Airports recruit NEXT GEN
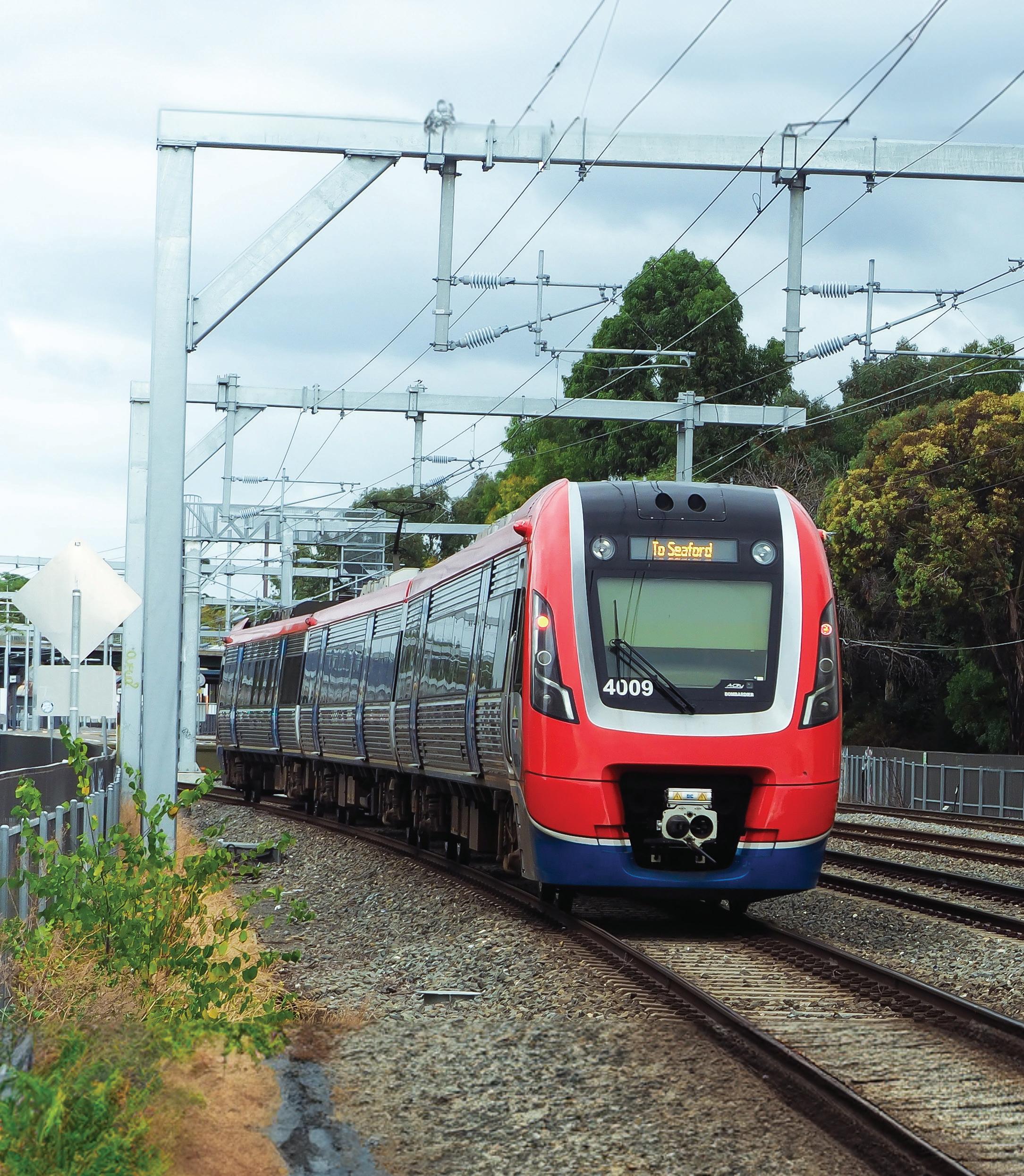
Airports recruit NEXT GEN
ORDERS UP: RMIT turns coffee to concrete
Protect your critical assets with the most reliable systems made in Australia.
Century Yuasa has been protecting critical power assets for 30 years with our local design, construct and onsite teams. Our DC systems are built with the best of global technologies and supported with the globally recognised Yuasa VRLA batteries which are the only batteries you can genuinely rely on to protect your critical assets and business services year after year.
To learn more about Australia’s own DC power systems, maintenance services, and the Yuasa range of VRLA batteries, visit our website.
For enquiries call 1300 364 877 https://cyb.com.au/industries-markets/industrial
Published by
Monkey Media Enterprises
ABN: 36 426 734 954
C/- The Commons, 36–38 Gipps St, Collingwood VIC 3066 P: (03) 9988 4950 monkeymedia.com.au info@monkeymedia.com.au infrastructuremagazine.com.au news@infrastructuremagazine.com.au
Editor April Shepherd
Assistant Editor Stephanie Nestor
Journalists
Tess Macallan, Kody Cook, Steph Barker, Yasmin Isaacs
National Media Executives
Rima Munafo, Brett Thompson, Ryan Sheehan
Design Manager
Alejandro Molano
Senior Designer
Luke Martin
Designers
Danielle Harris, Jacqueline Buckmaster
Marketing Manager
Radhika Sud
Marketing Associates
James Holgate, Rhys Dawes
Digital Marketing Assistants
Isabella Predika, Emily Gray
Publisher Chris Bland
Managing Editor
Laura Harvey
ISSN: 2206-7906
As we say goodbye to another year, and 2024 peaks over the horizon, I am sure many of you are excited for some R&R after what has been yet another eventful year.
Our last issue of 2023 brings with it two huge features; Airports and Rail, and two huge events; the Australian Airports Association (AAA) National Conference, and AusRAIL. To celebrate these two highlights in the events calendar, we have brought together some of the hottest projects in the sectors.
For rail, we cover Adelaide Metro’s new electric powered fleet (pictured on the cover), Parramatta’s light rail and New South Wales’ regional rail overhaul – showcasing regional, metro and suburban rail projects.
In the airport sector, we have an eye-opening piece from James Goodwin, AAA Chief Executive, discussing the industry’s career-drive, and we also hear from Perth and Ballarat airports respectively about the projects supporting the future of aviation.
Outside of these major features we cover some of the hottest topics in the industry at the moment, such as the Level Crossing Removal Project garnering global attention, gender diversity in the sector, and how cities are preparing for future population growth.
Industry leaders are looking to the future, as TasWater tells us all about their future-proof plan for Hobart’s water supply and RMIT researcher, Dr Rajeev Roychand, shares findings from a new report discussing how leftovers from your morning coffee can be turned into enhanced concrete to support sustainable construction.
As always, I look forward to delivering the latest news and content from the sector, and if you have a story idea or a tip, reach out – my digital door is always open.
GENDER DIVERSITY CRITICAL TO ADDRESSING OUR
SKILLS SHORTAGE
As the infrastructure sector continues to face a significant skills and labour shortage, we also face a very real solution — improving gender diversity.
TASWATER FUTURE-PROOFING GREATER HOBART’S WATER NEEDS
A new chapter of water security for 200,000 customers in southern Tasmania was written in September 2023, with TasWater officially opening its upgraded Bryn Estyn Water Treatment Plant (WTP).
MAXIMISING WATERPROOFING PERFORMANCE, LONGEVITY: THE VITAL ROLE OF MAINTENANCE
OPINION: AN INDUSTRY ON THE CUSP OF CHANGE
BANNING ENGINEERED STONE: PROTECTING LIVES AND ENSURING WORKER SAFETY
TURNING COFFEE INTO CONCRETE: RMIT STUDY BREAKS FRESH GROUND
As a country known for its thriving coffee culture, it’s no surprise that Australia generates 75 million kilograms of ground coffee waste every year. Most of this ends up in landfill, contributing to greenhouse gas emissions and exacerbating environmental degradation. To combat this, a team of RMIT University researchers are on a mission to transform discarded
into a
that
support
HOW MELBOURNE WATER IS KEEPING UP WITH A GROWING POPULATION
THE INVISIBLE WORK TOWARDS ACHIEVING A SUSTAINABLE FUTURE
BUILDING A RESILIENT ROAD NETWORK WITH THE NEW FITZROY RIVER BRIDGE
The Fitzroy River Bridge formed part of a vital freight route in Western Australia until it was permanently damaged following a cyclone, prompting the construction of a replacement bridge. With a disaster resilient design, the new bridge promises to support this remote road network by reconnecting communities and industries.
PARRAMATTA LIGHT RAIL DELIVERS SUSTAINABLE INFRASTRUCTURE
From its Australian-first innovative rail boot system to its award-winning green track, the Parramatta Light Rail Stage 1 project is leading industry best practice in delivering sustainable public transport infrastructure for the New South Wales community.
KEEPING RAILWAYS ON TRACK WITH INNOVATIVE REMEDIATION SOLUTIONS
HOW TAILORED LIDAR SOLUTIONS ARE CHANGING THE GAME
ADELAIDE METRO NET-ZERO PUBLIC TRANSPORT
In the pursuit of its net-zero emissions by 2050 target, South Australia is taking aim at its largest emissions contributor: transportation. Here Infrastructure Magazine explores what the future of sustainable public transport will look like in Adelaide as Adelaide Metro begins its transition to a zero-emissions system.
GETTING ON TRACK WITH NSW’S REGIONAL RAIL UPGRADE
In late July 2023, construction activities began to extend the existing rail siding at Coolamon, New South Wales. As part of the Fixing Country Rail Program, the project is aimed at removing freight bottlenecks, improving efficiency and making the state’s rail network safer for all services and customers.
PREPARE TO TAKE OFF WITH MY AIRPORT CAREER
Airports are bustling hubs of activity, connecting people, cultures, and destinations, but behind all the action exists a hidden world of opportunities.
INNOVATIVE TECHNOLOGIES FOR RAPID REPAIR AT AIRPORTS
DESTINATION WA: PERTH AIRPORT SUPPORTING REGIONAL AVIATION SERVICES
IOT & CLOUD COMMUNICATION
NHP’S MEDIUM VOLTAGE SOLUTIONS
STRENGTHENING OT CYBERSECURITY: A STRATEGIC IMPERATIVE
LEVEL CROSSING REMOVAL PROJECT’S DIGITAL SOLUTIONS RECEIVE GLOBAL RECOGNITION
For Melbourne residents, the Level Crossing Removal Project has become a part of daily life, as many locals take the city-wide works in their stride, with the knowledge that the transformational project will make the city safer and more efficient for generations to come. To make this momentous project as efficient as possible, the Victorian Government has utilised a plethora of digital solutions – garnering international attention, and awards.
RIVERLINK: A MODEL OF PROACTIVE SUBSURFACE RISK MANAGEMENT
IMPROVING SAFETY, EFFICIENCY IN RUGGED INDUSTRIES: THE BENEFITS OF VOICE RECOGNITION SOFTWARE
EARLY DETECTION: HOW SYDNEY WATER’S IOT ROLLOUT IS PREVENTING OVERFLOWS
With blockages and overflows being frequent problems for wastewater infrastructure, Sydney Water is undertaking a $15 million wastewater monitoring internet of things (IoT) deployment across its network. Already, Sydney Water is saving hundreds of thousands of dollars per month with sensors that can detect blockages before they cause damage.
6. EXPERIENCES AS A WOMAN IN ENGINEERING – MEET KATE FALLON
8. $70M MAJOR ROAD EXTENSION COMPLETE
9. $2M ENGINEERING SCHOLARSHIP PROGRAM TO SUPPORT WORKFORCE
10. WA COUNCIL TO TEST AUSTRALIA’S FIRST TRACKLESS TRAM
11. POWERLINK CALLS FOR LOCAL SUPPLIERS FOR COPPERSTRING 2032
12. MONARO HIGHWAY UPGRADE CONTRACT AWARDED
13. QUEST LARGEST BY LOCATION, FASTEST GROWING ACCOMMODATION PROVIDER IN NZ
Adam Copp was appointed Acting CEO of Infrastructure Australia in August 2022. An accomplished and transformational public sector leader, he has over 15 years’ experience in the Federal Government holding a range of policy, strategy and public affairs roles across infrastructure, workplace relations and the Council of Australian Governments. Prior to his appointment, Mr Copp was Infrastructure Australia’s Chief Operating Officer.
As Chief Operating Officer, Mr Copp was responsible for leading Infrastructure Australia’s Strategy, Finance, People & Culture and Digital Technology functions. He joined Infrastructure Australia in 2014 and set up the public affairs and stakeholder engagement function, before expanding his role across the other operational functions of the business. He is a passionate advocate for Reconciliation and First Nations engagement.
Principal Technical Safety and Risk Engineer, Kent
Kate Fallon has over ten years of safety engineering experience in the oil and gas industry. She has a wide variety of exposure in the industry, including knowledge and understanding of working on large-scale projects providing safety and risk engineering input and support. Ms Fallon joined Kent in 2022 as a Principal Technical Safety and Risk Engineer in Perth, Australia.
Chief Executive, Australian Airports Association (AAA)
James Goodwin is an experienced executive and non-executive director with a corporate affairs and public policy background, with a particular interest in the transport, aviation and infrastructure sectors.
He was appointed Chief Executive of the Australian Airports Association in early 2020 and successfully guided the AAA through one of its most difficult challenges in history.
He continues to lead the AAA in supporting its members and advocating for national airport policy to ensure the nation has a thriving aviation system that is safe, secure, competitive, and environmentally responsible, with a skilled workforce to benefit all Australians and visitors.
A former journalist and news presenter, he worked for major network news outlets in Sydney and Canberra, including several years in the Federal Parliamentary Press Gallery.
Chief
Executive Officer,Thoracic Society of Australia and New Zealand (TSANZ)
Vincent So is CEO of The Thoracic Society of Australia and New Zealand (TSANZ). TSANZ is the only health peak body representing a range of professions (medical specialists, scientists, researchers, academics, nurses, physiotherapists, students, and others) across various disciplines within the respiratory/sleep medicine field in Australia and New Zealand.
Dr Rajeev Roychand is a Postdoc Research Fellow working at RMIT University, Melbourne. He has more than 15 years’ experience in material research and structure design. He has published 46 high impact research papers and has secured more than $1 million in research funding. Nine of his research papers have extensively been covered by the international media. He is a recipient of the RMIT award for impact and collaboration (2022).
Michael Kilgariff Principal, Kilgariff AdvisoryMichael Kilgariff is a former CEO of Roads Australia and Managing Director of the Australian Logistics Council. In these and previous roles, he has developed a reputation for building strong working relationships across industry and government, with the aim of supporting and achieving outcomes that are mutually beneficial to industry, government and the community.
In recognition of his work in this area, Michael won the Transport and Logistics Executive of the Year in the CEO Magazine 2014 Executive of the Year Awards
Infrastructure Magazine caught up with Kate Fallon, Principal Technical Safety and Risk Engineer at Kent, for an exclusive Q&A where Kate shared with us her experiences as an engineer.
Kate discusses the importance of striking a balance between career and motherhood, emphasising the need for greater support and encouragement for women in engineering.
What made you choose a career in engineering?
I finished high school at 17 with my highest marks in mathematics and chemistry so a teacher suggested I study Engineering. When I looked at the number of women studying Engineering, Chemical Engineering had the highest percentage of female graduates and that was actually a key decision in choosing to study Chemical Engineering.
What are the advantages/challenges of being an engineer in a male-dominated industry?
Let’s be honest, Engineering and Oil and Gas has always been a “man’s world”. As a graduate, I would be in meetings and workshops and asked if I was the receptionist or HR. But in the past ten years there has been a huge shift in promoting women and ensuring we acknowledge and celebrate their successes. My current manager on the project I am seconded to is a woman and she is one of the best bosses I have worked with.
Choosing to be both an engineer and a parent I find often presents unique challenges to women. Women will usually take maternity leave when they have a baby. I know women that have felt rushed to return to their positions otherwise they would
be overlooked for promotions or career progression. I know women whose employers have made the assumption that their interests would now be with their kids and not their jobs and subsequently given smaller roles on projects.
We need to support engineers that choose to be mothers and encourage their return to work when they are ready, without holding their careers back or penalising them. We need to acknowledge that women, regardless of parenthood, are as much a part of the workforce and as important as the men who did not take any parental leave.
In recent years, I have seen companies install creches and offer flexible working arrangements to allow employees to be mothers as well as be part of the workforce which is truly amazing.
I am very fortunate to work for Kent, which is a company that embraces women and allows them the flexibility to do their job and do it well, as well as be a mother.
Is enough being done to promote/encourage women in engineering?
There could be a bigger push at the high school or university level to promote young women to study engineering. A few years after I graduated, some universities were offering women scholarships to study and there are now STEM programs in high schools which is great, but there is still more that can be done.
I joined WISE (Women in Subsea Engineering) and they hold regular events to celebrate women, which is a great way to bring people together.
What has been your biggest win throughout your time at Kent?
When the junior engineers realised they could approach me for advice. I joined Kent in a man-only team, where I am still the only female, so now I regularly look to support junior engineers by sharing my experience and knowledge. Hearing from them on their own work and career journeys, and sharing my own perspective, allows for transparency and open conversations that have created a great team dynamic.
The Queensland Government has officially opened the Sunshine Coast’s $70 million Bells Creek Arterial Road, which aims to reduce travel times to improve the state’s transportation into the future.
The State Government invested $35 million into the road’s construction and development.
Queensland Premier, Annastacia Palaszczuk, State Minister for Transport and Main Roads, Mark Bailey, and Member for Caloundra, Jason Hunt, officially opened the 8km extension of Bells Creek Arterial Road, completing the 11.9km link between the Bruce Highway and Caloundra Road.
Delivered as part of a $70 million project, the road was co-funded by development company Stockland and the State Government, aiming to provide a vital second gateway from the Bruce Highway to the southern Sunshine Coast.
The project has delivered significant economic benefits, including the creation of over 300 direct jobs and 550 indirect jobs over the life of the project, with Sunshine Coast business Shadforth Civil Contractors appointed to build the road.
Ms Palaszczuk, said, “The population of the Sunshine Coast is booming – one of the reasons our government put funding on the table to bring its construction forward from 2030.
“We promised the accelerated delivery of the Bells Creek Arterial in 2020 and today we are delivering on that commitment.
“More than 50,000 drivers use Caloundra Road every day so this brand new road will give those people a crucial second access to the Bruce Highway,” Ms Palaszczuk said.
“Our Big Build is not just a promise, it’s a guarantee. A guarantee that our government will build the roads, bridges, school, hospitals and infrastructure Queenslanders need now and in
Mr Bailey said the development of the Bells Creek Arterial Road marks the start of the government’s transportation projects across the state.
“Bells Creek Arterial Road now spans nearly 12km and will bust congestion on the Sunshine Coast, thanks to local member Jason Hunt’s tireless advocacy, and the workers who got the job done,” Mr Bailey said.
“As an avid bike rider, I’m excited to announce we’ve delivered improved active transport connections, including an overpass bridge from Baringa and Nirimba, helping more Queenslanders get outside and enjoy our great lifestyle.
“And that’s not all – over the next four years, the State Government is investing over $32.1 billion in road and transport projects all over Queensland, supporting 25,200 good, secure jobs across the state.
“We’re delivering more lanes, better roads and safer interchanges, helping Queenslanders get home sooner and safer.”
Featured image: Bells Creek Arterial. Image: Queensland Government.
Future Charles Sturt University students are being encouraged to apply for Transgrid’s engineering scholarships – a $2 million program aiming to boost the infrastructure workforce.
Applications are now open for 25 scholarships for first-year engineering students at the university’s Bathurst campus in 2024, under Transgrid’s Engineering Scholarship Fund.
The fund will support 100 engineering students at the university’s Bathurst campus between 2023 and 2026 to help grow a skilled workforce in regional Australia as the clean energy transition accelerates.
Executive General Manager of Major Projects, Gordon Taylor, said that Transgrid is delivering the critical infrastructure and priority projects identified by the Federal and New South Wales Governments to enable Australia’s clean energy transition.
“Our major projects such as EnergyConnect, HumeLink and VNI West will require world-class engineering expertise and we are delighted to support the next generation of engineers to help build our skilled workforce as we enable Australia’s renewable energy transformation,” Mr Taylor said.
“I encourage prospective students to apply for a scholarship with each recipient to receive $20,000 over four years to help meet the costs associated with their study, living expenses and learning resources.”
The first 17 engineering scholarships were awarded earlier this year, with recipients hailing from New South Wales regional centres including Albury, Bathurst, Dubbo, Orange, Port Macquarie and Wagga Wagga, as well as Victoria and Queensland.
Bachelor of Technology (Civil)/Master of Engineering (Civil) student, Olivia Tait, from Wagga Wagga, received a Transgrid scholarship to help with the cost of her studies, including travel to and from the Bathurst campus.
Ms Tait encouraged prospective engineering students to apply for a scholarship to help them realise their goal of becoming a professional engineer.
“Receiving the Transgrid engineering scholarship has really aided me in my studies and allowed me to focus more on my academic goals and progress my career goals,” Ms Tait said.
“I hope to become a professional engineer in the civil engineering field and make a positive change in the community and improve our community infrastructure.”
Charles Sturt Head of the School of Engineering, Mathematics and Engineering, Associate Professor Michael Kemp, said the Transgrid scholarships were a great addition to the paid internships already offered through the university’s engineering courses.
“A Transgrid scholarship will help a student in the earlier part of their course before the internship has started, with half the value being offered in the first year when it is most needed,” Professor Kemp said.
“This allows a student to fully engage from the beginning in the real world team based engineering challenges as well as starting the innovative and flexible ‘topic tree’, offered at Charles Sturt.”
Transgrid scholarships are open for commencing students undertaking a Bachelor of Engineering (Civil) (Honours) or a Bachelor of Technology (Civil)/ Master of Engineering (Civil) at Charles Sturt University.
Applications are now open for 2024, with the early bird round closing on 26 November and offers to go out on 12 December. Applications will remain open with a second round of offers to be made on 22 January.
Australia’s first Trackless Tram has arrived in the City of Stirling after a long journey from Shanghai, where it will soon be undergoing testing to determine its suitability for use along Scarborough Beach Road.
The $2 million business case and trial for the 30m-long Trackless Tram has been funded by the Federal Government, with the project being delivered with partners Curtin University, CRRC, Shanghai Electric and Infrastructure Technology Solutions.
Through the trial, a range of experts will examine how this technology works to help determine whether it can be implemented along Scarborough Beach Road.
Council said that, with its efficient and eco-friendly features, the trackless tram is part of Stirling’s vision for a sustainable region with a local focus.
It is hoped the tram will connect people to busy, vibrant areas, creating better accessibility and generating urban redevelopment within the Scarborough Beach Road Activity Corridor.
Representing the latest in sustainable mid-tier transport technology, Trackless Trams have the potential to achieve positive economic, business, transport, innovation and sustainability outcomes.
This new mode of commuting could be a game changer for Perth and encourage people to make the switch from cars to public transport.
City of Stirling said that it’s part of the region’s plan to reduce congestion, improve access to employment and contribute to urban regeneration.
As a net-zero emission vehicle the Trackless Tram will also support a reduction in carbon emissions as well as decreasing the number of cars on the road.
However, Council said it will require collaboration across community, business and government sectors.
The trial of the Trackless Tram will commence over the coming weeks and will run through to November, where locals and stakeholders will have the chance to ride the tram and be part of some user-experience testing.
In conjunction with event partners and sponsors, the City will also present a Net Zero Transit Symposium on 21 and 22 November at Rendezvous Scarborough.
Powerlink and its construction partners, UGL and CPB, have released 40 works packages for the CopperString 2032 project, giving local suppliers the opportunity to work on Australia’s largest transmission works.
These packages cover a range of activities and services, such as engineering, construction, environmental management, logistics, camp construction, haulage and communications.
They are designed to maximise the opportunities for local businesses and communities to participate in the
delivery of the nation-building project, which will stimulate new industries and innovation in the North West Minerals Province and aims to unlock the renewable energy potential of North Queensland.
Powerlink Executive General Manager for Major Projects, Ian Lowry, said the release of these packages sends a clear signal to the market that Powerlink is ready to start work.
“Since Powerlink took on this project earlier this year, we have been focused on starting work on the ground as soon as possible,” Mr Lowry said.
“Our process is not just about finding the best value for money, but also about finding the best fit for our vision. That’s why we want to hear from you, the local businesses and suppliers that know the region and identify who has the capability, capacity, and experience to deliver high-quality outcomes for the CopperString 2032 project.
“We want to work together to create a sustainable and resilient supply chain that benefits local communities along the CopperString line.
“This is an opportunity for regional businesses to register their interest in being a part of a project that will transform North and North-West Queensland for generations to come.”
Beele Engineering provide the ultimate solution for fire resistance, smoke-proof and gas-tight requirements in tunnels and underpass environments whilst fully capable to deal with Dangerous goods / Hydrocarbon applications.
The detailed design and construction contract for the Monaro Highway Upgrade Project, at the Lanyon Driveinterchange, has been awarded –representing a $70 million investment in this major corridor.
The contract has been awarded to local Australian Capital Territory company, Woden Contractors, marking a significant milestone for the project which is expected to start in 2024.
This contract aims to make the highway safer, improve travel times and support freight movements.
The contract includes:
♦ A new southbound flyover of the Monaro Highway over Lanyon Drive (including 3m wide sealed shoulders)
♦ Upgrading of the highway road pavement from David Warren Road through to Sheppard Street (including 3m wide sealed shoulders)
♦ A new widened bridge on the northbound carriageway over Dog Trap Creek just north of Lanyon Drive
Another major package of works for the interchange is planned for 2024, subject to environmental and other approvals.
This will include the removal of traffic lights at the Alexander Maconochie Centre and extension of David Warren Road to Lanyon Drive, with a new roundabout and signalised intersection
connecting with a new Monaro Highway off-ramp and Sheppard Street.
The Lanyon Drive interchange is being designed to minimise the impact on existing native vegetation in the area.
The landscaping plans are set to be finalised during the detailed design phase and focus on local and native species, prioritising tree planting, water sensitive urban design and biodiversity conservation.
Detailed design will soon be finalised with major construction works expected to start in 2024 and take around three years to complete.
Previous works on the Monaro Highway Upgrade have already been completed as part of a program of works jointly funded between the Federal and Australian Capital Territory Governments.
This includes completed safety improvements and new overtaking lanes on the rural section of the Monaro Highway between Old Cooma Road and Williamsdale Road.
Extensive utility works, which started in January 2022, have also been completed near Lanyon Drive in preparation for the flyover, including relocation and protection of major watermains and telecommunication networks.
The relocation of two gas mains is expected to be completed in the coming months, which are necessary before main construction works get underway on the new Lanyon interchange.
Federal Minister for Infrastructure, Transport, Regional Development and Local Government, Catherine King, said that the Federal Government understands the importance of investing in infrastructure that supports growing populations, reduces congestion and improves travel times.
“This project will provide a major economic stimulus to the Canberra and Monaro region including an estimated 700 jobs to be created during the detailed design and construction phases,” Ms King said.
“Projects like this are important to not only keep local people employed and businesses running, but also to provide the region’s community with better infrastructure and safer roads into the future.”
ACT Minister for Transport and City Services, Chris Steel, said that the Australian Capital Territory Government is building the infrastructure its growing city needs.
“Our investment in projects like this supports our growing population, improves safety and the efficient movement of people and freight,” Mr Steel said.
“The Lanyon Drive flyover is part of a program of works to improve safety on the Monaro Highway by removing dangerous at-grade intersections and separating traffic turning across the highway, in and out of the Hume industrial precinct and New South Wales.”
Quest Apartment Hotels have quickly become a trusted staple for travellers, with the hotel group currently having 40 properties across New Zealand, with two additional properties in Christchurch scheduled to open in the next 12 months.
The two new locations are Quest on Cambridge, due to open on the 15th November 2023 and Quest on Kilmore, due to open June 2024.
Quest Apartment Hotels aim to be traveller’s home, or office, away from home, complete with separate living, dining and sleeping areas, workstations and a fully equipped kitchen and laundry facility. Allowing guests to cook their own meals, do their own laundry, and relax with plenty of space.
Apartments are serviced daily; in house services include valet laundry and dry cleaning, babysitting services, grocery delivery and charge-back with selected local restaurants.
Quest attracts guests staying for days, weeks or months at a time, with the combination of flexible accommodation and services making guests feel like they never left home.
Quest is perfectly equipped to cater for families attending conferences, with locations close to all major conference venues in New Zealand.
To find out more, go to www.questapartments.co.nz
Quest has turned 25, and there’s a lot to celebrate.
STAY IN THE HEART OF CHRISTCHURCH
Quest on Cambridge opening this November. Enjoy introductory rates from $135 per night for stays from 15th November 2023 to 14th January 2024*.
OUR SUSTAINABILITY QUEST
We’ve replaced almost all single-use plastic toiletries with dispensersremoving 3.68 tonnes of plastic out of circulation. We’re also recycling old soap bars into new ones together with Soap Aid.
Find out more at soapaid.org
*Rates start at $135 for a studio and $155 for a 1-bedroom apartment all booked via the Quest App and the Quest website. All bookings must be for stays between November 15th 2023 to January 14th 2024 to qualify for the introductory rate.
QUESTAPARTMENTS.CO.NZ
As the infrastructure sector continues to face a significant skills and labour shortage, we also face a very real solution — improving gender diversity.
Recently, I participated in a panel discussion at the 2023 Women in Construction, Engineering, and Infrastructure Summit.
Facilitated by Infrastructure NSW Acting CEO, Janine Lonergan, and joined by Australian Constructors Association CEO, Jon Davies, and Maree Bridger, Department of Infrastructure, Transport, Regional Development, Communications and the Arts COO, the conversation covered a range of issues relating to diversity in the workforce.
Panelists all made the critical point that increasing diversity is imperative to the success of any workforce, especially at a time when labour shortages are a significant issue.
It is a well-known fact that the infrastructure sector is facing a critical skills shortage.
From our Market Capacity research, we know that this year public infrastructure projects are expected to face a shortage of 226,000 skilled workers.
While this skills shortage is not unique to the sector, what is unique is the lack of diversity across its workforce.
Insights from our Market Capacity research also reveal that female representation across the construction sector stands at just 14 per cent. For on-site roles, this number falls dramatically to just two per cent.
This hasn’t changed in over a decade.
In the face of critical skills shortages, the infrastructure industry has tried to power through by demanding more of its workforce. Put simply, workers have had to go harder and faster to meet project demands.
The result has been excessively long working hours, stress, burnout, job dissatisfaction and poor mental health.
It’s a complicated landscape in a sector facing a number of challenges, but this approach has made the industry an undesirable place to work.
In fact, we know through early findings of our 2023 Market Capacity research that over 50 per cent of apprentices and trainees who completed infrastructure training in recent years did not enter their intended occupation, while 20 per cent did not enter any infrastructure-related occupation.
So how can gender diversity lead to better outcomes?
Importantly, it is the morally right thing to do. We should strive for equity and inclusion as a normal way of operating. But the benefits of increasing gender diversity within any workforce, especially for the infrastructure sector, are incredibly rich and rewarding.
We all know diversity encourages a flow of different ideas, fresh perspectives and creativity that can drive positive change and innovation. For the infrastructure sector, greater innovation will be necessary for its survival in the face of stagnating productivity.
There are also significant economic benefits for increasing diversity. According to the World Economic Forum, companies with more diverse management teams have reported 19 per cent higher revenue. In addition, improving gender pay is estimated to improve the global economy by a staggering 26 per cent.
Then there is the significant cultural change that can follow by introducing greater diversity, which ultimately benefits everyone.
In the current climate, a significant benefit for the industry would be an increased pool of people to draw from to alleviate the pressure felt by the skills shortage.
The methods for increasing diversity in the workforce are clear and already laid out for us by bodies such as the Workplace Gender Equality Agency.
Companies need to develop diversity and inclusion policies, strategies and plans, and address key issues such as flexible working arrangements, while also embedding equality, diversity and inclusion KPIs.
From Infrastructure Australia’s perspective, in our Delivering Outcomes Report, we advocate for the embedding of equality, diversity and inclusion objectives through each infrastructure investment as part of a holistic and consistent approach to achieving this need.
Governments at all levels also have a role to play in leveraging the procurement process for public infrastructure projects to achieve this as well.
This is one of the most powerful tools available to governments to drive effective change and guide the industry towards achieving greater diversity.
Changing the way projects are delivered and adopting more innovative working practices can also be a powerful way to attract and retain more diverse workforces.
One example is for companies to switch to modern methods of construction such as off-site manufacturing, which can ease the physical burden for workers and provide more flexibility in the hours needed to deliver a project.
These are just a few key examples of how gender diversity can be improved within the infrastructure industry.
Although, there is one more key element for enabling gender diversity to truly be able to grow within the infrastructure industry, which is through strong leadership.
Senior leaders in the sector should be trained to fully appreciate the challenges and benefits of equality, diversity, and inclusion, and learn the best practice methods for achieving effective outcomes.
There are some really strong examples of leaders taking charge to make a difference.
The experience of Alison Mirams, founding CEO of Roberts and Co, is a shining example; real and impactful solutions were implemented under her leadership.
Solutions such as a five-day work week, which fundamentally changed workplace flexibility, equality, and health and wellbeing outcomes.
By relentlessly advocating for diversity, challenging the status-quo and connecting to the practical issues impacting women in the workplace, real change was achieved.
Then there is the leadership of Mr Davies to set the goal of having 75 per cent of members achieve the Workplace Gender Equality Agency Employer of Choice citation.
At the end of the day, all avenues need to be explored and adopted to drive greater gender diversity within the infrastructure sector if collectively we are to make headway in addressing the labour gap and productivity challenges.
Traditional security can provide reliable protection for critical infrastructure by actively monitoring and preventing theft or damage, so long as security personnel are onsite. Smart security systems can provide eyes where traditional security cannot, offering a comprehensive service that ensures buildings and assets are not left vulnerable.
Security guards cannot always be onsite and traditional camera systems cannot always be installed, especially on remote or occupied sites, leaving opportunities for potential criminals to break-in and cause damage.
However, smart security technology can complement traditional systems to provide responsive surveillance and active deterrence.
Spectur provides smart security platforms that can not only detect danger, but also actively deter threats. With a variety of applications, Spectur’s systems can keep an eye on remote sites, prevent break-ins and theft, monitor ecosystems and protect communities.
When paired with intelligent surveillance that utilises cameras, sensors and artificial intelligence (AI) to gather imagery and information, smart security systems can offer an all-encompassing service to keep critical sites safe.
For nationally-significant infrastructure, security is vital to prevent theft, vandalism or damaged equipment that would cause interruptions and delays. Developers and managers cannot afford guards or cameras to miss anything, especially if that means adding weeks or months onto a multi-year project’s timeline in order to fix damage or replace equipment.
If security guards are not onsite at the time of a break-in, the intruders are often long-gone by the time any personnel turn up. Deploying Spectur’s security systems can help deter any potential intruders on large construction
sites by responding to intruders before they break-in.
Spectur’s camera systems are selfcontained, smart platforms capable of capturing imagery and responding in real-time to threats. With AI-enabled cameras and sensors, Spectur’s systems can trigger alarms, identify number plates, detect motion and send out alerts to create a digital fence that actively prevents criminal activity.
When a building is left unoccupied and there is no staff around to monitor the site, it can become a target for intruders. Spectur’s camera systems can provide another set of eyes while security personnel are away.
But not all intruders breaking into unoccupied buildings will be potential criminals. Sometimes they are homeless people seeking shelter or children looking for fun. Certain sites are dangerous for the general public to enter, which means deterring intruders not only protects the site but also keeps people safe from harm or injury.
Especially for homes or schools left vacant during the holiday season, when there is no one around, a smart security system can provide assurance that a building is always being monitored.
Remote energy assets are particularly vulnerable to theft and vandalism, being far away from urban areas, hard to access and regularly left unattended. For many locations, traditional security systems such as cameras and security guards are difficult to set up or employ, so many asset owners have no choice but to do nothing.
However, Spectur camera platforms can be set up anywhere, since they are wireless and solar-powered, making them ideal for remote locations where there is no wired electricity or internet connection.
Unlike traditional systems, Spectur’s systems have a built-in 3G/4G modem to transmit data and are powered by solar PV and battery storage. While a regular camera would need to be set up close to an asset or on the building itself in order to be connected to power and internet, a Spectur platform can be set up on the perimeter of a site, meaning intruders can be stopped before they even make it onto the property.
When there is no one else around and traditional security options are not possible, smart security systems offer an alternative to protect these critical remote energy assets.
Traditional security has its limitations, with cameras being unable to respond to threats and security guards not always being on patrol. But, when paired with smart security systems, the additional capabilities of AI, sensors, remote functionality and more can fill in the gaps to make sure no site is left unguarded and vulnerable.
For more information on boosting your security system with smart capabilities using Spectur’s solutions, call 1300 802 960 to talk to our team and find the right solution for your unique onsite challenges.
A new chapter of water security for 200,000 customers in southern Tasmania was written in September 2023, with TasWater officially opening its upgraded Bryn Estyn Water Treatment Plant (WTP).
The project, which was TasWater’s largest ever capital works project, was delivered on time and under its $243.9M budget.
The new water treatment plant will provide safe, clean, and reliable drinking water for generations to come.
TasWater Chief Executive Officer, George Theo, said the opening marked a major milestone for Greater Hobart.
“This was a landmark day for southern Tasmania,” Mr Theo said.
“The new plant is able to treat 160 million litres of water per day. It’s been designed for future population and economic growth, with the potential to be expanded to treat another 40 million litres of water per day if required.
“The project is a story of infrastructure, economic benefits, current and future jobs, protecting and enhancing the natural environment, and providing opportunities for Tasmanians. It is also the story of TasWater’s dedication to securing the best possible customer outcomes now and long into the future.”
TASWATER’S LARGEST EVER CAPITAL WORKS PROJECT
Located north of Hobart in the Derwent Valley, the Bryn Estyn WTP is Greater Hobart’s primary source of drinking water, providing around 60 per cent of the water supplied to southern customers.
Water from Bryn Estyn winds its way through 433km of water mains and into 145 reservoirs before reaching the taps of customers in Hobart, Glenorchy, Kingborough, Brighton, Derwent Valley, Southern Midlands, Sorell and Clarence.
The original plant was built in 1962, with capacity augmentations in 1972 and 1992, and construction work on the current upgrade commencing in mid-2021.
All major structures, buildings, electrical and mechanical installations are now complete, with the new infrastructure commissioned, and the plant officially opened at an event on 22 September 2023, which gained widespread media interest in Tasmania and beyond.
TasWater’s General Manager Project Delivery, Tony Willmott, said the scale of the project is unprecedented for TasWater.
“In the early phase of the works, 11,456 cubic metres of concrete was poured, 2,800 tonnes of reinforcing steel placed, and more than 93,000 cubic meters of soil was excavated,” Mr Willmott said.
“TasWater is currently delivering a planned 10-year, $1.84 billion capital investment program for completion in the financial year 2025-26. The program is delivering important customer and environmental outcomes for the benefit of all Tasmanians.”
“During construction the project employed around 1500 people directly, and 500 indirectly,” Mr Willmott said.
“At its peak, around 150 people were working on site every day, generating benefits for Tasmanian businesses across the state.”
The Bryn Estyn project was delivered by TasWater’s Capital Delivery Office (CDO), an alliance with UGL Limited and CPB Contractors, along with their sub-alliance partner WSP, which will continue to deliver TasWater’s accelerated Capital Works Program through to July 2025.
It is a model that continues to directly support the Tasmanian economy, with more than 80 per cent of the total value of CDO packages being awarded to Tasmania-based suppliers, providing a significant economic boost for the local civil construction sector and its supply chain, growing the capability of the local contractor market for future projects.
TasWater’s Head of Water and Environment Services, Fran Smith, said the upgrade expanded the capacity for the organisation to deliver greater volumes of high-quality, safe drinking water for Hobart.
“To be able to treat and deliver 160 million litres of water every day, with every litre meeting the Australian Drinking Water Guidelines, is not a small task,” Ms Smith said.
“Each drop of water that has passed through Bryn Estyn has been subjected to a treatment process that includes filtration, ozone, absorption using activated carbon, chlorination, and now Ultra Violet disinfection for an extra layer of treatment.
“Just last year alone, across the state we undertook 273,000 tests to ensure Tasmanians could turn on the tap with confidence knowing their water is absolutely safe to drink, one test every two minutes.”
Mr Theo said TasWater was all about a customerfocused future.
“TasWater has a range of initiatives underway as we ramp up our customer and community focus and continue our journey to being the best service provider in Tasmania. The project takes us one step closer to realising our strategic vision ‘to unlock the full potential of water’ for a thriving Tasmania.
“We are proud of what TasWater is delivering, and the Bryn Estyn WTP is a prime example. While it is a story of a vast infrastructure project, it is also a human story for so many people, not least our customers, who will receive the benefits of the Bryn Estyn WTP upgrade for decades to come.”
In our home lives, we understand the value of maintenance. We wash our cars, check our gutters, vacuum our floors and look after our health. The same care and maintenance is applicable to the buildings we protect through waterproofing, because, when certain areas are neglected or left unchecked, the consequences can be damaging and costly.
Colin Picton, Fosroc ANZ Product Segment Specialist for Waterproofing and Joint Sealants, emphasises the importance of regular maintenance, and prompt rectification of any damage.
"Maintenance plays a crucial role in maximising the longevity and performance of waterproofing products," Mr Picton said.
"Keeping exposed areas clean makes it easier to check for cracking caused by movement or damage from falling debris.
"Checking for, and clearing, a blocked drain is far more effective and financially palatable than spending big money on re-waterproofing and the ensuing disruption it causes. Following a planned cleaning and maintenance program not only keeps the structure looking good, it will help avoid unexpected costs moving forward."
When it comes to waterproofing solutions, Fosroc ANZ's Nitoproof systems provide trusted, world-class results.
The liquid-applied range of membranes and topcoats, together with Nitoseal sealants, are made to withstand the toughest Australian conditions, and preserve the durability of the underlying structures it protects.
FOSROC’S TOP MAINTENANCE TIPS
Stay ahead with regular inspections
Create and action a scheduled maintenance plan in accordance with AS4654.2 2012. Pay close attention to joints, corners and terminations, and look for membrane cracking and blistering, bald spots or any other wear and tear. Storm damage from hail or fallen branches and debris can block drains. Record the inspection, including taking photographs.
Regular cleaning is essential for preserving the effectiveness of the Nitoproof system. Exposed to the elements, the membrane may accumulate dirt, debris, or other contaminants
that could compromise its performance. Clean coatings with a neutral pH cleaner or detergent and apply to the surface using a soft bristle broom. Rinse off thoroughly with clean water using low pressure spray. In coastal areas more regular cleaning may be required to prevent the build-up of salt contamination, every six months is recommended.
Keeping drains clear and functional prevents water accumulation, which can cause additional stress on the waterproofing membrane. Checking regularly, especially after storm or hail events will reduce the risk of leaks or structural damage.
Timely repairs for lasting performance
In the event of accidental damage or unforeseen circumstances, timely repairs are crucial for sustaining the performance of the Nitoproof waterproofing membrane. Before undertaking any repairs ensure the underlying cause has been identified and addressed. Any necessary repairs or maintenance should be carried out promptly by a suitably qualified contractor.
Commitment to waterproofing success
Regular inspections, proper cleaning, optimal drainage, and timely repairs are the cornerstones of effective maintenance. "Regular and comprehensive maintenance practices optimise the durability of any waterproofing system," Mr Picton said.
"By incorporating these practices into your routine, you can safeguard your structure, avoid costly repairs, and have peace of mind knowing that your waterproofing system is well-maintained."
The Australian infrastructure landscape is undergoing a profound transformation, marked by comprehensive policy reviews, and a noteworthy shift from transport infrastructure to renewables, electricity transmission, social infrastructure (such as water and hospital) and defence (in the north).
This era of change has left Catherine King, Minister for Infrastructure, Transport, Regional Development, and Local Government, contemplating two pivotal reports: the Infrastructure Investment Program (90 day) Review and the National Partnership Agreement (NPA) on Land Transport Infrastructure Projects
The 90-day Review, executed by an experienced trio comprising Mike Mrdak AO, Clare Gardiner-Barnes, and Reece Waldock AM, sets the stage for intense consultations between the Federal and State/Territory Governments.
Those negotiations are focused on three central themes: productivity, liveability, and sustainability. The liveability dimension is a nod to Prime Minister Anthony Albanese's urban vision, evaluating infrastructure based on its impact on the quality of life for people and communities.
The government's response to this 90-day review is eagerly anticipated by industry, and it's expected the response will coincide with the release of the Mid-Year Economic and Fiscal Outlook in early December.
The prevailing messaging from both is expected to emphasise fiscal and economic challenges, potentially necessitating a recalibration of the infrastructure agenda. Brace for funding cuts or delays for numerous infrastructure projects, considering an eye-popping $33 billion overrun in the infrastructure pipeline.
In the meantime, while these reviews are underway, the infrastructure spending tap has been turned off, causing many engineering consulting firms to feel the sting. Anecdotal evidence is mounting of large-scale redundancies by major consulting firms, which, in turn, will have a ripple effect on contractors who may find themselves bidding for a smaller pool of contracts up to a year behind schedule.
While this is all underway, Jane Halton AO PSM, a former senior public servant, was entrusted with overseeing the Independent Review of the NPA on Land Transport Infrastructure Projects, a critical mechanism through which the Commonwealth invests in land transport infrastructure in tandem with states and territories. As the NPA approaches its expiry date on 30 June 2024, the findings from this review will serve as the blueprint for negotiations surrounding a new Land Transport National Partnership Agreement.
This renegotiation will zero in on the project commitment and approval process, with a spotlight on administrative efficiency.
The 80:20 federal/state funding model in regional Australia is almost certain to be abolished given it is viewed by some in the government as a mechanism to favour regional electorates.
As part of the NPA Review, organisations like the Australian Owned Contractors Association and the Civil Contractors Federation are vigorously advocating for the government to meet its commitments in the Buy Australian Plan, to foster a more accessible and level playing field by implementing project package caps of $500 million.
The Buy Australian Plan aims to boost industry productivity and competitiveness by incentivising states and territories to embrace a set of rules, promoting opportunities for local mid-tier firms in bidding for significant infrastructure projects. One key component involves the subdivision of contract sizes to ensure they do not exceed $500 million in value.
There's also a pressing need for both industry and government to confront the monumental task of decarbonising transport. In 2020 the transport sector contributed around 18 per cent of Australia’s emissions, predominantly related to road-based transport, and a staggering 70 per cent of Australia's greenhouse gas emissions are tied to infrastructure.
The Commonwealth is resolute in its commitment to reducing greenhouse gas emissions, and while it's almost a given that Australia will miss its target of a 43 per cent
reduction below 2005 levels by 2030, it remains committed to the goal of net-zero emissions by 2050.
In response, the Commonwealth is crafting a Transport and Infrastructure Net Zero Roadmap and Action Plan to guide the reduction of transport emissions.
Furthermore, the Commonwealth is on the cusp of releasing an Infrastructure Policy Statement, aimed at establishing a comprehensive framework for both the industry and the government to navigate this new infrastructure landscape.
Simultaneously, the focal point of Australian infrastructure activity is shifting significantly from transport infrastructure to renewables, electricity transmission, social infrastructure and defence. This transformation is expected to be most pronounced in regional Australia, giving rise to a commensurate demand for a skilled workforce.
The latest Infrastructure Partnerships Australia Pipeline Report spanning from January 2022 to August 2023 highlights a substantial surge in energy-related expenditures, surging from $44.9 billion to $116.7 billion.
In contrast industry research and forecasting company, Macromonitor has predicted that while Australian major transport construction spending is at over $23 billion per annum, that will now start to tail off.
From a national perspective, the zenith of transport construction has been reached, with attention now firmly shifting towards renewables, transmission, social infrastructure and defence.
The Commonwealth has unveiled its monumental $20 billion Rewiring the Nation program, aimed at access to clean energy while striving to meet stringent emissions reduction targets.
A pivotal element of this initiative involves the construction of 10,000 km of new transmission lines, promising a substantial surge in infrastructure spending for regional Australia, driven by the renewable and transmission sectors.
While there are significant social license issues for transmission pending or currently in play, this sector will be a major contributor to regional employment and economic growth.
The realm of infrastructure is perpetually dynamic and exciting. However, the upcoming years promise not only a transformation in funding decisions but also a significant shift in the very nature and objectives of infrastructure development.
Michael Kilgariff is a former CEO of Roads Australia and Managing Director of the Australian Logistics Council. In these and previous roles, he has developed a reputation for building strong working relationships across industry and government, with the aim of supporting and achieving outcomes that are mutually beneficial to industry, government and the community.
Engineered stone (a.k.a. quartz or artificial stone) is a popular material widely used for stone benchtops in kitchens and bathrooms. However, recently this has come under scrutiny due to its health risks that it poses for workers, with the Federal Government considering a ban of the material.
The high levels of crystalline silica found in engineered stone pose a severe threat to the health and well-being of workers who handle it. These invisible silica dust particles are 100 times smaller than a grain of sand, so can travel deeply into your lungs where they wreak havoc – causing the lung disease called silicosis.
Recently, there has been an explosion of cases of silicosis in tradies, especially in stone benchtop workers. Silicosis is also a risk when working in any workplace which creates silica dust, such as excavation, mining, quarrying and mineral processing, tunnelling, construction, concrete or masonry, and pottery making, just to name a few.
Silicosis is the oldest occupational lung disease on record and is entirely preventable. More than 275,000 Australians are now at risk of cancer and lung disorders caused by silica exposure – that is, more than the entire population of Hobart and Launceston combined.
Curtin University researchers have shown that workers in trades have a 37 per cent risk of developing silicosis in later life. Monash University research published in June 2023 found that 28 per cent of Victorian stone benchtop workers had silicosis, and 21 per cent had advanced silicosis.
In the interests of protecting lives and ensuring workplace safety, a ban on engineered stone is a critical step towards a healthier and safer environment for all.
Engineered stone is produced by compressing ground stone such as crystalline silica and combined with resins. The crystalline silica content in stone bench tops can vary widely depending on the type of stone used.
Engineered stone benchtops can contain up to 95 per cent crystalline silica. Natural stone such as granite may contain from 20 to 60 per cent. It is the respirable crystalline silica released into the air which causes silicosis – no airborne silica dust, no silicosis.
Silica dust, generated during the fabrication and installation processes using engineered stone, poses a grave danger to workers. Silicosis is a debilitating and potentially fatal lung disease. Silicosis is irreversible, and its effects can be devastating, robbing workers of their lives and cutting short their careers.
The importance of prioritising workplace health and safety cannot be overstated. While measures such as dust control and personal protective equipment can help mitigate risks, they are not foolproof.
Despite reduction in dust levels and guidelines and regulations having been revised, instances of non-compliance or inadequate implementation are still common, leaving workers vulnerable to the dangers of silica dust exposure. A ban on engineered stone would eliminate this risk altogether in exposed workers, ensuring the highest level of protection for these workers.
Silicosis is silently progressive, usually only becoming noticed years after exposure to silica dust. Workers may not realise the severity of their condition until it is too late.
At TSANZ, we strongly advocate for a ban on engineered stone in Australia. By banning engineered stone, we have an
opportunity to prevent this silent suffering and protect the lives and livelihoods of many workers who are at risk.
Our members are the clinicians who diagnose and treat tradies with silicosis, and they tell us that this is the first and most important step to protect the workforce. Our tradespeople are getting sick, are forced out of employment, and die – for going to work every day to provide for themselves and their families, and that is simply not acceptable to us.
As a society, we have a moral and ethical responsibility to prioritise human lives over profits. While engineered stone has gained popularity for its aesthetic appeal and durability, the toll it takes on the health of workers cannot be ignored. Can your conscience cope knowing your faux stone benchtop contributed to a child or spouse losing their parent or partner?
By implementing a ban, we, as a society, send a strong message that the well-being of individuals should never be compromised in the pursuit of commercial gains or aesthetic appeal.
Advocating for a ban on engineered stone does not mean sacrificing progress or design options. It presents an opportunity to promote the adoption of safer alternatives that do not pose the same health risks.
The development and utilisation of materials which do not pose a risk of lung disease is possible and can create a safer work environment without compromising industry growth or aesthetic choices for consumers.
One of our trusted colleagues, Kate Cole, who is a certified Australian occupational hygienist, researcher, and thought leader in this area, has some great educational resources. Some examples of alternative materials she recommends include stainless steel, timber, and laminate. Stainless steel and timber (depending on the type) are highly durable materials, while laminate is a great low-budget option for homeowners who like to upgrade their kitchen as trends change.
Silicosis often affects individuals in their prime working and tax paying years, thus creating economic dependency
for workers who may have to rely on e.g., unemployment or disability benefits.
The treatment and management of silicosis requires specialised medical care, including diagnostic tests, medications, and sometimes lung transplantation. These expenses contribute to the overall healthcare burden and can strain healthcare systems. Besides being good public policy, it is in the Federal Government’s financial interest to address this issue head on and prevent rather than treat the disease.
Tradies who receive a silicosis diagnosis should consult with their employer and lawyer as soon as possible. It’s important that workers get the support and compensation they need and are entitled to, but workers’ compensation processes need to be followed.
We encourage any person who is concerned that they are suffering from a respiratory condition and who interacts with materials containing silica to have conversations with both their employer and legal representation as early on as they can.
Banning engineered stone is an essential step to protect the lives and health of workers who handle this material. Silicosis is a completely preventable disease and should not be occurring in the 21st century.
By taking decisive action, we can ensure that no worker suffers these devastating effects. By advocating for a ban, we affirm our commitment to workplace health and safety, responsible decision-making, and the wellbeing of our workforce and their families. Let us prioritise human lives above all else and work towards creating a safer and healthier future for all workers.
Vincent So is CEO of The Thoracic Society of Australia and New Zealand (TSANZ). TSANZ is the only health peak body representing a range of professions (medical specialists, scientists, researchers, academics, nurses, physiotherapists, students, and others) across various disciplines within the respiratory/sleep medicine field in Australia and New Zealand.
As a country known for its thriving coffee culture, it’s no surprise that Australia generates 75 million kilograms of ground coffee waste every year. Most of this ends up in landfill, contributing to greenhouse gas emissions and exacerbating environmental degradation. To combat this, a team of RMIT University researchers are on a mission to transform discarded coffee grounds into a valuable resource that can support a more sustainable construction sector.
The construction industry is one of the largest consumers of natural resources and a significant contributor to carbon emissions, making circular practices crucial for mitigating the impacts of resource depletion and climate change. From the repurposing of end-of-life work apparel to freeway noise walls made of plastic waste, circular initiatives are becoming increasingly prevalent across the sector.
Due to this need for more sustainable options in the sector, a team of engineers from RMIT University have published a study, Transforming spent coffee grounds into a valuable resource for the enhancement of concrete strength, that offers a new way to utilise coffee grounds.
Lead author, Dr Rajeev Roychand, said the motivation behind the research was reducing some of the 6.87 million tonnes of organic waste that ends up in Australia’s landfills per year, which contributes to three per cent of the country’s greenhouse gas emissions.
“Our research group discussed shifting our focus to diverting this waste from landfills and developing innovative solutions to transform waste into a valuable resource for different applications,” Dr Roychand said.
“Incidentally, this conversation happened over a cup of coffee in our team meeting. That’s why we decided to start with coffee grounds.”
The developed technique uses a low-energy process without oxygen at 350 degrees Celsius to turn used coffee grounds into biochar, which can then be used to make concrete 30 per cent stronger.
As the first study to prove that waste coffee grounds can be used to improve concrete, it has not been without its challenges.
“Organic waste in its raw form is detrimental to the concrete strength due to the organic compounds hindering the hydration reaction of cement,” Dr Roychand said.
“They need to be converted into biochar to make it compatible with concrete. But even to make biochar the process parameters are highly critical to deliver the best performance in its concrete applications.
“We started with raw coffee waste, which saw a significant reduction in concrete strength. This is because coffee waste leaches out organic compounds that hinder cement reaction, thereby negatively impacting its strength development. The team then worked on a method to break these organic compounds while preserving the carbon content, for that we used the pyrolysis process.”
Typically, pyrolysis – heating organic waste in the absence of oxygen – is carried out at higher temperature for the efficient thermal decomposition of organic waste. However, a key focus of the study was minimising energy use.
“We started with pyrolysing at a temperature of 500°C,” joint lead author Dr Shannon KilmartinLynch said.
“This saw significant enhancement in concrete strength compared to that of the raw coffee grounds in concrete, but it was still lower than concrete that does not contain any coffee waste.
“Since our focus was to minimise the energy consumption, we went for a lower pyrolysis temperature (i.e., 350 °C) and hoped that the lower decomposition could potentially help in improving the properties. It was a blessing in disguise. To our excitement, we noticed an improvement in concrete strength by almost 30 per cent.”
While the team’s research is still in the early stages, coauthor Dr Mohammad Saberian said the study is receiving plenty of attention from those who want to collaborate and translate the research into field applications.
“We are starting with field trials in collaboration with a local council and a few construction companies and we are hoping
Incorporating biochar into concrete offers several benefits. By significantly increasing the strength of concrete, the amount of cement content required can be reduced if needed. Furthermore, this waste to resource transformation creates the potential for diverting this waste from going to landfills in concrete applications, promoting sustainability and a closed-loop circular economy.
50 billion tonnes of natural sand is used in construction projects globally each year, with a considerable portion of this used in making concrete. This level of sand extraction has a significant impact on the environment, including habitat destruction, erosion, and disruption of river ecosystems. Coffee biochar could replace a portion of the sand that is used in concrete production, reducing that environmental impact.
Group Leader, Professor Jie Li, said, “The construction industry relies on continuous mining of finite natural resources to meet the ever-growing demand for the infrastructure development for the growing population.
“To keep this industry sustainable, we need to grab all innovative solutions that promote circular economy without compromising the mechanical and durability properties of the structural elements.”
to expand these trials internationally. We would be very happy to collaborate with local, state, and federal governments and construction companies willing to translate this research into field applications in different parts of the world.”
The construction industry has a long way to go until sustainability is fully integrated into everyday processes and projects. However, initiatives such as the recycling of organic waste, can support the sector to reduce its environmental footprint and drive sustainability forward.
The concrete industry is particularly well-positioned to contribute significantly to increasing the recycling of organic waste.
Dr Roychand said the research team will continue working on a range of waste materials and developing optimum process parameters for all forms of organic waste.
“There’s more groundbreaking research in the pipeline, so stay tuned.”
‘Transforming spent coffee grounds into a valuable resource for the enhancement of concrete strength’ is published in the Journal of Cleaner Production (DOI: 10.1016/j.jclepro.2023.138205).
Across the world, infrastructure projects wrestle with complex geotechnical challenges that quietly wait to trip up even the best planned road, tunnel, embankment, and foundation (plus many more), and it's not getting any easier for those in charge of these essential infrastructure projects.
Ground conditions can be unforgiving, deadlines unyielding, budgets restricting. Yet with any infrastructure project, geotechnical engineers are still expected to deliver an almost clairvoyant ability to predict how the ground will behave under certain conditions, and what that might mean for the asset during construction and throughout its life.
Engineers must assess ground behaviour and grasp the risks of settlement and impacts on neighbouring infrastructure, while facing the pressure of increasingly tough time and cost constraints. They have to feel confident they’ve got it right – now and in the days to come – and deliver a geotechnical analysis model able to support current and long-term decision making.
That means having tools they can trust to effectively see the future of the ground beneath their feet, and the asset built upon it.
In September PLAXIS celebrated 30 years of actively supporting the world’s geotechnical engineers, and giving them that ‘superpower’ (well, at least making it a lot easier).
In that time the software has developed from its core purpose as a user-friendly, finite element package, to become a resourceful, all-round companion for geotechnical engineers making critical, day-to-day decisions on the analysis of soil, rock and associated structures.
For example, in Australia, civil engineering consultancy WSP were faced with sand-capped, highly compressible peat swamp during the construction of a $165 million road extension project in Perth.
WSP Australia’s Principal Geotechnical Engineer, Shan Tom Wong, said, “If the approach embankments and bridge ramps were built without ground improvement, the peat would continue to settle significantly.”
However, the solution of driving concrete pillars through the peat to the stratum below called for 160 different design combinations to be analysed – an enormous task. By
automating the PLAXIS analyses, all 160 could be powered through easily, swiftly and efficiently, rather than doing them one-by-one, inviting errors and delays.
In a very different situation, the Laohutai mine in China faced the challenge of heavily laden mine trains inducing strong vibrations as they passed mine slopes and underground shafts.
Product Manager, Geotechnical Analysis, Sequent, Miquel Lahoz, said, “Safety was paramount with the possibility of slope or tunnel failure. “
Using PLAXIS 3D the Laohutai research team created a complex numerical model to simulate interactions between the rail track, slope, tunnels and underlying geology, and were reassured the mine could continue safely.
“Their predictions were validated with measurements taken on site and found to be stable with a safety factor of 1.2, well above the Chinese mining standard threshold,” Mr Lahoz said.
Unsurprisingly, the team said they valued PLAXIS for “its solid theoretical base, user-friendly interface, and strong logic for analysis in almost any geotechnical engineering field”.
Over the years, increasingly advanced iterations of PLAXIS have added creep or flow-deformation coupling through consolidation, simulating complex hydrological conditions, and determining how earthquakes or traffic flows can impact ground stability.
In addition to extensive geotechnical modelling capabilities, PLAXIS’ command-driven API has also been key in connecting it to other software, easily exchanging data, and automating model creation and the processing of results.
PLAXIS’ vision for the next 30 years revolves around several key pillars, including advancements in constitutive modelling and automated parameter determination, rock engineering, offshore geotechnical engineering, seamless integration with geological models, data-driven design and cloud computing. In short, it is and will keep constantly growing and evolving.
Now, three decades on from its original development at Delft University of Technology, PLAXIS fits seamlessly within Seequent’s broader range of products to boost interoperability and enhance communication within the industries it supports.
For over 30 years, PLAXIS has been trusted by geotechnical experts as the industry standard to perform advanced finite element analysis to solve common and complex geotechnical problems in soil and rock.
PLAXIS is more than just software; it’s a bridge connecting geotechnical engineering with a transparent approach to how structures interact with the subsurface, enabling better decision-making and ultimately ensuring the success of complex projects.
with a growing population
Over five million people live in Melbourne, with that number growing daily. As a result, the city’s sewerage infrastructure must be upgraded and expanded regularly to keep up with growing needs. This is why Melbourne Water’s tunnel boring machine – named Lucey – has been working hard underneath the Yarra to build the city’s eagerly awaited new Hobsons Bay Main Sewer.
The Hobsons Bay Main Sewer transports approximately 30 per cent of Melbourne's wastewater, sending it to the Western Treatment Plant, with the sewer main constructed in the 1960s and quickly approaching the end of its service life.
In order to make the necessary upgrades to keep it operating into the future, the Hobsons Bay Main will need to be temporarily shut down. Unfortunately, the needs of Melbourne’s waste network can’t be put on hold so easily.
To ensure the city continues to flow smoothly, Melbourne Water is funding a $206 million duplication project to reproduce the sewer, which will support the network while the original main is upgraded to modern standards.
Early works for the project began in 2021 and construction is expected to be completed in mid-2024.
Tunnelling works began in August of 2023, with Melbourne Water’s TBM, Lucey, operating at depths of between 24.5m and 27m below the surface of the Yarra, alongside the original sewer main.
The new 670m Hobsons Bay Main Sewer will stretch from Westgate Park, Port Melbourne to Scienceworks in Spotswood, under the Yarra River.
Melbourne Water’s Managing Director, Dr. Nerina Di Lorenzo, said that this major project forms part of a broader Melbourne Water capital infrastructure program that will enhance the reliability of the city’s sewerage network and services for the benefit of Melburnians today and for generations to come.
The Victorian Government, Melbourne Water, John Holland and Museums Victoria have all joined together to collaboratively deliver this significant upgrade project.
Dr. Lorenzo said that Melbourne Water is working hard to ensure that business as usual can continue for its neighbours, like Scienceworks and Grazeland, while considering the needs of the community and the impact these works have on everyone.
“We’ve developed a strong partnership with our delivery partner, John Holland. Our partnership extends over three years on this project, but has been ongoing as our long term partner on the Major Capital Delivery Water Framework,” Mr Le said.
“Our commitment to safety is of utmost importance to both companies. On the ground we hold joint safety forums, and mental health and wellbeing toolboxes, and these serve as a platform where we mutually learn from each other’s experiences, refining our practices for a safer work environment.”
John Holland Project Manager, Lucas Martinez, said that John Holland’s long-standing relationship with Melbourne Water spans over 20 years, including multiple tunnelling and deep sewer projects.
“With any project, it’s important to work directly with the client, and in all my experience I have found that open and transparent communication is the key to successful project delivery,” Mr Martinez said.
“We also have a close working relationship with the team at John Holland, who we appointed to construct the duplicate sewer,” Dr. Lorenzo said.
“Melbourne Water and John Holland project teams have been working on this for three years. We’ve established two working sites at Spotswood and Port Melbourne, constructed four shafts and started tunnelling works.”
Melbourne Water’s Project Manager overseeing the Hobson Bay Main Sewer duplication, James Le, said that collaboration has been central to the company’s approach.
“Working closely together we’ve been able to ensure that our efforts are aligned and that any challenges are addressed collaboratively. This partnership approach has not only helped us better understand the project’s goals but has also allowed us to find innovative solutions together, some of which resulted in securing significant financial wins for the client and project.
“As a result of our collaboration, we’re now about to expand our scope of works to include an upgrade of the North Drop Structure and being engaged for Early Contractor Engagement works to provide an optimal solution to the surrounding sewer assets that require rehabilitation.
“This approach allows Melbourne Water to maximise the efficiencies of having John Holland already mobilised onsite and tapping into the knowledge and experience of the team.”
Dr. Lorenzo highlighted the engagement with the local Spotswood Primary School, which selected the name ‘Lucey’ for the tunnel boring machine.
“Lucey is named after Lucey Alford, the first female Bacteriologist and the first woman employed by the Melbourne Metropolitan Board of Works (now known as Melbourne Water) as a scientist at the Spotswood Pumping Station.
“We’re also working with Westgate Biodiversity and Parks Victoria – as part of our Construction Environmental Management plan – to ensure we’re looking after the flora and fauna around the construction sites.
“We couldn’t successfully deliver the project without strong partnerships.”
Mr Le said that community engagement has been a key priority for the company.
“Regular collaboration meetings, open communication channels, and a shared commitment to project success have facilitated smooth coordination,” Mr Le said.
“We've teamed up with Scienceworks to inspire young minds about tunnelling works, engaged a local primary school to
involve the community, and partnered with the West Gate Biodiversity Group to enrich local ecosystems.
“These collaborations go beyond construction, fostering a community-driven and environmentally conscious approach to the Hobsons Bay Main project's success.”
Dr. Lorenzo said that Melbourne Water is aiming for net-zero carbon emissions on the project, which will be achieved via a number of initiatives.
“The project has an integrated sustainable design to reduce carbon. For example, we’ve been able to reduce carbon emissions by decreasing the amount of concrete needed.
“We installed a solar energy system consisting of 250 panels and batteries that will power our construction site sheds – which traditionally would have been diesel powered. Further, this solar infrastructure can be packed up and used on other Melbourne Water projects, which is exciting from an environmental perspective.”
Dr. Lorenzo said that electric vehicles are also being used to travel between work sites and rainwater tanks on both site compounds are reducing potable water usage.
“We’re also reusing and recycling everything we can, like soil which is being diverted away from landfill, and we even have an edible garden on site supported with composting. The environment is a major consideration for us.”
Mr Martinez said that he is incredibly proud of John Holland and Melbourne Water’s commitment to sustainability.
“Building infrastructure isn’t just about concrete and steel, for us, it is about ensuring a better and greener future for generations to come.
“We have embedded sustainability into the core of this project with a commitment to achieving net-zero, including solar power, sustainable concrete, alternative materials with reduced footprint, an electrical site vehicle and a comprehensive soil management program.
“We are very close to reaching carbon neutrality. This will be achieved by embedding sustainability in everyday operations and all decisions made by the whole team.
“This has enabled us to reduce the footprint by approximately 30 per cent from the original design, and we are currently working with the most reputable climate consultants and Melbourne Water to secure the most reliable and traceable carbon offsets offered by the industry.”
Mr Le said that the technical challenges associated with deep sewer construction need to be carefully considered and the complexity of working within a historically and culturally significant area makes every day interesting and enjoyable.
“It’s not every day that we tunnel under the Yarra River,” Mr Le said.
“The fact that we’re leaving behind a significant legacy that improves Melbourne’s sewerage infrastructure for generations to come is definitely worth getting out of bed for.
“This project has presented diverse challenges, each met with a strategic response. We've encountered the unexpected discovery of a culturally significant artefact during excavation, demanding careful preservation.
“Additionally, international procurement quarantine delays have required adaptive scheduling and resource management. Working around critical underground services throughout the construction period necessitated meticulous coordination and phased execution.
“These challenges highlight the complexity of the project, but through collaborative solutions and agile planning, we're able to successfully work through them.”
Mr Martinez said each project delivers its own set of challenges which is part of what he loves about the industry.
“While John Holland has a history of delivering diverse infrastructure projects, this one stands out due to its highly technical nature, high-risk profile and demanding scope of works and our commitment to achieving net-zero emissions,” Mr Martinez said.
“My experience has predominantly centred around the water industry. However, this project affords me the opportunity to apply my expertise within a different context and do so with a range of sustainability initiatives including solar energy, sustainable concrete and soil management.
“Along with the complexities of tunnelling under the Yarra River and coordinating with project stakeholders, these sustainable measures set this project apart, reflecting our commitment to environmental responsibility and challenging the status quo.
“This project has also delivered a number of successful social value initiatives – well beyond anything I have delivered in the past – as well as effectively achieving gender parity within the project team.”
the project, through recruiting and retaining top talent in an extremely competitive market, to managing and mitigating delays from international shipping delays in the post-COVID supply chain landscape.”
Mr Martinez explained that once the tunnelling is completed, the John Holland team will proceed with the live connections to the existing sewers and the permanent works.
“The live connections will involve working in the existing Hobsons Bay Main Sewer under live flows, which requires very detailed and careful planning in order to make sure there are no impacts to the existing sewer network and ensure the safety of everyone involved.”
Mr Martinez said that being a live asset, it’s critical to work in close collaboration with Melbourne Water Operations to ensure all their constraints and requirements are met.
“The permanent work will involve the installation of the maintenance structures that will provide Melbourne Water with access to the new asset once in operation, as well as the mechanical works (penstocks, stopboards), electrical and control scopes (power supply, instrumentation, CCTV) which will provide the asset with the required functionality to ensure safe and reliable operation for many years to come.”
Dr. Lorenzo said that Melbourne Water invests hundreds of millions of dollars per year into a wide range of critical infrastructure projects.
“The Hobsons Bay main sewer duplication project is a great example of the work that we are doing in this space for Melburnians.
“We’re looking towards the future and anticipating the evolving needs of a growing Melbourne.
“This project ensures our infrastructure is keeping up with future demand.”
In a sector as vast as infrastructure, promoting sustainable practices means addressing the complex needs of different projects, companies and utilities in a holistic way, to ensure long-term benefits for the environment and industry. Most initiatives focus on visible, above ground assets and services, but to achieve sustainability in the sector, we also need to look beneath the surface.
The phrase 'out of sight, out of mind' is, unfortunately, rather apt here. Underground operations form the cornerstone of every project, yet these unseen elements frequently escape our attention, despite their significant environmental implications.
Let's explore five key sustainability factors, and the ways experienced sustainability practitioners can guide the infrastructure sector towards a more sustainable future.
Underground activities in the infrastructure sector can disrupt natural habitats and contaminate soil and water resources. It is imperative to employ stringent environmental management strategies, which include exhaustive impact assessments and proactive protective measures. These steps are essential to establishing operations that are not only sustainable, but also coexist harmoniously with nature. Continual environmental monitoring and assessments are crucial to remaining informed about your operation's environmental impact.
The importance of Environmental Social Governance (ESG) reporting in meeting regulatory requirements and maintaining transparency must be considered. As industry leaders, we are responsible for pursuing sustainability beneath the surface while upholding rigorous environmental standards.
As the climate changes, our response should adapt accordingly. Extreme weather events pose a growing threat to service delivery and environmental sustainability. Prioritising infrastructure resilience through planning, stormwater management, and climate adaptation measures can minimise the effects of climate change. Collaborating with climate risk and mitigation experts can provide the necessary support, from natural hazard modelling to greenhouse gas
emissions reduction plans, strengthening the resilience of our infrastructure.
3. MATERIAL SELECTION AND USAGE
Traditional construction materials like steel and concrete have significant carbon footprints. We must embrace alternative materials with lower environmental impact and sustainable sourcing practices to escape this carbon-intensive cycle. Shifting our material selection towards greener options paves the way for a more sustainable future.
4. EFFECTIVE WASTE MANAGEMENT
Construction and maintenance activities generate substantial waste. We must outgrow the conventional "take-make-dispose" model, adopting recycling, reuse, and responsible disposal strategies. This approach minimises waste generation, diverts materials from landfills, contributes to a circular economy, and uncovers the overlooked potential of discarded resources.
5. WORKING HOLISTICALLY
Confronting sustainability challenges necessitates an integrated, holistic approach. This approach entails incorporating sustainable design principles, leveraging technological advancements, engaging stakeholders effectively, and driving ongoing monitoring and improvements. Collaboration amongst infrastructure companies, industry bodies like the Infrastructure Sustainability Council, environmental experts, and community stakeholders is vital for instigating significant change and accomplishing long-term sustainability goals beneath the ground.
Sustainability is a complex field; each company has unique factors to consider. If you find yourself seeking strategies to reduce your environmental footprint or boost your asset resilience – both above and below the surface – consider partnering with sustainability experts.
As a specialist provider of engineering and environmental services, Tonkin + Taylor brings your project ambitions to life.
With proven experience on large-scale projects across Australia and New Zealand, we are the specialist partner of choice.
From land development, transport, renewable energy, waste + resource recovery to water resource management, industry, and mining – we are passionate about creating and sustaining a better world together
The Fitzroy River Bridge formed part of a vital freight route in Western Australia until it was permanently damaged following a cyclone, prompting the construction of a replacement bridge. With a disaster resilient design, the new bridge promises to support this remote road network by reconnecting communities and industries.
In late December 2022, Tropical Cyclone Ellie crossed the Northern Territory coast and a subsequent tropical low settled over the Fitzroy Crossing, which caused significant damage to roads and bridges. This included several sections of the Great Northern Highway between Broome and Fitzroy Crossing in the Shire of Derby-West Kimberley, and the Fitzroy River Bridge.
The bridge was damaged beyond repair in the largest known flood to date – considered to have exceeded a one in 100-year flood event – cutting off access to communities and causing disruption to locals, tourists and the freight industry.
With the region left disconnected, plans to build a replacement bridge were announced within weeks and a procurement process, which would typically take nine months, was concluded in eight weeks.
A Main Roads Western Australia spokesperson said the Fitzroy River Bridge was the only sealed connection across the river in the vicinity of Fitzroy Crossing, meaning when it was damaged, local communities to the east of Fitzroy Crossing were cut off from key supplies and family members.
“This caused a significant amount of distress in the community and a high level of coordination was required between several agencies to provide
essential services whilst connectivity across the river was being restored,” the spokesperson said.
“The impact to the freight industry was also severe, necessitating major detours via South Australia and the Northern Territory, resulting in materials and food shortages and higher prices in remote locations.”
The Fitzroy River Bridge works are funded through the CommonwealthState Disaster Recovery Funding Arrangements, with design and construction to be completed by Main Roads Western Australia and a consortium comprising Georgiou Group
Pty Ltd and BMD Constructions Pty Ltd and BG&E.
Following construction beginning in May, the New Fitzroy River Bridge is scheduled to open by the end of 2023, more than six months ahead of schedule.
The bridge deck was launched span by span with a 36m segment positioned every four days until completed.
The eight bridge spans were constructed and launched incrementally from a launch pad located on the western side of the river. This construction method was selected to minimise the requirement for works to take place within the river channel, and safeguard the project against the potential of an early wet season.
The spokesperson said, while incremental launching techniques have been commonplace in Australia for decades, the speed at which the span construction, deck pour and launch were completed was unprecedented.
“Each new span was launched on average every four days,” the spokesperson said.
“This rate of progress was made possible due to a high level of collaboration with key suppliers and contractors to ensure that components such as bridge beams, bearings and concrete were made available at the time they were required and installed in a quick, but safe manner.”
By investing in disaster-resilient infrastructure, the new Fitzroy River Bridge project will reconnect east and west Kimberley communities and industries, opening up new economic opportunities for the region.
From the outset of the project, Main Roads and the Fitzroy Bridge Alliance have worked closely with local training providers, local government and other response agencies to maximise employment, contracting and partnering opportunities for local people.
“At the time of writing, over 130 locals have been employed on the project, a quarter of total construction hours are attributed to Aboriginal people and 19 Aboriginal-owned businesses have been awarded contracts associated with this job,” the spokesperson said.
“Workers have been involved in a variety of roles including traffic control, operating plant, and bridge labour.
“The project team has also assisted individuals seeking to start their own
businesses by providing business support, guidance when purchasing machinery and facilitating opportunities to gain experience using this machinery on different elements of the project.
“As the project approaches completion, Main Roads is liaising with other State Government agencies to identify ongoing opportunities for locals who have developed skills and business capacity as a result of the bridge build.”
The spokesperson said the new bridge will be six times stronger than the old bridge, as it is designed to withstand a one in 2000-year flood event.
“It will significantly improve the road network in a critical location, providing assurance to the freight industry, tourism operators and others who rely on the road network in the north west of Western Australia. Replacing the single-lane bridge with two lanes will also assist with transport efficiency and improve safety for all road users.”
As extreme weather events and natural disasters become more frequent, it is paramount to support the development of critical road infrastructure in remote Australia to ensure communities and industries can bounce back.
“The impact of ex-tropical cyclone Ellie in December and January showed the vulnerability of our road network to natural disasters,” the spokesperson said.
“Furthermore, the freight industry, tourism operators, logistics providers and local communities rely overwhelmingly on a safe, efficient and resilient road network in remote areas, particularly given the absence of other feasible and economical modes of transportation.
“This project has also demonstrated how infrastructure investment in remote locations can have a positive socioeconomic impact, through the creation of jobs and the circulation of money through the local economy.
“In August, The Australian newspaper reported how the community of Fitzroy Crossing had observed a significant reduction in crime and antisocial behaviour due to the opportunities created by the bridge build and other flood recovery efforts.”
From its Australian-first innovative rail boot system to its award-winning green track, the Parramatta Light Rail Stage 1 project is leading industry best practice in delivering sustainable public transport infrastructure for the New South Wales community.
The Parramatta Light Rail Stage 1 Infrastructure Works Package won the Outstanding Achievement – Sustainability Leadership Award at the Infrastructure Sustainability Council (ISC) Awards in 2023 – and there’s no secret as to why.
The project has so far reduced overall carbon emissions by around 80,000 tonnes during its enabling works and infrastructure delivery through a bevy of cutting-edge initiatives, some of which were the first time ever tried and tested in Australia.
In 2022, the project’s infrastructure works package achieved a Leading As-Built rating and record-breaking score of 104.35 by the Infrastructure Sustainability Council.
The project has been a catalyst for global sustainable design and has welcomed visiting delegates from the United States and Korea.
So, what put Western Sydney’s first light rail project on the map? We spoke with Parramatta Light Rail Stage 1 Project Director, Craig Paterson, to provide some insights.
ABOUT PARRAMATTA LIGHT RAIL STAGE 1
To understand how, and why, the project delivered sustainable benefits to enhance social and environmental community outcomes, one needs to understand the challenges of building in the dense urban environment of Sydney's second city: Parramatta.
Parramatta Light Rail Stage 1 connects Westmead to Carlingford via the Parramatta CBD and Camellia with a twoway 12km track and 16 light rail stops, and is expected to open to the public in 2024.
The route will link Parramatta’s CBD and train station to the Westmead Health Precinct, Cumberland Precinct, CommBank Stadium, the Camellia Town Centre, the largest museum in New South Wales ‘Powerhouse Parramatta’, the private and social housing redevelopment at Telopea, Rosehill Gardens Racecourse and three Western Sydney University campuses.
By 2026, around 28,000 people are expected to use the Parramatta Light Rail every day, with an estimated 130,000 people living within walking distance of the 16 light rail stops.
What’s more, the Parramatta Light Rail will reduce the need for people to travel by car around the Greater Parramatta region; taking the equivalent of 25,000 cars off the road (or 2.4 million t/CO2e) by 2041.
“While building in the heart of existing communities had its challenges, Transport for NSW prioritised innovative sustainable design and global construction practices in the project’s delivery to provide a future-proofed, well-connected and accessible transport system,” Mr Paterson said.
KEY SUSTAINABILITY INITIATIVES
Key measures that contributed to the Parramatta Light Rail Stage 1 project’s significant carbon emissions reduction included:
Micro-tunnelling under Parramatta’s CBD
Parramatta’s Church Street is a prominent dining and entertainment hub, with more than 60 eateries in the precinct alone.
Transport for NSW significantly reduced impacts on local businesses and patronage during early and enabling works to construct the Parramatta Light Rail, by using microtunnelling methods as an alternative solution to traditional excavation techniques.
Micro-tunnelling supported the project to limit the number of utility relocations, save energy and water and improve flood resilience.
"Resilience was a key driver when designing the Parramatta Light Rail, with significant challenges faced in Parramatta and Western Sydney, including flooding and extreme heat," Mr Paterson said.
Award-winning green track
Transport for NSW was faced with the challenge of integrating green space into a densely populated and existing urban environment.
In 2018, Transport for NSW commissioned Western Sydney University to develop feasibility studies for a green track in the Parramatta Light Rail project design, considering urban heat and practical solutions for cooling cities.
The result was the integration of a total of 1.3km of green track in three locations: the heritage-significant Cumberland Precinct, the historic Robin Thomas Reserve and Tramway
Avenue in Parramatta. It also uses 80 per cent less concrete than traditional track construction, resulting in improved environmental outcomes.
The project conducted prototype testing over 12 months using different grass species and selected the Zoysia ‘Nara’ native grass for its low maintenance, slow growth and heat resistance to match Parramatta’s urban climate.
1 green track was the first of its kind for New South Wales and contributed to the project being recognised with four national and two state awards since 2022.
“Already having a positive local impact, the green track is delivering urban cooling benefits and improved biodiversity,” Mr Paterson said.
The green track is maintained by an innovative irrigation system that features moisture-sensors in the soil to regulate water use and maximise environmental outcomes.
Unique rail boot system
Australia’s first high-attenuation rubber rail boot system was designed to encapsulate the embedded light rail track
to negate the need for a floating track slab, as well as reduce operational noise and vibration from light rail vehicles.
“The rubber boot construction was also designed to reduce maintenance by preventing corrosion and increasing the lifespan of the track,” Mr Paterson says.
Macro-synthetic fibres for track slab construction
New South Wales’ first use of macro-synthetic fibres in concrete track slab construction resulted in reduced steel reinforcement by ~2,466 tonnes.
These tiny fibres were used in the construction of track slab and footpaths to increase durability and performance, as well as deliver a more efficient method for undertaking construction.
“The fibres also mitigate potential stray currents from light rail operations, providing added safety benefits by minimising impacts to the railway and third-party infrastructure,” Mr Paterson said.
Bidgee Bidgee Bridge construction
Bidgee Bidgee Bridge, located over James Ruse Drive in Rosehill in Sydney’s west, boasts New South Wales’ secondlongest steel arch span.
Measuring 64m long and 16m high and weighing 1425t, the bridge was the biggest of the six bridges constructed for the Parramatta Light Rail project.
It stretches across six lanes of traffic on one of Western Sydney’s most heavily used traffic arterial routes, while also featuring part of the new 5.7km shared walking and bike riding path from Carlingford to Parramatta. This provides the community with expansive, never-before-seen views of Western Sydney.
The project used weathered steel for the bridge’s arch construction to minimise future maintenance and associated operational disruption for light rail passengers and sharepath users.
“By using Self-Propelled Modular Transporter installation of prefabricated bridge arch over a single night’s work, the project effectively managed traffic impacts on James Ruse Drive,” Mr Paterson said.
Smart LED lighting on shared path
The new 5.7km shared walking and bike riding path (active transport link) from Parramatta to Carlingford was delivered as part of the Parramatta Light Rail project.
It connects local homes, shops, schools, public transport and amenities, while providing health and environmental benefits, including reduced vehicle use, noise and emissions. The track features motion-sensor LED lighting to support energy efficiency and public safety.
"While work continues on the light rail project, which may impact shared path access from time to time; the shared path was opened ahead of light rail first passenger services to recognise and support the local community’s needs for an alternative travel option in the dedicated Carlingford-toCamellia corridor,” Mr Paterson said.
Transport for NSW remains committed to supporting businesses along the Parramatta Light Rail Stage 1 alignment before and during light rail construction, through to operations.
In 2018, Transport for NSW surveyed 85 per cent of street-level businesses (more than 330 businesses) along
the alignment to better understand their operation and business promotions.
A business reference group was established to facilitate consultation and collaboration with business owners and stakeholders, which informed the development of a business activation plan titled Activate Parramatta
Activate Parramatta has provided plenty of business support to date through initiatives such as events and activations, social media campaigns, and business support advertising in local publications.
Transport for NSW’s not-for-profit business partner, Realise Business, provided free one-on-one business support to more than 200 businesses during the project’s major construction.
Key sustainable social outcomes from this engagement with local businesses and stakeholders included how the project modified its construction hours in Parramatta’s key dining district to avoid working during busy meal periods for local businesses.
“A further outcome was achieved during COVID following consultation with the project’s business reference group of stakeholders, where Transport for NSW waived its contractual three-month construction embargo to fast-track major construction in the Parramatta CBD,” Mr Paterson said.
“This led to the project reopening the Church Street dining and entertainment earlier than planned, and this was further promoted by the launch of an extended activation campaign in the revitalised precinct during the busy summer months, providing a welcome boost to local business patronage.”
The project’s initiatives were underpinned by a best-practice approach towards considering sustainable outcomes across the project’s lifecycle.
This included outlining key drivers in the project lifecycle, using national and international benchmarks, implementing key performance incentives to encourage design excellence, engaging with an urban design panel to provide feedback on designs, setting goals, targets and pathways for the project and participating in external workshops to leverage global insights and methodologies.
“We also engaged with our major contractors to develop, and commit to, a joint-climate change risk assessment early in the process, thereby ensuring consistent application across the whole project lifecycle,” Mr Paterson said.
Another way the project is committed to sustainability is through its socio-economic targets.
“We engaged with social enterprises, Aboriginal businesses and aimed to develop a diverse workforce from various backgrounds including women in non-traditional roles, refugees, youth and underrepresented groups,” Mr Paterson said.
Mr Paterson said the project continues to seek ways to enhance the social, environmental and economic outcomes of the community as it moves towards the start of passenger services in 2024.
One way the project is doing this is through integrated transport options, including the Sydney Metro West, buses, ferries, active transport, as well as the planned Parramatta Light Rail Stage 2 which connects Stage 1 and Parramatta’s CBD to Sydney Olympic Park.
“We’re committed to continuing to seize opportunities to deliver a sustainable, world-class public transport system for the people of NSW,” Mr Paterson said.
Maintaining rail infrastructure and assets requires preventative maintenance strategies that provide quick and non-disruptive solutions for track subsidence. With millions of people taking advantage of Australia’s public transport systems, a delay caused by faulty infrastructure can bring the country to a halt.
When finding a solution to repair and strengthen rail assets, a fast, non-disruptive method is one way to prevent unnecessary delays to services.
Since 1989, Mainmark has been at the forefront of ground remediation solutions for subsiding rail assets, including station platforms, bridge relieving slabs, rail crossings, and rail ballast formations.
Mainmark’s cutting-edge technologies offer rapid, non-disruptive, and cost-effective methods to re-level rail infrastructure, strengthen subgrade soils, and address structural challenges.
One of Mainmark’s solutions is Teretek®, a unique solution that can deliver both ground improvement and re-levelling. Teretek® materials can fill voids, reconfirm support, and raise subsided pavements with precision.
Using a non-intrusive method, Teretek®, does not require extensive excavation, demolition, heavy machinery or disruption of services. The resin is injected through small holes, filling voids, re-establishing support, and providing targeted ground improvement to suitable compactable soils. With no curing time required, the asset is ready to return to full use as soon as the repairs are complete, making Teretek®,
a faster solution compared to traditional repair methods, and keeping railways on track.
Teretek® can also be used for targeted ground improvement to restore and enhance bearing capacity for weak or failing subgrades. Through the injection process, the expansion of the injected material compacts the adjacent soils and strengthens the subgrade soils, providing additional support.
Common applications include:
• Enhancing weak subgrade soils across railway networks and rail crossings
• Filling voids beneath rail platforms
• Raising subsided sections to original levels
• Bolstering rail ballast
• Restoring proper drainage and alignment
• Ensuring railway safety
Strengthening rail infrastructure involves finding long-term repair solutions instead of replacing critical assets. With a fast, non-disruptive solution like Teretek®, rail operators can save costs and prevent delays by remediating critical assets.
mini soundprotection wall with high absorbing surface
The new version of the STRAILastic_mSW adds a higher wall to the product range. This version is used for train speeds of up to 120 km/h.
¬ No foundation required for installation
¬ easy and quick installation
¬ Short delivery times > noise hot spots can be supplied with products quickly
¬ Closer to the noise source than any other sound protection
¬ Break-proof due to fibre-reinforced rubber compound with a cover layer of virgin rubber > UV and ozone resistant
¬ No material fatigue caused by vibrations or pressure and suction forces
¬ No problems with oversized loads
Due to the higher design, it gains even more effect in the area of the wheel.
STRAILastic_mSW 730 is fastened to both rails with an insulated, decoupled substructure or directly in the subsoil using ground screws.
STRAILastic_mSW 730 > mini goes maxi.
1. STRAILastic_mSW 730 new version of the mini sound protection wall
2. STRAILastic_IP the infill panel
3. STRAILastic_mSW the established mini sound protection wall
4. STRAILastic_A inox 2.0 rail dampers
As in many sectors, technological advancements are transforming the way in which rail transportation is managed, built, and monitored. The most recent gamechangers are LiDAR, digital twins and geospatial data, which, when used together, have the potential to truly change the industry as it exists today.
The monitoring of an asset is the very first step to harnessing the power of data, however, what makes or breaks a digital system is how the data is analysed post-collection. This sentiment couldn't be truer in the world of transport and rail, with the monitoring of track and surrounding assets an essential, yet time consuming job.
In conversations with experts in the rail sector, safety also emerges as a key focus for rail operators. Ensuring the safety of operators, maintenance workers, passengers, and freight is paramount when keeping vital transportation networks running.
Enhancing safety by providing accurate data for maintenance, planning, and operation is an ideal way that rail networks can switch their maintenance from reactive to proactive – this requires an extremely versatile and tailored approach, which data collection software cannot often provide.
Tech Mahindra Altavec, a leading provider of comprehensive rail network LiDAR and imaging solutions, knows that there is no one-size-fits-all when it comes to digital transformation journeys, which is why it offers a unique approach to ensure data is not treated like a hidden gem, but the main prize.
With a rich 30 year history in the rail industry, Altavec consistently delivers tailored outcomes, solidifying its position as a reliable and innovative partner in the rail sector.
Altavec's specialty lies in collecting, processing, and delivering field asset data for rail networks, combining state-of-the-art technology and surveying expertise to deliver high-quality results to demanding engineering audiences.
These solutions are unique for a plethora of reasons, such as:
♦ Individually customised design and configuration for each project
♦ All asset capture equipment in-house, employing multiple high precision Riegl LiDAR units, Inertial Measurement Units (IMUs), and Global Navigation Satellite System (GNSS) technology
♦ Various imagery options such as 360° panoramas, highresolution stills, and video
This comprehensive equipment allows for the most accurate and detailed data capture of rail networks, enabling rail
operators to make informed data-driven business decisions, with all the critical information at their fingertips.
Artificial Intelligence (AI) and Machine Learning (ML) are common buzzwords, with the uses for both extremely varied.
For rail, they can be integrated into existing projects to simplify maintenance and monitoring processes, save staffing costs, and reduce employee safety concerns.
For instance, instead of a crew having to search to find anomalies and maintenance issues, AI and ML algorithms can be combined with data collection efforts that utilise state-ofthe-art technology, including Riegl LiDAR units, IMUs, and GNSS.
This approach enables rail managers to identify, measure, and assess track assets with unparalleled accuracy, and facilitates the precise detection of defects, asset management, planning, and design.
Another innovation is Altavec’s Mechanised Track Patrols (MTP), which quickly has become a major talking point in the industry, emerging as the epitome of highquality, auditable data collection and analysis.
Through the integration of high-resolution digital imagery, accurate inertial and GPS data, and the ability to record data at any train speed, MTP enables offsite track inspections, seamless data integration with enterprise systems, and improved network availability.
This approach also involves empowering track walkers to perform inspections off-track using a desktop, boosting safety and preserving expert knowledge and skills.
MTP, as supplied by Altavec, offers several key advantages:
An example is the successful Measurement and Inspection Digital Twin (MIDT) project embarked upon by Altavec for Sydney Trains, which was an ambitious undertaking aimed at creating a comprehensive and highly accurate digital replica of the entire Sydney Trains network. This digital twin is far more than a passive mirror image; it's a dynamic tool that enables detailed inspections, measurements, and effective maintenance planning.
Over the course of five years, Altavec meticulously conducted surveys across the expansive Sydney Trains network. Deploying a formidable arsenal of state-of-the-art technology, including dual VUX-1HA Lidar scanners and 360° panoramic imagery equipment. The success of the project was not just about advanced technology; it was also about overcoming real-world challenges. Altavec's team needed to navigate through GNSS-compromised environments such as tunnels and urban canyons. Once the data capture was complete Altavec's team of geospatial professionals undertook the colossal task of processing the vast amounts of data. Raw information was meticulously transformed into a usable and accessible digital format.
♦ High-resolution digital imagery
♦ Accurate inertial and GPS data with sub-meter kilometrage
♦ Recording at any train speed
♦ Offline track inspections
♦ Integration of data with enterprise systems
♦ Increased network availability
♦ Enhanced employee retention and availability
The comprehensive digital twin, AI and ML, is an innovation that allows the rapid identification of potential issues, ensuring a safer and more efficient railway network. Altavec's involvement in the MIDT project not only transformed the way rail networks were managed, but also empowered Sydney Trains to operate with heightened efficiency
In the era of digital transformation, Altavec's MIDT project with Sydney Trains stands as a landmark achievement in the realm of digital mapping and geospatial solutions for the rail industry. This project sets a new standard in the railway inspection and management, ensuring our railways are efficient, reliable, and safer than ever before. Altavec continues to redefine what is possible in the world of rail network management and this partnership is a shining example of what is possible when innovation meets expertise.
In the pursuit of its net-zero emissions by 2050 target, South Australia is taking aim at its largest emissions contributor: transportation. Here Infrastructure Magazine explores what the future of sustainable public transport will look like in Adelaide as Adelaide Metro begins its transition to a zero-emissions system.
As one of the fastest growing sources of greenhouse gases in Australia, there is an urgent need to decarbonise the transport sector and encourage the use of clean and sustainable modes of transportation.
In South Australia, a series of cuttingedge clean fuel sources are currently being trialled across Adelaide Metro’s bus and train fleets, marking the beginning of an exciting journey towards a zero-emissions public transport system.
In late August 2023, Adelaide Metro welcomed two hydrogen fuel cell buses to its bus fleet as part of a two-year trial. The vehicles are based at the Morphettville bus depot and deployed on routes across Adelaide.
“Hydrogen fuel cell buses represent a rapidly emerging, green alternative technology,” Department for Infrastructure and Transport Chief Executive, Jon Whelan, said.
Testing is also well underway for South Australia’s first full electric battery bus, which arrived in January 2023, and a further nine full-battery electric buses are on order, pending the results of the trial.
It is hoped the six electric buses will join the existing fleet of 24 hybrid-electric buses already on the state’s roads. Further assessment is underway to inform a full transition plan and business case that determines funding requirements to achieve a zero-emission bus fleet.
“The rail fleet isn’t being left behind either – with the first hybrid-diesel train now in service. This train is fitted with the new Energy Storage and Recovery System,” Mr Whelan said.
The system works by storing kinetic energy generated when the train brakes to an onboard battery, converting it into electrical energy to power normal train operations –decreasing stress on the engine and fuel consumption by approximately 16 per cent.
These rail-cars have been coupled together and testing of the two-car train is complete. This is the first of 50 diesel rail-cars expected to be fitted with the hybrid system, with the trains to run on the Outer Harbor, Grange, Port Dock, and Belair lines.
The battery will also serve as an alternative power source, replacing the conventional diesel engine, to supply electricity auxiliary functions such as lighting and air-conditioning at the train platform within Adelaide Railway Station. This approach aims to reduce noise, emissions, and air pollution.
Installation of the Energy Storage and Recovery System on the remaining trains will be progressively rolled out, with all trains expected to be in passenger service with the new system by mid-2024. Once fully installed, Adelaide Metro will save an estimated 2,400t of CO2 emissions annually.
Marking a significant milestone, the Gawler line is now running exclusively with electric trains following the arrival of a tenth Electric Multiple Unit (EMU) in early August. The remaining two of the 12 new trains ordered are expected to be introduced into service by the end of 2023. In the meantime, diesel trains may occasionally run on the line due to maintenance and fleet improvements across the network.
The EMUs have been custom-fitted for the Adelaide Metro fleet by Alstom, a locally represented company engaged to provide maintenance services to the metropolitan train operator, Keolis Downer Adelaide.
Once the remaining EMU train enters service, Adelaide Metro will have a fleet of 34 EMU trains to maintain fully electric services on the Gawler, Seaford and
Looking ahead, the department is undertaking a feasibility study into the most appropriate zero-emission technology for the train fleet, for when the existing diesel trains reach retirement age in the early 2030s.
“By continuing to decarbonise our public transport network, we’re not only delivering a more sustainable future, but improving the experience for all our customers – with more efficient, quieter and safer services,” Mr Whelan said.
As well as being better for the environment, full battery electric buses offer a range of benefits for passengers. They offer smoother and quieter rides, while eliminating noise and fuel-based pollution.
The benefits of hydrogen-powered vehicles over battery electric buses include faster refuelling and greater range, which may be critical to delivering services to the outer metro areas and into the regions.
Hydrogen complements battery electric vehicle technology by providing a viable cleaner, greener, emissions-free technology that can power buses, trains or other heavy vehicles carrying heavy loads.
“Hydrogen fuel carries significantly more energy than the equivalent weight of batteries, which is important as the State Government evaluates future technology options, including powering trains on the Belair, Outer Harbor lines and Grange and Port Dock connections.
“Once the installation of the Energy Storage and Recovery System on the train fleet is completed, Adelaide Metro will save an estimated 2,400t of CO2 emissions annually,” Mr Whelan said.
Investing in public transport can encourage communities to reduce congestion, contribute to a greener future and save transportation costs. With the rollout of tap and pay technology, it’s becoming even easier for South Australians to travel sustainably.
In late July 2023, construction activities began to extend the existing rail siding at Coolamon, New South Wales. As part of the Fixing Country Rail Program, the project is aimed at removing freight bottlenecks, improving efficiency and making the state’s rail network safer for all services and customers.
Fixing Country Rail is a New South Wales Government program providing targeted infrastructure funding from Restart New South Wales for regional freight projects. With New South Wales’ regional freight volume expected to increase by 17 per cent to 311 million tonnes by 2036, improving the state’s supply chain network is critical.
As the largest regional contributor to agricultural production in New South Wales, the Riverina Murray region accounts for almost 13 per cent of produce across the state. Rail freight is among the most efficient methods of transporting big loads over long distances, with one freight train wagon able to hold enough grain to produce more than 150,000 loaves of bread.
Through a series of upgrades, Fixing Country Rail is set to improve capacity, access, efficiency and reliability of the regional rail network. The latest project under the program is a $11.7 million siding extension at Coolamon, west of Junee, which follows a successful business case completed as part of the 2020 round of the strategic freight program.
RAIL LINE EFFICIENCY
As a single line track, there are limited opportunities on the Junee to Griffith rail line to program efficient freight operations. Crossing delays occur during loading and shunting activities, particularly during the grain harvest and grain out loading seasons, impacting the main line.
Rail sidings, such as the one at Coolamon, serve a pivotal role in railway infrastructure by allowing trains to exit the main line temporarily. This creates a space for passenger and other freight services to continue their journey while a train undergoes loading or unloading activities.
The siding at Coolamon has been extended from 920m to 1,530m, enabling access for modern and more efficient freight trains up to 1,500m in length, which will help alleviate bottlenecks and congestion on the single line track between Junee and Griffith.
It is estimated that the extension of the siding will reduce passenger service delays for 3,879 passengers per month during peak grain seasons. As a multi-user siding, the upgraded Coolamon siding will be available to all operators.
designed to accommodate heavier freight trains with gross wagon weights of up to 100 tonnes, further enhancing the rail line's capacity and adaptability to modern freight demands.
Transport for NSW’s Regional Strategic Contracts Senior Program Manager, Simon Bingham, said the Coolamon rail siding extension is a crucial addition to improve operational efficiency along the Junee to Griffith line.
“We’re really excited about the Coolamon rail siding extension. It’s a win-win project, as it benefits freight
producers, operators and customers, as well as people using regional passenger trains,” Mr Bingham said.
“The project allows for improved scheduling of freight and passenger services on the line, as well as loading and shunting activities at the site. It will be more flexible and avoid conflicting paths, with trains able to use the new siding to load and unload while letting a train travelling on the main line to safely pass.”
Early site works on the Coolamon siding extension project were completed at the start of 2023, including material deliveries and project site set-up. Siding construction activities began in late July 2023 with Country Regional Network (CRN) Contractor UGL Regional Linx carrying out the works and up to 30 workers involved in the delivery of the project.
With commissioning achieved in late September, the siding is expected to be fully operational by mid-October 2023.
Several rail siding extensions and new rail siding projects have been delivered through Fixing Country Rail, including the $2.15 million rail siding in Temora West completed in mid2020, and the new $14.4 million siding installed at the Riverina Intermodal Freight and Logistics Hub completed in late 2021.
During the pandemic, some 2.3 million aviation jobs were lost globally, and Australian airports were some of the worst hit, with hard border closures both domestically and internationally significantly
lead individuals to excel in the field of aviation, irrespective of their initial entry point. There are no unskilled workers at airports,” Ms Meys said.
Australian airports.
ATTRACTING THE NEXT GENERATION OF WORKERS
All airport jobs are critical to maintaining a safe, thriving, and sustainable aviation sector. It doesn’t matter where you came from; it’s about where you are going and where airports can take you in your career. Whether you dream of working in aviation, security, hospitality, or any other airport field, Prepare to Take Off with the AAA’s My Airport Career website, is your passport to a world of aviation career possibilities.
My Airport Career is not just another career website; it's a gateway to a diverse array of career paths you might not have even considered at Australian airports.
With an airport career spanning 15 years across a diverse number of roles, AAA National Chair, and Executive General Manager – Planning and Infrastructure at Adelaide Airport, Kym Meys, launched the website in November 2023.
“Reflecting on my own journey, while I chose to embark on my aviation career by pursuing higher education, such a path is not a prerequisite for everyone. Dedication and passion can
“The role of My Airport Career is to become a one-stop destination for anyone seeking to explore the expansive world of airport related careers, providing in-depth insights into various roles at airports.
“The website features a wealth of information, including firsthand accounts from current employees, job profiles at airports and aerodromes, an interactive map to locate the nearest airport or aerodrome, and educational options to kickstart your aviation career.
“The interactive map feature on the website allows users to search for airport job openings near them. By simply inputting their location, users can discover exciting new career opportunities in
“The AAA is extremely excited to bring you stories from current employees in a wide range of jobs available across the sector. These are real-life success stories from individuals who pursued careers within the industry, sharing their own journey for those considering a career at one of Australia’s airports.”
INSIGHTS STRAIGHT FROM THE INDUSTRY
Employees featured include:
♦ Security Operations Specalist: Alicia, Perth Airport
♦ Aerodrome Reporting Officer: Matt, Parafield Airport
♦ Airside Works Coordinator: Nicolle, Adelaide Airport
♦ Senior Supervisor - Aviation Operations and Services: Dane, Canberra Airport
Consider My Airport Career as a gateway to an exciting world of possibilities, whether you are a high school graduate with a passion for aviation, a seasoned professional looking for a career change, or someone simply intrigued by the vast opportunities within the airport industry, My Airport Career offers the guidance and resources needed to prepare to take off.
As vital transportation infrastructure, airports provide critical services to support a variety of industries, from tourism to freight. But with high demand comes an increasing strain on aviation assets. In order to maintain this crucial infrastructure, airports need a fast, non-disruptive solution to remediate airport and taxiway subsidence.
High use can see vital airport pavement degrade, potentially resulting in accidents, damage to aircraft and vehicles, and service delays for passengers. This is why proactive remediation is paramount for keeping runways and taxiways operational.
Across Australia and internationally, ground-engineering specialist Mainmark, has been providing fast, non-disruptive & cost-effective solutions to remediate subsidence beneath commercial and defence airport facilities assets since 1989.
One of its solutions, Teretek® Resin Injection, is a technology that has been qualified, tested, and adopted by infrastructure authorities across Australia.
It offers a unique method for addressing voiding and loadbearing capacity issues in ageing infrastructure foundation systems, while avoiding the significant operational disruption and high costs often associated with pavement removal and replacement.
Teretek® materials expand in a controlled manner, allowing targeted placement to fill voids, reconfirm support, and raise subsided pavements with precision.
The application process does not require extensive excavation, demolition, or heavy machinery, as the resin is injected into the slab through small holes, filling voids and supporting the slab.
As soon as the repairs are complete, the slab is ready to return to full use, making Teretek® a faster solution compared to traditional repair methods. This means repairs can take place in only a few hours without disrupting services and causing delays for passengers, making it ideal for airports during peak travel periods.
Teretek® can also be used for targeted ground improvement to restore and enhance bearing capacity for weak or failing subgrades. Through the injection process, the expansion of the injected material compacts and strengthens the subgrade soils beneath the pavements, providing additional support.
Mainmark’s solutions and technologies are particularly well suited to address the complex challenges of airport pavement repair, including:
• The filling of voids directly beneath pavements to reconfirm support and limit deflection and deterioration
• Raising subsided pavements to re-establish design levels and/or drainage gradients
• To provide targeted ground improvement to weak subgrade soils
When faced with high demand for aviation travel, deploying a fast, non-disruptive solution is the only way to protect assets and keep airports running.
While other traditional methods require excavation or infrastructure replacement, Mainmark offers innovative and cost-effective ground engineering and asset preservation solutions to remediate slabs and pavements.
Finding ways to extend the lifespan of existing infrastructure, rather than replacing facilities and assets, can help airports save costs and avoid disruptions.
While traditional trade publications have quality audiences and high levels of trust, they can lack the full range of services to guarantee a return on your investment. And while traditional marketing agencies offer the latest marketing techniques, they don’t have the audience or the industry understanding the B2B sector needs.
Monkey Media is the missing link that brings together a trusted brand and powerful audience, with a complete agency offering.
TO FIND OUT MORE SCAN THE QR CODE NOW
In the 2022/23 financial year, over 14 million passengers passed through Perth Airport, with 5 million of those flying to regional areas within Western Australia. With surging regional passenger numbers, Perth Airport has started work on three key projects that will help cater for Western Australia’s growing regional aviation sector.
Australia-wide, passenger numbers are returning to pre-pandemic levels, with international and interstate flights steadily increasing. However for Perth Airport, there has been a boom in intrastate flights around regional Western Australia.
According to Perth Airport, in May 2023, almost 550,000 intrastate travellers passed through the airport, making it the highest single month regional passenger number on record. In June, regional passenger numbers were 39 per cent above pre-pandemic levels.
With the airport at capacity most days, these increasing numbers have highlighted the need for expanding aviation services and infrastructure.
Perth Airport is investing $80 million for three projects in the Airport Central precinct to underpin the future growth of regional aviation in Western Australia.
The projects include expanding the current Terminal 2 apron, building a new $35 million maintenance hangar for Virgin Australia Regional Airlines (VARA), and the development of a new Aviation Support Precinct to provide additional aviation support facilities for airport operators.
“The expansion of the apron provides operational flexibility for our airline partners within the Airport Central precinct and allows them to grow their business.”
VARA has committed to an Agreement for Lease of the new maintenance hangar and apron facility, expected to be completed by September 2024, which will allow VARA to operate more efficiently by consolidating its warehouse, storage, and engineering and maintenance office facilities in one location.
Perth Airport has engaged local construction partners West Coast Civil and Perkins Builders to deliver these important projects for Western Australia.
Perth Airport Acting CEO, Kate Holsgrove, said Perth Airport’s continuous and efficient operations are crucial for the viability of the $83 billion Western Australian resource sector.
“Following the last resources boom, the opening of Terminal 2 (T2) in 2013 made a significant impact on how efficiently the airport operated, creating more capacity and a greatly improved customer experience,” Ms Holsgrove said.
“Since opening more than ten years ago, the terminal has experienced a 54 per cent increase in passenger numbers. The apron has now reached capacity with aircraft parking on taxiways overnight to be ready for the early morning peak departures.”
With the need to prepare for the future development of the state underpinning these projects, it is crucial that Perth Airport is prepared for rising regional traveller numbers.
As this demand skyrockets, so do opportunities for industries such as tourism and the resources sector –supporting Western Australia’s economic growth.
The Western Australian Government’s joint venture with six participating airlines, the Regional Zone Cape Scheme, is encouraging regional travellers to visit Perth with over 150,000 capped airfares flown in the first 12 months.
“There are currently 38 overnight aircraft parking positions at T2, 18 of which are remote positions used for parking by airline partners from both T2 and T1D,” Ms Holsgrove said.
“Based on the demand of our airline partners, we will deliver an additional six remote parking positions by early next year, and we are also looking at delivering an additional eleven positions, providing 55 parking positions for T2 in the future –providing a 45 per cent increase in capacity.
VARA Executive General Manager, Nathan Miller, said the fleet renewal program is well underway and is set to strengthen resources and contract flying in Western Australia.
“The new facility will support the ongoing delivery of our fleet renewal program with the capacity to service our new larger fuel-efficient 737-700 aircraft, as we phase out our F100s,” Mr Miller said.
“It will also deliver greater operational efficiency enabling us to consolidate our maintenance, engineering and storage to one central base.
“This follows several key investments that bolster our operations and infrastructure in the state of Western Australia, including the establishment of a new local training base and a brand-new corporate HQ in the heart of Perth CBD this year.”
These new facilities and expansions promise to connect the state, with opportunities for additional aviation services and airlines to set up in Western Australia.
Ms Holsgrove said Perth Airport would also develop the Aviation Support Precinct near Terminal 2.
“This area will be reserved for operations that require airside access and apron areas for aeronautical operations, including hangarage, ground support providers, flight catering and airfreight logistics,” Ms Holsgrove said.
Alongside these works, Perth Airport is bringing together all its commercial air services at the Airport Central Precinct, connecting existing infrastructure in one location.
“Perth Airport’s vision to consolidate all commercial air services at Airport Central aligns with Master Planning dating back to the 1970s and we are excited to start the next stages of development.”
A transformation is coming for Ballarat Airport, with a runway extension project underway that will allow larger aircraft to pass through the airport. However, this runway extension promises much more than just more flights for the region, holding the potential to connect Western Victoria with the rest of Australia.
Ballarat Airport’s runway will be extended from 1,300m to 1,800m, creating opportunities to expand aviation services at the airport by allowing for larger commercial freight, firefighting and emergency aircraft.
The project is jointly funded, with the Federal Government contributing $3.8 million as part of its Regional Airports Program and the rest of the funds provided by the City of Ballarat. This comes after years of advocacy by the City of Ballarat to bring to life its long-term vision for the airport, as outlined in the Ballarat Airport Masterplan 2013-33, which aims to
improve transport connections, stimulate economic growth and encourage business expansion for Western Victoria.
Originally constructed in 1940, the airport was used as a training base for the Royal Australian Air Force at the beginning of the Second World War, but has since grown to offer a variety of services, including general and recreational aviation, emergency services and community hubs, such as the Ballarat Aviation Museum.
City of Ballarat Mayor, Councillor Des Hudson, said the airport provides valuable services for local and regional communities and organisations.
“The airport is home to an airline pilot training academy and a large aerial application business who are also one of Australia’s largest general aviation maintenance, repair and overhaul (MRO) organisations,” Cr Hudson said.
“It is also a well-established operational and training base for helicopter and fixed wing aircraft carrying out firebombing services.
“It accommodates twice weekly flights by air ambulance fixed wing aircraft and is also an alternative landing site for the emergency services that typically use the Ballarat Base Hospital heliport.
“The airport also enjoys an active recreational flying community centred around Ballarat Aero Club.”
However, Cr Hudson said the Ballarat and Western Victoria region suffers from a lack of connectivity to other locations in Australia, which means travelling interstate is costly and inconvenient for locals as they have to travel by road to Melbourne Airport.
“Ballarat is one of few Australian top 50 localities by population that does not have a scheduled passenger or freight air service,” Cr Hudson said.
“This reduces the city’s connectivity to other major population centres, Sydney for example, which restricts the ability for people to visit Ballarat without having to transit through Melbourne at great expense and inconvenience.
“An upgraded Ballarat Airport would greatly enhance the mobility of people in Western Victoria and connect the businesses in the region to the major population centres, supply chains and markets in Australia.
“The Ballarat Airport is located within the Ballarat West Employment Zone, and at the confluence of two major highways servicing Western Victoria. This has the potential to offer significant productivity improvements and increased market reach for those businesses that use aviation in their operations.”
Cr Hudson said the newly extended runway, once operational, will permit the operation of higher performance aircraft, which cannot presently be accommodated at airports in Western Victoria.
“In the short term, this will allow larger aircraft to operate passenger and freight charter services into Ballarat Airport or to have maintenance performed. With additional investment at the airport, the upgraded runway will allow the operation of aircraft capable of providing scheduled interstate airline services.
“The commencement of passenger and freight air services from Ballarat to locations around Australia would result in greatly reduced travelling times for businesses and for the more than 300,000 people who live in Western Victoria.
“There will also be the potential for Ballarat Airport to act as a base for the larger fixed-wing emergency services aircraft
which will improve the capability for emergency management and
With a longer runway, larger aircraft are able to land and take-off, opening up the airport to new and more frequent services. Supporting different industries, such as freight and tourism, the project would deliver benefits to both the local community and
“Productivity increases will occur because of the reductions in transport costs and improvements in transport quality due to aviation. An upgraded Ballarat Airport would allow day-return or overnight business trips, short leisure trips and urgent freight deliveries that would otherwise either be impossible or difficult from Ballarat.
“Additionally, Ballarat and the Western Victorian region contain world class visitor experiences that for many travellers are difficult to reach. Enhanced connectivity through an upgraded Ballarat Airport will encourage domestic and international tourism to the region with the commencement of direct interstate passenger flights.
“The enhanced capability, provided by the newly extended runway, will be explored in the updated Ballarat Airport Strategy and Master Plan 2023. This key strategic planning document, currently being developed, will provide guidance as to how the City can develop the airport to be a critical piece of transport infrastructure, thereby growing the economy and providing seamless connectivity to destinations and markets across Australia for the residents and businesses of Western Victoria.”
The runway extension is close to completion, with final works consisting of asphalting, line marking and lighting installation, which is expected to be completed in January 2024.
The full length of the extended airport runway will be able to be used once the new airport access road, Liberator Drive, is constructed. The Ballarat Airport will continue operating at its current capacity until this occurs and, to date, there has been limited impact on aircraft operations during the construction project.
Development Victoria is finalising the program of works that will deliver Liberator Drive and enable the runway to be used in its entirety.
Cr Hudson said that if the full economic benefit of the Ballarat Airport is to be realised, these additional stages of development will need to be funded and delivered.
“Stage 2 involves the upgrading and further strengthening of the existing runway pavement and Stage 3 would see the development of an airline terminal and associated passenger facilities, along with the construction of an aircraft apron parking area,” Cr Hudson said.
“We will continue to advocate for government support to partner with us to deliver the future stages of the airport upgrade. We see Ballarat Airport as well-placed to serve as the region's air transport hub and as a secondary airport for western Melbourne.”
NHP offers the ultimate personnel safety and asset protection with a complete range of medium voltage products and solutions, combined with long term support and service to rely upon.
NHP’s quality medium voltage range is manufactured in Europe and includes cast resin and oil immersed transformers, fixed and demountable switchgear, ring main units and protection relays. NHP can also design and manufacture customised kiosk solutions, including full MV/LV kiosks, outdoor enclosed MV switchgear substations and outdoor rated enclosed transformers.
Coupled with a local and experienced team of MV experts, NHP provides project solutions that focus on:
♦ Safety of people
♦ Reliability of product
♦ Availability of power
♦ Compliance to standards
♦ Customisation of solutions to meet your needs Features and benefits of NHP’s medium voltage range include:
♦ The ‘Arc-Killer’ quenching system, which quenches an arcing fault within 48ms
♦ No need to externally vent arc fault gasses
♦ Increased personnel safety and minimised switchgear damage
♦ Visible earth switch and in line isolation
♦ Highest levels of safety when testing cables
♦ Cast resin transformers with arc mitigation by design
♦ Switchgear and transformers with a 50-year design life
♦ Modern vacuum switching and load break technology
♦ Sets a new standard for reduced partial discharge
♦ Environmental (E3), climate class (C2) and fire behaviour class (F1)
♦ A demonstration and training facility at NHP’s headquarters in Melbourne
MAXIMISE SAFETY WITH NHP’S UNIQUE ‘ARC-KILLER’
NHP’s switchgear solutions feature a unique arc quenching system called the ‘Arc-Killer’, which quenches an arcing fault within 48ms for its air insulated switchgear and 25ms for its gas insulated ring main units.
Such a fast arc fault clearance rate not only protects people from danger, but also protects the switchgear panels from damage, ensuring maximum power availability and high reliability.
NHP’s dedicated project team ensures seamless project delivery while providing engineering support and flexible customised solutions. The company has also successfully delivered projects for over ten years in the defence, mining, healthcare, critical infrastructure and food and beverage sectors.
Services include:
♦ Engineering and local customisation
♦ Analysis and performance simulation
♦ Electrical and 3D design development
♦ Local manufacturing and factory acceptance testing
♦ Low and medium voltage servicing and support
♦ Training and product familiarisation services
For more information, please call 1300 NHP NHP or email nhpsales@nhp.com.au
Edge Technology.
Industrial Connectivity.
Camera-asa-Sensor.
Cybersecurity.
Unlocking future potential with digital transformation
Connect and protect people, assets and the environment
With a 30-year legacy of providing resilient industrial technology solutions, our experience connecting and protecting people, assets and the environment means we’re the preferred partner for solving IIoT, industrial networking, cybersecurity, asset management and asset visibility challenges.
Find out more.
As revealed in a recent State of ICS/OT cybersecurity whitepaper from SANS, a critical distinction has been made between Operational Technology (OT) assets and traditional Information Technology (IT) assets.
The SANS whitepaper states that, “While traditional IT systems primarily handle data at rest or in transit, ICS/OT systems oversee real-time changes in the physical world, managing physical inputs and controlled actions.”
This crucial difference underscores the need for organisations with critical operational environments to take a specialised approach to cybersecurity, as OT systems directly impact the physical realm.
The convergence of IT and OT represents a pivotal development in industrial operations. This integration not only yields a high level of operational efficiency but also provides a platform for operational empowerment, leading to enhanced innovation, streamlined costs, and improved overall performance.
This integration is no longer just a technological advancement, but a strategic necessity that allows organisations to adapt their operational processes.
Yet, with every stride forward, we encounter new challenges. As OT and IT systems integrate, a unique set of cybersecurity concerns becomes apparent. As more devices become connected, this convergence expands the potential attack surface, opening doors to vulnerabilities.
It's at this juncture that vigilance and proactive measures become paramount.
Dedicated resources for people and tools are vital in fortifying security programs to meet today's dynamic challenges. According to the SANS whitepaper, organisations investing in control system security are more likely to mature, detect, protect, and defend their critical infrastructure.
Encouragingly, a growing number of organisations are allocating budgets specifically for OT cybersecurity, with only 8 per cent lacking such provisions in 2022.
Looking ahead, respondents are directing these budgets towards key initiatives, with a strong focus on three key
objectives: increasing visibility, implementing intrusion detection tools, and finally, safeguarding networks with intrusion prevention tools.
Let’s look at these three in more detail.
THE THREE PILLARS OF CYBERSECURITY EXCELLENCE IN OT ENVIRONMENTS
Amplifying visibility into cyber assets
Network visibility is the cornerstone of a OT cybersecurity strategy, providing the necessary visibility and insights to protect critical infrastructure and maintain the integrity of operational processes.
Device discovery tools can help to build a comprehensive inventory of all connected devices, including legacy systems, IoT devices, and network components.
Vigilant intrusion detection systems
Keeping a watchful eye on the digital network is imperative. Intrusion Detection Systems (IDS) play a crucial role in enhancing OT cybersecurity by actively monitoring traffic and system activities for signs of potential security breaches or unauthorised access.
Empowering intrusion prevention measures
In addition to detection, prevention is crucial. Firewalls and access control systems play a pivotal role, carefully examining all network traffic based on preset rules.
Intrusion Prevention Systems (IPS) enhance this defence by not only identifying threats but also proactively blocking them in real-time. IPS can recognise and block malicious files, malware, and payloads attempting to infiltrate the network.
SECURING DIGITAL TRANSFORMATION
In a landscape defined by convergence, cybersecurity isn't just a necessity; it also represents a strategic advantage.
By adopting a layered approach to OT cybersecurity that includes visibility, IDS and IPS, organisations can reap the full benefits of digital transformation.
For Melbourne residents, the Level Crossing Removal Project has become a part of daily life, as many locals take the city-wide works in their stride, with the knowledge that the transformational project will make the city safer and more efficient for generations to come. To make this momentous project as efficient as possible, the Victorian Government has utilised a plethora of digital solutions – garnering international attention, and awards.
The Level Crossing Removal Project, which began in 2015, aims to eliminate 110 level crossings across Melbourne by 2030, including other network upgrades alongside the new elevated crossings, such as new stations and track duplications.
The major overhaul aims to improve community safety, reduce congestion on major roads caused by trains crossing, and support more sustainable transport for the future.
To complete this enormous project, Victoria’s Major Transport Infrastructure Authority (MTIA) established four alliances to deliver the program, one of which is the Southern Program Alliance (SPA).
This alliance consists of ACCIONA/Coleman Rail, WSP, and Metro Trains Melbourne, with one project in particular capturing the attention of the global infrastructure industry.
The Parkdale level crossing removal project involves rail and road removals, constructing a viaduct and building a new station along the Frankston line.
The project was awarded in late 2022, and is expected to be finished in 2025, with the overall cost expected to be $450 million.
The project was undertaken in a narrow corridor near heritage sites and required a multidisciplinary team, so to make this challenging process easier, lead design consultant, WSP, chose to adopt integrated digital solutions.
Leveraging open modelling applications and ProjectWise, powered by Bentley Systems, WSP established a digital twin to streamline workflows and help meet project objectives.
Using this web-based platform minimised rework and accelerated decision-making, which helped to reduce modelling time by 60 per cent and save 15 per cent in resource hours during the design delivery process.
Every year, Bentley Systems holds its 2023 Going Digital Awards in Infrastructure, honouring the work of Bentley software users who are advancing infrastructure design, construction, and operations across the globe.
Mr Patel explained that the scope of the project included removal of the level crossings at Warrigal Road, Mentone and Parkers Road and Parkdale, and replacing them with an elevated rail line. These works are alongside the construction of a brand new station at Parkdale, building the pedestrian crossing, car parks, and installing open spaces such as a playground, gathering spaces and open air gyms.
Mr Patel explained that working on multidisciplinary projects, such as rail projects, can be challenging as it involves multiple teams with varying expertise each working on different aspects of an initiative.
“To meet these challenges, a software solution was required that was versatile, dynamic and centralised to handle design challenges and stream processes,” Mr Patel said.
For a project this large, community consultation and messaging is key.
This year the awards, held on 11-12 October in Singapore, included two level crossing removal projects – one of which was the Parkdale project.
THE WINNERS WERE:
Category: Bridges and Tunnels
WSP Australia Pty Ltd
Southern Program Alliance
Melbourne, Victoria, Australia
Category: Construction
Laing O’Rourke
SEPA Surrey Hills Level Crossing Removal Project
Melbourne, Victoria, Australia
Jaimin Patel, Senior Structural Technologist, WSP, presented the Parkdale project for judging, explaining the magnitude of the project, and how digital solutions are helping to execute this futuristic design.
“This is a community based project, so most of the design and structure – everything – is focused on community,” Mr Patel said.
He also explained that ensuring there are no negative effects on the community was a paramount concern.
“With setting up digital models at the early stage, obviously we were able to use those models for animation.”
Mr Patel explained that “the biggest help” when it came to engaging with the community was setting up the digital models to allow his team to show residents how the new infrastructure would look, and that there wouldn’t be any major effect on their houses or businesses.
“By providing accurate data and 3D modelling capabilities in the early stage of design, this project will lead to an intergenerational legacy which impacts that extend far beyond the rail corridor itself. It'll change the way people move around.”
Lower Hutt is an urban centre of around 110,000 people, a short distance north of New Zealand’s capital city of Wellington. The city has outgrown its roots as a manufacturing hub and commuter suburb, into a thriving business and residential centre defined by the winding rivers that flow down the Hutt Valley (Heretaunga). But as it grows, as does the need for new and approved infrastructure.
RiverLink is a partnership between Greater Wellington, Waka Kotahi, Hutt City Council and iwi Taranaki Whānui ki Te Upoko o Te Ika and Ngāti Toa Rangatira to deliver crucial flood protection and river restoration work, improvements to public transport, walking and cycling routes, local roads and the State Highway 2 Melling Interchange, as well as urban revitalisation of the Lower Hutt city centre.
Te Wai Takamori o Te Awa Kairangi engaged Reveal in December 2022 to complete a comprehensive utility model that could be used to plan further investigations and inform partners on the status of the underground utilities within the planned project footprint in Lower Hutt.
The work was completed in two stages, with the first stage involving a comprehensive 2D desktop study. Reveal's team compiled information from various sources, including BeforeUDig and utility providers to ensure the data was up to date. This initial step ensured that the foundation of the model was built on accurate and reliable information.
Following the desktop study, Reveal performed a Ground Penetrating Radar (GPR) survey. The GPR data was processed and used to update the model from 2D to 3D, providing an even more comprehensive understanding of the subsurface infrastructure by adding crucial depth measurements to the model.
Samantha Smith, Project Manager – Utilities for Te Wai Takamori o Te Awa Kairangi, said, “One of the standout features of Reveal's model is its versatility. The model can be exported in various formats, making it compatible with our design software.
“This compatibility enabled seamless integration of the model into our planning and design processes, making it an invaluable tool. The visual presentation of the model is impressive, and the user interface is intuitive and easy to navigate.”
The Reveal team took only three months from project inception to deliver a fully-fledged unified utility model in a web-based platform for Riverlink’s designers and engineers to work with.
“One of the most significant benefits of using the Reveal model is its potential to reduce the need for invasive investigations. By highlighting unknowns and higher-risk areas, the model allows for targeted investigations and utility relocations planning. This approach minimises disruptions and costs associated with more invasive methods,” Ms Smith said.
“In conclusion, Reveal has proven to be innovative and forward-thinking in their field of subsurface utility investigations. Their diligent and thorough approach, coupled with the creation of a visually appealing and user-friendly model, has enabled us to plan further investigations, and inform our relocation design with confidence.”
With Reveal, you can eliminate subsurface risks, deliver infrastructure projects faster and minimise cost blow-outs and variations.
If you need to understand your underground, get in touch with the world’s leading subsurface experts.
PAs workplace accidents and staff shortages continue to commonly occur, digital transformation is essential to streamlining operational processes, driving productivity, and, most importantly, enhancing safety and security for workers.
articularly in heavy industries, digital transformation helps to automate processes, which reduces the need for human workers to be in risky environments around heavy machinery.
Across Australia and New Zealand, spending on Internet of Things (IoT) products and services – such as Artificial Intelligence (AI), cloud, and big data – is expected to reach $24 billion in 2026, with manufacturing, utilities, and transportation accounting for more than half (54.6 per cent) of the market share.
While IoT solutions are becoming increasingly critical for business efficiencies, they aren’t the only innovative solutions that have emerged as crucial deployments for heavy industries. More organisations than ever are investing in voice recognition software assistive technology to enhance their operations, increase efficiencies, and, ultimately, improve safety across job sites for workers in rugged industries.
Voice recognition as a tool has emerged from a primarily home-based utility to permeate – and enhance – rugged industries, by increasing the speed, accuracy, efficiency, and most importantly, the safety of operations.
On a fundamental level, it lets workers operate machinery, access data, and communicate hands-free, among other uses, reducing the potential for accidents on job sites.
There are multiple uses for voice recognition software assistive technology across rugged industries to enhance safety and efficiency in operations, including in the utility, transport and logistics sectors.
One of the biggest uses for voice recognition software assistive technology in utilities is its capacity to alert utility providers with updates on service interruptions and on-site safety. Primarily, this ensures frontline workers can quickly access key information while still easily and efficiently performing their tasks hands-free.
This is achieved by embedding on-demand AI via voice into rugged devices and tablets, which ensures technicians can complete hands-free references with their rugged mobile devices without sacrificing safety. For example, field workers
can access relevant information via voice commands to complete activities, while navigating freely on utility poles.
A key application for voice recognition software assistive technology in transport and logistics is the improvement of the safety of long-haul fleet delivery by empowering drivers to give commands or ask questions without diverting their attention from the road ahead, much like a consumer-grade GPS.
For example, drivers can use voice-activated navigation to access directions or receive updates on traffic conditions to reduce traffic waiting times, increase delivery throughput, and enhance driver safety by avoiding road incidents.
From a logistics perspective, workers in warehousing or distribution centres can improve speed, accuracy, and safety by using speech recognition to verbally confirm product picking.
Transportation and logistics environments can be overwhelmingly busy and full of competing noises. When it comes to voice recognition software assistive technology, solutions enhanced with noise reduction technology are essential in optimising voice-controlled solutions in a realworld environment.
Voice recognition software assistive technology's popularity has grown in many industries, including those operating in rugged environments like utilities and transport and logistics, by enhancing operations and improving safety. Businesses that continue to explore the applications of voice recognition software assistive technology across their operations will continue to uncover efficiencies without sacrificing worker safety.
Combining voice recognition software assistive technology with other IoT solutions allows businesses to take safety and efficiency to the next level, eliminating the need for select workers to be onsite and empowering other workers to operate at a distance, or more safely, depending on their roles.
As voice recognition software assistive technology continues to evolve, savvy businesses that make the leap today to new and innovative solutions will reap the benefits, as will their workers. Automation and innovation isn’t just for the future of rugged technologies; it’s for the now.
With blockages and overflows being frequent problems for wastewater infrastructure, Sydney Water is undertaking a $15 million wastewater monitoring internet of things (IoT) deployment across its network. Already, Sydney Water is saving hundreds of thousands of dollars per month with sensors that can detect blockages before they cause damage.
Set to be the largest project of its kind in Australia, the agreement will see Sydney Water install over 26,000 blockage detection devices across 4,600km of wastewater infrastructure by June 2024.
As of October 2023, Sydney Water has already installed 15,000 devices across its wastewater network that causes 70 per cent of overflows to waterways. The sensors detect about
20 blockages in the gravity wastewater network per month on average, saving approximately $400,000 in incident costs.
The devices, from project partners Kallipr and Metasphere, are data loggers attached to sensors that communicate regular data readings.
The sensors are installed on existing sewer infrastructure and frequently send back data readings, which are
pre-configured to trigger an alarm when certain thresholds are met – to indicate a potential blockage.
As the system detects blockages in wastewater pipes before they lead to wastewater discharge into customer properties and the environment, incidents can be avoided that could pose a public health risk and incur massive clean-up costs and result in reputation damage.
Sydney Water Head of Operational Technology, Craig Earl, is excited about the multi-million dollar initiative.
“This is a transformational project for Sydney Water,” Mr Earl said.
“We’re stepping into the Internet of Things with internet connected devices. We’re leading the industry on some of this new deployment, which is resulting in massive savings via early detection of blockages in our wastewater network.
“We’ve worked with other utilities around the country and industry partners as well. We’re really focused on that Australian ability to drive innovation, not just nationally but on a global scale as well.”
The majority of blockages are caused by tree roots penetrating pipes or access chambers, although grease and wet wipes also contribute to blockage build-up.
More than 11,000 sensing devices have been installed in the past 18 months, and the deployment work continues at a rate of between 200-300 devices a week.
The sensors can withstand high humidity and water immersion. The more than five-year battery life reduces the need for maintenance and site visits significantly. The devices can reliably and securely record and send data from remote and difficult-to-access areas by operating on the NB-IoT network.
Sydney Water’s Internet of Things Manager, Christoph Prackwieser, said the cost savings generated by the sensors have been considerable.
“So far, around 500 blockages at environmentally high-risk sites have been identified and cleared. We are saving $400,000 a month in avoidance costs with this technology,” Mr Prackwieser said.
Mr Earl said the results have been pleasing, with the data from the 15,000 devices currently installed creating a return every month on cost avoidance, plus the added benefit of protecting the environment.
Mr Prackwieser said the IoT technology is a game changer.
“The Internet of Things is a monitoring technology which allows us to securely connect these devices via the internet
to our systems. It’s been working very well and has generated good outcomes,” Mr Prackwieser said.
Mr Earl said the placing of the sensors is of paramount importance, so the utility has been very strategic about their placement; to maximise the ability to protect the environment.
“So many of our assets are around creeks and streams or places like Sydney Harbour where we’re installing these sensors, we’re ensuring we protect these special places,” Mr Earl said.
Installing the devices will allow Sydney Water to build on its highly successful wastewater management project. It is driving the digitisation of its existing wastewater networks and allowing for proactive management of blockage events within the infrastructure.
Mr Earl said he’s proud to be a part of the initiative and constantly shares his findings with his family.
“They know how passionate I am about this project and listen to my stories. They say to me ‘yes Dad, yes Dad’. They know it’s something that excites me and it excites me because I know we’re making a difference to this great city,” Mr Earl said.
Software,
Digital
Mapping, GIS & surveying
Condition
Construction
Airport
Smart
Freight & logistics
Funding/investment
Intelligent
Ports
AI
Intelligent
Roads
Sustainability
Disaster
Security
Signalling,
Rail
HYBRID ON DISPLAY AT AUSRAIL STAND 319
Innovative MEWP with Tier 5 engine & Stage V Technology for low emissions to reduce environmental impact
Key features of both MEWPs
• New fully integrated control panel with dynamic visual display
• 450kg basket
• Continuous 360° rotation and travel over the side
• 180° basket oscillation
• 16.68m max working height
• Available with new PA64 Pantograph (range 4.2m – 6.4m)
The only Hybrid MEWP with Stage V Technology to operate autonomously on a full battery for up to 50 hours work*
Melvelle Equipment Corp Pty Ltd 10 Rogilla Close, Maryland, NSW 2287 Australia
Phone: 61 2 4951 5244
Fax: 61 2 4950 1291 ABN: 55123570356 www.melvelle.com.au M.E.C.
Polymaster’s unique Enclosed IBC Bund solves many of the problems associated with IBC storage and chemical/fluid decanting in a weather resistant, purpose-built enclosure.
Æ Full weather protection – stops rain entering the enclosure
Æ Easy forklift loading with wide forklift access from both side and back
Æ 250ltr day tank
Æ Lockable cabinet to keep system secure
Æ Venting by two sides
Æ Viewing windows incorporated into the doors
Æ 110% bund capacity complies with AS3780
Æ Sight tube and low-level alarm available
Æ Chemical resistant – high grade polyethylene construction