Your 10-step guide to a greener and more efficient compressed air system manmonthly.com.au MANAGEMENT >> TECHNOLOGY >> SOLUTIONS SEPTEMBER 2022
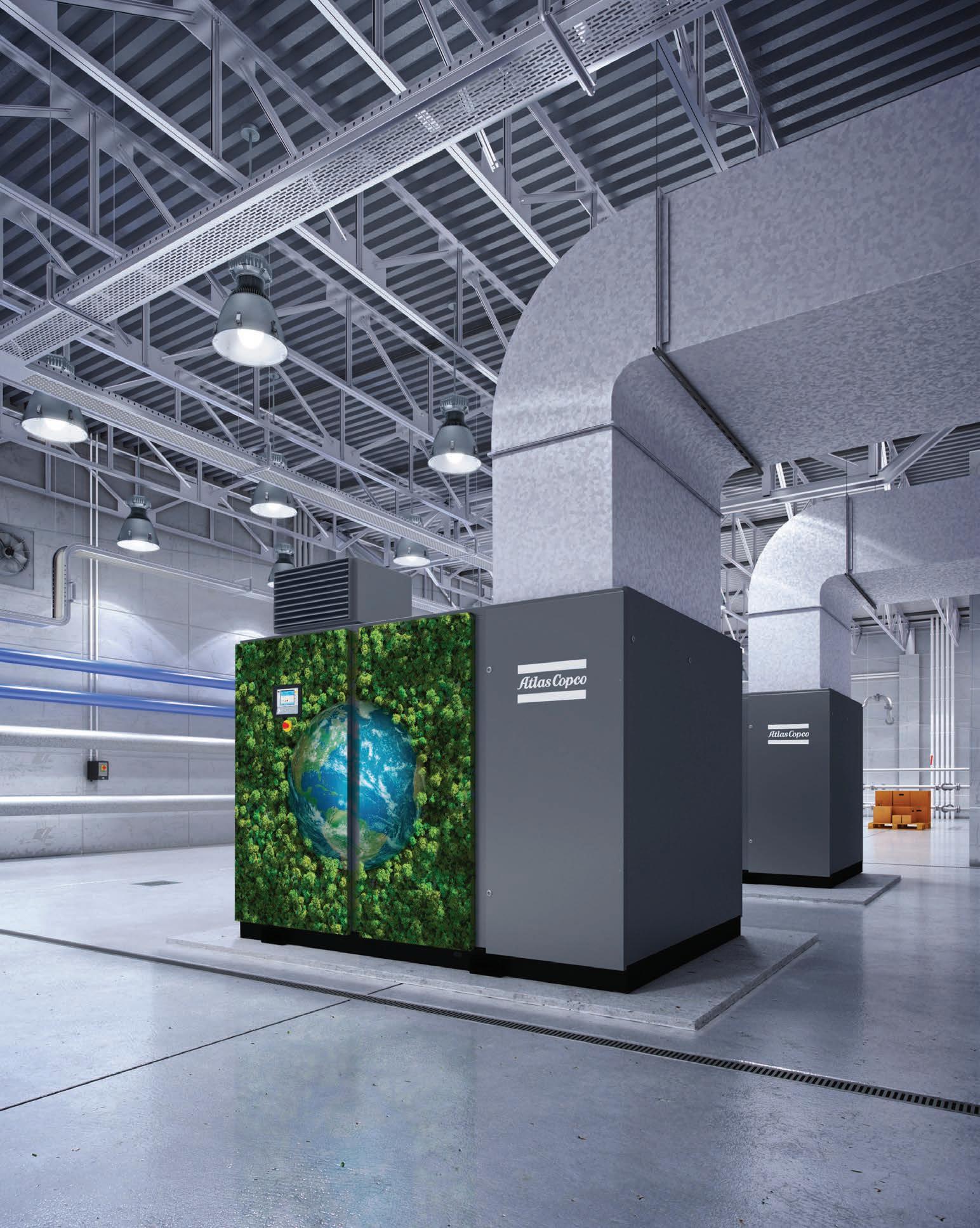
Scan
For a greener and more efficient production, the role that system maintenance (step 9) plays is very important. Companies should not only view maintenance as a means to ensure system reliability but also as an essential component of a total energy optimisation plan.
1. Application 2. Storage Distribution& 3. Air Quality 4. Air Volume 5. TechnologyCore 6. EquipmentControl 7.ControlSystem 8. Maintenance9.RecoveryEnergySystem 10. MonitoringSystem Scan to download the FREE 10-stepguide In past issues of Manufacturers’ Monthly, we focused on steps 1 through to 8. Now let’s finish up with steps 9 and 10!
The maintenance costs of a well-maintained compressed air system using genuine parts can be significantly offset by energy savings achieved by completing the maintenance on Systemtime. monitoring (step 10) is an extremely useful tool that helps you to always keep an eye on your compressor. With remote monitoring solutions such as Smartlink you can keep an eye on your compressor performance from anywhere and even via a smartphone application.
The most basic level of System Monitoring should alert compressor owners when their compressors are due for service and provide details of basic machine events such as machine warnings and shutdowns.
More advanced System Monitoring programs however can provide much more insight into machine reliability by undertaking smart health assessments, providing uptime KPI’s/reports and even making recommendations to protect your compressor uptime. These solutions are designed to also provide insights into, and trending of, energy consumption and machine usage. They can provide C02 calculations/ reporting and provide recommendations to reduce energy consumption so that you can always ensure that you system is operating to its highest level of efficiency. This is just like an external data logging system, but the detail is available in real time and at any time. Fact: Did you know there are more connected things in the world than people! Scan to download all of these steps again or contact 1800 023 469 and chat with one of our specialists.
it be great if there was a way to make compressed air systems more efficient whilst saving money and the environment at the same time? The bad news is that there isn’t one way to do that. The great news is that there are 10 ways! the QR code below!
The maintenance of the compressors in the system is particularly crucial for both energy efficiency and reliability because of how often they run.… did you know that if a car were to run 8,000 hours per year as some compressors do, service would be needed every 4-5 days?
Your productionmoregreenerguide10-steptoaandefficient Wouldn’t
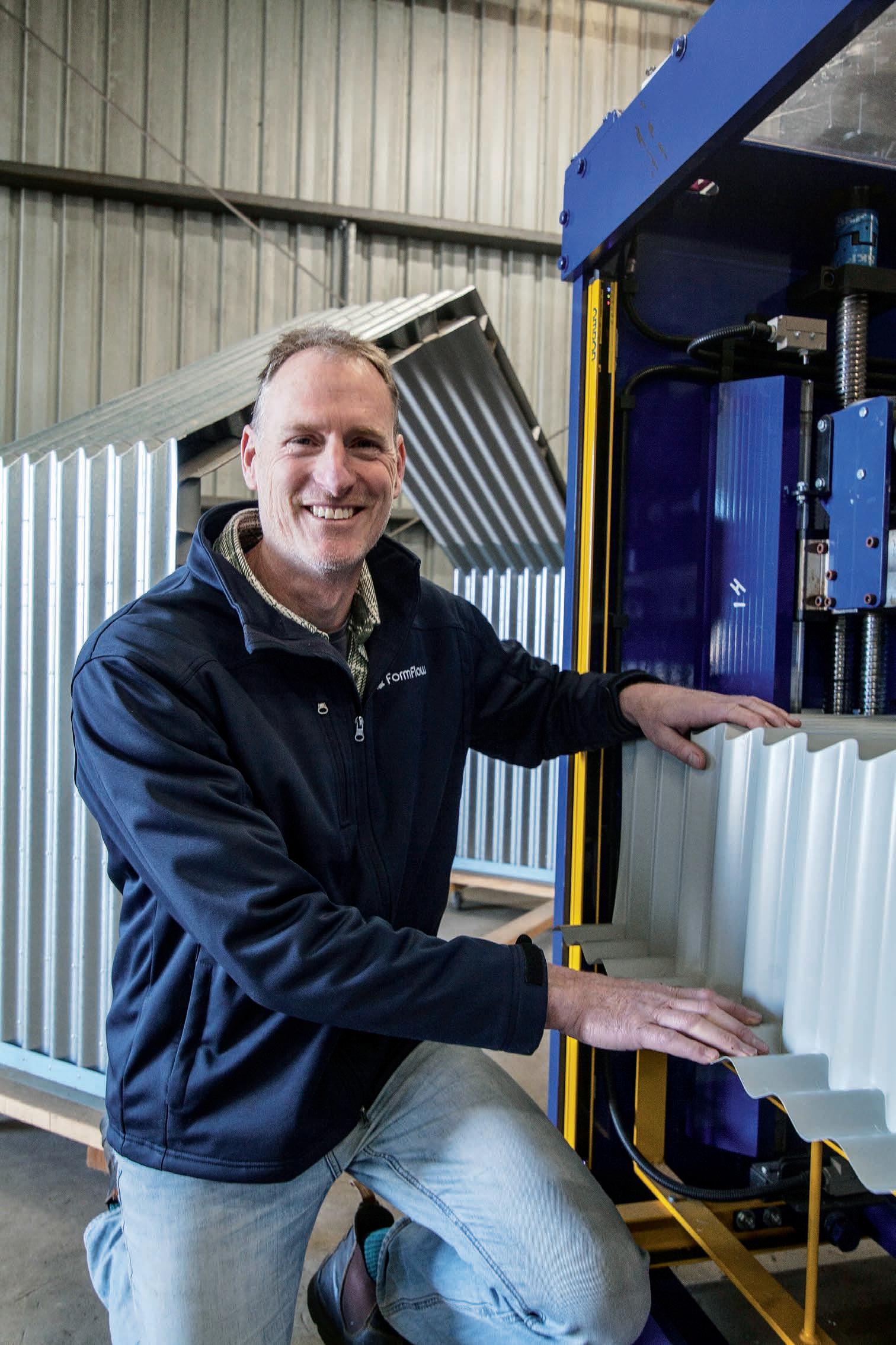
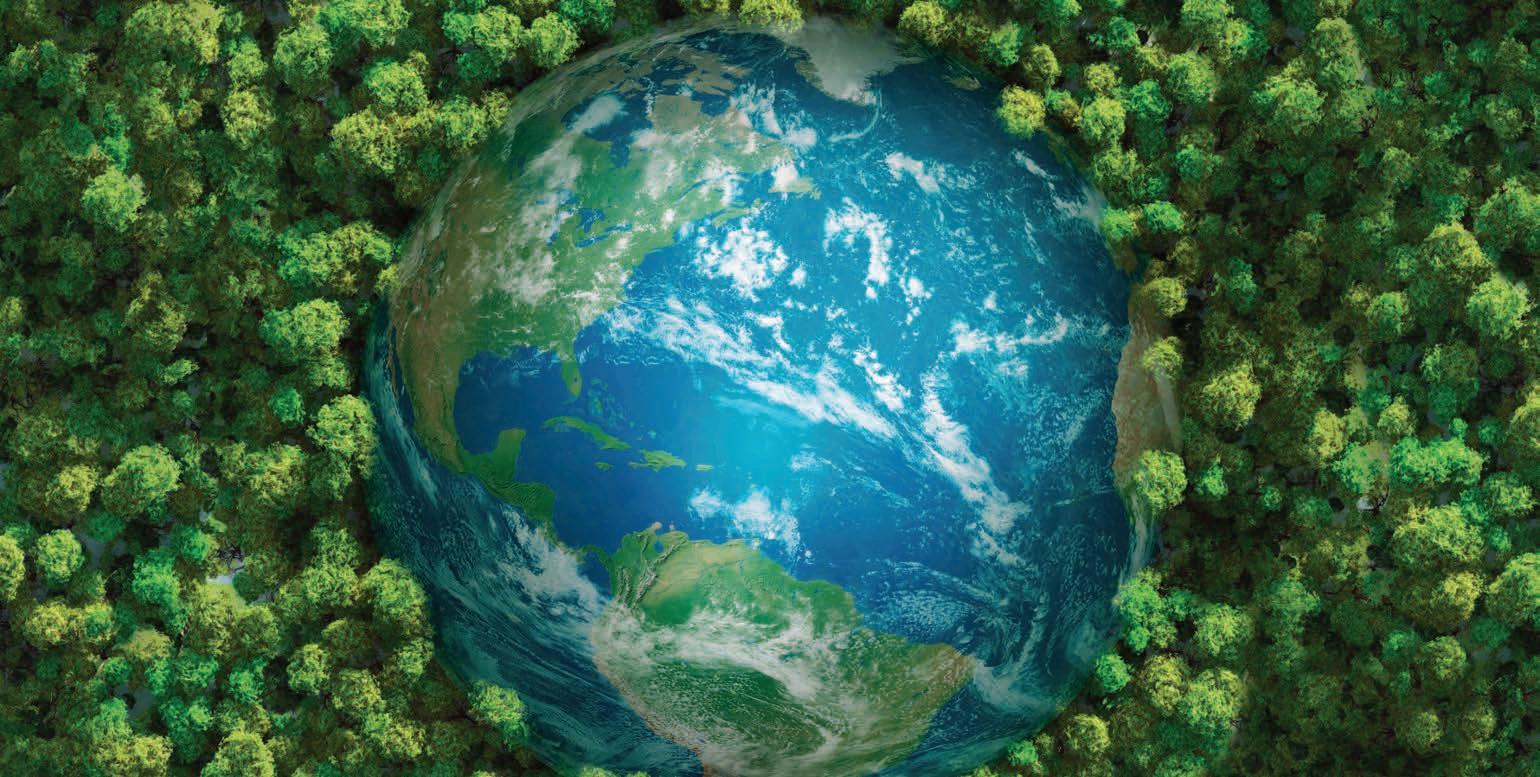
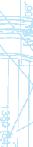

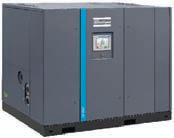
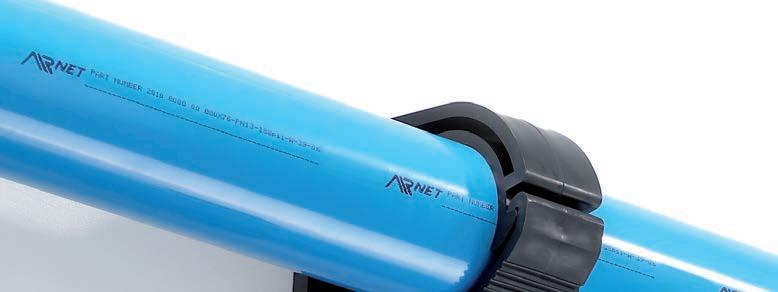
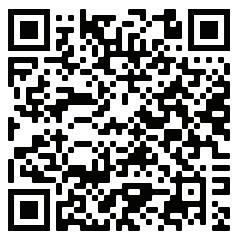
manmonthly.com.au MANAGEMENT >> TECHNOLOGY >> SOLUTIONS PP100007882ApprovedPostPrint Repairing electronics to save downtime 26 SEPTEMBER 2022 WORLD-FIRSTTECHNOLOGYBEND FORMFLOW: Giving the power back to engineers 46 Official Industry Partners Technology changing displacementmonitoring22
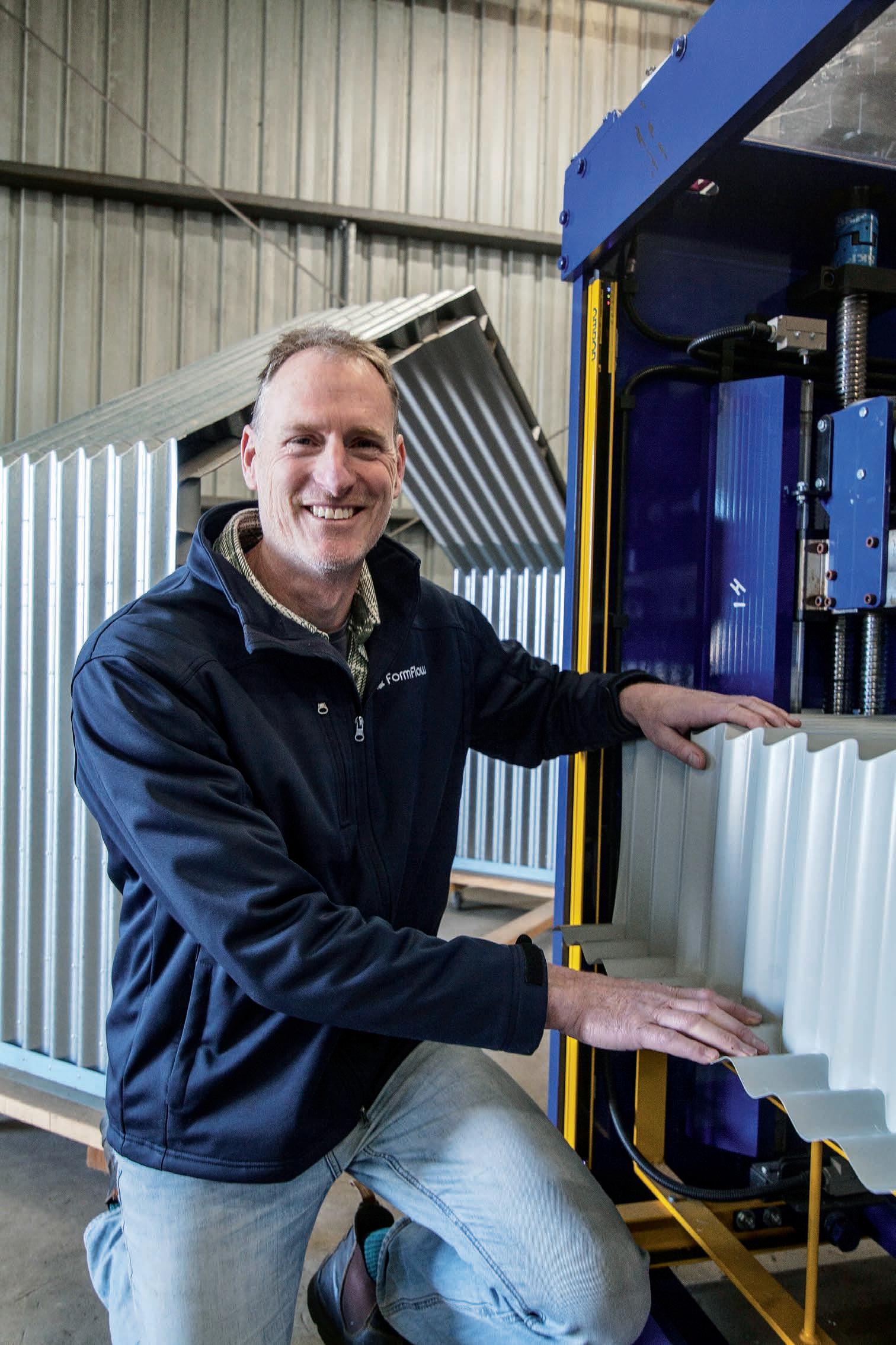
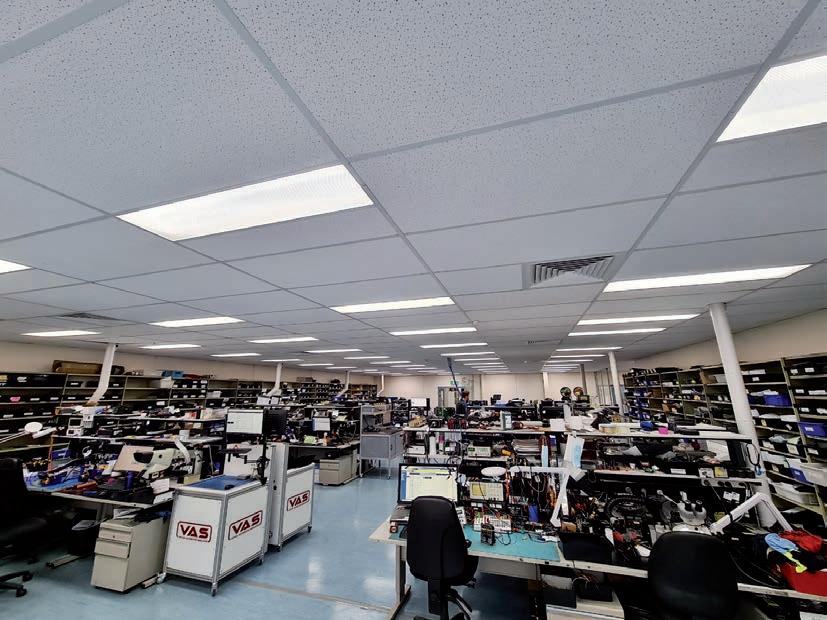
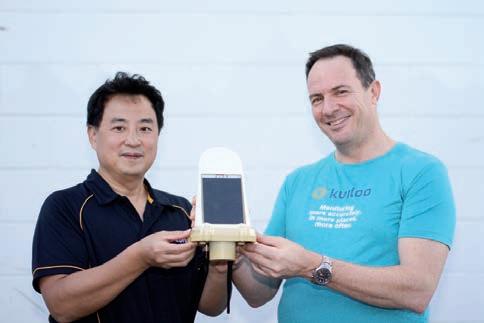
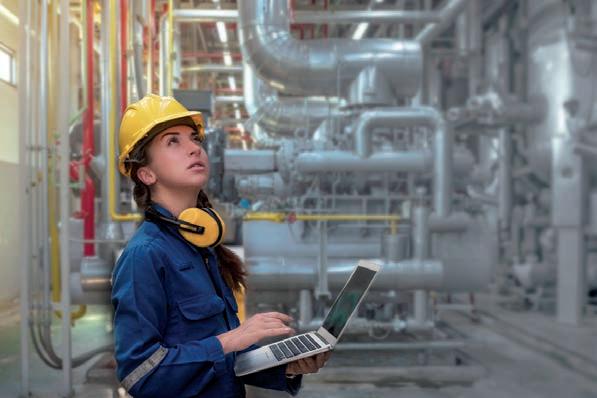
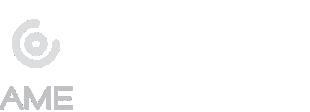
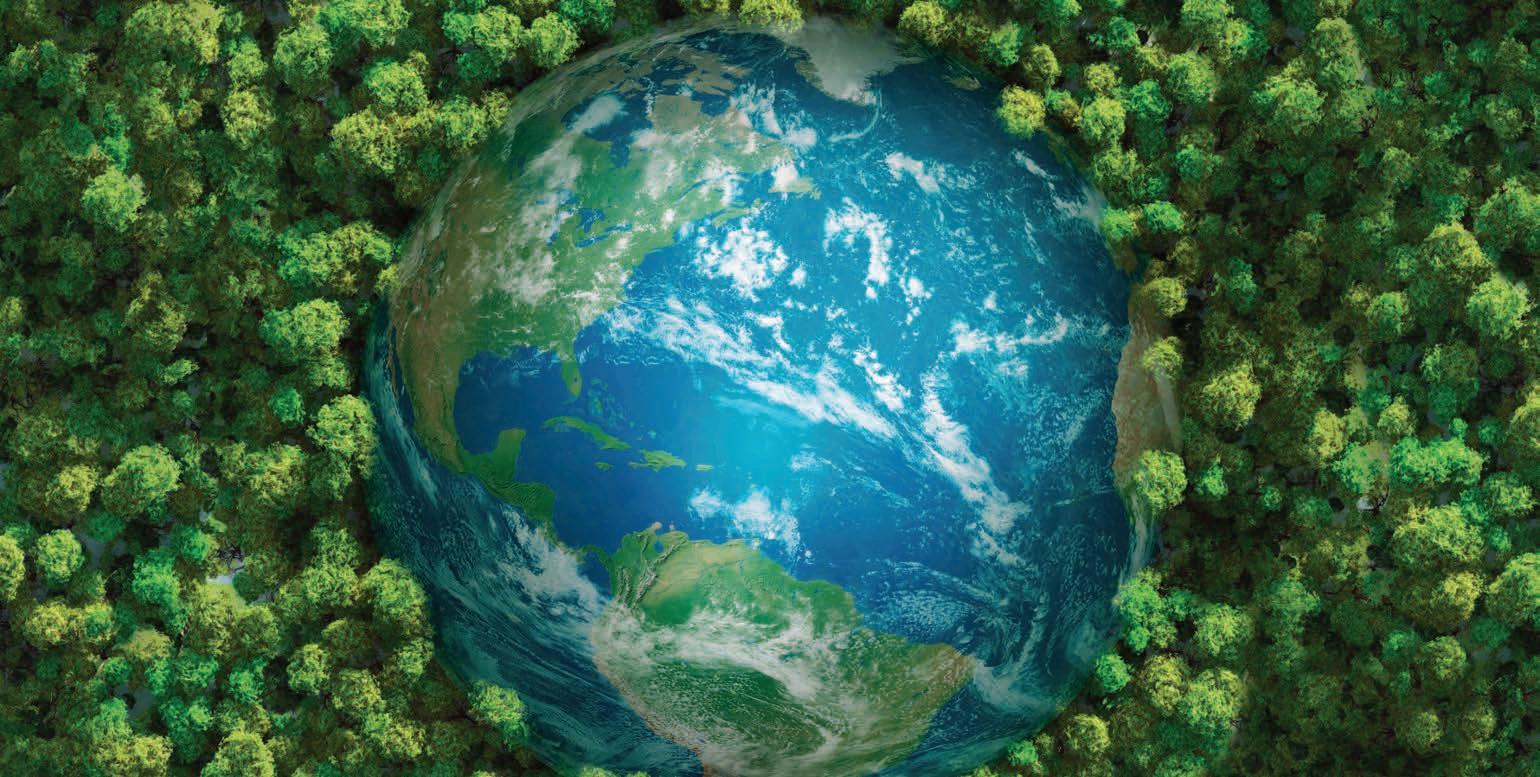
It’s funny how great ideas begin. Some are heavily researched, backed by extensive analytics. Some come from a light bulb moment – a simple observation can prompt creative minds to find a solution to a particular problem. In this case of this month’s cover story, FormFlow’s bending technology for corrugated steel was born out of one of these observations. The story goes, Duncan and his cousin were at McDonalds observing the casing for one of its famous apple pies, where you squeeze the packaging on the sides and push the ends in. All these years later, FormFlow’s technology holds a similar theory – basically inverting peaks into valleys to create shapes without damaging the material.
‘Inextensional’ is a geometric term meaning that the sheet cannot stretch or shear, and deformation is limited to a sharp bend. Read on to discover how FormFlow pioneered this innovation into real world applications and continues to grow its commercialisation journey.
For instance, Monitum is using world-first technology to track invisible movement in a structure or surface before any cracks show. The combination of a Global Navigation Satellite System (GNSS), the Internet of Things (IoT) and cloud computing technology delivers millimetre precise and accurate insights to help businesses manage risk.
In this edition of Manufacturers’ Monthly, we tell stories about SMEs breaking through the challenges of commercialisation because of outstanding innovation.
6 Editor’s Note 8 2012CommentNews@MMManufacturer Focus 24 Engineering Focus 28 Air Ventilation 30 Events – Land Forces 32 Electronic Repairs 34 Events – Women in Industry 36 Air Piping 38 Industrial Control 40 Air Compressors 42 Internet of Things 44 Compressed Air 46 Industrial Solutions 49 Supply Chain & Logistics 50 What’s New 51 Last Word
4 SEPTEMBER 2022 Manufacturers’ Monthly manmonthly.com.au For daily news visit manmonthly.com.auSEPTEMBER In2022side CEO: John Murphy Chief Operating Officer: Christine Clancy Group Managing Editor (Northern): Syed Shah Assistant Editor: Billy Friend billy.friend@primecreative.com.au Journalist: Alexandra Cooper alexandra.cooper@primecreative.com.au Production Coordinator: Michelle Weston michelle.weston@primecreative.com.au Art Director: Blake Storey Design: Kerry Pert, Aisling McComiskey Sales/Advertising: Danny Hernandez Ph: 0431 330 danny.hernandez@primecreative.com.au232 Subscriptions Published 11 times a year Subscriptions $140.00 per annum (inc GST) Overseas prices apply Ph: (03) 9690 8766 Copyright Manufacturers’ Monthly is owned by Prime Creative Media and published by John Murphy. All material in Manufacturers’ Monthly is copyright and no part may be reproduced or copied in any form or by any means (graphic, electronic or mechanical including information and retrieval systems) without written permission of the publisher. The Editor welcomes contributions but reserves the right to accept or reject any material. While every effort has been made to ensure the accuracy of information, Prime Creative Media will not accept responsibility for errors or omissions or for any consequences arising from reliance on information published. The opinions expressed in Manufacturers’ Monthly are not necessarily the opinions of, or endorsed by the publisher unless otherwise stated. © Copyright Prime Creative Media, 2021 Articles All articles submitted for publication become the property of the publisher. The Editor reserves the right to adjust any article to conform with the magazine format. Head Office 11-15 Buckhurst St South Melbourne VIC 3205 P: +61 3 9690 www.primecreative.com.auenquiries@primecreative.com.au8766 Sydney Office Suite 3.06, 1-9 Chandos Street Saint Leonards NSW 2065, Australia P: +61 2 9439 7227 Printed by: Manark Printing 28 Dingley Ave Dandenong VIC 3175 Ph: (03) 9794 8337 manmonthly.com.au twitter.com/Manmonthlyfacebook.com/Manmonthlylinkedin.com/showcase/manufacturer’s-monthly/ manmonthly.com.au MANAGEMENT >> TECHNOLOGY >> SOLUTIONS >> INSIDE >> Repairing electronics to save downtime 26 WORLD-FIRSTTECHNOLOGYBEND FORMFLOW: Giving the power back to engineers 46 Official Industry Partners Technology changing displacementmonitoring22 38Manufacturers’26 Monthly Contents Behind the cover
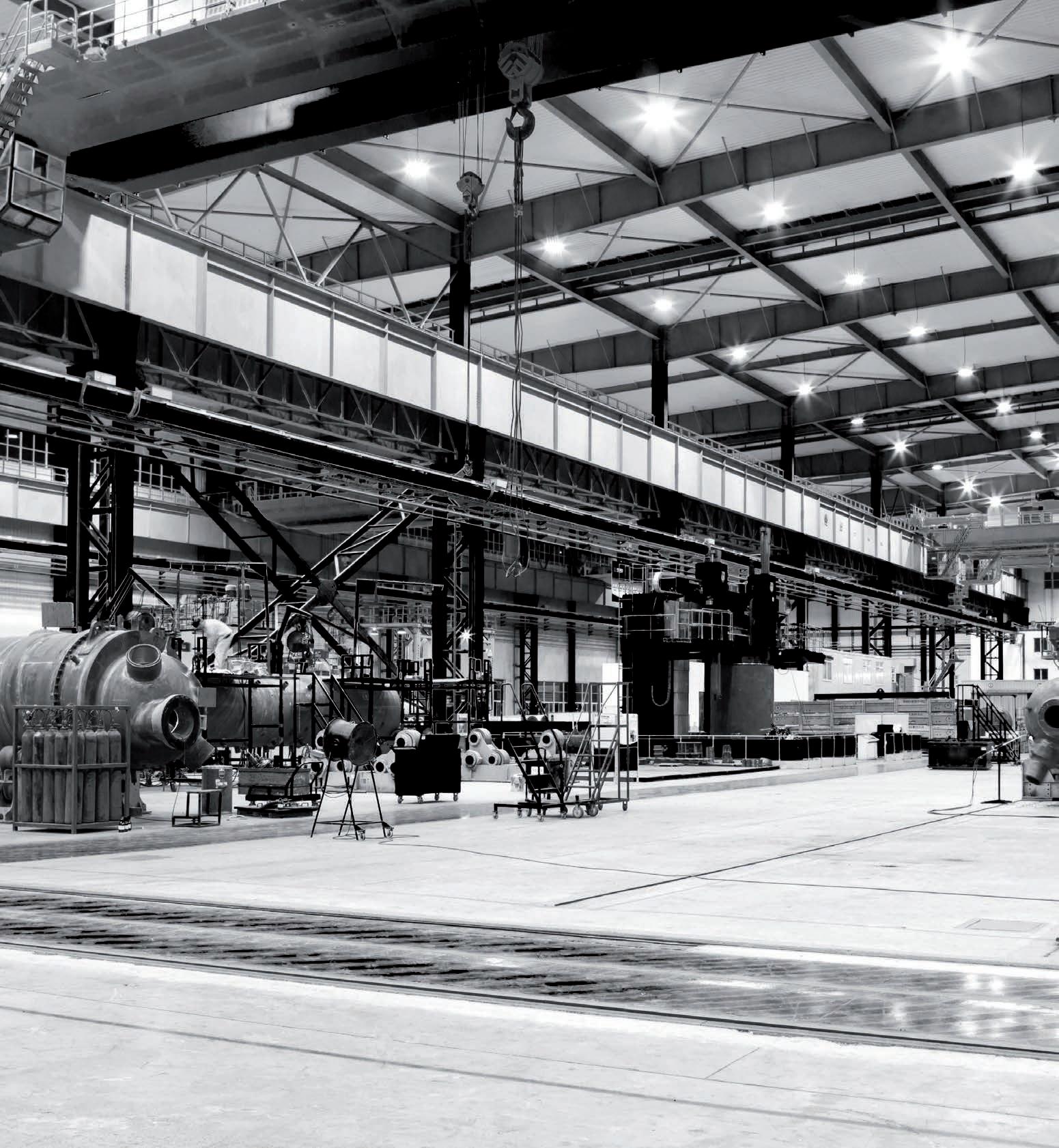

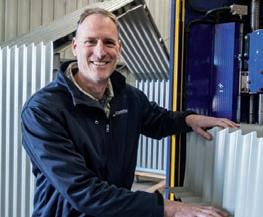



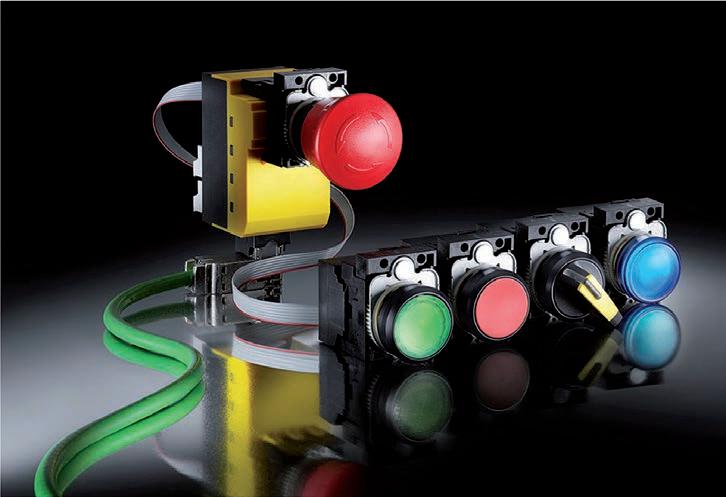
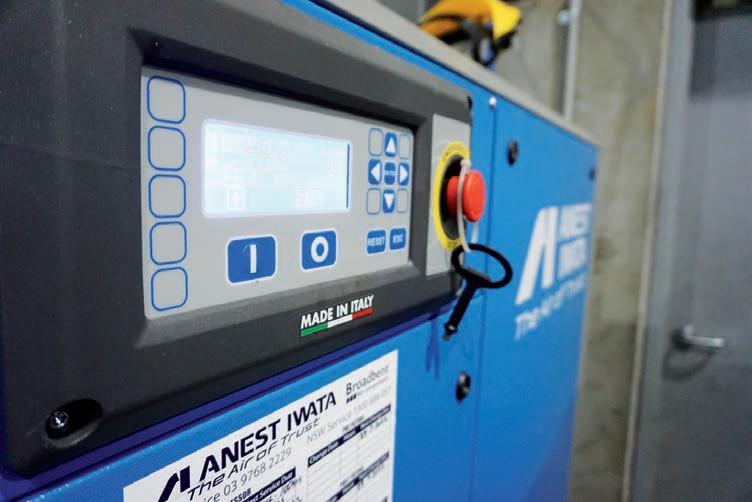
CALL 1800 800 878 OR VISIT NEWCAPS.COM.AUINGERSOLL RAND RM SERIES RELIABILITY, EFFICIENCY & PERFORMANCE 90 to 160kW oil-flooded air compressors High efficiency new design air-end Capacity improved up to 9% Specific Power improved up to 15% High performance IP55, IE3 Motor Low pressure system drop Integrated cooling fan with low power V-Shield Technology Small footprint, easy maintenance
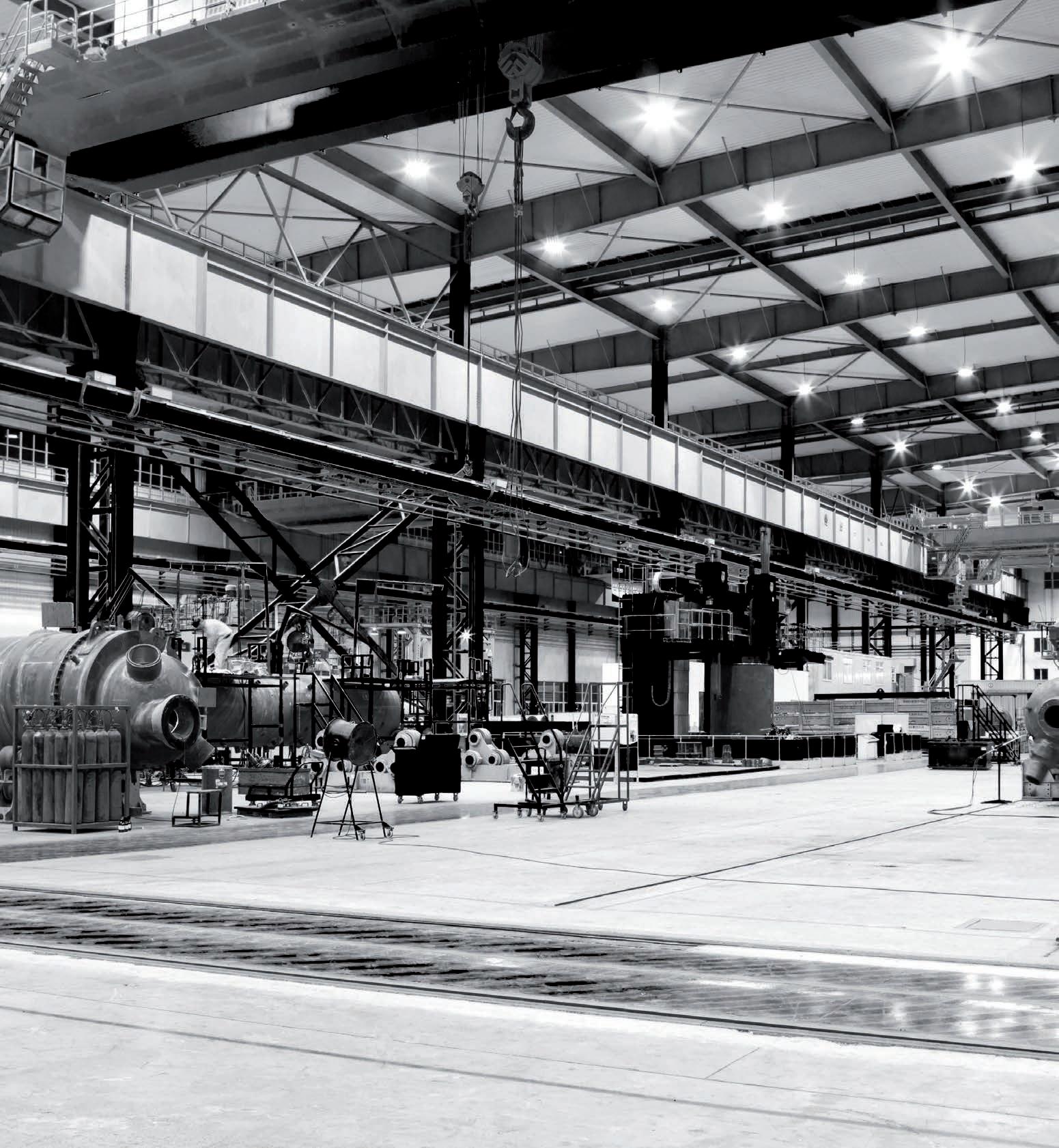

Although this term has been around since the mid-20th century, its importance has re-emerged as manufacturers grapple with the human and technological aspects of the interconnected IIoT. Managing both sides of this wave of technology means understanding how humans and machines fit together, and this does not just involve a user-friendly HMI.
The Modern Manufacturing Initiative (MMI) was welcomed by industry, but of course everyone cannot be pleased. The strategy was based off six key areas of manufacturing: resources technology and critical minerals processing, food and beverage, medical products, recycling and clean energy, defence and space. Upon being sworn in, Prime Minister Anthony Albanese pledged to “be a country that makes things again.” Part of this is his overhaul of the previous government’s initiatives, including a one billion dollar investment in advanced manufacturing.InJuly,reports that the Labor government had put a hold on the $1.3 billion in grants under the Coalition’s Modern Manufacturing Initiative certainly raised eyebrows. While the new government has said it will honour all contracts already signed under the scheme, a review is underway to determine whether the current manufacturing grants offer “value for money.” Industry minister Ed Husic has previously labelled the coalition’s manufacturing program as an “election slush fund,” but political squabbling aside, it’s essential the industry is given a clear idea of the road forward. Will SMEs be supported a long with large scale business? Will strategies be in place to upskill engineers and skilled workers which keep industry ticking? How will Australia embrace Industry 4.0? These are questions which are, for now, only partly answered. What we do know, without a doubt, is the fantastic stories about innovation and excellence within Australia’s manufacturing ecosystem.Today,the IoT for the industrial sector – the Industrial Internet of Things (IIoT) or Industry 4.0, depending on the organisation you’re from – is highly developed, and the global market for it is large. Accenture’s report Winning with the Industrial Internet of Things already stated that the IIoT market will be more than $19.63 trillion by 2030. The manufacturing industry is confronting the new reality of its structure as a “socio-technical system”.
A long-term vision, strategy and industrial policy required for Australian manufacturing IN October 2020, the Australian Government announced a $1.3 billion initiative as part of its national manufacturing priorities.
An existential issue confronting the industrialised world is the lack of growth in productivity, and Australia is no exception. Productivity growth in Australia, once at a healthy 2 per cent a year, has stagnated in recent years. However, the IIoT has some promise of increasing this number. With support from emerging technologies, such as AI, the IIoT has the potential to rapidly increase the value that manufacturers are able to extract from their assets.
Among other important stories to tell, this edition of Manufacturers’ Monthly showcases how SMEs are utilising advancing technology to improve their manufacturing processes.
SYED SHAH – Managing Editor, Manufacturers’ Monthly Editor’s Comment 6 SEPTEMBER 2022 Manufacturers’ Monthly manmonthly.com.au
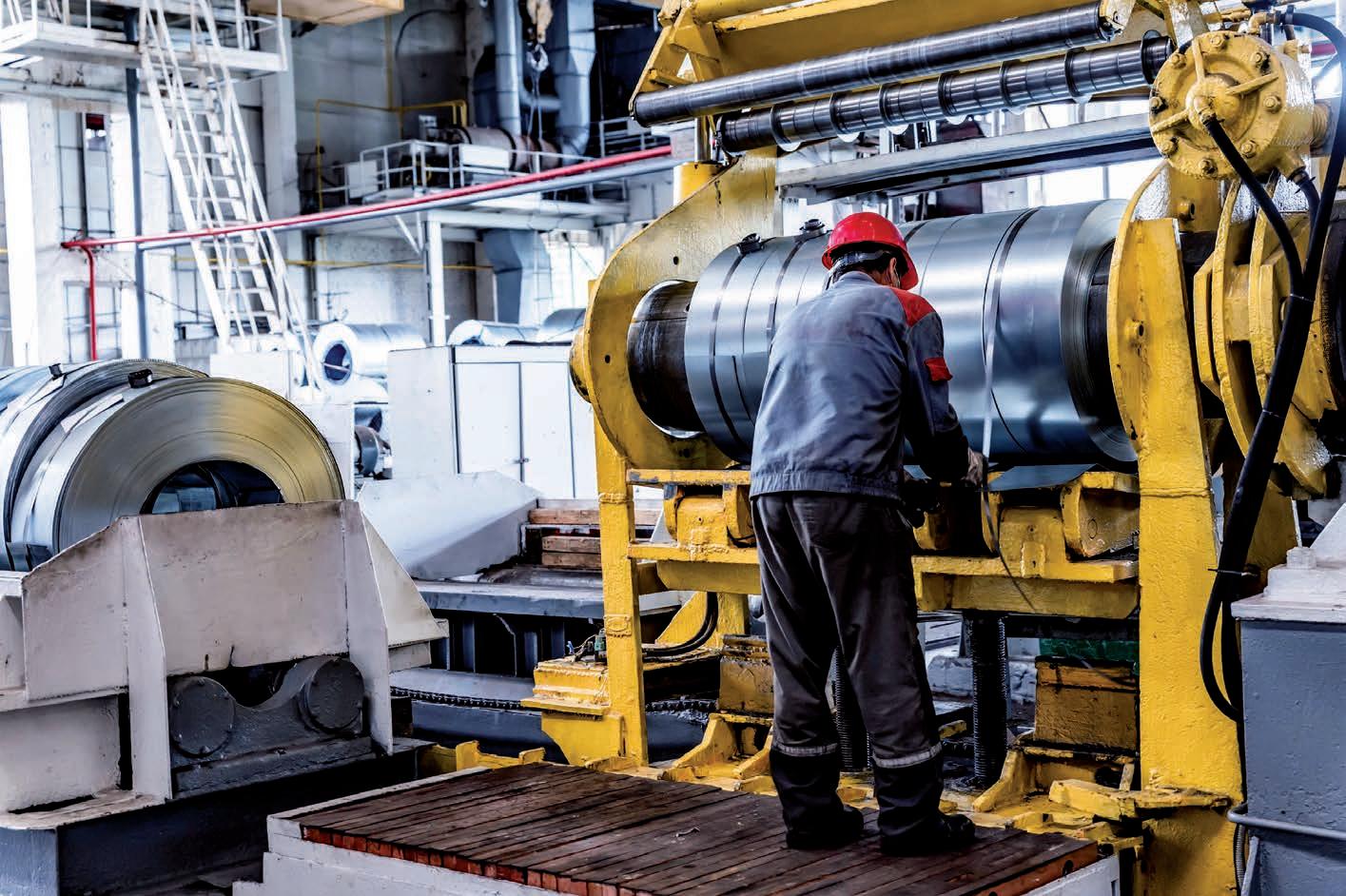
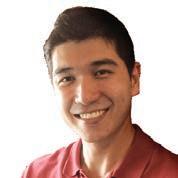
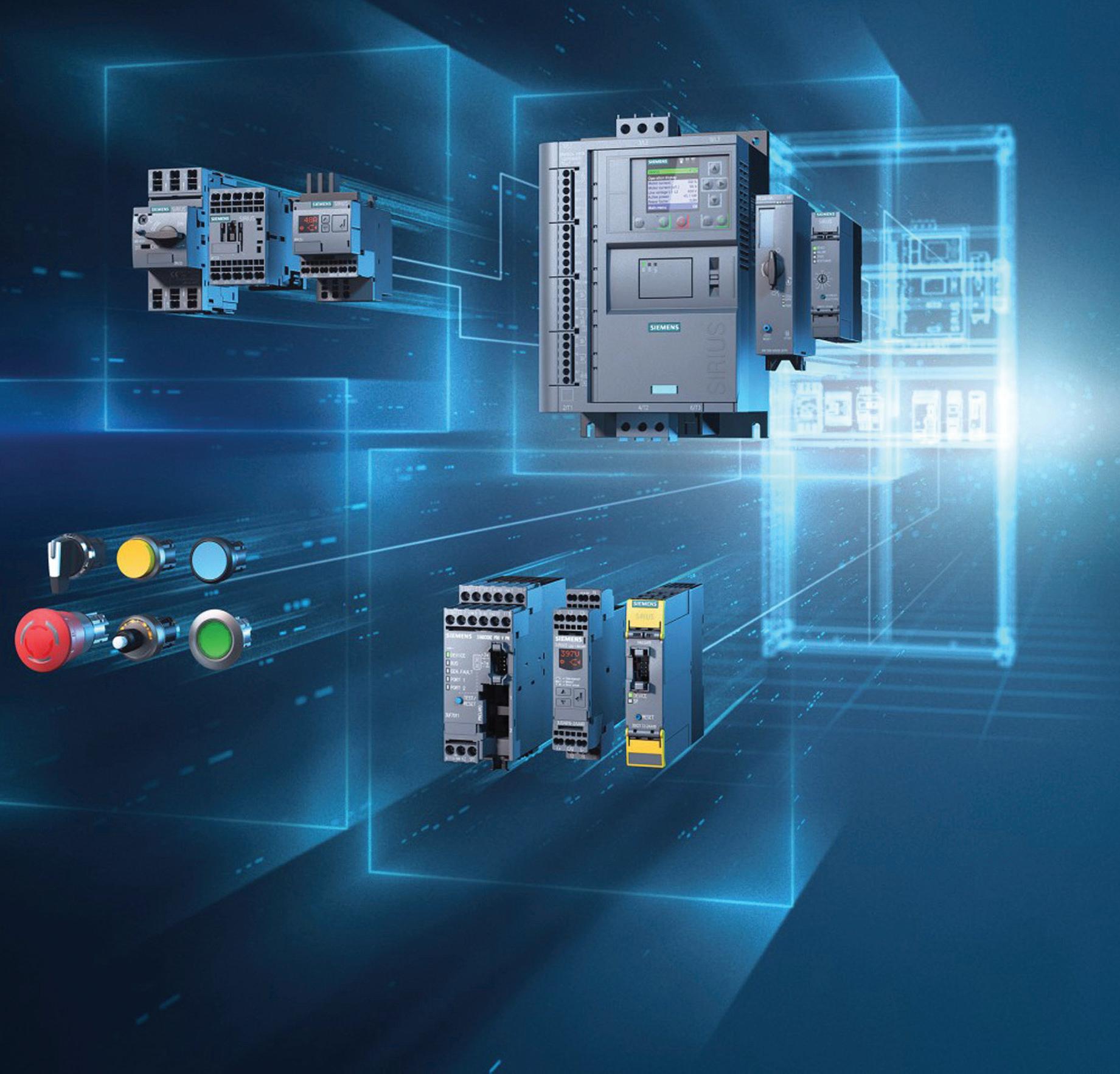
SIRIUS Industry Controls With Siemens SIRIUS from APS Industrial, you have exclusive access to a unique and comprehensive portfolio for every industrial control application. Thanks to their modular design and simple integration capability, these products can be designed and built into a control cabinet in a very simple NATIONALapsindustrial.com.auMONITORCOMMANDCONTROLway.DISTRIBUTORSOF
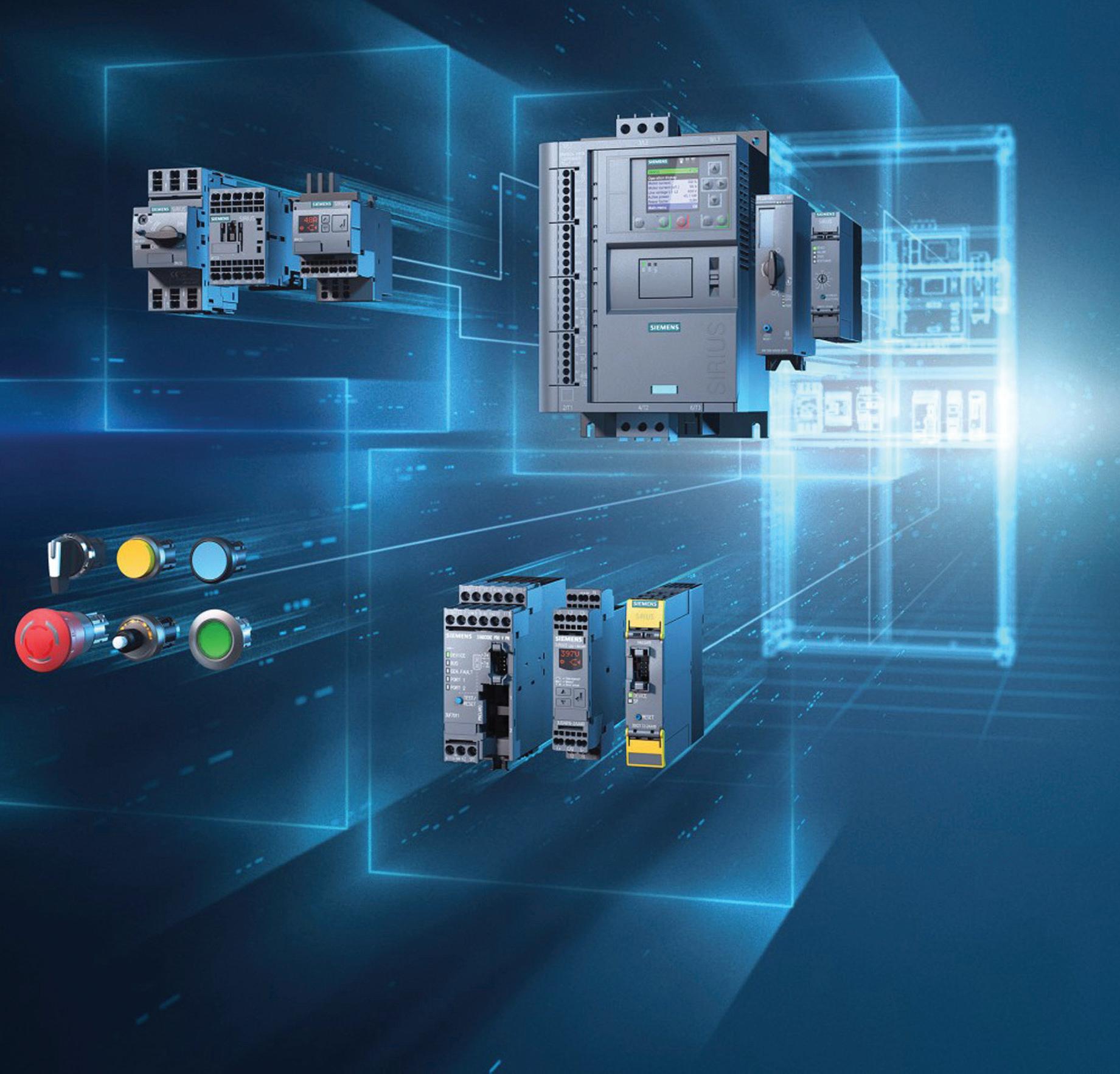
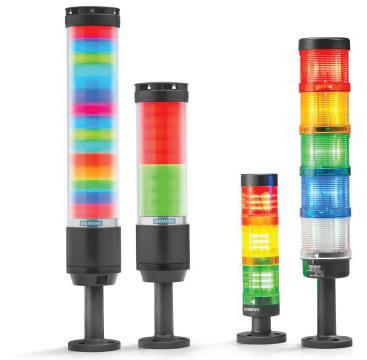
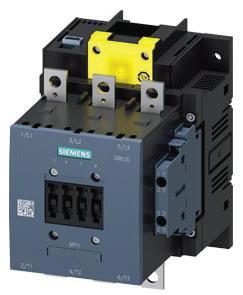
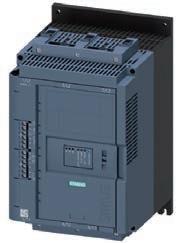
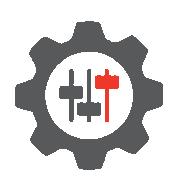

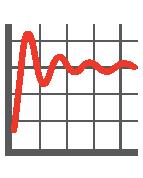
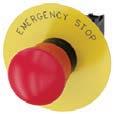
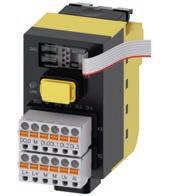




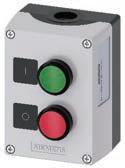



“Our members are also investing in their own welder training programs. BHP, Komatsu, JRS Manufacturing, Maxi-Trans and Precision Manufacturing Group have all established their own schools.
Australian senior managers are concerned about the lack of skilled staff in the recruitment market.
8 SEPTEMBER 2022 Manufacturers’ Monthly manmonthly.com.au GEOFF CRITTENDEN – CEO, Weld Australia Comment
WELD Australia has released the results of its 2022 Member Survey. The results demonstrate that significant concerns remain for Australia’s welding industry. In particular, Australia’s fabricators are being forced to turn down work due to a severe shortage of skilledAccordingwelders.to Geoff Crittenden, CEO Weld Australia, “Distributed in June 2022 and completed by approximately 140 companies, our 2022 Member Survey indicates that skills shortages, local content and sustainability remain high on the agenda for the welding industry.”
“When asked what they are most concerned about, 64 per cent of senior managers cited lack of skilled staff in an extremely constrained recruitment market. This comes as little surprise, with Australia facing a looming shortage of skilled welders – 70,000 additional welders will be needed by the end of the decade.”
We firmly believe in quality welding for structural safety,” said Crittenden. Inflation and rising costs were also of concern for approximately 23 per cent of respondents, followed by weak international supply chains (9 per cent) and reliability and affordability of power supply (4 per cent).
Aussie fabricators are turning down work due to skill Shortages Weld Australia has released the results of its 2022 Member Survey. The results demonstrate that significant concerns remain for Australia’s welding industry. In particular, Australia’s fabricators are being forced to turn down work due to a severe shortage of skilled welders.
“With a considerable volume of work being onshored in the wake of international supply chain disruptions, most Australian fabrication companies are so strapped for skilled welders that they are working at anywhere between 30 per cent and 50 per cent of their full capacity. They are being forced to turn down jobs because they simply don’t have the manpower to complete the work. This is having a major impact on production and causing delays throughout downstream industries including building and construction, mining, oil and gas, and manufacturing,” saidItCrittenden.islittlewonder that almost half (47 per cent) of survey respondents have a pipeline of work that extends for six months or longer—this protracted pipeline is necessary in the face of these ongoing skills shortages. By way of context, this is a marked increase on Weld Australia’s 2020 member survey results. In the wake of the COVID-19 pandemic, the most common answers were a pipeline of work that extended less than one month (at 28 per cent), one month (19 per cent), and two months (16 per cent). Given the concern over Australia’s looming skills crisis, it makes sense that 95 per cent of respondents support the concept of free TAFE, increased funding to upgrade TAFE facilities, or both initiatives. Clearly, the welding industry is looking to the government to help increase the supply of skilled labour over the coming years.
While industry appreciates the roll-out of government-funded TAFE places, it remains to be seen whether this initiative will translate into high completion rates. Moreover, while encouraging more students into TAFE is always a positive, government spending also needs to focus on resources for TAFEs, teachers and equipment—TAFEs need the right tools to teach this sudden influx of students,” said Crittenden.Industry is also investing in advanced welding technology to help overcome skills shortages. Over 28 per cent of respondents indicated that their company or the company they work for has purchased robots or cobots, and 25 per cent has invested in Industry 4.0 capabilities. A range of other types of technology were also mentioned, from drones and automated welders, through to various softwareDespitesolutions.theskills shortages, local procurement and content targets remain top of mind for the welding industry. 100 per cent of respondents confirmed that they would support Federal and State Government policies to increase Australia’s share of fabricated steel product to at least 75 per cent as part of a joint governmentindustry plan to grow the manufacturing industry.“Importantly, whether it is imported or locally manufactured, all fabricated steel erected in Australia must comply with Australian Standards. Weld Australia is committed to ensuring that no Australian lives are lost through an accident caused by non-compliant welding, without causing undue regulatory burden on industry.
Environmental sustainability and corporate responsibility Australia is rapidly moving from carbon fuelled power generation to a renewable energy system. In June 2022, Prime Minister Anthony Albanese announced more ambitious climate targets. Albanese pledged to cut carbon emissions by 43 per cent from 2005 levels by 2030, up from the previous government’s target of between 26 per cent and 28 per cent. Given these targets, private companies will play a key role, making sustainability a priority for many businesses. As such, our 2022 member survey asked a series of environmental sustainability focused questions.Welders are environmentally responsible. 30 per cent of respondents support the target of zero emissions before 2050; 20 per cent prefer cutting emissions by 43 per cent by 2030. In addition, 74 per cent of respondents would support a Federal Government package to help employees transfer from carbon intensive to carbon free industries.Clearly, Australia’s welding industry is already taking steps to reduce its carbon emissions. While 41 per cent of respondents have already installed solar panels to supplement power supply, another 53 per cent have installed LED or sensor lighting, 46 per cent have waste reduction programs in place, 46 per cent operate recycling, up-cycling or repurposing programs, and 13 per cent have a net zero carbon plan in place. When asked if an electric or hybrid UTE was available in Australia at a competitive price would you buy them for your company or employees as fleet cars, 50 per cent of respondents answered in the affirmative. Interestingly, 63 per cent of respondents would buy an electric or hybrid UTE for themselves. Corporate responsibility remains a growing area of focus for the welding industry. Over 63 per cent of respondents indicated that they have initiatives aimed at improving opportunities for women; 63 per cent promote opportunities for apprentices and trainees; 63 per cent have diversity and inclusion initiatives in place; 59 per cent have mental health and fitness
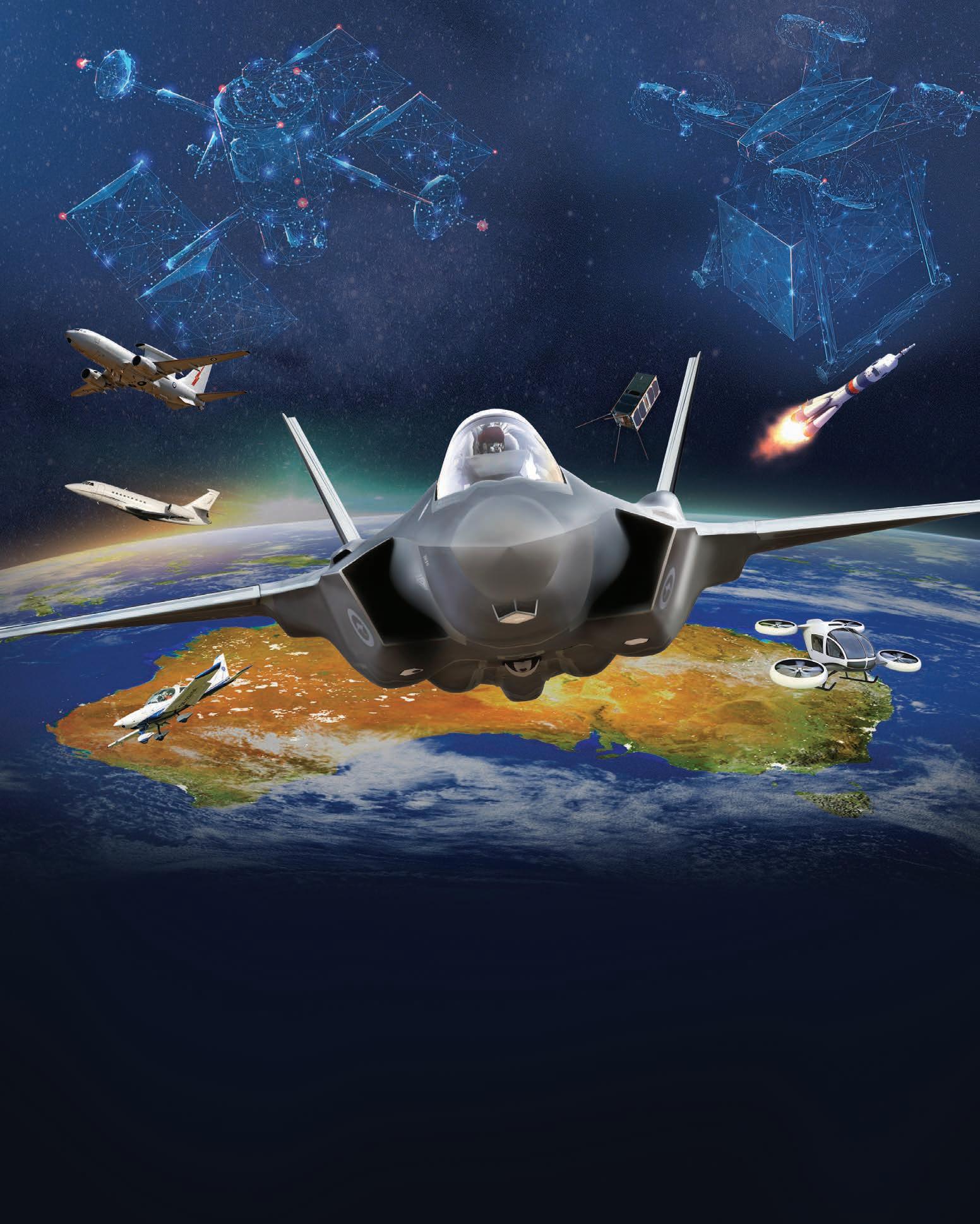
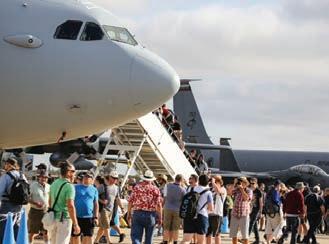
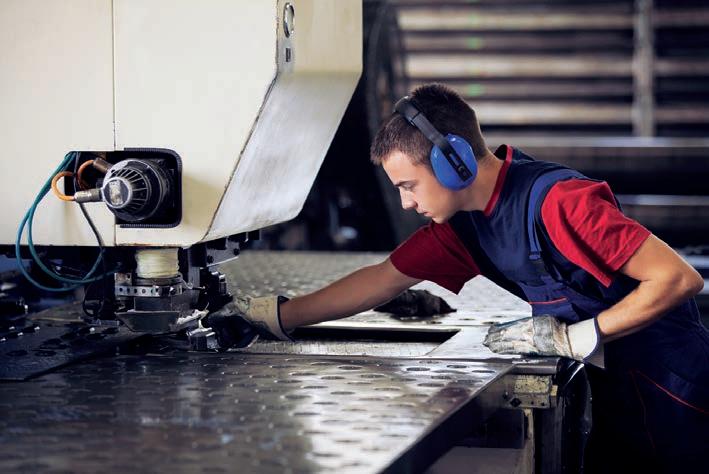
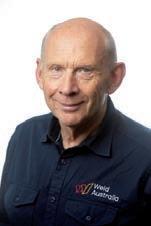
AUSTRALIAN INTERNATIONAL AIRSHOW AEROSPACE AND DEFENCE EXPOSITION 28 FEBRUARY – 5 MARCH 2023 Australia’s own international industry event, the most comprehensive aviation, aerospace and defence exposition in the Southern Hemisphere. PREVIOUSHIGHLIGHTSEVENT l 38,952 Trade Visitor Attendances l 698 Participating Companies l 41 International Air Chiefs and Representatives l 161 Official Delegations WWW.AIRSHOW.COM.AU
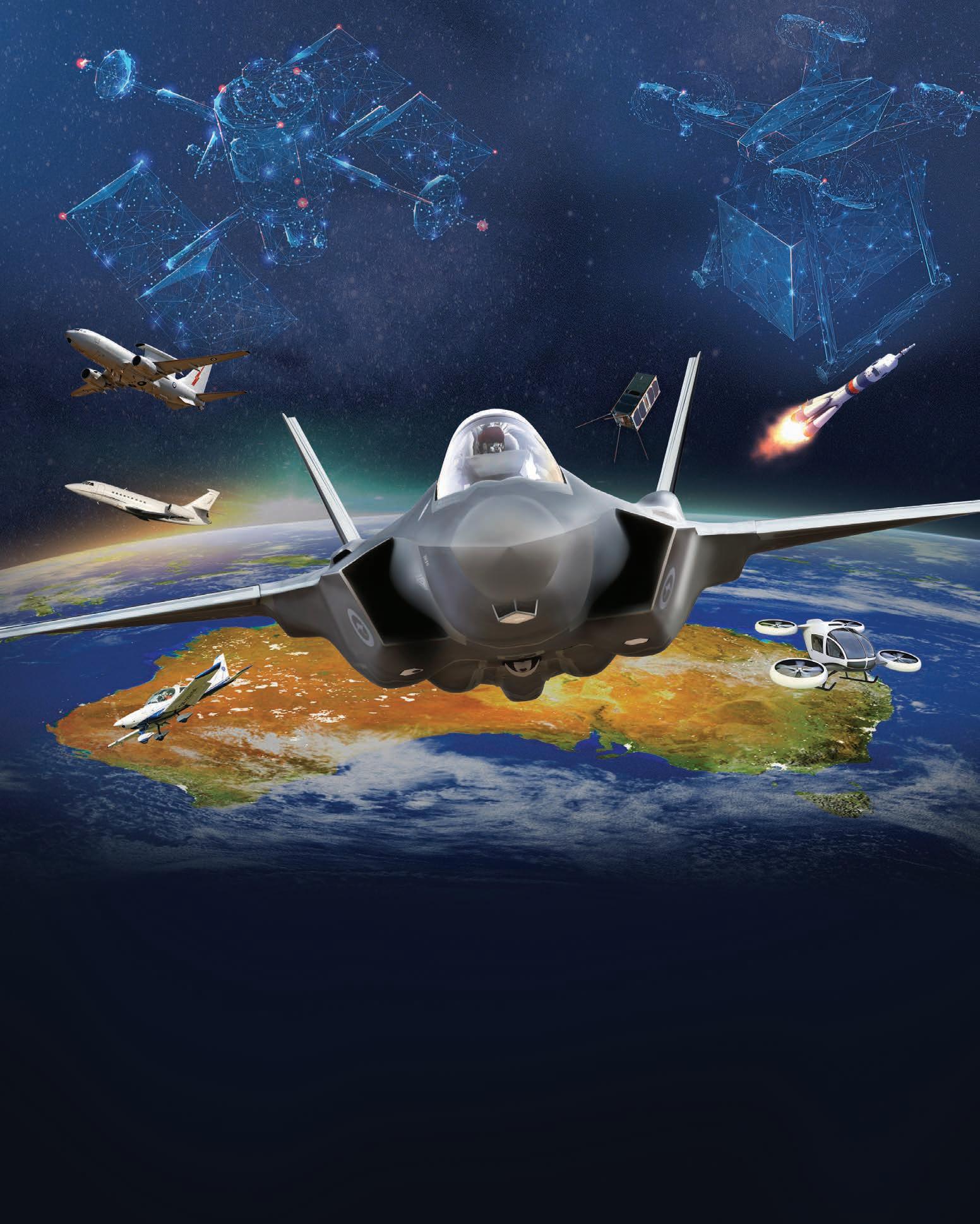
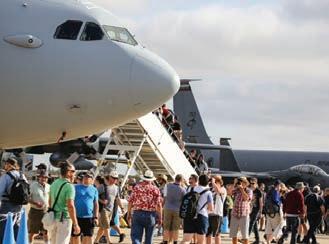
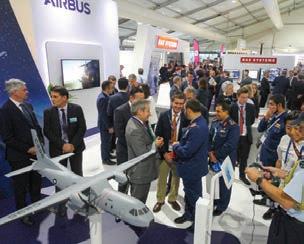
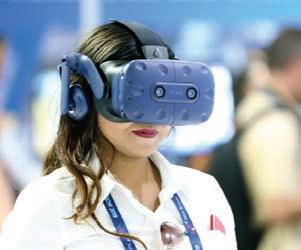
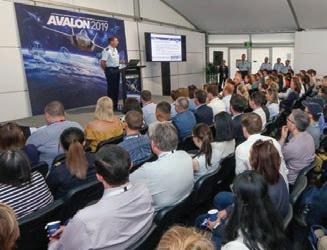
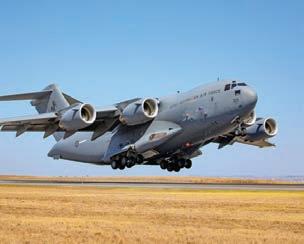
THE concept of manufacturingsovereigncapability has become a hot topic in Australia, and rightfully so, as the double hit of the pandemic and geopolitical issues has exposed significant gaps in Australian manufacturing capability and capacity.
‘Sovereign capability’ was a phrase more typically associated with specific industries, notably the defence sector. Now, in the face of international volatility, it is more commonly used to describe the building of Australia’s national scale, depth and resilience. To succeed in this endeavour, we need to focus on developing industrial capability in specific, targeted sectors where we have a comparative advantage (including through access to local inputs and resources) and where manufacturing acts as an enabling capability. We need to understand where we are different from other developed and industrialised nations and accommodate this in our policies, strategies, and investments.Thisrequires accepting that we can’t make everything domestically. As a nation of less than 30 million people, this would be neither economical nor feasible, and may also distract and dilute investment into areas where we can become global leaders, such as clean and new energy solutions, health and medical manufacturing, food, critical minerals value adding and specialised areas such as space and defence. While we have pockets of manufacturing excellence and exemplars across the nation, most of our manufacturers are micro-businesses focusing primarily on production.
IMCRC delves into why sovereign manufacturing capability has become such a hot topic and how Australia can accelerate its capacity to achieve this.
The drive for Australian Made must ideally also be a drive for Australian designed, engineered and owned. This is critical – we must invest in our ability to create uniqueness by designing and engineering complex products, processes, services and solutions that are significantly value add, digitally enabled and exportable. This will drive muchRealising the potential of our sovereign manufacturing capability
Comment 10 SEPTEMBER 2022 Manufacturers’ Monthly manmonthly.com.au
Focusing on developing industrial capability in specific, targeted sectors could be the key to improving sovereign capabilities across Australia.
The end of passenger vehicle production in Australia was one of the drivers of this need to transform. With it we saw the loss of significant industrial infrastructure where global multinationals drove best practice through tiered supply chains, creating opportunities for local manufacturers to export and expand internationally as part of a global network. In its prime, many suppliers to Australia’s automotive industry demonstrated our capability for production, but perhaps more importantly for design, engineering, innovation, logistics, operational and financial management, etc. – and did this at very aggressive price points to match global competition. So with these differences and challenges, how can Australia accelerate building sovereign manufacturing capability and capacity? Build design and engineering capability
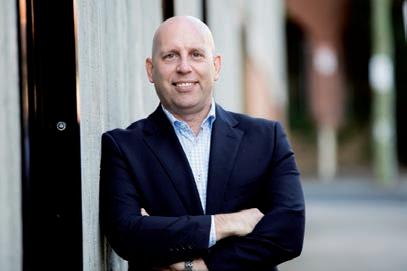
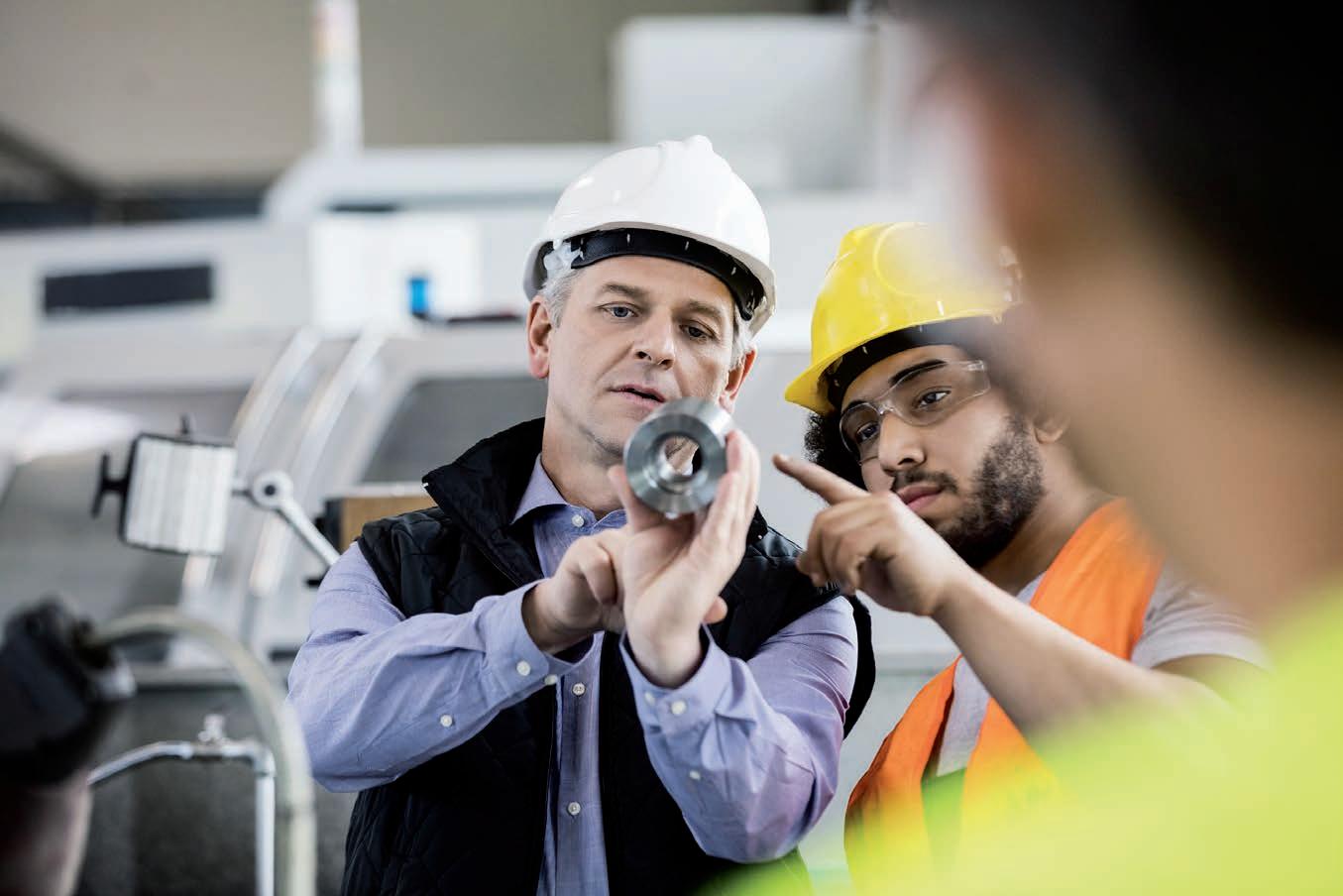
With the world rapidly digitalising, we can’t ignore the opportunity across industry to embrace Industry 4.0 to drive productivity and capture and create value. Much more can be done to educate and incentivise around this, including businesses being willing to collaborate to develop and implement Industry 4.0 solutions and business models.
Subhead: Growing the proportion of medium-sized manufacturers There is plenty of evidence that medium-sized companies provide the critical mass, capability, and ambition to drive innovation, productivity and growth. IMCRC’s futuremap® data shows the appetite for investment, Industry 4.0, and innovation is more active in a medium-sized company than in a large or small company. At this size, the business is more likely to have the management structure, credibility and finances in place to develop supply chains and export opportunities, support growth and collaborate. Thus, programs need to be developed specifically to increase the proportion of medium-sized companies that have the maturity to invest in and play leading roles in their sectors. Retaining local talent and creating opportunities We need to encourage and find ways to retain our talent, intellectual property, and investment opportunities within Australia and not lose them overseas. We have to create a more positive perception, or ‘brand’, of Australian manufacturing, positioning it as attractable and investable. This is needed at many levels, to interest primary school children in design and manufacturing, through to attracting equity and foreign investors.
Often, we look at skills development on a technical level, particularly for SMEs. Rarely do we consider investing in skills, development and education at the business owner or leader level to help them drive personal development, training, investment and innovation. Specific programs are needed to lift the capability and capacity of manufacturing SMEs to develop innovation, digital and green skills, as well as to embrace design thinking and collaborative partnerships.
Encourage more foreign investment into Australia
To grow our sovereign capability, we need to rethink the role and opportunity of foreign direct investment in Australia, and we need to do this quickly. Many nations are thinking this way and are actively attracting big investors into their countries. The potential benefits are enormous. You need only look as far as our defence sector to see that sovereign capability can and should be built in strategic, targeted areas, and in partnerships with nations and key industrial players within those nations.
SME Leadership and skills development
Government both as catalyst and purchaser We need a long-term vision, strategy and industrial policy with appropriate incentives and catalysts to lead Australia’s manufacturing industry towards it. The government is already driving discussions around local content requirements, including for small and medium enterprises (SMEs). At this stage it is still primarily about production, but its now timely to embrace the real opportunity for Australia to build capacity and capability, which is in design and engineering. Local content requirements for design would likely lead to local production and opportunities for Australian supply chains and may also incentivise startups.
At first, encouraging foreign investment might seem at odds with building sovereign capability. Sovereign capability can be built as ‘all Australian’ but it will take a very long time and, by being insular, we also risk losing connections with, and relevance to, global supply chains and activities. To grow our sovereign capability, we need to rethink the role and opportunity of foreign direct investment in Australia, and we need to do this quickly. Many nations are thinking this way and are actively attracting big investors into their countries. The potential benefits are enormous. You need only look as far as our defence sector to see that sovereign capability can and should be built in strategic, targeted areas, and in partnerships with nations and key industrial players within those nations. Multinational defence primes have played a significant role in strengthening the capacity and capability of Australian SMEs throughout the entire supply chain. As an example, IMCRC’s collaborative R&D investment with BAE Systems Australia is driving Industry 4.0 into shipyard manufacturing and supply chains. The project with Flinders University has led to the establishment of the Line Zero and Factory of the Future facilities at Tonsley in South Australia –which is building local talent and creating long-term opportunities for local SMEs.
And while programs of national significance (such as the Hunter Class Frigate Program) have a large role to play in attracting foreign investment, there are many other reasons as to ‘why Australia’. We have a long and proud history of manufacturing. We have a rich abundance of academic and research capability. We typically share common rules of law and standards of governance, respect for intellectual property, as well as common languages with other industrialised nations and strategic partners. Foreign businesses who invest into Australia often only strengthen that investment over time. By aligning with key investment sectors as outlined by the new Labor Government, we have a unique advantage. Take, for instance, medical manufacturing. Since 2016, global medical technology and Fortune 500 company, Stryker, and IMCRC have been co-investing in a five-year, $18 million R&D collaboration with RMIT University, University of Technology Sydney, St Vincent’s Hospital and others. By enabling Stryker to invest in and develop these partnerships and undertake innovative R&D, IMCRC’s project has led to Stryker establishing its first Australian R&D facility in Queensland. The medical research lab is designed to strategically complement Stryker’s global business while growing critical medtech design and manufacturing capability here in Australia. Opening this September, Stryker’s facility will create many highskilled, local jobs in engineering, science, clinical research and data analytics. In addition to job creation, foreign investments also generate opportunities for SMEs to develop the capability, knowhow and pathways to compete on the globalThere’sstage.no doubt that Australia’s focus on sovereign manufacturing is poised to create significant opportunities for our manufacturing sector, including for SMEs, but we must continue to think global while investing local. As IMCRC has found, with the right business model, incentives and partnerships, Australian manufacturing can be both attractive and investable for local SMEs and foreign businesses. This is also how Australian manufacturing can be thriving, relevant and globally integrated.
manmonthly.com.au Manufacturers’ Monthly SEPTEMBER 2022 11
needed business investment in research, development and innovation. This is not only applicable for industry. Research organisations also need to invest in design and engineering capability, ideally through partnerships with industry.
When we look at our well-known success stories, from Cochlear and ResMed to Carbon Revolution, RØDE and Blackmagic Design, we see that robust design and engineering capabilities, often honed through research and development (R&D), lie at the heart of their achievements. This is something we have seen echoed through the pandemic, with companies like Grey Innovation pulling together consortiums to design, engineer and locally manufacture critical items like ventilators, and Whiteley Corporation creating first-to-market COVID cleaning solutions. And, as Australia moves to increase sovereign manufacturing capability, there needs to be a renewed focus on investing in design, engineering and innovative R&D to really harness the opportunities within nascent sectors like critical minerals, clean energy and health.
Industry 4.0 investment
The Victorian Manufacturing Hall of Fame Awards highlighted the importance of local manufacturing this year.
The Awards showcased the breadth of products, machinery and equipment produced in Victoria, and recognised the people and businesses that are driving the sector’s success and growth. Minister for Industry Support and Recovery, Ben Carroll, congratulated the winners and finalists at the awards ceremony.“Victoria is Australia’s manufacturing state, and we are backing innovative companies to beat the best in the world,” Carroll“Thesesaid.awards recognise the contribution of our leading manufacturers that are developing new technologies and processes that help to create jobs throughout Victoria. We’re continuing to support our manufacturers because we want to expand what is made in Victoria – which will boost our economy.”Awards were presented across 14 categories including three new awards for Leader in Low Carbon Economy, Outstanding Responsiveness to COVID-19, and Leader in Diversity and Inclusion.Industrial design and advanced manufacturing business, Integra Systems was this year’s inductee. Based in Broadmeadows, the light metal products manufacturer also took out the award for Leader in Workforce Skills Development. Health technology company, Planet Innovation was awarded Manufacturer of the Year for large business and Outstanding Responsiveness to COVID-19 for its work in producing critical health products throughout the pandemic, including surface sterilisation and portable ventilators. Care Essentials, a healthcare manufacturer in Geelong, took out Manufacturer of the Year for medium businesses, and 3D printing company, Amaero Additive Manufacturing in Notting Hill was the small business winner.NCIPackaging received the inaugural Leader in Low Carbon Economy award for reducing its energy output by installing solar power across its Australian sites, while the Leader in Diversity and Inclusion award went to Elastomers Australia for providing more employment opportunities for Indigenous employees and women.
The other company awards were as follows:Leader in Industry 4.0: Coolon; • Leader in Innovative Product Development and Commercialisation: Foodmach; and Leader in Global Supply Chain Partnerships: Nissan Casting Australia. The awards for individuals went to:
• Honour Roll – Service to Industry: Patrick Boland and Pat McCluskey, ANCA;Woman Manufacturer of the Year: Andrea Del Ciotto, Osteon Medical; and
• Young Manufacturer of the Year: Benjamin Cheng, Eagle Lighting Victoria’sAustralia.manufacturing industry contributes around $30 billion to the local economy each year, supports around 260,000 jobs and provides more than 27 per cent to the nation’s manufacturing output. For more details, visit business.vic.gov. au/halloffame.
12 SEPTEMBER 2022 Manufacturers’ Monthly manmonthly.com.au News @MM
The Victorian Manufacturing Hall of Fame Awards has celebrated its 20th anniversary with a “Made in Victoria” theme, highlighting the importance of local manufacturing. The winners were announced at the Gala Dinner on 26 July at the Palladium at Crown.
Local manufacturing celebrated at Hall of Fame Awards
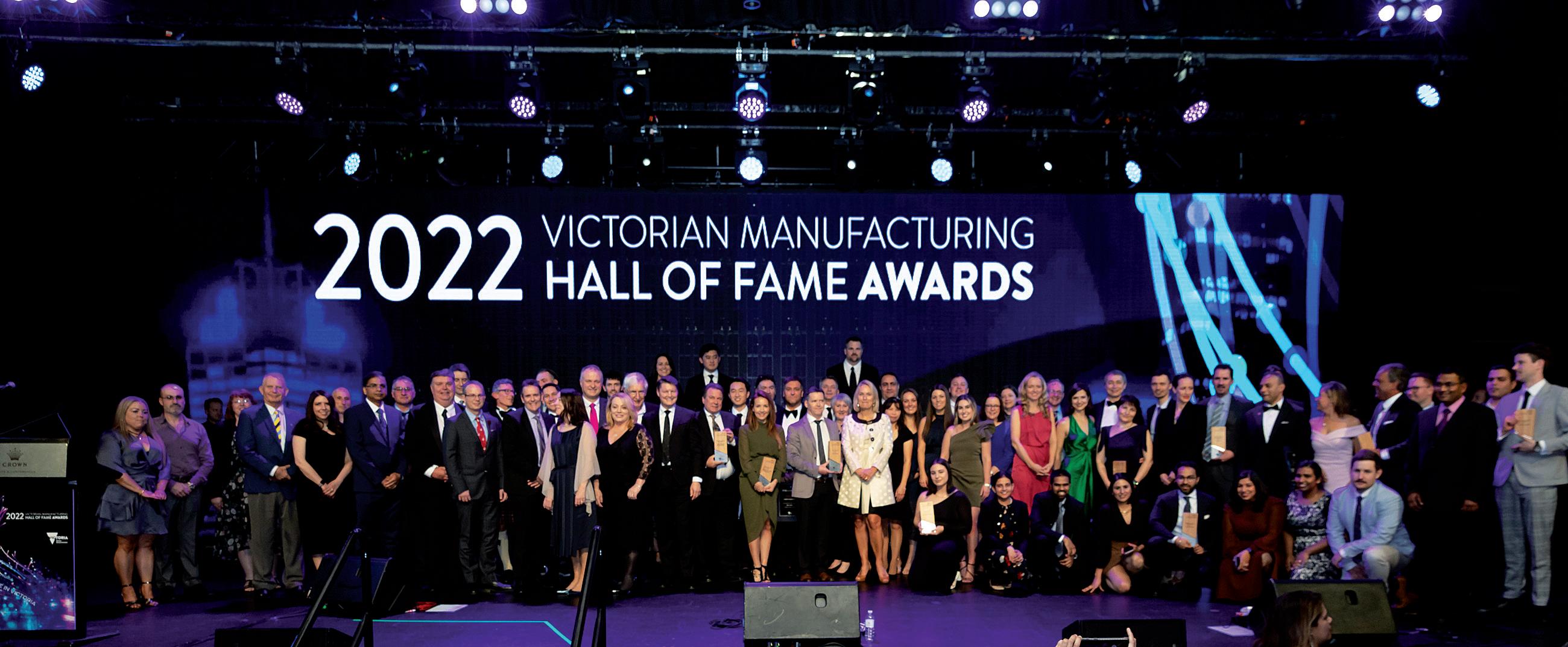
SMEs working on new advanced manufacturing solutions can sign up to the free, 10-week online Innovate to Grow program, to support their commercial idea by building their R&D knowledge, with 25 spotsUponavailable.completion of the program, participants may be able to access facilitation support, through CSIRO, to connect to research expertise nationally, along with dollar-matched R&D funding.
CSIRO director of Manufacturing, Marcus Zipper, said global supply chain disruptions highlighted the need to build Australia’s advanced manufacturing capability.“Advanced manufacturing plays an important role in so many sectors, with manufacturing contributing about six per cent of Australia’s GDP, from biomedical manufacturing to smart robotics and automation,” Zipper said.
TECHNOLOGYYOUCANTRUST AVAILABILITY SERVICEABILITYRELIABILITYAPRTNERSHIP SIMPLICITY DRD 60 - 100 IVR PM Interior Permanent Magnet Motor Variable speed drive Advanced reliability in compressed air Ceccato ceccato.au@ceccato.com1300Compressors555284 Advanced DRD IVR PM range of oil-injected screw compressors by Ceccato. 0922 Half Page Ceccato Man Monthly.indd 1 4/08/2022 4:57:52 PM
“Even though we know R&D drives innovation, it can be an expensive undertaking for businesses, risky and time consuming for those without the right guidance and support,” Feast said. “Through this program, participants will be given help to refine a new idea they want to explore and better understand mentor.”Theprogram is open to all companies, regardless of sector, who incorporate, or would like to incorporate, advanced manufacturing to improve their existing business“Evenoperations.thoughcollaboration is key in when they are thinking of exploring new innovation opportunities – our goal through this program is to up that percentage,” Feast said.
CSIRO’s Innovate to Grow: Advanced Manufacturing program commences 6 September. Applications close 22 August. R&D program to boost advanced manufacturing
manmonthly.com.au Manufacturers’ Monthly SEPTEMBER 2022 13 News @MM
Deputy director of CSIRO’s SME Connect team, Dr George Feast, said that to help businesses take their products or services to the next level, R&D was essential to better understand what opportunities might be presented to them.
CSIRO
CSIRO’s Innovate to Grow program will offer free R&D support to 25 SMEs.
The CSIRO is advancing Australia’s advanced manufacturing capability by providing free research and development support to help businesses develop new products or services through a new Innovate to Grow program.
“Building Australia’s advanced manufacturing capability is a key part of Australia’s recovery from the COVID-19 crisis, and much of this capability will be driven by SMEs, which make up 99.8 per cent of all businesses in Australia.”
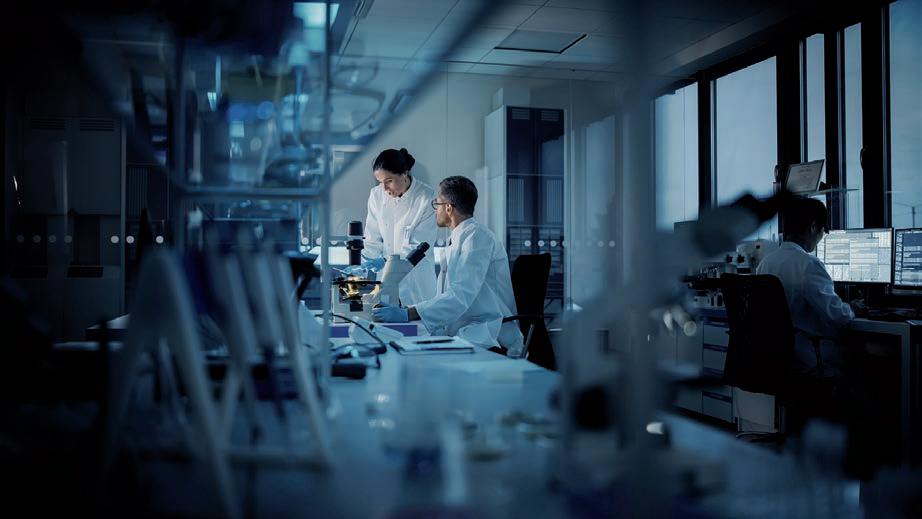
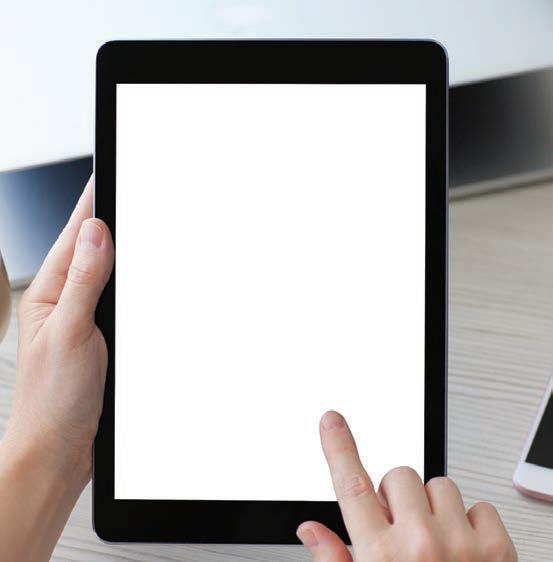
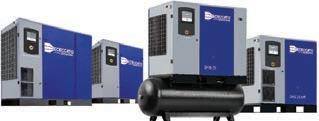
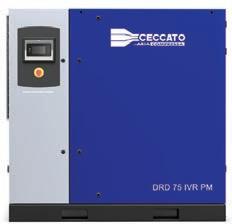

Jobs and Skills Australia will be a new independent agency, responsible for providing advice to government to underpin Australia’s response to current, emerging and future labour market and workforce skills and training needs, to improve employment opportunities and economic growth.
JSA will work closely with state and territory governments, as well as industry, employers, trade unions and training providers to ensure a shared understanding of the key issues facing Australia’s labour market. Minister for Skills and Training, Brendan O’Connor, said it is a critical priority for the government.“Asanation we are experiencing skills and labour shortages across industries that are vital to the health and wellbeing of Australians and our economy,” O’Connor said. “It’s vital to plan and to act to ensure that Australia has the skills it needs.”
14 SEPTEMBER 2022 Manufacturers’ Monthly manmonthly.com.au News @MM
The Australian Industry Group (Ai Group) Australian PMI dropped by 1.5 points to 52.5 in July, indicating a weaker rate of expansion compared to the previous month.
JSA will also examine the adequacy of the VET system in delivering these skills and make sure Australians of all backgrounds have the training and skills to access job opportunities now and in future.“Establishing an interim Jobs and Skills Australia director will enable its employers, unions and training providers, the skills and training sector, while forging towards addressing the nation’s skills crisis, contributing to productivity improvements, economic growth and creating more secure and better employment opportunities for Australian workers.”
Jobs and Skills Australia will be responsible for providing advice to government on skills and training needs.
The Australian government is taking immediate action to address the urgent skills crisis by introducing legislation to establish Skills Australia Jobs and Skills Australia (JSA).
Jobs and Skills Australia aims to address the skills crisis
Slower industry expansion shows need to address labour shortages
“The supply and labour constraints afflicting the Australian economy are weighing heavily on the manufacturing sector. Production and employment both fell in July, as manufacturers struggle with chronic labour shortages and supply chain interruptions,” Ai Group chief executive Innes Willox said. “New orders rose this month, but our manufacturers simply can’t meet this demand without more workers. Manufacturing has a key role to play in reducing the inflationary pressures facing Australia. To unlock the industry’s full potential, we need to promptly address skilled labour shortages.”
Key Findings for July 2022 Manufacturing activity slowed in July. Most sub-sectors eased but the metal products sectors recovered strongly. Labour challenges, supply chain disruptions and high energy prices remain the major structural constraints on manufacturing.Inputpricesdeclined for the first time since February 2022 but remain at very high levels. Employment declined, reflecting labour shortage pressures on manufacturing businesses. Most manufacturing activity indicators declined in July. However, new orders and sales strengthened, despite tight supply chain pressures.


Australia has highlighted a national and international approach in addressing stresses in global supply chain.
He said resilient global supply chains reinforced the prosperity, security and wellbeing of the partners“Collaborationnation.withinternationalisvitaltobuildingmoreresilient, transparent and diverse global supply chains,” Husic said. “That’s why Australia needs to work with like-minded countries to ensure access to essential goods and services are supported particularly when there is “Thedisruption.voicesofbusinesses, workers and community groups are central to these discussions as they are the first line of defence for maintaining well-functioning supply“Ourchains.government is committed to respond to important views raised by stakeholders at the Forum, including the need to ensure there is adequate workforce in times of crisis, the critical role of public procurement in strengthening and diversifying supply chains, and the need for substantial public-private partnerships to build critical supply chain resilience.”
“With Australia’s ongoing investments in building our supply chain monitoring capability, we are in a great position to work with interested governments, to provide advice and support collaborative actions to strengthen key global supply chains in a way that will benefit us all,”
Theshortages.government’s $15 billion National Reconstruction Fund will drive coinvestments in projects that address vulnerabilities in critical supply chain.
ARM Hub chair Emeritus, Professor Roy Green, said ARI status provided ARM Hub with greater credibility and access to expertise, to translate research into commercial applications for Australian manufacturing.“Ican’tthink of another facility in Australia that has ARI status, plus DGR, and is a facility where manufacturers and university meet that is external to a university campus but is in the industry and innovation ecosystem,” Green said. “It’s a fantastic opportunity for industry to leverage their R&D with the expertise of universities as well as tech companies in a way that is industry-driven, with the guarantee of an autonomous facility that is connected with universities but not necessarily following a university research agenda.”Stewart said ARM Hub provided industry with an agile, quick capability to run“Butprograms.wealso can take you on that journey of a longer-term innovation partnership, and conduct research for the TRL ones to twos, right through to TRL eight and nine.”
ARM Hub’s ARI status was also good news for the Hub’s university and research partners, Stewart said.
Meanwhile, the Buy Plan Australia will ensure that we can make use of government procurement as a major economic lever to strategically address supply chain risk.
Australia plans to strengthen its supply chain resilience
In September, the federal government will host a Jobs and Skills Summit, bringing unions, businesses, civil society and local governments together to build a bigger and more productive workforce and address skills
In a first for the Australian manufacturing ecosystem, the Advanced Robotics for Manufacturing (ARM) Hub has been awarded approved research institute (ARI) status.ARM Hub CEO Associate Professor Cori Stewart said ARI approval was awarded to not-for-profit organisations undertaking scientific research of value to Australia which had a suitably qualified research committee.“Weare the only independent manufacturing innovation hub in Australia to be granted this status, and it makes us a one-stop-shop for industry’s research and commercialisation needs,” Stewart said. “In addition to our commercial projects, this will allow us to run research programs, including philanthropic research, at ARM Hub and it will really help industry navigate how to get the diverse expertise and the IP and other resources it needs into its digital transformation programs.”ARMHub is a robotics, AI, and designled manufacturing centre established in 2020, that has worked to adapt international best practice from the UK Catapult innovation centres and US Manufacturing Institutes to the Australian context.ARM Hub supports the manufacturing industry to de-risk technology adoption, development, and commercialisation for Australian industry, by drawing together expert scientists, technical specialists, designers, and engineers from its university and CSIRO partner network to develop commercial solutions.
HusicThesaid.Global Supply Chain Resilience Forum was attended by ministers from the UK, Republic of Korea, Singapore, Indonesia, Japan, India, Canada, Mexico, Brazil, EU, France, Germany, Italy, Netherlands, Spain and the Democratic Republic of Congo.
“Each university has limited access to research programs due to having to prioritise projects, so ARM Hub can now help support industry, with our university partners, to access competitive research programs for strategic projects,” she said.
Australia has joined other nations to strengthen cooperation on global supply chains via the Global Supply Chain Resilience Forum, the largest multilateral forum focused on supply chain resilience. Minister for Industry and Science, Ed Husic joined the virtual ministerial forum, hosted by the US secretary of State, Antony Blinken and US secretary of Commerce, Gina Raimondo, to discuss collective longtermThestrategies.GlobalSupply Chain Resilience Forum complements Australia’s other international engagements on supply chains like the Indo-Pacific Economic Framework and the Quadrilateral Security Forum.Inthe meeting, Husic underpinned the importance of having both a national and international approach in addressing stresses in global supply chain, and the role of governments to step in and support businesses and workers where the supply of essential goods and services is at risk of significant disruption.
manmonthly.com.au Manufacturers’ Monthly SEPTEMBER 2022 15 News @MM
ARM Hub is awarded research institute status
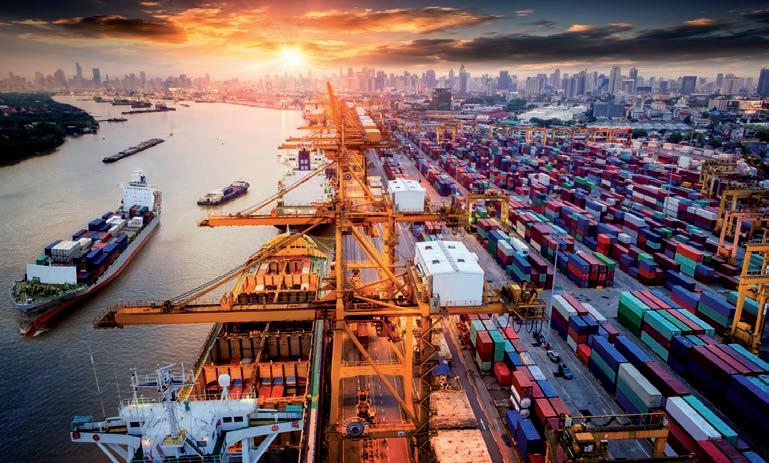
“Diverseco looks forward to delivering this unique business solution into the Northern Territory and has every confidence that it will be well received by local industry and create further commercial opportunities for local manufacturers,” Diverseco managing director Brenton Cunningham said.
presence in the NT will give local manufacturers direct access to leading technology and training resulting in skills, capability and jobs growth across the Thisindustry.”isthe latest co-investment awarded under the NT’s Advanced Manufacturing Ecosystem Fund (AMEF), which is administered by the Advanced Manufacturing Growth Centre (AMGC).
The project will see Diverseco and Charles Darwin University (CDU) codevelop four new robotic and automation micro credential qualifications tailored to the region and boost local skills and knowledge in advanced processes and machinery for the industry.
“By growing Territory capabilities in advanced manufacturing, we are expanding industries and export opportunities, creating new opportunities for investors and exciting job opportunities for Territorians.”
$4.45 million to boost advanced manufacturing in the NT NT chief minister with representatives from CDU, AMGC, Diverseco and minister for Advanced Manufacturing.
Diverseco will support the advancement of NT’s manufacturing industry by leveraging its and CDU’s manufacturing capabilities spanning defence, transport, logistics, agriculture, mining and waste disciplines, focusing on:
“Diverseco seeks to create solutions at the edge of possibility and the more importance we give to skill development, the more competent will be our youth.”
Manufacturers based in the Northern Territory will soon gain access to a multimillion-dollar advanced manufacturing facility housing robotic and bespoke automation products and services. This will support the implementation of technology such as robotic welders, automated pick and pack systems and product inspection services.
Diverseco and its project partners will provide on-site technical support and training services to local businesses seeking to adopt advanced technologies in their operations and support these businesses to upskill their staff. The facility will also be available to local business to demonstrate these technologies and develop tailored automated solutions for their individual year, AMGC and the Territory government have built a solid understanding of the manufacturing capabilities that exist in the Territory and the needs of the industry allowing us to support industry growth,” AMGC NT director Charmaine Phillips“Diverseco’ssaid.
• Automation solutions including industrial robots, collaborative robots (cobots), sortation systems, weighting solutions, dimension-weigh-scan systems, full packaging lines and industrial metal detectors;
“This exciting collaboration will support the advancement of the NT’s manufacturing industry by leveraging its manufacturing capabilities in the defence, transport, logistics, agriculture, mining and waste industries,” minister for Advanced Manufacturing Nicole Manison said.“Growing the Territory’s advanced manufacturing industry is a key part of our strategy to grow the economy to 40 billion by 2030 and create more jobs.”
16 SEPTEMBER 2022 Manufacturers’ Monthly manmonthly.com.au News @MM
• Bespoke, and advanced system integration solutions;
AMEF will provide almost half a million dollars towards this initiative, giving industry the ability to experience and test the latest in automation technology. The total project represents a $4.45 million investment into the NT’s manufacturing ecosystem.“Advanced manufacturing will be a major jobs driver of the future, and this new partnership will provide local minister Natasha Fyles said.
• Innovative and industry-tailored training to support for all the above capabilities.
The commitment will enable to local manufacturers wishing to advance their operations. It will also improve staff capability through access to the latest technology, training programs, design services, equipment implementation, and operations and maintenance activities.
• Extensive after-sales services, including equipment servicing, maintenance and spare parts; and
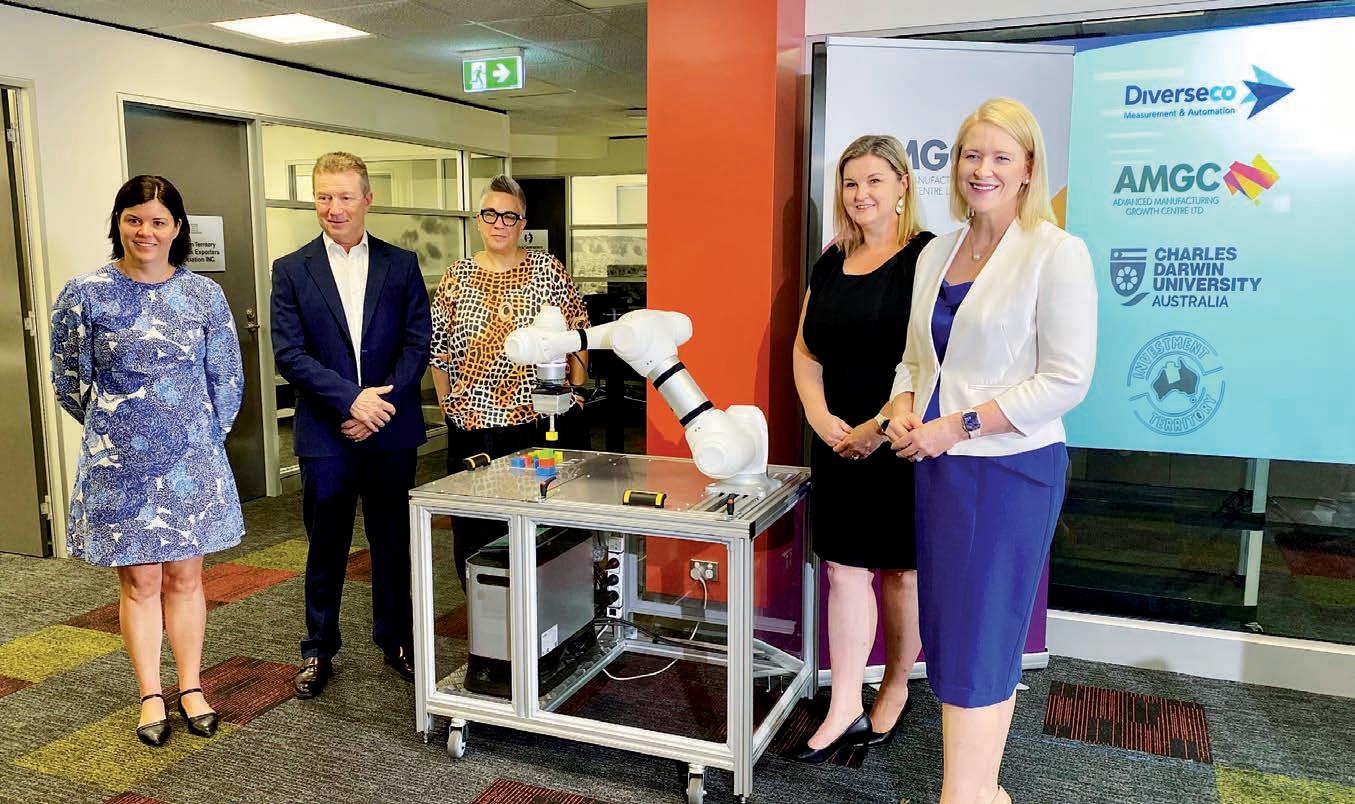
The new system was developed to process mesenchymal stem cells, a type of adult stem cell that can divide and differentiate into multiple tissue cells including bone, cartilage, muscle, fat, and connectiveMesenchymaltissue.stem cells are initially extracted from human bone marrow, fat tissue or blood. They are then transferred to a bioreactor in the lab and combined with microcarriers to allow the cells to proliferate.Thenew system combines four micromixers, one spiral microfluidic separator and one microfluidic concentrator to detach and separate the mesenchymal stem cells from microcarriers and concentrate them for downstream processing.
UTS researchers have developed a modular 3D printed microfluidic system.
UTS biomedical engineer, Professor Majid Warkiani, led the translational research in collaboration with industry partner Regeneus – an Australian biotechnology company developing stem cell therapies to treat inflammatory conditions and pain.
“While this world-first system is currently at the prototype stage, we are working closely with biotechnology companies to commercialise the technology. Importantly, it is a closed system with no human intervention, which is necessary for current good manufacturingMicrofluidicspractices.”precisely control fluid at microscopic levels and can be used to manipulate cells and particles. Advances in 3D printing have enabled the microfluidic equipment to be directly constructed, through rapid prototyping and building integrated systems.
manmonthly.com.au Manufacturers’ Monthly SEPTEMBER 2022 17 News @MM Nordfab’s CLEAN MOVEMENTAIR Join us in creating a safer, cleaner, more sustainable work environment. We are the leading supplier of high-quality dust and fume extraction products. High performance products Team of experienced engineers Over 20 year’s experience Part of Nordfab Ducting globally Local knowledge and support Friendly staff Quick turnaround contact@nordfab.com 1800 673 828 nordfab.com
Researchers from the University of Technology Sydney (UTS) have developed a 3D printed system for harvesting stem cells from bioreactors that could enable the high quality, wide-scale stem cell production in Australia at a lower cost.
“Our cutting-edge technology, which uses 3D printing and microfluidics to integrate a number of production steps into one device can help make stem cell therapies more widely available to patients at a lower cost,” Warkiani said.
Warkiani said other bioprocessing industrial challenges can also be addressed using the same technology and workflow, helping to reduce costs and increase the quality of a range of lifesaving products, including stem cells and CAR-TThecells.UTS study was recently published in the journal Bioresources and Bioprocessing. Stem cell therapy could become cheaper and widely available
While stem cells offer great promise in treating many diseases and injuries by replacing damaged cells, the current technology used is labour intensive, time consuming and expensive.
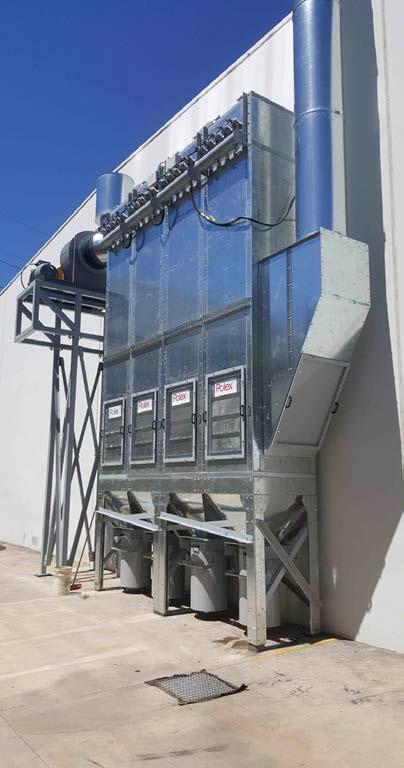
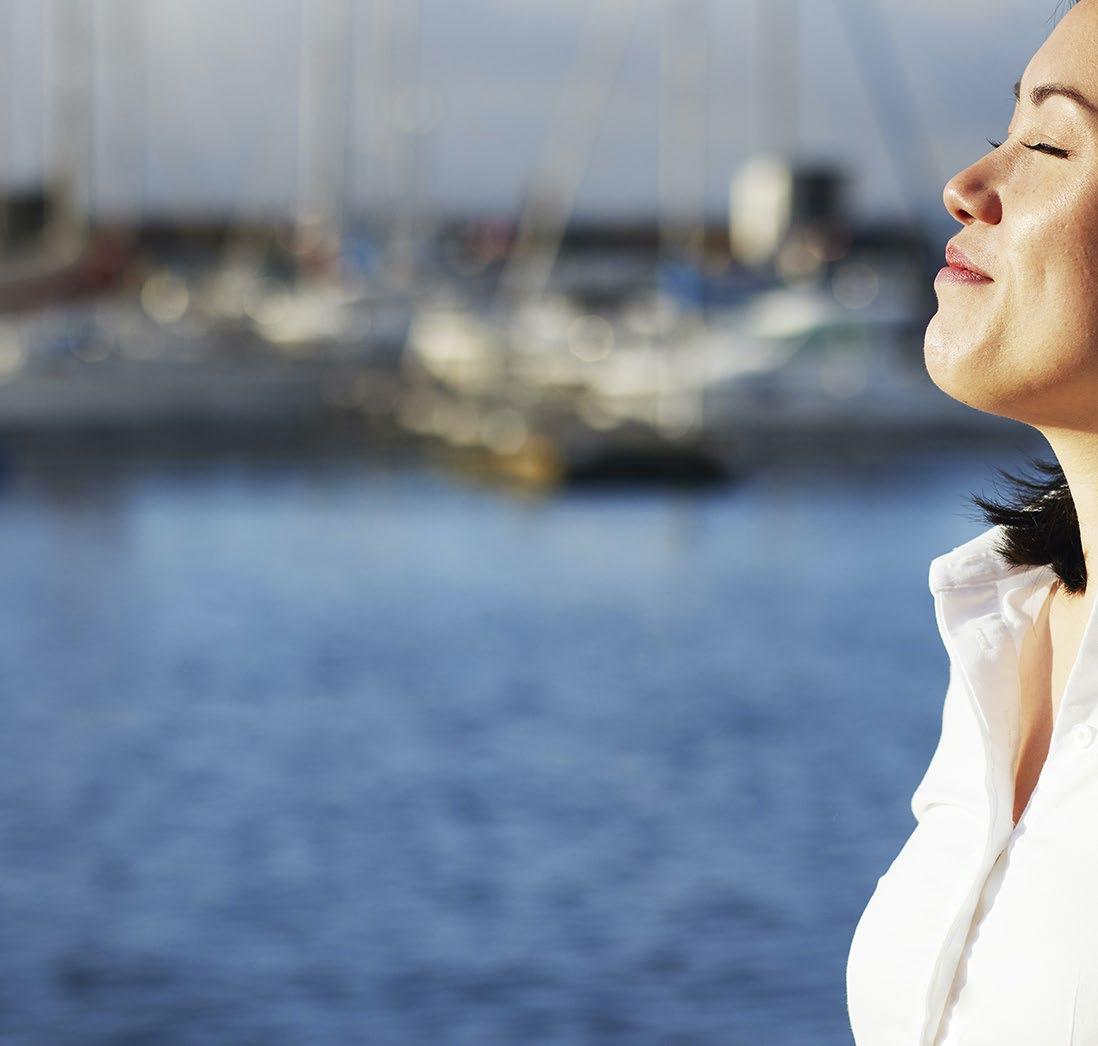
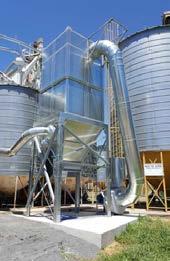
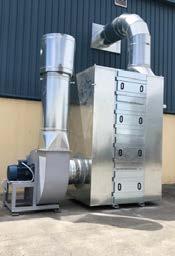

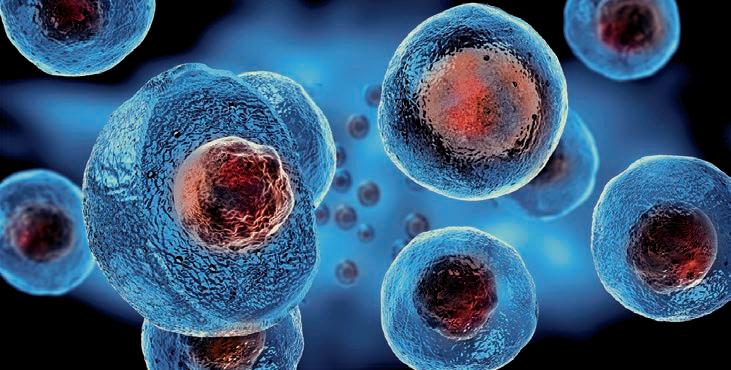
“Today’s signing here in Japan is a big deal for the Territory and for Australia –we will be building amphibious aircraft that will be exported to the rest of the world by the end of the decade,” NT chief minister Natasha Fyles said. “This exciting venture will create hundreds of jobs and upskilling opportunities for Territorians, while also injecting millions into our economy.”ShinMaywa manufactures the US-2 amphibious aircraft in Japan and are one of the few manufacturers globally of an amphibian aircraft. It has advanced knowledge in areas such as water landing safety, bird strike hardening and anti-corrosion, as well as significant engineering and manufacturing capabilities.TheNTwill become Australia’s first manufacturer and exporter of the iconic Albatross G-111T, an amphibious aircraft which can take off and touch down from land, snow, ice and water.
ShinMaywa manufactures the US-2 amphibious aircraft in Japan and are one of the few manufacturers globally of an amphibian aircraft. It has advanced knowledge in areas such as water landing safety, bird strike hardening and anti-corrosion, as well as significant engineering and manufacturing capabilities.TheNTwill become Australia’s first manufacturer and exporter of the iconic Albatross G-111T, an amphibious aircraft which can take off and touch down from land, snow, ice and water.
“Today’s signing here in Japan is a big deal for the Territory and for Australia –we will be building amphibious aircraft that will be exported to the rest of the world by the end of the decade,” NT chief minister Natasha Fyles said. “This exciting venture will create hundreds of jobs and upskilling opportunities for Territorians, while also injecting millions into our economy.”
The Albatross has a long and distinguished history but has not been commercially manufactured since the 1960s. It is a highly regarded aircraft and evidence through market studies have demonstrated that there is a strong demand for it to fill an identified gap in the global aviation market. This will be an exciting opportunity to build a new industry together with its associated supply chain which will create flow-on benefits for jobs, education and the economy in the NT.
“AAI would also like to recognise ShinMaywa as a world leader in Amphibious Aircraft. We are looking forward to cooperating with them as we grow our capabilities to manufacture the G-111T in the Northern Territory,” Amphibian Aircraft Holdings Group chairman Khoa Hoang said. “The G-111T will bring a much-needed transport capability to many countries to help in moving people, medical supplies, goods and services to remote and isolated communities.”TheNTgovernment is investing up to $10 million into Amphibian Aircraft Holdings Pty Ltd (AAH) through the Local Jobs Fund, to build upgraded versions of the Albatross amphibious aircraft in Darwin. This includes an agreement between AAH and global engine manufacturers Pratt & Whitney Canada. Once established in the NT, AAI will generate extensive value to the NT economy. The company forecasts an annual revenue of over $100 million by the end of the decade.
Shutterstock.com/BadkinCaroncredit:image
Amphibian Aerospace Industries partners with Japanese
The NT is aiming to export amphibious aircraft by the end of the decade.
Amphibian Aerospace Industries (AAI), a manufacturer based in the Northern Territory, has partnered with a Japanese amphibious aircraft manufacturer, ShinMaywa on new projects.
“The G-111T will bring a muchneeded transport capability to many countries to help in moving people, medical supplies, goods and services to remote and isolated communities.”
Amphibian Aerospace Industries (AAI), a manufacturer based in the Northern Territory, has partnered with a Japanese amphibious aircraft manufacturer, ShinMaywa on new projects.
The NT government is investing up to $10 million into Amphibian Aircraft Holdings Pty Ltd (AAH) through the Local Jobs Fund, to build upgraded versions of the Albatross amphibious aircraft in Darwin. This includes an agreement between AAH and global engine manufacturers Pratt & Whitney Canada.Once established in the NT, AAI will generate extensive value to the NT economy. The company forecasts an annual revenue of over $100 million by the end of the decade.
18 SEPTEMBER 2022 Manufacturers’ Monthly manmonthly.com.au News @MM
“AAI would also like to recognise ShinMaywa as a world leader in Amphibious Aircraft. We are looking forward to cooperating with them as we grow our capabilities to manufacture the G-111T in the Northern Territory,” Amphibian Aircraft Holdings Group chairman Khoa Hoang said.
“This investment is building a brandnew industry for the nation right here in Darwin,” Fyles said. “Both AAI and ShinMaywa will work together to make the Territory an Amphibian Aircraft manufacturing hub.”
The Albatross has a long and distinguished history but has not been commercially manufactured since the 1960s. It is a highly regarded aircraft and evidence through market studies have demonstrated that there is a strong demand for it to fill an identified gap in the global aviation market. This will be an exciting opportunity to build a new industry together with its associated supply chain which will create flow-on benefits for jobs, education and the economy in the NT.
“This investment is building a brandnew industry for the nation right here in Darwin,” Fyles said. “Both AAI and ShinMaywa will work together to make the Territory an Amphibian Aircraft manufacturing hub.”
Newmanufacturerroundofdefence research funding is now open
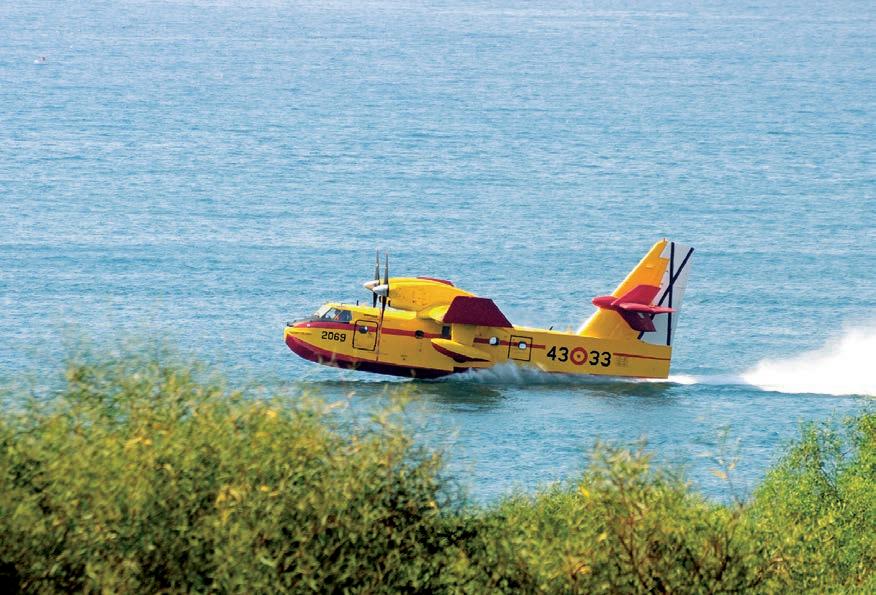
This program is delivering on the Tasmanian government’s 2021 state election commitment of $400,000 over four years to support women into leadership positions. Through these initiatives, more Tasmanian women than ever will be provided with the training and support they need to take on positions of leadership and influence.Byempowering women through leadership training, Tasmania can further support the advancement of women across its economy.Formore information and to apply for the program, visit the Tasmanian Leaders website.
“ANCA’s collaboration with IMCRC and CSIRO has accelerated the development of an innovative additive manufacturing technology which we believe has the potential to disrupt the $2.2 billion global cutting tool market,” he said. “Successful completion of this project will allow ANCA to commercialise the new hybrid additive manufacturing machine platform, grow our workforce and revenue and fill a significant gap in the global tooling market.”DrKathie McGregor, research director for Advanced Materials and Processes at additive manufacturing technologies more accessible to Australian industry.
Applications are open for new women’s leadership
Eight sessions will be held between September and November as part of the program.Applications are now open for 28 partial scholarships, which are funded by the Tasmanian government, with a small contribution required either by the participant or their employer.
“In keeping with CSIRO’s role of providing high-end research and development support to the Australian industry using state-of-the-art equipment and world class know-how, we have collaborated with ANCA to further develop a unique technology,” she said.
ANCA and CSIRO are working on a project that could disrupt the $2.2 billion global cutting tool market.
The state government recognises that women remain under-represented in a number of industries in Tasmania, which is why it is delivering on its plan to achieve gender equality through initiatives such as the I-LEAD Women in Industry Program.
Dr Matthew Young, IMCRC’s Manufacturing Innovation manager, said the IMCRC is pleased to be supporting ANCA’s innovation, and contributing to the growth of Australia’s advanced manufacturing ecosystem.
Australian industry will soon have access to an innovative additive manufacturing process for tungsten-carbide tools, via a nine-month $928,000 project between the CSIRO and a tool manufacturer, ANCA. Supported by the Innovative Manufacturing Cooperative Research Centre (IMCRC), the technology will enable affordable, high-performance tools to be manufactured using one platform, replacing the current production process of mould pressing, sintering, brazing and grinding.Nowin the advanced phase, the research is focused on refining the additive manufacturing technology ahead of ANCA taking the hybrid manufacturing platform to market.DeanMcBain, Research & Technology manager at ANCA, said the project had the potential to transform the way tungstencarbide brazed insert tools were made in Australia and across the world.
manmonthly.com.au Manufacturers’ Monthly SEPTEMBER 2022 19 News @MM
Onescholarshipplatform
to manufacture high performance tools
The Tasmanian government is supporting and empowering women to take up leadership positions in their chosen fields with $50,000 in funding to local organisation, Tasmanian Leaders, which will deliver the I-LEAD Women in Industry Program.Insupport of women’s leadership, the program is designed for women in traditionally male-dominated industries. It aims to support current and future leaders to develop the skills and knowledge they need to Expertssucceed.andprofessionals will share invaluable, tried-and-tested learnings and content in three key areas including personal leadership, strategic leadership, and business leadership.
“We expect the outcomes may enable and provide a boost to the local economy in terms of additional job opportunities and export income.”
“As ANCA and CSIRO’s R&D partnership generate significant benefits for Australian manufacturers, reducing costs and improving speed to market,” he said. “Once developed, this revolutionary technology can be applied to a range of cutting applications, creating significant global export opportunities and furthering ANCA’s position as a market leading manufacturer of cutting tools and equipment.”
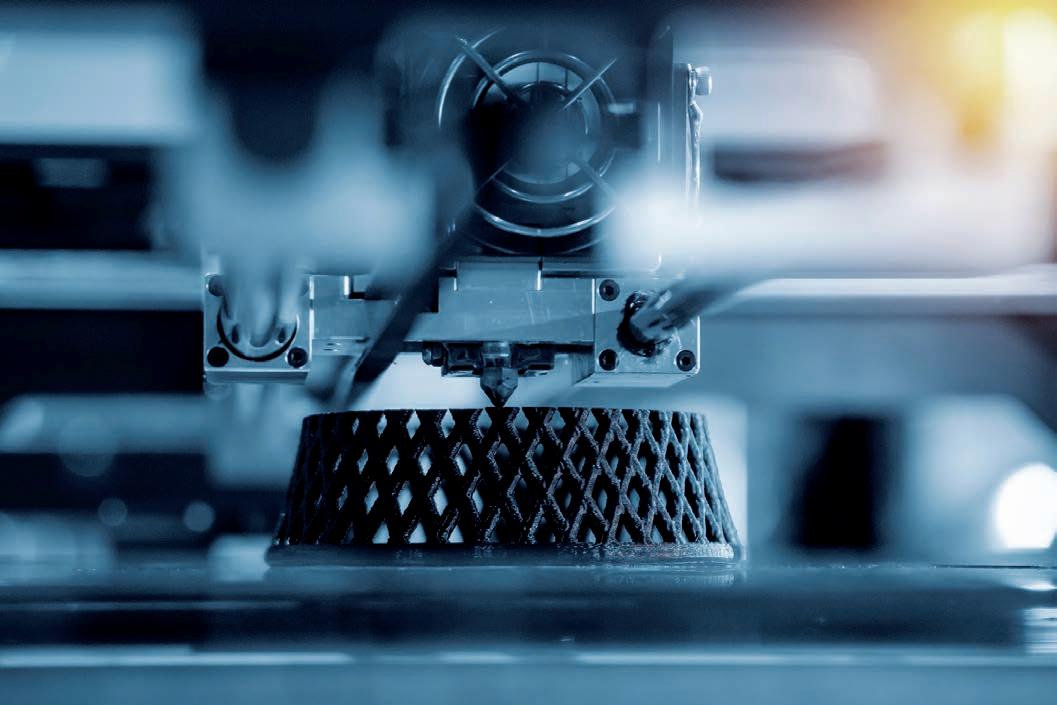
“There’s no one way of doing it. We’ve recently developed a process which forms a similar shape but in a different way, but it’s all about how you create the complex shapes. With carefully defined geometry you need to maintain the surface developability to ensure you don’t damage the material.”
Bringing bending ideas to life
DR Matt Dingle, FormFlow founder, began to explain the Australian company’s bending technology for corrugated steel by relating it to origami.
Billy Friend sits down with the company’s founders to find out how the technology is developing new building products, systems and manufacturing solutions.
The genesis for this innovation was engineering marvel, John Duncan, now 90 years old, and his late cousin Jim Duncan, who discovered the mathematical theorems of folding ‘intextensional’ curved sheet. The story goes, Duncan and his cousin were at McDonalds observing the casing for one of its famous apple pies, where you squeeze the packaging on the sides and push the ends in. All these years later, FormFlow’s technology holds a similar theory – basically inverting peaks into valleys to create shapes without damaging the material.
“Duncan was a brilliant academic with a practical understanding – he saw the potential of the type of process that we’ve eventually commercialised and set about with his cousin to develop the mathematics to be able to design those surfaces and make them work,” Dingle explained.Anengineer by trade, Dingle completed his PhD at Deakin University in partnership with Ford in 2001. This reawakened his love for developing ideas into working solutions – working both in product development and on his
Manufacturer Focus 20 SEPTEMBER 2022 Manufacturers’ Monthly manmonthly.com.au
FormFlow is founded on a world-first innovation with an Australian-made building material icon.
“The same theory applies to make this bend work,” he said. “By folding it in a particular way, you don’t stretch or compress the material at all, using surprisingly little force you can create the bends that we’ve created without damaging the coating.
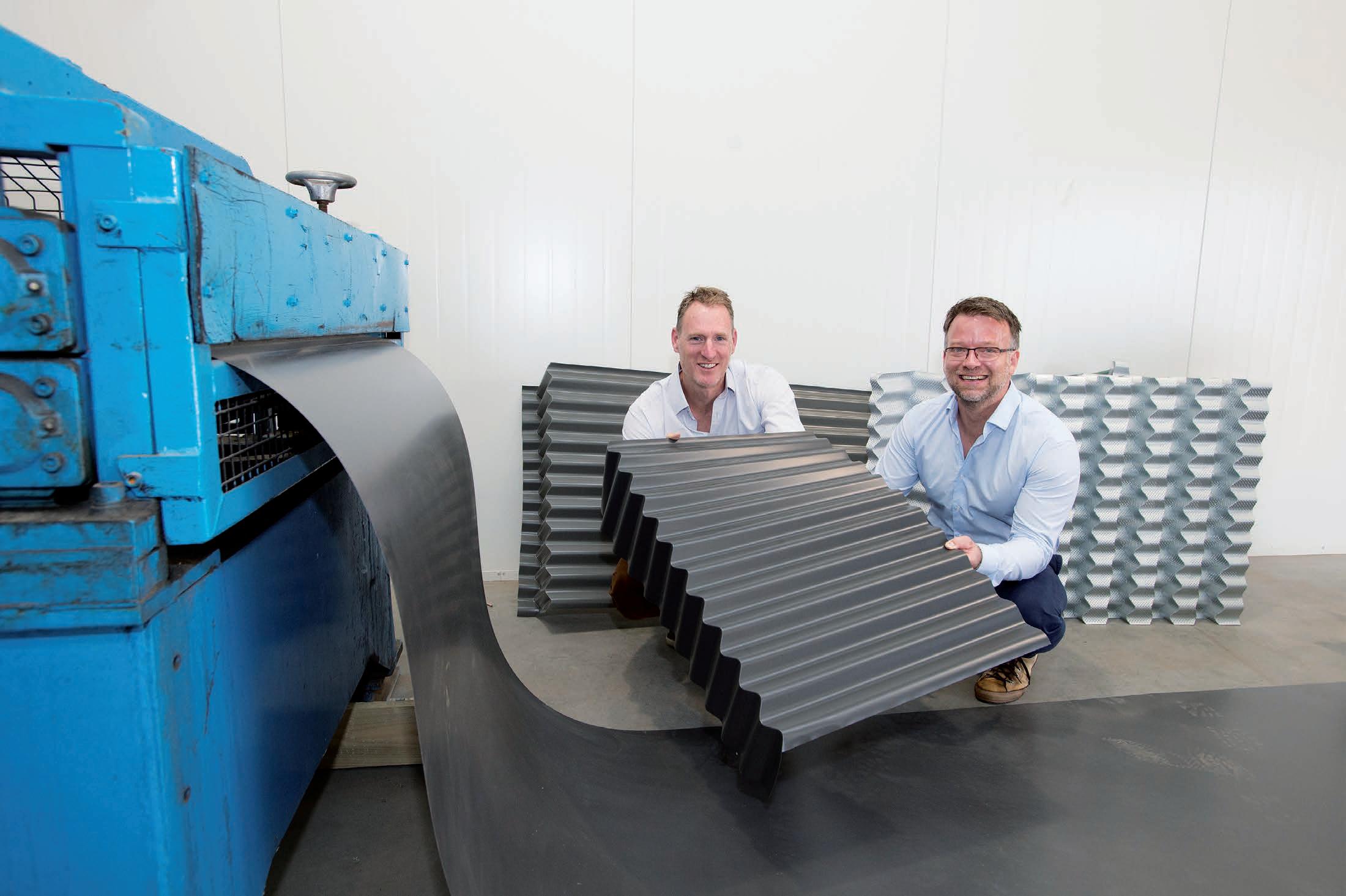
Monthly SEPTEMBER 2022 21
Unlike a typical build which starts with
Manufacturer Focus manmonthly.com.au
Manufacturers’
FormFlow uses its bending technology for its modular living spaces.
FormFlow Living’s modular construction FormFlow decided to embed its technologies into a commercial product, which forms the basis of FormFlow Living. The company’s range of pre-fabricated buildings can adapt to changing needs, whether that’s adding a home office or increasing the living space.
“The conventional construction approach involves a whole series of sequential processes and you obviously can’t finish one until the next one starts,” Dingle noted. “What we’ve done is divide the building up into a series of sub-assemblies, which can all be done in parallel. You can have a team of people and bring all these sub-assemblies together in one assembly line, which dramatically increases the throughput on a small footprint. If you’re going to do things in the conventional way, you need a massive factory to do it. We reckon you can do higher volumes than that in a pretty small footprint.”
foundations on site, FormFlow starts the building process in its factory in Geelong. Modular building is gaining momentum, but Dingle sees a lot of mistakes being made in a growing space.
A steel structural frame is welded and bolted together to form the bones of the new building, then particleboard flooring and prefabricated TRUECORE steel wall frames are installed. The highly developed production system works to speed up the construction process. While the steel is being welded and bolted together, FormFlow’s team at the factory are fixing the ply and insulation to the prefabricated wall frames prior to installing them. This means, once the steel is ready to go, the team can quickly and simply install the wall frames without the time-consuming act of plastering and painting. Key worker housing, flood relief, NDIS, social and affordable housing all contribute to
The world first metal forming process has now been used to create forwardthinking products for the building industry. The company has grown into using prefabricated building systems that complement the bend, leading to the expansion into manufacturing both commercial and residential modular buildings at its facility in North Shore, Victoria.
FormFlow co-founders Dr Matt Dingle and Dr Matthias Weiss.
academic project with the automobile manufacturer.Afterstarting his own engineering consulting company, he decided to join forces with some students he taught at Deakin University and an ex-colleague from Ford to start a company to realise the idea of developing a fully carbon-fibre wheel.This business adventure led to the establishment of FormFlow, where Dingle approached Geelong based engineering company Austeng for assistance in 2016 to develop a prototype machine to validate a new bending concept for corrugated steel. Following successful preliminary trials in September 2016, FormFlow was born.With the tutelage and research of Mr Duncan, FormFlow filed a patent and registered designs quickly after its inception, having worked long and hard on the basis of the idea before the company was founded. Over the next six months, FormFlow and Austeng collaborated on developing an industrial scale machine to bend commercial grade corrugated sheets.
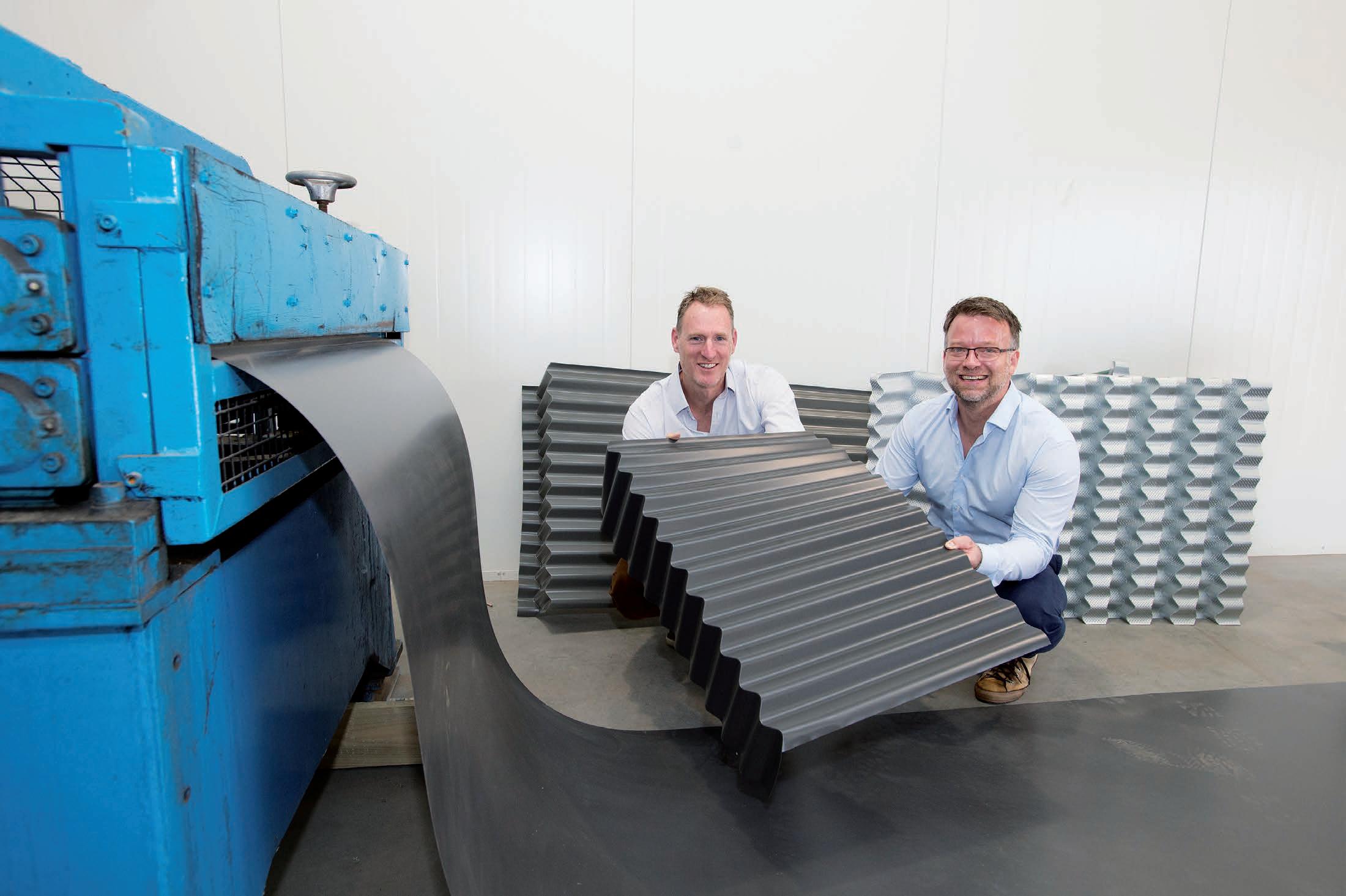
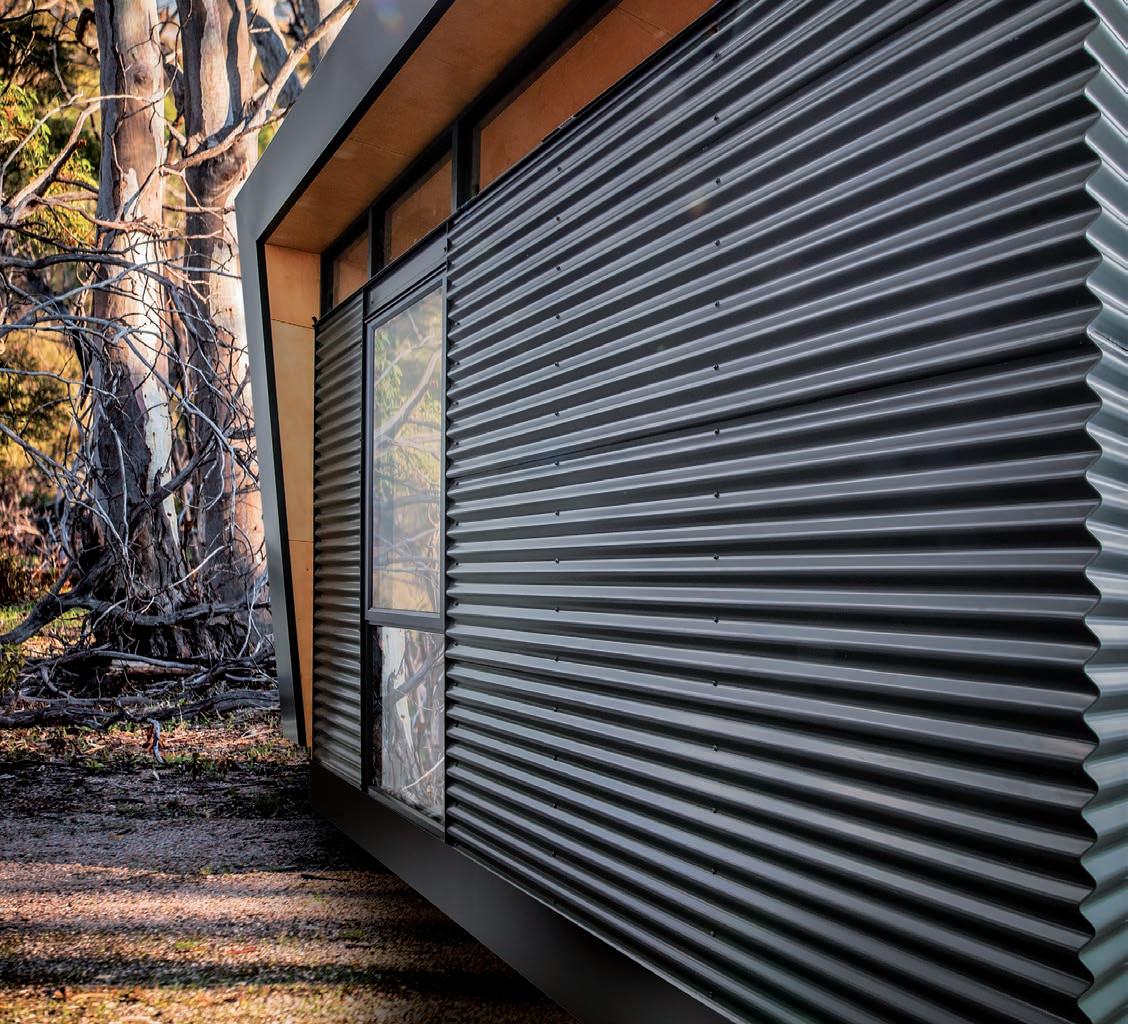
“We’re trying to take more of a manufacturing approach,” he said. “We spent a lot of time learning from what currently is in the market. Most of the companies that we see out there now are effectively just bringing construction under a roof so there’s not a lot of manufacturing thinking going on. It certainly brings some efficiencies to take a true manufacturing assembly line approach to building, this is where you’ll really start to see the benefits.”
To scale up FormFlow Living’s delivery model, the company will soon offer the building systems to customers under license and are also establishing its first regional manufacturing hub in South West Victoria later this year. Industry 4.0 innovations for steel forming Collaboration, rather than competition, is key to bringing forward FormFlow’s amazing technology to as many applications as possible, according to Dingle.“We are collaborating with the materials and engineering groups at Deakin University as well as the School of Architecture,” he said. “It’s absolutely vital as a way of exploring these bigger problems that you simply don’t have the bandwidth, or the capacity to deal with within your own business.”
FormFlow recently concluded a research collaboration with Deakin which delivered new commercial solutions for the steel forming industry. The project, supported by the Innovative Manufacturing Cooperative Research Centre (IMCRC), was designed to establish an Industry 4.0 manufacturing cell to control and optimise FormFlow’s corrugated steel bendingMatthiasprocess.Weiss, Senior Research Fellow at Deakin University and cofounder of FormFlow, said the idea of the project was to create a commercialscale forming process tracking the right variables to achieve consistent quality andWeiss,reliability.originally from Germany, studied material science and met his friend Dingle when he visited Germany to recruit Weiss for his PhD project. He is extremely experienced in rollforming related research and studies of ultrahigh strength metals for automotive and aerospace. Much of his recent research has been on further developing bending processes.“Based on the origami principle, you need to calculate specifically where you want the material to go and then calculate and develop the surfaces so that the material wants to go there,” he explained. “As soon as you force it, you’re
The C90 Bend is FormFlow’s flagship product. A laser system monitors the cross-sectional shape of the sheets.
the huge demand for quality, fast and sustainable housing.
22 SEPTEMBER 2022 Manufacturers’ Monthly manmonthly.com.au Manufacturer Focus
With less time on site, no exposure to the impact of weather conditions, a prefabricated home can get people into a new living space within weeks rather than months. FormFlow’s team continues to pioneer modular building design and manufacturing, combining Computer Aided Design with advanced technologies for process monitoring and quality control.“Weset up these small 1000 to 15,000 sqm sites wherever the housing is needed and have people employed locally to manufacture our buildings using our products,” Dingle said. “We’ve just gone through a process of developing a standard range of designs. One of the things we’ve learned in the last two years is that trying to do prefabrication with custom designs is really challenging – there’s always a lot of design work required so we’ve tried to look for standardisation opportunities.”
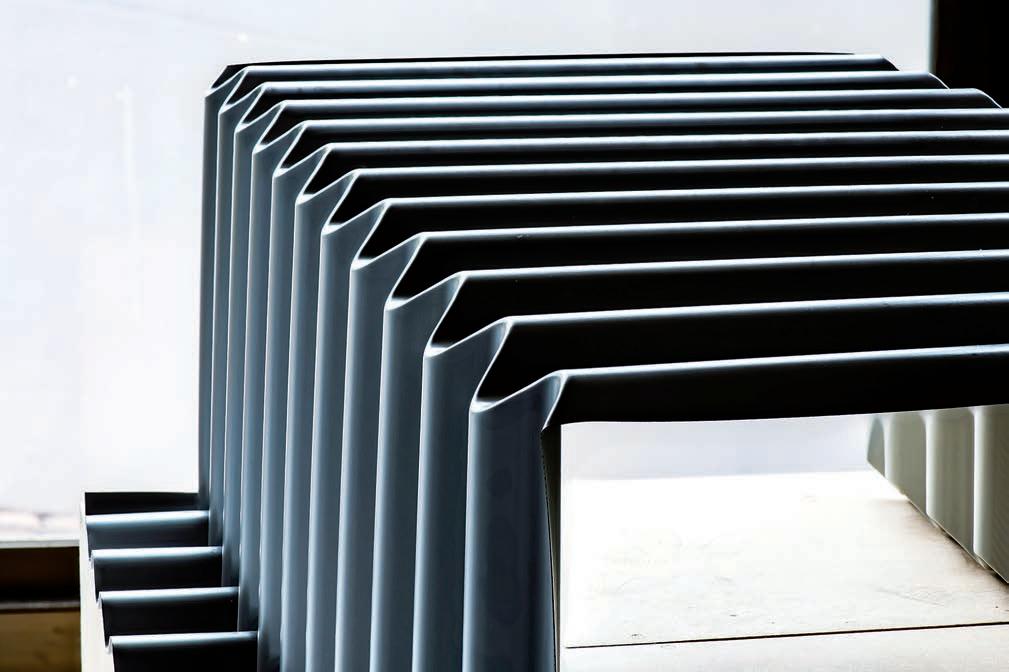
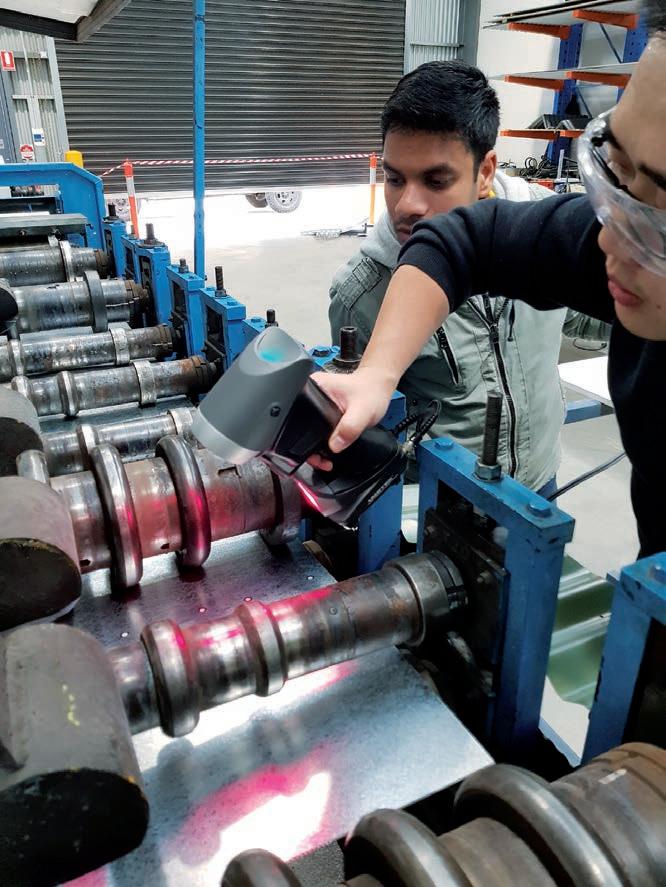
destined to fail. For me it was the perfect combination because it involves the prerollform material in the corrugated sheet with a process that technically should be a pure bend. For the last ten years I have been working on pure bending, where you can get even bad material to form ratherWhilewell.”undertaking fundamental research into the industry 4.0 solution, the project team identified additional outcomes that would deliver greater efficiencies.Thefirst is a 2D laser system that monitors the cross-sectional shape of sheets before and after bending and enables the manufacturer to perform continuous quality control.
Roll forming manufacturers have shown significant interest in the 2D laser system because it enables continuous, real-time quality control. The laser automatically measures the key parameters of the steel and provides the necessary data, something that is currently a manual, time consuming process.Thesecond outcome of the research project was an Industry 4.0 manufacturing cell capable of producing a corrugated corner bend from a flat sheet of steel. Weiss said having the flexibility to adjust the scope of the project enabled the team to develop completely unexpected, but more effective, solutions.
“Our research still focused on creating a high-volume manufacturing cell, but instead of implementing equipment to monitor and control the bend, we designed a new technology and forming process called the inphase continuous corner (IPCC),” he said. “IPCC means we no longer need to compensate for differences in steel corrugations or work with fixed lengths. We can instead take a flat steel sheet and form an easy-to-install bend in continuous lengths.”
The road to commercialisation is paved with lessons learned and obstacles, but undoubtedly this manufacturing start-up is more than on its way.
“It was a beautiful combination,” Weiss said. “We worked with Deakin’s mechatronics department for the laser. We had probably about eight people on this project from various areas all getting to a point where we could test the equipment and optimise it. If you really want to develop something new, working with a university is so useful.”
“By starting with the research fundamentals, FormFlow and Deakin were able to justify their non-traditional approach to problem-solving and develop products of significant benefit to Australia’s sheet metal manufacturing industry,” he said. “Once commercialised, the groundbreaking smart technologies will help standardise and validate suppliers’ material inputs and FormFlow outputs, creating affordable, high-quality products with minimal waste.”
“We want to move really quickly, which is sometimes a challenge,” Matt Dingle said. “The exposure from the market has been fantastic, but the next step has been developing a new market, informing the market and finding out the needs of the market to make the product“Whatsuccessful.we’vedone is incorporated our products into a whole range of prefabricated buildings so, we’re a builder in our own right now. We’ve decided to tackle the whole value chain because we feel we need to do that to explain to others how to do it. We want to continue to collaborate with others to bring the technology forward together.”
In working with BlueScope, FormFlow found there wasn’t an effective way of measuring the corrugated steel shapes. “With a corrugated shape, the depth of the corrugations, the spacing of them, and the overall amount of material from one peak to the next is what is important,” he said. “Funnily enough, there wasn’t a widespread sophisticated way of doing this. We now have a smart software which facilitates the use of the laser – we combined a relatively simple product with a user-friendly software so the operator can simply press a button and run the scan.”
manmonthly.com.au Manufacturers’ Monthly SEPTEMBER 2022 23 Manufacturer Focus
Within this project, FormFlow supported four internships and have students now employed at the company because of their excellent work.
In 2019, FormFlow licensed its foundation technology, the C90 bend, to BlueScope Steel in Australia to scale the business nationally and internationally.
The new continuous corner will reduce installation complexity and give a visually pleasing building appearance.
Dr Matthew Young, Manufacturing Innovation Manager at IMCRC, congratulated FormFlow and Deakin on the successful completion of their research collaboration.
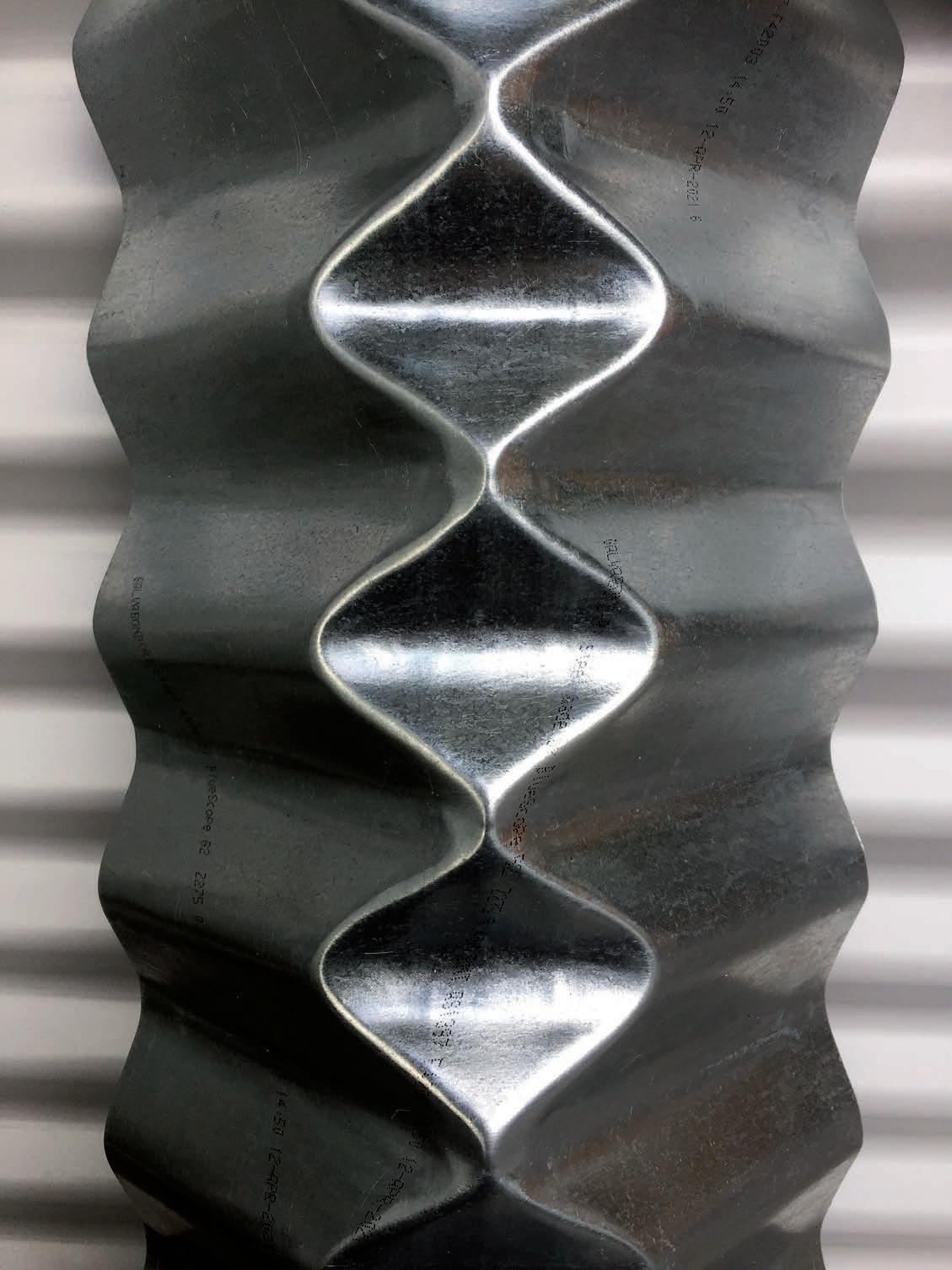
“Whenitems.people are working in deep being compromised,” he said. “We took the opportunity to essentially invent a new methodology of how we measure. That project was highly successful and gave birth to a company we called Monitum.”Monitum gained momentum after the success of this first automation project, expanding their portfolio to work on several large infrastructure projects, across Southeast Queensland. Most recently, Monitum achieved global industry recognition through its technology for real-time mapping of structural and geotechnical monitoring at the $4B AUD Queens Wharf project Tier 1 principal building contractors, their high frequency precise spatial data is delivered to the customer through a network of connected IoT sensors and cloud-based technology. The intelligent sensor networks provide accurate and meaningful data in real time, putting the power in the engineer’s hands to make the right decisions. A strong commitment to ongoing research and development has been crucial to sustaining Monitum’s growth.
TechnologyKurlooCreditImage
The Kurloo automated displacement monitoring device.
“We discovered the potential for GNSS when we used them to do realtime alerting on a really large excavation on the Toowoomba Second Range Crossing project,” Hellen explained. “We saw an opportunity for a new solution to be created, with the lower cost of precise positioning chips driven by the demand in drones, improved battery technology and a shift to greater levels of safety and remote operation.”
24 SEPTEMBER 2022 Manufacturers’ Monthly manmonthly.com.au Engineering Focus Monitum
YEARS into his career in measurement science as a consulting surveyor, the cofounder and CEO of Kurloo Technology; Lee Hellen, began his first commercial business in 2008. Three years later, Hellen’s team worked on the South Point project in Brisbane, with very heavily constrained tunnels and heritage buildings to deal with. Rather than taking manual measurements with instruments, the team wired the whole site with sensor systems and robotics to measure all the high-risk construction stability
Leading the way in automated monitoring with Kurloo Technology
Monitum’s continued innovation is shaking up the real-time structural and geotechnical monitoring space. Manufacturers’ Monthly speaks with the company’s managing director about the journey of its automated monitoring service – Kurloo Technology.
In 2018, Hellen saw a gap in the market for the use of Global Navigation Satellite System (GNSS) sensors in condition monitoring, with a convergence of new recently named Kurloo Technology.
In 2018, in partnership with the Innovative Manufacturing CRC and QUT, Monitum set out to research and develop a way to make precise positioning available to anyone, a domain previously only routinely operated by surveyors and geodetic experts. Their 3-year research collaboration project titled ‘Automated Monitoring and Analytics for Geotechnical and Structural Performance Using the Internet of GNSS Things’ would go on invent a commercialise more economical and simple way industry measures 3D displacement.Toachievethis, Hellen and his Kurloo Co-Founder and Chief Technical Officer Dr Charles Wang, partnered with Australian manufacturer IntelliDesign to design and manufacture the Kurloo low set out to design and develop a new solution to transform the way industry measures displacement.
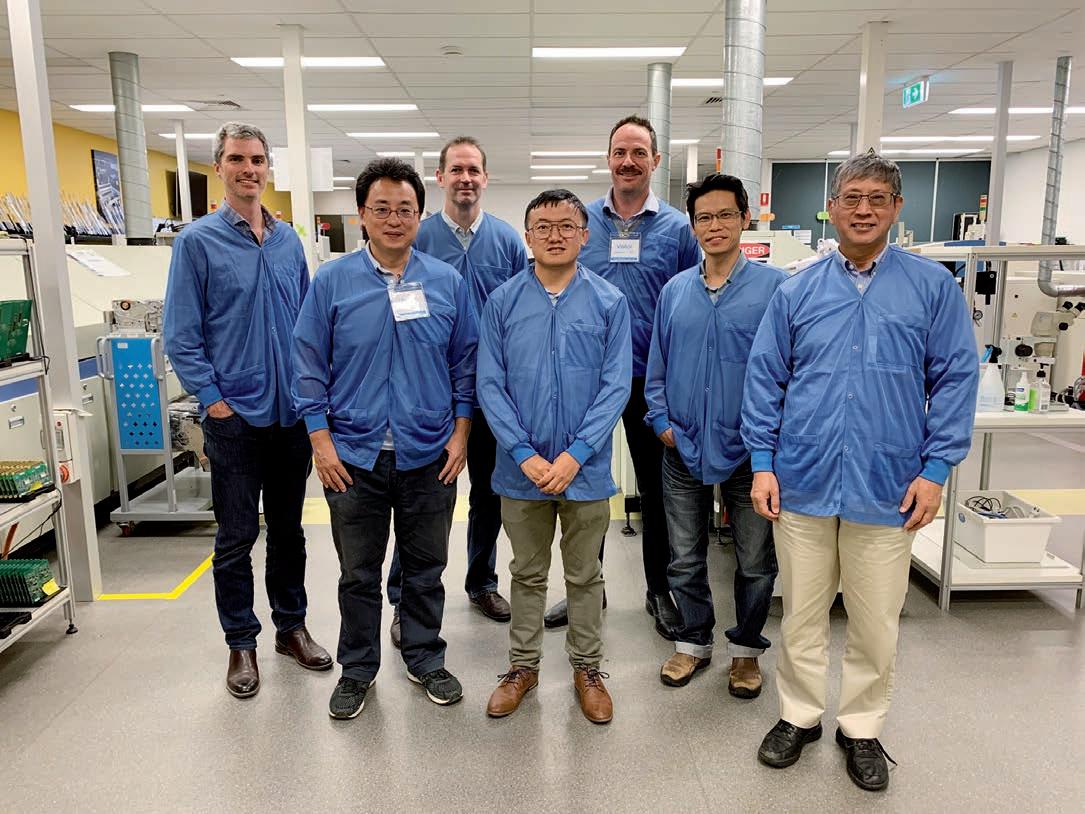
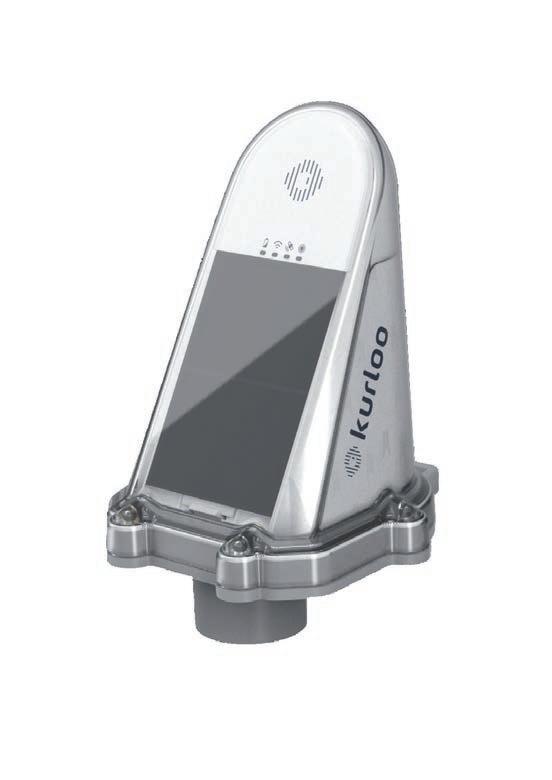
Kurloo can also be used for important scientific and environmental research applications like measuring ground surface movement in volcanos that can provide early warning of natural disasters.
Lee Hellen, Monitum managing director.ImageCreditKurlooTechnology
cost IoT GNSS devices in Australia. The project was made possible largely though the support of the Innovative Manufacturing CRC (IMCRC), who supported Australian manufacturing innovation and commercialisation.
A measure of accuracy often ignored is time, and traditional methods often arrive a week or two after the reading which means the site may have changed. Automation means you can get more frequent readings that are delivered quicker improving temporal accuracy and allowing correlation to events and behaviour with measurement.
“Monitum did some early work back in 2018 around developing our proof of concept,” Hellen said. “We bought some chipsets and tested some small circuits ourselves for around six to twelve months. To take it to the next level, we went to QUT and the IMCRC and explained the foundations we had – a customer base and market we know very well, we know the sensor will be successful in this market. We needed greater capacity in manufacturing and research which we didn’t have as a small business consulting company.”
Key to delivering the innovation within Kurloo was the cutting-edge geospatial research conducted by QUT’s project team, led by Professor Yanming Feng.“By combining Monitum’s deep understanding of the geospatial sector with QUT’s technical and research capabilities, we have overcome a significant barrier for industry and delivered a world-first product,” said Professor Feng. “The Kurloo devices are low power, built-in solar panel, high position, and can transmit data as remotely controlled from the cloud server. It is portable, low cost, easy to install.”QUT carried out the research for the whole system and worked with the manufacturer IntelliDesign for the design and testing of the device to ensure it works to meet the technical requirements. QUT has a team of 6 people in different areas, with research capabilities in electronics, networks, GNSS algorithms, software development, and geotechnical engineering.
As Industry lead partner in the research collaboration, Hellen couldn’t overstate the importance of the collaboration with QUT. Access to testing facilities and skilled interns and students helped to ramp up the capacity of the project.“When you work with a university like QUT, they can add a number of cross disciplines into your research,” he said. “Initially I partnered with some people that had precise positioning expertise, to work out how to automate the processing of GNSS signals into manmonthly.com.au
The applications for Kurloo are extremely broad, crossing over all kinds of high-risk infrastructure, transport and construction. Kurloo is ideal for monitoring the consolidated settlement of roadways and bridge abutments, stability of embankments and cuttings, hazardous fuel storage tanks, highrise buildings, dams, pipelines and other crucial infrastructure and many other environments.
Starting in 2018, an early research agreement was signed in 2019 and the first prototype was built in July 2020. To improve costly and labour-intensive geospatial data gathering techniques, Kurloo has leveraged Australia’s research and development capabilities to create an end-to-end displacement monitoring service. Hellen explained there are many benefits to such an automated solution.
“Kurloo provides the frequent, consistent and precise readings needed to help manage risk, and does so at a fraction of the price of traditional monitoring equipment,” he said. “A measure of accuracy often ignored is time, and traditional methods often arrive a week or two after the reading which means the site may have changed. Automation means you can get more frequent readings that are delivered quicker improving temporal accuracy and allowing correlation to events and behaviour with measurement. For example, you could have a large rainfall event or there could be some blasting done on a construction site and your readings will accurately track the impact of just before, during and after the event happens.”Thesecond benefit of an automated solution, according to Hellen, is the remote access and removal of the reliance of in demand highly skilled labour for routine measurement tasks.
“Trying to find a skilled surveyor is relatively finite at any time,” Hellen said. “Sometimes it’s also very difficult to put people in certain environments like a landslide area, so the automated sensors can measure while it all happens. Automating routine measurement tasks frees up your best people to do more productive and challenging work and makes you team more productive.”
Manufacturers’ Monthly SEPTEMBER 2022 25 Engineering Focus
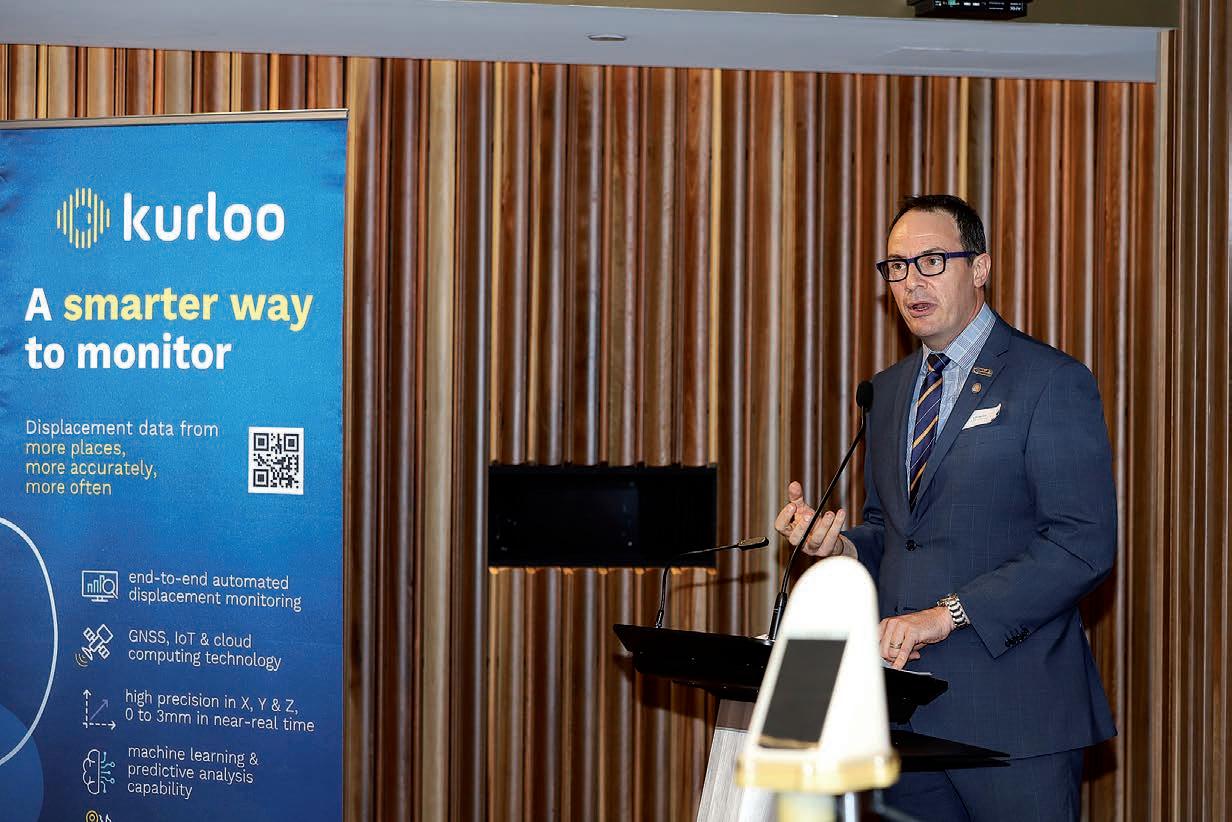
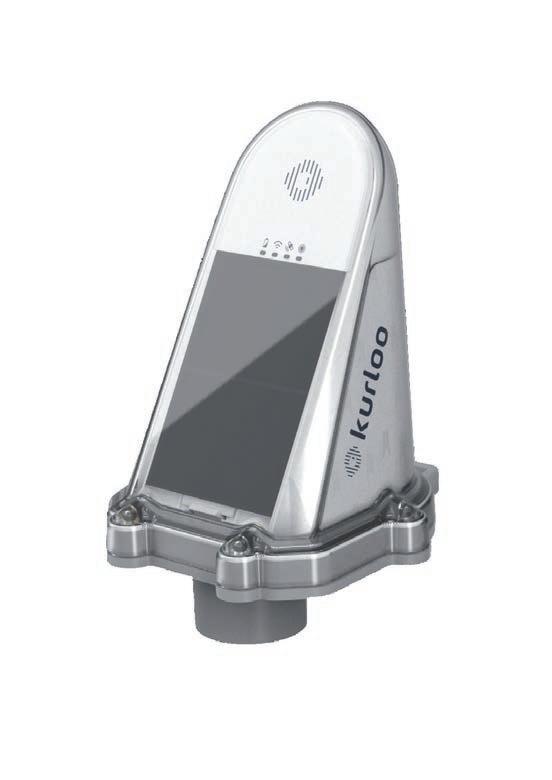
“In recognising the need for more innovative monitoring equipment, Monitum and QUT have utilised the power of advanced technology to create an economical, globally relevant monitoring service that fills a significant gap in the market,” he said. “And by partnering with local manufacturer Intellidesign, the Founders of Kurloo technology streamlined the development and commercialisation of its device and guaranteed its supply chain. The evolution of Industry 4.0 continues to generate new opportunities for Australian businesses to capitalise off technological innovation. By seizing them, businesses can develop more resilient offerings and extend Australia’s manufacturing capabilities.”
precise positioning on the earth. The university is broad, which allowed us to leverage people in geotechnical engineering, structural engineering, electrical engineering and different disciplines to really add several added dimensions to the project.”
26 SEPTEMBER 2022 Manufacturers’ Monthly manmonthly.com.au
David Chuter, IMCRC’s CEO and managing director, said IMCRC was thrilled to see Kurloo Technology successfully bridge the ‘valley of death’ to bring an Australian manufactured product to market.
Dr Charles Wang and Lee Hellen holding up a Kurloo monitoring device.
Lee Hellen explained that with the help of organisations like the IMCRC and QUT, you don’t need millions of dollars to commercialise Australian innovation.“Iwould encourage people to take their idea to universities and get help from someone like a for impact CRC,” he noted. “Set out to make it in Australia.
Engineering Focus
Like many Australian innovators, Monitum faced the challenge of being constrained by reliance on overseas manufacturers and supply chains, with sometimes months of lead time to receive a part from across the world. The execution of manufacturing Kurloo has been made possible, in part, by the relationship with local manufacturer IntelliDesign. “They’re a fantastic fit for our business,” Hellen noted. “They are a family-owned manufacturing company with a fantastic reputation for design and manufacture with similar types of products. They know how to create a device that they can made repeatedly at a very high quality using advanced manufacturing principles that can be globally competitive.”
“There is a lot more technical and academic rigor when you partner with a university rather than going at it alone,” he added. “Our product had a lot more credibility when we released it into the market because of the academic backing behind it and the reputation that comes with QUT.”
Working with a university with leading technical and academic experience can help attractiveness of a product, advancing the path to commercialization, according to Hellen.
Manufacturing the product using smart and intelligent techniques, with brilliant local people will give you a better product and a better chance of scaling and improving your value to customers over time.”
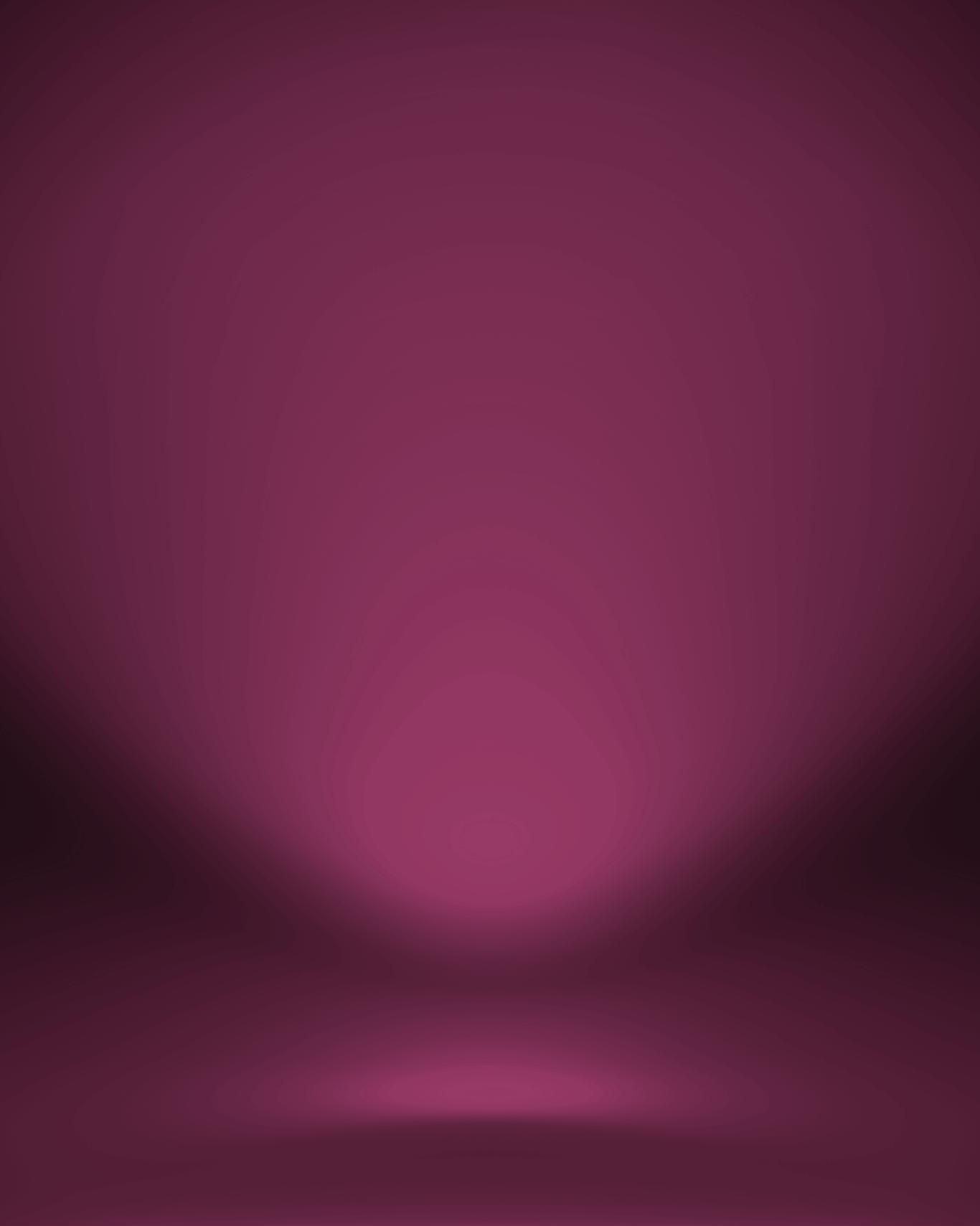
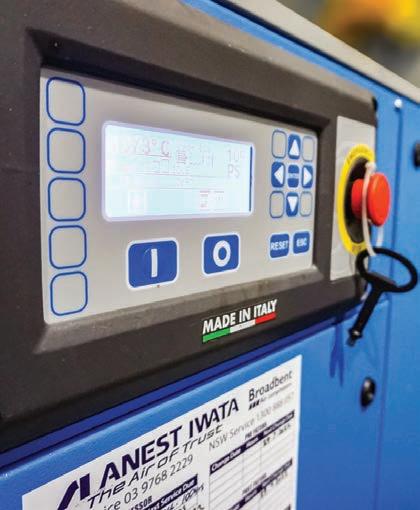
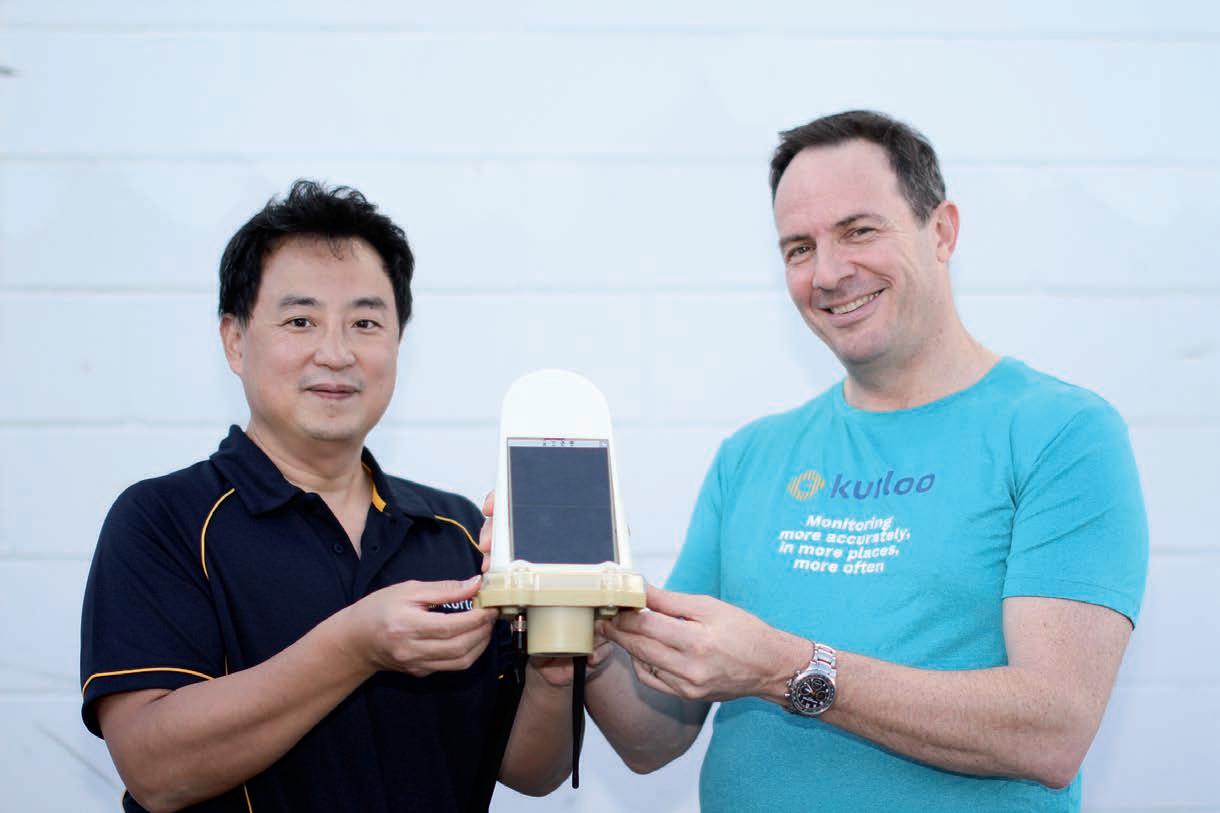
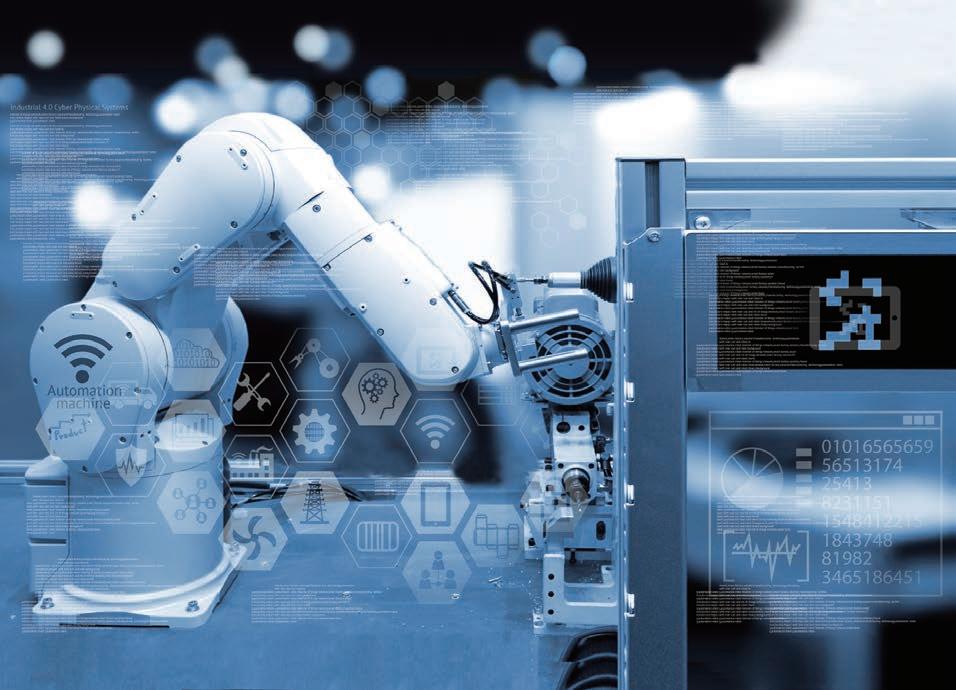
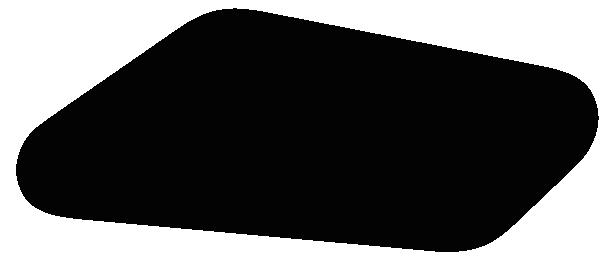
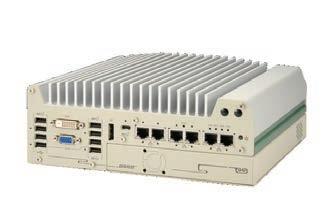
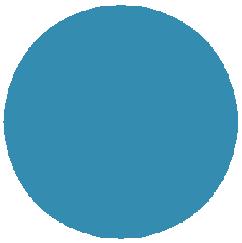
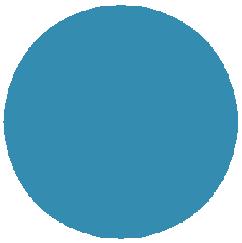
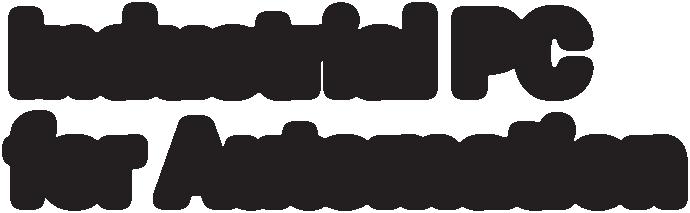
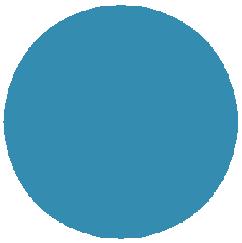
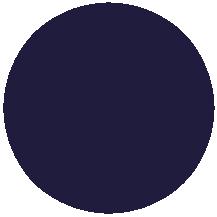
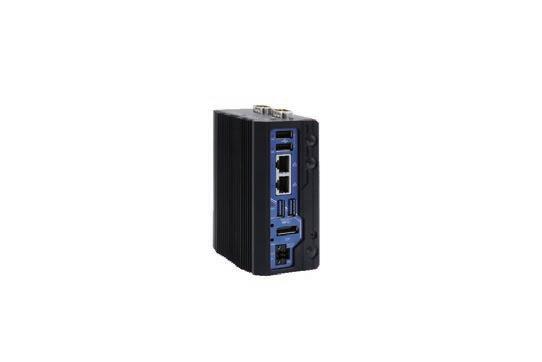
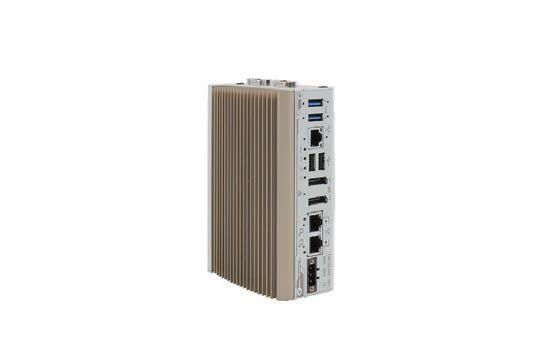
PROMPT ANALYSIS & REPAIR SERVICE INJECTRONICS INDUSTRIAL OFFER A UNIQUE SERVICE TO BUSINESS OWNERS, MANUFACTURING LINE MANAGERS AND SERVICE REPAIR AGENTS ALIKE. WITH A TEAM OF ELECTRICAL AND ELECTRONICS ENGINEERS, INJECTRONICS INDUSTRIAL CAN OFFER A FAULT ANALYSIS AND REPAIR SERVICE FOR MANY APPLICATIONS INCLUDING DIFFICULT TO SOURCE AND OBSOLETE ITEMS. INJECTRONICS INDUSTRIAL PRESENTS A NEW, TIME SENSITIVE AND COST AFFECTIVE OPTION WHEN IT COMES TO MAKING A DECISION ON YOUR INDUSTRIAL REPAIR. (Human Machine Interface) VFD (Variable Frequency Drive) Servo Drive Servo SpindleValvesDrives • Stepper Drives • PLC • Timer and Counters • Power Supplies • HV Generator • Industrial Computer • Motherboards • CNC Boards • Industrial Control Panels • Preventative Maintenance The range of repairs available include, but are not limited to: 1300 646ELECTRONIC?ANYTHING948.com.auindustrial.
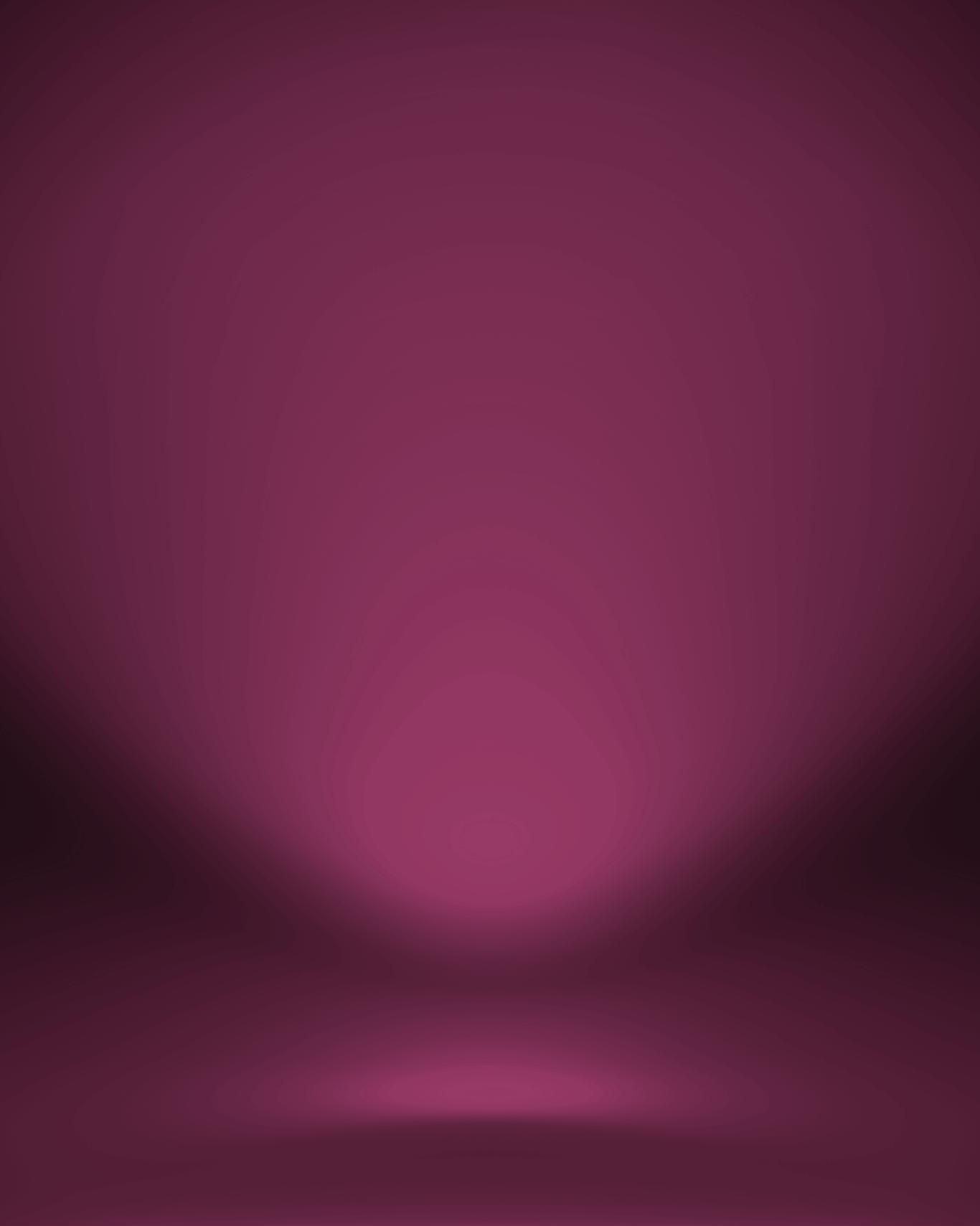
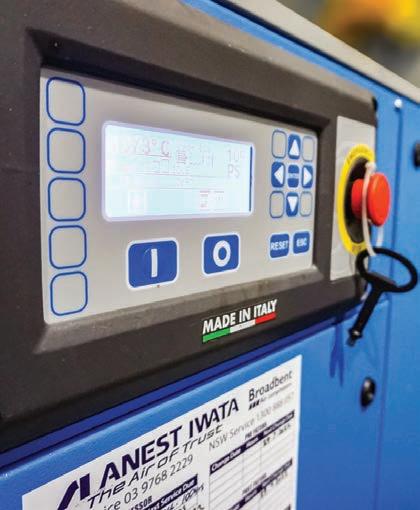
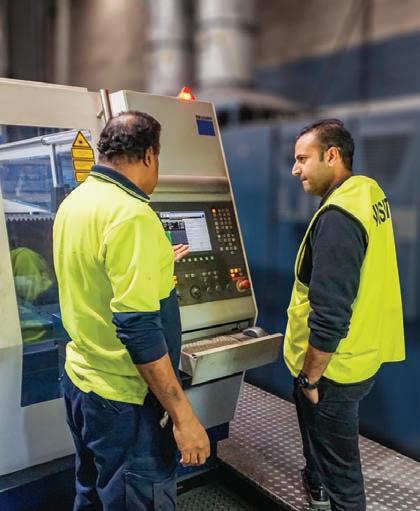
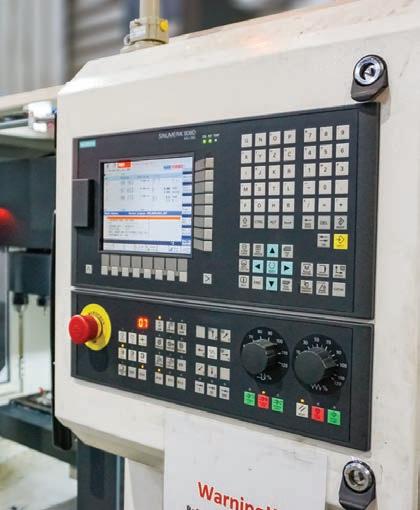

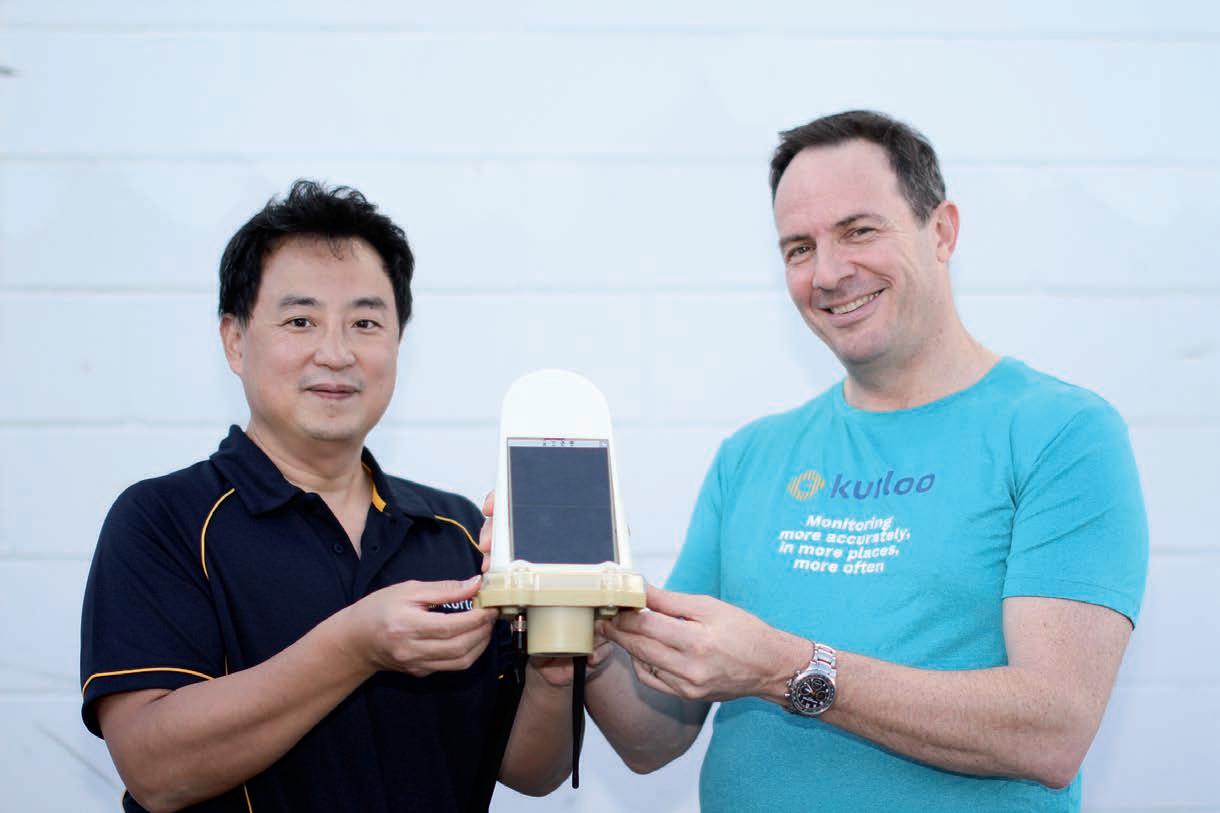
Like a vacuum, the dust collector filters dust and returns clean air either to the building or outside. Molly McCoy, Nordfab sales representative, shared the momentum the company is experiencing in the Australian market, after its recent acquisition of Ezi-Duct.
Another advantage of proper ducting is the reduction of cleaning costs, as McCoy – who has a background as a boiler maker – recounted one client’s factory floor was initially ankle deep in saw dust. Instead of relying on floor sweepers and spending time cleaning the floor, the feedback when working with Nordfab was simple: “I can see my factory floor again, what a relief.”
Modular ducting
A leader in ventilation ducting
Recent studies in America have face and eyes at work.
28 SEPTEMBER 2022 Manufacturers’ Monthly manmonthly.com.au
Nordfab’s ducting installation with Crusader Caravans at its new purpose-built facility.
Air Ventilation
The modular ducting system has been gaining popularity in the Australian market, according to McCoy, mainly due to its greater flexibility and quality to other systems. versatility to grow with a business, when changes are made to support growth or pivot towards certain operations, the quality of ducting doesn’t have to be compromised.“It’saclamp-based ducting system,” McCoy explained. “Galvanised sheeting is rolled and clamped together. Spiral ducting might be cheaper, but it has 15-25 per cent leakage rates. Having a modular ducting system allows you to take it apart and reconfigure easily like a Lego piece into different factory settings, whereas spiral ducting you have to cut up and fit into a fixed area.”
efficiency.A
Nordfab offers a variety of ducting products for process ventilation and dust collection. Monthly finds out how its team of industry experts is saving businesses money on installation costs while increasing efficiencies.
Spiral ducting is a rigid spirally wound tube manufactured of steel metal, most often galvanised steel, and has been air can more easily seep through the seam changed, which is why Nordfab’s modular system is so popular in the rapidly evolving industrial space. The thickness of the ducting is also an important element to its function, according to McCoy. “We usually 0.7 seven to one millimetre thickness figures, whereas other systems run at a minimum of 1.6,” she said. “We like to run our ducting a lot thinner – it makes it safer to hang on roofs and walls and is a lot easier and faster for the installers.”
“Within an industry where ducting is an OHS requirement, we try to keep costs as low as possible for the customer,” she said. “We achieve this by meeting with customers and visiting their site, so we can understand their personality and exactly what they want from us. The younger generations will continue to prioritise worker safety and happiness, so fitting the correct ducting system is essential for manufacturing operations.”
Crusader Caravans Crusader Caravans is a proud Australian manufacturer of caravans, with a facility in Epping, Victoria. The company uses high quality materials to craft individual
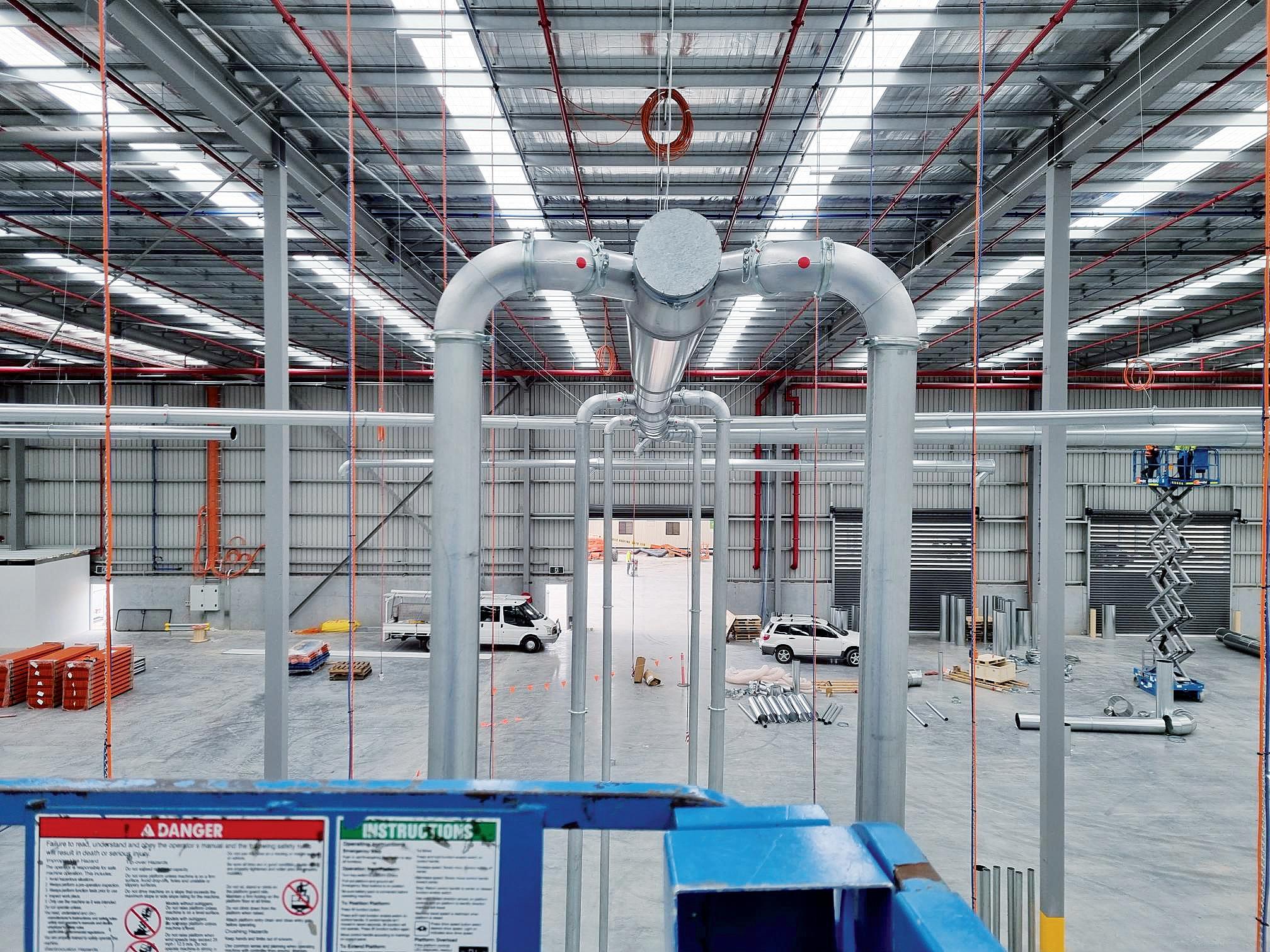
The thickness of ducting is an important element to its function.
“I was there for an hour or so looking at the kinds of machines and checking the sizing of the building,” she said. “The design process started from there – they gave us a layout and we initially spoke to them about five or six different ways we could design the system. They spoke about the ducting maybe being a showpiece as well, so we spoke about designing straight lines and keeping everything symmetrical.”
In January, Crusader Caravans reached out to Nordfab and McCoy met the team to have a look at the optimum ducting system to be designed and installed into the Epping manufacturing facility.
Nordfab’s factory manager for its Melbourne facility, James McIntyre, built most of the new system, with the addition of parts from the company’s Sydney warehouse.Sydneyhelped out and built a lot of the three-millimetre heavy gauge stuff, because with that size collector, we still needed to ensure that it’s an explosion proof system,” she noted. “We made sure when we put the design in that we had explosion proof panels, which worked out really well. In Melbourne, we try to fabricate as much as we can but we have the ability to get the larger machines from the head office in Sydney.”
When working around the customer’s budget, the Nordfab team decided upon a system which hadn’t been made before –the Econo 36000.
In Victoria, Nordfab uses two supremely experienced installing companies. Both installers were involved in the job for Crusader Caravan, and were provided the layout, full list of pieces, photos in a face-to-face meeting withWhatMcCoy.separates Nordfab from its competitors, according to McCoy, is its ability to fabricate in Australia and work in hand with its customers.
“We can deliver a lot faster,” she said. “Some companies we come across just provide more of a fixed system and tell you it will come in eight weeks. All of our sales reps have trade backgrounds, so we’re not there for the sale as much as making it work for the business. We know it’s going to cost thousands to stop running machines, so we look for the fastest and longest achieving option.”
manmonthly.com.au Manufacturers’ Monthly SEPTEMBER 2022 29 Air Ventilation
Nordfab pioneered an Econo 36000 for the customer.
“No one’s done an economic collector over the 15000 size before,” she said. “Usually it’s a modular dust collector (MDC), but we decided to do a shaker system which looks the same as the MDC, but it’s a bit thinner, cheaper and uses filter socks instead of cartridge filters.” MDCs are more expensive because of the pulse cleaning system, which involves air running through a valve system to clean the cartridge filters. The decision to design and manufacture an Econo for Crusader Caravans cut costs by around a third.“Alot of customers require MDCs because they use machinery which uses fine dust and needs a pulse system,” McCoy added. “Crusader, because they make caravans have such a large amount of machines but none of them were running anything too fine. I went out there and checked all the inlets and everything coming off all the consumables to each machine to discover the Econo 36000 could be used for what Crusader was trying to achieve.”
caravans with highly skilled tradespeople.
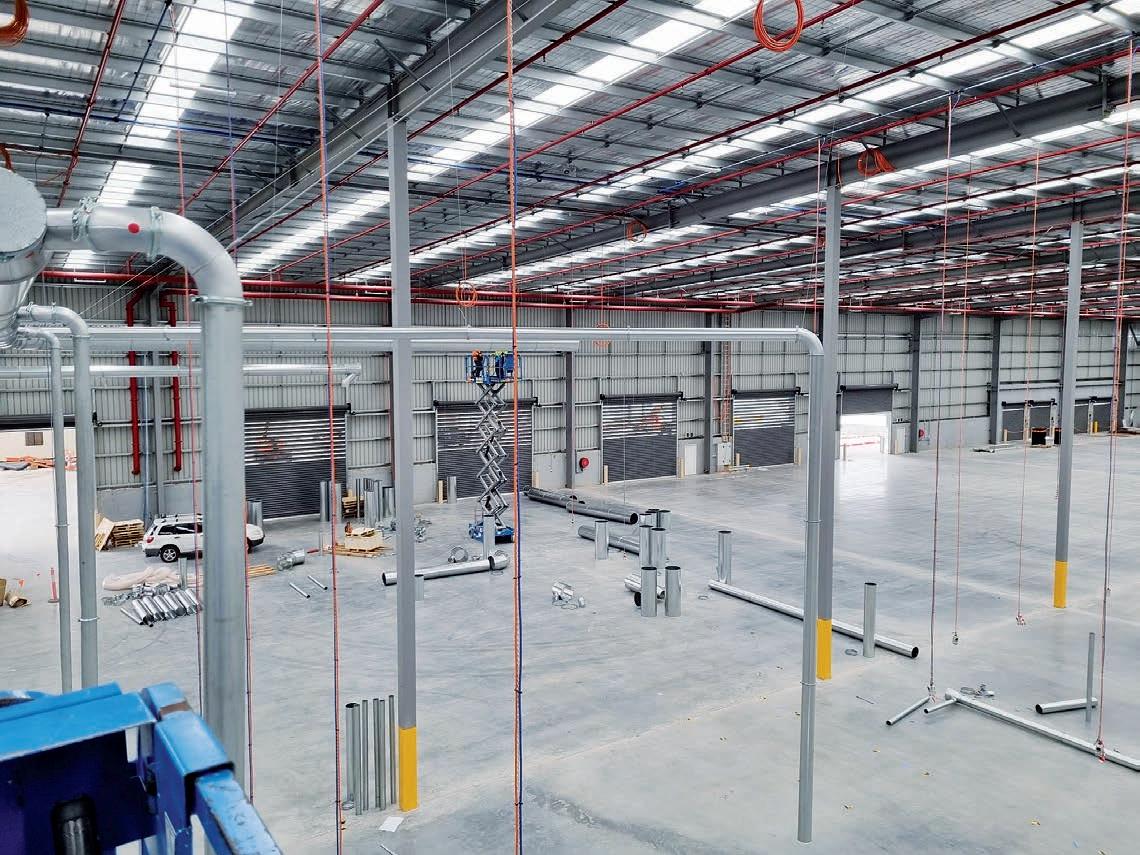
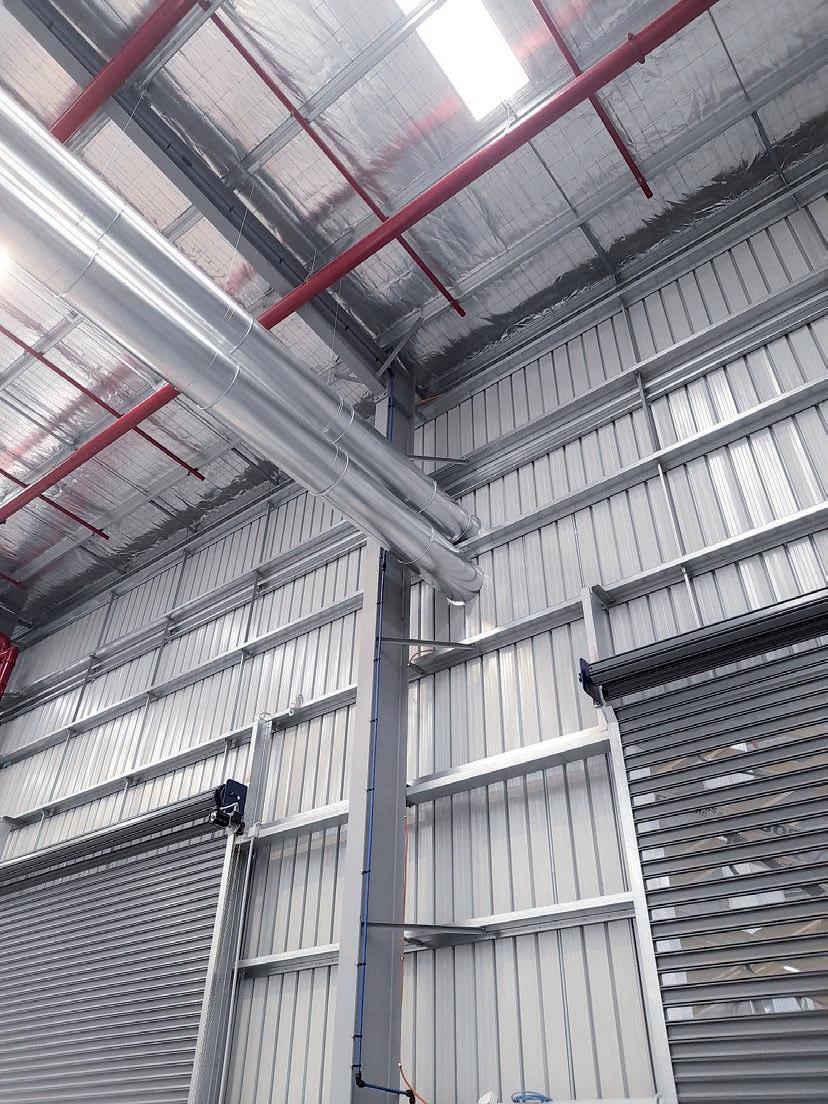
Subheader: Innovation Pitchfest
• Where future collaboration may be of benefit (and with whom). They will be more than a sales pitch, engaging a general audience in a tight, three-minute timeframe.
3. Deployable Biometrics. The explosion of bio measuring devices presents both and opportunity and risk. How does Army leverage this opportunity and guard against the risks in the battlefield of the future? The PitchFest offers serious exposure to a potential investment community.
• Application or end goal of the innovation.
Just weeks away from the Land Forces 2022 International Land Defence Exposition in Brisbane, the event’s program is strong in presenting new technologies and concepts that may one day form part of Australia’s defence capability.
WHILE the exhibition floor is expected to showcase the latest from the wide range of Australian and international defence companies present, Land Forces will also feature its two familiar means of highlighting specific technologies and their creators: the Land Forces Innovation Awards, and Innovation Pitchfest.
2. Information and Influence. The Army has a particular interest in being able to disseminate information to a diverse and disparate set of audiences in support of ADF operations – our region is home to a broad range of cultural groups, separated by mountains, vegetation, water and technological divides. How can 21st Century technology and innovation be employed to increase the efficiency and efficacy of information dissemination?
The sessions are an opportunity to showcase an innovative idea, technology, application or product in the early stage of its development (pre-commercialisation).
LAND FORCES 2022 National Innovation Award • LAND FORCES 2022 SME Innovation Award (including a $15,000 cash award)LANDFORCES 2022 Young Innovator Award (including a $15,000 cash Theaward)awards are open to Australian companies or the Australian subsidiaries of overseas parent companies. The innovation can be a new product or service or a new approach to business. Entries will be judged on originality and their understanding of user needs.
“The ideal innovation award candidate provides a solution to a known problem, or an advance that will materially improve an existing process or capability,” said Justin Giddings, CEO of LAND FORCES
1. Current events are highlighting that the proliferation of multispectral sensing means that the battlespace of the future will be highly populated with sensing, making it increasingly
And while the pitchers have their three minutes of potential fame, the Land Forces 2022 Innovation Awards will also highlight Australian industry developing the next generation of capability, be it a product, service or new way of doing business.Awards will be presented in the following categories:
Land Forces Innovation Awards
Innovation leading the way at Land Forces
Cutting-edge Australian companies and research centres participating at Land Forces 2022 will pitch their innovative ideas and technologies to the Australian and international community at the LF2022 Innovation PitchFest. Organised by the Defence Science Institute (DSI) in partnership with AMDA Foundation Limited, the Defence Innovation Partnership (DIP) in South Australia, Defence Innovation Network Thursday 6 October as part of the Exposition’s innovation program. This will be industry’s chance to present new products and R&D projects to an audience of potential customers, research partners and investors. This event will consist of three-minute pitches aimed at demonstrating Australian innovation, research collaboration and the development strengths of the pitcher’s idea or research project. Three-minute pitches must demonstrate: Uniqueness and novelty of the innovation.
30 SEPTEMBER 2022 Manufacturers’ Monthly manmonthly.com.au EventsSPEE3Dwasthe2021LandForcesSMEInnovationAwardwinner,fordevelopingabattlefield3DprintingsystemtoshortentheArmy’ssupplychain.
Pitchers are encouraged to take advantage of the fast-paced atmosphere of PitchFest, to hook and engage the audience with theirPresentationspresentation.will be judged by an expert panel with the top three recognised with a custom trophy. Present at PitchFest will be the Australian Army’s Future Warfare Branch, which is particularly looking for pitches that address the challenges or speak to the topics of:
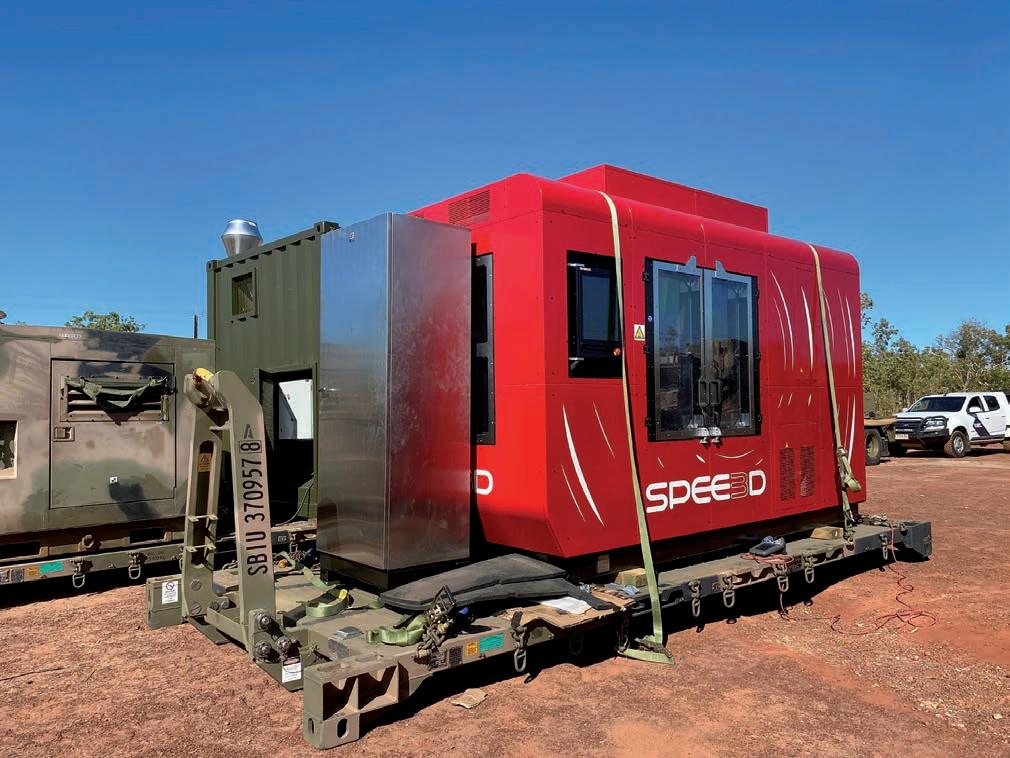
for
and
organiser AMDA Foundation Limited. “The ideal candidate is already at a development level that could see it fielded in a reasonable timeframe.”
some $455,000 in SME Innovation Awards and Young Innovator Awards since first presented in 2013. In 2021 the Land Forces Innovation Award winners included: National Innovation Award: Micro-X (South Australia) – for developing the world’s first development of computer models to predict how the armour on military vehicles will behave under the onslaught of an IED or land mine.
businessandjudgedentriesideacanprocess)newcompaniespracticalTheEngineeringWhight,(Queensland);Veivers,COMMENDATION:HIGHMrHarryDMTCLimitedandMrMackayCyborgDynamics(Queensland)awardsaredesignedforinnovators:individualsandwhointendtobringaproductorservice(orbusinesstomarket.Aninnovationbedefinedverybroadlyasanewthatgetsadoptedandused.SototheInnovationAwardsarenotonlyontheircreativitytechnicalmastery,butontheircase.
In addition, four Award contenders won a High Commendation:LANDFORCES 2021 National Innovation Award
For more information or
mobile, lightweight X-ray machine.
ideas.
• LAND FORCES 2021 Young Innovator Award
Micro-X won the 2021 Land Forces National Innovation Award, developing the world’s first
register, go to www.landforces.com.au manmonthly.com.au Manufacturers’ Monthly SEPTEMBER 2022 31 Events www.boge.net.au or (03) 5940 5913 High pressure piston and booster up to 40 bar(g) Oil free scroll compressors Medical, instrument, dental NEW generation series-4 screw compressors up to 160kW NEW full feature oil injected screw compressors 4-22kW For sales and service support contact your nearest BOGE partner NEW refrigerant compressed air dryer with sustainable, efficient and smart operation From 15-6,000 cfm
The Land Forces Innovation Awards and Innovation PitchFest provide platforms to highlight new Australian
The Land Forces 2022 International Land Defence Exposition will run from 4-6 October at the Brisbane Convention Exhibition Centre, Queensland. to
SouthManufacturingCOMMENDATION:SME(Victoria)COMMENDATION:HIGHDefendTexLANDFORCES2021DefenceInnovationAwardHIGHMilspecPtyLimited(NewWales)
“In keeping with AMDA Foundation’s mission to promote industry development, the awards are designed to encourage and reward excellence by Australian companies and emerging engineers and Awardsscientists.”program sees similar awards presented at the biennial Australian International Air Show and Aerospace & Defence Exposition at Avalon, and the INDO PACIFIC International Maritime Expo in Sydney.
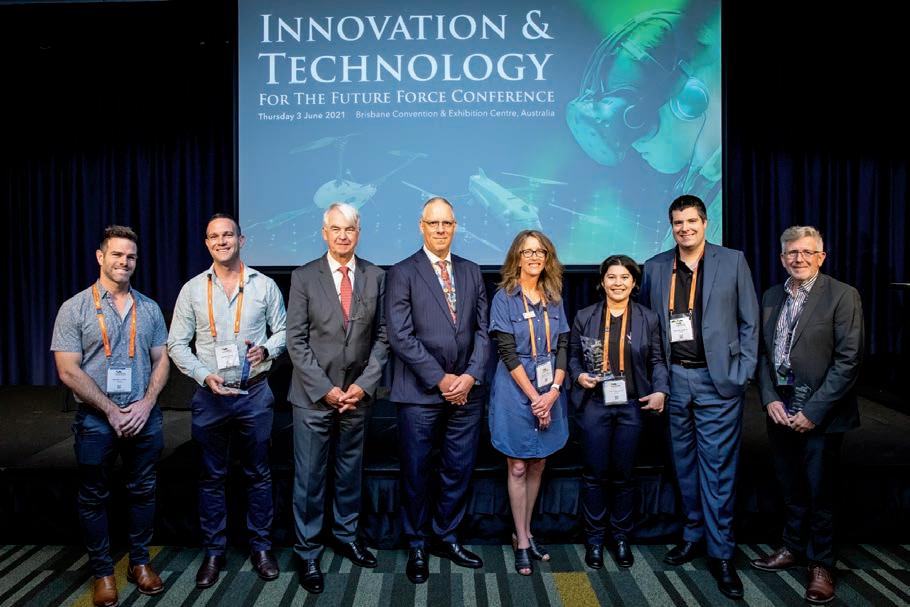
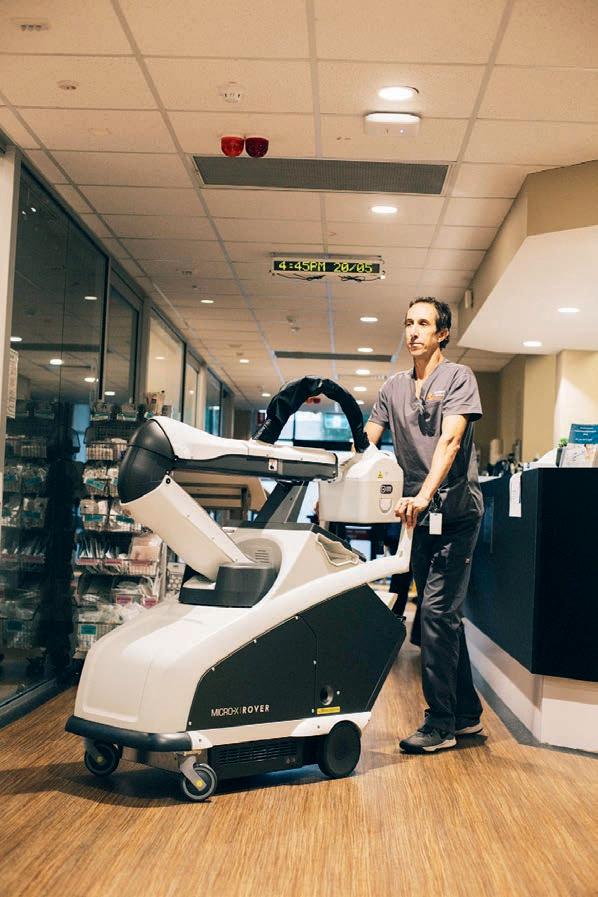
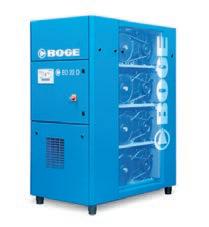
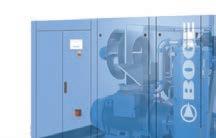
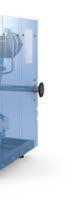
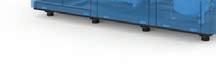
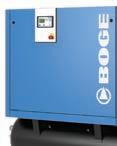
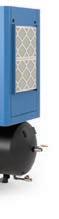
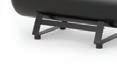
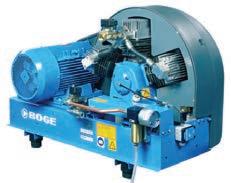
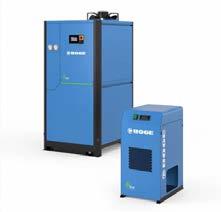
WALKING through Injectronic’s main facility in Hallam, Victoria, it was clear that the business has a strong focus on research and development, with a team dedicated to working on future products and repairs to be in line with emerging technologies.
Production line machines and other equipment are analysed to identify whether they can be repaired.
Building from a base of offering a unique service to the automotive market, Injectronics is starting to make a big impact in the industrial space. Billy Friend visited the company’s Victorian facility to learn how it is helping businesses avoid unaffordable downtime.
The business is an integral brand from the Innovative Mechatronics Group (IM Group), having supplied solutions for electronic and mechatronic components in Australia since 1983. Over the years, the business has earned a reputation for a unique skillset – having expertise to establish the route of a problem, and the capability to quickly turn around a solution lead to Injectronics becoming a leading supplier of quality new and remanufactured automotive electronic components.In2017,the IM Group was acquired by GUD Holdings and is now an important part of the GUD Automotive arm. Previously a privately owned company, Injectronics began to expand its footprint around Australia and take on successful expansion programs. To do this, the company invested in becoming closer to its customers, opening branches in Sydney, New Zealand and will soon add a facility in WesternRajbirAustralia.Singh,general manager remanufacturing, technology & operations, said the company’s expansion into heavy commercial vehicles like trucking Engine Control Modules and agricultural equipment, led to a simple realisation.
32 SEPTEMBER 2022 Manufacturers’ Monthly manmonthly.com.au
Electronic Repairs
The first point of call for industrial electronic equipment repairs
“People were not asking us how much, they were asking how long,” he said. “The cost of having a truck off the road is going to be much more than a repair, so they want a quick turnaround for that matter, which is why we opened more facilities around the country to reach the customer faster and reduce the price of shipping.” A dedicated team of technicians headed the new program for heavy duty Injectronics repairs, which formed the foundation of what the company is now doing in the industrial space for manufacturers. By collaborating with local businesses, Injectronics works with
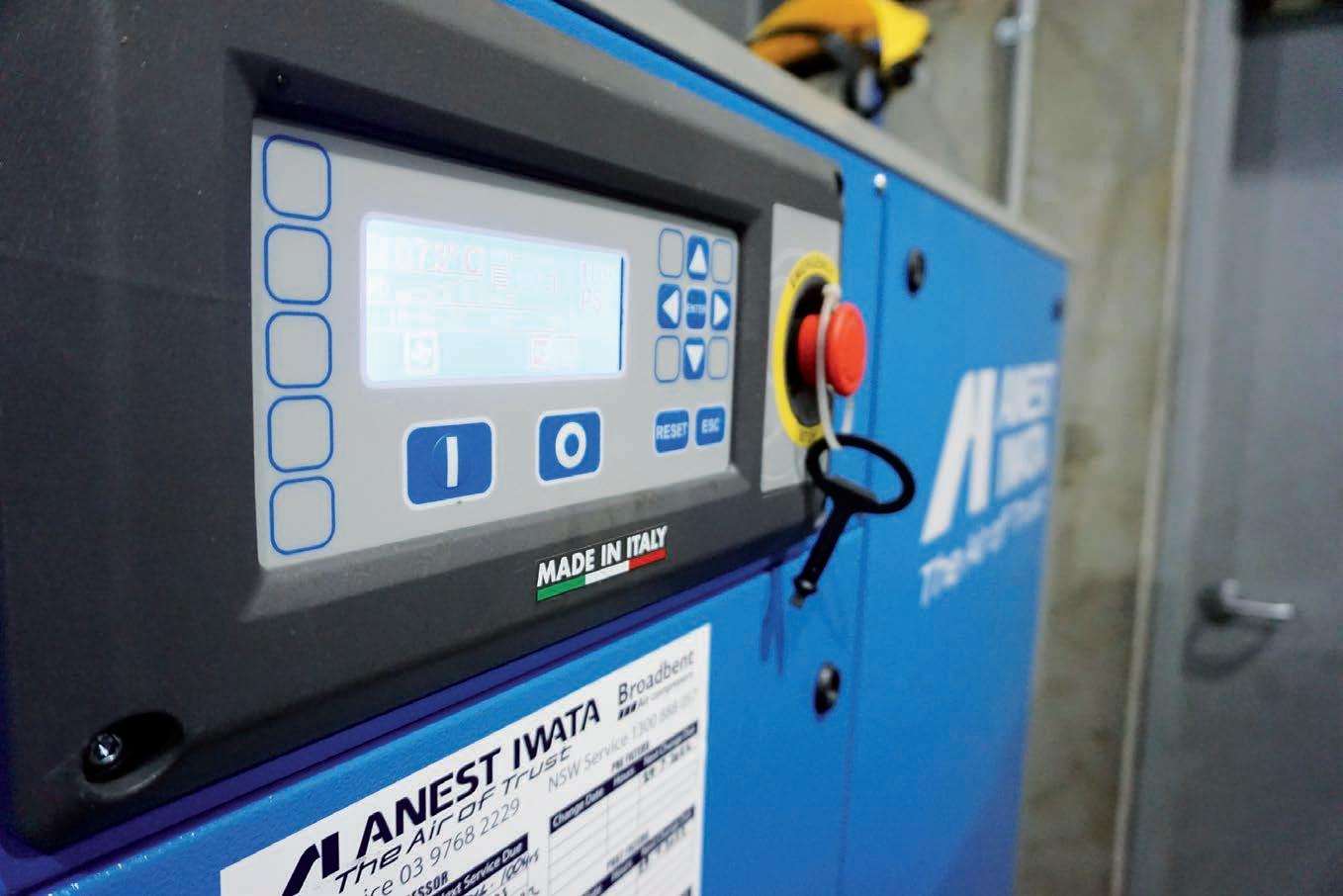
Singh had a very simple message for manufacturers, hoping that Injectronics can be the first point of check for faulty devices, equipment and machines.
Injectronics’ repair facility in Hallam, Victoria. Injectronics has invested in the latest technology to build its offering.
the customer to analyse production line machines and other equipment that has become faulty to identify – usually on the same day – whether it can be repaired. The industrial applications include control modules, industrial control panels, human machine interfaces, programmable logic controls and variable frequency drivers.
For these small to medium sized manufacturers, obsolete parts present a big challenge for when a machine breaks down. According to Singh, until recently the only option has been to replace the equipment with an upgraded system, costing money and time. In a production environment, multiple machines often perform the same functions. In this instance, when Injectronics identifies the fault and gets the machine up and running, it can also suggest a service for the other identical machines.Injectronics recently worked with a food and beverage manufacturer when its machine for making pasta broke down. The only option presented to the business was to spend $400,000 on a new machine, but it avoided the outlay by approaching Injectronics. Sometimes upfront cost isn’t the only motivator – businesses need to find ways to remain functioning at their efficient best when a new machine isn’t an option.“We had a customer with a pharmaceutical dispenser which dispensed a specific amount of fluid into a vile,” he said. “When it broke down, because it was a medical-grade machine, upgrading to new electronics wasn’t an not just the dollar value it’s about keeping businesses running.”
“Our electrical engineers have familiarised themselves with certain types of modules, which is handy,” Singh explained. “Once we see something, it’s in our system so we can apply, for example, the solution to the same Siemens panel in Western Australia just as we have done in Victoria. We see repetitive jobs which is a good thing about electronics. It’s all reverse engineering and we have that capability.”Sometimes, businesses wrongly assume a machine is faulty, when an extraneous problem is what is stopping its normal function. Singh calls this a no-fault-found unit, and it is extremely important to identify in order to avoid the ordering of spare parts, or a completely new machine. Last year, one of the control panels Injectronics was referred to had a fuzzy and hazy display from the customer’s side of operations. However, at the Hallam facility the display worked fine when the team powered it up. After ruling out environmental factors like heat, Injectronics advised the customer about where the problem might lie and explained how to disconnect all the devices to the ports and reconnect them one-by-one to identify the problem. Long story short, one of the cables was broken and causing the fault, so it was an easy fix to replace the cheap cable. “If the customer doesn’t receive that diagnosis from us, the electrical technician has already declared the display is faulty,” he said. “Without this testing, businesses purchase a new device and the same problemWhenoccurs.”youwalk into many manufacturing plants in Australia, the machines are decades old, because it is a significant investment to disrupt operations and place new machines in. By the same token, more traditional manufacturing processes like rollforming and fabrication don’t always require upgraded equipment and technology.
“The feedback we hear is there is fairly set standard and we are hoping to break that cycle,” he said. “When your machine breaks down, you call the electrician, who works out a certain device is playing Repairs
“We have proven there’s a need in the industrial market,” he added. “If a job is of high importance and extremely time sensitive, we can have all hands on deck to achieve that fast turnaround. We find the whole emotion around remanufacturing and repairing is changing in this country. The first instinct can’t be to throw something away – Injectronics provides feedback that could mean the difference between ordering a new part, repairing the existing, or uncovering that the part in question has no fault at all.” As Injectronics continues to provide solutions for industry, its service only grows in strength as it collates a database of common faults.
manmonthly.com.au Manufacturers’ Monthly SEPTEMBER 2022 33 Electronic
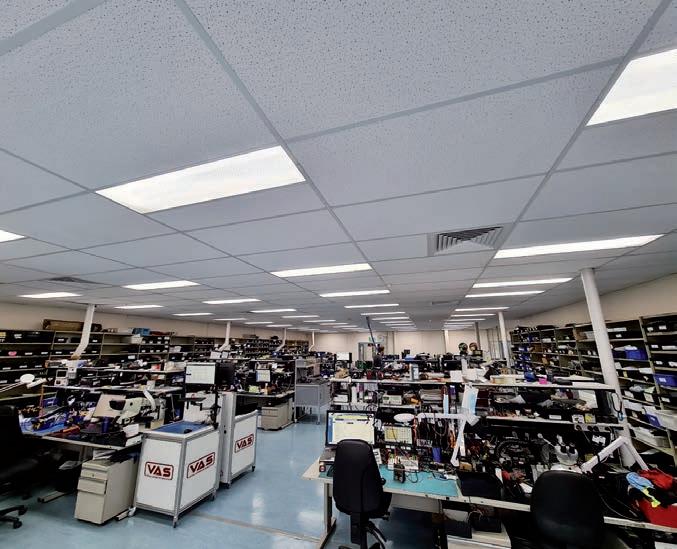
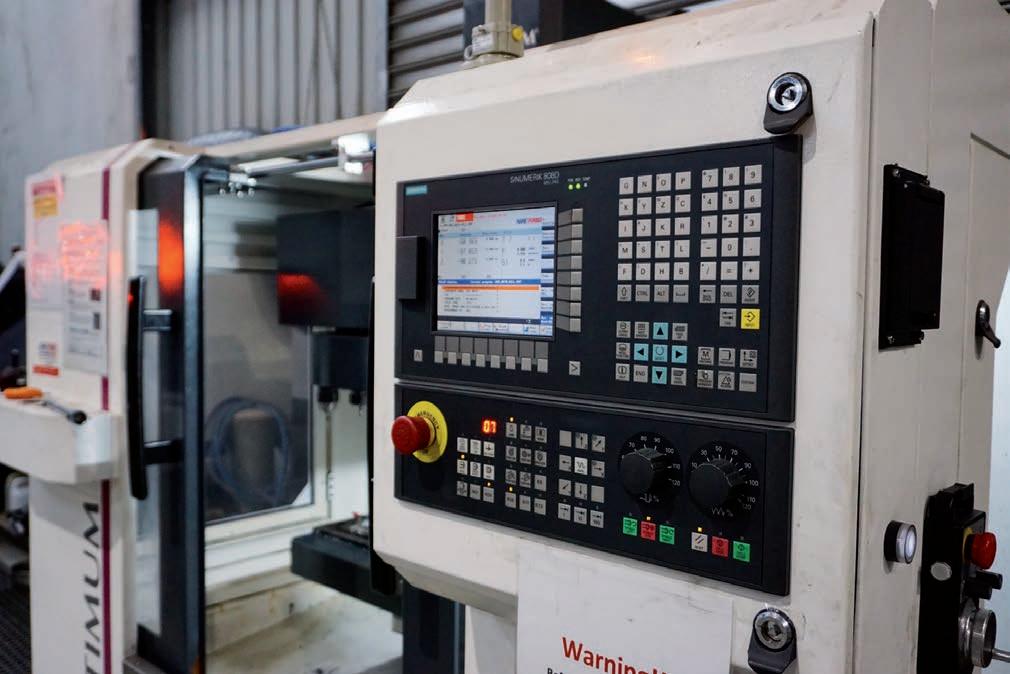
To book contact DANNY HERNANDEZ now danny.hernandez@primecreative.com.au | 0431 330 232 &AUTOMATIONROBOTICS In “the factory of the future”, innovative and more flexible technologies are helping the growth of fully automated production facilities. In November 2022 – we will showcase businesses in the automation and robotics space helping improve manufacturing Theprocesses.edition is an opportunity for businesses to demonstrate the extent of their services to the industries they serve. In every edition of Manufacturers’ Monthly, we’re proud to work with our commercial partners on content that helps connect you with your future customers. Booking deadline: 28 September 2022
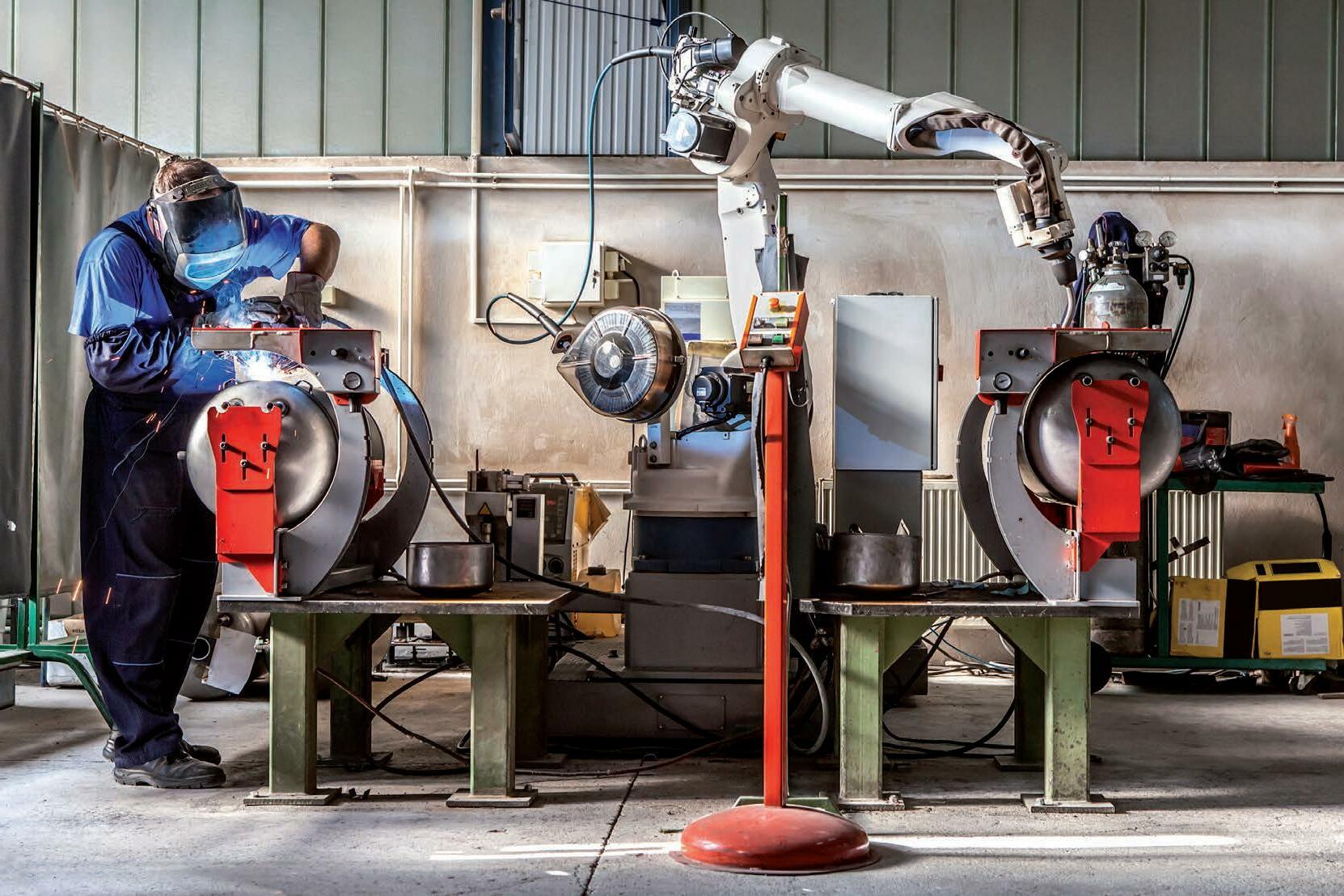
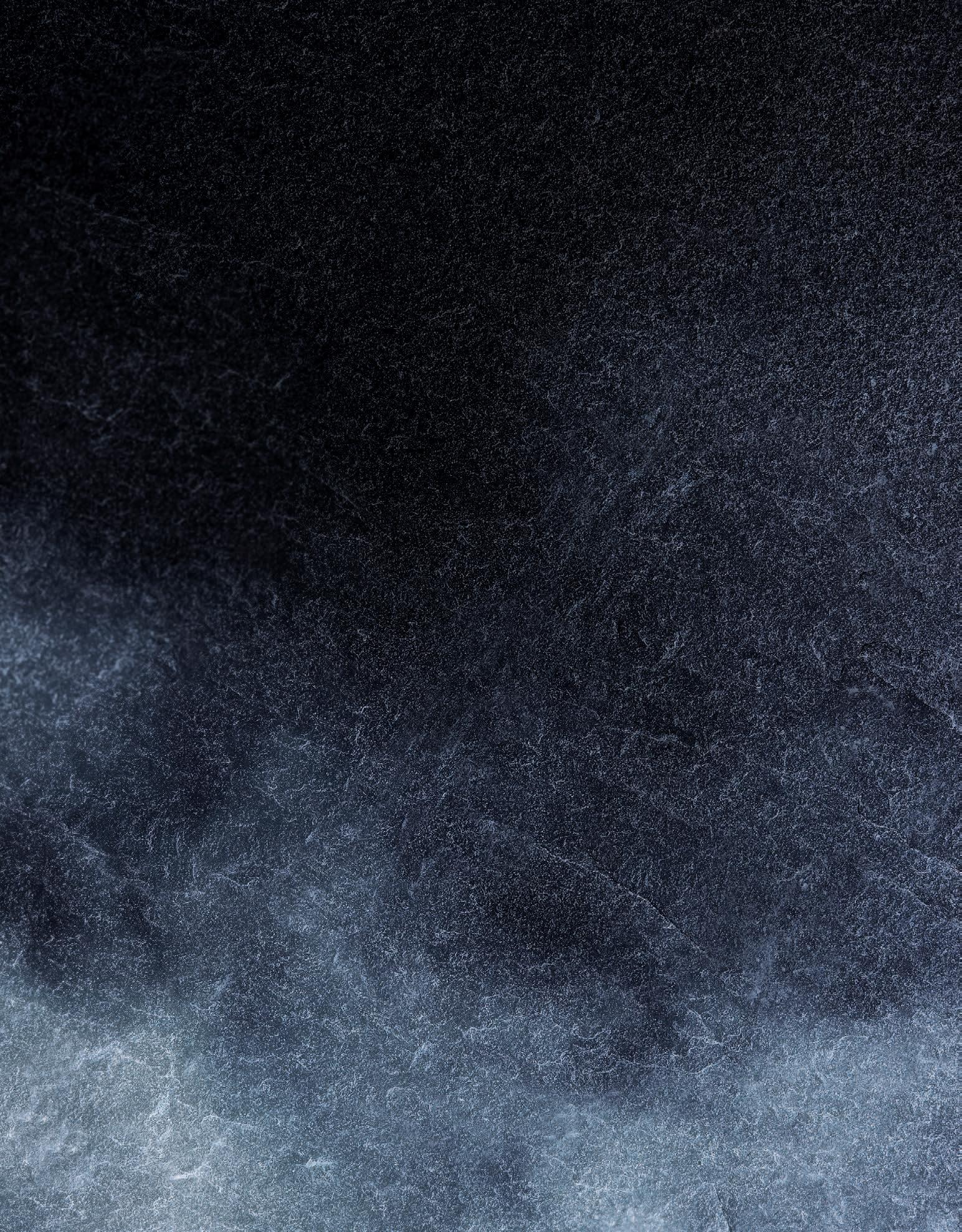
category are as follows: Business Development Success of the Year Jacky Magid
Bio Gro Jane La Nauze
Helen Tower - Seqirus Anika Talukder - BAE Systems Australia Safety Advocacy Award
Kelsey Smith - Roy Hill Emma Muller - Horizon United Group
The Women in Industry Awards will be presented in partnership with Manufacturers’ Monthly,
Judging for the fourth time, Fahey noted the breadth of nominations stood out to her this year. different projects and businesses that are put forward,” Fahey added. “It’s wonderful to also see the levels of people that are nominating. We’ve seen everyone from leading CEOs of very large, listed companies, right through to people that are working at the coalface of health and safety work like health and safety officers.”
Felicity Hall - CJC Management Annastasia Denigan - Qube Social Leader of the Year
All category winners will automatically go into the pool of finalists for the Woman of the Year Award.among others.
Nina McHardy - Fulton Hogan
Priya Perera - Department of Transport Stacey Davies - Daimler Truck & Bus
Julie Piccinin - BAE Systems Australia
Fulton
Michelle (Nikki) Cowper - Viva Energy Australia
“Anything that we can do to be showcasing the incredible roles that women play in the industry, support diversity and inclusion and certainly looking to promote for more females to join such an incredible industry is wonderful,” she said.
Excellence in Manufacturing
Excellence in Mining
Joana Feiteira - Transdev Sydney Ferries Industry Advocacy Award
Sarah Vogler - United Carriers
Ambrin Naaz Begom - M-Power Software
The for each-- Hogan
Barbara Pitsos - Fulton Hogan
Rebecca Healy - Boxhead Plastics
Joanne Jeffs - Fulton Hogan
finalists
Horizon United Group Sarah Marshall
Finalists are announced for the 2022 Women in Industry Awards
Te Ana Goeree - Viva Energy Australia
“I think something that’s very refreshing about the awards is that they are open to everybody. We are encouraging that profile of females that are working in the industry, and they’re working in such a variety of roles, and I think that’s a real strength of the process and the strength of recognising what women are doing for the industry and equally encouraging more females to join.”Allfinalists should be incredibly proud of the work they have
Jessica Ansell - Close the Loop Group
Sydney will play host to the Women in Industry Awards this year on 8th of September, recognising exceptional women across multiple sectors and shining a spotlight on their outstanding work in engineering and manufacturing.workinginourindustry,” the company said. “All nominees and winners are making their workplaces and communities a better place for future generations which closely aligns to our core values at Komatsu.”Oneof the judges, Kylie Fahey from the Institute of Quarrying Australia CEO, says this year’s finalists are an exciting and inspiring group for industry.
Uncle Charlies Saasha Callaghan - OLEOLOGY Sage Hahn
Women In Industry Awards
Stantec Australia Excellence in Construction Emma Muller
Excellence in Engineering Louise Adam - Aurecon Brenda Denbesten - BHP Sarah Stante - CaSE Maria Hill - Hitachi Rail
Deb Scown - Ampol Kari Banick - Linfox Danielle Bull - WesTrac Anne-Laure Saluden - Transdev Sydney Ferries
Sarah Coleman - idoba Maria Ruiz - ABB Australia
Rising Star of the Year
Yvette Mihelic - John Holland Mentor of the Year
Excellence in Transport Frances Ross - Ross Transport
Lina Goodman - Tyre Stewardship Australia
Gina Rinehart - Hancock Prospecting
manmonthly.com.au Manufacturers’ Monthly SEPTEMBER 2022 35
Biljana (Billie) Stanic - Martinus
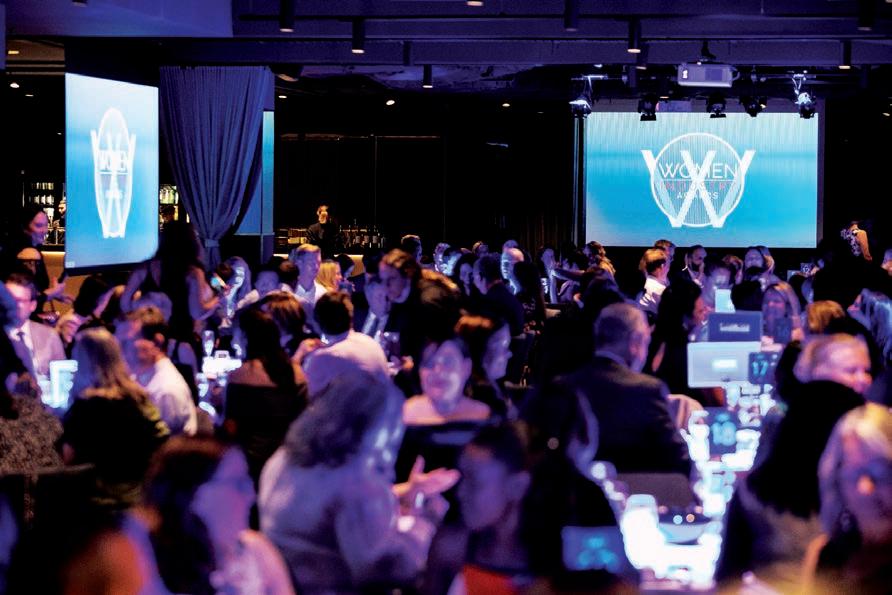
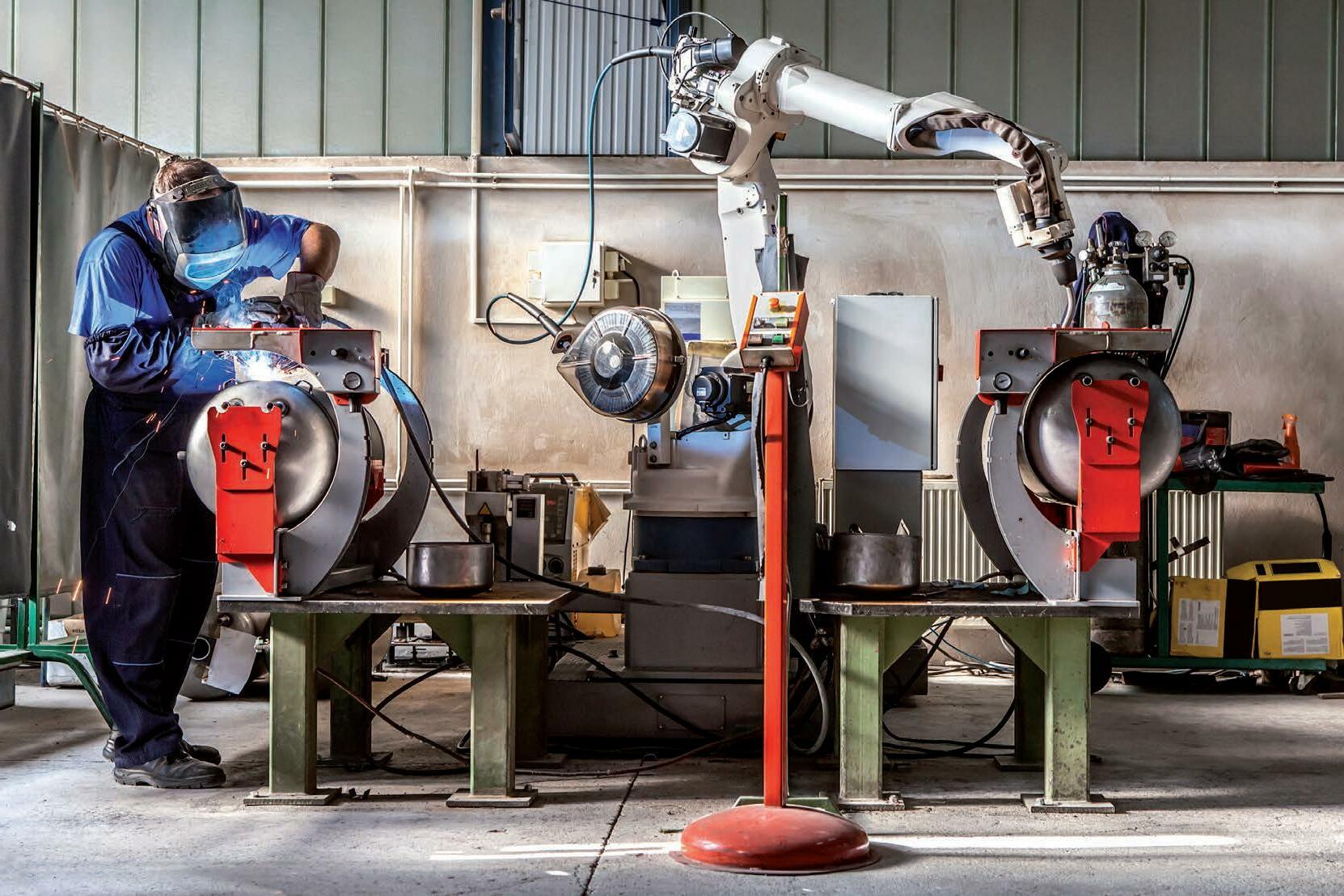
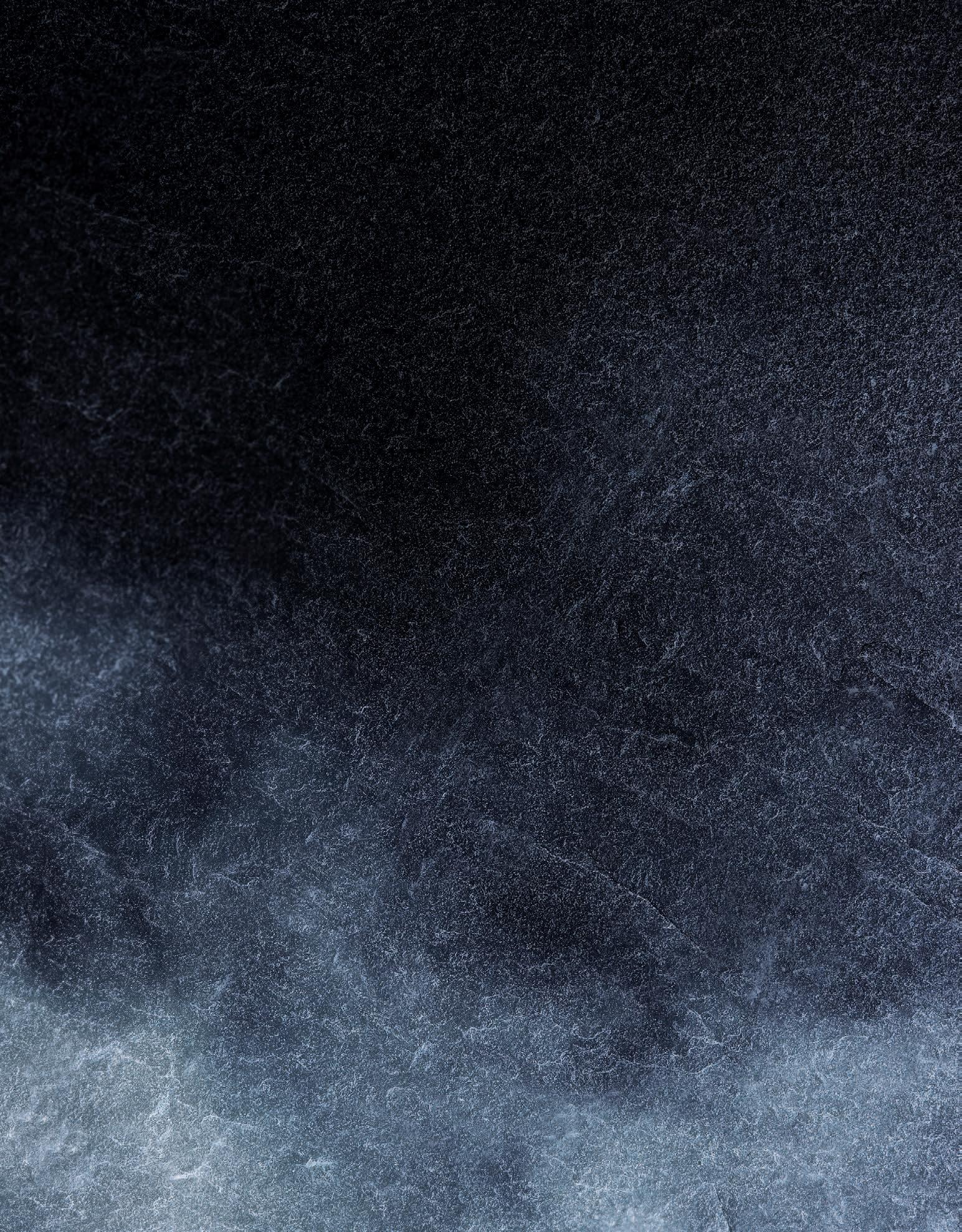
Well designed air piping systems ensure high quality compressed air reaches its desired point-of-use with the right pressure and flow.
Manufacturers’ Monthly discovers how the Airnet solution is helping Australian manufacturers protect the downstream manufacturing process thanks to consistently clean air.
AIRnet pipe and fittings are pressure rated and specified for most industrial applications where standard compressed air is required, including nitrogen generation, and rough vacuum installations. The system can be used to pressurise any machine process, product diverter apparatus, automation, and machining equipment, as well as common industrial air facilities like automotive assembly, distribution centres, loading docks, molding, cabinet, furniture, and service and repair centres.
Preserving the power of air
Owned by Atlas Copco, AIRnet is stocked in Melbourne, Brisbane and Perth branches – as well as the main distribution point in Sydney.
PHIL Shallvey, business development manager for AIRnet, spent the first ten years of his professional life in an engineering business specialising in pipe as a fitter and turner tool maker. He has since travelled the world heading sales teams for specialised industrial products. His journey has been upward all the way to his current role with AIRnet – which he finds exciting because of the myriad capabilities he sees in the solution.
“It’s a modular piping system to assist with the distribution of air from the compressor into a pipe network system which goes down and feeds whatever service is required – whether that’s a panel beater workshop, blow gun at a mechanics workshop or a plasma or laser cutter in an engineering workshop,” Shallvey explained. “Being owned by Atlas Copco, we can provide the customer with that complete turnkey solution. The supply of the air compressor, all the way through to the service point of the air can be done by the one company, which provides greater continuity and ease for customers.”AIRnetAluminium fittings and pipes can be removed, reconfigured and reused to move with a business’s changing demands. According to Shallvey, a burden of the past has been left behind with the absence of complex tools and no welding, AIRnet Aluminium fittings and pipes can be removed, reconfigured and reused to move with a business’ changing demands.
“We identified that we needed to capitalise on situations where our solution is needed right here right now,” Shallvey said. “We reset the whole product category and stock profiling, to the point where we’re overcoming the challenge of not having access to enough stock or the rightAluminiumstock.”
Over the last couple of years, the AIRnet brand has gained serious momentum in the Australian market.
36 SEPTEMBER 2022 Manufacturers’ Monthly manmonthly.com.au Air Piping
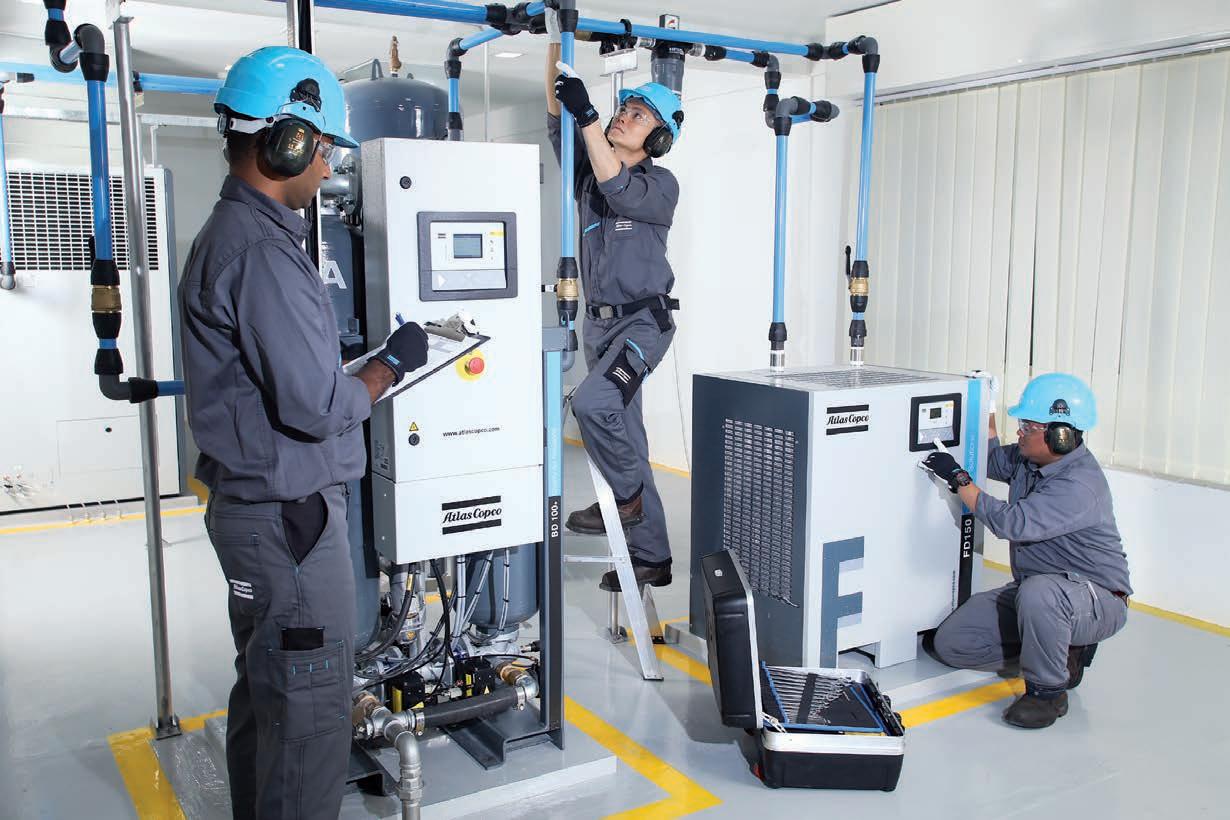

“The tool can allow the installers to design the piping system because all of the equipment data is already known by the system, where it chooses the right size of pipe almost instantly,” he said.
“The team can put together some mechanical drawings in the file you want, whether it’s a 2D PDF version or a full 3D CAD version of a system,” he added. “These can be provided to the customer free of charge, and it helps to create a really professional presentation to their prospective client.”
The AIRnet brand has gained serious momentum in the Australian market. AIRnet uses an easy-to-use push fit system.
“Turbulence and friction are the greatest enemies of a compressed air system because the compressor needs to work harder to be able to maintain and supply the amount of air that’s required. The improved smoothness creates better efficiency than the likes of black iron or steel.”From a design point of view, AIRnet’s research and development has ensured the product creates the least amount of resistance. AIRnet design technologies and innovations are based on technical expertise gained from Atlas Copco – more than 140 years of experience with pressurised air applications and equipment.“Having that longevity within the industry of making these products for industry creates a huge amount of experience,” he added. “A lot of research and development has gone into that to enable those fittings to be to be as efficient as they possibly can be.”
“Aluminium doesn’t have the corrosion factor steel does, and because it doesn’t corrode the internal surface of the pipe, it remains much smoother, allowing for less turbulence through the flow of the pipe,” Shallvey said.
manmonthly.com.au Manufacturers’ Monthly SEPTEMBER 2022 37 Air Piping
“Then it provides you with a Bill of Materials after you’ve finished the designing of it, which allows you to put a quote together. A medium to large job would take an installer anywhere from three to four days to work out everything and submit that as a quote to theThecustomer.AIRnet planner that can do all of that in about three hours – the aim is anyone with just a little bit of knowledge within the industry should be able to design a piping system relatively easily.”
AIRnet can save up to 70 per cent on installation time when compared to traditional piping systems – the previously complicated journey of designing and installing a piping system has been revolutionised by the AIRnet planner 2.0. The AIRnet Planner is a design tool – now available on the iPad – which enables a sales representative to design, visualise and create the Bill of Materials for total installation. The planner uses integrated calculations for compressed air, vacuum and inert gases with a database of thousands of pre-built and generic equipment models to help sales representatives simulate design as realistically as possible. Shallvey explained that ascertaining the correct diameter for a piping system is key. Pressure drop within a compressed air system is unavoidable, but it must be man¬aged for the system to achieve its maximum operational efficiency. Pressure drop wastes energy, it confounds compressor controls, and excessive pressure drop can adversely affect equipment operation and create quality issues with the work being performed by compressed air.
AIRnet also has access to a team of 20 design and mechanical engineers in its own design centre in India, which further aids the quick turnaround for customers.
gluing, or crimping required.
“So if the business grows over time, and they need to add more machines, it’s so easy to cut into the system, extend it, change or reroute it, without the use of any major tools because of the way that the couplings all fit together from 20 millimetres to 50 millimetres – it’s an easy-to-use push fit system.” This flexibility has to be provided without disrupting operations. Certain businesses can’t function without the compressed air for any period because they run 24 hours. In this case, by the use of valves, the AIRnet allows the required pipework section to be added without disrupting the current infrastructure. Once installed, the systems are joined and the extra piping becomes a part of the original system. A pressure drop of one bar results in a seven per cent increase of energy consumption, meaning a properly sized, leak free piping system is integral to keeping energy costs down.
“Being a modular system, it allows itself to be changed depending on that businesses’s requirements,” he noted.
An inadequately sized piping distribution system will cause excessive pressure drops between the air compressors and the points of use, requiring the compressor to operate at a much higher pressure in an attempt to over¬come these parasitic pressure drops, but an oversized piping distribution system design unnecessarily wastes money for businesses. The difference of just 10 millimetres in diameter can result in a 20 per cent increase on aluminium costs.
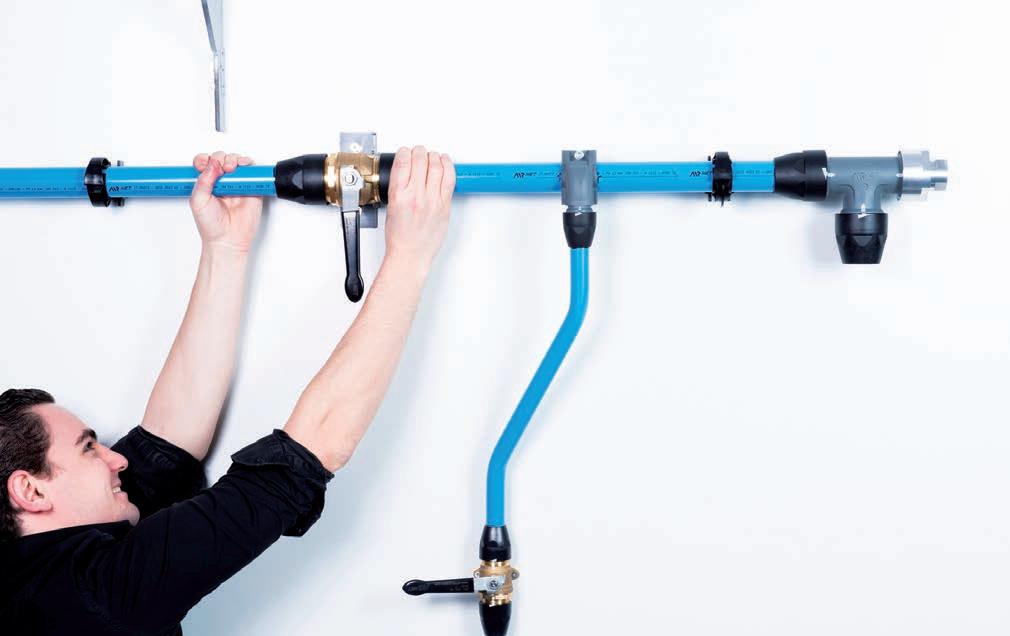
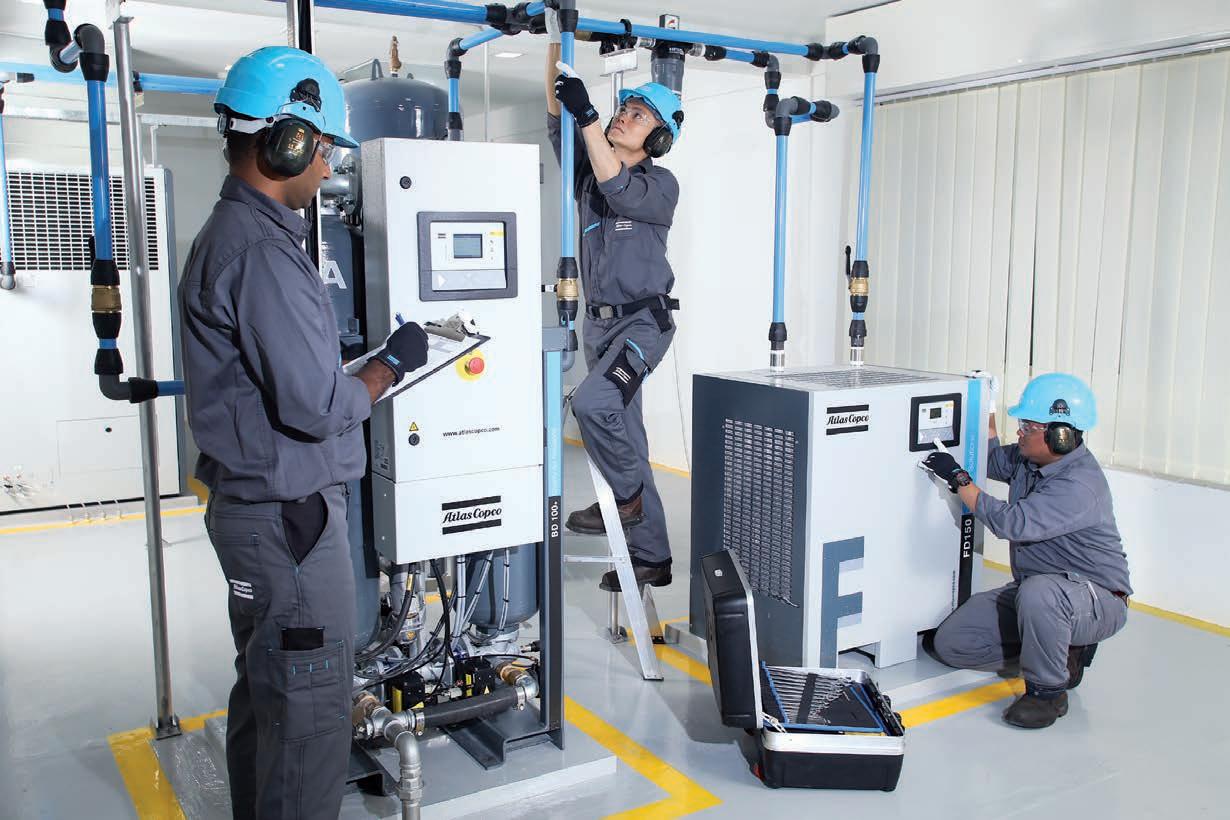
Different lighting effects: continuous, blinking, flashing and rotating Signalling modes: autoscale, filling level, signal column and individual Acoustic element: 10 adjustable tones, volume settable to 105dB Like the complete range of SIRIUS push buttons, the signalling columns also have an IP66 and IP69K rating, which means they can be hosed down by high pressure, making them ideal for food and beverage
“Theseapplications.featureswill see these signalling columns become part of your complete safety solution - where you can have alarms and red flashing lights signalling the machine is down or
Industrial Control 38 SEPTEMBER 2022 Manufacturers’ Monthly manmonthly.com.au
The Siemens SIRIUS range provides a flexible and robust solution for monitoring and streamlining production.
Robert Geppert, APS’ product manager, motor control, told Manufacturers’ Monthly that the newest
FROM factory automation and drives through to industrial control and communication, Siemens in partnership with local distribution partner APS Industrial, is at the forefront of technological innovations that enable manufacturers to maximise productivity, consistency and ROI in a competitive and highly demanding environment.TheSiemens SIRIUS control, command and monitoring range of products from APS promise to give users a more flexible and robust solution for monitoring and streamlining the production process.
addition to the company’s portfolio was an exciting one, bringing a number of new innovations to traditionally limited signallingAccordingcolumns.toGeppert, the new 8WD46 high-performance signal columns can be used universally in industrial applications and buildings, such as assembly lines, conveyor systems and shipping stations – making them an ideal complement to local food and beverage systems and “What’ssolutions.exciting about this new range is that it becomes part of our full signalling and command range. We already have high-performance push buttons and indicator lights, - electronically configurable signalling columns are now part of that,” he said.
Siemens solutions are designed to add value across every aspect of manufacturing operations.
Manufacturers’ Monthly sits down with APS Industrial’s Rob Geppert to focus in on the latest innovations within the industrial control portfolio, SIRIUS.
Driving productivity, efficiency, and sustainability through greater command, signalling and detection
“The range is very flexible which means instead of a customer having to buy multiple components and hold multiple spares, this is just one device that can be plugged in and programmed to provide the functionality that’s required.”
Multicolour LEDs allow to set more than 1M colours
“Our SIRIUS control range enables plants to indicate the status of a conveyor line or a packaging machine. By adding these new columns to the overall solution, users eliminate the requirement for multiple components to assemble your custom signalling columns.
Whether there is a need for colours, flashes, or acoustics, the 8WD46 signalling columns can be programmed to provide maximum flexibility which empowers the user to program what they need for their application.

“In addition to discrete connections, we also offer IO Link for integrating tightly into your automation system. In old school days you would hardwire a lot of signals to turn on whichever lights you wanted to whereas now it is just part of the automation and very easily, via the IO Link, the automation system can signal whatever is required.”
“It really fits in with the whole signalling and safety portfolio.” The wider flexibility of the signalling columns has a positive flow on effect on the rest of the production process, essentially helping with uptime.
As productivity and efficiency gains become more and more prevalent across the manufacturing industry, new innovations, like those from Siemens and APS, will continue to change the face of production.
“It certainly will help increase the plant uptime so that you can be warned before getting into shut down situations so that you can take proactive steps,” said Geppert.“With signalling columns in the past, you would effectively be limited to indicating whether a machine was on or off.“With this new column, you can do so much more - take tank levels for example. In this instance you might have 15 elements split up over your signalling column and each element will indicate whether your tank is empty, quarter full, half full etc. – ultimately giving you much better visibility of your process.”
manmonthly.com.au Manufacturers’ Monthly SEPTEMBER 2022 39
Industrial Control
Geppert also said that no matter what type of food or beverage product was being produced, all manufacturers and producers stood to experience material advantages by upgrading to this new style of signalling column. “It doesn’t matter if the process is, bread or brewing, they are all able to experience these benefits,” he said. “Typically, in those processes the user will buy packaged machines, like a conveyor or wrapping line. You can easily apply these signalling columns to each of those lines and have common indication right across your plant no matter which part of the line it is.”
Geppert said in addition to the SIRIUS industrial control portfolio, APS as the national distribution partner for Siemens also give local customers access to the full suite of SIMATIC factory automation solutions – a feat that gives customers access to everything under one roof to ultimately speed up process and“Timeproduction.tomarket is a significant advantage of the Siemens portfolio from APS Industrial. Because we can offer a full solution, we can get production up and running quicker than trying to integrate various suppliers into a solution,” he said. “Whether it be a push button or a signalling column, to a safety relay or limit switch, they can all be networked together to form part of the automation solution,” said Geppert. “Our clients will typically use integrators for the software and board builders for the switchboards and so on. At APS we provide the products that go into the solution and pre-sale support in terms of application guidance to assist the integrators, board builders and end users to get the best result.”
The SIRIUS ACT range of push buttons are central to effective control and indication. The new 8WD46 high-performance signal columns are perfect for industrial applications.
“When you are talking about food and beverage manufacturing, you are talking about batch control and so it’s important to have an automation system that can handle that batch production and it requires all sorts of sensors to control thatHavingproduction.afully integrated automation system, all from one provider, allows for faster engineering and enhanced functionality.Itisalldesigned to work together, and quality is a key driver in the food and beverage industry.”
someone has entered into an area they shouldn’t be in,” said Geppert.

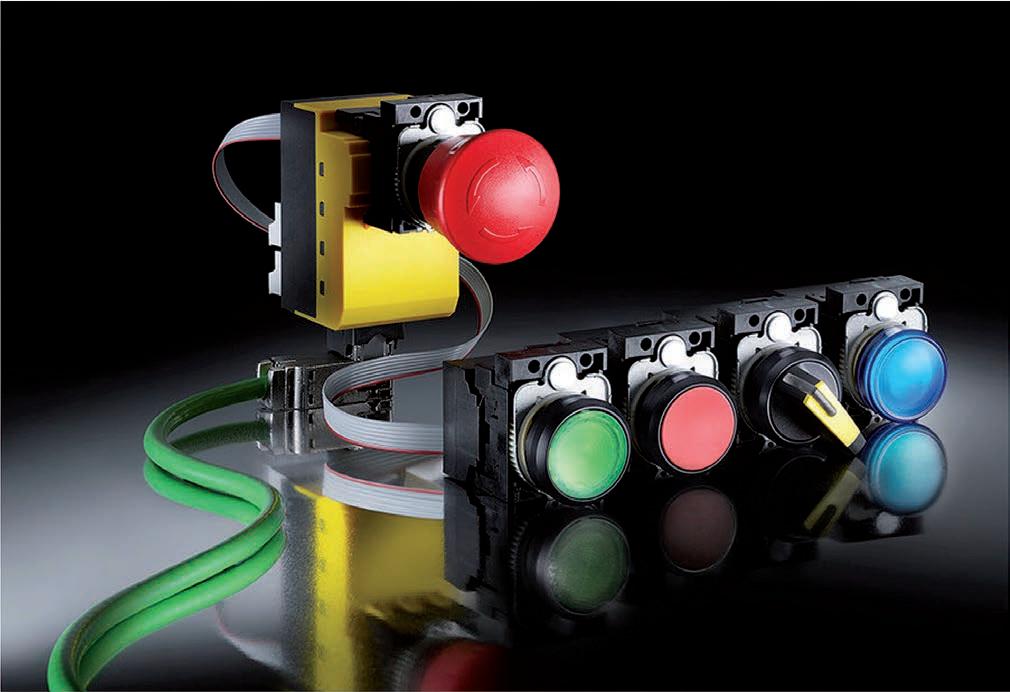
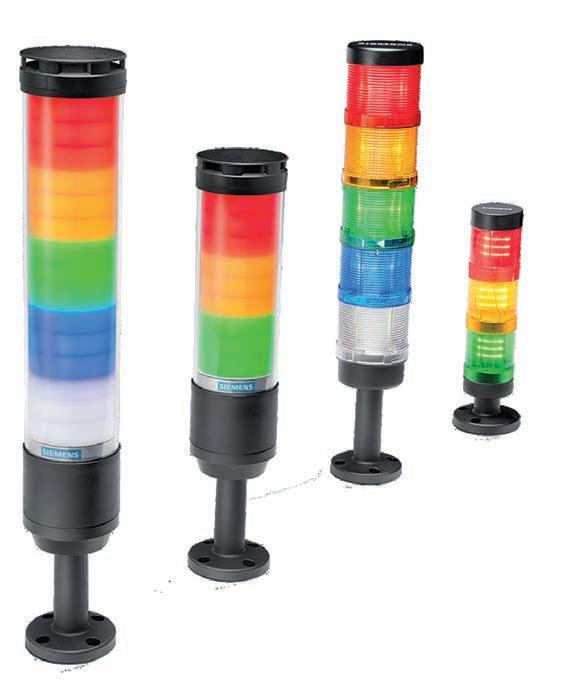
CAPS Australia has launched the new Ingersoll Rand RM Series of oil flooded rotary screw compressors. Manufacturers’ Monthly finds out the range of benefits the series offers manufacturers.
AUSTRALIAN manufacturers know that maintaining a highquality supply of compressed air throughout a huge number of their processes across the plant is as critical as any of the other utilities. Not only does the air need to be of the required quality, the systems which provide it need to be reliable for their entire lifetime.
a new range of compressors.
With ten branches located nationwide, the company focuses on making it easy Ingersoll Rand RM series
A complete solution for compressed air, gas production and power generation
Energy efficiency is also a crucial factor to consider due to the demanding usage requirements in the manufacturing environment.Withover42 years of providing proven compressed air solutions to this segment, CAPS understands all of these elements. solutions. It serves the manufacturing, mining, food and beverage, wastewater treatment, construction, oil and gas and more industries nationally and internationally.Withoverfour decades of experience under its belt, CAPS delivers innovative turnkeySolutions – offering the widest range of industrial air compressors and power generation solutions in Australia, including centrifugal blowers, compressed air dryers, pressure vessels, industrial generators and renewables.
40 SEPTEMBER 2022 Manufacturers’ Monthly manmonthly.com.au
It’s not that often CAPS Australia launch a brand new range of compressors to the market, but as Ingersoll Rand’s distributor in the country, CAPS says it’s really excited to be launching a completely new range of oil-flooded rotary screw compressors to the Australian market. The ‘M’ Series of compressors were introduced by Ingersoll Rand in the 1990’s and had evolved to a release of the RM220i series model in 2021. In 2022, CAPS introduced three new models bearing the RM nameplate. The new RM Series range will be available in 90, 110, 132 & 160 kW variants and a range of 7 through to 10 bar. features on the new RM series include: Single Stage RS series air-end, TEFC IP55 IE3 electric motor, Le-180 as well as a IP54 enclosed starter cabinet. These units also boast horizontal top arrangement of oil/ air coolers, allowing the compressor to operate in a max. ambient temperature of 46℃, V-shield technology and alarm and trip protection signal are sent via the Le180, avoiding unexpected failure. The RM series use the same air-end as found in the premium RS series, renowned for its efficiency. The RM Series has inherited the V-Shield technology taken from the RS series, using hoses with O-ring face seals, as well as the complete drive train being mounted on vibration mountingsThenew bearing system on the air-end improves service life and reduces friction loss. Overall, the air-end has 9 bearings in total four roller bearings to assist in the rotational process, three angular contact bearings to control the thrust load and two deep groove ball bearings to assist with the reaction thrust. Additionally, the air-end has an o-ring plane seal to eliminate any coolant spillage going into the motor. Compared with the models the RM series replaces, it offers an improved flow rate of approx. 9 per cent and a specific power improvement of up to 15 perControllingcent. the compressor is simple and powerful thanks to the (Le-180) Luminance Series Intelligent Controller. It features a full colour 7.6’ touch screen, delivering real-time system parameters, real time clock start & stop scheduling and built in graphic treading, a feature which was only available on the Xe145 controller on the RS premium series. It also has an onboard web page function, allowing operators to monitor and control their compressor remotely via a common web browser as well as motor temperature monitoring function. Full details of this new RM series range of compressors are available on the CAPS website at www.caps.com.au
CompressorsCAPSAustraliahaslaunched
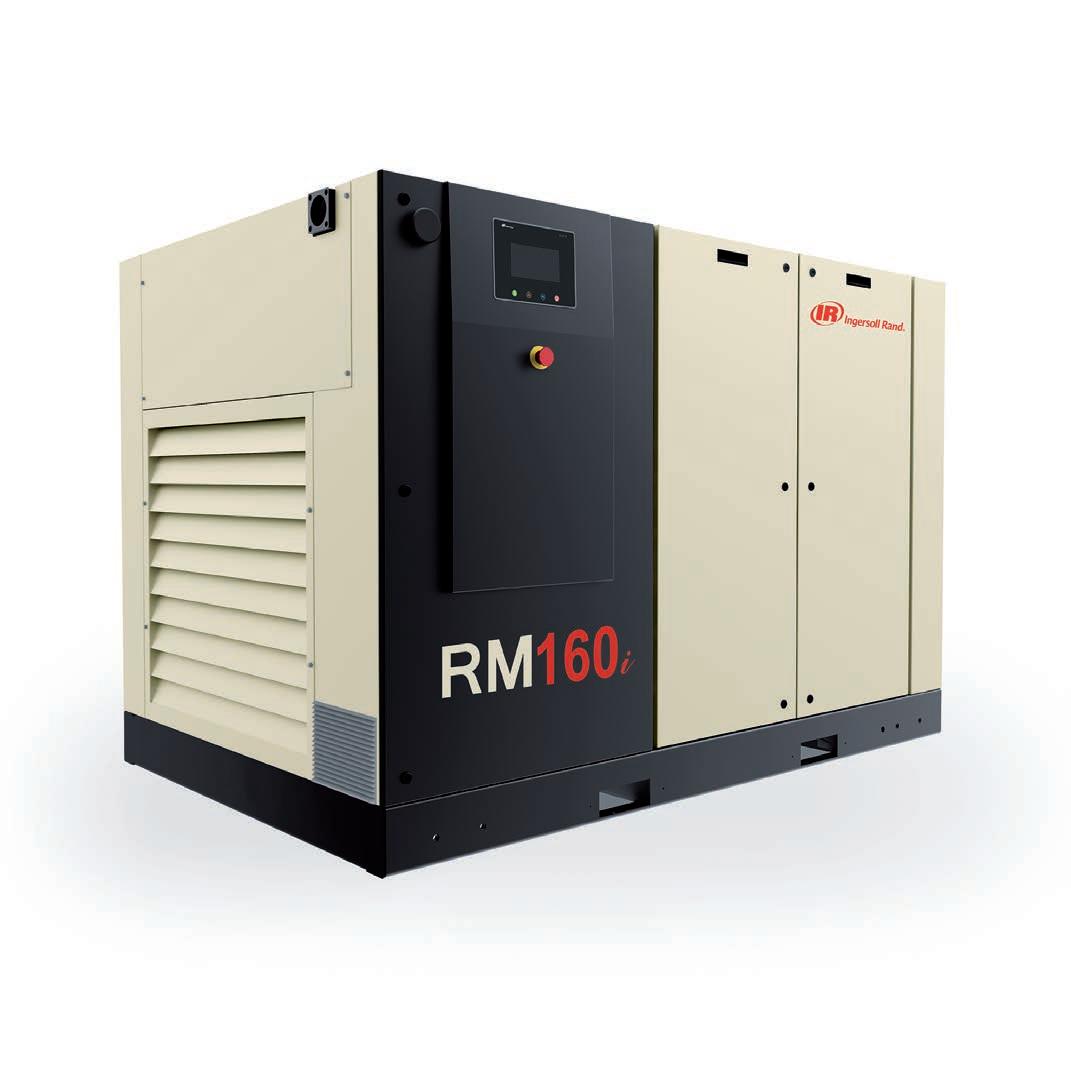
For further information, call your local CAPS Australia office on 1800 800 878 or visit our website www.caps.com.au
•Including:Rapid-response 24/7 support Fast, easy access to local expertise
solution provide; system design via its in-house engineers, build in Australian ISO9001 accredited manufacturing facility and commission a custom-built system, perfectly matched to individual requirements. and understand what these represent in terms of peace of mind in ensuring your manufacturing facility keeps on producing. One of the major advantages CAPS has as an independent company is that is not aligned to any specific OEM, so to perform seamlessly, CAPS offers a nationwide service network with the ability to service and repair your equipment. Its highly trained technicians continually update their knowledge, and have the model-by-model knowledge required to give the customer peace of mind. Its flexible range of smart air servicing packages are specifically designed to make the customer’s life as simple as possible.
• Spare parts from nine nationwide service centres Quick parts deployment
• Multi-brand trained technicians for on-call support Safety is a core value of CAPS, with a goal to never put people, plant or the environment at risk. Customers can be confident that technicians will be completely compliant to any site-specific safety requirements.
manmonthly.com.au Manufacturers’ Monthly SEPTEMBER 2022 Compressors41Registration Now Open Simulation, Autonomy and Innovation highlights at Land Forces 2022 Highlighting Australian Innovation: Innovation Awards | Innovation PitchFest HOSTED BY Australian EducationSimulationTraining,andConference Autonomy in the Joint Military Battlespace landforces.com.au For further information contact the LAND FORCES Sales Team: T: + 61 (0) 3 5282 0500 E: expo@amda.com.au PLATFORMS - EQUIPMENT - SUPPORT - TECHNOLOGIES Maintaining a high-quality supply of compressed air remains essential for Australian manufacturers.
Caps rental To round out its complete offer, CAPS Australia also have rental options available to meet short term or long term needs.

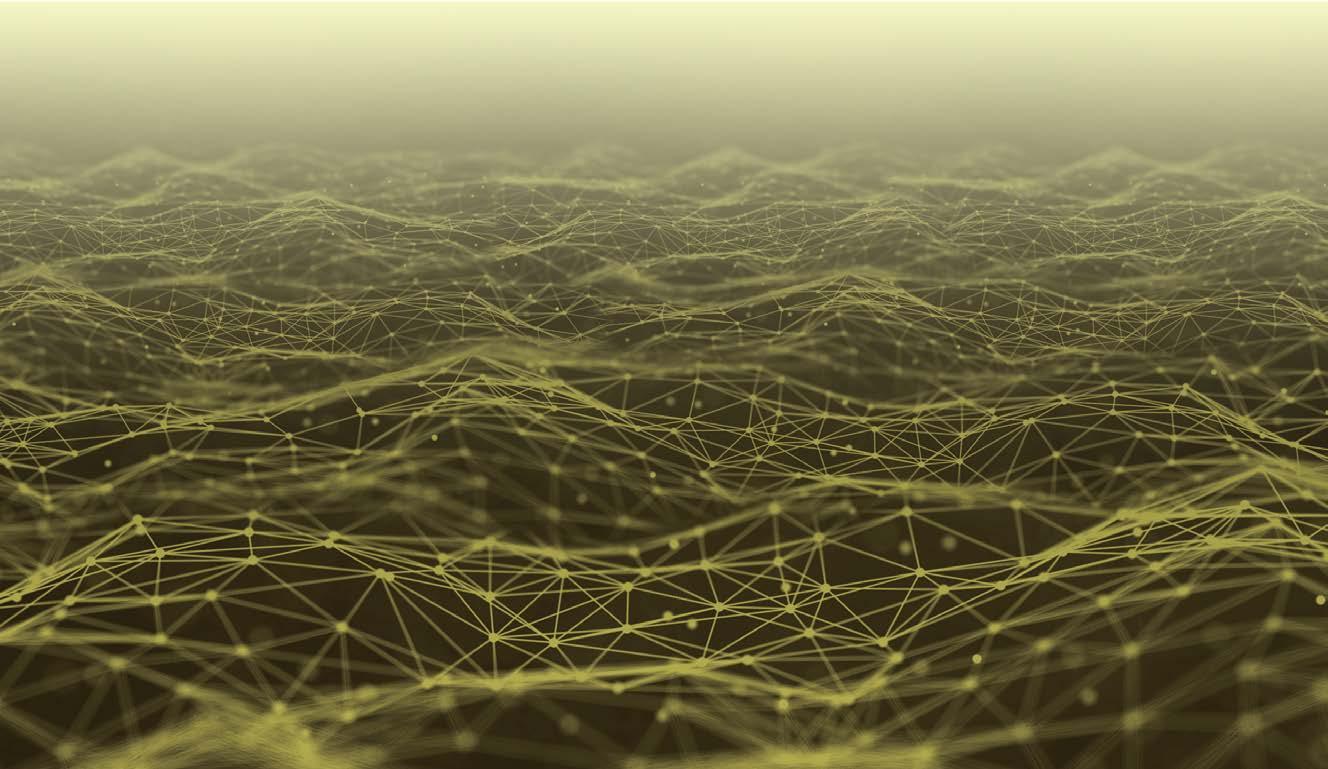
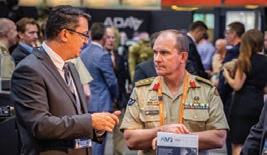
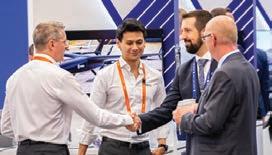

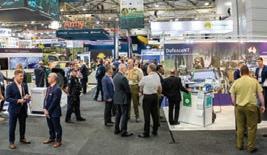
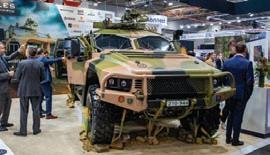
Moneo, Coertze explains the tool acts as ‘middleware.’“Moneowants to be sitting in the middle to act as the glue,” he added. “You collect parameters at the bottom, from the factory floor and put it into Moneo. After the data science and analysis, the data is pushed out to other platforms, because the factory may already have an overarching platform like an ERP system that sits on top. Being the link in the digital value chain is crucial.”
The Moneo solution Continuous evaluation of process data provides the basis on which sustainable and successful business decisions can be made. And in order to obtain such data from the manufacturing floor, reliable connection of sensors to IT infrastructure is essential.Moneocombines the level of operation technology with the level of information technology. Sensor data generated in manufacturing plants can be read and processed easily and used as the basis for sustainable corporate decisions. With its modular structure, Moneo consists of basic software plus applications – for example, condition
42 SEPTEMBER 2022 Manufacturers’ Monthly manmonthly.com.au Internet of Things
The sensor data generated in production plants can be processed to make sustainable business decisions.
The Moneo toolbox Historically, one of the major hurdles to be overcome when it came to integration of technologies has been the lack of ‘interoperability’, said Coertze. “It used to be the case that if you’d buy software from a certain vendor, it was proprietary, and you could only use products or services from that one particular vendor,” he said. “IoT has broken down the barriers because of its flexibility. Moneo was designed to push
The platformIIoT for industry As experts in forsensorsmanufacturestransformation,digitalifmindustrialandsolutionstechnicalprocesses.
The concept of IoT within the manufacturing industry is not a new one, ifm’s Freddie Coertze told Manufacturers’ Monthly, but effecting the implementation of IoT technologies within a business is a different story.
a customer for whom we performed some condition monitoring with Moneo, and the results were awesome. But notwithstanding the results – Moneo was still considered a ‘nice-to-have’ technology rather than a ‘need-to-have’ technology’.”Monthslater, ifm visited the same customer, and that customer had experienced a big breakdown in one of its power distribution boards, which took down the whole factory. “One of their bus bars just blew up because of power demand,” Coertze said.
Manufacturers’ Monthly finds out from national IoT business manager at ifm, Freddie Coertze, how the company is putting the power back into the engineer’s hands.
“The customer then realised that they needed to start properly monitoring their power – and that it could be done with Moneo. Suddenly, it became relevant to the business because they’d lost production. It was no longer a ‘nice-tohave’ technology, but something they needed.“Adoption of technologies such as Moneo is not a matter of people not knowing what they’re doing – it’s a matter
While Coertze noted that customers understand the value of IoT technologies at an engineering level, oftentimes engineering business units have struggled to sell the technology internally to the board.“Such technologies are well and good in theory, but if you don’t have tangible outcomes – ROIs tied to business KPIs –then you’re not going to be able to make the internal business case for them,” he said. “There are always competing business case internally such that they can reap the rewards on the operations ground.Andone area where ifm is really pushing to make such business cases is with Moneo, ifm’s powerful IIoT (Industrial Internet of Things) platform.
“We’ve moved beyond the stage of ‘Industry 4.0’ and ‘IoT’ as buzzwords that are new to people,” Coertze said. “I think everyone is familiar with those terms now, but the notion of digitising everything – that does still in many cases remain in the realm of ideas. What we haven’t had enough of is proving a tangible return on investment.” ifm is a manufacturer of industrial sensors and solutions for technical processes specialising in sensors, networking and control systems for a broad range of specialised applications.
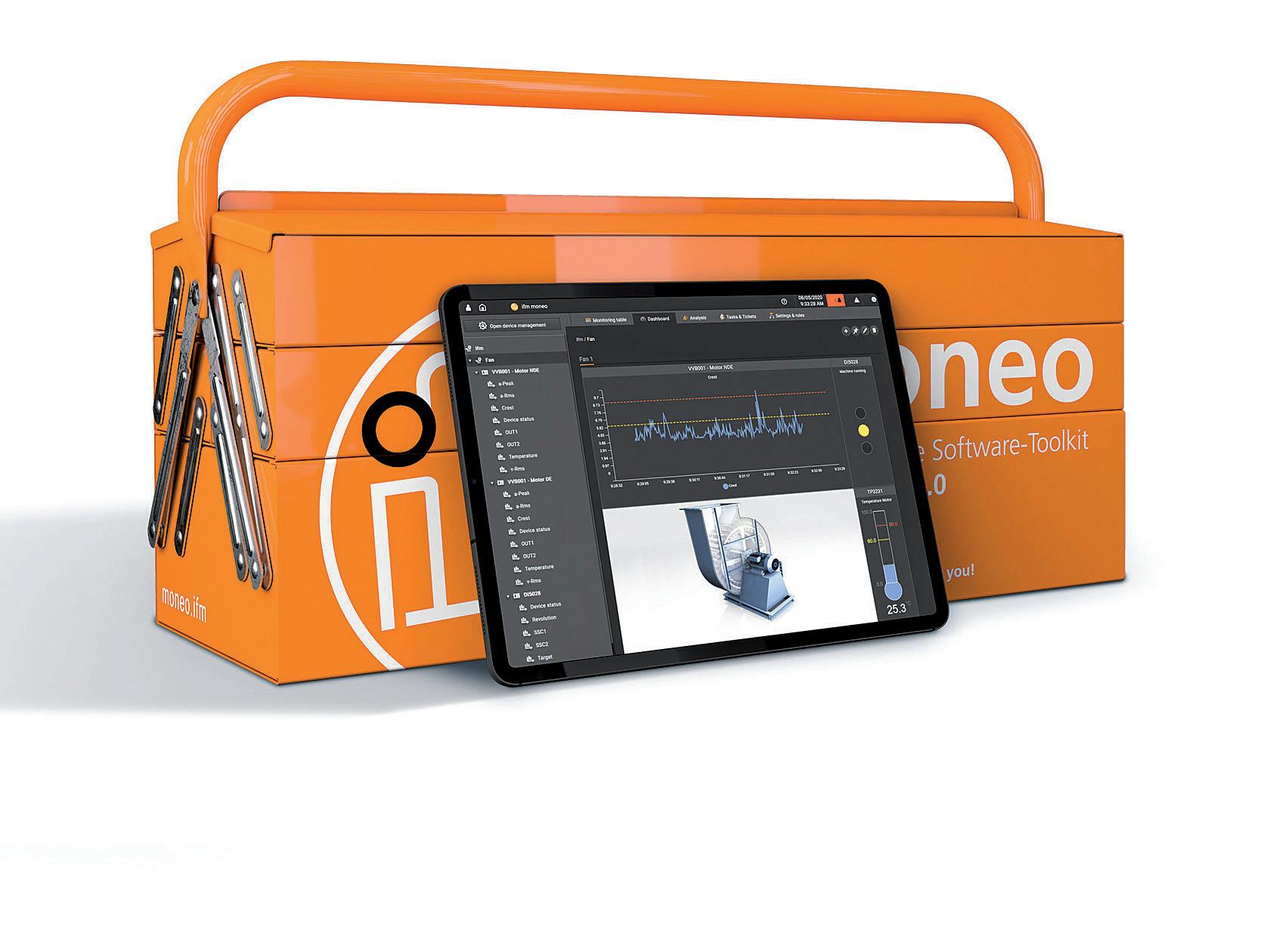
It’s often the case that engineers need sophisticated data analytics, but the data analysts within the company are often preoccupied in other domains of the business – for instance with financials or other corporate data beyond the manufacturing process floor. With Moneo, the power can be put back into the engineer’s hands, by providing sophisticated insights with respect to different sets of variables, without requiring the expertise of a pure data science person. The purpose of the tool is to monitor the critical process value (target variable) with regard to the production quality or the plant condition (e.g. temperature, flow, vibration, current consumption) on an ongoing basis.
and pull data from any platform, which is essential because oftentimes customers are dealing with legacy systems.”
The soft IoT tool helps engineers optimise manufacturing processes through early warnings and alarms.
The experienced ifm team will assess a particular business to understand its bottlenecks, identify inefficiencies and provide feedback on how they can improve.“Wewill then help them with building a proper scope by providing the right soft tools to make them more capable.”
“We really saw there are a lot of constraints an engineer will go through on this journey – where to start, what software tools to choose, how to design and understand the whole system,” he said. “ifm understands the common problems across all kinds of industry. This is more a unique service we do on-on-one for the customer.”
But in addition to breaking down external barriers between technologies, where Moneo excels is in its modular flexibility internally.
“It really resonates with industry because they are used to always having to consult with IT, but now the engineer can take back the power and do what they do best – trying to predict problems and fix things.”
Moneo converts sensor data into digital information, evaluates it and transmits it to the IT world.
“It’s easy to onboard devices themselves. Whether its temperature, pressure, flow, vibration, whatever the customer wants to monitor about the machines condition – they pull it into a five step wizard that will do all those things in the background, meaning they don’t even need to know anything about databases or data science.”
Consulting service
After seeing other IoT technologies fail to solve business problems, ifm is also offering its expertise and working with universities, to help students entering the industry.“Wewant to help people with their step into digital transformation,” he added. “Anyone can have the technology, but you always need to translate innovation into return on investment and gains in productivity.” Things
“The data science toolbox makes it easy for the engineer to start identifying problems,” Coertze said. “It’s easy to onboard devices themselves. Whether its temperature, pressure, flow, vibration, whatever the customer wants to monitor about the machines condition – they pull it into a five step wizard that will do all those things in the background, meaning they don’t even need to know anything about databases or data science.”
manmonthly.com.au Manufacturers’ Monthly SEPTEMBER 2022 43 Internet of
AI (assisted predictive maintenance) methods use a mathematical model based on historical data for a permanent target/ actual comparison between measured and predicted target values. This data enables the automatic and early detection of anomalies in a critical process value.
The adoption of IoT products and services has gained serious momentum over the last ten years in Australia. ifm now offers consulting to Australian businesses to help them fully profit from their foray into IoT, which was built out of a need in the market, said Coertze.
“The thing about Moneo is that you can focus its applications on various things – condition monitoring, process monitoring, energy monitoring. But one of the key applications – and strengths – is its Data Science toolbox.”
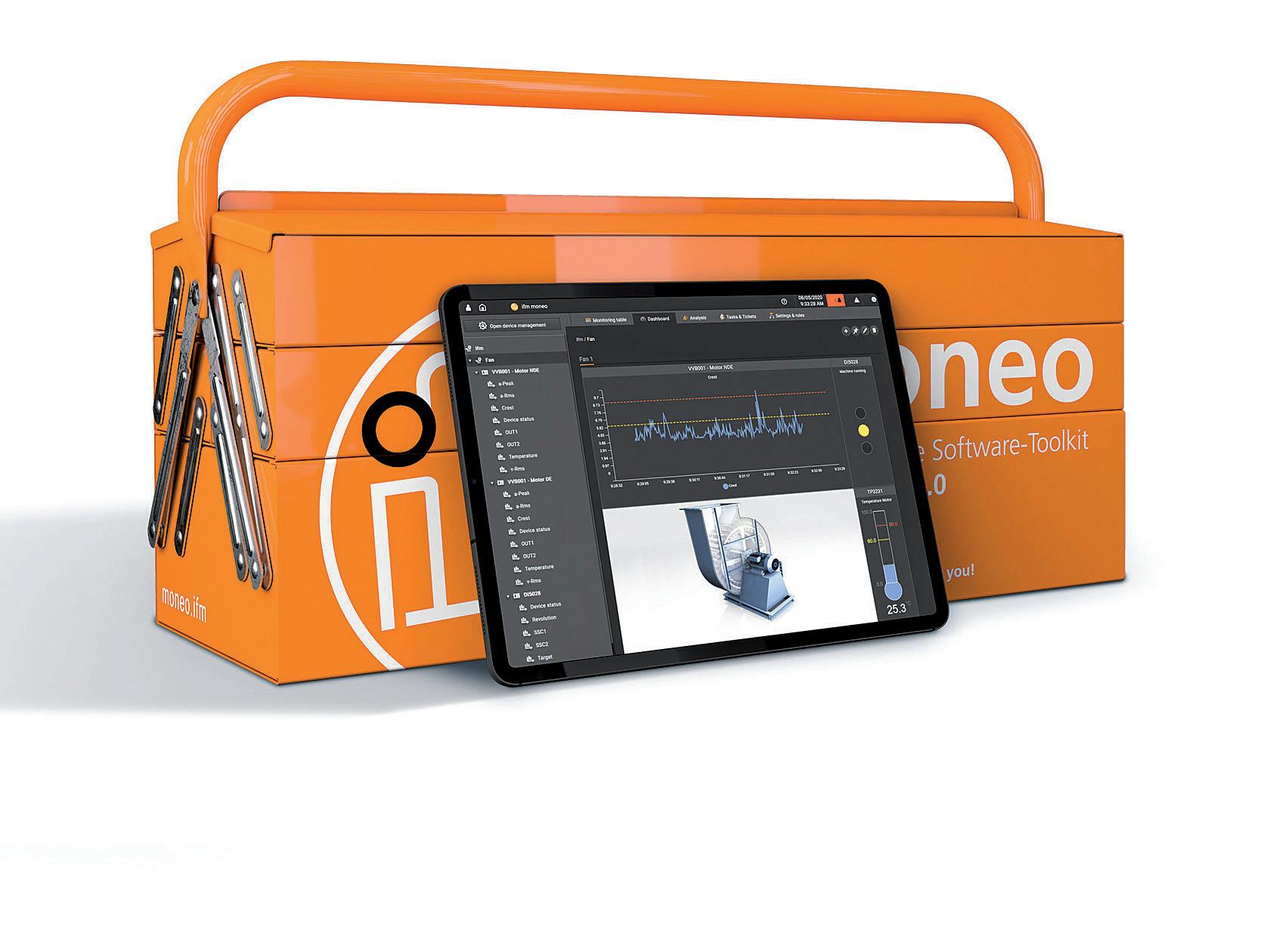
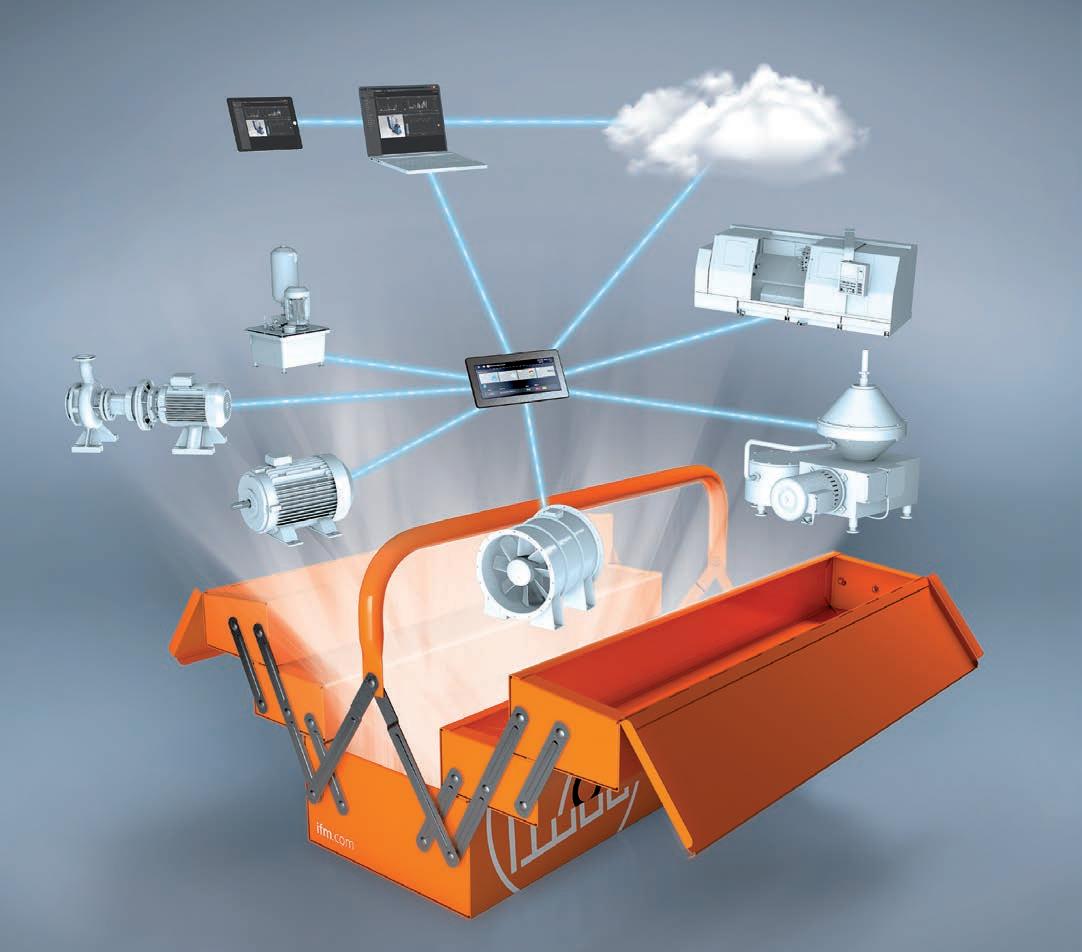
BOGE’s new DT refrigerant dryers ensure a stable pressure dew point, even in changing conditions. All models of the new DT series are characterised by low power consumption and low global warming potential.
All the models in the new DT series ensure a constant dew point of 3°C at a free air delivery of between 0.4 and 14 m³/min. With this strategy, the expert for compressed air systems ensures maximum delivery capability for its customers. Just like with the DS-2 series, the DT series refrigerant dryers all come with an “all-in-one” aluminium heat exchanger operated in a reverse flow process and containing a proven air/ air heat exchanger, evaporator and condensate drain.
Both BOGE refrigerated air dryer models DS-2 and DT-2 use the environmentally friendly and future-proof R 513 A refrigerant, with its low global warming potential, as standard, making all the Hermetically sealed refrigerant circuit The refrigerant circuit is hermetically sealed, rendering a leakage test by certified refrigeration engineer unnecessary.
Low global warming potential refrigerant
ROBUSTNESS, eco-friendliness and efficiency are the three main characteristics of the new DT series of refrigerant dryers from BOGE. The combination of innovative technology and intelligent control ensures a stable pressure dew point, even in changing environmental conditions. Thanks to the use of the future-proof refrigerant R 513 A as standard across the whole series, the refrigerant dryers are especially sustainable and have a low CO2 footprint. Additional advantages are energy-saving, reliable operation and numerous different monitoring capabilities. No compressor is without a refrigerant dryer – dry compressed air is required for almost any situation. In addition to the existing DS-2 series, BOGE has now launched a new range of products.
The new DT series of refrigerant dryers from BOGE Compressors combine climate protection with efficiency.
New BOGE refrigerant dryers for sustainable, reliable operations
44 SEPTEMBER 2022 Manufacturers’ Monthly manmonthly.com.au
Compressed Air
The hot gas/bypass valve present in all models keeps the pressure dew point at a constant 3°C, even in changing environmental conditions. As hot air is injected below a specific temperature, there is no danger of ice forming in the evaporator. And, in addition, the refrigerant dryer’s condensers are amply dimensioned, delivering reliable operation even for compressed air at an
Stable pressure dew point
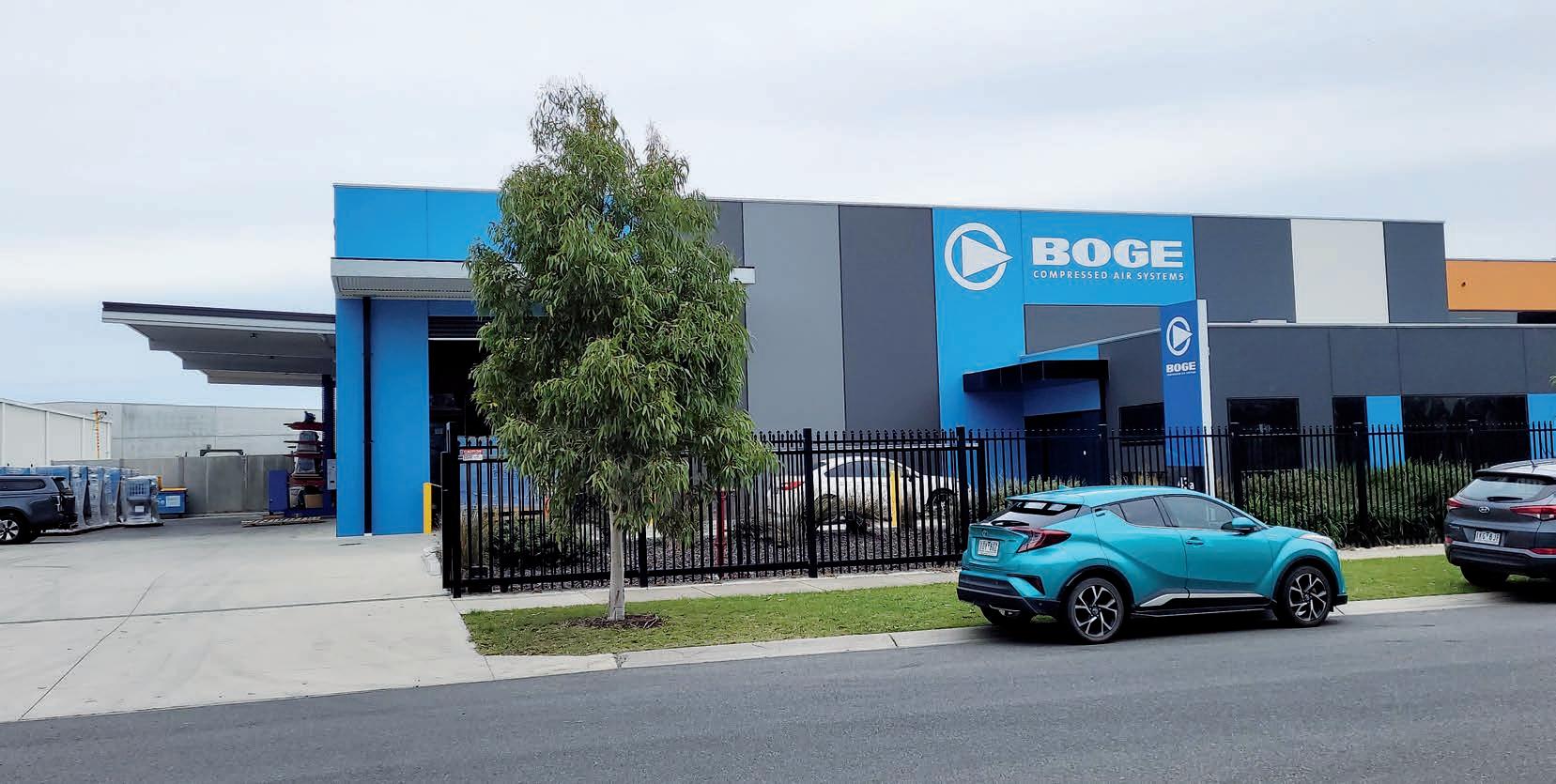
All models are characteristically low consumption. As the BOGE CCD 10 condensate drain used in the dryer has electronic level adjustment, any condensate that might form can be drained off without any pressure losses once a defined level has been reached. The DT 52 to DT 140 models offer even more savings potential: if the dew point is reached in partial-load operation, the control unit automatically switches off the compressor. The condensate in the heat exchanger then cools the compressed air until the dew point once again reaches the target value. Only once this happens does the cooling compressor come back on.
ensures maximum cooling air flow, which in turn has a positive effect on the pressure dew point. As a result, the refrigerant dryer is extremely robust and continues to operate even under the most challenging of circumstances.Allmodelsof the new DT series are characterised by low power consumption and low global warming potential. The new refrigeration dryers enable continuous monitoring of pressure and temperature via corresponding sensors. Control and reading take place via an LED status display. Reduced energy consumption
About BOGE Compressors
The new series from BOGE combines climate protection with efficiency.
manmonthly.com.au Manufacturers’ Monthly SEPTEMBER 2022 45 CompressedAir PREMIUM QUALITY HOISTING SYSTEM Production Electric Chain Hoists Heavy Duty Electric Chain Hoists High Demand Wire Rope Hoists
BOGE Compressors Australia Pty Ltd is a subsidiary Company of BOGE KOMPRESSOREN Otto Boge GmbH & Co. KG based in Germany. Whether for screw compressors, piston compressors, scroll compressors, turbo compressors, complete systems or individual devices, BOGE meets the most diverse requirements and highest standards – in a precise and quality-aware manner. BOGE solutions are used by all sectors of industry to supply compressed air for a wide range of manufacturing processes. The product is sold and serviced through a dedicated network of distributors throughout Australia and New Zealand. For more information, contact BOGE Compressors on (03) 5940 5913. Find your nearest BOGE distributor at www.boge.net.au.
Communication: Important parameters always to hand The refrigerant dryer’s control system permits continuous monitoring of the pressure and temperature thanks to a series of sensors. Unlike with the DS-2 series where a pressure switch disconnects the system in case of an emergency, in these new devices, the sensors take over the job. The pressure dew point can be quickly checked with the help of the LED status light. The new refrigerant dryers also come with a Modbus RTU/ RS 485 interface as standard, allowing you to detect alarm thresholds and display other relevant parameters. This data is then easy to forward onto an interlocking control device, master display or Building Management System.
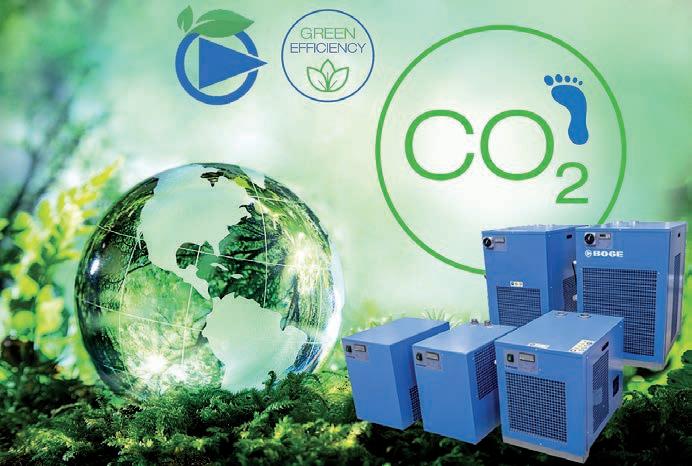
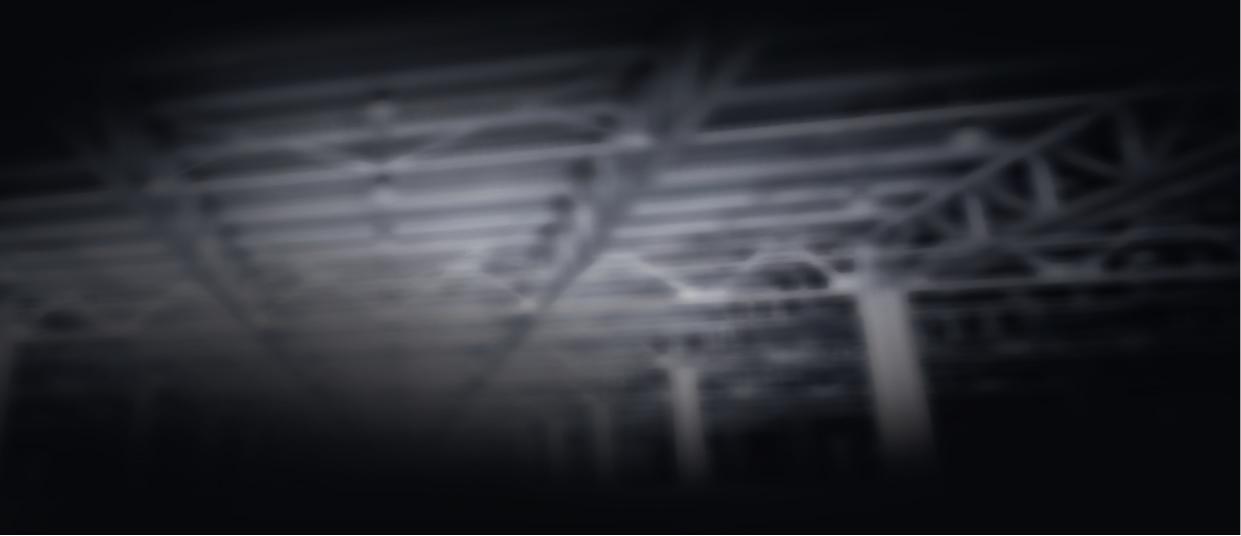

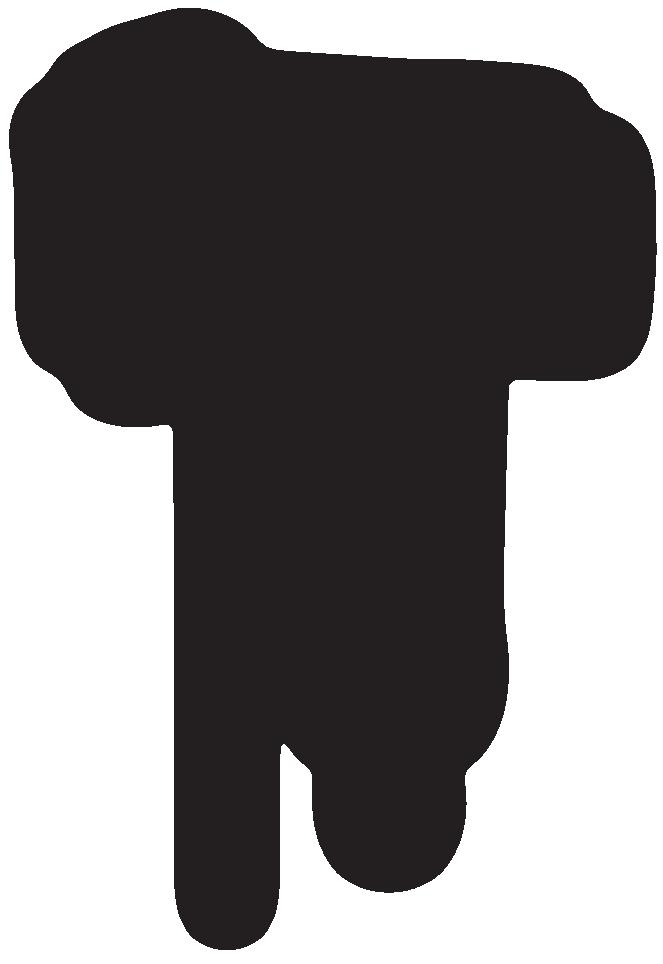

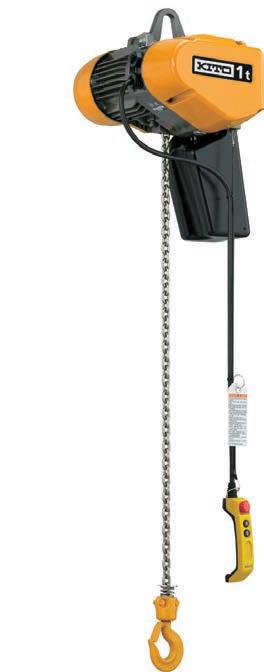
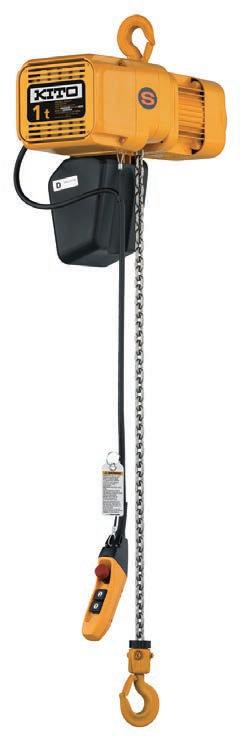

Whether it’s a finished wooden chair or hardwood floor, a wood-framed piece of art, or some beautiful exposed wooden beams that support the roof overhead –all of this begins at a sawmill where the wood is Australianprocessed.sawmills typically specialise in either a softwood such as radiata pine or a hardwood like Victorian ash or Tasmanian oak. For furniture and finished wood products, hardwood is the most common material of choice.
As a national distributor of industrial solutions, CBC has enjoyed a good working relationship with AKD for decades, according to Brian Crouch, senior accounts manager for CBC Geelong.“Ivisit AKD’s site every Friday
AKD was looking to upgrade the legacy couplings in their kiln, one of the key pieces of equipment on site used for drying and sorting the timber, according to Crouch. After heading out to site to take a look at the kiln’s existing couplings, Crouch recommended upgrading them to Regal Rexnord couplings to streamline productivity for the drying and sorting process.“The application is a high-heat and damp environment due to the organic nature of the timber logs,” explained Crouch. “I chose the Rexnord couplings high temperatures and moisture. I felt confident that the client would see an improvement and the solution turned out to be very successful.”
Gone are the days when timber milling was a backwoods operation. Modern timber processing mills like AKD now use advanced AI and automation processes to streamline their operations, according to Crouch. But that doesn’t discount the importance of monitoring every piece of equipment in the mill.
For more information about industrial solutions for sawmills and the timber processing industry, visit your local CBC branch today.
AKD thinks of timber processing and owning their own plantations as a form of environmental caretaking because the trees they harvest filter carbon from our ecosystem and lock it into the timber products they produce.
“The average Australian home uses about 14 cubic metres of structural pine which stores the carbon for the structure’s service lifetime – timber truly is The Ultimate Renewable resource and helps fight climate change,” Gatt said. “We plant and harvest, only to replant.”
AKD’s process from “stump to store.” “We take a long-term view when we establish a crop of trees. To produce the required strength characteristics in sawn timber for construction, it takes careful nurturing and tending until the trees are at least 30 years old at time of final harvest,” he said. “It all starts with growing a healthy right genetics in plant selection, and having the right planting spacings, weed control and nutrition regimes to allow for improved survival in the field in the early years. The young trees are planted in dense forests of up to 1,400 trees per hectare where they are closely monitored for health and hydration throughout the growing process.”
Branching industrial solutions for a local Australian sawmill
Industrial Solutions
Now more than 65 years old, Associated Kiln Driers (AKD) is today one of the largest softwood sawmilling businesses in Australia – supplying quality plantation pine products to timber merchants, retailers, fabricators and other manufacturers nation-wide. Employing more than 1,100 people across their Australian operations, AKD’s purpose is driven by a need to create opportunities for their employees, supported by a strong foundation of teamwork.“Allofthe team at AKD share a common purpose in creating a company that is truly sustainable and provides value to the world in high-growth sectors such as building and construction. And all of this begins with our planting process,” AKD resources manager Simon GattGattsaid.explained
“Every piece of wood is different and needs to be scanned to determine its strength, structure and any internal defects before being processed with the milling equipment,” he said. “Refining milling equipment to perform at the highest standard of operation ensures the production of optimal wood products.”
Although it’s easy to take for granted in daily life, much of the world is constructed from wood.
As one of the largest softwood sawmilling businesses in Australia, Associated Kiln Driers (AKD) is committed to creating sustainable value in high-growth sectors through its planting process.
getting involved in projects around the site, identifying existing or potential problems with equipment and looking for ways to improve the overall performance of their machines,” Crouch said.“AKD has state-of-the-art timber processing facilities including two timber mills and a woodchipper that operate on advanced AI and automation technology. I have had to familiarise myself with their equipment in order to provide more high-level engineering solutions for Recently,them.”
As a wholly Australian owned and operated integrated forestry and timber processing company, AKD has plantations and operations lined along the East seaboard in VIC, NSW and QLD.
46 SEPTEMBER 2022 Manufacturers’ Monthly manmonthly.com.au
AKD resources manager Simon Gatt explained the planting process, from stump to store.
Whereas, for residential and commercial construction products– such as wall frames, roof trusses, beams, studs, and posts – softwood is primarily used.
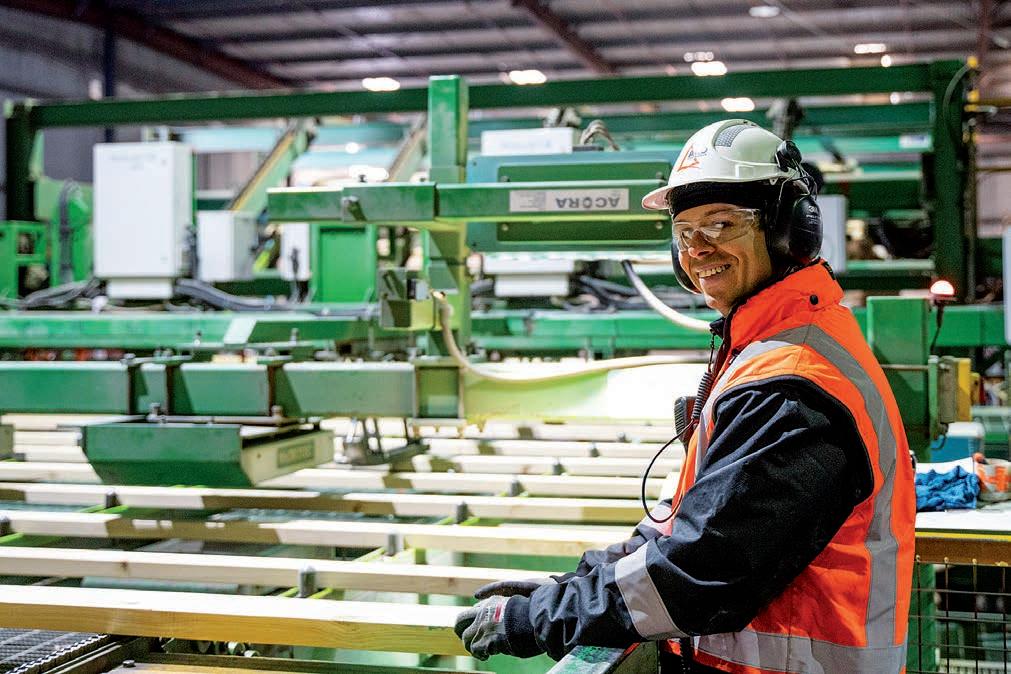
Industrial Solutions
Timken’s catalogue is founded on superior wear performance, but it’s the uniquely bevelled link plates and proprietary lubrication that make the Diamond® Agriculture Roller Chain stand out. The Diamond Difference begins with raw materials that meet exacting standards for metal grade, mechanical properties, carbon and alloy content to ensure minimisation of impurities that impact tensile and fatigue strength.
OEMs of harvesting equipment need to have confidence in the reliability of their designs, which means sourcing the best in power transmission genuine parts.
When it comes to agricultural equipment, machinery is only as strong as the agriculture chain that keeps it running. Manufacturers’ Monthly finds out why OEMs of harvesting equipment are utilising the Diamond Chain.
Featuring precision-ground pins, seamless rollers, and extruded solid bushings, this chain also undergoes a shot peening treatment to add a layer of compressive stress. Shot peening aids in mitigating fatigue failure when the part is exposed to repeated high loads. With the understanding that adequate lubrication can significantly extend a chain’s life, Diamond® have introduced a ‘hot dip’ process for enhanced corrosion protection. This initial lubricant technique incorporates protective additives to allow complete internal penetration and uniform exterior coverage.Additionally, all chains are preloaded to 50 per cent of their ultimate tensile strength, to firmly seat the pins and bushings. This process reduces initial run-in, and extends the service life of the chain. According to Sean Young, Regional General Manager at Timken, these unique design elements are the result of fieldbased research and design adjustments over many years.
“I have been with Motion Australia for 40 years, and over that time I’ve built a very strong rapport with the team at Timken,” he furthered. “We work collaboratively on customer projects every week, and I’m on the phone to them almost every day to discuss supply logistics. What we bring to the table from a sales and customer knowledge perspective, they deliver on quality and reliable product without fail.”
Diamond is a farmer’s best friend
manmonthly.com.au Manufacturers’ Monthly SEPTEMBER 2022 47
“Even before coming under Timken, the Diamond brand has been around for a long time, doing a lot of work on specialised applications for OEMs,” he said. “That history within Australia’s market is invaluable, and it gives our engineering teams a strong foundation from which to approach complex scenarios.”Forwell over 50 years, Timken has worked closely with Motion Australia to provide end-to-end solutions for a range of industrial sectors. According to Sean, a shared commitment to result-driven servicing helps both parties to understand customer processes and deliver excellent results.“Our experienced field crew work closely with Motion Australia’s product experts to implement fit for purpose power transmission componentry. We spend a lot of time liaising as a team to support customers, which we know significantly benefits the end user long-term.
Founded in 1890 as the Indianapolis Chain and Stamping Company, Diamond® Chain has been involved in many revolutionary feats of industrial design, including the Wright Brothers’ first motoroperated aircraft flight, and Henry Ford’s conception of automotive drive units. In 2019, Diamond® Chain was acquired by Timken – a global leader in engineered bearings and power transmission. As a Strategic Supply Partner (SSP) with Motion Australia, Timken is an established provider of critical machinery parts, such as the Diamond® Series Agriculture Roller Chain.“Timken are well-known for their outstanding catalogue of bearing products,” said Troy Markland, National Product Manager for Power Transmission at Motion Australia. “The Diamond® acquisition expands their power transmission offering, allowing them to carry a more full-spectrum solution package to agricultural equipment manufacturers.”Rollerchainis utilised to transmit torque between two sprockets of equal or dissimilar sizes. For agricultural applications, where environmental factors such as water and dust need to be factored in, Diamond® offers stainless steel, nickel or zinc plated and anticorrosion designs.
This chain is a highly valued component for harvesting equipment such as bailers and headers. The improved wear life of 30 to 40 per cent means that when they put these chains into application, they are going to last the full season.
“This chain is a highly valued component for harvesting equipment such as bailers and headers,” said Markland. “The improved wear life of 30 to 40 per cent means that when they put these chains into application, they are going to last the full season.”
Diamond brand products are made in America and held to a tighter range of performance than cheaper alternatives.
“This chain is incredibly popular, because the Diamond® brand has a strong reputation within the national market,” explained Markland. “We work hard to keep up with the demand, and have had to increase our ordering quantities for the agriculture sector every year.”
THERE are few environmentsworkingquiteas rugged as rural Australian farmland. While the nation is well known for its cattle rearing and dairy production, the soil and climate diversity also lends itself to the growing of valuable crops such as grapes, almonds, and olives. Agricultural activities account for over half of the country’s land use, with the production and export of fruit and vegetables on a steadyBecauserise. of the extremely timesensitive nature of the annual harvesting cycle, many of these agricultural operations simply cannot afford equipment break-down in the field. Every second that an olive or almond lies neglected on the ground, it decreases in value and quickly becomes unsellable.
“Rather than just selling a box off a shelf, Motion Australia works with us to inform these customers on our product value, which gives them the confidence to rely on us in the future.”
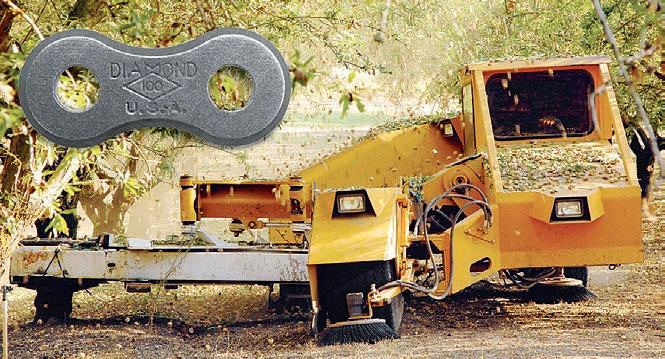
IN PARTNERSHIP WITH AUSTRALIA’S LEADING MANUFACTURING AWARDS NOW ON SALE
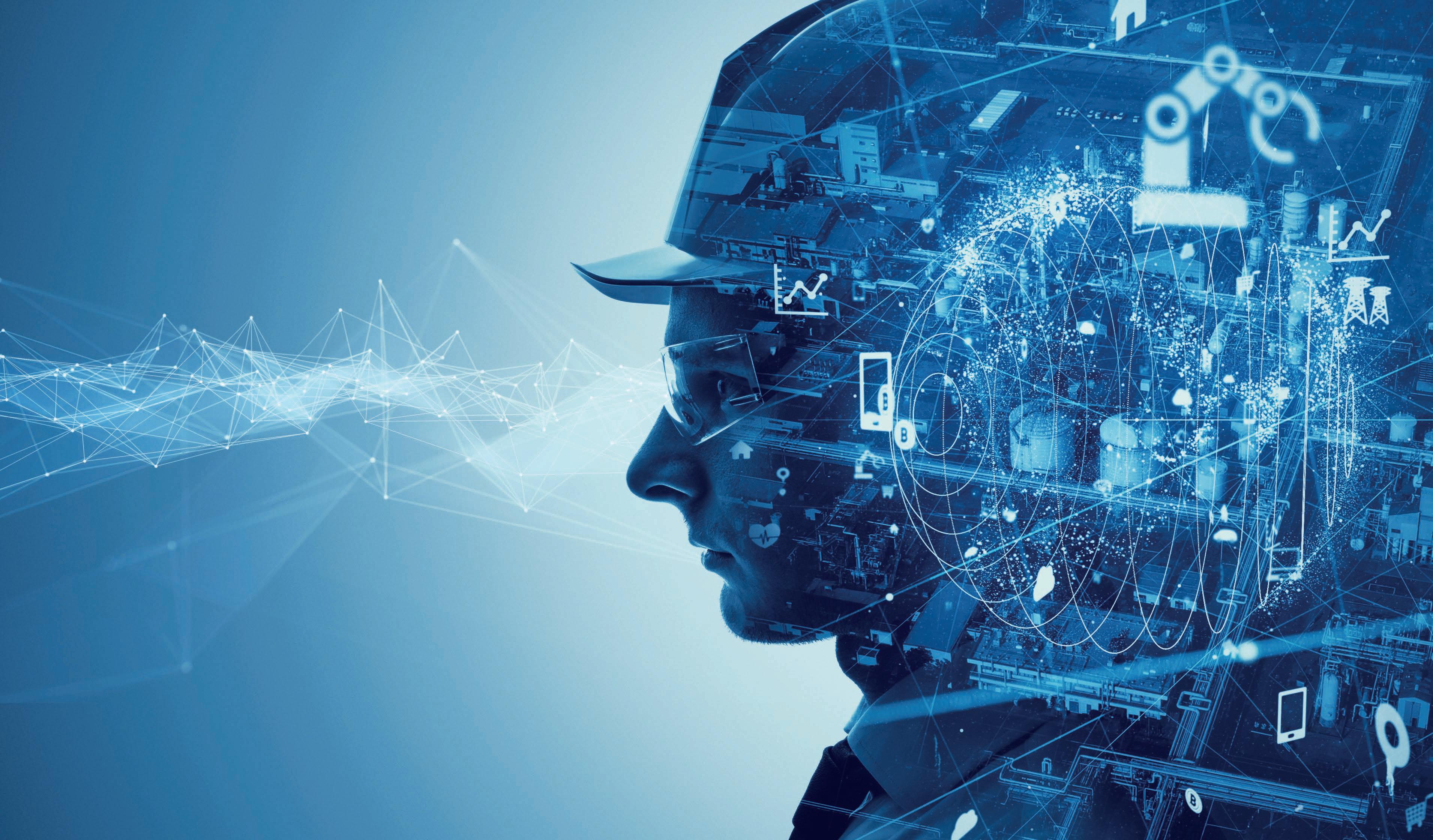
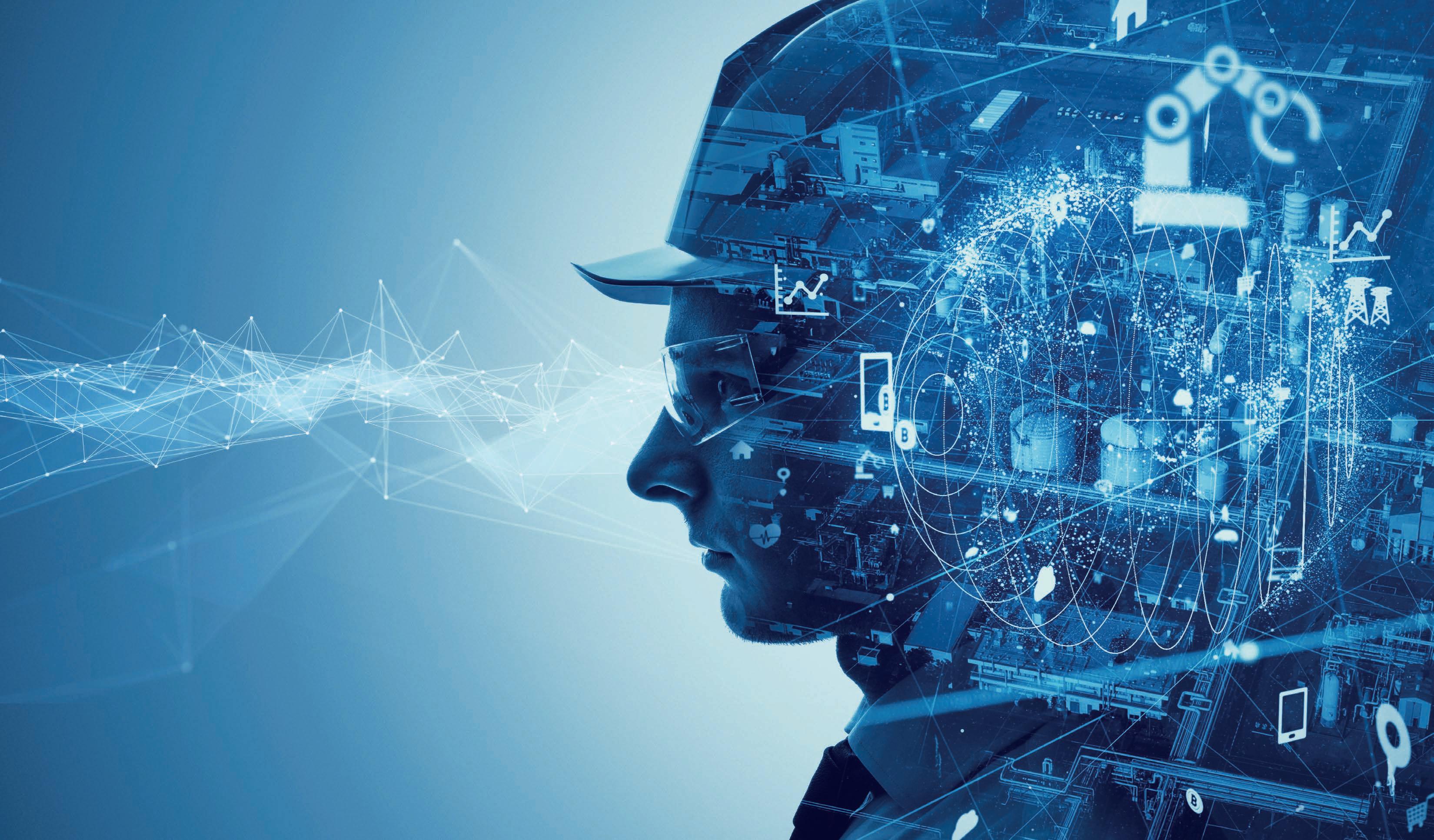
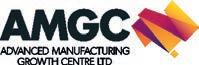
The Port Rail Transformation Project will make rail transport more competitive, cut the high cost of the last mile and reduce truck congestion at the port gate. It will boost rail’s share of the port’s transport task, which currently sees fewer than 10 per cent of containers handled by rail. It will also form a crucial part of the Victorian government’s plans for a shorthaul rail network connecting freight hubs in Melbourne’s north and west to the port.
The Victorian government has partnered with the private sector to develop the network. Operators of terminals located at Altona, Somerton and Dandenong South have been selected to build the new rail sidings and connections needed for the efficient operation of the network.Victoria will also be seeking additional interstate rail capacity to capitalise on the benefits being delivered by the Inland Rail Project.TheVictorian government is planning for a new intermodal freight precinct at Truganina in Melbourne’s west. The Melbourne’s outer north for development in the longer term. Victoria’s freight volumes are expected to grow to around 900 million tonnes annually by 2050, up from around 400 million currently. The new intermodal precincts will perform a key role in handling this forecast increase in the state’s freight volumes.
The Port Rail Shuttle Network will be key to the Victorian government’s plans to deliver importers and exporters new efficiencies in their supply chains by moving more freight onto rail. Rail has been underutilised in Melbourne for short-haul freight operations, with the entire metropolitan Rail is also seen as critical to the Port of Melbourne’s future success as container throughput triples by 2050.
• Lack of space to store and handle containers • Conflicts with competing land uses Road connections that generate amenity issues for nearby residential areasRailconnections that preclude double stacking of containers on trains A track layout that limits the efficient handling of longer trains. In the longer term, the development of new intermodal freight precincts will: Significantly improve the capacity of interstate freight transport in the north-south and east-west national corridorsComplement other improvements to the north-south intermodal rail supply chain with matching capacity and service level improvements Enhance national productivity by lowering the door-to-door cost of freight for interstate movements Create opportunities for urban renewal in the North Dynon area Reduce truck movements through Melbourne’s inner west Improve rail access for port-related freight by removing many nonport freight movements from the Dynon precinct.
manmonthly.com.au Manufacturers’ Monthly SEPTEMBER 2022 49
The proposed Port Rail Shuttle Network will establish terminals in the city’s west, north and south-east, where import containers are railed prior to delivery by road to their final destinations.Theproposed network promises an efficient and cost-effective alternative to road transport, as well as catering for empty containers and potentially interstate freight.
A cement train in Toorak. The Pacific National container train at West Footscray.
Supply Chain
The co-location of warehousing, distribution centres and other associated is handled mostly within the Dynon freight precinct. Dynon has a number of limitations that preclude a significant increase in capacity. They include:
T he investment will deliver new sidings and rail connections to Swanson Dock – home to two of Victoria’s three stevedores. Improving rail access to the Port of Melbourne was a legislated condition of the port lease negotiated between the Victorian government and the port’s new owners in 2016.
& Logistics
Port of Melbourne invests in rail infrastructure
The Victorian state government tells Manufacturers’ Monthly why exporters will be the big winners from Port of Melbourne’s investment in new rail infrastructure.
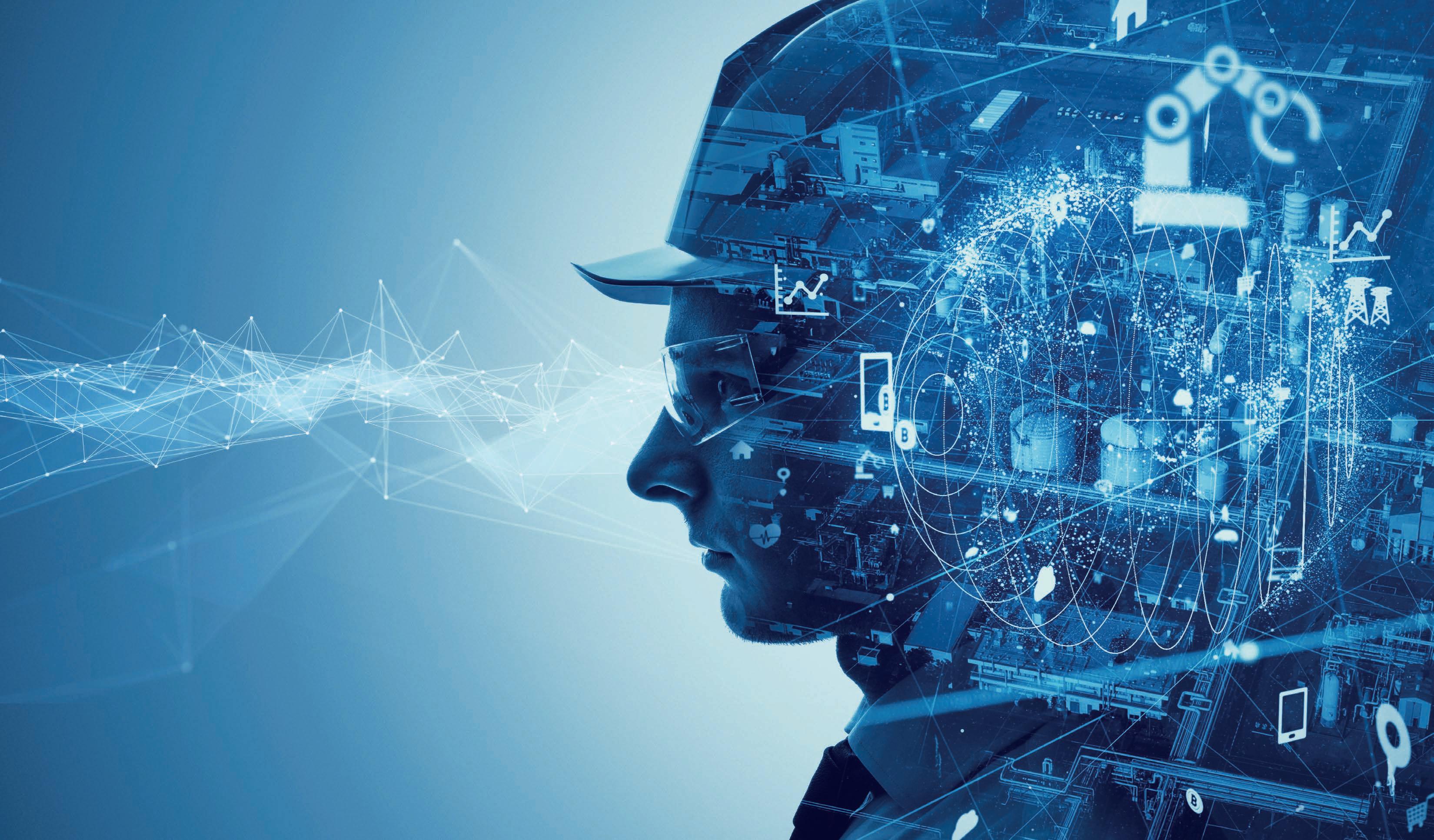
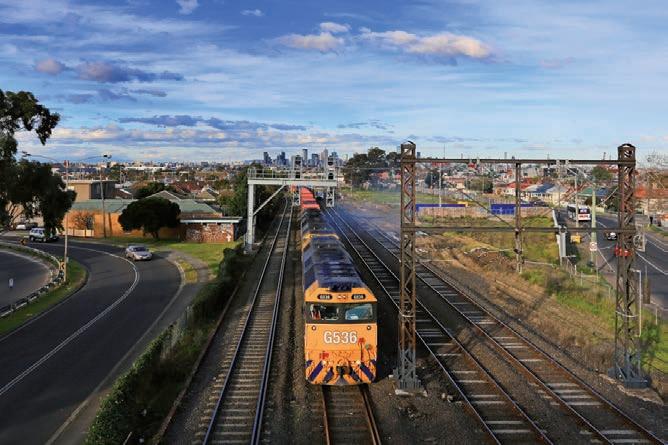
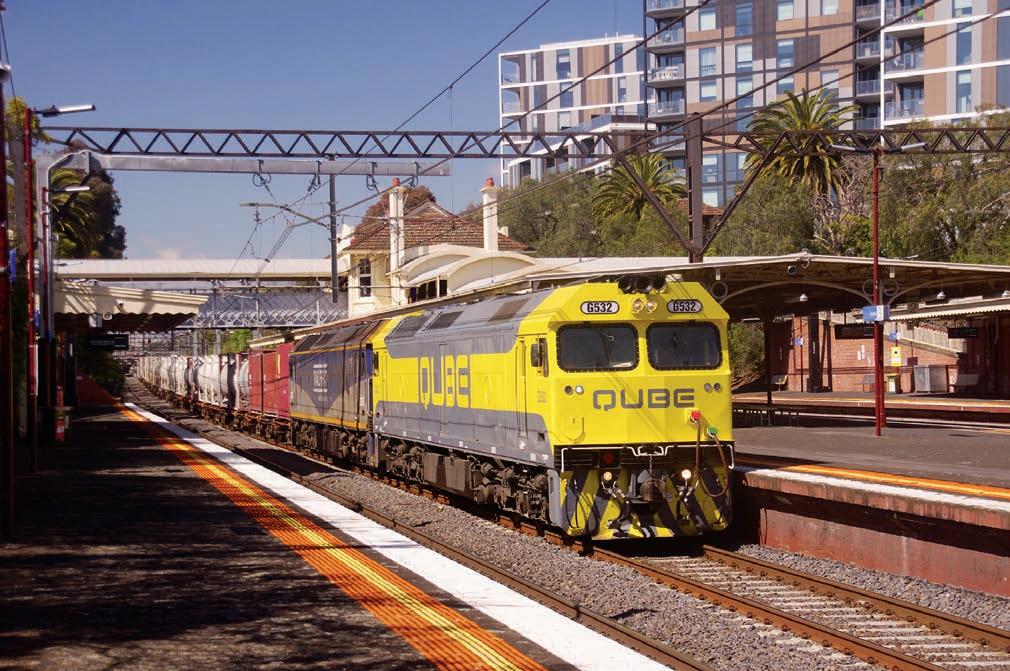
to the
•
Compressed air drives your processes and with it, the operational efficiency and performance of your company. Ceccato kept this principle in mind when designing the DRD IVR PM Screw Compressor. The oil-injected screw compressor with iPM motor technology offers your business a compressed air solution that adds value while also saving you money at the same Ceccato’stime.DRD IVR PM Screw Compressor can provide many user benefits to your production. These user benefits include: Minimal energy costs; User-friendly operation and maintenance; Reliable productivity and operational efficiency; Simple installation; A peace of mind investment. Ceccato understands energy costs represent about 70 per cent of the total operating cost of your compressor over a five-year period. That is why a major focus to your compressed air installation should be to efficiently reduce energy consumption. A variable speed compressor is superior to a fixed speed compressor in terms of energy savings as it perfectly matches air supply to air demand and avoids unload losses.
Company: Ceccato Compressors Australia Phone: 1300 555 284 Website:
and •
•
level
Xxx 50 SEPTEMBER 2022 Manufacturers’ Monthly manmonthly.com.au Brought to you by Neousys Technology, an industry-leading provider of rugged embedded systems, has unveiled the Nuvo-8111 series. Nuvo-8111 series is an expandable platform that features 4x PCIe/ PCI expansion slots. Compact and rugged in design, it supports up to a mid to high-end GPU for edge AI performance.Formachine vision applications, install a PCIe-Poe425bt, a 4-port 2.5GBASE-T with 802.3bt PoE++ PSE capability, or a PCIe-PoE454at, a 4-port 5GBASE-T frame grabber with 802.3at PoE+ to supply up to 90W of power to the end device, and turn the system into a powerful system for advanced factory automation, image recognition, product inspection, pick and place robots, and more.
•
The DRD IVR PM range combines Ceccato’s Imperium variable speed technology with their highly efficient drive train with iPM motor technology. They have evolved the energy efficiency of variable speed compressors to a new level, resulting in energy savings of up to 45 perWithcent.smart technical advantages and an innovative drive train technology, the DRD IVR PM is a revolution in the compressed air industry. With this revolutionary screw compressor, you can optimise your operation for superior productivity and quality. Take your performance and energy efficiency to new heights with technology you can trust.
Company: Neousys Technology Phone: +886-2- 2223-6182 Website: Neousyswww.neousys-tech.com/enTechnology releases the Nuvo-8111 series
Takewww.ceccato.com/en-auyourcompressed performance next
air

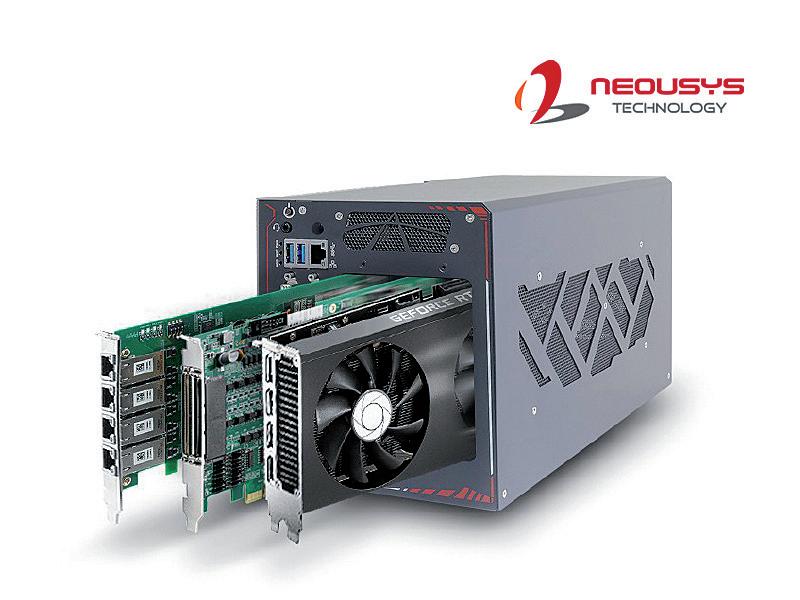
The ETIM product data model in Australia and New Zealand
Motor protection & motor control Contactors, overload protection relays, motor circuit protection breakers, soft starters, variable speed drives.
manmonthly.com.au Manufacturers’ Monthly SEPTEMBER 2022 51 LINDSAY LE COMPTE – General Manager (Construction and Infrastructure), Ai Group The Last Word
ETIM is a technical information model that enables manufacturers to upload technical data about their products into a common classification system so that building designers, builders, subcontractors and clients may easily understand and compare the technical aspects of individual, or groups of, products.Whether a business operates as a manufacturer, wholesaler or end user, the ETIM model enables quick, concise identification and data exchange between internationally operating parties, regardless of language. The model is in operation in over 20 countries. It is managed at a global level by ETIM International with chapters established at the local level to manage the conversion and operation of the model across jurisdictions. For manufacturers, having the technical data relating to their products contained within the ETIM international data standard is a significant benefit to their export capability, in addition to making it easier for local purchasers to identify what products work for Classificationthem. is a clear-cut way to logically structure product data. The ETIM model provides such a structure for technical products and ensures uniformity in shared product information. It includes the following categories or entities: Product groups • Product Synonymsclasses(Keywords) • VFeaturesalues • TheUnitsETIM model will be applied firstly to products in the electrotechnology sector followed by plumbing and heating, ventilation and air conditioning. The standard is also adaptable for general building products and tools. The ETIM Australia and New Zealand Chapter is supported by a group of Founding Members which reads like a who’s who of the electrotechnology manufacturing and distribution sector. These companies include ABB, APS Industrial, Eaton Electrical, Hager Electro, Legend Corporation, Legrand Australia, Metal Manufacturers Pty Limited (MMEM), NHP Electrical Engineering Products, Nexans Olex Australia, Phoenix Contact, Prysmian Australia, Siemens, Sonepar (Lawrence and Hanson) and Weidmuller.Addingstructure to the flow of technical information within the value chain, the ETIM model facilitates effective interaction between B2B professionals worldwide, which is why it is attractive to electrical wholesalers and distributors currently struggling with a myriad of different technical specification sheets and information relating to the products they sell. Selecting the right product solutions has never been more straightforward.ETIMisalsoadding a 3D process to its classification system. ETIM Modelling Classes (ETIM MC) is an extension to the basic classification model, specifying parameters for representation of products as 3D geometric objects. ETIM MC enables the uniform exchange of 3D product data among users and CAD software. It was purposefully developed as an extra layer around the core model, leaving the basic model untouched. In other words, no added complexity if you only use the basic ETIM classification! All of this bodes well for the effective implementation of Building Information Modelling (BIM) within the Australian and New Zealand construction sectors.TheETIM data model will be converted for use within the Australian and New Zealand jurisdictions by groups of industry experts working under the auspices of the Chapter’s Technical Committee.Thefirst two product areas to be addressed will be Power Distribution & Protection and Motor Protection & Motor Control. Other areas to be assessed include Industrial Components & Wiring Devices, Industrial Automation & Control and Energy Efficiency & Lighting. The likely scope of products within these areas include:
FOR many manufacturers, the acceptance of product classification is growing steadily with today’s extensive possibilities to compare products online a reflection of customers worldwide demanding transparency. Aspects of quality, delivery, reliability, logistical performance, pricing and supplier expertise are equally important in this regard. Digitally providing such objective and comparable product information saves all parties involved precious time – and therefore money. With this in mind, the national employer association Ai Group has partnered with ETIM International to launch ETIM Australia and New Zealand, which will be a game changer for the construction industry and its related manufacturing and distribution sector.
A final significant benefit of the ETIM model being implemented in Australia and New Zealand flows from the fact that it is free for industry participants and other users. The only cost will be a subscription fee for businesses to apply the model to their products and have a say in the future of the model in Australia and New Zealand through membership of the Chapter. Further information about ETIM Australia and New Zealand may be found at www.etim-aunz.com
Industrial components & wiring devices Enclosures, signaling (sight and sound), cooling and heating, timers & relays, push buttons and pilot lights, wire, cable and conduit, termination & wiring systems. Industrial automation & control Micro and modular programmable controllers and smart relays, motion, visualisation and reporting software, operator panels, industrial computers, gateways and networks. Energy efficiency & lighting Metering, CT’s, transducers, EV, power quality, building automation, solar, emergency lighting, commercial, industrial, LED and exterior lighting. Expanding the list of products available under the ETIM model, or making adjustments to the model, will be as simple as completing a request form to ETIM Australia and New Zealand.
The ETIM modeal allows manufacturers to upload technical data about their products into a common classification system.
Power distribution & protection Panel boards, power distribution chassis, load centres, circuit protection (MCB, RCD, MCCB and ACB etc.), earth leakage protection, switchboard monitoring, fuses and fuse protection, surge protection, transfer switching, switches (covering load break switches and isolators; GPO’s, plugs and sockets.
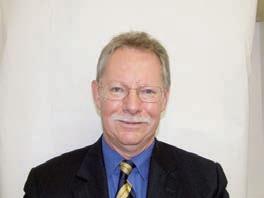
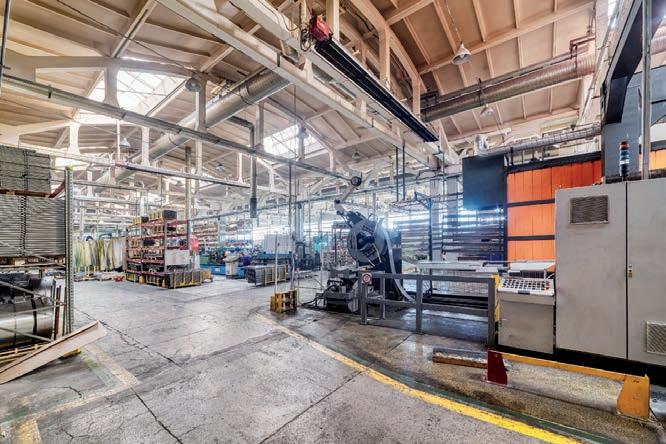
Predict and protect with Moneo ifm supports your journey into future proofing your operation The path to predictive maintenance just got easier with ifm. How much does it cost per hour for your machine to be offline? Moneo gives you the pre-packaged smarts to set up predictive maintenance at your plant. We’ve made it easier to protect your critical assets – both now and in the future. Knowing the condition of your machinery gives you peace of mind. It also allows you to perform maintenance at optimal times. The smart way to monitor your equipment 1300 365 088 sales.au@ifm.com | www.ifm.com/au


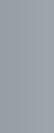






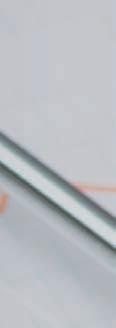
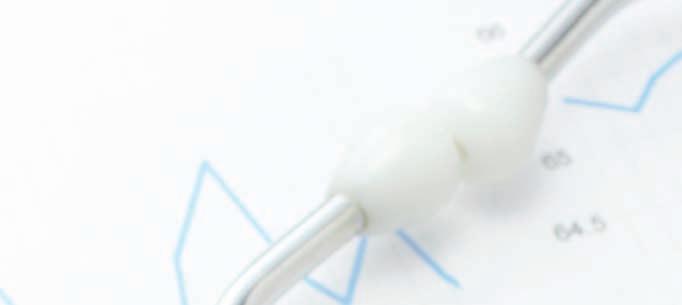
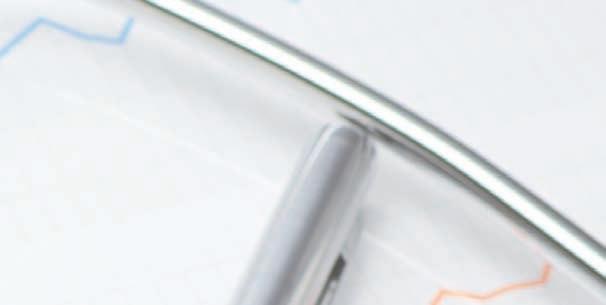
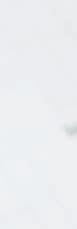
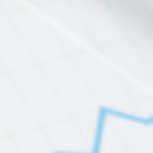

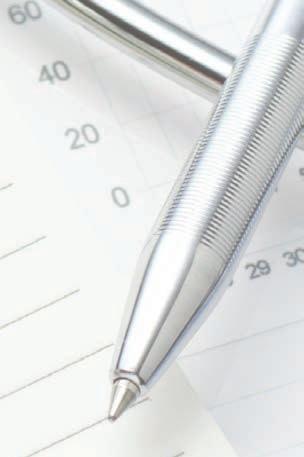
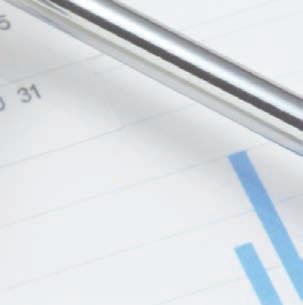
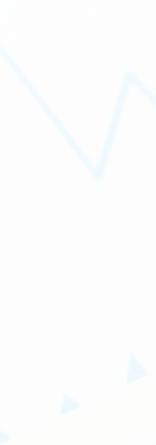

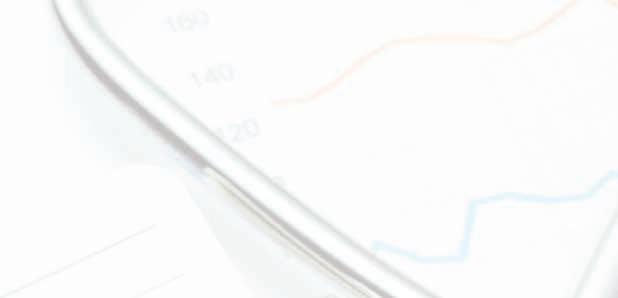

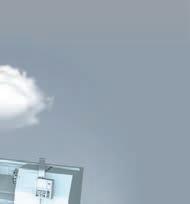

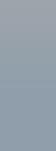
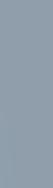
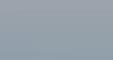

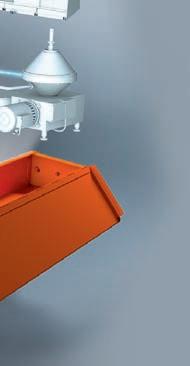
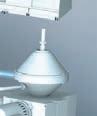
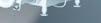
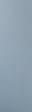





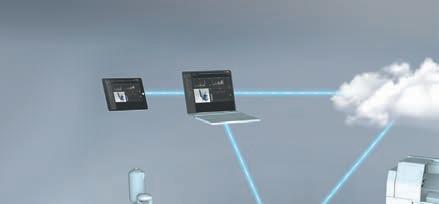

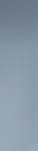
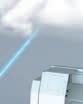
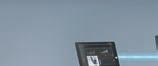




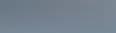

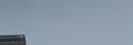


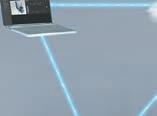
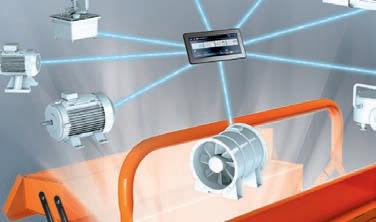
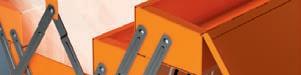
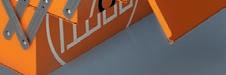
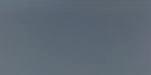
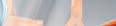

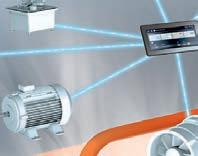

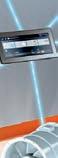
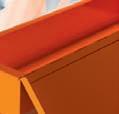


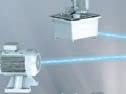
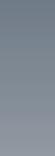
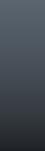
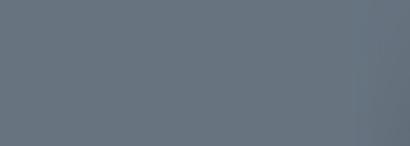
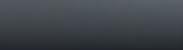
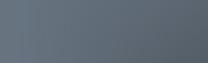
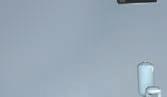

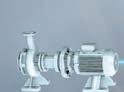
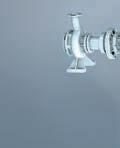

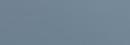

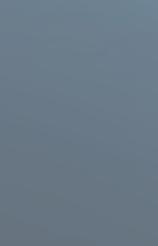

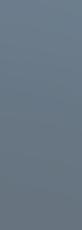
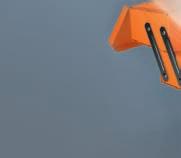

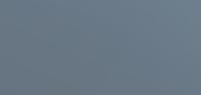
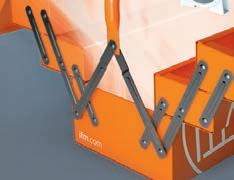
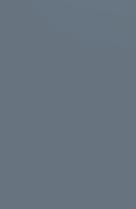
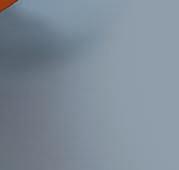
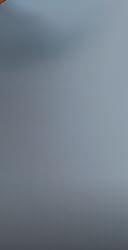
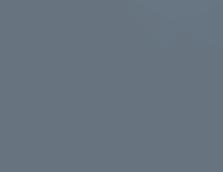


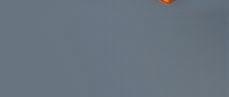

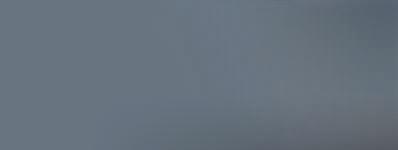

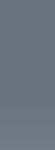
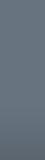
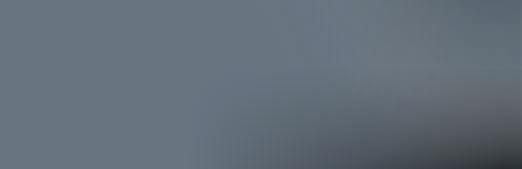

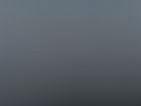
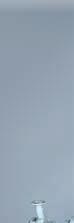
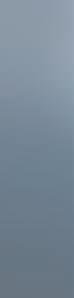
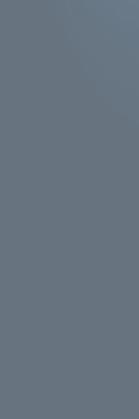







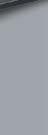
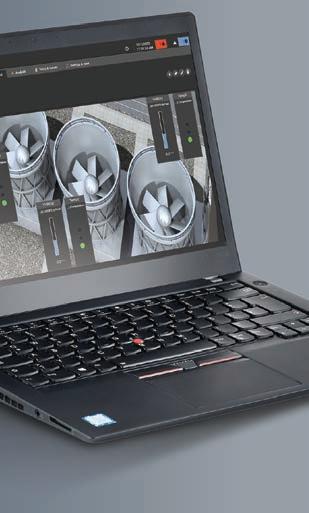
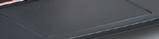
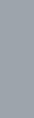
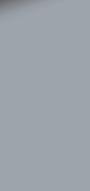

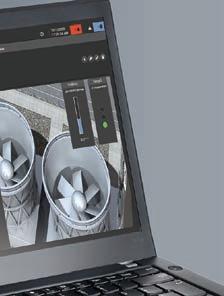
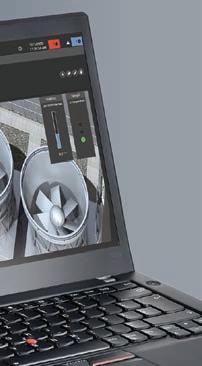


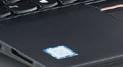
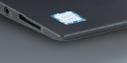



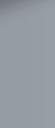
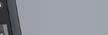



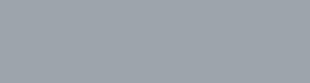


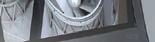
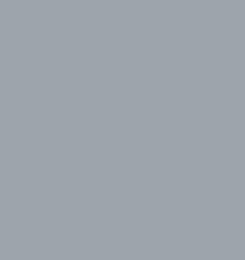
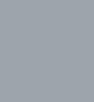

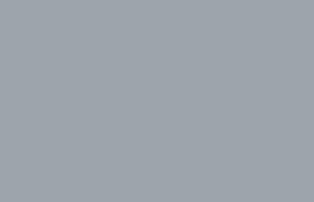

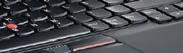

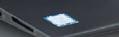






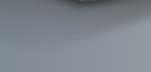




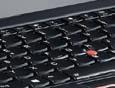

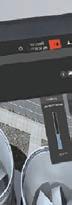
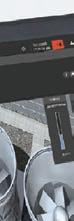
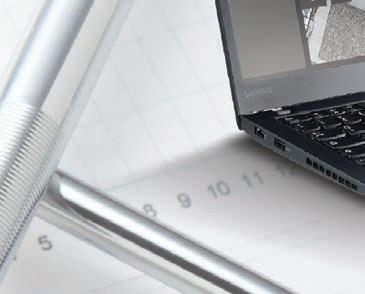
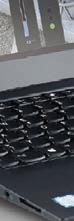
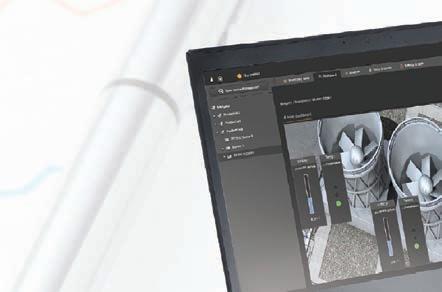
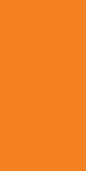
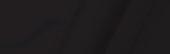
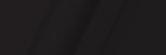

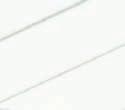
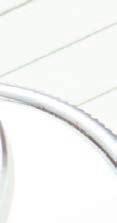
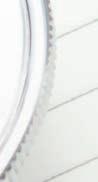

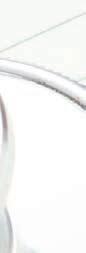
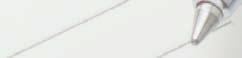

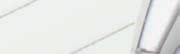



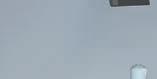

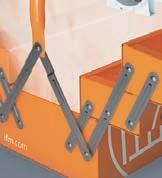
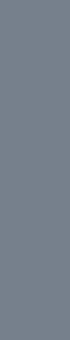


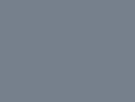




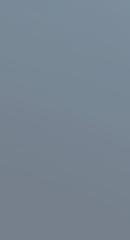



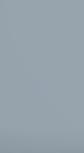
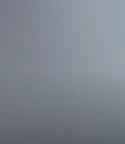



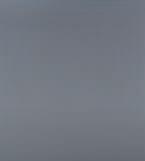

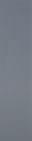
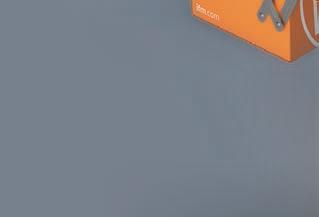


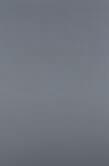
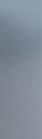



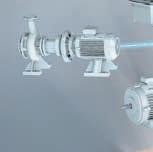

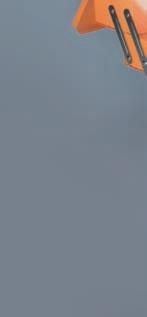

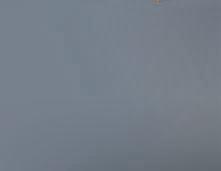



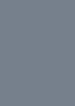



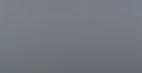








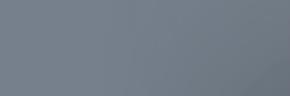

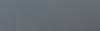

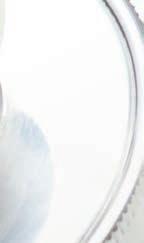
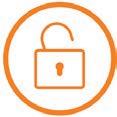





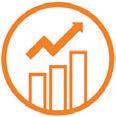
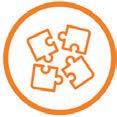
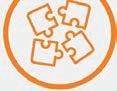
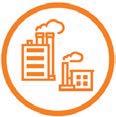

