
10 minute read
Industry news
LOGOS settles Moorebank Logistics Park and Qantas deals
Moorebank Logistics Park has an end value of $4.2 billion.
LOGOS Consortium has confirmed $2.47 billion of deals, acquiring Moorebank Logistics Park and Qantas’s Mascot site.
The historic acquisition of MLP will lead to the development of Australia’s largest logistics and warehousing infrastructure project, aiming to transform e-commerce capabilities in NSW and Australia.
LOGOS, together with Consortium partners, AustralianSuper, Ivanhoé Cambridge, TCorp (NSW Treasury Corporation) and AXA IM Alts, announced their entry into a binding agreement with Qube to acquire the MLP site in July 2021.
With an end value of $4.2 billion, MLP is Australia’s largest intermodal freight facility, offering industrial warehousing opportunities and rail-to-port connectivity. The site includes around 243 hectares of land which will be developed into high quality industrial property and infrastructure.
Darren Searle, LOGOS Head of Australia & New Zealand says the scale and technology of this project makes it one of the most exciting within the group’s $22 billion portfolio.
“Together with the LOGOS Consortium, we are thrilled to be moving forward with our collective vision for MLP, which is a fully automated port-to- site rail link and world-leading industrial and warehousing site,” he says.
“We are passionate about providing a logistics site of this scale, with this immense range of benefits, within a mere 30-minute drive of a major global CBD, as an Australian-first.”
LOGOS and its partners AustralianSuper and Abu Dhabi Investment Authority have also settled their acquisition of a 14ha Qantas site in Mascot for $802 million.
The logistics investor acquired the landmark deal in October, with intentions to develop a world class, multi-level logistics and office park development, changing the landscape of the Mascot precinct.
“The site offers unparalleled connectivity as a critical link to supply chains around the country given its central location and proximity as a key freight gateway for Sydney airport,” Darren says.
“Together with our partners AustralianSuper and the Abu Dhabi Investment Authority we look forward to activating our plans to develop a leading logistics estate on the site, improving the e-commerce and distribution opportunities in Sydney and creating thousands of jobs for the local community.”
“The settlement of both MLP and Qantas transactions today further expands our shared portfolio of logistics and last mile investments made jointly with AustralianSuper, and we are proud to work together with such established partners to further our shared commitment to advancing the logistics and distribution landscape in Australia.”
Truckies and businesses will be able to use a new digital tool with pick-up and delivery location information to transport Australian products more efficiently.
The registry contains operating hours, weight and height restrictions for vehicles, entry points, driver amenities and safety requirements for each site.
Barnaby Joyce, Deputy Prime Minister and Minister for Infrastructure, Transport and Regional Development says the tool will make it easier and quicker for freight operators to pick-up and deliver goods and take some of the stress out of their day-to-day work.
“Every Australian, everywhere, every day relies on freight. The National Location Registry will benefit us all by backing a more efficient supply chain for our businesses and truckies,” he says.
Industry participants include Woolworths, Coles, Sanitarium, PepsiCo, Toll, Linfox and Australia Post.
“For farmers, manufacturers and distributors, the Registry will reduce some of the hassle and time it takes to get their products to where they need to go,” Baranaby adds. “This will make life easier for the more than 50,000 small businesses involved in Australia’s road freight sector. These businesses can now encourage location owners to list their pick-up spots and other important information on this one Registry, saving time and effort.”
Scott Buchholz, Assistant Minister for Road Safety and Freight Transport says the Registry was kick-started by industry and for industry, with the support of the Government, to deliver the data the freight industry needs.
“A farmer that diversifies their plots to different crops and sets up a new processing shed can put this shed on the Registry so transport operators know exactly how to get in and pick up the produce to haul to markets,” he says.
“This will take some of the stress off our transport operators to find the new shed, ensure the produce is picked up quickly and smoothly, and means the farmer doesn’t have to give this information each and every trip.”
The Registry is a key element of the Australian Government’s broader National Freight Data Hub project, a $16.5 million investment to make a range of data available to support the freight industry. This includes the recently launched Supply Chain Benchmarking Dashboard, which is providing detailed and interactive modelling of Australian transport and logistics supply chains across 130 commodities.
The National Location Registry is managed by not-for-profit standards organisation, GS1 Australia.
Woolworths starts construction on first online fulfilment centre
Works have begun in the heart of Western Sydney on the supermarket Group’s first ever automated customer fulfilment centre.
Set to open in 2024, Woolworths’ Auburn Customer Fulfilment Centre (CFC) is being built by Vaughan Constructions and will be equipped with Knapp’s automation technology.
The technology will allow the hundreds of personal shoppers employed at the 22,000 sqm site to pick and dispatch up to 50,000 home deliveries a week across Western Sydney.
Annette Karantoni, Woolworths Director of e-commerce, says online grocery shopping is booming in Western Sydney as more and more customers look to reclaim time in their busy lives.
“Over the past two years alone, we’ve seen the demand for online groceries in Western Sydney more than triple. We need to continue investing in new capacity to keep pace with demand and rising customer expectations,” Annette says.
“The development of Auburn will provide a major boost to our same day delivery capacity in Western Sydney – unlocking faster and more flexible online shopping options for our customers. For added convenience, we’ll also offer pick up bays with a direct to boot service for local customers.”
The NSW Planning Department approved the State Significant development in June 2021.
Stuart Ayres, NSW Minister for Jobs, Investment, Tourism and Western Sydney, says the facility is testament to businesses evolving to meet the changing demands of a busy population.
“Investing in facilities like this creates quality jobs closer to where people’s homes are as we reshape the way we shop in a 24-hour economy,” he says.
The Auburn CFC is targeting a 5-Star Green Star Rating from the Green Building Council of Australia, with plans for rainwater harvesting, solar panels and electric vehicle charging facilities for delivery trucks.
Woolworths stores remain a key part of the e-commerce network, with investments continuing in Direct to Boot, in-store fulfilment and on-demand delivery. More than 80 per cent of online orders are fulfilled by stores. The development of the Auburn CFC builds on recent Woolworths investments in micro-fulfilment technology at its Carrum Downs, Victoria and Maroochydore, Queensland supermarkets.
Woolworths reported a 53 percent increase in e-commerce sales in the quarter ended September 2021 and they now account for more than 11 percent of all sales.
Container transport operators are experiencing between a five per cent to 20 per cent reduction in available staff.
The Container Transport Alliance Australia (CTAA) Director says industry players are facing the hardest conditions ever, with the Omicron variant adding to supply chain disruptions.
Staff shortages, terminal congestion and significant competition to secure vehicle booking slots are combining to create the difficult conditions, according to Neil Chambers from the CTAA.
“Container transport operators across Australia have reported to CTAA that they are experiencing between a 5 per cent to 20 per cent reduction in available staff, including heavy vehicle drivers, warehouse staff, forklift drivers, container unpack crews and administration, due to COVID infections and isolation requirements,” Neil explains.
“Compounding this are staff shortages at customers’ premises, as well as at international container stevedore terminals and at empty container parks across Australia, significantly delaying the movement of containers through the supply chain.
“As a result, transport operators are reporting operational capacity constraints, with transport yards operating between 70 per cent to over 130 per cent capacity.”
Neil says the reduction in capacity is because of delays in customer deliveries, and the need to stage empty import containers through transport yards while trying to secure de-hire slots at clogged empty container parks or container terminals that have reached capacity to receive returns.
“The current supply chain delays and the severe impact of COVID infections seem set to continue well into 2022,” he says.
“DP World Australia has notified industry that approximately 10 per cent of its workforce are impacted through either having contracted COVID-19 or are isolating at home with a positive case in their household. DP World says these numbers may increase as Australia works through the current COVID-19 wave.
“Vessel berthing delays at container terminals across Australia are still of significant concern, impacting all of the major stevedore companies. These delays are being felt most acutely in Sydney and Melbourne, with delays of between 2 up to 9 days, while a heat wave in WA is now affecting terminal productivity in Fremantle.”
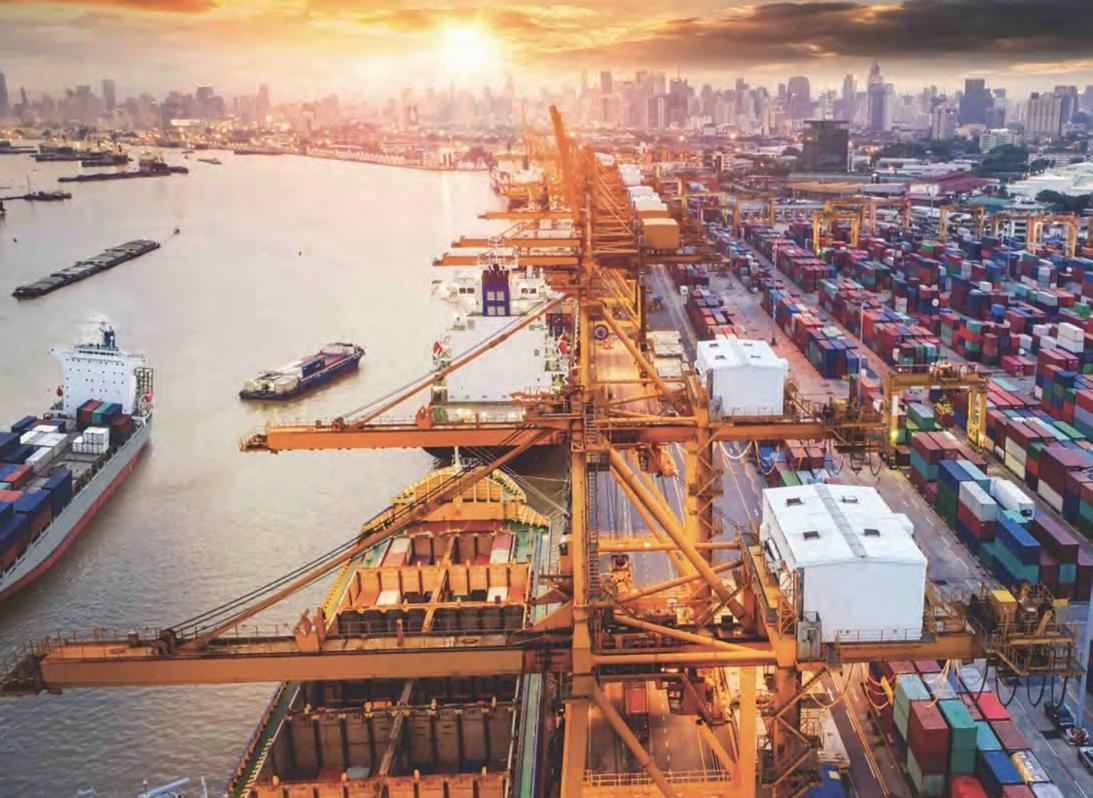
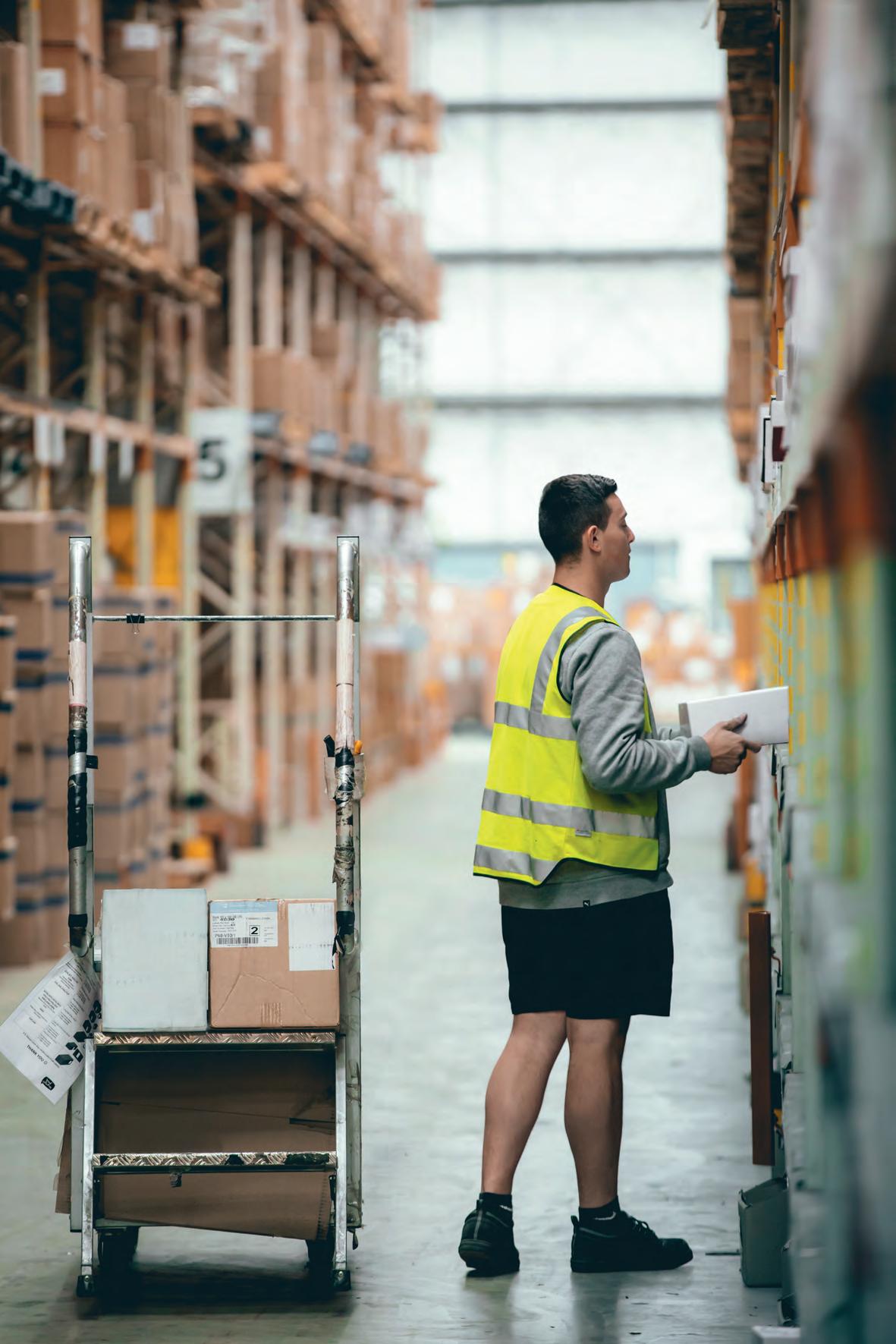
Taskforce set up to tackle AdBlue shortage
Testing waits halting supply chain
Scott Morrison gave the green light in December for a specialist taskforce to ensure the reliable and ongoing supply of diesel exhaust fluid AdBlue.
The announcement followed the Australian Trucking Association’s calls for a specialised effort to solve the supply shortage after talks broke down at a round-table discussion in early December 2021.
That month the federal government said multiple shipments of refined urea were on their way to Australia to provide two weeks’ cover for the market.
Advice provided to the Department of Industry, Science, Energy and Resources from AdBlue manufacturers is that this is within range of normal stockholding levels.
Industry is also reporting that other international supply chains are open and operating, a positive indication of ongoing supply options in the medium term.
ATA Chair, David Smith says the decision to establish the taskforce shows the AdBlue issue is now at the top of the government’s agenda.
“We’re think this is a good outcome. We have been calling for government to make resolving this issue a priority,” he says.
“It appears that Minister Taylor has listened to our calls and is putting the AdBlue shortage at the top of government’s priority list.”
Angus Taylor, Minister for Industry, Energy and Emissions Reduction says businesses and consumers buying additional stocks is unnecessary and unhelpful, and urged industry to continue operating as per usual and maintain normal levels of AdBlue.
“Global supply pressures, stemming from increased domestic use in China, have led to international issues in securing refined urea, which is key to producing AdBlue. This is exacerbated by the global shortage of natural gas, the essential ingredient used to make urea,” he says.
“I can assure Australians that the Government is working to ensure we do not face any shortages. We are pursuing a range of measures to address global pressures in the urea market. We will keep our trucks running and Australian motorists on the road.”
The taskforce will work across government and with industry to develop solutions to any potential future supply constraints. Options being explored include alternative international supply options for refined urea, bolstering local manufacturing capabilities and technical options at the vehicle level.
The Government is working with the Australian Competition and Consumer Commission (ACCC) and industry on whether an authorisation is needed to allow Australian diesel exhaust fluid producers to share information.
Industry bodies have called on governments to make rapid antigen tests available for the logistics sector, after some transport companies reported up to half of their staff are unable to work.
Freight & Trade Alliance (FTA), the Australian Peak Shippers Association (APSA) and the Container Transport Alliance Australia (CTAA) have noted instances whereby members (including freight forwarders, warehouse and depot operators) have received alerts from health regulators regarding people who have checked in at their premises testing positive.
Industry says many members are facing the predicament of having significant numbers of staff in isolation requiring tests to determine if they are safe to return to work.
Arthur Tzaneros, CEO of Australian Container Freight Services (ACFS), one of the largest trucking companies for the country’s major ports and whose clients include Coles, Aldi, Kmart and Bunnings, says there had been a 25-50 per cent shortage of drivers across the east coast during the past two January weeks.
The FTA hopes the genuine threat of grocery store shelves being empty will prompt faster resolution.
TWU national secretary Michael Kaine told Business Insider Australia that if the Morrison government doesn’t make rapid antigen tests free and widely
The supply chain industry is calling for free rapid antigen tests for workers.
available, Australia’s supply chain can be expected to buckle.
“Supply chains are starting to grind to a halt because of the virus. Now, these RATs are needed to clearly manage the spread of the virus because we need transport supply chains to be safe,” he said.
“And for so long as free and readily available testing isn’t there, then we’re going to continue to maximise the spread of the virus.”
