FLEET MANAGEMENT WITH
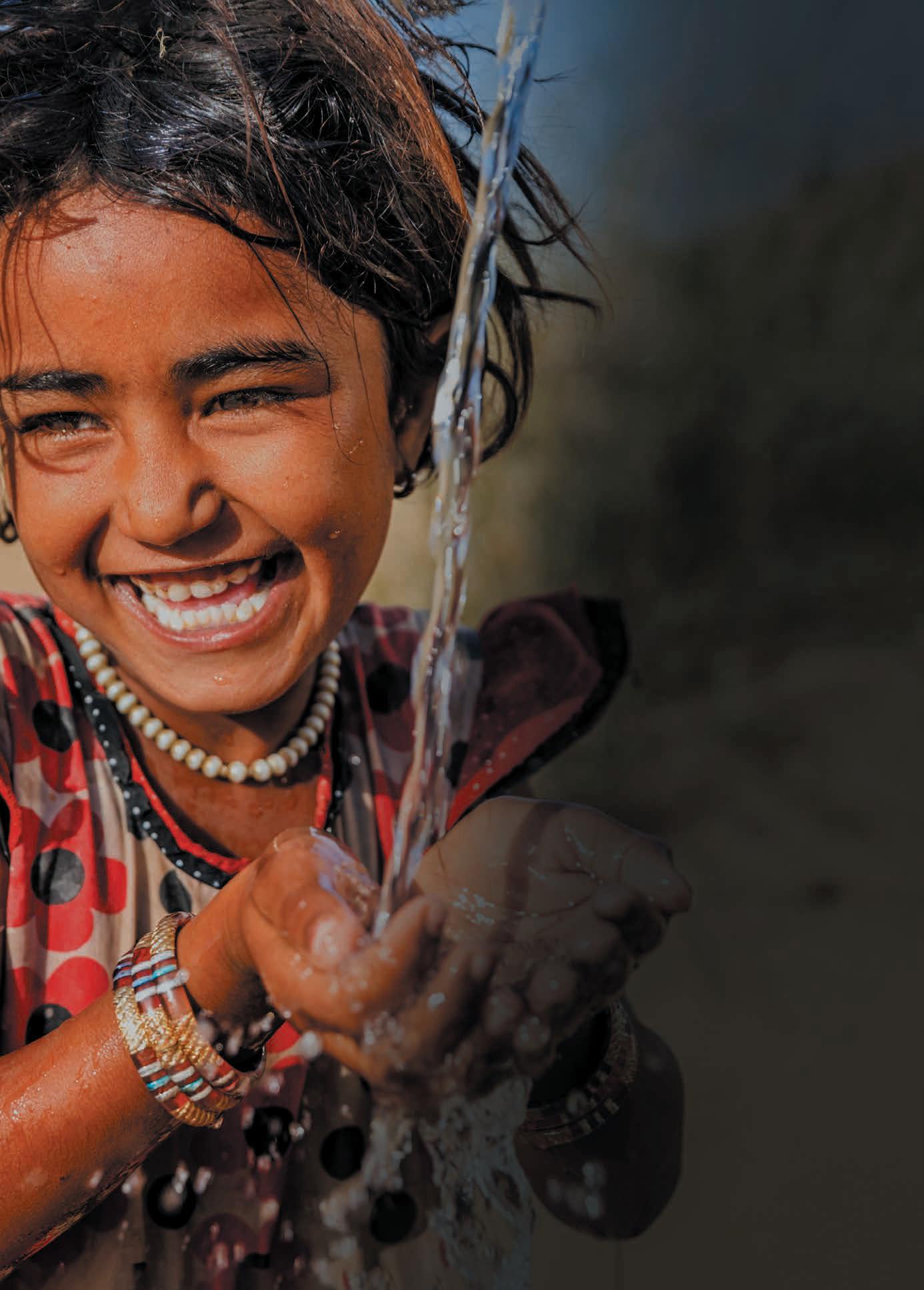
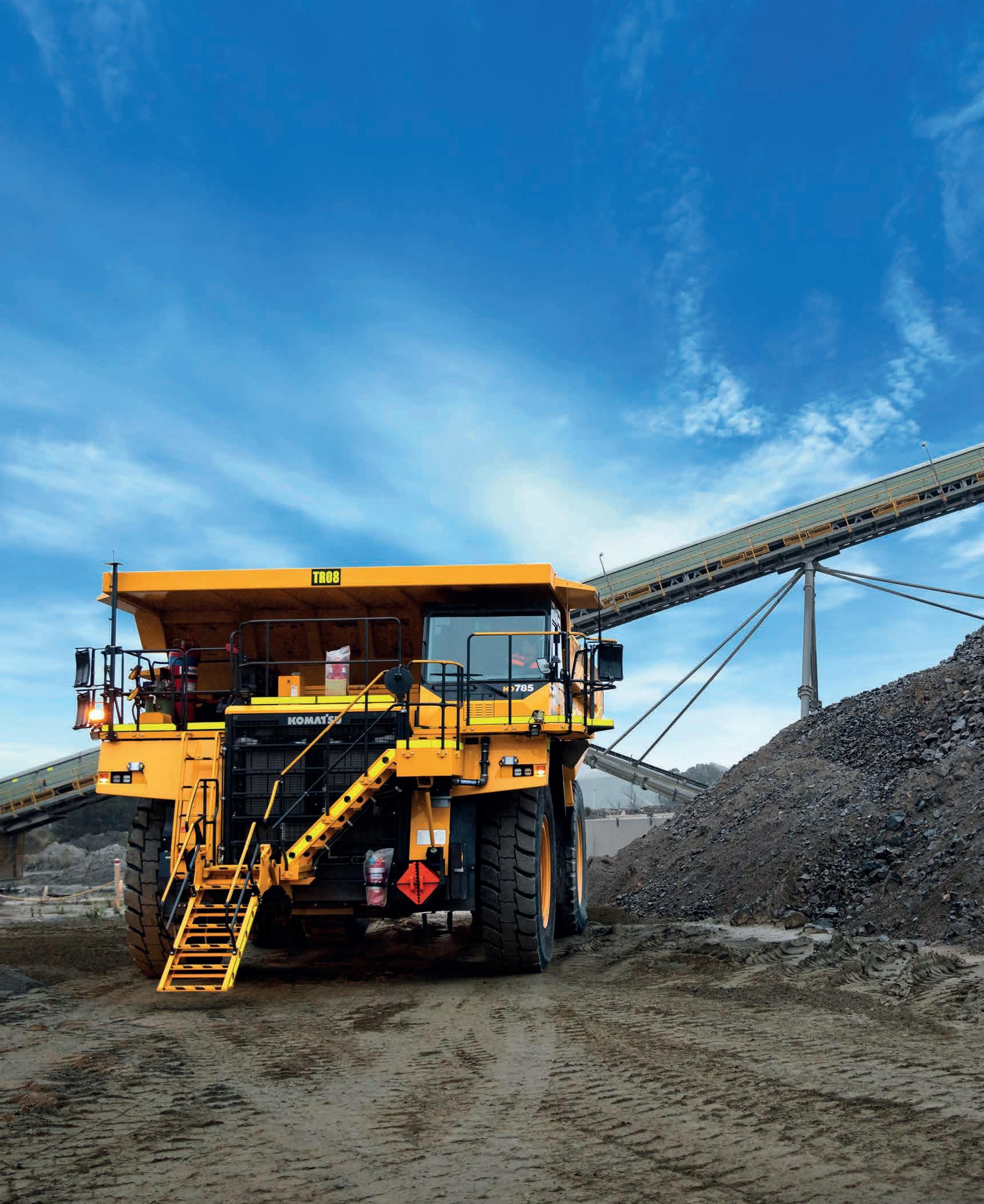
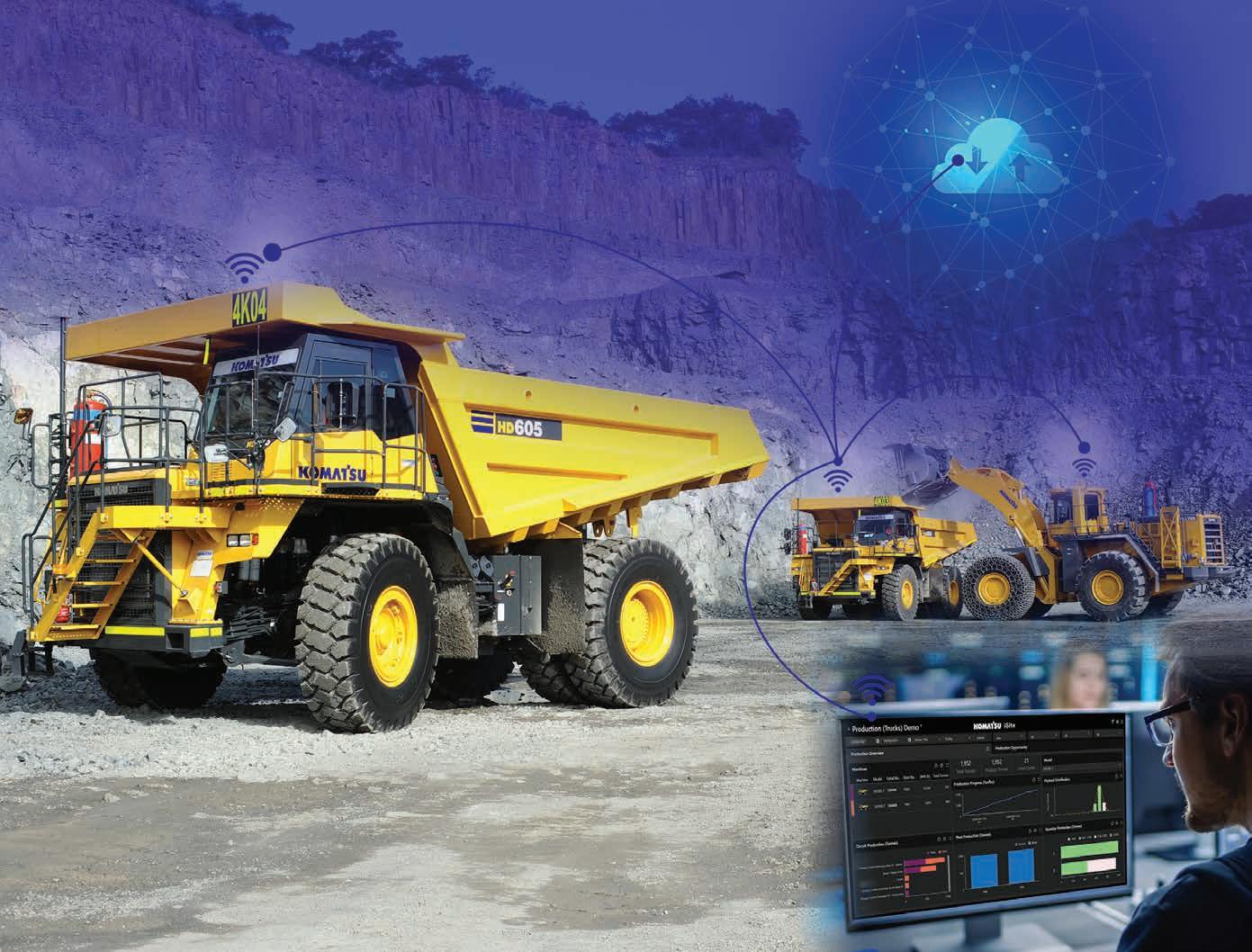
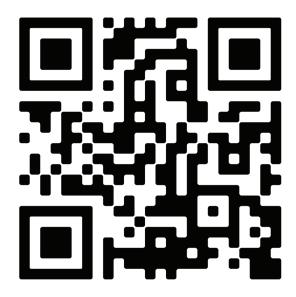
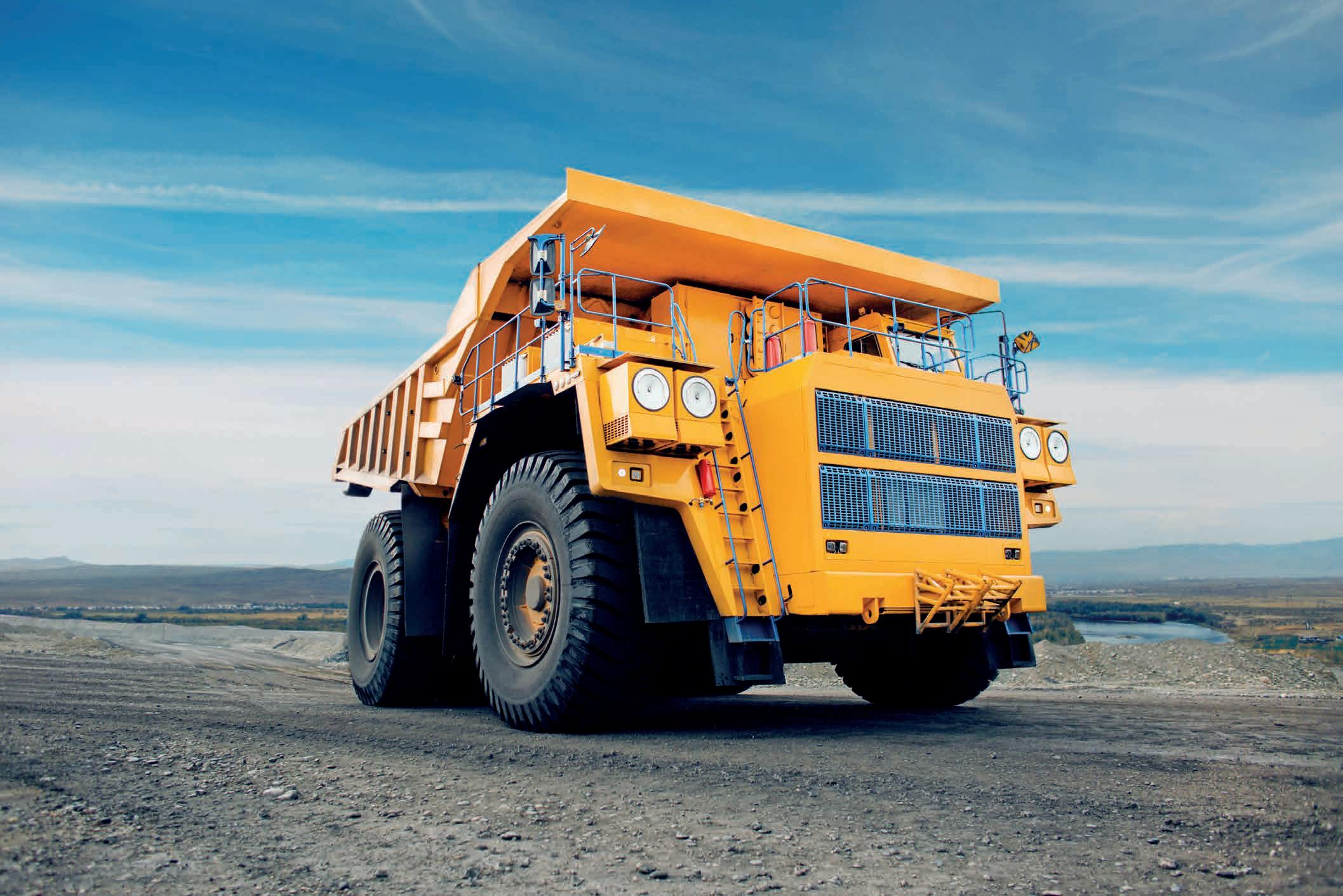
24 AIR SEAL FOR SMOOTH CONVEYING
The Essential Air Seal has opened up a new way for supressing dust.
26 DIVERTING WASTE FROM LANDFILL
Australian firm diverts more waste from landfill thanks to CDE’s solution.
28 JOY FOR KOMATSU
The Joy surface crushing equipment merged into the Komatsu portfolio.
30 CONNECTED MAP FOR CLEAR VEHICLE VISUALISATION
Volvo Construction Equipment unveils the Connected Map solution.
32 THE NEW GENERATION OF HITACHI
Hitachi Construction Machinery introduces new machines.
38 PLAYING THE PREVENTION GAME FOR SILICOSIS
Interview with Tracey Bence on the measures to prevent silicosis.
44 RECOVERING FROM A SINGLE PLANT
Terex Washing Systems’ FM Pentium plant offers dual purpose washing.
46 TURNING THE WATER OFF Kayasand on how quarries can turn the water off on aggregate washing.
48 TOTHINK EQUIPMENT
Boots on the ground experience for providing vibrating equipment.
52 A TEAM BUILDING EXERCISE
Jonny McMurtry from Precisionscreen shares management lessons.
COVER ADVERTISER:
Komatsu’s iSite fleet management solution takes real-time operational data from construction machinery on a site and allows for issues and bottlenecks to be identified, giving businesses the ability to improve their productivity. and get the most out of their machinery.
As I reflect on the content we have compiled for this edition, a repeated focus on ‘innovation’ shines through.
From broader adoption of smart fleet management tools on quarry sites to developing new products and concepts for digging, processing and conveying sand and aggregate, the sector seems to be embracing innovation at every level.
This, of course, is what’s expected of the quarry sector if it wants to keep up with its bigger brother, mining.
The fast pace at which mining is being transformed was not missed by Steve Franklin, founder of consulting firm Eltirus, when he attended the International Resource and Mining Conference (IMARC) late last year.
With a whopping 7800 participants, the event was an “eye opener” for the industry veteran who says he came out impressed with the technological innovations and the visions that mining sector has set for itself.
“Make no mistake, this change will come to our industry. Those who grasp it and work to make it their own will have a clear lead on their competitors. It will be a defining characteristic of their business and a selling point to the bright people they will need to hire to make it a reality,” he wrote in his note.
While mining has been transformed by technologies such as autonomous trucks and smart surveying drones, quarrying companies can benefit from the greater efficiencies offered by
battery electric equipment and fleet management tools like Komatsu’s iSite and Volvo Construction Equipment’s Connected Map.
On the processing side, concepts like Kayasand’s RCAS crusher and air screening technology and Terex’s FM Pentium plant are proving higher efficiencies for quarries.
Kayasand’s RCAS screen uses a unique combination of high-speed air flow and mechanical screen decks, while Terex’s FM Pentium plant can wash one grade of sand and one aggregate on a single chassis.
For safe conveying of material, Kinder Australia has come up with the Essential Air Seal, a combination of products that can seal dust around conveyors, thereby reducing exposure risks for operators.
Like every edition, we also shed light on safety issues related to the quarry sector. We speak with Tracey Bence, a certified occupational hygienist and current president of the Australian Institute of Occupational Hygienists to learn more about silicosis and what the quarrying industry needs to know about this occupational lung disease. Rebecca Crompton, director at FEFO Consulting and an experienced strategist for health and safety initiatives also writes about the importance of managing health and safety when contracting.
Finally, we hear updates from companies like Xylem, Komatsu, Hitachi, Kobelco, ToThink and CDE. Happy reading!
Tara Hamid EditorSMART FLEET MANAGEMENT TOOLS ON QUARRY SITES TO DEVELOPING NEW PRODUCTS AND CONCEPTS FOR DIGGING, PROCESSING AND CONVEYING SAND AND AGGREGATE, THE SECTOR SEEMS TO BE EMBRACING INNOVATION AT EVERY LEVEL.
Published by:
379 Docklands Drive Melbourne VIC 3008
T: 03 9690 8766 www.primecreativemedia.com.au
Chief Executive Officer
John Murphy
john.murphy@primecreative.com.au
Editor Tara Hamid tara.hamid@primecreative.com.au
Journalist
Lewis Cross lewis.cross@primecreative.com.au
Business Development Manager
Les Ilyefalvy les.ilyefalvy@primecreative.com.au
Client Success Co-ordinator
Janine Clements janine.clements@primecreative.com.au
Design Production Manager Michelle Weston michelle.weston@primecreative.com.au
Art Director Blake Storey
Graphic Design
Kerry Pert, Tom Anderson, Louis Romero
Subscriptions
T: 03 9690 8766 subscriptions@primecreative.com.au
The Publisher reserves the right to alter or omit any article or advertisement submitted and requires indemnity from the advertisers and contributors against damages or liabilities that may arise from material published. © Copyright – No part of this publication may be reproduced, stored in a retrieval system or transmitted in any means electronic, mechanical, photocopying, recording or otherwise without the permission of the publisher.
MOBICAT MC 120 PRO
MOBICAT MC 120 PRO
POWERFUL PERFORMANCE AND RUGGEDNESS, COUPLED WITH INTUITIVE, LOW-MAINTENANCE OPERATION . As the fi rst jaw crusher in the new PRO line, the MOBICAT MC 120 PRO features an impressively powerful crusher and the largest independent pre-screen in its class – for maximum performance up to 650 t/h! The new, intuitive SPECTIVE operating concept actively supports the user in finding the ideal setting for every task – quickly and precisely – simply by touchscreen. The MOBICAT MC 120 PRO: The intelligent power pack.
The IQA has made strides through the start of this year and will continue to do so as we head into the rest of the year.
With so much planned for this year in terms of training, events and growing our industry, it’s important for us to remember and pay thanks to those who are continually supporting the IQA and its members across the country.
It’s been said before, but it bears repeating – the IQA Branches are the lifeblood of the IQA - and we are committed to supporting them in all aspects of our business.
We are continuing to see an uptake and levels of success with our Young Member Network, in connecting and fostering the groundwork for successful and qualified young people who can take on the training and sage advice from the multiple veterans who are part of the IQA.
The IQA will again be hosting YMN tours and other events during 2023, to support and continually expand the training and opportunities that we can offer to the next generation of our industry.
Our annual diversity and inclusion day is once again set for the 1st of September and presents an opportunity to encourage broad involvement in our industry.
The diversity and inclusion days are an invaluable tool for our industry to spread awareness, provoke discussion and facilitate the inclusion of all into our industry.
We as an industry, have an aging profile. So as a group that supports the industry in so many ways, we all have a responsibility in reaching out and encouraging younger people to join.
It is vital that we accept and advocate for distributing knowledge from proficient members to newer members, to keep that knowledge alive and passed down in a productive way that facilitates the growth of the quarrying industry.
As part of that, I strongly recommend and encourage all members to keep their eyes open to all events as networking and developing these connections is paramount to what we are focusing on – growth.
Networking doesn’t end at those within the IQA. Giving back to communities and encouraging involvement from those outside to join in and spread the word is one of many ways in which we can encourage young people in the industry to become aware of the IQA and sign up so that we all can benefit.
The IQA has and will continue to offer opportunities, training and recognition across all of Australia for all people, in order to provide much needed support to our industry and continue to grow our industry.
As always, a massive thanks to our branch members, our committee members and the broader IQA community, without your continued support and contributions the IQA would not be as it is today.
Let’s keep working together as we grow the industry and forge long lasting connections through to the end of 2023 and beyond.
Duncan Harris President Institute of Quarrying AustraliaKNOWLEDGE FROM PROFICIENT MEMBERS TO NEWER MEMBERS, TO KEEP THAT KNOWLEDGE ALIVE AND PASSED DOWN IN A PRODUCTIVE WAY THAT FACILITATES THE GROWTH OF THE QUARRYING INDUSTRY.”
www.quarry.com.au
The IQA’s Strategic Plan 2020 to 2025 embodies the following vision, values and strategic priorities:
Vision:
Educating and connecting the extractive and associated industries.
Values: afe and sustainable environment. ersity and inclusion.
orking development skills, careers and life-long learning.
• Networking, connection, trust and communication.
Strategic Priorities:
• Maximise outcomes for industry through education and sustainable practise.
• Increase our relevance.
• A high performing and sustainable organisation.
IQA CONTACTS:
Phone: 02 9484 0577
Email: admin@quarry.com.au
Chief Executive Officer
Kylie Fahey
Company Secretary
Rod Lester
For all education, member and branch enquires please email: admin@quarry.com.au.
There are three specific areas where CO2 emissions can be reduced in a quarry operation. We work with sites to help them identify the opportunities for improvement, implement them and monitor the results, resulting in reduced emissions and lower cost per tonne. Talk to us about how we can help you meet your sustainability targets.
The Federal Government has finalised an interim board for Infrastructure Australia, as the organisation moves to a new governance structure. The current board will be replaced by three commissioners supported by an advisory board with experts from the infrastructure and related sectors and senior public service officials. Gabrielle Trainor AO will be appointed as acting chair of Infrastructure Australia, and Clare Gardiner-Barnes will be appointed as an acting board member. Existing board members Mark Balnaves, John Fitzgerald and Marion Fulker will also be
reappointed as acting board members. These appointments are for a period of up to 12 months, or less if there is an earlier transition to the new governance arrangements.
Chris Sutherland has been appointed the new chair of the Fremantle Port Authority, replacing Ross Love who served in the position for three years. Sutherland’s appointment will be effective 1 January 2023 and he will serve an initial two-year term. Sutherland has been a director of the Southern Ports Authority for the past two years. Prior to that, he has served for over a decade as the managing director and group chief executive officer of services firm Programmed.
Pekka Vauramo has had his contract as president and chief executive officer of Metso Outotec extended until the end of 2024. The extension followed talks between Vauramo and the board of directors at the Finnish quarrying, mining and construction materials processing solutions company. In October 2020, Metso Outotec announced that Vauramo’s contract was extended until the end of 2023. Pekka Vauramo started as Metso’s president and CEO in November 2018 and has continued as Metso Outotec’s president and CEO after the July 2020-completed merger.
Consulting firm Arup has appointed Tessa Knox-Grant as sustainable transport lead in Australasia. Knox-Grant will be joining the firm’s Cities, Planning and Design portfolio. She returns to Arup after almost 12 years in senior positions in the private and public sectors, including as a former executive director in the New South Wales transport department. Arup’s Cities, Planning and Design lead in Australasia, Jonathan Kinghorn said Knox-Grant’s appointment reflected the firm’s commitment to shaping more sustainable and inclusive cities and recognises the significant role of cities in building climate resilience through the use of sustainable infrastructure, urban greening, and renewable energy.
The new XD Series is engineered for the most demanding applications. Built on Kobelco’s rock-solid reputation for quality and reliability, these extreme duty machines feature a rugged machine body with comprehensive additional reinforcement where it matters most. These machines take strength and durability to an all new level – delivering increased performance across even the harshest work sites. Built for power. Built for reliability. Built to last. The new Kobelco XD Series.
Demand for materials for use in road construction projects is expected to grow to a peak of $7.6 billion in 2023-24, according to the second Infrastructure Market Capacity Report released by Infrastructure Australia.
Infrastructure Australia’s Infrastructure Market Capacity Program provides a national view of Australia’s infrastructure pipeline and the market’s ability to deliver on it. The 2022 edition shows that risks to on-time and on-budget project delivery have increased in the last 12 months, with demand for major public infrastructure projects climbing by $15 billion in a year.
Amid an increase in public and private sector infrastructure investment, Infrastructure Australia’s acting chief executive Adam Copp said the industry was also contending with a surge in supplyside risks in 2021-22 caused by continuing uncertainty in the global economy.
“Australia’s infrastructure sector is facing significant disruption to supply chains caused by the COVID-19 pandemic, volatile demand and more recently, the war in Ukraine. This is causing delays and cost escalations for imported items, while delivery risks are being compounded by
severe labour shortages that industry report as having the greatest impact on capacity,” Copp said.
“Industry also reports that fastrising costs and contracts that are increasingly allocating risk responsibilities to parties not bestplaced to manage them, combined with sharp declines in tier one contractor’s profitability observed in our 2021 edition, has contributed to a sharp rise in construction sector insolvencies in 2022. This leaves fewer companies to deliver the pipeline of work, with many already operating at 90 per cent capacity and above.”
The report finds that the fiveyear pipeline of major public infrastructure projects is valued at $237 billion – an increase of $15 billion in the last 12 months and equivalent to 6.7 per cent growth. Of this, transport accounts for 63 per cent of spend, with investment concentrated in New South Wales, Victoria and Queensland.
On the material demand side, the report finds the demand for materials for use in road construction projects is expected to grow to a peak of $7.6 billion in 2023−24. The cost of construction materials has risen by an average 24 per cent in the last 12 months.
The report deems labour scarcity as the single biggest issue faced by construction companies. As of October 2022, public infrastructure projects, including small capital projects, face a shortage of 214,000 skilled workers. In 2023, labour demand is projected to increase 42,000 to a peak of 442,000. This is more than double the projected available supply.
This year, Infrastructure Australia expanded the Market Capacity Program to investigate the potential to unlock new supply chains of recycled materials for infrastructure construction.
It found that based on current technology and standards, around 27 per cent of conventional materials used for road projects could be replaced with a range of recycled materials. This would mean substituting approximately 54 million tonnes of conventional materials used in roads infrastructure with approximately 52 million tonnes of recycled materials.
With advancements in technology and updates to standards, the tonnage of conventional materials replaced could rise to 43 per cent, replacing 87 million tonnes of conventional materials with 80 million tonnes of recycled products. •
“AUSTRALIA’S INFRASTRUCTURE SECTOR IS FACING SIGNIFICANT DISRUPTION TO SUPPLY CHAINS CAUSED BY THE COVID-19 PANDEMIC, VOLATILE DEMAND AND MORE RECENTLY, THE WAR IN UKRAINE.”
ADAM COPPThe five-year pipeline of major public infrastructure projects has increased by $15 billion in the last 12 months, the report finds.
Production targets. You need to hit them. We can help you do that with highcapacity crushing equipment that can be moved anywhere on your job site. Best of all, they’re compact yet powerful to get the results you need. Our crushing equipment won’t generate high levels of fine material and waste, setting you up for efficient cement production.
It’s the dependable equipment you need to hit your targets and confidently say your operations are … crushing it. komatsu.com/crushing
Streamline your quarry operations for optimal efficiency with feeder breakers that combine a material chain feeder and heavyduty crusher in a single machine.
Easy to maintain, operate and move to where you need it, our cost-effective reclaim feeders can help you start production quickly with faster delivery than engineered solutions.
With robust power and efficient designs, our sizers use technology that minimises aggregate fines without over-crushing material, which can lead to lower waste generation in your process.
Jointly funded by the Australian and the state governments, the biggest infrastructure build in New South Wales has had the third contract awarded for the Sydney MetroWestern Sydney Airport line.
The Parklife Metro consortium has been selected to deliver the Stations, Systems, Trains, Operations and Maintenance (SSTOM) contract for the project, following competitive tendering process. The consortium is planned to construct all six new metro stations between St Marys and the new Aerotropolis, and will be responsible for running the new Western Sydney Airport line for 15
years after it becomes operational. The contractors will also deliver a stabling and maintenance facility at Orchard Hills, and provide rail infrastructure and systems for the supply, commissioning and operation of a fleet of 12 new metro trains. The airport to metro build will serve to provide faster and more reliable metro rail services for locals and visitors to Greater Western Sydney. Federal infrastructure, transport, regional development and local government minister Catherine King said that the project is set to provide both an environmental stimulus and support for state employment.
“THIS PROJECT WILL CONNECT COMMUTERS AND TRAVELLERS WITH THE NEW WESTERN SYDNEY INTERNATIONAL AIRPORT, PROVIDING MAJOR ECONOMIC STIMULUS AND SUPPORTING MORE THAN 14,000 JOBS DURING CONSTRUCTION.”
CATHERINE KING
“The Australian Government is committed to delivering vital infrastructure for Western Sydney as part of a genuine partnership between levels of government that will enhance liveability and support the growth of industry and enterprise,” King said.
“This project will connect commuters and travellers with the new Western Sydney International Airport, providing major economic stimulus and supporting more than 14,000 jobs during construction.”
The awarding of the final contract coincides with another significant project milestone, with Sydney Metro – Western Sydney Airport becoming the first rail infrastructure project in Australian history to commit to being certified carbon-neutral from the start of construction through to operation.
All carbon emissions generated during construction and operation will be reduced and offset.
Having the project certified carbon neutral from construction to operation is in line with the Albanese Government’s goal of reaching emission reduction targets of 43 per cent by 2030, and net zero by 2050.
The Australian and NSW Governments are working together to deliver the city-shaping Sydney Metro – Western Sydney Airport line to coincide with the opening of Western Sydney International (Nancy-Bird Walton) Airport in 2026.•
Kobelco Construction Machinery has announced the opening of a new company owned dealership in New Zealand.
The establishment of Kobelco Construction Machinery New Zealand (KCMNZ) will enable Kobelco to streamline excavator sales and parts support across the country with a directto-market approach from 1 July 2023., the company announced.
From a new facility which will be opened south of Auckland, KCMNZ will handle all new Kobelco excavator sales from 1-85 tonnes, including demolition and specialist scrap and material handling machines. KCMNZ will also offer full aftersales service and support to its customers.
This new venture will streamline the
delivery process from the factory to endcustomer in the most timely and costeffective way. Specialist Kobelco-trained technical support will also be based in New Zealand, to provide technical expertise to support customers in achieving long-term success.
Kobelco Genuine Parts will be imported directly from the factory to the National Parts Distribution Centre south of Auckland, with an increase in parts inventory on the ground, for a quicker turnaround and less downtime for customers. Additional back-up support will continue in the form of an overnight freight service from the Sydney warehouse.
“Building market share and presence in the New Zealand market is a priority for
Kobelco,” Kobelco Construction Machinery Australia managing director, Paul Torrington, said.
“By implementing a direct-to-market strategy, with factory backing, we can provide customers with the high quality, yet cost-effective and efficient sales and support systems that Kobelco owners expect.”
The move is another sign of the Japanese brand’s commitment to growing its market position in New Zealand. Kobelco is also in discussion with current New Zealand Kobelco dealer MIMICO regarding an ongoing service and support arrangement to enable continuous service to customers currently supported by MIMICO branch locations. •
Heidelberg Materials has announced the acquisition of the Mick George Group, a leading construction and demolition waste recycler in the Eastern region of the UK, with an annual revenue of around £220 million ($400 million).
The Mick George Group specialises in bulk excavation and earthmoving services, demolition, and environmentally sensitive waste removal, complemented by waste management services as well as aggregates and concrete supply. The company operates four recycling facilities, eight waste transfer stations, eleven aggregates quarries, and ten ready-mixed concrete plants.
Recirculation of building materials from production to recycling is key to reach Heidelberg Materials’ target of offering circular alternatives for half of its concrete products by 2030.
Heidelberg Materials expects the acquisition would significantly strengthen the company’s circular materials offering whilst complementing its existing aggregates and ready-mixed
concrete business in the UK.
Last month, Heidelberg Materials announced the acquisition of RWG, a German construction materials recycling company, keeping in line with Heidelberg’s investment strategy to put a focus on circular economy.
The new acquisition adds a considerable recycling platform to Heidelberg Materials’ portfolio, supporting the development of innovative technologies for processing waste and upgrading it for use in the construction cycle as a valuable material.
“The acquisition of the Mick George Group is another significant step towards our target to offer circular alternatives for half of our concrete products by 2030. Pushing circularity and consequently recycling, reusing, and thereby reducing the use of primary raw materials is crucial to achieving Net Zero,” said Dr Dominik von Achten, chairman of the managing board at Heidelberg Materials.
“With the acquisition of the Mick
As part of the ongoing relationship Komatsu maintains with the Clontarf Foundation, Komatsu has showcased a newly built Komatsu Innovation Hub situated in Wacol that presents opportunities for young future leaders to learn about careers in both construction and mining.
A group of Year 9 and 10 future leaders were given access to the Komatsu Innovation Hub as part of their four-day camp across the Northern Rivers region of NSW, strengthening the company’s of the Clontarf Foundation.
The Clontarf Foundation is a non-profit organisation that assists in the education and employment of young Aboriginal and Torres Strait Islander men and more broadly works to improve discipline, life skills and self-esteem.
The future leaders were joined by Komatsu’s senior talent acquisition consultant, Samantha Zanevra and national operations manager–East, Scott Alexander, alongside apprentice Andrew Stuart.
The students were encouraged to explore the machinery and technology on display, with comments attributed to the students of ‘marvelling’ at the scale and scope of the size of machinery required for mining operations.
Speaking on the interaction and engagement of the students, Alexander said that the future leaders asked lots of questions and learned about the importance of a workplace being connected and working towards a common goal.
“We have so many great opportunities
George business, we are clearly moving towards establishing a truly circular materials and services offer in our UK business,” added Jon Morrish, member of the managing board and responsible for Western and Southern Europe. “I warmly welcome all 1,000 Mick George employees to Heidelberg Materials and look forward to further developing the business together.”
The acquisition is expected to be completed in the second quarter of 2023, subject to relevant competition authority approval. •
that these boys can join us for in a few years’ time if they want,” Alexander said, “it’s important they can see and be inspired by the options that they can consider for their future.”
Komatsu was recently named the NSW Training Award for Large Employer of the Year, with the accolade bring largely attributed to Komatsu’s innovative focus on apprenticeship training through its Apprentice Development System program.
Similar to the Clontarf Foundation’s approach, Komatsu equips apprentices and trainees with skills that go beyond the vocational training. These skills include but are not limited to: mental health awareness, public speaking, road safety and fatigue management, drug and alcohol awareness, and; a variety of business skillsets. •
“I WARMLY WELCOME ALL 1,000 MICK GEORGE EMPLOYEES TO HEIDELBERG MATERIALS AND LOOK FORWARD TO FURTHER DEVELOPING THE BUSINESS TOGETHER.”
JON MORRISH
It takes a different kind of brain behind the brawn. Fired up like a turbo diesel. Gears constantly churning. Hardwired beneath hard hats to solve problems, or avoid them altogether. With you and your crew at the helm, and Deere at your back. The workarounds, ideas and innovations that move earth, and your business, forward. Because that’s what it takes to win in the dirt. And that’s what it means to be Never Idle.
Deere.com.au/en/construction
amount of water available to our farmers and other businesses looking to expand their operations,” minister Butcher said.
The proposed works on Burdekin Falls Dam would include raising the spillway and abutments using concrete buttressing, raising and widening the saddle dams, and constructing a new saddle dam on the right bank.
To account for the increase in spillway height, the dam’s left and right abutments – the walls either side of the spillway – are also proposed to be raised.
The project will increase the dam’s storage capacity by 574,240 megalitres, boosting capacity to an estimated 2,434,240 megalitres. It would also provide approximately 150,000 megalitres equivalent medium priority water.
Associated works to support construction will include new water and wastewater treatment plants, resource extraction areas and associated access tracks, road works, worker accommodation camp, helipad, power and telecommunications. Recreation facility upgrades are also proposed.
The Queensland Government has endorsed raising the state’s largest dam, the Burdekin Falls Dam, by two metres. The project, carried out in conjunction with Sunwater, aims to address increased water demand in North Queensland.
The next stage of planning follows the Queensland Government’s initial consideration of Sunwater’s detailed business case (DBC), which outlined options to increase the dam’s water supply and longterm viability, alongside required safety improvements.
An independent assessment
demonstrated that projected water demand from the dam may exceed current availability by 2031 and that a raising of two metres would address this future need. This also considers growing demand from the emerging hydrogen industry in Queensland.
Queensland’s minister for water Glenn Butcher announced the works alongside local MPs Les Walker, Aaron Harper and Scott Stewart.
“Burdekin Falls is the largest dam in Queensland – at more than 1.8 million megalitres capacity – and raising it by two metres will significantly boost the
Sunwater chief executive officer Glenn Stockton said safety improvement works will ensure the dam continues to pass flood waters safely and complies with modern design standards and guidelines.
“We understand the critical role this dam plays in providing water security for the Burdekin and surrounding regions,” he said
Sunwater has begun preparation of the environmental impact statement (EIS), which will assess the potential environmental, economic and social benefits and impacts of the project.
Pending approval of the EIS and an investment decision, contractor engagement and procurement activities for the dam raising project would commence.
Sunwater expects to submit a draft of the EIS to the Queensland Coordinator-General in 2023. •
A quarry in the Otway Ranges in Victoria has been given a second lease on life, as a location for creative arts projects and events.
The abandoned quarry, which has an existing rehabilitation plan in place that is in line with government regulation, has been proposed to fulfil a different purpose with its rehabilitation by a Melbourne based couple.
The site is a 86,000 square metre Arkose Sandstone quarry, located within the Colac Otway Shire Council.
The Quarry has been in operation since the late 19th century as a source for local stone to use in road and rail building and as of 2014 has been abandoned.
With the quarry remaining under licence and currently going through rehabilitation, Joseph Norster and partner Millie Cattlin
have worked together to rehabilitate and transform the site into a permanent installation called “The Quarry”.
Speaking on the vision for the future of the installation and other projects, Norster said that the quarry was an ideal place for a creative program where rehabilitation would be the core interest of the area and of future projects.
“The quarry is a site for the development of experiments in building and architecture, creative practices, education and technology,” Norster said.
Norster and Cattlin has proposed an alternative rehabilitation plan for the quarry, that instead of blocking site drainage and allowing the pit to fill with water, the site would be left open to people, improve the health of the landscape and establish temporary
pavilions to facilitate events.
The Quarry Project is one of four sites to share in the quarry transformation grants recently awarded by the Victorian state government to inspire innovative plans to rehabilitate sites.
The other grants are with regards to currently operating quarries, with the Woolert Quarry end use masterplan and Montrose Quarry – end use feasibility assessment grants awarded to Boral resources and the Boggy Creek Biodiversity Corridor grant awarded to Burdett Sands.
The plan behind The Quarry project highlights the importance of rehabilitation and how quarries can look to creating value and use for the community once they no longer have material within. •
Located across the Darling Downs & Surat Basin, Queensland
• Rare opportunity to acquire a highly productive & exceptionally well developed investment in the quarry & transport industry
• Strategically located near major road, rail & resource sector projects
• 7 properties, 5 quarrys with 50+ years resource life-span
• Fully licenced, environmentally compliant & accredited operation
• Recently upgraded quality plant & equipment
• Fully integrated enterpise incorporating quarrying, processing & transport
raywhiteruraloakey.com.au
Expressions of Interest Closing Monday 3 April 2023 3pm
(Unless sold prior)
Geoff Byers 0437 732 494
Rod Wolski 0466 277 873
Tim Steele 0417 684 404
Ray White Rural Oakey
*approx.
The MOBICAT MC 120 PRO jaw crusher is extremely robust and delivers to the Kleemann standard with its low-maintenance operation.
With a focus on efficiency, performance and reliability the MOBICAT MC120 PRO jaw crusher has an efficient diesel-electric drive and can function with the use of an external power supply, making it an ideal fit for quarry activities.
The double-decker pre-screen has an extra-large screening surface of 3.5m square and swivels independently to ensure effective screening of fine particles in the feed material and higher throughput. The machine generates a reduction in wear in the crusher, by redirecting medium grain through the crusher bypass and the bypass flap integrated into the prescreen reduces adhesion for easy redirection of the material stream
The new 24-tonne ZW310-7 wheel loader from Hitachi has been designed to give powerful performance, low total cost of ownership, and exceptional efficiency. Built to the highest quality standards, it will significantly boost productivity at busy quarries and have a positive impact on profits.
Following on from the success of the renowned ZW310-5B model, Hitachi has introduced a new 4.5m³ bucket wheel loader suitable for rehandling and sales loading application in aggregate or sand quarries.
The ZW310-7 wheel loader offers a high level of productivity due to faster cycle times, high breakout force and loading capacity.
The operator comfort has improved with a redesigned cab equipped with seat mounted electric controls, joystick steering and reduced noise with low vibration levels.
The wheel loader also promises unrivalled safety and superb all-round visibility due to 270-degree bird’s-eye view camera, narrow engine hood and inbuilt safety systems.
Increased uptime is another key promise in the new Hitachi model, thanks to the robust and durable components, incorporated rear obstacle detection and easy access to maintenance points and components.
For more information, visit: www.hitachicm.au
The H Pumps offered from Toolkwip Pumps as part of the Selwood range, offer maximum performance and efficiency for high head, high pressure dewatering.
The efficient models offer total heads up to 158 metres, mechanical shaft sealing, Selprime automatic self-priming and emission compliant engines, making them Ideal for high head and high pressure applications and making them simple to operate and maintain.
The H150 has a capacity of 450 cubic meters an hour with a maximum pump speed of 1800 revolutions per minute (rpm) and four internal impeller blades to drive water pressure.
The Selprime priming method is a unique Selwood self-priming system that utilises a water tolerant diaphragm air pump. The design is environmentally friendly and lacks the problems of oil vapour emissions and oil emulsification.
The crusher unit also features an easy-to-use GEO setting option and has maximised crusher geometry through the use of the long crusher jaw, enabling high throughput with maximum reliability.
For more information, visit: www.wirtgen-group.com/en-au/
Red Star Anping has the ability to make polyurethane meshes to fit Derrick screens, such as TH48-30, TH56-42 and TH36-30, with other models available on request. The products from the team at Anping Red Star are well-known for their efficiency, high quality and outstanding performance on screening equipment.
An inventory has recently been set up in the company’s factory warehouse in Victoria, with the aperture size from 0.063 millimetres (mm) up to 4.5mm, providing solutions for business of all sizes.
Anping Red Star provides a door-to-door supply chain solution, to support businesses and provide long-lasting and effective poly-urethane equipment which works in conjunction with the largest equipment suppliers in the market.
For more information, visit: www.toolkwippumps.com.au
more
Tutt Bryant is now the Australian distributor of Jonsson’s crushing and screening equipment from Sweden.
Jonsson’s L120-330 double crusher encompasses the tried and tested Metso Outotec C120 jaw crushing unit and the powerful 400 horsepower (hp) Nordberg GP330 cone crushing unit with Jonsson’s pre- and post screens on the same chassis. The dual power provides flexibility for using an onboard generator, a site generator or mains electricity.
The onboard Jonsson Control System (JCS) enables the operator to upload data to the JCS cloud server from the belt scales, the automation system, the generator/engine monitors, as well as the alarm logs and fault diagnostics.
To submit new product and equipment releases, email: les.ilyefalvy@primecreative.com.au
The in-cab vehicle screen allows for monitoring and control of the crusher from an excavator. Mirrors, the crusher screen and camera feed from up to three cameras mounted on the machine can be viewed. Using this system, the operator can monitor the usage levels in the crusher to optimise production, start/stop the feeder, auto-stop and even read manuals, circuit diagrams or the spare parts’ lists that remains updated from the cloud server.
Transportable in only three pieces, this high capacity machine will drive efficient, low cost crushing on your projects for many years to come with the long serviceable life expected from Metso Outotec crushers. For more information, email Tutt Bryant at: metso@tuttbryuant.com.au or call 1300658 888
How Holcim is using Komatsu’s iSite fleet management system to drive production and safety breakthroughs, while reducing CO2 emissions.
As a global leader in sustainable and innovative building and construction solutions, Holcim is committed to driving its operations towards net zero. Over the past two years, the company has been implementing a ground-breaking fleet management system set to play a key role in achieving its aims.
In 2020, Holcim began working with Komatsu to pilot Komatsu iSite, a quarryspecific “brand agnostic” fleet management solution harnessing the power of the latest intelligent communications technology (ICT) developments, to drive production efficiencies at its Lynwood Quarry about 160 kilometres southwest of Sydney.
As a result of implementing the Komatsu iSite solution at Lynwood, Holcim has seen major improvements in production efficiencies.
These have included faster cycle times, more accurate truck loading, higher daily production rates, fuel savings of around 10 per cent, and significantly safer operation of mobile plant.
Dave Manning, Lynwood’s pit manager, who played a key role in implementing the system, described what has been achieved using Komatsu iSite at Lynwood as a career highlight.
“Working on this project, especially to get the benefits out of it that we have, has definitely been the highlight, seeing how it’s improved the site and benefitted the team,” he said.
The catalyst for seeking a solution like Komatsu iSite followed a review of the Lynwood operation by a team from Holcim’s head office in Europe.
“That highlighted some inefficiencies –which we were working through – but we weren’t getting there as quickly as we’d have liked to,” Manning said.
“We’d been using another system, but it wasn’t giving us what we wanted, so I sat down with Komatsu, told them what we needed to track, and how we’d like to get the data. They came back with a mining system that they were looking to pilot in the quarry industry.
“We jumped at the opportunity.”
The first stage of implementing Komatsu iSite at Lynwood involved fitting monitoring systems and in-cab screens to the face loading and haulage units.
This allowed the site managers to see where the trucks were throughout the load, haul and dump cycles, and for operators to see critical information about volumes and tonnages they were loading and hauling.
“The initial data we got was just a screen pinpointing where the trucks were, and we could draw some information out of that just by recreating reports,” said Manning.
“From that, we started to identify what were the main things we needed to get out of this system.
“And that’s where the creation of the dashboard comes into it,” he said. “Now I can log onto the dashboard and go into the utilisation, the production, the fuel burn and all those things that I wanted to know,at any point in time.”
The global Holcim team’s review showed the biggest inefficiencies were in Lynwood’s load and haul operation.
“To get the best out of the plant, out of the load and haul team, we needed to do something different. And with Komatsu iSite, we’ve achieved what we wanted in a fairly short time,” said Manning.
“Our consent for load-and-haul out of the pit at Lynwood is only 15 hours, between seven o’clock in the morning to 10 o’clock at night.
“We need to get as much rock out of the pit up to either the boot, the entrance chute to the feeder before the material reaches the crusher, or run-of-mine (ROM) to stockpile for the night, so we can feed the boot for 24 hours a day.
“Using Komatsu iSite, we were able to see where there were lagging factors,” he said.
“Now we’ve got data we can see where they are lagging, and what we need to do to fix them.
“The supervisors get emails every morning on how much production trucks are doing out of the pit. With this information they can see where the bottlenecks are.They can analyse that extra data to see if idle times are increasing or decreasing, or other trends.
“Then they’ll get together with me, and we go through anything cropping up that’s glaringly apparent, that we can deal with there and then.”
Before Komatsu iSite was implemented at Lynwood, a typical 15-hour shift would see 13,000 to 14,000 tonnes coming out of the pit.
“Since having Komatsu iSite here, we’ve seen some 18,000 tonne days out of the pit now, which has been fantastic. And that’s where we’re gunning for consistently,” Manning said.
“Being able to track and easily go and see what we’re hauling out of the pit to the boot or ROM and make sure we’re hitting those targets every day; that’s the single biggest benefit.
“Within three months of installing the system, we were seeing benefits. Within six months, we were achieving our truck loading KPIs. And within a year, the system had paid for itself,” he said.
One area where Komatsu iSite quickly paid off for Holcim has been its contribution to reduced fuel burn across the Lynwood operation.
This is a critical consideration for a company that is globally committed to sustainable operations and achieving net zero CO2 emissions as soon as possible.
One way to quickly reduce fuel burn is by eliminating unnecessary truck idling. Komatsu iSite has made a quick and effective difference here.
“When we were analysing the data coming
off the trucks, one of the elements we could log was the idle time for the trucks waiting in and around the pit,” said Manning.
“Being able to track idle time and utilisation allows us to manage fuel burn in particular.
“In terms of machine utilisation, you’re going to use the amount of fuel you use going up and down the haul road,” he said. “There’s not much we can change to that, other than road conditions, gradients and the like, which we’d put in place already.
“But now using Komatsu iSite, we’ve been able to get the operators on board so, if the truck’s just going to sit there with the engine running, they will turn it off.
“The truck fleet’s idle times have seen a six per cent improvement and similarly, wheel loaders have reduced from 14 per cent to seven per cent.
“We do have a fairly large footprint here at Lynwood, which means we make a fairly substantial contribution to CO2 emissions.
“Now with Komatsu iSite, we have been able to significantly reduce these emissions through running our operations far more efficiently, and by reducing idle times,” said Manning.
“I know in our discussions with Ampol, we’ve seen around a 10 per cent reduction in our fuel burn for our trucks out of the pit.”
Manning described the initial response from operators about having Komatsu iSite in their machines as being “somewhat sceptical”.
“There was a bit of Big Brother watching them, but we made it clear it’s not about that.
“It’s around getting the best out of the trucks, so we can help the crew work smarter, not harder,” he said.
“Once we started showing what we were getting out of it, the operators got on board. It became a bit of a competition between the day and afternoon shifts to see who could get the best production.
“The key to it was about being transparent with them,” said Manning.
“We’re now at the point where I had a guy on one of the new excavators who asked if it was getting Komatsu iSite. ‘It’d be good,’ he said. ‘We can see what I’m putting on the trucks and make sure they’re not ripping me off’.”
Komatsu iSite has also meant the days of walking around machines doing paper-based manual pre-start checks are over.
“Digital pre-start is built into it. When the operator gets in the machine, they’ll log on
and go through the normal pre-start for the truck, loader, digger, whatever it might be.
“If there’s any action item or critical item that needs to be addressed, it goes to our maintenance leading hand straight away, and he can get them addressed immediately.”
This ensures that critical items can be rectified urgently, while action items can be dealt with at the next service.
Since being introduced, a major benefit of Komatsu iSite at Lynwood has been to help drive a better safety culture.
In one instance, a supervisor doing their morning run had noticed evidence of a potential near-miss event, and asked Manning to play back the previous night’s video footage.
“I was able to rewind back and see evidence of a near-miss event. While we have
a strong reporting culture, we can use this type of footage to reinforce the importance of reporting near-misses which gives us additional opportunities to learn and improve further,” he said.
Manning’s team has also used Komatsu iSite to virtually eliminate truck speeding.
“When we first implemented the system, we could see we were getting a number of speeding violations every day,” he said.
“Pretty soon the team realised this, because we started presenting them with anonymised reports, showing them where we were having the alerts.
“Within six weeks, we were down to a handful. And now we don’t see any; at most it’s around two or three KPHs over, which is something we can manage.”
Manning said Holcim is now considering
how it may roll out Komatsu iSite to its other Australian quarry operations.
He’s had discussions with Holcim management in other states, and the company’s procurement team has been talking with Komatsu about purchasing Komatsu iSite-enabled machines for other quarry sites.
“We have an operations improvement team here in Australia now and one of their aims is to try and get more visibility across our sites.
“So, instead of having to ring me directly, they will be able to tap into the Komatsu iSite system from wherever they are, so they can look at the metrics and where we’re at – and then talk to me about some other improvements that they might identify that I may have missed.
An important reason why Holcim chose Komatsu iSite was because it was “brand agnostic”, so it can be used across all makes of equipment.
“Often at a quarry level, we don’t really get the choice in what machines we buy; that’s all handled by procurement. So, if we did have a Cat, or a Hitachi, or a Volvo machine, we could put Komatsu iSite on any of those machines.”
In the less than two years that Komatsu iSite has been operational at Lynwood, Manning said the biggest benefit has been the production efficiency improvements it’s driven.
“However, I’m not going to discount the safety side as well,” he said. “To be able to reduce the speeding events by as much as we did, as quickly as we did, that’s a major achievement in helping to prevent potential serious incidents.
“But to get the production efficiencies and payback as quickly as we have … well, we didn’t think we’d get it that quick. To get a less than 12-month payback for the system, that has been fantastic,” he said. •
United. Inspired.
Epiroc Drilling Tools has the broadest range of tophammer drill strings and related equipment of any supplier in the world. It means that you can look to one reliable and time-tested source for all your equipment needs. Each one of our products are designed for optimum performance in tophammer drilling applications on a price vs. performance basis. Whatever your needs, check out our many choices before settling for less.
epiroc.com/en-au
The Essential Air Seal, designed with a combination of products provided by Kinder Australia, has opened up a new way of supressing dust within quarries.
Providing the Essential Air Seal, a combination of specialised products that provide the ultimate dust seal around conveyors, Kinder is helping increase the efficiency and longevity of conveyor systems. Rather than contacting the conveyor belt, the seal suspends over the belt with zero contact, thus eliminating skirt friction and damage to the conveyor belt.
Traditional transfer points rely on a rubber or polyurethane soft skirting system to make contact with the conveyor. The solution from Kinder, however, hovers one millimetre (mm) above the surface of the belt, ensuring that the dust remains inside the system.
Quarry had the chance to speak to Kinder Australia’s business development manager, Sean Kinder, on how the multiple parts work together to form the Essential Air Seal system.
“The Essential Air Seal has come to be,” Sean said, “because of innovative European technology that we have found to complement our Kinder products.”
“We first became aware of the AirScrape and TailScrape technologies from Germany as a part of our research and development. From there, we began looking for specific products to complement our range.”
The system’s design starts with the AirScrape, a contact-free conveyor skirting and sealing system that acts as a side seal suspended over the conveyor belt. TailScrape, a proprietary and intelligent blade structure, combines with a K-Containment seal and a K-Sure belt support system from
Kinder to form what Sean described as the “ultimate team of dust suppressing products.”
“The arrangement of the lamellae, together with the movement of the material and belt, increases the suction effect, which in turn, keeps fine dust particles within the conveyor section,” he added.
“AirScrape works best with the one mm air gap underneath it and to do that, Kinder Australia’s K-Sure belt support system has provided the best support to enable the AirScrape to work as intended.”
According to Sean, designs for the equipment making up the Essential Air Seal system came as a part of a significant interest in contact-free skirting technology from Kinder’s customers. Switching to contactless design has many benefits for the industry, as Sean explained.
“The service life of the belt and conveyor components has been drastically extended and with that lessened damage to equipment. We have also been able to generate improved safety outcomes.”
The Essential Air Seal system is suited for the wider quarrying and aggregates industry, but has found particular use in the high dust environment that comes with cement production materials, such as clinker sand and gravel.
With health and safety at the “forefront of Kinder’s innovation ideas,” Sean said many Kinder products have been designed to minimise the spillage of materials and generation of dust and keep operations productive and safe.
“Airborne dust can create serious personal health risks if inhaled, not to mention other
site safety issues such as poor visibility and slip hazards,” Sean said.
“Dust can interfere with the correct functioning of conveyor componentry and cause extended shutdown periods and increased component replacement and maintenance clean-up costs.”
The Essential Air seal finds a secondary function in extending the time between scheduled servicing and downtimes. Using this system, other conveyor components suffer less wear due to reduced exposure to dust. Limiting the need for operators to go near the conveyors comes with additional safety benefits.
“Moving conveyor parts and exposed machinery have serious safety risks for maintenance workers and technicians. Pinch points, moving parts and moving materials increase the risk of slip, trip and fall hazards,” Sean said.
“Part of what we do is to limit the workers’ exposure, not just to dust itself, but also to the dangerous conditions that come about as part of the effect of dust on equipment.”
Kinder maintains a dynamic team of field application specialists and engineers, who are regular visitors at operations. The team at Kinder also provides inspections and guidance for various conveyor productivity improvements with their technical expertise and run regular training for customers, both in person and remotely via webinars.
“We want to open up discussions about common conveyor issues, and areas for improvement,” Sean said.
“Our engineers have designed and worked with the latest on the market technology, in order to provide the best, most effective dustsupressing solution available.” •
Victoria-based civil contracting and concrete recycling company Water Excavations has invested in an 80 tonnes-per-hour wash plant from CDE, in a bid to recover valuable waste.
Based in Mildura, a city in the northwest of Victoria, Waters Excavation has invested in a construction and demolition wash plant to recover valuable sand and aggregates from concrete waste.
As a family run business operating for over 55 years, Waters Excavation is an earth moving contractor to various feed streams including crushed concrete, scalpings and a fine sand deposit, working on a wide range of civil construction works from minor works to major government infrastructure projects.
Waters Excavation had set sights to reduce the amount of waste sent to landfill, not only to become more sustainable, but also to recover valuable material which they can resell to be repurposed in the local construction market.
In 2019, Waters Excavation first met wet processing experts CDE at global trade show bauma in Munich, Germany. The Australian CDE team worked with Waters Excavation to understand their needs and wants, to create a solution suited to them.
“We first met CDE a number of years ago and have since been building a relationship with the local Australian team,” said Michael Waters, the director of Waters Excavation. “We had heard great things about CDE’s technologies from another one of their Australian customers, which really firmed our decision to partner with them.”
CDE’s solution incorporates the EvoWash sand wash plant, the AggMax modular logwasher, a feed hopper and stockpile conveyor. Working together, these technologies enable Waters Excavation to produce five products for the local market.
CDE’s S20 hopper transfers feed to the plant. The feed conveyor includes an integrated magnet for steel recovery, ensuring that Waters Excavation can recover as much material as possible to divert more from landfill.
The high frequency Infinity D1-63 prescreen removes sand prior to the attrition process, with high-frequency screening action ensuring maximum sand removal, and the incorporation of the Infinity D1-43 screen dewaters organic and lightweight wastes liberated from the attrition process, enabling the production of two sands.
CDE’s RotoMax logwasher can be used in the processing of a variety of materials such as sand and gravel, crushed rock, construction and demolition waste material as well as a range of mineral ores and efficiently scrubs material for maximum attrition.
The incorporation of the AggMax modular logwasher’s upward flow rejects organics and other lightweight contaminants which are dewatered on the integrated trash screen, while the Infinity H2-60 sizing screen efficiently separates the material into three washed aggregates and allows the removal of sand liberated by the RotoMax’s attrition process.
Fines are passed to the EvoWash, a highfrequency dewatering screen with hydro
cyclone technology, which gives unparalleled control of silt cut points, allowing production of high value, in-spec product straight from the belt.
CDE’s pioneering solution is allowing Waters Excavation to produce high quality sand products to meet local demand, whilst also diverting waste from landfill.
Waters Excavation is producing five products thanks to CDE’s state-of-the-art wash plant. Products include two grades of sands; 0-2mm and a 0-4mm sand, as well as three aggregates; 4-10mm, 10-16mm, and 16mm-oversize.
One of the plant’s main features, Michael Waters said, is the ability to scrub aggregates of clay and float off lightweight contaminants such as leaves, sticks and light plastics.
“It’s been a real success,” he said. “I’m blown away with the level of contaminants we were able to remove from the waste stream and how clean the end products were.”
It’s a solution that could be replicated throughout regional Australia, which would have huge environmental benefits
“We’re delighted to see this plant up and running for Waters Excavation. Both of us are passionate about sustainability and recovering as much was as we can to be repurposed in local markets, contributing to a circular economy,” Daniel Webber, CDE’s Regional Manager for Australasia said.
“Plants like this are the future of the industry in their ability to minimise waste and maximise value, and we’re proud to share our expertise to create a solution which recovers and reuses valuable resources.” •
The Joy range of surface crushing equipment is now merged into the Komatsu portfolio, bringing together all surface products offered by Komatsu under the one banner.
Anew rebranding drive has been announced by Komatsu this year, with Joy’s surface crushing equipment, reclaim feeders, sizers and feeder breakers now being rolled out under the Komatsu branding as a part of an on-going process of integrating the brands into one Komatsu, while the underground mining equipment will continue with the Joy brand name.
The direction that the company is taking with bringing all Komatsu products under one banner is one that Matt Langbridge, Komatsu’s director of mining and crushing systems in the Australasia region, described as “creating value together”.
“A commitment to offering full product lines of high quality and high productivity equipment with consistent customer experience for quarries and surface mining operations is of key importance to Komatsu. The rebranding is going to take away any confusion people may have about our products,” Langbridge said.
In line with what is currently offered from existing Joy equipment, the Komatsu line of surface crushing products will persist with the unique crushing approach that prioritises energy optimisation and reduces the double handling of material.
Placing a focus on the company’s brand reputation, Langbridge spoke on how the product line will perform as effectively as expected from any Komatsu branded equipment.
“The crushing approach used in the Komatsu product line is different to traditional methods of crushing,” he said. Using tension instead of compression to crush aggregates, Komatsu crushers avoid generating high levels of fines or other waste material in the process.
The tension-based crushing allows appropriately sized material to pass through the crusher without further processing, which helps save energy by up to a 90 per cent when the machine is active.
“This ability to avoid re-handling the material and the time savings that result from the crushing materials being of the specified particle size are great examples of how we want to help businesses achieve their sustainability goals.”
Additionally, the crushers have a broad use in processing highly variable materials, which factors into the use of the machines in parts of Australia with high levels of seasonal variability.
“Being able to use the crushers through wet seasons, where the aggregates might not be in the ideal state to crush, is an important consideration for us as a business,” Langbridge said.
“We’re invested in not just the sustainability and environmental, social, and governance (ESG) targets for our customers, but also in sustainability from a business point of view.
“We want to ensure that people are able to operate year-round and our tension-based approach to crushing emphasises that.”
High levels of mobility and flexibility with which the machines can be used is another important consideration for quarrying operators when investing in equipment.
The Komatsu range continues to support the variable nature of the surface quarrying industry by providing a range of mobile options, with track mounted, wheel mounted or skid mounted options available.
“The options for our surface crushing equipment are designed with our diverse range of customers in mind,” Langbridge said, “to really drive home our purpose in creating value together.”
“What it means is that for a smaller quarry, you don’t need civil engineering work to install these crushers, screens and feeders. Once the equipment is on site, you can move pieces of equipment around with minimal effort.”
The surface feeder breakers and reclaim feeders from the product line also work directly with other Komatsu products, including wheel loaders, trucks and dozers. Integrating the line with pre-existing mobile fleet allows for ease of use of different equipment.
According to Langbridge, in line with what Komatsu already provides, the surface crushing equipment is designed with the quarrying space of Australia in mind.
As such, the crushers on offer are compact and feature a small size envelope that
Langbridge describes as being “atypical” in the industry.
“By integrating high capacity with small size envelopes, our crushers provide greater output, with a compact machine,” Langbridge said.
“The designs which we have put in place for the crushers allow them to have their own feed hoppers without the need for additional steel infrastructure around them.”
The compact nature of the crushers, feeds into the mobile and accessibility element of the product line, as the crushers do not require a specialised team to be on site to move the equipment.
Whilst changes are happening to the Komatsu surface product line, the Joy brand will continue to operate in the underground mining operations.
However, these changes extend to beyond
the colour of the machines and branding on the equipment.
Bringing the build quality of both equipment lines together is setting the framework for the future of the equipment that is to be offered to the quarrying industry.
Listening to the needs of customers, understanding issues and problems that present themselves and responding with a solution are all what Langbridge listed as “integral values Komatsu holds with regards
to customers,” which have persisted through his 25 years at the company.
“We’re looking to ways in which through our equipment, businesses can support a sustainable environment and contribute to communities,” Langbridge said.
“Optimising and creating value together with our customers and stakeholders is the philosophy that Komatsu wants to bring to the industry and the crushing product line is a true representation of that. “ •
Volvo Construction Equipment has unveiled the Connected Map solution, a positioning service which provides a visualised site overview for all machines and vehicles on site, including non-Volvo equipment.
Having the knowledge of where equipment is on site is invaluable to increasing productivity, especially as operations across all industry continue to increase in both size and scale.
Connected Map provides a real-time fleet management and personnel management solution, that is made easily accessible to all employees within a team.
The Connected Map solution is accessible via Volvo Co-Pilot, on smartphone devices and in the office, via the Office Portal web platform. The jobsite visibility is the main draw of the solution, as Azadeh Fazl Mashhadi, service offer owner site solutions at Volvo Construction Equipment said, when providing insight into how the technology functions.
“With Connected Map, users benefit from complete jobsite visibility,” Mashhadi said.
“It gives them a visual overview in real time of the position of every machine, every vehicle and every visitor on a site connected to the App, helping to make their operation more efficient and more productive.”
“The site management also have total jobsite visibility via the Office Portal, providing all the information needed to optimise traffic conditions for maximum productivity.”
The Connected Map solution works by extracting the positioning data from machine telematics or smartphone devices with SIM Cards and uploads it to a cloud-based Volvo platform.
“Regardless of branding on the equipment,
or whether they are a visitor on site,” Mashhadi said, “the Connected Map will visualise the position of any unit that has the app installed, making their position visible in either the Volvo Co-Pilot or on a smartphone.”
“For non-Volvo machines which are regularly on site, Volvo recommends fitting the machine with a generic/non-Volvo CoPilot with Map App.
“This can be purchased as an aftermarket option through a Volvo dealer.”
Connected Map will visualise a host of typical jobsite features and landmarks, including roads to assist operators in navigating around the site, loading zones, dump zones, speed zones as well as restricted zones for operators to enter.
Points of interest such as offices, workshops and fuel stations can also be visualised, which holds potential benefit for new or temporary operators.
Additionally, single lane sections can be defined on the map and used to notify the operator if another machine is approaching within the single lane section to avoid traffic congestion.
“What’s more, increasing the efficiency of transport operations can also help to cut travel times, minimise material mixing, lower fuel consumption and reduce emissions.”
For site managers, the Office Portal function of the Connected Map makes it easier to manage larger sites and even creates the possibility to manage multiple sites simultaneously.
In addition to the visualisation options, it also allows the Site Manager to react to the prevailing site conditions.
“The site manager can introduce measures such as one-way traffic or restricted zones,
Mashhadi said, “and communicate these changes to all users in an instant, helping to improve awareness, reduce accidents and increase productivity.”
Connected Map users can also find the positional data of their machine, thanks to the search functionality of the technology, which will look-up and find users or machines in real-time with the last machine position visible for up to thirty days.
“Connected Map makes it easier for the operator to become familiar with the site and know where everyone is – including visitors – helping to facilitate a more straightforward, safer, and less stressful operation,” Mashhadi said.
The Site Map application is available for free from the App Store and Google Play.
To begin using Connected Map and the Office Portal, Australians should get in touch with CJD Equipment, Volvo Construction Equipment’s only national authorised distribution partner in Australia.
Founded in 1974, CJD Equipment has been in the industry for a long time. CJD’s professionals have the skills and knowledge to support every type of operation and provide the right equipment.
Together, CJD and Volvo provide a full range of machinery suited to Australia’s unique landscapes and industry requirements.
These products are fully supported through a nationwide network of CJD’s branches, and carefully selected dealers and service agents, strategically positioned to ensure total support.
With fully equipped parts warehouses in every capital city, and dealers throughout major regional towns, CJD Equipment has the network in place to ensure businesses are well supported, no matter where their machines are. •
This year, Hitachi Construction Machinery will be officially launching new wheel loaders and excavators from its popular ZW-7 and ZX-7 series in Australia. Quarry finds out more.
Both owners and operators are set to gain from improvements in the new Hitachi ‘dash seven’ wheel loader and excavators as the new generation machines hit Australian shores this year.
Following on from the success of the renowned ZW310-5B wheel loader, Hitachi Construction Machinery Australia (HCA) is introducing the 24-tonne ZW310-7 model – a new generation 4.5 cubic metre wheel loader suitable for rehandling and sales loading application in aggregate or sand quarries.
Heralding a new era for digging, HCA is also launching three new models from its ZAXIS-7 large excavator series: ZX490LCH-7, ZX690LCH-7 and ZX890LCH-7. The Stage-V compliant large excavators promise up to 20 per cent in fuel savings, improved output and reduced life cycle costs compared to previous models.
Quarry sat down with HCA’s national product manager for wheel loaders David
Gallina and national product manager for construction excavators Bijesh Surabhi to learn more about the technologies embedded in the machines.
According to Gallina, new features in the ZW310-7 wheel loader mean higher productivity for the owners.
“The new ZW-7 wheel loader has been designed to give powerful performance, low total cost of ownership, and exceptional efficiency. Built to the highest quality standards, it will significantly boost productivity at busy quarries and have a positive impact on profits,” he told Quarry.
The new Hitachi patented Approach Speed and Rise Run control features contribute to lowering the cost of ownership, he explained. Short cycle loading operations are completed faster and more efficiently using the approach speed control feature with
a high level of productivity ensured by fast cycle times, high breakout force, loading capacity, and improved acceleration on inclines.
But that’s not all. There are other features in the ZW310-7 also contributing to higher productivity.
“As standard, the wheel loader operators can now work more efficiently and accurately thanks to the ZW-7 payload checker. It enables them to keep track of load weights in real time on the monitor and find out how much material is in the bucket or truck. The display shows when the bucket or truck is overloaded, so you can adjust the final load to achieve target capacity,” said Gallina.
“Combined with the new Stage-V compliant fuel-efficient engine with increased torque at lower revolution and intelligent computer aided lock up converter and transmission, you’re in total control to maximise productivity and increase efficiency.”
Operator safety improvements in the new ZW310-7 stand out, with the loader designed to offer better visibility, even in the reverse motion.
“The ZW310-7 allows for an unparalleled view from all angles, with superior visibility to the rear and either side of the narrow engine bonnet, combined with the aerial angle camera system, the operators have a 270° bird’s-eye view of the surrounding worksite,” said Gallina. “Safety is further enhanced by the intelligent anti-collision and warning system to alert the driver of any immediate dangers if anything is too close to the rear of the machine. The new standard intelligent system with improved vision helps protect the operator, site workers and the machine from potential hazards,” he added.
The operators of the new Hitachi ZW310-7 loader would also notice improvements with the redesigned pressurised cab, which offers more space, better quality, and a superior view of the surroundings.
“The ZW310-7 cab has one of the lowest noise and vibration levels in the market,” said Gallina.
The loader is equipped with seat mounted electric control multifunction lever and joystick steering, heated heavy duty seat with
horizontal suspension with a 75 millimetre wide seat belt with audible alarm. The armrest is integrated with a sub monitor controller (both dial and switches) to control the new high-resolution eight-inch secondary display on the right-hand A pillar.
“The new guidance display features provide the operator with a clear understanding of machine conditions, daily inspection reminders and real-time instructions to improve productivity and machine safety,” said Gallina. “During operation, the driver comfort is further enhanced by Hitachi’s new intelligent ride control function to prevent unnecessary machine pitching and vibration during load and carry cycles, keeping the operator in control and without fatigue.”
Hitachi’s new generation of ZAXIS-7 large crawler excavators, which continue to be manufactured in Japan, are also debuting in the Australian market this year, after a successful launch in the European market. According to Bijesh Surabhi, National Product Manager for Construction Excavators, the new generation of large excavators stand out for their Stage-V compliant engines, comfortable cabs and safety features.
The fuel savings benefit from a patented
Hitachi hydraulic system called Human and Intelligent Operation System (HIOS). The HIOS-V hydraulic system in the latest crawler excavators is a further evolution on Hitachi’s HIOS-IV, which facilitates quicker responses to more intuitive operator control.
“Through rigorous reviews focused on hydraulic loss, compared to the ZAXIS-6, Hitachi has achieved a reduction in fuel consumption of 11 per cent or more, and even greater performance when compared to the current ZAXIS-5 model sold in Australia,“ said Surabhi. “This hydraulic system also enhances efficiency in the swing, boom lowering and arm bucket roll-out. Productivity is further increased by the improved front speed for loading operations; and the increased engine output of the new ZAXIS-7 machines contributes to a higher workload. Operators now have the ability to alter the hydraulic priority between the attachment, arm roll-in and slew, so they can perfectly match the machine’s response to their operating style and preference. We have also retained the pilot operated hydraulic system (compared with an electric-over-hydraulic system), in order to maintain Hitachi’s legendary ‘hydraulic feel’.”
The fuel efficiency of ZAXIS-7 large excavators can also be controlled by using the new ECO gauge, Surabhi explained.
“Besides reducing costs, better fuel economy has a positive impact on environmental performance. The new excavators are Stage-V compliant, thanks to the combination of the Selective Catalytic Reduction (SCR) system, Diesel Oxidation Catalyst (DOC) and Catalysed Soot Filter (CSF).”
The cab comfort extends from the wheel loader to the excavators.
“The ultra-spacious cab is the perfect working environment for operators, offering reduced noise and vibration levels in the cab, which are both vital for the mining and quarrying industries,” said Surabhi. “Other new features include the synchronised motion of the seat and console – to reduce operator fatigue – and the adjustable console height with three positions to choose from. Easy operation comes from the ergonomic design of the console and switches, and the hi-res anti-glare screen is also easier to view.”
Job-site safety is enhanced by the exceptional view from the ZAXIS-7 large excavators. Operators can control their own safety, as well as that of those around them, thanks to the aerial angle camera system. It
have been built to last and maximise uptime. New engine parts enhance reliability, oil leakages are less likely and the durability of the trackframe has been improved,” said Surabhi. “In addition, the undercarriage of the ZX490LCH-7 has robust new components that prevent potential damage.
The ZX690LCH-7 and ZX890LCH-7 models are built with reinforced components that are ideal for the digging and loading of heavy materials. Strengthened to cope with the rigours of mining and quarrying, they provide lower costs over the machine’s lifetime.
”
The new ‘dash seven’ wheel loader and
The Australian designed Godwin NC80 rig pump from Xylem will be fitting into more mining drill rigs this year, with Xylem launching new variations into the market.
For years, the Godwin NC80 self-priming rig pump from Xylem has been a staple for drilling and shotcreting applications in underground mining. Products such as Sandvik’s DD421 jumbo have even opted to include this pump as an option in their original equipment manufacturer (OEM) package for sale to customers. Many others eventually retrofit the NC80 to their existing rigs, taking support from Xylem where necessary.
This year, Xylem is launching a new version of the Godwin NC80, with a 15-kilowatt (kW) motor. Earlier models had a 22kW motor. The new launch, as Xylem’s product and applications manager for the Godwin range, Jordan Thomson-Larkins explained, will make the pump applicable to a broader range of drills, including those manufactured by Epiroc.
Xylem has been manufacturing the Godwin pump locally, with a propelling technology borrowed from its flagship Flygt range of submersible pumps. Flygt’s innovative N-Technology features a semiopen N-impeller and a relief groove that work together to achieve self-cleaning ability. The shape of the impeller also means it’s well suited to passing of stringy and muddy water typical of drilling and shotcreting operations.
“The N-impeller and the insert ring allow stringy fibers to be passed through. We had
originally designed this product for the wastewater market, but it was later adapted to mining where we see a lot of similarities at a fundamental level. It’s perfect for pumping the shotcreting fibres, as it can chop the fibres in the process as well,” ThomsonLarkins explained.
According to Thomson-Larkins, Flygt’s N-Technology enables users to achieve substantial energy savings, often a minimum of 25 per cent compared to a conventional channel impeller pump.
The NC80 pump features fully automatic priming from dry to 8.5 metres suction lift. As a continuously operated venturi air ejector priming device, the pump also requires no periodic adjustment or control.
When compared with other models in its class, Thomson-Larkins said the NC80 also provided higher specifications, a better priming system, a better mechanical seal and a completely rebuildable wet end.
“Other products in the market generally do not include wear plates in their wet ends. Subsequently, they are basically thrown away. The NC80 is designed so that it can be rebuilt, thus extending the pump’s life, and reducing capital expenditure,” he explained.
A front and rear wear plate in the NC80 pump means the entire casing does not need to be replaced when servicing the pump. The mechanical seal in the standard NC80 pump is a silicon carbide dry-running high pressure oil bath mechanical seal, which according to
Thomson-Larkins is abrasion resistant and more durable than a tungsten seal.
“The silicon carbide has superior hardness, thermal conductivity and corrosion resistance compared to tungsten,” he explained.
Being a locally manufactured product, Thomson-Larkins said Xylem can offer customisation options where required. While the original pump comes with a hard iron wet end, other options such as cast iron and stainless steel are also available.
“We can also supply the unit in various kilowatts and with impeller diameters to suit the specified performance requirements,” Thomson-Larkins said.
Xylem’s in-house capabilities also mean the company can provide complete dewatering solutions to mines and quarries, beyond servicing and rebuilds.
“Xylem’s experience with dewatering solutions covers the entire water cycle. As such, we can guide customers on the product that best fits their needs,” said ThomsonLarkins.
Xylem will be launching the new 15KW Godwin NC80 Dri-Prime pump during the first quarter of 2023.
“This is a product that customers have been requesting for some time and we are very pleased to now be able to provide a solution that meets this requirement. They can trust us to back it up with our support and customisation capabilities to help them fit it onto their drill rigs,” Thomson-Larkins concluded. •
Crusher & Screen Sales Pty Ltd (CSSH) are the IMS distributor for Australia since 2012 and have been instrumental with IMS in developing plant for Australia conditions and requirements, there has been a strong emphasis on high quality plant for blending and pugging material for the quarry, construction industry, remediation of contaminated soils and blending of recycled products. The plant has been designed with large feed hoppers and capacity to service small to large operations with manual controls that in most cases have the ability to be fully automated insuring constant and accurate blending and reducing operator errors. IMS also manufacture a large range of wheel and track conveyors with production up to 2000 tonnes per hour and up to 45 meter long and screening plants.
CSSH and IMS together continual to improve their plant with feed back from clients and adjusting or adding new plant and ideas particularly in the blending of products to make previously discarded and recycled products into a sellable item, there is a strong desire by departments to add recycled concrete and other products into construction materials to reduce waste, landfill and raw material demands.
The IMS-PM1050-16Tb Track Pugmill is now the largest selling pugmill In Australia with capacity of up to 500 TPH, available in manual adding only water / liquids or fully PLC computer controlled and recording system adding cement, lime, or most powders etc. The PLC can be controlled by an iPad in the loader operating all the functions including
client or batch mix changes, loading truck and multiple trailers direct, stopping automatically once each item had been loaded with the correct tonnes and then restarted off the remote to repeat on the next truck or trailer. The recording system displays all batchers for the day and filing into projects or client names along with a summary of the total products used for the day for management control. All reports can be sent to the office or client showing the programmed percentages of each product compared to the actual results including a graph combining all the products processed. The control system can be integrated with other IMS products including electric modular blenders and pugmills offering up to four raw materials and multiple powders and/or liquids all blended at once.
•IMS- PM1050-16TB Track Pugmill with Silo option and full automation
•IMS – BP1200-9TB Track twin hopper blender with mixer
•Rubble Master (RM) Track 22x5 three deck screen
•Rubble Master (RM) Track 16x5 two deck scalping screen
•Rubble Master (RM) Track 18x5 two deck screen
•IMS – 24-meter track stacker with loader feed hopper
• IMS – 14-meter track stacker with five-meter loader hopper with tipping grid
•IMS- 20-meter track stacker with a 1200mm wide belt can produce 900 TPH and a 300mm rock
•IMS 15-meter wheel hydraulic stacker
Tracey Bence is a certified occupational hygienist, fellow and current president of the Australian Institute of Occupational Hygienists. Quarry reached out to her to learn more about silicosis and what the quarrying industry needs to know about this occupational lung disease.
Silicosis is an incurable lung disease caused by harmful levels of crystalline silica dust, usually over years. The main symptoms of silicosis are shortness of breath after exercising, chest pain, a harsh, dry cough and tiredness. But in the early stages of silicosis, there may be no symptoms. While chronic silicosis often results from exposure to silica dust over periods longer than 10 years, other versions of the disease, known as accelerated or acute silicosis, can lead to severe symptoms over a shorter period. If workers in quarries are exposed to high and freshly ground dust containing quartz, the risk of developing silicosis and even lung cancer cannot be ignored.
Unfortunately, there’s no cure for silicosis because once the lung is damaged, the damage cannot be reversed. But with enough awareness, the workers’ exposure and hence the risk can be contained, as Tracey Bence, President of the Australian Institute of Occupational Hygienists (AIOH) told Quarry
How prevalent is silicosis in the quarrying industry in Australia?
The sad truth is that we just don’t know. While laws have been changed in recent times to mandate the reporting of silicosis by medical practitioners, we know that not all workers who are at risk are being provided medical assessments and those assessments are not always of the highest quality. A study published by Curtin University predicted that 100,000 workers from various industries would be diagnosed with silicosis
and up to 10,000 Australian workers could develop lung cancer from exposure to silica dust. That’s why AIOH and many other health and worker organisations are supporting the National Dust Diseases Strategy and the proposed National Occupational Respiratory Disease Register so there is an obligation on doctors to report diagnosed silicosis and any link made to the exposure to silica dust.
What are the known causes of silicosis?
There are several illnesses caused by exposure to respirable crystalline silica dust, but silicosis is exclusively caused by breathing in very fine, mostly invisible respirable crystalline silica dust. Crystalline silica (Si02) is found in natural sources like sand, stone, quartz, but also in manufactured products such as concrete, and engineered stone.
The crystalline forms of silica, sometime called free silica can release dust particles so small (less than 10 micro meter or micron) that they are able to penetrate deep into the lung. The body’s inflammatory response to respirable crystalline silica is what causes lung cancer and silicosis.
What are the early symptoms? some of the symptoms for people with silicosis are shortness of breath after exercising, chest pain, a harsh, dry cough and tiredness. The early symptoms of silicosis are still not early because even once diagnosed silicosis only gets worse, progressing even after the person is no longer exposed to
respirable crystalline silica dust. There is no cure for silicosis. So, where we find a risk of inhaling the fine respirable crystalline silica dust in mining and quarrying workers, we must prevent exposure to this toxic dust.
Within the quarrying industry, who are at the highest risk of exposure?
Generally, occupational exposure risk is a factor of concentration and duration. In the case of silicosis risk, it is most associated with those tasks that involve high energy processes, mechanical equipment and freshly broken particles. Examples are crushing, screening, pulverising, blasting, drilling, dropping loads from heights, and even dry sweeping. In simple terms, the higher the amount of quartz in the material being disturbed, the higher the risk. So,
a focus on controlling silica dust levels is needed to keep people safe.
I would want people to learn more about the risks and how to control them through specific guidance from those in construction, mining and quarrying collated by occupational hygienists who are the people who go to sites all over Australia to measure silica dust and explain how to prevent silicosis. The advice can be found via www.breathefreelyaustralia.org.au and is called Breathe Freely Australia.
You mentioned silicosis is caused by the fine dust building up in one’s lung. How long does it usually take before there’s a risky level of build up?
There are many forms of silicosis. Chronic silicosis results from more than 10 years of exposure, but we are seeing accelerated silicosis now from exposure over less than 10 years, which is typically from excessive exposures in very uncontrolled environments.
One of the reasons why it’s tricky is that
when particles are smaller than 10 microns, they can hang in the air anywhere between eight minutes to 41 hours.
So, if you are dozing, crushing, moving a dusty load or breaking rock or aggregate, it takes far longer than you imagine for the fine dust to fall on the ground and no longer be in your breathing zone.
There doesn’t have to be a large cloud of dust for respirators to be recommended. It’s best to ask a hygienist or specialist in respiratory protection, what PPE you need to wear at work and when.
What are the recommended diagnostic tests and how frequently should they be done?
The best tests are those that measure for harmful levels of silica dust in our workplaces – not once the dust is in our lungs. But, if you are offered health monitoring, which may be described as a ‘silica medical’, make sure the doctor knows your occupational history and take any records of personal exposure (these may be available from an occupational hygienist or the regulator). Silica health monitoring should be offered to all
workers who are exposed to silica dust. Each state and territory has its own regulations for health monitoring for silica dust. For example in Western Australia, they have led the way for health by introducing five-yearly low dose, high resolution chest CT scan, which is known to give a much better picture of the damage caused by silica dust.
Measuring the dust concentration in air is the important first step to knowing risk to workers. Monitoring for respirable crystalline silica in air needs to be done by an occupational hygienist who is well trained in the equipment and method that must be used. It involves the worker wearing a small sampler around their breathing zone and attracting the dust onto a piece of filter paper using a battery-operated pump that runs for most of the shift.
Occupational hygienists measure the silica dust by capturing it on filter paper and that is how we know if harmful levels are getting into workers lungs. After the test, the filter paper is typically discoloured and dirty from the very fine silica dust. We then get the dusty filter weighed and analysed to get the concentration of silica dust and so quantify their personal exposure risk. If there is work in mines and quarries where there is risk of breathing in fine silica dust, the air should be monitored and the risk of life changing, irreversible harm from silicosis assessed and controlled.
What other measures are available to minimise risk for those working in the extractive industry?
We know how to minimise silicosis risk and it is all about preventing harmful levels of silica dust being breathed in.
Control measures that are known to be effective are:
• Mechanical, extraction ventilation;
• Dust suppression with water/wetting agents;
• Having pressurised vehicle cabins for keeping the dust out or filtering the air if it is getting in.
Other preventive measures include enclosure of crushing and conveying equipment, reducing speed of heavy vehicles on dusty haul roads, wetting aggregates and ores before they are dumped and reducing heights from which they are dumped to as low as possible. Hygienists recommend the avoidance of dry sweeping or using compressed air on anything that contains quartz.
If elimination of creating the fine dust is not possible, then protect the lungs with respiratory protection. Sometimes that means using a tight-fitting filtering P2 respirator, known as dust mask. When sealing properly and worn for as long as the fine dust hangs in the air (up to several hours) respirators can protect us from dangerous levels of fine silica dust.
What are some messages that AIOH is working to get across to help prevent silicosis?
This disease is preventable, we can control it, we need to measure it, then we need to move quickly to intervene. We don’t need to wait for someone to get silicosis or lung cancer. We can prevent it. All these preventative measures are wrapped up in the AIOH position on silica. Hygienists are the scientists of workplace exposure, and because we measure sometimes harmful concentrations of silica dust and know that silicosis is incurable, it’s clear to us what we have to do now – we’ve just got to be in the business of silicosis prevention.
My other key message is that there are always ways to work safely in mining and quarrying. We can certainly have healthy workers, with telling them about the hazards being step one. The workplace managers, engineers, people in charge of the resources and the policies should know enough about silica to make sure it gets measured.
The AIOH is so committed to preventing silicosis that we have compiled the best resources into a program called Breathe Freely Australia. I encourage all quarrying workers, managers, engineers, metallurgists, geologists and supervisors to learn how to breathe free of silica dust at: www.aioh.org.au •
Jason Freeman, Managing Director of Freeman Contracting Services, recounts why he bought the first Kobelco excavator for his business 12 years ago, and why he has stuck with the brand as his business has expanded.
When Jason Freeman bought his first second-hand Kobelco excavator nearly 12 years ago, his contracting business was much smaller than it is today.
Starting from humble beginnings in the late 1990s, the family-owned Melbourne business has grown substantially to now own a fleet of over 30 excavators, including 12 Kobelco units ranging from the two tonne Kobelco mini excavator to the 52-tonne SK500LC.
Freeman said what has not changed during this time, though, is the fuel efficiency and the reliability he can expect from his Kobelco machines.
Based at Little River in Melbourne’s west, Freeman Contracting Services started business in 1998 supplying fitters and boiler makers to the quarrying industry for quarry maintenance and fabrication.
As the team grew and the business was able to hire more competent tradespeople, it eventually moved to providing project work and campaign crushing. Today, the business provides a full range of crushing, screening, maintenance, demolition and equipment services to major quarries in the state.
“Our business has grown quite substantially over the years. At the peak times of business, we can have all of our 30 or so machines out working at quarries,” Freeman said.
With the industry struggling to produce trained operators fast enough to meet the increasing demand on the quarries, Freeman said his business was no exception.
“We pride ourselves not only in the range, quality and late model machinery, but also in the experience, knowledge and skills of our operators,” said Freeman. “We would have expanded our fleet size even further, but we are currently limited by the availability of skilled people.”
Freeman’s fleet features a complete range of equipment, from mobile cone crushers and jaw crushers to mobile screens, loaders and excavators.
In its excavator range, an SK500LC
and two 36-tonne SK350LC Generation 10 machines, purchased through local Kobelco dealer Melbourne Tractors, are among the latest additions to the company’s fleet.
Freeman said fuel economy was a key aspect for him in choosing Kobelco.
“These are fantastic machines and the best thing about them is that their fuel saving is excellent. Their reliability has been good, and the backup service is fantastic,” he told Quarry.
One way that the Kobelco SK500LC minimises fuel consumption is through the use of an innovative Boom to Arm hydraulic regeneration system. When lowering the
force generated by the boom’s weight as potential energy, redirecting pressurised fluid from the boom cylinder to the arm cylinder, which is used to extend the arm. This greatly reduces the need for the pump to supply oil to the arm cylinder during one phase of the dig cycle, thus saving fuel.
Kobelco’s ECO-mode control option helps further maximise the operating efficiency of the engine and other components to achieve much greater fuel efficiency. At the press of a button, the operator can choose the operation mode best suited to the task at hand and the working conditions, allowing the operator to choose between maximum productivity [H-mode], ideal balance [S-mode] or minimal fuel consumption [ECO-mode].
Using Kobelco’s GEOSCAN excavator remote monitoring system, data on fuel consumption and idling times can be monitored and used to indicate improvements in fuel consumption.
Cabin comfort was another parameter Freeman said he and his team appreciated in their Kobelco excavators.
“Our operators are happy with the machines. They are quite comfortable and easy to work with,” he said.
The Kobelco Generation 10 cab has falling object protection (FOPS Level 2) and its roomy dimensions make it comfortable for operators, as well as offering plenty of storage space. The cabin is mounted on long-travel viscous fluid filled isolation dampeners for minimal cab vibration and is pressurised to eliminate dust. This is in addition to excellent rear visibility thanks to the low engine cover and wide-angle rear-view camera that comes standard.
For hotter days, the large air-conditioner in the Generation 10 Kobelco has air vents on the back pillars that blow from behind and to the right and left of the operator’s seat. They can be adjusted to put a direct flow of cool/
warm air on the operator, which means a more comfortable operating environment.
Freeman noted the ease of servicing and maintenance with Kobelco. The Generation 10 Kobelco machines are designed with ample space in the engine compartment for a mechanic to do maintenance work inside. The layout also allows for easy access from the ground for many daily checks and regular maintenance tasks.
With full service packages available from Kobelco’s authorised dealers, including Melbourne Tractors, businesses like Freeman Contracting Services can access services year-round without a hitch.
With business booming and demand for quarrying contractors showing no sign of slowing down, Freeman said he considers more Kobelco machines in the future.
“These are fantastic machines. They do everything we need them to do, and I think we are going to see a lot more of them coming through,” he said. •
Saving time, money and providing a precise end product, the FM Pentium plant supplied by Terex Washing Systems is a must-have for dual purpose washing applications.
Maximising time and yield for material passed through a machine is a concern for all quarry operators. Targets are measured in price per tonne and subsequently tonnes per hour (tph) that are processed through a machine.
Utilising a novel screening method, the FM Pentium washing unit from Terex Washing Systems increases the efficiency with which quarries can wash sand and aggregates. It does this by being able to wash presized mixed sands and aggregates and discharging two saleable products.
The FM Pentium is a first of its kind for Terex Washing Systems, as sales manager Ben Willcox told Quarry.
“Normally when washing aggregates, quarry businesses would have to wash sand off as slurry,” Willcox said, “either treating the sand later or wasting it if they didn’t want to reclaim it.”
With the FM Pentium, that process can be skipped, as the sand can be washed away from the aggregate and then graded and screened as a separate product.
“Effectively, for operations that are processing both aggregates and sand, it’s cutting down on time which could be utilised elsewhere.”
A small footprint and high throughout rate further define the workhorse of the FM Pentium.
The FM Pentium takes the success of the FinesMaster range from Terex Washing Systems and builds upon it with its increased production and versatility.
The range combines a collection tank, a centrifugal slurry pump, a single or multiple hydrocyclones and a dewatering screen.
Emphasising Terex Washing Systems’ commitment to service, the FM Pentium units can be installed and operational on site in a single day.
“Every second that machines aren’t running, are seconds that our customers aren’t able to generate saleable material,” Willcox said.
“That is why we are committed and have the appropriate tools in place to get our machines up and running as soon as possible.”
Maximising throughput of material is of additional concern to quarries, with screening processes having the potential to be a natural bottleneck if raw material is not
being put through efficiently.
With a feed rate of 150tph for 0-40mm feed material and an output rate of 120tph for sand, even with the dual output, the FM Pentium is a contender for single material wash plants.
“Part of what makes the plant so effective is that it is cutting down on the number of plants necessary for operations,” Willcox said.
This is of particular interest for those
quarries that are solely producing one grade of aggregate and sand as a by-product. For plants that are just processing sand, it can produce a consistent and high-grade end product,” he added.
The consideration of waste has also been taken into account, with the plant as water efficient as other Terex Washing Systems installations.
“The slurry that would otherwise go to a tailings dam if there weren’t the tools to reclaim the water, can have value here,” Willcox said. “The fact that you have cleaner water going into the sump for future washing is a bonus.”
According to Willcox, there is currently one FM Pentium plant installed in Australia. Another one is in the planning stage and is set to be installed later this year.
Additionally, Terex Washing Systems is trialling an adjustable screen medium for these units, Willcox said.
“We have a patented screen that has
completed our rigorous NPPD test program.” “The adjustable medium will allow for one screen that can be changed to accommodate different sand and aggregate sizes, rather than requiring multiple screens of different sizes, the access to change media is beyond anything seen before.”
On a single chassis, the FM Pentium wash plant can produce one grade of sand and one grade of aggregate, filling a niche in the quarrying and aggregates industry.
There is stock available in Australia for the FM Pentium range to be tailored and fit to the needs of a variety of quarrying applications. •
OLI is the world’s top selling manufacturer of electric and pneumatic vibrators. The high level of customer service, guaranteed by 18 trading subsidiaries worldwide, and long-lasting and performing products make us always ahead.
Our vibrators are designed for industrial applications in all sectors, from the most extreme environments such as quarries, mines and foundries to the food and pharmaceutical.
Kayasand sees a future where quarries can turn the water off on aggregate washing by replacing their water-based washing systems with much cleaner and more precise dry washing systems.
When Japanese company Kemco first launched their innovative V7 sand manufacturing technology 20 years ago, they set out to revolutionise the way quarries produce concrete sand. They developed a new high-throughput, precision dry screening system that they called RCAS. This quad-deck dry screen combines the processing rate of air-classifiers, with higher accuracy than conventional screens and no dust emissions. It’s ideal for screening materials with high fines content or where accurate cuts of fine fractions are required. Kayasand has brought this same innovative technology to Australia, New Zealand, and the pacific islands.
The novel RCAS screening process uses a unique combination of high-volume air flow and mesh screen decks. It can accurately separate aggregates from 40 millimetres (mm) down to 75 micrometres (μm), and uses air to wash the aggregate rather than water. A blower creates an air-knife that raw material must pass through as it falls into the screening chamber. This blower spreads the raw material across a vibrating four-deck screen to maximise screen area utilization.
At the same time, a powerful dust collector sucks out ultra-fines from the coarse material before it even hits the screen deck. This, as Bram Smith, Kayasand’s general manager explained, results in cleaner aggregates passing through the screen and avoids blinding of screen decks caused by buildup of ultra-fines on the mesh.
“What you end up with is the throughput benefits of an air separation system, with the accuracy of a mesh screen system,” Smith told Quarry.
The action of the blower pushes the finer particles away from the feeder. This means the lightest particles travel further on the
screen, and spread more evenly, while the heavier particles drop down below the feeder. As material passes through the screen, a powerful counter current of air is sucked up through the decks and into the dust collector. It’s this reverse movement of ultra-fines in air through the screen decks that reduces the risk of blockage even further.
The combination of dust collector, skimmer and four screen decks, means the RCAS system can produce up to seven different precisely fractioned and de-dusted products from the feed. It’s ideal for a range of materials including quarry aggregates, limestone, recycled glass, recycled concrete, sand, quicklime and more.
According to Smith, there are many advantages offered by the novel screening approach. As well as higher throughput, which is typically double or more than that of conventional screens, it is also incredibly accurate. Installations in Japan achieve less than one per cent passing 0.075mm in the coarse aggregate fractions, while at the same time reducing the ultra-fines in the manufactured sand so it doesn’t need washing for use in concrete.
Perhaps the most exciting feature of the RCAS is the ability to eliminate water from the product screening process. As the ultrafines material gets extracted by the RCAS dust collector, there’s no need to wash the aggregate or the sand. Quarries can do without a wash plant and wash screens for final screening, and avoid the heavy costs of tailings management and waste minimization.
“In a quarry, you typically use water for three main purposes: wash down of plant and equipment, wash screens for coarse aggregate, and wash plants for manufactured sand. The latter two being the biggest
contributors to tailings,” said Smith. “If you remove those two elements and make them a dry process, you can have significant reduction in maintenance required for your silting ponds. Plus, the ultra-fines you extract using dry extraction can be used for other products.”
Smith said Kayasand’s goal is to help quarries slash their water demand by precisely screening sand without using water. This principle is embedded in Kayasand’s flagship V7 crushing and screening plant. It is designed to produce accurately graded concrete sand from any type of aggregate material. “We [at Kayasand] see a future where quarries can turn off the water on their aggregate washing process and replace it with dry systems that transform waste into products and by-products for use in all sorts of applications,” said Smith. “By removing the need for tailing control and the reliance on water, quarries can reduce costs and increased throughput.”
According to Kayasand’s Sales Manager, Frank Grech, the versatility of RCAS is a big benefit for quarries too.
“With products like limestone and recycled glass, accurately graded fractions find applications in a variety of markets. So, quarries can create a real value stream by tapping into those markets with their byproducts,” he said.
“Similarly, having a screen that de-dusts the coarse aggregate and crusher dust at the same time provides sand that is perfect for cement, concrete and asphalt production. By producing accurately cut fractions, the RCAS improves the consistency of those outputs.”
Versatility also finds another meaning when it comes to re-configuring the screening process.
“The RCAS screen is designed so that the screening decks are extremely easy to remove and replace. As such, a quarry can process one type of feed in one round and then change the configuration to produce other fractions or process a different material, with minimal delays.”
Reduced wear on the screen decks is another advantage in the RCAS. Although the use of an air blower and a dust collector, along with linear motion vibrating screens, can create turbulence inside the chamber, the elimination of water, and by extension cyclone systems, means less wear on screening surfaces.
“With RCAS, it’s the air flow that guides the material around, instead of it being dumped onto a screen. The screen area is used to greater effect, accuracy is preserved and there’s not the same wear and tear on the mesh system. It’s air with less wear,” Grech said.
Dust reduction is another side benefit of the RCAS screening plant. With the process taking place in an enclosed chamber and under negative pressure, any dust concern at the tertiary screening stage is eliminated.
“The dust collector is sucking the air at about twice the rate that the blower is blowing air. You can open the screen
chamber while it’s working and see the process in action. In most other plants, there’s too much dust to even get close to the screen.” The combination of high throughput, accurate screening and high efficiency in dry filler collection, makes the RCAS an ideal final screen for a variety of applications, according to Grech.
“If you need to screen products with
fine screen mesh, or deal with materials that have excessive amounts of fines, then this screening solution offers significant advantages,” he said. “Using the RCAS, you have a screening system that’s highly effective in cutting down to your desired fractions, controlling filler levels in the product, and producing a dry filler by-product, with no water, no dust and a lot of flexibility.” •
With beginnings in consultancy and design, ToThink Equipment brings boots on the ground experience to providing vibrating equipment for quarrying applications.
As important as having the most efficient machine on-site, is having the equipment knowledge to generate maximum impact and reward from the equipment.
This area is where Darren Toth and the team from ToThink Equipment stand out from the rest of the crowd.
Known primarily as ToThink Engineering, the business has registered a new addition in the form of ToThink Equipment that caters directly to the manufacture and distribution of vibrating screens, pan feeders and apron feeders to quarrying and extractive industry operations.
According to Toth, the development of ToThink Equipment stemmed from a desire to make machines and equipment that were designed by someone with experience in the extractive industry.
“With a commitment to manufacturing locally and supplying quality equipment, ToThink Engineering values the end build of the screens and feeders being not just to the quality that customers expect, but also to the quality that ToThink Equipment holds itself to,” Toth said.
The quality, which is a part of the offering from ToThink Equipment, comes from the partnership that ToThink maintains with suppliers such as Oli Vibrators.
As a distributor of Oli Vibrator motors, ToThink Equipment is backed by a trusted and well recognised motor manufacturer, further cementing the high quality the company aims to provide.
“We can put our hands on our heart and say that this machine won’t fail as it has an Oli motor in it,” Toth said.
Toth said having access to a good stock of Oli Vibrator motors locally and proximity to clients gave ToThink “an edge over larger companies in terms of lead times,” noting that “these bigger companies import complete machines from overseas.”
“One thing we have over larger companies
is that because we are manufacturing locally, we are in the same time zone as our customers,” Toth said.
“Knowing that they can come to us with questions and we’ll be able to get back to them on the same day and even get someone out to help them, is an aspect of our business which we’ve had really positive feedback from.”
Due to the local nature of ToThink, price of repairs and replacements also becomes lower, Toth said.
“When it becomes necessary to repair or replace parts for an original equipment manufacturer’s machine, there’s no debate whether or not to pay for freight overseas. We can dispatch the required parts to site within a couple of hours.”
“We want to support people in the industry with our machines,” Toth said. “We’re not hoping for our customers to need replacement parts, but if they ever do, they know that they’ll be able to get them as soon as physically possible and keep both their machines and outputs running at a high levels.”
All of the feeders and screens from ToThink are assembled in Victoria and, according to Toth, they can be designed with bespoke parts, depending on the needs of a quarry.
From Toth’s experience, the level of knowledge and understanding of vibrating equipment on quarry sites is “typically low.”
“A lot of the issues that we run into are that people are either unaware of how their vibrating equipment and feeders work, or they are operating them incorrectly. They might even have the wrong piece of equipment for the material that they are working with.”
“My team and I have experience and knowledge with these machines, so not only can we ensure that our customers are getting the machine that they need, we can also make sure they know how to use it correctly to increase the productivity observed on site.”
Toth said ToThink occupies a niche within the vibrating screen and equipment industry as it can quote and provide machines to fit specific needs.
“ToThink can provide machines that fit within the spaces of pre-existing machines on site, preserving the support structures present to save customers the cost of constructing entirely new infrastructure for ToThink’s screens.”
“Every second that machines aren’t running, is time that businesses aren’t able to generate profit,” Toth said. “The quarrying
industry needs all the support it can get currently and we’re aware of that, so by working with our customers we can provide these custom builds that incorporate what they already have.”
ToThink Equipment has a reputation for being well versed when it comes to vibrating screens and feeders. The company’s motto ‘Choose to Think’ reflects a desire to help
clients become self-sufficient with knowledge of their equipment.
“I’m committed to the industry and have given almost 20 years of my life to contributing to the industry,” Toth said. “I don’t want to help the industry by continually holding their hands. Rather, I want to see the industry thrive with the proper tools in hand to do so.”•
Eltirus’ team of professionals helps quarry operations improve their sustainability and enhance their efficiency with innovation. Eltirus Founder Steve Franklin writes about the state of innovations within the industry, reflecting on conversations from the International Resource and Mining Conference.
Irecently had the opportunity to attend the International Resource and Mining Conference (IMARC) in Sydney along with some 7800 other attendees. Over a threeday period, I attended dozens of different presentations by some of the best and brightest minds in the industry – from senior executives, to thought leaders, entrepreneurs and innovators. The experience was eye opening, impressive and thought provoking.
The impetus to attend came from one of our major clients – a senior manager who felt that the technological innovation that he was looking for was not going to be found within the quarry industry – and if not there, then where? After some debate, we decided that the best way forward was to look for solutions in a related field, in this case mining, and hence the visit to IMARC.
So, what did we find out and why do I think it has any relevance to our industry?
There was a strong acknowledgement by the presenters at IMARC that diversity and inclusion are important and in many cases these principles are now established
(or establishing) parts of many mining businesses. It was further noted that the next critical step for businesses was how they would meet the global challenge of decarbonisation – by way of example, it is expected that annual average demand for minerals to support decarbonisation will require a 60-100 per cent increase in output over the next ten years.
Interestingly, the mining industry also saw that their successful participation in global decarbonisation was the greatest opportunity the industry has ever had to reposition itself in terms of how the industry is viewed by the public. So, on the whole, there are exciting, challenging, and likely buoyant times ahead, working towards a common purpose of a decarbonised community.
The issue, of course, is how do you do achieve this? How do you turn ambition into strategy? The general view was that this would be achieved through the application of technological innovation, and as the
conference rolled forward, it was very clear that this was a topic forefront in most people’s minds.
There seemed to be two approaches. BHP was forthcoming in making it clear that they believed that the Australian mining technology sector was one of the best in the world and that they wanted to do everything they could to partner with it to leverage the advances.
In the same week, Rio Tinto advised the market that they were bringing all software development in house, setting up a group in Brisbane for this purpose.
Without getting into a debate about the rights and wrongs of these approaches, what is apparent is that there is groundbreaking and valuable technology right under our noses.
Whether it was autonomous haul trucks and equipment, battery electric trucks, advanced passive geophysical exploration tools or artificial intelligence (AI) driven diamond core logging and the smart software to make the most of these different technologies,
there was a group at IMARC displaying groundbreaking innovation.
It was also interesting to hear that the major companies were the ones pushing the manufacturers to create the electric and autonomous equipment they know they will need to achieve their sustainability targets. This is a welcome change. Some three years ago, my question as to when this technology was coming (to a senior manager of one of the major manufacturers) was answered with there was little interest in autonomous and electric equipment at that time. How things have changed!
If construction materials companies are to meet their sustainability targets, they will have to look outside of our industry. The concerning thing, however, is that they are going to go looking for those skills and technologies at the same time as they are already in short supply.
Whether the companies decide to develop these skills themselves or ask a partner –such as a dealer or a consultant – they may either not be available or be in such high demand that they will have to recalibrate their expectations for remuneration. This is such a problem within the mining industry that major players have had to create specialised autonomous technology training centres and develop whole new skill sets, training people from scratch to be able to deliver the type of services needed to support their autonomous technology.
At my presentation to the recent IQA National Conference, I predicted that autonomous and electric technology was likely five years away. More recently, my research would suggest that this timeframe
is likely to be significantly shortened, perhaps down to two to three years, from a technological sense. There is already a sixtytonne diesel haul truck running autonomous trials in Australia with the company concerned advising me that they will be ready to show it within three-six months. We are very much interested to go and see it in action and a quick ring around of key clients showed a great interest in attending the demonstrations.
We know that autonomous technology is on our doorstep and electric technology is not far behind, but I would posit that as an industry, we are not ready for it and further, that we need to make it a primary focus of our planning now, not later. We need to start preparing now – determining the skills needed, finding the people and training them, installing the communications bandwidth, the power and power storage capacity needed, designing our operations to accommodate these new machines and having the detailed plans and schedules needed to make them a success.
All of the speakers at IMARC who discussed these subjects had a clear secondary theme: change management. Specifically, they noted that operations needed help with new technologies to make it work and to
make it stick. It was not enough to introduce something new and expect people to figure it out. It requires real forethought and planning. They also want outcomes, not tools. One of the better sources of information on the change management that will be needed to bring autonomous and electric technologies to our industry can be found in the current (and upcoming) work of the Global Mining Guidelines Group (GMG) –well worth a look if you are interested in this area. They are currently working on the small autonomous haul truck (sub 100 tonnes) guideline and we at Eltirus are working with them to bring our experience of the construction and industrial minerals industry to this discussion.
Make no mistake, this change will come to our industry. Those who grasp it and work to make it their own will have a clear lead on their competitors. It will be a defining characteristic of their business and a selling point to the bright people they will need to hire to make it a reality, not to mention a make good of social responsibility and a major factor in determining both access to and cost of capital.
Will you ignore it until it’s too late, go for it alone or seek a partner? If it’s the latter, feel free to reach out to me. At Eltirus we have been studying this area for the past five years and we would be pleased to share what we know and compare notes. •
Jonny McMurtry, Chief Operations Officer at Precisionscreen, shares tips on how a company can keep its employees engaged, motivated and innovating.
The culture precedes positive results. It doesn’t get tacked on as an afterthought on your way to the victory stand. Champions behave like champions before they’re champions: they have a winning standard of performance before they are winners.
That’s a quote from Bill Walsh, the former head coach of American football team San Francisco 49ers and regarded by ESPN to be one of the greatest coaches in the NFL history.
Walsh’s quote was only one of the sports references in Jonny McMurtry’s presentation to Precisionscreen employees when he gathered the team for a number of culture building sessions throughout 2022.
Having recently completed his Master’s thesis in sports psychology and coaching with the University of Queensland, in conjunction with Rugby Australia, McMurtry has spent years studying what motivates young athletes, both on the field and away from high performance environments.
Lessons from the study, he said, have come in handy since he assumed the position of Precisionscreen’s chief operations officer in early 2022.
“I’ve been involved with Rugby Australia for over 16 years. Since I started my research with the University of Queensland, there was always the intention to introduce these
learnings into the workplace environment and to make Precisionscreen my case study. With the industry facing a shortage of skilled labour and the importance of retaining motivated team members, I think leading with empathy and understanding when in leadership or managerial positions is now more important than ever,” he told Quarry
As an Australian manufacturer involved in the design and manufacture of mobile screening, washing, crushing and recycling equipment, McMurtry said Precisionscreen has not been immune to the challenges of finding and retaining workforce.
“The industry-wide struggle in finding and/or retaining skilled labour, combined with a shift in our management structure and loss of significant amount of experience, led to our culture becoming an area of focus to help us retain our position as a designer and manufacturer of Australian machines,” he said.
“It’s not been easy but an internal focus on employee development and reaching out to new members of the industry by increasing the number of our apprentices and new trainees has helped us,” he added.
As part of this culture building exercise, McMurtry said the team has been engaged in a series of internal meetings, including a visit to the local footy field, to help them take onboard the management lessons and leadership techniques from his studies.
One management principle that McMurtry said he teaches and encourages line managers within Precisionscreen is to lead with empathy.
“The biggest thing is just understanding the person in front of you,” he said. “People carry a lot of baggage these days. We all lead very high information, high paced lifestyles. You might have a 60-year-old employee working alongside a 16-year-old apprentice. Their viewpoints on life, the skills they have, how they’ve developed their trade and even how they see the work-life balance can be very different from each other. So, what we try to instill in our senior and line managers is to understand the uniqueness of each individual through questioning, active listening and teaching or leading with compassion.”
This, of course, does not take away from the company’s own vision.
“Obviously, you have your morals and business ethics [to consider]. You’re aware of what’s important for the company, but at the same time being aware of what’s important to the individuals is critical so that you can get your message across, and have it heard, understood and appreciated at the same time.”
Another lesson McMurtry shares from his team building exercise is around building a
culture of honesty and accountability.
Burrowing from a well-known management lesson, McMurtry has been promoting the OARBED behaviour model within his team. The OAR part of the acronym stands for Ownership, Accountability and Responsibility, representing ‘above the line’ or ‘victor’ behaviour, while BED stands for Blame, Excuse, Deny, which is ‘below the line’ or ‘victim’ behaviour.
“Some of our biggest focus points this year are the mantras ‘focus on what is right’ as opposed to ‘who is right’ and not letting our fellow team members lie in BED (kicking out blame, excuses and denial) from our production process. We’ve worked hard to generate a culture of honesty and reflection to ensure we continue to grow and develop as a company and the individuals within,” said McMurtry.
“While we currently have a lean team, we want to make sure that the standards that we set are being met through the company so
that it doesn’t matter what position you’re in, it’s focusing on what is right as opposed to who is right.”
McMurtry said the outcomes from this team building exercise were already evident.
Recently, the team completed the design and manufacture of a bin feeder for safely loading bulker bags into existing Precisionscreen PLC pugmill units. The process, from concept discussion with the client to delivery onsite was completed within just six weeks – an outcome that McMurtry said was due to the “hard work and willingness to try new ideas of many employees.”
“One of the key theories that I come back to is the ‘Self Determination Theory’. This theory outlines three main areas which make self-determined and motivated individuals: autonomy (sense of control or input into their decisions and actions),
competency (recognised growth and development of themselves and their skills) and relatedness (sense of belonging to group or collective identity),” McMurtry explained.
But is it difficult to maintain a competitive edge as an ethical Australian manufacturer with the current market conditions?
“I don’t think it’s difficult at all. We obviously renumerate our employees adequately compared to industry standards; yet one of our big points of difference is the sense of purpose for our team: They get to see our machines designed, fabricated and finished. Australian machines, made by Australians, for Australian industries.”
“Ultimately what we’re trying to offer is a quality product that we can stand beside for Australian customers within the Australian market. That starts with our culture and making sure that we’re happy with the machines that we make. Beyond that, the score will take care of itself.” •
Rebecca Crompton, director at FEFO Consulting and an experienced strategist for health and safety initiatives, writes about the importance of managing health and safety when contracting.
Contractors are often engaged for their specialist skills or to assist with resource gaps. This can often lead to workers feeling under pressure to deliver and perform, particularly because the work is generally short in duration for a project or contract.
FEFO Consulting recently reviewed the benchmark data available through the Health and Safety Index and found Contractors were more likely to feel pressure to compromise safety whilst working compared with direct employees (25 per cent worse), and contractors are more likely to compromise safety by taking shortcuts (nine per cent worse).
Many may say, that is the contracting game – which is unacceptable morally and legally. Keeping people safe whilst they are working for or on behalf of your organisation must be at the heart of any contractor management approach, it can be easy to think contractor management and think compliance only.
When building out your plan to address contractor management in your organisation the initial step should be to consider the span of control and influence you have with the contractor in relation to health and safety.
Managing health and safety when contracting is not black and white. In, fact there are different risk profiles, different contract types and stakeholder requirements.
Once the assessment on the span of control is made, health and safety responsibilities and accountabilities throughout the duration of the work or contract can be applied with consideration given to a number of approaches:
• Organisation applie their safe systems of work.
• Organisation leads and directs the work.
• WHS performance captured.
Approach
• Contractor applies their safe systems of work.
• Contractor leads and directs the work.
• Organisation verifies contractual requirements.
• WHS performance captured.
• Contractor applies their safe systems of work.
• Contractor leads and directs the work.
• WHS performance not captured.
• When needed, the organisation will influence in accordance with the contract term.
If you set clear expectations early in the contractor lifecycle, this builds greater levels of trust, and can help to minimise the administrative burden of micromanaging contractors.
When considering contractor management industry leading practices, remember not all businesses are created equal. Different industries, needs, stakeholders and capability will influence decisions and what is practically needed to enable effective contractor management.
Qualities of industry leading practices may include some of the following activities:
• Use of third party prequalifying companies.
• Assessment of contractor safety performance.
• Risk rating for work to be perfomed by contractors.
• Placing contractors in charge of subcontractor safety and holding them to account to their standards.
• Verification of contractor safety periodically during the contract term. The different activities mentioned above may not be relevant to your organisation, so we recommend reviewing to ensure each item is fit for purpose. Further information on a practical, risk-based approach to contractor management can be found on our blog ‘Contractor Safety: How much is too much?’, including a free factsheet download ‘Six Steps to Contractor Safety’.
Rebecca Crompton is a director at FEFO Consulting, with experience in the end-to-end delivery of strategic health and safety initiatives that closely aligned with business performance and operational needs. Her core capabilities are in strategy, leadership development, management systems, critical risk management, contractor management, and critical incident response.
To understand more, register for the IQA Contractor Management online workshop scheduled for 18 April 2023. To register, visit the IQA website.
The Northern New South Wales sub-branch hosted three events across the Northern Rivers in November to mark the end of 2022.
The Respirable Crystalline Silica training workshop – which was at capacity – saw delegates learn from theory and practical examples at Holcim Teven Quarry. The program included a site tour and plant inspection with product demonstrations from Sandvik and Environmental Control Systems.
A Young Member Network (YMN) group
simultaneously enjoyed site tours of both Boral and Holcim Teven Quarries where both site quarry managers and supervisors generously gave their time to engage with the future leaders in our industry. To conclude the tours, Vanadium hosted a BBQ lunch for both groups.
On the same evening, a networking dinner attracted attendees from Newcastle, Armidale, Tenterfield, Warwick and Ballina. Sandvik and Environmental Control Systems provided presentations on their next level products and services. IQA would like to thank all attendees for a fantastic day in the north
There was plenty of fun and laughter at the inaugural IQA Queensland branch Trivia Night held in November. Queensland branch deputy chairperson Jason Egan was the perfect Trivia Master entertaining guests with his quarry jokes and keeping the night light with games, including the classic heads and tails.
Event sponsor AEG and the Queensland branch premium sponsors were given the unique opportunity to promote their company by providing several trivia questions relating to their organisations. The evening rounded off with a mix of movie, sport and music questions that trumped attendees from young to old.
The team from Ausrocks, otherwise known as “Aus-Rockers” on the night, took out the win. The wooden spoon prize went to “My Dancing Team has a Trivia Problem”, aka the young table, from Fulton Hogan. Special thanks go to prize sponsors, Ausrocks and Komatsu.
The Hunter sub-branch welcomed the first day of summer hosting its end of year networking dinner at Club Charlestown in Lake Macquarie. The afternoon commenced with a round of barefoot bowls and networking then settling in for an evening of relaxed formalities and a buffet dinner.
Guest speaker and event sponsor Chris Georgio of TASC Solutions provided an informative overview on the IQA’s leading range of technical and specialist training for the extractive and associated industry, covering professional development, mandatory competencies, upcoming education, and in-house corporate training tailored to your organisational requirements.
A lively bunch attended the Townsville Yacht Club on 18 November for a casino-themed games night. The event was sponsored by MS Fabrications, Sitech and Ritchie Bros, as well as our premium sponsors. IQA thanks them for their support of this event. The night was a great way to top off a successful year for North Queensland. The branch held several events this year in the Townsville region, including a golf day, a Health and Safety seminar, four dinner meetings, a golf day in Mackay and three events in Cairns.
The IQA’s Victorian sub-branch end of year networking dinner was held in Bendigo on 1 December with a record number of guests in attendance. More than 95 registered attendees enjoyed a fabulous dinner, which included a presentation from Rob Saxby, representing Komatsu, the event’s sponsor. Komatsu also donated a prize which was auctioned off with proceeds donated to the Black Dog Institute. Guest presenter, Richard Paterson from Basix 4 Blokes offered a compelling presentation about the importance of maintaining excellent mental health.
Members and non-members enjoyed dinner on 16 November 2022 and an informative presentation from Graham Lee, geologist at Graham Lee & Associates. Graham offered the attendees a glimpse into the ‘rock doctor’ world of in-situ resources found in the Illawarra and surrounding area, and the deposits within the greater Marulan area.
The presentation started with a mapping of all respective quarry and project locations that fall under the sub-branch area. He them moved through respective production, geology, and quality data. Graphical displays and pictures added a great visual appreciation as well.
The talk was well received by all and there were many interested patrons pursuing questions whilst networking. The crowd was very appreciative of Graham’s spiel!
The IQA’s Tasmania branch held a successful Tech and Social weekend tour of the Devonport, Ulverstone and the Latrobe area on 26-27 November. This year, a group of 33 attended the event. While Covid prevented
some local regulars from attending, we did have delegates from all over Tasmania, New South Wales, Queensland and New Zealand. After spending Friday night at the Argosy Hotel in East Devonport, the group got on the bus on Saturday morning to start the tour. Before leaving, Dugald Gray passed
around information of a Green Stone Adze (Axe head) which was found buried three feet down in a local gravel pit at East Devonport in 1935. This gravel pit would have been the original coastal shoreline and therefore also a camping area for the Tasmanian Aboriginal people. The Adze was found with remains of
ashes, seashells and other midden material. The Adze was made from Jade/Greenstone/ Nephrite material – likely from New Caledonia and brought to Tasmania by ancestors some 2000 years ago.
The first stop was just outside the local historic town of Latrobe, the location of the Mersey Valley oil fields. The oil fields were in boom times from 1910 to 1935, when the Latrobe oil shale fields produced an estimated 1.13 million litres of oil from historical underground workings. Amongst the Tasmanite’s early promoters was William Knox D’Arcy, who upon learning of the oil trade went on to found BP, having struck oil in one last desperate drilling attempt in Persia.
Second stop for morning tea was the famous Anvers Chocolates of Latrobe. Then onto Ulverstone, with a short stop at the Don to view a concrete underpass. This underpass was built for the highway many years ago, but in the wrong spot – so it was never used. Now, it stands in the middle of a paddock as a reminder to all to get the location right.
After lunch on the waterfront of the Leven River in Ulverstone, the group journeyed on to Simplot Ulverstone. Simplot was founded
by JR Simplot of Idaho, US, in 1929 and expanded into Australia in 1995 by acquiring iconic brands such as Edgells and Birds Eye. Simplot processes 270,000 tonnes of potatoes a year – and hoping to increase to 300,000 tonnes – purely for French fries. Last stop for the day was Spreyton Cider –which has been producing cider in-house since 2011.
Next morning, a smaller group ventured out to Devils road for a short walk to the location of the original underground workings for the Tasmanite Oil Shale operations. We found where the rope haulage/tramway used to be and one of the remaining adits. This was a fascinating visit and capped off what was a good weekend for all.
The IQA would like to thank Gary and Mary Richardson for their first Tech and Social weekend. Also, thanks to Stopford Drilling and Forze Explosives for sponsoring transport for the event. Shout out also goes to those who helped with historical and / or geological details around Tasmania Oil Shale. Dugald Gray, Professor Shane Pinner, ‘Buggie’ (Admiral Ron Bugg) and Peter Gray for connecting us with the Simplot tour.
Tasmanite Oil Shale is a siltstone, rich in the discoidal fossil algal cysts Tasmanites puntatus (10-70 per cent), which are 0.3 to 0.5 mm in diameter, amber to red in colour, and composed of “kerogen” which yields a variety of oils when heated and separated.
Tasmanite has advantages other Australian oil shales, because it can yield heavy hydrocarbons (e.g., a source of bitumen) as well a range of lighter petroleum products. The main fractionation products of oil derived from oil-shale include mineral spirits, gasoline, kerosene, diesel, lubricating oil, petroleum jelly, paraffin, bitumen, petroleum gas and impurities.
The oil shale was commercially worked by small companies and syndicates from around 1910 to 1935. The syndicates mined the shale from adits and shafts, conveyed it and crushed it, then heated the ore in a variety of retorts designed to distil oil from the hot gases.
The oil in the shale yielded about 130 litres per tonne of shale (range from five to 300litres/tonne), which compares favourably with other Australian and international oil shale deposits.
By 1911, when the government geologist W.H. Twelvetrees visited the field, the shale was being mined from a number of adits, transported via a rope haulage tramway to the treatment works, crushed, and retorted in a bank of four vertical retorts of a type pioneered by the mining company’s manager in New South Wales.
Mining activities were largely underground, generally involving simple manual methods based on the Bord and Pillar technique developed for coal mining. This approach was found appropriate for the average seam thickness of about five feet and the relatively faulted terrain, and was capable
of producing sufficient shale to feed the various processing plants erected by the successive operators.
Plans were developed to increase the level of shale production, utilising a mechanised Longwall technique, if and when the scale of the industry warranted, but these plans were never actuated.
Throughout the period, a wide range of different styles of retorts were employed to process the shale, with respective advantages and disadvantages pitted against each other.
In many ways, this ‘war of the retorts’ came to symbolise the development of the oil shale industry in the Mersey Valley.
On 30 June 2022, the Mining Safety and Health Advisory Committee (MSHAC) held the Respirable Crystalline Silica (RCS) forum in Brisbane. The forum had 70 industry stakeholders to discuss a range of topics including:
• current control measures to reduce dust exceedances;
• respirable crystalline silica size;
• lessons learnt from the coal mining industry;
• development of practical controls related to dust.
It was identified in the forum that there is still more work needed to ensure the controls that have been implemented across many of the quarries are maintained and monitored.
It is also imperative to ensure these quarries are functioning correctly and providing the desired reduction of dust at the source rather than having the dust become airborne.
It is essential that workers understand the risks and hazards associated with work activities and take the appropriate precautions.
Training in RCS explains what RCS dust is, the associated exposure hazards and your responsibility for controlling RCS exposure in the workplace.
For more information about RCS, or if you would like training for your team, contact IQA today.
For a full list of upcoming courses and to download a course catalogue, visit the IQA website.
Operator at Forze Explosive Services and Young Member Network (YMN) coordinator for Tasmania, Samuel Benson, talks about the importance of the YMN and the role it plays in the continued longevity of the quarrying industry.
What are the main benefits to joining the YMN and engaging with others in the industry through the YMN?
The mixed experiences and mixed knowledge and that cross pollination that you can be a part of by being able interact with other areas within the industry that you might not generally be exposed to.
For me personally, being identified as young member is fantastic when we do have the collective IQA events as it’s a signal to the more experienced members that I’m looking to learn and take on some guidance from those with more experience in the industry.
As coordinator of the Tasmanian YMN, what is some advice that you can share with the young people in and around the quarrying industry?
We have a smaller YMN here in Tasmania, but the community here and at the other IQA branches across Australia is an incredibly positive one, filled with opportunities to develop both my knowledge and career.
There’s so much collective industry knowledge shared here that can be accessed just by being involved.
The perception of the quarrying industry is incredibly important when it comes to the longevity of the industry, what role do the younger generations have to play when it comes to representing the quarrying industry?
We need engagement, both with other young people in the community and with the community in general. Things as simple as integrating ourselves as friendly faces and bringing awareness to the importance (and necessity) of our work in the communities we work near go a long way. A simple door knock is all it takes sometimes. In Tasmania, we have quarries and other operations that are part of sporting events, which can really help support the industry as we are showing that we are invested in our local communities.
What upcoming events are you most excited about from the IQA? Something that I’m looking forward to
I think that they’re quite important to the young members. I want to let young members in our community become aware that quarrying can result in a variety of careers, from operations to maintenance, management, and everything in between. There’s a range of trades that they can apply to within the quarrying environment. It’s aloo about getting in touch with them through outreach programs and events.
Has there been any long-lasting connections made through your time with the YMN?
Tasmania has a fantastic and well received IQA social weekend. Over the years, we’ve picked up all the names and faces of each other and it is really nice to be a part of this welcoming community. It’s a very diverse range of professions that are represented through the IQA within the industry and having everyone be in a social setting and able to share their experiences and opinions on things is incredible.
Is there anything you would like to share to help people join the YMN?
Reach out to the Young Member Network in your state. The coordinators are all on the IQA website and remember that the YMN is there for you. We are here to support you you’re your questions. We have access to a huge number of resources like training and qualifications. This support is not solely through the network, but also through the IQA as a whole.
And the best way to access it all is to reach
out and become a part of it as ultimately, we are about embracing members at all levels and really helping them progress through their careers to the position that they wish to get to.
IQA’S YOUNG MEMBER NETWORK:
The IQA’s Young Member Network (YMN) has been established to provide our young members and those that are interested in the quarry industry with guidance, support and an opportunity to develop successful career within the industry. Our national network has been established so likeminded young people can get to know their peers, share ideas and experiences, build key industry contacts and perhaps develop new friendships. The IQA’s Young Member Network is open to any IQA member 35 years old or younger.
What does the YMN provide for its young members?
1. Support and assistance in your current role by having a network you can turn to.
2. Forums and events at state and national levels targeted at young members, providing essential industry workshops as well as social interactions.
3. Guidance and advice on career paths with options for career development.
4. Assistance for those taking their first step towards professional recognition via the range of professional Development opportunities on offer.
For further information regarding the activities of the IQA’s Young Member Network please contact IQA on admin@quarry.com.au.
Training is one way to give your team the opportunity to discuss risk, controls and hazards in a safe environment and allow time to reflect on areas that can get missed in the day to day.
The IQA is a leading provider of training for the extractive and associated industries. Contact us today to help you plan cost effective training for your teams.
to decompose before they are covered by sediments and the process of fossilisation, which preserves their appearance, begins.
This is increasingly relevant, as up until a few years ago when work began at McGraths Flat, only four fossil spiders had been found in the whole of Australia. At McGraths Flat, researchers have so far unearthed thirteen spiders, which often are completely preserved.
A multitude of insect groups are also preserved in high levels of detail, which includes dragonfly nymphs, assassin bugs, cicadas and parasitoid wasps. Almost all of them represent species that are new to science and have not yet been named.
Though Australia is typically regarded as a dry and hot country, millions of years ago it was covered in rainforests. The McGraths Flat fossil site provides answers into the landscape of ancient Australia and additional information on how changes in climate impact ecosystems.
Every fossil provides a glimpse into a past world with plants and animals that are often very different to those that we can see today.
However, most fossils preserve only hard body parts like shells, bones, and teeth, which leaves palaeontologists with many questions about how organisms without hard parts looked like.
Equally challenging is the reconstruction of soft tissues, even if bones or other hard parts have survived.
A handful of fossil sites around the world preserve soft tissues of organisms, as such these sites are extremely important for studying how life has changed over time.
Given them the term “KonservatLagerstätten”, defined as fossil deposits that are known for exceptional preservation of fossilised organism, a team from the Australian Museum published an article in
the international journal, Science Advances, of a site found in Australia.1
Matthew McCurry, scientific officer and curator of palaeontology at the Australian Museum, was a primary author on ‘A Lagerstätte from Australia provides insight into the nature of Miocene mesic ecosystems’.
The Konservat-Lagerstätte site, located in central New South Wales, was named McGraths Flat, after Nigel McGrath who discovered the first fossils at the locality.
McGraths Flat provides unprecedented insight into the time of the Miocene, approximately 15 million years ago, when rainforests covered most of Australia.
The site contains a range of fragile and soft-bodied organisms that are normally missing from the fossil record, like insects or spiders.
Normally, soft bodied organisms tend
The site holds additional significance, because of how it holds information about how the changes in the climate impacted ecosystems. Through using pollen and spore grains preserved in the sediments at this fossil site, researchers were able to date the fossils to the Miocene epoch, a time where Australia changed dramatically. Widespread rainforests were replaced by the deserts and shrublands that now dominate the landscape and present in the fossils, is some evidence that the ecosystem was in a state of change. The pollen suggests that there might have been dryer habitats surrounding the rainforest, which indicates that rainforests in NSW might have already begun changing into dryer habitats at the time. Over the coming years, researchers have plans to continue excavating the site to learn more about the Miocene environment and to use the gathered information to better predict how modern Australian environments may respond to climate change. •
AUSTRALIA’S FIRST EVER ONLINE PORTAL DEDICATED TO BUYING, SELLING AND HIRING QUARRY EQUIPMENT.
For
We are a global team unified in a common purpose: creating advanced technology solutions to the world’s water challenges. Developing new technologies that will improve the way water is used, conserved, and re-used in the future is central to our work. Our products and services move, treat, analyse, monitor, and return water to the environment, in mining, quarry, public utility, industrial, residential, and commercial building services settings. We also provide a leading portfolio of smart metering, network technologies, and advanced analytics solutions.