ISSN 1838-2320 9 771838232000 08 SEPTEMBER 2022 $11.00 SCT Heaven’sLogisticsGate Innovation Fleet: South East Queensland Hauliers Mindset: Tiger Spider Test Drive: Hino heavy range Delivery: Fukushima Prefecture Industr y Fleet: McColl’s Transport Feature: Russell Transport Showcase: Heavy Vehicle Insurance Personality: Paul Walsh THE PEOPLE & PRODUCTS THAT MAKE TRANSPORT MOVE MAGAZINE Delivery Magazine inside: Pages 68-73. ® September 2022
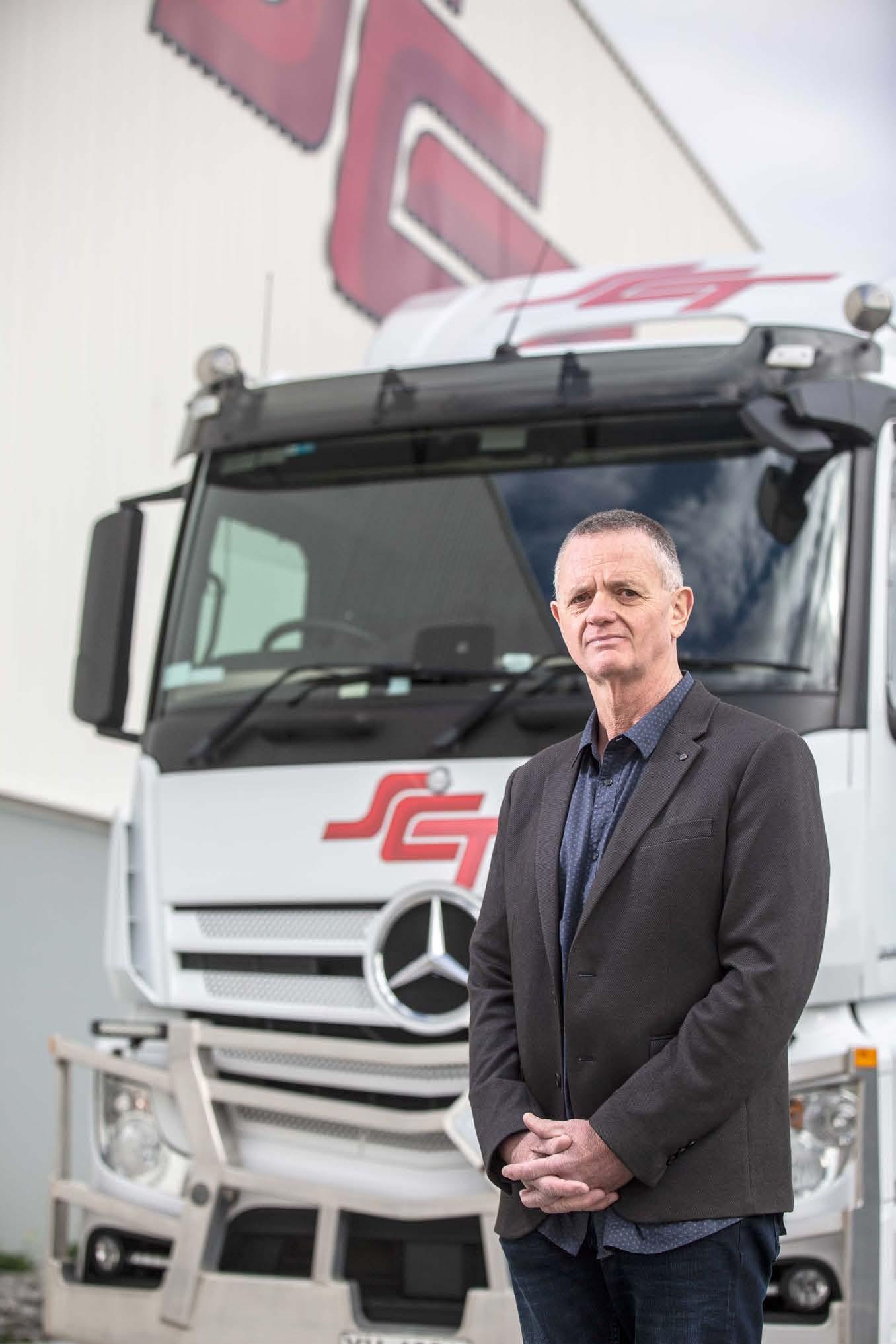
medium
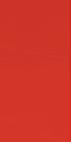

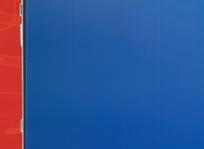
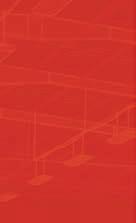
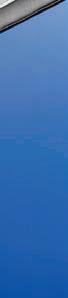




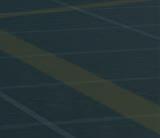

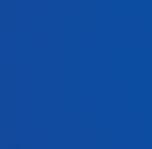
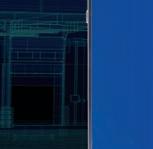
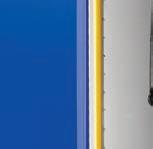

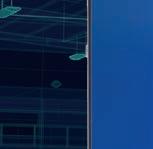

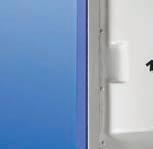
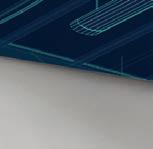
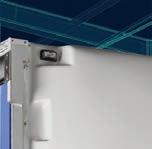
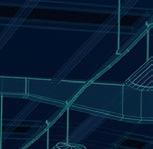
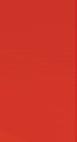

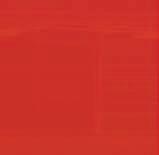
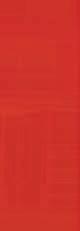
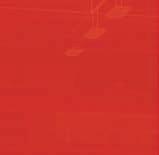

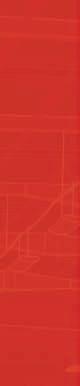
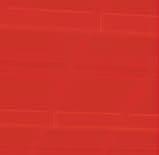
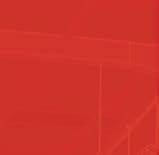


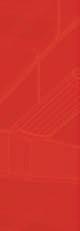

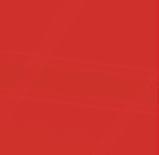
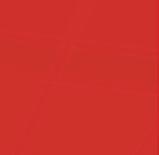
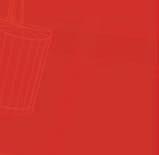
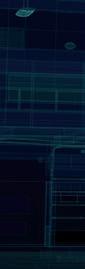



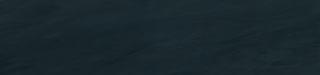



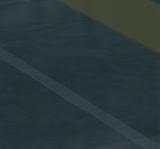
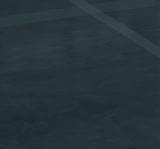
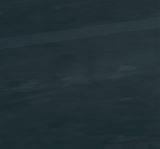
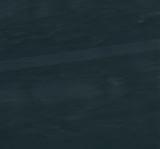
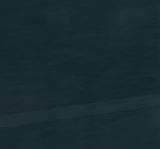

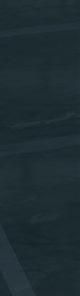
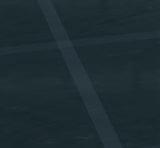
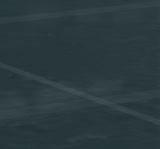

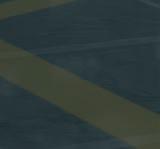

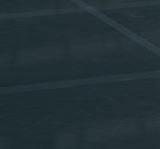
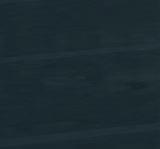
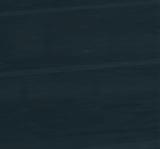
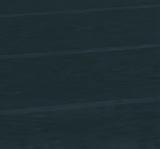

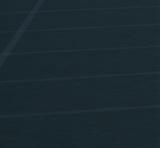


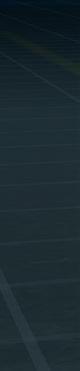



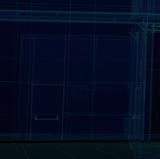
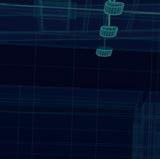

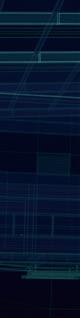
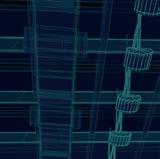

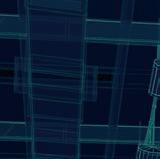

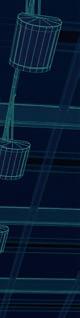

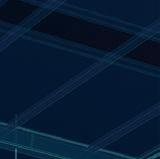
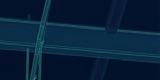

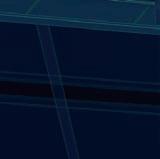
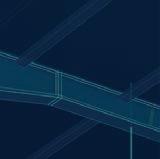
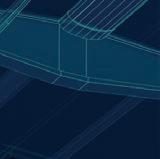
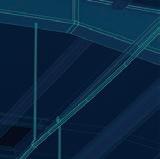
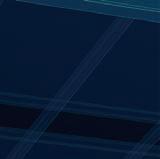
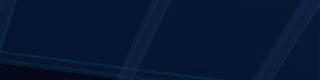
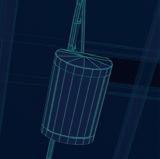

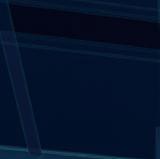
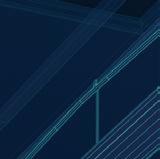
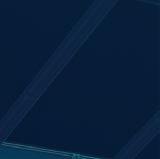

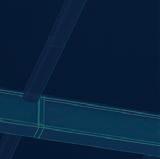
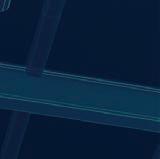
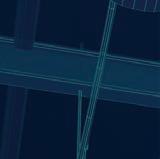
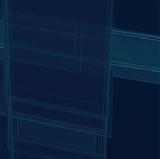
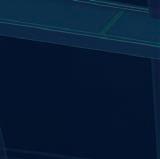
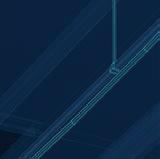
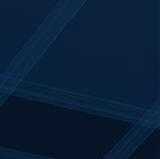
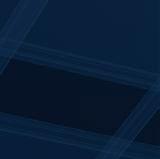
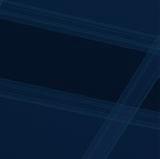

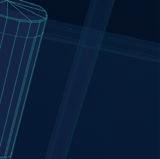
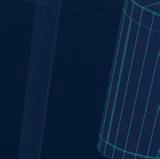
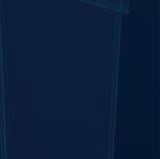
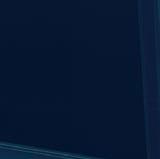
The duty
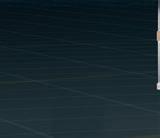
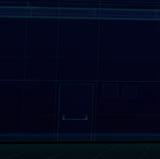
The Next Generation of Safety.
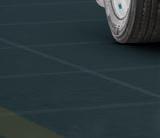
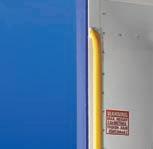
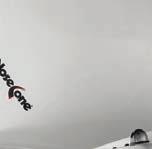

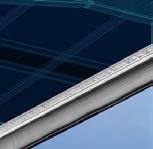
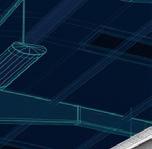

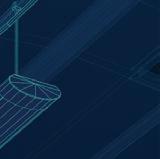
The new Isuzu F Series is our safest range of medium duty trucks ever. On selected models you’ll find Advanced Emergency Braking, Lane Departure Warning and Electronic Stability Control. Then there are standard inclusions like double side-intrusion bars, SRS dual airbags, digital reversing camera, LED headlights and a Cab Tilt Warning. And F Series trucks now come with a six-year warranty, too, so there’s one more reason to feel safe and sound. To find out more, visit isuzu.com.au. Safety features are for driver’s assistance only. Responsibility for the vehicle (including maintaining control, awareness of surroundings, and following road rules) remains wholly with the driver. Warranty is subject to the conditions outlined in the IAL New Vehicle Warranty. For further information please visit isuzu.com.au or contact your local dealer. FSA/ISZS1042
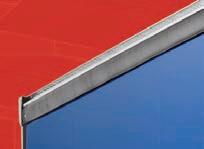
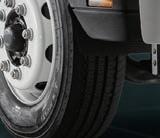
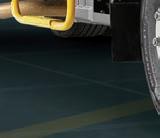
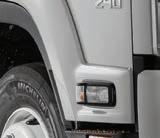
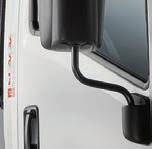
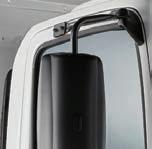
truck that’s big on safety.
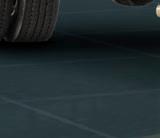
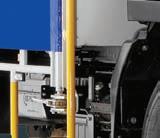
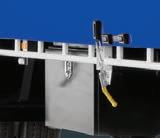
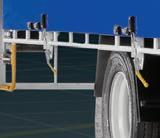



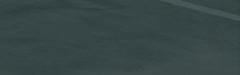
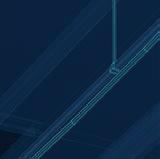
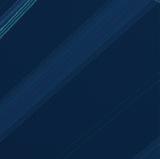
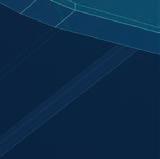

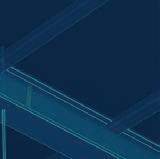



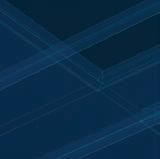
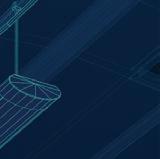
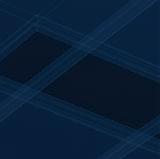
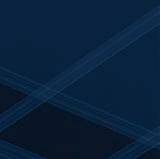
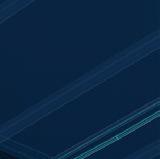


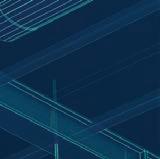
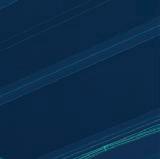

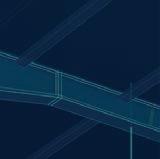
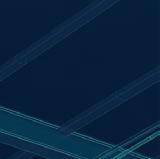
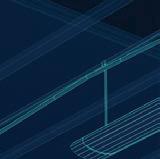

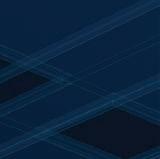
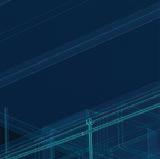
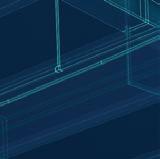
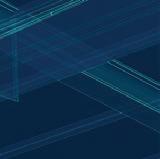
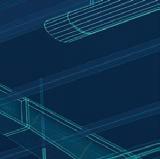


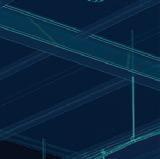
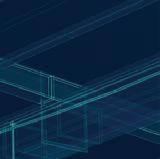
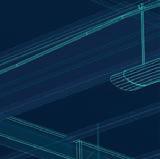

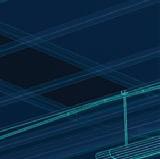
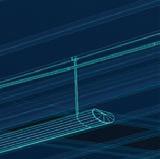
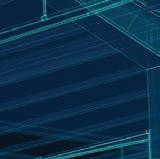
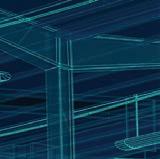
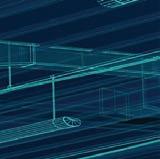
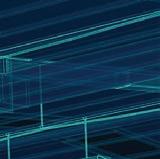

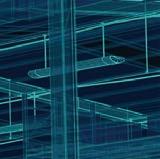
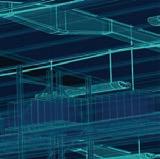
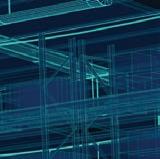
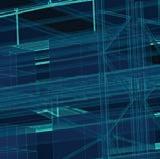
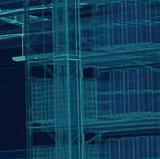
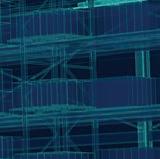
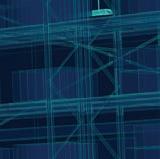

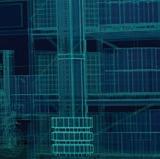
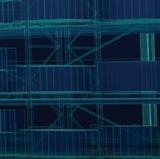

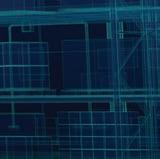
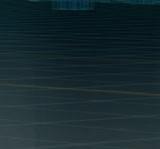
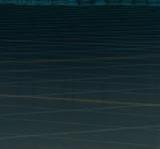
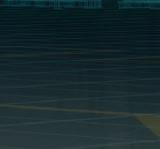
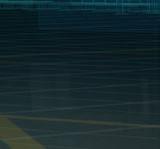
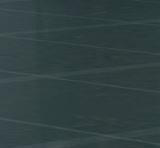
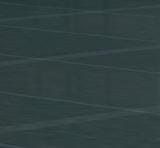

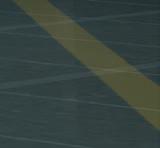
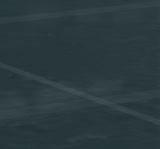
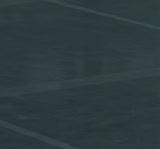
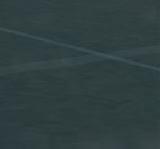
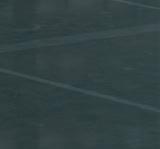
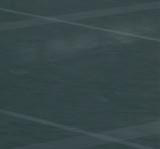
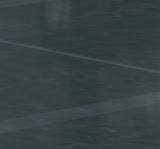

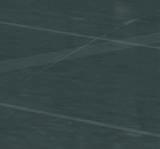
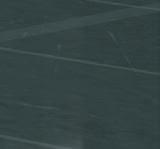



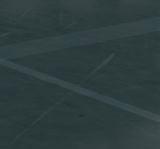
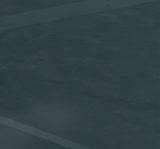
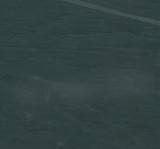

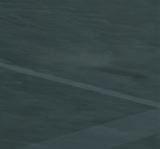
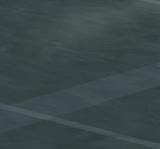
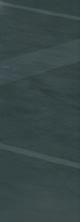





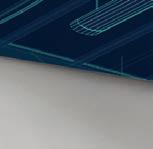

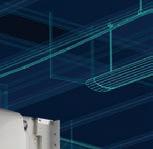
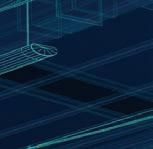
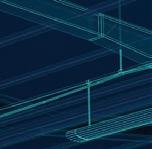

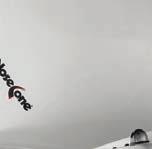
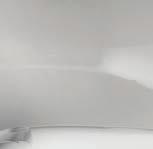
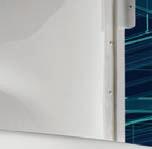

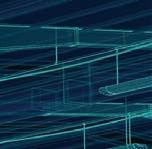
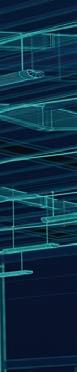
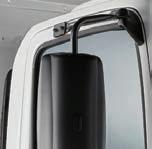
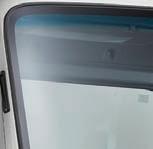
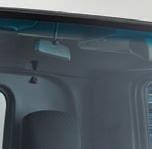
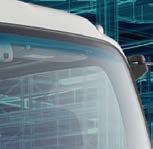

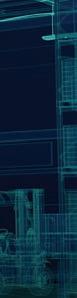
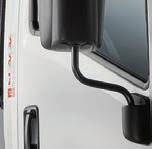

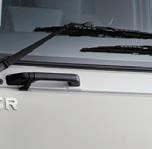
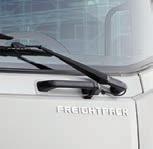
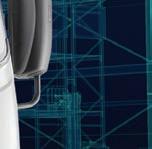
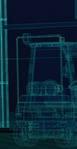


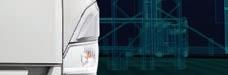
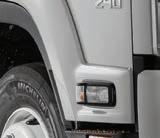

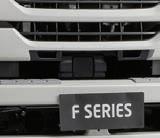
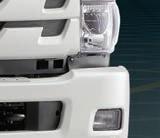
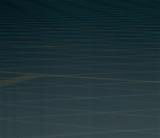

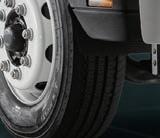
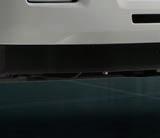
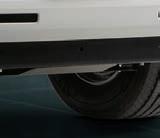
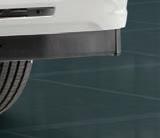
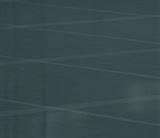


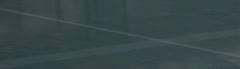



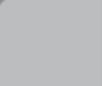
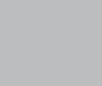
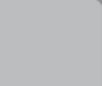



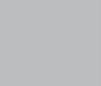
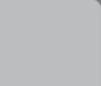

The new MAN generation redefines trucking in the modern age. Elevating driver fit, efficiency and economy, MAN optimises profitable working time. To put it simply, when it comes to trucks, MAN is the only choice. MAN. Simply My Truck.

THE NEW MAN TRUCK

TRUCK GENERATION. Roaring to life August 2022 SIMPLY MY TRUCK.


senior feature Peter Shields writer peter.shields@primecreative.com.auAshleyBlachfordashley.blachford@primecreative.com.au0425699819
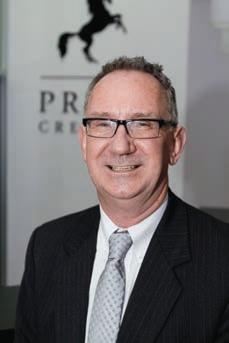
The right of refusal is reserved by the publisher.
The opinions expressed in PRIME MOVER magazine are not necessarily the opinions of, or endorsed by the publisher unless otherwise stated.
P: 03 9690 8766
www.primemovermag.com.au
SEPTEMBER 2022 $11.00
Annual rates: AUS $110.00 (inc GST).
SCT Heaven’sLogisticsGate
Fleet: South East Queensland Hauliers Technology: Battery Electric Vehicles Test Drive: Hino range Delivery: Fukushima Prefecture Industry Fleet: Feature:McColl’sRussell Transport Showcase: Heavy Vehicle Insurance Personality: Paul Walsh THE PEOPLE & PRODUCTS THAT MAKE TRANSPORT MOVE Delivery Magazine inside: Pages 68-73. ® September 2022
Australia’s leading truck magazine, Prime Mover, continues to invest more in its products and showcases a deep pool of editorial talent with a unique mix of experience and knowledge.


copyright
articles
William Craske | Editor
editor William william.craske@primecreative.com.auCraske
Handling placements for Prime Mover magazine, Ashley has a unique perspective on the world of truck building both domestically and internationally. Focused on delivering the best results for advertisers, Ashley works closely with the editorial team to ensure the best integration of brand messaging across both print and digital platforms.
PRIME MOVER magazine is owned and published by Prime Creative Media. All material in PRIME MOVER magazine is copyright and no part may be reproduced or copied in any form or by any means (graphic, electronic or mechanical including information and retrieval systems) without written permission of the publisher.
03 9690 8766 subscriptions@primecreative.com.au
Prime Mover magazine is available by subscription from the publisher.
Peter White | Journalist
MEET THE TEAM
For overseas subscriptions, airmail postage should be added to the subscription rate.
All articles submitted for publication become the property of the publisher. The Editor reserves the right to adjust any article to conform with the magazine format.
Ashley Blachford | Business Development Manager
journalist Peter peter.white@primecreative.com.auWhite
subscriptions
managing editor, Luke Applebee transport group luke.applebee@primecreative.com.au
design Kerry Pert, Aisling McComiskey
A seasoned transport industry professional, Peter has spent more than a decade in the media industry. Starting out as a heavy vehicle mechanic, he managed a fuel tanker fleet and held a range of senior marketing and management positions in the oil and chemicals industry before becoming a nationally acclaimed transport journalist.
ceo John john.murphy@primecreative.com.auMurphy
art director Blake blake.storey@primecreative.com.auStorey
Prime Creative Media will not accept responsibility for errors or omissions or for any consequences arising from reliance on information published.
Peter Shields | Senior Feature Writer
The Editor welcomes contributions but reserves the right to accept or reject any Whilematerial.everyeffort has been made to ensure the accuracy of information
John Murphy | CEO
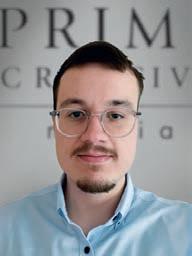
John has been the nation’s foremost authority in commercial road transport media for almost two decades and is the driving force behind Prime Creative Media becoming Australia’s biggest specialist B2B publishing and events company. Committed to servicing the transport and logistics industry, John continues to work tirelessly to represent it in a positive light and is widely considered a true champion for the growth of the Australian trucking and manufacturing industry.
F: 03 9682 enquiries@primecreative.com.au0044
design production Michelle Weston manager michelle.weston@primecreative.com.au
developmentbusinessmanager
client success Justine Nardone manager justine.nardone@primecreative.com.au head office 11-15 Buckhurst Street South Melbourne VIC 3205
Over the past two decades William has published widely on transport, logistics, politics, agriculture, cinema, music and sports
He has held senior positions in marketing and publicity for multinational businesses in the entertainment industry and is the author of two plays and a book on Australian film history. Like many based in Melbourne he is in a prolonged transition of either returning or leaving.
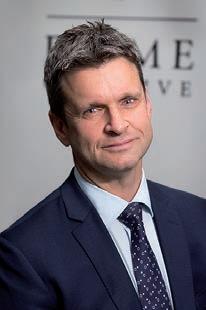
Having recently completed his Bachelor of Media and Communication (Media Industries) degree at La Trobe University, Peter brings a fresh perspective to Prime Mover Invaluable experience obtained during his time at upstart, La Trobe’s newsroom, has been supplemented by direct industry experience in a Council placement. Peter is looking forward to contributing to the magazine’s image as the leading publication for commercial road transport with his developed skills.
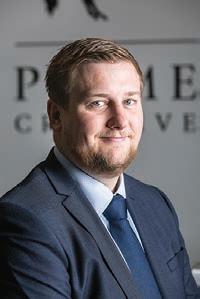
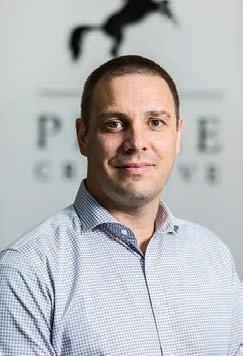

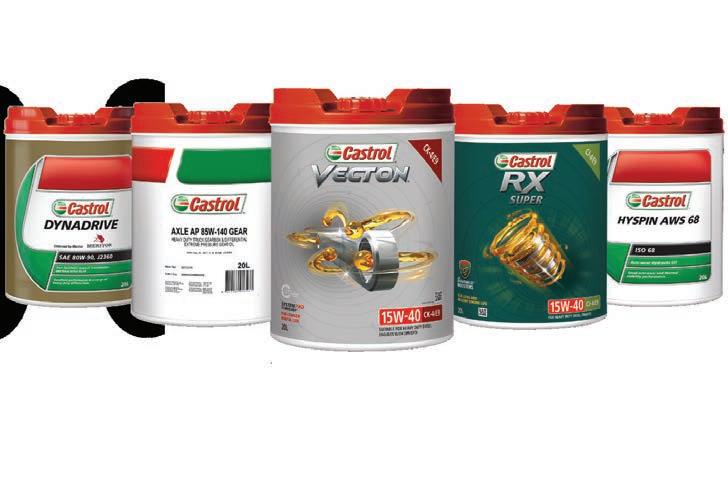
56 CONTENTS Prime Mover September 2022 60 66 30 STORYCOVER “We’ve found with the quads that we can move the bin and reduce the axle weights while the bin is still on the trailer.” 58
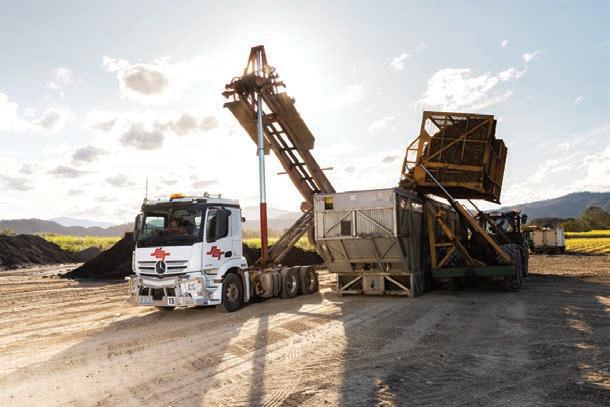

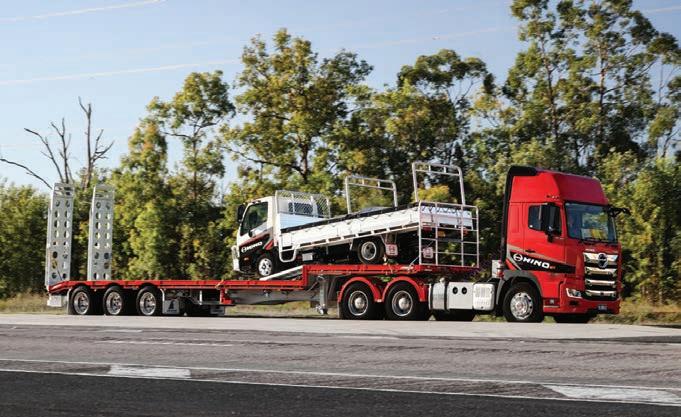
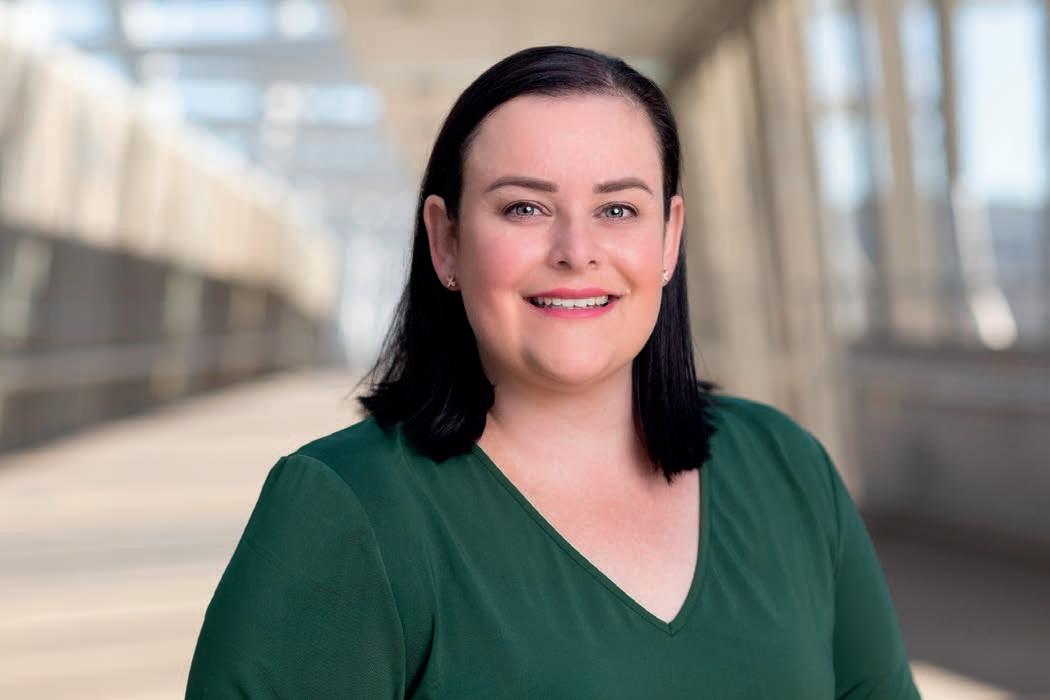
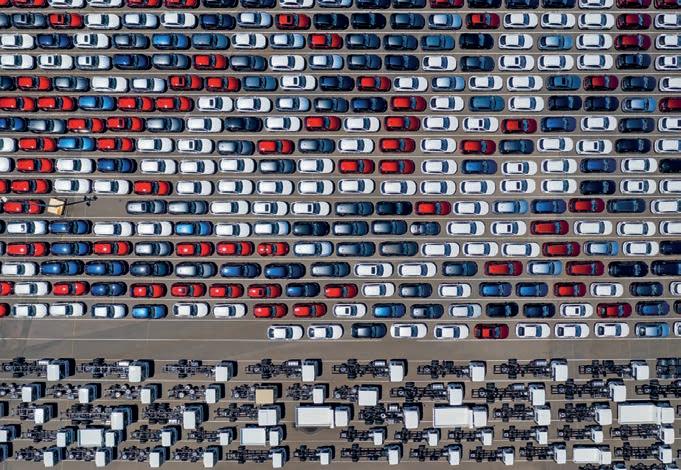
Even before it started moving oversized assets like goldmining machinery and exotic wildlife, South East Queensland Hauliers has, as part of a company-wide undertaking, been on mission to innovate.
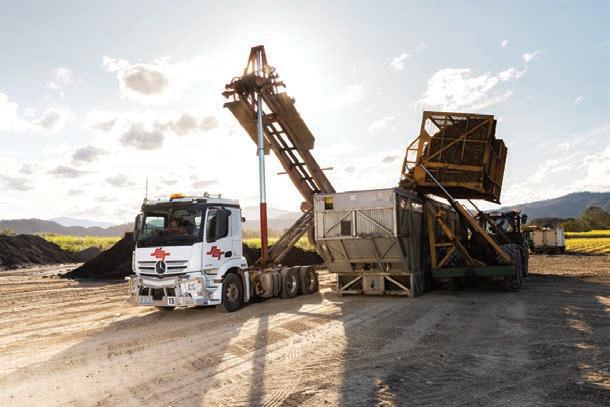
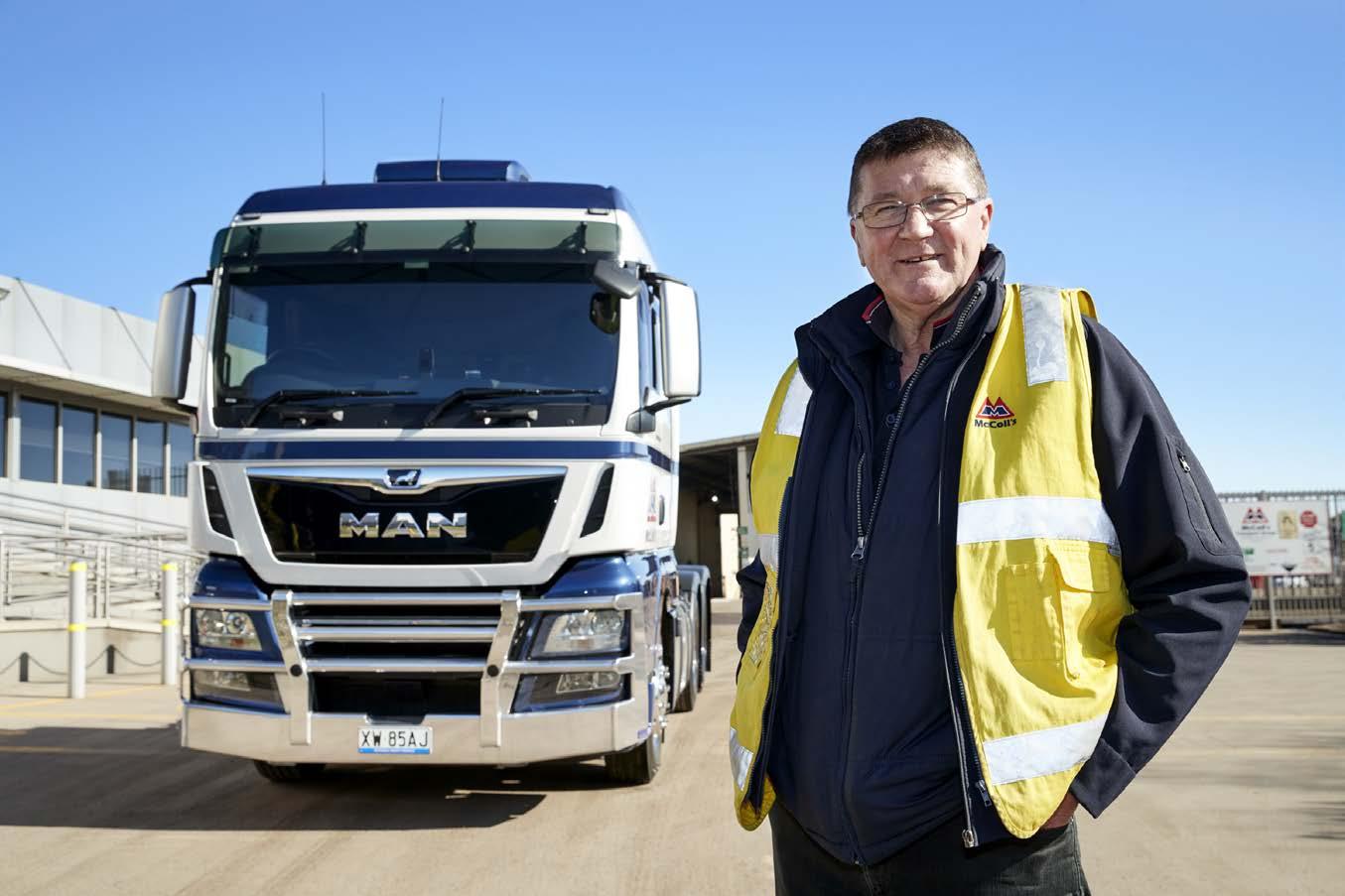
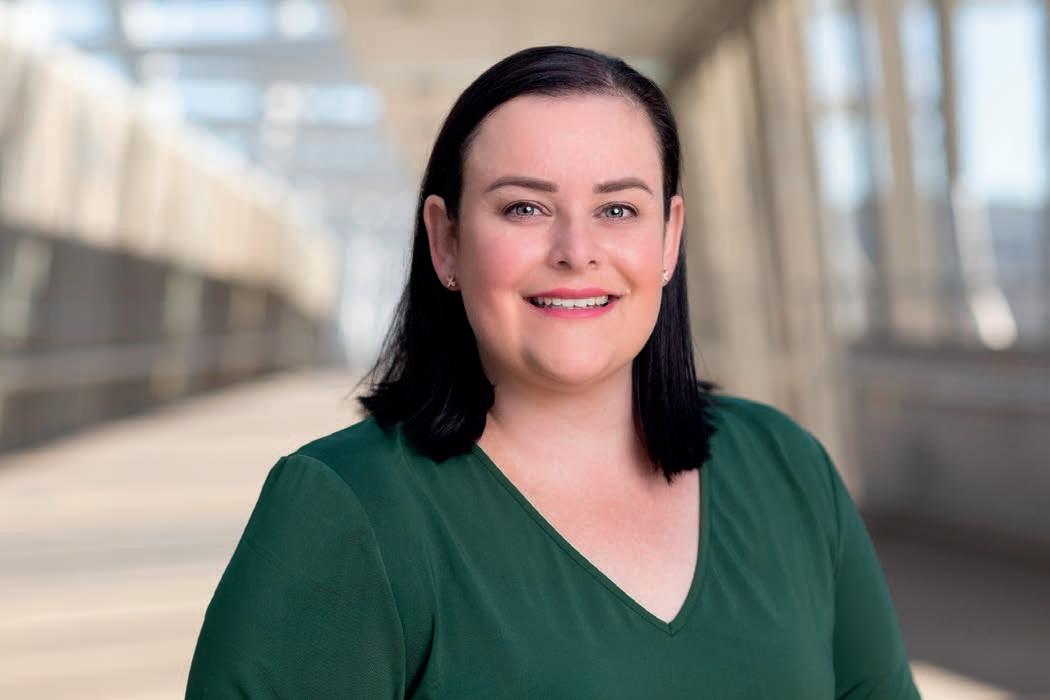
30 Heaven’s Gate
42 Highway to Heavy
TEST DRIVE
SCT Logistics has completed a daring replacement program of its dedicated sugarcane fleet in Northern NSW. A purpose-built PBS combination, hauled by new Mercedes-Benz Actros 2646LS commercial vehicles makes it unique to the industry.
36 The Lion King
Queensland’s Atherton Tableland and the Bruce Highway between Cairns and Townsville are at the start of Hino’s ambitious nationwide multi-vehicle assessment program.
FLEET FOCUS
60 Top of the Range
TRUCK & TECH
48 Load Star
Australia’s largest independent bulk liquid carrier of milk, food and chemicals, McColl’s Transport, is a company of influence in the national landscape of road transport.
Regular Run 08 From the Editor 10 Prime Mover News 28 Mindset 56 Insurance Showcase 64 Personality 66 Prime Movers & Shakers 68 Delivery 74 ARTSA-I Life Members 76 Truck Industry Council 77 Victorian Transport Association 78 Peter Shields’ Number Crunch Feature Stories THE LION KING36
Lack of availability of a previously preferred brand for a particular application led Russell Transport to consider DAF prime movers.
The solution to expeditious downturn, a decline in living standards and supply shocks, as far as two researchers at the Utah State University are concerned, can be found in a greater consumption of energy, not less. Austin Vernon and Eli Dourado are convinced that the shift in mindset for this to occur will happen once energy becomes superabundant. To achieve energy superabundance, society must go far beyond just replacing existing fossil fuel use with carbon-free alternatives. Theirs is a vision that insists on an increase of energy production by at least an order of magnitude fostered by cost declines achieved through advanced nuclear or geothermal technologies. Energy technology, in short, must be reimagined.
energy expenditures, at least part of the reason is a lack of vision of what we might realistically do with superabundant energy,” the report notes. Much of the paper, ‘Energy Superabundance: How Cheap, Abundant Energy Will Shape Our Future’, goes someway to supplying that vision. Econometric research has shown that higher energy consumption directly increases economic growth, contrary to a consensus that only richer countries demand more energy by virtue of wealth. Cheap energy decreases the cost of all the goods and services that use energy in their production. Of critical importance, it also helps with production of more and new goods and services in ways that are only economical when energy costs are low. In other words, the relationship between economic growth and energy consumption runs in both directions. Transportation, which accounts for about 20 per cent of global primary energy consumption, is deeply bound up with energy costs. It takes energy to accelerate objects and to keep them moving in the face of drag and rolling resistance. In a world of superabundant energy, it will be, according to the authors, one of the most explosive sectors enabling the number of kilometres travelled by both people and goods to increase prodigiously. Until then red tape masks our complacent, comfortable, consumerist depreciation.
stop the herd from being spooked. Australia’s Productivity Commission, as if wary of a fate worse than some burnt-out Depressionera horn player, cites the global surge of protectionism and the transition to net-zero emissions by 2050, as additional causes which will, under the siege of continued inflationary pressures, warrant productivity enhancing reforms. The Government having spent $16 billion in industry assistance for Australian businesses that needed support now wants to roll back that same assistance as conditions improve as a countermeasure to overheating the economy. The problem is conditions have not improved but don’t tell Wikipedia whose policies might have made former Iraqi Minister of Information Mohammed Saeed al-Sahhaf blush.
FROM THE EDITOR 10 september 2022
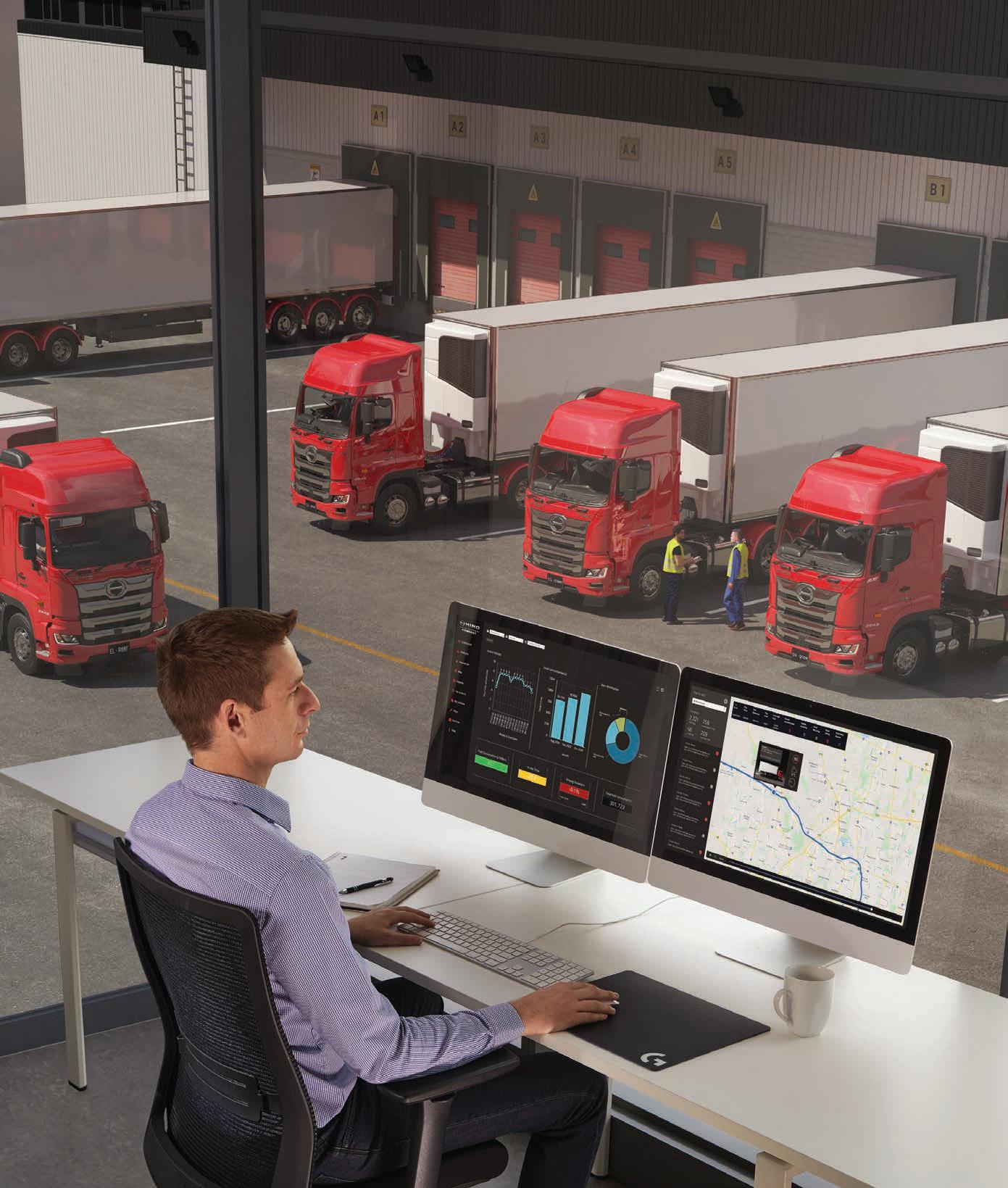
William Craske Editor
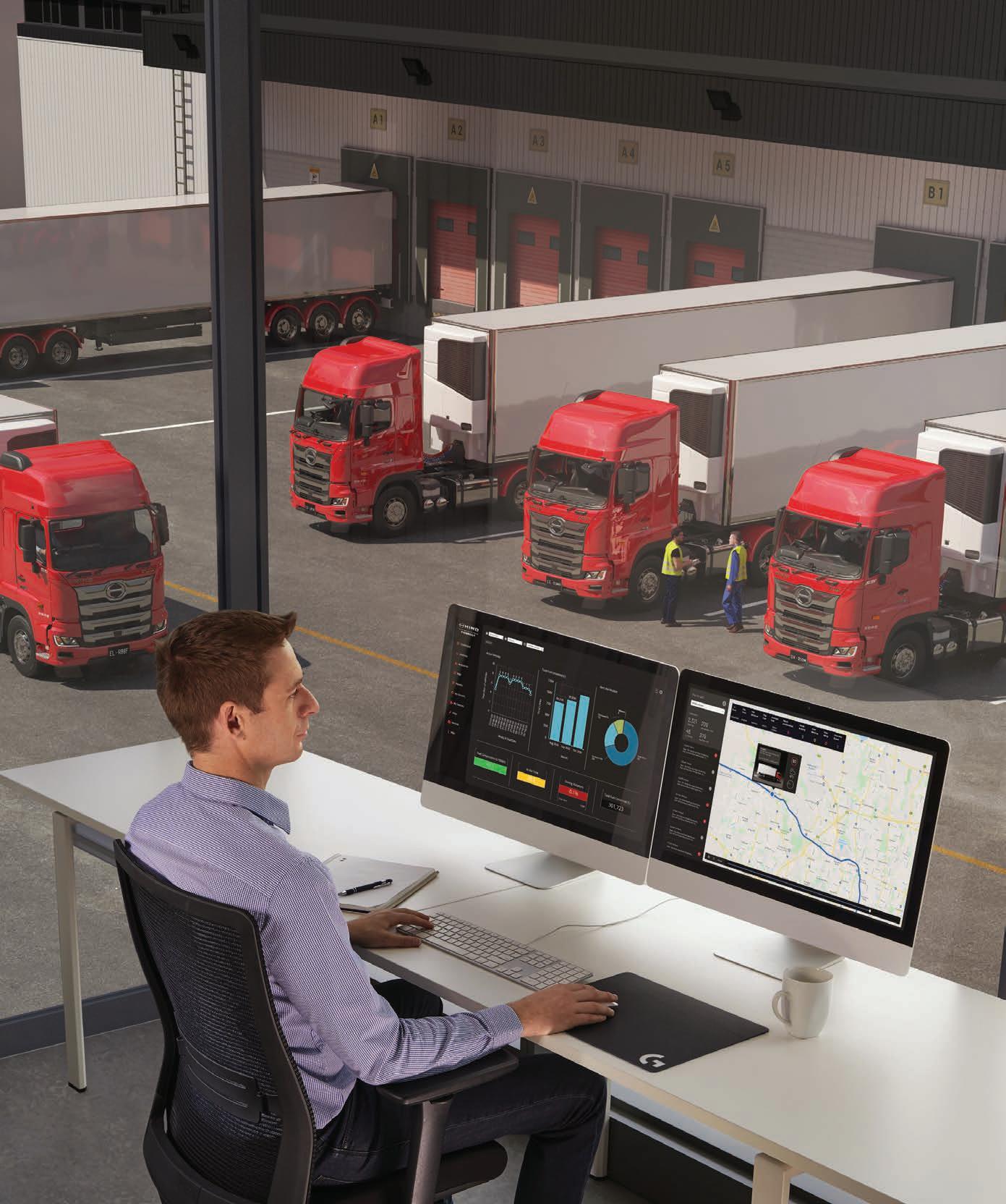
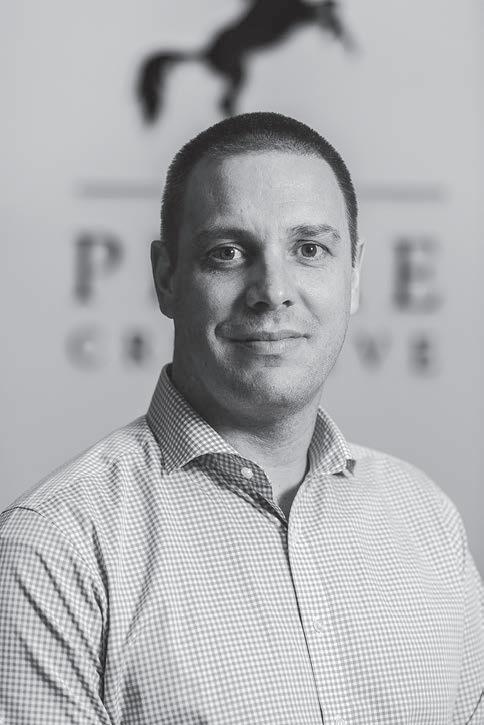
Bix Beiderbecke, the hell-raising jazz cornetist when he passed in 1931 was said to have “died of everything.” It was a prophetic obituary especially if you work in and around the construction industry, as many commercial vehicle operators do. Raw material suspensions. Fuel spikes. Trade tariffs. Government mandates. Labour shortages. Rate rises. Inflation. Energy destabilisation. It recalls the old saying if Lillee doesn’t get you Thommo will. Whole market sectors, for the moment, have been reduced to nervous 1970s English batsmen. The health of the global economy and the cause of its rapid diminution might matter less if they weren’t made to mirror polemical narrative effects driven increasingly by hegemonic economic powers. The progressive onboarding of the world, per James Poulos, into a networked system of constant communication has in the digital age, instilled a domino effect in which a crisis is but one sneeze away from a global catastrophe that some NGO, with its silent investors, has been patiently anticipating. Wikipedia, itself a non-profit, launched new restrictions on users to suspend edits made to its recession page. The network effect also can work the other way if the objective is to
“If our society remains suspicious of high
Rust Never Sleeps
XAVIER_HINO38841.11 HINO-CONNECT. NEXT-GENERATION TELEMATICS AND SUPPORT. Get connected to the only business telematics that combines key data tracking in real-time, remote diagnosis of vehicle faults and 24/7 alerts delivered to you and your Hino-Connect specialist for priority repair and service support. It is the total business intelligence solution designed to reduce costs, optimise driver and vehicle performance and improve safety. Hino-Connect. Now standard and active on all new 500 and 700 Series models. Find out more at hino.com.au THAT’S ANOTHER HINO FOR GETBUSINESSSUPERIORINTEL,CONNECTED



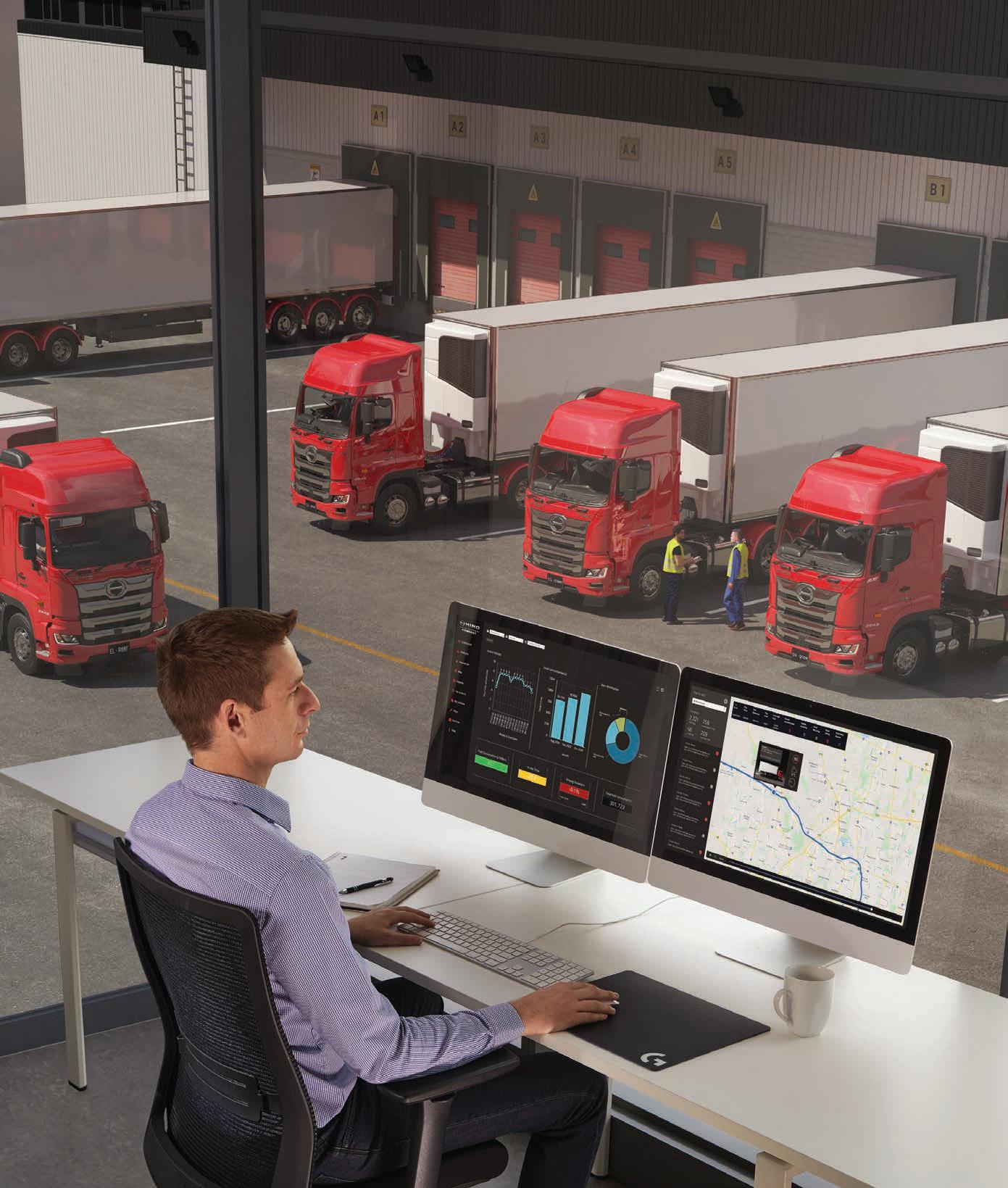
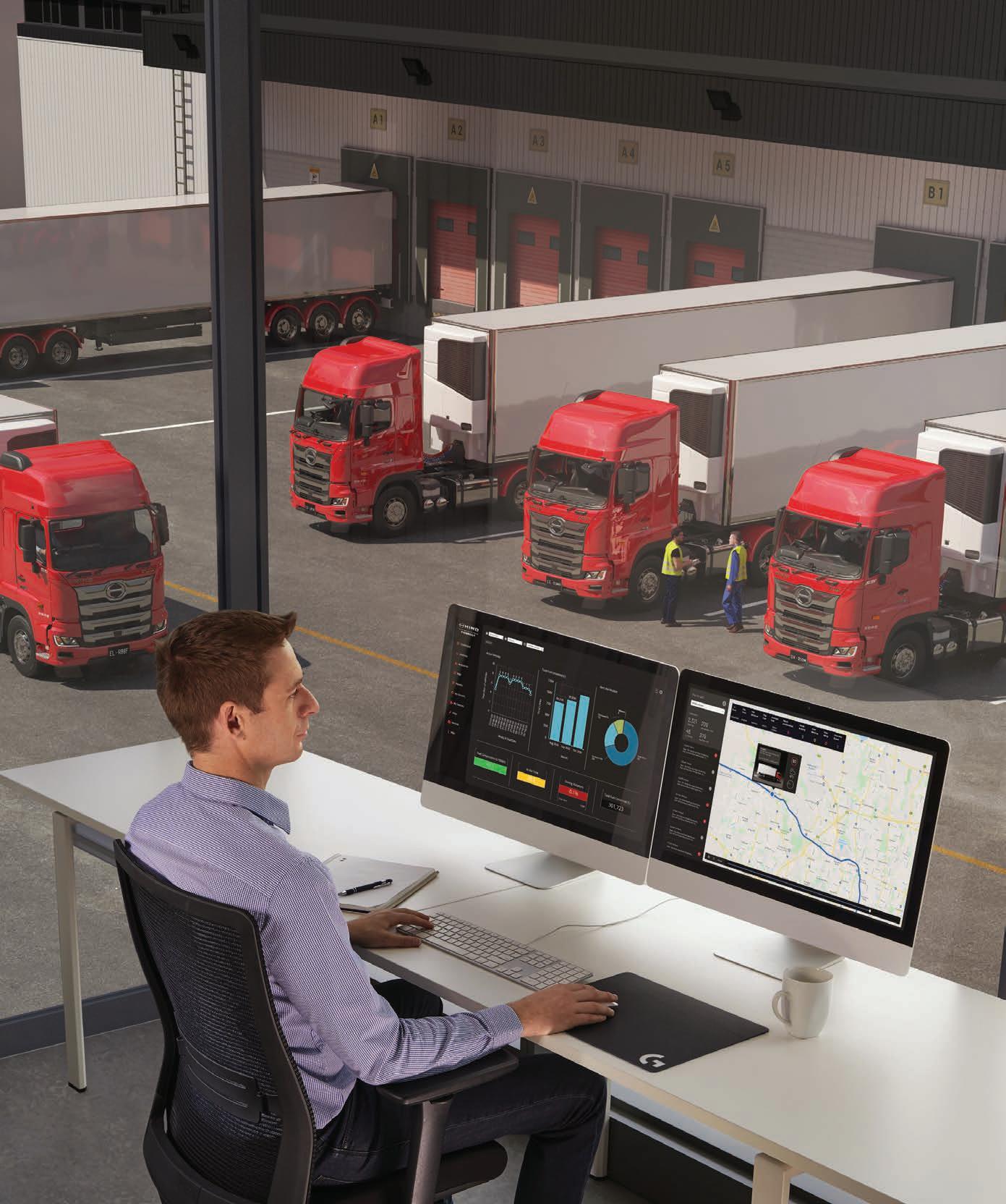
Cleary Bros chose the 2663 Actros, which features the 630hp 16-litre engine that also produces a hefty 3000Nm of torque. It is linked to a fully a 12-speed Automated Manual Transmission (AMT) with creep mode.
Cleary Bros also selected the Predictive Powertrain Control (PPC) system, which uses topographic map data to help the truck anticipate terrain and select the optimum shift pattern and engine response for maximum fuel economy. It also helps maximise the amount of time the truck spends coasting, driving down fuel Clearyconsumption.Broslooked into introducing an A-double as a way of boosting its productivity on the long runs the truck will cover each week.
“Our truck and quad-axle dogs have a payload of about 38-tonnes, but with this A-double Actros we are getting an additional 14 tonnes on every trip,” said Crandell. “That kind of productivity gain adds up pretty quickly.”
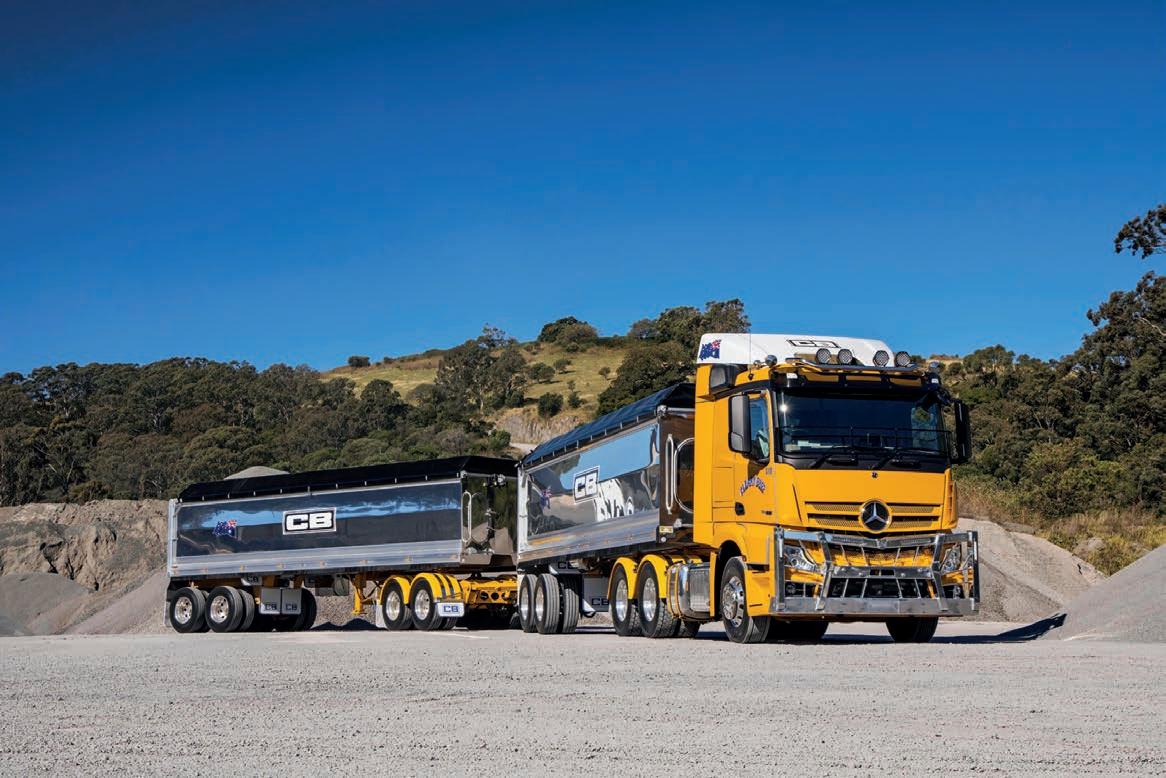
The new 630hp Actros A-double.
“We have been really impressed by the active safety features in our Freightliner Cascadia 116 and we know it uses the
Combination Mass of 74.5 tonnes, the PBS approved unit is ready to start delivering for the construction industry-focused operation based in Port Kembla. A Freightliner Cascadia 116, already working on the company fleet, introduced the Cleary Bros team to the advanced safety technology from Daimler Trucks which in turn convinced them to commit to the new 2663 “SafetyActros. is paramount in everything that we do, but it becomes even more critical when you are running higher productivity vehicles,” said Steve Crandell, Cleary Bros Transport General Manager.
PRIME NEWS
Like all Actros models, the Cleary Bros 2663 features the Multimedia Cockpit system, which consists of two large customisable tablet screens that present driver information in super crisp detail.
> Cleary Brothers launches first Actros A-double
Cleary Bros has introduced its first high productivity A-double. Pulled by a new Mercedes-Benz Actros, it affords the NSW-based transport company a 14-tonne gain over the truck and quad dog combination it has recently Withreplaced.aGross
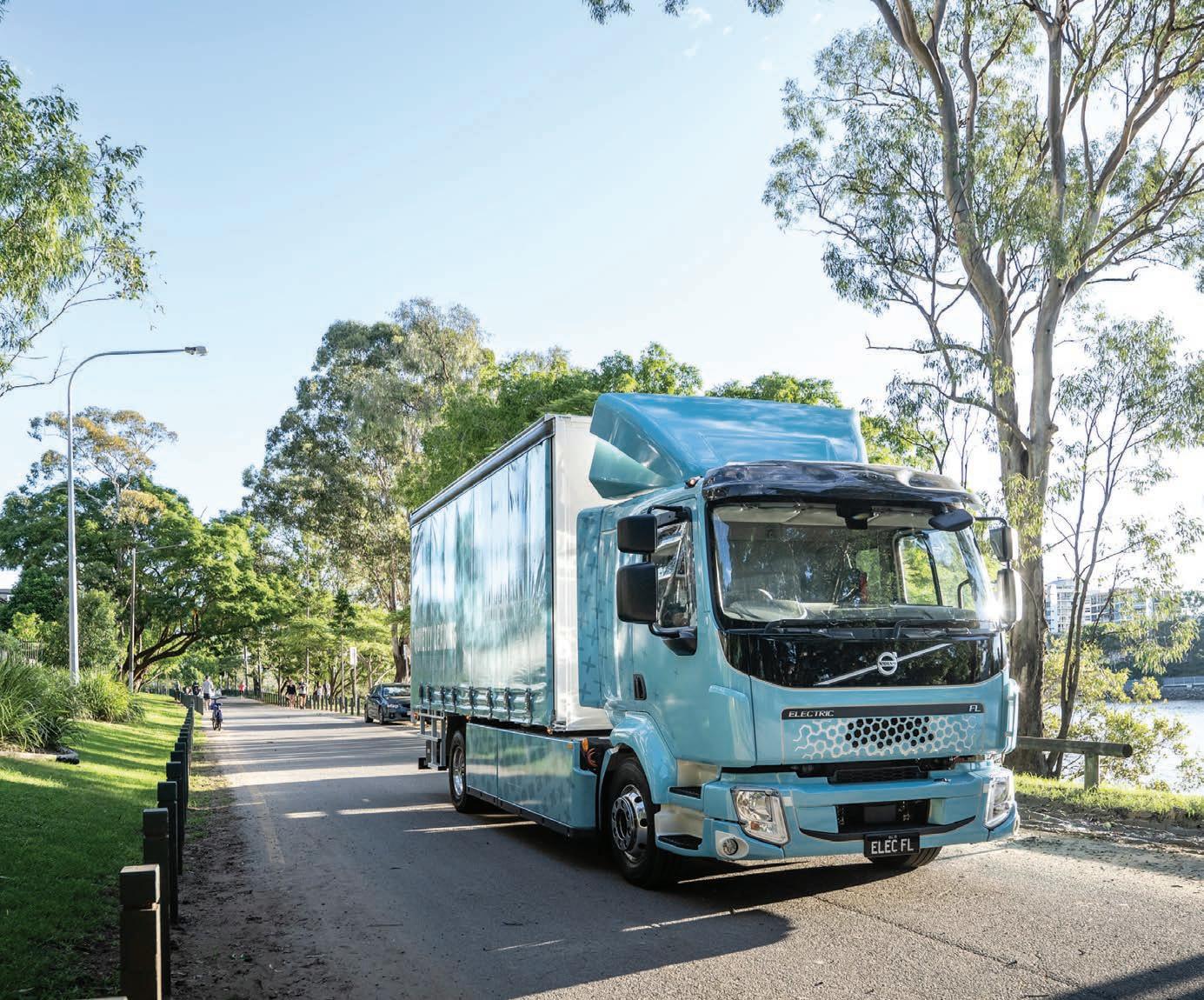
“We have been impressed by the
When the tailgate opens, the trailer airbags automatically release to drop down and improve the centre of gravity as the vehicle unloads.
All new Mercedes-Benz Actros models
The Cleary Bros safety-first approach extends to the aluminium Tefco trailer set, which features ABS, Electronic Braking System (EBS), Roll Stability System (RSS) and anti-burst hydraulics on tipping hoists.
“The performance of the 16-litre was certainly one of the reasons we chose the Actros,” said Crandell.
the fifth generation radar/camera Advanced Emergency Braking System (AEBS), which can now automatically perform full emergency braking for vehicles and pedestrians, as well as Lane Departure Warning System (LDWS) and Attention Assist (AA).
The new Volvo FL and FE Electric medium duty range meet the demand from society and customers for dramatic cuts in CO2 emissions. To simplify the transition to sustainable transportation, the trucks are offered together with service and support packages for electromobility needs.
The revolutionary new Volvo FL Electric
At Volvo Trucks, environmental care has long been central to our vision of the future. We care passionately about the world we live in, and as the shift towards electric vehicles gathers pace, we are more committed than ever to driving progress.
We are thrilled to announce the launch of our all-electric medium duty truck range for Australian transport operators.
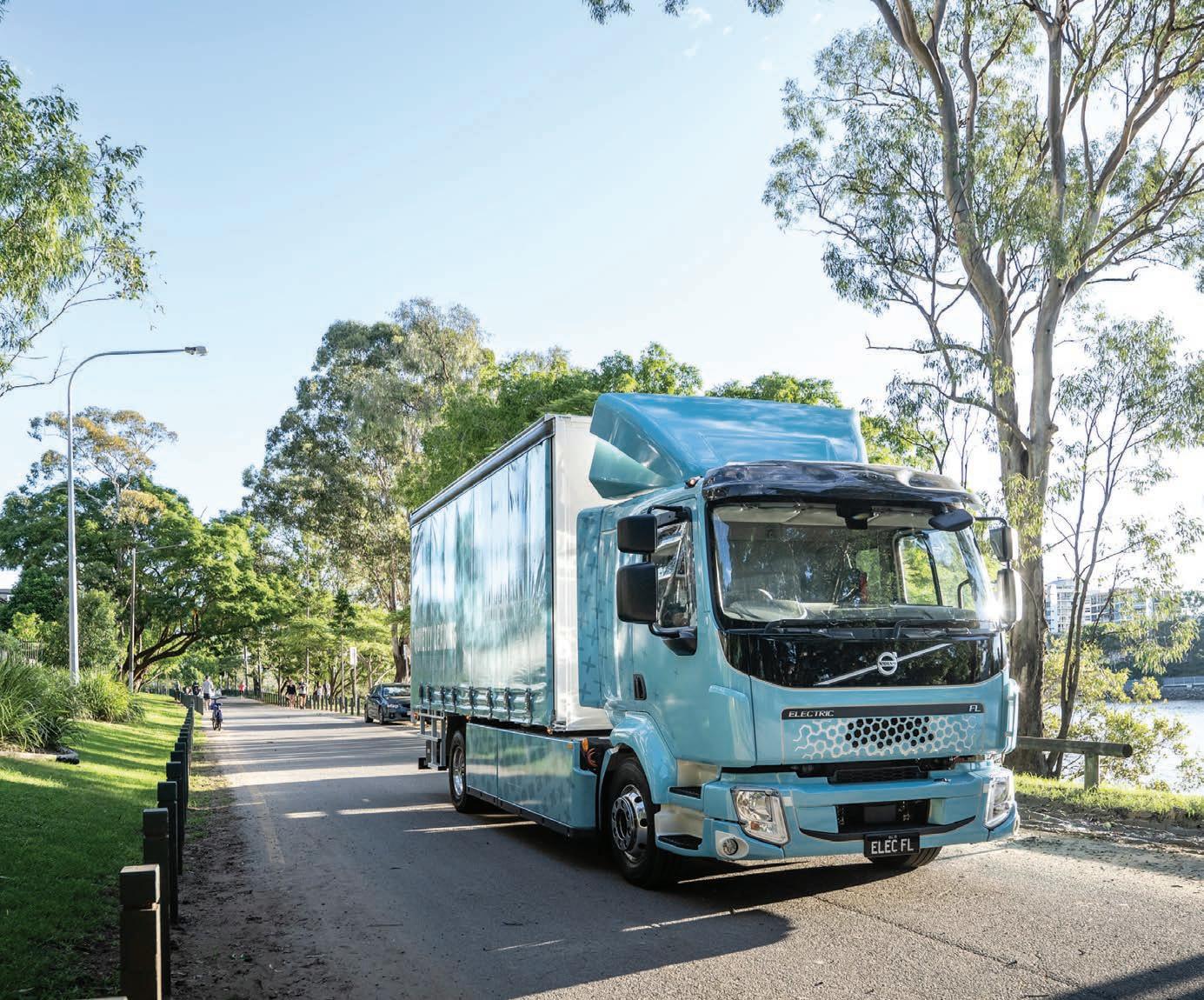
We are proud to partner with you in the transition to an electric truck future. Learn more by Volvovisitingwww.volvotrucks.com.au/electrictrucks.Trucks.DrivingProgress
We’re on Emission
PRIME NEWS 14 september 2022
east – places like Dandenong, Scoresby, Hallam and Braeside – and the Hume Freeway have had to leave the freeway network and travel along congested arterial roads through the north-eastern suburbs. The lack of a direct link between the north and south-east of Melbourne has been a brake on the productivity of the freight industry, and the completion of the Ring Road has long been high on the industry’s wish list.
North East Link will increase productivity for businesses by linking farms, industrial areas and distribution centres in the southeast with the Hume Freeway and key destinations in the north, including markets, freight hubs and Melbourne Airport. It will take 15,000 trucks off local roads a day and slash travel times by up to 35 minutes.
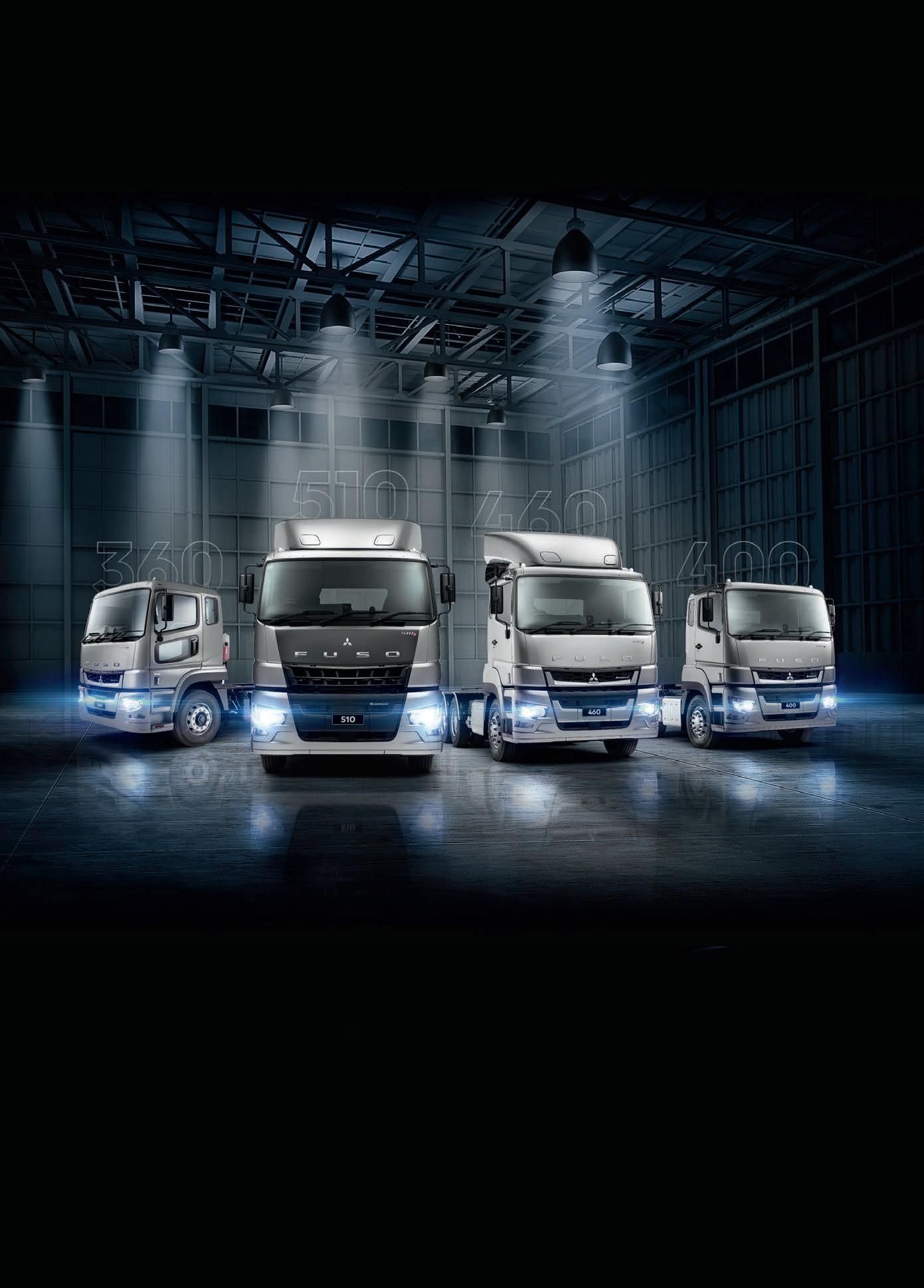
Livestock vehicles, trucks carrying dangerous goods and over-height vehicles that are banned from tunnels can avoid residential streets by using new ramps from the West Gate Freeway to connect to the port and fuel depots on Hyde Street. The West Gate Tunnel project is due to be completed in 2025. The other transport project revolutionising the movement of freight into and around the Melbourne metropolitan area is North East NorthLink.East Link will connect the M80 Ring Road with an upgraded Eastern Freeway, fixing the missing link in Melbourne’s freeway network. For decades, truck drivers needing access between the key freight-generating areas of the south-
Two further road projects are underway as part of Victoria’s Big Build that will, according to the Victorian Government, completely revolutionise the way freight moves around Melbourne. The West Gate Tunnel Project will deliver the road freight industry an alternative to the West Gate Bridge as well as direct access to Swanson Dock at the Port of Melbourne.
Road transport will get an easier run across Melbourne as a major freight route is upgraded and work gets under way on a further two. The second stage of the Monash Freeway Upgrade adds 36 kilometres of new lanes on the Monash and Princes Freeways between Clyde and Cardinia roads in both directions; between Warrigal Road and EastLink outbound; and between EastLink and Springvale Road inbound. The Monash Freeway supports more than 40 per cent of all commercial movements across Melbourne and as freight journeys continue to grow, the Monash Freeway Upgrade will help freight remain competitive by delivering travel time savings to key freight destinations. Stage 1 of the project – completed in 2018 –added 30 kilometres of extra traffic lanes to the Monash, increasing the number of lanes from four to five in each direction between EastLink and South Gippsland Freeway; and two lanes to three in each direction between South Gippsland Freeway and Clyde Road.
Two giant tunnel-boring machines have been ordered to help build North East Link’s 6.5-kilometre road tunnels. The mammoth machines – from German supplier Herrenknecht – will be among the biggest in the southern hemisphere and will each be 90 metres long, 15.6 metres in diameter and weigh around 4000 tonnes. The design, manufacturing, testing and transportation of the tunnel boring machines will take around 18 months. In 2024, they will be launched in Watsonia on their journey south toward Bulleen, with the road open to traffic in 2028.
>Monash Freeway upgrade enters next stage
By creating an alternative to the West Gate Bridge, the West Gate tunnel will allow broader use of combinations like longer B-doubles and A-doubles and new combinations like B-triples and AB-triples operating at their most efficient gross weight. The West Gate Bridge is restricted to vehicles with a gross mass of 68.5 tonnes, inhibiting the use of more productive combinations operating at higher weights by forcing them onto longer and less efficient routes to the port. The opening of the West Gate Tunnel will mean direct access to Swanson Dock for combinations like B-triples operating at 91 tonnes and AB triples at 113.5 tonnes.
A map outlining the changes to the M1 freeway in Melbourne.
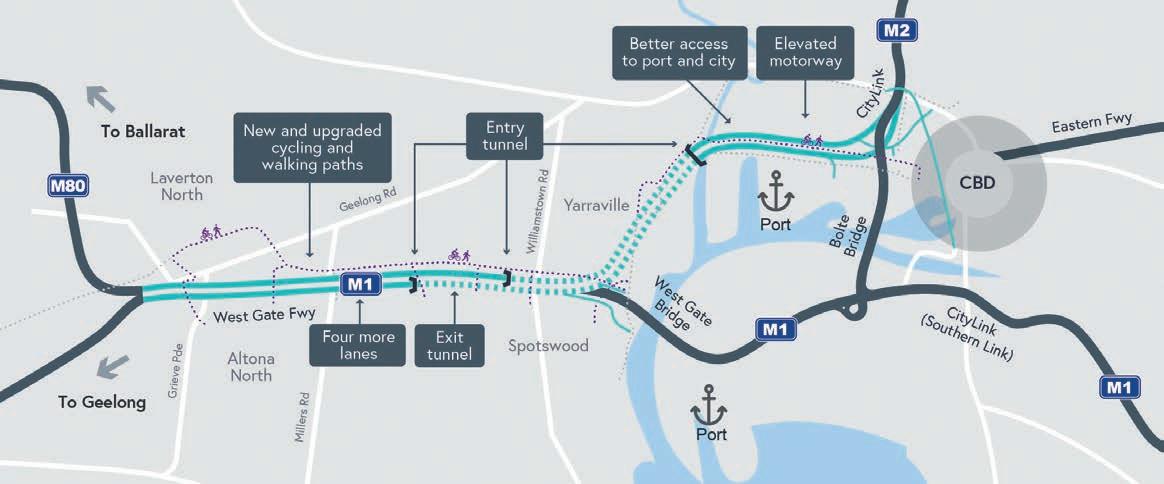
If you’ve got a challenge, we’ve got the Shogun for the Job.
COMMANDRESPECTTHESHOGUNRANGE
With a range of powertrains spanning from 360hp/1400Nm to a thundering 510hp/2500Nm, the Shogun draws on the latest in engine technology from Daimler backed by proven Japanese reliability. Available in 6x2, 6x4 and 8x4 rigid, as well as prime mover and tipper spec – there is a Shogun for every job.
TO FIND OUT MORE ABOUT THE FULL SHOGUN RANGE VISIT FUSO.COM.AU
As a Shogun driver, you get access to class leading safety including Advanced Emergency Braking with pedestrian detection, driver fatigue monitoring, active cruise control and adaptive LED headlights – all backed by Fuso’s classleading 5 year warranty as standard.
Respect is earned, not given. And for that reason, the Fuso Shogun range continues to provide some of the most powerful, fuel efficient and intuitively safe heavy duty trucks in Australia.
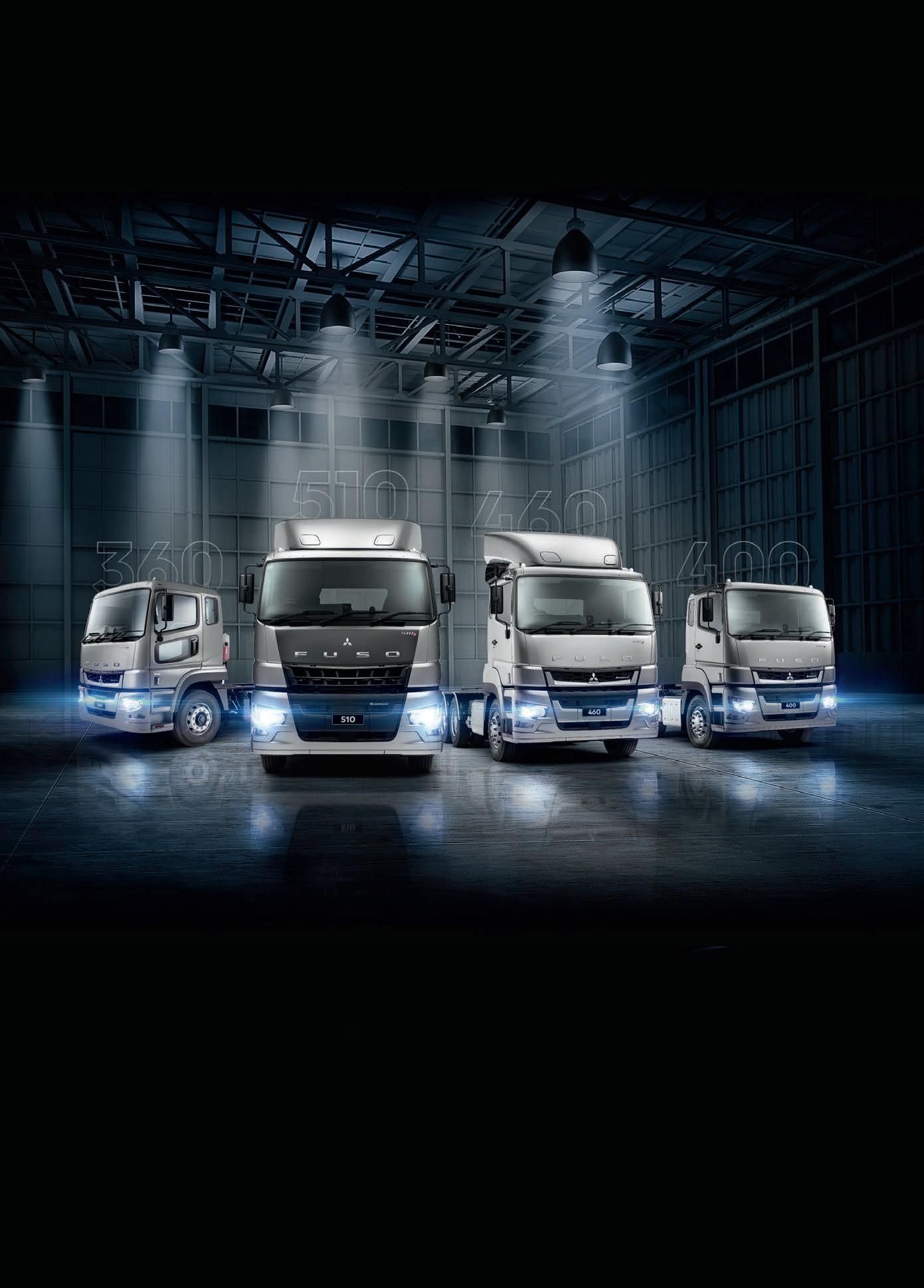
distribution business in Australia and New Zealand.
Transport and logistics company, Toll Group, has taken delivery of 11 new Euro VI Kenworths for its Olympic Dam and Cooper Basin operations.
During his first eight weeks at the helm, Capp has been travelling the country meeting with customers and many of the 2000 strong team at Scott’s Refrigerated “I’mLogistics.veryexcited to take the helm at Scott’s Refrigerated Logistics and deliver on its next stage of development and growth,” he said. “It’s hard not to be amazed at the scale of our business and its status as Australia’s largest integrated cold chain network. There are amazing
In 2003, he joined StarTrack and spent the next 12 years through its significant growth and evolution – five of those being a Director of Sales and a National
> Border Express reinforces executive stocks
> Toll Group takes delivery of new Kenworths
“Kenworth has been a trusted supplier of heavy vehicle prime movers to Toll for many years,” he said. “The dependability and the backup support of the product is crucial to our business and allows us to continue servicing our customers with limited downtime.”
PRIME NEWS 16 september 2022
Both vehicles feature a 15-litre Cummins X15 engine that produces 620hp and 2,700Nm of torque. Toll General Manager – Operations, Nathan Perrott, said the
Of the 11 Kenworths supplied with Cummins Euro VI powerplants, six K200s will be going to Toll’s Olympic Dam branch and five C509s to its Cooper Basin operations.
> Scott’s Refrigerated Logistics appoints new CEO
Kenworths were ordered for ongoing demand, and will be used to tow both trailer and tanker sets across Australia.
Just prior to joining Border Express, Friedel spent two and a half years with Maersk as Director of Sales of Oceania.
Manager, James Lindsay as Continuous Improvement Specialist, Allan Assoni as Logistics Planner and Robyn Holt as a HR Business Partner.
National cold carrier and warehouse specialist, Scott’s Refrigerated Logistics has appointed a new Chief Executive Officer and Managing Director. Former Glen Cameron Group CEO, Nicholas Capp was appointed to the position in May. Capp’s departure predates the recently announced acquisition of Glen Cameron Group by DHL.
“Our focus and what we will be known for is outstanding reliability whatever the conditions – excellent execution, day in, day out,” he said.
“Operationallycontinued. we aim to keep these vehicles for a minimum of five years,
C M Y CM MY CY CMY K
“These vehicles are designed for heavy applications in rough and remote terrains operating up to 155 tonnes,” he told Prime Mover. “Due to the severity of the operational terrain, the maintenance of these vehicles is critical to ensure reliability and longevity,” Perrott
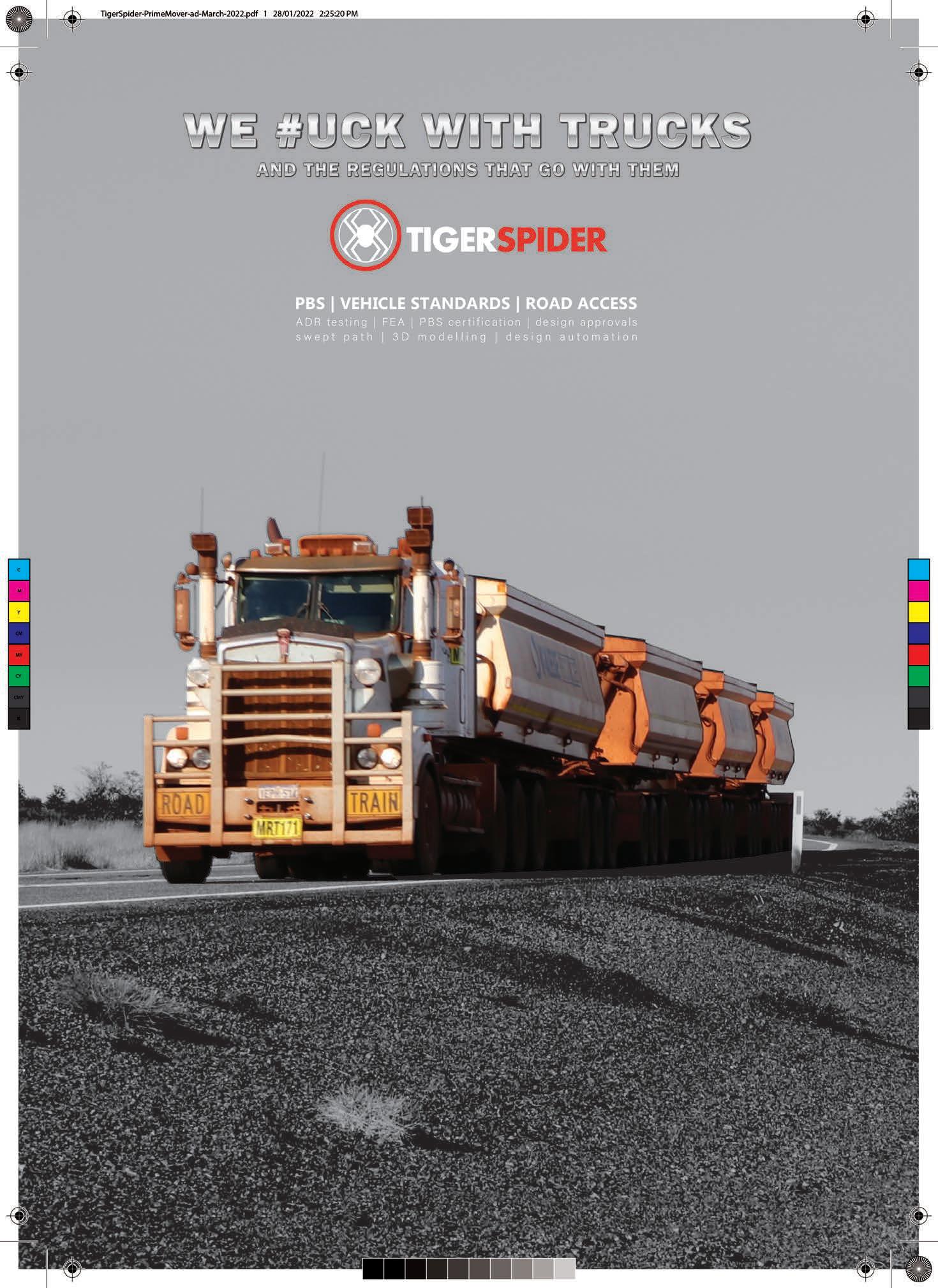
Australian transport company, Border Express, has appointed Kurt Friedel as its new Chief Commercial Officer. In his new role, Friedel will be leading the Account Management, New Business Sales and Customer Service functions nationally, with responsibility for more than 70 personnel and almost $400 million in turnover.
Friedel has a significant background in the industry dating back 20 years to his first role at Mayne Logistics Express, which later became Toll Priority.
his time at StarTrack, Friedel spent five years on the executive team of Ixom, the largest chemical
Kurt Friedel.
General Manager Commercial. Friedel said it was a pleasure to come onboard with the Border Express team. “I am thrilled to have the opportunity to join the Border Express team at such an exciting time,” he told Prime Mover. “We have an absolute commitment to be recognised by our customers as the industry leader in service, delivery and value, and we are investing in a broad range of initiatives to fulfil that commitment and create the platform to enable significant growth over the years Followingahead.”
“A massive array of products are being stored and distributed for leading producers, manufacturers and retailers across our eighteen depots nationally.” Capp’s role, as he sees it, is an opportunity to amplify the ongoing efforts of the team across its huge network.
Perrott said Kenworth has always been a reliable supplier and has limited downtime through its support.
He replaces Brett Lynch who had occupied the CEO chair at Scott’s Refrigerated Logistics since December 2020. Capp’s appointment is part of a raft of recent new managerial appointments at the private company that include Fiona Benjamin as National Project
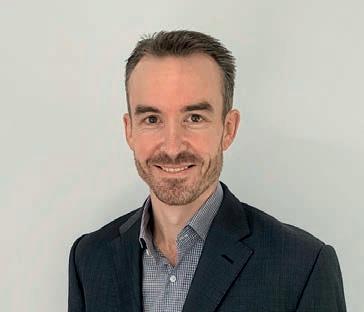
however, subject to the kilometres travelled we are able to extend the service life due to the service regime.”
stories and histories across the Scott’s business from fresh juices and avocadoes in WA, bananas and capsicums in the North, dairy out of the South or meat from all corners,” said Capp.
tigerspider.com.au | (03) 9537 1027 | 106/181 St Kilda Rd, St Kilda VIC 3182
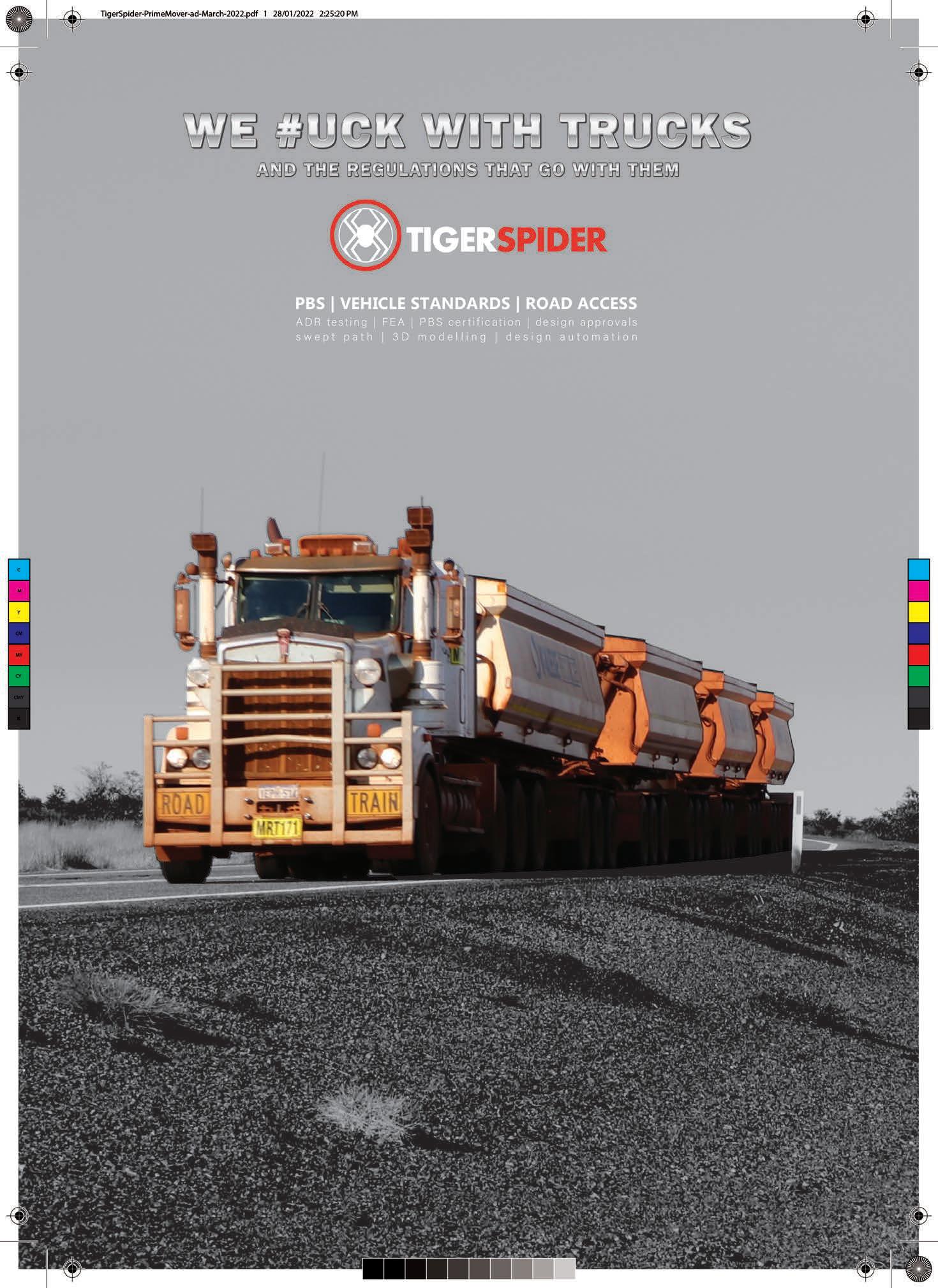
These vehicles, following an announcement by the National Heavy Vehicle Regulator, are approved to operate on the PBS Level 3A Mass Network that covers Victoria and New South Wales. Approval is based on the provision the vehicle combinations
“FFS is a strategically important acquisition and establishes Silk’s Port Logistics capabilities in Perth,” said Brendan Boyd, Silk CEO. “This will allow us to extend our elevated customer service offering nationally. FFS is an attractive opportunity, the businesses operating philosophy is highly aligned with Silk’s offering and will deliver operational efficiencies as well as further revenue growth. Silk also gains an exceptional team at FFS, who are the key to their success and will
> Ron Finemore Transport unleashes new 30m B-doubles
continue to drive significant value for FFS and the broader Silk business.”
exceed the overall length of 30 metres and meet the reference vehicle axle spacings for 30m quad-quad or quadtri TheB-doubles.gazettenotice expires 14 November, 2026. It came into effect on 18 July.
Regional road transport powerhouse, Ron Finemore Transport has introduced five new 30m B-double high cube combinations. The high productivity combinations that each carry 100-pallets were added to Primary Connect’s network in June.
FFS generates annual revenue in excess of $29 million as well as strong positive earnings and operating Thecashflow.acquisition is expected to contribute positively to Silk’s group earnings immediately and be earnings per share accretive from the first full year of ownership, before accounting for any potential synergies and integration costs.
The binding agreement to acquire the Fremantle Freight & Storage Group through the acquisition of head company Brightflow Enterprises was announced earlier today. The deal is subject to conditions precedent customary for a transaction of this nature together with final debt facility Establishedapproval. in 2000, Fremantle Freight & Storage (FFS) operates across four sites in metropolitan Perth and provides wharf cartage, warehousing, quarantine, fumigation and other complementary port-related services. The acquisition adds immediate scale to Silk’s WA footprint, consistent with Silk’s strategy to grow its ability to provide reliable Port Logistics solutions Further,nationally.the acquisition is expected to unlock demand from Silk’s existing blue
combination is currently being used in the Primary Connect network to transport ambient freight between Sydney – Wodonga and Brisbane –Wodonga, lifting each lane capacity by an extra 10 per cent. As well as reduced emissions and other environmental benefits, each of these new vehicle combinations will reduce truck movements on these transit routes by up to 80 less B-doubles a year. This partnership benefits the future growth for both businesses with safety,
A major strategic acquisition valued at over $30 million by Silk Logistics is expected to elevate its expanding national offering.
The acquisition is expected to complete before 1 September 2022, subject to customary closing conditions, including certain third-party consents. The acquisition price consists of $23.6 million payable upfront (subject to customary adjustments) with a further $7.8 million payable contingent on achieving agreed financial milestones for the period ending 31 July 2023. Additional consideration is payable in the event these milestones are exceeded, based on a percentage of the outperformance, but is not expected to be greater than $3.0 Silkmillion.has the option to pay 50 per cent of the $7.8 million and 100 per cent of any additional consideration in cash or Silk shares, based on Silk’s 30-day VWAP prior to 31 July 2023.
> Silk Logistics acquires Perth-based freight company
reliability, efficiency and sustainability at top of mind according to Mark Parry, Ron Finemore Transport Managing “RonDirector.Finemore Transport continues to make investments in higher productivity equipment as we seek to deliver to our customers safely, reliably and more cost effectively,” he said. “These investments are part of a continuous journey to safely increase productivity which benefits the community and helps reduce emissions per pallet carried.”
PRIME NEWS 18 september 2022
The acquisition of FFS will be funded through cash reserves and debt facilities (subject to approval).
Quad-quad B-doubles and quadtri B-doubles when longer than 30 metres are now eligible vehicles under the Victoria schedule of the National Class 2 Performance Based Standards (High Productivity) Authorisation Notice 2022 (No.2).
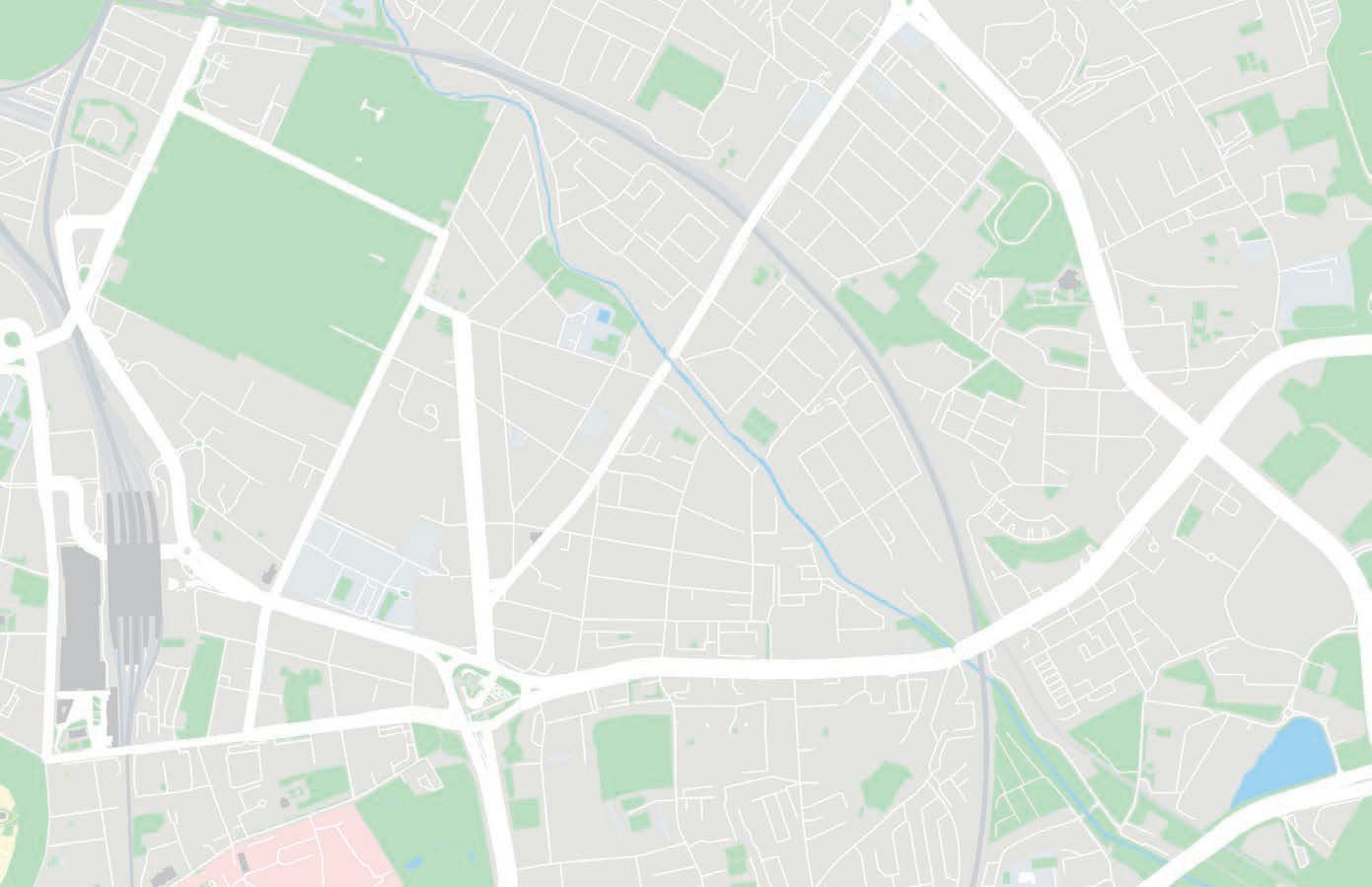
chip customer base as well as other potential cross-selling opportunities.
Primary Connect and Ron Finemore Transport have worked closely with trailer supplier engineers and relevant local government bodies to bring the next generation vehicles to life. The B-double high cube trailer
> PBS notice adds new vehicle combinations
Create a balanced program that rewards positive actions and communicates areas for improvement.
Video AI reviews all driving time to provide insights into behaviours to reward and areas to improve.
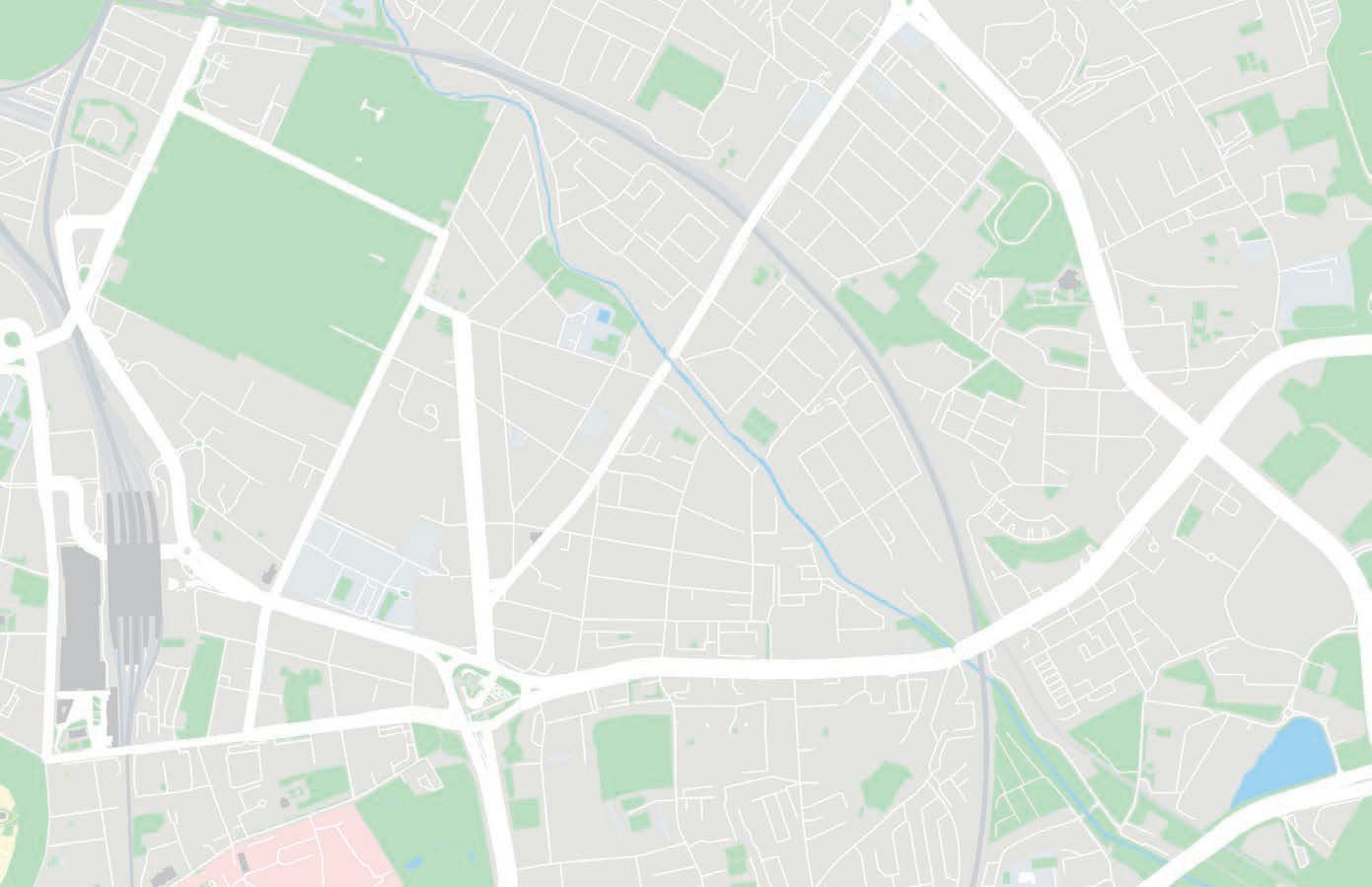
A new phase of intelligent driver safety is here. Where artificial intelligence turns video into meaningful insight, empowering you to drive change through personalised coaching and driver rewards.
SMART DASHCAM
A new approach to reduce risk by using video AI to protect your drivers

Digitise your coaching & training program with a dedicated driver app to help focus on performance.improving
1300 111 TeletracNavman477.com.au
Prevent incidents from occurring in real-time with audio alerts direct to the driver for dangerous events.
PRIME NEWS 20 september 2022
and sustainable supply chains,” he said as part of a media statement.
“Brad leaves the ALC with a strong and focused team, as well as a solid platform and strategy for membership growth,” said Davies. “We wish Brad all the best as he moves to take up a senior role in the public sector and we thank him for his leadership and contribution to the organisation and the broader industry.”
An average 1000m-long intermodal service from Dooen to the Port of Melbourne carries about $2.5 million worth of produce and the equivalent amount of freight to 70 trucks.
> ALC announces departure of CEO
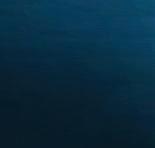
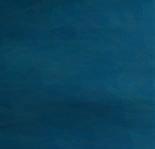
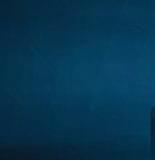
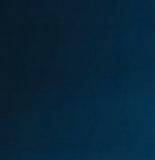
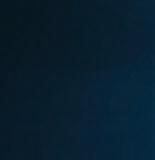
“For the Wimmera there is a lot riding on our capacity to send containers by rail,” she said. “Over long distances, trains burn less fuel and carry far higher
A scheme has been extended by the State Government to reduce rising truck numbers on Wimmera roads in Victoria.
on local government as our already fragile roads bear the brunt.”
volumes than road transport.”
“The subsidy has been steadily reducing since 2014 when $5m was offered to the four operators,” she said. “Unfortunately, for potential exporters, one-year extensions to the scheme may not provide enough long-term certainty for them to be able to make the shift to rail. And we know there are significant export projects proposed for our municipality that are now looking at their transport
The Victorian Government has allocated $3.5 million in its Budget for 2022/23 to extend the MSIS until 30 June 2023. The funding is shared between Dooen and other regional freight terminals at Shepparton, Mildura and Warrnambool. However Gulline said she wanted the scheme to do more to encourage change. She said guaranteeing the MSIS for at least three years would provide more certainty in the Wimmera’s rail freight capabilities and encourage more local companies to opt for rail over road.
The economic base of the Wimmera is heavily reliant on agriculture with tourism and social services regarded as active labour markets, one increasingly reduced in prominence by the presence of the other, following restrictions placed on the community through government intervention in the past two years. Gulline, who was elected mayor in November 2020, said the planned growth of mining in the Horsham area meant that rail freight would be even more critical in the future. Four of the world’s largest sand-mining projects have been planned within a 70-kilometre radius of Horsham. Gulline also wants to service this development by rail.
“Theoptions.beneficiaries of this scheme go far beyond the intermodal terminal operators,” Gulline said. Scheme for moving SCT containers to rail from road extended
“Never before has the supply chain been front and centre in the public debate and awareness around the freight and logistics sector to the national economy,” said Davies. “This is an important time for the sector, we believe that Dr Parson’s insight, knowledge and experience, combined with our members spanning the supply chain will build on ALC’s work to shape safer, more efficient
>

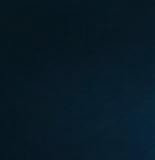

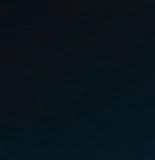
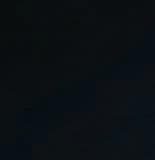
held executive leadership, research and public policy roles at a number of leading Australian institutions including serving as the director of a centre for supply chain and logistics and at two Universities. Wayfinder, an initiative focused on increasing female participation and diversity in the supply chain workforce, was launched by Deakin University in 2018.
The Australian Logistics Council (ALC) has confirmed the shock departure of CEO Brad Williams. In a surprise announcement, Williams has vacated the role less than 12 months after being appointed in August, 2021. The ALC has announced Wayfinder co-founder Dr Hermione Parsons as the new CEO. ALC Chair, Philip Davies welcomed the appointment and said Dr Parsons brings a wealth of knowledge and realworld experience across the end to end supply chain. Her career involvement to date includes the food industry, ports, economic issues, policy and research. “The ALC Board is excited to have appointed Dr Parsons to this key leadership role and we are all looking forward to working closely with her, as we continue to advocate for a stronger supply chain and support our members,”
said ParsonsDavies.has
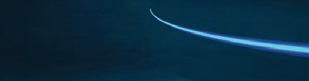
On behalf of the ALC Board, Davies extended thanks to outgoing CEO, Brad Williams, who is bound for the public sector, for his leadership and hard work.
The Mode Shift Incentive Scheme (MSIS) will be extended for another year, effectively keeping rail freight viable for Wimmera Intermodal Freight Terminal rail operator SCT.
The ALC Board and staff, according to the statement, remain focused on our national policy priorities and continuing to build momentum with government, industry and policy makers to affect positive change for the freight and logistics sector.
Under the program, SCT receives a small rebate for the cost of each container it puts on rail instead of sending it by road. About 15,000 containers of hay, grain and pulses are moved by rail per year on the service which runs three days per week. “With modern farming practices, we are seeing unprecedented levels of strain on roads in our municipality because so many trucks are delivering commodities to port directly,” said Horsham Rural City Council Mayor Robyn Gulline. “This not only damages our already failing road infrastructure but creates congestion in Horsham where trucks must travel through the centre of town, because, at the moment, there are no alternative routes,” she said. “The MSIS doesn’t solve the problem, but it certainly helps alleviate some of the strain that is placed
THE NEW D 190 FULL TIME PUMP HAS ARRIVED For more information contact Dana on 1300 00 DANA or visit us at www.Dana.com.au Strength • Power • Endurance ENGINEERED & BUILT IN AUSTRALIA
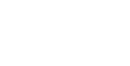

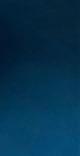
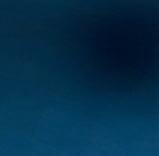
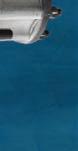
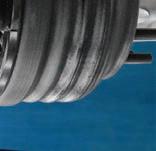

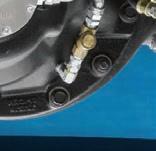
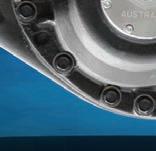
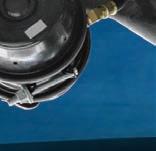

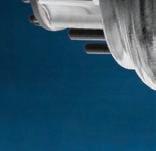
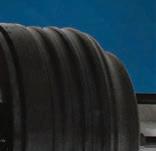

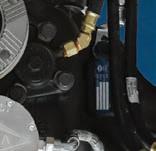
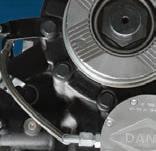
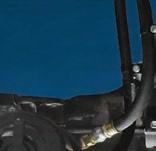
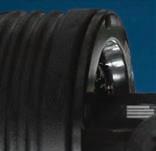
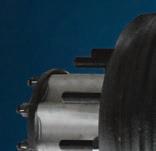
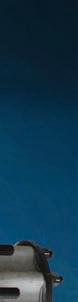
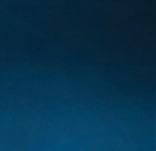

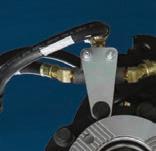
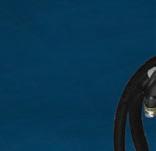

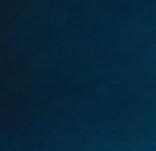
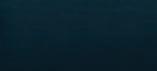
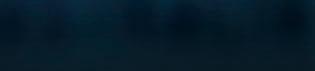
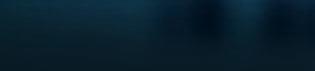
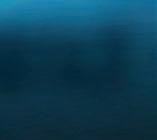
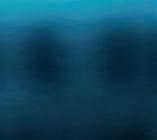

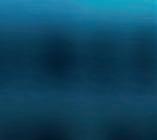
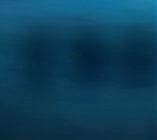


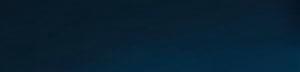
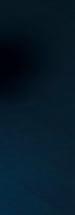
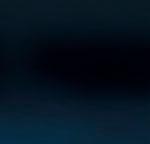
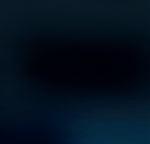
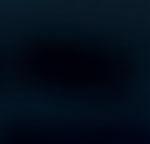
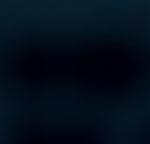
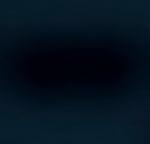
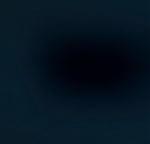

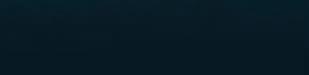
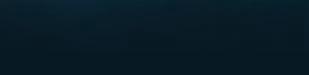
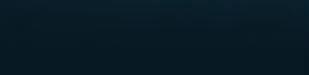

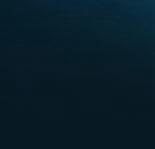


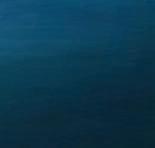
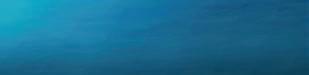
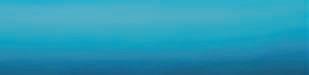
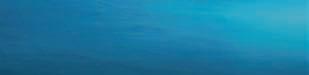
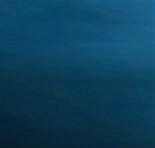
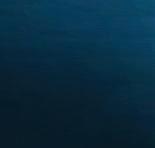
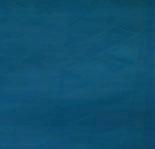
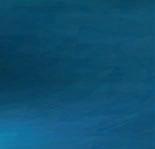
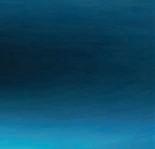
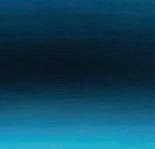
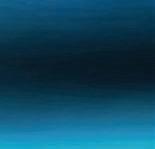
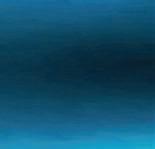
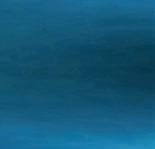
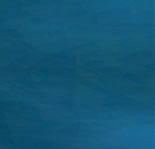
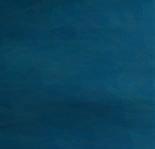

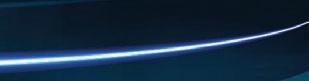
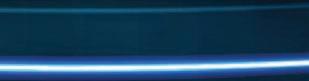
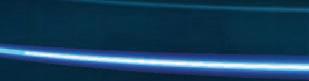
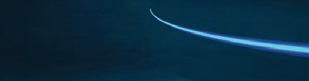
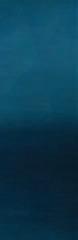
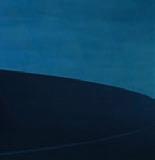

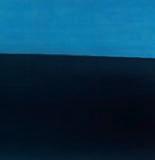

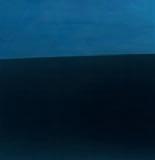
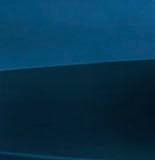

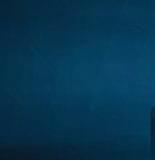
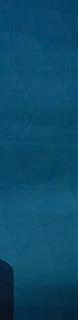
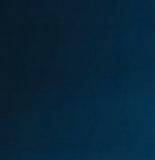
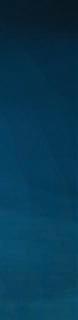
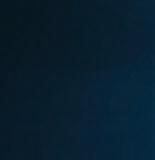
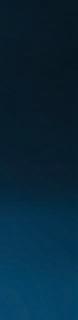
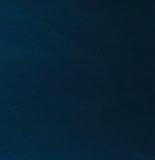
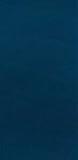

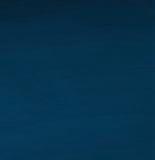
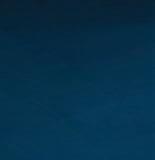
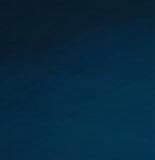
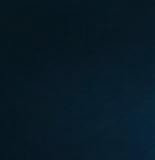


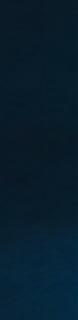

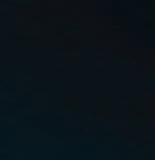
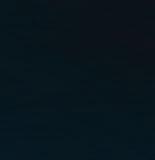

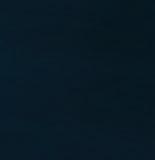
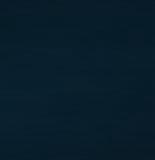

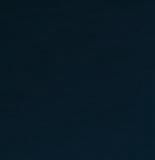
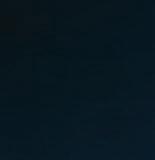
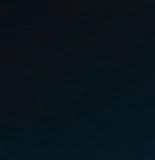
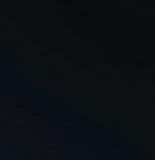
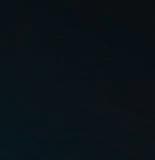

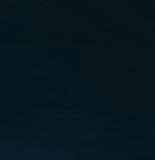
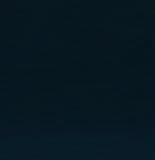
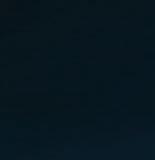

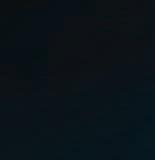
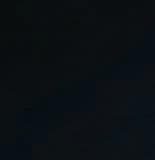
> Volvo
Volvo FL Electric Truck.
“Australia has long been stuck in the slow lane when it comes to electric transport uptake, but the ACT’s game-changing policy to phase out new fossil fuel powered cars is a welcome step forward,” said Climate Councillor Andrew Stock. “The ACT has set the bar for the rest of the country in reducing emissions from light passenger vehicle fleets, while also delivering lower pollution levels and a reduced reliance on expensive petrol.” announces landmark agreement
A landmark zero emissions agreement has just been signed between the ACT Emergency Services Agency and Volvo Group Australia. The agreement, which places VGA as preferred supplier of zero emissions heavy vehicles to the ESA, is believed to be a first for an Australian emergency services agency and firmly places both parties on the road to a fossil free future.
22 september 2022
PRIME NEWS
“The journey towards a zero emissions future isn’t just accelerating globally and that journey is fast gathering pace here in Australia.” said Martin Merrick, President and CEO Volvo group Australia. “Collaborations like the one we have just announced with the ACTESA are vital to help decarbonise our world and I applaud the agency for its commitment to being a part of this journey with us,” he said.
Volvo Trucks has committed to being fossil-fuel free by 2040 with production of electric trucks expected to begin at the Wacol site during 2025.

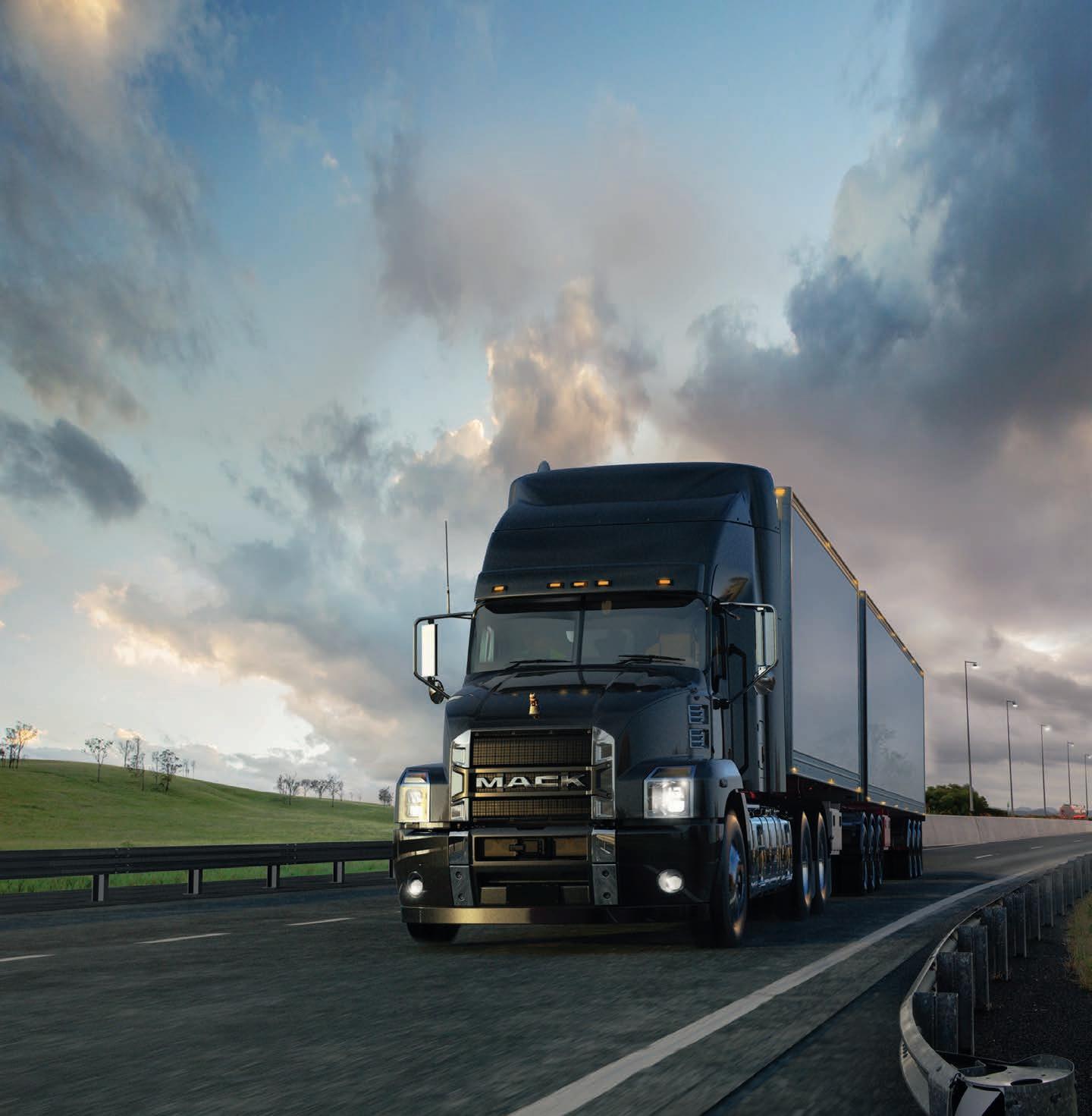
evolving towards an emissions free environment to improve the lives of many Emergencymore.”service support vehicles with zero-emissions capability are not currently available on the market. “The fulfillment of this contract will position the ESA as a leader in Australia for zero-emissions operational support vehicles,” says ACTESA Commissioner Georgeina Whelan. “At its core, the ACTESA strives to ensure the safety of our community, staff and volunteers. Making the transition to a sustainable fleet, subsequently contributing to the wellbeing of Canberrans and our environment, aligns with this key Forcommitment.”over50years, Volvo Group Australia has been manufacturing trucks in Wacol, Queensland. Volvo Trucks’ production facility in Wacol employs more than 700 people directly in the production process, supported by over 60 dedicated engineers.
“We are very aware of the trust placed in us to fulfil this role. Every day around the world lives depend on our vehicles, and we look forward to that trust
Earlier in the week, the Australian Capital Territory Government announced a plan to phase out light internal combustion engines by 2035. Under Australia’s first policy to phase out fossil fuel powered cars, it set an ambitious target of 80-90 per cent of new light vehicles sales being zero emission vehicles by 2030.
IT’S NOT THE END OF THE LINE THAT MATTERS. IT’S WHERE YOU START. ACTIVE SAFETY COMES STANDARD MACK CONNECT FLEET TECHNOLOGYMANAGEMENT DEALER NETWORK 82 LOCATIONS ACTIONMACK SERVICE BREAKDOWNEMERGENCY SERVICE When you’re running linehaul, you better get the best truck you can. And the smartest choice is a Mack Anthem, hands down. Mack Anthem delivers big time thanks to its strong service network, enhanced reliability and safety features. Purpose built for linehaul, it delivers all day, every day, and its enhanced fuel efficiency, superior driveline and total driver comfort make it the best way to get your business into top gear. Talk to your local dealer today, or visit MackTrucks.com.au/Anthem
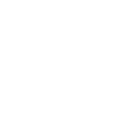
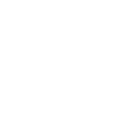
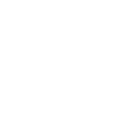
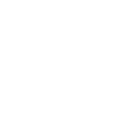
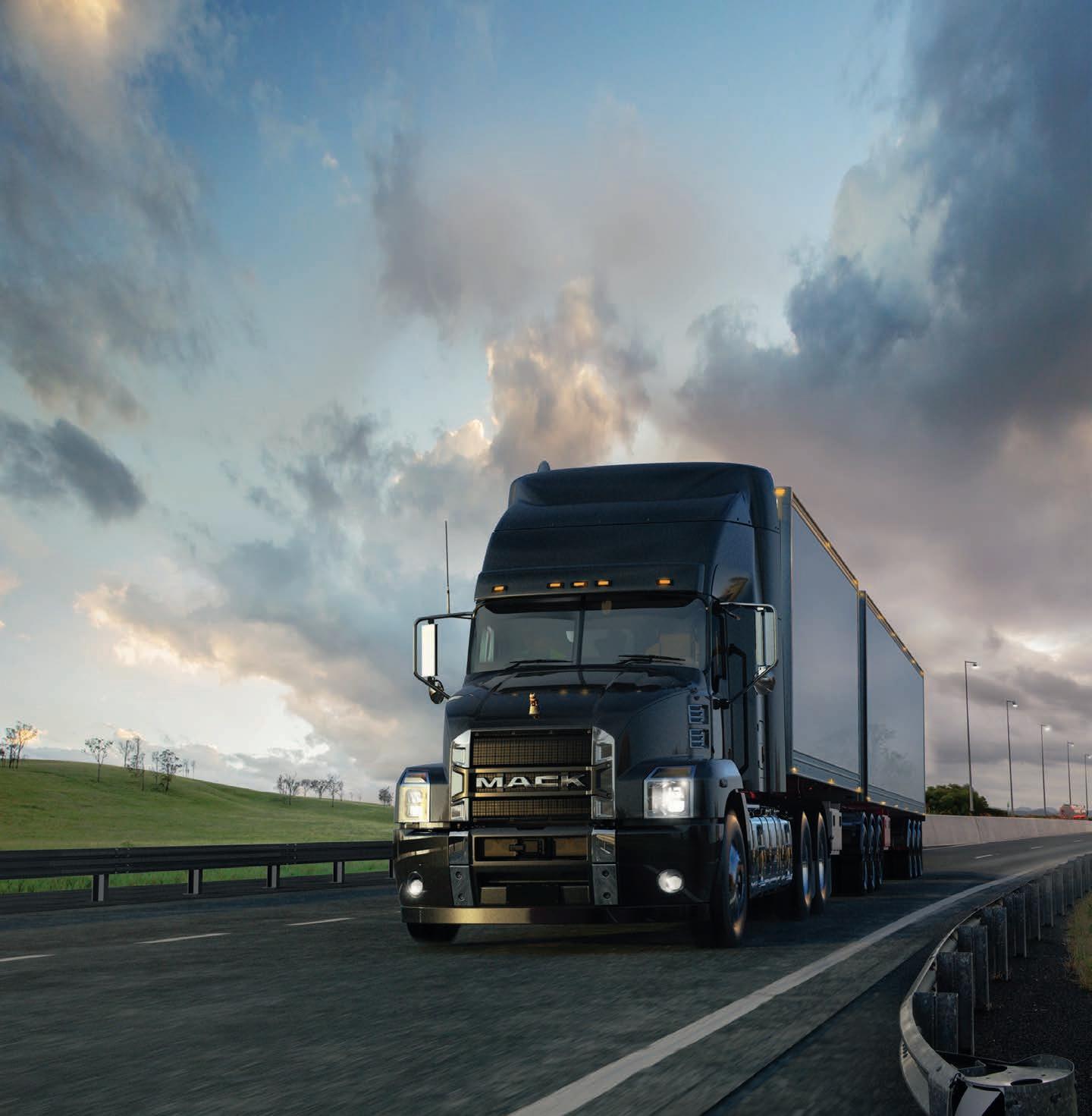
Reducing the more than 200 truck fires attended by Fire and Rescue NSW each year is one of the key objectives of a new guide issued by the NSW Environment Protection Authority. Preventing Fires-Truck Inspection Manual by the NSW Environment Protection Authority (EPA) aims to give truck drivers the inspection skills to identify and correct faults that have the potential to cause heavy vehicle fires that could endanger lives, livelihoods, and the environment.
Non-impact truck fires, according to Marler, were the cause of eight per cent of all heavy vehicle insurance claims.
Environmental Solutions. Many trucks catch fire because of mechanical or electrical faults that a trained eye could have identified. The Manual will provide a user-friendly guide, developed with the help of industry experts, to show truck operators how to inspect their vehicles and identify problems before they result in a fire. It also goes beyond prejourney checks, helping drivers identify faults – such as overheating brakes and electrical faults – while in transit and what to do if a problem develops on the open road that could cause the vehicle to catch fire.
during the current quarter.
Fenix Resources has signed definitive agreements to acquire 100 per cent ownership in haulage joint venture, FenixNewhaul. The transaction sets up Fenix as a fully integrated mining, haulage and logistics company and reduces operating costs it said in a statement.
The transaction is a key outcome from the board’s recent strategic review and provides Fenix with a vastly improved platform to evaluate and acquire further growth opportunities.”
“Truck fires are major incidents that can be extremely dangerous and result in smoke and water pollution, cargo loss, and extended road closures,” said Karen Marler, EPA Director of
“When the cargo is dangerous goods, the consequence can be particularly high and carry significant risk to the safety of drivers and road users and the environment,” she said.
“The EPA would like to see the Manual adopted as part of regular routine checks,” she said.
> Truck fires in crosshairs of new EPA guide
Marler said the Manual should be in the hands of the maintenance manager of every fleet and every heavy vehicle mechanic as well as drivers.
Value accretive, the arrangement will also ensure that the company now receives 100 per cent of profits and cashflows from Fenix Newhaul’s highly profitable haulage Duringbusiness.the June Quarter, approximately 340,000 tonnes of iron ore were hauled by Fenix Newhaul, slightly higher than budgeted levels of approximately 110,000 tonnes per month.
“Fenix’s ongoing ability to generate cash and profits was significantly improved during the quarter with the signing of the agreement to consolidate ownership of our road haulage joint venture,” said Fenix Resources Managing Director Rob Brierley. “The Fenix-Newhaul transaction is an important strategic initiative that will reduce our future haulage costs and result in cost savings and additional operational flexibility as well as supporting growth Fenix-Newhaulinitiatives.” was incorporated in October 2020 as a 50:50 joint venture company to implement the strategic alliance between Fenix and Newhaul. It was established to provide haulage and logistics services to Fenix’s Iron Ridge Project, in the Mid-West region of Western Australia, 490 km from Geraldton Port.
The innovative quad-trailer combination, relying on Volvo and Mack prime movers, has increased haulage capacity to approximately 140 tonnes per truck delivering cost savings on a per tonne basis. Currently there are 26 truck and trailer combinations in the Fenix Newhaul fleet, 18 of which are quad-trailer combinations. Delivery of the remaining seven A-trailers is expected to occur
Fenix Newhaul has now converted the majority of the haulage fleet to a quadtrailer configuration after a successful trial period conducted in late 2021.
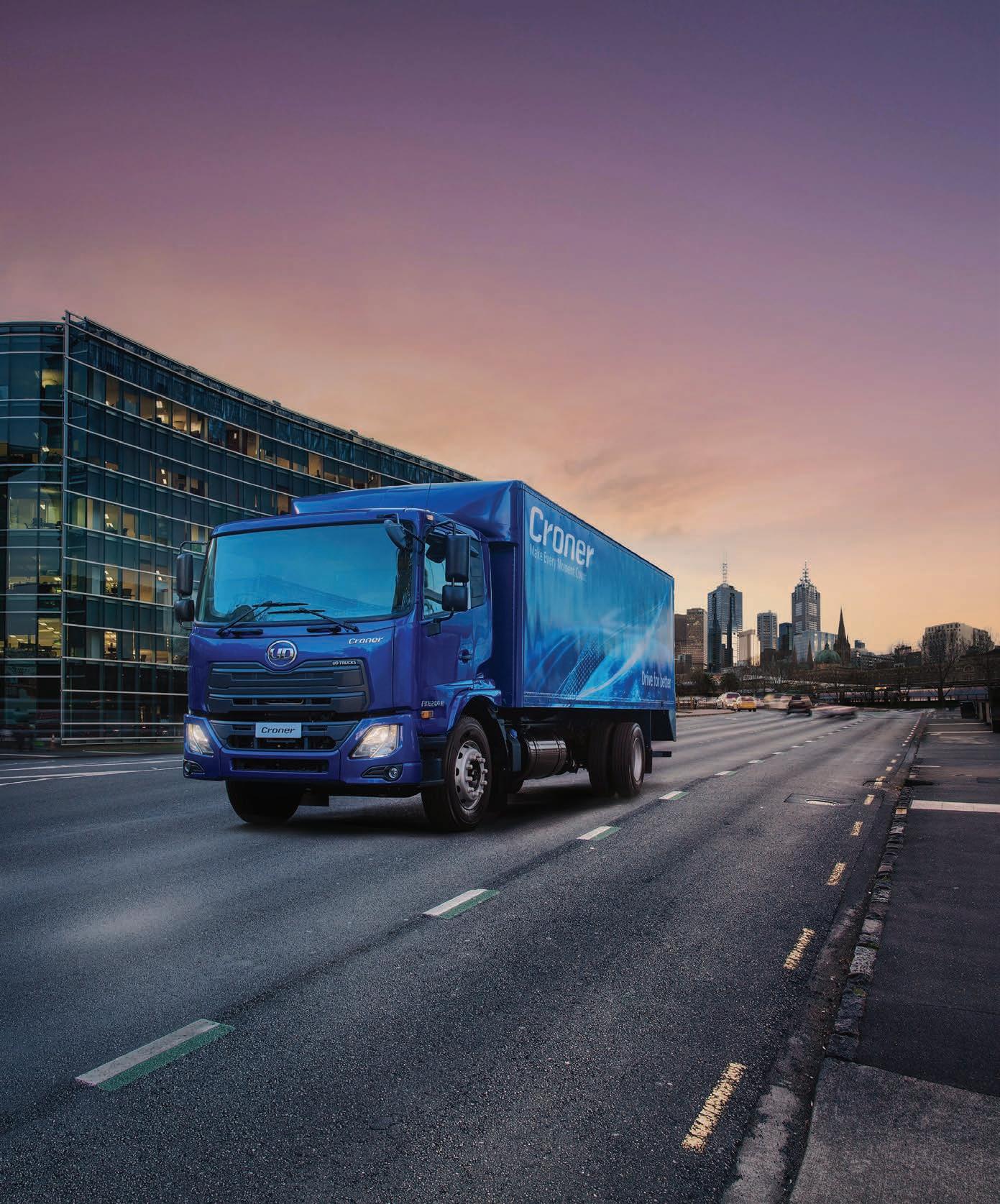
> Fenix assumes control of roadtrain business
“No driver wants to experience a truck fire and the actions needed to avoid
The disclosed transaction will involve upfront payment of $16.5million in cash and equity, including $7.5 million in cash consideration to be paid on completion; and 30,000,000 Fenix ordinary shares issued to Newhaul and valued at $9m based on the last closing price for Fenix shares of $0.30.
“In collaboration with Fenix, Newhaul has established a highly efficient haulage solution to connect Fenix’s Iron Ridge mine in the Mid-West, to the Company’s port operations in Geraldton,” said Craig Mitchell, Newhaul Founder and Executive Director. “This has been achieved by combining a modern, intelligent haulage fleet with a skilled and dedicated workforce, and strong systems and processes,” he said. “The entire Fenix-Newhaul team are excited to join with Fenix and contribute to building an even stronger and more scalable logistics business. We remain committed to supporting Fenix’s business and are particularly excited by their expansion plans in the Mid-West region.”
that outcome can be as simple as noticing chafing on high current cables, such as battery cables,” said Marler.
PRIME NEWS 24 september 2022
“Fenix-Newhaul is a highly profitable state-of-the-art logistics business which is an essential component of Fenix’s business success,” said John Welborn, Fenix Chairman. “Consolidating 100 per cent ownership is a smart move which will reduce our costs and provide operational flexibility. These advantages will make our business significantly more resilient and robust to commodity price volatility.
With its smart, intelligent design, the UD Croner is right at home in the CBD. Its tight turning circle, superior manoeuvrability and commanding visibility are all designed for comfortable, efficient city driving. Its high torque and money saving fuel efficiency ensures peak performance, and its proven uptime and reliability gets it noticed for being one of the hardest workers in town. Plus, for complete peace of mind, it’s all backed up by one of Australia’s best dealer networks.
To find out more, contact your UD Trucks dealer on 1300 BUY A UD or visit
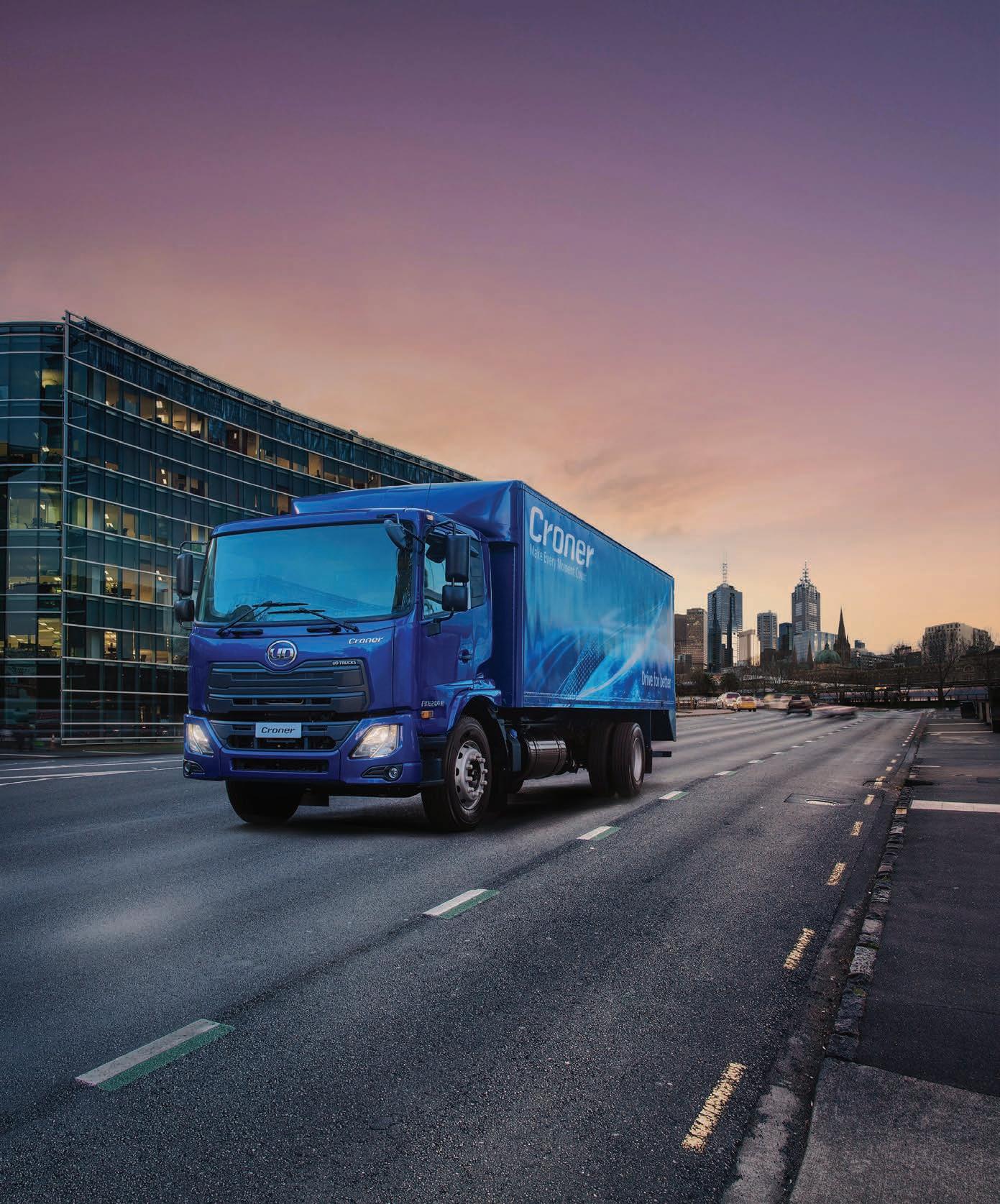
udtrucks.com/australia Follow us on
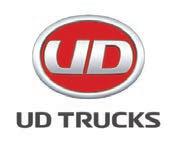


To perform in the city takes a special kind of truck. One that goes beyond the expected and leaves convention far behind.
Going the Extra Mile
Proudly part of Volvo Group Australia THE TRUCK AUSTRALIA
Into the city, out of the ordinary. TRUSTS
For over 85 years, UD Trucks have delivered ultimate dependability. No wonder this is the truck Australia trusts.
Beginning in 2025, MAN Truck & Bus will manufacture high-voltage batteries for electric trucks in large-scale production. The German company will invest around 100 million euros ($AUD151.6M) over the next five years at its traditional production site for combustion engines in Nuremberg. Eventually production capacities will be expanded to an estimated 100,000 batteries per year. The decision to invest in the battery production facility, which is expected to secure 350 jobs, was made in close cooperation between MAN Truck & Bus, employee representatives and with the active support of Bavarian politicians. It will also give Nuremberg’s traditional location a clear perspective for the future. Initially, the batteries, which along with the engines form the heart of electric commercial vehicle drives, will be manufactured manually at the MAN plant in Nuremberg in a small series production for about two and a half years.
It is anticipated that this will initially give MAN’s e-trucks a range of 600 to 800 Inkilometres.thenext generation of battery technology, ranges of up to 1,000 kilometres are expected by the year 2026. This will finally make the e-truck suitable for long-distance transport.
> MAN prepares for electric drive system transition
Around the middle of the current decade, the total cost of ownership for an e-truck and a diesel-powered one will be at the same level according to MAN Truck & Bus. MAN therefore expects customer demand for e-vehicles to increase significantly by then at the latest – assuming the appropriate charging infrastructure is in place.
the foundations for the large-scale industrialisation of electric drive systems for trucks and buses.
Construction of large-scale production is scheduled to start in mid-2023 and to be completed by the end of 2024. The news all but confirms MAN is laying
vehicle e-cluster ‘made in Bavaria’, consisting of the production of e-trucks at MAN in Munich, battery production in Nuremberg, research & development at both locations and cooperation with the respective colleges, universities and “Withinstitutes.our investment decision, we are securing around 350 jobs at the Nuremberg site and hundreds if not thousands of jobs in Germany,” he said.
“We are now starting to industrialise electromobility and continue on our path to climate-neutral mobility in commercial vehicles,” said Alexander Vlaskamp, Chairman of the Executive Board of MAN Truck & Bus SE. “It is a ground-breaking location and investment decision. At the same time, it is part of MAN’s transformation into a provider of sustainable transport solutions.”
“Such important decisions can only be made in close cooperation with all parties involved from the employer and employee sides as well as politics.”
The batteries are the result of complex assembly. Made of battery cells, which in turn are grouped into modules and combined in individual layers to form a battery housing (pack), the batteries will require high levels of know-how and strict safety standards. Depending on the range, a heavy electric truck will need up to six battery packs.
The production of heavy e-trucks will start at MAN in Munich at the beginning of Under2024.its “electrification” plans, a new chapter is now beginning for the Nuremberg production and development site, which will also increasingly take on tasks within the TRATON GROUP of which it is a member alongside Scania and Volkswagen.
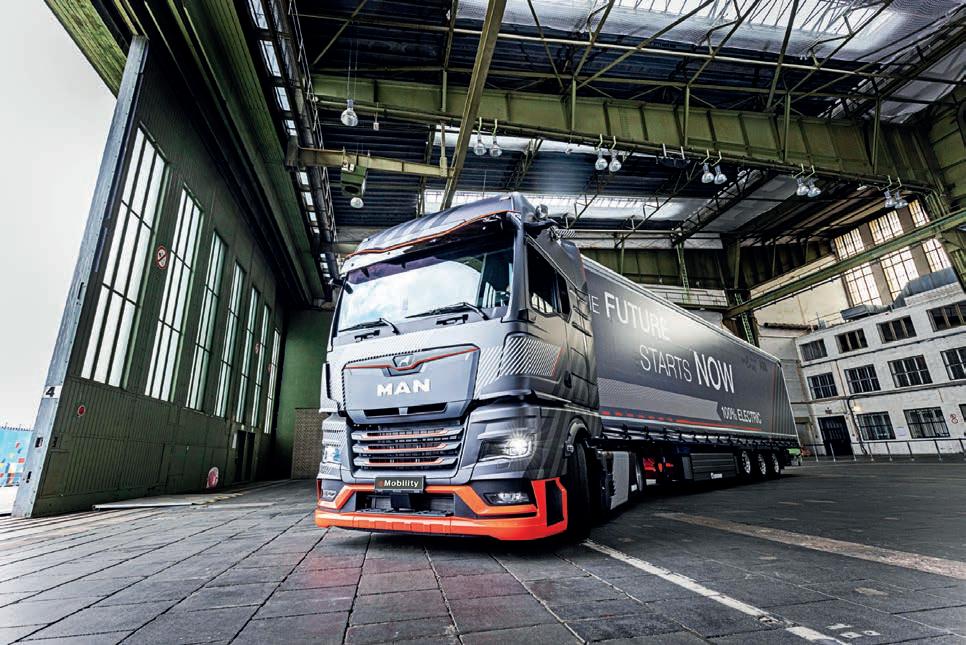
GLOBAL NEWS
The commercial vehicle manufacturer is receiving support from the Bavarian State Government, which has promised a contribution of around 30 million euros to energy research and technology funding for the period 2023 to 2027, provided that the funding and budgetary requirements are met. These funds will be used to conduct research in battery assembly, cell chemistry and development, battery safety, and ultimately battery recycling to ensure the sustainability of the propulsion mode.
26 september 2022
MAN eTGM electric heavy duty truck.
The investment, according to Vlaskamp, now paves the way for a commercial
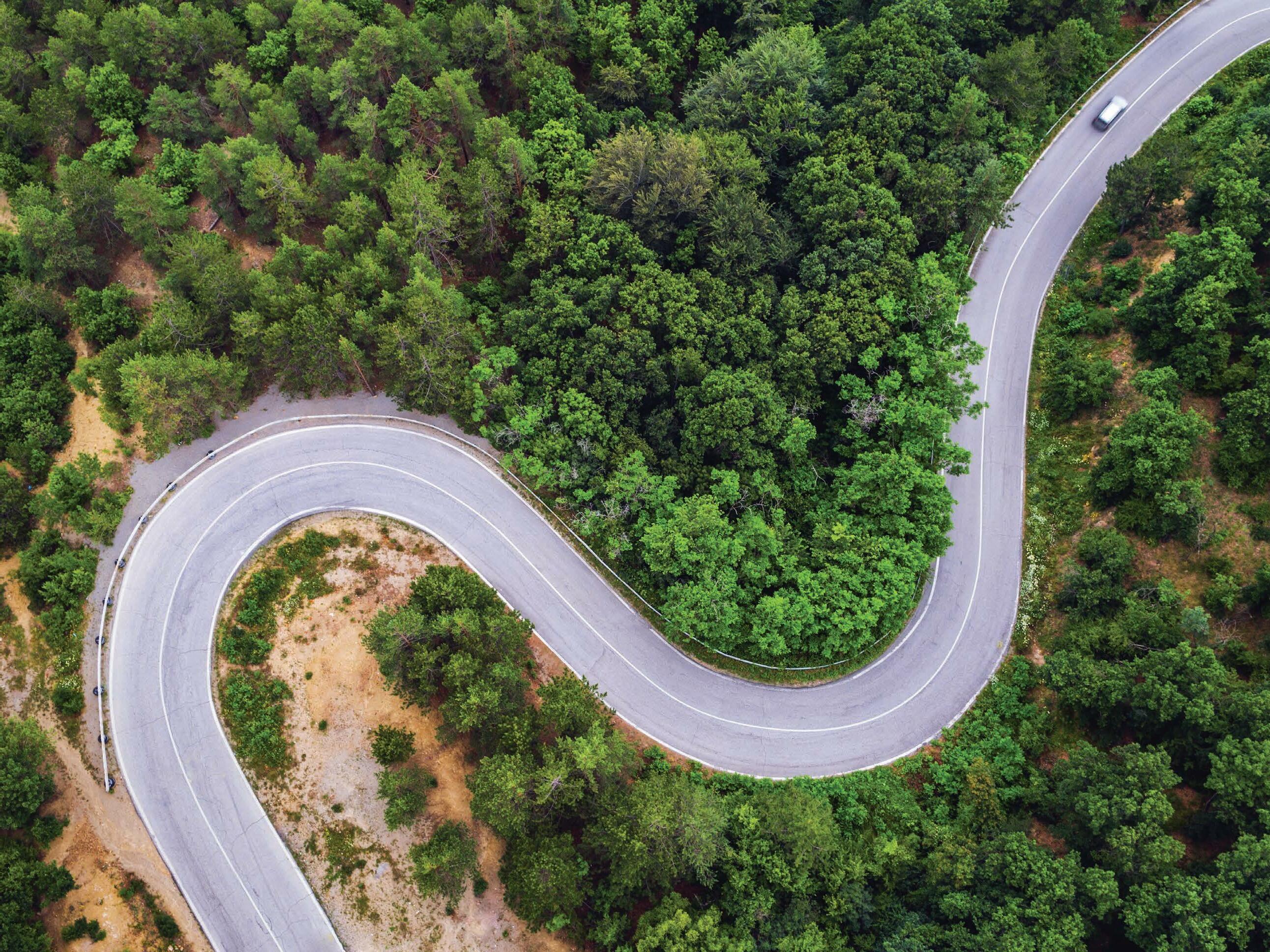
Marcus Coleman
At the same time, we reviewed offhighway operations further south and put a plan in place to modify equipment and increase payloads
Performance-Based Standards are delivering productivity for primary producers across the country.
K
HAUL OF FAME
by 25 per cent with GCMs north of 330 tonnes. It was a detailed review that involved analysis of truck frames, engines, transmissions, axles suspensions, steering systems, couplings and vehicle dynamics. We completed a comprehensive test program and were able to safely increase the productivity of that operation as well.
The significance of this result hit home when I was at the Heavy Vehicle Truck Technology (HVTT) Conference in New Zealand the following year. A researcher presented a case study of a PBS combination they’d developed for an iron ore mine in Sweden. The audience listed with great interest about what was essentially an A-double operating at around 90 tonnes GCM. Apparently, they had encountered some issues with vehicle stability. When I asked the presenter over dinner if they’d resolved the problems, he said that they were not operating because the iron ore mine had become unviable and was closed when the iron ore price dropped. This highlights just how critical freight productivity is for the international competitiveness of Australia’s bulk commodity exports. A few years back, Ken returned to NSW to help his brother Larry manage road freight operations for their 10,000 acres of cotton and wheat farms in the NSW
Tiger Spider Managing Director, Marcus Coleman, has more than 19 years’ of engineering consultancy experience in the heavy vehicle industry working for transport operators, heavy vehicle manufacturers and government. He is a professional PBS assessor, registered Chartered Professional Engineer (CPEng), registered Professional Engineer of Queensland (RPEQ) and RVCS Agent.
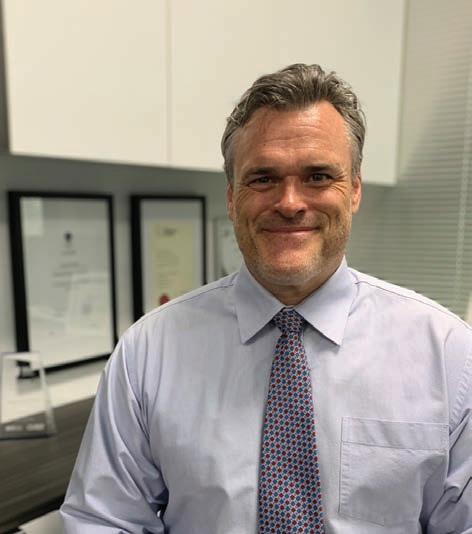
28 september 2022 SUPERANNUATION MINDSETOEM MINDSET
In the end we developed a range of 60-metre super quad, ultra-quad and quin roadtrain combinations and negotiated access to key roads in the Pilbara with Main Roads WA. The fleet was rapidly converted and contributed to the continuing viability of iron ore operations based on road freight. The road freight cost per tonne was reduced by around 15 per cent on volumes of 7 million tonnes per annum in one Withoperation.Gross Combinations Masses (GCMs) of 200 tonnes the 60m PBS roadtrains were a significant productivity improvement compared to AAB-quad roadtrains which typically grossed out at 165 tonnes.
en Walsh and I first met in late 2015 when the iron ore price plummeted to record lows. Ken worked for Process Minerals International (PMI) a subsidiary of Mineral Resources and was responsible for the road freight operations of the junior iron ore minor. I was called to Perth to meet with senior management and Ken to discuss how PBS could be used to improve road freight productivity in the Pilbara.
Walsh’s PBS approved A-double.
After reviewing the existing design and several phone calls do discuss the pros and cons of each, Ken eventually decided to apply for a permit with the existing A-double set in the knowledge that it was going to cost $10,000 or more for a bridge assessment. There were of course no promises from DOT Victoria about what weights would be achieved but based on the configuration and a review of the network I was reasonably confident that it would be a good outcome.
We completed the PBS Assessment and Certification relatively quickly but had to wait around 6 months for the bridge assessment to be finalised. Luckily, in the end it was a great outcome, and the productivity increase has been significant, going from a 43- tonne HML B-double payload to a 55-tonne payload. Meanwhile Ken was planning on purchasing two new A-double combinations. It wasn’t a straightforward decision because there was a potential for more weight with a tri-dolly and longer combination, but in the end the flexibility of operating a 30m combination on the 2B network was seen as the best way forward. In hindsight it was a great decision. The new A-doubles carry an additional three tonnes payload because the axle spacings meet the Victorian Reference
complying A-double combination?
Vehicle requirements and the purposebuilt A-double without slider has reduced tare weight with a tandem axle dolly optimised for operation on the PBS Level 2B network in Victoria and now NSW. The recent addition of the NSW network means Ken can operate an A-double to, and from, key ports in NSW, particularly Port Kembla, a significant grain and fertilizer export hub. Ken is now operating the two new combinations and would like to continue to use the existing combination but is concerned about more bridge assessment costs and time which means that it’s not a simple matter for a sub-contractor to hookup and go. Unfortunately, the bridge assessment process is very inflexible and despite the trailers being identical, a new prime mover means that the process must be started again, for another $10,000 and six months wait. It’s been relatively good times for primary producers and road freight in recent years given the global supply chain constraints and stimulus provided. But with interest rates rising and macroeconomic uncertainty ahead, there is always a risk that high commodity prices can drop like a stone. It’s important that we continue to improve road freight productivity to ensure that Australia maintains competitiveness in an increasingly volatile world.
primemovermag.com.au 29 SPONSORED BY
Riverina. It was great to get a call from Ken and discuss what possibilities PBS might offer.
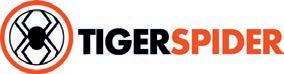
They had a Kenworth T909 towing a b-double tipper with sliding lead trailer which converted into a short roadtrain for the NSW roadtrain network. Ken wanted to get access into Victoria all the way to the Port of Melbourne and Port of Geelong to deliver grain as an A-double at 85 tonnes. Unfortunately, the existing combination with tri-axle dolly did not meet the required bridge axle spacings for access in Victoria and NSW were a long way from releasing their A-double networks. Substantial modifications to the existing equipment didn’t make sense and Ken was planning on ordering a new A-double set, but the lead time on that equipment was some time away and he wanted to continue to make use of the existing Unfortunately,equipment.configuring an A-double for Victoria isn’t straight forward. There are quite a few issues to consider and decisions to make. Firstly, is it best to operate a tandem-axle or tri-axle dolly? Secondly, do you want to stick within the 30metre PBS Level 2B requirements, or lengthen the combination up to 36.5m with the prospect of higher weights on some bridges? Also, is it worth persisting with existing trailing equipment or is it best to focus on a new
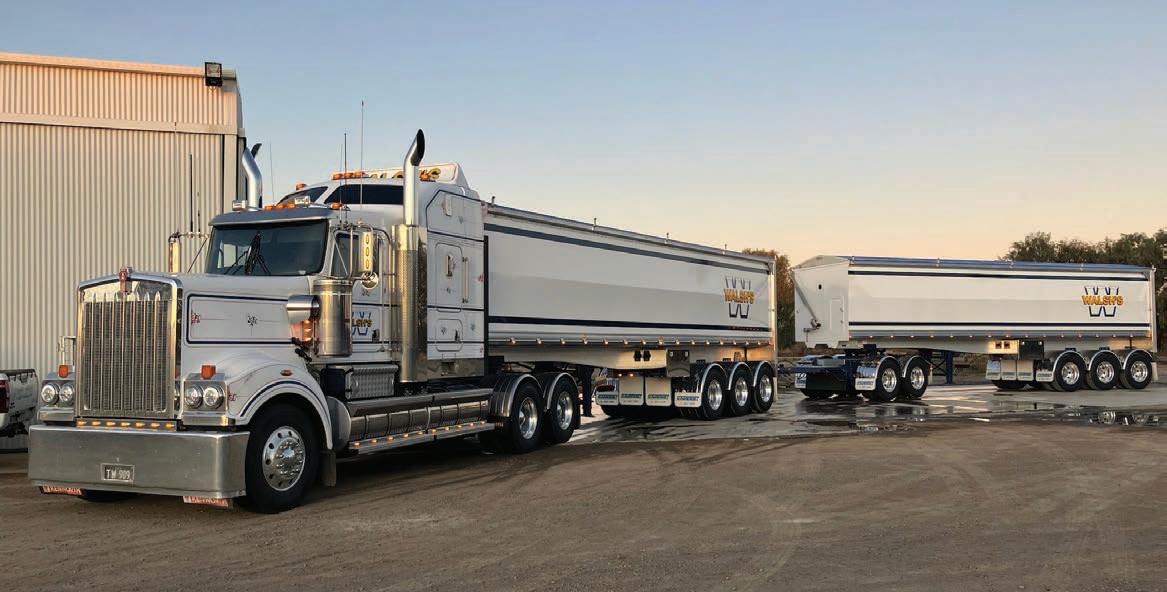
30 september 2022 COVER STORY
SCT Logistics has completed a daring replacement program of its dedicated sugarcane fleet in Northern NSW. A purpose-built PBS combination, hauled by new Mercedes-Benz Actros 2646LS commercial vehicles makes it unique to the industry.
HEAVEN’S GATE
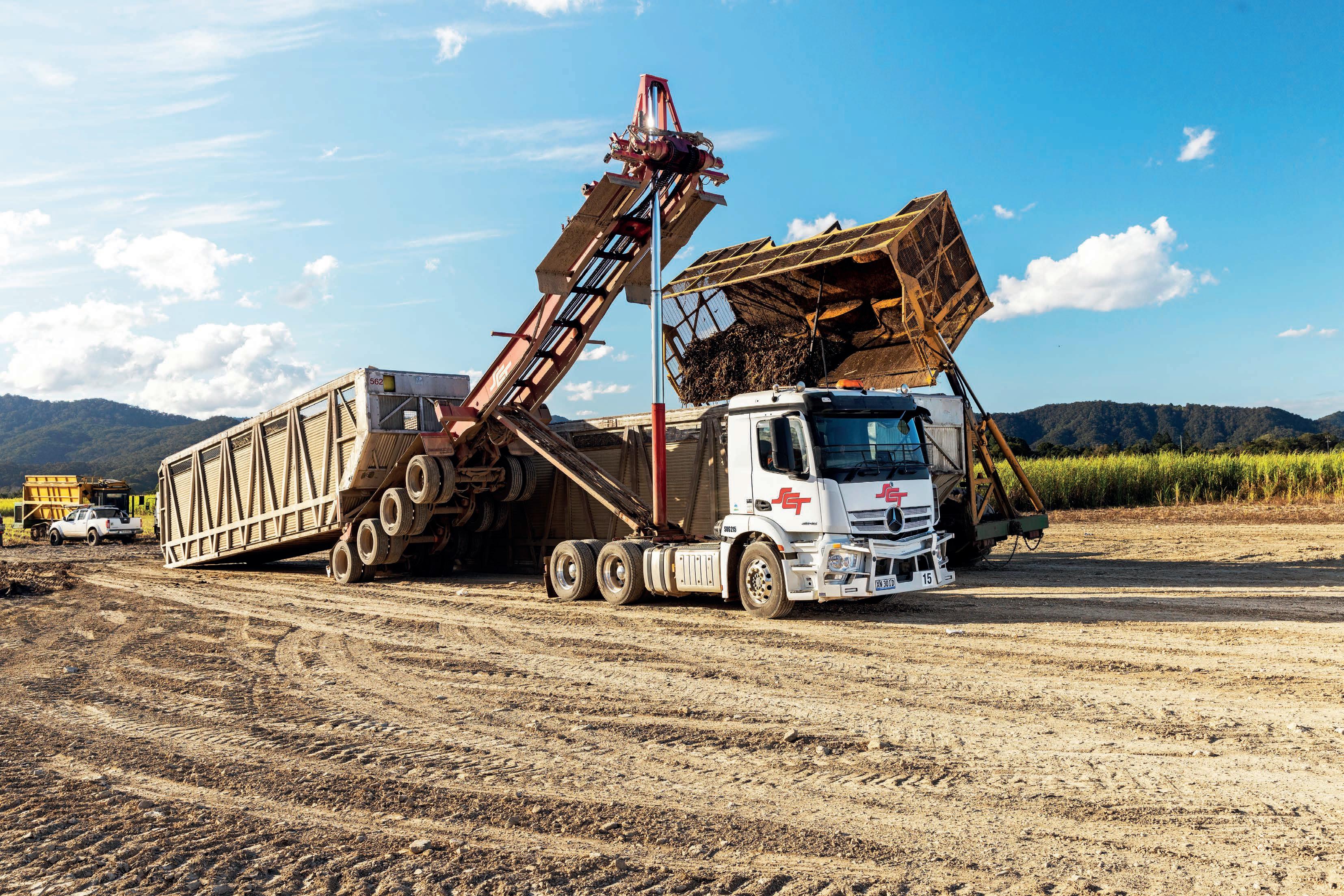
primemovermag.com.au 31
An adjustable bin lock system enables adjustments when the bin is suspended to correct axle weights as required.
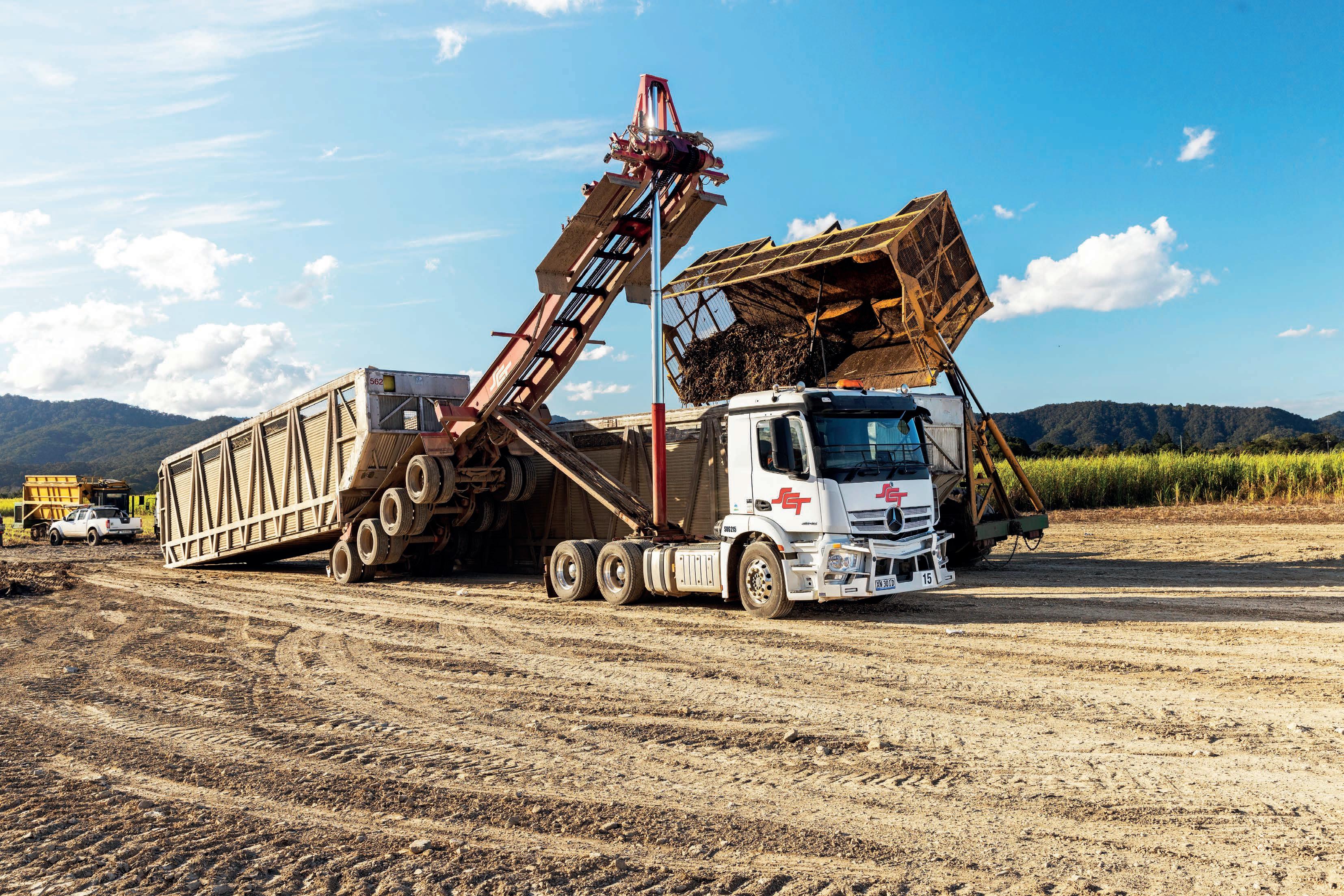
D
fleet of 31 trucks, embossed in the SCT insignia, roars to life. Since 2005, SCT Logistics has serviced the Sunshine Sugar account, ferrying its commercial vehicles between farm sites and the nearby mills. The trucks work 24 hours a day, seven days a week. A pick-up or delivery might only entail trips of a few kilometres, at the most a 150 km round trip, but the work is relentless. Farmers, tip harvested sugarcane into bins parked on cane pads or marshalling areas amongst the cane fields. The bins, which can carry up to 28-tonnes at a time, are retrieved by the trucks and delivered to the mill. A rear door on the bin opens, from which its contents are tipped from a purposebuilt trailer into a hopper at the mill
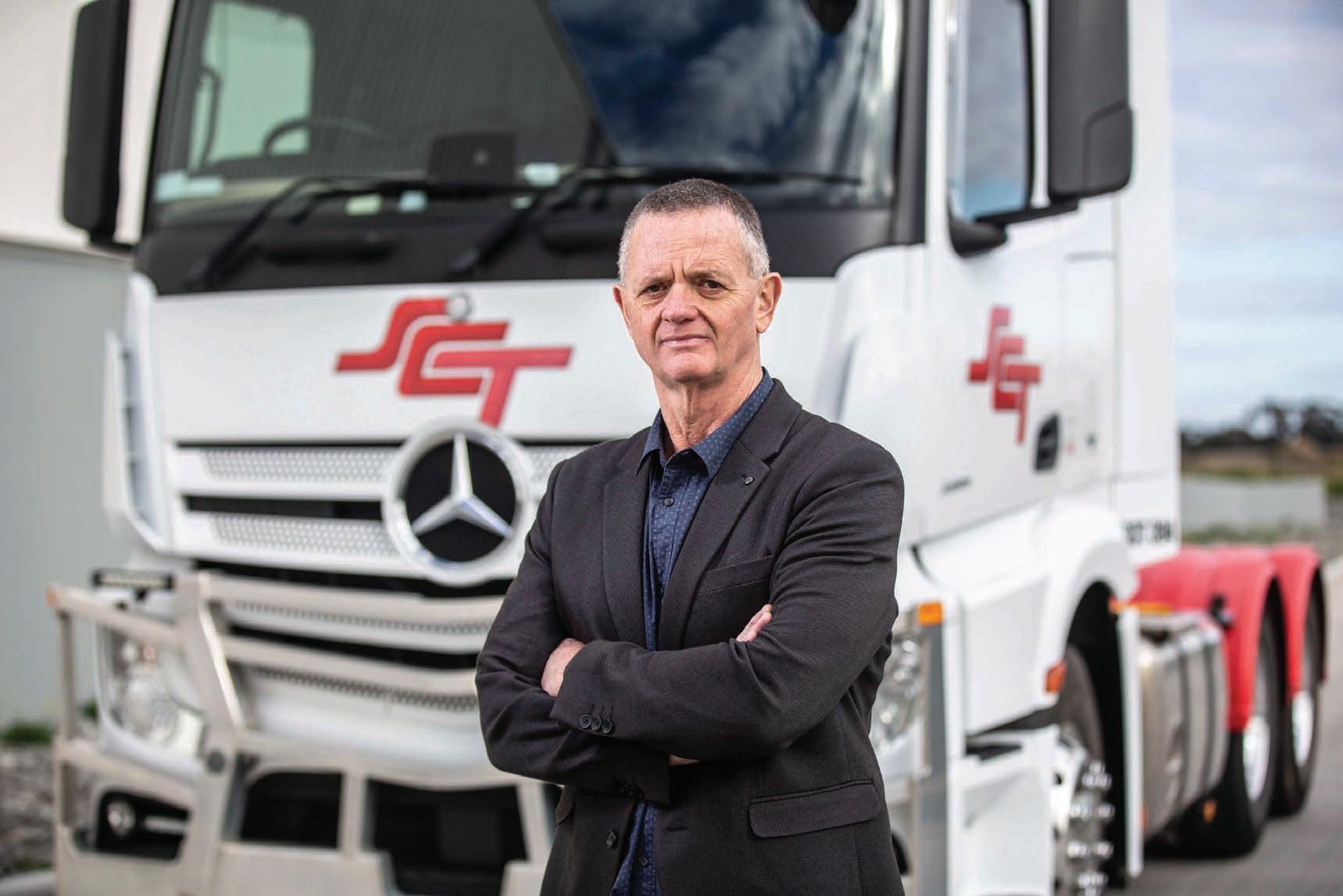
ense alluvial soils washed from volcanic mesa in the surrounds of Mount Warning have long made it a favorable agricultural region, with its sub-tropical climate well suited to growing crops. In the picturesque area outlined by the Tweed, Richmond and Clarence rivers in the Northern Rivers of New South Wales, the state’s sugarcane belt can be found.
Harvest typically commences in early June and lasts until December. In a good year, 2018 for example, the Broadwater
Michael Sommers.
There are some 500 independent sugarcane farmers in an area also home to banana plantations, beef farms, macadamia orchards, and fields of other fruit and vegetable crops. In recent years, sugarcane fields in the western part of the Richmond Valley have been
mainstay in the Northern Rivers region of SunshineNSW. Sugar, the banner with which the NSW Sugar Milling Co-operative and the Australian family-owned business, Manildra Group, sits under, operates mills in one each of the three main sugarcane-growing regions of the Northern Rivers. These are triangulated between sites — moving down the coastline — at Condong, Broadwater and Harwood. The Harwood Mill is the longest continuously running sugar mill in Australia, having commenced operations in 1874.
COVER STORY
With an ageing Kenworth fleet needing to be replaced, SCT Logistics, who already had an existing alliance with Daimler Truck across other areas of its business, opted to try something new.
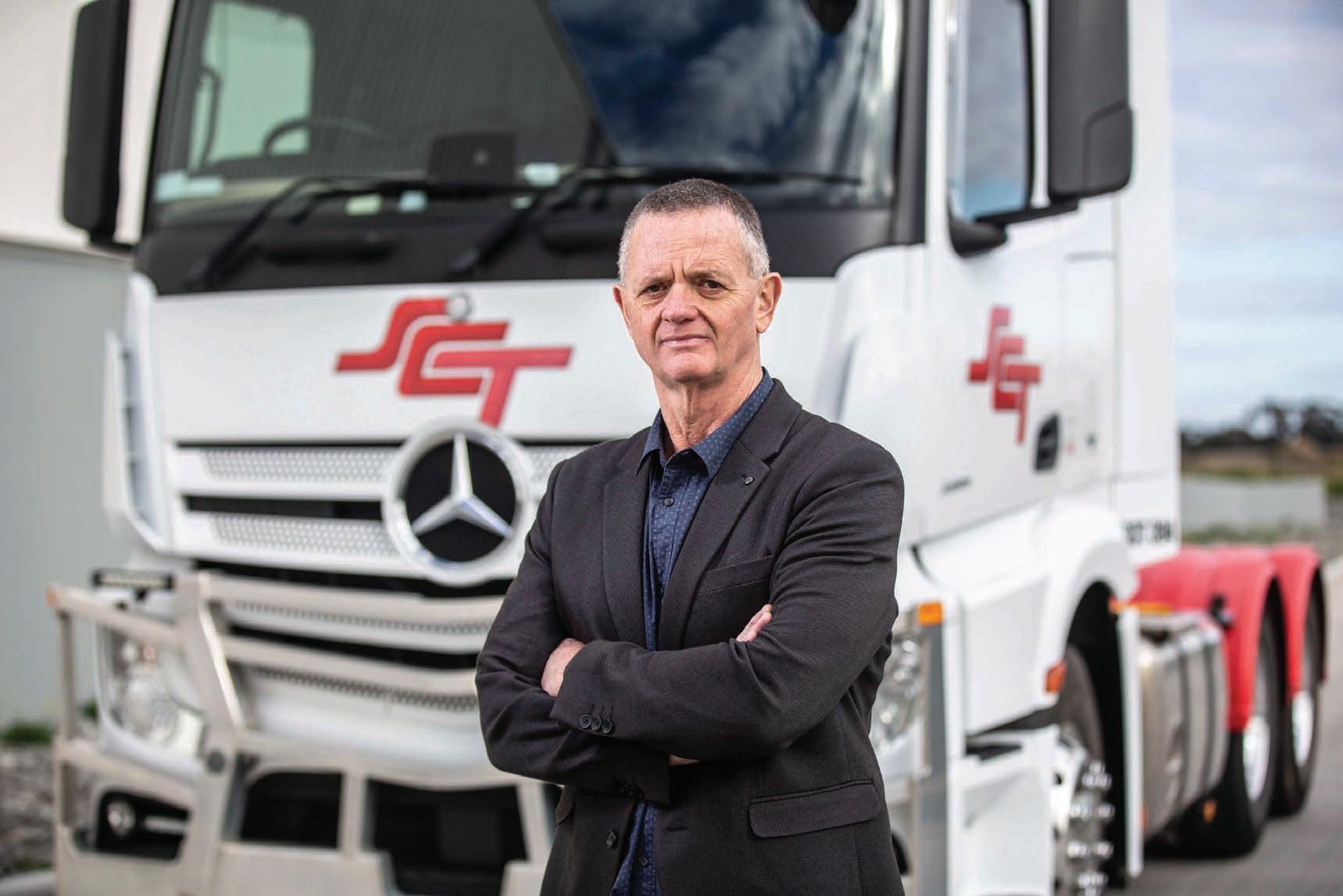
Up until 2019, SCT Logistics had been using Kenworths for the operation. That all changed two years ago when it introduced 16 new Euro 6 MercedesBenz Actros 2646LS trucks as part of a comprehensive fleet replacement program involving seven purpose-built quad axle skel trailers — the first of its kind approved under Performance-Based Standards (PBS).
The quad-axle trailing equipment is technically an over-axle tipping
“We worked out that we could get a better payload with the cabover Mercedes-Benz Actros, even though it is a heavier truck,” he says. “But with the axle and the wheel configuration, it actually gave us a better load profile. So, in the end we’ve managed to have a heavier prime mover but get an extra half-tonne payload.”
“Now we get that extra weight on the steer axle and the weight is distributed correctly,” he says. “We worked closely with Mercedes-Benz Trucks and MaxiTRANS to come up with the best payload-to-weight ratio and that’s where we ended up.”
It’s not viable, however, to go any longer, according to Michael, when taking into consideration the singularity of the combination and bins. It would throw out axle weights.
SCT Logistics National Fleet Manager Michael Sommers says payload advantages were a driving force behind the decision to update the fleet.
Tipping the purpose-built quad axle skel trailer onto its back wheels and axle.
Introducing a quad-axle trailer on the Mercedes-Benz Actros allowed SCT Logistics to increase its load capacity to 50.5-tonnes across each unit, with 27 tonnes assigned to the trailer, all the while maintaining a total vehicle length of under 19 metres.
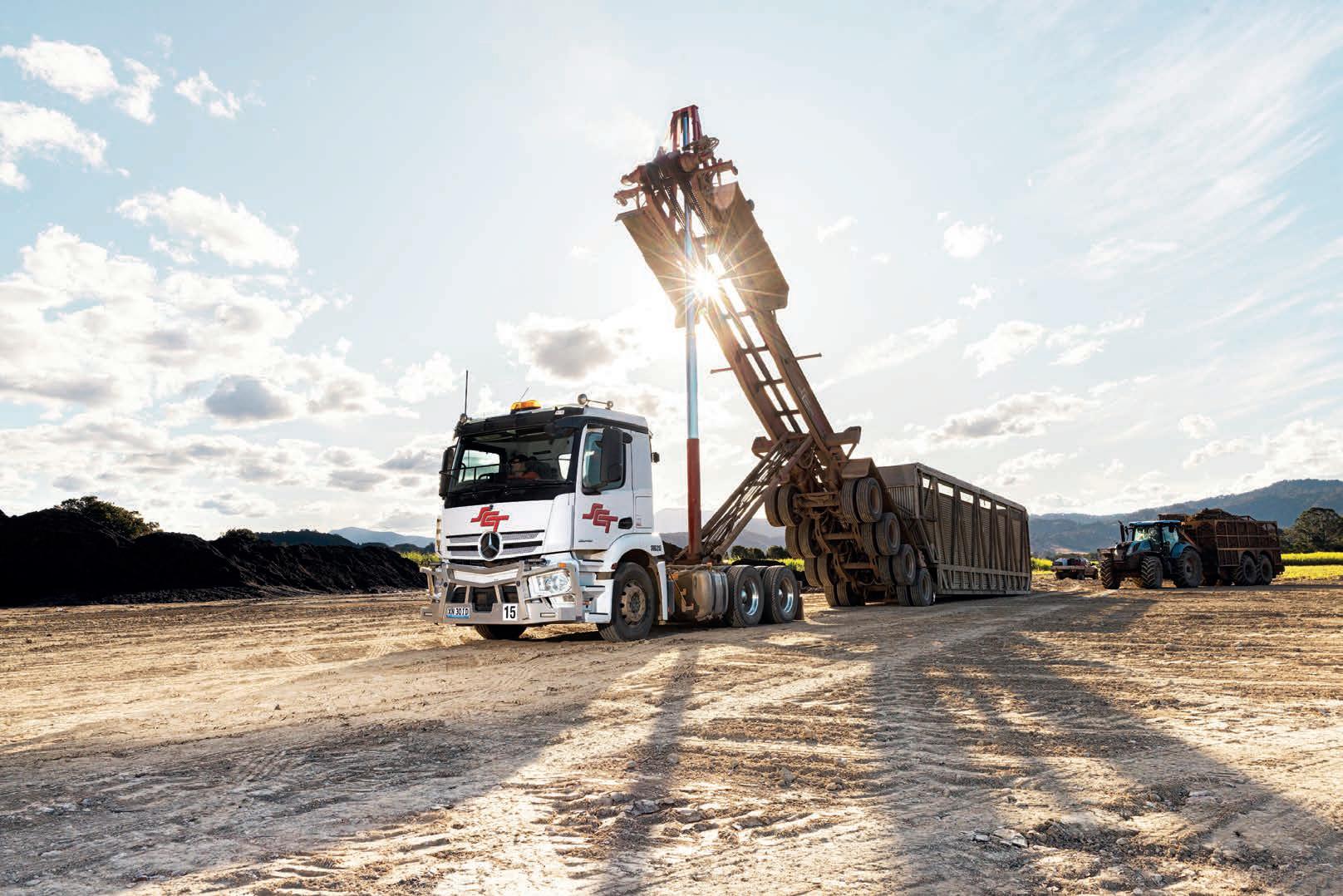
The operation is perhaps even more payload sensitive given the sugarcane
unknown. Therefore, any improvements to payload capacity on each vehicle is regarded as significant.
between distribution centres, but the payload requirement and apparatus of discharging it makes it a very different and intricate application, unique to not only this part of the world, but to the industry.
skel trailer. It has been sanctioned to 4.6-metres overall height.
An adjustable bin lock system was designed to enable adjustments of the bin when it’s suspended to correct axle weights as required. This saves time so that the bin doesn’t need to be lowered back down onto the ground. The application was not possible with tri-axle trailers. In the past, if a bin was not loaded properly on the pad, the load might move while it was being raised, triggering the onboard weigh system which would confirm that the axle weights had been exceeded. The bin would need to be returned and the load adjusted so that it could be picked up again within a legal load distribution. The new system is an exciting development as far as the mechanism goes for handling the materials safely and efficiently, according to Michael.
“SCT is a visionary company always looking outside the box,” he says. “As a family business it’s a pleasure to work for.”
Another 19 quad trailers were ordered in 2021, with the plan being to have all 26 units of the Mercedes-Benz fleet paired with quads.
In the commercial vehicle department, overseen by Michael, there are some 200 trucks and over 300 trailers. Around 1200 people are employed, including subcontractors with their own vehicles.
The option of having a fully maintained operating lease sweetened the deal
Trucks are usually ready to go a month prior to the new season. At this point SCT Logistics re-employs all its drivers. For those that don’t return, new drivers are found. That requires additional “Whentraining.you’ve got approximately 31 trucks, each being operated by three drivers, there’s up to 100 drivers who need to participate in some sort of refresher course or training,” Michael says. “It’s vital everyone is aware of best practice. Again, this takes time.” Service time was once measured in hours to factor in the heavy idle time of trucks operating the Power TakeOff (PTO). Now that information is recorded in MTData, the designated fleet telematics provider, along with driver
34 september 2022 COVER STORY
The first seven of these trailers went into action at the Condong sugar mill. As per 2018 figures, a total of 22,332 trips were made by SCT’s trucks to 136 different pick-up addresses for that one sugar mill. With PBS, those trips come down to 17,966 — a reduction of 4,366 truck
movements according to Michael. “Taking over 4000 truck and trailer movements off the road is a significant productivity gain,” he says. “When you’re working in these areas where the roads are mostly country roads used by local people, we want to ensure that safety comes first. It was a no-brainer for the Local Government Area (LGA). They told us that they would do that all day, every day.”
All trucks have an on-board weighing system and are registered in the Intelligent Access Program (IAP).
Truck trips completed in a season across all three mills exceeds 71,200; or they did up until now. Transit routes involve passage through five LGAs and require NSW RMS permits. Notwithstanding the occasional approval holdup, the LGAs have been supportive of the business model given the high scrutiny SCT Logistics places on its payloads and vehicle In-seasonconditions.maintenance of the vehicles is conducted every 14 to 21 days, scheduled to coincide with maintenance days at the mills. SCT Logistics runs the entire transport division. The workshop cleans all equipment thoroughly in the off-season. Splintering sugarcane spears tend to lodge in hard-to-get places and a comprehensive washdown for each mobile asset can take up to two days. Once completed, the vehicles receive a detailed inspection. Murwillumbah Truck Centre provides additional support when required.
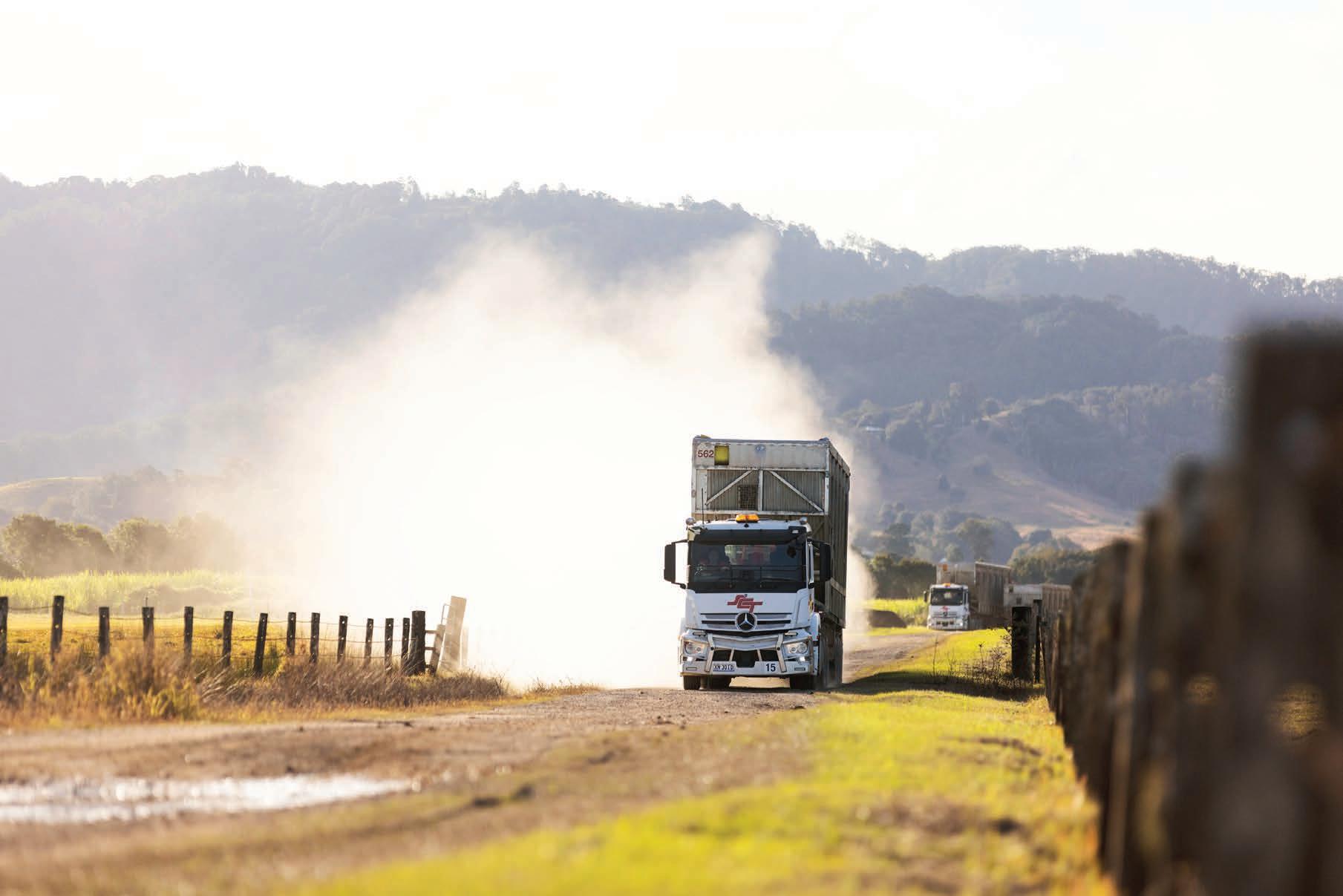
At the mill, driver prowess in the smooth-reversing Actros 2646LS dock the trailers at the cane tip, before tipping the trailer onto its back wheels and axle. A trolley on the top of the trailer slides down to the ground. It features a hook that goes over a latch on the trailer. It’s then chain-dragged all the way back up the trailer. Once it ascends to about the halfway mark, the trailer can be lowered whereupon the trolley is dragged to the front and locked in.
“We’ve found with the quads that we can move the bin and reduce the axle weights while the bin is still on the trailer,” he says. “If it’s legal, the driver doesn’t need to wait around any longer. MaxiTRANS went through the process with us of creating a design that we wanted so that the best axle-to-weight ratio was achieved.”
hours, fuel economy, mass declarations and any real-time metrics operations managers might need for assessment.
The company places an ever-increasing emphasis on improving safety and reducing its environmental impact as a business. Upgrading the NSW sugarcane fleet to a day cab Mercedes-Benz Actros 2646LS Euro 6, fits with this objective, but also helps realise another. By reducing operational costs, those savings can then be passed onto the customer.
It was near Murwillumbah, where Joshua Bray, an industry pioneer, whose
when it was obvious the MercedesBenz product was more cost effective to maintain over a five-year period, which is when SCT Logistics typically turns over its trucks.
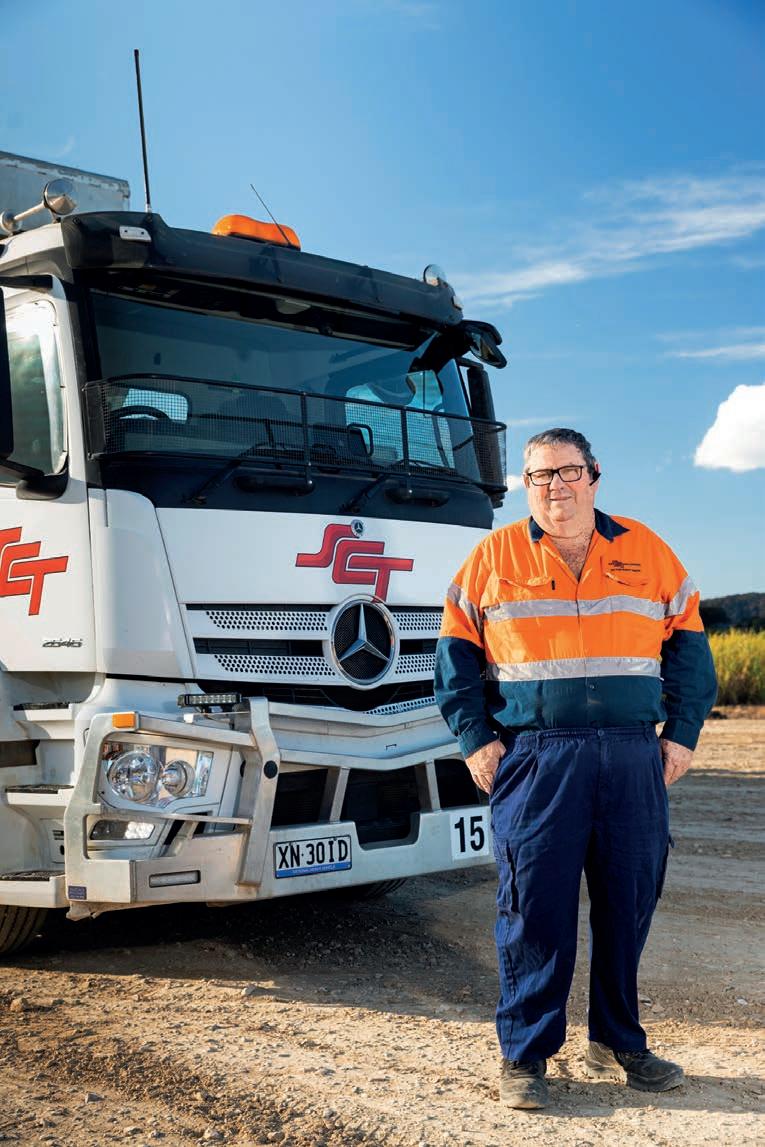
“In our arm of the business we’re going all in on European. Driver airbags, adaptive cruise control, lane departure warning and crash detection systems are all standard on the Mercedes-Benz. The benefits when compared to the previous trucks outweighed anything,” Michael says. “What we’ve got here is a heavier truck, but we’ve got half a tonne more payload. Daimler Truck made the whole process easier than what it could have been.”
Dominic Guinea, Condong Supervisor.
A Mercedes-Benz Actros 2646LS shuttles between sugar mill and farm.
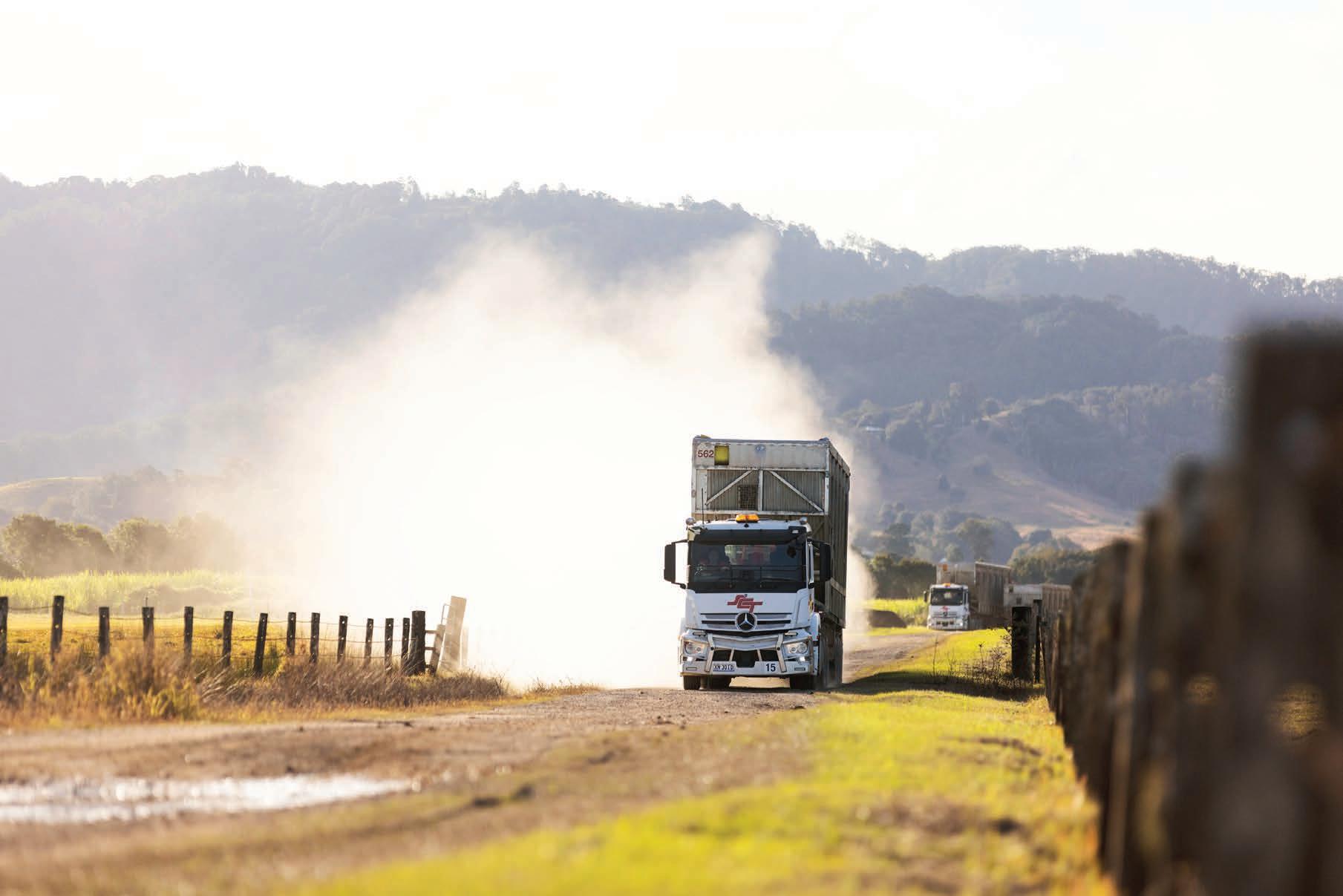
THE LION
36 september 2022 FLEET FOCUS MAN TGX 26.580 Euro VI. K
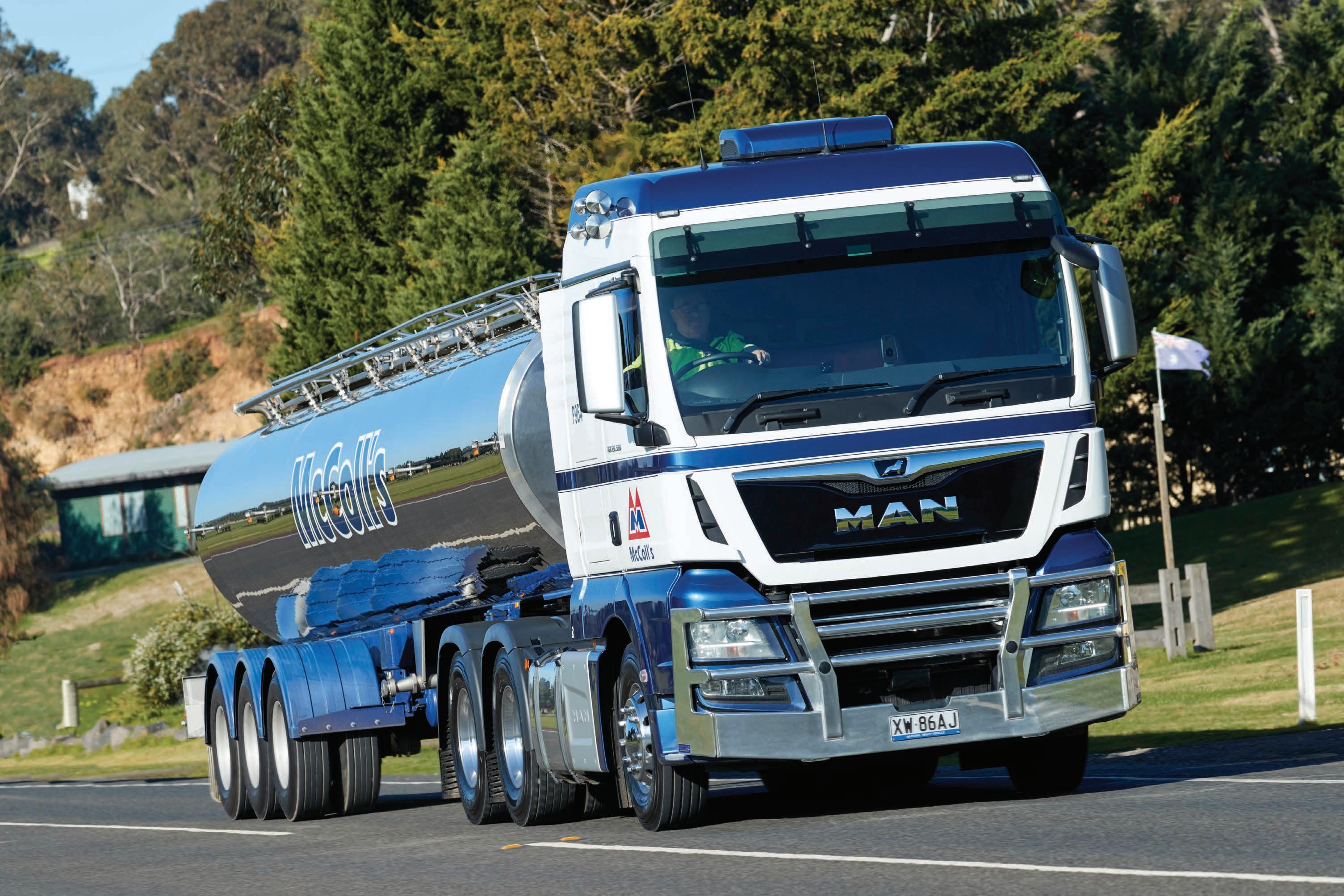
primemovermag.com.au 37 ING
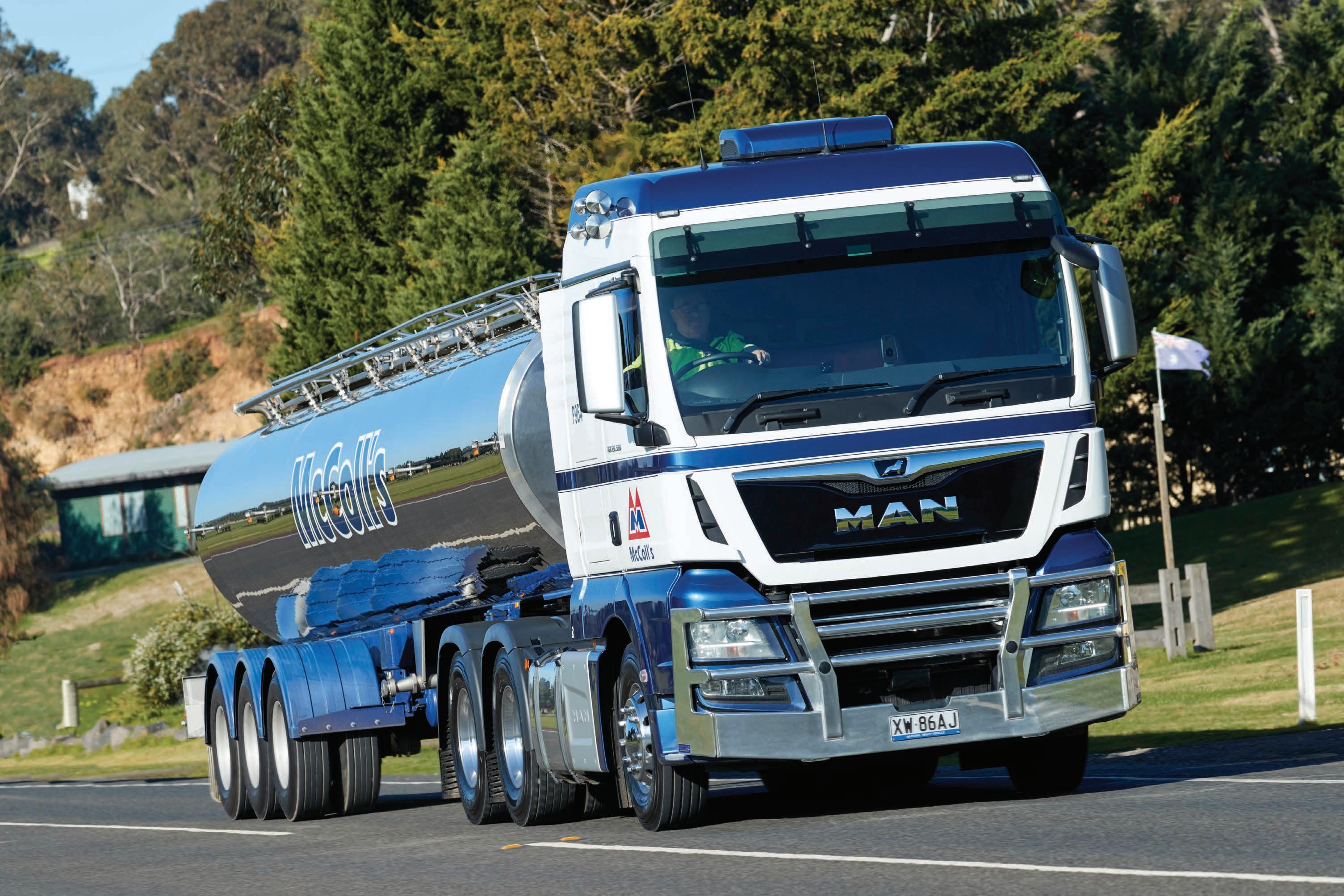
S
independentlargestbulk liquid carrier of milk, food and chemicals, McColl’s Transport, is a company of influence in the national landscape of road transport. The new MAN TGX 26.580s.

tates of general paralysis are not something blue chip businesses suffer from. That McColl’s Transport continues to expand following the divestiture of its general freight arm over a decade ago is an acknowledgement that the company knows what it does well, and it has plans in place to keep on doing it. A name long synonymous with handling bulk liquids in the main part on B-doubles and singles, wherever the application is more appropriate, McColl’s Transport situates its head office in Geelong but has depots spread out across Australia. The truck fleet involves three separate divisions. These are categorised as bulk food grade; chemicals, including dangerous goods; and farm milk collection and delivery.
movers have come online in recent months in Melbourne, providing another brand in the mix of OEMs it partners with nationally.
Theeconomy.”EuroVI
1300rpm. They are geared quite tall for fuel economy and that seems to be working quite well for them at the moment.”
Australia’s
With a higher ratio differential than McColl’s other brands, the D38 engine is doing less revs to get the same speed for better fuel consumption. Through the additional torque on these trucks being supplied, a vigorous 2,900Nm often between 930- and 1,350rpm, it’s working very well for Peter’s needs.
The two trucks offer a contrast between the other units in the fleet of 300 prime movers and the MAN prime movers that came before them.
“They are noticeably better than the previous model,” says Peter Shearer, McColl’s Fleet General Manager. “The bigger motor is also delivering superior fuel
A pair of new MAN TGX 26.580 prime
15.2-litre engine produces a maximum of 433kW with 2900NM of torque through a 12-Speed Tipmatic two pedal AMT. These new MAN units, at the minute, are mainly operating within the confines of Victoria. On a recent run to Adelaide, however, one of the drivers informed Peter that the new MAN TGX was 60 litres better on a return trip from Melbourne than the forerunner which had a smaller, 13-litre engine. It certainly gave Peter something to reflect on given the current inflationary cost of fuel.
“The drivers commented that it doesn’t sound like the truck is working because everything is so quiet,” he says. “The motor is not revving hard. It’s very smooth and quiet to McColl’soperate.”Transport, like many other carriers fighting to stay competitive, has had to manage fuel levies with vigilance this year. These vehicles will perform an estimated 200,000kms in a year.
“Some of the customers fuel levies were six monthly which is fine when it’s not moving much,” says Peter. “But in a volatile market it’s been something we’ve had to address with those customers to move to a monthly cycle in response to sudden increases in the price of McColl’sfuel.”have also had to have discussions with customers with price increases of
“The guys are more than happy with the performance of the new ones,” Peter says. “They did comment on the additional torque and how low the motor is revving at 100km/h. I think they’re only hitting
38 september 2022 FLEET FOCUS
“Chocolate when transported in liquid form has got to be kept above 40o and 45o celsius depending on the actual chocolate,” he explains. “Everyone thinks chocolate is a great thing to be carrying. But cold weather and chocolate don’t go together well. We’ve done chocolate for a long time.”
in moving chocolate. They will often underestimate the complexity of it.
primemovermag.com.au 39
The new MANs were ordered late last year, but not delivered until May due to delays with componentry supplies, par for the course in the current import market, specifically on turntables and bullbars.
that extra room and a bit,” says Peter. “The driver does five or six days straight. Even though it is primarily local work, he still lives in the truck. Little things matter when you’re spending so much time in them.”
It was on this food grade application that the fleet now services a new customer notably, the world’s largest chocolate manufacturer. As a brand, it turns out an estimated 1000 tonnes of chocolate a day, business to business. The product, at least locally, cannot be found on retail shelves.
The driver, who had happily driven an earlier generation MAN in the past, is expressly pleased given he considers it a superior and more comfortable vehicle for his ageing body according to Peter.
Despite only having recently entered the Australian market, the customer opened a brand-new facility in Campbellfield just last year. “They’ve got big plans for growth and we’ll grow right along with it,” says WhilePeter.one of the new Euro VI MAN TGX 26.580s was introduced specifically for this account pulling a single trailer at 46 tonnes GCM, the other has been acquired partly to persuade a well-regarded veteran driver, who was on the verge of retiring, to stay on. As a dedicated B-double quartered at Pakenham, in the outer southeast region of metropolitan Melbourne, it fulfils milk linehaul around the state.

If it had been available in the low roof cab, Peter might well have opted for the 640hp engine in the MAN TGX series. In the food grade division site access is as low as 3.7metres which limits the cab height of the trucks Peter can use.
Hot weather, as the presumption might go, would provide challenges for chocolate transportation. That is, Peter assures, not the case with summer conditions preferable.
New players in the market who bid for contracts soon find out the difficulties
AdBlue due to the shortage at the beginning of “AdBlue2022. has come back a bit in price but it’s a lot higher than it was prior to that shortage and we had to implement an AdBlue levy which we hadn’t had in the past,” notes Peter. “These additional operating costs are such a large part of our running costs.”
“Trying to keep chocolate warm is a problem,” says Peter. “You have to make sure your hoses are clean. If you leave chocolate in there it solidifies and it’s very difficult to get out once it goes solid. It’s a bit of a novelty for the first day or two but after that you can only eat so much of it.”
“The mid roof cab of the MAN fits in just nicely,” he says. “It gets in under 3.7 metres and it really maximises, the space for the drivers in the living area. You’ve got that extra 150mm which enables the driver to stand up when they’re getting dressed. It just makes it that much easier for them.” Ergonomics, even on such a micro level, will see macro dividends for customers and McColl’s Transport itself as it maintains standards and retains personnel. The bed size itself, compared to another marque, is 80mm wider.
“It doesn’t sound a lot but for the bigger guys it makes a world of difference with
“All the regular guys here said: ‘bugger driving that old heap.’ I thought I was king of the road because I’d come out of an old Mack R Model 320 Coolpower pulling a double roadtrain in WA,” he recalls.
“I thought these guys don’t know how good they have got it. Of course, farmers would buy whatever was cheap. We had old Diamond Reos and Fodens and a couple of Leaders with GMs in them. It’s a different game these days where they pretty much sit on 100 km/h wherever they go uphill and down dale.”
If he can get the MAN TGX 26.580s on PBS, providing they perform well and supply is not an obstacle, Peter might have up to 20 units running between Melbourne and Sydney by the end of the Trucks,decade. however, may need to be ordered up to two years out from deployment to meet current PBS requirements.
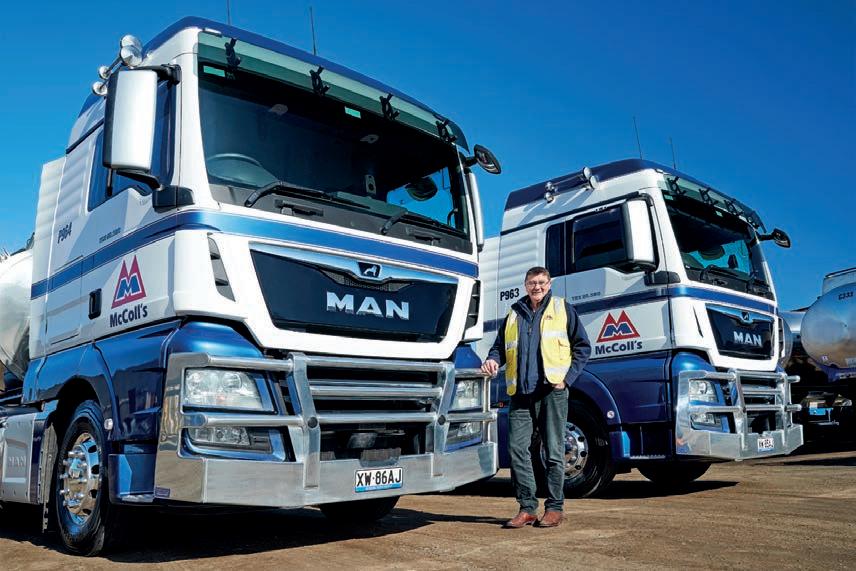
Peter Shearer.
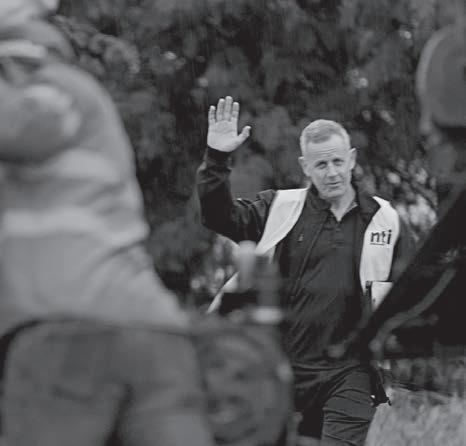
Insofar as there has been some movement between divisions when redeploying vehicles, it’s not on any scale. The farm trucks are unique as they run PTOs making it more difficult to swap them out. While the chemical fleet also carries DG adding extra complexity to the job. For the standard spec prime movers some exchanges are prone to take place. As it maintains long-term relationships with most of its suppliers, McColl’s has been fortunate to receive preferential treatment when procuring the likes of gearbox oil — another workshop essential in short “Oursupply.supplier has been managing to keep us in gearbox oil,” says Peter. “There has been a delay or two, but they have still
Being of a veteran ilk is, unfortunately, no great help for those trying to make sense of environmental forces seemingly beyond anyone’s control across the industry. For fleet managers that means a whole new approach to mobile asset turnover. It means leaning on procurement resources to find parts in non-traditional outlets and trialling equipment from non-traditional OEM “We’repartners.notused to things being in such short supply like they currently are,” he says. “What we have had to do is hang on to existing trucks for longer.”
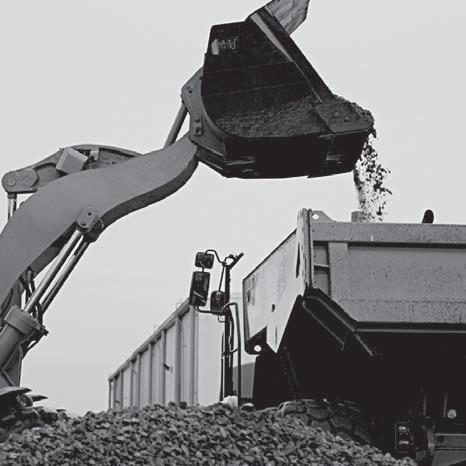
An eight bag electronically controlled air suspension helps with ride comfort as does an adjustable Isringhausen heated seat that provides, given the friendly interior, ergonomic room in the cabin which helps the driver manage circulation of his legs by allowing him to straighten out. Milk is the main product McColl’s carries in B-double tankers. These are fully loaded at 68.5 tonnes one way and travel back empty. Semi-trailers are on mass management approvals given the high volume of ISO tanks it moves around the country. A-doubles were not so typical as the footprint is outside the wide spectrum of Performance-Based Standards the fleet currently runs but according to Peter this is set to change.

“Sometimes you’re not sure what you’re going to have as far as trailing equipment and PBS units,” he says. “It’s crazy times.”
been finding it for us. There was also an issue with finding oil filters recently. Our spare parts people have been in the game a long time. They have got a few contacts that can search every supplier around and manage to get it for us. So far, we haven’t had to stop. I suppose turntables are probably the biggest holdup we’ve had to Latedate.”last year in a deal still being finalised, McColl’s Transport purchased a bevy of equipment from Peter Stoitse Transport, who chose to sell off its milk tanker assets to concentrate on general freight. Around 45 trucks came across to McColl’s as part of the deal and 134 tanks in total. That brings with it the challenge of sourcing turntables and steer axles for 26-metre “It’sroadtrains.beenquite a lot of equipment to get roadworthy,” says Peter. “Physically getting the roadworthies done has been challenging. Most suppliers in the space are struggling for labour with a shortage of Amechanics.”dieselmechanic by trade, Peter is from Geelong originally but ventured out at 20. He spent 15 years in Western Australia working on a commercial farm handling maintenance and operations. When he returned, he began driving at McColl’s part time. Now 20 years on he’s worked his way through roles as Linehaul Operations Manager, General Manager for Linehaul and moved across to Fleet last September when the long-time general manager went on long service leave.
“We are applying to have the MANs added to our PBS permit for A-doubles,” he says. “If we can get that sorted, we will run the MANs on the A-doubles too, which will take it up to 85 tonnes gross. We’ve put in for a design approval. The wheelbase is different to the other prime movers we run so we’ve had to reapply.”
The first truck Peter drove at McColl’s was an old big cab Mack UltraLiner with a Cummins engine. It was set at 520hp pulling a B-double.
40 september 2022 FLEET FOCUS
Terms and Conditions apply. You should read the PDS when choosing whether or not to acquire or continue holding a policy. Insurance products are provided by National Transport Insurance, a joint venture of the insurers Insurance Australia Limited trading as CGU Insurance ABN 11 000 016 722 AFSL 227681 and AAI Limited Trading as Vero Insurance ABN 48 005 297 807 AFSL 230859 each holding a 50% share. National Transport Insurance is administered on behalf of the insurers by its manager NTI Limited ABN 84 000 746 109 AFSL 237246. NTI.M015.1.29062021 We know what it takes to keep Australia moving. NTI is Australia’s leading specialist insurer for trucks, big and small; mobile plant and equipment; marine, cargo and parcels; plus Roadside Assistance for trucks. For decades, we’ve provided businesses with expert knowledge, first class repair networks, and superior claims service. With a vision to keep Australian industry working towards a safer and more sustainable future, we’re here to help keep you moving. nti.com.au
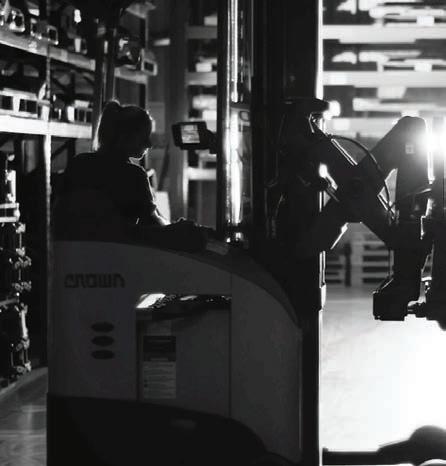
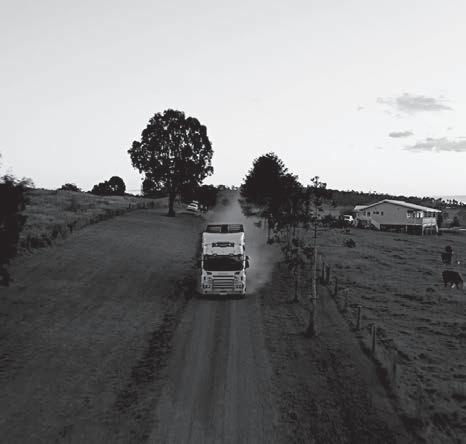
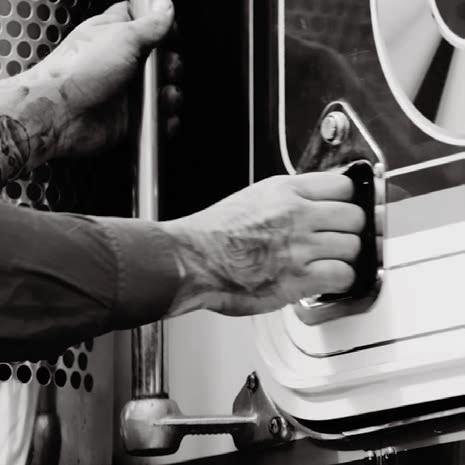

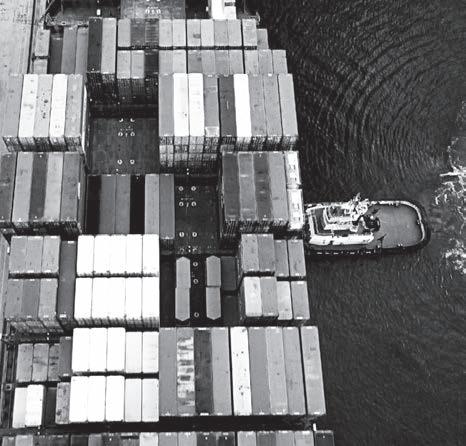
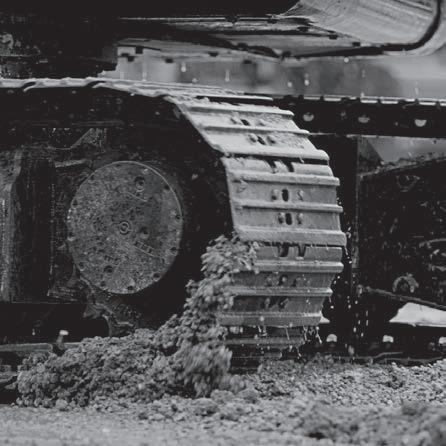
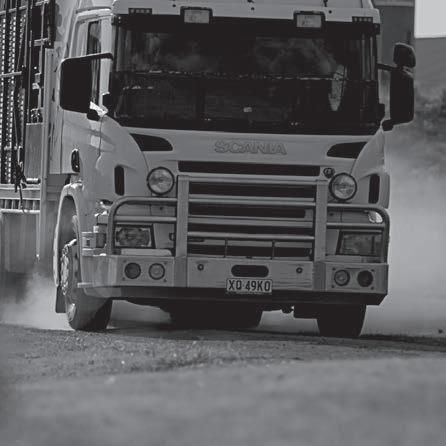
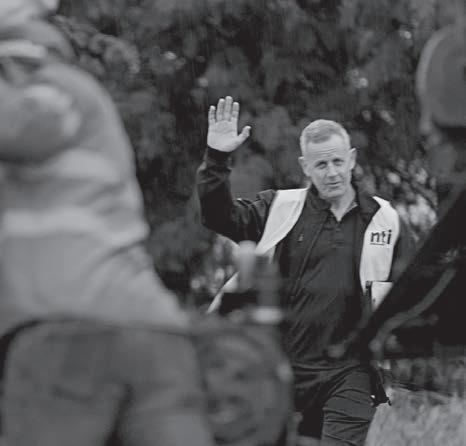
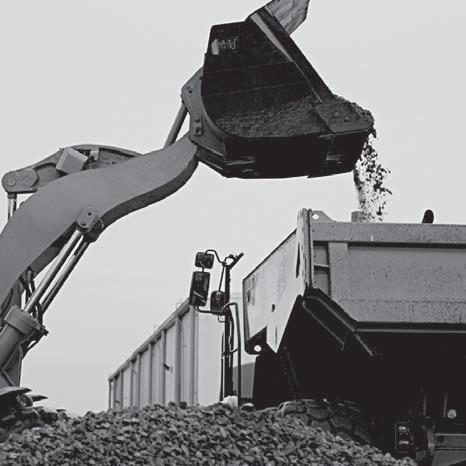
HIGHWAY TO
42 september 2022 FLEET FOCUS
Lack of availability of a previously preferred brand for a particular application led Russell Transport to consider DAF prime movers.
HEAVY
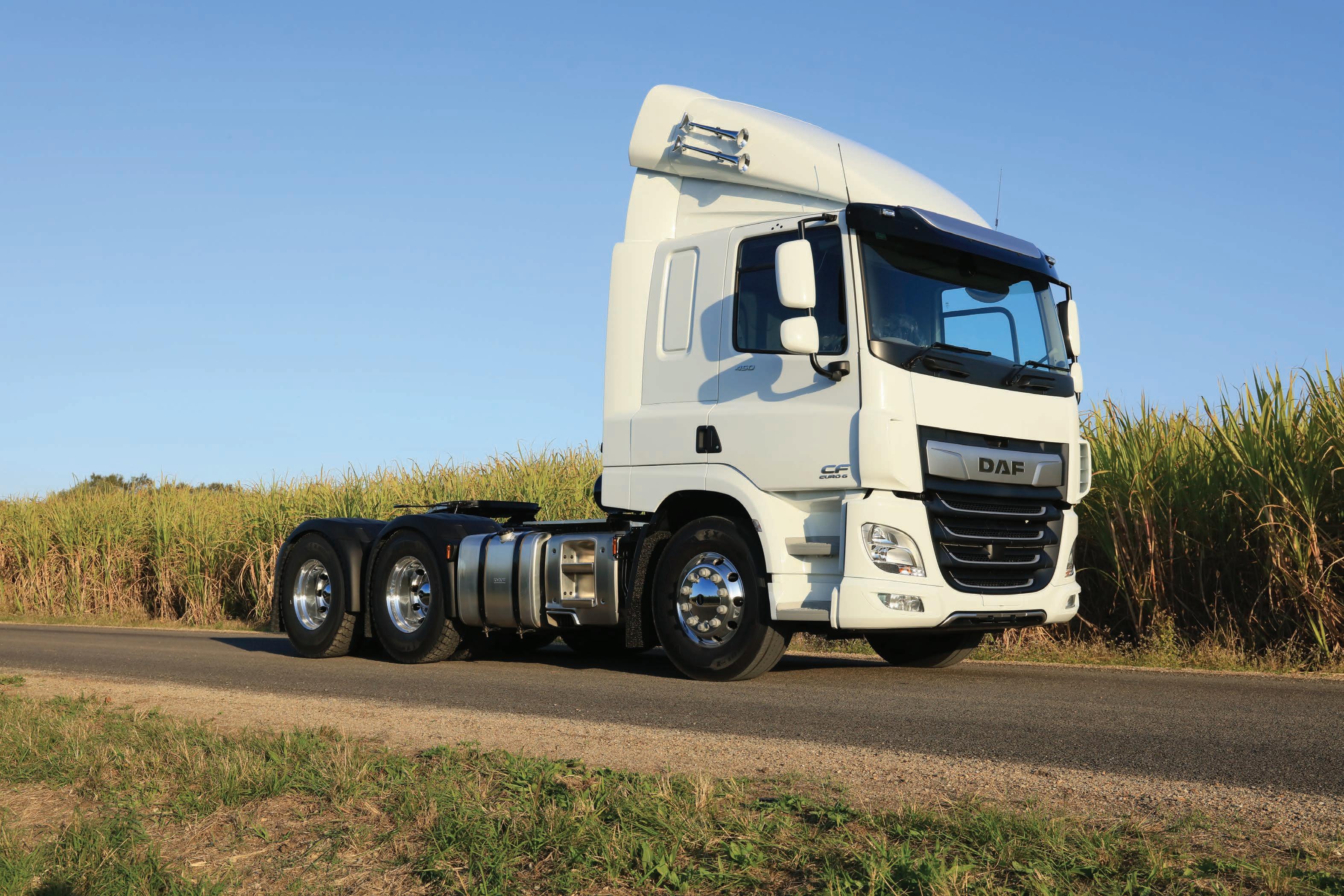
HEAVY
primemovermag.com.au 43
A new DAF CF450 in Yatala bound for Russell Transport.
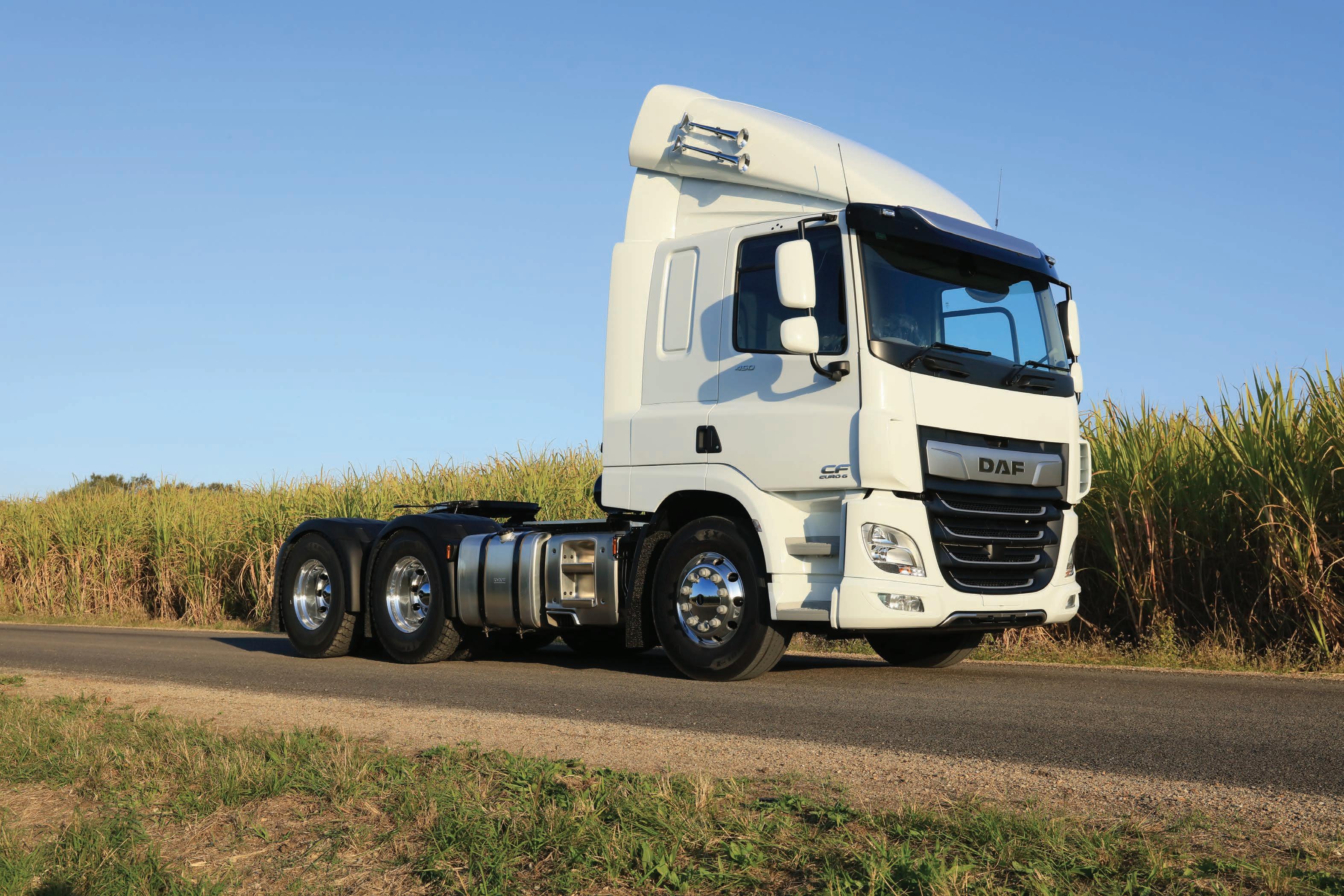
base fleet performing a similar process with the same products to destinations within a geographical area so we know where each vehicle will be operating.”
44 september 2022 FLEET FOCUS
In this highly competitive contract distribution operation Ken looks for economical and reliable vehicles which are also driver friendly.
Service is a key part of the culture in the overall business, which is divided into two divisions, one which encompasses industrial resource services including heavy haulage, lift and lock and lift and shift type operations, including lifting equipment, crane dry hire, terminal services, general transport, and specialised transport. The heavy haulage fleet is capable of handling loads up to 200 tonnes and has earned a reputation for successfully handling tricky loads ranging from locomotives to helicopters. The other side of business involves contract distribution.
inspection station, the workshop at the Eagle Farm head office has been the setting for a number of in-house engineering solutions to the emerging needs and changing demands of the company’s operations. Russell Transport employs approved personnel for modification and alteration work to ensure compliance with the Queensland Vehicle Standards and Safety
Isuzu’s decision to delete prime movers from its current available range meant Ken had to look at alternatives to service a particular contract the company had secured.
“I never place an order until I have actually signed the contract with my
In addition to being an approved AIS
“We’veRegulations.turned single drive prime movers into bogie drive body trucks, and four or five times we’ve taken out manual transmissions and fitted Autoshifts into different vehicles,” says Ken. “I bought two brand new Isuzu Giga prime movers and we put X12 Cummins engines in them. One has been on the road for about a year doing container work at the Port of Brisbane and I think we’ve got a world first – an Isuzu Giga with an X12 and an 18-speed Autoshift.”
“We class it as a cookie cutter,” says Russell Transport Director Ken Russell. “It’s the same offering each day with a
or 97 years Russell Transport has been a family run business, having commenced operations in 1925 as RB Russell Transport. Now in the hands of the third generation of Roy Bayley Russell’s descendants, the enterprise has expanded and diversified to become a leading provider of transport solutions including oversize and over mass heavy haulage, third party logistics and the Metro-Lift crane hire operation.
F
“We’re in stop-start traffic conditions and tight environments so the vision from the cab is important, and so is matching the truck to the application,” he Withsays.its diverse operations, Russell Transport runs a variety of prime movers from brands such as Isuzu, Mack and “WeKenworth.runsome big horsepower Cummins engines in many parts of the overall business where they match the applications such as A-doubles, roadtrains, and heavy haulage,” Ken explains.
If there is work which involves a longer distance away from the operational depots the base fleet can be supplemented with vehicles from other parts of the Russell business to perform the long-distance task.
Aerial view over Eagle Farm where Russell Transport’s main depot is located.
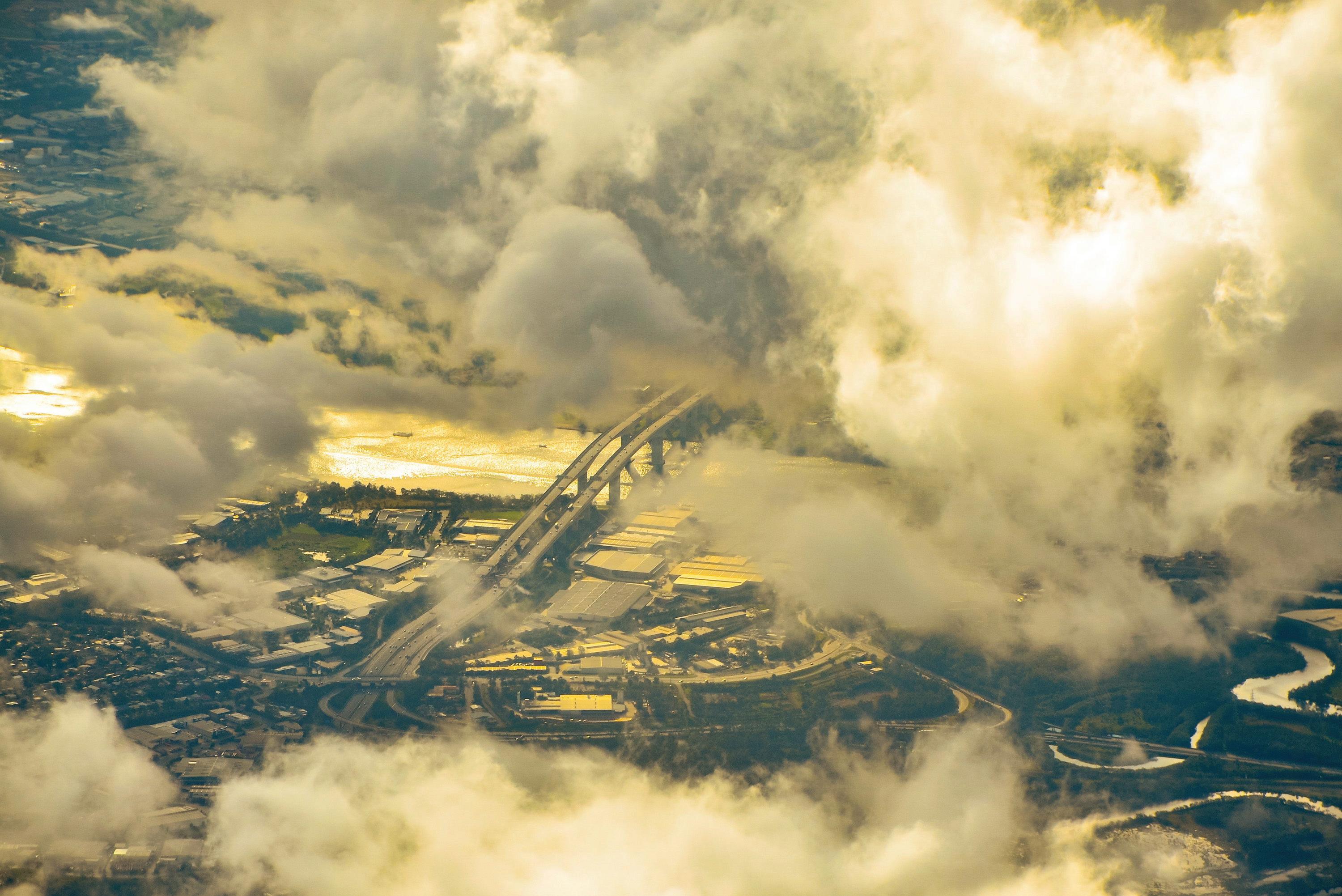
customer,” he says. “When you pick up 30 trucks’ worth of work in three months, you’re going to have a challenge to meet the additional demand. I was speaking about Kenworths with the guys at Brown and Hurley at Yatala, and they said we should really look at the DAF product. I’ve had some reliability issues with European trucks in the past and we’ve always mainly had American or Japanese trucks.”
“We think we have got the application right,” says Ken. “It’s all on bitumen and it’s 50,000 kilometres per year type of Thework.”DAFs commenced work in December 2021 and to date the team
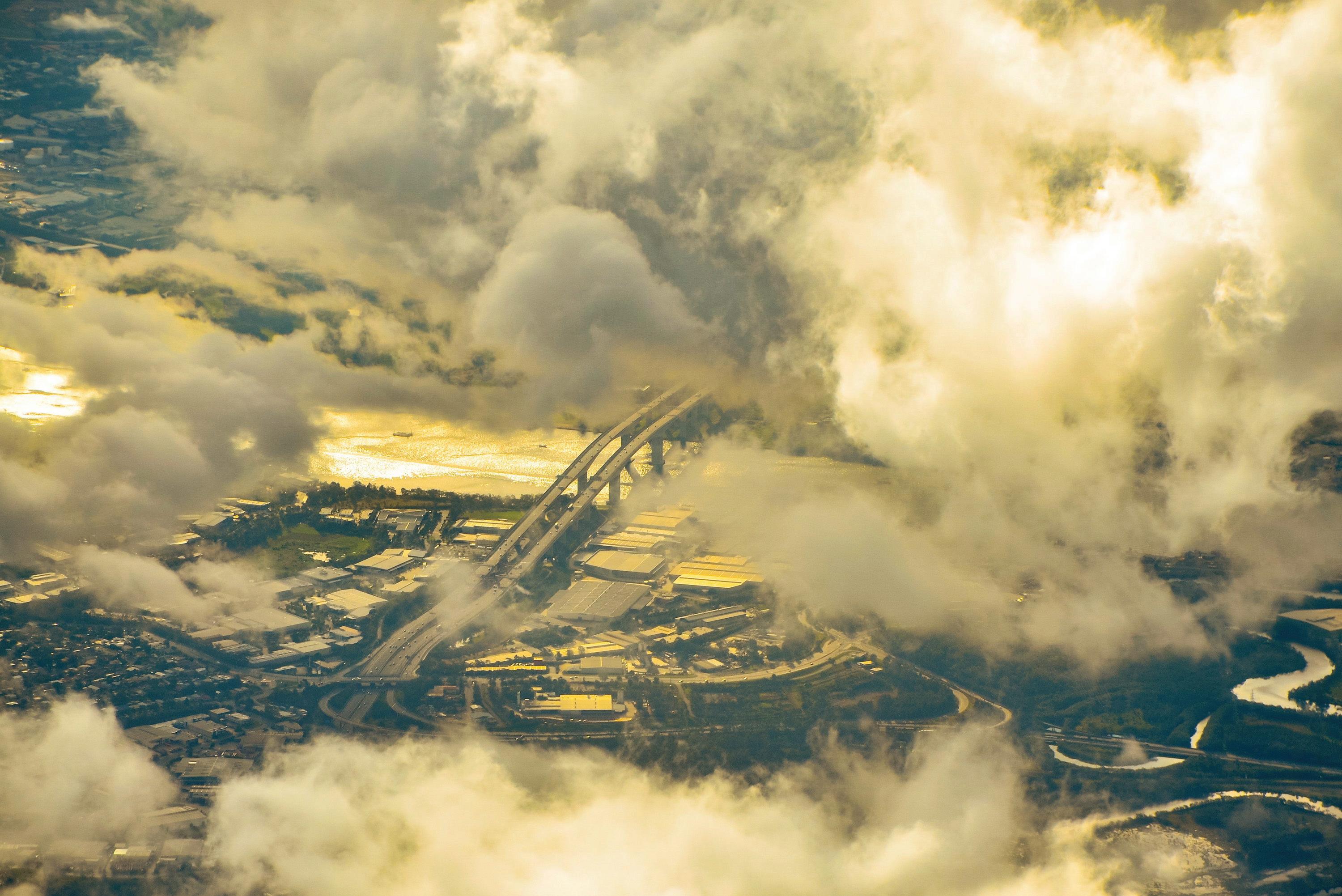
at Russell Transport have not fielded a complaint about any of the 15 trucks.
“If the Japanese trucks had been available I probably would not have looked at the DAF product,” says Ken, “Yet I’ve now become a loyal user of DAF in this application because they had the product there and they’ve supported it well.”
As the trucks are spread across two states, contract preventative maintenance programs apply to all of the 15 CF450s as well as six Kenworth T410s.
“We want that type of support,” says Ken. “We’ve done it with other European
Looking through fresh eyes has led to 15 DAF CF prime movers being added to the Russell Transport fleet. Eight DAF CF450s are now in Southeast Queensland mainly transporting 40 feet lengths of ‘I bar’ steel from an intermodal rail terminal and doing local deliveries of steel building products to construction sites in and around SevenBrisbane.ofthe
The new DAF CFs are Euro 6 rated.
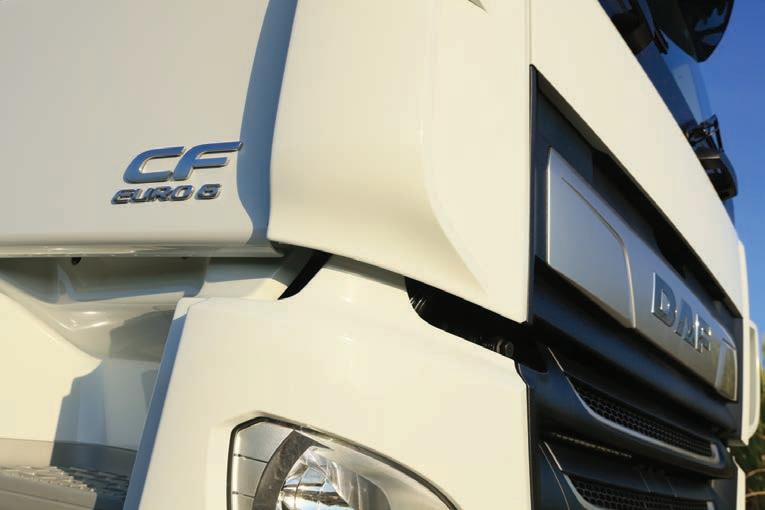
“After seven or eight months of operation not to have people whinging is a very good testament to the product,” Ken says. “When the DAFs arrived we had some of our people actually say these are the best trucks they had ever driven due to factors like comfort and Thevision.”DAFs are pulling single trailers and performing a single drop so at least half of the time they’re towing empty trailers. Ken is convinced the PACCAR MX 11-litre engines are a good balance of economy yet still have enough power to
primemovermag.com.au 45
do the job safely and efficiently, which matches the requirements in this type of urban distribution application.
DAF CF540 models are based in Adelaide performing deliveries of coil steel.
Ken observes, it can be a bitter pill to swallow as it still needs to be
their skillset and in many cases that’s fine, because all they have to do is pull buckles and open a curtain.”
46 september 2022 FLEET FOCUS
Winning the 2021 Primary Connect Small Carrier of the Year is just one of many indications that the team doesn’t merely pay lip service to their “Service You Can Depend Upon” statement, they embrace it and deliver upon it.
The DAF CF450s are operating around Brisbane moving ‘I bar’ steel.
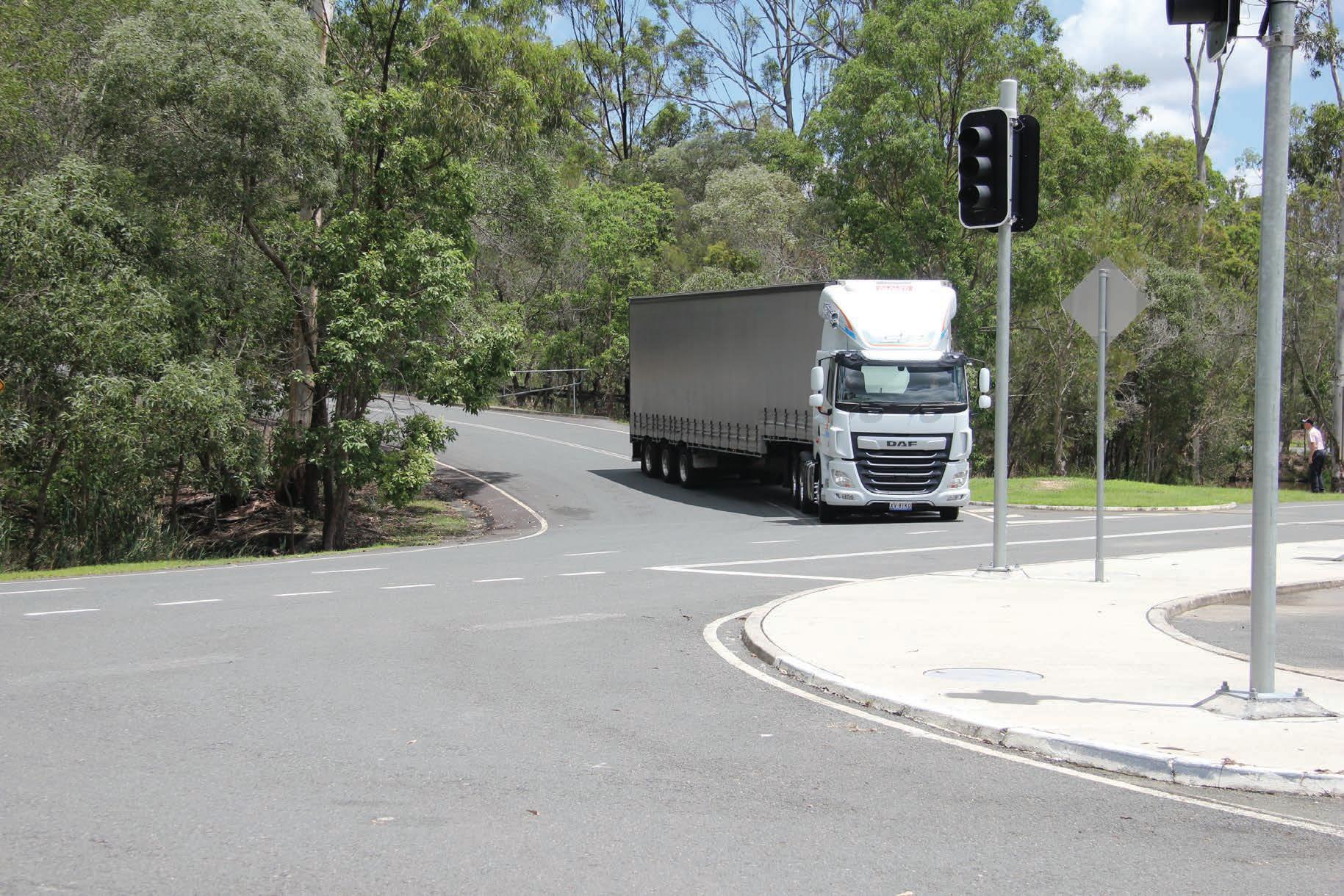
“Overarrangements.fiveyears in 80 per cent of cases we would have spent more than what the contract cost,” Ken explains. “Some of us were against the idea of paying up front and wanted to get the lowest cost over the life of the truck and pay for repairs as they happened, but the other side is knowing your cost up front, budgeting for it and you’ve protected Atyourself.”first,as
history in the hands of the same family (Ken’s dad Phil and sister Julie are also directors and well known and respected in the industry) provides some unique perspectives to current operations and challenges. Russell Transport was prepared to investigate alternatives when it came to obtaining trucks such as the DAFs to fulfil the needs of a specific application, and that same preparedness to consider the best way of handling particular circumstances extends to the industry’s well-documented shortage of
For almost 100 years Russell Transport has provided transport solutions across a broad spectrum of sectors which benefit their clients and their clients’ customers.
•
This information is general advice only and does not take into account your objectives, financial situations or needs. You should obtain and consider the relevant Product Disclosure Statement and Policy Wording (as applicable) from zurich.com.au before making a decision. A target market determination is available at zurich.com.au/GI-TMDs or by calling us on 132 687. The issuer of general insurance products is Zurich Australian Insurance Limited (ZAIL), ABN 13 000 296 640, AFS Licence Number 232507 of 118 Mount Street, North Sydney NSW 2060. ZU24335 V1 07/22 MuchLEWG-018915-2022
•
more than truck insurance.
•
This helps to reduce claims, keep your trucks on the road and build a more resilient business.
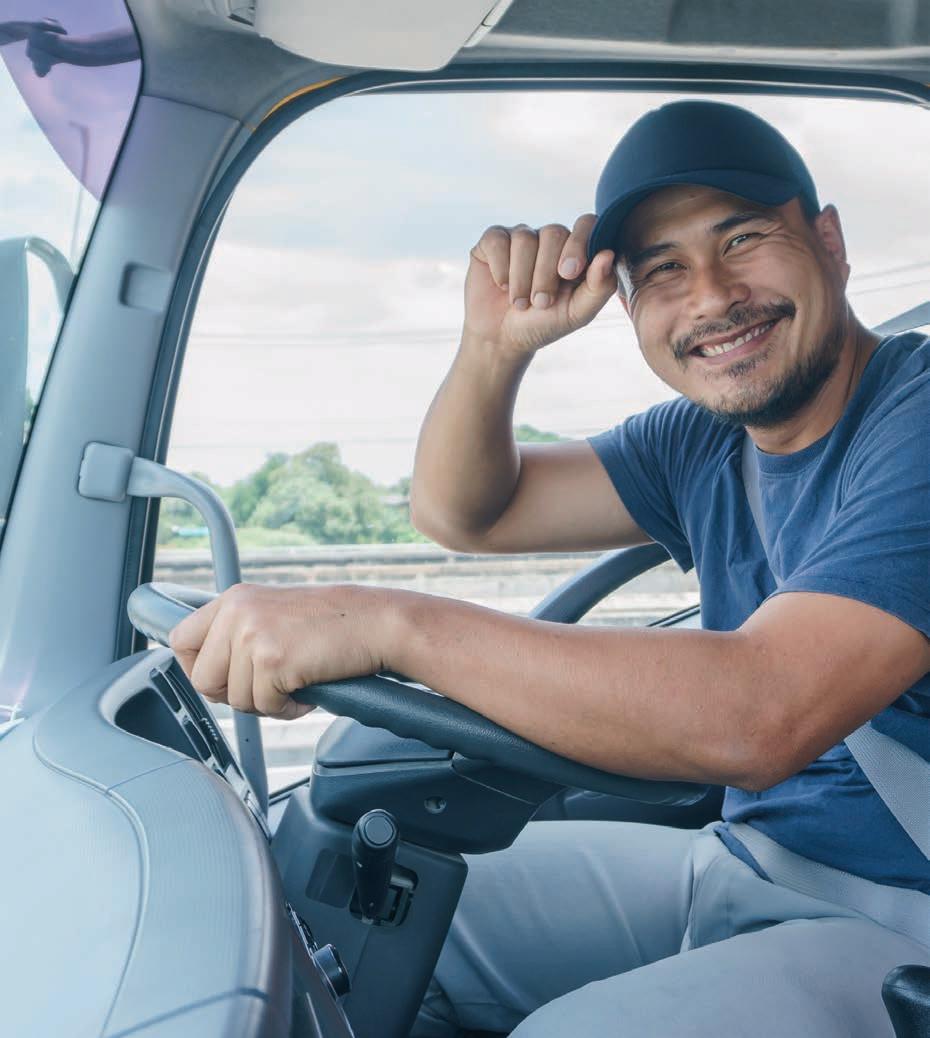
•
We
Zurich helps to improve safety in the trucking industry through marketleading fleet risk management services. work closely with customers to optimise: Business processes Fleet utilisation Fuel efficiency Driver behaviour
Ask your broker about Zurich today.
LOAD
48 september 2022 TRUCK & TECH
Even before it started moving oversized assets like goldmining machinery and exotic wildlife, South East Queensland Hauliers has, as part of a company-wide undertaking, been on mission to innovate.
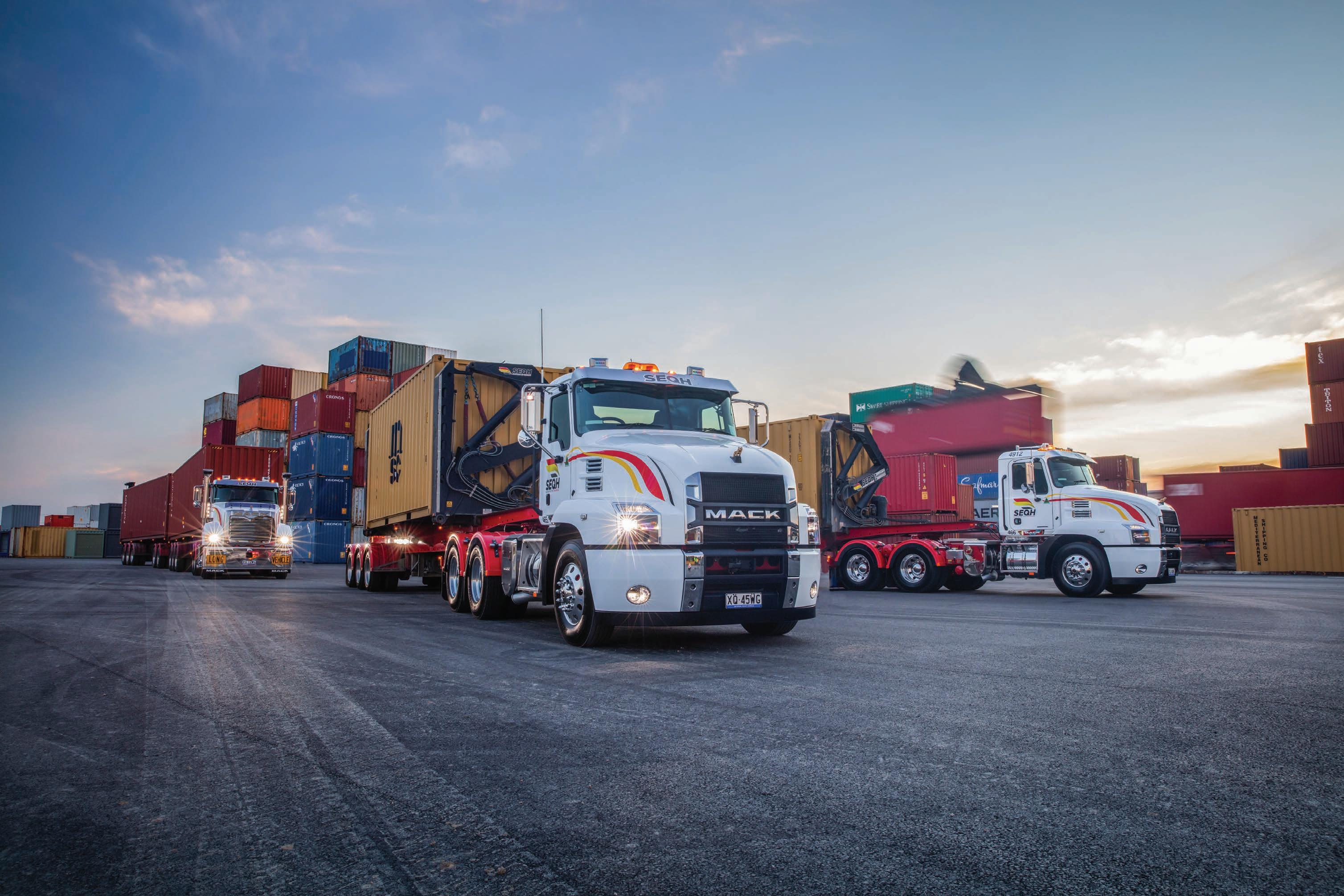
primemovermag.com.au 49 STAR
A Mack Anthem spearheads the SEQH container fleet Brisbane.in
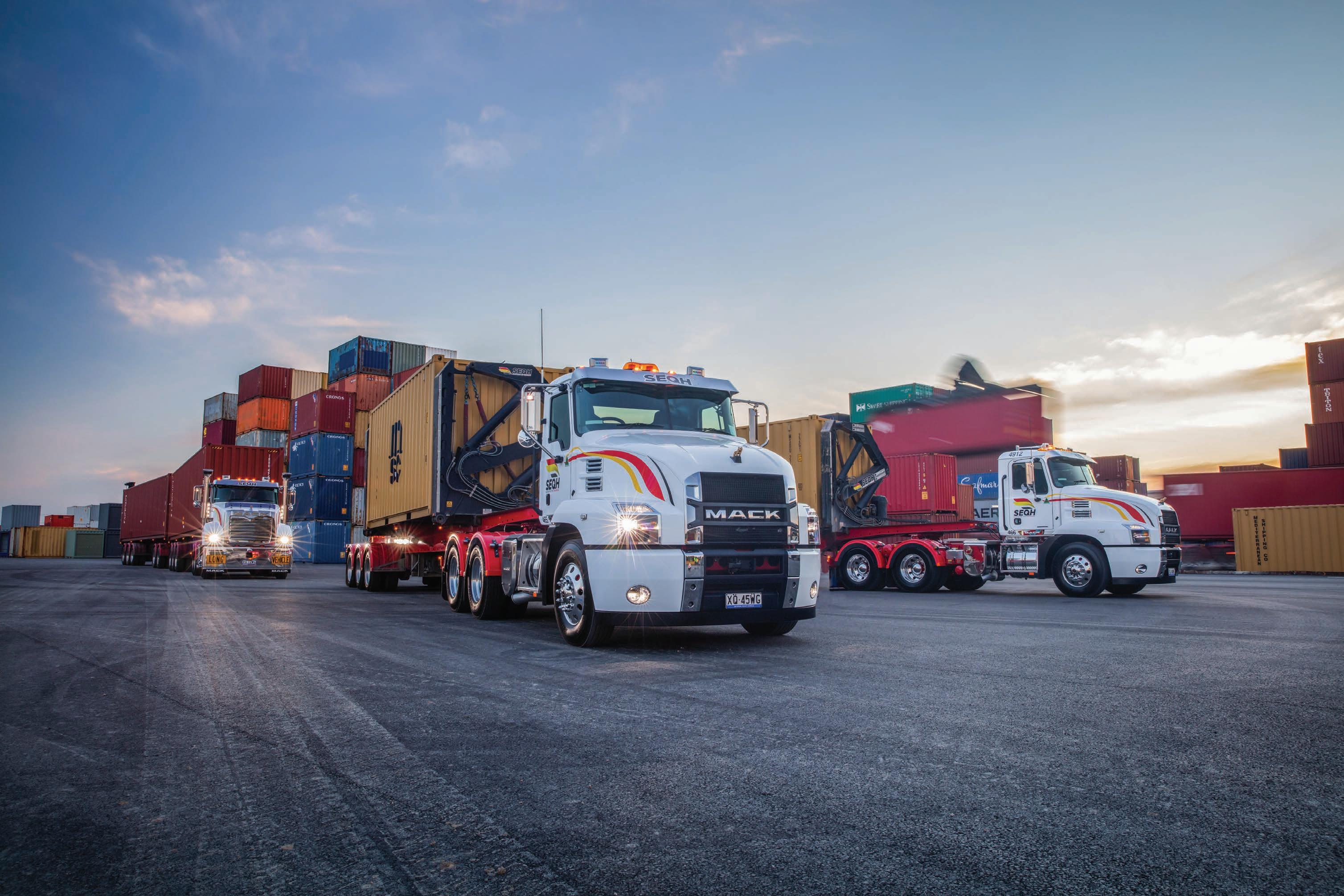
based in the Brisbane bayside suburb of Hemmant, this was the rare case in 2007. For strategic reasons, the company had wanted to own land rather than lease from the Port of Brisbane, seven kilometres away, prohibiting it from operating Super B-doubles, as was the custom of most of their wharf-side competitors. Following a couple of years of consultation with government agencies and OEM partners, they shifted to PBS-approved A-doubles, a decision that has proven both innovative and efficacious in levelling the playing field given the same zoning restrictions, when leaving the port area, no longer apply. The advantages of the A-double and
Director, has been a real gamechanger and not just for reasons advantageous to “Fromproductivity.asafety side of things, you have less trucks on the road” he says. “From the labour side of things, you have less drivers required, which in this market today, given the driver shortages, that’s ever so important.”
“From that point onwards, our business
The sun sets on the Mack Anthem gold bulldog.

Supporting the western region and the Darling Downs remains a major, if not central focus of the business. The company operates a depot at Wellcamp, near Toowoomba, where A-doubles descend daily from Brisbane. The fleet disperses 12 of its 80 prime movers out here to customer sites on afternoon and night shifts in double roadtrains or in an A-B triple combination. For longer distance jobs, disembarking from Roma, SEQH might run Type 2 roadtrains with three fully loaded boxes. The GCM on these units is well over 100 tonnes. Historically, operators running heavy containers from the likes of Roma, Goondiwindi or Moree, were, previous
50 september 2022
What’s more, it brings a cost competitive solution for customers, particularly, in the export markets. Supporting the agricultural sector by keeping costs down is fundamental for farmers to operate successfully and profitably according to Nathan.
handle freight, SEQH possesses the equipment on site to handle out of gauge heavy haulage cargo. There’s also a public weighbridge on site. That goes hand in hand with the bulk side of the business. Broadly speaking that’s what encompasses the full-service offering. South East Queensland Hauliers has a history that begins in 1956 and diverts with the purchase of the business in 1997 by current Managing Director Brett Plummer. His vision was to change the bread and butter model hinging heavily on tipper transportation and rapidly expand its marginal output as a containerised transport division to exploit the fast growing consumer economy.Notwithstanding eight Volvos and a solitary Kenworth, the remainder of the truck fleet is represented by Mack trucks – SuperLiners, Tridents, Granites and Anthems. The Anthems are in the main part operating around metropolitan Brisbane in the sideloader and single trailer fleet. The A-double units, a product of its long association with Haulmark Trailers and Mack, are being predominantly pulled by SuperLiners powered by a 685hp MP10 engine. In the last few years, SEQH have updated the permits allowing for the utilisation of Volvo FH16 units in the Theapplication.predominant value-add in its heavy
primemovermag.com.au 51 add value.”
“If they can pack more containers it
Making its customers tangibly more efficient is only part of how SEQH likes to add value.
“There’sloaders.only so much you can do with those delivery modes,” Nathan explains. “The moment that you put a container handler on site it increases your throughput on how much you can process and therefore pack.”
SEQH is customs 77G bonded and licenced for a biosecurity 1.1 facility. This means, for any containers marked for a rural destination they are able to provide a rural tailgate inspection. They can also provide general inspections,, fumigations and biosecurity washes of cargo or containers. They can also facilitate a customs overview if required. Reefer plugs have been installed on site for customers who have containers that need to be kept charged up. For awkward, ugly, oversized, hard to
Volvo FH16 on a regional assignment.
means they’re more profitable as well and the trade increases which helps us as we’ve got more containers moving on our trucks,” says Nathan. “The aspiring goal, which we’re proud to have achieved now, is to be a full-service wharf logistics provider and for us that means everything we do revolves around the core of moving import/export containers, however, it also branches off in that we offer warehousing services. If customers can’t unpack containers or can’t pack containers for export, we can offer that service. For some customers that’s not a part of their business. They want to get the freight to port but they don’t want to have a specific warehousing operation. They want to leverage off someone else. We can offer that Amongservice.”itsindustry accreditations

In some cases SEQH has actually positioned container handlers on site for its customers once they have exhausted the gains achievable from the more traditional model of trailers or side
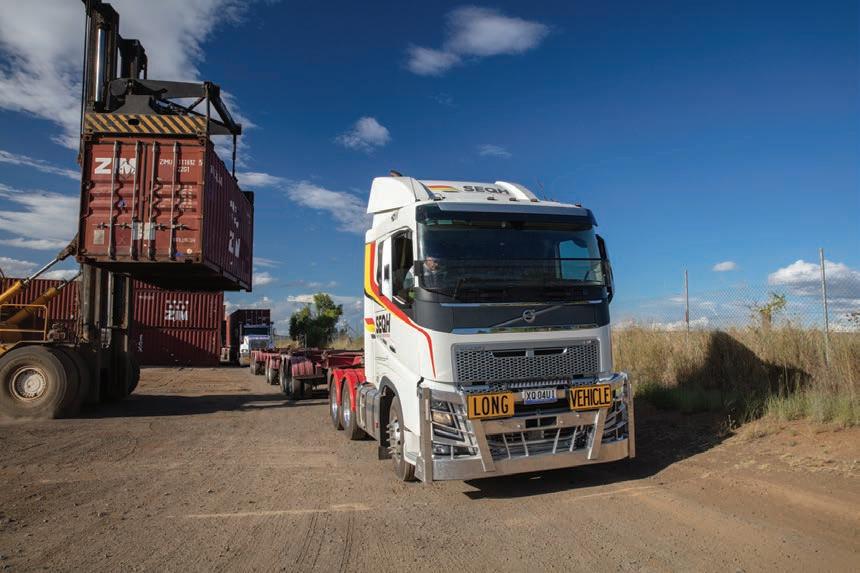
Volvo FH16 and Mack SuperLiner..
TRUCK & TECH
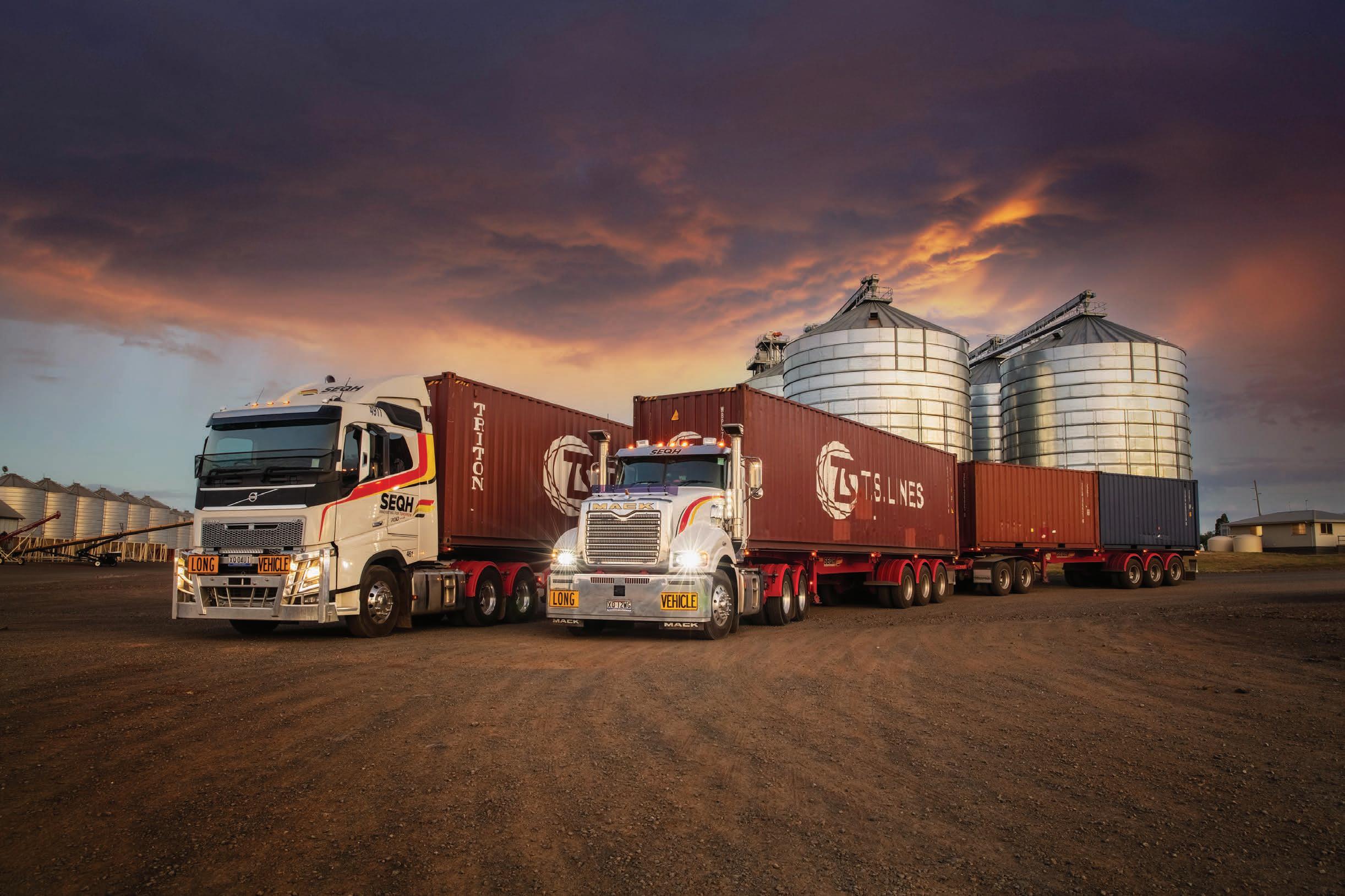
“If we’ve got a really heavy box and we need to send a trailer as well as a side loader to follow to lift that box off the ground there’s more cost, more inconvenience and labour,” says Nathan. “It makes it harder. Having the spread axle increases the weights meaning we can add more value to our network and the Fleetcustomer.”replacement is now a matter of escalated forward planning for carriers who have hitherto enjoyed short cycles when upgrading their vehicles. SEQH is no different in this domain. Purchasing arrangements for prime movers and trailing equipment is now being planned for the years ahead.
“Withissue.ushaving newer gear and reducing the average age of our fleet that then helps us to have more confidence that our average time on road is going to be better off because we’ve helped to reduce the average age of the fleet,” he says. “That’s to take pressure off our workshop labour and to respond to the reality that parts are hard to come by at the moment. You can’t rely on older gear like you used to.”
primemovermag.com.au 53
“We’ve placed orders early to have a better chance of getting our gear,” says Nathan. “At the same time, there has been opportunities whereby other companies have ordered trucks but haven’t actually ended up fulfilling that purchase when the gear comes online and we’ve been working with our provider and essentially doing last minute purchases when trucks have become available just to decrease the average age of our fleet and we’ve since then sold off more older equipment to try and relieve pressure in our workshop since there is two issues.”
For the moment SEQH is better equipped to avert the obstacles, which are many
animal around the crate so the carers and welfare of the animal to keep them in the find solutions to jam more cargo into the
36-tonnes in lifting capacity but fail when it comes to a legal axle spread in transit.
The first issue Nathan points to is the labour shortage of diesel mechanics in Australia. That will, in the current climate, extend the time frames for servicing and maintenance at a major truck fleet. Secondly, there’s the parts
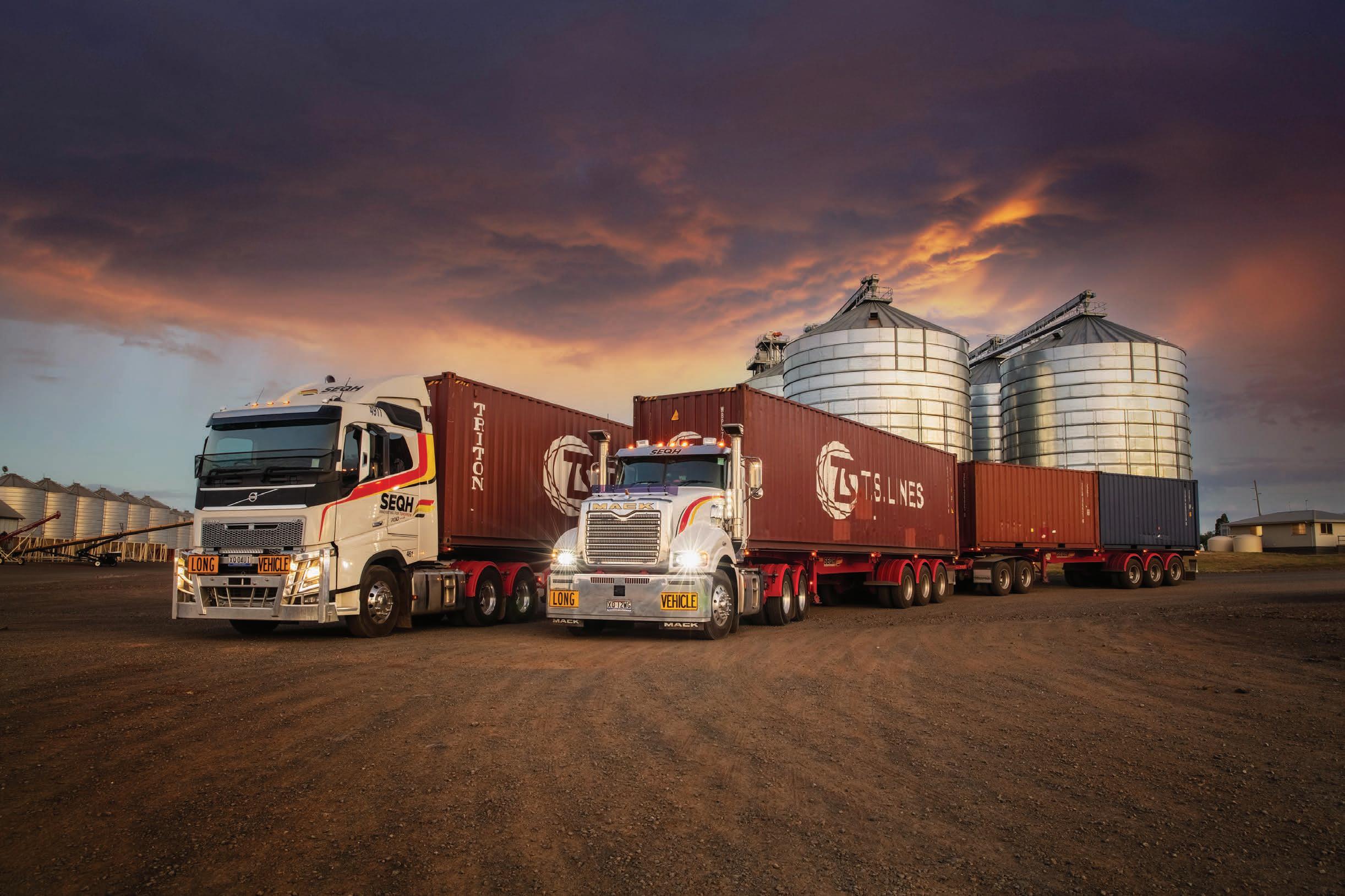
Over the years Nathan, too, has got the relevant licences to operate forklifts and heavy vehicles. When it comes to peak times, he’ll think nothing of jumping behind the wheel to help take the pressure off the allocators and to support the drivers on weekends. In that sense he says he got swallowed up by the industry.
Nathan took a circuitous route to road transport. His first career pathway following school was in fitness. At one stage he owned a personal training business with another fitness professional that was scheduling 400 PT sessions a week with eight different trainers. He sold that business but not before crossing paths with Brett Plummer. After time working for Kings Transport, Nathan was eventually offered a role at SEQH by Brett who is passionate and goal oriented, both great qualities for teaching.
“We’re trying to understand customer’s businesses. We’re trying to understand the economics. We’re trying to understand our people as they represent our company. I love spending time with our people to positively help them so that they have a career pathway. A lot of the time you’re trying to help people understand their purpose which gives them fulfillment when they’re exercising that purpose and growing.”
He adds, “Those are the crossovers and synergies that I see.”
Mack SuperLiner pulls an A-double.
That’s been a springboard for Nathan, who, in transferring to the road transport industry, discovers many similarities.
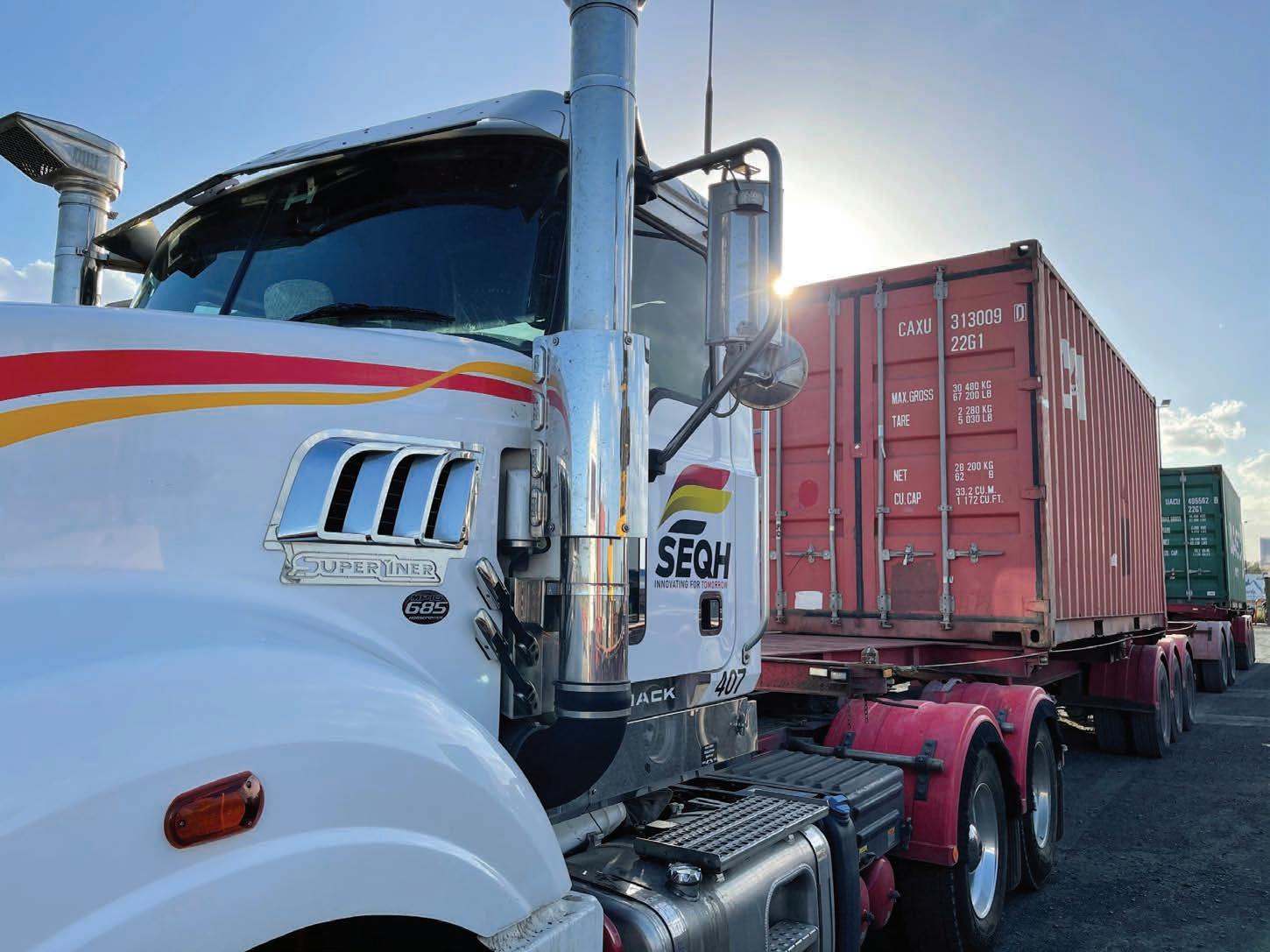
unhealthy people. I liked getting into people’s heads.”
TRUCK & TECH and soon accumulate for businesses that get caught with an over reliance on ageing mobile assets.
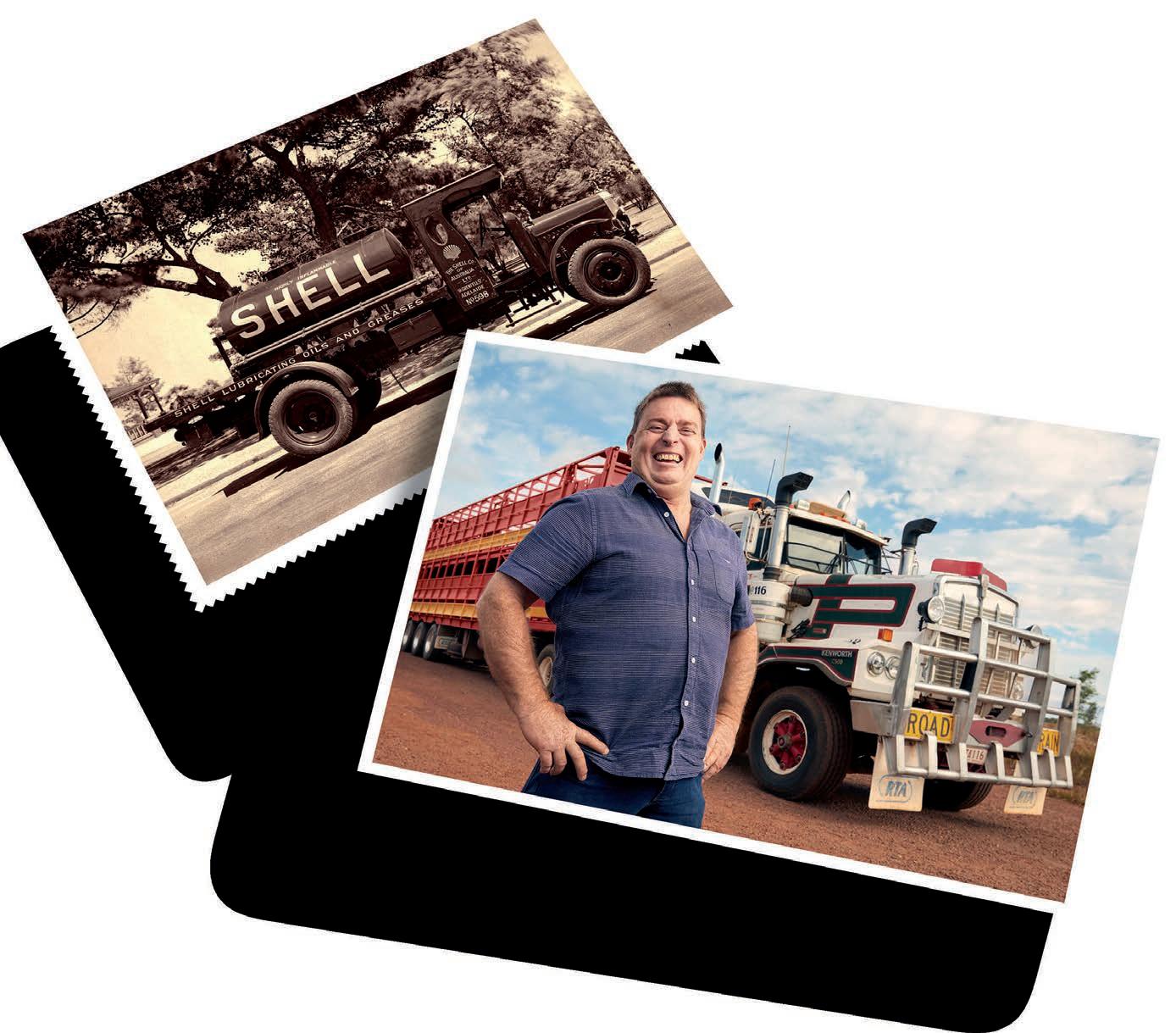
“The thing I loved about the fitness industry was I saw it as helping people change their lives,” he says. “We were very much focusing on helping unfit,
“That makes it very easy to learn from him and I have just sponged off Brett’s
knowledge immensely,” says Nathan. “He’s got very strong values within the company around work ethic and also helping customers, and working together as a team. He will jump in a forklift or into a truck if we’re really up against it.”
Fuelling Australia’s trucks since 1901.
We’ve come a long way since 1901. Today we offer a wide range of driver amenities, a national network of strategically located truck-friendly Shell service stations, and a price discount every time you refuel with Shell Card. And that’s just for starters.
Talk to us about Shell’s Australian Truck Network, and how we can help drive your road transport business towards a better future.
shell.com.au/trucknetwork SHELL AUSTRALIAN TRUCK NET WORK
For more than 120 years, Shell has been supporting Australia’s truck drivers with high quality fuels.
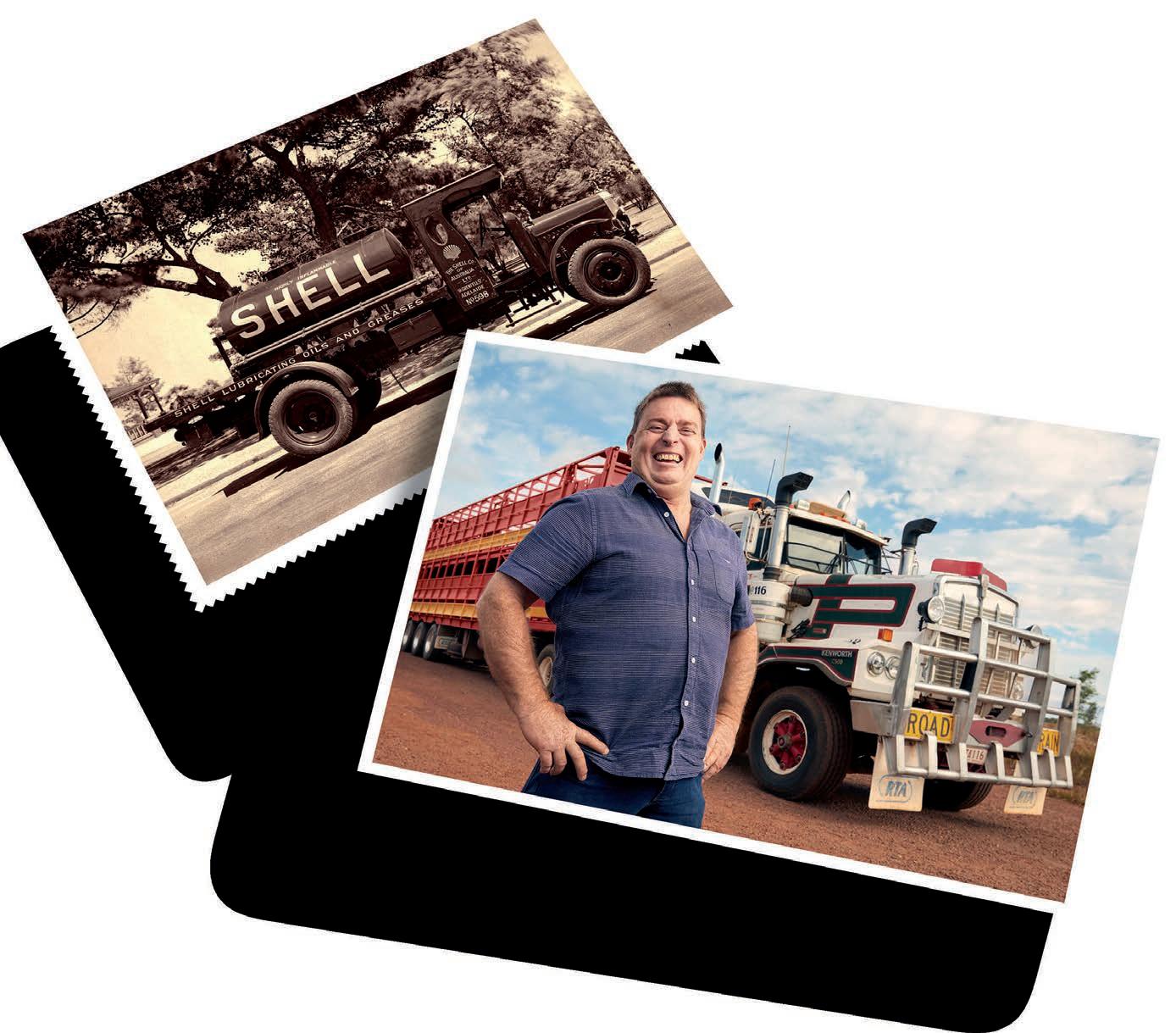
56 september 2022 INSURANCE SHOWCASE
“Weemissions.arealso partnering with a manufacturer and assembler of electric trucks to share knowledge and expertise, and to help their customers navigate challenges and risks as they embark upon these changes,” Mervyn says. “We also engage with a variety of government agencies charged with facilitating the changeover to alternative fuels, such as National Energy Resources Australia. We can now provide significant expertise, guidance and risk management to any business that wants to introduce electric vehicles and consider alternative fuelled vehicles into their fleet.”
“We are now equipped to help any customer navigate their way through this changing landscape, ensuring they make informed decisions, select alternative fuelled vehicles that are fit for purpose, and assist with all aspects of that change management process,” he says. “We risk assess their motor fleet risk profile and look at ways to improve controls and lessen exposures often reducing their crashes. While this assists our underwriters, it also improves the fleet’s own resilience and helps them deliver consistency.”
For decades, ZRS has helped fleet owners and operators understand their workrelated mobility exposures. With a purpose of supporting its colleagues with technical risk assessments and insights and a commitment to going beyond insurance, Zurich is able to offer a service truly unique and specific to the transport industry.
Alternative fuels are providing a realm of exciting options for commercial fleets. In this landscape, risk management, according to Zurich, will have a major role to play when it comes to a new set of compliance, safety and resilience challenges each option is likely to present operators.
use of replacement parts and paintwork repairs that are often an unseen addition to a fleet’s carbon footprint. Each time we avoid a crash we avoid unnecessary carbon
RISK MANAGEMENT TO THE
Many of ZRS’ mitigation strategies focus on driver behaviour, so when improving a company’s driving culture and behaviour, the process often comes with several benefits such as less crashes, a reduction in the total cost of crashes, and better fuel efficiency. Crash repairs will result in the
“We currently have Codes around the segregation of dangerous goods, and we need to consider the current situation when carrying bulk dangerous goods,” he says, “For example, ammonium nitrate when isolated from any source of combustion is relatively stable and diesel is
RESCUE
Mervyn Rea.
Z
“Our customers are not limited to those insured at Zurich, and so we work, principally with brokers, to service the needs of companies, regardless of whether Zurich is their insurer or not,” says Mervyn Rea, Head of ZRS AU/NZ. “Going

beyond insurance means we also focus on the uninsured aspects of risk too, and we’ve also built capabilities to assist with cyber, climate change and supply chain exposures. Hence, we are focused on helping business improve their levels of Zurichresilience.”recently hired two new members straight from fleet management roles with first-hand experience across the truck spectrum in rolling out electric vehicles in fleets they used to manage, with one of those being the largest electric truck fleet in the southern hemisphere at the time. Because of this, Mervyn says the company is even more heavily armed to accommodate any need for its customers.
urich Resilience Solutions (ZRS), born out of Zurich Insurance Group’s Risk Engineering network, is an expert in the field of risk management for alternative fuels. Conducting over 60,000 risk assessments each year and managing more than 800 international programs, Zurich offers its customers quality service with the benefit of 75 years of experience under its belt.
Implementing alternatively powered vehicles into a commercial fleet comes with considerable hidden costs and quite a few challenges. Even more factors are introduced depending on the type of cargo being carried with an alternatively powered fleet. As Fran de Sanary, ZRS Senior Risk Engineer says, it becomes much more complicated in the case of, say, dangerous goods.
primemovermag.com.au 57
According to Fran, when launching a new design, the OEM must also have in place global aftersales support, parts inventory, training and marketing – all of which takes time. He explains that effectively implementing alternative vehicles into a commercial fleet takes more than just simply purchasing the vehicle. The answer? You guessed it, quality risk management.
“I think it is important to note that implementation of alternative-fuelled vehicles into a fleet will at some point not be an option, they will be the only vehicles available,” he says. “Now the timing of that point is still in debate, however it is
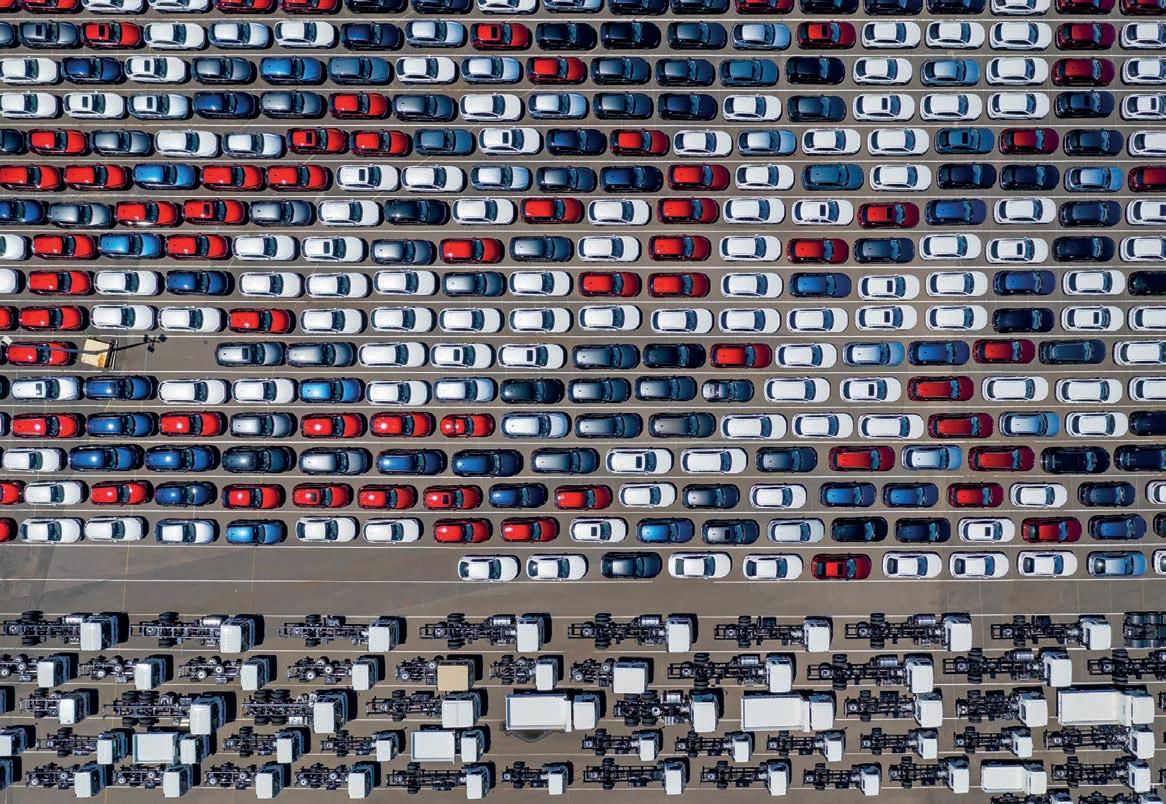
are given visibility, with a view that the risk improvement actions will not only provide a higher level of risk mitigation for the current operating environment but will prepare the client for the advent of the alternative fuels.
“The industry is now moving more rapidly towards full reliance on alternative fuels with a more defined pathway since the introduction of the first hybrids, and it is more likely now that the fleet of the future will consist of a mix of technologies, such as electric vehicles for local and last mile delivery and hydrogen fuel cell and hydrogen ICE for long distance and linehaul. This journey will be supplemented using green and synthetic Nowbiofuels.”there seems to be one overriding question: why have OEMs been reluctant to invest in hybrid technology despite its clear advantages in cutting overheads? Surely a lack of faith in the industry or safety can’t be a factor, with companies like Zurich leading the way in global risk management? Fran suggests it may
Work related mobility exposures are fast changing across commercial fleets.
alternative-fuelled vehicles,” he says. “The traditional time taken to develop and ultimately launch new conventional diesel fuelled vehicles into the market takes several years in practice. We only have to look at the development curve from Euro 4, 5 and now 6, and it must be noted these are only enhancements on the already proven base core design of the ICE engine. These have not been radical new designs such as fully electric or hydrogen fuel cell.”
classified as a combustible liquid only. Yet, when the two are mixed it can be highly Hydrogenexplosive.”fuel cell vehicles specifically will change the whole system of risk management for fleets. It will most likely be a whole new picture, with new practices and different procedures in place to complete certain operations. Fran says these changes will not only apply when changing from a diesel-powered fleet to that of hydrogen but will also be present when releasing a fleet of commercial electric vehicles onto our road network. “Risk mitigation processes will be integral in ensuring that the fleet is not only compliant to the evolving regulatory changes but aim in becoming best in class,” he says. “Risk management plays a crucial part in the fleet evaluation and measurement of the overall maturity of the business operating processes. It will also provide realistic risk improvement actions that would achieve a level of safety and compliance – not only meeting the compliance level, but it would be aiming
Brooke Caldwell.
58 september 2022 INSURANCE SHOWCASE
I
reduce prospective customers who will be less willing to use their services. The other significant factor is compliance. When major changes to legislation for Heavy Vehicle National Law came into effect in 2018, many operators needed to better understand what these changes would mean for their business and their responsibilities. Specialist insurer, NTI, here came to the fore. They have, in keeping with these environmental changes, continued to provide tools and resources for customers that have been well received — risk engineering is one
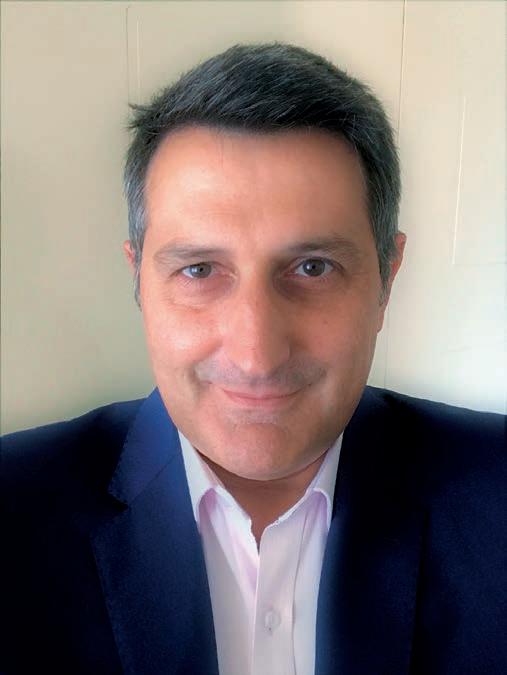
Paul Bressan.
of these resources.
RISKY BUSINESS
t’s a truism that accidents bring about disruption and expose companies to expenses that have long-term consequences. Heavy vehicle businesses that see a drastic decline in their incidents understand the benefits of this are legion. Not only does reducing incidents overall have a direct correlation on insurance premiums and productivity improvements but it also will have an impact on how the industry perceives the company. If a business is too frequently involved in incidents, it’s likely to increase costs, inhibit trust and
NTI provides, through its risk engineers, high levels of knowledge and experience that it can pass onto its customers to help them achieve best practice and significant gains.
In addition to helping customers operate more safely and efficiently, according to Brooke Caldwell, NTI National Heavy Motor Product Manager - Fleet, risk engineers can identify potential gaps in a company’s chain of responsibility (CoR).
“Our Risk Engineers are unique in that they’re industry specialists,” she says. “They have a working knowledge of the issues affecting our customers bringing a different perspective to their engagements.”
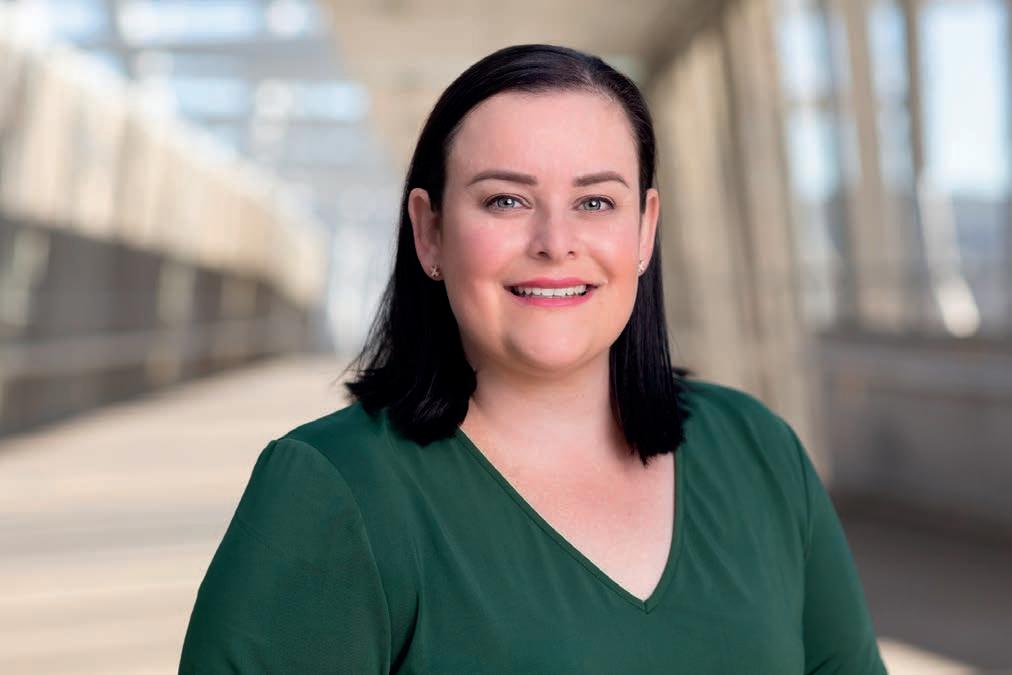
primemovermag.com.au 59
A full survey of a business can be conducted, tailored specifically to their needs, based on the inherent risks of the operations should a broker foresee any. This is usually where someone like Risk Engineer Paul Bressan comes in. He will be approached for guidance under these circumstances or to help identify the root cause of incidents by assessing the systems they have in place.
For its risk management department NTI were looking for someone with real-world industry experience. Paul, who joined in April of this year, has plenty of it having worked with major carriers like Toll and Border Express previously in safety and compliance roles. He sees, now more than ever, technology having an ever-increasing and ongoing role in risk management. That said, many experienced drivers and longstanding businesses, face challenges in understanding and adopting the types of technology that are available.
“We know there is a shortage of experienced drivers,” says Paul. “Faced with the challenges of fuel costs and COVID, many older or more experienced drivers have moved into early Aretirement.”riskengineer can help here, too. Engaging a risk engineer early, Brooke explains, can potentially help with identifying potential issues early like delayed vehicle maintenance which may lead to avoidable incidents as well as gaps in a companies’ driver management including selection, recruitment, onboarding and training practices to assist with safer operations.
“It’s surprising the number of smaller carriers that don’t tend to have a sound methodology behind their incident investigation – typically for common reasons.” he says. “Often they are not able to identify the root cause and even if they are, they may face challenges with communicating the cause to their staff and the wider community to avoid similar types of incidents reoccuring.”
centric, meaning we spend time with our customers and their broker to understand the business and operational needs to create a tailored report that combines unique customer insight with industry expertise along with bespoke recommendations and collateral.”
“Often it’s no fault of the truck driver. They just can’t see when someone has cut in or moved up beside them,” he says. “Something like that is simply addressed by having two cameras down the sides of the vehicles. The business in question has since installed sidefacing cameras across their fleet and the incident rate, in regard to those types of incidents, has dropped substantially.”
In what is proving a particularly tough environment for the moment, risk engineer engagements are helping to improve risk management and safety, as well as optimise customer processes.
“In our experience as Australia’s number one truck insurer, customers who engage our risk engineers have better business performance and more consistent insurance premiums,” says Brooke. “It makes the roads safer for everyone.”
“Clients will always have incidents, but we also want to reduce the severity of those incidents and ongoing consequences,” he says. “No business wants any vehicle off the road for any time. It does have an impact on their
Heavy vehicle operators, who may most benefit from a risk engineer, are usually looking to improve their compliance practices. Companies that are growing rapidly and need to stay on top of their operational commitments also will see significant advantages. How industry perceives a transport business is always important. How a transport company perceives itself is of equal note. Staff turnover and recruiting can belie broader cultural issues that may, in turn, undermine critical compliance requirements. Recruiting the right people for the right positions, however challenging, is only half the equation. Asset management and the maintenance systems in place for those vehicles can be considered the other half. The role of a risk engineer is to ascertain if the procedures and systems at hand are best practice and whether new technologies can be introduced to reduce claims and curb incidents. According to Paul it helps to educate and develop employees no matter whether they are new hires or existing staff.
Not long-ago Paul conducted a survey for a client that wanted to specifically address side collisions. Many of these had stemmed from drivers who were simply changing lanes and unaware they had a passenger vehicle in their blind spot. It was considered a behavioural issue, according to Paul, but there are, when all is said and done, a lot of blind spots in larger vehicles.
“Making sure that the business is involving the staff coming through is very important,” he says. “That also means educating them on new equipment and doing that all the way through prior to purchasing that new equipment. Early engagement is crucial. That helps and may even excite new drivers coming through.”
At present Paul is also consulting with another technology provider on fifth wheel sensors and cameras as part of research to develop a tool to mitigate dropped trailers, one of the high risks and most recurring type of incidents in the NTIindustry.issocommitted to business improvement, according to Brooke, it passionately believes in the benefits its risk engineers can bring to its customers’ business, that it offers this service at no cost. Heavy vehicle insurance, as NTI views it, should go much further than just paying claims after an incident. It should help reduce all exposure and in doing so assist a business be better making it more productive and efficient — hallmarks of a successful heavy vehicle operation.
“This leads to better staff retention and improved efficiency, and in turn less accidents, reduced repair costs and insurance costs,” she says. “Our approach to risk engineering is customer-
business. If we can reduce the incidents happening and even the time that those vehicles are off the road we see benefits across the board.”
RANGE
TOPOFTHE
Queensland’s Atherton Tableland and the Bruce Highway between Cairns and Townsville are at the start of Hino’s ambitious nationwide multi-vehicle assessment program.
60 september 2022 TEST DRIVE
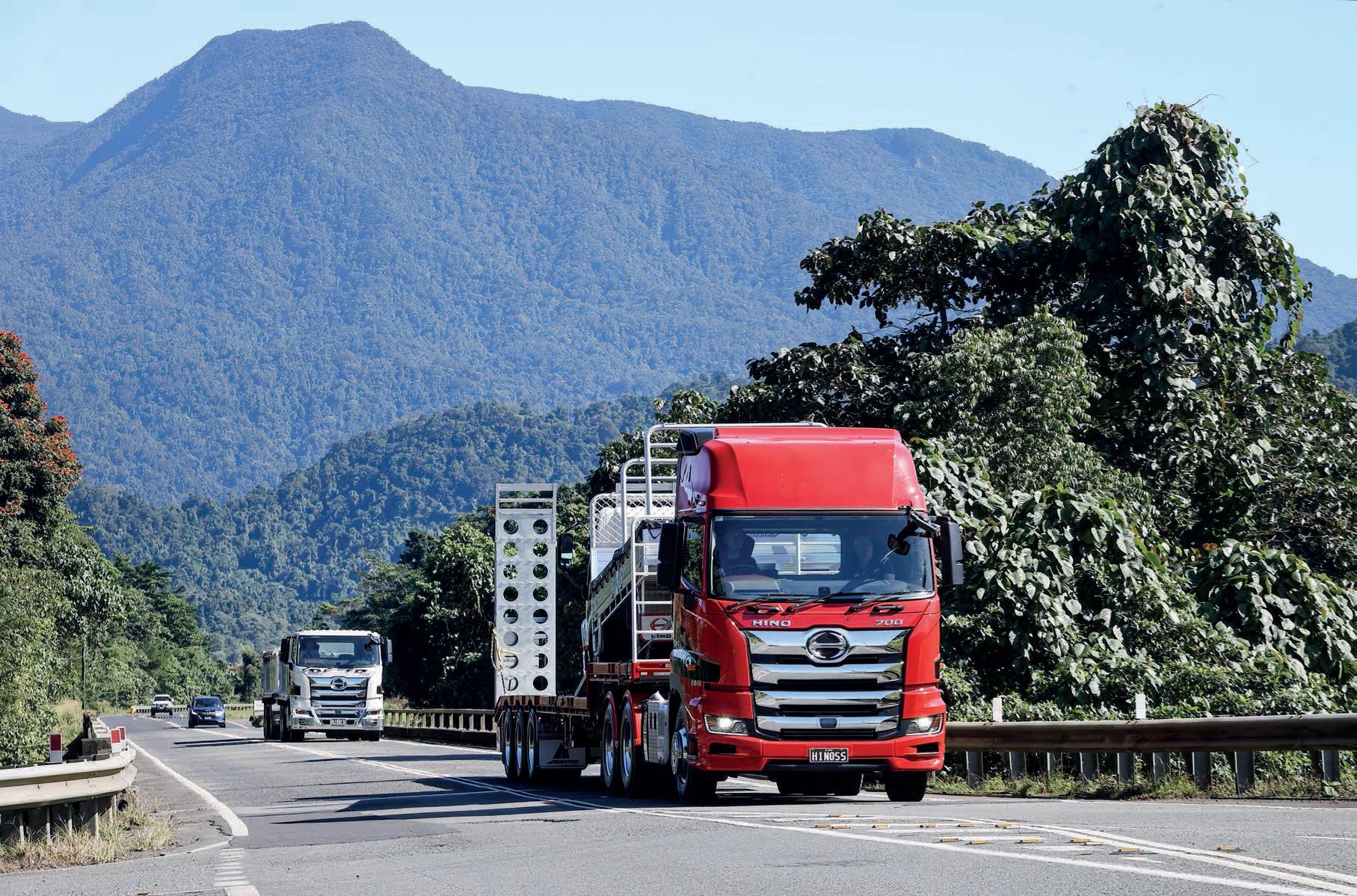
Hino’s current model line-up is relatively young. In 2017 Hino commenced the renewal of its range with the Wide Cab 500 Series which is currently the ‘oldest’ truck model at just five years. At the same time came the introduction of the Hino SmartSafe comprehensive safety package which uses technology to significantly improve safety for drivers, passengers and fellow road users. SmartSafe uses radar and cameras and includes a PreCollision System (PCS) with Autonomous Emergency Braking (AEB), Pedestrian Detection (PD), Lane Departure Warning System (LSWS) and Vehicle Stability Control (VSC).
In common with other manufacturers operating in the current global economic situation, Hino has the challenge of its orders significantly outstripping the source of supply, which has led to a number of pending strategic decisions. The widely acknowledged shortage of semi-conductors has been exacerbated by the COVIDinduced long-term lockdown of Shanghai
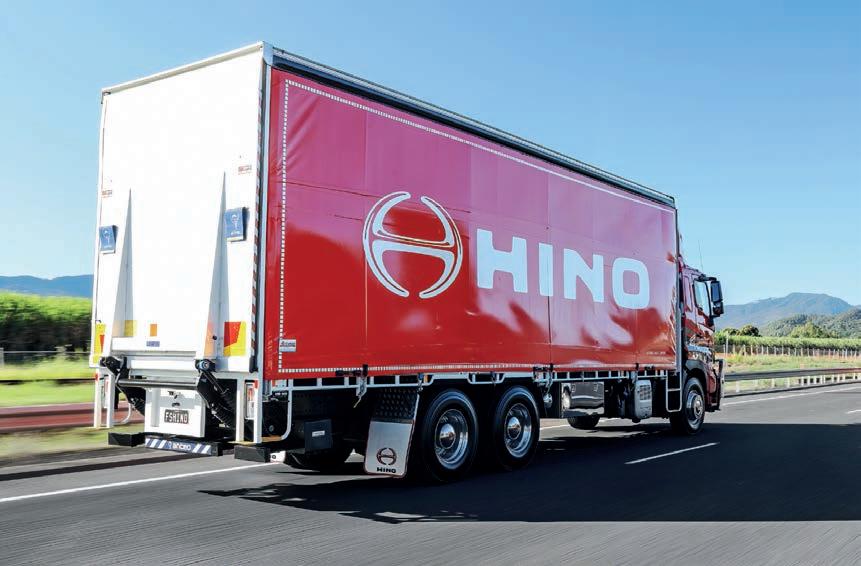
which is the source of components including tail-lifts and fridge units. This dilemma especially affects some Hino 300 Series models. Combine that with global shipping issues and the backlog of work facing local body builders and Hino has had to employ a realistic approach to such challenges and recognise what they can influence, and not waste time on things they can’t. Machiavelli’s advice is to not waste a good crisis, and this is the case of Hino not trying to be all things to all people, and to maximise its opportunities where they have an advantage.
The Hino 300 Series was launched in 2020 and the expanded range has seen the versatile 300 creeping into bottom end of the medium duty category with some models. Incorporating Hino SmartSafe, the 300 Series has set the benchmark
Hino 700 Series 13-litre 480hp curtainsider.
in Far North Queensland was deliberate, with the Atherton Tableland presenting challenges to the hill climbing and descending abilities of the Hino models involved and the Bruce Highway following the coast delivering a mix of metropolitan and highway conditions.
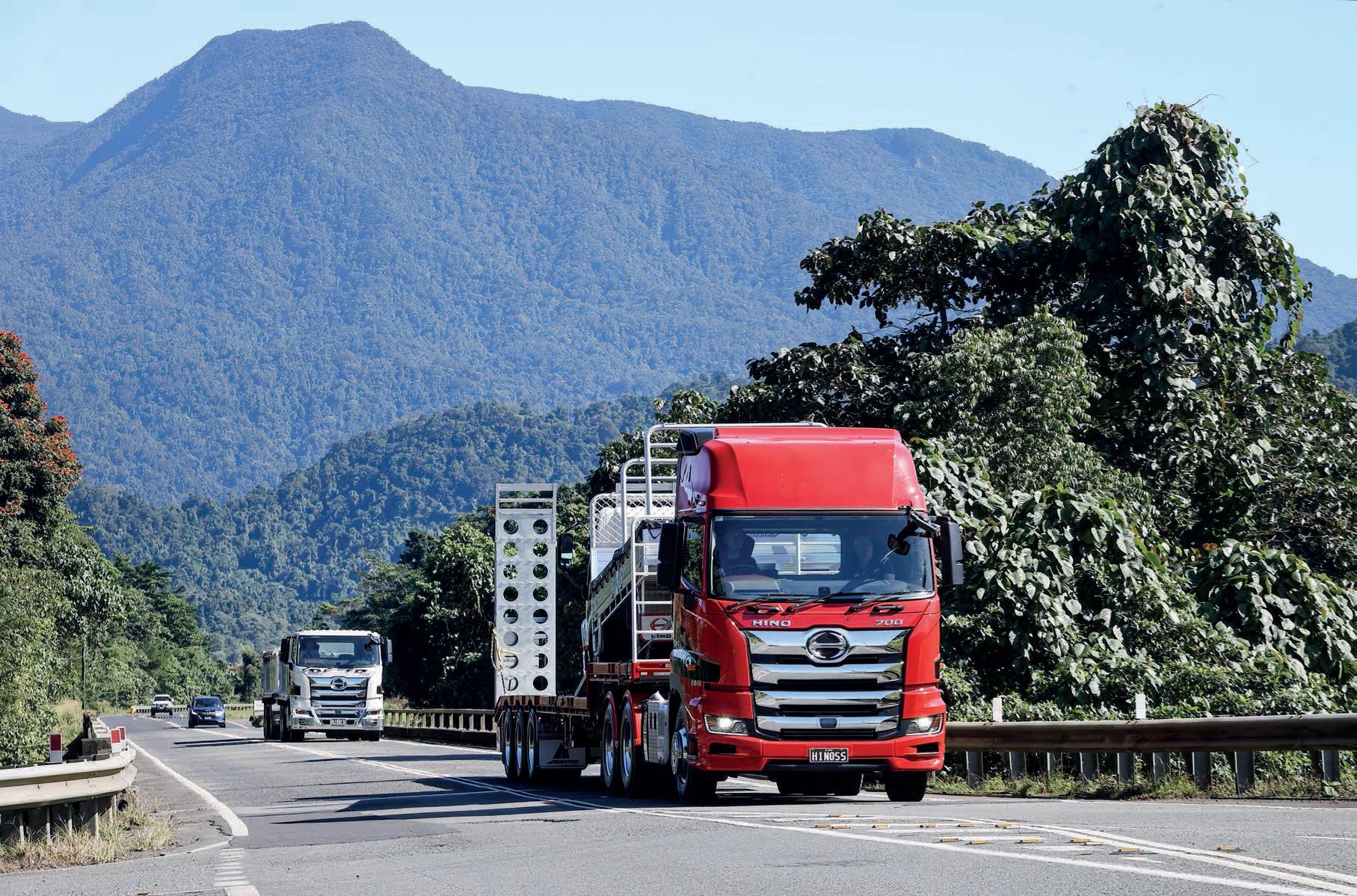
Hino 700 SS2848 with drop deck trailer tackles a steep grade on the Bruce Highway.
T
he past couple of years has seen the absence of the typical extensive product launch and test drive programs at which the industry, through its manufacturers, dealers, customers and media was able to experience a variety of a brand’s vehicles with the additional benefit of back-to-back assessments. Emerging from the forced hiatus brought about by COVID, Hino has not only assembled a comprehensive cross-section of its current models but crucially, provided group and one-onone access to its senior executives and key suppliers. The choice of the location
A multi-day event such as this requires meticulous planning and execution at an almost military level to be considered successful. Hino have definitely achieved this through a diverse range of its trucks, not just varied wheelbases of the same model. The line-up of demonstration trucks represents a $3million investment and includes models across the 300, 500 and 700 Series. This event is the beginning of a 130,000 kilometre around-Australia “road show” which will work its way through dealerships for the next six months providing local access for existing and potential customers to get behind the wheel. Where possible the road show will coincide with rounds of the Supercars championship where the all-new Hino Sports Deck will host an anticipated 1,700 customers over the period.
The first section of the drive involves climbing 800 metres of the Gillies Range up to the Atherton Tableland, using possibly the most convoluted main road in the country with a number of steep ascents and several 20 per cent pinches. Our ride for this section is a 500 Series crew cab FE1424 which is fitted with an Ekebol sliding tilt tray, which is a popular combination for automobile clubs and towing services. This particular unit sees service as the official recovery vehicle for the Supercars series. Thankfully it is not a damaged Supercar secured on the tray, but a rather sad example of why Mitsubishi no longer manufacture family cars in Australia. The tilt tray’s five-litre four cylinder engine provides ample power and torque (240hp and 833Nm) which is superbly delivered via the six-speed Allison fully automatic transmission. The interactions between the engine and transmission have been calibrated to make the most of the engine’s wide torque band without constantly shuffling between ratios. On such a twisty route the steering gets a thorough workout and delivers just the right amount of road feel without being too heavy. Descending from the plateau we take the wheel of a 700 Series FY3036 eight-wheeler which has been set up as a hook bin truck.
for safety, performance, efficiency and comfort and the use of true automatic transmissions has already proved to have been a good decision which is reflected in sales results.
Thanks to the 360hp engine’s Jacob’s Brake it only requires two brief instances of gently touching the brake pedal to hold a comfortable downhill speed because the Allison 4440 transmission self-shifted from sixth back to fifth and then to fourth in order to maximise the effect of the compression engine brake. A finger tap on the touch panel shifter console pulled the transmission back to third when negotiating the final and steepest section of the descent, with no need for the Electronic Brake System service brakes to be used. This particular truck is one of the last 8x4 models not to be equipped with the full Hino SmartSafe package including the unobtrusive Driver Monitor which is included in all Hino eight wheelers manufactured since August 2022. In recognition of the often extreme environments such as demolition sites in which hook bin trucks operate, the FY 8x4 has a rugged, yet smooth riding, six rod leaf spring rear suspension and is equipped with inter axle and cross locks on the diffs and also features load sharing front Onsuspension.severalsections of the flatter countryside both on the Tableland and on the coast highway between Cairns and Townsville, we get to experience two quite different Hino offerings in the 14-pallet Curtainsider market. The 26,000kg GVM 500 Series FR 2632 is powered by the nine-litre engine rated at 320hp/1,275Nm and backed by an Allison 3200 six-speed auto and is in a 4x2 configuration. The other curtainsider is a 700 Series fitted with the 13-litre 480hp/2,157Nm engine
Hino 500 FE1424 with tilt tray.
with the 16-speed TraXon AMT. With its 28,300kg GVM and 63,000kg GCM this spec is suitable for metro and regional rigid applications such as this test vehicle with it tailgate loader, as well as tipper and dog duties. Both of the Hino curtainsiders provide exceptionally smooth ride due to their four-point air suspended cabs being complemented by the latest generation ISRI drivers’ seats.
During our time with Hino executives, we are informed that the new 700 Series is already exceeding its predecessor’s sales by 20 per cent, with more opportunities expected once production can catch up with demand. This comes as no surprise as the Hino 700 in prime mover configuration presents a package worthy of consideration for many applications. The 700 Series prime mover participating in this event is a 6x4 with the 13-litre engine providing 480hp/2,157Nm. It utilises the ZF TraXon 16-speed AMT which is also equipped with the ZF Intarder and this SS2848 comes with an impressive GCM of 72,000kg. A similar spec 4x2 version is attached to the new Hino Sports Deck trailer which is a well equipped and executed mobile hospitality facility which forms an integral component of Hino’s increasing activities based around the Supercars motorsport calendar.
Hino customers benefit from HinoConnect, which is the next-generation of telematics and business intelligence developed in Australia which provides realtime performance data tracking, remote diagnosis of vehicle faults and dedicated Hino-Connect specialist support.
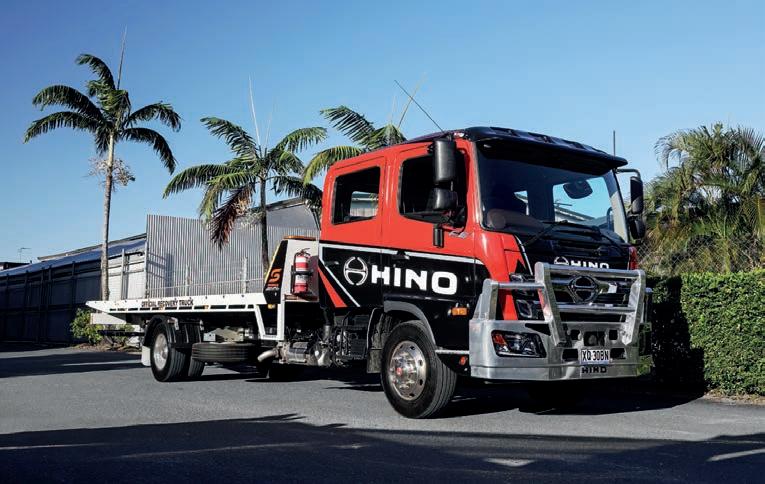
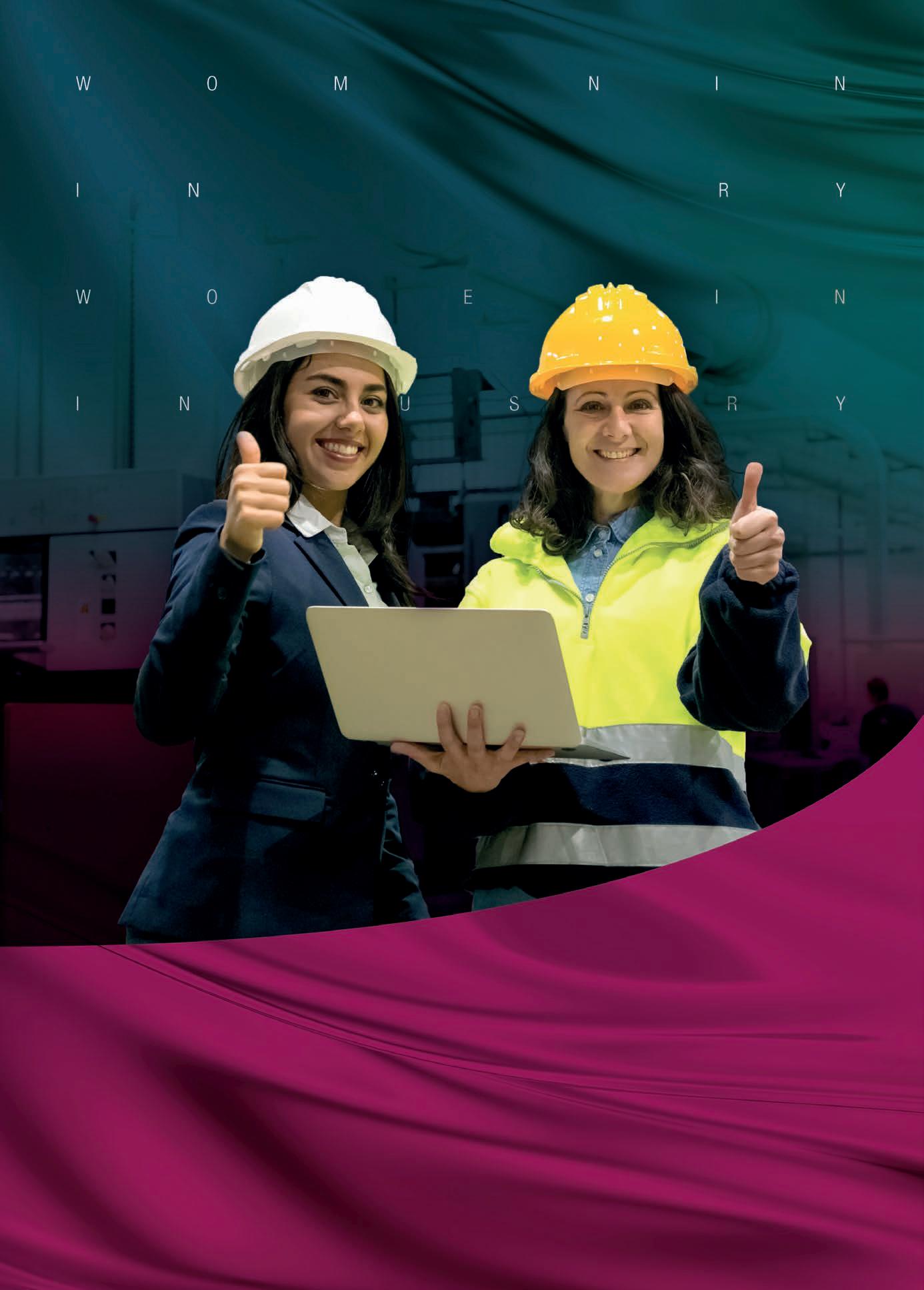
The Hino 700 Series was launched using a combination of sophisticated virtual and static formats in 2021 and while a select few media members (including Prime Mover) have had the opportunity to drive several examples since, it’s good to reacquaint as a group with Hino’s Heavy Duty contenders including a tipper and dog and a prime mover. All 700 Series meet the Euro VI emission standard using DPR and SCR. Standard auxiliary braking on the nine- and 13-litre 700 Series models is a Jacobs Engine Brake and the 13-litre models’ braking is further enhanced by the ZF Intarder fitted to the rear of the ZF TraXon 16-speed Automated Manual Transmission.
62 september 2022 TEST DRIVE
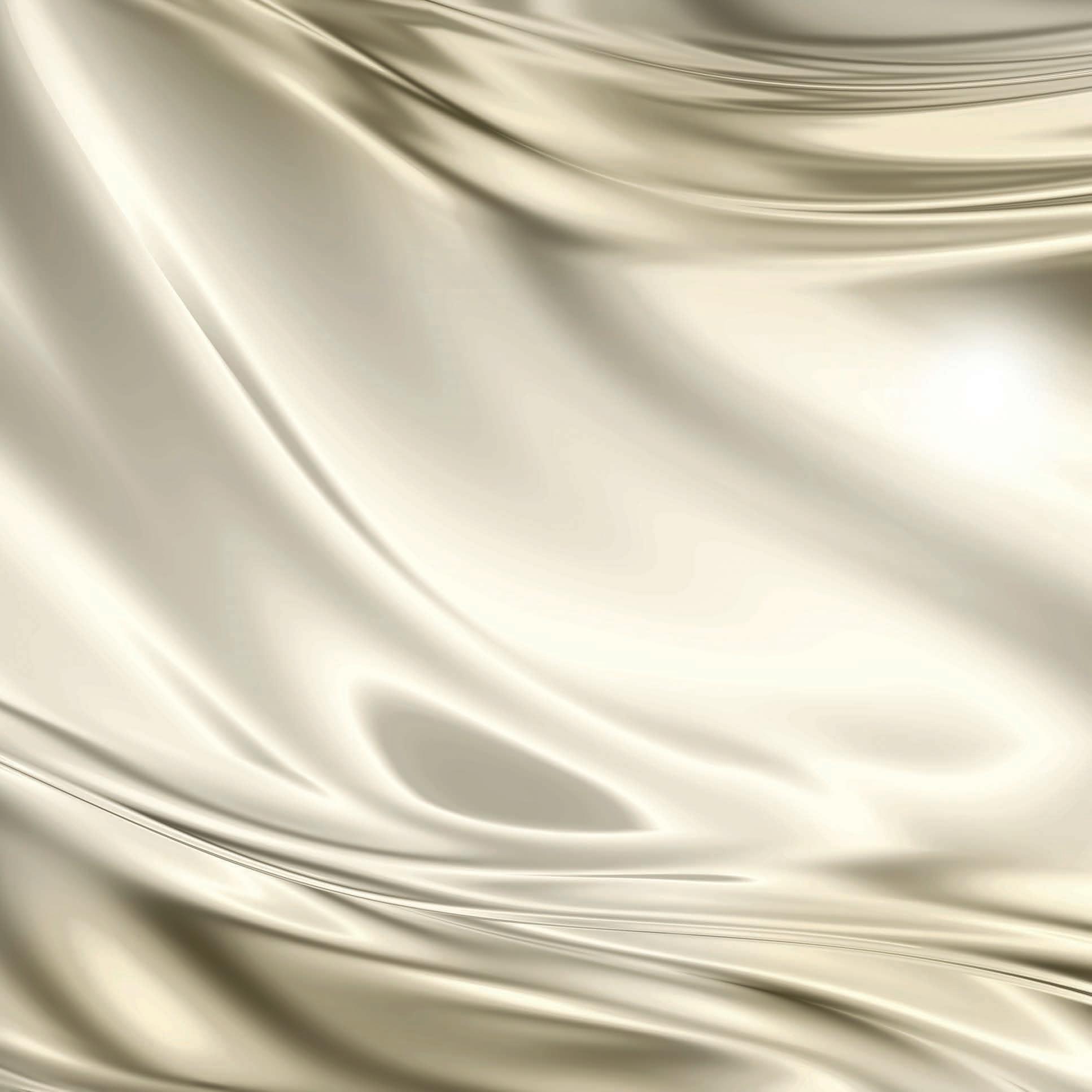
PROUDLY PRESENTED BY SEPTTHURSDAY8TH2022 MHD Supply Chain Solutions WOMEN IN INDUSTRY .COM.AU WOMEN IN INDUSTRY AWARDS AWARDS SPONSORS NOWTICKETSAVAILABLE
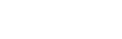
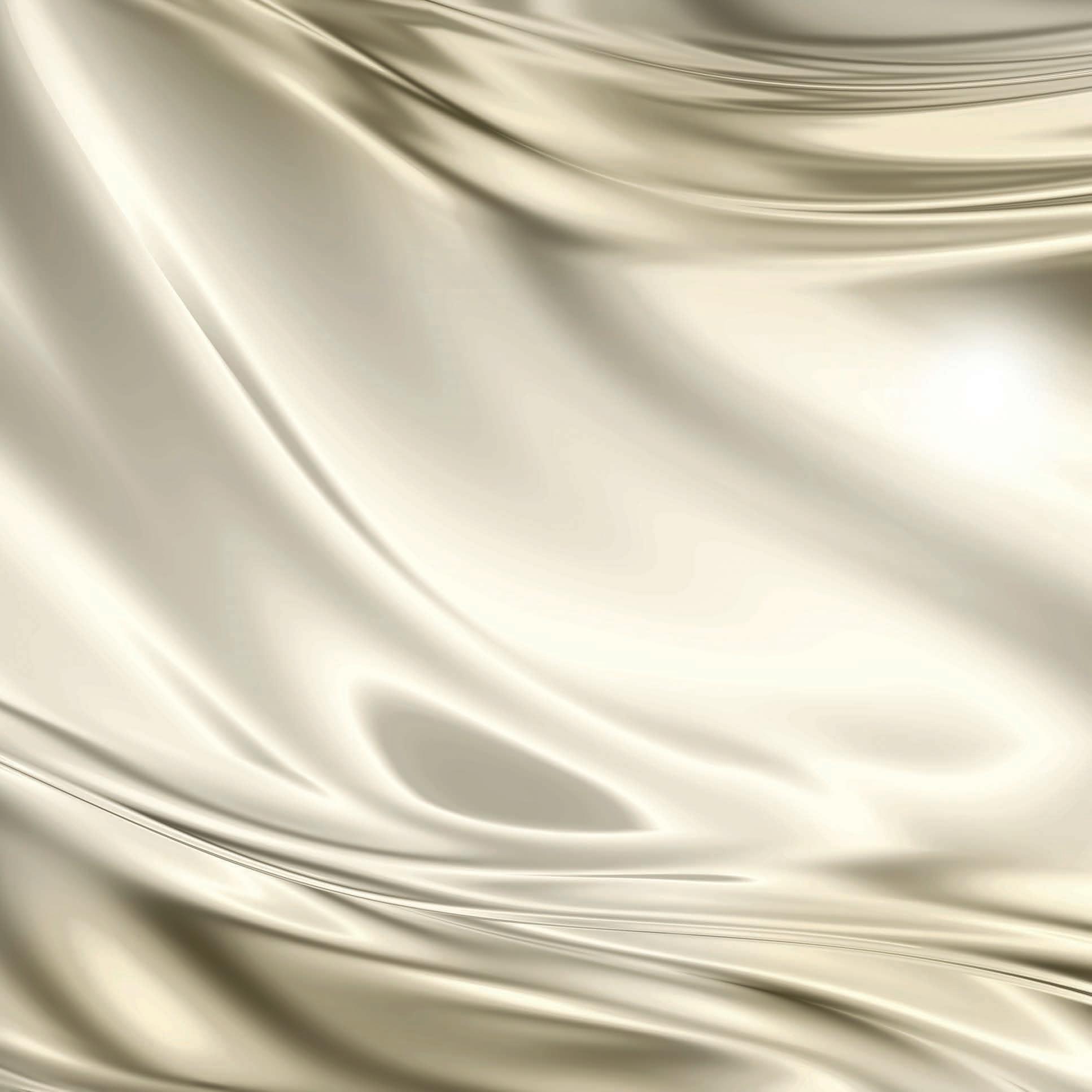
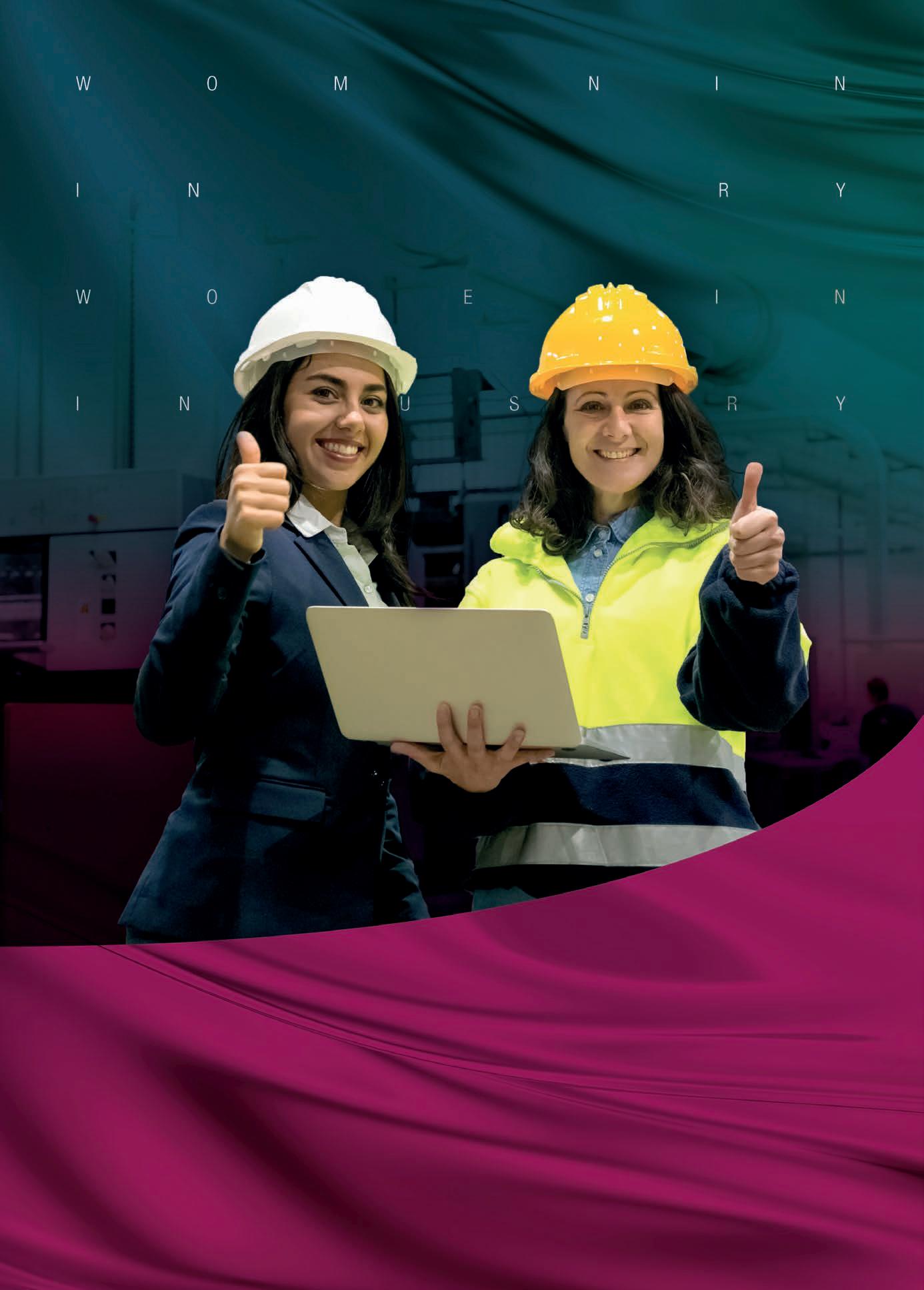
The promotion of vocational training and its benefits is part of the role of Paul Walsh who is helping to create clearer pathways for young and old alike to work within the road transport industry.
SOLV
PM: Why is road transport suffering so much from a shortage of people?
where suddenly it’s become critical. We rely on migrant workers in the transport industry and they went home. We had a growing freight task anyway, then COVID comes along and operators are parking trucks up because they can’t get drivers. We’ve also had the exponential increase in the freight task because consumers demanded change and want home delivery. Suddenly we’ve got a new set of job requirements for that last mile and it’s put a real microscope on this issue and we haven’t got enough people. Migration is one answer but it’s a short-term fix. It’s a part of the solution but we also need to look at how we skill people for jobs now and create future opportunities for them as jobs change. The heavy vehicle driver apprenticeship is not a panacea either. There is a combination of factors which needs to be put in play to make a difference, but each factor can impact and drive change. We try to be very clear in the messaging we’ve done around the apprenticeship that this is part of the solution, but it’s not the total answer.
of occupations but ultimately, it’s about skills and supporting people and supporting businesses. If they’ve got skilled people businesses are more productive.
64 september 2022 PERSONALITY
PM: The US reports annual driver turnover of around 89 per cent. Will an apprenticeship in Australia keep people in industry?
PW: That’s a recruitment nightmare and it’s a different market to ours’. My observation of the local industry is that typically once people come in, they tend to stay. There’s always going to be an attrition rate, but typically people stay within the industry because for many it’s
A
PW: I think it’s a couple of different reasons. We’ve been reporting driver shortages in the industry for as long as I care to remember but we’ve been able to manage the freight task in spite of that. However, we’ve had a unique set of circumstances brought on by COVID
Prime Mover: What got you into Paultraining?Walsh: When I finished driving, I moved into operations and then training and was the National Training Manager at TNT for a couple of years. About ten years ago it was suggested to me to work in the skills area which I’d always had an interest in. I wanted to be more involved in developing people and training opportunities. I’d taken on some nationally recognised training myself at one point in my driving career, and that set me on a path of undertaking a few more vocational qualifications to build my business skills and understand management processes.
ustralian Industry Standards (AIS) is focused on future skilling Australia’s workforce through working in partnership with industry, the vocational education and training sector, and governments. Paul Walsh is the CEO and is himself a former truck owner-driver.
PW: When I was at TNT we put a lot of people through vocational skills training. The transport industry typically has a lot of people who have never completed any vocational qualification, and some who have never completed high school. The first step was giving them recognition of the skills they have, which can be massive because many of them under-rate themselves and they just assume they were never good enough to finish school. By recognising their skills, whether it’s an equivalent trade level qualification at Cert III, or a more advanced qualification such as a Cert IV or a diploma, when they get awarded a qualification, they realise they actually have valuable skills. Not everyone wants to go to the next step, but it does create opportunity for people to consider what else they can do in their career
PM: What’s a brief overview of AIS’s PW:goals?
We create vocational qualifications which people can then use to recognise or develop their skills and knowledge. Part of our job is to actually promote vocational training and its benefits. We work in the transport industry and we also support the energy industry and there is a lot of synergy between the two. There may be different kinds
PM: What are some of the steps in improving skills?
PM: Should there be a stronger focus on recruiting 30- or 40-year-olds instead of younger people?
primemovermag.com.au 65
PM: What of the issue of the ageing PW:workforce?
Depending upon the statistics you look at, the average age is somewhere between 50 and 56. That’s a number that isn’t shifting and it’s telling us that for truck driving it’s often a career that people will pick up as a second or third or fourth or even fifth career. The average age is likely to remain high and obviously we’re all living longer so we’re staying in the industry longer. That’s not necessarily a bad thing but we do need to encourage younger people into the industry.
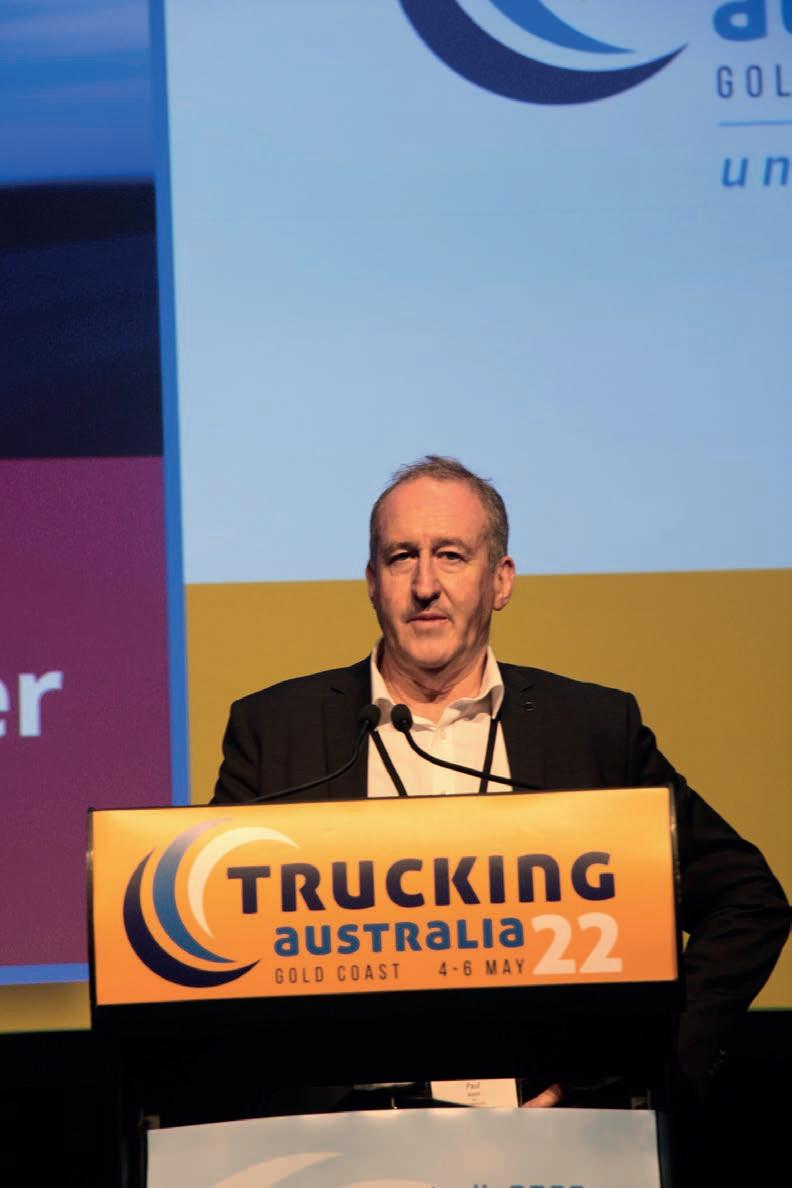
an opportunity or they change careers because the industry they were in has gone through change. These people are attractive to our industry because they bring a lot of transferrable skills and can be upskilled quickly. The other issue we often hear reported from industry is around the gap between school and truck driving, because there isn’t a clear pathway. They get out of school, go and do something else and then the industry has to try to attract them to join. One way of addressing that is the heavy vehicle driver apprenticeship which creates the pathway from school into industry. There is a way to do that even with the current graduated licensing scheme and various state associations are prosecuting that argument about changing to competency-based progression, which I support. We have a national vocational skills framework that is designed to assess the skills they’ve have, and to train and assess for the rest of the skills they will need. It’s important to note now that there is no push at this stage to mandate the apprenticeship to enter the industry. Let’s see if this starts to attract a new cohort and begins to make a difference. The underpinning aim is to demonstrate this is a professional career and is recognised as such. Some states are trialling arrangements where they are creating an entry pathway into a driving job where you do elements of the qualification to get you jobready and working. From there you can continue into doing the whole of the
Paul Graham.
apprenticeship qualification over time while you are on the job.
PW: People will often go off and try different things but by their late 20s or 30s they join the transport industry for
PM: What about the physical PW:demands?
ING
PM: Does the female gender provide an PW:opportunity?
Women make up less than four per cent of the truck driving workforce and that’s a huge opportunity when we need more drivers. Anything we can do as an industry to bring more women into the workforce is a really good thing for all of us. Women can change the dynamic in the workplace and the industry. They make great drivers and are often a lot more sympathetic on the equipment. There are fantastic careers in this industry and it’s not just truck driving. Jobs are going to change over the next five, ten, or 20 years which brings massive opportunities. The industry just needs to get the word out on how good it is.
THE SHORTAGESKILLS
When my father was driving trucks it was tough work and could give your body a bit of a beating. A lot of that has changed. It can still be pretty tough, but the equipment in today’s trucks, and the methods we use for manual handling have improved a lot, so the job is a lot more sympathetic to the driver than in the past.
a way of life, they like the culture of the industry and once they are in and have got through the first couple of years, they tend to hang in.
avid Muir has worked as a chemical tanker driver for Formula Chemicals in Sydney for the past four years and is acknowledged by the industry as a worthy recipient of the prestigious award which is sponsored by Teletrac Navman. The award is in recognition of David’s driving abilities as well as his dedication to the safe and efficient operation of the 26-tonne bulk tanker and the service he provides to
which holds 10,000 litres of various liquid chemicals such as chlorine, hydrochloric acid, sulphuric acid and sodium hydroxide. Driving a dangerous goods vehicle comes with its own set of challenges, especially in metropolitan traffic conditions where David is bound by legislation to not use any of Sydney’s ever expanding tunnel network and instead operates on the busier surface roads. As well as local Sydney deliveries, David transports bulk chemicals to many
D
Formula Chemicals’ customers. David came to Australia from the Scottish city of Edinburgh in 1990 and spent a decade driving State Transit buses around Sydney’s northern beaches where he says he learned to be patient in traffic. After moving with his family to the NSW Central Coast, David drove trucks for a local chemical company before signing on with Formula Chemicals four years ago. David is currently the main driver of the specialised rigid tanker
David Muir is the recipient of the Road Freight New South Wales Professional Driver of the Year award for 2022.
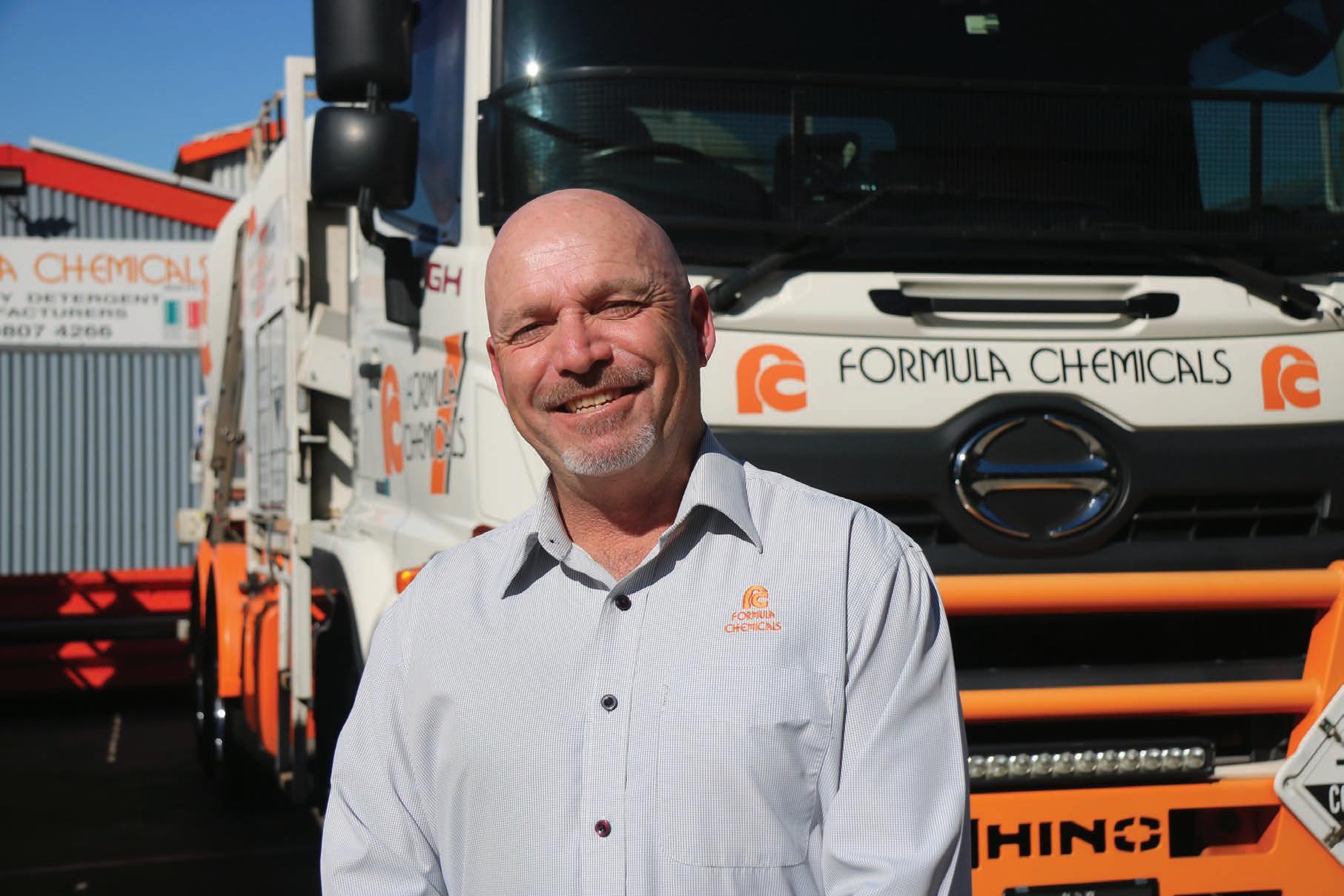
ACHIEVER
QUIET
66 september 2022 PRIME MOVERS & SHAKERS
In common with most truck drivers, David’s main concerns are other drivers not using indicators and cutting trucks off.
Delivering large quantities of dangerous goods involves a higher level of responsibility than, say, groceries and in addition to careful driving the operator has to ensure the unloading is carried out safely without spillages and that the correct product is transferred to its appropriate storage tank. David appreciates the chemicals carried are very important to the communities he delivers to.
David’s preference is not just to pull up on the side of the road in a truck rest area but instead take his breaks where there are plenty of facilities.
“They rely upon us,” he says. “A lot of little country towns have populations of only 500 people and their local swimming pools are pretty important for
“Here they are all automatics, and have got all the safety devices, as well as being a lot more comfortable,” he says. “Leigh’s (Formula Chemicals Managing Director Leigh Smart) reputation is for everything to be spot on. Once you leave this depot you know if you’ve done your correct checks, you’re safe on the road.”
“I normally stop at my usual places because I know they’ve got restaurants and toilets, and I can pull in, freshen up, use the bathrooms and get out and stretch my legs for 15 minutes,” he explains.
As a former under 10s and under 16s soccer coach, David’s interest in his own health and well-being means he doesn’t partake of the usual truck stop fast food meals when he is on an out of town trip. “I always take my own food so I’m not buying fast food,” he says. “I think it tends to make you sleepy. It’s not that I don’t eat it, but I tend to stay away from it when I’m driving. I’ll take a packed lunch with me with a muesli bar and some Davidfruit.”hasa personal policy of taking longer than the minimum required rest breaks stipulated by his Basic Fatigue Management accreditation.
David is an enthusiastic supporter of his Electronic Work Diary (EWD).
“If I’m on a long trip I stop for at least 15 minutes every two to three hours, and then, when I reach my destination, I’ll have at least another half hour break,” David explains. “On the way back I’ll do the same again and have a 15- or 30-minute break after the first couple of hours driving.” According to David he’s been doing the job for so long that he can plan his day the night before he “Ifleaves.I’m going down the Hume I know that it will take around two and a quarter hours to reach Sutton Forest so I can have my 15 minutes break, then go on to my destination,” he says. “A lot of drivers stretch it out to the maximum driving time according to the log book but I find that tiring. If you’re driving five hours solid, especially going down the Hume Highway, you’re just focusing on one strip of road. That’s why I’ll split it into four, sometimes five sections.”
David Muir.
primemovermag.com.au 67
them, especially in the summertime.”
“They don’t realise they are taking away our safe stopping distance in case of an emergency,” he says. “My top tips for drivers would be drive to the speed limit, drive to the road conditions, be patient and try not to get aggressive with other Daviddrivers.”appreciates the modern equipment operated by Formula Chemicals. At the previous company every vehicle was a manual.
“There are different challenges every day and you tend to challenge yourself to see if you can do better,” he explains. “Traffic can disrupt the schedule but I try to give myself plenty of time and I don’t rush.”
“That was 19 years ago,” he says modestly. Since receiving the award David feels that his already admirable attitude has been boosted and he is now even more customer focused, to the point he will frequently go out of his way to assist with components such as tank fittings.
“I’m happy what I’m doing and I don’t need to go anywhere else,” he says. “I’m 56 now and I’m happy with what I do and my lifestyle.”
NSW country centres including Wagga Wagga, Cootamundra, Young and Junee as well as west of the mountains to Orange and Manildra.
Dangerous goods vehicles in NSW are the subject of often intense scrutiny by a diverse group of authorities which includes the Highway Patrol, Transport for NSW through the Roads and Maritime Services which transitioned to the NHVR on 1 August this year, SafeWork NSW, the Environmental Protection Authority, and even the Federal Police. Through his dedication to safe operation David has been accident-free for the past 24 years and when asked when he received his last infringement notice the smile lines around David’s eyes indicate his pride in his remarkable record.
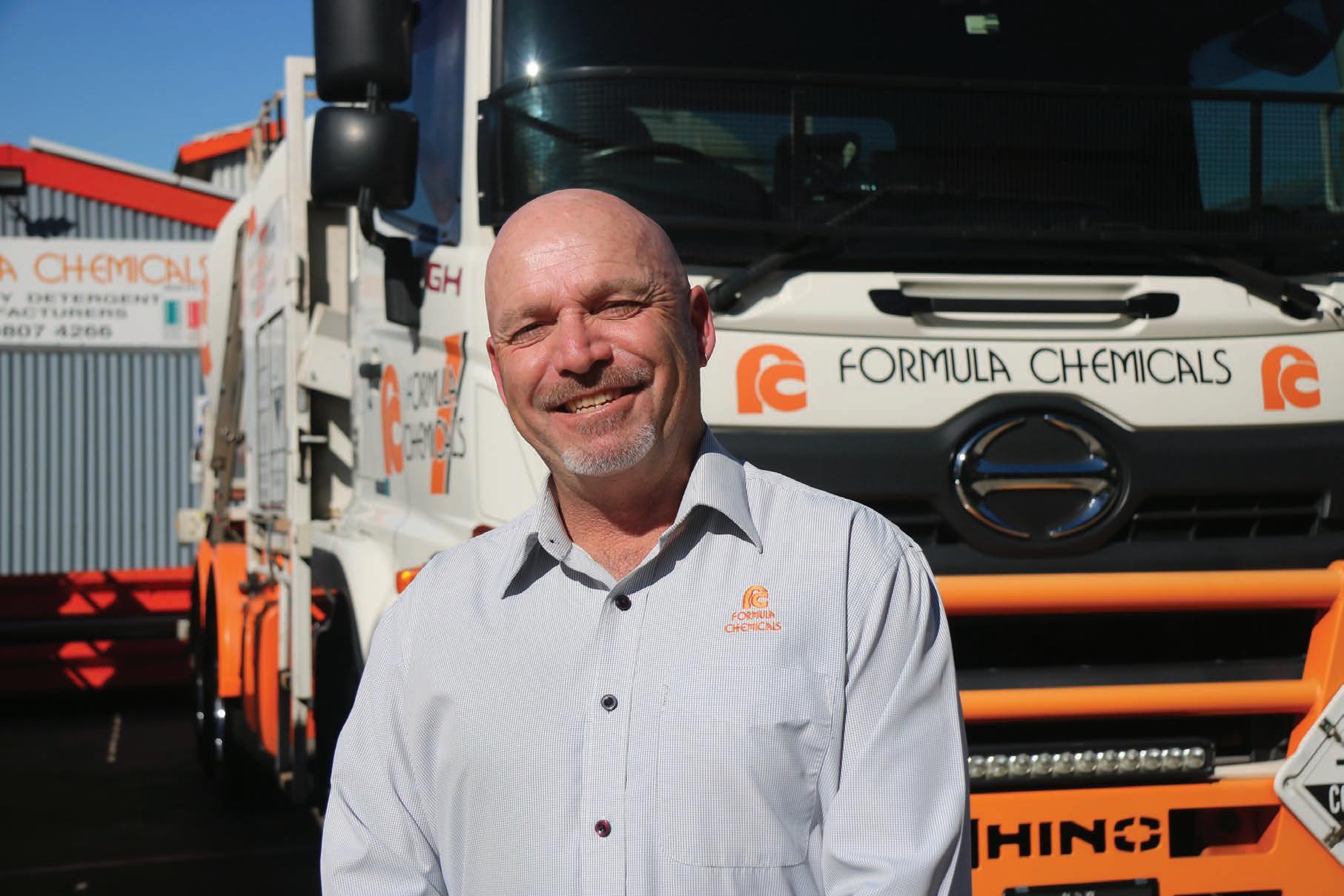
HILUX
“Thecustomers.significant suspension upgrades to the HiLux Rogue not only improve off-road capability but create a more stable and comfortable on-road driving experience,” he said. “Continuous improvement is a key facet of Toyota’s philosophy and has been clearly achieved by this latest HiLux premium Duemodel.”tothe vehicle’s suspension changes, roll rigidity has been enhanced by 20 per cent, improving steering feel when cornering and changing lanes. The HiLux will also receive a brake upgrade, with new rear ventilated disc brakes replacing the existing drum brakes for ‘enhanced braking performance’, and larger 17-inch front disc brakes replacing the predecessor’s 16-inch ones. Wide track overfenders and mudguards have been installed to house the increased track width, and the front body extension has also been widened to seamlessly integrate with the front bumper.
Toyota HiLux Rogue 4×4.
bodied Rogue, the HiLux’s core variants will receive a series of upgrades from Toyota as well.
Toyota has announced a massive performance and capability upgrade for the HiLux Rogue 4×4 flagship pick-up, which will be enhanced with a wider track and updated suspension package in the fourth quarter of 2022. The new dual-cab HiLux Rogue will see a track increase of approximately 140 mm in the front and rear, while the vehicle’s ride height has also been increased by 20 mm. To accommodate the track increase, the length of the HiLux’s front suspension arm and front stabiliser bar have extended, and the shock absorber angle has been adjusted to improve Rearefficiency.axle length has also been extended, dampers have been moved further out towards the wheels, and, for the first time on a HiLux, a rear stabiliser bar has been installed to enhance cornering stability and ride comfort. Toyota Australia Vice President Sales, Marketing and Franchise Operations, Sean Hanley, said the HiLux’s upgrades demonstrate Toyota’s dedication to
SR extra-cab and double-cab models will get new black 17-inch alloy rims, replacing its previous steel wheels. Body-coloured door handles will also come along for the ride for a more premium look. For the SR5 double-cab pick-ups (also included in the Rogue), extra active safety equipment will come as standard with the addition of blindspot monitor and rear cross-traffic alert for ‘greater on-road peace of mind’. A panoramic view monitor has also been added to the SR5s to help them manoeuvre in tight spaces, as well as puddle lumps which replace heated exterior mirrors. Its steering column lock has been replaced by an ID Box anti-theft immobiliser on automatic SR5 grades and above, which Toyota says will add an extra level of security when starting the car with the smart key.
NEW RANGE RECEIVES SAFETY, CONVENIENCE UPGRADES
Toyota is also planning on launching a new apex off-road HiLux variant, which
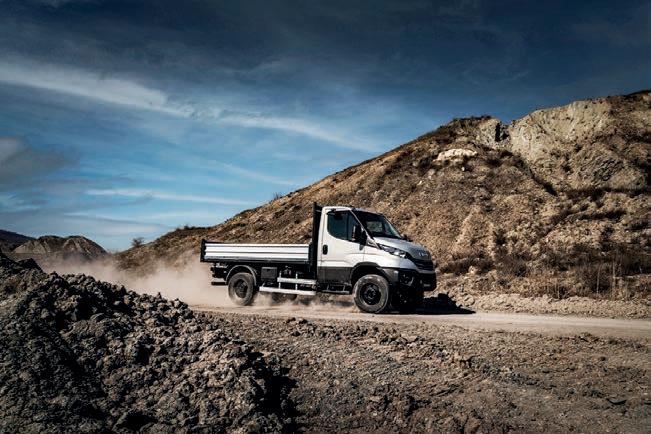
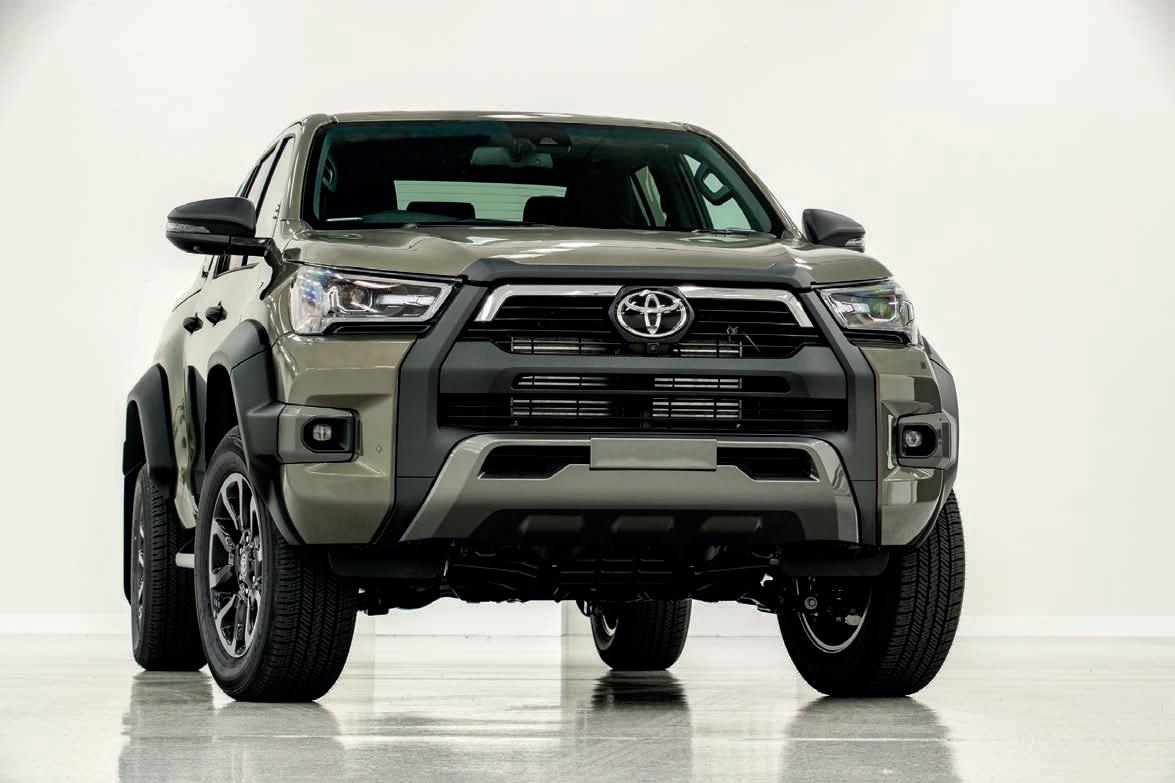
DELIVERY NEWS
68 september 2022
The new model will be available in single and dual cab variants with 7t GVM and three wheelbase options. IVECO’s 8-speed full automatic transmission is another important addition to the new release to provide a more relaxed driving experience in demanding off-road conditions.
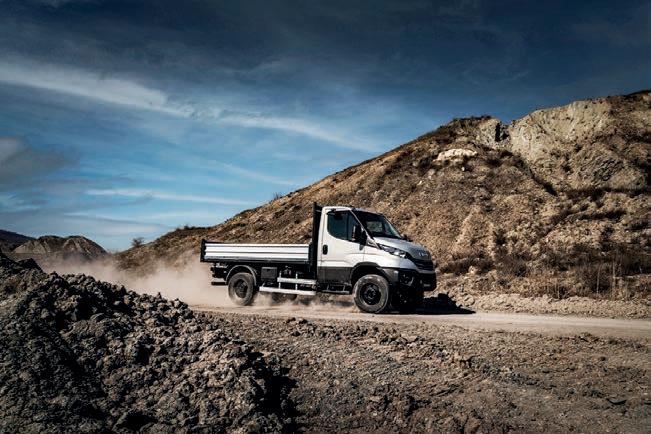
Canoo vehicles, the LDV is built on a proprietary multi-purpose platform (MPP) architecture that integrates the motors, battery module and other critical driving components. The LDV has a last mile delivery optimised cabin and customised cargo Canoospace.isutilising true steer by wire technology, reducing moving parts and cabin intrusion, resulting in more usable interior space, better driver ergonomics and the addition of a panoramic window to improve road visibility.
of refinement and independent front suspension to improve ride dynamics. Rear suspension remains parabolic three-leaf, ensuring the vehicle continues to offer generous load carrying abilities.
The LDV is engineered for high frequency stop-and-go deliveries and speedy vehicle to door drop-off, including grocery and food/meal delivery. Its customised interior is designed for small package delivery, at competitive per stop economics. The modular design and 120 cubic feet cargo volume are adaptable to evolve with customer needs which contributes to a decreasing per unit investment over time.
IVECO TEASES NEW DAILY 4×4
“We are proud to have been selected by Walmart, one of the most sophisticated buyers in the world, to provide our high-tech, all-electric, American made Lifestyle Delivery Vehicle to add to their impressive logistics capabilities,” said Tony Aquila, Canoo CEO and Chairman. “Our LDV has the turning radius of a small passenger vehicle on a parking friendly, compact footprint, yet the payload and cargo space of a commercial delivery vehicle. This is the winning algorithm to seriously compete in the last mile delivery race, globally.”
The full automatic integrates with the truck’s Euro 6, 3.0-litre turbodiesel engine, resulting in a flat torque band and extremely efficient use of the powerplant’s 132kW (180hp) and 430Nm. A six-speed manual transmission continues to be offered for those who prefer to self-shift. As standard, the new models feature centre, front and rear differential locks to provide high levels of traction offroad.
New IVECO Daily 4x4.
deliverymagazine.com.au 69
Canoo’s Lifestyle Delivery Vehicle.
WALMART MAKES HUGE EV ORDER FROM CANOO
American retail giant, Walmart has committed to purchasing 4,500 electric vehicles to be used for its last mile deliveries. The battery electric vehicles have been ordered from high-tech advanced mobility company, Canoo, to support Walmart’s growing e-commerce Havingbusiness.signed a definitive agreement with the option to purchase up to 10,000 units, Walmart is committed to deploying the Lifestyle Delivery Vehicles (LDV) as part of the company’s goal to achieve zero-emissions by 2040. While the LDV is expected to begin hitting the road in 2023, the companies have recently commenced advanced deliveries to refine and finalise vehicle configuration in the Dallas Fort Worth Canoo’smetroplex.fully electric Lifestyle Delivery Vehicle is an American-made commercial EV optimised for sustainable last mile delivery use cases. As with all
Full technical details on the new Daily 4×4 will be supplied closer to its official launch date.
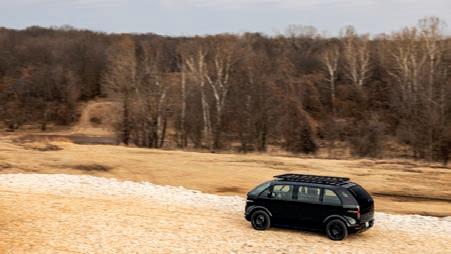
The latest generation Daily 4×4 cab chassis model has been teased by IVECO ahead of the vehicle’s proposed official Australian launch in the second quarter of 2023. As a favoured platform for expedition motorhomes, mining, exploration, forestry, emergency service work and similar applications that require extreme off-road ability, the new Daily 4×4 introduces new levels
The transfer box also has a PTO option, allowing power delivery to a broad range of ancillary equipment, from tipping bodies, to pumps and Andrills.expansion module with CAN open interface allows further customisation of bodies and accessories. Braking in the new model comes courtesy of ventilated disc brakes all round with ABS and Electronic Brakeforce Distribution, part of IVECO’s broader ‘ESP9’ program which offers a range of active safety equipment including Electronic Stability Program, Anti Slip Regulator, Hill Hold Control and others. The overall safety package also includes driver and passenger SRS AAirbags.raftof interior cabin changes have also been introduced to the new models to further improve ergonomics and connectivity.
Corcoran, currently Vice President Commercial Australia will assume the role of Managing Director, Australia and Papua New Guinea, effective 1 January 2023 and will report to Ken Lee, CEO Asia Pacific, DHL Express.
DELIVERY NEWS 70 september 2022
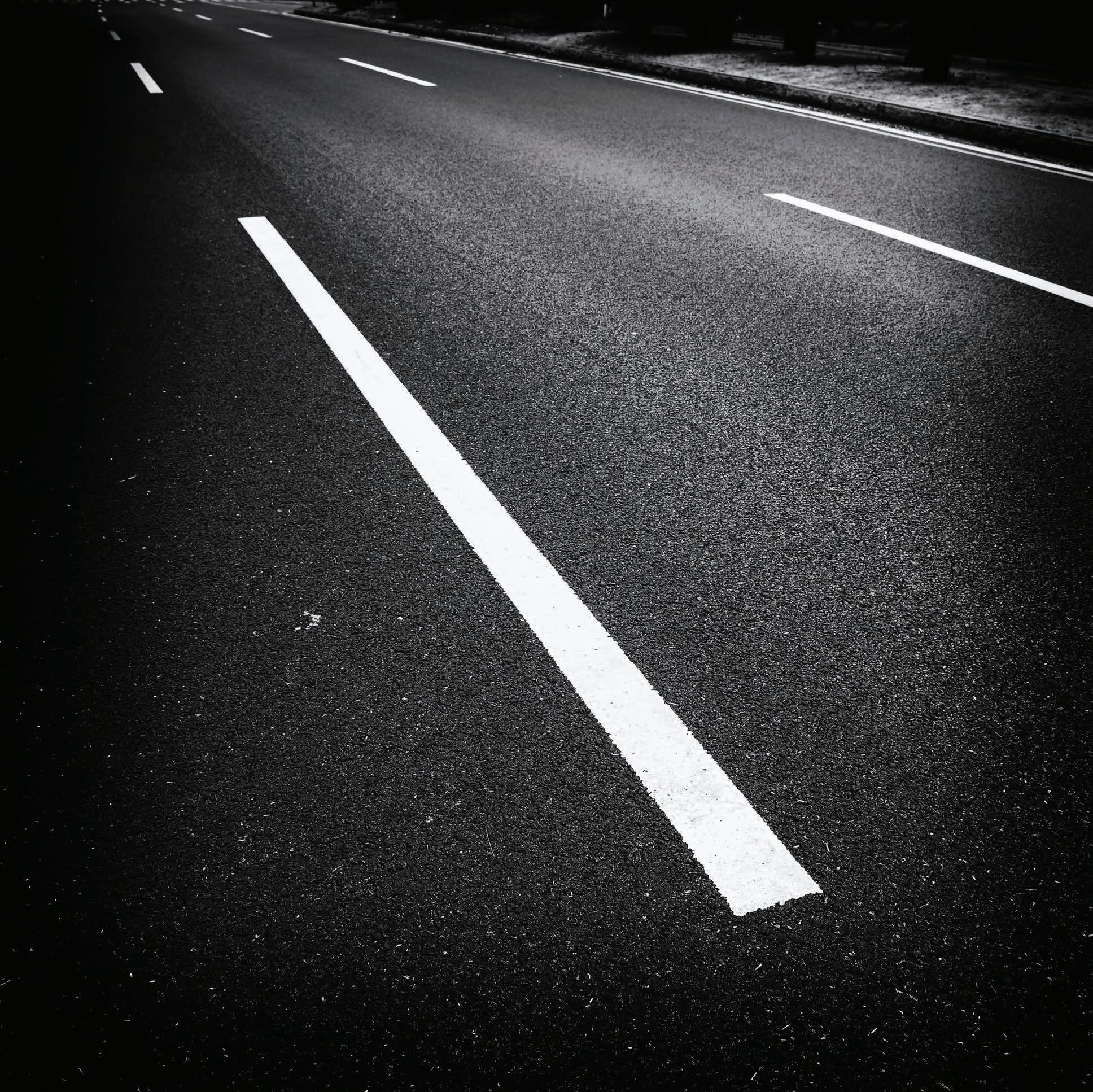
The six months from July to December 2021 were particularly strong as the impacts of COVID saw Australians turn to e-commerce like never before.
Popular buys were pet products (up 38 per cent YOY), tools and garden items (29 per cent) and products from major and discount stores (32 per cent), while baby products and athleisure items also grew. Recent End of Financial Year (EOFY) sales were also a boon for sellers of athleisure, sporting and outdoor goods, which were all up on the previous month.
Gary Edstein.
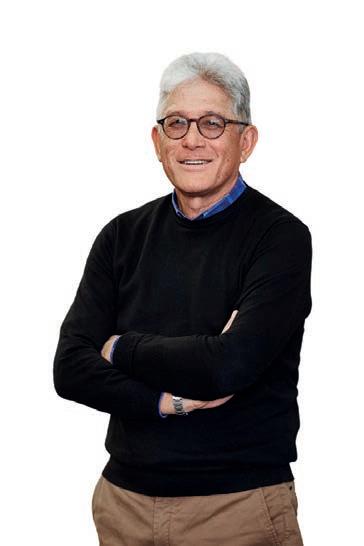
“As the Vice President Commercial Australia, Phil has led the commercial development of our business with a high-performing team, delivering consistent double-digit growth through unpredictable economic conditions,” said Edstein. “His customer-centric focus and advocacy for our culture of respect and results place us in a strong position going forward.”
Australia Post has delivered to 9.3 million Aussie households after fulfilling record online purchases in the past financial year. For just the second time ever, total households shopping online across the nation surpassed 9 million. This was up from 9.1 million the previous financial year, while online purchases grew almost 12 per cent.
With 26 years of experience with DHL Express, Corcoran’s appointment strengthens the business’s position with in-depth market knowledge and experience. Starting his DHL career in Australia in 1996, he has held various commercial and management positions across the Oceania region, including General Manager for Fiji and the Pacific Islands (2002), National Sales Manager New Zealand (2005), and since 2012, Vice President Commercial Australia.
With the Australian arm of the business established in 1972, this year marks the company’s 50th year of operations in the country.
AUSPOST SHATTERS ONLINE RECORDS
Under his strategic leadership, the company is now the market leader of the Time Definite International industry, growing its presence as a B2C brand. In 2021, DHL Express Australia was named the 2nd best workplace in Australia by Great Place to Work, and the company’s employee engagement
An average of 5.6 million households purchased something online each month in FY22, 1.5 million more than the average in NewFY20.South Wales, which experienced extended lockdowns last year, grew more
than 27 per cent year-on-year (YOY) and had the highest participation compared with its share of population, with around one in three purchases destined for the state.
The ACT (more than 27 per cent YOY) and Western Australia (14 per cent YOY) also saw significant growth in online purchases Moreyear-on-year.thanabillion parcels have been delivered via Australia Post’s online parcel management platform since its launch in 2016, and Australia Post Head of eCommerce Analytics Rose Yip said the growth in online shopping had accelerated beyond expectations throughout the “We’vepandemic.seen more than 900 million parcels delivered in the last three years alone,
“I am excited to see Phil Corcoran taking over the mantle. I am very confident that he will continue to build on the success with the support of a very knowledgeable leadership team in the Edsteinregion.”more recently spent 20 years leading the Oceania, Australia and Papua New Guinea regions. His career with DHL began in 1986 as Sales Manager, before going on to lead as Country Manager for the New Zealand and Pacific Islands business (1993), Australia business (1998), and a stint overseas as Director Express for Logistics Japan (2000) and Project Director, Asia Pacific Logistics Optimization (2002).
studies have consistently recorded scores over 90 per cent.
“Gary has dedicated his career to DHL and he has been instrumental in positioning DHL Express as a market leader in Oceania,” said Ken Lee, CEO, APAC, DHL Express. “He has increased our market share
DHL EXPRESS CONFIRMS LEADERSHIP CHANGES IN AUSTRALIA
and revenue, built the partner network and laid a solid foundation for future growth.
which says so much about how quickly e-commerce has grown in a short amount of time,” she said. “It’s now the norm for so many Australians, with more than five million households regularly shopping online every month, which is why we’ve not only increased our network capacity but we’re investing in more new facilities, technology and our fleet to set up a strong and sustainable network for the future.”
SAFETY APPLICATIONS & TECHNOLOGY
Integrated systems in commercial vehicle technology increasingly bring together a variety of applications designed, developed and tested to give the operator a safer, more efficient throughput in their operations. From the latest in electronic braking systems, tyre, temperature and driver monitoring to heavy vehicle visibility, whether in reflective tape to LED lights, a modern day truck is very much, when it comes to safety, the sum of its many parts. Changes in lighting conditions and visibility are considered key factors in driver fatigue with major innovations in LED lighting now a must on the latest high tech prime movers.Adaptive headlamps, daytime running lights, emergency stop lights, cornering lamps and enhanced vehicle visibility markings are must-haves for uniform fleets. It’s also now clear that the number of crashes involving heavy vehicles can be reduced if the driver of a heavy vehicle is informed of upcoming situations and given adequate warning of potential dangers. Electronic Stability Control.Trailer Roll Stability.Autonomous Reverse Braking.Antilock Braking Systems. Blindspot Elimination.Wheel Nut Indicators.These are just a few of the innovations that contribute to safer highways, drivers and businesses. Get involved in our upcoming showcase on safety applications and technology to inform potential customers of how your solution can change their world for the better.
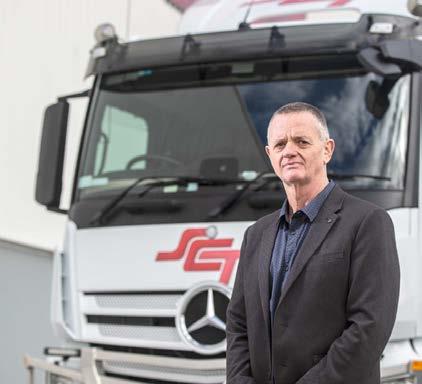
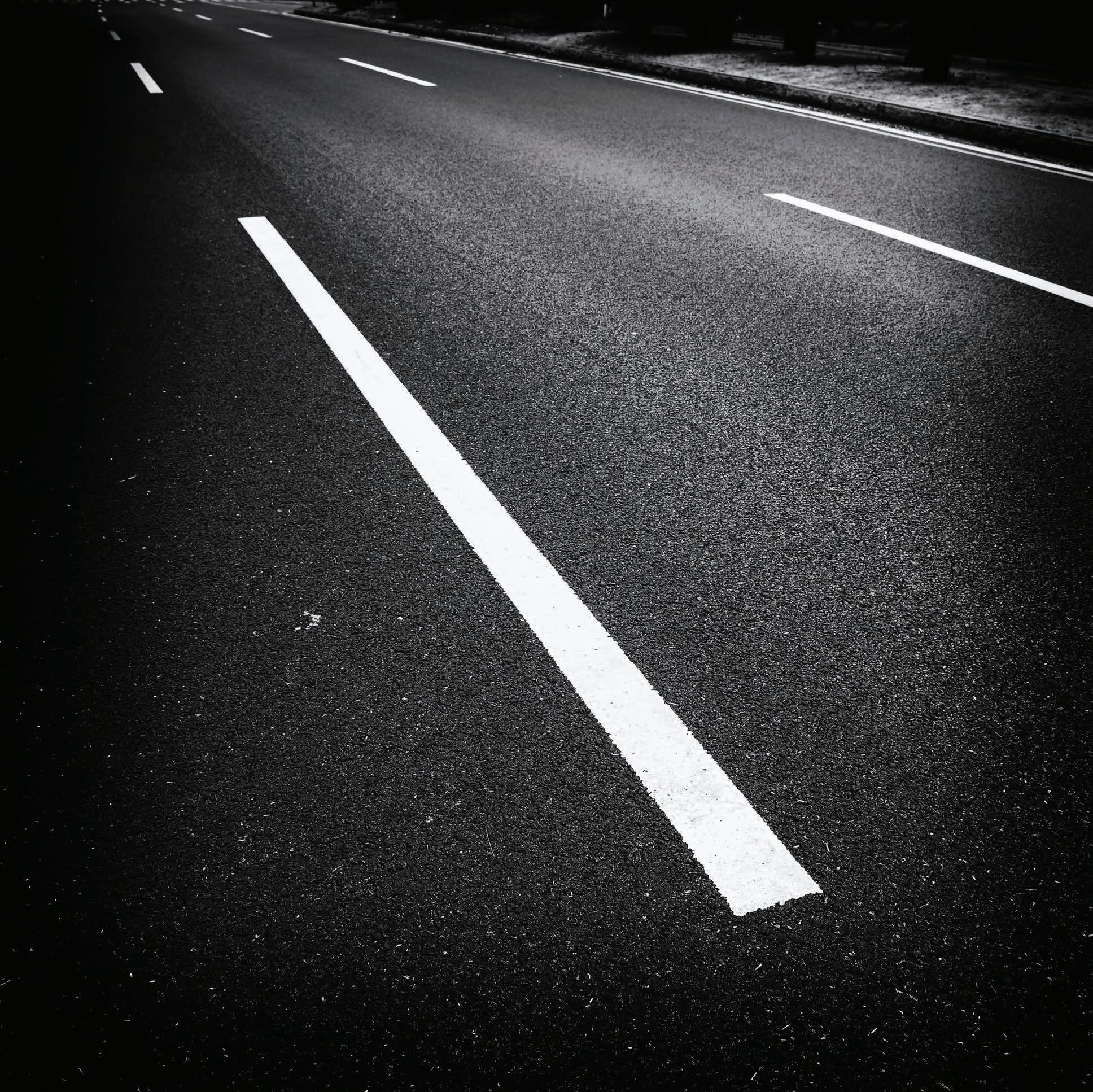
ISSN 1838-2320 9 771838232000 08 SEPTEMBER 2022 $11.00 SCT Heaven’sLogisticsGate Innovation Fleet: South East Queensland Hauliers Technology: Battery Electric Vehicles Test Drive: Hino range Delivery: Fukushima Prefecture Industry Fleet: Feature:McColl’sRussell Transport Showcase: Heavy Vehicle Insurance Personality: Paul Walsh THE PEOPLE & PRODUCTS THAT MAKE TRANSPORT MOVE Delivery Magazine inside: Pages 68-73. ® September 2022 ASHLEY.BLACHFORD@PRIMECREATIVE.COM.AU | 0425 699 819 TO BOOK IN PRIME MOVER CONTACT ASHLEY BLACHFORD NOW 22 SEP 2022
BOOKING DEADLINE
ADVERTISE IN OUR NOVEMBER 2022 PRODUCT SHOWCASE ON TRUCK SAFETY APPS & TECH.
list of others, aim to strengthen shared convictions and expand their circle of cooperation by steadily working towards the realisation of one of the world’s first hydrogen societies. Part of this process is contingent on the successful introduction of light-duty fuel cell electric trucks and establishing energy management systems that are integrated with their operational Inmanagement.collaboration with Commercial Japan Partnership Technologies (CJPT), the consignors and logistics businesses, infrastructure providers, and automakers will work together
FUTURE TENSE 72 september 2022
the essential urban infrastructure with provision to look at evacuation areas in times of Hydrogendisaster.produced in Fukushima,
ssential urban infrastructure and the role hydrogen will play as a new source of energy is the focus of an ambitious joint venture underway in Japan. Discussions between Fukushima Prefecture and Toyota Motor Corporation began in earnest June last year regarding initiatives for creating an implementation model involving hydrogen use in cities. Cities with populations of around 300,000 have been identified as the ideal test beds for the project before it is rolled out to similar-sized cities nationwide. The project initially concentrates on
which has a population density of 370 inhabitants per square kilometre, and hydrogen-related technologies developed in the city are set to be utilised.
A fuel cell electric vehicle proposed under the CJPT partnership.
Hydrogen truck technology undergirds a new project in Japan that aims to show what last mile logistics will look like in cities of the future.
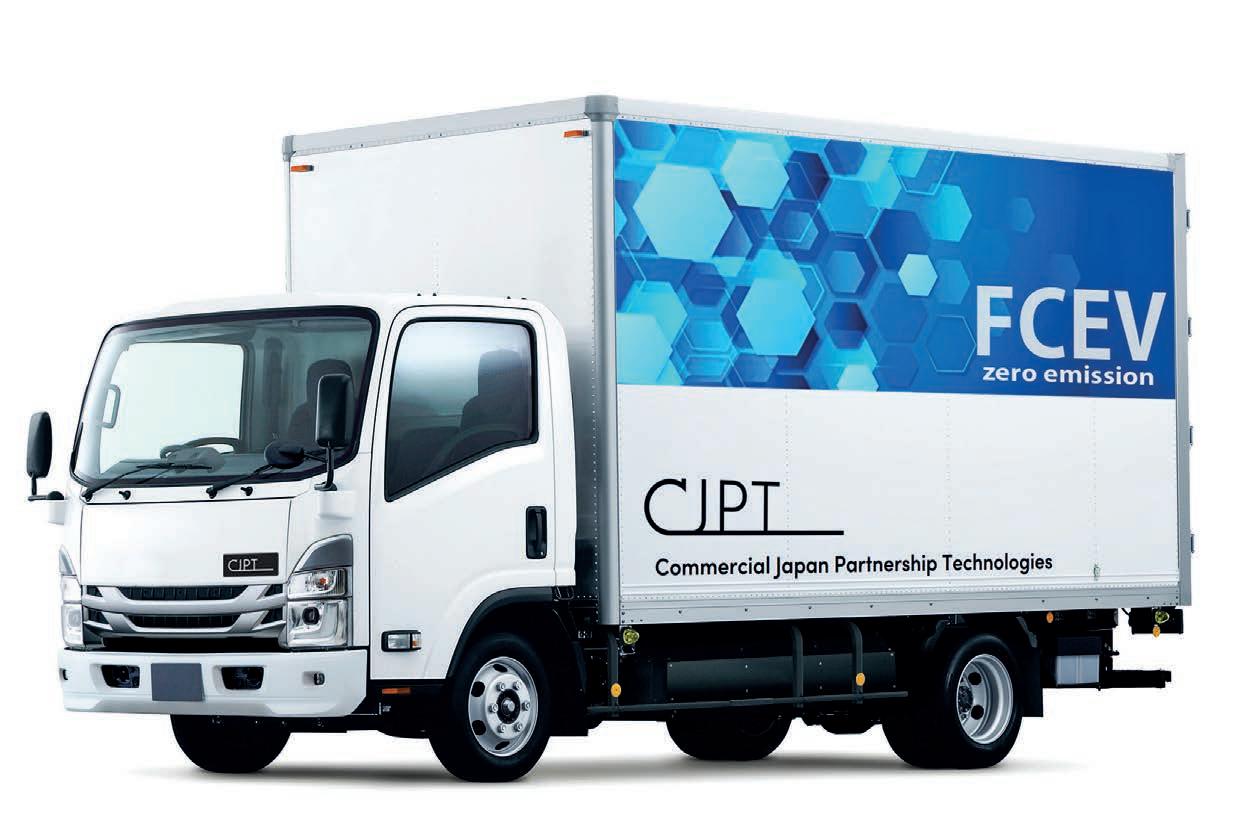
E
CITY LIMITS
Efforts are underway to establish what has been described as a sustainable society without any clear definition beyond reaching carbon neutrality by 2050 which brings it into alignment with World Economic Forum deadlines. Fukushima Prefecture, Toyota, and
60 light-duty fuel cell electric trucks will be introduced in Iwaki City and Koriyama City, and there are plans to introduce heavy-duty fuel cell electric trucks as well. Much of this working will hinge on the successful promotion of fuel cell electric vehicles whose intended use will be as varied as Toyotapossible.has,starting back in June, promoted the use of a mobile retail vehicle equipped with electrical appliances such as refrigerators and freezers in the towns of Namie and Futaba, in order to better understand the power generation capabilities of fuel cell electric vehicles.
The Fukushima project also seeks to increase the use of renewable energy and establish models that utilise hydrogen. Photosynthesis in plants, for one, is considered a promising avenue to reducing emissions through synthetic fuels based on electricity from renewable energy sources. Denso Fukushima’s plants will be used to showcase the implementation of hydrogen technologies. The local consumption of locally produced hydrogen is set to commence via development of new electrolysis equipment to produce clean hydrogen and combust it in the plants’ gas furnaces. In addition to the installation of stationary FC generators in offices to reduce carbon emissions, Fukushima Prefecture and Toyota will also begin implementation with a view to using them as a power source in times of disaster. The possibility of installing the FC generators in stores will also be studied.
Plants in Fukushima will be used to showcase the implementation of hydrogen technologies.
management. As convenience stores and supermarkets begin to introduce fuel cell light-duty trucks from January 2023, Toyota intends to build an energy management system that links the fleet management system of each company, vehicle travel information, and hydrogen station information. According to the plan, this system will provide optimal placement and operating conditions for hydrogen stations, avoid traffic congestion at hydrogen stations, and minimise vehicle and cargo downtime due to travel time to and from hydrogen
While having a highly pressurised tank to store hydrogen remains a prohibitive factor in hydrogen investment, researchers at Deakin University have discovered an energy-efficient way to capture hydrogen gas into a boron nitride powder. The powder has a large surface area relative to its volume, making it an ideal capture material. Once the gas has been absorbed into the powder, it can be transported at normal atmospheric pressure, which is deemed safer than a high-pressure tank or liquid hydrogen. The technique, according to the researchers, is also less energy-intensive and safer than the other storage alternatives. It’s these kind of breakthroughs, should they prove enduring in application, that offer glimpses of how the technology
of residents in local communities,” Toyota Motor Corporation declares in a statement. “By introducing vehicles capable of generating new value through the use of electricity and having a clean and quiet usage environment, this project will bring a range of benefits, including helping to make cities more convenient― especially those with ageing populations or those suffering from depopulation and will help promote the appeal of Fukushima Prefecture.”
Approximatelystations
Toyota, through these efforts, hopes to build a hydrogen utilisation model that can be implemented in various industries and regions. Details of these efforts would eventually be publicised by the joint venture partners to encourage uptake across other regions.
deliverymagazine.com.au 73
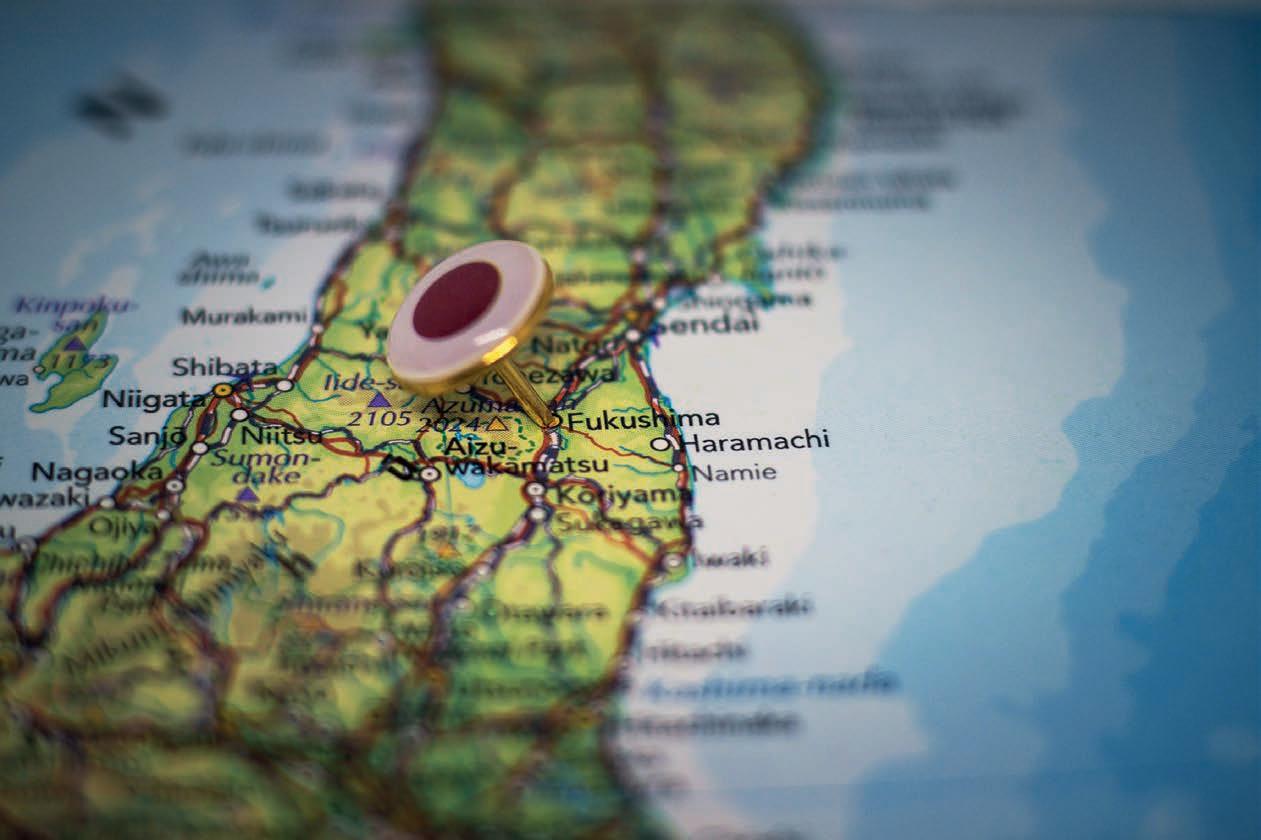
september 2022
INSIGHT | VICTORIAN TRANSPORT ASSOCIATION 74 december 2018 INSTITUTE
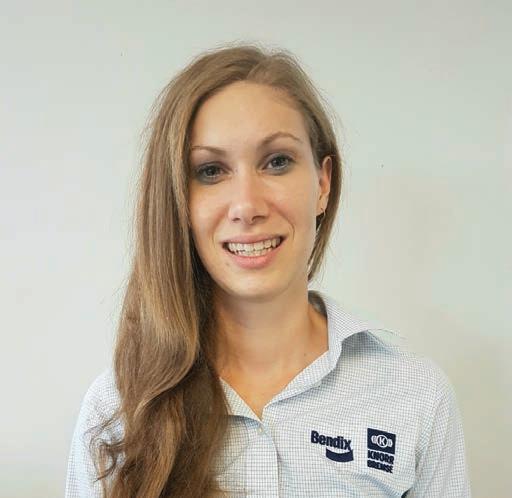
Electronic safety systems and recent heavy vehicle mandates – is it working?
• Vehicle Stability Functions (VSF) (Heavy Vehicles) and
From a data driven perspective, no. Anecdotally, yes. The data we require to be certain of the impact of the electronic safety systems for braking is not easily obtainable and in most cases, not tracked at all. There is addtionally no national road data or insurance level data allowing the operational status of the safety system to be confirmed for each incident. Annecdotal evidence and case studies support that there is a measureable positive safety impact of fitting electronic safety systems for braking to heavy vehicle combinations.
W
Both RSP and VSF features are often referred to in generic terms such as Electronic Braking Systems (EBS) or Electronic Stability Control (ESC). The mandated features allow for measurement of speed, lateral accelation, yaw rate, mass, vehicle COG and others to determine when to automatically reduce throttle
e’ve come a long way in Australia in the last decade with our collective focus on road safety and the role our heavy vehicles play. All levels of government and industry including work safe, large fleets and insurers have contributed to numerous programs in an attempt to reduce the number of serious incidents and deaths. These reductions don’t just benefit the public in saving lives, but also reduce the significant cost burden currently estimated as A$30Bn every year. Over the past decade, one of the key strategies taken by the federal government in consultation with industry was to mandate the fitment of electronic safety systems:
RACHEL MICHAUD
• Antilock Braking Systems (ABS) (Truck and Trailer)
application, engage engine brakes and apply foundation brakes to reduce or mitigate the severity of a heavy vehicle incident. There is no replacement for competent driving and the systems cannot prevent every incident, but they assist the driver in maintaining vehicle stability, reducing speed and giving feedback when vehicles are driving too close to the limit. At the beginning of 2010, it is believed that fitment rates were as low as 5 per cent for both heavy vehicles and trailers. Now the current proportion of trailers fitted with RSP is estimated as 27 per cent and for heavy vehicles likely between 30 per cent and 50 per cent, depending on the technology. Given mandatory fitments on new vehicles/ trailers, a 95 per cent coverage is likely to be realised some time in the 2030s as the rate increases year-on-year.
In the logging industry, the number of rollovers for VicForest went from 40 trucks per year to virtually nil following the introduction of EBS in 2010. The Monash University Accident Research centre conducted a study estimating that VSF or RSP would result in a 4 per cent reduction in fatal crashes and a 7 per cent reduction in serious injury crashes. This report analysed real road and crash data from varying jurisdictions between 2000 – 2013. Weighting factors were utilised to determine the likelihood of ESC preventing a crash based on location, nature of incident, road quality, speed and weather conditions. This estimate does not take into account the ‘learning potential’ of ESC systems and the gains in driver awareness which could also assist in the human factors portion which is quoted as accounting for the root cause quoted by one insurer to be of at least two thirds of all road incidents.
Have the number of deaths and serious injuries decreased in the past decade?
Yes if we look at the National Road Statistics which found the average number of deaths per year from 20082010 was averaged at 1426, now from 2018-2020 averaging 1106 per year. This is even with an overall increase of 17 per cent in the yearly number of tonnes per kilometres travelled by freight vehicles.
Given a reduction in deaths, can some of the recent reduction in deaths on our roads be attributed to the fitment of electronic safety systems for braking?
• Roll Stability Programs (RSP) (Trailers) also known as Trailer Electronic Braking Systems (TEBS)
Rachel Michaud, Senior Applications Engineer and Technical Account Manager, Knorr-Bremse Australia
Know what is fitted — Ensure that there are adequate visual cues to the driver via stickers/dash communication that safety systems are fitted. When jumping into a vehicle for the first time, fleets need to ensure drivers are taken through the safety systems fitted and understand the warning lights, tell tales and ways to use the features. Positive education and a shift in culture is required to encourage drivers that the systems are there to help, not to hinder.
Learn from near misses — Create a positive work place culture where near incidents are reported and discussed, rather than hidden. Consider driver reward programs where Truck and Trailer downloads are used to assess good driving patterns. For instance, looking for lower numbers of RSP interventions, lower number of high
A close circuit rollover test takes place.

pressure brake applications and rewarding drivers for improving their data as a sign they are improving their driving. Many good operators have already adopted these processes and are seeing tangible results in incident reduction, reduced brake wear and better equipment condition generally. We believe that pairing the ADR mandates and increases in electronic safety system fitment with the above four key points, will make a measureable impact on heavy vehicle safety. We, the safety systems providers, are dedicated to working with industry to communicate these important messages. What is the point of fitting a life saving system if it’s not plugged in? There is an urgency for those of us involved in safety and the heavy vehicle industry to do our jobs, do them well and see our drivers home safely.
Plug it in — Education on the trailer EBS power connection and ensuring that operators know this is a legal requirement to plug in, combined with regular checks by fleet managers to ensure that its plugged in. Warn and educate drivers on first offence.
Powered by
Ensure its operating — Education for drivers on the VSF/RSP warning lights on the dash. Look for visual and audible indicators (chuff test, power lights). Regular downloads to be taken (minimum of every single trailer service) from the VSF/RSP systems to check that the system is functioning and fault free, including observance of intermittent faults.
In preparation of this article the collective view from industry was that, ‘The fitment of ESC on heavy vehicle combinations contributes significantly to reduction in serious injury or fatality on our roads if the system is powered and operational and the driver is working with the system to complete their trips safely.’ What this means is, there is still work to be done. NTI’s Major Accident Investigation 2021 report stated that on average 35 drivers have been killed every year in heavy vehicle crashes over the past decade and many more are seriously injured. This makes heavy vehicle driving one of the most dangerous work places in Australia. Given this, how can we better work with and educate our drivers to give them the tools they need to get home safely? What can we do with respect to electronic safety systems and ensuring the mandates allow them to work and possitively impact the cause? Recent discussions with industry point to the below:

news COMMERCIAL ROAD TRANSPORT
primemovermag.com.au 75 ARTSA-I LIFE MEMBERS
Hopefully we have now seen the worst of the COVID pandemic. We have a new Federal Government elected on a strong mandate to deliver our Australian share of global carbon abatement over the next couple of decades. We also are witnessing the launch of twenty first century, zero emission, truck trials and new truck sales here in 2022, however we still have a RUC scheme that is reliant on diesel fuel revenue. Revenue that will decrease substantially over the next ten, or more years, as low and zero emission trucks become the norm. A scheme that does not reward operators for the take-up and use of those new CO2 emission reducing trucks. A road user charging scheme developed and still firmly entrenched, in the last century. TIC calls upon State, Territory and the Federal Transport governments to show some vision and look beyond the current RUC scheme and to instigate a substantial review of the PAYGO road user charging scheme in Australia. That work should investigate and develop a heavy vehicle road user charging scheme to take our country out of the twentieth century and into the twenty first. Paving the way to a safer truck fleet, one that leads to better health outcomes for all Australians, produces ongoing reductions in CO2 emissions from the road freight sector and provides operators who embrace low and zero emission technology with financial incentives whilst using these new vehicles in their daily businesses.
INSIGHT | TRUCK INDUSTRY COUNCIL 76 september 2022
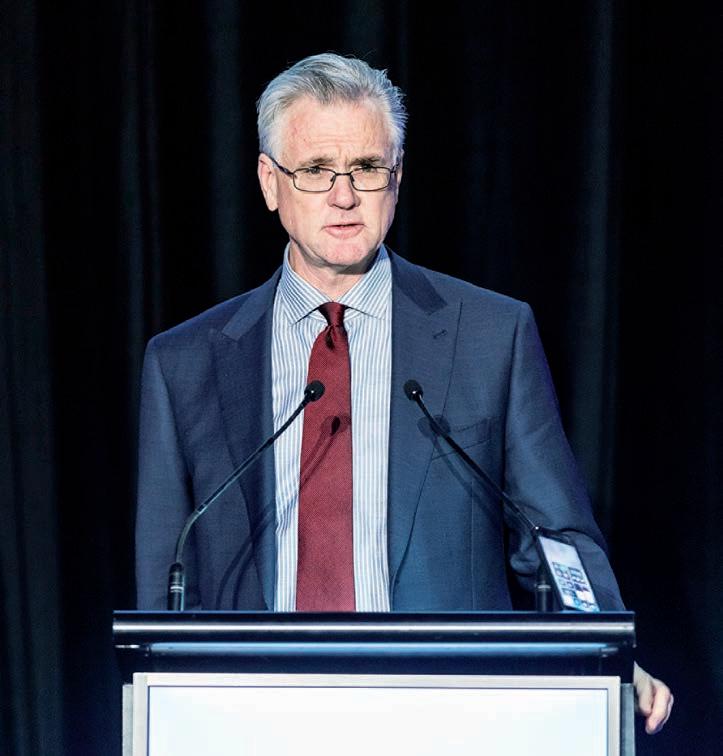
I
Zero emission trucks and road user charging
later in 2022, with a view to what future action needs to be undertaken.
our shores and certainly not taken hold.
So, roll on a couple of years, the RUC review was delayed due to the difficulties of consultation with industry during COVID, with the NTC making its final recommendations in December 2021 and the Ministers deciding to engage industry on a 2.75 per cent increase to heavy vehicle charges for the 2022/2023 financial year only. In announcing their decision, Ministers also indicated that they would revisit the determination
n early 2020, just before the world and Australia faced the first wave of the COVID-19 pandemic, the National Transport Commission (NTC) undertook a review of heavy vehicle pay as you go (PAYGO) charging fees in Australia at the request of, the then named, Transport and Infrastructure Council within the Council of Australian Governments (COAG). This was the first review of Australia’s road user charging (RUC) scheme in over four years. A preliminary study commissioned by the NTC identified that there was a substantial shortfall in the revenue generated by the heavy vehicle road user charge versus road spending. The study estimated that an increase to the RUC of 11.4 per cent in the financial year 2020/2021 would be required to address the gap. However, the NTC found, that if the PAYGO costing formula was applied, the calculated increase was much smaller, at only 3.7 per cent. This was because the formula uses qualified government road expenditure information from, then, 2016-2017 and not current year financial data. Further, COAG members were recommending only a 2.5 per cent increase be applied consecutively for the next two years, 2020 to 2022, justifying the smaller increase due to a then slowing economy, drought and bushfires, that collectively had led to reduced regional road freight movements. At that point in time COVID had barely reached
At the start of the 2020 RUC review, the Truck Industry Council (TIC) expressed an opinion that the NTCs analysis should be extensive and holistic, arguing the current RUC, that derived much of its funding from a diesel tax levy, was fundamentally flawed in light of a global movement to alternatively fuelled trucks, most likely to be powered by electricity and hydrogen. TIC postulated that the current RUC arrangements could not take Australian road transport deep into the twenty first century and that a significant overhaul of the current charging arrangements was required. TIC suggested a RUC scheme that ensures that all vehicles pay proportionally for the damage, or lack thereof, they contribute to our roads, the safety they afford all road users, the public health outcomes they generate and the carbon emissions that they produce, would be a fairer scheme.
The NTC rejected the Truck Industry Council’s calls for a wide-ranging review of the RUC, detailing that the scope of their actions was governed by the request set by the Transport and Infrastructure Council ministers. The review process was a somewhat benign examination of the PAYGO parameters. In TICs view, it was a missed opportunity.
Tony McMullan CEO, Truck Industry Council
The VTA is advocating for, and engaging with Government on, a more equitable solution so that the industry can benefit from the savings that others in the community have experienced and not be forced to increase prices or shut up Unfortunatelyshop. these recent price pressures are just the latest in a long line of challenges for the transport industry which includes driver shortages and issues around safety and licencing. But having worked in transport for a long time, I know just how resilient and innovative our great industry is. Already we are seeing progress, with the Victorian Government embracing the VTA’s Driver Delivery Program in order to create a pathway for skilled young drivers to enter our industry. We’re also seeing manufacturers embrace alternative fuel technologies to move towards a cleaner and more sustainable future — a topic recently explored at the VTA’s Alternative Fuel Summit. But these transitions take time. Until then, we need to reduce the cost of fuel for transport operators, the lifeblood that keep this country moving.
Peter Anderson CEO, VTA

The transport industry does not operate in a vacuum. We are the mechanism that gets produce into supermarkets, vaccines into clinics, clothing into retailers, whitegoods into kitchens and so much more. Anything that hurts transport
PETER ANDERSON
primemovermag.com.au 77 Powered by news COMMERCIAL ROAD TRANSPORT VICTORIAN TRANSPORT ASSOCIATION | INSIGHT

ustralians are facing their biggest economic challenge since the 2007 Global Financial Crisis – and there’s seemingly no end in sight for the near future. From the petrol bowser to the supermarket checkout, ballooning inflation and supply chain disruptions mean everyday Australians are paying more for essential items. And while the Government continue to introduce measures to ease these pressures and support businesses through these turbulent times, the transport industry has been overlooked. As a sector used to operating on very thin margins at the best of times, unless there is urgent and prudent action to lower our operational costs, Australians will start to feel the pinch more than they already are. In the July issue of Prime Mover, I called for an amendment to the Competition and Consumer Act 2010 in order to end the competition exemption that shipping liners receive. This followed research carried out by the Victorian Transport Association that found shippers have been achieving record profits all while transporting less cargo, highlighting the unfair burden being placed on the transport industry who are left footing the bill. And exponentially increasing shipping fees are just one of many issues our industry is grappling with. The rising cost of fuel was a major talking point for both parties at the recent election, with the Morrison
operators in turn hurts the Australian public. This is something that many still haven’t realised — but they need to before it’s too late.
A
Government halving the fuel excise in its Federal Budget, released weeks before Australians went to the polls. But not only was this saving not passed on to the transport industry, we essentially funded it through the removal of the Fuel Tax Credit. Operators were instead offered a paltry fuel saving that works out to around 4.3 cents per litre. Car drivers can get a bigger discount just by hanging on to their shopping receipt. Throw in increasing prices for labour, maintenance and parts and it’s clear that something has to give. While our industry has limited capacity to pass these costs onto customers, rising prices will eventually make their way down the supply chain to consumers, thereby offsetting the savings the cuts to the fuel excise were intended to create.
The impact of that would be far worse than a bigger grocery bill, as these small operators play an integral role in our interconnected supply chains and closures could potentially create a domino effect that would result in massive disruptions and gaps on shelves.
As price pressures rise for transport operators, something has to give
STUART ST CLAIR
For some smaller businesses, there’s a real risk that they’ll be unable to turn a profit under such gruelling fiscal conditions and will be forced to close.
PETER SHIELDS’ NUMBER CRUNCH 78 september 2022
The rise in the cost of living without any increase in real wages continues to bite, compounded by the costs of transport being the main factor in raising the prices of everything from bananas to B-doubles. The new truck market continues to be driven strongly along, with the widespread situation of demand outstripping supply due mainly to the increase in the road transport freight task and the impending cessation of the instant asset tax write offs. Companies will need to make a profit, not to overstate a point, before they have to be overly concerned with minimising the amount of tax that they pay. To wit, the blow out in the cost of fuels and electricity will have a significant impact on a lot of bottom lines.
with July 2021 and added 593 units to bring the YTD total for the category to 4,554, up 11.9 per cent compared with the first seven months of 2021.
DENNIS
SEA ELECTRIC
RENAULT
TOTAL 3494243795.1%
Medium Duty sales during July rose by 11.0 per cent compared
FIAT
DAF
Jul-22YTDChange
FORD
FORD
MACK
VANS
VOLKSWAGEN
VOLVO
HINO
FUSO
M-B VANS
RENAULT
MERCEDES-BENZ
CAB CHASSIS/PRIME
Light Duty trucks account for 1,377 of the July total, up 14.6 per cent on the July result of last year. The YTD accrual of 8,894 signifies an increase of 10.2 per cent.
Dollars and Sense
June’s result of almost 1,500 was always going to be a tough act to follow for sales in the Heavy Duty category due to the usual push to acquire deductible assets before the end of the financial year, yet July’s 1,067 is still 4.5 per cent more than in July 2021. The YTD total of 7,983 ‘big’ trucks is a remarkable 1,172 more than at the same point last year, demonstrating a growth of 17.7 per cent.
ISUZU 1090713329.1% 467 38414.7% 388 27396.3% 209 163015.3% 152 119432.1% 132 791 -22.9% 77 731 -5.8% TRUCKS 87 638 69.7%
It hasn’t taken long since the change of Federal Government for the blame game to get under way, with the ‘R’ word (recession) being increasingly mentioned. Treasury forecasts referred to by new Treasurer Jim Chalmers signalled a revised expectation that GDP growth in 2021-2022 will have dropped from 4.25 per cent to 3.75 per cent and the pre-election forecast of 3.5 per cent GDP growth during 2022-23 will drop to 3.0 per cent and for 2023-24 the forecast will drop from 2.5 per cent to just 2.0 per cent. In real terms that’s around $30 billion wiped off the economy over three years. It’s not all doom and gloom, however, when we look back at the growth of GDP during the 12 months to June 2019. It was just 1.4 per cent, the slowest rate of growth since the GFC.
The Truck Industry Council statistics for new commercial vehicles sales during July reveal 3,037 new trucks and 457 new heavy vans joined the national fleet. The year-to-date total for trucks of 21,429 maintains a year-on-year growth of more than 13 per cent compared with 2021. The total of 2,950 new Heavy Vans over the same period is a disappointing 30.8 per cent down, due to the widely held understanding that the availability of vehicles is the main constraint.

KENWORTH
IVECO
UD
FIAT
HYUNDAI 40 169 24.3% 46 167 81.5% STAR 20 165 -17.1% 6 48 108.7% 6 35 -69.8% EAGLE 1 24 -72.1% 2 7 30372142913.2% 181 1142-21.2% VANS 118 828 23.4% VANS 74 388 -48.4% VANS 35 292 -68.2% VANS 27 181 -10.4% VANS 22 119 -56.4% 457 2950-30.8%
VOLKSWAGEN
SCANIA 100 583 -14.0% 57 441 31.6% 43 311 -1.9% 53 278 36.3% 41 277 -13.4% MAN 20 227 37.6%
FREIGHTLINER
WESTERN
IVECO
TWU Nominees Pty Ltd, ABN 67 002 835 412, AFSL 239163, is the trustee of TWUSUPER ABN 77 343 563 307 and the issuer of interests in it. TWUS 7267 TWUSUPER offers tailored insurance for our members so they have financial peace of mind should the unexpected ever happen. This insurance protection is available for members young and old in any occupation, even drivers, loaders and forklift operators. Through life’s ups and downs, we’re here to help and support the people who keep Australia moving. Choose the fund that’s got you covered If you work in transport, choose TWUSUPER. Your VisitCall‘dangeroussupertransportfundcoversoccupations’1800222071twusuper.com.au/insurance approvedPayments inTWUSUPERby2020-21 $58.5m Many super funds don’t cover dangerous occupations like transport jobs. TWUSUPER is different.
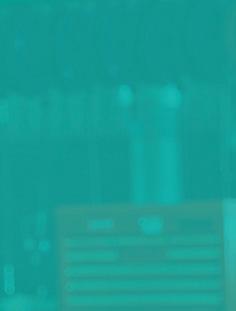
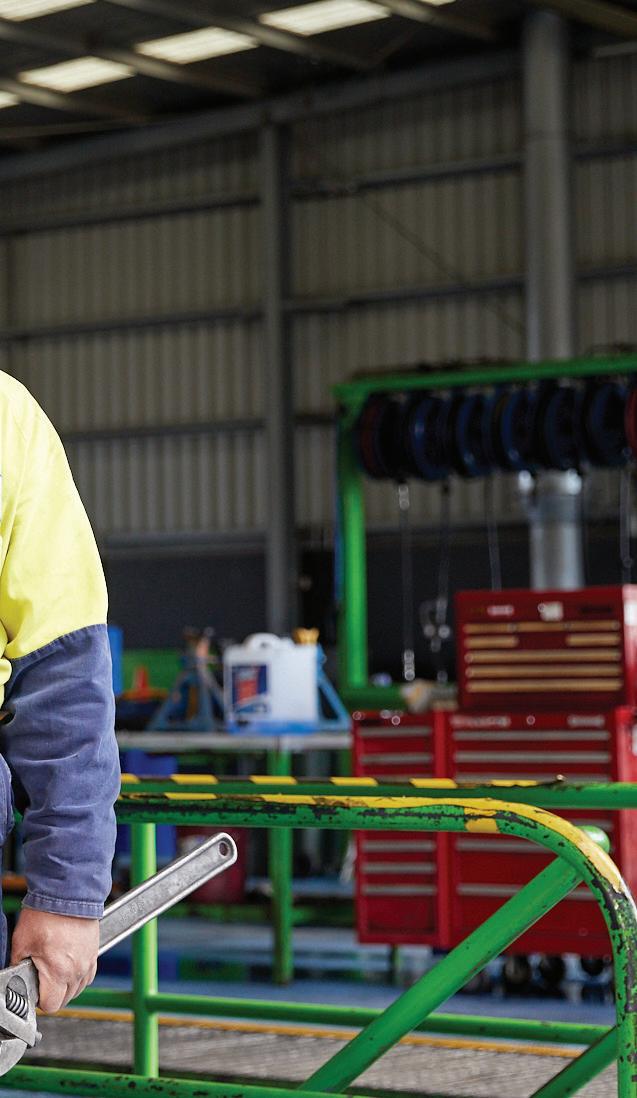
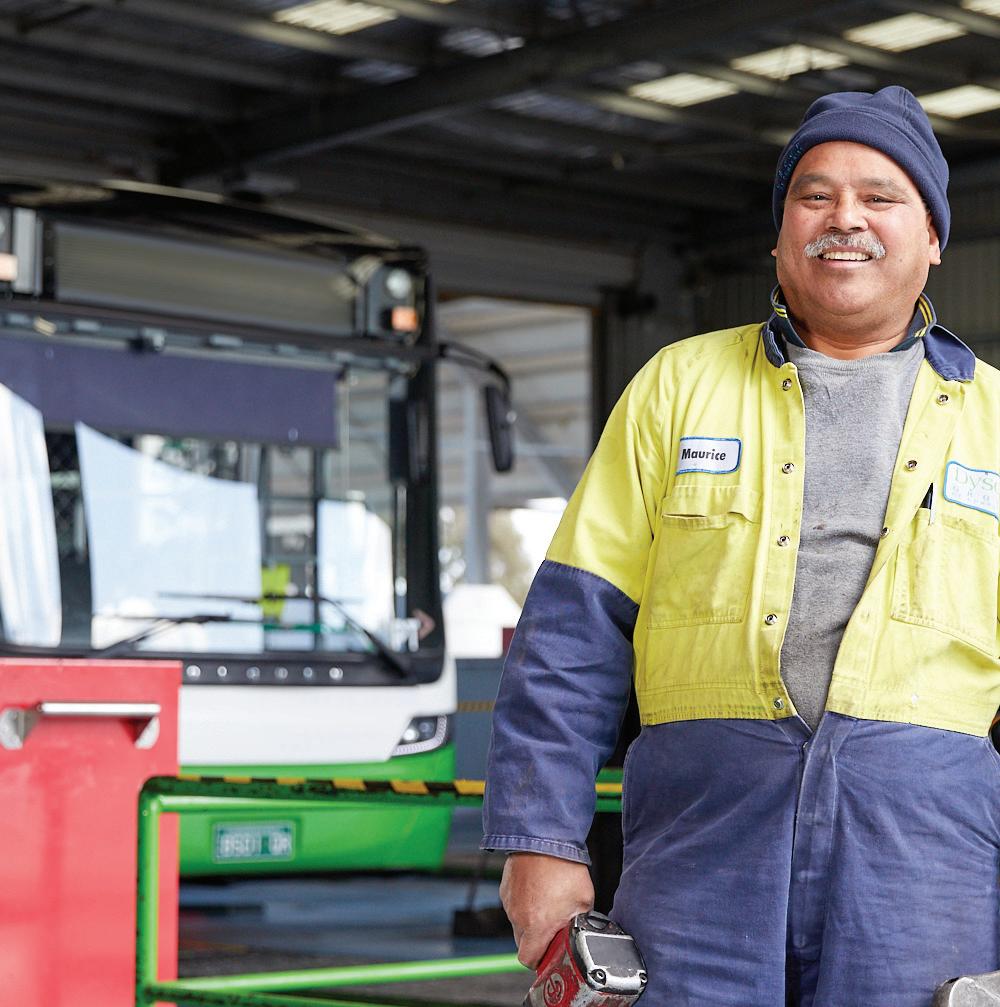
Fleet S avings and Carbon Footprint Calculator Discover how switching your engine oil could help your fleet generate cost and carbon savings. TRY THE CALCULATOR HERE ww w.shell.com.au/savingscalculator or scan the QR code Heavy Duty Diesel Engine Oil : CARBONNEUTRALDESTINATION
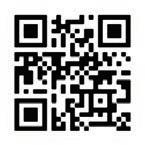
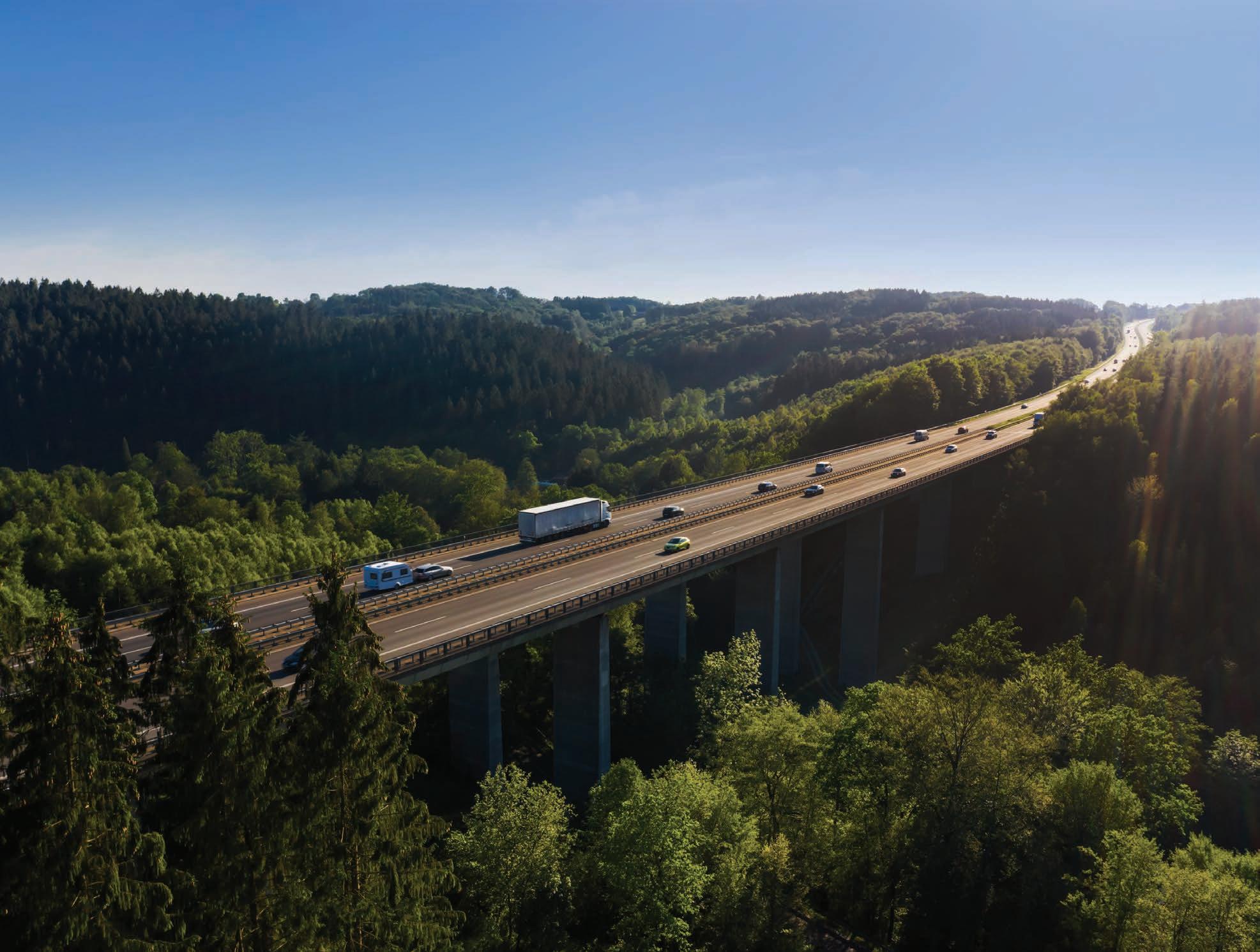