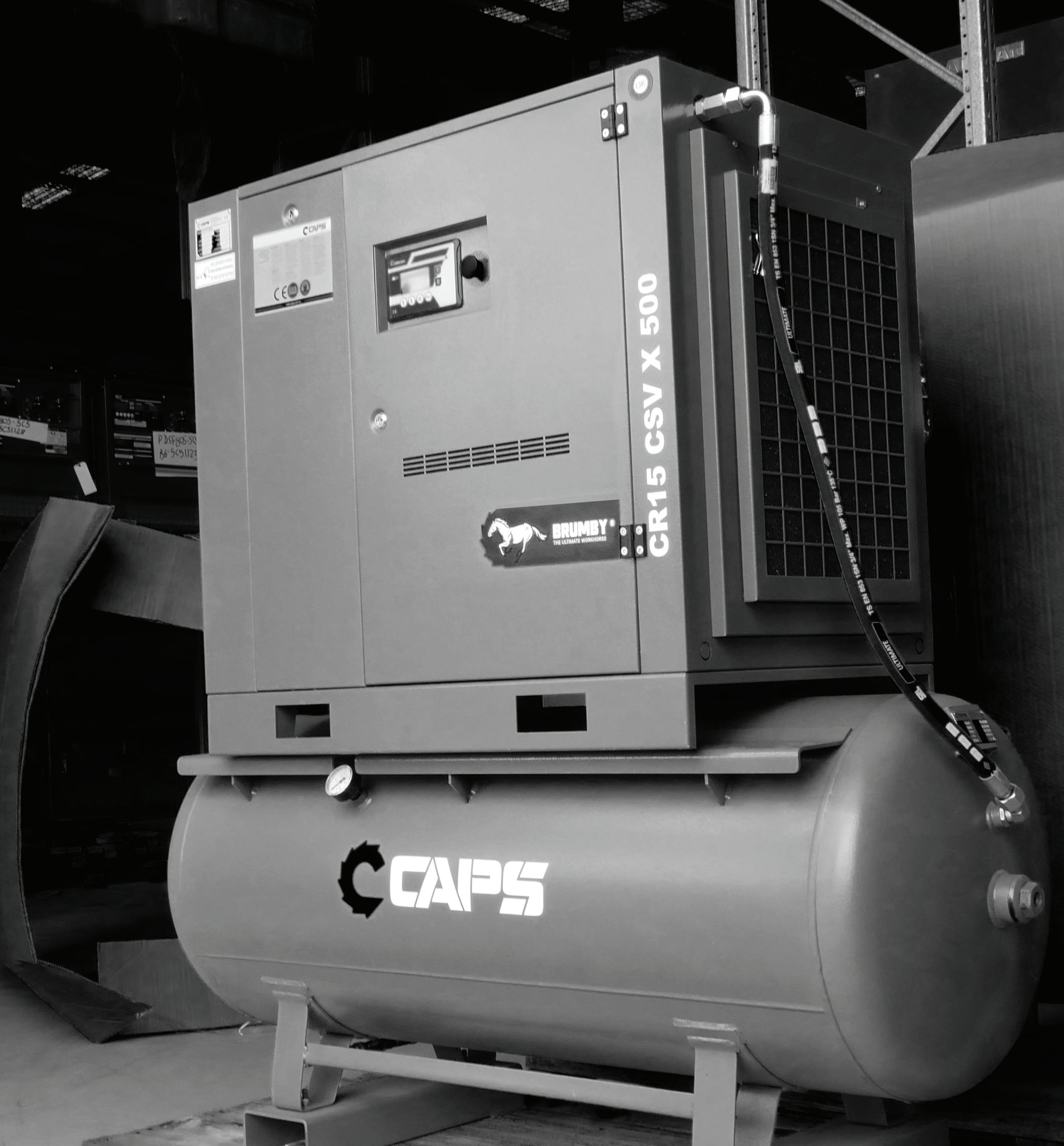
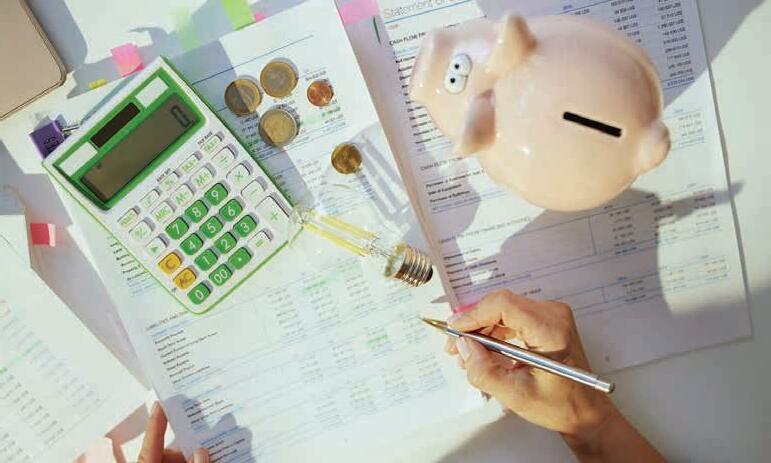
With over 40 years of experience under our belt, CAPS delivers innovative turnkey solutions.
CAPS Australia offer the widest range of industrial air compressors and power generation solutions in Australia, including centrifugal blowers, compressed air dryers, pressure vessels and industrial generators.
With nine branches located nationwide, it’s easy to get in touch with our knowledgeable team and get expert advice to ensure you purchase the right product for your requirements.
We have an extensive range of industrial equipment by world-renowned brands, including Ingersoll Rand, Kohler, AIRMAN and Pedro Gil.
Our products are built tough for Australian conditions and backed by our 24/7 service guarantee. Our flexible range of smart air servicing packages are specifically designed to make your life as simple as possible. They include:
•Rapid-response 24/7 support
•Fast, easy access to local expertise
•Spare parts from nine nationwide service centres
•Quick parts deployment
•Multi-brand trained technicians for oncall support
To round out our complete offer, we also have rental options available to meet your short term or long term needs.
manmonthly.com.au twitter.com/Manmonthly facebook.com/Manmonthly linkedin.com/showcase/manufacturer’s-monthly/
CEO: John Murphy
Chief Operating Officer: Christine Clancy
Managing Editor (Northern): Syed Shah
Editor: Billy Friend billy.friend@primecreative.com.au
Journalist: Mignon D’Souza mignon.dsouza@primecreative.com.au
Production Coordinator: Michelle Weston michelle.weston@primecreative.com.au
Art Director: Blake Storey
Design: Kerry Pert, Tom Anderson, Louis Romero
Sales/Advertising: Danny Hernandez
Ph: 0431 330 232 danny.hernandez@primecreative.com.au
Subscriptions
Published 11 times a year
Subscriptions $140.00 per annum (inc GST)
Overseas prices apply
Ph: (03) 9690 8766
Copyright Manufacturers’ Monthly is owned by Prime Creative Media and published by John Murphy. All material in Manufacturers’ Monthly is copyright and no part may be reproduced or copied in any form or by any means (graphic, electronic or mechanical including information and retrieval systems) without written permission of the publisher. The Editor welcomes contributions but reserves the right to accept or reject any material. While every effort has been made to ensure the accuracy of information, Prime Creative Media will not accept responsibility for errors or omissions or for any consequences arising from reliance on information published.
The opinions expressed in Manufacturers’ Monthly are not necessarily the opinions of, or endorsed by the publisher unless otherwise stated.
© Copyright Prime Creative Media, 2021
Articles
All articles submitted for publication become the property of the publisher. The Editor reserves the right to adjust any article to conform with the magazine format.
Head Office
379 Docklands Drive
Docklands VIC 3008
P: +61 3 9690 8766 enquiries@primecreative.com.au www.primecreative.com.au
Sydney Office Suite 3.06, 1-9 Chandos Street
Saint Leonards NSW 2065, Australia
P: +61 2 9439 7227
To kick off the new year, the February edition of Manufacturers’ Monthly dives into the world of compressed air solutions. Companies like Atlas Copco, BOGE, Pilot Air, CAPS and Energy Power Systems are leading the way in reducing energy costs through more efficient compressors and generators.
If contaminated, compressed air can lead to reduced performance, product spoilage and damaged
Printed by: Manark Printing 28 Dingley Ave Dandenong VIC 3175
Ph: (03) 9794 8337
production equipment, resulting in additional costs and unexpected downtime for site owners and operators. Compressed air is often referred to as the “fourth utility,” a vital cog in the manufacturing process. Elsewhere in the magazine, we tell stories of exciting new inventions, innovative solutions in major infrastructure projects and present expert commentary about the year ahead.
Choosing lower-carbon aluminium in your next project can reduce the embodied energy of your aluminium products by up to 75%* LocAl® Green (8kg CO2e/1kg AL) and LocAl® SuperGreen (4kg CO2e/1kg AL) are the responsible choice for a locally extruded, lower-carbon option in your next project.
FOR MORE INFORMATION VISIT: lowcarbonaluminium.com.au
POWERED BY
When compared with global average CO2e for primary aluminium production,
AUSTRALIAN manufacturing continued to show grit and strength in 2022, building on the momentum of emerging from the pandemic. As we enter a new year, both optimism and caution linger in the air of workshops and facilities around the country. Of course, inflation and economic uncertainty are concerns, as is talent challenges that may limit the industry’s growth momentum. Supply chain issues are still entirely relevant for every manufacturing sector, along with cost pressures and the threat of cyberattacks. The stories in the first edition of Manufacturers’ Monthly show industry is grappling with these challenges head on, and indeed overcoming adversity.
One often hears talk about the “end” or even the “death” of manufacturing in Australia: that economic activity in this country is more or less driven by resources, construction, services, agriculture, and not much more; that the sector that once dominated our industrial landscape –making up a quarter of Australia’s GDP in the decades after the Second World War – is no more. Indeed, for many outside the manufacturing industry, the manufacturing sector is frequently associated with Australia’s past; the dominant media narrative has it that the closure of large automotive plants in recent years marked a kind of terminal point.
While it is true that the sector is currently much smaller than it once was when at its peak in the 1960s, reports about the death of manufacturing in Australia are much like those rumours of Mark Twain’s demise in 1897: greatly exaggerated. Manufacturing remains a significant part of Australia’s economic activity, supporting 1.27 million jobs, according to a report from AMGC, Advanced Manufacturing: A New Definition for a New Era. Further, if Australia can stay at the top of the pack in innovative and advanced manufacturing techniques, technologies and processes, there remains much potential for the sector going forward into the future.
To keep the sector competitive, and to thus enable its further growth, industry leaders are increasingly looking to the productivity-enhancing potential of technologies and methods that come under the term Industry 4.0: robotics and automation, artificial intelligence and
machine learning, additive manufacturing (otherwise known as 3D printing), nanotechnologies and advanced materials, along with Internet of Things (IoT) sensor technology and data analytics.
Australia’s shift to net zero by 2050 has seen a strong increase in the demand for decarbonisation commodities. However, a number of mining and energy projects have been left vulnerable by inflation and logistics issues, making budgets difficult to reach with these increased sustainability expectations. It’s not only the big projects, manufacturers around the country are also feeling the pain of rising energy prices.
The Australian mining, manufacturing, construction and services industries price index rose over five per cent in the past year, which was the biggest increase since
the global financial crisis. In light of such challenges, the Ai Group has written to the Parliamentary crossbench to advocate the passage of the energy price intervention legislation to be proposed to Parliament this week, accompanied by clear signals for future energy investment and transition.
Innes Willox, Chief Executive of national employer association Ai Group, said there can be no doubt that the energy affordability crisis confronting Australia as a result of the invasion of Ukraine is serious, urgent and full of risks for industry competitiveness and households’ standard of living.
“The situation demands comprehensive action, even though – as Ai Group has consistently acknowledged – all the available response options have problems and complexities to manage,” he said.
“The combination of actions chosen
by the Federal Government, while far from perfect, is likely to be helpful overall in reducing energy affordability pressures on industry and households over the next few years and improving the long-term position of energy users. The rapid fall in wholesale electricity futures contract prices for 2023 since the October Budget, which has greatly accelerated since last Friday’s announcements, is a welcome sign of impact and will itself benefit many energy users. However, there are also important caveats and gaps at present. The caps will help, but nearly all large industrial energy users will have already contracted for supply in 2023, many of them at historically unprecedented prices.”
There is much to consider for manufacturing leaders heading into a new year. Manufacturers’ Monthly is excited to keep learning from industry and report the stories which are making a real difference to our sovereign capacity.
AWELD Australia member – who happens to be one of Australia’s largest mining and minerals companies – raised an important issue with me recently. This mining company is committed to creating a diverse workforce. They know that inclusive and diverse teams are good for their business; their research proves that these teams are safer, more productive and have a better culture. Having already implemented successful programs to increase the workforce participation of Indigenous Australians and women, the mining company has now turned their attention
to people living with a disability.
One has to wonder whether the manufacturing industry has considered employing this cohort of people. Are we doing enough to help people living with a disability find employment and gain a sense of fulfilment from contributing to society? Whether we like to admit it or not, we all have pre-conceived ideas about disabilities and the impact that they have on people’s ability to function as a productive member of a team.
The statistics
Around 1 in 6 (18 per cent) people
in Australia – or about 4.4 million individuals – are living with a disability.
Alarmingly, people with disability make up 37.9 per cent of the population living in poverty (despite only making up 18 per cent of the overall population).
One reason for this is that Australia ranks lowest among OECD countries for the relative income of people with disabilities. Overall employment rates for people with disabilities remain low, with workforce participation at around 54 per cent compared to 83 per cent for people without disabilities. Disappointingly, this labour force participation rate for people
with disability has remained largely unchanged over the last 20 years – it was 53 per cent in 2003.
In 2015, the Age and Disability Discrimination Commission undertook the Willing to Work: National Inquiry into Employment Discrimination Against Older Australians and Australians with Disability.
The Inquiry examined practices, attitudes and federal laws that deny or diminish equal participation in
CEO of Weld Australia, Geoff Crittenden, explains the importance of employers embracing a diverse workforce as Australia faces a huge shortage of welders.
employment for Australians with disability. The Inquiry Report was released in May 2016. Its key findings included the following:
1. Discrimination is underpinned by negative assumptions and attitudes that are held by many employers and throughout the community about the productivity and capability of people with disability and perceptions that they present a higher work health and safety risk.
2. Employers may lack knowledge, awareness and skills to develop inclusive workplaces, implement recruitment and retention strategies to support people with disability and meet their legal and regulatory requirements. They may also be unaware of government programs and supports that can assist them.
The thing is, these assumptions are simply incorrect. There are significant business benefits when employing someone with disability – benefits that have been confirmed in both Australian and international studies.
According to research by the International Labour Organisation, employees with disability are:
Reliable: People with disability take fewer days off, take less sick leave and have a higher retention rate than other workers. Safe Work Australia has confirmed that the costs to business of absenteeism and sick leave for employees with disability can be as low as 34 per cent of the cost incurred by their colleagues.
Productive: Once in the right job, people with disability perform equally as well as other employees.
• Affordable: Real cost savings are realised through reduced turnover, recruitment and retraining costs. People with disability have fewer compensation incidents and accidents at work in comparison to other employees.
Good for business: People with disability build strong relationships with customers and boost staff morale and loyalty by helping to create a diverse workforce. Teamwork is enhanced. It enhances the company’s image among its staff, community and customers with positive benefits to the employer’s brand.
The Soldamatic augmented reality welding simulators can be used to teach just about anyone to weld – people with depression, or autism, or PTSD. This training can then be followed with certification to ASNZS ISO 9606.
In a welding workshop, a person in a wheelchair or with any other physical disability is ideally suited to managing the work of two or three cobots. Alternatively, they could take on a role as a Welding Inspector.
Welding workshops complete Job Safety Analysis and Welding Procedure
Specifications for every job. They identify whether a particular welding job needs to be completed by a welder certified to AS/NZS ISO 9606, or an expert pressure vessel welder with 20 years’ experience. In much the same way these assessments are undertaken, industry could be identifying tasks that are suitable for people with a disability.
There are two major Australian Government funded employment services programs available to employers who wish to recruit people with disability. They are Disability Employment Services and Job Services Australia. Employers
in remote Australia can also access the Remote Jobs and Communities Program, which delivers employment services to people living in remote areas. For more information, visit: www.jobaccess.gov.au. There is a range of Australian Government funding initiatives if you employ a person with disability, including:
• The Employment Assistance Fund provides financial assistance for workrelated modifications, equipment and services to help people with disability get employment and perform their work as independently and productively as possible. The assistance is available to new and existing employees with disability.
For more information, visit: https://www.jobaccess.gov.au/ employment-assistance-fund-eaf.
• The Wage Subsidy Scheme offers financial assistance to employers who employ eligible people with disability who are registered with a Disability Employment Services provider. For more information, visit: business.gov.au/grants-andprograms/Wage-Subsidy-Scheme.
Disabled Australian Apprentice Wage Support is an Australian Government
incentive payable to an employer who employs an Australian Apprentice who satisfies the disability eligibility criteria in an Australian Apprenticeship. For more information, visit: www.australianapprenticeships.gov.au.
Job Access also has a detailed Employer Toolkit that includes information on disability employment basics, recruiting people with disability, getting your workplace ready and managing your team.
It is estimated that the economic benefits of employing people with disability would add over $50 billion to Australia’s Gross Domestic Product GDP by 2050 – but only if Australia were to move up into the top eight OECD countries for employment of people with disability.
With Australia facing a shortage of 70,000 welders by 2030, industry needs to consider accessing a diverse range of skilled and talented people. We need to take advantage of Australia’s untapped workforce to meet the needs of business. Smart employers recruit and welcome talent with disability.
In the majority of cases, people with disability are able to work and want to find a job. They simply need to be given the chance to show what they can do.
The Advanced Manufacturing Growth Centre (AMGC) has closed its $30 million Federal Government Commercialisation Fund, co-investing in a total of 61 Australian manufacturers.
The co-investment was received through an AMGC-managed program aiming to fast-track commercialisation and export high-tech and high-indemand products and services.
The program spans sub-sectors of: value add to resources, agriculture, forestry, and fisheries; transport; medical sciences; renewables, and low emissions technology; defence, space and, enabling technology – such as Artificial Intelligence (AI) and robotics.
Analysis of co-investment recipients reveals that manufacturers committed over two dollars ($2.30) of cash and in-kind contributions for every dollar of Federal funding. As a total, industry financial contribution and in-kind funding commitment tally $98.8 million – three times that of the initial fund allocation.
The strong contribution from industry,
manual roles – all within manufacturing.
Dr Jens Goennemann, managing director of AMGC, said the oversubscribed Commercialisation Fund proved there is significant demand from Australia’s local manufacturing industry to invest and commercialise worldleading ideas.
“Australia’s manufacturing industry has been the silent achiever over many years, growing its global customer base and investing for growth to take great local ideas to the world. In fact, demand for co-investment was so strong that the fund was oversubscribed by 300 per cent,” said Goennemann.
The final six projects to successfully receive co-investment include: Hygiene Co. (SA) – Recycling: Sovereign manufacturing of plasticfree wipes for medical, industrial, and personal use. The project removes reliance on international supply chains, while substantially decreasing CO2 emissions and waste from the importation of plastic-based wipes.
commercialisation of a manufacturing process to produce the red-pigmented algae to enhance the texture and colour of plant-based meat products. Total project commitment $2.93million ($525,000 from Commercialisation Fund)
Laronix (NSW) – Medical: Commercialisation of Bionic Voice, the world’s first and only smart naturalsounding artificial voice-box for people suffering from permanent voice loss. Total project commitment $817,536 ($408,768 from Commercialisation Fund)
Process Plants International (PPI) (QLD) – Resources Technology & Critical Minerals Processing: Commercialisation of a proven, proprietary anti-block sparge design using exotic metal printing for the minerals processing Pressure Oxidation (POX) autoclave industry. Total project commitment $441,000 ($220,500 from Commercialisation Fund)
Vypex (VIC) – Food and Beverage: Advanced 5.1-based Bluetooth system to track, trace, identify, and alert warehousing staff on items within the
Total project commitment $400,000 ($200,000 from Commercialisation Fund)
Optotech (VIC) – Medical:
Development of a new laser-based inspection system to quality assure locally manufactured and highly precise cochlear hearing devices down to two microns across 34 different parameters. Total project commitment $270,500 ($121,500 from Commercialisation Fund
“The final six Commercialisation Fund recipients demonstrate that the face of Australian manufacturing has changed, with medical devices, bio-manufacturing, recyclable materials, and laser inspection projects leading the global charge,” Goennemann added.
“As a nation, we should be investing more into our manufacturing capability. The COVID pandemic shone a light on how important local manufacturing capability is, and now is the time we need to back local companies to assist them in growing their global impact.
“This will deliver greater benefits at home with higher paying jobs, increasing
Dr Jens Goennemann, managing director of the AMGC with Energy Renaissance’s Brian Craighead.Australia now boasts a new manufacturing capability with the commissioning of the nation’s first, plant-based meat ingredient facility in Sydney.
Australians will soon be able to enjoy plant-based meat products made from locally sourced and processed grains via Australia’s first plant-based meat ingredient manufacturer, Sydney-based, Harvest B.
The company’s plant-based meat ingredients will offer a wholesale solution to consumer-facing food brands, manufacturers, and food service companies seeking a great tasting, clean-label certified, plant-based meat product that costs less than comparable animal protein.
The locally developed produce will assist efforts to decarbonise supply chains by offering a product that does not require a cold-chain solution and has a shelf life far superior to that of imported plant-based and locally sourced animal-based proteins.
This local manufacturing capability will enable substantive value to be added to high-quality local grains and other ingredients, while generating high-skilled local jobs. Furthermore, Harvest B has the potential to displace currently imported plant-based protein products while growing exports.
At the opening of the Harvest B facility at Penrith, Minister for Industry and Science Ed Husic said the facility is great news for Australian food brands and manufacturers.
“The Albanese Government is committed to revitalising Australia’s advanced manufacturing by backing companies like Harvest B. Supporting domestic capability in emerging technologies, including in areas like food production, will be a focus for the National Reconstruction Fund,” said Minister Husic.
“Australia has a strong reputation as producer of safe, premium, high-quality foods, and Harvest B will support domestic businesses to capitalise on the growing demand for plant-based protein foods.”
Harvest B Co-founders, Kristi Riordan and Alfred Lo, set about to address the growing global need to supplement existing energy, emissions, and land-intensive animal protein-based food systems with a novel plant-based approach while adding value to high-quality, locally grown grains.
“When investigating the plant-based protein market, it became apparent that there was not a single large-scale ingredient brand supplying highquality, locally made plant proteins to Australian food manufacturers. Now food manufacturers have the option to source locally developed products leveraging local inputs rather than resorting to international suppliers,” said Harvest B Co-founder and CCO, Alfred Lo.
“It made absolutely no sense that high quality, Australian grown produce is shipped offshore to be processed only for us to buy it back at higher costs as finished consumer products. It became quickly evident to Harvest B that there was a significant opportunity for this value add to be done in Australia, creating local jobs and greater export opportunities,” said Harvest B Co-founder and CEO, Kristi Riordan.
“To ensure we can grow our business, Harvest B invested heavily in research and development to create a novel product range that we believe exceeds the taste, texture, and price expectations of our consumers. In fact, industry and consumer feedback has been overwhelmingly positive to the point that we now have customers, both locally and abroad, approaching us.”
Leveraging locally grown grains and inputs, Harvest B will offer an initial output of 1,000 metric tonnes of product. Supplied to food brands, food manufacturers and food service providers, Harvest B’s plant-based proteins will then be converted into popular consumerfacing food products such as sausages, patties, mince, and the company’s own proprietary whole meat products.
Managing Director for the Advanced
Manufacturing Growth Centre (AMGC), Jens Goennemann, said Harvest B exemplifies how Australian manufacturers can value-add to the nation’s abundant natural resources.
“Australia is a nation blessed with abundant natural resources, yet we have relied too heavily on the luck associated with trading these commodities in a raw state. Like Harvest B, we should be leveraging our smarts and add value to these high-quality natural resources – right here in Australia,” said Goennemann.
With co-investment support from the Federal Government via AMGC and industry partners, including Woolworths’ venture fund (W23), Harvest B intends to initially develop 10 different product lines with substantial export into Southeast Asia which is already presenting opportunities.
The Australian Government has purchased 20 Lockheed Martin High Mobility Artillery Rocket Systems (HIMARS), and associated hardware, for an estimated cost of US$385 million.
HIMARS is a highly mobile, combatproven system that fires precision munitions ranging from 70 to 300 kilometres. Transportable by C-130 and C-17 aircraft, it is rapidly deployable and interoperable with partner nations.
Warren McDonald, chief executive, Lockheed Martin Australia and New Zealand said, “Lockheed Martin has been the leading designer and manufacturer of long-range, surface-to-surface precision strike solutions for more than 40 years. The Lockheed Martin developed HIMARS will provide Defence with unmatched mobile land-based firepower”.
James Heading, director of programs, strategic capabilities office at Lockheed Martin Australia’s Missiles and Fire Control said, “HIMARS employs a ‘shoot
and scoot’ capability which enhances crew and platform survivability in high threat environments. HIMARS can emplace, fire and relocate, and conduct reload in a matter of minutes, dramatically reducing an adversary’s ability to locate and target HIMARS.
“HIMARS enables a generational leap in capability for Australia, taking Defence from cannon artillery to LongRange Precision Fires that provide a 24/7 persistent, all-weather capability.
“HIMARS offers the Australian Defence Force the ability to use and share common munitions and to integrate into a coalition effort,” Heading said.
Lockheed Martin Australia is currently looking at options to provide ongoing support, maintenance and sustainment of the HIMARS and related equipment in Australia.
“Providing Defence with technical and logistical support, and sustainment services, offers opportunities for
Australian small to medium enterprises and provides local employment opportunities and benefits to the economy,” Heading added.
The first deliveries of the missile systems are expected in 2025.
Headquartered in Canberra, Lockheed Martin Australia employs
over 1,200 people in Australia working on a wide range of major programs spanning the aerospace, defence and civil sectors. Lockheed Martin Australia is a Department of Defence strategic industry partner in support of the Guided Weapons and Explosive Ordnance Enterprise.
Quantum computing startups and deep technology companies will be supported to advance their innovations through the New South Wales Government’s new $7 million Quantum Computing Commercialisation Fund.
Minister for science, innovation and technology Alister Henskens said NSW’s quantum ecosystem is uniquely placed to be a global leader of quantum technologies.
“Thanks to the NSW Liberal and Nationals Government’s strategic investment over the past decade, NSW is leading the nation in quantum research and development, boasting world-leading companies such as Silicon Quantum Computing, Diraq and Q-CTRL,” Henskens said.
“Our 20-Year R&D Roadmap recently identified our world class quantum ecosystem as an area of competitive advantage, and we want to help our State flourish in this area to create new jobs and industries which will grow the economy and help secure a brighter future for the people of NSW.
“This fund will target both startups and existing deep-tech companies to ensure that innovative projects are accelerated towards commercialising
quantum computing, maintaining our momentum and reinforcing NSW’s position as a global quantum centre of excellence.”
The NSW 20-Year R&D Roadmap sets out a 20-year vision for NSW to produce more world-leading new technologies, products and services, and develop and sustain globally competitive advantages
Vonda Fenwick has spent much of her illustrious career serving the manufacturing industry. Manufacturers’ Monthly sat down with the South East Melbourne Manufacturers Alliance CEO to reflect on her career as she prepares for retirement.
I was absolutely delighted when I was offered the role of CEO at SEMMA (South East Melbourne Manufacturers’ Alliance), in September 2019. I was on the inaugural SEMMA Board when the Association was formed 20 years earlier and understood why the association had been formed and the importance of the advocacy and support SEMMA provides for local manufacturers. SEMMA was born as a “Voice for Manufacturers in the South East.” I was so excited at the prospect of visiting all our members and touring their sites, getting to know their products and capabilities in order to better represent them and ‘sell’ the capabilities of the South East manufacturing region.
At the time SEMMA was formed, I was working in a manufacturing operations role in a highly vertically integrated scientific equipment company. As a highly successful export business with around 200 employees, our organisation was active in its support for the newly formed manufacturing association. Ironically, we saw our participation in SEMMA, as being more in the role of a ‘good corporate citizen,’ supporting micro and small to medium enterprises however, over the ensuing years, we had the need for SEMMA’s advocacy and support for our own organisation, in the form of advocacy
around complex trade and export licence issues. Further, they provided great, direct support across the spectrum of issues common to manufacturers.
After several months of settling in and developing, in conjunction with the SEMMA Board members – primarily manufacturers, many with their own businesses – our Strategic Plan to take us forward for the coming five years, I set about developing the operational plans, objectives and metrics to measure our progress against the new vision and strategy. Things were looking exciting and I had identified the two sectors we would target for growth – food for the first calendar year of 2020 and medical equipment for the following year in 2021.
The best laid plans and strategic goals were no match for what was to emerge in March 2020 to change our direction and upend our plans. COVID hit and we saw a period of dislocation and uncertainty like no other. Our support role and providing information and guidance on a daily basis became the norm for many months. Lockdowns and all of the rolling changes and new restrictions and guidelines kept us busy. Keeping on top of the latest government information in order to get it to members in a timely fashion became the imperative. Attendance at almost daily, on-line government briefings became commonplace.
We surveyed our members over a period of about 15 months to assess the impact of COVID. The results of the surveys were confronting. In the first month the uncertainties in the market meant order books dried up and employers were reluctantly shedding
staff – with predictions of many more to go had the Job Keeper wage subsidies not kicked in. Gradually confidence returned and with COVID site plans in place manufacturers, by September of 2020, were beginning to see orders flow and most now had different, COVID-induced issues to contend with; primarily supply chain issues and costs ballooning. Loss of key staff due to vaccination mandates hit just when orders were really starting to pick up and we had another period where members were really looking for support and guidance.
What achievements are you proud of during your tenure?
When I look back over my time with SEMMA I feel proud of how we managed to support our members during such challenging times and this was rewarded
Following today’s announcement from the Federal Minister for Skills and Training Brendan O’Connor MP, IBSA Group has been given the green light to create a new Jobs and Skills Council (JSC) to support manufacturing skills across Australia.
Sharon Robertson, CEO IBSA Group, said, “We are committed to establishing the industry- owned, industry-led
Manufacturing Jobs and Skills Council as soon as possible and getting on with the task of boosting manufacturing skills for employers and workers. Industry has consistently told us a skilled workforce is vitally important to them and the country as a whole.”
JSCs will provide strategic leadership in addressing skills and workforce challenges. They will identify skills and
workforce needs, map career pathways across education sectors, develop contemporary VET training products, support collaboration between industry and training providers to improve training and assessment practice and act as a source of intelligence on issues affecting their industries.
IBSA is encouraging all manufacturing employers, industry associations, unions,
by the fact that we actually grew our membership slightly during the worst of the COVID lockdown period. We recognised that our members were hurting financially and established the SEMMA Buying Group to use the power of negotiating group pricing to benefit members. The on-going skills shortages prompted us to develop our SEMMA 4-week basic welding skills course which saw our pilot programme successfully place 90+ per cent of our ‘graduates’ with SEMMA members. Importantly, our advocacy and representations to both State and Federal Governments meant that we ensured that the importance of manufacturing in Australia, the need for strong local content policy and the critical nature of SMEs in our supply chains were being heard at the highest levels.
training organisations and stakeholders to sign up to receive the most up-to-date news and alerts regarding the JSC.
The Manufacturing JSC is covering industries of manufacturing and engineering, light manufacturing including pharmaceuticals, print, food and advanced manufacturing. Emerging industries include defence and space technologies.
Australia’s biggest carbon emitters will now be forced to reduce their emissions by at least 30 per cent by 2030.
Minister for climate change and energy Chris Bowen has released reforms to the Safeguard Mechanism, which limits the emissions of 215 of Australia’s industrial polluters in oil, gas, mining, and manufacturing industries.
The reforms follow the Labor Government’s climate change bill that was passed in September last year, which ensures Australia’s emissions reduction target of 43 per cent and net zero emissions by 2050 will be enshrined in legislation.
Bowen explained that the 215 facilities were responsible for 28 per cent of Australia’s emissions, therefore, they will be responsible for 28 per cent of emissions reduction.
“We will start primarily by taking
the starting position as the emissions of each facility, and then between now and 2030 we will move to more of an industry baseline,” Bowen said.
“These proposed reforms have been carefully calibrated to deliver the policy certainty and support Australian industry needs through decarbonisation. There is much more to it than that, but these are some of the key points. This is pro-climate, pro-industry, pro competitiveness.”
The reforms to the Safeguard Mechanism have been proposed by industry heavyweights and big businesses, such as the the Business Council of Australia and the Australian Industry Group (Ai Group), to end policy uncertainty and enable a predictable emissions reduction pathway to net zero by 2050.
The Safeguard Mechanism was
put in place by the previous Coalition Government and requires facilities that produce over 100,000 tonnes of greenhouse gases annually (around 215 facilities) to keep their net emissions below a baseline.
The reforms aim to support businesses in reducing their annual greenhouse emissions by 4.9 per cent till 2030 and deliver 205 million tonnes of abatement to the end of the decade, equivalent to cutting emissions from Australia’s cars by two-thirds over the same period.
While major business groups have welcomed the reforms, concerns were raised about how local businesses could remain competitive with international counterparts.
“The Safeguard Mechanism positions released by the Government today are pragmatic and take industry input seriously, but clearly there is a lot more
work to do over the next few years by government and industry before these major climate policy reforms are fully bedded down,” said Innes Willox, chief executive of national employer association Ai Group.
“A core part of Australia’s climate balancing act is to build our competitiveness for the net zero emissions world that is coming without undermining our competitiveness in the messily transitioning world we operate in today.
A new independent report released has evaluated IMCRC’s manufacturing projects to deliver 4.2 billion in financial benefits and 6,000 jobs by 2030.
The Innovative Manufacturing Cooperative Research Centre’s (IMCRC) significant contributions to Australia’s manufacturing sector have been demonstrated with the release of an independent impact evaluation report into its 71 research and development (R&D) projects.
The Impact of the IMCRC, produced by leading economics, policy and strategy advisory firm ACIL Allen, examines the economic, social and environmental benefits that IMCRC has generated for its industry and research partners since its launch in 2016.
The findings of the report demonstrate the importance of R&D and the effectiveness of IMCRC’s industry-led business model in driving transformative commercial outcomes for Australian manufacturers.
2030. Further benefits to 2030 include:
The creation of over 6,000 ongoing full-time equivalent (FTE) jobs
The creation of 224 collaborations and new partnerships between researchers and businesses, including internationally, and of 22 new businesses or business models
Planned industry investment of $2 billion in future R&D
A reduction in greenhouse gas emissions of more than 3,300,000 tonnes CO2
Dr John Söderbaum, Science and Technology Director at ACIL Allen said the results of our analysis and the strong testimonies provided by participants in the case studies show that IMCRC’s industry-led model has resulted in significant positive impacts for the Australian manufacturing industry.
“There is also evidence that IMCRC’s approach has encouraged strong and sustained industry and research collaboration for project participants,”
relationships that have developed over the life of the CRC. It shows that the parties involved recognise the value of their collaboration and wish to continue
and demonstrates its consistent ability to drive innovation and deliver commercial outcomes for industry.
“Industry-led R&D holds the key to sector and building our sovereign capability
Air Liquide’s new patented cylinder top will help you work safely, gain greater performance and save you time and money.
ESSENTIAL SMALL MOLECULES FOR MATTER
Gangi Group is installing UV-C germicidal and lighting systems to automate the disinfection process in healthcare and aviation for the first time. Billy Friend finds out how the once small family-owned electrical contracting company has expanded to provide breakthrough solutions via an underutilised but proven technology.
SEBASTIANO Gangi came to Australia in 1966, and soon after established himself as a hardworking electrician in the South of Melbourne. His son, Robert, fondly recalls memories of working with his father, undoubtedly where a strong sense of work ethic was inherited.
“Growing up, I loved working with my dad,” he said. “I used to work on a Saturday or on school holidays. I remember working in a factory in Seaford and it was about six o’clock and we were still working together. Dad ordered pizzas and I remember singing this song with him which remains a great memory to this day.”
After living overseas, Robert returned to join the family business – with a focus on automation – to expand the integrated electrical solutions the company provides for various industries. A familiar fable, the COVID pandemic caused Robert to reassess and explore different areas for the business. Extensive research lead him to identify UV-C light had the capability to expand massively as an industry in Australia, eventually leading to the birth of germicidal light systems under Gangi Germicidal Systems (GGS).
UV-C was first used in the late 1800s to kill micro-organisms like bacteria, mould and viruses. Niels Ryberg Finsen – the first to employ UV rays in treating disease – won the Nobel Prize for Medicine in 1903 for inventing a curative lamp, which was successfully used through the 1900s.
The technology uses Ultra-Violet light in the germicidal wavelength range between 200 and 300 nanometres. The optimum wavelength for disinfection is 264 nanometres, which is located within the UV-C spectrum. When microorganisms are exposed to germicidal wavelengths, the high energy associated with UV-C light is absorbed by the DNA of bacteria and viruses.
When heavily researching UV-C, Robert discovered the technology has been proven to work for over 100 years and the first time it was used to disinfect municipal water supply was in Marseille, France, in 1908. So, if the technology has been around for so long, why has it remained such a small market – restricted to mainly food processing and water treatment – in Australia?
“I think we’re more risk averse in
Australia, which has its benefits but means you sometimes don’t explore the opportunities of new technologies,” he said. “We saw this as an underutilised technology, to help our healthcare system and beyond. When we started this, I was told it’s only a 30-million-dollar industry in Australia – is it really worth it? I think we are kidding ourselves if we think it won’t become much, much bigger than that.”
The light sources can be used for both surface and air disinfection. UV-C light sources can be placed within air ducts and HVAC systems to purify air. Because the light sources are contained within an enclosure, the UV-C disinfection can take place whilst spaces are occupied. The method can stop biofilm building up inside of a HVAC system, increasing efficiency and reducing maintenance.
After receiving a proof of concept for a bespoke UVC control system in early 2020, GGS went to market with the idea and was adopted in food processing, commercial offices, sporting clubs, schools and childcare facilities. At the height of the COVID pandemic, the proven technology was a natural solution to restrict the spread of the virus. At Bambini Early Learning Centre in the Royal Melbourne Children’s Hospital precinct, a trial program reaped tangible
results – the centre reporting a reduction in illnesses in the children.
“We went to expand the trial for the centre, but it wasn’t required because the system was working so well. For me, it was validation and something tangible to know how well the system worked, so we used that momentum,” Robert said.
For surface disinfection, knowing exposure time and where to place UV-C fittings is crucial and extreme caution is required when a disinfection cycle is taking place.
UV-C is a light source that is damaging to the skin and eyes, so humans can’t be in a room or have direct contact with the light source. The ozone layer protects us from UV-C produced by the sun in our natural environment. Robert knew to be properly implemented, the system needed to be completely controlled, so the team set about designing and developing control systems specifically for UV-C light sources.
Seemingly, the safety concerns and risks involved in dealing with this technology have limited the scope of its applications. The control system looks to put a stop to this, putting in various failsafe’s such as electronic locking systems and occupancy sensors to mitigate the risk of anyone being in the room while the UV-C was operable. It is the first of its kind to be fully automated in Australia, reporting when the lights are on and off, so the environment can be monitored.
“There was no point of me selling a system only on the basis of ‘when you leave at night, the lights come on,’ because we know that faults happen. It could be a faulty light or electrical circuit, so we had to design a system that not only has safety measures in place but also monitors the operation of the UV-C light sources.
Numerous fail-safes are in place to ensure the system is completely safe and 100 per cent automated, removing human error for a thorough disinfection.
The business complies with the ARPANSA (Australian Radiation Protection and Nuclear Safety Agency) guidelines, specifically mandated to minimise all human contact.
GGS has worked with different sporting clubs to provide safe, automated disinfection of training facilities and treatment rooms. From a practical standpoint, Robert explained the failsafes by referencing the system in place at a professional sporting club in Victoria. Gangi installed germicidal UV-C lighting in the HVAC system of the club’s sealed high-altitude training room. As the air circulates through the HVAC system it’s treated with UV-C light, which reduces the chance of airborne pathogens spreading. For high-performance organisations like professional sporting clubs, small changes can make a big difference. To disinfect the surface, the system was installed and automatically turns on when players leave the room.
Whilst developing and implementing systems for GGS, Robert and long-time friend Nathan Brown developed and manufactured the world’s first UVC patient stretcher disinfection chamber, now called the Lindo Chamber. Entering manufacturing for the first time, the start-up faced the challenge of partnering with the right manufacturer. Robert said he is learning from Melbournebased All Duct Fabrications as well as Swinburne University, so that GGS will open its own facility to continue to grow manufacturing capacity for Lindo products.
“I wouldn’t be here without collaboration,” Robert noted. “We continue to work with research organisations and brilliant minds at universities, but I think it’s important to collaborate and learn from other businesses as well. Whether in the disinfection ecosystem or any other start-
up business, I think you can learn from each other. We identified early that we didn’t have the full skill set.”
All Duct Fabrications re-designed the chamber so it could be put together in under 12 minutes. Originally called Clean Cart, the UV-C disinfection chamber was initially designed for shopping trolleys. After collection, the trolleys are rolled into the chamber and securely sealed for a button to activate the UV-C light to properly clean the trolleys.
To gain evidenced-based research, GGS engaged contract research organisation Eurofins Scientific to test the product in its laboratories. The chamber was proven to work, removing salmonella and E.coli from the trolleys in Eurofins’ testing environment.
The trajectory of the Clean Cart product took a turn when Robert had a conversation with a friend who flies with Air Ambulance Victoria.
“He saw the chamber, and said ‘Rob, that’s a perfect size for a patient stretcher.’ It dawned on us that healthcare could be terrific for this technology,” Robert explained. “The idea is to reduce resources, stress and costs by replacing the paramedic’s task of disinfecting a stretcher. A job which can take up to half an hour can be done by the chamber in under five minutes and the only manual labour involved is inserting the stretcher and removing it. Everything else is automated.”
Without the chamber, paramedics use chemical gloves and PPE to wipe down every surface, exposing them to potentially harmful pathogens and surfaces.
“Different paramedics have told us the reason they left the job was because they felt exposed to harmful chemicals, ruining their hands and feeling it in their lungs.”
GGS acquired Clean Cart in its entirety in 2022 and rebranded it to Lindo. Lindo was created to design, develop and manufacture innovative BioTech and MedTech products, using UV-C and “Bluelight” light sources.
The Lindo Chamber provides surface disinfection to a variety of health care equipment, including but not limited to, patient transport stretchers. Using germicidal lighting technology, the chemical-free form of disinfection not only reduces manual labour
for paramedics and other healthcare professionals, but also has a positive impact on the climate by reducing waste. Combined with an asset management and tracing system, the chamber is currently in use as a trial at Air Ambulance Victoria (AAV). It has been used successfully since October last year, with paramedics also using the chamber to disinfect other healthcare equipment like monitors and laptops. The success of the trial lead AAV to ask GGS to provide a permanent solution. Robert explained that the chamber is more than just a disinfection solution.
“We’ve expanded the monitoring system so that each stretcher provides provides an alert each time a stretcher is disinfected, saving that information to a database. We can then set the system to provide an alert when a stretcher hasn’t been disinfected for a certain number of days and provide a record of each time the stretcher was disinfected. This enables easy quality assurance, monitoring, and health and safety reporting.”
In May 2022, GGS was awarded an innovations connections grant by CSIRO to further investigate the viability of
blue light as germicidal light. The goal of the study is to analyse the difference between UV-C and blue light in disinfection and develop systems which work with blue light. According to Robert, blue light is a promising disinfection alternative in situations with little space and energy.
“Blue light has the same germicidal properties as UV-C, but takes a little longer to be effective. Because it is LED, we are now developing a chip in conjunction with a company in Finland that runs purely off 24 volts. So when you talk about the installation process into an aircraft, you can run it off of the power system without any transformers or drivers.”
The innovations grant will be used to fund a research project between GGS, the University of Melbourne, and the Peter Doherty Institute.
“Through CSIRO, by extension you get to work with universities and research organisations with a plethora of knowledge,” he said. “We are also working with the Swinburne University to build the next generation of the Lindo Chamber. We recently had a two-day workshop with them, which was fantastic. Founders of start-ups are
so involved, it can be hard to take a step outside and look in, which is incredibly important.”
After dissecting every aspect of the chamber with the university, GGS is now working on a more sustainable version of the Lindo Chamber, working with another local company to deploy an asset tracking and compliance digital platform. If a paramedic, for instance, notices something wrong with a stretcher, the chamber can take a photo and lodge a request so that the stretcher won’t be able to service again until it’s fixed. A product which started as a disinfection tool for supermarket trolleys has quickly transitioned to a completely new industry, and now has the ability to survey abnormalities in equipment to further reduce risks.
The collaboration also aims to establish a servitisation business model for LINDO and GGS.
“We haven’t found similar products on the market that offer the same level of technology. Along with the benefits for the healthcare industry, we believe that there will be a positive impact on not only the emergency patient transport industry but also other healthcare industries like Aged Care.”
CSIRO researchers have discovered strange diamonds from an ancient planet in our solar system could hold the key to making stronger and harder machine parts. Mignon D’Souza caught up with CSIRO researcher Colin MacRae to find more about the project.
FOR a few years now, scientists at CSIRO have been working on a project to confirm the existence of a mineral known as lonsdaleite.
Lonsdaleite is a rare, hexagonalshaped diamond believed to be found in ureilite meteorites from the dwarf planet’s mantle. The project team – with scientists from Monash University, RMIT University, CSIRO, the Australian Synchrotron and Plymouth University – recently found evidence of how lonsdaleite is formed in the meteorites, thus confirming its existence. The findings of the study – led by geologist Professor Andy Tomkins from Monash University – have been published in the Proceedings of the National Academy of Sciences (PNAS) journal.
Researchers have revealed a novel process in which the lonsdaleite is created, replacing graphite crystals in the dwarf planet’s mantle facilitated by a super-hot fluid as it cools and decompresses.
“We propose that lonsdaleite in the meteorites formed from a supercritical fluid at high temperature and moderate pressures, almost perfectly preserving the textures of the pre-existing graphite,” Professor Tomkins said.
“Later, lonsdaleite was partially replaced by diamond as the environment cooled and the pressure decreased.”
All of this sounds very scientific, but the discovery has extraordinary potential for the making of machine parts.
Professor Dougal McCulloch, director of the RMIT Microscopy and Microanalysis Facility and one of the senior researchers on the team, said the team predicted the hexagonal structure of lonsdaleite’s atoms made it potentially harder than regular diamonds, which have a cubic structure.
CSIRO scientist Mr Colin MacRae added that this is a potential breakthrough for manufacturing machine parts.
“This process isn’t normally possible because when you convert carbonaceous material through to diamond, it’s in a very
high-pressure medium where you can’t easily control the shape – you just jam everything together. Whereas here, the graphite is being transformed through to an ultra-hard material,” MacRae said.
The study used a range of cuttingedge science techniques on the largest sample of ureilite meteorites to date. At CSIRO, an electron probe microanalyser (EPMA) was used to quickly map the relative distribution of graphite, diamond, and lonsdaleite in the samples. This instrument, together with high-resolution transmission electron microscopy (TEM) at RMIT University, helped identify the largest lonsdaleite crystallites to date – up to one micron in size.
Dougal McCulloch and his RMIT team, PhD scholar Alan Salek and Dr Matthew Field, used advanced electron microscopy techniques to capture solid and intact slices from the meteorites to create
snapshots of how lonsdaleite and regular diamonds formed.
Professor Tomkins of Monash University said the study findings helped address a long-standing mystery regarding the formation of the carbon phases in ureilites.
“Nature has thus provided us with a process to try and replicate in industry. We think that lonsdaleite could be used to make tiny, ultra-hard machine parts if we can develop an industrial process that promotes replacement of preshaped graphite parts by lonsdaleite,” he explained.
Collin MacRae reinforced why the discovery was very exciting for industry – the unusual structure of lonsdaleite can help inform new manufacturing techniques for ultra-hard materials in mining applications.
“We often see graphite associated with
these diamonds. What’s really interesting for us, is that the lonsdaleite texture looks like it has the texture of graphite, which indicates very strongly that the formation processes simply allowed the atoms to transition from a graphite structure through to a long starlight structure,” MacRae explained
“It’s exciting because it means that potentially if you understand how to produce this material in the laboratory, which is supposedly harder than normal diamond, you could actually shape the graphite and convert it to limestone light and end up with shapes and materials.”
CSIRO’s Dr Nick Wilson said the collaboration of technology and expertise from the various institutions involved allowed the team to confirm the lonsdaleite with confidence.
“At CSIRO, an electron probe microanalyser was used to quickly map the relative distribution of graphite, diamond and lonsdaleite in the samples. Individually, each of these techniques give us a good idea of what this material is, but taken together – that’s really the gold standard,” he said.
To purchase a new cutting-edge electron microscope, CSIRO received special dispensation from the Australian Research Council (ARC) because the organisation has experts in that type of microscopy, with the ability to operate the equipment in-house.
Collin MacRae explained CSIRO’s proficiency in this space. “Our interest is in alternative materials for cutting materials for mining. That’s the reason why we’re interested in alternative materials like this. And so, we were completely supportive of analysing this problem with any company and we can see that potentially further down the track, we might end up with something that advances some mineral processing, exploration and similar areas.
“I’m an electron microscopist with a special interest in cathodoluminescence and software threat analysis,” MacRae explained his role in the project. “And that’s a unique capability that we’ve developed here over the last 15 to 20 years. We’re world experts in that area, and we’ve developed unique spectrometry and analytical techniques in that area. That proved to be through finding lonsdaleite. Because of lonsdaleite’s structure, there is a very strong image of luminescence when you struggle with an electron beam and so having cathodoluminescence, at least spectroscopy, has been the reason why we’re able to do this research.”
On the involvement of other partner universities and their collaborative efforts, MacRae said they had already been collaborating with Monash University and RMIT previously.
“In Scotland three years ago, we used advanced
techniques that we’ve developed using this new microscope to find samples of lonsdaleite. We took some samples to RMIT to Dougal McCulloch’s laboratory,” he explained.
“And they are world experts in carbon transmission electron microscopy – carbonaceous materials. Dougal has a lot of knowledge about how to make countermeasures materials as well. And so, he proved beyond any doubt that what we were looking at was, in fact, a one-star light structure as opposed to a simple diamond structure. That’s how the collaborations came about.”
Lonsdaleite’s discovery can now lead to its synthetic production, in the same way cubic diamonds are grown for use in industries like mining. Since lonsdaleite is much harder than a regular diamond, it can be used to create more durable machine parts.
Lonsdaleite has an added benefit according to MacRae, appearing to require lower pressures than its cubic cousin.
“If something that’s harder than diamond can be manufactured, that’s something industry would want to know about,” he said.
“Mining is one of the big areas for ultra-hard materials, where they can be used for cutting rocks. And so normally, these materials are fused diamonds in a silicon carbide matrix, and they do wear out. Therefore, we need to produce something that’s got harder materials than it’s going to wear. And it’s just going to be more efficient to operate them as well.
“Applications for mining are quite extensive. They could be useful for drilling nitrite. But certainly, the big application that we’re looking at is for the mining industry. That’s an exciting area for us.”
With the manufacturing industry more exposed to cyber attacks in recent years, Manufacturers’ Monthly speaks with RSM Australia’s cyber expert Ashwin Pal about the importance of understanding and dealing with the threats to the operational and information technology environments.
THROUGHOUT his 25 years in cyber security, Ashwin Pal has seen it all.
Now heading RSM’s Sydney cyber security division, Pal spent 18 years of his career working with system integrators in the field, building and breaking different systems. He has always had a part to play in the manufacturing industry, seeing the impacts of underinvestment and a lack of knowledge in this area throughout the years.
Cyber security incidents are growing exponentially globally, and manufacturing continues to be a key target. In June 2020, Australian beverage giant Lion was hit by a major cyber-attack that knocked out internal IT systems as well as operational technology, halting manufacturing and impacting customer orders. A second cyber-attack further disrupted the IT systems, prompting the company to strengthen its network defences while it continued to undo the damage from the first attack.
Global meat processing company
JBS Foods recently paid $14.2 million to a criminal cyber gang to end a five-day attack which halted its operations around the world, including in its Australian facilities. The five-day shutdown threatened Australia’s meat supply chain, with temporary staff lay-offs at some of the company’s plants and reports from farmers of shipments of livestock being cancelled.
According to Pal, probability and impact are the two reasons why manufacturing is a logical target for hackers.
“The probability for them getting through is going to be a lot higher because manufacturing is arguably behind a lot of other industries in terms of cybersecurity,” he explained. “The impact is much greater as well – when the factory floor shuts down, the cost is much greater because of all the inventory and raw materials involved.”
Because manufacturing revolves around operational efficiency, cyber
security can be easily overlooked. More often than not, technology on the factory floor is managed by workers focused on operations, who may not have the skillset to manage operational technology (OT) systems if something goes wrong. A huge
focus – rightly so – is placed on ensuring the operational technology is running constantly, but a sole concentration on keeping the lights on leaves vulnerabilities, which hackers can and have exploited.
“A lot of the equipment which comes in hasn’t been set up to be secure. The operational workers who set it up aren’t security focused, they are focused on making sure that robotic arm for welding is working, for example. They might not have changed the default administrative password. All it takes is someone to set up a wireless network from the factory floor and they have access to that robotic arm, which in turn can inject ransomware into the network and kill all the robotic arms.”
When RSM engages with a client, the team undertake a holistic assessment from cyber through to the OT environment. A thorough risk analysis using the appropriate standards is done in conjunction with penetration testing on both sides (IT and OT), giving the client the perspective of what they look like to a hacker.
“In between both exercises you see where the gaps lie and how exploitable they are,” Pal said. “In essence, we can provide advice to what a transformation program might look like for a client and make sure once they have climbed the mountain they don’t begin to slide down it.”
Just like with digital transformation, the temptation to completely uphaul an entire cyber security network at once might be pre-emptive and ineffective. It’s more useful to drip-feed improvements, beginning with the fundamentals. Pal explained that it’s important to isolate the “quick wins” first, which are quick to deploy and show runs on the board. Committing to a million-dollar project in this space can lead to executives running out of patience, killing it, leaving areas for hackers to exploit.
Pal also emphasised the importance of separating the IT and the OT environments.
“You cannot talk about manufacturing in one set. IT and OT are two different things with different purposes, levels of importance and impact. The threats for both are very different and they need to be treated separately.”
When hiring new people to help businesses sure up their critical infrastructure and data, Pal looks for one main quality.
“Cyber qualifications certainly help, but the key is having that curious mind,” he said. “It’s the desire to constantly look and understand for problems, to me that’s the differentiator.”
OT is crucial to automating and driving efficiencies within the manufacturing process. Traditionally, OT environments have not been as well secured as IT environments, which is a big mistake for manufacturing. Having no security on the factory floor opens the door for ransomware attacks locking up operations, costing far more money than an attack on the IT system.
“The impact of an IT incident in manufacturing is very, very different to say the impact of an IT incident for a company such as RSM, for example,” he said. “At the end of the day, for manufacturers, remaining operational and getting inventory out the door is all that matters. We take that philosophy into all our manufacturing clients who really appreciate it because they see we are identifying their major pain points, understanding the importance and potential impact on the business and acting accordingly.”
To hackers, OT environments can be seen as a soft underbelly without
the cyber security attention their IT cousins have had. OEMs aren’t cyber security experts themselves, so a lot of the vulnerabilities can stem from the equipment itself. The internet of things is becoming increasingly prevalent in the industrial environment, and with OT and IT environments converging, the Australian Government has recently created a voluntary code of practice for IoT equipment to protect itself from cyber-attacks.
RSM partners with companies who are experts in OT, providing specialised security tools and technologies for the challenge. Another obstacle with securing OT is it proliferates around facilities quickly, which only increases the attack surface. It can become difficult to keep track of every aspect of OT (asset discography) and without control over visibility, it is impossible to understand the vulnerabilities which need to be addressed.
“Cover the devices, the connections, architecture, network configuration, security configuration, etc.,” Pal said. “Update this information monthly as OT devices tend to proliferate. Without knowing what you have, you cannot secure it.”
Pal outlined a multitude of ways RSM helps protect OT, including: segregating and cloaking OT networks, ensuring
authentication, authorisation and lockout controls, intrusion detection, malware detection and backing up all critical data and configurations. On top of these strategies underlies people and process – personnel should be security-trained specifically for OT environments.
“They need to understand basic security concepts and controls that have to be implemented within the OT environment that they will be managing. Security policies for OT environments must be developed that outline the controls that need to be implemented and typically emphasise required areas. Without these, OT security will likely be ad hoc and exposed to numerous vulnerabilities.”
Operational technology and Internet of Things security company Nozomi Networks’ recent report looked at the challenges facing pharmaceutical manufacturing. Securing intellectual property and data from theft, identifying and preventing vulnerabilities in complex supply chains and preventing unplanned downtime headed the list of problems.
“Pharmaceutical companies are rapidly embracing tools and technology to gain operational efficiencies,” the report says. “However, automation and outsourcing increase risk and expand the threat surface. This makes it challenging
The same applies for the broader manufacturing industry, where the industrial IoT is opening up organisations to new cyber threats, partly because internet-connected sensors and devices are built for 24/7 reliability rather than security and the majority of operational systems are not up-to-date and remain unpatched.
The relative immaturity of cyber security for OT environments represents a challenge, but also an opportunity, according to Pal.
“It’s not too difficult to secure OT environments if we just focus on the basics,” he said. “This is where the IEC 62443 standard comes into play. We follow that stringently and have expertise on the laundry list of items which goes into securing networks.”
Massive financial implications aren’t the only threat cyber-attacks have on manufacturing, with breaches in OT leading to potentially devastating security implications. The factory floor is a dangerous place, often with heavy machinery being operated in different directions. Triton is a malware first discovered at a petrochemical plant in Saudi Arabia in 2017. The malware is designed to disable safety systems and targeted Schneider Electric technology. Coined “the world’s most murderous
hand/wrist/ankle surgeries, custom prosthesis and reconstructions for jaw joint osteoarthritis, trauma and cancer patients.
“The benefit of 3d printing is we can create a customised object very easily and quickly. We’re usually turning parts around for surgery within two days,” he said. “Someone might have gone through a trauma or accident and have a broken jaw, for example. The patient will have a CT-scan, the bio-medical engineer then plans the surgery and figures out what needs to be replaced or moved and a CAD file is generated and signed off by the surgeon. That file is passed to us, we manufacture the part which is delivered into surgery and put into the patient.”
Titanium is one of the few metals which is bio-compatible with the human body, lending itself perfectly for printing implants.
“Bones are lightweight but strong. Stainless steel has been used traditionally and is great for strength but they’re heavier. Titanium is that sweet spot that feels comfortable in the body,” he added.
“Suitability for the medical industry really comes down to process control – having complete control of all the parameters which go into making a part. It is really specified and we need to be really regimented in our internal processes.”
Leveraging off its success in the medical space, serving the aerospace industry has been a natural leap for Additive Engineering. The aerospace
industry is the largest customer of titanium alloy products. Titanium’s high strength-to-weight ratio, high temperature and corrosion resistance are favourable for applications including airframe structures as well as smaller components for jet/turbine engines, rotors, landing gears and compressor blades.
“We’re definitely still exploring other markets but we really just want to keep consolidating ourselves in being the number one provider for medical items in Australia,” Tevelein said. “Air Liquide has been fantastic working with us and we are looking forward to continuing on that path with them on board.”
“ADVANCE”, Air Liquide’s new strategic plan for 2025, is a milestone in the company’s history. It places sustainable development at the heart of the Group’s strategy and is built around 4 pillars;
1. Delivering strong financial performance
With ADVANCE, Air Liquide is taking action today while preparing the future. The Group is rising up to an ambitious challenge: maintaining its growth dynamic and improving its profitability while meeting its commitments to reduce CO2 emissions and investing in the markets of the future.
2. Decarbonising the planet ADVANCE will enable Air Liquide
WOMEN IN INDUSTRY NOMINATIONS ARE NOW OPEN. Now is your chance to nominate an industry leader who you believe is advocating for positive change and deserves to be recognised.
WOMENININDUSTRY.COM.AU
The Women in Industry Awards recognise outstanding women leaders from across Australia’s industrials sector.
PROUDLY PRESENTED BY
With more than 700 Australian and international companies displaying through a sold-out industry exhibition, flying displays featuring aircraft never before seen in Australia and a conference program already at capacity, the fast-approaching 2023 Australian International Airshow and Aerospace & Defence Exposition (AVALON 2023) is already evidence of a vibrant industry looking positively to the future.
TRADITIONALLY a venue for cutting-edge debate and highlighting new technologies, AVALON 2023 will provide a platform for engagement between Australian and international industry, government and academia, from Tuesday 28 February to Sunday 5 March, with “industry only” trade days from Tuesday to 2pm on Friday March 3.
This year’s event will feature conference sessions and exhibitor displays across the spectrum of aerospace, space, aviation and defence, from space industry development to electric powerplants, Advanced Air Mobility (AAM), business aviation, sustainable aviation and uncrewed systems.
AVALON 2023 will be first and foremost an engagement platform for industry, with formal networking
exhibitors connect with each other, key industry players and visiting military, government and industry delegations. It will also highlight and reward innovation in the Australian aerospace, space and defence industries, provide a focus for STEM and careers promotion and, through the weekend airshow, allow the general public to get closer than they ever have before to the military and civil aircraft that serve Australia’s defence and economy.
The packed conference program includes:
The Australian International Aerospace Congress (AIAC20), the preeminent aerospace forum in the region. The conference stream for AIAC20 will incorporate the 20th Australian Aeronautical Conference, the 13th International Conference
(HUMS) and the 12th National Space Engineering Symposium.
• The “Advancing Space” briefing, hosted by the Australian Space Agency, AusIndustry and Austrade.
“Defence’s Role in the Sustainable Aviation Fuel (SAF) Transition”, hosted by the Royal Australian Air Force and CSIRO.
The “Emerging Aviation Technologies: Challenging the Status Quo in Australia” conference, hosted by the Australian Association for Uncrewed Systems (AAUS).
The latest in the Australian Industry & Defence Network (AIDN) “Are You Defence Ready?” briefing series, to help SMEs pursuing defence business.
The Australian Business Aviation Association Members Meeting.
The Indo Pacific Military Rotorcraft
rotorcraft capabilities in the Indo Pacific), hosted by Boeing.
• The World Airports Conference
“Mission Possible: Net Zero Aviation in a Changing Global Environment”, hosted by prominent international aviation consultancy Airbiz.
“Delivering More Together – Defence Innovation, Science and Technology”, hosted by the Department of Defence: Defence Science and Technology Group.
As part of its mission to aid development of Australian industry, AVALON 2023 will again feature its Innovation Awards, designed to highlight and reward local innovation.
Twelve Australian innovators have been shortlisted for 2023, in a year when the cash prizes for two of the Awards have been more than doubled, to $50,000 each. The Awards are sponsored this year by Australian innovation and professional services consultancy Synergy Group.
Shortlisted contenders include a company that has developed the world’s first camera showing the stresses in the structure of an aircraft, a company applying the equivalent of a shark’s skin to reduce drag, and a young algorithm engineer helping to develop autonomous control systems for the next generation of combat drones.
Since the Innovation Awards were first presented at AVALON 2013, AMDA has presented Young Innovator and SME Awards to a total value of more than $485,000 across its major industry events.
AVALON 2023 will host a range of industry and public focused student engagement programs as part of the event’s formal careers and skills schedule.
Careers and Skills incorporates a range of programs designed to connect students of all ages to the aviation and aerospace industry and promote careers in the fields of science, technology, engineering and mathematics (STEM).
AVALON 2023 has engaged specialist education partners including aerospace training organisation Aviation Australia, the Royal Aeronautical Society Australian Division, industry recruitment specialist Kinexus and RMIT University, to present careers and skills events, including: Tech Zone (for all ages);
• Aviation Learning Paths (for secondary schools);
Program (for tertiary students); and
• What the 5th Gen Workforce Will Look Like (for industry professionals).
In addition to daily flying displays on AVALON 2023 industry days, the event will feature the southern hemisphere’s largest public airshow, from Friday 3 March to Sunday 5 March.
This will be the fifteenth Airshow event held at Avalon Airport, with a full flying program of Australian and international aerobatic performers, a vast
Enjoy all the perks of the city with the tranquillity of a country lifestyle. Cessnock City is perfectly positioned as gateway to the Hunter Valley vineyards and is surrounded by vibrant country towns and villages. Located just 30 minutes from Newcastle and 2 hours from Sydney, it is the ideal place to live, work and play.
Contact the Cessnock Airport Operations Coordinator during business hours Monday to Friday on (02) 4993 4228 to discuss commercial opportunities.
Download the Investment Prospectus at www.advancecessnock.com.au
array of modern military hardware from the Australian Defence Force and overseas air arms, together with antique, classic, and experimental aircraft both in the air and on the ground.
Highlights for 2023 will include a strong US contingent and the first Australian showing of the Republic of Korea Air Force Black Eagles display team, flying the Korea Aircraft Industries T-50 Golden Eagle.
AMDA Foundation CEO Justin Giddings said AVALON 2023 would be a welcome return to face-to-face engagement for the Australian aerospace, space and defence community.
“After COVID forced cancellation of
AVALON 2021, we are thrilled at industry’s obvious enthusiasm to return to AVALON for 2023,” he said.
“The sheer size and diversity of the industry exhibition, conference program and list of visiting military and civil aircraft will ensure this is the largest and most informative AVALON yet for industry. International delegation interest has been strong, the United States is sending its largest ever contingent of aircraft, and the Royal Australian Air Force is fully committed.”
Register now as a trade visitor for AVALON 2023 at www.airshow.com.au
Cessnock Airport is primed for growth, with its accessible location and close proximity to major freight routes and capacity to absorb future growth.
5 hectares of land is available for aviation operations, maintenance and manufacturing activities that is unencumbered by Defence and within an uncongested airspace.
Funded by the Black Summer Bushfire Recovery Grants Program
IN the 1870s, Eduard Franckel was a senior official at the Swedish State Railways. The railroad construction expert held a presentation in Stockholm, asking why there were no Swedish specialty companies for railroad materials, even though there were resources in the country. From this idea, AB Atlas was born.
From the different iterations of Atlas Copco throughout the years, there has been some truly remarkable stories, including on Australian shores. The Swedish company began its journey in Australia in 1950, with customers like the State Electricity Commission of Victoria, New South Wales Railways, Tasmanian Hydro Electric Commission, the Snowy Mountains Authority and numerous mines in Tasmania, New South Wales and Western Australia.
Atlas Copco has been involved in some of Australia’s major historical events. Take the year 1976 for example, where the first
in its
British female Prime Minister Margaret Thatcher was photographed in Victoria’s Broken Hill punching away with an Atlas Copco Panther rockdrill, wearing overalls, a hard hat and other protective gear. The following year, Atlas Copco helped the rescue mission of the Granville train disaster with its RH-series rock drills, a Darda rock-splitter and PRHS700 portable. Not every company has a dinosaur named after them, either. Thanks to assistance and equipment from Atlas Copco, paleontologist Thomas H. Rich was able to conduct excavations for ten years at Dinosaur Cove in the Victorian Otway Ranges. From layers of sand, mud and clay, which over a period of more than one-hundred million years had been pressed together into hard rock, a new species was discovered. In appreciation of the help received from Atlas Copco’s compressors, rock drills and pneumatic tools, the new discovery bears the company’s name – Atlascopcosaurus.
According to Atlas Copco Australia business development manager Roshan Kumbla, the company’s mantra has always revolved around energy efficiency. Increased costs across the global supply chain have hurt the hip pocket of Australian manufacturers, but reducing carbon footprints can directly lead to cost savings.
“Every product we release is at least 10-15 per cent improved in some way more than the previous one – our product evolution has been based on that,” explained Kumbla. “Compressed air production consumes a large amount of energy, which impacts a company’s bottom line as well as the environment.
Atlas Copco uses a 10-step guide to help companies lower their energy consumption and carbon footprint, which will translate into direct savings. When approximately 80 per cent of
your compressed air system’s cost is your electricity bill, these savings can’t be dismissed. Over the life of your compressor, by selecting the right initial compressor system, your business could save you 5 – 10 times the cost of your initial asset in power costs, and reduce your effective carbon impact substantially.”
More and more people are demanding governments take action on climate change, which is leading to new legislation in many countries, such as tighter emission standards and carbon taxes.
By the same token, many companies have realised that making their production greener beyond government mandates is not just good for the environment but also for business – and that it can shore up their long-term success.
“From our research and development of compressors, through our production processes and to the project planning of systems and service, we always strive maximise efficiency in the use of resources, and create the highest possible profitability and sustainability for our customers,” he said. “Regardless of the industry, Atlas Copco has effective and efficient solutions for compressed air, oxygen and nitrogen generation applications.”
150 years of continued innovation is certainly an impressive feather in Atlas Copco’s cap, but it isn’t enough for its customers to just take their word for it. To quantify the savings Atlas Copco’s compressors have in the short, medium and long term, the company performs a data logging service (AIRchitect), which allows a user to track and simulate energy use in a compressed air system.
AIRchitect can do the data logging for any compressor in the market, independently of the size and brand of the compressor. The core function of data logging is to get a full picture (every second of every day) of how your compressed air system is behaving, identify where energy is wasted, or
Atlas Copco’s reputable history has culminated
150-year anniversary. Manufacturers’ Monthly finds out about the company’s legacy of innovation, progress and how it continues to push the envelope towards sustainability and efficiency.
production is impacted, indicate how to improve that system, and finally simulate future system combinations that will deliver the most efficient, reliable and profitable operations to the customer. For instance, the third generation of Atlas Copco Variable Speed Drive compressors can save businesses up to 60 per cent on total energy costs.
“It records data for every one second of the operation,” Kumbla added. “For example, if the compressor is standstill or in unload power (the motor is running but it’s not delivering air), we will find out how often this is happening and translate it to a cost.”
By having multiple days of data, Atlas Copco can assist the business ownerto find new operational efficiencies, whether that’s running certain processes at different times or identifying when a compressor is running but doesn’t need to be, or simply by rebalancing when multiple compressors are running to maximise each compressor’s efficiency sweet spot. The innovative Variable Speed Drive (VSD) compressors help to avoid such inefficiencies in environments where the demand for air isn’t completely consistent and constant. As the name
suggests, a fixed speed air compressor operates at the same speed whenever it’s running. By design, it always draws the amount of power needed to meet the maximum compressed air demand, even if demand is less than maximum. Because the speed of the motor can’t change, whenever the demand for air changes, an air inlet valve adjusts to allow either more or less air to flow out.
In contrast, a VSD air compressor can operate anywhere in the range between its minimum and maximum speed, and it automatically adjusts the speed (and power usage) so production of compressed air matches demand in real time. When demand increases, the motor speeds up. When demand decreases, the motor slows down. This capability saves energy because the compressor doesn’t have to run flat out whenever it’s on, with a Free Air Delivery (FAD) increase of up to 21 per cent compared to fixed-speed models.
“By shifting to a variable speed drive, you can eliminate those energy losses laid out by the data logging we do,” he noted.
“In this way, the sales engineers and our authorised distributors become energy advisors, more than just selling boxes that compress and clean air. Atlas Copco
is built around its innovation but also backs that up with customer support. Our AIRchitect report is easy to understand and we have countless business owner testimonials relating directly to savings created from changing energy strategies.”
Atlas Copco’s constant drive for innovation is heavily supported by its investment in research and development globally across all products. Innovation leads to tangible results for customers, for instance, compressors which use 30 per cent less oil than competitors.
“It drives us to better ourselves and be better than our last product,” Kumbla said. “We think 10 to 15 years ahead at times. For instance, we were the first to implement VSD and the first to integrate dryers and package them off.”
Another advancement for Atlas Copco which continues to improve user productivity is its SMARTLINK program - a software which gives customers the ability to monitor their compressed air systems through a web interface. Remote monitoring is becoming one of the most critical needs of busineses today. SMARTLINK facilitates connectivity by
receiving signals from compressors in the field to help manufacturers avoid shutdowns, improve safety, reliability and efficiency in the compressed air system installed in their facility.
“No other competitor in the world has the level of connectivity with its compressors,” he said. “As well as this, you look at smart features like a Smart Temperature Control System ensuring optimal oil temperature and injection, Boost Flow Mode to temporarily exceed maximum compressor capacity and intelligent drains to limit energy use and service intervals.”
Atlas Copco has employees across Australia available for advice, planning, installation, service, maintenance and the optimisation of existing compressor systems and offer the range of services of a global compressor manufacturer. Choosing a compressed air product is always a big decision for any kind of business, so the experienced company does everything to actually prove how it will save money off the bottom line. This constant drive to serve the customer, in addition with a thirst for innovation, have combined to strengthen the company along its 150 year journey so far.
IN 1923, PWB began manufacturing chains in Australia. After over 90 years in Australia, Japanese heavyweights KITO Corporation joined forces with PWB to form the company as it stands today, with over 200 years of combined experience.
The safety of all users is at the core of what the company aims to achieve, not just within the organisation, but for the lifting industry overall. In conjunction with safety, KITO PWB has invested heavily into designing products which reduce downtime and foresee future problems before they happen.
With this in mind, Glenn Morgan, national hoist specialist, explained the
company’s advanced form of maintenance.
The inverter control in KITO PWB’s range of electric hoists is a dual speed variable frequency (VFD), which controls both hoist and trolley for optimum speed adjustability as well as lifting and lowering accuracy. The technology incorporates an easily accessible condition monitoring system via an hour meter and operation counter, which records the data of the number of hours used and the total number of times operated.
“It is all set out in the manual. It tells you when you need to change the oil, after how many operations you need to check the brake. It will even tell you when the Major Inspection is due, this is based
on actual usage, not on Calendar years,” Morgan said.
“This provides a pathway for appropriate preventive maintenance to be conducted to ensure the hoist is operational for when you need it.”
Operation-based maintenance helps to increase the operational life of hoists, decrease the maintenance cost and the amount of maintenance time on hoists and cranes, lower the risk of breakdowns and unplanned downtime, optimise operation and productivity and energy efficiency.
“Having the inverter as a standard feature is something that no other quality hoist has in the market,” he noted.
Hoists with condition monitoring
cover the full range of hoisting applications, with the powerful – ER2 Electric Chain Hoist & MR2 Motorised Trolley, the effective – EQ, EQS Electric Chain Hoist & MR2Q Motorised Trolley and the high-performance – RY Electric Wire Rope Hoist.
The standard inverter control for the dual-speed hoist provides soft start and soft stop to minimise impact and reduce shock loading, but can also customise the speeds meet the customer requirements. A low-load high-speed function on the EQ, EQS & RY Hoists allows for faster lifting speeds at low loads to increase productivity. The smooth start/stop and transition from slow to fast protects the
January, or the beginning of the year, is the best period of performing maintenance services for most industries. To welcome this season, Manufacturers’ Monthly assesses the benefits of KITO’s built-in condition monitoring system for general and preventative maintenance.
load and supporting structure and reduces load swing and bounce.
In some instances, crane service providers have not promoted KITO products, because of their superior durability. Minimal breakdowns and repairs are required for KITO’s equipment across a long period of time, losing opportunities for providers to make more money off repairs.
“From an end-user point of view, that quality and durability is what they want,” Morgan explained. “End users should be specifying KITO because they know their cost of ownership or runtime costs will be much lower compared to others. When you increase productivity and reduce ongoing repair costs it makes a difference in the long run.
“Lifting is one of the most dangerous things you can do and most people don’t actually give it the attention it deserves,” Morgan added. “The old adage of a chain is strong as its weakest link applies and KITO is always very conservative with its engineering, always over-engineering something to ensure complete safety. It’s probably this approach which translates to the company being the pinnacle of quality whilst still having a high market share.”
KITO is one of the few hoisting companies that manufactures both its own hoists and its own load chains. On top of that – KITO is the only manufacturer worldwide that nickel-plates its load chains. This combination provides the hoists with the unique benefit of safety and functionality, and excellent reliability.
KITO hoists are built to perform for years of trouble-free service. They are
Professional consulting services delivered across your project life cycle from strategy, procurement, and planning, through to project delivery.
Staff located in each of the eastern states and territories, providing localised service with national support.
robust and resistant to rough handling conditions. They continue to function well, even at fully rated capacities. Decades of specialised engineering and on-the-job testing has given the KITO team industry-leading intelligence on how to create the world’s sturdiest hoists, component by component.
National hoist business manager, Glenn Morgan, stands by the quality and engineering of the KITO hoist. “Honestly, there is no comparison on the market,” he said.
To support the KITO philosophy in delivering unmatched customer and end user satisfaction, KITO PWB has its own dedicated customisation workshop based at the Australian National Head office in Victoria. This is supported by a specialist team of hoist technicians who build customised lifting solutions not just for the Australian market but also for the greater Oceania region.
The workshop is designed to enable several technicians to be working simultaneously on multiple projects. From designing and fabricating chain buckets, specialised load cells and displays, travel limits, as well as assembling visual and audible alarms, remote control systems, close coupled trolleys and more. Every item passing through the assembly shop is fully function tested in accordance with AS1418 before it leaves the workshop.
No task is too big or too small. KITO PWB thrives on designing and delivering hoist and associated lifting solutions for all applications from small to large and complex challenges.
Expertise in bid and tender support, systems engineering and integrated logistics, training systems and e-learning programs, and project management services.
Our services are flexible and scalable and our attention to detail combined with industry best practice ensures that your business achieves success.
No matter what stage your project is in, our experienced defence consultants are qualified to add value and keep your projects moving forward.
systematiq.com.au
UNDOUBTEDLY, there are many industries that benefit from correct hose and cable management systems. JSG Industrial Systems is in the business of providing highly robust, functional, and practical hose management solutions to its industry customers.
With more than 100 years of experience, JSG understands the implications of poor hose management, especially in and around reciprocating or moving machinery, often resulting in premature ruptures and damage.
Wear, abrasions, kinking, being caught in machinery or affected by onsite vehicles cause damage to hoses and cables, leading directly to costly repairs and maintenance, unplanned downtime, and lost efficiency.
JSG Industrial Systems product manager for flow, James Slowgrove says workplace safety is also another key consideration, with problems arising from improperly stored hoses.
“Hose reels revolve around safety and operating efficiency. By effectively keeping
hoses off the ground when not in use, they remove potential trip hazards from the workshop floor or in the immediate area of a service vehicle,” he said.
“If the hose is not being used then they need to be wound back and stored correctly. We are reducing our operator time lost to injury through safely storing hoses.”
JSG provides hose reels that are designed to safely rewind and be correctly stored away from hazardous locations, including service vehicles and machinery sites. The company has an extensive range of high-quality products from leading suppliers.
Priding itself on being able to work with its suppliers, JSG shares technical information and makes continual improvements to manufacturing processes to maintain a competitive advantage in the market.
In relation to hose reels, JSG’s three key suppliers to industry customers are: Lincoln, Cobra, and Faicom.
JSG has an extensive history with Lincoln amidst mining, industrial and
commercial sites, leveraging off the company’s reputation as manufacturers of exceptional lubrication, pumping and hose reel systems.
Lincoln’s new generation springdriven hose reels are an open-style design for heavy-duty applications. They possess high-tensile frames ideal for harsh operating environments.
“Lincoln manufacture robust, functional and reliable hose reels, operating everyday across industry sites,’ Slowgrove explained.
Cobra hose reels are also open-style and can be supplied in manual, springretractable or direct-drive configurations. They are high-strength, with rigid frames and drum, and are designed for high flow rates with a large hose capacity and high duty cycle.
“Cobra provides a similar type of reel to those manufactured by Lincoln, with a focus on underground coal mining operations as their spring retracted reels contain no aluminium components,” Slowgrove added.
JSG has worked closely with Cobra to ensure the manufacturer’s air-assisted and hydraulic-driven reels, produced in a variety of sizes, can be used for diesel fuel, high-pressure grease, compressed air, and lubricating oils.
The Cobra hose reels are compact, designed for heavy-duty use in rugged environments.
Super swivels are used on the grease head reels to allow retraction even while under full pressure. The swivels have a full flow path and can withstand heavy slide loads.
Faicom manufacture reels tailored towards workshops and manufacturing
facilities, producing a variety of hose reels and cable reels that assist in minimising wear and improving operator safety. The MPRT curtain-support reels are used in the separation of welding, grinding, or painting sections within industry workshops.
“The Faicom range of products are very special, as each are designed specifically for a tailored application, whether it is for hot water washdown areas or oil transfer applications” he said.
“JSG’s hose reels are designed to cater for a large customer base, offering many applications.
“Our business is predominantly mining. We have two wonderful brands, Lincoln and Cobra, designed for these operations; however, with Faicom we can cater for niche applications where many of competitors do not.”
JSG’s many customers in different industries often require specific installation needs, according to Slowgrove.
“Hose reels are not straightforward; you have different fluids passing through them,” he said. “Chemical compatibility is crucial, not just in the hose but also in the hose reel.”
JSG prides itself on being a specialist in providing the right hose and reel for the right application.
“At the end of the day, if you are using a hazardous fluid; you don’t want that hose to leak; you cannot afford the hose reel to leak either,” Slowgrove noted.
“At JSG we offer a large range of products and expertise with a highly trained and knowledgeable sales team that understands hose management systems, and which ones are the most appropriate for the needs of our customers.”
JSG Industrial Systems’ new generation of hose reel systems are designed to withstand the toughest of manufacturing environments. Manufacturers’ Monthly finds out how the hosing solutions are leading to improved safety in various industrial facilities.
CAPS has partnered with a major manufacturer to the European market to create an affordable generator while still using premium quality components.
FOR over 42 years, CAPS has been Australia’s largest independent supplier of power generation and air compression products. With proven global engineering and export capabilities, the team of experts undertakes turnkey projects which include the design, supply, installation, commissioning, and provision of longterm maintenance support to Australian industry standards (ISO 9001:2008).
As well as being a master distributor of KOHLER and AIRMAN generators, CAPS has partnered with a major manufacturer to the European market to create an affordable generator while still using premium quality components. Some of the components include LeRoy Somer alternators, Perkins, Doosan or Baudouin engines, ABB breakers and industry renowned control systems.
CAPS fully supports and stands behind everything it sells – with a focus on guaranteeing generators will be high quality, dependable and suitable for your prime power or back-up power requirements.
Meeting tough industry testing and quality standards is the first step to the generator’s rapid response, powering up in seconds to deliver quality power during voltage and frequency changes.
In all CAPS generators are leading engine and alternator brands that have state of the art technology and have compliance with international standards.
Engines with low fuel consumption provide accurate speed setting and order, mount to the fuel pump and have mechanic or electronic type governors. The alternators have a bearing system which don’t need maintenance, with an electronic a type voltage regulator providing voltage setting.
The chassis is manufactured from steel that has features and durability for carrying the burden of a generator. Thanks to its rigid structural design
and anti-vibration mounts, it reduces vibration levels to a minimum. All chassis’ contain lifting lugs. In generators less than 1,600 kVA, the fuel tank is integrated into the chassiswith level indicators.
Compatible with 2000/14/EC directives, certified noise emission level
• 2 or 4 points transport possibility according to cabin size.
• Hidden exhaust inside the canopy
Emergency stop button located on the canopy Improved air suction channel to ensure homogenous cooling in the canopy
Radiator air outlet and exhaust with designed towards above
• Lid on cab that provides to be filled
up water and antifreeze easily to the radiator
• Amplified paint system against corrosion and rusting
• Improved performance in terms of sound insulation
Standard control panel, that is used in CAPS generators, ensures comfortable and safe usage. All measured and statistical parameters, operating modes, notice and alarms and condition of generator, are monitored easily from the control panel. On the front of the panel’s metal body has electronic control module and the emergency stop button and the panel’s metal body is made of steel sheet and is painted with electrostatic powder paint.
Australian manufacturers need to consider the risks associated with a potentially unreliable power supply. There are a multitude of processes critical to manufacturing plants and these processes could be adversely affected if there are any prolonged interruption due to an unscheduled grid failure. What would be the cost of losing production, plant, fridges, computers, lights, and staff not working for one hour, two hours or more?
Delivering a back-up diesel generator, especially for the manufacturing segment, involves several challenges, such as real estate constraints, rapid start-up along with performance and emissions issues.
This is why CAPS Australia’s complete solution provides; system design via our in-house engineers, build in our Australian ISO accredited manufacturing facility and commission a custom-built system, perfectly matched to individual requirements.
CAPS Australia only supply quality generators, and outside of our own range, we also distribute other major OEM brands such as KOHLER and AIRMAN generators.
KOHLER has 100 years’ experience in the power generation segment. CAPS has also introduced its own newly released range of generators built in Europe.
Both are made to the highest standards and have built a solid reputation as dependable mains backup generators. With sizes starting at 9kVA and going right up to 4,500kVA, CAPS can assist you with any backup generator requirement.
CAPS is also the Australian distributor for AIRMAN generators, which sit mainly in the prime power generation space. AIRMAN are synonymous with bullet proof Japanese built quality.
To ensure your back-up power equipment is always ready to perform when needed, CAPS offers a nationwide service network with the ability to service and repair your equipment. Our highly trained technicians continually
update their knowledge, and they have the model-by-model knowledge required to give you piece of mind.
Safety is a core value of CAPS, and our goal is never to put people, plant or the environment at risk. You can be confident that our technicians will be
completely compliant to any site-specific safety requirements you have.
For more information, call your local CAPS Australia office on 1800 800 878 or visit www.caps.com.au
Pilot Air manufactures Australia’s leading air compressor solutions for the Australian market. It’s an Aussie success story, and Manufacturers’ Monthly sat down with the company’s CEO, Martin Wyllie, to discover the secret to its success.
ATHER and son John and Eddie Pilotto founded the business in 1980, hence the name Pilot Air. John migrated to Australia after the second world war from Italy and worked in the compressed air industry, when he identified an opportunity in the higher-end quality market. As a naturalborn inventor, he and Eddie set about building Australia’s first reciprocating pump and air compressor units in John’s garage. John realised that fitting his air compressors with the best pumps available was of key importance, and he began importing Italian-manufactured pumps that were designed to do the job and do it with the utmost performance and reliability.
“John was focused on quality. He knew that building quality equipment would sustain the business and build its reputation. The pumps did cost much more than local or cheaper overseas products; however, it is this commitment to quality that still drives Pilot Air to this day. Our local manufacturing, supported by the parts we import from Italy, are the best money can buy and a big reason why Pilot Air is renowned for quality and consistency,” said Wyllie.
The 1980s was a pivotal decade for the business. The success of its rotary screw air compressor led the father and son to expand to a larger factory in NSW and continually refine and improve the design and componentry of the equipment. By the mid-80s, Pilot Air was importing the latest and most advanced pumps
from Italy. Known as the ‘NS’ series, these pumps formed a vital piece of the manufacturing process and forged Pilot Air’s reputation for high-end quality in the compressed air industry.
“We were the first in Australia to import Italian made pumps for reciprocating compressors. It wasn’t without financial risk. Our competitors were buying in cheaper parts; however, the business wanted to be known for quality and reliability first,” added Wyllie.
The quality first strategy paid off, and during the latter part of the 1980s, the business had moved to larger facilities to service the expanding demand and was importing the legendary Italian made ‘K”’ series pumps and manufacturing them into complete compressed air units. In 1987 Pilot Air released its first range of compressed air dryers and filters and was managing its large production facility in
Auburn, NSW, and its servicing facility in Silverwater.
Over the next two decades, Pilot Air established itself as one of Australia’s leading designers and manufacturers of complete compressed air solutions. Its name became synonymous with integrity, quality and service. With an enviable distributor network covering the coastline cities and the harsh Australian interior, Pilot Air launched its first range of variable-speed drive rotary screw air compressors in 2011. The business ran a highly sophisticated service and parts division, had manufacturing hubs in Sydney and Brisbane, launched the Quickline air distribution products and released the first scroll type oil-free compressors.
By the end of 2017, Pilot Air had relaunched the classic K series of reciprocating-type compressors with a host of updates and added features that continued the K series as the premium reciprocating air compressor on the market. Keeping innovation at the pointy end of development, the horizontal and vertical air receivers became part of the Pilot Air catalogue. In 2017 the company launched the ‘OFP’ range of oil-free type reciprocating compressors, with outstanding results.
An Australian and family business for over 40 years, the company has been designing, installing and commissioning compressed air solutions for some of Australia’s most prominent industrial and commercial brands. It boasts a distributor network that spans the entire country.
Today, Pilot Air is renowned for its extensive capability and unique customisation techniques for mid-tolarge-scale business operations. With clients ranging from iconic theme park operators to large distribution centres, logistics and material handling, civil and council, racing teams, hospitals, food and beverage and everything in between, Pilot Air is simply the best fit.
“Most of the industry has a fixed range of products that they will try to fit into the customer’s requirements. Sometimes you just can’t do that with an off-the-shelf product. A standard product is designed to go in a dry factory, but customers often come to us with a spec that requires a harsh or wet environment. In this case, we manufacture products to a high IP rating with specialised electric motors to be able to withstand those environments,” Wyllie explained.
Customised solutions include rotary screw or reciprocating air compressors, silent models for noise-sensitive environments, compact and portable models and oil-free systems.
Pilot Air leverages 40-plus years of experience mapping the technical specifications for the customer. The technical team will undertake a diagnostic examination of the site and purpose. Assessing power, location and air distribution, and using sophisticated software, the team analyses all variables, including peak and regular timetables. Using quantitative data, the team recommends a best-fit customised solution, based on performance, energy consumption, sound and space. The solution must pass a set of stringent quality control measures before its manufacture, testing, installation and commissioning.
“We comprehensively assess the
scope of what the customer needs. The machine is often done correctly, but air distribution through the plant is wrong. We specify the right distribution system, so the air travels efficiently to the machinery across the factory, avoiding having a Ferrari with retread tyres.”
The company’s strategy to remain solely invested in manufacturing the highest quality compressed air solutions has enabled the business to stay at the top of its game without the need for diversification.
“We have 45 staff with a 100% focus on air, so we don’t have to have many heads around different environments. We have in-house training where we specifically upskill staff to a point where they can understand the ideal size and type of machinery for the best outcomes and specify and install it correctly for the customer. We’ve got a range of partners that are also compressed air specialists. They have service teams that we use to fill the holes our team doesn’t reach,” he said.
Pilot Air protects any investment in its air compressors through its spare parts for current and superseded compressed air products. The company has a highfunctioning spare parts and servicing division that operates off and on-site.
“Our ethos is longevity; we want your capital purchase to be maximised over the product’s lifespan. That starts with offering a robust product, maintaining it, and keeping parts so that the investment
remains current for two decades or more. For that reason, service and spares are an integral part of the business – we want your business to stay up and running and your capital expense to be amortised over a long time,” explained Wyllie.
The last few years have thrown up challenges for the supply of parts worldwide. Not immune to the challenges, Pilot Air finds partners to maintain its expectation of quality.
“We’ve been doing this a long time and intrinsically partner with supply chain partners who have a similar ethos to us,” he said. “It’s always easy to find rubbish, regardless of your industry. We spend a lot of time working with our partners so they fit our business model.”
Pilot Air offers scheduled maintenance, preventative checks, on-site breakdown and in-workshop repairs. As well as routine maintenance, preparedness for breakdowns is key – ensuring the right people and spare parts are at hand to help the customer immediately.
“The cost of downtime, especially in manufacturing, can be very expensive,” Wyllie said. “We always recommend redundancy processes, but sometimes the smaller businesses don’t have that in place so it’s essential you can get them up and running quickly.”
Pilot Air: Australian-owned and family-owned, servicing the big end of town for over 40 years.
COMPRESSORS are used in different industries and guarantee a continuous supply of compressed air. Many elements can be adjusted if energy consumption or costs are to be reduced or the environmental footprint is to be improved. This is what BOGE has done, and the company now demonstrates with the advanced S-4 series how efficient, sustainable and reliable compressed air supply can be.
Whether as a direct work medium, as a pneumatic drive or to control valves and switches – compressed air is an important component of many industrial processes. This energy source is also used for power transmission as well as for transport or cleaning of materials. The applications are numerous, as are the requirements compressor manufacturers face.
With the S-4 series, BOGE’s developers and engineers have achieved a major breakthrough. The models have significant advantages when it comes to the following aspects:
Energy consumption
Sound insulation
Maintenance
• Longevity Sustainability.
Thanks to its robust technolog y as
well as numerous design improvements, the S-4 series quickly pays dividends. It is even suitable for use in sensitive and demanding environments, such as food technology. Furthermore, the compressors can also be used in areas with adverse conditions, such as the mining sector and foundries.
The airend specifically developed by BOGE is powered directly. The drive is hermetically sealed, very robust and therefore low-maintenance. No dust or dirt can get in and wear is significantly minimized – a huge advantage compared with belt-driven compressors. As an option, the speed can be controlled using a frequency converter and can therefore be perfectly adapted to the compressed air requirements.
Compared with the competition, the S-4 series models produce excellent free air delivery at low specific power consumption. These efficiency benefits are based on the revolutionary construction concept – the generously
sized components reduce internal pressure losses. Furthermore, BOGE’s airend is capable of achieving high efficiencies. The powerful, energysaving IE4 motors provide an additional advantage in terms of efficiency.
Flexible mounting brackets for the drive motor, airend and oil separation tank result in quiet operation. Oscillations cannot be transmitted, thanks to the smart fixing on the base frame. The generously sized cooling/ventilation unit with separate oil and air coolers additionally ensures sound-optimised cooling air. Furthermore, the sound pressure level is reduced by the radial fan’s low speed. In addition, sound insulation panels have been integrated to limit acoustic emissions to a minimum.
The compressor guarantees reliable operation with little need for maintenance. Oil separation, for example, takes place via a standing oil
separator with a central oil separating element. The innovative separation technology allows service lives of up to 9,000 operating hours. The cartridge can be replaced easily and conveniently. During maintenance, sound insulation panels and components can be removed or replaced using only a few actions. Access is provided from two sides. Oil and air coolers can easily be removed and cleaned via a tray.
The S-4 series models have previously been available in the range of 55 to 160 kW. BOGE has now extended this. Thanks to the new series with a range of 45 to 75 kW, companies and businesses with low compressed air requirements can now also benefit from the S-4 series advantages.
For the new models, BOGE reduced the footprint to 1.2 x 2 m, thus creating a compact design with cost benefits. The compressors feature the tried-and-tested airend and are characterised by all the S-4 series advantages mentioned. The efficient motors must also be highlighted here: Customers can choose between compressors with a fixed speed and IE4
Industrial advancement in the generation of compressed air
Manufacturers’ Monthly learns about increasing the efficiency and service life of compressors from BOGE, as well as the company’s new range of “tiny” screw compressors.
motor and frequency-controlled models with a permanent magnet motor. This reduces power consumption again compared with the previous models and increases free air delivery. Use of the efficient motors and low energy consumption is also accompanied by a reduction in CO2 emissions. BOGE has also improved user-friendliness again. For example, the operating element that is attached to the housing is now angled for optimised legibility.
Everything that distinguishes BOGE’s “big” S-4 series screw compressors is now available in the small performance segment between 45 and 75 kW. Each detail has been designed to have all the new models stand out with a reliable, quiet operation and top efficiency levels. With a footprint of merely 3.9 ft by 6.5 ft, the casing is extremely small, and since
screw compressors stand the test even in unfavourable conditions, thanks to the hermetically sealed, directly driven “Integrate Drive” air end which operates practically maintenance-free. High air output with low specific power input is a character trait of all new BOGE S-4 models in the “compact class”. The power consumption of e.g. the 75 kW model has been lowered by more than 12 per cent compared to its predecessor, and yet the quantity of compressed air was raised by almost 9 per cent.
Thanks to the changes made regarding technology, construction and design, the S-4 series compressors in the range of 45 to 75 kW – as well as the models in the higher power range – are suitable even for sensitive applications and demanding environments. They withstand dust and dirt. The models provide maximum reliability and are designed for a long service life. In combination with the smart control and other options, such as external heat recovery, efficiency
values can be increased again and maintained at the maximum level – all for a comprehensive optimisation of your compressed air system.
BOGE Compressors Australia is the Australian subsidiary of BOGE Compressors, a German manufacturer of compressed air systems and equipment. Based in Melbourne, the company offers a range of products and services,
including sales, maintenance, and repair of compressed air systems. BOGE Compressors Australia serves a variety of industries, including manufacturing, automotive, food and beverage, and healthcare. The company has a distributor network of experienced technicians and engineers who are able to provide technical support and solutions for compressed air systems.
In the latest installments of Crafted with Capral, Manufacturers’ Monthly finds out how the Australian aluminium experts are helping to create turn-key solutions for manufacturers in the construction and trasnport industries.
FROM its start as a Perth ducting workshop 50 years ago, Unique Metal Works has evolved into a highly diversified national business supplying many of Australia’s largest projects.
Its 350-strong workforce services mining, agriculture, architects, infrastructure and defence, operating from nine locations around the country.
Unique Metal produces OEM (Original Equipment Manufacturers) parts, equipment and components and is Australia’s largest laser cutting business, creating precise and intricate custom work, including building facades.
It also has plasma capability, welding facilities, CNC Pressing, metal rolling, and turret punches – all the equipment to produce quality aluminium products.
Unique Metal is a hybrid business, and its highly skilled people use thousands of
tonnes of aluminium annually.
Managing director Paul Figliomeni said its capability and diversification set Unique Metal apart.
“We’ve got capability beyond. We can cut, we can fold, we can weld, we can coat the product, whether it is anodizing or powder coating. We can provide a full turnkey service for our clients.”
Figliomeni described Unique Metal as complex and says it is difficult when people ask him what they do.
“It’s a matter of how long have you got? We can have up to 800 different projects underway at one site,” he explained.
“When it comes to sheet metal fabrication, we can provide a solution and tackle complex jobs. We can have input from the design phase to a project’s completion.”
Unique Metal’s portfolio includes manufacturing componentry for OEM
manufacturers and suppliers, for the RV market – for motor bodies and caravans, and boats and ships. The business also produces parking meters for councils around Australia.
Examples of large projects Unique Metal has supplied include metalwork and the façade for the Perth Stadium. It has recently been working on Australia’s largest reclad project - Central Park in Perth.
Importantly, Unique Metal continues to do small as well as large jobs.
Figliomeni delights in the response from small businesses who are “absolutely rapt that we can accommodate them.”
“Hopefully, they grow and come with us on the journey. We have had many businesses that have grown with us over the years,” he added.
Quality aluminium is essential to the Unique Metal business.
“It’s light and strong and is an easy material to work with. It also suits marine environments, and shipbuilding is a large market for us,” Figliomeni said.
“We use all grades from the marine grade 5083 to 5005, a far more bendable general-purpose aluminium. Façade manufacture generally requires a 5005 H14 CA55, and depending on the hardness specified, Capral accommodates us.”
Capral products are the first choice for Unique Metal – Figliomeni emphasised that Capral’s product range, technical knowledge and service stand out.
“We have worked closely with Capral for many years – almost since we have
been in business.
“We’ve got a great relationship. Capral offers solutions, good pricing, and reliability. We get our product when they say we will get it, and they keep us informed of any issues.”
Unique Metal takes advantage of Capral’s vast range of aluminium sheet and plate and sources standard and custom extrusions from Capral; Capral is its exclusive supplier for damper and louvre extrusions.
Figliomeni said the Capral team’s technical knowledge means they can advise on grades and standards, a critically important factor when complying with overseas and local specifications.
Where aluminium needs processing beyond Capral’s remit, Unique Metal often works with Capral to ensure Capral clients receive a seamless service.
“Whether it’s laser or plasma cutting, machining or rolling, we will generally step in,” he said.
Some of Figliomeni’s favourite projects using Capral aluminium include The Perth Optus Stadium, Crown Towers, Elizabeth Quay, and the entry to the Perth Zoo, which features a laser-cut lizard.
To watch the video of Unique Metal Works’ journey with Capral, scan the QR code.From its Victorian base, Australian automotive business HSP 4 x 4 Accessories has become a global leader in designing and manufacturing solutions that optimise the function of utility vehicles.
Innovation is at the heart of HSP’s business, which aims to create and distribute masterfully designed products that make work easier for vehicle users. Its ground-breaking products are often world-firsts and include the top-selling Electric Roll R Cover, Silverback Lid, and Tailgate Lock.
In addition to being 100 per cent Australian-owned, HSP makes and sources all of its materials locally.
Since 2007, brothers Massih and Masood Aimaq and lifelong friend Omer Dost have taken HSP from start-up to global leader.
Sales director Massih Aimaq is modest about HSP’s success but admits it feels amazing.
“But what is even better is that we have achieved our goal of designing and manufacturing in Australia, while most of our competitors have gone overseas.”
Massih said they needed to do everything in Australia “because we have control over our products from thinking of them to installing them on the utes of users.”
produce hundreds of products overseas to maximise profits. Instead, we design and manufacture bespoke products in Australia that improve how people interact with their vehicles.”
A feature of HSP’s innovation is taking technologies from non-automotive fields and putting them into vehicles.
“I think that’s why our products are much more forward-looking than some of our competitors and why we create products that other people haven’t thought of.”
One of the best examples of HSP’s approach is its Electric Roll R cover. HSP pioneered the electric roller cover, becoming the first manufacturer to introduce a fully electric roller shutter for utes. The Roll R is the world’s most advanced retractable ute cover. Its patented features work with factory sports bars, ladder racks, and crossbars, and users can control them with the vehicle’s factory remote or a mobile app. The cover is also priced lower than imported units with fewer features.
“It’s the most advanced ute roll top in the world; no other unit works with your factory remote and has a touchpad, mobile phone integration, and over-the-
and a factory in Alexandra in regional Victoria, where it recently added a larger, purpose-built production facility.
“We manufacture our Roll R cover at the new facility and do our aluminium extrusion work there as well,” he said.
“Our Alexandra workforce has a lot of specific skills; we have precision machinery there which is creating new skill sets. Our people there are great workers, and we are really happy to have them as part of our journey.”
When it comes to materials, Massih noted they couldn’t make their products without aluminium.
“Aluminium makes a lot of sense. When you look at a ute cover, you need to keep your items dry and secure under something that looks good. Aluminium is the best material to do all of that. It’s lightweight, durable, extrudable and has no limits in manufacturing,” he explained.
“We couldn’t make our products without aluminium. If we did, they wouldn’t be anything we would want to sell. Without aluminium, our products might not exist.”
Massih says HSP’s supply partnership with Capral has helped them on their
specific to a particular product and Capral accommodates our needs and offers quality, reliability, and quantity. There are a lot of synergies between us –they are a high-quality manufacturer that believes in manufacturing in Australia.”
Capral extrudes and powder coats all HSP’s aluminium to streamline HSP’s manufacturing process, supplying it prefinished and ready for fabrication. Using industry-leading powder coat finishes from Interpon, Capral can deliver to HSP the highest quality aluminium for its projects, eliminating the need for HSP to source finishing from a secondary supplier.
“Having access to powder-coated aluminium supplied to our door is important, it reduces our lead times, minimises the risk of damage to the material and ensures we have consistent quality finishes on our products every time. We choose to use the Textura black finish which is very modern, looks great but has anti marring properties and reduces the risk of scratches and marks on the painted extrusion,” Messih
Clearly, Capral is more of a partner than just a supplier to HSP.
“They understand where we’re trying
Industrial agriculture – including deforestation, the use of synthetic fertilisers, and widespread tilling – poses some of the biggest threats to soil fertility. Protecting the dwindling amount of healthy soil around the world is imperative for the future of food growing, with so many farmers looking to adopt less disruptive methods during the planting process.
THE act of tilling serves to mix crop residue, weeds, and animal manure into the soil, while aerating and warming the top layer. In doing so, however, it also loosens the plant matter from the surface. This leaves the area more susceptible to erosion by wind and water, leaving less healthy soil behind for each new season. Tilling can also compromise the soil biology, displacing the microbes and insects that contribute to its growing productivity.
In 1963, Jack Hine began pioneering the no-till movement from his family farm in Mansfield, Victoria. This practice was later advanced on the Southwest coast of Western Australia by his sons, Garry and Darryl, who adopted the no-till and zero-till farming practices on their family farm in Wellstead. Subsequently a new business called Direct Seeding and Harvesting was birthed from that farm, importing, and selling zero-till seeding equipment across Australia. In September 2017, the grandson of Jack Hine and nephew of Darryl & Garry, Stewart Mactaggart, took the reins from Darryl to run Direct Seeding, which is now based in Albany, Western Australia. Stewart is just as passionate as his uncles and grandfather about innovating new ways to perfect the zero-till farming system and promote the long-term benefits of stubble retention and soil cover.
“Zero-till farming is a niche market, but we’re starting to see a growing interest which has allowed us to come into our own,” Stewart enthuses. “In Australia, this transition is happening in part because there is an increasing need for more grass-fed livestock. There has been a substantial growth in the manufacture and sales of pasture seeding machines.”
Specialising in zero-tillage, precision,
and controlled traffic seeing equipment, the business harnesses multiple generations of broad acre farming experience to manufacture and distribute the best quality product for Australia’s unique environmental factors. In doing so, Stewart explains, they opt for only the highest-grade componentry that can be relied on to last.
“We have been using the NSK Agri Disc Hubs on our equipment for about six years, but recently began sourcing them through Motion Australia. They have been particularly valuable to us while we continue to innovate and develop robust equipment to suit our country’s unique farming conditions.”
Primarily used in the design of their Air Seeder Bars and Double Disc openers, the Agri Disk Hub bearing unit protects each piece of equipment from contamination, moisture, vibration, and heavy shock loads while in service.
“Where we are based in Western Australia, the soil is very abrasive and acidic, which leads to an increased chance of bearing failure, especially during years with more rainfall,” explains Stewart.
“Our country has some of the harshest operating conditions in the world, but zero tillage technology has come a long way in the last ten years. I can say that Agri Disc Hubs have definitely contributed largely to that.”
According to Russell Randal, Motion Australia’s National Accounts Manager for Agriculture, this relationship provides an opportunity for both businesses to leverage on their strengths in the market, particularly during an uncertain time for industrial business.
“When we initially got talking about how we could support their manufacturing process, they were very
excited about what we have to offer across the extended portfolio of hydraulics, power transmission and bearing parts,” he says. “We’ve helped Direct Seeding overcome gaps in their supply chain for a product that was already so integral to their design process.”
“The guaranteed lead times and exceptional service was another reason we switched to Motion,” Stewart adds. “There’s also the fact that they have a huge number of branches across Australia. By choosing a national supplier with ample stock on hand, we have no issues sourcing replacement parts for customers.”
NSK’s Agri Disc Hub units incorporate double-row angular-contact ball bearings to accommodate for heavy radial and axial loads. An O-ring seal protects the bearing from external aggregators, along with a cassette seal on the unit’s arm side.
“We initially opted for Agri Hubs because we needed something that was fully sealed against dust, dirt and water, and that doesn’t require manual greasing, which can put farmers at risk in the field,” says Stewart.
“We found that with some nongreaseable bearings, the seals just weren’t as durable, and we needed
• Higher contact angle allows higher axial loads
Optimised seal for long life
• Easy to mount
• Higher contact angle of 40 degrees Optimised interior design
something that could accommodate both sideways pressure and downforce, which is where the flexible load bearing comes in,” he furthers. “Over the years, it has performed extremely well on our equipment, and while there are certain limitations, we’ve converted over to them wherever possible.”
Understanding the everyday challenges faced by people in the agricultural industry is part of the job, says Stewart, and developing durable equipment that is low maintenance and easy to adapt is their number one priority.
“When it comes to OEM practices that are this specialised, you really need parts that are purpose-built for the industry.
NSK has hit the mark for agriculture with this product, and it gives both me and my customers peace of mind to know that they’re not going to fail during field service.”
Materials handling plays a crucial role in a variety of manufacturing sectors. Whether it’s the movement of steel in and out of a fabricator’s workshop, or the storage of machine parts inside a warehouse, establishing the best handling processes leads to greater efficiency across the board.
In April 2023, we will look at the latest innovation and advancements in this space.
In every edition of Manufacturers’ Monthly, we’re proud to work with our commercial partners on content that helps connect you with your future customers.
Booking deadline: 23 February 2023
To book contact DANNY HERNANDEZ now danny.hernandez@primecreative.com.au | 0431 330 232
Backplane Systems Technology is proud to present iBase’s ISR215, which is powered by an NXP i.MX 8M Plus applications processor built using 14nm LPC FinFET process technology. It reliably operates over a temperature range of -10°C ~ 60°C, across a variety of applications. The processor is backed by NXP’s longevity program, ensuring 15-plus years of supply from product launch.
The ISR215 provides high-performance and low-power capabilities for machine learning and vision applications, thanks to the powerful 1.6GHz Quad ARM Cortex-A53 processor with a Neural Processing Unit (NPU). Developers can offload ML inferencing tasks to the NPU while tapping the power of the ARM Cortex core, DSP, and GPU to handle other application programs. The ISR215 boasts a dual image signal processor (ISP) that features HDR, fisheye correction, and two HD MPI-CSI interfaces for up to 12-megapixel (MP) resolution cameras, an 800 MHz Tensilica HiFi4 DSP for audio/voice processing, and a high-precision GPU with 1080p and H.265/H.264 compression standards.
The ISR215 comes with flexible I/O configurations including USB, HDMI, and M.2 B-Key (3052) to accommodate expansion boards and modules with 5G, NFC, and QR code functionalities. Standard BSP support for Yocto and Android and design-in services are provided to help customers rapidly develop and deploy their innovations.
Key Features:
• NXP i.MX 8M Plus - ARM Cortex-A53 Quad Processor
3GB LPDDR4, 16GB eMMC & SD Socket for Expansion
• Embedded I/O, USB, HDMI, Ethernet
Supports M.2 B-Key(3052) for 5G Connectivity
• Ruggedized and Fanless Design
Company: Backplane Systems Technology
Phone: 02 9457 6400
Website: www.backplane.com.au
Beamex has expanded their successful PG pump family with the Beamex ePG, a revolutionary new electrical pressure pump for industrial pressure calibration applications. The Beamex ePG continues the company’s mission to provide better ways to calibrate for the industry, based on over 40 years’ experience of providing solutions for pressure calibration.
The Beamex ePG is a robust, portable battery-operated pressure pump that enables easy and quick pressure generation from near vacuum up to 20 bar (300 psi). With a fieldreplaceable, long-lasting battery pack, users can perform a large number of pressure calibrations on a single charge.
The Beamex ePG can be used together with any existing pressure calibrator, meaning users do not need to buy a new calibrator but can simply replace their manual hand pump with the ePG. It is very intuitive to use, with coarse and fine adjustment buttons to easily generate the required pressure. The Beamex ePG can also be serviced by the user to simplify maintenance.
When the Beamex ePG is used together with the Beamex MC6 family of calibrators, it enables fully automatic pressure calibration where the MC6 calibrator automatically controls the ePG. This optional feature will be available in the near future with a firmware update to the Beamex ePG.
“Calibrations in the process industry are often performed in the field, and typically a manual hand pump is used for pressure generation. But a manual hand pump is laborious to use, especially if you need to do several calibrations or pump a higher pressure,” says Antti Mäkynen, product manager at Beamex. “Based on requests from our customers for easier pressure calibrations, we developed a new technology that enabled the creation of the Beamex ePG.”
Company: AMS Instrumentation & Calibration
Phone: 03 9017 8225
Email: sales@ams-ic.com.au
Website: www.ams-ic.com.au
IT would not be news to anyone reading Manufacturers’ Monthly that skills were at the top of the agenda for both businesses and governments in 2022.
Everywhere you look there is evidence of the widespread skill shortages being experienced right across the Australian economy.
In shopping centres and commercial areas across the country, ‘help wanted’ signs are a practical reminder of the widespread labour and skills shortages currently constraining a broad range of everyday Australian businesses.
The message is the same when you talk to CEOs and leaders of large companies. They talk about having a new business model to implement and scale, a new technology to adopt or just an increase in customer demand – but they say they’re constrained, because they’re struggling to secure the right people with the right skills to get the job done.
An Ai Group skills survey released in November last year – Listening to Australian businesses on skills and workforce needs – has sounded yet another alarm on the skills shortages and gaps plaguing the Australian economy.
Our survey of close to 350 business leaders from a wide range of Australian companies asked them about their skills and workforce needs and challenges and they told us there are plenty – and they
are increasing and changing.
Businesses are telling us there’s a widespread and acute shortage of technicians and trades workers, the mainstays of many enterprises and a bedrock of our economy overall. Well over half the businesses in our survey report that their skills needs have increased in relation to technicians and trades workers in the past year, and 71 per cent reported difficulties meeting their needs when it came to these vital workers.
This finding alone should ring alarm bells. Technicians and trades workers construct and maintain our buildings, roads and infrastructure, build and run our essential services, telecommunications, transport and logistics networks, and manufacture our goods. They take years to train and, quite simply, we cannot function without them.
Another startling and consistent response from employers is the number of businesses reporting a lack of basic digital skills and describing improving basic digital skills as their No.1 priority. And when businesses were asked which workers would be the focus for digital training and upskilling, the answer again was technicians and trades workers.
This should be low-hanging fruit for policymakers. Focusing on improving basic digital skills across the workforce could drive significant productivity uplifts, as more of us learn to work with
and harness available technologies more effectively.
Australian businesses are also feeling the effects of the transition to a clean economy, with about a quarter reporting either emerging or increased skill needs as a result.
And while some things change, some stay the same. Foundation skills – like literacy and numeracy – remain a perennial issue for businesses. Three out of four employers said they were affected in some way by low levels of literacy and numeracy. Nearly one in five said they were highly affected.
When businesses were asked what they considered to be driving skill shortages, 68 per cent cited “growth in demand” and 35 per cent attributed it to supply chain challenges or disruptions.
Both factors speak of playing catch up or pivoting to deal with uncertain and dynamic markets. As we all seem to have learnt in 2022, this uncertainty is the new normal.
So, what are businesses planning to do?
There was very strong support for training and development, with 82 per cent of businesses intending to either maintain or increase the amount they spend on staff training in the next 12 months. The proportion of businesses intending to employ skilled migrants also rose sharply, from 7 per cent in 2021 to 44 per cent in 2022, evidence of a widespread intention to make strong use of skilled migration
channels as we emerge from Covid-19induced restrictions.
Ai Group’s survey reinforces what all the other economic indicators and analysts are telling us: we need to focus on skills like never before. The Jobs and Skills Summit highlighted the scale and size of the challenge we’re facing. It also created the shared goodwill and momentum to enable real change.
We want, and need, Australia to continue to be a productive and prosperous nation. However, we know that this will only happen if our workforce has the skills and smarts to self-assuredly navigate uncertainty, break through inertia and step up to solve new and emerging problems.
We need to develop our own workforce, not just to simply sustain what Australia has built to date, but to confidently tackle new challenges and new frontiers. Our current workers, including those in the last third of their careers, are valuable commodities worthy of our investment. The upcoming next generation is gold.
When it comes to the answers, all roads lead to education and training –skilling, re-skilling and upskilling – at scale. It’s complex, but it can be done.
The results of our survey should be a call to arms for us all.
Download Ai Group’s Skills Survey here: go.aigroup.com.au/skillsurvey
Compressed air is one of the top energy consumers in industrial plants. 45% of all industrial applications use hot water or steam. 50% of compressed air systems have big heat recovery potential. There are increasing incentives for reducing energy and CO² and with increased energy prices, creates a huge market demand for energy savings.
Energy savings - reduction of energy costs
CO2 reduction - reduction of environmental impact
5 sizes fit all - standardisation
Standard connections kits - fast installation
Stand-alone unit - simple installation and serviceability
Atlas Copco’s Smartlink technology gives you the ability to monitor your equipment via real time data. Depending on the chosen service plan, we can also monitor the equipment, allowing you to identify variations in operation and update maintenance schedules and visits to improve uptime and reliability.
1873 - 2023