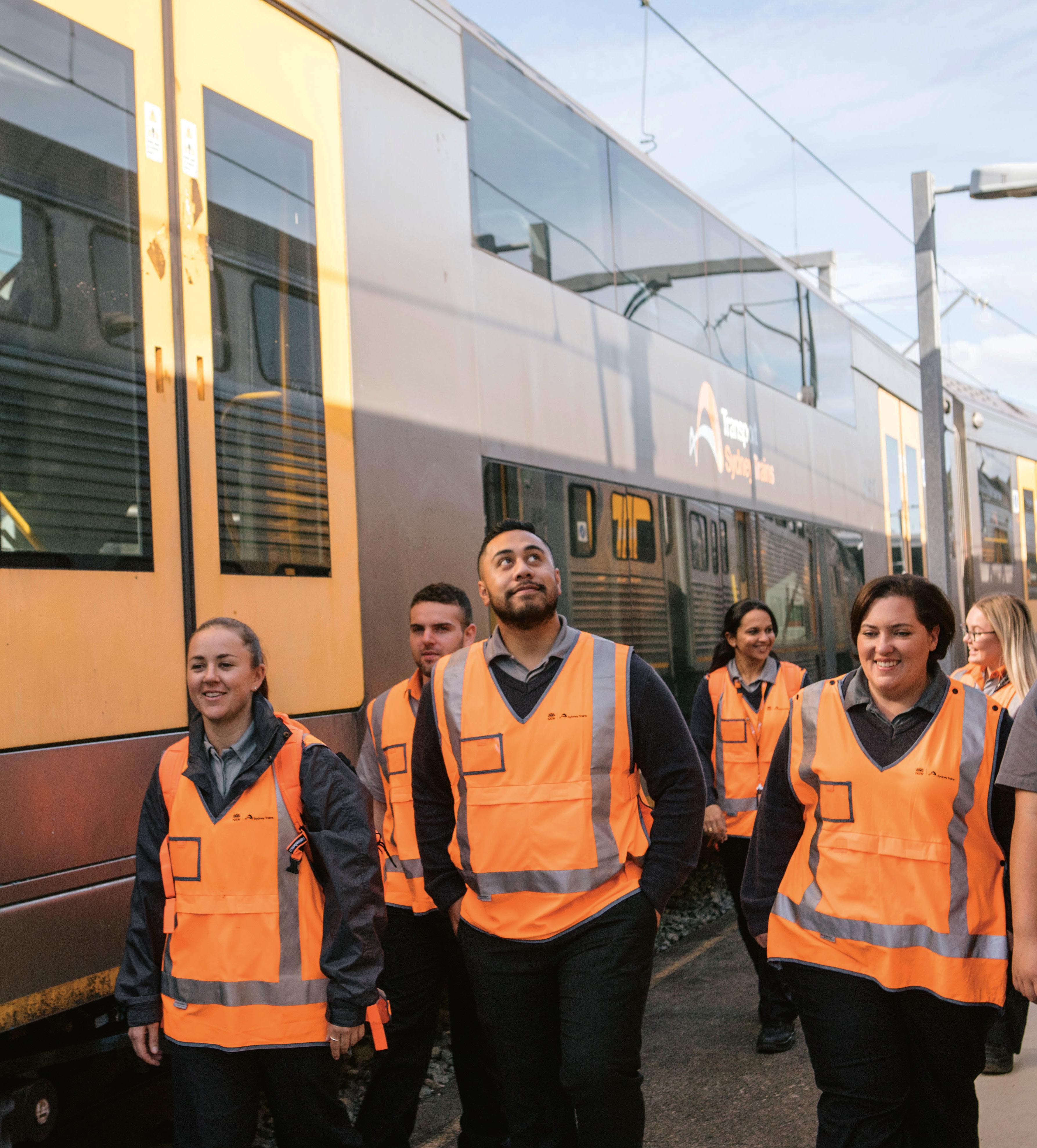
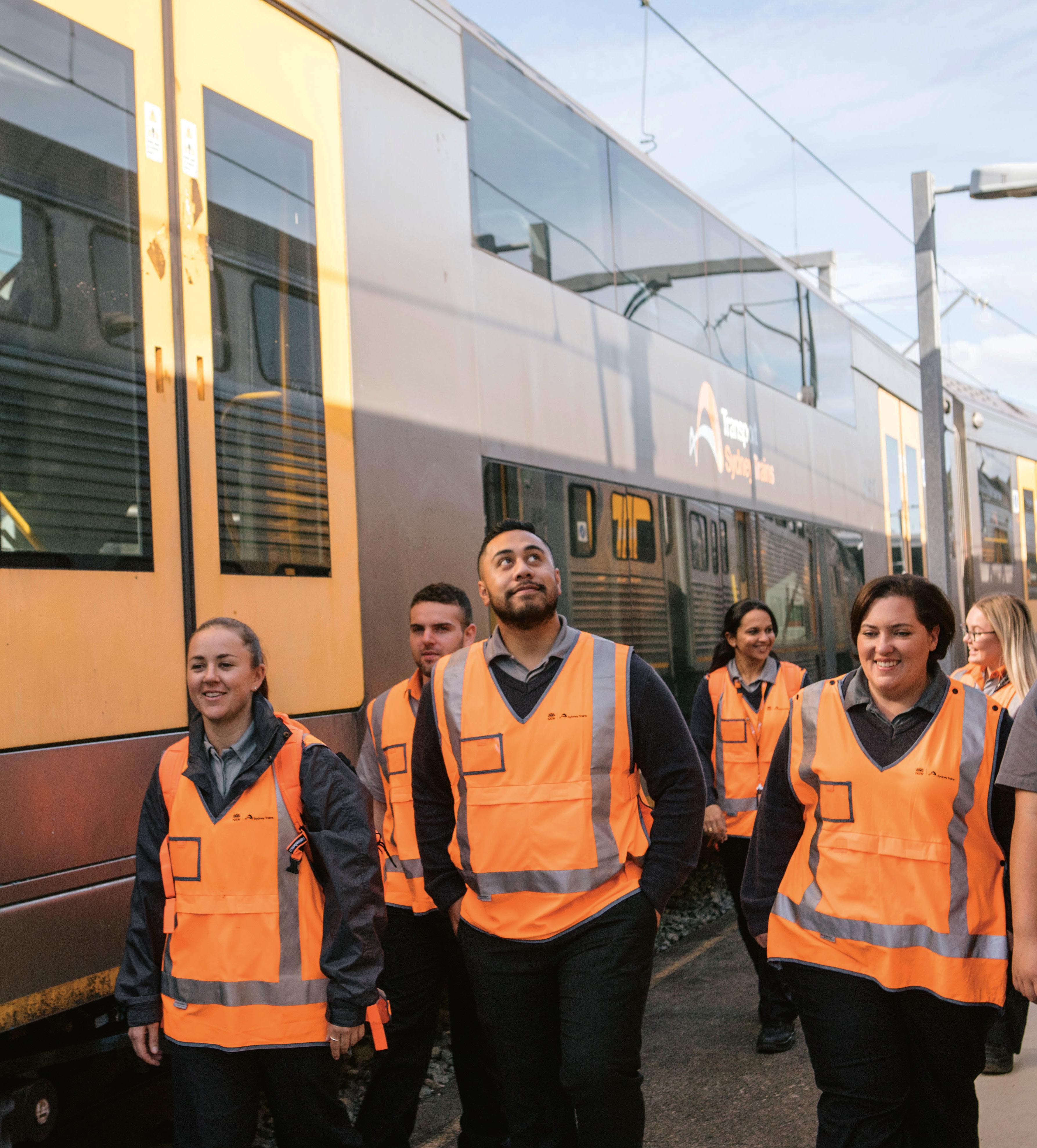
WORKFORCE FOR THE FUTURE
Fosroc’s
range

• Gun grade sealants – suitable for use in vertical and horizontal joints, including potable water storage
• Fire rated, fuel resistant, chemical resistant and biodegradation resistant sealants
• Pouring grade sealants – designed exclusively for horizontal joints in floors and pavements
Future Proof.

Published by
Monkey Media Enterprises
ABN: 36 426 734 954
C/- The Commons, 36–38 Gipps St, Collingwood VIC 3066
P: (03) 9988 4950 monkeymedia.com.au info@monkeymedia.com.au infrastructuremagazine.com.au news@infrastructuremagazine.com.au
Managing Editor
Jessica Dickers
Journalists
Stephanie Nestor, Tess Macallan, Tayla Oates
National Media and Events Executives
Rima Munafo, Brett Thompson
Design Manager
Alejandro Molano
Senior Designer
Luke Martin
Designers
Danielle Harris, Ozlem Munur
Marketing Manager
Radhika Sud
Marketing Associates
James Holgate, Jackson Barnes
Digital Marketing Assistants
Natalie Ta, Rhys Dawes, Isabella Predika
Publisher
Chris Bland
GM Growth and Strategy
Laura Harvey
ISSN: 2206-7906
Cover image Copyright: State of New South Wales (Transport for NSW).
EDITOR’S WELCOME
As Adam Copp, the Acting CEO of Infrastructure Australia, says in his article in this edition, Australia’s infrastructure market is currently at a critical juncture, with a variety of challenges combining to create a perfect storm.
The sector has a massive major project pipeline underway and planned for the future, but is struggling to meet this demand due to skilled worker shortages, increased material costs and supply chain delays, and the critical need for productivity reform across the board. This is also while dealing with the impacts of climate change and ensuring our infrastructure is built with sustainability in mind.
As always, we’ve tried to tackle these challenges in this edition, including an in-depth look at attracting and retaining workers. There is, however, some great progress happening in this space.
In Melbourne, we have the Victorian Tunnelling Centre helping to train new tunnel workers by using two replica tunnels that can simulate different conditions that occur on real tunnelling projects. Meanwhile in the rail sector, the National Transport Commission (NTC) has established the National Rail Skills Hub to address skill shortages and provide a platform for collaboration to create a more skilled and mobile workforce.
These initiatives, and others, are starting to make an impact on the way we’re dealing with training and skills demand. These will help meet demand for some of the major projects underway, some of which we’ve
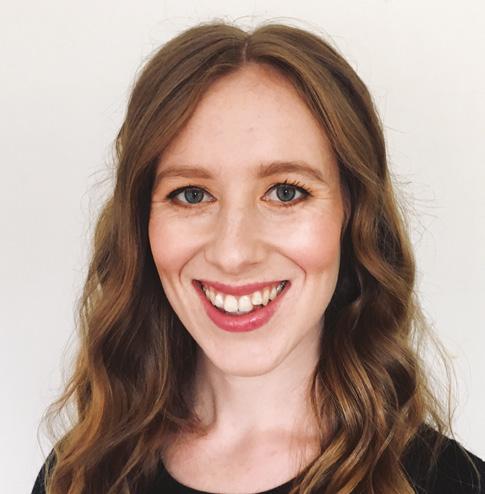
highlighted in this issue – including the Suburban Rail Loop and Coffs Harbour Bypass.
Another key aspect that plays a part in all of these conversations is digital transformation, as more and more infrastructure organisations are implementing innovative digital technologies to help increase productivity, and reduce costs. The need for digitally minded workers is also a growing concern.
Our Software, communications and connectivity feature takes a closer look at this conversation, in particular on page 48, where we have global construction business advisor Shivendra Kumar exploring the most important part of any company’s digital transformation – its people.
On a more personal note, we have some exciting changes happening here at Infrastructure. After leading this magazine for the last seven years, this will be my last issue of Infrastructure. I have loved covering this industry over the years and working closely with the sector's best minds so I sincerely thank all of our contributors and our readers for their overwhelming support. I look forward to seeing the exciting direction the team takes the magazine.
Jessica Dickers Managing Editor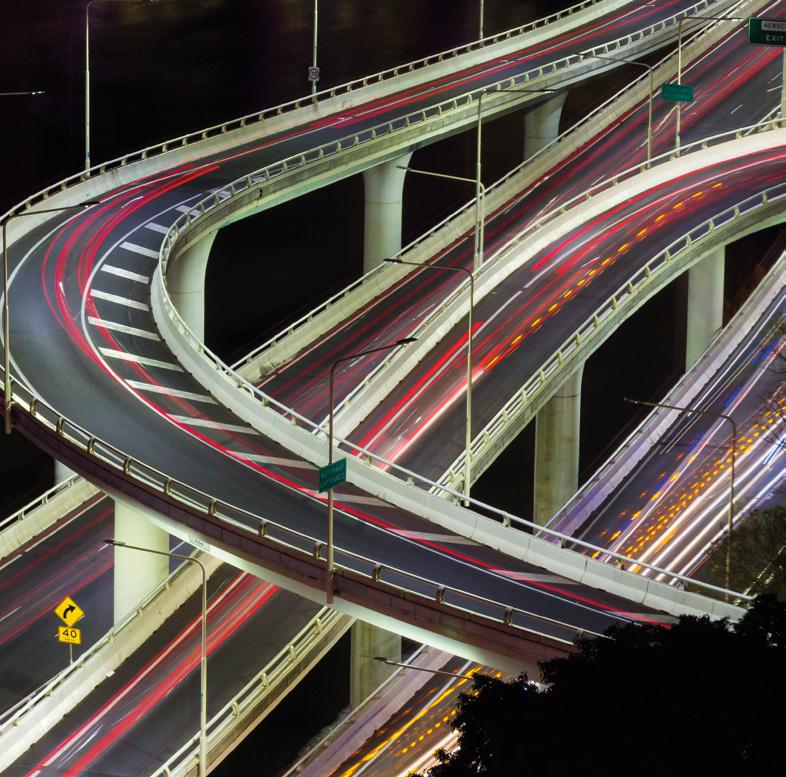
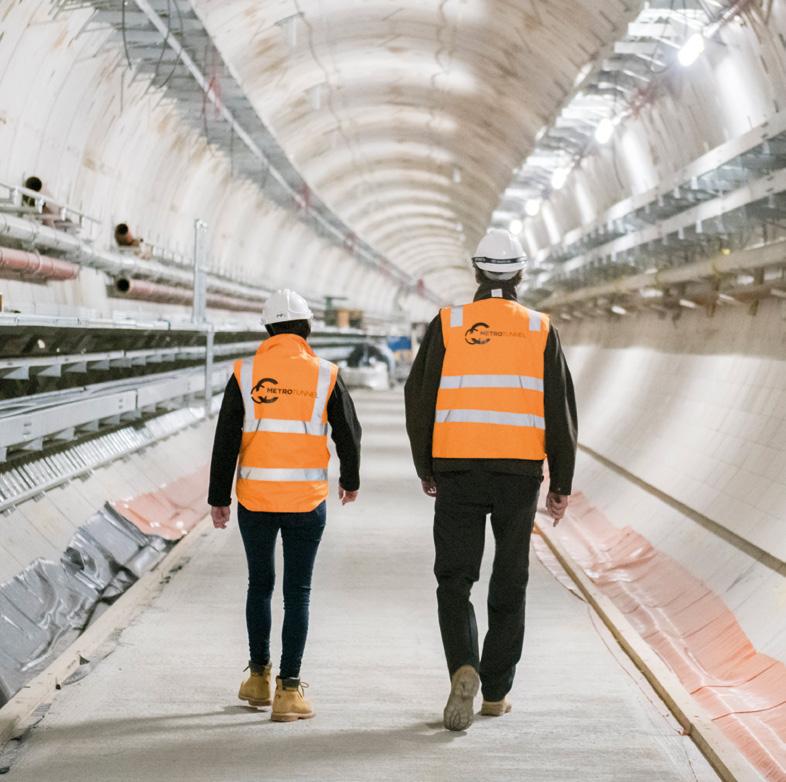
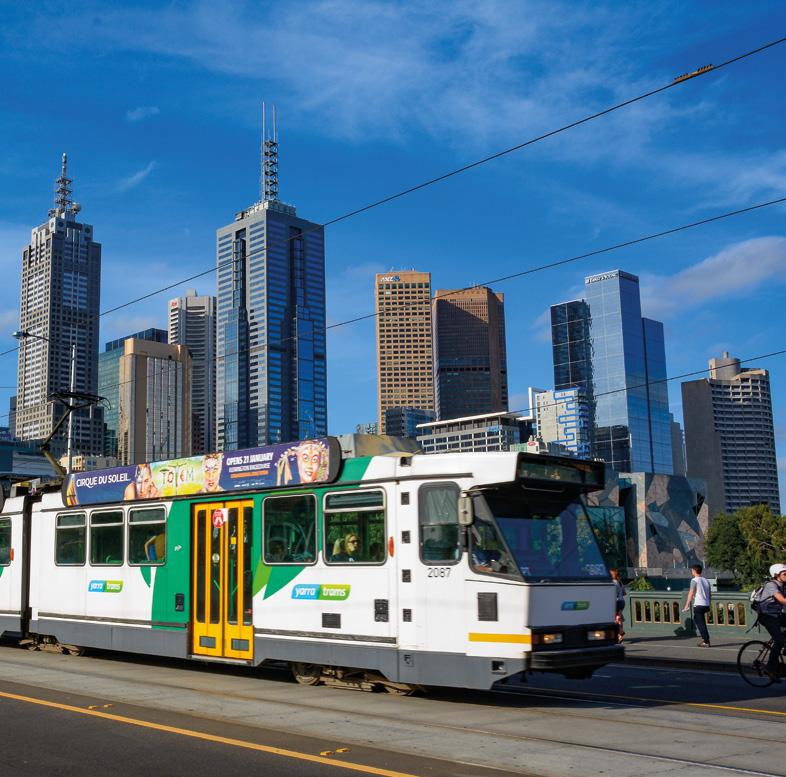
TO WEATHER THE STORM, WE MUST REFORM
AUSTRALIA’S INFRASTRUCTURE MARKET IS AT A CRITICAL JUNCTURE
Unprecedented demand from a massive major project pipeline combined with the lingering symptoms of the COVID-19 pandemic have created a perfect storm that is bringing construction companies to their knees and threatening budget blowouts that will hit the public purse.
EXCELLENCE IN CIVIL CONSTRUCTION
AT 2022 CCF NATIONAL EARTH AWARDS
Freeways, rail bridges, drainage and cycle facilities were just some of the projects recognised at the 2022 Civil Contractors Federation National Earth Awards.
It’s no secret that these are challenging times for many organisations engaged in the delivery of infrastructure across Australia. Over the past year, a multitude of negative pressures – any one of which would in themselves represent a major issue – have combined to produce a storm of such force that parties of all sizes across the industry are feeling the effects.
COFFS HARBOUR BYPASS
DO YOU KEEP REMOTE, TEMPORARY AND UNWIRED SITES SECURE?
KEY ISSUES THAT WILL DEFINE INFRASTRUCTURE IN 2023
Australia’s infrastructure sector is feeling the pinch like never before, as the peak of investment committed during the pandemic begins to bite.
THE RIGHT CABLES FOR TUNNELS AND OVERHEAD
THE MOST IMPORTANT PART OF DIGITAL TRANSFORMATION
Infrastructure companies are undergoing digital transformation programs to create new investment opportunities, more efficient operating models, and greater sustainability. While the technologies implemented are important, the most crucial element of this process is actually understanding the impact on your employees. This is referred to as maintaining the human perspective.
HOW A BETTER UNDERSTANDING OF GROUND CONDITIONS HELPS TACKLE RISK
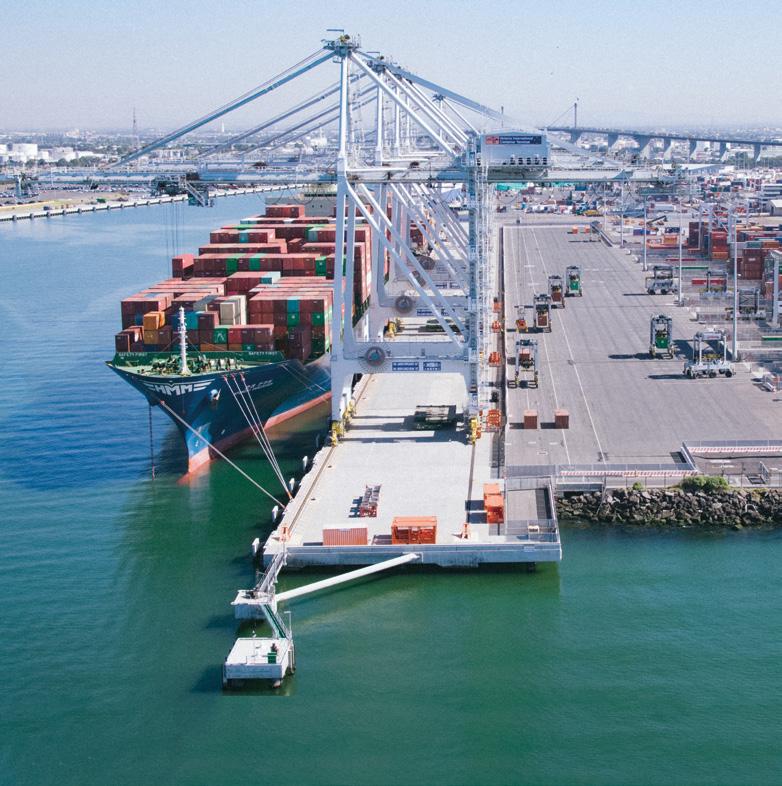
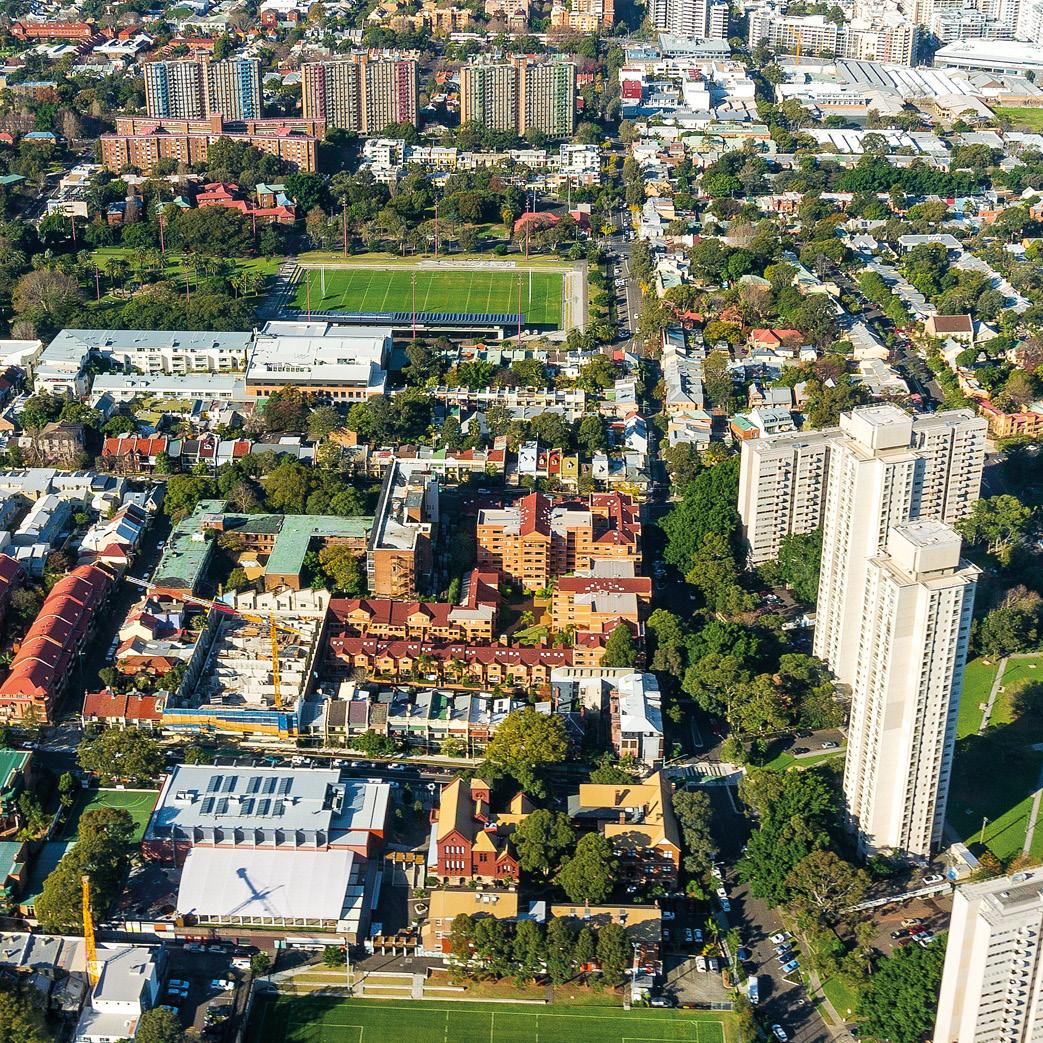

SOFTWARE,
A CASE FOR STRATEGIC ASSET MANAGEMENT: ECOLOGICAL VS TRADITIONAL INFRASTRUCTURE
HOW IOT, CONNECTIVITY AND EDGE COMPUTING CAN SUPERCHARGE REGIONAL AND RURAL AUSTRALIA
EXPANDING NBN CONNECTIVITY TO JUST ABOUT ANYWHERE
SPATIAL & GIS
FROM LANDS, TO SEAS, TO STARS –THE FUTURE OF GEOSPATIAL
Ahead of the Locate23 Conference in May, Infrastructure Magazine spoke with Bradley Slape, Surveyor-General of South Australia, to explore the current applications of geospatial data and technologies in the infrastructure sector, shared challenges and future direction, as well as why he thinks land applications should be prioritised over sea and space.
SIGNALLING, TRACKING AND CONTROL
SYSTEMS
ATTRACTING THE NEXT GENERATION OF RAIL SIGNALLERS
Victoria’s Big Build is on the hunt for the next ‘unicorns’ of the rail industry to take part in fasttracked training to fill vital signalling jobs.
TRAINING AND SKILLS
TRAINING TOMORROW’S TUNNEL WORKERS
GROWING A RAIL WORKFORCE FOR THE FUTURE
Australian rail is experiencing an unprecedented level of investment. To ensure its success the National Rail Skills Hub is helping the industry double its workforce and improve skills portability.
REGULARS
1 EDITOR’S WELCOME
4 CONTRIBUTORS
76 ADVERTISERS’ INDEX 76 FEATURES SCHEDULE
6 FEDERAL GOVERNMENT PASSES NEW HIGH SPEED RAIL AUTHORITY BILL
6 VIC’S BIG BUILD DIRECTOR GENERAL STEPS DOWN
7 ROUND THREE OF REGIONAL AIRPORTS PROGRAM ROLLED OUT
8 SYDNEY METRO ST MARYS STATION CONTRACT AWARDED
8 EXTRA $65 MILLION FOR NSW BYPASS PROJECT
9 WEBUILD COMPLETES ACQUISITION OF CLOUGH
10 $80 MILLION ACCELERATED FUNDING FOR PACIFIC HIGHWAY
10 CONTRACT AWARDED FOR $7 BILLION TRAIN PROGRAM
12 STREAMLINING THE ACCOMMODATION SECTOR
13 $400 MILLION INTERMODAL FREIGHT TERMINAL TO BE BUILT IN MELBOURNE
14 SOPHISTICATED CYBERATTACKS POSE NEW CHALLENGES FOR CRITICAL INFRASTRUCTURE
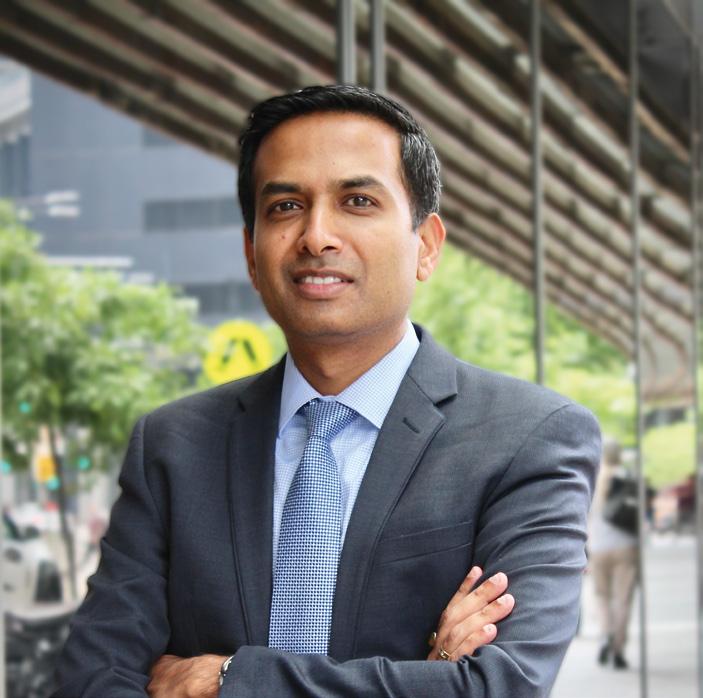
Shivendra Kumar
Principal Consultant,Shivendra and Co
Mr Kumar is a global construction business advisor and owns the consultancy firm, Shivendra & Co, where he helps small to medium construction businesses increase their growth potential and profitability, improve their processes and execute business strategies.
He is using his extensive industry experience from previous roles at large infrastructure organisations, including Siemens and Downer, to transform the construction industry from the ground up and be a voice for Australia’s contractors. Mr Kumar also interviews infrastructure’s biggest names for the The Competitive Contractor podcast.
Romilly Madew Chief Executive Officer, Engineers AustraliaPreviously Ms Madew was CEO Infrastructure Australia (IA), where she was responsible for overseeing IA’s critical role in helping governments prioritise projects and reforms that best serve our communities.
Before joining Infrastructure Australia, Ms Madew was CEO of Green Building Council of Australia for 13 years. In acknowledgment of her contribution to Australia’s sustainable building movement, she was awarded an Order of Australia in 2019.
In her capacity as CEO of Engineers Australia, she sits on the STEM Champions of Change committee. She is also currently a Member of the Australian Academy of Technology & Engineering (ATSE) Infrastructure Forum, and Director Placemaking NSW Board; among many other associations.

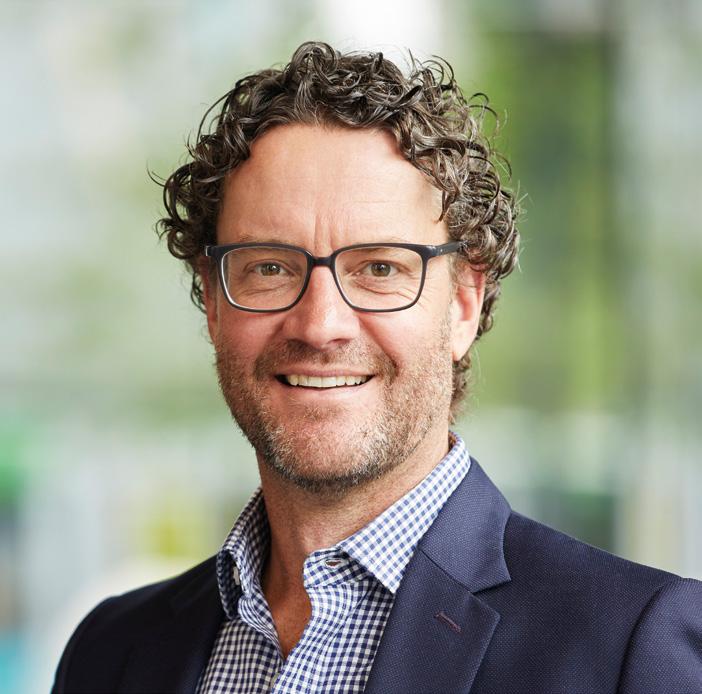
Melbourne
As Chief Executive Officer, Mr Cannon oversees the strategic direction and operations of Port of Melbourne. He brings to the role over 20 years of commercial strategy, finance, legal and corporate governance experience. Mr Cannon comes to Port of Melbourne from global logistics group, Toll Group, where he was Chief Financial Officer and Chief Strategy Officer.
Prior to Toll, Mr Cannon spent nearly a decade at ASX-listed Asciano Limited, which then owned the Patrick ports and Pacific National rail businesses. He holds a Bachelor of Commerce and a Bachelor of Law (with honours) and is also a graduate of the Advanced Management Program (AMP) at Harvard Business School in Boston.
Contributors
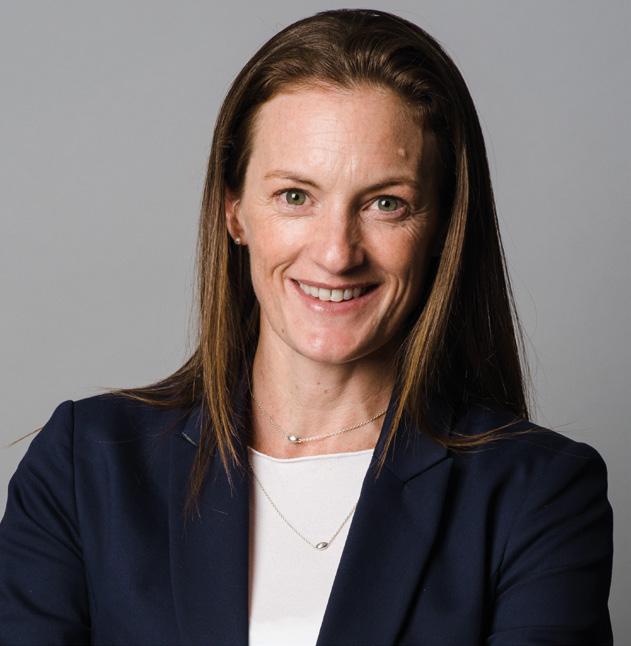
Mandi Mees
Head of National Rail Skills, National Transport Commission (NTC)In her six years at the NTC, Ms Mees has led national reform initiatives to introduce new driver distraction and personal mobility device laws, to improve heavy vehicle policy, and is currently catalysing change in how the nation reports on vehicle fleet emissions. Today, her work is to accelerate access across Australia to skilled labour in rail by leading the development of the National Rail Skills Hub.
Prior to the NTC, Ms Mees led policy advocacy programs with Roads Australia, was the Deputy Mayor of the Macedon Ranges Shire and had an extensive international career in advertising and communications across the pharmaceutical, IT, financial and engineering services sectors.
Adam Copp
Acting CEO, Infrastructure AustraliaMr Copp was appointed Acting Chief Executive of Infrastructure Australia in August 2022. An accomplished and transformational public sector leader, he has over 15 years experience in the Australian Government holding a range of policy, strategy and public affairs roles across infrastructure, workplace relations and the Council of Australian Governments. Prior to his appointment, Mr Copp was Infrastructure Australia’s Chief Operating Officer.
As Chief Operating Officer, Mr Copp was responsible for leading Infrastructure Australia’s Strategy, Finance, People & Culture and Digital Technology functions. He joined Infrastructure Australia in 2014 and set up the public affairs and stakeholder engagement function, before expanding his role across the other operational functions of the business. He is a passionate advocate for Reconciliation and First Nations engagement.
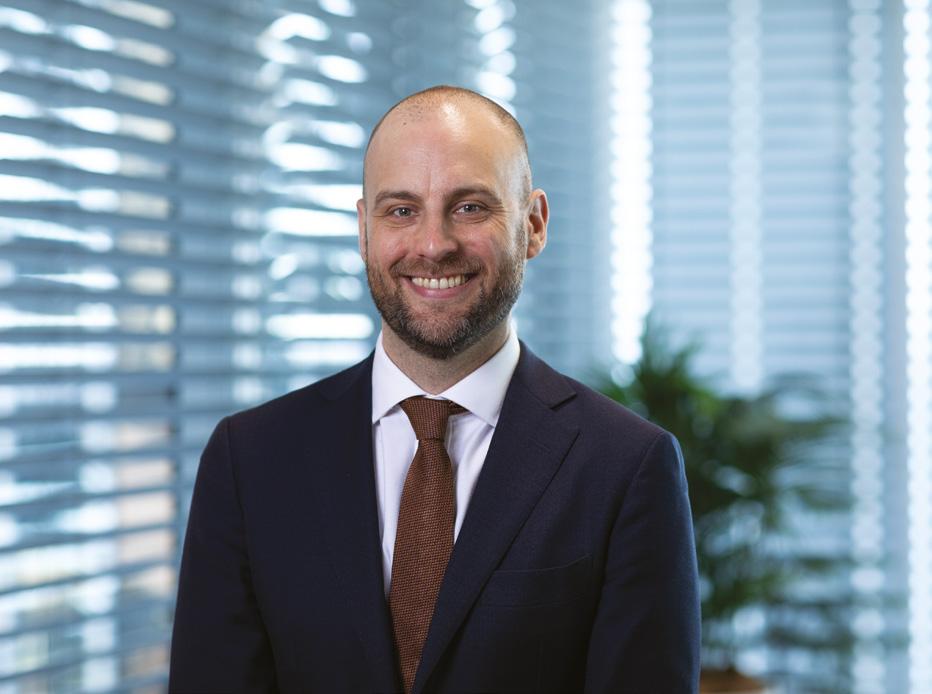
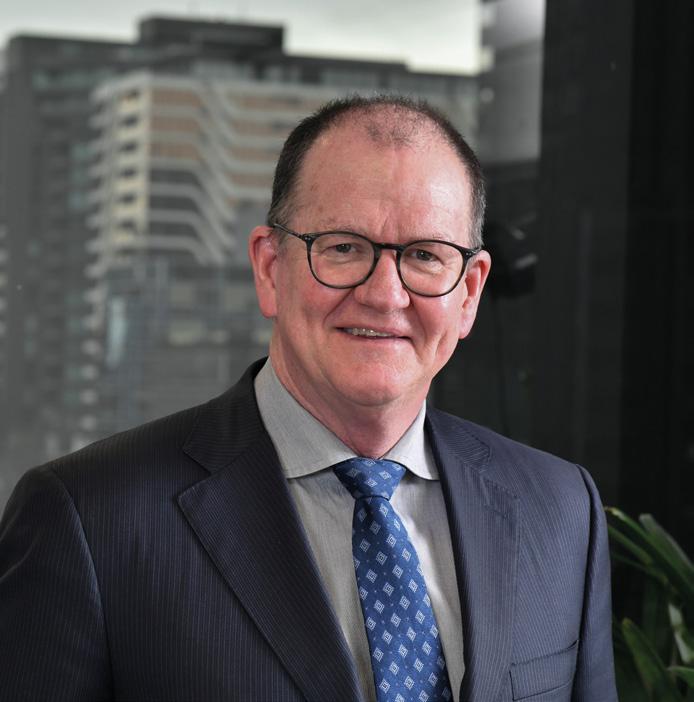
In this and previous industry association roles, Mr Kilgariff has sought to build strong working relationships between industry and government, with the aim of supporting and achieving public policy outcomes that are beneficial to the economy and community.
He brings to Roads Australia a keen understanding of the major economic, social and government policy drivers, combined with a broad understanding of the key issues affecting the transport industry. In 2014, Mr Kilgariff won CEO Magazine’s Transport and Logistics Executive of the Year award. He also completed the Cambridge University Judge Business School Advanced Leadership Programme in 2017.
FEDERAL GOVERNMENT PASSES NEW HIGH SPEED RAIL AUTHORITY BILL
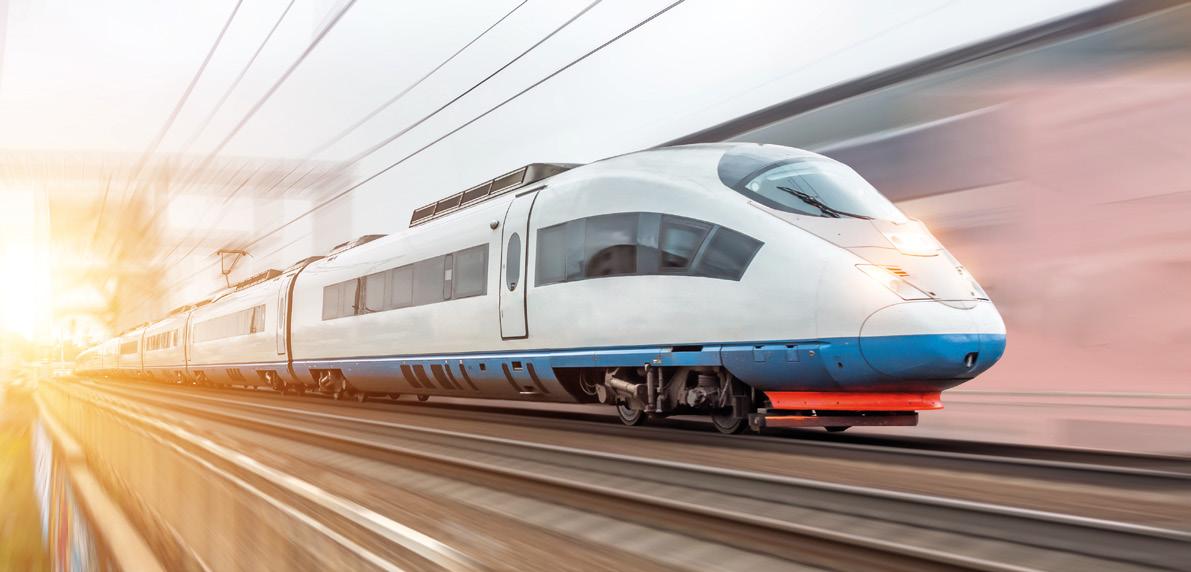
The Federal Parliament has passed the new High Speed Rail Authority Bill 2022, marking the start of the High Speed Rail Authority establishment, as well as supporting and developing a high speed rail network in Australia to connect major cities to significant regional locations.
The Authority will provide independent and impartial advice on the policy and standards of high speed rail; and plan, identify and secure corridors. The Authority will also oversee the construction and operation of the high-speed rail network, and coordinate with state and territory governments, industry, business and communities to enhance Australia’s long-term rail investment.
The Authority will build on previous work, including the comprehensive study commissioned under former Infrastructure Minister and now Prime Minister, Anthony Albanese, that found high-speed rail was not only viable, but would return over $2 for every $1 of investment.
A high-speed rail network could allow passengers to travel between major cities and significant regional cities at speeds exceeding 250km/h.
The passage of the Bill delivers the Federal Government’s election commitment to establish the Authority which will start work on the $500 million down payment for the planning to secure corridors and commence early works for the Sydney to Newcastle section of the high-speed rail network.
While the Authority works closely with the New South Wales Government on this section, it will continue to advance plans for other sections of the high-speed rail network, which will eventually connect Brisbane to Melbourne, with stops in Canberra, Sydney and regional centres.
The Authority will be overseen by a Board which will include experts from the rail and infrastructure sectors. The Authority has begun recruiting board members who will be selected through a merit-based process, including the Chair, to ensure the board is composed of people who have the appropriate skills, qualifications, knowledge and experience to best bring high speed rail to fruition.
VIC’S BIG BUILD DIRECTOR GENERAL STEPS DOWN

CSince the election of the Victorian Labor Government in 2014, Mr Hannett has overseen an unprecedented construction blitz across the state.
Mr Hannett has led the Big Build as it grew from the removal of 50 level crossings to now 110 by 2030, the construction of the Metro Tunnel, and a $100 billion pipeline of transport projects across Victoria, employing more than 50,000 workers.
Victorian Premier, Daniel Andrews, said Mr Hannett has led the historic Big Build program of works that has transformed the state and created tens of thousands of jobs.
“Corey’s passion for the sustainability of the construction sector, and the safety of workers on the ground, have been hallmarks of his leadership and I thank him and wish him, and his family well for the future,” Mr Andrews said.
Mr Hannett will be replaced by the current CEO of the Level Crossing Removal Project, Kevin Devlin.
Mr Devlin has worked alongside Mr Hannett on the delivery of Victoria’s Big Build and is uniquely placed to ensure the ongoing success of the program.
Mr Devlin will start as Director General following Mr Hannett’s departure in late March 2023, allowing time for a seamless transition and the opportunity to move quickly to fill his role at the Level Crossing Removal project.
ROUND THREE OF REGIONAL AIRPORTS PROGRAM ROLLED OUT
The Federal Government’s Regional Airports Program will see 44 airports across regional Australia be made safer and more accessible, with the airports sharing in $27.9 million of funding under round three of the Regional Airports Program.
Some of the airports that received funding in the third round of grants include:
NEW SOUTH WALES
♦ The Kempsey Shire Council – $5,000,000 for the resurfacing of runway, Pilot Activated Lighting (PAL) upgrade and all-weather ambulance shelter at Kempsey Airport
♦ The City of Broken Hill – $4,998,048 for upgrades to aircraft pavement movement areas at Broken Hill Airport
VICTORIA
♦ The Campaspe Shire Council – $2,350,000 to resurface and upgrade the airstrip, extend the main runway, reseal taxiway and aprons, improve drainage, replace PAL to LED threshold lights, install patient transfer station and dedicated aeromedical helipad at the Echuca Aerodrome
♦ The East Gippsland Shire Council – $1,546,379 for the construction of a patient transfer station and dedicated taxiway/apron for medevac aircraft at Bairnsdale Airport
QUEENSLAND
♦ The Central Highlands Regional Council – $1,592,932 for the remediation of runways, graded areas and drainage works at Emerald Airport
♦ The Gladstone Airport – $864,204 for surface sealing treatments to rejuvenate five main aprons and one taxiway
SOUTH AUSTRALIA
♦ The Coorong District Council – $193,125 for the sealing of an unsealed section of primary runway, pavement rehabilitation of secondary runway and taxiways, primary runway lighting replacement and line-marking at the Tintinara Aerodrome
♦ The District Council of Mount Remarkable – $139,819 for the replacement of runway edge and hold point lighting at the Booleroo Centre Aerodrom
WESTERN AUSTRALIA
♦ The City of Busselton – $218,810 for an apron upgrade and sealing to apron and taxi lane area and associated linemarking at Busselton Margaret River Airport
♦ The City of Greater Geraldton – $168,327 for surface restoration and resealing of the runway at Geraldton Airport
TASMANIA
♦ The Burnie Airport – $428,450 for the resurfacing of Taxiway A and additional $417,160 for the application of surface treatment to all aircraft movement areas at Burnie Airport
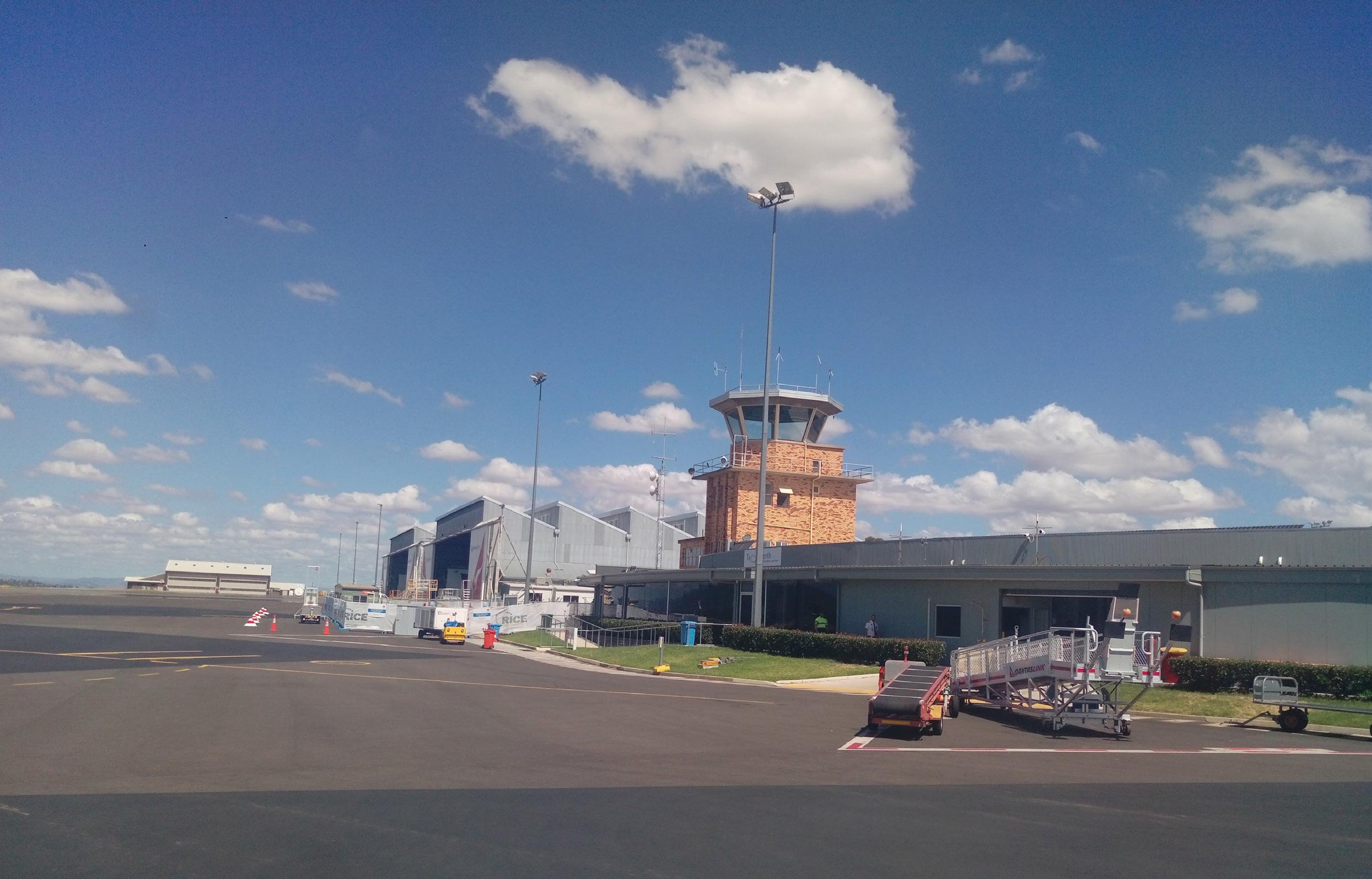
♦ The Airlines of Tasmania – $241,550 to repair and strengthen the runway, taxiway and apron pavements and aircraft hardstand at the Cambridge Aerodrome
For the full list of successful projects, please visit: www. infrastructure.gov.au/infrastructure-transport-vehicles/ aviation/regional-remote-aviation/regional-airports-program

ASYDNEY METRO ST MARYS STATION CONTRACT AWARDED
$82.5 million contract for the St Marys Station transformation project, part of the Sydney Metro –Western Sydney Airport mega-project, has been awarded.
Laing O’Rourke was awarded the contract to build a new footbridge at the station.
The Sydney Metro – Western Sydney Airport project is jointly funded by the Federal and New South Wales Governments at an estimated cost of $10.5 billion, with the Federal Government contributing $5.25 billion. Work on the footbridge is expected to commence in April 2023 and is expected to be completed by the end of 2025.
Federal Minister of Infrastructure, Transport, Regional Development and Local Government, Catherine King, said, “The 55-metre-long concourse will provide customers with fast and easy connections to all areas of the station.
“New metro rail will be the transport spine for the Western Parkland City.”
The fully accessible concourse will enable commuters to seamlessly transfer between new metro platforms and suburban trains on the T1 Western Line.
It will also link to a new pedestrian plaza at the northern end of the footbridge and allow commuters to transfer from the newly expanded multistorey carpark at Harris Street.
EXTRA $65 MILLION FOR NSW BYPASS PROJECT
The Federal Government is working with the New South Wales Government to address critical infrastructure needs of the New South Wales south coast, allocating an additional $65 million for the Nowra Bypass planning project.
The additional funding will bring the total joint commitment with the New South Wales Government to $105 million and will allow for robust planning and preparatory works to occur on this priority project for the people of Shoalhaven.
A bypass is expected to ease traffic congestion, reduce travel times, improve safety for all road users and increase amenity for the community and businesses of Nowra.
Federal Infrastructure, Transport, Regional Development and Local Government Minister, Catherine King, said, “We are committed to working with the New South Wales Government to deliver good infrastructure investment that creates jobs, builds opportunity and unlocks economic growth and productivity.
“By easing traffic congestion and improving safety through Nowra, a bypass will improve the liveability and workability of the region – supporting freight, local businesses and tourism,” Ms King said.
The $105 million Nowra Bypass planning project is being funded by both governments, with the Federal Government committing $97 million and the New South Wales Government committing $8 million.
The addition of a new plaza and entry on the northern side of the existing rail corridor will provide quick and easy access to the existing station and generally improve connectivity in St Marys.
This space will include green areas, kiss and ride, bicycle storage and the opportunity for future development.
The Federal and New South Wales Governments have a shared objective to have the Western Sydney Airport line operational when the airport opens for passenger services in late 2026.
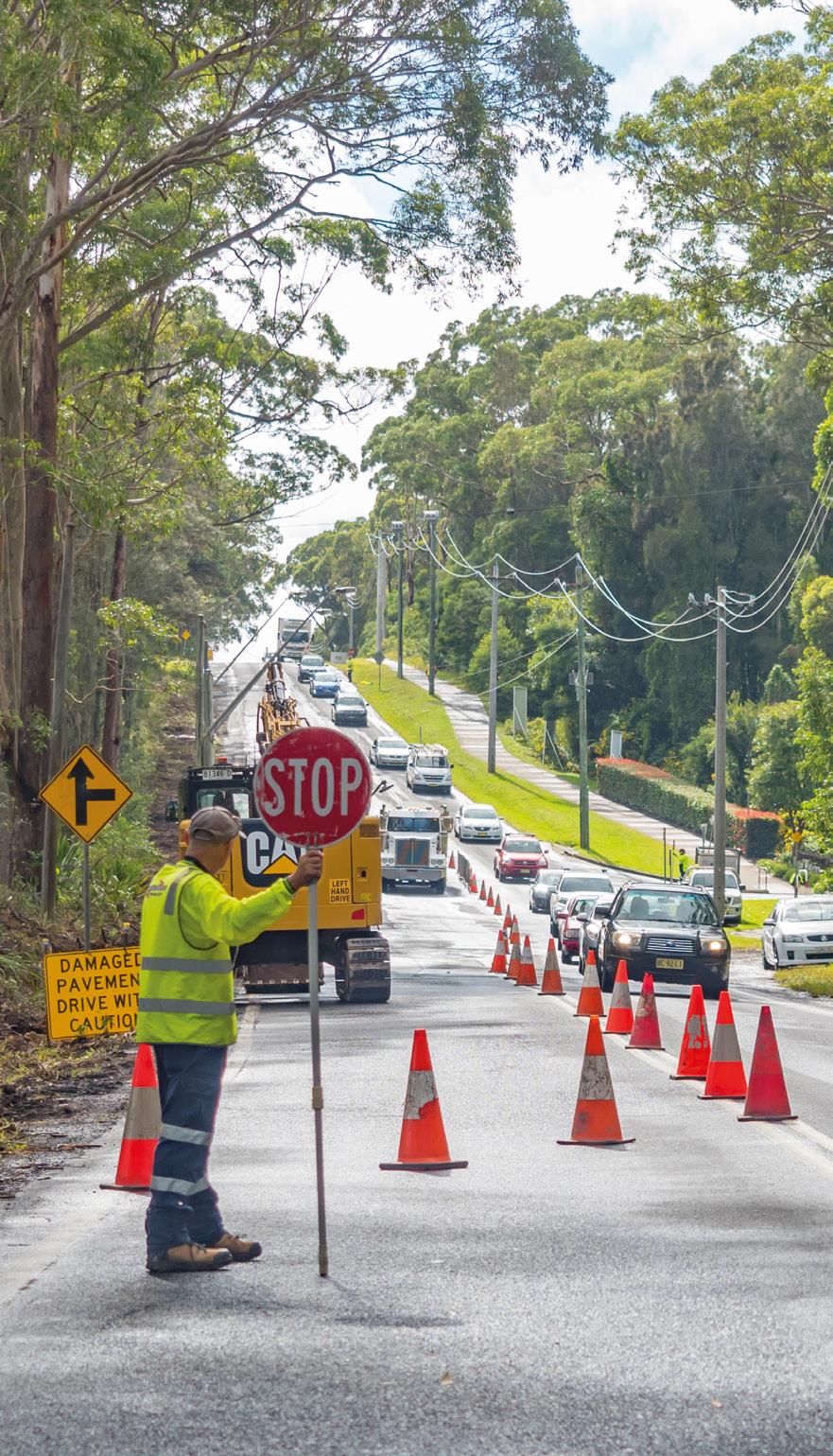
WEBUILD COMPLETES ACQUISITION OF CLOUGH
Following Clough entering voluntary administration at the end of 2022, the acquisition of Clough assets and operations by Webuild has been completed. The approval by creditors ensures the continuity of Clough’s projects in Australia and Papua New Guinea, as well as workforce employment.
The combined group will have more than 3,000 employees in Australia and a total workforce of 83,000 in the 50 countries where it operates.
The acquisition includes Clough’s organisation, including offices, trademarks, credentials, business references, senior management and
office personnel, as well as more than $6 billion worth of projects in backlog.
In early February 2023, Webuild assumed operation and control of Clough’s activities in Australia and Papua New Guinea.
In addition to Clough’s stakes in projects held in common with Webuild – strategic infrastructure projects Snowy 2.0 and Inland Rail – the Group took the stakes, under restructured terms, in the Waitsia gas project, Lombrum naval base, Tallawarra power plant, as well as projects for which Clough is preferred bidder, such as Perdaman’s Ceres urea plant.
Following the acquisition, in Australia alone, Webuild’s order backlog will reach

a combined of $18.5 billion, confirming the Group’s focus on markets with a low-risk profile, including Italy, Europe, Australia, and the US.
The acquisition of Clough assets and operations will safeguard around 1,000 jobs and guarantee the continuity of Clough infrastructure projects that are among the most important being built in Australia and Papua New Guinea.
Among the projects acquired by Webuild is the construction of part of the Sydney Metro-Western Sydney Airport project that will connect the city to the new airport. The Group is working on the North East Link, the missing section of Melbourne’s beltway.
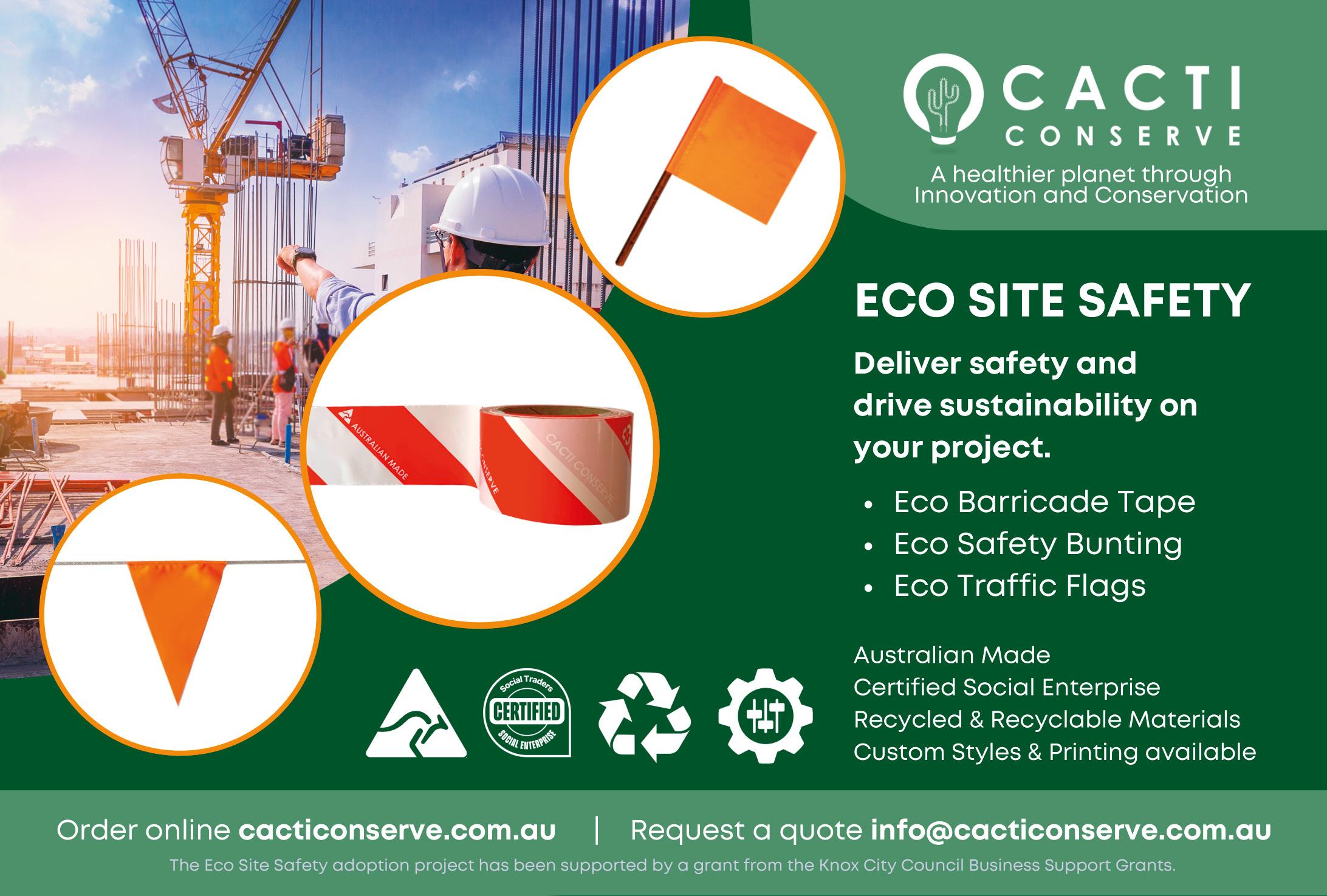
$80 MILLION
ACCELERATED
FUNDING FOR PACIFIC HIGHWAY
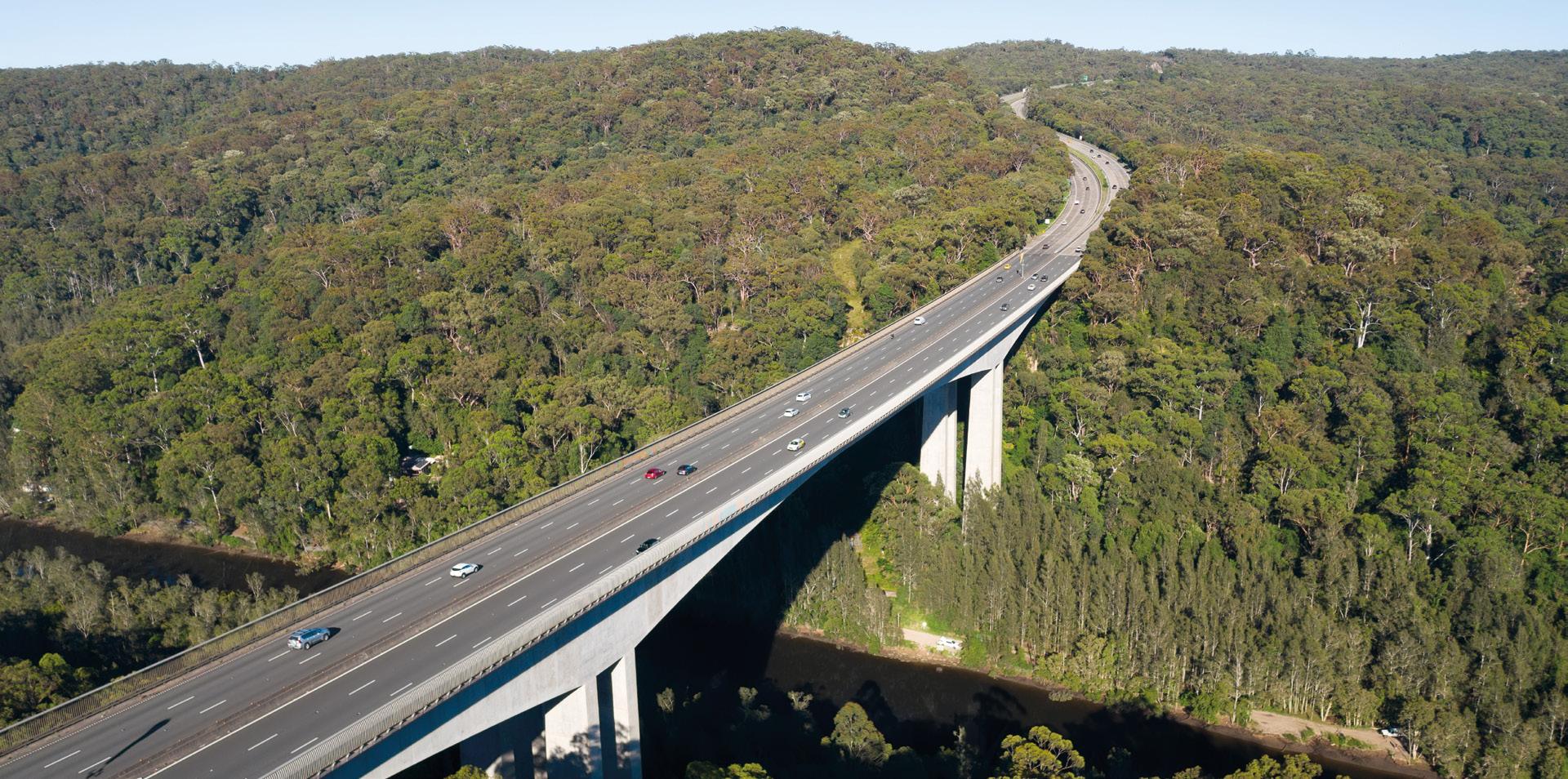
The Pacific Highway – Wyong Town Centre project will receive $80 million fasttracked funding by the Federal Government.
Prime Minister Anthony Albanese, said, “The Pacific Highway is one of Australia’s busiest and most important urban arterial roadways, making investment in its improvement vital.
“With the population of the Central Coast projected to increase by about 75,000 over the next two decades, this announcement ensures we are delivering for the future.”
The Federal Government is contributing $336 million towards the
project, with the New South Wales Government committing $84 million. The contribution will help the New South Wales Government to expedite delivery of this priority project on the Central Coast.
New South Wales Premier, Dominic Perrottet, said, “The New South Wales Government has a clear long-term economic plan backed by a $112 billion infrastructure investment to deliver the roads and infrastructure needed to keep our state moving.
“This includes significantly upgrading what is one of the country’s busiest highways, to help ease congestion through Wyong so that local residents
and visitors can get to where they need to quickly and safely.”
The $420 million project will upgrade the Pacific Highway through Wyong, duplicating the highway between Johnson Road and Cutler Drive.
The existing Wyong River road bridge will also be replaced with two new road bridges, increasing clearance heights for River Road and South Tacoma Road.
The works are currently in the planning phase, with the delivery schedule to be determined as planning and development works progress.
CONTRACT AWARDED FOR $7 BILLION TRAIN PROGRAM
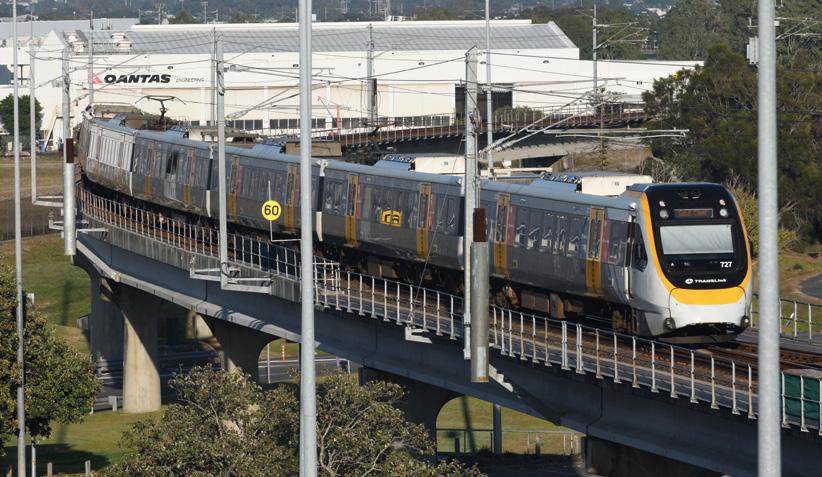
The Queensland Government has awarded the contract to build and deliver 65 next generation trains in the Maryborough region.
The project is part of the Queensland Train Manufacturing Program and is set to create hundreds of jobs for manufacturing workers. The contract has been awarded to Downer.
Queensland Premier, Annastacia Palaszczuk, said the initial plan was to
build 20 new trains in Maryborough but planning indicated a need for another 45 trains.
“That means 800 good, secure jobs here in Maryborough to deliver 65 trains,” Ms Palaszczuk said.
“This will be a game changer that secures the future of manufacturing for Maryborough.
“Downer has a strong track record of delivering here in Australia, and around the world, so Queensland’s future fleet is in good hands.”
Downer was one of three shortlisted applicants – selected after a robust procurement.
The trains will be built at a state owned facility, set to be constructed 25km north of Maryborough at Torbanlea. Construction of this facility will begin later into 2023.
Queensland Transport and Main Roads Minister, Mark Bailey, said the program would also deliver ongoing new rail maintenance jobs at facilities in SouthEast Queensland.
“The proposal put forward by Downer offered strong value for money, leadingedge accessibility and a modern design, whilst delivering maximum benefit to the region and to our great state,” Mr Bailey said.
“What we want is a superior level of service for commuters and tourists alike as we respond to population growth, the Olympic and Paralympic Games and beyond.
“The Palaszczuk Government will now work closely with Downer to undertake detailed design on the trains to ensure they are customer-focused and fully accessible for passengers.”
• Vehicle and Equipment Finance
• Business Acquisition
• Shareholder buyout
• Unique Working Capital Solutions
• Trade and Debtor Finance
• Sole Traders to ASX Listed businesses


“A great sounding board to understand our options”
MV Technology Solutions
“Used their Network to help us grow, a great record of assisting other businesses in rail, transport and infrastructure” DeMaher
“Good at developing simple solutions to complex financing needs. We scoured the market and reviewed many products and options, they worked tirelessly to ensure a solution that met our needs rather than supplying us with an off the shelf facility ”
Sabre Rail Australia
“From the initial acquisition of our business, working with us when our region was affected by floods, the expansion plans and fleet The Finance Consultancy have funded for us have really deepened our relationships with suppliers and subcontractors. They understand our business, work with our accountant and our days of getting donuts from the bank are over.”
Customised Gas Australia


www.thefinanceconsultancy.com.au
Chris Slack: 0415 305 502 theteam@thefc.com.au
STREAMLINING THE ACCOMMODATION SECTOR
Quest, New Zealand’s largest serviced apartment provider, is setting more records for NZ’s accommodation sector and has a clear message for developers: get in touch.
In the next three years, Quest Apartment Hotels NZ plans to open ten new properties. Three of these are set to open in 2023, including Quest Mt Maunganui and Quest Hastings in May, and Quest on Cambridge in Christchurch in July.
Beyond that, plenty of other locations across NZ could house new Quest facilities as Whangarei; New Plymouth; Hamilton CBD & surrounds; Wellington CBD, Kilbirnie and Newtown; Dunedin; Timaru; and Auckland’s Greenlane, Ellerslie, Onehunga, Grafton and the CBD, have all been on Quest’s radar.
The Quest brand represents over $1.2 billion in property value, with 40 facilities in NZ and Fiji. Despite the challenges that came with the pandemic, Quest still managed to open five new properties in Palmerston North, Takapuna, Mt Eden, Queenstown and at 256 Lambton Quay in Wellington.
Quest COO, Adrian Turner, said its model has business solidity and the base to bounce back and operate in turbulent conditions.
“The current sales quarter tracking suggests a high degree of resilience in our model and market. Demand is
already ahead of projected budgets, and we expect it to remain so for the next 12 months at least – predominantly driven by the private sector. We’re proud to be the leading apartment hotel provider in every region where we operate,” Mr Turner said.
EMBRACING TECHNOLOGY AND EVS
Many of the new businesses registering with Quest’s network are SMEs – a market sector that represents a significant portion of their clientele.
“We’ve received bookings from more than 1,700 new companies across our properties since the travel border was removed from around Auckland in mid-April. These companies, along with our established clients, are attracted to the ability for self-catering and eatingout being charged back to their room, so they receive a single bill at checkout,” Mr Turner said.
Staying ahead of the technology curve is also a key client mindset – something the Quest App has managed to successfully do.
“The app has streamlined the booking process for customers, allows them to remotely check-in, unlock their room and even book a Hertz rental car with extremely competitive partner rates,” Mr Turner said.
An increasing number of corporate clients are also converting to EV fleets which is why EV charging facilities are now standard in new Quest developments.
The story of Quest NZ began in 1998 when Stephen Mansfield took on Master Franchisor Rights, and soon after opened Quest Auckland and Quest Wellington for corporate travellers. The first purpose-built Quest was opened in 2002 – Quest Parnell.
Quest is the largest and fastestgrowing apartment hotel operator in Australasia, with over 170 properties located across Australia, NZ, UK and Fiji. Quest Apartment Hotels is the largest provider of serviced apartment-style accommodation in NZ with currently 40 Quest properties. The company prides itself on a local focus and ownership in each of its regions. Quest delivers accommodation and services to meet the needs of the NZ corporate traveller.
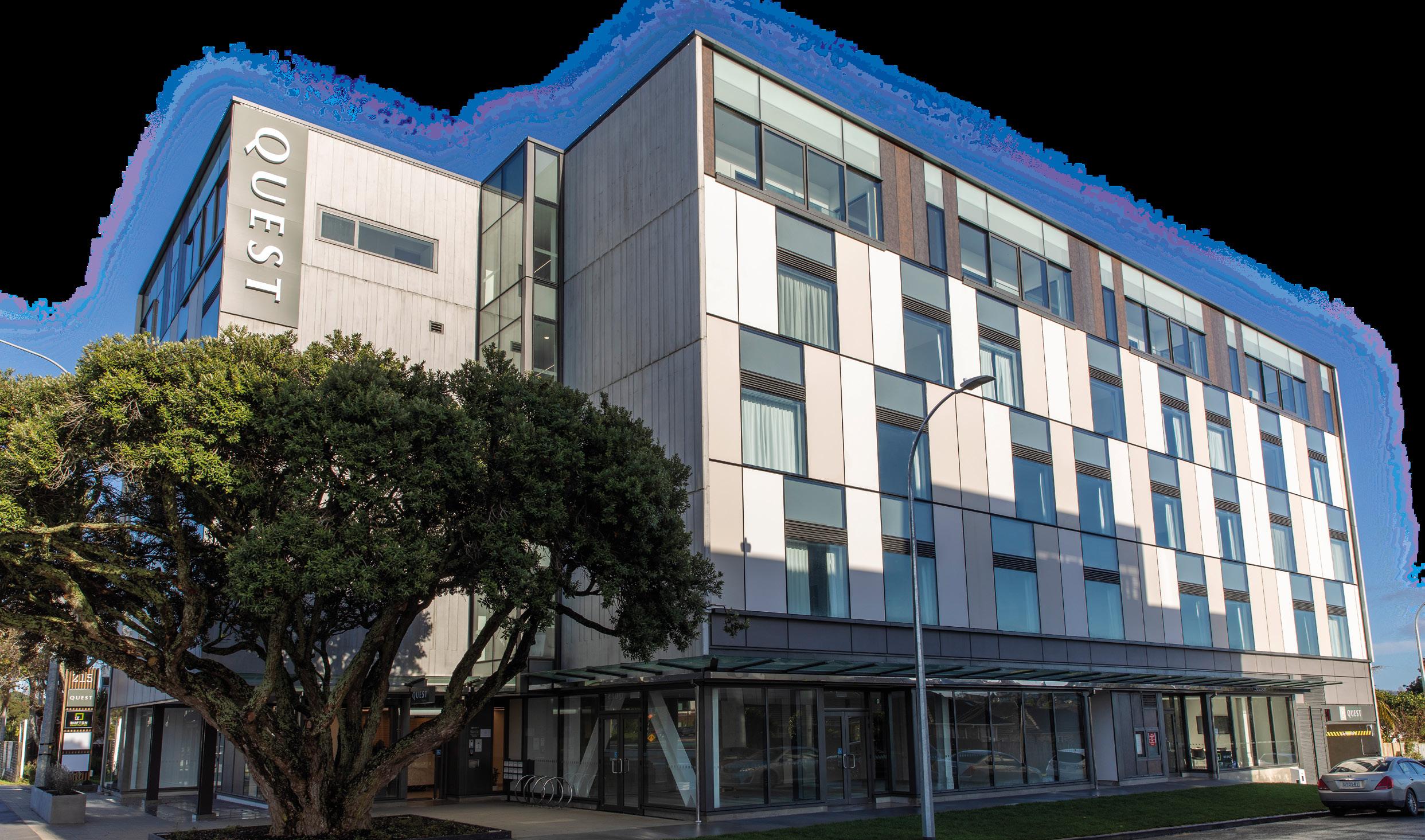
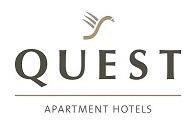
$400 MILLION INTERMODAL FREIGHT TERMINAL TO BE BUILT IN MELBOURNE
A$400 million intermodal freight terminal will be built in Melbourne’s north, following private sector investment from Intermodal Terminal Company (ITC).
Construction will start soon on the Somerton Intermodal Terminal, which will be a key node in the Australian and Victorian Governments’ $58 million Port Rail Shuttle Network.
The terminal will create jobs, remove thousands of truck movements from suburban roads, reduce carbon emissions, and increase efficiency as well as safety for producers, farmers, freight operators and exporters.
Federal Minister for Transport and Infrastructure, Catherine King, said, “The Port Rail Shuttle Network will not only enhance the strategic importance of local freight and logistics operators – it
will also deliver efficiencies and costsavings for businesses.”
When at capacity, ITC expects the Somerton Intermodal Terminal to take 500,000 truck trips off Melbourne’s roads – equivalent to 454 million truck kilometres. Each year, it will also save 451 million litres of fuel and reduce carbon emissions by 189,000 tonnes.
The Federal and Victorian Governments both want to move more freight by rail in the state. By 2050, the Port Rail Shuttle Network is expected to move 30 per cent of Melbourne’s containers by rail from Somerton, Altona and Dandenong South to the Port of Melbourne, avoiding thousands of truck trips on roads each year.
The Port Rail Shuttle Network will enable trucks to deliver or pick up containers from these hubs in outer metropolitan Melbourne instead of driving to the Port of Melbourne, which
is in turn investing $125 million for on-dock rail infrastructure to cater for these shuttle trains.
The Somerton Intermodal Terminal will be built at the Austrak Business Park and is forecast to create 190 jobs during construction and a further 50 permanent jobs for Victorians once the terminal is operational in 2025.
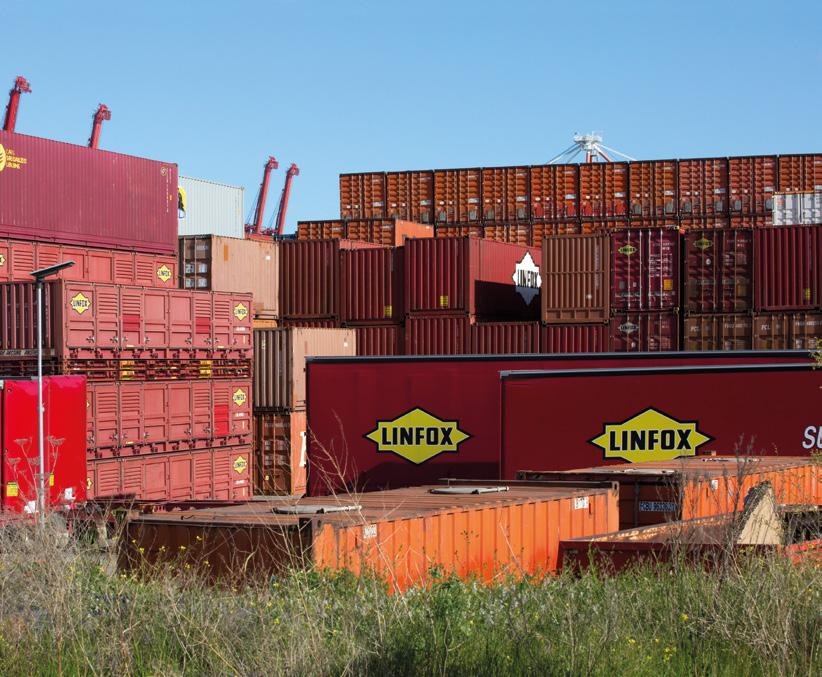
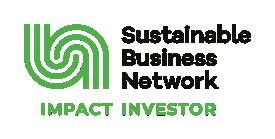
We’re opening more doors for sustainability.
We’re committed to changing our business inside and out, to become more sustainable. As an Impact Investor of the Sustainable Business Network, we’re on a relentless mission to be even better for the environment. With brand-new EV charging stations, solar panels, and refill toiletry dispensers being installed at Quest Apartment Hotels across Aotearoa, our mission is already underway.
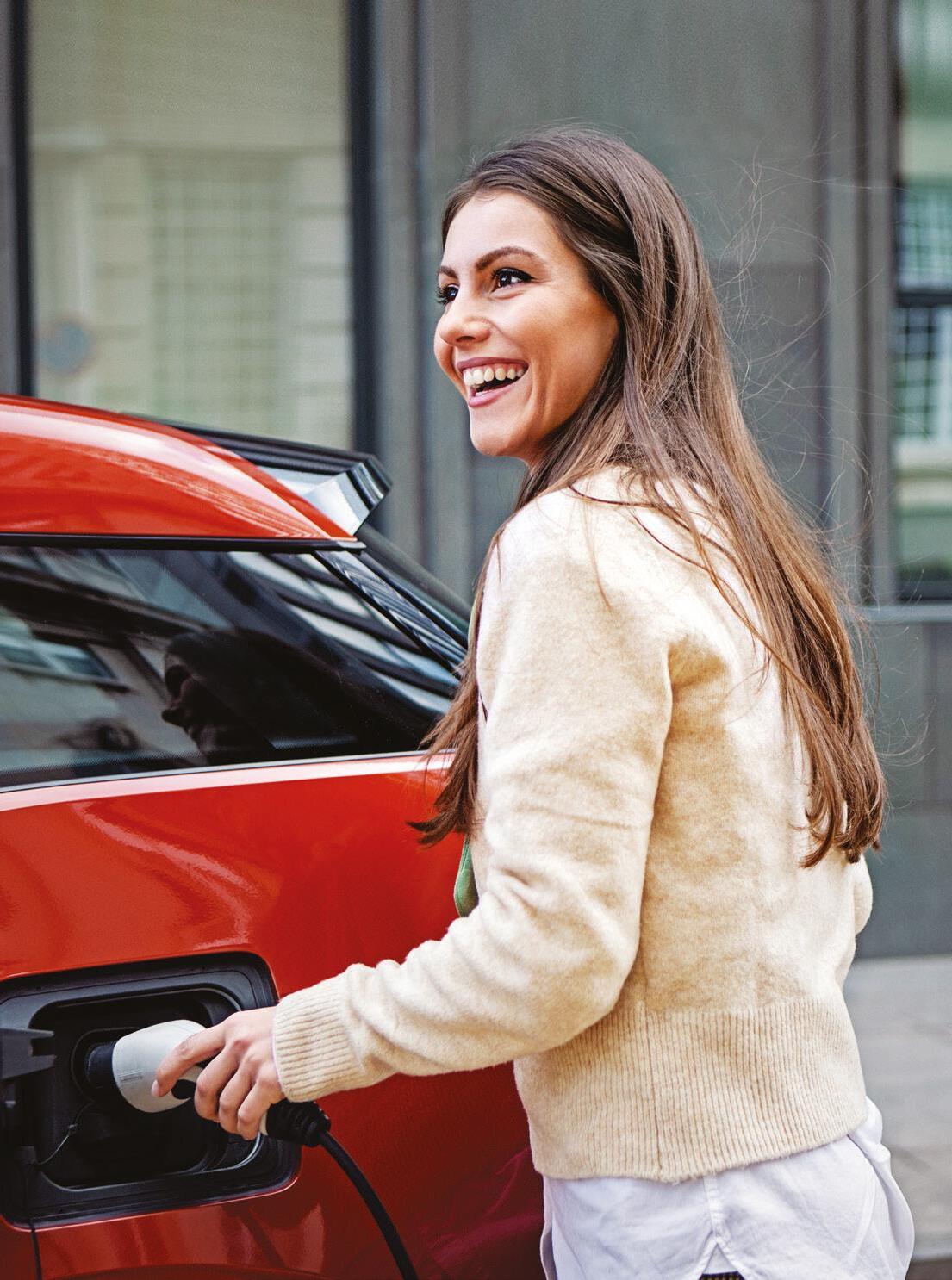
SOPHISTICATED CYBERATTACKS POSE NEW CHALLENGES FOR CRITICAL INFRASTRUCTURE
Cybercrime is on the rise in Australia, and the new Risk Management Protocol signed off by Minister for Home Affairs and Cybersecurity Clare O’Neil in February makes it clear – being prepared to respond to a cyber incident is not enough. Ongoing risk management and operational resilience is now a regulatory expectation, not to mention a business imperative.
According to The Australian Cyber Security Centre (ACSC), cybercrime in Australia has increased by 13 per cent YOY from 2021 to 2022. A number of these attacks, most notably state-sponsored attacks (attacks carried out with the active support of national governments), are also directly targeted at Industrial Control technologies. In April 2022, the Australian Government amended the Security of Critical Infrastructure Act 2018 (SOCI) introducing a new, enhanced cybersecurity obligations framework for Systems of National Significance (SoNS). This amendment, and a number of other considerations, are combining to require the entire industrial sector to review their approach to cybersecurity as the threat levels continue to increase.
THREAT 1 - CYBERCRIME HAS BECOME A MATURE BUSINESS
Cybercrime has reached business maturity, evolving from underground, fragmented communities to mature, self-regulating marketplaces that favor efficiency. Adopting the Software as a Service (Saas) business model, Ransomware as a Service (RaaS) is a
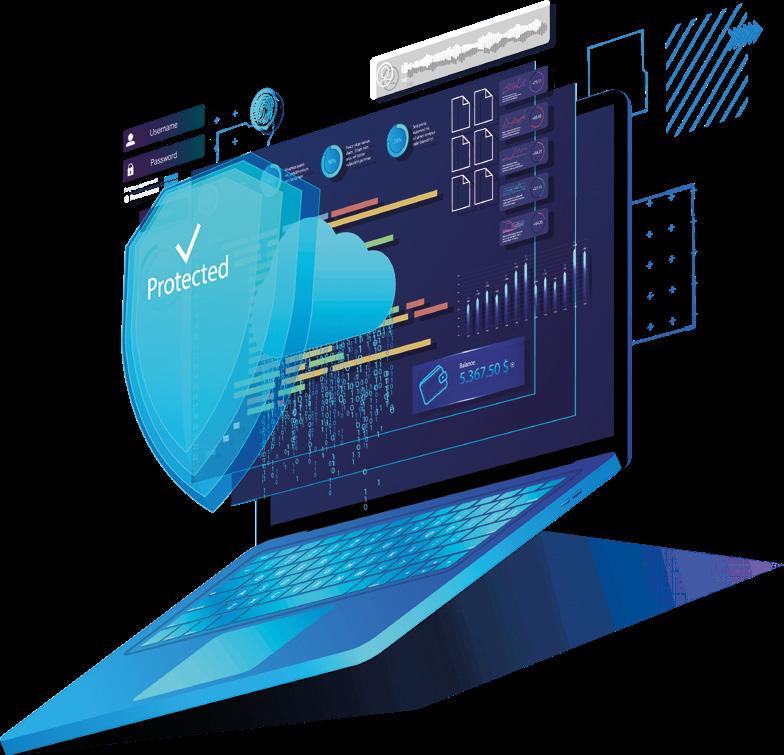
subscription-based model that enables its customers to use already developed ransomware tools to execute attacks.
If successful, the RaaS provider earns a percentage of the ransom payout. RaaS businesses now advertise online, providing their services for any parties willing to pay, and post job openings, looking for employees that can write malicious scripts that can bypass security measures.
THREAT 2 - CYBERATTACKS HAVE GROWN IN SOPHISTICATION
Just as Artificial Intelligence and Machine Learning continues to increase efficiency and productivity for the business world, so too does it provide significant technological evolution for those using it for nefarious means. Artificially intelligent attacks can now sneak into a network, listen in, and explore what sort of AI or Machine Learning you are using for your operations.
Through developing a deeper understanding, these attacks can then tweak your processes, causing your own AI to take actions on malicious information. Smart scripts are also written that don’t activate until they can work to the core of a network.
One ransomware attack against a European OT R&D firm lay dormant for a month before it wrote shell scripts to network servers.
THREAT 3 - IT/OT CONVERGENCE IS CREATING MORE ATTACK SURFACE FOR ATTACKERS TO ENTER THROUGH
The IT/OT convergence is providing many benefits to industrial operators around the world, however connecting operational technology can leave security gaps, and this is creating more paths for attackers to enter, and more opportunities for cyber disruption. Several well-known attacks used
vulnerabilities created by IT/OT convergence, including the Triton malware attack that shut down Saudi Arabia’s Red Sea refinery, which targeted safety systems throughout the refinery and put it at risk of explosion.
Attackers around the world no longer view IT and OT as distinct, partitioned regions, so it is important going forward that IT and OT security are discussed as one.
INCREASE THE SECURITY OF YOUR INDUSTRIAL NETWORKS
To secure network infrastructure, global technology leaders in the IT/ OT space are developing secure and reliable networking solutions. Intrusion detection and prevention systems can identify and mitigate cyberthreats in IT/OT environments by providing real-time network visibility, secure remote access, signature-based security, network segmentation, virtual patching, threat intelligence, deep packet inspection, centralised security management, and containment of malicious activities. These devices meet IEC 62443 cybersecurity requirements and are specifically built for industrial environments.
LEARN MORE ABOUT THIS TOPIC WITH MADISON TECHNOLOGIES
If you need help building, optimising or scaling cybersecurity in your organisation, Madison Technologies recommend booking a discovery session with its technical team, where you can take a deeper dive into the unique challenges of your operations. It will listen to your requirements and recommend a solution that fits your needs. Visit www.madison.tech or phone 1800 72 79 79 for more information.
Industrial technologies for future infrastructure.

Digitally transforming critical operational environments to unlock data insights and business intelligence.
o Intelligent Cameras
o Temperature
o Level
Connectivity.
o Wired
o Wireless
o Mission Critical
o LTE/Mobile
o Analytics Sensors & Edge Devices .
Platforms & Applications .
o On Premise
o In-cloud
o Visualisations
o Location + more
o IoT
Connect and protect people, assets and the environment
With a 30-year legacy of providing resilient industrial technology solutions, our experience connecting and protecting people, assets and the environment means we’re the preferred partner for solving IIoT, industrial networking, cybersecurity, asset management and asset visibility challenges.
Cybersecurity.
o Secure technology for IEC 62443 standards
Find out more.
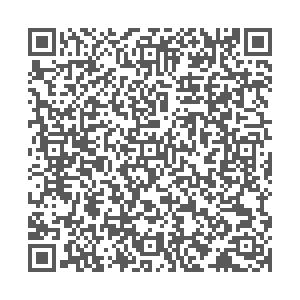
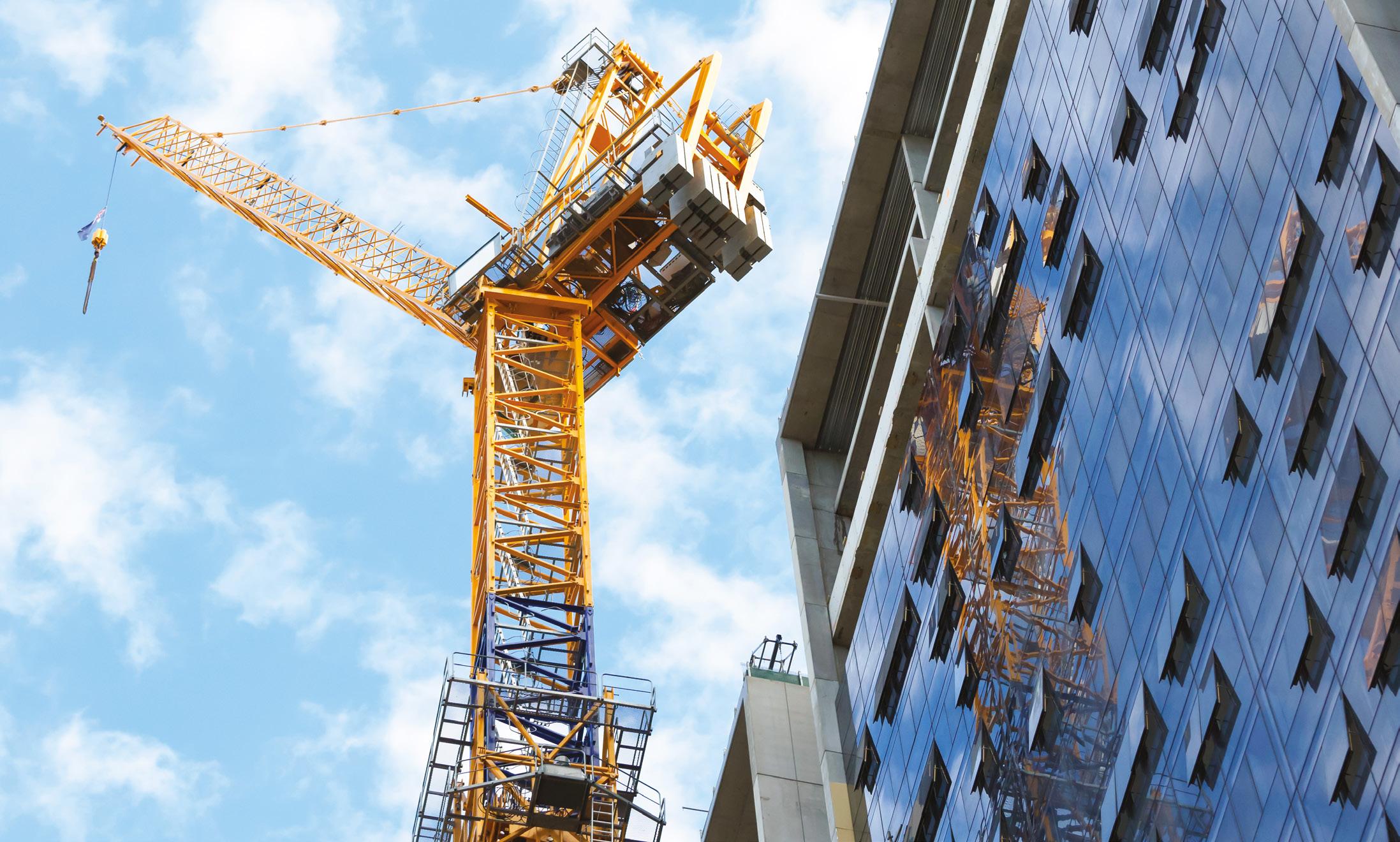
AUSTRALIA’S INFRASTRUCTURE MARKET IS AT A CRITICAL JUNCTURE
By Adam Copp, Acting CEO, Infrastructure Australia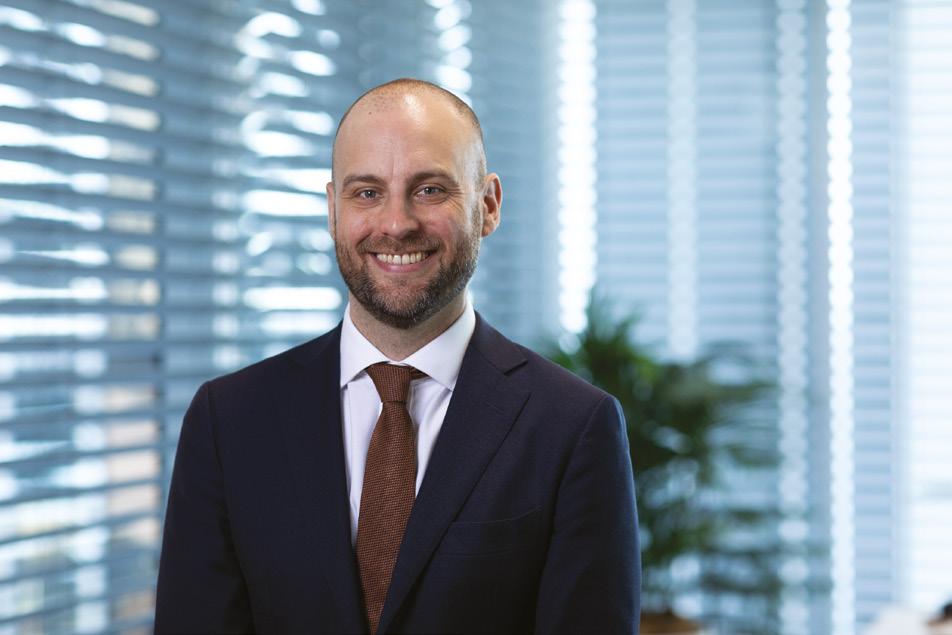
Unprecedented demand from a massive major project pipeline combined with the lingering symptoms of the COVID-19 pandemic have created a perfect storm that is bringing construction companies to their knees and threatening budget blowouts that will hit the public purse.
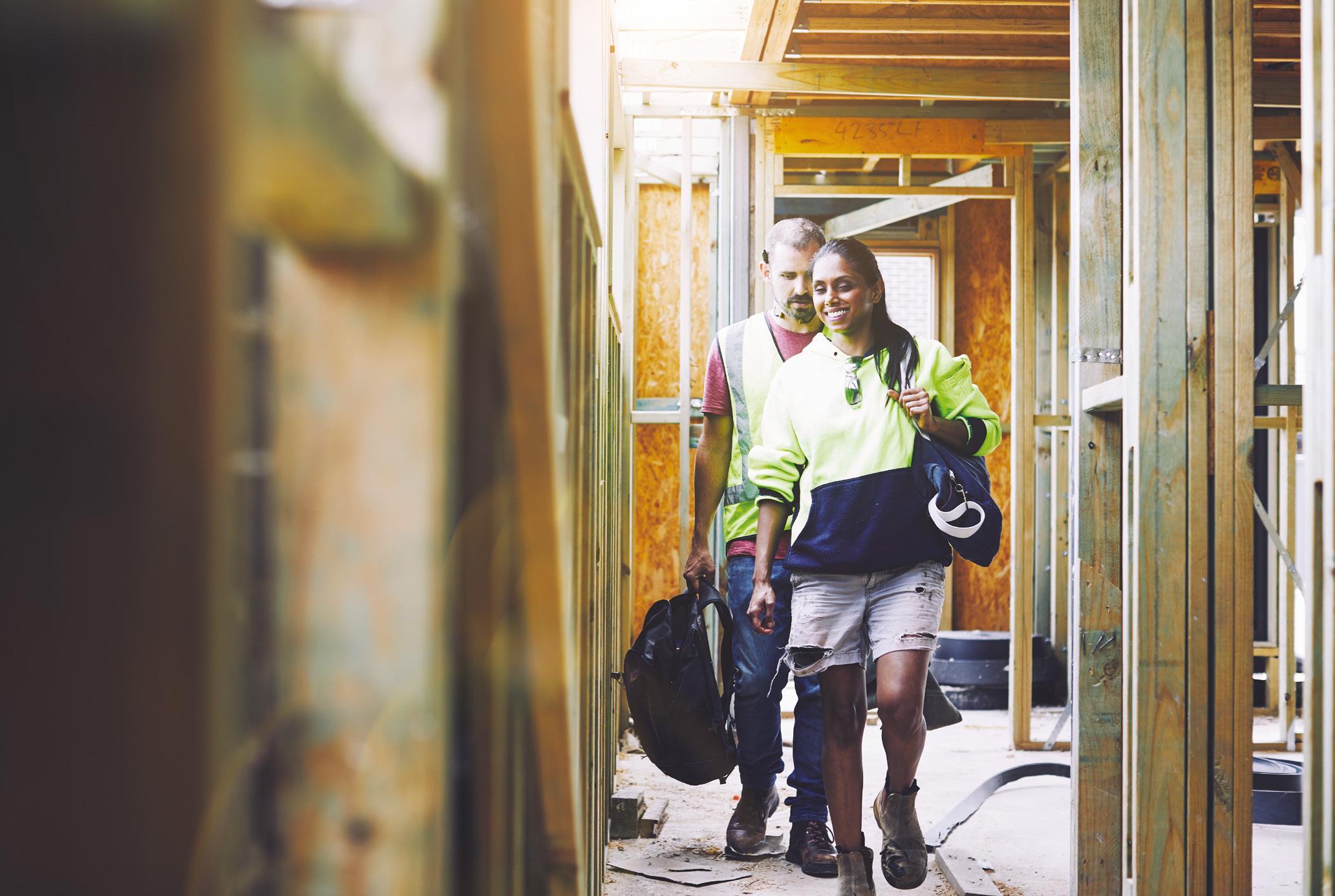
was already struggling with low productivity.
The Prime Minister and First Ministers requested Infrastructure Australia undertake this research at the Council of Australian Government in March 2020. Since then, we’ve been working with state and territory governments and industry across Australia and the globe to investigate the issues and find a pathway forward.
REPRIORITISING THE PIPELINE
The first and most immediate step governments can take to alleviate the pressure is to look at its current pipeline and reassess its priorities based on the current capacity constraints within the market.
We saw the NSW Government take this step last year, reprioritising the Beaches Link as well as other projects to mitigate against delivery risks and we know other jurisdictions are working on this as well.
Of course, these are difficult decisions. Delaying projects means communities need to wait longer for the roads and transport projects promising to make their lives easier. There are political implications too. But something has to give – if governments don’t proactively take control, the market will likely do it for them.
The end result could be budget blowouts and delivery delays that ultimately mean the taxpayer gets less infrastructure for their buck.
ATTRACTING TALENT
When it comes to having the people available to do the work, supply will not even come close to meeting the demand this year based on current projections.
In 2023, labour demand is projected to grow by 42,000 to a peak of 442,000 which is more than double the available supply expected.
Our research shows that labour scarcity is the single biggest issue facing construction companies.
This is an industry ripe for cultural reform.
We know many construction workers are suffering from bullying, unrealistic deadlines and long and inflexible
hours with limited opportunities for career development. The job takes a toll physically and mentally.
Safe Work Australia statistics show that the construction sector had the third highest rate of fatalities across all sectors, with 24 fatalities in 2018.
Australian construction workers are also 70 per cent more likely to take their own lives than employees in other industries. This is unacceptable.
Against this backdrop, it’s no surprise the sector is failing dismally when it comes to diversity and attracting women. Women make up just 12 per cent of the construction workforce, most of which work in clerical or administrative roles – that’s not good enough for a sector that is Australia’s third largest employer.
An industry with a healthier gender diversity balance will help address the current cultural issues facing the sector. We need to do more to attract young women to the industry and we need the industry to make diversity and inclusion a business priority.
The reality is, you can’t be what you can’t see – we need more women in leadership roles across the industry.
Already there is some good work happening in this space, including the work of the Construction Industry Culture Taskforce to develop and implement a new Culture Standard for the industry.
The 2022 Jobs and Skills Summit also delivered action in this space with the Australian Government and states and territories agreeing to a $1 billion one-year National Skills Agreement to provide additional funding for fee-free TAFE in 2023 while a longer-term agreement to drive sector reform and support women’s workforce participation is negotiated.
The Australian Government also committed to strengthening existing reporting standards to require employers with 500 or more employees to commit to measurable targets to improve gender equality in their workplaces.
INNOVATION AND DIGITISATION
Innovation is one of the key tools we have to make change, improving productivity and attracting and retaining men and women to work in the exciting industry that construction is.
A switch to manufacturing and off-site prefabrication is one way we can ease the physical burden for our construction workers and drive a better work/life balance, reducing safety hazards along the way.
More widespread adoption of digital twins which enable the simulation and rehearsal of all aspects of construction can identify hazards, or better ways of doing things, as well as reducing risks, not to mention costs.
Everyone in our sector, from government to the local tradie, is experiencing the impacts of these unprecedented challenges. Let’s take this opportunity now to work together and drive real change to set the industry up for a healthier future.
EXCELLENCE IN CIVIL CONSTRUCTION RECOGNISED AT 2022 CCF NATIONAL EARTH AWARDS
Freeways, rail bridges, drainage and cycle facilities were just some of the projects recognised at the 2022 Civil Contractors Federation National Earth Awards.
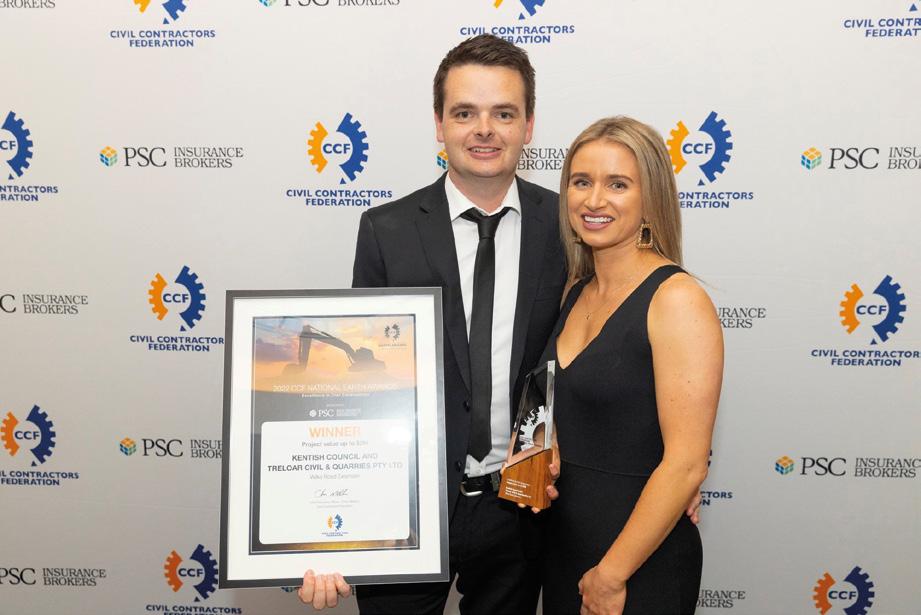


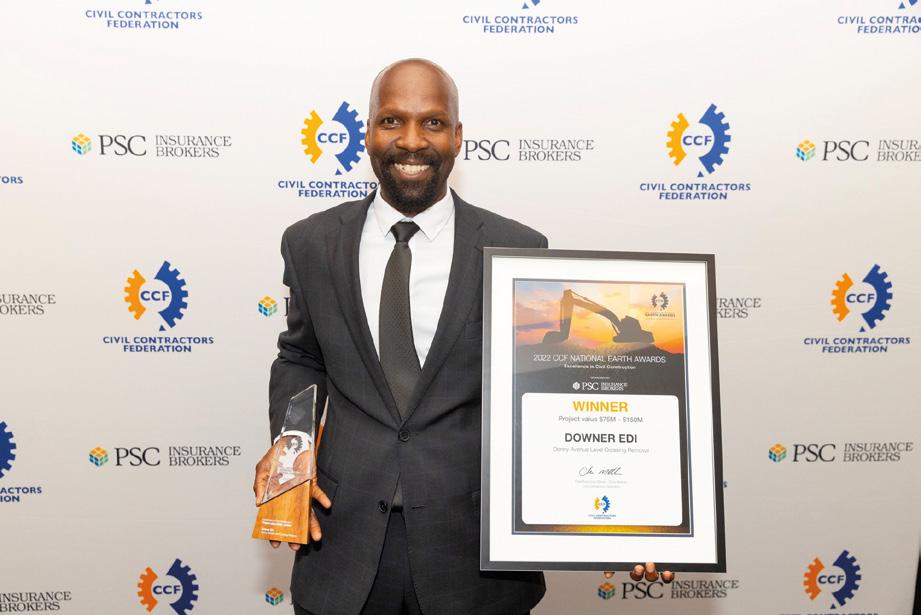
Award winners were announced at a Gala Dinner in Canberra, where 250 people from across the civil construction industry gathered to recognise 47 finalists, all of whom were category winners at the state and territory level.
The CCF National Earth Awards are the most prestigious awards in civil infrastructure, with the annual award ceremony attracting hundreds of entries each year.
Projects nominated for the CCF National Earth Awards are judged against a range of criteria, including the management of project, construction, safety, quality and project stakeholders.
Winning projects also demonstrated how they positively contributed to people development and training outcomes, including how they improved the capability of the industry by identifying and developing future leaders; prioritised cadetships, traineeships and apprenticeships; and maximised opportunities for Indigenous Australians.
Category winners also demonstrated best practice innovation, including how new technologies improved safety outcomes, minimised impact on members of the public and supported the delivery of projects in challenging locations.
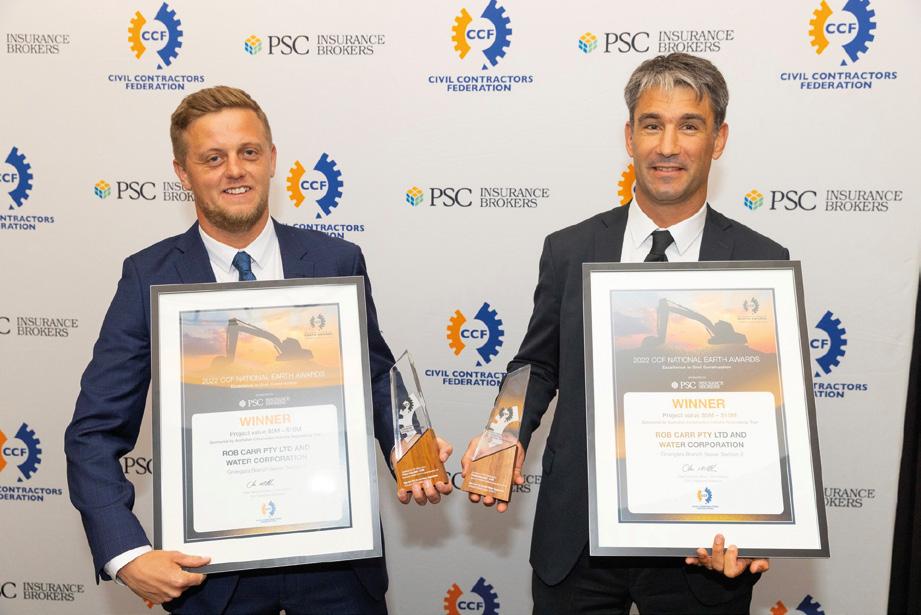
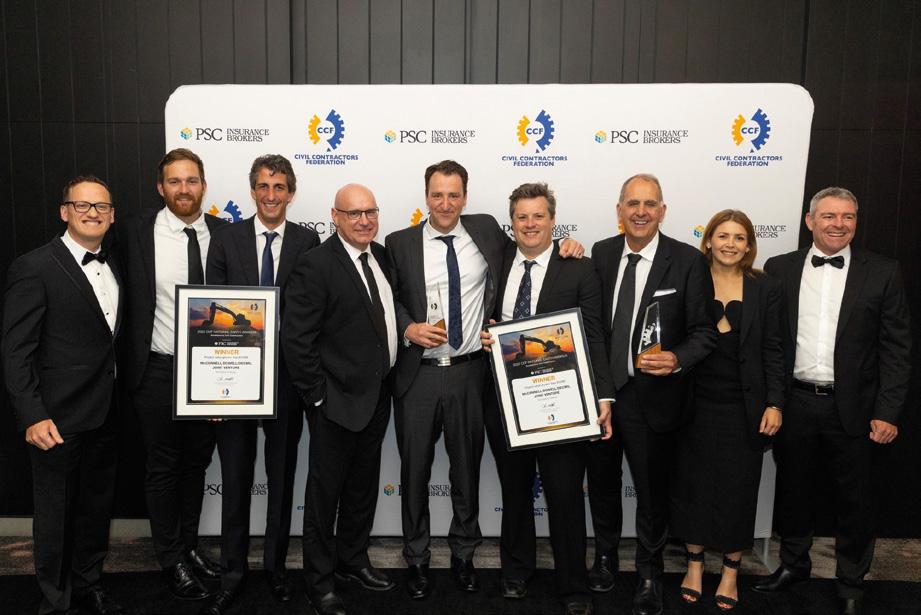
Award winners also demonstrated how they met and exceeded all necessary environmental requirements such as replanting of vegetation to offset project works, utilising recycled materials, mimimising waste to landfill, use of non-potable water, and maximising energy from sustainable energy providers.
CCF was fortunate to have the Hon Catherine King, Minister for Infrastructure, Transport, Regional Development and Local Government address the dinner who said, “Events like these are important in recognising the contribution you make big and small and the importance of your industry in the economic prosperity of the country.”
The evening was also highlighted by the awarding of a CCF Lifetime Membership Award to Adrian Grainger from Tasmania in recognition of his enormous contribution to the civil construction industry at the state and national levels.
CCF has already kicked off the 2023 CCF National Earth Awards, with planning underway to hold award ceremonies at the state and territory levels. Winners of those awards will progress to the CCF National Awards which will once again be held in Canberra on 10 November 2023.
The winners of the 2022 CCF National Earth Awards are:
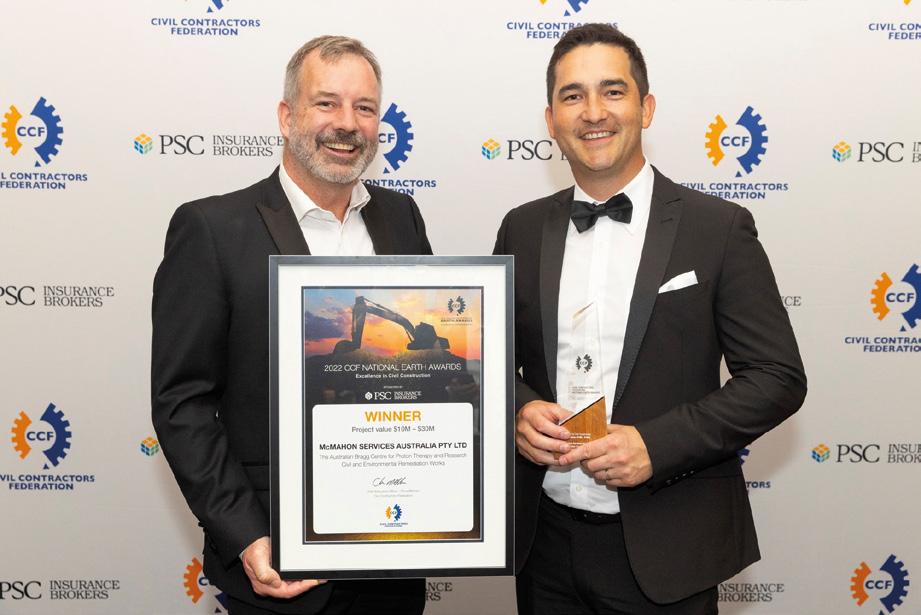
The Australian Bragg Centre for Proton Therapy & Research – Civil and Environmental Remediation Works Site investigations, demolition, bulk earthworks and remediation for the basement and bunker levels of the new $500 million Australian Bragg Centre in Adelaide’s BioMed City precinct.

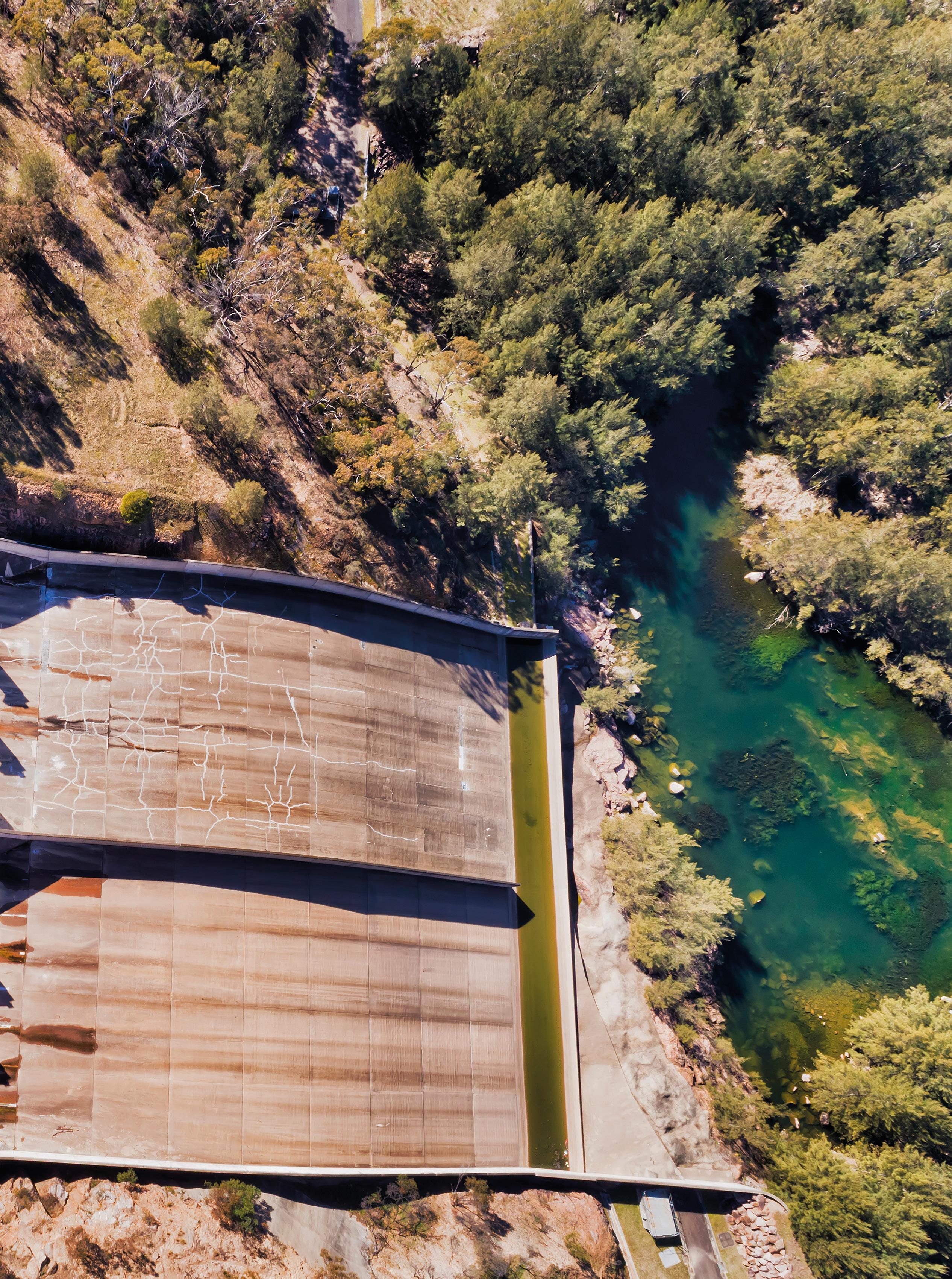
THE KEY ISSUES THAT WILL DEFINE INFRASTRUCTURE IN 2023
By Peter Colacino, Partner, Avista Strategy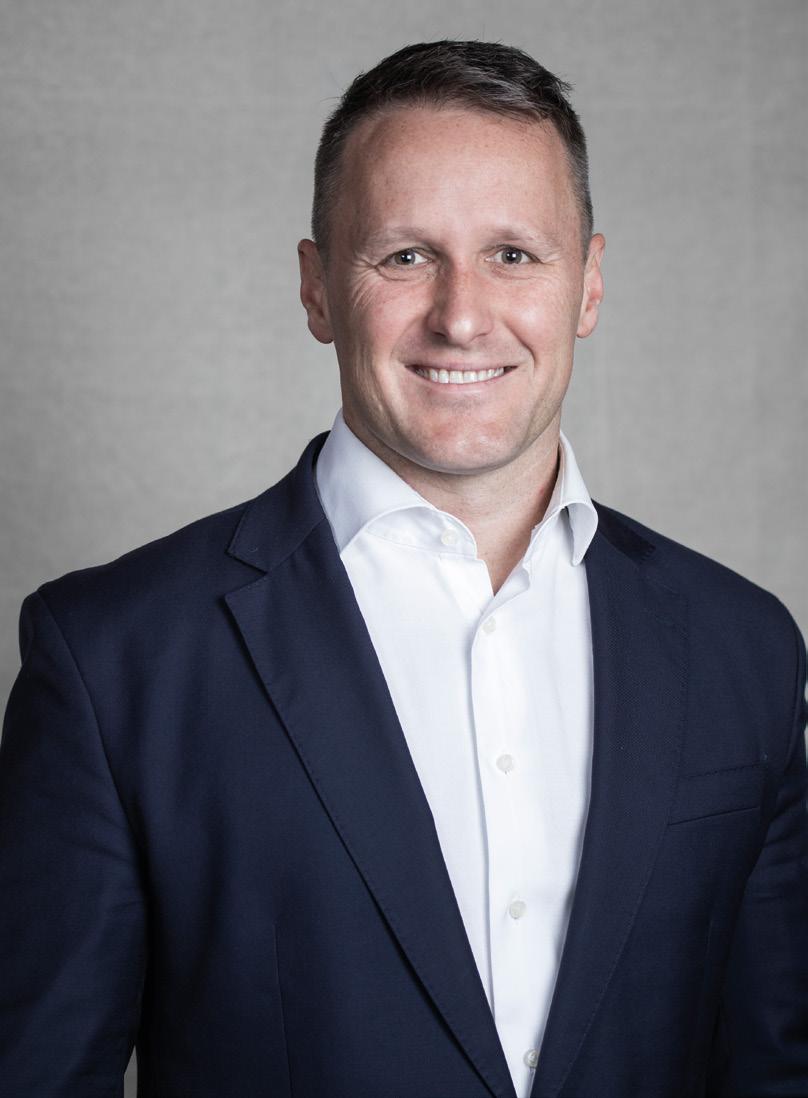
Australia’s infrastructure sector is feeling the pinch like never before, as the peak of investment committed during the pandemic begins to bite.
As investment approaches levels exceeding the previous all-time peak for construction and building work in Australia, and with public infrastructure now constituting over two-thirds of the total construction spend, public investment is crowding out capacity for the private sector to access the skills and resources it needs.
While the notion of constraint is not new for a sector that has faced a shortage of key skills for time immemorial, the breath of the issue is presenting unexpected challenges.
THE NEED FOR PRODUCTIVITY REFORM IS REAL AND IMMEDIATE
The reality of a finite market is now visible with governments forced to respond with productivity reform.
Governments are moving to embrace collaboration with contractors and the supply chain to realise innovation and reform. This increased collaboration can unlock potential efficiency savings of up to 20 per cent.
Some governments are also acknowledging the fluidity and connectedness of the national market. State governments, notably New South Wales and Victoria through the Construction Industry Leadership Forum (CILF), are now several years into a journey to reform the sector. Western Australia has commenced a considered process of co-design with industry to consider reforms to support the sector, and Tasmania is active in managing the combined demands of public and private construction work.
Reform in the media-shy water sector has been less visible, however, led by Sydney Water’s Partnering 4 Success initiative, a series of utilities are following suit with their own collaborative delivery model reform processes.
The role of industry as an active champion and participant in these reforms sets them apart from past efforts led by government alone. Industry is looking to government for signals of preparedness to do things differently, and a willingness to invest in reform to bring digital transformation and modern methods of construction.
War in the Ukraine rippled through the Australian building industry with sanctions impacting $80 million worth of Russian timber imports, particularly laminated timber beams critical for housing construction. The shortage of timber and other materials has flowed through to further escalate the cost of housing.
These constraints all existed before the Australian Government’s Housing Accord, a commitment to build an extra one million houses over five years from 2024. Constraints in the international market, the increase in demand and the focus on timber as a sustainable material presents an opportunity for the Australian timber industry to innovate and deliver new products to service the gap in the market.
As expected shifts in interest rates flow through to the home building sector, there is a potential for a downturn in activity.
However there remains a question on the consequences in light of the Housing Accord and pent-up demand to service commercial projects.
The supply chain is responding to the emergence of constraints with the adoption of new (and some old) materials and approaches. The use of recycled materials and timber present significant opportunities to reduce the sector’s ecological impact while also alleviating capacity constraints. As Infrastructure Australia’s Market Capacity Report found, more than 27 per cent of the material used in road maintenance can be replaced by recycled materials.
A NEW APPROACH TO CLIMATE RISK AND RESILIENCE IS NEEDED
The water sector will also be at the forefront of reform to respond to climate change adaptation and mitigation.
Our land of droughts and flooding rains has been brought into stark focus over the past twelve months as many catchments deal with the compounding impacts of La Niña and extreme weather events.
A wetter, warmer Australia is one more prone to flood and to the need for drought resilient water supplies. Ensuring the resilience of water supplies to the impacts of flood and fire, as well as managing the inundation of stormwater infrastructure, is a critical challenge for a sector that faces significant knowledge gaps about the condition and capacity of its assets.
The significant changes to the landscape of resilience agencies adds a complicating factor. After significant mismatches between expectations and reality in the role of resilience, the leading agencies in the sector have been disbanded, so what’s next for resilience?
The focus must be moving beyond the notion that every asset or community can be fortressed against hazards. Climate adaptation is an infrastructure challenge. Not only are 79 per cent of emissions enabled by the sector, but 89 per cent of the costs of climate adaption will be met by the sector. This challenge requires deep pockets. So, instead, we need to think more holistically about the likelihood that a disaster will occur and how communities and the systems that support them can respond efficiently and effectively.
SOCIAL IMPACT IS THE NEXT FRONTIER OF SUSTAINABILITY
As communities emerge from the impacts of disasters resulting from natural hazards, the focus on sustainability must broaden beyond the ecological to include economic, social and governance considerations.
While recovering communities navigate the challenging interactions of physically rebuilding, business recovery and local employment, the broader focus of sustainability discussions will turn to a more complete and complex set of social issues.
From responding to the challenge of workforce diversity and gender in the sector, to the potential impacts of an
Indigenous Voice, and understanding how local voices can be more completely embedded into infrastructure decisionmaking, particularly on a diversity of issues such as resilience (and fire management), we have the opportunity to reopen sustainability as more than a response to climate change.
FREE MARKET IS OUT, INTERVENTION IS IN
The uncertainty of market conditions, the scale of change required to lead the carbon transformation and the focus on social dividend has brought market intervention back into vogue.
While intervention in the infrastructure sector has crept back over recent years with the re-emergence of government delivery entities, the formation of new government businesses and hybrid delivery models, this trend can be expected to accelerate as governments look to manage multiple risks and control price escalation.
The State Electricity Commission proposal put forward by Victorian Labor ahead of the 2022 election shows the significance of the potential change. However, it is not unique, with a shift away from privatisation prominent in the political dialogue in New South Wales, South Australia and elsewhere.
GREAT ASPIRATIONS WILL REMAIN OUT OF REACH WITHOUT GOOD GOVERNANCE
From Indigenous governance to market regulation and the cascade of post-election Australian Government reviews that enter implementation, and could commence following the New South Wales election in March, the nature of sector governance will come squarely into focus.
The interface between market policy and governance reform will present as a focus in the political dialogue with asset controlling entities, such as NSW TAHE, the focus of election jostling. The important role of commercial diligence, and the focus on optimising assets beyond core services, should not be lost to governance changes.
The focus of governance discussion would ideally focus squarely on delivering outcomes for the community and ensuring the aligned behaviour of stakeholders. The UK Institution of Civil Engineers’ Infrastructure Governance Code, released earlier this year, lays the foundation for good behaviour, while it is the role of elected government officials to clearly define the outcomes and aspirations of infrastructure services in response to community needs and expectations.
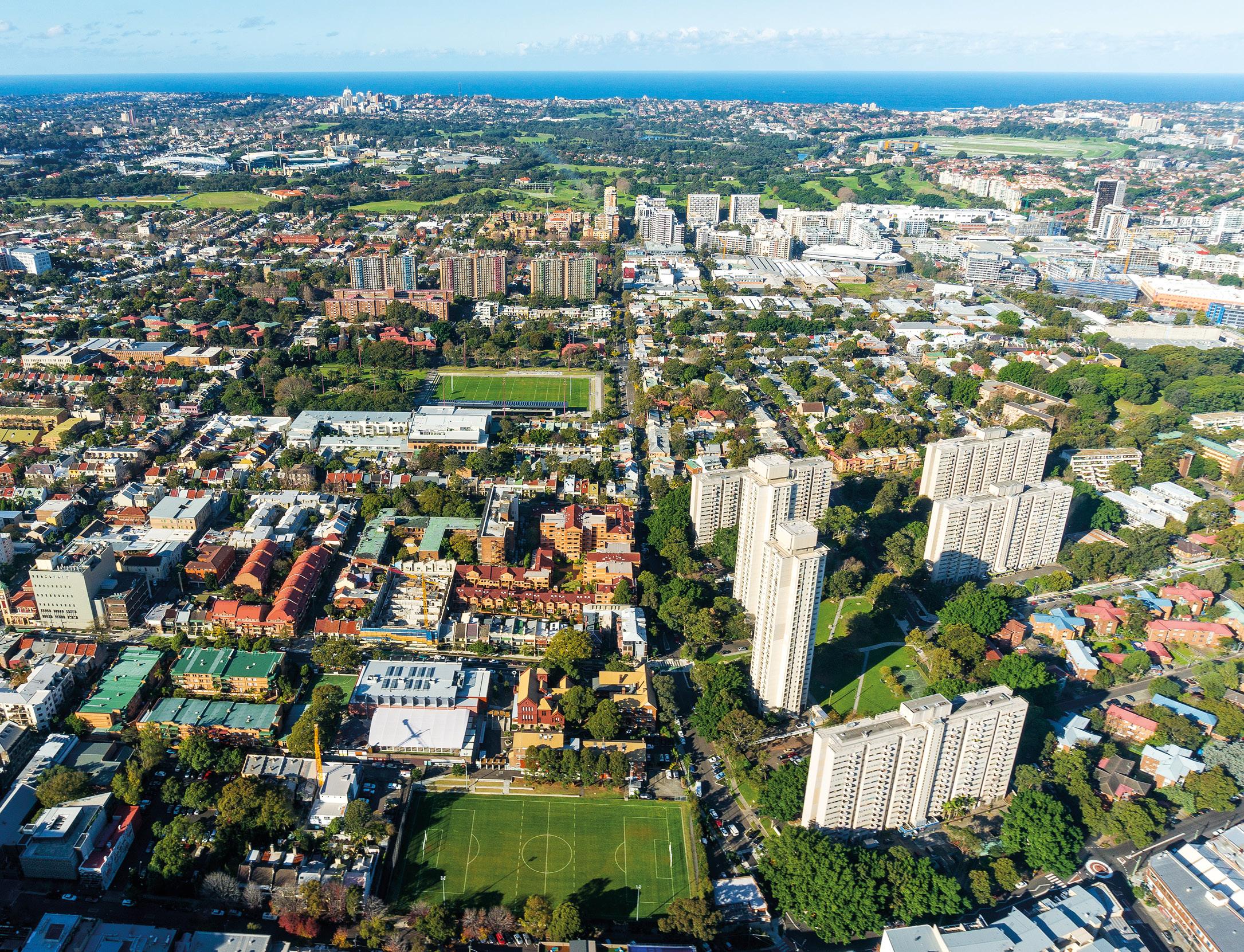
SELECTING THE RIGHT CABLES FOR TUNNELS AND OVERHEAD TRANSPORT SYSTEMS
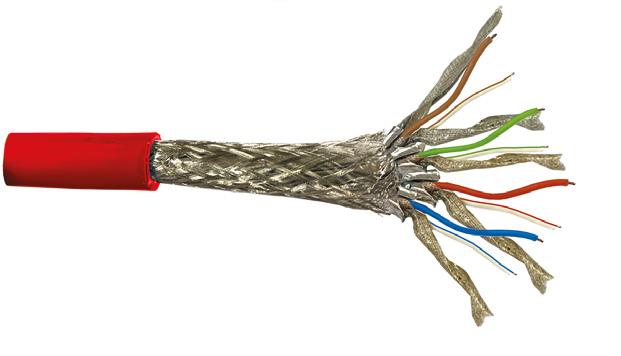
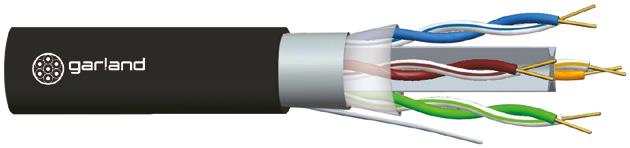
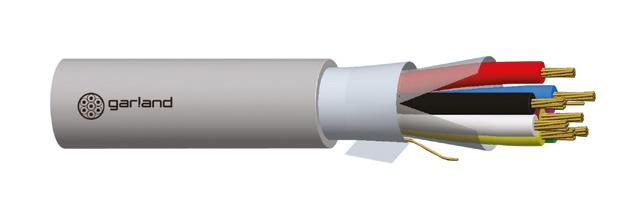
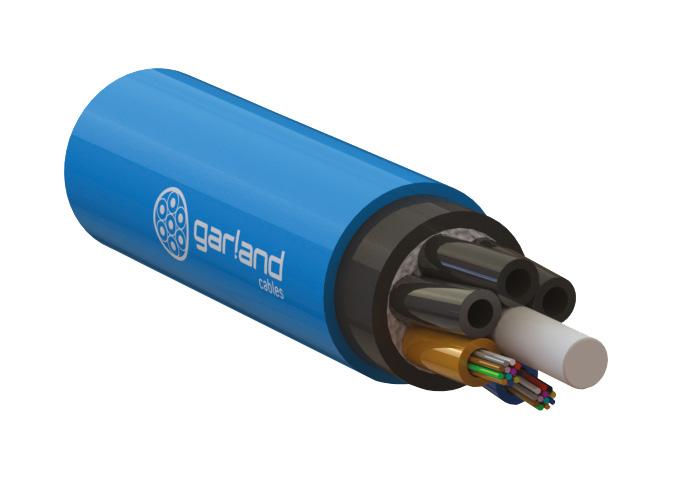
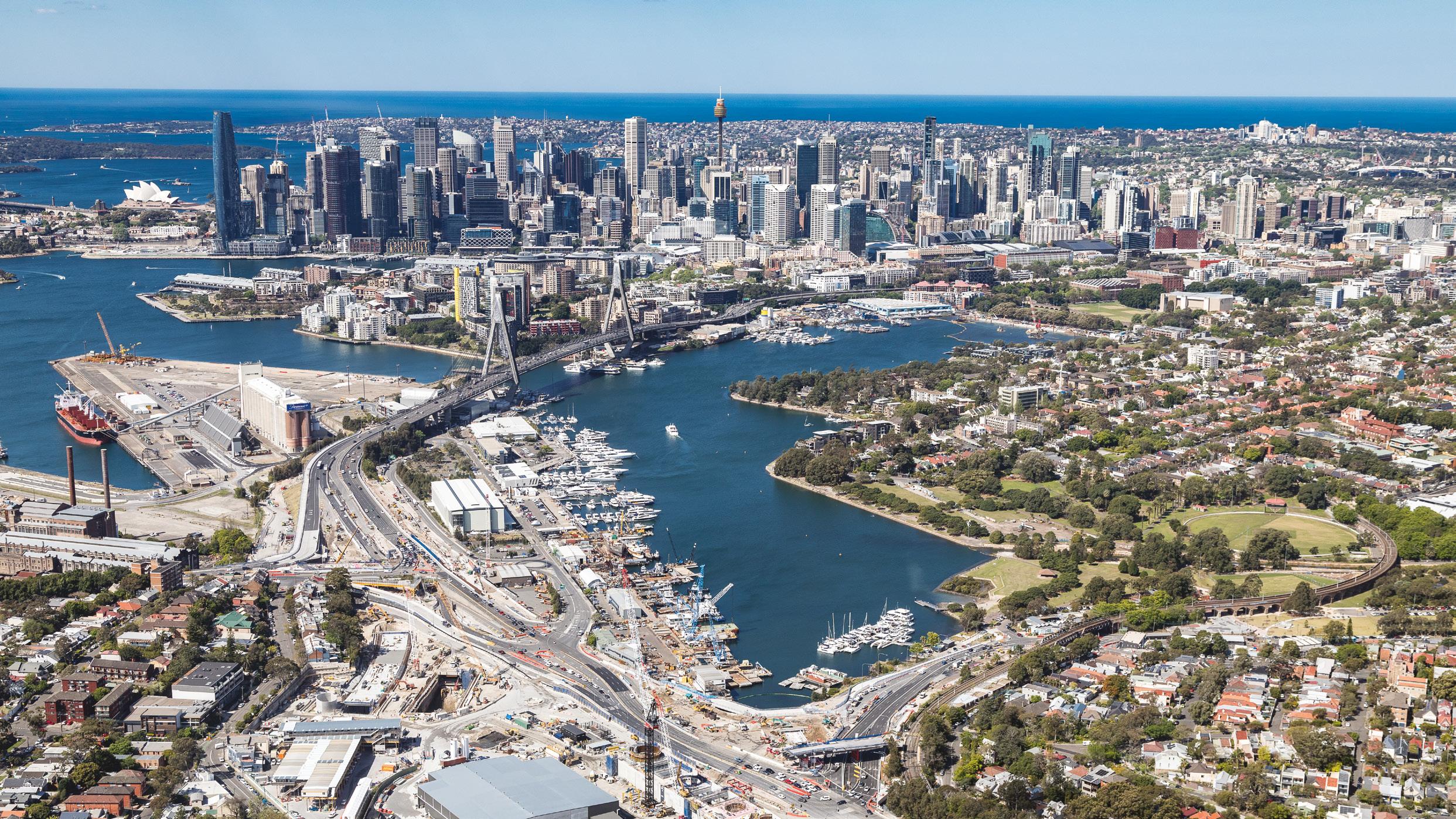
Australia has seen a dramatic increase in imports in recent years, up 34 per cent from 2020 to 2022. This significant rise has created an increased demand for infrastructure to facilitate the import, storage and distribution of these goods. As Australian capital cities continue to become increasingly dense, building and cabling tunnels and overhead transport systems demands additional requirements that aren’t present in traditional surface transport systems.
For example, tunnel cabling needs to not only be flame retardant but, depending on the application, may also need to continue to operate under fire conditions, often referred to as a circuit integrity cable.
There are a number of standards that specify the performance these cables need to meet under fire conditions including IEC 60332 and Australia’s own AS/NZS 3013. Fire within a tunnel can also result in loss of life due to toxic and corrosive gases released when plastics burn, so the use of Low Smoke Zero Halogen (LSZH /LSOH) materials is preferred or often mandated for these installations.
Again there are a number of national and international standards that govern these characteristics such as IEC 607541 and IEC 60754-2 that assess the amount of halogen gas released using various methods, and IEC 61034-2 that grades the level of smoke generated when burned.
To help manage all these various requirements, there are other standards that combine all the various characteristics into a single rating, hoping to aid and simplify the selection of cables. Typical of these standards is AS/NZS 4507 that uses its own classification system to combine the various requirements into a single rating and using this approach can help simplify requirements.
Some cable types do not easily fall into these standards. For example, AS/NZS 3013 cannot be applied to optical fibre cables although this is often requested by designers
or legislators. Navigating these various demands can be confusing and difficult. The situation is further complicated by the sheer range and variety of cables required for modern control and monitoring systems.
SUPPLYING CABLES TO AUSTRALIA’S BIGGEST PROJECTS
Most of these systems are custom designed for the application, so standard ‘off the shelf’ cables are not normally available and require custom cable designs to be offered. These designs go through several iterations as the circuits are tuned for optimal performance, ease of installation and cost. All these factors put a huge demand on the cable supply and this can get exponentially more difficult as the number of cable suppliers increases.
Madison Express understands these issues and has focused on building its portfolio and expertise in this area to provide a number of solutions for cabling infrastructure. By focusing on security, communication, control, and transport cables, Madison is able to offer solutions for several of the cable supply packages often associated with these major projects.
With both its own Garland brand and a number of reputable international brands including LEONI and R&M, Madison has already supplied several projects including the Sydney Metro Northwest Project, WestConnex M4-M5 Rozelle Interchange Tunnel, the Western Roads Upgrade in Victoria and Grafton Prison.
Your trusted partner for network infrastructure solutions
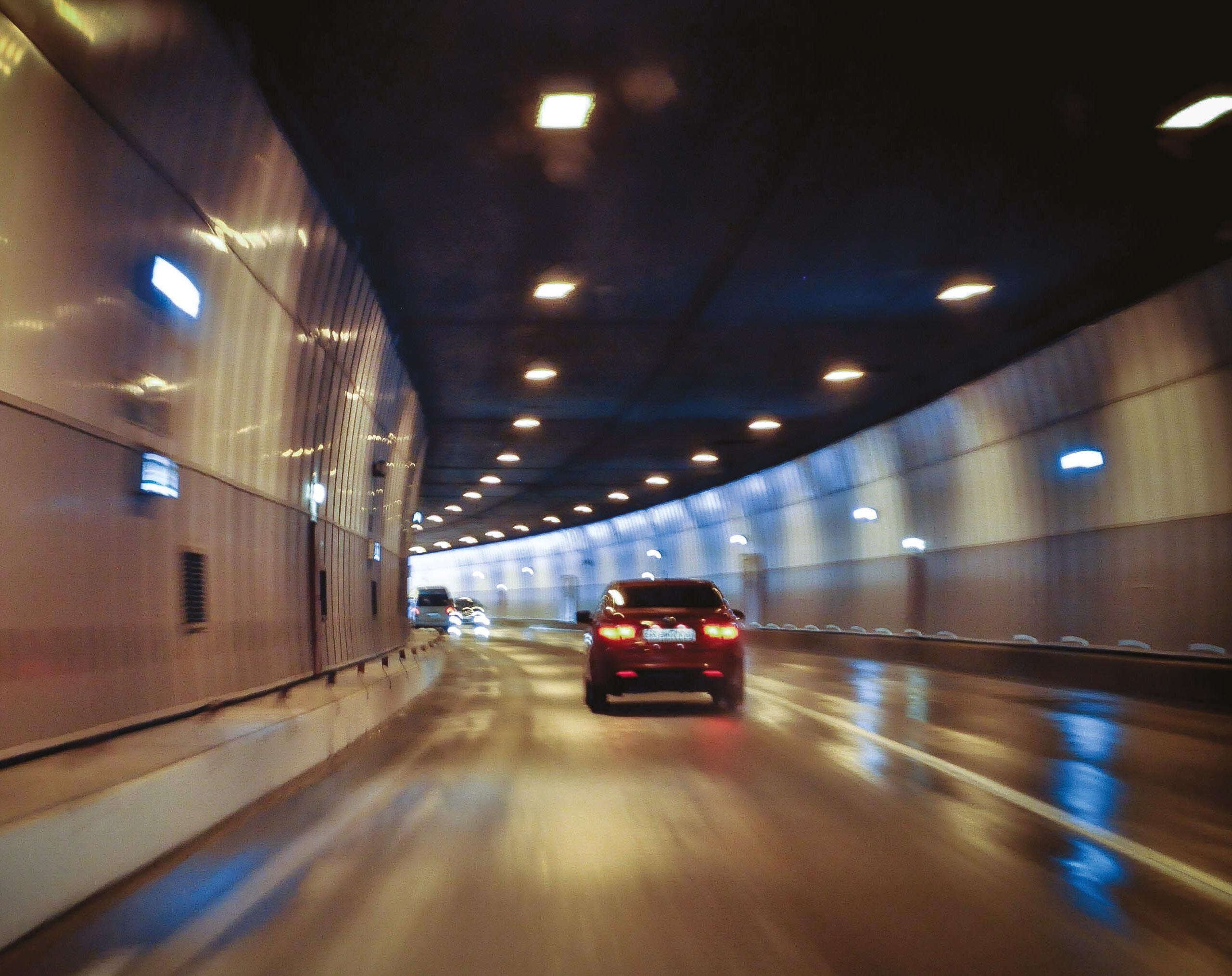
Madison Express distributes a range of Fibre and Instrumentation cable and connectivity solutions suitable for your next project. We can source and custom-make cable designed to match specific technical and environmental requirements.
9 Copper and optical fibre network cabling infrastructure
9 Copper and optical fibre connectors, patch panels, adaptors and wall & rack mount enclosures
9 Copper and optical fibre patching systems and accessories
9 End-to-end cabling system warranties
9 BEP-approved Garland Pro Series PVC cables for Green Star Installations
With over 30 years’ experience, Australian-owned Madison Express is one of the most well-known and respected names in the cabling and connectivity industry. Our end-to-end solutions are always at the technological forefront thanks to our dedicated research and development team. We pride ourselves in our ability to provide expert advice and support across all our product lines, and also assist in all aspects of pre and post-sales support.
SUBURBAN RAIL LOOP POWERS AHEAD
By Stephen Cauchi, Suburban Rail Loop AuthorityMelbourne’s Suburban Rail Loop (SRL) has taken another significant step forward, with Expressions of Interest to open for the next major works package – the contract for design, construction and operation of all tunnel systems and infrastructure for SRL East.
SRL East will deliver 26km twin tunnels and six new underground stations between Cheltenham and Box Hill – transforming public transport in Melbourne’s east and south east and creating up to 8,000 jobs during construction.
The new contract includes the trains, tracks, signalling and communications systems, as well as the maintenance depot and stabling facility. It also includes a 15-year term to operate and maintain SRL East.
Expressions of Interest will open this year, with final selection expected in 2025. It is a major procurement milestone for the 90km orbital railway and follows a tremendous year of progress for Victoria’s biggest-ever infrastructure project in 2022. In September, three global industry leaders were shortlisted to build the twin tunnels for SRL East, with tunnelling to start in 2026.
Early works for SRL East started in Clayton in mid-2022 and will ramp up through 2023, with works to be launched in Glen Waverley, Burwood, Monash, Cheltenham, Box Hill and at the stabling facility in Heatherton.
Two of the four stages of SRL are now underway – SRL East and SRL Airport (being delivered by Rail Projects Victoria) between Melbourne Airport and Sunshine.
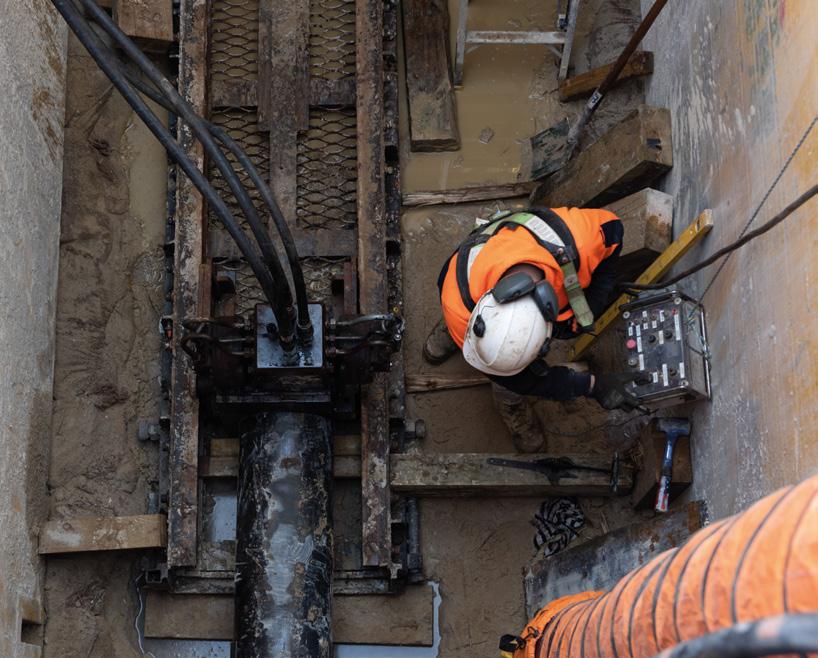
RESPONDING TO THE NEEDS OF A GROWING CITY
Melbourne is growing rapidly and needs a public transport system to meet the challenge. Victoria’s population is expected to reach around 11.2 million by 2056, with Melbourne to be home to around nine million people – a global city the same size as London today. Suburban Rail Loop is the first new suburban rail line in Melbourne since the Glen Waverley line opened in 1930.
SRL will change how people move around Melbourne –setting a new benchmark for modern, convenient and efficient public transport. More than 80 per cent of Melburnians will experience reduced travel times with shorter, faster and more reliable journeys, as well as less congested roads.
Minister for Suburban Rail Loop, Jacinta Allan, said Suburban Rail Loop will create thousands of jobs and deliver the critical wheel on the city’s hub-and-spoke train network.
“Victorians recognise Suburban Rail Loop is the project our growing city and state needs and these major works contracts are a crucial milestone as Suburban Rail Loop steams ahead,” Minister Allan said.
SRL East will deliver six brand new underground stations – at Cheltenham, Clayton, Monash, Glen Waverley, Burwood and Box Hill – with trains running by 2035.
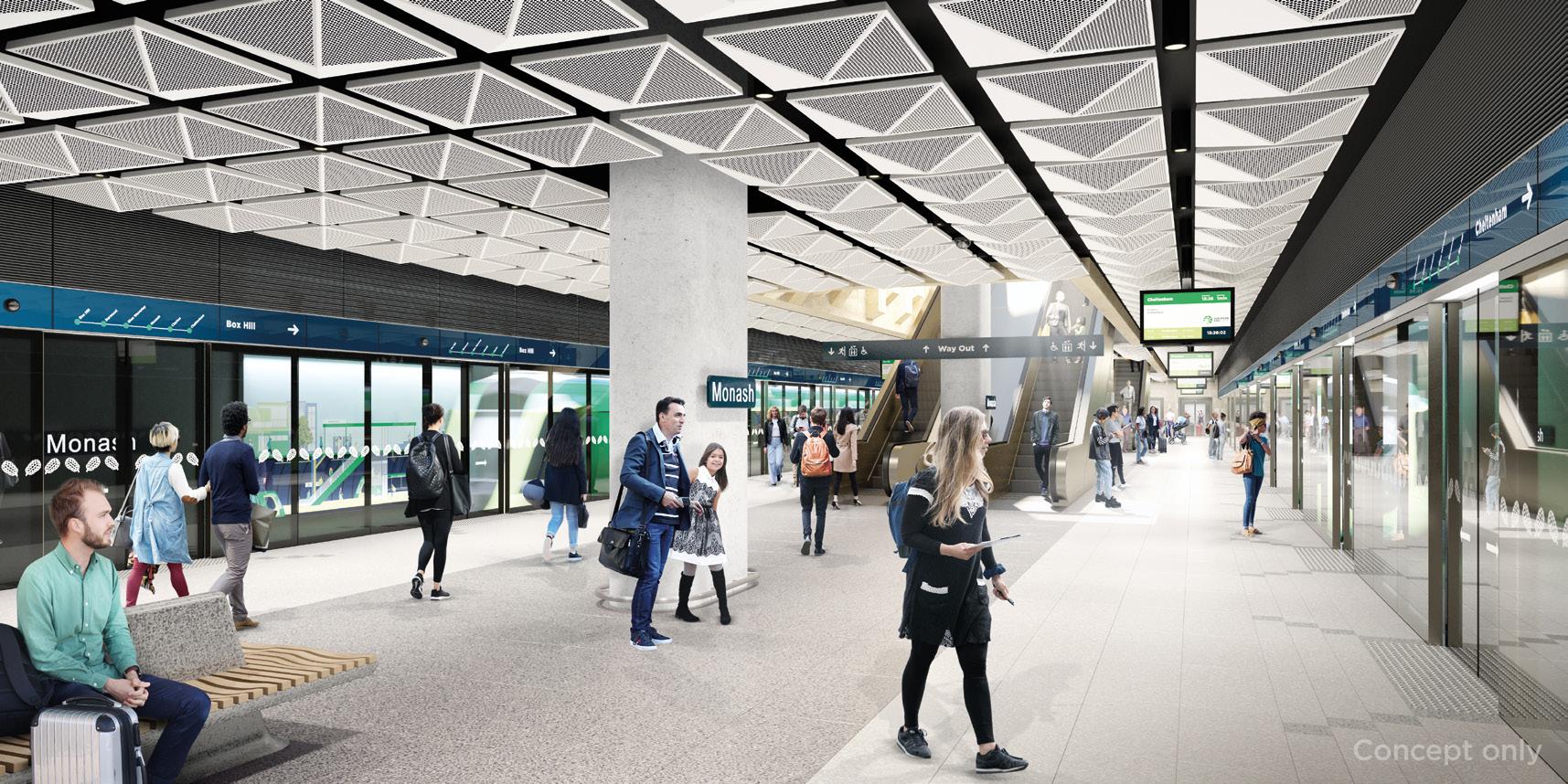
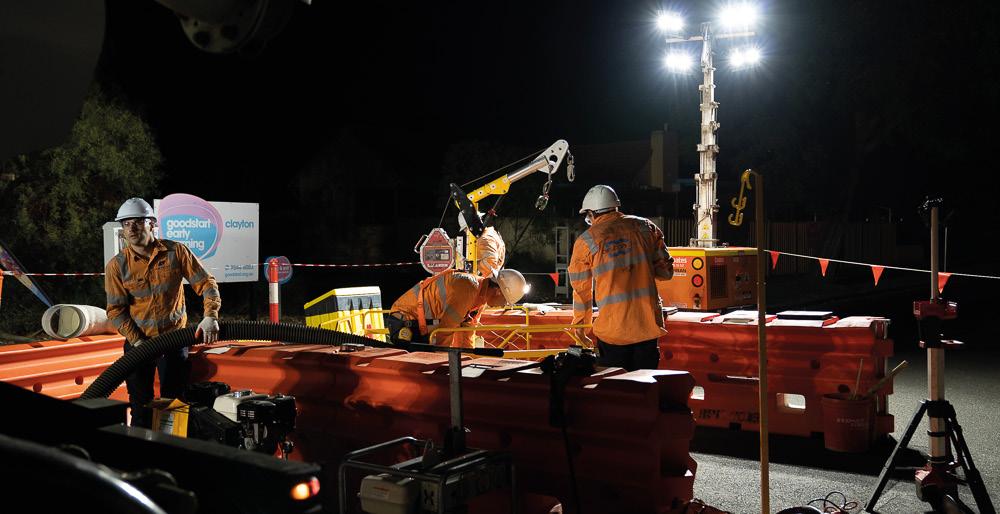
LOOP
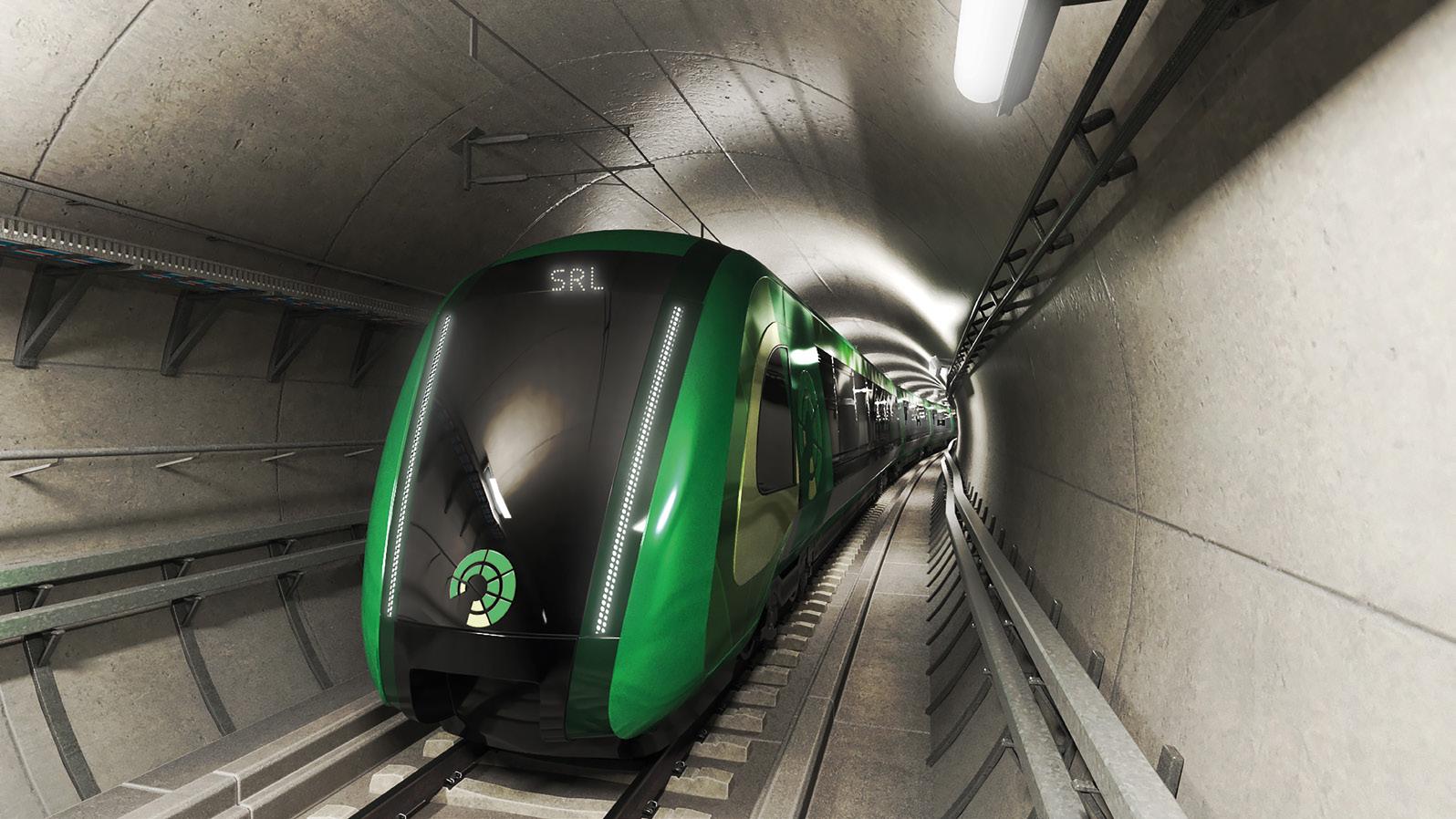
SRL Airport will help deliver the long-awaited rail connection from Melbourne Airport to Sunshine and is scheduled to open in 2029.
SRL North from Box Hill to Melbourne Airport and SRL West from Sunshine to Werribee are in the early stages of planning and development.
Suburban Rail Loop will not only connect to every major existing line between Cheltenham and Werribee, it will deliver direct rail access to many areas for the first time.
SRL East will provide rail access to Monash and Deakin Universities; SRL Airport will provide stations at Melbourne Airport and at East Keilor and SRL North will offer rail service to La Trobe University and Westfield Doncaster for the first time.
“Suburban Rail Loop won’t just transform our public transport system – slashing travel times and easing congestion – it will help manage how our city grows, creating a long pipeline of jobs and training opportunities,” Minister Allan said.
“With trains running by 2035, SRL East will open up access to key education, health and employment centres in Melbourne’s east and south east, relieving pressure on roads and slashing congestion and travel times across the network.”
SRL East is estimated to cost between $30 and $34.5 billion.
The Victorian Government has so far allocated $11.8 billion to the project, while the Federal Government has made an initial commitment of $2.2 billion. The SRL Airport stage is fully funded through a State and Federal Government partnership.
Beyond the many jobs delivered during construction, SRL will create major economic activity centres around the new stations, transforming Melbourne into a city of multiple employment centres.
The section of line from Cheltenham to Melbourne Airport is forecast to become Melbourne’s busiest rail line by 2051.
SRL will slash travel times across the network, with the average one-way journey 40 minutes faster than a public
transport journey today.
The estimated travel time between most SRL stations will be around three to four minutes.
From Cheltenham, for example, commuters will save between 40 minutes to an hour when travelling to either Monash, Glen Waverley or Burwood. It currently takes 56 minutes for a student to travel from Ringwood station to Monash University. With SRL, this will be slashed to just 25 minutes.
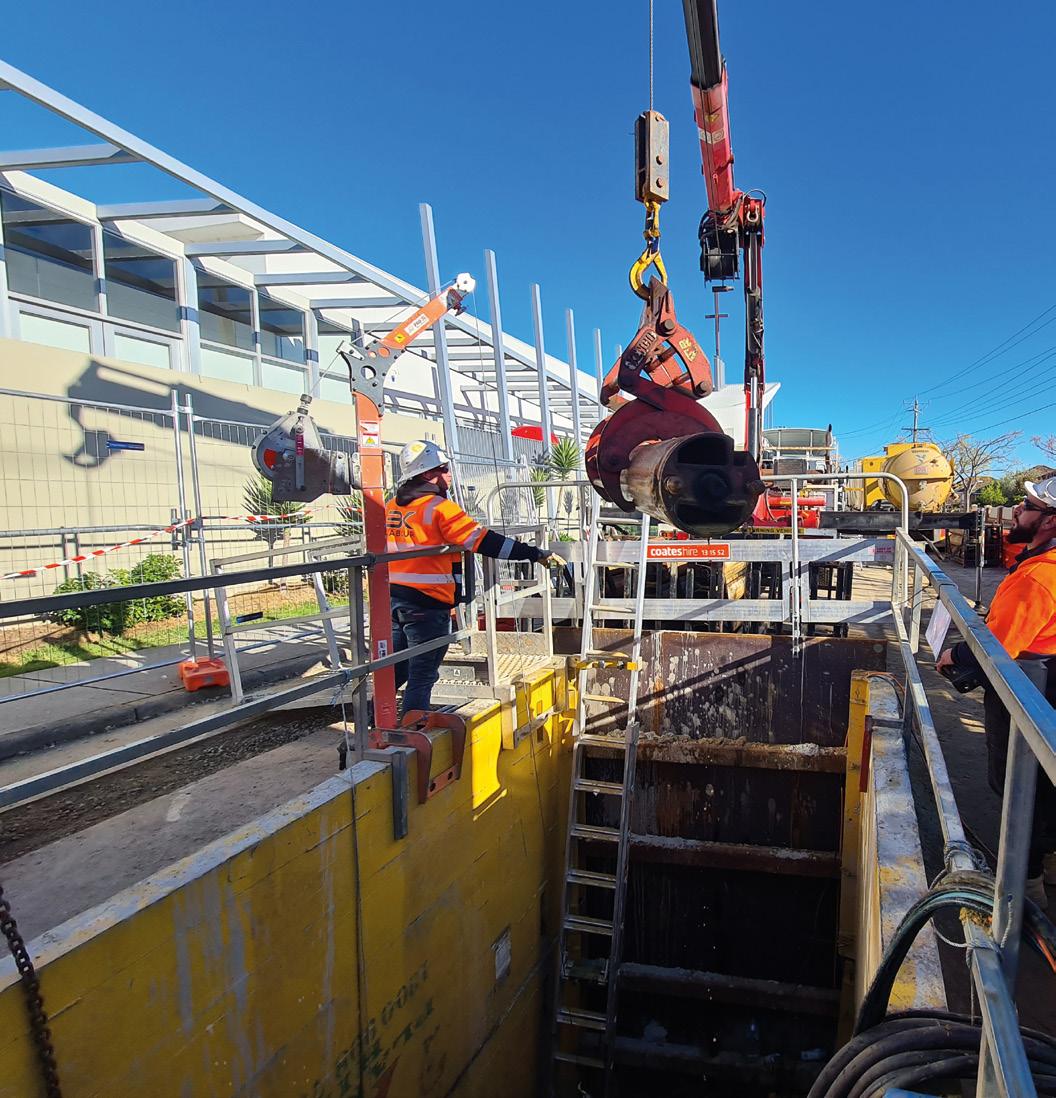
SRL will be a ‘turn up and go’ service. Trains will initially run every six minutes in the peak between Cheltenham and Box Hill and frequency will increase as future stages are delivered. Ultimately, service frequency will increase to a train every two minutes.
SRL East and SRL North will be a standalone line, using a different gauge (standard) and power system (alternating current) to the rest of the Metro Trains network. It means SRL will be able to use state-of-the-art systems without having to retrofit technology into the existing network.
The new automated, four-car trains will be comfortable and easy to access, with low internal and external noise, quality passenger information systems, and ergonomic seats. Carriages will have dedicated spaces for wheelchairs and passengers with special needs, as well as flexible use spaces for prams, assistance animals and other uses.
With SRL North connecting to Melbourne Airport, the train interior will be configured for flexibility and ease of movement, and with capacity for fit-out of convenient luggage storage.
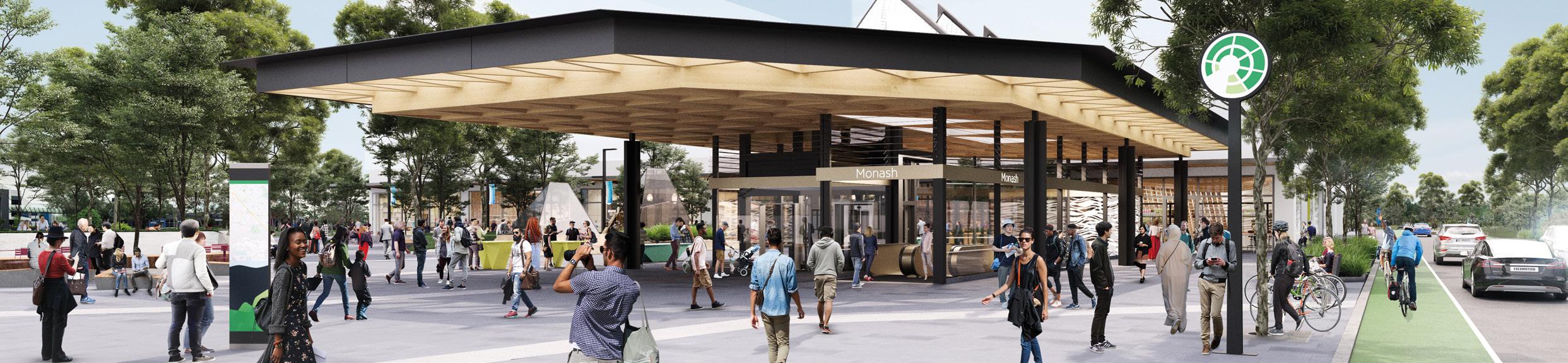
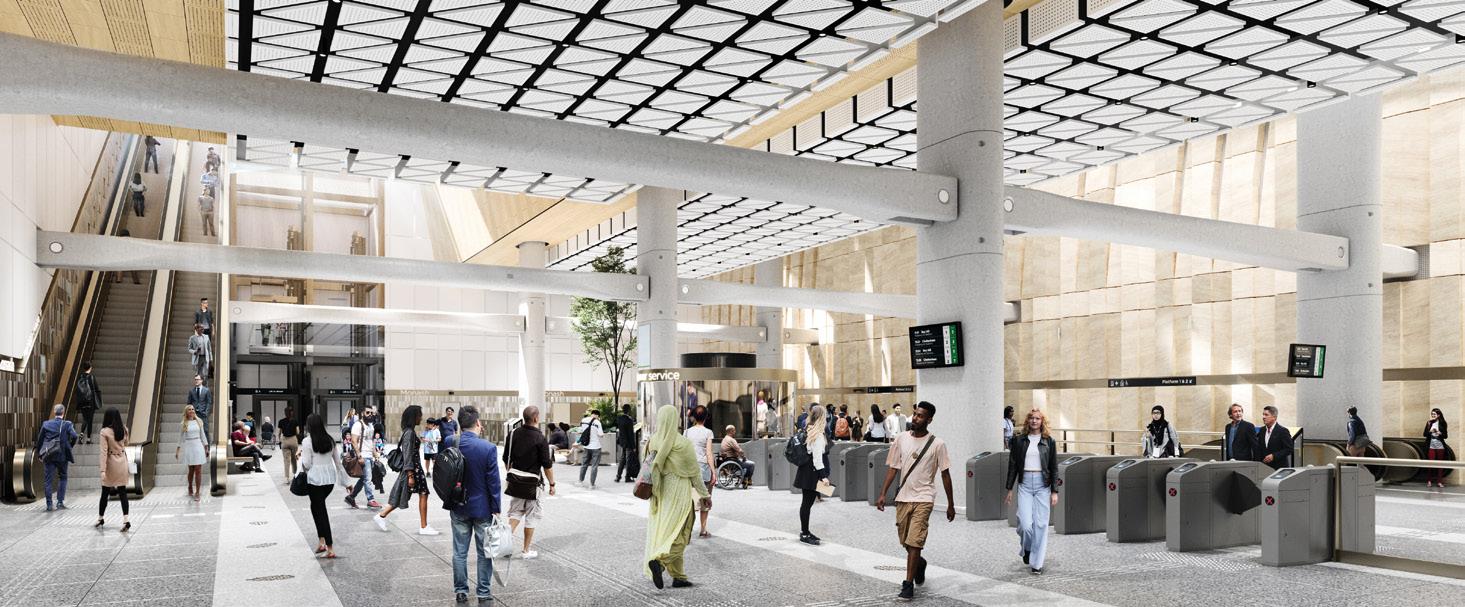
MORE THAN A RAIL LINE
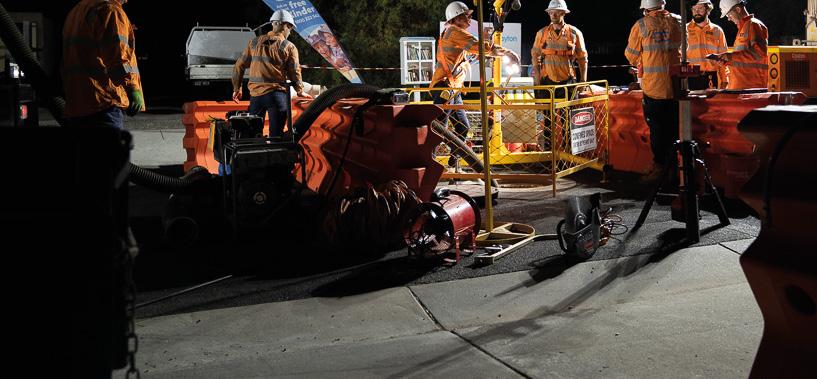
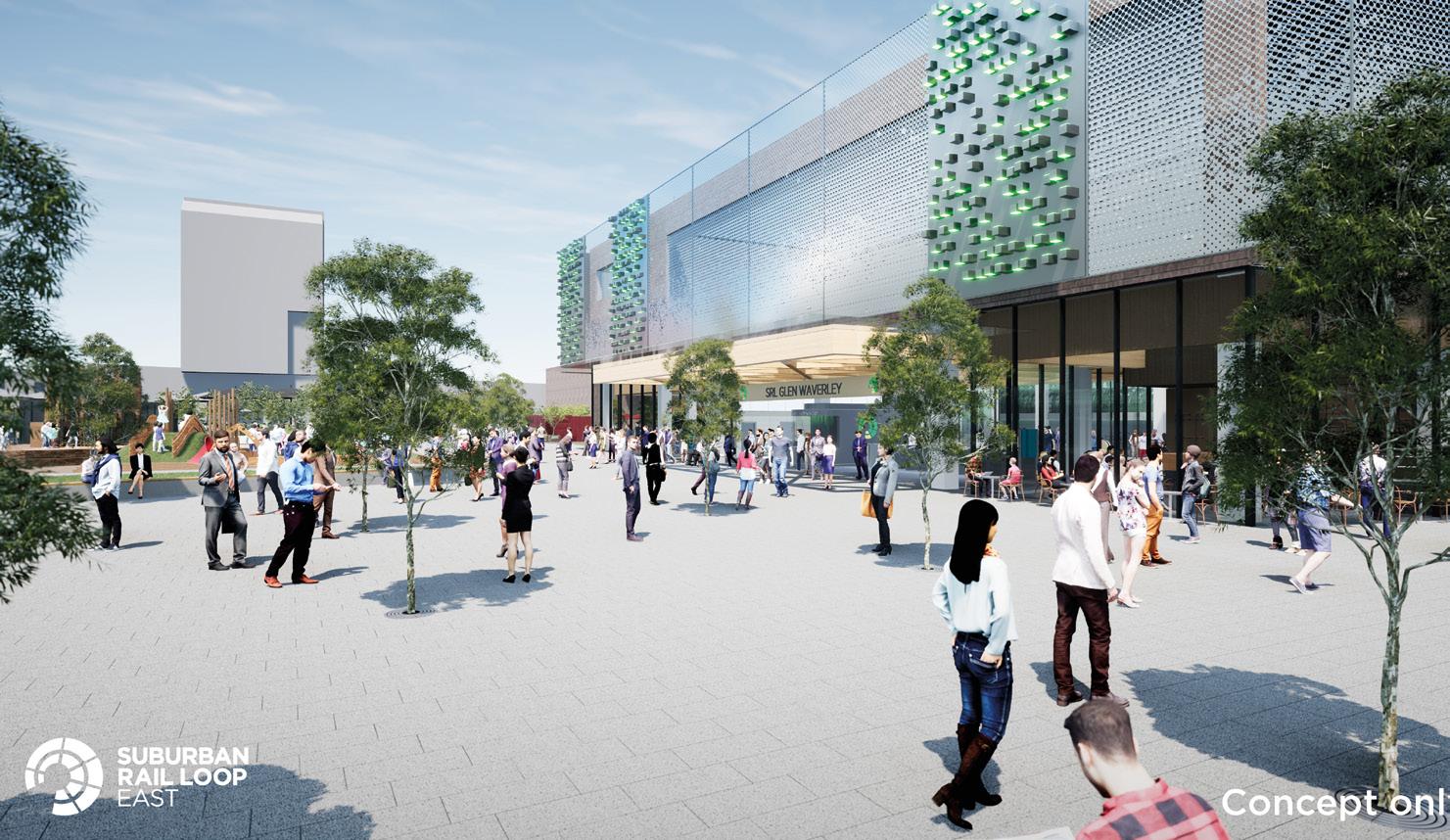
SRL Precincts around the new underground stations from Cheltenham to Melbourne Airport will be home to almost 550,000 jobs by 2056 – about the same number of jobs as there are in the Melbourne CBD today.
This means more than eleven per cent of Melbourne’s jobs will be located in the broader areas around SRL stations –almost as much as the 13 per cent in the central city. 165,000 of these jobs will only be delivered because of the transport benefits offered by SRL – bringing more jobs closer to where people live – all within a short walk from a station.
“This multi-faceted project will reshape how we grow in the decades ahead – creating major employment centres in the middle suburbs with more housing options, services, and open and public space all a short walk from an SRL train station,” Frankie Carroll, Chief Executive, Suburban Rail Loop Authority, said.
“The Suburban Rail Loop Authority has been engaging with community members, local councils and stakeholders about the opportunities to invest in and revitalise the neighbourhoods around the new stations, and this important precinct planning work will ramp up in 2023.”
Crucially, SRL will give regional Victorians much better access to job opportunities, education and health services and bring metro Melbourne and regional Victoria closer than ever.
Eight regional lines link Melbourne to centres including Geelong, Ballarat, Bendigo, and the Latrobe Valley. They will connect to SRL through transport super hubs at Clayton, Broadmeadows and Sunshine.
Regional Victorians will be able to travel to and from key destinations across Melbourne’s suburbs without having to go through the CBD. This will cut 80 minutes on average from return public transport trips and open up previously
inaccessible jobs in high growth employment areas.
Regional students won’t have to miss out studying at a major education institution in Melbourne because it is too difficult to get to. SRL will mean students have direct connections to Monash, Deakin and La Trobe universities and Box Hill Institute. Access to Deakin University from Wallan, for example, will be around 45 minutes faster with SRL East and North – making it within an easily commutable travel time.
Travelling to world-class healthcare will be more convenient with SRL stations to be built close to Monash Medical Centre, Monash Children’s Hospital, Monash Heart Hospital, Box Hill Hospital and Austin Health.
Significantly improved travel times between the regions and Melbourne’s middle suburbs will make regional centres and towns more attractive for investors, visitors and tourists. For example, a resident of Heidelberg could save an hour on a return public transport trip to East Gippsland by transferring at Clayton.
A BIG YEAR AHEAD FOR VICTORIA’S BIGGEST INFRASTRUCTURE PROJECT
For SRL East, a major focus in 2023 will be the ramping up of early works to prepare for major construction to start in 2026.
The first phase of early construction includes preparing sites for the launch of tunnel boring machines, moving and protecting underground services, and undertaking ground improvements, geotechnical investigations and road modifications.
After the completion of major underground service relocation works in Clayton, early works this year will extend to other SRL East locations.
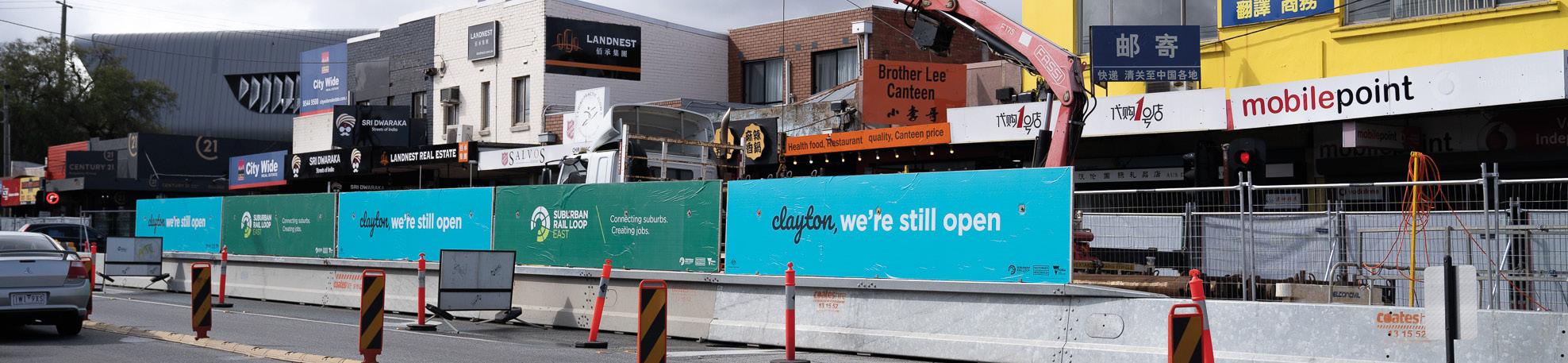
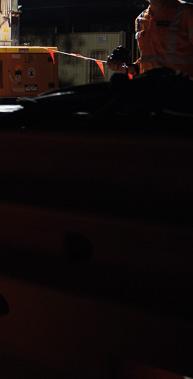
Works will start in Glen Waverley to relocate water, power and communications services. This will be followed by work at Monash. At Box Hill, a tram terminus on Whitehorse Road will be temporarily moved ahead of construction of the Box Hill SRL station.
Construction is also underway to build a new park and playground in Burwood to offset land required for station construction.
This phase of works will create hundreds of local jobs, and opportunities for the next generation of skilled workers. Around 14 per cent of the total hours are being undertaken by Victorian apprentices, trainees or cadets.
A recruitment drive is now underway for hundreds of workers, including engineers, supervisors, planners and environment experts, with a focus on encouraging more women and Indigenous Victorians into the industry.
As well, the first tunnelling contract will be awarded later this year. The three shortlisted bidders are:
♦ CPB Contractors, Acciona Construction Australia and Ghella – This consortium has experience in Brisbane’s Cross River Rail, Sydney Metro, Vancouvers’ Broadway Millenium Subway and the Caulfield to Dandenong Level Crossing Removal in Melbourne
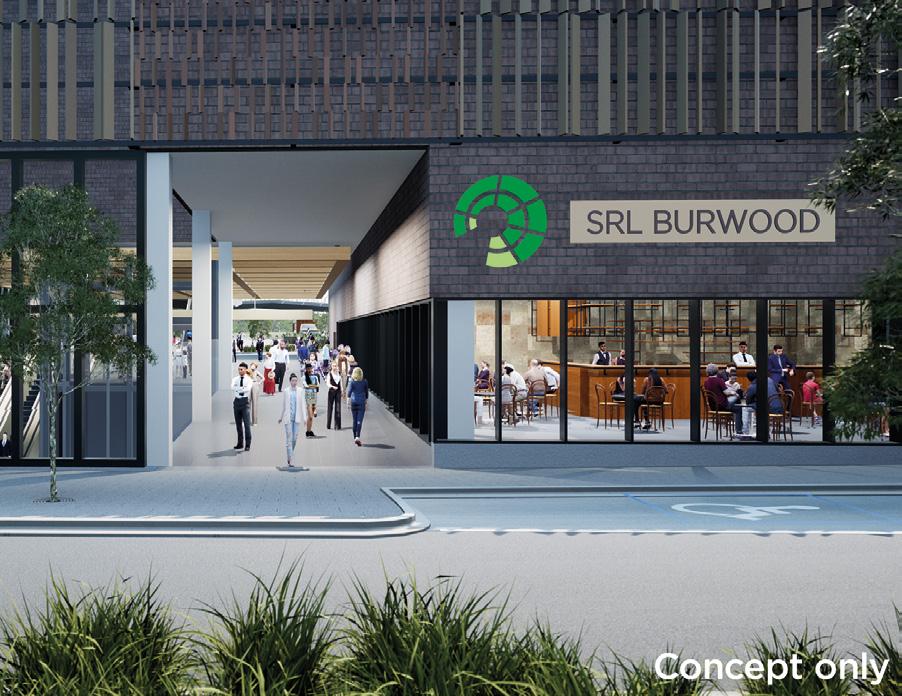

♦ John Holland and Gamuda Berhad (trading as Gamuda (Australia) Branch) – These companies have experience building Melbourne’s Metro Tunnel, Sydney Metro Northwest Tunnel and Malaysia’s Klang Valley Mass Rapid Transit, and both are currently constructing the MRT project in Singapore
♦ Webuild S.p.A and GS Engineering and Construction Australia – Companies with experience in projects including the North East Link tunnels in Melbourne, the Forrestfield-Airport Link in Perth, and Copenhagen’s Cityringen Metro
Two of the three bidders will be awarded tunnelling contracts – one from Cheltenham to Glen Waverley, the other from Glen Waverley to Box Hill.
The Cheltenham to Glen Waverley contract will be awarded late in 2023, with tunnelling expected to start in 2026.
The second tunnelling package from Glen Waverley to Box Hill will be awarded in 2024. Construction of SRL East will create a long-term pipeline of work, generating thousands of local job opportunities and helping train the next generation of skilled workers. SRL East and SRL North will support up to 24,000 jobs across the Victorian economy.
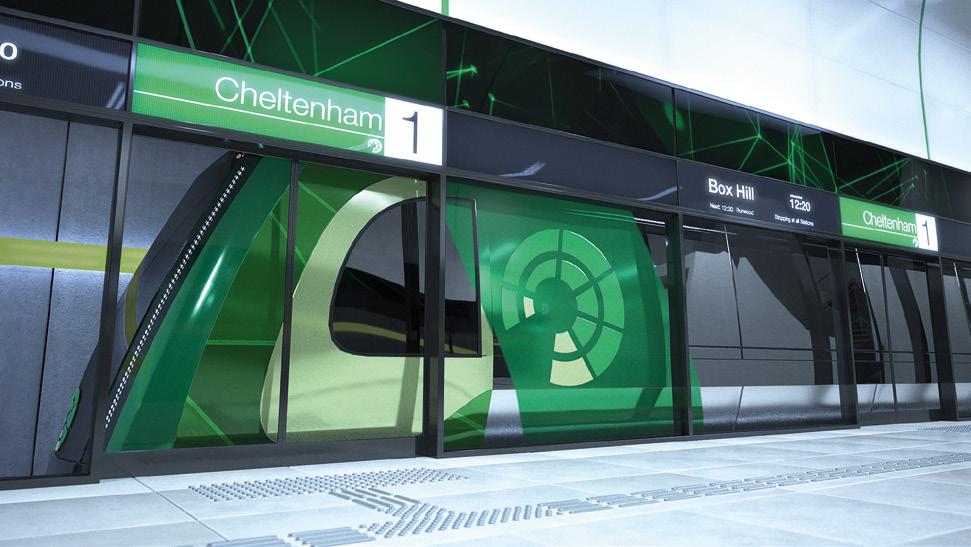

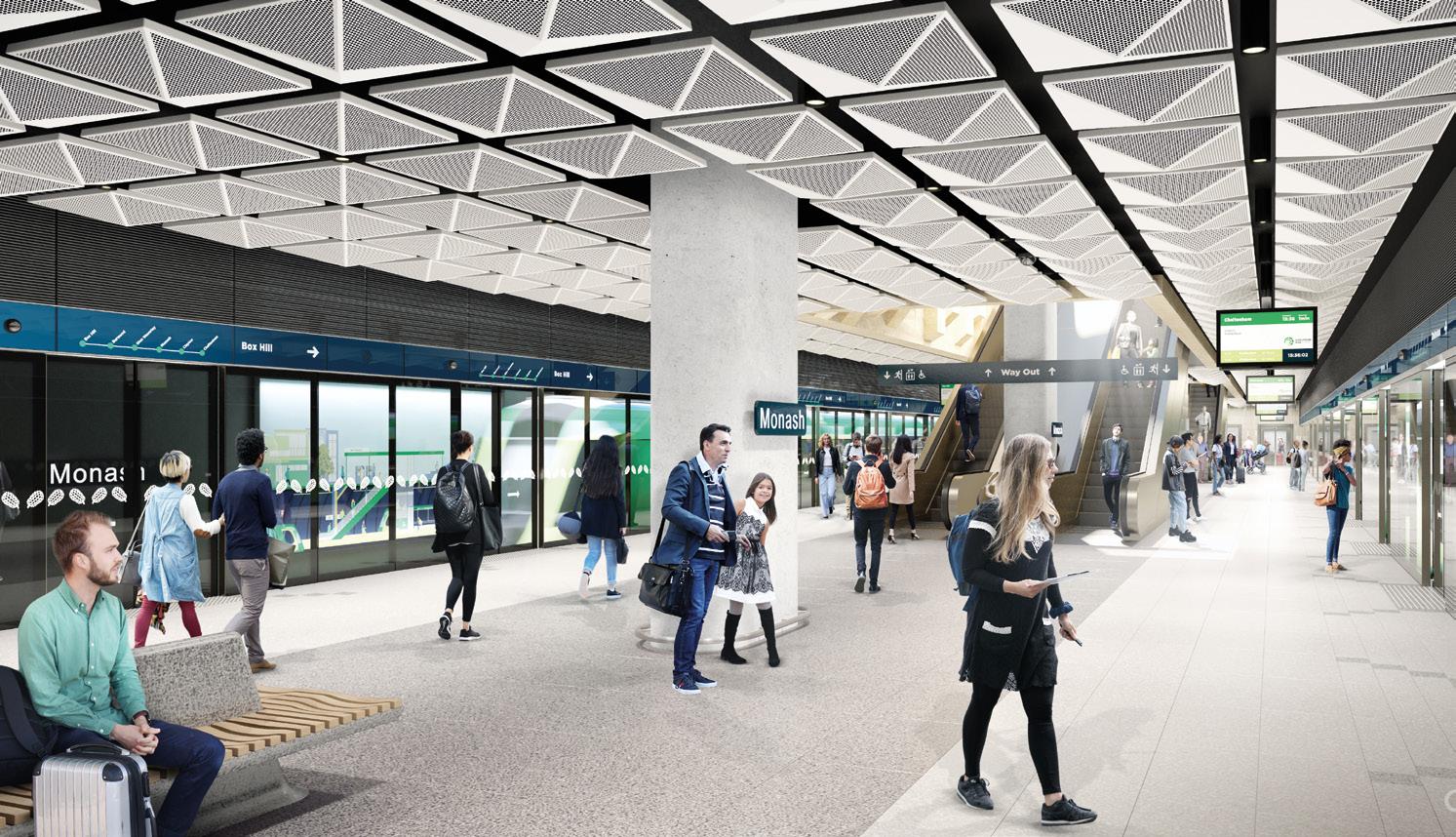
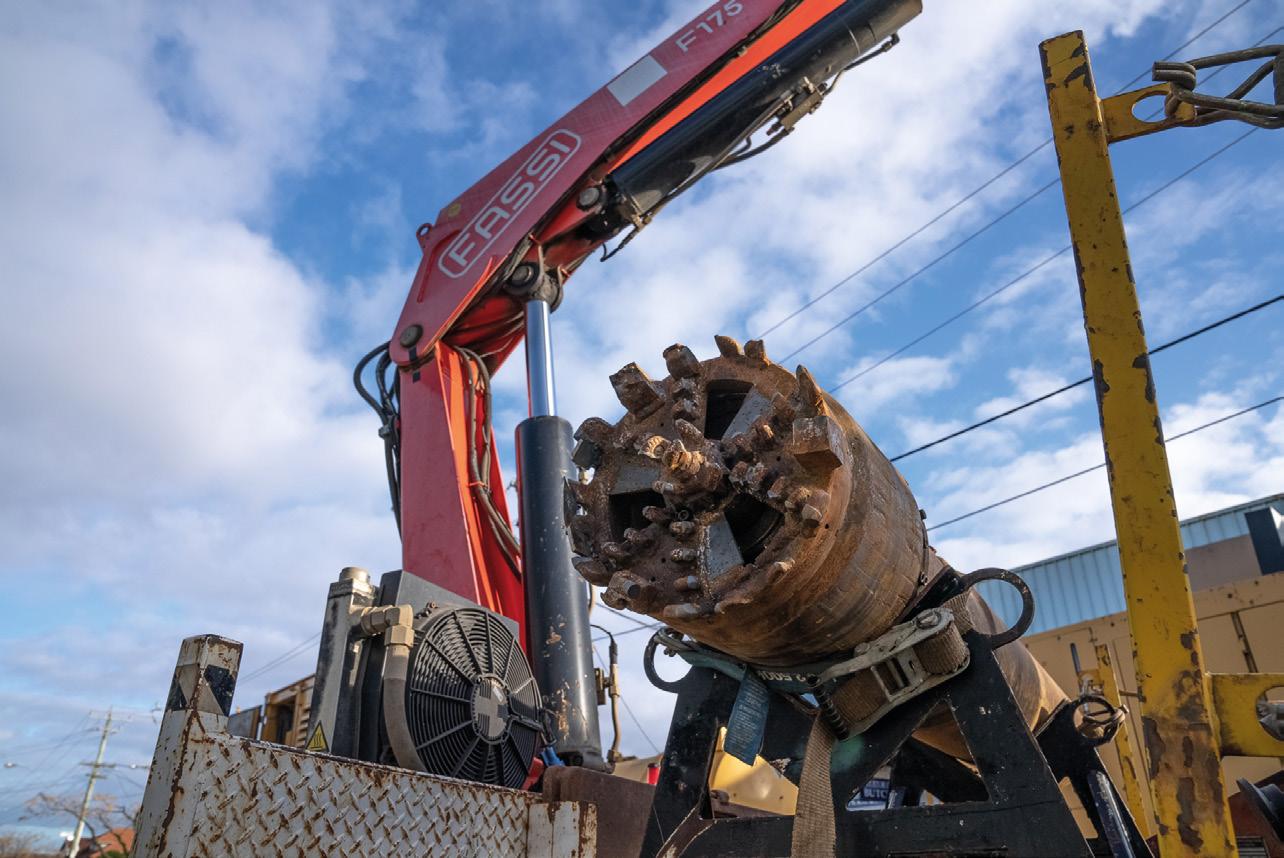
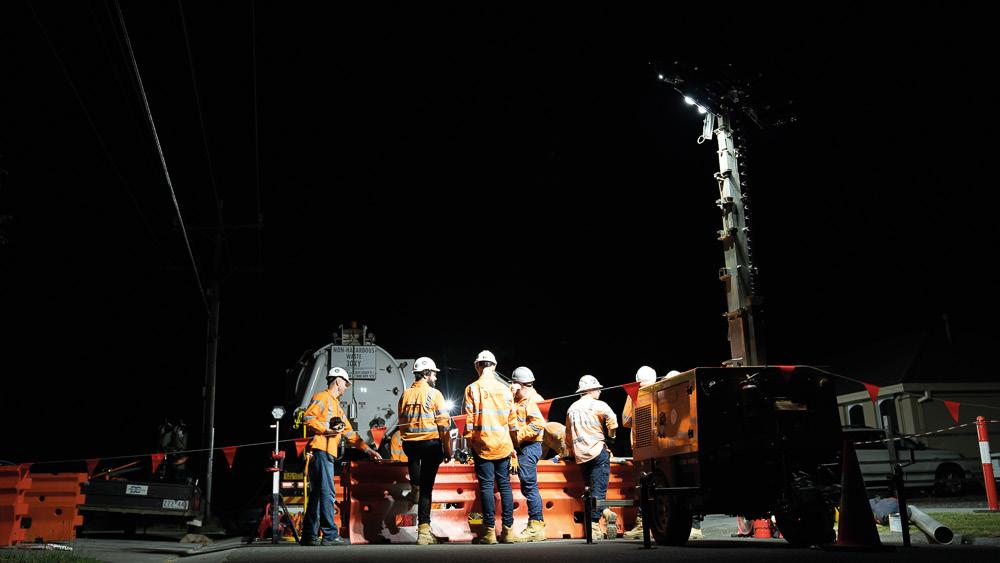
MEDIUM VOLTAGE SOLUTIONS THAT ARE BUILT TO LAST
NHP’s medium voltage (MV) products and solutions include a range of switchgear manufactured in Belgium by its quality manufacturing partner Switchgear Company (SGC), transformers manufactured in Italy by Trafo Elettro, and customised kiosk solutions manufactured in Australia by NHP.
The MV switchgear is high quality and packed with safety features. The range consists of the DF-2 and DF-2+ air insulated panels and the DR-6 and DR6+ gas insulated RMUs.
NHP’s MV transformers include both cast resin and oil immersed types, which can be supplied enclosed or unenclosed. NHP can also customise kiosk solutions, including full MV/LV kiosks, outdoor enclosed MV switchgear substations and outdoor rated enclosed transformers.
Coupled with a local, experienced, customer centric team of MV experts, NHP excels at providing project solutions that focus on safety for people, reliability of product, availability of power, compliance to standards, and customisation of solutions to meet customer needs.
Features and benefits of NHP’s medium voltage range include:
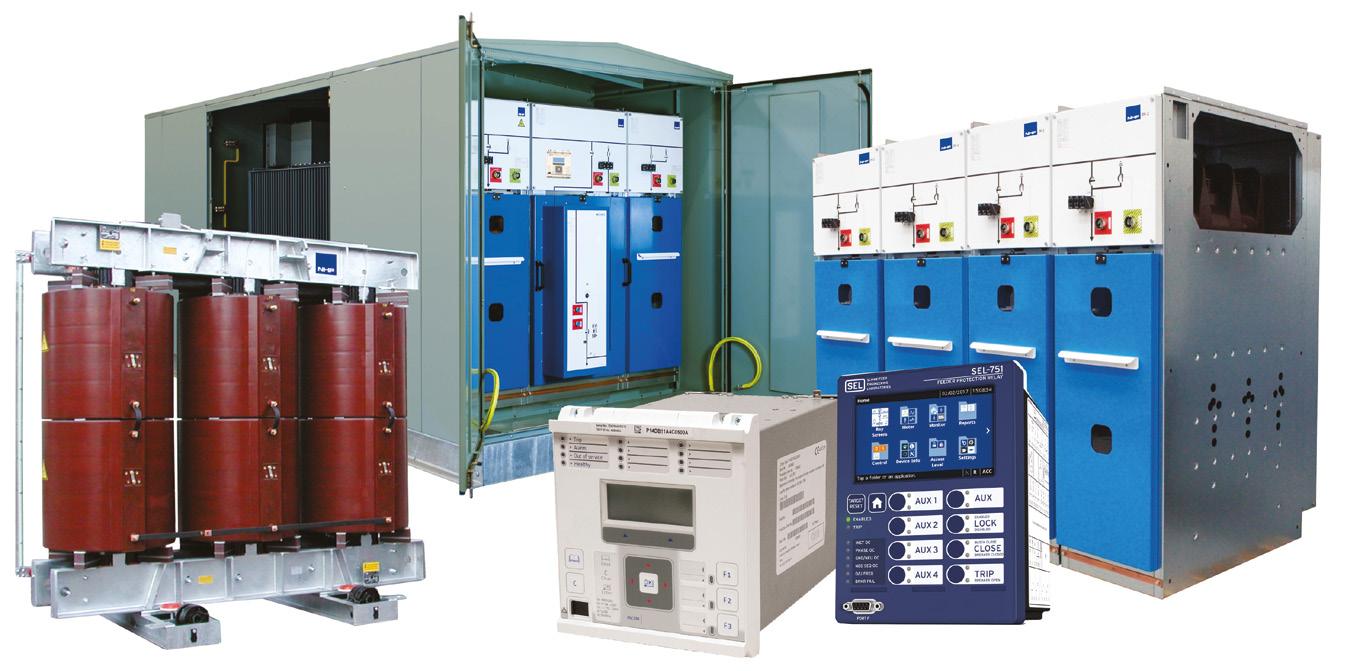
♦ ‘Arc-Killer’ quenching system quenches an arcing fault in less than 50ms
♦ Visible earth switch and in line isolation
♦ Highest levels of safety when testing cables
♦ Cast resin transformers with arc mitigation by design which reduce the risk of fire
♦ No need to externally vent arc fault gasses
♦ Switchgear with a 50-year design life
♦ Modern vacuum switching and load break technology
♦ Proven performance
♦ Sets a new standard for reduced partial discharge
♦ Most advanced method in HV winding fabrication
♦ Environmental and climate class tested
A GAME CHANGER IN PERSONNEL SAFETY
NHP’s DF-2+ MV air insulated switchgear (AIS) panels feature a unique arc quenching system called the ‘Arc-Killer’, which can quench an arcing fault in less than 50ms. Such a fast arc fault clearance rate not only protects people from danger but also protects the switchgear panels from damage, ensuring maximum power availability.
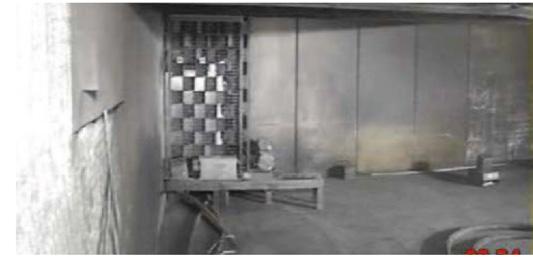
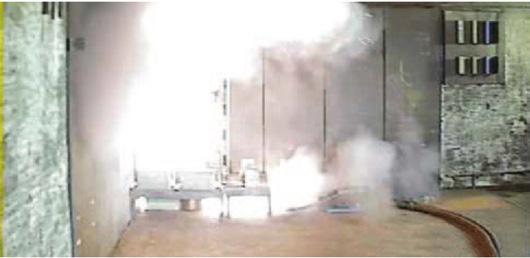
Furthermore, the DF-2+ panels include a visual earth switch to provide maximum safety for electrical operators and maintenance staff. DF-2+ switchgear panels have achieved a substantial install base over the last ten years, becoming the product of choice in many applications including airports, water treatment plants, defence, mining, hospitals, food and beverage, manufacturing and many more.
The DF-2+’s modular design allows simple and custom-made combinations of MV cubicles to be created, which are suitable for primary and secondary MV applications. The combination of cubicles is unlimited, so very complex diagrams of distribution and transformer switchgear can be compiled through the endless spectrum of possibilities.
DF-2+ WITH THE ARC-KILLER PROVIDES A MARKET LEADING B-FLR INTERNAL ARC CLASSIFICATION
Most MV switchgear on the market today will offer an ‘A-FL’ internal arc classification. This means the ‘safe’ boundary to the front and lateral side of the panel is 300mm. Obviously for HV operators or maintenance staff, this is not a practical working distance.
However, DF-2+ panels have an internal arc classification (IAC) to category B, FLR 20kA 1 s. (F = frontal, L = lateral, R = rear) which provides a safe working boundary of 100mm. As a result, the operator is protected against the consequences of an arc, whether they stand in front of the switchboard, next to it or behind it, allowing a truly practical working distance.
For more information, please contact your local NHP Account Representative on 1300 647 647 or go to nhp.com.au/MV
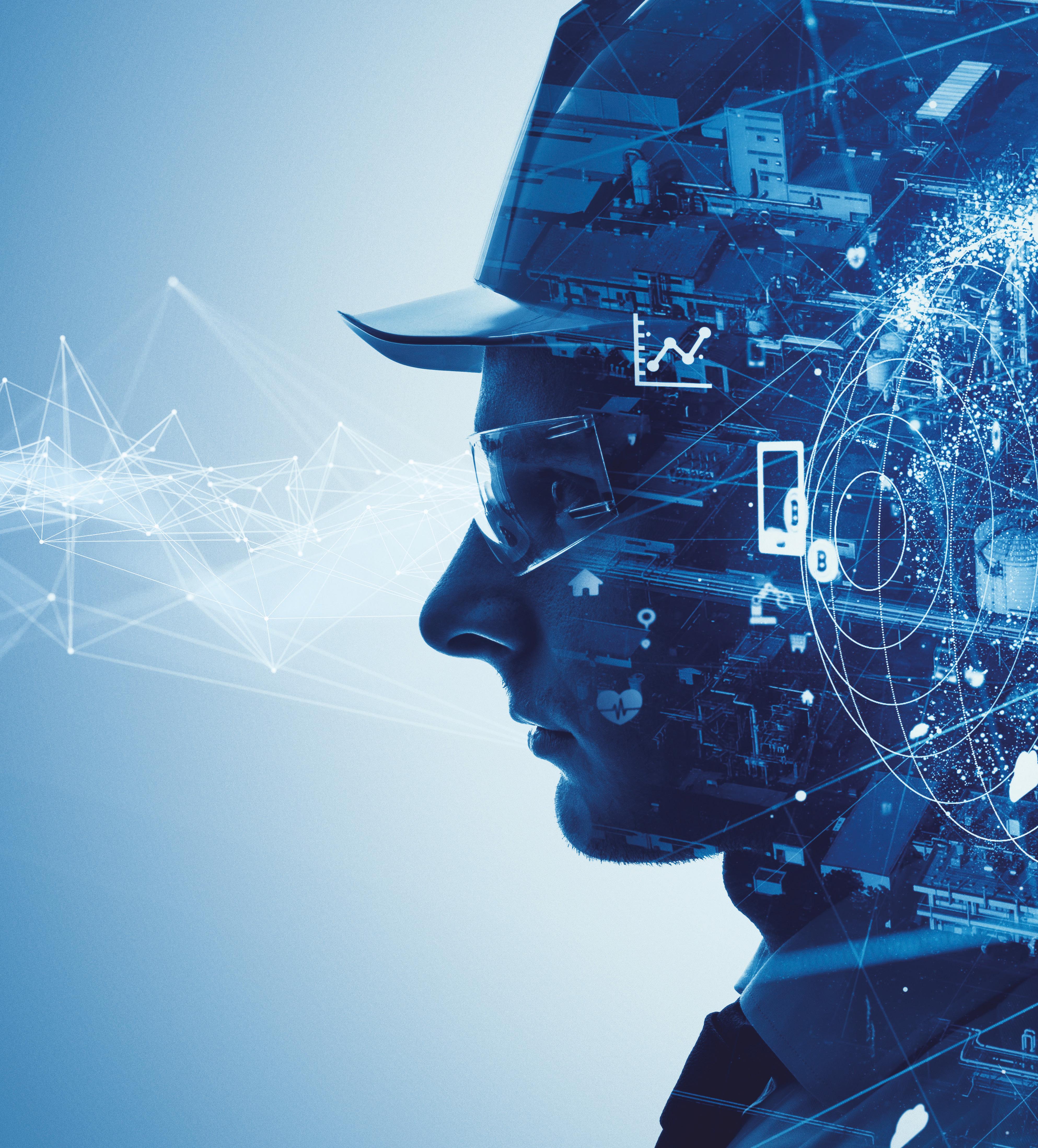
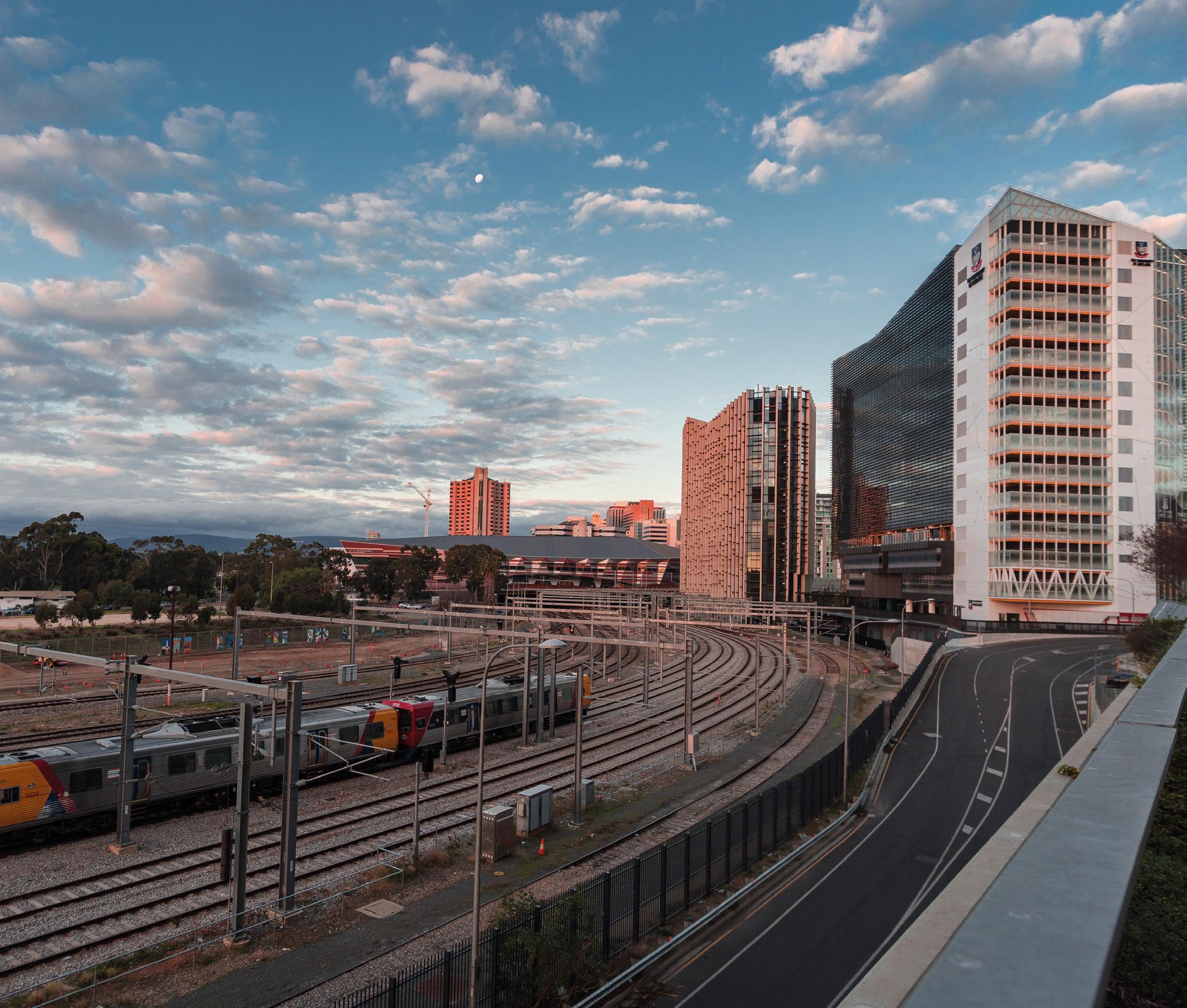
THE DISCUSSION SHAPING THE FUTURE OF TRANSPORT

This is particularly important as the population grows and consumer behaviours change.
For Australia to thrive, we need a robust and reliable transport system, adjustable to the unknown and ready to meet the demands of the future.
By Romilly Madew AO, Chief Executive Officer, Engineers AustraliaAustralia’s transport system underpins our economy and the wellbeing of our communities. It’s vital that there is continued investment to provide safe, sustainable and efficient movement of people and freight throughout Australia and the world.

So how do we move the dial? As a starting point, greater collaboration will be needed between policy makers, planners, engineers and governments to ensure we are moving towards a shared vision of the future.
This vision needs to be bi-partisan, have consideration of the challenges and opportunities, and needs land-use planners, transport planners, engineers and others, collaborating to help lessen the reliance on inefficient transport modes and creating more locally sustainable communities.
There are nearly 20 million vehicles registered in Australia with 20 per cent of these registered as freight vehicles. In addition, Australia has some of the world’s busiest domestic air travel routes and being that we are an island, has a heavy reliance on ports. Transport
in Australia accounts for over 18 per cent of Australia’s greenhouse gas emissions. This includes emissions for the combustion of fuels by road, rail, aviation and shipping. In addition to this, the built environment globally accounts for 40 per cent of emissions annually. Reducing emissions in the transport sector will be needed to help Australia reach the legislated emissions reductions targets, which include a 43 per cent reduction on 2005 emissions levels by 2030 and net zero by 2050. Technological advancements will play a part, however future projects will need to focus on the impacts of climate change, and how sustainability and resilience principles will be embedded. Planners and engineers will need to come together to build communities which lessen an individual’s need to travel and for necessary travel, pivot the system away from a heavy reliance on less efficient transport modes, such as cars. Achieving this will require collaboration, a greater use of technology, social engineering and a bold vision for what can be, rather than what has been done.
MANAGING THE TRANSPORT SYSTEM HOLISTICALLY
Engineers Australia’s Future of transport discussion paper puts forward ideas on how this can be achieved to elicit discussion and shape a way forward for the sector. Better use of urban informatics, developing land as mixed use, integrating and prioritising more efficient transport modes, and planning and modifying streets and neighbourhoods to be more connected are some areas identified which should be prioritised. Land development plans may currently exist; however, they don’t always provide sufficient attention to the transport networks and funding required to connect these developments. Systems engineering principles also need to be applied. In many cases, projects are currently planned incrementally, instead of being viewed as a component of a greater system. Utilising a systems approach will aid in planning and managing the transport system in a holistic manner. By applying systems thinking the network is examined as a whole, understanding the relationships and

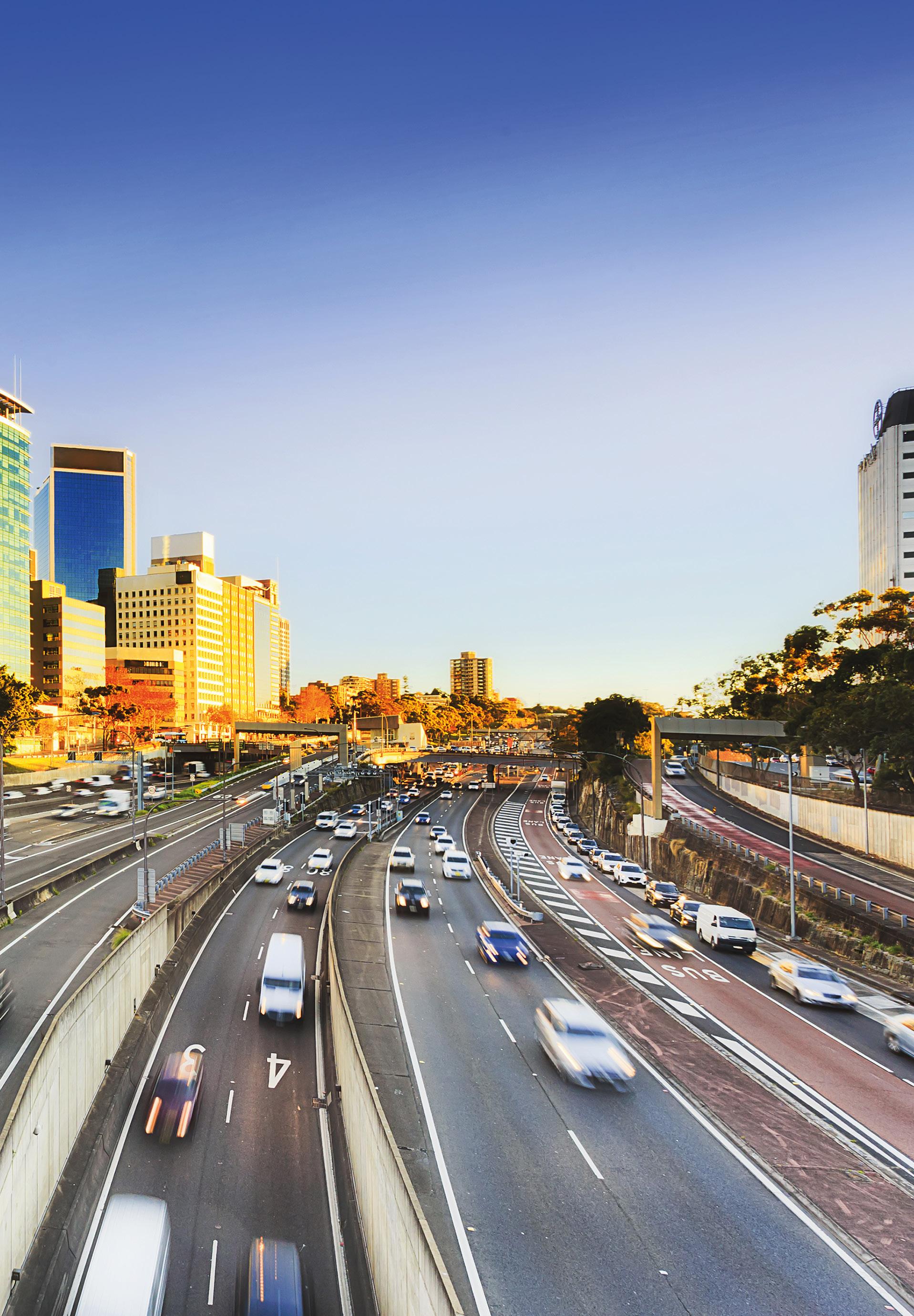
interconnection between transport modes, infrastructure, the community, government policy and regulations. It will further allow for consideration of all the stages of the systems lifecycle, from design through to construction, operation, maintenance and decommissioning. This is particularly important as we move to a more sustainable infrastructure sector and transport system.
In conjunction with this, the transport system will be aided and challenged by rapidly changing technology. Engineers will be at the forefront of this, both developing these new and emerging technologies, whilst also integrating them into the system. Take micromobility for example. Integrating micromobility into the system has multiple benefits. These new modes are shifting the first mile/last mile conundrum often facing planners. Integrating them will also require a change in transport infrastructure which can have positive
effects on society if designed and integrated correctly.
APPLYING UNIVERSAL DESIGN PRINCIPLES
Another area identified was the importance of embracing the concept of universal design, supporting planners and engineers to help to future proof the system. Universal design allows for more equitable participation in the transport system and therefore should be embraced to allow for the creation of environments which can be used by more people. The theory of universal access allows for a system which can be used by everyone taking into consideration the needs of people with disabilities and other mobility challenges as well as financial constraints and those who face additional socioeconomic barriers.
The benefits of applying universal design principles is that it improves people’s quality of life and their
independence. It can also facilitate a system which can integrate more modes of transport. For example, the integration of micro-mobility mentioned previously. In some instances, this will require more spacious pathways, ramps and a focus on safety by design. This has benefits for parents with prams, greater wheelchair access and mobility devices used by the elderly. This is just one example of how applying a systems thinking approach, collaborating, being more inclusive and designing based on future trends, can benefit the system. Engineers will be at the forefront of the future of transport in Australia. Through greater collaboration, new funding models, better integration of technology and by viewing transport as a complex and interrelated system, we can ensure transport continues to contribute to Australia’s economic and social prosperity.
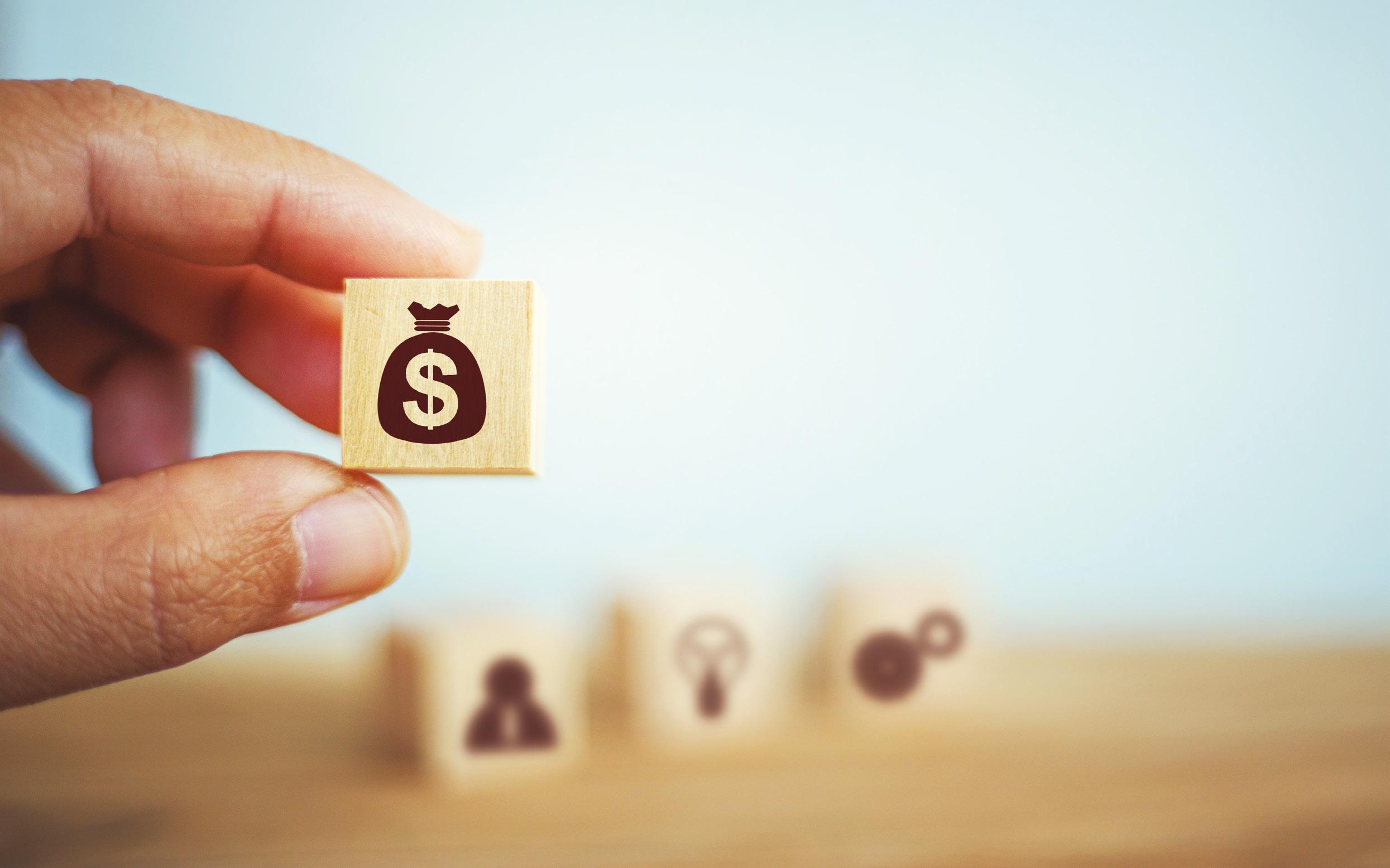
WHAT ARE YOU REALLY WORTH?
By Ben Townsley, Managing Director, PronamicsThroughout the Australian infrastructure industry, companies are managing billion-dollar contracts yet going into administration due to poor risk mitigation and cash flow management, so job security is no doubt always in the corner of your mind. If you’re an estimator, you can easily get a new job, but are you getting ahead?
You’re worth more than your hourly rate. Achieve more, earn more and enjoy industry recognition without having to work more by using exceptional estimating software. Then the only thing you’ll be doing more of is enjoying life.
REACH YOUR GOALS
Estimators that become industry leaders are the ones who acquire skills and experience. They get the best positions and compensation because they leverage their tools and global network to create profitable opportunities for their company. They also work smarter, not harder, so they maintain a healthy work-life balance – preserving their physical and mental health, and establishing themselves as reliable and valuable team members.
Is becoming a respected, coveted and well-compensated industry specialist part of your career plan?
DON’T BE HELD BACK
It’s scary to think that there are estimators doing multimillion-dollar calculations in repurposed, unsuitable software, putting their fate in the hands of aging, unsupported and unmaintained applications, or even stitching together old spreadsheets to create a tender for submission. Pronamics has seen how those who cling to familiar yet inefficient ways end up paying for it – mentally, personally, financially and professionally. Is your software impeding your success?
CHOOSE WISELY
Companies that attract and retain good estimators are the ones that value them. They give them the tools, training, support and experience needed to grow and succeed. Key
decision-makers partner with companies who uphold their commitments when delivering products and services to their most valuable resource – their team.
The software estimators use is no exception. Security, accuracy, clear workflows and configurable reporting are essential. Within the application’s ecosystem there must also be comprehensive support offerings, dynamic multi-user systems to support flexible working arrangements and accessible opportunities for users to upskill.
Development must include industry collaboration and upgrades released to align with industry trends. In a world where cost management is critical, the software must also be affordable. Have you chosen your estimating tool wisely?
WHY CHOOSE EXPERT ESTIMATION?
More than 30 years ago Pronamics’ founder, an experienced and well-respected estimator, provided estimators with the first purpose-built, accurate and affordable estimating software on the market. Now, with over three decades of comprehensive industry use and feedback, Expert Estimation has evolved into one of the world’s most powerful, professional and versatile estimating applications.
Since then, Pronamics has been transforming ‘mehstimators’ into expert estimators. The philosophy ‘more done – more fun’ permeates every aspect of the user experience. Partnering with Pronamics means you will have access to exceptional software. You’ll also enjoy unrivalled personalised support, an exclusive professional network and incredible career opportunities.
Pronamics has the tool and the team to make your measurable outputs spectacular. Time to find out what you are really worth.
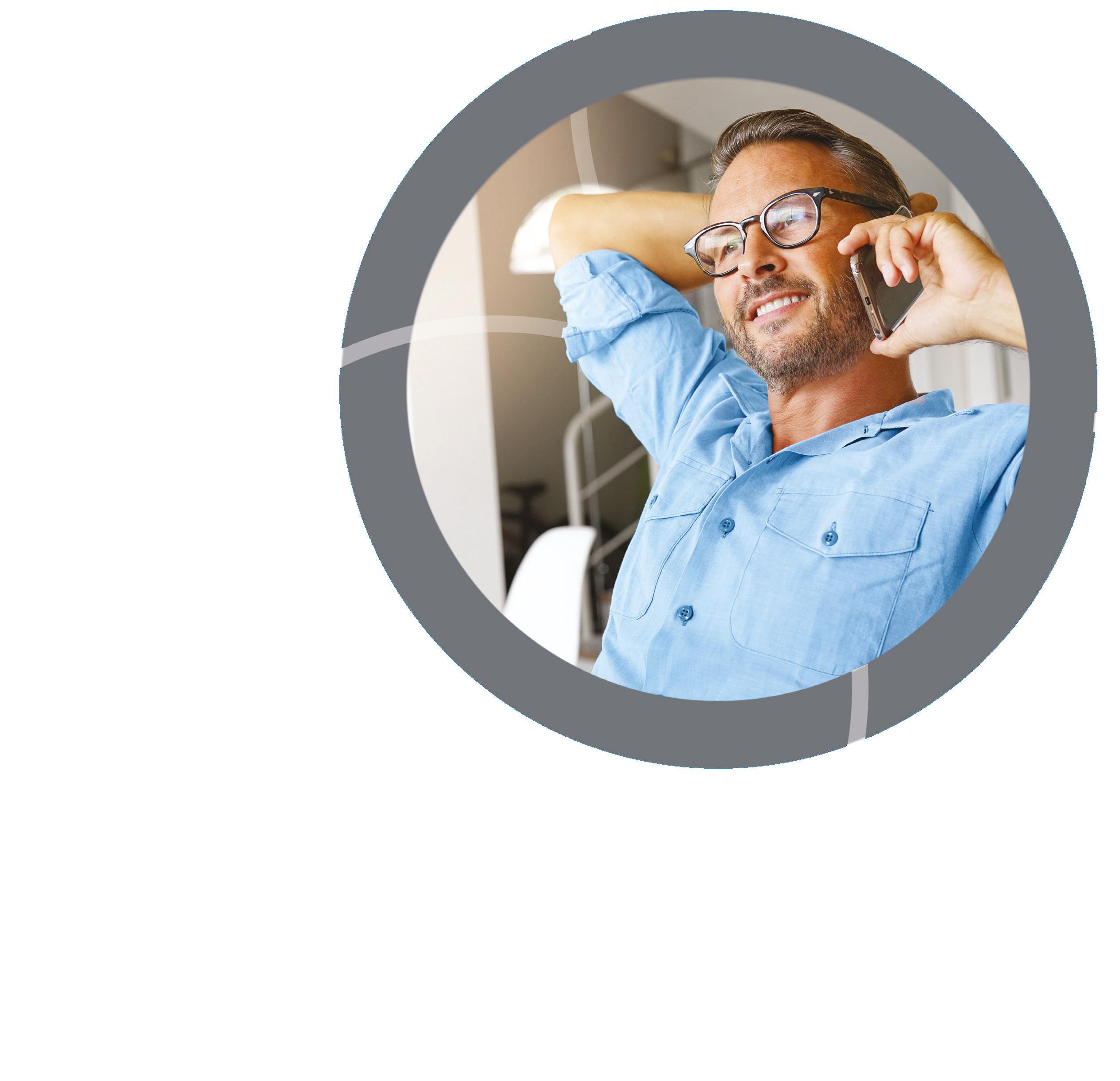
Software solutions for Australian infrastructure.
Pronamics Expert Estimation delivers both power and flexibility to make tendering simpler. Use a range of approaches to create complex, transparent, reportable and repeatable estimates.
CLEAR WORKFLOWS
Navigate from the building blocks of your tender through to the final dollar figure, then produce transparent and customisable reports.
TEMPLATES AND FORMULAS
Save time by replicating existing projects and modifying for current tenders. Tried and tested formulas reduce risk of error.
MULTI-USER COLLABORATION
Work remotely as a team and share project data easily and safely, with configurable security and permissions.
MANAGE SUPPLIER QUOTES
Accurately compare supplier pricing for goods and services and get a true idea of the costs involved.
SCAN TO LEARN MORE
Start your 30-day free trial and find out how Expert Estimation can make your life easier.
TO WEATHE R THE STO R M, WE MUST r EFOR M
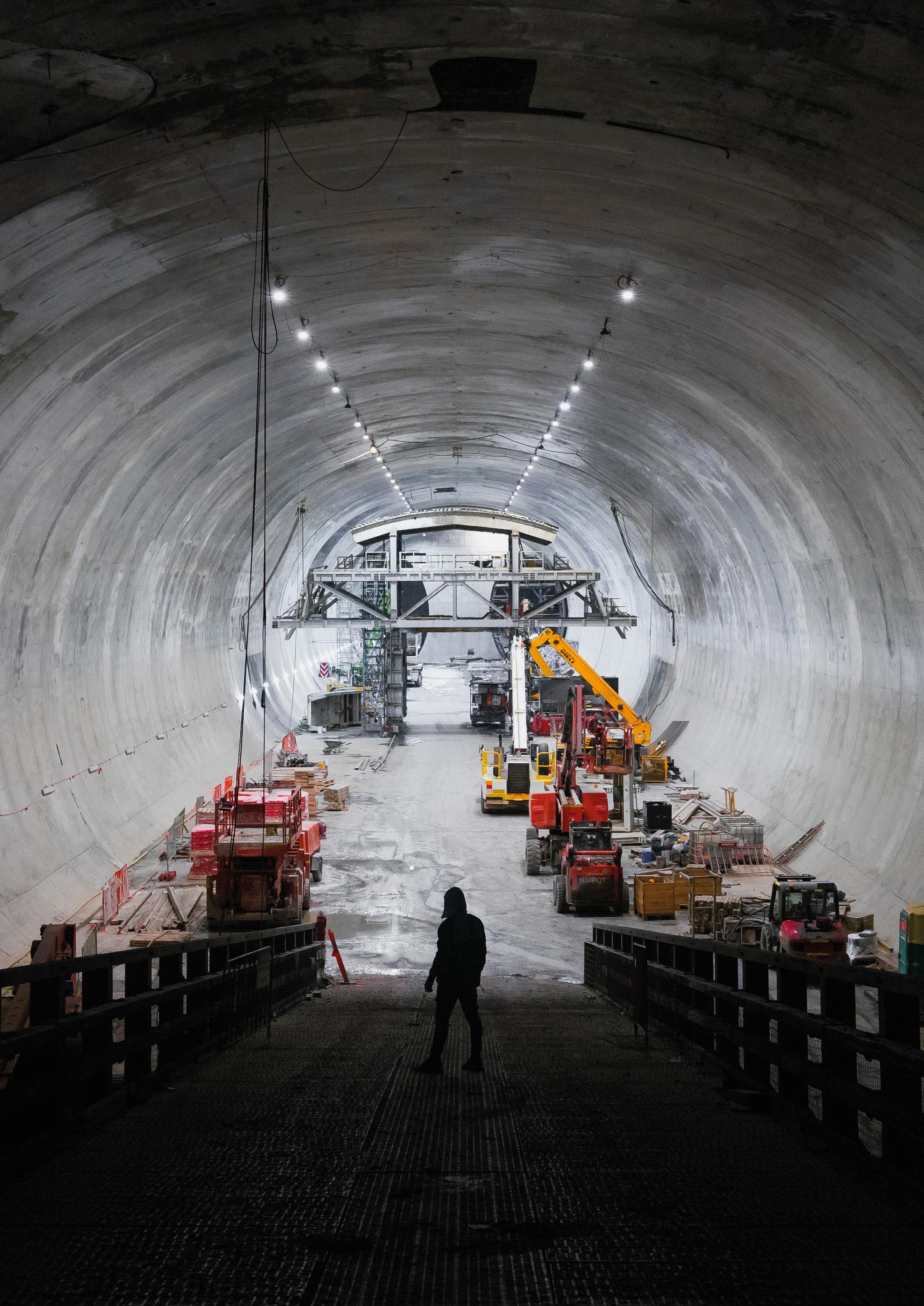
It’s no secret that these are challenging times for many organisations engaged in the delivery of infrastructure across Australia. Over the past year, a multitude of negative pressures – any one of which would in themselves represent a major issue – have combined to produce a storm of such force that parties of all sizes across the industry are feeling the effects.
Because COVID-19 has now dominated the economic narrative for three years, the temptation from some commentators is to look upon the conditions now afflicting the sector as entirely a product of the pandemic. But that misses something more fundamental.
Yes, some of the inflationary pressures and labour shortages in the economy have been exacerbated by COVID-19. However, to lay the blame entirely at the feet of the pandemic overlooks some of the industry’s other structural weaknesses.
Recent economic analysis of the industry (including by Deloitte) has specifically called out the need for additional flexibility in contracts and for collaboration over combativeness, particularly in the allocation of risk.
These issues were present long before COVID-19, and unless industry and governments can deliver some fundamental reform, they will endure long after the pandemic recedes into memory.
Indeed, the year before the start of the pandemic, RA and its members identified that serious and major issues in the way transport projects are delivered needed to be remedied. This is essential if Australians are to get best value for money and best project outcomes for the investments being made.
These critical issues included risk definition and allocation, increase in project size and complexity, lack of visibility of a long-term pipeline of work, inadequate timeframes to assess risks, inadequate time in the design phase for innovation and improved design solutions, inadequate engagement between governments and industry during the design stage, and deficient education and immigration approaches to provide the required workforce skills and diversity in the workforce for the industry.
THE INDUSTRY’S MOST PRESSING ISSUES
RA produced its first Procurement Reform Report: Recommendations and Strategies in September 2020, which identified some of the ‘green shoots’ being seen in procurement reform across several states and territories. That report made a series of recommendations as to how governments and industry could collaborate to drive further reform and put the sector on a more economically sustainable pathway.
Of course, much has changed since September 2020. Most notably, there has been a substantial deterioration in both the economic and geopolitical climates, which is having a deleterious impact on the planning and delivery of infrastructure. Significant and increasing supply chain and hyper escalation
challenges including for materials, plant and equipment, and supporting transport logistics are having significant impacts on the way contracting is undertaken. Added to this are labour supply challenges, with Australia at near-full employment leading to worker and skills shortages across the market.
With these factors in mind, RA convened workshops in the second half of 2022 to consider, update and (where necessary) recalibrate some of the initial report’s recommendations to reflect this new reality. This resulted in RA’s Procurement Reform Report Update: Momentum for a sustainable transport sector, released in December 2022.
The update report calls attention to the most pressing issues now confronting the sector, such as:
♦ Cost escalation, foreign exchange rate volatility, and hyper-inflation for construction materials and manufactured items
♦ Increasing pressures on wage and labour costs

♦ Often unreliable timeframes for the tendering process and inconsistent approaches to bid cost reimbursement
♦ Lack of skilled resources with near full employment and low skilled migration levels
♦ Difficulty in adopting innovation, including the use of new methods and recycled materials within the existing contracting approach
♦ Access to, and cost of, professional indemnity and project insurances and inappropriate cascading of requirements to project partners, including principal arranged insurance
♦ Increasing importance of visibility of operations and maintenance pipeline and the need to reform procurement in this area in line with capital projects
♦ A more collaborative approach is needed for appropriate risk allocation and mitigation between clients, contractors and subcontractors
While these issues aren’t necessarily unique to the delivery of transport infrastructure, the cost of inaction in this sector will have widespread ramifications for stakeholders.
For governments, the risk lies in an inability to deliver the planned transport infrastructure for the community.
This increased uncertainty around real project costs and timeframes will ultimately lead to a loss of confidence from the community in project planning and delivery.
For industry, inflexible contract arrangements, unrealistic risk allocation and unsustainable cost pressures are leading to increased risk of business failure, reduced investment in resources and career opportunities for the workforce. Without reform, we risk withdrawal of more industry players from the sector and all the associated economic and well-being consequences that flow from that.
For the wider community, the ongoing risk is that the full value of the transport infrastructure investment made via their tax dollars is not realised, due to planning and delivery practices that are no longer fit-for-purpose.
ENHANCED PRODUCTIVITY GROWTH RECOMMENDATIONS
The updated report provides a realistic and comprehensive reform pathway that will drive better outcomes for all these parties by incentivising collaboration, reducing adversarial approaches and allowing the community to get the best value for money and the best project outcomes for the investments being made.
Importantly, the report also provides concrete examples of good practice and innovation in procurement that are already being delivered by industry, to help promote knowledge sharing and stimulate the development of creative and truly collaborative solutions.
RA’s recommendations are all centred around enhanced productivity growth in the sector by:
♦ Encouraging more collaborative approaches to contracting and risk allocation
♦ Reducing regulatory barriers to innovation
♦ Embracing circular economy opportunities to improve sustainability
♦ Ensuring that industry training programs are equipping our workforce with the right skills
♦ Improving the wellbeing of our workforce by sharing knowledge and successes in initiatives that improve industry culture
Given the challenging conditions that the market now faces, this is the right time to make further progress on procurement reform. A sustainable, productive and successful transport infrastructure sector where the whole industry works together for better outcomes is an imperative. The recommendations in RA’s report will help bring this objective to fruition.

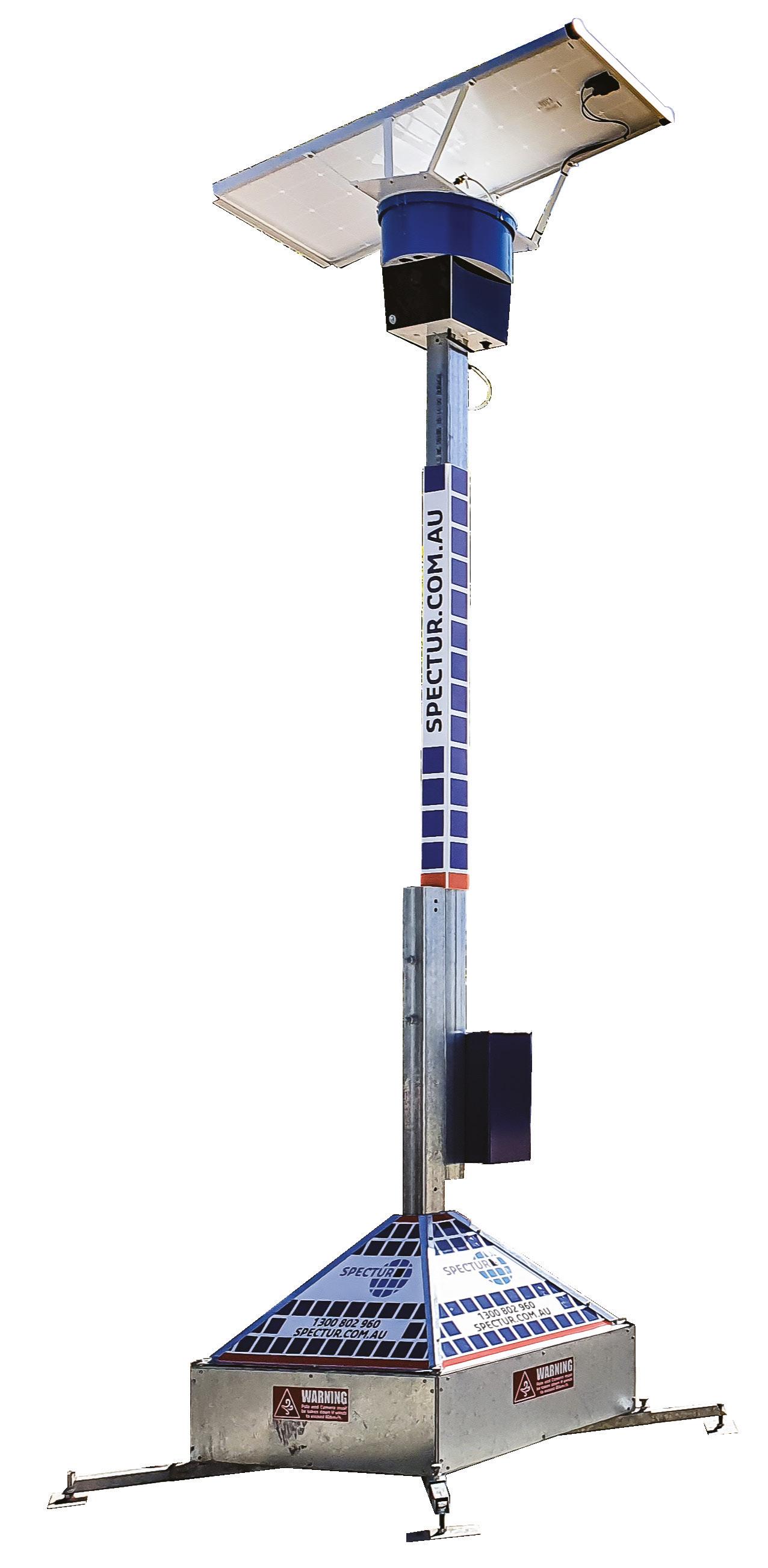
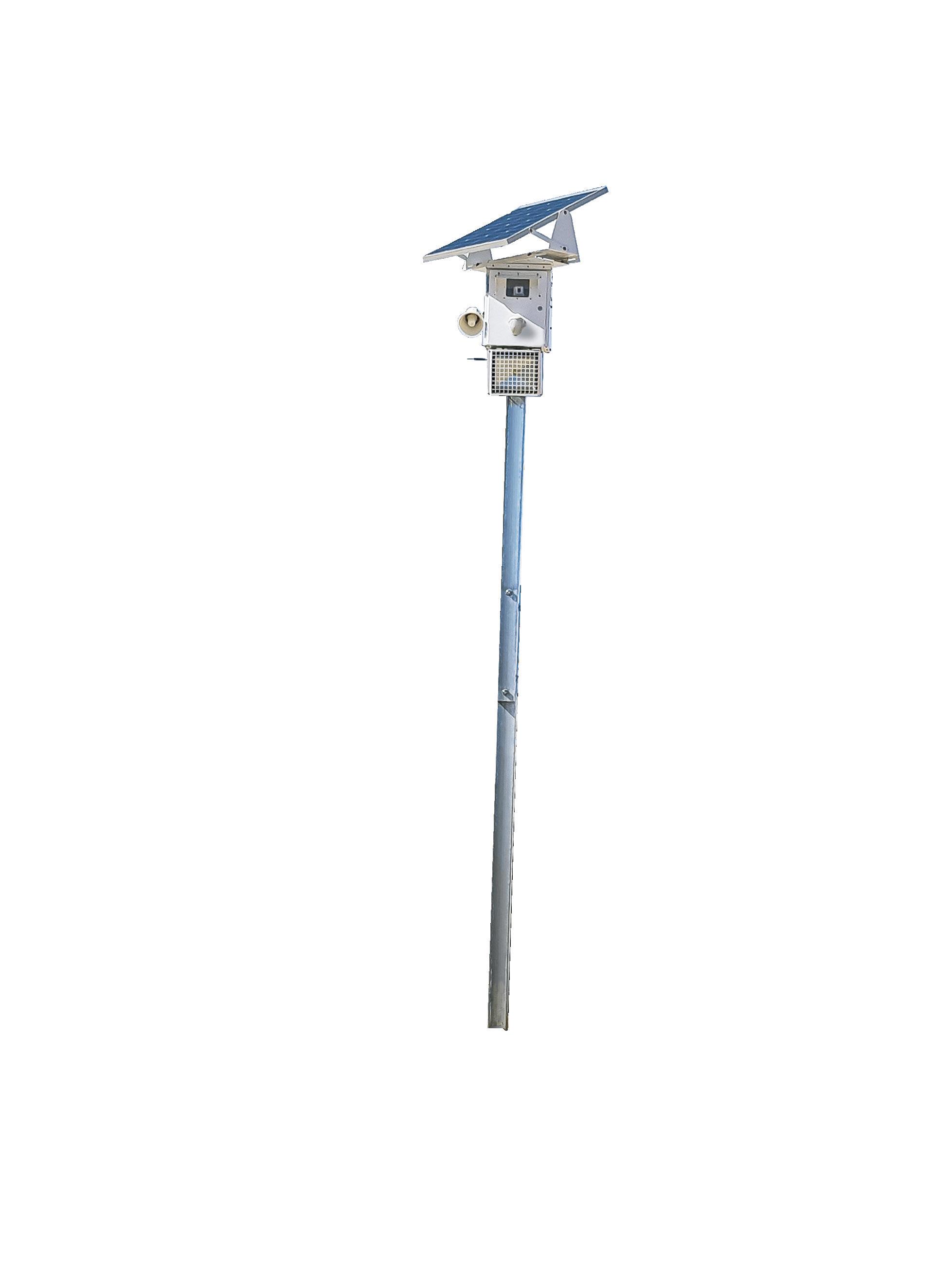
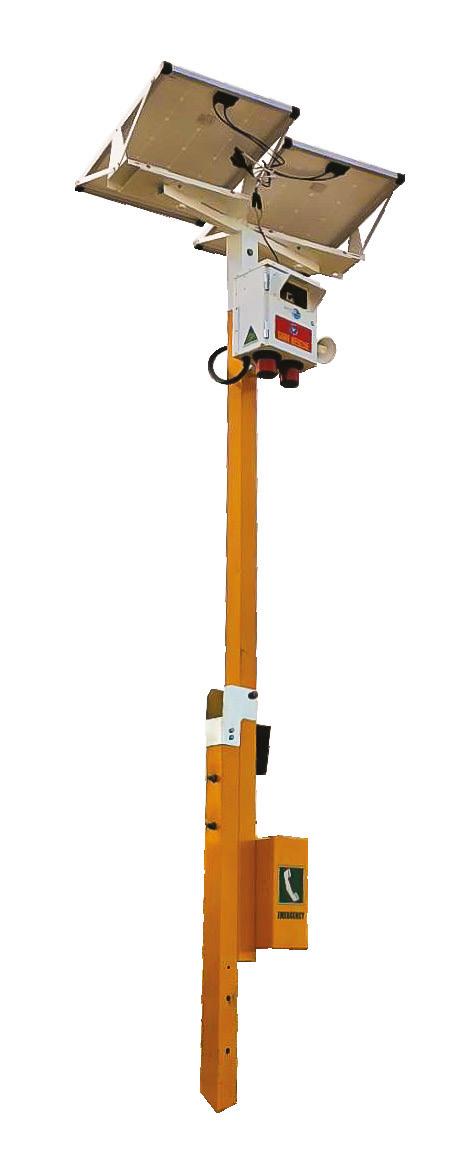
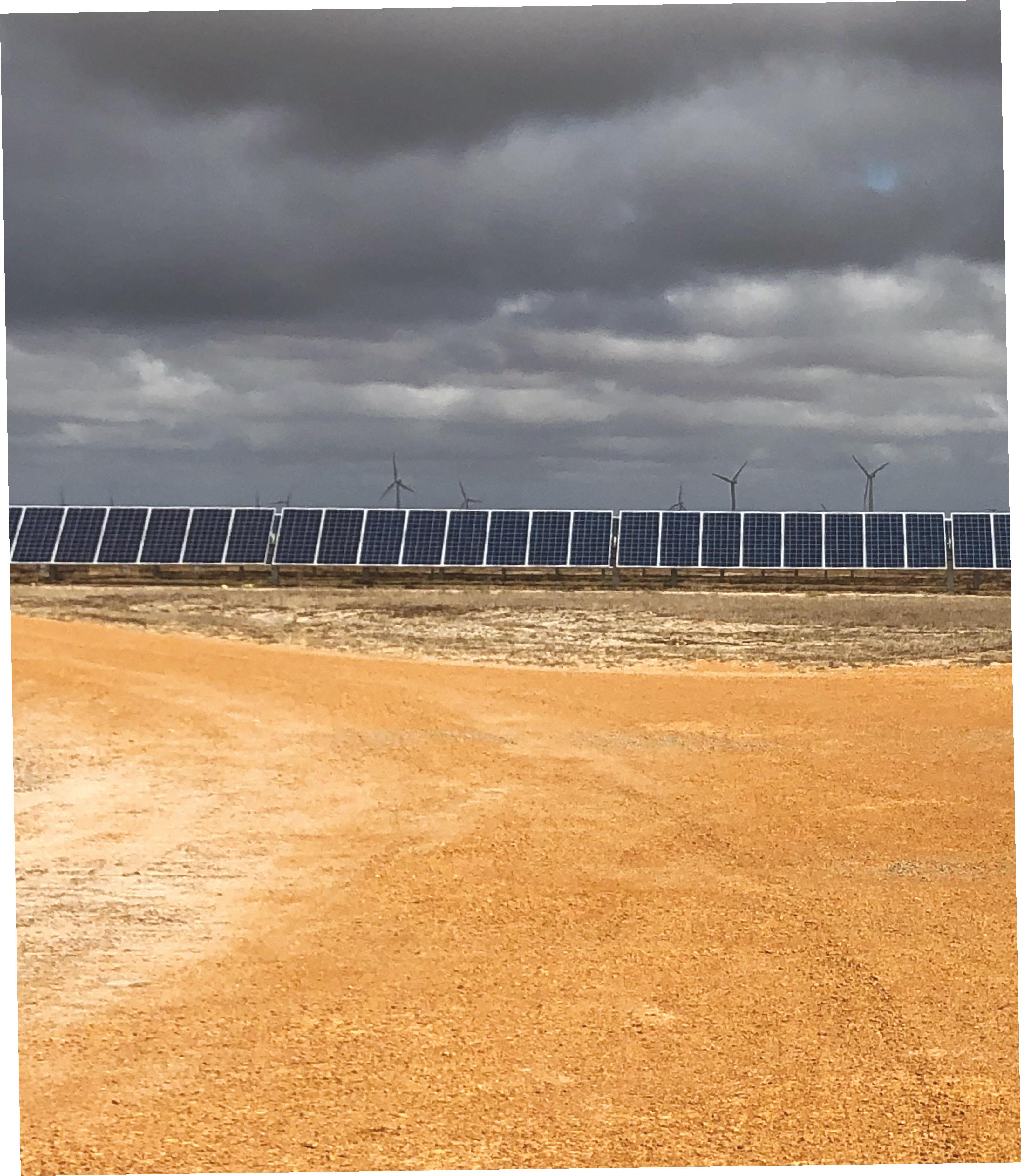
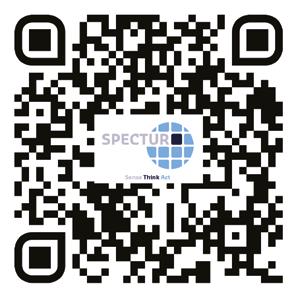
AN INNOVATIVE SEWER ABANDONMENT SOLUTION FOR NORTH-EAST LINK
The early works for Melbourne’s North-East Link project posed a technical challenge: decommissioning the old, recently bypassed sewer pipework below the new motorway. The sewer needed to be filled in a way that removed any risk of collapse once the road was operational.
Running for around one kilometre below Bulleen Road lay a complex series of pipes of varying profiles that needed to be filled with a solid material stronger than the surrounding ground. Achieving this would mitigate the risk of the aging sewer asset collapsing once the motorway was built overhead.
The series of pipes were up to 2.74m2 in cross-sectional area, meaning each metre of length could contain up to 2,740L in volume.
One way to do this was to excavate and remove the old sewers, however much of the pipes’ length lay 20m underground. The pipes also criss-crossed other subterranean infrastructure including gas mains, water mains and telecommunication cables. Plus, the pipework ran directly below a very busy road that could not be closed during the day. This meant excavation and removal was not a viable option.
Another method was to create plugs at various points and then pump concrete into the voids, but conventionally placed concrete is not very flowable over long distances and experiences shrinkage (decrease in volume) as it cures. This would potentially create a gap along the top of the fill, meaning the structural integrity and complete abandonment of the sewer pipework could not be guaranteed.
The project required a more effective solution, which is where Mainmark’s vast experience in below-ground utility abandonment came to the fore.
Mainmark is a renowned global leader in geotechnical and asset preservation solutions, specialising in foundation subsidence repairs. Its proprietary cellular concrete material and technical expertise made it the preferred partner for this significant infrastructure project in Victoria.
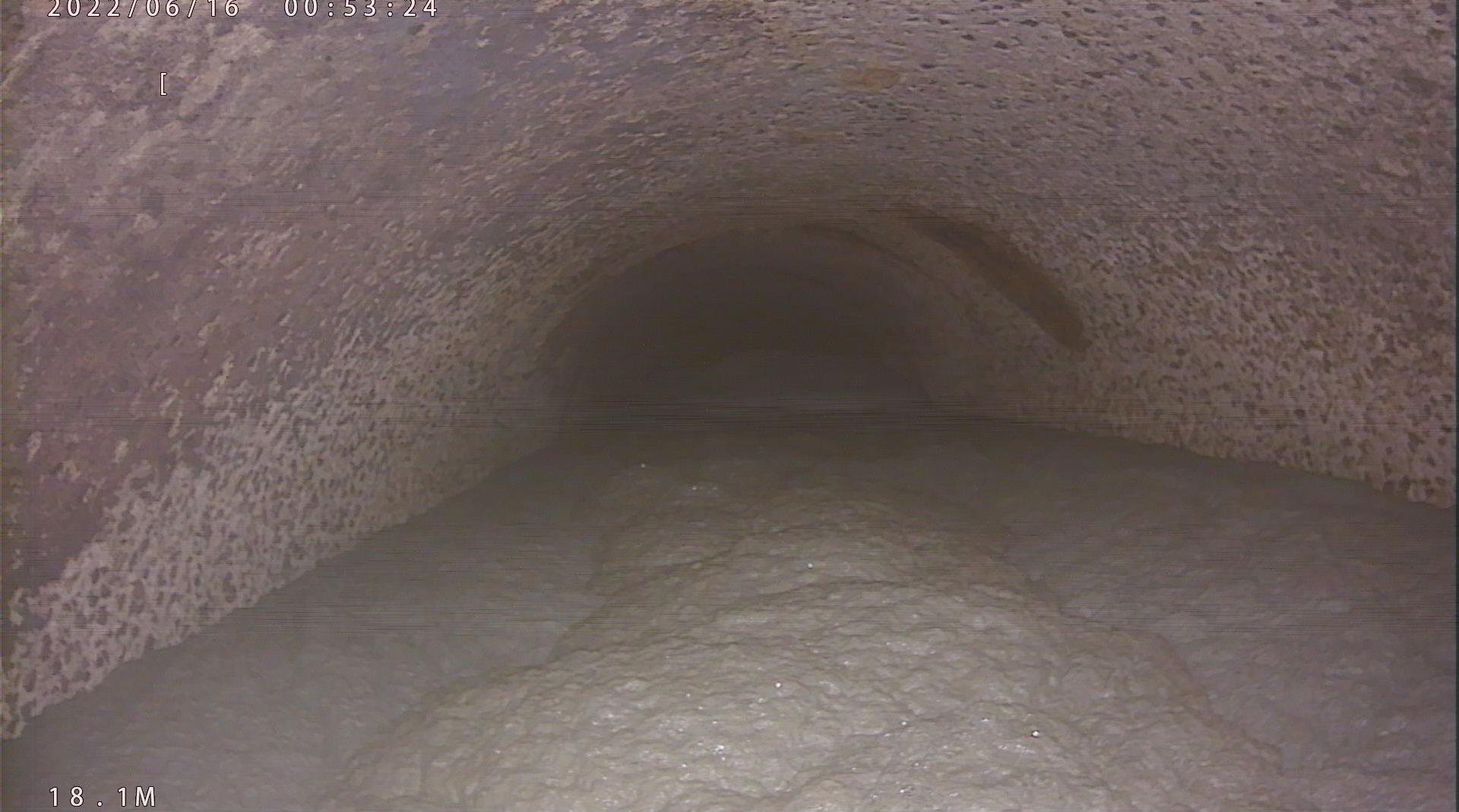
MEETING THE TECHNICAL CHALLENGES
The scope of the project included filling the large sewer main below Bullen Road, as well as the filling of smaller reticulation sewer lines feeding into the mainline, including reticulation manholes.
Max Kudrenko, Mainmark’s Regional Manager (Southern Region), said accessing the pipework was very technically challenging. The concept was straightforward – fill a sewer with grout – but the methodology to get it in there, and be certain that it was full, was the hard part.
“We rolled out every night, six nights a week for about three months, precisiondrilling small, 75-millimetre diameter
holes directly down from the surface. These drills broke into the top of the sewer. Through those holes, we inserted PVC injection sleeves,” Mr Kudrenko said.
Terefil®, Mainmark's proprietary solution of low-density cellular concrete, was injected into the abandoned sewer pipework.
Mr Kudrenko said that on site the crew utilised a specialty batching process.
“Conventional concrete agitators come to site delivering a water and cement slurry, and we then introduce specialty treated engineered surfactant into the slurry to produce Terefil®. It develops properties that make the material very suitable for backfilling of voids or pumping very long distances, as well as producing a lower density material,” Mr Kudrenko said.
However, for this project, the concrete batch plants were unable to supply the site with cement slurry. Supplying such a project with the quantities required overnight would negatively affect their day-to-day capabilities.
“So, in what was another small, technical triumph, we ended up utilising a volumetric mixer. That meant every single night we essentially had a mobile concrete batch plant, rather than agitators, on site,” Mr Kudrenko said.
“The Terefil® fills more volume with less cement, so it’s more cost-efficient and has a smaller carbon footprint. It’s aerated, so the final compressive strength is not as high as concrete, but the result is still much stronger than the surrounding soil, which the client required.”
RESULT: A QUALITY-ASSURED FINISH
Not only did Mainmark enable the project to surge ahead without risk of ground collapse, it also boosted the client’s confidence in the result with a clear and measurable quality assurance process.
“Throughout the works, we had an inspection test plan that outlined conditions to be met. Every 20 minutes of each shift, we took density samples to ensure the ingredients for the Terefil® were at the correct levels. We constantly measured each ingredient, too,” Mr Kudrenko said.
“We had a live video feed of what was running through the grout line and into the sewer pipe so we could watch what was happening in real time. That also offered video footage as documentation of the material filling to the crown of the pipe."
“We’d also regularly collected samples from the sewer pipe itself, after the Terefil® had been pumped in, to ensure what arrived in the pipe was the correct mix.”
During every shift the Mainmark team would collect test sample cylinders of the product being placed underground.
“Those samples were tested by an independent, third-party lab to prove that, after 28 days, the Terefil® had hardened to the specified strength,” Mr Kudrenko said.
The Mainmark team spent a great deal of time developing a methodology to ensure the work would be completed on time and within budget amidst the various technical, engineering, geological and community-based challenges.
Mr Kudrenko said it was a real testament to his team.
"During project meetings, our team was the only one that identified several aspects that others had overlooked. We pointed out that the methodologies initially proposed were not feasible, as they would have resulted in increased costs and exposure to project risk, instead reducing them." Mr Kudrenko said.
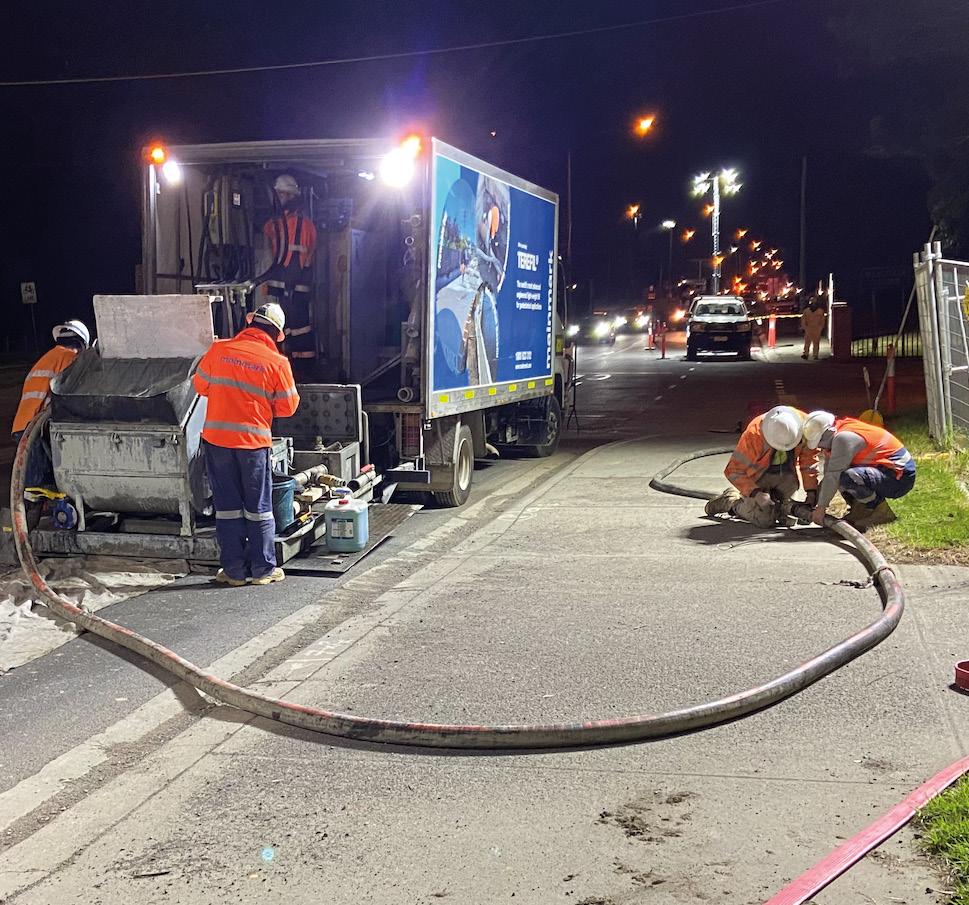
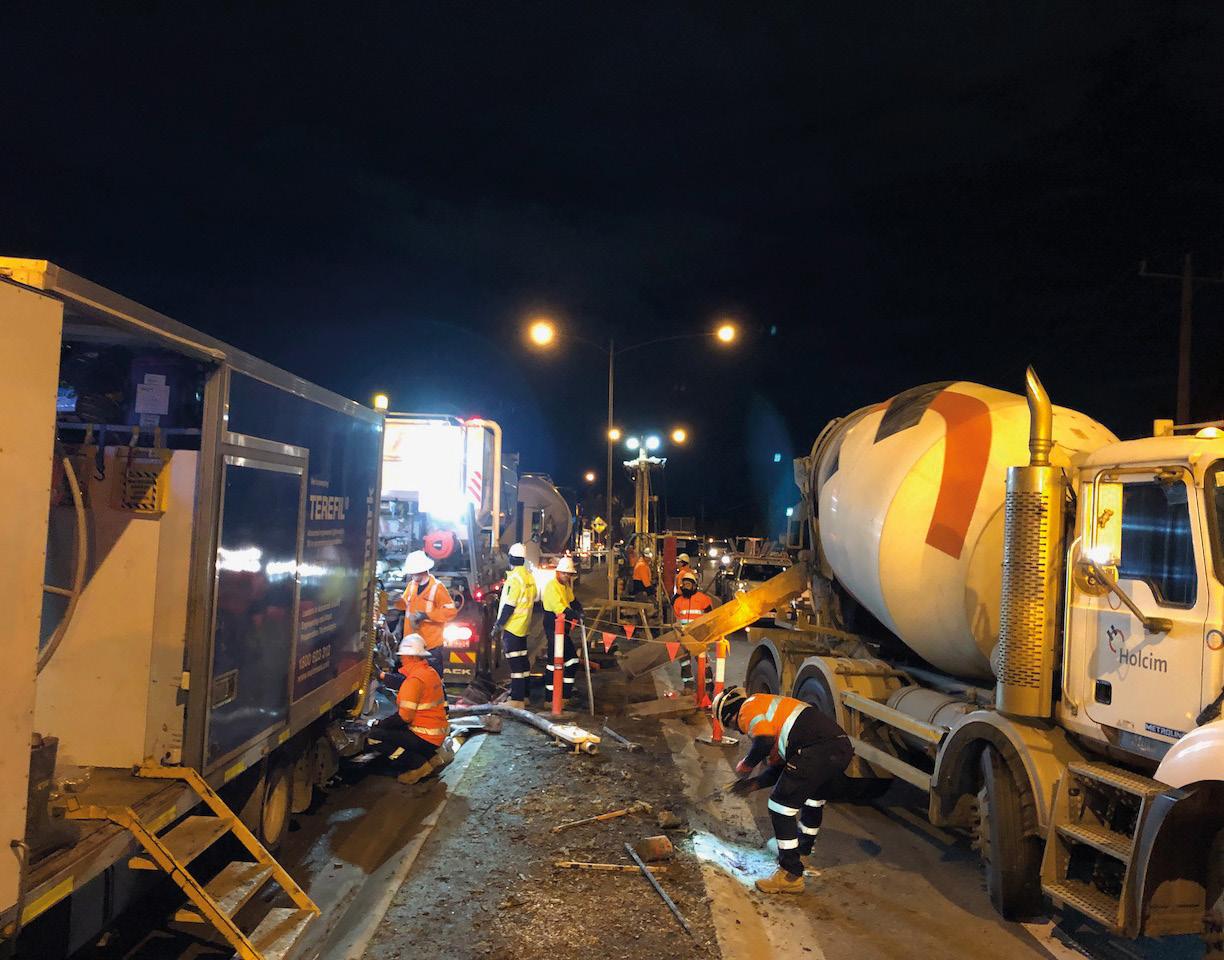
The project in numbers
» 4000 cubic metres, or four million litres, of Terefil® injected
» 60 nights of work
» 850+ metres of sewer pipe filled, including mainlines, reticulation lines, manholes and access pits
» Live testing the quality of the Terefil® every 20 minutes throughout the entire project
» The project was safely completed ahead of schedule and within budget
THE GAME-CHANGING COFFS HARBOUR BYPASS
A multi-billion dollar bypass of the Pacific Highway – a well-known thoroughfare of trucks and tourists – will reduce traffic for the Coffs Harbour community and boost tourism to this jewel of the NSW North Coast.
Transport for NSW North Regional Director, Anna Zycki, said the $2.2 billion bypass was a jointly funded project from the Australian Government and NSW Government that would improve the daily lives of thousands of residents and visitors.
“When complete, the bypass will transform travel in this region by diverting 12,000 vehicles away from the CBD each day and saving motorists around 12 minutes off their trip,” Ms Zycki said.
“This is one of the biggest ever projects in the Coffs Harbour region.”
The contract to build the Coffs Harbour bypass has been awarded to a partnership between Ferrovial Construction and Gamuda Berhad, known for the purposes of this project as Ferrovial Gamuda Joint Venture (FGJV).
FGJV Project Director, Daniel Perez, said it was thrilling to be part of what will be the final piece of the puzzle for the journey between Sydney and Brisbane.
“The Pacific Highway is a major contributor to Australia’s economy and the Coffs Harbour bypass will be a key link in this vital piece of the nation’s infrastructure,” Mr Perez said.
“Our team is already working with the local community and local supply chain to maximise job, training and investment opportunities for the Coffs Coast region.
“Partnering with local stakeholders and the community to respect the traditions and customs of the Gumbaynggir people and helping to protect the region’s unique natural environment will be vital parts of a successful project.”
Major work will start later this year and the bypass is expected to be open to traffic from late 2026.
THE ROAD TO PROGRESS
In coming months, the Coffs Harbour community and motorists will start to see the bypass taking shape as major work starts.
The upgrade will deliver four lanes of divided motorway bypassing the Coffs Harbour CBD, taking thousands of vehicles out of the centre of town and saving motorists time by avoiding up to 12 sets of traffic lights.
Deputy Project Director, Rochelle Hicks, said early work started on the Coffs Harbour bypass last year.
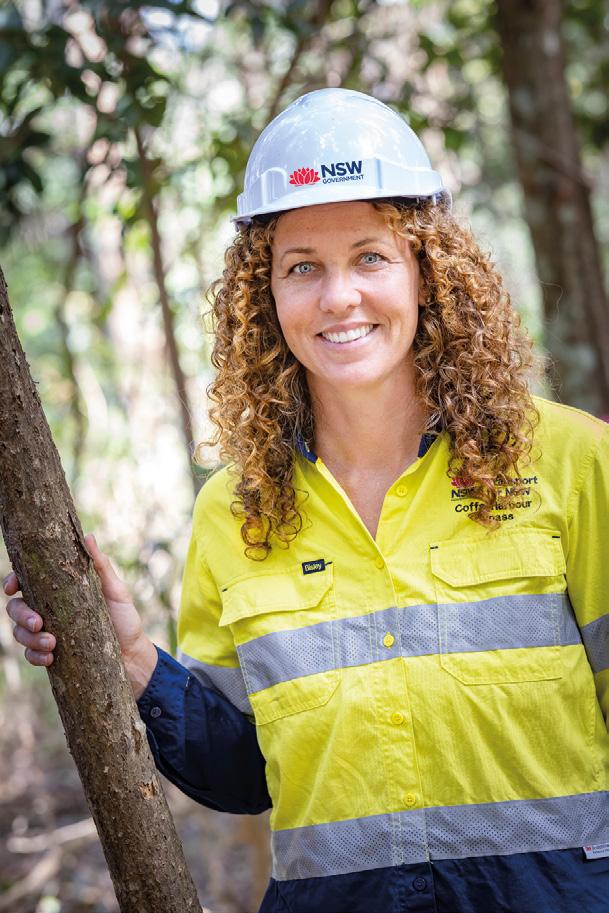

“Ferrovial Gamuda Joint Venture has been busy establishing its site team and progressing the detailed design with Arcadis,” Ms Hicks said.
“Arcadis was engaged by Ferrovial Gamuda as the lead designer of the detailed design phase of the bypass.
“Transport for NSW has been responsible for delivering the utility relocation, at-resident noise treatment, demolition and construction of the new rural fire shed.”
The key features of the bypass include three tunnels at Roberts Hill, Shephards Lane and Gatelys Road; three interchanges at Englands Road, Coramba Road and Korora Hill; a bus interchange at Kororo Public School; and formalising the bus stop facility at Coramba Road.
It will also include bridges over and under the bypass to maintain connections with existing local roads and properties; fauna connectivity structures to enable animals to travel over and under the bypass; and noise mounds and noise walls including 14km of low-noise pavement.
“One of the first steps for major construction is the approval of the Construction Environmental Management Plan (CEMP),” Ms Hicks said.
“Shortly after CEMP approval the Coffs Harbour Bypass Team will establish the site with environmental, safety and traffic controls. Major construction will start in March with visible bulk earthworks around the middle of the year followed by the start of tunnel construction.”
CHALLENGES AND INNOVATIONS
Ms Hicks said there were only a few locations on the east coast where the Great Dividing Range meets the Pacific Ocean, and Coffs Harbour is one of these.
“With the landform and the subtropical climate, one of our biggest challenges will be earthworks and managing wet weather impacts during construction,” Ms Hicks said.
“We are also tying into a very busy existing Pacific Highway at the northern and southern ends of the project, and traffic
staging will be a challenge to ensure local and travelling road users have minimal delays.
“The project team has been challenged to be highly innovative with the procurement, design and delivery of the bypass project.
“We have adopted risk sharing mechanisms in the contract and Transport for NSW has kept ownership or shared risks on a number of items including wet weather, geotechnical information and contamination.
“During the major contract procurement, we challenged industry to be innovative on the technical standards and design, and to progress beyond a business-as-usual approach.
“We have fostered a culture of forward thinking to build a high-quality motorway that provides the best value for money.
“Transport for NSW and the Ferrovial Gamuda Joint Venture are aligned with targeting innovation and working together to deliver the project.”
BUILDING A LEGACY TOGETHER
Ms Hicks said the Ferrovial Gamuda Joint Venture and Transport for NSW would deliver the Coffs Harbour Bypass as one Coffs Bypass Team.
“Working together in this collaborative way as one team will provide a focus on efficient problem solving,” Ms Hicks said.
“There is just about every combination of construction scenarios to develop and deliver from complex bridges, hard rock drill and blast tunnels and millions of cubic metres of earth to move.
“This is combined with a steep, subtropical greenfield construction and a busy existing motorway to tie into at both ends. I’m excited to see this shift in the construction industry and openly focusing on collaboration to work together to achieve positive outcomes.”
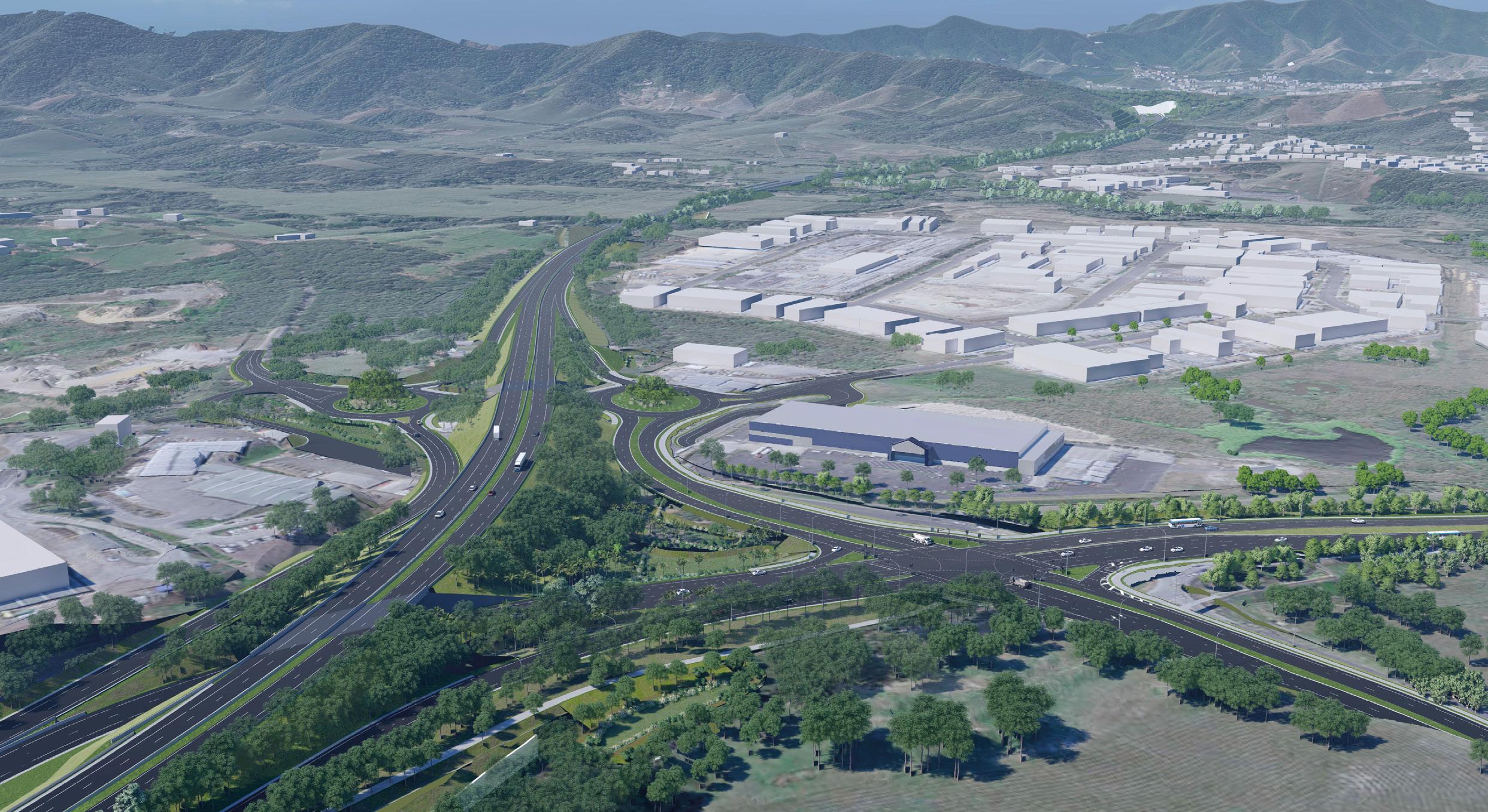
HOW DO YOU KEEP REMOTE, TEMPORARY AND UNWIRED SITES SECURE?
No matter the location, critical infrastructure needs to be monitored to ensure continuous functionality and asset security and safety. But when infrastructure is located in a remote location, far from wired internet or network power, asset owners need a robust solution that can reliably provide eyes and protection at all times.
When it comes to security, being able to see what is happening anywhere at any time can make all the difference for infrastructure owners. But in remote locations, or at temporary jobs or unwired sites, surveillance options can be limited.
Remote sites can also bring challenges associated with buried services, earthing systems, shared ownership or leasing and other constraints that make excavations or engineering changes to existing infrastructure and assets complex, timeconsuming and expensive.
As a result, setting up security systems in hard to reach or temporary locations can become unfeasible or costly to install. In these situations, utilities and critical infrastructure owners have often been left with no other choice but to do nothing and hope for the best.
However, it is possible to find a solution that can meet the unique requirements of remote assets, ensuring critical infrastructure in remote and temporary locations can remain operational and secure.
NO SITE TOO REMOTE
Around Australia, there are many assets and construction sites situated in physically remote or temporary locations. With traditional camera systems or limited security personnel, there is very little network operators can do to prevent any harm or damage to equipment or buildings.
But a lack of access to power or wired internet is no longer an obstacle when protecting remote assets. Spectur designs and manufactures surveillance and warning systems with the ability to function off-the-grid. Spectur’s systems offer eyes at all times on key infrastructure and assets, to assist with monitoring and security.
Substations, marshalling yards, sidings, construction sites, pumping stations, telecommunication towers, power generators, dams and many more sites are often located in remote or temporary locations, where it is difficult to regularly send out personnel to monitor assets.
With Spectur’s security solutions, personnel can have a real-time live view of assets without having to be on site. At any time and anywhere, asset owners can check changing conditions to ensure personnel and assets are safe.
DECISION-MAKING WITHOUT HUMAN INTERVENTION
What makes Spectur’s systems truly unique is that as well as being able to operate off-grid, they also have the ability to sense, think and act in response to a range of stimuli.
With a system that can sense and make decisions – all without human intervention – asset owners can have peace of mind that critical assets are protected even when there is no one around.
Spectur’s systems use cameras to capture images, detect motion and offer the ability to remotely monitor sites. Utilising artificial intelligence (AI), the systems distinguish real threats from false alarms, and then act to broadcast a pre-recorded warning, flashing lights or alarm.
These actions deter trespassers; and the ability to distinguish between real and false alarms ensures asset owners are not bothered by sensors mistaking moving wildlife or foliage for an intruder.
The AI is also fully programmable and can be provided by third parties onto the devices and in the cloud, allowing specialist applications such as fire detection, flood monitoring, people counting and other applications to be added and deployed remotely and flexibly.
For example, Spectur cameras can identify number plates to determine which vehicles are meant to be on the property and which are not. When unapproved licence plates are identified, alarms can sound and online alerts sent, alerting asset owners of the security breach.
SELF-CONTAINED SYSTEMS
Spectur camera platforms can function off-the-grid because they are completely wireless. Powered with solar panels and rechargeable batteries, there is no need for a wired power connection as each station, consisting of four cameras, can operate for five days when fully charged.
On top of that, an in-built 3G/4G modem, with amplified antennas or even satellite connectivity ensures transferring data, communications and more is possible, no matter where the system is located.
As a result, Spectur’s systems are fully self-contained and do away with obstacles associated with installing costly and intrusive surveillance equipment.
Setting up a Spectur system requires no trenching, excavating or digging to set up cables. This not only removes the need for going through a long approval process for permits, but is also less intrusive for the local environment.
Spectur’s systems can also be made transportable by setting them up on a concrete block or trailer. This is ideal for temporary locations, and also gives options for permanently located assets or sites.
A fully wireless and self-contained system also means that these cameras don’t have to be installed on buildings. Spectur systems can be positioned on the perimeter of an asset or property to stop people before they can even scale a fence.
By the time an intruder has entered a property and reached a critical asset, it’s often too late. Preventing intruders from even breaching the perimeter of an asset ensures criminals are deterred well before they can damage assets, equipment or buildings.
ACTIVELY LOOKING OUT FOR TROUBLE
Surveillance systems aren’t just used for preventing property damage, they can also ensure on-site safety for both workers and members of the public.
Not all intruders who enter these sites are looking for trouble – some may be thieves or vandals, but sometimes it’s children or teens looking for fun or a homeless person seeking shelter.
These sites can be very dangerous to non-professionals, with the risk of electrocution, injury, or even death. Spectur solutions can act as a deterrent to prevent intruders from entering the property and potentially hurting themselves.
EYES AT ALL TIMES
When overseeing assets in remote or temporary locations, peace of mind means having eyes at all times. Whether it’s checking for damaged equipment, checking if flood levels have risen or deterring intruders, Spectur’s systems keep critical assets safe and sites operating.
For even the most remote assets in Australia, Spectur’s surveillance and monitoring solutions offer self-contained, wireless, responsive, solar-powered and easy-to-install security and protection systems.
For more information on remote surveillance and monitoring systems using Spectur’s smart solutions, call 1300 802 960 to talk to our team and find the right solution for your unique onsite challenges.
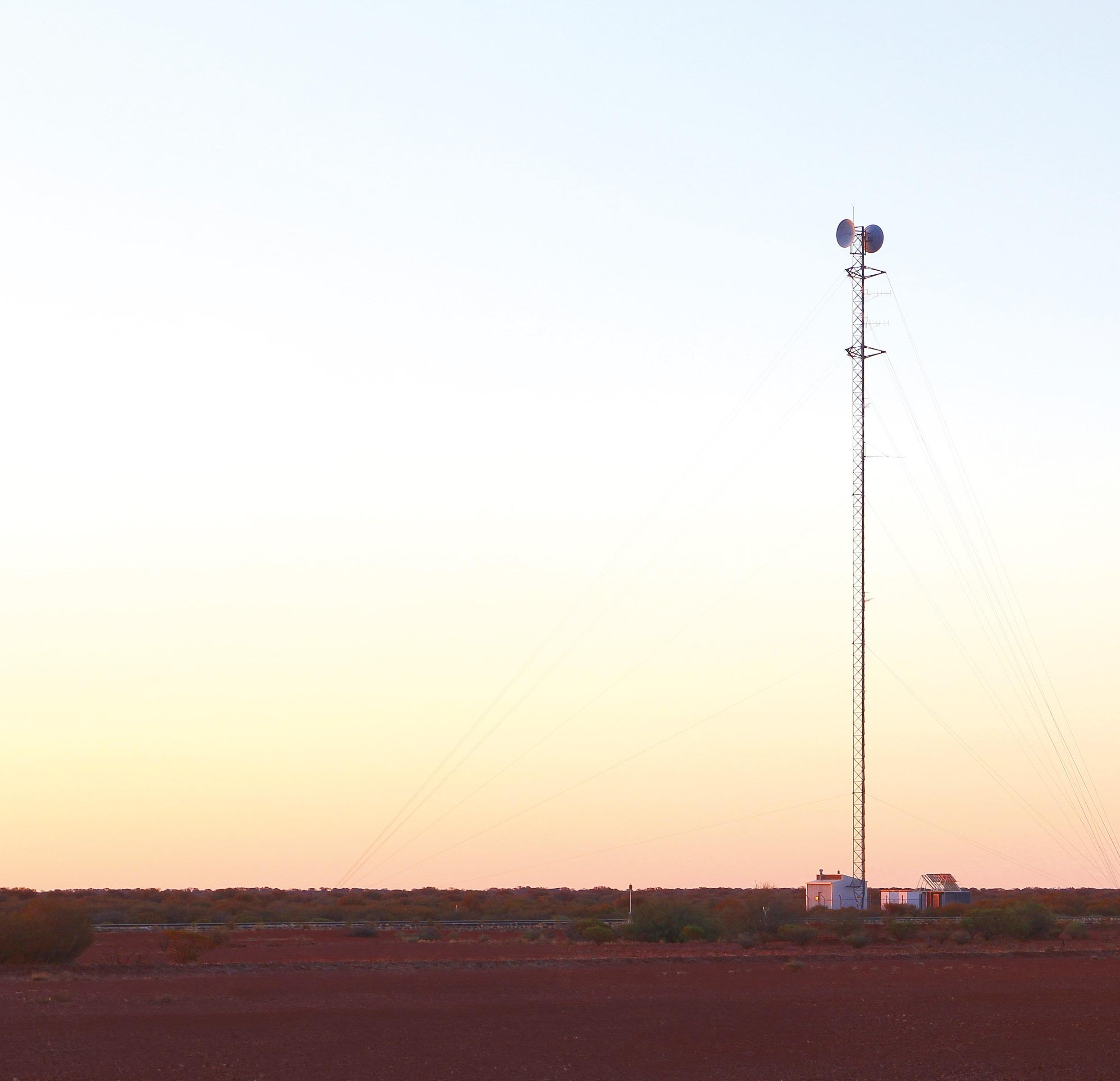
Even the most remote infrastructure can be protected with Spectur’s surveillance systems.
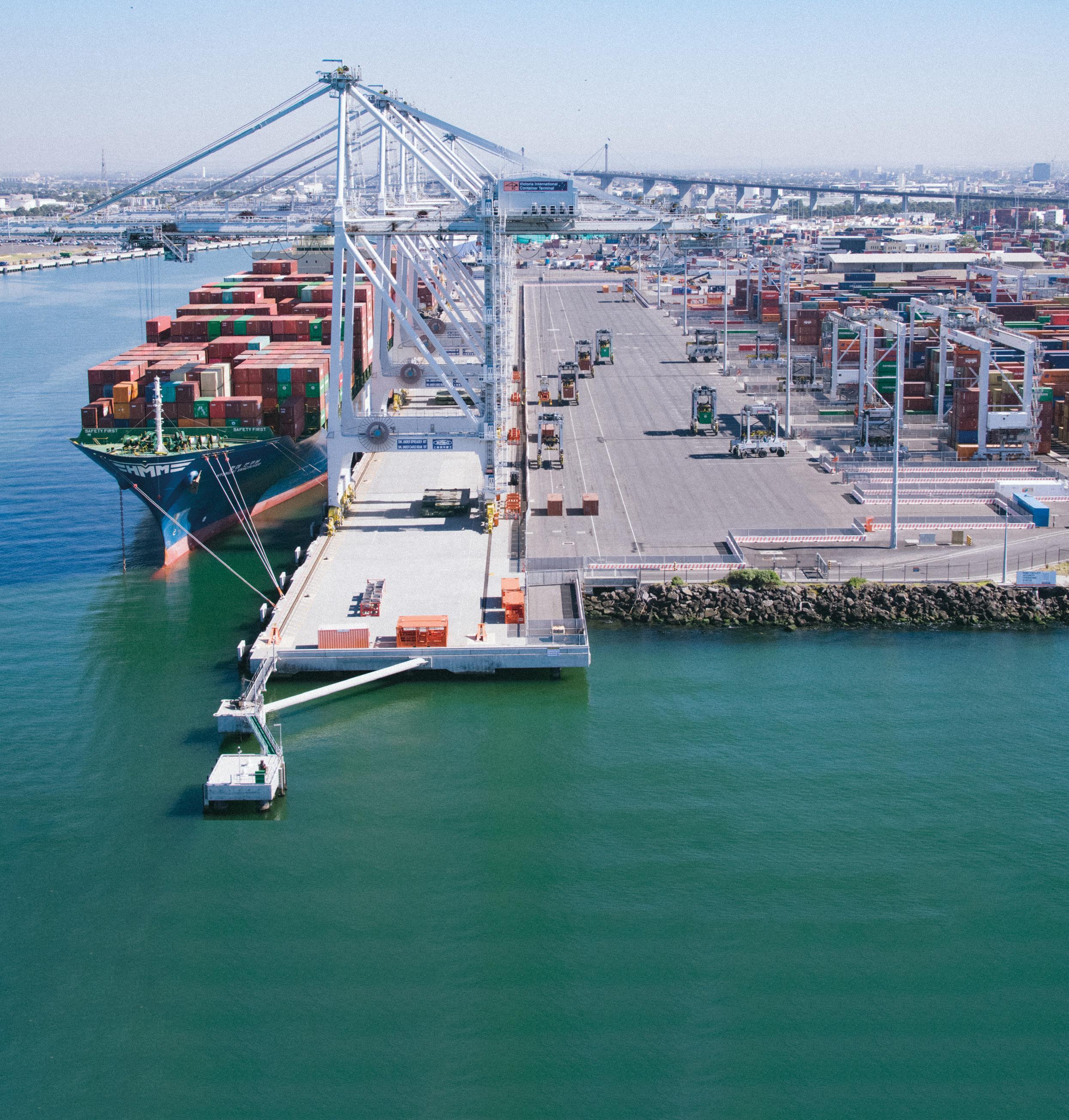
SUPPLy CHAIN INFRASTRUCTURE INVESTMENT CRITICAL TO PRODUCTIVITY
Ongoing private investment in supply chain infrastructure is a necessary part of ensuring Australia’s resilience and productivity, says Port of Melbourne Chief Executive, Saul Cannon.
Prior to COVID, supply chain matters rarely made headlines. However, pandemic-related delays in goods ranging from medicine to furniture, electronics and automobiles, alerted many Australians to the fragility of the globalised trade system.
Port of Melbourne Chief Executive, Saul Cannon said recent disruptions and congestion at both the global and local level demonstrate why we need an ongoing focus on building supply chain resilience.
“We must not waste the lessons in resilience we have learned over the last three years,” Mr Cannon said.
“Australia is still a relatively small market by international trade and shipping standards, and we need a stronger strategic
focus on our global positioning to ensure that Australia is appropriately positioned to respond to growing trade demand and changing market dynamics.”
Port of Melbourne is planning for, and investing in, port projects to maintain efficient operations and respond to capacity needs.
Port of Melbourne is investing more than $2 billion in projects over the next decade or so, on top of the approximately $420 million already spent since the State Government privatised the port in 2016.
“It’s about ensuring that we have the right infrastructure in the right place at the right time to deliver for Victoria and beyond,” Mr Cannon said.
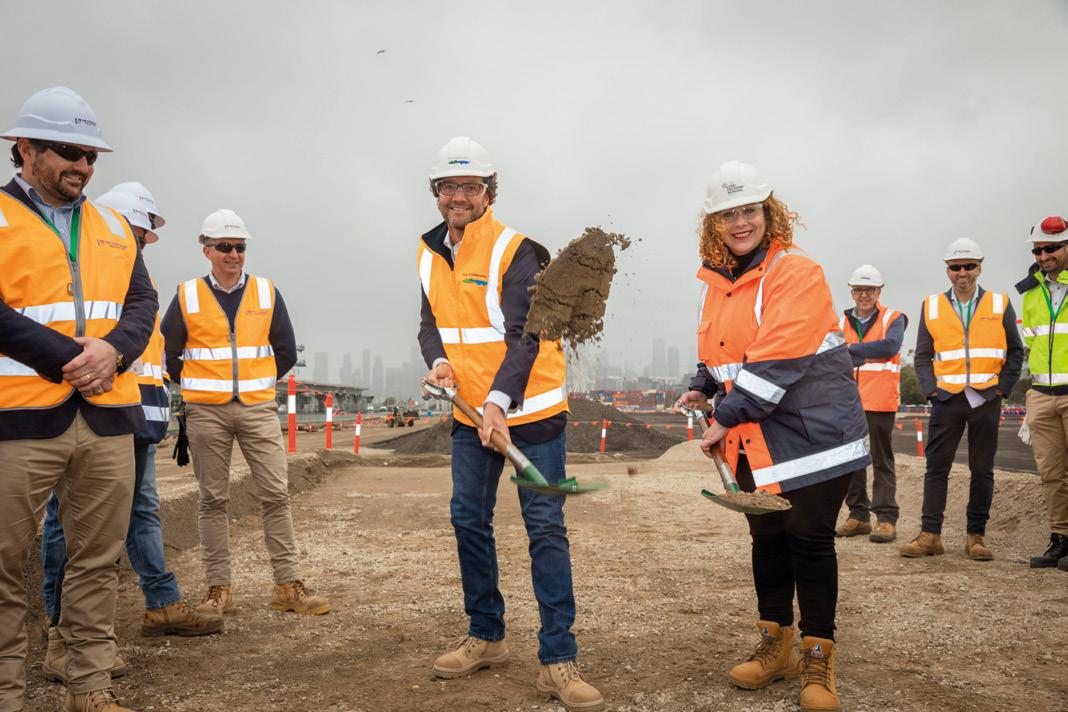
PORT RAIL TRANSFORMATION PROJECT
The Port Rail Transformation Project is well underway, involving the development of a rail terminal adjacent to Patrick’s container terminal at Swanson Dock. This is on track to be complete by mid-2023, and it will support the Victorian Government’s Port Rail Shuttle Network, providing direct rail connections from the port to major freight hubs in Melbourne’s north, west and south-east.
The $125 million project will see more containers moved by rail more efficiently, by-passing roads in inner Melbourne.
Mr Cannon said that moving freight by rail can move far more containers in a single trip than trucks can. For example, a 600m long train can carry 84 containers compared with a B-Double truck which has an average capacity of three containers.
“There are significant benefits to moving freight off roads and onto rail. These benefits include lower carbon emissions, improved safety, and decreased air pollution,” Mr Cannon said.
WEBB DOCK EAST EXTENSION PROJECT
The Webb Dock East Extension Project is also underway and will restore Webb Dock East to a two-berth terminal, as it was designed to be. The project involves demolishing a redundant section of concrete and extending the quay line by 71m. This project is also on track to complete around Q3 2023.
Mr Cannon said the project is an important part of a 30-year investment strategy, designed to create a more efficient and productive port that helps to strengthen Victoria’s economy.
“We are seeing a rising number of larger vessels calling at the port and our current infrastructure at Webb Dock East at times does not allow for two larger size ships to berth at the same time,” Mr Cannon said.
SWANSON DOCK WEST REMEDIATION PROJECT
Planning for the Swanson Dock West Remediation Project is also well underway.
“Swanson Dock West wharf structures must be remediated and upgraded to enable us to continue to handle container vessels for the next 50 years,” Mr Cannon said.
A project milestone was reached in January 2023, with the awarding of a contract for Stage 1 of the project to construction giant McConnell Dowell, which includes the remediation and upgrade of the existing wharf structure.
“The existing Swanson Dock West wharf is of varying ages and forms of construction. Sections of the wharf are close to or beyond the typical design life of 30 years and as a result, major remediation is needed,” Mr Cannon said.
PORT CAPACITY ENHANCEMENT PROGRAM
Finally, Port of Melbourne is in the early stages of its Port Capacity Enhancement Program (PCEP) – a significant infrastructure program aimed at developing a fourth container terminal.
Mr Cannon said the port is currently engaging with stakeholders to ensure that our planning takes into account relevant feedback in relation to the development of PCEP.
“Supply chain infrastructure has long lead times, so we need to plan now for the longer-term future. For ports, that means addressing the trend in larger vessels and ensuring we have the capacity to meet trade demand,” Mr Cannon said.
“We are committed to meeting our stewardship obligations to manage, operate, maintain and develop the port for the benefit of the economy and the state.”
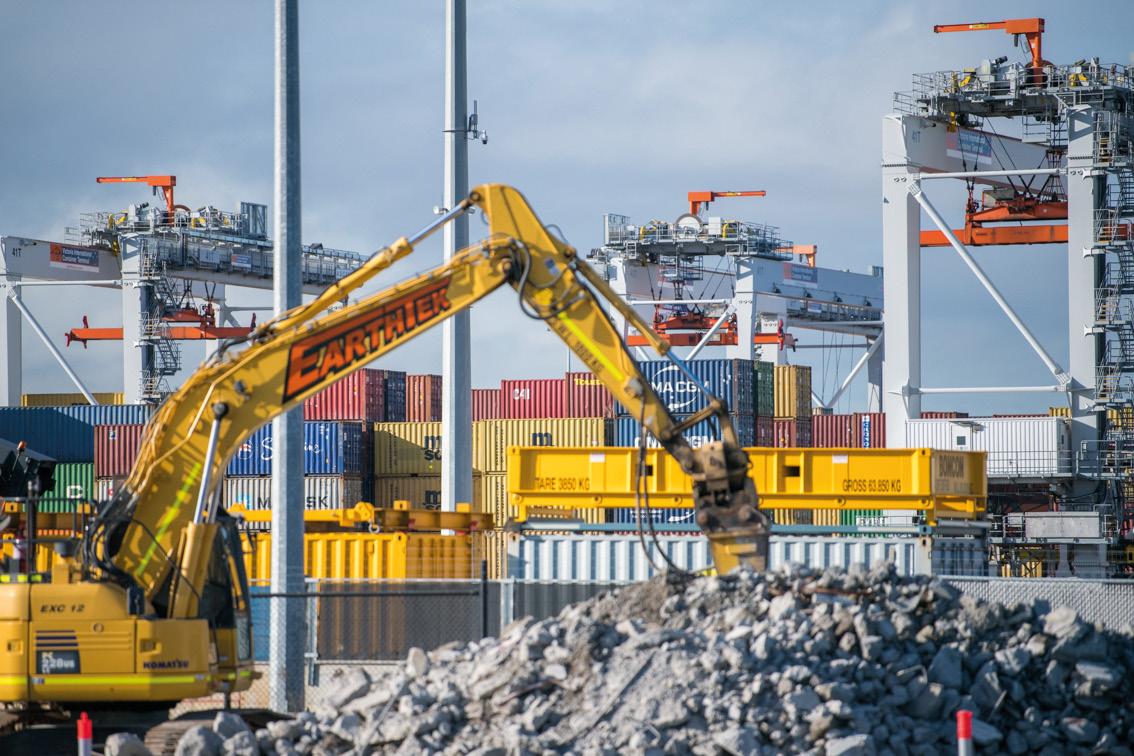
For more information on Port of Melbourne’s current projects, please visit www.portofmelbourne.com/current-projects. View its 2050 Port Development Strategy at www.portofmelbourne.com/facilities-development/port-development-strategy/. Or learn more about the Port Rail Transformation Project at www.portofmelbourne.com/facilities-development/port-rail-transformation-project/.
THE MOST IMPORTANT PART OF
DIGITAL TRANSFORMATION
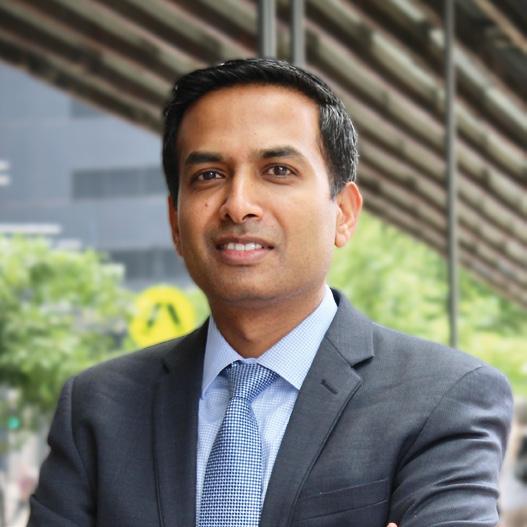
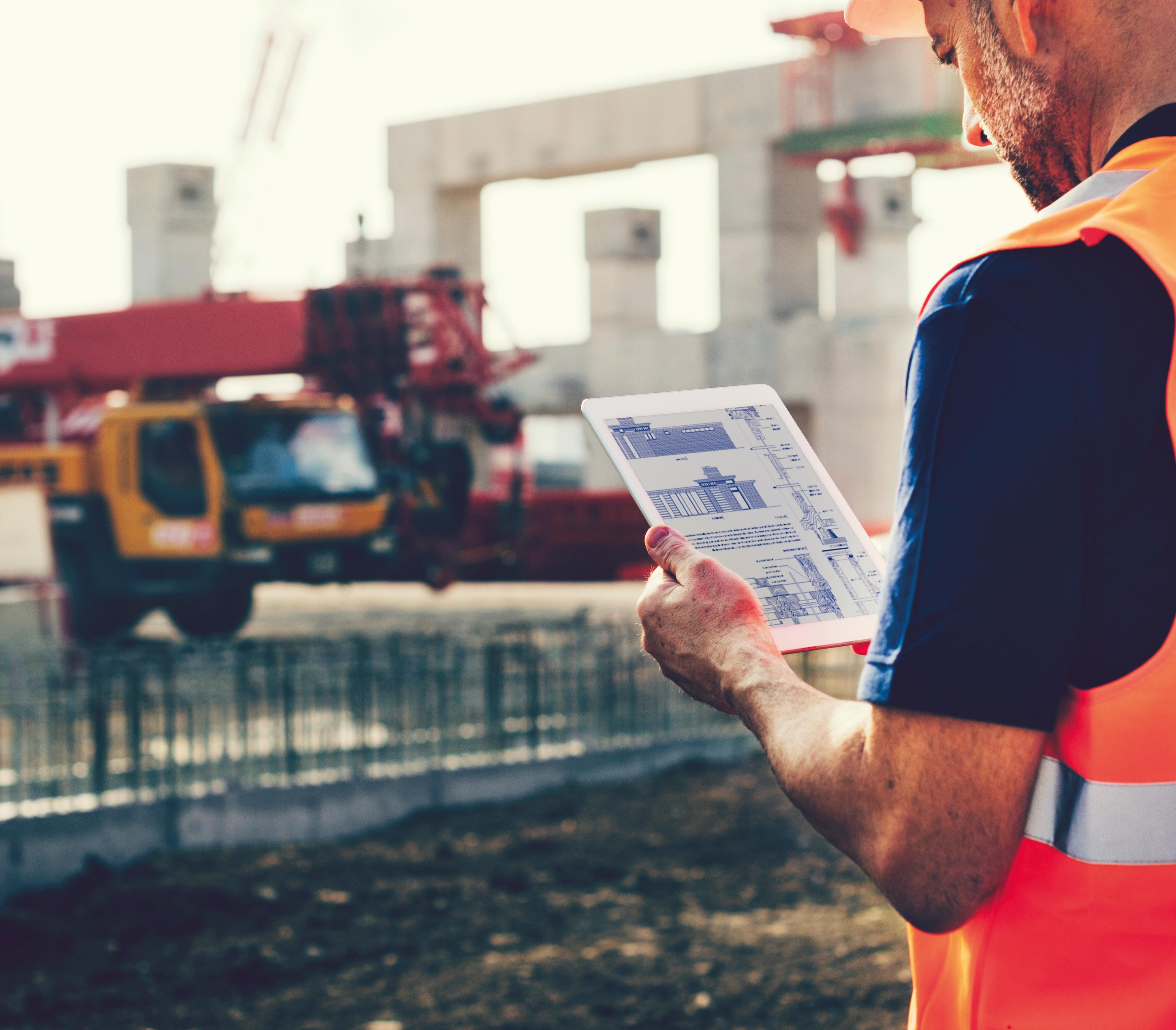
Infrastructure companies are undergoing digital transformation programs to create new investment opportunities, more efficient operating models, and greater sustainability. While the technologies implemented are important, the most crucial element of this process is actually understanding the impact on your employees. This is referred to as maintaining the human perspective.
n its 2022 report Delivering Outcomes, Infrastructure Australia found that digital transformation will drive productivity and innovation in infrastructure delivery and that digital is a “core enabler to achieving transformational change across the sector”.
The report found that project outcomes could be enhanced by applying a ‘digital by default’ approach, but that the “potential transformative benefits of digital remain largely unharnessed by government and industry stakeholders”.
Throughout the infrastructure sector, the goal of digitisation is always the same: to increase efficiency and minimise unnecessary spending or processes.
But how do you make sure your digital transformation attempt does not end futilely?
How do you ensure that your digital transformation actually makes a significant improvement to efficiency so you’re not wasting the money you invested?
How do you avoid becoming the construction company that implemented cloud technology for its field staff without actually solving any of their day-to-day problems?
How do you reduce the likelihood of getting to the end of your multimilliondollar digital transformation project and only using half of the digital tools you introduced?
And how do you not become the business that delivers its digital transformation project six months late because the business is operating well without it?
To ensure your construction company does not end up dealing with these issues when undergoing a digital
transformation journey, you must maintain the human perspective.
The ‘human perspective’, or in other words, your employee’s perspective and engagement with the digital transformation implementation process, is the most important element of any digital project, and if it’s not prioritised, you’ll see the consequences.
Let’s look at how you can maintain the human perspective.
ENGAGE YOUR EMPLOYEES
The human perspective is critical to the success of your digital transformation because without it, employees aren’t encouraged to support the change for the long term.
This is important because we’re not just referring to the IT team and vendors that implement or build your system, it’s about getting all of the employees
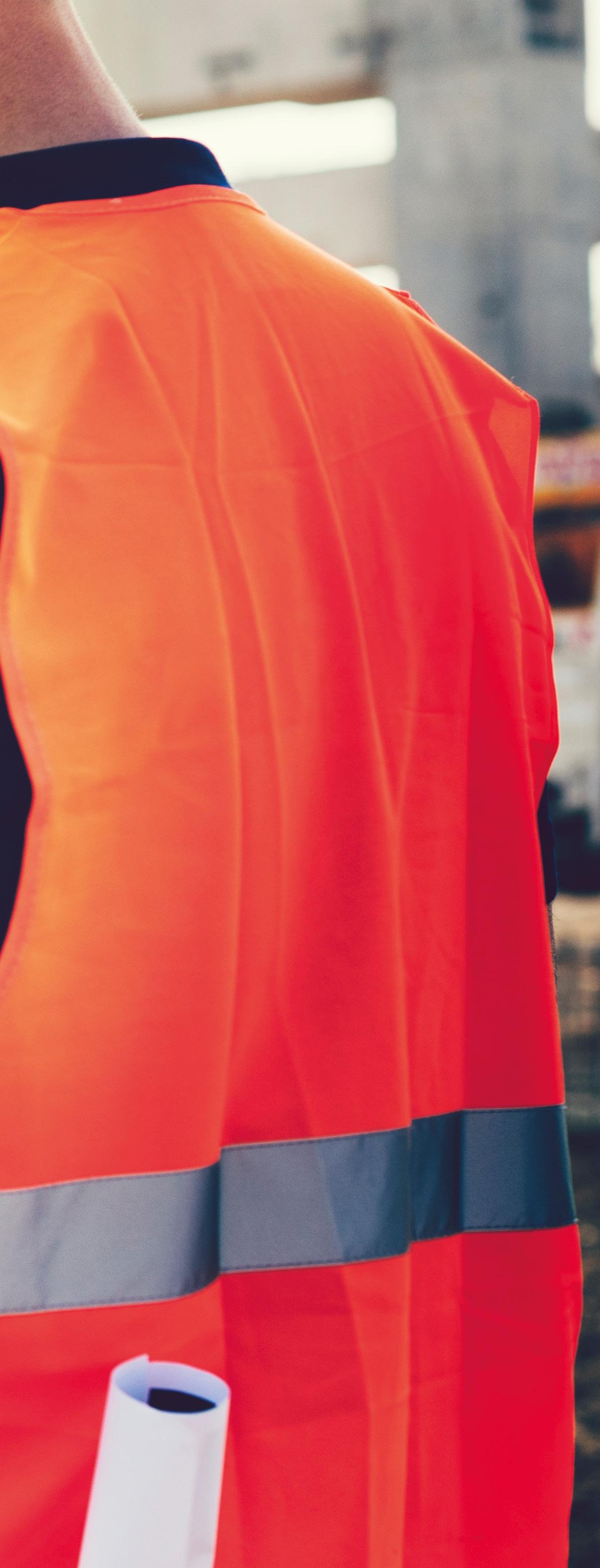
who will end up using this technology on board from the start.
Digital transformation is about more than implementing new technology or applications, it’s a process that involves changing and modernising the habits of employees so they can be more productive. In short, you’re not just giving them new tools, you’re also teaching them how to use those tools properly.
As with other transitions, this process requires a strong commitment. If you are a company director or the person driving this transformation, you need to make it clear to your employees how this digital transition correlates with their needs, as they are the ones on the ground running the day-to-day operations.
If they understand the ‘why’ of what the company is doing, and how it impacts their daily roles, they will be more motivated to ensure its
success. If this isn’t communicated properly, some employees could start to feel unsupported, which can result in low morale, then a growing sense of detachment, and finally loss of ‘ownership’.
It’s this scenario that can cost your company great talent and resourceful people – a challenge that is even more prevalent now with industry-wide skills shortages and a sector struggling to meet growing construction demand.
This often starts when a company asks employees to change from an in-house built application that has been created on a dependable software platform and has been used for a while, to something completely new, or conversely, when a company won’t give employees the necessary progress update that they need to remain engaged.
TALK TO PEOPLE DIRECTLY
While more and more construction companies are digitising, you shouldn’t fall into the trap of implementing technology for the sake of it, because it’s what everyone else is doing. For the digitisation process to work, the new technology needs to be solving specific challenges in your business.
To make sure that your company and its employees actually need the change – whether it’s a software update or new infrastructure – you need to talk to them directly.
Before announcing an initiative or plan, talk to your employees during weekly update meetings or speak with the project managers and department heads to gather more information that may either support your ideas, or inform you that a change like this isn’t necessary just yet.
It doesn’t have to be with a large group of people, but your direct presence will give the impression of accessibility and openness to your team. This could enable a deeper connection and ignite a spark that gives people a good sense of direction at work, making the implementation easier.
This process also reduces the risk of your digital transformation projects failing because employees can give you feedback and information from their daily working processes, which can be added to your plan to make it more detailed and prepared for any future issues.
While this feedback can be helpful, if on the other hand, you feel that the software change is important
nonetheless, you can do your own research by forming a specific team to test the possibilities of you pushing the transformation to happen.
As a decision-making executive, you might persuade people more by stating the fact that your long-term vision, and the change it involves, will cause disruption in the company and possibly the wider industry, to prepare yourself for the impending responsibilities and decisions that will come with navigating your plan.
After you have collected all of this information, I suggest processing the data with a third party. This could be a vendor or an acquaintance in the company, someone who can process the information you have objectively. This is important because if you handle it yourself, you may cherry-pick the feedback that supports your stance. By rechecking the data together, you will also be able to see a detailed perspective on the situation you are facing, and identify the best way your transformation plan can be successfully executed.
TECHNOLOGY SHOULD NOT MAKE US LOSE OUR HUMANITY
Always remember to put the human perspective of your employees and colleagues first to maintain a sense of understanding between you as the decision-maker, and the people who will be affected by your choices. Entire businesses improve when employees perform better, and they’ll do this when they feel happy and supported.
The simplest way to do this is to engage with them, include them in your plans, and give them a say in how the transformation process will impact them. By incorporating the human perspective in your digital transformation, your company and your employees will experience a holistic transformation and become a future-fit and future-ready enterprise to face the challenges of tomorrow.
And if you don't, your company will notice the consequences.
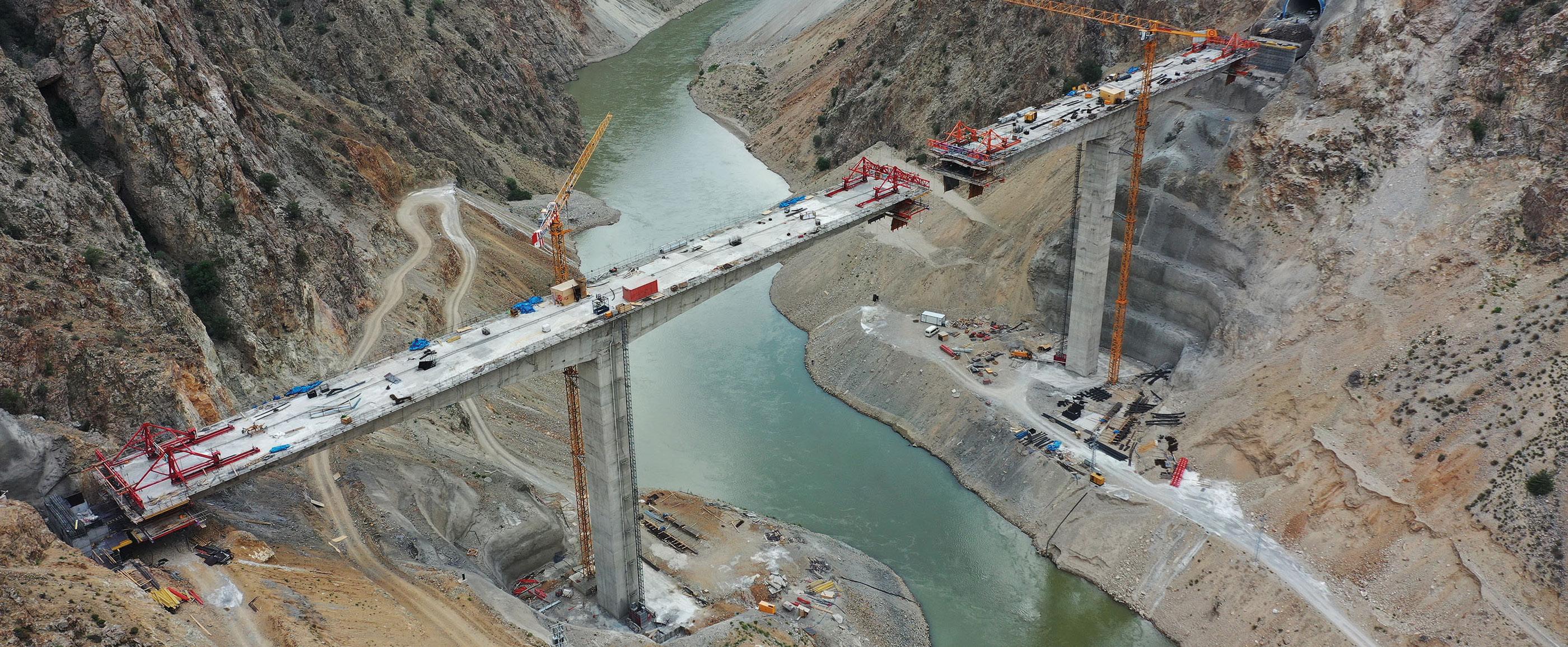
HOW A BETTER UNDERSTANDING OF GROUND CONDITIONS HELPS TACKLE RISK
What are the leading causes of delays, disputes, and major claims in infrastructure projects? A recent CRUX Insight Report placed ‘unforeseen physical conditions’ in the top 10.
Pat McLarin, Civil Director, at Seequent, the Bentley Subsurface Company, said managing ground risk is a live industry issue. Mr McLarin has more than 20 years experience as a product manager in the research and development of geospatial hardware and software, with a focus on subsurface solutions during his last six years at Seequent.
“Unearthing the unexpected can completely derail a project, with changes coming at significant cost,” Mr McLarin said.
As teams react by sourcing new equipment, bringing in fresh expertise, or training team members, project progress can often stall or halt completely.
“Rather than accepting the status quo, the latest in digital innovation can help bring a better understanding of the geological complexities at every stage of your project,” Mr McLarin said.
SHORTCUTS COST IN THE LONG RUN
A deeper understanding of the subsurface is crucial for infrastructure design and construction.
“Geotechnical engineers responsible for this essential earlystage phase are under the pump to ensure it’s done accurately, as well as efficiently,” Mr McLarin said.
But when project owners look for ways to cut costs, speed up production, or maximise construction dollars, it can be quickly compromised.
The CRUX study brings this to light. Globally, the trend is clear – taking ground investigation shortcuts can lead to a multitude of challenges down the track.
“The squeeze on geotechnical teams shows no sign of letting up and so the industry must learn to adapt,” Mr McLarin said.
“Adapting means meeting the demand for speed while still delivering accurate, usable insights. Digital innovations that quickly and easily collate geotechnical data into 3D models can bring deeper insights, deliver more value and support better decisions.”
Seequent’s 3D implicit modelling solution helps assess geological risk.
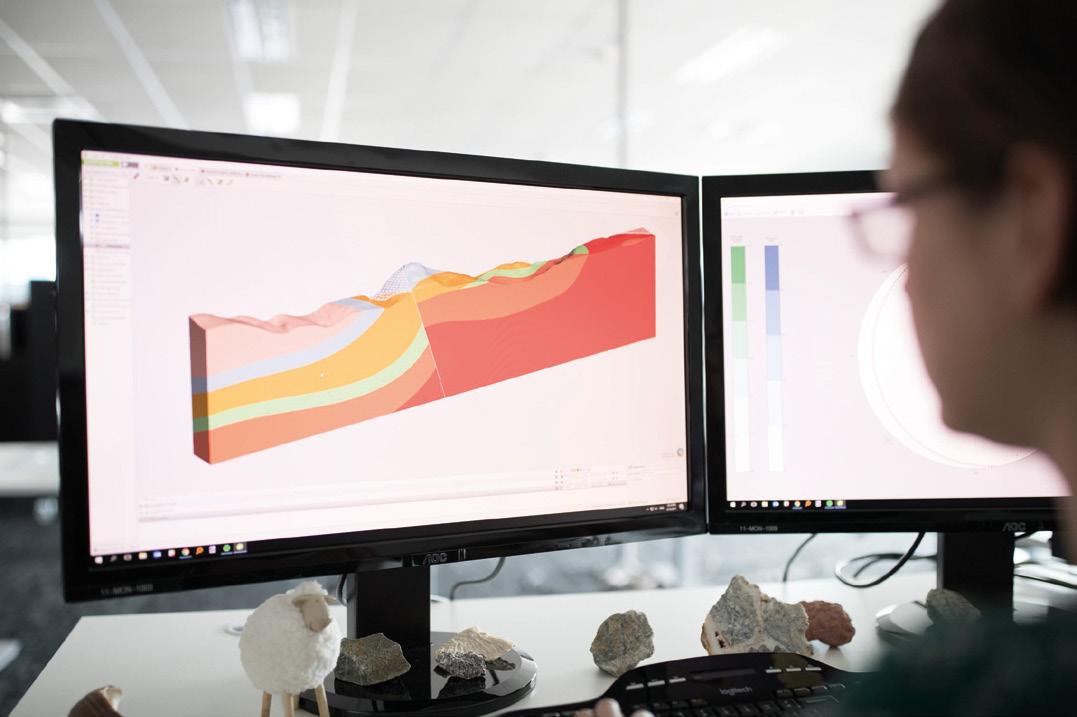
MAKING A DIFFERENCE ON MELBOURNE TUNNEL PROJECT
Mr McLarin leads Seequent’s strategy for civil infrastructure and participates in open standard development to raise the profile of the geotechnical disciplines in BIM and digital twins.
Digital modelling, digital twins and BIM technologies were identified in the CRUX Insight Report as helping project teams manage complexity and work smarter.
The West Gate Tunnel project in Melbourne is one of a multitude of complex infrastructure projects currently underway worldwide where Seequent software has made a difference.
The project involved an exhaustive investigation of geological risk, led by geotechnical services firm WSP Golder. It used the 3D implicit modelling solution offered by Leapfrog Works to help assess geological risk and communicate that to a variety of stakeholders.
“Our subsurface software helps you easily combine all geotechnical information into auditable workflows for teams, contractors and joint ventures,” Mr McLarin said.
“This means everyone has the latest insights and can collaborate on a shared up-to-the-minute understanding of the subsurface, to make faster decisions and quickly progress a project.
“As we build back better, digital transformation will become the norm for ground engineering on infrastructure projects, allowing faster project delivery, with more certainty and to achieve a better outcome.”
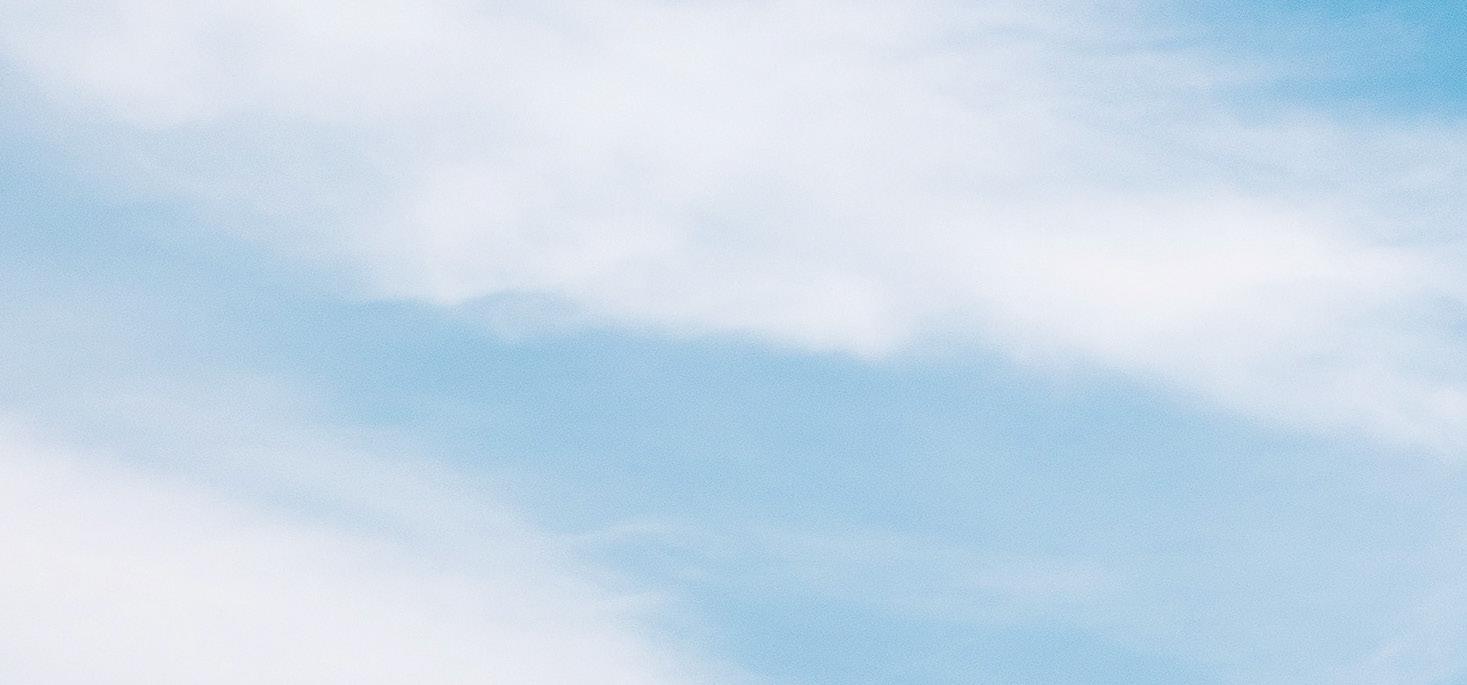
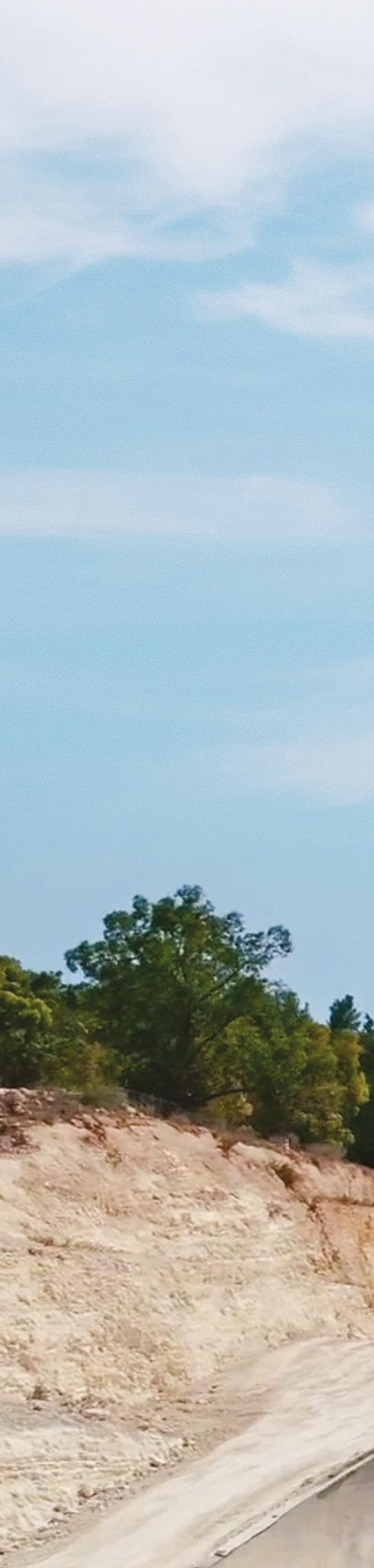
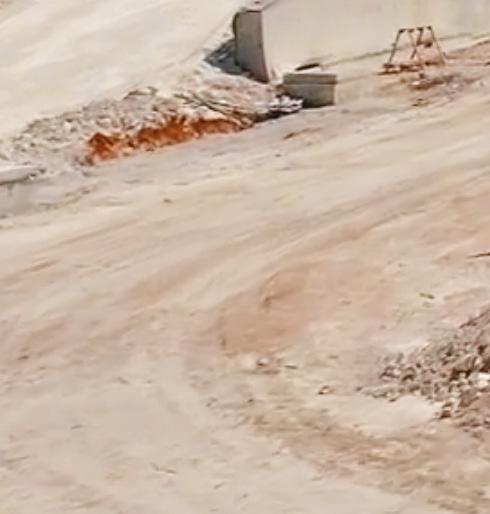
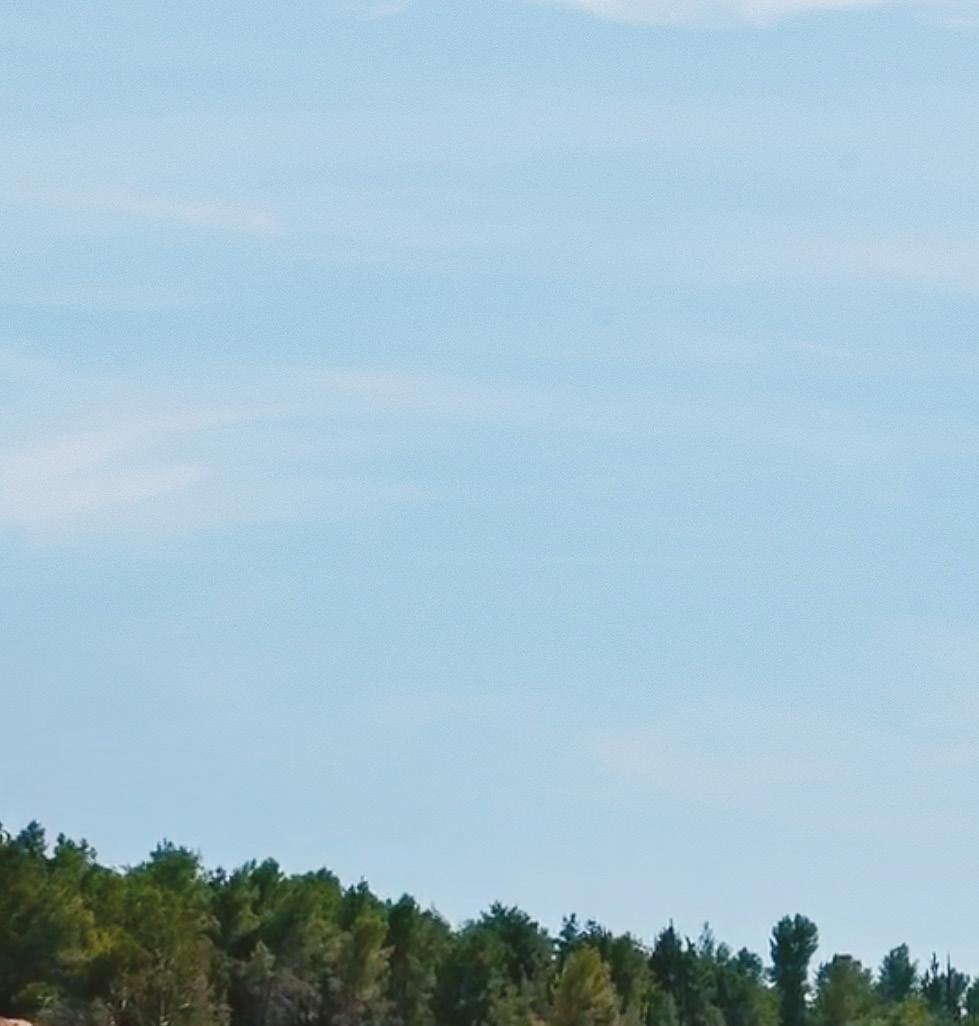
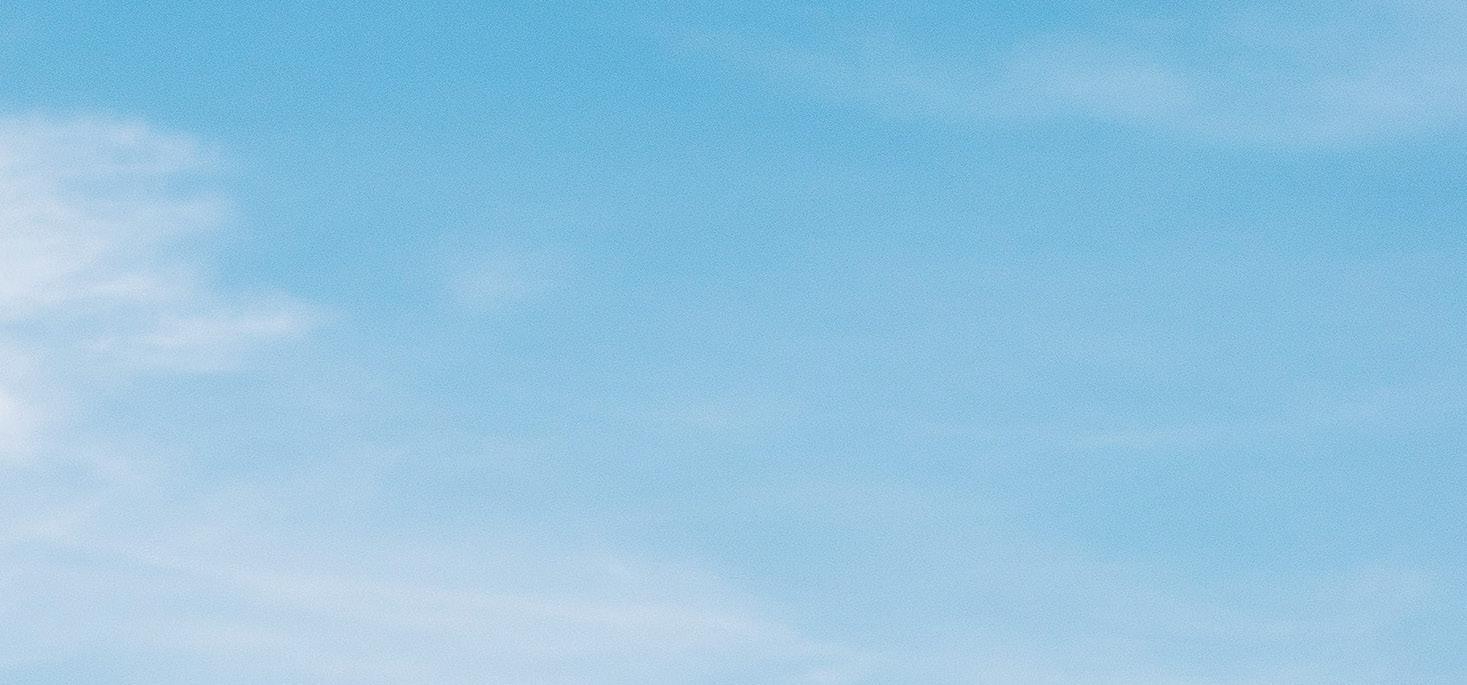


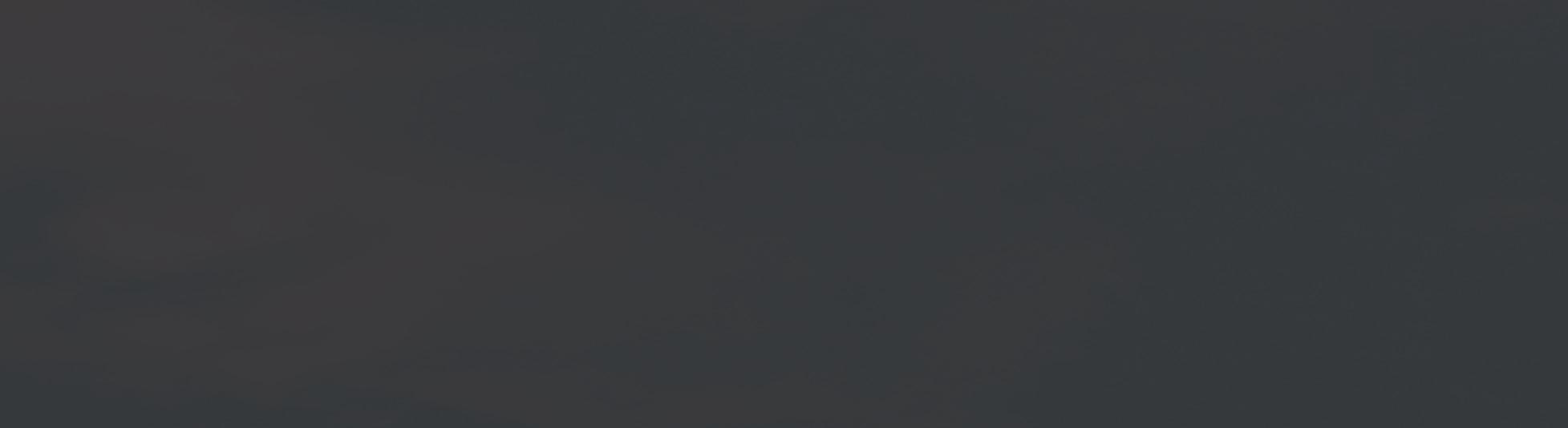
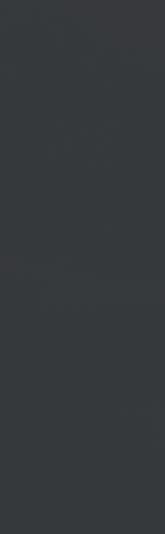
When you collaborate around a shared understanding of ground conditions, you can deliver projects faster with more certainty and achieve a better outcome.
Geotechnical Engineers, Engineering Geologists, and Geophysicists use our software on infrastructure projects to plan, design, and construct roads, rail, bridges, tunnels, buildings, dams and levees.
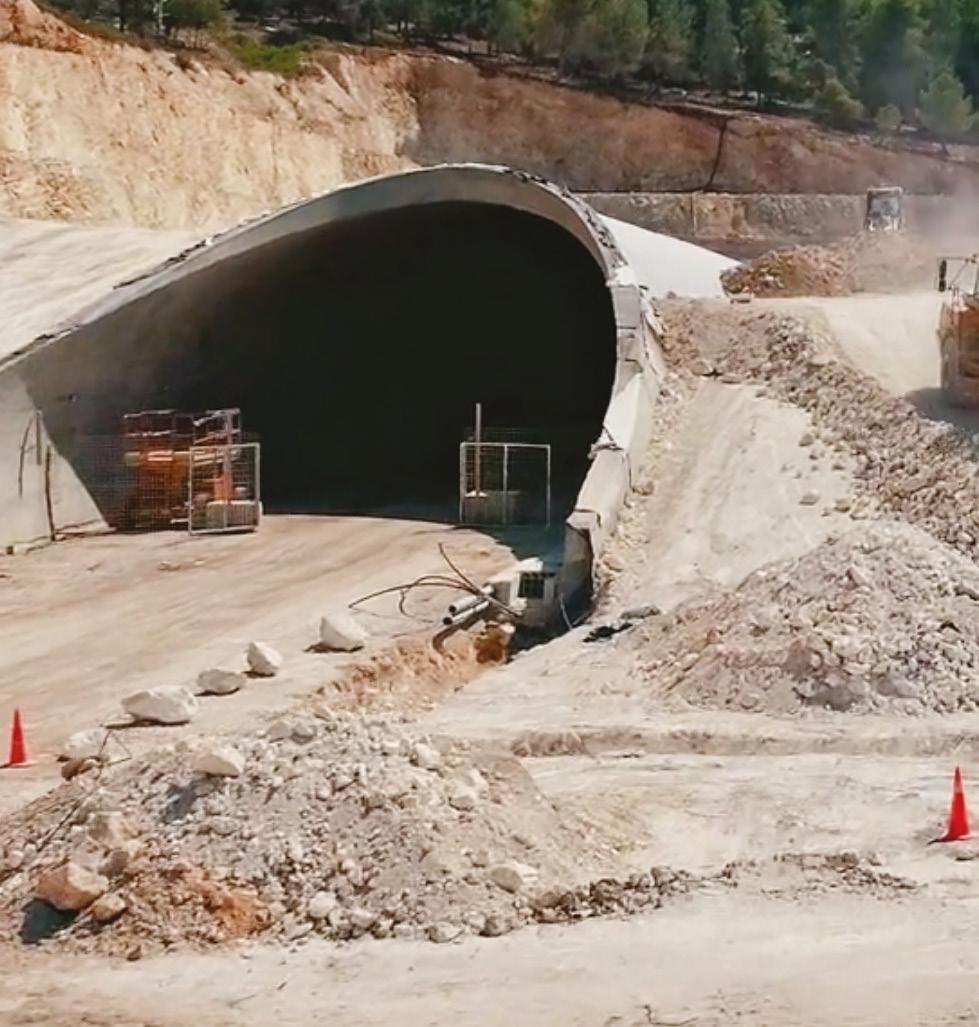
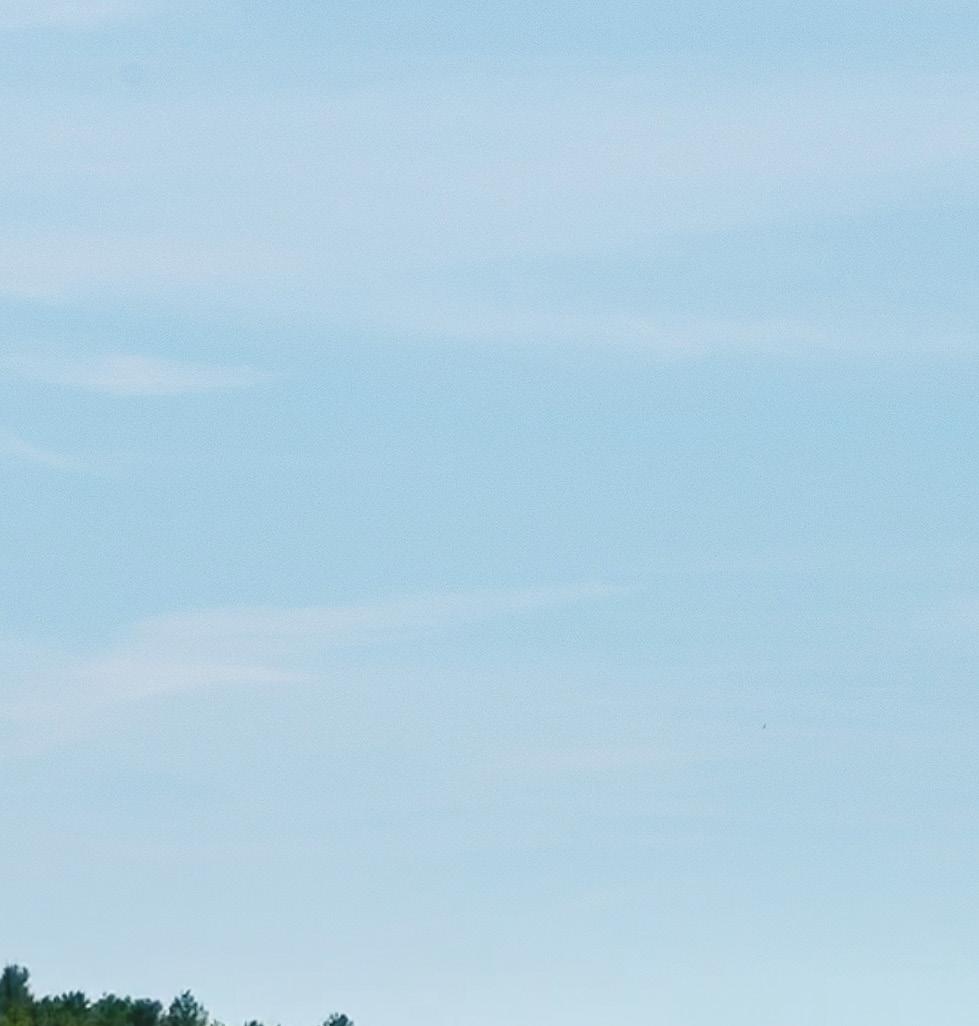
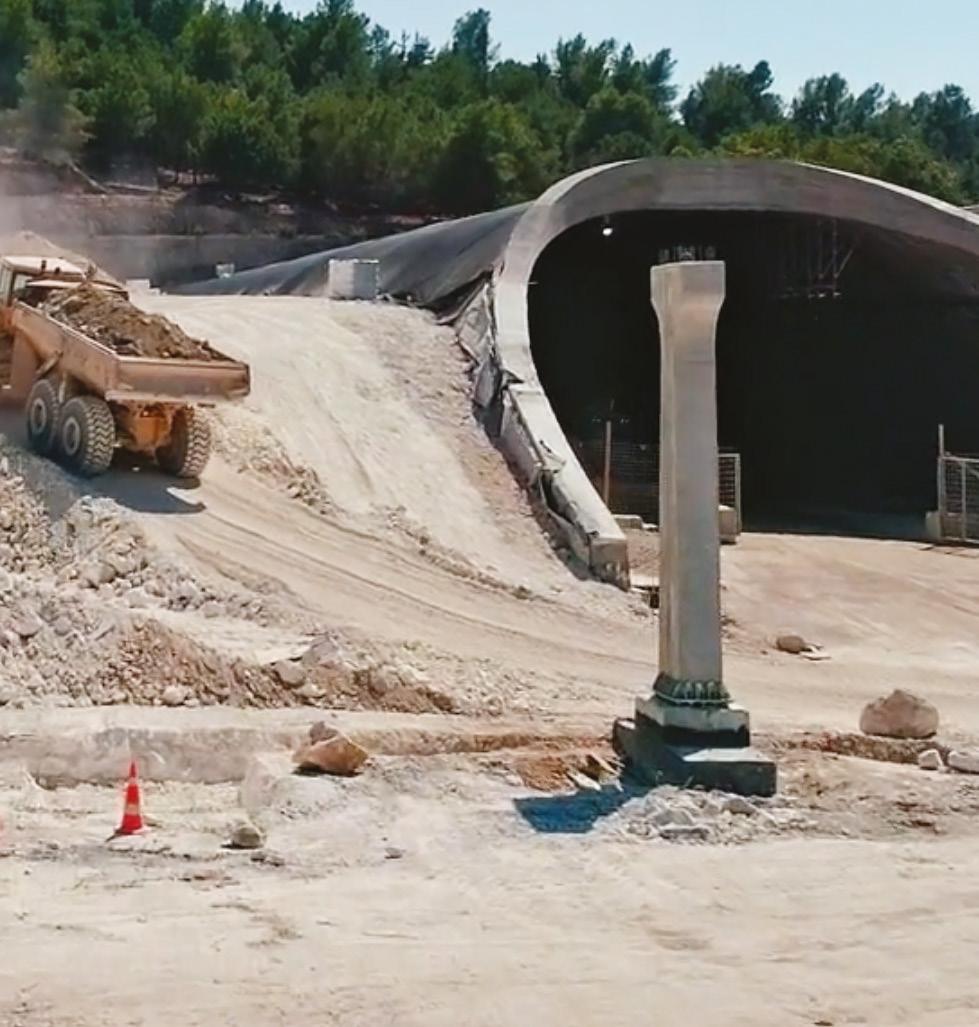
See how civil engineering projects are succeeding with our software worldwide.
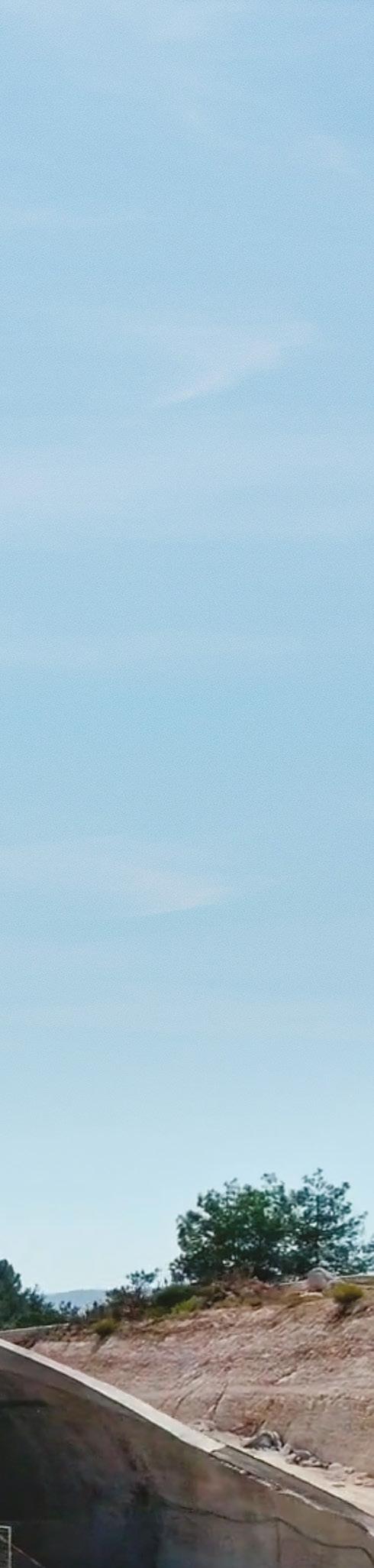
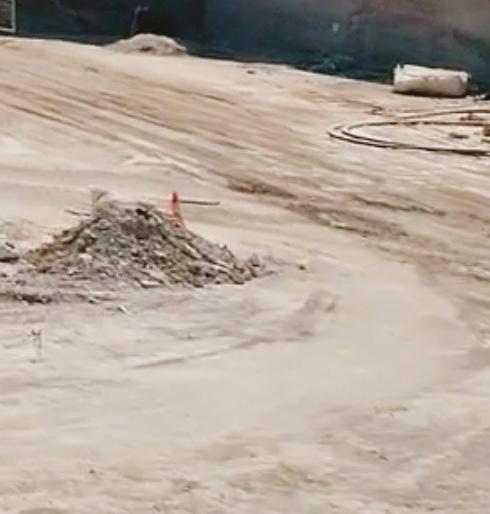
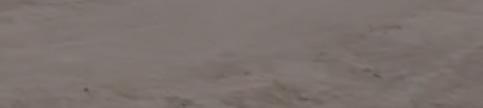
THE TECHNOLOGY SUPPORTING
CANBERRA’S BIGGEST INFRASTRUCTURE PROJECT
By Tess Macallan, Journalist, Infrastructure Magazine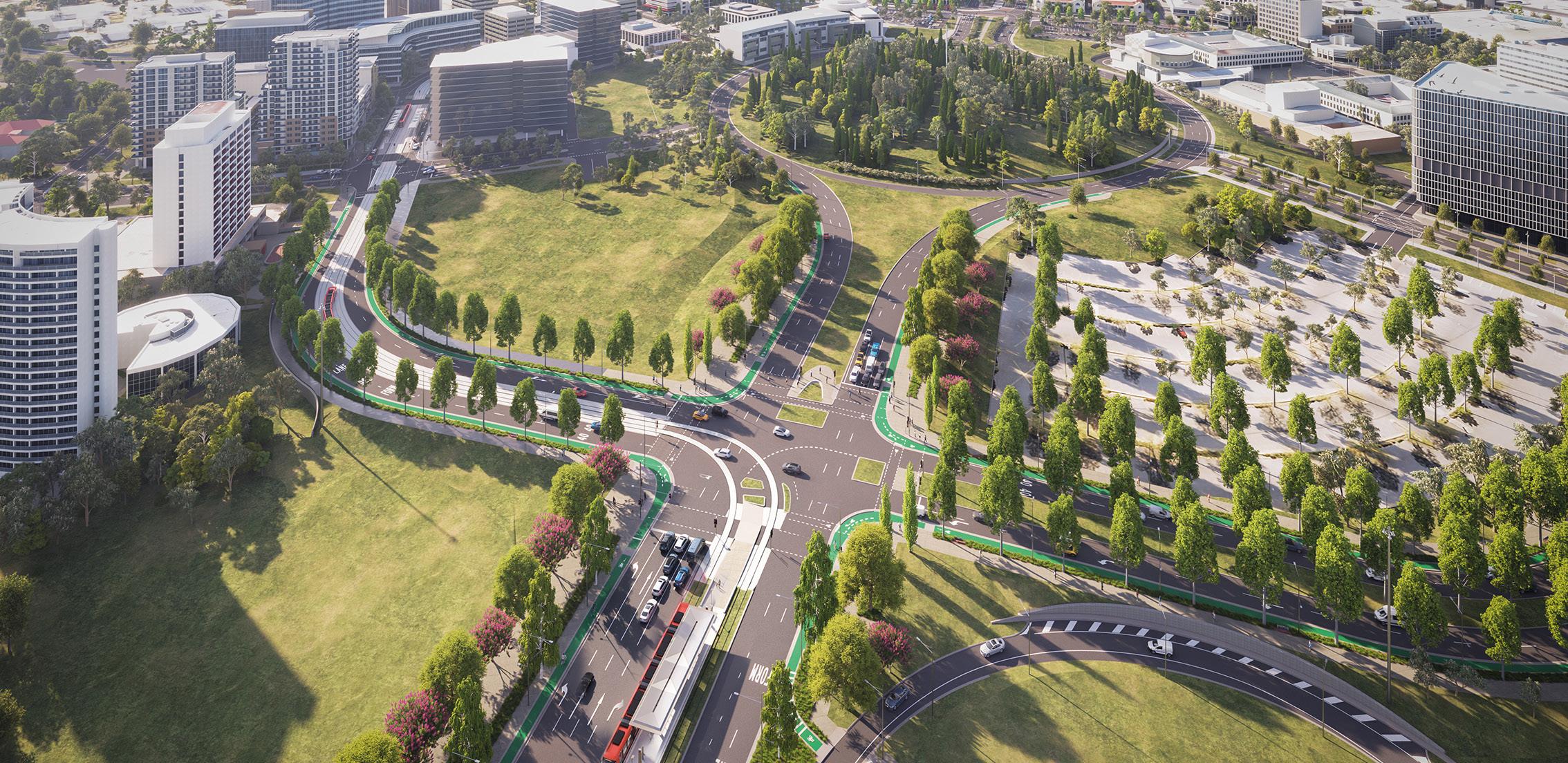
Raising London Circuit is one of central Canberra’s most significant road projects since the 1960s, with the new interchange benefiting pedestrians and cyclists and enabling the Light Rail to Woden project to proceed. However, as with many major projects, road users will be impacted throughout the construction. The ACT Government is addressing these disruptions by implementing smart traffic monitoring technology.
The Raising London Circuit project involves increasing the level of London Circuit approximately six metres – to the Commonwealth Avenue level – and creating a signalised intersection. Raising London Circuit is a critical step in extending Canberra’s light
rail network, allowing for a seamless integration of light rail infrastructure. Once the project is complete, construction can start on the first stage of Light Rail to Woden, Stage 2A – City to Commonwealth Park. Stage 2B will take the light rail from Commonwealth Park all the way to Woden.
Light Rail to Woden is projected to transport 39,000 passengers a day once operational, supporting Canberra’s growing population.
Australian Capital Territory (ACT) Minister for Transport and City Services, Chris Steel, said Light Rail to Woden is the biggest infrastructure project in the history of the city.
“The project will make Canberra better connected and more sustainable, support thousands of jobs and cut future traffic gridlock as we grow,” Mr Steel said.
However, Raising London Circuit is also set to benefit the city as a standalone project, aiming to provide a better connection between the city and Lake Burley Griffin.
Australian Capital Territory Chief Minister, Andrew Barr, said, “Connecting
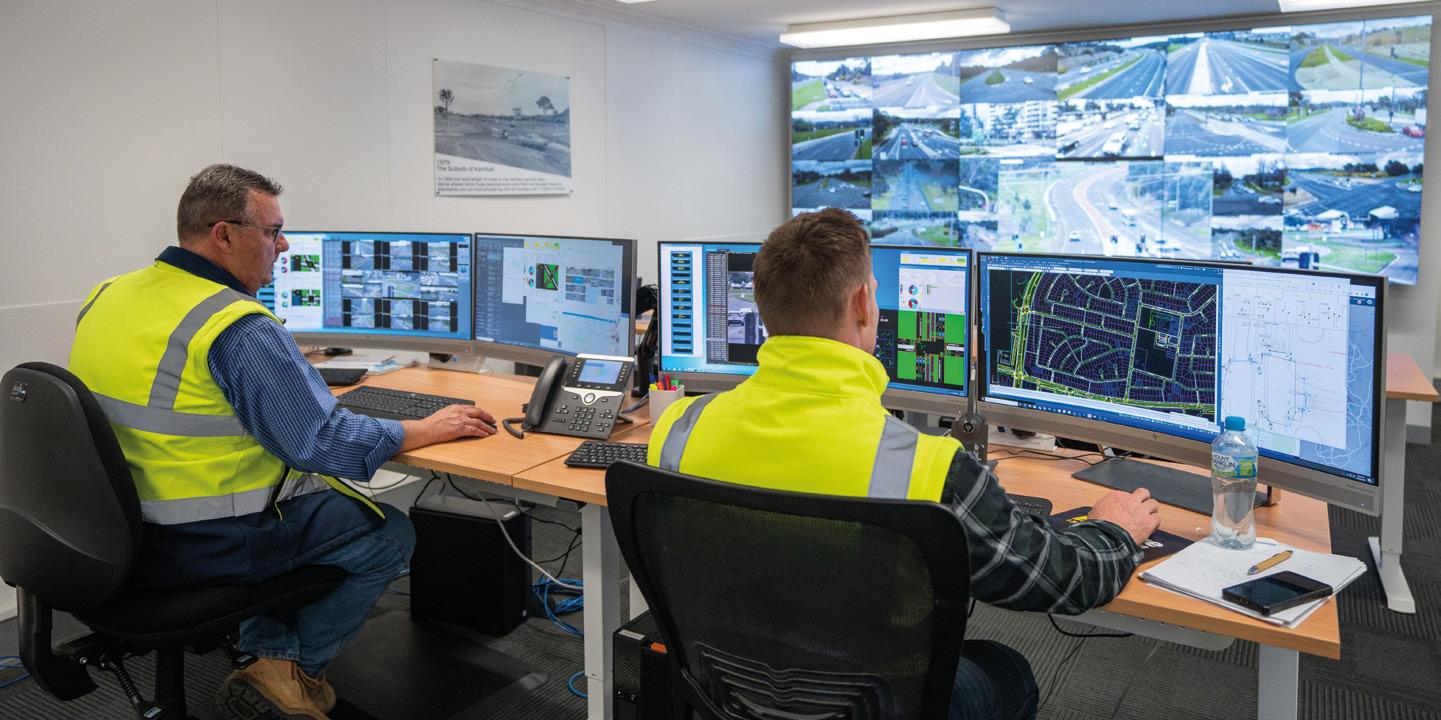
London Circuit to Commonwealth Avenue is a significant step forward for light rail, activating the southern part of Canberra’s CBD, Canberra Theatre precinct and providing better connections to the Acton Waterfront.”
The project includes new footpaths and pedestrian signals to offer more options for those walking around the city. Pedestrians and cyclists will also benefit from the inclusion of dedicated bike lanes.
“We are not only building the platform for light rail to turn from London Circuit onto Commonwealth Avenue, but removing barriers for cyclists and pedestrians moving through the southern part of the city,” Mr Barr said.
Construction works for Raising London Circuit began in October 2022. This included the installation of temporary traffic lights and a new bus lane at the northern side of Vernon Circle.
A new footpath and pedestrian signals on City Hill between Constitution Avenue and Edinburgh Avenue are also now open, providing a safe connection for Canberrans and visitors to walk, e-scoot and cycle across the city centre.
In December 2022, the ACT Government announced the temporary closure of London Circuit between
Edinburgh Avenue and Constitution Avenue and the permanent closure of the two western cloverleaf ramps leading into the city.
Providing an update two weeks after the closure, Mr Steel said, “The Government has been closely monitoring the traffic around the city during construction and as expected, there has been some disruption on certain road corridors since the closure of the southern section of London Circuit and the two cloverleaf ramps on Commonwealth Avenue.”
MANAGING TRAFFIC DURING CONSTRUCTION
The raising of London Circuit will have major impacts on traffic conditions in Canberra.
The ACT Government’s early traffic analysis indicated that without intervention, construction impacts would lead to congestion and delays, with flow-on impacts across the entire road and public transport network.
To manage disruption, the Government is installing around 40 additional Bluetooth sensors across the city’s road network, alongside 30 new cameras to provide live updates to motorists and public transport users.
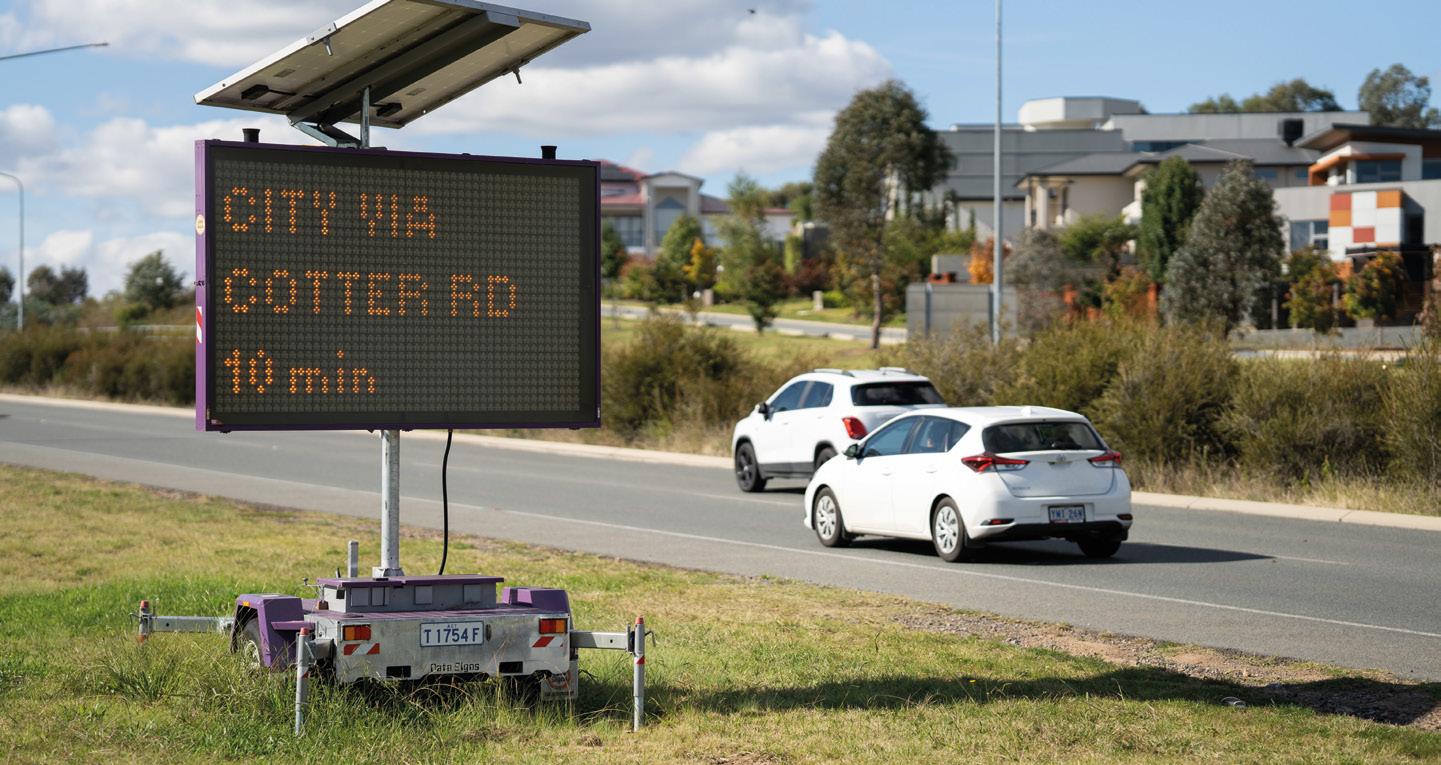
20 Bluetooth sensors have been installed as of February 2023. Supply chain issues have impeded the arrival of the new cameras but it is expected that they will all be installed by mid-2023.
“To reduce traffic impacts associated with the delivery of light rail and other major public and private projects in the city centre, we’ve been investing in smart technology to better manage our traffic network during construction and beyond,” Mr Steel said.
At Canberra’s traffic management centre, additional staff have been employed to ensure live coverage during the busiest times of the day.
Mr Steel said that although disruption is unavoidable, these measures ensure better management of traffic lights and provide motorists with live updates on signage as construction progresses.
“The data collected from the traffic network will be used to convey directions to motorists before and during travel on the best ways to move around the city during the construction period,” Mr Steel said.
“Better surveillance of our roads throughout the day will also mean we can respond more quickly to events like accidents holding up traffic.”
When areas of the network appear to be congested, staff are dispatched out in the field to investigate. From there, the public is notified through variable messaging signs.
Roads ACT will also communicate with other areas of the ACT Government and they will send out notifications through social media.
Although it is too early to see full results from the technology, continuous monitoring through the Bluetooth sensors has allowed for better accuracy.
In February 2023, Mr Steel said the ACT Government was keenly monitoring conditions and looking for ways to improve the commutes of Canberrans.
“Major infrastructure projects now under construction are disruptive but they will ensure that our city is better connected, sustainable and vibrant in the long term,” Mr Steel said.
With the raising of London Circuit expected to be completed in 2024 and Light Rail works to continue in the coming years, the implementation of smart technology will continue to support Canberra’s traffic management system.
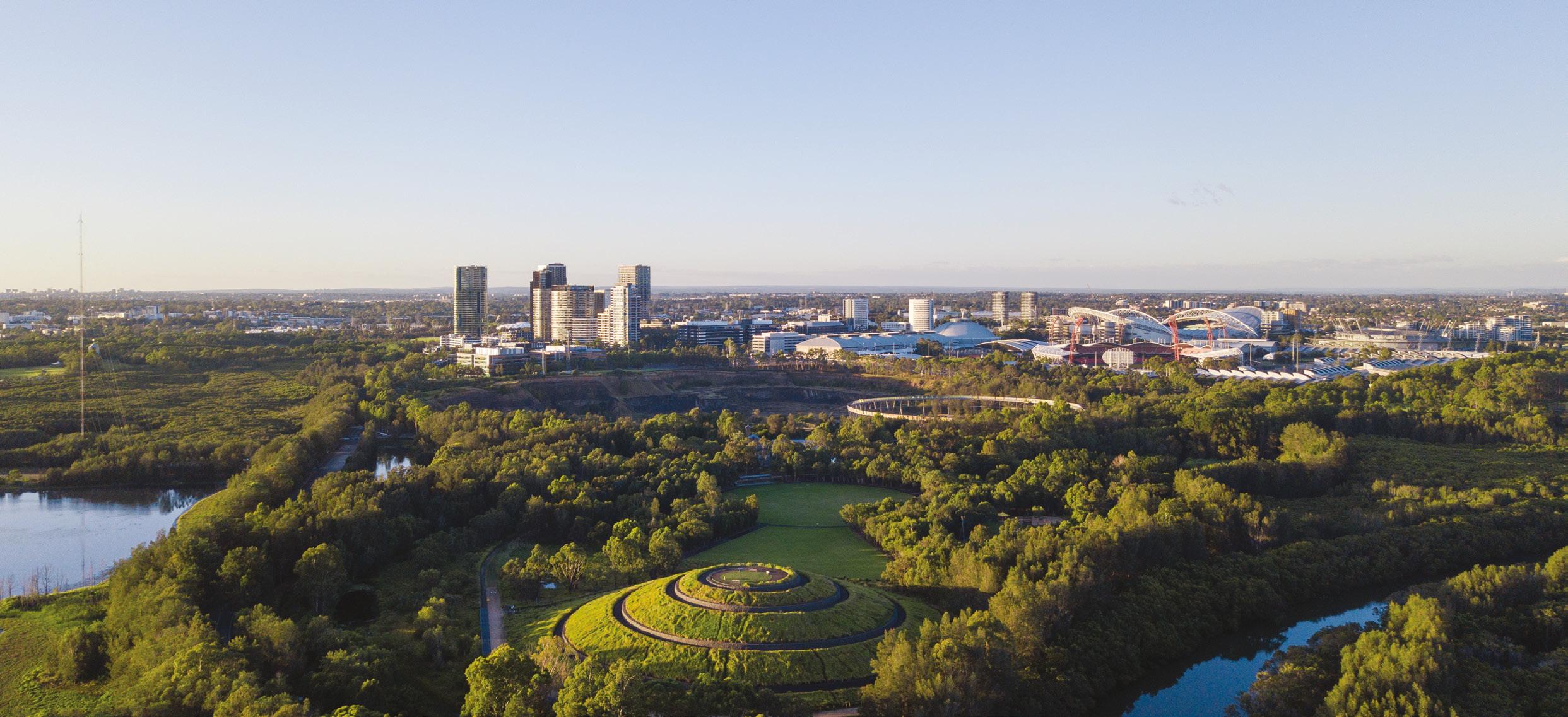
A CASE FOR STRATEGIC ASSET MANAGEMENT: ECOLOGICAL VS TRADITIONAL INFRASTRUCTURE
The requirements for assessing and maintaining ecological assets such as waterways and wetlands are vastly different to that of traditional assets.
Ecological assets are complex and can be unpredictable in their performance and lifecycle management needs. They require tailored, site-specific adaptive maintenance to keep them in good and serviceable condition and can be severely affected by the impacts of climate change, particularly when their condition declines and they become less resilient.
Conventional asset management was largely developed for traditional assets whose performance and lifecycle management needs are predictable, well understood, and supported by industry guidelines and standards.
Given the complexity of ecological assets and the many ‘levels of service’ they provide to the community, they are incompatible for integration with existing asset management systems. This has proven to be a conundrum for local authorities and councils whose role it is to maintain them. It has also resulted in a lack of financial planning and thus maintenance is often reactive rather than proactive.
STRATEGIC ASSET MANAGEMENT PROVIDING A SOLUTION
Recently, Brightly, in partnership with E2Designlab, developed a strategic asset management framework to address the unique needs of ecological assets for the Sydney Olympic Park Authority (SOPA).
SOPA is responsible for managing the ecological assets around Sydney Olympic Park, including waterways, constructed wetlands and bioretention systems which are critical for stormwater conveyance, harvesting, and treatment. In addition, SOPA is also responsible for maintaining habitat ponds for the endangered Green and Golden Bell Frog and vast mangrove and saltmarsh wetlands.
Given the complexity of the assets, SOPA found existing programs were not sufficient in delivering the required funding and management tools for the assets.
Under constrained resource capacity, a number of SOPA’s ecological assets were degraded.
SOPA needed a bespoke program to manage the overall asset portfolio to sustainably deliver the required levels of service, control risks, and drive continual improvement now and into the future.
Brightly and E2Designlab worked with SOPA to guide their long-term management and restoration.
Sally Boer, Director at E2Designlab said, “We brought together a multidisciplinary team with skills in environmental engineering, ecology, and strategic asset management to develop these resources.
“Once we had the right skills on board for the project, we needed to understand how to create a solution that would meet SOPA’s brief.”
CREATING A FRAMEWORK, PLAN AND CONCEPT DESIGNS
The team distilled the project into these key stages:
Develop a strategic asset management framework
The team reviewed relevant internal and external materials to understand SOPA’s ecological assets, environmental obligations, and current asset management processes, systems, and requirements.
Undertake an asset audit
The team undertook an audit of 158 ecological assets to understand their current condition, risks, levels of service and maintenance and rectification requirements.
Develop an asset management plan
Using the information uncovered to deliver the framework the team was able to develop an asset management plan capable of sustainably delivering required levels of service, managing risks, and driving continual improvement in the asset portfolio over the next 20 years.
Develop concept designs
Once the plan was approved, the team was able to prepare concept designs and costings for different options to restore degraded assets to a good and serviceable condition.
David Horseman, Strategic Asset Management Services Manager at Brightly, said, “Working with E2Designlab we were able to collaboratively address the needs of SOPA in managing this complex but vital ecological asset portfolio through strategic asset management.”
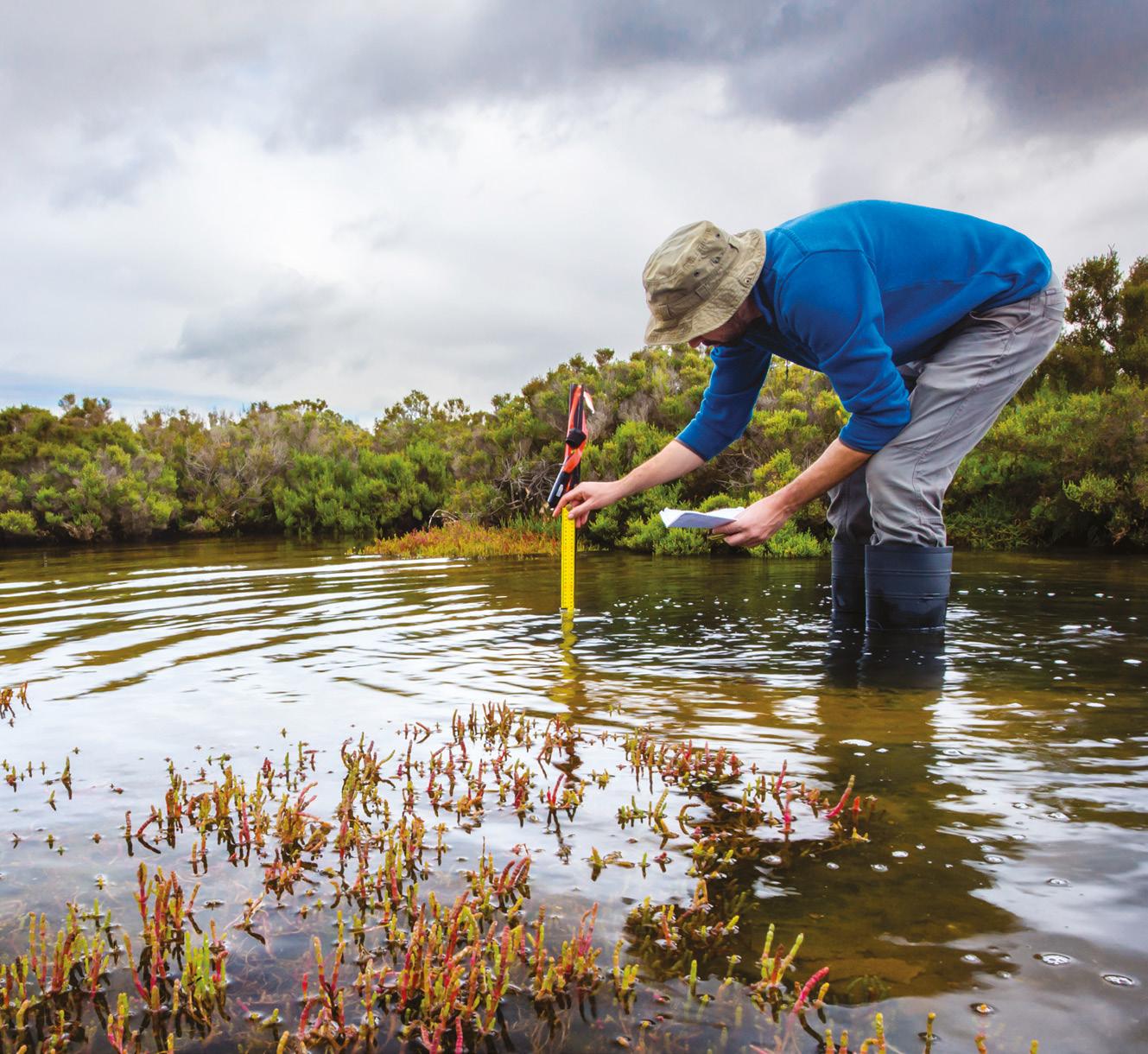
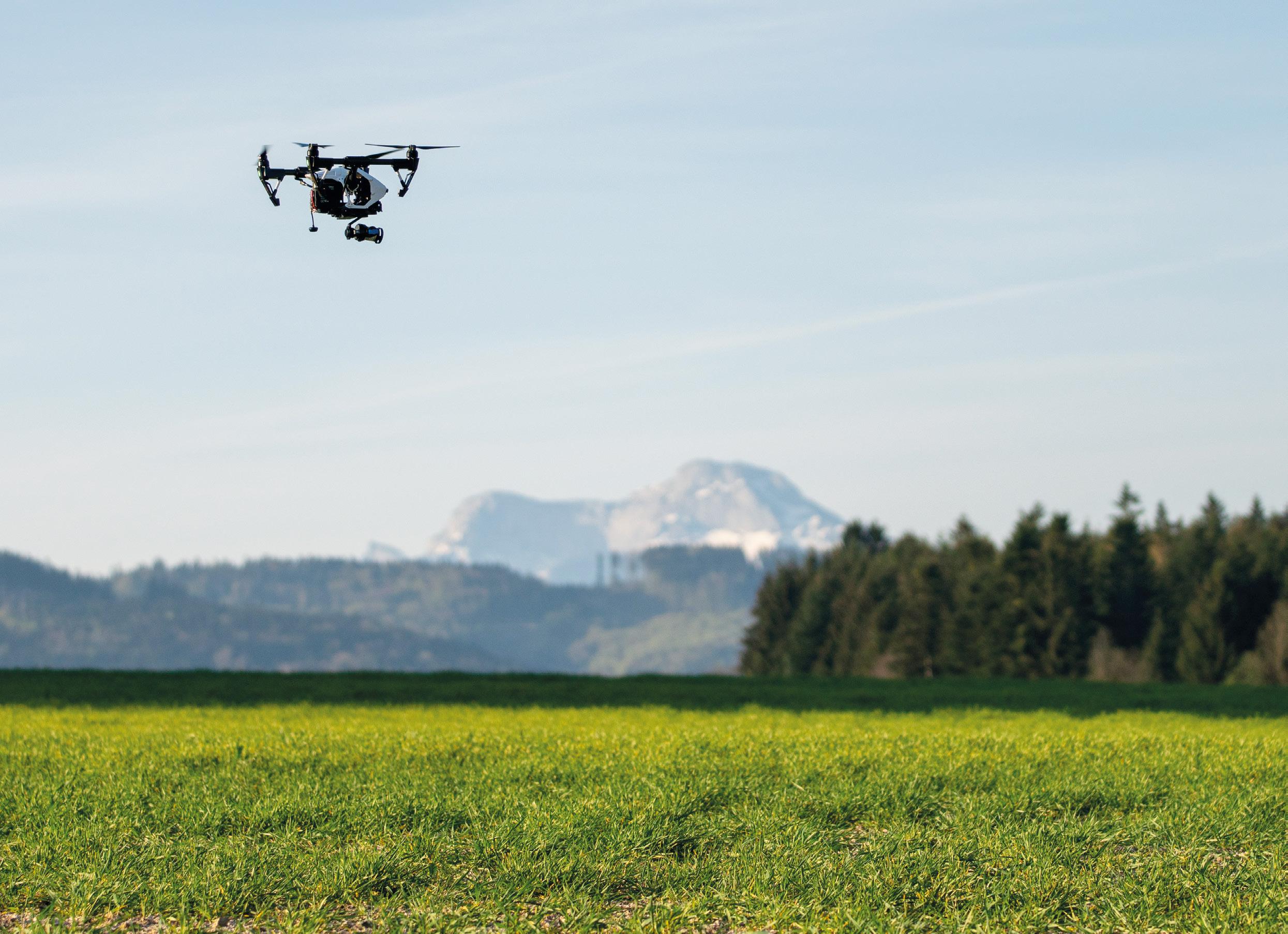
HOW IOT, CONNECTIVITY AND EDGE COMPUTING CAN SUPERCHARGE REGIONAL AND RURAL AUSTRALIA
By Nam Nguyen and Nadeen Jayasundara, Co-Chairs of the IoT Alliance Australia (IoTAA) Collaboration WorkstreamWhile it’s acknowledged that Regional Australia has a Digital Divide versus metro urban areas, this disadvantage is often focussed on voice, mobile and broadband connectivity. The demand for data is relatively the same (or arguably greater) for regional communities and businesses. The success of Internet of Things (IoT) solutions has the potential to supercharge regional economies and improve livelihoods, or worsen the divide.
The Internet of Things (IoT) refers to connecting devices or systems with embedded sensors to the internet so that they can send and receive data remotely. IoT, in effect, is all about data. It’s about collecting appropriate data, storing, processing and transforming it into insights, enabling targeted data users to act for their particular purposes and benefits.
WHAT IS IOT?
To be successful, IoT solutions need three critical elements:
1. IoT sensors/devices – required for data generation, and often they generate large volumes of it
2. Connectivity – some form of connectivity is required to transport data to and from IoT devices/ sensors. It is mainly for transporting data from IoT devices to the cloud for storage and processing. Without connectivity, there is no Internet of Things
3. Data Analytics, AI/ML, Storage and Computing – sensor data needs to be cleansed, transformed, processed, and analysed using
artificial intelligence (AI) methods such as machine learning (ML) to derive insights for business decisions or inputs to drive process automation. Often these tasks are done centrally in cloud platforms, on servers in data centres typically located in or near the major cities Additional infrastructure is required on top of the above elements to make any IoT application accessible to end users, compliant with regulatory requirements, and purposeful.
Successful implementation of IoT applications needs reliable IoT devices, the availability of digital connectivity and access to connectivity, and computing resources for data storage, processing and enrichment, i.e. artificial intelligence/machine learning. There are examples of successful IoT deployments from multiple industry sectors in Australia, from smart cities to smart buildings, construction, utilities, manufacturing and logistics, and the entertainment sector, to name a few. The majority of these IoT deployments, however, are found in urban or populated areas, where there are multiple connectivity options, and access to
public or private cloud computing resources is not of any concern, regardless of the requirements of the IoT solutions, such as bandwidths, the volume of data, and or latency.
The most common connectivities for connecting IoT devices to cloud platforms are:
LoRaWAN – an LPWAN, or low power wide area network technology that uses a licensed-free spectrum, the ISM band. LoRaWAN coverage delivered by many LoRaWAN network providers
SigFox – an ultra narrowband technology that also uses the ISM band and is provided by a private operator. Coverage is generally based on enterprise requirements, which are often private and therefore not available for public use
LTE-M/NB-IoT – public LPWAN, cellular-based technologies provided by the telcos, and coverage is extensive, from 80 to 98 per cent population coverage, depending on each cellular operator. There is only one provider of LTE-M network
LTE – broadband network with extensive coverage by all three telcos. All three Australian telcos have LTE networks with wide bandwidths, with downlink speeds of up to one Gbps, and can transport large volumes of data between devices/edge and cloud 5G – the next generation cellular technology from LTE. It offers large bandwidth and faster speed and can support many more IoT devices per cell than LTE. 5G coverage is not as extensive as LTE but is growing gradually
Ethernet LAN via Fixed NBN (National Broadband Network) – also widely available to most homes and businesses. NBN speeds vary from tens of Mbps to one Gbps.
Wi-Fi – is widely available to homes and most businesses.
The real value of IoT is unlocked when IoT data is sent to IoT platforms, often in centralised servers and data centres, for storage, processing and analysed with the use of artificial intelligence such as machine learning.
HOW IS THIS DIFFERENT IN REGIONAL AND RURAL AUSTRALIA?
Most population areas have choices for connectivity and access to cloud computing platforms. In contrast, in sparsely populated regional and rural areas, public cellular (LTE) networks and NBN fixed services do not extend beyond most regional centres,
leaving regional businesses and consumers with no or limited connectivity. NBN has been the only service provider offering satellite broadband services. However, it still falls short of regional business requirements in terms of bandwidths and speeds.

Despite having limited connectivity to the internet, it has not stopped the deployment of IoT solutions and innovation in regional areas. Many smart IoT use cases have found their way to farms, mine sites, paddocks, water and environmental monitoring, local council services and public safety, and regional businesses and industry hubs. IoT devices are connected through a local network, using LoRaWAN, Sigfox, private LTE networks, or other private radio networks such as Taggle. New, innovative IoT satellite networks are emerging, offering narrowband, nonreal-time services. More broadband satellite providers such as Starlink are starting to offer new innovative services that would be more attractive to regional areas.
Technology plays a major role in innovation. The lack of digital infrastructure, i.e. connectivity in regional and rural Australia, and local access to cloud computing and data centre resources directly affect IoT performance through low latency, realtime data and decision-making, costs and productivity.
HOW EDGE COMPUTING CAN HELP UNLOCK THE VALUE OF IOT DEPLOYMENTS IN REGIONAL AUSTRALIA
Edge computing brings computing power, data storage, and networking capabilities closer to IoT deployments. There are different implementations of edge computing. Edge computing can also be known as:
On-premises/on-premises edge – where computing capabilities are geographically close to the IoT devices. Usually hosted on-premises and owned by the enterprise.
Edge cloud – where computing capabilities are implemented in regional,
distributed edge cloud, or edge data centres. An example could be an edge data centre in the regional/rural areas providing computing capabilities. Edge cloud is usually hosted by data centre operators.
Implementing edge computing with IoT deployment can bring many benefits, including:
♦ Edge computing can solve real-time problems. By processing IoT data as near the sources as possible, results can be made available in or near realtime, enabling immediate decisions and consistent experiences
♦ Instead of constantly sending data to the cloud, only results are sent, reducing connectivity costs. Edge computing reduces the amount of data that needs to be sent away to a centralised cloud-based location
♦ Real-time IoT applications such as process automation can be realised with edge computing as latency can be significantly reduced and performance increased
♦ Edge computing also reduces IoT security risks associated with cloud computing, as data is not centrally stored, thus increasing resiliency IoT deployments with edge computing capabilities enable improved IoT performance through low latency, real-time data and decision-making. This can bring significant cost reduction and increase productivity.
Regional deployment combined with the growing importance and innovations in sustainability (energy, land, water, food), AgTech and precision farming, smart mining and intelligent transport, provides the opportunity to supercharge regional and rural Australia economies and communities.
These views are of a personal nature in representation of IoTAA only. For more information, please visit iot.org.au.
Expanding NBN CONNECTIVITY TO JUST ABOUT ANYWHERE
nbn is making some great leaps forward in innovation, but imagination can be just as important.
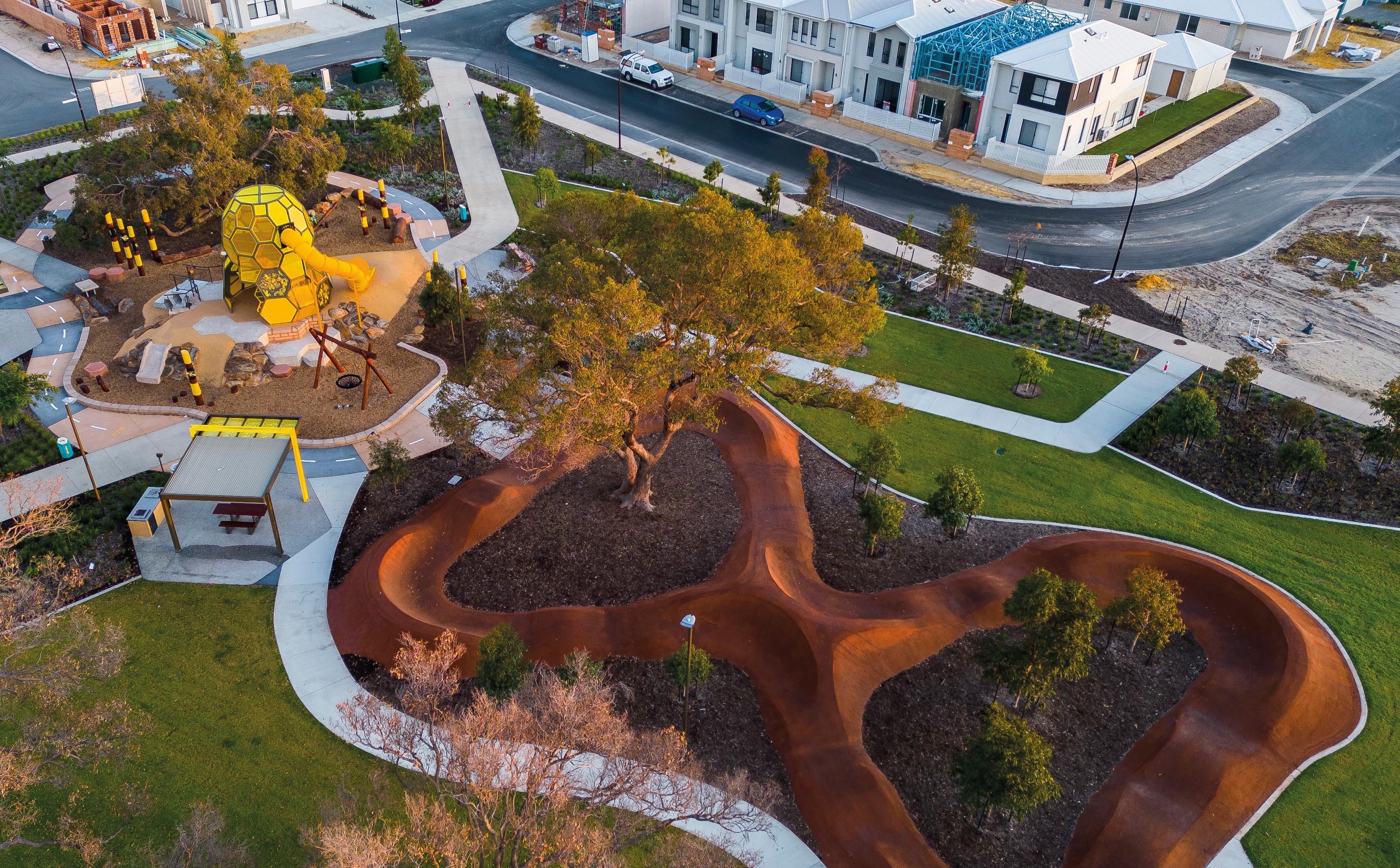
If you can imagine it, you are halfway to making it. Picture a new park in a new estate in Western Australia. In that park, there's a small device no bigger than your thumb connected to a light pole. And through that device, the community benefits from the power of broadband connectivity via nbn® fibre.
That park could have high-performing Wi-Fi for anyone who visits there. A new father could sit in the fresh air videocalling his parents while his newborn sleeps in a pram. Kids could play e-games against each other while taking a break from the BMX track. A university student could write her assignment on a smart bench that has USB ports and wireless chargers for her devices.
You could even work from home – not shackled to your dining table – but in the outdoors, surrounded by the grass and trees, living your best life. At the same time, you're leveraging everything you need from the cloud.
Suppose you push your imagination further – this small device and its fibre connectivity power a small weather station, allowing the developer to regulate the irrigation at the park and
at one of its display homes just down the road. It's saving water and money – and sparing all of us the spectacle of sprinklers watering grass that's about to be soaked by rain.
Property developers, the people building future communities, would know they're creating an environment where people want to live, and businesses want to trade. And that's great for developers, business owners and your way of life.
You don't have to imagine that because that's already happening with nbn's newest product, nbn® Smart Places*.
THE POWER OF THE NBN NETWORK OUTDOORS
Brabham Estate, built by leading national property developer Peet and in collaboration with Development WA, is located 20km north-east of Perth’s CBD. This innovative community is one of the program locations where an nbn Smart Places device has been installed on a light pole in a public park.
This WA example is one of 35 trials across the country. nbn Smart Places is
a fascinating product that proposes to take the power of nbn beyond homes and businesses. It proposes to deliver broadband services via nbn fibre to just about anywhere. It’s designed to allow nbn to satisfy the current thirst for digital connectivity that will only grow into the future. But, because it's essential, nbn must stay ahead of that demand.
If you look at the last six years, data use has tripled. As a result, the need for broadband will reach levels never seen before over the next decade as the internet continues transforming the world and how we live.
One of the ways nbn plans to meet that demand is through nbn Smart Places. This new equipment – miniaturised, ruggedised and reversepowered network connection devices – can create fibre connections just about anywhere. It will enable the power of the nbn network to be delivered to demanding outdoor locations that aren't serviceable using standard equipment.
As you can now imagine, the possibilities are just about limitless.
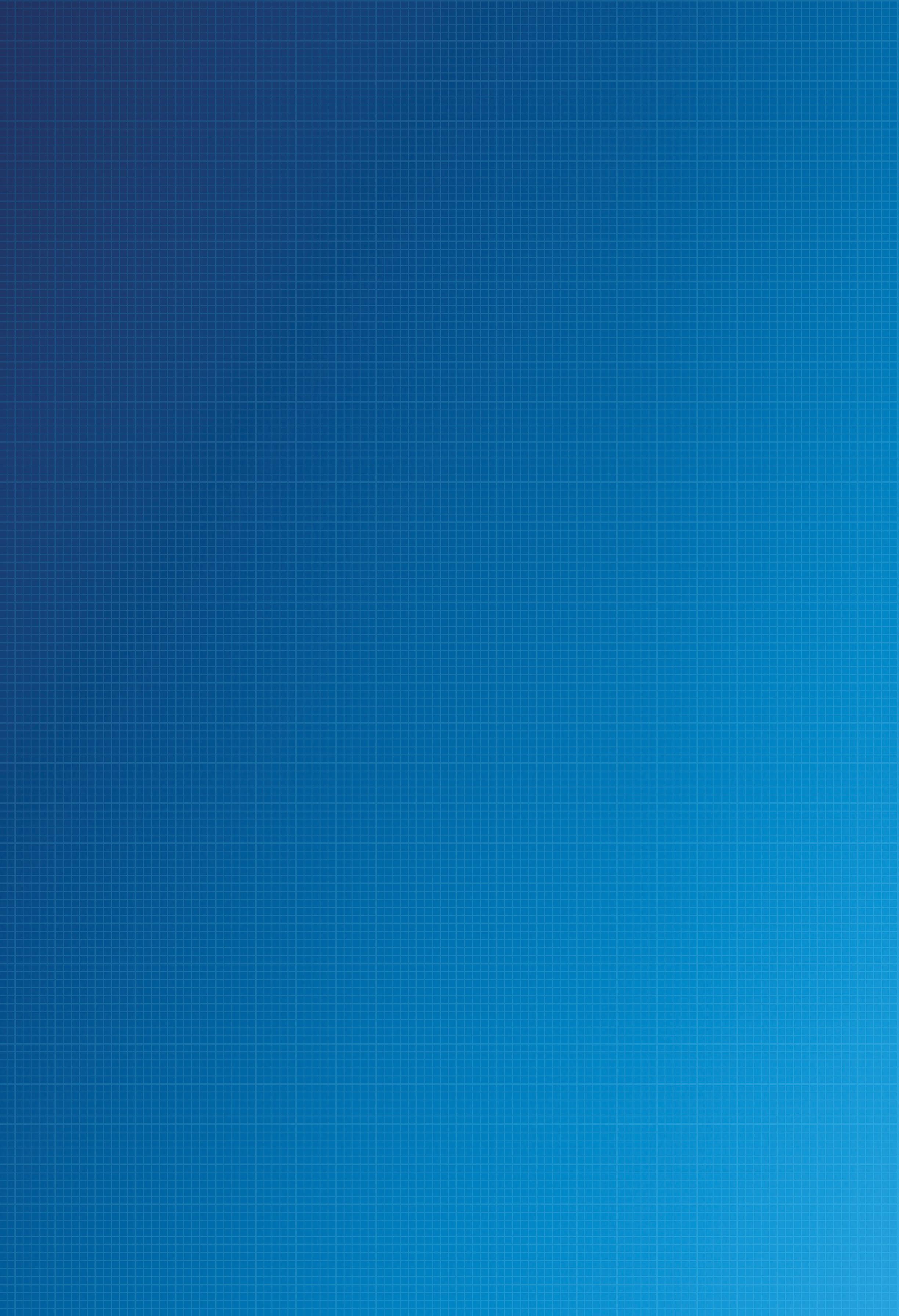
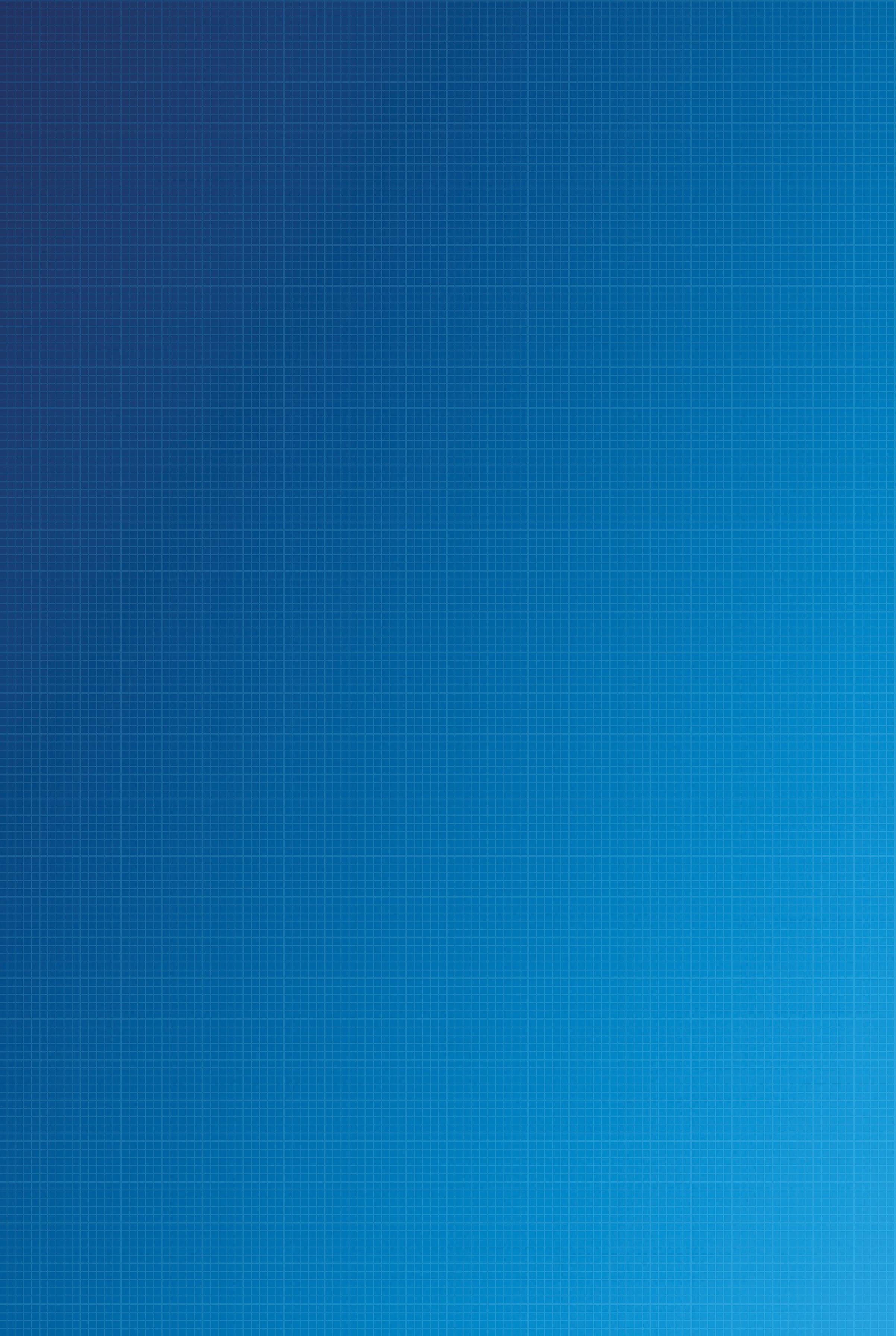
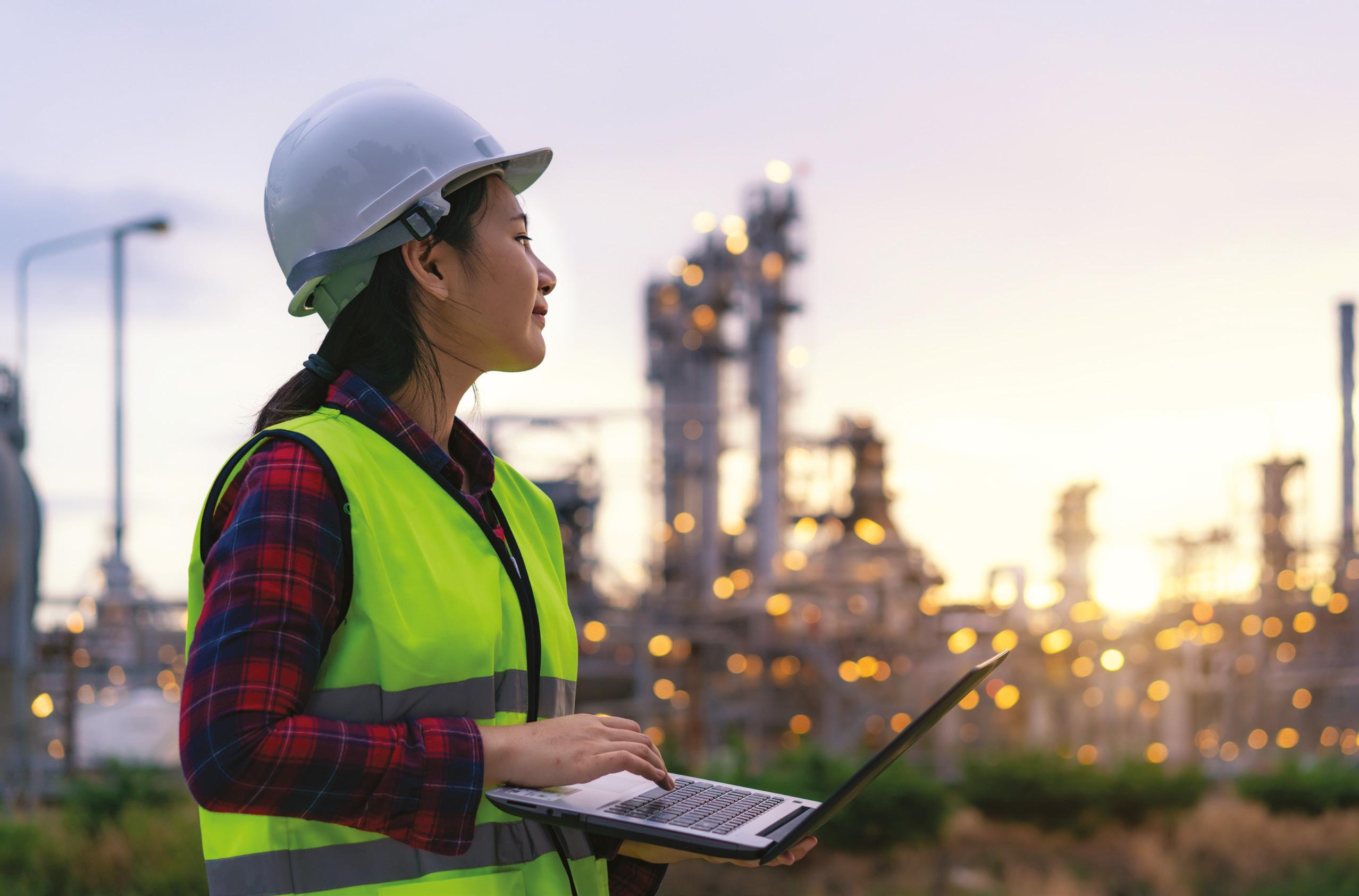
FROM LANDS, TO SEAS, TO STARS
– THE FUTURE OF GEOSPATIAL
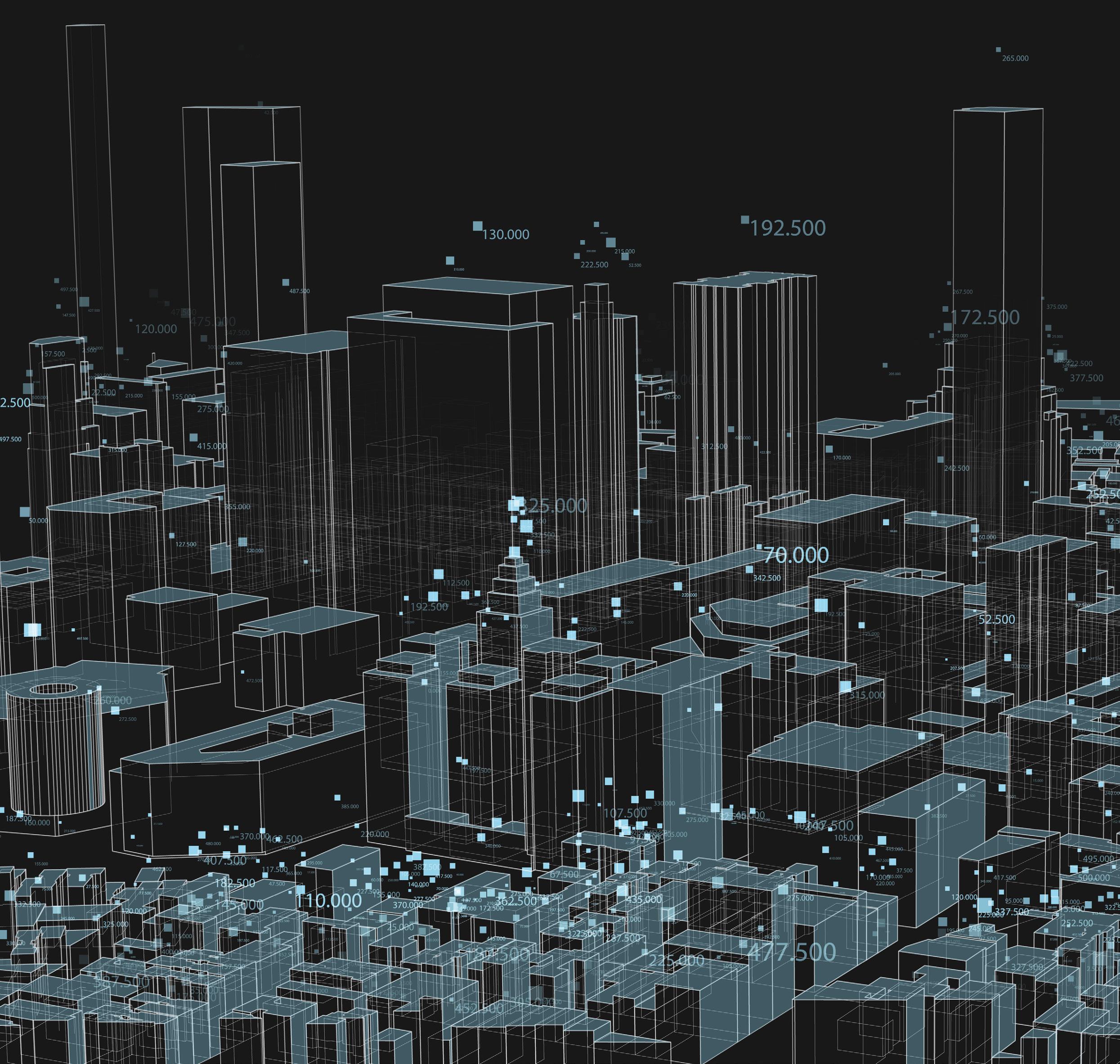
Ahead of the Locate23 Conference in May, Infrastructure Magazine spoke with Bradley Slape, Surveyor-General of South Australia, to explore the current applications of geospatial data and technologies in the infrastructure sector, shared challenges and future direction, as well as why he thinks land applications should be prioritised over sea and space.
Bradley Slape has been in the role of Surveyor-General of South Australia, Land & Built Environment Planning and Land Use Services at the Department for Trade and Investment for just over 12 months, following an extensive career working in both the private and public sectors.
Mr Slape said he believes geospatial data and technologies underpin Australia’s infrastructure sector, making them an extremely important, if not critical, component of the industry.
“Whether it’s design, set out or as-built data, it’s all geospatial. Geospatial data is essential for machine guidance for construction, and engineering surveyors use the latest positioning technology to ensure machine guidance and automation is maximised on infrastructure projects,” Mr Slape said.
Mr Slape said he sees the analytical tools associated with geospatial data to be having the biggest impact in today’s world, compared to other applications or technologies.
“Combining any type of data with geospatial data allows informed decision making and better business outcomes,” Mr Slape said.
“South Australia has a fully digital planning and design code that allows users to identify what they can and can’t do on a property at the click of a button, all underpinned by spatial data. Artificial Intelligence and Machine Learning are also at the cutting edge of the geospatial industry.”
DEBATE AT LOCATE23
Mr Slape will be a keynote speaker at this year’s Locate23 Conference – Australia’s premier geospatial conference that provides a unique opportunity to learn about the latest trends and applications in geospatial technologies.
He will be a part of the panel discussion that explores this year’s theme of ‘Geospatial Evolutions | From Lands, to Seas, to Stars’, with his experience fitting perfectly in the representation of ‘land’ as he has had a strong focus on cadastral surveying.
In terms of which of these areas should be the geospatial industry’s priority, Mr Slape unsurprisingly believes it should be ‘lands’, coming from his work as a licensed land surveyor, but is keen to debate further at the event.
“Clearly, satellite positioning plays a major part in the land and sea geospatial industries and I’m looking forward to participating in the opening plenary panel session to discuss the connections that Enrico Palermo, Head of the Australian Space Agency, sees between lands, seas and stars,” he said.
SHARED CHALLENGES AND SOLUTIONS
While these are three very distinct areas and applications, they also have the potential to share the same challenges and therefore be able to learn from each other. Mr Slape said one of the shared challenges he sees is a shortage of skilled workers and a lack of general awareness of the geospatial industry in the community.
“This is likely to be a major hurdle for filling the resource gap to sustain the infrastructure projects planned for Australia. Collectively creating awareness of the geospatial industry is paramount to attracting resources into the industry and sustaining a level of expertise,” Mr Slape said.
These challenges have been a priority for Mr Slape in his role as Surveyor-General of SA, but in a different way than he was initially expecting. Four months into the role it was announced that the existing surveying degree in SA would not be taking any more students and the course would teach out the current students. Since the announcement, the Surveyors Board and Mr Slape have been focused on establishing a new surveying degree in SA.
He said discussions with another local university have so far been extremely positive and it is looking promising that there will be a new surveying degree in SA from 2024.
“The termination of the degree set me back quite a bit as when I was appointed Surveyor-General I wanted to put my efforts into increasing student numbers in the existing course and promote surveying as a career,” Mr Slape said.
“I am now turning my attention to the promotion of the profession and creating an awareness of surveying to high school students so that the existing TAFE courses and new degree can attract the student numbers required to make them viable.”
In addition to promoting the industry and providing more opportunities to train professionals to help meet the huge demand for skills, Mr Slape also said he sees the future direction of Australia’s space and spatial industry to be a collaboration of these industries like we’ve not seen before.
“It’s inevitable that the industries will both evolve and converge over the coming years. As the Australian Space Industry advances, I think we will see applications between the space and spatial industries that will build on the existing earth observation connections.
“Geospatial data underpins earth observations, imagery is only meaningful when combined with other data and the geospatial industry provides ‘the other data’,” Mr Slape said.
Locate23 conference will run from 10 – 12 May at the Adelaide Convention Centre. For more information, and to register, please visit locateconference.com.
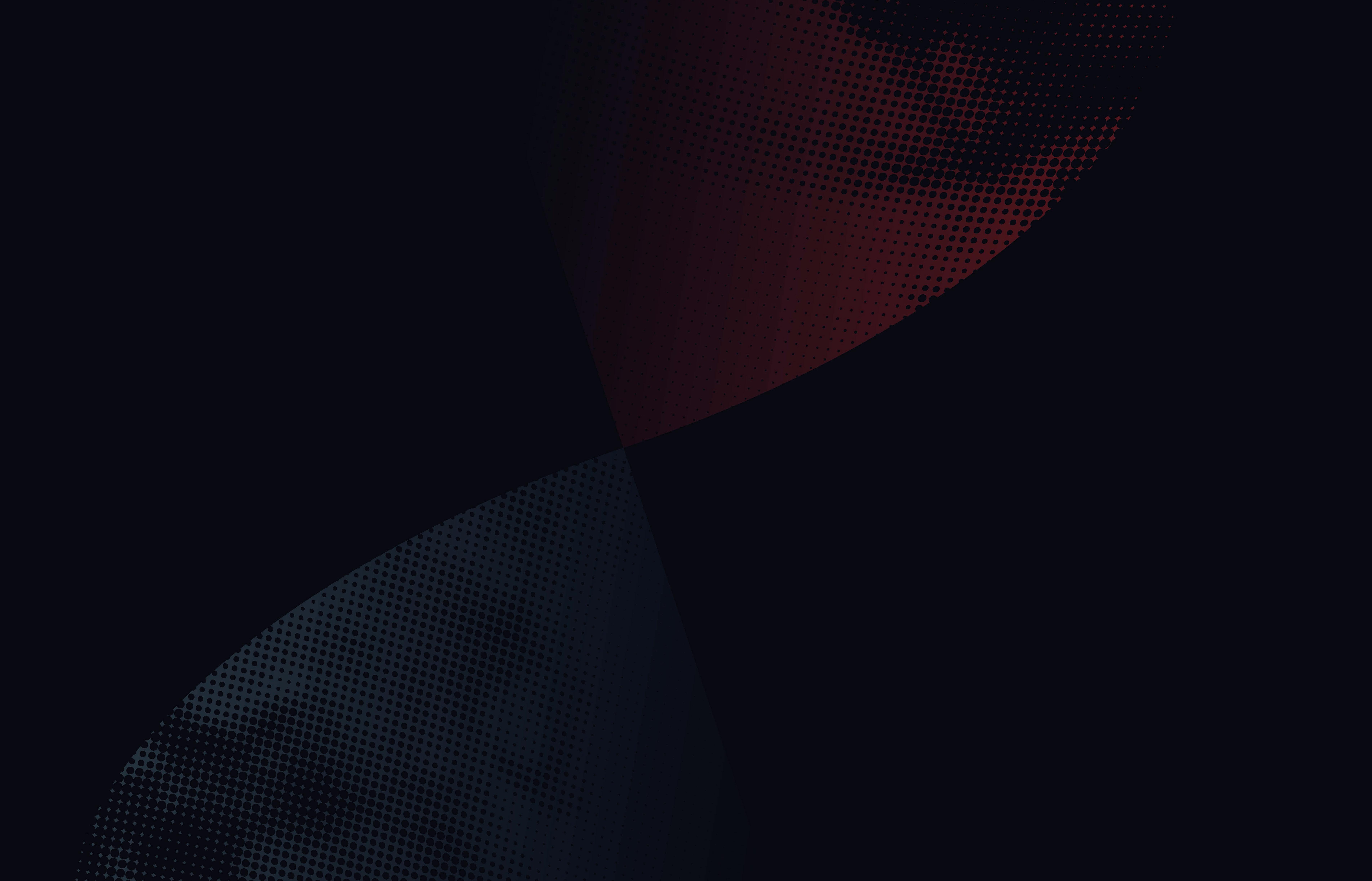
The missing link in your B2B Marketing Strategy
While traditional trade publications have quality audiences and high levels of trust, they can lack the full range of services to guarantee a return on your investment. And while traditional marketing agencies offer the latest marketing techniques, they don’t have the audience or the industry understanding the B2B sector needs.
Monkey Media is the missing link that brings together a trusted brand and powerful audience, with a complete agency offering.
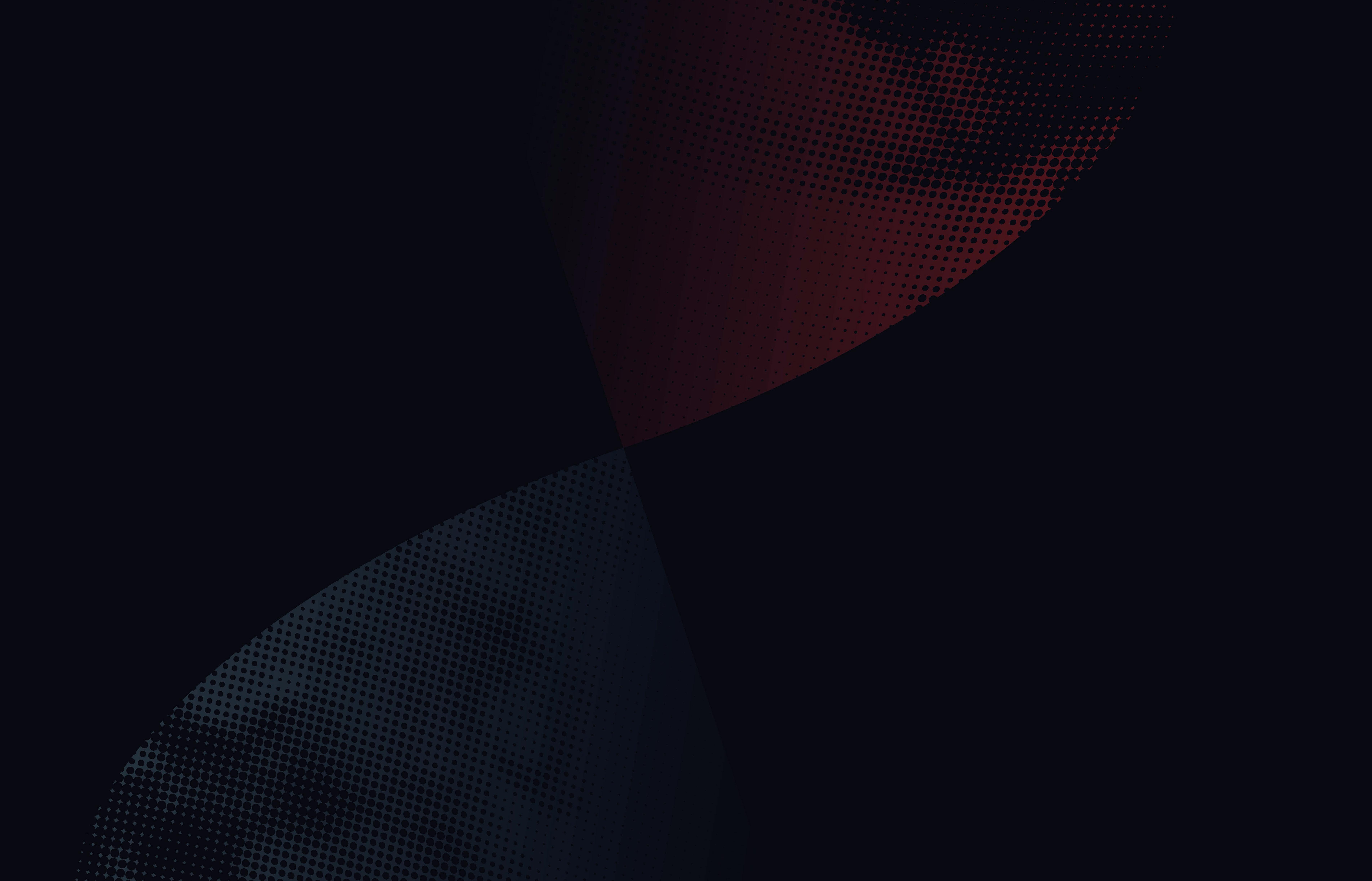
TO FIND OUT MORE SCAN THE QR CODE NOW
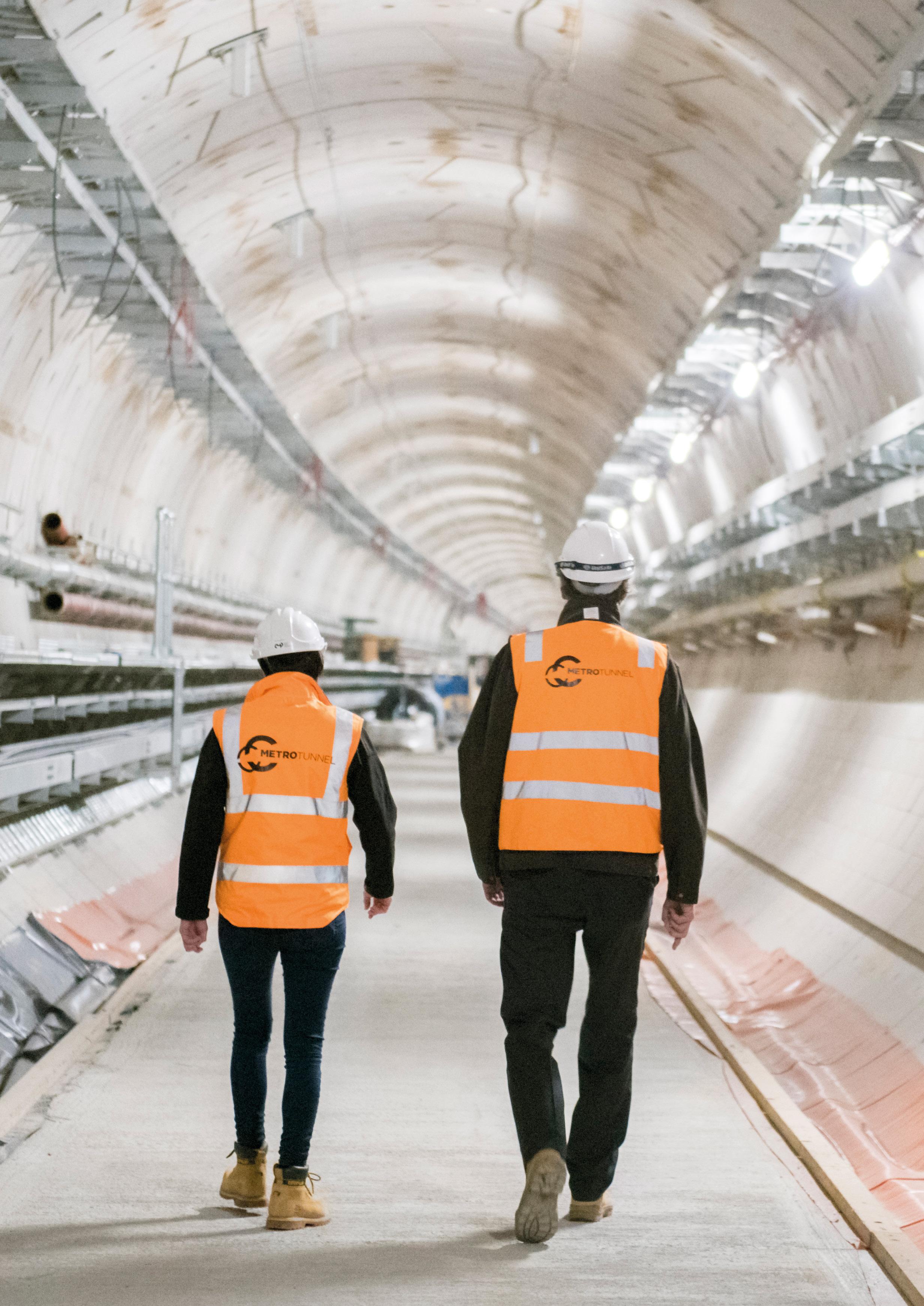
ATTRACTING THE NEXT GENERATION OF RAIL SIGNALLERS
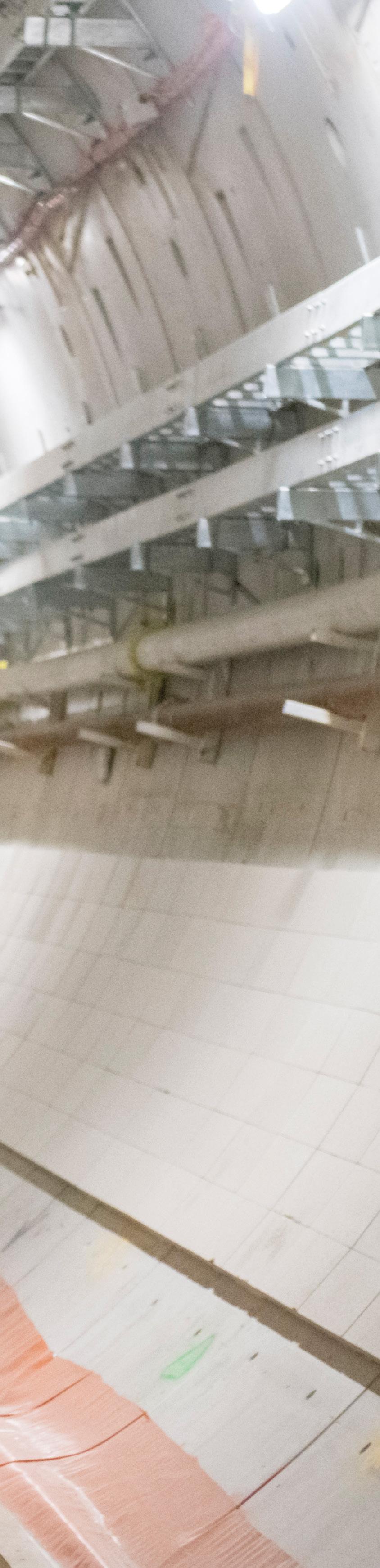
Victoria’s Big Build is on the hunt for the next ‘unicorns’ of the rail industry to take part in fast-tracked training to fill vital signalling jobs.
Train signalling is the nervous system of any rail network. It’s the complex system of wires, computer software and mechanical equipment that allows trains to run safely.
When there is any incident involving signalling, specialists are called in to fix the problem. However, these specialists are also busy delivering the unprecedented $90 billion investment in transport infrastructure.
As level crossings are removed, signalling is upgraded. As the Metro Tunnel is built and commissioned, signalling is required. As we plan and begin work on the Suburban Rail Loop and Melbourne Airport Rail, signallers are designing, installing and testing the systems that will make it all work.
Often referred to as the ‘unicorns’ of the rail industry, experienced rail signallers are fast becoming a rare commodity.
Due to the pipeline of transport infrastructure projects under Victoria’s Big Build, there is a need to find the next generation of signalling specialists.
The industry is looking to secure the skills and knowledge required to transform signalling systems to the latest modern technology, while maintaining safety and ensuring services continue to run with maximum reliability.
The most impacted and in demand roles are principal testers, testers in charge, and senior designers. Over the next 15 years the number of people working in these roles is expected to triple. That means there’s now opportunities for hundreds of graduates to get trained and employed.
NEW ONLINE COURSE TO FAST-TRACK TRAINEES
The Major Transport Infrastructure Signalling Strategy Taskforce, in consultation with industry, has released a new suite of online, streamlined training to enhance the way Victoria’s major rail projects are rolled out through quicker, more accessible, and more certain training pathways for vital rail signalling resources.
Victorian Minister for Transport and Infrastructure, Jacinta Allan, said this new suite of online, streamlined training is a step in the right direction, paving the way for qualified signalling resources to get on the ground, getting work done.
“There are more than 20,000 people working on the 165 rail and road projects that make up the Big Build – but we need and want more,” Ms Allan said.
The training is an important step towards plugging resourcing gaps as the program of works gets bigger, and the aging demographic retires from specialist roles. The e-learning module means these essential ‘unicorns’ of the rail industry can be prepared and out on the ground faster, helping to build, upgrade and maintain the ever-growing network.
To become a rail signalling engineer, you need a degree in electrical, science, mechanical or information technology plus have more than five years of experience as a professional engineer in similar fields.
Under previous processes, you’d then be mentored, an often time consuming and unclear road to signalling work. The new system allows would-be signalling engineers to complete the e-learning needed to demonstrate they’re ready to start their Signalling Assistant Designer role and commence their upskilling journey to becoming a qualified Signalling Designer, or Tester and beyond.
Competency and Skills Development Lead on the MTIA Signalling Taskforce, Mathew Sekulitch, said this new training creates a clearer pathway to becoming a Signalling Designer and Tester, putting the focus on getting on the ground and delivering in the field.
“It’s a great way to fast-track your way off the bench, and onto the field where you can make a big difference,” Mr Sekulitch said.
The modules were deployed in March 2022 and updated in July post an industry review period and are recognised by both MTM and V/Line, again streamlining the entry process to work on both networks. Additional courses are being developed in 2023 to support upskilling workers in other Signalling Design and Tester roles.
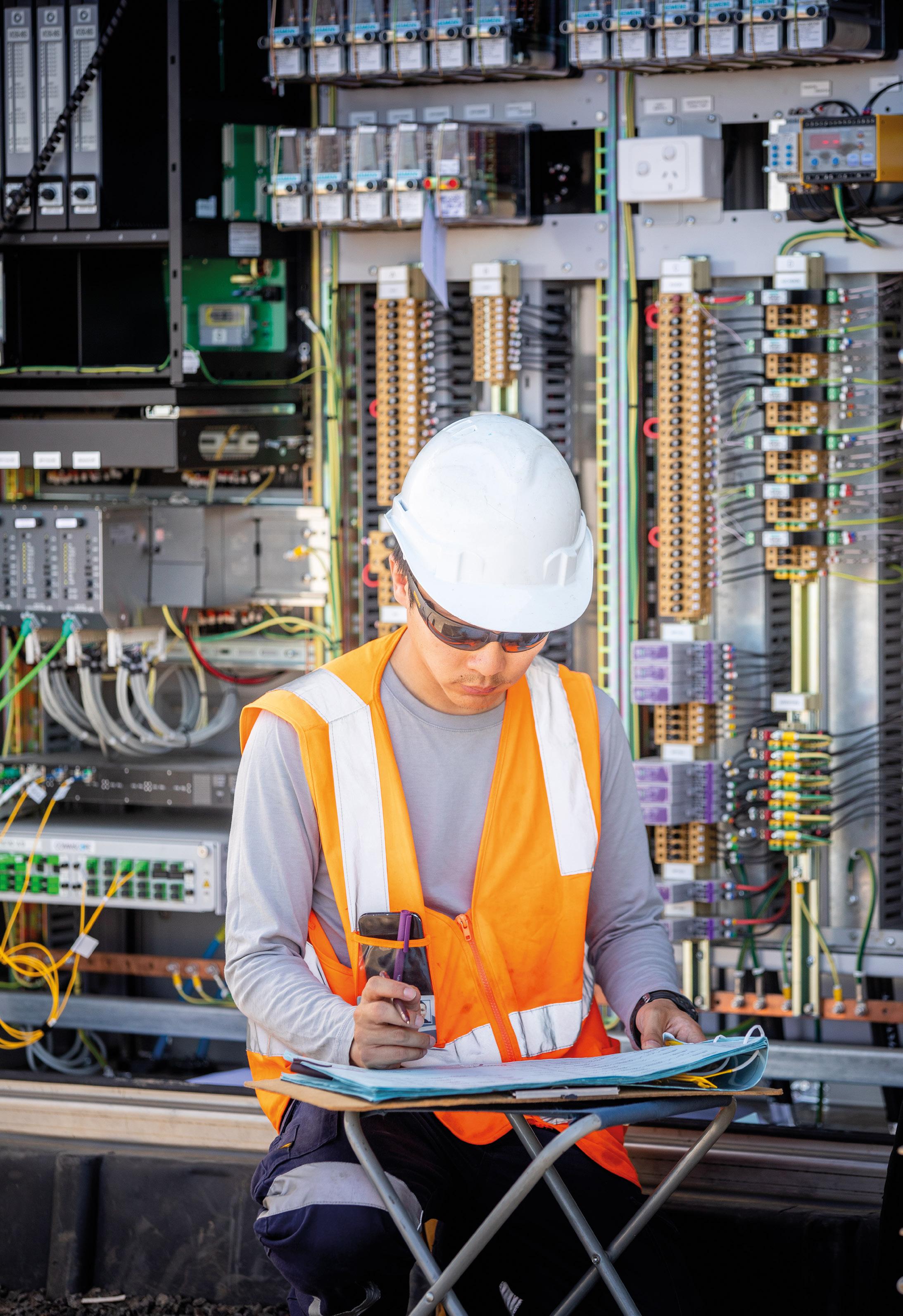
The skills and expertise of signalling resources are expected to be in increasing demand. As a graduate, you can expect to earn about $70,000 a year and, as you progress, there is capacity to earn even more in senior management roles in testing and design.
UPDATES TO TRAIN SIGNALLING
Major Transport Infrastructure Authority Director General, Corey Hannett, said signalling is a crucial part of the network and in high demand.
“This online training will help us get more designers competent and able to hit the ground running to help improve our rail system,” Mr Hannett said.
The government has also endorsed a new, proactive system that will allow safe, smaller distances between trains, boosting network capacity – allowing more trains to run, more often.
The European Train Control System (ETCS) has been endorsed as the preferred technology for addressing Victoria’s long term rail signalling needs.
The ETCS is being used in New South Wales, Queensland and New Zealand, and supports mixed traffic including metro, regional and freight trains.
The current signalling system allows a maximum of 18 trains per hour (tph), the new system will allow 24tph – or a 30 per cent improvement.
Other benefits include less trackside equipment, reducing maintenance, boosting reliability and reducing operating costs.
The system will also integrate with the Communications Based Train Control (CBTC) to be used on the Metro Tunnel and likely to be used on the Suburban Rail Loop. CBTC is most suitable for these projects.
Now the system has been endorsed, investigations to identify a suitable pilot site to better inform future projects has commenced.
RETIRED RAIL
SIGNALLERS AND THE NEW ENGINEERS REPLACING THEM
Name a Melbourne rail project from the past 30 years and Ron Cranston and Selvadurai ‘Selva’ Nithianandan have worked on it.
Rail signalling engineers Ron Cranston, 69, and Selvadurai ‘Selva’ Nithianandan, 67, have worked alongside each other for 25-years on some of Melbourne’s most iconic rail projects including:
♦ Melbourne Underground Rail Loop – the City Loop
♦ Jolimont Rationalisation which saw Flinders Street rail yard reconfigured to accommodate construction of Federation Square
♦ Upgrades on all but a few regional and metropolitan rail lines
♦ Level crossing removals
Mr Cranston started his career in 1975 and retired in July 2022, while Mr Nithianandan started in 1986 and is paring back his hours in anticipation of retiring soon. The Metro Tunnel will be one of the final projects they work on – the biggest underground rail project since the City Loop.
In practical terms, Mr Cranston and Mr Nithianandan are two of the only ‘unicorns’ in the country who know how to work systems like ‘geographical interlocking’. They’re known as the guys you call when you have a signalling problem.
These systems are being phased out – but remain in situ at busy interchanges including Southern Cross Station, near Jolimont and Bell Street, Preston.

Mr Cranston said signalling isn’t complicated, there’s just a lot of it.
“It’s just a bunch of lines and cross sections on a piece of paper, until you see it in real life. We would never have thought Melbourne would have the population to support the Metro Tunnel,” Mr Cranston said.
Mr Nithianandan said he loves sharing his knowledge and industry experience with engineers who are entering the industry.
“Ron and I are good friends, we’ve solved many problems and helped each other a lot over the years. We’ve helped a lot of other people too,” Mr Nithianandan said.
“The industry is small, everyone gets to know your name and everyone wants you to work on their project.”
Both men have passed on decades of knowledge to the next generation of signalling engineers, including Priannka Kumar, 35, who counts both as significant mentors and has worked with them on projects including:
♦ William’s Landing
♦ Pakenham East Depot
♦ The Regional Rail Revival
Ms Kumar said she first met Mr Nithianandan when he was seconded into her team as a team leader, and then upon meeting Mr Cranston, found him to also be very professional and polite.
“Selva cares about the person as well as the task. If you’re not sure of where to go or what to do about something, he’s the first person I would call. He just shares that information freely, and doesn’t hold information back. If you show that initiative, he’ll show it back.
“Ron will take the time to work through with you how to solve the problem, rather than just telling you the answer. He doesn’t just answer the ‘what’, he answers the ‘why’ as well,” Ms Kumar said.
In a growing trend, these highly experienced industry technical specialists are reaching the end of their careers with a wealth of knowledge now hopefully passed on to the next generation.
TUNNEL WORKERS TRAINING TOMORROW’S
By Tess Macallan, Journalist, Infrastructure Magazine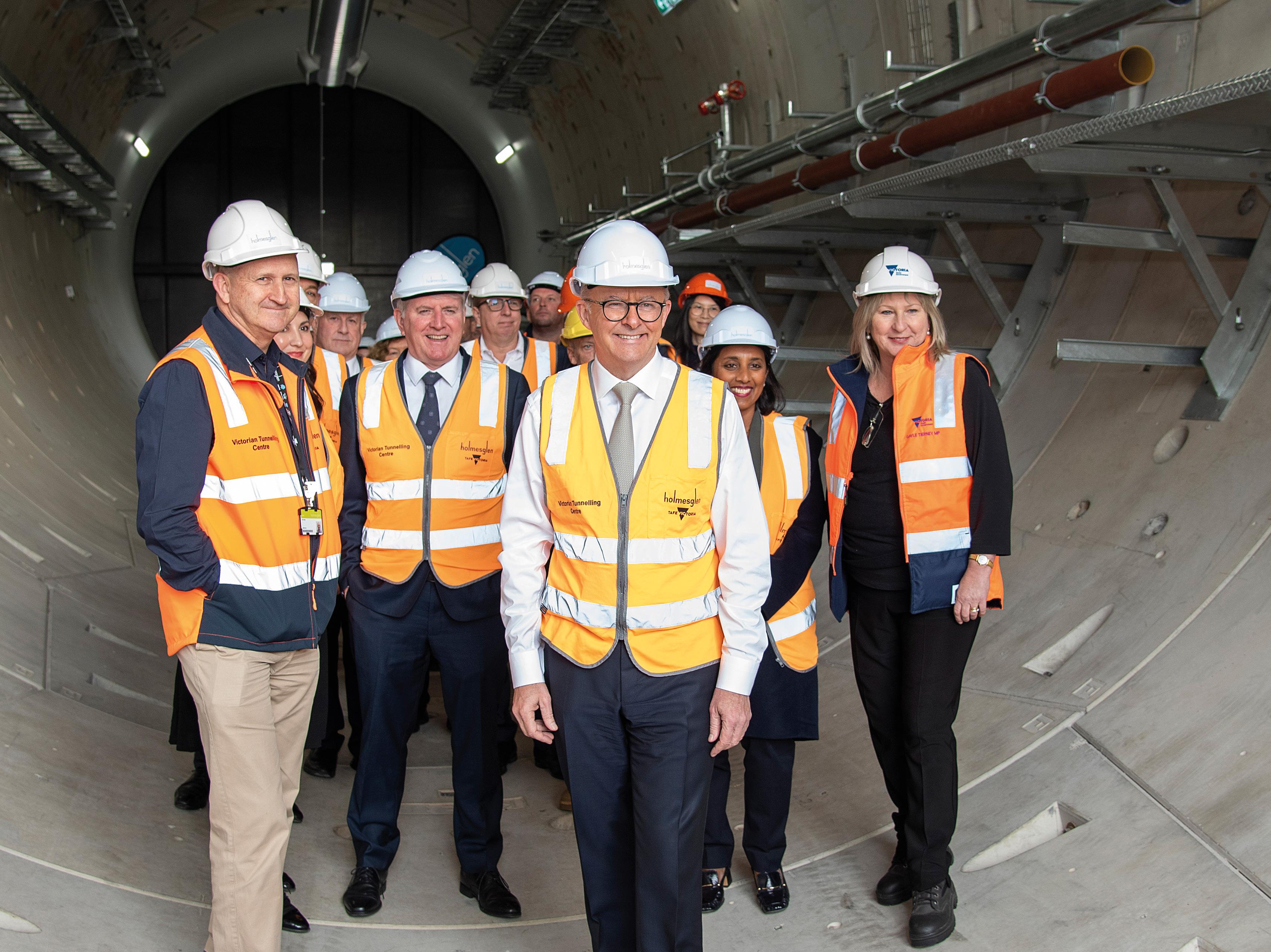
Across Australia, ambitious multi-billion dollar road and rail projects are in development. However, with ongoing labour shortages, state and federal governments need to ensure there are enough workers with the necessary skills to get these projects to the finish line. That’s why the Victorian Government invested in a training centre designed specifically to equip workers with the skills required for the state’s upcoming tunnel projects, including the North East Link and Suburban Rail Loop.
In 2020, the Victorian Government opened the $16 million Victorian Tunnelling Centre (VTC) at Holmesglen Institute’s Drummond Street campus at Chadstone. The facility features two replica tunnels, multi-purpose engineering work rooms, concrete lining spray simulators and virtual reality experiences. The centre has the capacity to train up to 5,000 workers a year in underground construction and maintenance,
including training for tunnel boring machine (TBM) operators.
Holmesglen’s Associate Director of the Centre for Energy and Infrastructure, Dr Ross Digby, explained to Infrastructure why the centre’s two replica tunnels are a game-changer when it comes to educating the next generation of tunnel workers.
“One is a segment lined tunnel that will normally be constructed with a tunnel boring machine. It's 25m long,
7.2m external diameter, and has been constructed with segments that were from the Metro Tunnel Project across our partnership project in Melbourne,” Dr Digby said.
There is also what is known as a road tunnel or a mined tunnel, which is the width of a three-lane freeway. Dr Digby said this would have been constructed using a long drill or road header. With these two tunnels, the centre is able to cover the main tunnelling
methodologies used in the construction of most road tunnels.
The facility is a first for Australia in providing students with the opportunity to learn within both replica mined and bored tunnels on one site.
Major projects currently in progress in Australia, such as Cross Yarra Partnership’s (CYP) work for Melbourne Metro, Sydney’s WestConnex , Brisbane’s Cross River Rail and Snowy Hydro 2.0, involve the construction of tunnels, and utilise a mix of civil and underground tunnelling equipment, including TBMs. Therefore, it is vital that Australia has a workforce capable of operating safely in these complex and potentially hazardous environments.
AUSTRALIA’S SKILLED LABOUR SHORTAGE
The global pandemic has contributed to labour shortages around the world, and Australia’s infrastructure sector is not immune to these challenges. Infrastructure Australia’s 2022 Infrastructure Market Capacity Report found that as of October 2022, Australia’s public infrastructure projects were facing a shortage of 214,000 skilled workers. Projections estimate this number will peak at 248,000 in 2023.
The report states that public infrastructure will continue to face significant workplace skills shortages until at least early 2026 and that action must be taken in both public infrastructure planning and workforce training to ensure Australia can see through the completion of infrastructure works.
Infrastructure Australia said projected growth is largely driven by major projects, which make up about 70 per cent of demand. The workforce demand for major public infrastructure projects will peak at almost 306,000 in 2023, close to double the demand in 2020, and triple the demand in 2016.
Further complicating the issue is that Australia’s public infrastructure sector has ever-shifting needs, due to new processes, equipment or technology. As Infrastructure Australia’s report notes, if workers do not update their skillset, employers can have difficulty finding people to fulfill roles. Although a sector can appear to have a large workforce, those workers may not have the right skills or their knowledge may be out of date.
KEEPING UP WITH THE INDUSTRY
To address these challenges, stay ahead of changing tunnelling technology, and provide dedicated training for its major projects, the Victorian Government funded the centre through Rail Projects Victoria. The centre is purpose-built and Holmesglen Institute engages an industry advisory group, comprising senior players from Australia's tunnelling industry, to advise and guide on how to best prepare trainees for a future in tunnelling. From the outset, the centre’s services have been underpinned by rigorous training methodology and a strong commitment to safety and best industry practice.
Dr Digby said the tunnelling centre is more than just a training facility. It works alongside Monash University, with its doctoral students undertaking specialist research at the centre.
“It's a place where we get industry together to demonstrate new equipment, demonstrate new procedures, and get people in to understand about careers,” Dr Digby said.
With tunnel boring machines becoming increasingly ubiquitous across Australia’s infrastructure projects, Dr Digby said the centre is working on how to upskill workers in the operation of this technology.
“We're continually refining and building our programs to meet the needs and to work with the current technologies that the tunnelling industry is using. It's changing all the time.”
In providing new tunnelling technologies in use by industry, the centre aims to be a place workers can return to during the course of their career.
“We're not just providing them at the start of the process, it's a lifelong journey,” Dr Digby said.
THE ADVANTAGES OF SIMULATION LEARNING
The centre uses a range of digital technologies to help trainees experience a tunnel environment without exposing them to any potential hazardous they may encounter on an actual work site. These include HoloLens, virtual reality, and mixed reality.
The centre has a long drill and a rock bolting simulator, which allows for high level specialised training in a simulated environment.
With the mixed technology the centre uses – HoloLens glasses from Microsoft – Dr Digby said students get to experience a simulated version of very dangerous equipment right before their eyes.
On top of digital technology, the centre uses different methods to create a sense of realism inside the training tunnels. This includes temperature controls in the tunnels, putting water in them, and replicating the sounds of an operational environment.
“We can put smoke in there if need be. We can do anything we want really to completely replicate what it's like to be in that underground environment, be it a segment lined tunnel, or be it a road header mined tunnel,” Dr Digby said.

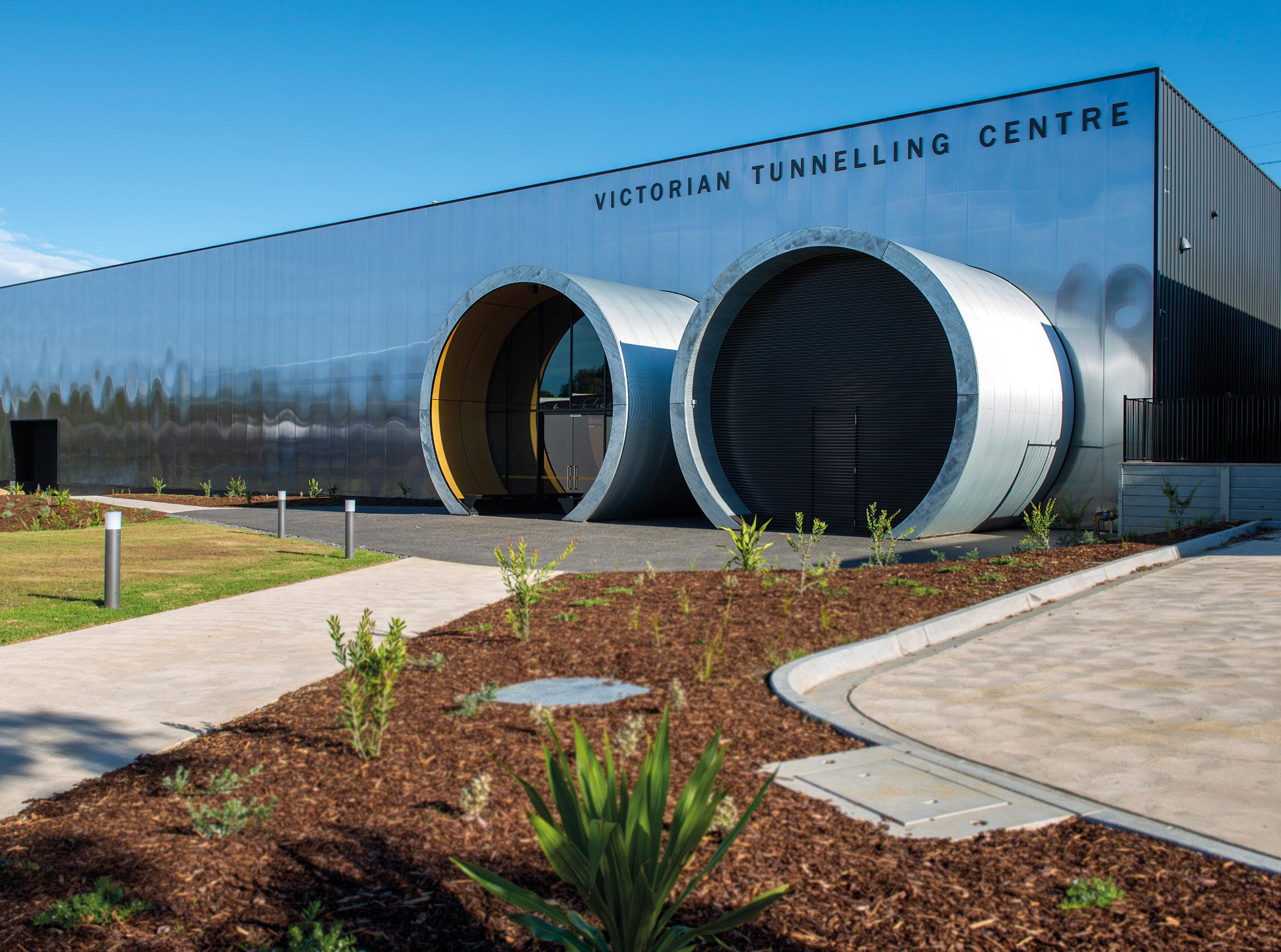
READY FOR ANYTHING
Tunnelling work comes with a high amount of safety hazards. There’s the risk of collapse, falling rocks, confined spaces, fires and water inrush. TBMs and other heavy machinery also have the potential to be potentially hazardous.
This poses a difficulty in educating workers, as they cannot just go inside a real tunnel environment. Prior to the Victorian Tunnelling Centre, training courses would rely on traditional teaching methods, including diagrams and videos, to assist trainees in their learning.
Dr Digby said providing a practical learning environment for students is really important, particularly when it comes to emergency situations.
“If something’s happened and they’ve got to undertake an emergency procedure, and they’ve only read about it in a book or role-played it in the classroom, it just doesn’t work,” Dr Digby said.
Now with these tunnels, the centre is able to contextualise the training and enhance it by putting equipment or things like refuge chambers in there to
create a realistic simulated operational environment.
Dr Digby said recreating emergency situations is important because in a real world situation, a worried or distraught worker will only increase the risk of danger to themselves and others.
“If you're down in the tunnel and you start freaking out, you're not only putting yourself at risk, you're putting other people at risk,” Dr Digby said.
The centre’s 20 seat refuge chamber allows students to practice for the event of an emergency.
“We identify what are the really high risk situations or equipment intensive situations that the trainees will experience when they're working, but create them in a safe way in the tunnel environment, so they can experience exactly what it's like without actually having to be put at risk, and put others at risk as well. It also improves the safe movement of workers around equipment and effectively manages space in the tunnel during a project.
“There are carefully designed training scenarios our expert trainers can put in place down there, which are designed
to make people feel uncomfortable, so they understand which tunnelling roles are or aren’t for them. Our focus is on health and safety, teaching new skills and helping trainees develop their future career,” Dr Digby said.
However, what could make one person cut and run from a career in tunnelling could be the reason someone else decides this is their dream role.
AMPLE OPPORTUNITIES
Dr Digby said a benefit of the facility is that it attracts people who might not have considered tunnelling previously.
“People need to understand that there are careers in tunnelling,” Dr Digby said.
Those studying at the tunnelling centre can earn Certificate and Diploma qualifications as well as safety-based training for working underground.
With tunnelling works for Victoria’s longest road tunnels – the North East Link — underway, the VTC will play a major role in producing a skilled workforce that can get the job done safely and to the highest international standards.

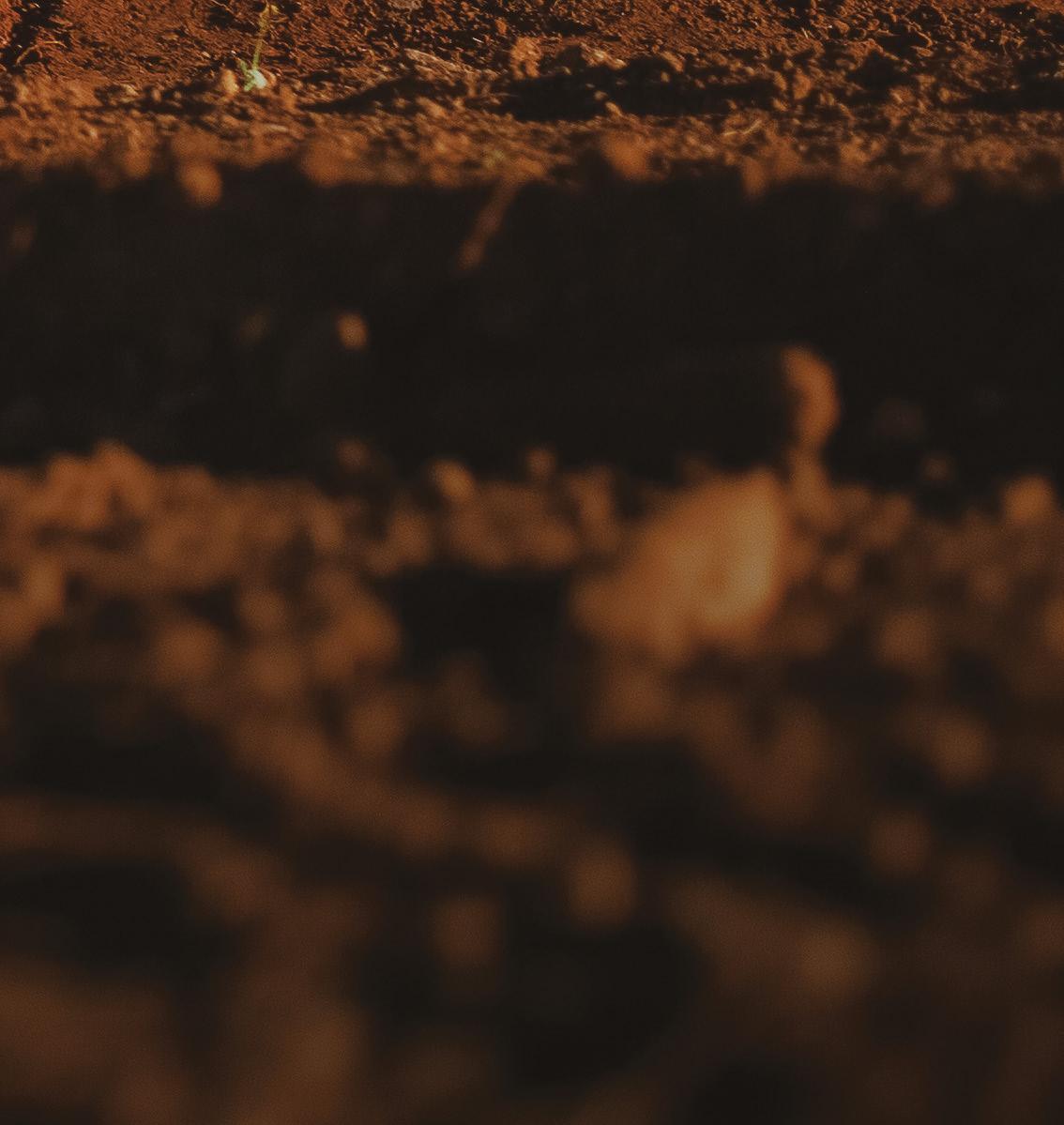
You can’t always choose your deadline. But you can choose how you get there. Introducing Deere’s new Mid-Size Excavator E210-II. Combining a spacious, operator-friendly cab with the exceptional performance and precise control you need, you and your team can get the job done faster, more efficiently, and on budget, every time. Choose not to compromise. Talk to your local dealer, today.
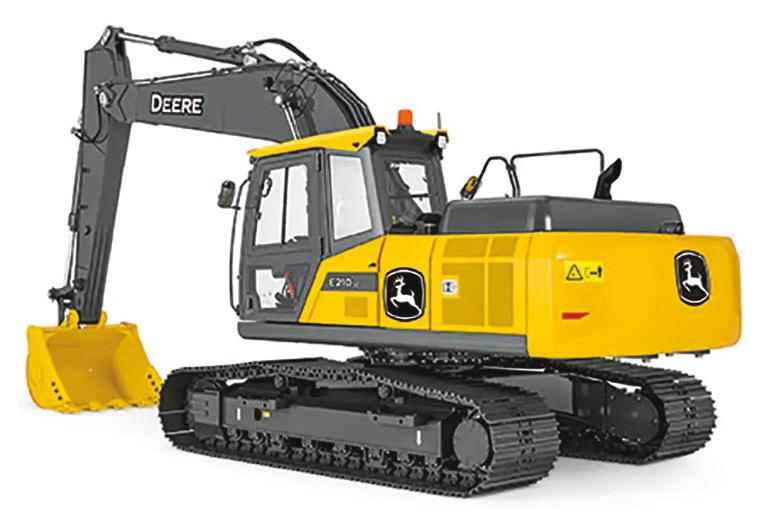
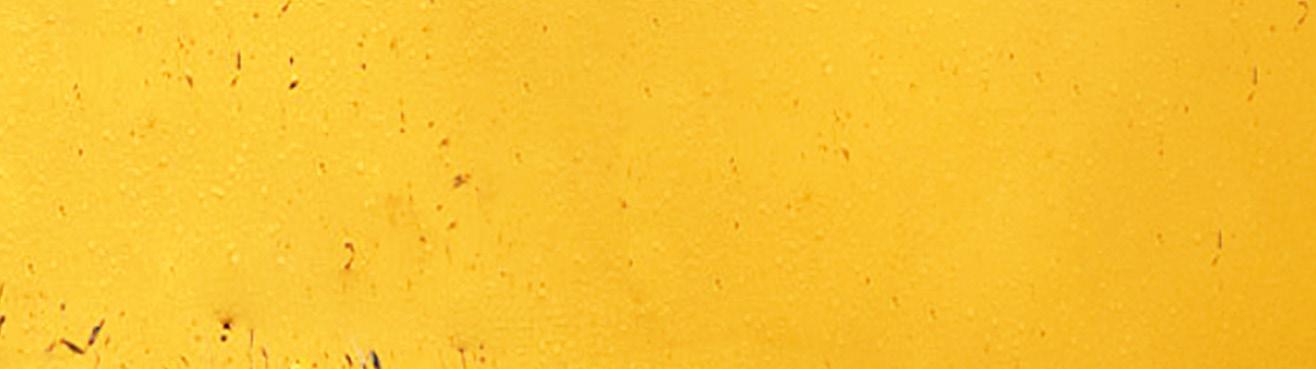
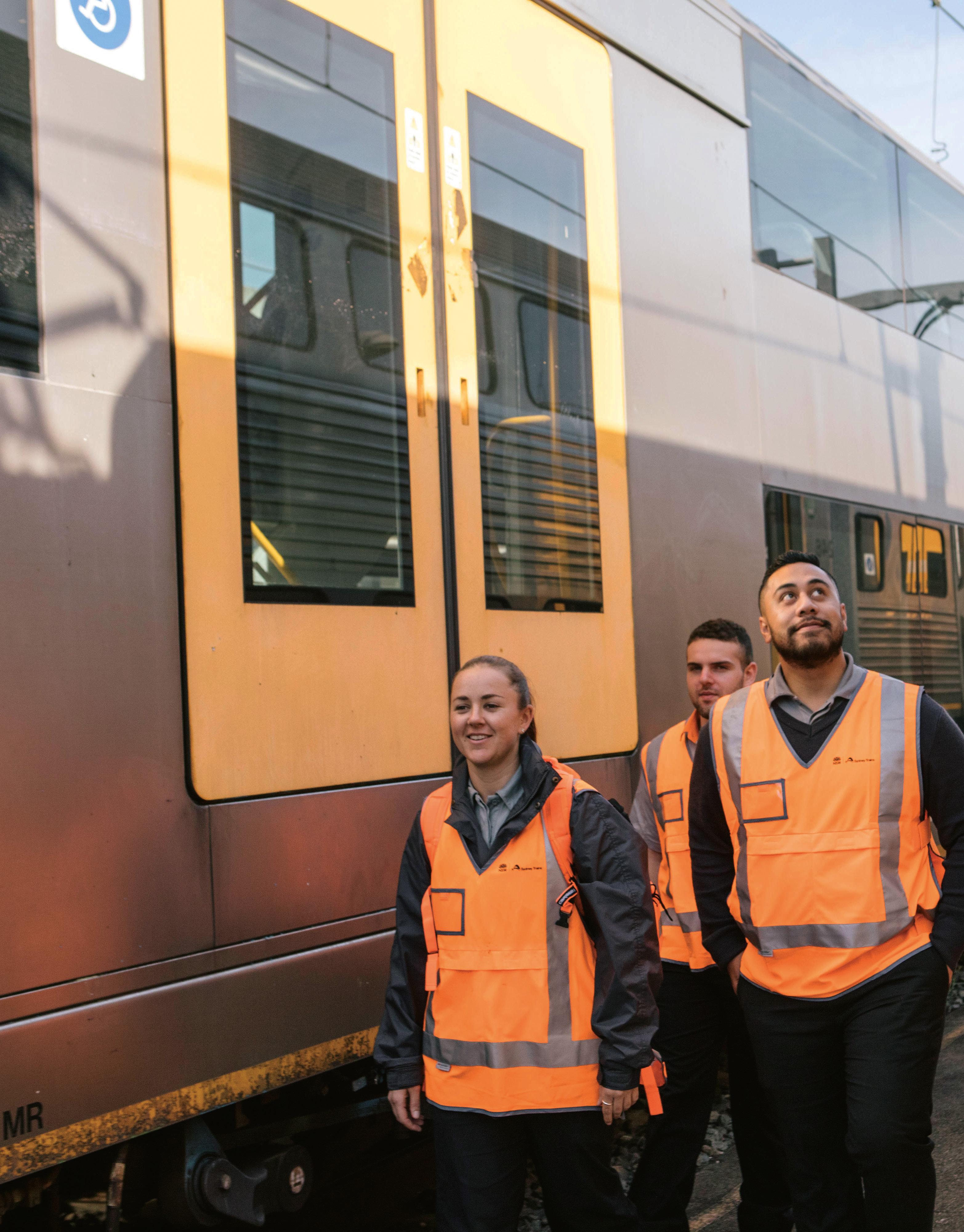
GROWING A RAIL WOR k FORCE FOR THE FUTURE
Australian rail is experiencing an unprecedented level of investment. To ensure its success the National Rail Skills Hub is helping the industry double its workforce and improve skills portability.
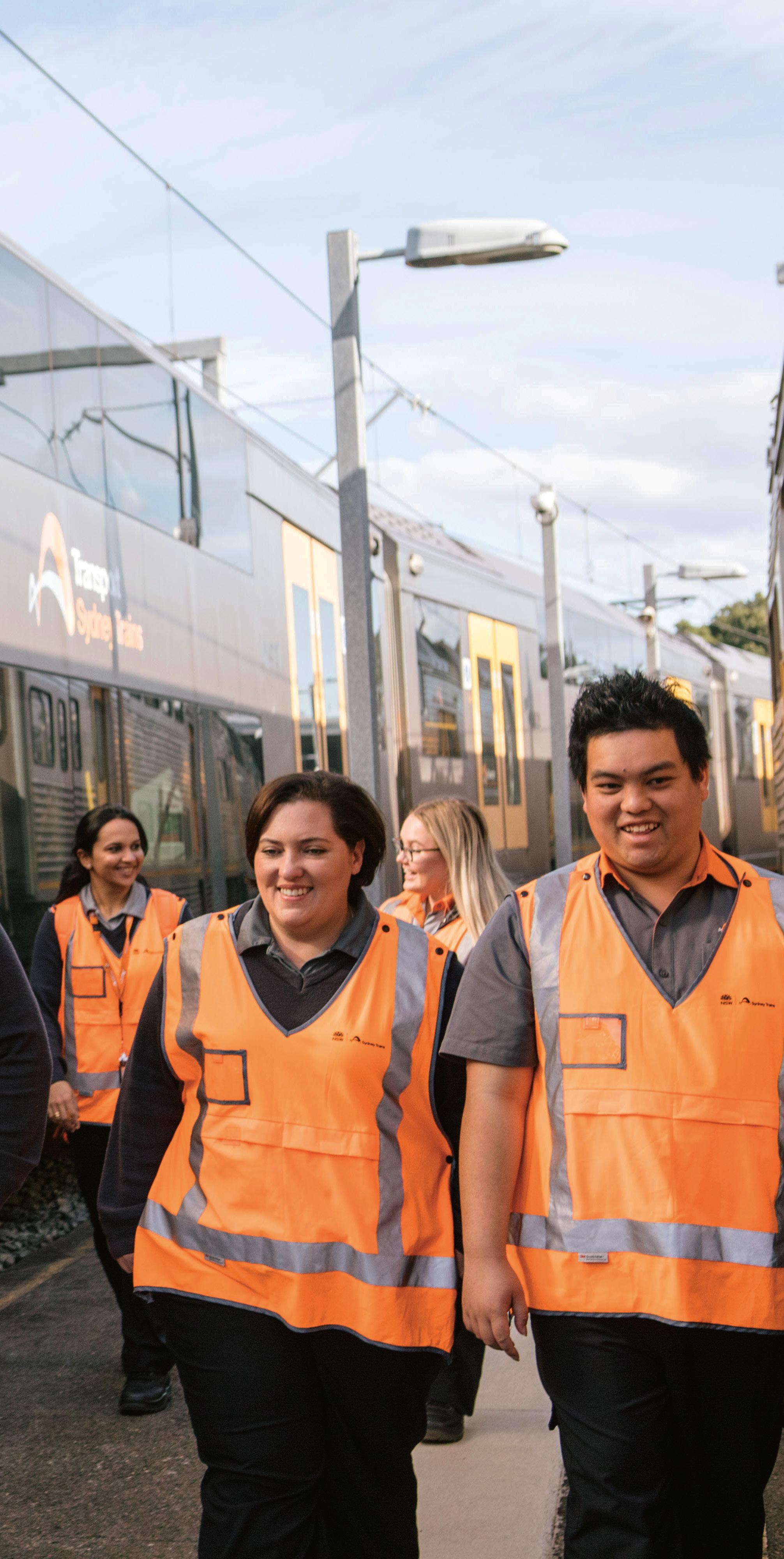
An estimated $155 billion will be invested over the next 15 years to expand and modernise Australia’s rail networks.
More than 70,000 additional people with all kinds of skills are needed to design, build and run the rail system which is being modernised with new digital systems and technology.
As part of a plan to improve the interoperability of rail systems nationally, National Cabinet has asked infrastructure and transport ministers to identify the training needed for the operation of digital rail systems and other new technologies.
Just as important as recruiting new people with digital skills will be retaining experienced workers to ensure the smooth transition between old and new parts of the rail network.
To achieve this, the National Transport Commission (NTC) on behalf of all governments is working with industry to attract a younger, more diverse cohort of workers, retain existing expertise and rethink how it trains its people.
The National Rail Skills Hub has been set up by the NTC to bring education and transport sectors together to address skill shortages and provide a platform for collaboration to create a more skilled and mobile workforce.
Launched by Minister Catherine King in December 2022, the National Rail Skills Hub is working with public and private organisations to put rail on job seekers’ radar and improve and accelerate training pathways.
It is focused on:
♦ Making it easier for all Australians to enter rail at any stage of their career
♦ Aligning the needs of rail enterprises with the VET sector, defining clearer training pathways with qualifications recognised across the country
♦ Attracting a new generation of workers, with a focus on women and young people
♦ Identifying and preparing the industry for skills of the future
Copyright: State of New South Wales (Transport for NSW).
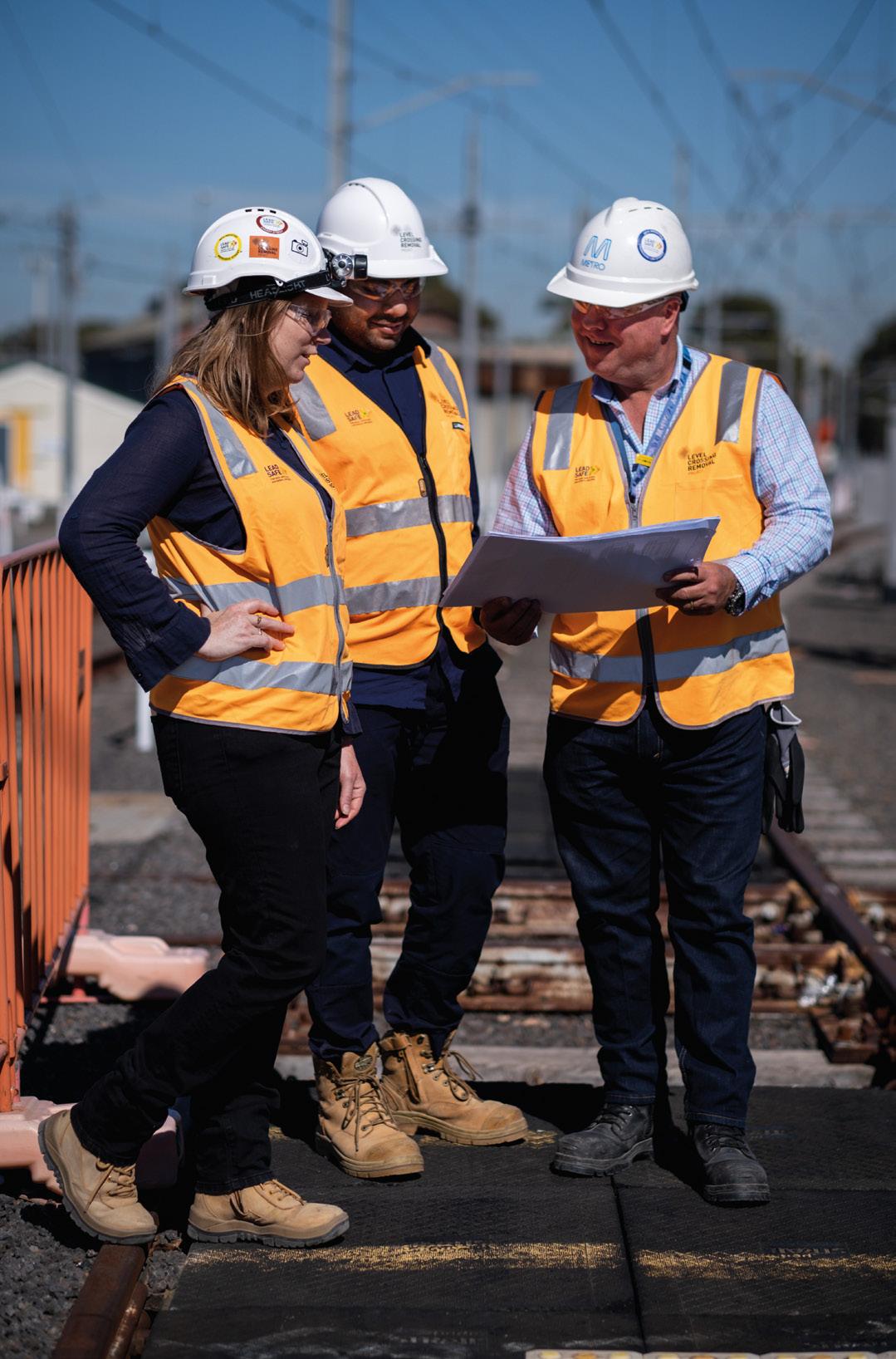
NATIONALLY RECOGNISED QUALIFICATIONS AND TRAINING
Australia’s rail system reflects its history and the evolution of separate state-based networks and private systems with bespoke rules, standards and training approaches.
With 29 networks, three different railway gauges, and eleven separate signalling systems, rail training has been fragmented and conducted at an enterprise level with a lack of clear career pathways or entry points. In many cases, workers’ skills and qualifications are not recognised beyond the enterprise they train in.
NTC’s Head of National Rail Skills, Mandi Mees, said the lack of mutual recognition and portability of skills is the biggest drain on talent, especially in highly technical areas like signalling.
“This impacts productivity and is compounding the skills shortage,” Ms Mees said.
“The National Rail Skills Hub is working with industry and educators to develop a national approach to training, with qualifications that are recognised across
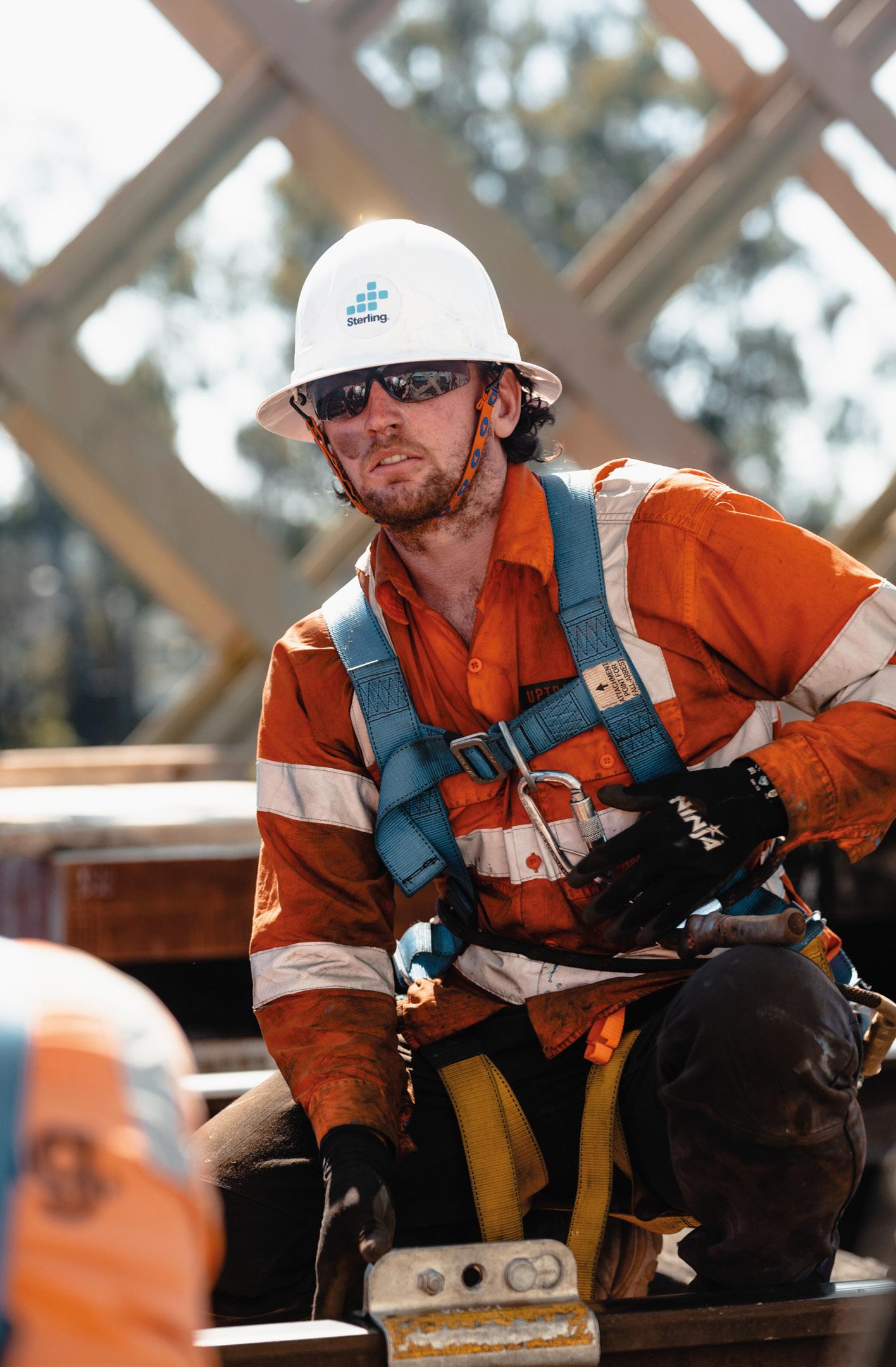
the country improving workers’ ability to move around to meet demand.”
The Hub is working with the Australasian Railway Association (ARA) to improve skills portability for drivers, track workers, signallers and other in-demand skills. This includes the development of nationally recognised qualifications and a model for delivering rail skills training.
Digital courseware for Certificate IV in Rail Network Control has been developed first and will be housed on the Hub’s digital platform where it can be accessed by registered training organisations (RTO) across Australia.
Currently there are 10 RTOs accredited to deliver the course. By offering course material for free, the Hub is encouraging more organisations to provide the training and freeing up trainers’ time to focus on quality of delivery.
A pilot program for a national Safely Access the Rail Corridor (SARC) accreditation is also underway.
SARC accreditation is required for anyone working in a rail corridor. However, it is not nationally recognised so a rail worker who completed their
SARC competency in New South Wales has to retrain to work in Queensland. The pilot will show how a national approach to developing and delivering entry level rail training courses could work.
COLLABORATION AND RESOURCE SHARING
Through its digital platform, webinars, forums and pilot programs, the National Rail Skills Hub is bringing the education and transport sectors together to tackle the skills challenge. It is encouraging rail enterprises to share resources, training materials and strategies that have been successful at improving skills and attracting workers.
For job seekers, the platform provides training pathways, showing entry points, training requirements and opportunities for career progression. More than 30 pathways are being developed with the Department of Employment and Workplace Relations (DEWR) and Industry Skills Australia. Ongoing work with the Australasian Railway Association and Engineering Education Australia (EEA) is identifying ways job
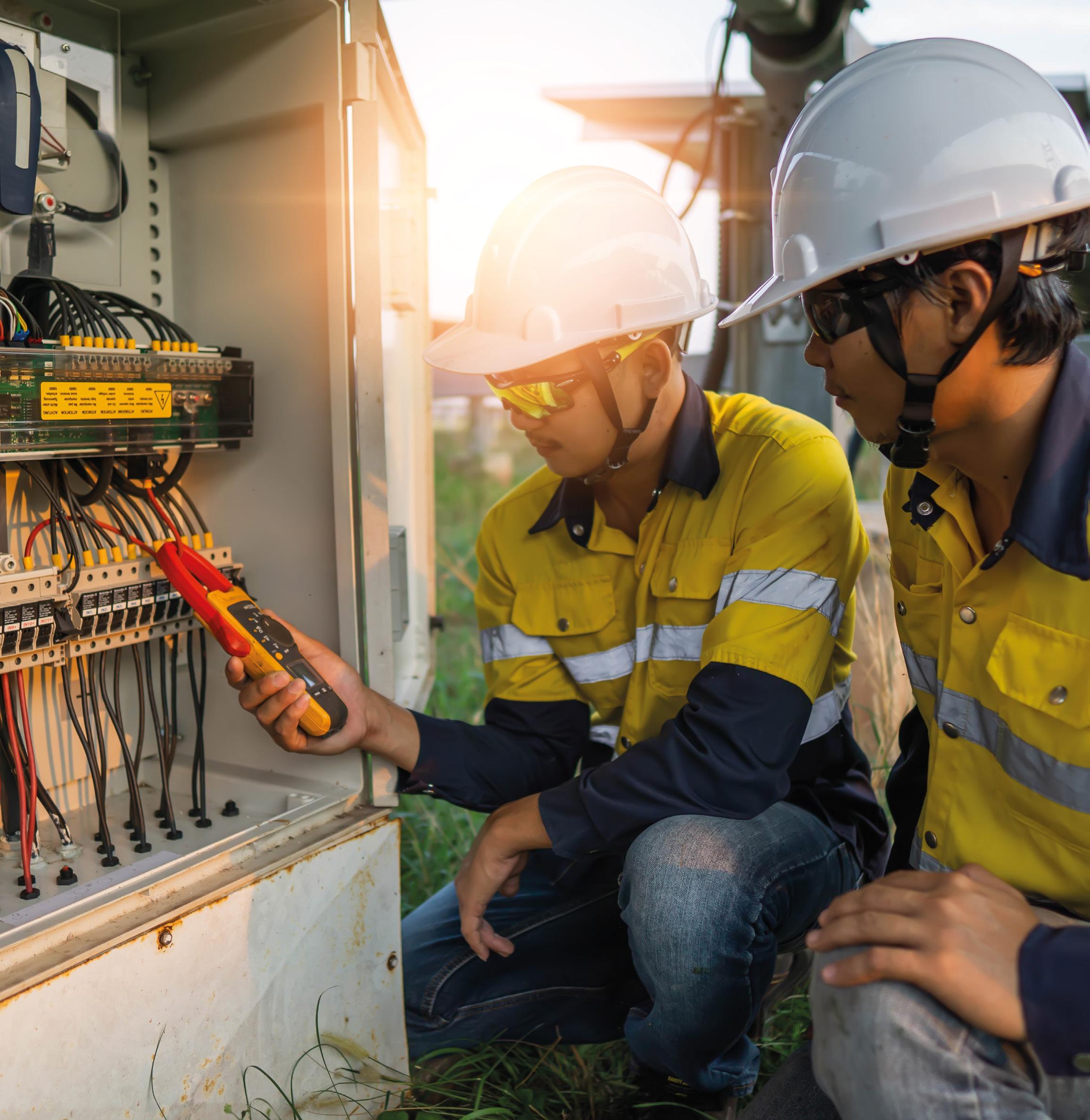
seekers can accelerate their training to the most in-demand rail roles.
To help lift rail’s profile as a career of choice, the platform features profiles of people working in diverse rail roles, from train driving to cyber security. The workers give insights into how they entered rail – in some cases this is straight from school, in other cases it’s after a successful career in another industry, or having spent time at home parenting. They talk about the experiences their jobs present and the impact of new technology.
SKILLS FOR THE FUTURE
Rail is forecast to move more passengers and larger volumes of freight than any other mode across Australia’s major cities and freight routes. As a new generation of train signalling and control systems is introduced and integrated with existing networks, old and new skills will be needed.
National Cabinet acknowledges this challenge and has identified a nationally consistent approach to training, mutual recognition of qualifications and finding workforce solutions to meet
future demands, as key priorities of the national rail reform program.
To gain a better understanding of what new jobs and skills will be required, the Hub is undertaking a digital skills gap analysis.
The training models it is currently developing can then be used to ensure any gaps are easily plugged, maximising the benefits from the interoperable rail networks of the future.
The National Rail Skills Hub is a key component of the National Rail Action Plan (NRAP), endorsed by Australia’s infrastructure and transport ministers.
FEATURES SCHEDULE & ADVERTISERS’ INDEX
June
Freight

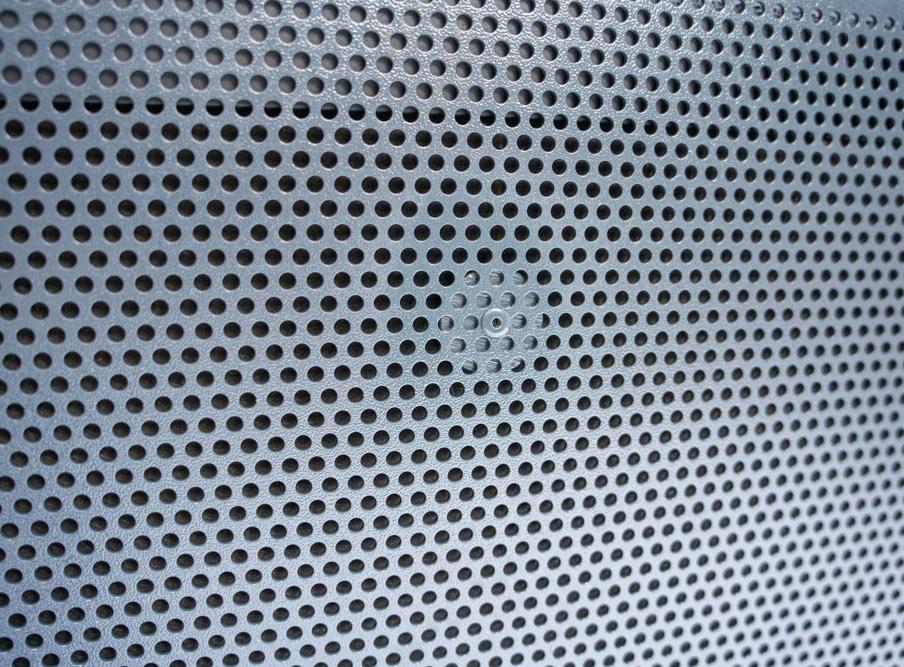
The new 2.0 surface
From now on all of the STRAILastic sound protection systems are equipped with the new generation highly absorbent acoustic surface.
Constructed from several layers and materials, it combines all the advantages of individual materials.
Benefits at a glance
¬ No foundation required for installation
¬ easy and quick installation
¬ Short delivery times > noise hot spots can be supplied with products quickly
¬ Closer to the noise source than any other sound protection
¬ Break-proof due to bre-reinforced rubber compound with a cover layer of virgin rubber > UV and ozone resistant
¬ No material fatigue caused by vibrations or pressure and suction forces
¬ No problems with oversized loads
The basic material remains a durable and stable rubber compound. The insulating e ect of the elements and properties of rubber are now complemented by an absorbent surface.

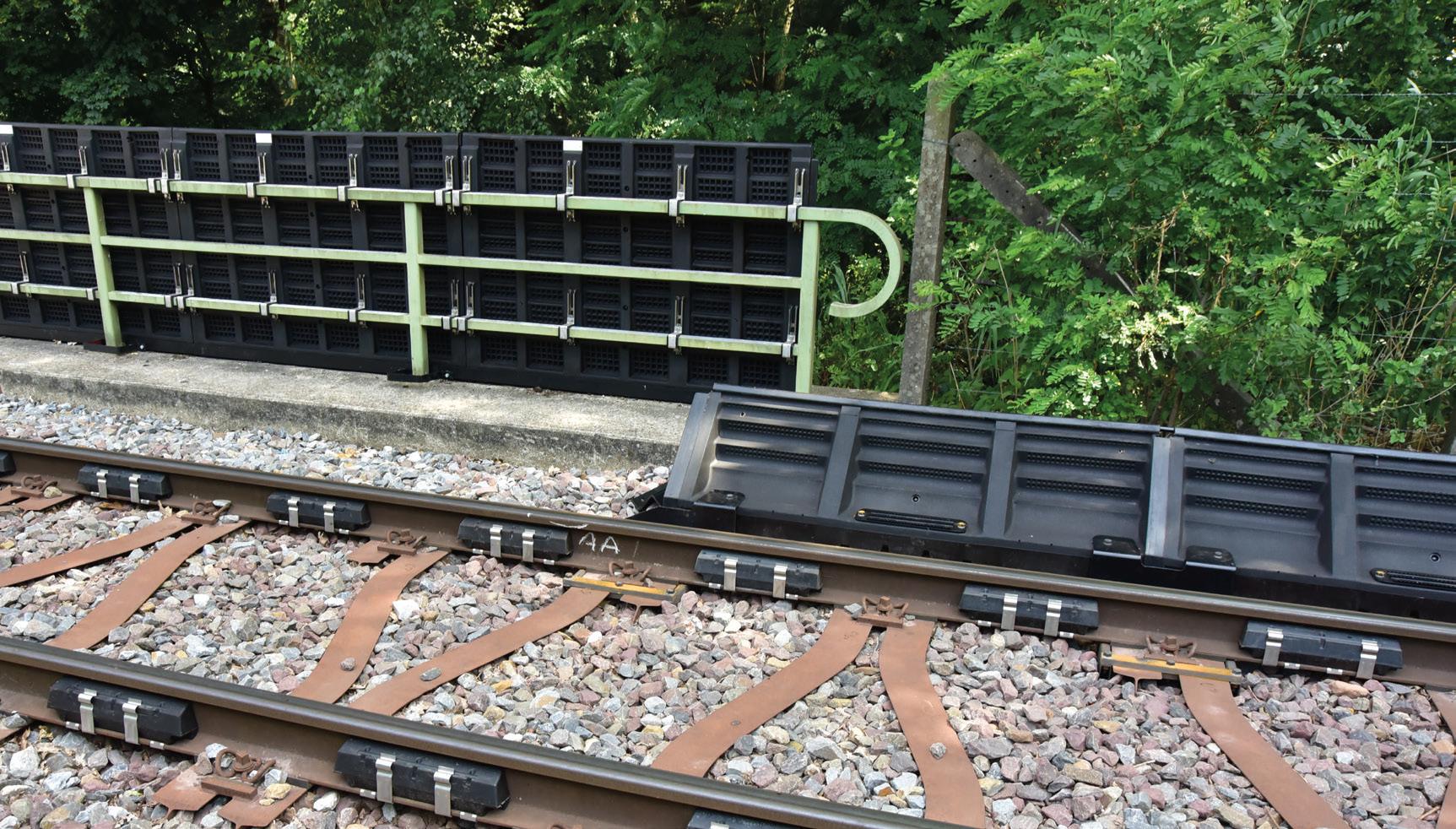
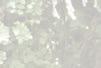
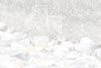
Secure IBC storage & decanting solutions
Polymaster’s unique Enclosed IBC Bund solves many of the problems associated with IBC storage and chemical/fluid decanting in a weather resistant, purpose-built enclosure.
Æ Full weather protection – stops rain entering the enclosure
Æ Easy forklift loading with wide forklift access from both side and back
Æ 250ltr day tank
Æ Lockable cabinet to keep system secure
Æ Venting by two sides
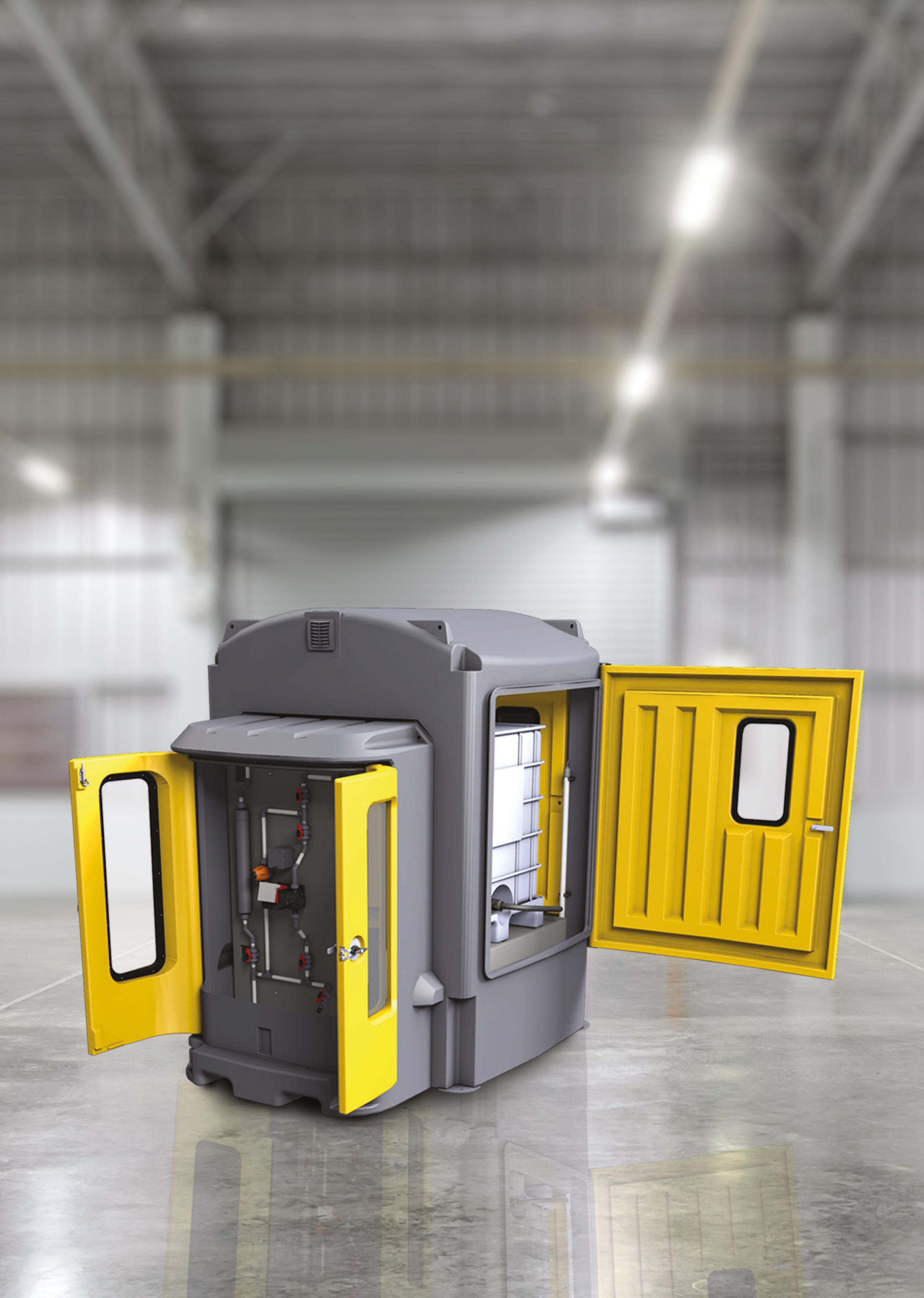
Æ Viewing windows incorporated into the doors
Æ 110% bund capacity complies with AS3780
Æ Sight tube and low-level alarm available
Æ Chemical resistant – high grade polyethylene construction