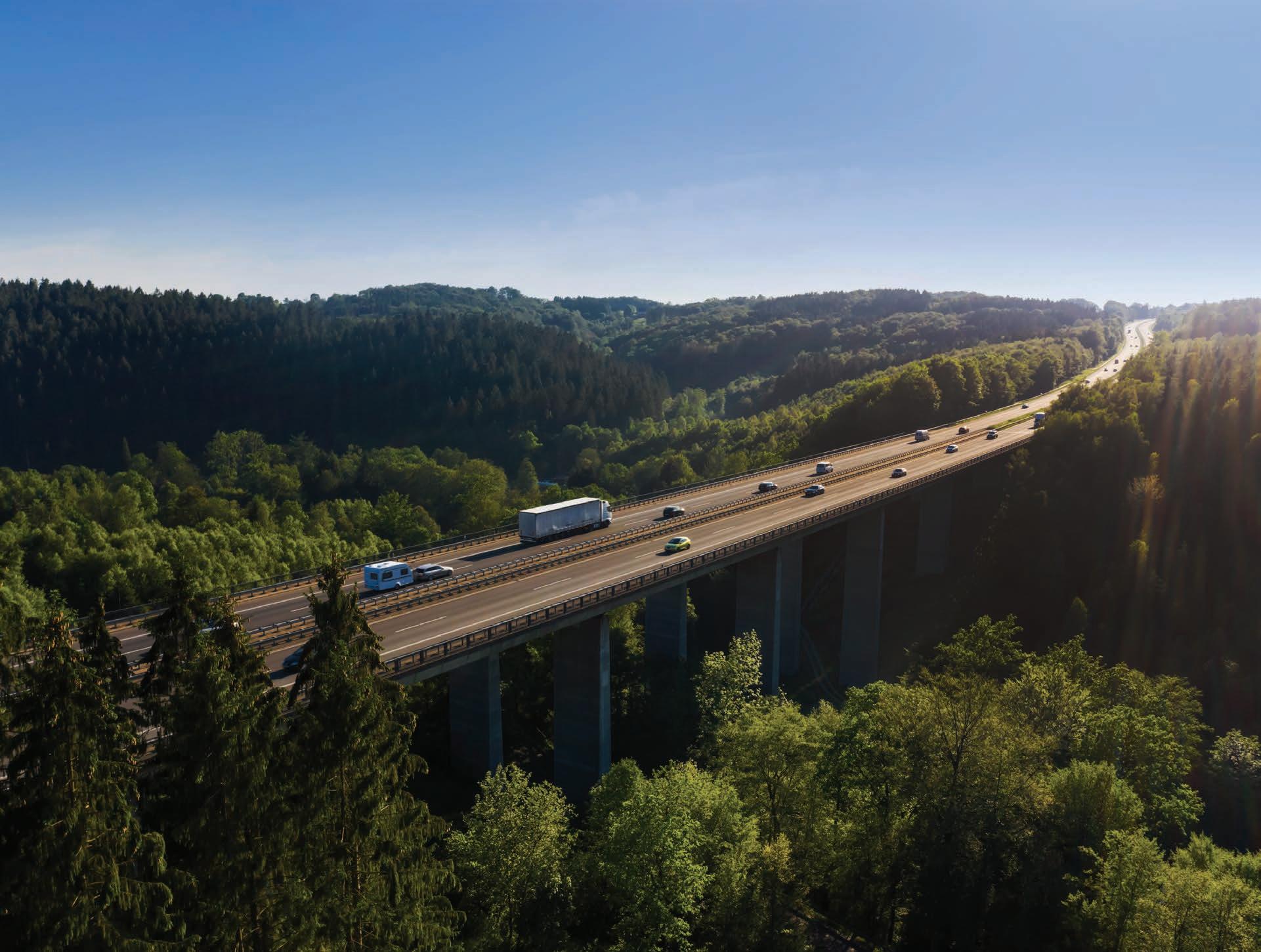
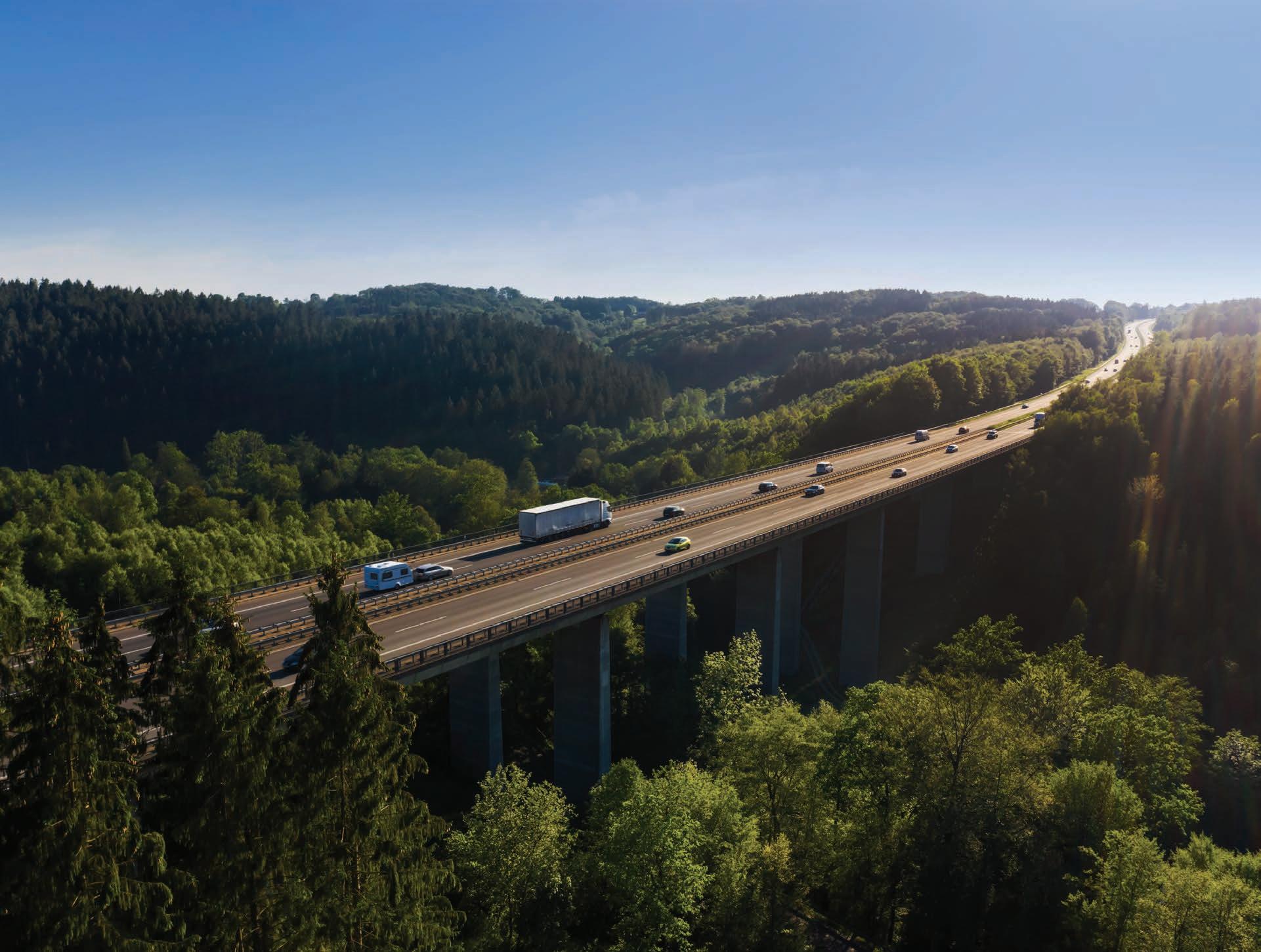
Toll Tomago Balance of Power
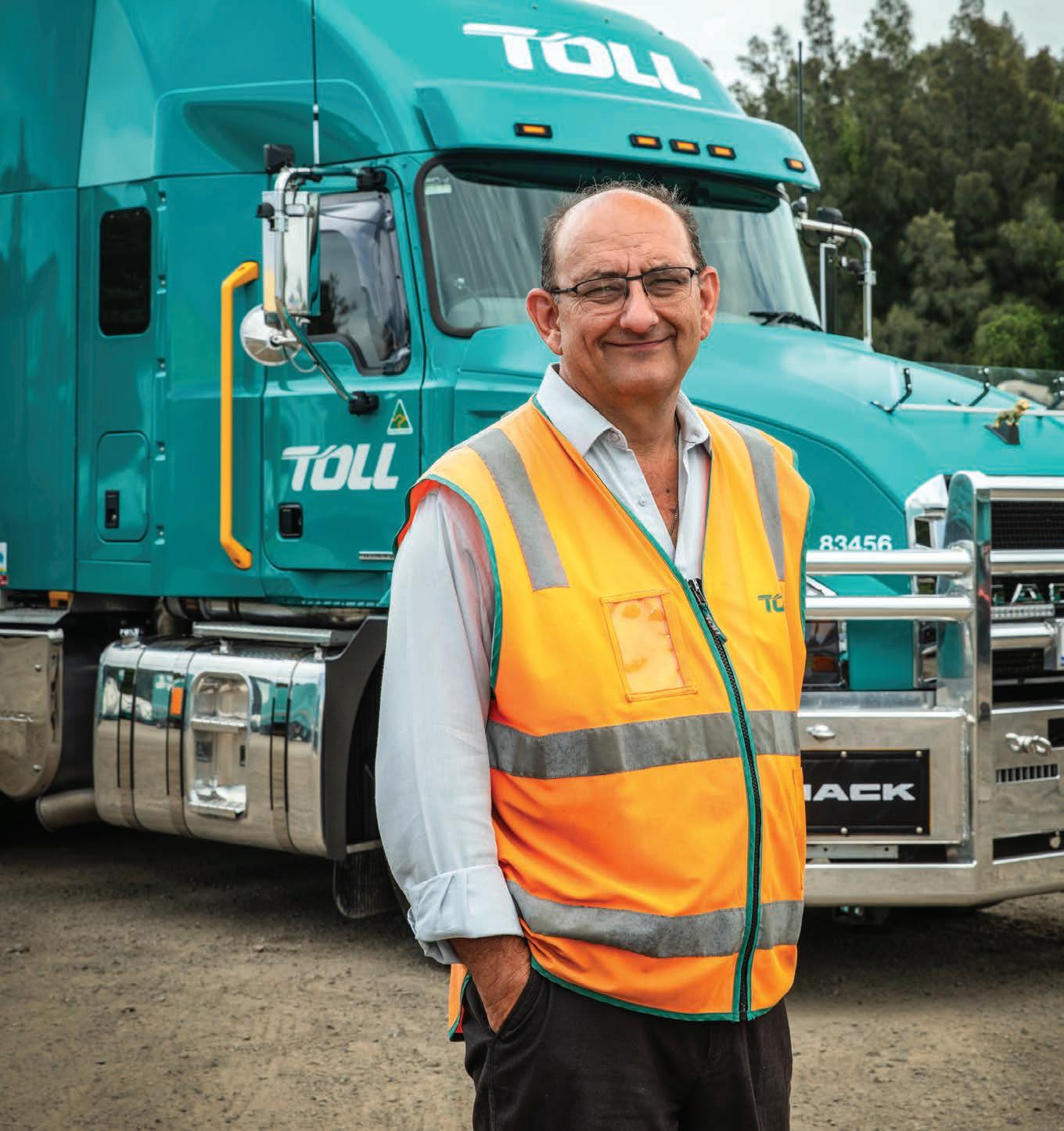
INDUSTRY
Carrier: Blenners Transport
Trades: Sydney Side Plumbing
Spotlight: Scully RSV
Personality Profile: Damian Smethurst
INNOVATION
Fleet: Nubco
Feature: Eureka Concrete
Technology: FleetSeer
Test Drive: Volvo FH16 780hp


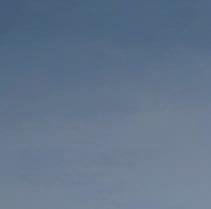
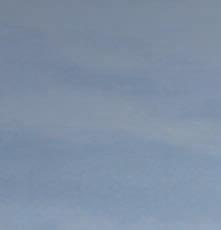

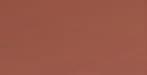
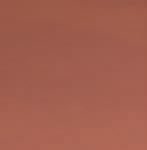
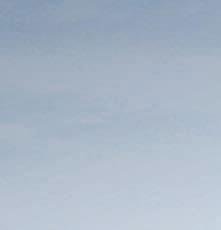
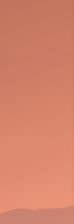



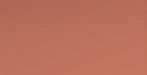
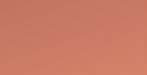
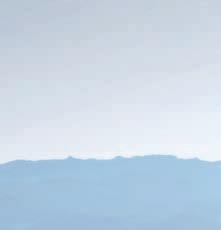
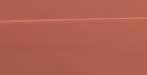


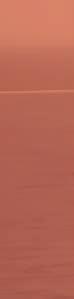

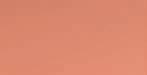

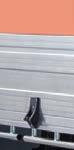

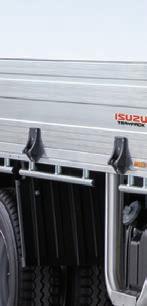
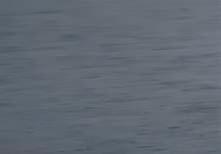

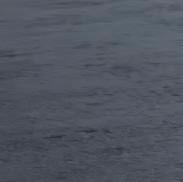
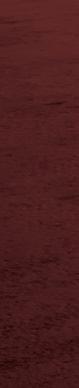

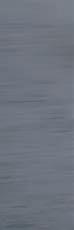
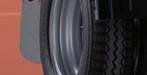

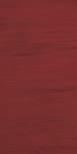



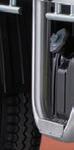
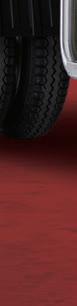



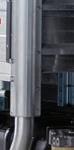


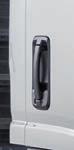
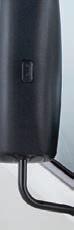

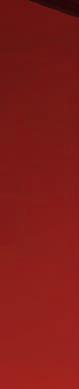
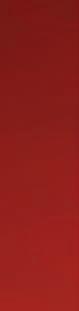

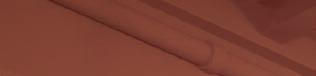



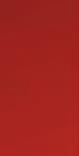

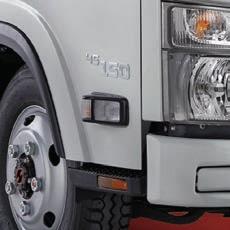

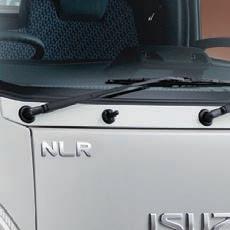
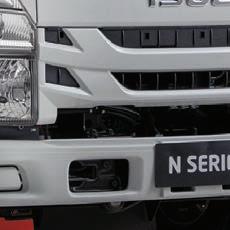

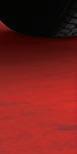
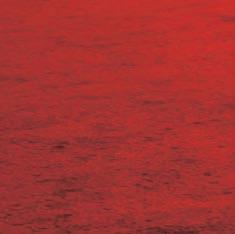

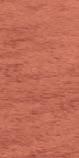



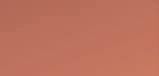
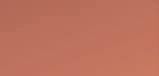
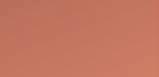
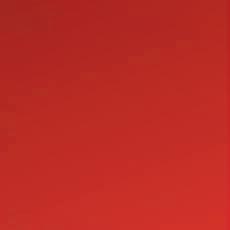


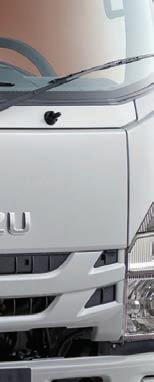


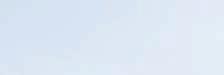
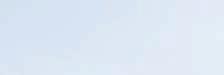


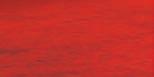
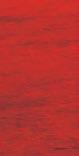


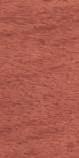


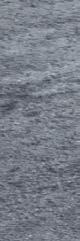


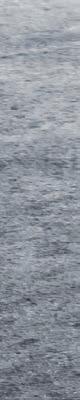
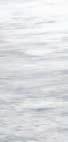

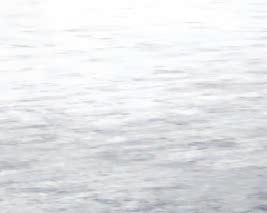
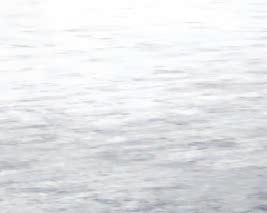
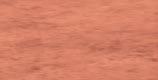

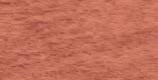
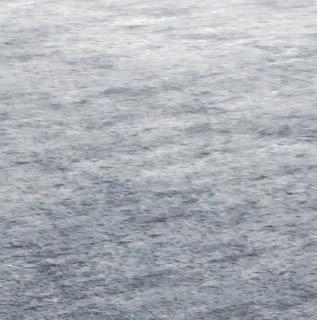
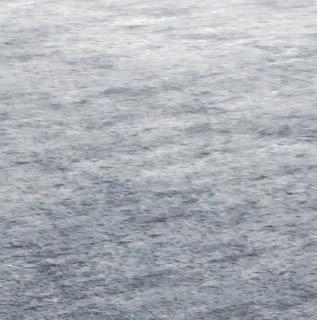
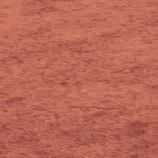



MEET THE TEAM
Australia’s leading truck magazine, Prime Mover, continues to invest more in its products and showcases a deep pool of editorial talent with a unique mix of experience and knowledge.

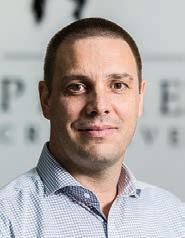
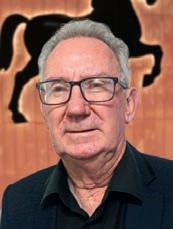
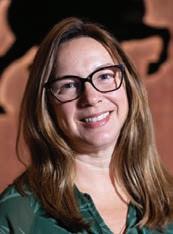
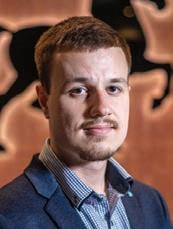
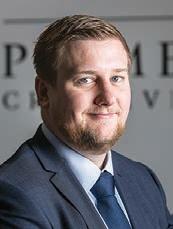
Christine Clancy | COO
With more than two decades of experience as a media professional, Christine has worked in newsrooms across Canada, Vietnam and Australia. She joined the Prime Creative Media team 12 years ago, and today oversees more than 43 titles, including a dozen print and digital transportation titles. She continues to lead a team that focuses on continuous improvement to deliver quality insights that helps the commercial road transport industry grow.
William Craske | Editor
Over the past two decades William has published widely on transport, logistics, politics, agriculture, cinema, music and sports He has held senior positions in marketing and publicity for multinational businesses in the entertainment industry and is the author of two plays and a book on Australian lm history. Like many based in Melbourne he is in a prolonged transition of either returning or leaving.
Peter Shields | Senior Feature Writer
A seasoned transport industry professional, Peter has spent more than a decade in the media industry. Starting out as a heavy vehicle mechanic, he managed a fuel tanker eet and held a range of senior marketing and management positions in the oil and chemicals industry before becoming a nationally acclaimed transport journalist.
Louise Surette | Journalist
Louise joins Prime Mover after nearly 25 years as a writer. Starting her career as a reporter at the Toronto Star, she has spent much of the last 15 years as a design writer and editor. In 2020, she was shortlisted on the Richell Emerging Writers Prize list. Originally from Nova Scotia, she lives in Melbourne with her two children.
Peter White | Journalist
Peter has completed a Bachelor of Media and Communication (Media Industries) degree at La Trobe University, and he brings a fresh perspective to Prime Mover. He gained valuable experience at Upstart, La Trobe’s newsroom, work that has been supplemented by direct industry experience in a Council placement. Peter has a strong interest in commercial road transport, and in contributing to Prime Mover’s efforts in growing the industry.
Ashley Blachford | Business Development Manager
Handling placements for Prime Mover magazine, Ashley has a unique perspective on the world of truck building both domestically and internationally. Focused on delivering the best results for advertisers, Ashley works closely with the editorial team to ensure the best integration of brand messaging across both print and digital platforms.

CEO John Murphy john.murphy@primecreative.com.au
Editor William Craske william.craske@primecreative.com.au
Managing Editor, Luke Applebee Transport Group luke.applebee@primecreative.com.au
Senior Feature Peter Shields Writer peter.shields@primecreative.com.au
Business Ashley Blachford
Development ashley.blachford@primecreative.com.au Manager 0425 699 819
Art Director Blake Storey blake.storey@primecreative.com.au
Design Kerry Pert , Louis Romero, Tom Anderson
Journalists Peter White peter.white@primecreative.com.au
Louise Surette louise.surette@primecreative.com.au
Design Production Michelle Weston Manager michelle.weston@primecreative.com.au
Client Success Salma Kennedy Manager salma.kennedy@primecreative.com.au
Head Of ce 379 Docklands Drive, Docklands VIC 3008 enquiries@primecreative.com.au
Subscriptions
03 9690
All
Copyright
PRIME MOVER magazine is owned and published by Prime Creative Media.
All material in PRIME MOVER magazine is copyright and no part may be reproduced or copied in any form or by any means (graphic, electronic or mechanical including information and retrieval systems) without written permission of the publisher.
The Editor welcomes contributions but reserves the right to accept or reject any material.
While every effort has been made to ensure the accuracy of information
Prime Creative Media will not accept responsibility for errors or omissions or for any consequences arising from reliance on information published.
The opinions expressed in PRIME MOVER magazine are not necessarily the opinions of, or endorsed by the publisher unless otherwise stated.

www.primemovermag.com.au



30
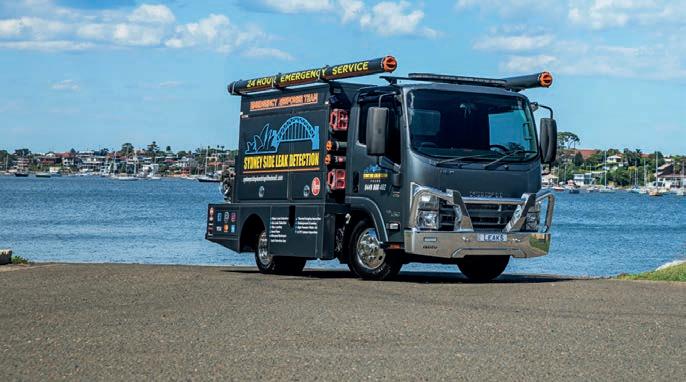
46
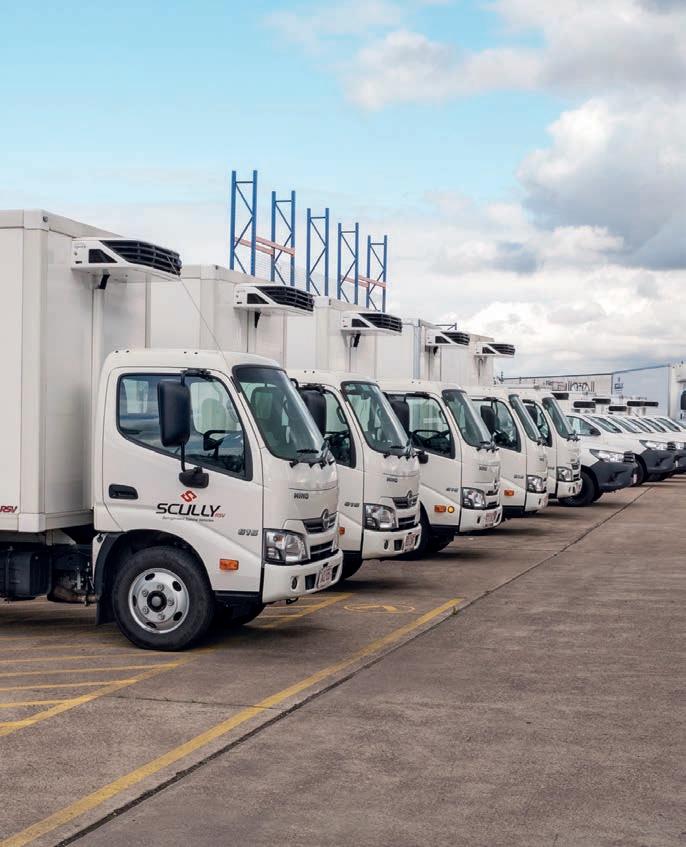
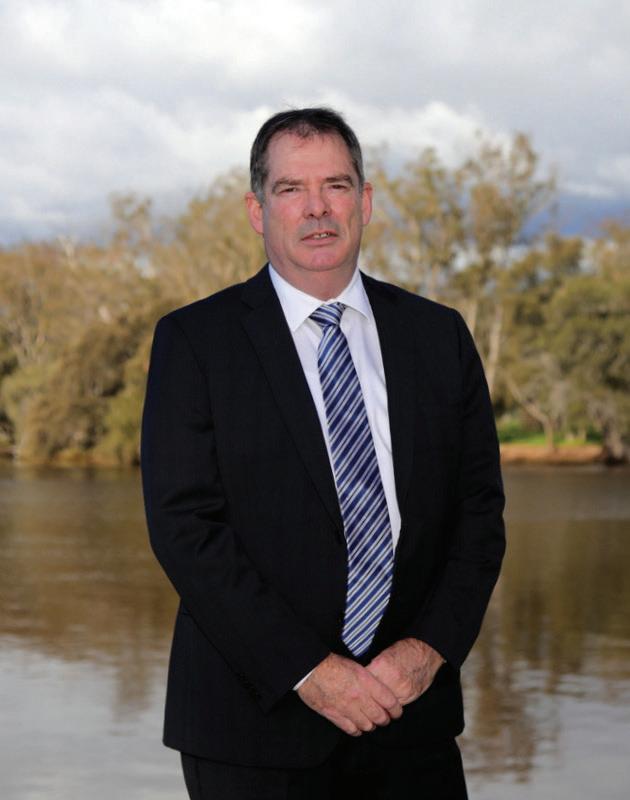
64

COVER STORY
“Toll has an RFP in the market that involves significant expenditure across the next two financial years. That will involve a strict procurement process to reward the work accordingly.”

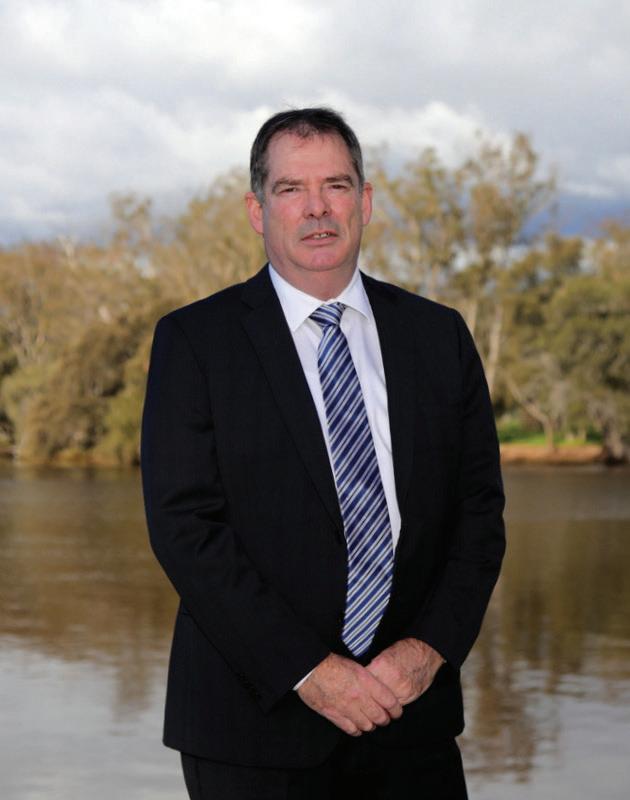
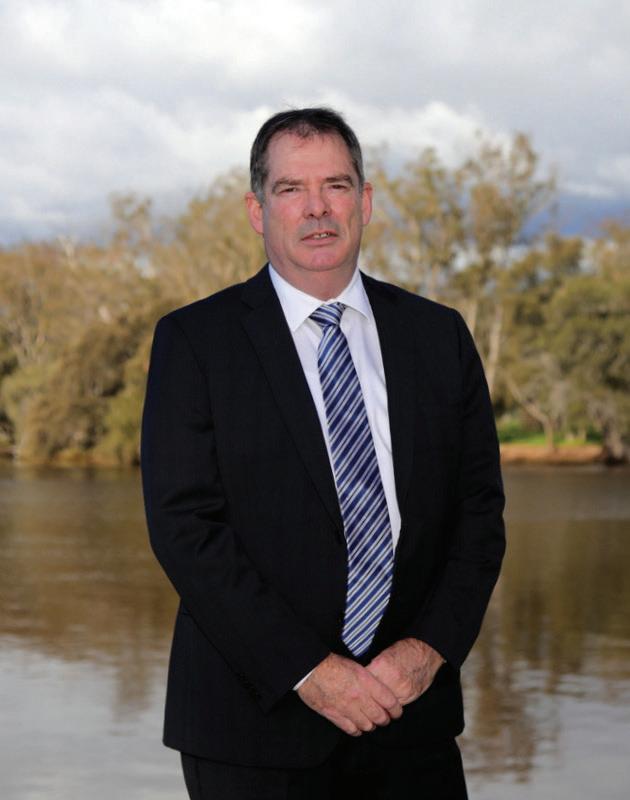

Prime Feature STORIES
FLEET FOCUS
24 Balance of Power
A specialty unit within Toll Resources at Tomago is set to introduce a new fleet of Mack Anthems as part of its dangerous goods transport operations.
30 Turning Point
North Queensland cold carrier, Blenners Transport, has unveiled a $17 million new transport facility in Cairns.
34 Steel of Approval
For more than 40 years Nubco has been a reliable supplier of steel and industrial products in Tasmania.
TRUCK & TECH
38 The Right Mix
Third generation, family-owned concrete company, Eureka Concrete, puts serious hours on its trucks in Ballarat. It chooses TRP as its local parts retailer and Cummins Meritor as its preferred supplier of drive axles and differentials.
42 Margin Call
Dead running is often considered a necessary evil for many fleets unable to schedule backloads for their assets. FleetSeer
STEEL OF APPROVAL 34
is a new tool that enables greater visibility across truck movements to improve profitability on problem routes so that the margins, as McColl’s discovered, can be better balanced.
TEST DRIVE
58 Breaking the ICE
Volvo Trucks has unveiled in Sweden an improved line-up, showcasing a range of aerodynamic and safety updates to the FH and FM as well as a new 17-litre engine and Prime Mover was there to drive it.

One need not work in media to have marketing cross their path. In a consumer society it’s a fact of life. Every. Single. Day. Pick up a breakfast cereal. Sit at a train platform. Take a shower. Brand names stare back at you. Your phone, just like Amazon, collects your data so that it can bring messages from marketing departments tailored to your time of day. It’s nearly dinner time. Hungry? You will be. Everything that can be seen and heard can be packaged. Turn on the radio for a progress report from your favourite sport. Commercial demands of broadcasting have turned a score update into a mantra of advertising slogans. In Texas they might call it all hat, no cattle.
Bait and switch, whereby the product being promoted is not the one nally sold, has long had a negative association as a practice in advertising. Sometimes this is not by choice. When demand outstrips supply, however, we invariably end up in unfamiliar places. Unfamiliar places are places of interest. Tourism is based on this principle. But in the unfamiliar place we tend to get lost. It only took two weeks for the Smashed
Bait and Switch
Jack, a new burger at American fast food chain Jack in the Box to disappear. It was eight years in the making.
“We unfortunately failed on this soft launch,” said a widely quoted Jack in the Box spokesperson.
But did they? The amount of additional traf c it helped drive into stores would likely have also been measured. It’s doubtful it failed at this metric.
Sometimes products, to make them more marketable when they are considered dead on arrival, are sold as something else.
The greatest movie ever made about a concrete pour is one of these. Sold as a psychological thriller, the 2003 movie starring Tom Hardy as the titular character, Locke, essentially plays like a one man solo. The entire movie consists of a man driving a BMX X5 at night conducting several otherwise intense phone conversations ahead of a 315 metric tonne concrete pour for a 55 storey building of which he is chie y responsible. The logistics alone make for palpable urgency.
A genre, at least to my knowledge, for this type of experience doesn’t yet exist. That’s not something that should be held against it. But in the marketplace of products, it certainly limits its reach. Supposing such a category
existed already, Locke, as matchless as it is, occupies a lonely position. For a marketer that’s not a good place to be. The founders of Michelin tyres certainly found a way around this conundrum. You don’t have to appreciate ne dining to have come across the term Michelin star. Restaurants can live or die on having their Michelin star taken away. Brothers Édouard and André Michelin, in 1900 published a guide for French motorists to encourage greater travel by car in France. Nearly 35,000 copies of this rst, free edition of the guide were distributed. It provided information to motorists, such as maps, tyre repair and replacement instructions, car mechanics listings, hotels, and petrol stations throughout France. As a cross-marketing exercise it remains a brilliant promotion which has taken on a whole new life of its own. The case in point is few people today associate the one product with the other.
It’s not yet clear though whether the Michelin Man is a cautionary tale of what happens when indulging to excess at these ne dining establishments.
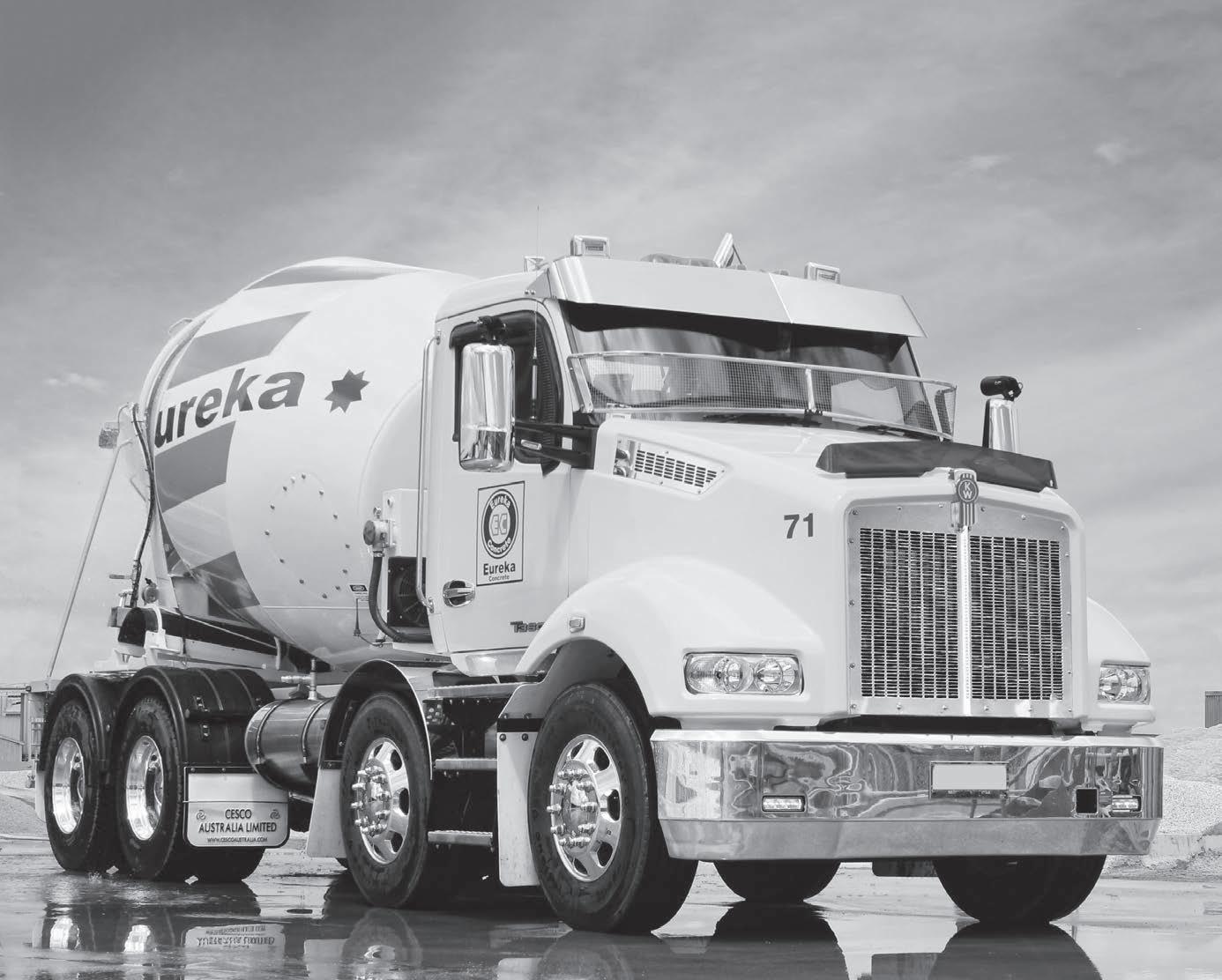
READY FOR WORK
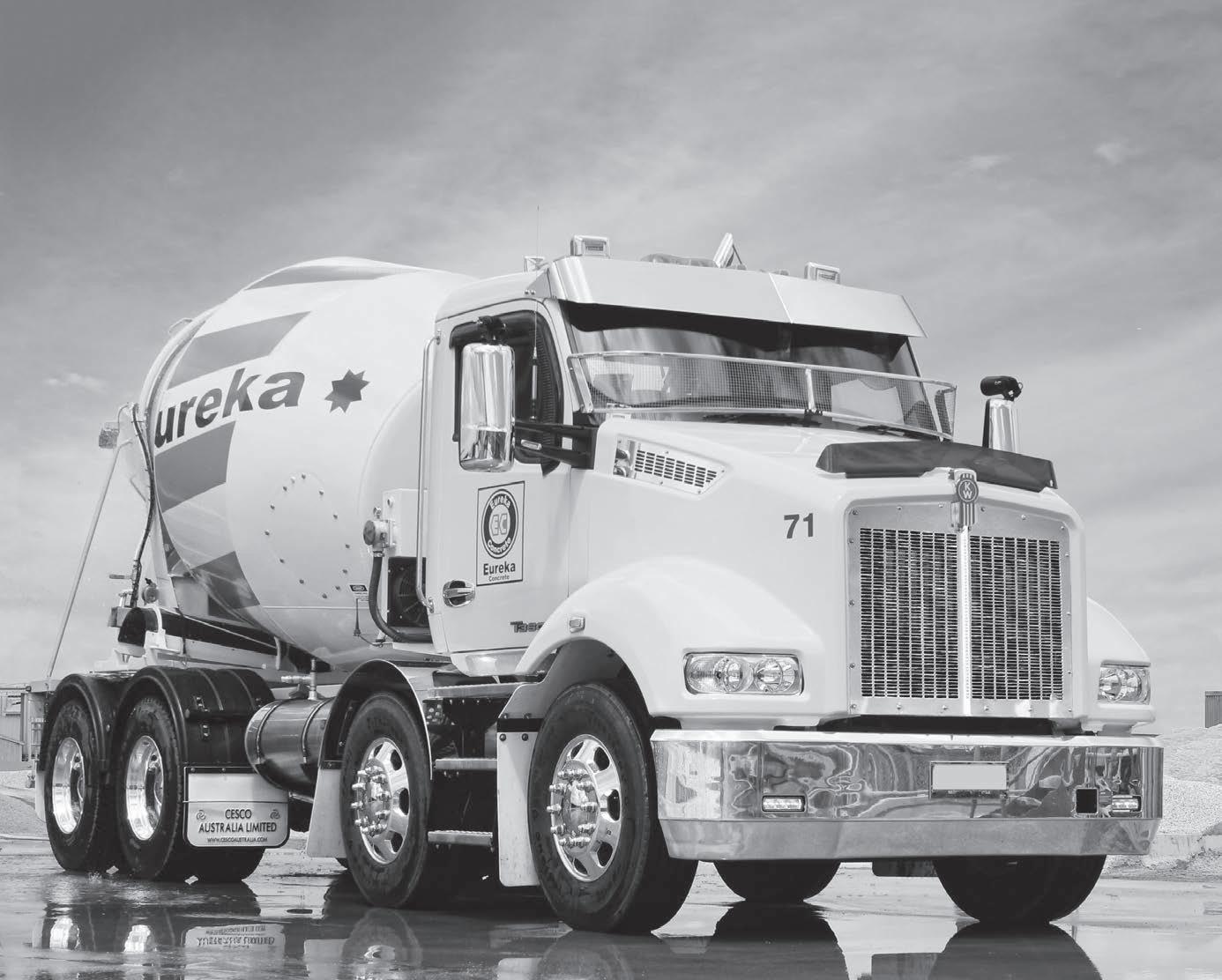
MERITOR MT-14X TANDEM AXLES
• Large inter-axle differential with high torque (2,780 Nm) capability for durability and longer life.
• Oil pump lubricates the inter-axle differential to prevent damage during
loss of traction.
• Driver controlled differential lock maximises traction in and around construction sites.
• Built in Australia and proven to perform in heavy-duty vocational applications.
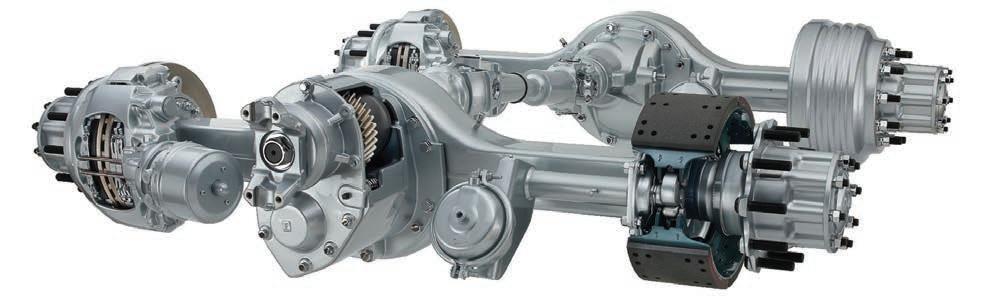
> Toll introduces new A-double-rated Kenworths
Two new Kenworth T610 SARs have been delivered to Toll in South Australia. Operating under Performance-Based Standards (PBS), the new Kenworths have been assigned A-double duties for bulk fuel cartage.
One of the trucks will deliver jet fuel from a fuel terminal to Adelaide airport. The other is transporting fuel across the broader network in metropolitan Adelaide and South Australia.
The jet fuel tanker combination is expected to travel approximately 1,300 kilometres each week, delivering around 3,000,000 litres.
The second vehicle, meanwhile, covers anywhere up to 4,200kms each week.
These new vehicles will replace ageing Kenworth trucks and mark the first two Euro VI engine vehicles to be used in its South Australia fuels fleet.
The T610SARs have been chosen to ensure compliance with the requirements and maximise available payloads. Both are powered by a X15 Cummins engine rated at 525 horsepower and 97-tonne GCM.
All Toll standard safety features are fitted, including a driver fatigue and on-board telemetry system.
Deployment of the new Kenworth T610 SARs fits with Toll’s policy of investing in the latest available technology where possible.
The drivers are reportedly happy with
the comfort and handling. Kenworth’s reliability in performing the task and the service back up provided by the local dealership, CMV Trucks, made these the best choice according to Toll.
“The existing Kenworth fleet has operated reliably without any significant downtime issues,” said Shaun O’Flaherty, General Manager Global Fleet Management, Toll Group. Toll currently operates 15 Kenworth prime movers in the South Australia fuels fleet.
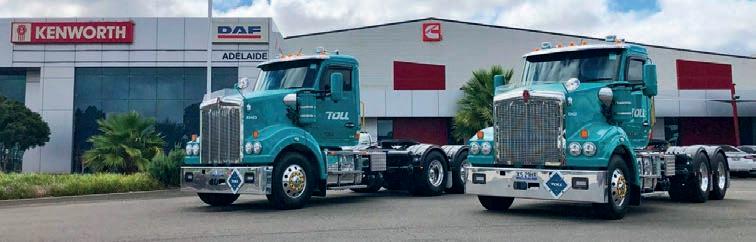
> NSW freight strategy gets independent advisory council
The NSW Government has announced policy reform program to address the key issues facing the freight industry in the state.
The program will deliver prioritised and practical policy reform focused on the key current and emerging challenges facing the NSW freight task. It will be led by Transport for NSW under the leadership of an Independent Advisory Panel of eminent experts all who have deep experience in the freight and logistics sector reporting to the Minister who will assist in the development of a new freight strategy for the State.
The panel will consist of Kerry Schott AO, Lucio Di Bartolomeo and Hermione Parsons. This policy reform will focus on the different parts of the supply chain, with ports, rail, road and intermodal facilities all considered as part of a coordinated supply chain to determine the right policy framework to optimise safety, sustainability and productivity.
NSW Transport Minister Jo Haylen said a more productive freight sector can deliver reduced costs for businesses and lower retail prices for ordinary people right across NSW.
“Our freight network is still too disjointed and inefficient with policy and infrastructure bottlenecks right across the supply chain,” said Haylen. Immediate priorities for the panel will include consideration of the determination of compensation to be paid by the Port of Newcastle for increasing container operations as part of NSW port policy. The panel will also review and consult with industry on the recommendations made by Ed Willett’s review of the port regulatory framework and the regulation of the movement of containers at Port Botany.
The program will identify short, medium and long-term actions for Government to support the ongoing improvement of freight transport across NSW.
The freight task in NSW is a complex and evolving with a need to respond
to advances in technology and a move toward net zero emissions, the ongoing development of major infrastructure, the changing ports landscape, national harmonisation policies and global trade fluctuations. Expectations are that the Freight Reform Program will deliver a comprehensive strategic reform agenda to optimise freight transport to benefit NSW communities.
There will be comprehensive stakeholder consultation undertaken as part of this program. It is intended that the first phase will follow release of a Discussion Paper and is expected to occur in the first quarter of this year.
“Safe, sustainable, and productive freight transport is critical to support the people, businesses and industries of NSW,” said Haylen.
“I am pleased to be able to announce the beginning of this significant reform agenda to inform government policy and provide an evidence-based action plan that will optimise the freight transport network in NSW.”
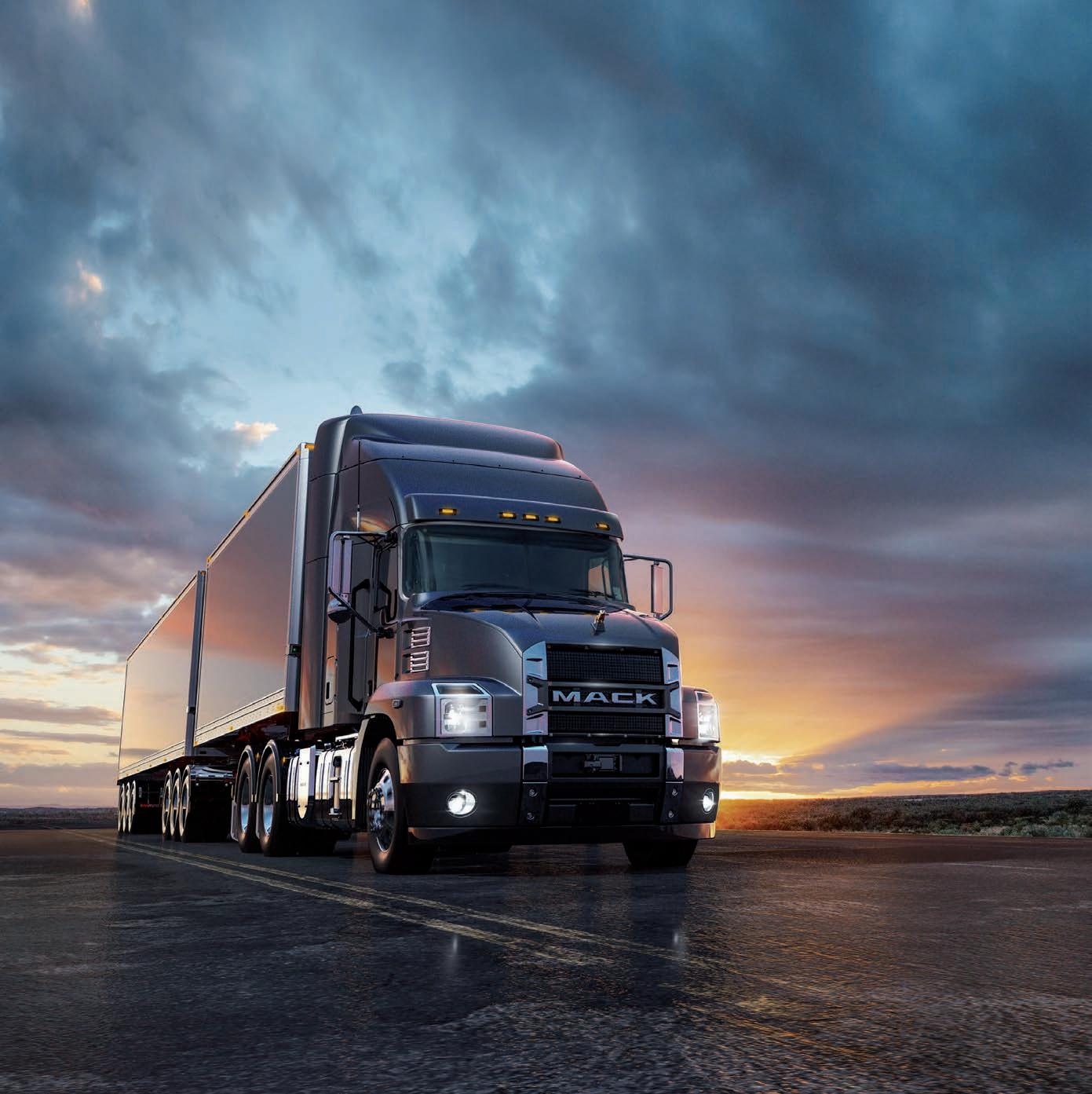
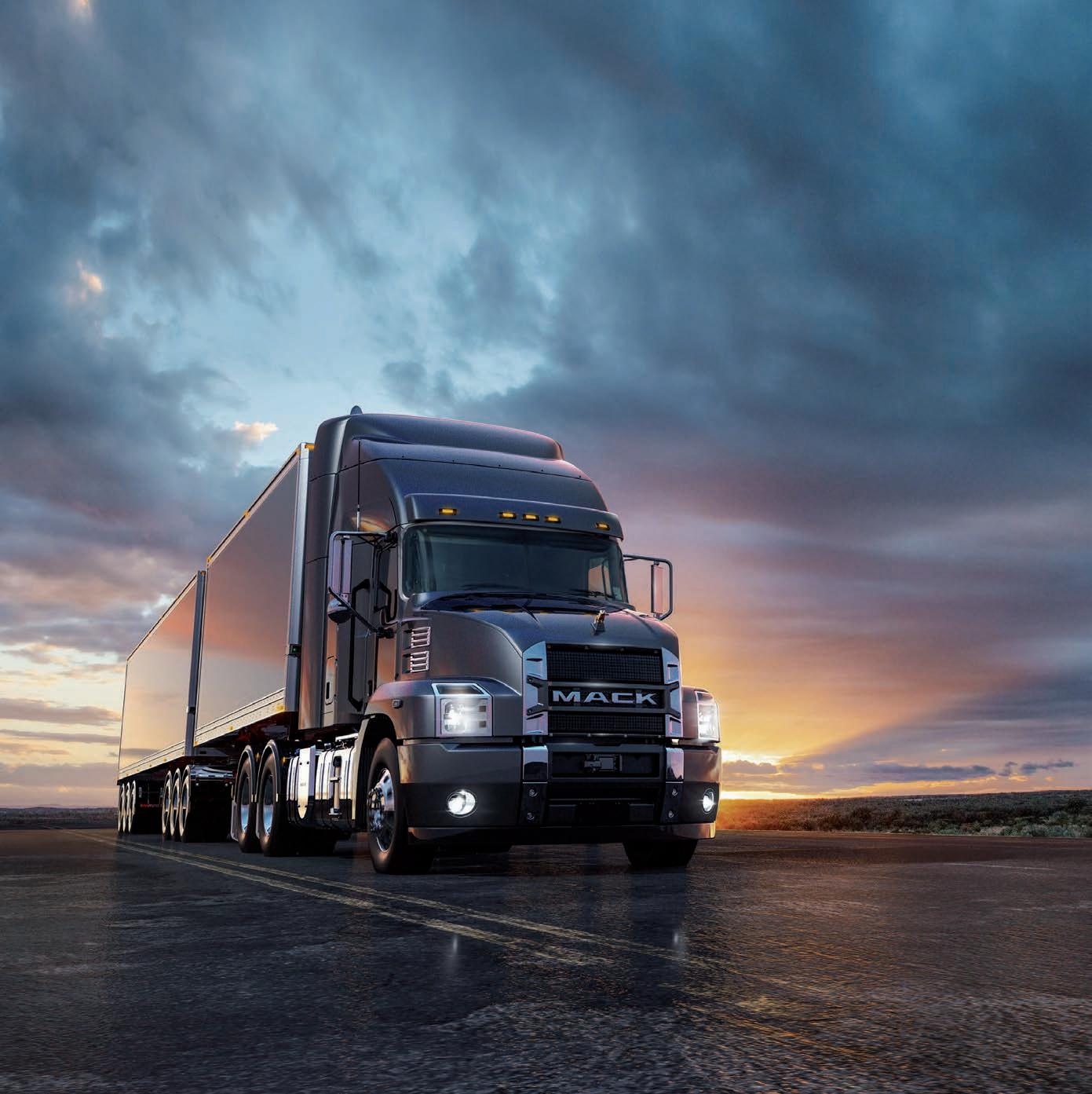
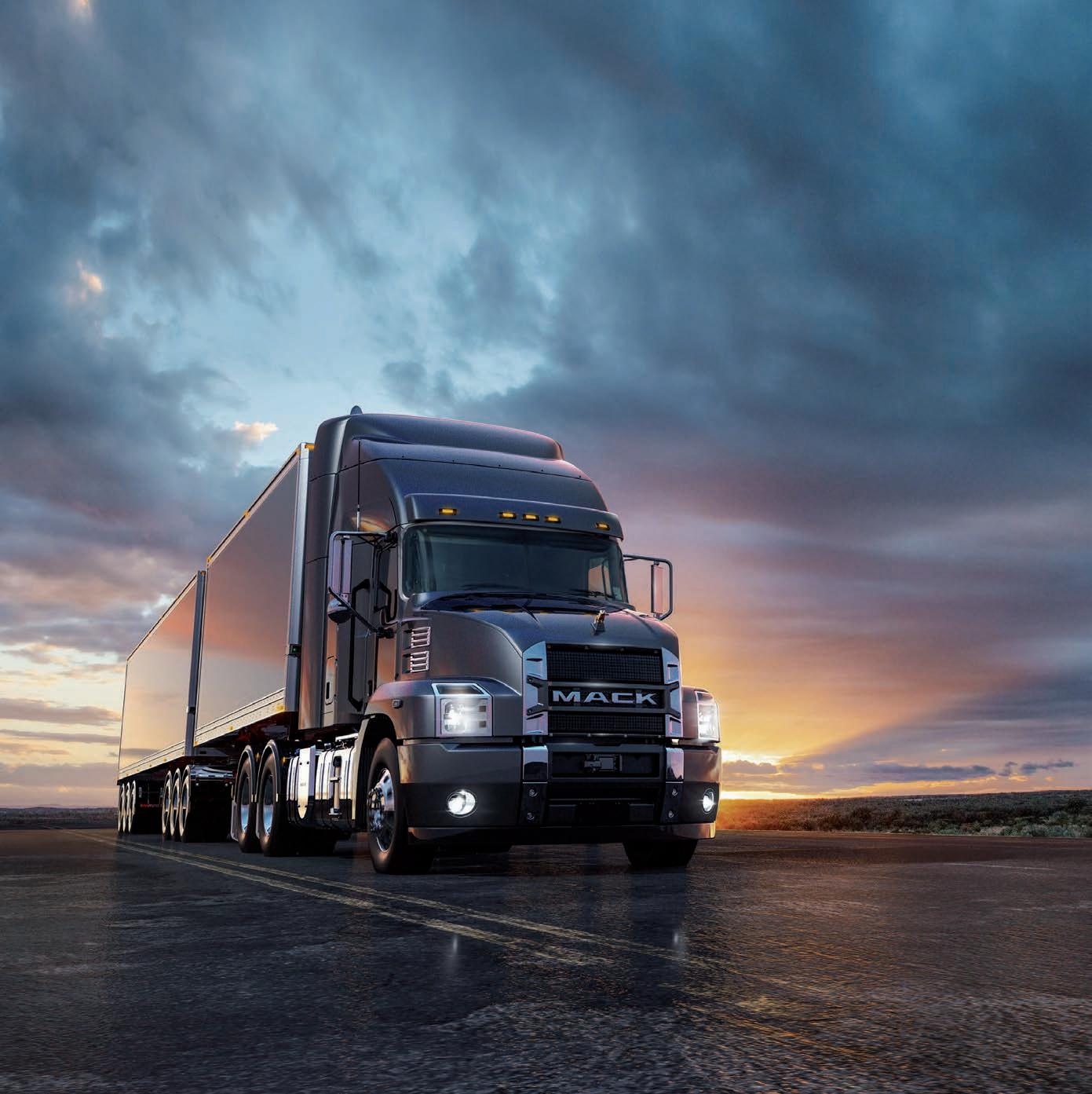
MAKE HISTORY WITH MACK
Mack started manufacturing in Australia back in 1963, and since then, we’ve gone from strength to strength. Along the way, Mack Anthem has been a big part of our success, thanks to its outstanding performance in tough line-haul assignments. Anthem delivers maximum uptime, improved fuel efficiency, sophisticated safety and unbeatable driveability, and its powerful Mack MP8 engine is specifically designed for B-Double work. Plus, the smart mDRIVE automated manual transmission means changing gears is far more efficient. Make your own history with Mack, and talk to your dealer today, or visit MackTrucks.com.au/Anthem
> Legend Logistics launches new business
Legend Logistics has launched Legend Mechanical Services. Initially established to solely look after the Legend Logistics business, the new service located in Laverton North, provides a tailored heavy vehicle service and maintenance schedule, and is aimed particularly at fleets and owner-operators with vehicle needs.
Routine servicing, as well as preventative maintenance repairs and assessments all fall under the business remit. The market difference, however, is that the new business can provide 24 our servicing to save the customer downtime.
Over the past two years Fleet Manager Anthony Gregson said both he and Legend Logistics Managing Director Troy Eiken had been inundated with enquiries from heavy vehicle operators and fleet managers for assistance. That was the prompt, according to Gregson, they needed to open the doors to wider industry.
“LMS was born with the sole goal of bringing back old school mechanical
mentality and combining a state-ofthe-art facility with the latest in Jaltest diagnostic tooling,” said Gregson. “Our facility also includes modular hoists and fully automated oil systems that provide the specific oil to meet environmental and OEM specifications, full engineering and fabrication services, road worthy and air conditioning repairs, break down service, induction compliance, among other services.”
There are benefits for fleet owners or single vehicle operators — LMS caters to both.
“With 24-hour servicing and repairs we can meet the truck’s maintenance needs while the driver is having his hard earned rest break ready to jump in the truck in the morning, meaning in most instances, a saving to the owner as the truck won’t have any down time,” said Gregson. Alongside Gregson there is a trainee apprentice and four qualified mechanics with over 100 years of combined industry experience. Gregson himself has amassed 20 years as a qualified
> Lowes announces annual driver award
For the third year in a row, Lowes Petroleum has acknowledged company driver commitment to road safety with an annual Professional Driver’s Award. With over 200 drivers transporting millions of litres of fuel a year across hundreds of thousands of kilometres of rural roads, the awards criteria included reviewing drive cam alerts, logbook and fatigue breaches and incidents like crossovers and speeding.
Drivers are nominated by their peers across the 500 plus staff with nominations tripling since their inception in 2021. As one of the judges, General Manager of Health, Safety, Security and Environment (HSSE) Bernie Morris said while all their drivers operated to best practises, the awards were an added incentive ensuring Lowes drivers were the best in the business.
“We assess the nature of the nominations around customer service,
the care drivers showed for their vehicles, the commitment to their depots and to the team they work with,” he said.
“The priority is always safety. In one instance of dash cam footage, you can see a motorcycle barely missing a fuel tanker head-on after breaking multiple road rules.”
Morris said it was crazy to consider what a driver goes through in their daily experience.
“We have even had footage where it is obvious the person has pretty much fallen asleep before waking in the nick of time,” he said. “The vision is testament to our drivers’ abilities to not only read the road, but also anticipate actions by other road users that could be dangerous.
“Most of us go to work each day knowing that our immediate workspace is a safe environment for us to work in. Our drivers don’t have that luxury: everyday road conditions, the weather, vehicle issues
mechanic for Caterpillar and later as a specialised freight driver.
“Knowing just how to fix trucks isn’t enough in this world,” he said.
“Understanding how these vehicles operate in their day-to-day roles is extremely important to the preventative maintenance and diagnostics. At LMS we have found holes in most maintenance programs and the time spent in workshops when it’s not needed.”
Having the capability to service and maintain trucks and trailers 24 hours a day fills a niche that Gregson believes is highly sought after in the industry and will have positive results on drivers so that they can have their required rest breaks without compromising time on the road. The initial response from the market has been more than encouraging. “We are currently looking for more skilled mechanics that are passionate about trucks to help grow LMS and cope with the demand we are receiving,” said Gregson.
and the public create dangerous work environments.”
For winning driver, Albury’s Mick Woodham, the award speaks volumes about the company’s commitment to road safety as well as acknowledging their importance to the business.
“I was pretty impressed, to be honest, that the company did these awards,” said Woodham. “I didn’t really know much about them and was blown away because I didn’t expect it. I really appreciated receiving it.”
A career driver, with more than 30 years of truck driving under his belt, Woodham said safety was always paramount, with planning around everything from weather and road conditions to rests stops to manage fatigue.
“In a day in the life of driving trucks you don’t know what you will encounter whether that is animals on the road or motorists overtaking recklessly,” he said.
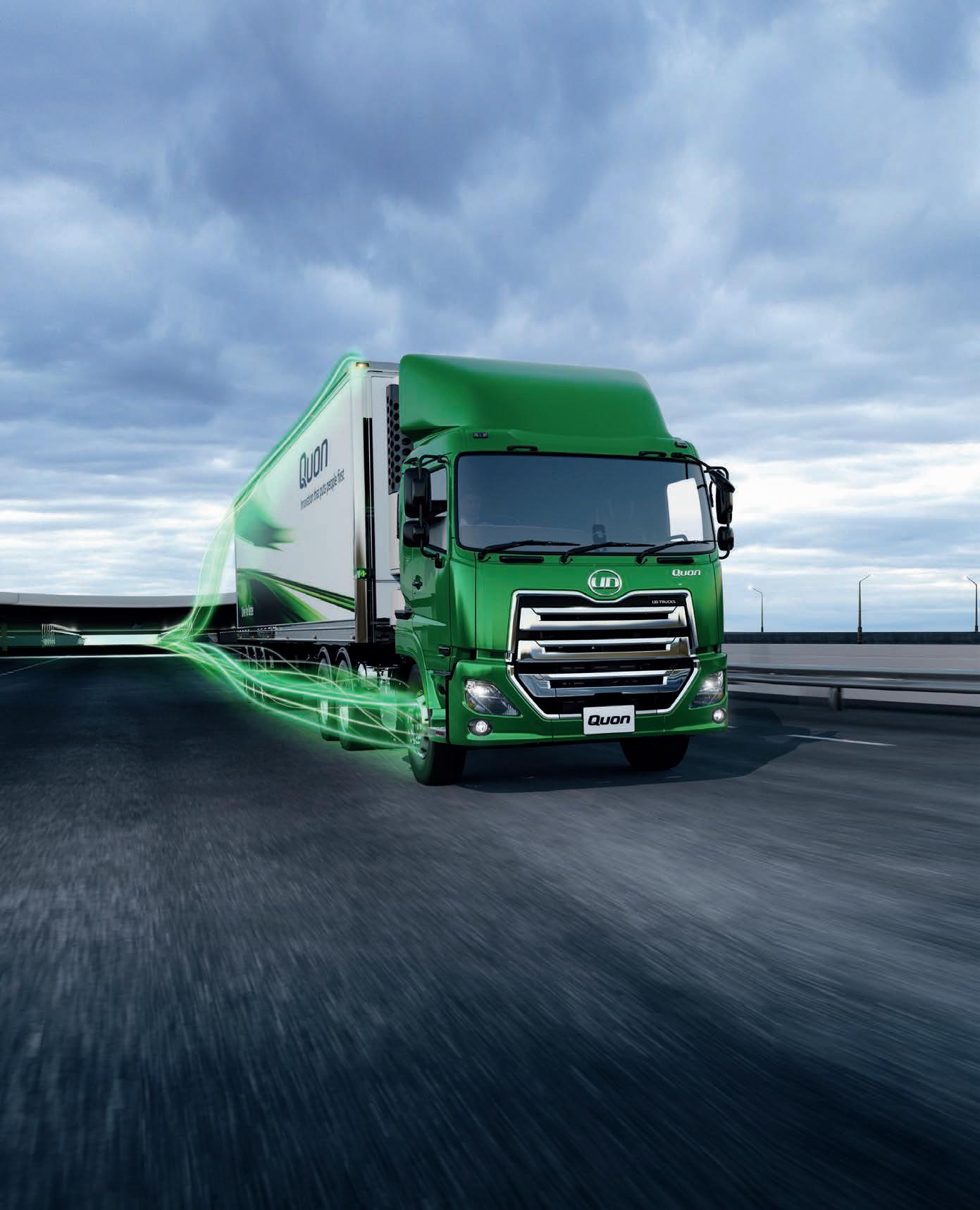
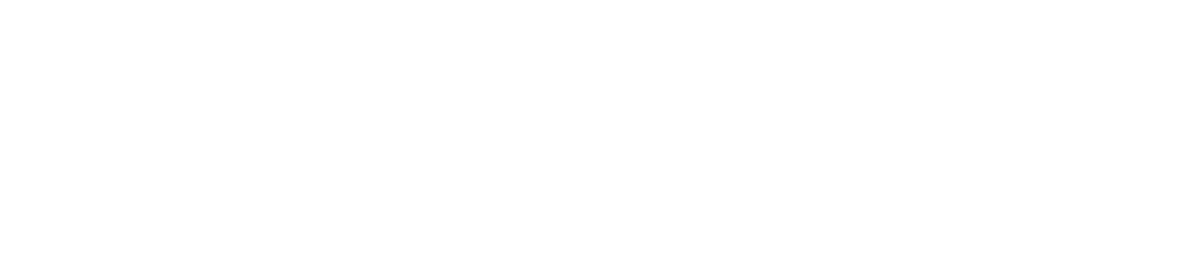
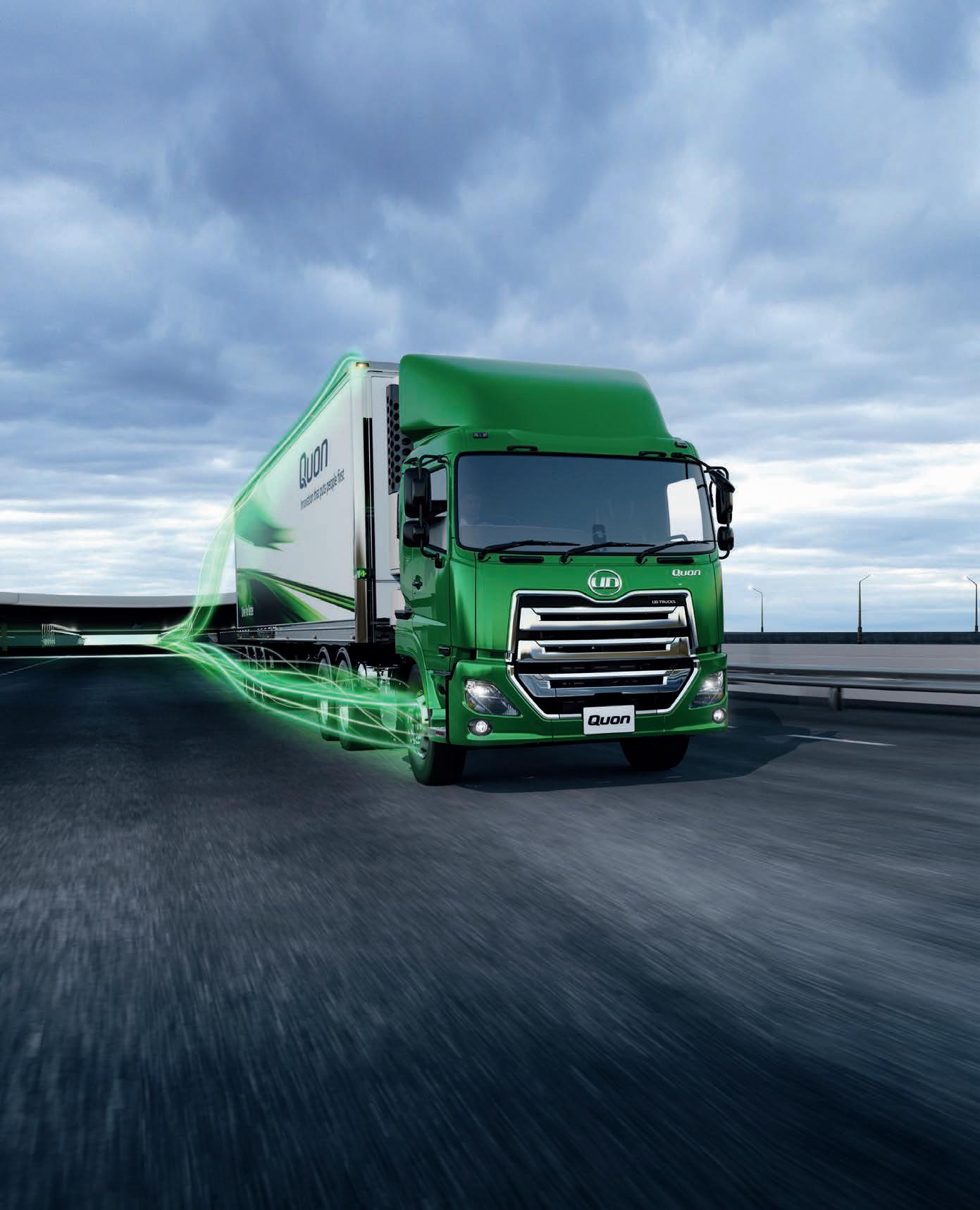
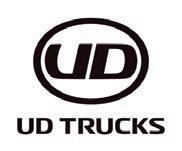
> Tony Innaimo Transport adds K220s, unveils new depot
General freight carrier, Tony Innaimo Transport, has moved into a new facility in Brisbane. Located in Berrinba, only minutes from the Logan Motorway, the 95,000m2 site features two 20,000m2 sheds joined together by a 6,000m2 awning over an undercover drive through area for loading and reloading.
There’s also 10,000m2 in pallet racking which brings it in line with the company’s Arndell Park site which features 20,000m2 of shed, with 10,000m2 rack spaces in addition to internal hardstand.
Formerly occupied by CEVA Logistics, the Berrinba facility expands upon Tony Innaimo Transport’s other depots in Canberra, Sydney, Yass, Wagga, Newcastle and Melbourne.
Some 40 linehaul dedicated prime movers and 25 rigids will visit the site over a weekly period to handle unloads and reloads.
There are 28 container docks and nearly 10,000m2 of external hardstand space which makes it a legitimate truck and trailer purposely built transport depot.
The depot will be used primarily for cross docking. On one side unpacking containers from the wharf, road and rail and building pallets will be performed for the Spotlight Retail Group. General distribution will take place on the other side of the depot where freight profiles are mixed and matched on the rigid and semis before they go

out for deliveries.
The site, leased initially for sevenyears, is fully secure with electric fences. Being centralised it’s ideal, according to Jamie Kemp, Queensland State Manager Tony Innaimo Transport, as a depot for the locations in their network.
“There’s a lot of potential here and we’ve got a lot of people who work for Tony’s business who treat it as their own so they’re always striving to do what’s best,” he told Prime Mover “Tony is one of the best, most downto-earth people you can meet. He puts a lot of faith in his people.
> Hazell Bros acquires business unit from Downer
Tasmanian construction and transport specialist, Hazell Bros, has made a strategic acquisition. The family-owned 80-year-old company late last year acquired the VEC Civil Engineering business from the Downer Group. Included in this acquisition is the VEC Precast Manufacturing and Steel Fabrication Workshop, assets that are anticipated will contribute to the overall growth and diversification of Hazell
Bros operations.
As part of the acquisition, Hazell Bros has welcomed approximately 60 new individuals into the business.
That brings its total workforce to 800 employees. VEC Civil Engineering is based in Ulverstone, Tasmania.
“These additions complement our existing robust civil construction capabilities and position Hazell Bros for even greater success in the years
“This site opens up a lot of opportunities for growth for the business and people here.”
The fleet has also added one new Kenworth K220 with three more on order this year. As the business expands owner Tony Innaimo continues to invest in new equipment. “Everything he buys is new,” said Kemp. “These K220s come with Icepacks and creature comforts to look after the drivers, automatic gearboxes, Cummins Euro V X15, 600hp, 2.8-metre Big Cab, Meritor axles, custom air coolers, microwave and TV.”
to come,” Mary Mickan, Hazell Bros Business Improvement Manager told Prime Mover. “This is a significant step in our long-term plan to expand our presence in the northern region of the state,” she said.
“The acquisition not only broadens our geographic reach but also enhances our capabilities and strengthens our position in the civil construction sector.”
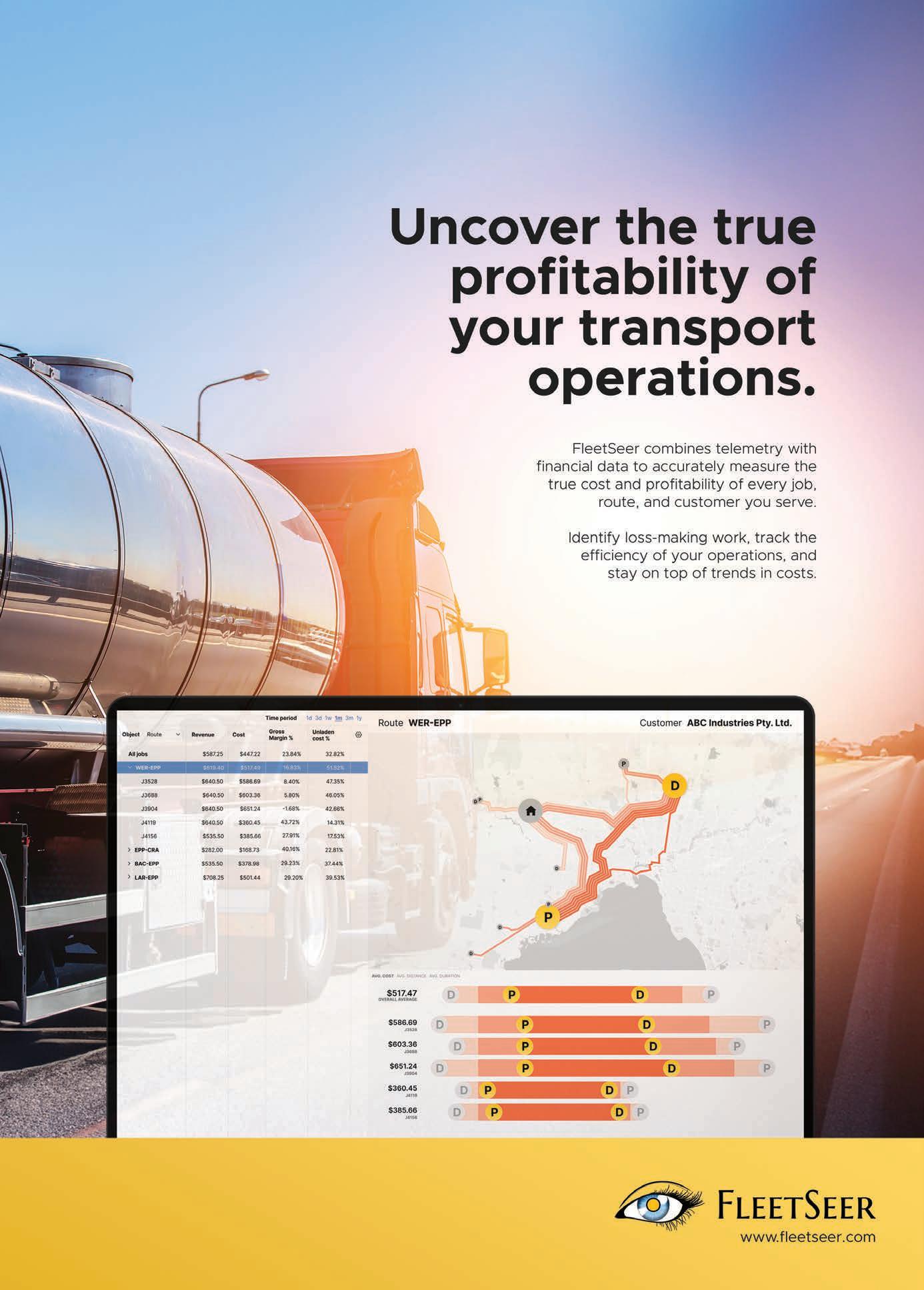
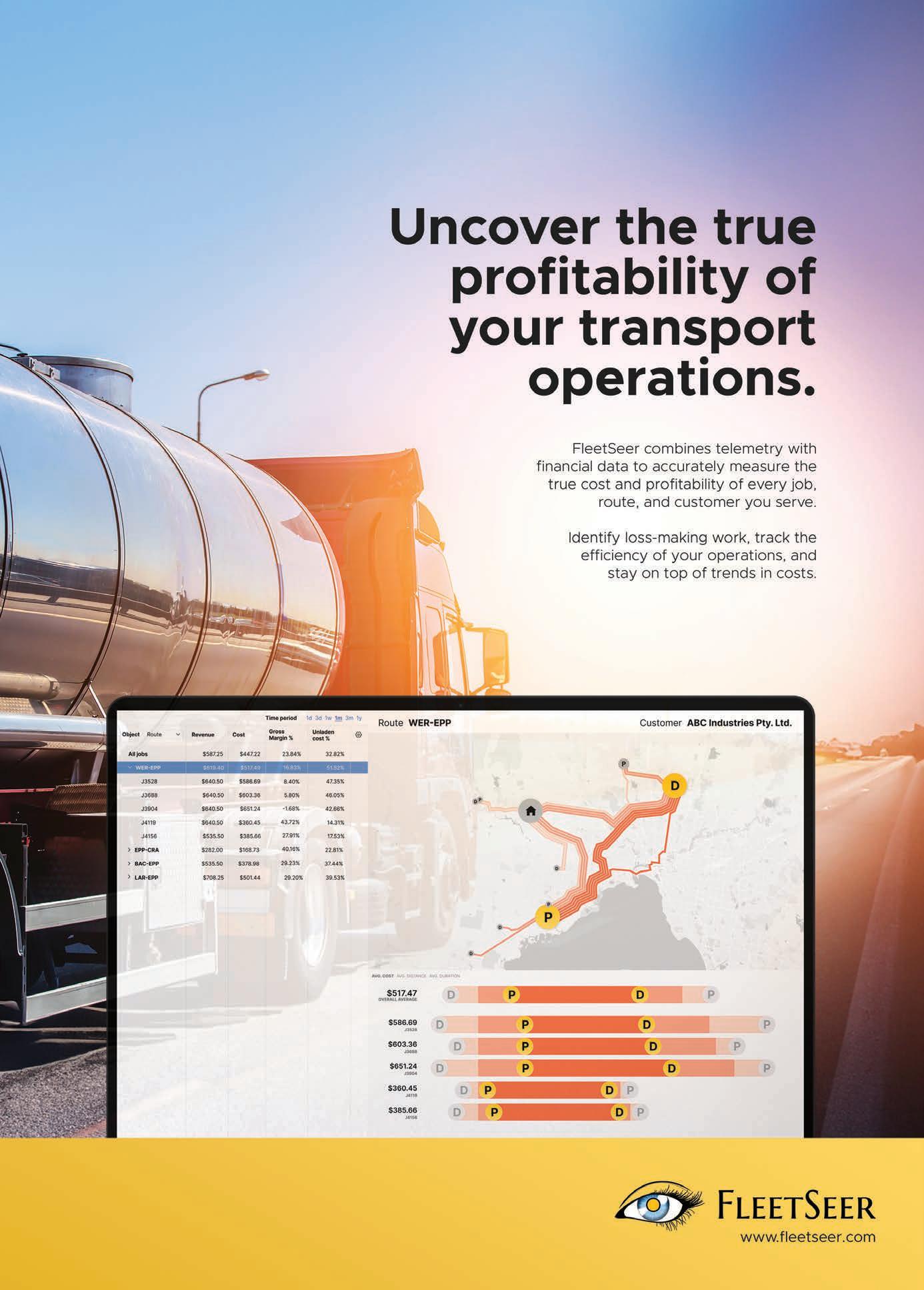
> Austmix lands 21 Mack Metro-Liners
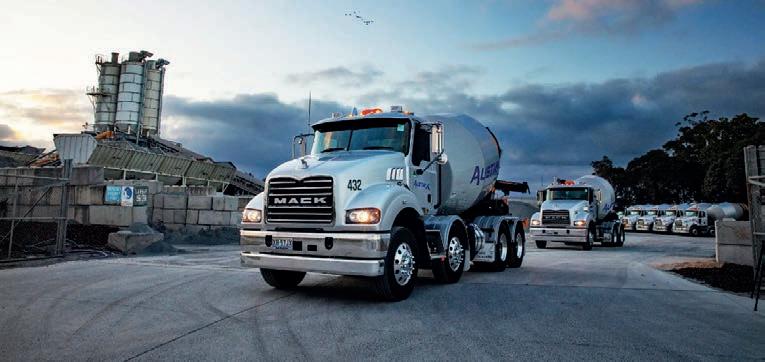
Concrete delivery specialists Austmix have bolstered their significant truck orders with Mack. Following on from 21 new Mack Metro-Liners delivered to it last year it will add a further ten units later in 2024.
Upgrades to its plant in Pinkenba to a twin-alley and opening a new singleally plant in Burleigh Heads underpin recent surges in the company’s output. “We got tired of saying ‘no’ to people because we didn’t have enough trucks to deliver orders,” said Managing Director Jim Venn. “When we won the contract for the Gold Coast Light Rail we had no option but to expand.” Austmix have been aligned with Mack for its agitator trucks for over 25 years.
“I’ve consistently found them to be the best truck for the job,” said Venn. “ “When you’re carrying a product like concrete that simply has to be delivered on time, those things count.” According to Venn, the height of chassis rail on the Metro-Liner is positioning perfectly.
“When you’re putting a rotating barrel full of a moving semi-liquid on the back, a low centre of gravity is critical, and the Metro-Liner is a very balanced truck,” he said.
The Metro-Liner is also an ideal fit for Venn’s personal favourite barrel, produced just a few kilometres away by another home-grown manufacturer, Cesco.
“The Metro-Liner takes the Cesco barrel beautifully,” he said. “The wiring harness in truck has everything preconfigured so it fits perfectly with the cameras and other hardware.
“Mack has a lot of experience with agitators and they’ve thought this stuff through. It’s all pre-built in there if you know where to look,” said Venn.
When ordering the new trucks, Venn and his team worked with VCV Australia and Mack, making small adjustments to the design. These decisions were motivated in part by wanting to make life easier for the drivers.
“We asked Mack to switch the position of the radio in the cab and fit stiff blocks in the suspension,” he said. One such change sounds trivial but is critical to the whole operation of delivering concrete.
“Trucks these days are configured to turn themselves off if they’re idling for more than a few minutes,” said Venn. “You can’t have that with an agitator— that barrel has to keep turning—so Mack tuned the new Metro-Liners so they won’t turn off. This is a small detail, but it shows the attention to detail and Mack’s understanding of the business.”
> Flex Contract Logistics enters SA market with latest acquisition
Flex Contract Logistics will enter the South Australian market with the acquisition of Lobethal Freightlines & LF Warehousing and Distribution, effective January 22, 2024.
Based in Adelaide, Lobethal Freightlines is expected to bring a wealth of expertise and resources to the Flex team. This acquisition not only bolsters Flex’s fleet with additional equipment but also establishes a significant presence in a key market where Flex has been servicing, but not formally represented.
After being founded in 2021 by Managing Director Lachlan Boyd, Flex developed a five-year strategy to become a major force within the
transport and logistics industry.
In a statement Flex said it had exceeded its own expectations, growing significantly over the first two years with transport depots in Melbourne, Sydney, Brisbane and now Adelaide.
The acquisition of Lobethal Freightlines aligns with Flex’s strategic vision of becoming a national logistics provider.
“By expanding into Adelaide, Flex is now better positioned to serve its customers with enhanced regional coverage, faster response times, and a more comprehensive network,” Boyd said. “The acquisition is another steppingstone towards Flex’s five-year plan.”
In April 2023, Flex announced the
acquisition of Doug Hayes Transport — its first.
“It is a testament to the hard work, discipline, and commitment from each and every one of our employees & dedicated sub-contractors that allow us to do this,” said Boyd. “Whilst the acquisition in April had its challenges as most do, nine months later we are proud to say the Flex brand is well engrained across the Eastern Seaboard. We will never waiver on our commitment to our customers, to provide them a service that they cannot fault, and we will continue to take them on our journey.” Flex now services full loads and palletised freight right across the country, in all major capital cities.
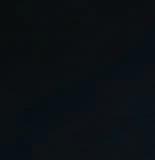

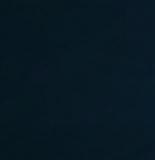
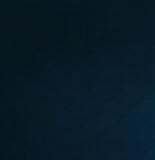
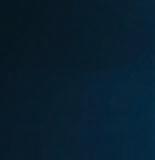


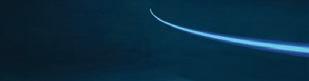
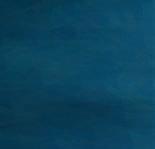

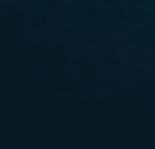
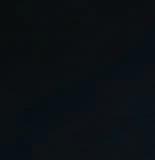
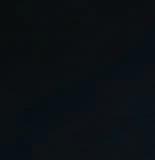
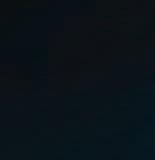
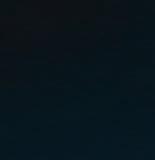
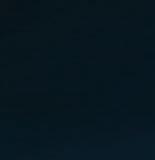
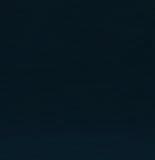






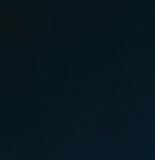

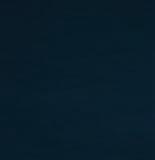
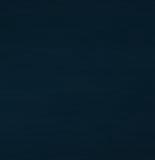

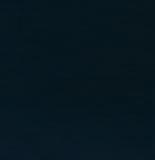
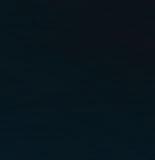
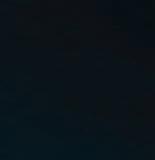
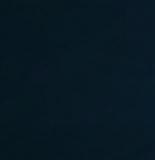
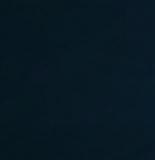
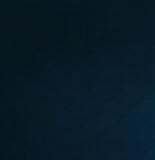
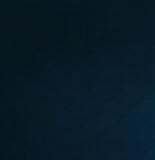
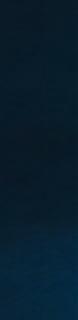
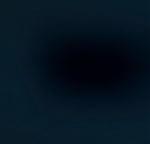
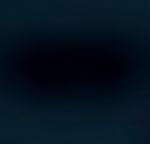
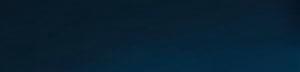

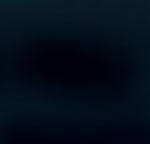
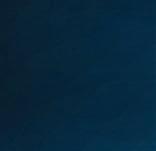
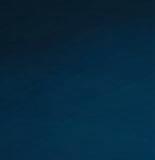
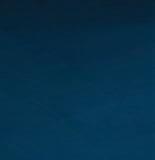
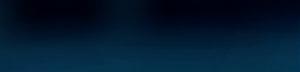
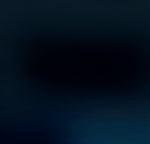
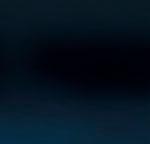

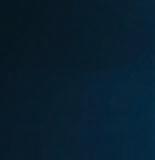
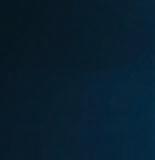
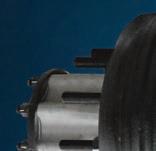

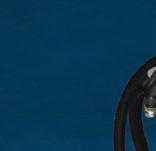


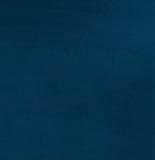
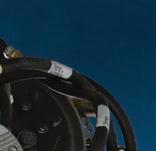
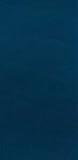
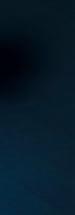
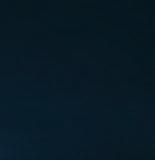



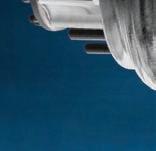
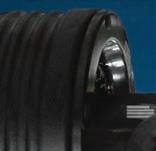

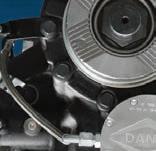
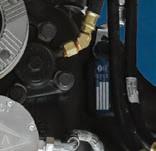



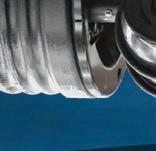
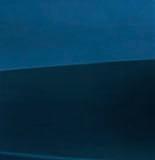
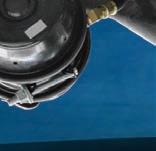




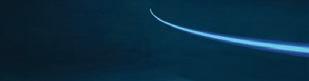
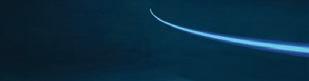
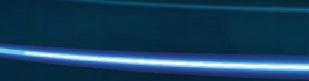
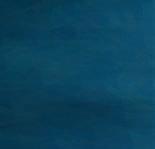
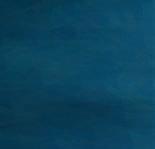

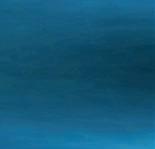
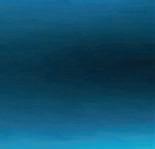




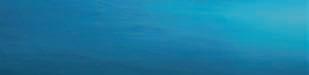
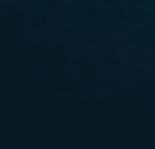
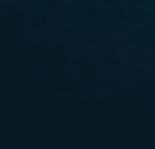
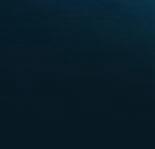
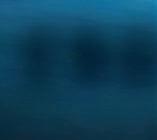
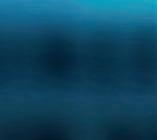
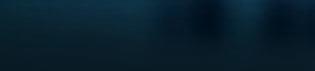
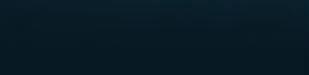



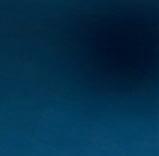
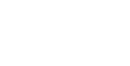

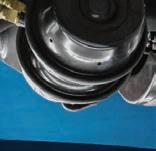
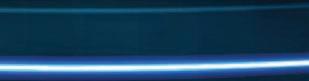

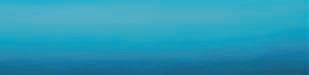
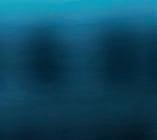
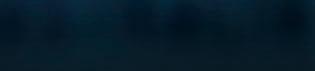
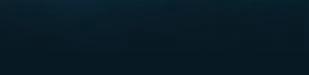
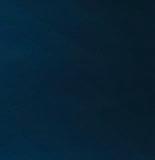

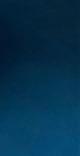
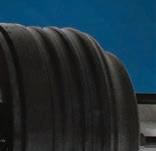

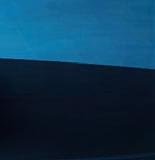
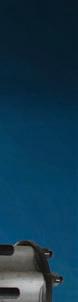
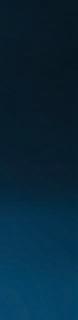
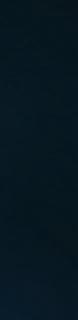
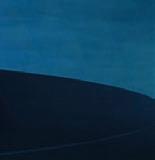
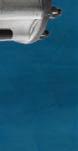
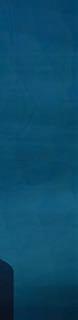
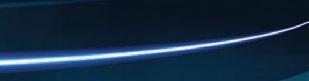
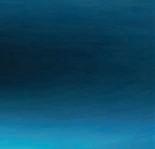
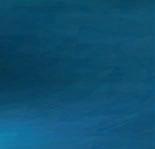
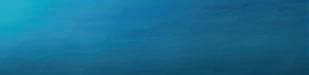
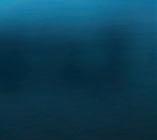

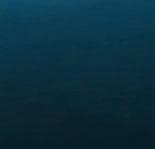


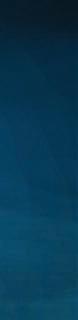
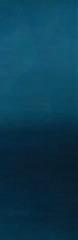
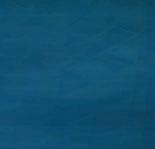
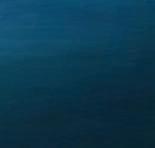
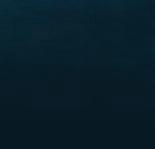
> Qube makes major solar energy investment
As part of its latest solar energy investment, Qube is preparing to transition all of its light vehicles to electric. Qube Director of Bulk, Todd Emmert, unveiled Qube’s new 268kW solar and 309kWh battery system which have taken its Picton, Western Australia, facilities entirely off the grid.
Qube employees and customers were joined by Member for Forrest, Nola Marino, and the Mayor of Bunbury, Jaysen
de San Miguel, to celebrate the launch.
“This is an incredibly exciting day for Qube and a great step forward in our ambition to be a sector leader in the transition to a lower carbon future,” Emmert said.
“Today we welcome Qube’s first fully ‘off-grid’ facility thanks to the solar system installed across the roof tops of Qube’s warehouse, maintenance and administrative facilities, which feed a
> JCT Transport & Logistics announces new venture
Dedicated same day haulage specialist, JCT Transport & Logistics, has launched a new business division. The JCT Express Haulage venture involves the expansion of its service profile which will include ad hoc services alongside the dedicated, permanent hire, and contracted logistics options it already provides.
This marks JCT’s competitive entry into the general freight sector where it aims to offer customers premium service options ranging from couriers to taxi trucks and right through to semi-trailers
and B-doubles.
“With many years of expertise and a team of dedicated transport professionals, we are well-equipped to provide clients with top-tier transport solutions which through careful consultation, we tailor to the unique and specific needs of our clients,” said Shaun O’Connor, JCT National Transport Manager.
With a focus on dedicated, permanent hire, and contracted solutions, JCT will continue to offer premium crane truck services as it expands and enters the
giant 300kWh Battery Energy Storage System on site.”
Emmert revealed that Qube is also welcoming four light electric vehicle chargers to its Picton site.
“My hope is that Qube’s Picton site will provide a template for what is possible with the right mix of available space and technology and will become the first of many ‘off-grid’ facilities in the Qube network,” he said.
general freight market this year.
“Our commitment to quality, safety, and excellence remains unwavering, and we look forward to continuing to serve our much-valued customers and transport partners with the highest level of service across both divisions throughout 2024 and beyond,” said O’Connor.
Based in Epping, Victoria, the 40-truck strong fleet consists of rigid crane trucks, extended reach crane trucks, semi cranes, semi-trailers, prime movers, Tautliner and pantechs of all class types and more.
> Former Kings Transport executive starts role at Austrans
David Spink has commenced his role as new Chief Executive Officer at Austrans.
Effective 15 January 2024, Spink’s appointment will leverage his 18 years of logistics experience as the company looks to drive future innovation and growth. His previous roles included Chief Commercial Officer and Chief Operating Officer at Kings Group as well as National General Manager at Kings Transport.
“Known for his expertise in driving growth, managing P&L, and leading large teams, David has a track record of securing significant contract wins and spearheading strategic initiatives,” Austrans said in a statement. “David’s appointment underscores Austrans’ commitment to innovative leadership and excellence in logistics services.
“With an MBA and extensive experience in business development and technology integration, he is poised to enhance Austrans’ operational efficiency and service quality.” The move fits with major changes at the Melbourne-based business which announced a new fully leased industrial estate for the last available building at Premier Logistics Hub – Altitude, Bankstown Airport in August last year. The new facility offers 14,615m2 of warehouse and office accommodation.
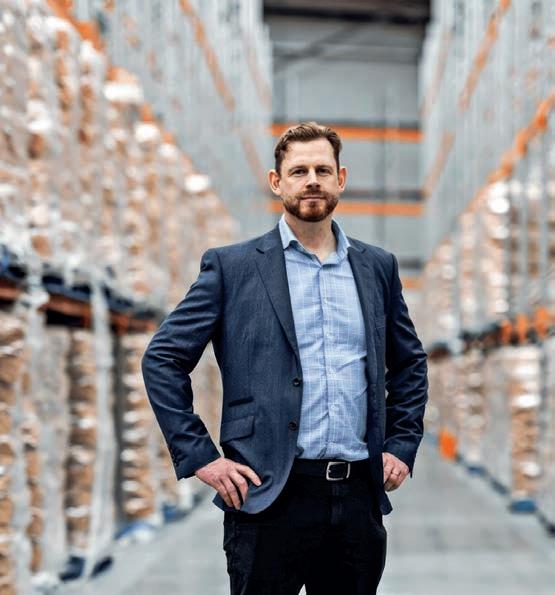
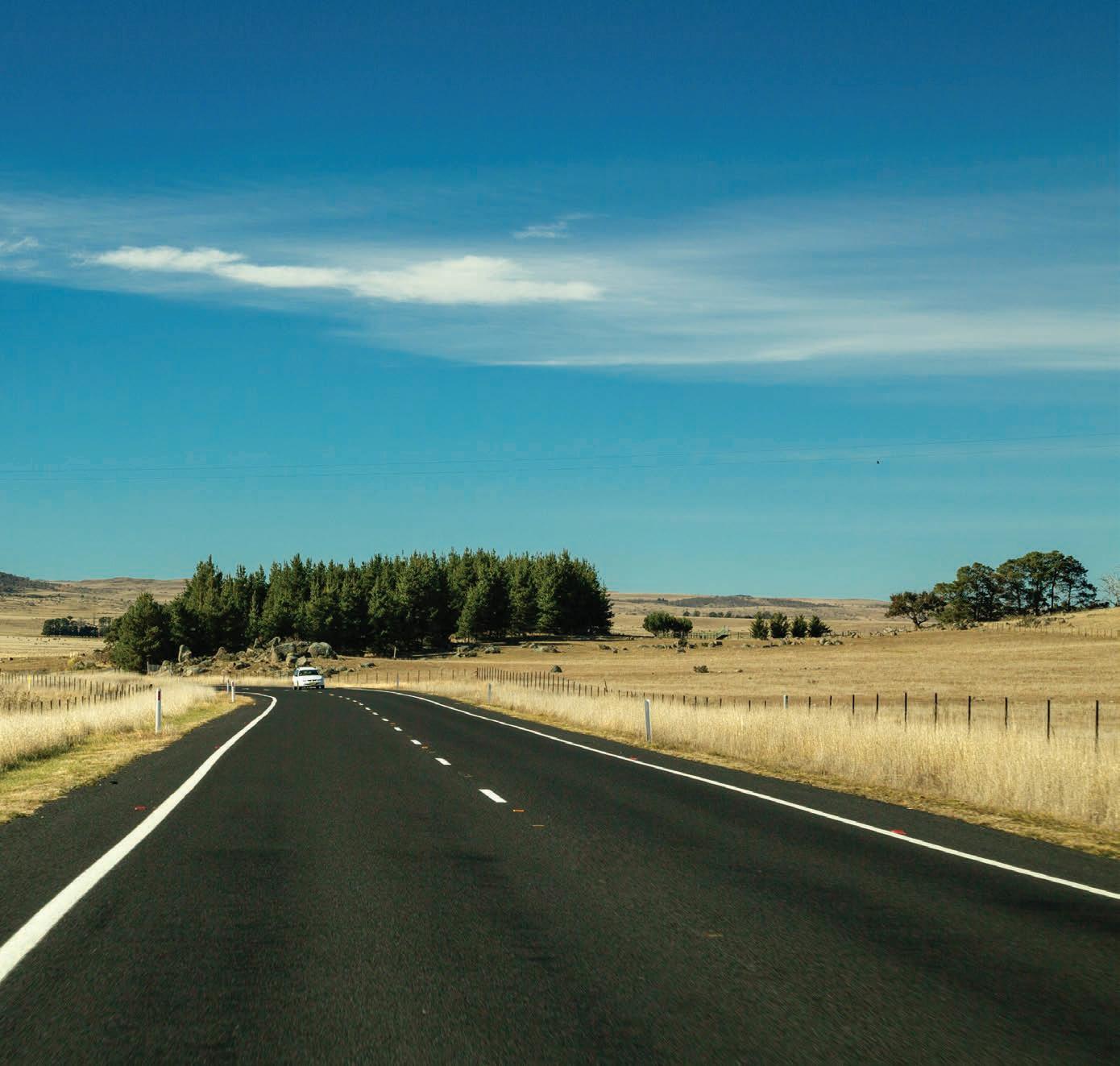

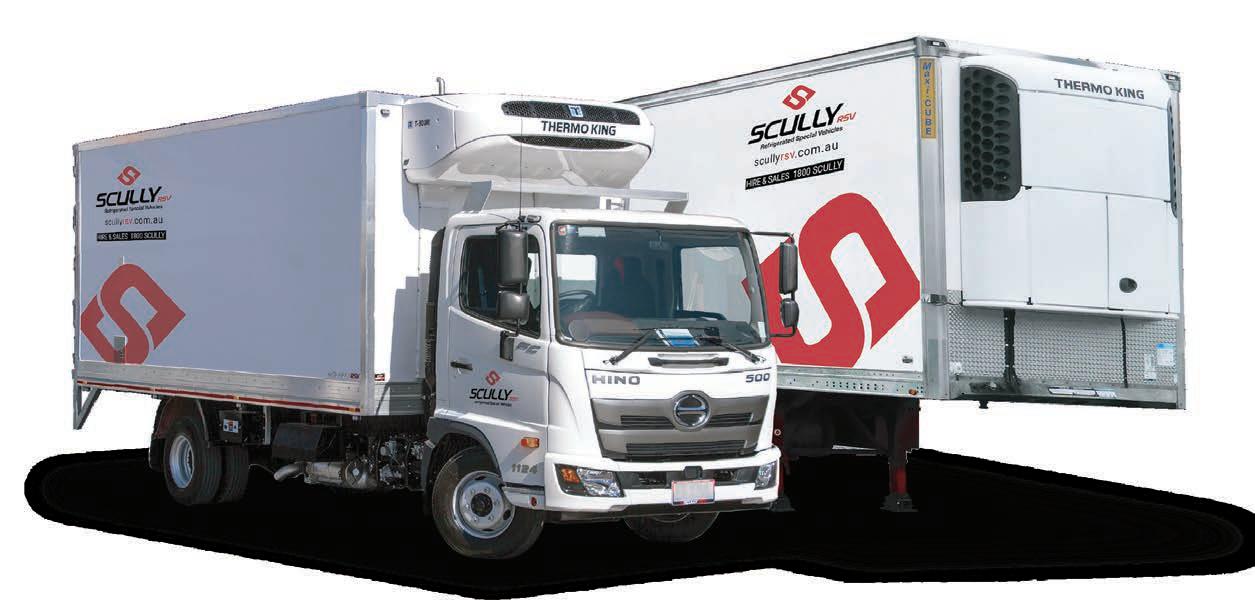
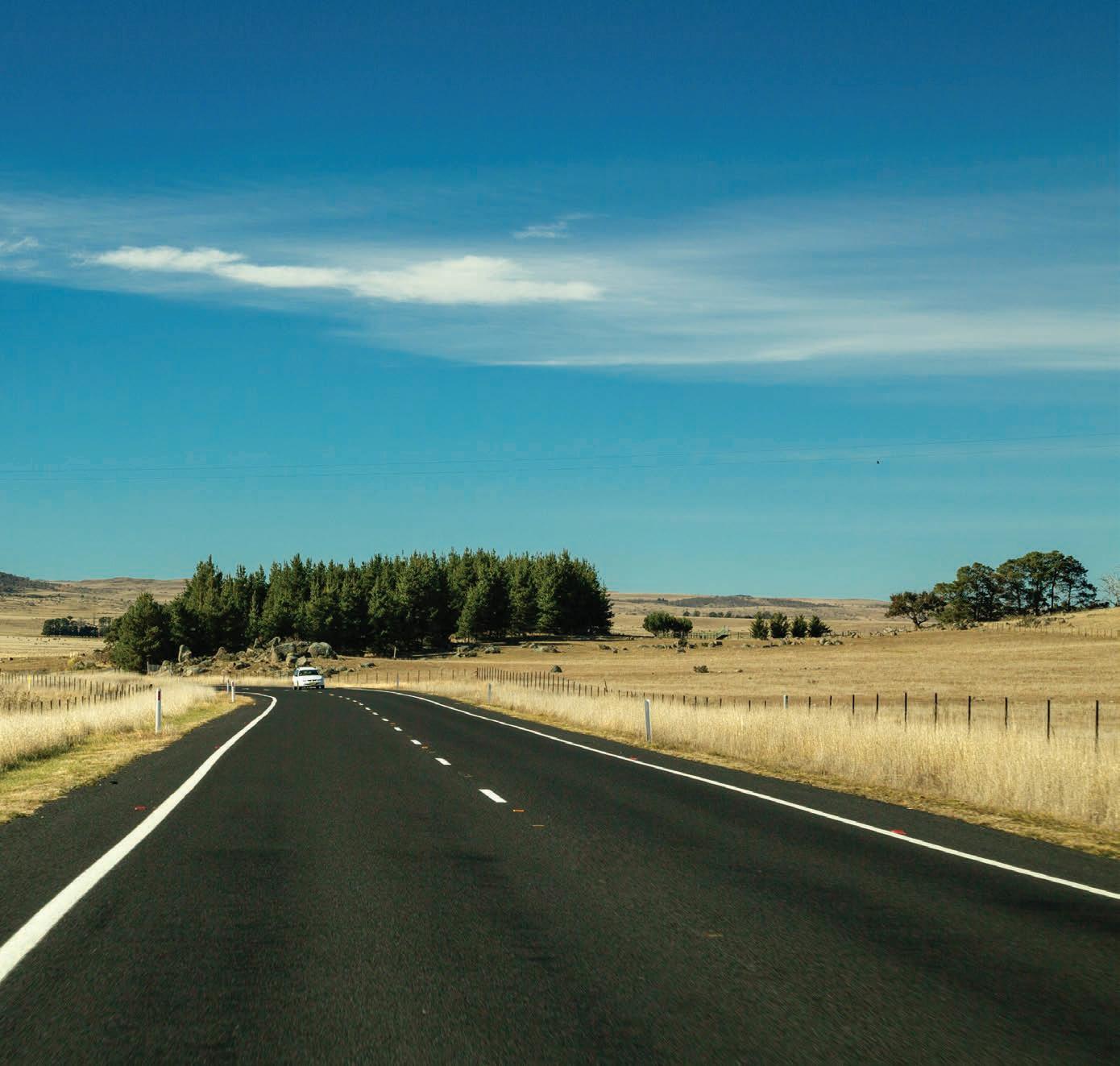
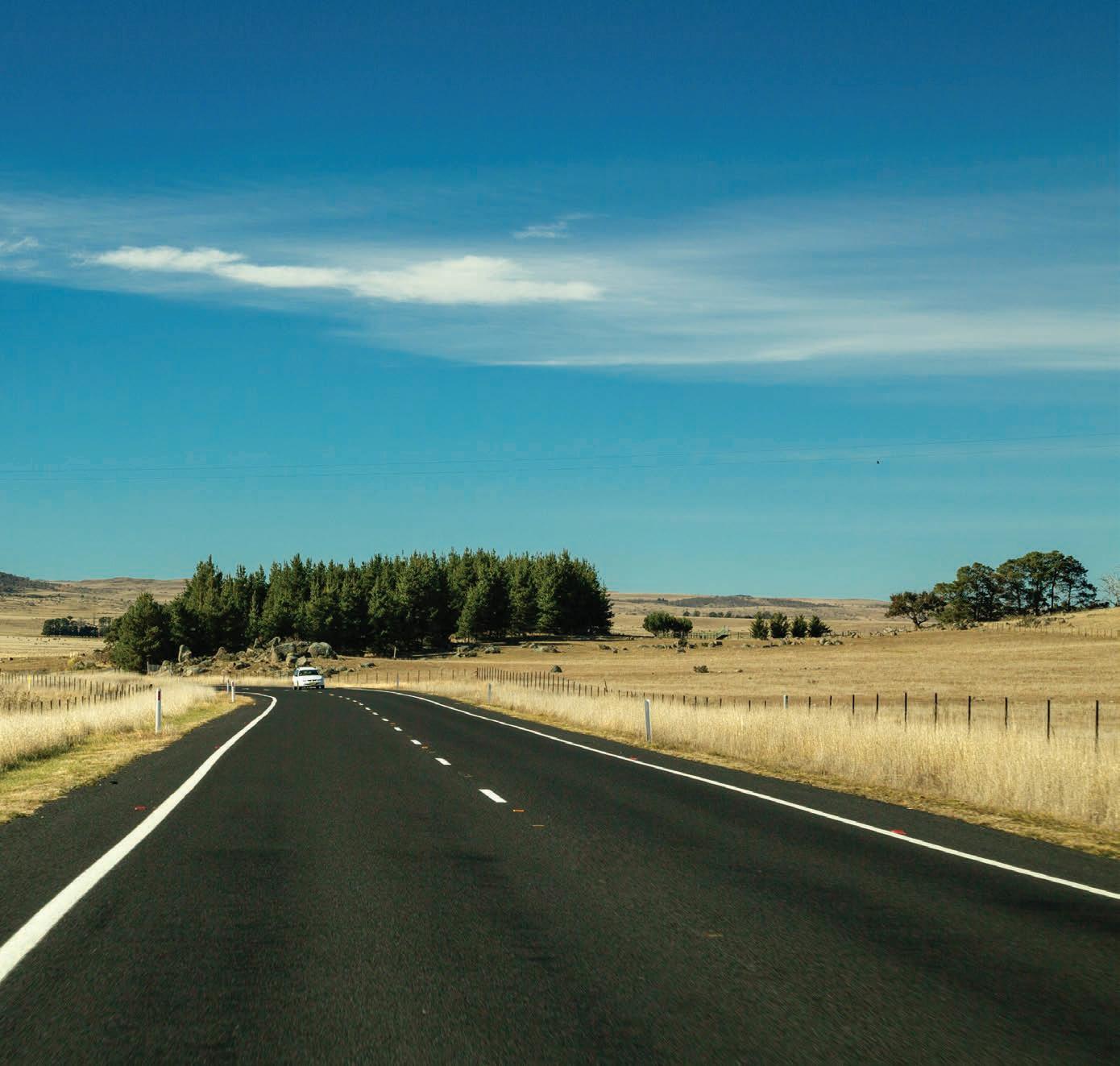
The SafetyCulture platform enables a more efficient and optimised inspection capture and reporting system for vehicle compliance and safety. Delivered via a QR code scan, users can launch and complete the vehicle inspection in less than 30 seconds.
Scully RSV is proud to be bringing this initiative to market with Safety Culture and leading the way in keeping our communities and their families safe. It’s another great example of delivering on the customer promise, that Scully RSV fleet is managed to the highest levels of quality, safety and reliability.
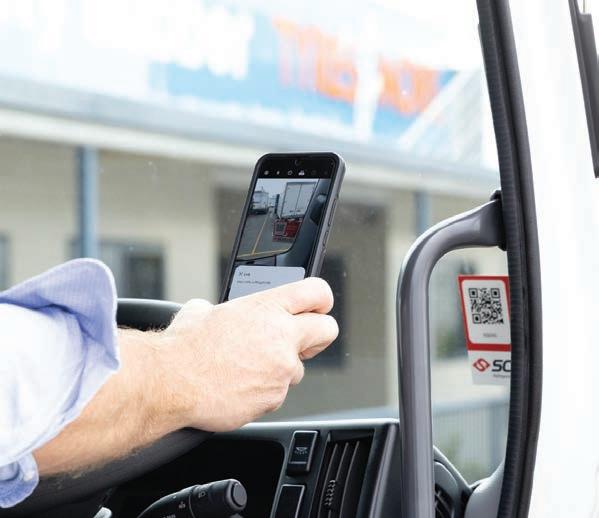
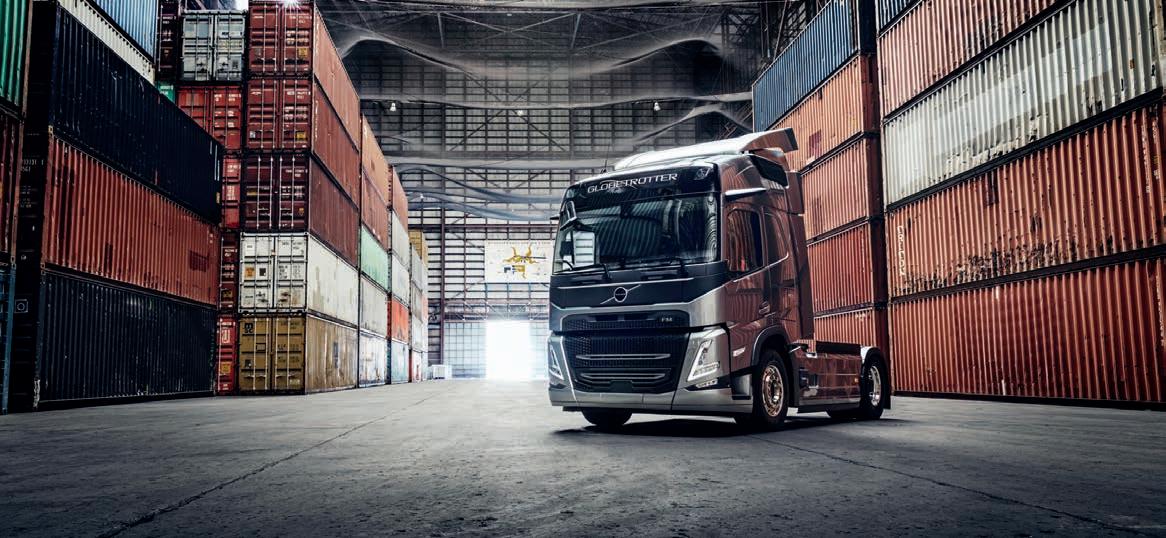
> Volvo reveals revamped heavy-duty lineup
Volvo Trucks has unveiled an improved lineup, showcasing a range of aerodynamic and safety updates to the FH and FM as well as a new 17-litre engine. Driver appeal, safety and efficiency are at the forefront of arguably the biggest revamp of the Volvo FH since the launch of the fourth generation FH platform in 2012.
Both the FH and FM cabs have also received significant aerodynamic improvements. However, the most noticeable feature is the addition of the optional Camera Monitoring System which replaces the traditional left and right mirror assembly.
CMS gives a wider field of view than a standard glass mirror and is able to shift that view accordingly as an articulated combination negotiates turns and intersections. Another outcome is the aerodynamic and efficiency gains of not having mirror housings on the side of the cab.
The A-pillar mounted CMS screens can also be activated remotely from the sleeper for additional security while the driver is resting. In addition, the FH range has expanded with the addition of an ‘extended front’ variant dubbed the FH-Aero, available for the European market.
At the global launch in Sweden, an
entirely new flagship 17-litre platform was revealed. The D17 engine is equipped with a single efficient turbocharger that boosts engine responsiveness, improving driver experience.
Volvo’s innovative patented wave piston design optimises combustion and reduces emissions, while the new injection system ensures, according to Volvo Trucks, the best fuel economy and the increased peak cylinder pressure enables high power output. Power ratings for the Australian market are yet to be confirmed.
Volvo Group Australia President and CEO, Martin Merrick, is confident the new D17 engine will be a game changer for linehaul, regional and heavy haulage customers across Australia.
“This engine has been subjected to a brutal local testing program in some of the harshest conditions and some of the highest weights this country has to offer to ensure the uptime and productivity that Volvo Trucks customers have come to expect,” he said. “Regardless of driveline, whether ICE or BEV, the Volvo FH will continue to deliver efficiency, safety, power and comfort for Australian drivers and I for one will be very proud to see the first of these new trucks roll off our Wacol
assemble line mid-2024.”
Volvo’s I-See technology has been refined to save energy and carbon emissions, using a cloud-based topographic map to optimise driving and enable more driving time in cruise control mode that can both save energy and give more relaxed driving. Updated brakes are also included with Volvo patented drag-free brake discs, pads and hubs, improving the braking capacity, reducing energy consumption and emissions.
All engines are available with 13- and 14-speed Crawler and Ultra-Low Crawler I-Shift AMT transmissions as well as the traditional 12-speed. The new FH16 600 will also benefit from the option of a new low-drag I-Shift variant for highway applications. Inside, the FH features a revised audio system and the addition of interior styling and branding upgrades.
“This latest iteration of the Volvo FH is the cleanest, most efficient, and most powerful truck we’ve offered Australia customers yet,” Merrick said. “With the Volvo FH having just celebrated 30 years of delivering unparalleled levels of safety, performance and efficiency, it’s fitting that the revamped Volvo range has raised the bar in these areas once again.”
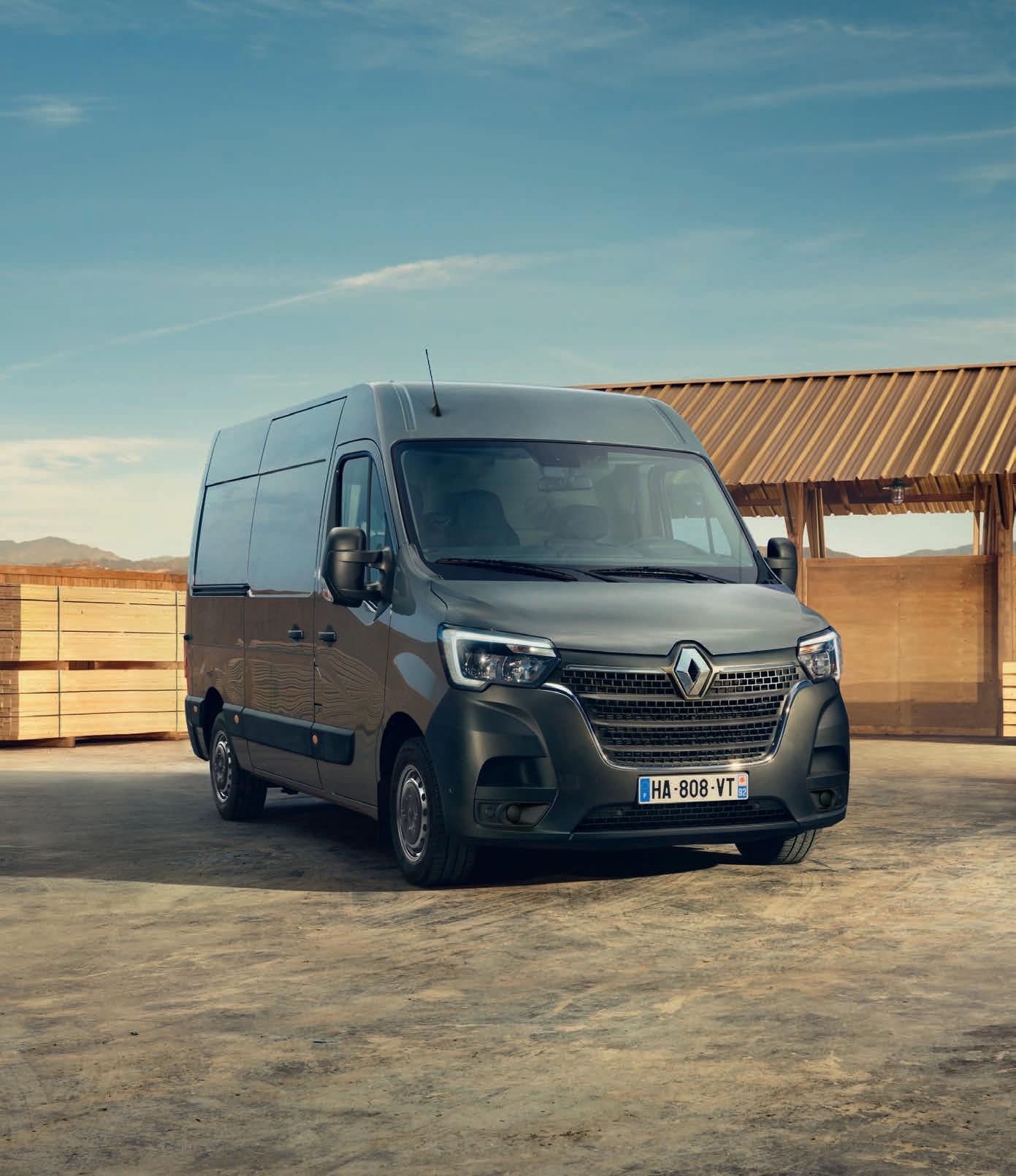
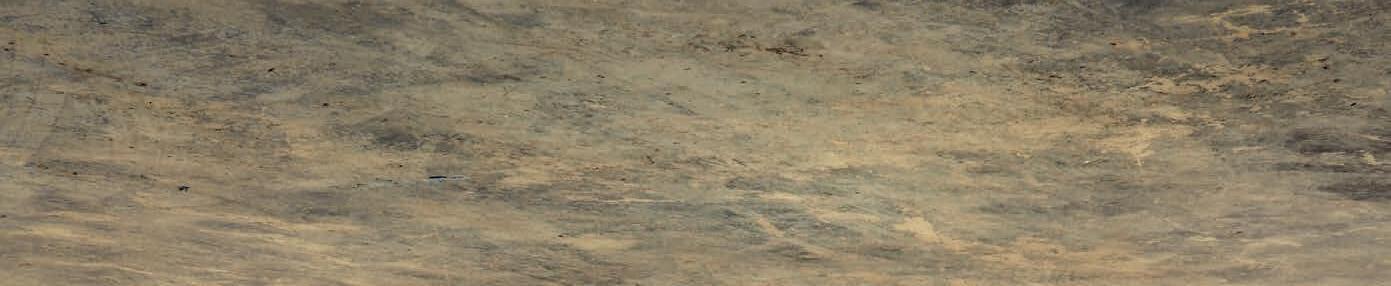
RENAULT MASTER
cargo carrying powerhouse
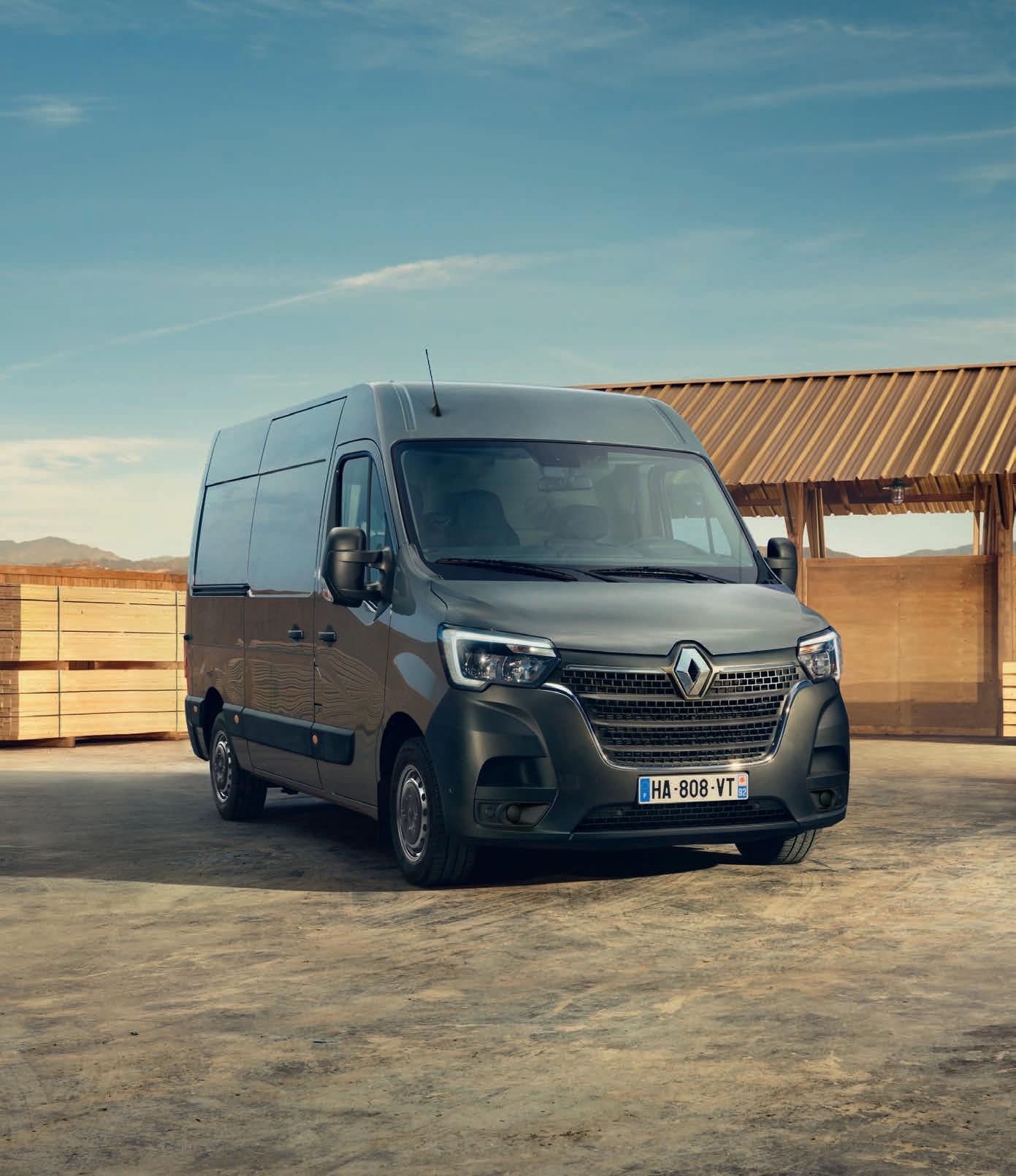
with up to 17m3 of cargo volume and a choice of configurations, there is a Master Van for any business.
plus, with a 100L fuel tank and long service intervals, you can hit the ground running every day. stock available now.
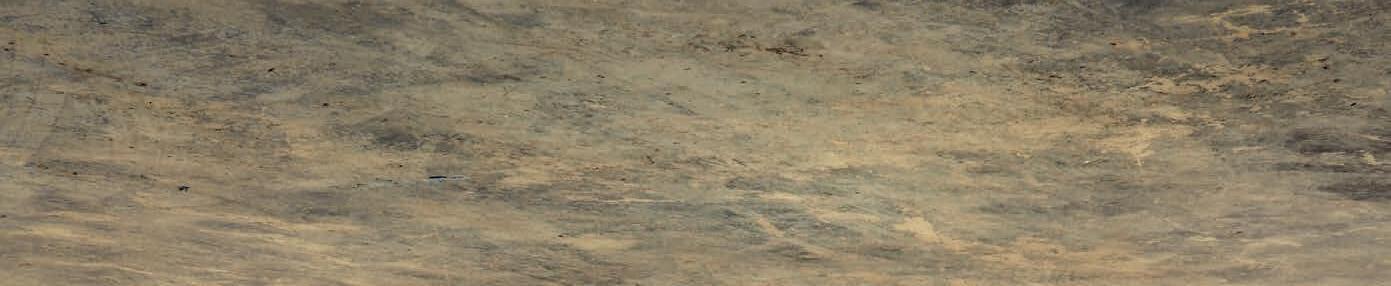
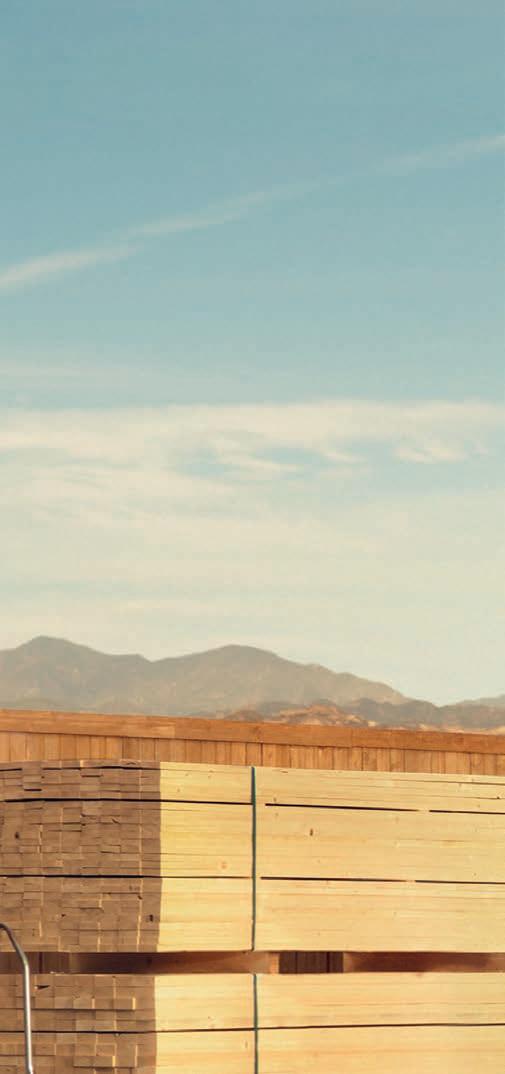
> Coyote Container completes historic trip in fuel cell truck
Port cartage and drayage specialist, Coyote Container, has successfully completed a 400 mile journey in a Nikola Tre Fuel Cell hydrogen truck. The trip from the Port of Oakland to the Port of Los Angeles in Long Beach last week involved hauling a container on a single trailer with a 17.7 tonne GVM.
William Hall, Managing Member and Founder of Coyote Container drove the Nikola over the often hilly 643-kilometres which involved climbs through the Altamont Pass in the Bay Area, Grapevine Canyon further along the I-5 interstate through to Tejon Pass with an elevation of more than 1200 metres. This was followed by a steady descent to Pier C in Long Beach with a rest break for Department of Transport compliance in Lost Hills.
“The truck is a dream to drive and I arrived at Pier C with about 140 miles of remaining range,” said Hall. “I drove conservatively and did the steep climbs at 40 mph much as I would in a diesel with that load profile, though I could have easily gone 55.”
In 2023 Nikola produced 42 trucks and wholesaled 35 Class 8 Nikola hydrogen fuel cell electric vehicles (FCEV). These are reportedly the only US designed and assembled Class 8 hydrogen fuel cell electric truck on the road today. Of the seven trucks produced but not wholesaled, three are being used in an extended field test with a fleet partner in Colorado, two are in continued validation and engineering and two are being used for service training/customer demos.
Assembled in Coolidge, Arizona, the FCEV commenced serial production on 31 July 2023, with the commercial launch on 28 September.
“As an owner of this trailblazing technology, I expect that there will be many lessons learned along the way and came prepared to deal with it,” said Hall, who experienced a glitch at the end of the trip in a hydrogen tank valve that is housed inside one of the five hydrogen tanks. Nikola dispatched a repair team within 30 minutes to look at the issue.
As a safety precaution, the entire set of
tank valves closed and shut down the fuel cell according to Hall.
“I still got my load into the terminal on the battery which had 20 miles of range at reduced power,” he said. “Overall success in the trip with the load delivered in safe and efficient manner.” Nikola President and CEO, Steve Girsky was pleased with the outcome.
“Coyote Container’s historic California trip with their Nikola hydrogen fuel cell electric truck represents the incredible capabilities of our technology and its countless possibilities,” he told Prime Mover. “We’re grateful for our trailblazing customers and partners who inspire us as we continue toward our vision for a zero-emissions future.”
Late last year Nikola formalised a definitive ten-year agreement with FirstElement Fuel (FEF). The collaboration enables Nikola customers to access fuelling services at the new FEF multi-use heavy-duty truck station situated strategically near the port in Oakland, California. Additonal fuelling locations are expected by Q2, 2024.
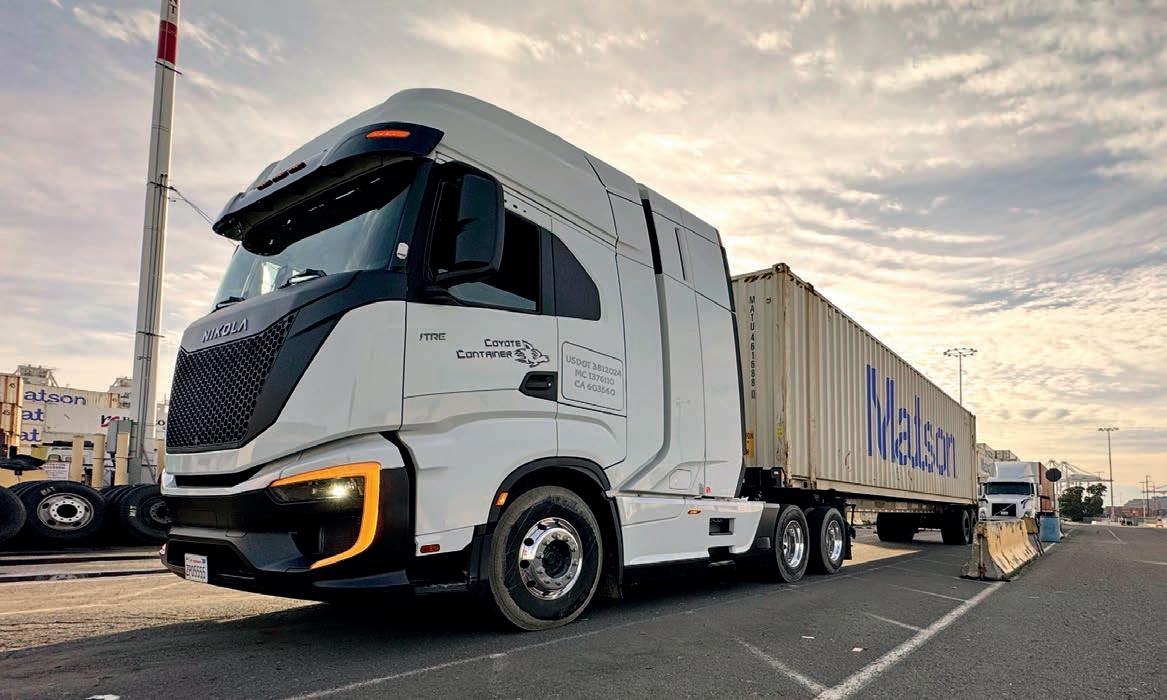

Our Difference. Your Advantage.
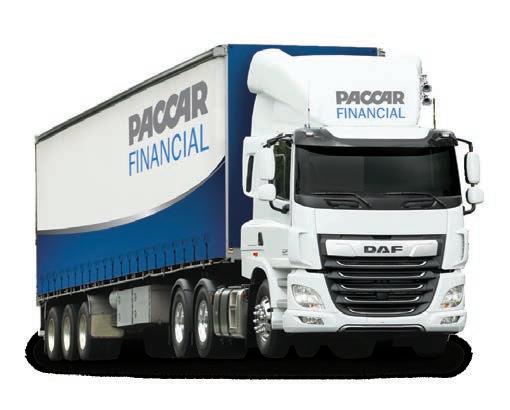


Exclusive member offers
PACCAR Financial Advantage is an exclusive loyalty program for PACCAR Financial customers. It is free to join and offers discounts on a variety of products to keep your business moving.
To find out more visit paccarfinancial.com.au/advantage or speak to your local finance manager.
POWER BALANCE OF
A specialty unit within Toll Resources at Tomago is set to introduce a new eet of Mack Anthems as part of its dangerous goods transport operations.
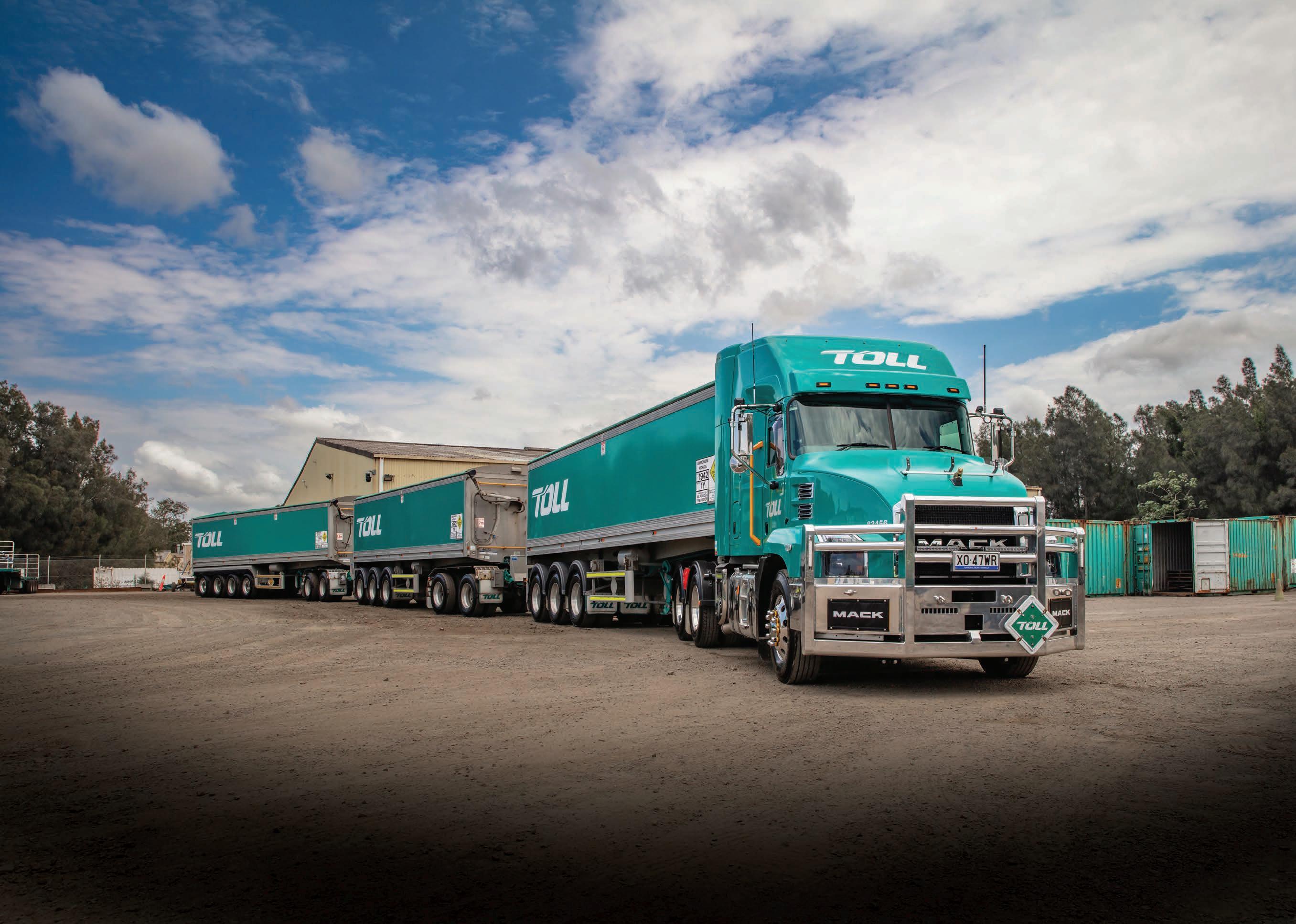
Among the specialty wings in the vast and varied operational footprint of the Toll Group can be found the Security Sensitive business unit at Tomago, a national subvertical within Toll Resources and Industrial division. From here multitrailer con gurations are hauled all over the local region and country, contingent upon the task. Principally,
the Security Sensitive business is an operation that supports the mining industry in the Hunter Valley for the distribution of explosive precursors or ammonium-based explosives and other dangerous goods. Trucks in the eet that regularly service the local region aren’t necessarily limited to it. They will, as part of the distribution routes, range predominantly across the eastern seaboard, from Adelaide right up to the

Bowen Basin with occasional dispatches also to Tasmania.
In the Tomago site alone, there are 46 active trucks that operate alongside nearly 100 staff. Trent Markham, Service Supervisor for the Workshop is one of them. He overlooks a team of ten that handle maintenance scheduling, parts ordering, stocktake and general everyday communication with other vendors and customers.
“The Toll business was founded in the Newcastle region, so there’s a rich history for the company here,” he says. “Being one of the last remaining truck units for Toll in the area is a source of pride. Having a new eet of trucks join our depot keeps alive the spirit of what founded the business.”
The rst two Mack Anthems in the new eet of trucks to which Trent refers, are from an initial batch of ten units on
order. These trucks, the rst Mack prime movers at Tomago for two decades, are split evenly between 36-inch walk through sleepers and day cabs. A 13-litre 535hp MP8 engine with a 2600nM torque rating power both specs. The sleeper cabs, which also feature a 36-litre refrigerator, will be allocated to individual drivers while a roster system is used for the day cab trucks. These new Mack Anthems are
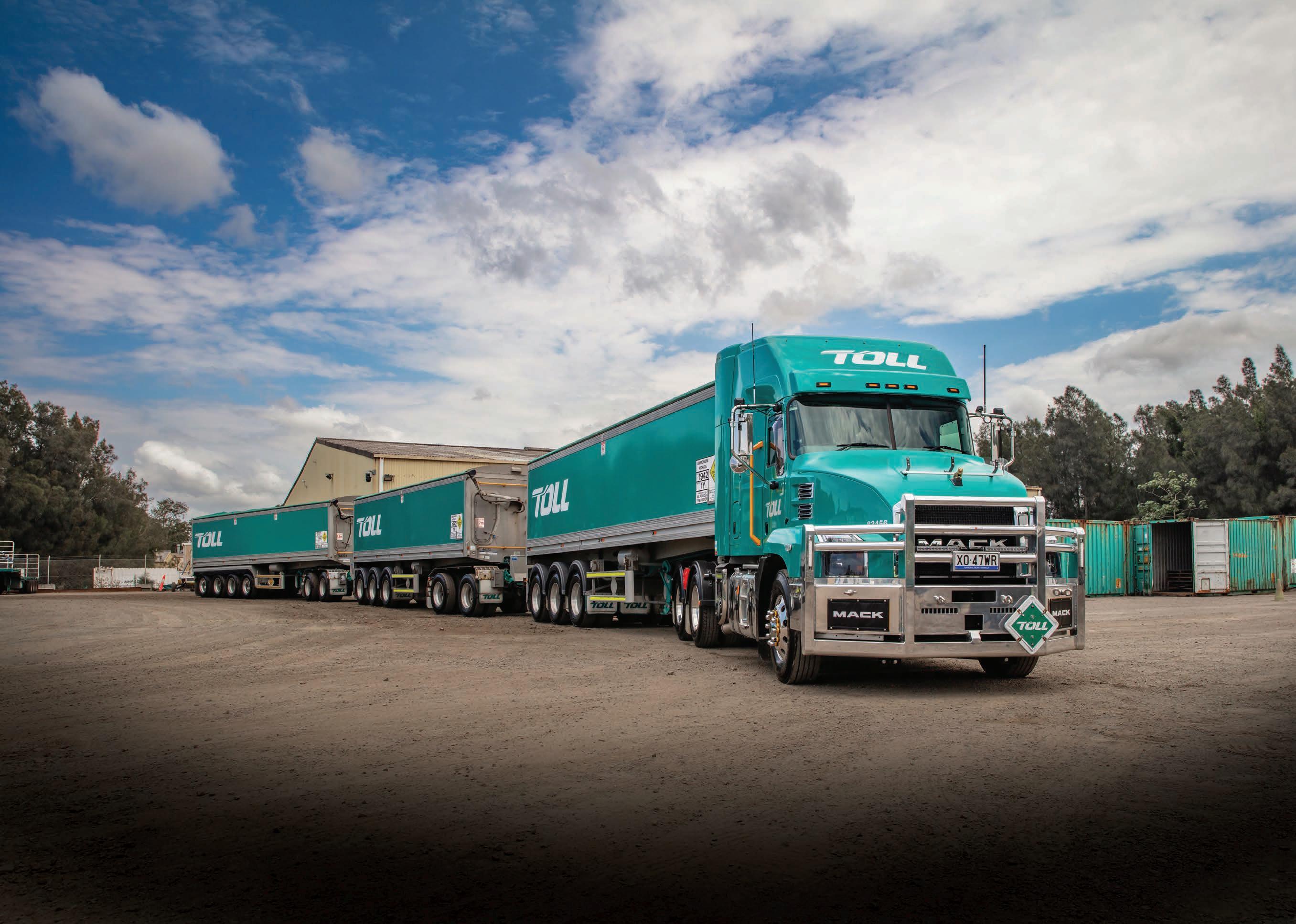
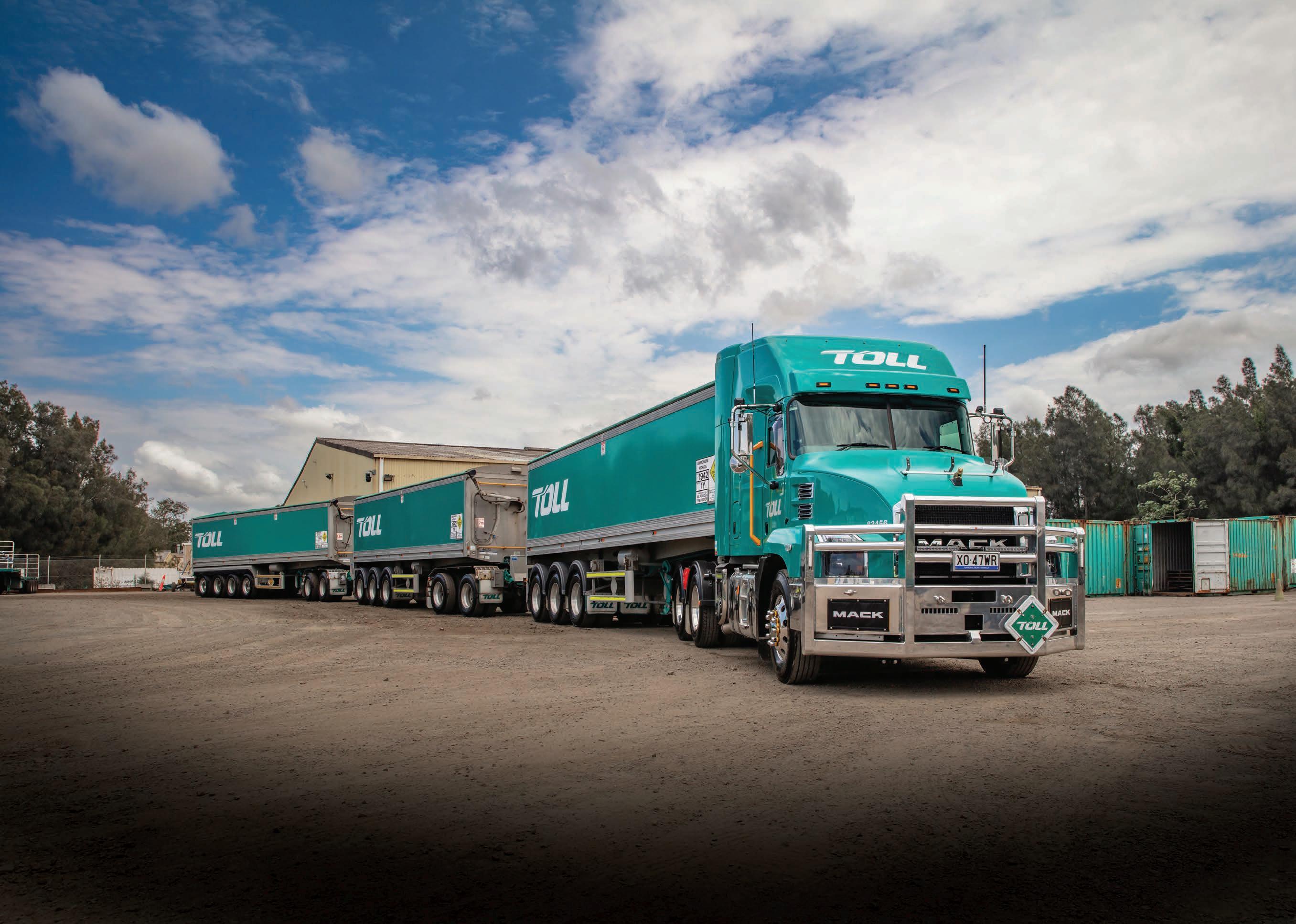

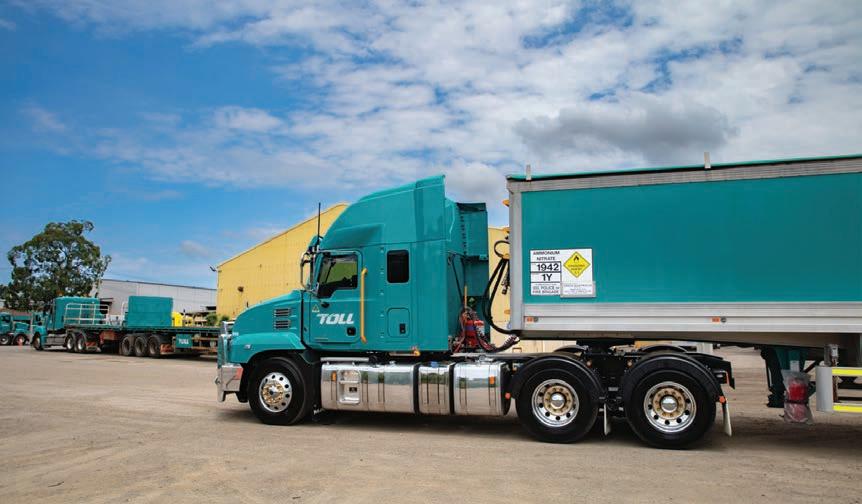
rated to 90-tonnes in either cab speci cation.Whatthisdoe s is afford Toll the option to run A-double and B-double combinations while giving them the opportunity to extend the con guration s, when appropriate, in the future. Delivery of the trucks was time critical in that it aligned with certain contracts and load requirements according to Mitch Brooke, Toll Group National Manager Fleet & Maintenance. “The introduction of a new batch of vehicles like these Anthems is very important to us for our operational uptime and that’s why the decision has been made to bring in the new vehicles
in order that we meet our customer demand and expectation,” he says. “In terms of trailers they will do everything from barrels to end tippers, belly dumpers to at tops — a wide range of trailer types and con gurations.”
Transport Operations Manager, Paul Nicou has been with the business for 22 years. He came across to Toll in 2006 when it acquired the nal shareholding of the R&H Transport business bringing the site under their control.
“There’s been a signi cant change in the work that we do,” he says. “Now there’s a more specialised focus on dangerous goods whereas the site initially
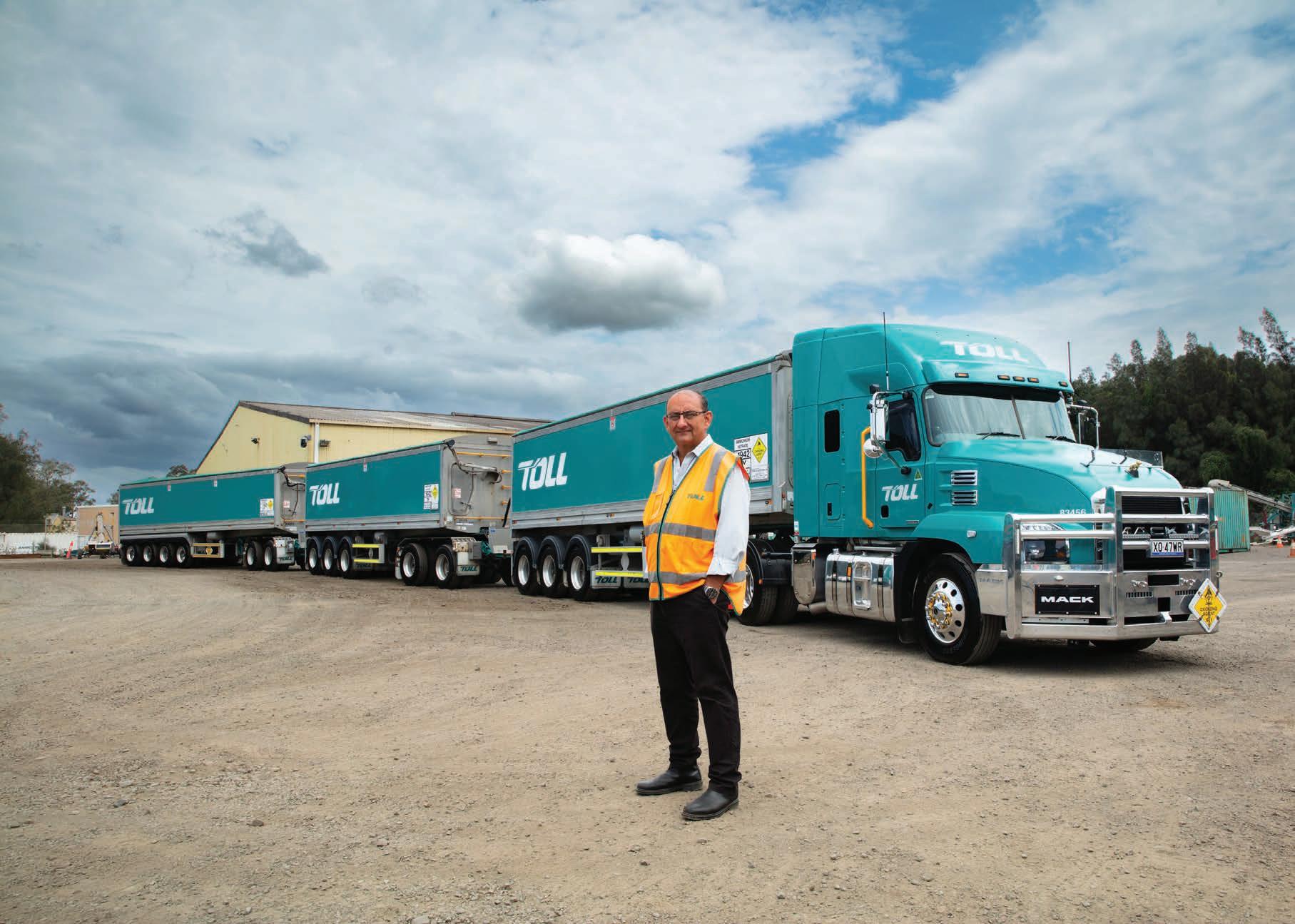
moved the likes of general freight and aluminium.”
Chris Yourell, Toll Group General Manager Dangerous Goods Transport, has been with the company for 18 years having joined after the full acquisition of R&H Transport.
“Interestingly, these are the rst Macks in the business unit,” he says. “We did a review and along with our preference to move to a single platform on the driveline we had a clear cost of life cycle bene t.”
Mack’s ability to meet the asset requirements which are very speci c to a trailering eet that features
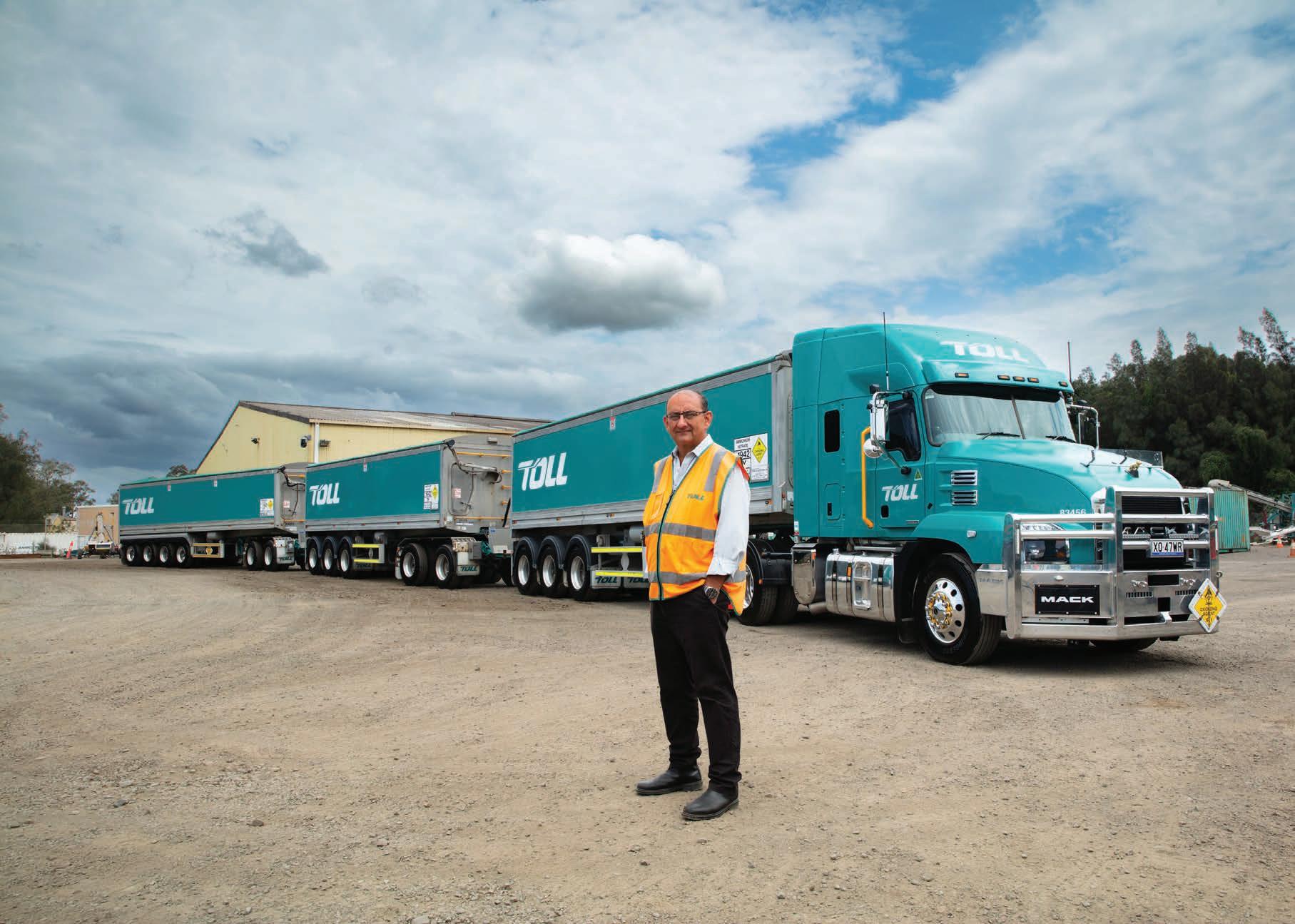
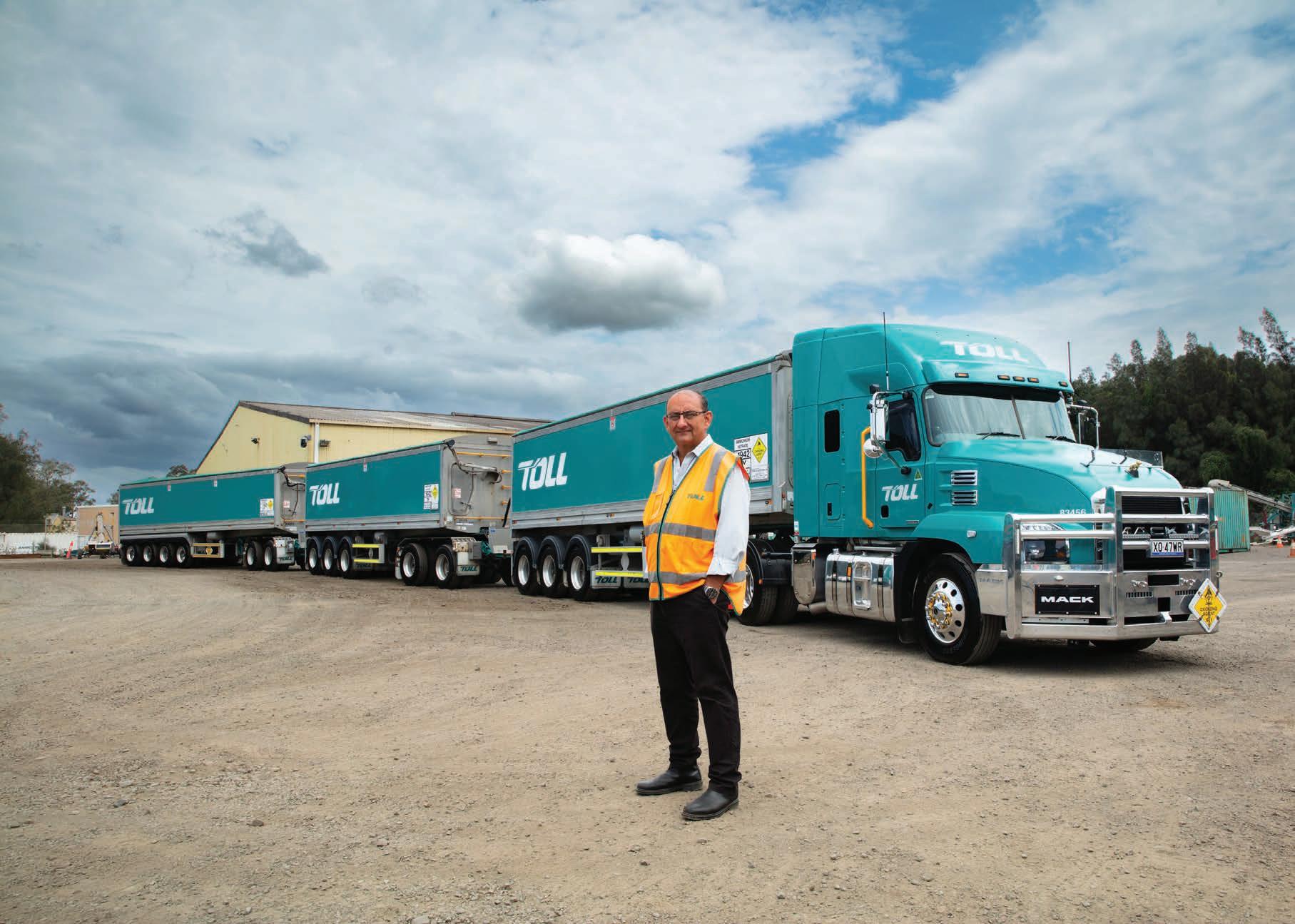
A-doubles, tri-quad B-doubles and quadaxle singles
The prime movers must also be compliant with the dangerous goods code. In addition to battery isolation and GPS tracking, re suppression is mandatory on the engine bays and on the hubs. Temperatures on the hubs, but also the trailers, are monitored and feeds back into the cabin so that if a driver receives an alert for an elevated temperature, he can deal with it immediately.
“The eet needs to be compliant to meet that regulatory framework when operating at a major hazard facility,”
says Chris. “The drivers need to have a very good understanding of the requirements of pick-ups and deliveries in these facilities.”
All drivers out of Tomago are DG (dangerous goods) quali ed and must receive a security clearance to load and discharge the various trailer combinations.
A new vehicle platform brings with it new architecture and a different driver experience. To get the most out of the trucks, driver training is necessary, and this service has been provided by Mack to Toll’s inhouse driver trainers.
“Obviously, we have got a change
management process so that’s all been completed and now drivers are being passed out to operate and to maintain the eet,” says Chris. “It wasn’t a case of go visit a dealer and pick up your truck. Mack had people on site in our Tomago operation handing over the assets and training our people. Now we’re looking forward to getting the remainder of the new eet embedded into the operation.” The rst unit has kindled great interest among staff at the site, not in the least the drivers. The lucky operator, Trevor Archer, who has piloted the rst truck as a B-double tanker set to Melbourne return on a couple of occasions and into

some mine sites, is “ecstatic” about his experience according to Trent.
“The driver said it rides like a dream,” he recalls. “He thinks it’s the best thing since sliced bread.”
This marks Trent’s twelfth year at Toll. He began as a boilermaker repairing tippers and at tops. After completing his diesel mechanic apprenticeship, he worked on the oor for another six
years before moving up to a day shift team leader and then the supervisory role he now holds. He’s had ample opportunities to service a wide range of bonneted American style trucks. Having worked across all 46 vehicles, he says his experience with the Mack product was negligible until these latest Anthems arrived. Since then, he has managed to go on some drives and the
driver comfort and lighter Mack Air Ride suspension are immediately noticeable. “Comfort-wise the crew are more than happy with them,” he says. “The bunks are great as are the long-range tanks and the bigger fridges and the lighting in both the interior and exterior is fantastic.”
The new Mack Anthem is in full possession of the latest advances in

lighting technology and features LED roof clearance lamps and daytime running lamps that provide better expansion according to Trent.
“The square chunky headlamps behind the bullbar give the Anthem not only a better distance but spread,” says Trent. Paul, who notes convenience is now a major factor for his drivers, agrees.
“There’s good vision and everything
in the cab looks well-appointed and prepared,” he says. “With good facilities easily within reach and easy to operate, it’s a very tidy truck.”
The grab handles are safety yellow for better visibility in low light, ensuring drivers can have three points of contact whenever they exit or enter the cab. Along with the other accents, such as the re ectors which are mounted
above the windshield, the tanks and splashguards, are at one with the Toll ‘green’ colour scheme.
“The new Anthems look rugged and the MP8 engines are tough,” says Trent. “When you’ve got the gold dog on the front of it you know it’s all Mack and Volvo genuine parts. It makes our life easier given the trucks are easier to diagnose and easier to get parts being that it is a single platform.”
With the biggest eet of heavy vehicles in the country working across several divisions and then smaller units beneath those, Toll must excel in both selection and exclusion of its asset mix.
“We’ve gone through an extensive exercise to determine how we best operate and refresh our eet,” says Shaun O’Flaherty. “In the process of that journey we’re looking to drive down the average age of vehicles and operate the most reliable and fuel-ef cient eet that’s possible.”
Based in Melbourne, Shaun is the leader of the Global Fleet Management team. He’s been at Toll for seven years having been active in several positions previously. His role is to acquire the optimal eet suitable to the task and provide that service to the business units who run the contracts.
“Toll has an RFP in the market that involves signi cant expenditure across the next two nancial years,” says Shaun. “That will involve a strict procurement process to reward the work accordingly.” Mack, and Volvo by extension, have been a longstanding and important OEM partner of the Toll business.
“The Mack Anthem from all accounts is a reliable and relatively new prime mover and we’re really excited to take ownership,” says Shaun. “Mack has been an integral component in the eet anatomy of Toll over many years and we’re really excited to take delivery of this parcel of new Mack Anthems set to enter our operations in the very near future.”
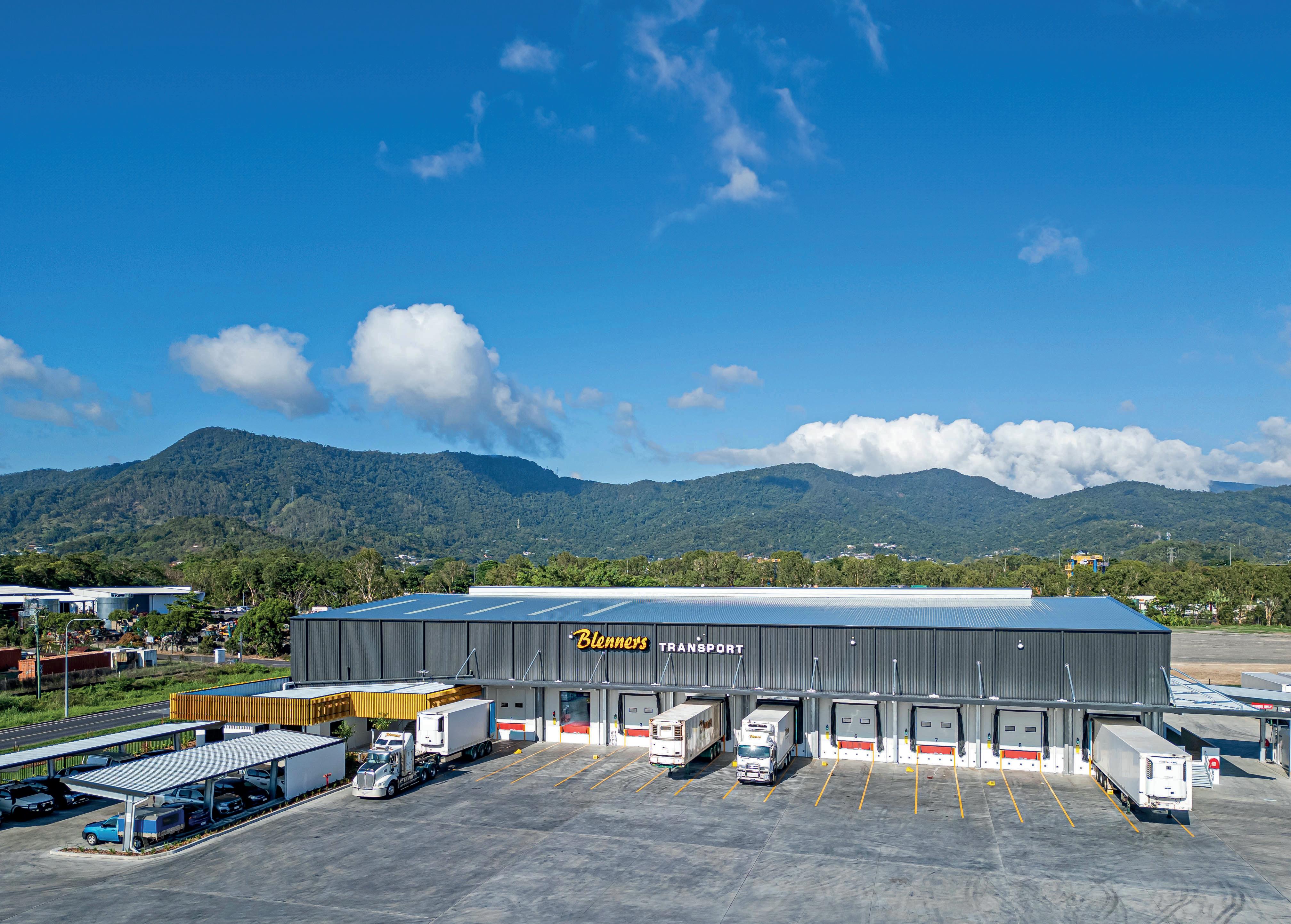
POINT TURNING
Blenners Transport has unveiled a $17 million new transport facility in Cairns.
Nearly ten years of farming — bananas initially and some sugarcane later — took place before Les Blennerhassett branched out into moving his own cargo by road in 1988. That business, more commonly known as Blenners Transport today, moves fresh produce to market nationally from Far North Queensland where its head of ce is situated in Tully, along the Cassowary Coast two hours south of Cairns.
The Cairns depot has just been replaced.
The business, a week before Christmas last year, moved into a new $17 million state-of the-art facility on a 16,000m2 site.
The footprint of the new building, which itself takes up 3,200m2, is considerable and dwarfs the previous site.
It’s a major distribution point for the region and the Atherton Tableland, a
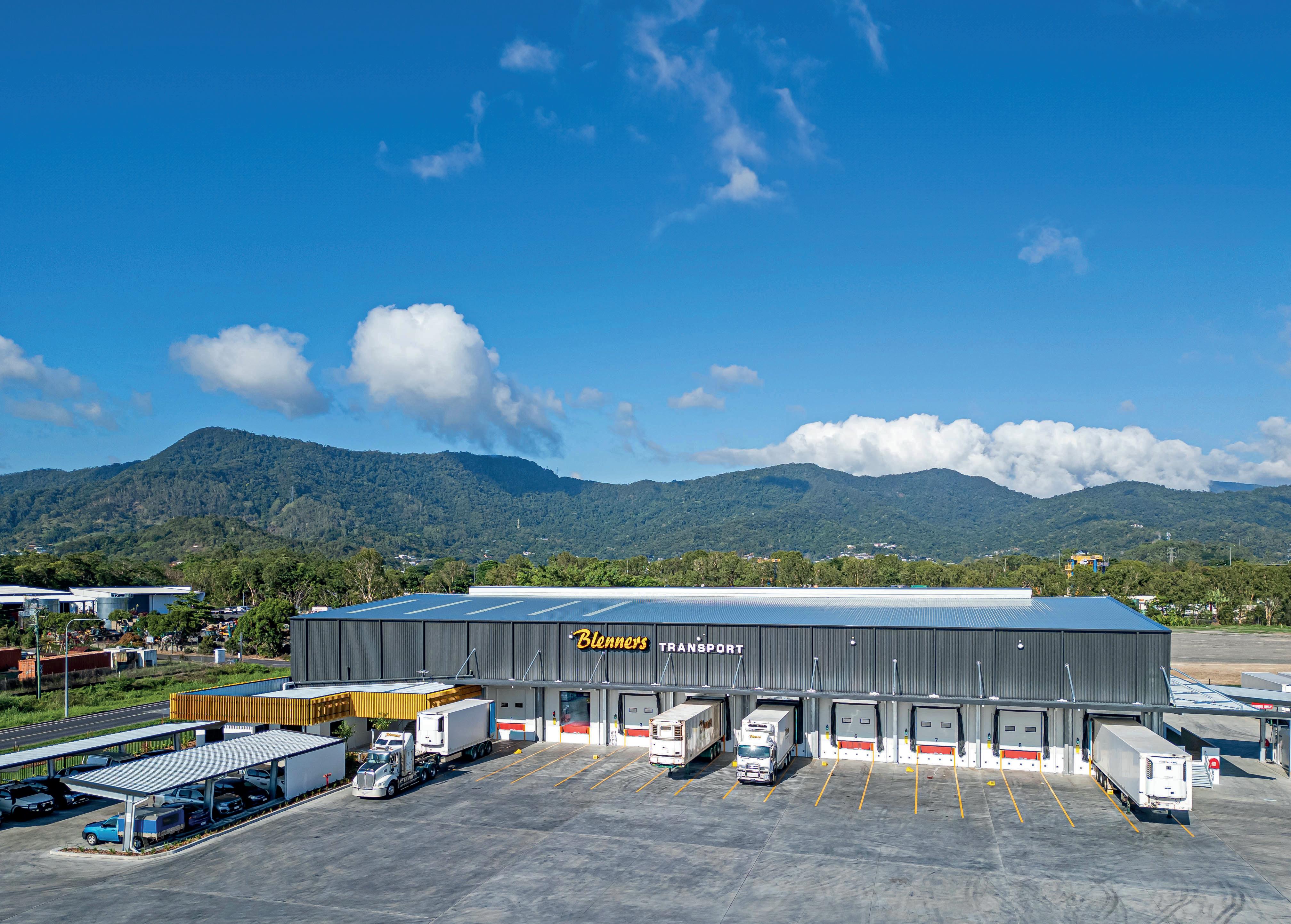
sprawling food bowl to the west that produces mangoes, avocados, bananas, blueberries and citrus varieties, all which Blenners moves to every capital in Australia.
Designed and built by Keir QLD, the depot features nine docks with freezer and chiller storage, and dry storage in addition to hardstand and washbays for Blenners’ own daily transport activities. The dry storage area has provision to hold 600 pallets while freezer/chiller capacity is now 900 pallets.
Being a main node for its linehaul freight, 12 dedicated vehicles work out of here full-time servicing Cairns and the nearby Tablelands. With that said, it’s no small provincial operation.
Blenners Transport operates 180 prime movers in its national eet, all of them Kenworth and riding on Meritor
drive axles. The most consequential development in the eet, outside of its recent monogamous commitment to the PACCAR bonneted truck, is the adoption of Performance-Based Standards of which there are a growing number of vehicles now at work nationwide.
Blenners is approved to run 18 PBS B-doubles with 38 pallet capacity and two 26-pallet PBS singles. Into Melbourne, 2680 kilometres away or 29 hours uninterrupted, it runs four 44-pallet PBS roadtrains and a new Kenworth T659 was recently purchased explicitly for this leg. “PBS represented a signi cant change to our business and the scheme continues to drive opportunities for us,” says Les. “To give us that extra capacity while allowing us to go straight into town without having to drop a trailer is one of the many bene ts.”

Already on order are eight new 42 pallet B-doubles sets con gured as 16-pallet leads with 26-pallet rear trailers. These will be designated east coast linehaul duties between Brisbane and Cairns. A pair of new Kenworth K220s, the latest model from the OEM, have been speci ed for this B-double haulage with seven more in the pipeline.
“We save a lot more on extra fuel and drivers wages now that they are pulling 38 pallets instead of 34 and it will improve more when we start pulling the 42s,” says Les. “It’s an advantage to us as drivers are now hard to nd. What we can do now is move many more pallets in any given week with the same number of drivers.”
The preference, at least on the heavy vehicle eet, customarily is for a 4:11 differential ratio. The new K220s, however, are being operated slightly lower on a 3:9 diff ratio for added fuel saving given the Cummins X15 engine and Endurant XD Pro 18-speed automated transmission can effectively talk to each other. The drivetrain produces 550hp with a maximum output of 2000 lb/ft.
“The drivers are nding it smooth to operate,” says Les. “It’s a good ride. Our rst was an early demo model and we’ve just added a brand-new unit.”
PACCAR are going to provide additional airbag support for the rear of the cab next
month something its predecessor, the K200, didn’t possess. The small airbag, which can be tted by the customer to the K220, will help take out cabin kick when passing over railway crossings and rutted roads more common in ood prone areas. The Queensland food market has a big presence in Perth, and as a result, so does Blenners. Because of the two-week turnaround, Blenners runs 28 roadtrains of its own to Perth every fortnight. Last week alone it completed 20 return trips on roadtrains using its own trucks as well as subcontractors.
The roadtrains travel down through the middle of Queensland via Charleville and Cobar, then Broken Hill, Port Augusta, Ceduna and then onto Perth. On shorthaul the Kenworth T410, powered by a PACCAR MX-13, is favoured.
PUD work is equally important. The eet operates 45 Isuzu FXZ and FXY 1500s that it nds reliable and robust across its eight depots where the conditions are, for the most part, hot and humid. The Isuzu eet is currently being turned over to an eightwheel spec. Very soon every Isuzu will have an Allison automatic gearbox.
“There’s less wear and tear moving to the automatic transmission, so we’ve changed to Allison and we seem to be having a good run with those,” says Les.
Tully is widely considered one of

Australia’s wettest towns. It holds the record for the highest daily rainfall at 1140 mm. Annual rainfall recorded at the Tully sugar mill is 4000mm. These can be trying conditions on equipment. When asked if Isuzu lives up to its reputation for reliability, Les is quick in response.
“What’s the top-selling body truck in Australia? What’s the top selling prime mover? I never buy on price. I always buy on quality,” he says. “The Isuzu is as good as gold. Grease them and change the oils, and away you go, especially now that we have gone to the automatic transmission.” He feels similarly passionate about his prime movers.
“They say you can’t afford a Kenworth and I say you can’t afford not to have a Kenworth,” Les continues. “Some of my Kenworths are ten to 20 years old and if we give them a bit of a freshen up or put them online for sale or out on the street, they sell in ve minutes. When you look at the whole-of-life cost of a truck Kenworth is by far superior. When you’re going to get rid of the other brands, you’re going to burn more than the 30 or 40 thousand dollars you saved at purchase point.”
Recent years have occasioned an expansion of the company footprint. Blenners now services the major meat industry wholesalers and the extra capacity at the new depot accommodates the uptick in


extra freight that also requires temperaturecontrolled storage like that for frozen chickens. With state-of-the-art ammonia refrigeration, the new facility is a major upgrade on the previous depot, which was operational for some 15 years.
The build took just on ten months to be completed. Over Christmas Blenners had over 150 pallets of ice in storage to cope with local demand. Australian Liqour Marketers is storing alcohol during the wet season for when inevitable disruptions impact road and rail. Some 300 pallets of alcohol will be moved out from the Blenners depot in Cairns intermittently by April.
“It’s great we’ve now got that capacity and you get all those little add-ons that help pay the power bills,” Les says. Inbound from Brisbane it receives goods from food suppliers like IGA, Bidfood, PFD Foods and many independent grocers. In Cairns a new tug is used to move the 80 refrigerated rail containers in the eet to the rail line which is only 500 metres away.
Blenners Transport employs 550 people, nearly all of these are based in Queensland where all eight of its depots are located between Brisbane, Rockhampton, Mackay, Townsville, Tully, Cairns, Mareeba and Innisfail.
Moving produce from a region vulnerable to cyclonic conditions brings with it
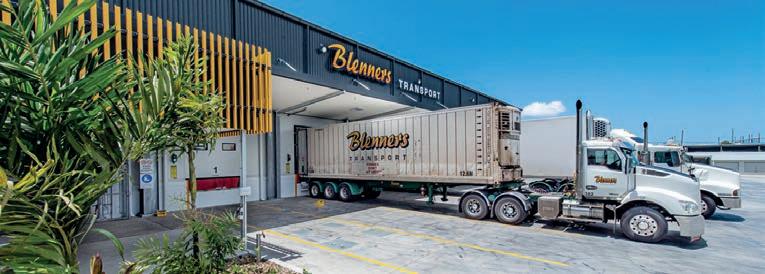
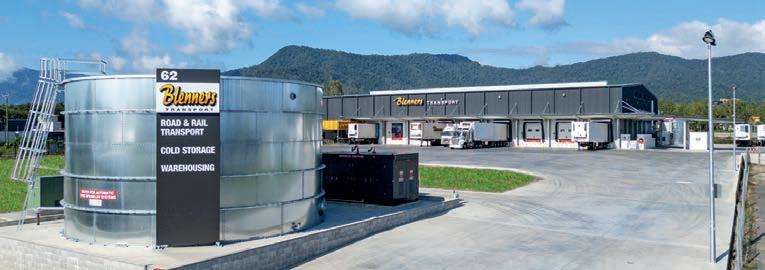
unique trials and a greater sense of resilience. Ahead of these severe lowpressure events, Blenners Transport can be overloaded the week before by growers, especially the banana farmers who need to cut as much as they can.
“They want to get them into boxes rather than pick them up off the ground,” explains Les. “Instead of a big plump banana everyone will be cutting skinny to get them into boxes.”
Unlike the mango tree, a banana tree will blow over in a severe storm. Mangoes although more tolerant to higher winds, and not unlike lychees, do need colder conditions to ower.
“The mango crop was down last year because there was no winter up here,” says Les. “Without that seasonal change it was a small clearing. The avocado crop, however, looks like it is going to be as big as the previous year.”
According to the Australia Trade and Investment Commission, Australia is the third-largest consumer of avocados in the world, at 4.5 kg per person each year. In 2022–23, the nation produced 10,685 tonnes of avocados, valued at more than $58 million. That makes Australia one of the world’s top 20 producers, led by Mexico, Colombia, and Peru.
The new depot is more than equipped to help store and distribute the latest
bumper crop of avocadoes or any other perishable goods, for that matter. It represents yet another crucial turning point for the business — and there’s been several. When QRX in 2002 pulled out of Tully, a market Les could never get a start in, Blenners snapped up many of their growers and essentially doubled in size. That was followed by a move into the Mareeba area after Cyclone Larry in 2005 to carry mangoes after the banana crop was effectively attened by the cyclone. The drop in productivity was extreme. Blenners went from transporting 110 loads of bananas a week to moving just six. Now it’s one of the major produce carriers out of Mareeba.
On that score, Cairns represents another major milestone. With the additional docks the trucks, according to Les, can be unloaded and reloaded at twice the speed compared to the previous site.
“It’s pleasing we can turn around our trucks a lot quicker,” he says. “It’s made a massive difference. Instead of all the drivers sitting out in the street waiting to get into the dock when there was only four, they can come back to the yard and drop the B trailers on them and put the A trailers on, get them unloaded and get out of there. It’s going to be a big labour-saving exercise.” He adds, “There will be a massive saving in hours of the week.”
STEEL
For more than 40 years Nubco has been a reliable supplier of steel and industrial products in Tasmania.
Established in Devonport in 1983 Nubco has evolved from humble beginnings to become a leading supplier to both trade and DIY customers of an extensive range of power and hand tools, steel, fasteners, hardware components, welding equipment, trailers and trailer parts, tool storage solutions, machinery and other industrial products. Nubco now has seven stores strategically located throughout Tasmania and supported by an in-house eet of eight trucks with the most recent acquisitions being three extra-long wheelbase Hino 500 Series FM2628 rigid trucks.
Operating its own eet of delivery vehicles is an important factor in Nubco being able to provide solutions for its customers. Predominately the trucks are used to carry and deliver steel products and reinforced mesh up to nine metres in length on the custom-built steel bodies and the latest Hino’s also have the capacity to carry up to 12-metre lengths of structural steel utilising the certi ed heavy duty racks which also incorporate cross bars mounted to the cabin’s roof.
“We chose Hino, as the vehicles are well suited for our multiple applications,” says Todd Cordwell, Nubco’s State
Operations Manager.
“We go to variable sites and we understand delivering long and dif cult to handle products and having the right truck for the job is paramount to us.”
Based at the company’s Hobart head of ce, Todd has been with Nubco for 17 years. His background is in the fast-paced environment of retail management with one of the ‘big two’ supermarket chains.
The Hino FM 2628 6x4 trucks are equipped with airbag rear suspensions and Effer chassis-mounted cranes. The
custom body trays were manufactured in Launceston using steel provided by Nubco.
Access can often be challenging when delivering to locations such as building sites and safety is always the priority, especially when negotiating unstable ground and in close proximity to power lines.
“We have a process where our people will go through a pre-delivery check list,” explains Todd. “We will try to eliminate every safety hazard or awkward possibility the drivers might
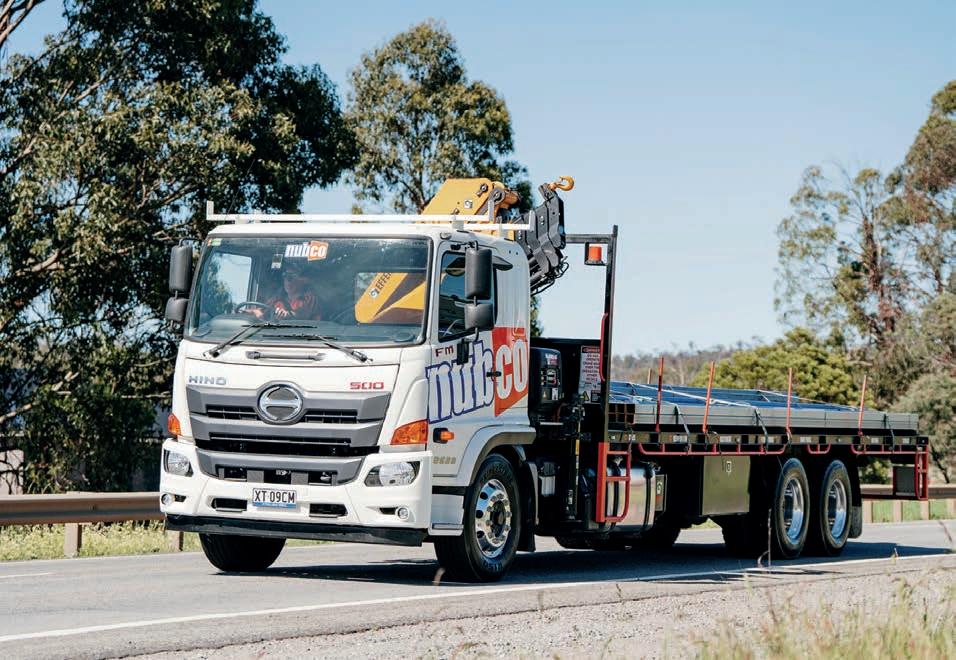
STEEL
run into on a site. We ask the customer to ll out the paperwork honestly so we can ful l our delivery commitments to them.”
In addition to the dangers presented by power lines, other practical factors such as the turning circles of the trucks, gate openings and tree branches need to be considered.
“These Hino trucks we are running are
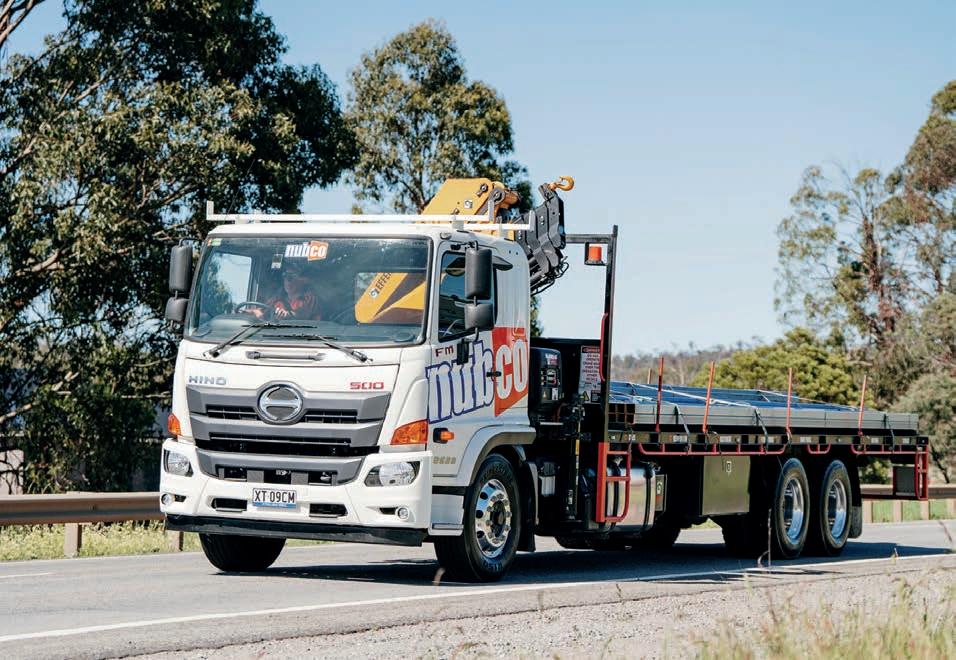
OF APPROVAL
the size of a bus, so we need to be able to turn a bus around on site,” says Todd. “We make sure we can get in and out and do everything we can to eliminate surprises when we get to a site.”
Nubco’s transport operations began with six metre bed medium rigid trucks without cranes delivering steel to customers and as the business built up it has progressed to trucks with eight-
metre long bodies and chassis mounted cranes. The load capacity is increased by the tment of overhead load racks which, although initially restricted to less than one tonne, proved the concept and have been further developed. The six-metre bodied trucks remaining in the eet still perform well in tighter suburban situations where the longer vehicles may have access problems.
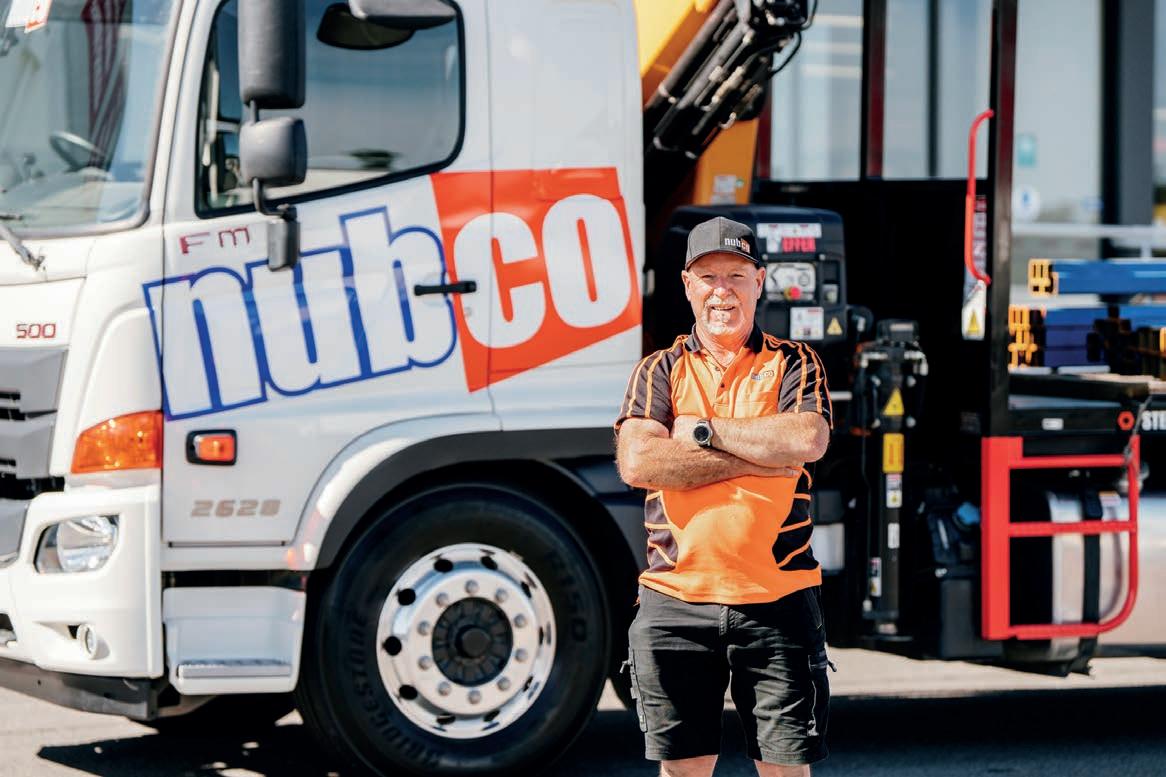
“With these latest Hino trucks, we’ve been moving from Medium Rigid to Heavy Rigid and we’ve been able to double the payload carried on the bed and also been able to get extra capacity up top on the racks as well, which has been good for carrying structural steel beams and reinforcement mesh,” says Todd.
Handling heavy and slippery steel product can de nitely be a challenge but for the time being the Heavy Rigid option from Hino has been a good t for the Nubco operation.
“There have de nitely been some growing pains, and it’s been a bit of a journey, but that’s a good thing,” Todd says. “We’re still evolving and have still got lots of things to consider and at some stage, depending upon the direction, we might go to extendable
semis, who knows?”
The drivers are required to be pro cient in load restraint procedures as there can be a variety of Nubco’s products being carried at any one time.
“It’s the typical logistical things you’ve got to work through,” says Todd. “The trucks are packed depending upon the product mix. There can be mesh on the bed and steel up on the top racks, and then some consumables and smaller items on board to be delivered.”
Operating the cranes adds an extra dimension to the drivers’ tasks and training in safety awareness is important to the Nubco team.
Dale Richardson is a Launceston based driver who is valued not just for his driving and crane operating skills, but for his attention to the safety aspects required by his job.
“There’s ‘drivers’ and then there’s drivers,” says Todd. “But Dale is certainly a top operator who is dedicated to safety.”
Although the trucks are seldom anywhere near their maximum weight capacity, the con guration of a truck tted with a crane and its associated components, such as tanks for the hydraulic oil, can lead to premature wear and tear on the front tyres as well as the front axles and suspension components. This has been more evident with the earlier Medium Rigids and the newer heavier capacity Hinos have not had the same issues.
Servicing is performed under a contract with the local FRM Hino dealerships. Todd considers this type of arrangement a better alternative to ad-hoc servicing using third party workshops.
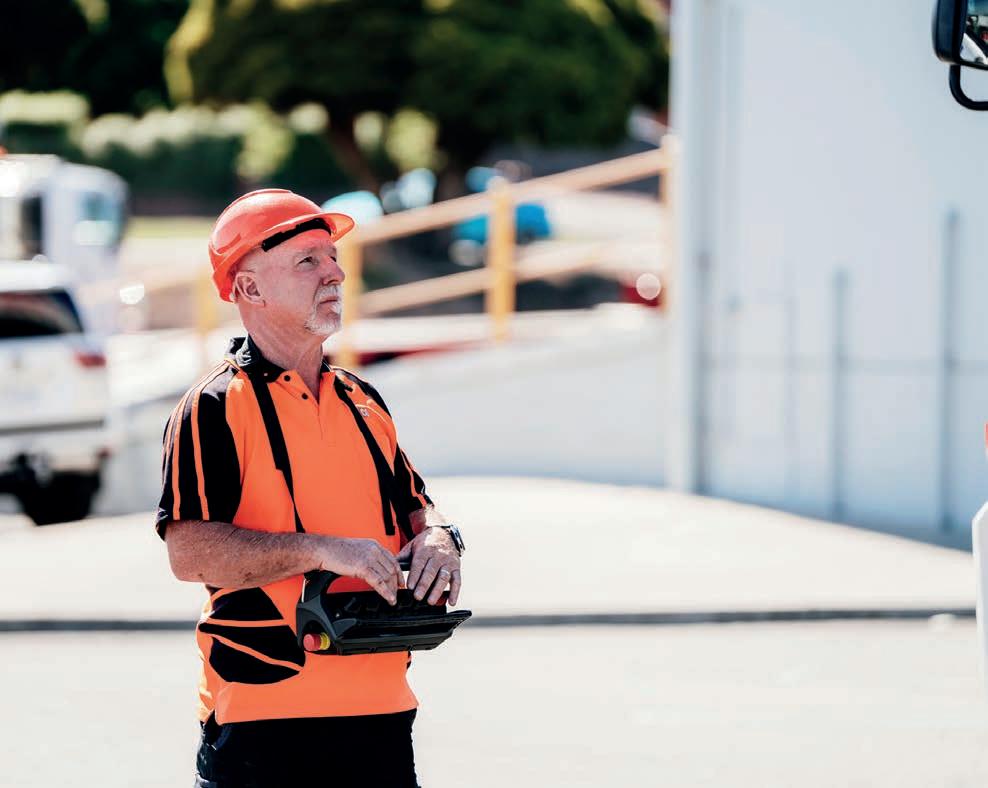
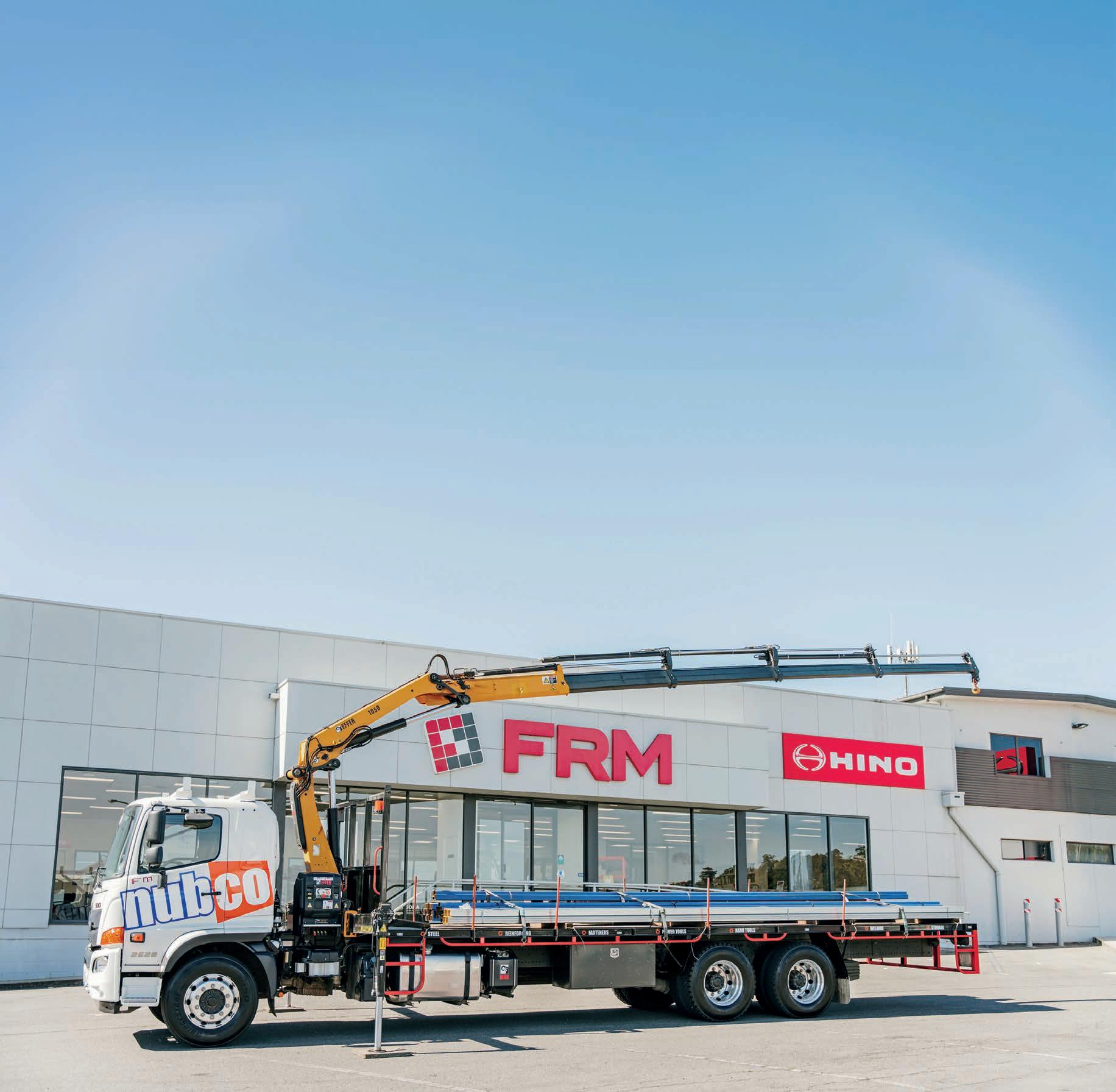
“We nd it a lot more ef cient and we don’t receive any nasty surprises,” he says. “We know what we are paying which assists cash ow and it helps with peace of mind as well.”
The drivers generally operate for set times between 7.30am and 3.30pm.
This allows them to be on site early particularly when delivering for builders. Although driver fatigue isn’t a fundamental issue, all drivers carry logbooks in case they have to operate more than 100 kilometres from their home bases such as when performing stock transfers between Nubco’s warehouses and stores.
The Hino’s eight-litre 280-horsepower engines have proven adequate for the tasks expected of them, as have the Allison 3500 six-speed full automatic transmissions.
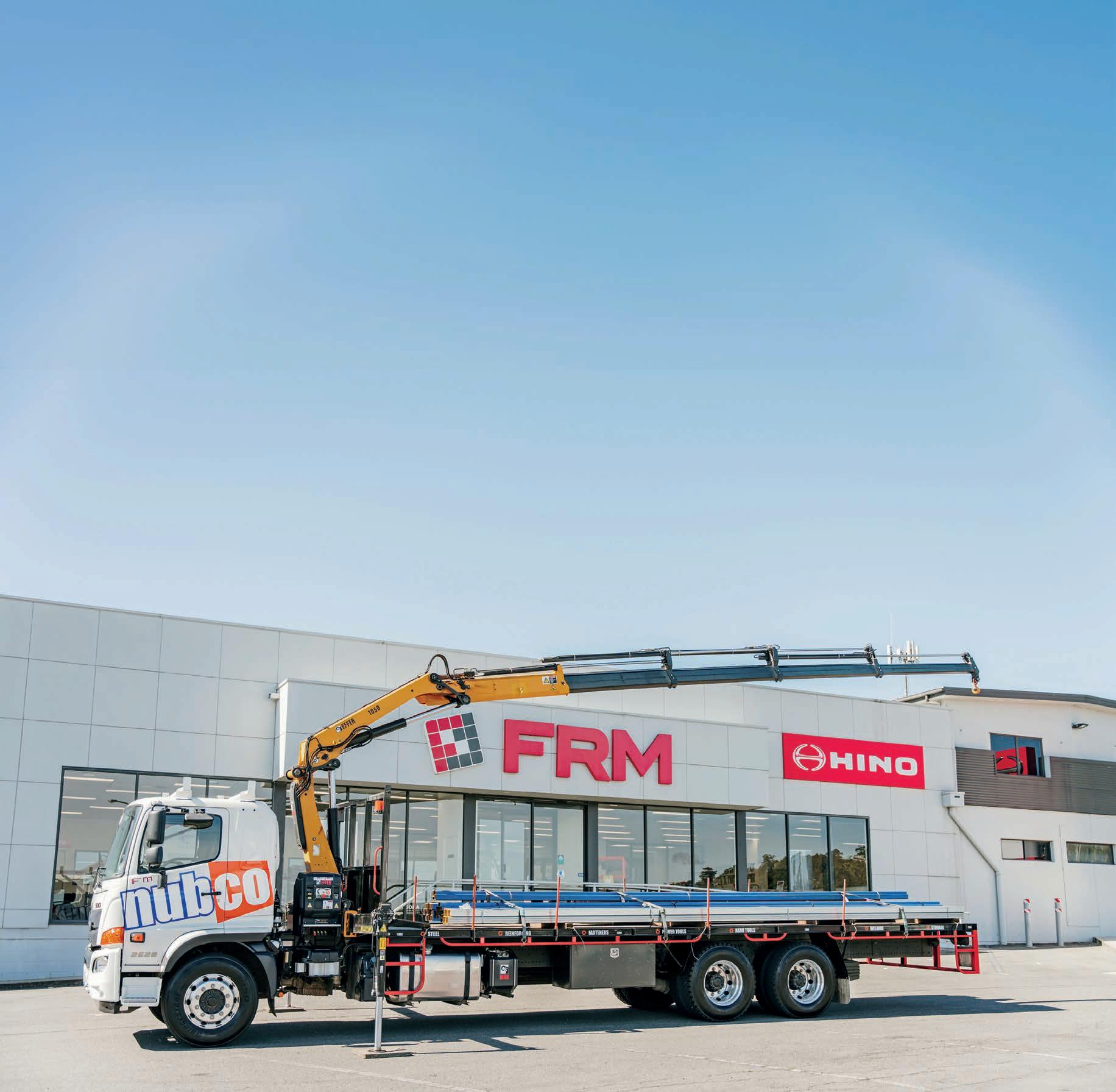
Understanding the customers’ businesses as well as their own has helped put Nubco in the position of being the ‘go to’ industrial product and steel supplier
throughout Tasmania. Not to mention, the safe and reliable operation of its inhouse eet has been a major contributor to the success of Nubco.
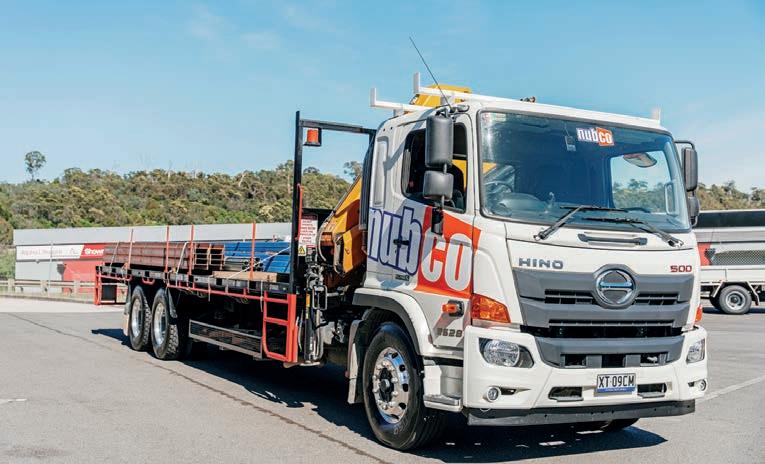

MIX THE RIGHT
Third generation, family-owned company, Eureka
Concrete,
puts serious hours on its trucks in Ballarat. It chooses TRP as its local parts retailer and Cummins Meritor as its preferred supplier of drive axles and di erentials.
The story of Eureka Concrete, a regional Victorian business begins in La Trobe Street, Ballarat in 1972. For more than 50 years the business, founded by Graeme Beaston and now run by his four sons Jason, Troy, Luke and Dominic Beaston, has processed and delivered concrete for the Central Highlands region where it has steadily forged a reputation for reliability and quality service. In addition to the multiple sites it operates in Ballarat, Eureka Concrete also has plants in Avoca, Beaufort, Ballan and Maryborough. The company employs 60 full time staff with another 15 sub-contractors.
General Manager Troy Beaston believes Eureka creates a competitive environment in the market because its opposition is dominated by multinational businesses.
“Being a family orientated business, we can give that personal advice and trust to our clients,” he says. “What differs us from our competitors is we provide backup service and support.”
Eureka Concrete runs several models in the vocational space including T360s, T358s and T359s from Kenworth for its 8x4 agitators, larger tri-axle 10x4s and some tipper trucks, which are the most recent additions to the eet. There are 45 company owned heavy vehicles before factoring in subbies.
Despite dealing with limited access on most sites the newer tri-axle trucks are delivering more payload and that outweighs any issues of manoeuvrability. The 9-metre barrel (up to 8.2 cubic metres) improves on the 7.2-metre capacity on the 8x4s, making them ideal for the bigger jobs on commercial projects and industrial sheds.
These Kenworth T360s have reversed the placement of the lift-axle which is commonplace at the rear of most trucks of this type. Eureka Concrete has moved the lift-axle to the front to counter its high frequency for having to back into sites while it also increases power to the drive.
“With the lift-axle in front of the drive axle it works a lot better to accommodate
that extra reversing required of drivers at many sites,” says Will Beaston, who is Head of the Workshop and the grandson of the now retired company founder. “The way to do it is to have the tandem drive wheels at the back doing all the driving and the lift axle oating around. That’s the way we have set it up.”
While Kenworth is the main brand of choice Eureka does have a few UDs, Macks and Mercedes-Benz trucks.
Meritor’s 14x tandem drive axle is standard gear in a lot of vocational segments. Eureka Cement spec it widely on their Kenworth and Mack vehicles. “It comes down to reliability,” says Will. “We’ve never had any problems with that product ever.”
The 14X tandem drive axle have succeeded Meritor’s longstanding 140/145 series, but conveniently feature the same axle housings, brakes, hubs and drums as the predecessor. A major difference is the larger main differential bearings in the forward rear axles that improve durability. The robust inter-axle differential is also 20 per cent larger
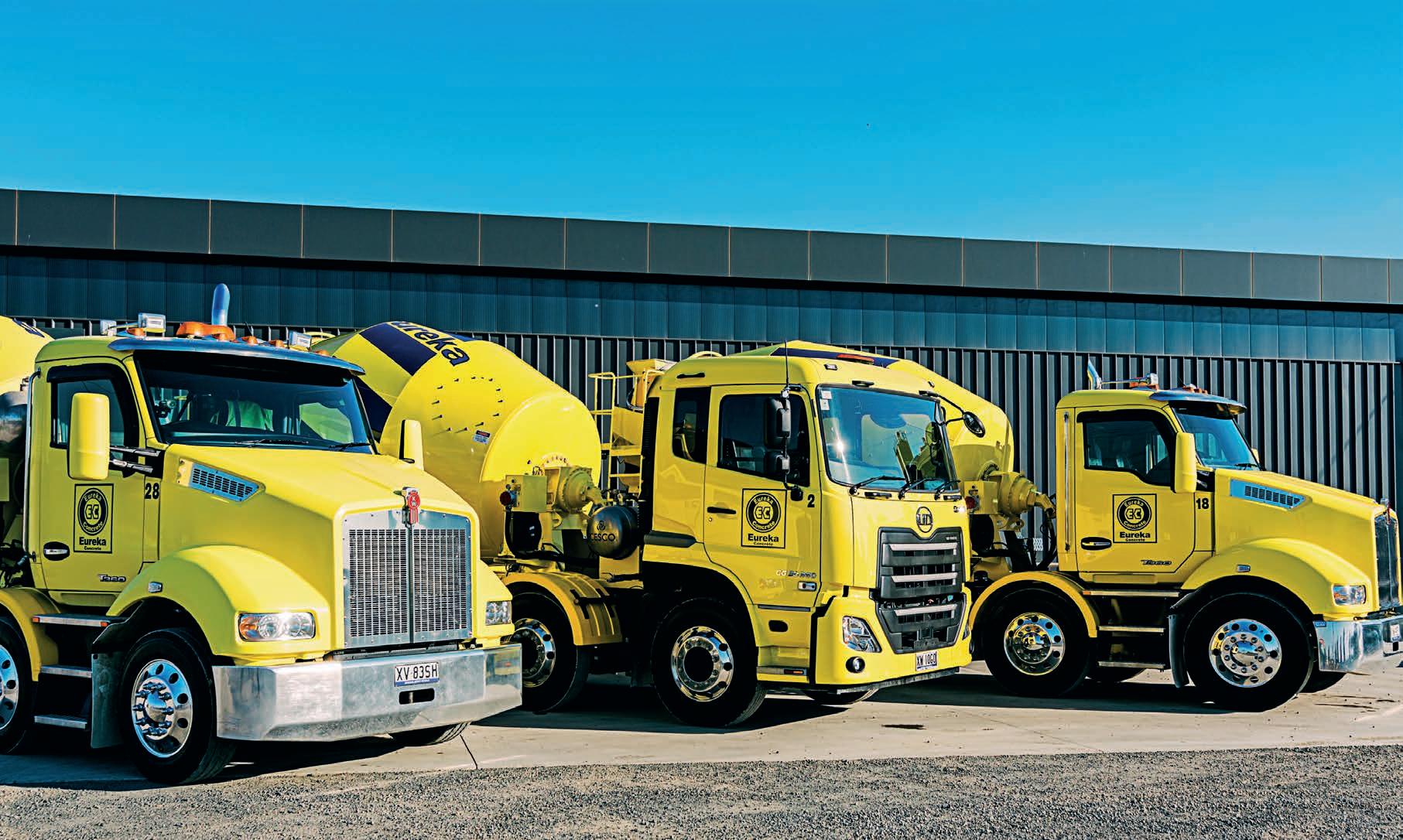
to comfortably handle today’s higher torque engines.
The Eureka Concrete workshop employs a specialist who services all the differentials in the eet. Oils in the diffs are changed between 100,000 and 150,000kms. The trucks receive a service every three months or between 300 to 500 hours, depending on what comes rst. This involves changing engine oil lters, fuel lters and air lters. During this process the brakes and suspension also get a general check over. Most of the repairs and servicing on the Kenworth product takes place in the workshop. When it comes to the condition and durability of the equipment Will is at the coalface.
“Meritor’s braking system is pretty good,” he says. “Because our agitators aren’t doing much highway work the brakes are nearly always in great condition. We work on the brake drums,
brake shoes, slack adjusters and seals. When the wear is there, we will tend to those accordingly.”
The business has had to keep pace with the recent housing boom and ongoing demand for commercial and civil infrastructure. Going the extra mile for the customer, no matter if they are only at the prospective stage, is inherent in the business. Even when at capacity for scheduled jobs, Eureka Concrete will take on more work should a customer need it. A steady stream of residential jobs offsets the civil works like kerbed roads and footpaths while lucrative windfarm projects have become a growing source of revenue in recent years. Bases for wind turbines involve signi cant concrete pours like the one Eureka did at the Skipton Wind Farm. They now operate a Con-E-Co batch plant for projects of this scale.
“The mobile plant we can put anywhere
we want at any location and distribute concrete from there,” says Will. “It can go anywhere in Victoria or Australia for that matter.”
The faster, mobile plant relies on a bin system. In the legacy plants they normally load by weights with front end loaders. With the bin system a bucket is poured directly into the hopper and from there that hopper will pivot and distribute it into the belt.
With so many jobs, big and small, in the of ng, Eureka Concrete can’t afford to have vehicles parked up waiting on parts. A major diff problem, after all, can immobilise the truck.
“We’ve had one diff in my time, which is seven years, malfunction,” says Will. “That’s not a bad record and that is going back ve years. Meritor is a very good product.”
A simplicity of design helps. Tapered dowels for the differential
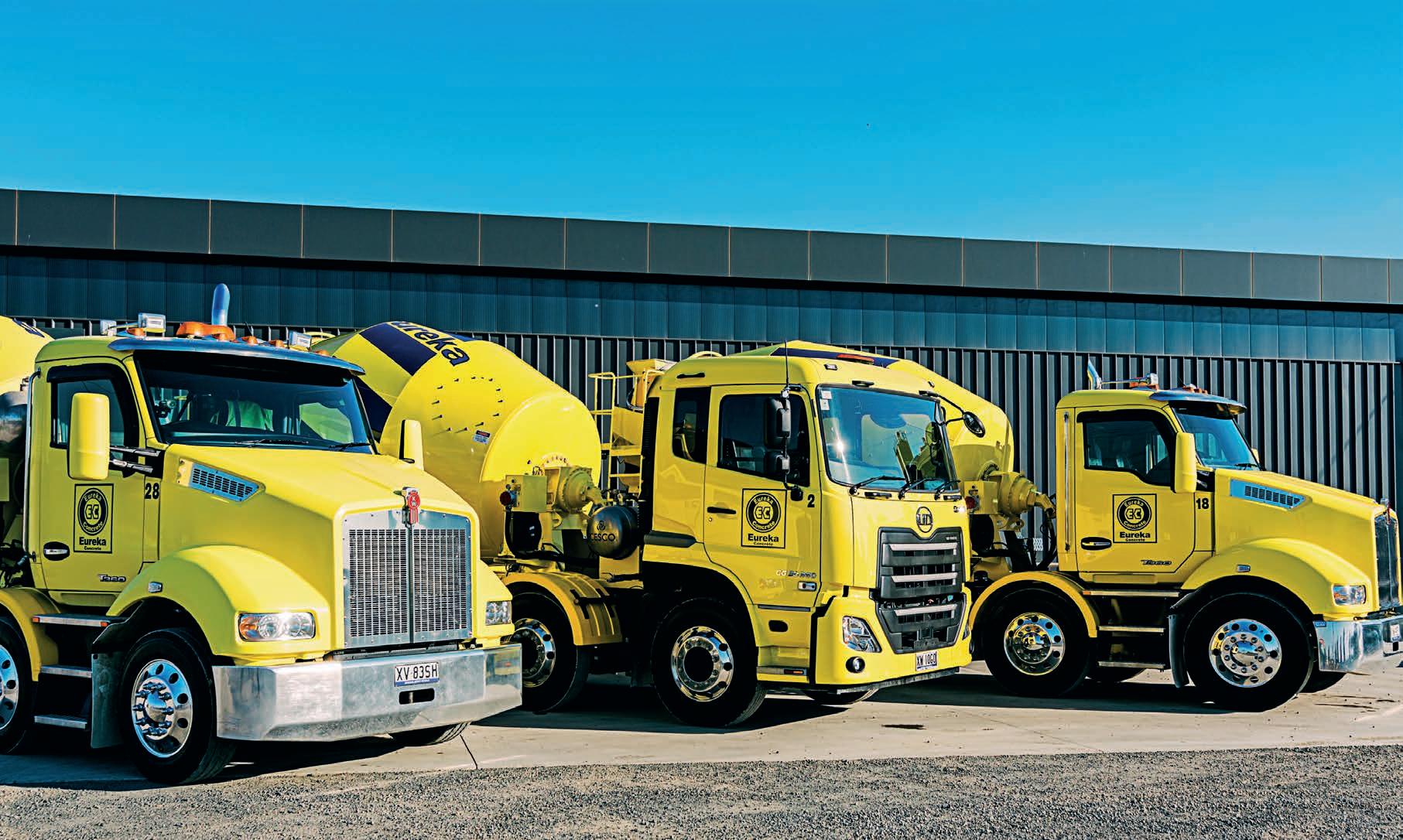
carrier to axle housing installation on the forward rear axles are in only four locations. This helps reduce stress points. The parts support is also excellent
according to Will despite the eet being based in a regional town.
“TRP do a really good job in supporting Eureka Concrete,” he says. “I need the parts inside a couple of days and TRP probably do the best service in Ballarat. They rarely don’t have something in stock for us and since Supervisor Andrew Davidson took over it has improved dramatically.”
Offering reliability to a business that values it so much to the point it underpins its very ethos, goes a long way in fortifying the relationship.
“There’s no need to be looking elsewhere,” says Will. “If something is not broken, we’re not going to change it.”
Service routines throughout the mobile assets are tracked via a Fleetware product. It helps to ascertain hours of use on the trucks for scheduling.
Drivers are also a big help. The vast majority have been designated their own truck and often understand the nuances of the vehicles, day-in and day-out, better than anyone according to Will.
“They do a prestart check every day where they jot down their hours, kilometres and note anything that might be off with the truck that morning,” he says. “That will be generated as a message and get sent out to me. I will book in the truck for a service and the repair that needs
to be done for that truck that’s had the prestart check.”
Across the eet the Cummins ISL 8.9-litre engine is the most prevalent power plant with an ISC 8.3-litre engine speci ed for the tip trucks.
Very few of the engines have thrown a piston to Will’s memory.
“That’s very good given the engine hours are up well over 24,000 hours of operation,” he says. “That’s a decent record. Some of the trucks have gone more with no issues at all.”
The memo for Eureka is not to treat its concreters and customers as just numbers. Delivering personalised service and great product reliably stems from that.
“Graeme Beaston before he retired used to run around pies and pasties and drinks for the concreters and customers,” recalls Will. “He was giving back as much as he can. As a family business our reputation is important and wordof-mouth in the local areas, we work is something we rely on. We treat all customers with respect.”
In the immediate community the company presence is palpable. Eureka Concrete supports many organisations in Ballarat and the surrounding district by advertising, sponsoring and spending within the local towns.
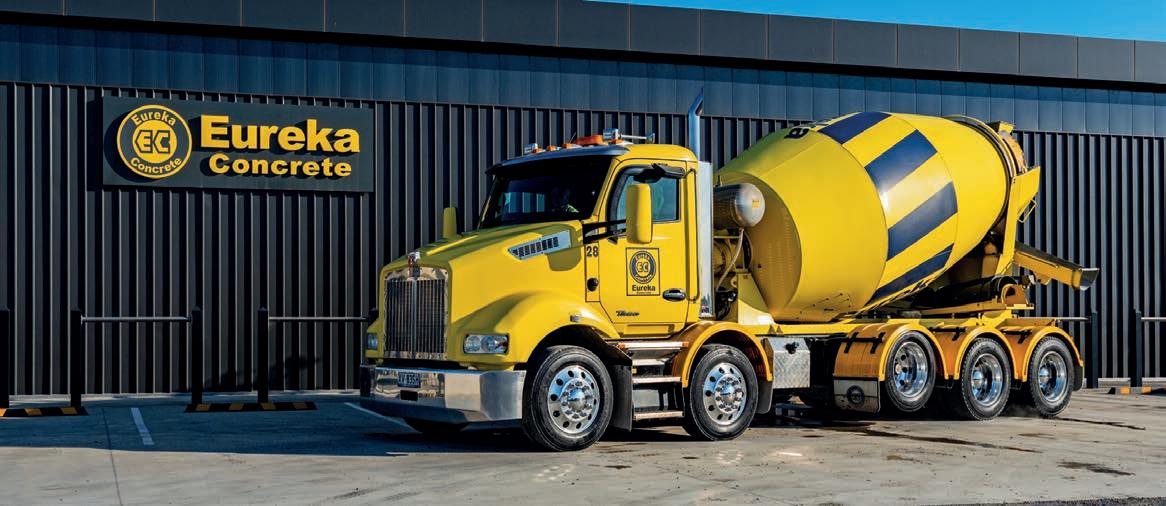
MARGIN
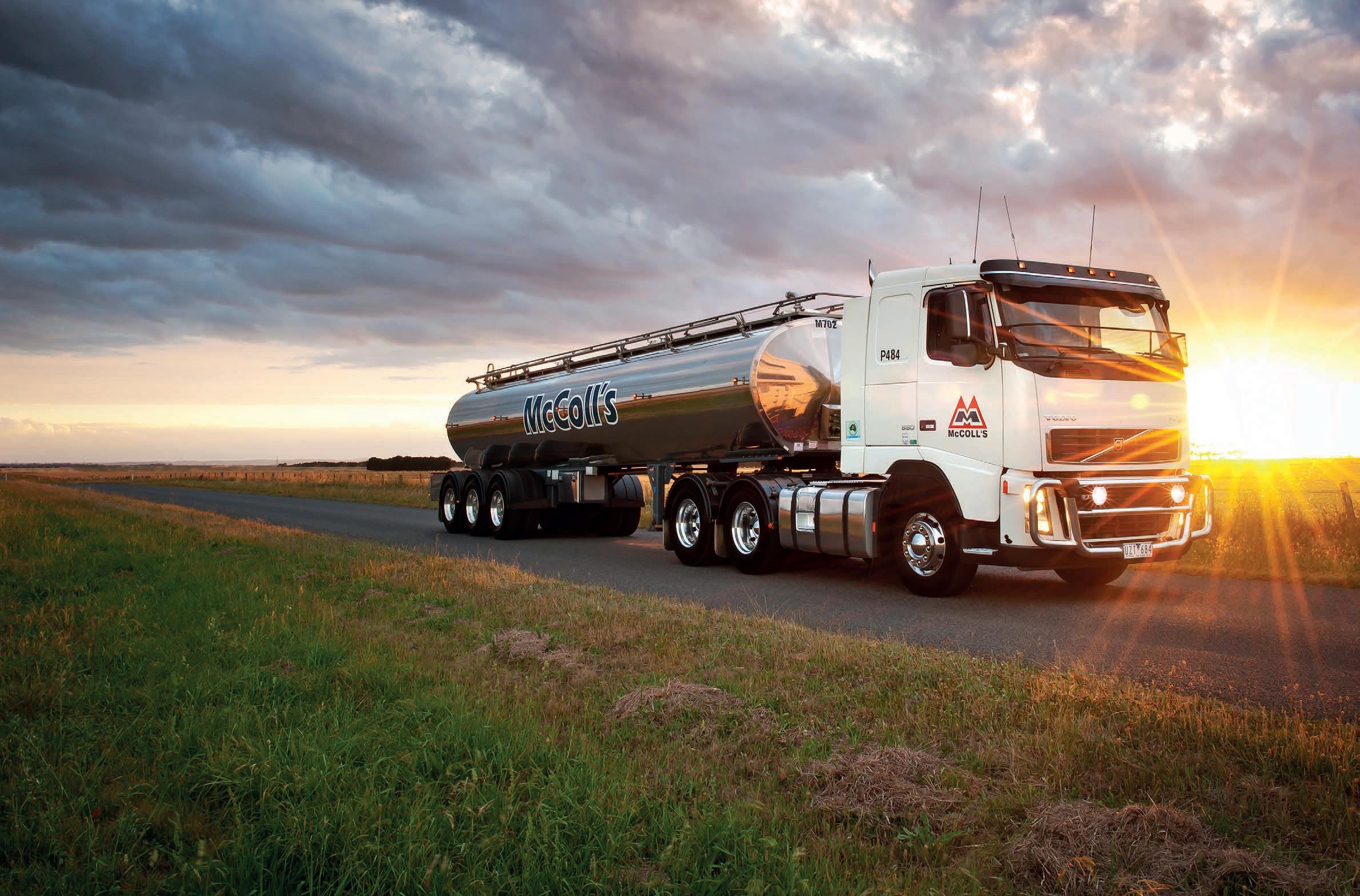
Dead running is often considered a necessary evil for many eets unable to schedule backloads for their assets. FleetSeer is a new tool that enables greater visibility across truck movements to improve pro tability on problem routes so that the margins, as McColl’s discovered, can be better balanced.
FleetSeer, the brainchild of Harvey Lee and Mark Szabo, provides revenue monitoring, pricing with data-driven cost estimates and the ability to identify loss-making work.
These solutions were all sought after by McColl’s Transport, a leading business in the competitive milk tanker segment where the fundamentals don’t change, even while changes are visited upon operations almost daily, sometimes with little warning. To better determine the pro tability of its trucks, and it possesses well over 130 prime movers, McColl’s approached data-driven transport solutions provider, FleetSeer to delve into one of its established systems. Using machine learning, FleetSeer gathered data on individual trucks based on an hour-by-hour and day-byday basis.
Good prices, based on accurate estimates of cost, can prevent low-margin business from ever showing up in the rst place.
“What happens is that we can either do some pricing with a bunch of optimistic assumptions in it, or we can get a solid understanding of what the actual costs are likely to be and hopefully come to an agreement,” says Simon Thornton, McColl’s Transport CEO. “That’s the visibility they have provided us: pricing with intelligence behind it.”
FleetSeer integrates with a variety of data sources to drive new analytical capabilities for businesses by simplifying and then communicating the complexities inherent in transport operations.
Operational data that is collected, for
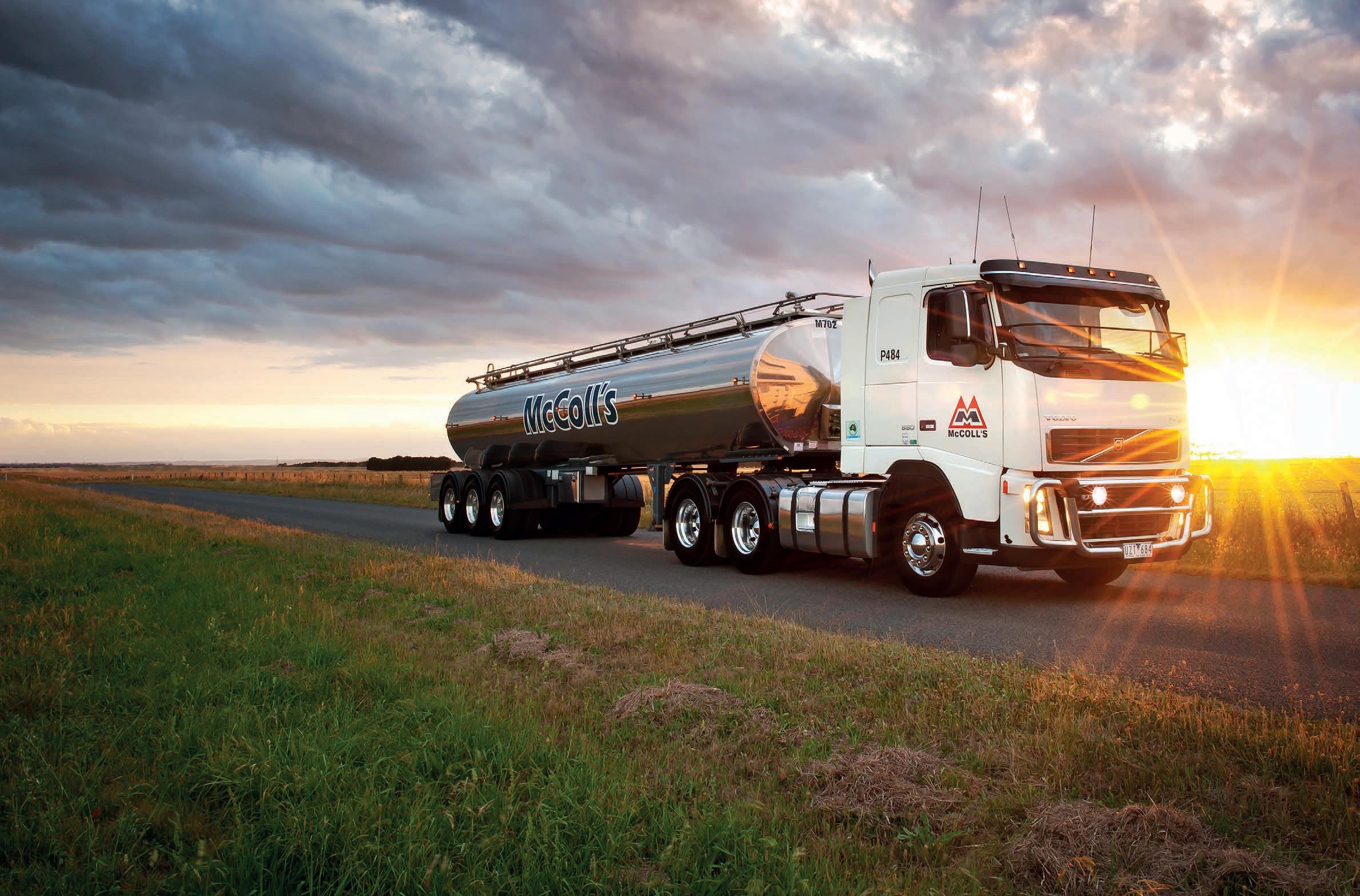
example from the transport management system, is usually aimed at invoicing the job, rather than tracking the costs. Since dead running is an overhead, it is rarely tracked by basic operational systems, and invariably becomes an invisible cost according to Harvey Lee, FleetSeer Chief Executive Of cer.
“A key insight here is that before FleetSeer, it was very dif cult, if not impossible, to really pinpoint where and when the dead running was occurring,” he says. “Schedulers might have pithy insights into their own patch of operations, but the knowledge is not kept in a structured dataset allowing
others such as price managers to use it to make accurate decisions.”
For McColl’s that was demonstrated in combining data from sources previously not in alignment and lling gaps in observations. Having access to very good near-term historical data is key according to Simon.
“Knowing what happened in the past week can help you to see where you went down the wrong track, whether it’s a job with super high margin or super low margin,” he says. “That alone can allow you take the necessary and timely corrective action.”
A business that, for instance, relies on a
few 60 per cent margin jobs and some zero per cent margin jobs averaging out to north of 30 per cent, can encounter a problem, according to Simon.
“Ideally you want everything in a tight band,” Simon says. “That way, you’re not making it all incredibly attractive for someone else to pick off the good ones but also, so you don’t have potholes all over the place with the bad ones.”
He adds, “The biggest thing we can do is identify those potholes and stop doing those runs.”
Adaptations are necessary especially in milk tanker transportation. Heavy rain in one region might increase production. Vehicles therefore need to be redeployed. A job originating in Melbourne and destined for Ballarat would, on the balance of numbers, require a Melbourne-based truck, meaning it would be loaded out of Ballarat and return home empty. That’s not a deal breaker. But what happens when the customer calls and there is no truck available in Melbourne on the day? McColl’s in that situation, as Simon explains, would send a truck
from Geelong.
“Suddenly you’ve got these extra kilometres in there,” he says. “Something that might have had an acceptable margin suddenly doesn’t. And so FleetSeer is able to identify all the runs that we are doing on a run-by-run basis and consolidate that to see trends over months so that we know how closely the jobs that we are doing match up to the way that we process them.”
At any one time every transport company has a high quantity of trucks running around. Some of these are pro table while others are not.
“You just hope at the end of the day that the ones that made money made more than the others lost,” says Simon. “With FleetSeer we can see where those potholes are and even if all we do is avoid the bad ones and keep going with the bits that make money, then life is pretty good.”
McColl’s, when all is said and done, already knows which routes make money above the operational average. A consistent pricing process is applied but it’s often a process as reliant on
B-double tanker.
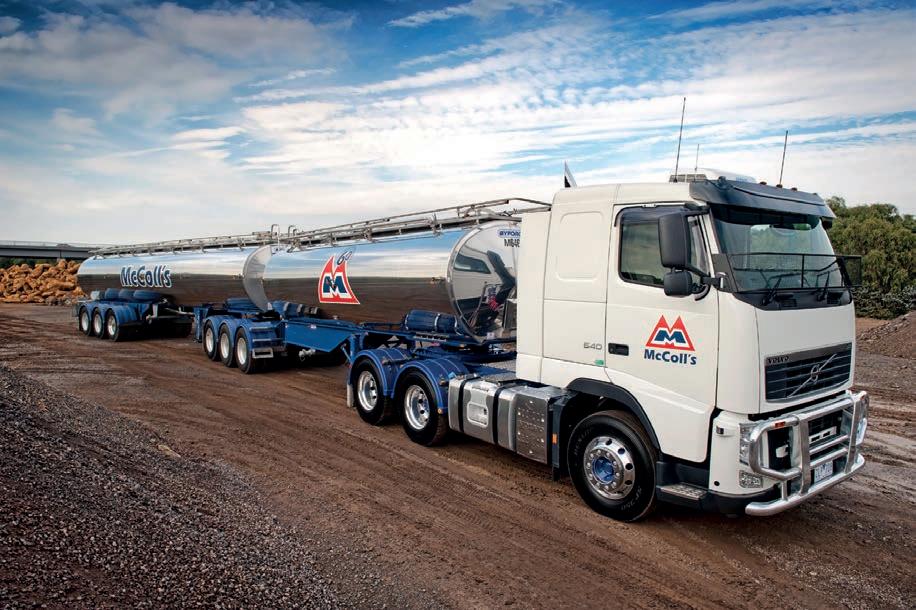
luck as it is good management. For instance, when an extra backload suddenly becomes available. In that case McColl’s is dealing with a big margin for which it becomes very
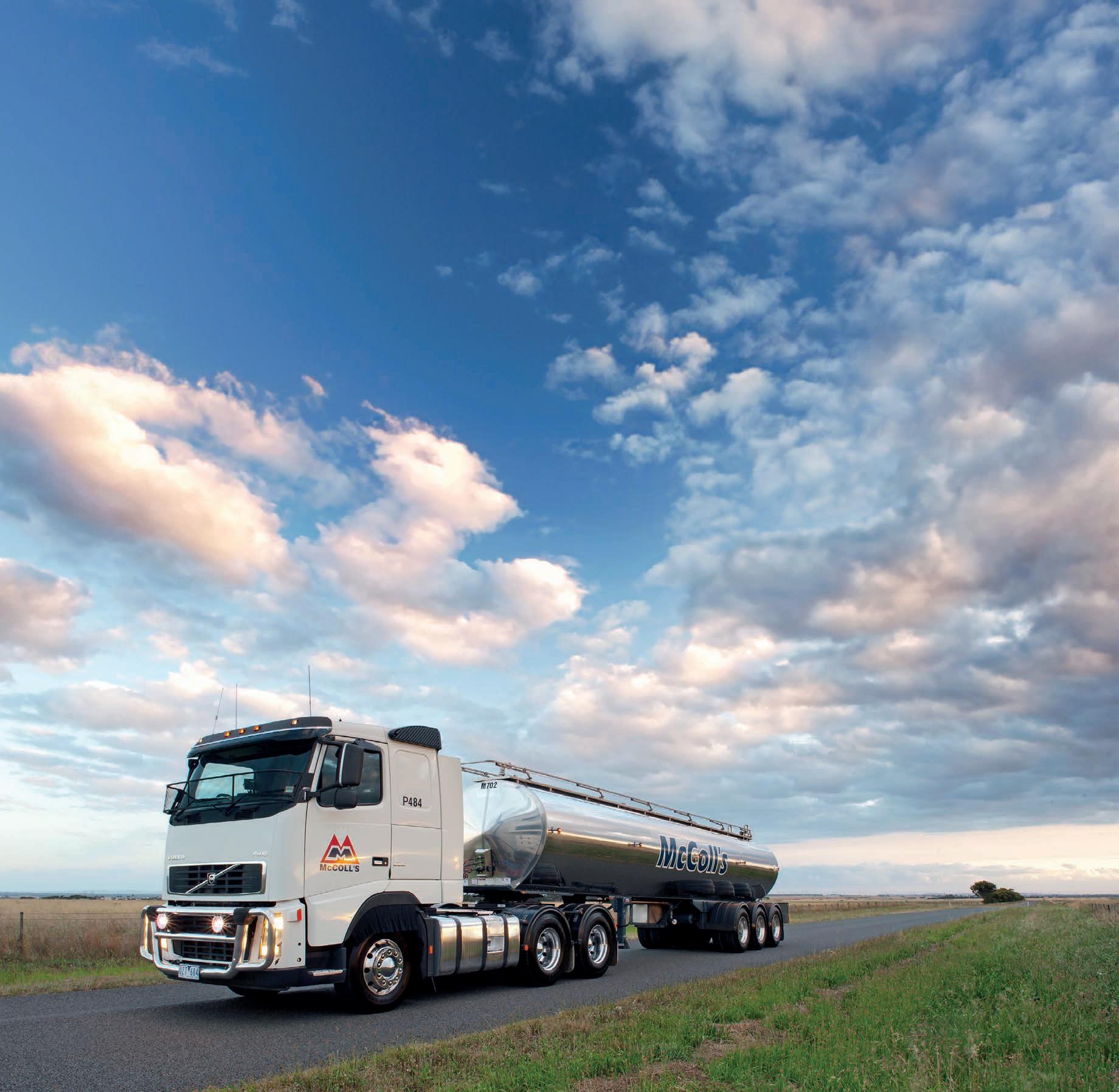
conscious of and naturally protective.
“Losing either the up leg or back leg suddenly becomes a concern,” says Simon. “We’ve got to be very careful somebody doesn’t come and pick off one half of it and nd the things that used to make money don’t make money anymore.”
The volume of backloads can uctuate from week to week. Commitments made because of regular backloads that were factored into the original task and, when
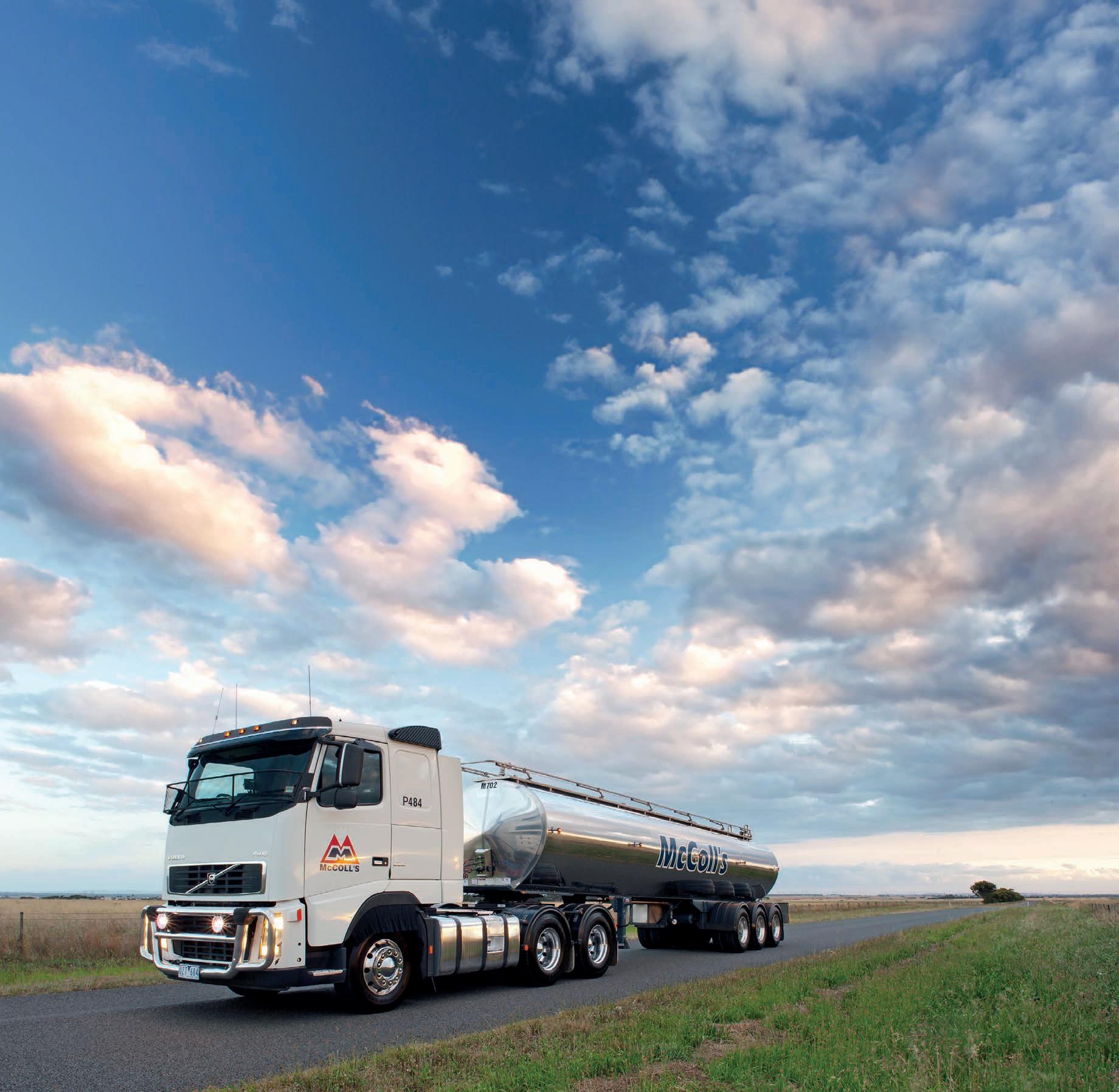
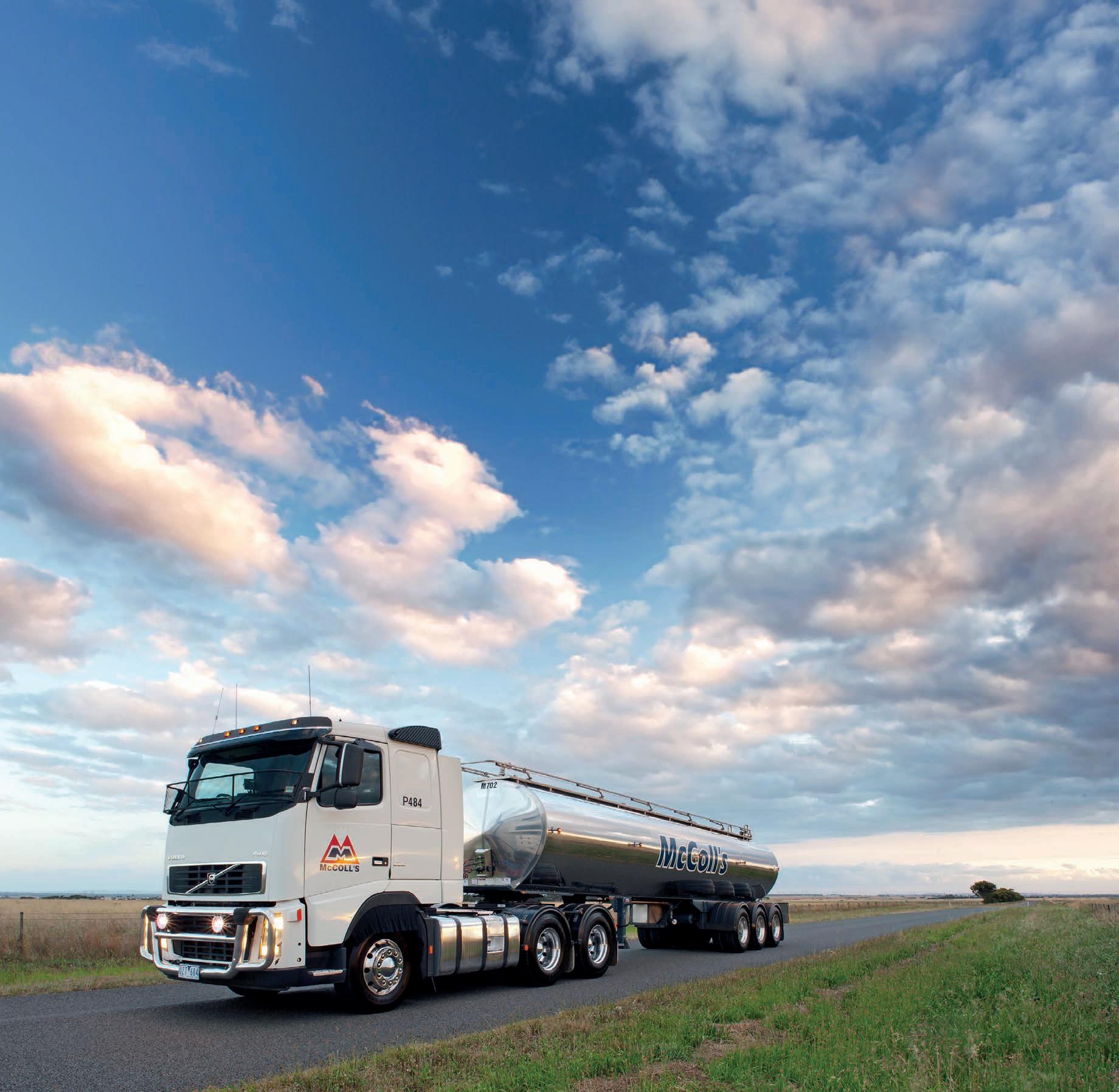
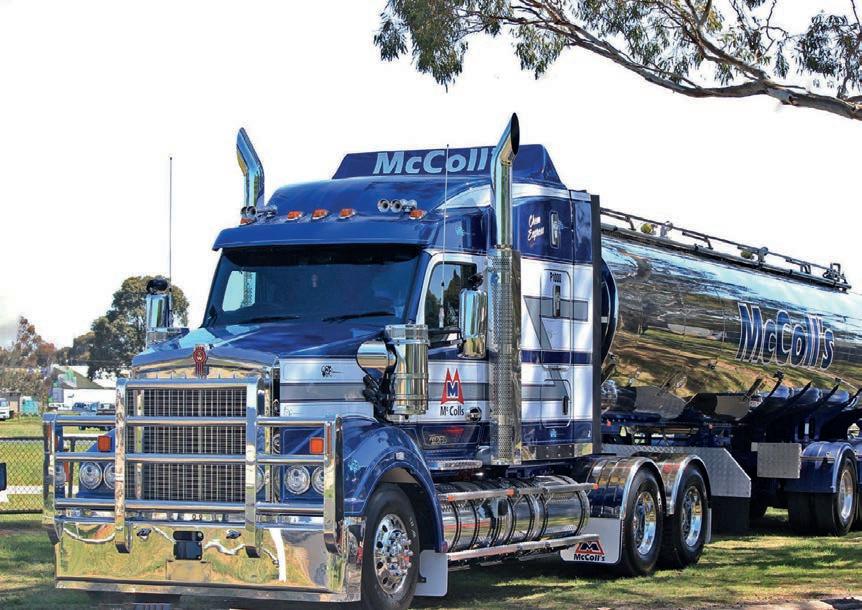
removed from the inventory, can mean costly dead running just to honour the agreement.
“The question for us is about what do we originally assume in the pricing and whether a diversion from that is an option.” says Simon. “The FleetSeer system has helped us identify where these anomalies are.”
Most of McColl’s work is not contracted to individual tanker allocation or locked at a particular price point. They’ll agree to prices with their customers but if there is a leak somewhere that doesn’t work for them, they’ll make it known to the customer that the leg in question, given it no longer has a backload, can’t be serviced at the same price. If, per chance, another backload becomes available McColl’s is happy to go back to the original price. By being able to quickly identify these problem areas, running up big losses can be avoided. Working with FleetSeer in these instances encourages better strategic decision-making.
“Everyone talks about sustainability but mainly when they’re talking about that they’re talking about reducing CO2 in
the environment,” says Simon. “There’s another component to sustainability, which is to have businesses that can keep making enough of a return on their assets so that they can still come back and do it again tomorrow. Lots of transport companies have failed that test unfortunately. Is it because they couldn’t choose the right trucks to do the work in? Is it because they couldn’t hire the right drivers or nd enough drivers?
Probably not. Mostly it will be some commercial thing often lost in the noise in the bigger business.”
FleetSeer can be compared to a CT scan according to Simon. As a commercial diagnostic tool, it helps eets to ush out the hidden malignancies they might feel but overlook.
“There aren’t that many people who are that smart and good with data and are prepared to work in the transport industry to make a living,” he says.
“Mostly the people with that kind of data size move in the nancial markets and make a fortune there. The guys at FleetSeer, for one reason or another, have chosen to be in the transport market, and we nd it very helpful.”
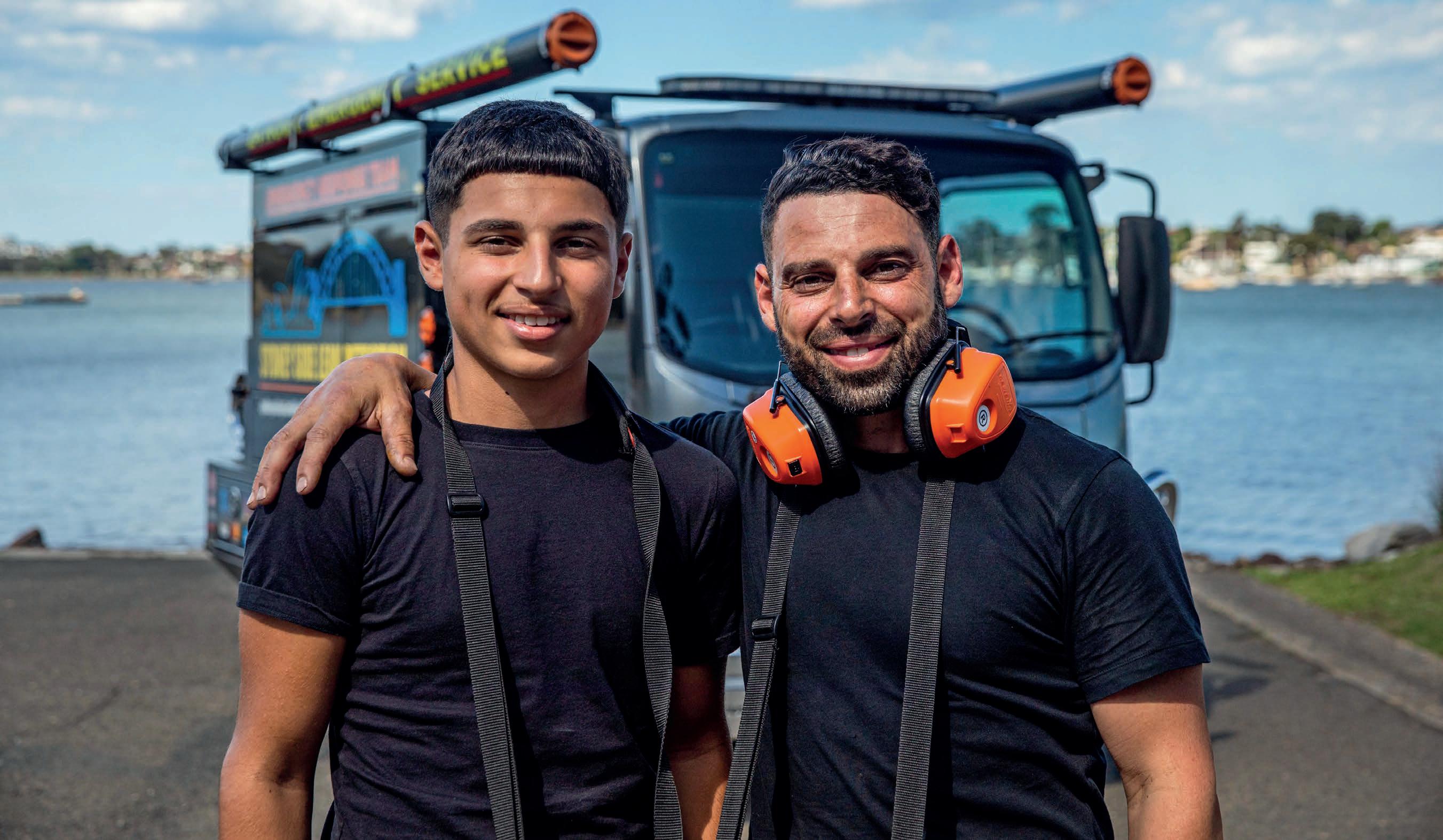
LIMEL LEAKS
IGHT IN THE
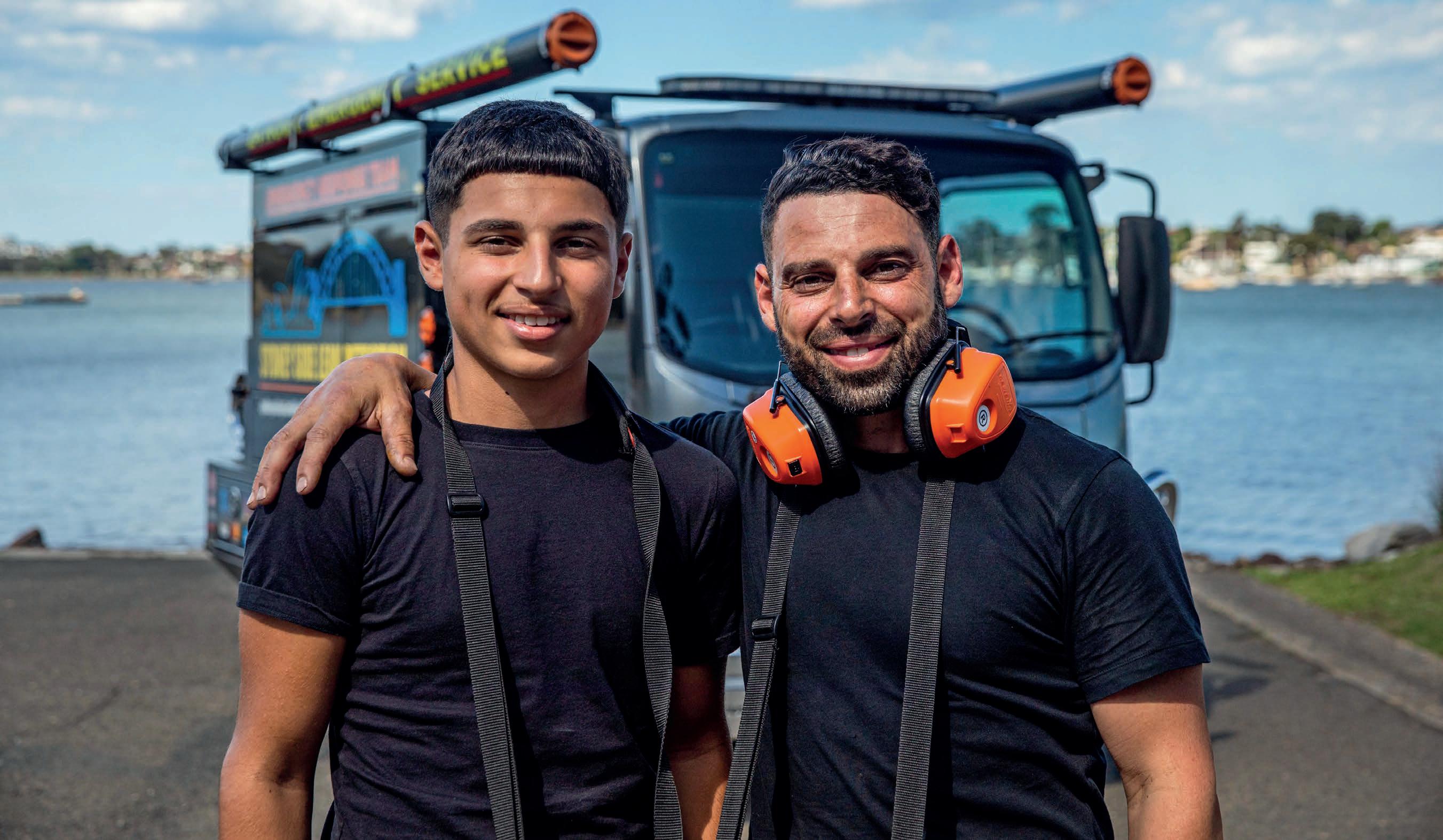
Mohammed Mourad had no intention of becoming famous, but a combination of a passion for detecting leaks, a social media account and a standout Isuzu truck has made him a plumbing sensation.

It all started when Mohammed’s 15-year-old son took some videos of his dad at work, interested in the way he detected leaks. Little did the owner of Sydney Side Plumbing know just how much interest there was in what he did for a living.
“It’s crazy how much people love watching us work,” he said. “My son put up a couple of videos on Tik Tok and Instagram and before you knew it, we had close to a hundred thousand followers. People just seem to really like leaks. I think they nd it satisfying.”
The videos, set to catchy music, show Mohammed using various detecting equipment and locators to nd leaks in business and homes.
Mohammed didn’t always want to be a plumber, but his father, a builder, pushed him into the trade, believing it to be a good prospect.
“I didn’t like it at all,” he said of the rst few months. “I didn’t like the jobs and I always felt sick, but dad told me to get my license and then decide.”
By the time he did get his license, Mohammed had gotten over the smell
and found himself enjoying working for a company specialising in leak detection. He then eventually set up his own business.
His current social media popularity might make him the envy of his fellow plumbers, but he also has something else
they seem to covet.
He has turned his NLR 45-150 Isuzu Traypack into a customised plumbing workshop on wheels, complete with standout signage, and often elds calls from people in the industry who want help creating a similar truck
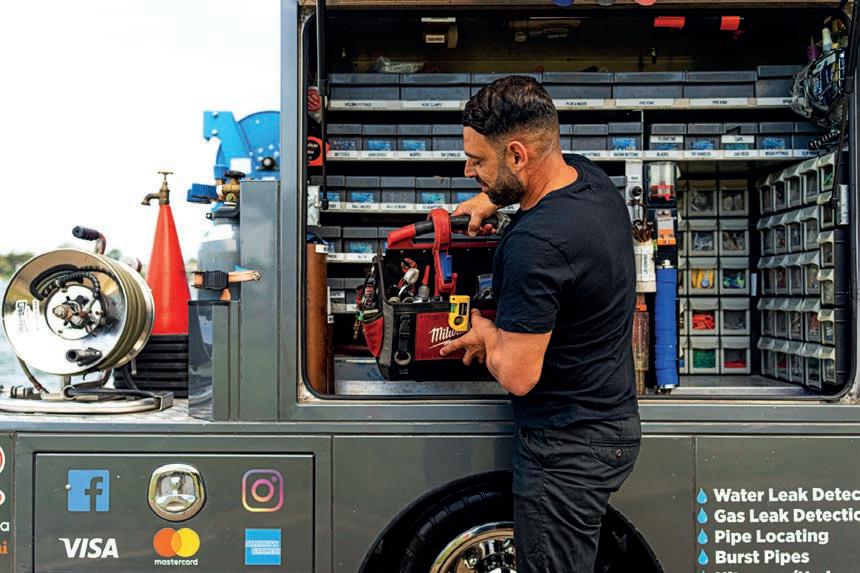
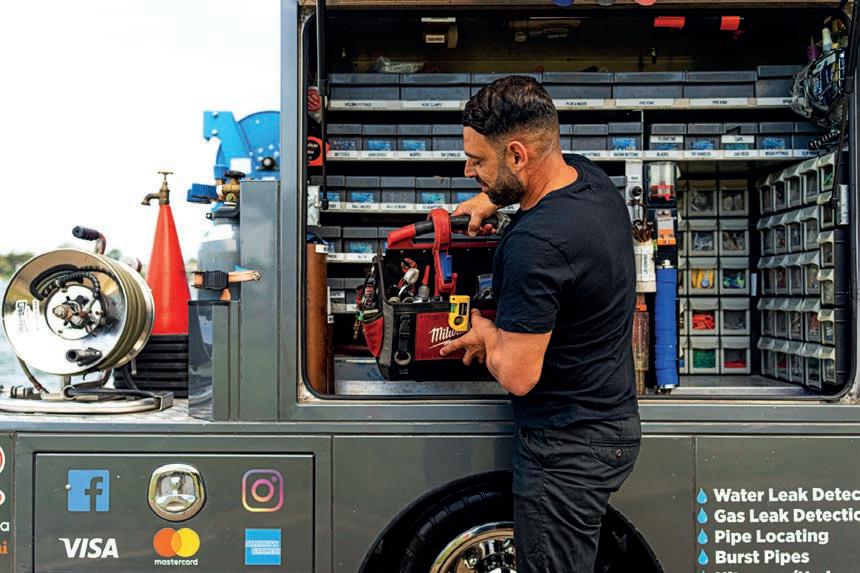
“I wanted to build something on the truck so that I didn’t have to waste time going back and forth to Reece for things,” he said. “I wanted to have every single pipe and tting on board. This way if we get called out to an emergency, I have the right things I need to x it.”
Mohammed Mourad. Owner, Sydney Side Plumbingfor themselves.
Back when he was in the market for a vehicle, Mohammed recalls, he wanted something that he could organise with customised boxes to t everything he would possibly need for a job. That way he wouldn’t have to wait for parts and could x the problem quickly and ef ciently.
“I wanted to build something on the truck so that I didn’t have to waste time going back and forth to Reece for things,” he said. “I wanted to have every single pipe and tting on board. This way if we get called out to an emergency, I have the right things I need to x it.”
Mohammed said his truck has made Sydney Side Plumbing a standout from the crowd, able to take on even the biggest jobs and nish them without stopping to collect parts or equipment. The NLR 45-150 Traypack serves Mohammed’s bespoke plans perfectly and he likes the look of its design over the competition’s. His model is powered by a 4JJ1-TCS engine that produces 110kW at 2,800rpm and has 375Nm of torque. It is a 4 -cylinder, 5-speed manual transmission with a gross vehicle mass of 4,500 kg and a gross combination mass of 8,000 kg. He now has one more Isuzu trucks getting tted-out to suit his business’s needs.
“Everything has gone perfectly, and we’ve had no issues,” he said. “The service is fantastic which is why I recommend them to everyone.”
Even better, Mohammed won a prize pack from Isuzu Trucks in its Merry Truckmas competition, winning fuel and parts. Mohammed’s son still takes videos and helps him at work after school and on weekends. In fact, he is showing some impressive skills.
“He’s better at locating pipes than I am now,” Mohammed said. As for following in his dad’s footsteps, Mohammed said there was no pressure.
“Although my dad pushed me into this direction, I am grateful, but I don’t want to push my kids into anything,” he said. “I tell my kids to do what they want to do, but I think he really does like it.”
SMART TECHNOLOGY
Manage compliance with Teletrac Navman’s fleet management solutions
TN360 provides the tools to help eliminate guesswork. See past the day-to-day to identify and mitigate risks that would previously have been invisible for a safer and more productive operation.
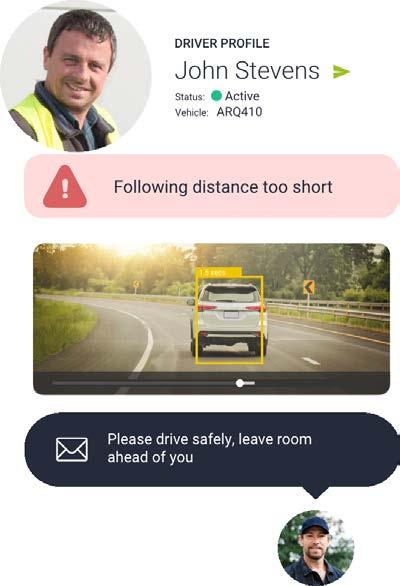
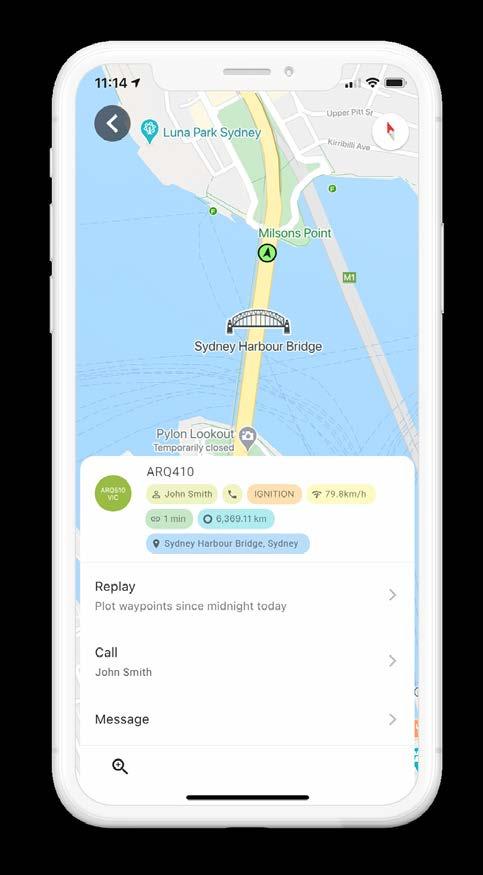
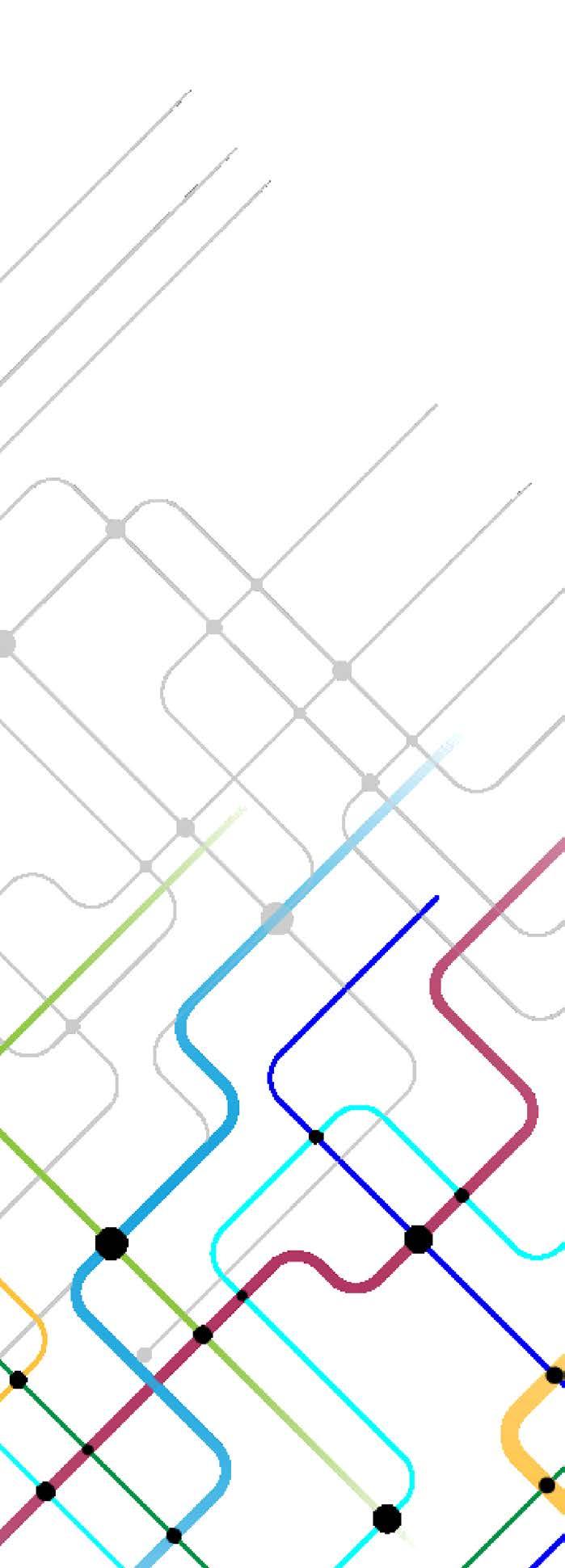
FIRST FLEET
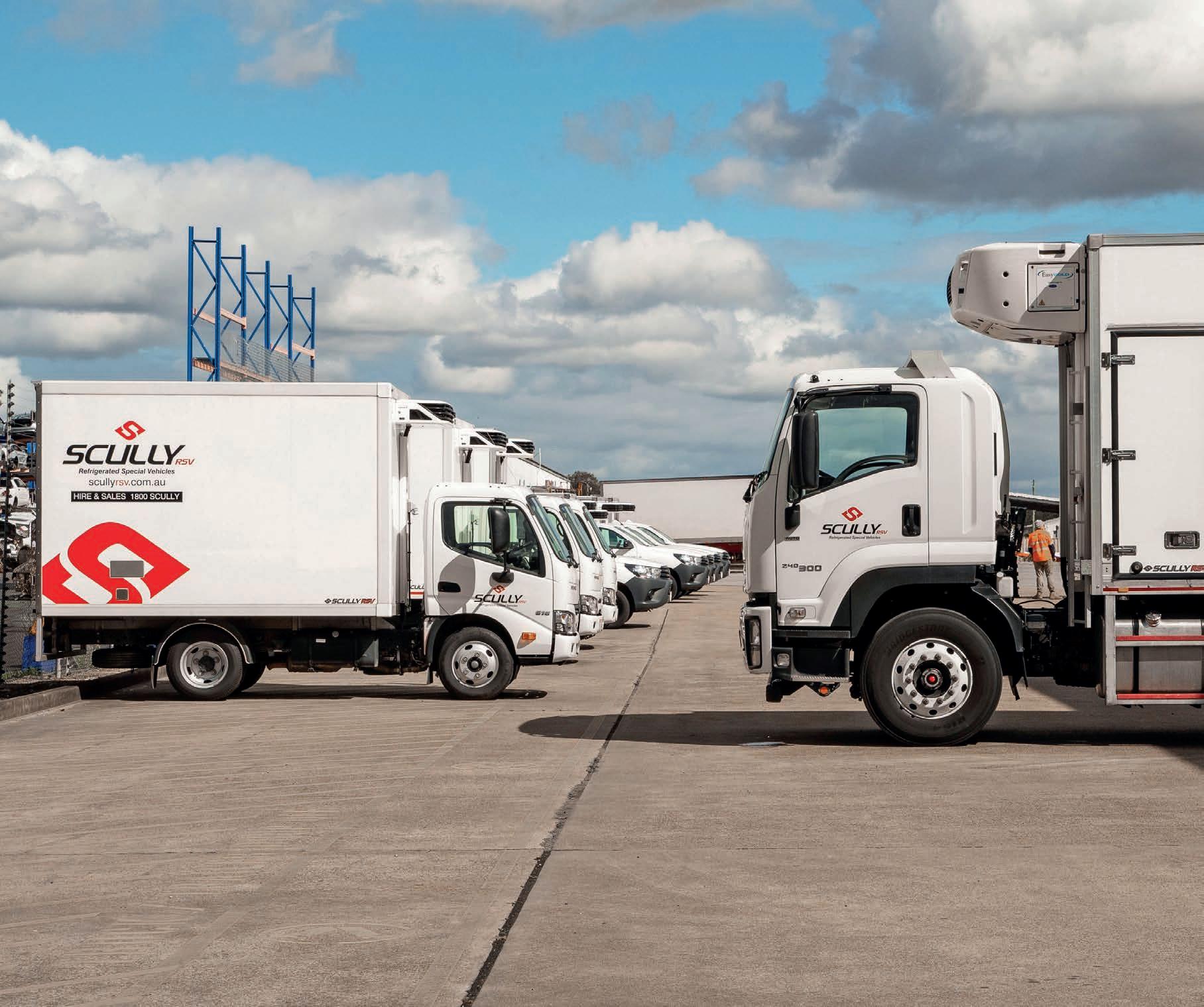
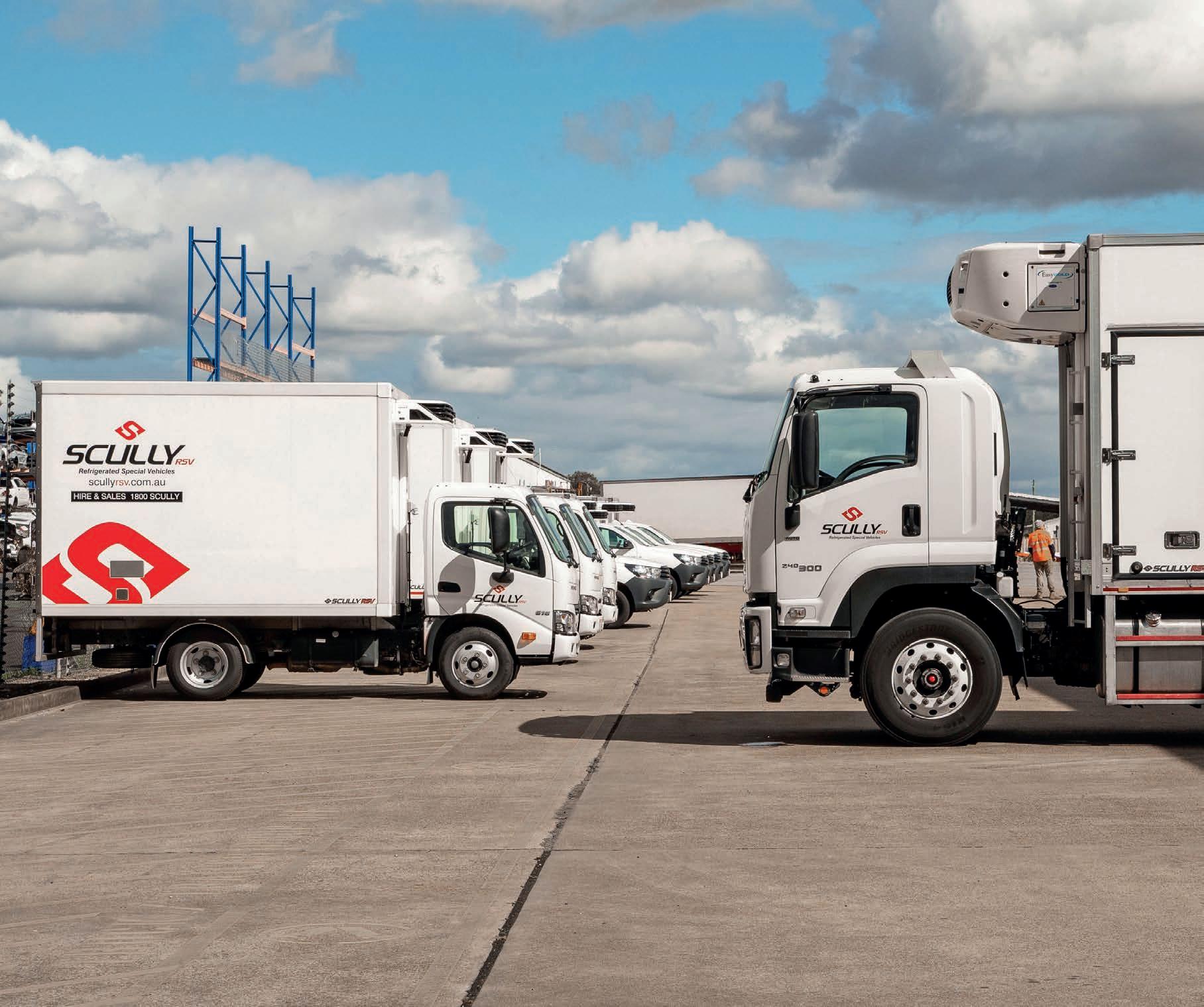
Accompanying its wide o ering of vehicles, Scully RSV has a range of long-term hire solutions which operators have much to gain from.
In making the decision on whether to hire a vehicle or purchase one, there are many factors which may come into play. With bene ts on both sides of the coin, owners and operators may lean towards one option as opposed to the other based on their individual needs.
There are signi cant advantages to choosing the rental option, though, as the burgeoning success of refrigerated truck rental and long-term hire eet Scully RSV, makes evident. Renowned for its rental solutions and dominant position in the market, Scully RSV has built its success on the foundation of its vehicles for short- and long-term hire.
“Long term hire is so much more than just providing an asset to a customer on a regular basis,” says Andrew McKenzie, Scully RSV CEO. “For us it starts with ensuring that asset is always at the leading edge of technology, ef ciency and safety which is part of our duty, through to providing total eet management solutions.”
Ranging from utes to 14-pallet trucks and a eet of A- and B-double trailers, Scully RSV can build customised solutions for hire and sales, with over 1,000 assets available.
A bene t popular with customers who hire vehicles with Scully RSV is the one monthly fee for 24/7 call out support, servicing, registration and insurance. Scully RSV also builds on this with exible terms, as it understands that circumstances can change. Its long-term hire option allows customers to access signi cantly reduced rates with ease of exit, should the business change.
By renting with Scully RSV, customers can preserve business capital for other projects.
Scully RSV implements what Andrew calls a thorough eet replacement program as it can cycle through its vast array of assets, which helps to ensure
the customer is always able to access the latest in vehicle technology and safety. “We’ll reach out to our customers and notify them of our upcoming replacement program cycle and swap out their vehicle for a new model,” he says. “This ensures minimal business disruption and keeps them on the road in a quality and reliable vehicle tted with the latest in refrigerated transport technology.”
One particular area Scully RSV both excels and takes pride in is building a total eet management solution for its customers. This involves looking at their eet in totality according to Andrew. “We work with the customer on understanding what is their core eet that they want to own on their balance sheet and what is the ex within their organisation in terms of contracts and eet demands that they need support with,” he says. “Fleet management is often a mixture of new sales and a mixture of long and short-term hire assets across rigids and trailers.”
The other advantage of long-term hire through Scully RSV, Andrew points out, is that it can lessen the burden associated with asset management.
“We have a dedicated team around the country that provide industry leading eet management solutions,” he says. “The size of our eet and the scale of our geography makes it easy to service both national and local eets.”
Vehicles can be tailored to suit individual needs — meat hangers, doors, tail lifts, ooring and body size, for example, are all able to be speci ed.
Scully RSV also takes care of the service and maintenance schedule, so that customers can focus on running their business. And when it comes to the speci c vehicle’s end of term, customers can upgrade it for a new one or simply return it.
At present Scully RSV is seeing demand
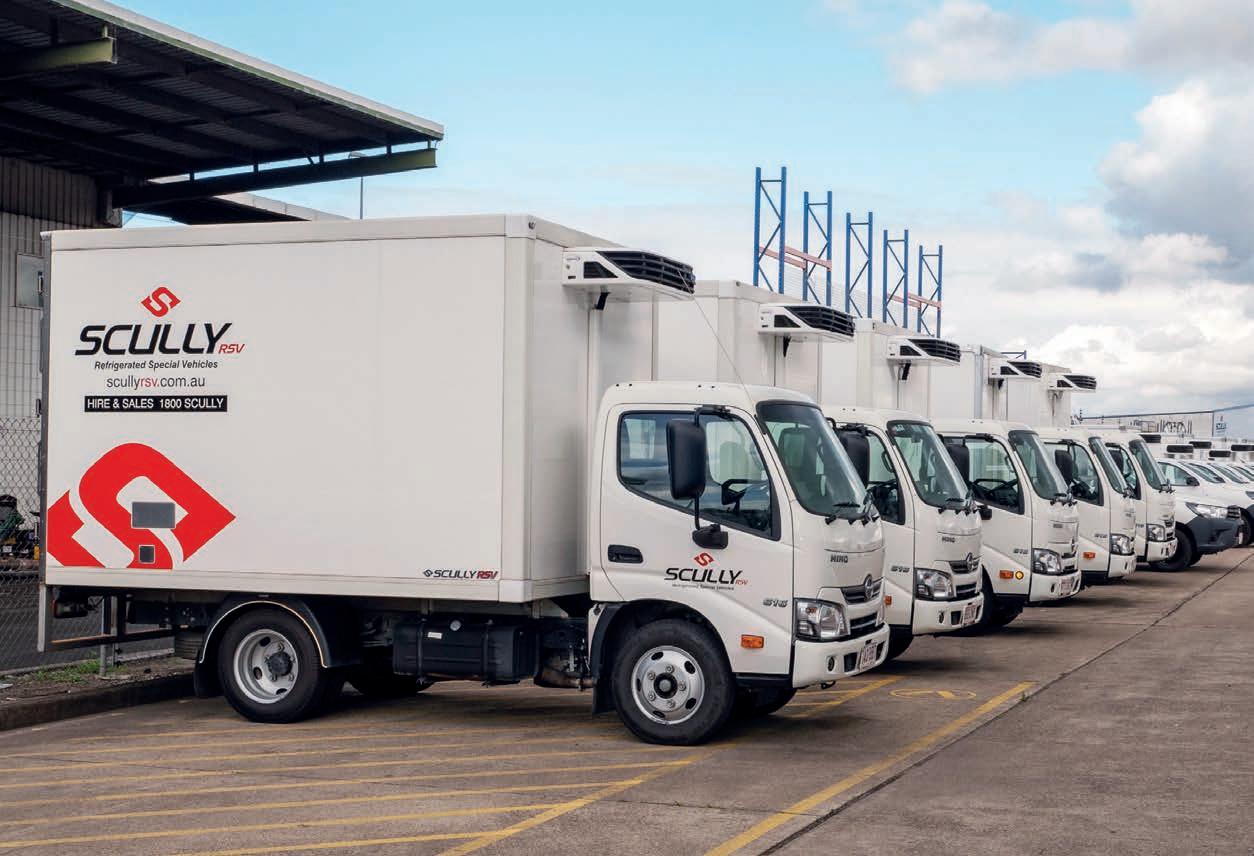
in fast growing companies where transport isn’t their core business. Maintaining a eet and the subsequent COR obligations, in addition to asset management, is always something that is going to be dif cult and that’s where Scully RSV adds signi cant value.
“Our customers fully leverage the bene ts of partnering with a refrigerated transport solutions provider as opposed to adding a eet team or eet department to their business,” says Andrew. “This is where our customers lean on us and unlock eet management that is more than just giving an asset at a given time. Our people are readily available and take care of the eet so our customers can take care of their business. That’s the difference between Scully and our competitors. We build out for our customers, the full partnership with our teams as opposed to just hiring them an asset.”
The other main differentiator for Scully RSV in the competitive eld of refrigerated transport solutions, is its unique manufacturing process. Using panel materials from a local supplier in New South Wales and sourcing Australian steel it assembles and builds each and every unit inhouse in Brisbane. It is this business model which Scully RSV has mastered over the past 30 years, with extensive manufacturing experience in supplying Australia’s refrigerated needs.
It was essential that Scully RSV, as a full-service provider, constructed its new industry-leading manufacturing facility in Rocklea, Queensland, last year.
To keep up with unprecedented demand for the product as well as refrigerated transport equipment, Scully RSV tripled its manufacturing capacity with this new facility. Featuring the industry’s latest manufacturing technology, the 12,000m2 warehouse ushered in a new
era for Scully RSV and has successfully enabled it to manufacture up to 60 rigid bodies a month.
The new head of ce joins Scully RSV’s ever-expanding national network of locations in Queensland, New South Wales, Victoria and Western Australia. Collectively this expanding footprint allows for the OEM to support the size and scale of the latest eet requirements of national companies in its growing portfolio.
With 24/7 call out support and 24/7 standby included, as well as vehicles from the industry’s leading suppliers, Scully RSV is a trusted partner in refrigerated transport solutions. Now, with the help of its new facility, Scully RSV is able to offer its customers longterm rental solutions in any corner of the country. As a market leader in refrigerated transport solutions, Scully RSV has the scale to service the nations refrigerated needs.

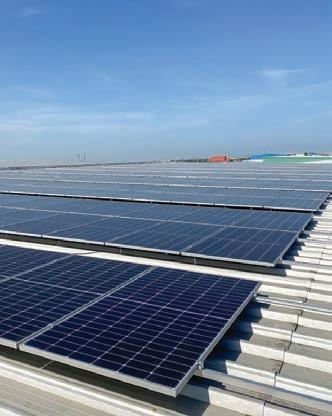
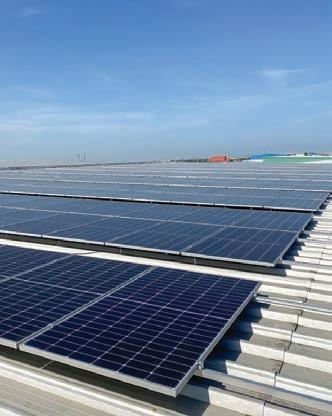
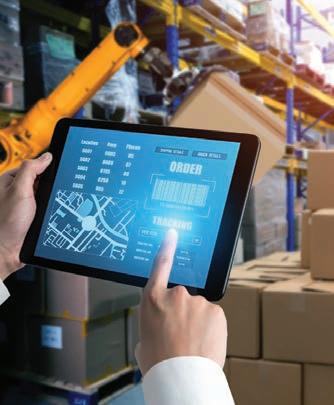
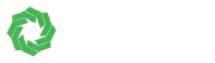
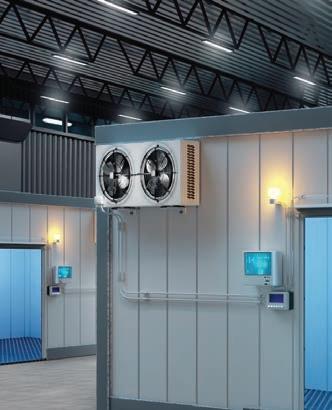
WINNING THAT SEASON

Brisbane-based All Purpose Transport has been recognised with a major award.
Conceiving a plan and putting it into practice is one way for a business to test its current perspective. Seeing those plans succeed and receive wider recognition, as has happened recently at All Purpose Transport (APT), vindicates the merit behind them. For All Purpose Transport that acknowledgement came at the Australian Training Awards where the company received the Large Employer of the Year award for their exceptional training program ‘Project APT’. In the 11 years since it was launched,
Project APT has helped more than 500 employees and owner-drivers to achieve formal quali cations. Back in 2012 APT identi ed it had an ageing workforce that needed revitalisation. A fortuitous meeting with a representative from the Department of Transport and Main Roads in Queensland set the wheels in motion, leading to the creation of a comprehensive training program with TAFE Queensland.
“We were presented with an exciting opportunity, and we realised we could elevate our entire workforce,” says Paul
Kahlert, All Purpose Transport CEO. The initiative now known as Project APT was launched to attract and retain talent during a mining boom in Queensland. With an average worker age of 47, APT created a training program for skills development and marketing, given truck driving was perceived commonly as a second-choice career path with high turnover.
Last year the program achieved a 70 per cent retention rate among owner-driver contractors.
APT has over 110 operational and

administrative employees along with more than 260 owner drivers operating small vans through to B-doubles. A signi cant percentage of the workforce comprises migrants, including refugees who have gained formal quali cations. Communication, especially with non-native English speakers, was an initial hurdle that APT overcame with comprehensive training methods, including one-on-one sessions and multimedia tools.
The company also made strides in diversity, notably in operations and warehousing roles. While driving positions remained male-dominated, other areas saw a more balanced
gender representation, attributed to technological advancements and the shift in required skill sets.
Women now account for about 40 per cent of the operations team, marking a signi cant demographic change.
Belinda Polglase, APT’s Head of People and Safety, is one of the growth stories within the organisation, which has since gone onto interstate expansion, having risen up the ranks herself.
“It’s not just about work skills. It’s about personal growth,” she says. “The training has helped our staff in life, fostering goal-setting and nancial management, which, in turn, has strengthened our workforce community.”
The company offers a variety of transport and delivery services from express couriers to refrigerated cold carrying, new furniture deliveries and removals, to taxi trucks, general freight and warehousing.
APT’s extensive eet now features 14 electric vehicles, making it one of the rst transport companies to introduce battery electric trucks for large and bulky home deliveries in Queensland according to Kahlert.
“We now have 14 electric vehicles undertaking over 10,000kms each week,” he says. “We’ve created better people and, consequently, a better business.”
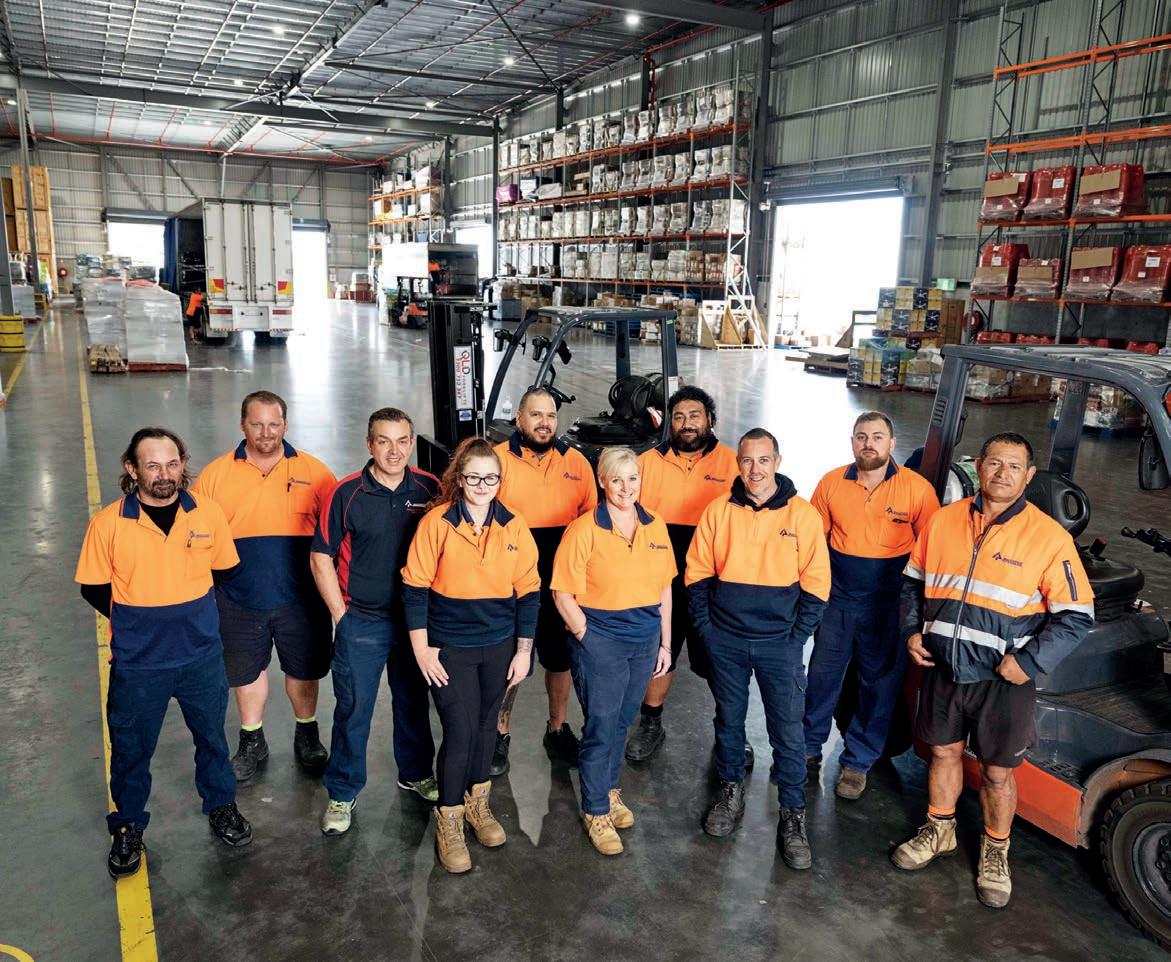
PRO PUBLIC
The recent Port Botany Landside Improvement Strategy decision is a signi cant victory for Road Freight NSW.
Road Freight NSW (RFNSW) has welcomed the release of the Final Report into the Port Botany Landside Improvement Strategy (‘PBLIS’) — with a key recommendation that it remains in public hands. The decision was being hailed as a ‘big win’ for RFNSW and its members, who had lobbied the NSW Government against any moves to privatise PBLIS. To wit, RFNSW had longmaintained that the PBLIS has delivered the most productive port in Australia and
that any sale or administration of PBLIS by a third party, such as the private port operator, would undermine the solid productivity gains so far delivered by PBLIS across the supply chain.
RFNSW CEO, Simon O’Hara was fully supportive of the nding to which, under current arrangements, Transport for NSW (‘TFNSW’) administers the Regulation describing it as “appropriate at this time.”
“From our perspective, there’s a real bene t in keeping the PBLIS under the watch of
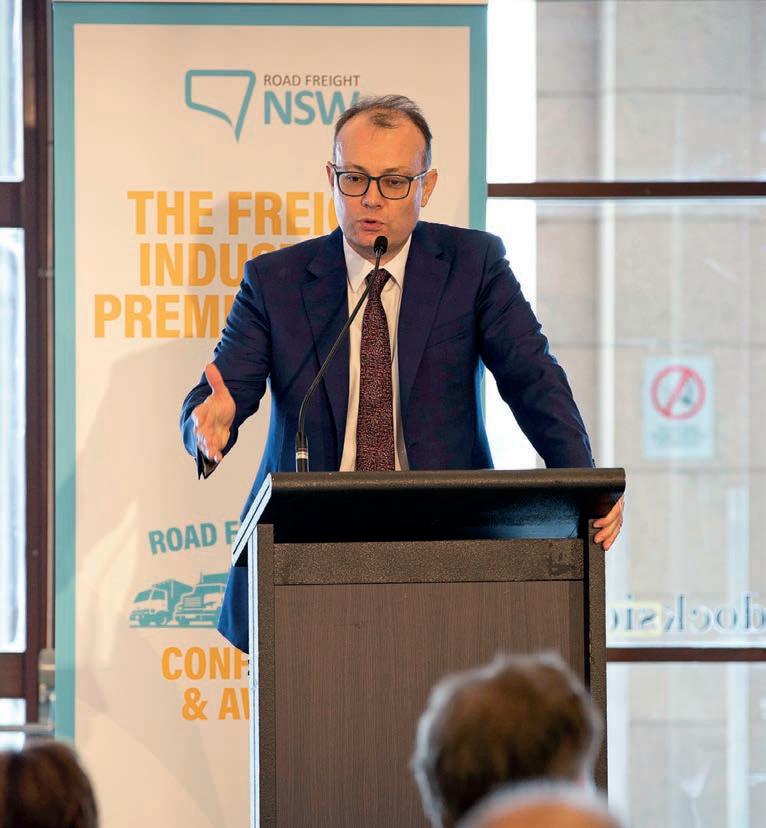

TFNSW, not only for the good of trucking operators, but for the wider community,” he says.
It was a reward for much time and tireless effort by O’Hara and his team.
Lopez Bros Transport Business Development Manager Ann Lopez was full of praise for the stance taken by O’Hara and his team, with the announcement serving as a timely reminder for why the container transport business remained a proud and long-time member of Road
PERTY
Freight NSW.
“Announcements such as this one today are a signi cant reason why we continue to do so,” says Lopez.
“Congratulations Simon O’Hara for your work on this.”
As one of its main 2023 election priorities, O’Hara was particularly pleased that the Government had listened to RFNSW’s concerns about privatising PBLIS.
“Whilst we support some of the report,

we need clari cation on a number of the PBLIS recommendations,” he says. These include, among others, recommendation 6 ‘removing the power for regulating stevedore charges’ in light of ongoing struggles by trucking operators to cope with stevedores’ ever-increasing terminal access fees; the removal of A and B carriers under recommendation 10; and recommendation 17 ‘certi cation requirement for container transport road operators and lastly the proposed new booking slot regime.
“We are mindful of the unique Sydney family run business demographic for landside operations at Port Botany,” says Simon. “We need to ensure that our
member businesses, who perform a vital role in the supply chain remain pro table, create jobs with decent pay and careers, continue to deliver productivity gains for the Australian community, see PBLIS as t for purpose.”
The state-based advocacy group for heavy vehicle operators was looking forward to engaging with the NSW Government as part of the review into the state’s freight industry.
The policy reform will identify short-, medium- and long-term actions and deliver a comprehensive strategic reform agenda for the Government to support the ongoing improvement of freight transport across NSW.
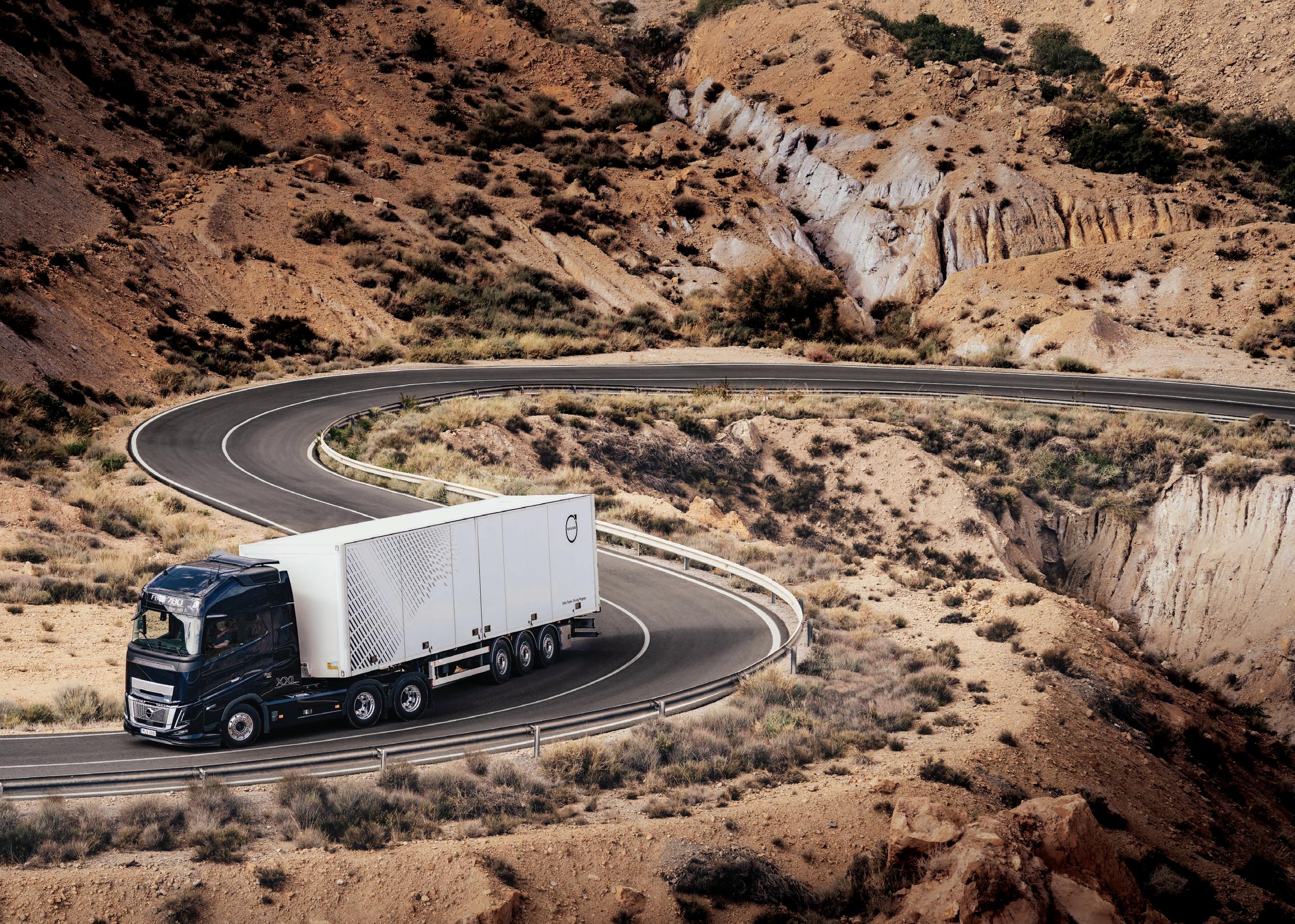
BREAKING THE
A new big bore diesel engine, comprehensive changes to cab aerodynamics and a pathway to an alternative propulsion future are just some of the key elements in Volvo’s new line-up.
ICE
Volvo has kicked off 2024 with quite a bang, starting with the launch of its new VNL conventional cab in the United States with an all-new platform capable of accommodating the latest in diesel technology as well as the powertrains of the future. This will include battery electric, fuel cell electric and internal combustion engines using diesel and alternative fuels such as natural gases as well as hydrogen. The VNL features the rst 24-volt electrical infrastructure in the North American trucking industry and the multiple active safety features introduced in this new generation of Volvo trucks will be the standard for the future commercialisation of fully autonomous trucks.
On the other side of the Atlantic in Sweden, a signi cantly re-engineered Volvo FH16 was the main news with comprehensive improvements in aerodynamics to further enhance fuel ef ciency, and a new 17-litre “big bore” engine which can be rated up to 780-horsepower and 3,800Nm of torque, which gives back to Volvo the horsepower bragging rights.
In addition to a bore size 5mm larger than the to-be-discontinued 16-litre engine, the other main difference is the
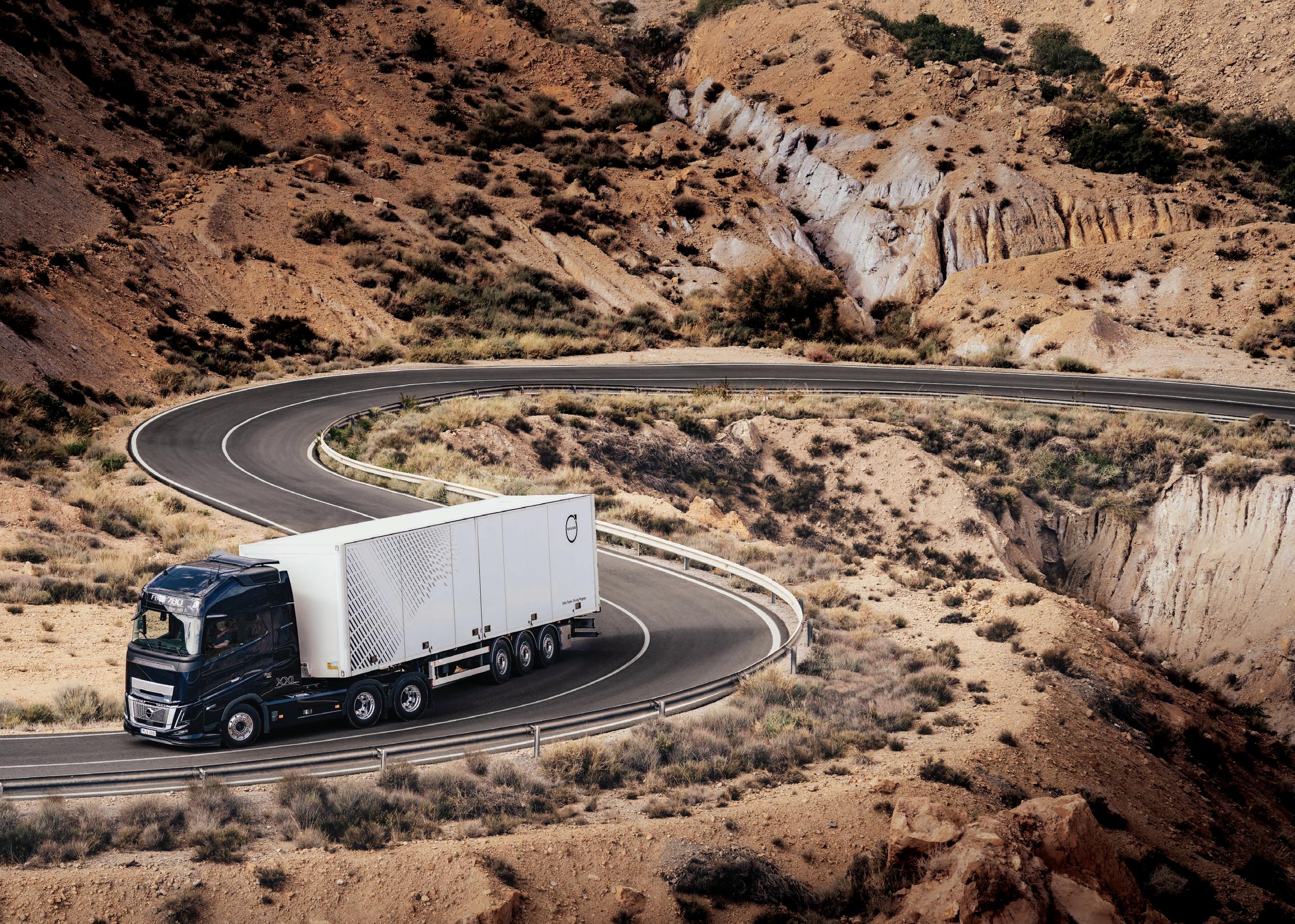
tment of a single variable geometry turbocharger which, as well as improving engine response and power, contributes to an over-all reduction of engine weight by 70kgs. Despite the larger 17-litre engine, the FH16 nomenclature for the truck remains, as Volvo consider this to be model branding rather than a description of what’s under the cab. The new engine is referred to as the D17 and many of its components are carried over from the D16.
Other ratings for the 17-litre are 600hp/3,000Nm and 700hp/3,400Nm. All variants utilise Volvo’s innovative patented wave piston design to optimise combustion and reduce emissions, while the new injection system ensures the best fuel economy, and the increased peak cylinder pressure enables the high-power outputs to be maintained.
The D17 engine is certi ed to run on biofuels including HVO (Hydro-treated Vegetable Oil). The Volvo engine brake has been long acknowledged as one of the best in the business and with the 17-litre it provides an impressive up to 540Nm of engine retardation. There is only one very short descent on the Volvo test circuit we are using, and the engine brake effectively slows the trucks without any need for the service brakes. Similarly, coming down
from around 80 km/h on the more open sections to almost a standstill to perform a U-turn, was achieved with almost no application of the wheel brakes which now feature Volvo’s patented low drag design as a contributor to fuel ef ciency. This section of road was shared with other traf c including tippers involved in the earthworks associated with the construction of Volvo cars’ battery plant. Volvo’s I-Shift transmission has been equipped with polished gears which reduce internal friction losses to save fuel and to also deliver even quicker shifts. The oil change interval for the gearbox has been taken from 450,000 kilometres out to 800,000 kilometres.
The wheelbases remain the same with the front axle location also unchanged, although the new FH cab is 240mm longer than its predecessor. This is taking advantage of some EU vehicle length rules changes enacted in 2019 which are intended to encourage the design for improved aerodynamics for commercial vehicles. Those new rules mean that the Volvo XXL cab, so popular in Australia, is now available to the European market, adding 600 litres to the interior capacity. Both the FH and FM cabs have received signi cant aerodynamic improvements including seals around openings for
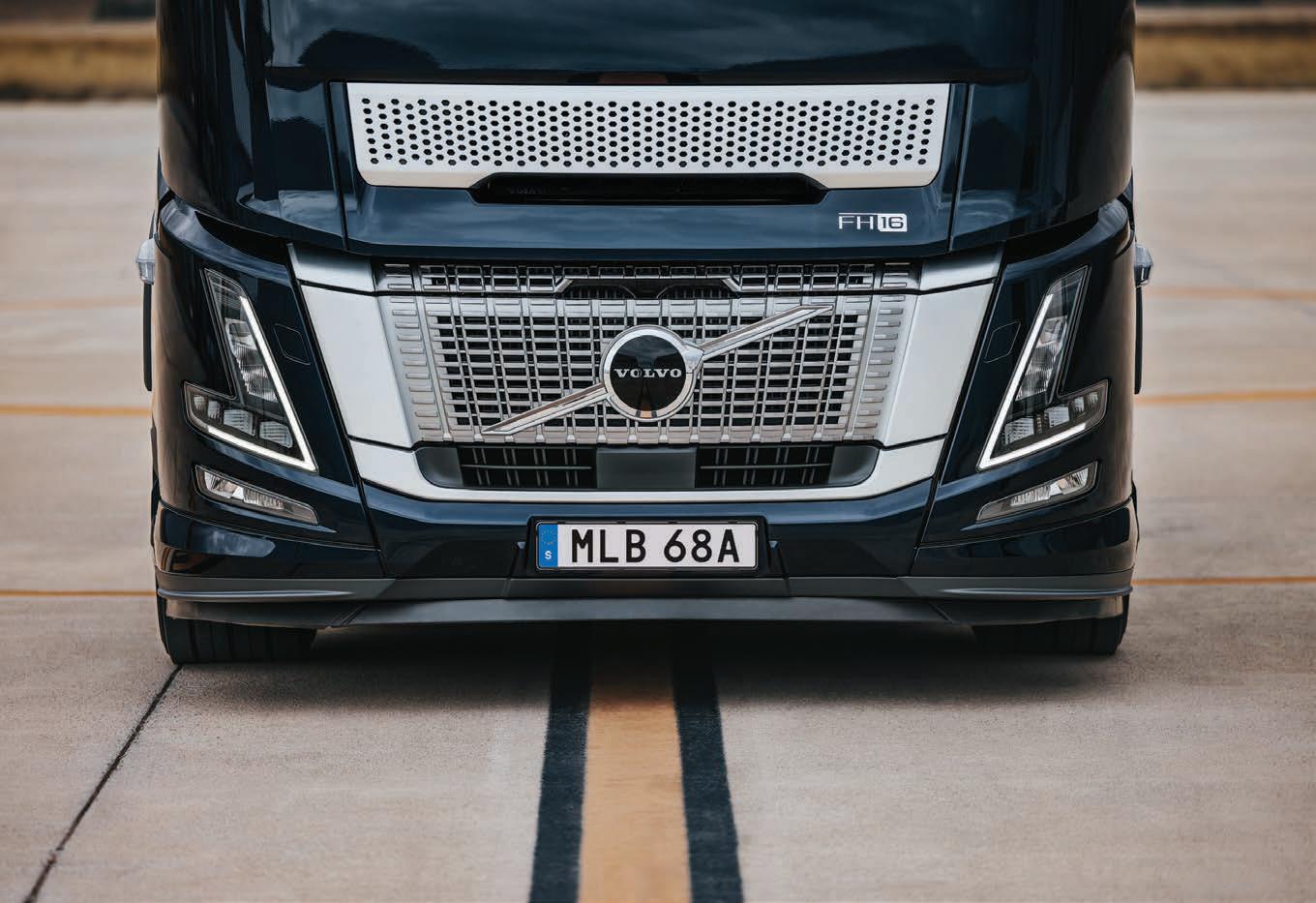
components such as lights. A noticeable feature is the addition of the optional Camera Monitoring System (CMS) that replaces the traditional left and right mirror assemblies and provides a wider eld of view than a standard glass mirror and can shift that view accordingly as an articulated combination negotiates turns and intersections as the view will pan dependent upon the position of the steering wheel. An additional outcome is the aerodynamic ef ciency gains of not having mirror housings on the side of the cab.
Driving with the CMS technology very quickly becomes second nature. While our short experience is during the rather limited daylight hours in Sweden during mid-winter, a demonstration of the CMS capabilities in darkness, low light and changing light (such as entering and leaving tunnels or reversing into dark warehouses) shows that the CMS’s incorporation of infrared lighting provides a substantial improvement to rear and side vision on the screen displays.
The passenger side screen is three centimetres longer than the one tted to the driver’s A pillar to account for the longer distance from the driver’s eyes. Adjustable reference lines provide the driver with an accurate view of the end of the trailer(s). The A-pillar mounted CMS screens can also be activated remotely from the sleeper for additional security
while the driver is resting. The mid-winter conditions in Sweden at the time of our visit also affect the presentation of the trucks due to the grime from driving through snow slush. A bene t of the CMS is this common problem is alleviated and clear vision remains on the internal display screens. The new lower grill section opens out to become a platform for use when cleaning the windscreen as well being used as a seating bench complete with integrated cup holders in case the driver is in the mood for a roadside picnic.
Winner of the International Truck of the Year 2024 award, the Volvo FH Electric Aero version impresses, as does a natural gas powered 500hp FM rigid with a side tipper body. This engine utilises an initial shot of diesel to initiate the combustion of the gas rather than using spark ignition. Unlike diesel, natural gas does not ignite due to compression alone, so this technology overcomes that issue at the same time as maintaining a high engine compression ratio which retains the effectiveness of the engine brake. A 780hp FH16 is at the launch in Gothenburg, connected to what can be best described as Europe’s closest combination to an A-double, with an overall length of 34.5 metres and loaded up to a gross combination weight of 64 tonnes. It tracks remarkably well due to the integration of a steer axle on the quad axle front trailer and, at this weight, the
power and torque of the 780hp engine make light work of the 12 per cent grade on the test circuit.
Volvo has taken a “little drops make a mighty ocean” approach to its quest for improved fuel ef ciency (regardless of the particular fuel being used) and the changes to the laminar air ow of the new FH Aero cab deliver an 11 per cent aerodynamic improvement which will translate in the real world to a ve per cent improvement in fuel economy which is maximized at normal highway speeds when air resistance is the biggest consumer of energy. Other changes include revised cooling ducts and a higher rear plate over the chassis behind the cab.
There is no current timeline for the introduction of the enhanced FH Aero cab into Australia and it will most probably be restricted to electric versions when it eventually becomes available here. Australia has proved to be the largest market globally for the FH16 model, while Greece is Europe’s biggest recipient of the FH16.
As is almost the standard situation at truck launch events, there are very limited opportunities to experience a comprehensive driver test but the few short kilometres we are able to drive across a number of models in the new Volvo line up only serves to whet our appetite for more when they are available to be assessed under local conditions.

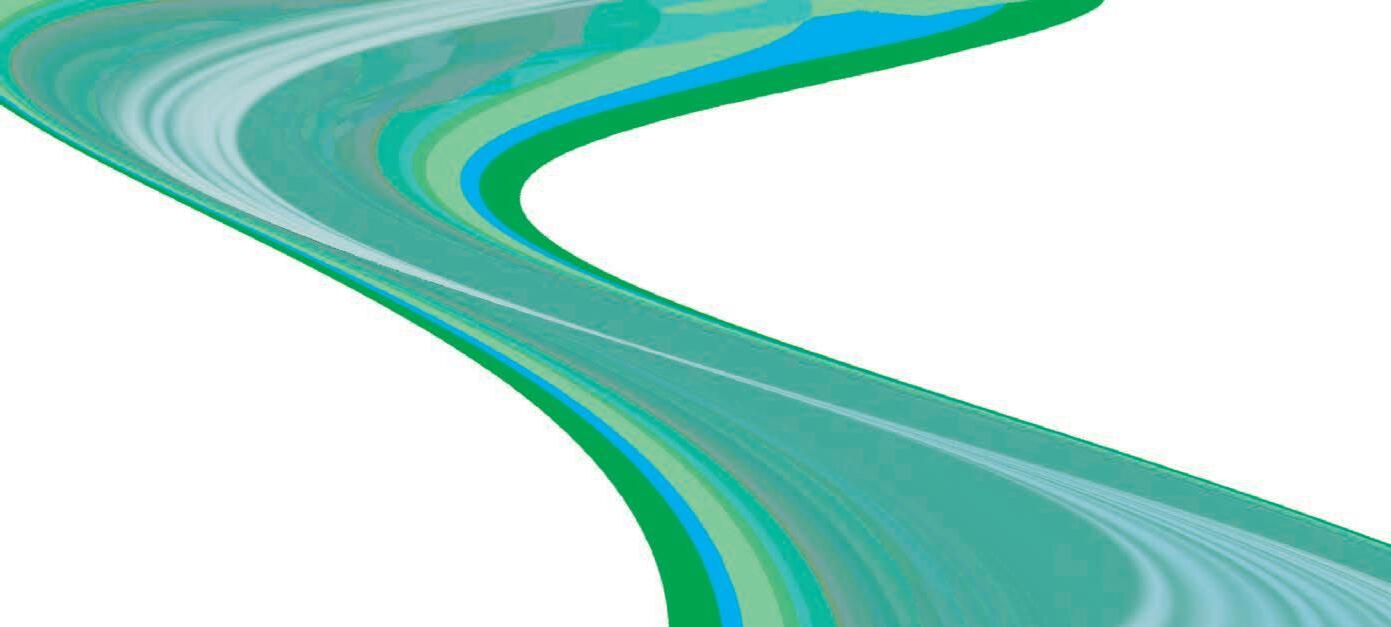
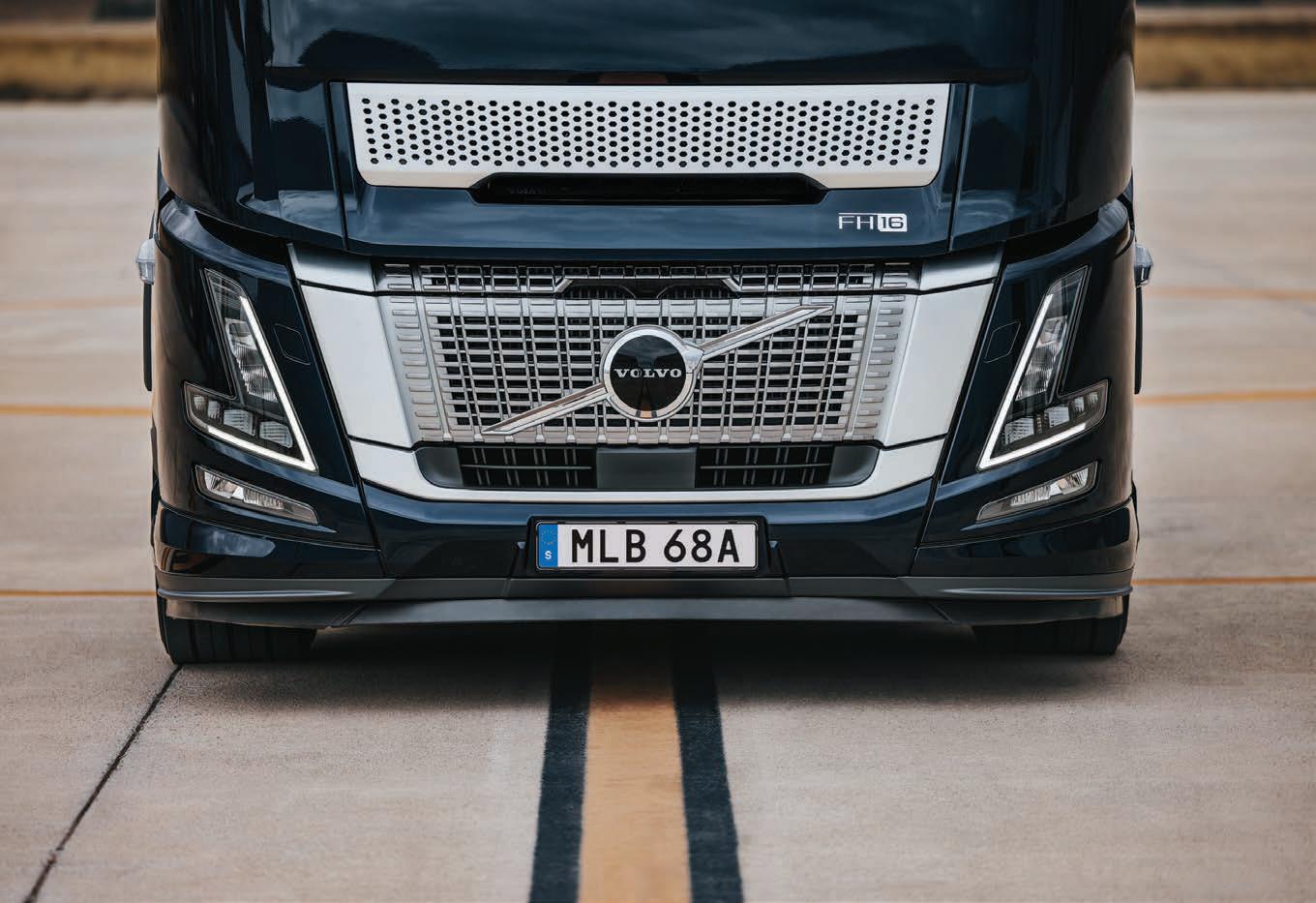
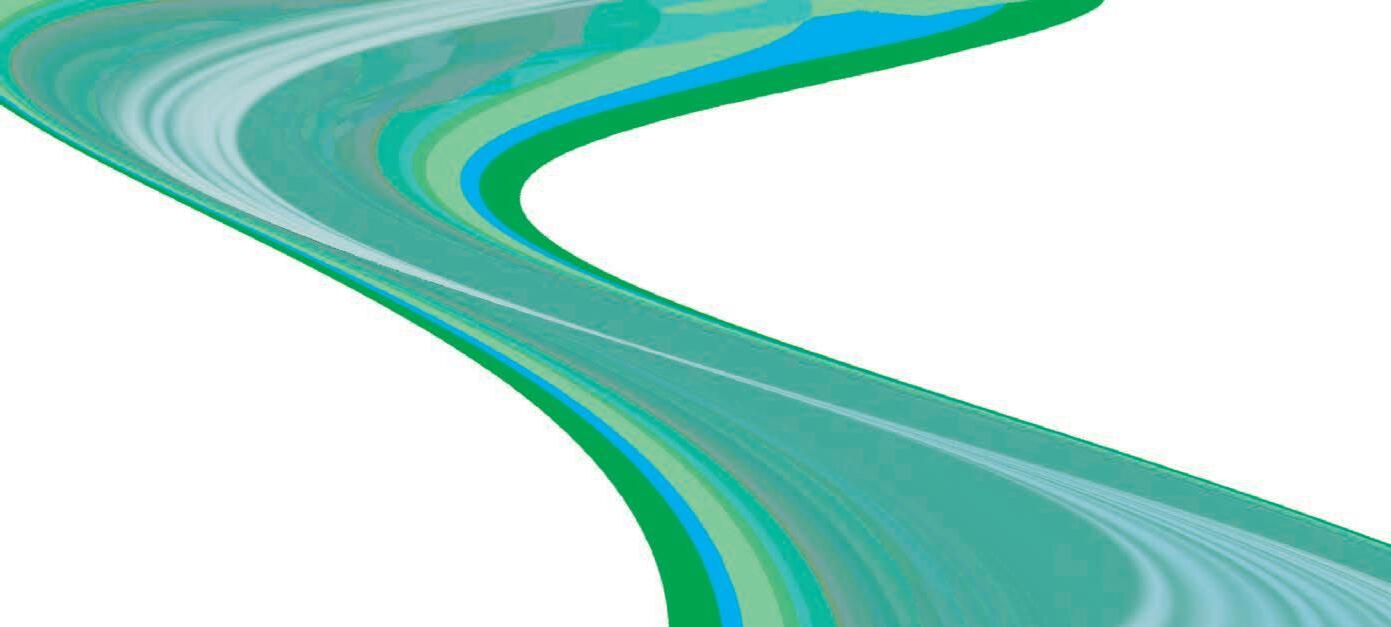

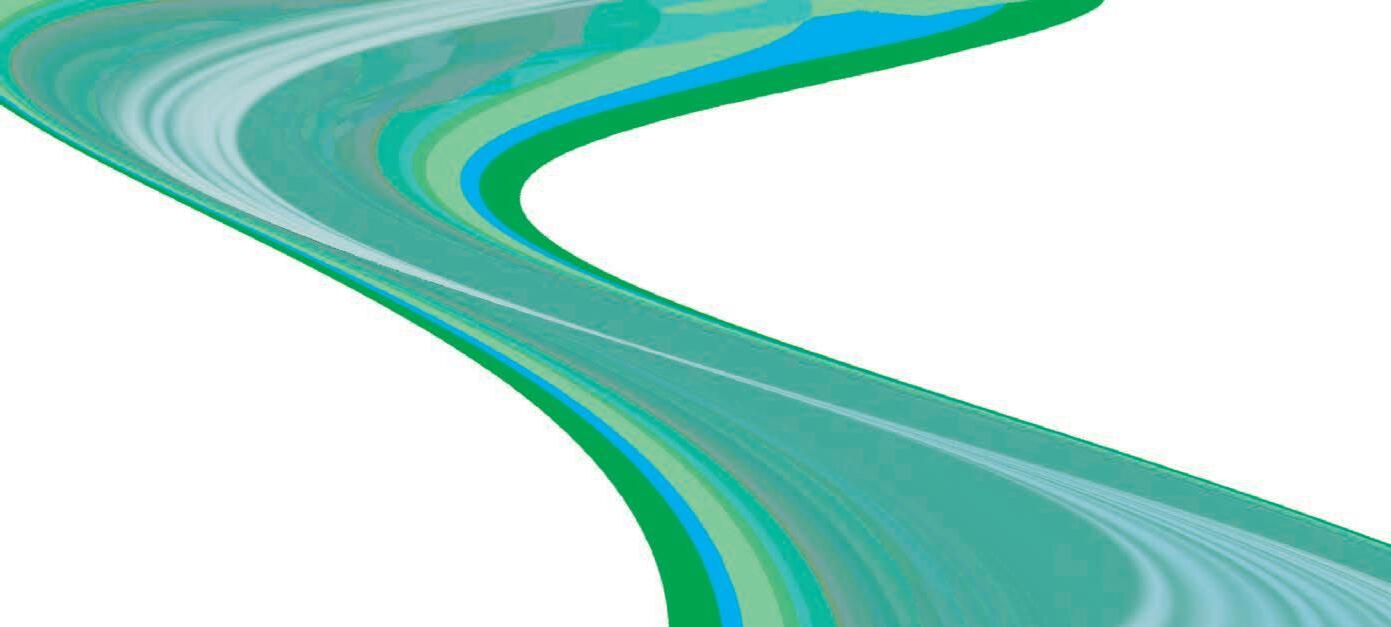
DO YOU KNOW A DRIVER OF CHANGE?
WOMEN IN INDUSTRY NOMINATIONS ARE NOW OPEN.
Now is your chance to nominate an industry leader who you believe is advocating for positive change and deserves to be recognised.
PROUDLY PRESENTED BY
Thurs 20 June, 2024
The Women in Industry Awards recognise outstanding women leaders from across Australia’s industrials sector.
KING PIN
An
extensive resume across engineering, production, operations and the aftermarket has
primed Damian Smethurst for his latest role at PACCAR Australia.
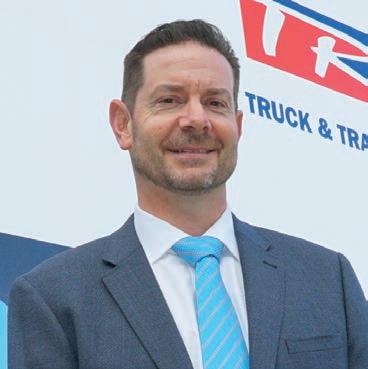
Damian Smethurst assumed the role of PACCAR Australia Managing Director in May 2023.
Prime Mover: What’s been your journey prior to become Managing Director?
Damian Smethurst: I was at IVECO originally out of university and saw a pretty cool graduate program ad for Kenworth and I knew that’s where I wanted to be. I’ve been at PACCAR for 26 years. I’m a manufacturing engineer by quali cation and I spent the rst ten years of my career in materials and supervising the factory oor and getting to understand the manufacturing side of the business. That’s also where I started to learn to work with and manage people. I became the plant manager in 2007 just as emissions changes drove a huge surge in demand. We had an American running the plant at that stage and he received the call back home and gave me the reins. We had massive orders and we got to 20 new trucks a day by the end of that year. Still to this day I think of that year as my most stressful and also my most rewarding.
PM: What happened next?
DS: The next ve or six years I was the factory’s Operations Director and it’s still fair to say the factory is my rst love. I then went into engineering and product development and spent the next seven years as Chief Engineer leading the engineering team through various
product programs including starting with the tail-end of the K200, followed by the T610, T410 and the T360. Then another move to aftermarket as PACCAR Parts Australia General Manager as well as responsibility for the dealership in Laverton. That role gave me a different perspective on the business and lots more exposure to customers and dealers. I was over there for the last ve years before getting the tap for this role back in May last year.
PM: Has your progress through those various roles helped in providing a good understanding of the PACCAR products?
DS: It has helped having a broad understanding of the product, customers and dealers, and also the suppliers. I really do value my time in the aftermarket gaining an understanding from a parts and service perspective of what’s required to keep trucks on the road and operational, and factors such as uptime and availability of parts and service support.
PM: Coming off a record year in 2023 how to you see the next couple of years in relation to the industry in general and PACCAR in particular?
DS: It’s hard to see the market dipping too far and I certainly don’t foresee any cliffs. It’s always been cyclical, but always in an upward trajectory. When I started, we were doing three trucks a day, we’re at 20 a day now.
PM: Does that strong demand put too much pressure on supply?
DS: To a point. We’ve got a fairly solid back-order list, which we need to keep reducing. We don’t like our customers having to wait too long for their trucks, so we and our dealer network are working hard every day to be as responsive as we can to what is unquestionably record demand.
PM: Is there a requirement for additional manufacturing capacity in order to achieve that?
DS: No doubt. We could be doing 30 trucks a day and perhaps still not meet the current demand. We’ve got some restrictions in a few areas of the plant and I’m hoping to help remove those bottle necks.
PM: Has the closure of the IVECO plant affected PACCAR’s suppliers much?
DS: Not really. Ten or 15 years ago we encouraged many of our local suppliers to broaden their customer base and obviously IVECO was a part of that. I’m disappointed to see them stop local manufacturing because I think it was good for our customers that our local suppliers could utilise a secondary customer with IVECO. More of their eggs are in the PACCAR basket now. We’ve tried to open our doors where possible to some of their employees.
requirements and that doesn’t change whether it’s Kenworth or DAF. Kenworth has built its reputation on that and we feel that having our core engineering team here, and the ability to design locally, has been fundamental.
The manufacturing site here provides a huge advantage and we are really proud of the fact we have remained here and
is it just the costs of manufacturing are too high here?
DS: I think all those things. We are a long way away and that does increase the cost base, and the volume is relatively low on a global scale. We are the smallest PACCAR plant and will always be that, but we work hard to ensure our products offer our customers value.
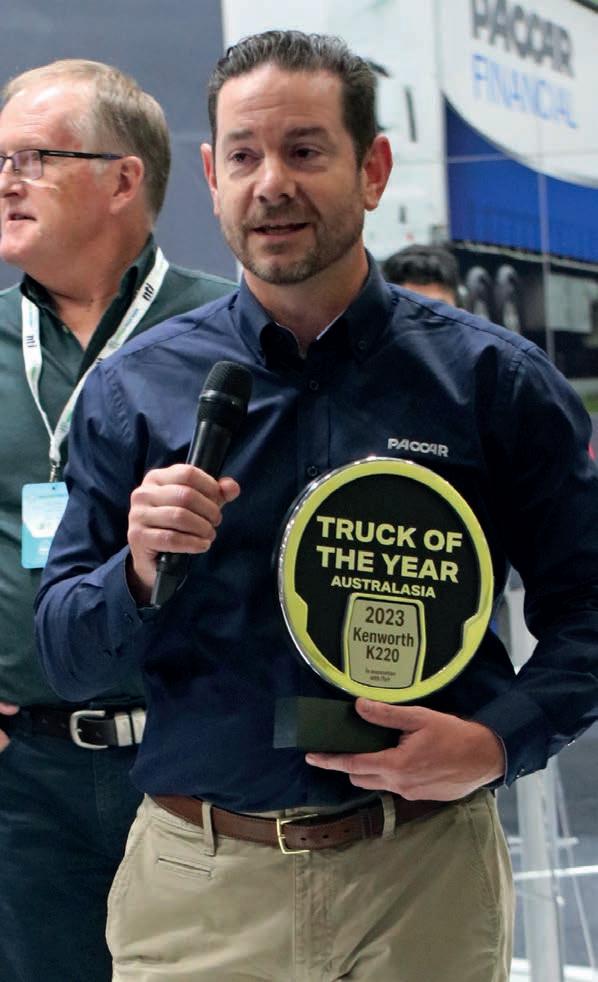
PM: As a local manufacturer what are the challenges and advantages?
DS: For both brands the advantage has always been just having local knowledge and insight into local applications and customer
plan to remain here for many years into the future. But if you clean sheeted and started again, it may be dif cult to get enough capital to make the investment. We are so fortunate others had the nous to open this facility in 1971 and continue to invest in it.
PM: Is that because we’re isolated or
PM: Kenworth is renowned for being such a strong brand. Is that something that has been conscious or is it just something that the market has come up with as things have progressed?
DS: We’ve been here for 50 years and have got a lot of runs on the board and that reputation is well earned. We do invest in the product and the support of the product. That’s what builds the reputation rather than anything we’ve tried to generate.
PM: The DAF XG+ is expected to be a game -changer for DAF. Will it have an impact on Kenworth?
DS: I don’t believe so. The beauty of having DAF and Kenworth is that there is very little overlap in terms of application. They appeal to different types of customers. The XG+ is going to be able to stretch its legs a little bit in terms of engine capacity and become an option for a lot more eets. DAF is an amazingly engineered product, and what we are doing is taking the best cab that we believe is available on the market and pairing it with an appropriate engine that can push it into the upper echelon of the heavy-duty segment. We don’t believe at all that it will compete with Kenworth.
ENGAGE RULES OF
Western Roads Federation was established to provide a relevant and united voice for the road transport industry operating in Western Australia. Cam Dumesny has been CEO for nine years.
Growing up in country
Victoria where his father was a heavy vehicle mechanic, Cam Dumesny joined the Australian Army where he was an of cer specialising in logistics and then technology during postings in Australia, the United States and the United Kingdom. After leaving the defence force Cam has drawn upon the skills and experience he acquired and found a natural t in providing advocacy for the road transport industry.
“I wouldn’t do it if I didn’t enjoy it,” he says. “I sometimes feel like I’m representing an under-dog industry which is grossly under respected for what it does. We don’t argue our business case very well because we’ve never made the case to the politicians and the community about how much value we add to the economy.”
Operators are sometimes their own worst enemies. Cam acknowledges that some need to better understand the true costs of operating and charge accordingly to provide the necessary accruals for factors such as maintenance and tyres and unexpected costs.
“They all need to be factored into the price,” he says. “I sometimes wonder if people are buying a lifestyle. It is a lifestyle industry in a way but at the end of the day it’s also a business.”
In his no-nonsense approach to advocacy Cam is aware of the
challenges. One of which is to make the industry important to the economy and government.
“If we can get them to accept that we are worth a quarter of a trillion dollars to the economy then it’s a lot easier to get investment in better roads, better rest areas, and better training for our industry,” says Cam. “We are out arguing for those all the time, but they don’t see that the investment is going to help improve the economy of the country.”
Because of the vast emptiness of much of Western Australia the road infrastructure doesn’t always have the same visibility as perhaps the Hume or Bruce highways.
“Out of sight, out of mind,” says Cam. “Which leads to another problem which is the disparity of investment in infrastructure which is increasingly in capital cities. Recent reports show the Victorian government is about to spend 40 times the Victorian annual road maintenance budget just on 15 kilometres of freeway in Melbourne.” Cam sees the situation not being con ned to Western Australia.
“The quality of our regional freight network is just absolutely below average and is maintained to a bad standard,” he says.
Extreme weather conditions too often show up the lack of all-weather sealed roads which brings road freight to a
standstill or requires lengthy diversions to enable vital freight items to be delivered. Regular seasonal disruptions in places such as the Kimberley region require trucks to travel from Perth to Darwin via Port Augusta as there is no alternative route.
“We’ve still only got two sealed roads across Australia and they are 2,000 kilometres apart,” says Cam. “If the gravel Great Central Road was sealed it would provide an alternative to the Kimberley route that would only be about 100 kilometres longer. Being able to travel from Kalgoorlie and Laverton through to Alice Springs saves about 1,200 kilometres on the alternative through Port Augusta. You could seal that road for around $2 million per kilometre, so around $2 billion to seal all the way from Laverton to Alice Springs. $2 billion does about four kilometres of freeway in Sydney. Yet it’s really hard to win the argument, although one opens up the nation and the other saves about ve minutes.”
The Western Australian Government took the decision not to participate in the Heavy Vehicle National Law administered by the National Heavy Vehicle Regulator which doesn’t surprise Cam.
“At this point there hasn’t been a compelling reason for WA to join and the Northern Territory is in a similar situation,” he says. “Bear in mind that
MENT
statistically the large majority of WA freight occurs within the state without much cross-border movements and most the remaining freight from the east comes via rail.”
WRF has established a strong relationship with the local mainstream media and is recognised as the “go to” body for all things involving road freight.
“We don’t go picking ghts against rail or air or sea because we need all four modes working together,” say Cam. “We’ll obviously advocate for road but we also recognise the importance of rail, sea and air in the freight mix, so we advocate for a freight strategy that’s inclusive and having that approach opens us up a bit more to the general media.”
Having the WRF adopt an apolitical approach has been important as well. “We can’t be politically biased,” says Cam. “You’ve got to be able to represent issues to all political parties so we’re not on the outer if there is a change of government.”
An example of the bene ts of this philosophy has been in enlisting the Greens to support the use of High Productivity Vehicles capable of moving four 20-foot containers from the Fremantle port using trucks with lower emissions and higher-level safety packages.
“The industry sees modern, safe, and lower emission trucks but the community sees some landscaper using 30-year old truck to shift their bobcat around and belching black soot,” says Cam. “As far as they are concerned that’s a ‘truck’ yet his core business is the bobcat, the truck just gets them from job
to job. But that’s what they see, and we pay a penalty for it.”
With that said, Cam has concerns that the image of the industry is not improving. “We had a higher pro le during COVID but governments, collectively both state and national, have lost interest in it as has the community,” he opines. “The
industry has is itself,” says Cam. “People like Heather Jones [Pilbarra Heavy Haulage Girls] and Glen “Yogi” Kendall get out and try to advocate that it’s a good professional industry, but then you get drivers on social media attacking them and pulling them down.”
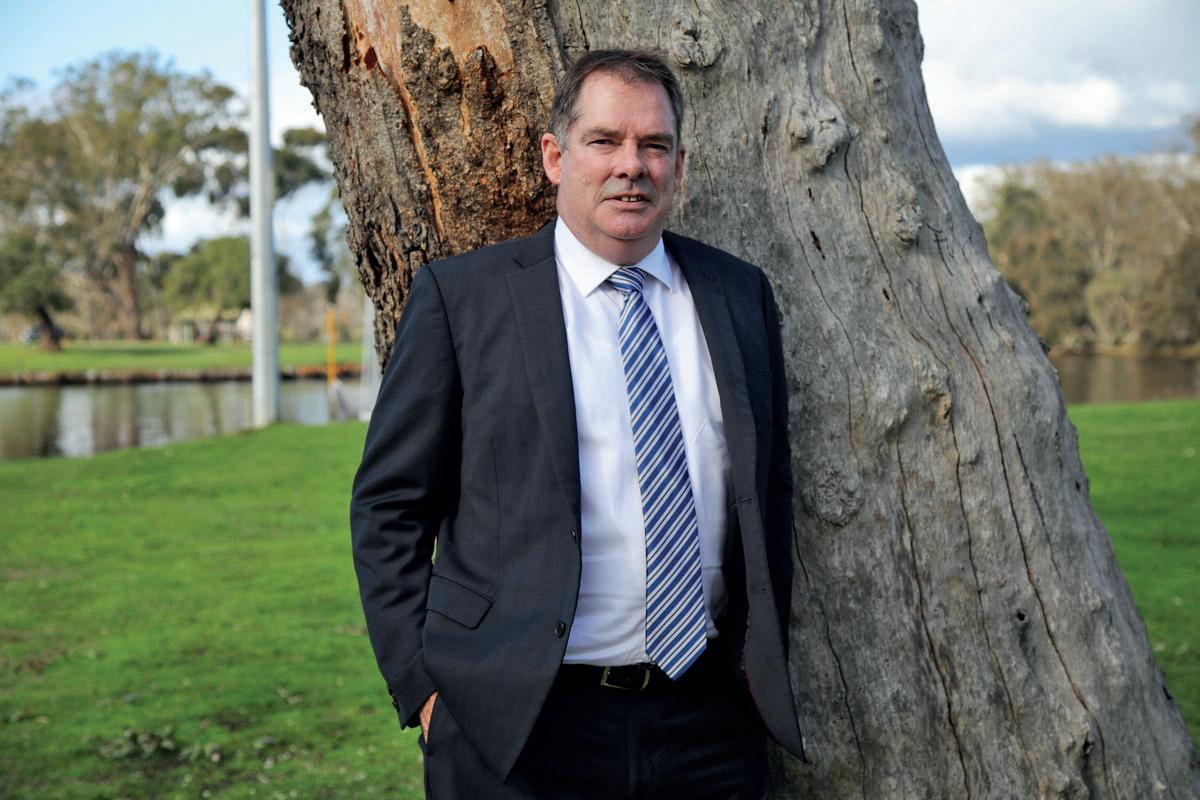
only time we get a good pro le is when there is a ood or re disruption and the community goes without, and it’s the trucks that roll in. We never capitalise on it in terms of wins for our industry and it’s just a short-term blip on the mainstream media.”
Social media can, perhaps too often, deliver mixed coverage.
“There is a very entrenched opinion of truck drivers and the transport industry and often the biggest problem the
Despite that, the WRF’s united approach is paying dividends in terms of recruiting and training as well as obtaining funding for facilities such as rest areas.
“We work with the livestock association and the TWU and we don’t agree on everything but work on what we do have in common,” says Cam. “You can make some differences by working together such as achieving the $50 million allocated by the Government for heavy vehicle rest areas.”
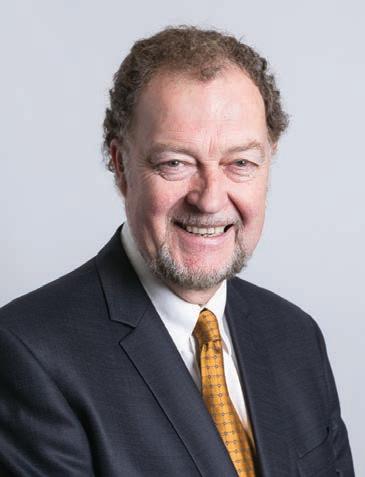
Modi cations to heavy trucks, trailers and buses need to be approved by an accredited person called an Approved Vehicle Examiner (AVE), who will issue a certi cate and af x a plate to the vehicle. The NHVR can also approve a class of modi cations. I have written several articles about the need to reform the approval process — see my articles of August 2023 and February 2021. This article is about key technical requirements arising from the National HV Modi cation Code of Practice – VSB 6.
What modi cations need to be approved? In the National Heavy Vehicle Law, a modi cation is: (a) addition or removal of a component from the vehicle; and (b) a change to the vehicle from the manufacturer’s speci cation. A repair that reinstates the original speci cation using OEM parts is not a modi cation and doesn’t need to be approved. A change that implements a manufacturer’s optional speci cation using original parts is not a modi cation. Keep good records if you do this work.
A change that does not make the vehicle non-compliant with a vehicle standard is not a modi cation. Examples are installing aerials, air conditioners, additional approved lights, tipper covers, headlamp shields and manufacturer’s wheel and tyre options. The latter covers non-original tyres and rims that are within vehicle
Heavy vehicle modifications — key requirements
manufacturer’s speci cation. There are some modi cations in the grey zone such as beacon lights installed on the cab roof or the status lights on trailer refrigeration units.
What are the heavy vehicle standards?
These are technical rules and mass and dimensional limits that are in (a) the Australian Design Rules (ADRs), the Heavy Vehicle National Law and its Regulations (or state law for Western Australia and Northern Territory) and any state/territory registration requirements that get published in a government gazette. Requirements in mandated codes of practice should also be assumed to be HV standards. There are other technical standards that may be applicable to plant equipment that may be installed onto a heavy vehicle. These arise from the occupational work health and safety regulations in the state/territory jurisdictions. For example, vehicle loading cranes, DG tanks and some tip truck hydraulic systems must satisfy work-safety technical standards. Large air tanks could be prescribed pressure vessels. The AVE cannot issue these approvals.
Can the manufacturer’s dealer approve modi cations? No. A dealer is legally required to obtain an approval certi cate for modi cations conducted to new vehicles before rst registration. For example, if you purchase a tray truck or a new tip-truck and tip-trailer from an OEM truck dealer, approval certi cates should be provided. These requirements were not enforced until a couple of years ago. This has created a signi cant increase in demand for AVE services.
When should the AVE get involved?
Before work starts. This seems obvious but is commonly not done. Getting an AVE at short notice when work is nished is likely to be dif cult. Great frustrations will occur for the
owner. The AVE should oversee the modi cation, do some calculations, and check the plans or sketches beforehand. That way, the work will proceed smoothly.
What documents are required? There should be dimensioned plans, drawings or sketches. The modi er should keep a technical le that fully describes the modi cation, identi es applicable technical standards, and justi es the design against vehicle standards. The technical le should be available to the AVE but need not be provided. Take many photos when the modi cation work is being done!
Are there any general strength requirements in VSB 6? Yes. Code J, Body Attachments and Code H, Chassis Modi cations specify a general Factor of Safety for strength members of at least 3. For point loads such as tipbody pivots, the Factor of Safety should be at least 6. The Factor of Safety is based upon maximum static loads and referenced to the yield strength(s) of the structural materials. Permanent distortion occurs at yield strength. An unwritten law for chassis and subframe design is: Make only gradual changes to strength in a highly stressed region. Strength transition avoids stress concentration.
Body attachment requirements: Most rigid trucks have a tray, body or tank attached. There are no technical standards in the design rules (ADRs) or in VSB 6 for the tray, body or tank. Because of this the body does not require an approval. For example, there is no approval code for the structural integrity of a body or a tank. The attachment of the body does need an AVE approval, because these are rules relevant to dimensions, lights and general safety. A key consideration is the strength of the chassis ladder in conjunction with the body subframe. Calculations are needed to show
that the chassis ladder is adequately strong. VSB 6 does not explicitly consider dynamic loads. It is assumed that a static Factor of Safety of 3 will be adequate to cope with these undetermined dynamic loads. The AVE should question this assumption.
Twisting of the chassis ladder just behind the cabin can be excessive because there is often a short unreinforced section of the chassis ladder between the stiff subframe and the stiff cabin cross member and transmission mounts. ‘Torsional stiffness’ mainly arises from structural elements positioned above or below the chassis ladder. VSB 6 provides guidance that the forward body-chassis attachments should be exible so that the twist is spread. No requirement to calculate torsional stiffness exists in VSB 6, but a successful design will transition the torsional stiffness. Another problem is that fatigue failure sometimes occurs in chassis ladders. Fatigue failure can occur at much lower stress levels than yield stress.
Can U-bolts still be used? A question that often comes up is whether bodies and trays can be attached using U-bolts. VSB 6 allows U-bolts if a ‘strength tube’
is used to prevent the c-section of the chassis rails from distorting. Also, two diagonal brackets are needed on each rail to prevent the body from rocking back and forward. I prefer to see bodies attached by side plates with a forward exible (external) bolt-down mount. Can high-strength chassis rails be safely extended? Cutting, extending and rewelding a high strength chassis rail can be done by a specialist modi er. The rail should be cut on an angle and the join should be away from any crossmember. The inserted chassis rail section should be the same steel as the original rail and the rails will need to be pre-heated and then welded by an accredited welder. An added rail reinforcement will always be needed and this should overlap the join by at least 500mm. Don’t forget to transition its strength!
What about the pulling forces applied by a towbar or drawbar?
A truck or trailer with a heavy-duty towbar also needs a heavy-duty chassis ladder at the back, or for a trailer drawbar, strength at the front. The design needs to allow for the additional pulling loads. A guide to these is the test forces for towbars and drawbars
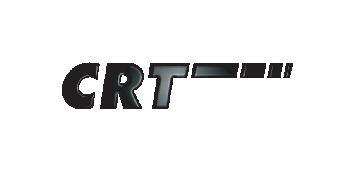
speci ed in ADR 62. Calculations are required. For trucks, the rear suspension rail reinforcement will probably need to go right back to the towbar. How can brake system modi cations be proven? Brakes are complicated! Changes of brake set-up including using non-genuine linings could be a modi cation! VSB 6 provides little guidance about how to certify signi cant brake system changes. If an axle is added or substituted, brake calculations are needed. Continued compliance with the design rules must be proven. The ARTSA brake calculator provides a tool that could be used — see my July 2023 article. Changes to advanced (smart) brake systems will probably require help from the brake supplier’s specialist. The AVE probably can’t do this work.
Operators need to have a basic understanding of the legal requirements for two reasons – 1. to stay legal and 2. to avoid insurance disputes. If a HV has been modi ed, there should be modi cation plate af xed to it. Keep it safe!
Dr Peter Hart, ARTSA-i Life Member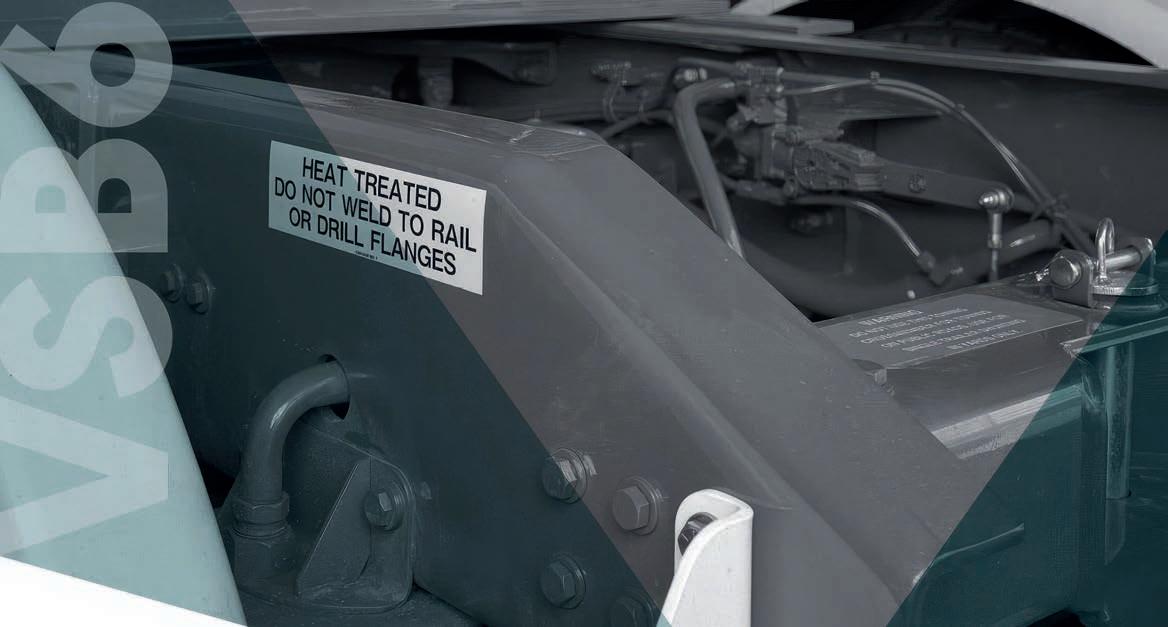
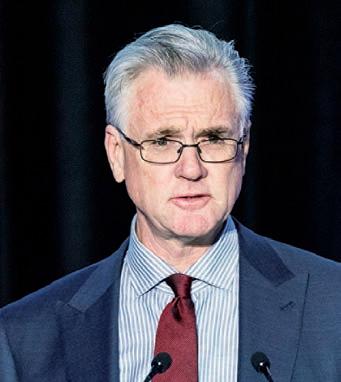
As I detailed in my column last month, 2023 saw a new all-time record set for new heavy vehicle sales in Australia, with a total of 47,757 heavy, medium and light truck and vans delivered across the nation. However, that was not the only sales record broken last year, with the Truck Industry Council’s T-Mark sales data showing that a total of 367 low and zero emission trucks sold in 2023. At rst glance this appears to be a quite modest number given the size of the total new truck market last year, except the sales gures do not tell the broader story here.
These 367 low and zero emission truck sales represented an almost four-fold increase in sales over 2022, when only 99 low and zero emission trucks were sold. That is a signi cant year-on-year increase not seen by any other truck segment, or vehicle type. Furthermore, approximately 90 per cent of these low and zero emission truck sales were made with no governmental (federal or state) nancial assistance. As the vast majority of these truck sales was made without assistance, one has to presume that there is a positive business case to be made for low and zero emission trucks in many applications and operations. A deeper dive into the T-Mark sales numbers for these trucks reveals the type and use cases of many of these vehicles. Eighty-three per cent are Light Duty trucks, primarily used for city/urban
Low and zero emission truck sales take off
deliveries. A further 16 per cent were Medium Duty trucks, again the majority of which are destined for that metro type distribution role. Just 1 per cent were Heavy Duty trucks and all of these were rigids. There were no Heavy Duty prime mover low, or zero, emission sales in 2023, potentially an indication of limited product availability, however equally, an indication that these power technologies currently have limited opportunities for this application in Australia, where high power muti-combination diesel prime movers prevail.
A leading factor in low and zero emission Heavy truck availability and take-up is Australia’s restrictive dimensional and mass regulations. Currently limited to 2.5m maximum vehicle width, most of the rest of the world is 2.55m, or 2.6m, Australia’s “narrow” truck width regulations are a signi cant roadblock to new low and zero emission Heavy trucks that are only being designed for the majority of the world and their “wider” regulations. Australia accounts for less than 1 per cent of global truck sales, hence we are in no position to dictate unique truck designs for such limited truck sales. In a positive move, in late 2023 Assistant Minister Carol Brown signed off on Australia Design Rule changes that will allow 2.55m wide trucks on our roads if they are tted with a number of new safety technologies. However, that good news has been tempered somewhat by the delay in updating inservice regulations that are currently still preventing the use of 2.55m wide trucks in Australia. A roadblock that may take a further six months to address.
Limited axle masses are another key issue for the ef cient operation of Heavy Duty low and zero emission trucks in Australia. While Europe allows up to a 2000kg axle mass increase for these truck types to offset the additional mass of batteries, hydrogen tanks, etc, Australian governments currently offer no such mass concessions. In Australia, the additional weight of these trucks must be borne by the operator who simply has to reduce the payload of the truck, meaning less freight carried compared to a diesel truck, to ensure they legally comply with our “minimalistic” weight regulations. This issue must be addressed by government.
TIC and our members are very conscious that the Australian road transport industry must actively move to reduce its carbon emissions and as such, TIC members will be rolling out more new low and zero truck models in 2024 and beyond. However, there must be recognition of Australia’s limiting heavy vehicle dimension and mass regulations by all levels of government, federal, state and local. This recognition must be accompanied by positive changes that will allow globally designed trucks to operate ef ciently on our road networks. Further, governments need to consider the appropriate nancial incentives to drive change to a low carbon road freight transport future, one that will see our ageing diesel truck eet replaced with new, safer, cleaner and greener trucks. An outcome that will bene t Australia and all Australians.
Tony McMullan CEO, Truck Industry Council
As another Australian summer draws to a close it’s instructive to re ect on three months of incredible uncertainty at ports around the country, particularly the Port of Melbourne which experienced almost routine-like industrial and cyber-security unrest, and disruptive political activism.
The usual pre-Christmas speculation about supply chain challenges were super charged for stevedore DP World Australia as prolonged industrial action with the MUA, along with a cyber-attack, heightened concerns freight customers and consumers would be hit with delays and shortages.
Webb Dock stevedore VICT was also a regular victim of unrest with political protestors disrupting loading and unloading of Israeli- agged ships, with the ow-on effects felt by landside operators and further down the supply chain.
Thankfully, DP World contained the cyber-attack and associated retail shortage fears were allayed — toys, clothing, homewares, and other Christmas wishlist items were in good supply thanks to customers anticipating delays and keeping warehouses stocked. The industrial dispute is making its way through the Fair Work Commission, and Victoria Police have responded effectively and quickly to disruptions at VICT.
A silver lining of these activities has been regular media reports of the myriad of issues at play at the waterfront, helping to
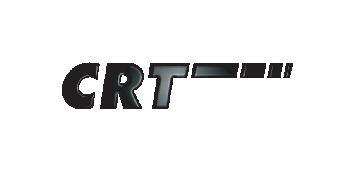
Summer disruption underscores waterfront reform urgency
educate Australians about the intricacies and sensitivities of supply chain management, and the repercussions for them as freight and logistics consumers.
Coming off 18 months of rising interest rates and in ation, Australian consumers have a deeper understanding of why they are paying more now because of what’s happening overseas. Geopolitical con ict, rampant post-COVID labour shortages, and global supply and demand imbalances, regularly feature on the evening news as reasons for higher prices in the economy. Australians may not like paying more for goods and services, but at least they are appreciating the reasons for it.
This isn’t to say we should lay down and accept price hikes and higher costs that are out of step with community expectations, which is where government can step up and enact reform. The cost of moving goods in and out of Australia, and more generally worldwide, is increasing exponentially due to higher global container shipping rates, which are making things everywhere more expensive than they should be.
In January, the Drewry World Container Index increased by almost a quarter (23 per cent), with the composite index increasing by 82 per cent compared with the same period in 2023. Generally, prices for freight coming from China are skyrocketing with rates on boxes from Shanghai to Los Angeles, New York, and Rotterdam up almost 30 per cent; conversely, prices for returning boxes decreased around 2 per cent, highlighting the imbalance.
The VTA has long advocated for reform that would contain super pro ts earned by shipping liners, who currently can access a wide suite of exemptions from
Australia’s competition law. Part X of the Competition and Consumer Act (2010) needs to go because it allows shippers to agree on freight rates and quantities and the kinds of goods to be transported on trade routes. Such cartelism has been outlawed in the United States and its complicity unheard of in other parts of the business world.
Unfortunately, landside road freight operators servicing stevedores will be worse off from all this unrest, with freight customers, primary producers, and consumers, paying higher prices for disruption and uncertainty.
Complicating things even further for the landside operator are the comparatively lower margins they charge, providing them with less capacity to pass on higher costs in full, and run the risk of losing business by not doing so. While the rate of in ation is easing, prices continue to increase in the economy. Now is not the time for landside operators to expose their businesses to nancial risk by limiting cost recovery.
Attaining greater port ef ciencies and reducing clogging and congestion for in and outbound trade will be a major issue this year, underscoring shipping super pro t reform urgency and for landside productivity improvement to offset seaside disputes.
If we cannot resolve serial waterfront disruption there is a heightened potential for the kind of sovereign risk creation that will give manufacturers, primary producers, and shippers pause to reconsider Australia – with its higher costs –as an export market. Such a scenario must be avoided at all costs.
Peter Anderson CEO, VTAOut of the Red
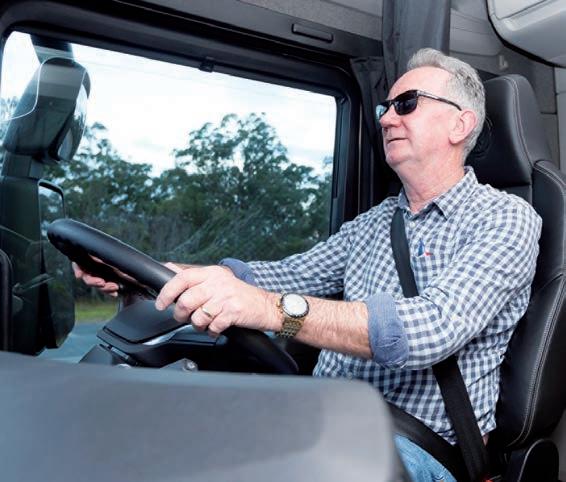
One month does not a year make, particularly if the month in question is January. Public holidays and the popularity of the period for employees to take annual leave in line with summer school vacations contribute to a general ease off in Australian business across the board during the month in most years. For the new truck industry in Australia, after a couple of back-toback record years the relative respite of a ‘quieter’ month in terms of new truck registrations would have been unlikely to raise even mild concerns among many of the OEMs and their dealers, and they would remain encouraged by the more than healthy order banks most are currently holding.
The Truck Industry Council reported 2,211 new trucks for January, which was 167 units less than in January 2023 (-7.0 per cent) but still a solid start to the year, especially considering that January 2022 achieved a smaller 1,927 units, and the industry went on to set a record for that full year.
During January the Light Duty sector provided 823 new units, which was 205 less than during January last year (-19.9 per cent). The Medium Duty market segment achieved a modest month-on-month gain of 34 units in its monthly total of 440 (+8.4 per cent) and Heavy Duty trucks once again surprised with the highest numerical result of 948 units which may have only been four more than in January 2023 (+0.4 per cent) but still a strong result especially when the dollar value of the bigger trucks is taken into account.
The ‘big’ van sector had a particularly good month during January, helped along by several eet deliveries. The total of 492 units was 85 more than in January 2023 (+20.9 per cent) and with several new models slated to be available the rst half of the year, the situation looks encouraging. The reality of strong demand combined with limited availability is likely to be exacerbated even further by the political tensions in the Red Sea region in terms of the supply of commercial vehicles and

components mainly from European manufacturers as well as adding to landed costs if sea freight is forced to be carried out via the Cape of Good Hope.
Numerous manufacturers have agged new models coming to the local market during 2024 and the interest and development of low and zero emission trucks will contribute to the dynamic of what continues to be a healthy industry.
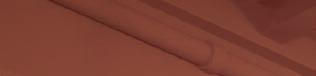
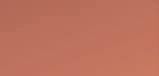


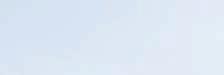

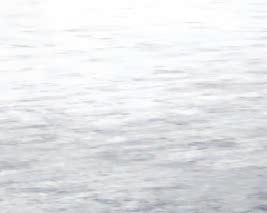
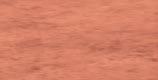

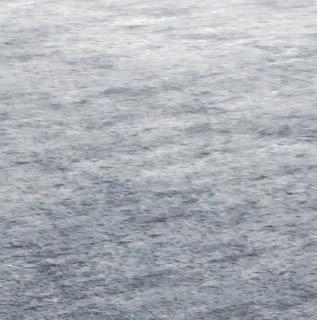



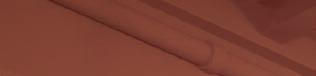
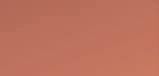


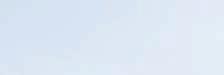

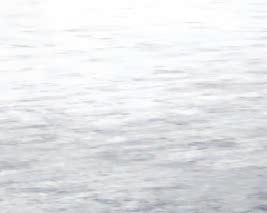
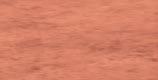
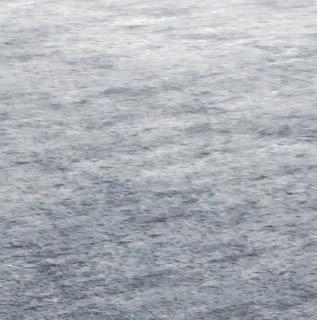

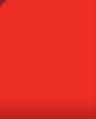













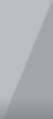
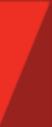






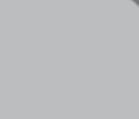

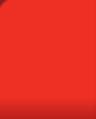

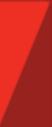
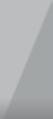













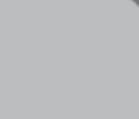

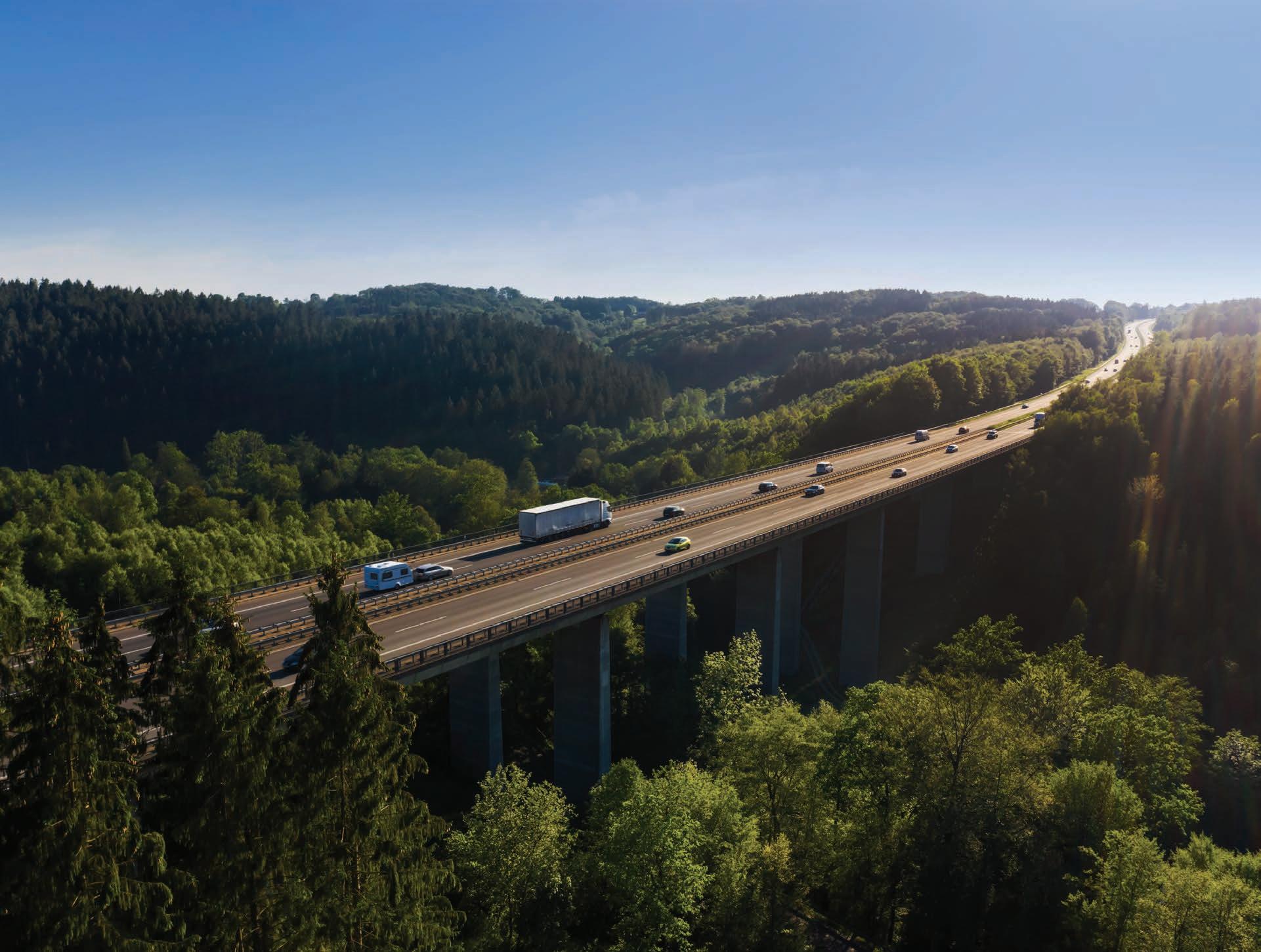
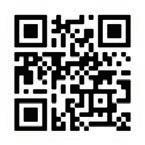