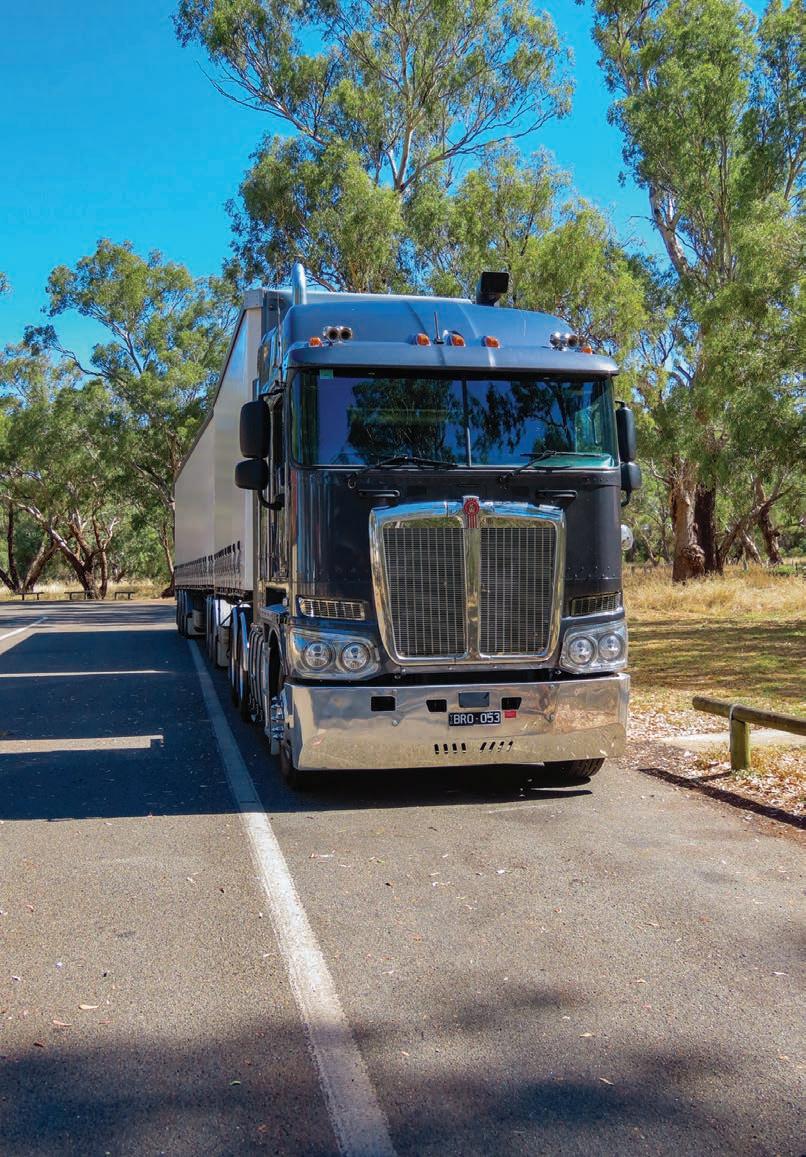
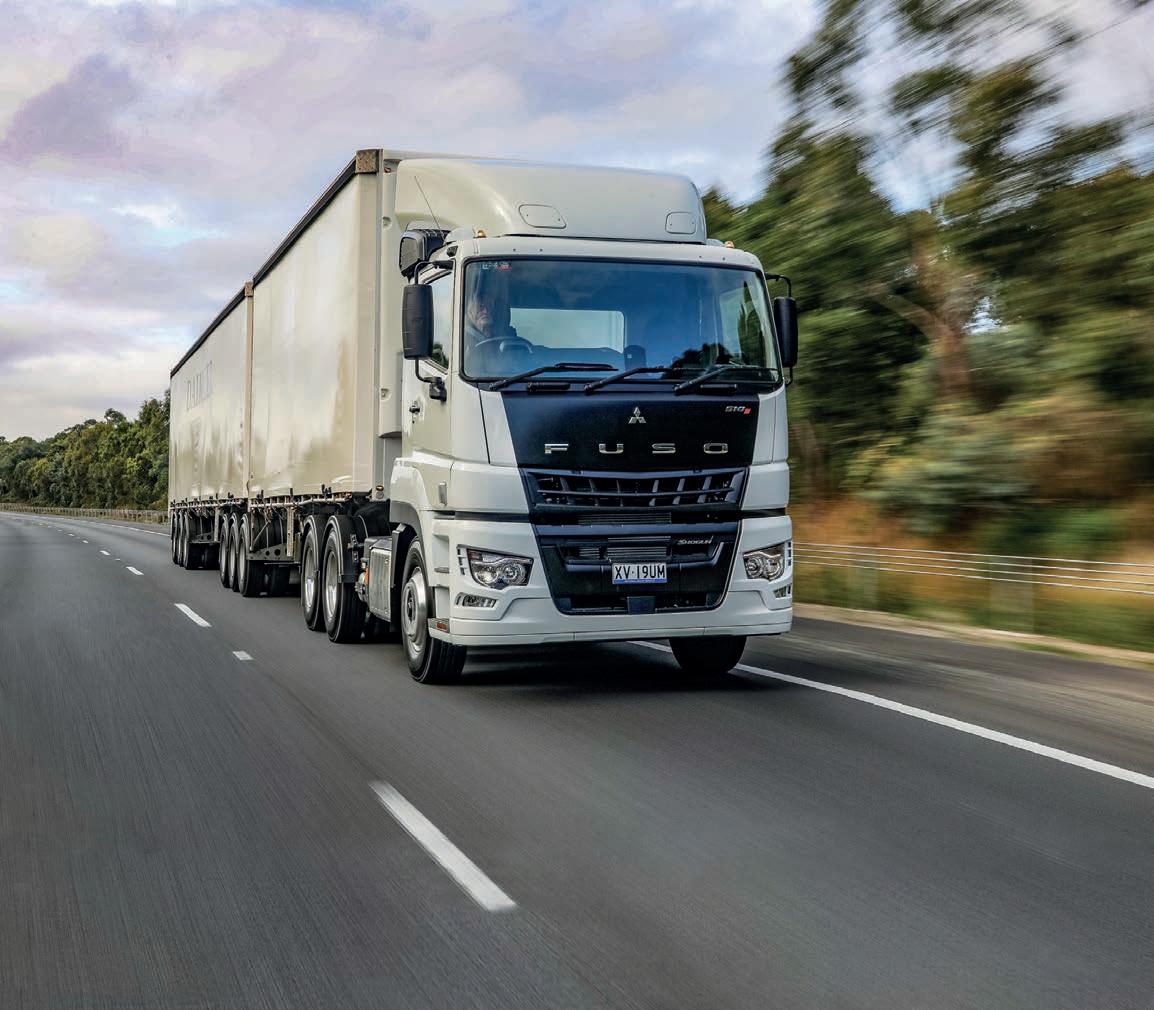

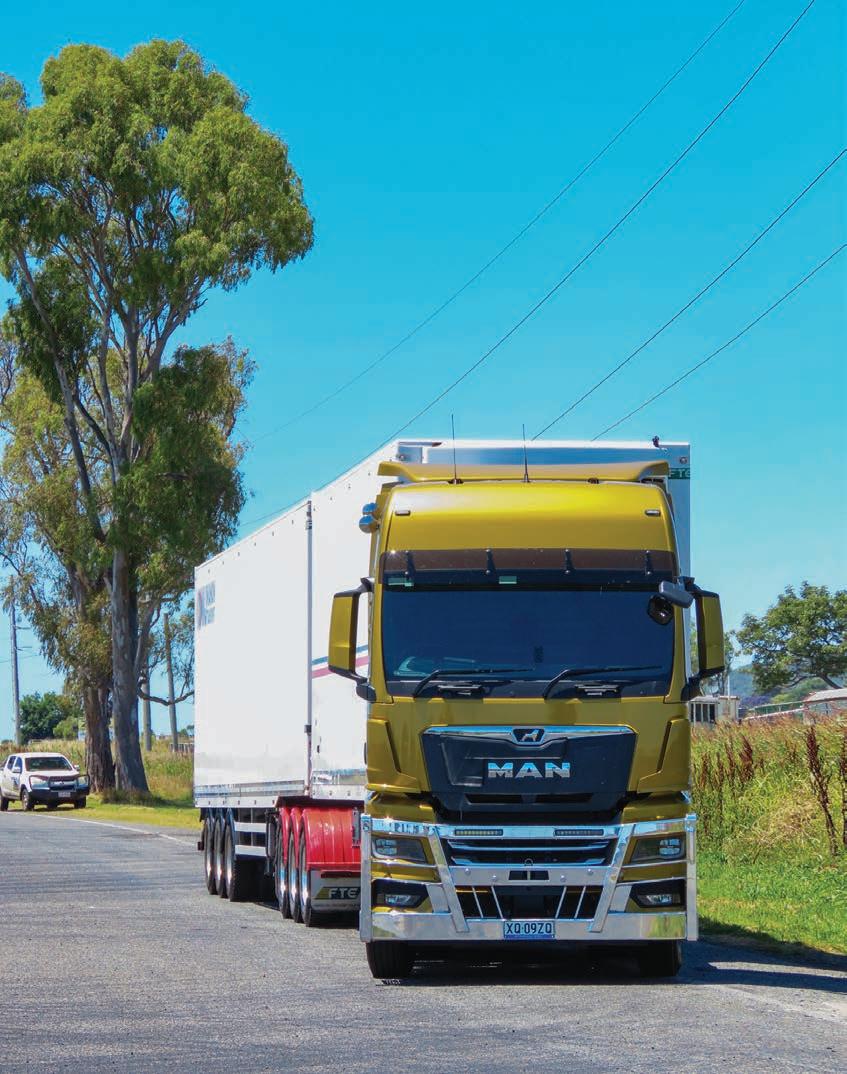

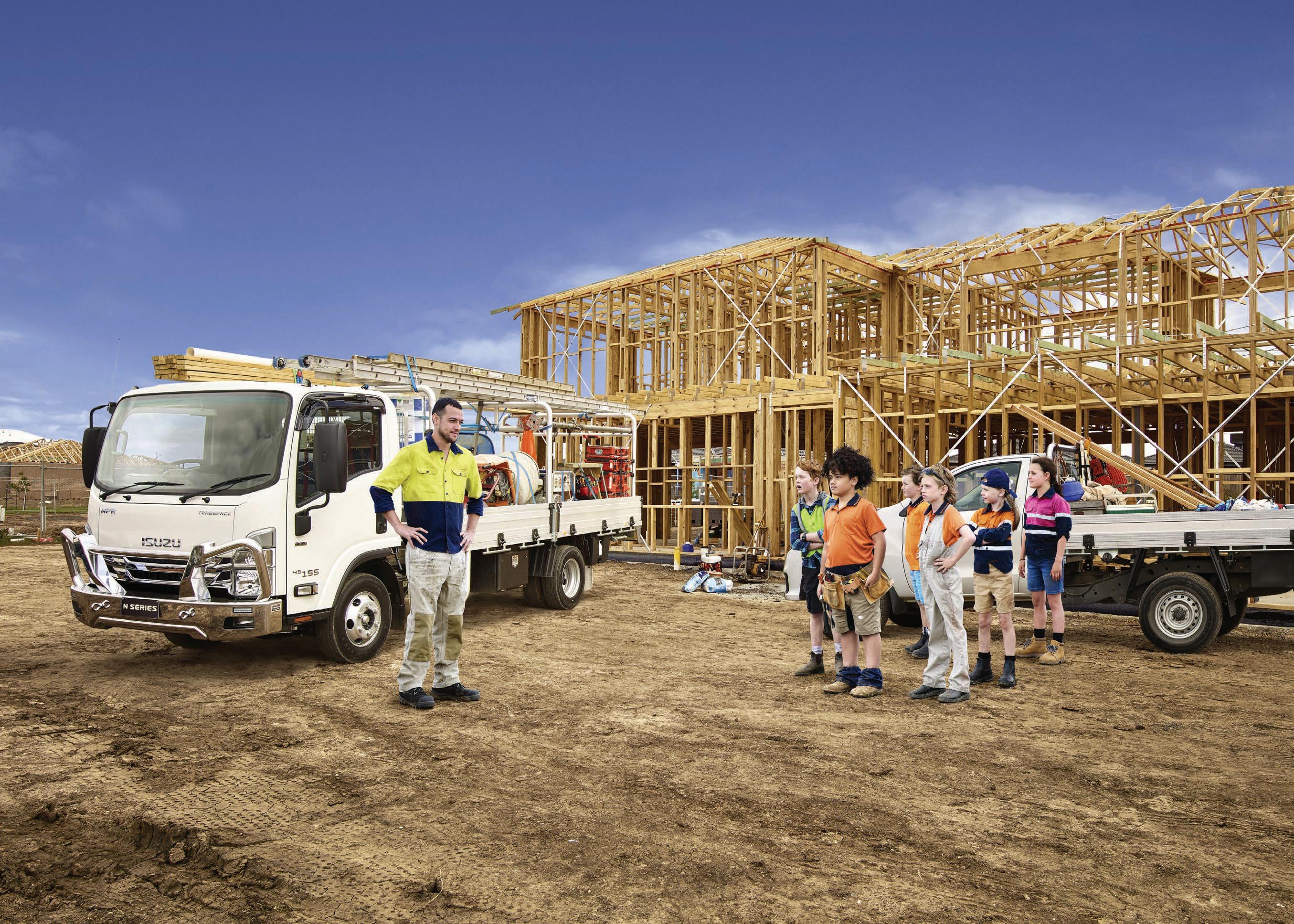
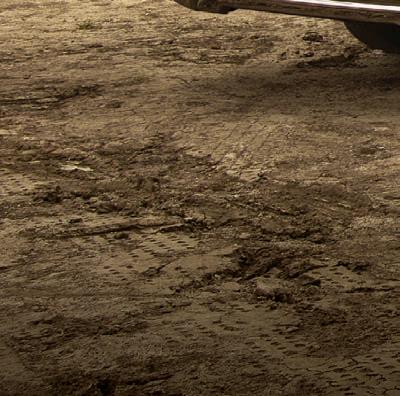
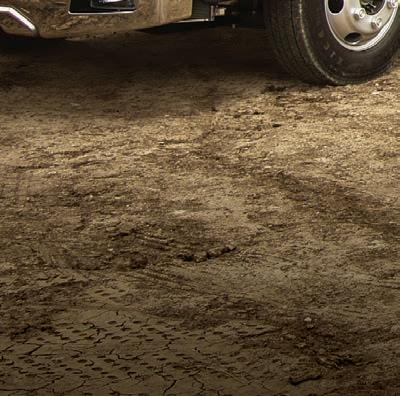
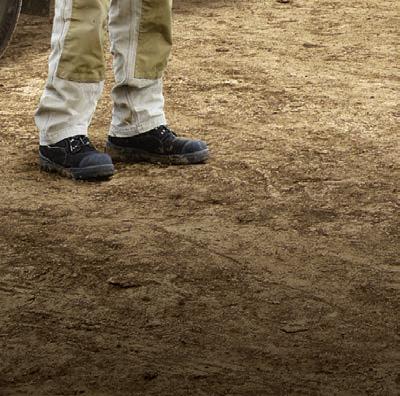
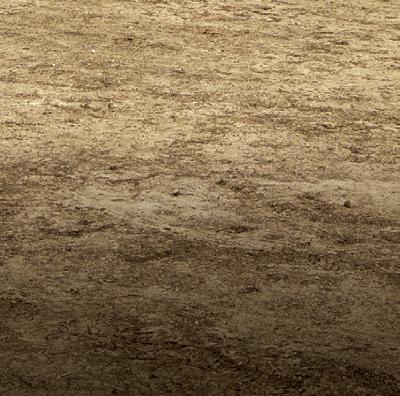
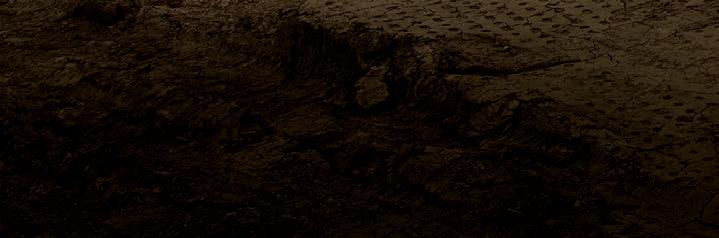

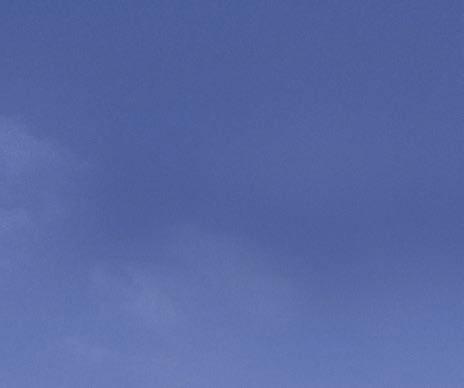

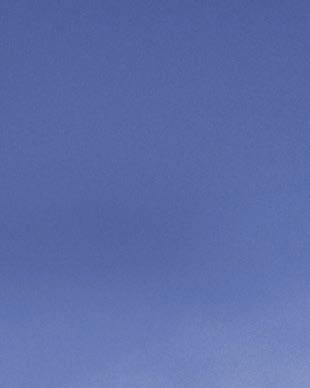
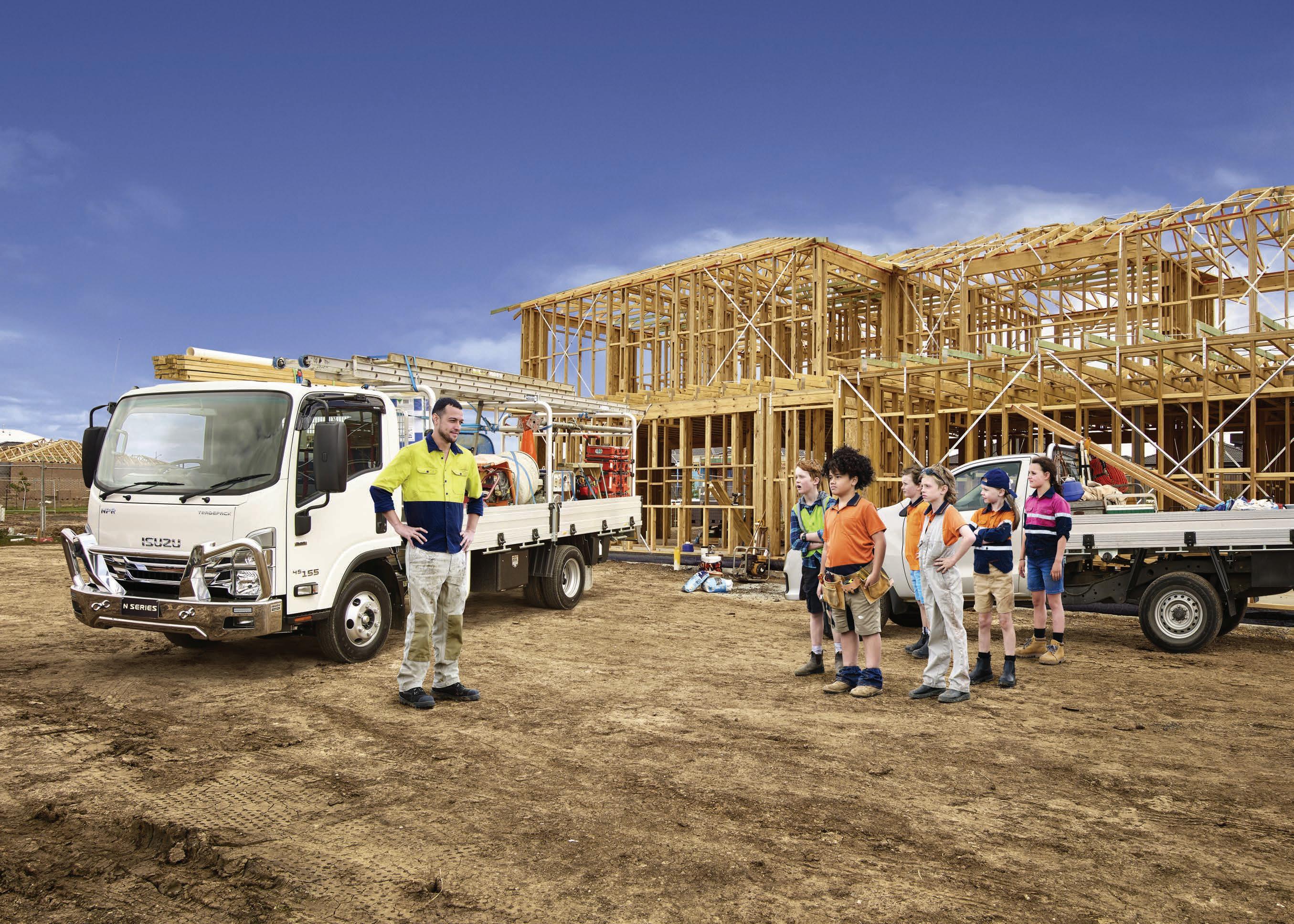
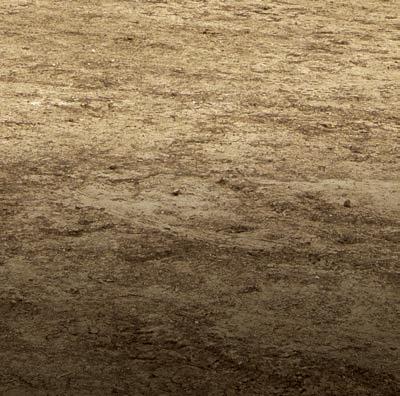
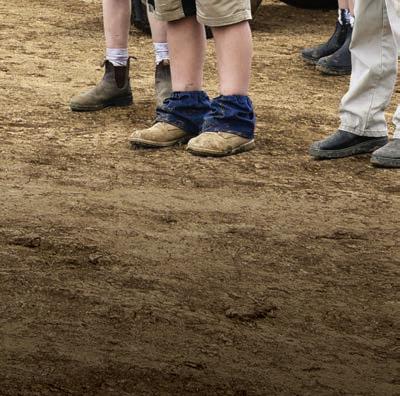
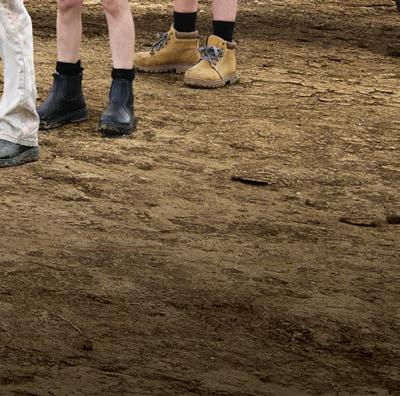
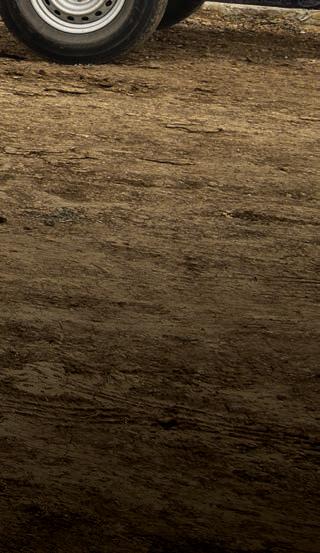
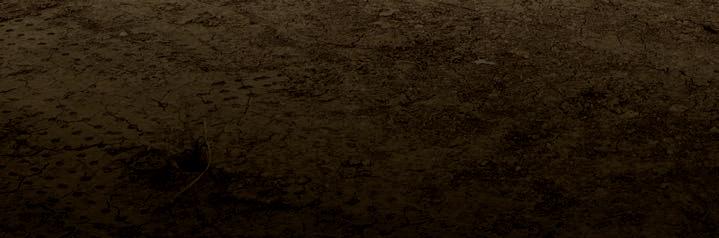
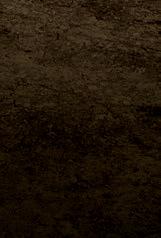










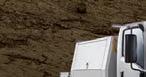




































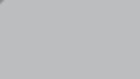
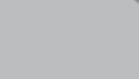




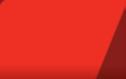


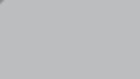
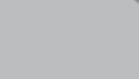
PUBLISHED BY Prime Creative Media Pty Ltd
ABN 51 127 239 212 379 Docklands Drive, Docklands VIC 3008 Australia
It’s that time of year again, with the truck and trucking industry poised to get together at the main show in Australia, the Brisbane Truck Show. There is plenty of anticipation going around about what may or may not be on show this year. Stretched supply chains mean that exhibitors may not have been able to get the desired truck/trailer/engine/component into the country in time due to the ongoing problems getting gear into the country at the right time.
Any missing items will hardly be noticed as there will be so many new and innovative displays this time around. Our industry is embarking on the early steps through a revolution, as we veer away from the technologies which have sustained trucking for over a century, into the brave new world of zero emissions trucking.
The will be new fuels, new concepts, new brands and a first opportunity for many to get a peek at what trucking could look like in 30 years time. It will be a chance for everyone to get up close and personal, touch and feel what kind of trucking industry they will be working in the future.
However, the Brisbane Truck Show isn’t all about the equipment, it’s mainly about the people. This is our tribe’s chance to get together, often since the last show two year ago. This is the opportunity to get all of the gossip, renew old friendships and make new ones.
A lot of the fun at the show is accidentally running into an old friend on one of the stands or catching up with former colleagues in their new roles or as showgoers. There is plenty to do, plenty to see and a hell of a lot of information to take in.
Although trucking and truck making are highly competitive industries, they are also communities, where we all share some common attitudes and beliefs. For an industry so diverse and also constantly on the move around the country, this is a chance for a lot of us to be in the same place at the same time and simply interact.
For myself personally, this show will also mark a major first. PowerTorque in Australia has got together with Trucking NZ to develop, judge and award the Truck of the Year Australasia and we will be presenting the trophy to the winning truck manufacturer for the first time at the show.
This will be the chance to reflect on what we are looking for in a truck and what we need from our trucks, now and into the future. A chance to celebrate what we all love about the trucking industry and the trucks we drive.
Telephone: 03 9690 8766
Fax: 03 9682 0044
Email: enquiries@primecreative.com.au
Chief Executive Officer: John Murphy
Managing Editor: Luke Applebee
Editor: Tim Giles
Contributors: Paul Matthei
Correspondent: Will Shiers (UK)
Advertising Manager: Trevor Herkess: 0411 411 352, trevor.herkess@primecreative.com.au
Client Success Manager: Salma Kennedy, salma.kennedy@primecreative.com.au
Production Manager: Michelle Weston
Circulation & Subscriptions Manager: Bobby Yung
Designers: Blake Storey, Kerry Pert, Tom Anderson, Louis Romero
Official Media Partner:
REGISTERED BY Australia Post - ISSN 1445-1158
SUBSCRIPTION
03 9690 8766
subscriptions@primecreative.com.au
PowerTorque Magazine is available by subscription from the publisher. The right of refusal is reserved by the publisher.
Annual rates: AUS $60.00 (inc GST). For overseas subscriptions, airmail postage should be added to the subscription rate.
DISCLAIMER
PowerTorque Magazine is owned and published by Prime Creative Media.
All material in PowerTorque Magazine is copyright and no part may be reproduced or copied in any form or by any means (graphic, electronic or mechanical including information and retrieval systems) without written permission of the publisher.
The Editor welcomes contributions but reserves the right to accept or reject any material.
While every effort has been made to ensure the accuracy of information, Prime Creative Media will not accept responsibility for errors or omissions or for any consequences arising from reliance on information published.
The opinions expressed in PowerTorque Magazine are not necessarily the opinions of, or endorsed by the publisher unless otherwise stated.
EDITORThere are certain things most trucking operators need to be able to do, but there are challenges to tasks like remote running in Queensland, which require a specialist with the ability to handle a complex operation in difficult conditions.
PowerTorque, in association with NZ Trucking, is introducing the Truck of the Year Australasia Award for the first time in 2023.
With the launch of the new S-Way model bringing the truck brand’s range on the Australian market up to date, is this new model range the way forward for Iveco?
As part of its examination of the future development of alternative fuels for the trucking industry, PowerTorque looks at the road to zero emissions.
With the world looking for zero emission transport solutions, one company, Cellcentric, jointly owned by Daimler Trucks and Volvo Group, is moving forward with fuel cell technology to be included in their heavy vehicle product portfolio.
Some trucks look to be designed for a particular task, and Tim Giles finds when driving a Western Star 47X as a tipper and dog, it is a truck within its comfort zone.
Times have changed and engine makers no longer just supply an engine. There’s much more to the story and PowerTorque looks at the Detroit which comes with the X Series Western Star.
26
08 NEWS AND VIEWS
Isuzu announced the new N Series models, Scott’s are in limbo after the operation went into receivership and much, much more.
74 THE EFFLUENT CODE
The NHVR has registered an industry code of practice called ‘Managing effluent in the livestock supply chain’.
82 MAKING CUSTOMERS PAY IS PART OF BREAKING THROUGH THE PAIN BARRIER
NatRoad CEO, Warren Clark, takes us back to our youth, where we probably first heard the term ‘no pain, no gain’ from a coach.
88 I DRIVE BY MYSELF
Going Global got a taste of things to come when he hopped aboard a Freightliner Cascadia self-driving truck.
92 HELPING TO SHAPE LONDON’S SKYLINE
PowerTorque’s European Correspondent, Will Shiers meets a man who has built up several successful tipper firms, helping to shape London’s skyline in the process.
88
With the introduction of the K220, Kenworth have gone through a process of updating a classic truck while keeping the central character of the K Series ethos.
• Supporting drivers for more than 50 years
• Seating – on a higher level
NatRoad has come out in support of broader industry calls for a freeze on heavy vehicle charges in 2023-24. NatRoad’s response to a National Transport Commission’s (NTC) consultation paper aligns with the submission from the Australian Trucking Association (ATA).
“We are both asking for a freeze on charges next year and for increases in the two financial years after that to be limited to 2.75 percent,” said NatRoad CEO Warren Clark. “We also agree with the ATA’s call for a lower remote area road user charge set at half the national road user charge rate.”
Warren said continuing high fuel costs is just one of the burdens that trucking businesses are expected to absorb.
“Inconsistent and poorly communicated state border closures, purchasing COVID-19 related PPE, higher AdBlue costs and the impact of the previous government’s six-month fuel tax cut are all hitting our industry,” said Warren. “From 1 April to 18 August 2022, some 2,000 heavy on-road transport operators had to negotiate payment arrangements with the ATO because of the fuel tax Budget decision.”
The Hyundai Mighty electric truck is reckoned to be a continuation of Hyundai’s sustainable commercial vehicle momentum. The Mighty electric follows on from XCIENT Fuel Cell, the brand’s first-ever hydrogen-powered heavy truck, currently deployed in Switzerland and California.
Mighty electric has an estimated laden range of approximately
240km, a zero-emission workhorse for metropolitan and last-mile deliveries. It has a 120kW, 320Nm electric motor, and is powered by a 114.5kWh battery system with rapid charging capability from 10 per cent to 100 per cent in under 70 minutes.
Hyundai have said that the XCIENT Fuel Cell prime mover is currently being assessed for a potential trial in Australia.
The Heavy Vehicle Rest Area Steering Committee held its first meeting in Canberra, chaired by Senator Glenn Sterle, it was the first time that truck drivers have been at the table directly informing decisions that will impact their work through increasing access to new or improved heavy vehicle rest areas.
The four industry representatives and five truck drivers discussed their priorities for the roll-out of the Government’s $140 million commitment to the building or upgrading of rest areas for heavy vehicles.
“Having truck drivers at the table involved in the delivery of our rest areas election commitment was a key part of the
announcement made by Minister Catherine King and Senator Glenn Sterle during the 2022 election.”
“It was a real privilege to attend part of the first day of the Committee’s meeting,” said re, Carol Brown, Assistant Minister for Transport and Infrastructure. “The shared knowledge and experience of members of the Committee will deliver heavy vehicle rest areas in the most efficient locations.”
It was back in 2007 that Australia last saw a new shape Isuzu launched on the truck market. Since then, the Australian truck market leader has introduced a series of upgrades and add-ons, but no all-new models appeared.
Now in 2023, the Isuzu organisation in Japan has announced the new N models with the new F Series due to follow close behind. It can be anyone’s
guess as to how long it will be until these new designs and models will flow though to our truck market, but there are a few encouraging signs.
Automatic Emergency Braking Systems are to become mandatory in Australia in 2025. The solutions employed to meet this mandate are pragmatic add-ons, rather than long term sustainable technology. Isuzu may look to rush some of the
new models though to maintain supply at the leading edge of technology.
One of the majot changes announced for N Series is the most obvious one, a genuine battery electric vehicle out of the Kawasaki plant and aimed to fulfil a fast growing demand around the world for zero emissions transport. It will be Isuzu’s first massproduced Battery Electric Vehicle.
Volvo Trucks Australia has just delivered the first Volvo Electric truck sold Down Under to global logistics giant GEODIS. The 6x2 FE Electric will be put to work transporting parts from GEODIS’s Matraville NSW headquarters to Volvo Group Australia’s Minto NSW Parts Distribution Centre on the Southwestern outskirts of Sydney.
Daily energy demands are met by 50kWh AC charging at
the depot end of the 47km route. The FE Electric is fitted with four batteries on board and offers 266kWh capacity and is capable of hauling a 7-tonne payload. The truck also makes use of a 225-kW/850Nm dualmotor driveline with a 2-speed automated transmission.
Operational range is quoted at up to 220km depending on battery configuration and application.
Brown and Hurley Kenworth DAF Caboolture has been named Kenworth Dealer of the Year for 2022. Caboolture is the latest Brown and Hurley full-service dealership, opening its doors in 2015.
The award was presented at PACCAR’s annual dealer event where the Caboolture dealership was also named Cummins Dealer of the Year for 2022.
Kenworth DAF Adelaide has been named the 2022 DAF Dealer of the Year. This is the first time Kenworth DAF Adelaide has been awarded the accolade since its introduction in 2002. The award was presented to Kenworth DAF Adelaide Managing Director, Jonathan Crawford.
Cummins announced it will unveil its most advanced ever big bore diesel truck engine at the Brisbane Truck Show. The entirely new 15-litre platform, known as the X15D, will deliver the highest-ever outputs for a Cummins truck engine while setting new standards for fuel efficiency at ultra-low emissions levels.
“With the all-new X-series platform, Cummins is taking the internal combustion engine to a next generation level, capable of meeting future ultra-low emission standards with a low-to-zero carbon fuel capability,” said Mike Fowler, Director of On-highway Business for Cummins Asia Pacific.
There is no set date for release of the X15D in Australia and New Zealand. “The X15D will only be released when we are completely satisfied with its reliability and durability in meeting the harsh demands of the Australian B-double duty cycle,” said Mike.
NatRoad says it’s time to address high Performance Based Standards (PBS) regulatory costs and expand the as-of-right access to agreed networks. NatRoad calls the National Heavy Vehicle Regulator’s ‘Performance Based Standards 2.0’ discussion paper ‘a mixed bag’, conceding that many of its proposed reforms are improvements.
“We know that these are issues that the NHVR has to refer to the National Transport Commission (NTC) under current legislation,” said NatRoad CEO Warren Clark.
“So let’s get on with that and change the scheme so it’s based on performance requirements and not prescriptive ones.”
The PBS scheme should be better used as a mechanism for promoting the uptake of safer high-productivity vehicles, according to the Heavy Vehicle Industry Association. In HVIA’s view PBS 1.0 was successful in sparking innovative approaches to vehicle designs but was less effective at opening access for those vehicles. To be successful, PBS 2.0 needs to tackle this issue.
Daimler Trucks Albury has taken out the Daimler Truck Australia Pacific Dealer of the Year Award for 2022.
“Daimler Trucks Albury represents a remarkable success story, having thrived since David Warren and the team took hold of the reigns in early 2020,” said Daimler Truck President and CEO, Daniel Whitehead, when he presented the award to Daimler Truck Albury Dealer Principal, David Warren, at a ceremony in Melbourne.
The National Heavy Vehicle Regulator has announced that operators of agricultural equipment in South Australia and Victoria are being advised that the following notices will be revoked by the end of February 2023: the South Australia Class 1 Agricultural Vehicle Mass and Dimension Exemption Notice 2019 (No.1) and the Victoria Class 1 Agricultural Vehicle Exemption Notice 2018 (No.3). These two notices will expire 28 days after the revocation notice has been published.
Operators in both states can operate under the National Class 1 Agricultural Vehicle and Combination Mass and Dimension
Exemption Notice 2020 (No.1), which provides a harmonised approach to agricultural equipment movements across Australia.
In South Australia, the national notice allows nationally consistent mass limits greater than those provided under the state notice, and night travel in the national notice meets or exceeds authorisations provided under the state notice and associated night travel bulletins.
The Victorian notice is being revoked as the NHVR national maps have now been updated to reflect the state networks. Network access under the national agricultural notice is the same as under the state notice.
“A highly respected local, David leads a highly motivated team that has reinvigorated the Mercedes-Benz Trucks, Freightliner and Fuso brands in the region and raised customer support to remarkable levels. Daimler Trucks Albury is clearly a deserving winner of the Daimler Truck Dealer of the Year award.”
Paccar Parts Australia announced Brown & Hurley Kenworth DAF Darra as the 2022 Paccar Parts Dealer of the Year. Performance in areas including customer support, sales growth, parts availability, retail marketing activities and training, are assessed by the judges.
“Highly deserving of this award, on behalf of Paccar Parts, I would like to congratulate everyone at the dealership for their hard work and dedication, setting an excellent example for the industry.” said Damian Smethurst, General Manager of Paccar Parts Australia.
“Darra’s parts sales growth was above average for 2022, but it was their continued investment in its people and facilities and their commitment to parts availability and customer satisfaction that set them apart. They are setting an excellent benchmark for the industry by providing an exceptional customer experience. Congratulations!”
Australia Post has taken delivery of its first Volvo Electric vehicle, as part of a six-month trial. The Electric FL utilises four batteries to achieve an energy capacity of 265 kWh and has a range of up to 300km depending on application and the payload is up to 5,500kg.
The electric driveline provides 425Nm of torque, which is delivered to the rear wheels via a 2-speed automated transmission. Electric FL maintains a full suite of active safety systems including Autonomous Emergency Braking.
“It’s very rewarding seeing these vehicles go into service after so
much hard work ensuring they are the right fit for both our market and the applications they are being put into,” said Tim Camilleri, E-mobility Manager, Volvo Group Australia. “These vehicles are proving themselves day in and day out around the globe.”
Hino Australia are introducing Alloy Tray and TradeAce Built to Go models to its Hybrid Electric range from July 2023.
“Rising fuel prices and an increased focus from customers wanting to minimise their environmental impact has seen sales of Australia’s only Hybrid Electric light-duty truck soar,” said Daniel Petrovski, Department Manager, Product Strategy for Hino Australia.
“Not only do our Hybrid Electric models meet Euro 6 exhaust emissions standards, but recent real-world trials comparing
the proven Hino Hybrid Electric truck against a traditional diesel equivalent revealed a 22 per cent reduction in fuel use and CO2 emissions.”
LIFT UP TO 30,000 LIFT UP TO 30,000
PowerTorque’s publisher, Prime Creative Media (PCM), announced a new partnership between Healthy Heads in Trucks & Sheds (HHTS) and Australian Truck Radio (ATR).
PCM and ATR said they are proud to support HHTS for the great work they do within the transport industry. People who work in the road transport, warehousing and logistics industries
have long faced challenges relating to mental health and wellbeing.
“We know that stigma around mental health in this sector is a key risk factor and barrier for help-seeking,” said Naomi Frauenfelder, HHTS Chief Executive Officer. “As such, the primary objective of many of our resources and programs is to drive a reduction in mental health stigma and improve access to information.”
Mercedes-Benz Trucks has delivered the first batch of Actros units as part of a 120-truck deal with SGGS.
The Brisbane-based operator runs all over Australia, with an emphasis on ‘crossing the paddock’ between Perth and the East Coast, and already operates 37 Mercedes-Benz Actros trucks as part of its 80-plus truck fleet.
The first Actros joined the SGGS fleet back in 2018 and the team was impressed by its reliability, fuel efficiency as well as the full-suite of active safety features.
“That truck has been great and the Actros just keeps getting better and better with each new model,” says SGGS General Manager, Adam Fraser. “The fuel savings are excellent. It soon adds up when you do the kinds of distances that we cover.”
After starting out in the trucking industry working for a number of well known characters in the trucking industry, Kent Baillie has become one of those characters himself, running an operation from Pittsworth in Queensland and hauling general freight west from Brisbane into all of the remote areas of that vast state.
His job title is now Managing Director of Mt Isa Carriers, but it has been a long hard road for Kent, both figuratively and in reality, a long dusty road across the Sunshine State and into the Northern Territory.
Originally from Millmerran, on the road from the Queensland/NSW border at Goondiwindi to Toowoomba, Kent, did mess around with trucks in the paddock as a child, his father worked as a truck driver.
“By the age of 10, we were loading trucks,” says Kent. “It was expected every day after school, every week and every holidays. He worked for Lill and Alexander. Later, he became the boss of Lill and Alexander but prior to that he had his own truck. Dad was a Darwin runner with an old B-model Mack. He also ran across the paddock to Perth and then in those later years, he became a manager, but he had been Lill and Alexander’s first employee.
“When he retired, he retired from there as the boss, so for all us
boys our first job was with Lill and Alexander, they were a very reputable long-standing company and when the owner died, they just decided to close it up.
“When we stopped working for Lill and Alexander, in 1993, I bought my first truck and everyone reckoned I was a fool for doing it. I bought an old day cab, a W-model Kenworth, and my brother had one as well. A lot of people thought we were nuts. We would run Brisbane to Darwin in a day cab and sleep on the load or across the seat or whatever. Often a pillow against the window, we couldn’t afford a bunk.”
They were carting for TNT Express and Brambles. He recalls banking his two checks for those first loads. Time and experience taught him some hard lessons, and through hard work gained a reputation for reliability.
The business had three trucks running to Darwin when Kent’s wife left him and he had to look after his children, the youngest of which was youngest 10 months old. At the same time a family friend, Graham Porter, who had his own transport business, suffered a heart attack. They asked Kent if he would come and run their operation for two weeks.
“I went and helped Graham for two weeks and the rest is history,” says Kent. “I invested in the place when times were tough and we became
There are certain things most trucking operators need to be able to do, but there are challenges to tasks like remote running in Queensland, which require a specialist with the ability to handle a complex operation in difficult conditions.
partners, and just five years ago, I bought out his share and we just kept managing Mt Isa Carriers.”
The original Mt Isa Carriers operation was established in 1965, in Mount Isa, by Graham, and Kent used to subbie for him. By the time Kent took over they were running some old gear and the operation was spending too much money on maintenance, a situation which Kent has turned around since taking over.
“I’d done all the figures and we bought one our first new Mack in 2012,” says Kent. “I said to Graham, we’ve just got to have it otherwise we’re just not going to survive. We had it for five years. six years, and we put 1.4 million kilometres on that thing. He was against M-drive and he was against the MP 10, but over the six years we never once put a spanner on that truck. When we traded it in, Mack was shocked it still had the original turbo.
“Now, that’s all we’ve got, the MP 10s, and then we’ve got the 700 and a 600 Volvo. Everything we run is road train. Plus we’ve got a few local trucks that run to Brisbane and around. We own our base here in Pittsworth and
our depot in Townsville, but we lease in Brisbane.
“We’re doing a daily service across from Townsville to Mt Isa, so we cover all of that area too. We’ve been up there for seven years, we have a perfect crew. That’s where the latest Mack went to, ‘Hillbilly Deluxe’.”
The Townsville depot services direct to Mt Isa, while the trucks heading West from Pittsworth make a number of stops heading West, starting in Barcaldine, where the operation has got a number of agents around that area, covering Longreach down to Tambo and further West.
The operation runs a wide selection of trailers from mezzanine deck curtain siders to flat tops, drop decks, ramp trailers and pantech trailers for some parcel freight (as agents for most of the major players in parcels). The operation can service, virtually, the whole of North-Western Queensland.
“We’ve done nothing but grow, and the reason is a mixture of things,” says Kent. “However, what we’re seeing now, is people are sick and tired of the big boys, who are my only opposition and I won’t get that work because they are part of national deals with them for the whole country. We handle every drop of grog to Cloncurry and Julia
Creek, so every drop of alcohol in those areas comes from us.”
One of the strengths of the operation is their local agents, and the policy is Mt Isa Carriers don’t care if it’s a parcel or if it’s a full load, whether it’s a few boxes or a stack of tyres.
“It’s all about the driver now and I’ve been old school,” says Kent. “I think they’re spoiled, compared to what we had. People can’t believe that I ran to Darwin without a bunk. That’s just what we had to do, and now we’ve got tracking on everything. The new trucks have got bloody TVs and microwaves. On the Macks, we’re running the 60-inch sleeper and the Volvos have the XXL.
“The whole scope of the industry has changed. Like the fatigue management and everything else. Do I agree with it 100 per cent? No. Do I think it’s working? Yes, but I think it could be made somewhat easier on the driver. I would like to see us go the way of WA, where the focus is not on the driver, it’s on the company. It forces businesses to do the right thing. We’re a small business and we do the right thing. So why can’t others?
“I think with electronic work diaries,
we’re going to end up there. We’ll have electronic diaries ready before the end of 2023. I’m all for it. We do trip plans now. I want to do it, to make sure that these boys are not pushed. Everyone knows our schedule and we’re pretty good at it.
“If it helps clear scum out of the industry, which I think still needs to happen.”
Mt Isa Carriers has 27 trucks on the road and there are 52 staff altogether. The largest depot is at Mount Isa, because it’s a receiving depot where there are van drivers, body truck drivers, semi drivers.
“This year I brought on a general manager, he’s an ex-corporate exec and he’s helped us make even further changes, because he understands the systems,” says Kent. “Then I’ve got Darren in here handling operations and I’d be lost without him. Five years ago, I was doing all this myself and now Cassie, my wife has come in here and taken a heap off me, as well.
“You only survive by change, you’ve got to constantly change. It’s the little things that these guys handle for me, they’re picking up things that used to take up time, and we’ve
had another record year. The whole scope of buying has changed now. Somewhere like Mount Isa and the surrounding area have discovered online shopping. The parcel freight in 2022 tripled, so we’ve changed from the old consignment notes and gone electronic
“We use TransVirtual, and it tells me everything. We used to have customers ring up and say, could you send a POD? That would take time, but now they can have it within minutes of delivery. Because we’re agents for various customers, we’ve got it set up so it appears as an offline consignment note under the customer’s name.
“We also went over to Xero and now everything’s live real time. We can invoice and bill every day. When I go back 10 or 15 years ago, at the end of the month we’re sitting around the kitchen table with a pile of paper until two o’clock in the morning, and we were tired. That was a big killer years ago, cash flow.”
“When I first started doing Darwin, you knew absolutely everyone on that run,” says Kent. “If it was nighttime,
we could still pick out any truck going the other way, by the time and by the configuration of their lights or whatever. It was only in the early 90s and for triple road train drivers, there wasn’t many of us.
“Back then, we had to hook up our triples in Mount Isa. Then it came back 230km to Morven and then it came back another 90km to Mitchell. Now it’s another 85km closer to Brisbane, at Roma. Apparently, soon we’ll be talking about Toowoomba, which is 350km closer. There’s more and more road trains on the road, whereas we were the big boys back then.”
Getting trailers in the right place at the right time is always a bit of a juggling act.
The operation has single trailers coming up the Toowoomba Range on the 160km drive up out of Brisbane, arriving at the Pittsworth depot. At this point, they are hooked up as double road trains and head West. One of the trucks will be doing. a ‘dog’ run, heading out of the yard as a double road train and traveling to Roma.
At Roma the dog trailers are separated and then added to the other doubles, turning them into triple road
At Caltex, we are committed to providing the most advanced premium industrial lubricant technoloiges available for every kind of operation – from mining to agriculture, power generation to construction, trucking to global marine.
trains for the run to Mount Isa, another 1330km further. The dog runner picks up a couple of trailers returning from Mount Isa and runs them back to Pittsworth. The whole system works like a sort of constant conveyor belt.
The system for running to and from Townsville with triple road trains is much less complicated. Triples can run all of the way from Mount Isa into the pads at the Port at Townsville and these are then broken up to run as doubles, under permit, across from the Port to the Mt Isa Carriers yard.
Every driver works on standard hours trips have been arranged to ensure drivers do not need to drive any more than 12 hours a day. The relationship with customers has developed to the point where Mt Isa Carriers will tell a customer when any freight can get delivered, and not the other way round.
“I refuse to be pushed,” says Kent. “So, my drivers all work on standard hours and we are constantly checking them, every week. Whena driver comes in, he’ll hand his logbook sheets into Sharlee and then we’ll check them against the tracking. We don’t want them breaking any laws. I refuse to overload, we’re old school, and I want to keep it way. It’s a really
fine line between wanting to keep that old school culture and when you’ve got to bring the technology into it.
“I have done million-dollar deals on a handshake. People these days still find that hard to believe. If a customer’s got a problem, every single customer that I have, has my mobile number. You’re not going to go to a call centre. If they’ve got a problem, they’re going to ring me and I’m going to sort it out for them. The only thing I have to sell is a service, that’s all I’ve got, and that’s what wins them over.
“A lot of companies fail to understand that it is a service industry. I have had a delivery from a major company recently. They lost it, then delivered it to the wrong place. It took six weeks for them to actually acknowledge they’d stuffed up and would replace it. Every time I spoke to someone different and so you’d have to start again from scratch. We don’t have that here.”
Mt Isa Carriers has got a workshop, but a lot of the maintenance is outsourced on the newer trucks, under maintenance contracts. They also have good relationships along the routes
with people who can help out if a truck or trailer has problems.
As it is for many in the industry getting drivers is an issue, with the fleet’s drivers having an average age in the early fifties.
“I’ve got a young driver here, Jayden is just about to turn 23,” says Kent. “He wanted to drive road trains, so we’ve brought him through. He was in a body truck, we gave him some local work, then a couple of dog runs. He’s now in one of the new Macks and he’s not 23 yet, and a lot of big businesses won’t do that. I’ve had to take special insurance coverage on him.
“You’ve got to be able to do this, you’ve got to give them a go. To Jaydon’s credit he is unbelievable, a good kid, a good operator, he listens, but they are few and far between.
“He will go a long way. I hope he stays forever, but being young, who knows. Someone has to have this trust and put them in a truck. I’m running trucks and trailers worth a million dollars and then the freight on top of it. You don’t want idiots behind the wheel and that’s why a lot of big companies won’t employ people under 25. I’m unprepared to take that special coverage out on them.”
With up to 600 horsepower and 2,050 lb-ft of torque, the big bore workhorse provides efficient and dependable power and performance without compromise. Detroit’s advanced technology also means GHG17 requirements are met through innovative fuel efficiency resulting in lower emissions.
This power, performance and efficiency prowess is backed by our industry-leading warranty and extended coverage packages that ensures the highest level of support for our customers.
Combined with superior fuel economy and the absence of a midlife change out, the DD16 delivers an enviably low total cost of ownership and maximum uptime.
This is all backed by our well-established and extensive national service and support network which, together with our highly skilled factory-trained technicians, means you can count on getting the right advice when you need it.
With Detroit, there’s no compromise.
PowerTorque in association with NZ Trucking are introducing the Truck of the Year Australasia Award for the first time in 2023.
This year sees the arrival of a major initiative to increase the profile of the truck industry in Australia and New Zealand and emphasises the importance of trucks to our nations’ wellbeing and prosperity.
Truck of the Year Australasia (ToYA) will be presented at the Brisbane Truck Show in front of the media and will also serve as an opportunity for the truck industry, as a whole, to promote its importance to our economy.
In 2023, the first ToYA will be awarded to the truck which meets criteria based on those used globally by the other three International Truck of the Year (IToY) awards already in existence, in Europe, South America and China, but also taking into account the particular characteristics of the Australasian truck markets.
Truck of the Year Australasia is a positive initiative which will shine a spotlight on the excellence of the product hauling freight on our highways. There is general media interest in the award, which will further enhance that spotlight. Also, with the help of the close connections with our fellow jury members and access to trucking industry publications around
the world, it is an opportunity to showcase this Australasian excellence internationally.
To choose the winner, a jury of five people will assess the trucks nominated. Apart from Tim Giles, Editor of PowerTorque and Dave McCoid, Editor of NZ Trucking, we have asked Charleen Clarke from South Africa to make up a third IToY representative. The other two jurors have yet to be decided, but will be either industry experts or journalists, without brand affiliations, one from Australia and one from New Zealand.
The award is our region’s development adding to the International Truck of the Year (IToY) award family, which was originally launched in 1977 by the British journalist and legendary Editor of TRUCK magazine, Pat Kennett. Today,
the 23 jury members from magazines throughout Europe have been joined by ‘associate members’ in the growing truck markets of Australia, New Zealand, Brazil, Japan, China, India, Iran, and South Africa. Altogether, the combined truck operator readership of the 24 IToY full-jury members’ magazines and those of its 10 associate members exceeds 1,100,000.
Here in Australia, the period around the Brisbane Truck Show is the obvious time and place to make the announcement of the award, as it is one of the few occasions when all of the Managing Directors and CEOs, of all of the truck manufacturers operating in the Australian truck market, are in the same room. The presentation of the award will alternate between Australia and New Zealand, with the 2024 award being presented in New Zealand.
Deciding on which truck is to be named Truck of the Year Australasia is not one just of thinking about a personal favourite, it is about understanding the requirements and preferences of the trucking industry in both Australia and New Zealand.
Australasia presents truck makers with challenges unlike those it faces elsewhere in the world. Trucks are working in the harshest conditions, extreme heat, sub zero temperatures and mountainous topography at weights up to and over 200 tonnes in some cases and the trucks are running at higher speeds than most of the rest of the world.
Unlike the other regions in the world, Australia and New Zealand utilise trucks from Europe, North America and Asia, often loading these trucks to much higher weights than they are designed for in their domestic markets.
The main criterion for the nomination and the election of any truck as ‘Truckof-the-Year Australasia’ should be its contribution to the standards of safety
and efficiency of transport of goods by road in Australasia. The five judges use their experience to draw out the overall effect of the new vehicle and make a judgement call on the weighting of each segment of the criteria.
Any truck which fulfils the criteria and which has a GVM of 4.5 tonnes or above is eligible. The truck must contain considerable technological improvements. A minor facelift, for instance, does not make a truck eligible. The truck nominated must be reasonably new, shall be produced in series and shall be ordered, according to an official price list.
Choosing the nominations for the 2023 Truck of the Year Australasia has been complicated by the effects of the pandemic on the flow of technology and vehicles at a time when travel and supply chains have suffered major disruption.
As a result, the judging panel has allowed some fluidity with the dates the trucks were launched but insisted that
any contenders need to be available in both Australia and New Zealand.
The trucks nominated are, in no particular order:
• MAN TG3
• Kenworth K220
• Iveco S-Way
• Fuso Shogun 510
All of them have been driven by, at least, Tim Giles and Dave McCoid. In following years, we hope to enable other jury members to sit in the driver’s seat as well.
The following articles in this magazine describe the driving experience of the Kenworth and the Iveco, and readers can catch up on the Fuso and MAN, in articles from previous issues here, by scanning these QR codes:
There is no doubt about the biggest date on the truck world’s calendar in Australia this year. The date is May 18 and the event is the Brisbane Truck Show in Brisbane. Visitors can expect to see more innovations and a much more varied offering of truck types on the stands.
The world is changing and the drive towards zero emissions targets has seen vast sums invested in different technologies, many of which will be seen for the first time at BTS23. We have seen a smattering of electric trucks at BTS in the past, prepare for a much higher proportion of the vehicles on display offering the ability to reduce trucking’s carbon footprint, some by a little and some by a lot.
Although the way ahead is not clear, in terms of carbon reduction, we do know it’s coming and the trucking industry will be one of those most radically affected by legislation to reduce carbon. The pressure is already
on to make reductions from customers and the demand means show goers will be checking out the possibilities, while also reminiscing about the good old days, when diesel was the only show in town.
It won’t be just a couple of small electric trucks, it may be full ranges of electric trucks. It won’t be just electric power, watch out for some surprising hydrogen powered options too. Top selling brands like Isuzu and Kenworth will be explaining their probable route to target zero, as will many other brands.
It won’t just be the current truck brands on display, the new electric and hydrogen power technologies have seen a number of new players enter Australian truck market. They will all come with variations on the zerocarbon theme.
However, don’t forget the traditional truck product, which will also have a major presence. Alt-power may be the way of the future, but new diesel-
powered trucks are going to be with us for quite a long time to come, as the Australian trucking industry comes to terms with the practicalities of reducing carbon emissions.
One of those traditional dieselpowered trucks will be displaying the fact that it has received the honour of winning the inaugural Truck of the Year Australasia award, which will be announced at the BTS.
Of course, the manufacturers of the trailer being pulled or the bodies which are fitted to these future trucks will also be on hand to demonstrate their latest offerings, some able to reduce emissions, as well.
The trucking industry is about to go through a period of flux, where old certainties are no longer certain and new paradigms will appear, as the way freight is transported is moved over to the new world, where what was once was good is now bad and whole new industries are growing up to take the trucking world forward.
The Brisbane Truck Show 2023 is going to feature a lot of new names and faces as well as some more familiar ones, as the truck industry looks forward to a lot of new technologies, power sources, combinations and components.
Drive
The new IVECO S-WAY range takes the on road and liveability experience to the next level.
Drivers enjoy a SAFER driving experience with world class driver assist technology. The S-WAY cab maximises aerodynamics, while the Fuel Efficiency System continuously evaluates conditions boosting PERFORMANCE. The driving ergonomics and cab have been reimagined and designed for supreme COMFORT.
S-WAY makes tomorrow safer, more productive, and even more comfortable. iveco.com.au
It’s been about a year since the Kenworth K220 was first unveiled to the waiting Australian trucking public. The launch of the K220 was something which the truck drivers of Australia had been waiting on for some time. The new design did not disappoint.
This major upgrade and redesign comes at a crossroads for Kenworth and Paccar, where the tried and trusted method used by the Kenworth brand in the past needs amending. It is not possible to continue with some of the legacy systems and technology of the past. It comes into conflict with the fast-moving pace of new legislation around trucks on our highways and the introduction of a much higher level of sophistication in overall truck systems
Another factor which influences new trucks being brought out by the Paccar group, or any of the other global truck makers, is to develop the product they are selling to use more components which can be used globally across all of the brands in the group.
Therefore, we have a truck which uses the same basic cab concept as the first Kenworths built in Bayswater in Victoria back in 1971, but with a cabin interior layout much improved, even when compared to the K200.
There’s also a large amount of new technology in the driveline. It’s still the Cummins X15, but the adoption of the Adept concept, where the engine and the Eaton AMT transmission communicate at a high level, is a significant advance.
There is even more sophistication on tap with the latest AMT from Eaton, the Endurant XD, which brings this North American transmission into the same ballpark, previously only occupied by the European AMT transmissions.
It was with some excitement that Tim Giles climbed up the steep metal ladder into the cabin of the new K220 for a two day test drive hauling a B-double set from the KW HQ at Bayswater to Tamworth in rural New South Wales.
The plan was to head out of the
Bayswater plant and head across country through the Yarra Valley and on up towards Benalla. After some time on the Hume Highway the truck detoured through Wagga Wagga, before returning to the Hume at Gundagai and settling to spend the night at the Big Merino in Goulburn. The following day involved a run into Sydney, making use of the North Connex to keep rolling out to the Hunter Valley and up to the Liverpool Plains and the final destination of Tamworth.
The Cummins X15 engine on the test truck is the Euro 6 version, and at the moment, it is possible to buy a Cummins engine with a Euro 5 system, but that will end when the ADR 80/04 rules comes in, November 2025.
Cummins X15 is the standard engine in the K220 and on this test truck, the power is set at 550 hp and the torque at 2050 ft lb. As usual, a wide variety of options are available from Kenworth when thinking about horsepower, transmission, rear axle.
Cummins engines now all come standard with the ADEPT software, which offers features such as Smart Coast and integration with the adaptive cruise control. The set-up includes an overrun system which brings in the engine brake in when speed goes over a preset speed to reduce the speed of the truck.
The X15 now comes with a switch to enable and disable DPF burn off. If the truck is in a situation where a DPF burn off might be a problem, then the driver can disable it, or can enable the burn off when the truck’s in a position to do one safely.
Transmission options include the tried and true Eaton RoadRanger and also Eaton’s latest offering, the Endurant XD.
The Bendix Fusion system, which includes active cruise control, automatic emergency braking and a suite of safety systems is an option
• 30 + years in the market place
• Clean, grease-free fifth wheel
• More cost effective
• Easy to fit
• Consistent steering characteristics
• Environmentally friendly
• Australian designed & manufactured
• Used by some of the most highly respected companies since 1990
With the introduction of the K220, Kenworth have gone through a process of updating a classic truck, while keeping the central character of the K Series ethos.
at the moment but when we get to January 2025 the AEB will be mandated on all new trucks and then it ceases to be an option and becomes standard.
The transmission on this test is the Eaton Endurant XD, which is an allnew box, which has been developed as an AMT from the ground up. Out on the road, this box is definitely a revelation, it is a game changer for North American designed transmissions. It combines the robust nature of the classic Eaton transmission with the high-level electronic sophistication we normally associate with AMTs developed in Europe.
In this brave new world, where Roadranger skills are no longer a given in the trucking industry, this is the kind of AMT Kenworth need
to enable their customers to help them cope with the skill levels at the younger end of the workforce.
Of course, there is still a manual option available in the Kenworth range, but PowerTorque expects the experience of fleets, when they get their hands on the Endurant XD, to change a few minds and we can expect to see the proportion of trucks coming down the Bayswater production line fitted with AMTs to increase.
It has been a long climb back for Eaton after the less-than-ideal performance of the Autoshift and the limitations of the design of Ultrashift, in computerising the Roadranger. However, the team at Eaton have achieved an excellent quick changing, flexible and intuitive transmission, which a driver can leave in auto most of the time and get the job done as well as they can with the traditional box, if not better.
It’s a three by three by two box, with all of those gears able to combine to give the driver 18 gears, this design combination means there are three reverse gears available to the driver, and for certain applications that number can be increased to six reverse gears. This option would be useful on tasks like spreading gravel, in road work situations.
The Endurant is also available with a 0.7 overdrive reducing the rpm required at 100 km/h. The rear diffs on the truck tested were 1:4.11 which is quite a standard diff in a Kenworth, meaning the engine is sitting at 1650 rpm at 100km/h.
Taller diffs are available which would bring the revs at cruising speed down to 1550rpm or even 1450rpm at 100km/h, if the freight task allows and the desire for better fuel economy is there.
With the Endurant XD, the driver can choose to use it completely manually and just paddle the steering column stalk up and down. In some situations, this may be useful when the terrain is particularly difficult or the load problematic. This transmission is smarter than that and will make the right changes at the right time 99-plus per cent of the time.
Leaving it in auto mode but keeping an eye on the truck and then
At Volvo Trucks, environmental care has long been central to our vision of the future. We care passionately about the world we live in, and as the shift towards electric vehicles gathers pace, we are more committed than ever to driving progress.
We are thrilled to have launched our all-electric medium duty truck range for Australian transport operators.
The new Volvo FL and FE Electric medium duty range meet the demand from society and customers for dramatic cuts in CO2 emissions. To simplify the transition to sustainable transportation, the trucks are offered together with service and support packages for electromobility needs.
Come and visit us at the Brisbane Truck Show Stand #49, Hall 3 between 18 - 21st May and learn how we can partner with you in your transition to an electric future.
Learn more by visiting www.volvotrucks.com.au/electrictrucks.
Volvo Trucks. Driving Progress
intervening using the paddle when needed is a far better option and one which makes for more relaxed driving and reduces distraction. There is always the easy option, to leave it in auto and see how it copes.
In most driving tasks that is going to be sufficient. The skill of the driver will be knowing when to intervene and when to leave it alone. Add into this scenario the use of the active cruise control and the driver then becomes a virtual steering wheel attendant who has to keep an eye on things.
Quite a lot of the dashboard is a carry over from the K200, with some major differences. However, the picture in behind the dash is all new. The whole electronic system is now a multiplexed one, with components communicating along the common CANbus around the vehicle. This level of sophistication is vital to drive the safety systems which are mandated on new trucks for 2025.
The most obvious symbol of this change is the 15-inch screen in front of the driver. This is a pleasing curved shape and the figures and dials on the screen have a crisp 3D-like look to them. Gone are the days of the small fuzzy screen which couldn’t be seen in bright sunlight.
This can be made as busy or as sparse as the driver prefers. There is a ‘dark mode’ where the screen is mainly dark and displays the rpm, a digital speedo, gear selected and cruise setting. To this can be added fuel and coolant, various air pressures, oil levels and much more. It is up to the driver to turn on as much as they need.
No matter which instrumentation is set on this screen, if some kind of fault occurs, a notification of what has gone wrong will appear on that screen as an alert for the driver.
This screen is also the driver’s interface with the Bendix Fusion system which uses the camera in the windscreen and the radar in the front bumper to monitor the road ahead of the truck. This system enables the active cruise control, where the truck will maintain a speed, but also maintain a safe preset distance to any vehicle ahead.
Importantly, the Fusion also controls
and activates the automatic emergency braking system, which has been mandated for 2025. This activates engine and service brakes to bring the truck to halt in an emergency situation.
On the display, the system shows current following distance and what length of following distance has been set by the driver. An image of a car will appear when it detects a vehicle in front and then alerts will activate and lights will flash, if the system has concerns about closing speed, or the possibility of a collision.
To the left of the larger screen there’s the AVN, an eight-inch audio visual unit, including radio, navigation,
and control of music streaming from a connected device. Underneath this is the aircon with controls familiar from the T610 models, but for a system which has been redesigned specifically for the K220.
Further to the left we come to the DIN spaces where one or two UHFs can be fitted, or the operator may want to fit a data screen from a telematics or monitoring system. To the left again is another space for any auxiliary dials the operator wants to include, although these are also digital gauges which are designed look like the legacy analog ones.
Underneath the panels there’s a
row of switches, another aspect of the interior design which is reminiscent of the T610 interior. The operator can reorder and change the layout of them and can also add or delete switches, plus they can also be programmed through the data unit.
To the right of the switches there’s the ‘duckbill’ trailer brake lever, replacing the steering column handpiece to activate the trailer brakes, to straighten up a combination. The system also has a hill start aid which can be turned on and off, next to the duckbill.
This truck also has a lane departure warning system included. If the truck is operating on narrow lanes with white lines the system can be turned off, but after 11 minutes it will turn back on again.
There’s a switch to activate a systems check so the truck will go through the 13 systems on the truck before setting off on a journey. This also goes through and checks all of the light circuits to make sure there’s no dead globes or LED malfunction.
Drivers now have the ability to switch the bunk lights on and off from the dash and there is also a command panel in the bunk so the driver doesn’t have to get out of bed to switch the lights off. This really is Kenworth coming into the modern world.
The control panel in the sleeper has a pair of USBs, a 12-volt socket and a LED light on a stalk. Not only can you turn the lights on and off, but also control a bunk cooler, and there’s a digital alarm clock.
Cabins still come in the standard format of either a 2.3 or a 2.8 metre length, the offering is similar to that offered in the K 200. Sizes available vary from a 1.7m long day cab with a flat roof to the 2.3m sleeper with raised or flat roof or the 2.8m sleeper, only available with the aerodyne style roof.
Spending the night in the bunk of the 2.3m cabin was a pleasant experience, the wriggle room is comfortable and there is plenty of storage to suit the requirements of most drivers. There is an under-bunk fridge,
the controls in the bunk work well and the bunk itself is very comfortable and large enough to make up for the layout, which can feel less spacious than the smaller European sleepers.
The truck’s automated and safety systems handle what the driver wants and what the Fusion system can see with the radar and camera. It will head down the highway and travel, as instructed, at 100km/h, but when it comes up behind a slower vehicle it will back off to maintain a safe following distance. If the vehicle slows even more, the truck will bring in the engine brake to slow it further and will apply the brakes if needed.
The engine brake on the X15 seems more effective than it has been in the past, when coupled to the Endurant XD. The retardation starts with compression braking on half of the bank of cylinders, this is followed by the full bank coming into play and finally the AMT changes down a gear and ups the engine speed another
No ma tt er the driver or the job , the End ur ant Series fr om Ea ton Cummins has the automated transmission for your fleet. Each product reflects our commitment to best-in-class fuel efficiency, performance, and uptime.
200rpm to further increase retardation. These three retardation modes are available to the driver manually by pulling back on the right-hand steering column stalk, as well as being utilised by Fusion.
There are times where driver intervention is needed. If the Fusion slows the truck, the driver can steer into the outside lane and the truck will continue at cruising speed. If there are upcoming opportunities to overtake, the driver takes control by just touching the accelerator and then moves closer to the vehicle to prepare to overtake.
The driver themself can choose just how much to get involved. The truck’s systems are not taking away the driver’s choices and autonomy, they are offering options to make their life a little easier.
Unfortunately, on this test, the truck was one of the original evaluation vehicles, used for the launch and initial road testing. Its setting wasn’t optimal and the system was the first fitting of the first generation of the system. It was clear what the system wanted to do, but it didn’t always get its timing right. By the time these systems are being fitted in the first run of K220s rolling down the assembly line in Bayswater, there should be a seamless feel to the driving experience as the different functions interact more precisely.
The K220 still has similar limitations to those of its predecessors. There is not a flat floor and the raised roof design is a much improved one compared to the old Aerodyne, there is a feeling of more space. The geography of the cabin does not leave
much room for moving around in the 2.3m cabin, but there is enough.
There is no getting away from the difference in ingress and egress from the cab. The need to climb up a ladder, shuffle across a step and then duck down into a door is far from ideal. The fold out steps are still an option, but one which a low proportion of customers take up.
There is no cab suspension on the K220 at the moment and it’s obvious from the ride that this is the case. The ride from the parabolic springs on the chassis is acceptable and is much improved over previous generations of the K Series, but not as smooth as its European rivals. There is a cab air suspension system under development by Kenworth and that should be available in the near future, stay tuned.
While no one can predict the future with absolute certainty, we’re confident it’ll be brighter with the new Scania Super. Our new powertrain has already gained a reputation for not only providing the smoothest drive on the road but also being the most fuel efficient in it’s class. Our new 13-litre platform, which now extends to 560hp, delivers a fuel saving of at least 8 %* allowing you to increase your fuel efficiency while also reducing greenhouse emissions.
But it doesn’t stop there. As with our new V8 engine family the Scania Super 13L engine can also run on B100 biodiesel**, further reducing your CO2 emissions by up to 80% with no adverse impact on engine performance.
So if you’re ready to meet the commercial and environmental challenges of today and tomorrow, you’re ready to meet the all new lean green Scania Super.
Contact your nearest Scania Account Manager or go to www.scania.com.au to find out more.
With the launch of the new S-Way model bringing the truck brand’s range on the Australian market up to date, is this new model range the way forward for Iveco?
The last five years have seen big changes for Iveco in Australia, with the end of one of the longest selling truck models in Australian history and the ceasing of truck production at the iconic Dandenong assembly plant, originally, built by International Harvester.
The new reality for Iveco in Australia is one of rebuilding a truck brand, importing global models and adapting them to the Australian trucking industry conditions in a way which can bring the latest developments in Europe, direct to Australia, without the long delay between a truck launch in Europe and the commencement of
production here.
As new models are being developed in Europe, the Australian team can work on the adaptations required here and then build the new models in a synchronised program in Europe, with the assembly plant in Madrid assembling the trucks for Australia alongside the European versions.
The first model arriving from the new Iveco system is the S-Way, a complete model range which has been available in Europe for some time. This selection of models will be added to as Iveco refines the process and can offer a full range, as it did in the past.
“We had to make some decisions about what we were doing in regards
to our local factory and we went through that process quite seriously,” says Michael May, Iveco Australia New Zealand Managing Director. “We were looking as to how we could quickly get ourselves up to speed with the latest technology in Europe and the company collectively made the decision that the best way to do that was to bring in the product that we built for the whole world, South America, Europe and our region, Asia, Australia and the Pacific, from the Madrid plant.
“It was a challenging time for us, but we did a really good job with the sundowning of the factory in the right way and it’s given us an exciting opportunity to align. Now we’re
aligned with the latest product that’s coming out of Europe.
“We haven’t lost the engineering and the validation teams that we have down under. We’ve built a good strong core of engineers, and we’re going to continue to grow that. We’ve got a Customer and Innovation Centre, in Keysborough, Victoria, which we have moved into.”
Iveco has completed the local development of the Acco dual control, designed to replace the long serving Acco which dominated the waste sector for so long. This is expected, by Iveco, to be an important part of its product range, moving forward.
“We’re going to be looking into opportunities for us as a region to lean into new methods of propulsion, validation and potentially autonomous testing and validation,” says Michael. “So, these are where we want to lean forward, linking to the universities continuing to grow, and grow that part of our business.”
Certain aspects of the new range will be familiar from the former Stralis range with three different cab options, the Active Space, the Active Time and the Active Day configurations for long distance, intrastate and local respectively.
This range also brings the Euro 6
set of engines to the brand, in fact, the emissions level is at the lowest iteration of Euro 6, Step E, of the exhaust emission limits. Three engines are fitted to these trucks, the Iveco Cursor 9, Cursor 11 and Cursor 13.
The Cursor 9 is a 8.7-litre engine which produces 360hp from 1,530 to 2,200rpm and 1,650Nm from 1,200 to
fuels like biodiesel or HVO to reduce carbon emissions.
Further down the drive train is the Iveco Hi-Tronix AMT, available in 12- and 16-speed configuration. This is sourced from ZF and is the Iveco version of the Traxon AMT found elsewhere in European trucks. Drivers can intervene and change gears manually with a steering wheel mounted paddle, if it is required.
There is also an Eco-Fleet feature which can be turned on by the driver with the aim of maximising fuel efficiency by keeping the rpm levels well within the most efficient band. This can be further enhanced by the use of the Hi-Cruise feature, which uses cruise control, preloaded topographical mapping and learned behaviour over routes it has used in the past, to make correctly timed gear changes, to maximise fuel efficiency.
With a mandatory deadline in 2025 for automatic emergency braking, the S-Way also includes a full suite of safety systems including the usual abbreviation suspects like: Advanced Emergency Braking System, Brake Assistance System, Adaptive Cruise Control, Lane Departure Warning System, Electronic Stability Program with ABS (disc brakes all round) and ASR (Anti-Slip Regulation), Hill Holder and Driver Style Evaluation plus Driver Attention Support (DSE + DAS).
The DAS system checks the driver’s level of attention by analysing steering wheel movements. If a state of drowsiness is detected, a message on the screen and an audible signal prompt the driver to take action and take some rest.
1,530rpm. The next step up in power is to the Cursor 11 and the 11.1-litre engine pumps out 460hp from 1,500 to 1,900rpm and 2150Nm of torque from 925 to 1,500rpm.
The top power option is the Cursor 13 which, at 12.9 litres, has two power output options. The 530hp version produces maximum power between 1,600 and 1,900rpm and torque of 2,400Nm from 950 to 1,500rpm.
One step further up the power ladder comes a Cursor 13 with a rating of 550hp from 1,605 to 1,900rpm, and torque produced at 2,500Nm from
1,000 to 1605rpm.
The Hi-eSCR emissions control technology is a single after-treatment system featuring passive DPF (Diesel Particulate Filter) where regeneration does not require driver intervention. The system does not use EGR to control emissions. Iveco reckon this technology has many benefits for the truck buyer with reduced fuel consumption, a lower tare weight and no requirement for additional cooling, as passive DPF regeneration occurs at a lower temperature. All of these engines are also able to use alternative
“The truck is designed in Germany, Italy and Australia/New Zealand thanks to the local engineering team and validation team,” says Emiliano Foieri, Heavy Duty Product Manager at Iveco. “We’ve done millions of kilometres and thousands of hours of validation in ANZ. The vehicles are assembled in Spain and the engines are coming from France, plus one engine from China.
“It’s not like the old days when each market was completely different. This is a global system, a global product, but we are heavily involved in the development to make it specific for us
MAN’s TGX 26.510 is trucking redefined. Featuring the generous GM cab and powered by MAN’s technologically-advanced 510hp 13L Euro 6 engine with over 390hp of engine braking, the TGX will go the distance.
Come and see us in the main hall to learn how our new MAN truck generation boasts excellent driver fit, great efficiency and economy features, optimised uptime, and makes for a strong business partner.
in Australia. We have to carry bigger loads bigger than the European ones, our cooling strategy is different to the Europeans. So, all these things are designed to cope with the Australian conditions. The trucks as they are in Europe, they’re not usable at this the end of the world. We have spent years trying to design the S-Way ANZ.”
Visibility is improved in the new models with a new mirror design, which is helped by the fact that the doors have a full window, with no quarter light. The cabin redesign has also reduced the drag coefficient by 13.5 per cent, which equates to a claimed three per cent improvement in overall fuel consumption.
The wider Active Space cabin is available on trucks fitted with the 13-litre engine. The Active Time is the mid size cabin used on other prime movers and is also fitted with a bunk, but it is only 2.3m wide instead of the 2.5 in AS. There’s also Active Day, which is mainly used in waste applications, but also for other day-cab operations. There’s also the low roof and the high roof option
on AS and AT.
Iveco has gone over to using the European telematics system in its truck, as opposed to the local Australian system it offered previously. The driver can interact with it via the multimedia system.
Although there was limited time at the wheel at the recent launch of the S-Way from Iveco, there was a chance to get a handle on what the driving experience with the new models is like. The first impression is of a stylish European truck with a distinctive stylish sweep to the front grille. There will be no missing these new models as you meet them on the highway.
The climb up into the driver’s seat is simple, even in the wider AS cabin, as you would expect of any European truck. Inside, sitting in the driving position, the dashboard has been updated and now has larger screens both in front of the driver and on the central binnacle of the wraparound dash.
The surprisingly large steering
wheel has plenty of buttons, as we have come to expect. Disconcertingly the cruise controls are on the right, whereas most of the competition have them on the left. However, the steering feel is positive and reassuring.
The right-hand stalk on the steering column controls the engine brake and the left hand one the usual wiper, indicators and light. Once the engine is fired up the driver simply presses the buttons on the dash to their left to select drive and sets off down the highway.
This is where the marriage of the Cursor engine and the Hi-Tronix AMT come into their own, the gears and the acceleration come in smoothly, without fuss. The driver simply uses the right foot to convey how they want the truck to behave and it responds instantly, flicking up though the gears beautifully.
The smoothness of the deceleration matches that of the acceleration. Simply pull back the engine brake control to get a controlled move down through the gears and the ability to change the rate of deceleration with
the engine brake control. It is out on the road where this truck comes into its own.
The visibility improvement from the new mirrors is clear. Although the mirrors remain relatively large the blindspots of old have been reduced. Instrumentation and controls are also clearly defined and easy to find.
For a modern European truck, it is becoming increasing rare to have a large handle to activate the engine brake and a hand-piece to brake the trailers, but they are still here in the S-Way. Iveco haven’t gone to simple buttons and switches, yet.
On the narrower AT and AD cabins the dashboard runs straight across from the driver’s side to the passenger
side. Therefore, the information screen to the driver’s left has been placed centrally on the dash. To aid visibility, the whole unit has been hinged and can be pulled out to face the driver if needed or folded back out of the way when cross-cab access is needed.
Overall, driving the S-Way is a pleasant experience and one which many drivers will appreciate. The integrated driveline functions very well and seamlessly. The active safety systems are equally well integrated and do their job without hitch and also without fuss.
The question is inevitably, will this range of trucks be the one to drag Iveco back into contention in the
Australian truck market and get onto the contender’s list of trucking fleets? There is also an Acco replacement waiting in the wings to bolster the chance of a return to favour in the vocational market for the brand.
Success on this front will depend on a number of factors. One of those factors is the quality of the engineering, fit and finish, as well as suitability for the task. These models, as tested, seem to be a possible solution and could help the brand lift its sprits and its sales. If this product invigorates the Iveco team and its network, then they will have the product to make a mark in the Australian truck market once again.
THE SMOOTH POWER ON STEEP TERRAIN, THE BUNK SPACE, TROY HAMILTON, HAMILTON CONTRACTING
As part of its examination of the future development of alternative fuels for the trucking industry, PowerTorque road to zero emissions.
Although there is an inevitability about the trucking industry moving to a zero emissions model, there is no defined plan or timeline for the us to follow. There is no clear picture of what the technology mix will be, and no idea which technology will achieve the desired emission reduction.
At the moment there are a number of competing technologies being developed, but little knowledge about how those technologies will play out, which will succeed and which will fall by the wayside. Battery electric trucks are going to predominate in shorter freight transport tasks, but where the cut-off point, between electric and other technologies like hydrogen fuel cell, hydrogen internal combustion engines (ICE) and fuels like biodiesel,
is impossible to estimate, at this time.
One thing is certain, and that is uncertainty, the time period between the introduction of the first zero emission vehicles and the point at which the fog of uncertainty about the effectiveness of each technology clears is going to be a long one, the length of which we can only guess at, in 2023.
The North American Council for Freight Efficiency (NACFE) has come up with the term the ‘messy middle’ for that uncertainty, the period when road transport fleets will be faced with a number of powertrain options including advanced diesel, renewable fuels, natural gas, hydrogen, hybrids, battery electric power and hydrogen fuel cells.
There will be no single right solution and the variety of choices will make it difficult for operations to work out which options are suitable for their particular freight task.
“While this period can be complicated, NACFE regards it as a time where trucking will have
to evaluate many options and look beyond just the truck to the infrastructure needed to support that truck,” says NACFE in its ‘The Messy Middle - A Time For Action’ report.
“It is critical that fleets have reliable data on which to base their decisions in order to make proper choices. There are new dynamics at play
in the trucking industry including changing customer and stakeholder expectations, the introduction of new engines, regulations and incentives, operational changes, and other factors including fuel price instability and uncertainty about the second life of some of the alternative fuelled vehicles.”
To combat the extreme pressures that heavy duty vehicles such as Cement Agitators, Garbage Compactors or City Route buses are exposed to, Bendix has created Bendix Protrans™HD.
Protrans™HD has a heavy-duty formulation designed to cope with high temperatures found in constant braking and full GVM loading which requires a higher performance brake pad.
Find solutions for every brake job at www.bendix.com.au
There are a number of factors trucking operations will have to get up to speed on: the maturity of the technologies, the range of the vehicles and route flexibility, infrastructure, vehicle integration, and available incentives.
The idea of waiting to see how all the pieces of this technology and policy puzzle play out is not an option, now is the time to prepare for the impending radical changes. The trucking industry will need to get firm answers and direction from government and suppliers as to the likely timeline, for legislation, incentives and the availability of each technology option, as well as the infrastructure to support it.
Everyone involved needs to lay out their plans, the OEMs, suppliers, utilities, charger manufacturers, regulators, fuel companies, hydrogen suppliers et al. The plans cannot be marketing hyperbole or political promises, there needs to be clearly defined markers on the route to zero emissions as well as realistic predictions of the new technology’s capabilities and certainty of fuel or energy delivery timelines, and certainty of supply.
Trucking operators will also need
to do their due diligence. They will need to interrogate suppliers to ensure the claimed emission levels are, in fact, realistic and quantifiable. There are disputes between the different energy sources as to which of them are genuinely capable of zero emissions.
Jurisdictions and regulators will need to be quizzed by the industry about future plans and their impact on what emissions levels will be allowed, where and when. Certainty on this topic is going to be hard to find with our election cycle in Australia, but certainty will be needed by both the trucking industry and its suppliers on future regulatory developments.
Operators are going to have to drill down into their own businesses and look at the freight task’s requirements and come up with alternative scenarios to suit the alt-power options, at a point when a definitive answer on range and suitability may not yet be clear.
Businesses will also have to factor in the way energy pricing and supply options will develop. Those who are going to supply electricity will need to ensure a grid capable of supplying the energy needed in the right locations.
The cost and volatility of the fuel pricing for hydrogen or low emission diesel is also something which needs to be investigated and some level of certainty, of sufficient and stable
supply, provided by suppliers.
Even in the Australian truck market, which is some way behind those in Europe, North America and China we can start to get an idea of how the likely options will roll out.
The first zero emissions trucks to make an appearance are the light and medium duty battery electric vehicles (BEV). These are the simplest solutions and the kind of freight tasks they handle are the low hanging fruit of carbon free trucking.
For these trucks tare mass is relatively unimportant, they often run short distances in urban environments and are parked up back at their depot at night. This means the charging issue can be solved by relatively low power chargers back at the depot, over a period like eight hours. The trucks already running on the road in Australia, like the SEA Electric, Fuso eCanter and the electric Volvo FL trucks are all working in freight tasks which fit this kind of profile.
Over time, the number of these trucks will increase as the concept becomes more familiar and will accelerate, if incentives are introduced to increase the take up of low carbon emission trucks. As the take-up
increases the BEVs will start to appear in tasks which are not quite so suitable for the basic BEV.
Operators will start to find the limitations of the BEV and turn to other alternatives like hydrogen fuel cell, for example, when the limitations created by long charging times or trucks with a relatively low range become an issue.
Although there are plenty of hydrogen powered trucks being given a lot of publicity, there seems to be more hyperbole than high performance in the hydrogen fuel cell truck world at this moment. However, there are some notable exceptions like the 50 Hyundai Xcient fuel cell trucks handling a number of freight tasks around Switzerland.
This technology is maturing fast and all of the major truck manufacturers have evaluation models on the road in one form or another.
One limiting factor is likely to be supply infrastructure for hydrogen, and more particularly for green hydrogen, which gets fuel cell technology closer to zero carbon in a well-towheel sense. The development of a substantial supply infrastructure is going to take time, but Australia may be able to become a leader in this area with our abundant sunshine, which is ideal to produce solar power to run electrolysers and use them to use desalinated water to make green hydrogen.
The fact that these technologies are all new, in development and likely to need serious investment to get up and running as well as time to mature for our market, means that there is going to be quite a long period before the picture clears and the road to low emissions becomes evident.
However, during this period the pressure from large corporate customers and other transport clients is going to be building on their road transport suppliers to move towards carbon zero. They will be reducing their carbon footprint and expecting all of their suppliers to do so as well.
At this point supplying low carbon road transportation becomes a selling point and a way to compete in the market. This will be happening at a point where the electric and hydrogen solutions cannot fulfil demand and the infrastructure to support them is not up and running.
This is where the messy bit comes in. There are a number of halfway houses on the road to zero carbon, which can be used. Trucking operators may be able to offer interim solutions, to reduce carbon emissions during this period while the truly zero carbon solutions are developing and maturing.
One has been on the Australian market for some time and that is the diesel hybrid drive train which has been shown to reduce fuel use, and
therefore carbon emissions by up to 20 per cent in many urban delivery tasks. Solutions which may come to the fore in this period are fuels like biodiesel and other renewable fuels, which can reduce effective carbon emissions by up to 80 per cent in a conventional diesel engine, or natural gas, either as LNG or CNG which emits up to 20 per cent less carbon dioxide than diesel.
There is also work going into hydrogen ICE, which could offer an interim, or even a permanent, technology which uses so-called grey or blue hydrogen before a supply of green hydrogen comes on stream.
The fact is the paradigm for powering trucks in Australia will be completely changed over the years between now and 2050. For 120 years road transport has been able to keep the wheels of the world economy turning using just one fuel and one technology, diesel.
Over the next thirty years, the picture looks set to completely change and freight will be transported by road using a variety of energy sources, depending on the freight task, the location and the local resources. There will not be one simple solution but a whole raft of more complex solutions, and it might get messy.
There is unlikely to be any real introduction of hydrogen powered trucks in Australia, from Volvo, until the second half of the 2020s, reckons Paul Ilmer, Vice President Emerging Technology Business Development at Volvo.
“The second half of the decade for fuel cell electric platform introduction and hydrogen injection is still an unknown,” says Paul. “It’s also dependent on development of synthetic fuels as well because you’re adding the complexity of hydrogen injection.
“From a hydrogen perspective, in the second half of the decade, we’re aiming for the same range as a diesel
truck. That’s our corporate aim, and then, from a tonnage perspective, we should be able to handle a B-double comfortably, but it’s still to be tested, it’s really a validation question.
“So far, we’re not seeing many technical issues. In terms of supply, the trick is going to be ensuring supply on freight routes, making sure that hydrogen is available on the freight routes we all use now.”
Hydrogen suppliers will need to adapt to the needs of the trucking industry, rather than the trucking industry changing its behaviour to suit hydrogen suppliers. The introduction of hydrogen for combustion engines
can’t be disruptive. Operationally, Paul feels fuel distribution needs to be very similar to the set-up today.
There is a dynamic between the large corporations and the truck manufacturers, which is going to have to play out in order for one to be able to sell hydrogen to the trucking industry and for the truck makers to be able to sell hydrogen engine trucks to the industry.
Both will need to invest, but need the other to guarantee the demand, both for fuel and for trucks. In Europe, Volvo and Daimler have jointly financed a large number of electric charging facilities to ensure infrastructure to charge the electric trucks they want to sell. A similar deal, or government intervention may be needed for hydrogen in this chicken or egg type scenario.
There is no point in selling 200 hydrogen trucks without refuelling infrastructure being there, but there’s no point in investing in a servo with a hydrogen bowser, if there are no hydrogen trucks passing.
“There’s a consortium looking to set up hydrogen refuelling here, when the truck makers have trucks,” says Paul. “We’re completely transparent. But, I’ve seen over the last 12 months
There is a lot of talk about hydrogen as an alternative source of zero emissions fuel, but is there a hydrogen road map, and when will it arrive here in Australia?“There’s a consortium looking to set up hydrogen refuelling here, when the truck makers have trucks.”
an absolute tsunami of enquiry, and I think the infrastructure probably has an opportunity to go earlier than the truck supply.”
At this point, it is difficult to plan more than a couple of years ahead, because the way fuels like hydrogen will play out is uncertain. A hydrogen fuel cell could be here by 2026, but it also may not be until 2029.
“We’re being quite transparent when we say the second half of the decade for fuel cell trucks, because we don’t know, for example, what they mean to Europe, North America or Australia,” says Paul. “It allows us to have a kind of honest development transparency, we need to work out which market comes first, where the support is set up in that market, is it suited to some markets more than others, because of climate, road condition, and things like that.
“What we do know, though, is Australia is a priority market, because of the abundance of demand and the signals that we’re getting around hydrogen infrastructure.”
Volvo is probably going to end up with quite a mix of alternative power vehicles and will have battery electric,
certainly fuel cell and, probably in certain applications, a hydrogen combustion engine.
Volvo says it is open to whatever technology works for any application, that has the lowest carbon profile. By the time we get to 2030, there is likely to be a mix of technologies and energy delivery systems and energy types and how one or the other suits different applications better than others will become clearer. So far, it’s quite obvious that battery electric is going to suit urban distribution around the city.
Battery electric is the first cab off the rank and the range issue will decide where the cut-off point between battery and fuel cell will come.
“We’re assuming with electric, we’re going to be in the vicinity of 350 to 400 kilometres range,” says Paul. “You can only fit so many batteries on the chassis. So I think that that sort of 3-400km mark will be the cut-off for battery. Then, for applications beyond that, we’re going to be relying on hydrogen energy storage. I think there’ll be incremental gains around battery electric, including truck design, around aero, reducing energy losses along the driveline.
“I still think so much of it is about the driver, the guidance that you give
them by way of telemetry gauges that show when you’re consuming energy or producing energy, has a big impact. We see that the driver still has a 20 to 30 per cent impact on the range.”
There is a good deal of uncertainty around combustion engines, going into the future. At the moment the diesel engine is the only viable fuel but on the way to a zero-emission hydrogen engine, there are some staging posts offering reductions in carbon emissions, including HVO (biodiesel) and biogas, which can reduce carbon by up to 80 per cent.
“HVO will lower the carbon profile, and my opinion is, once we get good supply, I actually think it could be here to stay,” says Paul. “There’s some applications where the internal combustion engine is going to be around for a long time. Thinking about heavy, long applications, renewable diesel is a great alternative. It’s a pragmatic alternative too, it’s not pie in the sky, it’s a real alternative.
“Even from a hydrogen perspective, when you look at quads and things like that. I don’t know if we’ll be able to solve those. We should be able to solve it with HVO, for example.”
With the world looking for zero emission transport solutions, one company, Cellcentric, jointly owned by Daimler Trucks and Volvo Group, is moving forward with fuel cell technology to be included in their heavy vehicle product portfolio.
Cellcentric has been developing and building hydrogen fuel cells for cars for some time, but ever since its takeover by Daimler and Volvo, the company has pivoted to concentrate purely on developing fuel cell technology for the truck market.
PowerTorque met up with Matthias Jurytko, Cellcentric CEO at the IAA Transportation show in Hanover and got the lowdown on how this cutting edge tech is coming along and how it will power trucks in the not-too-distant future. Standing next to a 150kW fuel cell system, Matthias explained where the project is heading.
“We’re 50/50 owned by Daimler Trucks and Volvo Trucks, and we are the main supplier for a fuel cell system,” said Matthias. “We’re using two 150kW systems in a twin system to make a 300kW (408hp) system. With a small battery that gives us enough propulsion power to move European trucks, for example, with 41 tonnes at 80km/h cruising along a motorway.”
A hydrogen fuel cell works by using hydrogen gas as the fuel source. Hydrogen gas is stored in a tank on the truck and is then fed to the fuel cell. The fuel cell contains a membrane and two electrodes that are separated by a catalyst. The catalyst helps to break down the hydrogen molecules into protons and electrons. The protons pass through the membrane, while the electrons are forced to flow around the outside of the cell, creating
a potential difference and therefore an electric current.
The current produced heads down the line to a power distribution unit and this then transfers the power to either an electric motor or to the vehicle’s battery. It is at this point where it will be down to the truck OEMs to determine how they want to operate their system, as they develop their own distribution strategy. For Cellcentric, the fuel cell system and the hydrogen supply are the only components inside the scope of the project. The rest is up to the individual manufacturers.
“Both Daimler and Volvo define the specifications to which we have to develop this technology, they are both on the same side, trying to get to the right fuel cell,” said Matthias. “However, when it comes to the application of the technology in the trucks, they are in competition.
“There’s a couple of things we are developing right from scratch, we are setting the standards and then there is the challenge of preparing for mass production, which will be happening in the second half of this decade. These are the challenges we have.”
Cellcentric is working to produce a fuel cell that is as light as possible, but also capable of handling a range of up to 1000km. Critical factors include service lifetime, data requirements, durability, as well as the power output, which should be able to match current diesel drivelines.
The fast acceleration in fuel cell technology in recent years means the strategy has to be flexible, no-one can be sure exactly where hydrogen is heading.
“This is the biggest challenge this industry has ever seen,” said Dr. Andreas Gorbach, Head of Truck Technology and Member of the Board of Management Daimler Truck at the IAA. “It’s decarbonisation, digitalisation and a supply crisis. From a decarbonisation standpoint, talking about propulsion systems, it’s certainly transforming what we have today, from diesel into zero emission,
battery electric and fuel cell.
“We’ve been doing everything with one technology for 120 years, but the diesel ‘one size fits all’ solution won’t take us into the future. So, it’s battery electric and hydrogen based propulsion. Daimler Truck and the Volvo Group jointly established Cellcentric as a joint venture for development, manufacturing, industrialisation and commercialisation of fuel cell systems.
“Three things are important, we need great products, second, we need the infrastructure and third, it needs to have a good total cost of ownership case for our customers. That massively depends on energy cost, electricity versus diesel versus hydrogen. This is why we will also see them develop at different speeds in different regions because energy prices, tolls and other things will differ around the planet significantly. These are the three things we need, great product, infrastructure and the right energy prices.”
Cellcentric has been involved in a long fuel cell development process but is now moving over to the next phase of the story. It is now gearing up to produce the fuel cells at high volumes,
which should, in the long run, bring down the price of the individual units to make the technology more viable for the trucking industry.
Cellcentric has decided that the 150kW stack will be its main building block into the future which will work for most truck applications as well as stationary power, heavy applications, ships and trains. It can be used as a single unit or multiple set of units for any application (a stack of three fuel cells equates to 612hp for the driveline).
The individual units are approximately 230kg, therefore, two units producing the 300kW will weigh in at 460kg. Add to this the battery which fuel cell designs need between the cell itself and the electric motor and then there is the mass of the electric motor which powers the driveline. However, the latest electric drivelines on show at IAA use an e-axle, a drive axle which includes the motor in its assembly, reducing tare.
Daimler intends to use liquid hydrogen in its trucks, which has a high energy density, this is just one of the methods of on-truck storage. Other truck makers are using hydrogen gas tanks and others are storing the hydrogen onboard in the form of ammonia.
The reason Volvo and Daimler came together to invest in Cellcentric was because they realised the vast research and development costs to get their own fuel cell system up and running would be prohibitive, driving them to come up with an agreement around the pooling of research resources, just for the fuel cell itself.
Although the core of the propulsion system will be the fuel cell, both Daimler and Volvo are likely to diverge in their approach to the other onboard systems. Both have evaluation vehicles on the road now but are likely to come up with different systems and protocols around the fuel cell itself.
“We both believe in using fuel cell technology as one cornerstone to decarbonise transport and when we were scouting the topic some years ago, on a supplier basis, it was very clear to us that there was nothing available off the shelf, for fulfilling our tough requirements,” said Lars Stenqvist, Chief Technology Officer Volvo Group. “We then had discussions about whether we should we start to develop something internally and we came to a conclusion that the effort was far too big and our volumes were not sufficient to do this on our own.
“Then the Daimler team knocked on the door, with a proposal, because they had come to the same conclusion, saying if we combined our joint resources and our joint volumes, then we would be a significant player in this industry. That’s how it all started.
“So now we have Cellcentric up and running, a 50/50 joint venture and it’s our intention to develop fuel cells and produce them in high volumes, and then to act as a tier one supplier. We will install the fuel cell systems in our vehicles. But it’s important to state that, on a vehicle level, we remain competitors.
“This is what it takes to take society from a brown platform to a green platform, sometimes you work in partnership, even when your competitors, and yes, we are open to sell to third parties, what we are looking for is big volumes.”
With undisputable road presence and trusted reliability, there’s no place you’d rather be than behind the wheel of a Kenworth.
Some trucks look to be designed for a particular task, and Tim Giles finds when driving a Western Star 47X as a tipper and dog, it is a truck within its comfort zone.
There is something about tipper and dog work which is not the same as other freight tasks. The requirements are different, and so are the preferences of the transport operators. Many will only run a bonneted truck in this application and, in fact, they do predominate around Australia in this role.
Getting on board a new Western Star 47X tipper, with a quad dog on behind seems the most natural thing in the world. The Bruce Highway from Brisbane to Mackay was the route, and negotiating the many and varied road works en route was the frustration.
The first thing to say, when approaching this combination, is that the 47X looks designed specifically for this task. It has the no-nonsense look we expect from a tipper, and there’s enough shiny metal on the front to satisfy the tipper driver.
Climbing up inside the cabin, this is a North American truck and feels, to a certain extent, like its predecessors. There’s enough switches and dials to satisfy the traditionalists and only
a relatively small information screen directly in front of the driver, which gives a hint of the arrival of modern technology.
Under the skin, of course, this is a very modern truck. There is the Gen 5 Detroit DD13 engine putting out 525hp (386kW) and with the classic 1850 ft lb (2508Nm) of torque, when needed. This is the latest iteration of the engine, the state of the art from the Daimler Group.
Axles front and rear come from Meritor and this truck runs with an industry standard 1:3.42 rear axle ratio
The wiring is multiplexed with a high level of sophistication to run the engine, the Detroit DT12 AMT, plus the myriad safety systems which are onboard and mandated from 2025. The DT12 uses the Performance Off-road package, ideal for this kind of work.
The safety package is the Detroit Assurance Active Brake Assist, which includes active cruise control and automatic emergency braking. The system does have an off switch, and the ACC can bring the truck’s speed down to to zero km/h. It also has ABS,
stability control, Sideguard Assist and also the Detroit lane departure warning system with a 15 minute timeout.
This is a thoroughly modern truck, but it is still ‘Western Star enough’ to satisfy those who prefer to be a little more old school. Getting that blend of ancient and modern right can be a fine balance, and Western Star seem to have come close to pulling it off.
On the test, it was possible, if the driver is up for it, to have driven this 47X for most of the day with just active cruise control on when running on the highway. This tells us the system is doing its job and making sure that it stays a safe distance from vehicles in front. The radar and video combination sense and react to vehicles they need to without too many false alarms.
Sometimes a slow car in the lefthand lane, or a sign close to the road on the outside of a right-hand bend will make the system cut the revs or apply a little braking, but a split second later it is back on the throttle. If not the driver
simply presses the throttle or moves the truck across the lane slightly, to avoid any issues
The radar unit in the windscreen is actually quite large, covering a work diary sized area of the opening.
Once the driver sets the desired speed and the preferred following distance, the active cruise control does exactly what it is supposed to do, and the driver doesn’t need to do anything. It is quite responsive, as the truck starts to get into the climb the truck waits, and then decides whether it’s going to grab a gear or not.
Climbing, it is quite happy to sit at around 1200 rpm and let the torque do the work. There’s plenty of pulling power on hand to get the job done. The AMT is responsive, and it changes quickly. The changes are very certain, there is no ponderousness about it, no lag time between gears.
What’s different, from when you drive an AMT in a European truck with the same sort of setup, is that the changing process makes a lot more noise. It’s very much the same with the engine noise, there is a lot more in cabin sound than in its European equivalent.
You can actually hear the gear changes being made and this is clearly a deliberate design style choice. US drivers must prefer to get more feedback from the driveline that those in Europe, who don’t need to hear the sound to know the truck is working hard or changing gear. It’s simply a style thing.
During the 10 hour drive north from Brisbane the truck did its job without
fuss, it’s very comfortable. easy, relaxed driving, sitting in a comfortable cabin. The driver can just let it do its business.
This setup, with its wheelbase at 4925mm and a standard day cab is what you might call the Hanson specification, or suitable for any operation similar to that. It doesn’t have large fuel tanks. It is actually quite nicely set up to run tipper and dog with a busy schedule.
From the driver’s seat, there the central binnacle to the left, with a basic radio fitted which has got a USB you can plug into. Below this there’s three old fashioned gauges, an air gauge and two temperature gauges. Below this, again, is the air conditioning controls. To the right of them is a space, which can have a large information screen fitted, but in this case is home for the set of switches to control the various systems on the dog trailer. Operators can choose between entertainment system screen or switches, when the screen becomes available.
There is a series of power outlets to run whatever the driver needs in the cabin. Below this is three banks of switches, all different shapes and sizes. As the system is now multiplexed, the operator can configure all of these switches wherever they prefer, to suit both applications and personal taste. Also here, are the maxi-brakes and the trailer brake hand-piece, nice and traditional.
Directly in front of the driver there is a very clear screen with a menu across the top. The test truck is configured
with the speed, outside temperature and the current state of the cruise control system as a default view. To the right is the gear being used and how many seconds the truck is behind the vehicle which is ahead, when one is detected.
To the left and right of this screen are the more traditional gauges. There’s tachometer, oil pressure and fuel to the left, and speedo, air pressure and coolant temperature, to the right.
Directly in front of the driver’s right knee and out of the driver’s eye line is the switch which turns the lights on. Indicators, main beam and wipers are controlled by the left-hand stalk, while the right hand one controls the transmission and engine braking. Pressing the button on the end sends the AMT to manual and driver paddles the stalk up and down to change gears.
One of the issues from the past has been the failure of the doors to seal properly when closed. This has been overcome and the doors are well sealed, but this does mean the door needs to be closed quite firmly, to be properly closed.
The seats are large, wide and comfortable and from the driver’s seat the visibility is quite good for a bonneted truck, matching equivalent competitors. The kerb mirror on the passenger side can be augmented by the Sideguard Assist which will tell the driver there is a vehicle on the passenger side with a triangular white light on the A pillar and a warning if the left indicator is activated.
After driving this shift in the Western Star 47X, the take away is that this truck does exactly what a tipper and dog operator would want from it. There is power and torque to handle the job without much fuss. The safety systems work effectively out on the highway and the driver can relax and be comfortable in their seat.
From the outside it does look like a Western Star and sometimes in the tipper game appearance is important. There’s probably enough cues in the design to satisfy the traditionalist driver. They can change gear manually if they really want to but can leave it all to the computer if they care to.
The level of sophistication required in the modern truck means that any component not only has to do its job but also communicate with the rest of the vehicle. It is both sending out data, for the rest of the vehicle and using data to do its job better for the improved efficiency or safety of the whole truck.
With the release of the latest offering from Western Star, the brand has moved forward several stages from a basic truck to a much more sophisticated and connected whole. It is a communications system on wheels, like all newly released trucks.
The mandating of some safety
systems and the move forward to the ADR 80/04 exhaust gas emissions regulations has introduced the need for more data to be flowing around the vehicle and for the various systems to be able to communicate and interpret data in real-time as the truck is travelling along and to take actions based on that data.
Western Star come out of the Daimler Trucks stable and manufacture in the US. Therefore, the electronic control systems are dealing with a Detroit based environment. The engine, transmission, rear axles and several other systems are out of the Detroit order book. One of the new additions to the truck’s
ecology is Detroit Connect.
However, let’s start with the engine. There are two engines available from Detroit in the X Series. There’s the DD 16 and the DD 13 Gen 5. The Gen 5 is the new classification of Detroit and is used to differentiate between the progress of the various iterations of the DD13.
Gen 1 was the original version of the 13 litre, Gen 2 saw it change to meet US EPA 10 emission rules by using adblue, Gen 3 never got into Australia, Gen 4 is the engine that’s in the Cascadia in Australia. This new Gen 5 is now in production, with similar emissions to Gen 4 but with improved fuel economy. There’s quite a few internal differences in this new engine including compression ratio, the shape of the pistons, the way fuel and air flows inside the engine, with an improved swirl motion.
The main significant difference is in the after-treatment system. The SCR system is in a box which is physically smaller, but has a larger DPF inside, with improved surface area, from a single DPF instead of two smaller ones. This enhances two elements, it reduces back pressure, reducing fuel consumption and secondly it also substantially increases the time between regeneration events.
Regeneration parameters on the original DD13 started after 20 hours, but on both DD16 and DD13 Gen 5 this has pushed out to 125 hours. In fact, on the DD13, in particular, and to a certain extent on the DD16, if the service cycle is anything other than a high idle time application, it manages the temperature well enough to get close to a position where it never
Times have changed and engine makers no longer just supply an engine. There’s much more to the story and PowerTorque looks into the package from Detroit which comes with the X Series Western Star.
needs a regeneration.
In addition, if an operation does have periods where the engine does have to idle for long periods, they can choose an option which auto elevates rpm when required. The engine senses the exhaust temperature is getting a bit low, in a high idle time application, and it pushes the idle speed up to about 1000rpm.
There is also thermo coasting, which is essentially the system going to engine brake on three cylinders, and fuel on the other three. It powers itself against the engine brake, which puts quite a lot of heat through the exhaust. There’s no net change in torque and the system only activates when the truck is in cruise control.
Detroit reckon the driver doesn’t notice any difference, other than the engine sounding a bit odd. The driver
ARE TWO ENGINES AVAILABLE FROM DETROIT IN THE X SERIES. THERE’S THE DD 16 AND THE DD 13 GEN 5. THE GEN 5 IS THE NEW CLASSIFICATION OF DETROIT AND IS USED TO DIFFERENTIATE BETWEEN THE PROGRESS OF THE VARIOUS ITERATIONS OF THE DD13.”
can be just cruising along at 100km/h and sees a green light illuminate, on the dash. The whole process can take around 20 minutes on the road.
According to Detroit, by retaining EGR, good fuel consumption gains have been retained. The engine was always designed to have EGR and has, historically, had a low failure rate on EGR valves, coolers, piping or turbochargers.
Depending on the duty cycle
the truck is working in, the system will choose its own mix of emission control. It can use all EGR or all SCR, or a mixture of both, depending on the load and any other parameters which might effect the exhaust gases. The data from engine management, NOx sensors, torque needed, enables the engine management to calculate its requirements and the solution which suits it best.
By using this mix and match
“THERE
process the engine can run hotter, with higher combustion temperatures burning fuel more efficiently. These higher temperatures do mean higher NOx in the exhaust but fuel efficiency is improved and the SCR can handle the NOx.
The DD13 and DD16 engines now being used in Australia are the same as those used in North America and no longer a specific engine for Australia. The DD16 still has turbocompounding included in the system, where an air turbine is connected to a gear train that feeds power back onto the flywheel.
The automated transmission, the Detroit DT12, is now common across the Daimler heavy duty offering, globally, and so will be the main transmission offered in the X Series from Western Star. However, this is a brand which will also be specified with a manual transmission. in the Australian market, the Eaton RoadRanger is available, but the Detroit DT12 AMT should be regarded as the standard offering.
There are two versions of the new AMT available, both are called DT12 and from the same family. The OV is the overdrive version of the box and the HE is designed for
high efficiency. With HE being the AMT to be specified to get the most out every litre of fuel on linehaul type operations.
The OV version of the box is specified when the AMT needs to be able to cope with situations like off-highway work. It’s got a whole feature set, which is designed to be useful for things like a rocking mode which helps the truck to get free when it gets stuck in gravel.
In this OV transmission there are two versions available, the OV and the OVX. The difference between the two is essentially that the OV will go up to 62.5 tonnes GCM and OVX doesn’t have a weight limit on it.
According to Detroit the testing in road train has shown the AMT to be very effective, despite only using 12 gears instead of the traditional 18. The take-off feature has worked well when compared to a manual clutch as, it is claimed, the control in the automated manual is much more precise. It knows exactly how much heat it’s putting into the clutch and differential and releases takeoff power at the right rate to minimise risk.
There’s a feature called Powerlaunch, which lets you bring the engine revs up well up above 90 per cent of engine torque. It then brings the clutch in at the right
speed to pull away from stationary. To activate it, there’s no switches, the driver simply puts their foot all the way through and the control system does the rest.
In Australia, all the Western Stars that have the AMT use the control stalk to move between different driving modes. These modes are many and varied, but when the end customer orders the truck, they can choose which modes they require and how the AMT will behave.
There will be fleet customers which want a truck to default into economy mode after it is keyed off, but others will prefer the AMT to stay in the chosen mode until next time the truck is fired up.
Other operators may choose the option to make manual gear changing available at relatively low speeds, but remove that option from the driver when the truck is travelling at highway speeds, to enhance fuel economy on long high speed runs, but give the driver
flexibility when manoeuvring at slow speeds.
There are a number of systems involved in Detroit Connect, they’re all one system but they perform lots of functions. The familiar fault codes
give the ability for a operator to see the health of their trucks. Is there maintenance they need to do now? Or is it something to look at next time it comes in for service?
The driver can see what’s happening on the screen in the truck and also the fleet manager back
at base gets the same read-out to monitor the truck’s performance and status, at the same time. Every Western Star with the Detroit engine has five years of Detroit Connect included in the price of the truck. The system will use any mobile network which is available to send back the data.
The system will give the fleet manager the reports and historical data to enable them to monitor both truck and driver behaviour. It’s also looking at the whole life of the engine and tracking performance. The system will also interpret data if there is an issue and recommend changes. If there is not a simple solution, if the issue is more complex, it’s possible to go through the data with somebody from Detroit to work out what to do next.
If the customer prefers they can get the same reports Detroit provided in the past when a technician plugged diagnostics into the truck. The difference now is it comes back to the operator online and live.
The operator can get a remote download, do a remote update of parameters and software. If they want to change the speed on a setting, remote shutdown times or operating temperatures of that system, they can do it remotely. If they want to move a truck from being in their regional fleet to being in a home-based fleet, they can just hit the button and action the software updates on the system on board.
There is also a safety analytics
package interpreting data from all the safety systems which are fitted to the truck. Detroit Connect will record 60 seconds before and 15 seconds after what happened for any particular event.
From the driver’s point of view, a warning may come on and then
go away, but from the operator’s point of view, they can look at a list of trucks and see which ones have got the most occasions of any particular safety issue. From here they can drill down into the data to identify other issues.
If a problem regularly occurs the operator can set the system to flag particular issues in order to monitor some behaviours which have been identified. This can be an alert when something happens, or the ability to check on particular problems periodically.
The system does not currently have a process where the driver can log into each truck when they start a shift. There is also no method of connecting other safety systems, which may fitted into the truck, so that all of the information from the truck can appear on one screen, back at base.
Since 1963, Mack has been designing and building trucks to handle Australia’s unforgiving conditions. Mack Titan has always taken on the toughest of road train, triple and quad assignments, tackling long distances and big payloads with ease. Its powerful Mack MP10 engine delivers up to 685hp and 2,300 lb-ft torque, while the innovative mDRIVE automated manual transmission delivers the grunt to the gravel with the minimum of effort. Titan delivers excellent fuel efficiency and low emissions, making it the ideal truck when you’re clocking up the k’s. Make your own history with Mack, and talk to your dealer today, or visit MackTrucks.com.au/Trucks/Titan/
PowerTorque visited the Daimler plant at Tramagal, Portugal, which has been building light duty trucks in Portugal for the European market for well over 20 years.
The plant at Tramagal produces around 12,000 trucks a year, with numbers rising again this year. Portugal is a relatively small country, with a population of just 10 million, but it is an energetic country, well motivated and well educated. The Lisbon region is home to many tech start-ups. Daimler Truck also has a growing connectivity software business in the region.
The reason for Daimler to set up the factory in a small town outside of Lisbon, begins with taking over a facility, which was started in 1964 by the Bois de Ferreira family producing military trucks. There was a professional truck making business on the site, which was taken over by Mitsubishi Motors. Later, after Daimler took over the commercial vehicle arm of Mitsubishi, the plant became part of Daimler Trucks Asia.
“Our business relations in the company, our interface, our counterparts, they sit in Japan, they sit in Kawasaki, with very few in Germany,”
says Arne Barden, CEO, Mitsubishi Fuso Truck Europe. “We were the first to build the eCanter, in 2017 and we have a lot of experience in building electric trucks.”
This Daimler plant has been building light duty trucks in Portugal for the European market for well over 20 years. The Canter has a large market share in Portugal, with significant sales also in Italy, France and Germany.
Although this plant produced all of the eCanters sold in Australia, so far, the next generation models for our market here will be sourced from a full-scale assembly line, recently completed in Japan, which can build both diesel engined as well as electric Canters.
In 2014, the first prototype of the eCanter was produced at Tramagal. Now, the next generation eCanter has already gone into production at the plant, with its next generation battery, e-axle and a number of other innovations.
At the moment, the number of work hours needed to build an eCanter is
higher than those needed to build a diesel truck. Battery and e-axle fitment take extra time, but as numbers ramp up, Daimler expect the eCanter to use as much manpower as its predecessors.
Due to the issues created by a production line handling very powerful electric systems, Daimler grades staff at ten different levels, depending on training and skill levels. only staff at higher qualification levels are allowed in parts of the production line where the high voltage systems can be accessed.
Arne Barden started his career in the Wörth Plant in Germany where Mercedes Benz trucks are assembled. Later, he went to India, for six and a half years and was responsible for the factory setup of the Bharat Benz plant there. He later worked on the launch of heavy duty trucks for the Indonesian market. From there he headed to Kawasaki in Japan, where he was head of supply chain management for four and a half years. Taking on the job in Tramagal saw him returning to Europe but to a much milder climate than that he could expect back in Germany.
When you’re running a trucking business, or you’re out on the road, trust is everything. You need a team behind you that you can rely onpeople you know are always on your side.
At UD Trucks, we have one of the widest networks of sales and service experts dedicated to your success. From local dealership managers to finance specialists, from performance specialists to truck technicians, our people take the time to get to know your business, and they work with you like they’re part of the team.
To find out more, contact your UD Trucks dealer on 1300 BUY A UD or visit udtrucks.com/australia
Managing the many facets of a transport fleet is plenty of work, but planning for natural disasters such as bushfires and unpredictable flood seasons adds another layer of pressure.
Rogers Transport, a family-run transportation, freight and logistics business, was hit hard during the Queensland and New South Wales storms in early 2022.
“We had about three and a half metres of water through the truck depot, and we lost 26 trucks in total, about half of those were rigids and the other half were prime movers,” says Rogers Transport General Manager of Operations Brad Rogers. “It’s taken us a while to get back on our feet.”
The flooding was a massive blow to the Rocklea-based business, thankfully however Brisbane Isuzu was on hand to offer support.
“We’ve been purchasing trucks from Brisbane Isuzu for decades,” says Brad. “We lost 15 rigid trucks, so the team at Brisbane Isuzu moved quickly to assist
us. We’ve recently taken delivery of another six new F Series trucks, and we’ve got another six on order.”
With four FVL 240-300 Freightpacks and four FVM 210-300 Freightpacks on the road around the clock, the company introduced a ‘one driver, one truck’ policy which meant that each driver is solely responsible for the truck they operate daily.
It has been a huge success so far, with truck drivers taking obvious pride in the Isuzu F Series trucks they pilot, with reduced mechanical and maintenance issues and next to no problems when it comes to upkeep, cleanliness and presentation.
The Freightpacks come with a curtain side body that allows for easy access for unloading goods.
With space for 14 pallets in the Freightpack the FVLs and FVMs require a killer engine to keep the trucks running and move the heavy loads. Powered by Isuzu’s tough six-
cylinder 24 valve SOHC 6HK1-TCS engine, Brad’s customers won’t be let down.
Loading the F Series Freightpacks and checking goods is a breeze thanks to the removable rear step which facilitates installation via a tailgate loader. Lightweight side gates are easy to fold back, but durable enough to keep heavy loads secure while on the road and within the rough and tumble of loading.
“Rogers Transport drivers love their Isuzu trucks,” says Brad. “They’re comfortable, they’re straight forward to use, they’re easy to work with, there’s plenty of parts available for them, and the reliability is on-point.”
There are big things in the works for Rogers Transport over and above the F Series fleet expansion.
The company is also moving into a huge purpose-built facility in the Port of Brisbane, consolidating their three locations into one depot with a wealth of storage and a serious footprint for expansion.
Natural disasters are one of those things which always on the minds of truck fleet owners, especially those in Southeast Queensland.
“We’ve just signed a lease on a new facility out at the Port of Brisbane, so we’re going to amalgamate all our three sites,” says Brad. “It’s an exciting time for us, with 55,000 square meters of yard! We can’t wait to continue building our fleet with Brisbane Isuzu because they have proven time and again to be relied upon.”
The fleet expansion and new location mean that Rogers Transport can deliver on their range of freight and logistics services including container movement, warehousing, local distribution and interstate freight transport, in an improved capacity.
Founded by Gary and Val Rogers over three decades ago, the successful freight and transport business moves hardware and paint supplies up and down the southeast coast of Australia.
Brad is the second generation of Rogers to take up a key role within the transport operation. Growing up under the tutelage of his hard-working parents, Brad is familiar with trucking and what it takes to keep the fleet on the road and drivers happy and satisfied.
Swiftly securing new trucks to continue servicing their long-term clients has made a world of difference for a business that prides itself on reliability and attention to detail.
“We’ve got a couple of trucks with over a million kilometres still running with original engines, they have excellent performance and longevity,” says Brad. “The trucks with a million kilometres are the first ones we bought over 15 years ago, and they are in fantastic working condition. We’re big on our preventative maintenance and servicing, to
look after all our trucks, no matter their age.
“All our servicing is done in-house by the team here and we use genuine parts from Brisbane Isuzu. Parts are always readily available and if there’s a delay it’s because the parts are on a truck up from Sydney or Melbourne and we’ll have them within a day or two.”
Adding further efficiencies, the latest F Series models to join the fleet came with some changes and upgrades that the team has had to adapt to.
“The new trucks all have automatic transmissions,” says Brad. “It was a change at first, but the guys are loving them. They’re loving the new AV unit and the creature comforts that Isuzu offers. Swapping to the automatic transmission was due to availability initially, but the feedback from the guys has been great. They love them, so we’ve continued to spec the new trucks with automatics.
“It’s simpler to have auto when driving through traffic these days, the roads in Brisbane are only getting busier and busier.”
Now that the fleet is growing and the new facilities are ready, it’s only a matter of time until the Rogers Transport team can get back to doing what they do best: moving freight throughout Southeast Queensland and delivering warehousing solutions to their clients.
In December 2022 the National Heavy Vehicle Regulator (NHVR) registered an industry code of practice called ‘Managing effluent in the livestock supply chain’ or the ‘Effluent Code’.
Sponsored by the Australian Livestock and Rural Carriers Association, the Effluent Code provides practical guidance, to parties in the livestock supply chain who influence or control heavy vehicle transport activities, to help minimise effluent spillage into the road network.
Importantly, the Code makes it clear that managing effluent in transit is the responsibility of everyone in the livestock supply chain.
With guidance from an NHVR Code Advisor, the Code was developed by an industry working group. Organisations involved included producer groups, livestock transporters, sale-yard managers, feedlot managers, processors, government departments, enforcement bodies and animal welfare advocates. This group identified the activities involved in livestock transport and proposed relevant best practice controls to eliminate or minimise effluent loss in transit.
Of course, effluent is an unavoidable by-product when livestock are transported by road. Did you know that cattle can defecate 12 to 16 times a day, and sheep can lose around 4 per cent of their live weight as effluent in a 24 hour period?
The factors that affect livestock effluent production include the species and condition of the livestock, its access to water, feeding pattern and stress levels prior to loading, climate and weather conditions, and the length and characteristics of the journey. Though transporters are aware of these factors, they can only control some of them. Transporters rely on
other parties to prepare livestock for transport, provide accurate information and assist with the disposal of livestock effluent produced during the journey.
Modern livestock trailers are designed with ventilation and non-slip floors to provide for animal welfare and keep valuable livestock safe and in good condition. Transporters who travel through urban centres generally have effluent capture tanks installed on their trailers, but these have limited capacity.
Some effluent spillages have little impact on remote or rural roads, but with increasing urbanisation effluent spillage has a greater effect on the safety and amenity of road users and of residents in local communities. Impacts could include the risk of a vehicle (particularly a bicycle or motorbike) slipping and losing control.
While road safety is the primary focus of the Heavy Vehicle National Law, there are many other reasons for the livestock supply chain to be proactive when it comes to managing effluent in transit.
For example, biosecurity is one of the biggest risks to domestic livestock production. An incursion of foot and mouth disease (FMD) would devastate our market access costing the nation up to $80b over 10 years. Like many other diseases, parasites, pests and weeds, it can be spread via livestock effluent.
The livestock industry’s social licence may also be tested by effluent spillage in the road corridor. Large or repeated spills near towns or urban areas can harm the reputation of the whole of the livestock supply chain. Food culture in Australia increasingly focuses on ‘paddock-to-plate’ marketing, and transport is a critical element of that narrative.
And of course, effluent can become
a significant animal welfare issue if containment within a livestock trailer becomes the only option.
Transporting livestock is a very challenging job and the people who work in the industry are passionate about it. Like many involved in heavy vehicle transport, livestock carriers would appreciate better recognition and understanding of their role and skills, as well as better roads and better facilities, like rest areas with toilets, improved access to showers and healthy food options for drivers, and truck washes and effluent disposal facilities, for livestock transport vehicles.
Operators and drivers love the lifestyle, they’re proud of their trucks and they care about the welfare of the animals that they move daily from farms, feedlots and sale-yards to farms, feedlots, sale-yards and processors. Of course, there are elements of the job that are frustrating, and one of these is managing livestock effluent in transit when you have limited options for its containment and disposal.
Managing livestock effluent is a whole of supply chain responsibility. That’s why the Effluent Code includes information for off-road parties about the things that they can do to help minimise effluent loss. By working together, to eliminate or minimise livestock effluent spillage we can improve road safety, animal welfare and biosecurity outcomes, protect the environment and support the sustainability of the livestock industry.
Livestock transport operators have been the only link in the supply chain expected to manage livestock effluent in transit and keep it off the road. Drivers have been regularly fined for effluent infringements, others in the supply chain have avoided responsibility But all that is about to change, says the ALRTA.
Introducing the Australian Made 406MHz GPS Personal Locator Beacon from GME, the MT610G.
The MT610G is a super-compact, lightweight PLB, offering an impressive 7-year battery life and a 6-year warranty.
Featuring an integrated 72 channel GPS receiver, high-intensity LEDs, IP68 Ingress Protection, and an inherently buoyant design, the MT610G is designed to meet and exceed the latest international standards, ensuring enhanced peace of mind for the outback trucker.
gme.net.au/plb
One of the strengths of the LBRCA Conference is that it gets rural operators to stand up in front of their peers and talk about the issues which affect them all. There are experts on the stand as well, but it is the real world stories from trucking operations which regularly hit the mark.
One of the topics under discussion was the problem of finding drivers and then retaining them when they are found.
“We have a workshop which does a lot of truck repairs, and that’s where I got a lot of ideas from,” said Mick McCulloch, Managing Director of McCulloch Bulk Haulage. “We compete for drivers and mechanics with the mining industry. Everyone’s situation is a little bit different, when you look at where you are losing
Mark Fletcher, a third-generation truck driver, has been awarded the 2023 LBRCA Young Driver of the Year at the LBRCA Annual Conference in Tamworth.
The LBRCA Young Driver Award recognises outstanding young drivers under 35 who demonstrate a best practice approach and commitment to driving and safety.
The Award, sponsored by SafeWork NSW and the LBRCA, includes a trip worth $5,000 to the USA, where Mark will gain an understanding of international bulk transport and handling practices and attend the Mid-America Trucking Show (MATS), the largest annual heavy-duty trucking event in the world.
your drivers to. Our problem is the mines and lifestyle.
“The workshop runs a five/four roster and the blokes work 10.5-hour days and the do five off, four on and then five on, four off. So, they are working two weekends on and two weekends off. The night shift does 36 hours a week and the day shift does 36.5 hours a week. That gives us a very good coverage.
“Driving a truck, you might work ten days straight on AFM, and then they want two or three days off. We are trying a driver situation where they are working seven days on, seven days off. We increase the productivity of the truck by about 35 per cent. Obviously, our wages are a lot higher, because we are paying for their week off as well. We started it in January and it’s been a great
Nominated by his employer Mick McCulloch Director of McCulloch Bulk Haulage, Mick is pleased Mark’s commitment and passion to the heavy vehicle industry has been recognised.
“Mark is 24-years-of-age and is now driving a new B-double combination carting bulk commodities throughout regional and rural NSW. This is a huge achievement in such a short period of time and testament to Mark’s ‘always give 100 per cent’ attitude,” says Mick.
Mark has grown up around trucks and says that driving them isn’t just a job, it’s a passion, and one that he hopes to keep doing until the day he retires.
Mark is a well-respected employee, a worthy recipient, and a brilliant role
success. The number of phone calls I have gotten from drivers that want to do it is unbelievable. The problem is you have to manage two drivers per truck, and we are working on that.”
Mick also points to the problem that truck drivers are not classified as skilled labour. His operation can bring in mechanics on a 482 temporary shortage skilled visa from overseas, but not drivers. Mick’s operation is making progress, unfortunately, not everyone can work on the kind of shifts he uses, because there isn’t enough weekend work for everybody, but it has improved driver retention.
One of the examples of the work Mick has put in over the last few years is the winner of the LBRCA Young Driver of the Year (see below).
model for the rural transport industry. He will assist the LBRCA to promote rural transport as a viable, rewarding, and long-term career choice for young people throughout 2023.
This year’s Livestock and Bulk Carriers Association Conference took place in Tamworth with a wide range of topics brought to the fore, including driver shortages among others.Mark Fletcher, 2023 LBRCA Young Driver of the Year.
With the Telstra 3G closure on its way and the landscape of the industry vastly changing every year, it’s the perfect opportunity to embrace the benefits of the latest smart telematics and fleet management systems.
Teletrac Navman’s fleet management solutions give you actionable insights to streamline your operation for faster response times, improved safety and better service.
Recently, NatRoad CEO, Warren Clark told the National Heavy Vehicle Regulator (NHVR), “There is no doubt that telematics has the potential to make operators’ lives easier by improving safety, efficiency and productivity.” The association says greater adoption of telematics could help the road transport industry meet the challenge of a growing freight task, as long as it’s regulated fairly and transparently.
It’s true that a future-proofed transport business relies on clear insight into the who, what, when, where, and why of its drivers and assets to improve business outcomes – but to get the best results, it’s critical your business starts with a foundation of trust from a source you can rely on.
100% visibility with this perfect pair
When a Teletrac Navman TCA TypeCertified device is paired with the AI-powered TN360 fleet management software, which provides the information, security, and surety you need and more. It enables data from vehicles and assets to be securely communicated as key metrics such as trip distance, vehicle engine, and
safety data, which are all viewed as analytics within TN360. This gives the business access to high-definition GPS tracking within maps, real-time vehicle updates, and customisable dashboards. With this perfect pair of telematics and fleet management software, you’ll have the visibility to ensure drivers and vehicles are operating safely and efficiently.
TN360 allows you to work smarter with two-way instant messaging, digital forms, and proof of delivery without waiting for drivers to report in. Plus, you can access job dispatch and work via the SmartJobs feature which leverages in-cab and mobile devices and supports popular TMS platforms such as TMW, SAP, and Oracle.
Take the stress out of improving driver safety with our Electronic Work Diaries (EWDs) and Smart Dashcams. Teletrac Navman’s NHVR-approved EWDs are an electronic alternative to written work diaries, delivering realtime alerts with accurate fatigue break information, ensuring drivers never miss a compliance break.
The Smart Dashcam uses forward and driver-facing cameras, telematics data and advanced onboard sensors to monitor driver performance against key safety and performance metrics. With this data at your fingertips, you can identify areas for improvement and reinforce positive driver behaviours to keep your fleet safer than ever.
The best bit? Its cost-effectiveness – the Transport Safety & Regulatory Bundle represents less than 7 per cent of a local operator’s variable costs.
For a typical interstate operator, it’s 1.8 cents per km whilst providing access to increased productivity, Smart OBM, EWDs, paperless objective evidence, AI cameras, proactive risk mitigation and the ability to manage compliance by exception.
Leverage our professional services, network of solutions specialists, customer support, and more to ensure you get even more value out of your software.
Meet some of our industry experts at the Brisbane Truck Show - Stand 104, Hall 4
Step into the future this Brisbane Truck Show as it shines a spotlight on the increasingly important role smart tech is playing in the industry.
Your trucks can provide a goldmine of information that can reduce costs & boost productivity.
Dashboards, Insights, Analytics & Reports
Digital Documents, Checklists & Forms
Route Compliance & Job Execution
Vehicle Maintenance & Scheduling
AI-Enabled Camera Solutions
Driver Behaviour & Electronic Work Diary
Engine & Performance Management
Compliance and Health & Safety
With the power of AI, TN360 delivers real-time visibility to all your vehicles, assets & equipment across your business. Experience fleet visibility that delivers intelligence instantly. From driver safety through to productivity, monitor your operation in real-time to make smarter decisions.
Get all the tools you need to get connected.
It seems that few are against safety improvements, most want cheaper groceries/productivity but many are against larger vehicles, whilst a majority want their goods delivered but do not want trucks. The situation needs to be changed whereby larger high productivity freight vehicles (HPFV) gain greater access while delivering the productivity the population yearns for by way of reduced costs whilst delivering safety improvements.
Somewhat commonly seen in the HPFV arena, are AB-triples, B-triples and to a lesser extent BAB-quads and ABB-quads. Recently there has been some promotion that BA-triples are OK, so what has changed? Previously it was commonly considered (the NHVR included) that an AB-triple is a better performer than a BA-triple from the same vehicle units.
Operators promote ABB-quads over BAB-quad because of their on-road dynamics. If it is about improving the ‘standard,’ shouldn’t then the ‘best’ performance option be promoted?
Outside of PBS, AB-triples certainly have a positive history, if operators prefer BA-triples (whatever their reasoning) then there should be benefit in requiring that configuration to be assessed in accordance with PBS Safety Performance Standards (PBS).
Victoria has an insatiable appetite for PBS, everything is a road to PBS. Modular B-triples and AB-triples were embraced by NSW RMS under the Road Train modernisation project. Relatively simple, here is the performance criteria if you comply, then here is the applicable network.
But regardless of whether it is an AB-triple versus a BA-triple or an ABB-quad versus a BAB-quad, the key requirement is ACCESS.
Whilst gaining Access is a minefield, it really should not be that way. There have been many projects and documents prepared as to how to complete access assessments, but most seem to be more focused on how it can
be stopped rather than how to make it happen. I recently had an example of a B-triple awaiting access approval, at that stage it had been parked for more than 120 days. With so much history of approvals, we must stop forcing the known good performing safe and productive combinations to go through the cost and drag of PBS.
Access that is based on reference vehicles is extremely limiting as most reference vehicles are not real vehicles. The burden is always on the operator, with some routes having multiple mass restrictions, then the operator is expected to determine the minimum applicable to the task and the route.
If the bridge structure is an unknown it will be impossible to readily establish reasonable assessments for networks. I have been in a couple of detailed discussions around bridges and access. The problem with bridge assessments is the fact that design history of the asset along with the current status need to be known. The design status of many structures in local government areas are unknown and there are nearly 400 local government authorities (LGAs) (excluding Western Australia). Therefore, without the appropriate information, it is difficult if not impossible to conduct a proper assessment.
The NHVR has a bridge access project, the Strategic Local Government Asset Assessment Project (SLGAAP) in progress that has considerable potential for the many structures with unknown design and history. It was stated that some 24,000 LGA structures could be included in this project, where structures could be categorised into ‘bridge families’, such that several structures would be assessed and then all structures in that family would be considered accordingly. A lot of work, but seemingly a positive way forward.
When the bridge issues are resolved Access should be simple,
there is good reason it could be like the smorgasbord at the local club, the menu having very different courses, and my proposed Access Smorgasbord menu has five (5) key options: Length; Height; Swept Path Performance; Gradient; Bridges (axle spacing mass schedule).
• L ength (intersection stacking etc), Pavements and Bridges, do not differentiate between PBS and other vehicles, so the first task, remove that mystery. Similarly, access should not be commodity limited (except maybe in disaster or emergency with specific cooperating conditions). Mass management in conjunction with telematics should be the precursor, non-compliance should be actioned appropriately, this will allow the Factor of Safety applied to structures to be reduced.
• Height - options including up to 4.3m and up to 4.6 metres
• Swept Path Performance - options, generally in accordance with PBS safety levels.
• Gradient - the maximum gradient on networks should be information held by the road owner/manager, if they do not know how can they appropriately assess and access application.
• Axle spacing, group mass and GCM - this is difficult. An axle spacing mass schedule has a place for not only bridge assessment by also for vehicle designers, noting that where short simple spans are involved and only two or maybe three axle groups can impose mass at once, GCM is rarely a factor.
By providing multi layered access maps the access smorgasbord would then provide the operator with a ready assessment of access and remove the unacceptable delays and incurred costs in considering access.
Road and access managers need to deliver a simple process for Access, remove the need for permits and Safety and Productivity will follow.
Optimize your fleet with data-driven insights and AI powered by the #1 global telematics provider.
Geotab’s AI-driven platform transforms real-time data from any source into actionable insights that provide measurable business value, help reduce fleet’s emissions and costs while improving operational efficiency. Optimize your fleet’s performance and stay ahead of the competition.
geotab.com.au
NatRoad CEO, Warren Clark, takes us back to our youth, where we probably first heard the term ‘no pain, no gain’ from a coach.
No Pain, no gain’ was probably uttered by a sports coach or physical education teacher at the end of a lung-busting training session, or after the team we’d been thrown into had been flogged by a margin of nightmare proportions.
If you’re a heavy vehicle operator in 2023, the last person you want to hear delivering that ‘no pain no gain’ phrase is your accountant or business manager. Like it or not, financial pain is a constant and deep-seated feature of the current business environment.
It’s a measure of the industry’s resilience and professionalism that most operators are still in business, given today’s cost pressures. Most of us
understand the term viability to mean the ability to live, grow and develop.
Viability should be the word on everybody’s lips right now, particularly our industry where profit margins for many are so thin. Coming to terms with the so-called ‘pain points’ is a starting point for any business that’s looking to make itself viable.
NatRoad recently commissioned research by economists to better understand what needs to change to ensure road transport can sustain itself as industry in Australia now and into the future. Our research project tapped into more than 170 firms, most of them employing five drivers or fewer and turning over up to $2 million per annum.
Those operators told us, unsurprisingly, that the cost of fuel is their number-one pain point right now. Some 93 per cent rated it as ‘very important’ or ‘important’, well ahead of compliance with regulation (69 per cent) and labor costs (59 per cent). Of course, the relatively low rating for labour costs was likely because our respondents were mostly owneroperators.
But large or small, nobody is immune to high fuel prices. It’s just that the smaller operators feel that pain the most. According to globalpetrolprices. com the price of diesel fuel in Australia in mid-March was $1.81 per litre, a significant drop from $2 at the start of 2023. It topped $2.20 in mid-2022 and it’s an issue that’s not going away soon, given the state of the global economy and the ongoing war in Kyiv.
Of course, those financial pain points can be addressed and operators were asked what were the factors in play if they were to succeed. The
top-rated was the ability to pass through costs (such as fuel and tolls) to customers. Some 78 per cent of respondent ranked it important or very important.
Others were effective cost control (72 per cent), winning/retaining customers through non price factors (59 per cent) and having an appropriate pricing policy (58 per cent).
Again, it was no surprise to learn that only eight percent of operators say reducing their carbon footprint is ‘very important’ for them to be viable. It’s not that they don’t care; these businesses are simply too busy trying to keep their heads above water.
The vast majority of businesses do not even measure their emissions at this stage of the game. That may have to change, but the ball is very much in the court of the government policymakers.
And the driver shortage? The ability to retain or hire drivers was the secondhighest pain point for businesses turning over more than $10m per annum, but rated 11th for smaller businesses, probably again because most of them are owner-drivers.
All this sends a message to government that our industry is at a critical point. We are an essential service and a cornerstone of this country’s economic wellbeing. Surely we deserve some sort of practical relief in this year’s Federal Budget.
The National Heavy Vehicle Regulator has released the survey results targeted to enhance safety across the Heavy Vehicle Industry, writes Dave Hourigan the NHVR Chief Regulatory Policy and Standards Officer.
Commencing with the National Heavy Vehicle Regulator at the start of 2023, one of my first priorities was to analyse the findings of the 2022 Heavy Vehicle Industry Safety Survey results. I am pleased to say the results of the survey, which have now been released publicly, encouragingly highlights industries improvement in safer practices and general understanding of enhancing safety across the sector. This survey was held in June, July and August last year to provide the NHVR with greater insight as to how the heavy vehicle industry manages its safety responsibilities.
As the safety regulator for the heavy vehicle industry this survey serves an important role in helping the NHVR to better understand the safety perceptions and practices in our industry to tailor future initiatives to address safety gaps.
This is the third iteration of the survey and I want to congratulate the 5,750 respondents who took part in the survey because it demonstrates the priority the heavy vehicle industry has for improving safety.
The results provided excellent insights about the heavy vehicle industry management of safety responsibilities. It informed us that there has been an increase in safer practices applied by those employed in the heavy vehicle industry, as well as an increase in a better understanding of heavy vehicle safety technologies.
Typically, those who completed the survey were:
· Managers (43 per cent)
· Drivers (41 per cent)
· Employed in a business based in Victoria (49 per cent), New South Wales (20 per cent) or Queensland (15 per cent)
· Delivering loads that comprised
general freight (20 per cent) or primary production/farming (20 per cent)
· Transporting their goods locally (59 per cent)
· Employed in a business that has two to ten staff (60 per cent) and have been in the industry for 20 years or more (53 per cent)
Overall, safety management across the industry was found to have increased since our last survey done in 2020, with notable improvements in the uptake of a basic Safety Management System (SMS) where 65 per cent of respondents now have an SMS for their business. This is an encouraging result, but it also tells us that we still have a lot of work to do to increase SMS uptake. In addition, 98 per cent of respondents found the SMS materials available from the NHVR very helpful.
Having an effective SMS is one of the best ways to ensure you have a safetyfocused business and are complying with your safety duty obligations under the Heavy Vehicle National
Law (HVNL). One way for operators to be more aware of an SMS and how to implement one can be found in the materials that we provide on our website. We have an array of guidance materials, including an SMS roadmap that can help operators to put this system into place for their business.
Encouragingly, there was an increase in respondents who have a better understanding of heavy vehicle safety technologies. When considering a vehicle upgrade, several safety technologies stood out:
· Antilock Braking System (ABS) (77 per cent)
o Those employed in the bus, dangerous goods, and waste sectors are most favourable
· Features that reduce blind spots (68 per cent)
o Those employed in the bus, construction/landscape products, steel, and waste sectors are most favourable
· Reversing safety systems (64 per cent)
o Those employed in the bus, government including local government, and waste sectors are most favourable
Despite almost two-thirds of respondents indicating awareness of side and rear underrun protection systems, only 33 per cent of respondents indicated they would consider that technology when upgrading a vehicle. Those employed in the dangerous goods, waste, and containers sectors were more favourable to considering side and rear underrun protection systems when upgrading a vehicle.
We were also able to capture the various views that people in the industry, based on their years of experience. We listed ten different safety features in the survey and of those ten, respondents who had been in the industry for five years or less placed a higher rating of importance for many of the safety features, compared to those that have been in the industry for 20 years or more.
In recent years, we’ve been pleased to see an increase in the uptake of Performance Based Standards (PBS) scheme for heavy vehicles. In the survey we were able to capture some of the views PBS operators had. When purchasing a new vehicle, PBS operators typically consider ABS, stability control systems, and features that reduce blind spots as most important.
In addition, those that are PBS owner-drivers are more favourable to the following safety management practices:
· Review risk controls in their business
· Commit to having a dedicated safety person in their business
· Hold regular meetings to discuss safety issues
· P rovide ongoing communication to staff about safety
· Attend safety meetings or events
· Keep and maintain records of safety training
PBS has been picked up by
industry as a major driver of efficiency, with lower operating costs and higher safety benefits for the network. To hear from PBS ownerdrivers that they are prioritising safety in the management of their business is highly encouraging. We’re hoping to see a continued increase in the uptake of PBS vehicles in the months and years to come.
Throughout 2023 we will be engaging widely to use the results from the survey and help address the most critical safety risks. We will do this by delivering more targeted SMS and Chain of Responsibility messaging and information to address gaps and increase awareness across different sectors.
“When I first approached the ATA team about them creating a report on the trucking industry, I stressed that I wanted it to be positive, which might sound strange considering I’ve called the conditions facing the industry as ‘the
This includes fixing the national truck laws, where the ATA will now expand our national Road Transport Act proposal into a chamber-ready bill which can be introduced into the Federal Parliament. We highlight that if Australia fails to achieve vision zero on road safety, it will be one of the most significant failures of public policy.
David Smith, Australian Trucking Association Chair says that he stands by the ‘perfect storm’ description. We have a combination of age-old issues such as access combined with the global pandemic, natural disasters and supply chain shortages.
The cost of doing business seems to rise every month and it’s not going away any time soon.
Then there are the long-term challenges. Skills and driver shortages. Inadequate roads and a broken system for funding this vital infrastructure.
There’s a complete lack of rest areas and proper facilities. We need greater ambition for improving safety and boosting productivity. Despite years of workshops and meetings from never-ending reviews, we still have broken national truck laws.
And now, just over the horizon is a future of great transition, with zero emission vehicles and automation fast becoming a reality. On top of all of this, we have to keep the economy moving.
These are all very challenging
issues but you’ll note I asked for the ATA report to be positive. And I still believe it’s the right call. You see, there’s a positive story to tell about the trucking industry and it’s important we show the light as well as the shade.
And so the ATA has created ‘Trucking Australia – the Report’ which is a snapshot of trucking today and into the future. One of the most positive things about trucking is our ability to work together. We are great at putting differences aside and pulling in the same direction. The report reminds us that it has been the work of state and sector trucking associations, the ATA’s members, which have stood up and fought for the industry.
Our member associations were critical to working through some of the major challenges with the pandemic, such as state border closures. They’ve also secured key wins for industry, including funding critical roads, rest areas and effluent disposal sites. The report also sets out the key issues and long-term challenges that the ATA is addressing, together with our members.
Governments must also implement minimum rest area standards, and mandatory road service level standards to guide road funding decisions to where that investment is most in need. There is also a pressing need for national reform of road user charges, and development of a national transport workforce strategy.
We must also enable the opportunities that will come from future and emerging technologies. We face a future of great transition, trends of decarbonisation and automation are coming, even if they might feel disconnected from our day-to-day challenges. But these transitions will reshape our industry.
Future transition and technology do not wait and getting them wrong can leave once successful businesses as a footnote to history. There’s no point putting our collective heads in the sand. None of this is going away so we’re best off trying to understand and embrace the opportunities.
But we have now arrived at a pivotal moment. A watershed. A time when the burden of the last few years, the unresolved long-term challenges, and the beginning of significant future transition, have all arrived at once.
How can the industry possibly navigate this challenge, and find its way to a better future? To secure the future of our industry, we must face this moment together.
perfect storm’.”
The Strategic Local Government Asset Assessment Project is assisting road managers to better understand their assets, through engineering assessments and supported decision-making for heavy vehicle access.
Better decisions
Safer roads
Enhanced productivity
For more info, visit nhvr.engagementhub.com.au
Daimler Truck plans to introduce series-production driverless trucks in the United States by 2030. Gianenrico Griffini, Italian Trucking Editor and President of the International Truck of the Year Jury, got a taste of things to come when he hopped aboard a Freightliner Cascadia self-driving truck on the highways around Albuquerque, New Mexico, USA.
We don’t have to wait years to see selfdriving trucks on public roads. They are already a reality in the United States, with some prototypes based on the Freightliner Cascadia platform. Built by Daimler Truck North America, the semi trailers, equipped with Level 4 automated driving systems, are undergoing field tests in actual operating conditions on interstates around Albuquerque, New Mexico.
Albuquerque is the HQ of Torc Robotics, a company acquired by Daimler Truck in 2019. Torc develops the software, integrates, and fuses the inputs from different sensors, such as cameras, lasers, radars, and lidars, to allow safe automatic driving on high-traffic density highways. A lidar is a device that measures the distance from an object by a laser beam and returns high-resolution three-dimensional information on the surrounding environment.
The validation tests do not occur in confined areas but on multi-lane highways with a standard prime mover, trailer combination of 80,000 pounds (about 36.29 tonnes) at the maximum cruising speed allowed in the States of 65 miles per hour (just under 105 km/hr).
For safety reasons, during road tests, a human safety driver, assisted by a Torc Robotics engineer, is always ready to take complete control of the truck if a risky situation arises. The safety driver
also has a crucial role in providing the software specialists with the feedback to program the onboard computer according to a prudent, safe, and fuel-conscious driving style, without hard braking and harsh accelerations.
Daimler Truck’s decision to develop autonomous driving solutions first in the United States depends on multiple factors. Firstly, the States have the most branched and extensive motorway network globally, and the speed difference between trucks and cars is not as high as in the European Union. Moreover, US highways represent a more structured environment than an urban situation. There are lanes headed in the same direction, and it’s easier to predict where cars are supposed to be going. In this environment, the Freightliner Cascadia can handle most traffic situations: lane mergers, merging into traffic from a ramp, changing lanes, and slowing down or speeding up.
The US legislative framework is also favourable since the only counterpart the truck manufacturers deal with is the US Department of Transportation (DoT), which is proactive in facilitating the introduction of technical innovations.
Furthermore, self-driving eighteen-wheelers respond to clear business cases and market needs, such as a continuous increase in freight demand transported by road
(a 30 per cent increase is expected by 2030) and a growing shortage of heavy vehicle drivers.
According to the American Trucking Association estimates, unfilled driver jobs slid to nearly 78,000 units in 2022, down about four per cent from more than 81,000 in 2021. It’s still a considerable number that is bound to skyrocket, according to ATA forecast, to more than 160.000 units in 2031. This shortage is due, among other reasons, to a significant
number of retirements and the industry’s failure to recruit more women, who account for eight per cent of the overall workforce.
In developing autonomous driving solutions for the States, Daimler Truck has focused on a specific business case: connecting one logistics centre to another (hub-tohub) along a motorway. When the truck arrives at the destination hub, a professional truck driver takes it to the final unloading point.
In March 2022, Torc Robotics created a special advisory board, TAAC, Torc Autonomous Advisory Council, with leading companies in the sector, such as Schneider, Covenant Logistics, Penske Truck Leasing, and Ryder System, to foster collaboration and better understand the challenges faced by logistic companies.
The TAAC comprises key freight industry players who will provide strategic guidance to Torc as it
integrates with the freight network and tackles challenges beyond highway driving. The goal is to introduce Level 4 series vehicles by 2030. The platform used to develop autonomous driving solutions is the Freightliner Cascadia. With an annual sale volume of around 85,000 -100,000 units in a normal sales,
it’s the best-selling heavy duty prime mover in the USA.
In 2022, Freightliner had a market share of 42 per cent in the heavyduty segment, which reached a fullyear total sale volume of more than 254,000 vehicles (compared with about 222,000 units in 2021).
For safety reasons, the experimental Cascadia has many redundant systems. There are redundant (and independent) systems for the foundation brakes, steering actuation, vehicle data transmission network (CAN-Bus), and parking brake. The primary and secondary Electronic Braking System (EBS) Controllers, in particular, offer precise and reliable controls to decelerate the truck and the trailer.
Should the primary EBS encounter any critical faults, the secondary EBS will take over to execute a safety procedure called Minimal Risk Maneuver (MRM). Two servo motors electronically assist the steering gear. Should any one of the servo motor experience a fault, the second unit takes over entirely to provide the required steering commands to execute the MRM procedure.
Finally, anti-hacker protection (Cyber security), which is of paramount importance in developing autonomous driving solutions, has been fully addressed by Torc engineers. Although Daimler Truck North America did not disclose any figures about autonomous driving vehicle sales forecast, it expects that self-driving vehicles will manage six per cent of freight volume by the end of this decade.
The latest addition to our growing Ultima family, Narva’s all‑new light bars provide high performance and extreme durability in tough Aussie conditions.
• MARKET-LEADING BEAM PERFORMANCE
• SUPERIOR CONSTRUCTION
• CUSTOMISABLE LOOK
• UNPRECEDENTED WARRANTY
Find a job you enjoy doing, and you will never have to work a day in your life,” says Aiden Kelly, quoting American writer Mark Twain.
He’s general manager at North West London-based Kingscote Haulage, and the job he’s referring to, and has been enjoying for the last 44 years, is moving muck. During his ‘lifetime of lorries, quarries and tips’ he’s worked on some of the England’s capital city’s biggest civil engineering projects, moved
millions of tonnes of muck, and helped to shape the current skyline.
Aiden’s story starts in 1979, when as a teenager he began working for his father Frank Kelly’s London-based tipper firm, Power Presses and Plants.
“I remember the first job,” says Aiden. “We had 70 trucks working on a job, including 35 of my father’s, and we moved 750,000 tonnes of muck. I would open the weigh-bridge at 5.30am, and stay there until sunset. It was such an experience for me, and I learned so
PowerTorque’s European Correspondent, Will Shiers meets a man who has built up several successful tipper firms, helping to shape London’s skyline in the process
much, including how to drink!”
Hearing him reminisce about the jobs he carried out in the late-1970s and early-1980s, and talk about the people he worked with, is like listening to a who’s who of the current London muck-away world. Over the last half a century the Irish have made a massive impact on London’s construction industry, with most of today’s biggest tipper operators and construction firms being Irish-owned, and Aiden and his father knew them while they were just starting out.
He explains that most arrived in London from Ireland with a few quid in their back pockets, and with hard work and good business acumen, built up massive fleets of tippers. This is exactly what happened to Frank Kelly, who
left Ireland for London at the age of 16, soon finding himself a job as a fitter. Once he had enough money saved up, he bought himself a truck. By the 1970s he’d built up a fleet, and was working on some big projects in the south east of England.
Then, in the early 1980s, the entire business, with its 45 trucks, was sold on. But not content with that success, the father and son team did exactly the same again, building up another successful firm, and selling that too.
Having repeated the cycle a few times, more latterly on his own, Aiden decided it was time for a change. From now on he would use his vast knowledge, and impressive list of contacts, to do exactly the same for large contractors that required
a haulage fleet.
“I used to do a lot of work for Brian Murly at Mann Construction, and ended up doing all of his muck,” recounts Aiden. “He suggested that I should let my own thing go, and build up a muck-away division for Mann Construction instead. So that’s what I did. Brian was like a mentor, and gave me the belief to do what I do now.”
Having made a success of this, Aiden went on to do exactly the same for a well-known concrete frame company.
“It’s a large £600m (A$1.1bn) business,” says Aiden. “They offered me a lucrative job to build up a haulage division for them. We started with one lorry, and five years later we had 75 lorries, tips, a recycling facility, and
were turning over £25m (A$46m) a year. But in this role, after a length of time you become an expensive commodity, and you’re expendable.”
It was time to look for another opportunity. So, a few years ago, Aiden got in touch with Brian Morrisroe, the founder of the Morrisroe Group, one of the UK’s leading concrete frame specialists. It was spending a lot of money on muck-away, and he suggested that it should invest in its own tipper fleet. His offer was accepted, and in early 2020 Kingscote
Haulage was founded.
“My timing wasn’t great,” admits Aiden, who found himself attempting to start the company just as the UK was plunged into its first Covid lockdown. “I had just ordered my first lorries, which led to a few jittery times.”
But he needn’t have worried, as construction was quick to bounce back, and thanks to his impressive list of contacts and connections, he found enough work out there to get this fledgling company established.
“The longer you are in the industry,
the more contacts you have,” says Aiden. “So obviously I have a fairly large list. So, I got on the phone and raised what work we could. I was very lucky.”
Although Aiden has run most marques over the years, including Magirus-Deutz, Foden, and more recently Mercedes-Benz, on this occasion he opted for Scania. “I ran Scanias some years back,” he remembers. “They’re just a great workhorse, and go on and on.”
So, a fleet of 10 P-series XT410s and
XT450 eight-leggers were ordered, and all fitted with Fitzgerald tipper bodies.
Attempting to rapidly grow a fleet is always going to present challenges, but these are magnified when faced with unprecedentedly long lead times for new vehicles. With Scania quoting 21 months for a second batch of trucks he decided to buy some used vehicles. Consequently today, in addition to 23 Scanias, you’ll find a pair of Volvo FMXs, an FM and an FM grab in Kingscote Haulage colours.
All new trucks are taken on fiveyear R&M contracts, with Aiden looking to dispose of them after this time.
“There’s a reason why people don’t keep their trucks any longer than five years, and that’s because they start to get a wee bit expensive to run,” says Aiden.
At the present time there are 27 trucks on the fleet, with another seven on order. All are equipped with a plethora of safety devices, to help protect vulnerable road users. This includes lower glazed passenger doors, cameras and audible left-turn alerts. However, unlike a growing number of London-based operators, Aiden has so far avoided low-entry cabs, preferring Scania’s P-series over its L-series.
“They’re great if you’re running on roads all the time, but not if you’re going onto landfill like we do,” Aiden explains.
He’s also yet to consider adding any zero-tailpipe-emission trucks to the fleet, but doesn’t rule out battery-
electric in the future. But, he says they would need to make sense from both a practical and cost perspective.
But what he is considering in the very near future is hydrotreated vegetable oil (HVO), which is growing in popularity in the UK as a less-polluting but slightly dearer alternative to diesel.
Despite a UK-wide driver shortage, Kingscote Haulage hasn’t struggled to put bums on seats, and doesn’t employ any agency staff. Aiden says this has a lot to do with treating drivers with respect, which is confirmed by right-hand-man Delroy Lucas, who has recently come off the road to train as Kingscote Haulage’s new transport manager. He says Aiden always treats his staff with respect, which is reciprocated in loyalty.
“It’s about having the right attitude,” says Aiden. “The bigger the fleet, the bigger the churn you have, which can’t be helped. But we try to keep as many settled as we can. And I always talk to them like humans, rather than barking orders at them.”
Whereas Aiden normally plans to stay in roles like this for five or six years, on this occasion he says he’s in it for the long-haul and is ‘here to finish the job I’ve started’.
While he doesn’t have ambitions to grow the fleet above 35 trucks, over the next decade he intends to turn Kingscote Haulage into a £30m (A$55m)-a-year business. He’s in the process of adding both landfill and recycling, with significant
announcements expected over the next 12 months. He says landfill and recycling facilities are important strings to have in any muck-away operator’s bow, since they add stability, and keep trucks busy during quieter periods.
“My aim is always to build up the muck-shifting part as quick as I can, and then put in additional landfill and recycling elements,” says Aiden. “When you’re disposing of materials, and then recycling, you’re always loaded.”
Over the years I’ve interviewed countless people who have built up successful haulage firms. Maybe even two during the course of their working lives, but never several. With this in mind, I’m intrigued as to what he believes is the secret to his success.
“At one time in my life I would have said being competitive, but these days it’s more about alliances than competing with people,” says Aiden. “Also, I have a reputation in the muckshifting world for never letting anyone down. If I take on a job, I finish it. I always keep to a deal, and I guess that pays off in the long run.”
To quote Mark Twain again: “There are basically two types of people. People who accomplish things, and people who claim to have accomplished things. The first group is less crowded.” Aiden Kelly definitely falls into the former group.
Allison products make their vehicles, and ultimately their business, more productive.
In the trucking and heavy vehicle industries, productivity can make or break a business. Allison automatic transmissions have a reputation around the world for quality, reliability and durability because they are designed and built to last.
When downshifting, the Allison transmission never misses a gear, the technology makes it impossible. Electronic controls ensure that the transmission is in neutral any time the driver leaves the cab, and the transmission automatically interlocks with equipment like rear door or ramps for added safety and security.
Allison Transmission is the choice of the transport industry. Fleet owners and operators understand that when it comes to reliability, productivity and ease of operation, no-one comes close. That’s why Allison is Australia’s number one choice for fully automatic transmissions in medium duty and light heavy duty truck sales.
“Australia is Allison’s third largest market behind the USA and Canada,” says Robert Cavagnino, Australian Sales Manager for Allison Transmission. “We have a quality product and work very closely with OEMs to be able to articulate what is needed for the harsh Australian environment.”
Allison Transmission is the world’s largest designer, developer, manufacturer and distributor of fully automatic transmissions for medium duty and light heavy duty vehicles. And it’s why over 300 hundred of the world’s most highly regarded commercial and military manufacturers specify Allison products.
But why do they, and thousands of other businesses globally insist on putting Allison transmissions and hybrid propulsion systems in their vehicles? Put simply, it’s because
They can also help you do more work in less time, which is basically the name of the transport and distribution game. How do they do that? They provide superior startability, faster, more fuel-efficient acceleration, higher average speed, more kilometres per day and as result of all that, increased productivity.
“With greater reliability comes greater productivity,” says Cavagnino. “We know that our customers rely on our transmissions to make their vehicles spend less time being maintained, and more time making their business profitable”.
Every transmission, no matter how well designed and built, will require some level of servicing. And for that, Allison has an extensive network of 43 authorised distributors and dealers across Australia and New Zealand.
Safety is, of course, a huge factor when it comes to medium and light heavyduty vehicles. And in this area, Allison comes to the fore once again.
“With Allison Automatics, there’s no clutch or manual gear changing.” says Cavagninos. “So driver attention and awareness is maximised, and both hands stay on the wheel during gear changes. And in trucks or buses, that’s exactly where hands belong.”
Better manoeuvrability is another huge advantage of an Allison Automatic.
When driving uphill or downhill with a heavy load, Continuous Power Technology allows Allison fully automatic transmissions to deliver uninterrupted engine power to the wheels, for improved overall manoeuvrability. The Allison Automatic gives you great control and makes the time you spend out on the street as productive as possible.
Allison’s torque converter creates an infinitely variable gear ratio that further manages power to the wheels. Using just the accelerator means drivers can more precisely control vehicle speed, have more control on gradients, and ultimately protect the driveline from shock and reduce long term vehicle wear and tear.
Once you’ve tried Allison transmissions, you’ll never shift. You’ll never go back to changing gears manually again. Having no clutch will be your greatest ally in those clutch moments.
Because when you add it all up, you’ll realise that Australia was made for Allison Automatics. And that’s exactly why Allison Automatics are made for Australia. To find out more about the Allison product range visit allisontransmission.com.
It’s often said that without trucks, a country stops. In a country as vast as ours, that’s certainly true. Trucks travel thousands of kilometres every day of the year, keeping Australia moving.
Hendrickson, through unrelenting pursuit of innovation and quality, is positioned as a leading global manufacturer and supplier of heavyduty mechanical, elastomeric and air suspensions; integrated and nonintegrated axle systems; parabolic and multi-leaf springs; tyre inflation systems and bumpers and trim components to the commercial transportation industry.
Global manufacturing is a feature of Hendrickson’s operations, utilizing the latest technology and systems to integrate supply and logistics from its various international location to meet specifications and high quality standards expected from Hendrickson customers.
“Like many others, in last couple of years, we’ve been impacted by global supply chain challenges, but we’ve further enhanced our fairly sophisticated supply chain model enabling us to stay ahead of the disruptions,” says General Manager, Arthur Mitsel. “Our ability to manage supply chain by working
closely with our customers, suppliers and logistics providers meant we continued to support local demand with our broad product offering without compromising on quality.”
“We pride ourselves on being a technology driven organisation which focuses on developing and manufacturing innovative suspension. We design and manufacture our own suspension, staying one step ahead of technology is a big part of Hendrickson globally.”
The Hendrickson story began in 1913 with the founding of The Hendrickson Motor Truck Company by inventor and businessman Magnus Hendrickson. This small Chicago-based manufacturing company built trucks, often equipped with cranes or dump bodies. Eventually Hendrickson sold the truck manufacturing operation to focus solely on suspension systems and related components.
In May 1973 Hendrickson Australia commenced operations, assuming the distribution of the Hendrickson suspension range from the previous
distributors. Hendrickson’s first MD, Lynn Brown was already involved in the trucking business and knew a lot about it. In the earliest days, Hendrickson Australia operated out of his home in Mount Waverly (Melbourne) with the first parts shipment being delivered onto his nature strip, a delivery that probably wouldn’t meet today’s industry standards or amuse the neighbors. Luckily the Australian warehouse now equates to 11,500 sqm and today Hendrickson Asia Pacific has responsibility for Australia, Japan, Southeast Asia, and New Zealand. One of Hendrickson Australia’s foundation products, the RT walking beam suspension was ideally suited for the construction industry (where the volume of truck sales was going in those developing economies). The RT suspension paired with a developing Australian market meant rapid growth for Hendrickson. So rapid that today Hendrickson Australia prides itself on a product offering which includes suspensions to on and off road commercial trucks and trailers
This year, 2023, is the year when one of the stalwarts of supply to the truck industry celebrates a major milestone, 50 years of Hendrickson in Australia.
including military applications.
“Our value proposition as a team is to provide bespoke solutions to various markets. So, we’ve got an extensive engineering group, probably more so than some of our competitors. It’s really about taking American technology and customising it to the various Australia market requirements, legislations conditions and so forth.
In 2008 Hendrickson moved to its current location in Dandenong South. Since that time, the business has continued to grow distribution and support throughout the region. The product range has also greatly expanded to encompass axles for trailers and suspensions to suit trucks, trailers and buses also including very heavy-duty suspensions for mining applications.
Within the local engineering department, Hendrickson have been at the cutting edge of design and validation tools for many years. In addition to being one of the first in the industry to implement 3D Computer Aided Design (CAD), Hendrickson utilises a range of advanced Computer
Aided Engineering (CAE) techniques including Finite Element Analysis (FEA) and Multibody Dynamics (MBD) simulation tools.
Alongside these computational techniques, Hendrickson invests heavily in physical validation. This includes physical fatigue testing on test rigs within the on-site R&D laboratory, certification testing and in field data acquisition. These tools are utilised during the product development process to ensure Hendrickson products are up to the task in the Australian market.
In March 2022 Hendrickson Australia expanded its operations by securing the adjacent facility within its current location. The additional facility substantially increased Hendrickson’s operations enabling its ongoing growth within the region.
At the time of Hendrickson’s Australian 50th anniversary, the latest expansion marks Hendrickson’s ongoing commitment to supporting its customer’s growth within the region by leveraging proven expertise and an ever-evolving quest for innovation
within the heavy commercial vehicle industry.
Incorporated within the expansion is a state-of-the-art customer engagement centre which allows Hendrickson to further develop its product training programs and continue to partner with Industry key stakeholders and customers.
“Our vision is to continue to support the industry and our customers in
their pursuit of improved productivity and safety within an ever-demanding commercial environment.” says Arthur.
“The industry is going through a significant disruption, and we expect that to accelerate over the next decade or so, with the introduction of alternative fuel, commercial vehicles,” says Arthur. “Hendrickson is well positioned to support these changes with new technology. Part of our value proposition is about innovation, but not just innovation for innovation’s sake, it is around innovating to add value to our customers.”
“As our customers transition to new technology, we have got a whole lot of programs to stay ahead. Our value has been around improving the total cost of ownership of the vehicle for our customers. With batteries being introduced the vehicles become a little bit heavier, so weight advantages and reducing the weight of the
vehicle overall will become a bigger component.”
The engineering facility has developed into a highly skilled and equipped group with the disciplines tailored to the needs of the Asia Pacific region. It can take a concept, develop and prove it, then ultimately bring it to production. “We see that as a big opportunity for Hendrickson to continue to grow and support our customers. Our product tends to be efficient in its design and we look at how well the product packages in a vehicle.”
The early years of Hendrickson in Australia were very much framed through the Hendrickson family influence. People are the backbone and key to the success of any organisation and as the years have rolled by it has been the people at Hendrickson during the past 50 years who have and continue to shape the company’s growth. “Something that is really important and dear to my heart is really in terms of people. I’d like to think that we’ve built a very good culture over my time here, and we’ve got engaged and loyal staff members” says Arthur.
Some of the longer serving staff members with over 15 years service include Andrew Martin (MD & VP International Operations), Arthur Mitsel (GM Asia Pacific), Tracie Hart
(HR Executive Manager), Simon Iyer (DOF International Operations), John Stewart (Sales & Marketing Executive Manager), Evan Edmonds (Trailer Product Coordinator), Plant Operatives Kim Nguyen, Nga Kareroa, John Colverd and Guna Dissanayake; and Sales Team members Matt Huigens, Brad Sleath and Patrick Duncan. A true testament to the culture at Hendrickson is the 10 Year Club Annual Luncheon where both past and present employees with 10 years plus under their belts come together to celebrate, reminisce and enjoy an afternoon seeped in Hendrickson Australia history. The group currently boasting 31 members and a combined tally of over 400 years’ industry experience.
Some of the Hendrickson team will celebrate 50 Years with customers at a Cocktail Event during the upcoming Brisbane Truck Show in May, where they are pleased to welcome a couple of their US based division heads from both truck and trailer divisions who will be attending and help celebrate the 50 years. An all-staff event will take place in June where the team can celebrate the business collaborative success and Hendrickson Australia can show its appreciation to a team of over 120 employees who continue to support Hendrickson’s growth at every level.
Indiana based Cummins Inc recently launched a range of zero emission technologies including a number of recent acquisitions under a new brand; Accelera.
Cummins breakthrough technologies have reduced the company’s product emissions by more than 90 per cent over the past 25 years, and the new brand Accelera will continue to advance the company’s path toward a zero-emissions future. Recent zeroemissions highlights that Accelera will continue to build on include completing the acquisition of Meritor and it’s ePowertrain (formerly Blue Horizon) solutions as well as the Siemens Commercial Vehicle business which produces high performance electric drive solutions. The recent acquisitions add to an already existing portfolio of electrolyser, fuel cell and battery solutions.
Cummins recognises the future demand for clean and green technology is not going to be satisfied by a one size fits all approach. The new brand Accelera is therefore advancing a range of zero-emissions solutions, including hydrogen fuel cells, batteries, e-axles, traction systems and electrolysers, to sustainably power a
variety of industries from commercial transportation to chemical production. Both a components supplier and integrator, Accelera is focused on decarbonising applications like buses, trucks, trains, construction equipment, stationary power and carbon intense industrial processes.
Over the past several years, Cummins has invested more than US$1.5 billion in research and technology, capital and acquisitions to build Accelera’s leadership and technological capabilities. The entity is now a global leader in zero-emissions technologies, providing battery electric and fuel cell electric solutions across commercial and industrial applications with hundreds of electrolysers generating hydrogen around the world today.
“Achieving our goal of reaching net-zero emissions by 2050 requires leveraging our entire portfolio of businesses,” said Jennifer Rumsey, Cummins President and Chief Executive Officer. “As we have continued to lead in and advance the engine-based solutions that power our customers’ businesses, we have also built the broadest combination of zeroemissions technologies dedicated to
the commercial vehicle industry like battery electric and fuel cell electric powertrain solutions and electrolysers for green hydrogen production.”
“Establishing Accelera reinforces our commitment to leading in zeroemissions solutions and highlights our unmatched ability to leverage our deep understanding of our customers’ needs and applications, technical expertise and extensive service and support network to walk hand in hand with our customers throughout the energy transition.”
MT-160 ADVANTAGES
• Australia’s most popular heavy-duty axle
• Available in Linehaul (Pumpless) or Vocational (Pumped) configurations
• Built tough to suit Australian conditions
Carrier Transicold unveiled its first trailer concept powered by a dedicated hydrogen fuel cell fridge unit at last year’s IAA Transportation exhibition in Hanover, Germany.
It is not just the truck power plant that needs to move towards zero carbon emissions. The same should apply to diesel-powered truck accessories. The introduction of a hydrogen powered refrigeration unit demonstrates a commitment by Carrier Transicold to electric and sustainable temperature-controlled transport solutions.
The fuel cell system was specifically developed to integrate within the chassis of Carrier’s Vector transport refrigeration unit. The system is said to deliver zero direct emissions without a reduction in performance or refrigeration capacity.
Developed in close cooperation
with Bosch and PowerCell Sweden, the new hydrogen fuel cell technology will be coupled with Carrier Transicold’s Vector HE 19 trailer unit. Central to the new system is the integration of the Bosch 48-volt automotive battery, which directly interfaces the fuel cell with the refrigeration unit, removing the need for a standalone engine or a separately mounted buffer battery system.
“Carrier Transicold continues its electrification journey, providing an electric solution in every area of the temperature-controlled transport market, from vans through to multitemperature trailers,” said Victor Calvo, Vice President and General
Manager, Carrier Transicold. “The new hydrogen-powered Vector concept is a major step forward for the company and we’re delighted to demonstrate the future of transport refrigeration for customers. We are committed to exploring every avenue to reduce emissions and deliver better sustainability for customers, and hydrogen fuel cell technology is extremely exciting.”
The hydrogen fuel cell technology delivers the same level of autonomy as existing diesel engines used in the standard Vector units. By using a hydrogen fuel cell system, customers can maintain operations with the legacy products, but without any of the associated emissions.
The new fuel cell system is powered by hydrogen tanks coupled with an electric power distribution unit (PDU). The PDU is used to convert the direct current provided by the fuel cell into the alternating current needed to operate the refrigeration unit. The refuelling time for the new concept is equivalent to a standard diesel engine and, depending on the tank size, can also achieve a similar autonomy range.
The combination with the Vector’s existing all-electric E-Drive technology, a mainstay of the company’s trailer systems since 1999, eliminates the need for the mechanical transmissions found in belt-driven truck and trailer refrigeration systems, making it ideally suited to operate on the electric power derived from the hydrogen cell, while delivering increased efficiency and reduced risk of refrigerant leaks.
Launched in 2020, a first demonstrator version was presented
in 2021 by Carrier and Bosch with the hydrogen fuel cell system placed in a frame under the trailer chassis. The advanced version presented in 2022 at IAA goes one step further and integrates the hydrogen fuel cell within the standard Vector chassis.
When the ‘FresH2’ fuel cell project moved to its first road test phase, it hit the road in France. The hydrogen fuel-cell powered refrigeration unit, Vector HE 19, from Carrier was fitted to a semi-trailer manufactured by Lamberet.
The development of this solution has been carried out at the Bosch site in Rodez, France, and it went into service with the European specialist in temperature-controlled food transport operation, STEF, in September 2021.
FresH2 comprises a fuel cell powered by hydrogen tanks, to which an electronic unit is added, enabling it to convert the direct current provided by the cell into the alternating current needed to
operate the refrigeration unit.
“The FresH2 project perfectly illustrates our passion for innovation and reflects our commitment to a sustainable cold chain, particularly through the electrification of our product lines,” said Jean-Pascal Vielfaure, Managing Director France and Southern Europe, Carrier Transicold. “With the FresH2 project, we are pleased to contribute to the energy transition and participate in developing a hydrogen-powered solution of the future for semi-trailers. Thank you to all of our partners for their commitment and trust.”
The Hino 300 Series Hybrid Electric light-duty truck is the perfect solution for your business. Delivering up to 20%* fuel and emissions reductions - with no recharging or range limitations, it has led the way for over 15 years. It’s the first and only light-duty Hybrid truck to meet Euro 6 exhaust emissions standards and customers can also benefit from a 16% reduction in maintenance costs. Driven by Toyota Group technology, experience Australia’s only Hybrid Electric truck that reduces your operational cost to gain a genuine competitive advantage. Harness the Hino Hybrid Electric today! Find out more at hino.com.au