interface and construction methodology challenges to explore and test options with our clients and partners, a willingness to challenge whether there is a better way – all leading to better project outcomes.”
Dr James McConnellInnovation,TechnologyManagerExecutiveGlastonbury,General-Engineering,andDowell
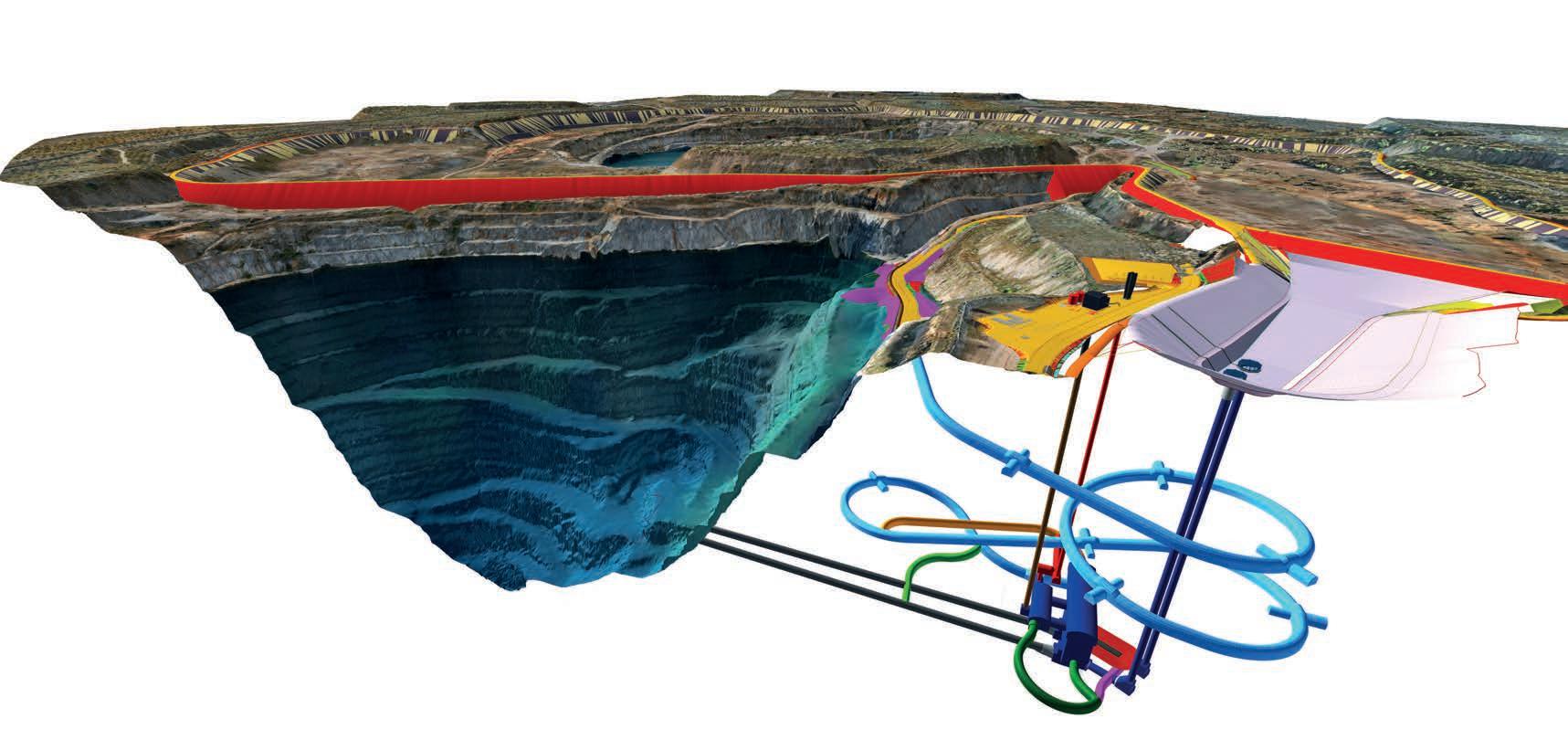

construction sector globally. The construction industry draws far too much on resources around the globe and can play a huge role in challenging and addressing this generational problem.Projects like the Kidston Pumped Storage Hydro Project will help redress some of that broader sector impact as we work towards a more sustainable future. Once completed, the project’s entirely new approach to largescale energy storage will generate enough electricity to power 143,000 homes for 8 hours. Glastonbury says he wants to play his role in helping the business continue in their journey to increase health, safety, quality and productivity in construction. “At the front door of the business there is an invitation to come and join us, but with a clear statement that we want to be creative in how we approach the industry. I think people can recognise that as a trait of the business,” says Glastonbury.“Beingopen about that creative culture provides the platform or fertile ground and certainly makes it much easier to start having conversations with project teams around a new technology or process.”
Creative construction
On the Hūnua 4 major watermain project in Auckland McConnell Dowell’s in-house survey team used LiDAR scanning to capture the existing conditions and produce highly accurate point clouds of the pipe jacking trenches and TBM reception shafts
There is an ever-increasing shift in the construction industry towards procurement models such as early contractor involvement (ECI). Clients are looking to find partners that they can work with at earlier stages to help explore options and then shape a solution, often to inform a financial investment decision or to accelerate getting a project delivered.“Withthe increased general industry trajectory towards this style of engagement, we are often working collaboratively with an owners team and engineering partner to test and validate or rule out options. This environment certainly opens the door to more industry innovation,” says Glastonbury. “We certainly see more of that style of working and there are some interesting opportunities that go with that. For instance,
COVER STORY
18 INSIDE CONSTRUCTION August/September 2022

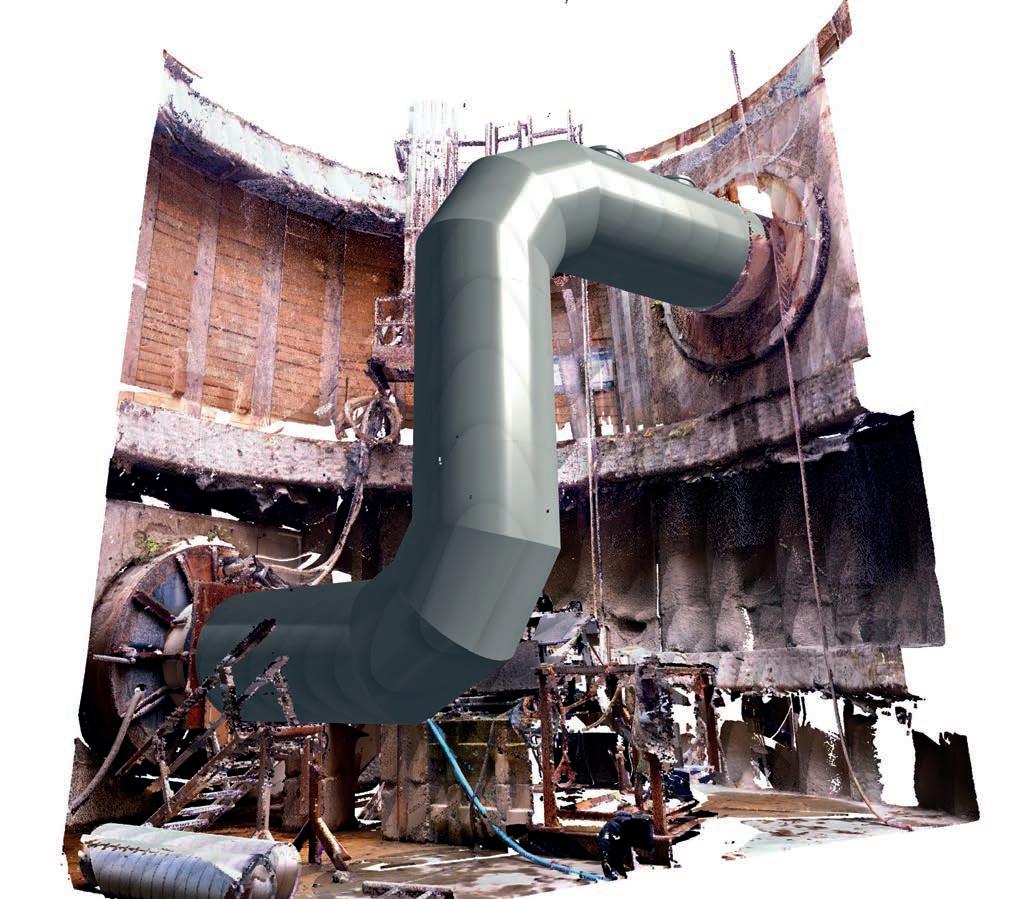
“What we’re talking about in the early definition phase of working with clients is working in the “grey space”. You’re working at a level of ambiguity that requires particular attributes. Practitioners need to be happy to sit in the undefined or the creative space and explore and test options for a little longer to achieve a better outcome, after which you might hand it over to a delivery team to take a well developed plan through to construction completion.“Therearealso obviously some deeply technical skills required when you’re trying to define a scheme such as a renewable energy project. You can’t be in there without the requisite technical skills and something like a Pumped Hydro Scheme requires highly specialist skills and a team that can leverage lessons along the way. “We’re quite selective in what we approach in the market. We’re a business that has some rich experience in particular market sectors and thrive on delivering more complex projects by helping our clients arrive at a complete solution. We don’t simply want to be seen as just constructors, we’re creative thinkers and innovators as well as constructors.”TheKidstonPumped Storage Hydro Project received funding from ARENA (Australian Renewable Energy Agency) as part of their Advancing Renewables Program and is a great example of a valuable contribution in the move towards a more renewable power network in Australia. “The project is currently underway and it’s hugely exciting. There’s a team of people that know they’re working on a world first and
we can start to leverage data-sets to test and validate options more quickly than traditional practice, drawing on a big pool of knowledge from your previous portfolio of experience. It allows you to have different conversations and explore and layer on information to build insights in a way that the industry perhaps hasn’t done in the past.”
McConnell Dowell recently completed the Mordialloc Freeway in Victoria, which won the EnvironmentalawardSustainabilityInfrastructureCouncil’sforExcellenceinOutcomes
“I think there’s a huge opportunity in the world thatbeanddiscussionaandconstructionofdatathatforusisliveandregularpoint,we’llcertainlydoingmoreonfront.”
www.insideconstruction.com.au INSIDE CONSTRUCTION 19

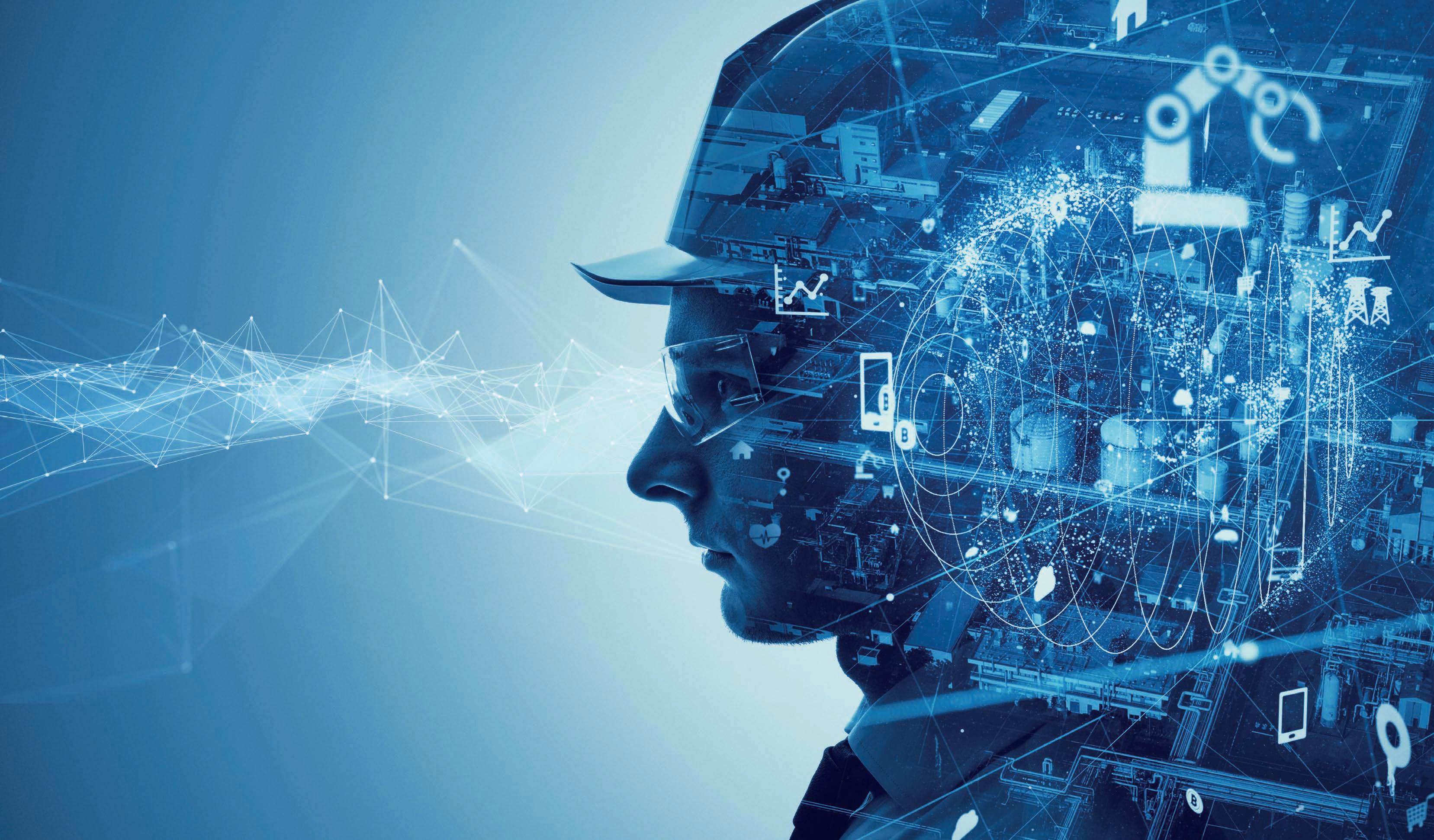
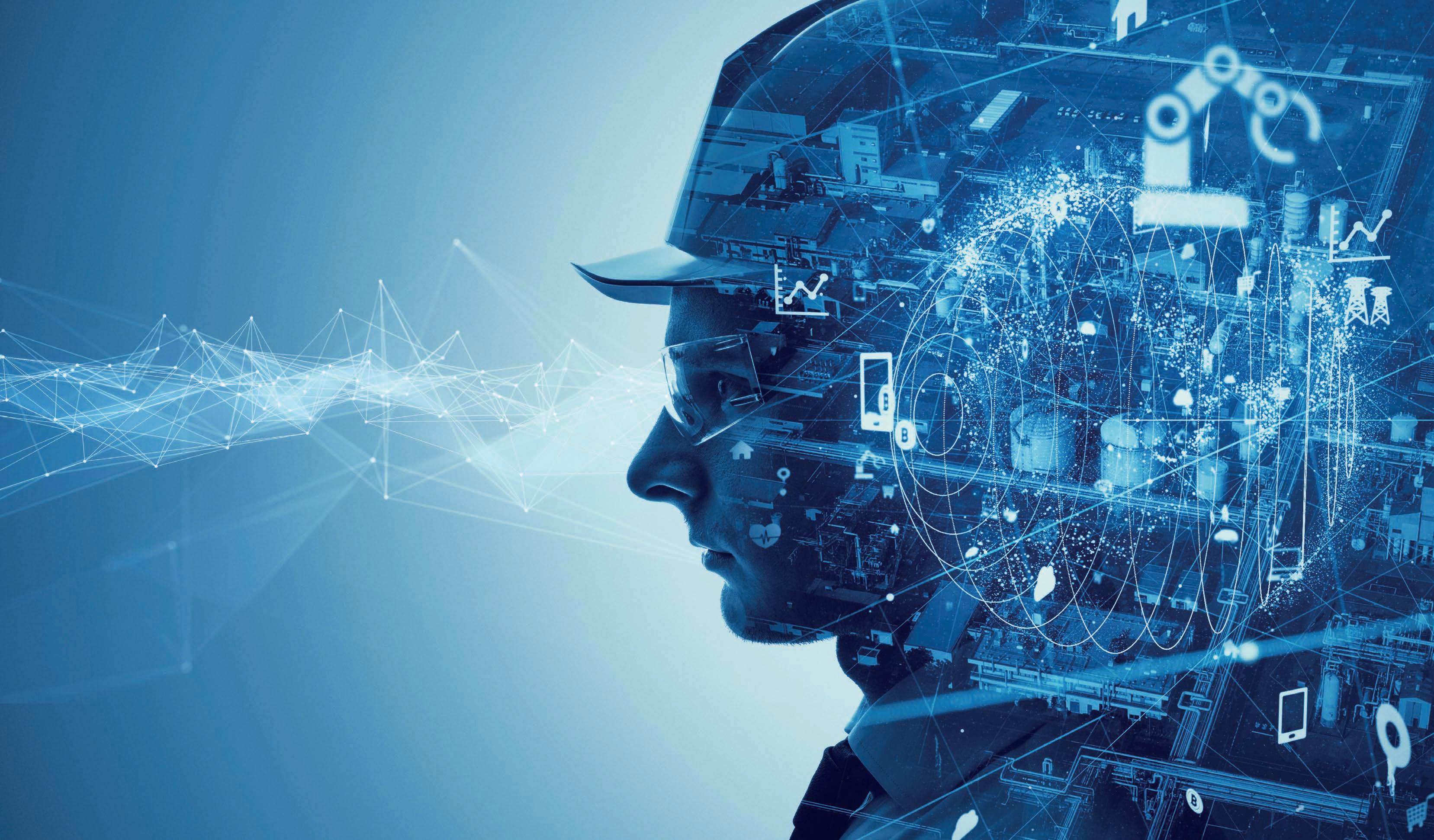
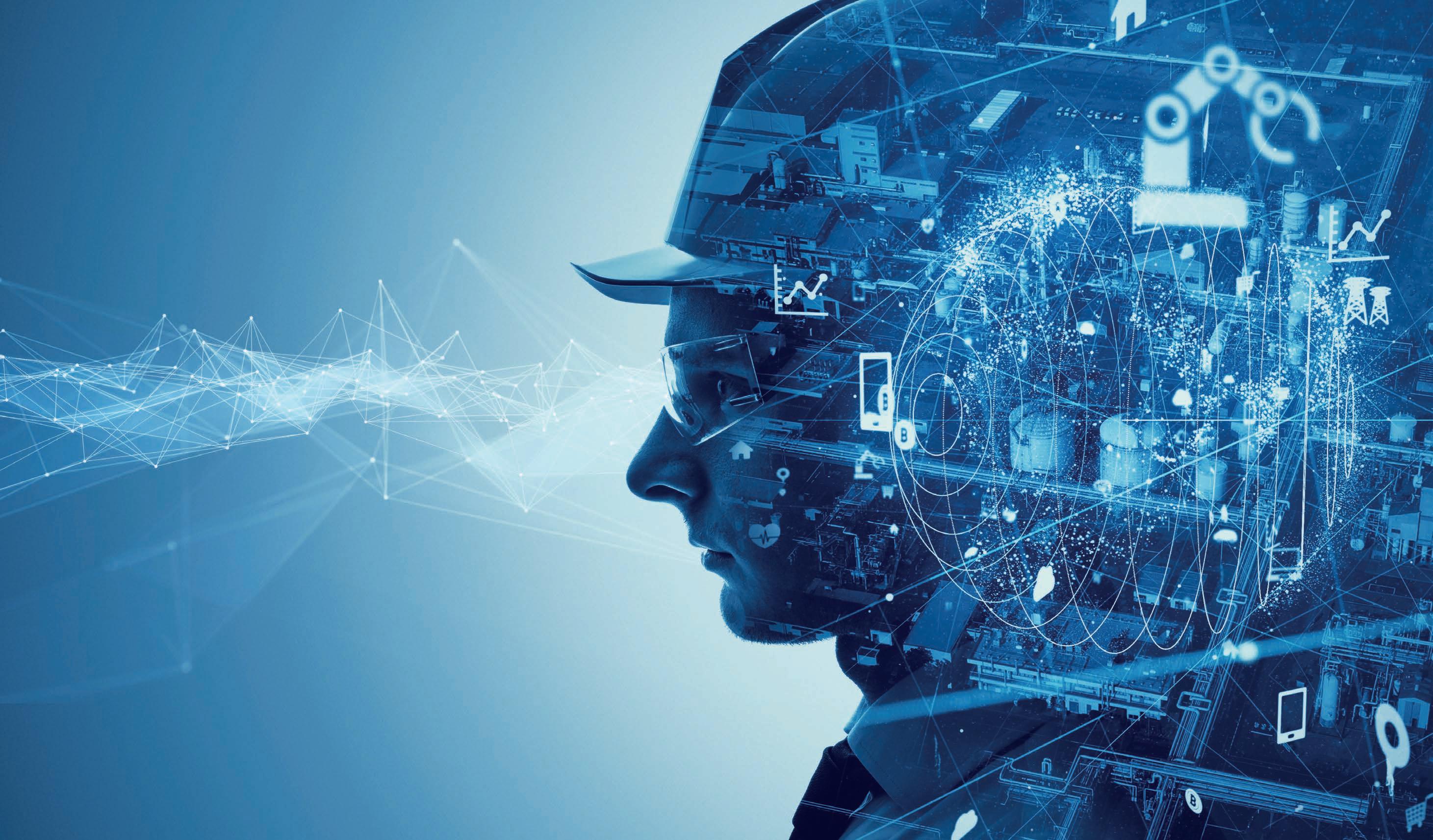
IN PARTNERSHIP WITH AUSTRALIA’S LEADING MANUFACTURING AWARDS ARE NOW OPEN
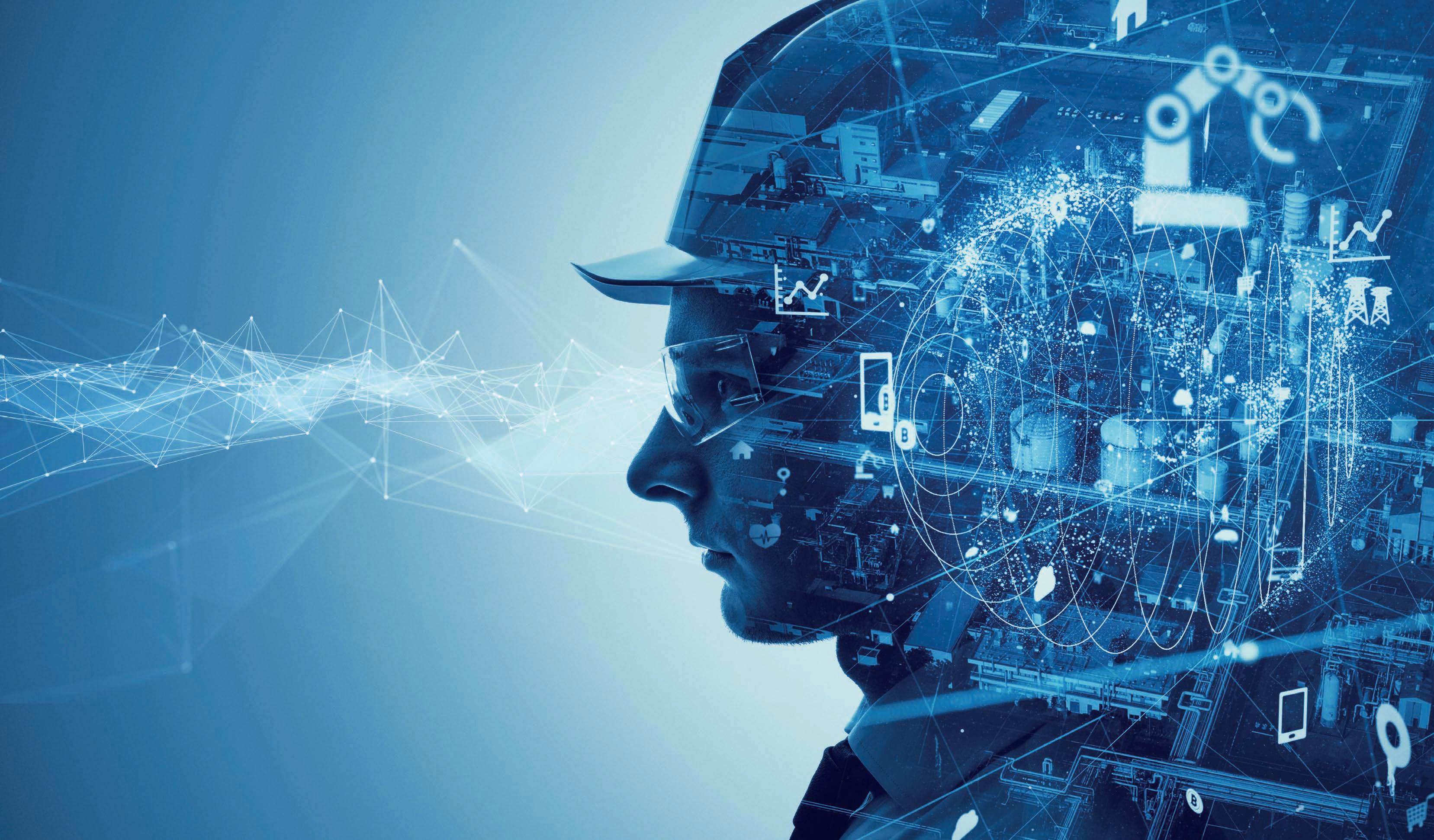
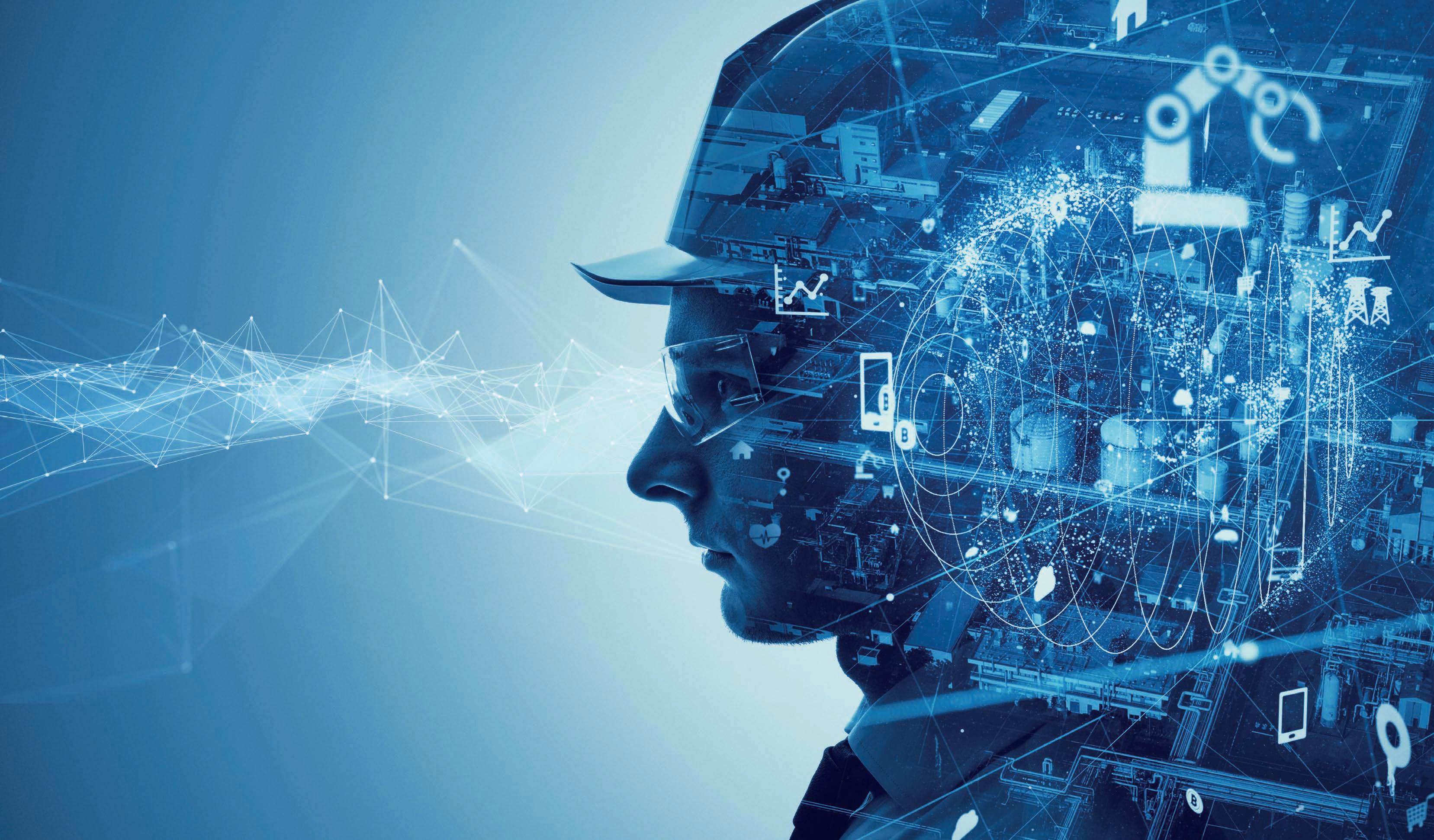
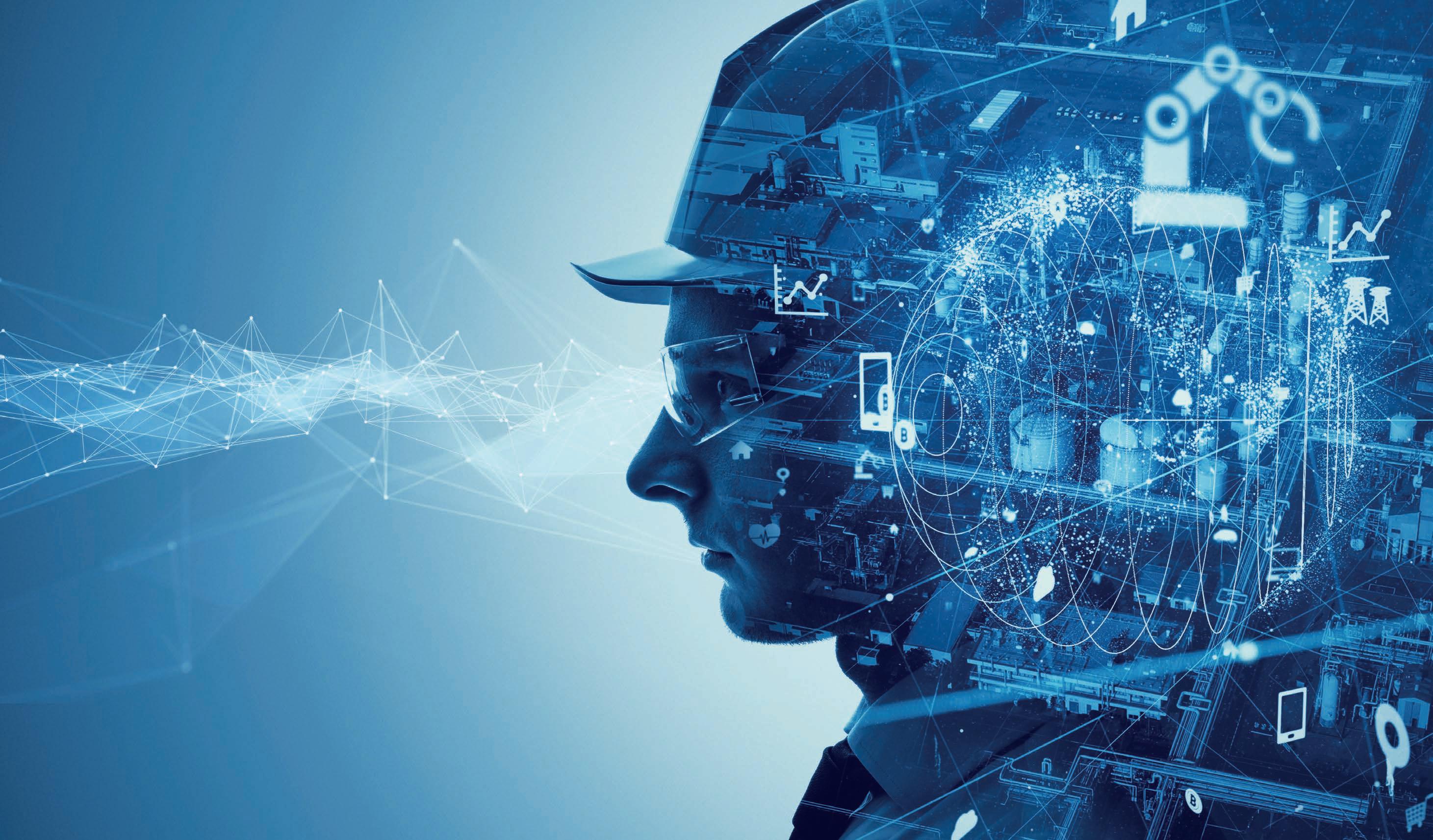
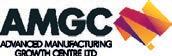
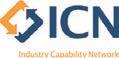
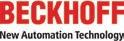
www.insideconstruction.com.au ISSUE 01 AUGUST/SEPTEMBER 2022 Exploring Creative Construction with McConnell Dowell’s Executive General Manager – Engineering, Dr James Glastonbury EnergyShift Helping with the Focus ShowcaseConTechonsafelyatWorkingheights MediaOfficialPartner Inside Construction is a multi-platform publication for the Australian construction industry. It provides a leading source of construction news and insights showcasing the very best that the construction industry has to o er. Or visit www.insideconstruction.com.au, select Magazine Subscription and use our easy online form to subscribe today! Scan this QR code subscribe!to
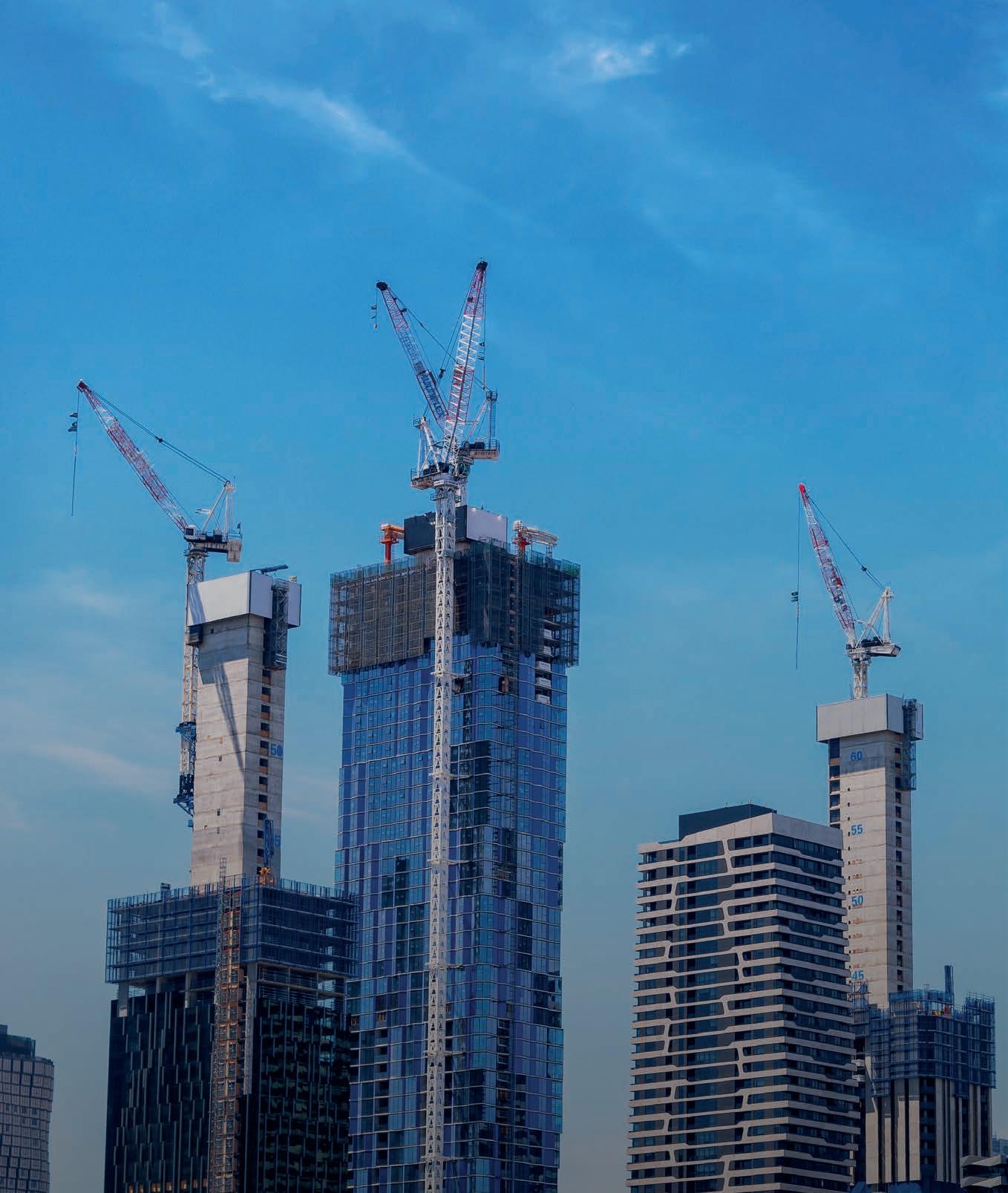
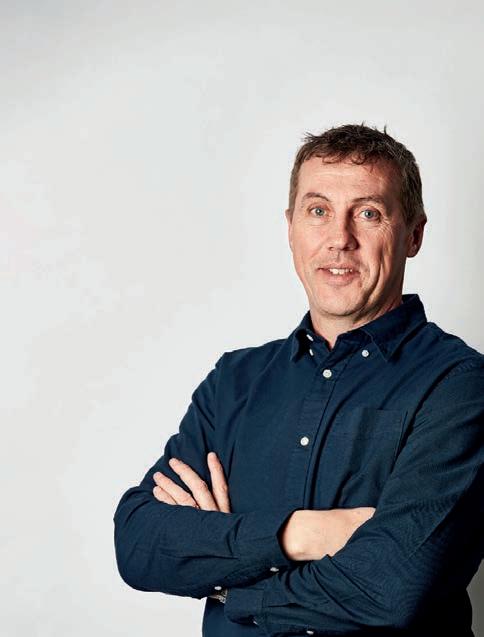

Trimble Viewpoint: scrap constructionthe silos ConTech
FEATURE
The power of ConTech
Truly connected construction is possible through technology Over the years project management and project management software for construction has evolved in massive ways. Many of the tools and methods we use today have been tried and tested over centuries, but much has changed in ways our predecessors could never have imagined. As technology has advanced so have the ways in which we plan, construct and develop everything from bridges, schools to skyscrapers, hospitals and everything in between. It’s an industry that is constantly innovating and if you want to stay at the top of the pile you need to be prepared to move with the rapidly changing times. As construction and technology both become more advanced the traditional siloed approach to managing construction projects becomes problematic. This perspective can lead to real problems in the efficiency of a project which could cause irreparable damage both to the project and a company’s brand. Instead, today’s modern construction projects need a connected, real-time construction management experience. This allows the data, workflows and complexities of projects to be easily shared, analysed, discussed, communicated and understood, and result in meaningful action across every phase of the construction project. Trimble Viewpoint has 11,000 plus employees and more than 1,200 construction technology patents worldwide. The company’s approach to creating connected construction environments with the introduction of their innovative software has seen it become an industry leader in
www.insideconstruction.com.au INSIDE CONSTRUCTION 23
“Our global product strategy, software.”managementwithyoureveryefficientlyOurthethatalsosolutionsconnectsOneConstructionTrimble,notonlyourownbutit’saplatformconnectsindustry.productsmanageaspectofbusinessdatadriven
In the construction sector, technology holds the keys to unlocking productivity – improving efficiencies, reducing costs, increasing speed of delivery and delivering better outcomes. Construction companies are increasingly looking for innovate ways to plan, design, and build. This month we caught up with industry leaders in the ConTech space to explore the technology solutions shaping the future of construction.
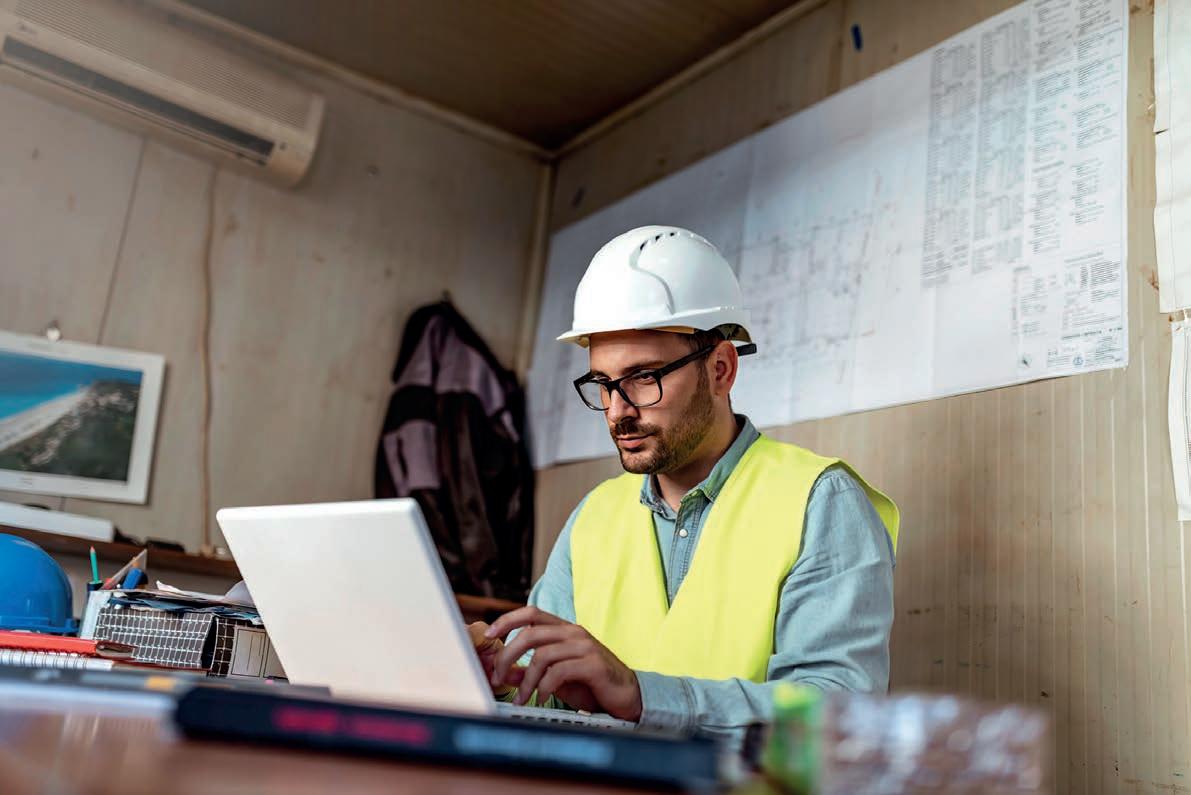
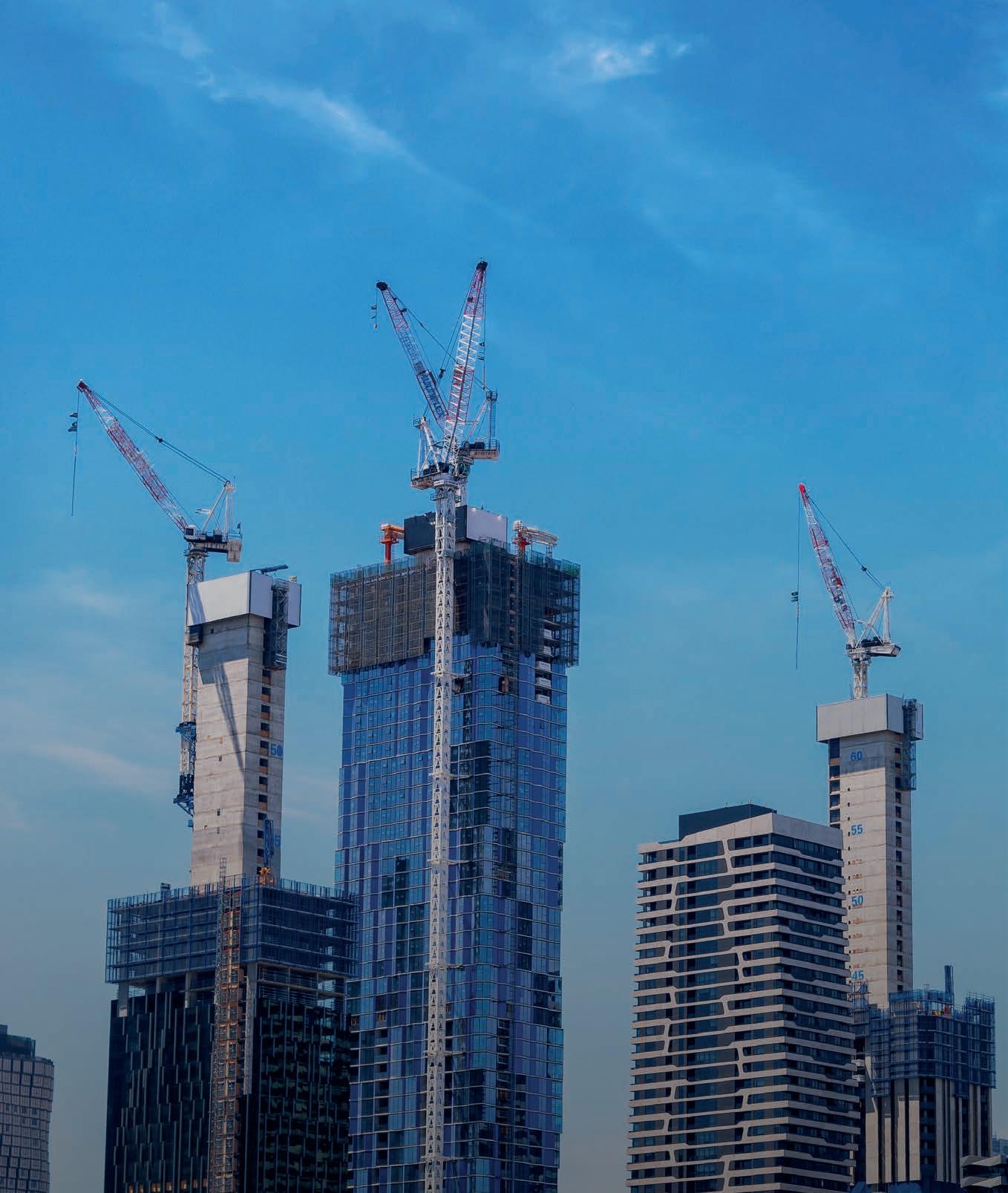
version. Moving from a paper system to a digital system doesn’t necessarily make a company more efficient. In most cases it simply just shifts the problems to a new place. Having a single point of access and information for the various aspects of a construction project can do wonders for efficiency. Bringing together everyone to collaborate under one platform with a single source of unified data is proven to have a meaningful impact on the success of a project, meaning constructors can keep their team and clients happy at the same time. But the connected construction experience can also offer so much more than this; the benefits are truly wide-ranging. Bringing everyone together earlier in the process can help identify potential choke points later in the project that might not have been noticed if working in silos. This can result in everything from fewer change orders and less wasted time and materials right through to lower project costs, which in turn means more profit.
“And that drives efficiency, it drives accuracy, it means less rework and in turn that generates cost savings, reduces risk and improves margins.”Collaboration also offers the potential for innovation, as people come together to share the construction technology sector. Andrew Tucker, APAC senior product manager for Trimble Viewpoint says a connected construction environment is necessary for ANZ contractors’ success. “Our global product strategy, Trimble Construction One, not only connects our own solutions but it’s also a platform that connects the industry. Our products efficiently manage every aspect of your business with data driven management software,” says Tucker.
Construction project management software needs to be connected with real-time data and workflows in order to be efficient and successful and keep project teams on the same page. The siloed approach just doesn’t cut it anymore.
“Data connectivity is critical right through the ecosystem of stakeholders from the extended teams of architects and engineers to project managers and finance teams,” says Tucker.
Moving the problem isn’t solving it
A 2020 survey highlighted that nearly a quarter of all construction companies are using six or more separate applications to manage their daily operations. On top of this Trimble Viewpoint’s recent research found that some 48% of project managers said their project management software had only basic or no data and workflow connections among the other software systems in their company. When the systems and applications don’t talk to each other then problems start to arise. Most commonly, companies have had to manually input the information in several different places, leaving a wide margin for humanHavingerror.multiple versions of the same document across various platforms then brings with it the potential headache of ensuring everyone is working from the right
FEATURE ConTech
24 INSIDE CONSTRUCTION August/September 2022
“Trimble Construction One means everyone in the business is working on the same set of data. There’s no double data entry, there’s no working on old plans, everyone’s working on the same set of data at the same point in time.
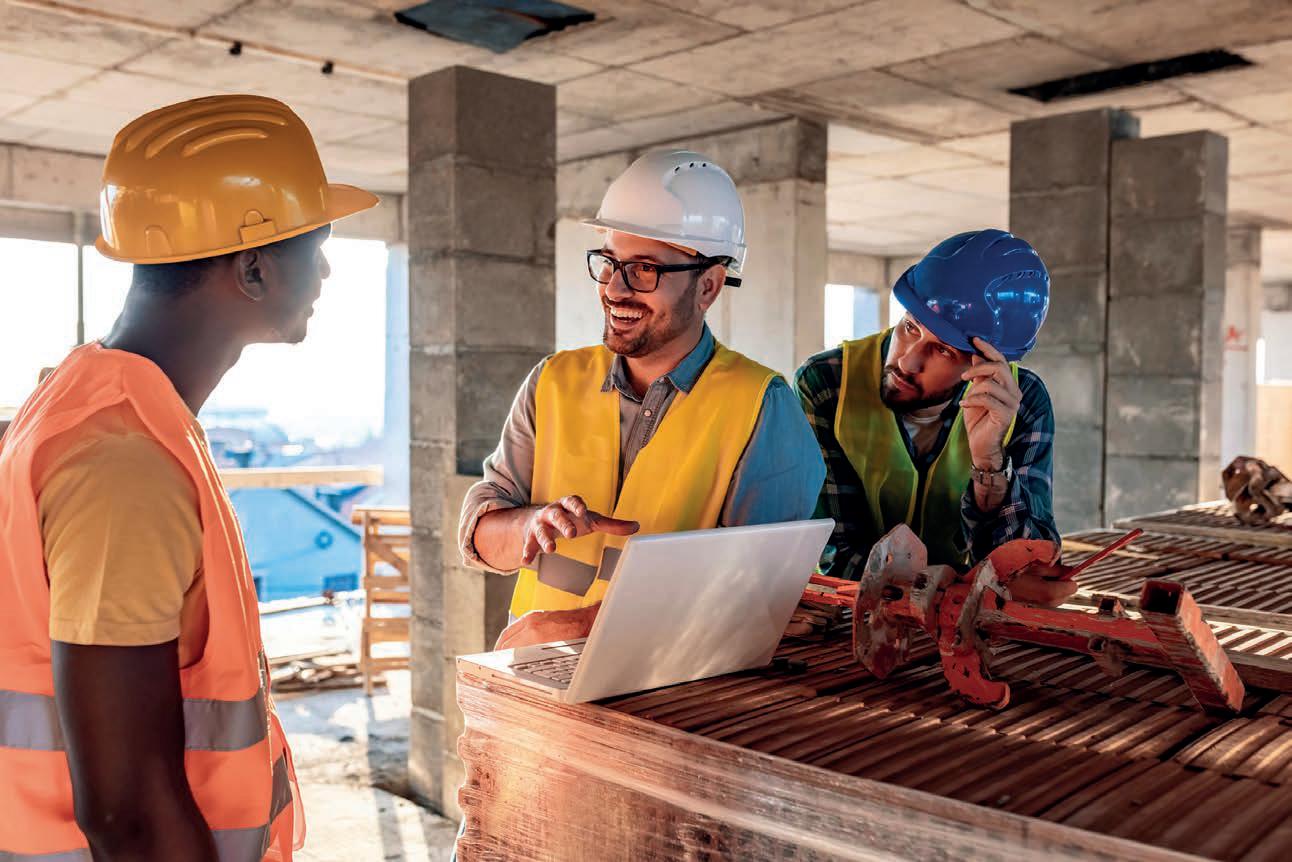
“ESG and sustainability is hugely important to us here at Trimble Viewpoint,” says Tucker. “With everyone working from the same set of data, it means you’re building it right the first time. It means there’s less rework which drives down material usage and makes everyone more efficient throughout the entire construction lifecycle. Trimble Construction One has an immediate impact on“Takesustainability.abulldozer for example. Previously you would have to work to a 2D plan, you’d have to have someone driving the bulldozer around, you’d have a surveyor going out and checking the levels, you’d be filling and cutting and repeating that work until the levels were correct. Today a bulldozer can be connected directly to the digital model and it becomes a 3D printer of the landscape. It means we can deliver automated machine control into things like bulldozers, they can then automatically operate to the millimetre and get it right first time. And that’s just one example of how, by connecting the digital and physical world, we can really make the industry more efficient and more sustainable.” Change it up and reap the benefits It’s probably a pipe dream to imagine that silos will ever truly be a thing of the past, but that’s no reason to stand idly by. The old mantra of ‘we’ve just always done it that way’ simply doesn’t cut it if businesses want to stay relevant and profitable. Tucker says it’s important when making the step to software integration that businesses find a connected construction suite from a reliable technology vendor and ensure the connected project management software includes automation tools to simplify matters.
www.insideconstruction.com.au INSIDE CONSTRUCTION 25 ideas and knowledge, which can only really be a benefit for construction businesses and potentially the industry as a whole. Scrap the silos The evolution of the construction industry is not going to stop anytime soon. As technology continues to advance the industry will need to follow suit as new concepts and ideas come to fruition. Scrapping silos and embracing connected construction workflows is vital. The silos that have become common in construction are hampering the industry now and not only from an efficiency perspective. Removing them can also reduce human error, improve sustainability, streamline complex workflows and crucially, save businesses money.
Visit Trimble Viewpoints website for more on its products and services at www.viewpoint.com/en-au/ “Companies that are taking that step to invest in and adopt incompetitivegettingthatthetechnologiesconstructionnewarecompaniesarereallytheedgetoday’sworld.”
Today technology is playing a large role in bringing project teams together, even when they’re physically disconnected, and the right connected cloud solution can facilitate teamwork and collaboration. “Companies that are taking that step to invest in and adopt new construction technologies are the companies that are really getting the competitive edge in today’s world,” says Tucker.“It’savery difficult market at the moment so it’s important now more than ever to adopt new technologies that are the key to downward pressures on cost, preserving your margins and making your business more efficient.”
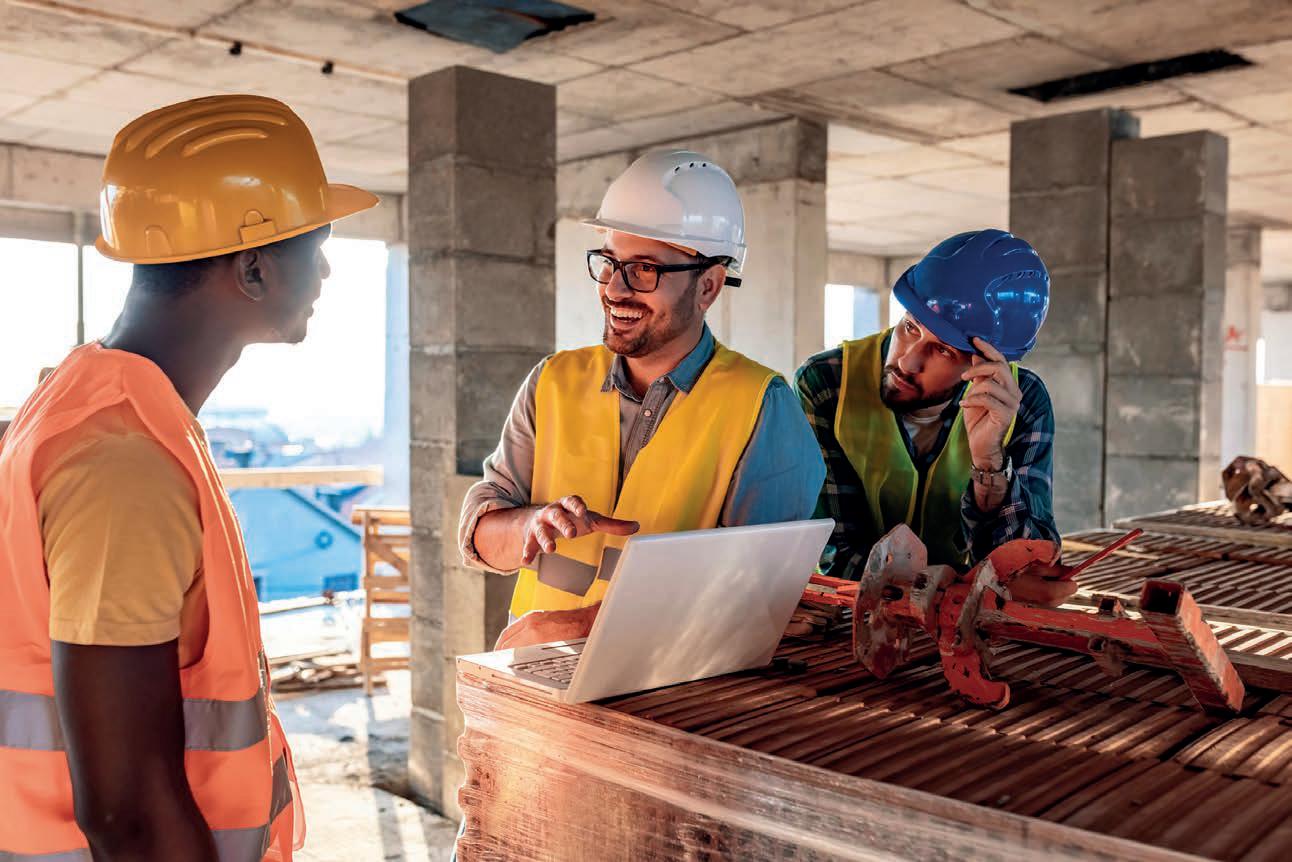
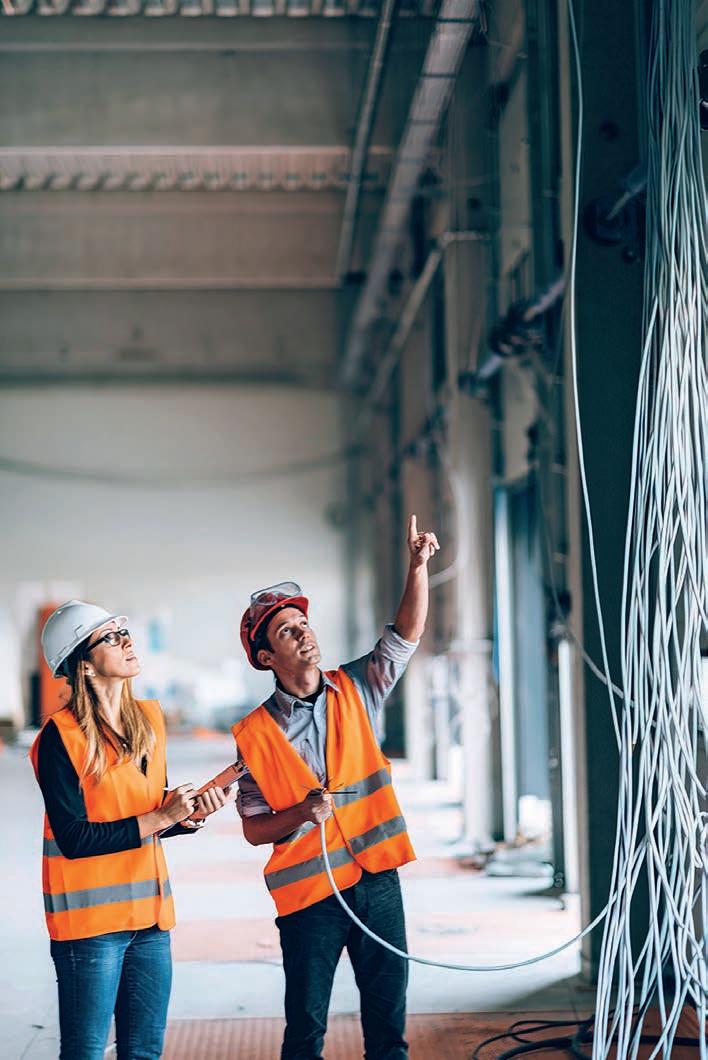
A realistic approach According to this year’s GCPO report, which surveyed construction professionals from the Americas, Europe and APAC, APAC respondents are now the least likely to have a clear digital transformation strategy, yet they are most likely to take a disjointed approach where different parts of the business invest in technology according to their own needs. This contrasts sharply to last year, when the region had more organisations with clear integrated digital transformation strategies. Rob Bryant, EVP for APAC at InEight, offers an explanation. “What we’re seeing is a bit more sober thinking. As recently as last year, there was a lot of buzz and excitement around digital transformation and digitalising processes,” he says. “Now respondents are seeing the reality of what’s involved and that it takes a lot more than just installing software. It’s changing organisational processes. It’s considering everything right through the supply chain to the construction methods used on-site. So perhaps last year, we caught the tail-end of a wave of initial enthusiasm that led to a lot of investments in point solutions, and now the next step is to recapture that enthusiasm and momentum and apply it to more integrated thinking.”
APAC respondents are also most likely to want their organisation to fund technologies that help keep them updated with real-time information, a feature of organisations with more integrated digital strategies and connected data.
Working to enhance communication Disconnected digital adoption is also impacting APAC communications, efficiency and project performance. When asked about the biggest challenges to projects being completed on time and on budget, APAC organisations are now most likely to cite communication gaps and/or inadequate communication with stakeholders and inefficiencies arising from non-standardised systems and processes.
26 INSIDE CONSTRUCTION August/September 2022
In the InEight Global Capital Projects Outlook (GCPO) report for 2021, APAC was the most technologically forward-thinking global region surveyed. Yet this is an achievement the region has been curiously unable to replicate according to this year’s 2022 report. Is this a case of first-mover disadvantage? Or perhaps experience has given a more informed, mature view that has tweaked the balance between enthusiasm and realism?
The construction industry is changing how it thinks about, and approaches, its most essential processes. There is a clear demand for more accessible and actionable insights among employees and digital transformation is now seen as the greatest opportunity for future growth.
Encouragingly, however, the region is now most likely to cite digital transformation as the biggest growth opportunity in the comingImprovedyear.data analytics is seen as the technology most critical to success over the next one-to-three years.
Brad Barth, Chief Product Officer at InEight, weighs in on these developments. “A patchy approach to digitalisation hampers projectwide collaboration, communication and standardisation. It also prevents organisations connecting the data dots to identify broader growth opportunities,” he offers.
FEATURE ConTech
InEight: a maturing view on construction digitalisation
“Progressive project delivery models such as design-build and integrated project delivery increasingly demand a level of multiparty visibility, collaboration and integration that will require more integrated digital strategies. A typical project we worked on in Australia required real-time communication and oversight across a complex partner network spanning 12 design and delivery organisations.”APACcompanies also now prioritise narrow, short-term concerns such as organisational efficiency or cost savings over holistic, higherorder needs such as improved productivity or preserving knowledge when it comes to the benefits of a greater technology investment. “When organisations see technology as delivering short-term individual benefits such as time or cost savings, this leads to suboptimal implementations,” Barth continues.“Thosethat view technology as fundamental to scaling the overall business, informing smarter decisions, and identifying broader business risks and opportunities adopt more holistic, joined-up strategies.”
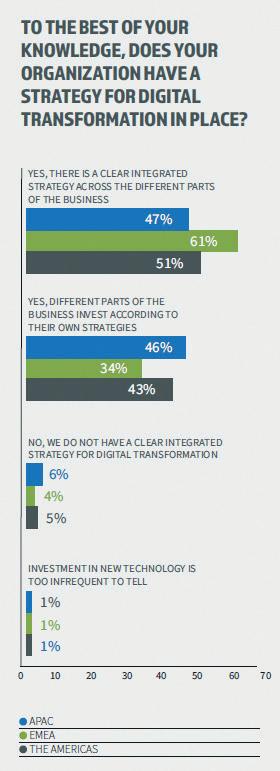
Stepping up sustainability
“There are a lot of sustainability leaders in APAC, and the recent election in Australia, for example, shows how the tides are shifting in the region. That said, in terms of construction, we’re at the start of this journey and a lot will depend on effective standardisation,” he says.
“At the moment, stakeholders are pulling in different directions and lack a unifying framework for what good practice looks like. For example, owners prioritise things like energy efficiency and sustainability in the operational performance of the finished project, whilst contractors are more interested in the materials and construction processes used. There’s a big role for technology and data to provide some alignment right from the beginning.”
Looking to the Future APAC’s early digital lead has eroded somewhat as others have caught up. The next step will be for the region to regain its momentum and adopt more integrated approaches to digital transformation based on holistic thinking and higher-order needs. This will unlock the heightened efficiency, transparency, standardisation and collaboration essential to many modern project delivery models and contracts.Fortunately, there is clear and unabated desire in APAC for new technologies among employees. The key will be aligning digital transformation across all departments and divisions based on a holistic view of technology as fundamental to collective performance. About InEight InEight provides field-tested project management software for the owners, contractors, engineers and architects who are building the world around us. Over 575,000 users and more than 850 customers worldwide rely on InEight for real-time insights that help manage risk and keep projects on schedule and under budget across the entire life cycle. From pre-planning to design, from estimating to scheduling, and from field execution to turnover, InEight has powered more than $1 trillion in projects globally across infrastructure, public sector, renewable energy and power, oil, gas and chemical, mining, and commercial. For more information visit InEight.com “Those that view technology strategies.”holistic,adoptopportunitiesrisksbroaderidentifyingdecisions,informingoveralltofundamentalasscalingthebusiness,smarterandbusinessandmorejoined-up
www.insideconstruction.com.au INSIDE CONSTRUCTION 27
One important field in which APAC leads the world is sustainability. Eighty-three percent of APAC organisations have invested in improving sustainability compared with 74% in Europe and 82% in the Americas. They are most likely to achieve this through lean construction, internal training, or collaboration with external partners such as consultants to improve processes. For Bryant, this is an exciting development.
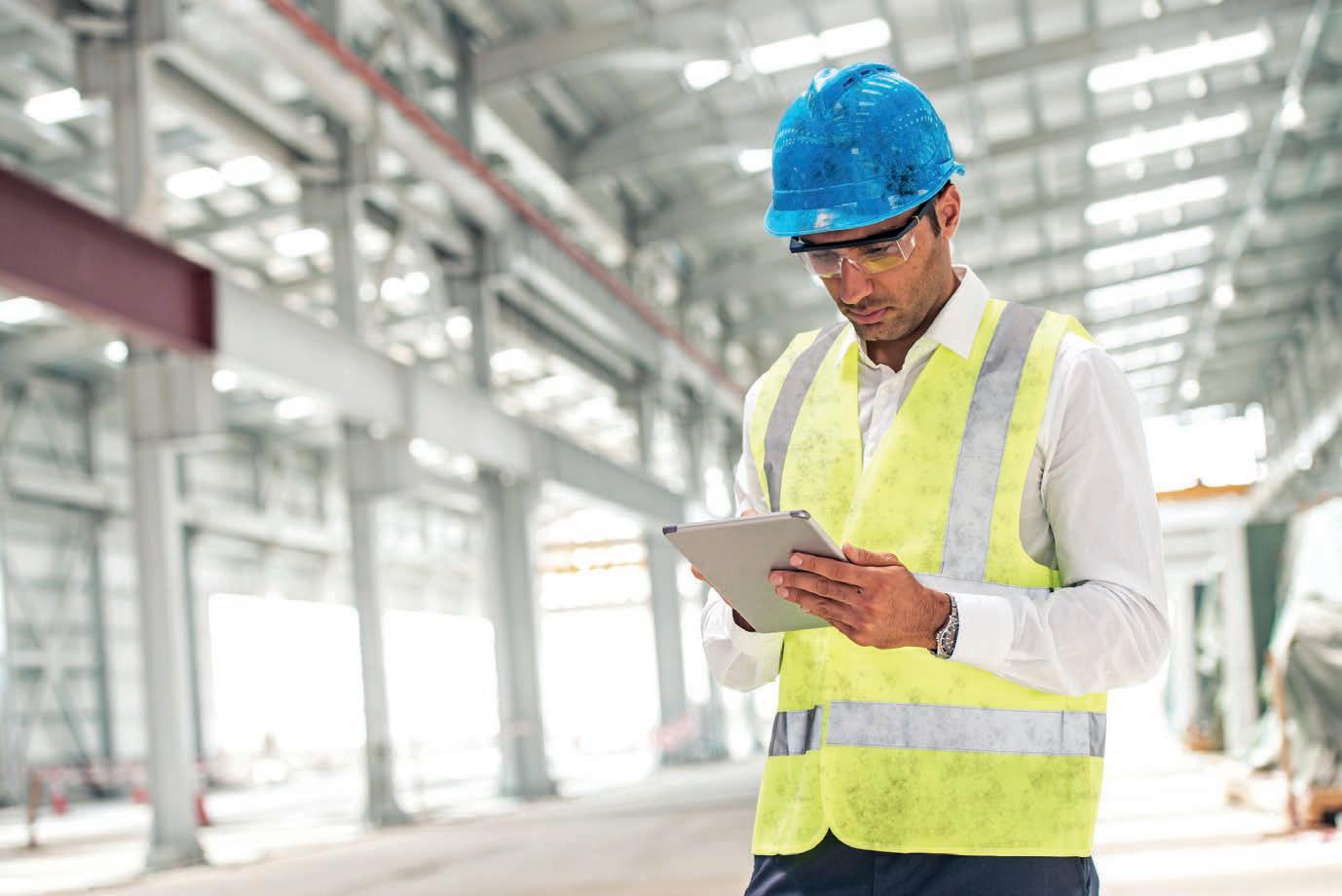
No matter what sector of construction you’re in, you’ll leave CONEXPO-CON/AGG with new ideas, new relationships, and new opportunities to grow your business, and your place within the industry. This isn’t just North America’s largest construction trade show, it’s taking construction to the next level. LEARN MORE AT CONEXPOCONAGG.COM 250,000sqm of exhibits / 130,000 attendees / 1,800 exhibitors / 150 education sessions TAKING CONSTRUCTION TO THE NEXT LEVEL.2020AttendeeMissy Scherber, T. Scherber Demolition & Excavating MARCH 14-18 / 2023 / LAS VEGAS / NEVADA
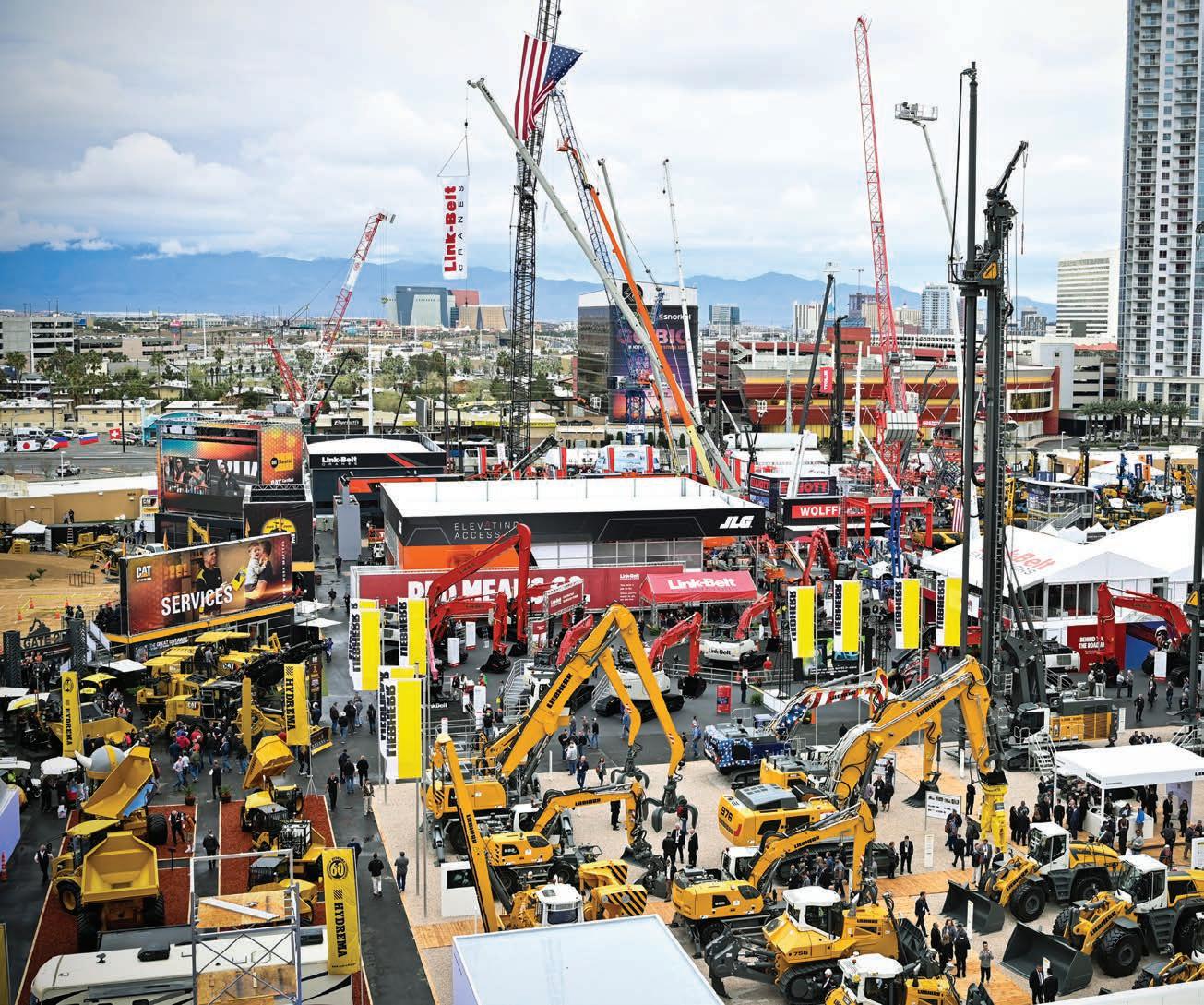
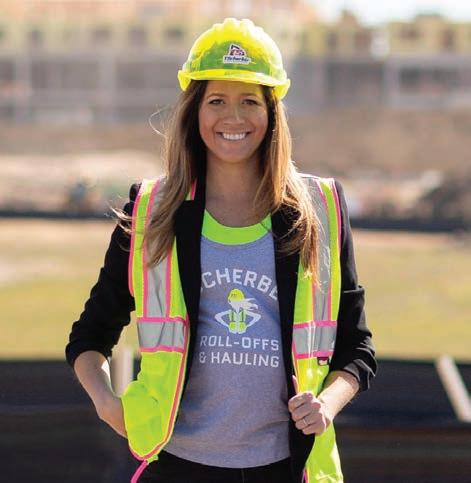
The problem is each individual product they purchase then just sits on an island. The first step they usually take is to build these islands within their business and eventually get to a point where they realise they need a better way to manage their data.”
COINS transforms the construction industry
A leader in construction management software and services, COINS provide end-toend business solutions through technology that can be tailored to a particular customer’s needs. Their complete product suite is called COINS Construction Cloud and provides COINS with the flexibility to address different markets, primarily in the construction, engineering, home building and service sectors. Their services are designed to support medium to very large, complex projects across the four different sectors. In construction and speciality engineering, COINS implement their software to coordinate and manage large workforces and increase productivity, profitability and certainty. In home building and property development, the technology supports optimising a parcel of land and optimising estate and building design not only to meet societal demand, but also to make best use of the environment.
Jim Farrer is approaching three years in his role as Managing Director for COINS and has a diverse technology centric background across financial services, aerospace, manufacturing and major projects. His extensive experience has seen Farrer identify the unique set of challenges and opportunities the construction industry needs to address. “Construction should probably be declared as a bit of a crisis,” says“TheFarrer.construction industry operates on very thin margins using lots of effort, resources and human capital to complete complex projects. The productivity and profitability are really lagging compared to most other sectors. “Many smaller companies that decide to take a step forward by utilising technology might simply have an accounting package or use things like spreadsheets to run their business, or some of them might only have an accounting package and use intuition and experience. That can work, but once you go to scale up you start to outlive the capability of those baseline products.
Craig Dovey, Project Controls Manager, Georgiou Group says their project managers were spending a lot of time on admin, trying to work out if costs and forecasts were accurate. “We needed to be able to quickly and accurately see how whole projects were tracking and what their daily costs were, in real time,” says Dovey. That’s when they engaged COINS. By introducing COINS Construction Cloud to a business, the company is then able to access Georgiou Group was able rationaliseto the variety of products they were using down to a much smaller set.
The construction industry is somewhat lagging in the adoption of technology compared to other industries and COINS are tackling that problem head on with their collaborative working model.
FOCUS COINS Software
Construction Industry Solutions (COINS) is setting a benchmark for positive industry change in construction driving collaborative working through innovative software. COINS Construction Cloud transforms the way construction industry professionals communicate, engage and manage complex projects.
GroupGeorgiouImage:
www.insideconstruction.com.au INSIDE CONSTRUCTION 29
“What happens from there is companies start to add in specialised products when they have a particular problem in an area, for example their estimating might not be great, so they’ll buy an estimating product.
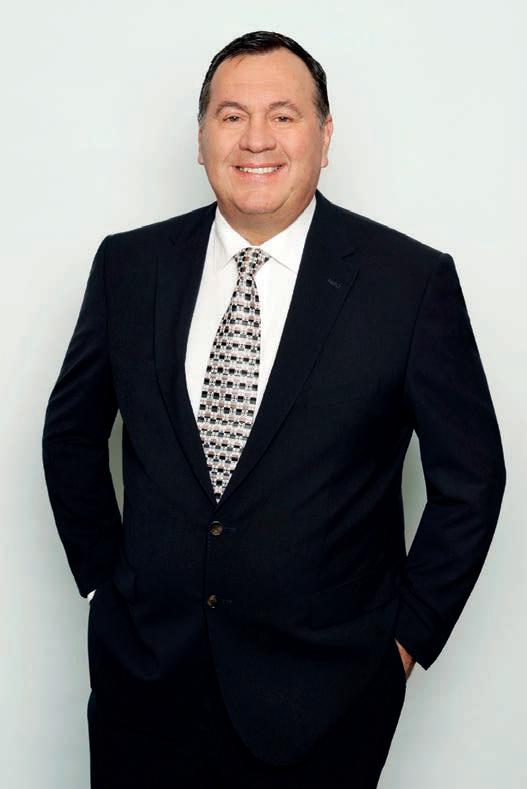

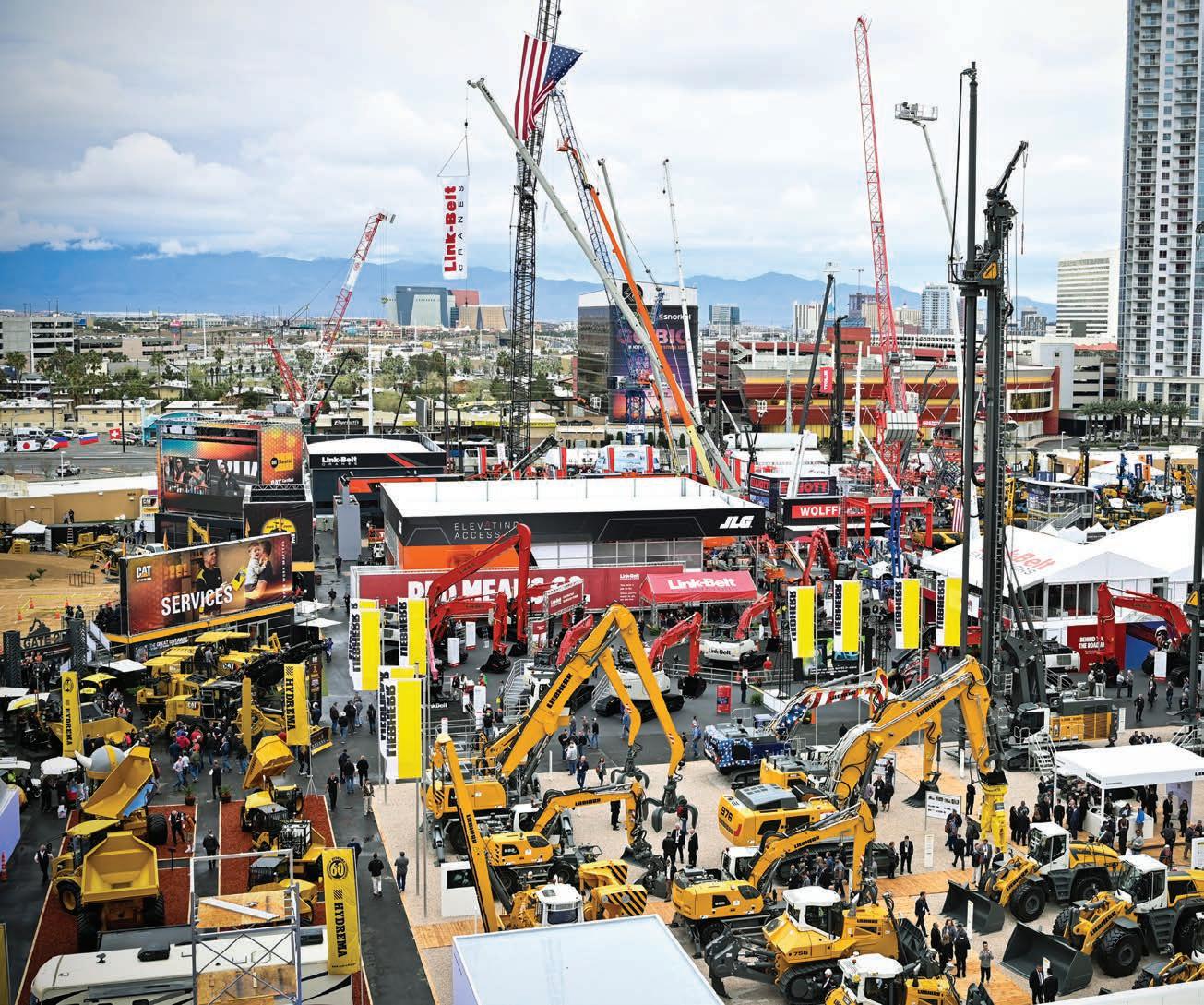
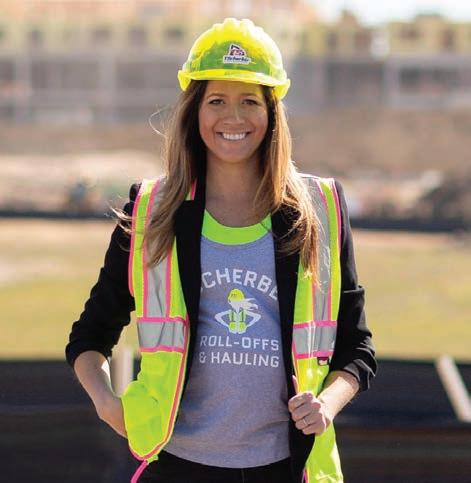
How
30 INSIDE CONSTRUCTION August/September 2022 their data in an integrated system where it’s all in one platform with one source of truth.
During their work with Georgiou Group, a national civil building and construction company, COINS quickly realised they’d encountered a company with a great vision and willingness to embrace technology.
FOCUS COINS Software
At the most fundamental level, COINS technology enables the processing of all transactions and the capture of all data associated with those transactions. For example, somebody may purchase a piece of material or equipment for a project and there are end-to-end processes for the purchasing of items that are ultimately going to increase productivity on that project. Those costs need to be costed to a project, bills need to be paid, bank accounts need to be maintained and cash balances monitored. Every single transaction, being a payment to an employee, purchase, lease of a piece of equipment or someone’s labour time being spent on a project is captured and managed by COINS software. The technology facilitates transaction processing. You can order or pay for materials and in the course of facilitating those transactions, COINS software captures all of the data in near real time so that people have a live picture of what’s happening in the business. At an incremental level, businesses have complete visibility of what’s going on. They don’t have purchasing sitting in one system, people and payroll sitting in another and construction sitting in another – it’s all in one place. Transactions and activity can then be aggregated up to look at project performance and how a project is going versus original budget and its intended cost. does it work?
Having accumulated a multitude of specialist systems the organisation was keen to streamline project management.
“We met them at a point in their journey where they were seeking a single integrated platform, and so COINS was contracted by them to put our system in which replaced a lot of those individual specialist systems.”
The Georgiou objective was to consolidate down to fewer platforms, get a single source of truth and build their confidence in one integrated system. But more than that, they were looking to expedite month-end processes.Beforethe introduction of COINS construction management software, it would take Georgiou Group time and extra manual effort to gather company data for review. They can now get that picture very shortly after months end with much less manual intervention.“Itwasalsoabout connecting different parts of the business. They no longer have the construction teams operating in isolation with the only communication or engagement being what they say to head office over the phone or via email. They are now connected in via the data and technology. It’s brought their whole picture to life,” says Farrer.
“All of the functions were very good at doing their particular task, but the systems weren’t talking to each other causing inefficiencies and inconsistencies. Georgiou Group fundamentally didn’t have trust in what they were seeing across their individual software packages,” says Farrer.
Georgiou Group were able to rationalise the variety of products they were using down to a much smaller set which has great advantages in term of costs and maintenance.
“A customer might ask a contractor to build 10kms of road for X million dollars. That cost build-up comprises of things like plant hire, people, materials, provision for risks and opportunities,” says Farrer. “The COINS system allows you to keep a
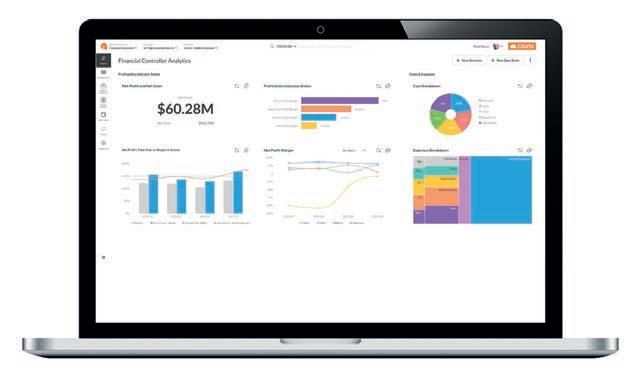
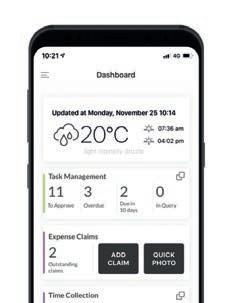
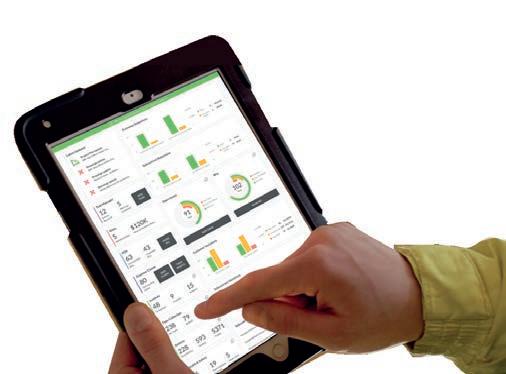
By sourceplatformwhereintegratedtheirablecompanybusiness,CloudConstructionCOINSintroducingtoatheisthentoaccessdatainansystemit’sallinonewithoneoftruth
GroupGeorgiouImage:
At large, COINS are a company dedicated to inspiring positive change in individuals, communities, businesses and industry.
“It was also inteamsconstructionhaveTheyofdifferentconnectingaboutpartsthebusiness.nolongertheoperatingisolation.”
www.insideconstruction.com.au INSIDE CONSTRUCTION 31 very close eye on how things are progressing. So that transactional activity management aggregates up to a project layer. You might have a very large construction organisation that consists of many companies and each of those companies may have many projects and every project has many components. By aggregating all the information and data together, they have a complete picture of what’s going on, what’s working well, what’s not working well, what needs attention and what’s meeting expectations. “It allows organisations to, with that knowledge, address opportunities and in addition to that live picture, project performance into the future. This allows then for long range workforce planning, long range planning of capital and other sorts of investments.”“That’showour COINS Construction Cloud brings everything together and can support transformation in the construction industry.” Collaboration is a vital element of the COINS operating model and through that they strive to shape the industry to a better set of behaviours. “Georgiou is a great example of this. We have an extremely collaborative and trusted relationship that benefits us, benefits them, benefits their customers and benefits society because we’re actually working together,” says Farrer. “Some traditional practices in construction, and they’re still there today, sees the customer engage a contractor to do a job, that contractor then engages subcontractors and the associated risks cascade through the supply chain. We need to establish better transparency throughout the process to avoid devolvingAccordingrisk.”tothe Australian Securities & Investments Commission (ASIC) the construction industry records more insolvencies each year than any other sector, with nearly 25% of all insolvencies in Australia being a construction company. There are also staggering statistics of high rates of suicide in the“Someindustry.construction companies tend to feel as a purchaser they have this ultimate right over the supplier. We break that paradigm. With our customers the way we work is collaboratively. They have responsibilities, we have responsibilities, we have collective goals, we work together – and we find that model is very successful. If that model was perpetuated across the industry at large, and that’s what we try to do, I think you’d see a much more transparent industry,” says Farrer. As well as their commercial software and technology side of the business, COINS also actively give back a large portion of their profits to society through COINS Foundation. The Foundation was established by COINS to support a wide range of social initiatives across the globe from arts and social change organisation Big hART and Wynyard Yacht Club’s Sailability program in Australia, to expanding the PEAS network of schools in Uganda and DFN Project Search in the UK which supports the transition of young people from education through to careers.
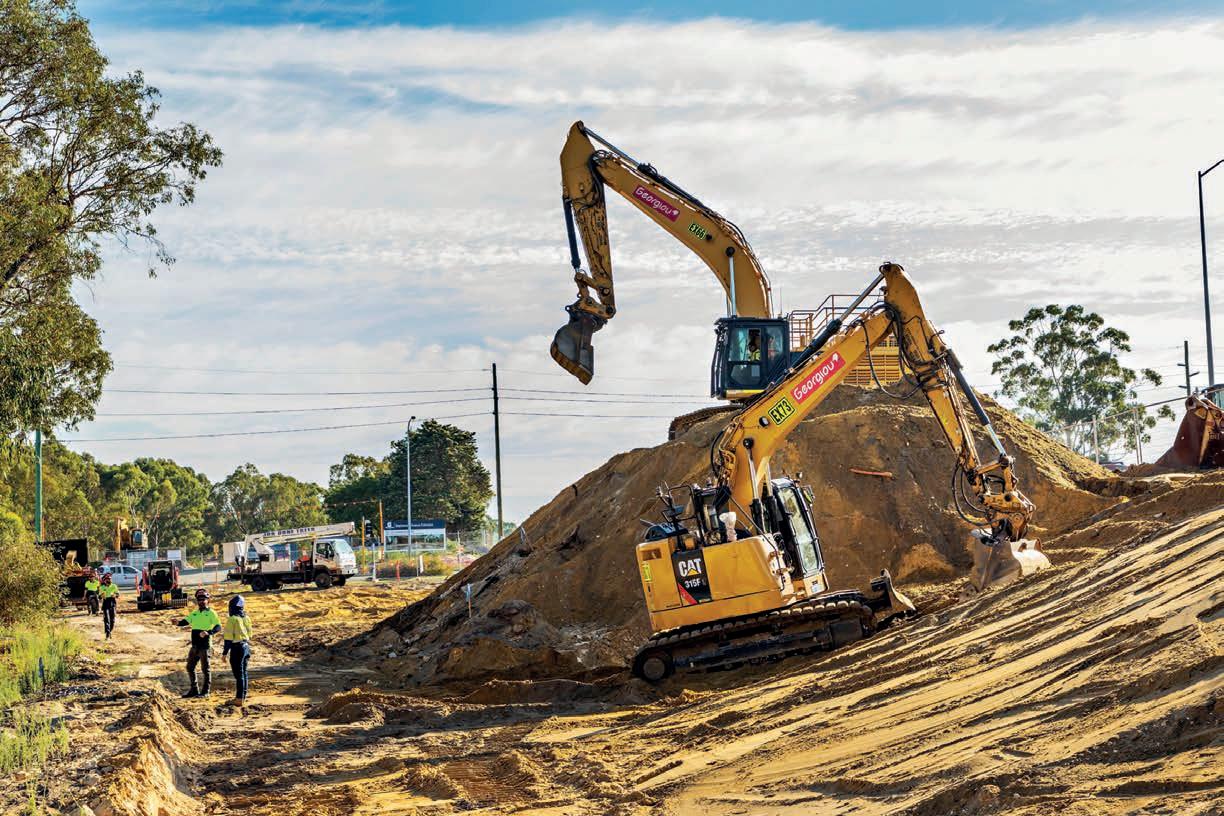
CONQA – a digital tool specifically designed for photo.asofbyandimproving–workingsubcontractorsinconstructionisreducingrework,safetyreducingadminmakingthetaskqualityassuranceeasyastakingaHere,
One New Zealand company making its mark in Australia wants to change this attitude towards QA through developing an easyto-use digital tool conveniently accessible to everyone with a smartphone. With the QA platform CONQA, the aim is to put this process where it belongs – at the heart of every job undertaken on site to reduce rework, raise standards and improve health and safety. Finding the problem Recent reports have looked into trends in the construction industry, showing Australian construction companies spend on average one in every eight hours, or 12 per cent of their time, on rework. And, despite the low levels of digitisation in the construction industry, 43 per cent of respondents said that they believe that technology will help improve resource efficiency through fewer errors.
For construction companies worldwide, a key cost in any project is the amount of rework that has to be done to fix mistakes that have accidentally occurred as different subcontractors complete their work. Although quality assurance (QA) is already in place as a measure against this, it is often seen as ineffectual and merely an administrative burden pushed to the end of the line when work has already been completed.
to get involved Words Cat Fitzpatrick Images
CONQA Co-Founder and CEO Daniel O’Donoghue explains how the digital revolution is coming, smartphone CONQA
Mark of quality
One such digital technology hoping to improve standards and generate significant cost savings is CONQA – a QA platform that subcontractors have on their phone, making it easy for them to complete their Inspection Test Checklist (ITC’s) and Inspection Test Plans (ITP’s) as they go, and upload a picture of the completed work to show the finished result. Not only does it ensure that a job has been completed correctly the first time – it also helps subcontractors feel confident in their work and remove the arduous task of tickbox paperwork down the line.
“CONQA was started by myself and two There is communicationimprovingreworkbyconstructiontodigitalpotentialhugeforsolutionsreducecostsonsitesminimisingand
FOCUS CONQA Technology
and you need little more than a
CONQA is the brainchild of three friends from New Zealand who identified a gap in the industry for a more intuitive and user-centric approach to managing QA.
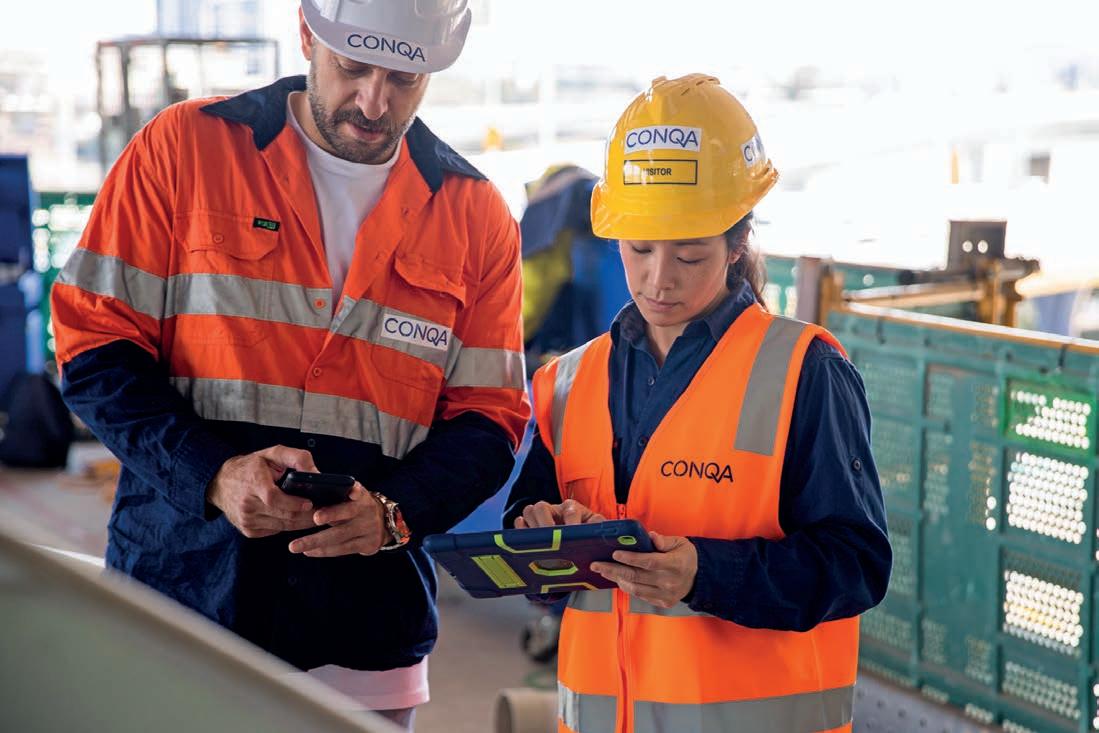
www.insideconstruction.com.au INSIDE CONSTRUCTION 33 friends of mine, and we basically wanted to solve big problems with technology,” explains Daniel O’Donoghue, Co-Founder and CEO of CONQA.“Westarted off with the idea of wanting to build a business that could have an impact, but not necessarily a clear idea of what the business would do. So, we searched for problems that could be solved with technology and looked into a few different sectors.”Having studied engineering at university, O’Donoghue reached out to friends who had become civil engineers on large-scale construction projects and asked them what problems they were facing in their day-today work. This is where QA came up – the series of checks needed to be undertaken to make sure a job has been performed correctly. However, the approach to QA had made it an inconvenient and time consuming boxchecking exercise often delayed until the end of the month, when mistakes had already been made. “A common mechanism for QA is with a checklist, much like you would use when you go to the supermarket,” says O’Donoghue. “You’ve been to the supermarket 1,000 times, and you know how to go around the supermarket, but you still make a list as a prompt, so you don’t forget things. And it’s the same thing in construction – they’ve done a lot of this work before, they know the key steps, but the reality for them was, because it was so cumbersome, they ended up signing off all of these checklists at the end of the week, or the end of the month.”
“Those handshakes and human contact – actually getting in front of people – that’s still a really important aspect for a lot of the contractors we work with and is really important to us. Having people on the ground in those markets has been about building great connections with the contractors we work with.”
Minimising rework
He says that this would be like a pilot filling out their pre-flight checklist, designed to ensure that the plane is safe to take off, after the flight has already landed at the other end. “Approaching QA in this way means it has zero impact on rework,” he says. “That was the catalyst for building CONQA. From that point, we researched the industry quite heavily and spoke to a lot of people at the ground level who are having to do this task. We tried to understand why it was such a pain for them and what can be done to make it easier. The key thing that they would always say was that it just had to be a simple solution.”
The core issue that CONQA is tackling is reducing the amount of rework subcontractors have to do on a project. One issue currently is that it’s difficult to truly understand the scale of rework taking place and the cost it incurs because the data isn’t tracked.
One study undertaken by the Get It Right Initiative in the UK in 2015 looked into the most economically significant errors in construction and their causes and found that avoidable errors cost around five per cent of a project’s value. This is around £5 billion per annum across the sector in the UK. With unmeasured and indirect costs added in, this rises to somewhere between 10 and 25 per cent of a project’s costs due to causes such as inadequate planning, ineffective communication and a poor culture around quality“Reworkassurance.triplesthe cost for a subcontractor, because they’re paying to do it the first time, they’re paying to do it the second time, and then it’s the opportunity cost of what they could have been doing with that time,” says O’Donoghue.“Also,ifasubcontractor has to go back into an area to redo work, this has a ripple effect on every other contractor who follows them. It can cause chaos, with people working around each other. And, if you do that 100 or 1,000 times on a project, you can start to see why it Contractors can represent up to of the workforce. If they aren’t at the table, how do you expect the industry to change? 80%
Based in Auckland, New Zealand, the team put together the CONQA platform as a way for subcontractors and their employees to easily mark off the steps of a particular job, remind themselves of what needs to be done and quickly take photos as they go, removing the burden of admin and a pile of paper. The concept quickly grew, and now CONQA has expanded over the pond to open up three Australian offices in Melbourne, Brisbane and Sydney.“Construction is still quite a face-to-face industry,” says O’Donoghue of CONQA’s growing presence in Australia.
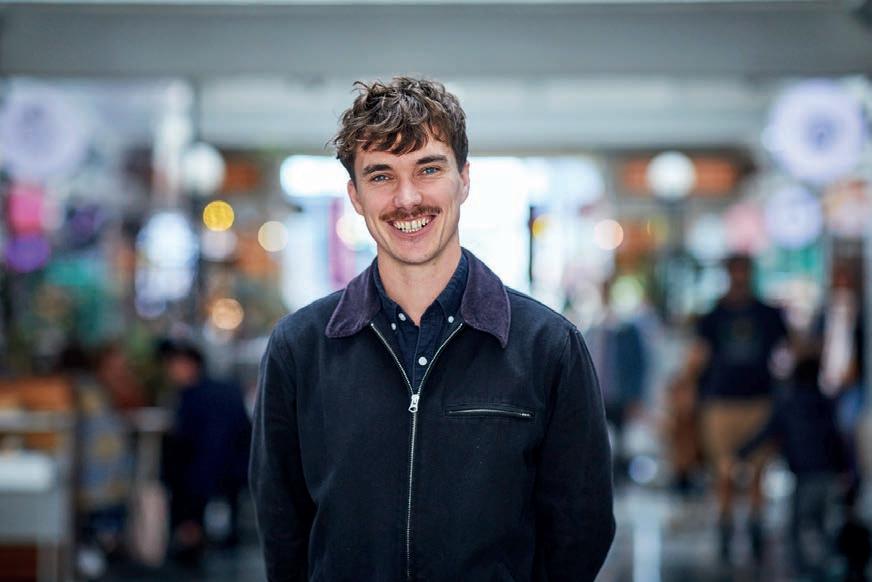
“The type of the construction work that a subcontractor may be doing on site will vary, even within a company,” says O’Donoghue.
“We want to minimise and prevent as many mistakes as possible,” explains O’Donoghue.
“The end user is someone who works for a subcontractor. Whether it’s plumbing or pouring concrete, subcontractors are the ones who are organising the labour and they are the ones who need to check that what has been done is correct before they hand it back to the head contractor, who gets the next trade
This is where CONQA comes in as a way to tackle mistakes and ensure the correct processes are followed every time.
“This is why we tailor our software for the specific needs of a business and a particular project. That’s what makes CONQA work well. We trim out all of the fat that could effectively bog people down on site. By keeping it clean and simple, with only the information that they need and not the stuff that they don’t, it makes it a lot faster and, therefore, a lot more engaging for them.”
Safety focus Huge savings can be made in reducing the time and materials wasted on redoing work, but there’s the reduction on the physical and mental toll of rework on a labourer as well. Australian construction consultant John QA, as a practice, should sit with the subcontractor. CONQA takes the old checklists, which are often written down on paper, and optimise these for the crew as they work – breaking down each project into a folder structure on the mobile app. This contains all of the activities that will be done for a particular job in an easy-tofollow“Eachsequence.ofthoseactivities will have an Inspection and Test Plan associated with it and the user will go through and complete that using their mobile phone, taking photos as they go, which addresses the problem of rework,” says O’Donoghue. “They capture the evidence of their work to demonstrate to anybody looking at it later that they’ve done the process well, as well as capturing the conditions that surround their work, which helps from a liability perspective. Once done, they just put their phone back in their pocket and they get on with their day.
How does it
34 INSIDE CONSTRUCTION August/September 2022
“That’s the key – to try and make this process, which is important but not very enjoyable, as fast and easy as possible. And then, from that work being done on the front lines, the information that comes out of that process is relevant to a lot of other stakeholders as well, principally the head contractor. It can also be used to help communicate progress and support claims from a cost perspective.”
What’s clear is this definitely isn’t a one size fits all process – CONQA takes an individual contractor’s work needs into account to tailor the platform to individual needs and make sure it’s as useful as possible for the company
“And this is also true for the mistakes that can cost them money, which are the things that you end up putting on a checklist to prevent them from happening. Sometimes it can vary to an individual team level, depending on their experience. In most projects everything’s very bespoke – very rarely do you see two buildings that are the exact same, or two roads being built under the exact same conditions. Due to their nature, tasks will vary. There are common threads, but the way projects are set up will differ.
FOCUSwork? CONQA Technology
becomes such a productivity killer. It’s costing time and materials if you’re redoing work, so it becomes a big financial burden.”
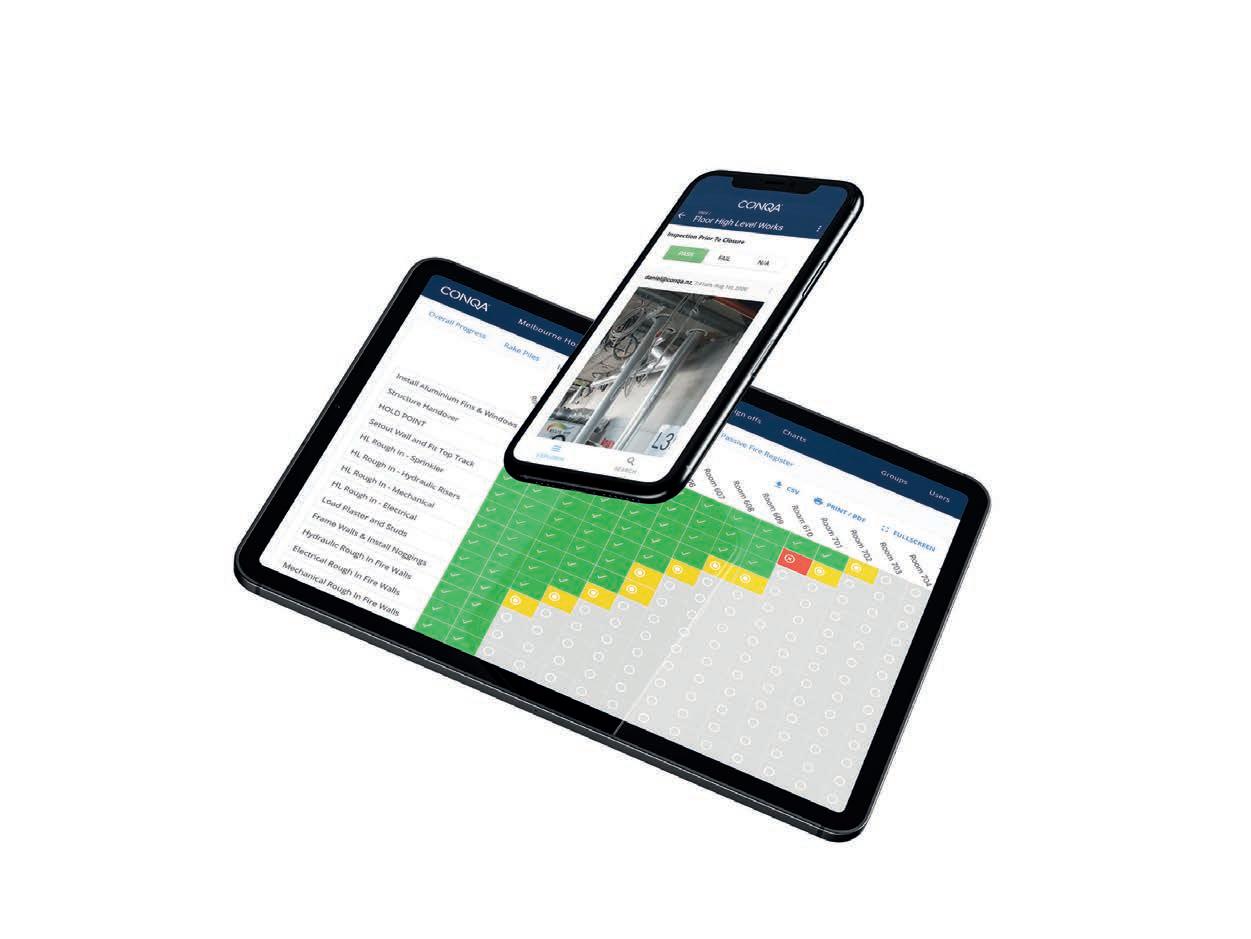
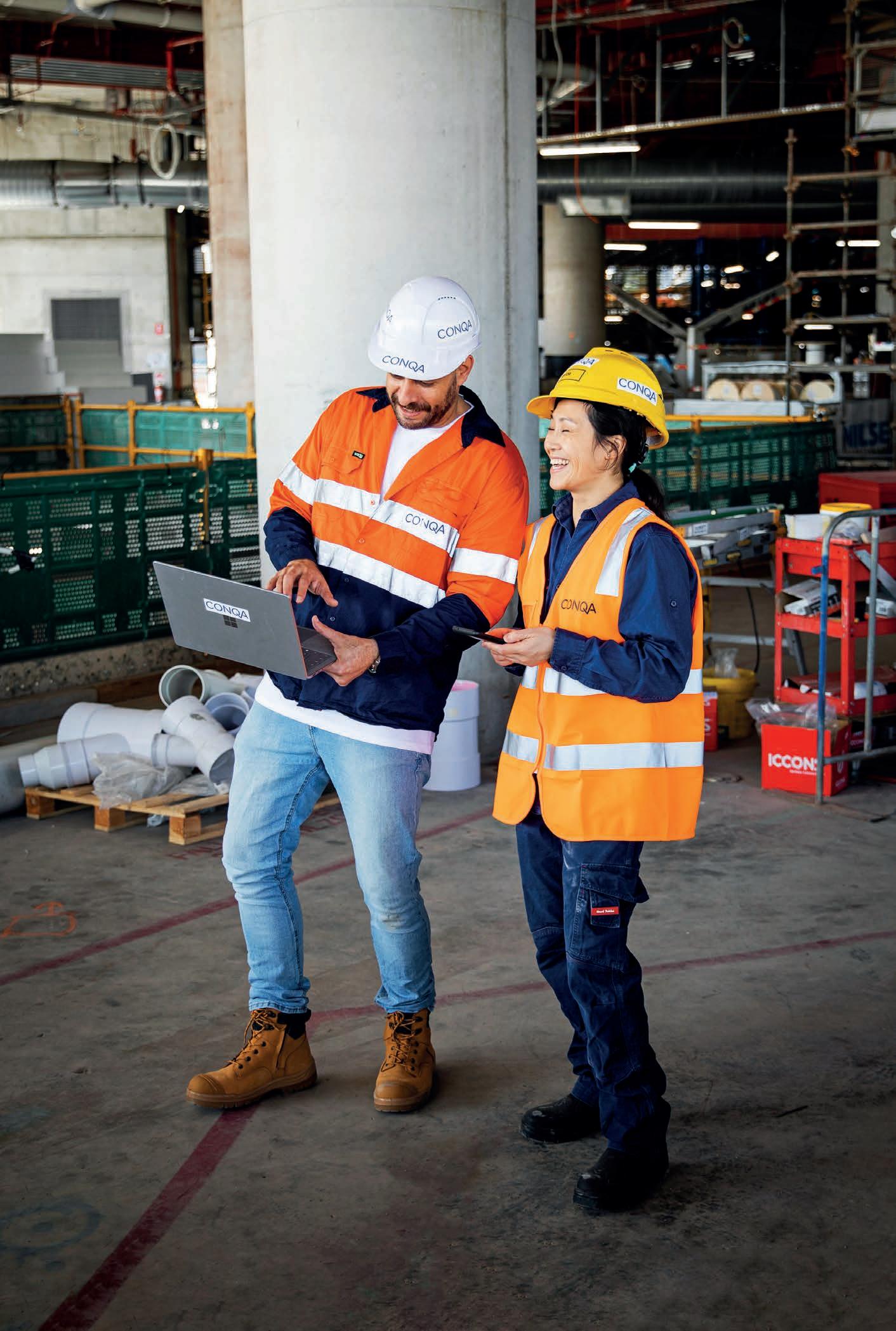
35www.insideconstruction.com.au INSIDE CONSTRUCTION As well as reducing rework finishedoverallstandardsimprovesassuranceimprovingcosts,qualityonsitesafetyandthequalityoftheresult
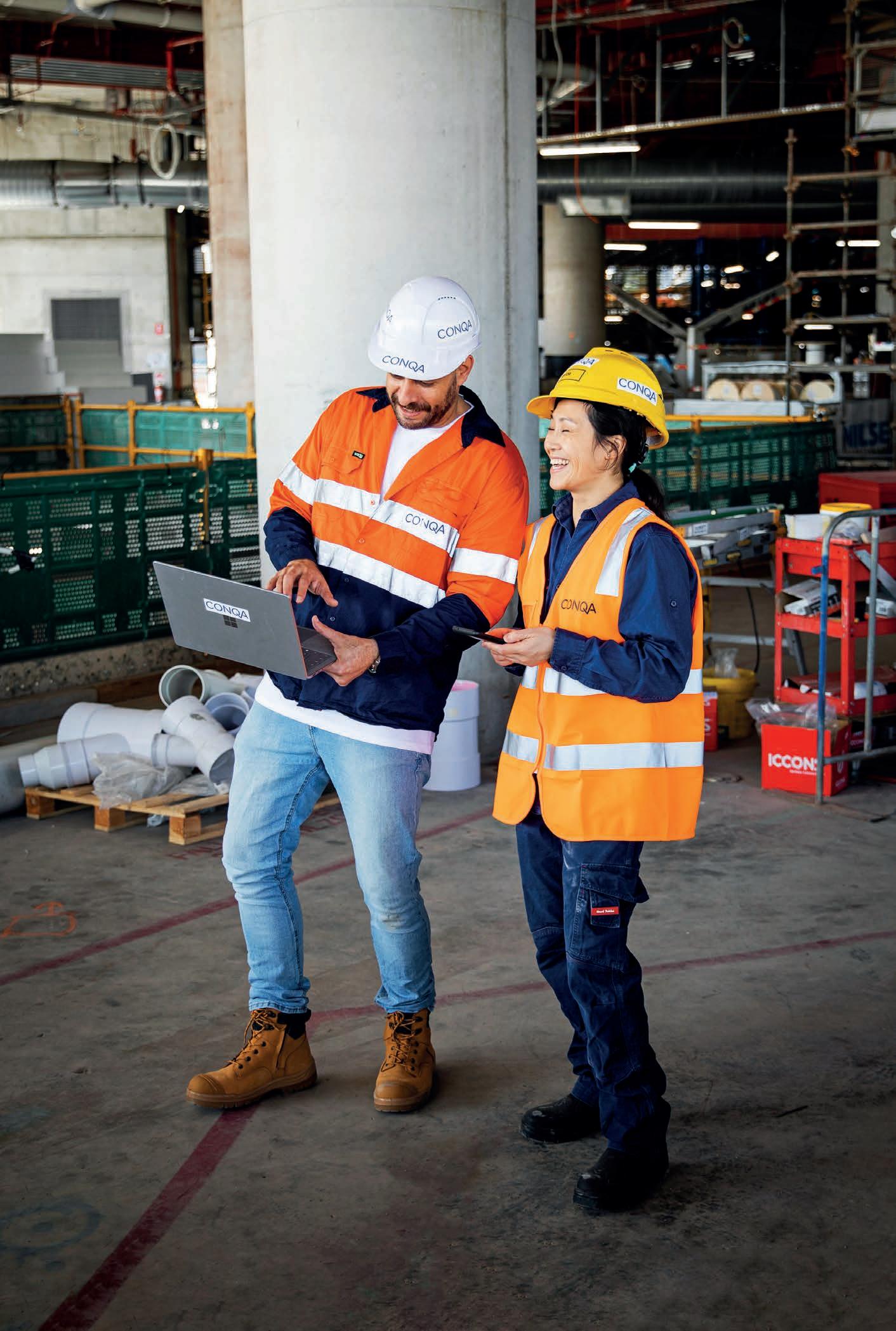
Also key has been subcontractor engagement, says O’Donoghue, and focusing on these businesses and their workers is how the industry can improve its utilisation of digital tools. However, a lot of the time, subcontractors aren’t involved in these discussions of what can be improved through using new “Subcontractorstechnology.canrepresent up to 80 per cent of the workforce,” he says. “And if they aren’t at the table, if they aren’t part of that digital conversation, how do you expect the industry to change? All of the construction work, the actual nuts and bolts of it, comes together at the site. Therefore, you’ve got to get subcontractors engaged. “I think a mistake we often see made is that businesses are waiting for the younger generation to come through and they really miss the opportunity. There are people who’ve been on site for 30 years, who are incredible at their jobs and know how to run a team well, but they might not be as tech savvy as some
36 INSIDE CONSTRUCTION August/September 2022
Morrison from Frontline Coach looked into the impact of rework on health and safety incidents and found that there was a 70 per cent higher chance that a worker would be injured during a rework activity than the originalO’Donoghuejob. says that this is because if a subcontractor team is going back in to redo work, it’s an ad hoc process where the conditions will have changed, other work may have to be undone to fix a problem and the planned sequence of events and who is supposed to be on site starts unravelling.
FOCUS CONQA Technology assurancearoundandcommunicationineffectiveplanning,tocostsofbetweenSomewhereaproject’scanbedueinadequateapoorculturequalityand 2510%%
“But disputes will arise around who has to pay for rework and those costs aren’t always factored in. This can put a lot of tension on a relationship between parties and cause a lot of mental“That’sstress.oneof the big motivating factors for us in that we’re not only helping businesses to become better and more profitable. We’ve got great stories of customers whose teams are able to go home on a Friday afternoon instead of having to go back on site and fix things up over the weekend. They know their job has been done well, and they can go home and enjoy time with their families. Minimising rework has a lot of positives to it.”
“And it’s not just the physical health and safety,” he adds, “it also has a big impact on mental“Constructionwellbeing.has a lot of issues with mental health. We partner with Mates in Construction and their research has shown that you’re six times more likely to die from suicide than you are from a from a health and safety-related incident if you work in construction. When there’s a mistake, there’s not always objective information as to who’s caused it and how it was caused. And most of the time it’s just natural human error.
Digitisation of the industry Although a solution to improving QA on site and reducing rework has been found, a challenge for CONQA has been addressing the lack of familiarity to digital tools within the construction industry and ensuring that the CONQA platform is something that everybody can use, and would be interested in using, even for those who are more used to having a pen and paper on hand. In terms of digitisation, the construction industry is far behind other industries such as media or finance but there are huge benefits that could be achieved by adopting digital technology on construction sites, says O’Donoghue.“Digitalsystems have had a lot of positive impacts on how various industries work,” he explains.“Theycreate feedback loops that you can use to track and monitor information, which is practically impossible to do on a paper-based system. You minimise double handling and can ensure that the information captured is relevant and available immediately. Processes can be made easier and sped up. “The challenge for the construction industry is that, apart from off-site manufacturing, it’s all site-based and the use of technology is limited compared to businesses based in an office. Therefore, we had to optimise our software for the tools that subcontractors have available – the most universal of which, from a digital perspective, is a phone. That’s what we’re focused on, really making sure that the software can be done super easily and cleanly on a phone, because even a tablet is impractical – you’ve got to remember to take it with you or people don’t have it on them all the time. Having this system available in the pocket is key.”
CONQA is looking to challenge the idea that QA is a waste of time and that on every project there will be a list of things missed or mistakes made that have to be redone. “Once a subcontractor starts to be engaged and rework rates start to drop, they start to have better commercial protection and have the ability to support their progress claims. They save themselves a lot of time and it makes it easier for the teams on site, who’ve got a tough job before you add the admin workload on top of it,” says O’Donoghue.
“Some of the most successful contractors that we work with are using benchmarking and apply CONQA across their projects to lift their standards up so the whole company is benefiting from lessons that they learn. It’s fostering a culture of continuous improvement and using the software to help support that. “The great thing about quality assurance is that it’s coupled to work verification. If someone has gone through and checked that they’ve done the work correctly, you’ve got a much higher level of confidence in that work. It can then be signed off and the area is ready for the next party to go in. “QA has the ability to help inform the status of work, which is relevant to so many parties, particularly to the head contractor, who’s trying to coordinate many subcontractors. They can see the status of each subcontractor and make sure that the QA is aligning with the work that they’re completing. And the information captured is also useful for some of the compliance elements as well as the dayto-day running of a construction project.” “I asked one of our customers why he uses CONQA, and he said ‘because your product works’. Once you have it functioning, a company can become more productive. They operate better, they communicate better, they can provide information to their clients, which helps their brand, and it helps to minimise liabilities. There are a lot of other derived benefits that come from your QA process just doing its job.”
Visit CONQA’s website for more on their product and services at www.conqahq.com year.“One of the key things that they’ve said is that it keeps their supervisors actually supervising their most valuable asset, which is their labour force,” says O’Donoghue. “Rather than being back in the office doing admin, they’re out in the field, watching the work, making sure it’s at the right quality, so that they can deliver a great product to their client. And they’ve got the records to help back it up. So, from their point of view, it was about engaging their team with the QA process. Everyone’s found it easy to use and engage with. At the basic level, all we’re trying to do is make sure that the QA process actually functions.”
www.insideconstruction.com.au INSIDE CONSTRUCTION 37 of the younger generation. By not bringing them to the table, so much opportunity will be missed.“Focusing on clean, simple, and easy-to-use solutions that won’t alienate those people who can add so much value is important for the industry. If they wait five to 10 years for younger people to move into leadership positions, or running crews on site, those who can get their existing workforce digitally enabled now are going to be well ahead of them by O’Donoghueyears.”says that by working with subcontractors directly, he’s seen behaviours shift, with workers who were initially reluctant to use the new tool be surprised at how easy CONQA is to use and quickly become advocates for it. He says having the visibility available of who is doing work well helps drive engagement, which is critical to changing attitudes to QA and how it is undertaken.
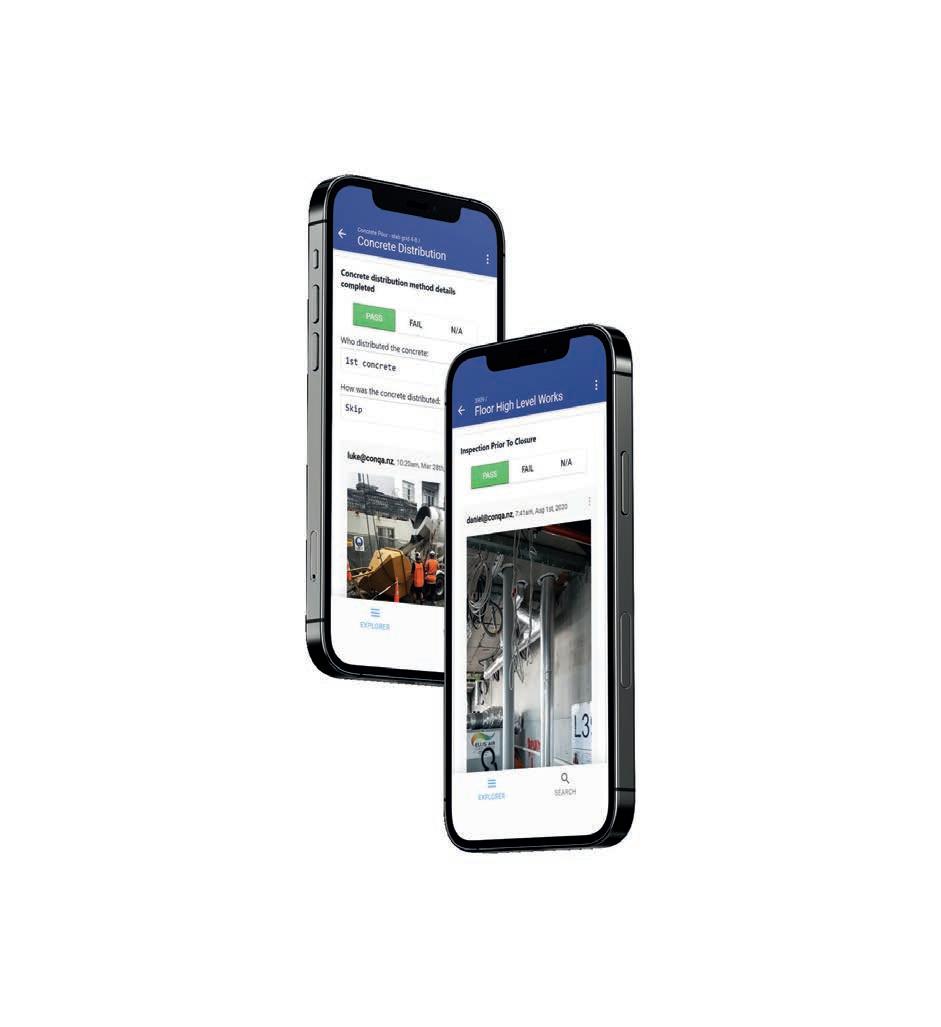
www.insideconstruction.com.au The Inside Construction weekly e-newsletter is your leading source of construction news and insights showcasing the very best that the construction industry has to o er. or visit www.insideconstruction.com.au, and click the “Join our newsletter” box on the bottom right to subscribe to our weekly newsletter! Scan this QR code newsletter!subscribetothe
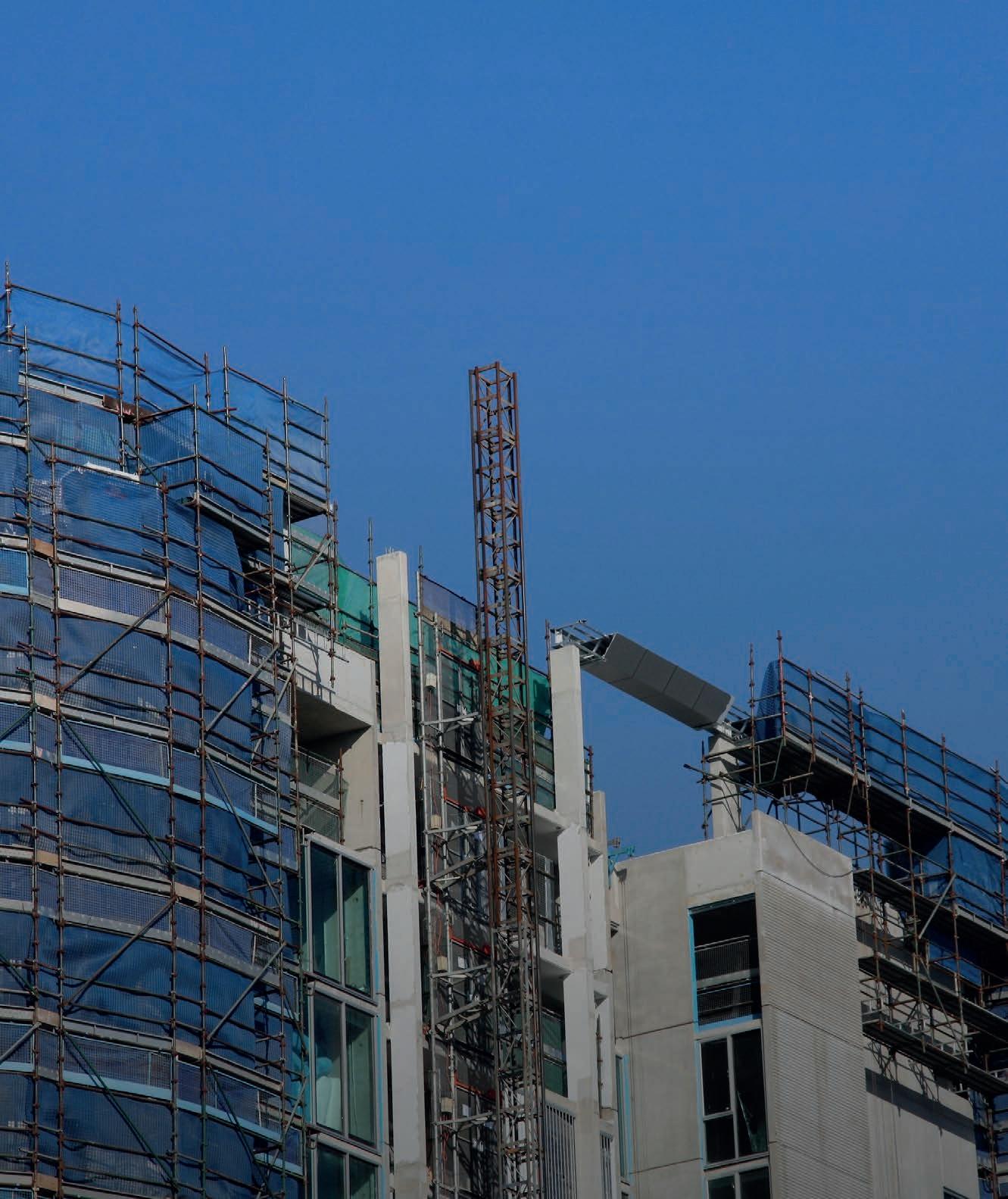

WAHA is dedicated to supporting and influencing the ongoing development of safe practice, equipment innovation, systems and product design, continuous education of all stakeholders, and the operational competency of all persons working at height and in confined spaces. As a professional membership organisation, WAHA is a centre for the working at heights, safety, engineering, and design communities to come together to advance safety, increase knowledge, and advocate for best practice in the discipline.
WAHA is a voice for industry, and its industry membership tiers reflects leadership in the WAHAfield.utilises an internal audit process for its Gold and Silver Members to ensure all members represent best practice and to maintain WAHA’s position as a leading advocate for safety and as an effective agency for change on current and emerging issues. Individual and Student Members represent a community of engaged professionals from a variety of industries with an interest and incentive to enhance safety in the workplace.
www.insideconstruction.com.au INSIDE CONSTRUCTION 39
The team at Inside Construction, in partnership with Cranes and Lifting magazine has been working with the Working at Heights Association (WAHA) and a number of WAHA members to bring you news and information about working at heights safely. It is a critical topic for the construction and cranes sectors and all too often we read about injuries and worse as a result of safe working at heights practices not being adhered to. These features are designed to reinforce the importance of adopting the correct working at height practices, products, and training programs to ensure all workers in our industry leave for work in the morning and return home safely at night.
WAHA is a centre for the working at heights, disciplinepracticeadvocateknowledge,safety,tocomecommunitiesandengineering,safety,designtotogetheradvanceincreaseandforbestinthe
FEATURE Working at heights safely
Importance of height safety systems
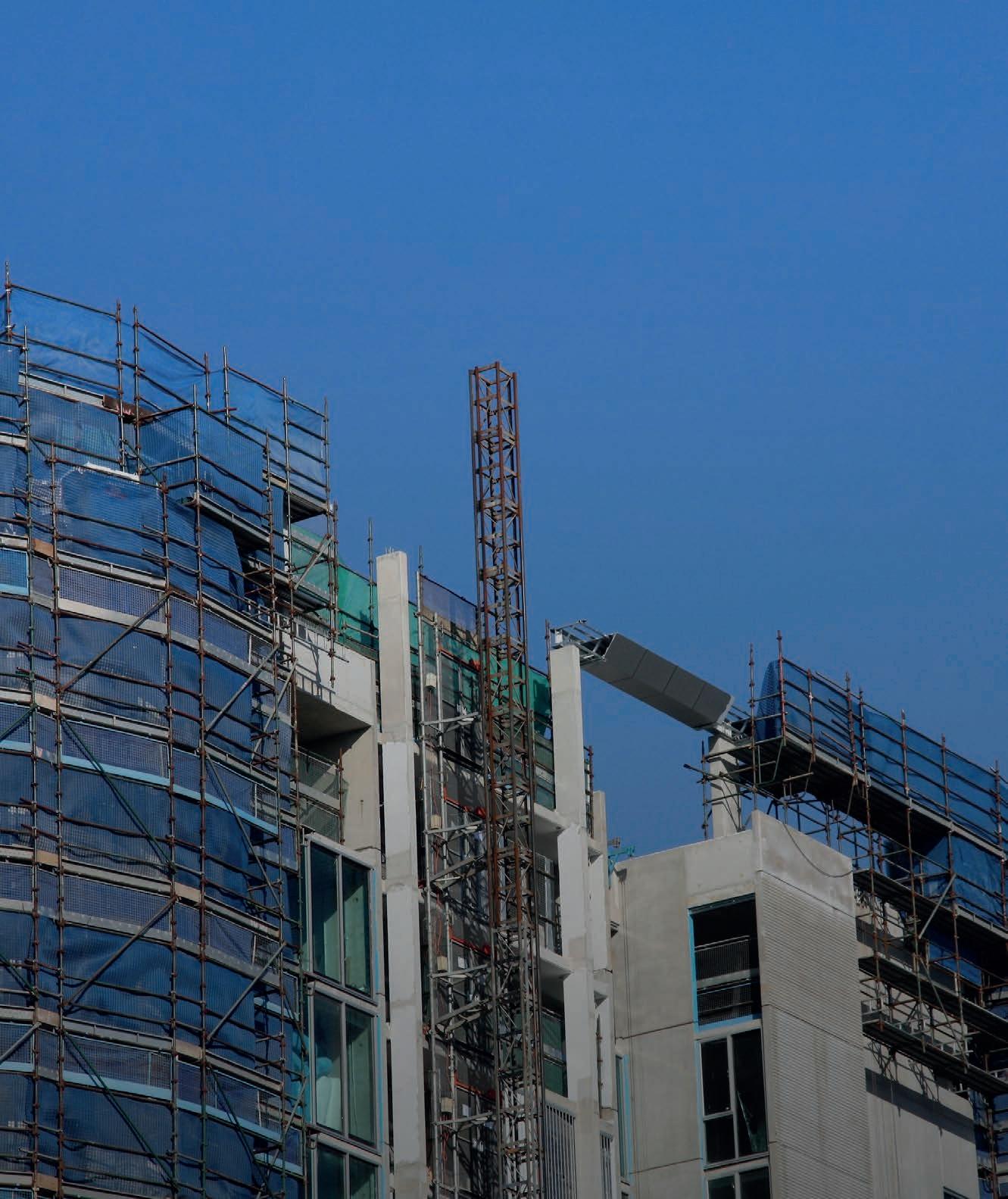
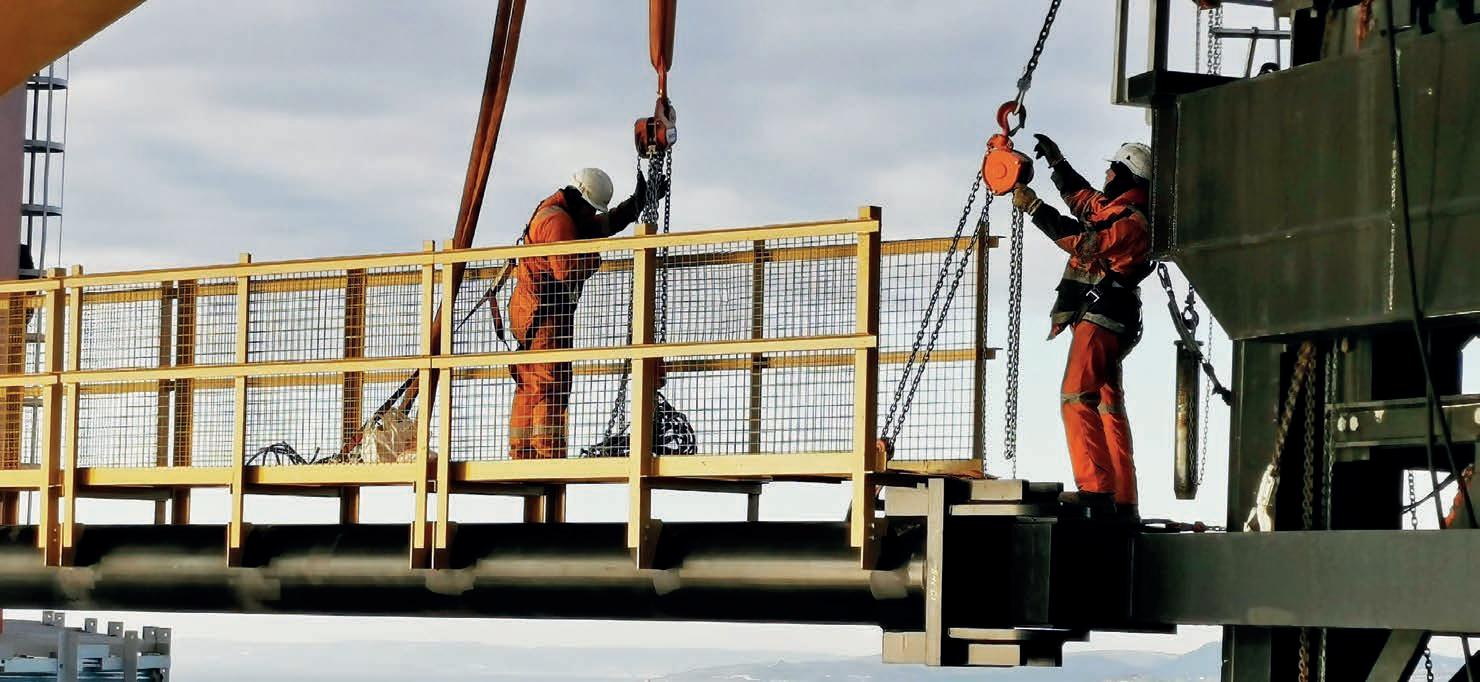
40 Paramount Safety has recently become a part of PIP Global – an AustralianqualityandmissionParamountwhichannouncementhighlightsSafety’sfordevelopingoffering highproductsforthemarket.
“One of the things that we understand foremost is that, in a mature industry such as the materials handling, lifting, rigging, and height safety industries, pretty much anything that has been thought of has already been done,” said Sugden.
Innovation in a matured industry – not likely?
The Linq chain block and lever hoists are products that have been designed by Sugden and the team at Paramount. The Linq Elite range of chain blocks has an innovative seven-bearing crank for enhanced longevity, resulting in bespoke gearing, giving a really low hand chain or lever effort.
The key to innovation in the lifting and materials handling industry is mainly the result of listening to the industry, understanding the challenges and being solutions-focused. ParamountSafety began “out of a small shed” in Perth in the early 1990s, laundering cotton safety gloves for reuse, but quickly recognised the opportunity to grow its own line of personal protective equipment.
The passion for safety underpinned every decision made by Paramount to expand, leading to the development of the Linq range of lifting and rigging equipment.
“If aliens did not build the pyramids, and in fact it was humans, then you can bet some form of lifting technique would have been used to do so,” said Paramount Safety’s Linq chief technical officer Stephen Sugden.
“The industry has gotten to the point where the only way that you can really develop and innovate is to understand the specific needs of a particular industry and then solve the issues endemic to that industry. This lead to the Linq brand’s innovative and class-leading products for the safety-critical industries of lifting and Paramountrigging.”Safety’s Paul Bozkurt is the category manager for Linq and recognises that every jobsite is different, so Paramount must adjust accordingly. “We often find ourselves being called into consult directly with the industry on behalf of our country-wide distributors, for our safety products in the construction, lifting, and mining industries,” he said. Stephen Sugden has been developing lifting, rigging, and height safety products since the 90s right across the globe. Since joining the team at Paramount’s Linq and PIP Global’s network, he continues to use his extensive experience to develop products in reaction to industry specific needs.
The introduction of the dust gasket feature for both the ranges of chain blocks and lever hoists prevents dust ingress to the working gears and contamination of greased moving parts whilst in use in high-dust environments.WorkinginAustralia poses a number of challenges, especially when working in harsh environments such as building sites and mines, but the dust gasket feature designed by Paramount lowers wear and tear, and improves safety. Whilst the need for innovation is ongoing, as it is a response to industry needs and feedback. Sugden and the team at Paramount strive to ensure the highest levels of safety.
“Any faults, in particular designs over say the last 100 years, have been mostly rectified and changed, or have just been accepted. As a result, innovation has slowed because the at heights safely
FEATURE Working
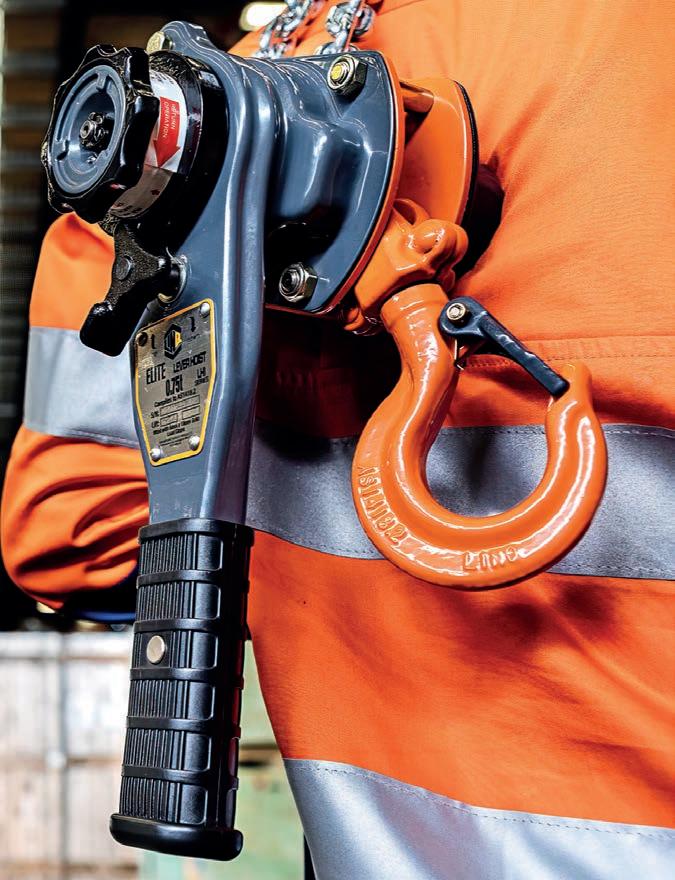
CONSTRUCTION
41 cost of innovation is very high compared with the offerings from a 1,000 parts assemblers in the general market. “That dust cover has been on my design list since the 90s, when I was supplying lifting product into African mines, so it’s not often that you get an opportunity for company as large as the PIP Group and Paramount Safety to listen to your ideas,” Sugden said. The Linq Elite range of chain blocks and lever hoists require less effort – for example on a one-tonne Linq chainblock the effort to raise the load is less than 26kg compared to the 33kg per tonne effort that is typical of others in the Australian market. “That’s almost a 30 per cent advantage in terms of effort. Over time this mechanical advantage helps to improve safety as operator effort is significantly less,” said Sugden. All Linq lifting chain blocks and lever hoists utilise steel lock nuts as opposed to nylon. This helps eliminates premature replacement due to lock nut failure, wear from environmental issues such as heat, and UV. Steel lock nuts also allow for safe reuse at service time. “We have identified that one of the big issues in Australia is how to keep the product operating safely for longer. This calls for tighter This ensures that consistency in manufacture process is maintained and proven to the highest standards each batch, every batch. “Our product is not a no-name import with a label slapped on for marketing purposes by an anonymous assembler of dubious source.
The Linq products continue to be developed and push the lifting sector forwards Paramount safety value safety above everything else and deliver this with its Linq products
“We are the manufacturer and our bespoke, OEM-appointed, ISO accredited facility that “We often find ourselves being called industries.”liftingconstruction,productsforwideofindustrydirectlyconsultationintototheonbehalfourcountry-distributors,oursafetyintheandmining
“Linq blocks are locally designed, locally developed, manufactured using our parts on a vertically integrated ISO manufacturing facility covering forging, stamping, heat treatment, case hardening and assembly, all under one roof as can be seen by the forging and stamping of our brand on all parts, including our load chain.
“What this means is that this is our product – we have total responsibility for it. We get that Australian law says that if you are the importer then you are the manufacturer, but we’ve taken that many steps further.
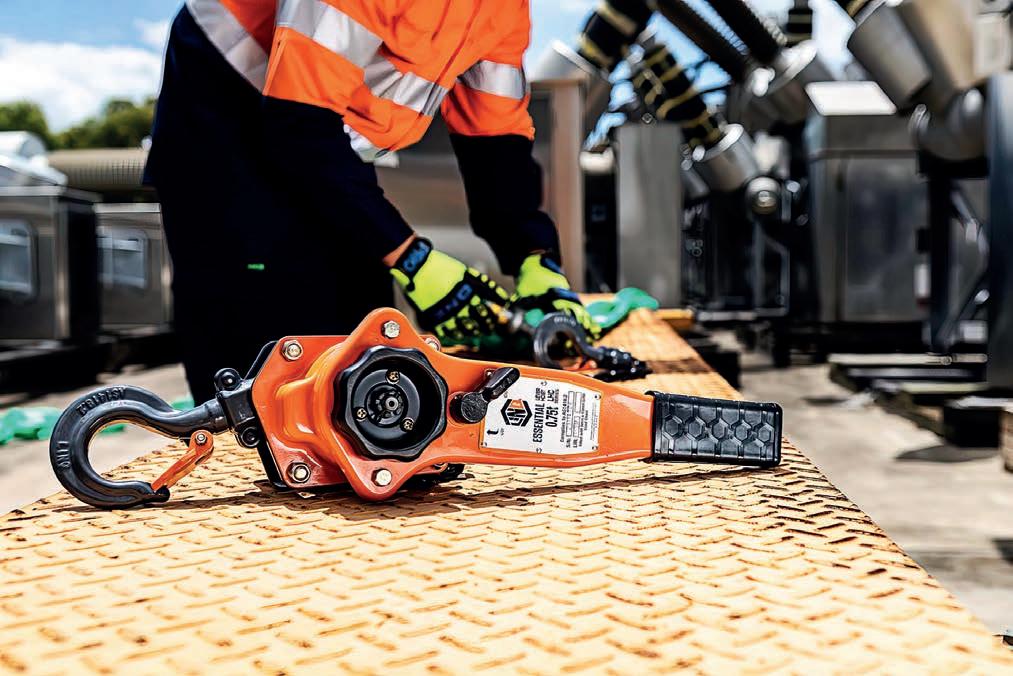
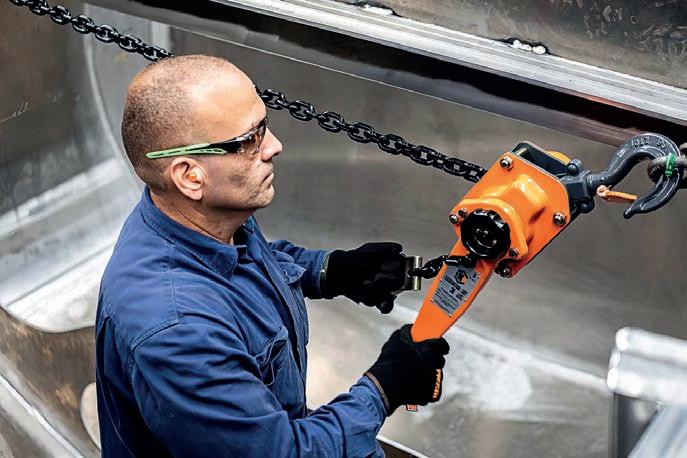
The importance of training when working at height
Construction sites can be described as transient, dynamic, and complex environments, and because construction workers spend most of their time on site, they are exposed to a higher risk of injury and even death. In 2021, Safe Work Australia acknowledged that working at heights is the leading cause of serious injury and death, with the construction industry unfortunately leading the way.
Vertical Horizonz Australia (VHA) was established in 2001, delivering height, confined space, rescue, and work health & safety (WHS) training to industry. Since then, it has become an expert in its selected industries and cemented itself in the Australian vocational education and training (VET) sector. Here it delivers nationallyrecognised training to the residential and civil construction, energy, and transport industries. With a head office and major training centre based in Brisbane, VHA can provide training at its head office or onsite. Additionally, VHA retains the capability to deliver training nationally and internationally at your place of work.Considering the Australian construction industry is predominantly small businesses with 97 per cent employing 20 workers or fewer, there is a reliance on the masses to do the right thing. However, variables such as not having a training schedule, poor or no WHS policies, time pressures, cost, and workplace pressures all contribute to the reluctance by businesses to source and undergo industryrelated working at heights training. James Moohan from VHA has noted that when workers have minimal training it results in poor practices. “For example, often we discover trainees have not been shown how to correctly check and fit a safety harness, only been shown how to utilise a non-adjustable 2m lanyard when working under restraint, or were even exposed to working at height during their training,” he said. “This can result in utilising unsafe equipment, modifying systems to allow working at variable distances, and encouraging poor workplace practices. Our training shows the trainee how to use height equipment correctly, in a controlled safe environment, while working at height,” Moohan said.
42 INSIDE CONSTRUCTION August/September 2022
Vertical Horizonz has offeredandcontinuesVerticalimportanceAsconstructionsafetyimportancerecognisedhistoricallytheofheightintheliftingandindustry.firmbelieversintheoftraining,Horizonztodevelopimprovetrainingbythebusiness.
FEATURE Working at heights safely
Training is a pivotal part of working safely at heights and Vertical Horizonz offers a range of training for those working at height Vertical Horizonz offers a range of different areas for training to ensure those who participate have a range of skills

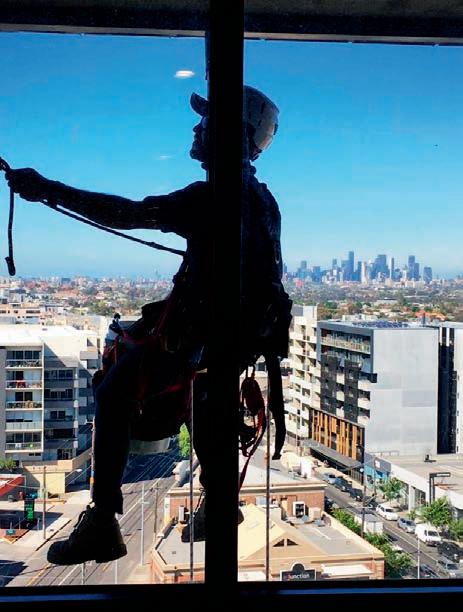
Training vital for safelyworking
After training, the skills acquired allow people to complete even the most challenging tasks at height safely
www.insideconstruction.com.au INSIDE CONSTRUCTION 43
“The highest possible force a human can sustain before receiving significant injury is achieved after falling for 0.35 seconds. This equates to a height of 600mm.”
This demonstrates that the training provided by VHA helps to change behaviour, translating to a change in attitude. Inevitably, changing the way risks are viewed and assessed and best work practices are instigated. As members of the Working at Height Association, VHA is part of a national body dedicated to developing a pathway to better safety standards. In 2020 there were 194 work-related fatalities, 36 in the construction industry, with 22 caused by falling from height. 25 to 44-year-olds accounted for 32 per cent and, shockingly, over-55-year-olds account for 44 per cent of fatalities. In the same period machinery operators and drivers had 67 fatalities, labourers 41 and managers 35 fatalities.Somerecent training provided by VHA includes: working at heights, height rescue, and confined space consultation for Powerlink Queensland; a bespoke training package for Contract Resources, nationally and internationally, involving heights and confined space rescue, breathing apparatus, and risk assessment within inert environments; and working at heights for a wind turbine construction client in Vietnam.
Paul Thew from Contract Resources has recognised how pivotal the training has been for his “Workingteam.in nitrogen-saturated environments is extremely hazardous, and one false move can literally mean the difference between life and death,” Thew said. “At Contract Resources we see training as the number one reason we have an unblemished safety record in relation to work in a nitrogen atmosphere.“InanAustralian first, Vertical Horizonz, in cooperation with Contract Resources, designed an extremely advanced training program to ensure the safety of our workers. The solution was completely bespoke and set a new standard for the petrochemical industry internationally,” Thew said. International research supports training as the recognised strategy to improve safe work performance. As a construction worker you are more likely to suffer a fall from height when you do not attend a safety training course. Additionally, behaviours such as carelessness, misjudgement, or over confidence, are major causes of serious harm or death from a fall at height.“Vertical Horizonz has spent the last two decades imparting specialist knowledge about working at height around the globe. Our ethos of ‘real training that saves lives’ has set our benchmark for quality training, by specialists, to industry,” said James Moohan. Brain Nowakowski of Sundriven Solar confirmed: “After my staff attended one of the VHA’s height’s courses, they now talk about the risks and work processes for each job prior to starting. One of them keeps on top of contractors on site, pulling them up when they aren’t doing things right.”
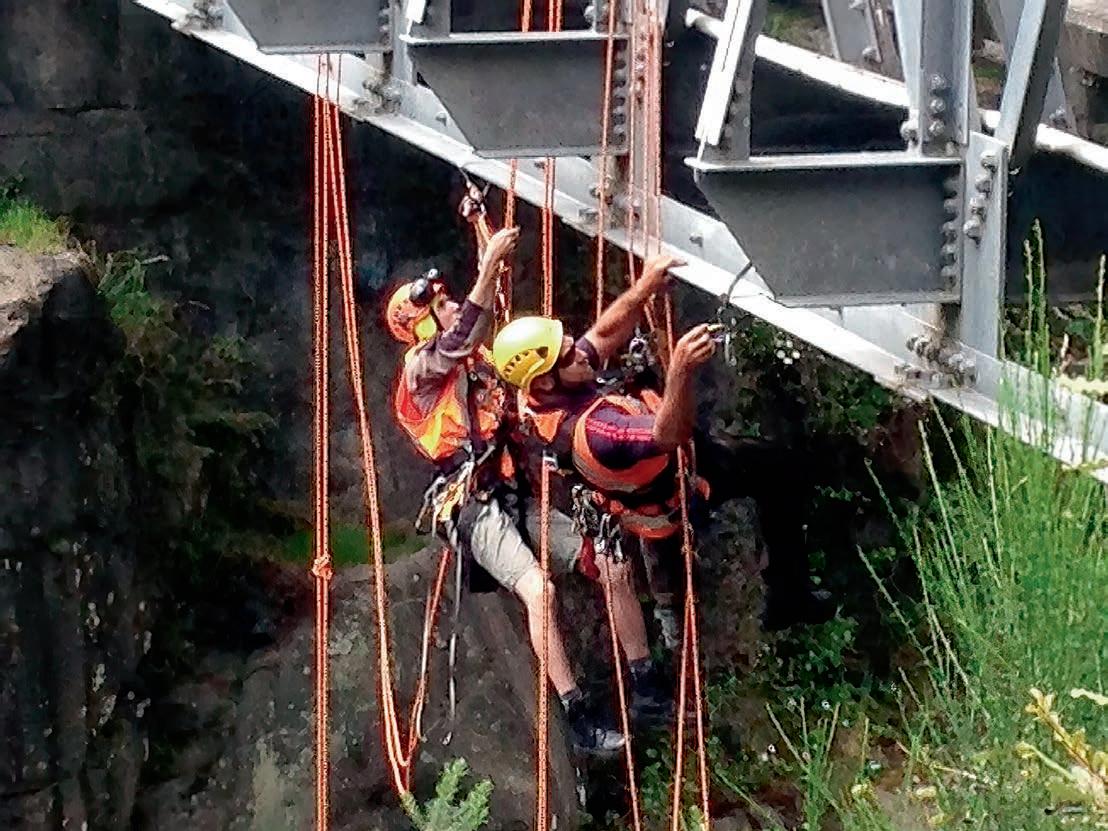
Blackwoods have introduced on-site industrial vending machines as a safe inventory solution for Canada Bay Council. Blackwoods have been providing first-rate solutions to their customers for over 140 years and today boast a catalogue of over 300,000 products. Australia’s largest provider of industrial and safety supplies, Blackwoods recently partnered with City of Canada Bay introducing on-site vending machines to solve the councils inventory problem.
In October 2020, after an internal realignment, Canada Bay Council realised it couldn’t have staff in its stores department 24-7, and consequently management sought solutions from its suppliers. As part of its proposal, Blackwoods suggested the placement of an on-site industrial vending machine to manage the council’s critical inventory, most of which was Personal Protective Equipment (PPE). “Like most businesses we all had to realign our thinking during the Covid Pandemic. Our first priority is to keep staff safe and to do this we need access to key PPE items 24/7.
44 INSIDE CONSTRUCTION August/September 2022
FOCUS Inventory solutions
Blackwoods introduce on-site vendingindustrialmachines
Blackwoods, which has a diverse range of inventory solutions, is always looking at ways to improve business practices for their customers, and their partnership with the City of Canada Bay is a great example of what can be achieved when customers and suppliers work together. The City of Canada Bay is a thriving local government area in the inner west of Sydney, Australia’s most populated city. It covers 19.82 square kilometres and has a residential population that is pushing towards 100,000.
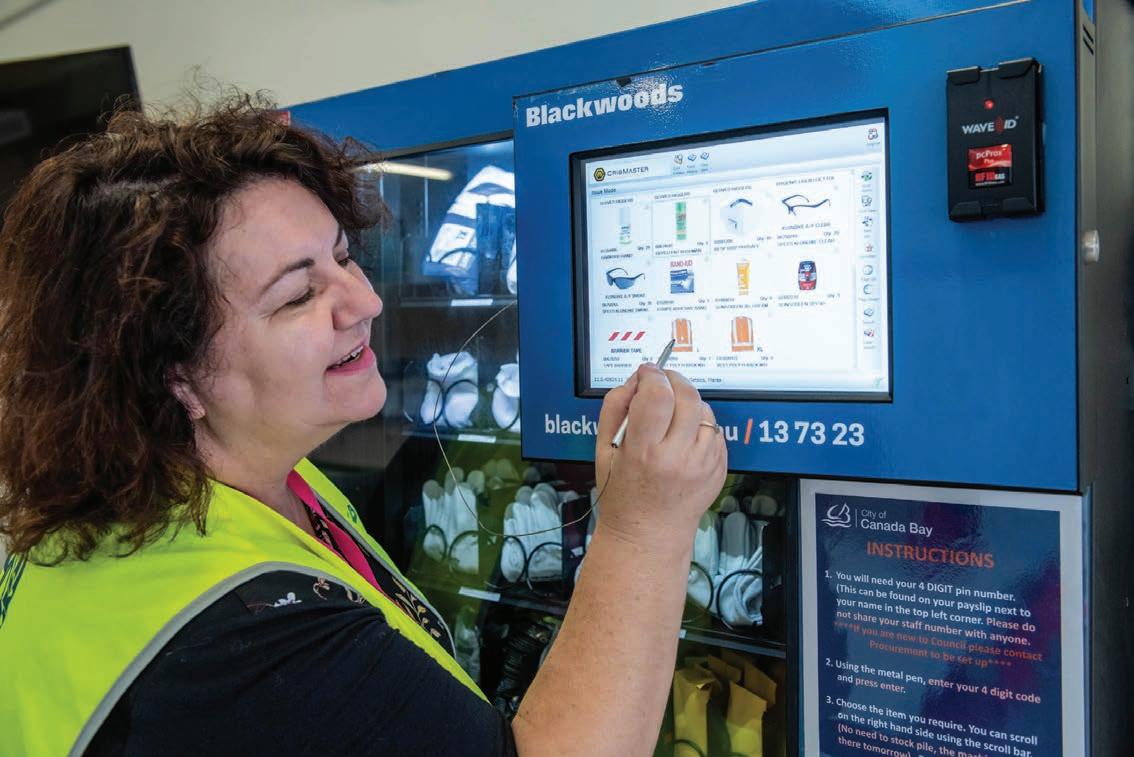
The vending machine became the most cost effective, space saving and logical solution,” says Marea Getsios, Procurement and Fleet Manager of Canada Bay City Council. Canada Bay Council became the first council in the Sydney Metropolitan area to adopt the vending machine solution. Ben Lawes, Inventory Solutions Specialist of Blackwoods says the benefits for the council have been widespread.“Aswellassite approved PPE, the vending machines have given the council a distribution point for Covid related items such as hand sanitiser, antibacterial wipes and disposable respirators. The machine reordering process is automated and through usage reports and stock on-hand reports, we can help the customer avoid stock outs of critical PPE which would impact their work schedules,” says Lawes. The on-site vending machines provide the council with the much needed access to inventory 24/7 for essential safety and PPE items, increasing productivity and reducing the time staff need to spend off-site. Benefits have also included a reduction in consumable spend, improved safety and compliance and greater visibility of usage among staff ensuring the approved PPE is being utilised at work sites. Further to that the vending machines are an innovative technology that provide automated reporting and management of key product trends. The touch screen interface disperses the chosen item in just four seconds and Blackwoods regularly re-stocks each machine ensuring all stock is maintained at high levels. Getsios went on to say, “At first our staff had a bit of a chuckle and were disappointed it didn’t dispense soft drink or chocolate bars, but now they are all grateful that our council has prioritised their safety by ensuring key PPE is available around the clock for easy access. There has been a reduction in the hoarding of items such as face masks, sanitisers and gloves.”Thesuccess of the on-site vending solution underlines the versatility and value of Blackwoods. Not only are Blackwoods an Australian supplier of products, but their technical expertise ensures they find solutions for all their customers. Blackwoods recognise the critical importance of having efficient access to inventory around the clock, even in the most remote of workplaces. “If the site has a need to change items in the “The relatedpointagivenmachinesvendinghavethecouncildistributionforCoviditemssuch
www.insideconstruction.com.au INSIDE CONSTRUCTION 45
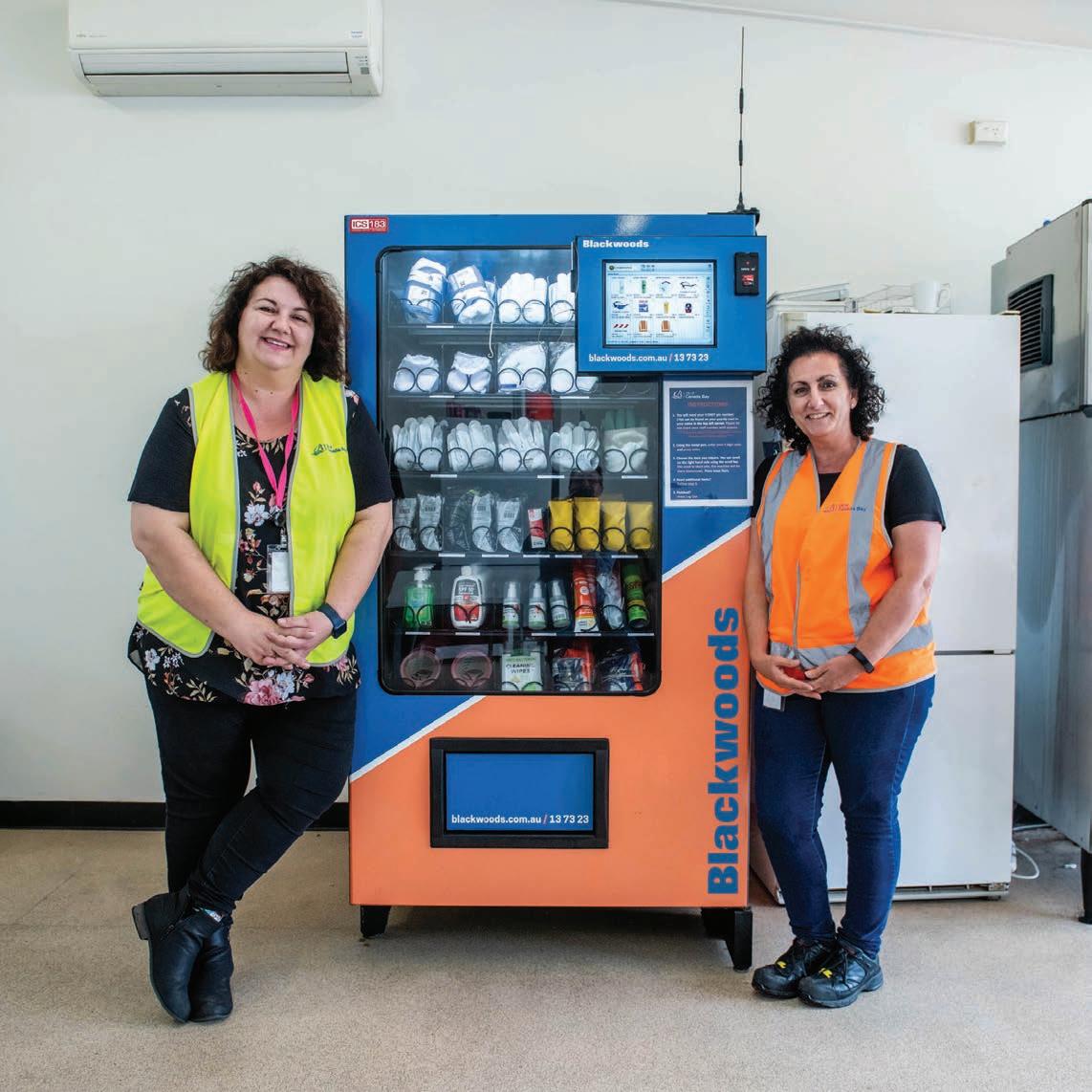
46 INSIDE CONSTRUCTION August/September 2022
The urgent need for the construction industry to change and become more sustainable was the genesis for the event. This is an industry that suffers from lagging productivity growth, a lack of diversity, lack of innovation, shortage of resources, poor mental health and slim profit margins. Despite various attempts, the industry has failed to shift the dial and now is the time to bring about widespread change. The industry has a lot of answers and tools, it just needs to actually implement and use them – and it can only do this if it works together. Setting the tone Setting the tone for what can only be described as frank and fearless discussions, the Australian Constructors Association’s President Mr Duncan Gibb introduced the L-R: Cathy Hayes, Seved Robin, Skye Mason & Gabrielle Trainor
The construction frog is boiling slowly in the pot – we need to find a way to crank up the heat to make it jump out! Be bold, be brave, and do it together as an industry – that was the takeaway from this year’s Future of Construction Summit (FCON22). Partnering with FuturePlace, the national representative body for major contractors, the Australian Constructors Association brought key issues to the forefront of discussions at the newest national conference for the construction sector, FCON. Promoted as the ‘must attend’ industry event, FCON22 did not disappoint. Almost 500 industry leaders and stakeholders attended the 2 day event held in Sydney from 4 - 5 May. With a stellar line up of speakers from government, industry and the supply chain, attendees were invited to join discussions about much needed reforms and the opportunity for a more productive and sustainable industry.
EVENTS FCON 2022
Future of Construction Summit 2022

L-R: ACALaslett,GreenRitchieandCraigformerPresident.
Massive prize for productivity
The FCON22 agenda reflected the three key pillars the Australian Constructors Association believes support a sustainable industry: positive industry culture; equitable and aligned commercial frameworks; and sufficient capability, capacity and skills. Strengthening these pillars has proven to be a difficult task as each of these pillars are interconnected and improvement in one requires improvement in all. This interconnectedness was highlighted by discussions at FCON and reinforced that message that the construction industry needs to work FCON22together.attendees widely accepted the position that it is time to increase collaboration and break through the areas of trust and value that have let the industry down. Through a mix of panels, fireside chats, presentations and roundtables, attendees were presented with honest discussions in a bid to start rebuilding trust in the industry. This included exploring the importance of all stakeholders having an understanding and empathy for each other’s drivers in order to better align on a more sustainable and productive future path for the industry.
www.insideconstruction.com.au INSIDE CONSTRUCTION 47
A fireside chat between the Australian Constructors Association CEO Jon Davies and Vice President Scott Cummins reiterated the need to get above projects and think about value for money to the industry. Mr Cummins went on to declare, “There is a massive prize for productivity, but we need a system that encourages and promotes it.”
Future of construction agenda
summit saying the industry needs to break through the clichés and forge new industry partnerships. Referencing clichéd stereotypes in the industry such as consultants only being interested in putting bums on seats to produce conservative designs, contractors only being interested in consultant’s PI policies and passing risk to the supply chain, clients only being interested in lowest price/maximum risk transfer and so on. Mr Gibb said, “Our individual success is tied to each other’s success and is not mutually exclusive. We can and must do better. And doing that will require a frank discussion about changing the way we have always done things.”
Underpinning the three sustainability pillars is a $15 billion opportunity to improve industry productivity and with the skills shortage knocking at the door the need for greater productivity and innovation led discussions on day 2. It was clear that there is not one silver bullet, there are a range of things to do collectively as an industry. The capability and capacity panel agreed the industry is changing and moving forward, but it needs to continue “As an industry we’ve shouted safety health…thewhisperedand world is changing and momentum is building. Bottom line this is imperative.”tothisofthetheproductivityhaveweconversationaallneedtoabouttheofindustryandsustainabilitytheindustry,isn’tanicedoit’san
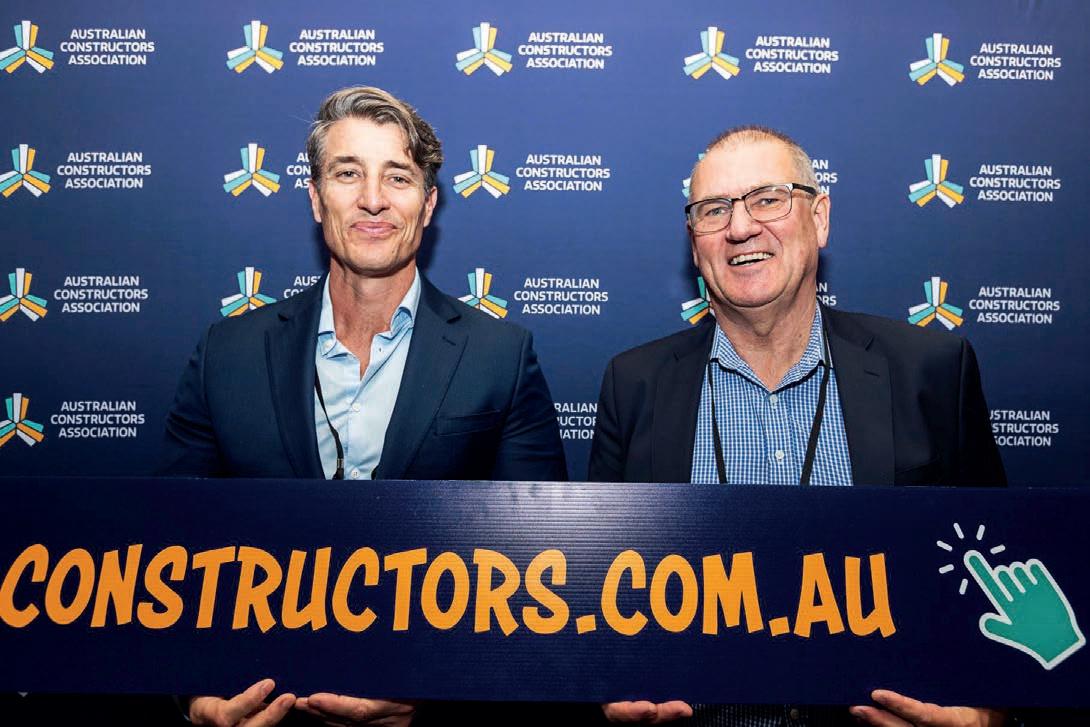
The technology leaders panel reported that the construction and technology worlds are colliding. There is so much data in existence, but how do we effectively use it?
48 INSIDE CONSTRUCTION August/September 2022 industry to attract and retain workers. Some of the levers discussed included technology adoption, improved focus on environmental sustainability and adoption of the new Culture Standard developed by the Construction Industry Culture Taskforce.
things.”alwaystheaboutfrankthatbetter.canexclusive.notsuccesstosuccessindividualistiedeachother’sandismutuallyWeandmustdoAnddoingwillrequireadiscussionchangingwaywehavedone EVENTS FCON 2022
Speaking of technology, people are the construction industry’s biggest asset and in discussing technology at FCON, speakers reiterated that it is really about augmenting those great people with better technology, making them more efficient, safer and more informed with data. It is going to take courage for digital to meet construction with a people firstBeyondagenda.the three pillars and technology, FCON also highlighted the importance of environmental sustainability which recently emerged as a key focus area for the Australian Constructors Association. If the construction industry really values moving to net zero and the reduction of gross CO2 emissions, it must that incentivise all stakeholders to invest together to reduce carbon emissions via design as well as developing new construction methodologies. This was one of the many important points made during the sustainability panel discussion. Changing culture Infrastructure Australia estimated that the construction industry is about to face a shortfall of 105,000 workers and this was before the major flooding events on the East Coast caused significant damage to infrastructure and increased demand for workers even further. Only 12 per cent of our workforce are women and this number declines to 2-3 per cent for blue collar workers. With construction workers six times more likely to die from suicide than a workplace incident, is it any wonder the industry is struggling to attract and retain enough people to undertake the record pipeline of work ahead. If we want to keep our workers safe, attract new talent and keep pace with the growing demand for infrastructure, we need to tackle the big issues that have plagued our industry for decades. Construction Industry Culture Taskforce Chair Gabrielle Trainor AO spoke on changing culture to address gender diversity, “Our
L-R: ScottViceJonAssociationConstructorsAustralianCEO,DaviesandPresident,Cummins
Emerging technologies and digitalisation drive efficiencies and capture data. However, if people don’t trust the data, and don’t use it, or it’s not meaningful, we’re not productive.

In the words of Utopia!”brickalongaco-opetitioncollaborationfroghavespeech,inCEOAssociationConstructorsAustralianJonDavieshisclosing“Wetoboilthetostimulateandfordigitaljourneytheyellowroadto
www.insideconstruction.com.au INSIDE CONSTRUCTION 49 working hours and mental health and the work being undertaken by the Construction Industry Culture Taskforce – a partnership between the Australian Constructors Association and governments of NSW and Victoria.“Asanindustry we’ve shouted safety and whispered health…the world is changing and momentum is building. Bottom line this is a conversation we all need to have about the productivity of the industry and the sustainability of the industry, this isn’t a nice to do it’s an imperative,” Trainor said. The national culture standard developed by the Taskforce was a key discussion point at FCON22. The Culture Standard provides a framework for clients and contractors to work together to improve the conditions for workers in the construction industry. It proposes a set of standards be incorporated into procurement processes to improve worker time for life, wellbeing, and diversity and inclusion. Following the public consultation in late 2021, the Culture Standard is now being piloted in NSW and Victoria on a range of projects and contract types. It is anticipated that the evidence base supporting broader adoption of the standard will be finalised by the end of 2023. Subject to the findings, governments Australia-wide will be called upon to adopt the standard through procurement processes in each jurisdiction. Industry at its best
L-R: Jon Davies, Sarah Marshall and WhitneyJayne
The turnout and enthusiasm at the newest national construction conference was a heartening reminder that the industry is at its best when it works together. Australian Constructors Association Vice President Scott Cummins summed up the themes perfectly saying, “It’s all about collaboration. It is about getting the early involvement of our contractors, sub contractors, designers and the supply chain and everyone working together to take on the challenges that we are confronted with today. It is about using innovation and technology and increasing the productivity of the entire industry to solve the problems that we are confronted with to deliver great infrastructure for the whole of Australia.”Fromterms such as ‘co-opetition’ – where industry competitors also collaborate to achieve mutual benefits for the industry, to ‘reverse mentoring’ – where younger workers and older workers connect and learn from each other, countless insights were shared that resonated with the audience. Don’t lose the sense of urgency Discussions from FCON22 promised to bring about transformative change at an accelerated pace. The Australian Constructors Association has not lost sight of this promise and is advocating strongly and partnering with government and industry to bring forward change.Planning is underway for FCON23 to be held in Melbourne from 3 - 4 May 2023. Audiences can expect to see a reinvigorated agenda with industry headwinds like material price escalation a prominent feature. In the words of Australian Constructors Association CEO Jon Davies in his closing speech, “We have to boil the frog to stimulate collaboration and co-opetition for a digital journey along the yellow brick road to utopia!” Find out more at constructors.com.au
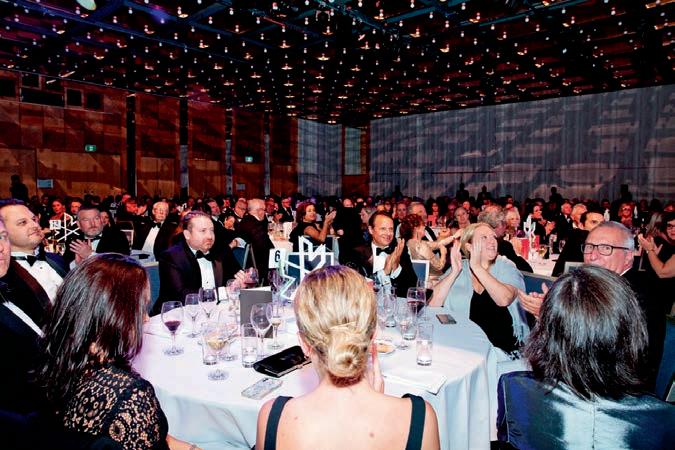
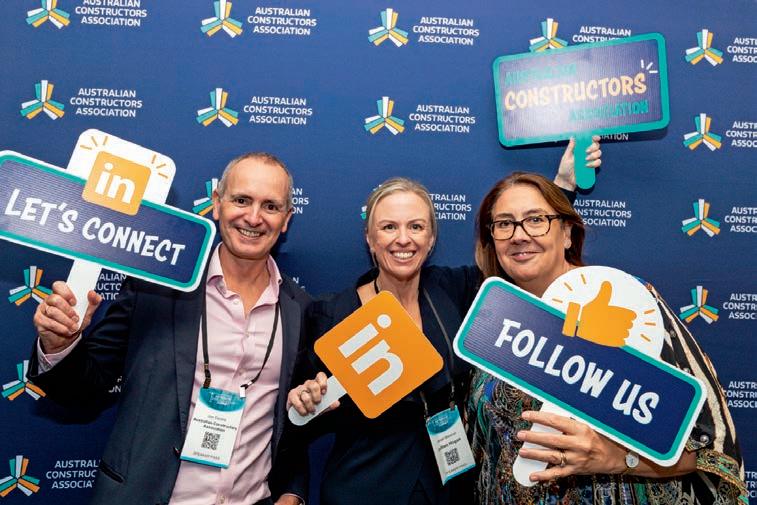
Today she is a project manager for Coulson Operations, an organisation that operates 5 childcare centres across Northern NSW and has been contracted to lead a high-profile job to build an integrated childcare centre on the Gold Coast. Coulson Operations are partnering with Autism Australia to deliver the project, and Keiley says further details will be announced in the coming months.
It’s been a process, but the job is amazing and it’s a unique build that I am proud to be a part She is also the National Association of Women in Construction (NAWIC) Women on Tools Committee (WoT) Chair. NAWIC is an organisation supporting, promoting, and advocating for change within construction and non-traditional trades for women. They educate, empower and connect women in the industry. NAWIC Queensland is made up of 7 committees and Keiley chair’s the WoT committee.“Myroleas Committee Chair for the Women on Tools Committee sees me lead a team which specifically supports ladies and male allies that are ‘on the tools’ such as apprentices and tradies. We like to make sure the voices of lady tradies are heard within the broader construction industry and among corporate construction workers, as tradies often have different needs, concerns, and ways of doing things,” says Keiley. It’s been an interesting and inspiring journey for Keiley. Following the completion of her trade in 2008 with Custom Plumbing Services, she was the second ever trade qualified, female plumber in Canberra, ACT. She says throughout her 20 years in construction the industry has improved exponentially in supporting women to take up blue-collar roles.
“It’s a technically challenging build because it lies within a very low lying, flood prone area. We’ve had to do a lot for flood mitigation. We’ve had a lot of compliance issues because we’re not only dealing with the building code but we’re dealing with the Childcare and Education Department requirements as well.
PEOPLE Profile Rachael ProjectPlumberKeiley:toManager
Rachael Keiley’s career in construction spans almost 20 years across plumbing and building, both on and off the tools. Now in a project management position for boutique developer, Coulson Operations, the plumber by trade is heading up an exciting, new project soon to be revealed to the public.
50 INSIDE CONSTRUCTION August/September 2022
Kicking of her trade as a plumber in 2003 at the Canberra Institute of Technology, Keiley has had a diverse career taking on roles in commercial construction, plumbing, maintenance, heritage and rural work, estimating and project management.

Keiley’s career has led her to construction project management, but she says she’ll always be passionate about plumbing. During the building boom in the early 2000s, she went looking for a role in the automotive industry and was unable to get a start. She then jumped at the first job that she was offered, which happened to be plumbing.“Allthese years later I’m so grateful that I started my career in plumbing. I’ve had such an amazing career specifically because of a plumbing company giving me a start. The universe had something in store for me and today I still think about where I would be if I was a mechanic,” says Keiley. With a long history of experience and industry expertise, Keiley has some great advice for people thinking about starting a career in the construction industry.
Association of Women in Construction and other associated organisations to raise the profile of tradeswomen and break down some of that bias,” says Keiley. After finishing her trade, Keiley dabbled in and out of construction before being headhunted into an estimating role with a plumbing company in 2009. She then made the move to Queensland and into commercial construction where she found herself working on high rise projects. “Over the past 20 years, bathrooms and kitchens, restructuring the roof and adding on an extension. “On weekends, after hours and during holidays I’m working on my own projects, mainly within residential and live-in builds.”
“My advice for girls coming through is don’t recreate the wheel, we’ve got a sisterhood in the construction industry and there’s a lot of us here now, so reach out to your support system and don’t be afraid to lean on them. We’re here to share advice and help support you. Those old days of poor culture are now getting eradicated.”
www.insideconstruction.com.au INSIDE CONSTRUCTION 51
“When I joined the ofbreaktradeswomenraiseorganisationsother(NAWIC)ConstructionofAssociationbyamazingtimeasthewomenveryclub.veryyearsindustryconstructionnearly20agoitwasmuchaboy’sItwasn’tcommonfortobeontoolsasmuchitistoday.OverI’veseenworkdoneTheNationalWomeninandassociatedtotheprofileofanddownsomethatbias.”
“People need to take construction seriously as a career because the benefits and pathways are vast. I started as a plumber, I ended up as a builder, I had a construction company, I went into development and now I build for someone else,” says Keiley.
L-R: (upper) Shannon Box, Jasmine Bullock, Becky Fisher, Kat Worth, Tash Kirchner, Rachael Price, Jasmine Turnbull, Radmila Desic, (lower) Carlie Low, Rachael Keiley, Toni Hillman, Ruth Gunaseelan Rachael Keiley, Project Manager


communities,” says Marshall. “The most positive aspect about working in the industry is by far the incredibly talented people you get to work with and learn from every day and the community members you meet along the way. Our industry employs people from all corners of life which brings together lots of interesting experiences and stories.”Marshall has a passion for driving infrastructure sustainability, reducing the stigma of mental health issues, driving improved leadership and career pathways for the blue collar workforce, increasing Indigenous engagement and procurement, workforce employment, community engagement, skilling and training and driving improvements in all areas of diversity.
Previously with Abigroup and Lendlease as an Executive General Manager, Marshall drove mental health initiatives on a national and global scale. In a first for corporate
An accomplished construction and infrastructure executive, Sarah Marshall has spent her professional career spearheading positive cultural change in the construction sector.
52 INSIDE CONSTRUCTION August/September 2022
SarahPEOPLE
sustainabilitypeople,ChampionMarshall:forsafetyand
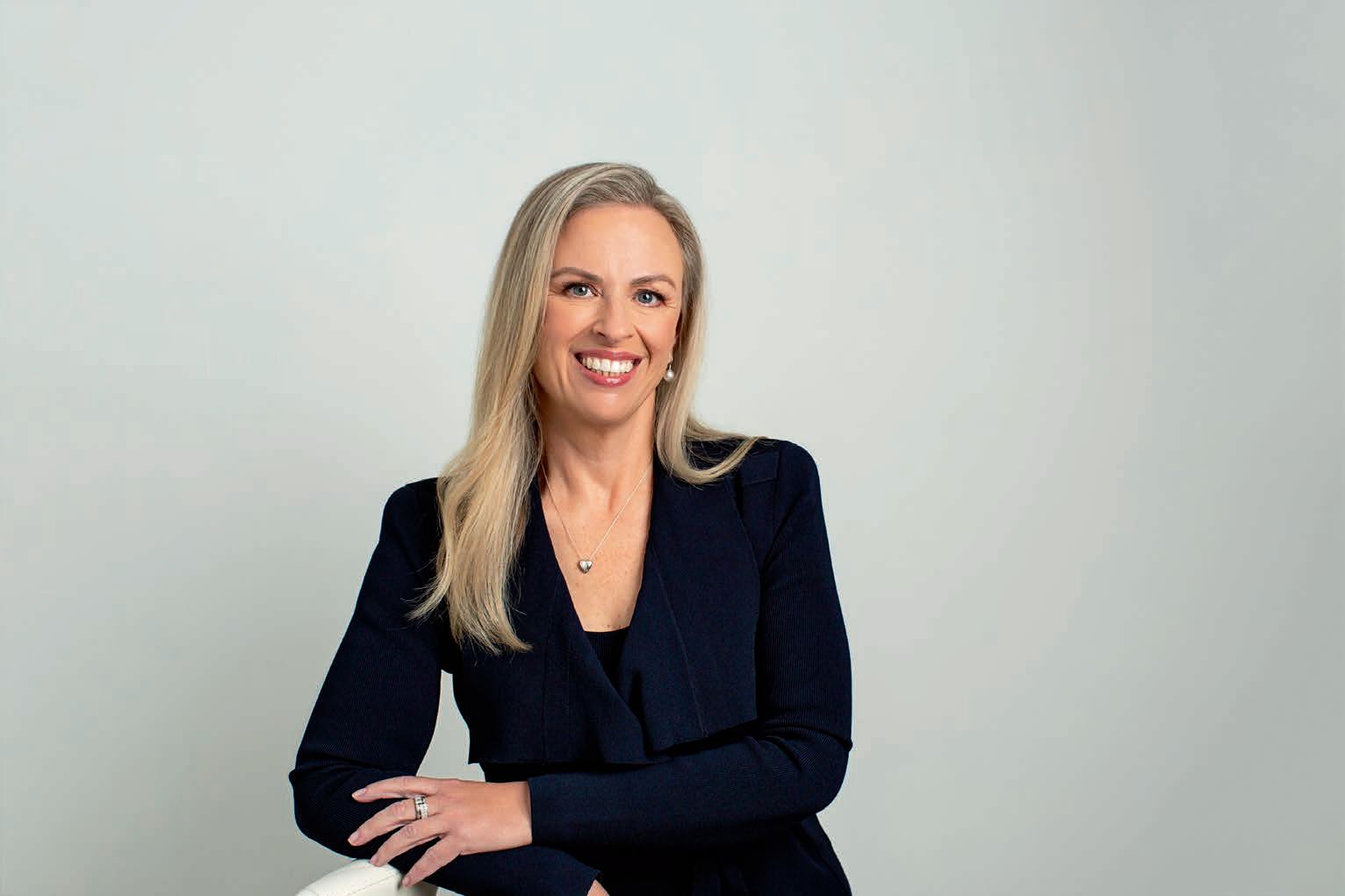
“The most positive aspect stories.”experienceslotsbringsoffromemploysway.meetmembersthefromwithyoutalentedtheindustryworkingaboutintheisbyfarincrediblypeoplegettoworkandlearneverydayandcommunityyoualongtheOurindustrypeopleallcornerslifewhichtogetherofinterestingand
www.insideconstruction.com.au INSIDE CONSTRUCTION 53 Australia, in 2009 she formed a partnership with Beyond Blue which started a wave of conversation and change across the industry. The Beyond Blue partnership represented an innovative approach to business partnering with a non-for-profit organisation to raise awareness of depression and anxiety disorders in the construction industry. It paved the way for other businesses and organisations to follow suit and develop their own mental health initiatives and partnerships.Marshallisdedicated to working collaboratively to drive widespread industry change. She is a Board member of the Australian Constructors Association (ACA) and Executive Sponsor of ACA’s Capability and Capacity Board Committee. She is also Chair of the Capability and Capacity Group within the Construction Industry Leadership Forum – a collaboration between the ACA and the governments of NSW, Victoria and Queensland. Further, Marshall is Deputy Chair and Board Director at the Infrastructure Sustainability Council (ISC). During her time working with these boards and industry associations, Marshall has helped drive improvements to industry culture, including greater female and Indigenous participation. She has been a strong advocate for the new industry culture standard developed by the Construction Industry Culture Taskforce and, in particular, the ‘5-Day Working Week’. She has also helped establish learning and development guides for construction engineers in partnership with the ACA and Engineers Australia.Marshall’s commitment to driving industry change has seen her well recognised by the construction industry through multiple awards. In 2015 she won the Lendlease Employee Excellence Award for Vision and Values, in 2014 Marshall was titled the WME Corporate Sustainability Leader, in 2013 she was a top 2 finalist at the Telstra Women’s Business Awards, in 2011 she took home the Lendlease CEO Award for Sustainability and Corporate Leadership and in 2002 she won the National Association of Women in Construction Award (NAWIC) for Outstanding Achievement in Innovation. “Whilst it is always so humbling to receive an award for my work, there is part of me that is often very uncomfortable with the recognition. The work that I have done around raising awareness of mental illness, improving the culture, attracting more women and diverse groups to the industry is, I believe, something that all good leaders should be doing as part of their day jobs,” says“TheMarshall.thingabout awards that I enjoy the most is the process of working with the individuals and teams who have nominated me. Taking the time to stop and reflect on the difference that we are making to the industry and peoples lives is something we do not do often.“Attimes they seem like small incremental changes but over time they really do make a difference and we must continue to focus on the end game. “I also acknowledge the importance of having representation of senior leaders like myself in the mix for awards – I truly believe that ‘you can’t be, what you can’t see’, so whilst the nominations are often very uncomfortable for me, I know that they are so valuable for younger females coming up the ranks in our industry to remind them that they are worthy to hold space with their male counterparts.” On top of her impressive professional career, Marshall regularly gives back to the community through pro bono, volunteer and community work, from organising Charity Bike Rides raising awareness of constitutional recognition of Aboriginal and Torres Strait Islander peoples or men’s health, to her previous role as an Ambassador for Beyond Blue. In every organisation that Marshall has worked for she has been a voice for change, motivating and inspiring real and meaningful change both at a company and wider industry level. “The construction industry is an incredibly rewarding industry, but it can be tough at times,” says Marshall. “Industry culture and diversity is changing for the positive and I will continue to strive to make sure that there is a role for everyone no matter your gender, cultural background, previous experience or employment status.”
2. Asset sustainability Earthquakes, fires, high winds, flooding. The US alone experienced 14 different $1 billion or higher disasters in 2019, the fourth highest year on record; and it’s estimated that natural disasters now cost Australia $38 billion per year. Our industry plays an important role in solving the asset sustainability challenge. As one Australian engineer executive stated, “The one and only thing we need to pay attention to is climate change; floods, fires and rooves blown off houses.”
1. Technology adoption Those interviewed spoke of the progress we are making in the use of new technologies such as drones and lidar scanners. However, challenges remain. As one engineering executive put it, “Clients are asking for rigorous digital delivery ahead of its time. It’s making people crazy, costing dollars, and we don’t get the benefit of the beginning of technology adoption. We’re on a journey together, and owners are pretty rational about it.” One client stated, “Technology is not making us faster because we are swimming in data.” Continuing to crack the technology adoption code will be critical to gains in productivity in the coming decade for our industry.
Words Dr Gretchen Gagel
Looking back upon 25 years of project excellence and forward to the challenges we face as an industry
Serving as one of the four judges for the 25th anniversary of the Australian Construction Achievement Award in 2022 was an uplifting event that solidified the tremendous pride I feel for our industry. This collaboration between the Australian Constructors Association and Engineers Australia represents the spirit of collaboration we value so deeply in the construction sector. To hear each nominated project team passionately explain how they worked together to solve technical challenges, to engage the next generation and local communities, and to achieve outstanding results, was remarkable. What I also appreciate about our industry is that we continue to strive for improvement.
54 INSIDE CONSTRUCTION August/September 2022
Earlier this year, in collaboration with study sponsors the Construction User Roundtable and Construction Industry Institute, I interviewed forty-four construction industry leaders in Europe, Australia, Asia, and the United States to explore current trends, issues and solutions. These six key themes emerged:
PEOPLE Opinion Dr backGagel:GretchenLookingandforward
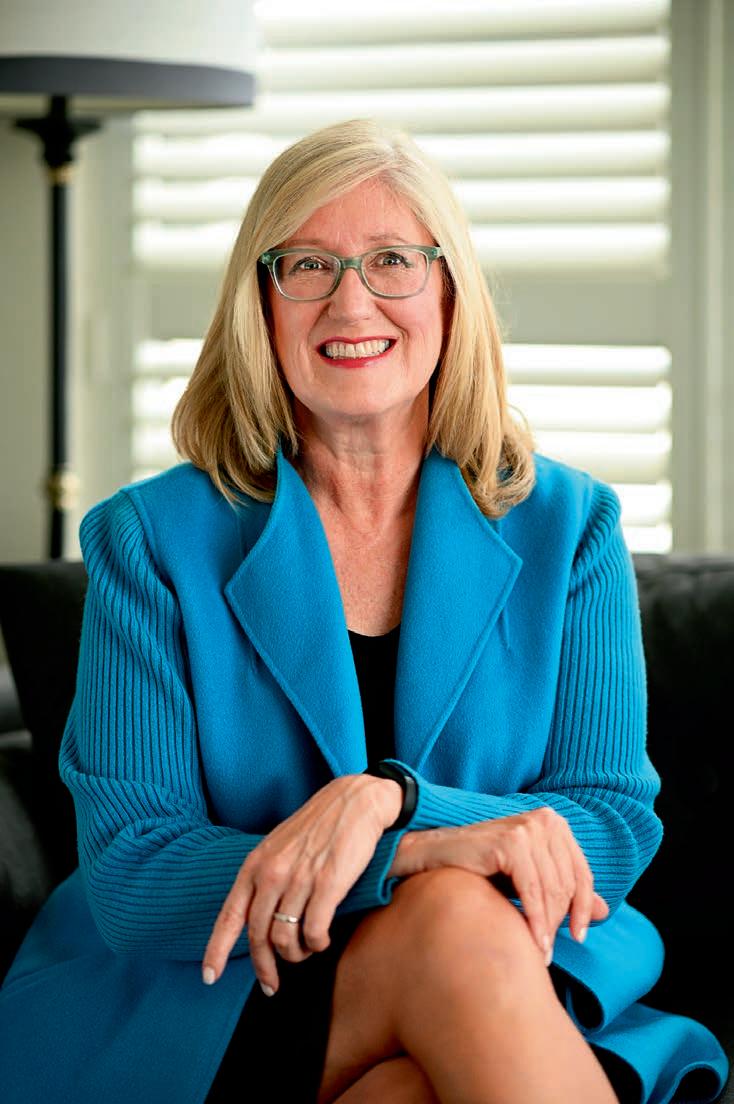
Our industry frequently exhibits complicated power dynamics that do not contribute to the highest levels of productivity and value. As one client study participant stated, “These are masterservant relationships that start with the procurement models.” Another client participant stated, “Trust issues remain. It’s in our culture, our contractual norms, our ways of working. People are protective of transparency, worried about liabilities and potential claims.” But we are seeing improvement in collaboration and a recognition that longer term, trusting supplier relationships pay off. As one global client stated, “What helps us? Really good, longer-term strategic relationships with vendors that improve everyone and provide greater transparency. It’s not standard practice, but it’s getting better.”
Our industry has made great strides in addressing physical safety concerns, and now understands that being one of the leading industries for suicide is not acceptable. Participants shared many examples of progress. As one global contractor stated, “People are getting the message, and we are destigmatising talking about it. We’ve trained our supervisors for the signs to look for. Our safety award program for the first year had two awards for helping people in mental distress. We need client support to make it work as clients that ‘get it’ and treat us like human beings make the difference.”
3. Supply chain and estimating More than half of those interviewed feel that we’ll be dealing with supply chain issues for more than four years, and that estimating has become “guestimating” at best. One global pharmaceutical company indicated that “missing a $0.25 part in a cable tray caused a three-month delay.” However, we have also seen incredible agility in keeping projects going in the face of supply chain adversity. We’ve also seen collaboration in repricing projects to ensure that clients continue to receive value and suppliers make an appropriate profit.
4. Power
www.insideconstruction.com.au INSIDE CONSTRUCTION 55
5. Labour shortage
A leading Australian contractor shared this: “For the last decade, we’ve trained people to be connectors with a two-day training course and stickers to identify them to help with mental wellbeing.” This is progress.Weneed to continue to recognise the tremendous successes of our industry through vehicles such as the Australian Construction Achievement Award; and continue to face our industry challenges head on. It’s through collaboration, trust, and innovation that we will drive progress and change for a better industry more capable of serving the needs of our society.
6. Mental wellbeing
This is a global issue with Australia alone forecast to project a 100,000-person shortage in construction by 2023. The great news on this front is that improving our image and our work practices to ensure we are attracting the top talent of the world is a significant area of focus. The efforts of the Construction Industry Culture Taskforce are but one global initiative to solve this problem. Attracting a more diverse workforce is also critical. As one person stated, “This is an acknowledgment of the reality that diversity makes a difference and that diverse teams are better at problemsolving and innovation.”
We need headchallengesourcontinueAward;AchievementConstructionthevehiclesindustrysuccessestremendousrecognisecontinuetototheofourthroughsuchasAustralianandtofaceindustryon
Dr. Gretchen Gagel is Chair of Brinkman Construction (US), a member of the National Academy of Construction (US), a member of the Construction Industry Culture Taskforce (AUS), and an affiliate professor at the Australian National University and the University of Denver. As President/Managing Director of Greatness Consulting Pty Ltd she continues to advise organisations within the construction industry on optimising capital program delivery and developing talent. You can hear more from Gretchen on her Spotify podcast, “Greatness”. For a copy of the study discussed please reach out to her directly at ggagel@greatnessconsulting.com.
competencesiteConstructionsafety&
receive micro credential learning on formwork return home safely at the end of the day. This program will provide specific formwork skills and positive awareness of the industry risks by providing practical learning outcomes to benefit workers. The activity will focus on the individual formworker to allow that person to increase their safety knowledge and skills, allow them to become more employable, more connected to the industry and their peers and increase motivation and enthusiasm in the industry.Theeasy to access micro credential learning
The time was right for the Australian Formwork industry to take control of change, innovate and adopt new technology to assist in a new education pathway to improved safety, that delivers massive benefits to all concerned in the industry. As FIA President, Jason Andrijic, states, “There is an opportunity right now to upskill workers and provide a new learning pathway for new entrants and ensure a future skilled labour force, that is competent, safe and productive.”
56 INSIDE CONSTRUCTION August/September 2022
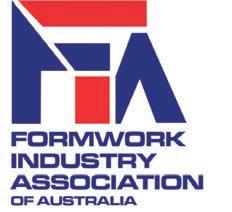
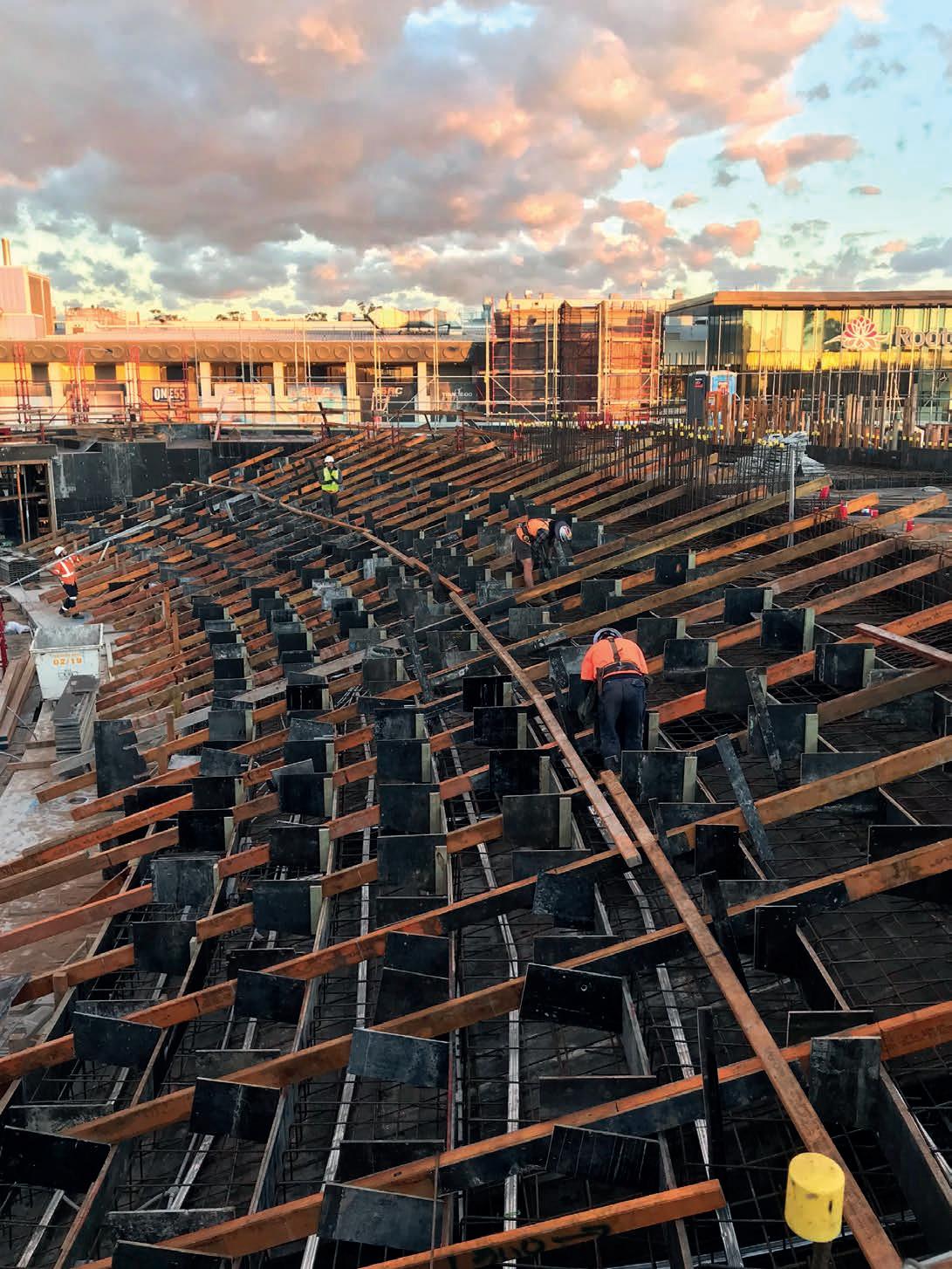
How can you help? The easiest way to get involved and to help create industry wide and recognised minimum levels of safety is to support the FIA and become a member. With its achievements over the past year, the FIA has demonstrated that by working together there is mutual benefit as a strong industry body to achieve outcomes otherwise not possible by going it alone. Further information
1. Introduction to WHS and the Formwork Code of Practice 1 .1. Awareness of formwork code of practice 1 .2. W hat does a Code of Practice Cover? 1 .3. Common Formwork Hazards 2. Controlling common formwork hazards 2 .1. Access & egress 2 .2. Manual handling 2 .3. Penetrations 2 .4. Handrails 2 .5. Silica dust 3. Risk management 3.1. Risk tools/documentationassessment
4. Consultation 5. Different types of Formwork
The FIA will then develop the next stage of the education pathway in consultation with industry and government training services to build a worker’s skills, learning, confidence, and capabilities and improve site safety and competence.
www.insideconstruction.com.au INSIDE CONSTRUCTION 57 program will be accessible to workers at toolbox talks, pre starts or other times in the shed via mobile learning and is a record they can take with them. With video and image-based learning, along with gamification, it is hoped to engage workers in learning, tackle the language barriers and prepare workers for further learning.
Current situation
The Safe Formworker pilot program is voluntary and whilst it does not form part of any legislative or regulatory scheme, it will assist formwork companies, construction companies and business owners to meet their obligations under the WHS legislation including the Formwork Code of Practice. For further information on the program, please contact the Formwork Industry Association CEO, Michael Sugg on 0401 326 161 or via formworkassociation.com.aumichael@
The Pilot program was released in early July and will have 300 workers complete the program by the end of October 2022. Once the initial statistics have been gathered and additional funding achieved, the program will be rolled out to the industry. Already, those involved in the pilot have expressed positive feedback and shared ideas on how the program can be developed further to meet industry needs.
What is program?the Developed in consultation with the formwork industry the program is a pathway for workers to receive micro credential learning on formwork specific WHS issues. Initially 5 courses with 12 lessons, the program will be administered by the Formwork Industry Association and include: “There is opportunityan right now to andislabourfutureandforlearningprovideworkersupskillandanewpathwaynewentrantsensureaskilledforce,thatcompetent,safeproductive.”

58 INSIDE CONSTRUCTION August/September 2022
Hyper-escalation of construction costs for contractors locked into fixed price contracts is emerging as one of the biggest challenges and one that, if not addressed, could significantly impact on the ongoing sustainability of the industry. Service stations can increase prices within hours of the oil price going up and
Solution needed for constructionescalatingcrisis
Words Jon Davies, CEO Australian AssociationConstructors
Jon Davies, CEO, Australian solutions.inflationconstructionAssociationConstructorslooksintocostandindustry
The headlines tell a depressing story of increasing failures of construction businesses caught in an escalating crisis. Covid caused significant delay and disruption to many projects and led to a massive increase in the number of projects as governments sought to stimulate the economy. The increase in work caused huge demand for workers, with Infrastructure Australia forecasting a 105,000 worker shortfall in the next 12 months. Flooding events and ongoing wet weather on the East Coast further delayed projects and increased demand for workers – and then Russia invaded Ukraine. Oil prices skyrocketed and along with them the price of energy intensive construction materials like steel, cement and asphalt. Other material prices such as timber also increased as they became harder to source and took longer to arrive as supply chains buckled. Double digit inflation for an industry with single digit profit margins was always going to be a recipe for disaster but more so for one that is required to lock in prices for projects that can take years to construct. This industry already accounted for almost 25 per cent of insolvencies in Australia and more worrying, is one whose workers are six times more likely to die from suicide than a workplace incident.
ASSOCIATIONS Australian Constructors Association
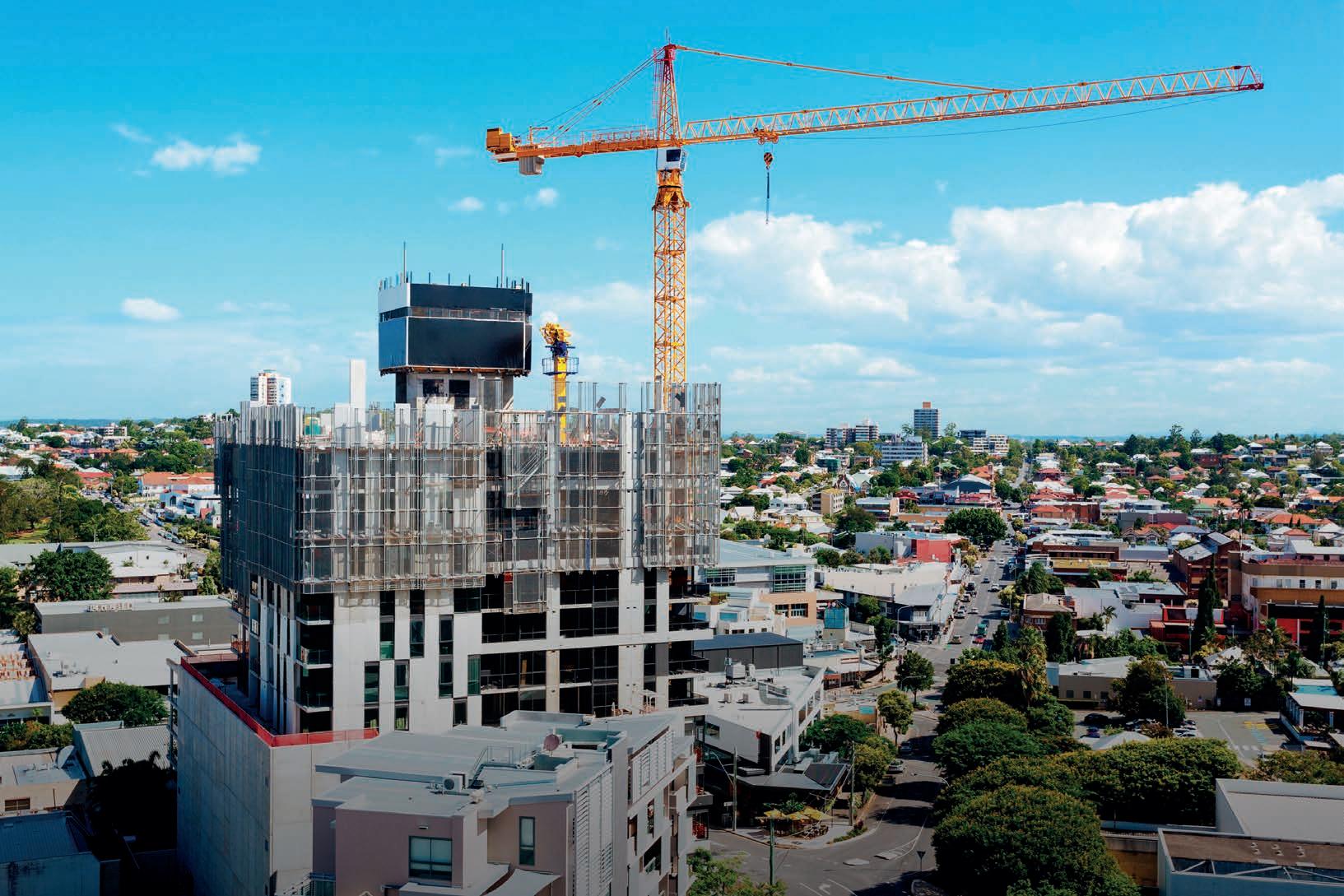
www.insideconstruction.com.au INSIDE CONSTRUCTION 59
dealtfluctuationsensuremechanismstransparentshouldcontractsforwardcontaintofuturearewithfairlyJonDavies,CEO,AustralianConstructorsAssociation
supermarkets increase the price of tomatoes within days of supply being disrupted, yet construction companies are expected to provide fixed prices that include for a range of unknown and unpriceable risks like inclement weather, material price escalation and diversion of utilities that don’t appear on any drawings. The industry is seeing examples of price rises over a 12-month period of up to 70 per cent and yet clients continue to expect fixed prices. The industry cannot continue to bear the cost of these steep price increases – some costs will need to be passed on to halt the growing trend of insolvencies. The Australian Constructors Association’s latest report, Construction cost inflation – Ways to address and escalating issue, highlights the impact of increasing costs and calls on government to take action both in respect of current and future contracts to ensure that the contractor is not left out of pocket for what is an issue that is well beyond their reasonable control. It is not in anyone’s interest for this situation to continue. When contractors fail the impacts ripple throughout the complex network of contractors, consultants, suppliers and sole traders that is the construction industry.Capacity is lost, impacting the industry’s ability to deliver the governments’ pipeline of projects and therefore realise the associated economicUltimately,stimulus.thisisa shared problem –government, contractors and the supply chain are in the immediate firing line, but company failures impact the wider economy. It is in the client’s best interests to work with the contractor as the cost of doing so will be far less than the cost and or delay to a project if the contractor fails. Some government clients are starting to include provisions for cost escalation, known as ‘rise and fall’ provisions, which the Australian Constructors Association applauds. However, these are often limited to a particular type of contract or particular commodity when the problem is much more widespread. We need to fundamentally change a system that encourages contractors to compete against each other to price and take on unpriceable risk like material price inflation. To its discredit, the industry has been all too willing to participate in this system.Going forward contracts should contain transparent mechanisms to ensure future fluctuations are dealt with fairly. This also means contractors should not make windfall gains if price falls. Projects should not be deferred or cancelled as this can have unintended consequences worse than the problem trying to be solved. Asset owners can keep to budget by using pre agreed positive/negative variations to adjust the scope to account for material price fluctuations or other risks for that matter.
The industry needs to become more financially sustainable to properly focus on important issues such as improving productivity, sustainability and innovation.
Going
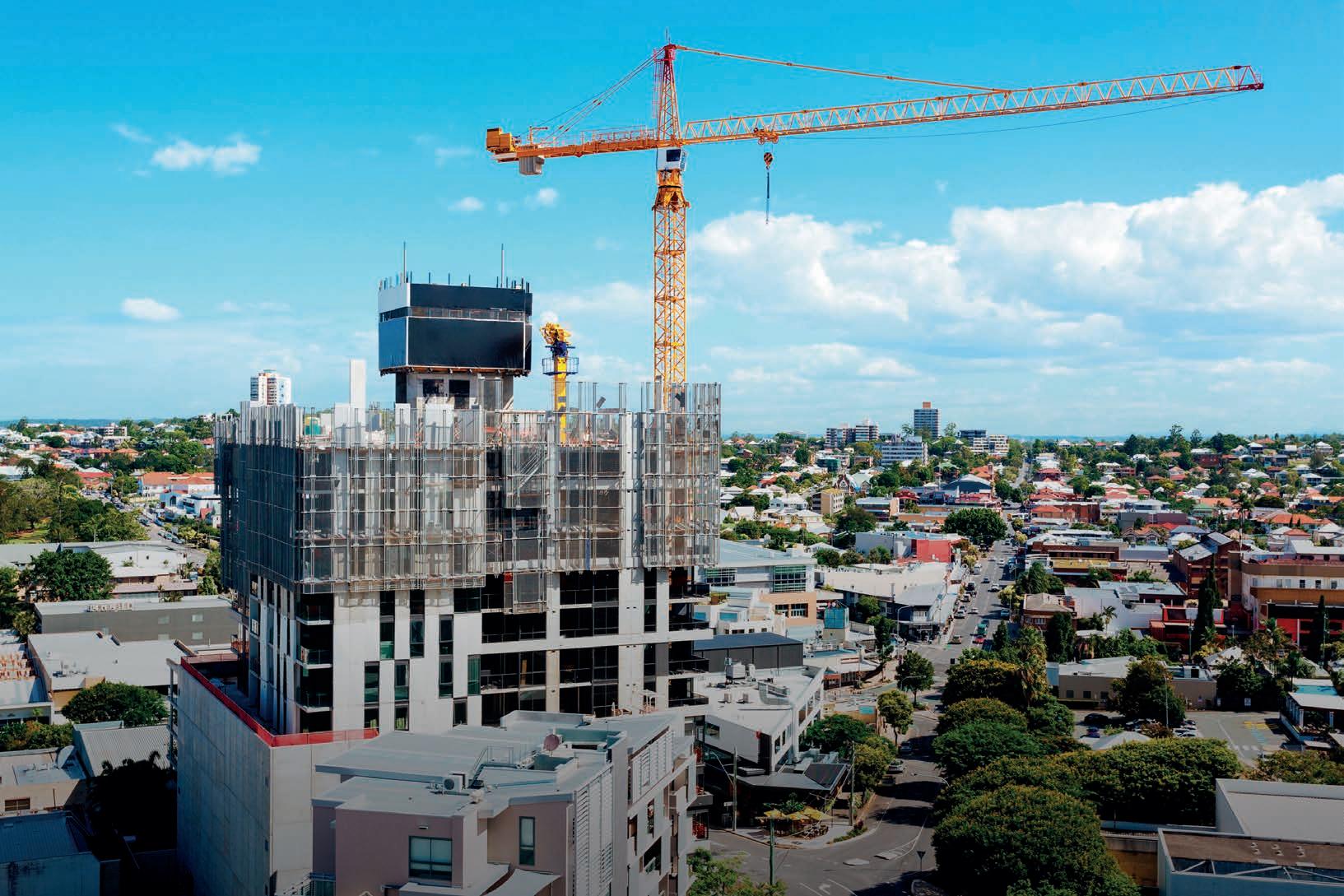

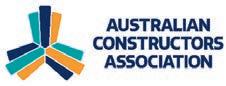
Association
Master Precaster to save builders time and mitigate risk Master Precaster grew out of discussions with tier one quality managers. Evidently, a precaster having ISO certification wasn’t enough to warrant that systems and procedures were actually being practiced on a dailyMasterbasis.Precaster membership requires the precaster to pass an audit where they are assessed on their QSE practices as well as a range of other benchmarks like track record, technical expertise, factory capability, industry Precast Concrete
ASSOCIATIONS National
While Covid continues to run rampant, the construction industry is busier than ever. In the main, National Precast members are manufacturing to fulfil orders booked well into the future. As the peak body for the precast industry, National Precast addresses a number of industry matters with government and Standards Australia, offers new initiatives and its members themselves bring new offerings to the table.
60 INSIDE CONSTRUCTION
Secondary lifters declared an unsafe practice National Precast has had an ongoing dialogue with the Queensland’s Office of Industrial Relations (OIR). It started some years ago after discovering that the requirement for secondary – or backup –lifters, had snuck its way into the State’s Code of Practice (a requirement which only exists in Queensland, let alone the rest of Australia or throughout the world). Together with industry professionals –including the major suppliers of lifting componentry Reid Construction Systems and Leviat – and other peak bodies such as Master Builders and the Crane Industry Council, National Precast has declared secondary lifters unsafe and encouraged the OIR to remove the requirement. Letters have been sent to relevant ministers and the opposition. Understanding grouting – available as a guide and as online learning Tight construction programmes can result in grouting becoming a secondary consideration and that can have serious consequences. Consequently, imparting engineers, builders and precast installers with a better understanding of their requirements when it comes to grouting precast elements, is imperative. We have now produced guidance in the form of both a Guide and an online learning module. Both are available via nationalprecastonline.com.au.
Association Australia
From the desk of the CEO Master Precaster Austral Precast has DoubleBrickbothintroducedthePanelsystemandWall Australia
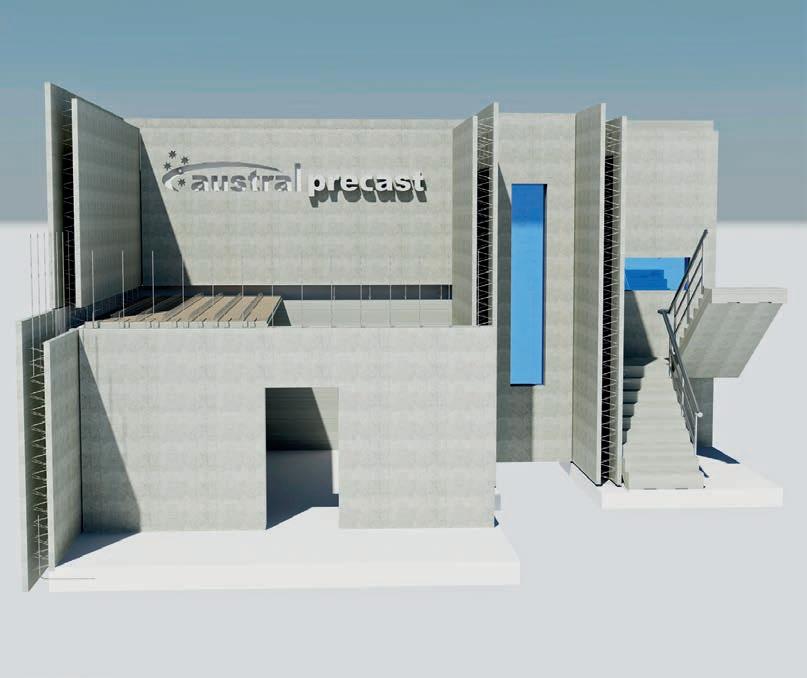

Master initiativePrecaster
The Master Precaster initiative removes risk as it assists a builder doing their due diligence on a precaster.
Panel Brick and Double Wall update traditional offerings Panel Brick is a brilliant solution that capitalises on two of Austral Precast’s core is a unique product involving the prefabrication and connection of two precast concrete panels to form a services cavity, which eliminates the need for metal or timber studwork.
REZICAST offers a system whereby precast homes can reach lockup in just 10 days
delays to programmes which can be very costly once a job has started. Master Precaster is designed to take the load off builders, who don‘t always have the resources to properly do their due diligence on a precast manufacturer before awarding a tender. Using a Master Precaster does the checking for the builder and mitigates their risk. New member initiatives Meanwhile some new member initiatives have hit the market. Master Precaster Austral Precast has introduced both the Panel Brick system and Double Wall, while REZICAST offers a system whereby precast homes can reach lockup in just 10 days.
Panel Brick is on show in St Paul’s Terrace Apartments in Brisbane’s Fortitude Valley, while Double Wall has recently been used in Astina Suites at Penrith, NSW. Lockup in 10 days Precast housing has been given a boost with a new system that capitalises on the reliability and high quality of precast, to dramatically speed house building. Started in the ACT by founder Mick Johnson, REZICAST is licensed to builders and offers a unique way to connect panels and deliver housing that is fire and flood resistant, as well as acoustically and thermally efficient.
www.insideconstruction.com.au INSIDE CONSTRUCTION 61

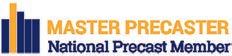
62 INSIDE CONSTRUCTION August/September 2022
The heavy equipment expo, CONEXPO-CON/ AGG, comes to Las Vegas, Nevada only once every 3 years and is an industry leading event not to be missed. The show brings together the construction community from all over the world with over 130,000 industry professionals and guests attending each year. Co-located with CONEXPO-CON/AGG 2023, the International Fluid Power Exposition (IFPE), will also bring together the fluid power, power transmission and motion control industries.
CONEXPO-CON/AGG 2023 has been selected by the U.S. Department of Commerce for the Trade Events Partnership Program (TEPP) and is set to showcase the latest trends, innovative technology, and products from 1,800 equipment manufacturers. Building new relationships in the construction community and discovering new equipment, services and people in the industry is what the show is all about. Every product category and construction field will be covered at the 2023 event including: AsphaltAggregatesssociations
& Organisations Business Operations Concretearthmoving & Material Handling lectrical & Mechanical Power Transmission Products - IFPE Engine HaulingEquipmentnginesComponents&DrivetrainsComponents • IFPE • Industrial Hydraulic Products - IFPE • Infrastructure Maintenance • Jobsite Safety & Operator Awareness • Jobsite Support & Tools • Land Clearing • L ifting (Aerial & Cranes) • Mobile Hydraulic Products - IFPE • Personal Safety • P neumatic Products - IFPE • Portable Power • Related Products & Services - IFPE • Technology Solutions • Traffic Safety • Trucking • Underground Construction • Water Hydraulic Products - IFPE Exhibitors will cover over 250 thousand square metres to bring you the latest and greatest in construction. The show will also host over 150 Education Sessions providing attendees the opportunity to obtain cutting edge information for today’s fast paced construction environment. Want to attend? Head to www.conexpoconagg.com/vegas and fill in your details to receive more information about attending the show and go in the draw to win a flight to Las Vegas, USA. EVENTS CONEXPO-CON/AGG 2023 CON/AGGCONEXPO-2023 North MarchtradelargestAmerica’sconstructionshowreturnson14-18,2023. • A stec Industries Inc • C ASE Construction Equipment • Caterpillar Inc • Hitachi MachineryConstructionAmericas Inc • Hyundai EquipmentConstructionAmericas • John Deere Construction & Forestry • KOBELCO MachineryConstructionUSA • Komatsu • Liebherr • K-Tec / Ashland • Link-Belt Cranes • McCloskey International Ltd • Sandvik Rock Processing Solutions • SANY • Superior Industries • Terex Corporation • Volvo Construction Equipment • Wirtgen Group • A nd many more… Top exhibitors CON/AGGCONEXPO-2020

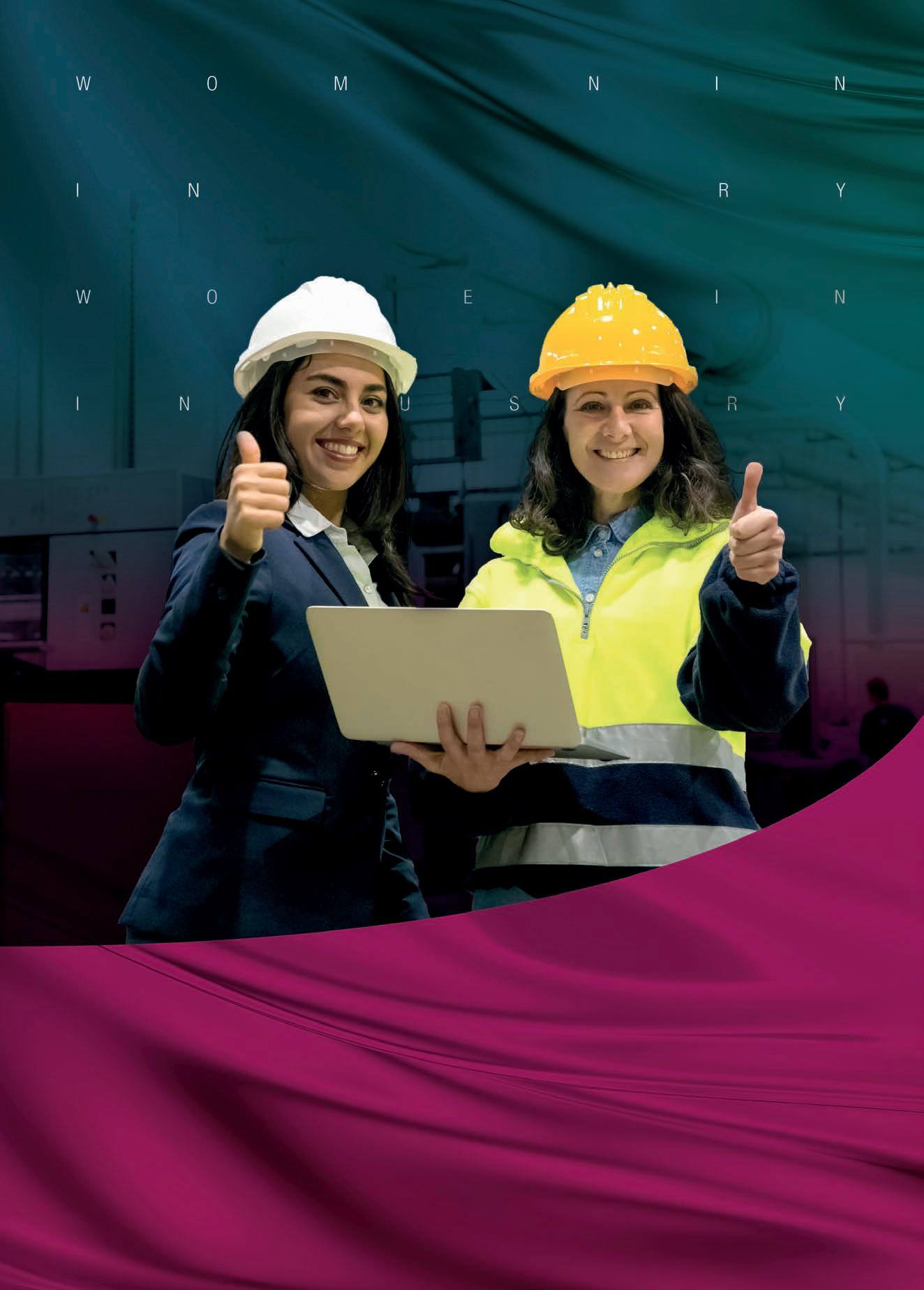
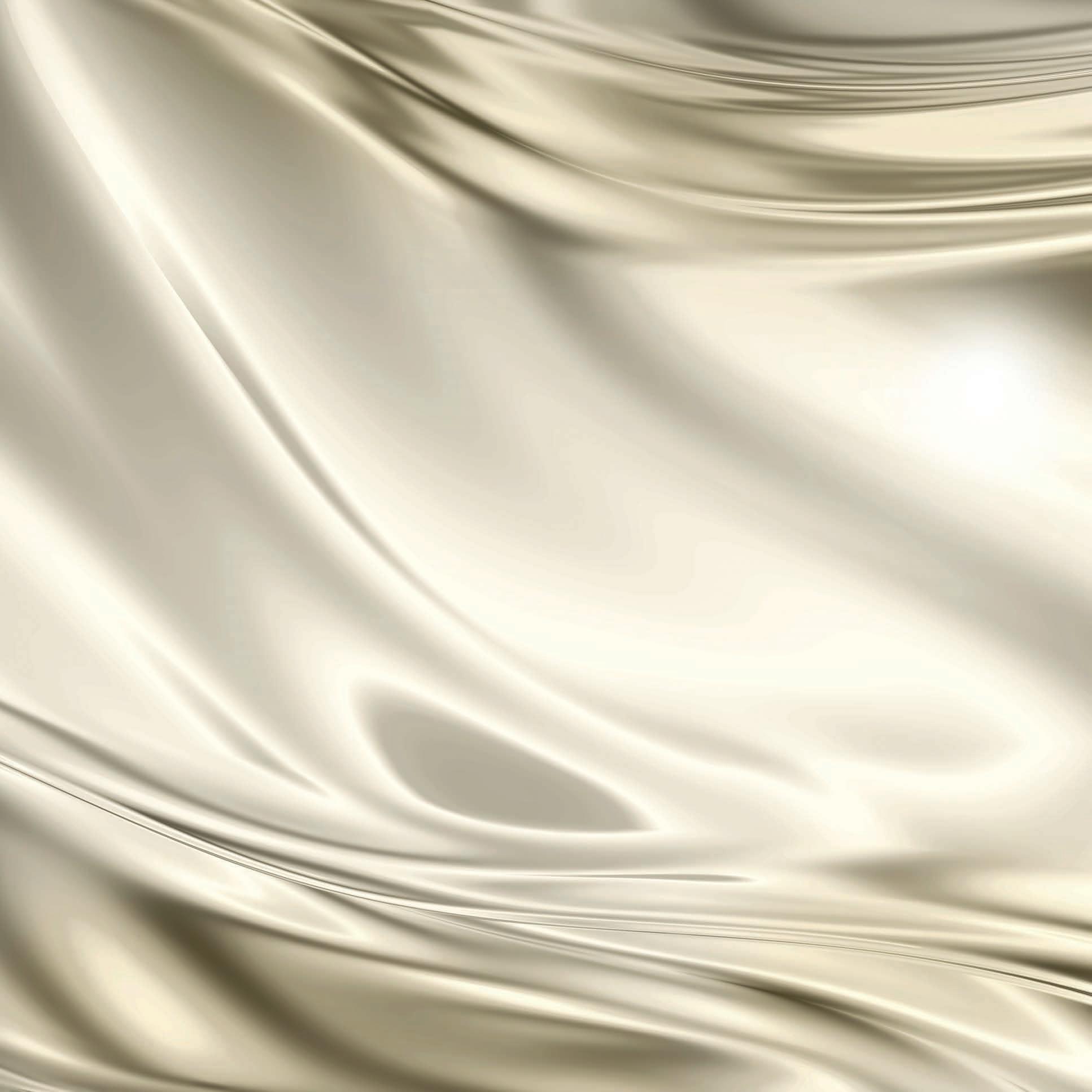
PROUDLY PRESENTED BY MHD Supply Chain Solutions WOMEN IN INDUSTRY .COM.AU WOMEN IN INDUSTRY AWARDS AWARDS SPONSORS NOWTICKETSAVAILABLE SEPTTHURSDAY8TH2022
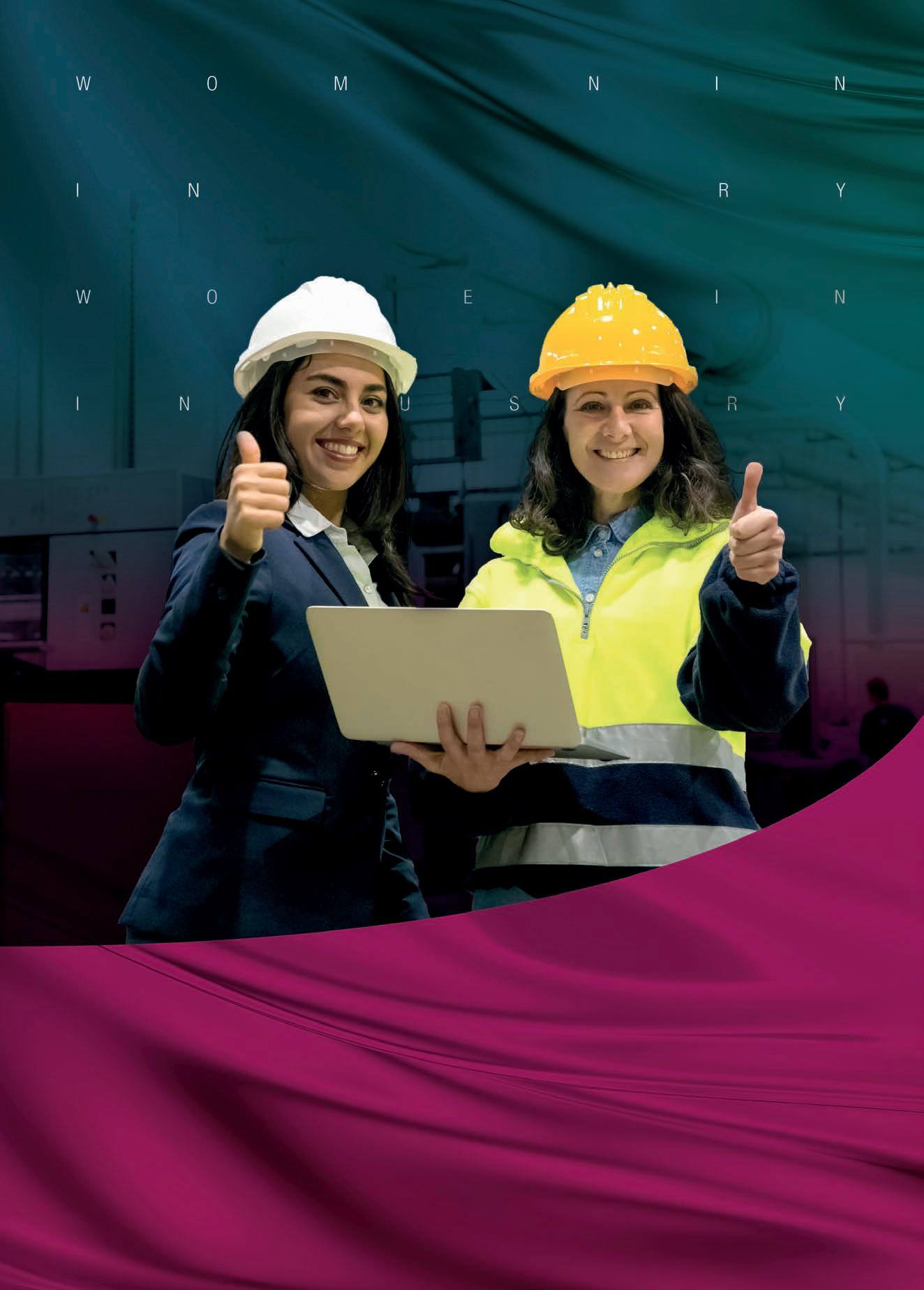
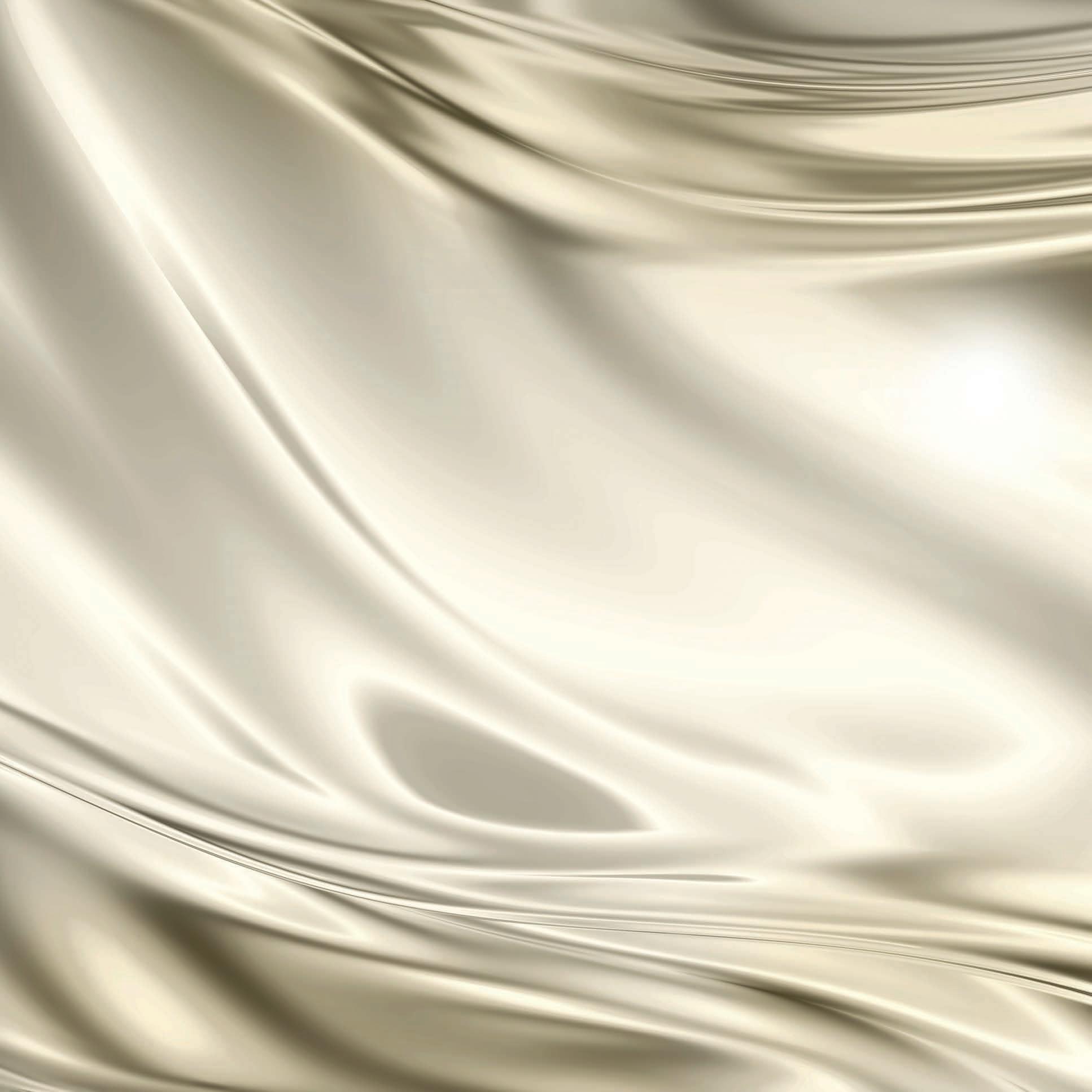
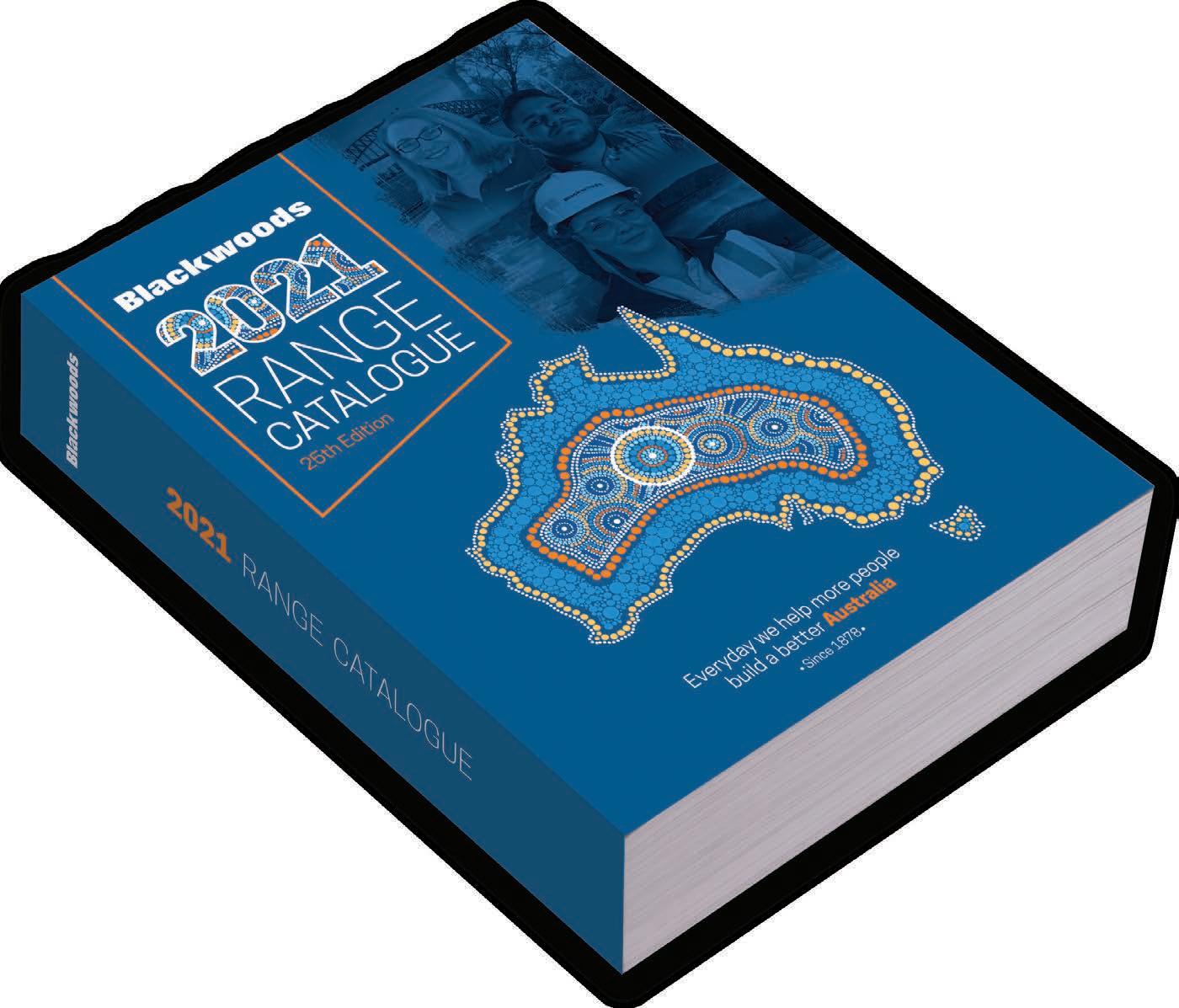
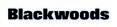