
5 minute read
Industry Focus
Distinguished Professor Arnan Mitchell at the Micro Nano Research Facility, located in RMIT University’s Melbourne campus.
Launching Australia into the global space race
Caroline Tung interviewed researchers at RMIT to find out more about a prototype being developed in Australia that could help determine if humans can settle on the Moon.
ATEAM of researchers at RMIT University in Melbourne have joined the great space race with a pioneering invention. And, they are on the way to putting Australia on the world map in space manufacturing.
The protype device, called MAPrad, is one tenth the size of existing ground penetrating radar (GPR) systems, which allows those using it to see more than 100 metres below ground level, almost twice as deep compared to existing technology.
The aim is to send the device into space to identify minerals, ice deposits, or voids such as lava tubes on the moon that can support potential human settlement.
Start-up CD3D has now received a grant from the Australian Space Agency’s Moon to Mars initiative to further develop the prototype with RMIT, including testing it by mapping one of Earth’s largest accessible systems of lava tubes.
CD3D CEO and RMIT Honorary Professor, James Macnae, said their unique geophysical sensor had several advantages that made it more suitable for space missions.
“MAPrad is smaller, lighter and uses no more power than existing ground penetrating radar devices, and yet, can see up to hundreds of metres below the surface, which is around twice as deep as existing technology,” he said. “It is able to achieve this improved performance, even after being shrunken to a hand-held size, because it operates in a different frequency range by using the magnetic rather than the electric component of electromagnetic waves.”
The magnetic waves emitted and detected by the device measure conductivity and electromagnetic wave reflections to identify what lies underground. Voids and waterice provide strong reflections, while various metals have high conductivity at unique levels.
“MAPrad’s initial development was specifically focused on facilitating drone surveys for mining applications, but it has obvious applications in space where size and weight are at a premium, so that’s where we’re now focusing our efforts,” Macnae said.
The multi-stage project is currently a feasibility study. The researchers will then seek to validate whether the structure will survive the launch. The next phase is to prepare the device for deployment.
The researchers will also seek approval to scan one of the world’s largest accessible systems of lava tubes at the Undara caves in Far North Queensland. The tubes have diameters of up to 20 metres and some are several hundred metres in length.
The specialised radar system was developed in partnership with Canadian company, International Groundradar Consulting, in a collaborative research project funded through the AMIRA Global network.
Successful field tests have since been carried out in Australia and Canada using a backpacked prototype for mining and mineral prospecting.
Industry Focus
RMIT University engineer, Dr Graham Dorrington, said they would traverse the park above the caves to detect the voids below, some of which have not been completely mapped yet.
“We know the dimensions of the main tubes, so comparison with surface scans to check accuracy should be possible,” he said.
“Undara will be an excellent testing site for us, since it’s the closest thing on Earth to the lava tubes thought to exist on the Moon and Mars.”
The immediate concern is mapping ice-water deposits on the Moon and getting a clearer picture of the resources available there to support life.
Dorrington said their system could be mounted on a space rover, or attached to a spacecraft in low orbit to monitor for minerals on future missions, and for lava tubes on later missions.
“After the lava tube testing later this year, the next step will be optimising the device so as not to interfere or interact with any of the space rover or spacecraft’s metal components, or cause incompatible electromagnetic interference with communications or other instruments,” Dorrington said. “Qualifying MAPrad for space usage, especially on the Moon, will be a significant technical challenge for us.”
The team will use the unique capabilities of the Micro Nano Research Facility (MNRF) and the Advanced Manufacturing Precinct and are also looking to collaborate on later stages of development with specialists in spacecraft integration or organisations with payload availability.
RMIT is setting up space validation facilities for testing the functionality and endurance of devices such as MAPrad.
MNRF director, Distinguished Professor Arnan Mitchell, described the project as a multidisciplinary effort, and is keen to showcase the university’s capabilities to industry.
“To make the MAPrad as rugged as possible and also as lightweight as possible, we’ll try integrate it, so make it as much a solid block material as we can,” he said.
Some questions the team will answer through standards testing include how the device will survive the launch and the vacuum leaving Earth, as well as the temperature changes in space.
Mitchell is confident that the standard tests for satellite validation will be accurate indicators the MAPrad will survive, based on previous testing.
“My team has a lot of experience in ruggedising things for defence applications like being able to survive on helicopters, which are very vibration-prone environments, so they’re similar requirements to survive the launch,” he said. “Once they’re actually in space, there’s much less of that physical wear and tear.
“It’s more how to survive the vacuum, will it survive the radiation, and there’s no atmosphere on the Moon to protect the structures from the Sun.”
Mitchell hopes that delivering on this high-profile project will attract more industry organisations to connect with RMIT’s Advanced Manufacturing Precinct and MNRF.
The MNRF currently has more than 450 researchers accessing its fabrication facilities to do rapid prototyping at both the nano and macro scale.
“From my perspective, we’ve got some of the most sophisticated advanced manufacturing, research and developments tools in the world at RMIT. I don’t think that it’s very well-known,” Mitchell said.
“I think if you can demonstrate that you can miniaturise something using these tools, and it can survive launching into space and operate on the Moon, it’s a clear message that there are many things that you could also be doing here on Earth: from sensors in the Outback to automotive, electronics to agriculture, you can do all sorts of things.”
RMIT has facilities available to print objects from the nanometre scale (almost to the scale of molecules), to integrated circuits, things the size of the radar sensor (to millimetre scale), and right up to things the size of turbine blades.
“We have an extraordinary array of capability, and we’ve worked very hard to make it accessible to people outside of academia,” Mitchell said. “We really want to bridge the gap between academic research and industrial application. There’s a lot of mechanisms and support to make that happen.”
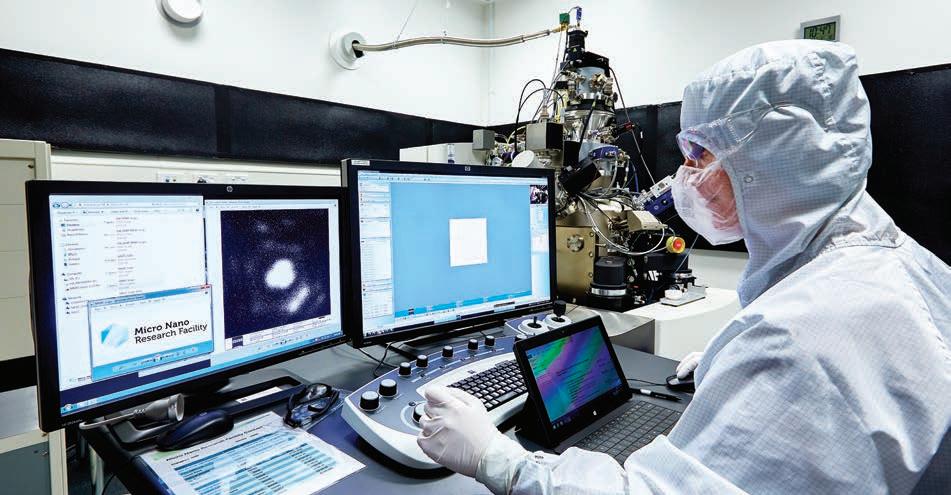
The MAPrad is much smaller that the size of existing ground penetrating radar systems. A researcher views computergenerated space data at the Micro Nano Research Facility in Melbourne.
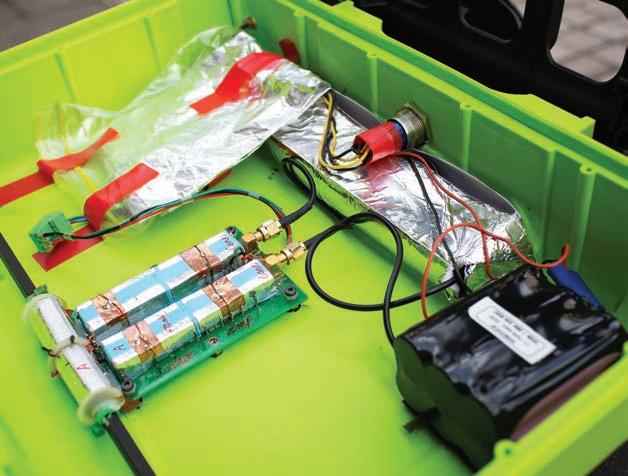