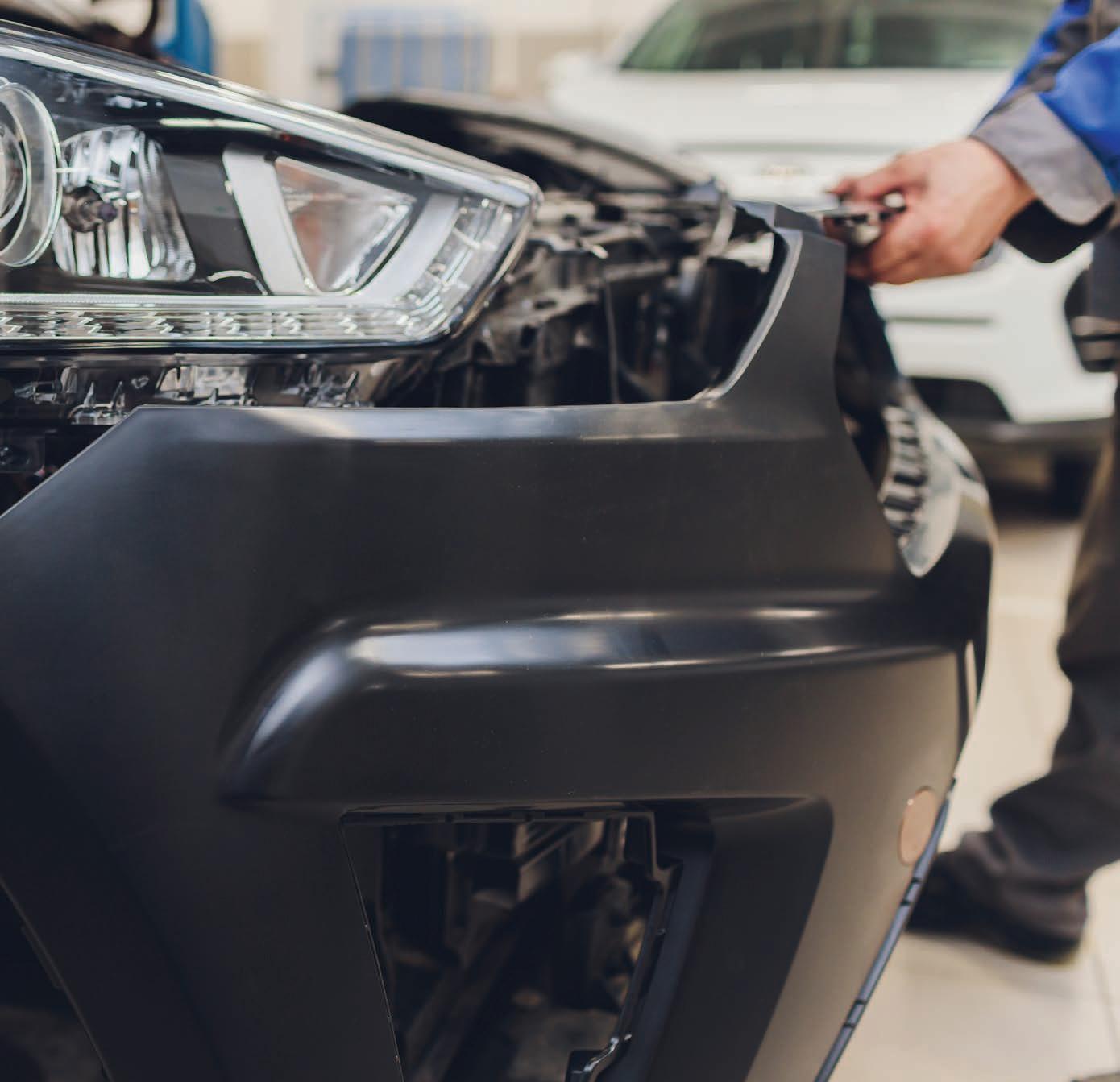

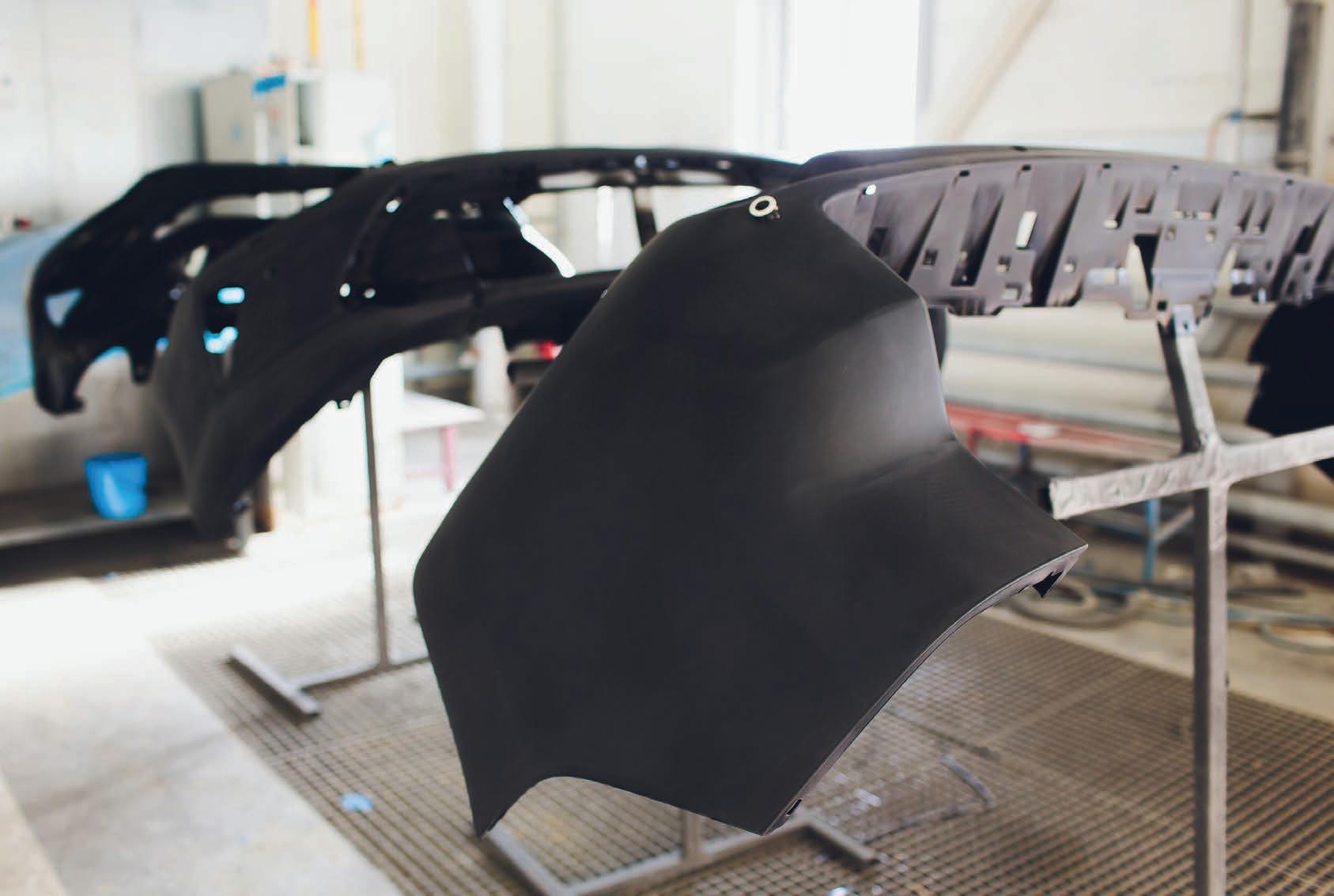
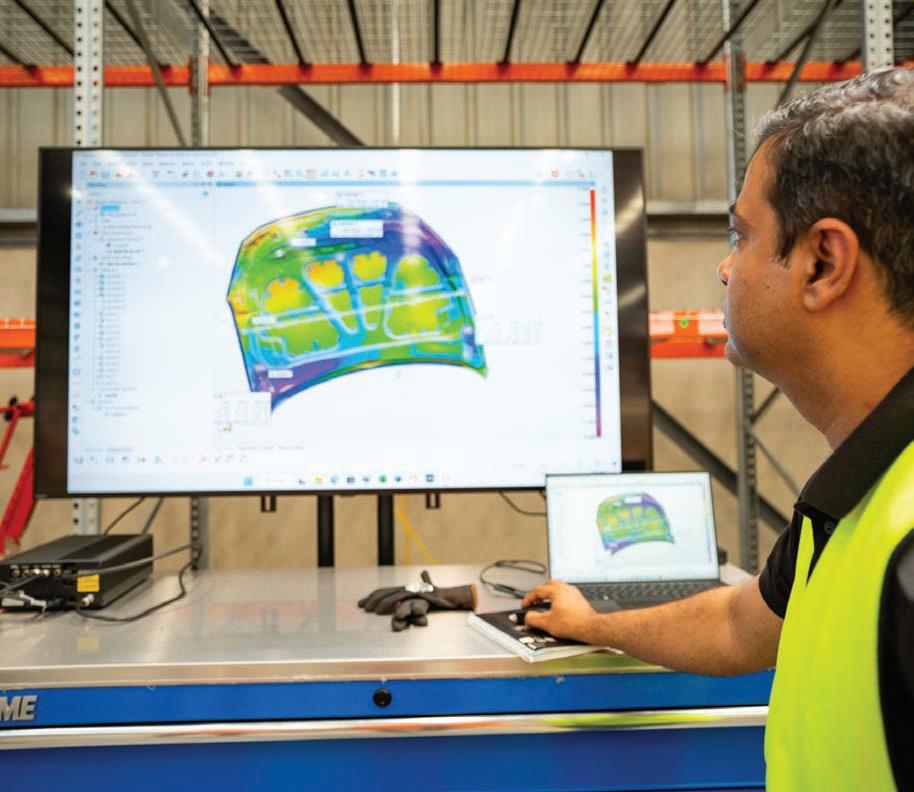
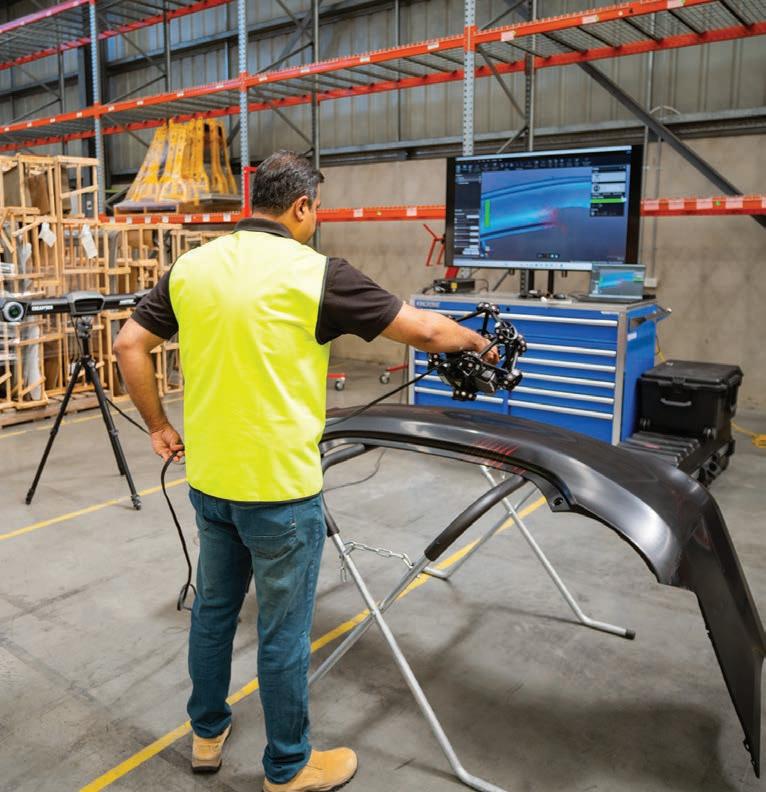
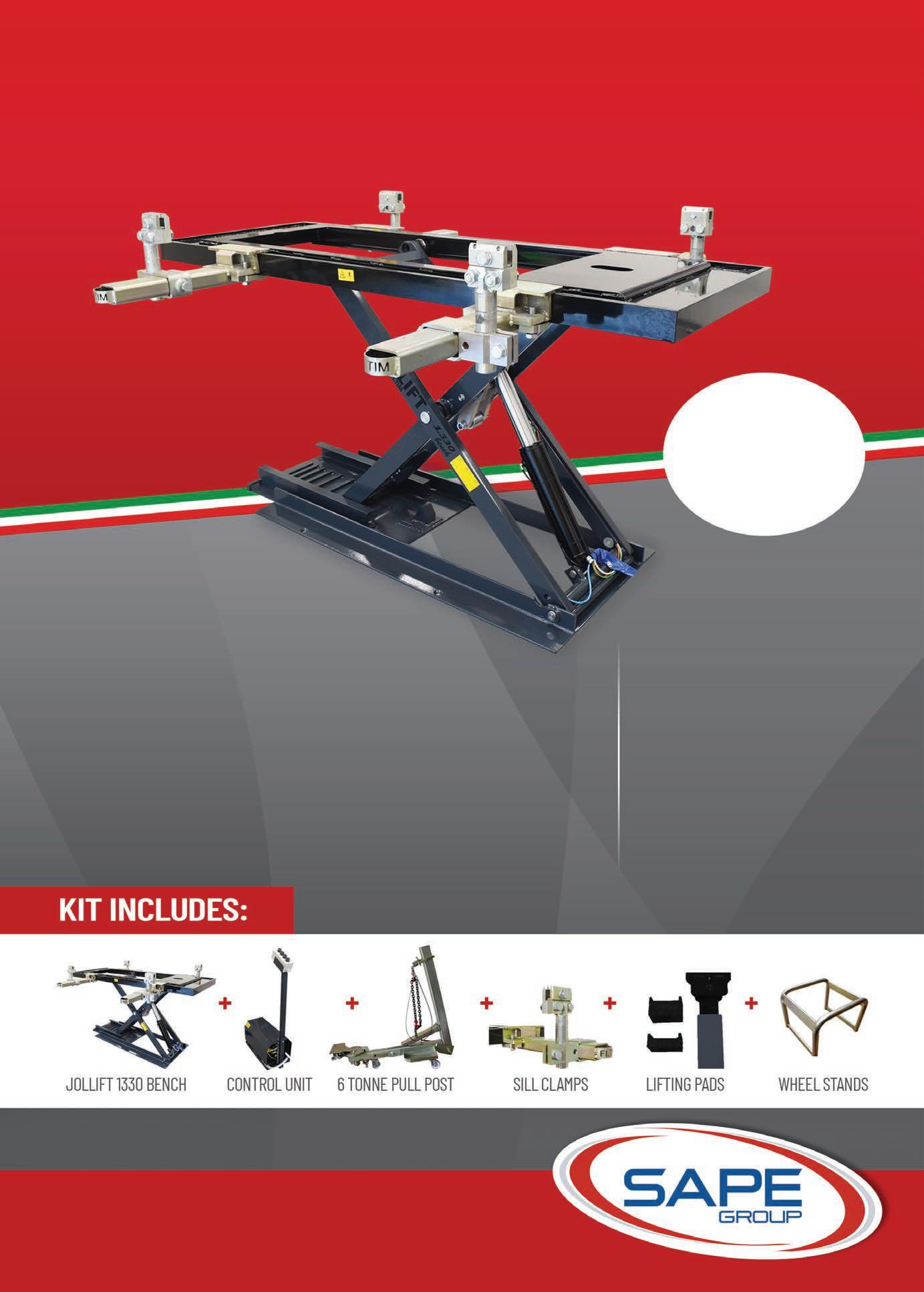
ACM Parts’ range of quality assured aftermarket parts guarantee material, fitment, and functionality, offering peace of mind when selecting an aftermarket part. This range includes collision parts, lighting, and cooling components to suit a large range of major makes and models.
ACM’s Aftermarket range is focused on quality and reliability. You can rely on every part to meet all the OEM lifecycle performance standards — offering repairers an easy, fast, and cost-effective solution for sourcing parts.
Each collision part has been individually verified to ensure fitment, functionality, and quality. To guarantee this before moving into production each part undergoes thorough assessment testing against its genuine equivalent.
For more information on our wide range of ACM Aftermarket Parts with nationwide delivery call our customer service team on 1800 226 727.
The end-to-end digital ecosystem bringing advanced, game-changing technologies to your collision centre
Confident colour selections anytime, anywhere!
Thanks to its advanced cloud-based digital colour platform, PPG LINQ Color puts all the colour identification information you need at your fingertips 24/7, on any Internet capable device, such as a PC, tablet or smart phone. A next-generation user interface, combined with an intuitive workflow and rich graphical colour representations, makes this the perfect tool for making confident colour selections at anytime and anywhere.
PPG MagicBox is a clever piece of electronic hardware which wirelessly connects the paint shop computer, spectrophotometer and scales, allowing information to seamlessly flow between them. In addition, remote sensors within PPG MagicBox monitor ambient conditions to help painters make the right mix for the job.
Follow us online!
PPG Refinish Australia & New Zealand
CEO John Murphy john.murphy@primecreative.com.au
COO Christine Clancy christine.clancy@primecreative.com.au
SALES DIRECTOR Brad Buchanan bradley.buchanan@primecreative. com.au 0413 672 403
EDITOR Eugene Duffy eugene.duffy@primecreative.com.au
BUSINESS DEVELOPMENT MANAGER Kerri McCauley kerri.mccauley@primecreative.com.au 0404 898 362
PUBLISHED BY Prime Creative Media 379 Docklands Drive, Docklands, VIC 3008 03 9690 8766 www.primecreative.com.au
DISCLAIMER
The National Collision Repairer is published by Prime Creative Media, 379 Docklands Drive, Docklands. This publication is copyright. Apart from any fair dealing for the purpose of private study, research, criticism and review under the Copyright Act (1968), no part may be reproduced by any process without written permission. Enquiries should be addressed to the publisher. The publisher believes all the information in this publication to be correct at the time of printing, however is not in a position to make a guarantee to this effect and accepts no liability in event of any information proving inaccurate. Prices, addresses and phone numbers were, after investigations and to the best of our knowledge and belief, up to date at the time of printing. It is also not feasible for the publisher to ensure that advertisements which appear in the publication comply with the Competition and Consumer Act (2010). The responsibility must therefore be on the individual, company or advertising agency submitting the advertisement for publication. Whilst every endeavour has been made to ensure complete accuracy, the publisher cannot be held responsible for any errors or omissions. Copyright AJMF Solutions Pty Ltd
Welcome to the latest edition of National Collision Repairer, where we bring you insights into the dynamic and ever-evolving collision repair industry in Australia.
You may notice several elements that are new to this edition; a new look, a new editor and a new owner.
But with these changes you can also be assured we will continue to bring you all the best elements you have come to expect from the industry’s leading magazine.
We hope the new design is a more modern look to match an industry often at the forefront of innovation.
As the new editor, I hope to reaffirm and build on the strong ties and industry relationships of the past, making it an even better magazine for a changing industry moving into the future.
And the new owner, Prime Creative Media Publishing who recently acquired The National Collision Repairer magazine, is fully committed to further solidifying its presence in the automotive industry. Prime Creative Media has a strong history of supporting the transport and automotive sectors through publications like Trailer Magazine and Prime Mover Magazine, as well as the recent addition of Australian Car Mechanic to its stable of products. With The National Collision Repairer, Prime Creative Media is expanding expertise and service to this vital sector. We remain dedicated to Prime Creative Media’s three pillars of purpose; to help grow individuals, businesses and the industries that we serve.
We have collaborated closely with former owners Joe and Josephine McFadries to ensure the exceptional service The National Collision Repairer is known for throughout the industry is carried on.
This is a magazine about the collision repair industry, produced for the collision repair industry.
In this issue there are multiple discussion points for the industry beginning with the recently released 2023 Australian Road Toll Report which provides valuable data on road safety trends.
We are also thrilled to highlight the growing adoption of zero and low-emission vehicles in Australia with battery electric
vehicles accounting for an impressive 8.8 per cent of June sales, indicating a shift towards sustainable and environmentally conscious transportation. As the automotive industry continues to embrace green mobility solutions, we can look forward to a greener and cleaner future for our roads.
We are proud to showcase the Women in Collision initiative launched by Auto Parts Group (APG), which offers invaluable support and recognition to female trade apprentices in the collision repair industry. This program not only fosters diversity and gender equality but also addresses labour shortages in the industry. By empowering and nurturing talented female apprentices, APG is contributing to a thriving and inclusive workforce that will shape the future of collision repair.
On the forefront of innovation, BMB Prestige Collision Repairs’ achievement of the prestigious I-CAR Gold Class Collision status serves as a testament to the industry’s dedication to staying ahead of technological advancements. By investing in continuous learning and training, BMB Prestige Collision Repairs exemplifies the commitment of collision repair professionals to provide top-notch services and meet the evolving needs of customers.
As we celebrate the achievements and progress in the collision repair industry, there are some amazing, and safe vehicles out there too. BMW Australia’s announcement of a new six-cylinder petrol variant for its flagship X7 Sports Activity Vehicle promises to elevate driving experiences to new heights. With cutting-edge technology and performance, the X7 xDrive40i embodies the spirit of innovation defining the automotive industry.
Our publication remains steadfast in its commitment to celebrating the progress, achievements, and positive transformations shaping the collision repair industry. We extend our heartfelt appreciation to all professionals, technicians, stakeholders, and enthusiasts who play a vital role in creating safer roads and driving positive change.
We hope you have a delightful read filled with inspiration, insights, and a sense of pride, knowing we are in lock step on the transformative journey the collision repair industry undertakes.
Eugene Duffy Editor The National Collision RepairerThe Australian Road Toll Report gives insight into risk factors, trends, gender and age disparities as well as a look at individual state and territory road fatalities, as the nation inches towards zero fatalities.
The 2023 Australian Road Toll Report by financial company Savvy is part of its ongoing research into Australian demographic trends and statistics. Key highlights from the report include:
• Most statistically probable fatality is a male vehicle driver between the age of 40 to 64 years of age
• National road toll for 12 months to April 2023 was 1,204, up 4.3 per cent from last year
• Seven per cent increase in Australian road fatalities among women over the last 12 months
• Most road deaths recorded by drivers of vehicles (48.6 per cent)
• Deaths per 100,000 population stood at 4.6, which has been decreasing since 1995
• Australia is ranked 20th out of the 36 OECD countries for road fatalities
Between 1965 and 1985, the average annual Australian road toll stood at 3,378 – arguably the most dangerous period on
national roadways.
Thanks to better driver education, stricter laws around drink driving and seatbelt wearing, and improved driver safety technology, this average over the twenty-year period between 2001 to 2021 dropped to 1,379 – 41 per cent of what it was back then.
As Road and Highway Authorities around Australia encourage drivers to head Towards Zero – a year without road fatalities – the 12 months to April 2023 saw 1,204 deaths on Australian roads, an increase of 50.
“Australia has made great strides since 1995 to combat the road toll. Continued driver and road user education, improved safety features in cars, and upgraded infrastructure will all contribute to reducing the road toll to as close to zero as possible,” said Adrian Edlington, a spokesperson from Savvy.
“Driving to suit the conditions, taking regular breaks on long trips and of course having the right kind of insurance will all help.”
According to BITRE, Australia’s road incident fatality rate was 4.26 per 100,000 population ranked 20th out of the 36 OECD nations (2020).
Between 2011 and 2020, this fatality rate fell by 25.4 per cent, compared with the OECD median of 34.6 per cent. While we are well behind the UK (2.26 fatalities per 100,000 people) and Germany (3.27), we are still ahead of New Zealand (6.01) and the United States, which has a fatality rate of 11.78 individuals per 100,000 head of population in 2020.
“If we take out the Northern Territory, which has taken many steps to curb its excessive road toll through tougher penalties and reduced speed limits in remote areas, we fare quite well against the rest of the world in terms of fatality rates,” Edlington added.
“Of course, we acknowledge that on an individual level, no road fatality is acceptable and more needs to be done to continually bring numbers down.”
Auto Parts Group (APG) has announced its Women in Collision initiative, with ten $1,000 Würth tool awards available to women in the collision repair industry.
The Women in Collision initiative is open to all female trade apprentices in the collision repair industry, regardless of the company they work for, and nominations can be made by the apprentices or their employers. Participants are asked to provide a 25-word statement showcasing the apprentice’s passion, commitment, and vision for the collision repair industry as part of the application evaluation.
Ten apprentices will be selected to receive a $1,000 Würth tool voucher each, which can be redeemed via the Würth tool online portal. Unique login details will be provided to each of the selected recipients.
“It’s no secret the collision repair industry is facing labour shortages, especially when it comes to apprentices, who often struggle to afford the necessary tools to succeed. Auto Parts Group is committed to providing you REAL ADVANTAGE, through material workforce support,” APG said in a media release.
“We believe in our industry and feel that this is a great way to back the next generation of female apprentices. It’s also an opportunity for you to secure your workforce and support the growth of your business.
“Even if you don’t have a female apprentice, we encourage you to spread the word and help support the broader industry.”
To participate in the Women in Collision campaign, visit the APG’s website and fill out the application form before August 20th, 2023.” More details available at autopartsgroup.com.au
Axalta Coating Systems, a leading global coatings company, has announced that it has selected a new Australian refinish distributor, AJP Industrial Supplies, based in Mackay, Queensland.
The decision aligns with Axalta’s commitment to the refinish market and ongoing focus on servicing regional areas of Australia.
Established in 2008, AJP Industrial Supplies has built a strong position in the local Mackay market, servicing a range of industrial customers in the mining, construction, agriculture, and transportation industries.
As part of the agreement with Axalta, AJP Industrial Supplies will distribute Axalta’s Spies Hecker, Syrox and Duxone refinish brands, helping expand their position as a leading coatings supplier in central Queensland.
“We selected a distributor that could provide customers with a simple, relationship-focused buying experience and a commitment to service,” said Stephen Morris, Axalta’s territory business manager in Queensland.
“Partnering with AJP Industrial Supplies is an obvious choice, as they have an outstanding reputation in the Queensland market, supported by a competent technical team.”
“We were looking for an opportunity to further strengthen our business with the addition of a highly reputable brand in the automotive refinish industry,” added Malcolm Henri, AJP Industrial Supplies’ Operations Manager. “Their support has been excellent and we are excited by what the future holds.”
Axalta is a global leader in the coatings industry, providing customers with innovative, colourful, beautiful, and sustainable coatings solutions. From light vehicles, commercial vehicles and refinish applications to electric motors, building facades and other industrial applications, its coatings are designed
to prevent corrosion, increase productivity, and enhance durability.
With more than 150 years of experience in the coatings industry, the global team at Axalta continues to find ways to serve more than 100,000 customers in over 130 countries better
every day with the finest coatings, application systems and technology. For more information on Axalta and its products, please visit axalta.au or call 1800 292 582. AJP Industrial Supplies can be contacted at (07) 4998 5299.
Australian customers took delivery of 124,926 new vehicles during June to mark the end of the 2022-23 financial year – an increase of 25 per cent compared to June 2022.
This result also marks an 8.2 per cent increase compared with the six-month period of January to June 2022 and is the highest June result since 2018.
FCAI chief executive Tony Weber said the continuing sales growth was encouraging, especially considering the ongoing issues relating to vehicle supply.
“The end of the financial year has traditionally been a strong month for vehicle sales,” Weber said.
“Indications from our members are that demand for new vehicles remains solid, but the supply is not yet at a point to meet this demand. To put it simply, if we could have landed more vehicles, this would have been a record June result.
“Also, we will monitor the broader economic conditions and their potential
to impact vehicle purchasing decisions by fleets, businesses and families during the second half of this year,” he said.
Sales of zero and low-emission vehicles continued to grow with 16.6 per cent being battery electric, hybrid or plug-in hybrid models.
Battery electric vehicles accounted for 8.8 per cent of June sales and make up 7.4 per cent of new vehicle sales during the first half of 2023. The Tesla Model Y recorded 5,560 sales, making it the second highest-selling vehicle behind the Toyota Hi-Lux (6,142).
“The early adopters of the new powertrain technology continue to push up the sales of electric vehicles across the country,” Weber said.
“The steady introduction of new battery electric models across all model segments at more competitive price points is critically important as we deal with the challenges of supplying electric vehicles that meet business and
The Australasian New Car Assessment Program (ANCAP) announced it has awarded the first-ever Mazda CX-60 its full five-star safety rating.
ANCAP praised Mazda’s all-new premium mid-sized sports utility vehicle (SUV) for its all-round performance when tested against its strict 20202022 assessment criteria.
The first-ever Mazda CX-60 achieved record scores for Child Occupant Protection (93 per cent) and Vulnerable Road User Protection (88 per cent).
The CX-60 was awarded full scores for protection of the driver and child occupants during the Side Impact Test, and to the driver in the severe Oblique Pole Test.
ANCAP also awarded full points for the effectiveness of the centre airbag
fitted to the front seating row, which is designed to reduce occupant-tooccupant contact and occupant-tovehicle contact.
A variety of innovative technologies underpin the safety performance of the CX-60 and gained it the full five star ANCAP rating for all CX-60 models in Australia and New Zealand.
These include Mazda’s Skyactiv Multi-Solution Scalable Architecture, the company’s latest structural and body concept which combines advanced mechanical design with high-strength materials, including 1,800 MPa-grade metals. In addition, a suite of advanced onboard safety systems support drivers and occupants, some of which are Mazda-firsts. These include Smart Brake Support, which
personal consumer needs at prices the mainstream buyers can afford.”
Sales across every State and Territory increased apart from the Northern Territory which recorded 1,085 sales, a reduction of 2.7 per cent compared with June 2022. In the Australian Capital Territory, sale numbers increased by 24.9 per cent (1,856); New South Wales 15.6 per cent (37,020); Queensland 27.5 per cent (28,029); South Australia 28.3 per cent (7,974); Tasmania 22.3 per cent (1,923); Victoria 31.8 per cent (33,966); and Western Australia 33.2 per cent (13,073).
Toyota led the market with a total of 20,948 vehicles sold. Mazda recorded 9,706 sales followed by Hyundai (8,215), Ford (7,753) and Kia (7,551).
The Toyota Hi-Lux was the highestselling model with 6,142 sales. Tesla Model Y recorded 5,560 sales followed by Ford Ranger (5,334), MG ZS (3,756) and Toyota RAV 4 (2,858).
uses a forward-sensing camera to help reduce the likelihood of an accident by applying the vehicle’s brakes if needed, and See-Through View, which displays an image on the instrument panel screen that lets the driver effectively see through the front and rear corners of the CX-60 when manoeuvring.
Other advanced technologies include Lane Departure Warning, Lane Keep Assist and Blind Spot Monitoring.
“The CX-60 is Mazda’s most advanced new model to date,” said Vinesh Bhindi, managing director of Mazda Australia. Its concentration of design, technology and comfort makes it the ideal premium mid-sized SUV and today’s announcement by ANCAP underlines its impressive safety performance.”
CGU Insurance has finalised a distribution agreement with ANZ, to become the general insurance underwriter for ANZ retail banking customers for motor, home, and landlord insurance products.
CGU, part of IAG’s Intermediated Insurance Australia (IIA) business led by group executive Jarrod Hill, is one of Australia’s leading commercial, rural, and personal lines insurers.
Mr Hill said, “ANZ is a company that aligns well with the values and purpose of CGU, and our broader IAG business. As purpose driven organisations, we are committed to delivering market leading products and services to our customers.
“We’re excited about the mutual benefits and enhanced customer experiences this agreement will deliver. CGU’s continual focus and investment in strengthening our digital capabilities along with our well-established claims expertise to effectively manage claims, particularly during major natural peril events nationally, were fundamental in securing this agreement.
“We look forward to working with ANZ on this long-term relationship, where our emphasis will be on delivering increased customer value through a streamlined, digitally enabled model and high-quality products and services.”
ANZ managing director for retail banking Kath Bray said, “We’re pleased to partner with CGU to bring our customers continued support for their insurance needs and further improve their financial wellbeing.
“We know CGU will be able to provide high quality service and support for customers who want to protect the things that matter most to them.”
The agreement complements IIA’s strong history of distribution through Financial Institutions, further enhances and leverages the scale of its Intermediated Personal Lines portfolio and contributes to its target of achieving a $250 million insurance profit by FY24, with the business continuing to optimise its portfolio and enhance its digital capability.
When did you join the industry?
1993
What was your first job in the industry?
An apprentice OTR tyre technician.
What do you like about the industry?
The people and the relationships that I have formed over the years.
What could the industry improve on?
I would not say that I dislike anything, but I would say that we could do more in the industry to promote it and attract new talent.
What keeps you awake at night?
The occasional noisy neighbour.
Who is your biggest inspiration?
My old CEO at Continental between 1997 and 2003. He not only ran the company well but was a real people person. I was a junior rep at the time, but he took the time to know all his team and develop us.
If you could change one thing, what would it be?
More trips to the outback.
What do you do when you’re not working?
Spend time with my family and go on 4WD trips when opportunities arise.
Who in the world would you most like to meet?
Donald TrumpI-CAR Australia and AMA Group have announced that BMB Prestige Collision Repairs has been awarded the prestigious I-CAR Gold Class Collision status.
Gaining Gold Class for OEM facilities is a straightforward process given the variety of delivery methods including hands-on training, live and virtual classrooms and online options.
OEMs can streamline upskilling technicians with I-CAR Australia’s Road to Gold Program, which provides a clear path to Gold Class accreditation.
“With the amount of OEM training delivered by I-CAR, it was fairly simple for us to gain the status. Training becomes second nature for our technicians as with the changing technology, everyone must keep on top of it. The I-CAR Gold Class
program really embedded that,” stated Ian McInnes, centre manager of BMB Prestige Collision Repairs.
With the remote locations of shops across Australia and the ever-changing working environments due to COVID, I-CAR Australia makes it even easier to gain Gold Class accreditation with its large range of online courses.
“COVID really changed the way training is delivered. I-CAR’s online courses supported the team to continue their training as much as possible while minimising the disruption from COVID,” McInnes concluded.
EVs with aluminium body structures will be increasingly present in the Australian car industry within the next few years.
Training on how to repair these new
aluminium alloys is now more important than ever.
I-CAR Australia provides best-in-class training programs that are developed to keep the collision repair industry and body shop owners ahead of material and technological changes.
“If facilities are not keeping up with technology training they will be left behind. AMA Group and I-CAR work closely to schedule courses to fit into the needs of the business and maximise the ability of our team to complete their training. AMA Group has a clear goal to work toward I-CAR Gold Class status in all its facilities,” explained Scott Donnelly, technical training, prestige & OEM manager at AMA Group.
“This training is not just a nice to have but a must-have,” added McInnes.
Solera Inc. the leading global provider of vehicle lifecycle management softwareas-a-service (SaaS), data, and services, has introduced its new AI-powered collision repair suite in Australia.
The announcement comes as part of Solera’s continuous and ongoing launch of its full suite of vehicle lifecycle services in Australia, which is a key market in the brand’s global expansion plans. To help drive digitisation in the industry, Solera brings technology solutions spanning insurance claims, vehicle servicing, repairs and recycling, and property insurance claims.
Solera is aiming to tap into the growing automation market, having driven accelerated growth recently via its innovative Qapter platform and integrated technologies, and is now bringing its AI-driven visual intelligence (VI) suite to the market.
Solera’s Qapter VI, is a global, modular, and flexible platform that leverages AI technologies to provide exponential value to the vehicle claims industry and will increase automation and reduce cycle times via:
• Intelligent damage detection via guided image capture, reducing the cost of risk inspections
• Enabling efficiencies for repairer estimators via automatic initial assessment of vehicle damage
• Expediting parts ordering to improve cycle times, reduce parts fraud and CO2 emissions
• Improving partial or total loss triage decisions
• Accelerating claim resolution and settlements, benefiting both insurers and repairers
“Solera’s vehicle lifecycle management SaaS, data and suite of services provide a range of innovative solutions that will empower insurers, repairers and recyclers in Australia to digitize, upscale and improve the customer experience of their offerings,”
said Chris Iacovou, managing director, Solera APAC.
“Australia has always been highly regarded in the international automotive claims and vehicle repair segments, and Solera is excited to support the continued growth and digitisation of this dynamic market. We want to support businesses to increase their profitability by streamlining operations, improving customer satisfaction, and expanding market reach.”
Bradley Gannon, automotive CEO at Capricorn added, “Partnering with Solera has enabled us to revolutionise the automotive industry in Australia and New Zealand, via the development of Capricorn Service Data, powered by Solera Autodata.
“The partnership has equipped Capricorn with a powerful resource to support workshops to deliver exceptional customer service, streamline diagnostics and conduct efficient vehicle repairs. It powers the most comprehensive auto repair solution for the automotive aftermarket.
“Together, Capricorn and Solera are dedicated to bringing cuttingedge solutions and technology to our community, enabling businesses to thrive and excel in this dynamic industry.”
The business currently provides claims and supply chain management solutions to the top five insurance companies operating in Australia, via its suite of global data and technology solutions.
Eliminate wait times for wheels
Reduce repair cycle times and increase efficiency and turnaround
Use in the paint booth to avoid over spray Load capacity tested to hold 1134kg each
The Australasian New Car Assessment Program (ANCAP) tests of the Genesis Electrified GV70 and Electrified G80 have seen both models earn the program’s maximum five-star safety rating.
Additional frontal offset and oblique pole tests confirmed the integrity of the battery and the safety of the high-voltage electrical system, to see each model’s existing five-star safety ratings extended to include the EV variants.
With the addition of Electrified GV70 and Electrified G80, alongside GV60, the entire Genesis EV model line-up is now rated five stars by Australasian independent vehicle safety authority ANCAP.
“The excellent 5-star performance of the Genesis model range in ANCAP testing provides the best possible endorsement of the safety technology inherent in our battery-electric powertrains, as we continue towards a sustainable motoring future,” head of Genesis Motors Australia, Connal Yan said.
Both Electrified GV70 and Electrified G80 come equipped standard with an impressive array of advanced active safety and driver assistance technologies.
Key safety features of the electrified GV70 include:
• Eight airbags – including front centre side airbag
• Active bonnet
• Blind-Spot Collision Avoidance-Assist (BCA) – Rear/Side
• Blind-Spot View Monitor (BVM)
• Driver Attention Warning (DAW), including:
• Leading Vehicle Departure Alert
• Forward Attention Warning (FAW)
• Forward Collision-Avoidance Assist (FCA), including:
• Car/Pedestrian/Cyclist detection
• Junction Turning/Junction Crossing function
• Lane-Change Oncoming/Side function
• Evasive Steering Assist function
• High Beam Assist (HBA)
• Intelligent Front-Lighting System (IFS
• Intelligent Speed Limit Assist (ISLA
• Manual Speed Limit Assist (MSLA
• Lane Keeping Assist – Line/RoadEdge (LKA-L/R)
• Lane Following Assist (LFA)
• Parking Distance Warning (PDW) (Front & Rear)
• Parking Collision-Avoidance Assist –Reverse (PCA-R)
• Multi Collision Brake (MCB)
• Rear Cross-Traffic Collision Avoidance-Assist (RCCA)
• Rear Occupant Warning (ROW) – logic type
• Safe Exit Assist (SEA)
• Smart Cruise Control (SCC), including:
• Stop & Go function & Machine Learning
• Surround View Monitor (SVM) w/ 3D surround view
• Trailer Stability Assist (TSA)
• Tyre Pressure Monitoring System (TPMS)
Key safety features of the Electrified G80 include:
• Ten airbags – front, front centre side, driver’s knee, front thorax & pelvis, rear thorax and curtain
• ABS / ESC / BAS / HAC / VSM
• High Beam Assist (HBA)
• Active Bonnet Lift System
• Blind-Spot Collision Avoidance-AssistRear/Side (BCA-R/S)
• Blind-Spot View Monitor (BVM)
• Driver Attention Warning (DAW)
• Emergency Stop Signal (ESS)
• Intelligent Speed Limit Assist (ISLA)
• Forward Attention Warning (FAW)
• Forward Collision Avoidance Assist (FCA), including:
• Car/Pedestrian/Cyclist (FCA-CAR/
PED/CYC)
• Turning/Junction Crossing (FCA-JT/ JC)
• Lane-Change Oncoming/Side (FCALO/LS)
• Steering Assist (FCA w/ ESA)
• Lane Keeping Assist-Line/Road-Edge (LKA-L/R)
• Lane Following Assist (LFA)
• Manual Speed Limit Assist (MSLA)
• Multi Collision Brake (MCB)
• Parking Distance Warning: Forward/ Reverse (PDW-F/R)
• Rear Cross-Traffic Collision Avoidance-Assist (RCCA)
• Rear Occupant Alert (ROA)
• Safe Exit Assist (SEA)
• Smart Cruise Control w/ Machine Learning (SCC-ML)
• Surround View Monitor (SVM)
• Front & rear seatbelt pre-tensioners
• Parking Collision-Avoidance Assist –Reverse (PCA-R)
• Pre-Active Adjustment Safe-Seat (PAS) – front passenger
• Pre-Safe Seat Belt (PSB) – front seats
• Rear outboard ISOFIX / Top tether child restraint
• Tyre Pressure Monitoring System (TPMS)
The Australasian New Car Assessment Program is Australia and New Zealand’s independent voice on vehicle safety. ANCAP crash tests cars and conducts performance assessments of safety features and technologies to provide a star rating that indicates relative safety performance.
Since 1993, ANCAP has published independent safety ratings for thousands of new vehicle makes, models and variants, allowing a comparison between vehicles and a key vehicle selection factor for consumers.
With the snow season officially well underway, RACV is urging Victorians to prioritise safety on the roads as driving conditions can become more dangerous during winter.
Over the next months, weather conditions are more likely to change frequently resulting in wet, icy, and foggy roads, making it harder to see, stop and navigate.
RACV general manager for automotive services Jackie Pedersen said it was imperative that motorists took a safety-first mindset to work together to reverse the tragic trend of lives lost on Victorian roads in 2023.
As of 8 June, Victoria’s road toll sits at 140 lives lost on the year to date, up 35.9 per cent from last year, the highest number of deaths at this stage of the year since 2018.
“Even one life lost on our roads is too many, which is why we need to take our responsibility to drive safely seriously,” said Pedersen. “Victorians
will know all too well that weather conditions – and driving conditions –can change quickly, so it’s vital to plan ahead wherever possible.”
RACV has posted six tips for safe driving in winter conditions:
1. Slow down: travel just a little slower, even on roads you know well.
2. Keep an eye on the weather: be aware of changed conditions and heed any weather warnings particularly when travelling in areas where extreme weather is more common.
3. Maintain a safe braking distance: it takes much longer to stop in the wet, so extend the distance between you and the car in front to at least four seconds.
4. Take care of your vehicle: ensure your car’s safety equipment, windscreen wipers, batteries, lights, and brakes are working correctly.
5. Check your tyres: tyres must have plenty of tread depth (no less than 1.5 millimetres) and no damage.
6. When in doubt, pull over: it is never worth the risk to drive in conditions you’re even the slightest bit unsure of.
“Motorists also need to keep pedestrians, cyclists and motorcycles at the forefront of their minds as they are much more difficult to see in low visibility conditions,” added Pedersen. “Snow chains are a must-have when heading to the snow and you should make sure you test-fit them before you leave.”
RACV has also published tips for safe driving in snowy and icy conditions, emphasising that specialised snow chains topping the list.
For more information on road safety and driving and maintenance tips, visit www.racv.com.au.
We
Auto Parts Group (APG), the leading independent supplier of collision parts in Australia, is going from strength to strength under the stewardship of James Knox, the company’s dynamic new CEO, who joined APG roughly seven months ago.
“I’ve been in the industry for quite some time,” Knox said. “I’ve been part of the automotive repair industry for the last 20 years covering insurance, smash repair and now collision parts.”
Originally working in Corporate Finance, Knox soon transitioned to the insurance industry, where he found himself engaging more intimately with the ins and outs of auto repair.
“About 20 years ago, I started at Suncorp and ended up as the CFO of the Personal Insurance business, running a portfolio called Suncorp Insurance Ventures, which was our supply chain private equity arm,” he said. “This portfolio had investments in Capital Smart, ACM Parts and Home Repair, introducing me to the smash repair industry.”
Knox’s understanding of the collision repair industry expanded when he served as the inaugural CEO of Repairhub, which gave him first-hand insight into the operational challenges and opportunities present in the sector.
“I spent four years there, expanding it from just five shops to just under 20 when I left, making it the second largest smash repairer in the country,” Knox said. His role at Repairhub is where he initially crossed paths with APG, as the company was one of his major suppliers at the time.
APG’s dedication to providing a comprehensive and convenient service is central to its operations. The company ensures quality control and
expedited deliveries with their dedicated delivery team, as well as around-theclock support with their phone-based customer service teams.
Such dedication – together with its internal work culture – impressed Knox immediately.
“The founder of APG, Stephen Campbell, and I have known each other for 10 years. Knowing APG as I did, and admiring their work, when it came time for the founder to step back from the business, I was brought on to take over the CEO role.”
Under Knox’s leadership, APG, formerly known as All Crash Parts, has solidified its position as a trusted partner in the automotive industry. Boasting an extensive product range covering more than 45 vehicle manufacturer brands and a substantial inventory of over 44,000 SKUs, the company has an unwavering commitment to offering top-quality parts for a competitive price.
“We are not just collision parts providers; we aspire to be trusted partners in the industry, seeking to provide our customers a real advantage,” Knox said.
Looking forward to celebrating its 30th anniversary next July, APG has already achieved a significant milestone.
“Our biggest milestone is becoming the largest and leading independent supplier of genuine and aftermarket replacement parts in the country,” Knox noted with pride.
APG’s successful expansion is apparent from the numbers. “We now have national coverage with over 10,000 customers nationally serviced through our five distribution centres,” he added.
The company’s dedication to growth
and service is clearly reflected in other recent initiatives: a new warehouse in Sydney has already been launched, and construction is underway for a new facility in Brisbane.
However, these new facilities are not just about increasing APG’s physical presence. They’re integral to the company’s broader mission of catering to the increasing demand for alternative parts in the automotive market.
“Our main goal is to support the growth we’re experiencing and the demand for alternative parts,” Knox said. “This past year, we’ve grown about 20 per cent as a business and are reaching a point where we are outgrowing our infrastructure.
“These new facilities will support our push into not only our genuine range but also expand our certified aftermarket range.”
Under Knox’s guidance, APG’s impressive trajectory is set to continue well into the future. As it gears up to celebrate its 30th anniversary, the
James Knox, CEO of APG.caught up with James Knox to look at his impressive personal story, how a one-time investment banker became CEO of an industry-leading collision parts supplier, what advice he has for those starting their careers, and his plans for boosting Auto Parts Group’s success.
company’s commitment to innovation, quality, and service remains as strong as ever.
As a relatively new CEO inheriting a very strong company, Knox has high ambitions for what he can contribute to the company’s future success.
“We aim to continue the corporatisation of the business, growing our professionalism as an entity,” he explained. “We also want to drive the push into the aftermarket opportunity, which will require changing perceptions within the industry and among our customers.”
Innovation and technology also play critical roles in APG’s ongoing growth and Knox’s forward-looking strategy.
“Technology has always been a significant part of our business, along with our depth of service and capabilities,” Knox said. “For instance, we have APGiQ, our online sales and service portal, where customers can order parts, check availability, understand list prices, and track their product from being picked in the warehouse through to delivery.”
At the heart of APG’s success is a strong
commitment to nurturing meaningful relationships within the industry. “Indeed, a significant part of what we’re trying to accomplish as a company is to partner with our customers. This critical aspect of partnering with the industry is something we don’t take lightly,” Knox said.
APG’s commitment to industry partnership extends to maintaining a proactive presence in the field. The company employs on-road, Territory Managers to stay connected and responsive. Knox’s own approach includes actively engaging with customers: “I personally get out there and speak with customers as much as I can. I love it. And it’s essential to always keep your ear to the ground and learn from what customers are telling us.”
Beyond interpersonal connections, APG participates in industry initiatives to foster and consolidate stakeholder relationships. By way of illustration, Knox pointed to APG’s support of initiatives like the Women in Collision promotion and its foundational partnership with the Australian Collision Industry Association (ACIA).
Recognising the challenges faced by its partners, APG advocates for better
remuneration from insurance companies and brings awareness to profitability concerns in the collision repair industry. “We understand that advocating for better remuneration from insurers and raising awareness about profitability are important challenges for our partners.”
Believing that profitability can be boosted through options such as certified aftermarket and independent genuine, APG actively promotes these options. This approach is paired with support for partners, pushing for better pricing from insurers, and sponsoring industry initiatives – forming a comprehensive strategy for industry growth and sustainability. The complex remuneration landscape has traditionally resulted in a bias towards OEM dealer products. Knox and his team tackled the issue by highlighting the lack of incentives for repairers to choose more economical parts.
Knox put forth a concept called Shared Value to address the issue. The principle behind this concept is simple: if insurers want repairers to opt for less expensive parts, they need to provide the right incentives. “If you want a repairer to source a more cost-effective part for your car, if you want to shift the mix to
more certified aftermarket or alternative parts, you need to incentivise the repairer to do so,” he said.
APG’s mission to tackle this challenge involves raising awareness and pushing insurers to reconsider their remuneration models. Knox noted that this engagement has led to positive shifts in the industry, with Suncorp lifting its non-OE dealer parts remuneration to 80 per cent of OEM list for all alternative parts.
“It’s a significant challenge for us, but through constructive engagement, we’ve seen a positive shift in the market.”
In his position as CEO of APG, Knox has gained significant insights and wisdom that might prove valuable for those seeking to enter the industry.
NCR also asked him what advice
he’d give someone at the beginning of their career.
Firstly, Knox stressed the importance of being practical, commercial, and datadriven in your approach. Understanding the ins and outs of your business, using data to guide decisions, and holding people accountable are all essential for success.
“Any good leader needs to understand their business and use data to inform decisions or identify issues and hold people accountable. That’s a significant part of what I’m driving at APG.”
Another crucial aspect Knox underlined is the need to act decisively. He believes that even if you might only get 90 per cent of decisions right, this is better than making no decisions at all.
“It’s about being prepared to make that call, and then measuring,
monitoring, and following through with it.”
Finally, as a career progresses, Knox emphasised the importance of investing in people.
“Another key takeaway is the importance of taking care of your people,” Knox emphasises. “They are everything.
“Building great teams is something I truly enjoy, along with the interactions I have with people, both customers and employees.”
It’s this blend of business acumen, decisive action, and a people-first mindset that aspiring professionals should look to emulate as they navigate their own paths in the collision repair sector.
And it’s a blend that James Knox embodies and exemplifies as CEO of Auto Parts Group.
THE CTR9 AND CTR7 FULLY AUTOMATIC WELDERS COME WITH A NEW, REVOLUTIONISED LIGHT-WEIGHT TRANSFORMER GUN.
With its 355° swivel handle and ergo-grip, it enables perfect working positions for anyone, for any job. The gun is supported by a telescopic arm in a durable and lightweight extruded aluminium that can be easily adjusted both vertically and horizontally.
A compact power unit with a low centre of gravity gives mobility and stability, while a 16,000-amp transformer and CANBUS communication ensure a perfect weld every time.
T TRADE-IN DEAL:
The Trade-in deal is offered in conjunction with our Special Deals ‘Promotion’ on Car-O-Liner CTR9 and CTR7 Spot Welders, which means we will trade any type of spot welding system regardless of age or condition.
ACM Parts has unveiled its latest venture: a cutting-edge Aftermarket range of replacement parts. Adam O’Sullivan, executive general manager for ACM Parts discusses the company’s commitment to stand out as a leading supplier and deliver top-tier replacement parts.
In an industry where quality and precision are paramount, ACM Parts Australia has risen to the challenge with the launch of its innovative Aftermarket range.
Boasting a comprehensive selection of collision parts, lighting, and cooling components, the new range guarantees material excellence, precise fitment and unmatched functionality. With a meticulous verification process in place, ACM Parts aims to instil peace of mind in its customers, assuring them that every Aftermarket part surpasses OEM lifecycle performance standards.
ACM Parts’ foray into the Aftermarket realm is not just another offering; it is a testament to the company’s dedication to meeting the evolving needs of the Australian car park. In a candid Q&A session with the National Collision Repairer, Adam O’Sullivan, executive general manager for ACM Parts, revealed that the Aftermarket range was not born from assumptions but carefully matched to real-life parts demand data. “We create a range that our customers need and want today, and which is relevant to the diverse Australian car park,” he emphasised.
To achieve this, ACM Parts underwent months of rigorous supplier reviews and employed key criteria focusing on supplier parts development sophistication, manufacturing, and quality control processes. Several international trips to suppliers in Taiwan and China were undertaken to validate and exceed ACM’s standards for the new Aftermarket range. This unwavering dedication to quality and fitment assurance sets ACM Parts apart from the competition.
Ensuring that every Aftermarket part performs precisely as intended is a priority for ACM Parts. To achieve this, the company has employed a comprehensive fitment testing process, emphasising collaboration with chosen key suppliers with extensive experience in supplying both Aftermarket and OEM parts worldwide.
The process involves 3D scanning and Computer-Aided Design (CAD) analysis of each part in the Aftermarket range. “We have undertaken our own 3D scanning and CAD analysis of this range as well as physical vehicle fitment trials where required, to ensure complete confidence in this range,” said O’Sullivan.
One notable tool in this fitment testing process is the ‘Creaform MetraSCAN’ scanner, which plays a vital role in building a CAD reference file of the Aftermarket part. This reference file is then overlaid with the Genuine CAD file, ensuring that the Aftermarket part fits perfectly, offering quality fitment assurance. With this meticulous approach, ACM Parts can guarantee the proper performance of each collision part, making them a preferred choice for discerning repairers.
When it comes to replacement parts, ACM Parts works closely with global supply partners to ensure that every Aftermarket part not only meets but also surpasses the durability and requirements of equivalent OEM parts. Material specification and validation information is provided to ensure
that every part upholds OEM lifecycle performance standards.
“Our Aftermarket range meets or exceeds the requirements and durability of the equivalent OEM part,” assured O’Sullivan. This commitment to quality and reliability is central to ACM Parts’ mission of offering repairers an easy, fast, and cost-effective solution for sourcing parts.
ACM Parts’ new Aftermarket range is a
Ensuring that every Aftermarket part performs precisely as intended is a priority for ACM Parts.
Thatcham Research and Innovate UK’s Impact of BEV Adoption on the Repair and Insurance Sectors report finds all parts of the Motor Insurance Claims process will need to adapt to support the transition to Battery Electric Vehicles (BEVs).
Automotive risk intelligence company Thatcham Research has issued a report, funded by the UK Government’s innovation agency (Innovate UK), that highlights the technical and practical differences between BEV and ICE (Internal Combustion Engine) vehicle insurance claims processes.
The report examines potentially significant implications for motor insurers, their supply chains and in turn, consumer acceptance.
Despite newer BEVs featuring high fitment levels of ADAS (Advanced Driver Assistance Systems) and passive safety technologies, they are not risk or incident free.
Due to the nascent nature of the industry, BEV incident claims are currently ~25.5 per cent more expensive than their ICE equivalents and can take ~14 per cent longer to repair. Road collisions involving a BEV can be catastrophic for the vehicle as understanding and competence in rectifying the damage continues to develop.
The most significant challenges identified by the report originate from the high voltage (HV) battery. BEV batteries represent a substantial percentage of the original vehicle value and are therefore rapidly presenting negative impact to the economic model of vehicle repair.
Although there is a relatively small number of BEVs in the market, there is an understandable but concerning lack of affordable or available repair solutions and post-accident diagnostics.
Thatcham Research’s data-driven modelling shows that in 2022, 9,400 vehicles were potentially involved in collisions resulting in battery inclusion in the repair. This is estimated to reach
up to 260,000 vehicles annually by 2035.
Adrian Watson, head of engineering research, Thatcham Research, comments, “Without meaningful change, there is a strong likelihood that claims costs will continue to rise disproportionally.
“Much of the motor insurance industry is yet to adapt to mass BEV adoption challenges, and the implications remain unquantified on repair capacity, training and skills, cost, and the lifetime sustainability of BEVs. This lack of awareness means many BEVs are often deemed irreparable, leading to premature write-offs because of high battery cost and the lack of value the UK ecosystem can recover from them.”
Government guidelines state that due to potential fire risk, damaged BEVs awaiting repair should be stored in an outside quarantine area, at a safe distance of 15 metres from other nearby objects.
As such, an outside storage space with capacity for 100 ICE vehicles, would allow for the safe quarantine of just two BEVs, representing a potential 98 per cent reduction in repair capacity. The cost incurred through following recommended quarantine protocols of 48hrs will add a minimum of £60 to every claim, the report states.
If the vehicle cannot be safely stored at the repair centre there will be further costs associated with transportation to
and from an alternative location, storage at the alternative location, along with a longer duration of hire vehicle.
Watson comments, “This could result in a measurable rise in associated claim cost and duration, negatively impacting on the BEV ownership experience.
“This presumed rise in cost is a result of just one element of the BEV claims process flow. However, there are many other factors which may also result in further insurance premium costs due to the differing processes that follow a BEV collision.
“These range from limited access to battery diagnostics to enable a better understanding of battery health and potential repair options, to the increased weight of a BEV creating challenges to roadside recovery and a requirement for body shops to make costly investments in specialised repair skills and equipment.”
“It’s important to reiterate that most, if not all, of the outcomes highlighted by the report could be avoided with the right solutions in place,” said Watson.
The report’s authors would suggest investment in further cross-industry work to identify more detailed solutions and to make direct recommendations about a range of interventions or support to accelerate those solutions. For example, by understanding the needs of vehicle manufacturers, repairers, insurers, and salvagers to optimise the supply of new/refurbished/recovered batteries in vehicle repair.
Dutch paint and coating manufacturing company AkzoNobel is investing in two new manufacturing and research and development (R&D) facilities to utilise advanced technologies and create step-change improvements in North America.
The facilities include a pilot manufacturing plant in Huron, Ohio and a new R&D centre in High Point, North Carolina.
Huron’s new pilot plant is one in a network of pilot plants globally and supports AkzoNobel’s Packaging, Marine and Automotive businesses.
The state of Ohio serves as AkzoNobel’s largest footprint in North America, with locations in Huron, Strongsville, Springfield, and Columbus.
The company’s community of North America R&D Centres supporting the
Performance Coatings businesses includes – in addition to High Point – laboratories in Troy, Michigan, Strongsville, Ohio, Houston, Texas, Flying Hills, Pennsylvania and Lancaster, South Carolina.
The company has said its R&D Centres are transforming its investment in science and technology and give customers direct access to sustainable product development.
“We are capitalising on data analytics to transform our manufacturing processes and enabling the flow of information from the laboratory to the factory floor to our customers, generating agility to changes in the marketplace and meeting customer needs,” said John Griffin, North America regional director for AkzoNobel.
“The new R&D Center serves our
Wood Coatings business and brings together teams of researchers from diverse disciplinary backgrounds to create new solutions for our customers and immediately send it to the manufacturing production plant.”
AkzoNobel has active operations in over 150 countries and the company supplies sustainable and innovative paints and coatings through its portfolio of brands including Dulux, International, Sikkens and Interpon.
BASF Group is hoping for a return to better market conditions in the remainder of 2023 following lower than expected sales across its global network.
The company reported a 24.7 percent decline in sales to 17.3 billion Euros in its latest financial result for its operations in the second quarter of 2023.
BASF group has also adjusted its outlook for the remainder of the year to come.
BASF chairman Dr. Martin Brudermüller described it as a result of the tough market environment.
“We faced low demand from our key customer industries, except for automotive,” Brudermüller said at a
company release of the results.
The company reported the decline in sales was mainly driven by lower prices, primarily in the Chemicals, Surface Technologies and Materials segments.
Lower sales volumes as a result of weaker demand weighed down the sales performance in all segments.
Income from operations were €1.0 billion in the second quarter of 2023 below the figure of the prior-year period of €1.3 billion.
“Almost all segments contributed to this with significant declines in earnings, in particular the Chemicals and Materials segments, “ Brudermüller said.
“Surface Technologies achieved slight earnings growth.”
The 2023 SEMA Show in Las Vegas will feature a fully customisable hands-on education program which includes a line up of world-class seminars at the SEMA Women in Automotive Symposium.
Attendees can take advantage of the robust SEMA Show Education schedule to create a best-in-class professional development experience during the SEMA Show (October 30-November 3) and throughout the year.
The SEMA Women in Automotive Symposium is designed to provide a resource for women to network, mentor and participate in professional development programs geared toward helping them accelerate and advance in their careers and business.
This inaugural event–taking place in Room N258 on Wednesday, November 1, from 11:00 a.m.-4:00 p.m., will help women address common challenges faced by women in the industry, find solutions, gain new tools, and learn essential skills to drive business and career advancement.
Executives, general managers, middle managers, department heads, emerging leaders, diversity managers and related automotive professionals will benefit from several sessions, beginning with an inspiring opening keynote called “Drive: How to Gain and Maintain a Competitive Advantage” led by twotime racing champion and entrepreneur Julia Landauer, who has 21 years of competition under her belt, most recently starting the No. 44 Chevrolet in the NASCAR Xfinity Series.
Following will be a power networking luncheon and fireside chat called “Communication Secrets, Secrets of Success and Maintaining a Success Mindset.” This session will be led by FOX Sports Reporter Amanda Busick and feature Carolyn Jackson, vice president, brand strategy, Barrett-Jackson.
This interactive session will see Busick
interview Mullany-Jackson for career insights and thoughts on the tenacity and determination of a committed and dynamic team, a leadership state of mind, empowerment, and challenges, plus the achievements of her career as a top female executive in the automotive industry.
Rapid-fire-style workshops are next on the schedule, with four 15-minute sessions designed to help attendees engage, discover, and connect with subject-matter experts and thought leaders on small-business strategies and industry topics, including:
• “Becoming A Woman-Owned Certified-Enterprise,” led by Melanie White, CEO and owner of Hellwig Products.
• “Self-Branding: The ACTION Behind Building Your Personal Brand,” led by Jacki Lutz, senior manager marketing communications, corporate at Sensata Technologies.
• “The Power of Mentorship, Sponsorship and Allyship as a Strategy for Success,” led by Deanna Singh, managing partner at Uplifting Impact.
• “Make the Jump! Four Steps to Becoming the Authority in Your Industry,” led by Shaundra Dineen, award-winning motivational speaker and podcaster.
The program concludes with a moderated conversation with industry executives in a session designed to teach how action leaders are working toward gender equity and insights into the most significant challenges and opportunities facing the industry today.
“The further you advance in your career, the more important it becomes to hear directly from senior executives about the critical issues on their radar–and how you can also prepare to address such challenges as you progress through the ranks. We’re looking forward
to providing this opportunity, and so much more, to the women in the industry as part of this inaugural SEMA Education program,” said Pamela Brown-Matthis, SEMA director of education.
The “Driving the Future of Automotive: C-Suite Insights” panel, co-hosted by SEMA Businesswomen’s Network, will be led by industry executives explaining what they are doing personally to support women leaders through mentoring, sponsorship and modelling effective allyship, followed by a Q&A session.
Moderated by Cheryl Thompson, the president and founder of Center for Automotive Diversity, Inclusion & Advancement (CADIA), the one-hour session also features panellists Kim Less, vice president, aftermarket at Nissan North America; Subi Ghosh, executive vice president, Strategic Partnerships & Marketing at Stream Companies and partnerships chair at Women of Color Auto Network; Jayme Blasiman, founder of Femanic Garage and founder and coowner of Women’s Motor Fest; Matilda Johnson, chief experience officer at City Classic Cars; and Axel Cooley, president of Metallon.
The SEMA Women in Automotive Symposium is free for all 2023 SEMA Show attendees. Online registration for the SEMA Women in Automotive Symposium is available online.
Jaguar Land Rover (JLR) and Allianz Partners have launched a new program, Simply Drive, to give clients instant and complimentary insurance cover for the first month.
The embedded insurance program will enhance the purchasing experience for Range Rover, Defender, Discovery and Jaguar clients across Europe.
The Simply Drive service will be available on all new vehicles, offering clients the convenience of immediate and complimentary insurance cover for the first month of ownership, making their purchase quicker and easier.
This seamless service is the first product from JLR’s new, long-term partnership with Allianz Partners, a world leader in Business-toBusiness-to-Consumer insurance and assistance services. Over the next year, the insurance offering will be available across eight European
markets and epitomises the modern luxury purchase experience for Range Rover, Defender, Discovery and Jaguar clients.
François Dossa, executive director, strategy and sustainability for JLR said, “Our ambition is to offer clients a truly modern luxury experience in all that we do, and we are delighted to be working with Allianz Partners to enhance our clients’ modern luxury ownership experiences.
“We have co-created an innovative mobility solution offering our clients the benefit of convenience and assurance of seamless, immediate insurance coverage from the first moment they purchase their new vehicles.”
Jean-Marc Pailhol, member of the board and head of global strategic partnerships at Allianz Partners said, “This program marks the beginning of a long-term partnership
with JLR to deliver superior digital and innovative solutions and peace of mind to clients.
“We are proud that JLR appointed us as a partner of choice for supporting their Reimagine strategy and by making car insurance a ‘by default’ component and seamless experience in their client car purchasing journey.”
The Simply Drive service went live in Germany this month and will be rolled out across Austria, Belgium, France, Italy, Portugal and Spain over the next year.
The product will be integrated into the vehicle purchasing journey for Range Rover, Defender, Discovery and Jaguar clients.
The program is enabled through technology developed by simplesurance, as a key pillar within Allianz’s platform strategy, to allow seamless integration of Insurance products across markets.
If you have ever wondered how SATA manages to continually come up with industry-leading designs, backed by precision engineering, a trip to the home of SATA needs to be on your bucket list. It’s an eye-opening experience, says Matt Sbizzirri, PPG product specialist for associated products, who visited SATA’s high-tech facility at Kornwesthiem, Germany.
SATA GmbH & Co. KG is a global leader in the field of wet paint technologies and, besides Germany, supplies distribution partners in around 100 different countries.
“SATA employs just under 250 people and every one of them is very driven to continue SATA’s long-term reputation for being the very best. No one wants to put that at risk, so they handle every step of the production process with care and an incredible level of precision,” says Sbizzirri. For example, the tolerance during the manufacturing of a SATA spray gun is just 0.008mm – anything outside that is rejected and I actually saw this happen during my tour. It’s important to note that SATA has not been tempted to move any of its production to another country where it might be cheaper but also more difficult to maintain the SATA level of quality.
“The parts for every single SATA spray gun are manufactured at their Kornwesthiem plant, assembled on site and then double-checked for quality and spraying performance by a SATA person who is obsessed with perfection.”
“My visit also gave me a clear insight into how SATA has been able to make continuous improvements that have shifted the benchmark for spray equipment performance over the decades,” Sbizzirri added.
“For example, the onsite repair department is right next door to the SATA R&D department so that
information flows quickly and easily between them. Each day, the repair department actually prepares a report on the warranty work and other repairs it’s doing and that is sent to the SATA CEO, the head of quality control, the head of export and the head of R&D.
“They spend time every day discussing the issues to look for trends and develop solutions. Everything is taken very seriously and a super important part of that is feedback from customers around the globe who are actually using the products, whether it’s a spray gun, an air hood, a filtration system, etc.
“For example, I know that SATA see Australia and New Zealand
as a significant part of their global strategy and they really do hold us in high esteem. You quickly realise that the reason SATA equipment carries premium pricing is because it’s worth it – you get what you pay for!”
“SATA really enjoys the relationship with its customers and it’s very open to receiving visitors. Whether you are a SATA user, a SATA enthusiast or just from the industry, I would highly recommend a visit. However, the SATA team will need some notice so please reach out to your local SATA distributor or direct with SATA Germany,” Sbizzirri concluded.
everything you need to know about an obsession that dates
Sbizzirri provides insights.
The National Collision Repairer met repair centre manager Nazeer ‘Naz’ Ali back in May this year when he was recognised as National Rising Leader of The Year at AMA Group. Despite a demanding schedule, Ali made time to update us on how he’s doing at Capital S.M.A.R.T.
Born and bred in Melbourne, Ali did a bricklaying apprenticeship and moved into landscaping before an opportunity arose at Capital S.M.A.R.T. Since joining the company there’s never been any doubt his career path was heading for the fast lane of management.
“I left school around 15 or 16,” said the 28-year-old with a smile. “I was actually bricklaying for two-and-a-half years and got qualified, then went into landscaping because I thought my career path was going to be through the construction industry. But the work ran out.
“My friend Nathan got me the job with Capital S.M.A.R.T. about seven years ago at the Dandenong site doing the parts role, and the rest is history. I moved on to Blackburn with Keven Glen, estimating at the front door, and then moved on with him to Marlborough to learn production, then to Callum Downs.”
The early times at Capital S.M.A.R.T were good for Ali.
“I always felt Capital S.M.A.R.T, from the beginning, even before the AMA takeover, always recognised young talent,” recalled Ali.
“I’ve seen a few of the guys who worked their way up. They were only a couple of years older than me, all tradesmen or in parts or estimating roles as well, so I feel like Capital S.M.A.R.T AMA definitely recognises young talent coming through.”
When asked about his transition to AMA, Ali said he found great opportunity
and recognition.
“I won the award for AMA Rising Leader of The Year, so that’s always great as well (laughs), “but it didn’t really affect us too much. It meant a couple of different suppliers and a couple of different processes, but all in all the business stayed the same: we’re just fixing cars.”
In a demanding and intense role with the company, it’s the people and the work environment which keep Ali keen. “I love coming into the team every day, you know, seeing some new faces, some of the guys who’ve come along with me for the ride and everyone coming up.
“We face challenges every day, even two to three years post-Covid. There are always supply issues, staff issues, and so on. But I like a challenge. I like coming in every day and putting in the work with a very tight crew.”
A strong advocate for a customercentric-based business model and a mentor and model for other aspiring youngsters in the company, Ali spends his free time in the gym, pursuing an amateur career in Muay Thai and kickboxing, and when asked about his ‘dream’ car could only laugh and offer, “To be honest, nothing fancy. Probably a four-wheel drive of some sort. I’d love a HiLux.”
Where does this active and committed manager see himself in five years’ time?
“In five years?” pondered Ali, deep in thought. “In the next couple of years, I’d like to be in a support crew, bringing up the next generation of managers and leaders, showing them the ropes, showing them how it’s done.’
If Nazeer Ali sets that as a goal, National Collision Repairer has no doubt that’s where he’ll be.
IAG’s ongoing support and sponsorship of these awards is greatly appreciated, as is the support from I-CAR Australia, who donates two training courses valued at over $500 to each Future Leader of the Industry.
Aaron Samphier sits down with The National Collision Repairer to discuss how Fix Auto Macarthur’s integration into the Fix Auto network has led to its sustained growth and success, driven by streamlined processes, comprehensive support, and a strong customer-centric approach.
In the dynamic world of collision repair, where constant changes in technology, customer expectations, and market demands reign supreme, independent repairers face numerous challenges in staying ahead of the curve.
However, for Aaron Samphier, director and owner of Fix Auto Macarthur, a strategic decision to join the Fix Auto network two years ago has proven to be a game-changer. With the rebranding of his shop in 2021, formerly known as AAA Malibu Paint & Panel, Samphier’s venture into the world of Fix Auto has been marked by continued growth, providing valuable lessons for others in the industry.
The relaunch of Fix Auto Macarthur was the result of months of meticulous preparation and dedication. Samphier
spoke with enthusiasm about the process, “Fix Auto worked with us to review our business from top to bottom, we took the opportunity to look at everything from receiving customers into the business, estimating work, undertaking the repair process through to how we handover completed cars at the end of it all.”
This comprehensive approach allowed the team to identify areas for improvement and ensure that their customers would receive a professional and top-notch experience.
Joining the Fix Auto network provided an opportunity for Samphier and his team to reevaluate their existing processes and elevate them to new heights.
“Like most repairers, we believed we
always had good processes in place,” he said. “However, it has been insightful to review these with a fresh perspective and now support them with strong branding and materials.”
The support and branded tools from Fix Auto have added a layer of professionalism that resonates with customers and instils confidence in their choice of repair shop.
Scott Holden, the state general manager of NSW and QLD, praised Samphier and his team’s customerfocused approach.
“Aaron has a great facility, a passionate team of people, and a really positive culture in his business. Everyone is extremely customer focused.” This customer-centric approach, combined with the support and scale provided
by Fix Auto, has positioned Fix Auto Macarthur for elevated success as part of the world’s largest independently owned repair network.
Fix Auto’s assistance during challenging times has also been instrumental. The pandemic brought about uncertainties and lockdowns but Fix Auto managed to provide a fleet company that helped Fix Auto Macarthur weather the storm. Samphier’s determination and resilience during these difficult periods further strengthened his relationship with the Fix Auto family.
Stuart Faid, head of Fix Auto in Australia and Asia, acknowledged the challenges faced by the network during the COVID-19 pandemic. He shared, “Covid has impacted our anticipated growth trajectory this year. The reality is things are not getting any easier in the industry and for those remaining independents out there. Whether it’s Covid or consolidation, the odds are increasingly against us. Uniting to achieve strength in numbers, scale, and unification is the surest way to secure
our businesses against the challenges ahead.”
Aaron Samphier shared his experience as part of the Fix Auto network, emphasising the advantages of being part of a larger group while retaining independence. Having started in the industry almost two decades ago, he saw the potential for growth and improvement by joining Fix Auto. And the results have been impressive: “Our revenue has doubled since joining the Fix Auto network,” he proudly stated.
The transition into the Fix Auto network brought numerous benefits, from refining existing protocols to improved negotiation with insurers. “Having the backing of a corporate company helped fine-tune the company and was what I believe made a massive difference in the success of the company,” Samphier explained. Furthermore, the focus on customer experience and service has been instrumental in enhancing the shop’s reputation and attracting more clients.
Fix Auto Macarthur has found its niche as a non-drive centre. Samphier
explained the difference between drivable and non-drivable shops, explaining how their shop efficiently handles repairs for non-drivable vehicles, saving their customers time and hassle and allowing the business to cater to a niche market.
Looking back on his decision to join Fix Auto, he confidently affirmed that it was one of the best choices he made for his business.
“It was worthwhile joining the group, and I started seeing benefits from day one.”
As Fix Auto Macarthur continues to thrive and grow, it serves as a shining example of how partnership, resilience, and customer-centricity can propel a business to new heights. With Fix Auto’s global support and an unwavering commitment to excellence, the future is bright for Fix Auto Macarthur and the entire Fix Auto network in Australia. As the industry evolves, one thing is certain: Fix Auto Macarthur will remain at the forefront, delivering outstanding services and customer experiences in the years to come.
Hyundai Motor Company announced it is launching an expanded ‘Goal of the Century’ (GOTC) global communication campaign with various brand initiatives for the FIFA Women’s World Cup Australia & New Zealand 2023.
The news follows the recent announcement of Hyundai Motor’s renewed partnership with FIFA, which amplifies the company’s scope as an official mobility partner to include air mobility and robotics, both innovative future business sectors for the company.
The new campaign builds on GOTC activations initiated during the FIFA World Cup Qatar 2022 that reflect Hyundai Motor’s commitment to Sustainable, Innovative and Humane efforts around the world. With the expanded GOTC campaign, Hyundai Motor aims to combine the history of women’s football and the company’s vision to sponsor the Women’s World Cup via a new, more humane brand message that includes ‘Women + Inclusivity’ as key concepts.
“This year, Hyundai’s Goal of the Century campaign expands on its previous efforts to create a sustainable world by focusing on social inclusivity for women,” said Sungwon Jee, senior vice president and global chief marketing officer at Hyundai Motor Company. “The campaign embraces womanhood by not only supporting the FIFA Women’s World Cup 2023™, but also by celebrating the
legacy and history of women’s football.”
“Looking back at how far women’s football has come, Hyundai has an optimistic view of the future,” Jee said. “As a longtime supporter of the game since 1999, Hyundai aims to continue fostering inclusivity and equality throughout the sports world.”
As part of the new campaign, Hyundai Motor released a global campaign video whose central message, “How Far We’ve Come,” stands as a tribute to the remarkable history of women’s football.
It commemorates the significant progress achieved and highlights the enduring partnership between Hyundai Motor and the Women’s World Cup, spanning an impressive 25 years and encompassing seven tournaments since 1999. The film features some of women’s football’s most legendary moments from 1850 up to the present day.
Hyundai Motor is sponsoring a special exhibition, ‘Calling the Shots: Faces of Women’s Football,’ at the FIFA Museum, during the FIFA Fan Festival in Tumbalong Park, Sydney, from July 20 to August 20, 2023.
The exhibition celebrates the heritage of players, staff and supporters who have contributed to the development of the Women’s World Cup so far. Hyundai Motor is also highlighting the sustainable construction of the museum via the use of recycled materials.
To further increase awareness of
the GOTC campaign and spread its message to football fans, Hyundai Motor is resuming its partnership with Common Goal to support women’s football-related activities. The company is sponsoring the ‘Global Goal 5 Accelerator’ program, which focuses on developing women role models for young footballers and expanding opportunities for women to participate in football.
Hyundai Motor is also sponsoring Festival 23, an eight-day youth festival of ‘Football for Good,’ to be held in Sydney during the FIFA Women’s World Cup 2023’s quarter-final week. Through this festival, the company will celebrate the game’s social impact, bringing together young girls for a combination of educational workshops and cultural programs.
In cooperation with FIFA’s digital platform (FIFA+), several game programs, such as ‘Trivia’, ‘Hyundai Goal of the Tournament’ and ‘Hyundai Match Predictor,’ will be operational during the tournament to help spread the campaign message to global football fans.
Kia
Christine Dicker of Motorama Kia Moorooka has made a podium finish at the 6th biennial Kia Service Advisor World Competition, coming home with a bronze medal and continuing Australia’s legacy.
Dicker earned her place in the global finals following her win at the local
finals earlier this year, in which she beat five other finalists to be crowned the Australian champion.
Representing Australia and her dealership, Dicker travelled to Seoul, South Korea in late June to compete in the final competition alongside 44 other finalists from 42 nations. Consisting of a written test and multiple practical tests,
the final round aimed to evaluate the contestants’ capabilities in customerfacing scenarios and knowledge of on-site responses.
“This is an achievement I will never forget – I will take home the skills I have refined and share them with our team so that our customers get the best experience we can deliver,” Dicker said.
BMW Australia will enhance its successful X7 flagship Sports Activity Vehicle (SAV) line-up with a new sixcylinder petrol variant that will launch towards the end of this year.
The X7 xDrive40i is powered by BMW’s renowned six-cylinder TwinPower Turbo engine – which also features in the new BMW X5 and X6 – and integrates 48-volt mild hybrid technology to deliver new levels of performance and efficiency characteristics.
It generates maximum output of
280kW with peak torque of 520Nm – a figure that can be boosted to 540Nm with input of the 48-volt mild hybrid system.
The new-generation mild hybrid technology comprises a crankshaftmounted starter generator integrated into the transmission housing.
The generator is used as a starter motor to fire the combustion engine and recuperates kinetic energy during coasting and braking. The accompanying 48-volt battery powers the generator, stores recuperated
energy and powers the onboard electrical system.
The new six-cylinder engine partners with an eight-speed Steptronic Sport transmission including shift paddles on the steering wheel. Engine power is channelled to the road – or unsurfaced terrain if required – via the intelligent all-wheel-drive system BMW xDrive.
The new X7 xDrive40i will join the X7 xDrive40d and M60i – both of which launched late last year –with specifications mirroring that of the former.
Following another year of high performance throughout the national dealer network, Mitsubishi Motors Australia Limited’s (MMAL) executive and senior management have been undertaking a national roadshow to celebrate the achievement with dealers, their families, and regional staff.
The centrepiece of these celebrations was the announcement of the Distinguished Dealer Awards for 2023.
MMAL CEO, Shaun Westcott, and other members of the executive were on hand in Sydney, Melbourne, Brisbane, Adelaide and Perth to personally congratulate the seven winners from around the country.
Established in 1981, the Mitsubishi Motors Australia Distinguished Dealer Award is the highest accolade available to Mitsubishi dealers.
The award seeks to celebrate success across sales, aftersales and customer experience at a dealership and is a true representation of the hard work and effort which staff at dealerships put in, as part of a team, throughout the previous year.
This iteration saw a solid cross-section of regional and metro dealers take the award, demonstrating the success that can be driven by performance across the country, while it also saw three
dealerships take the award for the first time.
Mitsubishi Motors CEO Shaun Westcott remarked “The Distinguished Dealer Awards sets a high bar for dealers across Australia, as we seek to continually exceed our customer’s expectations by demonstrating excellence across the business.”
“Each year becomes increasingly competitive as we see the quality delivered by our dealers nationally, across sales, after sales and customer experience.”
“This year is no different as we see a selection of consistently high performers continue to deliver and take out the awards, while there are some new achievers entering the field as well. This is great news for MMAL and its customers, and we look forward to seeing what our dealer network will achieve in 2023 and beyond.”
The 2023 Mitsubishi Distinguished Dealer winners are:
• Wayville Mitsubishi notches up its 6th gong as a Mitsubishi Distinguished Dealer winner.
• Melville Mitsubishi is receiving the dealer award for the first time in its history, with new dealers since 2020.
• De Maria Mitsubishi has taken out its’ third consecutive award this year having won in 2021, 2022 and now 2023, after winning this award overall for the seventh time.
• Warragul Mitsubishi operator Craig Turnbull took over Warragul Mitsubishi in the last five years and has taken out the Mitsubishi Distinguished Dealer Award for the first time in its history.
• Werribee Mitsubishi have achieved back-to-back awards in 2022 and 2023. A consistently a high achiever, they have won the award now six times in the dealer’s history.
• Suttons Mitsubishi Arncliffe, a familyoperated business celebrating 80 years of operation, achieved its award for the first time in their history
• Ross Gray Mitsubishi has achieved the dealer award for the fourth time in its history in 2023, with previous successes in 2009, 2012 and 2021.
Jaguar South Africa has revealed the six female artists participating in the 2023 #GiveHerACrown campaign. Championing a diverse range of artistic disciplines, the women were chosen for their unique and ground breaking work which celebrates female creativity and empowerment.
The 2023 campaign will see each artist create a bespoke piece aligned with the theme of “Celebrating the exquisite details of women”. Each art piece will portray a story that aims to not only inspire but encourage women to embrace their uniqueness and individuality. Jaguar firmly believes in empowering women and celebrating their fearless spirits and creativity, to express their inner selves to the world.
Launched in 2020, #GiveHerACrown is an empowerment platform that uses the power of storytelling and the arts to make a difference in the fight against gender inequality. #GiveHerACrown, empowered by Jaguar, has played an important role in uplifting female artists, providing them with a platform to showcase their talents and share their stories.
As Jaguar reimagines its all-electric, modern luxury future within the JLR portfolio of brands, a focus on Diversity and Inclusion remains a top priority for the corporation. As a global business, building a rich and inclusive culture that reflects our communities is central to our commitment. As part of its strategy, the company has set several global objectives, including the target to have 30 per cent of all senior leadership positions held by females by 2026.
Employee-led networks, supported by the central Diversity and Inclusion team, and the Diversity and Inclusion Board co-sponsors, Barbara Bergmeier and François Dossa, are also advocating for gender equality in the business and more widely in the industry.
It is this expressed commitment to diversity and inclusion that attracted the involvement of talented filmmaker Linda Notelovitz from Life Design. Notelovitz will turn her camera on the six artists,
bringing to life their unique and inspiring stories Along with sharing their stories, the short films will focus on the behindthe-scenes of the artists’ creations.
These bespoke art pieces will join the Crown Collection, which is the exclusive collection of artworks produced each year by the artists of the #GiveHerACrown campaign. This year’s collection is curated by ARRCC, a highly regarded and accomplished interior design and décor studio based in Cape Town.
This year’s Crown Collection will be revealed and exhibited at The Melrose Gallery on 10 August and will remain on display until 25 August. As in previous years the proceeds from the campaign will go towards the Crown Bursary Fund to benefit a selected number of aspiring female designers.
Representing a diverse range of art disciplines, the 2023 artists are:
1. Andiswa Bhungane: a brilliant and upcoming resin and acrylic painter, who describes her work as luxurious and multifaceted.
2. Beth Diane Armstrong: a creative sculptor of large-scale projects. Her focus has been on creating monumental artworks made of stainless steel.
3. Helena Hugo: a seasoned portrait artist who prefers to portray individuals who are often overlooked.
4. Lara Klawikowski: a consummate professional and skilful fashion designer, Lara designs wearable art and unique womenswear.
5. Shelley Mokoena: a talented fashion designer who prides herself in creating bold yet understated pieces that turn heads.
6. Sonja Swanepoel: a diverse and multitalented sculptor and landscape architect. Sonja creates contemporary art for environmental awareness.
Notelovitz, director & producer, Life Designs, said, “As a woman filmmaker, being asked to create a film campaign for #GiveHerACrown 2023 can only be described as a full-heart experience. Meeting and working with the six unique female artists, all complex and bright, and each one very talented was more than I imagined it could be.”
Craig Mark, director of the Melrose Gallery said, “The Melrose Gallery is pleased to host the launch of this year’s ‘Give Her a Crown’ collection. We recognise the need to support woman empowerment and this project is a welcome addition to our annual ‘Woman’s Month’ programme curated by Ruzy Rusike.”
Irene Kakooza, communications manager, JLR South Africa & Sub-Sahara Africa, said, “Jaguar believes in the power of innovation and creativity, not only when pioneering products but as a way to solve society’s biggest issues.
“At a time when the world, and South Africa, desperately need to focus on empowering, recognising and protecting women, #GiveHerACrown is an ideal and much-needed platform. We are proud to be a part of the initiative for the third year in a row.”
The increasing use of aluminium in automotive manufacturing will impact the collision repair industry, requiring specialised training and equipment. I-CAR Australia recommends shop owners and technicians start adopting an upskilling approach to their business model to prepare for this transition.
In 1970, aluminium only accounted for two per cent of car components; today, this number is increasing to over 15 per cent and is expected to rise to 24.9 per cent or even greater for electric vehicles (EVs) by 2030.
EVs require greater range and one of the best ways to achieve high range is weight reduction. Aluminium is the preferred material to use for reducing the overall weight of EVs. For instance, the latest all-aluminium vehicle from Range Rover is 39 per cent lighter than its steel predecessor.
The use of aluminium in automotive body structures for electric vehicles is one of the largest growing material components being used, the demand for aluminium in EVs will near ten million tonnes by 2030 this is a ten-fold increase from 2017.
So why should we care about the increased use of aluminium when it only seems to be used in electric vehicles?
The Australian market is still slow to adopt EV purchases due to two major reasons: range and price. These two factors are about to change very quickly, not in the next decade but in just a few years.
Australia is such a vast country and consumers are demanding EVs to have a similar range to that of current internal combustion engine (ICE) vehicles. EV makers are forever trying to figure out how to increase battery range for future EV models. Newer technologies such as lithium vanadium phosphate, aluminium-ion batteries and solid-state batteries always seem to be on the horizon and never implemented, but
this is all about to change.
Toyota confirmed its long-awaited solid-state battery technology at the “Let’s Change the Future of Cars” technical workshop in Japan this June, with its latest offering of solidstate EV battery technology with a 1500km range. The technology will be introduced in 2027, which includes the Toyota Crown E.
Next-generation lithium-ion batteries is set to be launched in 2026, with a range of approximately 1000 km, with solid-state batteries arriving around 2027- 2028 with a range of 1200 kilometres and increasing to 1500 kilometres.
With the improved driving range of over 1000 kilometres for upcoming
EVs, this marks a turning point for the Australian market.
While the driving range of EVs will meet consumer demands within the next few years, the cost is still an issue. Current costs of mainstream EVs are in the $60,000 to $100,000 range, with a hefty second-hand EV market. With used Teslas selling for around $50,000 to $60,000, it is hard for the average Australian to purchase a reputable EV that compares anywhere near what you can get in a combustion engine for around $15,000 to $25,000.
But there is a silver lining in the future. EV costs are projected to drop, with Tesla implementing plans to reduce EV Costs by about 50 per cent in the next five years. MG
and BYD planto launch the first sub-$40,000 (ex-onroad costs) EVs in Australia this year. Sedan and SUV EVs are forecasted to be cheaper to produce than equivalent ICE vehicles by 2026.
EV manufacturers have implemented a range of cost-cutting manufacturing techniques and one of these is the use of aluminium body structures. But how can this be more cost-effective when aluminium can cost 20-50 per cent more than steel?
Sub-header: The solution lies with giga casting
Giga casting cuts manufacturing and production cost significantly and is currently implemented by Tesla with its giga press.
The giga press is a series of highpressure aluminium die-casting machines where molten aluminium is injected into the cold-chamber casting mould at high velocity resulting in around 30 completed castings an hour. Tesla’s giga press simplifies assemblies from 70 parts to just two to three large castings. This has greatly simplified its
production line, which has resulted in the reduction of around 600 robots for the Model 3 and will reduce Model Y’s rear underbody manufacturing cost by 40 per cent.
Tesla is not alone in using this technique. Toyota has recently announced a similar process at its “Let’s Change the Future of Cars” technical workshop. The Japanese automotive manufacturer will incorporate a simple slim vehicle body structure through giga casting for future EVs. Other manufacturers including General Motors, Hyundai and Volvo will also be incorporating similar processes. Additionally, Chinese manufacturers like NIO and Xpeng, as well as Tesla have plans to cast a full vehicle body structure in one single piece.
Sub-header: How will this impact the collision repair industry?
With electric vehicles set to increase in range and affordability, we should see a sudden projected uptake of EVs in the Australian market. Due
to an ever-increasing number of manufacturers adopting giga casting techniques, there will be a large shift from traditional multi-sectioned steel body structures to aluminium body structures with only three or fewer sections.
Other ICE vehicles are also turning to aluminium as their choice of material due to its advantages. Aluminium can absorb twice as much energy as steel in a crash, have larger crush zones, and does not rust like steel.
As vehicle body structures, panels, crumple zones, and extrusions are increasingly being made from aluminium, technicians in the collision repair industry need to understand how to best repair high-grade aluminium alloys and adopt best practices when welding or working with aluminium to ensure structural safety and compliance.
A big misconception is that it is easy to adapt to aluminium, but this is far from the truth. Welding aluminium is about chemistry and every metal
reacts differently from thermochemical reactions. The learning gap is even greater as newer EV structures are manufactured with a blend of advanced alloys.
Workshops looking to incorporate full-scale aluminium repairs need to understand that aluminium and steel do not mix and can be extremely corrosive to each other. Workshops need a separate space to carry out repairs as steel shavings can cause irreversible damage to aluminium surfaces. Dust generated from grinding and sanding can become explosive. Workshops will therefore require dedicated aluminium dust extraction systems.
Further, tools and other specialised equipment will be needed to be taken into consideration. One cannot use the same steel grinder on aluminium bodies, or it will cause galvanic corrosion. Other equipment like aluminium MIG welders vary in price from $4000- $14000 with certain original equipment manufacturers (OEMs) requiring using only approved equipment for repair.
There are three main differences
when welding aluminium versus steel. Molten aluminium is harder to see while welding as it does not change colour when heated, and more preparation and pre-treatment is required when working with aluminium. Lastly, thermochemical differences are important to note – welding aluminium at very high temperatures can cause the metal to decay which can result in safety issues. Aluminium’s melting point is 660.3°C and aluminium oxide is 2072°C.
Technicians repairing aluminium panels must also understand how the material moves when heated, as aluminium does not have “metal memory” like steel. Things like pushing out a dent can cause stress to the material and lead to microfractures in the material. Aluminium has high thermal conductivity and heat travels throughout the panel rather than in a concentrated spot. Aluminium becomes permanently changed if heated past a certain point, therefore, technicians need to heat the area with a digital temperature set heat gun for heat control.
There are certifications available for OEMs to repair modern vehicles with aluminium materials or advanced technologies like HV batteries and ADAS. More and more OEMs are requiring certified repair technicians within the collision repair industry. This will only continue in the coming years as vehicles become more advanced.
I-CAR Australia recommends shop owners and technicians start adopting an upskilling approach to their business model to allow an easy transition into aluminium repairs and other technological advancements.
I-CAR Australia provides a range of advanced training programs for the repair of aluminium that is specifically designed for upskilling and certifying technicians within the collision repair industry. It currently offers hands-on training and certification for aluminium welding for Tesla OEMs, as well as a range of online and classroom courses for non-OEMs. Soon, I-CAR Australia plans to expand their hands-on training to other OEMs, which will prepare technicians for this sudden push to aluminium.
• Self-piercing rivets
• Flow-form rivets
• Countersunk flow-form rivets
• Solid rivets
• Solid self-piercing rivets
• Blind rivets
• Blind rivet nuts & bolts
• Pressing out
• Backshaping
• Calibration
• Hole punching
• Stamping
FOR VEHICLE REPAIR
FULL SET
• 1x Workstation inc. XLogic
• 1x Short stroke cylinder SSC 40mm
• 1x XPress power pack
• 1x ea Blind rivet adapter BR 20/50
• Tool box RS-06 V4 (JLR)
• 1x Blind rivet nut adapter BRN 50
• 1x Tool box RS-04 (BRN 50)
• 1x ea C- arm GC 80/40, 80/120, 140/240
• 1x Spiral compressed air hose 4m
STANDARD SET
• 1x Workstation inc. XLogic
• 1x Short stroke cylinder SSC 40mm
• 1x XPress power pack
• Tool box RS-06 V4 (JLR)
• 1x ea C- arm GC 80/40, 80/120, 140/240
• 1x Spiral compressed air hose 4m
UP GRADE SET
• 1x Workstation inc. XLogic
• 1x Short stroke cylinder SSC 40mm
• 1x Spiral compressed air hose 4m
Approved and recommended by OEMs.
• Metal detection
• Gun force pressure
• Current control
• Time control
• Data storing
The National Collision Repairer Lifetime Achievement Awards began in 2007 and was created to acknowledge the dedication and commitment of the men and women who have contributed to the collision repair industry over and above their “day job”.
The criteria for induction are a minimum of 20 years in the collision repair industry, contributions to the industry beyond the scope of their local area, contributions to the industry beyond the scope of their direct employment and nomination from within the industry.
We extend our congratulations to the recipients of the Life Achievement Awards, acknowledging their invaluable contributions and recognising that their lifetime dedication to the industry has played a significant role in shaping it into the vibrant and cutting-edge field it is today.
There are now 57 inductees on the Honour Roll, including the winners of the 2023 Lifetime Achievement Awards – Ben Chesterfield, Scott Donnelly, and Morry Corvasce.
A full house of invited guests, including sponsors, collision repairers, suppliers, insurers, and previous inductees, gathered at the Pullman Sydney Hyde Park to congratulate the three 2023 lifetime achievement award inductees earlier this year in June.
The Roll also includes five international recipients from New Zealand, the United States, and Sweden, who have not only contributed to the
development of the industry in their own countries but also left an indelible mark on the Australian collision repair landscape. This award recognises the recipients’ perseverance, contributions, and experience, which amounts to a staggering total of over 1,900 years.
Importantly, we continue to attract
sponsorships from veritable who’s who of the collision repair industry, many of whom have been with us since the inaugural awards. So, once again, we take this opportunity to express our gratitude to the individuals and their organisations who support this initiative that truly does “honour the past”.
HELD ANNUALLY, THE RECIPIENTS OF THE NATIONAL COLLISION REPAIRER’S LIFETIME ACHIEVEMENT AWARDS ARE INDUCTED AND HONOURED FOR THEIR OUTSTANDING SERVICE TO THE COLLISION REPAIR INDUSTRY.2023 inductees Ben Chesterfield, Scott Donnelly and Morry Corvasce.
Capricorn Rising Stars is a prestigious award that recognises talented automotive apprentices with initiative and commitment to the industry. The 2023 winner, Chelsea Bowers, wants to mentor others and promote automotive trades as a career option for the next generation.
Australasia’s largest automotive cooperative, Capricorn, is proud to announce its 2023 Capricorn Rising Star from Queensland, Chelsea Bowers.
The prestigious achievement award recognises talented apprentices who show initiative, thirst for knowledge, and commitment to the automotive industry.
Chelsea Bowers, from John Edwards Automotive in Geebung, Queensland, is exceptionally talented. Last year, she was a Top 5 Finalist, and has taken the top prize this year.
“I began my journey in automotive when I started a school-based apprenticeship in grade 12. I took every Wednesday off and worked alongside a brilliant mentor who taught me so much. I found my love of cars again when I was restoring a 1964 Buick with my friends in my spare time,” Bowers said.
“I decided I wasn’t finished with the trade and I was determined to come back and finish my apprenticeship. This is when I found John at Bosch and the rest is history. I love my job more than ever and I have never once felt out of place. We shared the same values of honesty and communication.
“As I re-entered the trade, I met a few women in all different trades who had gone through exactly what I had gone through and had a whole network of tradeswomen I could turn to. Everything I went through got me to where I am now. It has taught me resilience, both mental and physical strength, passion and most importantly, the drive to share my story so no one ever feels as though they need to go through the same thing.”
Bowers said that coming from a humble workshop has accelerated her growth and provided great benefits as an automotive apprentice.
“Being in a small workshop, I feel as though I’m very involved and included in my work for any job that comes along. I like to put myself out of my comfort zone and choose to do difficult jobs
so I can learn quickly and accurately. I also do a lot of external training outside of work hours that can help improve my knowledge and confidence. I like to network on behalf of my workplace so I can expand my people skills and get comfortable talking to people so I can communicate with my customers at work on a more personal and relatable
level,” she said.
“I love that every day is a different challenge and a different opportunity to learn something new. Something that keeps me going when times get difficult, is thinking about how far I’ve come in my journey and how I can use my story to inspire the next generation of people looking to get into the automotive trade.
I’m very grateful to be in a positive workplace that appreciates me, and we can all get along and help each other out with anything.”
Through her apprenticeship, Bowers has built strong connections with her customers and is dedicated to providing personalised service.
“One of our regular customers runs a not-for-profit women’s shelter. We have a very strong, trusting relationship with these people. Every time they come in, our hearts break hearing the stories they tell us about what they go through. When they bring their car into our workshop, we stock the boot with donated nappies, sanitary items, soaps, toilet paper, shampoos and conditioners, and anything else they need at the time as a thank-you for helping those in need. It’s only a small gesture but it does go a long way. We make sure the women who come into their care who have cars are well looked after as well with their car services and maintenance needs,” she explained.
When asked about her long-term goal, Bowers shared, “I have a vision that one day I will own the workshop I am currently employed in, and I have my apprentices that I closely mentor. My long-term goals that accompany this vision is running hands-on workshops at schools teaching basic car maintenance and safety, as well as encouraging students to consider a trade-in automotive as their first career option
post-school.
“I am very passionate about the next generation of tradies who will soon dominate the industry. I look forward to continuing to break the stigma of what the image of a mechanic looks like in people’s minds.”
According to the owner of John Edwards Automotive, Sam Lawson, Bowers is not only an advocate for women in trades but serves as an inspiration for future generations.
Chelsea Bowers has won a $5,000 cash prize from Castrol and a Capricorn Rising Stars Trophy. The winning workshop, John Edwards Automotive, has received a 12-month Repco Autopedia subscription along with enrolment in the Workshop Whisperer’s Service Advisor Pro online program.
Brad Gannon, Capricorn CEO Automotive said, “The 2023 Capricorn Rising Stars Apprentice of the Year was selected from an impressive 550+ apprentices nominated by Capricorn Member businesses located across Australia and New Zealand. This competition highlights the importance of apprentices to the Australian and New Zealand automotive aftermarket industries.
“The competition also seeks to encourage new talent to join the industry, ultimately generating more qualified automotive repairers to ensure the industry’s continued future growth and strength. Big thanks to
our Members who nominated their talented apprentices along with award sponsors Castrol, Repco and The Workshop Whisperer who made this competition possible.”
Stay tuned for the return of the Capricorn Rising Stars competition in 2024.
To find out more and be part of the Capricorn community, visit www.capricorn.coop.
If you are looking for a premium body filler that can handle any filling scenario, from deep filling to final filling of pinholes, you need to check out the Dolphin product range from U-pol.
U-pol is renowned for advanced chemical technology, and the Dolphin premium body filler range is a perfect example
Dolphin fillers are designed for the professional automotive refinish market to improve workflow and produce highquality surfaces ready for painting in the shortest time possible.
Talk to any refinish professional that has used the Dolphin body filler range and they will tell you the top three reasons why they choose Dolphin:
1. Easy to sand: By far the biggest reason for choosing Dolphin. Sanding takes time because it is the final step (apart from blowing and wiping down). It produces the final surface to be painted and so must be done correctly. Dolphin fillers are easy to sand, even after long periods of curing, and leave a smooth and even finish with minimal effort.
2. Ease of use: Dolphin fillers are workable, stick to a wide range of substrates, and cure quickly ready for sanding. Fast-curing technology is designed for professionals, but is not suited to weekend warriors who need a bit more open time. Dolphin fillers also have excellent adhesion and durability, making them suitable for both metal and plastic repairs.
3. Easy to apply: Dolphin spreads easily and smoothly, resulting in less time sanding and less waste. Unlike some fillers, Dolphin does not sag or slump and can be applied in thin or thick layers without compromising quality. Dolphin also has low shrinkage and low porosity, which means fewer pinholes and less risk of cracking or staining.
The Dolphin body filler range is designed to be a system with a Dolphin variant optimised to provide faster results for each stage in the panel repair process:
Dolphin Premium
This is a high-performance lightweight body filler that can be used for filling deep dents, holes, rust damage, and other major defects. Dolphin Premium has excellent spreading and shaping properties, high adhesion and flexibility, and low shrinkage and porosity. It can be applied over bare metal, galvanised steel, aluminium, fibreglass or directly over epoxy primer. It cures in 20 minutes and can be sanded with P80-P180 grit paper.
This is a two-component polyester finishing glaze that can be used to fill pinholes, scratches, and other minor defects. It has a smooth creamy texture that spreads easily and self-levels, leaving a fine finish that requires minimal sanding. It can be applied over bare metal, existing paintwork or directly over body filler. It cures in 20 minutes and can be sanded with P180-P320 grit paper.
This is a fast-drying, easy-sanding polyester stopper that can be used to fill minor imperfections such as scratches, stone chips, pinholes, and dents. It can be applied over bare metal, existing paintwork or directly over body filler. It has excellent feathering properties and can be sanded within 15 minutes of application.
This is the latest product in the range and provides outstanding self-levelling, cures in 6 to 8 minutes, produces an ultra-fine finish, and can be used straight out of the pack with its large easy-pour nozzle.
Dolphin Speed Glaze is ideal for spot repairs and small areas where speed and convenience are required. It can be applied over bare metal, existing paintwork or directly over body filler. Dolphin Speed Glaze can be sanded with P320-P400 grit paper.
Labour is by far the biggest cost in the panel repair process and the Dolphin Body Filler system will get you through preparation to applying paint faster.
Time is money – don’t let less advanced body fillers bog you down.
Find out more about the Dolphin Body Filler range on the U-pol website: u-pol. com.au. You can also contact U-pol at (02) 4731 2655 or info@u-pol.com.au
Digital technologies are becoming increasingly powerful catalysts for innovation across industries worldwide and in the automotive sector, it is a market size expected to reach nearly US$7 billion globally by 2030.
In simple terms, AR adds a virtual world on top of a physical one, blending real and virtual components together to enhance the user experience. This delivers significant benefits across the value chain in the automotive industry, streamlining processes for everything from design and manufacture to testing, fine-tuning, and even sales. One of the biggest benefits it delivers to the industry is in automotive repair.
Technology advances have led to modern vehicles with increased complexities—such as advanced digital features, increased sensor usage, and more autonomous functionalities— which have stretched the boundaries of traditional repair shops.
In short, more complex vehicles need more complex maintenance and repairs. Consequently, the industry has seen a surge in the use of AR, supported by AI and Internet of Things (IoT) to support repair.
Four key applications of AR have emerged as game-changers for the automotive industry:
1. Remote diagnostics: Increased demand from drivers and vehicle owners for near-real-time vehicle assessments has led to a growth in the use of AR and AI to support remote diagnostics. Smart glasses enhanced with AR and AI technologies, or rugged tablets tethered with a rugged IP camera, let technicians use diagnostic software in real-time to conduct remote system health checks for vehicles quickly and efficiently.
The rugged device lets technicians automatically collect vehicle data and share it for remote analysis while
inspecting the vehicle. Combining these technologies with skill of human technicians means repairers can assess the vehicle more accurately to ensure its system operates within its specific design parameters.
It also streamlines diagnostic assessment, reduces time to repair, and avoids potential downtime. This can lead to lower costs and increased customer satisfaction.
2. Remote expert support: The need for more complex repairs has led to an increased demand for skilled technicians that are capable of properly servicing modern vehicles. As technology advances rapidly, it can be difficult for technicians to keep on the leading edge of transformation.
However, AR can be used to enhance technicians’ capabilities by providing them with digital twins that let them blend physical and virtual worlds for quick and efficient troubleshooting. With remote expert support and using a digital twin, technicians and mechanics can visualise a digital repair and make any necessary corrections or tweaks in the digital world before applying the repair to the physical vehicle or part.
3. Intelligent step-by-step troubleshooting:
AR can also be a valuable tool to help guide mechanics and technicians through a comprehensive diagnostics process to identify potential issues, eliminating guesswork and reducing inefficiencies caused by hard-to-solve root cause failures.
The biggest benefit of AR’s application in this capacity is the potential to leverage AI and machine learning (ML) to automatically review server data for other similar failures on record, and
continuously use the most up-to-date techniques, best practices, and methods to repair issues. This can help to significantly improve first-time fix ratios for repairers as well as save time.
4. Predictive maintenance:
AR lets automotive repair shops futureproof their services with predictive maintenance capabilities. Repairers can consolidate vehicle information, repair history, and diagnostic software data, and then use AR to effectively extrapolate a component’s lifecycle and provide trend-based failure predictions.
Taking this more proactive approach lets repairers empower their customers to optimise maintenance timings and avoid potential breakdowns, saving both time and money.
AR delivers essential benefits to repairers that will significantly expand the capabilities of repair shops, measurably boosting efficiencies and knowledge for technicians and mechanics that manage complex repairs. AR enhances automotive repairs by leveraging the spatial relationships of actual vehicle components and giving technicians a robust toolkit to improve repair efficacy, speed, and quality. Ultimately, this translates to a more efficient service for customers.
AR’s fusion with automotive repair is a powerful example of technology’s transformative capacity. By enhancing remote diagnostics, intelligent troubleshooting, predictive maintenance, and expert support, AR is not only revolutionising automotive repair but also paving the way for the industry’s digital future.
US shop owner Barry Dorn said he doesn’t see “who is winning” as the time involved with processing supplements grows.
“My concern is that we all lose that trust with that customer,” Dorn said.
He was speaking during a panel discussion on supplements during this spring’s Collision Industry Conference (CIC), “They see a $1,000 photo estimate turn into a $20,000 repair plan. The trust is lost. The customer knows somebody is lying to them. They just don’t know who.”
He said it’s also hard on frontline employees – both at shops and insurance companies – who must “go through this frustrating, laborious process,” and might question if it’s something they really want to continue to do – at a time when there’s already a labour shortage.
“It’s almost cruel and unusual punishment,” concurred Mike Giarrizzo, CEO of DCR Systems, which operates eight collision repair shops under partnerships with dealers. He said his company explains to customers what to expect.
“We tell them we’re going to provide their insurer with every bit of evidence and documentation necessary to fix the vehicle correctly,” he said. “We’re going to go out of our way to provide any information that their insurer needs and convey what needs to be done and why. But we can’t control the way they respond to that.”
Darrell Amberson of LaMettry’s Collision in Minnesota pointed to the cycle time ramifications of getting supplements approved. He said his company looked at 25 insurance jobs from each of four of the company’s locations.
“Virtually all of them got one supplement, the vast majority had two supplements, and some had three or more supplements,” Amberson said, noting that about three-quarters of the
100 jobs were non-DRP.
“The average response time, from the time we submitted the first supplement, to when we got the response from the insurer, was 4.2 days. When you looked at the DRP jobs, those were obviously much lower because we get an almost immediate response. Those were less than one day.”
But one of the larger insurers had an average response time of over six days and another over eight days.
“And I’m not talking about resolution. I’m just talking about a response,” Amberson said. “This is detrimental to all of us, including the insurer. My question is: How long is it going to take the insurers to figure this out so they can get response times down? Those of us who have been around a while recall a time when non-DRP response times were far less than that.”
Andrew Batenhorst of Pacific BMW Collision Center in Glendale, California, said his shop also measures insurer
response time.
“And I have a conversation with the local [claims] managers about how they’re doing,” Batenhorst said. “If we get measured all the time on [key performance indicators], I like to flip the table back on them, and a lot of them are really surprised by what we show them. Having that open conversation can make a difference. Not every carrier is going to be open to that. But one by one, if you start opening up a dialogue, and you realise there’s a way to talk about these things, you can make a difference. They have different metrics than we do, obviously, but we all need to figure this out together.”
Two of the panellists representing the insurance industry during the CIC discussion shared their perspectives on what could improve the supplement process. Consultant Roger Wright, a former vice president of claims at a large
insurer, sees a role for the automakers.
“We really need the OEs to help clarify some of the procedures they have,” Wright said. “They just don’t make sense to insurance companies, and that’s why they’re so resistant sometimes to paying for certain things.”
Wright said the pandemic may have sped up insurers’ move toward “no-touch” or “low-touch” claims processing, but that transition started at least a decade ago to reduce claims processing costs.
“That’s measurable to the guys in the Ivory Tower,” Wright said. “They can’t control severity. Severity is a by-product of the technology we have today and the complexity of the car. So, what’s important to the insurance executives, is controlling [claims processing] costs. That means finding a way to handle claims faster – not necessarily better, but faster. Unfortunately, it’s caused this [supplement] dilemma we have that’s gotten worse.”
Wright said while many shops are doing better at blueprinting and documentation, much of the industry still isn’t, also contributing to supplement processing issues. Phil Langley, vice president of client services for SCA Claim Services, agreed.
“I can guarantee you that already today – it’s what, about 11 o’clock –we’ve probably already had 100 shop
visits where someone from our company shows up and no one is there to even show us where the vehicle is,” Langley said. “If we could work on that, that would be a good first step.”
He said after working with hundreds of insurance companies and thousands of shops, each with their own processes, some industry standardisation would help.
“We’re caught in the middle most times on the supplement process. We don’t get paid in general to write supplements. When we have to come back, that’s a cost. It’s factored into our cost of doing business, but when there’s no documentation, or if we can’t find the vehicle or there’s nobody there to walk through the vehicle with us, we almost have to start over.”
Aaron Schulenburg of the Society of Collision Repair Specialists agreed that shops that aren’t providing adequate photos, OEM procedures and other documentation to support the supplements they submit need to start doing that.
“But a big part of the problem is that if the repair industry does a better job of meeting those expectations, there should be a change in outcome,” Schulenburg said. “I think where the frustration rises is there are so many
shops who have prioritised doing exactly that, and are doing it very well, and instead face almost a more difficult challenge” in getting supplements approved.
Shop owner Dorn agreed that shops should provide good documentation supporting the supplements they submit.
“But I think that needs to be a twoway street when there’s a denial,” Dorn suggested. “If we have to fully document why we are doing something, I think the other industry stakeholders need to document why they’re not [paying for] it.”
Dorn said he sees the industry at a turning-point in terms of supplements.
“We can’t continue to go down this path,” he said.
“Fundamental change has to happen. We have to get away from the archaic ways that we’ve been doing things for 30 years. Everyone is frustrated.
“No one is winning. No one is happy about this. So, let’s agree we have to change the process.”
John Yoswick is a freelance writer based in the US who has been writing about the automotive industry since 1988. He is also the editor of the weekly CRASH Network (www.CrashNetwork. com) and can be contacted by email at john@CrashNetwork.com.
In the fast-paced world of collision repair, efficiency, safety, and adaptability are the pillars upon which success is built. With space constraints and fatigue being common challenges faced by repair professionals, the need for an innovative solution has never been greater. Enter the ERGO LIFT 1000 ROLL – a game-changing vehicle lift that’s set to transform the way collision repair experts operate and optimise the limited workspace.
The ERGO LIFT 1000 ROLL is a versatile powerhouse, capable of effortlessly lifting and moving a substantial 2.5 T vehicle, all thanks to its advanced compressed air operation. This cutting-edge technology ensures smooth and precise manoeuvres, allowing technicians to focus solely on the repair process, without the burden of
manual lifting.
Its four support arms are engineered to automatically lock in place, providing a secure grip on the vehicle during the lifting process. Furthermore, these support arms are fully adjustable, catering to various chassis types with ease.
• In its minimum position, the lift sits 10 cm above the ground, saving valuable space within the already limited confines of the garage
• With a maximum lifting height of 95 cm, repair professionals can work standing up, reducing fatigue, and promoting a healthier working environment.
• Complies with the stringent EN 1493 standard, which specifically
relates to vehicle lifts, ensuring that operations are conducted securely and efficiently
• Equipped with four optional wheels, it is mobile and highly manoeuvrable Technicians can effortlessly position the lift wherever required, minimising downtime and enhancing workflow within the garage.
• The ERGO LIFT 1000 ROLL boasts an impressive load capacity of 2.5 T and has undergone rigorous factory testing up to 3.8 T. Combining efficiency, adaptability, and safety in one compact package, the ERGO LIFT 1000 ROLL vehicle lift has set a new standard in the industry.
WITH
and tyre makers unique opportunities to enhance rubber performance, simplify manufacturing processes and promote a healthier environment, PPG Agilon performance silica is a breakthrough technology.
Now, new PPG research has demonstrated nearly 50 per cent energy savings for tyre makers, along with the ability to cut manufacturing time by a third, compared with conventional technology.
Unlike traditional reinforcing fillers, PPG Agilon silica is created by precipitating silica and silane together and delivering them as a single, finished compounding solution. As a result, tyre makers can eliminate the entire manufacturing step required in
conventional technology in which highdensity silica undergoes a reaction with silane.
Other benefits include increased mixer fill factor, higher silica loadings, reduced mixer temperature, and lower water consumption. End users also receive significant benefits when PPG Agilon silica is used in tyre treads, in the form of improved fuel efficiency and traction and extended treadwear.
It’s a win/win for efficiency and sustainability, according to Anurag Raj, PPG customer sustainability business partner, Specialty Coatings and Materials.
“PPG Agilon silica products are engineered to extend the tyre industry’s ‘magic triangle’ including lowering rolling resistance for improved fuel efficiency, increasing traction for
In the ever-evol-paced world of collision repair and automotive protection, innovation and performance are key factors that can make or break a product. When it comes to surface coatings, professionals, and enthusiasts demand nothing less than the best. That’s where Le’Mix 2K Protective Texture Coating shines, delivering unmatched protection and durability.
1. High gloss – high solids – black or tintable
Le’Mix 2K boasts a captivating high gloss finish that enhances the visual appeal of any surface it graces. The high solids content ensures superior coverage and protection, leaving nothing to chance when it comes to safeguarding valuable assets.
2. Lightning-fast drying
Time is of the essence in the collision repair industry, and Le’MIX 2K understands the importance of efficiency. With its rapid-drying formula, this coating accelerates the repair
process, allowing professionals to deliver top-notch results in record time. Whether air-dried or low-backed, Le’Mix 2K ensures a swift turnaround without compromising quality.
3. Excellent filling properties with excellent adhesion
Le’MIX 2K’s impressive filling properties make it a reliable choice for repairing damaged surfaces. It seamlessly integrates with the substrate, leaving no room for imperfections. Its exceptional adhesion guarantees a strong and enduring bond, ensuring long-lasting protection.
4. Defying the elements – shield against damage
The rigours of daily life can take a toll on vehicles and other surfaces. Le’Mix 2K steps up to the challenge, resisting chemicals, stains, corrosion, impacts, scratches, chips, and even the harmful effects of UV rays. With Le’Mix 2K, surfaces remain unblemished and resilient, maintaining their pristine appearance for years to come.
improved safety and handling, and durable construction that extends the useful life of tyres,” Raj said.
The new research shows that PPG Agilon silica can play an even more important role in the transition to sustainable mobility and contribution towards multiple UN Sustainable Development Goals.”
For more information, visit www.ppgsilica.com.
5. Re-coating abilities
Le’Mix 2K’s brilliance doesn’t end with its initial application. It can be effortlessly re-coated with solvents, waterborne basecoats, and 2K topcoats, ensuring compatibility with various automotive finishing systems. This adaptability not only streamlines the repair process but also showcases the product’s commitment to user convenience.
For collision repair professionals and automotive enthusiasts seeking a true game-changer in the realm of surface coatings, Le’Mix 2K Protective Texture Coating is the ultimate choice. Its performance, durability, and versatility make it an indispensable asset in any automotive arsenal.
To learn more about this product and explore its diverse range of applications, visit the official website at www. lemix.com.au.
Le’Mix
Axalta Refinish has launched its global training academy, with tailored face-to-face, live virtual, and e-learning options to enhance skills for automotive refinishing experts.
The Axalta Academy, a state-of-theart global training platform for refinish professionals, is launching globally in 15 languages to empower refinishers to maintain and improve their specialised competencies with top-class training
The platform adjusts to the way in which they work and is backed by Axalta’s unrivalled, industry-leading expertise.
Paul Polverino, Axalta ANZ’s national training manager says, “The Axalta Academy has been designed with our customers in mind. It puts them in a different class. We’re sharing knowledge about cutting-edge, digital tools and application techniques, as well as demonstrating how we’re championing innovation and continuous training.
“With three distinct ways in which to consume this best practice, the Axalta Academy is flexible, convenient, and effective, which is exactly what busy, ambitious and aspiring body shops need. We easily align information to a body shop’s training requirements. The Axalta Academy is also a perfect resource for our upcoming apprentices.”
The Axalta Academy resources have been thoughtfully packaged, depending on the user: apprentice, painter, body shop manager or body shop owner. Each has its own content, tailored specifically for each one’s individual goals – whether that’s kick-starting an automotive refinishing career with the basics for apprentices; keeping up with the latest products and techniques for painters; supporting processes and maximising earning potential for body shop managers; or boosting productivity and maintaining the competitive edge for body shop owners.
For maximum flexibility, the Axalta
Academy has different training streams on its online platform through which best practice knowledge can be delivered. Once registered, users simply create their profile and then have a choice of three types of training based on their requirements: face-to-face, live virtual or e-learning.
Face-to-face: Highly experienced Axalta instructors lead all face-to-face training courses, which are held at world-class Axalta training facilities across the world. These hands-on sessions provide both theoretical and practical aspects of every step of the refinishing process. Users have access to country-specific calendars where they can apply for different courses. Live virtual training: These live-stream technical training events come direct from the Axalta training facilities around the world. They deliver customised distance learning that saves the time and cost of travel as well as time out of the body shop. A calendar of country-specific live events shows what’s availablerefinishers simply click a link and register. Participants also have the opportunity to ask questions and
interact with the trainer.
E-learning: The e-learning material in the Axalta Academy includes a library of interactive instructional content on topics from digital colour matching and plastic repair to special finishes and basecoat systems. This library will be continuously added to and expanded. Polverino concludes, “The Axalta Academy is a one-stop-shop for all refinish training needs, whether that is improving skills or increasing productivity. It will ensure you get the most value out of the paint products you use.”
Axalta Academy is fully accessible and optimised for Android and iOS and can be accessed via a PC, laptop, tablet, or smartphone. The platform is available in English, as well as a further 14 languages, which will be launched throughout Q2 and Q3 2023 – Chinese, Dutch, French, German, Indonesian, Italian, Japanese, Korean, Polish, Portuguese, Spanish and Swedish, Thai and Vietnamese.
For more information about Axalta Academy and to register, visit axalta. au/academy or contact Axalta Coating Systems on 1800 292 582 or info-ANZ@axalta.com
$21,999 SALE +GST
Looking for a space saving repair bench with all the features of a large bench? With the Jollift 1330 Fast Repair Bench you can now equip each work bay with a quality Italian manufactured car bench. The flexibility of the modular design means that multiple benches can share one pull post, one set of clamps and one set of wheel stands, which makes it totally affordable for each work bay to have its own repair bench.
• Fast repair bench
• 6 tonne pull post
• 100mm lowered height
• 1300mm lift height
• 3000kg lift capacity
• Estimating, assembly and disassembly