
6 minute read
Comment
GEOFF CRITTENDEN – CEO, Weld Australia
Keeping Australian welders safe: Weld Australia’s free welder safety resources
WELDING is a safe occupation when proper precautions are taken. But, if safety measures are ignored, welders face a range of potentially dangerous hazards that can cause electric shock, or even a fatality.
Within the last month alone, Weld Australia was enlisted to investigate two separate accidents that saw inexperienced welders sustain serious electric shocks. In both instances, the young men were hospitalised for assessment. While they both made a full recovery, this was more by luck than judgement.
The first electric shock occurred during the arc start process, with the welder using high frequency TIG. Several conditions combined to create a highly dangerous situation. The welder was wearing inappropriate clothing and Personal Protective Equipment (PPE), including a defective glove, and the return lead was connected to an old, rusty workbench. So, when the welder leant on the workbench, he unintentionally became a part of the circuit, which had 6,000 volts coursing through it.
The second safety incident that Weld Australia investigated could have easily resulted in a fatality. Another inexperienced welder was TIG welding and it appears that the filler rod made contact with the live tungsten electrode. At the time of the incident, the welder reported an electric shock in his left forearm, with the point of the current return path unknown. A week later, the welder reported cramp-like pains in both his left arm and left leg, suggesting that the return path was via his left leg. In Weld Australia’s opinion, this welder is fortunate to still to be alive.
Accidents and serious “near misses” on the rise
The problem is, these are not isolated incidents. Accidents and serious ‘near misses’ are happening in workshops right across Australia every week. These accidents are less likely to occur in the largescale state-of-the-art workshops owned and run by Australia’s major fabricators – they have in-depth Workplace Health and Safety plans and procedures in place. Rather, these accidents are happening in small welding workshops, car body repair shops, home garages, and farm sheds.
Perhaps most concerning of all, these sorts of safety incidents could well become even more common. According to one of Australia’s major tool retailers, their single largest seller since the outbreak of the COVID-19 pandemic has been Gas Metal Arc Welding (GMAW) machines.
In all likelihood, these GMAW machines are being purchased by owners of small workshops, tradesmen without welding qualifications, and home DIY enthusiasts – most of whom do not know how to weld, or how to use a GMAW machine properly.
Weld Australia warns electrical safety must be taken seriously.
Electrical safety precautions in welding
Electrical safety must be taken seriously when welding. Electricity is a vital part of welding work, but when mishandled it can result in serious injury and death. Between 2014 and 2016, seven people died due to electrocution while working.
According to Safe Work Australia’s Welding Processes Code of Practice, electric shock or electrocution can occur through
direct contact with an electrode, live parts, a work piece, or through contact with a device such as an unearthed cable or tool. The risk of electric shock can be exacerbated by moisture and high humidity, both common in welding environments.
Both welding professionals and inexperienced enthusiasts need to familiarise themselves with the processes required to minimise the risk of electric shock. Simple actions such as checking that equipment is dry and well maintained and installing shut down mechanisms such as fuses and low voltage safety switches can save lives. Ensuring that anyone who welds is equipped with the knowledge and safety equipment required is key to preventing serious incidents such as those recently investigated by Weld Australia.
Welding safety resources
Weld Australia has a wide range of welding safety resources, many of which are available to the public – completely free of charge.
Technical Note 7: Health and Safety in Welding
This Technical Note gives guidance on health and safety practices in welding, cutting and allied processes such as brazing, soldering, pre- and post- weld material treatments and metal spraying, for the prevention of injury, ill health and discomfort, as well as damage to property, equipment and environment by fire, and explosion.
Various Chapters deal with:
• Basic principles of safe working • The main hazards and safety measures in welding, cutting and allied processes • Precautions required in particular working situations
Technical Note 22: Welding Electrical Safety
Although electric arc welding can be performed perfectly safely, there are circumstances when there is a substantial risk of electric shock. Precautions against this risk include use of properly maintained equipment, correct protective equipment and sound work practices. With reference to Industry best practice, Technical Note 22 addresses how to safeguard a person against electric shock, reviewing elements such as: equipment, the human body, the workplace Australian Standards.
Education is the key to ensuring that anyone who welds is safe. Employers, professional welders and DIY enthusiasts alike must invest in thorough and up-to-date training to ensure an in-depth understanding of the risks associated with welding, the mitigation strategies that can be used, and the equipment available to prevent accident and injury.
If you know someone who is welding without the proper training or experience, be sure to pass along Weld Australia’s free resources. All of these resources are available via the Resource Centre on our website: https://weldaustralia.com.au/
Weld Australia sponsors the Endeavour Awards
Weld Australia is proud to support the Endeavour Awards once again in 2021 by sponsoring the award for the Best Industrial Internet of Things Application. This award will recognise the most outstanding application used in a smart factory to improve the manufacturing process.
It is advanced manufacturing processes that rely on innovative technologies and methodologies like IoT, robotics and automation are helping to make welding a safer profession. For instance, the use of robots and co-bots (particularly in confined spaces) helps to remove welders from immediate exposure to welding fumes, ultraviolet radiation, heat and sparks.
In the wake of a year where uncertainty was the only certainty, it is time now more than ever to celebrate the resilience of Australia’s manufacturers. Their ability to be innovative, collaborative and responsive to manufacturing demand shows just how good Aussie manufacturers can be. Local manufacturers banded together, establishing working groups and prototyping complex products (like ventilators), bringing them to market in record time.
Weld Australia is delighted to take this opportunity, alongside our fellow sponsors, to spotlight those manufacturers excelling in their field, and to celebrate the Australian manufacturing industry across the board.
Safety incidents such as electric shocks are becoming more common with inexperienced welders.



Transport Industry (Alu decking)
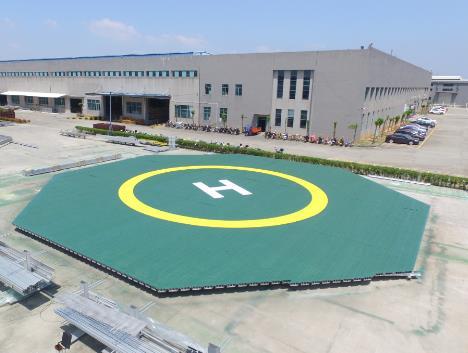
Heliport (total solution)

Coaches (Alu frameworks)

Hull (5383 super structure)
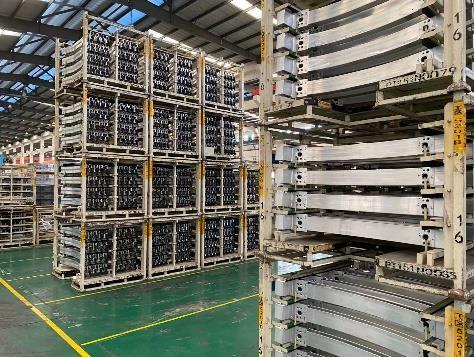