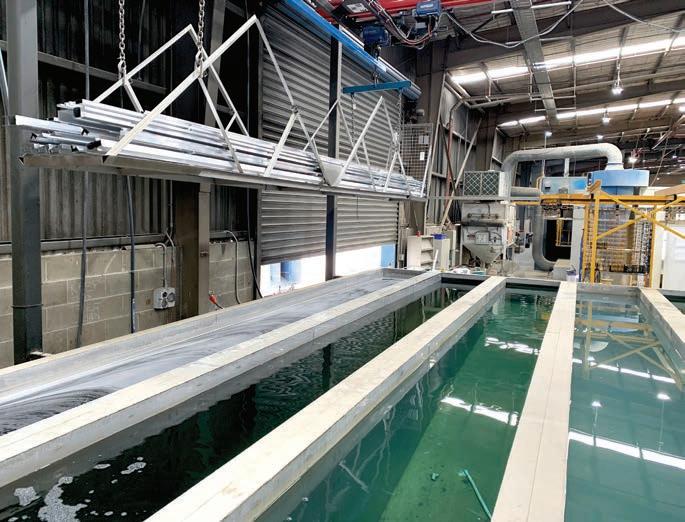
5 minute read
Anodising
Custom protective coatings: The future of metal manufacturing
The benefits of protective coatings for machined components are well known – but manufacturers can take this a step further. Working closely with a specialist coating supplier gives manufacturers the ability to provide custom, project-specific finishes and offer a tailored, quality service to their customers.
MANUFACTURING metal components is more than simply machining parts based on a drawing. Fabricators and metal manufacturers need to be attuned to their customers’ needs, delivering high-quality and long-lasting parts. Choosing expert surface finishers to supply protective coatings such as anodising and powder coating can help manufacturers meet their customers’ requirements for durability, including corrosion, abrasion, heat and chemical resistance, as well as colour preferences.
However, with specialised projects for industry priority areas such as defence coming more into focus in Australia, manufacturers may need to think outside the box to deliver the highest quality products possible.
Seeking the advice and support of specialist protective coating and surface finishing providers allows manufacturers to go beyond simply checking the boxes for corrosion or abrasion resistance. By determining which finish – or finishes – meet customers’ specific requirements and working to create customised finishing solutions, manufacturers can provide an unparalleled quality service, build grater customer trust and stronger customer relationships.
Defence manufacturer Milspec Manufacturing has garnered a reputation as one of Australia’s most precise, reliable contract manufacturers, providing brushless alternators and portable power systems to supply chains across the globe. When Milspec received project specifications for a crucial land project for Kongsberg Defence Australia, they sought a way to fulfil the strict requirements needed to ensure the metal components could withstand the harsh conditions they would be exposed to.
“Defence projects require very specific finishes, because of the very harsh conditions they parts are exposed to and the stringent global standards they must comply with,” said Milspec general manager, Neil Morrison. “To ensure customer satisfaction we needed to find a finisher who could collaborate with us at every step to achieve exactly what the customer required.”
Teaming up with DECO Australia – the South West Sydney surface finishing experts – assisted Milspec in achieving the highly custom finish required for the project.
DECO Australia, who have collaborated with a wide range of engineering, aerospace, automotive, medical and defence manufacturers, are driven to provide specialist finishing solutions to meet unique customer needs. Their tailored services and willingness to work with customers mean they are able to set up specialised production lines and even create custom finishes.
When project requirements call for a niche finish, working with a surface finisher can yield unprecedented positive results. The use of duplex finishes, which combine the benefits and properties of multiple surface treatments, can optimise production and performance for complex projects.
Milspec’s project specifications called for a very specific grey finish to meet international standards, as well as the removal of surface contaminants, corrosion resistance and the application of multiple finishes to different areas of the component. While this may have initially appeared to be a challenge, DECO has a history of developing duplex coatings – one of their most notable examples being the one-of-a-kind finish on the façade of the Hong Kong Tai Kwun Arts Precinct. To achieve the required finish for Milspec’s project, DECO set about developing an efficient coating system, blasting the parts with plastic media, masking certain areas before anodising the components, to ensure different coatings could be applied to different areas of the same product, and applying a custom grey finish to other areas.
“DECO’s innovative approach meant instead of sending the part to multiple suppliers or offering an alternative that wasn’t quite what was specified, we could utilise a coating system that met the exact specifications,” said Morrison.
As well as providing creative solutions, working with surface finishers allows for more thorough quality testing. Manufacturers can closely observe initial trials, discussing adjustments and approving prototypes to get the best final result.
Before working on Milspec’s
DECO works with customers to customise protective coatings. Processes like hard anodising helps manufacturers meet durability requirements.

Anodising
order, DECO undertook a first article inspection, along with anodic coating weight and neutral salt spray testing, providing a report and prototype for Milspec to evaluate. This provided proof of performance of the coating system before starting the project and allowed the manufacturer and end customer the confidence in the process prior to DECO processing the project.
Rather than outsourcing parts internationally – a costly, drawn-out process that increases lead times, pairing with a local finisher can also help manufacturers deliver orders in a timely fashion, using Australian companies rather than relying on overseas suppliers.
The grey finish required for the Kongsberg project was not typically found in Australia – meant the project could have been sent offshore to achieve the correct finish. However, DECO’s innovative nature meant the surface finishing provider were willing to go above and beyond to meet the project’s finishing requirements.
“DECO, as an Australian Family Business, is fully committed to providing sovereign industry capability,” said DECO’s Industrial Business Manager Richard Hamber. “That means researching and coming up with innovative new ways to meet customer needs. If there’s a finish you can’t get here in Australia, we will find a way to source it – providing that niche service and meeting those very specialised customer needs here in Australia.”
The fact that DECO was able to source the required grey dye and apply it onshore represents a significant step forward – the ability for manufacturers to seek creative, innovative finishing solutions and build closer, more involved relationships with finishing providers and their customers to create more tailored results.
Milspec and DECO’s combined success illustrates the significant benefits manufacturers can access when working with innovative coatings providers. By moving away from standard finishes and charting new finishing territory, manufacturers can aim for greater customisation and an improved ability to meet the increasingly specific requirements for significant Australian and international projects, such as aerospace and defence.
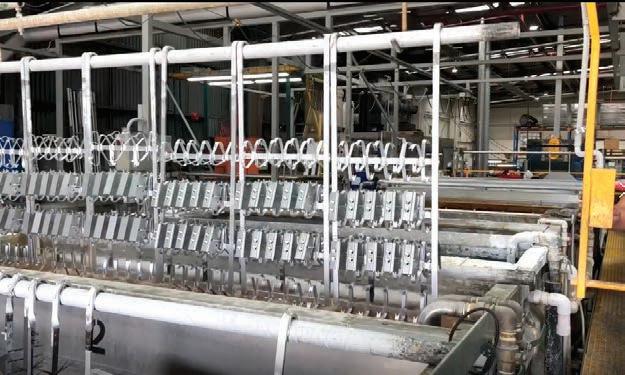
DECO offers services to help businesses set up specialised production lines, and can also create custom finishes.
For more information on DECO Australia’s finishing services, visit deco.net.au/protective-coatings For more information on Milspec Manufacturing, visit milspecmanufacturing.com. For more information on Kongsberg, visit www.kongsberg.com

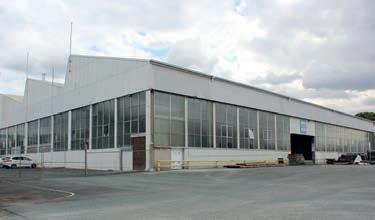
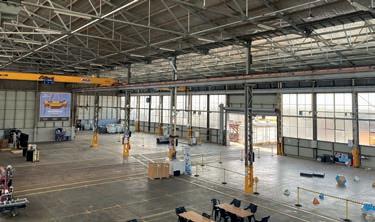