TRANSPORT OF THE FUTURE: INTELLIGENT, SAFE, AUTONOMOUS

UPPING CONCRETE’S SUSTAINABILITY FACTOR
TUNNELLING THROUGH: EASING CONGESTION IN MELBOURNE’S TRAIN NETWORK
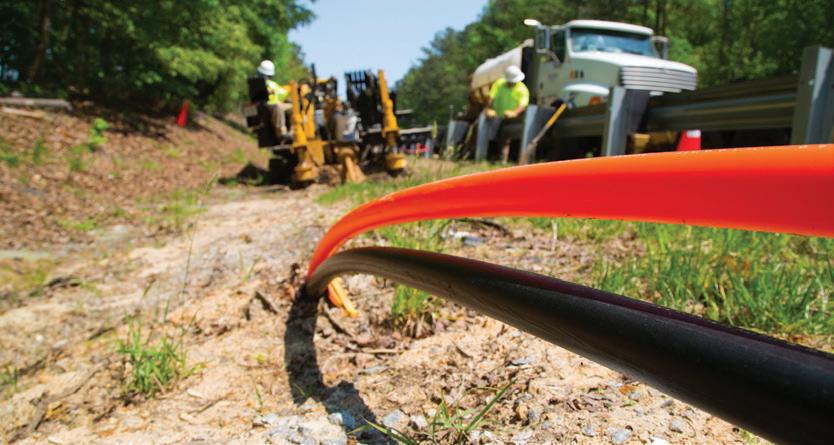
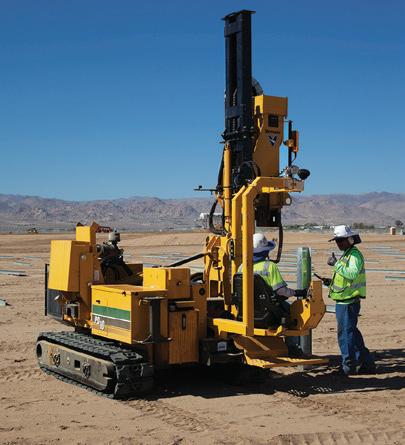
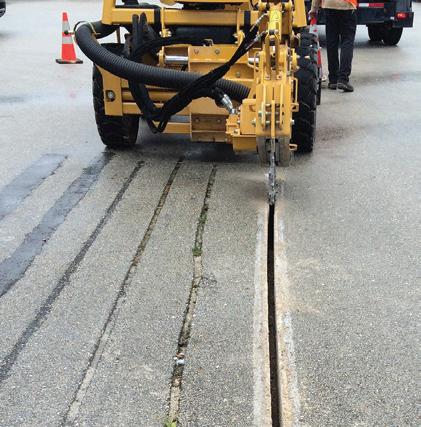
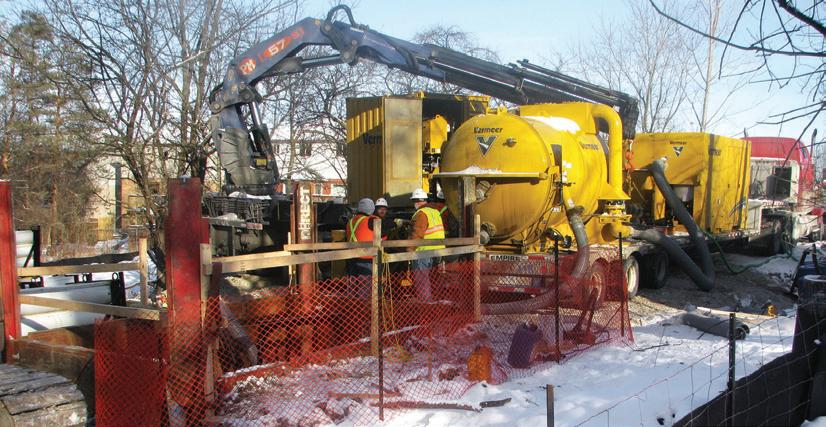
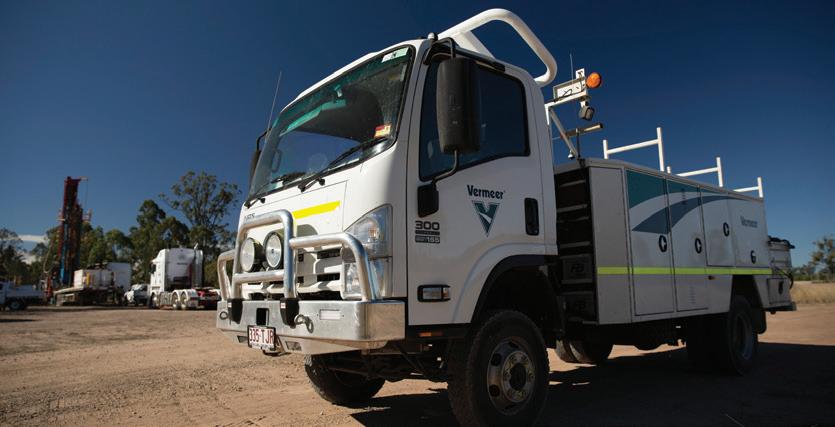

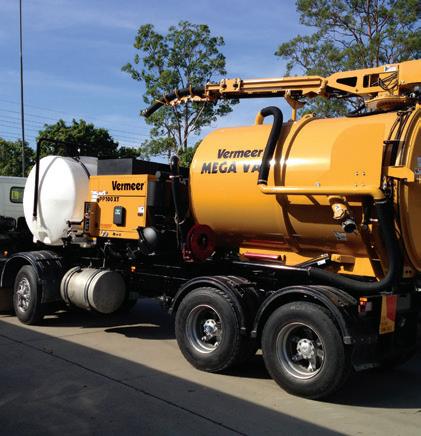
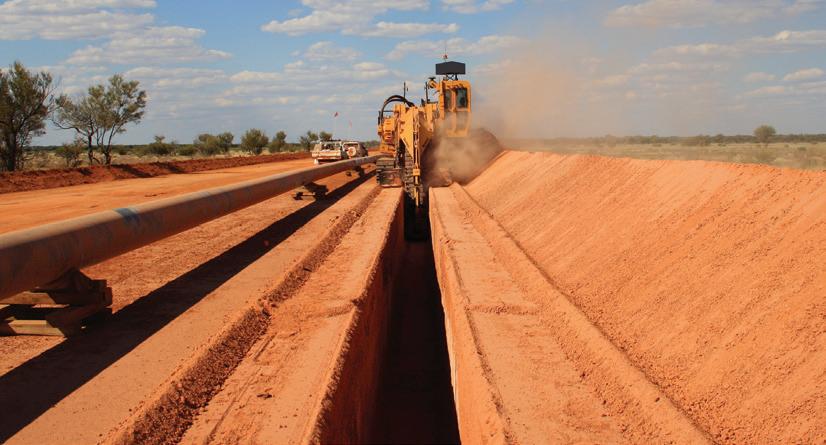
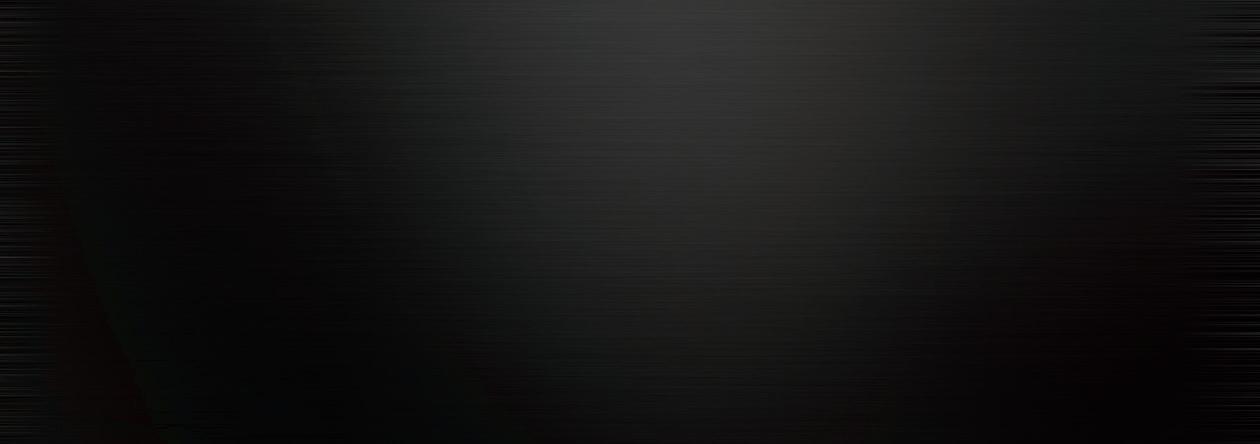
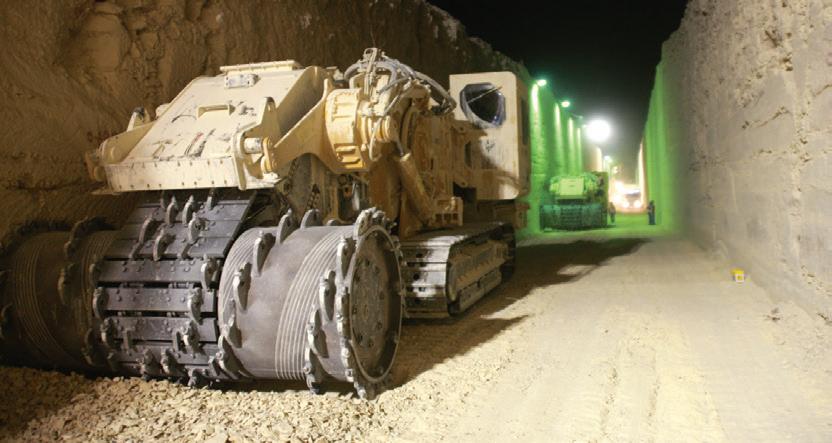
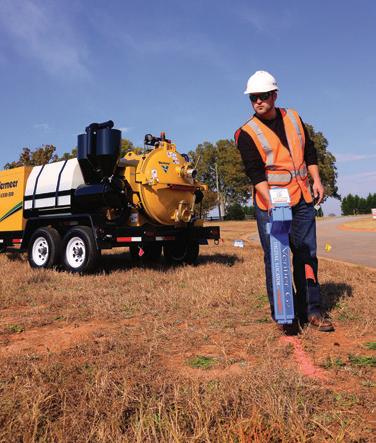
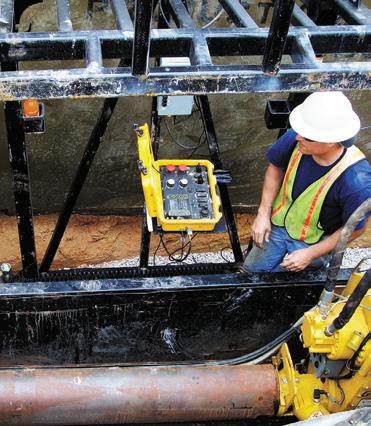
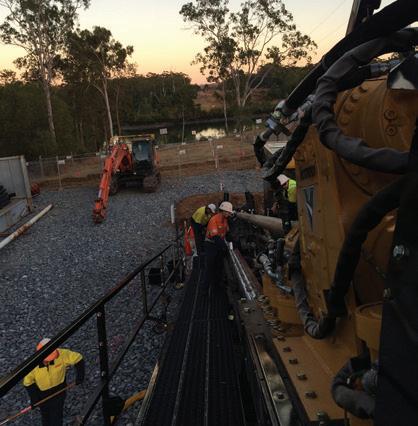
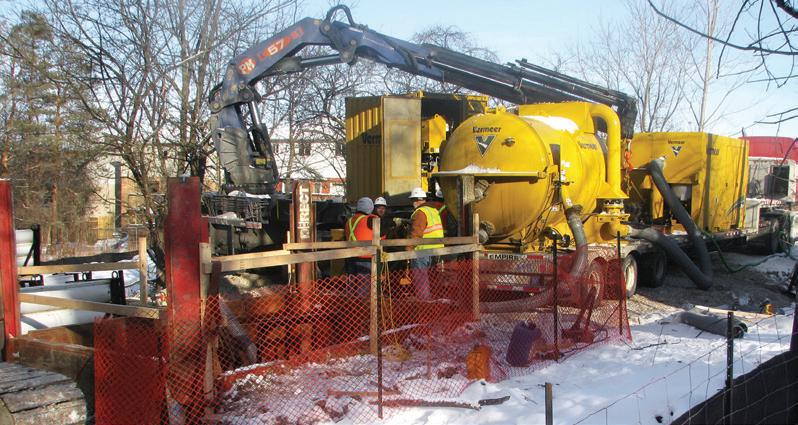
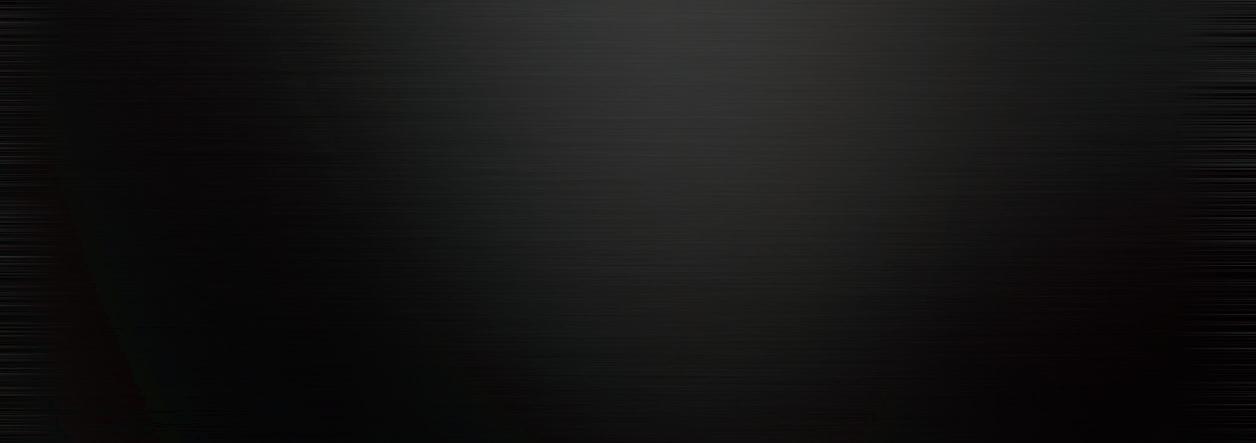
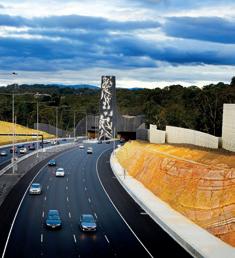

TRANSPORT OF THE FUTURE: INTELLIGENT, SAFE, AUTONOMOUS
UPPING CONCRETE’S SUSTAINABILITY FACTOR
TUNNELLING THROUGH: EASING CONGESTION IN MELBOURNE’S TRAIN NETWORK
Irecently attended the Australian Asphalt Pavement Association’s 17th International Flexible Pavement Conference, where I was lucky enough to listen to some of the leaders in the road industry discuss the key challenges, opportunities and trends coming up for the industry.
There were three key themes that jumped out at me at this event:
4,921
6,660
Published by
Monkey Media Enterprises
ABN: 36 426 734 954
PO Box 1763
Preston South VIC 3072
P: (03) 9988 4950
F: (03) 8456 6720
monkeymedia.com.au info@monkeymedia.com.au infrastructuremagazine.com.au news@infrastructuremagazine.com.au
Editor
Laura Harvey
Senior Associate Editor
Jessica Dickers
Contributing Editor
Michelle Goldsmith
Associate Editor
Lauren Cella
Marketing Director
Amanda Kennedy
Marketing Associate
Mathew Walker
Marketing Consultant
Aaron White
Production and Customer Service
Titian Bartlau
Senior Designer
Alejandro Molano
Designer Jacqueline Buckmaster
Publisher Chris Bland ISSN: 2206-7906
1. Our population is growing, and this is going to have significant implications for the road infrastructure we plan and build in the future
2. We need to look more closely, as an industry, at the things we can do to make the construction of our new roads safer for workers and road users
3. We need to find innovative ways to deliver the road infrastructure we will require in the next thirty years, given the significant size of our country, and the relatively (in global terms) low number of taxpayers we have to fund our future roads
There’s no doubt that the challenges laid forward for the road industry as a whole is significant – but on a positive note, I’m a big believer that challenges are huge drivers for innovation. The opportunities for all of those in the road industry are there to be grabbed with both hands.
One such opportunity is innovation in safety, which will be a big driver of future growth for the road industry. We’ve explored this in more detail in our article on page 56, where we take a closer look at the industry’s efforts to improve the quality of roadside safety barrier installation and maintenance.
Another area of innovation, which rightly receives plenty of interest, is that of intelligent transport systems. The drive (pun intended!) within the industry to establish intelligent transport options, such as driverless cars, continues to gather momentum. In this issue we take a closer look at the recent trials being undertaken on Melbourne’s EastLink to test the compatibility of the
existing freeway with some of the latest vehicles on our roads, which already have a number of automated vehicle technologies that are inching them closer towards full hands-off-the-wheel capability. You can read more about these trials on page 60.
Innovation, of course, is a common theme across all sectors that make up the infrastructure industry, and this is particularly the case when it comes to asset management. In August, Infrastructure magazine hosted its first event, Asset Management for Critical Infrastructure, where we gathered some of the country’s leading managers of critical assets, to discuss innovation and a range of other topics of key importance to the asset management sector.
When it comes to asset management, innovation is vitally important, and it’s incredibly exciting – but it must be balanced with the need to adhere to standards and maintain the strict controls and balances that are required to effectively manage assets, such as power, road and rail networks, safely and efficiently.
It was a thrill to bring so many members of the industry together to consider and debate the key issues, and we’re looking forward to bringing Infrastructure readers more industry events in the future – watch this space!
Laura Harvey EditorI’m keen to hear your thoughts and feedback on Infrastructure Drop me a line at laura.harvey@monkeymedia.com.au or feel free to call me on 03 9988 4950 to let me know what you think.
Queensland and Northern Territories largest range of paving equipment, parts, technology, service and training, Hastings Deering is committed to supporting you from the ground up. Call 1300 991 263 or
We are focused on building relationships that extend well beyond machines. That means sharing our expertise to help you select, acquire, operate and maintain your paving equipment, then standing by your side to keep that equipment – and your business – running smoothly. Invest with confidence knowing it’s more than just parts, service and support. It’s a partnership designed to deliver more for you.
CRANE SPOTTING
ASSET MANAGEMENT’S BEST GRAPPLE WITH INNOVATION, STANDARDS AND SUSTAINABILITY
Leading managers of critical infrastructure in Australia gathered in Sydney in August to discuss some of the most pressing issues facing the asset management industry.
OUTSTANDING ACHIEVERS RECOGNISED BY THE ARA
Individuals and organisations from across the Australasian rail industry were awarded for their outstanding achievements and innovations in rail at the recent Australasian Rail Industry Awards Gala Dinner.
Twice a year, the RLB Crane Index measures crane activity as an indicator of construction sector health across Australia. In this article, we take a look at where cranes could be spotted during the second quarter of 2017, and what this tells us about the industry.
ACCURACY IS BOOMING
NEW VISION OF OUR URBAN FUTURE
A Victorian Council faced with rapid growth is embracing new technologies to deal with the challenges that come with a booming population.
ANTI-VIBRATION SOLUTIONS FOR AUSTRALIA’S RAPID URBANISATION
WATER
CROSS YARRA PARTNERSHIP TO BUILD
The Metro Tunnel will connect some of Melbourne’s busiest train lines, freeing up space in the crowded City Loop, which is currently operating at capacity. Some of the world’s best contractors have just been selected to build the tunnel, Victoria’s biggest ever public transport project.
TUNNELLING INDUSTRY NEEDS
SIMPLIFIED DOZER OPERATION ON CONSTRUCTION SITES
Designed to quickly move large quantities of materials on construction sites, dozers, with their enormous size, can cause serious injury if not operated properly.
WHEN THE RUBBER HITS THE ROAD: RECYCLED TYRES CREATE STRONGER CONCRETE
Engineers have developed a more resilient type of concrete using recycled tyres that could be used for concrete structures like buildings, roads, dams and bridges while reducing landfill waste.
MAKING CONCRETE GREAT AGAIN
ENERGY INFRASTRUCTURE
ADDRESSING THE ENERGY TRILEMMA: FINKEL’S RECOMMENDATIONS TO IMPROVE POWER INFRASTRUCTURE
The Australian energy industry is currently dealing with an energy trilemma: how do we transition to sources of energy that are clean, affordable and abundant?
THROUGH THE LOOKING GLASS: THE FUTURE OF AUSTRALIA’S SOLAR PROJECTS
TRANSFORMING ENERGY NETWORKS AS THE INDUSTRY EVOLVES
MINERALS CONFERENCE LOOKS TO NEW SILK ROAD
IMPROVING THE QUALITY OF ROADSIDE SAFETY BARRIER INSTALLATION AND MAINTENANCE
It has been acknowledged for some time now that the installation of roadside safety barriers in Australia could be considerably improved to provide better outcomes for road users.
China’s Belt and Road Initiative will take centre stage when resource industry heavyweights gather for this year’s International Mining and Resources Conference (IMARC), to be held from 30 October to 2 November at Melbourne’s Convention and Exhibition Centre.
EASTLINK TRIALS AUTOMATED VEHICLE TECHNOLOGIES
Vehicles are on the way to enabling hands-offthe-wheel driving on freeways, with trials of automated vehicle technologies underway on one of Australia’s largest tollways.
EVOLVING TRANSPORT TECHNOLOGY
RIGHT IN A CHANGING ECONOMY
Australia’s cities are changing, and as a result, the way we move goods to their ultimate destination is changing too.
ENGINEERING AND CONSTRUCTION TECHNOLOGY: A NEW ERA FOR MOBILITY
New technologies are transforming all stages of the engineering and construction process, with the potential for companies to realise significant improvements in efficiency, safety, collaboration, and mobility.
CULVERTS
BUILDING A BRIDGE WITH A HOUSE SLAB
MidCoast Council recently adopted an innovative approach to replacing an existing river crossing along one of its rural roads, utilising residential house slab technology – also known as waffle pods – in what is believed to be the first time the system has ever been used to create an insitu concrete box culvert.
08 PLAN FOR NATIONAL FREIGHT AND SUPPLY CHAIN EFFICIENCIES 10 NORTH EAST LINK CORRIDOR OPTIONS UNVEILED 12 SMART TECHNOLOGY INTRODUCED ON PERTH FREEWAYS 14 NEW ENTITY ANNOUNCED TO BUILD WESTERN SYDNEY AIRPORT 14 ROAD RENEWAL BRINGS JOBS TO QUEENSLAND 15 NEW CHAIR OF INFRASTRUCTURE AUSTRALIA
Michael Kilgariff is the Managing Director of the Australian Logistics Council (ALC). ALC is the peak national body representing the major and national companies participating in the Australian logistics industry, with a focus on national supply chain efficiency and safety. Since his appointment to the position in 2009, Michael has worked closely with industry and government to elevate the needs of freight efficiency and safety. Michael holds a degree in Economics from the Australian National University, and is a graduate of the Australian Institute of Company Directors’ diploma and advanced diploma courses.
Professor for Geotechnics and Underground Constructions at the University of Leoben
Robert Galler graduated from the Mining University Leoben, Austria, in 1993. He obtained a Ph.D. in Subsurface Engineering at the University of Leoben in 1997. From 1997 to 2007 he worked with Geoconsult ZT GmbH, Salzburg, Austria as Project Manager in Design and Construction of Underground Structures. Reference projects are the New High Speed Rail Link between Cologne and Frankfurt in Germany; the tender design for the Semmering Base Tunnel in Austria; and the Preliminary Design for the Brenner Base Tunnel. Since November 2006 he is Full-Professor for Subsurface Engineering at Montanuniversität Leoben, Austria. Furthermore he is Head of the Department Mineral Resources Engineering as well as Head of the Department “Zentrum am Berg”, a 1:1-scale underground research and development centre as well as a training and education centre for all aspects of underground structures.
Partner, Herbert Smith Freehills
Peter Davis is a partner at international law firm Herbert Smith Freehills. He specialises in energy, resources and infrastructure law. He has acted on a number of significant acquisitions and disposals in the energy industry and regularly assists with key commercial contracts including power purchase and connection arrangements and provides advice in relation to the National Electricity Rules and jurisdictional regulation and reform to industry participants and regulators. Peter works closely with infrastructure investors, energy retailers and generators, renewable project proponents and their financiers. Peter has been listed in Best Lawyers in Australia in the practice area of Energy Law since 2014. Peter holds a LLB (Hons) and BEc from the University of Newcastle and is a member of the Australian Resources & Energy Law Association (AMPLA).
Guy commenced at Western Power in December 2011 as Operations Commercial Manager. He was later appointed Head of Business Planning and Reporting before joining the Executive Management Team as Chief Financial Officer in February 2015. He was appointed Chief Executive Officer in July 2016. Guy brings a wealth of international, financial and operational experience across a diverse range of sectors, operating and residing in a number of continents including Asia, Africa, Europe, North and South America, and Australia. He is also a Leadership WA 2013 Alumni, graduate of the Australian Institute of Company Directors (AICD) and a Fellow of the Association of Chartered Certified Accountants (FCCA).
With over 20 years’ experience across transport and business, Susan is eager to harness the benefits that technology can deliver to business and the Australian community. Through the global network of ITS Associations and participating as a member of the Board of the ITS World Congress, Susan has strong linkages with the international ITS community, ensuring Australian advances can be shared overseas while also keeping abreast of international developments in this rapidly evolving field. Other affiliations include: Convenor of the Austroads Connected and Automated Vehicle Industry Reference Group and a member of the Steering Committee for this activity; member of the National Transport Commission Industry Advisory Group; member of the national Transport Commission Industry Advisory Group; member of Monash University Institute of Transport Studies Industry Advisory Board; and member of the Space Cross Sectoral Interest Group, established under the Trusted Information Sharing Network for Critical Infrastructure Resilience. Susan has built a career in consulting and in industry to look at collaborative solutions involving government, industry and academia. This industry experience is combined with professional qualifications including a Bachelor degree majoring in Environmental Management and an MBA from Melbourne Business School.
The Australasian Railway Association (ARA) has created a new ten point plan identifying key areas of improvement to help guide long-term decision making and drive efficiencies in rail freight.
The ARA submitted its Ten Point Plan to Creating Greater National Freight and Supply Chain Efficiencies to the Department of Infrastructure and Regional Development’s inquiry into National Freight and Supply Chain Priorities.
Danny Broad, Chief Executive Officer of the Australasian Railway Association, said, “The ARA supports the development of a national freight and supply chain strategy to guide long-term decision making and investments by both government and industry.
“With Australia’s freight task expected to grow by more than 80 per cent between 2011 and 2031, combined with our national population expected to increase to 30.5 million by 2031, it is critical that we act now to ensure that we are able to meet the freight needs of tomorrow.
“The ARA, on behalf of the rail industry has identified ten areas that require attention to enable greater efficiency and productivity for rail freight.
“They include linking future infrastructure funding to the delivery of reform, commitment to a competitively neutral policy approach to ensure domestic rail freight markets can operate as far as possible on a level footing with other modal choices, a national framework for corridor protection, equitable access pricing for road and rail, as well as Commonwealth, State and Territory Government investment into rail.
“Other areas for improvement also include maximising efficiency on the existing network, addressing ‘externalities’ that impact upon the Australian community negatively, supporting technology developments, addressing jurisdictional inconsistencies, and continuing to identify ways to address challenges associated with different track owners.”
At NHP, we’re closer than you think. With locations across Australia and New Zealand, and representatives in your local city, town and regional community, we understand your speci c needs.
Together with our extensive network of global partners, we o er choice in product, choice in technology, choice in service, choice in support and ultimately choice in how you deal with us –whether that be in person or online, where and when you need us.
NHP ELECTRICAL ENGINEERING PRODUCTS 1300 NHP NHP | nhp.com.au |
This enables NHP to customise solutions for the local market, bringing to life smart and secure technologies that automate production, control power and manage energy. To nd out more, visit nhp.com.au/more/localchoice
The Victorian Government has unveiled the four potential corridor options for the North East Link, which aims to ease congestion in Melbourne’s north east and take trucks off local roads.
The four possible corridors have been determined through extensive works spanning the entire north-east, including geo-technical investigations, traffic modelling, environment studies, and discussions with community groups, businesses and local residents.
Each corridor has been assessed against a range of measures including key local concerns such as reducing congestion and getting trucks off residential roads, as well as the impact on urban areas and the environment.
Each of the options identified begin at the Ring Road in Greensborough and connect to either the Eastern Freeway or EastLink, and all will involve tunnels, new surface roads and bridges.
Corridor A – This 11km corridor would follow the Greensborough Highway south using existing freeway reserve and connect with the Eastern Freeway near Bulleen Road.
Corridor B – This 24km corridor would provide a direct connection from the M80 to EastLink. It would not require
upgrades to the Eastern Freeway.
Corridor C – Similar to Corridor B, this 26km corridor would connect to EastLink and not require any upgrades to the Eastern Freeway.
Corridor D – This 40km corridor would connect with EastLink south of Ringwood and travel east using part of the proposed Healseville Freeway Reserve.
Victorian Premier Daniel Andrews said “For decades the North East Link has been put in the too hard basket – this is the missing link Melbourne desperately needs to slash congestion and stop the rat runs in the north east.
“We said we would look at all options and that’s exactly what we’ve done. This is about making sure we get this project right.”
The Government is expected to determine the preferred corridor by the end of 2017.
The Victorian Budget 2017/18 provided the first $100 million for the North East Link to undertake design, planning and pre-construction works, ahead of contracts being signed in 2019 and construction commencing in 2020.
The Minister for Roads, Luke Donnellan, said, “For too long local roads in the northeast have become default freeways. North East Link will fix that – carrying 100,000 vehicles a day and creating 5,000 jobs.”
Perth’s 300,000 daily freeway commuters now have access to real-time estimates of journey times on overhead electronic signs.
The live travel time estimates aim to inform motorists of traffic conditions ahead and reduce driver frustration.
The time estimates are calculated using existing in-road vehicle detection sensors and a new smart technology system.
Every few minutes, the system uses an algorithm that considers distances and current average travel speeds to estimate travel times, which are then published on the overhead electronic freeway signs in real time.
Minister for Transport Rita Saffioti said “In a first for Perth, the State Government is using smart
technology to communicate freeway travel times to motorists in real-time.
“Displaying travel times will reduce driver frustration by providing motorists with a quick understanding of the current road conditions ahead and giving them an estimated time of arrival to key freeway exits.
“They are also able to make more informed en route travel choices by being able to change their journey based on the displayed travel times that can be used as a guide.
“This is a great example of a lowcost, high-impact solution to improve traffic flow and get the most out of our existing infrastructure.”
Travel times will automatically be displayed on nine selected freeway signs during both morning and afternoon peak periods on weekdays.
Supply and service of high pressure hydraulic Equipment.
Supply, service and annual inspection of all rigging and height safety equipment.
Full turnkey engineering of custom lifting solutions, from concept to engineering to manufacture, commissioning and training..
Load testing up to 100T
PLC controlled synchronous jacking and skidding systems.
Hydraulic Gantries to 1000 tonnes
Electric and Pneumatic Hoists and winches.
Specialised Heavy hydraulic lifting solutions are supplied to customers w ho are unable find anything to suit their needs on the market.
Federal Minister for Urban Infrastructure, Paul Fletcher, and Western Australian Senator Mathias Cormann have confirmed the incorporation of the multi billion dollar corporate entity that will deliver the Western Sydney Airport
WSA Co is the next significant step in the Government’s priority to deliver a second airport for Sydney. With an investment of up to $5.3 billion in equity, WSA Co will operate as a Commonwealth Company, prescribed as a Government Business Enterprise.
WSA Co will be chaired by Paul O’Sullivan who is the current Chair and former Chief Executive of Optus. Mr O’Sullivan’s business leadership expertise makes him highly credentialed to lead the company delivering Western Sydney Airport.
Mr Sullivan’s experience leading an infrastructure business as it established market share against a long established incumbent will be of great value as Western Sydney Airport is planned and constructed before commencing operations by 2026.
Mr O’Sullivan will be joined by Fiona Balfour, Tim Eddy and Christine Spring as directors of WSA Co.
Mrs Balfour has over 35 years’ experience across a range of industries. She is a long-serving airline executive and is currently a member of the Airservices Australia board.
Mr Eddy has over 30 years’ experience in professional services with a focus on commercial transactions, most recently as Managing Partner Operations, Oceania, Ernst & Young.
Ms Spring is an expert in aviation infrastructure and airport operations, as well as a civil engineer with approximately 20 years’ experience. She has a focus on planning and construction of significant capital development projects in the aviation industry.
The board’s early priorities will be to recruit its CEO and senior management, and to commence procurement of construction activities.
To complement the experience of the directors announced, the Government expects to appoint further directors in coming months, with a further focus on construction expertise and experience in Western Sydney.
A$6.5 million road renewal package of works has been completed in North West Queensland, boosting jobs in the region.
Acting Minister for Main Roads, Steven Miles, said the works were part of the Queensland Government’s fasttracked $140 million road safety and road network renewal works package to boost employment in the region.
“We are committed to accelerating works as fast as possible to help improve infrastructure and create jobs right across Queensland,” Mr Miles said.
“This package alone delivered an average of 21 jobs in Mount Isa, Normanton, Hughenden and Camooweal.
“Transport and Main Roads is continuing to identify longerterm projects which will improve infrastructure and create jobs across Queensland.”
Fast-tracked works completed as part of the road safety and renewal package in the North West included:
♦ A culvert replacement on the Flinders Highway near Hughenden
♦ Maintenance and preservation works at intersections of the Barkly Highway (Mount Isa-Camooweal) with Gardenia Street, Goroka Street, Diamantina Developmental Road, Milne Bay Road and Northridge Road
♦ Maintenance and preservation works on the Burke Developmental Road (Normanton-Dimbulah)
♦ Maintenance and preservation works on the Gregory Downs-Camooweal Road
“The fast-tracked program of works includes road resurfacing and sealing, line markings and lighting, bridge upgrades, culvert replacements and intersection upgrades,” Mr Miles said.
The Federal Government has appointed a new Chair of the independent Infrastructure Australia Board, following the retirement of Mark Birrell.
Infrastructure Australia CEO, Philip Davies, welcomed the appointment of Julieanne Alroe, who brings extensive experience from the aviation sector to her new role as Chair.
Ms Alroe is a highly qualified executive who has more than 30 years’ experience in commercial airport management and operations, infrastructure management, strategic planning and corporate affairs.
Ms Alroe was a member of the Infrastructure Australia Board prior to her appointment as the new Chair, and is currently the CEO and Managing Director at Brisbane Airport Corporation.
In addition, Ms Alroe has held board
positions with Tourism and Events Queensland, and is President of the Queensland Futures Institute.
Her previous board appointments include the position of Chair of Airports Coordination Australia, and the Airports Council International Safety and Technical Standing Committee. She was also a board member of The Queensland Theatre Company, Australia Trade Coast, and the International Grammar School Sydney.
Ms Alroe said that she was honoured to be appointed as the new Chair of Infrastructure Australia’s Board.
Julieanne Alroe replaces Mark Birrell who joined the Infrastructure Australia Council at its inception in 2008 and was appointed Chairman of the Infrastructure Australia Board in May 2014.
“I want to thank Mark for his
dedication and incredible service to Infrastructure Australia over the last nine years,” Ms Alroe said.
“Under Mark’s stewardship, Infrastructure Australia has become a trusted advisor to governments, industry and business leaders around the country, with a strong policy voice and widely recognised mandate to lead reform.
“Mark played a crucial role in leading the development of Infrastructure Australia’s first Audit and Plan which have established a platform for our ongoing policy and reform agenda.
“I look forward to continuing this important work, advocating for nationally significant infrastructure investment and reform.”
Ms Alroe will begin her new role in September 2017.
Sydney Metro is a once-in-a-century infrastructure investment which will shape the future of Australia’s biggest city for generations to come.
Services start in 2019 on Stage 1, the AU$8.3 billion Sydney Metro Northwest project. From 2024, metro services will extend under Sydney Harbour and through the central business district of Sydney as part of Stage 2, delivering 31 metro stations and 66 kilometres of new metro rail.
The biggest urban rail infrastructure in Australian history, Sydney Metro is the first fully-automated railway system in Australia. New technology like platform screen doors – common around the world – will be used for the first time in Australia.
For Australia’s only global city, new metro rail means a new world-class rail service which will easily and quickly connect customers to where they want to go.
The state government of New South Wales has now announced the Sydney Metro West project – Sydney’s next big rail infrastructure investment, a new proposed connection between the central business districts of Parramatta and Sydney.
Industry engagement has now started and Sydney Metro is seeking input – both locally and internationally – to ensure a market led and innovative approach in the project’s development.
For more information, contact the Industry Engagement Team industry.sydneymetro@sydneymetro.info www.sydneymetro.info/industry
Leading managers of critical infrastructure in Australia gathered in Sydney in August to discuss some of the most pressing issues facing the asset management industry, at a conference attended by asset owners, utilities and senior figures from within the infrastructure sector.
Asset Management for Critical Infrastructure was held from August 16–17 at the Swissôtel in Sydney, providing more than 70 members of the asset management community with an opportunity to learn from the industry’s best, network with clients and colleagues and discover some of the latest innovations when it comes to the art of managing critical infrastructure
The expert panel of speakers lined up for the event was spearheaded by two keynotes – Steve Doran, Director of Infrastream and Chair of the Sydney Chapter of the Asset Management Council, and Antony Sprigg, CEO of the Infrastructure Sustainability Council of Australia.
Mr Doran’s keynote presentation, Leading innovation in asset management, kicked off day one of the conference, and gave delegates plenty of food for thought on the topic of innovation.
According to Mr Doran, strong industry competition and shareholder perception that companies are not future-proofing are two of the critical reasons why innovation has become a necessity for today’s asset managers, rather than a luxury.
Mr Doran warned delegates that they needed to consider risks such as their traditional technologies becoming
obsolete, and more agile start-ups providing more cost-effective solutions when weighing up how heavily to invest in innovative new methods of managing assets.
During his presentation Mr Doran also provided advice to delegates on balancing innovation with the risk that inherently comes with it - something that doesn’t always come naturally to managers of critical assets.
“While at one extreme there may be standards that are compulsory via legislation that should not be by-passed due to say commercial risk exposure, there will also be many that are effectively only optional guidance or allow significant leeway,” Mr Doran said.
“Perhaps the most relevant example to us all as asset managers are the ISO 5500X suite of asset management standards. Earlier this year, due to my passion for innovation and role in the field of asset management, I performed an analysis of clauses throughout these three standards to determine whether innovation and ISO 5500X were ‘friends or foes’.
“Refreshingly the outcome of this analysis was that these standards do not restrain us from innovating. The ‘how’ we implement management of assets is up to us and the only real innovation limits in this case are preconceptions and misconceptions and
the nature of our interaction with the key stakeholders around us.”
Antony Sprigg’s keynote presentation provided the opening for day two of the conference, with his presentation focusing on The role for ‘sustainability’ to inform and evaluate asset management for critical infrastructure.
According to Mr Sprigg, the last few years have seen a shift in industry attitudes towards sustainable thinking when it comes to our assets, and in his presentation he explored the role a sustainable approach to asset management should play in Australia’s future.
Mr Sprigg urged companies to think about sustainability as an essential part of their planning, rather than just something extra.
“Often when referring to sustainability the response is really around financial sustainability, rather than the genuine reflection of sustainability which is triple-bottom line; social, economic and environmental,” Mr Sprigg says.
“There needs to be a bit of a mindset shift to go beyond five or ten-year thinking, and look at a genuine whole of life context.
“Thinking about longer-term issues will be respected, because you’re putting the asset, the community and the client’s ultimate responsibilities first. I think there’s inherent benefit with that.”
The keynote presentations were supported by a number of speakers who
directly manage assets themselves, all of whom shared fascinating insights into the way their businesses are currently managing their assets for optimum current and future performance.
Peter Harcus, General Manager of Asset Strategy Gas at Jemena, discussed recent changes in Australia’s energy landscape, which have led to Jemena adapting its approach to managing pipelines.
“The increasing cost of energy –particularly the recent increase in gas costs domestically – has heightened the need for Jemena, and other members of the industry, to demonstrate that we are efficient and prudent in our investment and operating decisions,” noted Mr Harcus.
According to Mr Harcus, this need to demonstrate value for customers is complementary to another key trend in the gas industry – much greater scrutiny of gas providers’ social license to operate.
“Today, energy consumers want to know that when they turn on the lights or use an electrical appliance that they are accessing reliable, safe and efficient energy, that is also helping to reduce carbon emissions.
“Gas absolutely has a role to play in this energy future, and we need to be far more proactive and transparent in explaining the merits of gas as a safe, reliable, efficient and clean fuel that will continue to play an important role in the Australian energy mix.”
Also providing the asset owner’s
perspective was Paul Higham, Head of Service Planning and Asset Management for Sydney Water, who explored the way in which a consumer-centric view of asset management can drive innovation for the water sector.
Mr Higham outlined the considerations Sydney Water takes into account when it comes to planning its asset management program, with particular emphasis on the organisation’s $2.2 billion growth planning projects.
“Our number one priority is meeting the needs of our customers when developing our asset management programs,” he said.
“Sydney Water, like many other utilities, is an asset intensive organisation. In recent years we have moved from an asset-centric view of the world to a more customer-centric view of the world. After all, assets are a means of providing essential services to our customers.”
Mr Higham also said that finding the right balance of service and affordability is paramount in Sydney Water’s approach to managing existing assets with the development of new assets.
“Innovative thinking seeks to get more out of existing assets before new investments are considered.”
Representing the rail industry was Michael Killeen, Asset Manager at NSW TrainLink, who explored the topic Establishing the desired balance of cost, risk and performance in his presentation.
Mr Killeen explored what companies
need to be doing to balance cost, risk and performance in order to deliver an asset management program that is truly outcome driven.
According to Mr Killeen, a considerable challenge for asset managers in the rail industry is highlighting the importance of an outcome-focused program to stakeholders.
“There is a real tendency to measure processes and inputs in the rail industry. An outcome focus identifies and gets the organisation aligned to objectives that make a real difference to customers.”
Mr Killeen said there are two things that asset owners can do to best communicate the outcome focus and balance between cost, risk and performance to stakeholders.
“The first step here is to engage with stakeholders and understand from them what is important – what makes a measurable difference to how they perceive value.
"The second part of this discussion is identifying and objectively assessing things that will make a real difference to those measures.”
The program for Asset Management for Critical Infrastructure included two panel sessions, allowing speakers to interact and freely discuss some of the key issues they face on a daily basis.
On day one, the speakers representing asset owners – Paul Higham, Peter Harcus and Michael Killeen – participated in the Predictive Maintenance Panel, where they discussed some of
the techniques they’re all using to predictively maintain their assets.
The panelists discussed recent innovations when it comes to predictive maintenance, and highlighted the factors most important to them when considering various predictive maintenance technologies.
On day two, delegates enjoyed the Innovation Panel, led by Andrew McAlpine, Asset Performance and Systems Manager at TransGrid, and comprised of keynote speaker Steve Doran, Keith Paintin, Principal Consultant Asset Management at Jacobs and Greg Tyrrell, the Executive Director of the Australian Association for Unmanned Systems (AAUS).
During this session, the panelists considered how innovative asset owners currently are when it comes to the management of their assets, and discussed some of the innovative technologies they are each excited about.
During both sessions delegates had the opportunity to ask their own questions of the panelists, which led to some lively discussion of the topics at hand.
Asset Management for Critical Infrastructure allowed delegates plenty of time to network and get to know other members of the asset management community a bit better.
On day one, delegates participated in a formal networking session in the form of the Speed Networking session. During this session, all delegates had the
chance to meet between five and seven of their fellow delegates, and compare notes on their individual roles within the industry, the useful information they’d picked up during the sessions so far, and to consider potential opportunities to work together in the future.
Feedback from delegates from this session was particularly positive, with many noting that the timing of the session – right before lunch on day one – allowed particularly fruitful conversations to continue and go into further detail over the extended break.
At the close of day one, delegates also enjoyed a more informal networking drinks, where they were able to continue conversations started in the speed networking and meal break sessions in a relaxed environment.
With plenty of opportunities to connect with colleagues, combined with the intimate nature of the event, delegates left the event particularly pleased with the new connections they were able to make over the two day event.
The inaugural Asset Management for Critical Infrastructure was a highly successful event, with delegates commenting on the quality of the speakers, the depth of the presentations and the surplus of networking opportunities as the key benefits of attending the event.
The second annual Asset Management for Critical Infrastructure will be held again in August next year - keep reading Infrastructure in print and online so you can stay up to date with all of the details about next year’s event.
Individuals and organisations from across the Australasian rail industry were awarded for their outstanding achievements and innovations in rail at the recent Australasian Rail Industry Awards Gala Dinner.
The Australasian Rail Industry Awards are hosted by the Australasian Railway Association (ARA) the member-based association that represents passenger, freight, track, manufacturing, construction, supply and other rail companies in Australia, New Zealand and Indonesia.
The awards are also supported by the Institution of Railway Signal Engineers (IRSE), Railway Technical Society of Australasia (RTSA), Rail Track Association Australia (RTAA) and the Permanent Way Institution (PWI).
Over 400 representatives from various sectors of the rail industry attended the sold out dinner to acknowledge the contributions of the twelve category winners.
The award categories and winners are as follows:
♦ Career Achievement Award – Ben Lombardo, Speno Rail Maintenance
♦ Customer Service Award – Metro Trains Melbourne
♦ Employee Engagement Award – NSW TrainLink
♦ Frank Franklyn Young Rail Specialist Award (RTAA) –James Donovan, Metro Trains Melbourne
♦ Freight Rail Excellence Award – KiwiRail
♦ Innovation and Technology Award – Sydney Trains
♦ Permanent Way Institution Young Achiever Award (PWI) –Rebecca Coffey, Lycopodium
♦ Safety Award – Australian Rail Track Corporation
♦ Systems Engineering Award (IRSE) – Zdenka Wright, Metro Trains Melbourne
♦ TrackSAFE Award – NSW TrainLink
♦ Workforce Diversity Award – Brookfield Rail
♦ Young Rail Professional Award (RTSA) – Gordon Baulch, Metro Trains Melbourne
ARA Chief Executive Officer Danny Broad congratulated all of the winners for their outstanding achievements and contributions to the rail industry.
“It was exceptional to see so many talented individuals and committed companies within the rail sector awarded for their excellence, passion and dedication to the rail industry,” said Mr Broad.
“Included amongst the twelve award recipients was Brookfield Rail, awarded for the Workforce Diversity Award for their significant impact on enhancing diversity in its workforce across the past decade, including their achievements in
addressing workforce gender imbalance and their approach to gender pay parity to create a greater workplace for all rail workers.
“The final award for the evening, the Career Achievement Award, recognised Ben Lombardo for his contribution as a leading pioneer and innovator in the Australian rail industry since the early 1980s, when he took over the leadership of the Speno business in Australia, driving key value add technology
development, innovation and the introduction of specialised maintenance technologies into the Australian rail maintenance industry.”
Proceeds from the Australasian Rail Industry Awards go towards the TrackSAFE Foundation, a registered Harm Prevention Charity established by the industry to endeavour to reduce near collisions, injuries and fatalities on the rail network resulting from suicide and reckless behaviour.
A Victorian Council faced with rapid growth is embracing new technologies to deal with the challenges that come with a booming population.
Wyndham City Council, in Melbourne’s outer west, has employed holographic mixed technology to provide stakeholders with a first-hand three-dimensional vision of what the future holds for the city.
Dubbed WynLens, the headsets use Microsoft Hololens technology to transform how the Council presents and uses city data.
With the latest Census data showing Wyndham is the fastest growing municipality in Victoria, Project Director Adam Mowlam, said the Council was faced with unique challenges. With the population growing at such a rapid rate, it’s important to find innovative and fresh ways to deal with the challenges.
“Our WynLens solution presents interactive threedimensional models and data overlays holographically,” said Dr Mowlam.
“Mixed reality is used to firstly present a three-dimensional vision of our future city, and secondly, lay the foundation for a revolutionary decision making tool.
“This brings abstract and technical ideas to life, making themes and issues easier to understand for a wide range of stakeholders.
“In a first for any government anywhere in the world, urban planners and economists at Wyndham City use this technology to understand planned developments and for investment attraction purposes.”
WynLens uses both aerial and Google Map style base maps to present a model of the city that can be zoomed in and out, displaying three-dimensional proposed buildings with information. WynLens also has the ability to toggle data layers, much like a geographic information system.
Dr Mowlam said the traditional approach of governments –presenting two-dimensional data through tables, spreadsheets and charts – does not always provide the insight that stakeholders and investors require.
“Traditional approaches provide very limited information to decision makers, and citizens often struggle to interpret what is being presented to them,” Dr Mowlam said.
“Research has shown that the visualisation of threedimensional form taps into a human cognitive process that we are more significantly capable of understanding meanings more quickly and precisely.”
Dr Mowlam said the tool is now at the point where it will expand to the next stage, ready for public sector-wide adoption.
“This project stage will significantly expand our capabilities. Cloud hosted data will be streamed to the WynLens platform, allowing stakeholders to visualise both static and live datasets, such as traffic, underground assets and air quality,” Dr Mowlam said.
“Our organisation is committed to advancing urban innovation to revitalise our city, and this includes bringing local government, other tiers of government, business, universities and leaders together so we can all work collaboratively and approach large city-wide problems innovatively.”
The creation of the holographic mixed-reality model uses drone imagery, 3D modelling, 3D visual design and a range of geospatial tools. The project was incredibly complex – every step was an adventure into the unknown and required agile thinking and entrepreneurial spirit. Approaching unexplored
greenfield technologies like holographic computing requires an open mindset, and an environment supportive of calculated risk taking.
One of the huge benefits of mixed reality is collaboration. The project team has enabled WynLens to be operated by a host to control the holograms, however this is difficult in large spaces due to the time required to anchor the project space in the real world. The team is currently establishing Spectator View, which allows an audience to see a 2D representation of the world the WynLens users are seeing.
The Council last year created a portfolio dedicated to the Smart City space, with a focus on exploring and embracing new and emerging technologies to change the way the city operates.
Councillor Aaron An, who holds the Smart City portfolio, said new technologies develop at an exponential speed, and a key objective of his portfolio was to identify and deploy new technologies that have the ability to connect, engage and inform residents.
“Smart Cities are driven by citizens who demand better services, and our job at Wyndham City Council is to facilitate that interaction,” Cr An said.
“This technology has endless opportunities when it comes to engaging with citizens, and we look forward to rolling it out to consult with our community on planned developments, and even use it as an education tool.
“We are changing the way we work, engage with citizens and other stakeholders, how we partner with other organisations across the public, private and voluntary sectors, and the way we respond to future challenges.
“Smart technology like WynLens helps us to not only manage infrastructure and resource consumption better, but also engage more effectively with our residents.”
Limitless in possibility, WynLens was initially used to provide an improved visualisation of the urban environment, with a particular focus on planning content including more than 30 current development proposals, ranging between three and 20 storeys across the Werribee City Centre. The project started with four planned developments in Werribee’s City Centre.
The Council’s vision for the four sites, in a public-private partnership, is to revitalise the town by creating a multi-storey carpark, 300 residential apartments, 5,000 square metres of office space, and retail and dining outlets. The plans also include the construction of 100 serviced apartments, a childcare centre, and a community learning hub.
Through a competitive process, Wyndham City selected The Burbank Group and The Pelligra Group as the developers to transform the sites.
Using known parameters, including cadastral boundaries, planning zone height controls and proposed building designs, a three-dimensional digital representations of these buildings can be produced on site.
“It helped us to understand the built environment, and evaluates scenic beauty, anticipate changes in views, and integrate visual aspects during the process. It also, of course, saves time and costs in having renders drawn up for every project,” Cr An said.
The project has already received a huge positive response in the sector, having won the prestigious National Award for Excellence in Local Government earlier this year.
Upon presenting the Council with the award, Fiona Nash, the Federal Minister for Local Government and Territories, described the project as “extraordinary”, acknowledging its potential to be rolled out across the country.
“The WynLens project enhances community engagement and improves planning outcomes by allowing residents to visualise local surroundings using interactive 3D and immersive landscapes,” Minister Nash said.
“In developing WynLens, Wyndham City has succeeded in employing cutting-edge technology to improve its local community’s understanding of planning and development proposals.”
For government agencies like Wyndham City, the ability to simulate future scenarios and mapping of IoT sensors across different city systems through holographic representations is the next stage of computing and fundamental to future cities.
For more information on WynLens visit www.wyndham.vic.gov.au
Taylors recently presented Reality Model evidence at VCAT to demonstrate how a proposed dwelling extension related to the existing built form. This cutting-edge 3D technology provides a unique perspective on the neighbourhood character, visual amenity, overlooking and overshadowing aspects of a proposal.
Taylors’ Reality Models are based on sound survey principles that ensure accuracy and reliability, and are generated by:
● Capturing hundreds of overlapping drone images
● Incorporating ground-based survey data to ensure accuracy
● Superimposing the proposed design in its correct real-world location
● Producing a game-like interactive interface that can be operated in real-time
“Reality Modelling has the potential to revolutionize how development proposals are presented, understood and evaluated. The ability to view an environment from any angle, in real-time, is a truly powerful method of communication.”
Alastair MacColl – Taylors 3D Modelling & BIM Manger, Licensed Surveyor and Expert Witness
contact us:
www.taylorsds.com.au Melbourne | Brisbane | Christchurch | Jakarta
The Rushmore Building in Manhattan. The Getzner experts elastically decoupled the individual floors of the 41-storey building to minimise rail-generated vibrations.
With its innovative solutions, Austrian specialist Getzner Werkstoffe minimises this structure-borne noise, benefiting people and their surroundings.
“Dense urban areas, with transportation, industry, offices, residential areas and public space next to each other, pose a challenge in the field of vibration isolation,” says Thomas Dorfner, Regional Sales Director Asia Pacific at Getzner Werkstoffe.
“Professional vibration isolation benefits not only the people living and working in the area. It also reduces lifecycle and maintenance costs of the capital investments.”
To reduce vibrations in urban areas, Getzner developed high-tech materials like Sylodyn®, Sylomer® and Sylodamp®, that can be modified to meet specific requirements. In Australia and New Zealand, the innovative Getzner solutions reduce noise and vibrations in multiple city centres.
Getzner has completed countless successful international projects in urban centres in recent years, including the Rushmore Building in New York’s Upper West Side. This two-tower highrise complex was constructed directly above an AMTRAK railway tunnel, and
Australia is one of the world’s most highly urbanised countries, with around nine million of the country’s 24 million people living in two cities – Melbourne and Sydney. And urbanisation is going to continue in the coming years, according to experts. This rapid urbanisation poses challenges for city planners, as metros, railways and industrial applications cause vibrations that affect people as well as buildings.
consisted of two railway lines carrying 25-ton axle loads, and a planned future metro line. Due to the proximity to the railway line, rail-generated vibrations were a major concern.
“Getzner’s solution was to elastically decouple the individual floors of the 41-storey building. A very sophisticated solution, in which two stories were completely decoupled in terms of vibrations,” said Mr Dorfner.
Not far from the Rushmore Building is another luxury condominium, The Touraine, a 15-storey residential building containing 22 exclusive residences. The location in the historic Upper East Side of Manhattan, immediately adjacent to three subway lines with more than 1.000 daily trains, is as exclusive as it is worrisome in terms of noise and vibrations.
Using Sylodyn® material from Getzner, the construction project managers subsequently developed an innovative bedding for the condominium building which offered protection from vibrations. Specifically, elastic foundation and wall supports made from the high-tech polyurethane were used to good effect under the foundation of the building and on the surfaces of the foundation walls.
In London, Getzner was responsible for isolating vibrations on a very busy 2.5km long section of the London Underground in the city centre. Sylodyn® sleeper pads protected the track superstructure and reduced the level of vibrations caused by the railway traffic. The Getzner experts faced similar urban challenges in Berlin, with the Hampton by Hilton at Alexander Square, which is located next to busy tram lines and above a planned metro line. Thanks to the bedding of the building on Sylodyn® mats, structure-borne noise was successfully reduced.
Elastic shielding of buildings. Getzner’s high-tech vibration isolation solutions benefit not only the people living and working in the area, but also reduce lifecycle and maintenance costs.
Victorian water corporation Grampians Wimmera Mallee Water (GWMWater) was previously using numerous disparate systems, and was seeking an integrated enterprise solution that would provide it with a single source of truth for all its business information.
Mark Williams, Managing Director at GWMWater, said, “Integration has been a key driver for us at GWMWater. We have shifted very much away from best of breed systems, as we look to improve our overall operational efficiency and productivity.”
GWMWater implemented TechnologyOne Financials, Human Resource & Payroll, Property & Rating, Corporate Performance Management, Supply Chain and Asset Management products to form an integrated enterprise solution.
These products are the key components of TechnologyOne’s preconfigured OneWater solution, which was developed in collaboration with more than 60 utilities and infrastructure organisations.
THE BENEFITS
TechnologyOne’s enterprise solution has enabled GWMWater to transform its business by breaking down business silos and centralising information.
The single modern platform and consistent interface has reduced training and improved the user experience for staff.
“As we’ve added more TechnologyOne products it has made it easier to share information across different departments,” Mr Williams said. “We’ve created a single point of truth for all data, so it isn’t splashed across multiple systems. When you
use a common platform across the organisation, and staff from different areas need to access each other’s data, it forces a discussion that we weren’t previously having.
“TechnologyOne’s software has given our people the information they need at their fingertips. For GWMWater, TechnologyOne has been an enabler of business efficiency.”
GWMWATER’S PERSPECTIVE
GWMWater provides water services to 70,000 customers across a geographic spread of 62,000 square kilometres, which is about 30 per cent of Victoria.
Brendan Nitschke, Manager, Knowledge Systems at GWMWater, said, “When we were using best of breed systems, it was really hard to integrate them.
“When you’re dealing with multiple vendors, they can be reluctant to integrate with competing business systems. We would end up with our data across multiple systems, and were never sure which was the original or accurate source.
“It is much more seamless now that we have all our information in the one system.
“We no longer need to work with multiple vendors or administer multiple systems, and we have been able to save a lot of time by reducing the amount of training our staff need to undertake.”
Mr Williams said TechnologyOne’s software has also provided GWMWater with a future-proof solution, enabling it to better mobilise its workforce and embrace smart mobile devices.
“We have improved productivity quite significantly by having hand held tablets for our asset management workforce.
“We have made more efficient use of our workforce by making the information available instantly to field workers. They can record what they’re doing seamlessly in the field, rather than having to do paper-based recordings and come back into the office to enter it manually.”
The Metro Tunnel will connect some of Melbourne’s busiest train lines, freeing up space in the crowded City Loop, which is currently operating at capacity. Some of the world’s best contractors have just been selected to build the tunnel, Victoria’s biggest ever public transport project.
The $11 billion Metro Tunnel Project is the biggest public transport project in Victoria’s history and is ranked a high priority on Infrastructure Australia’s Priority List.
The project includes the construction of twin nine-kilometre rail tunnels under Melbourne connecting three of the network’s busiest rail lines. This will create capacity from day one of operation for 39,000 more passengers in peak periods, with seamless transition to the existing City Loop to create a true, international-style metro network.
Construction for the project has been divided into four key packages of work. Each will be delivered by a different
consortium of expert companies through differing procurement models.
The Melbourne Metro Rail Authority is the Victorian Government body responsible for overseeing the delivery of the project.
Dividing the work into packages is regarded as best practice for delivering large-scale infrastructure projects, as it reduces delay and cost risks while increasing diversity of expertise and the quality of the project.
The Tunnels and Stations package of works includes the design and construction of the twin nine-kilometre tunnels and five underground stations, as well as the provision of maintenance and other services during the operating
term. This package was procured through a Public Private Partnership and is worth up to $6 billion, making up the bulk of work for the project.
In July, the Victorian Premier, Daniel Andrews, and Minister for Public Transport, Jacinta Allan, announced that the Cross Yarra Partnership (CYP) was the preferred bidder for this package. The consortium comprises nearly 80 companies including Lendlease Engineering, John Holland, Bouygues Construction, Hassell and Capella Capital. CYP was selected as the preferred bidder following an extensive competitive tender process with some of the world’s most experienced construction and tunnelling contractors.
The rigorous evaluation process asked respondents to provide a proposal that addressed a number of evaluation criteria. Against the evaluation criteria CYP’s proposal presented the best design option and value for money.
CYP brings together some of the most experienced designers, builders and project managers in the world. Its members have worked on many of the biggest international rail projects in recent history, including the Crossrail in London, Singapore Metro, Gautrain Rail Link in South Africa and Express Rail Link in Hong Kong. As such, its proposal brought together a local and international architectural team to design new train stations and precincts for the Metro Tunnel, which will be among the best in the world.
The Tunnels and Stations package will create more than 5,000 jobs, including apprentices, trainees and engineering cadets, and CYP will spend 88 cents in every dollar on local content, including labour. This exceeds Victorian Industry
Participation Policy’s requirement of 84 cents for this contract and as a result, CYP will drive job creation throughout the supply chain.
CYP’S
The complexity and size of the Metro Tunnel means its construction presents many challenges. CYP proposes using a number of construction techniques to help ensure the Metro Tunnel is delivered safely and efficiently while minimising impacts to local residents and business.
The new Arden, Parkville and Domain stations, and the entrances to the tunnels, will be built using a technique known as cut and cover. This type of construction involves using excavation equipment to dig a large trench or rectangular hole in the ground, which is then covered by a concrete deck. Once the deck is in place, surface activity can resume as construction works continue below. Concrete panels are then used to form the various levels and internal structures, similar to the construction
of the underground basements of high rise buildings.
CYP’s design for the underground station at Arden includes the creation of new public space around the station and three feature skylights that will bring natural light into the station concourse. To reflect the precinct’s rich industrial heritage, local clay bricks will be used throughout the station and the integration of a water feature at the station entry will enhance sensory connections with the environment.
The CYP station design for Parkville includes an additional entrance outside the Royal Melbourne Hospital, bringing the total number of entrances to four. Changes to Barry Street and Grattan Street will see the creation of new public space, with increased tree canopies and opportunities for outdoor dining and seating.
The station at Domain will feature a floating timber canopy which will bring natural light into the station concourse and pedestrian underpass. It will create
a new train-tram interchange on St Kilda Road, relieving pressure on the world’s busiest tram corridor. The Albert Road Reserve will be enlarged and landscaped to create new public open space for the local community and travellers.
Both stations within the CBD, according to CYP’s proposal, will feature a “trinocular” platform design – an underground construction technique used overseas including Haussmann-St Lazare station in Paris and the iconic Moscow Metro. Three overlapping tunnels will be mined via road headers to create a wide open platform space with vaulted ceilings, providing clear lines of sight and easy navigation for commuters. This construction technique is uniquely suited to the CBD's highly variable geological conditions. As a result of the trinocular design, the platforms are widened by more than seven metres, bringing the total platform width to around 19 metres – one of the widest metro platforms in the world.
Swanston Street will remain accessible
and open to trams while the Metro Tunnel’s CBD South Station is built, due to the construction of access shafts up to 11 storeys deep being dug adjacent to Swanston Street at City Square and behind the Young and Jackson Hotel, where the station entrances will be. These shafts will transport machinery, equipment and workers underground to excavate and line the station caverns below the surface of Swanston Street. This construction approach reduces disruption at surface level and is used on tunnel projects overseas, particularly in constrained city environments.
CBD South will have a direct underground connection to the Degraves Street Subway that will allow commuters to seamlessly interchange between the Metro Tunnel and City Loop services at Flinders Street Station. New lifts will be provided to improve universal access at both ends of the Degraves Street Subway, making this connection fully accessible to all passengers.
Passengers will access CBD South from
eight different points – including an extra entrance at City Square. The other entrances will be at Federation Square, the Degraves Street Subway, Flinders Street, Swanston Street, Cocker Alley and Scott Alley.
The station design at CBD North will have a direct underground connection to link the station with the Melbourne Central concourse, providing a seamless connection between the Metro Tunnel and City Loop services. Literature Lane will be extended to connect Little La Trobe Street with La Trobe Street, and passengers will be able to access the underground station from this new network of laneways. The station entry at Franklin Street is designed with an accessible roof, creating a new public space for passengers and the students who attend the adjacent RMIT University.
Financial close and contract award for this package is expected later this year.
Mining engineer Professor Robert Galler has led many cutting-edge European tunnelling projects. Here, he discusses some of these, and touches on the topics his presentation at the forthcoming Australasian Tunnelling Conference might include.
AProfessor of Geotechnics and Underground Constructions since 2006, Professor Galler also juggles a long list of board appointments, consultancies and R&D projects in the European tunnelling industry.
Austria’s 175-plus-year-old University of Leoben, where he holds his professorship, has a deep history in the field, and was the country’s first university to have a chair of tunnelling.
Pre-professorship, Galler spent a decade at Geoconsult, leading its industrial construction division and heading several major projects, including the Cologne-Frankfurt high-speed railway link.
“We did the design for some quite difficult tunnel projects,” he recalls. “The most exciting sections were to underpass the BAB A3 – a very important motorway link between Cologne and Frankfurt – with a side wall gallery tunnel construction, as well as to build a deep
open pit just parallel to an about 30m high motorway dam construction.
“For both, we had to find special solutions to get approvals for the construction. As I was also the responsible geotechnical engineer, I spent two days of every week for more than one year on the construction site.”
The following large-scale project was the tender design for the Semmering Base Tunnel, over 20km long, which was stopped for political reasons. A new route is currently under construction, and work on the final stage began last year.
“After that I was engaged in the Brenner Northern access tunnel route (about 40km of tunnels split up into eight different lots) where I was the project leader for the design for several lots,” he recalls.
“After that project I was the project leader for the design of the largest railway tunnel of the world – Brenner Base Tunnel.”
A current effort Professor Galler leads is the Zentrum am Berg (ZaB) facility, scheduled to open next year.
The innovation and training hub is located inside Styria’s Mt Erzberg, on the site of a former underground iron ore mine. The complex features five tunnel shafts and 3km of tunnels, which will be used for R&D testing on a 1:1 scale, as well as simulating emergency situations and other training situations.
Its material describes it as offering real conditions “under a large variety of topics like geotechnical monitoring, numerical simulation for geotechnics, research on safety and security, testing of equipment for fire detection and fire protection, risk management, thermo and aerodynamic issues, long-term stability and durability of materials or maintenance of underground infrastructures”.
Other focus areas, says Professor Galler (under his chair about ten research projects are currently running) are the
RICAS2020 underground compressed air energy storage project and in reclaiming tunnel excavation material for reuse onsite or by industrial users.
The latter area was explored in the 2012-2015 DRAGON European Commission (EC)-funded project, for which he was project coordinator.
The project addressed the fact that excavated material is usually dumped in landfill, and there is untapped opportunity to reuse it. It developed a system integrated onto tunnel borers and described as achieving “the automated bypass analysis, online classification and in-stream sorting” of this material.
The steps, as described in an EC summary, involve excavation by the borer’s cutting wheel, load monitoring characterisation on rock properties,
material discharged by belt conveyor, sampling using a hammer sampler, crushing and conveying, microwave moisture analysis and x-ray elemental analysis, photo-optical grain size analysis, then in-stream sorting of the material based on the online classification results.
All steps take place completely underground, and the recycled material could be used onsite in concrete aggregates, or elsewhere, for example in cement or steel manufacturing.
At the time of writing, the topic for Professor Galler’s keynote has not been chosen by the Australasian Tunnelling Society.
Depending on the eventual selection, he says attendees could expect to learn more about long-term stability of tunnels tests and results, results
from testing several 30-40 year old tunnels, the development of resourceefficient and advanced underground technologies, or results from the EU project DRAGON.”
When asked to name a major shift in the industry that he finds concerning, Professor Galler nominates a loss of skilled workmanship.
“It drives the industry in a direction to work with staff which is not understanding the technology quite well,” he offers. “This drives up the number of accidents, but also drives down the quality of the result (the underground structure). As this situation will even get more dramatic in the future, we – the university together with the industry – have to find solutions.”
Professor Robert Galler is speaking at the 16th Australasian Tunnelling Conference in Sydney from 31 October–1 November 2017. The conference will explore the theme Challenging Underground Space: Bigger, Better, More. Only held every three years, the Australasian Tunnelling Conference draws together the best designers, contractors, suppliers and key clients under one roof – don’t miss out on this fantastic opportunity, register now at ats2017.com.au.
The Cat® PM620’s capabilities are going beyond face value after one Australian firm has found a suitable application deep underground as part of Sydney’s WestConnex project.
As a heavy earth moving firm specialising in underground tunnel and shaft works, SU Tunnel and Civil Services requires a range of specificallydesigned plant and tunnelling equipment to undertake these complex projects beneath the Earth’s surface.
Working on projects such as the Lane Cove Tunnel in Sydney, the Burnley Tunnel in Melbourne, and more recently tunnelling works on the M4 East section of Sydney’s $16.8 billion WestConnex project, high-end, customised equipment has always been a must for the company.
Mark Moore, SU Tunnel and Civil Services General Manager, said the company needed to purchase a compact road profiler that could be modified to operate safely in a tunnel environment and could run continuously for almost 24 hours a day.
“We’ve always bought Komatsu or Hitachi Construction machinery, but the recent developments in Cat products and the conversations we had with Hastings Deering guided us towards the PM620,” said Mr Moore.
Launched late last year, news of the new PM620 has spread quickly, with Cat equipment dealer Hastings Deering showcasing the new model through a range of demonstrations, one of which Mr Moore attended.
“We also held our own trial in New South Wales and tested the machine in a quarry under different working conditions, and it was just so good,” he said.
SU Tunnel and Civil Services investigated different profiling machines available on the Australian market and Mr Moore said the PM620 stood out, primarily because of its dust suppression system.
“We shopped around extensively for a PM620 machine, but the dust suppression systems and the single engine, rather than double, was a winner as it helps reduce emissions,” he said.
“We’ve had all sorts of different machines. Cat have obviously invested the time and money into this new model, making it a worthwhile product.”
Seeing the machine in action helped SU Tunnel and Civil Services decide that the PM620 was the right machine for them. In April, it purchased its first Cat PM620 – the first of the new profilers to be sold in Australia.
The company’s PM620 was commissioned and commenced on site that same month.
While Mr Moore asserts that profilers such as the PM620 are better known in the road and asphalt space, this particular machine proved an asset to the SU Tunnel and Civil Services crew working on the WestConnex project.
“The modified dust suppression system is very good.
Hastings Deering assisted in building in extra spray capabilities, which has made it a lot safer, but has also given us the ability to work the machine 24 hours a day,” said Mr Moore.
The integrated Cat Grade Control on the machine automatically controls the rotor depth and cross slope to a preset cutting depth, which also proved a major benefit for the project team.
“The 3D grade and slope control guidance system works well in the tunnel environment, which is another safety benefit as it takes operators on the ground out of the equation,” explained Mr Moore.
“It’s very operator friendly and easily serviceable for maintenance. It’s definitely got that ease of service and Cat has definitely done its homework with these machines.
“It’s also 40 per cent quieter than other profilers out there,” he added.
SU Tunnel and Civil Services is investigating other tunnel projects in Sydney and Melbourne where it’s PM620 can make an impact, and is looking at purchasing more profilers in the future.
Mr Moore said the relationship between SU Tunnel and Civil Services and Hastings Deering is relatively new, however it’s the beginning of a fruitful partnership.
“Hastings Deering have backed and provided us with great support. The upfront effort that they’ve made to modify the machine to suit our requirements has been fantastic,” he said.
“They spent about three days in the tunnel commissioning the machine and WesTrac (another Cat dealership) have been providing backup service and support.
“The PM620 is proven in the European and US markets, but not yet in Australia. Typically, our industry sees this machine
550 + ATTENDEES
60 + SPEAKERS
65 + EXHIBITION BOOTHS
Twice a year, the RLB Crane Index measures crane activity as an indicator of construction sector health across Australia. In this article, we take a look at where cranes could be spotted during the second quarter of 2017, and what this can tell us about the industry.
Consulting firm Rider Levett
Bucknall (RLB) first tasked its Oceania Research & Development and Communication teams with counting cranes in late 2012, based on the theory that the number of cranes in the sky correlated with levels of overall construction activity. Since then, the RLB Crane Index has been released
twice a year, with the second quarter (Q2) 2017 index being the tenth edition. Each edition, crane numbers across Australian cities are indexed against those of the base period, Q3 of 2013, which were indexed to a value of 100, and compared to those of preceding periods to provide a city-by-city measure of changes in crane activity over time.
COUNTING CRANES ACROSS AUSTRALIA
The results of the most recent RLB Crane Index closely reflect general infrastructure and construction trends across the country.
From a base of 100 at Q3 2013, the total crane index value for Australia has now risen to 245 in Q2 2017.
While there has been a slight decrease
in crane numbers since the most recent previous edition of the index in Q3 2016, with Australia’s total number of cranes onsite in key cities dropping from 666 to 654, these figures are still indicative of a significant increase in construction activity over the past five years.
While crane numbers decreased over the Q3 2016–Q2 2017 period in most cities, Sydney and Melbourne saw
significant increases in crane activity. This is representative of more general changes in economic activity in recent years, with New South Wales and Victoria leading the charge, while Western Australia, Queensland, and the Northern Territory are feeling the crunch post-construction phase of the mining boom.
Fuelled by rising house prices, the residential sector dominates when it comes to crane deployment.
The 548 cranes working on residential developments across Australia by the end of the assessment period made up around 84 per cent of total crane activity.
Overall, Australia’s residential sector saw a net gain of nine cranes since the last index.
The only other sectors to show growth in crane numbers were the health, retail, and civil sectors.
NUMBER OF CRANES REMOVED / ADDED
omm e rc i
E
R
H
O
SYDNEY RESIDENTIAL SKYLINES DOMINATE
In addition to being the only cities that saw crane numbers rise, Sydney and Melbourne host the majority of Australia’s active cranes, with 51.1 per cent and 22.3 per cent respectively.
Sydney continues to be Australia's crane hotspot, with a ten per cent increase in cranes since the previous count.
From an index value of 332 in the previous edition, the index has grown to a value of 363. This represents 334 individual cranes on the skyline within and around Sydney, up from 305 in Q3 2016.
During the index period, Sydney saw 147 cranes erected on new projects and 118 removed for projects completed or nearing completion.
The increase in crane numbers reflects growth in the amount of construction works being undertaken within New South Wales, which grew by 13 per cent overall over 2016, with residential activity up by 21 per cent and nonresidential up by five per cent (Australian Bureau of Statistics).
Construction activity is concentrated along the main northern, western and southern corridors of Sydney.
Of all the cranes that can be spotted in Sydney, 87.4 per cent (or 292 individual
cranes) are deployed on residential developments. This amounts to 45 per cent of all Australian cranes and 53 per cent of all residential cranes in Australia.
Since the last report, Sydney has added 128 cranes within the sector and 94 have been removed.
The total residential construction work done in NSW represents only 31 per cent of the national total, yet commands 53 per cent of all cranes working on residential projects. This may reflect different approaches to construction and development. Another point of difference is that unlike other Australian cities where crane activity clusters closer to the city centre, many cranes in Sydney are located in the suburbs.
Sydney cranes working in nonresidential sectors include 13 (or 3.9 per cent) working on commercial construction projects, and seven cranes (or 2.1 per cent) working on transport developments in the civil sector, in addition to smaller numbers working on education, health, civic, or other projects.
Melbourne is Australia’s second hub of crane activity, and saw an eight per cent increase in its RLB Crane Index over the assessment period, reaching an almost
AUSTRALIA NET CRANE MOVEMENT BY CITY NUMBER OF CRANES REMOVED / ADDED
record high of 225 (up from 208).
Melbourne cranes now number 146, up from 131 in Q3 2016, a net gain of 15 cranes. Over the period 92 cranes were added and 77 removed from construction sites.
Crane numbers tell a similar story to construction work figures for Victoria, which were up six per cent in 2016. Increases in construction activity are largely being driven by residential work, which increased by ten per cent while non-residential work decreased eight per cent.
Within Melbourne, 43 (30 per cent) of cranes are located in the CBD and surrounding suburbs, the eastern suburbs host 28 (19 per cent), the northern suburbs have 30 (20 per cent), the southern suburbs have 35 (24 per cent), and the west have ten (seven per cent).
Residential sector construction projects account for 83.6 per cent of all cranes deployed in Melbourne. This represents a total of 122 cranes, up from 109.
Meanwhile nine cranes (6.2 per cent) are deployed on projects in the commercial sector, health and education sectors have four (or 2.7 per cent) each, hotels have three (2.1 per cent), and retail and civic have two (or 1.4 per cent) each.
Outside of Melbourne and Sydney, Brisbane currently has the most cranes erected on construction projects at 12.4
per cent of total cranes. This is despite the city seeing a drop in crane numbers from 95 to 81 since the previous index (correlating to an index of 213, down from 250 at Q3 2016). The vast majority of cranes in Brisbane, at 72 (or 88.9 per cent) are servicing residential projects. Smaller numbers are active on commercial or other projects.
The Gold Coast boasts 30 cranes (or 4.6 per cent of total cranes), down from 34 at the time of the previous count. This decrease was largely the result of seven cranes being removed from the Commonwealth Village project. Twentyeight (or 93.3 per cent) of the cranes are working on residential developments, with the rest working in the hotel sector.
Crane numbers in Adelaide remained unchanged since the previous index, with 15 cranes deployed across the city (2.3 per cent of the total active cranes counted across Australia). Adelaide’s cranes are deployed primarily on health and residential projects (seven cranes, or 46.7 per cent each), with the one remaining crane working on an education sector project.
In Canberra, eleven cranes commenced on projects and 16 cranes were removed from sites since the last count. Total cranes in Canberra now number 19 (2.9 per cent of total cranes), down from 24. The residential sector still dominates, accounting for 14 cranes (or 73.7 per cent).
Commercial, education, and retail projects each had one crane, and two cranes were working on projects fitting into the ‘other’ category.
Of Australia’s remaining active cranes, 24 (or 3.7 per cent) are working on projects in Perth.
Perth’s RLB Crane Index fell by 50 per cent to 65, due to the completion of 16 construction projects resulting in total crane numbers declining by 24 cranes.
This is reflected in the 2016 Construction Work Done numbers. The ABS reported that Western Australia’s work done for the 2016 calendar year fell by 34 per cent.
Cranes in Perth are deployed on residential (37.5 per cent or nine cranes), hotel or commercial (16.7 per cent or four cranes each), retail (8.3 per cent or two cranes), civic (4.2 per cent or one crane), or ‘other’ (16.7 per cent or four cranes) projects.
Crane numbers in Newcastle experienced a similar decline.
Newcastle’s RLB Crane Index fell from a high of 113 (for the last two editions of the index) to 50, a decrease of 55% per cent.
Four cranes now dot the skyline around Newcastle, down from nine, all of which are sited on residential projects. Two new cranes were erected and seven removed during the assessment period.
Only one crane was operating in Hobart by the end of the assessment period (down from four). This crane was deployed on a retail sector project. No cranes were operating on developments within Darwin.
The RLB Crane Index provides a number of interesting insights into construction sector trends across Australian cities, in regards to both project types and locations.
While construction activity may have declined overall due to completion of large construction projects in a number of cities, causing a slight decrease in crane numbers across Australia, residential sector projects, especially in Sydney and Melbourne, are significant growth areas.
Additionally, total Australian crane activity has more than doubled since the 2013 baseline.
For a quick way to assess construction industry health in your city, it turns out it pays to keep an eye on the sky.
Australia’s first dynamically controlled positioning system for a sea crane for the accurate material placement of breakwalls has been installed on the NSW south coast.
Building Shell Cove marina on the NSW south coast involves multiple complex designs, testing the limits of machinery and positioning technology to deliver the project accurately and on schedule.
Coastwide Civil is the main contractor for the job and has invested in a Liebherr LR1280 sea crane to construct the breakwalls for a 300-berth marina and inshore boat harbour.
As the design includes multiple shelves, levels and troughs, along with a variety of different materials, knowing that the correct material has been placed in the right location is paramount to the job’s success.
To ensure accurate material placement, Coastwide Civil enlisted the assistance of Topcon’s Australian distributor, Position Partners, to fit GPS machine control technology to the crane.
In an Asia-Pacific first, Position Partners worked closely with Topcon Positioning Group Europe and Liebherr to fit Topcon 3D-MC positioning technology to the crane.
NSW Field Services Manager Gary Campbell said “There have only been a couple of other installations of this type in the world, so it was exciting to have the opportunity to see firsthand what is possible, and the initial results are extremely promising.”
Unlike traditional crane positioning systems that involve mounting GPS antennas, sensors and cabling to the machine’s boom, Topcon and Liebherr’s development team partnered to create a solution that enables the Topcon
positioning technology to talk directly to the machine and keep all positioning components away from the working end of the machine.
“Keeping the antennas, sensors and associated cabling away from the boom and moving parts of the machine is paramount, not only to maintain consistent accuracy but also to reduce exposure to the elements and salt water,” Mr Campbell explained.
Mr Campbell added that maintaining precise positioning with such long distances from the positioning sensors, whilst compensating for current, wind and the sheer size of the boulders being placed, is no mean feat.
“The crane is able to move a ten-tonne boulder in a single grab, which means it’s going to move in the wind and water, and the positioning technology needs to compensate for that,” he said.
“Topcon’s software also measures from an array of around eight points for each rock rather than just one, because one point isn’t going to give you accurate data on a boulder that’s a couple of metres across,” he added.
To complete the reporting loop, Coastwide Civil has introduced sonar measuring technology to scan the bottom of the seabed and sea wall to produce a render of the different levels. The sonar data is then transferred back to the Topcon machine control system using Position Partners’ Tokara telematics technology.
“Using the sonar technology in conjunction with Topcon machine control enables accurate as-builts to be captured and fed back to the crane to keep the design on track with minimal re-work,” Mr Campbell said.
“It’s a great result to see what can be achieved through cooperation between Topcon and Liebherr’s engineers, local knowledge and experience and a customer who pushes the boundaries to find a better way to build.”
Growing infrastructure demands around the world are creating tremendous challenges and opportunities.
Topcon works to stay a step ahead, by creating solutions that incorporate technology advancements into the way you work today and tomorrow, transforming the way infrastructure is built.
Our integration of high-accuracy positioning, high-speed imaging, cloud-based information management and down-to-earth simplicity creates higher productivity, enhanced quality and improved sustainability. With Topcon, you can stay ahead of your competition and meet the challenges of Infrastructure growth.
Watch Topcon Positoning Systems President and CEO Ray O’Connor’s Bloomberg “NEXT INFRASTRUCTURE” interview: www.topconpositioning.com/Infrastructure.
Let’s discuss your next project: 1300 867 266 | www.positionpartners.com.au
Designed to quickly move large quantities of materials on construction sites, dozers, with their enormous size, can cause serious injury if not operated properly. The new iGD CoPilot from Leica is designed to increase productivity and ease operation on construction sites, reducing the risks of dozer operation by helping to decrease fatigue and stress on operators.
Morten Nissen, Leica Geosystems Machine Control Division product specialist, said the new iGD CoPilot is designed to simplify dozer operations on construction sites when not using 3D or 2D machine control, and can be used by all dozer operators, no matter their training level.
“We designed this new function for three reasons: to improve the productivity of new operators; to decrease the learning curve of less experienced dozer operators; and to decrease fatigue and stress on all dozer operators.”
Mr Nissen said the iGD CoPilot makes sure that the dozer will make a straight smooth push, without any waves.
“This can be used in any situation where a flat surface is needed or material is needed to be moved.
“This function will make less experienced operators more effective, it will make experienced operators even more productive, and remove some of the daily stress. Further, site safety levels will be increased due to having less fatigued operators running dozers.
“A more focused and alert operator is a much safer operator, decreasing the risk of accidents and increasing the general safety level of the job site.”
Mr Nissen said this function is unique to the iGD CoPilot, and is a revolutionary design for dozer operators.
“Now the engineer, manager or surveyor can operate the dozer without totally destroying the surface.”
Mr Nissen said it can be used on an existing Leica iGD2 solution or for a new installation only with iGD CoPilot.
“The new functionality will be available in Leica iCP32 software as of August 2017 to selected markets. Customers can download the new version of software from myWorld.”
The new iGD CoPilot will also available as part of the new Leica iCON iGD2 software which utilises SP14, a state-of-theart inertia sensor.
This dual axis high speed sensor combined with iCON software technology enables the dozer to establish and maintain a height and slope by referencing the blades’ current or set position. This adds an extra mast and laser sensor, allowing operators to work independently of the slope direction if needed.
The iCON iGD2 software is a stand alone system requiring no other reference meaning, no laser or GPS/TPS (3D) use.
The machine can be set to a site reference benchmark or pre-defined height and cross slope. Once set, the automatic blade control takes over and all operators have to do is concentrate on steering the machine.
The Leica iCON iGD2 system can dramatically increase machine utilisation, productivity and optimise material usage on any earthmoving and fine-grading contract. It can be used with a wide range of sensors and combines ease-of-use, and unrivalled flexibility with a powerful and intuitive user interface.
The key to the Leica iCON grade iGD2 system lies in its unique PowerSnap™ concept – a single docking station allowing operators to easily and quickly exchange machine sensors and control panels, depending on the project needs.
Contact CR Kennedy Survey Solutions for more information on the new iGD CoPilot or for any other information on machine control at www.survey.crkennedy.com.au.
Engineers have developed a more resilient type of concrete using recycled tyres that could be used for concrete structures like buildings, roads, dams and bridges while reducing landfill waste.
The researchers, from the University of British Columbia (UBC), experimented with different proportions of recycled tyre fibres and other materials used in concrete – cement, sand and water – before finding the ideal mix, which includes 0.35 per cent tyre fibres, according to researcher Obinna Onuaguluchi, a postdoctoral fellow in civil engineering at UBC.
Recycled-rubber roads are not new; asphalt roads that incorporate rubber “crumbs” from shredded tyres exist in the US, Germany, Spain, Brazil and China. But using the polymer fibres from tyres has the unique benefit of potentially improving the resilience of concrete and extending its lifespan.
“Our lab tests showed that fibre-reinforced concrete reduces crack formation by more than 90 per cent compared to
Are you a contractor that goes through the hassle of calling your local ready-mix company, placing an order and waiting around for that company to deliver it to the construction site?
But what if you didn’t have to do all that? What if you could decide exactly when and where you want your concrete, and usually for less money?
This is possible when using a volumetric concrete mixer for road and bridge repair, utility jobs and more. Unlike traditional concrete mixers that combine ingredients for concrete before delivery, volumetric concrete mixers hold the dry and wet materials in separate compartments, measure them by volume, and mix on-site as needed.
Cemen Tech volumetric mixers produce concrete in a way that is completely different than the traditional process of hiring the local ready-mix company to mix and deliver it to you – on their schedule and at more cost. Volumetric mixers allow you to produce the exact amount of concrete needed – where you need it, when you need it and for less money.
INCREASE YOUR PROFITS. DECREASE YOUR DOWNTIME. EXPAND YOUR CAPABILITIES.
regular concrete,” said Onuaguluchi. “Concrete structures tend to develop cracks over time, but the polymer fibres are bridging the cracks as they form, helping protect the structure and making it last longer.”
UBC civil engineering professor Nemy Banthia, who supervised the work, said the environmental and industrial impact of the research is crucial. Up to three billion tyres are produced around the world every year, generating close to three billion kilograms of fibre when recycled.
“Most scrap tyres are destined for landfill. Adding the fibre to concrete could shrink the tyre industry’s carbon footprint and also reduce the construction industry’s emissions, since cement is a major source of greenhouse gases,” said Banthia, who is also the scientific director of UBC-hosted Canada-India Research Center of Excellence (IC-IMPACTS), a centre that
develops research collaborations between Canada and India.
“We use almost six billion cubic metres of concrete every year,” added Banthia. “This fibre can be in every cubic metre of that concrete.”
The new concrete was used to resurface the steps in front of the McMillan building on UBC’s campus in May. Banthia’s team is tracking its performance using sensors embedded in the concrete, looking at development of strain, cracking and other factors. So far, the results support laboratory testing that showed it can significantly reduce cracking.
The research has received support from IC-IMPACTS; Tire Stewardship BC, the non-profit that manages British Columbia’s tyre recycling program; Atlantis Holdings; and recycler Western Rubber Products, which processed the fibres.
While concrete is very durable, if left unprotected it can be susceptible to corrosion, dilapidation, cracks and discolouration. When this occurs it can compromise the integrity of the structure, reducing its lifespan and making it an eyesore. However with the correct preparation and surface coating, old and damaged concrete surfaces can be made almost new. Here we discuss how the application of the correct construction resin can make concrete great again.
Before: Unprotected concrete is susceptible to corrosion, dilapidation, cracks and discolouration.
According to Chris Bauer, head of flooring at Hychem, one of the main challenges to concrete rehabilitation revolves around education and quality.
“When rehabilitating concrete surfaces the final result is dependant not only on the quality of the product used but also the quality of the installation. You can have the best product on the market but if the surface isn’t prepared or the product installed correctly you won’t achieve optimum results,” Mr Bauer said.
“At Hychem, we work closely with a network of licensed installers that have been selected due to their extensive experience applying coatings.
“We also pride ourselves on our market knowledge, and being able to advise clients on what the best products are for their application. We have open communication with both the installation contractor and the end user to ensure that the client gets the product they need and not what they think they need.”
Another important factor that needs to be taken into consideration is the conditions that a product will be subject to.
“We are conscious of the fact that Hychem products will often be used in the middle of winter in Tasmania and the
peak of summer in Queensland. Because of this we rigorously test our products to ensure they consistently perform across a wide variety of temperatures ranging from 10°C to 40°C,” Mr Bauer said.
“As we also manufacture our own products in Australia we are able to deliver products quickly and provide personalised solutions.”
Concrete is subject to a variety of conditions depending on where it is installed. Conditions such as heavy traffic, and exposure to harsh chemicals and weather conditions can cause unprotected concrete to breakdown over time and become unsafe, unhygienic, and unsightly.
According to Mr Bauer there are a number of options available to rehabilitate concrete flooring depending on the specific needs of the client.
“Hychem offers a range of resins for a variety of applications such as kitchens, wineries, airport hangers, bridges, roads and car parks,” Mr Bauer said.
“For example Hychem’s Polyac BDM – PMMA trafficable membrane system for roads and bridges is fast curing so contractors are able to complete large projects and have them ready for service within the same day or night.
“This means we can not only rehabilitate corroded concrete with minimal downtime and disruption, but it also provides substantial cost savings through labour savings.”
Water and wastewater infrastructure is subject to numerous chemical and atmospheric conditions that can cause concrete to corrode.
As this infrastructure ages and deteriorates there is a greater emphasis placed on rehabilitation.
According to Colin Murphy, Product Manager at Hychem, an epoxy liner such as Hychem’s TL5 is perfect for rehabilitating old water and wastewater infrastructure, making it look brand new and extending its life into the future.
“TL5 can be applied directly onto damaged concrete and has a coverage of in excess of 6mm in one application which means only one coat is needed,” Mr Murphy said.
“We designed TL5 specifically to provide long-term fast-turnaround protection of water assets and it has been tested for over 20 years in Australia’s varied and harsh environments.”
For more information, please contact Hychem on (02) 4646 1660.
The Australian energy industry is currently dealing with an energy trilemma: how do we transition to sources of energy that are clean, affordable and abundant? The Finkel Review, released in June, outlines a range of recommendations to help the industry move towards this goal, and here, Peter Davis takes a closer look at the recommendations and how they will help the industry reach its lofty goal.
The Independent Review into the Future Security of the National Electricity Market by Chief Scientist Dr Alan Finkel (Finkel Review) saw a committee of energy market experts recently make 50 recommendations aimed at addressing the energy “trilemma”; the challenge of achieving secure and reliable energy supply while reducing carbon emissions and ensuring affordability for consumers.
While the proposal to introduce a Clean Energy Target (CET) has dominated political and media discussion, its real focus is ensuring the security and reliability of the power system.
While the fate of the CET remains to be seen, the Council of Australian Governments has endorsed all the remaining 49 recommendations of the Finkel Review and the implementation process has begun.
HOW DID WE GET HERE?
Blackouts in South Australia, and loadshedding in NSW during the summer peak contributed to a growing political realisation that Australia’s National Electricity Market has become vulnerable, with significant concerns arising in relation to power system security (the ability to deal with sudden system shocks) and reliability (the availability of generation to meet demand).
The causes of this decline in security and reliability have been hotly debated however it is clear that the fall in the
proportion of synchronous generation in the energy mix has been a major contributor. Large synchronous generators (such as coal, gas or hydro) naturally support system security through the inertia inherent in their operation and provide reliability through controllable dispatch.
Historically the National Electricity Market has been dominated by large scale synchronous generation, and the current regulation largely takes this support for granted. For example, services that support system security (known as ancillary services) are relatively undervalued in Australia in comparison to other jurisdictions such as the US and the UK, and capacity is not separately recognised and valued.
As renewable generation has been progressively added to the market, and aging synchronous generators have been removed, current regulations based on the assumption that security and reliability would be provided as a natural consequence of the generation mix require re-examination.
The Finkel Review calls for transmission network operators (TNSPs) to provide and maintain a particular level of inertia determined by the Australian Energy Market Operator (AEMO) for each region or sub-region by mid-2018.
This envisages TNSPs providing or contracting for inertia services, or
synthetic inertia through fast frequency response services. These services could be provided by existing synchronous generators, utility scale batteries or very fast load shedding schemes.
Critical questions still to be resolved include how AEMO will establish the appropriate level of inertia in the system and what will be the consequences for a TNSP for failing to contract for or achieve the requisite level.
Threshold questions also include how the inertia services should be provided and their cost determined and allocated. For example, would the usual Regulated Investment Test for Transmission mechanism apply, and could any assets acquired by the network operator to provide the service itself form part of the regulatory asset base provided solely by third parties or otherwise on a ringfenced basis under market or negotiated contracts?
The Australian Energy Market Commission is currently working through these issues and its draft determination is due in November 2017.
One of the most striking recommendations in the Finkel Review is the Generator Reliability Obligation which provides that if a “new” variable renewable energy (VRE) generator wishes to connect in a region that is close to the limit of minimum dispatchable capacity , that it must provide an amount of new dispatchable
generation capacity from within the same region. That dispatchable generation capacity cannot come from existing sources.
A key question for the many renewable generation projects currently approaching financial close or in construction is when this new recommendation may take effect and when it does, what generators will it apply to? Could it, notwithstanding Finkel’s comments about “new” generation, be applied retrospectively given the current boom in renewables construction?
A further question that seems to naturally arise is whether, in order to be effective, the policy may expand to include a requirement on generators to ensure that the dispatchable plant it installed or contracted is available at particular times or in particular conditions. For example, a utility scale battery could be required to maintain a particular level of charge.
The overlap between the Generator Reliability Obligation more broadly, and the potential for TNSP’s to have a need to purchase synthetic inertia services, may support the entry of a new type of market participant who could operate batteries or small or mediumscale dispatchable plant to meet VRE generator and TNSP requirements through market contracts while trading any the excess dispatchable capacity.
The Generator Reliability Obligation could impose major costs and complications on VRE generators connecting to areas of the NEM with a high concentration of VRE generation.
A perennial issue for generators is the fact that the country’s transmission networks are built to support load rather than facilitate the dispatch of generation facilities. It is generally up to individual generators to fund the network extensions and augmentations required to accommodate new projects.
The Finkel Review acknowledges these issues. It proposes a greater role for central planning and coordination in transmission development together
with an implicit acknowledgement that planning decisions should facilitate the efficient connection of future generators (particularly for renewables) and not simply current applicants. The Review proposes development of an integrated grid plan to support ‘renewable energy zones’ on a nationwide basis.
The Finkel Review also contemplates government funding to assist in the establishment of transmission infrastructure in advance of individual generators applying to connect. Various state governments have shown a willingness to directly or indirectly provide financial support to the development of renewables projects in their States, often through certificate procurement or subsidy arrangements. As contemplated by the Finkel Review a viable alternative to these arrangements could be the funding of augmentations to constrained transmission networks in areas with high renewable resources.
In an effort to further manage system security the Finkel Review also recommends that all “existing large generators” be required to provide a ‘binding’ three year notice prior to closure. The intention of such a policy is clearly to provide investment certainty for new entrants and to provide the best opportunity for replacement generation to be developed.
This requirement is no doubt driven by the recent closure of large generators such as Victoria’s Hazelwood Power Station and echoes the “Contracts for Closure” process contemplated by the Commonwealth Government at the time the carbon price mechanism was introduced.
The difficulty with such a scheme seems to be in its administration and enforcement. It is not clear what penalty would be applied should a generator close without giving three years’ notice. It is also not clear what mechanism would be used to force a generator to close if, having given notice, it preferred to remain open at the nominated date for closure.
In recent years there has been an increasing focus among policy makers on the risk that inadequate cyber security poses to Australia’s critical infrastructure.
Responses include the creation of the Critical Infrastructure Centre, the development of the Joint Cyber Security Centre (currently in Queensland, but expanding to New South Wales and Victoria) and the inclusion of cyber security-related obligations in foreign investment approvals and energy network operating licences.
The Finkel Review calls for yet another layer of cyber security oversight for the energy sector with new measures to include annual reporting on cyber security preparedness by all industry participants (including routine testing and employee training). These measures would be administered by a new Energy Security Board in consultation with the Australian Cyber Security Centre and Commonwealth Department of Energy.
The challenge for the Energy Security Board will be to ensure the entire energy sector has appropriate security measures in place while avoiding inconsistency or any inefficient doubleup with the compliance requirements to which many industry participants are already subject.
Much will now turn upon the manner in which the high level and conceptual recommendations in the Finkel Review once transformed into law and policy change.
Affordability, the third and most politically charged arm of the energy trilemma (and the one that receives the least attention in the Finkel Review) is now likely to come under the greatest scrutiny as the cost of improving Australia’s energy security and reliability must now be determined and allocated between industry participants and consumers.
Australia’s energy future came into the spotlight once again, following the release of the Finkel Report. The report highlighted the role of renewable energy, such as solar, to reduce power prices, and increase the reliability and security of energy in the country. Here, we look at the opportunities and challenges for investment in largescale solar provided by the report.
The Independent Review into the Future Security of the National Energy Market, also referred to as the Finkel Report, was handed down to the COAG Energy Council by Australia’s Chief Scientist Alan Finkel on 9 June 2017. It sets out 50 policy recommendations based on four key outcomes: increased security, future reliability, reward customers, and lower emissions. While the report opens up a number of opportunities for the growth of renewable energy to help achieve these outcomes, there are also issues that need to be considered.
OPPORTUNITIES
One of the key recommendations put forward by the Finkel Report is the adoption of a Clean Energy Target (CET).
The report states, “A Clean Energy Target will encourage new low emissions generation into the market in a technology
neutral fashion. Under this mechanism, new low emissions generators such as wind, gas, or the combination of coal with carbon capture and storage, will receive incentives to enter the market.”
The CET also provides renewable energy developers new opportunities by creating an alternative to the Renewable Energy Target (RET), which is scheduled to top out large-scale generation at 33,000GWh in 2020.
While the report recommends that the RET is not extended, the CET would take over its role in encouraging new low emissions generation.
The CET would provide eligible generators with certificates for the electricity they produce in proportion to how far their emissions intensity is below the threshold. These would allow renewable energy generators to negotiate and enter into longer-term PPAs as electricity retailers would be obliged
to purchase these certificates to demonstrate that a predetermined share of their electricity came from low emissions generators.
This in turn will lead to greater investment, including the construction of new large-scale solar, as parties are provided greater security that their investment will be recovered.
While the Finkel Report opens up new opportunities for the investment into new large-scale solar projects, it also increases the costs.
The report recommends the adoption of a new Generator Reliability Obligation, consisting of new obligations for variable renewable energy generators such as solar connecting to the NEM, to ensure reliability is maintained. One of the options to achieve this reliability is the inclusion of battery storage with new projects.
Jeff Lawson, National Construction Equipment Sales Manager at Vermeer, said that the additional need for infrastructure such as batteries will increase the price of construction.
“In the long-term, batteries will increase a solar projects’ energy output and revenue, but the initial increase in construction costs needs to be addressed,” Mr Lawson said.
“One way to offset this extra cost is to use equipment that will make construction more efficient, reduce the risk of project delays or added installation costs, while producing high-quality work.
“For example, Vermeer’s PD10 pile driver has GPS guidance and automation features, ensuring piles can be installed cheaply compared with other foundations such as anchor systems, ballasts or hybrid racking systems.
“The PD10 uses an inclinometer with auto-plumb and a laser-controlled post-depth-control feature to make sure each pile is installed exactly in place, resulting in improved efficiency and productivity while consistently maintaining accuracy.
“Australia is already experiencing a solar boom, and under the CET this can continue to grow beyond 2020 - even with the additional costs of batteries - if contractors can offer developers solutions that drive down costs of construction, ensuring new developments remain an attractive investment option.”
The amount of change we’re currently seeing in the energy industry has had significant implications for Western Power, Western Australia’s state-owned electricity provider. New technologies – including renewable energy sources and battery storage – are naturally having an impact on the way Western Power approaches is day-to-day operations.
For Western Power, a traditional energy network operator with both transmission and distribution functions, and with high solar PV penetration on one side and substantial renewables projects on the other, the broader shift in the traditional energy chain of generation, distribution and retail is being keenly felt.
“We are currently experiencing a greying of the lines between generation and distribution, and distribution and retail,” noted Mr Chalkley.
“The advent of battery storage on one side, as well as smart meters and big data on the other, is also providing a challenging environment for distributors. Add to this grid defection from solar PVs and large-scale renewables, and you have a real melting pot.”
For Mr Chalkley, it’s been important that Western Power recognises this evolution as an opportunity, rather than a threat.
“The challenges we’re facing can be overcome with changes to current legislation and regulation, which haven’t kept pace with industry changes,” said Mr Chalkley. “We are also in a strong position as a trusted provider to test and pilot the new technologies that have emerged. This will counter the revenue decline as solar PV continues to grow.”
Mr Chalkley believes that the disruption being seen in the industry, in the form of new technologies, will significantly challenge the business to consider the best investments when it comes to new asset planning.
“I believe that the disruption has added another step, very early in the planning stage, that challenges whether the traditional form of investment will be the best solution.
“Our traditional network assets and solutions have long lifecycles and long payback periods – but new, emerging
The energy industry is undergoing a period of significant change, the likes of which has never been seen before in its 100-plus years of existence. The transition of energy networks from being one-way providers to two-way networks with renewables integrated is being felt particularly keenly in Western Australia, and we sat down with Western Power Chief Executive Officer Guy Chalkley to discuss his plans for moving his grid successfully into the 21st century.
technologies could make these assets obsolete over a short period of time.
“We do not have all the answers yet, but we remain committed to safety and reliability, whilst we wait for a fuller view of impact of disruption or alternative investment solutions.”
For Western Power to sufficiently take advantage of the opportunities renewables provide – rather than be threatened by them – Mr Chalkley firmly believes the utility needs to take the right approach to integrating renewables into their network.
“Renewables need to be connected in the right places and with the right level of investment in the network to enable their efficient use,” said Mr Chalkley.
“The current network wasn’t designed for renewables, or the two-way flow of electricity for that matter. We do need a good forward picture and plan of what and where future renewables are likely to be located, so we can prepare the network for the changes that will take place.
“This needs to be done at a high level so that we are not simply adding piecemeal, point solutions. A longer term view has to be taken that secures the network for future generations utilising a mixture of renewables and traditional generation.”
One of the key points to consider is the fact that there is a wide variety of emerging technologies out there, that can be considered for implementation into the network. As Mr Chalkley said, there is no one “silver bullet” solution to meet the brief of providing energy that is reliable, affordable and clean.
“All of the new solutions provide customers with alternative options that
can be better than existing options,” noted Mr Chalkley. “And ultimately, this can only be good for the customer.
From a network position, the customer’s particular set of circumstances has to be considered to deliver the most efficient solution possible, to meet their needs for safe and reliable energy.”
To that end, Western Power is moving forward with a number of projects that incorporate innovative technologies that answer customer needs.
“We are piloting a large-scale microgrid in an edge of grid eco-tourist town, a battery storage system in a remote town that suffers above average outages, and a stand-alone power system in a farming community with below average reliability,” said Mr Chalkley.
“Along with these physical projects, demand management tools are helping shape customer behaviours, which is proving to be a smarter investment than the traditional sub-station build in urbanised areas.
“These are four of many options that we will be continue to pursue in the future. As an organisation, we need to work now to be more prepared for higher levels of PV and batteries on customer premises, as well as technologies such as ‘peer to peer’ trading.
“Western Australia has very good sun, wind and wave resources, with global technological partners queuing up to partner and test their projects in an environment that can provide an available site. The fact that land is available and the population is sparse has become an advantage.
“Add to this people who have always got things done and delivered often in adversity, and you have an excellent mix for the future.”
The focus on integrating solutions into the network that offer the best benefits to customers is a sentiment echoed in other areas of the business, particularly when it comes to affordability.
The transformation program that Western Power embarked on at the beginning of Mr Chalkley’s tenure is already delivering significant savings in terms of customer bills, and importantly, safety and reliability has not diminished.
“We also want to improve the process for access and with new technologies, better communication and by taking the time to listen, we believe the customer experience has improved and will continue to improve.
“One of the things that you realise quickly as a monopoly is that we have responsibilities. We are embedded in the community, our employees are also customers and we all reside in the community. Fundamentally the customer has little choice but to use us in some form.
“It is important that we treat people with respect and act with integrity, this involves actively listening to and engaging with our customers and the community to identify and implement innovative solutions that take their input into consideration.
“We aim to engage with the community early and proactively to address social impacts. We engage across a broad platform of stakeholders and community members, from people who are potentially impacted by new or existing infrastructure – through to our regionally based community investment program that aims to make a meaningful contribution to our communities.”
21–23 November
SPEAKERS INCLUDE:
Sir Terry Morgan CBE, Chairman, Crossrail UK
Gerhard Kress, Director Mobility Data Services, Siemens AG
Hon Anthony Albanese MP, Shadow Minister for Infrastructure, Transport, Cities and Regional Development, Shadow Minister for Tourism
Neil Scales OBE, Director-General, Department of Transport and Main Roads
Howard Collins OBE, Chief Executive, Sydney Trains
Emma Thomas, Director General, Transport Canberra
Bob Herbert AM, Chair, Australasian Railway Association
John Fullerton, CEO, Australian Rail Track Corporation
Nicole Stoddart, Managing Director, Construction Services, ANZ, AECOM
René Lalande, CEO, Transdev
Loretta Lynch, Managing Director, Keolis Downer Gold Coast
Alan Beacham, Executive General Manager Rail & Defence, UGL
Nick Easy, CEO, Queensland Rail
Michael Bailey, General Manager Railroad Operations, BHP
Danny Broad, CEO, Australasian Railway Association
Roy Cummins, CEO, Port of Brisbane
Stephen Troughton, Deputy Secretary Infrastructure and Services, Transport for NSW
Michael Miller, CEO, Downer Rail
Damien White, CEO, TasRail
Andrew Dudgeon, Managing Director, Bombardier
Paul Gill, Managing Director Signalling, Alstom Transport
> > And many more
AUSTRALASIA’S LARGEST RAIL CONFERENCE + EXHIBITION
Sponsorship and exhibition opportunities at AusRAIL PLUS 2017 are highly sought after. Ensure you book early to position yourself in front of rail leaders. Contact Deborah Bocock on 02 9080 4348 or email deborah.bocock@informa.com.au
It has been acknowledged for some time now that the installation of roadside safety barriers in Australia could be considerably improved to provide better outcomes for road users. To correct this situation, a number of members of the road safety industry in Australia have come together to establish a scheme that will standardise the training of all personnel involved in the installation of roadside safety barriers across Australia, and achieve optimal safety outcomes for all road users.
In 2011, VicRoads was approached by a number of barrier installation companies and product suppliers with serious concerns regarding practices the industry was engaging in that were likely to compromise the performance of safety hardware.
VicRoads began investigating work practices in 2012, and over a 12-month period, VicRoads randomly inspected a number of routes that received large quantities of permanent barriers. By the end of the 12 months, VicRoads had seen considerable evidence to realise the concerns raised were valid and worth taking action on. Typically, hardware was not being installed in accordance with both VicRoads’ specification requirements and the licensed product suppliers’ requirements.
The investment made by all stakeholders to develop, improve, and to receive acceptance by the respective road authority for any new road safety hardware device is significant. But despite such an investment of effort, there is little or no process or governance around who can install these devices, and limited understanding by the industry on how to specifically design barriers using the systems. This is the critical missing link in this entire process to realising the full potential of our investment in road safety and saving lives.
Following the investigations from VicRoads, in 2013, Roads and Maritime Services sponsored an industry forum in Parramatta, convened by the Austroads Safety Barrier Assessment Panel (ASBAP). The forum was well attended by 66 stakeholders, all concerned with manufacturing, supplying, hiring, renting, installing and maintaining safety barriers in Australia and New Zealand. There was overwhelming support at the forum for improvement to the industry.
Preference was expressed for a national system that not only ensured conformance across states, but created uniform standards and a level playing field for both construction and maintenance across Australia and New Zealand.
The industry and road authorities felt the creation and adoption of a national training and accreditation scheme, not only for the installers, but for designers, engineers, surveillance personnel, and others involved in deploying the correct safety hardware at the right location, constructed in accordance with standards, was paramount.
In response to this need to nationalise and standardise the safety barrier installation industry, a Working Party (WP) was formed by ASBAP from volunteers at the forum representing the industry and road authorities. This WP consisted of 14 representatives from all
Australian states (apart from Tasmania) and, initially, two representatives from New Zealand.
By November 2013, the WP had concluded that to save reinventing the wheel, Australia may benefit from adopting an existing national scheme for safety industry barrier training and accreditation.
It was noted that the UK has the only culturally similar national scheme in an English language framework; and that this solution for industry training and accreditation was effective and responsive to changes in product, standards, laws and regulations.
It was also agreed that in order to roll out a similar scheme in Australia, the WP would benefit from the assistance of the administrator of this scheme, Lantra Awards.
The UK standard was developed in the 1980s to harmonise differing UK county technical standards into a single national standard for training and accreditation in alignment with quality assurance and quality management scheme (QMS) standards. A sector scheme is a bespoke QMS for organisations working on the UK road network, designed to ensure a properly trained and competent workforce in the UK highways industry.
The sector schemes are based on
the ISO 9001:2008 standards, but do not duplicate them. Rather, they interpret them specifically for highway maintenance activities. In the UK there are currently 31 sector schemes, with 14 administrative bodies supporting these schemes.
Sector scheme 2B – Vehicle Restraint Systems is the relevant sector scheme with regards to safety barrier industry accreditation. The scheme applies to all aspects of road safety barrier systems made from parts manufactured off site, for example, the design, the installation, the audit, the maintenance, and the repair of a safety barrier. This sector scheme has been successfully organised and run by Lantra Awards for almost 30 years.
Since operation commenced, sector scheme 2B has offered considerable benefits for road authorities, installation companies and the general public. These include:
♦ Fewer deaths and serious injuries of road users and road workers
♦ Uniform installation and maintenance standards, meaning a longer lifespan for road barrier systems
♦ Guidance on continual maintenance and expectation, meaning a longer lifespan for barriers
♦ Guaranteed minimum standards for all installation and maintenance companies, as only qualified companies are contracted by road authorities
♦ The job being done right the first time, making it more efficient and cheaper to deliver installations in the long run.
Once it was established that the Austroads WP would benefit from the expertise of Lantra Awards, conversations between the two groups began early in 2014.
After a number of meetings between the two parties, both over Skype, in the UK and in Australia, Lantra Awards put a Training and Accreditation Proposal to Austroads early in 2016.
In July 2016, representatives from Lantra Awards visited stakeholders in Auckland, Melbourne, Brisbane and Sydney, presenting their proposal. In November 2016, Austroads offered Lantra Awards a contract to develop scheme 2B into a workable scheme for use in Australia and New Zealand.
The plan is to implement the scheme in Australia and New Zealand as an independent, quality-assured training regime.
All installers and labourers would undertake a one day foundation barrier course to complement, rather than duplicate the existing qualifications available to industry employees.
Installers would then be required to undertake a two day general installation course, where they would learn the theory behind safer roadside barrier installation.
Product proprietors would also develop product-specific training courses to a given template, running over the course of a day, for any installers using their particular products.
All installers would be required to complete an online logbook confirming their practical experience, and independent assessment of the competence of installers in the workplace would take place regularly.
Following the signing of the contract in November 2016, the two parties are now moving towards implementing this scheme in Australia and New Zealand.
It is expected that the timeline to establish and begin teaching the courses outlined above will take approximately six to twelve months.
It is expected that the transition period, during which everyone is trained in the relevant courses, will be approximately two years.
The initial contract period between Austroads and Lantra is a minimum of eight years. This is the foundation period which will enable the scheme to be established, and allow for time to assess candidates with basic training over one five-year period.
Apart from the basic training course, it is expected that during this period some advanced courses will be introduced and some product specific courses will be offered to enable the industry to develop talent and meet the expected demand for continuous personnel development.
Vehicles are on the way to enabling hands-off-thewheel driving on freeways, with trials of automated vehicle technologies underway on one of Australia’s largest tollways.
EastLink’s 40km road network is the largest privately operated network in Victoria. EastLink is the major north-south transport artery in Melbourne’s east, connecting the Eastern, Monash, Frankston and Peninsula Link freeways. EastLink is Melbourne’s fastest road and safest freeway, with traffic averaging 250,000 vehicles per day.
Production vehicles with Level.2 automated vehicle technologies are already on Australian roads, at progressively lower price points, and with increasing numbers. Level.2 means partial automation of steering, acceleration and braking. At least one of the driver’s hands must be on the steering wheel at all times.
One of the most widely implemented automated vehicle features in these cars is highway autopilot.
Today, highway autopilot generally means a combination of lane keeping assist (the vehicle steers itself within the lane) and adaptive cruise control (the vehicle adjusts speed via acceleration and braking to maintain a safe distance to other vehicles), with onboard sensors dynamically monitoring the presence of other vehicles and road users. In freeway conditions, this supervised driving allows a more relaxed driver load when used according to the vehicle manufacturer's guidelines.
Some of the latest vehicles also include autonomous overtaking, which the driver initiates by flicking the indicator stalk. The vehicle finds a safe overtaking opportunity, autonomously implementing the overtaking manoeuvre with indicator signals.
Emergency auto-braking, already available, will be supplemented by automatic collision avoidance, involving a combination of steering and braking.
While vehicles are now reading speed limit signs to inform motorists and provide warnings when the speed limit is exceeded, the next innovation will be automatic adjustment of speed to the prevailing limit.
Over the next few years, technology step changes such as these will be combined together by vehicle manufacturers to enable Level.3 conditional automation, with all aspects
of the driving task automated under certain circumstances (for example, hands-off-the-wheel driving on freeways). The driver must be ready to take back control when prompted by the vehicle. This will of course be subject to legislative changes in each jurisdiction.
Some of the latest vehicles on sale today already have the necessary hardware sensors to take the vehicle from the current Level.2 highway autopilot all the way to Level.3 handsoff-the-wheel driving on freeways.
This will be achieved through software upgrades (at regular service intervals or by auto-download via wireless data networks) together with high definition maps for automated driving and sensor augmentation where necessary.
Therefore testing the compatibility of existing freeways such as EastLink with the latest Level.2 vehicles is a useful task to provide early warning of any incompatibility, so that it can be addressed by vehicle manufacturers and freeway operators. This will expedite the development of Level.3 hands-off-thewheel capability.
As the operator of a major freeway, EastLink needs to assess the envelope within which Level.3 hands-off-thewheel capability will safely operate. Which parts of EastLink, or the whole network? At what times, or all of the time? Under which conditions, or all conditions?
These are some of the practical purposes of the EastLink trials, making them the first of their kind in Australia.
The trials are being undertaken by EastLink in partnership with VicRoads, the Australian Road Research Board, La Trobe University and RACV. While EastLink, which complies with VicRoads’ freeway standards, is the main test site, trials also include stretches of other VicRoads freeways.
Although the trials are being conducted for the benefit of EastLink and VicRoads, trial results will be disseminated nationally, and freeways across Australia may benefit from adjustments made by vehicle manufacturers as a result of the trials. EastLink trials have already been
conducted with vehicles provided by a range of manufacturers including BMW, Honda, Mazda, Mercedes, Mitsubishi and Volvo. The most recent technology demonstration involved the new Tesla Model X. Additional manufacturers, including Audi and Toyota, will soon be providing vehicles to assist the program.
The trials have already identified opportunities to improve the compatibility between new technologies and freeway infrastructure. For example: Line markings:
♦ Good quality of line markings –including reflectivity and luminosity – on both sides of the lane are essential to avoid “dropouts” of the lane keeping assist function, and to help a vehicle maintain its position centrally in a traffic lane. Partly driven by the trial results, EastLink has recently repainted 100 per cent of its line markings.
♦ Gaps in contiguous line markings should be avoided, as this may lead to dropouts of the lane keeping assist function or unintentional lateral movement.
♦ In construction zones, the use of temporary yellow line markings conflicting with white line markings is incompatible with the lane keeping assist function, causing dropouts. The automated functions in different vehicles may dropout with varying amounts of advance warning. When planning traffic management for construction zones, road operators will need to consider whether lane keeping assist dropouts are acceptable on a case by case basis.
Speed signs:
♦ Consistency of speed signage (format and placement) and maintaining line of sight visibility will enable more reliable interpretation by vehicles.
♦ Speed signs on freeway exit ramps or side roads need to be located well away from the main carriageway so they are not confused for main carriageway signs.
♦ Conflicting or confusing speed signs should be avoided, as vehicles find it very difficult to determine the correct speed limit under these
circumstances. This could occur within a construction zone where there is poor implementation of traffic management plans, or in circumstances where different speeds apply to different vehicle types (e.g. a lower speed limit for trucks).
♦ Variable speed signs are increasingly deployed on Melbourne’s freeways. Roadside variable speed signs are read very well by some vehicles, while other vehicles are not yet reading them reliably.
♦ The flashing annulus feature on variable speed signs (when speed is lower than normal) is not expected by some vehicles, impacting recognition.
♦ In general, overhead speed signs, which are an increasingly common format on Melbourne’s freeways, are not yet read reliably by vehicles. Lane control signs:
♦ Overhead lane control signs (lane open or closed) are increasingly common on Melbourne’s freeways. However, they are not yet recognised and used by vehicles.
Vehicle manufacturers and freeway operators are now able to work on taking advantage of these opportunities to further improve Level.2 performance, which will pave the way for the introduction of Level.3 capability.
Road operators across Australia, informed by their knowledge of the infrastructure on their roads (including line markings and signage) and the capabilities of Level.2 automation systems already appearing in vehicles, may wish to make some input into a nationally consistent operational domain on the road network.
With Level.3 hands-off-the-wheel driving on the way, it’s envisaged that freeway operators will need to communicate directly to autonomous vehicles, for example to communicate a change in conditions or the operating environment (for example, an emergency incident, congestion event, or lane or freeway closure).
As part of the EastLink trials, connected vehicle transceivers are being installed at three of EastLink’s tolling gantries, to create a section of EastLink enabled for V2X communications.
Initial testing has been focused on verifying the compatibility of connected vehicle communications (5.9 GHz) with the existing DSRC tolling tag communications (5.8 GHz).
Next, the trials program will conduct
on-road tests of different message types.
EastLink received a Special Commendation award from the Australia & New Zealand Driverless Vehicle Initiative (ADVI) for these trials of automated vehicle technologies.
EastLink will continue to is raise
public awareness of automated vehicle capabilities, and will be communicating the progress of the trials via email newsletters to 360,000 EastLink customers, and by media engagement (with extensive coverage already achieved on TV, print, radio, industry and automotive news media).
When I first joined ITS Australia, I spent many hours explaining to people what ITS stood for. Today, ITS is widely recognised as the abbreviated form of Intelligent Transport Systems and it is an accepted part of the vocabulary across governments, business, learning institutions, and increasingly in the community.
What has also changed is the breadth of the industry. Transport, vehicles and infrastructure are still very much at the heart of the ITS industry, but increasingly falling under this umbrella are industries which were once considered fringe or even futuristic.
The ITS industry has evolved and it continues to transform. New technologies are being developed and deployed at a rapid rate, creating new opportunities in Australia and internationally. Today, nearly every Australian state conducts at least one connected and automated vehicle trial, with South Australia recently announcing Australia’s first vehicle to pedestrian technology trial where vehicles interact directly with pedestrians’ and cyclists’ mobile phones to improve safety on the road network.
End users have also changed their behaviours and demands. Mobile smart devices have enabled consumers to access information on-the-go and they expect accurate, real-time information and options.
Global ITS leaders, including traditional and newly aligned industries, will converge in Brisbane to discuss how the landscape is changing and what this means for industry and consumers. The Australian Intelligent Transport Systems Summit is Australia’s largest industry-led ITS Summit and, aptly themed Transforming Transport, is hosted by ITS Australia in partnership with the Queensland Department of Transport and Main Roads.
International keynote speakers include Steve Shladover, Program Manager, Mobility, at the California PATH Program,
and Anthony Ferguson, Deputy Director, Traffic and Technology Division, Department for Transport, UK. Mr Ferguson said he was struck by how much Britain and Australia had in common in terms of transport technology when he attended the 23rd ITS World Congress in Melbourne last year.
“I feel ITS does not have the prominence it should, bearing in mind how it affects our daily lives. The rapid evolution of communications technology is creating possibilities that could bring ITS right into the mainstream of transport thinking,” said Mr Ferguson.
Big Data, the Internet of Things, access, analytics and realtime assessments increasingly underpin intelligent transport systems. ITS Australia, as set out in our report, Smart Transport for Australia, recommends all real-time dynamic data from government should be freely available, that strategies should be implemented to ensure reliable and ubiquitous network coverage, telemetry, cyber security and data integrity.
Kath Johnston, Manager Data and Analytics, Policy, Planning and Investment at the Queensland Department for Transport and Main Roads specialises in complex congestion problems. She said the challenge is not technical, but commercial and cultural.
“The fourth industrial revolution is here,” said Ms Johnston. “Increasing data volumes, computational power and connectivity, the emergence of analytics and businessintelligence capabilities, new forms of human-machine interaction and dissemination to the physical world are set to disrupt current business models in a range of industries. Transport is one such industry.”
Zac McClelland from VicHyper is leading the Southern Hemisphere’s only hyperloop project and will discuss the project’s potential at the Australian Intelligent Transport Systems Summit.
Increasingly influencing transport technology are industries once considered distant, but now very much aligned and integrated with intelligent transport – for example, payment gateways for private and public transport users who expect to pay for services with a swipe of a finger online. Convenience, choice of travel and payment systems have developed to the extent that the concept of Mobility as a Service (MaaS) – another phrase unheard of just a few years ago – is one of the fastest growing sectors in the ITS industry. MaaS is a key contributor to Smart Cities and the liveability of our cities, suburbs and regional communities.
Hyperloop travel was certainly not on the agenda at last year’s ITS Summit. This year, the prospect of travelling in air-tight pods flying in near-vacuum tubes at 1000km/h is a genuine talking point. VicHyper is leading the Southern Hemisphere’s only hyperloop project and Zac McClelland, Project Leader, expects technology to significantly reduce travel times and costs, reduce the carbon footprint, and increase travel safety.
“The technology is already there. Even though a Hyperloop hasn’t been made before, all the systems are used somewhere else. We move eight million domestic passengers a year
between Melbourne and Sydney, and around five million a year between Sydney and Brisbane. We’ve got the resources and knowledge, the energy from solar power, it’s just ideal.”
Also reflecting the evolving nature of the industry, are the ITS Summit technical tours and exhibitors which cover a wide range of advanced technologies not previously available including access to behind the scenes intermodal facilities, wireless innovations, intelligent sensors and scalable data flow solutions.
Australia’s intelligent transport systems industry is leading the way in assessing, facilitating and monitoring the transformation of the way we transport people and freight. ITS is increasingly influencing decision making and positively impacting the economy.
As Mark Jackman, Regional President, Chassis and Vehicle Safety Systems, Robert Bosch Australia, explained, “The ability to move freight and people for business and leisure is key to our economy and wellbeing. Every intelligent city requires a smooth and efficient transport system, and a vast and decentralised country like Australia is the perfect place to design and test Intelligent Transport Systems.”
Australia’s cities are changing, and as a result, the way we move goods to their ultimate destination is changing too. The Australian Logistics Council has made a series of recommendations to the Australian Government to help make sure our freight strategy is fit for purpose as we move forward.
In the lead-up to the 2016 Federal Election, the Australian Logistics Council (ALC) urged the development of a comprehensive National Freight and Supply Chain Strategy to address these challenges.
The Federal Government subsequently agreed to undertake the development of such a strategy during the Prime Minister’s Annual Infrastructure Statement to the Parliament in November 2016.
ALC believes the inquiry and the subsequent development of a National Freight and Supply Chain Strategy
represents an ideal opportunity to establish a high-level framework that will facilitate the safe and efficient operation of Australia’s supply chains, which will:
♦ Provide an integrated and efficient freight transport and supply chain network for Australia’s international and domestic supply chains
♦ To the fullest extent possible, ensure that policy settings and regulation are competitively neutral between the different freight transport modes
♦ Allow freight operators to innovate and increase the productivity
of the freight logistics services they provide, in order to improve outcomes for consumers, Australia’s industries and the wider economy
♦ Contribute to continuous improvement in the safety of all freight logistics operations, as well as improved societal and environmental outcomes
The lived experience of Australian society over recent decades points to increasing levels of urbanisation. Effectively, this means we are trying to do more in a limited physical space.
In particular, resurgence in the desirability of inner-city living, coupled with rapid rates of population growth, present some urgent challenges for our freight logistics industry.
The essential items which most Australians take for granted in everyday life – food to eat, household appliances, clothing, medications and vehicles to name just a handful – are generally not grown or manufactured close to the places where most of us live.
These commodities must be transported from their point of origin to the retailers from which we purchase them, or otherwise delivered directly to our doorsteps from ports, freight depots or warehouses.
Yet, as we create more populous cities, it is fast becoming apparent that our existing planning regimes and approaches to development fail to adequately prioritise the movement of freight.
The congested state of many major freeways and key arterial roads, as well as traffic gridlock within cities themselves, is a constant source of annoyance for many Australians. However, more than simply being an irritation, these problems are symptomatic of a far deeper issue.
Capacity constraints in the road network are not only a problem for motorists – they also impose significant costs on the freight logistics industry.
The disruption to the supply chain that occurs because of road congestion, as well as capacity issues afflicting ports, airports and rail freight facilities all have an impact on the cost of moving freight – and ultimately, the prices paid for goods by Australian consumers.
Indeed, congestion on our roads alone is already costing the Australian economy some $16 billion a year. Without remedial action, that cost is projected to rise to more than $50 billion a year.
With the National Transport Commission projecting Australia’s freight task will grow by 26 per cent over the next decade, it’s clear that unless corrective steps are taken quickly, the safety and efficiency of Australia’s supply chains are at enormous risk.
Australia’s supply chains do not stop at state borders. Our economy is national – and accordingly a nationally consistent approach to infrastructure and the regulation of freight movement is required.
In an ideal world, a national economy should be managed by the national government. This includes the responsibility for the development of the infrastructure and regulatory settings necessary for the nation’s supply chains to operate safely and efficiently.
In many circumstances, the Australian Government has encouraged the development of individual pieces of infrastructure through financing. However, many of the decisions relating to the planning and delivery of such projects are made by state and/or local governments.
This is the reality of Australia’s federal structure.
Like all other industries, the freight logistics sector must work within the restraints imposed upon it by the Australian Constitution.
The unfortunate by-product of this constitutional reality can often be duplication and delay in achieving the sort of policy reform that industry –and the entire economy – badly needs.
However, recent policy initiatives announced by the Federal Government, including the formation of an Infrastructure Financing Unit within the Department of Prime Minister and Cabinet, appear to indicate a desire on the part of the Commonwealth to become more active regarding infrastructure and planning issues.
Certainly, it would be enormously helpful to the freight logistics industry – and to the economy more broadly – if the Federal Government could do more to ensure a greater consistency of approach to infrastructure development and planning issues among the various jurisdictions that play a role in such issues.
Of course, it is imperative that greater Federal Government involvement results in more consistent outcomes, and does not simply add to the complexity and cost of infrastructure development in Australia.
Over the last six months, ALC has worked closely with its members, freight logistics industry participants and governments at all levels to work through many of these issues, and develop a comprehensive roadmap which sets out many of the challenges being faced by industry, as well as identifying some practical solutions.
The resulting document, Freight Doesn’t Vote, represents ALC’s final submission to the Inquiry for National Freight and Supply Chain Priorities
It recommends reviewing a number of regulatory practices that inhibit the efficient movement of freight, such as curfews and bans on freight vehicles, as well as identifying opportunities for the Federal Government to incentivise good planning practices and encourage the take-up of new technologies that can deliver better outcomes.
The submission does not shy away from recommending initiatives that may be politically challenging – particularly around greater Commonwealth involvement in planning, as well as road pricing and investment reform.
However, the reality is that Australia’s economy is being transformed by population growth, by technological change and by the changing behaviour of ever-more discerning and empowered consumers. Like all other industries, the freight logistics sector must adapt to an economy in transformation.
Moreover, given the exponential growth of the middle class throughout Asia, and thus the importance of exports to Australia’s continuing economic performance, becoming a world leader in supply chain efficiency and safety is not merely desirable, but essential.
The engineering and construction industry is at the cusp of a new era, with a proliferation of technology start-ups developing solutions to change how companies design, plan and execute projects, and to combat issues that have dogged the sector for decades, such as difficulties with mobility, and compiling and sharing project information.
These improvements are especially important at a time when construction projects are becoming increasingly complex and expensive, and the pressure to improve costs, timelines and efficiency is increasing.
In order to assess the range of solutions currently available or in development, and their potential benefits, McKinsey & Company analysed more than 1,000 construction start-ups
and their products. To investigate how engineering and construction companies can better navigate this changing landscape and improve their strategies to deploy new technologies, they also reviewed responses from a survey of over 200 senior executives in the industry.
The resulting report provides a range of insights into how technological innovation is shaking up the sector, and how companies can make the most of the opportunities this provides.
While start-ups were developing tools across the entirety of the construction project lifecyle – including the design, preconstruction and construction phases – the majority of new
New technologies are transforming all stages of the engineering and construction process, with the potential for companies to realise significant improvements in efficiency, safety, collaboration and mobility. A new report prepared by consulting firm McKinsey & Company, titled The new age of engineering and construction technology, shines light on some of the key innovations transforming the industry, and how companies can best deploy them for more efficient, mobile workflows.
technology products targeted the construction phase. These included enterprise resource planning systems, which are used throughout construction.
Technologies developed for the construction phase generally addressed use cases in three main categories: onsite execution, digital collaboration, or back-office integration.
Solutions for onsite execution primarily focused on:
♦ Safety
♦ Quality control
♦ Field productivity
Solutions for back-office integration focused on:
♦ Enterprise resource planning systems
♦ Equipment management
♦ Scheduling
♦ Materials management
Solutions for digital collaboration focused on:
♦ Document management
♦ Design management
♦ Performance management
♦ Contract management
While many of the start-ups examined were simultaneously developing tools for multiple construction use cases in the same category, fewer were developing cross-category solutions.
Frequently, many of the biggest challenges and unexpected issues that arise during a construction project occur onsite. As a result, various mobile solutions are being developed to better integrate workflows, increase productivity, and enhance safety and quality in the field.
Innovative tools to enhance field productivity provide the capabilities to track crew deployment in real-time, manage project staffing, and track onsite productivity at a trade and worker level.
For instance, some tools track the active working hours of each team member onsite by analysing data from wearable GPS devices, or by allowing workers to enter information about their activities, location and hours into mobile devices in the field.
Additionally, technologies that enable team members in the field or elsewhere to remotely access and update important project information in real-time can result in significant productivity improvements and reduce unnecessary datahandling.
Other field productivity applications help companies to manage project staffing across skilled trades or to monitor onsite productivity at the trade or worker level. With one tool, for instance, managers can immediately retrieve data on actual project hours, budgeted hours and remaining hours.
Other solutions focus on improving safety outcomes in the field. These solutions include tools enabling real-time reporting and tracking of safety concerns or incidents via workers inputting data onto mobile devices, like smartphones and tablets, enabling faster response to problems and better data. Additionally, many solutions enable safety warnings and tips to be rapidly disseminated to the entire workforce, through real-time alerts.
One area identified as gaining significant momentum in recent years was safety monitoring enabled by wearables and virtual or augmentedreality tools.
New quality assurance solutions allow managers to inspect remote sites via photos taken in the field and tagged with various information including geographic coordinates, while others allow workers in the field to update and track their punch lists in real-time.
The use of GPS during projects, particularly those related to transportation, has already increased the accuracy of project specifications. This, in turn, increases efficiency and accuracy during onsite execution.
In the future, leading engineering and construction companies hope to create autonomous quality-control systems by combining new technologies and artificial intelligence with other tools, including GPS and building information modelling (BIM).
While most tools in the onsite execution cluster fall into these areas, construction start-ups have also developed products to assist with many other onsite activities, including supply chain logistics.
A variety of innovative solutions have been developed to better integrate back-office functions to exploit valuable project data.
Many of these tools focus on giving project managers and other staff members onsite or elsewhere immediate access to real-time backoffice data on their mobile devices.
Key focuses of back-office integration solutions include scheduling, managing equipment and materials, and enterprise resource planning.
Scheduling solutions enable tasks to be created, assigned, prioritised and tracked in real-time, and mean that work plans and schedules can be delivered immediately to workers, wherever they might be stationed at the time.
Materials and equipment management
Tools for materials management allow vital construction materials to be identified, tracked and located across the entire supply chain, through GPS tracking or mobile data input. Likewise, equipment management solutions enable tracking and management of the construction-equipment fleet.
Enterprise resource planning
Enterprise resource planning solutions frequently focus on work order management, remote monitoring building systems, predictive analytics for system management, mid to small project management, and asset management.
These include tools to allow contractors to see which change orders a company’s customers have approved, including those for which they have not yet paid.
The various parties involved in successfully executing a construction project – including architects, engineers, project managers, and construction contractors – are more numerous and widely dispersed than those in most other industries.
However, they need to communicate frequently, since certain changes, such as a seemingly minor modification to a materials order, could significantly increase timelines or costs if made too late or not effectively communicated to all parties. This creates a need for mobile solutions enabling more effective collaboration and making sure all parties are on the same page at all times, with the most accurate up-to-date information.
Key areas of innovation in digital collaboration technology include document management, design management, performance management, and contract management.
Document management
Many start-ups are creating tools that let companies upload and distribute documents across all sites, track changes to them, search all projects across phases, and record all decisions made about their content.
For instance, changes to digital documents made in the field can be input on mobile devices and distributed immediately, keeping information up-to-date for all parties and removing the need for changes to paper documents to be transcribed.
In some cases, document management tools can also serve as a permanent repository, providing easy access to past records.
Design management
Staff on engineering and construction projects often need to update blueprints and other design documents while onsite.
Rather than returning to the office to complete such tasks, as these workers would have done in the past, innovative technology enables them to make changes in the field. For instance, one mobile platform lets staff add markups, annotations and hyperlinks to blueprints.
Other design management solutions on offer enable the visualisation of drawings and 3D models onsite on mobile platforms such as tablets and smart phones.
Performance management
With innovative performance management tools, managers can update and immediately share information (including workforce data) in the field, particularly during the crucial pre-construction and construction phases.
Available tools also offer capabilities for real-time monitoring of project progress and performance, and enable updates and past reports to be viewed on handheld devices.
Some performance dashboards can automatically import field data, simplifying the process of collecting information.
Contract management
Contract management tools have been developed to help staff with a variety of critical tasks including updating and tracking contract compliance checklists, and collecting and disseminating information about client and contractor communications that occur when contract terms are renegotiated.
According to McKinsey & Company, it is vital for engineering and construction companies to invest in the right new technologies and deploy them in the right way, in order not to be left behind in a rapidly changing industry.
The report suggests that following four key steps can maximise a company’s chances of successfully taking advantage of innovation:
1. Create a focused digital strategy and organisation
♦ Determine performance goals and identify digital tools that help achieve them
♦ Appoint a group or leader to take responsibility and drive results
♦ Analyse current IT systems and determine if they can support new tools
♦ Identify gaps and set timelines for resolving them
2. Turn projects into test labs
♦ Identify potential use cases and launch tool pilots during projects
♦ Measure key performance indicators, celebrate success, learn from failures, and encourage widespread rollout of promising programs
3. Let data lead the way
♦ Revise fundamental business processes to support digital solutions
♦ Simplify the process for piloting and deploying digital solutions
4. Increase investment in digital solutions
♦ Contemplate M&A deals with technology companies
♦ Identify potential investment partners
♦ Establish “listening posts” in the industry
The report concludes that “companies that place the right bets now will probably be the industry leaders in the next ten to 15 years if they match their greater investment in technology with a company-wide commitment to change”.
MidCoast Council recently adopted an innovative approach to replacing an existing river crossing along one of its rural roads, utilising residential house slab technology – also known as waffle pods – in what is believed to be the first time the system has ever been used to create an insitu concrete box culvert.
While the end result appears deceptively simple, it meets many of the requirements for council works, being cost effective, fit for purpose and environmentally friendly and providing an improved level of service to the residents who use the road.
The crossing on Belbora Creek Road, known as Causeway #1, was originally
a concrete causeway, with a small concrete pipe installed adjacent to the southern shore. After the neighbouring Gloucester Council upgraded other causeways along Belbora Creek Road users reported that Causeway #1 had become a dangerous and substandard piece of infrastructure.
Preliminary investigations into the existing crossing revealed that the causeway consisted of three or four different generations of concrete slabs bounded by kerb logs poured at different levels. The standard upgrade
of a causeway is to rip it out, remove the existing causeway, install concrete box culverts at the bed level and reinstate the causeway slab over the top of the box culverts which effectively lowers the upstream impoundment to bed level. This was the initial design thinking for this upgrade also.
Plans were prepared; however, the 45° skew of the road in relation to the creek made this a relatively expensive construction method. In addition, Council construction crews were extremely wary of this
as a methodology, having lost their groundworks to rainfall events on several other comparable projects during recent wet years.
With significant creek flows occurring at this location, the potential for Council to construct a bridge that remained flood-free at the ARI 100-year or one per cent Annual Exceedance Probability (AEP) level was quickly discounted, and a number of alternate solutions were assessed based on the philosophy used in downstream upgrades in the neighbouring Council.
Local consultant Matrix Thornton Consulting Engineers (MTCE) was contracted to develop potential solutions and provide a suite of possible alternatives. MTCE evaluated 20 different options, including girder logs, precast concrete beams, steel
girders, box culverts, plastic arches (as used in sewer trenches), Bondek slabs over concrete piers and waffle pod construction.
The evaluation looked at construction costs of the various elements, the pros and cons for each, and provided a method diagram for many of the options.
Being engineers who had designed many house slabs using the waffle pod technology, MTCE was comfortable with this method of construction and advocated for it, noting the potential negatives of some of the other alternatives and the specific advantages of the waffle pod product. MTCE noted particularly the speed of construction, the ability to leave the existing causeway in place, and minimising disturbance to the creek bed. While a unique solution for a causeway replacement project, they inspired confidence to proceed with
Waffle pods have been used in house construction for many years. First developed in South Australia to cater for the highly reactive clays of Adelaide, they have become widely used across Australia. The pods are boxes, 1.09m square and varying in height. Depths of 175, 225, 300 and 375mm are available to suit different ground conditions. They are made of light Styrofoam, much like an old coolite surfboard. These boxes are basically void formers that suspend a concrete slab over the boxes between concrete beams that are formed between the pods. For houses, this creates a stiff slab that is very strong. For the waterway area of this project the pods were arranged on the causeway for the pour and
subsequently removed to create a skewed insitu box culvert resting on the old causeway. The pods, stacked two high and two wide, created openings 2.18m wide and 0.6m high in the box culvert sections. Beyond the waterway, the pods were placed on the road and remain in place. The size of the pods was reduced as the road rose out of the causeway until it basically joined back to the level of the top of the new causeway. These approach pods significantly reduced the amount of concrete that was used in the abutments.
Removal of the pods from the causeway was considered a challenge. The pods were wrapped in plastic to prevent adherence of the concrete. MTCE engineers tested varying amounts of solvent required to cause the pods to collapse, primarily to prevent any excess solvent leaching into the river. Ultimately this solvent process proved too slow for the contractors who found that mechanically breaking up the pods with a crowbar and shovel, and removing
the material by hand, was the quickest method. The Styrofoam of these pods held together well, so there was very little breakout and the pieces were easily removed, collected and stored.
When these pods were first introduced into NSW, legislators foresaw a problem with the leftover sections of pods becoming a litter problem, and determined that the manufacturer or supplier must collect all unused portions of the Styrofoam for re-use in the manufacturing process. On this project, all left-over foam was packaged into large bags and the supplier picked it up and returned it to the manufacturer for recycling.
The design was by no means straightforward. The initial plan sets contained only three pages. The final plan set that went to tender was 20 pages, containing numerous cross sections detailing the various stages of construction as foreseen when working with the existing structure.
The old causeway was found to consist of a number of concrete slabs separated by gravel cobbles with the edges held in place by old timber. The design called for the removal of these old timbers. The voids left were replaced with concrete beams. These edge beams also provided an opportunity to widen the causeway. The legs of the skew culvert rested on the old causeway. At these points, holes were drilled through the various slabs, shear connectors installed and grouted into the cobbles below.
The potential for overturning of this structure was similar to the Gloucester Shire Council causeway bridges. This was overcome by extending the legs of the culvert upstream and fixing them to the bedrock below. In order to ameliorate the problem of floating debris that was apparent on the downstream structures, these extensions were designed with a sloping face to act as deflectors channelling debris through or over the boxes.
An open tender went out for the project, and as may be expected of a new-design construction system, the tendered prices varied wildly, reflecting the unknown nature of working in a waterway on an old existing structure using an untried construction system.
Local building firm Reece Construction won the tender and the project was completed successfully and without mishap in eight weeks, with a road closure period of only three weeks.
The waffle pod system provided a quick, cost-effective method to install a low-level culvert over the existing concrete causeway. This method
reused and built upon the existing infrastructure, provided a higher level of service to the road and in this instance preserved significant aquatic habitat and irrigation access upstream of the structure. Clever design also provided fish passage through a fish ladder utilising the existing pipe.
Local tradesmen were comfortable with the construction method which did not require specialist or large lifting equipment. Thoughtful and clever design overcame potential issues with the project, and this design and construction methodology may be a useful tool for other councils dealing with similar rural causeways and looking for a cost-effective solution.
The author wishes to acknowledge the efforts of Phil Miles, Senior Leader Asset Planning at Greater Taree City Council; and Phil Thornton and Carey Molloy, engineers at Matrix Thornton Consulting Engineers; for their efforts in helping to prepare this paper. The full paper can be viewed online at www.apas.org.au/apas2017
China’s Belt and Road Initiative will take centre stage when resource industry heavyweights gather for this year’s International Mining and Resources Conference (IMARC), to be held from 30 October to 2 November at Melbourne’s Convention and Exhibition Centre.
Chief Executive of the AustraliaChina Belt and Road Initiative (ACBRI) Jean Dong will introduce the topic, as part of IMARC’s spotlight on the impacts of infrastructure both on resource extraction and the international commodities market.
IMARC General Manager – Asia Pacific Anita Richards said the Belt and Road Initiative would be a defining piece of infrastructure in the 21st century, with far reaching effects on the dynamics of the global resources market.
The government of the People’s Republic of China proposed the Belt and Road Initiative (BRI) in 2013 – a plan to construct a continuous land route connecting Asia with the Middle East and Europe – loosely following the route of the ancient Silk Road.
In order to be completed, the BRI will require the involvement of over 60 countries, and the Asian Infrastructure Investment Bank estimates that it will require $8 trillion of investment from 2010 to 2020.
“The BRI will require the input of a huge range of industries, and vast quantities of resources to complete,
which will have long-term consequences on trade movements in commodities,” Ms Richards said.
“The world has never seen an infrastructure project of this scale, and the opportunities for the resources sector presented by the BRI cannot be understated.”
Honorary Auditors of the BRI, ShineWing Australia, will be exploring the opportunities for infrastructure development at the upcoming IMARC conference.
Matthew Schofield, Partner of ShineWing Australia said “We are very excited to be a long-term supporter of IMARC. It gives us opportunities to be part of the leading-edge discussion around new possibilities and opportunities for both inbound and outbound investment for the energy and resources sectors. Networking with visionaries is a great way to engage in meaningful dialogue with our clients.”
Conference goers will also have the opportunity to hear from Jeyakumar Jankaraj, CEO of Adani Australia, as he discusses the challenges and opportunities with their Carmichael coal mine and rail project in Queensland.
This will be followed by a presentation from AECOM, who have recently been appointed by Adani Australia to carry out survey and design work for the Carmichael Rail Network, linking Galilee Basin mines to the broader network.
“Infrastructure plays a pivotal role in any mining project and Adani provides a perfect case study in how the presence or absence of the right infrastructure is often the factor that determines a project’s viability,” Ms Richards said.
“Delivering infrastructure presents a range of unique challenges, and unique opportunities, to the resources sector.
“Resources companies and consultants alike need to have a firm understanding of both global and local infrastructure trends.”
For more information please visit www.imarcmelbourne.com, or contact the conference team:
International Mining and Resources Conference
T: 03 9021 2031
E: info@imarcmelbourne.com
W: www.imarcmelbourne.com
November 2017
AusRail Airports
Asset management
Deadline: 6 October 2017 March 2018
Security and critical infrastructure
Sustainability IoT & cloud communication
Land access Excavators/earthmovers/plant
Construction standards and codes Landscaping and Vegetation Management
DISTRIBUTION
AusRail Plus Australian Airports Association Conference
Deadline:
Big
Tolling
Road design
Pits and poles Skills and training
Noise and vibration DISTRIBUTION
Bridges
Deadline: 16 February 2018
Signalling, tracking and control systems
Road marking Condition monitoring and maintenance
Spatial & GIS Urban transport corridors
Software, communications and connectivity
DISTRIBUTION Core18
Tunnels Energy infrastructure
Deadline: TBC
Smart Infrastructure Safety and risk management
ITS Concrete Freight Mobility
Energy infrastructure Culverts
Cranes & heavy lifting When infrastructure intersects
DISTRIBUTION TBC
PARTNERS
If you haven’t seen Australia’s spectacular West, this is the ARSC conference for you! The Australasian College of Road Safety (ACRS), Austroads, ARRB Group and Curtin Monash Accident Research Centre (C-MARC) invite you to attend the largest road safety-dedicated conference in the Southern Hemisphere. The 2017 Australasian Road Safety Conference (ARSC2017) will be held in Perth at the beautiful Crown complex from Tuesday to Thursday 10-12 October 2017.
With a theme of “Expanding our horizons”, ARSC2017 will showcase the regions’ outstanding researchers, practitioners, policy-makers and industry spanning the plethora of road safety issues identified in the United Nations Decade of Action for Road Safety: Road Safety Management, Infrastructure, Safe Vehicles, User Behaviour, and Post-Crash Care. ARSC2017 will bring with it a special focus on engaging all levels of government and community, from the city to the bush, to move Towards Zero. The comprehensive 3-day scientific program will showcase the latest research; education and policing programs; policies and management strategies; and technological developments in the field, together with national and international keynote speakers, oral and poster presentations, workshops and interactive symposia.
ARSC2017 is expected to attract over 500 delegates including researchers, policing and enforcement agencies, practitioners, policymakers, industry representatives, educators, and students working in the fields of behavioural science, education and training, emergency services, engineering and technology, health and rehabilitation, policing, justice and law enforcement, local, state and federal government, traffic management, and vehicle safety.
Perth is a beautiful contemporary city, set amidst the natural wonder of the picturesque Swan River and the world’s largest inner city park, Kings Park. It is also the gateway to the West’s iconic Margaret River wineries, white sand beaches, Rottnest Island with its unique quokka population, and bohemian ocean-side Fremantle. Now’s the time to plan that long-considered WA holiday!
For more information on ARSC2017, past conferences, to submit your abstract, or to receive regular conference updates visit www. australasianroadsafetyconference.com.au or contact the Conference Secretariat on (08) 9389 1488 or ARSC2017@eecw.com.au
ARSC2017 also offers unique branding opportunities for organisations in road safety and injury prevention. See the website for further details.