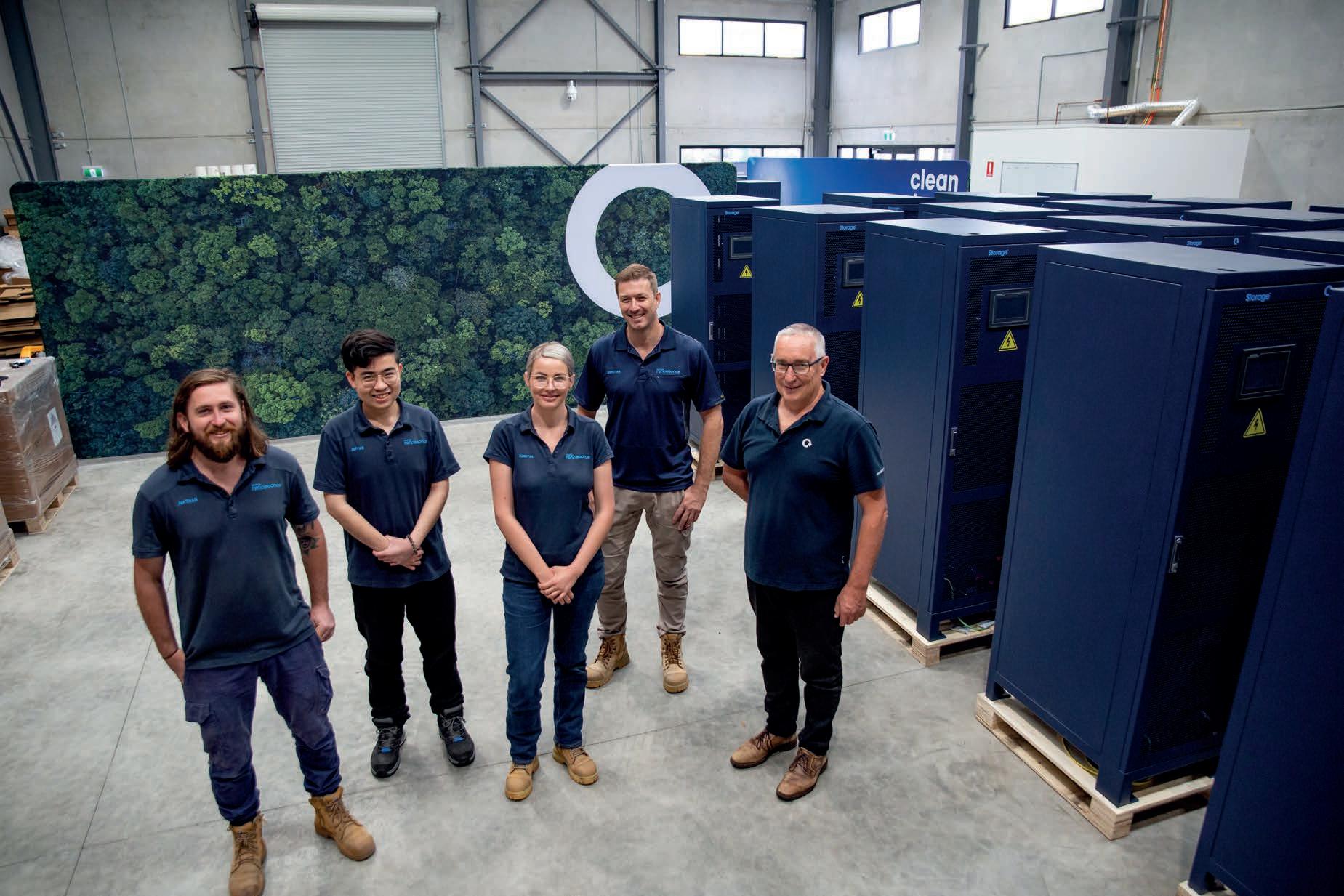
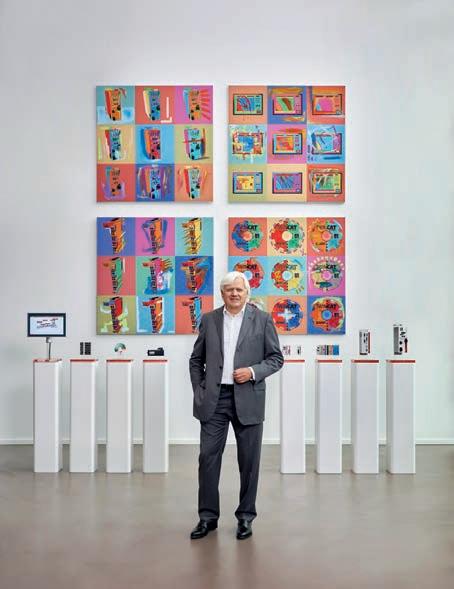
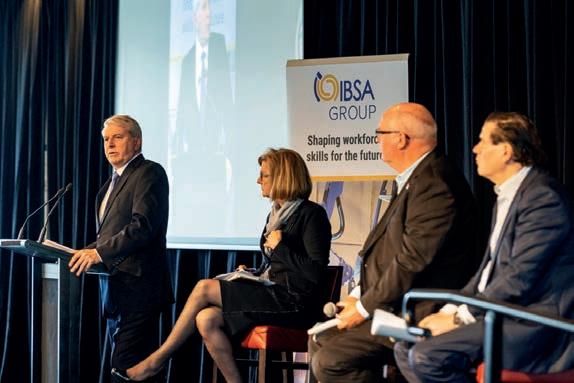
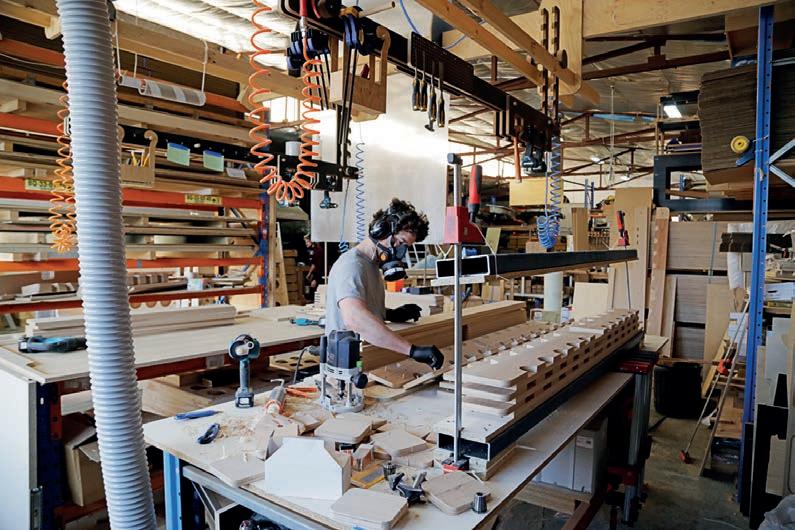
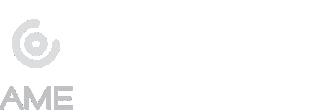
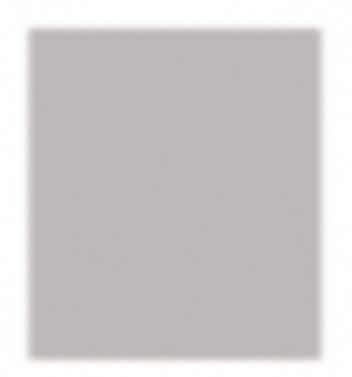
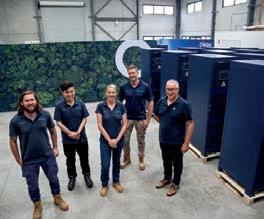
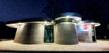
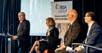
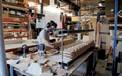
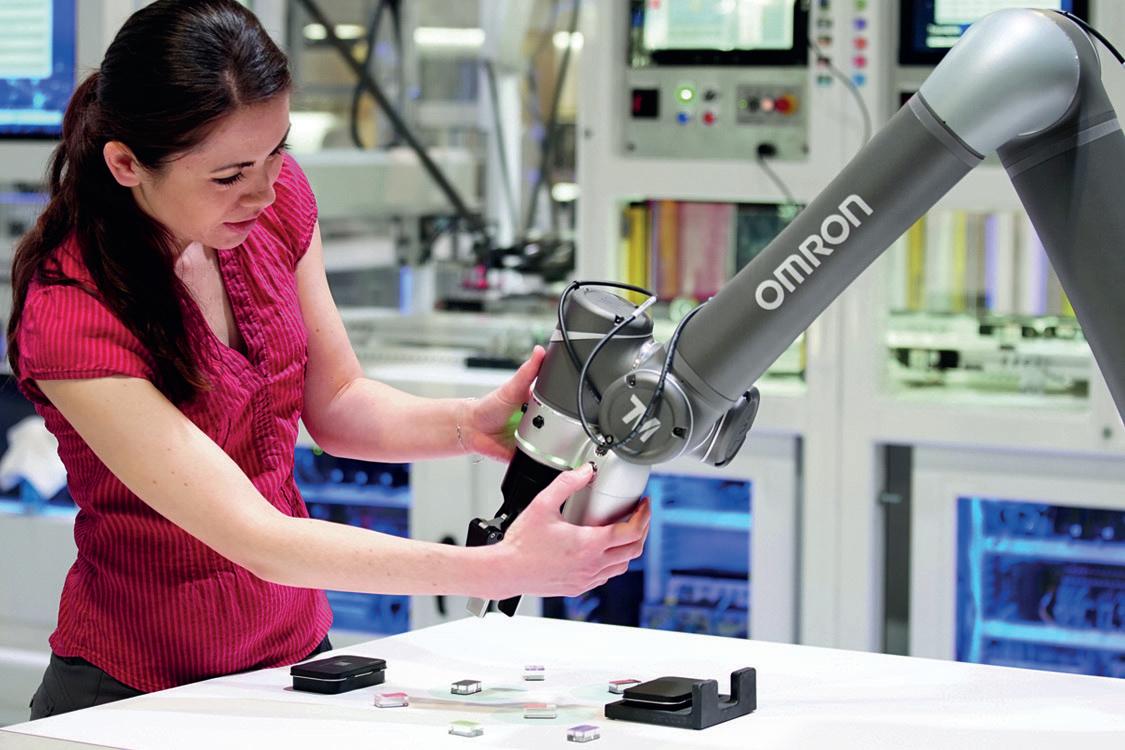
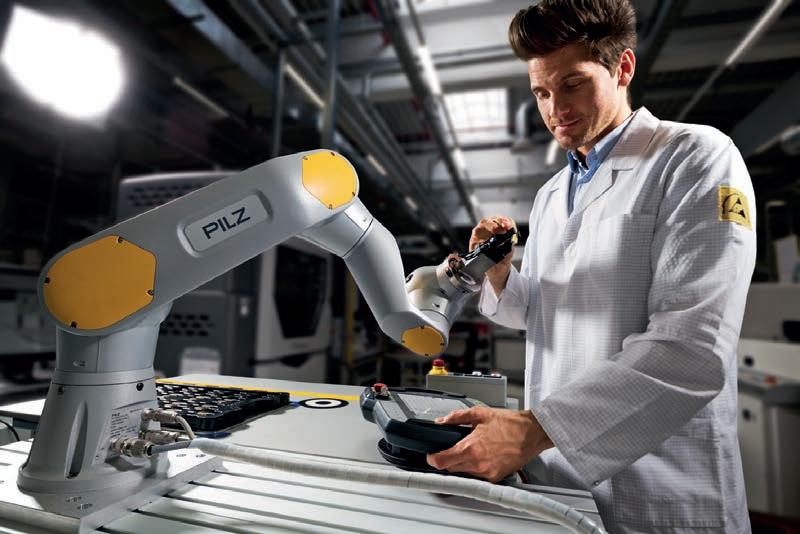
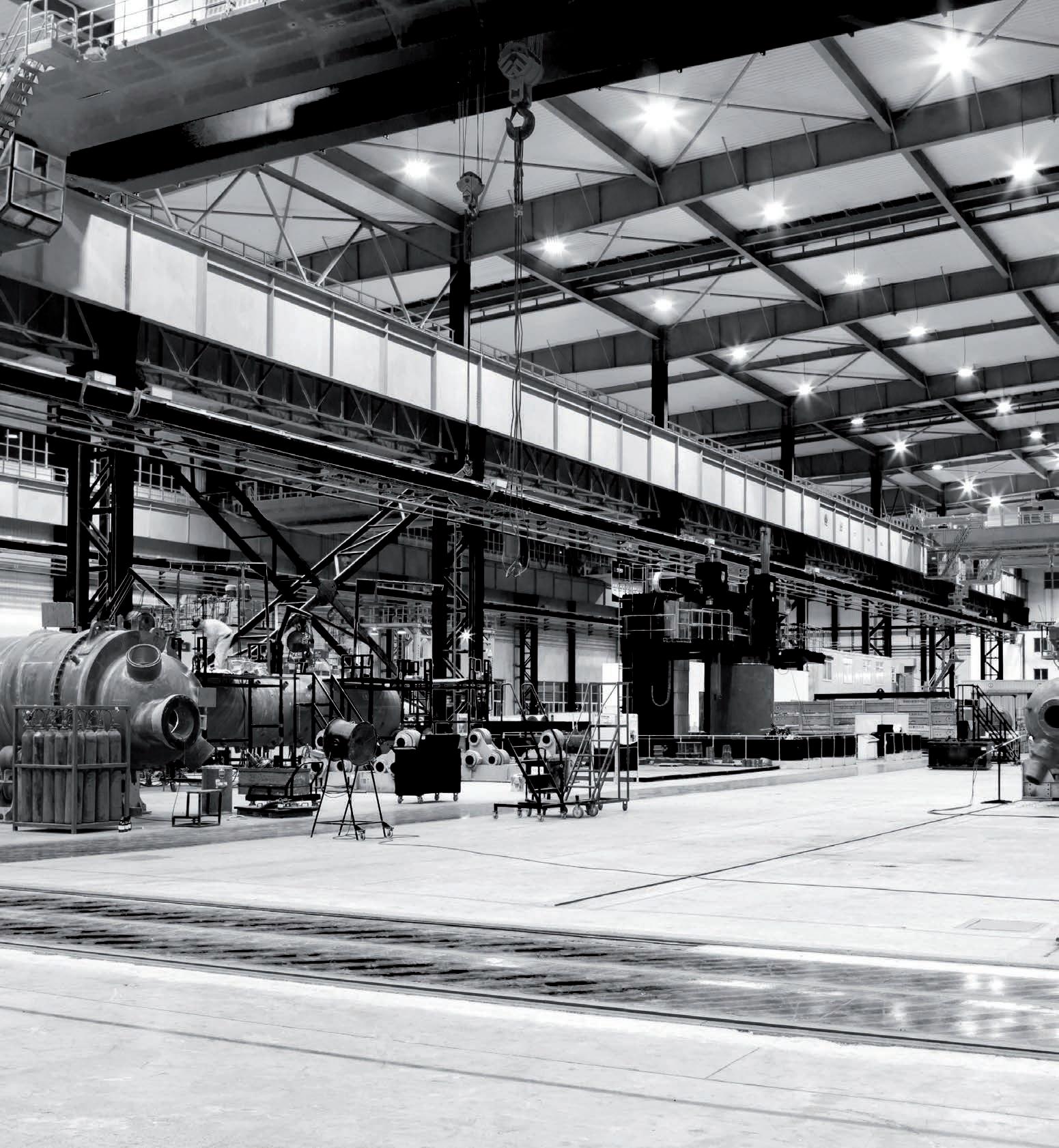
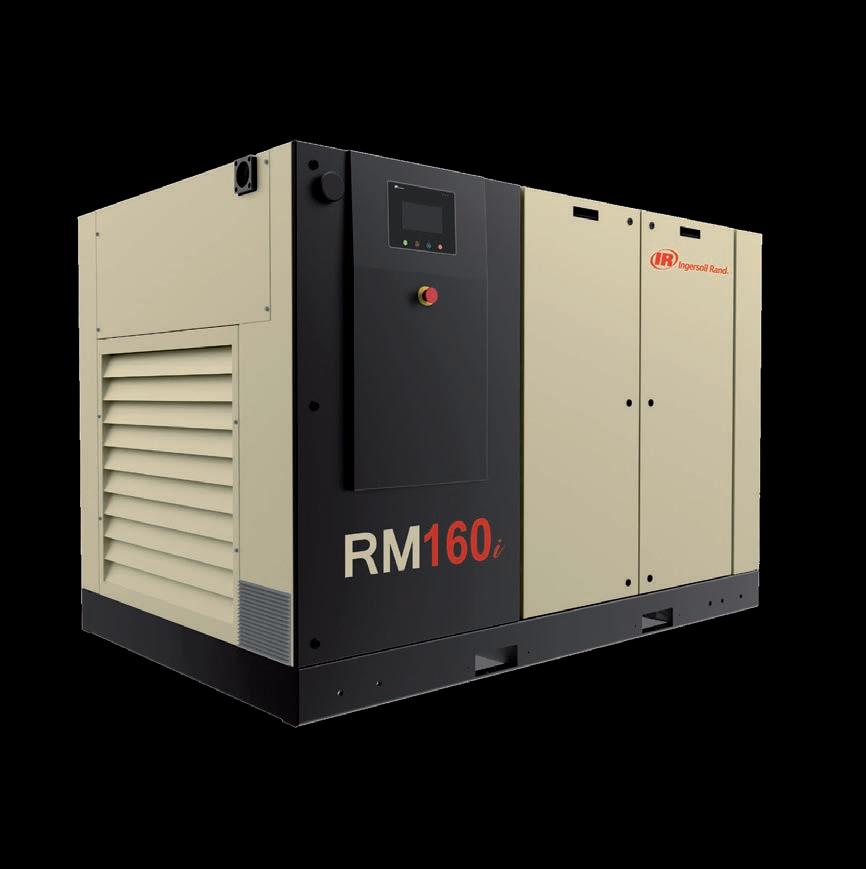
THE opportunity that Australia, and the world, faces when it comes to the introduction of robotics and automation is not one that is often understated. In Australia alone, there is the potential to unlock $315 billion dollars of value over the next decade through the application of digital technologies, according to the Digital Innovation report, prepared for CSIRO’s Data61.
Digital technologies have the potential to radically transform jobs that until now have been the exclusive domain of humans, for example, aged care, education, health, and financial services. But all this won’t come as news to the one industry that has been grappling with these issues for over half a century. In 1961, the first industrial robot was introduced to a manufacturing
production line in Trenton, New Jersey. Its name was Unimate #001 and the client was General Motors.
More than 50 years on, when other industries raise concerns of the replacement of humans with robots, they should perhaps talk to a local manufacturer and listen to their story. Although the number of people employed by manufacturing businesses in Australia has fallen since the late 1980s, the past two years have seen an increase, just as manufacturing enters Industry 4.0, its next phase of technological innovation. This suggests that there is no simple binary of human robot replacement, and that rather, when manufacturers adopt new technologies, they are increasingly doing so to grow the value of their workforce and the products they produce. This
in turn spurs greater employment as dirty, dull, and dangerous tasks are automated, allowing people to take on higher value work.
Industry and Science Minister Ed Husic recently called for Australia to be be at the forefront of critical technology development. The Labor Government is setting up a new consultation period on the most crucial technology categories as part of its goal to reach 1.2 million tech jobs by 2030.
The 2021 national priority list featured 63 technologies across seven categories, including advanced materials and manufacturing, artificial intelligence, computing and communications, quantum and biotechnology. There’s no doubt robotics can be an area of improvement in this country, helping manufacturers suffering from skills shortages.
In this edition of Manufacturers’ Monthly, we are speaking with those manufacturers at the edge of this technological curve.
Driven by the potential of technology, new business models are opening up for manufacturers to grow their business. Manufacturers in Australia are analysing the data they gain from IoT-enabled devices, using their expertise and developing software built off the data that comes from making. These software platforms, whether they be standalone programs or mobile apps, are then another source of revenue and naturally, employ more people.
Taking in sum, it is increasingly evident that when it comes to technology, whether that be robotics, big data, or automation, manufacturing is wanting to lead the way.
AUSTRALIA’S prison population continues to grow at a rate that is four times that of the general population.
According to the most recent figures from the Australian Bureau of Statistics, from 30 June 2020 to 30 June 2021, the total number of Australian prisoners increased by 5 per cent to 42,970. Australia’s overall imprisonment rate also increased by 5 per cent from 205 to 214 prisoners per 100,000 adult population. This rate well exceeds that found across countless nations, from Scandinavia, Western Europe, Canada and the United Kingdom, through to Iraq, Saudi Arabia, China and New Zealand.
Alarmingly, Aboriginal and Torres Strait Islander prisoners make up 30 per cent of all prisoners in Australia. And yet, in the 2021 Census, just 3.2 per cent of the total population identified as Aboriginal or Torres Strait Islander.
In the 12 months to 30 June 2021, Aboriginal and Torres Strait Islander prisoners increased by 8per cent to total 13,039 people. Not surprisingly then, their imprisonment rate also increased by 5 per cent to 2,412 prisoners per 100,000 Aboriginal and Torres Strait Islander adult population.
Let’s compare those figures: 214 prisoners versus 2,412 prisoners per 100,000 adult population.
Clearly, something doesn’t add up.
As at 30 June 2021, the median age was 32.8 years for Aboriginal and Torres Strait Islander prisoners. When comparing the prison population to the general adult population, prisoners are much younger – 2 in 3 (65 per cent) prisoners were under 40, compared with about 2 in 5 (40 per cent) in the general adult population.
According to the latest statistics, on an average night, there were 819 young people in detention, most of whom (at 83 per cent) were aged 10-17. Half (or 410 of the 819) of all these young people were Aboriginal or Torres Strait Islanders. And yet, Indigenous Australians make up just 6
per cent of the Australian population aged 10-17. What is causing this disparity? Is it endemic institutionalised racism?
And, possibly most concerning, once Aboriginal and Torres Strait Islander prisoners enter the correctional system, finding their way out can be tough. The latest report from the Australian Bureau of Statistics showed that 78 per cent of Aboriginal and Torres Strait Islander prisoners had experienced prior adult imprisonment.
All these statistics paint a clear picture: our prison population is rapidly expanding, Aboriginal and Torres Strait Islanders account for an overwhelmingly disproportionate percentage of prisoners, and they are increasingly younger people and reoffenders.
So, then what is being done by our governments to help alleviate the situation?
According to the latest figures, the Australian Government directly spends around 1.5 times as much on Indigenous people on a per-capita basis compared to the general population, amounting to $14.7 billion per annum. However, given the alarming statistics cited above, it remains to be seen whether this funding is being directed in the most effective fashion.
With the National Agreement on Closing the Gap coming into effect on 27 July 2020, it was hoped that government funding might be reallocated to the initiatives where it was needed most.
The National Agreement sets out ambitious targets designed to change the way governments work to improve life outcomes experienced by Indigenous Australians. The two most pertinent targets are:
Target 6: By 2031, increase the proportion of Aboriginal and Torres Strait Islander people aged 25-34 years who have completed a tertiary qualification (Certificate III and above)
to 70 per cent.
Target 11: By 2031, reduce the rate of Aboriginal and Torres Strait Islander young people (10-17 years) in detention by at least 30 per cent.
Over two years on and, according to the Closing the Gap Implementation Tracker, the vast majority of commitments are either delayed, or ‘not reportable’. Meanwhile, the incarceration and recidivism rates of Indigenous Australians increases year-on-year. Existing funding and programs are not closing the gap –in fact, they seem to be exacerbating it. Indigenous Australians are not receiving the education or the support they need to improve their own life outcomes.
Australia needs practical rehabilitation and vocational education and training (VET) programs that can help alleviate recidivism for Aboriginal and Torres Strait Islanders.
A 2015 study by the Australian Institute for Health and Welfare found only 38 per cent of prison entrants surveyed had attained year 11 or 12. Just 20 per cent of Indigenous entrants had completed the same level of education, and Indigenous dischargees were more than twice as likely as non-Indigenous counterparts to have only reached year 8 or below.
The introduction of VET programs as part of prisoner rehabilitation offers opportunities for Aboriginal and Torres Strait Islander prisoners to reduce this disadvantage, increasing the likelihood of successful reintegration into the community and reducing the risk of reoffending.
A recent study confirmed that participation in VET whilst incarcerated helps prisoners to remain custody free post-release. In fact, prisoners who successfully completed VET were 60 per cent more likely to remain custody free at two years post-release; and 78 per cent more likely to remain custody free at five
years post-release.
VET and rehabilitative efforts are generally successful in reducing recidivism. In fact, there is some evidence to suggest that without rehabilitation, sanctions and incarceration alone may result in increased rates of reoffending.
Given the proven success of VET programs for prisoner rehabilitation, in 2022, Corrections Victoria expanded the VET Centre of Excellence model to deliver Fusion Welding to ISO 9606 certification standard to complement their Metal Fabrication industry at Langi Kal Kal Prison. Federation University delivers the training program with the support of Weld Australia and on-site prison industry staff.
As part of the program, augmented reality training was introduced to expand the welding skills of the prisoner learners to meet international standards. A welding workshop sits alongside the augmented reality training room so that participants can work on projects to use and practice their welding skills in the physical as well as virtual environments.
To participate in the program, prisoners are invited to submit an Expression of Interest and then selected through an interview process. Up to eight participants can be accommodated in the intensive 14-week program.
The ability to gain and maintain employment post-release is equally as important as training when it comes to the successful reintegration of former prisoners into the community. And yet, few ex-prisoners are able to find meaningful work. Prisoners often come from a socio-economic group that already faces difficulties in gaining employment. They generally have high levels of drug
Weld Australia CEO Geoff Crittenden writes about Australia’s prison population and providing employment opportunities to the disenfranchised.
even more difficult for prisoners to find a job. Combine all this with Aboriginal and Torres Strait Islanders heritage, and securing meaningful work becomes near impossible.
According to the Australian Institute of Health and Welfare fewer than 1 in 4 (22 per cent) of former prisoners nationalwide report that they have paid employment organised to start within two weeks of release from prison. This can also be exacerbated at times by parole conditions that make full-time employment more difficult to manage.
The VET Centre of Excellence model links participating prisoners with prospective employers and pre and post-release support service providers. These connections provide prisoners with sustainable pathways to employment and support to reintegrate to society postrelease.
Australia’s skilled welder shortage has reached critical levels. According to the results of our 2022 Member Survey, when
constrained recruitment market. With a considerable volume of work being onshored in the wake of international supply chain disruptions, most Australian fabrication companies are so strapped for skilled welders that they are working at anywhere between 30 per cent and 50 per cent of their full capacity.
They are being forced to turn down jobs because they simply don’t have the manpower to complete the work. This is having a major impact on production and causing delays throughout downstream industries including building and construction, mining, oil and gas, and manufacturing.
Industry is already at capacity, with Weld Australia’s members turning away projects because they cannot find enough welders to complete the work. We have known for some time now that Australia will have a shortfall of at least 70,000 welders by 2030. Alarmingly, this projected shortfall of welders does not account for Australia’s move from carbon
These types of practical, long-term training and rehabilitation programs are so important. They equip prisoners with knowledge and give them practical skills that they can use on release. They help give prisoners purpose, particularly Aboriginal and Torres Strait Islanders. They build self-esteem and respect, and give prisoners the confidence to change their own life outcomes and build a successful future, particularly as postrelease employment as a welder is almost guaranteed.
We need a justice system that acknowledges the culture of Aboriginal and Torres Strait Islanders, and provides for that in delivering a fair equitable justice system. Australia needs practical, long-term measures and funding for VET and training programs in correctional facilities, as well as alternatives to prison, and real support for people on remand.
Taking this a step further, we need
Wales Government has invested heavily in Weld Australia’s Advanced Manufacturing School Outreach Program. Why can’t other state governments, or the Federal Government, invest in this program for Indigenous communities nationally? Why aren’t we giving Indigenous children the same opportunities to learn and access training?
I urge Minister for Indigenous Australians, the Hon Linda Burney MP, to support the funding of VET education, training and employment pathways for Indigenous Australians—both within prisons and the broader community. Reallocating even a small portion of the $14.7 billion spent every year could offer huge benefits for Indigenous Australians and industry. With a looming welder shortage in Australia, secure employment in the fabrication industry can give Indigenous Australians the power and confidence to improve their own life outcomes.
manufacturers,
union leaders, peak bodies and training providers together to share strategies to address the skills crisis. When interviewing SMEs and different organisations every month for stories in this magazine, a common thread is the lack of skilled manufacturing workers available in this country.
The Forum highlighted the need for a collaborative and systematic approach, with government and industry working together to seize the opportunities that lie ahead. For instance, the requirement for better dialogue between government and industry was jointly raised by Australian Manufacturing Workers’ Union national president Andrew Dettmer, and Ai Group chief executive Innes Willox.
Willox reiterated that any skills
education must be linked to produce outcomes. Dettmer also called to address the lack of support mechanisms in the current system for young apprentices moving between employers.
Panel discussions broached topics like engaging the workforce and locking in opportunities, addressing labour shortages, the impact of new technologies and the skills system response.
While a range of strategies can be adopted, including use of skilled migration, there’s little doubt skilling Australia’s workforce is central to futureproofing the national economy.
According to the National Skills Commission, 60 per cent of businesses are currently recruiting and 30 per cent of those report recruitment difficulties. The manufacturing industry is having more
and trade occupations are in shortage. This increased competition for labour supply will mean that employers will need to develop new ways of identifying, attracting and skilling up the workforce.
So, Manufacturers’ Monthly caught up with CEO of IBSA Sharon Robertson, to ponder what solutions Australia can and should deploy to ease the problem continuing to rear its head in the manufacturing industry.
The day was a big success, starting with its participation. It was well attended by the key leaders of our manufacturing sector and our skills sector. Minister O’Connor was very generous with his
O’Connor has actually just asked to meet with me again to talk through some of the outcomes of the forum.
It was a great opportunity for collaboration. And that collaboration wasn’t just amongst the key players here in Australia, but internationally too. I think Australia’s manufacturing and skills sectors have forged and further developed relationships through the forum discussions, which is evident by a number of the follow ups – international organisations want to continue the dialogue going forward, because the challenges that we’re facing here in Australia are similar to everywhere else.
About collaboration, one point that’s jumped out at me, was the changing language from the Minister about government working as a partner with
CEO of IBSA Group, the long time shaper of workforce skills and supporter of the manufacturing
Addressing the skills crisis with real collaboration
industry. I felt that was a really positive shift in language. Equally, Innes Willox of the Ai Group, one of our presenters in the morning and discussed the importance of listening to industry. He said that’s the key to improving our skill system. So obviously, we’ve taken his comments onboard and are looking at how to better achieve that at an operational level.
We’re all abundantly clear that we need new skills, not just for the advancements in technology, but the new skills that are needed to fill the gaps in our supply chain are things we’ve not done here before. So, that means not just obviously a new set of skills etc, but more importantly a new way of actually providing that training and skills. One of the things that came through in the discussions is that we need toadapt and adjust the way we’re delivering skills – the sophistication in thinking is really encouraging. While there is still a place for face-to-face delivery, the needs and expectations of learners are changing. The forum identified the importance of industry having different types of skills responses available, including online learning, workplace simulations and augmented reality.
Industry and training providers will need to work together to deliver contemporary insights into training new skills. There is important discussion to be had about how we respond to industry training needs in a way that has value for the employer, the individual and industry.
challenges and opportunities for the sector to respond to. And we are certainly keen to look at how we can drive some of the outcomes from the Summit, which had clear overlaps with the conversations that were had at IBSA’s Forum. It’s about building on those relationships that have been forged through this and extending those to sharing lessons learnt and collaborating in a more comprehensive way at every level. How do we influence and shape the reform, so it provides the opportunities that we talked about for the manufacturing sector in particular?
or various others to re-enter the workforce. Other untapped cohorts include those who are disadvantaged and women.
A case in point, the NDIS is not connected to our sectors in a way that readily identifies where the employment opportunities could or should be. So, you can see that there’s a lot of linkages that haven’t been made within our government, systems and society to actually start reprogramming how we think about things. There are some great examples where disadvantaged people have been able to step into the workforce. I think we should be doing more to help employers to do that. It’s about looking at things differently and providing the employers and the system with the mechanisms and tools to respond to this shortage, not just trying the same thing and expecting a different result.
promotion about how it’s operating now in more highly automated, clean and specialised areas, not the traditional paradigms of long hours at dirty factories not necessarily attracting the highest skill levels. It’s quite the opposite these days, as you know.
I think career counsellors, as a case in point, could do more to help reposition the opportunities, particularly in advanced manufacturing and also the scaffolding of people’s careers in and out of manufacturing. It’s so broad and doesn’t mean you’ll be quarantined, if you choose a career in manufacturing.
Skills is such a pervasive issue across the across the whole sector that it’s not just about looking to the government or TAFEs to provide a skilled workforce. Employers need to get involved in the debate and the discussions, whether on a local level with other similar employers or on a broader national level. One way or another, the more employers can be involved in the debate and in what types of skills are needed, the better the outcomes will be.
One of our speakers at the forum, BAE Systems, spoke about working on qualification innovation including things like work-based engineering degrees, where people work alongside studying. This means they come out with job ready skills, as opposed to spending years doing the study and then needing several more years to be truly job ready. It’s a much stronger integration of traditional qualifications and vocational education and training.
We’re certainly competing against many countries for skilled migrants. We can’t talk to what the skilled migration system needs to do as that’s a little bit outside our purview. It is clear that we need to look at different ways of addressing the labour shortage.
There’s been a number of discussions, not only at our forum, but also at the summit, about looking for some of the cohorts in Australia that could potentially fill the gaps in our labour market at the moment. A number of initiatives have been
Number one is the basics about doing a better job of not only promoting but describing the role. For example, traditionally, manufacturing roles have been described in classic ‘blokey’ ways. The female cohort could be overlooked because they don’t describe roles in a way that’s attractive to them. Overall, there’s huge opportunities in the manufacturing sector.. It certainly needs to have more
We need to provide much stronger and more effective scaffolding between VET and higher education, so people can move from one to the other to support their skills development needs. At the moment, I think individuals, particularly young people, are faced with the challenge of choosing which way they go. I don’t think it should be an either-or option.
In summary, let’s ensure we continue the discussions about improving skills and addressing the labour shortages in manufacturing. The more collaborative and engaged the whole ecosystem can be, the better it will be for workers, employers and the nation as a whole.
One of the takeaways from the skills summit was the the increase in migrant workers to 35,000 per year. How do we attract more skilled migrants?
WHEN the term ‘Industry 4.0’ was first coined in the early 2010s, much hype ensued around the concepts of automation, digitalisation and the Internet of Things. Twelve years on, you and I know and understand the benefits of Industry 4.0, but why do we still see evidence of many manufacturers being reticent about getting involved?
In my role as Director Industrial Transformation at IMCRC, I have spoken to many manufacturers, mostly small to medium enterprises (SMEs), through futuremap – IMCRC’s business diagnostic designed to help manufacturers demystify Industry 4.0 and assess their business maturity.
And through these conversations, it is clear manufacturers’ awareness of Industry 4.0 has grown. But despite this and the barriers to entry lowering, many are struggling to integrate enabling
technologies into their businesses. In fact, when I look at aggregate results of futuremap, one response stands out: only 24 per cent of manufacturers find the time to regularly discuss industry 4.0 as a leadership group.
It is time to acknowledge this is not a tenable position going forward. Technology is advancing so rapidly that we no longer have years to think about adoption. If we’re not doing it now, we risk being left behind.
However, it is fair to say the last few years have taught us many lessons. Lessons about embracing the unknown. Lessons about resilience. We have all become far more amenable to change. And I believe there is an opportunity for leadership to embrace this mindset and bring forward the shifts required in our manufacturing base.
Let’s talk about the reasons why it’s time to ‘get on’ with Industry 4.0.
Industry 4.0 is a force multiplier. Having successfully invested in a project portfolio of 71 research and development (R&D) collaborations, IMCRC has consistently seen opportunities breed opportunities –often in surprising forms.
In its infancy, Industry 4.0 was largely seen as a tool to lift productivity. And while this is still a critical benefit for many manufacturers, it also offers them the opportunity to invent or reinvent their offerings and strengthen their competitive position.
Take, for example, leading hydraulics and automation control solutions company HYDAC Australia. In 2021, HYDAC embarked on a 12-month collaboration with Deakin University and IMCRC to develop a cutting-edge virtual reality training environment. The technology was initially intended to
support the maintenance and repair of hydraulic products.
However, with a robust demonstrator now available, the HYDAC team are finding companies are approaching them for support and ideas for their own implementation of virtual reality training. As a result, a new business stream is opening for HYDAC.
These days employees are likely to be more comfortable with innovative technology than leadership. Augmented and virtual reality have become native environments for many. We are seeing increasing investment in personal devices to support this trend, with the likes of Meta and Apple betting heavily on hardware to move this way of working into our daily lives.
Another example is smart phones,
Why now is the perfect time to ‘get on’ with Industry 4.0Around one quarter of manufacturers regularly discuss Industry 4.0 as a leadership group.
and wants, training us to expect accurate, well presented and instantly accessible data. Employees will rightly expect our manufacturing performance data to also meet this benchmark, as will our customers and suppliers.
With digital technologies such as additive manufacturing, sensors and data analytics becoming more and more accessible at home, it is likely companies have employees who possess a skill base that can add value in the workplace.
We have seen this shift echoed in IMCRC’s futuremap workshops. When it comes to the adoption of Industry 4.0 technologies, many manufacturing SMEs are now saying the internal push from staff is greater than the external demand from customers.
By embracing the digital revolution, businesses can create a culture for their staff that feels relevant and supports society’s evolution. And at a time when
Perhaps the biggest incentive for action is the growing need for manufacturing to move towards net zero. With the Australian Government committing to a 43 per cent reduction in emissions by 2030, we will be expected to move quickly.
The risk here is that manufacturers consider challenges like net zero and Industry 4.0 adoption as competing in the context of a busy steady-state workload.
I would argue that the opportunity here is to bring the two issues together, with Industry 4.0 seen as a key enabler.
For example, by optimising specific technology or adopting new software with energy-saving functionality, we can achieve reductions in energy consumption.
Similarly, newer and more innovative technology can reduce a business’ carbon footprint by replacing traditional
manufacturing processes. Consider digital twins. By integrating digital twin technology, a manufacturer can more accurately test scenarios, improve product quality and control, and more efficiently balance resources across a complex supply chain.
If we think of the digital and clean energy transformations as being inextricably linked, we are more likely to achieve mutually beneficial outcomes and
grow the impetus for getting on board.
As a manufacturing SME, you are uniquely positioned to embrace the digital revolution due to your size, agility and entrepreneurial culture. And as a manufacturing leader, it’s on you to make it happen. Be the instigator of change. Understand your barriers to uptake and remove them.
Be bold. Be brave. And if you’re going to do Industry 4.0, do it now.
HYDAC Australia collaborated with Deakin University to develop a virtual 3D training solution. HYDAC Australia’s VR/AR training solution teaches staff to safely service and maintain important hydraulics systems and components.Minister for Infrastructure Catherine King said a local Tesla manufacturing plant would be “absolutely” welcome in Australia when releasing a consultation paper for a new national electric vehicle (EV) strategy.
The consultation paper seeks views on proposed goals, objectives and actions for the National Electric Vehicle Strategy, to ensure Australians can access the best transport technologies and help meet emission reduction targets.
King’s statement indicates the federal government’s enthusiasm to ramp up local car manufacturing, including manufacturing EVs, and reduce emissions in Australia.
The paper stated: “Australians are being sold some of the highest emitting cars in the world.
On average, new passenger vehicles in Australia have around 20 per cent higher emissions than the United States, and around 40 per cent higher emissions than in Europe. We need to catch up to the rest of the world when it comes to transport emissions.”
The paper also notes ramping up local manufacturing as a key goal;
other goals include making EVs more affordable, expanding EV uptake and choice, reducing emissions, and saving Australians money on fuel.
King’s comments come as Robyn Denholm, Tesla board chair, spoke about reviving Australia’s auto industry by manufacturing EVs.
“Australia is in a unique position because we have the minerals here that other countries don’t have,” Denholm said to the National Press Club in Canberra recently.
“The supply chains for the electric vehicle and the lithium-ion storage batteries that are key for renewable energy are being formed now.
“I do think the private sector and government need to work together. I don’t think that incentives are required because most business people will see the exponential growth that’s going to happen over the next period of time in those minerals.”
At the unveiling of the consultation paper, minister for energy Chris Bowen commented on realistic expectations of manufacturing EVs in Australia.
“The economics of electric vehicle manufacturing are very different to traditional internal combustion engines, whether it’s full vehicles or those components of vehicles along the way,” Bowen said.
Nutromics has raised an additional US $14 million for its wearable diagnostic platform, with investment from Dexcom Ventures, VU Venture Partners, and Artesian Investments.
The latest round of funding will support an expansion of clinical studies, expansion of their research and development team and investment across both Australian and United States hubs. Nutromics plans to raise more funding in 2023 following in-vivo clinical studies.
Nutromics is developing a wearable diagnostic platform that uses DNA technology to enable tracking of multiple targets in the human body using a single patch. This is the first
technology of its kind that is both a platform and proven to work on the human body.
The DNA sensor technology will provide clinicians and patients with continuous and real-time diagnostic information ranging from hard-to-dose drugs, like vancomycin, to biological markers for conditions such as kidney disease.
“We are aiming to cause a paradigm shift in diagnostic healthcare by essentially developing a lab-on-apatch. A lack of timely and continuous diagnostic insights can strongly impact outcomes when dealing with critical disease states.
“With this strategic industry and VC investment in us, we see more confidence in our technology and hope
Nutromics
to accelerate our growth, as the need for our platform in the lab diagnostic space is urgent,” said Nutromics’ co-founder and CEO Peter Vranes.
“And as I said at the outset, the more we have an electric vehicle market in Australia, the more that will support electric vehicle component –and indeed, potentially more in due course manufacturing.”
Nutromics was founded in 2017 and has seen exponential growth over the last year, raising over US$20 million to date for its wearable diagnostic platform.
World-leading aircraft manufacturer, Bombardier, has chosen Victoria for its state-of-the-art Asia Pacific engineering operations headquarters.
The new engineering headquarters will deliver maintenance, repair and overhaul services, acting as a central depot and providing ground support for all Bombardier aircraft across Australia, New Zealand and the Pacific.
Bombardier’s Melbourne Service Centre at Essendon Fields will also create 65 new high-skilled new jobs.
In addition, it will deliver opportunities for students and graduates as Bombardier is set to partner with Victorian universities and TAFEs to develop specialised aviation servicing training.
Minister for Industry Support and Recovery Ben Carroll visited the centre, and said the Victorian state government is supporting world-leading businesses to invest in the state because they will boost Victoria’s booming economy and bring
high-skilled jobs.
“This is a significant win for Victoria to have Bombardier choose Melbourne as its base, further cementing the state as a global leader in innovation,” Caroll said.
Bombardier executive vice president Jean-Christophe Gallagher said, “The introduction of the new Melbourne Service Centre continues to illustrate how Bombardier is transforming its
aftermarket footprint around the world – and establishing high-paying aerospace careers in Melbourne.
“We look forward to deepening our ties with the local community by working with local schools to establish an invaluable aerospace pipeline that will train and develop highly skilled maintenance technicians for years to come.”
Australian company MoTeC – a global supplier of automotive electronics used by racing teams in some of the world’s premier motorsport series – has been acquired by global heavyweight Bosch.
The Melbourne-based company and its global network of 250 dealers officially became part of Bosch Motorsport – a business unit of Germanbased Bosch Engineering GmbH – on 1 September.
The MoTeC brand is well-known among racing professionals and motorsport fanatics, with MoTeCequipped cars competing in premier racing series such as Le Mans, NASCAR, FIA GT, Australian V8 Supercars, IndyCar, Dakar Rally and World Superbikes. Australian professional services firm RSM Australia leveraged its global network of offices and industry contacts
to generate international buyer interest and negotiate the sale of the privatelyowned company for an undisclosed sum.
RSM Australia National Head of Corporate Finance Glyn Yates said the final outcome was a great result for both parties and an example of the strong level of deals activity still occurring in the mid-market.
“We’re seeing a continued strong level of activity from the privately-held end of our market,” Yates said.
“There’s still plenty of interest from onshore and offshore for the right asset – assets that have strong underlying cash flows, strong and sustainable margins, longer-term contracts in place and or long-term relationships with customers. These are the business fundamentals driving value in the current environment.”
Bosch Motorsport vice president Dr Klaus Boettcher said MoTeC was the perfect fit for Bosch Motorsport.
“The acquisition of MoTeC fulfils Bosch Motorsport’s strategic goal to extend its product portfolio and distribution to serve additional racing series and the racer market,” Dr Boettcher said.
Former MoTeC owner and managing director Phil Morris said his goal for the sale of the business was to ensure the longevity of the MoTeC brand – which had been built over 30 years – and to further cement its world-leading reputation in the motorsport industry.
”I am delighted that the MoTeC brand and its Australian legacy will continue to thrive under Bosch’s ownership and that customers around the world will continue to benefit from the technical
Bombardier has approximately 80 business aircraft customers based in Australia – many of which are based in Melbourne – as well as customers who fly in and out of the country.
The aircraft manufacturing company is a global leader in aviation, specialising in designing, manufacturing and servicing business aircraft. Its worldwide fleet of about 5,000 aircraft are used by a variety of multinational corporations, charter providers, governments and high net-worth individuals.
Bombardier adds to the list of aviation engineering firms the Victorian state government has recently supported, including aircraft composites manufacturer Quickstep Holdings Limited to expand its facility in Tullamarine and the Qantas Group to establish its principal engineering line maintenance hub at Melbourne Airport.
Victoria’s international aviation sector directly employs 6,700 people and supports thousands of other jobs.
knowledge and expertise of MoTeC’s dedicated and experienced staff who are the engine room of the business,” he said.
RMIT researchers have used supercomputers to speed up the search for a key ingredient in the next generation of lithium-metal batteries.
The team, led by RMIT University, in collaboration with the CSIRO, say the work could potentially increase storage capacity by ten-fold compared with today’s technology.
Senior lead researcher Michelle Spencer, a professor of Chemistry and deputy director of RMIT’s STEM Centre for Digital Innovation, said the team used supercomputers to develop an ultrafast way to screen hundreds of potential molecules that could make suitable electrolytes for lithium-metal batteries.
“This work could benefit anyone wanting to use electronic devices, such as mobile phones and laptops, or electrified transportation like electric cars and future electric planes for commercial air travel,” Spencer explained.
“Our work is only a small component of the large body of work being done
in the rechargeable battery space, and electric flight for large-scale domestic and international travel is still a long way off.”
According to Spencer, despite rapid advancements, lithium-ion batteries still face several challenges related to the stability of the electrolyte.
“Organic-based electrolytes used in lithium-ion batteries are not compatible with batteries using lithium-metal as the anode, as they tend to decompose when exposed to the metal,” she said.
The research, which also involved RMIT PhD scholar Dale Osborne and CSIRO scientists Dr Michael Breedon and Dr Thomas Rüther, is published in the Journal of Materials Chemistry A.
Osborne said the team can identify specific features or molecules that might perform better and recommend them to experimental groups to test in the lab.
“The computational approach we’ve developed dramatically speeds up the screening process, which would traditionally be prohibitively expensive and
time consuming if each candidate molecule were to be experimentally synthesised and tested in the lab,” Osborne added.
The team is investigating further modifications of the electrolyte molecules that might widen their electrochemical stability, pushing the boundaries of battery storage capacity.
The researchers use supercomputing
facilities at the National Computational Infrastructure (NCI) facility in Canberra and the Pawsey Supercomputing Centre in Western Australia.
“We are also using RMIT’s RACE Hub to analyse our data and produce highresolution animations that help us to interpret our data and communicate our research findings,” Spencer said.
General Atomics Aeronautical Systems Inc. (GA-ASI) is working with Conflux Technology on the design and manufacture of a new Fuel Oil Heat Exchanger (FOHE).
GA-ASI is developing this enhanced thermal solution for its MQ-9B SkyGuardian and SeaGuardian Remotely Piloted Aircraft.
GA-ASI is a leading developer of unmanned aircraft, and Conflux is a thermal management system solution company headquartered in Australia.
Conflux is a pioneer in mastering additive manufacturing for heat exchanger applications. The two companies have worked together since 2018 to develop heat exchangers for aerospace.
“GA-ASI wants to optimise and augment the performance of our current units by minimising the differential pressure across the FOHE,” said Stephen Eiting, vice president of Manufacturing Operations for GA-ASI.
Another GA-ASI objective is to develop an AM heat exchanger design that can be 3D printed, post-processed, and
Technology said their mission is to heat exchanger performance.
“For our project with GA-ASI this means
class team and agility to do it right.”
The two companies have worked on four different AM projects since 2018.
GA-ASI and Conflux Technology are designing and manufacturing a new Fuel Oil Heat Exchanger for aircraft.
General Atomics Aeronautical Systems Inc. (GA-ASI) is working with Conflux Technology on the design and manufacture of a new Fuel Oil Heat Exchanger (FOHE).
GA-ASI is developing this enhanced thermal solution for its MQ-9B SkyGuardian and SeaGuardian Remotely Piloted Aircraft.
GA-ASI is a leading developer of unmanned aircraft, and Conflux is a thermal management system solution company headquartered in Australia.
Conflux is a pioneer in mastering additive manufacturing for heat exchanger applications. The two companies have worked together since 2018 to develop heat exchangers for aerospace.
“GA-ASI wants to optimise and augment the performance of our current units by minimising the differential pressure across the FOHE,”
said Stephen Eiting, vice president of Manufacturing Operations for GA-ASI.
Another GA-ASI objective is to develop an AM heat exchanger design that can be 3D printed, post-processed, and bench-tested. As part of this most recent purchase order, Conflux will produce a fully functional prototype unit that can be tested by GA-ASI.
Abe Masoud, business development manager of North America for Conflux Technology said their mission is to heat exchanger performance.
“For our project with GA-ASI this means drop-in replacements that remove thermal load and maintaining a compact profile, while also increasing performance to meet higher system demand,” Masoud said.
“When you are leading the charge on advanced technology, you need a world class team and agility to do it right.”
The two companies have worked on four different AM projects since 2018.
Most recently the two teams have leveraged AM to develop a cold plate
heat exchanger (HX) that provides additional cooling capacity for its highdissipation Line-Replaceable Unit (LRU) used in various GA-ASI’s UAS platforms.
Minister for Energy and Climate Change Chris Bowen says Australia’s car manufacturing industry could be reborn with a local electric vehicles sector to produce cars for local and international markets.
The comments were made at an energy forum in the US, where the minister recently test-drove an all-electric ute, which he declared “hugely” popular in the US but is unavailable in Australia because of “poor policies.”
Speaking to the media last week, Bowen told The Australian Financial Review Australia can make electric vehicles, after the death of the automotive industry in 2017.
“Not only do I think that, so do the electric vehicle manufacturers,” he said. “There’s work to do to make that more viable in Australia, but the economics of an electric vehicle are a lot different to the economics of making internal combustion engine [cars].”
“We have a range of policies which no doubt will be looked at in due course. I believe we can make key components of electric vehicles and indeed electric vehicles totally in Australia.”
Speaking to the media, Bowen said a range of policies will be looked at in due
course.
“Australia and Russia are the only two developed countries without fuel efficiency standards – that’s something that will be discussed.”
Australian Tesla chair Robyn Denholm recently spoke at the national press club, suggesting Australia should play a role in the rapidly expanding electric vehicle and battery manufacturing sector.
Recently, Australia’s first lithium-ion battery giga-factory came a step closer to realisation with the conclusion of Energy Renaissance’s pilot program. The facility will house over 700 employees and initially produce up to 300-megawatt hours of energy storage annually, scaling to 5.3-gigawatt hours of energy storage per year via its ground-breaking battery system. When in operation, the facility is
expected to contribute $97.5 million to the Australian economy.
Queensland premier Annastacia Palaszczuk has also stated that she would back an EV factory if Tesla decided to build one in the Sunshine State. In July, the Albanese government made electric vehicle tax cuts one of its first orders of business, hoping to further encourage EV take-up across Australia.
Global medical technology company Stryker has opened its Australian research and development (R&D) lab in Brisbane, Queensland as part of a partnership with the Innovative Manufacturing Cooperative Research Centre (IMCRC).
Located in Brisbane’s Herston Health Precinct, a collaborative community of health facilities, medical research institutes, universities, and organisations, the R&D lab will focus on digital, robotics, enabling technology and advanced manufacturing research.
The lab established with the support of the Queensland government, the University of Queensland, Queensland University of Technology and Metro North Hospital and Health Service to accelerate the translation of research within Australia’s medical technology ecosystem.
Stryker’s investment in the R&D Lab stems from its five-year, collaborative research project with IMCRC, RMIT University, St Vincent’s Hospital, University of Technology Sydney, University of Sydney and University of Melbourne.
The IMCRC project, which commenced in 2017, combined 3D printing, robotic surgery and advanced manufacturing to create patient-specific bone implants to treat bone cancers and tumours.
CEO and managing director of IMCRC, David Chuter, congratulated Stryker on the opening of its lab and recognised its ongoing contribution to Australia’s medtech manufacturing ecosystem.
“As a company at the forefront of medical technology, Stryker’s expanded presence in Australia will generate
significant opportunities for researchers, universities and local industry, creating skilled jobs and pathways for collaboration,” Chuter said.
“IMCRC is delighted that, following our successful collaborative R&D partnership, Stryker has invested in this landmark R&D facility and deepened their commitment to medical research innovation in Australia.”
Maurice Ben-Mayor, president of Stryker South Pacific, said Stryker’s project with IMCRC demonstrated the importance of collaborative, open R&D and helped shape their current approach to innovation.
“We are delighted to take our next steps in Australia and support its future as a world leader in medtech with the opening of our R&D lab,” Ben-Mayor said.
“With its world-class research institutions and highly skilled workforce, Australia has the capabilities Stryker needs to develop and produce the next generation of innovative medical technology.”
“By supporting the establishment of meaningful partnerships between research institutions and industry, and by providing the right incentives and framework, we can deliver critical, globally relevant innovations that lead to local medical manufacturing opportunities,” Chuter added.
“We must continue to attract more globally leading businesses like Stryker to invest in Australia and utilise our worldclass research and innovation expertise, especially where this can enhance our manufacturing capabilities.”
UNSW engineers have developed a new 3D printing process that prints solid-state polymer electrolytes (SPE) into any shape desired for use in energy storage.
Researchers have said the 3D printing process of such material could be particularly useful in future medical devices where small, intricately designed energy storage offers a number of benefits.
The research team from UNSW’s School of Chemical Engineering is led by professor Cyrille Boyer, and includes Dr Nathaniel Corrigan and Kenny Lee.
Solid-state electrolytes are a key component in solid-state batteries but traditionally suffer from poor performance due to low ionic conductivities or poor mechanical properties.
However, in a paper published in Advanced Materials, the team from UNSW reports their 3D printed SPE offers high conductivity, as well as robust strength.
“Nobody has 3D printed solid polymer electrolytes before. Traditionally they have been made using a mould, but previous processes did not offer the ability to control the strength of the material, or to form it into complex shapes,” said Lee.
“With existing solid-state electrolytes when you increase the mechanical strength of the material, you sacrifice a lot of the conductivity. If you want higher conductivity the material is much
less robust. What we have achieved is a simultaneous combination of both, which can be 3D printed into sophisticated geometries,” he explained.
“This polymer electrolyte has the potential to be a load-bearing energy storage material. Because of its strength, it could be used as the actual structure of small electronics, or in aerospace applications, or in small personal medical devices given our 3D printing process can be very intricate and precise.”
Although the SPE developed by the UNSW team is regarded as a highperformance material, the researchers said it can be manufactured using inexpensive and commercially available 3D printers, rather than sophisticated engineering equipment.
The SPE described in the paper is composed of nano-scale ion-conducting channels embedded in a rigid crosslinked polymer matrix. It is produced via a process known as polymerisationinduced microphase separation (PIMS).
To showcase the versatility of the material, the researchers 3D printed an intricate map of Australia which was then tested as an energy storage device.
Corrigan said that one of the other benefits of this SPE in energy storage devices is the fact it increases the cycling stability, which is the number of charging and discharging cycles until its capacity is
reduced to a certain amount.
“In our paper, we show that this material is very stable and has the ability to charge and discharge over thousands of cycles. After 3000 cycles there was only roughly a 10 per cent drop,” Corrigan said.
The researchers said 3D printing could also reduce wastage compared to other
traditional forms of manufacturing and reduces costs since the same machine can be used to produce a variety of differently shaped materials.
In future, they believe product designers could utilise their SPE to create items with a much higher energy storage density.
BAE Systems Australia and EPE have announced a technical partnership to demonstrate advanced autonomous capabilities in Australia at Land Forces 2022 in Brisbane.
The two organisations will collaborate on the development of autonomous technologies through BAE Systems’ Unmanned Ground Vehicle (UGV) program, which began this year.
Focused on implementing BAE Systems’ advanced vehicle management systems on to UGVs, the collaboration with EPE aims to develop soldier support systems for the Australian Army.
As Australian agents to the HDT Hunter WOLF (Wheeled Offload Logistics Follower) UGV platform, EPE
was initially contracted to provide platform, integration and engineering support as well as test facilities, using the company’s state-of-the-art UGV test and evaluation facilities in south-east Queensland.
Operating within a multi-domain autonomy architecture, the program focuses on the integration of UGV mission systems to enable prototyping that will develop certifiable mission systems.
BAE Systems Australia managing director for defence delivery, Andrew Gresham said they were pleased to partner with EPE to help develop and grow sovereign autonomous capability in Australia.
“It’s critical for businesses like ours to collaborate with Australian industry so we can successfully support the ADF and, working with companies such as EPE provides opportunities to work as one team, creating an environment that fosters innovation,” Gresham said.
“Having access to the EPE’s unmanned ground vehicle platform and magnificent test facilities here in South-East Queensland has helped us make significant advances in ground autonomy technology, and we look forward to furthering this work together.”
BAE Systems Australia is an industry partner and the Land Domain Lead to government agency
Trusted Autonomous Systems Defence Cooperative Research Centre.
Commercialisation of this technology will be accelerated through these collaborations.
EPE’s director innovation and commercialisation Ben Sorensen said. “It’s been an extremely positive experience working with BAE Systems on a shared pursuit of a multi-domain, collaborative and autonomous robotics for Defence at our MILTECS test and assurance facility.
“Our technical teams are working collaboratively, both virtually and face-to-face, to advance the technology, enhance capability and significantly derisk future Defence programs.”
Scientists have said that rare diamonds from an ancient dwarf planet in our solar system could lead to the production of ultra-hard machine parts.
A team of researchers, including those from Australia’s national science agency, CSIRO, have confirmed the existence of lonsdaleite in ureilite meteorites from the dwarf planet’s mantle.
Lonsdaleite is a rare, hexagonalshaped diamond believed to be much stronger and harder than its more typical cubic cousin. Lonsdaleite is named after pioneering British crystallographer Dame Kathleen Lonsdale.
The research is led by Monash University, in collaboration with CSIRO, RMIT University, the Australian Synchrotron, and Plymouth University, and was published in the Proceedings of the National Academy of Sciences (PNAS).
The study provides clear evidence of lonsdaleite’s formation in nature, offering options for synthetic production that could make more durable machine parts.
Lonsdaleite’s existence has been previously questioned, but his study has used a range of cutting-edge science techniques on the largest sample of ureleite meteorites to date, and provides clear evidence of its existence.
CSIRO scientist Colin MacRae said the discovery could have enormous implications for industries like mining.
“If something that’s harder than diamond can be manufactured readily, that’s something industry would want to know about.”
At CSIRO, an electron probe microanalyser (EPMA) was used to quickly map the relative distribution of graphite, diamond, and lonsdaleite in the samples.
The flagship instrument, together with high-resolution transmission electron microscopy (TEM) at RMIT University, helped identify the largest lonsdaleite crystallites to date—up to one micron in size.
CSIRO’s Dr Nick Wilson said this collaboration of technology and expertise allowed the team to confirm the lonsdaleite with confidence.
“Individually, each of these techniques give us a good idea of what this material is, but taken together—that’s really the gold standard,” he said.
The study, led by geologist professor Andy Tomkins from Monash University, reveals a novel process in which the lonsdaleite is created, replacing graphite crystals in the dwarf planet’s mantle facilitated by a super-hot fluid as it cools
and decompresses.
“We propose that lonsdaleite in the meteorites formed from a supercritical fluid at high temperature and moderate pressures, almost perfectly preserving the textures of the pre-existing graphite,” Professor Tomkins said.
“Later, lonsdaleite was partially replaced by diamond as the environment cooled and the pressure decreased,” he added.
Typically containing large abundances of diamond, ureilite meteorites are the only major suite of samples available from the mantle of a dwarf planet.
The parent asteroid was catastrophically disrupted by a giant impact while the mantle was still very hot, creating the ideal conditions for lonsdaleite and then diamond growth as the pressure and temperature decreased in a fluid and gas-rich environment.
Queensland premier Annastacia Palaszczuk has announced a clean energy future for Queensland, which includes the biggest pumped hydro scheme in the world.
A new dam in the Pioneer Valley near Mackay will supply half of Queensland’s entire energy needs with clean, reliable and affordable renewable energy.
The dam is one part of a $62 billion Queensland Energy and Jobs Plan. The plan also includes:
70 per cent of Queensland’s energy supply from renewables by 2032, 80 per cent by 2035;
Two new pumped hydros at Pioneer/ Burdekin and Borumba Dam by 2035; A new Queensland SuperGrid connecting solar, wind, battery and
hydrogen generators across the State; Unlocking 22GW of new renewable capacity – giving 8 times the current level;
• Publicly owned coal-fired power stations to convert to clean energy hubs to transition to, for example, hydrogen power, along with jobs guarantees for workers; Queensland’s publicly-owned coal-fired power stations to stop reliance on burning coal by 2035; 100,000 new jobs by 2040, most in regional Queensland; 11.5GW of rooftop solar and 6GW of embedded batteries; 95 per cent of investment in regional Queensland;
• Building Queensland’s first hydrogen ready gas turbine; and
• Projects subject to environmental approvals.
The Premier said the visionary plan will set Queensland up for the next century
“This plan is all about cheaper, cleaner and secure energy for Queenslanders. It is about turbo-charging new investment in new minerals, batteries and manufacturing,” she said.
“Renewable energy is the cheapest form of new energy. This plan makes Queensland the renewable energy capital of the world. It also takes real and decisive action on climate change providing the biggest commitment to renewable energy in Australia’s history.”
Deputy premier Steven Miles said the two new pumped hydro facilities would be bigger than the Snowy Mountains hydroelectric scheme.
“We will use cheap solar electricity during the day to pump water up the mountain to store it. Then at night we can release the water to generate electricity. It’s like a giant battery,” Miles explained.
Minister for energy, renewables and hydrogen Mick de Brenni said the Energy and Jobs Plan ensured Queensland’s power generators remain in public ownership.
Treasurer Cameron Dick said Queensland’s energy transformation will provide the greatest jobs opportunity in a generation and will bring manufacturing back to the regions.
and business planning to enter manufacturing at the ‘Renaissance One’ plant in Tomago, just north of Newcastle in the Hunter Valley. A few years ago, the company was told it wasn’t possible to manufacture lithium-ion batteries in Australia. Once operations are shifted at the start of next year, Renaissance One will be the first gigawatt facility in the country with the aim to expand to five gigawatts per annum whilst manufacturing battery cells.
Before the company’s inception,
sparked an idea to leave his successful business, to bring clean, stored energy to Australians.
With access to a high-talent pool of engineers, Chilcote and Craighead brought experts together to ask a simple question – what’s the best action to take for renewable energy?
At the time, Australia was almost completely reliant on wind and solar –with the exception of pumped hydro, there was no baseload renewable energy sources.
“We found problems with the current lithium-ion batteries in the Australian context: They weren’t manufactured with an eye on the hotter Australian conditions, they were a safety risk as the chemistries were prone to catching fire, it was difficult to install them in rugged, remote locations and there was a lack of cybersecurity and sovereign energy capability for the defence industry.”
Chilcote has over 25 years of experience in executing major lump sum risk projects in the power industry,
where he said it took around four years –and many frequent flyer points – to fully grasp the battery industry and technology providers.
“Pre COVID, manufacturing was a bit of a dirty word. It’s now more widely accepted that we should manufacture locally, but there’s still a lot of people with battle wounds from the exit of the car manufacturing industry, for example. The tide has turned but it’s still relatively slow in Australia.”
An over-reliance on raw commodities
Renaissance is set to operate Australia’s first lithium-ion battery manufacturing giga-factory. Billy Friend sits down with managing director Mark Chilcote to discuss the company’s energy mission to be a catalyst for sovereign supply and security of Australia’s clean energy storage systems.
clean stored energy to the fore
battery value chain can play an important role.
“My view is pretty simple. Mining is going to increase, but it will change. I think it will be less than ten years until the coal industry is insignificant. The continued environmental impacts we’re seeing like typhoons, earthquakes, bushfires will drive change and companies like Energy Renaissance will be the catalyst to drive this change.
“We’ll give long term supply agreements for people that then
develop their businesses but we won’t go upstream. Australia is the only country in the world with all the minerals for lithium-ion batteries. For the transition, it will take government, miners, lithiumion battery manufacturers, defence to all play a part.”
Following the completion of an Advanced Manufacturing Growth Centre (AMGC) co-funding program, the reality of Australia’s first lithium-ion battery giga-factory is only around the corner. Initiated to design, commission and operate a pilot lithium-ion battery manufacturing plant – dubbed Project ‘Apollo’– the pilot facility was designed to develop, test and document the technology, systems and processes and commence operations to supply to customers ahead of full-scale manufacture. The company currently operates at its ‘Apollo’ facility in Tomago producing up to 4MWh of batteries per month and serving customers across Australia.
“With the support of organisations such as AMGC, CSIRO and the Innovative
Manufacturing CRC, we have been able to develop a world-leading lithium-ion battery for domestic and export use and soon, we hope to expand the impact of this program to add value to Australia’s abundant raw materials by embarking on cell manufacture,” Chilcote noted.
Completion of the pilot program was a crucial step in Energy Renaissance’s scaleup program before its moves into the custom-designed, 4,500-square-metre ‘Renaissance One’ manufacturing facility. The plant will produce up to 300 Megawatt hours of energy storage annually, scaling to 5.3 Gigawatt Hours, or 5.3 billion watts, of energy storage per year via its ground-breaking battery system.
Completion of the pilot-facility program follows on from an earlier AMGC co-invested project where ER and CSIRO first developed a proprietary battery system (‘superRack™ and superPack™’), which is a unique plug-and-play prismatic cell system. This is combined with the Renaissance BMS™ which is a CSIRO-developed cyber-secure battery management system comprising custom circuit boards, software, and wiring and gives ER a competitive advantage in the
global battery market.
“First, we had to get product to market, in the field and operational,” Chilcote explained. “The battery industry is very immature and the interface between batteries and inverters is confused at best. We had a fairly steep learning curve on that interface. We didn’t have any problems with our batteries, but we did have a learning curve on the system.”
ER’s superStorage™ products will be the first lithium-ion battery energy storage system and battery management system that currently uses 92 percent of Australian components for its manufacturing in Australia, with the company already supplying batteries to local customers for use in industrial and commercial applications. Its SuperStorage™ platform will monitor, benchmark and self-diagnose battery performance autonomously and efficiently, supported by human intervention to develop customer specifications and deliver customer service. Energy Renaissance has taken the learnings from its pilot program to avoid costly mistakes in its automation and
robotics design.
“Buying an automated system wasn’t going to be useful unless we knew how to do it manually. We spent a lot of time assembling and manufacturing manually in the Apollo project and now we’ve taken the learnings from that and with the help of Bosch, we’ve engaged them to do our automation system design.”
The collaborative project, worth $1.47 million, was supported through a $525,072 co-investment administered by AMGC and matched by Energy Renaissance, with project partners contributing a further $427,681. Project participants include CSIRO, ATB Morton and Maccor. Energy Renaissance forecast $95.7M in revenue directly related to this project (excluding the larger Renaissance One facility) over the next 5 years. Energy Renaissance will move into the new facility at the end of this year and expects to be fully operational around March 2023.
After looking at locations all around the country for its flagship facility, Tomago was chosen because of its proximity to a deepwater port and university in Newcastle as well as CSIRO’s energy hub. Energy Renaissance gets custom steel
fabrication from nearby in Newcastle, circuit boards from Penrith, NSW, plastics from Queensland and the components in its batteries are all sourced from local suppliers.
Leveraging local suppliers and supply chains, the company’s aim is to offer products that are as close to 100 percent Australian content as possible, with the company already at 92 percent as it relies on imported battery cells that are not currently manufactured in Australia. This number wasn’t achieved overnight, said Chilcote.
“18 months ago, we were 100 per cent import, buying basically everything out of China” Chilcote said. “We made a priority list of what we would onshore. We picked Australian suppliers with an attitude and belief in themselves with a long-term vision.”
To demonstrate this journey, Chilcote referenced a partnership with Academy Sheetmetal, a family owned Newcastle sheet metal manufacturer.
“When we first approached them, they were around three times more expensive than China,” he said. “Like us, they weren’t willing to accept this, so we did a lot of value engineering with them and changed the design to suit their machinery. Off the back of that, they have
bought new equipment and robotics to be more efficient and we are now almost sole-sourcing the metalwork from them.”
Printed circuit boards and injected moulded plastics are also sourced locally, but computer chips will continue to be imported in the foreseeable future, said Chilcote. Part of Energy Renaissance’s next step is to manufacture battery cells using the raw materials Australia is lucky enough to possess. The company is hoping to confirm financial investment decision on the battery cells in June of next year and begin manufacturing after 12 months at the Renaissance One
“We’re trying to build up both the local industry and the industry in Australia.
So in the near future, we’ll have a production of energy that’s not only cheap, but we’ll also have sovereign supply and sovereign security of our energy storage systems,” Chilcote
“So the problem we’re solving is if we can make clean energy cheaper and more reliable, then we help Australia bridge the gap between fossil fuels today and renewable energy tomorrow. The vision back in 2015 was all around Australian products and people and reducing the impact of the environment – we’ve never swayed from those two pillars.”
Dr Jens Goennemann, managing director of AMGC said Energy Renaissance is proof positive that Australia can be a world leader in the renewable energy industry.
“Energy Renaissance’s approach typifies how we should be seeking to
move away from our reliance on raw commodities and tap into our abundant human, commodities and manufacturing prowess to transform it into complex goods for local and export markets,” said Goennemann.
“Energy Renaissance didn’t stop when they developed a battery for hot and humid climates, they embarked on commercialising the technology and we are pleased to have been there to assist them – they are a shining light for others to follow.”
Part of the superStorage platform, the battery management systems (BMS) developed in collaboration with CSIRO has three attributes which separate it from systems bought off the shelf. First of all, to satisfy government and defence contracts, the BMS is the only known cyber-secure system in the world. The BMS is more accurate than counterparts, which lends itself to the future of ‘energy as a service.’
“If you’re going to be trading through a battery, then it needs to be very accurate and it needs to know when it should trade. We will use machine learning so the batteries learn when to trade,” Chilcote said.
The third unique advantage of the Energy Renaissance solution is particular attention to cooling to make the batteries far superior in Australian conditions.
“The temperature of the battery is important, but what is more important is the consistent temperature of the
batteries,” he added. “The BMS is designed to anticipate batteries at the top naturally heating more than those at the bottom to solve this problem.”
Fourth-generation dairy farmers John and Rochelle Pekin and owners of the Nikep Dairy Farm have felt first-hand the impact of the price of grid electricity in recent times. Adding to the financial pain, the farm initially had an unreliable grid electricity supply that required them to have a backup diesel generator to power its operations, especially in the afternoons as high-power demands from around the farm’s location meant it was most vulnerable to brown outs.
Working with Energy Renaissance, the owners had a 250kW rooftop solar system and a 520kWh Renaissance superRack™ installed, which now provides 95 per cent of the farm’s energy requirements. The
Nikep Dairy Farm is saving $70,000 every year on energy and fuel bills, but John Perkin said the switch wasn’t just based on finances.
“Investing in clean energy goes beyond economic considerations for us as dairy farmers. We want to inspire others to do something now because we’re making our farm more sustainable, which is better for the environment,” he said.
“Being an Australian dairy farmer, we want to support a local battery manufacturer like Energy Renaissance. It’s important for us to support local manufacturing as it creates jobs, and it is great for our economy – just like what we’re doing here for the Aussie dairy industry. If the day comes when we need support for our batteries, I feel reassured that we’re in the same country as Energy Renaissance and we’ll get the help that we need.”
In time, Mark Chilcote explained Australia’s defence industry will be the biggest market for Energy Renaissance, followed by special-purpose electric vehicles. The company will continue its current offering for static storage, as the demand for lithium-ion batteries will only increase in homes, agriculture, factories and mining.
Instead of competing against other forms of green technology, Energy Renaissance sees an ecosystem where different technologies can bounce off each other.
“Ultimately trains, ships and heavy haulage will become hydrogen. There are uses for flow batteries, pumped hydro and others – we don’t think it’s one technology which will win the race.”
The other consideration for lithiumion batteries, Chilcote noted, is the likelihood of the battery chemistries
advancing and changing within the next decade or two.
“We’ve been very careful in the design of our platform to be chemistry agnostic,” he said. “This means we can change as the chemistry evolves. Hopefully the technology changes because of one of our Australian universities, but it will evolve.”
In order to manufacture battery cells, Energy Renaissance has to buy the raw materials out of China and Taiwan, despite them being mined in Western Australia. The opportunity is there, Chilcote said, to flip the page on this, and turn our wealth in mined materials from an Achilles heel to a manufacturing advantage.
“We have to start actioning whatever can be done in that upstream supply chain to help people develop that industry. We won’t have energy security until government and industry can achieve this.”
Space Tank Studio is a business makerspace and manufacturing incubator helping local designers and innovators build new to-market products with global potential. Billy Friend spoke to Scott Anderson and Holger Dielenberg about the makerspace’s ambitions for the near-future after successfully pivoting through the COVID-19 pandemic.
NEWideas and start-ups inject excitement into Australia’s manufacturing ecosystem. Without innovation and different approaches, Australia risks losing the opportunity to be a player on the world stage, as well as an exceptional manufacturer of things on its own shores. Currently, the players who are new to the game face major hurdles and barriers to access what they need to succeed.
Holger Dielenberg, Space Tank Studio founder, explained that the purpose of the business makerspace is to play a foundational role in the bigger picture of Australian industry – to help innovators and niche manufacturers transform creative ideas into working prototypes with a viable commercial proposition so they will become the engine of Australia’s
design economy.
“There are not many avenues for entrepreneurs to access the industrial equipment, network and education they need to achieve this,” he said. “Most of Australia’s accelerators aren’t focused on traditional manufacturing or advanced manufacturing – there’s a heavy bias towards app development software.”
Dielenberg spent 7 years working in Europe where he noticed the development of co-working spaces that focused on creative manufacturing. When he returned to Melbourne, his mission was to merge the incubator model with the creative makerspace model.
“I had spent many years building shared warehouse models for creative use in the 90’s. These types of space are valuable because they support thousands
of creative makers and help to maintain a vibrant creative maker culture. But after experiencing the European models and studying the emergence of the Maker movement in the USA, I realized that a commercial mindset in creatives at a grass roots level was missing. Helping people who make physical things get off the ground and supporting their commercial growth, – no one had done it as an incubator model,” he explained. “In 2013, I found a warehouse in North Coburg and started building. We brought together all the fundamental equipment and technology components under one roof, but also the commercial mindset to help develop ideas from napkin, to bench, all the way to business.”
Space Tank has supported over 800 early-stage manufacturers and designers
in its 8 years of operations, and won numerous awards for providing specific support to startups. Dielenberg, along with co-founder Scott Anderson, is looking to scale equipment offering in the Coburg North facility, which includes a wood workshop, welding bay, laser cutting, 3D printing, CNC milling, bronze forge, spray booth and co-working fabrication space.
Manufacturing contributes over 20 per cent of Victoria’s economic output – an estimated annual output of $204B – but startups are lacking in sectors that rely on manufactured goods, according to Dielenberg.
Sadly, he said, it is little wonder why Australia has lost major aspects of its manufacturing capability.
“Buying manufacturing equipment
“You must learn how to make products that take advantage of current and future technology developments, but more importantly, you must consider your go to market strategy. Building a business case doesn’t happen overnight and infact for most creative entrepreneurs it is an afterthought,” Dielenberg added. “We have programs such as the Bench to Business program to make people better entrepreneurs.”
The Bench to Business program is one of three of Space Tank’s training initiatives, helping develop better, more successful founders and applied technology startups. The program is for individual founders, emerging product developers and designers who have a passion and drive to take their concept from napkin sketch all the way to market. The content is across three areas: human centred design, prototyping for design and business and marketing.
in Australia is prohibitively expensive,” he said. “The knowledge to use that equipment can be a challenge. A lot of people enter the world of making and innovating via insights they have gained from their professional activities or from left field inspiration – they don’t want to do a three-year degree; they want to hit the ground running. Australia’s geographic isolation from international markets, relatively small population and high labour rates are against them. Emerging entrepreneurs need to run a lot leaner in the early days considering the long lead time to get to market. Combine these challenges with an incubator/accelerator support network that only caters to App developers and the hurdles for manufacturing startups can be insurmountable.”
The challenges are plenty, resulting in much of the high-end prototyping and advanced manufacturing equipment being used in large corporates, bigger business and universities. Outsiders don’t have the ability to wander into these spaces, but we are seeing more disruptors and early adopters put their hat in the ring, as evidenced by the stories being told in this magazine this calendar year.
So what do start-ups and SMEs require to commercially succeed? Dielenberg said Space Tank sees opportunities to bridge the gap in the are of what is being labelled
‘Applied Technology’.
“We can leverage efficiencies of scale by providing affordable access to highend equipment as well as the training to use that equipment – the mentoring on how to use efficient advanced manufacturing workflows to process ideas and prototypes quickly and convert a concept to a commercialisation right from the get-go,” he said. “No one can
afford an entire factory from day one but renting a studio space with affordable access to equipment lowers barriers to entry. In particular Australia has an advantage in product development where physical and digital worlds meet.”
Every entrepreneur has to start somewhere, so providing our brightest brains with the right education and training is crucial.
Scott Anderson joined Space Tank in 2017, bringing commercial and corporate experience to help grow the business makerspace into a venture studio ‘startup factory.’ “There needs to be a number of building blocks in place to build a successful startup factory,” said Anderson. “In addition to access to equipment and facilities and creating better founders, we need strong corporate collaboration, manufacturing focused accelerator programs and community.”
Space Tank understands the
importance of corporate backing, which is why it is working on establishing a CoLab Venture Studio model, bringing together corporates, domain subject matter experts, manufactures and designers to ideate solutions in a defined problem space. The purpose of this is to validate and develop proof of concept solutions, allowing corporates to outsource innovation and commercialisation. It isn’t a new concept around the world, but Space Tank is wanting to make it work on our shores.
“Community is an import element to success,” Anderson continued. “Having those conversations in the corridor and bouncing ideas off the right people with an ecosystem around that is valuable. For instance, if someone needs access to specialist services outside of our offering, we can point you in the right direction via our large industry network. We want to look to continue to scale this as well.”
Applied technology combines digital and physical products and systems. Smart products incorporate the use of IoT, sensors and connectivity to genuinely enhance and change our lives. Globally, the bulk of startup activities come from
app development, but Anderson and Dielenberg both echoed that the days of App startups with highly inflated valuations and ‘unicorn’ investor hype are reaching market saturation.
“We think that the app space is overcrowded,” said Anderson. “Apps are now used in nearly every aspect of our lives and the App market is beginning to repeat itself. We’ve seen valuations go down but a lot of people are still chasing the unicorns – the billion dollar valuation – which are as rare as hen’s teeth.”
Balance needs to be restored in the startup ecosystem, according to Anderson, with the next steps to support the integration of physical and digital innovations in areas like medical, mobility, clean economy and smart city technologies. This will underpin job growth in future focused economic sectors. For designers and manufacturers, the end of ‘app hype’ marks the opening of a new opportunity space – applied technology.
Dielenberg first used the term ‘Applied Technology’ in a 2018 Melbourne Knowledge Week presentation. The term is now being used more commonly to describe Australia’s modern design and manufacturing landscape. With the help
of government funding, Swinburne University and RMIT are now starting to offer diplomas and degrees in applied technology, which are engineering and digital technology courses developed in conjunction with industry partners.
Space Tank has always supported creative and niche manufacturers like furniture makers, lighting designers, jewellers, set and prop designers. But Dielenberg feels more focus needs to be placed on makers using technology.
“We have supported the growth of some innovative product developers like Bastion Cycles using ergonomic 3D design and carbon fibre and 3D printed titanium, Eutropia Aerospace micro rocket propulsion systems, Jaunt Electric Vehicles, UpperLimbCo orthotics, Freo2 oxygen delivery systems and Freeform Composites carbon 3D printing technology. Our goal is to increase our support for these kinds of startups.”
“We can fit around 25 businesses at a time at Space Tank and help them grow. Innovators can now make a ‘dumb’ product smart and combine things in ways never before possible, which can help Australian entrepreneurs to overcome business scaling challenges like the tyranny of distance, our small population, gender imbalance and high
labour costs.”
To support this mission, Space Tank is looking at scaling its equipment and programs to attract even more hightech startups. “We think there is a good opportunity to grow Space Tank’s CoLab Startup Factory concept in new design/innovation precincts such as the Brunswick Design District and Fishermans Bend,” said Anderson.
Launch Vic have been very successful in growing the state’s startup ecosystem, but Anderson explained that the Government has an opportunity to ensure balance between App and Applied Technology startups.
“Thanks to Covid, political vision for sovereign manufacturing and strengthening Australia’s supply chains are finally catching up with public and industry opinion,” Holger said. “A shared and immediate challenge facing our governments, businesses and institutions, is to transition our society from an economy based on finite resources with limited options, to a future where infinite knowledge and creative enterprise create unlimited opportunities to thrive.
“Creatives, entrepreneurs, designers, engineers and startups will be the most important people leading the way.”
Beckhoff Automation’s global managing owner, Hans Beckhoff, and Nick Psahoulias, managing director of Beckhoff Automation, Australia, speak exclusively with Manufacturers’ Monthly about the company’s growing global presence, and the human touch needed in automation technology.
HANS Beckhoff, founder, owner and managing director of German giant Beckhoff Automation, has seen a lot in the past 40 years of steering the family-owned business.
Currently one of the top three PC control technology companies in the world, Beckhoff tells Manufacturers’ Monthly how that level of experience has helped the company navigate the latest COVID-19 crisis. While the nature of the pandemic took many by surprise, Hans Beckhoff said that the company saw some kind of crisis as inevitable. And like with every crisis, it’s being prepared that’s critical in seeing it through successfully.
“In the Western world, capitalism rules
the business and it’s typical for capitalism that you have cyclic business,” he said.
“This means every five to ten years you would have a crisis that would go on for a few years, something like this. As a company you should foresee such a crisis and you should be able to go through it in terms of financial stability.”
In a globalised economy, Hans Beckhoff was particularly aware of how a crisis can affect supply chains. The company had anticipated the Euro crisis and had learned to prepare for the effects of the disruption.
“What we learned is that you need have your own warehouse filled up with material,” he added. “One of our business philosophies is that we should have at
least between four to six months of raw material in stock physically in our own warehouse.”
Despite the interruptions, Hans Beckhoff noted he was happy to be in a position to support his customers as business continued strong. All that was needed was to have the supply. The challenge came with the international shipping crisis, so the company has had to adapt to longer delivery times.
“We are doing our very best and have invested a lot of money in this,” he noted.
The result is a company that has continued to see growth and is well placed to see even more growth in the future. With a total worldwide result of 1.182 billion euros, the company increased
its sales in 2021 by around 28 per cent in comparison to 2020. “This is a great result that we are incredibly proud of,” Beckhoff noted.
“In the end, we managed to go through the crisis without any serious implications to the business,” he said. “There was a small slowdown that had already started in 2019, before COVID-19 hit, and which is now ending. We will see a big boom coming.”
Hans Beckhoff is preparing for major growth in the automation technology market.
“We have a lot of incoming orders this year,” he said. “And my prediction is that this ‘boom’ will go on – we are seeing it in all parts of the world – so it’s not only
China, but also America and Europe.”
“Every year we introduce evolutionary technology into the market and every 5-7 years we try to introduce revolutionary technology. The intelligent transport systems XTS and XPlanar are revolutionary. They are really changing the way machines are built,” says Hans Beckhoff, who also highlights the new MX-System as such an innovation, which was introduced late 2021.
“The MX-System offers a flexible, space-optimised and intelligent system solution and sets a new level in industrial automation by completely replacing the conventional control cabinet. In June 2022, we presented ATRO as another innovation. Our new concept for robotics applications is a modular system from which the right robot kinematics can be put together extremely flexibly for any application. Furthermore, we will introduce our new vision hardware this fall. Our product range will be extended by cameras, lenses and illumination. We
have already introduced the TwinCAT Vision software in 2017.”
Automation Down Under Australia, naturally, fits well within Hans Beckhoff’s vision for growth. Australia is in the middle of embracing a manufacturing transformation, with increased automation, which has been viewed by the government and the business community as critical to its future.
In Australia, Beckhoff Automation is headquartered in Melbourne, operating under the leadership of managing director Nick Psahoulias. The warehouse and main sales team are based in the south-eastern suburb of Oakleigh.
Psahoulias is confident of the market strategies the company has adopted locally. After seeing the results of the past year, he is already making moves to expand into other states.
“We grew by 25 per cent in 2020,” Psahoulias told Manufacturers’ Monthly
“We saw this as an opportunity not to play cautious, but actually to reinvest in ourselves and make sure we had the best sales and best support team we could.
“This has proven to be the right decision, as it’s been a good year. Going forward our next location will probably be Perth once we find the right person for the opposite side of the country.”
This expansion in Australia represents a fraction of the success Beckhoff Automation has experienced worldwide. Founded in 1980, the company built it success on powerful PC-based control technology. Since then, Beckhoff Automation has risen to become one of the world’s foremost specialists in electronic and software-based automation of machines, processes, buildings, and devices, using the features of a PC, and combining it with automation technology, IT with OT. Hans Beckhoff explained that the company’s philosophy is centred on PC-based control, where certain types of high-tech
components are required to facilitate machine control with reactions speeds below a millisecond.
“If it comes down to controlling a very fast packaging machine or measuring a fast data rate, or if you need a faster reaction time, then Beckhoff Automation is a safe bet to go with,” he said. “Its PC-based technology can perform up to one 100th millisecond of real reaction time, which is normally not possible with most standard machine controls that run around a millisecond or longer.”
Industrial PCs are the base for machine intelligence, and Beckhoff’s engineers and other specialists develop the motherboards to optimise the operating systems. Beckhoff Automation specialises in applications in all areas related to PC control, from packaging, to wind and solar power, even battery production.
The company also specialises in automation functions like the sequential logic of a machine project, as well as algorithms for robotics, CNC application for standard motion applications, pointto-point movements, measurement technologies and artificial intelligence for vision.
“It’s about high tech on a big level and application know-how on the customer level,” Hans Beckhoff added. “Our customers can rely on this know-how chain and it’s very important to me – as the managing director and owner of the company – that this know-how chain is always improving, covering more fields and, most importantly, is stable. Our engineers stay with Beckhoff for a long time.”
All this expertise is combined in one automation suite software package, TwinCAT (The Windows Control and Automation Technology) – and Hans Beckhoff’s passion for the project is clear. It turns almost any PC-based system into a real-time control with multiple PLC, NC, CNC and/or robotics runtime systems. Whether it is communication to the cloud or to a linear PC system, everything found within TwinCAT can be used on standard PCs – which makes a powerful system easy to use.
“TwinCAT is a connection system between the different parts of the IO technology, drive technology and PC technology,” Hans Beckhoff explained. “From the smallest control to the biggest
and most advanced, everything is proven with TwinCAT. Our customers have a good, powerful base for all different types of applications.”
Beckhoff Automation also offers a multitude of technologies to the market, which are available in Australia. This includes their input output (IO) products, such as their IO box modules, which are IP67 protected. The company is one of the main global producers of IO products.
“What is now typical for all our friends in general automation technology, there is an IO in the form of an electronical component that looks a little bit like a terminal and electrical formula,” Hans Beckhoff said.
“This idea, brought to market in 1995 by Beckhoff at the Hannover Messe trade event, proved to be viable. The basic idea was to develop it at Beckhoff through industrial mechanics and housings. We were a strong hardware and software company then, but we were still relatively small-medium. Unfortunately, we did not get a patent for it then, and so, of course, all automation manufacturers copied the idea three years later. Today, bus terminals have been developed
as a standard component with our automation technology.”
In terms of acquired growth, Hans Beckhoff said they are always looking to expand, buying up smaller companies with great ideas, and are looking to be at the forefront of technology leadership.
Most of the business is based in Europe, 25 per cent in Asia, 10 per cent in North America. With 40 subsidiaries (including Australia) as well as partners in more than 75 countries, Beckhoff Automation is able to provide the customers with complete and optimal support.
With such a global presence, maintaining a strong team has been key for Hans Beckhoff. He said that it’s the trust in his staff to deliver for customers that is essential to the management of his business across the globe. For him, because automation technology is complex, it is important to be supported by good people. He puts great emphasis on the importance of customer service and why he wants that to be present in the Australian market with
“Beckhoff Automation is a high-tech company with traditional values and I as the manager of the company have placed a great focus on making sure the specialist engineers and are the best in the business at what they do. Now, I want to make sure our customers have access to them, and this results in building on getting new customers who trust us.
We are winning customers, not losing customers and I am proud to say that the ones we started with in the 1980s, they’re still with us,” he said.
“We’re not only selling hardware and software, but also inspiring trust because a machine builder has to trust the control supplier – they both depend on each other. Our customers can talk to all our engineers and our engineers in most countries are available locally, we have good specialists in Australia as well.
“On one side we like to be a worldwide high-tech company, which is driving technology, which is of the utmost quality available. On the other side, we want to be – and we are – the local, friendly neighbour and engineer, who is available just around the corner.”
1. RoboHelix
RoboHelix has developed and introduced the world’s first fully automated robotic flight-forming machine and has secured an international patent for it.
RoboHelix chose to work with Beckhoff Automation’s complete solution for its process and were able to remove the technical element of flight forming and have a solution that enables anyone to form superior flights without any experience. With an integrated product combining software and hardware, RoboHelix has been able to extend the original system, rendering traditional machines obsolete and added further job functionality to the manufacturing workflow.
“RoboHelix uses electric motors to actually bend and twist these flights into a precise shape,” Nick Psahoulias said. “What this means is that this could be made from the local machine shop down the road from a manufacturing plant. When they need a spare set of flights made, they send them the drawings and within a couple of hours they can have a fully formed auger, ready-made.”
“This innovation is very important for anyone from a food processor who needs to move cookie dough down a production line, or a mining company that needs a new drill manufactured. The innovation behind this product is they’ve taken a really traditional, ancient application like the Archimedes screw and turned it into a real IoT device where you can order it online. It gets made and delivered in a quantity of one.”
“This is a real success story for this innovation. Taking something ancient and making it a new process.”
Another example is Modra, who placed its trust in Beckhoff Automation’s platforms to manufacture its creel machines for carpet weaving.
“Traditionally, all of these reels of fabric would be hand-loaded into a carpet weaving machine,” Psahoulias said. “This means all the colours had to be pre-determined, all the links had to be known, and there is a lot
of operator interaction with making carpet.”
“A carpet-making wall has 500 reels of thread on there and an operator would go and pick the right colours of the threads and put it through the needles and have the machine ready to go. What this does is automate the entire process. So here you might have each cassette of reels, you might have 100 reels in there, and what this machine does is automatically wind the empty reels with the right colour of thread and then puts them back into the cassettes, ready to be put into the weaving machine.”
“The operator no longer has to do anything by hand, all they have to do is transpose the cassette from the loading machine to the weaving machine.”
The transposing of the cassette from the loading machine to the weaving machine is the next step for Modra. Ninety-five percent of Modra’s business is exported, so everything it does is remotely configured and remotely supported, lending itself well to PC-based technology. The company is based in Victoria, but the machines are used all around the world.
In the early days of the COVID-19 pandemic, there was a panic for more ventilators. A State Health Department asked a local engineering firm how quickly they could make ventilators in Australia. This company designed and developed the ventilators in around six weeks.
“It was very, very fast R&D and we were using factory available products, so there was nothing custom-made here,” Psahoulias said.
The ventilator technology was based on the TwinCAT software.
“The entire intelligence was based on TwinCAT. Through the software, the interface for the nurses was so natural that they were able to learn how to use these ventilators within 15 minutes,” Psahoulias added.
“I think the law allows 45 minutes for training on such a device. So it was that intuitive that it was quickly adopted and awarded a contract to build 100 systems. And as we know, these were very much needed for this year.”
Beckhoff customers.Manufacturers’ Monthly investigates CAPS Australia’s latest engineered instrument air project, which will utilise over 2.8 megawatts of installed Ingersoll Rand air compressors and four huge zero loss desiccant dryers from its German partner FST.
FOR over 41 years, CAPS has been Australia’s largest independent supplier of power generation and air compression products. With proven global engineering and export capabilities, the team of experts undertakes turnkey projects which include the design, supply, installation, commissioning, and provision of long term maintenance support to Australian industry standards (ISO 9001:2008).
CAPS’ flexibility is a major attribute with its ability to provide for a reciprocating, rotary screw, portable diesel or centrifugal air compressor, engineered around a particular customer’s needs. To help manufacturers, stock is key, and having the largest range from the world’s leading industrial air compressor manufacturers means the Australian company provides for a huge range of applications.
According to Andrew Fraser, Engineering & Manufacturing Manager at CAPS Australia,customer confidence also
plays a role in the selection process. CAPS is a renowned supplier of compressed air and power generation systems and the company has built a positive reputation for being reliable and customer-service oriented.
“One of our advantages, is that all the work is performed locally. Our engineers are all Australian-based and have a thorough understanding of Australian standards requirements. This extends to state-based design and plant registration authorities such as WorkSafe and Workcover OHS requirements,” Fraser explained. “We stay close to the customer throughout the process, including aftersales. We’ve got nine branches across the country and always strive to provide our services in a timely manner.”
Depending on the needs of the client, CAPS can provide a complete ‘endto-end’ service to clients. This usually entails a site visit from one of CAPS specialists where they will work with the customer to get an understanding of the
application and requirements for the custom-build. They will then send this information to the engineering team who will provide drawings of the vessel. Once the design has been agreed to, CAPS will continue the build and then provide installation.
CAPS also work with independent third-party design and quality assurance inspection bodies such as ICD, Bureau Veritas or LRQA where required. They have expertise in AS1200, AS1210, AS3920, AS 3788, AS4037, AS4458, AS4343, AS3992, AS2791, ASME VIII, ASME IX, EN286-1 and more.
CAPS’ capabilities are demonstrated in a recent project involving eight 355kW Ingersoll Rand flagship oil-flooded rotary screw air compressors and four zeroloss desiccant dryers from their German partner FST.
The customer originally contacted CAPS Australia with the request to
generate bulk clean, dry instrument air, with maximum energy efficiency whilst balancing the capital equipment and infrastructure installation costs. This would allow the customer to meet the required compressed air quality and demand under worst case ambient conditions. CAPS determined a customised equipment solution was needed to meet the site environmental standards with safe and simple automatic operating requirements while also complying with the client specifications.
CAPS’ expertise lead to the decision to design, build and supply a heavily customised air compressor and dryer package.
The Ingersoll Rand flagship oil-flooded rotary screw air compressors and zeroloss desiccant dryers were completed with factory acceptance testing, passed final client inspections, customised with outdoor mods, high dust filtration,
packaged pre filters and enhanced safety electrics.
“The two stage RS355ie compressor has a full load specific efficiency of six kilowatts per metre cubed per minute positioning it at the cutting edge of outright rotary screw air compressor efficiency,
delivering a huge 69 metres cubed per minute of free air delivery at 8.5bar,” Fraser said. “The compressor features an IE3 heavy duty 96 percent efficient drive motor, designed specifically to Ingersoll Rand’s exacting specifications. It’s Capable of continuous full load delivery in ambient temperatures as high as 46°C without deration.”
The RS355 series comes standard
with the Xe145 full feature controller that includes the ability to communicate to customer communication systems with Modbus RS485 or Modbus TCP/IP protocols.
“The XE145 controller can sequence 8 additional machines without use of external master controller and integral web server feature included for monitoring compressor statuses via a connected browser,” he added. “For additional safety the compressor has also been fitted with incoming power isolation so that safe power isolation is required prior to the opening of electric enclosure. The electrics inside this enclosure are compliant with the applicable requirements of the ISO3000 standard.”
Once more, every pressure relief valve has been re-tested and certified to AS1271 standards and a protective cover for the Xe145 controller provides IP65 weather and UV protection.
The RS355 compressor’s high dust two stage filtration system has an innovative primary mechanical separation panel including dust collectors.
“This panel was followed by a high efficiency high-capacity air filter element,” he noted. “The primary mechanical separation system ensures the maximum service life of the critical air filter element even in the harshest and dirtiest of environments.”
Packaged pre filtration ensures the cooling airflow is pre cleaned prior to entering compressor, which provides long term protection for oil cooler and air after coolers in dirty and environments.
The packaged pre filter element is easily accessible for routine maintenance.
The project includes four large desiccant dryers with the capacity to produce up to 8000 normal metres cubed per hour or 4700 cfm dried to -40 degrees Celsius pressure dew point, at pressures as low as 6.5bar. Pre and Post filters on the driers ensure the air is treated to ISO8573 class 1.2.1 standards.
“To operate with maximum energy efficiency, these dryers also configured as zero loss heat regenerative to ensure no valuable upstream compressed air is lost through inefficient purge cycles,” Fraser explained.
Additionally, the dryers have an air to water inlet heat exchanger to optimise the compressed air even on the hottest of Western Australian days. An automatic redundant dryer capacity available at all times, for critical plant instrument air needs.
The dryer also includes a PLC controller mounted in a stainless steel IP 65 enclosure and the controller has the ability to communicate with the site DCS via Modbus TCP IP.
All in all, because CAPS is an independent business which is not tied to a particular OEM, it is able to search the world for the best matching piece of equipment tied to the customers’ requirements. The Australian company continues to deliver end-toend solutions based off its in-house engineering expertise.
Compressors play a crucial role in a variety of manufacturing environments. Manufacturers’ Monthly investigates the seven most important compressor demands, and why Atlas Copco variable speed drive (VSD) machines meet all of them.
ATLAS Copco offers both variable speed drive (VSD) and fixed speed compressors because each types offer advantages in specific circumstances.
As the name suggests, a fixed speed air compressor operates at the same speed whenever it’s running. By design, it always draws the amount of power needed to meet the maximum compressed air demand, even if demand is less than maximum. Because the speed of the motor can’t change, whenever the demand for air changes, an air inlet valve adjusts to allow either more or less air to flow out.
In contrast, a VSD air compressor can operate anywhere in the range between its minimum and maximum speed, and it automatically adjusts the speed so production of compressed air matches demand in real time. When demand increases, the motor speeds up. When demand decreases, the motor slows down.
The first VSD range of compressors were first made in 1994, manufactured in Atlas Copco’s Belgium factory. The latest VSD ranges are made in multiple factories around the world.
The variable speed drive adjusts the compressor’s speed (RPM) by means of an inverter. Instead of sending all the power directly into a traditional AC motor that runs at full capacity, the inverter provides the VSD compressor only with the specific frequency required to meet the current demand.
Gabriela Harris, Atlas Copco communications manager, said this capability saves energy because the compressor don’t have to run at full capacity whenever it’s on.
“You can think of VSD like the accelerator in a car, which allows you to vary the car’s speed according to road conditions, level of traffic and whether you’re in a hurry,” she noted.
The ability to adapt motor speed to the fluctuations in air demand means VSD air compressors can be the best choice for a
huge range of industries.
Some manufacturers offer retrofitted fixed-speed compressors with an add-on inverter as VSD units. These compressors should come with a disclaimer. According to Harris, to get the most out of VSD technology, a compressor must be designed, built and tested as a VSD compressor. All components, not just the inverter, must work together to deliver the maximum energy savings and a reliable operation.
“That is why Atlas Copco VSD compressors clearly outperform the pretend ones,” she said. “Because only a dedicated design and custom-built, quality components will get the most out of the VSD technology. There is indeed a growing demand for VSD units, especially where energy costs are increasing, and demand of air consumption is not consistent. VSD give an attractive Return on Investments (ROI), which can be easily quantified and calculated with our data loggers. Contact us to know how much
energy can be saved. We carry significant local stock of VSD, right from 7-90kW range and focus on increasing it to align with the future demands.”
In order to continually innovate and create the most specific solutions for manufacturers, Atlas Copco invests heavily in research and development.
“Significant investment in research and development helps develop new solutions that improve our customers’ performance, providing energy efficient compressed air solutions,” Harris said. “Continuous interactions with customers, connectivity and data-driven insights are key to understanding the customer’s requirements.”
Atlas Copco VSDS machines come equipped with a new element, a FerriteAssisted Synchronous Reluctance (FASR) motor, a Neos Next Inverter, and Smart Temperature Control (STC) System.
The Neos Next Inverter provides
IP54 dirt protection and combines the functionality of one electrical cubicle into a compact unit. Lastly, the STC ensures ideal injection temperature control. With all these components included, the GA VSDS air compressor is a powerful machine that adapts its performance to its operational environment – and to your needs. Also, with optional Energy Recovery, these machines can re-use up to 80 per cent of heat generated.
“Benefits offered by the FASR motor include IE5 efficiency (which is the most premium motor on the market), and the way they’re constructed without rare earth metals reduces your carbon footprint and saves on unsustainable rare earth metals.”
For maximum connectivity, the VSDS are equipped with SMARTLINK technology and OPC UA. SMARTLINK provides real-time data, insights, and analytics to help maximize performance. OPC UA helps you integrate our VSDS seamlessly into your smart factory.
Each company has different compressed air needs, which is why it can be hard to decide on the best air compressor. Atlas Copco says manufacturers don’t need a standard solution, they need the compressor that is just right for you. A variable speed drive (VSD) machine delivers exactly this flexibility. If compressed air flow changes throughout the day, this equipment will match those needs. Designed for various applications, including heavy industry, woodwork, textiles, recycling, pulp & paper, chemical & petrochemical, and general manufacturing, an Atlas Copco VSD compressor offers lots of options for a custom compressed air solution.
“If you work across different applications requiring varying levels of air flow, a VSD air compressor will definitely be the right choice. In some instances, they provide an all-in-one solution.”
Reliability is a crucial factor with any air compressor setup, especially when downtime adds unexpected operating cost expenses. To maximize performance and efficiency, you’ll want a machine that is versatile, connected, and easy to install, maintain, and monitor. The Atlas Copco variable speed drive GA VSDS air compressors come with the latest innovations to keep your factory operating smoothly. With their Neos Next inverter, Boost Flow and Limp Modes, and Smart Temperature Control (STC) System, they’re wellequipped to help avoid downtime.
When maintaining any machine, you’ll want to invest in OEM replacement parts and a service plan with certified technicians. With proper care, Atlas Copco air compressors are built to operate for a long time. By following the recommendations below, your equipment should keep going for years to come.
Although generic non-branded parts are cheaper upfront, they could increase your company’s overall operating costs and expenses. By using generic parts for your machine, you increase the risk of breakdowns, downtime, and loss of air flow and
and cut into potential revenue.
If you use more than one air compressor, you might want to add an Equalizer 4.0 central control system. This connected technology helps you operate multiple compressors efficiently while minimizing individual wear.
With stricter emissions regulations, and increasing gas and fuel prices, it’s now more important than ever to reduce electricity consumption wherever possible. Depending on your country, you may need to act quickly. Electricity consumption makes up more than 80 per cent of the cost of owning and operating an air compressor. Atlas Copco’s VSDS air compressors produce maximum air flow with the lowest possible electricity usage. With features including a state-of-the art drive train, the Neos Next inverter, and a Smart Temperature Control (STC) system, they can reduce energy consumption by up to 60 per cent.
Although it may not seem costeffective to replace old machines, doing so could save on wasted energy consumption.
When choosing an air compressor to work with your smart factory,
connectivity, in addition to other innovations. The VSD model comes with features like SMARTLINK and OPC UA for maximum control and integration. It also has unique innovations like Boost Flow and Limp Mode, and a Smart Temperature Control (STC) System.
Adding SMARTLINK monitoring technology to any air compressor puts you in charge. This feature from Atlas Copco provides real-time air system status updates and monitors energy use. SMARTLINK also comes with an easy-to-use mobile application. In addition, you can opt for an Elektronikon Touch 4.3-inch display for access to customizable timers and controls.
With OPC UA, you can connect all your production equipment in one system. This integration includes machines beyond air compressors. When combining OPC UA and SMARTLINK data technologies, you’ll tap into secure, efficient connectivity to keep your smart factory running.
If you have your compressor on the production floor, rather than in a separate utility room, you’ll want a quiet solution. Industrial compressors don’t always have to be loud, especially the latest models. Since VSD air
noisy than fixed speed models.
Industrial air compressors come in a variety of sizes to meet different industrial application needs. When deciding between a large or small air compressor, it’s important to consider your pressure requirements. If you need to push or move heavy objects, a big machine with lots of force is likely the solution. To determine size, you’ll also need to calculate how much air flow you’ll need on a daily basis.
Although it might seem smart to plan for future expansion, investing in a machine that’s too big for your needs could be wasteful. As always, our team is here to help evaluate your air flow needs and guide you through the process.
Low emissions will be mandatory for businesses in the future and are quickly becoming the norm.
If you use industrial compressors in your operations, chances are you could benefit from the latest energy efficient equipment to meet today’s and tomorrow standards. The best way to begin achieving low emissions is with a comprehensive energy and emissions assessment of your operations.
Compressors
This month marks a major milestone for OMRON, a global automation giant with a proud history spanning nearly 90 years. The company has announced a striking new name and unveiled an innovative plan for the future to drive its operations in Australia and New Zealand over the next decade. OMRON Oceania will now be known as OMRON Automation and Robotics to better reflect the company’s core business. In this interview, OMRON Automation and Robotics managing director Henry Zhou explains how the company and its customers will benefit from this latest transformation.
MRON automation business’s new trading name in Oceania represents an important milestone in the company’s proud history. What has been the main reason for the
Our new company name reflects what we do and who we are – a forward-looking company providing automation solutions based on our advanced and futuristic concept of innovation-Automation. This is a new chapter for our company and our customers and people remain our top priority. We will continue to deliver outstanding service to help our customers, employees and society to grow
Our customers will continue to benefit through an expanded range of automation and robotics products and industrial solutions. Our exciting and advanced technology based on innovative-automation will enable end users to Work Smarter, Earn More and, most importantly, Have More Fun!
The global pandemic has drastically changed the business landscape. What are the biggest challenges now facing industry in Australia and New Zealand?
Businesses across the globe have faced unprecedented challenges over the past two and a half years. Supply chain disruption and skills shortages are causing major headaches for industry in Australia and New Zealand. Businesses are also dealing with surging inflation, soaring energy and material costs as well as steadily rising interest rates and global
these challenges industry must transform. More manufacturers are now looking to “onshore” – to bring their operations back into the region. This onshoring – empowered by automation and robotics solutions – is helping them to achieve supply chain resilience and become more competitive globally. And with smart automation, businesses can address current chronic skill shortages, so that team members do not have to perform mundane, repetitive or hazardous jobs.
OMRON is now working closely with Government and leading education institutions, including Universities and Technical and Further Education (TAFE) to develop advanced training programs. Also, OMRON’s state-of-the-art testing laboratories are helping to improve skillsets to prepare the local workforce for the highly skilled jobs that will help society
Within the next decade, I firmly believe Australia and New Zealand markets will see the dawn of the new “Golden Age” of manufacturing. This technology revolution will bring great opportunities for manufacturers in the Oceania region.
The surging demand for Food, Life Sciences and Logistics will further enhance the strong position of Oceania manufacturers globally. In addition, new technology is rapidly being developed for emerging industries, such as the transition to electric vehicles (EVs) and the emergence of exciting new digital technologies, which will open new doors
of industry sectors. This will provide some outstanding opportunities for Australian and New Zealand businesses now and well into the future.
OMRON is a company with a longterm commitment and plans to help businesses overcome their challenges and social issues in the manufacturing sector and achieve success over the future decades.
Based on the thought of
“Empowering people through automation”, our Shaping the Future 2030 (SF 2030) long-term vision focuses on key areas such as food and commodities, logistics, medical, EV (Electric Vehicle), digital devices and advanced manufacturing. We see huge opportunities for those sectors in Australian and New Zealand markets. OMRON’s products and services are perfectly aligned to meet their future needs.
Our major advancements in Robotics, Artificial Intelligence (AI), Machine Learning and Advanced Automation will help local manufacturers to stay ahead of the curve. This long-term commitment will give our customers and partners clarity and great confidence going forward.
There are many companies globally that provide automation products and services. Why should businesses choose OMRON – what’s your main point of difference?
Firstly, we’ve been around for over 89 years. We are a global company with a strong international professional and partner network. Innovation is an integral part of our DNA. We continue to invest heavily in R&D. This commitment to innovation has cemented our place each year as one of the World’s Top 100 Global Innovators (by Clarivate 2021).
Secondly, we offer the widest range of automation and robotic solutions in
the industry. Our advanced technology can be seamlessly integrated into one unique platform, making it extremely easy and efficient to implement. And our ground-breaking technology helps us stand out from the crowd. We are a company renowned for a number of ‘world firsts’ in automation, machine vision and robotics.
Finally, in Australia and New Zealand, we have built a proud track record of service over the past 40 years. Our cutting-edge advanced automation and robotics products are backed with solid customer support, including extensive training and engineering services.
All those qualities make us unique in the marketplace and give our company, our customers and our partners a big advantage.
When companies consider investing in new technology, they must do three things –minimise risk, maximise return and ‘future proof’ their new investment. They should look for effective and efficient solutions that provide a strong return on investment (ROI). It is best to start with a small investment with a big-picture outcome. This gives a business scope to scale up and helps to minimise risk. To ‘future proof’ their investment, businesses should always choose a leading supplier that can offer the latest technology and innovative solutions –and provide ongoing support. They should look for a long-term partner that can support their products. A reliable partner with a proven track record.
customers and employees to unleash their full potential and transform into sustainable and innovative factories. With our ambitious long-term Vision for the Future, OMRON Automation and Robotics will continue to improve lives and contribute to a better society.
Manufacturers’ Monthly learns from Pilz Australia about important considerations for safe robot application and how the company works with robot manufacturers and automation companies on designing technical specification for human and machine collaboration.
THERE is hardly any other machine that catches the imagination of humans as much as robots. They are the perfection of machines due to their larger degree of freedom in terms of diversity and the scope of their activities. Robots ultimately express the human aspiration to have machines that participate in people’s lives and assist them in every situation.
In today’s industrial era, closer collaboration between humans and machines is on the rise. Collaborative robots, known as ‘cobots’, are designed to work alongside humans to augment and enhance performance. It keeps humans at the centre of robotic interventions. The strengths and advantages of the machines such as reliability, endurance and repetition accuracy are therefore combined with the knowledge and flexibility of humans.
Cobot applications vary significantly, but in general, they are used to extend human’s physical capabilities, enabling them to perform more high-value tasks. For example, a cobot arm could do the heavy lifting required to pick and place items, while a human performs corresponding tasks requiring dexterity and judgement. In humanrobot collaborations such as these, the workspaces of the humans and robots overlap spatially and temporally.
This presents many challenges to safety as there is no one way to ensure a safe robot application. There are many aspects that need to be considered to achieve a safe and secure human-robot collaboration. Following the right processes however is key to ensuring the application is as safe as possible. Performing a detailed risk assessment of the application, implementing appropriate safeguards, followed by a
1. A risk assessment is carried out at the beginning
Risk assessment involves determining the applicable harmonized standards and regulations, the limits of the machine, the risks within each life phase of the machine, the actual risk appraisal and assessment and the recommended approach to reduce the risk. It is important that each hazardous area is considered individually and without protective measures.
2. The central role of validation The safety concept and system
In contrast to risk assessment, each hazardous area is considered with protective measures in validation. For this, the robot application must be in a state such that it is ready for delivery.
In accordance with the standard, various methods must be applied for the validation, including visual checks, practical tests and measurements. Validation includes, among other things, the verification of the required performance level PLr, a fault simulation (2-channel triggering, crossfault, etc.), overrun traverse measuring if the HRC application is to be made safe using speed and separation monitoring, checking of
use of the power and force limiting method.
3. Touching without injuring Collisions can be mitigated in various ways: Through design and technical protective measures such as the rounding of edges and corners and reduction of the speed of the robot movements. Finally, it must be validated by means of a measuring method whether the possible collisions are harmless from a technical safety perspective.
4. Measurement of force and pressure in accordance with ISO/TS 15066
As for all measurement methods, these types of measurements
must be comprehensible, traceable, and reproducible. The Pilz Robot Measurement System (PRMS) examines human-robot collaborations (HRC), recording force and pressure.
The force measurement device is equipped with springs and sensors to measure the forces exerted on the human body. The nine different springs have different spring force constants and are used in force measurement to recreate the various body regions.
Pressure indicating films are used to measure the local pressure and compare it with the limit values specified in the standard. A convenient software tool is available for validating and digitalising force measurements and for generating test reports.
One can either buy or rent the collision measurement set PRMS depending on business needs. The set includes:
1-day practical product training including HRC measurement technique
• Force measurement device PRMS Pressure indicating films
• Compression elements
Scanner for evaluating the pressure indicating films Sophisticated after sales package –including calibration and software
product training depends on the rental period.
To date, at least, there is no one safe robot or one safe sensor technology that covers all possible scenarios from the applications in terms of safety. The requirements in relation to the safety technology always depend on the respective application. Safe robot cells only come about when everything is taken into consideration – robots, tools and workpieces as well as the
review. The safe HRC application is therefore ultimately the result of the interaction of normative basic conditions, a complex risk assessment that is based on this, the selection of a robot with the corresponding safety functions, the selection of suitable additional safety components and, finally, validation.
As a member of the international standards body, Pilz has actively collaborated with robot manufacturers,
PRMS
collaboration in the industrial environment. Pilz also provides support for the implementation of relevant standards and directives. Jointly with the customer, the experts at Pilz work out a globally optimum safety strategy for robot applications along the life phases of the robot system through to CE marking and employee trainings which has up-to-date and practical content pertinent to robot applications.
CNC Design has recently expanded its longterm partnership as the Australian distributor of Swiss manufacturer Güdel to distribute products throughout five countries in Southeast Asia. Manufacturers’ Monthly speaks with CNC Design sales manager Michael Sutherland about the advantages of linear tracks for robots in an automated environment.
in 1954 by Alfred Güdel, the Swiss company has grown from a single precision machine shop to a global business with operations in more than 20 countries.
The Güdel Group is a manufacturer of high-precision machine components,
part of CNC Design’s portfolio for many years in Australia. Michael Sutherland, sales manager, said the company’s linear tracks & modules are in line with the trend of more automation in manufacturing.
“The track motions are commonly
The TMF-4-B is a robot drive axis specially designed for a range of handling and welding robots.
extended reach or extended range for the robot with welding applications, and secondary carriages allow accessories to be carried,” Sutherland said.
Güdel’s focus on quality translates to a resistance to challenging environmental conditions including dust, paint & weld splatter. They also have engineered special options for very cold environments used in warehousing, with optional anti-
corrosion elements for the guideways
“You can get linear tracks up to 100 metres in length, so it’s fairly unlimited in terms of what you can do with the seventh axis,” he explained. “They come in a range of sizes from TMF-1 to TMF-6, which gives you the ability to handle small to the biggest capacity robots.”
“Linear tracks are not the core expertise of the robot manufacturers, but they are Güdel’s strength, so businesses have been able to focus on their robots and have the tracks supplied.”
Linear tracks for the overhead installation of robots can enable the ideal configuration for different product processes. The TrackMotion Overhead (TMO) gets the robot off the floor, taking up less space and improving the safety of the working environment.
“The basic problem the TMO is solving is allowing the robot to work above or beside the machine or process it’s operating on, which saves that floor space where you would’ve had a track bolted to the floor. Depending on how you want your robot to work, you can put it in different orientations on the overhead tracks.”
These different orientations are split into three configurations – elevated, wall-mounted and ceiling mounted. The ceiling mount
configuration is popular for machinetending operations where the robot wants to be above the machine the workpiece and it can reach down into the machine, pick up a part, move it to the next operation and drop it back down.
“In general, the track motion again extends the work envelope beyond just the typical arc reach pattern of the robot,” Sutherland noted. “We extend that to a much wider area by putting it on the track and putting it on the overhead track allowed us to also have a lot more reach down into the work envelope compared to the floor mount. Robots are a large capital purpose, so people really want to make the most of them. By putting a robot on a track, you can greatly increase the working envelope of the robot.”
Synonymous with safety and productivity, Sutherland explained Güdel products can help remove operators from dangerous environments.
“In what our customers are doing, Güdel helps remove the risk of people being in areas where robots are handling large, heavy and awkward products,” he said.
For more information, visit cncdesign.com.au/gudel-modules-components, gudel.com/products/linear-tracks-for-robots/tmf or gudel.com/products/linear-tracks-for-robots/tmo
Manufacturers’ Monthly explores the three pillars behind recent manufacturing investment attraction in the Hunter Valley’s Greater Cessnock.
City Council is playing its part in supporting local manufacturing. A new initiative means investors to the region will be provided with economic data, a business concierge service for projects that create 10 or more jobs and an efficient planning approval service and planning advice and guidance.
Tony Chadwick, economic development & tourism manager, explained the council’s vision for manufacturing in the region.
“Of the 19 different industry sectors, economic data shows that manufacturing is a key driver in exports, employment and local expenditure. Manufacturing is second only to the construction industry as a key economic driver in the greater Cessnock economy at this time,” he said.
“100 direct manufacturing jobs will create a further 81 indirect jobs, highlighting the importance to our region. By comparison 100 direct accommodation and food service jobs will
create 21 indirect jobs. So for this reason manufacturing is a focus for our team.”
The Hunter Valley is Australia’s oldest wine region, but the region is making more than internationally acclaimed drops.
Being located in Australia’s oldest wine region, the Cessnock LGA generated revenue of $407 million from wine manufacturing in 2021. Other significant revenue generating manufacturing sectors are:
Chemical manufacturing: $423 million
• Metal and metal product manufacturing: $133 million
• Food manufacturing: $80 million
Saw mill and wood products: $30 million
Beer manufacturing: $21 million
Other products: $59 million
The LGA covers approximately 1,950 square kilometres and forms part of the Lower Hunter. European settlement since the 1820’s saw the establishment of pastoral lands, the coal mining industry,
the viticulture industry and more recently a thriving tourism industry. While mining was the principal industrial base and source of employment in the Cessnock Region for the first half of the twentieth century, changes in the mining industry, including deepening coal seams and automation, has led to the closure of mines in the area.
With supply chain security a desire for Australia, the Hunter having good electricity supply and an abundance of industrial land, we see manufacturing as playing an important role in our future. With 1198 hectares of industrial land zones, a population growth rate of over 2% and ready supply of labour from Cessnock and surrounding towns, there is an excellent opportunity to expand our manufacturing base.
The Hunter Valley is know for its scenic beauty – the natural landscape is a big part of attracting different businesses.
Cessnock is characterised by large areas of steep, heavily vegetated terrain in the south and east, as well as flat, cleared areas surrounding the town of Cessnock and neighbouring urban areas. The flat terrain around the Cessnock township contains some of the largest remaining remnants of the valley-floor vegetation in the Hunter Valley.
Heritage is at the heart of the Cessnock LGA – several hundred items of heritage significance, including items of indigenous, built and natural significance contribute to its true ‘country town’ character.
Key to a manufacturer’s success is the ability to transport and distribute products. Cessnock has excellent transport infrastructure, is positioned on transport routes and is in close proximity to the Port of Newcastle and the Newcastle airport.
Port of Newcastle is the largest port
on the East Coast of Australia. As a global trade gateway for more than 220 years, the Port delivers safe, sustainable and efficient logistics solutions for its customers.
With a deep-water shipping channel, capacity to double trade volumes, available portside land and berthside connections to the heavy rail network, few Australian ports can match the unique capabilities of Port of Newcastle. The Port creates jobs and generates more investment in the local community, This contribution has been valued at $1.6 billion to the Lower Hunter economy and 9,000 local jobs per annum.
The Newcastle airport is Australia’s sixth largest regional airport. In the New South Wales Government’s eyes, the airport is the regional hub of Australian industry participation supporting the Joint Strike Fighter fleets in the Asia Pacific region.
Further to this, Cessnock Airport is primed for growth and is ready to leverage from opportunities from surrounding regional airports, including Newcastle and Bankstown. Its accessible
location, proximity to major freight routes and capacity to absorb future growth means the airport hosts a number of complimentary aviation businesses and has a growing demand for pilot skills and training (fixed wing and rotary).
Kurri Kurri has 64 hectares of IN3 industrial zoned land, with both greenfield and brownfield sites available, as well as 216 hectares of IN2 industrial zoned land at Black Hill.
“The NSW Department of Planning and Environment are currently reviewing the development application to redevelop the former Hydro aluminium smelter plant at Kurri Kurri,” Chadwick said.
“This 2,000ha site has a mix of industrial and business zones as well as 2,000 new residential homesites. The site offers excellent connectivity to nearby centres of Kurri Kurri, Cessnock, East Maitland and Central Maitland with access to Newcastle City only 40 minutes away via the Hunter Expressway. Other sites are available at various locations throughout the region.”
Weld Australia is proud to sponsor the 2022 Endeavour Awards for the category of Best Industrial Internet of Things Application. This award will recognise the most outstanding application used in a
Research Program scheme and is focused on collaborative robotics in advanced
The aim of the Centre is to improve the collaborative robotics capability within Australian manufacturing by training the next generation of manufacturing leaders, researchers, and technicians with collaborative robotics expertise. Headquartered at Queensland University of Technology (QUT), with two other locations at The University of Technology Sydney (UTS) and Swinburne University, the Centre is expected to build the human and technical capability needed to underpin Australia’s global competitiveness in advanced
The Centre is working to accelerate the pace of the adoption of cobots in Australian industry through five research programs that address both the technological advances and the human and design factors that need to be considered when implementing collaborative robotics.
Through this research and its implementation, the Centre will support manufacturers in creating a digitallycapable workforce of the future and
a safer, more efficient and globally competitive Australian manufacturing industry.
The Centre’s multidisciplinary team of researchers are working in collaboration with industry partners, including B&R Enclosures, Cook Medical, Weld Australia, InfraBuild, IR4, TU Dortmund University, and the ARM Hub (Advanced Robotics for Manufacturing.
Together, QUT and Weld Australia are offering practical solutions to
Access to full range of research projects, outcomes from research including IP that can be used within your field.
Flexible and adaptive approach to research and its application to mirror the needs of your business.
Access to international and national experts in the field, free of charge.
Collaboration with other companies who have similar challenges and the opportunity to work together to
Cobots are designed to work alongside human employees, assisting employees with work that may be too dangerous, strenuous, or tedious. This helps to create a safer, more efficient workplace without eliminating jobs. Cobots are easily programmable and are capable of ‘learning’ on the job. In welding, cobots can be used for several purposes, from joining metal parts and holding parts steady for workers, through to sorting hardware using a vision system.
Cobots are specifically designed to share the workspace with human beings, making automation easier for businesses of all sizes, particularly SMEs. Cobots are generally versatile, lightweight, require relatively little space, and are much easier to program than their industrial counterparts. They can also capture large volumes of data that can be deployed in areas such as predictive maintenance.
Robots and cobots play an essential role in creating lean manufacturing processes, helping reduce or eliminate redundancies, errors, bottlenecks and waste. The right type of technology can help eliminate workflow delays and duplications and accelerate entire processes through the automation of individual tasks.
The integration of cobots into production processes is proven to deliver superior quality outcomes and higher repeatability. Any process that improves weld quality and repeatability is worthwhile. Welding is not just a commodity, or a simple, straightforward process. When welds
fail, the results can be disastrous. A poor-quality weld can be hugely expensive, and can cause massive damage, injuries, and even fatalities.
With increased productivity, quality and repeatability, manufacturers are able to leverage new domestic and export markets. Increases in productivity enable manufactures to deliver on changing customer needs and mass customisation, while maintaining a sustainable competitive advantage.
The use of robots and cobots has the power improve safety for welders and manufacturing workers. As automation reduces routine, dangerous manual work, workplace injuries are expected to drop by as much as 11 per cent. For instance, the use of robots and co-bots (particularly in confined spaces) helps to remove welders from immediate exposure to welding fumes, ultraviolent radiation, heat and sparks.
A move towards the use of robots and cobots will unburden the average Australian of two hours of the most tedious and manual work each week. Approximately 62 per cent of low-skilled workers will experience improved job satisfaction, and wages for non-automatable work will increase by around 20 per cent. Introduction of cobots into production lines allow businesses to make better use of human skill and innovation, with machines taking over mundane tasks so that employees can focus on critical thinking, quality and creativity.
Brought to you by
Neousys Technology, an industry-leading provider of rugged embedded systems, today released their latest compact fanless computer, the Nuvo-2600 series.
Powered by Intel Elkhart Lake quad-core processor, Nuvo-2600 series provides up to 1.8x the CPU performance over its predecessor, Apollo Lake. Featuring rich I/Os and a flexible patented expansion Cassette module, the Nuvo-2600 is an ideal embedded system for industrial applications such as machine vision or logistics automation. With an optional ignition power control, Nuvo-2600 series can also be applied to AMR applications.
Nuvo-2600 series comes with a variety of I/O ports that feature practical connector interfaces and flexible function expansion slots. It has four Gigabit PoE+ ports via RJ-45 connectors with screw-lock mechanisms to secure camera or Lidar connections; a frontaccessible 2.5” HDD tray accommodating a 7 to 15mm 2.5” SSD/HDD up to 5TB; two miniPCIe expansion sockets for WiFi, CAN bus, COM, or DIO expansion.
In the Nuvo-2600 series line-up, the Nuvo-2600E features a patented Cassette module to install an add-on PCIe card such as a GbE frame grabber, or EtherCAT motion control card. Nuvo-2600J has a Neousys patented SuperCAP UPS module that features 2500 watt-second energy capacity to sustain operation during power outage until shutdown, or provide a steady stream of electrical current to protect the system.
“Enclosed in ruggedized compact dimensions, Nuvo-2600 series features an Intel Atom x6000E quad-core processor, wide temperature fanless operation, 4x PoE+ GbE ports, and flexible expansion from mPCIe, PCIe, or a SuperCAP UPS,” Neousys Technology product manager Kaichu Wu said. “It is the perfect multi-purpose embedded computer for machine vision and autonomous warehouse applications.”
Company: Neousys Technology Phone: +886-2-2223-6182 Website: www.neousys-tech.com/en/
Backplane Systems Technology is proud to present iBase’s OFP-151-PC-NVK, which is an openframe 15-inch panel PC and a SCADA (Supervisory Control and Data Acquisition System) management solution. It displays the real-time status of equipment such as freezer, air conditioning, lighting system and power metre, and serves as a communication bridge between sensors and the cloud to instantly transmit equipment operating status.
The platform features modularized functional blocks for easy customisation across all venues in the retail industry. The upgradeable OFP-151-PC-NVK panel PC comes with easy to mount, open-frame modular design with optional coloured frames. It supports IP65 front panel protection against dust and water and is built with industrial-grade components to ensure reliable performance with fanless operation in temperatures of up to 50°C.
OFP-151-PC-NVK is installed with the Novakon iFACE Designer, a comprehensive objectoriented UI/UX graphics editing tool that utilises numerous industrial automation standard protocols, mainstream brand name PLC drivers and universal IoT cloud protocols. Allowing, the platform to provide easy connectivity among diversified industrial equipment and devices, such as sensors, power meters, controllers, PLCs, IO modules, and IoT cloud platform.
15” Open-Frame Panel PC with Novakon iFACE Designer Software;
• Powered by Intel Pentium QC N4200 Processor with IP65 Front Panel Protection; Four-in-one Management Systems Including Freezers, Air Conditioning, Lighting System and Power;
Works as a Backend Facility for Monitoring and Managing Parameters in Intelligent Retail Environments;
• Optimises Overall Power Consumption and Avoid Down-Time;
Trend Chart Display and Log Report Export of Historical Data;
• Alarm Notification of Equipment/Device Status through Email/LINE App; Supports Modbus RTU/TCP/ASCII, OPC UA, Restful API, MQTT; Mitsubishi, Siemens, Rockwell, Omron, CODESYS... PLC drivers; and Supports Charts, Alarm, Macro, Data Log, Recipe, Scheduler, Report, VNC, OpenVPN, FTP, SQL...Software Functions.
Company: Backplane Systems Technology Phone: (02) 9457 6400 Website: www.backplane.com.au
AUSTRALIA’S prosperity and security fundamentally depend on trade. Whether it is through multi-billion-dollar export industries or connections to global supply chains for imports, no part of our economy or society isn’t deeply intertwined with trade.
Like many countries, Australia’s trade links to the world were significantly disrupted at the height of COVID-19. Shipping delays, product shortages and snap lockdowns threw global supply chains into chaos. It was a difficult reminder of how important trade is for Australia.
Fortunately, many of the acute interruptions of the pandemic are beginning to lift in 2022. But as Australia reconnects with the world, we are finding that the global trade system is rapidly changing.
Emerging technologies – particularly digital and clean energy – are shifting the focus away from goods and on to technology and services. After the shock
of COVID, businesses are moving away from hyper-extended supply chains to favour ‘resilient’ trade networks. Growing geopolitical conflict is also affecting the trade system, with trade sanctions and protectionism now a fact of life.
This new world demands a fundamental reappraisal of our trade strategy. To help navigate this transition, Ai Group has developed a policy report: Australia’s new trade agenda. This report ‘future casts’ five global-level trends that will shape the what, how and who of trade through the 2020s. It also maps how government and businesses can rethink their strategies for success.
The five trends that will define Australia’s trade future are:
• G eopolitics and protectionism
During periods of political and economic disruption, many governments turn to trade barriers for national security reasons. Recent examples include the US-China trade
war, trade sanctions on Russia following its invasion of Ukraine and food export bans during the COVID pandemic. These protectionist measures threaten the integrity of the open trading system on which Australia relies. They can close off markets for our exports, raise the cost of our imports and disrupt supply chains for critical goods. Managing geopolitical risk effectively will be essential for trade success in coming years.
The digitalisation of the economy is also transforming what and how we trade. Digitalisation creates new products to be traded, such as digital content and services delivered across borders. It also opens new methods for trade, utilising e-commerce platforms and paperless trading technologies.
As most trade rules were written in the pre-digital era, they urgently need to be updated for the technologies
of today. Governments will need to collaborate and create new international agreements customised for digital trade. Businesses will need to ‘digital-proof’ their trade operations to remain globally competitive.
As the world moves towards net zero carbon emissions, most governments are adopting carbon pricing mechanisms. But to prevent so-called carbon leakage – where polluting industries simply migrate across borders – they are also developing systems to price the embedded carbon in traded goods.
Carbon pricing in trade offers opportunities and risks for Australia.
We will need to decarbonise many of our exports, particularly minerals and metals, to avoid paying carbon levies in key markets. But it will also open new opportunities for exporters who can demonstrate the use of renewable
energy who will be able to command a price premium for low-carbon products.
As geopolitical tensions have increased, it has proven very difficult to strike new global trade deals. Many governments have instead looked to plurilateral agreements –amongst smaller ‘clubs’ of likeminded countries – to advance the trade agenda. Australia is party to ten such plurilateral agreements under negotiation now.
The emergence of these instruments will change the logic of trade from a ‘global’ to a ‘club’ outlook.
Governments will need to decide which partners to work with, on which issues and in which club formats.
Business will need to reconfigure commercial strategy to exploit opportunities these clubs create, particularly in the digital and clean energy sectors.
While the pandemic was the initial cause of supply chain disruptions
in 2020, political factors are now perpetuating the challenge. Rising protectionism for food, technology and pharmaceuticals are constraining global supply. Russia’s invasion of Ukraine has caused a global energy crisis. China’s ongoing COVID-zero policies are disrupting the factories central to global value chains. Resilience, rather than pure efficiency, has therefore become an increasing focus in supply chain management.
Governments are directing industrial policy toward securing critical products, such as semiconductors and critical minerals. Businesses are building more diversity into their supply chains and exploring ‘friend-shoring’ strategies to relocate production to more trusted partners.
Australia will not succeed as a trading nation if we maintain a business-as-usual approach to these emerging trends.
Each poses risks to our existing trade relationships, which we are already
experiencing in the form of supply chain disruptions. But they also open opportunities to develop new trade ties that can support 21st century industries.
The Government must reconfigure its trade diplomacy to these new realities. For two decades, Australia has focused on opening new markets for exports via bilateral free trade agreements (FTA). While this strategy has proven successful – we now have FTAs with all our main partners – it has also hit a natural limit.
It is time to look towards a new form of trade diplomacy focused on rule-making. Each of these trade trends in some way involve rules – over how digital trade is conducted, how carbon is priced, how protectionism is limited. And the emerging trade clubs, rather than the World Trade Organisation, will increasingly be the venue at which these rules are decided.
The most important thing Government can now do is ensure Australia has a seat at the table whenever new trade rules are being devised, and work with likeminded partners for the best results possible.
Business will need to adjust to a more complex and difficult trade environment. Since the 1990s, the trends of globalisation and liberalisation have made it progressively easier to be a tradeengaged business. But as protectionism returns and supply chains come under stress, more risk-attune trade strategies will be required.
There is no one-size-fits-all model for how business should adjust. The five trends affect different markets in different ways. But across all of them, the value of diversity will prove critical. Businesses with narrow trade relationships are more exposed to risk than those with broader ties. And diverse traders are better placed to exploit emerging opportunities.
Australia has pivoted its trade outlook before, and we can do so again. If we can get our trade settings right now, we can ensure Australia remains a great trading nation well into the future.
Read Ai Group’s policy report – Australia’s new trade agenda – here: https://go.aigroup.com.au/tradereport Jeffrey Wilson says Australia must look at a new form of trade diplomacy focused on rule-making.