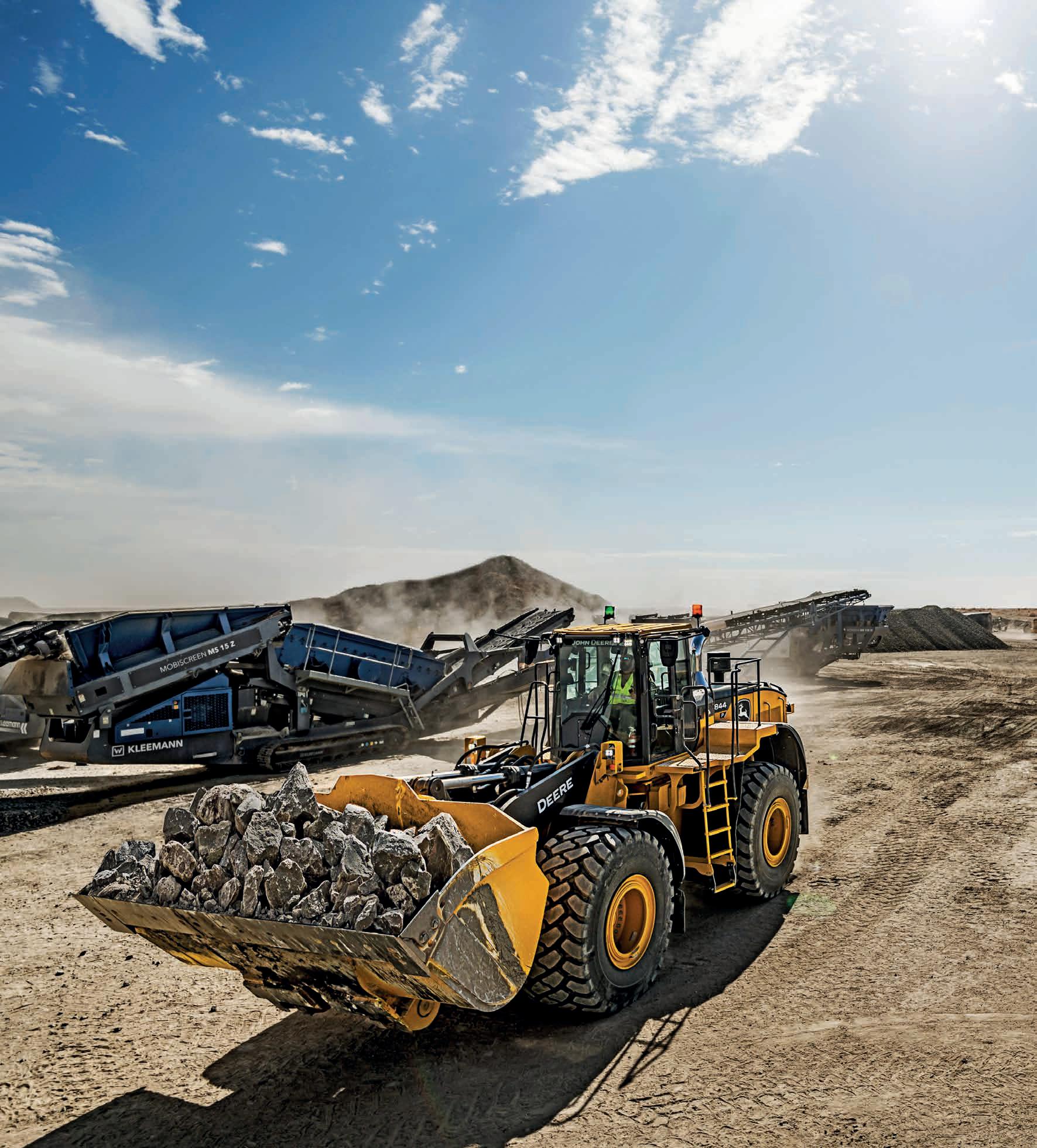
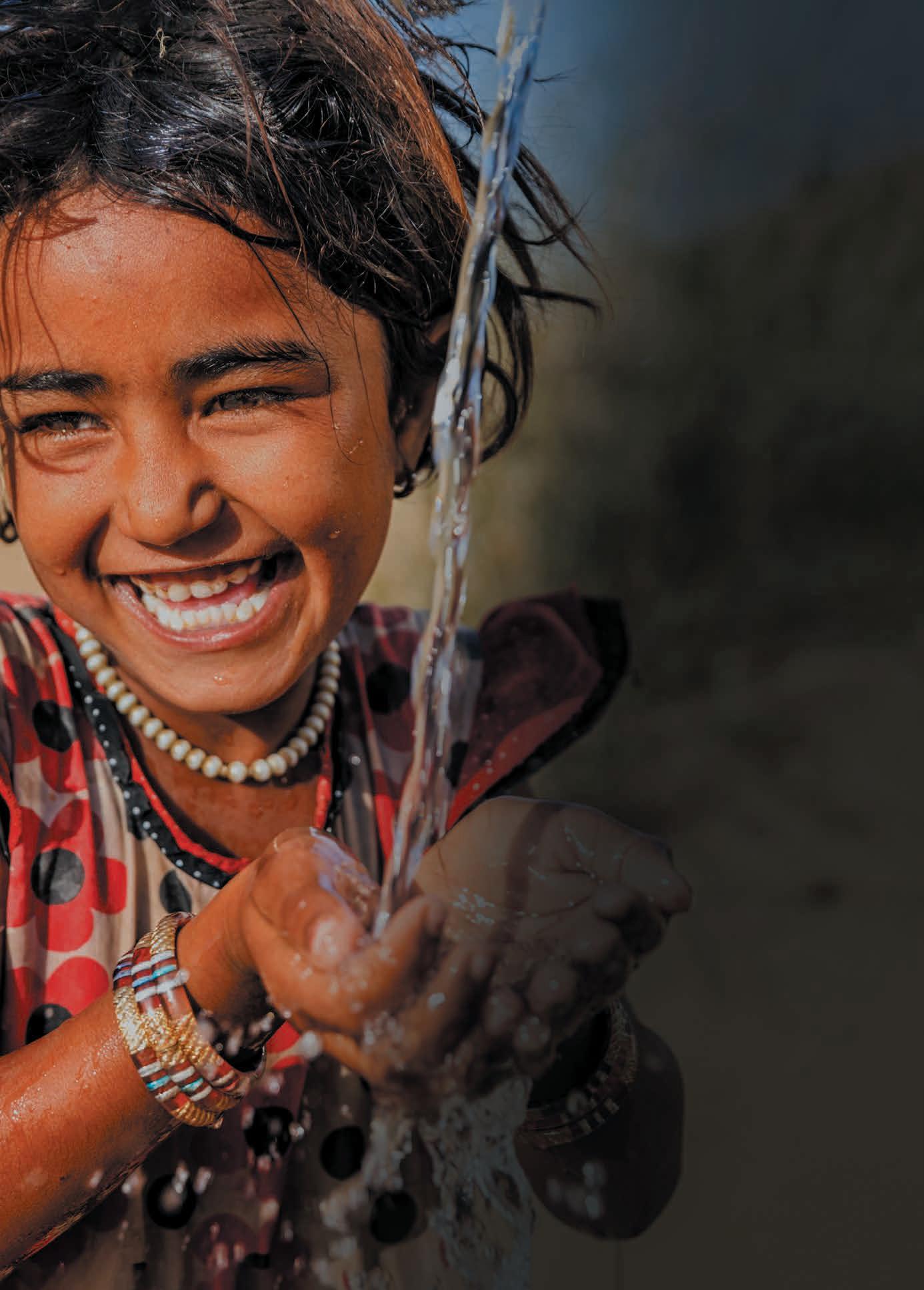

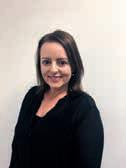
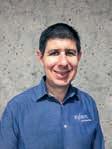
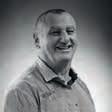
Durable frame and dump body, lowers Total Cost of Ownership over the life of the truck
Descend at a safe speed with Automatic Retard Speed Control (ARSC)
Premium operator comfort Comfortable cab Comprehensive visibility
Fuel consumption reduced up to 7% percent compared to the previous model
1300 566 287 |
McPherson Strut Front Suspension provide an improved ride
Smaller Turning Radius (8.7m) for tighter benches and haul roads
Quarry sat down with managers and decision-makers from the quarrying industry to hear their vision for 2023. Interviewees include:
• Sam Russell, Director, Institute of Quarrying Australia
• Karen Poulton, Marketing Manager, John Deere
• Matt Wessel, Director of Strategy, Product Marketing and Engineering, Xylem
• Steve Franklin, Chief Executive Officer, Eltirus
• Cameron Ballentine-Jones, Executive General Manager, Komatsu Australia
• Greg Mumford, Sales, Service and Marketing Manager, Caterpillar
• Jonny McMurtry, Chief Operating Officer, Precisionscreen
• Ben Willcox, Sales Manager, Terex Washing Systems
• Jeff Gray, Director of International Sales and Mining, Superior Industries
• Grayden Leaver, Executive General Manager, CJD Equipment
• John Andersen, Manager, Crusher Screen Sales and Hire
• Daniel Webber, Regional Manager, CDE
• Paul Doran, Business Development Manager, Tutt Bryant Equipment
• David Smale, Regional Managing Director, Astec Australia
• Phillip Agius, General Manager, Delta Rent
• Sean Kinder, Business Development Manager, Kinder
Quarry people are a humble group of people. Or at least that’s the impression I’ve had in the short time that I’ve been interacting with the industry. They go about doing their jobs quietly – a job that sets the tone for so many other downstream industries.
That said, quarry people are also a resilient bunch. They have to be. There’s too much at stake here. Millions worth of developmental projects rely on quarries to supply them with raw materials.
Throughout 2022, the quarrying industry was thrown into the deep end, with supply shortages, shipping delays and tight labour markets. Demand, on the other hand, was larger than ever. The floods on the east coast certainly did not help.
As I spoke to many business and industry leaders in the quarrying space for this edition, some messages were echoed louder than others. All of their companies had found ways to get through and come out stronger on the other end. Whether it was by setting up support closer to their customers, or bringing orders forward to overcome shipping delays, they reflected an industry confident in its ability to thrive amid turbulence.
Karen Poulton from John Deere summed it up best: “…quarry people are a resilient, innovative and supportive group of people that dig deep and get on and do what needs to be done.”
With that, 2023 is looking to be a year of expansions for many. New product lines, particularly battery-driven
and hybrid machines are on the horizon by most major equipment manufacturers. Equipment suppliers and plant providers are investing on telematics, fleet management and automation technologies, and service providers are increasing their boots on the ground.
It’s also shaping up to be a good year for material innovations, with Australian companies making headways in areas of carbon capture technology for cement and manufactured sand to produce low carbon concrete. These innovations, and more, will be topics we’ll explore in detail throughout 2023.
We’ve also included in this issue a special report from the Asia Pacific finals of Caterpillar’s Global Operator Challenge, which was held in Tokyo in October. The finalists, including two Australians, will be competing in the global finals in March at the 2023 CONEXPO in Las Vegas.
Debuting this edition is a new section called People on the Move, which is dedicated to tracking new appointments and movements of top executives within the quarrying and construction industries. If you are an industry key player and your organisation has had new appointments, please feel free to reach me and share the news with me. We are happy to help keep people in the quarry industry connected and informed.
Tara Hamid EditorBY
Published by:
379 Docklands Drive Melbourne VIC 3008
T: 03 9690 8766
www.primecreativemedia.com.au
Chief Executive Officer John Murphy john.murphy@primecreative.com.au
Editor
Tara Hamid tara.hamid@primecreative.com.au
Journalist
Lewis Cross lewis.cross@primecreative.com.au
Business Development Manager Les Ilyefalvy les.ilyefalvy@primecreative.com.au
Client Success Co-ordinator
Janine Clements
janine.clements@primecreative.com.au
Design Production Manager Michelle Weston michelle.weston@primecreative.com.au
Art Director Blake Storey
Graphic Design Kerry Pert, Tom Anderson, Louis Romero
Subscriptions T: 03 9690 8766 subscriptions@primecreative.com.au
The Publisher reserves the right to alter or omit any article or advertisement submitted and requires indemnity from the advertisers and contributors against damages or liabilities that may arise from material published. © Copyright – No part of this publication may be reproduced, stored in a retrieval system or transmitted in any means electronic, mechanical, photocopying, recording or otherwise without the permission of the publisher.
BE A YEAR OF EXPANSIONS FOR MANY. NEW PRODUCT LINES, PARTICULARLY BATTERY-DRIVEN AND HYBRID MACHINES ARE ON THE HORIZON
MOST MAJOR EQUIPMENT MANUFACTURERS.
As a leading supplier of rock excavation equipment for more than 145 years, we believe that innovative mining technologies such as automation, interoperability and battery are the future of our industries. We boldly drive a vision for a future of digital automation, as this will enhance productivity, energy efficiency and safety for customers. As such, we are investing in making mining smarter.
With the holiday season behind us, the coming year is certainly what I look forward to. I hope everyone has had time to enjoy some well deserved time off and are ready to hit the ground running with a busy year for what the IQA has planned.
At times of beginnings like this, I think that it is important to remember our mission statement and what the IQA aims to achieve: Educating and connecting our extractive and associated industries.
The IQA is the leading provider of technical quarry training, specific quarry courses and quarry manager training for the extractive industry within Australia and we are on track to exceed those commitments to the industry as we crest halfway through our 2020-2025 strategic plan.
The importance of our organisation to the industry and additionally, to the success of the talented people within the industry, cannot be stated enough.
The IQA has and will continue to offer opportunities, training and recognition across all of Australia for all people, in order to provide much needed support to our industry and to continue to grow our industry.
No better time then to also recognise and congratulate those who have been with the industry for an incredible length of time. It’s with great thanks that I can congratulate both our 30 and 40 year members. Without the wealth of experience and industry knowledge held by these members, we would be sorely lacking.
Looking to the new as well, we have seen a tremendous success with
out Young Member Network, to connect and foster the groundwork for a strong industry in the next generation.
Our Queensland, South Australia and New South Wales Young Member Tours were of a great success and though they are a step in the right direction, as an industry, we need to do everything we can to continue this reception and growth of promising young people of all walks of life into the industry.
Our IQA branches have a very full calendar for 2023, with networking opportunities and involvement with key industry topics as a focus for this year.
We remain firm in the support of our branches and strongly recommend that all do their part to engage and support these events.
Once again, we are keeping our fingers on the pulse of the education and training for this year, with the accessibility and diversity we offer as part of the IQA, being supported through the innovative use of digital tools and training planned for this year.
I would like to say a special thanks to our branch members, our committee members and the broader IQA community, without whose support and contributions the IQA would not be as it is today. Lets keep working together as we achieve goals and smash targets through to the end of 2023.
Duncan Harris President Institute of Quarrying Australiawww.quarry.com.au
The IQA’s Strategic Plan 2020 to 2025 embodies the following vision, values and strategic priorities:
Vision:
Educating and connecting the extractive and associated industries.
Values: fe and sustainable environment.
• Diversity and inclusion.
• Working development skills, careers and life-long learning.
• Networking, connection, trust and communication.
Strategic Priorities:
• Maximise outcomes for industry through education and sustainable practise.
• Increase our relevance.
• A high performing and sustainable organisation.
IQA CONTACTS:
Phone: 02 9484 0577
Email: admin@quarry.com.au
Chief Executive Officer
Kylie Fahey
Company Secretary
Rod Lester
For all education, member and branch enquires please email: admin@quarry.com.au.
RECOMMEND THAT ALL DO THEIR PART TO ENGAGE AND SUPPORT THESE EVENTS.”The Institute of Quarrying Australia Educating and connecting our extractive industry
Jason Adams has been promoted to president of Superior Industries, the US-based bulk materials handling solutions specialist. Adams has previously successfully launched the company’s construction management group and eighteen months ago, was promoted to senior vice president and in that role. Adams has continued to lead the construction management team, in addition to the sales, manufacturing, and aftermarket departments and carries that experience forward to his new role as president.
The Australian Sustainable Built Environment Council (ASBEC) has appointed a new president, Tanya Cox, as Professor Ken Maher AO steps down after seven years in the role. Cox is a non-executive director of various ASX-listed and unlisted boards, is the former chair of the Green Building Council of Australia and World Green Building Council and was previously chief operating officer of Dexus Property Group for 11 years. Cox enters the role with tribute to the previous work done by Maher.
Peter Tompkins will be appointed chief executive officer and managing director of the Downer Group, following the retirement of Grant Fenn in February 2023. Tompkins joined Downer in 2008. Following Downer’s acquisition of Spotless in 2017, he was appointed project director for the Royal Adelaide Hospital Public Private Partnership, and led the integration of Spotless into Downer as chief executive of Spotless. He has served as chief
Global process solutions provider company McLanahan has appointed Lee Hillyer as director of sales – mineral systems. Hillyer will be leading efforts to further expand the business and establish McLanahan as a supplier of processing solutions within the coal, minerals, and other mining sectors in markets outside of North America..
AUSTRALIA’S FIRST EVER ONLINE PORTAL DEDICATED TO BUYING, SELLING AND HIRING QUARRY EQUIPMENT.
For
THE CODE WAS DEVELOPED IN CLOSE CONSULTATION WITH WORKERS, EMPLOYERS AND TECHNICAL EXPERTS ACROSS QUEENSLAND.
monitoring to check dust controls are effective
• providing health monitoring to at-risk workers, with clearly defined triggers for testing based on level of risk
• consulting with workers, as well as training, education, instruction and supervision of workers.
The Code was developed in close consultation with workers, employers and technical experts across Queensland, building on international best practice to ensure silica dust is managed safely and workers are protected in the construction industry and the manufacturing of construction materials.
The Queensland government has approved a new code of practice for managing respirable crystalline silica dust exposure in construction and manufacturing of construction elements.
The new code, which commences on 1 May 2023, is Australia’s first silica dust code of practice for the construction industry. It applies to all construction work as well as the manufacturing of materials such as bricks, blocks, tiles, mortar and concrete.
The code outlines how duty holders
can meet the requirements of Queensland’s work health and safety legislation, including eliminating or minimising exposure to respirable crystalline silica (RCS) at work by:
• using tried and tested dust control methods that prevent silica dust from being generated or being released into the air, including water suppression and on-tool dust extraction
• using appropriate respirable protective equipment to safeguard at-risk workers
• using exposure data from air
Crystalline silica is a common mineral found in many building materials, such as bricks, blocks, pavers, tiles and mortar; concrete and cement, including products such as fibre-cement sheeting and autoclaved-aerated concrete; as well as most rocks, sands, and clays.
Tasks such as cutting, sawing, grinding, drilling, polishing, scabbling or crushing materials that contain crystalline silica can generate RCS.
RCS particles are so small they cannot be seen under ordinary lighting and stay airborne long after larger particles have settled to the ground –the small particle size means it is easily inhaled deep into the lungs (<10 µm). •
Heidelberg Materials is set to acquire RWG Holding, which is an integrated provider in the demolition and construction materials recycling sector in the greater Berlin area.
According to Heidelberg Materials, the acquisition, which is subject to approval by the relevant antitrust authorities, will strengthen its circular materials offering to meet the growing demand for sustainable building materials.
According to Dominik von Achten, chairman of the managing board at Heidelberg Materials, processing of concrete demolition waste will allow Heidelberg Materials to increasingly prioritise recycled aggregates
over primary raw materials and to offer ready-mixed concrete with a high recycling share in the greater Berlin area.
“With the acquisition of RWG, we are substantially strengthening our activities in the circular economy,” said Achten. “We want to offer circular alternatives for half of our concrete products by 2030. In this regard, the recovery of building materials and concrete recycling make a decisive contribution and are key to achieving our ambitious sustainability and CO2 reduction targets.”
The acquisition, which is expected to complete in the first quarter of 2023, includes three recycling centres across
Berlin and a demolition business with an annual revenue of around 50 million euros ($77.3 million).
Heidelberg Materials is focused on driving innovative technologies to process concrete demolition waste and upgrade it for use in the construction cycle as a valuable material.
The acquisition complements Heidelberg Materials’ existing Berlin footprint. In Germany, Heidelberg Materials offers significantly CO2-reduced concretes with recycling content as part of its sustainable EcoCrete portfolio. •
Global construction material company Cemex is launching new decarbonisation projects in three of its global cement plants, where it will use game-changing carbon capture, utilisation, and storage (CCUS) technology developed by Australian company Calix.
In November, Cemex announced that it will be conducting three Front End Engineering (FEED) studies to scale CCUS technologies at its plants in Germany, Poland, and the US.
The studies fall under the scope of a new global license agreement with Leilac, a subsidiary of Australian technology company Calix. The agreement enables Cemex to leverage Leilac’s highly efficient direct separation technology, to capture carbon dioxide (CO2) at a low cost in its operations.
The cement and lime industries have relatively high CO2 emissions and are responsible for around eight per cent of global CO2 emissions.
The majority of CO2 emissions are released directly and unavoidably
from the processing of the raw materials – not from the combustion of fossil fuels.
Calix’s technology re-engineers the existing process flows of a traditional calciner, indirectly heating the limestone via a special steel vessel. This unique system enables pure CO2 to be captured as it is released from the limestone, as the furnace exhaust gases are kept separate.
The solution requires no additional chemicals or processes, and minimal changes to the conventional processes for cement.
In an ASX announcement, Calix Managing Director and CEO Phil Hodgson said Calix was working closely with Cemex to progress the three projects, as well as a global licence agreement, currently under negotiation, covering Cemex’s global operations. “Calix and Leilac will continue to work with Cemex towards the shared goal of decarbonised cement and lime,” he said.
Leilac, Calix’s 93 per cent owned subsidiary focused on the
The construction industry is a critical pillar of the Australian economy, producing upwards of $437 billion in revenue and approximately nine per cent of the nation’s Gross Domestic Product in 2022.
The sector has a projected annual growth rate of 2.4 per cent over the next five years and as it grows, so does the requirements for the quarrying and aggregates industries to supply raw materials to the construction industries.
The boom of the construction industry directly affects and assists the quarrying industry, with greater spending and returns being proportionately reflected in the raw materials required from the aggregates industry.
With investments in new and existing infrastructure projects in every state and territory, the Australian Government’s national rolling 10-year infrastructure investment pipeline will increase from $110 billion to $120 billion, significantly boosting the sector.
Featuring an exhibition, conference
and awards across the two days of the expo, the 2023 Inside Construction Expo: Engineering the Future presents an ideal environment to focus on and discuss answers to the significant challenges facing both the construction industry and, by extension, the extractive materials industry.
Opening discussion regarding the skills shortage in the construction sector, the continuing digital transformation of the construction industry and the overall safety values in the construction industry, the expo is a not to be missed opportunity to join the conversation and engage with others in the industry to develop solutions to these issues.
The conference will focus on major projects and civil construction, with the conference and world-class exhibition providing a platform for construction equipment and companies, alongside industry leaders, to present ideas and equipment that are best suited to the current concerns in the industry.
decarbonisation of cement and lime, and Cemex have a longstanding partnership.
In Australia, both Adbri and Boral are working with Calix to establish plants for low emission lime and cement production. Adbri has committed to a FEED study underway for its decarbonisation project with Calix and Leilac to develop the world’s first commercial scale process for low emissions lime. Separately, Calix is engaging with Boral to explore the feasibility of developing a CCUS project at Boral’s cement and lime facilities in the NSW Southern Highlands, targeting 100,000 tonnes per year of CO2.
Both projects are currently awaiting funding from the Australian Government’s new Carbon Capture Technologies program, announced in the Federal Budget 2022-23, through which the government will provide $141.1 million over ten years as part of a realignment of investment in carbon capture technologies. The program is expected to open in 2023.•
The centrepiece to the event will be about Victoria’s Big Build, expanding out to showcase construction on other significant infrastructure taking place around Victoria. With the exhibition spanning 15,000 square metre across 10 bays at the Melbourne Convention and Exhibition Centre, Inside Construction Expo provides the best opportunity to companies to meet with their target audience. •
To find out more information and to enquire about attendance and exhibiting, visit: www.insideconstructionexpo.com.au
“CALIX AND LEILAC WILL CONTINUE TO WORK WITH CEMEX TOWARDS THE SHARED GOAL OF DECARBONISED CEMENT AND LIME.”
PHIL HODGSON, CALIX MANAGING DIRECTOR AND CEO
The federal government has set up a unit within the Department of Infrastructure, Transport, Regional Development, Communication and the Arts dedicated to identifying ways the portfolio can help achieve net-zero carbon emissions.
Led by Ian Porter, the new unit is planned to identify how the infrastructure industry can work across government and with others in the industry to help achieve netzero and improve the resilience and longevity of transport networks and supply chains in the face of increasing extreme weather events.
As currently planned, the unit has relevance to the aggregates and construction materials industry, as the flow on effect of ensuring the lifespan of supply chains is important to quarries and other plants reliant on efficiently transporting materials to location.
The unit will support a cross-portfolio net-zero taskforce, that is planned to advise the federal government on ensuring regional Australians benefit from Australia’s transformation to a renewable energy superpower.
Porter brings significant experience in climate change, energy and
“IAN PORTER BRINGS A WEALTH OF EXPERIENCE THAT WILL SUPPORT THE NEW NET ZERO UNIT’S CRITICAL WORK TO TAKE OUR TRANSPORT AND INFRASTRUCTURE CLIMATE CHANGE POLICY, RESEARCH AND ENGAGEMENT TO THE NEXT LEVEL” CATHERINE KING, MINISTER FOR INFRASTRUCTURE, TRANSPORT, REGIONAL DEVELOPMENT AND LOCAL GOVERNMENT.
sustainability policy, as well as working across government, public service, consulting and the notfor-profit sector – including most recently heading up program delivery for Climateworks.
“Ian Porter brings a wealth of experience that will support the new net-zero unit’s critical work to take our transport and infrastructure climate change policy, research and engagement to the next level,” Minister for Infrastructure, Transport, Regional Development and Local Government Catherine King said.
The decision to form the unit builds on important initiatives already underway across the portfolio, that include creating a net-zero council to promote sustainable aviation fuels in this country and consulting on fuel efficiency standards for light vehicles to support the National Electric Vehicle Strategy.
The unit forms part of the government’s commitment to reduce greenhouse gas emissions by 43 per cent below 2005 levels by 2030 and achieve net-zero emissions by 2050.
The unit will help to advance the government’s emissions commitments by connecting government agencies, industry and climate experts together to translate the latest research into action, while ensuring climate expertise is embedded into policies and investments. •
A new Main Roads office will be established in Manjimup in Western Australia next year, as part of the state government’s decision to return road maintenance back in-house to the transport agency.
Western Australia’s Minister for Transport Rita Saffioti this week visited the site of Manjimup’s old Department of Education building, which will be re-purposed into a new Main Roads office for the South-West region.
The new office – which will accommodate around 20 employees – is being established in preparation for increased road network management responsibilities in the region.
The Western Australian government is investing $48.8 million over the next
six years on new regional staff housing, depots, and offices funded from operational savings realised through the transitional change.
The decision follows an initiative by the Western Australian government in Apri this year to return road maintenance jobs in-house. The initiative is expected to create 660 permanent jobs within Main Roads, including 490 in regional Western Australia.
Road maintenance contracts have been outsourced by Main Roads since 2000. Under the current arrangement, there are five network maintenance contractors engaged by Main Roads, delivering more than $400 million of maintenance and improvement works throughout the state each year.
Once fully implemented across the state, the initiative is deemed to create savings of more than $25 million a year and increase employment opportunities for regional WA.
Already, 41 road maintenance workers in Wheatbelt have become the first to transition to in-house delivery by Main Roads in October – with works in the Mid-West Gascoyne Region to be brought in-house next.
The South-West and Great Southern will transition to in-house road maintenance with Main Roads when existing network contracts expire in late 2023.
The last region will be the Kimberley, which will be brought in-house when the current contract ends in January 2026.
The Manjimup office is expected to be operational in March 2023. •
Operations Skill Set is a fantastic example of how the McGowan government is working with industries with skills shortages to train the jobready workers they need to continue delivering for our state,” Ellery said.
“Its success in producing more than 230 workers for the transport and logistics, civil construction, and mining industries since it was launched last year further highlights our Government’s commitment to supporting industries to meet critical workforce needs.
The Western Australian government’s $6.1 million Heavy Vehicle Driving Operations Skill Set has hit a key milestone, with 232 people now employed after acquiring heavy rigid (HR) licences through the program. The program, which started in April 2021, has been developed in collaboration with multiple industries and in direct response to the truck driver shortage emphasised during the Covid pandemic. It aims to train up to 1,000 workers to combat skills shortages in WA’s transport industry.
The qualifications and opportunities for employment additionally have relevance to the quarrying and mining industries, with HR licences essential for many tasks on site. Providing theoretical and practical hands-on truck driver training at the state-of-the-art Driver Risk Management facility located
near Perth Airport, the program aims to train 1,000 job-ready workers to combat skills shortages across the quarrying, construction and transport industries.
Since the program began in April 2021, 232 graduates of the program have gained employment following their completion. Additionally, there has been a strong uptake from women in the program.
According to the WA government, around 30 per cent of participants in the course have been women, increasing the representation of women in the traditionally male-dominated field of truck driving.
With a focus on providing accessibility for skill building, Minister for Education and Training, Sue Ellery, said that the training offered is designed with the intent to make participants job-ready.
“The Heavy Vehicle Driving
The Queensland government has released the ‘Future Infrastructure: Private Investment’ discussion paper, to incentivise private bodies to invest in state infrastructure needs.
The paper outlines and clarifies the ways in which the Queensland government plans to support the private sector with respect to the investment into public state infrastructure projects.
With the release of the paper comes the acknowledgement that the continued economic growth of Queensland requires collective and collaborative investment in priority areas alongside the private sector.
Speaking on the release of the discussion paper, Queensland’s Deputy Premier and Minister for Infrastructure Steven
Miles speaking at the Australian Financial Review’s National Infrastructure Summit in November said it aimed to provide the industry with “greater clarity in infrastructure investment opportunities” in Queensland.
“We’re committed to encouraging more private sector investment to work with the Government in shaping Queensland’s future,” Minister Miles said.
“The release of the ‘Future Infrastructure: Private Investment’ discussion paper, signals our intent to do this, and tells the private sector that Queensland is the place to invest.”
The discussion paper provides a platform for targeted industry engagement with expressions of interest open to be involved
“This program provides participants with real hands-on experience and practical hours in heavy haulage to help them become job-ready, and get more skilled drivers on our roads.
“It’s also great to see such a high number of women taking part and those delivering the course supporting more women into an occupation that has traditionally had very low numbers of them.”
The six-week metropolitan course is available through Central Regional and South Regional TAFEs – in collaboration with industry – and is free for eligible participants. The course has also been expanded to regional areas with a 10week program now running in SouthWest WA due to the success of the initial program. The program ultimately aims to train 500 new workers in HR licences and upskill 500 existing workers from HR licences to Heavy Combination and/or Multi-Combination licences.•
in this engagement in early 2023.
Minister Miles said the Queensland government aims to continually develop infrastructure investment opportunities along with a better understanding of potential barriers to investment and how the government can better apply existing levers to achieve greater infrastructure investment.
“By being clear on our priorities and working closely with industry, we can better identify where and how these partnerships can deliver Queensland’s future infrastructure,” he said.
“As our population grows, so too does the need to cater for that growth, with liveable communities always at the centre of our decision-making and planning.” •
“THE HEAVY VEHICLE DRIVING OPERATIONS SKILL SET IS A FANTASTIC EXAMPLE OF HOW THE MCGOWAN GOVERNMENT IS WORKING WITH INDUSTRIES WITH SKILLS SHORTAGES.”
SUE ELLERY, WA MINISTER FOR EDUCATION AND TRAININGThe program’s aim is to train up to 1,000 workers to combat skills shortages in Western Australia.
Life is all about making the most of opportunities. The five Australian finalists, who in October competed in the Asia-Pacific finals of Global Operator Challenge, were treated to a life-changing week-long experience in Tokyo, where they went up against the best operators from Japan, Indonesia, India, and Philippines. When the dust settled, two Australians stood tall as the best operators in the Asia-Pacific region.
For Australian competitors Patrick Doheny (Victoria) and Nick Thompson (South Australia), the adventure is set to continue as they go on to compete in the global finals in March at the 2023 CONEXPO in Las Vegas after placing first and second runner-up, respectively.
As per the Australian state qualifying events, the Asia-Pacific Finals revolved around three challenges, in which the competitors were scored based on time, quality of work and safety. With the competition spread over two days and no leader board scores displayed, it was anyone’s guess right up to the presentation who had performed the best in the eyes of the judges. As it turned out, it was speed and time that the judges were most
focused on. Time penalties were added to the competitor’s overall score for any indiscretions or mistakes made along the way.
The Australian team consisted of a great bunch of characters that did a fantastic job of representing their state and dealer. Jake Myers from Western Australia shone
as a standout performer. He has stepped into a different role at his work and hasn’t been operating machines for a year or so. Myers was awarded the prize for safety and performance, which truly showed the quality of his work.
who put in three impressive performances across the competition and missed out on making it to the top three. Aiden Lee from Queensland rounded out the five Australian finalists, and if it weren’t for a couple of penalties on his first challenge on the first day, where a few nerves just got the better of him, he also would have been a real candidate for the top three.
The first challenge of the three was the “Big Dig” Excavator Challenge, where competitors operated a Next Gen Cat 320 with 2D GRADE technology and 0.8 cubic metre bucket. The objective was to dig a 6000-millimetre (mm) trench to a depth of 900mm with a three metre (m) flat bottom and a three metre 30 per cent slope.
The second challenge was the “Load & Go” Medium Wheel Loader Challenge, where competitors operated a 950M Z medium wheel loader. The objective was to load and carry material, achieving a target payload of nine tonnes (9000 kilograms). The course was around 200 metres long, and competitors needed to make two passes to reach the nine-tonne.
The final challenge was the Mini Excavator challenge, where competitors in the Cat Next Gen 303CR handled materials softly and precisely put them into specific features around the course. Elements included manoeuvring around the tight course without
touching cones, dropping balls and raising flags in designated stands.
At the end of the competition, the Japanese contestant Masato Imai took out the event with a fantastic performance, with two Australians, Patrick Doheny from William Adams and Nick Thompson from CavPower coming in second and third.
Chatting with the two Aussie lads about their experience, Thompson shared his excitement.
“This whole experience from start to finish has been amazing, from the Japanese people and experience to the quality of the event, amazing food and opportunity to have my first overseas experience here in Japan. The fact that in just three or four months, I’ll be heading to Las Vegas with Pat as the AsiaPacific finalist is just mind-blowing,” he said.
“When I decided to enter the local CavPower/Cat competition in South Australia, I didn’t think for a minute that this amazing journey and experience was about to unfold. Coming to Japan alone was massive on its own, but to now have the Global Finals in Las Vegas to compete in, has blown my mind. The Caterpillar team deserves a huge pat on the back for the quality of this event.”
Doheny also shared his experience. “In the loader challenge on the first day of competition, I didn’t feel like I had performed
well, so when I had the excavator challenge on the last day of competition, I knew I had to step things up. Luckily for me, it went extremely well, and I felt like I nailed that challenge. Overall, this whole experience has been fantastic, from the food to the amazing Caterpillar team who did an excellent job at putting on this huge event and also my dealer William Adams back at home in Victoria. I just can’t thank everybody involved enough.”
From the Global Operator Challenge event location in Chichibu to the streets of Harajuku and Shibuya, the Australian competitors were treated to an amazing Japanese experience. After having a chat with all the Aussie competitors before the announcements of the final results were made, it was clear that there was one consistent theme that shone through, and that was just how happy each of the competitors was that they grasped the opportunity with two hands to compete in the Cat Global Operator Challenge.
The Cat Global Operator Challenge, being held in March 2023 at CONEXPO in Las Vegas, will identify the world’s best operator from over nearly 40 countries, where more than 80 Cat dealers from around the world have held local, one-of-a-kind competitions.
We wish our two Australian Global finalists all the best in what will surely be yet another amazing adventure and opportunity with the Cat team. •
Sam Russell sits on the Board of Directors for the Institute of Quarrying Australia. He’s also the General Manager of Aggregates for Holcim Australia’s Western Australia division. Speaking on the importance of community engagements, he says environmental and social impacts has never been more important for quarries.
What were some of the biggest achievements for the Institute of Quarrying Australia (IQA) in 2022?
The year 2022 was a highly successful year for the IQA. Membership continued at historically high levels, and we delivered training across the country to a huge number of students, both face-to-face and online.
The IQA National Conference, held in March after several COVID delays, was the biggest and best IQA conference held to date. IQA’s chief executive officer Kylie Fahey and the team delivered an event that was educational and fun, and the attendees clearly enjoyed it.
The presidential handover was held in Perth for the first time and was incorporated into the annual general meeting and the Gala Dinner. Our new president and board were ushered in, and we are looking forward to the next phase for the organisation.
Last but not least, this is an opportunity to thank Shane Braddy for his presidency over the last three years. He was critical in leading the organisation and the industry through an unprecedented period and handed over the reins with the organisation in great shape.
How did the quarrying industry perform as a whole through 2022?
The quarrying industry navigated a challenging year with COVID impacts, extreme weather events and difficult economic conditions driven by the war in Ukraine.
Thanks to the resilience and innovation of our people, we were still able to keep our people safe, and continue delivering for our customers and the community.
Importantly, the construction industry continues to provide critical services and products to our community and will continue to do so – from the roads we drive on to the houses we live in.
In your opinion, what’s a promising change happening within Australia’s quarrying sector?
Safety and innovation continue to improve as we see less people hurt whilst doing their job. Community engagement continues to develop as the industry builds closer relationships with Indigenous Australians and people living in our local area.
We are seeing more sustainable operations with rehabilitation, technology and energy transition occurring at a rapid pace.
The use of batteries and hydrogen is expected to reduce the impact of our industry significantly over the next decade.
What do you foresee to be key challenges for the industry over the next two to three years?
Unstable global political environment – the ongoing war in Ukraine and its impact in particular; challenging labour conditions with continued low unemployment and skills shortages; economic factors including high inflation; and continuing to ensure the health and safety of our people as Covid waves continue to come.
The IQA works hard for operators in our industry, in three main areas – training, advocacy and networking.
Training is one of the focus areas for the IQA, and there is a large range available for operators from one-hour online workshops all the way to diplomas. There are digital training sessions as well as face-to-face options. We have a full range of material for all aspects of quarrying that is recognised by the industry, so there’s no need to create your own material or go on an exhaustive search for material elsewhere. Importantly, if you don’t see what you want, contact the IQA. We are constantly
looking to develop new options for our members and would love to hear from you.
The IQA provides regular networking events, which allow operators to catch up with what’s going on across the industry, identify any training opportunities and just have a bit of fun as well!
Lastly, the IQA engages in advocacy on behalf of the industry. This makes the industry a better place to work for everyone and helps the community understand the great work that we do.
What are the main goals IQA aims to achieve in 2023?
Launching the personal learning cloud is our primary goal for 2023 – this will provide real time accessible and online training via a simple platform. We believe it will bring a lot of value to our members and, more broadly, the industry.
And of course, we will continue developing and delivering our training programs and our networking events across the country.
Any last words?
Our industry is in a great position to support our communities and our people for the future. Keeping our people safe, improving our environmental and social impact, and delivering the products and services our community relies on is even more important than ever. Industry groups such as the IQA, our organisations and ourselves as individuals all play a part in building the future we want to see. I encourage you to get involved directly and to be part of it.
IQA is a professional body for quarry operators and suppliers throughout Australia, with membership open to all individuals. To learn more about IQA’s training, networking and advocacy activities, visit: www.quarry.com.au
From your perspective, how did the Australian quarrying industry perform during 2022?
Year 2022 has brought continued skilled labour shortages, higher transport costs, increased wage costs to attract and retain staff, planning and implementation of sustainability and diversity and inclusion initiatives and management of multiple regulations across different states. Whilst supply chain has improved, it’s still not where we all need it to be and if that wasn’t enough, let’s not forget about the devastating impact of flooding. All of this, coupled with strong
supportive group of people that dig deep and get on and do what needs to be done.
Which John Deere machines are most popular within the Australian extractive industry? Are there particular features in these machines that quarries are particularly interested in?
We’re seeing loads more of our production class wheel loaders and crawlers in quarries. The new 904 P-Tier wheel loader is built off the success of the 844L aggregate handler. It’s purpose-built for the rugged demands of the aggregates industry and is equipped
has automation of repetitive tasks like return to dig, return to carry and bucket shake to help new operators become good and all operators become less fatigued.
On our 1050K crawler, we introduced a suspended double-bogie undercarriage. It can absorb vibrations caused by rough operating conditions, the 1050K rides smoother and is more durable than previous models. A reduction of peak vibrations in the cab by up to 75 per cent helps operators carry on in comfort while moving faster, boosting production. But that’s not all. Both Extended Life and Heavy-Duty undercarriage
Karen Poulton is the Marketing Manager for John Deere Construction and Forestry Division. She reviews some of the most popular John Deere products for the quarrying industry and why they hit the mark for safety, efficiency and innovation.John Deere’s new 904 P-Tier wheel loader is a two-pass loader with the ability to automate repetitive tasks.
collectively racked up over a million machine hours. This loader is unique in that it runs four electric wheeled motors, which allows the system to recover energy and send to the power electronics to manage where the most efficient path for energy to go. This allows the machine to be highly productive in the pit face while managing wheel slip. This means operations can process more material while burning less fuel. This helps reduce the 944K’s overall environmental impact.
required power to charge the machines at the right time, in the right place. We’ve already made investments in some of the technologies that will be needed with our recent purchased in a battery company called Kreisel Electric, which produces innovative battery technology for e-mobility and stationary systems.
The journey also includes focus on improving diesel engine and vehicle efficiency as well as technology to support
renewable fuels that emit less harmful emissions. We’ve made investments in Illinois-based start-up company, ClearFrame Engine Technologies, who are dedicated to the development of clean engine technology. Their technology enables low-carbon fuels such as ethanol or other renewable fuels to be integrated into compression ignition engines, offering a sustainable solution without compromising engine performance.
products. What sort of programs and services are accessible and why should quarries use them?
Our remanufacturing program reduces our impact on the environment by reducing our reliance on raw materials through the reuse of parts. This enables us to eliminate waste and reduce energy use compared to manufacturing new parts. By bringing parts back to the original specification, our John Deere Reman business provides quality remanufactured products such as engines, drivetrains, hydraulic and electronic at a lower price point than new parts and provides alternatives to customers looking for value and uptime. In 2021, we recycled 12,609 tonnes of material through our remanufacturing process.
What else do you foresee to be major challenges for the Australian extractive industry over the next two to three years? Recruiting a skilled, diverse and dynamic workforce will continue to be a challenge, as is attracting more women and young people to the industry. Also managing inputs, not just from a dollars and cents perspective but from an environmental perspective.
How can John Deere best assist its customers with meeting these challenges? Our latest model wheel loaders help new operators become good, quicker. They are easier and more intuitive to operate, we feature automation of repetitive tasks and the inclusion of an advanced vision system and a rear object detection system boost operator confidence.
What other innovations are your products adopting to promote safety?
No one ever said safety second! The new 904 P-Tier wheel loader has obstacle intelligence features such as Advanced Vision System – an industry-first for loaders. This provides a wider field of view than conventional mirrors. It also increases the visibility to sides of the machine by integrating digital cameras on the rear-view and side mirrors and combines these views into a dedicated single display in the cab.
The 904 P-Tier also offers an improved rear
object detection system. This feature overlays projected vehicle reversible path within the same dedicated monitor, enhancing the operator’s experience and situational awareness. It also provides an audible alert of objects behind the machine that increases in intensity as objects get closer.
By combining cameras, radar and machine learning, obstacle intelligence gives operators eyes in the back of their head.
John Deere offers programs, services and advice beyond the installation of key mobile
All of our equipment is equipped with JDLink onboard telematics. In addition to monitoring your maintenance and machine performance, you can gain actionable insights and have a data driven conversation with operators. To meet sustainability targets you need a base line to start and to monitor from. JDLink provides that machine data now and on an ongoing basis and the subscription is free.
We’re excited to continue to be active members of the IQA at both national and branch levels. People in the quarry industry are some of the nicest, most humble and generous people we have the privilege of working with. Here’s to an amazing 2023.
For more information about John Deere’s quarrying equipment and services in Australia, visit: www.deere.com.au
It takes a different kind of brain behind the brawn. Fired up like a turbo diesel. Gears constantly churning. Hardwired beneath hard hats to solve problems, or avoid them altogether. With you and your crew at the helm, and Deere at your back. The workarounds, ideas and innovations that move earth, and your business, forward. Because that’s what it takes to win in the dirt. And that’s what it means to be Never Idle.
Matt Wessel is Xylem’s Director of Strategy, Product Marketing and Engineering for Australia and New Zealand. He offers input on how quarries can fulfil their sustainability goals with smarter water management.
Looking back at 2022, how did the Australian quarrying industry perform?
The quarry industry should be proud of its resilience throughout 2022. As the nation began to emerge from the Covid pandemic, many parts of the East Coast of Australia were continually challenged by flooding and extreme weather events and the whole sector faced inflationary pressures impacting operating costs and labour shortages in a very tight employment market. Despite these challenges, the quarry industry continued to work hard to deliver aggregates such as stone, gravel and sand that are the
building blocks of Australia’s building and construction industry.
What were some highlights for Xylem from 2022?
The Xylem team in Australia has had another strong year partnering with customers in various sectors including the quarry industry. Our team has enjoyed the opportunity to reconnect with more of our customers face to face as pandemic restrictions eased. This has allowed us to stand side by side with customers investigating and solving their water challenges right at the source.
Additionally, our team was very excited to move into our new head office in Sydney that saw us significantly expand our warehouse, service, local assembly and testing capability in a brand new 10,000 square metre facility – that is twice the size of our previous facility. This allows us to continue to deliver improved customer experiences via additional stockholdings and local assembly to provide products, solutions and services to the Australian market with increased speed.
What are some of the most popular Xylem products in the Australian extractive industry?
It is definitely our pumping solutions via our strong Flygt and Godwin brands. These extremely robust Swedish (Flygt) and English (Godwin) dewatering pump portfolios bring with them a combined 250+ years of experience in the toughest applications around the globe. However, I believe Xylem can make an even bigger contribution to the quarry sector as the industry’s partner in complete water cycle management via our full portfolio. Xylem’s proven mechanical, process and digital solutions in water treatment and water quality monitoring can provide quarries with the ability to effectively meet their environmental obligations and sustainability targets.
Have you noticed any changes in the industry’s approach to water security/efficiency?
The quarry industry continues to evolve as the bar is lifted in the areas of environmental protection and sustainable operations. This in turn is driving a strong focus on the management and value of water in quarry operations. It is no longer just enough to produce high quality aggregates, but it is equally as important how a quarry achieves this in an environmentally responsible and sustainable way. Xylem continues to
partner with our quarry sector customers to introduce them to already proven technologies that support them in these areas of complete water management.
What external factors are driving decisionmaking for quarries when it comes to choosing water solutions?
There are a range of external factors shaping decision making for on-site water solutions. Uncertainty and challenges in global supply
chains, higher fuel/energy costs, labour shortages and extreme weather has seen an increased focus on higher quality, increased efficiency and more robust solutions that have extended lifetimes. Additionally, rising interest rates will likely see capital expenditure approvals start to tighten and water infrastructure investments won’t be immune here. Xylem’s premium and high efficiency product portfolio, local aftermarket service support and rental fleet provide our
quarry customers a level of comfort as they tackle these challenges.
Does Xylem have any innovative products or services to launch in 2023?
Xylem continues to expand our digital offerings that supplement our well-known mechanical products like our pumps. This enhances these products to become digitally smarter water solutions, delivering higher efficiency in everyday pumping by using real
time analytics and data to help make better decisions with processes using water.
What do you anticipate will be a major challenge for the Australian extractive industry in the next three years?
Net Zero and related sustainability targets that are being embraced in unison by governments and private industry are incredibly important focus areas to ensure we leave the planet in healthy shape for future generations.
The Australian extractive industry, like all industries across the globe, will be working through the challenges of delivering on these sustainability commitments against the backdrop of global economic uncertainty, extreme weather conditions and labour availability challenges with an ageing population.
Achieving these important but lofty targets will require collaboration across the sector and the support of key partners with specific domain expertise.
How can Xylem assist the industry with meeting these future challenges?
Xylem is uniquely positioned to support the industry in solving their water challenges that form part of this sustainability challenge. The combination of our unmatched premium portfolio of pumping, treatment, testing and monitoring equipment, plus our local team of water domain experts and access to a global Xylem network of experience means we can be a trusted partner for the industry in the water space. This allows quarries to maintain focus on optimising their extractive operations with the comfort that their water challenges are in good hands.
Any final words?
Our local communities rely on a vibrant quarry sector providing the building blocks for the construction of infrastructure and services we take for granted, like our homes, schools, hospitals and roads.
Whilst the Xylem team remains focused as a company across the region to live our tag line: “Let’s Solve Water”, we’re all very driven by our purpose to live in a world where water is not a barrier to human health and prosperity, and that continues to drive us to solve water challenges with our customers and communities
The best way Xylem can help our quarry customers is to be a trusted water management partner – and a way we can do that is by coming to site and evaluating every point that water touches the business and offering a “water audit”, which includes inspection advice or site audit advice. We want to track and trace water usage and help customers understand how they can better use water.
For more information about Xylem Australia and New Zealand’s water management solutions, visit: www.xylem.com/au
How did Eltirus perform during 2022? Any highlights from the team?
We had a tremendous year, bringing on new clients and working with some of the most interesting construction materials businesses in the region. In 2022, we re-branded the business from Cement and Aggregate Consulting to Eltirus. It was our biggest year so far in terms of research and development activity. Bringing on new staff and systems has fundamentally added to our capabilities and how we help the industry. A primary highlight for us is the development of Enable, our site-wide data collection and analysis system, that we now have in daily use with a major quarry operator.
In your view, what factors are driving investments in the quarrying industry?
I think most operators are more focused on meeting the high demand from the various infrastructure projects in play rather than major investments.
Following from the above, have you noticed any trend changes in recent years?
There is an increasing (and necessary) focus on diversity, inclusion and mental health as primary areas for the industry to address. It is good to see that the mining industry has (in the main) embraced these challenges and is working diligently on making them a reality while now also focusing on decarbonisation. This may be a guide for our own industry in the foreseeable future.
What are some challenges facing the extractive industry over the next 3-5 years?
I attended the International Mining and Resource Conference in Sydney in November. A consistent message there was that the companies saw the decarbonisation of their own businesses (and the broader economy) as their primary objective and that technological innovation – such as autonomous electric technology – was key to achieving this.
Central to this is the need to find the resources to drive this technical change, and there was much debate about whether companies should develop the technology and skills internally or rely on external partners, particularly given the skills shortages attendant to both approaches – problems that are going to be potentially even more difficult for the quarry industry to manage. By way of example, construction material businesses don’t generally have a technical services department with large numbers of geologists, mining engineers and the technical specialists with the skills and time to embrace and develop the processes and systems needed to make this change – if not, who will do it?
How is Eltirus placed to help quarries address these challenges?
Our realisation was that autonomous electric technology would not be workable in a quarry that didn’t have effective survey control, known geology, a well-defined operational plan and a means to collect the data produced by each of the systems and analysed in such a way as to provide the “levers” to better control operations.
Technical innovation is at the core of our business, and we have a well-defined and proven decarbonisation strategy for construction material businesses that has been built in conjunction with key stakeholders in the software and technology areas and specifically with major players in the autonomous and electric haul truck space.
Which new technologies in the quarrying industry are you most excited about?
The primary area of interest for us now is autonomous electric haul trucks, and autonomous technology generally. We are heavily invested in this area through involvement with manufacturers and with the Global Mining Guidelines Group in the development of international guidelines
for the use of small autonomous trucks. This technology is much closer than most people realise, and significantly more cost effective. We are starting to see the advent of Autonomy 2.0 – where the truck is “smart”, rather than relying on external processing to direct it. This will really change how we look at these types of technologies. We are planning to take an industry group to visit with one of the key players in the quarry autonomous truck field in early 2023 and have been delighted by the positive interest and take-up.
What are Eltirus’ key objectives for 2023?
Our primary goals are to help clients know what’s in the ground, to extract it sustainably and to ensure compliance with both internal and external stakeholder requirements. Our focus this year is twofold: First is getting the message out that major innovations such as autonomous electric haulage, advanced data analysis and resource optimisation strategies are here now (or will be, in the very near future) and that they pay significant dividends environmentally, socially, and economically. The second goal is ensuring that we are the partner of choice for companies adopting these technologies to ensure that they have the planning, systems and support necessary to make innovation a reality and to be a collaborative partner they can trust.
The industry is ripe for innovation through digitalisation and autonomous operation – to name but a few key initiatives. The companies that are wholeheartedly adopting these exciting new technologies and making them their own are gaining a substantial advantage over their peers. We are very honoured to be a fundamental part of these transitions.
For more information, visit: www.eltirus.com
Cameron Ballentine-Jones, Executive General Manager of Customer Support at Komatsu Australia, shares why he thinks the quarrying industry is at a critical economic juncture.
How did 2022 look like for Komatsu Australia? Do you have any milestones or highlights to share?
With the supply chain challenges caused by Covid and the buoyant period for the Australian economy, our biggest success has been to be able to deliver on the majority of customer needs. We’ve had a huge volume of equipment to deliver across all sectors. On top of that, we’ve also succeeded in supporting our customers with parts and aftermarket services, in what I would call an unprecedented year of market demand.
What are the most popular Komatsu machines in the extractive industry currently?
The rigid dump trucks, including the Komatsu HD785, HD605 and Hd405 dump trucks are the busiest ones.
In the loader products, we’ve recently sold some of the big Komatsu loaders from the WA900 series. The WA600, WA500 and WA480 loaders remain staple loaders for quarries.
In excavators, the PC850 and PC700 excavators are the most popular. From the smaller loaders, machines in the range of the WA320, WA270 and WA200 make up the majority of the products that we’ve been delivering this year.
From your perspective, have there been changes in what customers are looking for in their machinery?
Customers are looking for innovations in products, and that innovation comes down to three areas: The first is safety and how our products can support and enhance their safety performance. The second one is productivity and the third one is in the environmental, social, and governance (ESG) area.
Customers are looking for innovations that lead to lower fuel burn or machines that have lower emissions.
How do Komatsu’s products help quarries achieve more sustainability?
Since about 2018, we’ve been delivering Tier-4 engines on all our machines. That product already helps deliver significant reductions in particulate matter released into the atmosphere. Komatsu Corporations has also released its global roadmap, which sets a vision of achieving zero net carbon emissions by 2050 and sets a target of reducing carbon dioxide emissions by 50 per cent and raising the ratio of renewable energy use to 50 per cent by 2030 from 2010 levels. The quarry industry often has constraints around financing. Realising this, we’ve come up with a range of flexible options to support our customers to reduce fuel consumption, optimise engine life and rebuild and recycle components so they can get a longer life out of their existing machines.
Which unique Komatsu technologies help quarries achieve more efficiencies?
One of our products in the quarry space is Komatsu iSite. It’s a locally developed hardware and software solution that is designed to improve productivity, reduce fuel use and allow customers to manage their fleet more holistically. It’s a manufacturer agnostic product, so it can be installed on any piece of equipment and our customers are already adopting it with great enthusiasm.
A second example is what we call our Smart Construction Dashboard, which enables customers to measure and track their quarrying activity. We support that with drone technology to monitor the landscape and provide inputs into the 3D modelling and using AI-driven algorithm, we help the customer quantify and refine their production.
What do you anticipate being key challenges for the quarrying industry in the next two to three years?
I think issues related to energy cost and ESG compliance will become even more
prominent. Access to skilled workers is a global issue which impacts everybody. In our company, we’ve invested heavily in apprentice training. We recently enrolled 80 new apprentices for next year, so we have a steady input of apprentices. Safety improvement will be another continued focus area. From an economic point of view, we are about to enter an interesting financial landscape, both globally and locally. This will mean flexibility in managing assets and the costs associated with those will be even more important for our customers than they were before.
How is Komatsu positioned to help quarries meet these future challenges? At a global level, Komatsu invests significantly on research and development and will continue to do so. Our job as distributors is to collect the voice of the customer and feed that back to the manufacturing team. But there’s also local innovation happening at a local level, particularly around information management like iSite and Smart Construction Dashboard. Another initiative that we’ve undertaken for some years is to arm all our service technicians with digital technology so they can review the information in advance of arriving to a site and resolve it with minimal delay. They even have access to our global network for troubleshooting. We call it ‘Fix at First Time’ and it helps give our customers more uptime. It also helps remove technicians from the line of fire to advance safety for our customers. Engaging closely with customers at a specific site level is more important in quarrying than anywhere else. With our service digitalisation, we are in a good position to support our customers.
For more information about Komatsu Australia’s earthmoving products, visit: www.komatsu.com.au
1300 566 287 | komatsu.com.au
Komatsu iSite offering provides site and project management personnel with an “at a glance” production visualisation of any quarry or major civil construction site.
Komatsu iSite gives the user a real time animated overview of every movement of production machines – and the material they are extracting, shifting or placing.
Call us today on 1300 566 287 to find out how Komatsu iSite can help your site.
Looking back at 2022, how did the Australian quarry industry perform?
The quarry industry performed very well. The residential construction market, the civil infrastructure projects being undertaken and expansion of mining infrastructure all helped to support the growth in the quarry industry.
What were some highlights for Caterpillar from 2022?
Highlights were the ability to bring new technology and equipment to the quarry industry. This enables our customers to achieve better productivity and efficiency, which is also aligned to the industry’s focus on sustainability.
What are some of the most popular Cat machines in the extractive industry?
The most popular product category from Cat this year was our medium wheel loaders. The 980/982 medium wheel loaders specifically, which were revealed at the national Institute of Quarrying Australia (IQA) Conference, have been very well received since their
launch, by customers both in Australia and New Zealand.
The 982 medium wheel loader comes equipped with a Cat C13 engine and very importantly, features that make step changes in fuel efficiency and productivity such as Cat Payload and a new autodig feature.
Which equipment technologies do you foresee to be of greater interest for the extractive industry over the next few years?
I think technologies that measure payloads accurately and efficiently will become more and more relevant, as well be technologies that enable customers to reduce their fuel consumption – both to improve their fuel efficiency and to reduce their carbon footprints.
Does Caterpillar have any innovative products to launch in 2023?
We will be completing our Next Generation line-up of our medium wheel loaders in 2023, which we are very excited about. That will mean all of our medium loaders will become
was and what to expect for the
equipped with the latest technology in Australia, so more customers will be able to experience the difference of our next generation products.
What do you anticipate will be a major challenge for the Australian extractive industry in the next three years?
I think the acquisition of new people into the quarrying industry is the primary concern, both in attracting new people in and also in training these fresh people to be able to perform advanced duties. There are a lot of older people leaving the industry and taking that knowledge with them with no one to pass it on to. Additionally, how to respond to the challenge presented by sustainability is another key challenge.
How can Caterpillar assist the industry with meeting these future challenges?
The first is through training offered by Caterpillar and the Cat dealers. We have a well-established training programs that comprehensively teaches operators and rewards the business. The second way is through our technology that helps with the sustainability challenges I mentioned. The new engine technology that we have helps reduce fuel consumption. We also offer technology that enables customers to gain higher levels of productivity and increased sustainability, through the virtue of trained operators using these machines.
Any final words?
At Caterpillar, we are committed to supporting our customers in Australia, which is shown through our ongoing support and our sponsorship of the IQA –which we see as a very important pillar of the industry. We’ll continue this support strongly in the future.
For more information, visit: www.cat.com/en_AU
Jonny McMurtry, Chief Operating Officer at Precisionscreen, observes that the industry is now, more than ever, keen to utilise products efficiently.
How did 2022 look like for Precisionscreen in terms of company performance? What were some key milestones?
After a Covid affected period of 12 to 24 months, which was full of uncertainties and changes for us, our focus was on gaining some stability. Having lost a lot of experience in some of our management figures leaving the company, we decided to focus on Australian manufacturing as opposed to a blend of importing and manufacturing. Looking back at our achievements, we can call it a success because we grew as a company, not just in terms of sales and turnover, but also because we were able to retain all our staff and introduce new members to our team. We even launched two new products in the market over the past six weeks, which were developed internally using ideas from our line managers and different people within the company. Both products were developed organically by understanding what our customers’ needs and requirements were.
Which of Precisionscreen’s products are most popular in the quarrying industry?
Our Scorpion range, including our reclaimer and pugmill units continue to grow in volume and have a new addition to the range in our Scorpion stacker, wheeled hopper/conveyor unit. The newest addition to our Scorpion family, our Scorpion Stacker plant comes with galvanised extended hopper, e-lanyards for main conveyor, suitable guarding, engine bay enclosures, fitted with large eight cubic metre hopper and extended jib conveyor for 6500 millimetre discharge height and powered by Perkins power pack and in-house developed hydraulic system.
Has Precisionscreen introduced new products or upgrades?
Alongside our recently introduced Scorpion Stacker unit, we have recently introduced new units such as a bin feeder for safely loading bulker bags into our PLC pugmill
units. We also had modifications to existing units such as track mounting our PLC pugmill unit. The new Bin Feeder system was developed in only six weeks, from the point of discussions with the client to being completed and working onsite, which is an example of the team’s hard work and willingness to try new ideas.
What do you foresee to be major challenges for the quarrying industry in the next three years?
Access to skilled labour, increasing cost of imported goods and raw materials prices plus running costs of machines including electric power systems and diesel, combined with the quarry industry’s ability to meet or match the demands of materials required for expected increase in infrastructure and development.
How has Precisionscreen set itself up to face those challenges?
Firstly, we contacted local education facilities that do apprentice training and we offered placements or work experience for some young college students to both introduce new ideas to our business and hopefully new, enthusiastic young adults into our industry. We also tried to develop our new skills and techniques with our existing employees within the team, making sure the employees we have are fully proficient and up to date with the certifications expected for our industry. To tackle the overseas or imported costs, that ties in with our focus on local manufacturing. We’re not trying to compete against every type of machine in the market. What we’re trying to do is offer alternative solutions which can be manufactured in Brisbane, using local manufacturing and local suppliers for innovative and reliable products and services, fully developed in Brisbane. We are trying to counter-act those increasing costs and the limited supply by offering alternative solutions with the end user in mind.
Have there been changes in market demands from your perspective?
Over the past 12 to 24 months, our most sought-after product has been our PLC Pugmill. I think the industry is trying to maximise production volumes or generate sellable products as effectively as possible. Where in the past a lot of resources might have gone to waste, more customers are now trying to get as many materials as they can from their crushing and screening processes.
I don’t necessarily think that the expectations or demands from the industry have changed or substantially increased, but I think the customers are expecting more effectiveness and improved efficiencies from their processes.
Going into 2023, what does Precisionscreen aim to achieve?
Our focus for 2023 is new product development and the growth and strength of our company’s culture.
We are still looking to develop new or diversification of Precisionscreen product lines, such as electric driven screen plants and modular crushing plants. With the increasing price of diesel, we want to develop some direct electric or electric over hydraulic crushing and screening options, particularly for our customers in metro areas who have access to good electricity sources. We will also focus on niche areas and offer solutions for sand washing processes, which includes the re-introduction our fines recovery pod to help customers with water recycling for washing processes and extracting fine material.
Ultimately, what we’re trying to offer is a quality product that we can stand besides, be proud of and support for years to come which Australian customers within the Australian market can rely on.
For more information on Precisionscreen’s screening and crushing solutions, visit: www.precisionscreen.com.au
What were some milestones for Terex Washing Systems in 2022?
Terex Washing Systems (TWS) celebrated 62 years of serving the industry in 2022. We also launched two new products. One was the FM Pentium washing plant, and the other was the introduction of our VacRecover product.
The FM Pentium is a patented product by TWS. Its design goes against the traditional screening process in the way that you’d normally take off size fractions from smallest to largest by feeding all the material on the top and the smaller size fractions coming out from underneath. With the FM Pentium, we feed the larger material from the bottom and then pump up and take off the sand from the top deck. It’s a unique product that can deliver several configurations in a smaller footprint. Globally the product has been well received by the industry and our customers.
The VacRecover is a recovery unit that best suits the recycling industry, specifically the processing of what would be otherwise considered ‘waste’ material from hydro-excavation/vacuum trucks. The principal is that a vacuum truck vacuums up wet slurried material, be it sand, soil, or rocks, and the VacRecover unit helps in the recovery of sand and aggregate through separation and dewatering, while also helping recover water.
What services does Terex Washing Systems provide to customers apart from product supply?
We are a one-stop-shop for customers looking for washing solutions. We supply, install, maintain everything from feed to filter presses and as well as smaller standalone solutions.
We work with our customers to provide bespoke solutions for their specific
needs. Right from the start we have our dedicated, in factory, applications teamwork with the customer to define their needs, laboratory testing is carried out, and then our engineering team design the plant and full solutions to their needs. We also provide a full project management service to deliver, install and commission the plant and it doesn’t stop there, we provide aftercare support 24/7 through our regional support networks to ensure maximum uptime and efficiency of your plant.
TWS can also provide a range of finance options through Terex Financial Solutions to help the customer pay for their solution.
What are the key aspects that quarries look for in their wash plants?
Have you noticed any trend changes in recent years?
Of course, everybody is keen to manage resources these days and eliminate waste, we have seen a large increase in the demand for our wash recycling products often from quarries that would have been traditionally processing only natural materials. Capital equipment costs can sometimes be a barrier to quarries changing their business model and producing more of their product from recycled sources, and we think increasingly government incentives will also assist with driving forward that adoption, which can only be a good thing from a circular-economy standpoint. Additionally, I do see more interest in water conservation and the awareness that water in these operations is a critical resource also to be managed.
What do you foresee to be key challenges facing the Australian quarrying industry in the next few years?
We are currently facing a massive shortage of sand, particularly in those states where there has been flooding.
From our end, we help the customers as much as we can.
Additionally, speeding up sign offs and licensing would help quarries release more sand reserves to the market.
What are some areas where TWS can help the industry overcome their existing and/or inherent challenges?
Because of all the labour shortages and the increases in demand, everybody is so busy these days. Being able to provide turnkey solutions to our customers means TWS customers can take advantage of the increased workload and build new plants with minimal hassle. Whether TWS is building the plant, or the customer is building it themselves, we can help them bring all the pieces of the puzzle together. We have the widest in-house product portfolio of any equipment manufacturer in our space. We can also help quarry managers with optimisation through their plant to get the most out of their crushing, screening and washing plants.
What will be Terex Washing Systems’ goals in 2023?
We want to continue to provide innovative and bespoke solutions tailored to our customers’ needs.
We’ll continue to invest in our products and team to be able to provide a first-class service to our customers.
We will also make continued investment in our headquarters to enhance our lead times, where we have managed to maintain industry leading lead-times despite all the headwinds of the past two years.
For more information about Terex Washing Systems’ washing products and services, visit: www.terex.com/washing/en
Jeff Gray is the Director of International Sales and Mining at Superior Industries, which is renowned worldwide for its crushing, screening, washing and conveying solutions. He sits down with Quarry to discuss the latest in the world of bulk handling and equipment processing, and what the company has planned for this year.
How did Superior Industries perform in 2022? Were there any highlights you’d like to share?
It was a great year, we saw near record levels of revenue, and we’ve seen the bottom line start to work its way back up after the prices of raw materials stabilised, which led to some stability in the business.
We are also very excited that we will be launching two new product lines for cone crushing this year. We’ve had a cone crusher in our portfolio, but with the two new lines, we are leaping into sectors that we couldn’t play in before. This gives us the opportunity to fulfill some application specific needs, as well as the needs of customers that have preferences for certain styles of cone crushers.
The new products will be introduced at CONEXPO in March 2023 and first launched in North America, followed by a launch in the Australian market within six to twelve months, if not sooner.
Which Superior Industries’ products are most popular within Australia’s quarrying sector?
Our conveying, washing and screening product lines all have a very good penetration in the Australian market. Australia is among our top five markets globally.
service the slag industry in Australia as far as processing steel slag.
From an efficiency point of view, are there common pinch points in quarries that your products can address?
The most common thing that we see in aggregate processing plants is that they’ve been asked to produce more of certain products and you always want to have your crushers maximised and fully utilised, but as we try to push the productivity of the plants, a lot of times the screen area limits our finished product output. So, as we push our plants to higher and higher tonnes per hour rates, we need to make sure that we look after our screening area. That’s a cautionary tale.
How has Superior Industries adapted to the challenges around supply chain for timely product delivery?
in a position now that we need to partner with our dealers to ensure that they have the inventory at their facilities to service the installs for Australia. We are doing this by putting in resources in Superior Industries to help our dealers achieve that, to make sure they have the right parts in place, at the right time.
What do you foresee to be a key challenge for the Australian extractive industry in the short term?
I think for Australia, the economy, where the government is trying to curtail the rate of inflation through interest rate hikes, could be a challenge for the sector. That’s always a fine line to walk for any economy. If those [rate changes] are enacted too quickly, it can bring some things to a halt, specifically for the commercial and municipal construction and road projects. That’s a potential challenge that we’ll keep an eye on.
In 2023, what are Superior Industries’ primary goals?
Significant expansion of our manufacturing capacity, for both equipment and for conveyor components. Those are two areas where we saw demand outpacing our ability to maintain what we feel are reasonable lead times, so that’s a big effort and one that we are working through with our plants.
What
The main thing that ties into sustainability is our activity in the steel slag processing market, as well as the concrete and asphalt recycling markets.
The slag market is one where we’ve become very active in, and we’ll expand globally.
Some of our customers in the US also
For many years, it was not uncommon to be able to complete any piece of equipment in 16 to 20 weeks or less and ship it. Today, the lead times are double or in some cases longer. For our manufacturing operations, one thing that we looked at was that we have six manufacturing locations around the world. Some locations have a larger pool of potential workers, so we’ve looked to see who has the best access to adding capacity and that’s where we’ve moved our investments in facilities to help us grow. From our distributors’ standpoint, it’s kept them more on point as far as looking at their inventory of equipment and making sure they are replenished on time. I think our distributors, that is Tricon on the East Coast and 888CSE on the west coast for conveying equipment, have done a good job of trying to stay ahead with the availability of the most popular product sizes. We are
Another goal this year is to add a stocking and servicing dealer in Western Australian for our crushing and screening equipment, as well as for our washing equipment. In the east coast, we want to enhance our crushing inventory with our dealer Tricon.
For more information about Superior Industries’ product line, visit: www.superior-ind.com
Grayden Leaver, Executive General Manager of Sales and Marketing at CJD Equipment, says a shift to more sustainable equipment is imminent for the quarry industry.
How has CJD Equipment performed since last year this time?
We’ve continued to have solid results over the last 12 months. CJD Equipment is fortunate to be involved in an industry that has been far less affected than other industries during the pandemic. We have been able to maintain our operations and maintain the livelihoods of all our dedicated staff.
What predominant factors drive demand for construction machinery in the quarrying industry?
One of the main drivers for construction machinery has been the government’s Infrastructure Investment Program, which has created a copious amount of road and infrastructure projects across the country. This investment has led to a growth in demand of raw materials, driving more business for our customers. In the past year, we have also seen a push for more customised machinery specific to its application. Customised machinery is often configured to interact with ever evolving site management tools which benefits sites for productivity, efficiency, safety and sustainability.
How has CJD adjusted to these demand changes?
At CJD Equipment, we have been granted the opportunity to lean on our 30-year partnership with Volvo Construction Equipment (Volvo CE) to adjust to the demand changes. Volvo CE desires to be an industry leader in this space, and they are continuously looking at ways to adapt to market demands. Volvo is well known for its focus on site and operator safety, providing industry leading offerings. Technologically, we can improve our current range of construction equipment, to ensure continued development in efficiency, safety and application. Through Volvo’s industry leading offerings, we have been able to make a shift towards site management and evolve the
productivity services we have to offer – which covers everything from site simulations and EcoOperator training [course] to Connected Maps and a high level of productivity data. In the last 12 months, Volvo has also taken huge strides in electromobility, alternate fuels and fossil free steel. Whilst some of these developments are short term and will be seen in the next 12 months, the shift to sustainable equipment will be a long-term development. We are having several discussions with customers around the journey CJD Equipment and Volvo are on in this space.
What are some of the most popular Volvo CE machines in the quarrying industry?
Some of the more popular machines are the L260H loader, the EC950E excavator along with the A40G, A45G and A60H articulated haulers. We also have seen a number of enquiries or the last 12 months on the R100 rigid hauler.
Has appetite for hybrid machines or alternate fuels increased in view of rising fuel costs?
Yes. We have recently released the Volvo EC300E Hybrid excavator, with more to come. There is a lot of work being done behind the scenes in the area of hybrid machines, motion systems and energy recuperation from Volvo, which we believe will lead to far more significant savings in the future.
With regards to the above, what options does Volvo CE currently offer to customers in Australia?
Currently we have the hybrid EC300E excavator available to customers. The EC300E Hybrid offers the same levels of controllability and performance as the standard EC300E, with up to 15 per cent increase in fuel efficiency and has the ability to work in ECO mode and Hybrid mode simultaneously. We also have the EC250E Hybrid and EC350E Hybrid excavators available as indent order.
What challenges do you foresee for the quarrying industry over short term?
I believe the quarry industry will continue to have challenges in staffing, human resources and machine availability. However, I think the biggest challenge is the journey into electromobility, alternate fuel, automation and sustainability. I think equipment manufacturers, dealers and customers alike know the world is evolving. The journey to bring that to Australia and the quarry industry could, at times, be long and confusing, with new processes and directions. The exciting part is that we as an industry can play a positive role in building the world we want to live in.
How can CJD assist the extractive industry with meeting these future challenges?
CJD and Volvo CE can continue to assist the industry through the continued refinements of existing products, the implementation of new technology and electric construction equipment. This in turn will assist with developing more sustainable products, along with world-class site management, productivity support and packages, to ensure safety and productivity for those in the quarry industry.
Finally, any forecasts or promises from CJD Equipment for 2023?
One of CJD Equipment’s major targets will be to commercially launch the Volvo electric range of compact excavators in the next 12 months. We are very excited about this project. We also plan to spend a lot of time working with our quarry customers in the areas of site management and productivity services. We will continue to provide the highquality products, service and support that the quarry industry has come to expect from CJD Equipment and Volvo CE.
For more information about Volvo CE products and CJD’s programs and services, visit: www.cjd.com.au
Volvo’s range of excavators are the perfect combination of power and stability, no task is too tough. With superior digging force, quick cycle times and outstanding fuel efficiency, you can expect smooth operation and increased productivity in the most demanding environments.
Feel the Volvo difference today.
Crusher Screen Sales and Hire specialises in sale and hire of plants Australia-wide, from crusher and screens to conveyors and mixing equipment. The company also provides services around soil remediation and is the Australian distributor for IMS. Manager John Andersen speaks with Quarry about what the company has been up to.
How was 2022 for Crusher Screen Sales and Hire? Can you share some milestones?
Some challenges of 2022 were supply issues and increased prices of plants and shipping costs. This led to some products waiting months to get on a ship. To top that off, we were then hit with cost increases. In some cases, parts have been in short supply or there has been extended delays in obtaining them. So, the big milestone for us was being able to meet those challenges and not letting our clients down.
Which were the most popular Crusher Screen Sales and Hire products within the industry?
There has been good demand for sale and hire of the IMS-PM1050-16TB track pugmill that is fully automated. IMS offers this highcapacity track pugmill, which is specifically developed to produce high quality material blending for stabilising road based materials with the addition of water and cement or lime. The track pugmill can also be used for blending at asphalt plants, for cold emulsified asphalt mixing (cold mix), for roller compacted concrete (RCC) and for flowable backfill material. They are working on a lot of the major infrastructure projects throughout Australia, meeting the required specifications of blending products. There has been a large demand for most products serving the quarry and construction industries and we expect this to continual next year.
Have you noticed changes in what the industry is demanding from suppliers such as yourself?
There has been such a demand for plants that some clients have had to wait months for delivery or [they’ve had to] purchase another machine, which might not have been their first choice. This has also led to increased demand for second hand plants, resulting in price increases. If the contractor has won a
project and needs a specific plant, they may have to take what is available, be it new or second hand.
What support does the company provide beyond your core products?
Besides servicing and making sure parts are available, we spend a lot of time and money automating the IMS pugmills and blenders, improving the product to ensure it remains a market leader in this field. It is already gaining a larger market, not only in the quarry and construction industry, but also in remediation projects. Some states and councils are requiring recycled products to be blended with quarry products to reduce landfill and utilise a reusable product instead of waste.
What’s one key challenge you anticipate for the quarrying industry in 2023?
Shortage of skilled workers and plant shortages, which could negatively affect the
it reduces [risk of] operator error and supports management that their product is meeting the specifications. It also helps produce supporting reports that can be overseen without having to be on site. A lot of virgin quarry materials have difficulty meeting the standard with some of the new specifications that have been introduced. The range of blenders and pugmills we offer will resolve this problem. Of course, the quarry is picking up extra costs on plant purchases and operating costs, but it’s still cheaper than having a product rejected on a construction site or sitting as a rejected product at the quarry. The companies that embrace the changes will have an edge over their competitors for major projects and get considered by the head contractors and authorities.
Finally, what are your goals for 2023?
Much the same as last year, keeping service
Crusher & Screen Sales Pty Ltd (CSSH) are the IMS distributor for Australia since 2012 and have been instrumental with IMS in developing plant for Australia conditions and requirements, there has been a strong emphasis on high quality plant for blending and pugging material for the quarry, construction industry, remediation of contaminated soils and blending of recycled products. The plant has been designed with large feed hoppers and capacity to service small to large operations with manual controls that in most cases have the ability to be fully automated insuring constant and accurate blending and reducing operator errors. IMS also manufacture a large range of wheel and track conveyors with production up to 2000 tonnes per hour and up to 45 meter long and screening plants.
CSSH and IMS together continual to improve their plant with feed back from clients and adjusting or adding new plant and ideas particularly in the blending of products to make previously discarded and recycled products into a sellable item, there is a strong desire by departments to add recycled concrete and other products into construction materials to reduce waste, landfill and raw material demands.
The IMS-PM1050-16Tb Track Pugmill is now the largest selling pugmill In Australia with capacity of up to 500 TPH, available in manual adding only water / liquids or fully PLC computer controlled and recording system adding cement, lime, or most powders etc. The PLC can be controlled by an iPad in the loader operating all the functions including
client or batch mix changes, loading truck and multiple trailers direct, stopping automatically once each item had been loaded with the correct tonnes and then restarted off the remote to repeat on the next truck or trailer. The recording system displays all batchers for the day and filing into projects or client names along with a summary of the total products used for the day for management control. All reports can be sent to the office or client showing the programmed percentages of each product compared to the actual results including a graph combining all the products processed. The control system can be integrated with other IMS products including electric modular blenders and pugmills offering up to four raw materials and multiple powders and/or liquids all blended at once.
•IMS- PM1050-16TB Track Pugmill with Silo option and full automation
•IMS – BP1200-9TB Track twin hopper blender with mixer
•Rubble Master (RM) Track 22x5 three deck screen
•Rubble Master (RM) Track 16x5 two deck scalping screen
•Rubble Master (RM) Track 18x5 two deck screen
•IMS – 24-meter track stacker with loader feed hopper
• IMS – 14-meter track stacker with five-meter loader hopper with tipping grid
•IMS- 20-meter track stacker with a 1200mm wide belt can produce 900 TPH and a 300mm rock
•IMS 15-meter wheel hydraulic stacker
Daniel Webber, CDE’s Regional Manager for Australasia, shares some of his experience on efficient and safe management of sand washing plants in quarries.
This year was very successful for CDE, it couldn’t have gone any better with new and existing projects that we are involved in. Like the rest of the industry, we had some challenges with inflationary pressures such as increased raw material costs, and we worked diligently to reduce the impact on our valued customers. As a business we decided to focus on what we could do to minimise the effect on them whilst still offering innovative solutions. In 2022, internally we focused on operational efficiencies. So, while it’s been a challenging year with some of the economic situation, it’s been another successful year for us and the processes we’re delivering to our projects in the region. We have five new CDE plants across the country in the construction and demolition sector and in natural materials sector we delivered a solution for Walker Quarries in New South Wales.
The growth and development of our local team. We have doubled our boots on the ground this year and we’ve also invested in over half a million worth of new spare parts stock in the region. It’s a significant investment for our business and the right one for our customers, and we’re proud to be delivering that. We’ve also signed a deal with Rino Recycling for a highly integrated and automated waste processing plant in Pinkenba in Brisbane. This will be commissioned in late 2023. We’re really excited about that as well.
CDE has been very active in the sand washing and waste recycling space. But do you have any other areas of focus in the quarry industry?
We’re always going to be strong in sand washing – wet processing is our sole focus. It’s the core and the backbone of our business. So that’s the first thing when people think about CDE in the quarrying
space and we’re going to continue to be at the forefront of that. What’s emerging now is a lot more focus on tailings management downstream, and the responsible use of water. There is opportunity in tailings thickening, dewatering and maximising water recovery. We expect that trend to continue in 2023.
Based on your experience, how can quarry operators extend the life of their equipment and parts?
I think one of the big things is not to stress their assets. There’s always a temptation to push equipment beyond its limits. And processing equipment will generally run outside of its design capacity. But it will generally come at the cost of uptime and maintenance. This comes right back to that purchasing decision and selecting equipment with an eye to operate in its optimal zone. You shouldn’t buy a 100 tonnes-an-hour sand plant and run it above capacity and expect it to run flawlessly. It should be operated below its design capacity, and you are going to get a lot better life out of the asset.
There’s always a temptation once a capital decision has been made to rush out and buy something that is available right now but sometimes the quickest solution isn’t the right solution. I think people need to get past that temptation and think about the lifecycle of the asset. Maybe waiting for the right equipment takes a couple of months, but it will mean a lot less downtime and optimal performance in the long run.
In addition to your core products line, do you provide additional services to the industry?
Yes. What a lot of people probably don’t know is that we can facilitate a lot of washing and scrubbing testing. That can involve testing a particular grade of sand to see if it’s good enough quality to produce specialist products as glass filter, frac sand and the likes. Or it can be just the production of larger quantity
of marketing samples to drum up off-take. So, if people are trying to add value to their resources, they can pick up the phone and we can certainly help with sample processing and determining what products can be made from their resources.
From a safety perspective, are there dangerous practices in the industry that you think can be avoided? Please explain. For me, it always comes back to the basics. With electrical equipment, tests and tags, as well as strong lock/out isolation procedure are essential. Also, with wash plants, there will be times when you must work from heights. I think people these days are very good with discipline when it comes to working from heights, but the one thing that is sometimes overlooked is dropping from heights and the risk of falling objects pose for below the work front – securing tools and establishing. An exclusion zone below should become second nature just like the use of a safe elevated work platform and harness. Everyone should get home safe, every day.
Do you have any other advice for quarry operators?
Ongoing training of operators and managers is vital, and so is staying up to date with technology. I also think that engaging experts is vital. Social media has infiltrated not only our personal lives but our working lives as well. There’s a lot of content online. Some of it is good, but some of it is only skin deep and people can get led astray if they are only referencing that data, which might not even be practical to our local market. There are a lot of excellent, independent consultants in the quarrying industry across Australia, and from what I’ve seen, we have some of the best professionals in the world. So, get good advice and you’re on the right way to making good decisions for your business.
For more information about CDE’s services, visit: www.cdegroup.com
How did Tutt Bryant Equipment (TBE) perform in 2022?
It was a record year for us in terms of equipment sales. We experienced unprecedented demand, not just from the quarrying industry, but also from infrastructure, mining and waste industries. Part of the reason, I believe, was that we were bullish and had placed ample stock orders well in advance, so we had good stock inventory across the country to meet the demands of existing and new customers.
In your view, how did the quarrying industry perform during the year?
Quarrying, as an industry, was not as seriously impacted by Covid as other industries, given that we were fortunate enough to be classified as an essential industry. If anything, we saw a ramp up of activities as governments increased their infrastructure spending to fuel a Covid recovery. Like all industries, however, we and our customers had to adapt to keep our staff safe to enable us to continue to work.
What has TBE done to adapt?
With many new customers coming to our business, we’ve had to increase our interactions, both with the customers and with Metso Outotec and supply chain to make sure that we can get the equipment that our customers need here on time. We required more vigilance on reporting shipping delays and we’ve tried very hard to do everything that we possibly could to meet customers’ expectations; which I believe is proven by the fact that we had such an outstanding year.
We are trying to grow our service team so with the current shortage of skilled labour, we have and continue to recruit from overseas. We also have a training academy being developed internally to enable us to train people and develop our own capability to service/support the machinery.
Which of TBE’s products are most popular in the quarrying industry?
Metso Outotec’s crushers have been around for about four decades, so a lot of serious practitioners prefer a Metso Outotec jaw crusher. The LT106 or the LT120 jaw crushers are the primary crusher options for many customers as these crushers are rated to crush very high compressive strength materials.
In our portfolio, we also have a combination machine called the LT220D, which has a cone crusher and a triple deck screen mounted on one chassis. We’ve sold many of these machines lately as they suit smaller contracting companies or people that move regularly and want low fuel usage machinery.
But our biggest seller is probably the LT1213S impact crusher. They are in a class of their own as far as productivity and reliability are concerned and customers are very happy with their performance.
Have you observed any change in appetite for new technologies in the industry and how is TBE addressing those?
In general, a lot of the operators are looking at the introduction of diesel-electric machines so they can become more cost effective and reduce their emissions/ energy usage. This is something that Metso Outotec has identified globally and is developing an entire line of diesel-electric products, to be gradually rolled out in the next few years. I see that as a real growth opportunity, not just for our company, but also for customers to differentiate themselves from their competitors by having low-cost, high-production equipment capability.
Smart and remote fleet management is another thing that allows customers to reduce their cost per tonne of crushing. Metso Outotec has a fleet management
system called Metrics, which is standard on all our units in Australia. Metrics is a cloud-based fleet management tool that customers can use to monitor the performance of their machine from anywhere in the world. That’s currently being updated and will be rolled out in the new year as a more user-friendly system with more information for analysis.
Do you foresee any challenges for the industry in the next three years?
Shortage of skilled workforce remains a challenge for most industries, and one that I believe will take time to correct. From our end, with our recruitment drive and training academy, we are doing all we can to ensure our staff are adequately trained so that when our customers have a service issue or a breakdown, then we can help them get back to operational status as quickly as possible.
What are TBE’s key goals in 2023?
In addition to rolling out the updated Metrics system, we have recently received a new line of products from a Swedish subsidiary of Metso Outotec called Jonsson. They only make diesel-electric equipment, and their version of Metrics goes into more detail and incorporates live belt weighing, even allowing the operator to monitor the performance and the temperature of some components of the crusher with live data. Jonsson’s mobile crushers are for the bigger end of town, from 140 tonnes and upward, so it’s not going to suit every application. But if you wanted large mobile crushers in your quarry pit, well these things will certainly do the job. Obviously, our goal is to deliver some units into Australia in 2023.
For more information about Tutt Bryant Equipment’s Metso Outotec mobile range and services, visit: www.tuttbryant.com.au
Metso Outotec Lokotrack ST mobile screens give you high screening capacity and excellent productivity with a range of feed materials.
ST4.10™ is ideal for large-scale aggregate production where closed circuit process is used for producing aggregates for concrete and asphalt sands, road base and building foundations. Its 5’ x 20’ triple deck screen produces four end products. The wide feeding box and adjustable discharge height on 10 m conveyors makes it a powerful aggregate screen in closed circuit crushing processes.
For more information, contact metso@tuttbryant.com.au
Follow us on:
David Smale, Astec Australia’s Regional Managing Director Australia Pacific, shares insights on what the quarrying industry has been experiencing and the role of companies like Astec in helping the industry overcome challenges.
How has Astec Australia performed over the past year? What have been some key milestones?
Astec’s number one commitment always is to our customers and continuing to meet that commitment has meant we’ve grown substantially over the past year, both geographically and internally. Our objective has been to strategically position people where they can most effectively support our customers, and that has meant bringing new people into the business. Even in this tight labour market, we have been able to attract the right people into the company. Many of our excellent team members have been with Astec for more than ten years. That kind of stability has a significant impact on a company’s culture and a positive flow-on impact for customers. For example, our team has a zero-tolerance policy for not responding to customer calls, because the person on the other end of the line might have an emergency and it’s our job to be there when they need us. It also has positive impacts for our people. Take our safety culture, for example; recently we achieved 1500 days with zero recordable incidents. It is a significant milestone, but one our team is constantly striving to surpass.
Supply chain issues continue to impact international markets. Every company has had to negotiate supply delays of critical components and materials and that, coupled with shipping disruptions, has meant increases in prices and lead times. Overall, though, I think at Astec, we have been able to anticipate and mitigate those issues. That is not to say we have resolved them completely, but we remain focused on finding solutions and, as always, supporting our customers is our highest priority.
Restructuring our geographical presence has helped us meet our business KPIs and better service our customers and our dealers’ network. Whereas in the past, our
dealers had to work with our factories internationally, they can now work with us at a local level, and we can connect them to the right people across our global network to receive the support they need.
We have also expanded our presence in markets including New Zealand and the Pacific Islands, particularly around supply of materials solutions such as cone crushers and screens. Our dealer in New Zealand, Turnco, is performing well and we are delighted to have them onboard.
Astec has also made significant progress this year in expanding and improving our technology platform. We have recently established a global digital group which is working on standardising digital control systems across all our businesses. This follows Astec Industries’ acquisition of a company called MINDS, a leader in plant automation control systems and cloudbased data management in the asphalt industry. As we strive to enhance control of our equipment for asphalt customers, we’ll look to extend MINDS’ capabilities into other areas of our business, including materials solutions and aggregate and concrete plants.
From your perspective, how has the quarrying industry performed over this period?
The quarry industry is performing well, mainly because it is working to keep up with everything that’s happening, particularly along the eastern seaboard – from the high level of activity in Victoria to the Western Sydney Airport project in New South Wales, to projects in Queensland in preparation for the 2032 Olympics.
One of the things we are seeing is industry and governments working in a more collaborative way; governments are inviting industries and associations to the table. As we head towards the Olympics, in
particular, Queensland has really embraced this collaborative model of working with industry. Together we are developing a strategic plan that will enable and support industry to deliver projects critical to the success of the Olympics. Governments and industry in other states, too, are seeing this model as an effective way of delivering major construction and infrastructure projects.
In your opinion, what are some major challenges for the quarrying industry today and how is Astec prepared to manage those challenges?
Continuing issues around supply chain logistics, inflation, and the availability of skilled people remain the key challenges. At Astec, we have recently appointed a regional logistics manager. His role is to interact with the factories, shipping lines and freight forwarders to help us stay on top of those supply issues. We’ve also taken other measures to try to reduce lead times and minimise delays for our customers, and that has meant having to forecast industry needs up to 18 months in advance.
Another major challenge is people. Our customers tell us they can get trucks but can’t get drivers or operators. The lack of skilled people is the one thing that’s going to cap our capability as an industry. Astec is working very hard in this space, including with governments here and around the world. We’ve had discussions with the Queensland Minister for Transport about our own efforts, and letting him know we are keen to work with his government on its initiatives around the problem. Astec’s global international human resources manager is also doing a lot of strategic planning around ‘people and inclusivity’. The aim is to make sure we cast the net as wide as possible when we are inviting people to work for us.
Which Astec products are currently most popular in the quarrying industry in Australia?
Our product lines continue to be well received by industry. Our roller bearing cone crushers are a good example of that, as are our horizontal, inclined and high-frequency screens.
The high-frequency screens continue to surprise our customers with their capability and versatility, particularly in waste recycling applications and very fine material sizing. Also, the Astec multi-frequency screening technology is gaining recognition in the mining industry.
More recently, we have had good success with our tracked pugmills, too. Our range of tracked crushing and screen equipment supplied into Australia has expanded with four new models being delivered in 2022, and more new model releases planned for 2023. This worldwide demand on our tracked crushing and screening plants has necessitated the expansion of our
manufacturing facilities to keep up with customer requirements. All our new products are performing very well in the market and there are more on the way.
Astec global recently appointed a new vice president of operations international. What will be the implications for Australia?
Yes, Martin Dummigan is our new vice president of international operations. Martin was president of Telestack before our business re-structured to become OneAstec. His role is to optimise production capability across our international factories. While that’s a mid- to long-term plan, we do expect it will help deliver products to our market more efficiently and cost effectively.
What are Astec’s major goals/focus areas in 2023?
That’s easy. Continuously improving service and support for our customers remains our core focus, just as it has always been. We will continue trying to mitigate supply issues, and continue working closely with our customers so we can identify potential problems before they arise, and if they do, resolve them quickly. Our focus always is to support our customers so they can get on with the job of delivering essential infrastructure.
For more information about Astec’s global capabilities, visit the Astec Industries website: www.astecindustries.com
Our company was founded on innovation and we are committed to helping our customers succeed. Astec - we’re built to connect.
With unmatched strength from rock to road, connection is at the heart of everything we do. At Astec, we design and manufacture products used to build the infrastructure that physically connects the world. But it’s the connections we make with people that drive us forward.
One of the things we are seeing is industry and governments working in a more collaborative way; governments are inviting industries and associations to the table.
”
Phillip Agius is the General Manager of Delta Rent, one of Australia’s largest suppliers of low hour hire plant and equipment. He shares how Delta Rent is the ideal partner for quarry operators to optimise the cost and efficiency of their fleet.
How was 2022 for Delta Rent? Can you share some milestones?
After the challenges of the last few years, we’ve experienced growth and development across our industry over the past twelve months. During 2022, we expanded our operations in the Queensland and Northern Territory mining markets, and now have a record number of quarry sites active nationally. Operating one of Australia’s largest privately owned hire fleet of specialist plant and equipment, along with offering personalised 24/7 service, Delta Rent is committed to being at the forefront of new technology, and we continue to invest in our constantly evolving diverse fleet.
What support does the company provide beyond your core products?
Our personalised support – accessible 24/7, Australia wide – is what sets Delta Rent apart. Our onsite workshops provide around-theclock servicing, with original equipment manufacturer (OEM) backed support, service, and technicians.
Our low hour fleet, with full OEM GPS tracking and telematics reporting, provides our clients with access to superior performing equipment, enabling them to deliver the level of service their customers expect.
Delta Rent’s clients benefit from our experience, service commitment, fleet size and mix – giving them the security of knowing that whatever and wherever the job, we’ll be partnering with them to help maintain customer expectations and enable them to deliver high levels of service.
What’s one key challenge you anticipate for the quarrying industry in 2023?
Every industry is staring down the coalface of rising operating costs, and staff shortages. We’re no different! Agility is crucial to ensuring continual rising costs, along with general operational challenges, are accounted for and managed appropriately.
How has Delta Rent set itself up to support its customers with potential challenges?
At Delta Rent, we’re constantly exploring options to keep our overheads, equipment, fuel, repair and maintenance costs manageable to enable us to continue to meet customer demand and exceed expectations. We’re working with our client partners to minimise fleet operating costs, including maximising the use of fleet optimisation technology. We’re also committed to ensuring we have the best team in the business –providing our clients with continual reliability and superior service standards. Staff training and retention is a key component to our ongoing success.
In your view, is the quarrying industry taking full advantage of fleet optimisation technologies available on the market? Our diverse fleet of equipment includes all major OEMs, providing our clients with the ideal choice for every situation. Incorporating the use of OEM-supplied telematics systems, our clients benefit by being able to measure equipment utilisation, how many cycles they are doing, whether they are over-speeding, how much fuel they are burning, what gear
Sean Kinder, Business Development Manager for Kinder Australia, says with tighter regulations on noise and dust
more important than ever for quarries to revise their processes.
What innovations has Kinder introduced lately?
The interest towards Airscrape has been exceptional ever since we introduced it to Australia. AirScrape is a specialised conveyor sealing and skirting system which acts as a side seal, suspended over the conveyor belt. It has been proven to reduce the spill and dust formation at transfer points and other critical sections in the conveyor chain, whilst not making any contact with the conveyor belt.
What support does Kinder provide beyond your core products?
Kinder’s team of engineers have allowed us to go above and beyond in developing solutions to suit the needs of the market,
as well as customised products to suit individual customers’ requirements. We have a dedicated engineering team, as well as many of our field/projects team members, including myself, are qualified as engineers. We have expertise in the fields of mechanical, aeronautical, chemical and electrical/electronics engineering.
What’s one key challenge you anticipate for the quarrying industry in 2023? Excessive dust and noise continue to challenge the industry. As well as being a significant productivity issue, the increased proximity of residential areas to quarries means that it is now more important than ever to meet the requirements of having a site that is as unobtrusive as
possible, safe for workers and residents, and meeting regulations.
How is Kinder set out to address that?
Our dust and noise management solutions are always highly sought after by quarry operators. We have developed ‘The Essential Air Seal’, which is a dust containment combination that we believe to be the absolute industry benchmark when it comes to containing dust. Incorporating our K-AllShelter conveyor belt covers can physically contain any dust from escaping, whilst protecting the conveyed material from wind, precipitation, heat and humidity.
For more information, visit: www.kinder.com.au
control, it’s
Health and safety expert Mark Wright writes about how heavy vehicle compliance requirements can be harnessed to build a highperformance culture.
For many organisations, Chain of Responsibility (CoR) requirements outlined in the National Heavy Vehicle Laws are seen as a compliance activity and burden. The fear of prosecution, reputational damage and compliance breaches often creates a knee-jerk reaction that is often unsustainable. What if heavy vehicle compliance could be harnessed to build a high-performance culture and commercial opportunities?
In November 2022, the National Heavy Vehicle Regulator (NHVR) published a prosecution of three directors for primary duty offences. This is a common reminder of why legal compliance is important. This fear of compliance does not always need to be the primary concern. Round
eight of the Heavy Vehicle Safety Initiative (HVSI) to fund new projects to deliver a safer heavy vehicle culture was recently launched. The Australian government has committed over $4 million towards Round right of the HVSI. Submissions are now open and close on 5pm AEST Monday 20 February 2023.
For more information on the HVSI program, including the submission process and eligibility, visit: www.nhvr.gov.au/hvsi
To go beyond basic legal compliance, consider the capabilities needed to enable effective leadership and a highperformance culture. The table below compares low and high maturity mindsets when fulfilling your Director and Officer NHVL due diligence obligations.
Due Diligence Legal / Compliance Focus Leadership Focus
Mark Wright is a trusted risk, health and safety professional with a career working in senior leadership positions, non-executive director board roles and work in over 15 countries. Wright is the managing director of FEFO Consulting and Health and Safety Index with partners and clients in Australia, New Zealand, UK, Europe, and Americas. He has a genuine interest in sharing learning and helping organisations make effective choices with data led insights.
IQA is delivering a virtual workshop on Chain of Responsibility on 30 March 2023. To register, visit the IQA website. If you would like training for your team, contact IQA today.
a) Knowledge Acquire health & safety knowledge. Build a growth mindset by harnessing the collective intelligence and experience of diverse teams. Look externally and benchmark leading practices.
b) Understand Understand the nature of operations, hazards, and risks.
Seek to understand and actively listen. Consciously build deeper and more trusting relationships during interactions.
c) Resources Ensure appropriate resources and processes.Know how and when to leverage resources. Consider cross functional work groups, support functions and Business Process Outsourcing (BPO).
d) Information Receive and consider information and respond in a timely way.
Have a leader narrative for use in their day-to-day communication. Have great, connecting conversations about the things that matter.
e) Compliance Implement processes for compliance.Go beyond basic compliance and feel energised by connecting personal and professional purpose to objectives of the organisation.
f) Verify Verify resources and processes for (a)–(f).Know how to put all of this to use in during the day to day and consciously shape culture through actions, a thriving work environment, rituals, and behaviours.
The IQA’s final Victorian branch event for 2022 was held on 22 November 2022 at the Australian Road Research Board (ARRB). Attendees were treated to a laboratory facility tour by ARRB’s national laboratory leader Shannon Malone, as well as a
presentation by ARRB chief operating officer Dr Richard Yeo. The event was rounded out with a presentation from Carlos Pardo, lifecycle manager at Sandvik – which is one of IQA Victoria’s major sponsors. Pardo spoke about reliability and protection packages. The event also provided attendees with a wonderful opportunity to network and connect.
The West Australian Branch held its annual Golf Day in November 2022. The event enjoyed record attendance and the IQA welcomed many new faces and long-time supporters. Wonderful weather and the course at Joondalup Resort meant players enjoyed networking, fun and a bit of healthy competition. Sponsors got behind marshmallow drive, “beat the pro” and other prizes.
In the first place was the RUD Chains team, with players including Novak Anfuso, Eugene Chai, Marcus Haines and Christopher Pope. The second place winner was the Equipment Placement team. Taking home third prize was the WA Limestone team. Rudd Industrial and H-E Parts came fourth and fifth respectively. Winner of the NAGA Award this year was 888 Crushing & Screening.
At the post-game event, players enjoyed canapes, networking and celebrated the wins and challenges of the day. The IQA WA branch thanks all the wonderful players and sponsors for the day.
On 18 November 2022, the IQA North Queensland branch convened at the Townsville Yacht Club for their end of year function. The event was sponsored by MS Fabrications, Richie Bros and Sitech.
The networking event saw a good mix of quarries and suppliers with the theme being “Casino”. Using funny money, “punters” were able to bet on Blackjack and Roulette tables.
This event wrapped up a successful year in North Queensland. Throughout 2022, the branch held six events in the Townsville area (including a golf day, one ‘Health and Safety’ seminar and four dinner meeting), one golf day event in Mackay and three events in Cairns (a golf day and two dinner meetings).
The next event from the branch will be a dinner meeting in February 2023. Keep an eye out in the January newsletter for a full calendar of 2023 events.
The Sunshine Coast turned on the weather, providing a beautiful day for Women in Quarrying (WIQ) and the Young Member Network (YMN) to tour Hanson’s Glasshouse quarry.
his own career pathway into the industry. Wilson was joined by two of his female staff Kirsty McDonald-Clifford and Sarah Moffat, who shared their own experiences and pathways demonstrating two very different avenues into the industry.
On return to the Beerwah Hotel, everyone enjoyed pub style lunch whilst listening to Geoff Wilson from Beyond Blue, who shared his story of hope, recovery, and resilience in dealing with depression and anxiety conditions. He provided tips to help others in the workplace that may be battling with mental health.
The IQA thanks Chris Wilson and the team from Hanson Australia who helped make this day all the more special. Special thanks also to the Queensland WIQ major sponsor John Deere/Kleeman and YMN major sponsor AusRocks for their continued support.
The final IQA South Australia branch dinner for 2022 was held at the Norwood Football Club in Adelaide. Guest presenter was the legendary Michael Aish (former Norwood SANFL footballer), who provided a great insight into the highs and lows of his football and personal career.
The SA branch thanks its sponsors for their continued support, which goes a long way to ensuring that the branch remains relevant, vibrant and effective for its members.
On 15 November 2022, the IQA delivered the ‘Plant and Equipment: Safety, Compliance and Best Practice’ workshop at the WesTrac Institute at Tomago in the Hunter region of New South Wales. This is one of the new courses launched by the IQA in 2022 and addresses the safety issues associated with supervising the operation of plant and equipment in quarries.
The workshop was delivered in collaboration with the NSW Hunter subbranch, who secured the exceptional training facilities at WesTrac Institute in Tomago. The institute is a world class training facility, made up of 14 general classrooms, two labs and a five-bay workshop. The number of programs offered at the WesTrac Institute is extensive, with new programs developed regularly to meet staff and customer training needs, and the general requirements of the industry. Additionally, the location was ideal to support the delivery of the workshop.
Quarry operators and work health and safety (WHS) staff took part in the full day on-site workshop, which included a behind the scenes look at the WesTrac Tomago facility, viewing operational areas such
as the impressive 12,000 square-metre parts distribution centre, new machine assembly area, the new dig-pit/machine demonstration area, and the state-of-the-art machining and reclamation workshop.
The IQA thanks WesTrac for welcoming IQA members and non-members and for providing an insight into the Tomago facility. Both the IQA and WesTrac look forward to future opportunities to work together.
Thinking about corporate training? The IQA can deliver this workshop and others, on site or in training facilities. To book your corporate training, please contact the IQA on 02 9484 0577 or email: education@quarry.com.au
A key service of the IQA is to deliver corporate training to the industry. On 27 October 2022, the IQA delivered the ‘Supervising for Safety’ workshop for Boral Cement at its Marulan South limestone mine in New South Wales.
A total of 21 frontline leaders, supervisors and managers took part in the full day onsite workshop. Seen as an essential building block to instil good safety practices, the
‘Supervising for Safety’ course enabled the group to re-focus on their site supervision and safety culture.
Boral Cement at Marulan recognises that site leadership has a duty of care and an obligation to provide a safe environment for employees and recommends the course to other Boral sites and companies.
• Verification of Competency – 31 Jan 2023, 1pm-5pm
• Quarry Materials Production and Quality Management – 7 Feb 2023, 10am-5pm
• Plant & Equipment – 16 Feb 2023, 12pm4.30pm
• Hazard Identification – 22 Feb 2023, 12pm-1pm
• Introduction to Quarrying – 23 Feb 2023, 1pm-5pm
• Introduction to Safety & Health Management Systems – 28 Feb 2023, 1pm-2.30pm
• Slope Stability for Operators – 9 March 2023 9am-12pm
[The event times are all Australian eastern daylight times.]
For a full list of upcoming courses and to download a course catalogue, visit the IQA website.
IQA is supported by its members and many longstanding members. Annually, the IQA recognises those members who reach the significant mile stone of 30 and 40 years membership.
The IQA branches took the opportunity at many end of year celebrations to recognise those members who reached the 30 years and 40 years milestones.
The IQA would like to thank these members for their loyalty to the institute and their ongoing dedication and contribution to the industry.
GRADE NAME COMPANY
Fellow James Chalmers
Associate Det Barmin Oatram Finacnce
Member Peter Brownsdon Hanson
Member John Carroll Boral
Associate David McKelvie SAFEmix
Fellow Ross Outen TBA
Fellow David Pallot Hanson Vic
Member Nicholas Palmer R. N.B. Trading
Member Clifford Regan Kimberley Quarry
Fellow Rodney Street Boral
Memeber John Flynn Terex Jaques Australia
Associate Mark Taylor Cavil Power Products
Associate Ross Whiting Benedict Industries
GRADE NAME COMPANY
Hon. Fellow Daniel Duke
Member David Francis
Associate Stephen Bond FLSmidth Abon
Fellow Ian Laws Joest Australia
Member Robert Wearn Mulgoa Quarries
Associate Geoffrey Price MLine Supplies (NT)
Member Brian Humphries Canberra Sand & Gravel
Fellow Anthony Ward Tony Ward Consulting
Fellows are the leaders and senior managers of the quarrying and aggregates industry, recognised for their contributions, expertise and achievements. Quarry had the chance to sit down with recently appointed IQA Fellow, Greg Dressler, to celebrate his appointment and explore his long involvement with the industry.
IQA Fellows are an exclusive group of seasoned professionals with significant industry acumen and experience.
Demonstrating leadership by supporting the IQA and industry networks and espousing professional development and lifelong learning and upholding industry standards, the recognition of a Fellow from the IQA represents those who have actively worked in the best interests of the industry.
An IQA member since July 2004, Dressler currently occupies the position of quarry manager at Hanson Quarries, having been in previous quarry manager positions since 1998.
Active in the quarrying community and invested in the development of education within the industry, Dressler is the current chairperson of the IQA Hunter sub-branch and was appointed from IQA member to Fellow in September 2022.
What have been some of the experiences and lessons you’ve learned in your career that have stuck with you?
I’ve been working in the industry for 36 years, so there’s probably not a day that has gone by where I haven’t learnt something. One thing that really stands out is environmental management. At the end of the day, we are working in a way that impacts the environment and learning how to mitigate that impact and to plan appropriately is a number one priority. There’s inherent risk with our work and everything that we do on site every single day. It’s important to remember that risk to get people home safe. I think if you care about people, it goes a long way in making sure that you’ve got the right systems and processes in place.
What are some of the challenges facing the quarrying, aggregates and extractive industries?
Currently, there is a very high demand for infrastructure projects, housing developments and the likes in the Greater Sydney area. As such, there is a surging demand for construction materials. That’s challenging as an industry as demand is outstripping supply. In addition, we’ve seen
some trouble in attracting people to the industry, which plays into the larger issue of the communities we operate near and what the community thinks of the extractive industry. It’s important for quarries to be close to market to be able to get the product into those markets at a reasonable cost. However, being close to communities poses issues around impacting those communities. So what we as an industry need to work towards is educating the public to help them understand the necessities of our industry.
How does the IQA help to support training and education within the industry?
Support, training and education levels within the industry would not be nearly as high without the support from the IQA. We’re a relatively small and a heavily regulated industry. To help work with that, the IQA is offering specific training that is applicable to operating a quarry. We’ve seen that technical training in and around the obligations for environmental management is the true way to help the industry. The training being done specifically for quarrying applications is so important, as the only closely related industry is the mining industry but there’s a lot of key issues that don’t overlap. In terms of running seminars, training events and functions to help people get in contact with others, the IQA facilitate that professional growth within the industry. That is exactly why we need the IQA.
What positive things have been going on within the industry from within?
The industry is trying to diversify its people, both within and from outside the industry. This is being done through encouraging younger people to enter the industry and making the industry more equitable and supportive for women. We’ve seen that in action, with a lot more women in the industry now. Bringing diversity to the workplace is just another strength of the industry because we’re not limiting ourselves to what we’ve always had, we’re looking to embrace change and
look forward to cementing the future of the industry.
Your work and commitment to the industry is extremely commendable. Is there any moment from your past with relation to the industry that you are particularly proud or fond of?
When I was fairly new into my quarry supervisor/manager role, it was around the same time that the change in legislation was going towards risk-based legislation. The site I was working at was purchasing a new drill rig and the team and I couldn’t get past the fact that we had a drill rod that was rotating but was exposed and had no guard. As a group, we came up with a solution whereby we built a pressure switch into the operator’s seat so when the operator got off the seat with a small time delay, it would stop the rotation. We went to receive an award for that years ago. That was me being a part of an industry innovation that I look back on fondly. These sorts of innovations are still happening within the industry, though I think these moments need to be shared from us older people. We need to act as mentors for younger people, to show them that innovation can happen from within. Additionally, it’s not easy getting the qualification and neither should it be. So we need to be supporting the industry from within as much as possible and the best way to do that is through the IQA.
evolutionary tree of the fossils.
This method was part of an extensive and ongoing investigation, with lead author Dr Stephen Pates, a postdoctoral fellow at the University of Cambridge and senior author Dr Joanna Wolfe, a research associate at the Department of Organismic and Evolutionary Biology at Harvard University.
The study was used to compare the new fossils with 57 other living and fossil arthropods, radiodonts, and panarthropods, determining the place of the fossils in the history of arthropod evolution, with the researchers designating a new taxon for the species, Mieridduryn bonniae, with the larger specimen designated the holotype.
At this point in time, the status of the smaller specimen was left open, reflecting these different possibilities.
“The size of the smaller specimen is comparable to some modern arthropod larvae – we had to take into account this possibility in our analyses,” said Wolfe.
The relatively small but scientifically important fossils are some of the first findings from this important new Ordovician fauna.
Botting and Muir continue their work in the small quarry in the sheep field with more still to come.
This deposit, located in a sheep field near Llandrindod Wells in Wales, was discovered by independent researchers and Llandrindod residents Dr Joseph Botting and Dr Lucy Muir, Honorary Research Fellows at Amgueddfa Cymru, the National Museum of Wales.
The quarry is well known as one of many local sites yielding new species of fossil sponges, with two new fossils species being discovered at the site.
“This is the sort of thing that palaeontologists dream of, truly soft-body preservation,” Muir said, “we didn’t sleep well that night after the discovery.”
Upon research, the fossils were determined to be from the Ordovician Period and provide insight into the evolutionary development of modern day arthropods.
The fossils of creatures that have been found to exist over 500 million years ago are substantially different from their modern day counterparts, but only recently have been studied to the extent that they now provide crucial understanding of the evolution of arthropods.
As one of the most diverse and robust animal phylum on the planet, including a large variety of invertebrates such as spiders, some bees and spiders, the knowledge of their past and expected future development is crucial to ensuring the survival of these species.
In an article published in Nature Communications, Ordovician opabiniidlike animals and the role of the proboscis in euarthropod head evolution, The researchers used phylogenetic analyses, to determine the age and position in the
“Even the sheep know we are on to something special here, they usually come to watch,” Muir said.
The fossils and the information they present emphasise the secondary use that quarries have in discovering the origins of the earth and those that live on it.
“It was important to assess the implications of some features, such as spines on the appendages or a carapace, evolving convergently with radiodonts in our analyses,” Wolfe said.
Whatever the eventual conclusion of the origin of these fossils, they remain as important hallmarks in the evolutionary history of arthropods. •
We are a global team unified in a common purpose: creating advanced technology solutions to the world’s water challenges. Developing new technologies that will improve the way water is used, conserved, and re-used in the future is central to our work. Our products and services move, treat, analyse, monitor, and return water to the environment, in mining, quarry, public utility, industrial, residential, and commercial building services settings. We also provide a leading portfolio of smart metering, network technologies, and advanced analytics solutions.