AN EFFECTIVE DRONE PROGRAM
The introduction drones has had a revolutionary effect on a range of industries, quarrying chief among them.
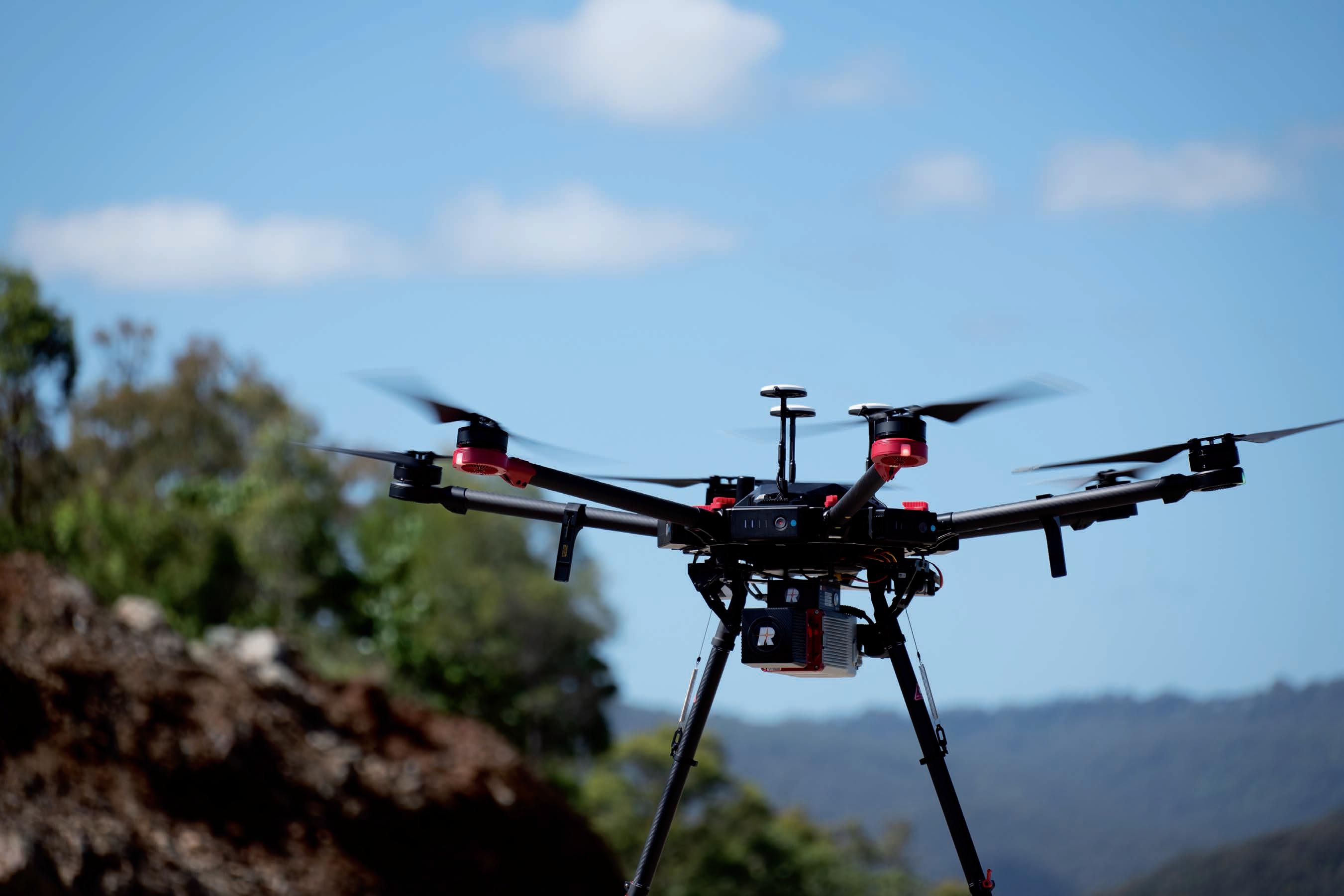
POWERING TO THE RIGHT SOLUTIONS
SKF understands the need to approach a quarrying issue with a holistic view.
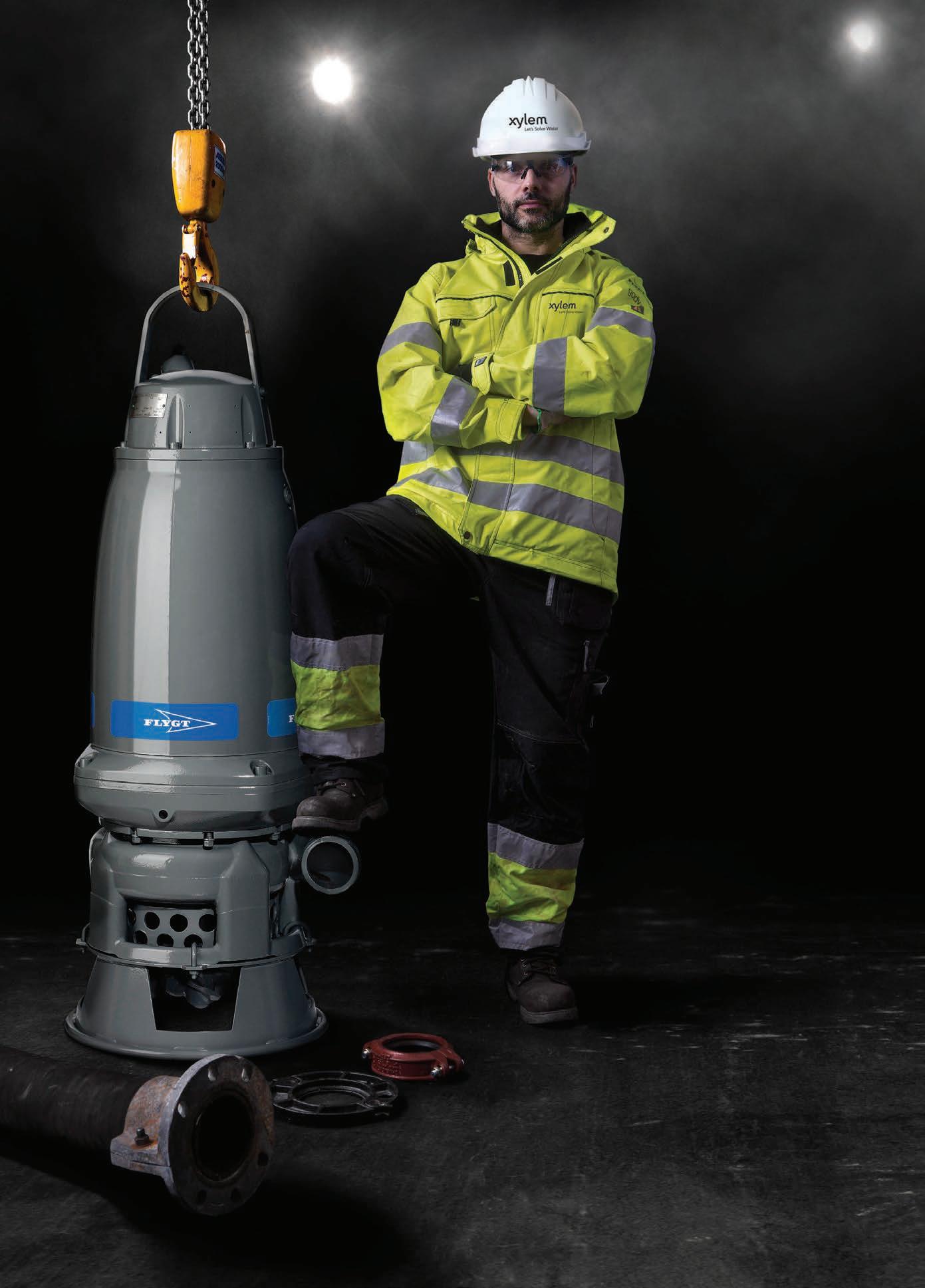
The introduction drones has had a revolutionary effect on a range of industries, quarrying chief among them.
SKF understands the need to approach a quarrying issue with a holistic view.
Smart Construction technologies are creating lucrative business opportunities for quarries through integrated connectivity solutions. Komatsu’s Smart Construction is a complete digital transformation package, encompassing everything from intelligent machines, to drone data, fleet management solutions and a whole suite of applications, aftermarket solutions and services.
Call us today on 1300 566 287 to find out how Komatsu’s Smart Construction can help your site.
A deep dive into the rehabilitation of quarries that are no longer in use.
SKF understands the need to approach a quarrying issue with a holistic view.
Embedding sustainable practices is critical in ensuring the long-term success of a business.
Limestone has been used across the world for thousands of years.
Maxam is ready to provide experience, tools, technology and services to help clients perform efficiently and effectively.
Together with the Digital Data Chain Consortium, VEGA wants to advance the digital twin of its instruments.
After earning a degree in environmental science, Mikayla Schwarz never thought she would end up working in the same industry as her dad.
MAXAM is the leading provider of integrated blasting solutions to the Australian quarries and construction industry with the largest and most comprehensive national network of operational depots and supply hubs dedicated to providing explosive products and specialist services to over 200 sites nationally.
MAXAM is focusing on customer solutions, bringing a new perspective to the explosives industry. This new process is based on adding value and helping reduce customers’ total cost of ownership (TCO) through the intelligent application of explosive energy to drive significant downstream savings in drilling, haulage and crushing costs .
MAXAM’s best practice process ensures that desired outcomes are met and risks managed through experienced people applying solid processes that are supported by advanced design and analysis tools. In this way, the company provides experience, tools, technology and services that help clients perform their engineering projects efficiently and effectively.
Contact MAXAM for your local specialist: +61-7-3717 1818
It seems we say it every year – or at least we have since the start of 2020 – but the last 12 months has been a period of major change.
Ever since Australia began to emerge from the COVID pandemic and started its first tentative steps on the path to living with the virus towards the end of 2021, industries have seen a lot of movement in terms of staff.
There has been considerable change across the entire country.
And so it is in the extractive industries.
At two conferences I attended in recent months, the conversations I most commonly overheard or were involved in seemed to be some variation on the idea that lots of people were leaving or – just as crucially – entering the industry.
As you’ll no doubt read on the next couple of pages, Institute of Quarrying Australia (IQA) President Shane Braddy is finishing his time in the role.
Having been President since 2019, Shane was on board at the start of the earth-shifting pandemic and helped to steer the IQA (and, indeed, the quarrying industry) through perhaps the most tumultuous period in its history.
He helped put the protocols in place to keep people safe and allow the industry and its professional body to continue thriving.
On behalf of the publication, I’d like to thank Shane for his enormous efforts over the past three years.
It’s safe to say those efforts will not soon be forgotten.
Looking at this latest issue of the magazine, the October Quarry is full of the usual top-notch content the industry expects.
Eltirus founder Steve Franklin takes us through how a company-wide drone program, including the software to process the data from these
machines, has had a revolutionary effect on quarrying.
From accurate stock management to improved collaboration across the business, an effective drone program can be a major boost to any quarry operation.
But that program takes time and effort to set up, and Franklin outlines what needs to be done to ensure a business gets the most out of its investment.
Elsewhere in the magazine, we feature the usual great content about the best and brightest pieces of equipment for the extractive industry, from rugged on-the-ground machines to finely tuned digital solutions.
We also shine a light on a great example of quarry rehabilitation and take a close look at limestone, the true multi-use rock.
Getting back to the idea of transition, I’d like to thank our outgoing editor, Maria Highland, for all of her hard work on Quarry
Maria may have only been on the publication for a few months, but she made a genuine impact and worked tirelessly to produce a rich and full magazine every month.
Maria leaves Quarry in a better place, and I’ll always be grateful for her unwavering efforts.
But Maria’s absence of course opens the door for a great new Quarry editor, who will start on the publication before the end of the year. In the meantime, I will step in as a ‘guest editor’ for the time being.
The time for transition is here – and it’s very exciting.
Paul Hayes Editor“ON BEHALF OF THE PUBLICATION, I’D LIKE TO THANK SHANE FOR HIS ENORMOUS EFFORTS OVER THE PAST THREE YEARS. THOSE EFFORTS WILL NOT SOON BE FORGOTTEN.”
Published by:
11-15 Buckhurst Street
South Melbourne VIC 3205
T: 03 9690 8766
www.primecreativemedia.com.au
Chief Executive Officer
John Murphy john.murphy@primecreative.com.au
Editor
Paul Hayes
paul.hayes@primecreative.com.au
Business Development Manager Les Ilyefalvy les.ilyefalvy@primecreative.com.au
Client Success Co-ordinator
Ben Griffiths ben.griffiths@primecreative.com.au
Design Production Manager Michelle Weston michelle.weston@primecreative.com.au
Art Director
Blake Storey Graphic Design
Kerry Pert, Tom Anderson
T: 03 9690 8766 subscriptions@primecreative.com.au
The Publisher reserves the right to alter or omit any article or advertisement submitted and requires indemnity from the advertisers and contributors against damages or liabilities that may arise from material published. © Copyright
– No part of this publication may be reproduced, stored in a retrieval system or transmitted in any means electronic, mechanical, photocopying, recording or otherwise without the permission of the publisher.
As this is my last President’s editorial, I would like to share what I have learnt over the past three years, where we are now and where we are going, and to recognise and thank those who have supported me and the IQA.
I have had the enormous privilege and honour to help contribute to the progress of the IQA’s vision and objectives as a director, Deputy President and as President, including as Chair of the IQ International Presidents Committee.
When I became Deputy President, I could see how much there was to learn. Fortunately, we have a great onboarding process for the incoming President.
My sincere thanks to IQA Company Secretary Rod Lester, who oversees what is the most rigorous governance process and procedures that I have ever experienced. Anyone who wants to participate on a board should strongly consider the IQA as an excellent pathway to gain first-class experience and education as a director.
The past three years have seen many challenges, which we have largely overcome. The pandemic arrived just as I started my time as President and presented the most significant event in our long history.
First and foremost, we had to protect our members and supporters. We developed and implemented COVID-19 protocols, systems, processes and awareness programs.
We responded positively, quickly and effectively, postponing several events, including the October 2021 IQA National Conference that was eventually held in March 2022. Of course, that too almost didn’t happen as we undertook our risk assessment review. But the conference was ultimately held, and what a celebration it was. I have this wonderful memory seeing our members finally mixing after two-and-half years of mostly virtual meetings and events.
As a result of significant revenue reduction due to delayed (and in some cases cancelled) events, we had the added responsibility to protect the IQA’s hard won financial position, which had improved after merging with the Australian Institute Quarrying Education Foundation (AIQEF) in 2020.
We were fortunate to receive support from the Federal Government that enabled us to keep our entire administration team employed at a time where there was so much uncertainty.
Our state branches and their subbranches performed magnificently, holding events when they could, with people attending in great numbers. Having previously been a Victorian Branch committee member, and later Chair, I know how strong and dedicated our members are in every branch and sub-branch, and I knew their resilience could weather any storm.
And weather the storm we did. We have more members than in 2019, the Women in Quarrying program has gone from strength to strength, and our educational programs have been revamped and developed so most can be delivered virtually or in-person.
I am thankful for our CEO Kylie Fahey. I finish my time proud that we have the first female CEO who is making such a difference to how the IQA is managed and perceived, which is extremely important when collaborating with state regulators and employer bodies, such as Cement Concrete and Aggregates Australia (CCAA).
We have excellent relationships across the spectrum of industry suppliers, employers, employer representative bodies and government, which will pay dividends as we implement our transformation and growth projects and programs.
It makes me proud to see how far the IQA has come since I first became a member in 1989. However, we are not complacent nor comfortable, and understand many of the transformation projects are still be implemented.
1989. HOWEVER, WE ARE NOT COMPLACENT NOR COMFORTABLE, AND UNDERSTAND MANY OF THE TRANSFORMATION PROJECTS ARE STILL BE IMPLEMENTED.
The IQA’s Strategic Plan 2020 to 2025 embodies the following vision, values and strategic priorities:
Vision:
Educating and connecting our extractive and associated industries.
Values:
• A safe and sustainable environment.
• Diversity and inclusion. Working development skills, careers and lifelong learning.
• Networking, connection, trust and communication.
Strategic Priorities:
• Maximise outcomes for industry through education and sustainable practise.
• Increase our relevance.
• A high performing and sustainable organisation.
Phone: 02 9484 0577
Email: admin@quarry.com.au
For all education, member and branch enquires please email: admin@quarry.com.au.
We recognise there is significant work to be done, and we are guided by our strategic plan priorities:
• Maximise outcomes for industry through education and sustainable practice
• Increase our relevance
• Ensure a high performing and sustainable organisation
Your IQA Board has commenced a significant review of where we are today and where we need to be. Comprehensive market analysis has been completed, identifying eight key result areas in which projects are currently being scoped.
The Board has committed significant investment to support these transformation
projects, and I will watch with pride as they are delivered.
We identified the burning platform for transformation early in 2020 and we must remain focused, maintain momentum, and stay on the right track.
The Board has approved funding in the FY23 budget to conduct an external review of our strategy, programs, and delivery mechanisms. This will help refine and shape projects in the eight key result areas.
I wish the incoming President, elected at the Perth AGM in September, his or her deputy, returning and new directors all the very best. I assure you, our members, that we are in very good hands.
Thanks to the many who supported me during my three-year term, especially to my wife Julie and my family, who have encouraged me throughout.
To all our members and supporters, thank you for remaining committed to the past, present and future of the IQA. It has been a privilege and honour to have served you and I will continue to support the IQA wherever I can.
All the very best of health and happiness for the future.
President Institute of Quarrying Australia (2019–22)
Vapes and e-cigarette devices have been linked to global spontaneous combustion over the last 12 months.
Vapes and e-cigarette devices have been linked to spontaneous combustion events in the US, UK and Australia over the last 12 months.
The WA Department of Mines, Industry Regulation and Safety (DMIRS) last year received a report of an incident at a mine where a vape battery spontaneously ignited in a worker’s pocket while travelling in a utility.
The potential risk and consequences of a vape battery explosion and fire in
an underground mine, quarry or in the vicinity of an explosives magazine or fuel facility are potentially catastrophic and as such then DMIRS has made note of the danger.
The department’s director of dangerous goods and petroleum safety Steve Emery has highlighted the key actions required to avoid the hazards associated with vapes.
This event is consistent with reports of other vape devices spontaneously
combusting in the US and UK, some of which have resulted in fatalities. The vast majority of those injured have been people with vape batteries in their pockets when they exploded.
Those carrying devices on-site were also found to have had conductive materials such as coins or keys in their pockets, which increases the likelihood of a short circuit occurring.
A recent study led by researchers at George Mason University estimated there were more than 2000 visits to US emergency rooms from 2015–17 for vape burns (thermal and chemical) and explosion-related injuries.
A Health NSW fact sheet states that “the products available in Australia use a wide variety of parts and are sourced from many different manufacturers, including overseas manufacturers where safety and quality controls are unknown”. This which includes the quality and safety of the lithium-ion batteries used in vapes.
Given the potential consequences of these occurrences, the risks associated with vapes being carried on quarry sites, particularly in potentially hazardous areas, should be reviewed and preventive and control measures developed and implemented. •
Rino Recycling has invested in a new automated waste processing plant in Pinkenba, Qld, in partnership with CDE and Turmec. The plant will provide the construction industry with a quality alternative to virgin quarried material.
Integrating wet and dry processes, the hybrid plant is set to improve waste recovery rates in the Brisbane metropolitan area and divert high-value construction materials away from landfill.
The plant will have the capacity to recycle more than 800,000 tonnes of material every year to meet the growing demands of the region and will divert an additional 90,000 tonnes of waste from landfill.
The recycling solution is also expected to save over 8400 tonnes of carbon entering the atmosphere. The project also features
an automated aspect to minimise the need for operator intervention.
The plant will accept a variable waste stream comprising of commercial skip and bin waste, hydro excavation waste, crushed concrete, and excavated fills.
CDE and Turmec will engineer an interconnected system to accept incoming feedstock.
Feedstock will initially be processed via Turmec’s dry mixed recyclables plant to separate fines and removes contaminants before processing through CDE’s advanced wash plant solution to produce a range of recycled sand and aggregates of virgin material quality.
Linked by a network of conveyors, waste material will transition between the wet and dry systems without manual input.
“The completion of this integrated hybrid plant will be the first of its type around the world and will pave the way for the future of recycling,” Rino Recycling general manager Daniel Blaser said.
Operating alongside the core processing plant will be CDE’s Hydro:Tip solution to handle non-destructive digging muds with ease and efficiency. This will enable Rino Recycling to process waste mud in a costeffective and responsible manner while recovering recyclable materials that can be re-sold to generate additional revenue.
According to CDE business development manager Jason Hartmann, the hands-off approach is a defining feature of the plant. .
“This solution from CDE and Turmec will increase the total availability and throughput of the plant,” he said.•
An effective drone program is a fundamental part of modern quarry operations. We can work with you to identify your needs and provide an end-to-end solution consisting of the right drone for your business, all the accessories and software and training needed to support you every step of the way. Talk to us about how we can help you build your drone program and get you in the air.
Adbri reported that revenue has increased up to $812 million.
Leading construction material and lime producer Adbri reported revenue has increased up to $812 million at the end of financial year (FY) 2022.
Adbri has reaffirmed a commitment to execute strategic priorities to deliver business improvement and growth through a focus on reducing cost and improving operational efficiency to transform the lime business.
Discussing the challenges faced by the business and the execution of strategies for the future, Adbri’s managing director and chief executive officer Nick Miller said that the cost-reduction strategies employed by the company will shape growth in the future.
“We have delivered another period of top line growth, with increasing volumes across the majority of our product lines as strong demand continued in the construction and mining sectors, despite significant disruption to the business as a result of severe weather events on the east coast of Australia,” Miller said.
“The company has actively managed its pricing strategy to partially mitigate significant inflationary pressures while continuing to execute our costreduction program to deliver savings and protect earnings.
“Adbri enters the second half in a robust financial position to advance
key strategic initiatives including the Kwinana Upgrade project, the Kalgoorlie kiln definitive feasibility study and the performance of recent acquisitions.”
Following the impressive results, Adbri has also announced the recent appointment of Dean Jenkins as an independent non-executive director.
Jenkins is an experienced executive who has held senior leadership positions across the transport, manufacturing, engineering, energy and resources sectors both in Australia and overseas.
His appointment is part of the Adbri board’s commitment to restore a majority of independent directors following the recent retirement of long-serving independent non-executive director Ken Scott-Mackenzie.
Through the growth of concrete and aggregates, enhancing capability in infrastructure and actively managing land holdings, Adbri has plans to increase an already solid financial position through 2022.
“We expect growth in underlying earnings for 2022, driven by increased contributions from cement, concrete, aggregates, masonry, joint ventures and recent business acquisitions, subject to weather, inflationary headwinds and traction with out-ofcycle pricing,” Miller said. •
Sand and gravel supplier Burdett’s has invested in a dredge and dry-fed wash plant from CDE at its new greenfield site in Lang Lang, Victoria.
The company wanted to relieve pressures on its existing operations, maximise operational efficiency and add value to existing products. CDE designed and installed a 250-tonnes-per-hour wet processing solution to produce highquality washed sands.
The plant incorporates a dual EvoWash sand wash plant, dredge sump, infinity design ProGrade screen, feed hopper and dual sliding blending conveyors.
EvoWash screens and separates smaller sand and gravel fractions via an integrated high-frequency dewatering screen. CDE’s ProGrade screen separates out the 15mm and +5mm fractions, delivering a high powerto-weight ratio and reducing power consumption.
The have an independent spray bar assembly protected from vibration, helping to ensure durability and allowing Burdett’s to meet production targets.
CDE’s classification and dewatering technology increases the accuracy of separation and delivers high-quality
product with less than 15 per cent moisture content straight off the belt, eliminating the need for drying.
Burdett’s needed a plant with flexibility to take a dry excavated feed and a dredge feed. The conventional mining process of extracting material from water and leaving it to dry and dewater is extremely labourintensive and increases operational costs.
CDE commissioned a dredge feed system, so once Burdett’s reaches the water table it can dredge wet slurry feed to the plant. This removed the intermediatory step of dewatering materia, reducing operational and labour costs. •
United. Inspired.
We’ve been involved in the mining and steel industry since the 15th century. All that know-how is built into all our rock drilling tools – for your benefit. Our Rock Drilling Tool Selector is design to help you find exactly what you need to optimise your operations. Ultimately, that means excellent hole quality and low-cost drilling for you.
New Hope Group has surrendered environmental authority and mining leases for the site, which was subject to open-cut coal mining in the 1980s.
New Hope made the decision to backfill the voids, reshape and rehabilitate the area to meet community expectations, chief executive Rob Bishop said.
“The extensive rehabilitation works were conducted between 2014 and 2017, with ongoing works undertaken over the past eight years,” he said.
“Our progressive rehabilitation program at New Acland returns mined land to agricultural and conservation uses while contributing to the region’s agribusiness industry.
The Chuwar coal mine in Ipswich, Queensland, is the first open-cut coal mine in Queensland to be fully rehabilitated. The Queensland Government critically assessed
the project and concluded that all rehabilitation requirements had been met in full, deeming the site safe, stable, non-polluting, and able to support grazing.
“To date, more than 740ha of land has been rehabilitated at New Acland. At the time of the Queensland Government’s announcement, it was the largest single area of certified rehabilitation for an open-cut coal mine in Queensland.
“To put the size of the area in context, the certified, rehabilitated land at New Acland covers about 300 Suncorp Stadiums.”. •
CEMEX will expand trials of zero-emission concrete mixers after successful trials across Europe.
The mixers were first tested in Poland, following initial trials in Germany and France, among others. The trials used the Putzmeister iONTRON e-mixer fully electric ready-mix concrete truck.
The prototype vehicle is 100 per cent powered by electricity.
The manufacturer provided a mobile charging station for use during the trials, which enabled the concrete mixer to be charged from 20 to 100 per cent in eight hours.
“Transport is one of the key areas where CEMEX is striving to reduce carbon emissions,” CEMEX mobile equipment fleet and category manager – Europe Craig Hooper said.
“Our company is constantly looking for new, more environmentally friendly transport solutions, hence the decision to conduct extensive pilot studies to verify the possibilities offered by electric concrete mixers.
“The positive results of the trials in Europe now allow us to think positively about the potential implementation of these vehicles, which will bring CEMEX closer to achieving its climate goals.”
CEMEX joined the First Movers Coalition in 2021. As part of this move, the company has committed to accelerate innovation and development of decarbonisation technologies in heavy road transport services.
The planned investment in zeroemission vehicles will contribute to the fulfilment of these commitments.
It is also another step in the implementation of CEMEX’s ‘Future in action – Committed to net zero CO2’ strategy towards being a zero emissions company.
The strategy was announced in February 2020 and outlines goals CEMEX intends to achieve by 2030.
This includes plans to be below 475kg of CO2 per tonne of cementitious material. This is the equivalent to a 40 per cent reduction (according to its 1990 baseline).
CEMEX also has plans to reduce the carbon content per cubic metre of concrete to 165kg. This is the equivalent to a 35 per cent reduction (according to its 1990 baseline) and to reach 55 per cent in clean energy consumption. •
John Deere has an unrivalled reputation globally for dependable quality, proven reliability, outstanding durability, and strong performance. And now excavators designed, built, and backed by John Deere are available for you to put to work right here in Australia. Ergonomic automotive-quality styling, 7” touch-screen monitor, and intuitive controls deliver maximum productivity all day long. Together we’ll meet even the toughest demands.
It’s a New Day and a New Deere.
Scan to learn more
The awards are an invaluable opportunity to recognise not just the nominees and winners, but the hard work and dedication of all women in industries such as mining, road transport, manufacturing, engineering, logistics, bulk handling, waste management, rail and infrastructure.
Marshall has been leading the Fulton Hogan team as general manager for over three years, while also serving as board director for the Australian Constructors Association. She has spent her career spearheading positive change in the industry by driving sustainability, improving culture, and driving improvements in gender diversity.
The 2022 awards were sponsored by Atlas Copco, Weir Minerals, and Komatsu. Commenting the awards, Komatsu expressed pride in its sponsorship.
Recognising and celebrating the contributions made by women in the industrials sector, the Women in Industry Awards took place in Sydney on September 8.
Fulton Hogan general manager Sarah Marshall was one of the big winners for the construction and quarrying industry, taking home the Excellence in Construction and Woman
Fulton Hogan was a major winner for the night, coming out on top in multiple categories with Joanne Jeffs, Barbara Pitos and Nina McHardy awarded the Social Leader of the Year award, Safety Advocacy award and Industry Advocacy award, respectively.
The Women in Industry Awards are held each year to recognise the exceptional work and dedication of the
“Komatsu is proud to once again be a sponsor of the Women in Industry Awards to celebrate the successes of the incredible women working in our industry,” the company said.
“All nominees and winners are making their workplaces and communities a better place for future generations which closely aligns to our core values at Komatsu.”
The Excellence in Mining award, sponsored by Weir Minerals, went to idoba chief executive officer Sarah Coleman.
Coleman is a knowledgeable mining and management consulting executive with experience in operations, improvement, innovation, technology, and asset management. She founded leading business improvement company ImpRes in 2010, and now heads idoba as its CEO.
Other winners from the night included:
Sage Hahn– Business Development
Success of the Year
Louise Adams– Excellence in Engineering
Rebecca Healy– Excellence in Manufacturing
rances Ross– Excellence in Transport
Danielle Bull– Mentor of the Year
• Helen Tower– Rising Star of the Year (sponsored by Atlas Copco).
Are you looking for a dynamic excavator to suit your quarry or your large civil project? Komatsu’s PC700LC-11 combines powerful digging force with a variety of working modes to maximise productivity and efficiency.
This unit is in the 70-tonne-class range and has 327kW (439 HP) at its disposal to suit all of your applications. The bucket capacity can be tailored to suit specific on-site material and/or fleet requirements.
The PC700LC-11 is designed and manufactured by Komatsu Japan and is an integral performance package. The unit comes standard with Komatsu’s Komtrax (remote telemetry system) to ensure easy monitoring of operational performance and usage.
The PC700LC-11 has a host of features to benefit your business and is backed by Komatsu Australia’s service and support network. Is this the machine for you?
More information: Komatsu Australia, komatsu.com.au
Polyurethane (PU) tension mats are used for impact- and abrasionresistant applications, offering long lifetime, more flexibility and low noise.
The water resistance of PU panel, with the taper apertures, is also able to achieve a high screening efficiency and is suitable for all types of materials, from limestone to coal to iron ore.
Generally speaking, the lifetime of the PU tension mat is 3.9 times greater than the rubber one, and 8–10 times greater than the conventional steel screens.
This means the maintenance cost and downtime can be reduced considerably.
Hong Hui JV is able to make not only the screen panel, but the specially designed hooks or capping strips, as well as the bolt hold-down system if required.
More information: Hong Hui JV, hhjv.com.au
MeshTracer is Rajant’s personnel- and asset-tracking software advances site security and situational awareness.
One of the most effective mustering and tracking, incidentmanagement, and communication platforms on the market today, MeshTracer uses real-time location system (RTLS) technology to identify people and assets going into and out of an entrance, located in a zone or in a particular area of a site.
The software is easily adopted, highly adaptable, and simple to use. When integrated with a client’s incident policies and equipment, MeshTracer provides an enhanced solution for every facility and personnel.
More information: SmartTech Australia, smarttechaustralia.com.au/ solutions/wireless- networks/rajant-kinetic-mesh-networks
Many contractors are finding that the shape of the aggregate is the key to success.
The VSI crusher uses a rock lining spinning rotor to accelerate material, which is then impacted in a highly energised rock lined crushing chamber. Likewise, the Australian-designed VSI crusher has hydraulically variable/adjustable crusher drive, dedicating 350kW drive to the rotor itself.
Powered by Cat C-15 engine and ifm control system, and designed and setup in Precisionscreen’s Brisbane factory, this unit is built for Australian conditions and includes heavy-duty belts and triple-seal conveyor bearings.
More information: Precisionscreen, precisionscreen.com.au/ equipment-sales/crushers/precisionscreen-trackcrush-pv350-vsi/
To submit new product and equipment releases, email: les.ilyefalvy@primecreative.com.au
Since Rostrevor Group was established in 2019 it has worked to service the recycling, quarrying, construction and mining industries with crushing and screening services.
The privately owned company, which is based in Victoria, has set out to be the safest and most reliable contract crushing company. With a focus on the highest standards of quality, Rostrevor wants to grow into a company with the widest range of capabilities of any crushing contractor in the state.
Rostrevor Group takes pride in being a unique specialist in supplying a large range of crushing and screening service on a contract basis throughout Victoria. It uses the latest in high-production equipment, manned by experienced personnel, and it’s proud to say the team maintains an outstanding safety record. Using the services of Rostrevor Group Crushing & Screening means you gain a fully independent service that is safe and dependable.
More information: Rostrevor Group, call 0409 847 079 or email daisy@rostrevorgroup.com.au
Xylum’s HL270 pump is a Godwin product that is primarily used in mining.
The increasing depth of open-pit mines is creating a demand for higher-pressure watering pumps, but there a few pumps available that can be optimised for such conditions.
That’s where the HL270 comes in.
Designed specifically for open-pit mining, the HL270 is a durable, highpressure pump that can operate in tough conditions, removing water from deep mines with few to no booster pumps.
It also features a new interchangeable pump end designed to work with existing high-powered engines – it’s a ‘plug and play’ solution.
The HL270 comes with two seal options: mechanical and glandpacked; and two material options: cast steel and duplex. Its improved reliability and safety help to reduce maintenance costs, and remote monitoring and control available via Xylem Field Smart Technology is especially valuable on-site.
More information: www.xylem.com/en-au
Ritchie Bros. will be holding its National Unreserved Auction from 12–13 October at 8.00am AEST. The auction will be held online through the company’s unreserved auction format. Those who want to inspect the machinery before they buy can do so at the auction site prior to the auction going live.
Ritchie Bros. is trusted globally to provide fair, open and honest auctions, with free bidding and registration.
A global asset management and deposition company, Ritchie Bros offers customers end-to-end solutions for the buying and selling of used equipment.
The company auctions everything from heavy equipment to trucks in Australia and across the world.
Among the 500-plus items for sale in the October auction are a 2013 Komatsu D85PX-15R crawler tractor and a 2016 Kobelco SK135SR-3 tracked excavator, both of which are expected to sell quickly.
There are also over 30 trucks, 190 machinery attachments, and 80 consumer items that will go live on the day of the auction.
More information: Ritchie Bros., rbauction.com.au, ironplanet.com.au
Drones allow for accurate stock management and improved collaboration across a business.
The introduction of cost-effective drones – and the software to process the data from them – has had a revolutionary effect on a range of industries, quarrying chief among them, according to Eltirus founder Steve Franklin.
As for any photography, light plays an important part (by definition) when using a drone.
Given the drone is moving while the photographs are being taken, you need as high a shutter speed as possible, preferably something like 1/1000th of a second. This is not always possible during the winter or periods of heavy overcast, and it can be important to know how to manually control the drone camera shutter speed to make the best of the light.
Likewise, it’s important to always try to fly with the sun as high in the sky as possible, or in such a way so as to ensure that faces are not left in shadow (easier said than done in winter). A shadowed area cannot be recreated accurately in photogrammetry.
As mentioned earlier, there are two basic ways to fix the location of the photographs: either while they are being taken or afterwards.
Our experience is that the best way to determine the locations is as they are taken, using a drone that has a high accuracy GPS
Plot of a GPS signal against a known mark over time, showing why a correction is important.
So why do we need a correction signal?
Isn’t GPS good enough on its own?
The reality, unfortunately, is that it is not. An
shows how much drift can occur, hence the need for correction.
The drift also occurs vertically. A correction service works by providing (in real-time) the difference (also called a delta) recorded by a base station on a known point between the GPS location it is receiving.
It’s important to note that for this to work, the drone must be continuously receiving this signal via a 4G connection (which doesn’t always work in remote areas).
The second approach to fixing the location of the photographs is to correct the positions after the flight. A good example of this is the Propeller PPK solution, which produces excellent results and does not require a correction signal while in flight (we deploy this solution to clients in remote areas).
A variation on the second approach is the use of GCPs, where we create marks on the ground in known locations (they must be accurately surveyed by a surveyor) and correct the photograph locations from these known locations on the ground. The problem is that you need to have a lot of GCPs, and you need to maintain them to ensure that they don’t get buried, overgrown, shadowed, blown up or moved, etc.
While this approach is workable, our experience is that it’s far more timeconsuming and error-prone in practice and not one we recommend.
To create a three-dimensional image using a drone, we employ a process known as photogrammetry. This is a technology that has been around a long time but is now greatly simplified by improved technology.
In essence, it works like this: if you can see the same point in at least three different photos and know the location of each photograph precisely, you can determine the location and height of that point. Hence the comment earlier about picture quality – the blurrier or less detailed the photo, the harder it is to use it for accurate photogrammetry.
Once the photographs are collected, they need to be “stitched together” either by you (using Pix4D or AgiSoft software) or by using a cloud-based service (eg Propeller or Drone Deploy) to do the work for you.
The DIY approach makes sense if you really want to control the whole process, but it requires high skill levels and a lot of computing power.
While we use this approach for specialised jobs, we would generally recommend that a cloud-based approach is more workable for quarry sites.
As mentioned earlier, drones are a great way to collect accurate stockpile data, but they can also be used to provide a much broader set of data that is valuable for site-planning.
One of the benefits of using a platform like Propeller or Drone Deploy (to name just a couple) is that the data can easily be viewed, manipulated, and shared by stakeholders.
Our experience is that of the many platforms known as Trimble Stratus) provides the best balance of features.
We particularly like the fact that it is 3D-only (rather than a hybrid 2D/3D approach), finding this much better for collaboration.
Lastly, you also need to have a standardised
• Survey accuracy checks
• Flight recording
• Drone maintenance recording
• Checking compliance with CASA rules
If you haven’t seen it before, software like AirData can be an invaluable way to help
Like all operations that rely on finite resources, there comes a time when a quarry will meet the end of its life cycle.
The question of what happens to a quarry once it’s no longer in use is not something most need to think about, but as Extractives Strategy Taskforce chair John Krbaleski notes, the question is considered more often than one might think.
“A quarry may be temporary, but it supplies critical materials for our daily lives and the possibility for the future of quarried land is endless,” he said.
The resources that once sustained the quarry will eventually be exhausted, and the quarry will need to be rehabilitated.
This rehabilitation plan is normally determined as part of the quarry approval process, and will often involve replacing the original topsoil, reproducing waterways, and replanting local trees.
The process of rehabilitation is normally a continuous one as the operation moves from one section of the quarry to another. Ongoing rehabilitation work is important to ensure a self-sustaining environment once operations are completed.
In some cases, quarries are completely redeveloped into parklands, sporting facilities and even housing estates.
This is exactly what happened to Karkarook Park.
Karkarook (Aboriginal name for ‘sandy place’) Park is a recreational and sporting space that spans 10 hectares in the southeast Melbourne suburb of Heatherton.
The site of the park has a varied history, originally used for flood retarding, market gardens, and horse agistment before being turned into a sand quarry.
In 1997, Parks Victoria entered into a partnership with CSR Limited and Boral Resources to extract sand from the site and then rehabilitate it to form a new recreational lake, wetlands and parkland.
The park is now described as a recreational oasis and those who visit can see nothing of the former sand quarry on the surface.
But it is not just Karkarook Park that has been created from a former quarry site.
In fact, many of Melbourne’s most wellknown parks – including Fitzroy Gardens and Albert Park Lake – were once quarries that operated in the 1830s and ’40s. Some of these parks were rehabilitated from Melbourne’s first quarries.
Arguably the most famous post-quarry park is the Royal Botanic Gardens Cranbourne, an award-winning contemporary space that was once a sand quarry that functioned for more than 50 years.
“I’ve been working within the industry since the 1980s, I’ve seen active quarry sites change greatly over that time and many of them are now unrecognisable,” Institute of Quarrying Australia (IQA) president Shane Braddy said in a statement in February 2022.
“One of the best projects I’ve had the pleasure to be involved with is Karkarook Park in Heatherton, a large site on the corner of Warrigal Road and what is now the Dingley bypass.”
Karkarook Park provides one of the most diverse habitats for different animal species in Victoria. More than 100 species of birds and a wide range of fish call the park their home.
Indigenous trees, shrubs, grasses, and aquatic marsh vegetation help to balance the needs of the 160,000 yearly visitors with the needs of the local environment.
“A former 40-hectare sand quarry is now a leisure and environmental haven that forms a key part of the area’s green wedge alongside residential, retail and business areas,” Braddy said.
“Along with the partners of that project, we were honoured to receive many awards for that work when the park opened in the early 2000s.”
Quarry rehabilitation is also an important topic for the Victorian Government, which in March 2022 announced the Quarry Transformation Grants to accelerate the rehabilitation of former quarry sites across the state.
“Quarries are essential in securing affordable materials for Victorians, the process of transforming these spaces for community uses will also create jobs in the future,” Victorian resources minister Jaala Pulford said.
“The Victorian Government is committed to promoting innovation in our quarrying sector”, Krbaleski noted in the publication The New Lives of Old Quarries
The grants saw a total of $550,000 made available to four successful applicants in two categories – small quarries and larger operations.
Victorian quarries are required to rehabilitate their sites to a safe, stable, and sustainable standard under the Mineral Resources (Sustainable Development) Act 1990, and these grants will take the pressure off future recipients.
Many rehabilitated quarries are transformed into lakes, as their locations provides a great option for water and fishing.
“Metropolitan man-made lakes typically come with good access and transport options, well-designed fishing spots and their proximity to a large population make them perfect family fishing spots,” Victorian Fisheries Authority chief executive officer Travis Dowling said.
“It’s great to be able to offer good quality inland fishing opportunities via these former quarry sites.
“Looking at the number of quarries on the outer areas of Melbourne, I think we will see future generations of anglers wetting a line at more places than we can today.”
Karkarook Park boasts an impressive lake of 15 hectares and makes a perfect spot for canoeing, kayaking, or sailing. Rainbow trout and red fin can be found in the water.
The Karkarook Park lake was completed and filled in 2004, just three years after sand extraction was completed. By transforming a quarry into a recreational space at the end of its lifespan, those in the business can ensure
Quarries are key local employers, and their rehabilitation leads to a wide range of ongoing careers like park development and management and flora and fauna conservation.
Quarrying has long been an essential part of the Australian economy, and proper rehabilitation can ensure that no quarry site ever goes to waste.
“We can only extract the rock and sand once, whether it’s for the construction of roads, bridges, homes or hospitals,” Braddy said.
“However, we can leave behind some amazing community assets that become the centre of
A major quarry operation is nothing less than a finely tuned machine, with seemingly innumerable pieces of rotating equipment required to keep it running smoothly.
The prospect of a busy quarry operation can be overwhelming for some, particularly if one of the key pieces of equipment is not functioning correctly. But for SKF it presents a welcome challenge to focus on customers’ specific needs.
As a leading global manufacturer of bearings and associated products with more than a century of experience, SKF understands the need to approach such a situation with a clean and intelligent view, and its new power transmission range of solutions is part of that view.
As SKF’s contract manufacturing and quality manager for power transmission Lloyd Brown told Quarry, the company does not just work with its partners to replace faulty components, but rather to assess the situation in order to understand the causes and repercussions of any issues the rotating equipment might be having.
“A customer may come to SKF with a concern on a bearing, and when investigated sometimes it is as obvious as alignment or a seal arrangement or a lubrication issue,” Brown said.
“However, it is not at all that uncommon when investigated that we find that the power transmission configuration surrounding the bearing could be a contributing factor to the issue.
“Sometimes the conditions of the processes or the equipment change (such as speed, loads, and temperatures); however, the original design of the equipment remains the same.”
SKF has expanded its primary offering of bearings, seals, and lubricants with a wide range of power transmission solutions.
The pain points highlighted by Brown can create a domino effect throughout a quarrying operation, causing premature wear, vibration and failure of components across the plant. This encompasses many aspects of a quarry’s operations, such as a high-speed, low-torque pumps and fans drives, as well as higher demand drives on cone crushers, ball mills,
The quality of SKF pulleys can significantly extend belt life.
hoists, elevators, conveyors and blowers. SKF’s extensive power transmission solutions are designed to address the various needs of a quarrying plant and its equipment.
SKF sprockets are made from high-quality steels and can be further adapted for high performance.
The new range of XP2 V-belts caters to high-power belt drives, while heavy-duty roller, mill and conveyor chains and sprocket drives provide highly abrasive assurance.
“We also offer a number of flexible shaft couplings that are perfect for quarries and mining, such as our grid couplings, gear couplings, disc couplings, or our elastomeric SKF Flex tyre couplings, FRC couplings and even jaw couplings,” Brown said. “Additionally, we have an excellent range of standard shaft bushings including taper bushes, QD bushes, and our FX keyless locking devices commonly used in conveyor drum pulleys.”
In order to ensure the quality of its products lives up to the company’s holistic approach to helping its customers, Brown said SKF power transmission products meet a range of globally recognised compliance standards.
“SKF power transmission products are designed and manufactured to meet international standards including ISO/DIN and ANSI/BS/AGMA. Our power transmission products are also fully RoHS and REACH
compliant,” he said.
Of course, it’s in the interest of all – the customer, SKF, and the quarrying industry – that SKF’s power transmission offerings are reliable, ensuring its range of bearings,
seals and lubricants remain part of a reliable operation.
“Granted that our SKF main core product is the bearing, the full transmission system has a direct influence and impact on the performance and service life of the rotating shafts and bearings,” Brown said.
“With our SKF power transmission offering, you are guaranteed that the products you use meet the same strict quality standards that the SKF brand name stands for.
“With SKF’s focus on its strong product offering consisting of bearings, seals, lubrication and power transmission, combined with our portfolio of connected technologies capabilities and our vast experience around rotating equipment performance, we are able to offer improved service life and predictive maintenance to increase efficiencies and reduce running costs.” •
Visit skf.com/au to learn more.
With a relationship spanning more than a decade, these two leaders in the quarrying sector understand the value of working hand-in-hand.
Rocktec Technology is a leading original equipment manufacturer (OEM) located in Matamata, New Zealand. Focused on the quarrying sector, Rocktec delivers a wide range of solutions targeted predominantly at quarry and bulk material handling projects.
In a bid to widen its scope of service and its footprint, Rocktec was acquired by Skookum Technology in 2021.
Skookum was founded over 25 years ago and is one of Australasia’s leading suppliers of forestry and bulk handling equipment.
Reflecting on the rich history of the company, Rocktec material handling specialist Jason Tapper said it recently celebrated 30 years in business and is going from strength to strength.
“Our roots remain firmly planted in the quarrying sector and while we service customers globally, our primary focus remains the Australasian market,” he said.
One of Rocktec’s key differentiators is its ability to problem-solve.
“We pride ourselves in tackling complex issues through customised solutions, rather than selling ‘off the shelf’ products,” Tapper said.
“The majority of our customers can attest to our tailored solutions for the quarrying sector.”
The company has evolved over the years to service the bulk material handling sector. Its range of products includes apron feeders, crushers, feeders, screens and more.
Demanding sectors like quarrying and bulk handling require robust, quality solutions matched by service and communication.
“Communication is a big factor for us,” Tapper said.
“Suppliers should communicate when things are good and when things are bad.
“Having open lines of communication is critical to the success of each project and we rely on our suppliers to deliver.”
And meeting these requirements is the gearmotor manufacturer Bonfiglioli.
“They’re easy to work with, supply us with the information required and are backed by sound technical engineering,” Tapper said.
“Of course, we need a robust quality solution so we aren’t looking for the cheapest solution, but rather a quality solution that can stand up to the environment and last in the long run.”
According to Bonfiglioli New Zealand sales manager Paul Savage, the relationship began around 13 years ago and some projects between the two companies require as many as 20–30 gearboxes.
“We work closely with Rocktec on each and every project to clearly understand
the scope, deliverables and deadlines,”
Savage said.
“We understand that their solutions are generally tailored and that there is no room for error.”
Tapper agrees and said he also understands the value in having such a close working relationship.
“In larger projects, we work with Bonfiglioli to reduce the number of variable components and to provide standardised product across the plant,” he said.
The team from Bonfiglioli aligns closely to Rocktec on every project.
“We don’t supply from a catalogue – each solution is fit for purpose,” Savage said.
Savage outlined several key projects on which the two brands collaborated.
“Six mobile hoppers were designed, built and sent from New Zealand to Western Australia,” Savage explained.
“Rocktec chartered a ship to transport six hoppers – weighing in at 64 tonnes each.”
To increase stockpile capacity, Rocktec took part in a conveyor project on a plant that could only manufacture in dry weather.
“The solution was used to maximise the stockpile volume that could be kept in sheds,” Tapper said. “We developed a large
conveyor over two land levels. In addition, we designed a lightweight auger system to distribute product across the shed.”
The Bonfiglioli gearboxes used can withstand the high-dust environments and harsh weather conditions.
“We generally make use of Bonfiglioli’s A series, HD series, if over 75kW, or planetary gears, for apron feeders,” Tapper said.
Both companies exhibited at this year’s NZ Quarry Show in July.
“This was another opportunity for our brands to showcase their relevant technologies and the ‘power of two’,” Savage said. “Our partnership with Rocktec is something that we are very proud of.” •
Visit bonfiglioli.com/australia/en or rocktec.co.nz/ for more information.
The updated Next Gen Cat 966, 966 XE, 972 and 972 XE wheel loaders with simple-to-use technologies and operator features are boosting efficiency and productivity.
Bringing a host of standard technologies to the 8–9-tonne wheel loader line, the updated Cat 966 and 972 series increases operator efficiency, delivering consistently high bucket fill factors to increase productivity by up to 10 per cent.
The machines’ design extends fluid and filter change intervals to reduce maintenance costs up to 15 per cent when compared to the previous models, the company said.
The Caterpillar designed and manufactured continuous variable transmission (CVT) of the Next Gen Cat 966 XE and 972 XE loaders improves fuel efficiencies up to 35 per cent compared to the previous powershift models.
All models in the updated 966 and 972 loader series feature standard Cat Payload with Assist for accurate weighing of bucket
payloads, so operators can load to target the first time, every time. Real-time data is fed to the operator display and allows manual tip-off function to improve final bucket adjustments and truck load accuracy.
The new Cat Autodig with Auto Set Tyres deliver consistently high bucket fill factors for the updated medium wheel loaders.
Providing fully automating bucket loading, Autodig improves fill factors and decreases loading time. Working in conjunction with Autodig, Auto Set Tyres promotes proper loading techniques to significantly reduce tyre slip and wear.
Similar to the 980 and 982 loaders, the updated 966 and 972 models allow customised profiles for customer-specific application, and new application profiles set
multiple machine parameters with the press of a button to optimise settings for the job.
Selectable on-screen job aids, along with streamlined new layout, facilitate loader operation and allow operators of all experience levels to be more productive.
Optional Cat technologies help to further increase productivity and operation profitability of the updated series.
Cat Payload with Assist offers Tip Off Assist to automatically adjust the final bucket load to match hauling unit target, as well as enhanced list management, site integration and extended scale features.
The Cat Productivity subscription provides detailed and comprehensive actionable information for the site on a smartphone, tablet or computer. The Tip Off Assist button helps operators remove the guesswork and accurately hit their targets every time.
Deep system integration of the CVT powertrain, engine, and hydraulic and cooling systems as part of the Next Gen Cat 966 XE and 972 XE design results in significantly increased performance and fuel efficiency. Without the torque converter of mechanical drive systems, the loaders independently control engine revs per minute and machine speed to provide efficient digging, fine control, and operation.
According to Caterpillar, operators will experience smooth, fast acceleration and high speeds on grade with the CVT design. Machine manoeuvring on grade is enhanced through speed-hold and antirollback features.
Delivering optimal loading efficiency in the pile, advanced rimpull control helps to reduce tyre wear. Beyond saving fuel, the lower rated engine speed of the XE models reduces component wear and makes for quieter operation.
The 966 and 972 series design extends maintenance intervals to 1000 hours and eliminates the 500-hour service intervals, Caterpillar said.
This means the loaders spend more time at work, while an integrated optional Autolube reduces daily maintenance and increases component service life.
Access to hydraulic and electric service areas helps to make servicing the loaders fast and easy
“Without a doubt, all these design updates reduce maintenance costs up to 20 per cent for the Cat 966 and 972 models,” the company said.
The new loaders feature Caterpillar’s next generation of ride control that works as a shock absorber to improve ride quality over rough terrain.
Making for a quieter work environment, the cab includes sound suppression, seals and viscous mounts to decrease noise levels. A wide door that unlocks remotely from the ground, along with inclined steps, improves cab ingress and egress.
Shipped with a seat-mounted electrohydraulic joystick steering system as standard, the Next Gen 966 and 972 machines offer precise machine control with
minimal arm movements, increased comfort, improved loading accuracy and more legroom for the operator. An HMU steering wheel is available as an option for the 966 and 972 powershift models.
The loaders’ new dashboard and highresolution touchscreen display are designed to provide intuitive and user-friendly control, and multiple air suspension seat options include heating or heating and ventilation to provide greater comfort.
The new range of wheel loaders is also built with safety in mind, with enhanced features such as standard monitored seat belts with an optional exterior beacon, and a cab windshield that extends from floor-to-ceiling to improve visibility.
In addition, a standard rear-vision camera and large mirrors with integrated spot mirrors provide all-around visibility.
Cat Detect radar to alert operators to hazards and a 360° multi-view vision system are options that provide an extra level of monitoring around the loaders to advance safe operation. Similar to a car, Cat Detect technology’s audible and visual alarm sounds when the operator is reversing close to objects behind them.
Available in capacities from 2.8–14m3 for the new 966 and 972 loader series, Cat Performance Series buckets balance shape against the machine’s linkage for higher fill factors and better material retention.
Fusion Quick Coupler buckets permit rapid work tool changes without leaving the cab, so the loaders move quickly from task to task. •
Visit cat.com/en_AU.html for more information.
Embedding sustainable practices is critical to ensuring the long-term success of a business as the world moves towards a greener global economy.
Viva Energy Australia, a Shell lubricants macro distributor, and Shell Lubricant Solutions provide a range of options to help businesses achieve operational excellence and reduce their environmental impact.
Reducing CO2 emissions is at the top of the business agenda across all industries, including construction and quarrying, as tighter regulations and consumer demand mean a shift towards a low-carbon economy.
But the pressure to maximise output while increasing productivity creates operational challenges. The COVID pandemic has further increased these pressures, and construction companies have found it difficult to keep up with demand due to dwindling workforces.
And the demand is clearly rising, with the industry predicted to expand by 35 per cent over the next decade.
“Minimising the environmental impact of industry is not a new concern, but recent years have seen an increased focus and the acceleration of action,” Shell Lubricant Solutions vice president – global marketing B2B and OEM lubricants Troy Chapman said.
“Around the world and across industries, companies are setting ambitious targets to decarbonise their operations.
“This presents businesses with the challenge of finding practical solutions to help protect the environment while also meeting the ever-present demand for higher productivity, complying with rapidly changing legislation and strengthening their licence to operate – all while optimising their total cost of ownership.”
Construction faces a delicate balancing act: how to meet demand and drive profitability while improving its environmental impact and reducing emissions.
Shell lubricants help businesses to use more sustainable practices that serve to avoid or reduce emissions, and can provide opportunities for CO2 offsets.
These practices include improving equipment performance and energy efficiency, investing in carbon-offsetting programs and offering carbon-neutral premium lubricants, such as the Shell Naturelle range.
Construction operations are increasingly located in remote and diverse locations.
It is vital to develop innovative solutions that ensure businesses can flourish while preserving these sensitive environments.
Shell Lubricant Solutions offers a range of readily biodegradable lubricants that help businesses to grow safely and sustainably.
Shell Naturelle S2 Hydraulic Fluid is a biodegradable hydraulic fluid for advanced performance in environmentally sensitive areas. Using an EAL (environmentally acceptable lubricant) like Shell Naturelle provides an effective way for companies operating near environmentally sensitive areas to manage their impact on ecosystems by protecting soil and groundwater with low ecotoxicity lubricants and maintain their licence to operate.
New regulations and industry practices are also encouraging businesses to manage waste in a more efficient way. Shell lubricant products are designed to extend equipment life to help reduce waste and encourage the recycling of used parts.
The plastic pails used for the Shell Naturelle range currently include 25 per cent postconsumer recycled resin. These solutions comply with the latest 2020 EU Ecolabel requirements and help reduce plastic waste to landfill.
“Increasingly, there is a realisation among companies that making a tangible difference means looking at not only their own operations but also their whole supply chain,” Chapman said.
“Customers are increasingly seeking sustainable solutions that contribute to a company’s broader sustainability targets.”
As the world progresses towards a more circular economy, businesses are finding
ways to reuse, recycle or repurpose products. Working with a partner with the right expertise enables businesses to unlock the ability to increase profitability and sustainability.
Shell Lubricants and Viva Energy Australia work with business partners to reach their sustainability goals by educating maintenance managers on the performance benefits of regenerated oils with base oils, and reviewing the use of sustainably sourced raw materials such as re-refined base oils and bio-derived materials. Shell lubricants can also provide peace of mind that the products meet regulatory requirements.
Shell Naturelle carbon-neutral lubricants present an easy choice for construction businesses. They protect equipment, the environment and productivity.
•
For more information, contact the Viva Energy technical help desk (Shell Lubricant Specialists) on 1300 134 205 or technicalhelpdesk@vivaenergy. com.au
Shell Naturelle S2 is an environmentally acceptable synthetic hydraulic fluid.
Australia has long been at the forefront of limestone quarrying, with the rock used in everything from environmental sustainability to construction.
Limestone has been used across the world for thousands of years.
A natural sedimentary rock, limestone can be traced back to the Egyptian pyramids; of course, it’s now used for more everyday things like roads and architecture.
In fact, it seems almost every important building one can think of, from houses of parliament to Windsor Castle in the UK, has
the main source of calcium carbonate.
The world uses about 5000 million tonnes of limestone every year. While Egyptian quarries still hold the monopoly on the amount of mined limestone, Australia is a strong contender.
New South Wales, in particular, has an impressive stash of limestone, with more than 400 separate known deposits.
Perhaps the most famous deposit in the state is the Mudgee-based Mudgee Dolomite & Lime (MDL) quarry. The MDL operation is located in the state’s north-east and has been
operation since the 1830s, blasts 3.5 million tonnes of rock per year and is the source for up to 60 per cent of all cement products used in the state.
Limestone from quarries across the country is used in a variety of ways, including some that are less well-known.
For example, lime is often used for water treatment, with municipalities using it for portable water softening and to remove impurities from drinking water.
Elsewhere, it is used for pulp and paper, as lime assists with the chemical-
plants, industrial facilities, and medical and hazardous waste incinerators. Lime absorbs and neutralises sulphur oxides from the gases, helping to prevent acid rain while reducing hazardous emissions.
And, of course, the dominant use for lime is in roads, with the Romans putting it to use in
use any mechanism at all, it was usually a horse and cart.
A 2021 analysis conducted on stone tools recovered from a former Roman outpost in Italy highlighted how the ancient civilisation utilised collaboration between geologists and archaeologists to acquire the correct
and seemingly from one source”.
The Industrial Revolution later saw the use of gunpowder become more common in limestone quarrying, which helped to significantly sped up the process.
Although limestone quarrying more recently experienced a setback during the COVID-19 pandemic, it is expected that the industry will bounce back.
According to ‘Australia Lime Market Report and Forecast 2021–2026’ by Expert Market Research, the market should see a two cent bump in compound annual growth 2022–26.
The growth is due to rising government investments in construction and increasing populations and urbanisation.
“The construction industry in Australia maintained a significant growth rate over the last few years, especially in the South Wales and Victoria regions,” the
“This development has played a key role in growing the sales of limestone to the construction industry.”
The report also indicated that environmental uses are the fastest-growing use of lime, with stone being used to comply with air, drinking water, sanitation, and solid waste rules.
There is no doubt that Australia will continue to be a key player in providing the world with one of its oldest known construction materials. •
The original limestone casing on the Bent Pyramid at Dahshur, Egypt.Quarries are a notoriously rough and rocky worksite, a tough place that requires a dozer that can handle the harsh terrain.
Enter the John Deere 1050K Crawler Dozer.
With suspended double-bogie undercarriage that can absorb vibrations caused by rough operating conditions, the 1050K is designed to ride smoother and be more durable than previous models.
That smooth ride is ideal for operators.
According to John Deere, the dozer’s reduction of peak vibrations in the cab by up to 75 per cent helps operators carry on in comfort while moving faster and ultimately boosting productivity. And less vibration equals less component wear.
In addition, extended life and heavy-duty undercarriage options with sealed and lubricated track (SALT) are available to match a customer’s specific application, which helps to make for an even smoother and more productive ride.
The 1050K’s dual-path hydrostatic transmission allows operators to push a full load through turns without losing material, while the John Deere PowerTech engine delivers a strong power-to-weight ratio to provide the traction needed to push more material.
The John Deere final tier 4 (FT4)/ EU Stage IV PowerTech diesel engine delivers proven performance in mining, quarrying, roadbuilding, and other largescale applications. It is also efficient, with the Standard Eco mode maximising fuel economy without loss of performance, automatically adjusting engine RPM and transmission settings based on load to burn up to 15 per cent less fuel depending on application.
This all adds up to users getting more done with minimal extra effort.
The 1050K dozer is designed to be easy on the person in control.
Electro-hydraulic (EH) mean the machine is grade-control ready. This makes adding a system as easy as “plugging in the components, calibrating, and going to work”, according to John Deere.
Low-effort controls command blade curvature, and the full-featured hydrostatic drivetrain helps to deliver predictable response at all times and virtually eliminate jerky or abrupt movements.
An ergonomically correct joystick provides intuitive, low-effort control of steering, direction, and ground speed. The fact the joystick is detented means it doesn’t require an operator’s constant touch or attention, and it employs a thumb-actuated travelspeed-control switch.
In addition, total machine control (TMC) monitor allows the operator select decelerator mode and response, forward/ reverse ground-speed ranges, steering modulation, F-N-R shift rate, and forward/ reverse speed ratios for improved control.
The 1050K’s rugged rear rippers are configured either as a larger single shank or in a row of three evenly spaced shanks.
This means operators can choose the style to match the application, whether they’re working in quarrying, mining, roadbuilding, land-clearing, site development, or general earthmoving.
“Heavy-ripping single-shank ripper delivers concentrated force to break up rock, hard
packed or frozen soil, and concrete,” John Deere said.
“With an overall beam width of only four feet, eight inches, and maximum penetration of three feet, seven inches, you can get in and dig deep.”
The 1050K has been designed to minimise daily maintenance time.
Large-hinged doors provide access to dipsticks, fill tubes, maintenancefree batteries, and vertical filters, while convenient service points make quick work of the daily routine.
“Easily cleaned cooler design features a standard reversing fan that automatically back-blows the cooler cores at pre-set intervals,” the company explained. “(Users can) simply press a button to actuate the reversing cycle when needed.
“Remote lube banks provide easy access for lubrication of crossbar and C-frame pivots. Separate hydraulic and hydrostatic reservoirs eliminate the possibility of crosscontamination.”
The operator station tilts a full 70° in only minutes for wide open drivetraincomponent access.
With so many of the 1050K crawler dozer’s features having come directly from customer feedback, John Deere has designed a machine suited to the people working the rough and rocky terrain of a quarry site every day.
The 1050K is a rock-solid machine that will show up day in and day out, ready to tackle the high-production demands of the job. Get to work. Stay at work. Enjoy the work. • Visit deere.com.au/en/index.html for more information.
Maxam is working to bring a new perspective to the explosives industry.
As a global company specialising in energetic materials, Maxam is ready to provide experience, tools, technology and services to help clients perform efficiently and effectively.
Maxam is a leading provider of integrated blasting solutions to the Australian quarry and construction industry.
The company is home to what it describes as “the largest and most comprehensive national network of operational depots and supply hubs dedicated to providing explosive products and specialist services to over 200 sites nationally”.
Maxam is focusing on customer solutions, bringing a new perspective to the explosives industry. This new process is based on adding value and helping to reduce customers’ total cost of ownership (TCO) through the intelligent application of explosive energy to drive significant downstream savings in drilling, haulage and crushing costs.
The company’s best practice process is designed to ensure that desired outcomes are met and risks managed.
Maxam said this is done via its network of experienced employees – more than 5000 professionals working around the globe – applying solid processes that are supported by advanced design and analysis tools.
In this way, the company is able to provide experience, tools, technology and services that help clients execute their engineering projects efficiently and effectively.
Maxam is also able to put its skills and experience to use in much larger projects, including the DigiEcoQuarry – Innovative Sustainable Aggregates Systems project.
Described as “a significant breakthrough in process digitalisation and automation capabilities for the aggregates sector”, DigiEcoQuarry aims to design, develop and validate an innovative quarrying system (IQS) comprising sensors, processes, tools and methods for data capture, processing and sharing to provide integrated digitalised, automatic and real-time process control for aggregates quarries.
As part of its work in the DigiEcoQuarry project, Maxam will develop innovative technologies of its X-Energy platform in a quarry of the Hanson group, a member of the project consortium.
X-Energy is, according to Maxam, the first solution in the aggregates industry that integrates selective energy application in a fully digitalised mine cycle.
“It combines the most advanced explosives technology in the market (Smart Rioflex) and a set of digital tools for optimised blast design and execution,” the company said.
“The X-Energy application allows a mine to customise the design and execution of each individual blast and integrate it to the requirements of downstream operations.
“The benefits in enhanced safety, reduced impact to the environment, optimised rock fragmentation, efficient use of energy, higher production, and reduced costs help mines become more competitive and more sustainable.”
In the context of the DigiEcoQuarry project, X-Energy digitalisation tools like the Maxam Blast Center, X-Logger and RIOBLAST, combined with smart explosives and adaptive delivery systems, will enable quarries to leverage data and the use of selective energy to enhance safety, reduce environment impact, and optimise TCO
“Maxam is delighted to be part of the DigiEcoQuarry project,” MAXAM’s senior technical advisor Vicente Huelamo said. “We look forward to developing new technologies of our X-Energy platform specifically for the aggregate industry.
“Our focus would be to improve rock fragmentation, wall damage, ground vibrations, and airblast overpressure. The work will also help improve the performance of downstream operations.” •
Visit maxamcorp.com to learn more.
Users can access GPlus Live on a mobile, tablet or desktop.
Gcompliance via a simple interface from any device and location.
A personal dashboard allows GPlus Live users to individually tailor their interactions with the platform and collate data, manage compliance, schedule activities and see results in real-time.
Groundwork Plus originally developed GPlus Live to manage information internally after being dissatisfied with much of the off-the-shelf software designed for other industries.
Five years on, and with the benefit of feedback and the development of new modules and capabilities from on-the-ground trials, Groundwork Plus is formally releasing GPlus Live to the industry.
Groundwork Plus now has a designated team of programmers, data managers and trainers to assist users in tailoring the platform to suit site-specific requirements and business preferences and ensure the system is utilised to its maximum potential.
• Testing and quality
Groundwork Plus’ NATA-accredited geotechnical laboratory uses these modules to efficiently manage, store and report data.
“GPlus Live can be used to track trends, compare variables and automate reporting,” Groundwork Plus director Tegan Smith said.
“Actions can be scheduled in the dashboard calendar and reminders and notifications set to ensure actions are not missed or are easily delegated via the system digitally. GPlus Live lets users to set triggers and alerts, ensuring compliance is managed proactively.”
Users can also store and manage essential data like inductions, insurances, qualifications, and emergency contacts.
“GPlus Live assists users to manage environmental compliance, plant and equipment maintenance requirements, or fill in safety and health e-forms, registers, and checklists,” Smith said.
“Our clients can have peace of mind when it comes to security,” Groundwork Plus director Clayton Hill said.
“Users can securely log in to GPlus Live on their mobile, tablet or desktop with a PIN and two-factor authorisation. The system is protected by data encryption and has automatic and regular cloud database back-ups.
“Clients also have control over the level of access provided across their business. Permission levels can be set so users only receive relevant notifications and can access specific data easily and efficiently.
“Whether you are an operator, supervisor, quarry manager or executive, GPlus Live is a proactive tool designed to manage compliance and performance in every facet of operations.” •
Visit groundwork.com.au for more information.
Production systems are home to mechanical, electrical, electronic and software components.
Together with the Digital Data Chain Consortium, VEGA wants to further advance the digital twin of its instruments.
Transparent data exchange between manufacturers and users is an almost limitless topic. To make progress in this area, many individual solutions, including some proprietary ones, have to be brought together under one roof.
The Digital Data Chain Consortium, of which VEGA as a founding member, wants to make documents and data accessible to all by means of a digital-type label.
What looks like a complete system out on the factory floor rarely turns out to be a unified whole when viewed up close: every production system is home to mechanical, electrical, electronic and software components from many different manufacturers.
This represents a complex multiplicity that makes itself especially felt when things are not running smoothly; for example, when a
sensor needs to be re-parameterised, a valve sealed or a fuse replaced.
How efficiently a machine – or even an entire system – can be repaired or serviced largely depends on how quickly the necessary data is available.
Do the relevant documents first have to be laboriously searched for in a folder buried under stacks of papers? Is the manual locked away in a dusty cabinet somewhere? Is there a PC database where information on the component in question stored – hopefully up-to-date – and readily retrievable?
According to the Digital Data Chain Consortium, a data solution that promises greater productivity looks quite different. The consortium’s goal is to make all system components clearly identifiable.
“It’s all about having secure and accessible data in the cloud instead of in individual databases”, VEGA product manager Florian Burgert said.
According to Burgert, significant savings are possible when data is available in this way.
“The situation today is that companies often have to integrate legacy data into existing applications,” he said. “Searching for and collecting data can be time-consuming, as it may be scattered around the country or even around the world, or stored on the computers of different manufacturers.”
As a manufacturer of level and pressure instrumentation, and founding member of the consortium, VEGA developed the new “DIN SPEC 91406” standard together with wellknown process automation companies.
The aim of the proposed standard is to make equipment management easier by using distinct and unambiguous digitaltype labels. Users should benefit as much as manufacturers, who can perform faster updates with far less printed material.
The new labelling, which is only recognisable as a QR code on the housing of the device, has everything that might be required, namely all manufacturer information relating to the product. And when required, the data can be called up with any mobile device at any time.
In practical terms, this means traceability extends from production to ordering and Visit vega.com/en-au to learn more.
TheInstitute of Quarrying Australia (IQA) and Cement Concrete & Aggregates Australia (CCAA) have again joined forces to present CMIC23 as the pre-eminent conference for the construction materials industry.
As the eighth Construction Materials Conference, CMIC23 carries the theme, “Adapting to a new environment”.
The organising committee, chaired by Charlie Stoneman (Hanson), will present an engaging program, with the event being held in Brisbane from March 15–17 2023.
“The program is designed to challenge our thinking and assist our leaders to adapt and evolve in a very challenging business environment,” Stoneman said.
“The program will showcase influential speakers from within the industry, as well as leading global experts, who will provide insights on the dynamics that are impacting or will impact our sector.”
The conference commences with the Industry Innovation Day and Trade Exhibition on March 15. Stoneman said the day will showcase a series of short (10–15-minute) presentations by representatives of member companies, industry bodies, partners and suppliers, showcasing the innovation and best practice that exists within the industry. Anyone involved with the industry is invited to submit papers for consideration to be included in the Industry Innovation Day.
Ellen Fanning, award-winning current affairs journalist and an exceptional moderator and facilitator, will be the MC for CMIC23. With a wealth of experience in communications, politics, social, cultural and business issues, Fanning will facilitate discussion and consideration during the keynote and plenary presentations across the following sessions:
Adapting to a new macro environment – Focusing on the economic and international environment
Adapting to a new energy and supply chain environment while adopting decarbonisation pathways
Adapting to new customer, community and workplace environments
How does our industry adapt to the new environment? Presentations and a facilitated panel discussion on our industry’s future
“The trends impacting on the macro environment for our industry are changing and this will be a key focus in session one,” Stoneman said.
“We are really excited to have engaged one of Australia’s best-known economists in Chris Richardson to present on Australia’s economic environment. We will have many more exciting speakers to announce in the coming months.
“The social program for CMIC23 will again be a highlight and we are excited to work with our sponsors to bring first class social events to life.”
Hitachi is hosting the welcome reception following the Innovation Day in the Watermall within the Queensland Art Gallery. The Hitachi Welcome Reception will showcase one of Australia’s most outstanding public concrete architectural works – a fitting tribute to the role our industry plays in the built environment and cultural aspects of our communities.
On Thursday evening Komatsu will ensure the Brisbane Convention and Exhibition Centre’s Plaza ballroom will be transformed to celebrate a gala atmosphere. As host of the gala dinner, Komatsu will ensure delegates and partners enjoy a night celebrating the industry in an entertaining environment.
The conference will conclude on Friday March 17 with the Industry Leaders Breakfast, which will be held at the iconic Victoria Park Golf Course.
“The theme for the breakfast is ‘Leadership and building resilience to adapt to the new environment’,” Stoneman said
“The breakfast is an exciting addition to the program and will conclude a highquality conference with two leading speakers who will leave delegates feeling motivated and energised.
“The breakfast format is being planned to provide a distinct finale to the conference, giving delegates a unique opportunity for networking while providing distinctive yet engaging content in a more relaxed setting compared previous events.” •
Unlock the potential of your quarry materials with CDE’s advanced wet processing & water management technology.
CDE experts will design a customised solution guaranteed to boost production efficiency, increase yield and grow profitability by delivering consistent in-spec sand & aggregates.
The SA branch annual general meeting (AGM) was held at the Kooyonga Golf Club Friday 19 August, with over 80 guests in attendance.
Michael Sheppard, a representative of valued branch sponsor SMS Geotechnical, provided a brief insight into the company’s operations and services, while the branch also welcomed new member in Crystal Kennedy.
The Victorian branch hosted the Winter Quarry Night at the Australian-first tunnelling training centre.
The facility includes a replica mined tunnel and rail/tunnel boring machine, similar to the Metro Tunnel, along with a full-height entrance, two multi-purpose engineering and technical workshops and training facilities.
Attendees experienced tunnel shaft and concrete lining spray simulators, virtual reality experiences, a cutter head, a refuge chamber
and materials required. (Quarry will provide an in-depth report on the Bridgewater Bridge Project in an upcoming edition.)
The 24th Annual North Queenland Branch Golf Day was held in September in Townsville. The event continues to be one of the most popular on the north Queensland calendar, with registrations selling out weeks before the event.
There were plenty of laughs and a great opportunity for people in the industry to take time out of their busy schedules to network.
Winners:
• Best Nett (sponsored by Nordev) – Bituminous Products team 2; Andrew Thompson, Robert Mitchelton, Darren Caddy and Brett Galea
• Best Gross (sponsored by Komatsu) – Fulton Hogan; Bradley Hamilton, Wayne Abrahmse, Brad Gibson and Lyndon Hiscock
• Runner Up Nett (sponsored by Hastings Deering) – Boral; Paul Blake, Colin Phillips, Bevan Hill and Peter Brett
Growth Minister for Police, Fire and Emergency Management, and Liberal member for Braddon,
newly appointed minister shared his priorities for
The Northern Region branch provided a special opportunity to complete the IQA slope stability training at Hanson’s Sancrox Quarry.
The quarry recently featured in the NSW Resource Regulator Roadshow presentation, showcasing the challenging ground strata and slope stability conditions presented on-site.
Facilitated by principal geotechnical engineer and geotechnical group manager Ralph Erni, attendees were able to understand the difficult and challenging ground conditions with multiple examples of practical solutions and controls to manage the risk of geotechnical hazards.
The workshop was be followed by a sub-branch networking dinner in Port Macquarie. Thank you to the dinner sponsor, Screenmasters Australia.
Visit the IQA website for more dates on slope stability training.
The new Bridgewater Bridge project is the largest transport infrastructure project in Tasmania’s history. Project leaders for updated attendees of the scope of the project, including
Face-to-face training is back. Following a very disrupted schedule, the IQA has scheduled a number of new courses that are being offered in-person:
• Supervising for safety
• Plant and equipment: Safety, compliance and best practice
• Slope Stability
• Respirable crystalline silica
• And more Upcoming sessions:
• Electrical awareness – October 13 (Perth)
• Introduction to safety management systems
– October 13 (webinar)
• Quarry products technical training – October 25 (virtual workshop)
• Electrical awareness – November 2 (virtual workshop)
• NAGA prize – Orica team 2; Derek Brakels, Dean Morrison, Vaughan Milton and Damien Burns
• Longest Drive Hole 4 (sponsored by Ritchie Bros.) – Glenn Betts
• Longest Drive Hole 11 (sponsored by Construction Sciences) – Ken Goldie
• Nearest the Pin Hole 2 (sponsored by Wirtgen Group) – Nathan Billings
• Slope stability for operators – November 3 (half day virtual workshop)
• Respirable crystalline silica – November 8 (virtual workshop)
• Introduction to quarrying – 1November 10 (virtual workshop)
Revised courses on hazard identification and emergency management will be released in October. Visit the IQA website for details or email education@quarry.com.au
The NSW 2022 Quarries and Concrete Health and Safety Conference, co-hosted by the IQA and CCAA, will be held on October 19. Visit the IQA website to review the full program. Visit www.quarry.com.au for up-to-date scheduling of courses in your state.
If a course is not listed, please contact the IQA admin@quarry.com.au and we can discuss your training needs.
golf day in Townsville is one of the most popular days on the north Queensland social calendar.
• Nearest the Pin Hole 2 (sponsored by Wirtgen Group) – Stuart Munn
• Chipping competition (sponsored by Achieve)
– Aon; Fabio Lucano, Gill Christiansen, Shaun McLaren and Greg Wilson
• Putting competition (sponsored by Lincom –Bituminous Products team 1; Chris Byrne, Cal Lee, Simon and John Warren
A special thanks to our sponsors, without whom the day could not go ahead:
Catering – RLA Finance Australia
Drinks carts – Oricia and Drillmaster NQ
Hole sponsors
Ritchie Bros.
Bituminous Products
BQC Quarries
Soil Engineering Services
Impact Drill & Blast
omatsu
Markwell Group aro Software
Douglas Partners
• Competition sponsors
Construction Sciences
Ritchie Bros.
• Wirtgen Group
Achieve
Lincom
Queensland branch and Central Queensland sub-branch members and others in the industry enjoyed a day of product demonstrations at Rock Trade Industries,
followed by dinner, networking and the AGM.
The day commenced with presentations on SEM versus drill and blast, particle-sizing in mechanical rock cutting, and case studies on technology for all over the world.
Vermeer Australia then ran its first official demonstration event of the T1255 single-sided direct drive surface miner.
Attendees at the AGM enjoyed a presentation on the MacIntyre Wind Farm project, one of the largest wind farms in Australia. The MacIntyre Precinct involves the design and construction of over 2.5 million cubic metres of bulk earthworks and civil works to create over 220km of roadways and access tracks to more than 180 turbine locations.
As part of the construction of the wind farm and overhead transmission lines (OHTL), a variety of ancillary infrastructure is proposed, throughout the construction and operation phases. This includes a quarry/ borrow pit area.
•
A full list of branch and sub-branch committees for 2022–23 will be reported in the November edition of Quarry.
For over 40 years, Bonfiglioli, in conjunction with the leading players in the industry, has developed applications for mining such as conveyors, bulk materials handling, crushing, grinding, slurry processes and many more.
When high output torque, robust reliability and long operating life must be achieved, choose Bonfiglioli.
I have grown up in the industry my whole life, with my parents owning a quarry and earthmoving business.
I love the diversity of all the different sites I go to. Every site is different, whether it be
vegetation communities present dependent on the region that I am in.
I also love meeting new women in the industry across the sites and the important roles that they do, whether they are a weighbridge operator or truck driver.
It is pretty inspiring, really.
Organisation and a diary on hand is key. I am often described as a high achiever, and I love being on a range of committee groups within my local community. My first year of work was a bit of a wake-up call that I can’t be on every committee, and it is totally fine to say no or commit at 50 per cent.
I am still in a few committee groups outside of work, but I have certainly toned it down a bit to a healthier level.
Knowing what you know now, what advice would you give yourself in your first week in the industry?
Be open to new opportunities.
I know not just about my environmental knowledge, but more about the operational side of a quarry, and the legislative aspects.
Can you share a challenging moment and how you worked through it?
I will be honest, I sometimes get nervous going to a new quarry or mine site that I have never been to before. Especially with all of the trucks and access roads, I never want to end up in the wrong space or get in someone’s way.
If I am going to a new site, I either get another colleague to come with me, or the site manager is usually only a phone call away. They are always happy to help or to drive me around to where I need to get to.
None at all.
You can’t be what you can’t see, so what advice would you give women who may never have thought about the extractive industry?
It’s not just men driving trucks. The whole industry is so diverse and there is so much room to grow in any direction that you wish.
Studying environmental science at university, I never thought I would be working in the same industry as my dad.
It is pretty special. •
A recent archaeological dig at a quarry in Scotland found evidence of a potential Roman battle on a former ironworking settlement, with some findings dating back to around 2000 BCE.
The multi-phase Bronze Age through to Iron Age site has been discovered during pre-quarrying investigations at Lochinver Quarry near Elgin, Aberdeenshire, thanks to funding from Tarmac and support from Archaeological Research Services and Aberdeenshire Council.
Tarmac is a UK-based business that provides sustainable construction materials, road contracting and building products.
Archaeologists working at the Lochinver Quarry found several dozen buildings dating to the Bronze Age and Iron Age (circa 2000 BCE to 100 AD), along with findings such as iron furnaces, domestic hearths, rubbish and storage pits, timber enclosures and cremation burials.
Evidence of ironworking at such a large scale is rare, marking it as an exciting find for the team.
Radiocarbon dating of some artefacts date them to the end of the first century AD and suggest the settlement was abandoned after burning. The archaeology team suspects this might indicate evidence of the Roman battle of Mons Graupius, the exact location of which remains a mystery.
“This is a genuinely exciting find unlocked by the quarry project and by carrying out proper and professional investigation in advance,” Tarmac estates manager Stephen Cowan said.
“The expertise and enthusiasm of the archaeology team have really brought things to life and engaged everyone.
“It has also been good to also share the findings on the ground with the wider community and everyone is keen to see what else will be revealed in the later laboratory analysis.”
Dr Clive Waddington of Archaeological Research Services and the director of the site called it “a rare and important site”.
“(It) provides an exciting opportunity to further understanding of later prehistoric life, early metalworking and the impact of Rome in the far north of Britain,” he said.
“This is a topic that is still relatively poorly understood and one that is in need of
at Lochinver, to shed new light on these important, though neglected, parts of our history.”
It is hoped the site will provide important new evidence that will help to address questions surrounding the battle of Mons Graupius, as well as the impact of the Roman invasion on the Iron Age tribes of Scotland and its legacy for local communities.
Laboratory analysis forms the next stage of this work, which researchers hope will provide more information on the subjects.
“The remains from Lochinver Quarry are an exciting discovery with huge potential to improve our understanding of Bronze Age and Iron Age life in north-east Scotland,” Aberdeenshire Council archaeologist Bruce Mann said.
“We now look forward to the program of post-excavation analysis, which will reveal much more about the date, function and significance of these structures.” •
Visit archaeologicalresearchservices.com/ projects/lochinver-quarry for more information.
Daniel McEvoy is a Reliability Engineer at Motion Australia. His main focus is working with customers to reduce risk and increase reliability of their critical plant. Condition monitoring is one of the ways we effectively do this, and it is part of Daniel’s day-to-day role. The team can help identify, track and trend potential faults on critical pieces of equipment, reporting problems back to the customer so they can be proactive with their maintenance strategy rather than reactive. This helps the customer save money with unnecessary down time. Daniel has a range of skills which enable him to conduct vibration analysis, oil analysis, infrared thermography etc. Daniel also notes that correct installation of parts is a major benefit to plant uptime. as it provides our customer with the best opportunity to maximise service life, and reduce down time and unwanted production losses. Other day-to-day tasks for Daniel include training, consultation, root cause analysis and corrective services.
1 What’s your favourite word?
It would be a toss-up between, sure, mate or grand.
2 If you could win an Olympic medal for any sport, real or fake, what would it be?
Fixing things.
3 If you could change your name, what would it be?
Mr. Fix it!
4 What was your favourite subject in school?
Applied Technology
5 What’s your hidden talent?
Surprisingly, bowls
Daniel has a range of skills which enable him to conduct vibration analysis, oil analysis, infrared thermography etc.
During a time of uncertainty for the global supply chain and skills shortages across many industries, uptime is everyone’s most valuable resource. The mines and quarries sector is learning to adapt, employing new technologies and approaches to help equipment communicate through advanced condition monitoring.
Grant Gray, General Manager –National Sales at Motion Australia, says that even amongst the growing need for raw materials across infrastructure and construction, quarrying operations will need to embrace the benefits of Industry 4.0 if they hope to remain competitive.
“Most consumers are noticing the widespread challenges when veggies are out of stock at the supermarket, or their favourite restaurant is closed two days a week due to staffing issues,” he points out. “But these problems are heavily impacting resource sectors as well, along with an inordinate demand
for raw material – so having increased visibility on the health of equipment is paramount.”
In a rugged quarrying environment, gearboxes and other parts are often subject to contaminants, extreme temperatures, and heavy use. Whether it’s a crusher, roller, pump or screen, even the most reliable equipment can experience unexpected failure. But according to Grant, it’s all about the smarter allocation of time and people power to keep ahead of the game.
“The increase in material demand also puts more load and stress on quarrying equipment – we’re moving a lot more product now, and we’re moving it faster, for longer. It’s vastly more productive to have maintenance fitters staying on top of equipment upkeep and scheduled change-outs, rather than continually spending time attending to broken gear. This is where a remote or online monitoring solution can make all the difference.”
While online condition monitoring has been a reality for some time, Grant says that flow-on challenges from the Covid-19 pandemic have forced many businesses to take stock and evaluate the potential strengths of predictive maintenance solutions.
“I think historically there has been a view that this is a tool reserved for the big players within the sector,” he reflects. “And that just isn’t the case anymore; the costs around
implementing it, even on single site operations, has come down significantly, and the return on making that investment is evidently worth it.”
Echoing this sentiment, Michael Greelish, National Business Development Manager at Motion Australia, points out that reliability and consistent production is only capped by the extent of a site’s predictive maintenance plan.
“We do a lot of remote monitoring for quarries, particularly on crusher machines,” he says. “Rather than letting them run to failure, it’s more beneficial to keep an eye on their ongoing performance and address any necessary repair or replacement in a timelier manner.”
Even in smaller quarrying environments, the integration of online condition analysis to one or two crushing machines has proven beneficial in the long-term. Sensors can replace the need for regular maintenance checks, freeing up time throughout the day that might be better invested elsewhere on site.
A correctly installed digital framework allows operation managers to have greater visibility on the health of each piece of equipment, closely analysing factors like speed, vibration, pressure, and temperature of different moving parts. Compared with traditional, frequency-based monitoring approaches that depend on manual
labour, the generated data offers an increased likelihood of identifying subtle changes to the machine’s behaviour.
“Catastrophic breakdowns on crushers and screens always start with something small,” Grant explains. “A little vibration, or small drip from a seal. Then all of sudden the gearbox has got no oil in it, and all the metal parts are grinding without lubrication, so you’ve got excess heat building up.”
“Of course, ultimately, the whole thing explodes, costing hugely in downtime and repair,” he continues. “So, the question we ask ourselves is, what could we have done if we’d known? If we’d noticed that high frequency sound coming out of the machine, or slight uptick in temperature before it wasn’t too late?”
As experts in the supply and maintenance of critical quarrying equipment, Motion Australia is well placed to assist with this level of monitoring, analysis and support. The Quarry Roadmap industry guide outlines key pain points often seen on primary and secondary pieces of equipment, suggesting practical solutions based on the team’s extensive knowledge.
“Now is the time to be having these conversations with us, so we can come to your site and offer added value to increase your production,” urges Grant. “These issues around supply chain aren’t going away overnight. With the global demand for raw material, we will continue to be heavily invested in ensuring uptime for quarries.”
Scan to take a look at Motion Australia’s Industry Solutions Quarry Roadmap.
belts, so they called us in to organise a solution,” he recounts. “Our power transmission specialists looked over the crusher and identified where there was cracking due to heat, as well as some marking that indicated excessive slippage.”
width. They weigh about half of what a standard V-belt would and are nonself-igniting to mitigate fire risk.”
In many ways, crushers are the heartbeat of a quarrying site, working constantly to break down large pieces of raw material while contending with high vibration, dust and other contaminants. On a recent site visit to a quarrying and materials recycling plant in Melbourne’s west, Motion Australia successfully carried out a drive belt upgrade that has led to significant cost and downtime savings.
The customer’s primary cone crusher was running off a 250KW electric motor and experiencing rapid changeover requirements due to an accelerated wear life on the belt assembly. According to Rob Michelson, National Product Manager for Belts at Motion Australia, the standard V-belts were not capable of meeting the site’s high volume production rate.
“The customer was only getting two to six weeks life out of their previous
“We suggested the Gates® Predator® V-Belts as the best solution going forward,” he continues. “They’ve been running on there for about three months now and in down time alone this change-out has saved them around $90,000. They’re extremely happy with the outcome, as are we.”
Rob suggests that realistically, if belts are requiring replacement more than once a year, a drive analysis is required to assess where improvements can be made.
“The added benefit of this customer’s upgrade is that they were able to go from using ten belts down to six,” he points out. “This has helped provide better overhung load and increase the drive’s bearing life. It’s a bit more compact and creates a much more robust unit.”
Achieving the right amount of tension on any belt application is critical. Too loose, and it will likely experience excess heat or premature wear. Setting them too tightly, however, will result in added strain on the shaft and bearing components.
Rosynes Hernandez, Product Manager for Power Transmission at Gates® Australia, says that while standard belts usually feature polyester tensile cords, the Predator’s aramid alternative offers a maintenance-free solution that won’t require constant re-tensioning.
“The Predator’s aramid core is the strongest available in V-belt construction,” she says. “It’s what pulls and holds the tension to transmit high rates of power. The grip on the pulley is seriously firm, and the curved sidewall ensures a clean, even wear across the
Rather than using a standard rubber material, the Predator® belts are constructed from a chloroprene compound, which boasts superior resistance against both heat and oil. Able to handle up to 2.2 times more power than similarly sized standard V-belts, they also include a bareback cover for added protection.
“The great thing about the double layer fabric cover is that it reduced friction and heat build-up, but also allows for a small degree of potential slippage,” says Rob. “In these crushing units, there is often a lot of high shock load, so if the drive belt can be a little forgiving without losing power capacity, that’s ideal.”
As part of the equipment analysis, Motion Australia’s power transmission specialists used the Gates® Design Flex® Pro™ Software to obtain a comprehensive reading on the drive’s performance and health. This offered a better understanding of the required changes, so that relevant on-site training for installation and aftercare could be carried out.
“All of our power transmission managers are currently travelling around Australia to get this program downloaded into our customer’s systems,” says Rob. “It’s going to give them better visibility over their drive performance on a range of different machines, to make sure that they aren’t
over or under designed.”
The professional Design Flex® Pro™ portfolio allows users to save on time by identifying the most suitable belt products to fit each unique piece of equipment. It can print, email and create PDF files of these design specifications to streamline the
estimation of energy consumption, belt pull, cost savings and overall transmission capacity.
“A lot of people already have their eye on the Gates brand when they come to us for these types of applications,” concludes Rob. “They’ve garnered an incredibly strong reputation in
the Australian industrial market as a robust product that’s designed for the harshest operating environments.”
“These premium belts, hand in hand with such an industry-informed analysis program, truly gives customers the best possible outcomes that will stand to last in the long-term.”
From Rockhampton to the Pilbara, the mining and quarrying networks in Australia are widely spread out, with many operations taking place in geographically remote locations. This can mean that sourcing everyday equipment sometimes proves difficult, and inventory management requires more than a little forward-thinking.
Enter Motion Australia’s diverse selection of vending solutions –designed to combat supply chain costs and downtime by allowing 24/7 access to the most frequently used tools, PPE and consumable products.
According to B2B eCommerce Manager Brenton Finch, overconsumed and misplaced items account for a considerable portion of overspending on many industrial sites, having a serious impact on the bottom line.
“What makes our machines unique is that they work in tandem with the CribMaster software, which is really the key to monitoring stock levels and configuring things like controlled access,” he explains. “It lets the user know exactly what they’ve got on hand, notifying them when they need to reorder. This allows for smarter resource
allocation for each particular job, team or individual employee.”
The On-Site Solutions system can be tailored to suit each user’s requirements and project layout. It can either print a simple stock report on a regular basis, or even generate automatic re-ordering back through the nearest Motion Australia branch.
“Having that added traceability is hugely beneficial in a number of ways,” points out Brenton. “It reduces downtime spent looking for and ordering items, because it can ensure constant product availability. Using this solution, there
should never be an instance where something is inconveniently out of stock, because it will have already flagged the system and triggered a reorder ahead of time.”
Additionally, it allows the business to reduce overall batch quantities, and avoid wasting costs on over-ordering. Instead of the business ending up with three times the amount of bearing lubricant than what is actually required, it will make the whole process more streamlined by reducing redundant stock.
“What’s more,” Brenton says, “it promotes a huge cost saving related to lost or damaged equipment, because it has constant records of who is accessing the machine at what time, for whichever specific task. It does this through individual ID numbers or a swipe card required for access – this is entirely configurable depending on how much information the site manager wants to keep on hand.”
Ideal for high-use consumables, PPE, general shop supplies and cutting tools, the ToolBox unit resembles a regular food and drink coil vending machine. The userfriendly touch screen interface allows individuals with approved access to retrieve items easily throughout the day, mitigating the need to visit a stock room or travel off-site for parts.
Each product is clearly visible through the glass front panel, and stored between coils of varying depth and width. Available in either six or seven shelf options, it can store up to 60 individual SKUs at any given time.
The next step-up in Motion’s vending portfolio is the ProStock – designed to hold small, pre-packaged maintenance, repair and operations (MRO) items. Much like the ToolBox, it can be used to stock PPE, cutting tools and general shop supplies, but is also suitable for welding consumables and electrical components. It has a much higher SKU capacity of up to 560 items, and can be reconfigured as stock rotates through.
Venturing into larger capacity solutions, the WeighStation is a double-door
cabinet which offers more versatility in product size. It can carry about four to five times the stock volume of the standard coil machines, including small to large MRO consumables, abrasives, and general shop supplies.
The precision scale technology offers accurate reporting on changing stock levels, and the easily accessible storage trays ensure timely replenishment.
For storing frequently used tools and larger items in a convenient location on site, the ProLock is a fully configurable storage container with up to 24 individual lockers. Best suited to durable and calibrated tooling, it can also factor restricted access to items requiring inspection prior to use. Cordless power tools can be placed on charge while inside, making it easier to keep track of everything in the one place.
“Larger sites might also consider our upscaled inventory solutions, such as the AccuCab decentralised tool store, or an RFID Storeroom, which features secure gated entry and much larger holding capacity,” says Brenton. “The
1. The end-user takes whichever items they need from the dispensing unit.
2. The process software downloads the usage information throughout each day. It then alerts the local Motion Australia branch about which items need to be replenished.
The quarrying industry can pose significant health and safety risks to employees if quarry managers don’t take steps to ensure a safe working environment.
According to Work Safe Victoria, there are more than 900 quarries in the state of Victoria that range in size from locally owned and operated quarries to large scale operations that are owned by conglomerate investors and global mineral powerhouses.1
Victorian quarries produce a range of materials that supply other Australian industries. Whether it is cement, stone or aggregates like rock, gravel and sand used in the building and construction industry or mineral soil for agriculture, Australians depend on quarried materials for every aspect of their lives.
And yet, regardless of the size of a quarrying operation or the crucial role it plays in Australian life, the risks and hazards quarries pose always remain the same because of the nature of the working environment.
It may seem obvious that falling rocks could be a big risk on quarrying sites, but there are many ways that this can occur on various pieces of quarrying equipment, according to Steve Hittmann, Category Manager for Industrial Drive Systems and Mobile Final Drives at Motion Australia.
“Quarrying equipment is designed to move heavy rock material upwards, downwards, and side to side. This could be in the form of an inclined conveyor belt or a bucket elevator,” says Steve.
“Now imagine for a second that an incline belt conveyor that is about 30 or 40 metres long has heaps of crushed rock on it going uphill to another location on site. In total, that conveyor could have 10 tonnes of crushed rock on the incline.”
“Now if the drive on that conveyor
cuts out for whatever reason– an equipment failure or a power outage–the drive and the conveyor belt will start running backwards down the incline and the 10 tonnes of crushed rock will go with it, landing at the bottom of the conveyor, with any luck nowhere near any pedestrians. But the damage that it can do is catastrophic.”
These kinds of dangerous situations are not uncommon on quarrying applications. As a result, Victoria’s Occupational Health and Safety Act of 2004 issued strict regulations for quarrying sites that ensure these dangers are minimised as much as possible.
Installing backstops and anti-roll back technology on inclined conveyors is just one of the required precautions that every quarry must take on equipment to stay within the bounds of OHS laws, but it is a very important one.
“Australia-wide, any piece of equipment that is inclined by more than four degrees, is required by law to have anti-roll back technology in place,” expounds Steve.
“Fortunately, Motion Australia suppliers that we work with like Regal Rexnord have been proactive in designing solutions to address the dangers of quarrying applications with their Falk True Hold NRT Low-Speed Backstops solution.”
For more than 125 years, Regal Rexnord has been globally recognised for their forward-thinking innovation in the fields of power transmission. Regal
Rexnord acquired the Falk brand in 2005, ushering in a new range of power transmission solutions which now includes safety products for industrial applications.
On a basic level, the Falk True Hold NRT Low-Speed Backstops are a failsafe solution for elevated and inclined equipment, as they allow it to rotate in only one direction. An example is in the case of an inclined quarrying conveyor - the belt line can rotate up the incline,
1. Suitable for dusty environments
Dual, double lip contact seals on each side of unit protect against lubricant leakage and contamination.
2. Longer service life
Grease purgeable exclusion seals create a barrier for contamination and enhances seal life, reducing maintenance costs and extending the life of the seals.
3. Low maintenance generous lubricant capacity
The units maintain optimum oil splash for internals and optimum cooling of the Backstop. The cooler operating temperature enhances oil life and seal life.
4. Visual lubricant check
A standard oil site glass allows operators to verify lubricant levels visually.
but it won’t rotate backwards. If the machine tries to roll back, the Falk True Hold NRT Backstops will stop it. But in addition to providing substantial safety benefits, the Falk True Hold NRT Low-Speed Backstops also have a number of other capabilities, according to Steve.
References: 1. Worksafe Victoria. Quarries health and safety guide. https://www.worksafe.vic.gov.au/ quarries-health-and-safety-guide
5. Performs optimally under variable temperature, humidity, and moisture
The Falk 3-micron Airmax Breather prevents moisture from entering during the inhalation cycle and allows moisture to exit and evaporate as the NRT reaches normal operating temperature. This prevents water contamination and eliminates oxidation of rotating elements.
6. Positive holdback operation Ramp and roller backstopping mechanism performs a wedging action of the cylindrical rollers compressed between the inner cam and outer race assuring immediate prevention of roll back rotation.
7. 100,000 full load cycle rating
Backstop mechanical design capabilities meet or exceed the life of most or all system components. NRTs can run longer than the expected system design life.
Other features and benefits
• Proven speed and load functionality
• Ideal for high vibrational applications
• Dual sets of fasteners and gaskets on seal cages
• Versatile installation potential
• Extended torque capability with load balancing on hydraulic load sharing system
• Maximized tonnage capabilities
• 3-year Heavy Duty Warranty
Falk True Hold NRT Backstops use anti-rollback technology to failsafe quarrying conveyors.
The inside of fluid power machinery is complex, and subject to some of the harshest conditions on mining sites. To address this, Gates® has designed a fit-for-purpose range of industrial-grade hoses, ideal for transporting water and emulsions between hydraulic components.
The Megasys® portfolio offers increased performance and flexibility, facilitating peak plumbing and routing in compact applications. Capable of reducing expenditure by up to 64 per cent, they are easy to install and require fewer bent tube fittings. With such diverse capabilities within the range, it’s important to select the most suitable hose for each individual system.
The Gates® Megasys® range is separated into two main categories:
Wire-braid hose – M3K, M4K, M5K, M6K, MXT, MXT-XTP
These are constructed using high-tensile steel wire and are tested to 600,000 cycles.
Spiral-wire hose – EFG3K, EFG4k, EFG5k, G8K
These are constructed from four to six alternating layers of spiralled, high tensile steel, and are tested to up to one million impulse cycles.
Xpiral hose – MXG4K-XTP, MXG5K-XTP
Built with Gates patented Xpiral™ woven spiral technology, MegaSys MXG™ 4K/5K hydraulic hose is lightweight, highly flexible and qualified to one million impulse cycles. MXG™ 4K/5K exceeds the performance of wire spiral constructions, but with the lower weight and flexibility driven by Gates materials science technology.
Identification laylines are printed along the side of each product, and are used to
communicate critical information about its specifications. This offers increased efficiency for purchasing or organising stock on site. In addition, hoses in the MegaSys® line are distinctly colourcoded to quickly and easily view pressure ratings.
• YELLOW: 8,000 PSI, G8K
• ORANGE: 6,000 PSI, EFG6K
• RED: 5,000 PSI, M5K/EFG5K/MXG5K-XTP
• PURPLE: 4,000 PSI, M4K/EFG4K/ MXG4K-XTP
• BLUE: 3,000 PSI, M3K/EFG3K
Alongside the respective colours, each hose description label will list the I.D number, bend radius, psi working pressure, SAE and European standards, and important features such as flame resistance.
To makes things easy to remember, Gates® recommends using the STAMPED method for running through hose selection criteria:
S = Size
T = Temperature
A = Application
M = Material to be conveyed
P = Pressure
E = Ends or couplings
D = Delivery (volume and velocity)
The inside of a hose diameter can vary, and must align with pressure requirements to avoid excessive turbulence. If possible, check the printed measurement on the side of the old hose that needs replacing. If this has worn off, cut the original hose and carefully measure the internal diameter to match up with the new product.
Both fluid and ambient temperature need to be considered when putting together a new hose assembly. The selected product must withstand the minimum and maximum temperatures that it will experience in service.
Noting where and how the hose assembly is going to be installed will help to determine an optimum selection. Some questions to ask in this process are:
• What is the fluid compatibility?
• What are the environmental conditions and potential risks?
• What are the routing requirements?
• Are the government and industry standards being met?
• Are there unusual mechanical loads?
• Is a non-conductive hose required?
Ensure that the hose tube, cover, couplings, and O-rings are compatible with the water, oil emulsions, or glycol solutions being used. Take care in this selection where gases are present.
Noting the system pressure is one of the most important steps. The published working pressures must be equal to or greater than the relevant system pressure rating. If the hose experiences pressure spikes beyond this, the product life will shorten, so this is not recommended.
Proper sizing of transport efficiency can be ensured by checking the original hose I.D. against the new one. If any relevant aspect of the system has since changed, use the Nemographic Chart to make an exact measurement.
In the quarrying industry, the success of a quarrying operation depends on the performance of equipment in the field. To optimise productivity and keep operational costs down, quarries need to operate like a well-oiled machine with all equipment running at peak performance.
However, due to the nature of a quarrying site and the arduous operating environment, quarrying equipment is subject to a lot of wear and tear from the effects of harsh chemicals, rust and corrosion, and the ingress of moisture and contaminants.
As a result, quarry maintenance departments face a tremendous amount of pressure to keep equipment wellmaintained to curb the costs of incidental breakdowns and premature equipment failures, according to Steve Keown, National Product Manager for Lubricant and Chemicals at Motion Australia.
“Equipment maintenance and repairs significantly impact an operation’s bottom line. A large majority of quarrying equipment is custom made to fit out a site’s specific requirements, so it is an expensive investment,” says Steve.
“In addition to this, any downtime that is experienced on equipment incurs costs to productivity, time, and labour,” says Steve. “Therefore, when equipment and componentry experience an incidental failure– the repair process is critical to controlling operational costs.”
For the team at Motion Australia, helping quarries protect valuable equipment and assets means determining maintenance solutions that can reduce downtime and labour costs. While at the same time, aiming to improve the performance and longevity of equipment and componentry in field.
“There is always a risk during the repair process that a component could be damaged or require a replacement, particularly during disassembly,”
explains Steve. “In the instance that the component manufacturer is overseas, and a part or component needs to be imported, that increases downtime and costs on an operation.”
For a practical solution that addresses some of the quarrying industry’s most critical pain points, Steve recommends the CRC 5.56 Multipurpose Lubricant.
“The CRC 5.56 is a timeless solution that we have supplied to many of our biggest customers in the heavy industrial market over the years,” says Steve. “On quarrying applications it’s ideal for lubricating and protecting fasteners, shackles, pins, bushes and hinges¬ in hard-to-reach locations.”
“It is one of Motion Australia’s bestselling products to the Australian quarrying segment– and well recognised across generations of maintenance workers as an essential ‘toolkit in a can’ on site for its ability to eliminate the need for destructive disassembly on expensive equipment,” furthers Steve.
“The CRC 5.56 facilitates the quick removal of components and releases rusted parts which saves time and labour on repairs.”
According to Melanie Mangos, Head of Industrial Sales at CRC Industries Australia, Australian heavy industry consumes a significant volume of CRC 5.56 every year because the effectiveness of the formula has the ability to save operations thousands of dollars in repairs and downtime– reduced to the cost of a single can of 5.56.
“The CRC 5.56 embodies many of the values and principles that CRC was founded on,” says Melanie. “As a global leader in developing premium quality aerosol lubricants and anti-corrosion formulas, we have built on a foundation of more than 60 years globally of experience supplying premium maintenance products to the heavy
• Saves time and labour on repairs
• Lubricates and penetrates rust and corrosion
• Facilitates quick removal of components
• Assists in non-destructive disassembly of expensive assemblies
• Actuator ‘straw’ nozzle for hard-toreach locations
• Fast acting formula
• Provides an environmental barrier for fasteners, shackles, pins, bushes, and hinges
• Protection from moisture with a protective film
• Self-healing properties
industrial market.”
Ideal for mining and quarrying equipment due to its ability to provide a barrier to strenuous environmental conditions, the CRC 5.56 formula can be used safely on metal, alloy, rubber, plastic and painted equipment. Additionally, the actuator on the nozzle allows for easy access to hardto-reach componentry.
“The product is versatile and unparalleled when it comes to breaking through any rust or corrosion and clearing away scale and dirt. CRC call the product ‘A toolkit in a can,’” explains Melanie. “The formula is fast acting and penetrates rust and corrosion to release parts and components. While at the same time, adding a protective layer of self-healing film that prevents ingress of moisture and contamination.”
“The 5.56 is part of the reason CRC has become a household name and you would be hard pressed not to find one in every MRO workshop in the country,” concludes Melanie. “It’s not uncommon to find a can of 5.56 in a tradie’s truck, toolbox, or workbench, and for older generations to pass this product down to the next generation as a staple.”
The materials extracted from quarrying operations are often transferred to a processing plant, manufacturing facility, warehouse, or workshop where they will be transformed into products. Regardless of where these materials end up, fresh air in these spaces is essential for limiting exposure to the dirt and dust
that come with them.
SafeWork Australia has issued a warning to employers about the health safety risks associated with working in conditions that have inadequate airflow. By law, Australian employers are now required to ensure their working environment has an effective ventilation system.
In a nutshell, ventilation means replacing contaminated air with fresh air. But when it comes to creating safe, healthy working environments, it’s important for site managers to equip their workspaces with powerful, efficient, heavy-duty mechanical ventilation systems, according to Troy Lopez, General Manager at Fanmaster.
fans: For keeping air moving in industrial workspaces
Ventilation methods work by expelling stale air and introducing fresh air from outside. These units can be either fixed or portable. Fixed ventilation methods include hooded roof fans, wall exhaust fans, axial flow fans, and industrial louvered fans designed for industrial sites and agricultural buildings. Portable ventilation units include portable fume collectors, mobile man coolers and compact air blasters.
3. Coolers
The Fanmaster
Hooded roof fan extracts heat, smoke, dust, or fumes from buildings. When used in conjunction with coolers, the hooded roof fan helps to keep the temperature down during hot Australian summers.
“Improper ventilation causes stress on the body, inducing discomfort, exhaustion, and heat stroke in workers. Industrial activities such as welding, drilling, grinding, and even transporting materials emit harmful dust, dirt, and contaminants that can cause long-term respiratory and neurological diseases,” he says.
Cooling units such as evaporative coolers and air conditioners also help improve air quality and air circulation through movement and distribution. Another option is that of misting fans –which supply a fine mist (which quickly evaporates) during operation, helping to create cooling breezes.
Which option works best for you?
and
made from high quality steel
Fortunately, the ventilation, cooling, and extraction experts at Fanmaster have site managers covered with a few effective methods for ventilating industrial workplaces:
1. Industrial fans for air circulation
Fans can make people feel cooler and more comfortable due to the breezy, chilling effect they create. Fans that improve air quality by extracting contaminants and stale air include:
• Mobile Mancoolers: These portable fans that extract contaminants are often used in the mining and quarrying industries because they are suitable for confined spaces on underground operations
• Commercial pedestal fans: Available in a wide range of sizes
• Fixed wall fans: Ideal for use in a range of working environments
• High-volume-low-speed (HVLS) ceiling
In some cases, working environments might require a range of solutions to ensure quality air flow. The best way to start is by speaking to an expert to determine the best solution for your situation.
Fanmaster has been an Australian familyowned-and-operated business for over 21 years. The company specialises in the import and manufacture of cooling, heating, ventilation, and extraction systems and offers extensive knowledge in their field to the industrial sector.
As a supplier to Motion Australia’s network of businesses, this adds an additional layer of technical support and mechanical engineering know-how to Fanmaster’s mission to bring fresh air and thermal comfort to Australian industry.
Visit your local Motion Australia branch and speak to a technical representative today to find the best ventilation system for your quarry.
In many Australian maintenance workshops, the LOCTITE® name is associated with efficient repairs made easy. Now, thanks to LOCTITE PC 7218’s new and improved formula, repairing worn parts and protecting equipment on mining and quarrying applications is easier than ever before.
For more than 20 years, the LOCTITE PC 7218 wearing compound has set the standard for high performance wear resistance for the mining and quarrying industry. LOCTITE PC 7218 is a two-part ceramic filled epoxy paste designed to protect, rebuild and repair high wear areas of processing equipment. Applications such as cyclones and separator bodies, dust collectors and exhausters, pump liners and impellers, fan blades and housings, chutes/ hoppers and elbows/transition points can benefit from the surface protection that LOCTITE PC 7218 wearing compound provides against abrasive materials and erosion.
LOCTITE PC 7218 can also be used for filling gaps, patching and lining pipes, walls, internal surfaces, and tiled areas.
By rebuilding surfaces with LOCTITE PC 7218, maintenance workers can restore
and reinforce them with abrasion resistant coating.
With the recent upgrade and re-release of the LOCTITE PC 7218 formula, LOCTITE has taken maintaining this high-quality standard one step further with improved adhesive and wear resistance capabilities, and the removal of ingredients subject to the 2018 Amended Poisonous and Deleterious Substances Control Law.
To stock up on supply of the LOCTITE® PC 7218, visit your local Motion Australia branch today.
Based on preliminary testing done, LOCTITE materials scientists found that the new LOCTITE PC 7218 formula compares favourably to the former product in three key areas:
1. Strength at high temperature: The new product shows 62% higher tensile shear strength at 80°C.
2. Heat aging property: The new product maintained the same shear strength at 80°C.
3. Abrasion resistance: The new product has improved the weight loss ratio by more than 50%
A leading iron ore ship loader in Western Australia was experiencing wear on the inner face on one of their chutes. The chute was catching iron ore from a fall of approximately six meters lasting only 10 weeks a repair cycle, before requiring patching or replacement.
In under five hours, the inlet chute was prepared and rebuilt using LOCTITE® PC 7218 wearing compound as a ‘cold fix’ requiring no Hot Work Permit. The result was chute life doubled to 20 weeks and the company accrued significant cost savings by avoiding chute replacement and a reduction in labour hours. 10 weeks of production in, the chute was practically still in newly repaired condition.
On a quarrying site, vibrating screens, also known as ‘shaker screens’ play an important role in mineral processing. Much like sifting sand through a sieve, a shaker screen is primarily used for sorting quarried materials to size.
The principle of a shaker screen is relatively simple: they are typically inclined over shafts that have motorised drives that cause the shaker screen to vibrate rapidly.
Depending on the arrangement, the screen moves in a linear or elliptical motion to create centrifugal force. This force causes the smaller particles to crumble and fall to a feed below, while larger sized materials move overhead.
Shaker screens are typically a lowmaintenance, low-cost piece of equipment that allow operators to maintain a good level of control over the flow of material that is otherwise heavy, abrasive, and difficult to handle.
Despite of all the benefits of vibrating screens to the mineral processing industry, the downfalls seem to exceed them in terms of the service life of shaker screens and frequent breakdowns. In short, most shaker screens just don’t work very well.
According to Michael Greelish, the National Business Development Manager at Motion Australia, the most common reason that vibrating screens break so frequently is because the bearings fail.
“The screen manufacturers are not at fault, as they design the screens to withstand immense stress from materials being fed continuously through cycles of crushing and sorting.
If the stress levels remain to testing standards, the screen is likely to be reliable and resilient with the life of the machine,” says Michael.
“The problem is not with the screens themselves; it is with component failure. The internal componentry experiences extreme levels of fatigue and rapid wear under the stress of constant circular, linear, and elliptical forces against abrasive materials,” he continues.
“When the quarried materials are fed onto the screen decks, their movement is relatively volatile, and these uneven movements can put additional stress on internal componentry. The force is hard to predict and even harder to contain–often causing one side of a screen to fail prematurely.”
Michael emphasises that quarries rely
• X-life quality = 70% longer life than standard bearing types
• Bainite heat treatment for temperature stability up to 200°C
• Surface hardened cage for high wear resistance
• Cage guided by outer ring better accommodates centrifugal forces
• Tighter OD and ID dimensional tolerances for better control of fit in housing and on shaft
• Durotect CK hard coating on bore for reduced fretting corrosion and shaft wear
on the performance of their vibrating screen applications for their production.
“A quarry’s overall production output is contingent on the performance of their shaker screens, and the performance of the screens is determined by the suitability of the bearings for the application,” he says.
For quarrying managers, shaker screens pose a difficult engineering problem that often requires outside consult to solve. This is where Motion Australia and their longstanding supply partner Schaeffler enter the equation.
“We have been partnering with Schaeffler to work with quarrying customers for many years, and this includes performing joint site visits and two-fold engineered bearing solutions for shaker screen applications,” says Category Manager for Industrial Bearings at Motion Australia, Tony Tormey.
Tony specialises in providing bearings solutions for heavy industrial applications that “solve problems for customers, rather than create them.”
“A vibrating screen needs to have multidirectional capabilities, so it requires a spherical roller bearing solution that is purpose designed and built to accommodate the extreme stress of these movements,” says Tony.
From their state-of-the-art engineering and manufacturing facilities in Germany, one of Schaeffler’s most recent innovations is their patented Durotect CK bearing surface coating that went into the design of their FAG T41D Shaker Screen Bearings.
“When it comes to bearing solutions for shaker screens, the Schaeffler FAG T41D Shaker Screen Bearings are unparalleled in the market because of the cutting-edge Durotect CK surface technology used in the construction of the bearings,” highlights Tony.
Specifically designed for shaker screen applications, the T41D Bearings have a thin layer chromium bore coating to the inner ring bore which alleviates fretting corrosion, and offers superior wear resistance, greater load carrying capacity and longer service life.
shaker screen applications, the T41D Bearings are part of Schaeffler’s X-Life portfolio, which stands for ‘extended life’ of the bearings.
X-Life bearings are all heat-treated for temperature stability and high wear resistance and resilience under centrifugal force, making them even more well suited for shaker screens.
The T41D Bearings have further surface treated cages and tighter dimensional tolerances for better housing and shaft fitting.
“Quarry managers will often approach us at Motion Australia and ask how they can improve the structural integrity of the shaker screens on their site to reduce stress and avoid production losses,” says Tony.
“I tell them if they want to drastically improve the life of their shaker screens and avoid any loss of productivity, the T41D bearings are the answer,” he concludes. “In some cases, they will even outlive the screen– problem solved.”
In the quarrying industry, off-road light vehicles are often used for the efficient transport of personnel and supplies around or between sites. Some are employed to venture underground, carrying loads of material or equipment through confined and hazardous spaces.
Much like the human body, trucks and cars have a plethora of internal components that work together to keep the whole system moving. Within a light vehicle, the drive shaft serves to deliver torque from the transmission to the differential, then onwards to turn the wheels in motion. A drive shaft designed for a sportscar will be different to that in a quarry site truck, which is where industry knowledge from the team at Hardy Spicer comes in. Michael Walton has been working at Hardy Spicer for over a decade, and has recently stepped into the role as Branch Manager in Townsville. He says that with nine centres located across Queensland, New South Wales and Western Australia, the group is wellplaced to liaise with key players in the quarrying space to ensure the best possible fit for their on-site four-wheel drives.
“Many years ago, we worked with some mining companies to develop a greaseable front CV joint for their fleet’s light vehicles,” he says. “That greaseable front feature meant that they didn’t have to disassemble the whole vehicle to carry out lubrication maintenance.
Around the same time, we innovated our heavy-duty mining specification drive shaft.”
The shaft’s Hardycoat® nylon splines offer 30 per cent longer life than standard steel alternatives. Additionally, the rubber lip seal and boot give superior protection against dirt, dust and water. The complete shafts, universal and greaseable CV joints available from Hardy Spicer are all interchangeable with standard parts from commonly used car makes.
“Our drive shafts are being used in quarries for both above ground and underground applications,” Michael enthuses. “We also have the biggest line of heavy-duty universal joints that are greased through the cap, featuring triple lip seals and teflon thrust pads, giving them a much longer life than a lot of standard OEM replacement parts.”
Each Hardy Spicer service centre is equipped with purpose-build engineering machinery, including press up benches, electronic balancers, and weld lathes. This gives them the capability to balance drive shafts perfectly to meet ISO standards before they go into service, ensuring the prevention of excessive spline wear, yoke, tube or weld failure.
“We can either repair or overhaul existing shafts, or design and build a completely new one to suit almost any application,” says Michael. “Whether it’s a light vehicle or heavy piece of machinery, these custom-built, high performance parts are built to last.”
According to Michael, the team can also carry out fitting of universal joints, couplings and centre bearings, ensuring the safest possible end result for longterm service in the field.
“For example, I’ve recently been working with a customer on a custom job for a two-piece shaft, which has a special parkbreak through the middle,” he explains. “We can do unique flanges, or different shaft lengths. There’s not much we can’t do or won’t try to collaborate with the customer on to find a solution.”
“We’ve supplied these drive shafts to many sites across Australia over the years, and often times people are so happy with their performance that they come back to request fitment on their personal vehicles,” he concludes. “That’s a real demonstration of how satisfied they are.”
Nothing can slow quarry production down like wet conditions. When water permeates the quarrying process, the extracted minerals, gravel, and sand quickly turn to sludge and slurry which are common by-products of daily quarry operations.
As a result, quarries heavily rely on effective pump applications to manage and control the ingress of water on site, and keep production running.
Pump systems in general vary in their ability to withstand the rugged conditions of heavy industrial applications, according to Troy Markland, National Product Manager for Chain and Ironware at Motion Australia.
“The performance of a pump system depends entirely on how it is assembled - from design and manufacture to the sealing and power transmission components,” he says.
“Slurry and sludge pumps use greater or lesser degrees of centrifugal and hydraulic force to displace watered down materials, and in most cases using a specialised dewatering pump is the most efficient and cost-effective solution for a quarry.”
Consequently, it is necessary for quarries to make some considerations when designing and fitting slurry pump assemblies, highlights Troy.
“Slurry pumps typically consist of two shafts– one for driving and the other being driven,” explains. “Power comes from the motor and transfers to the turning shaft through a coupling arrangement.”
“Ensuring a pump system is fitted with the right coupling components is critical to the performance of the application, as any heavy vibrations and loads can cause cracks and fractures on drive equipment,” he explains.
“Furthermore, pump systems are often located underground and requiring heavy lifting and rigging equipment to install. So, they can be difficult to maintain and repair if there is an issue.”
According to Troy, joining two aligning drive shafts is very difficult to do without any deflection and misalignment. Therefore, preventive maintenance on coupling components starts at the point of installation on pump systems.
From Motion Australia’s portfolio, Troy often suggests Fenner coupling solutions to quarrying customers for the most robust drive shaft solutions that can stand up to the abrasive nature of sludge and slurry.
“The Fenner Fenaflex Tyre Couplings are the preferred choice for both aboveground and below ground pump applications due to the Fenaflex tyre, it can accommodate a high degree of misalignment – up to four degrees,” he explains.
For below ground applications, a FRAS rated (Fire Resistant Anti-Static) tyre is recommended.
“The rubber tyre also does a good job of softening vibrational force through absorption,” he adds. “Making them very versatile and flexible on heavy load and high torque applications.”
Working closely with Fenner application engineers, Troy has gained a good understanding of fitting the Fenner Fenaflex Tyre Couplings on quarry pump applications, putting together a brief installation guide for quarry operators to refer to.
•
Firstly, all mating surfaces of the assembly taper balls and flanges, and taper lock bush bores should be cleaned to remove any debris that might impede assembly.
• Before placing the flanges on to the shaft, loosely place the bush into the taper lock bore and align the half holes correctly.
• Remove clamping rings and screws.
• Place loose clamping rings onto the mover and drive machine shaft before locating coupling flanges.
• If keys are required, side fitting keys with top clearance should be used.
• Once the clamping rings and flanges are in place, tighten the fixing screws to the required torque* detailed in the instructions supplied with each bush.
• For keywayed flanges, place on the shaft, locate keyway, and tighten screws.
• Bring the shafts into alignment, taking into consideration end-float and misalignment.
• Measure the gap between the shaft to the appropriate distance.
• Lay a straight edge across the flanges in several areas to check that they are aligned parallel to one another.
• Open the tyre and place over the coupling flanges ensuring it is seated properly, closing the gap of the tyre.
• Replace the clamping rings over the flanges and tighten the clamping ring screws evenly until the correct screw torque is achieved.
• There should be no metal-to-metal contact between coupling flange and clamping ring.
• Run the coupling under load for a test period, if possible and check the torque to ensure it is correct.
*Always refer to the manual for each product for torque ratings.
With sustainability on the forefront of the of the agenda for mining, quarrying and heavy earth moving companies, suppliers have experienced a huge uptick in the demand for zero impact cleaning products in recent years.
“Heavy industry has shifted with the move toward greater Corporate Social Responsibility. New standards and regulations from local and governing bodies have motivated companies to buckle down on their sustainability targets,” says Michael Greelish, Motion Australia’s National Business Development Manager.
“As a result, mining, quarrying and resources managers are now seeking to procure greener product solutions that will offset the environmental footprint of their operations. And in many instances, the green product solutions we supply now take precedence over standard products.”
When it comes to leading the charge on developing greener products for heavy industry, CRC has managed to stay ahead of the curve with the introduction of their Bio-Degreaser formula. Bio-degradable, non-toxic, pH balanced, and water soluble– CRC’s Bio Degreaser offers next generation green cleaning technology without compromising performance.
“With our innovative Bio-Degreaser, we are purposefully demonstrating our commitment to Corporate Social Responsibility and setting a new standard for cleaning and degreasing solutions,” says Melanie Mangos, Head of Industrial Sales at CRC Industries Australia.
On quarrying site where dust, dirt and contaminants are prevalent, it’s necessary to routinely degrease parts and components to keep them in working order.
The CRC Bio-Degreaser is an industrial strength, robust, concentrated formula
that is non-abrasive, non-flammable, non-corrosive, and solvent free. Safe for use on most metal surfaces, the Bio-Degreaser is capable of cleaning engine and motor parts, generators, compressors, bearings, chain, screens and hydraulic systems– quickly and effectively.
“CRC Bio-Degreaser is an extra heavyduty cleaner, its formulation penetrates to dissolve tough grease, oil and contaminants – safely. Our diverse end users love the strength of its cleaning solution,” says Melanie.
“CRC Bio Degreaser is water soluble and works well on all metals and alloys which is one of the reasons our customers trust the product,” she concludes.
As a world leading supplier of premium quality aerosol and bulk lubricants, anti-corrosion and maintenance products, CRC has enjoyed a prosperous working relationship with Motion Australia and their customers in the mining and quarrying sectors for decades. Both companies acknowledge the importance of reducing the environmental footprint of the heavy industrial sector.
For more information on CRC BioDegreaser and CRC’s range of environmentally friendly cleaning and degreasing products, visit your local Motion Australia branch and speak to one of our experts today.
CRC Bio Degreaser is water soluble and works well on all metals and alloys which is one of the reasons our customers trust the product.
Eliminating the risk of fire hazards and combustion is critical to keeping quarrying environments safe. For this reason, where the frequent use of explosives and harsh chemicals takes place, it is important that large pieces of machinery are adequately safeguarded against static charge.
In 2020, Gates® introduced the PowerGrip® GT®4 high-torque synchronous belt to the Australian and New Zealand market. Constructed from rust-resistant ethylene elastomer (EE), this narrow, high-capacity drive belt is meticulously engineered to address durability, efficiency, noise reduction, and streamlined installation.
Importantly, it minimises the amount of friction and the build-up of heat caused by repetitive shock loads. Constructed in alignment with the ISO 9563 testing methods, this belt falls within the specified electrical resistance properties needed to safely operate in an explosive or fire-prone environment. Essentially, it is sufficiently conductive to dissipate electric charge that may form as the drive unit runs.
“One of the biggest challenges that quarries face is making sure that all stages of operation are compliant for the safety and wellbeing of personnel,” points
out Michael Greelish, National Business Development Manager at Motion Australia.
“A straightforward way of doing this is opting for machinery and parts that are up to code, and designed with the industryspecific risks in mind.”
The PowerGrip GT4 is ideal for most types of heavy-duty quarrying equipment, such as driving pumps, fans, conveyor systems, drills and earth moving machinery.
After just a couple of years in the field, the product has already set a new industry benchmark for its impressive power ratings. This is largely due to the company’s extensive research and development efforts, combining decades of technical knowledge with the latest in power transmission science.
Compared to the previous GT®3 series, this newer synchronous belt has boasted superior performance in all operating conditions. To combat a lack of consistent manufacturer standards for developing power rating tables, Gates has undergone a thorough rating development plan to ensure accurate modelling results.
Available in 8MGT and 14MGT pitches, the PowerGrip® GT®4 is a narrower band, without compromising on transmission capacity. This allows for more compact
• High tooth jump resistance
• Reduced environmental impact
• Improved safety and ergonomics
• Lubrication-free capabilities
• Chemical resistance
• Wide temperature range of -40°C to 120°C
• No stretching
• Various available widths of 20, 30, 50, 85mm (8MGT) or 40, 55, 85, 115, 170mm (14MGT)
drive assemblies, and mitigates fatigue or strain during installation and change-outs.
In contrast to many other elastomer synchronous belts currently on the market, they are not fabricated from chloroprene, which harbours performance limitations and can have a negative impact on the environment. Instead, Gates® has pioneered an ethylene elastomer technology, which offers increased resistance to oxidation, heat, extreme weather, brake fluids, oil and grease. Paired with the internal fibreglass tensile cords and patented tooth profile, Michael says they are the next generation for optimum quarrying capacity.
“A fantastic feature to consider is that they require no lubrication or re-tensioning, which reduces huge amounts of downtime and maintenance costs,” he enthuses.
“At Motion Australia, we stock a broad catalogue of Gates® products including compatible sprockets and pulleys, and our power transmission experts are available to carry out site inspections to audit individual customer requirements.”
One of the greatest logistical challenges for quarrying operations is transporting materials from one location to another on site. The heavy loaded, vibrational, and abrasive nature of moving quarried materials requires a sturdy and efficient method of transport– the most convenient of these being a classic belted conveyor system.
Anyone who has visited a quarry, will be familiar with the intricate web of conveyors that spans across the site–some troughed; some flat; and some slanted for uphill and downhill movement. A classic quarry conveyor system consists of belts, pulleys, bearings, and rollers that feed materials in and discharge them out by way of chutes for transport, sorting, and processing.
Of these parts and components, the most critical for the success of a quarrying conveyor system, are the bearingsaccording to Michael Greelish, National Account Manager for Mining, Quarrying and Resources at Motion Australia.
“Bearing failures are one of the primary causes of downtime on quarrying conveyors and this is often due to how they are installed,” he says. “Correctly measuring the internal clearance of the bearing is difficult to get right on installation. In many cases, the bearing ends up being fitted too tightly so it breaks during production, or too loosely so it spins on the shaft.”
“It is very important to install conveyor bearings correctly with the proper fit up, so you can get the optimal performance and service life out of the bearing. A step-by-step fit up that includes checking and using gauges to install the bearings will ensure a prolonged bearing life on quarrying applications,” he emphasises.
For Michael, determining the best bearing solutions for quarrying conveyors and working with suppliers to ensure correct installation is a huge part of Motion Australia’s offering to the quarrying industry.
However, there are some suppliers, like Australian Timken, that set the standard
in terms of providing reliable bearing solutions for these types of applications, he notes.
“In particular, the Timken® Spherical Roller Bearing Solid-Block Housed Unit has established itself in the market as the strongest housed bearing unit of its kind– providing exceptional resilience and strength under extreme operating conditions– and that standard remains unparalleled in the industry,” says Michael.
An example of how the Timken® Spherical Roller Bearing Solid-Block Housed Units perform in quarrying conveyor applications happened recently when a quarrying customer who was experiencing issues with the tail bearings on their quarrying conveyor approached the Motion Australia team.
“The bearings were getting buried by dirt, dust, and contaminants – causing shutdowns every few months and costly bearing replacements,” explains Michael.
“But after a successful trial on one of their conveyors with two Solid-Block Housed units, the customer replaced all
the bearings on their conveyors with the Timken units.”
According to Mark Davies, National Mining Manager at Australian Timken, the success of the Timken® Spherical Roller Bearing Solid-Block Housed Units is due to their superior manufacturing and construction methods.
“The housing is made from solid cast steel and the bearing is fitted inside the housing at the factory level,” explains Mark. “The internal clearance is pre-set at the point of sale, and the sealing arrangement is prefitted to lock in grease and protect from the ingress of dust, dirt, and contaminants.”
“In addition to this, the units are available in a host of shapes, sizes, sealing arrangements and locking systems. We have six different internal locking mechanisms: V-Lock, Double V-Lock, Concentric, Eccentric, Tapered Adapter, and the Double-Nut Tapered Adapter,” elaborates Mark.
“Of these, the Double-Nut Tapered Adapter has been tailored specifically for conveyor pulley applications as an easy screw and lock mechanism that eliminates the need for complicated installation processes.”
In recent years, providing bearing installation training to quarrying sites has become an integral part of Motion Australia’s business offering.
“In the case of the Timken® Spherical Roller Bearing Solid-Block Housed Units, if the installation is done right, it should be a quick and easy process of simply locking the unit onto the shaft with no fitting required,” says Michael.
Furthermore, he notes, Australian Timken plays an active role in working with Motion
• A two-row spherical roller bearing
• Black oxide inner ring
• Six different primary seals against inner ring
• Machined solid feet
• Housing tolerance: J7 > Light Interference fit
• Standard Relief Valve
• Optional open or closed steel or urethane seal covers (bolt on)
• Five axial locking styles
• Easy to change from fixed to floating
• Housing can be supplied with Standard Powder Coat or special order Nickel, Zinc, or Urethane coating
• Housing manufactured from cast steel
Australia’s quarrying customers to provide on-site training for Timken® Solid-Block Housed units.
“We regularly supply Timken® Spherical Roller Bearing Solid-Block Housed Unit installation training to customers,” he says.
“In conjunction with Australian Timken engineers, we teach customers how to correctly install the Timken® Spherical Roller Bearing Solid-Block Housed Units. This training includes all staff on site–from the apprentices to the fitters to the engineers.”
Currently, Motion Australia is also offering their Quarry Training Session– a workshop with a focus on skills sharing and upskilling, that covers training on fitting conveyor bearings, V-Belt tensioning, and alignment procedures.
“This is not an online program. We bring training rigs out to the site and concentrate mainly on the fitting of spherical roller bearings because they are a bit more specialised in their installation requirements. We teach the staff how to measure and calculate radial internal clearance and the reduction of it once the bearing is fitted up by allowing staff to work on the rigs,” says Michael.
“It is a two-hour training session with no digital component or online modules, and no PowerPoints,” he concludes.
“We understand the best way for a lot of tradespeople to learn is by doing. So, this truly a hands-on training.”
For more information on Motion Australia’s Quarry Training Sessions and Timken® Spherical Roller Bearing Solid‑Block Housed Unit training, contact your local Motion Australia branch today.
Lance Brett has been working in mechanical seals for over 35 years. Now a National Product Manager at Seal Innovations, he is excited to bring their new Heavy Duty Slurry Seals onto the market for Australian customers.
“We’re really pleased with the quality of these seals and how they stand up in terms of wear life and reliability,” he enthuses. “It perfectly complements the rest of our product range and offers new potential for our involvement in the mining and quarrying sectors.”
The role of a sealing application cannot be overlooked, especially in resources where they act to secure valuable materials while they are being processed. Slurry is formed when water combines with ferrous and non-ferrous raw material, such as rock and soil between 1mm and 25mm thick. In mining, there are several types of pumps used in the transport of large volumes of slurry to mineral processing plants, where it then undergoes a separation process.
The solids within slurry can often prove highly abrasive, contributing to the accelerated wear life of critical parts, including seals. This problem can be amplified in a hyper saline environment, which may cause crystallisation of material around the surface.
The new Heavy Duty Slurry Pump Seal from Seal Innovations can withstand the harshest operating environments, providing maximum seal life in mining, quarrying and dewatering applications. The abrasion resistant metal components, along with silicone carbide faces, create an open design which reduces flush water and product dilution.
“This seal unit has been specifically designed for handling slurry concentration of up to 40 per cent solids by weight,” explains Lance. “It is an incredibly robust construct mechanical seal which is best suited to rugged mining and quarrying environments. Differently to standard O-ring designs, it is a rotating assembly, offering accurate installation with no special tools required.”
What’s more, the smooth, elastomercoated cone spring increases the product’s reliability with an even spring load to the seal’s faces. This ensures minimal wear or clogging, in operating pressures up to 300 psig (20.7 bar).
“We have introduced this product to fill a prominent need in the market for miningsuited slurry pump parts,” Lance elaborates. “It’s a really exciting addition to our portfolio of industry leading seal products, and we’re already taking it to some of our most
valued customers as an upgrade solution on troublesome equipment.”
He adds that, in addition to a comprehensive catalogue of sealing products, the business also provides aftermarket engineering and repair services from some of their centrally located branches.
“We can repair and overhaul slurry pump units as well as seals from our workshop in Brisbane, and we can repair any type of slurry seal from our Melbourne workshop. Everything is repaired back to manufacturer specification, and thoroughly tested for performance before re-entering the field.”
Technicians from Seal Innovations regularly visit customer sites, utilising their comprehensive knowledge of seal engineering to carry out audits, training and installation services. In line with their motto – “keep industry moving” – they strive to meet each customer’s unique requirements and offer a one-stop-shop for all sealing needs.
Think Water’s foundation principle is that water is our most precious resource and must be treated with efficient management practices. Established in 2007 from a collection of independent businesses, the Think Water group now spans 51 stores across both Australia and New Zealand, specialising in irrigation, pumping, and filtration system design.
“We are heavily involved in our local mine and quarrying industries, and a large part of that is providing the best hosing equipment, which we source through Advanced Industrial Products (AIP),” says Andrew Carrier – Managing Director at Think Water Peats Ridge. “We have been working alongside them for around 25 years, and our own customers have come to trust the excellent quality product for a broad range of applications.”
As part of Motion Australia’s businesses, AIP operates out of its head office in Darra, Queensland, with strategically located branches in Brisbane, Mackay, Wetherill Park, and Sunshine West down in Victoria.
One of the key products that Think Water sources through AIP is the Powaflex Pumpman rubber layflat hose. It is available either as a simple discharge hose, or pump assembly complete with Bauer couplings and Band-It preformed clamps. Designed to meet Australian
industry standards, it demonstrates high performance with extreme reliability.
“Increased levels of rain on the east coast have meant that a lot of underground quarry sites are experiencing flooding, which restricts access and slows down operations,” Andrew explains. “The Pumpman hose offers a very resilient and flexible solution for the efficient dewatering of these areas. Additionally, the high abrasion and temperature resistance defends the product from wear and tear, so the user gets a much longer wear life.”
Capable of transporting both water and slurry in tough operating conditions, the Pumpman rubber layflat is also suitable for washdown and irrigation purposes, with a pressure rating of 150psi (10 bar).
“We have never had any complaints from our customers using the hose, and no news is good news with these sorts of products,” Andrew furthers. “Just the fact that businesses continue to re-order the same units indicates that they are performing really well.”
Stephen Marley, Area Manager at AIP, says that it isn’t unusual for rainwater or seeped groundwater to collect in quarries, so sites need a dependable solution that can handle the transport of large amounts back above ground and away from the area. He adds that a long-
standing relationship with Think Water allows for the best possible solution to reach end-users in Australia’s northeastern quarrying region.
“We take a lot of pride in building close relationships with customers like Think Water, because at the end of the day, this extends beyond a purchase-supply situation,” says Stephen. “We offer technical support and create a sense of reliability that we will deliver on short turnaround times, with a diverse catalogue for almost any application.”
Andrew echoes this sentiment, reflecting on the continual benefits of working together to help customers get premium results with consistency.
“The communication has always been very positive. They are a fantastic company to deal with, and the service that we get is terrific. Our close relationship is a testament to what can be achieved when industry knowledge and customer service come together.”
An extended selection of Powaflex and compatible products are available through AIP’s national supply network, including rubber lay flat hoses, Powaflo valves and Powafit fittings.
On a quarry site, a well-engineered conveyor system can boost productivity by automating much of the transportation process and creating efficiencies that otherwise would not be possible at the ground level.
But engineering a quarrying conveyor system is not a straightforward process. Designing a conveying system for a quarry site requires specialised knowledge to assemble the right parts and components into a working system that will run smoothly once switched on.
According to Motion Australia’s Tony Tormey, a disproportionate number of breakdowns on conveyor systems are due to a bearing’s failure. “Bearing service life is a critical consideration for quarry conveyor systems because a bearings failure can mean a catastrophic halt in production and maintenance costs in the five figures,” he says.
As Category Manager for Industrial Bearings Solutions at Motion Australia, Tony works closely with quarrying customers to deliver bearings solutions that can perform on heavy industrial applications such as conveyor systems used for transporting quarry materials on site.
“The rolling elements on a quarrying conveyor are subject to a large volume of heavy loaded materials and strong vibrations running around the clock during production hours. This is why selecting the right bearings for a quarrying conveyor system is critical to the success of an operation.”
Sharing in his passion for bearings solutions, Tony has the benefit of working
closely with NTN, which has a joint venture with CBC, one of Motion Australia’s businesses.
NTN and CBC have enjoyed more than 50 years of successful partnership in the bearings industry. Together, the two businesses have more than a century of combined technical and engineering knowhow they can draw on for designing and developing bearings solutions for heavy industrial applications.
For this reason, many quarry operators turn to NTN and Motion Australia for assistance in developing tailored bearings solutions for their site.
Most recently, Tony has been directing customers towards the new NTN ULTAGE range of bearings for quarrying conveyor applications, which he says are picking up speed in the quarrying segment due to the performance and longevity.
“The NTN ULTAGE were designed to be the next generation of standard highperformance bearings for the most demanding applications in heavy industry,” says Tony.
Constructed from premium grade steel with a special heat treatment processing, the NTN ULTAGE bearings can support heavy loads, higher operating speeds and maintain stability up to temperatures of 200 degrees Celsius. The result is higher load ratings, greater tolerance to vibrations, reduced operating temperatures and up to three times longer service life when compared to conventional bearings.
Available in a variety of sizes and types, the NTN ULTAGE range is versatile and flexible in offering specialised and industry-specific bearings solutions.
For quarrying conveyors, Tony recommends the NTN Sealed Spherical Roller Bearings, which incorporate unique design lip seals that remain steadfast under misalignment and pressure for preventing any ingress of contaminants or moisture. Additionally, the bearings are pre-lubricated with long-life grease that requires no
cleaning or regreasing after the bearings are fitted.
Bearing’s compact design means less complex housing sealing is used to achieve better results. The internal design consists of a pressed steel cage and a streamlined curvature design that was adopted from the NTN EA series bearings. The EA design is well-recognised in the industry for its lighter and more compact design and topping the industry’s highest load ratings.
NTN and Motion Australia are invested in the design and development of engineered bearings solutions that can be tailored for quarrying sites to speed production and streamline automation.
Industry leading, dynamic load rating
Testing shows over three times extended bearing life
Optimised internal geometry that distributes bearing stress
Heat treated steel construction capable of handling 200°C
20% higher speed capacity
Available in the 223xx series with a cylindrical or tapered bore
Available with bore diameters of between 40mm and 170mm
Available on request for the other series and bore dimensions
Manufactured according to specification EF800
According to Safe Work Australia, noise exposure is the most common preventable cause of hearing loss, which research suggests may contribute to a range of other health concerns including tinnitus, increased heart rate, muscle tension, and fatigue.1
Workers in the mining and quarrying industries are frequently exposed to loud, explosive, grinding, scraping and crushing sounds in close proximities and for extended periods of time. Noise-induced hearing loss (NIHL) is a permanent condition, is a permanent condition, and 100% preventable.
The E-A-R™ Push-Ins™ earplugs from 3M are designed to protect the wearer from noise exposure levels, particularly low-frequency type noise in industrial environments. Constructed with slow recovery polymer foam and joined by a handy PVC cord, they are both washable and reusable with no rolldown required. In addition, these earplugs feature an insertion stem, which eliminates the need to handle the tip when fitting, for a more hygienic approach.
When it comes to critical pieces of PPE, checking that the product meets industry standards can ensure the best possible defence against work-related injury. The E-A-R™ Push-Ins™ are fully compliant with the Australia and New Zealand AS/NZS 1270:2002 certification scheme, and have been tested against the European EN352-2:2002 basic safety requirements.
Fit testing can ensure that users are getting optimal protection from their ear plugs. While most earplugs will have the SLC80 rating printed on the box, this may not be accurate to the size and shape of every worker’s ear canal. Finding the best fit for each individual
will be determined by their Personal Attenuation Rating (PAR).
Designed to be compatible with the E-A-R™ Push-Ins™ and other ear protection products from 3M, the E-A-Rfit™ Dual-Ear Validation System harnesses F-MIRE technology to quantify accurate hearing levels within just five seconds per ear. This can help to eliminate guesswork around the efficacy of different earplugs, with a system that it both portable and durable for on-site testing at any time.
Step 1: Set up the testing station
Install the software onto your computer via the provided flash drive or 3M website. Set up the speaker and microphone assembly, before connecting the system via the USB port.
After set-up is complete, have the test subject insert the earplugs as they normally would before entering the worksite. Then, attach the microphones to each side by inserting the metal probe tube fully into the test plug. Use the subject’s eyewear temple bars to hang the microphones in an upwards pointing direction.
Anybody working in environments where there is a risk of noise induced hearing loss can benefit from thorough fit testing for ear protection.
Position the speaker around 12 inches away from the subject, and then hit ‘run test.’ In less than five seconds, the system will generate a personal attenuation rating, indicating accurate reduction levels provided by the fit. Results will reflect the effectiveness of the person’s fitting method, and whether they require additional training in the use of hearing PPE.
Anybody working in environments where there is a risk of noise-induced hearing loss can benefit from thorough fit testing for ear protection. This might include newly hired employees, employees exposed to high noise areas or to toxic chemicals, and those with assured temporary threshold shift (TTS)/ standard threshold shifts (STS). Ideally, this testing is not a one-time event. Follow up is always recommended to provide opportunity for ongoing and refresher training.
References: 1. https://www.safeworkaustralia.gov.au/ system/files/documents/1702/workrelated_ noise_induced_hearing.pdf
Quarries play a vital role in Australia’s extractive industry, facilitating the production of raw material –such as sand, rock, and gravel – for civil infrastructure and residential construction developments. In contrast to mining, the quarrying landscape comprises of mostly smaller scale sites1 which rely on fewer primary pieces of equipment to bear the load of high intensity output.
Because of this, if a critical part of a machine goes down it is essential that repair can be carried out quickly, as every second of downtime will likely be expensive. To answer this need, CRAM is offering expert repair and overhaul on exciter gearboxes typically used on vibratory screens.
With humble roots in the small NSW town of Unanderra, CRAM is now a globally recognised specialist in fluid power, electro-hydraulics, and tailored engineering services. Their full-spectrum offering entails industryleading refurbishment and repairs on key equipment across the resources, manufacturing and construction industries.
“Exciter boxes essentially sit up the top of a quarrying screen to make the whole thing shake, putting it out of balance so the material gets sifted through,” explains Michael Greelish – National Business Development Manager at Motion Australia.
“So usually what happens when the bearings or other components reach the end of their wear life, is they’ll take the box off and send it back to the screen manufacturer to get repaired. This is usually quite expensive for them, whereas CRAM now have the facilities to strip, inspect and report on these gearboxes with more efficient cost and timeframe parameters.”
According to Michael, CRAM has many years of experience catering to the mines and quarries sector, and an excellent track record of providing holistic solutions for customers. From fabrication and tube work right through to mechanical overhaul and hydraulic schematics, they work closely to Australian standards and are dedicated to troubleshooting complex projects.
“The great thing about the Mackay workshop is that it’s centrally located for so many coal mines and quarrying sites up in Queensland,” he continues. “So instead of having to send their units all the way back to Sydney or Melbourne, they can save on freight and get a much faster turnaround. This can be particularly important for instances where there is no spare gearbox on site, and the machine can’t operate during repair time.”
Tony Harmsworth, Branch Manager at Mackay, says that there are generally two reasons why an exciter may need
attention - either it has experienced an abrupt failure, or it’s up on hours and in need of an overhaul.
“Nine times out of ten, if it’s a premature issue that’s occurred it will be to do with shortened bearing life or lack of lubrication,” explains.
“When it arrives at the workshop, we check all the journals first. Then we go over the condition of the gears and reclaim them back to spec or replace components like bearings and seals where needed. After that, the housing gets blasted, and we do a fresh coat of paint so by the end it’s as good as fresh out of the box.”
Both Michael and Tony agree that this initiative is only the latest benefit to come about from becoming part of the Motion Australia network.
“Because we liaise with the teams across other branches like CBC, Seal Innovations and Hardy Spicer, our customers really benefit form a true one-stop-shop for broad categories of servicing types,” says Tony. “We’re all about creating long lasting relationships, and a strong sense of trust in our commitment to deliver high quality support,” he resolves.
References:
1. https://nationalindustryinsights.aisc.net. au/industries/mining-drilling-and-civilinfrastructure/extractive-industries-quarrying
In the mining industry, draglines are a key piece of excavation equipment that have largely maintained the same design and functionality since they were first invented in 1904 by John W. Page, owner of Page Engineering Company.
Essentially a giant walking shovel– using large buckets, rigged wires, and a boom arm– draglines operate similarly to cranes in their ability to hoist large volumes of extracted materials from pit to pile.
Since their intended purpose has always remained relatively the same, there hasn’t been a lot of technological innovations for draglines that have emerged in the past 100 years– in fact, it’s not uncommon to see draglines that are decades old still in operation.
However, there has been advancements in the part and components used in the operation of draglines, particularly power transmission systems, according to Motion Australia’s Steve Hittmann.
“Draglines can be retrofitted with the latest driven part technology to improve their speed, efficiency, and performance in field,” remarks Steve. “But the most notable issue with draglines is the tremendous amount of power they require to operate them. And as most mine sites have fleets of draglines, these requirements can impact an operation’s bottom line significantly.
As National Category Manager for Mechanical Drive Systems and Mobile Final Drives, Steve’s expertise is vast and includes extensive knowledge of gearing, motors, couplings, brakes and clutches.
“Choosing the right power transmission components is more important than many mining operators may realise,” says Steve. “A good quality power transmission solution for a mining operation is one that can accommodate torque, sheer and compressive forces, vibrations, and high speeds. Ideally, it would also be failsafe, maintenance friendly, and reduce downtime on production.”
Recently, when a major coal mining operation in Queensland approached Motion Australia for a power transmission solution for their dragline fleet, they went
out to the site to assess the application requirements and determine the best course of action.
“We met with the engineers who were responsible for maintaining their dragline fleet,” he explains. “The site was after a solution to minimise maintenance on their fleet and improve operational efficiency. The existing gear couplings required regular lubrication and were expensive to change out, as the complete coupling assembly needed to be replaced when they reached their fatigue life”
Motion Australia deferred to one of their partners in supplying engineered power transmission solutions– Australian Timken–to assist with providing a solution to the coal mining customer, with specific emphasis toward the Timken Quick-Flex® Coupling.
Brad Womersley, Regional Sales Manager at Australian Timken, recommended the Timken Quick-Flex® couplings to power the hoist, drag and propel machinery. “We chose the ‘fit-and-forget’ Timken QuickFlex® 3150 Couplings for their maximum tolerance to force, minimal maintenance, and ease of installation,” says Brad.
“The easy fitment in the envelope design means no metal-to-metal contact and eliminates the need for lubrication. Furthermore, service life of our Quick-Flex® Couplings typically matches that of the equipment itself, which is ideal for draglines that will be in-field for years for reducing the total cost of ownership.”
The Quick-Flex® 3150 Couplings were installed on three of the coal mining site’s draglines. Since then, the customer has reported that the couplings have been operating faultlessly, according to Steve.
“This was a win for both Motion Australia and Australian Timken because the success on the initial machines opens door for the rest of the site’s dragline fleet,” he concludes. “In an industry like coal mining that often operates on legacy equipment, processes, and procedures, this could mean future engineering opportunities and further growth for us in the coal mining sector.”
• Motor to gearbox (low torque/high speed)
• Gearbox to driven equipment (high torque/low speed)
• Motors to pumps
• Any driven shaft
• Versatile design that is interchangeable with most coupling arrangements and can be standardised across a site
• Able to withstand up to two degrees of misalignment
• Dampens vibration and withstands repeated high shock load to the equipment
• Available in standard, single-ended spacer, double-ended spacer, or spined hub designs
• No metal-to-metal contact
• Designed for continuous and peak torque levels. Split cover options help resist axial separating force under high torque.
• Four bore options available to meet customers’ needs: Bored, Bushing, Splined and Mill Motor style.
• Four insert choices for varying torque needs
• Withstand temperature up to 176°C
Choose from Type NRTH for both low speed and semi-high speed applications and Type NRT for heavy-duty high torque applications. Size-for-size TRUE HOLD Backstops provide more system holding power than any other backstop. Plus, Longlife designs and our ability to engineer and manufacture complete, integrated drive packages, assure that you get the ideal system for your needs, whether it’s a single, tandem or multiple backstop configuration.
Titan’s Recovery Puller Winch is ideal for every recovery situation. The rope gripping system is easily disengaged, allowing smooth installation of the wire rope. Allows you to operate the winch without the need for any other powered device, when you are in off-road isolated areas.
These high performance and sealed bearings, belonging to the ULTAGE range, are designed to operate in harsh environments and on equipment requiring extended maintenance intervals. This series is suitable for applications as diverse as steel industry, paper making industry, mines and quarry conveyors, textile, handling equipment as well as elevator transmissions.
Tapered roller bearings can carry radial loads and unidirectional axial loads and offer high capacity. These bearings are used widely in machines with relatively severe loading conditions, usually in various combinations of opposed or combined single-row bearings.
The Fanmaster IHR8-22-6-3 Hooded roof fan extracts heat, smoke, dust, or fumes from buildings. When used in conjunction with coolers, the hooded roof fan helps to keep the temperature down during hot Australian summers.
Schaeffler OPTIME is an easily scalable Condition Monitoring solution, developed for various purposes in industry, recommended for a range of rotating machines with a speed of 120 rpm*-5000 rpm.
ITW’s Molygear has a high load carrying capacity providing lasting lubrication on heavily loaded gear boxes. Formulated from molybdenum disulphide, other applications for the Molygear industrial gear oils include worm drive and conveyor drive gear boxes that are found in the mining, quarrying, heavy earth moving and mineral processing industries.
LOCTITE PC 7218 is a 2-part, grey, epoxy based surface coating for metals. Ideal for protecting against coarse particle abrasion or erosion, or for rebuilding worn parts. It is designed for parts such as cyclones/separator bodies, dust collectors/ exhausters, pump liners/impellers, fan blades and housings, chutes/hoppers and elbows/ transition points.
Specifically designed for shaker screen applications, the T41D Shaker Screen Bearings have a thin layer chromium bore coating the inner ring bore which elevates fretting corrosion, and offers superior wear resistance, greater load carrying capacity and longer service life. These bearings are heat-treated for temperature stability and high wear resistance and resilience under centrifugal force –making them even better suited for shaker screens.
The SUPERDRAULIC HVI HI TEMP range of high viscosity index, high temperature anti wear hydraulic fluids is available in Viscosity Grades 46, 68 and 100. It is formulated using the same chemistry as the Superdraulic range however is formulated with shear stable polymers making it suitable for use in applications where extra harsh conditions and heat are common.
CRC 5.56 is a multi-purpose product with superior penetrating power that breaks through rust and corrosion while it clears away scale and dirt. Eliminates the need for many disassembly operations. Lubricates for smooth action, and silences annoying squeaks and squeals. Protects metals against corrosion and displaces moisture to help start wet engines.
Fenaflex Tyre Couplings are highly elastic, lubrication free couplings that tolerate large amounts of misalignment in all planes as well as offering simple installation and inspection without disrupting the drive. The Fenaflex coupling also has excellent shock absorbing properties while reducing vibration and torsional oscillations.
These push to fit, foam earplugs are easy to use again and again, reducing waste. Poly bag keeps earplugs clean and accessible for re use. Blue stem makes insertion and removal cleaner and easier. Noise Reduction Rating (NRR)* 28 dB. CSA Class AL. Test compatible with 3M™ E A Rfit™ Validation System. *The NRR may overestimate the hearing protection provided during typical use. 3M recommends reducing the NRR by 50% for estimating the amount of noise reduction provided. 3M is Leading the Advancement of Hearing Conservation™.
These extremely popular bearings are made to contend with hot, high-speed and heavy load conditions, offering seven times the service life of generic counterpart products. They can also withstand long periods of lubricant contamination and provide a 20 per cent improvement on seizure resistance. Offering less than half the rate of wear then generic bearing options, the Hi-TF has been designed following comprehensive research and development.
Providing longer operating life due to their improved crack fatigue strength, wear strength and peeling resistance characteristics, especially when the lubricant is contaminated. The EA bearings provide advantages due to their compact design, longer operating life, and longer intervals between maintenance and inspections.
The CRC SmartWasher systems employ a natural process called bioremediation to degrade and remove contaminants from the cleaning fluid, allowing re-use of the cleaning fluid. The CRC SmartWasher is part of the CRC Greenlight program, which offers a diverse range of environmental cleaning products that are smart, safe, and effective.
Heavy-duty ductile iron housing withstands shock loads. Exclusive Magnum no-leak seal design. Horizontal split-housing allows easy disassembly for maintenance. 31 unit sizes, up to 3M lb-in (340 kNm) torque.