Training Taking

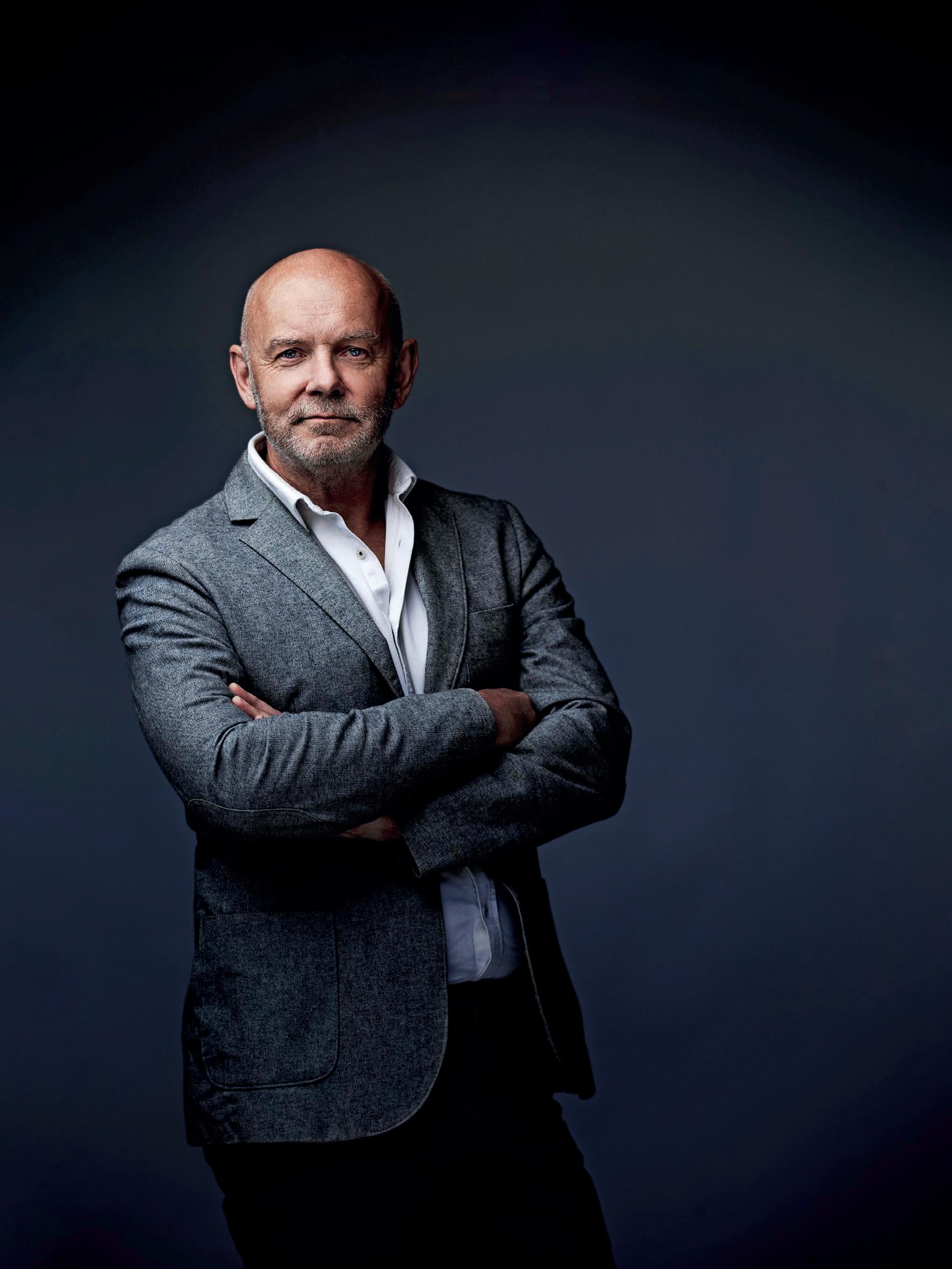
The easy way to submit and assess progress payments
Many construction businesses use spreadsheets to manage, submit and approve progress claims. But this is time-consuming and error-ridden, potentially leading to payment delays, failure to comply with regulatory obligations, and causing friction between main contractors and subcontractors. There’s a much better way.
Payapps is the cloud-based collaboration tool that makes submitting and approving payment claims easier and faster than ever before. Payapps helps main contractors and subcontractors work better together to make progress claims and approvals simple and seamless, with a single, accurate and transparent view of every contract from project start to finish.
Ditch the spreadsheets today. Learn more at payapps.com/insideconstruction
Area9 Lyceum builds 21st century skills and competencies through one of the world’s first fourdimensional learning platforms, Area9 Rhapsode.
Dr. Gretchen Gagel catches up with Gabrielle Trainor, Chair of the Construction Industry Culture Taskforce (CICT), to discuss sustainable construction.
Project Manager for Multiplex drives positive change, managing complex and unique projects around NSW.
Bitumen and Asphalt Production Foreperson for Downer seizes opportunities.
NAWIC champions women in construction.
ACA boasts new era for construction.
An insight into Advanced Precast’s success.
FIA’s advocacy success.
Lentune’s Supplier Invoice Automation enables a streamlined, cloud-based workflow for construction businesses.
Mad Cat Constructions deploys a suite of Trimble solutions on their small machines.
The Green Building Council of Australia leads the sustainable transformation of the built environment through their Green Star rating system and key pillars.
Makinex launches Hybrid Power Systems to generate clean power on construction sites, reducing diesel consumption and improving power efficiency.
Construction software company Payapps is taking action to create a more sustainable future for the construction industry, achieving Climate Active carbon neutral certification in Australia.
McConnell Dowell look for new ways to reduce their carbon footprint, led by the company’s Executive General Manager of Health, Safety, Environment and Quality.
38
Earth Friendly Concrete develops absolute zero cement concrete technology that works through ordinary concrete supply chains.
42 Eliminating material waste with Matrak Matrak software simplifies the complexities of material tracking and presents huge potential in tracking emissions resulting from the use of materials.
Blackwoods’ assess, inform, equip model provides end-toend safety solutions.
Following the successful launch of our first print magazine, we’re pleased to bring to you the October 2022 edition of Inside Construction, filled with the latest news and insights into the construction industry. This month we delve into ‘Green Construction’ and showcase the industry leaders forging positive change in the sustainability space.
Rising material costs, fewer skilled workers and a series of supply chain disruptions all pose challenges for the industry, and yet we’re seeing an immense push for change - from both industry organisations and the private sector, to develop a more sustainable built environment in Australia.
The developing trends and techniques in built sustainability are reshaping the industry for the better and are fundamental to the future of construction.
This month, we hear from some of the leading construction companies doing their part for the environment. We’re seeing an increase in the use of sustainable construction materials in current and planned builds, resulting in lower carbon emissions. Products like Wagners Earth Friendly Concrete, a zero cement geopolymer concrete, can reduce a projects carbon footprint by up to 80 per cent when compared to ordinary concrete.
In the sustainable technology space, Makinex has developed Hybrid Power Systems to generate clean and efficient power on construction sites, reducing site diesel consumption by over 90 per cent.
New technologies are being used to reduce material waste and reordering. Last year alone, Matrak’s solution to material tracking saved around 30 shipping containers of materials in over 180 projects.
Construction businesses are also pivoting their operations to align with the initiatives of organisations like the Green Building Council of Australia (GBCA), which we can proudly announce as an official Inside Construction media partner.
Our team has worked closely with the GBCA to present this month’s ‘Green Construction’ feature, sharing the latest facts, trends and figures of sustainability in the built environment.
It’s not just construction companies that are vital to the sustainable future of the industry, but also the workers on the ground. Australia’s construction workers are the drivers of positive change, including women like Gabrielle Trainor, Chair of the Construction Industry Culture Taskforce, who is pushing for the adoption of a Sustainability Culture Standard across the industry.
Organisations, like the National Association of Women in Construction (NAWIC), are striving to help champion and empower women, like Gabrielle, in the construction industry to reach their full potential.
The Inside Construction team is thrilled to share news of an official media partnership with NAWIC. Our partnership aims to empower women in construction and forge a brighter future for the industry.
We hope you enjoy the read.
John Murphy
Christine Clancy
Sarah Baker sarah.baker@primecreative.com.au
Ashley Grogan ashley.grogan@primecreative.com.au
Brad Buchanan bradley.buchanan@primecreative.com.au
Daz Woolley
Art Director
Blake Storey blake.storey@primecreative.com.au
Michelle Weston michelle.weston@primecreative.com.au
Adele Haywood adele.haywood@primecreative.com.au p: +61 0403 500 544
Glenn Delaney glenn.delaney@primecreative.com.au
Marcus Walters
Head Office
Prime Creative Pty Ltd 379 Docklands Drive, Docklands, Victoria 3008 Australia p: +61 3 9690 8766 f: +61 3 9682 0044 enquiries@primecreative.com.au www.insideconstruction.com.au
+61 3 9690 8766 subscriptions@primecreative.com.au
Inside Construction is available by subscription from the publisher.
The rights of refusal are reserved by the publisher
All articles submitted for publication become the property of the publisher. The Editor reserves the right to adjust any article to conform with the magazine format.
Inside Construction is owned by Prime Creative Media and published by John Murphy.
All material in Inside Construction is copyright and no part may be reproduced or copied in any form or by any means (graphic, electronic or mechanical including information and retrieval systems) without written permission of the publisher.
The Editor welcomes contributions but reserves the right to accept or reject any material. While every effort has been made to ensure the accuracy of information, Prime Creative Media will not accept responsibility for errors or omissions or for any consequences arising from reliance on information published. The opinions expressed in Inside Construction are not necessarily the opinions of, or endorsed by the publisher unless otherwise stated.
One of Australia’s leading contractors, John Holland, has seen the benefits of a new health and safety learning platform – Area9 Lyceum’s Rhapsode – saving the company more than 12,000 hours in training time.
Rhapsode uses an AI algorithm built on the experience of more than one billion data points to support each learner exactly as a personal teacher would, but at scale. The platform measures and assesses the learner as they move through the content, filling the gaps in critical safety knowledge that standard e-learning fails to deliver.
More than 30,000 million learners worldwide use Area9 Lyceum’s learning platform, which delivers truly personalised training.
This month we caught up with Jono Bonifant, Director & CEO of Lentune, to explore the company’s Supplier Invoice Automation software.
The first of Lentune’s now suite of construction management products, Supplier Invoice Automation enables a streamlined, cloud-based workflow for construction businesses. The smart accounts payable software greatly reduces supplier invoice processing, provides a real-time picture of each invoice, and gives the user greater control over their cost management.
One company reaping the benefits of Lentune is construction machine and equipment supplier, Wacker Neuson who has seen the time required to process, approve, and store supplier invoices reduced by over 50%.
Bonifant and Matthew Watson, Finance Manager, Wacker Neuson look into the advantages of moving away from manual handling and data entry. Pages 18-20.
Australian civil and commercial contractor, Mad Cat Constructions has deployed a suite of Trimble solutions on their small machines.
Mad Cat Constructions Director and Project Administrator Trevor Reynolds turned to Trimble dealer, SITECH Construction Systems, for a solution after identifying challenges around small machine productivity.
John Holland users are taking 20-30 minutes less to complete Rhapsode courses than previous approaches and John Holland estimates that Rhapsode has saved the company 12,800 hours to date, closed gaps in critical health and safety knowledge, and is enabling improvement in the company’s approach to critical health and safety risk management.
Dr. Khurram Jamil, President –Strategic Initiatives for Area9 Lyceum and Martin Smith, Group General Manager Health, Sustainability and Climate, John Holland share the benefits of Rhapsode and its innovative learning formula. Pages 13-17.
The Mad Cat fleet is now equipped with the latest in Trimble technology. Reynolds, along with Shane Wright, Account Manager, SITECH, describe how the introduction of Trimble Solutions has saved Mad Cat time and money, increased employee satisfaction and improved safety on site. Pages 22-25.
Founded by brothers Shane and Brett Hodgkins, Matrak is changing the way construction teams manage their projects.
The Hodgkins brothers, Shane CEO and Brett CTO, developed Matrak as an end-to-end material tracking
platform to simplify and support the complexities of tracking and managing materials.
Last year alone, the Matrak team estimated they saved around 30 shipping containers of materials in over 180 projects. Hutchinson Builders are one of the companies seeing the sizeable value of the Matrak platform.
Shane, Brett and Jacob Baldacchino, Façade Manager at Hutchinson Builders look into the Matrak platform, its huge potential in tracking emissions resulting from the use of materials, and its capability in eliminating the need for material reorders. Pages 42-43.
Blackwoods invests time and expertise in their customers, an approach that resulted in a quality solution to worker safety on the West Gate Tunnel Project (WGTP).
In November 2020, construction was underway at the West Gate Tunnel Project (WGTP). As with all Tier 1 construction companies, health and safety is a core value and WGTP (CPB Contractors) were looking at an effective engineering solution to control Silica dust exposure whilst undertaking jackhammering activities. They turned to Blackwoods who delivered a retrofit dust suppression system.
Blackwoods’ Terry Meachen, Major Projects Manager and Drew Dauncey, Technical Safety Specialist recount the WGTP and their solution to improve safety on site. Pages 44-45.
Simplify the complexities of construction supply chains with the leading material tracking platform.
Contact us today at www.matrak.com/demo
The Green Building Council of Australia (GBCA) was formed with a purpose to lead the sustainable transformation of the built environment.
This month the team at Inside Construction has worked closely with the Green Building Council of Australia to highlight the fantastic work companies are doing in the ‘Green Construction’ space.
GBCA CEO Davina Rooney has worked in the construction industry for over 20 years and is advocating for more conversation and action around sustainability in the construction industry. The GBCA is leading the way for change through four key pillars – rate, educate, advocate, and collaborate.
Rooney presents the top opportunities for construction companies to reduce their carbon footprint in today’s environment.
Makinex has launched Hybrid Power System’s (HPS), a system that uses solar and battery technology to generate clean power on construction sites. The fundamental goal of the product is to reduce diesel consumption by over 90%, with one recent customer reducing their diesel consumption by 99% over a 3-month summer period using the system.
The HPS product, over its development cycle, has morphed into
the company’s recent launch of a subbrand – Makinex Renewables. Makinex Managing Director Paul Weaver details the advantages of clean power, reducing diesel consumption and the company’s passion for renewable products.
Construction software company Payapps is taking action to create a more sustainable future for the construction industry, achieving Climate Active carbon neutral certification in Australia in 2021.
Their mission to develop and provide software to make life easier for its users has reduced the need for paper globally in over 30,000 construction companies, saving approximately 20 tonnes in paper each year.
Jessica Widdicombe, Senior Finance Manager at Payapps, has been with Payapps for 4 years and led the process for the company to achieve Climate Active carbon neutral certification.
Widdicombe encourages other construction companies to be a part of the carbon neutral journey.
McConnell Dowell employees are constantly looking for new and innovative ways to reduce their impact on the world around them. Leading the charge is Samantha Johnson, the company’s Executive General Manager of Health, Safety, Environment.
Evidenced by the company’s large portfolio of sustainably managed
projects around the globe, the Port Kembla Gas Terminal - Marine Works project is a perfect example of McConnell Dowell’s commitment to reducing, or eliminating where possible, negative environmental and social impacts.
Johnson delves into several projects completed and underway by McConnell Dowell, their mission to reduce their carbon footprint and the sustainable solutions the company has adopted across their operations.
Wagners Earth Friendly Concrete (EFC) has been reducing the carbon footprint in the built environment with their geopolymer concrete. Over the past 10 years, with over $20 million dollars of their own investment, Wagners EFC developed a zero-cement concrete technology that works through ordinary concrete supply chains, proven globally in commercial construction and infrastructure projects.
The company has now established a market in London, securing several partners in the UK to set up EFC producers in multiple locations – one being the High Speed 2 (HS2) project.
Talking about the project, Jason Zafiriadis, Wagners EFC’s Chief Commercial Officer explains the huge carbon emissions EFC can save compared to traditional cement made concretes.
Dr. Gretchen Gagel caught up with Gabrielle Trainor, Chair of the Construction Industry Culture Taskforce (CICT) this month, to discuss sustainable construction and the Culture Standard being adopted across the construction industry in Australia. Trainor joined the CICT in 2020 and is a key driver of the new Culture Standard initiative, developed by the NSW and Victorian Governments, and the Australian Constructors’ Association, together with other industry leaders and researchers. Trainor is a non-executive director and advisor whose experience covers over 25 years on boards in the public and private sectors.
Jade Nicholson , Project Manager with Multiplex Constructions, has worked on a range of projects including the Charles Perkins Centre at The University of Sydney Camperdown and M&L Hospitality’s redevelopment of 161 Sussex Street, Sydney. More recently Nicholson worked on a commercial building, with the purpose of the project to bring together 10 displaced entities in the healthcare system and deliver a purpose-built building which focused on collaboration. Nicholson is now delivering a high school in Mosman for School Infrastructure, with her team using new technologies such as a new digital materials handling booking system.
Emily Jennings, Bitumen and Asphalt Production Foreperson for Downer started with the company in 2017, seizing opportunities for career growth every step of the way. Depending on what her team has on for the day, Jennings could be doing anything from blending bitumen, operating the asphalt plant, loading sprayers and bulkers with bitumen, or driving a loader, forklift, HR truck or bobcat. She has helped manufacture and deliver high specification bitumen to Ayres Rock and Alice Springs airports, and continues to work on a range of projects including the Darwin Rail Terminal as well as upgrades to Darwin and Tindal Airports.
The National Association of Women in Construction (NAWIC) has come on board as an official media partner of Inside Construction
NAWIC’S vision is to create an equitable construction industry where women fully participate and their core policy is to achieve 25% female participation in the construction industry, by 2025 (#25by2025).
The organisation provides a forum for its over 7,000 individual members and over 150 corporate members to meet and exchange information, ideas and solutions.
Members have an opportunity to expand personal and business networks, maintain awareness of industry developments, improve skills and knowledge, and contribute to other women in the construction industry.
Lauren Fahey, NAWIC’s General Manager, introduces the organisation, their goals, and shares the latest data from their member survey conducted earlier this year to highlight the need for industry action.
Jon Davies, CEO Australian Constructors Association (ACA) represented the construction sector at this year’s 2022 Jobs and Skills Summit. He took the opportunity to put construction on the nation’s radar and to emphasise the need for change.
The CEO’s message was simple – ‘change will only happen if government, industry and unions leave behind the baggage of history’.
Speaking under the banner of creating safer, fairer and more productive workplaces, Davies outlined the importance of the construction industry to the Australian economy.
The ACA’s idea for the Summit was a new ratings initiative called the Future Australian Infrastructure Rating – FAIR. Essentially, FAIR would rate government funded projects on how well they performed against key reform areas such as improved productivity. The FAIR initiative could be included in the next iteration of the National Partnership Agreement as a requirement for all federally funded projects.
Joining the National Precast Concrete Association Australia (National Precast) in 2015, Advanced Precast has seen consistent growth over its almost 40 years in business.
As an effort to showcase the important work being undertaken by the precast concrete industry around Australia, Inside Construction interviewed Brett Foster, Operations Manager, Advanced Precast.
Advanced Precast joined National Precast after identifying the advantages of being around a network of likeminded people.
The company was established in Melbourne in 1985 and today employs 160 people comprising construction workers, engineers, detailers and administrative staff. Since those early years, the company has grown to become one of Australia’s market leaders in the field of precast concrete within the building sector.
The Formwork Industry Association (FIA) has successfully advocated the reinstatement of the Certificate III in Formwork/Falsework until 31 December 2023.
Following extensive campaigning at both federal and state level by the FIA, the Australian Skills Quality Authority (ASQA) agreed to extend the transition period of CPC31511 - Certificate III in Formwork/Falsework.
The decision extends the transition period for ASQA registered training organisations, to continue training assessment and issue Australian Qualifications Framework (AQF) certification.
The FIA is also currently piloting a new Safe Formworker program and negotiating a new education pathway with governments, which includes a new Certificate III in Formwork with a focus on infrastructure, and a pathway for accessible learning with accredited and unaccredited training, as well as ‘recognition of prior learning’ (RPL) for mature and existing workers.
Area9 Lyceum builds 21st century skills and competencies through one of the world’s first four-dimensional learning platforms, Area9 Rhapsode™
In the construction sector, the safety and wellbeing of its employees is paramount. One of Australia’s leading construction contractors, John Holland, has seen the benefits of a new health and safety learning platform - Area9 Lyceum’s Rhapsode.
Dr. Khurram Jamil, President – Strategic Initiatives for Area9 Lyceum, says Rhapsode according to estimates from John Holland, has saved them more than 12,000 hours in training time and delivered more effective targeted training to its employees.
“Founded by physicians and computer scientists, and headquartered in Copenhagen and Boston, Area9 Lyceum combines more than 20 years of research into human factors and cognition,” says Khurram
“With cutting-edge computer science and artificial intelligence (AI), we transform learning outcomes for millions of learners and businesses like John Holland.”
“Across construction, mining, manufacturing, health care, finance and corporate education, Area9 Lyceum brings scientific rigor to transform learning outcomes at scale globally.”
John Holland employs over 5,300 staff and more than 1,300 contractors working on projects across Australia and New Zealand. After years of predominantly classroom training, the company included international adaptive e-learning provider, Area9 Lyceum, to its blended approach to learning following successful trials in early 2020.
Speaking of Rhapsode Martin Smith, Group General Manager Health, Sustainability and Climate, John Holland says, “The personal approach for each learner was found to reinforce their journey, as opposed to the traditional ‘one size fits all training’.”
Higher-quality data enabled the business to measure the effectiveness of the training at individual, group, and site level.
Khurram says many current e-learning platforms provide a ‘one size fits all’ approach, not taking into account individual learning needs.
“We have profound insight into the way individuals learn, and how their needs
change over time. Every learner is unique – Rhapsode delivers truly personalised learning at scale, cutting training time in half, guaranteeing proficiency, and making lasting impacts on careers and business outcomes,” he says.
“With more than 30 million learners having used Area9’s methodology, it is based on peer-reviewed scientific research about what works in learning, combined with empirical evidence collected over many years.”
John Holland has worked with Area9 Lyceum to complete the development of 15 health and safety courses based on John Hollands safety-critical procedures and started to move its key health and safety technical training, and non-technical learning, into Area9 Lyceum’s adaptive learning platform.
The company has also committed to providing its training courses to a range of
John Holland employs over 5,300 staff and more than 1,300 contractors working on projects across Australia and New Zealand.
“Across construction, utilities, mining, manufacturing, health care, finance and corporate education, Area9 Lyceum brings scientific rigor to transform learning outcomes at scale globally with over 30 million learners.”
John Holland’s leadership recognised the value of personalised training and made the decision to move all health and safety critical procedural courses to Rhapsode. 15 procedural health and safety courses have so far been delivered and they have been adapted to support specific projects John Holland is delivering, including the Metro Tunnel project underway in Melbourne.
“By taking a scientific approach, Rhapsode knows how to measure the impact of training, and how to dynamically reorient the learner when appropriate as they work through the course content,” says Khurram.
“By adapting moment-by-moment and over longer periods of learning, this allows the learner to speed through things they already understand and zero in on what matters for this learner, short term as well as long term.
“Rhapsode supports individual needs, measures confidence, and improves the engagement and learning experience for each
The Rhapsode software allows global management requirement courses to be tailored to both subcontractors and leaders, and to refine the focus of the learning objectives and outcomes.
“The results from a full year of integrating our health and safety critical procedural courses into Rhapsode have been excellent - all key metrics have been exceeded by this partnership,” says Martin.
Rhapsode uses an AI algorithm built on the experience of more than one billion data points to support each learner exactly as a personal teacher would, but at scale. The platform measures and assesses the learner as they move through the content, filling the gaps in critical safety knowledge that standard e-learning fails to deliver.
The software is particularly adept at measuring levels of ‘unconscious incompetence’ – the ‘I don’t know what I don’t know’ - where a learner is not aware that they lack knowledge about a task they are undertaking, or believe they are carrying out activities and tasks in accordance with procedures even though they are not.
In the context of construction health and safety, this poses a significant risk both to the individual and the surrounding workforce. However, Rhapsode reporting shows that the
average level of ‘unconscious incompetence’ for people completing the course is reduced from 25% to less than 1%, significantly increasing the learners understanding of the procedural content in task planning and execution..
“The difference in this platform is the AI ability to move each learner to a higher level of understanding,” says Martin.
“This has a significant and positive impact on health and safety risk management as Rhapsode helps each learner understand their learning gaps.”
The Rhapsode software has identified thousands of significant gaps in the competencies of learners. “But the key to the success of this innovative platform is the elimination of the gaps and each person reaching 100% proficiency on the content. This is a very different outcome to the standard compliance ‘tick and flick’ e-learning,” says Martin.
“We now have detailed data from individuals, works sites, subcontractors, and across the organisation that shows the elimination of these knowledge gaps and the positive impact this can have on the management of critical safety risks,” says Martin.
Martin says courses at John Holland are taking 20-30 minutes less to complete than previous approaches. The AI-based solution can determine an individual’s proficiency profile around the course content and support each learner personally, so it moves quickly through the areas with high competency and spends more time on learning and content across areas where there are gaps.
For John Holland users, the average time to health and safety proficiency has been halved across all courses. John Holland estimates that Rhapsode has saved the company 12,800 hours to date, closed gaps in critical health and safety knowledge, and is enabling improvement in the company’s approach to critical health and safety risk management.
Keeping the focused educational content to areas where learner knowledge is low also helps maintain learner focus. “It deters them from glazing over the content they assume they already know, even if they do not,” says Martin.
“Because the adaptive learning platform tells the learner that they need more information
on a topic before delving into that educational content, the learner recognises that all the information being provided is information they require and do not fully understand already.”
Khurram says Area9 Lyceum’s approach is to work closely with businesses to support their needs and requirements including with direct employees, new starters, and subcontractors.
“Rhapsode AI algorithm allows each learner to engage in a personalised learning journey through the course to achieve 100% proficiency, a key difference to standard e-learning proven across millions of people in a wide range of industries,” says Khurram.
For company’s looking to replace their current training or learning processes with Rhapsode, Khurram says the process is straight forward.
“Our partnerships start with small starter projects working closely with the subject matter experts in the business to build a course to be used across a number of employees,” he says.
“This is an efficient and effective way to assess the value of adaptive learning for the company which is integrated into their existing LMS allowing single sign on for employees.”
“From this pilot we continue to work with organisations in building more courses, supporting improvements in competency, saving time, engaging employees and enhancing business outcomes.”
“By taking a scientific approach, Rhapsode knows how to measure the impact of training, and how to dynamically reorient the learner when appropriate as they work through the course content.”
Jono Bonifant joined software solutions provider Lentune in 2014, and together with Lentune founder Matthew Reid, has transformed the supplier invoice process in construction with Invoice Automation software.
Jono Bonifant is the Director & CEO of Lentune, and for the past six years has partnered with Lentune’s Founder, Director & Software Architect Matthew Reid to simplify and refine the supplier invoice process in construction.
When Jono joined Lentune as Commercial Manager in 2014 he and Matthew noted businesses lacked insight around their invoice processes and identified the demand for a streamlined solution. “We started looking at the construction industry and discovered many companies were still tied to a lot of paper, and the painstaking task of data entry, when it came to supplier invoices,” says Bonifant.
“During a build, contractors can be inundated with invoices from their suppliers which, without automated invoicing, takes a lot of time for their accounts team to enter the data and process the information.”
Bonifant and the Lentune team then set about their goal to develop a project management system around the financials
of construction, and the Supplier Invoice Automation module was born.
The first of Lentune’s now suite of construction management products, Supplier Invoice Automation enables a streamlined, cloud-based workflow for construction businesses. The smart accounts payable software greatly reduces supplier invoice processing, provides a real-time picture of each invoice and gives the user greater control over their cost management.
Bonifant says the software was created out of a large focus to eliminate the use of paper to improve sustainability, but first and foremost was developed to remove the need for data entry to improve productivity on site.
“It takes around 75% of an administration team’s time to enter and process invoicing data. By removing data entry from the invoicing process, productivity improves significantly,” says Bonifant.
“The traditional invoicing workflow generally starts with an invoice arriving which is then printed off and, at some point, passed to the
boss for sign-off. The last thing that happens is the invoice is put into a financial system, with the whole process sometimes taking up to eight weeks.”
Bonifant says through Lentune technology all invoicing information is found in one platform and is available in a visible and accurate format as soon as the document is received from the supplier. It can give you a running total of project spend and if used with the Lentune app to create purchase orders, Lentune can tell you the total committed costs before project invoices have come in. By using Lentune software which has been developed specifically for construction, it can empower construction professionals to control and manage their job costing efficiently.
One company reaping the benefits of Lentune is construction machine and equipment supplier, Wacker Neuson. Prior to installing Lentune, the business had a manual paper-based supplier payments system.
Matthew Watson, Finance Manager, Wacker Neuson says the manual system wasn’t efficient and relied on lots of manual handling and data entry. “Our system also didn’t meet our lean objectives nor our environmental goals of reducing waste, including paper waste, where possible,” says Watson.
“Wacker Neuson offer zero-emission battery technology in many of our products and we take this ethos right through our business.
“Lentune helped us automate our accounts payable system. We moved away from manual handling and data entry onto Lentune’s digital cloud-based software. We find the optical character recognition functions within Lentune fantastic. This functionality really helps cut down data entry and drive efficiencies.”
Watson says their workforce is now able to process invoices more quickly since moving to the all-digital accounts payable model.
“We measure efficiency by the number of keystrokes required to enter, approve and process an invoice. Lentune, with its optical character recognition technology and improved user interfaces, has helped us reduce keystrokes to enter a supplier invoice by 75%,” says Watson.
“Lentune also has a great document storage feature which really helps with documenting the vendor invoice approval process.”
According to Watson Lentune has helped Wacker Neuson reduce the time required to process, approve and store supplier invoices by over 50%.
The construction industry is currently facing challenges from inflationary material costs to an increasing skilled labour shortage, but we’re seeing more businesses tackle these challenges with the adoption of new technologies and systems.
“Ultimately if your business doesn’t have good systems in place, it can result in staff that are swamped with paper trying to keep up with the running of their projects, and customers who are worried about cost blowouts. You should also consider the reputation that will come from the downfall of these things going wrong,” says Bonifant.
“By adopting a solution that gives accurate and timely information to everyone in the business, it can improve employee wellbeing and help retain staff in the current competitive construction environment.”
During the beginning of the Covid pandemic, the need to be able to complete a job away from the office increased sharply and continues to do so. It accelerated the conversation around mobile working solutions and systems that allow construction professionals to work on the move.
Constructors need information on the go, out in the field and they need to be able to complete the job away from the office. Mobile working has become more than commonplace, it’s the new norm. Bonifant says the best way to manage a project on the go is with cloud-based software.
“Having systems that are mobile and user friendly is paramount to a quality solution. Our cloud-based system allows the user to access all supplier invoices anywhere there is an internet connection with the click of a button,” says Bonifant.
Simplifying operations, Lentune’s Invoice Automation system breaks workflow down into three simple stages.
The check stage allows the administrator or accounts team to do their due diligence and ensure the data captured by the system is accurate. The system generates a visual PDF of the supplier invoice based on the data which can then be reviewed in seconds, checked in and delegated to the appropriate person.
“Lentune helped us automate our accounts payable system. We moved away from manual handling and data entry onto Lentune’s digital cloudbased software.”
Invoice pricing can be checked against agreed supplier pricing before invoice approval.
Once the first stage is complete it provides visibility for the rest of the workforce to see what costs have been assigned to each project. Supplier invoices then move into the approval stage where team members approve the invoices that have been assigned to them.
Following approval, the third stage is processing. Lentune picks up any approved invoices and automatically sends them to the business’s accounts package to be paid. To further simplify the process Lentune can integrate with the business’ existing
Bonifant says delegated authority is also an important feature of the invoicing system. “We all want to give our team ownership to do their role well, but we also want to make sure we’re not giving them control over things outside of their responsibilities,” says Bonifant.
“Delegated authority is a powerful tool for making sure people stay on task and only have authority over the tasks assigned to them. Lentune allows the administrator to select who in their business has the authority to view, amend and approve supplier invoices.”
“The user can be specific around who can approve invoices on what job and to what level. It gives them a lot of control around how they structure their business.”
From a dedicated dashboard, Lentune gives the administrator full visibility and oversight regarding the supplier invoices that need to be processed. They can see who in their team has invoices assigned to them that haven’t been actioned, how many and what the value
“In terms of chasing things up, Lentune does the grunt work for you. Accounts teams have the information in front of them rather than having to sift through loads of data to see what invoices are still outstanding,” says Bonifant.
Lentune also provides the user with immediate access to back costing information and historical invoicing, ensuring accurate
The outdated manual systems of shuffling through piles of paper and data entry are quickly becoming a thing of the past. Lentune’s Invoice Automation software can save time and effort for everyone in the
solar and battery technology to generate and store reliable, clean power without the need to be connected to an overhead power network.
is a combination of highly efficient solar panels, high-capacity battery storage and a backup generator that ensures 24/7, environmentally friendly power.
HPS is the only solution in the world that goes wherever you need it. Simply transport to your site and within moments, clean and constant power is at the ready.
The HPS system is a game-changer for any site that needs to be maintained. It removes the dependency on generator power, lowering refuelling and servicing costs.
Australian civil and commercial contractor, Mad Cat Constructions has deployed a suite of Trimble solutions on their small machines. Its fleet is now equipped with the latest technology, including the Trimble Earthworks Grade Control Platform and Trimble WorksManager Software.
Mad Cat Constructions (VIC) PTY LTD, established by Trevor Reynolds and Jim Knight, is a civil contractor based in Warragul, Australia. Mad Cat operates a large fleet of specialist machinery and attachments to facilitate civil and commercial projects for road corporations, councils, developers and large construction companies.
Effectively use machine control on small machines to gain productivity advantages.
• Trimble Earthworks Grade Control Platform.
• Trimble WorksManager Software.
• Trimble Siteworks Positioning System.
• Improved productivity.
• Greater accuracy.
• Safer jobsite.
• Less waste.
• Increased profits.
Mad Cat Constructions employs an experienced team and manages a large fleet of specialty machinery and attachments to facilitate a range of projects, from road and bridge construction to demolition and erosion control around Victoria.
Since its inception in 1995, the company has invested in advanced technology to streamline operations, and drive productivity and quality. After identifying challenges around small machine productivity, Mad Cat Constructions Director and Project Administrator Trevor Reynolds says the team turned to local Trimble dealer, SITECH Construction Systems, for a solution.
“Our teams were spending too much time interpreting and working off 2D plans. We also had no connectivity between the office and the field,” says Reynolds.
“We needed a streamlined solution to improve the efficiency and productivity of our small machines, so we approached SITECH Construction Systems.”
“Our fleet – which includes excavators,
graders and skid steers with various blades and scoops – is now equipped with the Trimble Earthworks Grade Control Platform.
In the background, Trimble WorksManager Software wirelessly transfers data such as 3D designs to the Earthworks systems on the construction site along with the Trimble Siteworks Positioning Systems.”
Mad Cat Constructions deployed Trimble Siteworks Positioning System (SPS) integrated with Trimble WorksManager Software. The SPS system makes use of Real-Time Kinematic positioning (RTK) to capture accurate points of plus or minus 10-20mm, without the surveyor having to manually level the pole.
Shane Wright, Account Manager, SITECH says the Earthworks Grade Control Platform and SPS Rovers receive RTK corrections via the internet with the Trimble Internet Base Station Service (IBSS).
“IBSS allows you to get highly accurate Global Navigation Satellite System (GNSS) positioning for site positioning or machine control,” says Wright.
The Trimble Earthworks Grade Control Platform was installed on the Kubota machine at Super Groups before being delivered on site.
The SPS base station receives GNSS data from satellites, the data is then processed by the base station into RTK data before being sent to Trimble WorksManager – Trimble’s cloud base software. WorksManager then sends the RTK corrections data via the internet to the Earthworks Grade Control machines and SPS rovers to ensure accurate positioning onsite.
Wright says Mad Cat Constructions also use WorksManager for data transfer. “Traditionally with machine systems, the surveyor would have to use a USB stick, plug it in to a computer to download the designs, then walk out to the machine and plug it into the control box and download the design data” he says.
“WorksManager removes that manual process, and transfers all data via the cloud, directly to the machines.”
Mad Cat Constructions operators can now upload their design into the WorksManager software, allocate the machines they want the design to go to, and the chosen machine pulls that design from the cloud.
“It’s a streamlined process that removes the need for manually carrying and collecting data,” Wright adds.
On the machine control side of the business,
Trimble Earthworks Grade Control Platform allows operators to view 3D models of a site, overlaid onto existing ground – and allows users to access cut/fill information, slope data and other bench points, and reference points in context.
Mad Cat Constructions is using the Trimble Earthworks Grade Control Platform, Trimble’s latest offering in machine control systems. The Grade Control Platform allows operators to view 3D models of a site. The model is overlaid onto existing ground and users can access cut/fill information, slope data and other bench points, and reference points in context.
Operators especially like the Trimble Earthworks ‘Autos’, or automatics mode, which automates the boom and bucket operation while the operator controls the stick for consistent, high accuracy finished grade in much less time.
Just recently, Mad Cat began construction on a large subdivision project in Victoria. The project scope included all civil works, from initial bulk earthworks and utility installs through to completed roads and footpaths. During planning for the project, crews wondered if the same technology-enabled
advantages gained on big machines could be realised on small machines for things like drainage, power and communications trenching, and footpath preparation.
The Mad Cat team knew that a Kubota U55-4, a 5-ton tight tail swing excavator powered by Kubota’s 47.6 HP direct injection engine, would be ideal for activities in narrow space. They needed grade control software – and automatics – to further drive operator productivity.
Working with SITECH, and the team at Victoria-based Kubota dealer Supergroups, Mad Cat installed Trimble Earthworks with automatics on the U55-4, one of the smallest machines the system has been used on.
“As we are running other equipment already with Trimble Earthworks and automatics, it was very easy to implement with a few adjustments – we basically put it straight to work,” says Reynolds.
“We simply upload the prepared project design using Trimble WorksManager into the cloud and the machine loads the files and away we go.”
While Mad Cat has not yet calculated the exact return on investment, Reynolds says, “It’s a no brainer.”
He points to one example of laying electrical tape over power conduits. “We don’t need to mark out trench locations, mark the depth or have someone measuring,” he says.
“We don’t have to worry about locating other services nearby.
“The operator just gets in and digs to the correct depth and position.
“Another benefit is the ability to deliver perfectly in-line trenches for utilities to the specified depth with no over digging. The accuracy reduces spoil that has to be removed from the site and requires less time to dig and verify depths.”
Reynolds says the introduction of Trimble Solutions has saved time and money, increased employee satisfaction and improved safety on site.
Bottom line, he concludes, “There are fewer people involved in the same activity and we’re more accurate. Having the Trimble Earthworks Grade Control Platform, Trimble WorksManager Software and Trimble Siteworks Positioning System has been a game changer.”
This month the team at Inside Construction has worked closely with the Green Building Council of Australia to highlight the fantastic work companies are doing in the ‘Green Construction’ space.
The Australian construction industry continues to charge forward despite global supply chain pressures, labour shortages and cost inflations. Nationally, there are a plethora of projects in the pipeline and, as the industry continues to see rapid growth, we’re seeing an increase in construction companies looking to pivot their operations to more sustainable models.
from embodied carbon and 28%of emissions come from the building and construction sector globally.
These staggering statistics have seen a surge in conversation and action around sustainability in our industry and organisations like the GBCA are leading the way for change.
“Buildings have about 40% of the global carbon budget, they use about 50% of global materials, and they’re fundamentally important to our health and wellbeing.”
In 2002 the Green Building Council of Australia (GBCA) was formed with a purpose to lead the sustainable transformation of the built environment. GBCA CEO Davina Rooney has worked in the construction industry for over 20 years, and says she’s seen sustainability strategies have gone from being a ‘nice to have’, to something that’s at the top of the industry’s agenda.
“Buildings have about 40% of the global carbon budget, they use about 50% of global materials, and they’re fundamentally important to our health and wellbeing,” says Rooney.
“This year the GBCA celebrates our 20th anniversary. Over the past decade we have seen the construction industry make huge strides in creating a more sustainable built environment, but we still have a long way to go.”
According to the 2021 report from the Clean Energy Finance Corporation, Australian buildings and infrastructure: Opportunities for cutting embodied carbon, up to 10% of national greenhouse gas emissions come
Rooney says they do this through four key pillars – rate, educate, advocate and collaborate.
“We rate buildings, which is to set the standard for best practice through our rating system GreenStar. We educate by working with industry, running conferences, training and thought leadership series on the latest sustainability topics. We advocate, partnering with government to set strong standards and sensibly transition innovative ideas into regulation,” she says.
“To bring all this together, we collaborate with industry. We now have over 600 members who we work with to make positive change happen and deliver new models, and ways of working, at scale in the built environment.”
Many people and businesses don’t know how integral Green Construction is to climate change says Rooney. The decisions we make throughout the life of a build can have enormous impacts on the future of construction.
“There’s no reason why all new buildings shouldn’t be designed to be net zero, highly efficient, powered by renewables and fossil
fuel free – the technology to support the transition exists now,” says Rooney.
“The next huge focus for the sector is the materials that we all use. This is what we call the hard to abate part of the sector. Our partners in manufacturing are doing amazing work, but one of the big roles of construction companies is to create a business case for change.
“I was speaking to one of the big manufacturers in the last week and their low carbon concrete range has caused their market share to quadruple in the last year. That’s because of key construction companies looking for more sustainable options.”
Pushing for sustainable alternatives in the construction industry has been a big focus for the GBCA since their inception, but Rooney says working with the industry to take innovative ideas to scale across every project is paramount.
The GBCA’s Green Star rating system is recognised internationally and is one of the largest and most comprehensive of its kind in
companies for sustainable incentives on their projects.
“Over 55-million-sqm’s of building space and over 40% of CBD office space in Australia is Green Star certified. What we find is there’s an enormous amount of area for improvement in this space as we work with our partners,” says Rooney.
“The key opportunity here is for all of us to take sustainability and try and deliver it in every project, every day.”
In the past few years, we’ve seen a green rush of people putting in designs to the highest construction standards, with a focus on delivering buildings that are decarbonised for the future.
Sustainable and environmentally friendly construction is increasingly becoming of top importance to everyone in the supply chain, from clients and constructors to materials suppliers and sub-contractors.
“The only way to achieve a 40% reduction in embodied carbon by 2030 is by everyone in the industry working together,” says Rooney.
“Whether it’s using more sustainable products or reducing waste during a build, Green Construction is critical to creating a prosperous future for our nation.”
carbon by 2030 is by everyone in the industry working together.”
Davina Rooney, CEO, Green Building Council of Australia.
Inventing and designing efficiencydriven products for over 15 years, Makinex has launched a system that uses solar and battery technology to generate clean power on construction sites.
For over 15 years Makinex has been identifying inefficiencies in the construction sector, and inventing products to make contractors more efficient, safe and profitable.
Ingrained in Makinex’s culture is a passion for challenging conventional methods of work, and after identifying the need for a more sustainable power solution on site, the team invented the Hybrid Power System (HPS).
The Makinex team saw the opportunity to create the HPS product 4 years ago, with a core competency of providing clean power to construction sites and reduce diesel consumption.
Makinex Managing Director Paul Weaver says that over time the product has morphed into a range of Hybrid Power Systems from 10kVA, up to 90kVA.
“The fundamental goal of the product is to reduce diesel consumption by over 90%, particularly in remote site locations,” says Weaver.
Makinex was founded in 2004. From humble beginnings in Sydney, NSW the company now has a presence in 14 countries, 50 employees, products carried by more than 4000 equipment hire and rental companies, and over 1000 reseller and OEMs.
The delivery of their latest product, the HPS, adds to their extensive offering of efficiencydriven solutions.
Weaver says the HPS is having success in remote site locations where typically they burn through a lot of diesel needing power for often 24 hours a day, seven days a week.
“Our system uses solar and battery technology to generate and store power without the need to be connected to an overhead electricity network, reducing diesel consumption on site and providing an efficient power source,” he says.
“We’ve made the generator component of the system the third wheel, designed to only kick in when the solar is not producing enough energy for the batteries to recharge.
“The system, manufactured here in Australia, has built in smarts that can be used by the customer to monitor and manage power. For example, if there’s a particular time of day that the noise levels need to be restricted, the system can be controlled so that the generator kicks in at certain times.
run for long enough to manage that without having the generator kick in.”
The functions in the system also allow the customer to monitor fuel consumption so they can get firsthand access, through their computers, of how much diesel they’re burning, and measures the reduction of carbon emissions.
When the HPS came about 4 years ago, Weaver says the conversation around carbon emissions wasn’t as strong as it is today. The increased price of diesel, which has been creeping up over the past year or two, has now put it at the front and centre of their customers’ minds.
“The third component that has contributed to the success of the product is tier one companies employing sustainability managers who are tasked with sourcing products like the HPS in the market,” says Weaver.
“I really enjoy dealing with people in the sustainability space. Though they’re not technically set up to understand the product to the level of an engineer or site manager, they’re the ones who are introducing our products to those key people in their business.
“We’re increasingly seeing with tenders the expectation of a green or environmental
benefit to what and how they’re building. Many companies are no longer prepared to accept a jet diesel generator on site that’s going to burn through 3, 4 or 5 litres of diesel an hour.”
The Makinex HPS delivers outcomes and results that help companies meet their sustainability goals. The system doesn’t rely on other energy sources or other elements of the process to come together, it can be commissioned on site in less than 5 minutes and supply instant power. In the main, the HPS delivers a great outcome for the environment, cost savings and efficiency.
A recent case study conducted by Makinex showcases the value of the system. One of their customers in northern NSW, using a 45kVA HPS, reduced their diesel consumption by 99% over a 3-month summer period. They used just 30 litres of diesel over the 3 months, unlike some traditional diesel-powered methods which can use that amount in just 6 hours.
“Our system provides a considerable financial benefit to the customer, and those that have bought or are hiring units currently are coming back for more,” says Weaver.
“We have now shifted our focus over to our supply chain and production. We’re investing more in that area so that we can fulfil the need that the market is creating for us, so that’s exciting in itself.
“The industry has a high expectation for quality products that last, so we often overengineer and over-design our products to ensure they’re reliable and of the highest quality.”
The HPS product, over its development cycle, has morphed into the company’s recent launch of a sub-brand – Makinex
Renewables – where they are designing and building sustainable and renewable technologies for the construction sector.
Weaver says there’s a few products in the pipeline that the market hasn’t seen yet that came about from conversations with their customers.
“We’ve been talking to our customers and asking questions around what they’re powering and how we can provide better products. It’s amazing how many ideas have come back to the table, and it allows us to
continue to develop great products in the renewables space,” he adds.
The continual pursuit of a better way is something that Makinex strives for and has been the catalyst for shifting the business to create sustainable, renewable products. The company has developed a reputation in the industry for bringing quality products to market, and their latest HPS is just the beginning of Makinex’s renewable
Energy levels and fuel consumption can be monitored, and noise levels can be controlled, making HPS intelligent and transparent.
As a continuous source of clean power, HPS excels in remote locations, eliminating diesel fuel dependence.
“Our system provides a considerable financial benefit to the customer, and those that have bought or are hiring units currently are coming back for more.”
Construction software company Payapps is taking action to create a more sustainable future for the construction industry, achieving Climate Active carbon neutral certification in Australia in 2021.
In 2021, the Payapps team made the decision to pursue carbon neutral certification through Climate Active, a partnership between Australian businesses and Government.
Achieving the certification later that year, the company has continued to put their best foot forward to improve their carbon footprint.
Payapps is a cloud-based collaboration tool for the construction industry, assisting contractors and subcontractors to simplify and expedite the payment approval process. Their mission to develop and provide software to make life easier for its users has reduced the need for paper globally in over 30,000 construction companies, saving approximately 20 tonnes in paper each year.
Founded in 2014 by Melbourne born Lincoln Easton, Payapps was developed to remove traditional, inefficient methods of managing progress claims. Easton found that many construction companies experienced friction when it came to managing progress claims and saw the potential for a Software as a Service (SaaS) platform focused on collaboration and efficiency.
Jessica Widdicombe, Senior Finance Manager at Payapps says the product has since become an efficient, sustainable, and globally recognised progress claims solution. “As well as improving efficiencies on construction sites, Payapps reduces the need
for paper helping our customers to achieve their goals in reducing their environmental impact,” she says.
Widdicombe has been with Payapps for 4 years and led the process for the company to achieve Climate Active carbon neutral certification.
“Our product is a clean technology by nature that helps reduce risks and promote efficiencies within the construction industry and so going carbon neutral ourselves presented as a logical next step,” says Widdicombe.
“Our leadership team is very passionate about sustainability, so when the opportunity arose to achieve a state of carbon neutrality, everyone was on board.”
Digitisation presents one of the greatest opportunities for the construction industry to achieve net zero emissions. With technologies like Payapps forging sustainable solutions for the industry, it’s becoming increasingly important for companies to be more receptive to adopting innovative technologies.
Although the Australian construction industry is slow-moving in the uptake of technology, technology-aided operations will one day become ubiquitous across the sector. Industry organisations like the Green Building Council of Australia are driving change in built sustainability, and green technology like Payapps is a major factor in driving this change.
“Many of our customers have key values around sustainability, and we want to support them by recognising Payapps can have a positive impact on their business and the environment,” says Widdicombe.
“We are able to show action, real intent, and commitment to carbon neutrality through our Climate Active certification. We aim to showcase the amazing benefits of technology in the sustainability space.”
The process to achieve carbon neutral certification, and maintain it each year, included a relatively small investment for a great initiative, Widdicombe says.
Payapps met the requirements of the Climate Active Carbon Neutral Standard by measuring their emissions, reducing where possible and offsetting remaining emissions.
“The first and biggest part of the process is calculating your carbon emissions. We had
help to get started from our major shareholder IFM Investors’ and an environmental consultant Pathzero, who guided us and helped us identify initiatives to achieve the certification. Pathzero’s SaaS solution enabled us to calculate our Greenhouse Gas (GHG) emissions, identify ways to reduce our impact, and look at ways to offset our emissions,” says Widdicombe.
The Payapps platform provides progress payment visibility across the supply chain, including subcontractors, and helps businesses involved in the process reduce their own carbon emissions. By reducing the need for paper, it also saves on the transportation, storage and archiving of documents, furthering its sustainability benefits right through the supply chain.
“We’re proud to be supporting our clients to become more sustainable by using the Payapps software and also playing our part here in the office,” says Widdicombe.
“We have introduced a number of initiatives to reduce our carbon footprint, including reducing our electricity consumption and waste, as well as recycling where possible. All Payapps employees are encouraged to do their part, whether it be reducing travel time or using efficient modes of transport.”
Payapps has also started an education process following their certification, largely for their Australia based employees, to provide their staff with everyday steps they can take to reduce their emissions.
“The education sessions are still in the early stages of development and we’ll continue to evolve them each year,” says Widdicombe.
According to the ACT Government’s ‘No Waste Paper and Cardboard factsheet 2022’ the average office worker uses approximately 50kg of paper, or 10,000 sheets of A4 paper, a year. Widdicombe says Payapps offices are almost paperless.
“We educate staff to look at the things we use day to day – like marketing materials, printed documents and electricity – and collaborate to find alternative, sustainable solutions,” she says.
Currently going through their second year of the certification process for the last financial year, Widdicombe says Payapps is continuing to be proactive in the sustainability space, always looking for ways to improve.
“Our headcount has doubled over the last 12 months, and the economy has opened back up. Our first year of certification is a low baseline to measure against considering everyone was in lockdown, so naturally our emissions will increase as the business grows, but we’re actively trying to reduce our emissions on a per employee basis moving forward.”
“Our goal is to continue to support industry pillars around sustainability and encourage other companies in construction to be a part of the carbon neutral journey.”
Payapps is an efficient, sustainable, and globally recognised progress claims solution.
“We have introduced a number of initiatives to reduce our carbon footprint, including reducing our electricity consumption and waste, as well as recycling where possible. All Payapps employees are encouraged to do their part, whether it be reducing travel time or using efficient modes of transport.”
Inside Construction weekly
is your
this
to
Throughout their global operations McConnell Dowell holistic approach to every project, embracing practices that help minimise environmental and social impacts.
Led by Samantha Johnson, the company’s Executive General Manager of Health, Safety, Environment and Quality (HSEQ), McConnell Dowell employees are constantly looking for new and innovative ways to reduce their impact on the world around them.
Johnson says in planning a project, the company looks into the impact that project could have on the environment and surrounding communities.
“In the planning phase, we put together an extensive plan to minimise the impact a
On the Eastland Port Wharf 7 Upgrade project in New Zealand, McConnell Dowell collaborated with their customer to innovate and deliver some outstanding sustainability outcomes.
we look at things like how we can reduce carbon, embrace the circular economy and minimise waste and pollution,” says Johnson.
“Our community and people are also of top importance to us here at McConnell Dowell. Our objective is to work with and for the community, keep everyone safe, embrace diversity and inclusion, and support and develop our people.”
Evidenced by the company’s large portfolio of sustainably managed projects around the globe, Johnson says the Port Kembla Gas Terminal - Marine Works project is a perfect example of McConnell Dowell’s commitment to reducing, or eliminating where possible, negative environmental and social impacts.
The NSW project involves the conversion of an abandoned coal terminal site to a gas import facility at Port Kembla to bring flexible additional energy supply to the eastern seaboard of Australia. “Driven by our engineering teams, we’ve been able to alter drilling work on the Port Kembla Project to save approximately 20,000 litres of diesel, which is around 54 tonnes of carbon emissions saved,” says Johnson.
“We’ve converted and removed several temporary works which has greatly reduced negative impacts on the marine environment,
which has in turn saved us steel and another 45 tonnes of carbon emissions.
“Similar to that we’re also completing the Eastland Port Wharf 7 Upgrade in New Zealand where again, by changing the piling design, the team has managed to save tonnes of carbon emissions as well as reduce the impact on the environment and community.”
McConnell Dowell was awarded the design and construct contract to rebuild Wharf 7 by Eastland Port in Gisborne, New Zealand in early 2022, following a successful six-month value engineering exercise.
The Wharf 7 contract is part of stage one of the $60 million Twin Berth Project which will enable the safe and simultaneous loading and unloading of up to two handymax, 180-200m long ships.
Using digital engineering and animation capabilities to refine the staging, McConnell Dowell’s engineering team has maximised value and sustainability on the Wharf 7 Project.
Speaking on the project, Johnson says, “Through a design refining process, we have been able to remove the need for 49,000 tonnes of hardfill by using 70% less steel and 50% fewer piles than the original design.”
“Social impacts have been reduced with
The Narre WarrenCranbourne Road Upgrade project is the fourth Major Road Projects Victoria (MRPV) contract awarded to McConnell Dowell. The others being the Echuca Moama Bridge, the Mordialloc Freeway, and the current Healesville - Koo Wee Rup Road Upgrade.
minimised disruption to port activities, and a drill and drive method to mitigate noise and vibration during piling.
“The marine environment, (Rua Koura (crayfish puerulus)) local ecology and seabed will be minimally affected due to the projects innovative design and construction strategy.”
Construction on the wharf began in April this year, with works expected to be completed in October 2023.
Johnson says more customers are now accessing loans that are purely dependent upon the plans being able to demonstrate a carbon zero or reduced environmental impact.
“We have combinations of customers who are using green finance, and their shareholders who are very interested in sustainability, and the environmental, social and governance (ESG) space,” says Johnson.
“Their shareholders are looking to invest in sustainable projects, and then we have our shareholders who are asking us to become more environmentally friendly and sustainable.”
“We have drivers coming from both sides. It’s great because then, when you add into the mix the advances in engineering, and all the technology that’s available now, it’s as though everything is coming together cohesively to allow us to achieve the best possible environmental and social outcomes.”
When McConnell Dowell tend for a project, Johnson says their teams working collaboratively with the client and the community are essential to environmental and social planning.
There may be a need for additional investment in innovative technologies or sustainable materials, or research and collaboration with the surrounding communities. The client needs to be able to see the value and outcomes that arise from their investment.
“Every project is different and has a different set of factors affecting what we’re going to construct. Whether we’re working towards reducing our carbon footprint or planning a project that benefits the community during and after construction, collaboration is key,” says Johnson.
“If we can see a different way of going about construction that’s going to have a much lower carbon footprint and be kinder to the
environment, then absolutely we’ll put that forward to the client.”
On the social side, Johnson and McConnell Dowell teams strive to make a positive contribution to the communities they work in through strong stakeholder engagement and consultation, providing local employment opportunities and seeking community feedback on every project.
The company also prides themselves on being proactive with social support and investment initiatives, such as supporting local Men’s Sheds, integrating Aboriginal artwork and working with local schools.
Recently, McConnell Dowell’s team on the Major Road Projects Victoria’s (MRPV) Narre Warren-Cranbourne Road Upgrade project held a working bee, hosting 10 student leaders from Cranbourne Primary School. Their team worked alongside the students to spread 15 cubic metres of mulch, refreshing garden beds across the school grounds.
Cranbourne Primary School Principal Lachlan Yeates says the working bee was a great learning experience for the students.
“We’re excited to be working with MRPV and McConnell Dowell to help support student leaders in becoming more environmentally aware,” Mr Yeates says.
“We greatly appreciate the time and resources volunteered by the project team to beautify the school grounds.”
In Victoria, government contracts require the contractor to use a certain portion of their spend on either local or social procurement. This can involve working with minority groups in the community, purchasing from social enterprises and providing employment for people from disadvantaged communities.
Johnson says regardless of whether there is a contractual requirement for local and social procurement, McConnell Dowell look to do it for every one of their projects. “It just makes sense,” says Johnson.
“There are huge benefits out of working with the community and working with some of the more diverse areas of the community. It brings about positive experiences and outcomes for our teams and the groups that we work with.”
“The local community tends to know if there are environmental hazards or areas of concern, so we’re committed to working with them from the outset of the project. That
“Our community and people are also of top importance to us here at McConnell Dowell. Our objective is to work with, and for, the community, keep everyone safe, embrace diversity and inclusion, and support and develop our people.”
can be right from the tender period when we haven’t even won a project yet, and it continues throughout the project’s lifecycle.”
In 2021, McConnell Dowell, in joint venture with Decmil, took out the Excellence in Environmental Outcomes Award at the Infrastructure Sustainability Council Gala Awards for their Mordialloc Freeway Project (MFP).
The MFP, a 9 km freeway link in Victoria, incorporates interchanges, bridges over wetlands and a shared user path. McConnell Dowell implemented a range of sustainability initiatives in response to waste crisis and shortage of quarry materials, creating what they call ‘Australia’s greenest freeway’.
“We were able to save thousands of tonnes of otherwise waste material to construct asphalt pavements, stormwater drainage pipes, noise walls and concrete reinforcing mesh, resulting in a 27% reduction in embodied energy,” says Johnson.
The MFP project team were able to divert 97% of construction waste from landfill, lay 321 tonnes of recycled road base and asphalt, and reuse 570 tonnes of plastic in 32,000 m2 of noise walls.
“We’re extremely proud of our effort in using innovative new technologies and processes to complete the MFP project to a high environmental standard,” says Johnson. Judges from the awards were equally
impressed with the project. One judge said, “The focus on reduced truck trips, local sourcing and recycling is a powerful way to improve industry practices.”
“The MFP demonstrates the potential cost benefits of improvised sustainability practices while supporting development and scale-up of local industry.”
As a global company, McConnell Dowell has a goal to reach carbon zero operations by 2050, but Johnson says they’re continuously striving to improve and kick ESG goals. Many of their goals are technology dependent and efforts to achieve those goals can be seen across their operations.
To improve their carbon footprint, McConnell Dowell is introducing solar generators instead of diesel-powered generators. “Whether it’s saving water or electricity, reusing and repurposing waste, or using less materials to achieve the same result, we’re always on the lookout for sustainable and environmentally friendly solutions,” says Johnson.
“Much of the plant we use is not currently available to either be electrical or hydrogen fuelled, so we have to wait for the technology to catch up. This doesn’t stop us from doing the best we can with the resources we have.”
Visit McConnell Dowell’s website for more on their projects and services at www.mcconnelldowell.com
“There are huge benefits out of working with the community and working with some of the more diverse areas of the community. It brings about positive experiences and outcomes for our teams and the groups that we work with.”McConnell Dowell, in joint venture, completed the Mordialloc Freeway Project (MFP) four weeks ahead of schedule in late 2021.
Established as an initiative of Australian construction materials company Wagners in 2010, Earth Friendly Concrete has since seen rapid growth, delivering sustainable geopolymer concrete across the globe.
Over the last 10 years, Earth Friendly Concrete® (EFC®), established by Wagners, has been reducing the carbon footprint in the built environment with their geopolymer concrete.
According to VDZ’s 2012 report –Decarbonisation Pathways for the Australian Cement and Concrete Sector – Australia consumes an annual per capita of approximately 450kg’s of cement. The report also states emissions from cement manufacturing accounted for 6-7% of global CO2 emissions in 2021.
The Wagners team saw the opportunity to play their part in reducing the impact construction has on the environment, developing an absolute zero cement solution to eliminate the climate impact of cement on the built environment.
Jason Zafiriadis, Wagners EFC’s Chief Commercial Officer says the decision to establish EFC came around the time there were talks of a carbon tax in Australia.
“EFC came from a real focus on understanding the bigger drivers of carbon emissions, and cement use was identified as an opportunity for change,” he says.
“If the cement industry was a country, it would be the third largest emitter of CO2
“To make a tonne of cement, you effectively need to bake two tonnes of lime, and a tonne of that gets released as CO2 into the atmosphere just through the chemical reaction, let alone all the energy you need to
Zafiriadis says Wagner’s aren’t afraid to take the hard road on things and solve the hard
The difficulty to create a cement free concrete was to make the product behave relatively like ordinary concrete in application. Over the past 10 years, with over $20 million dollars of their own investment, Wagners EFC developed a zero cement concrete technology that works through ordinary concrete supply chains, proven globally in commercial construction
“Our concrete can achieve around 80% of what you can achieve with ordinary concrete. We can achieve the full compressive strength range that ordinary concrete can deliver; we have better durability, which is important for
marine and sewer; and we can deliver specialty applications with better flexural tensile strength, which is important for large scale, pavements, roads, airports and the like,” says Zafiriadis.
“We have better shrinkage and no heat of hydration, ideal for large scale concrete pours for large raft beams or wind tower bases. That’s really tricky to deal with in respect to shrinkage and heat of hydration, and so we are actually a better technical solution for those applications.”
Wagners is now investing even more of their own funds to scale up the EFC business in southeast Queensland, to make the Wagner concrete plants Earth Friendly Concrete® and ordinary concrete capable.
Over the past two years, the company has established a market in London, securing a number of partners in the UK to set up EFC producers in multiple locations – one being the High Speed 2 (HS2) project.
The HS2 project is a planned high speed rail link from London to Birmingham, the largest rail infrastructure ever in Europe.
Wagners has been working with Capital Concrete using its EFC on the project. In November 2021, it was estimated more than 900 m³ had been used for the HS2’s structural works piling mats and 2 km³ for haul roads and bases for cranes – saving 270,000kg of carbon.
“We’re seeing a huge uptake of EFC in Europe driven by their sustainable policy environment, yet we’re finding the Australian construction and infrastructure industries are more hesitant,” says Zafiriadis.
“Europe’s policies are really being driven and motivated to reduce their carbon footprint with new and innovative methods. What we’re finding in Australia is, as a nation, we have ambitious, high-end policy drivers to achieve net zero by certain dates, but the only real driver to achieve that at the moment seems to be through offsetting or a reduction in energy usage in the operation of a building.”
The traction Wagners EFC has been getting in the UK has resulted in the company setting up a large-scale state-of-the-art production facility in London, which has been under construction over the past 12 months.
Expected to be completed in the next five to six weeks, the facility will enable them to deliver their technology at scale to a much wider customer base.
The company’s next step is to secure a facility in Germany, following the success of three major contracts in the country to pull through EFC technology into sewer infrastructure.
“Three of Germany’s largest precasters have been doing development work with our technology in sewer infrastructure projects. They’re leveraging our product not just because we have a much lower carbon footprint, but from a durability perspective, we deliver a product that lasts,” says Zafiriadis.
“We have been certified by Germany’s Deutsches Institut fur Bautechnik (DIBt), who certified our technology for that application which is a huge step.
“These project’s also get better end-oflife out of our concrete because when they measure the circularity of that infrastructure, the concrete can be crushed up and used as aggregates.
“It’s not just the carbon footprint that is important as we look to do things differently in infrastructure. It’s also the circular economy, how we can reduce the amount of energy and raw materials that we use in building works, and how we measure the end-of-life use through the things that we’re building.”
Zafiriadis says EFC is also working hard with Australian standards to work towards a standard for geopolymer concretes.
“We’ve been putting the hard yards in on the building codes and certification area, which helps manage risk. Currently we have a 50-year design life spec with Queensland’s Department of Transport and Main Roads and work with industry bodies like the Materials & Embodied Carbon Leaders’ Alliance, driving embodied carbon reduction initiatives across the building and construction industry. We also support the initiatives of the Green Building Council of Australia and have just become top tier members of the Infrastructure Sustainability Council,” he says.
“We want to start becoming more involved to help their clients maximise their ratings through the embodied carbon innovation streams of their rating system. Our EFC technology is an ideal solution to the challenge of cement emissions.”
The way EFC technology works is it replaces ordinary cement with industrial waste byproducts like fly ash and blast furnace slag –the products that most concrete supply chains
have an abundance of in major industries, economies and markets.
The concrete producer will use their existing supply chain of raw materials and swap out the cement with fly ash and slag. EFC then supply their chemical activator, the EFC Activator System, and that allows those materials to perform like ordinary concrete during the batching process.
As far as the concrete producer is concerned, there is very minimal change to the way they make concrete, with the EFC activator solution added at the point of production.
“It then goes into the back of an ordinary concrete truck and goes to site like an ordinary concrete supply chain would. It’s also placed like ordinary concrete would be,” says Zafiriadis.
“We can reduce the carbon footprint by up to 80% when compared to ordinary concrete, so it’s a huge carbon footprint reduction that we can deliver for new construction and infrastructure works.”
When talking about the hesitance of Australian companies adopting EFC’s sustainable solution to concrete, Zafiriadis says he empathises given the challenges holding them back in today’s industry climate, such as material costs and low margins.
“Those that do want to step forward, to lead the charge with using new technologies and innovations in the projects they’re involved with, will be the ones that will prosper,” he adds.
“Contract frameworks are set up to motivate and drive the contractors and the subbies to deliver measurable outcomes for sustainability, innovation or engineered benefits, and gives them scope to pull through new techniques.
Although, it’s done in a manner where that risk is being shared.
“We can reduce the carbon footprint by up to 80% when compared to ordinary concrete, so it’s a huge carbon footprint reduction that we can deliver for new construction and infrastructure works.”Earth Friendly Concrete® was used to construct the Pinkenba Wharf on the Brisbane River, claimed to be the greenest wharf structure in the world.
Mettle completed a six-storey building, 112 Alfred St, in Brisbane’s Fortitude Valley using Wagners Earth Friendly Concrete®
anything different if there’s too much risk involved, so the change has to come from the client side, public and private sector.”
Construction services company Mettle is one Australian company proudly using the EFC product. The company completed a six-storey building in Brisbane’s Fortitude Valley using EFC.
Director of Mettle Marc Kenney was the major driver in using the concrete technology, despite advice from within his circles not to take the risk.
“Marc had a vision for the building and that was to have a strong sense of community and place. The project had a biophilic design throughout the building, and he drove the use of EFC through all structural applications,” says Zafiriadis.
Kenney adds, “Being both the developer and builder of 112 Alfred St, we were afforded the luxury of being able to make decisions around the products we used. We chose EFC to primarily build the structure because someone had to go first, and we were eager to try something different that was paired with the biophilic design principles of the development.”
“Being a first for EFC’s use in a multi-level insitu application, there were certainly a number of challenges in terms of mix design and educating our workforce in how to work with it. Wagners stood shoulder to shoulder with us along the journey which was invaluable and appreciated. The finished product stands out in terms of its off-form finish which is both clean and striking.”
In Australia, EFC was also used on the
“There’s about 20% of the applications that we can’t achieve, such as the same finishing or flatness as ordinary concrete, and we don’t hide from that. We have processes where we can get around that, or in some rare instances we will suggest using ordinary concrete for particular applications.
“Even though concreters are a little wary at first, once we start working with them, they’re incredibly impressed with the product.”
Matrak is supporting over 250 projects to reduce risk, material waste and improve efficiency, through their innovative construction material
Matrak’s sustainable solution to material tracking is changing the way construction teams manage their projects. The company’s material tracking platform was designed to simplify and support the complexities of tracking and managing materials — building visibility throughout the entire supply chain.
Matrak co-founder Brett Hodgkins experienced the frustrations of manual material tracking firsthand, working for his dad’s façade company for five years from 2010. Alongside his brother, Shane Hodgkins, the pair developed Matrak – an end-to-end material tracking platform.
CEO and Co-founder, Shane Hodgkins says end-to-end material tracking is an inevitable shift for the industry. “It’s a shift that’s been progressing for a while, but has accelerated over the past few years,” he says.
“Our platform enables anyone, from manufacturers and installers to logistics and builders, to track the materials they are using for different projects, through all of the different stages of the project’s lifecycle and keeps everyone on the same page.”
A building can be seen as a sequence of materials getting to the right place at the right time, with the proper quality. When something goes wrong in the materials process during a build it can result in financial penalties, and many cases, delay the entire project.
“Basically, we’re trying to remove a lot of the adversarial nature between companies,” says Shane.
“The Matrak platform allows everyone in the supply chain to be on the same page and not have any risks associated with materials on their projects, giving people time to focus on getting the job done.”
CTO and Co-founder, Brett Hodgkins says there’s many elements that make their platform a sustainable solution for the construction industry.
“Because the platform allows the user to track materials as they are being handled, issues can be resolved before things get shipped,” he says.
“Shipping costs are significant, so by removing the risk of having to reorder materials, Matrak saves the associated reorder costs as well as saves the time it takes to reorder and have the materials shipped to site.”
“You have all of the material tracking information in front of you on the dashboard,
including who in the supply chain has handled the materials.”
Last year alone, the Matrak team estimated they saved around 30 shipping containers of materials in over 180 projects. Shane says a lot of it has to do with risk prevention. Even if your materials are in the right spot, Matrak allows you to have certainty.
“We also haven’t come across any other systems that allow this level of granular material tracking across different stakeholders,” says Shane.
Traditional processes of material tracking in the industry, such as excel sheets and email communications, become quickly outdated once the data is recorded or sent. The value that comes from having large amounts of material tracking data, all timestamped and tracked through everyone in the supply chain is palpable.
When it comes to tracking carbon emissions, Matrak presents huge potential in tracking emissions resulting from the use of materials. There’s an increasing push by organisations like the Green Building Council of Australia and government bodies for construction companies to invest to cut national emissions across the built environment.
According to a report from the Clean Energy Finance Corporation (CEFC) – Australian buildings and infrastructure: Opportunities for cutting embodied carbon – embodied carbon in the production of building materials is responsible for 28% of emissions from the building and construction sector globally.
When a company has to reorder materials, the emissions generated by the entire process need to be considered, including the resource extraction, manufacturing and transportation of the materials to site.
“There’s a lot of data and information out there about the emissions used in the design of a build, but very little about actually bringing the project to life and things such as material reorders,” says Brett.
“Matrak eliminates the need for reordering, which can lead to a reduction in emissions that would have been generated in the process.”
Hutchinson Builders are one of the companies seeing the sizeable value of the Matrak platform. Jacob Baldacchino, Façade Manager at Hutchinson Builders says life before Matrak was far more complicated.
“Beforehand, prior to Hutchinson Builders, my role had me flying overseas, just about every week or two, to verify that what we were paying for and what we were agreeing to was happening. I also found information getting lost in translation with the different languages and cultures I was working with. Having Matrak, which is in multiple languages when needed, sharing the same information on both ends has been a gamechanger. It’s made it a lot easier for us,” he says.
Mr. Baldacchino says Matrak has allowed them to see the project’s productivity as far back as procurement and production.
Before joining Hutchinson Builders, Mr. Baldacchino has seen a number of companies negatively impacted by traditional methods of material tracking. “Let me give you an example,” he says.
“With traditional methods, you might order and receive a container of materials. It might be running late so the container is rushed to site. Then you’re faced with a bill of materials that need to be ticked off and accounted for one by one. If that’s not done, it’s near impossible to keep track of the materials ordered, whether they were all there and of the right quality, so finding what you needed becomes more difficult than just ordering replacements locally in some instances.”
Matrak not only accounts for all ordered materials, but it gives you real-time transparency and visibility to see what’s arrived on site, what’s on its way and what still needs to be shipped.
“Personally, I think we’re only seeing the start of what you can get out of the platform. The Matrak team have been fantastic in adapting the platform to our needs,” says Mr. Baldacchino.
“It gives us a sense of security that we have done everything we possibly can to make sure that what we’re providing is the best of the best.”
The construction industry is fast paced and for companies to maintain a good reputation, projects need to be completed on time and on budget. Shane and Brett had this at front of mind when developing the Matrak platform, delivering a simple and efficient product that even the busiest of people could use.
The platform can collect the drawings from the project a company is running, like
elevations or shop drawings, and then extract a bill of quantities from those drawings to provide visibility of what items are needed to complete the project before it commences.
From there, the user can print a QR code or ticket of the drawings, which are interactive and can be colour coded as completed. The software then shares all the information with everyone else in the supply chain who are using the platform.
On top of their sustainable product, Shane says Matrak also has their own sustainability goals as a company.
“We’re a member of the Materials & Embodied Carbon Leaders’ Alliance (MECLA), specifically because we’ve got all this information on the materials going through the supply chain. It means that by connecting that information with not just the manufacturers, but also their sources of raw materials, we can track the embodied carbon within a construction project,” says Shane.
“We’re currently delivering early pilots on embodied carbon tracking with façades because they’re quite carbon intensive to begin with. I think the whole team here are excited because we think that we can make a big impact in the industry, just by creating the visibility of embodied carbon in materials that doesn’t exist anywhere else.”
Sharing their finals thoughts, Shane and Brett say it’s inevitable that material tracking use in the construction industry will accelerate in the near future.
“To us, it seems illogical to have large, complex and expensive projects with teams having no visibility on the different materials they are purchasing and using. Relying on pen and paper or excel is becoming a thing of the past, and for good reason,” says Brett.
“The innovative, forward-thinking construction companies and leaders that see the benefits of a quality platform like Matrak are those who are going to drive positive change in the industry.”
“The Matrak platform allows everyone in the supply chain to be on the same page and not have any risks associated with materials on their projects, giving people time to focus on getting the job done.”
The Matrak app will create a Bill of Materials from your drawings and make them interactive for real-time updates.
Industrial and safety equipment provider, Blackwoods focus on ensuring workers are protected when it matters most. The company’s approach to safety extends far beyond supplying safety products.
Blackwoods invests time and expertise in their customers, an approach that resulted in a quality solution to worker safety on the West Gate Tunnel Project (WGTP).
“It’s what we refer to as our assess, inform, equip model. At each stage of the process, we collaborate with customers to make sure they receive the correct products, information, and training,” says Drew Dauncey, Technical Safety Specialist, Blackwoods.
Blackwoods work with their clients to identify hazards, review safe work practices, and check safety equipment usage to deliver expert recommendations. Their team of Technical Safety Specialists leave no stone unturned when it comes to safety, from producing workplace and product-in-use surveys to facilitating product trials and fit-testing.
“During assessment we also identify any hazards and conduct work practice and safety equipment usage assessments. We then implement solutions based on a workplace’s specific requirements,” says Dauncey.
content, industry insights and key resources relating to new and emerging safety issues.
“We help our customers stay informed by sharing our technical expertise, as well as giving product training and presentations,” says Dauncey.
By providing technical expertise and implementation support; product identification, selection, and sourcing guidance; and access to fit-for-purpose products that comply with applicable standards; Blackwoods ensure their customers are equipped for any project.
“We aim to provide customers with product selection guidance, sourcing, delivery, and post-purchase support in line with the relevant standards,” says Dauncey.
Respirable Crystalline Silica (RCS or Silica dust) is a significant safety issue for many in the construction industry, and a leading cause of lung cancer and other illnesses. It’s not surprising an Australian syndicate of safety orientated businesses are leading the way with an innovative home-grown solution, including Blackwoods.
In November 2020, construction was underway at the West Gate Tunnel Project (WGTP). As with all Tier 1 construction companies, health and safety is a core value and WGTP (CPB Contractors) were looking at an effective engineering solution to control Silica dust exposure whilst undertaking jackhammering activities.
“Civil construction requires significant concrete structures to create the infrastructure needed for road and tunnel construction. Jackhammering is a large component of the work, particularly during pile break back activities,” says Richard Cain, Senior Health & Safety Advisor at the West Gate Tunnel Project.
In November 2020, construction was underway at the West Gate Tunnel Project (WGTP).
“Workers’ health and well-being is our top responsibility, and new innovative solutions need to be found to keep Silica exposure levels below the Occupational Exposure Standard.
“Taking into consideration the lessons from the stone masonry industry, we were keen to find industry changing solutions to combat the risk to health of construction workers. We’ve worked with Blackwoods for many
years and have assisted in solving many of the unique problems our projects typically present.”
Following the launch of Safety Spotlight late in 2020, the WGTP team looked to Blackwoods to improve respiratory protection on site. With PAPR systems making their way to workers, a desire to find an ‘Above The Line Control’ and engineer Silica dust out of the process entirely (and not just rely on PPE), was now on the table. Once again Blackwoods was engaged to help solve the problem.
“We knew dust suppression systems were being trialled in the USA but with nothing available here in Australia, the WGTP team shared photos and links on the system and asked the question ‘can we make it here?’,” says Terry Meachen, Major Projects Manager at Blackwoods.
“So, we engaged our supply partner, Dixon, and they jumped to the idea in a bid to develop a retro-fit system specific for jackhammers.
“The WGTP team were very keen on a locally developed and manufactured system to promote local content on the project. Currently an additional person must be available to spray water on the job to keep the dust down.”
With Dixon, an innovator in the hose coupling industry, onboard, trials began in March of 2021 and continued through to June.
“Many configurations and spray nozzles with varied spray patterns and flow rates were used and tested on site at WGTP. Instead of just a simple spot test here and there, we trialled it day and night, in different weather conditions and over long periods with a goal to be below the Australian exposure standard of 0.05mg/ m3,” says Meachen.
After much trial and error, one flow nozzle proved successful, keeping the concentration of RCS below the Australian occupational exposure standard of 0.05mg/m3 over eighthour work shifts during the month-long final trial.
“There was a tremendous amount of effort applied to getting this right amongst the parties involved. It took a bit of time, but we eventually got there. In fact, we achieved consistent average readings below 0.05mg/ m3 over the month. This was a pleasing and exciting discovery for all,” says Matthew Dicker, Health & Safety Manager, West Gate Tunnel Project.
controls must be in place that meet or exceed the benefits of the Dixon system across its Victorian sites.
Cain adds, “We believe this will spark a number of initiatives to suppress Silica dust across a variety of different applications. We thank Terry, Blackwoods and Dixon for all their efforts in working to reduce the risk to our workers.”
Blackwoods’ team of Technical Safety Specialists are experienced in a wide range of industries and invest time with customers to understand the specific hazards they face. They share knowledge so that customers are equipped to ensure that every employee, contractor and visitor returns home healthy and injury-free.
“Our solution to control Silica dust exposure on the West Gate Tunnel Project (WGTP) is a great example of our end-to-end safety solutions,” says Dauncey.
“The Blackwoods technical safety team help customers get the right product, technical knowledge and training, to achieve the best result.”
“Workers’ health and well-being is our top responsibility, and new innovative solutions need to be found to keep Silica exposure levels below the Occupational Exposure Standard.”Following the launch of Safety Spotlight late in 2020, the WGTP team looked to Blackwoods to improve respiratory protection on site.
This month, Dr. Gretchen Gagel caught up with Gabrielle Trainor, Chair of the Construction Industry Culture Taskforce (CICT), to discuss sustainable construction and the Culture Standard being adopted across the industry in Australia.
‘Green construction’ isn’t just about sustainable development and the environment. It’s also about the people we attract to the construction industry and how we create a sustainable future. During my nearly 40-year career in construction, I’ve had several opportunities to work with groups focused upon creating a significant shift in the industry. For example, in 2017, I worked with the US Construction Industry Institute (CII) to create a “Manifesto for Change”, to address several systemic issues in our industry.
I was thrilled to be asked to join the Construction Industry Culture Taskforce (CICT) in 2020, a group of dedicated government and private industry individuals.
Their focus is upon securing the long-term sustainability of the industry through the broad adoption of a Culture Standard in Australia. I sat down with CICT Chair Gabrielle Trainor to talk about the initiative.
Gretchen: Gabrielle: Why is it so critical that we focus upon the sustainability of the construction industry in Australia?
Gabrielle: The case for a strong focus on the sustainability of our industry is overwhelming.
The scale of the construction industry has significant impacts in several areas:
1) Environmentally – in terms of our total scope greenhouse gas emissions and the way the built form affects humanity, heritage and our natural world.
2) Socially – considering the quality-of-life construction can deliver to communities, offset by the human costs in doing so.
3) Economically – the sum of those parts achieving the equilibrium of all costs and all benefits.
From the CICT’s point of view, we have concentrated on the construction industry workplace, at the infrastructure end initially, and its need for change.
There have been many projects seeking to address gender, diversity, mental health and wellbeing for decades, yet the statistics have not moved. However, our industry, clients and stakeholders have recognised that serious change is urgently needed. The momentum is palpable, here, and internationally.
The most obvious self-interested perspective
is that we need over 100,000 people in the industry, almost immediately, to fulfil the infrastructure pipeline that is presently committed. Despite great achievements, ours in not an industry of choice, especially among women (12% of the workforce), and increasingly among young men.
There have been great inroads on physical safety – to everyone’s credit – but a wider lens reveals workers’ lives and wellbeing take a second place to the need to deliver projects on time and on budget.
We need to focus, together, on an integrated approach. We need to require cultural change as part of a new bargain for construction projects. I strongly believe, and the evidence supports, that holistic culture change will create a more diverse, safe and productive industry.
Gretchen: If we’re sitting here 10 years from now talking about the successes achieved by CICT, what are the highlights?
Gabrielle: Our Culture Standard, developed by the NSW and Victorian Governments, and the Australian Constructors’ Association, together with other industry leaders and researchers, seeks to tackle three key domains of industry culture together. They are working hours, gender diversity and wellbeing. Our Standard requires active plans, self-set targets and programs to be included in tenders for infrastructure projects as requirements of the procurement process.
By 2032 I foresee, that following the success of our pilot projects, the Standard has been adopted in government policy nation-wide and is required for all client projects – public and private. That’s our aim and to get there will be an extraordinary moment.
In a decade, it would be great to see subcontractors, and everyone in the supply chain for projects, supported in implementing the Standard.
The goal is, by 2032, to see women account for a vastly greater percentage of the construction industry workforce. The industry should be seen as a great industry to work in for all – where jobs are rewarding; where everyone is welcome, encouraged, developed and respected; where projects create extraordinary satisfaction; and where the statistics on diversity, mental health and wellbeing have shifted.
In the future, I see the industry recognised as
a leader in sustainability in all its aspects –they all go hand-in-hand.
Gretchen: We’ve both seen initiatives like this in the industry before. What makes this one different? Why will it succeed?
Gabrielle: The Culture Standard is different to the many other efforts to improve the industry because:
It is a truly collaborative approach involving government, clients, industry and researchers. It has also had support and engagement from the union movement.
It seeks to tackle industry culture holistically. This recognises working hours, diversity and wellbeing are interrelated – addressing one at a time, independently, will not move the needle as far as is urgently needed.
It uses the procurement process as the vehicle to require change. The platform is burning, and change will not happen unless it is part of the contractual requirement for all proponents, equally. Reform will not happen unless the playing field among contractors is level and support is given through the whole of the supply chain.
T he Standard is strongly evidence based. Our research testing the application of the Standard on a number of pilot projects will demonstrate, we believe, that productivity will improve if projects are procured under the Standard.
Having said that, the Standard itself addresses workplaces. It will take time for change to be felt and as we know, the complex societal and broader contracting environment also needs to change. We need sustained effort across the entire spectrum.
Gretchen: How can people become involved?
Gabrielle: The first step is to go to our website and get in touch. We are keen to hear people’s experiences and suggestions as well as projects willing to test the Standard as a pilot.
You can read about the elements of the Standard and the research behind them at cultureinconstruction.com.au
Gabrielle Trainor AO is a non-executive director and advisor whose experience covers over 25 years on boards in the public and private sectors. She is a member of the boards of the Victorian Government’s Major Transport Infrastructure Authority and listed investment company WAM Global. She is a director of the ACT City Renewal Authority, the Western Parkland City Authority and Built Pty Ltd. Gabrielle is a member of the Western Sydney University Foundation and a trustee of the Charlie Perkins Education Trust. She chairs the Construction Industry Culture Taskforce, a joint project of industry, academe and the NSW and Victorian governments.
Dr. Gretchen Gagel is Chair of Brinkman Construction (US), a member of the National Academy of Construction (US), a member of the Construction Industry Culture Taskforce (AUS), and an affiliate professor at the Australian National University and the University of Denver. As President/Managing Director of Greatness Consulting Pty Ltd she continues to advise organisations within the construction industry on optimising capital program delivery and developing talent. You can hear more from Gretchen on her Spotify podcast, “Greatness”.
“In the future, I see the industry recognised as a leader in sustainability in all its aspects –they all go handin-hand.”Gabrielle Trainor, Chair Construction Industry Culture Taskforce (CICT).
With her determination, perseverance and resilience Jade Nicholson is making her mark in the construction industry. Now a Project Manager with Multiplex Constructions, Nicholson has worked on a broad range of projects which have each shaped the professional she is today.
When it comes to passion, Nicholson has it in droves. Coming from an all-girls school in Sydney where construction was never spoken about as a career choice, the now Project Manager for Multiplex paved her own path into the construction industry.
“I’ve always lived and worked by my motto – if you want to see the change, you’ve got to be the change that you want to see,” says Nicholson.
So, following school graduation and a 12-month gap year in Europe, Nicholson changed her university preferences to pursue a degree in Construction Project Management at University of Technology, Sydney.
With her father, uncles and cousins playing various roles in the construction industry–Nicholson says it has a strong influence on her career - “I’ve always loved architecture; I’ve always loved buildings; so, choosing a degree that marries those two things was second nature to me,” she says.
“My dad said to me, ‘Jade, do you know what you’re getting yourself into’, and suggested that I get a job in the industry to understand foundationally what it’s about.”
Nicholson took her dad’s advice, and in her first year of university secured a role as a building cadet for Laing O’Rourke. She spent five years with the company whilst studying for her degree, navigating the ropes of the fast-paced construction industry and full-time study.
In 2012, with her degree in hand and industry experience, Nicholson secured a Site Engineer position with Multiplex. “There’s always been something about Multiplex that has resonated with me. It’s a company I knew I wanted to be a part of,” she says.
Nicholson was quickly promoted to Project Engineer in 2015, then Design Manager in 2016, before achieving a long-term career goal of becoming Project Manager in 2021. “I’ve been in the industry for nearly 16 years and so far it’s been a very rewarding career. If I look back and I think about the diversity of projects that I’ve worked on, the people that I’ve worked with, what I’ve learnt and how much I’ve grown, I find it incredibly rewarding and fulfilling,” says Nicholson.
When speaking of the projects she’s worked on, Nicholson says she’s proud of every single one, particularly during her time with
Multiplex. “The thing about the projects I get to work on is they’re all unique, they’re all complex with different challenges, but with them comes an amazing opportunity to grow, develop and hone your skill set,” she says.
Though, Nicholson says there are a few projects that have had a major impact on shaping the Project Manager she is today, like the Charles Perkins Centre at The University of Sydney Camperdown.
Her first project after joining Multiplex, Nicholson worked with architecture firm FJMT to deliver their bold design for the Centre which was completed in 2013. As Site Engineer, she was responsible for the facade and the structural steel which were both key architectural elements for the project. Nicholson was awarded the National Association for Women in Construction (NAWIC) Achievement in Construction, Refurbishment and Fitout for her role in delivering the project.
“It’s a beautiful looking building with an amazing atrium. There’s a structural steel stair that cantilevers off and transitions by 15-degrees each level. It’s clad in a moulded plasterboard that wraps and adjoins the atrium balustrade, which has resulted in a ribbon like effect. The prefabricated engineering solution meant we mitigated considerable work, health and safety risks which also resulted in an installation that provided improved construction efficiencies,” says Nicholson. “It was a difficult build that I can proudly say we finished on time.”
In 2014, Nicholson started on another complex project, helping to deliver M&L Hospitality’s redevelopment of 161 Sussex Street, Sydney, now the Hyatt Regency. The project included refurbishment of the existing hotel, the construction of a new 3,450 square metre convention centre and a 25-level tower constructed over the Western Distributor.
Nicholson says this job in particular taught her about the importance of good stakeholder management, communication and why managing expectations is key. “We were doing construction works 24/7 in a 24/7 operational hotel. In order to balance construction activities with hotel operations, we would have daily meetings with hotel management. I worked with them to understand their operations whilst clearly outlining our works
“I’ve always lived and worked by my motto – if you want to see the change, you’ve got to be the change that you want to see.”
and the impacts they would have. There was a lot of collaboration and compromise made by both parties, which is key to any successful project,” she says.
“In the end it was a successful job that I now reflect back on and appreciate how much the project shaped who I am.”
In 2015, the Sussex Street project ended up being recognised by the Australian Steel Institute (ASI) and was awarded the Site Award at its National Health & Safety Excellence Awards.
More recently Nicholson worked on a commercial building, with the purpose of the project to bring together 10 displaced entities in the healthcare system and deliver a purpose-built building which focused on collaboration and integration. Completed in 2020 for Health Infrastructure, Nicholson managed the jobs entire design from beginning to end having worked front end to secure the project for Multiplex.
Now the Project Manager is delivering a high school in Mosman for School Infrastructure, managing a team with 35% female representation. Nicholson is incredibly passionate about the positive careers that exist within the construction industry and can see firsthand the benefits of diversity and inclusion. She is an advocate for women in construction and an advocate for creating inclusive teams. Right now, Nicholson says, “The team is thriving; it makes me proud to see everyone go about their work, collaborating in delivering what is another very complex project in a fully operational environment.”
Her team is using new technologies including a new digital materials handling booking system, and although there was some resistance in using it in the beginning, she’s starting to hear great feedback on the ground.
“The efficiencies and productivity we’re getting out of the technology are immeasurable, but more importantly the data we are capturing and able to use to inform our approach to materials handling is worth it,” says Nicholson.
When talking about the best thing about her job, Nicholson says it’s the diverse mix of people she gets to work and interact with every day.
“On one hand I might be dealing with a
complex engineering/buildability issue with engineers and architects, or sitting in a client meeting outlining our approach to a particular element of work. But on the other hand, I’ll be onsite having a discussion with a subcontractor who’s been doing their craft for 40 years,” she says.
“The people that I get to work with in all facets of the industry, from clients to consultants, subcontractors and the Multiplex team, are diverse and all bring something different to the equation.”
Another rewarding aspect of her job is seeing a job through to completion. In the construction industry projects have the ability to shape and influence people’s lives. Society is surrounded by the built environment and the buildings Nicholson works on today will be a part of the community long into the future.
“For me, being in the construction industry is not a career, it’s a lifestyle choice, and there is nothing more satisfying then finishing a job and obtaining Practical Completion,” says Nicholson.
Her advice for anyone looking for a career in the construction industry is, “Be your authentic self, value what you bring, and back yourself. A career in the construction industry is incredibly rewarding. It’s a dynamic industry, with every part offering unique opportunities and challenges. Don’t forget to speak up for what you want – my advice is be overt.”
“For me, being in the construction industry is not a career, it’s a lifestyle choice, and there is nothing more satisfying than finishing a job and obtaining Practical Completion.”Jade Nicholson, Project Manager, Multiplex Constructions.
In her 3 years as Bitumen and Asphalt Production Foreperson for Downer, Emily Jennings has manufactured thousands of tonnes of asphalt for projects throughout greater Darwin.
Emily Jennings, Bitumen and Asphalt Production Foreperson for Downer, started with the company in 2017 as a Traffic Controller. She didn’t always aspire to work in the construction industry, but after completing a social science degree at university after school, Jennings wasn’t sure what career path she wanted to follow.
“I went travelling around Australia until I decided what I wanted to do and arrived in Darwin in 2017. I started a role as a Traffic Controller for Downer where I gained an insight into the world of bitumen and
In this role, Jennings spent most of her time working for Downer’s spray seal crew on various projects in remote areas of the Northern Territory, including several urban asphalt projects around Darwin. Jennings says she found the process fascinating and loved being a part of it.
When the opportunity arose for Jennings to join the Downer production team in 2019 as a trainee Operator, she jumped on it. “I was nervous and unsure of what to expect,” she
“It was also intimidating being the only female in the crew, but over 3 years on I couldn’t be happier with the decision I made to join the production team.”
Jennings says her crew is responsible for safely and efficiently manufacturing bitumen and asphalt for various projects around the Northern Territory, and her typical workday varies. The hardworking operator starts every morning by doing a prestart meeting with the production team, and throughout the day, oversees the operations of the crew to ensure all daily targets are met in a safe manner.
“Working with bitumen can be extremely dangerous. It is heated and stored at temperatures of up to 200 degrees, so all processes must be followed carefully to avoid serious incidents and injuries,” says
Depending on what her team has on for the day, Jennings could be doing anything from blending bitumen, operating the asphalt plant, loading sprayers and bulkers with bitumen or driving a loader, forklift, HR truck
“My favourite thing about my job is that it never gets boring. It’s not a typical nine-to-
five job, and every single day is different,” says Jennings.
“In my few years with Downer, I have already been given so many opportunities to learn and progress within my role and there’s always more to learn.”
Jennings has played a significant role in several projects during her time with Downer. She has helped manufacture and deliver high specification bitumen to Ayres Rock and Alice Springs airports. She’s also manufactured thousands of tonnes of asphalt for a number of projects throughout greater Darwin including the Darwin Rail Terminal, new housing estates and industrial subdivision, as well as upgrades to Darwin and Tindal Airports.
Recognised for her commitment and enthusiasm throughout her career, Jennings took home the Australian Flexible Pavement Association’s Field Worker of the Year award in 2020. This year she won the National Association of Women in Construction’s (NAWIC) Tradeswoman of the Year 2022 award.
“I’m proud of my achievements, but the thing I am most proud of is being able to help welcome and encourage new people, particularly women, into the construction industry – especially those who, like myself, have no previous experience,” says Jennings.
When talking about her role, Jennings says being able to work in a team is one of the most important aspects. “With lots of different crews and people working at Downer, being able to communicate efficiently with everyone around me to achieve a common goal is essential,” she says.
“My goals for the next number of years are to remain working within the construction industry.
“I see Downer as a long term career with plenty of opportunities for personal and career growth. I aim to keep learning and progressing in my current role by improving my leadership and communication skills and gaining more valuable experience.”
Jennings says her advice for someone looking for a career in the construction industry is to be open minded and willing to learn from those around you – “I still learn new things every single day.”
In 1995, the National Association of Women in Construction (NAWIC) was formed. Over the 27-year history, NAWIC has become a peak body championing the diverse collective of women in construction.
Our vision is to create an equitable construction industry where women fully participate and our core policy is to achieve 25% female participation in the construction industry, by 2025 (#25by2025). We know that real change happens at 30%. We know we are sitting at 13% and we know that striving for 25% seems like a huge task. We all need to do our part in achieving this goal. We all need to strive to achieve more equality, inclusion and diversity in the construction industry.
growing network with NAWIC organisations spanning across the world in places including America, England, New Zealand and South Africa.
Words Lauren Fahey, General Manager, The National Association of Women in ConstructionThe National Association of Women in Construction (NAWIC) provides a forum for its members to meet and exchange information, ideas and solutions. Our members have an opportunity to expand personal and business networks, maintain awareness of industry developments, improve skills and knowledge, and contribute to other women in the construction industry. We are also part of a
We proudly represent over 7,000 individual members and over 150 corporate members and we welcome women (and men) in construction from all walks of life, cultures, ages and career stages. We truly value the support of our members, sponsors, dedicated volunteers, and our wonderful staff, and are inspired by the amazing achievements women are making in this industry. “You can be what you can see!” is our mantra; sharing and celebrating the achievements of women in the industry to inspire a new generation.
After launching our member survey earlier this year, we know that 73% of our members experienced gender adversity during their career. This data confirms what we knew
anecdotally and makes immediate action even more of an imperative. It is time for changemakers.
By removing the entrenched cultural barriers through changemaking programs such as our Male Allies, it will improve the perception of the industry, attracting more young females to construction.
As Australia’s 3rd largest industry for employees and GDP contribution, it is our job to continue supporting women. A lift in female recruitment and fixing the leaky pipeline will result in a significant leap for women. We must also ensure more is being done to achieve pay parity.
Whilst there are issues the industry faces, there are also many positives. We know that 80% of our members believe the role of women in construction is changing for the better and 80% feel respected and valued as much as their colleagues. We can see businesses are focusing on inclusion and diversity and I am confident that we will build a better industry together.
“We know that 80% of our members believe the role of women in construction is changing for the better and 80% feel respected and valued as much as their colleagues.”General Manager, The National Association of Women in Construction.
The 2022 Jobs and Skills Summit put a spotlight on the need for change in construction to secure a brighter future for the industry. Australian Constructors Association CEO, Jon Davies, proudly represented the sector at this year’s Summit, sharing a simple but important message.
Walking into the marble foyer of Parliament House on 1 September 2022 was memorable to say the least. With great excitement and some nerves, I was there to represent the construction industry at the highly anticipated 2022 Jobs and Skills Summit. For our industry, this was the opportunity to put construction on the nation’s radar and to emphasise the need for change. My message was simple – ‘change will only happen if government, industry and unions leave behind the baggage of history’.
Speaking under the banner of creating safer, fairer and more productive workplaces, I had the privilege of outlining the importance of our industry to the Australian economy but, as I said in my speech, ours is an industry that could and should be so much better.
As Australia’s third largest industry, employing 1 in 10 of the working population, construction offers some of the most exciting and rewarding careers. But this very industry runs on wafer thin margins and accounts for 25 per cent of all insolvencies in Australia. It operates in deeply embedded ways and has been notoriously slow in adopting digital technologies – according to global consulting firm McKinsey just hunting and fishing have a worse track record.
commitment, a positive step forward was the announcement of a tripartite National Construction Industry Forum. The forum will comprise representatives from government, unions and business, including the Australian Constructors Association.
This is an exciting opportunity for the industry, and we need to grasp it with both hands. This is our opportunity to work together to transform, as other sectors have, so we can emerge as a worldwide leader and industry of choice for future generations of workers. With a focus on improving the sustainability of the industry, the group’s priorities are likely to include addressing the cultural issues that are preventing women from joining the workforce, addressing the industry’s poor mental health, developing industry capability and capacity and improving productivity.
A happy workforce is a productive workforce and improvements in culture will go a long way in easing the capacity constraints facing today’s constrained labour market. The construction industry needs a further 105,000 workers right now, which is over half of the annual government’s target skilled migration intake.
By Jon Davies, CEO, Australian Constructors Association.While in the last decade great progress has been made to improve the physical safety of the industry’s workers, the same focus needs to be applied to addressing other issues that have, by comparison, been neglected. Of critical importance is the need to improve the culture of the industry. Women make up only 12 per cent of our workforce and that percentage dwindles to single digits for trades. Disputes are common, stress is an issue and workers are six times more likely to die from suicide than a workplace incident. The problems are not new. They have been around for decades, and they are slowly killing our industry.
It was clear at the Summit that everyone wants to see change – government, industry and unions – and for the first time I could see a genuine commitment from all to be better partners to each other. Reflecting this
Australia is also facing worldwide competition for workers – particularly in the construction sector. The strategy of investing big in infrastructure in response to Covid is a worldwide trend and, unlike previous booms, getting people on planes has become a lot harder. The lure of our golden beaches and warm sunny weather is not enough to counter migrant concerns over high cost of living, bushfires, floods and Covid lockdowns, not to mention the opportunity to work on once in a lifetime projects like the Saudi Arabian Giga Project Neom. It is fair to say the shine has come off Australia.
Onto the topic of training, who are we going to train? We are technically at full employment. Yes, increased investment in training is necessary; however, in today’s high employment environment it will just upskill from lower skilled industries to higher skilled ones. Whilst this is still a laudable aim, it will not address the skills shortages we are facing. The answer must be finding ways to improve
productivity – doing more with less. If we could just halve the gap in productivity growth between construction and other major industries, we could be saving $15 billion annually and, importantly, significantly reduce the number of resources needed to deliver the record pipeline of work.
Government holds the key Government holds the key to unlock productivity gains. The Federal Government can leverage the money it grants to the states, to drive improved outcomes. Our idea for the Summit was a new ratings initiative we call the Future Australian Infrastructure Rating – FAIR. FAIR provides a mechanism for the Federal Government to ensure reforms are implemented. Essentially, FAIR would rate government funded projects on how well they performed against key reform areas such as improved productivity and increased female participation. Federally funded projects undertaken by state government delivery agencies would be given a rating that would
be published, leading them to strive for better outcomes for their stakeholders.
The FAIR initiative could be included in the next iteration of the National Partnership Agreement as a requirement for all federally funded projects. If implemented, FAIR will help governments address the industry’s skills shortage and unlock productivity gains, and in the process strengthen the industry.
The Summit was a positive step forward. It secured a commitment to work collaboratively together and led to the formation of the new National Construction Industry Forum. But to move from incremental improvements to the transformation that is required our industry needs a disciplined client, a responsible client, a model client who will help us to move in the right direction. That client is government and that is exactly why the Australian Constructors Association has proposed FAIR. It is time to commit to a FAIR way forward for construction.
A happy workforce is a productive workforce and improvements in culture will go a long way in easing the capacity constraints.L-R: The Hon Tony Burke MP, Minister for Employment and Workplace Relations; Jamila Rizvi, Deputy Managing Director, Future Women; Oanh Tran, Principal Solicitor, Young Workers Centre; Paul Zahra, CEO, Australian Retailers Association; Joanne Schofield, National President, United Workers Union; and Jon Davies, CEO, Australian Constructors Association.
of Australia’s market leaders in the field of precast concrete within the building sector. In 1999 Advanced Precast expanded its base of operations into NSW, ACT and then in 2005 into the QLD market. We now service Melbourne, Sydney, Canberra, Brisbane, Gold Coast and the surrounding areas.
Can you briefly describe your company’s current workforce and technical capabilities?
Joining the National Precast Concrete Association Australia (National Precast) in 2015, Advanced Precast has seen consistent growth over its almost 40 years in business. This month, Advanced Precast’s Operations Manager Brett Foster gave Inside Construction insight into the company’s success.
Precast concrete is an important contributor to Design for Manufacturing and Assembly (DFMA) methodology, offering ever important productivity benefits to construction. As an effort to showcase the important work being undertaken by the precast concrete industry around Australia, Inside Construction interviewed Brett Foster, Operations Manager, Advanced Precast.
How long have you been a precaster and how did the journey begin for your company?
Brett: Advanced Precast was established in Melbourne in 1985. Since those early years, the company has grown to become one
Brett: Advanced Precast currently employs 160 people across all three states comprising construction workers, engineers, detailers and administrative staff. Our in-house engineering, detailing, manufacturing, and construction expertise has enabled the company to promote and lead by example in the delivery of innovative and cost-effective precast solutions for building structures.
What has been your biggest or most interesting precast project to date?
Brett: With almost 40 years in the game our list of interesting and exciting projects is a very long one. To name a few of the standouts amongst this list:
• L akeside Stadium, Albert Park VIC (Besix Watpac)
• Epica Apartments, Chatswood NSW (Mirvac)
• Coburg Station VIC (John Holland)
• Swinburne University – Advanced Technologies Centre, Hawthorn VIC (Kane Constructions)
• T he Arthouse, South Brisbane QLD (Mirvac)
How long have you been a National Precast Concrete Association Australia member and why?
Brett: We joined 7 years ago. We saw the advantages of being around a network of likeminded people. It was apparent that other organisations like ours were also experiencing similar issues or challenges; and that it is an opportunity to work through some of the industry wide issues. The education aspect is extremely rewarding, very relevant and current.
What do you like most about the precast industry?
Brett: Everything that precast stands for and all the numerous advantages that precast offers – to name but a few:
• Speed of construction which in turn leads to major cost savings: Approximately 1 – 2 days and more per floor saving which in turn results in reduced overall construction times.
• Faster return on investment (including any interest outlaid) due to early settlements.
• Manufacture is carried out in controlled conditions without weather and other factors that affect other disciplines.
• L abour efficiencies and optimal workmanship.
• Site labour, amenities and builder prelims are all massively reduced, and the flow on possibilities from this is endless.
We are a combination of the construction team and the documentation team.
Everything we build is built on paper first. Potential issues are sorted out up front and collaboration is optimised ahead of time where the pressure of instantaneous decision making is significantly reduced or eliminated completely.
Where do you see the precast industry heading in the next few years?
Brett: With skilled labour shortages at an alltime high level, the reduction of on-site labour that precast offers is hugely advantageous.
This issue is only increasing as skilled migration levels are low. ‘The great resignation’ continues to play havoc in the industry across the board.
Technological advances in the factory are moving exponentially versus the on-site construction advances. With a widening gap comes greater supply demands for alternatives and hence a pickup in the use of precast.
The Technology Age will enhance the opportunities for automated factories and factory machinery more than in past eras. There is also a need for a rethink and rationalisation on some of the standards that are currently impeding the whole concrete industry, as well as shortages/excessive lead times in certain materials.
until 31 December 2023. December 2023.
The decision was made on 24 May 2022 with support from the following:
• State Regulators - Victorian Registration and Qualifications Authority; and Training Accreditation Council Western Australia.
• A rtibus Innovation in their role as the Skills Service Organisation.
• Construction Industry Reference Committee.
• Feedback from RTOs delivering the qualifications.
This allows the Formwork industry to continue to employ apprentices and access relevant funding to assist with wage bills. It also enables the industry to access training and demonstrate education and learning targets now required for most government projects to secure projects and work.
Furthermore, it enables the FIA to continue to campaign for improved safety within the industry. The FIA provides access to Australian wide standardised and consistent formwork safety training, to enable workers to return safely home to their families at the end of the working day.
This extension is granted to all ASQA registered training organisations (RTOs) delivering the CPC31511 - Certificate III in Formwork/Falsework until 31 December 2023.
The Training Accreditation Council, and Victorian Registration and Qualifications Authority, will consider extending the transition period for the same training product for TAC or VRQA registered RTOs,
qualification as the significance of changes would not provide the expected learning outcomes for existing learners.
The decision extends the transition period for ASQA registered RTOs to continue training assessment and issue Australian Qualifications Framework (AQF) certification.
CPC31511 - Certificate III in Formwork/ Falsework will remain on relevant ASQA registered RTOs scope of registration until the end of the extended transition period, unless withdrawn from scope prior.
The FIA is currently piloting a new Safe Formworker program and negotiating a new education pathway with governments, which includes a new Certificate III in Formwork with a focus on infrastructure and a pathway for accessible learning with accredited and unaccredited training, as well as ‘recognition of prior learning’ (RPL) for mature and existing workers.
This will ensure Australian Formworkers are ready for learning, have a clear education pathway to learn at their own pace through micro-credential learning and provide access for apprenticeships to address the labour and skills shortage. Above all it will ensure improved safety, quality and productivity of Australian Formwork.
Don’t miss out - for more information and to keep up to date on the training developments, head to the FIA website and become an FIA member: formworkassociation.com.au/join-us