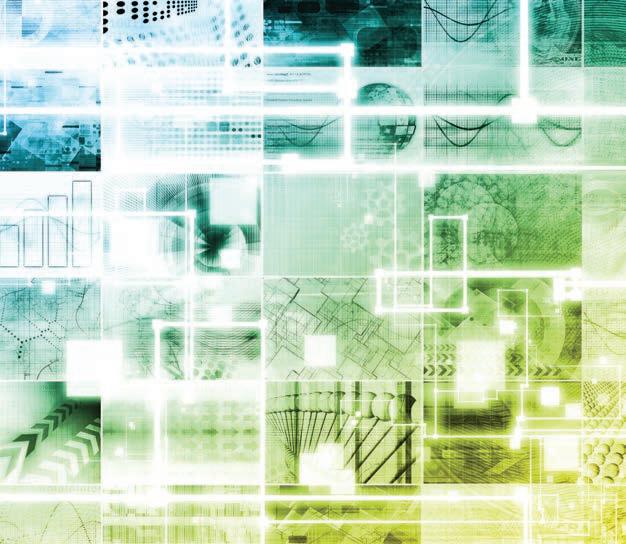
4 minute read
The Last Word
MARK PETERS – State Director, Queensland and National Projects Director
Commercialisation for a sustainable manufacturing future
SINCE the Advanced Manufacturing Growth Centre (AMGC) was established in 2015, we have helped more than 215 manufacturers and 24 research institutions undertake collaborative projects. These projects have commercialised innovative products and services that embrace the entire manufacturing value chain.
As one of the key leaders responsible for evaluating and managing AMGCs co-funded projects, I have the honour of seeing first-hand the talent and smarts that reside on our shores. I have the privilege to work with individuals and companies to help them advance, scale up, and commercialise, hence the reason our latest funding program is labelled AMGC’s Commercialisation Fund.
Prior to the Commercialisation Fund, AMGC facilitated over 80 projects nationwide. These co-funded projects are expected generate more than $1.2 billion in revenue and create 2,361 direct jobs and 8,474 indirect jobs. All of these projects illustrate that Australia is home to a highly skilled, adaptable, and enthusiastic manufacturing industry.
This enthusiasm is backed up by solid commercial acumen and a global market hungry for our innovative goods. One of AMGC’s co-funded projects is – quite literally – generating power from thin air. Cool Mine is developing Air2Volts, an uninterruptible power supply (UPS) that will deliver an inexpensive, reliable supply of electricity to power monitoring, communications, and control systems in underground mines. Air2Volts relies upon thermoelectric generator (TEG) technology which converts compressed air into usable electricity.
Cool Mine is a perfect example of the manufacturing multiplier effect, with jobs generated across the entire manufacturing value chain. In developing its innovative products, Cool Mine has capitalised on the highly skilled design and engineering capabilities available here in Australia, and as the businesses moves into the production, sales and service phases, even more jobs will be created.
It is this multiplier effect that is enabling Australian manufacturers to realise the opportunities presented by international markets and global supply chains. Take, for instance, iOrthotics, Australia’s premier manufacturer of custom-made orthotic devices.
Established in 2009, iOrthotics recently invested in new technology: fusion jet printing. With targeted research and development, and co-funding from AMGC, iOrthotics can now manufacture over 20,000 additional pairs of orthotics annually, while slashing their annual plastic landfill waste.
The result? iOrthotics has expanded into the US market, creating a new market for Australian made products.
Magnetica is set to do the same. As an industry-leader in the field of magnetic resonance imaging (MRI) technology, Magnetica is commercialising a coil system that will see the company become an OEM of an extremity and musculoskeletal (MSK) scanner, ready to export to overseas markets.
Traditional MRI scanners are enormous, weighing around 5 tonnes – or two Toyota Landcruisers. The sheer weight greatly restricts the installation and movement of MRI machines. The smaller size and significantly reduced weight of Magnetica’s MSK scanner will mean that the system can be deployed in substantially more clinical settings, from neonatal units, through to sports sites and defence applications. There is no other machine on the market that can compete with this Australian innovation.
Australian manufacturers are creating products and services that are export-worthy, and in return, they are strengthening our sovereign manufacturing capabilities to solidify local supply chains.
With the help of AMGC co-funding, Black Sky Aerospace recently became the only Australian manufacturer of solid-state rocket propellant and motors. Australia has never had the ability to manufacture its own rocket fuel, making this a major milestone in securing Australia’s national sovereignty within the burgeoning space sector.
Black Sky Aerospace is adding value to the nascent space sector value chain, as well as into fully developed industries like defence. Their locally manufactured rocket fuel will have wide-ranging impact on Australia’s growing space industry. Unlike liquid fuels, solid fuels are easier and safer to transport, store and use. With this new capability, Black Sky Aerospace will give Australian manufacturers the opportunity to test and trial their products in comparatively more affordable launches, before sending their products into space.
Also in aerospace, AMSL Aero’s Vertiia—an electric VTOL (Vertical Take-off and Landing) aircraft—will soon take to the skies. Vertia combines the vertical take-off and landing capabilities of a helicopter with the efficient high speed flight of a fixedwing aeroplane. This next generation technology is starting to attract interest from the likes of Uber and the Royal Flying Doctor Service.
Much like the finalists of this year’s Endeavour Awards, all of these projects demonstrate the talent and innovation that is alive and well in Australia’s manufacturing industry. As an incubator for STEM skills, advanced technology and innovation, Australian manufacturing is leading the way in techniques as diverse as 3D printing, robotics, and composites, and in sectors that range from medical and mining, through to aerospace and defence.
Clearly, by embracing the entire manufacturing value chain, Australian manufacturers are capably expanding their reach into international markets, strengthening our sovereign manufacturing capabilities, solidifying local supply chains, and building opportunities for the next generation of talented minds.