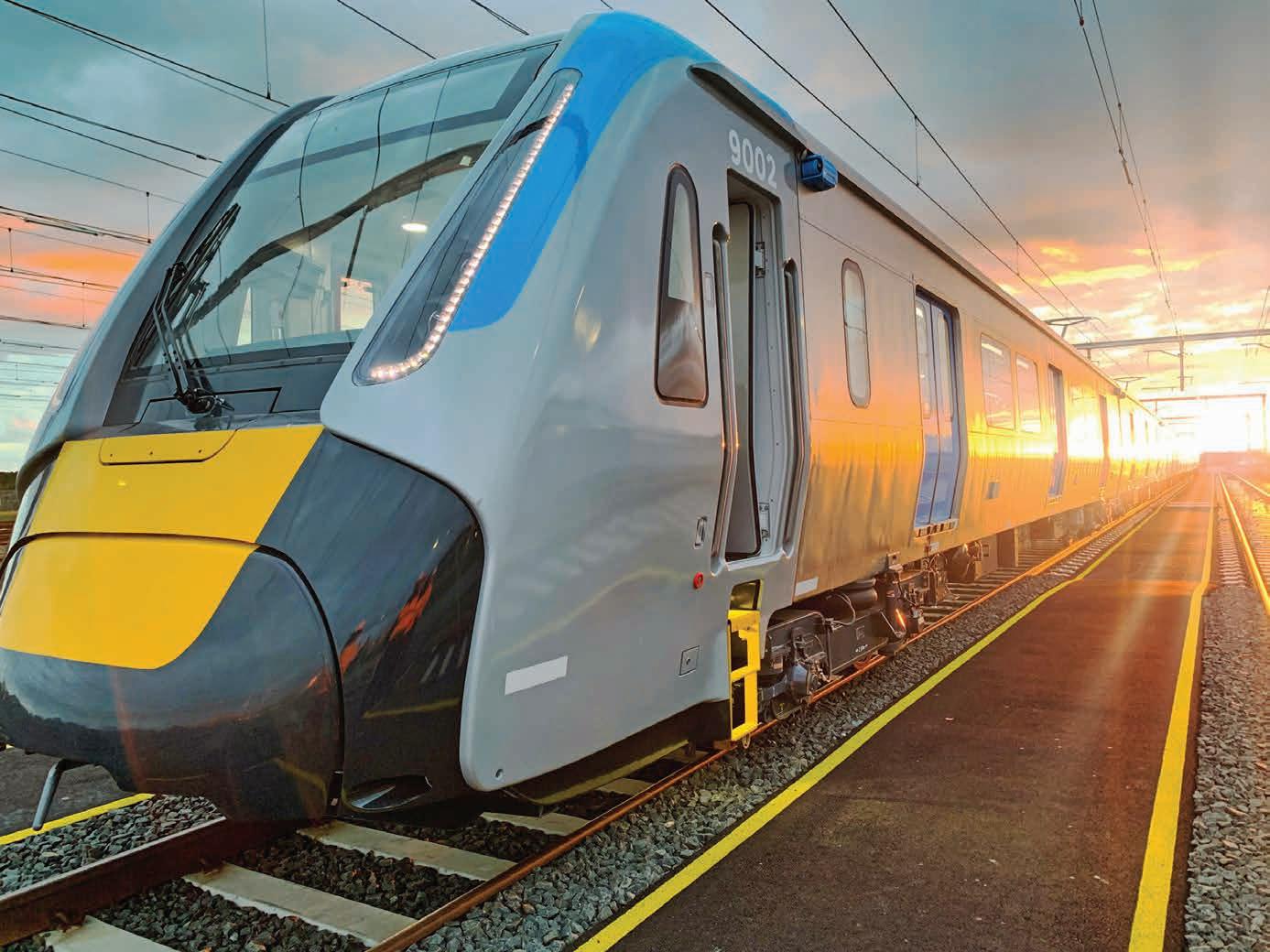

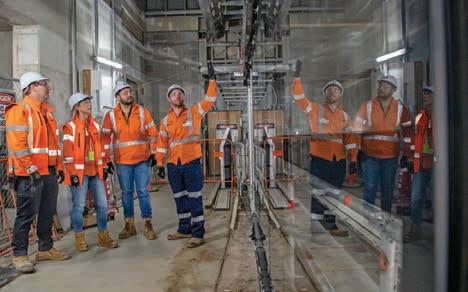
PAGE 22
PAGE 32
PAGE 42
ISSUE 3 - APRIL 2024
Published by:
379 Docklands Drive Dockalnds, VIC 3008
T: 03 9690 8766
www.primecreativemedia.com.au
Publisher
John Murphy
E: john.murphy@primecreative.com.au
Chief Operating O cer
Christine Clancy
E: christine.clancy@primecreative.com.au
Managing Editor
Mike Wheeler
E: mike.wheeler@primecreative.com.au
Editor
Joshua Farrell
E: joshua.farrell@primecreative.com.au
Business Development Manager
Alex Cowdery
M: 0422 657 148
E: alex.cowdery@primecreative.com.au
Client Success Manager
Salma Kennedy
E: salma.kennedy@primecreative.com.au
Design Production Manager
Michelle Weston
E: michelle.weston@primecreative.com.au
Art Director
Blake Storey
E: blake.storey@primecreative.com.au
Design
Caterina Zappia
Subscriptions subscriptions@primecreative.com.au
www.RailExpress.com.au
The Publisher reserves the right to alter or omit any article or advertisement submitted and requires indemnity from the advertisers and contributors against damages or liabilities that may arise from material published.
© Copyright – No part of this publication may be reproduced, stored in a retrieval system or transmitted in any means electronic, mechanical, photocopying, recording or otherwise without the permission of the Publisher.
The bumper period of rail works is continuing at the start of 2024. The funding across passenger and freight services is a major injection for rail, but also into broader communities where these works are being completed.
At the start of the year Inland Rail celebrated one year of construction in Victoria. The benefit for local Victorian communities has been immense.
Inland Rail has spent $45.1 million with 196 Victorian businesses and employed 732 locals on the Victorian section of the project.
The project started work at four sites in 2023 – Barnawartha North, Glenrowan, Wangaratta and Seymour-Avenel Road, Seymour. Steady progress has been made with Barnawartha North completed and Glenrowan close to completion.
When governments invest in rail, they are investing in the communities around them. It is similar around the suburban rail loop projects in Melbourne.
The team of almost 1,000 currently working on the Suburban Rail Loop have already clocked more than five million hours on site. At least 10 per cent of all hours to be worked on the project will be delivered by cadets, apprentices and trainees.
The eastern seaboard of Australia is heavily investing in rail, bringing more people into the sector for long-term sustainable jobs, all of which bodes well for the years ahead. The focus on apprentices in the Suburban Rail Loop will ensure young talent is joining rail, helping the industry plan for the future ahead.
Similarly to Victoria, Queensland has announced $2.75 billion in funding to connect the Sunshine Coast to Brisbane.
The project will run through communities such as Nirimba, Caloundra, Aroona and Birtinya. These works, if funding is matched by the Federal Government, will be vitally important in supporting local businesses and communities in Queensland.
It is an exciting time in the rail sector. With so many projects underway, the industry will be eager to see the benefits in the years to come.
It has been enjoyable putting together the
April edition of Rail Express
This month has a focus on digitalisation, a critical development for the rail sector to help bring the industry to the forefront of modern technology.
Siemens has brought digitalisation into the fray to support sustainability on Singapore’s Downtown Line. The digital solution allows the rail team to closely monitor ageing infrastructure to minimise downtime and ensure network availability at all times. It will also help get more Singaporeans on public transport in order to meet lofty sustainability targets.
Further in the magazine you will see a deep dive into Brimble’s human-to-machine interface (HMI). The system allows the company to minimise downtime and simplify the processes it has on site, to keep machines working for longer, and reduce the number of accidents.
The cover story explores Martinus and its solutions for the infrastructure space. The organisation is aiming to disrupt the norms in the construction space with forward thinking ideas, evident on its involvement on the Inland Rail project.
This edition also gave an opportunity to delve into the world of light rail bridges and bridge strikes. There was no better case study then the Montague Street Bridge in Melbourne. The infamous bridge has been struck many times and Rail Express spoke with Naomi Dickinson from the National Transport Research Organisation to learn more about improving safety around the bridge and such structures more broadly.
Finally, we will explore the Frankston to Stony Point extension that was recently proposed by Federal opposition leader Peter Dutton. We include the history of the proposal and what locals are looking for from a potential train line.
You will also find regular comments from the Australasian Railway Association, Rail Track Association Australia, RISSB and the PWI.
Happy reading!
RYAN BLACK
EMAIL: rblack@mancoeng.com.au
PHONE: +61 401 748 873
BRYAN BLACK
EMAIL: bryan@manco.co.nz
PHONE: + 64 21 960069
mancorail.com.au
mancorail.co.nz
The NSW Government has announced seven new stations will receive upgrades as part of an $800 million commitment to accelerate accessibility at stations across NSW.
Thousands of commuters will benefit from the rollout of the program designed
to make public transport safer and more accessible, particularly for vulnerable members of the community.
The 136-year-old Macquarie Fields Station is one of seven new stations in line for an upgrade. The station has never been fully accessible, with the city-bound Platform 1 only accessible via stairs.
Transport Minister Jo Haylen explained that Macquarie Fields Station has been in need of a facelift.
“We know the community has been advocating for these improvements for a long time and they will soon have the opportunity to have their say on this muchneeded project,” she said.
More than 10,000 passengers travel through the station every week and the community is home to 2,000 people aged over 60, many of whom have been campaigning for lifts for more than eight years.
Upgrades to Macquarie Fields Station will
Works to upgrade the T3 Bankstown line are almost complete as Sydney Metro readies the line for conversion to metro standards.
Over a 31-day shutdown of the N line from Sydenham to Bankstown, work was undertaken as preparations continue before the final conversion, which will take place during a 12-month shutdown of the line starting between July and October 2024. The shutdown is set to take place after the launch of City metro services between Chatswood and Sydenham.
It will also be closed over the April school holidays. Once completed, the work will see a metro train running every four-minutes in the peak, bringing turn-up-and-go services to the people of southwest Sydney. Some stations on the line currently only receive a train every 15 minutes at peak times.
In January, more than 600 trades worked on the line daily, which added up to more than 150,000 hours.
In January, further work also took place on the Metro North West Line to allow train testing with the new City metro line. The
include a new footbridge with lifts, stairs, a covered walkway to the platforms, a new family accessible toilet, improved lighting and CCTV. There will be six accessible parking spaces, two new accessible dropo spaces and a relocated bus stop on Railway Parade. Access to the station will be improved with a new pedestrian crossing and signage.
Having completed early stakeholder engagement with vulnerable members of the community, Transport for NSW will undertake targeted stakeholder engagement over the coming months. The community will be invited to have its say on the draft concept design toward the end of the year.
Construction is expected to begin in late 2024, following the development of planning approval documentation, with work taking around 18 months to complete.
Other stations include Moss Vale, Lewisham, Gri th, Bardwell Park, Chester Hill and Queanbeyan.
extension of this line means communities of northwest Sydney will have a direct public transport link into the Sydney CBD for the first time.
The weekend shutdown enabled the rigorous testing and commissioning program to continue ahead of the mid-2024 opening of the City line and seamless integration with the existing Metro North West Line. This ongoing testing and commissioning activity included:
• Eight trains operating on the line at one time, doubling the previous maximum of four.
• 33 trains completing the full journey between Tallawong and Sydenham.
• Trains travelling between Tallawong and Sydenham, at times at maximum speeds, simulating the turn-up-and-go service of a train every four minutes.
• Systems integration testing, including train and platform screen doors, passenger information displays, help points and announcements in all stations.
• Dynamic noise and vibration testing on the train, stations, in the new metro tunnels and in basements of buildings located above the alignment.
With over 120 years’ experience in automatic metros and rail mass transport, we o er safe, innovative, and high-performing public transport.
At RATP Dev, we are committed to providing tailor-made mobility solutions to cities like yours, for a better lifestyle and sustainable urban growth.
ratpdevaustralia.com.au
Through
RAIL
Digital engineering
Auckland’s City Rail Link (CRL) project has completed installation of the second and final railway line below the central city.
The newly laid 3.4 kilometres of track will carry trains underground north from Maungawhau Station at Eden Terrace and connect with the two new central city ones – Karanga-a-Hape and Te Waihorotiu – and downtown’s Waitematā Station (Britomart). CRL’s southbound line was installed last year.
Dr Sean Sweeney, Chief Executive for CRL, said there is plenty to celebrate.
“Completing the two tracks brings us one big step closer to the next phase of the project – testing trains inside the tunnels mid-year, and from there handing CRL over next year to Auckland Transport and KiwiRail, who will operate and maintain it,” he said.
CRL’s main contractor, Link Alliance, and railway infrastructure company, Martinus New Zealand, installed the track on what is one of the steepest sections of railway in New Zealand. From Maungawhau the line
drops 70 metres to Waitematā, which sits below sea level.
At its deepest point, CRL runs 42 metres underneath Auckland’s busy Central Motorway Junction.
The final section of the northbound line was installed near Te Waihorotiu Station.
The project’s tunnel boring machine, named in honour of Maori rights activist Dame Whina Cooper, excavated most of the tunnels to clear the way for track laying. Other sections of tunnel, near Waitematā Station, were built by first digging trenches and then covering them over.
Link Alliance Project Director, Francois Dudouit, says conditions under Auckland were challenging with tight curves, a steep gradient and no room for heavy machinery to pass.
“We became New Zealand’s first construction organisation to gain a Rail Operators and Rail Access Provider licence under the Railways Act – an innovation that gave us the flexibility we needed to plan the job and get it done to the highest standard,” he said.
The focus for 2024 shifts to train testing and the fit out of the stations and tunnels, alongside landscaping and urban realm enhancements. The fit-out programme includes the installation of lifts, escalators, security systems, CCTV, electricity, signalling and communications.
All track laying across the project’s three sites is now complete. Altogether, New Zealand’s largest transport infrastructure project laid 11 kilometres of line. In addition to the underground lines, new tracks were laid at Maungawhau to connect CRL and the Western/North Auckland Line, and a short section of track was laid at the eastern end of Waitematā (Britomart) Station.
Over three years, CRL’s project-wide track laying programme used more than 1100 tonnes of steel, poured almost 11,000 tonnes of concrete, laid 4,000 sleepers and completed hundreds of rail welds, which smooth out the ‘clickety-clack’ joins where track sections meet, to give Aucklanders a smoother ride.
Inland Rail’s Narromine to Narrabri (N2N) project has received approval from the Australian Government Department of Climate Change, Energy, the Environment and Water under the Environment Protection and Biodiversity Conservation Act 1999.
This Australian Government approval follows New South Wales Government approval and is a key step in the staged approach agreed to by the Australian Government in its response to the recommendations made by Dr Kerry Schott for getting the delivery of Inland Rail back on track.
The approval will underpin the next stage of the design for the N2N project, Inland Rail’s longest section of track comprising more than 300 kilometres of new track in mid northwestern New South Wales, helping provide more certainty that Inland Rail can be built to an agreed budget and time frame.
When constructed, the N2N project will link the completed Parkes to Narromine and Narrabri to North Star Phase 1 projects providing new freight capacity and improved connectivity to ports on the east coast and westwards via Parkes to Adelaide and Perth.
Rob Storey, Inland Rail Director PreContracts explained that the N2N project is a key link in the future Inland Rail supply chain.
“Now that we have a full suite of approval conditions, the survey and investigation activities are critical inputs to the next stage of design and securing the land needed for the N2N project corridor.
“Inland Rail acknowledges the important input from the community, local landowners and businesses during the approvals process and remains committed to working with stakeholders.
“Inland Rail will support the shift of more goods onto rail, meaning faster, more reliable freight; safer, less congested roads;
Final designs for the new road bridge that will remove the dangerous and congested level crossing at Station Street, Beaconsfield have been released.
Incorporating feedback received from community consultation in 2023, the updated designs maintain Beaconsfield’s village atmosphere and reflects the community’s desire for easy pedestrian and vehicle access around the new road bridge, while blending in with the natural surroundings of the suburb.
The boom gates at Station Street, Beaconsfield will be gone for good and the new road bridge open in 2025.
Minister for Transport and Infrastructure Danny Pearson announced works are ramping up to take cars over the Pakenham Line, which will improve safety and provide better access for the local community.
“The final designs are in, and major works are in full swing to remove the dangerous and this congested level crossing, making local roads safer and easing tra c for road users,” he said.
“When the crossing is removed it will bring the Pakenham Line one step closer to being boom-gate free, transforming the way people work, live and travel in Melbourne’s south-east.”
Construction crews worked around the clock south of the rail line until late February to prepare for major piling works, ahead of the bridge foundations being completed later this year.
Further up the line, work continues to remove the level crossing at Brunt Road, with the new road bridge set to open in 2024 – a year ahead of schedule.
These works, along with another three
and fewer emissions.”
Moving forward, the N2N project team will continue to engage with NSW and local government and the community as it undertakes necessary activities to further inform the design of the N2N project.
These activities include surveys and on-site investigations to help provide more certainty that Inland Rail can be built to an agreed budget and schedule.
Inland Rail is committed to ensuring that the final design of the project addresses and appropriately mitigates potential impacts to the environment and social amenity in accordance with the approvals of the Federal and NSW governments.
level crossings being removed at Main Street, McGregor Road and Racecourse Road, will make the Pakenham Line boom-gate free – boosting safety and easing congestion in Melbourne’s south-eastern suburbs.
Work is progressing well at the new premium Pakenham Station – which is set to o er improved accessibility facilities to passengers.
The metropolitan rail line is also being extended 2km as teams work to build the new East Pakenham Station.
Other improvements for passengers on the line will include the Metro Tunnel, which will create a new continuous rail line from Sunbury in the west to Cranbourne and Pakenham – lessening travel times and adding 45 per cent more peak capacity. With testing now underway, the Metro Tunnel will open in 2025, a year ahead of schedule.
ALSTOM CBTC RANGE: World leading high-capacity signalling
Construction of Cross River Rail’s Albert Street station has reached a major milestone, with key sections of the cavern completed.
Crews have made progress underground, completing the mezzanine level – where people will take the final escalators down onto the station platform – and the platform itself.
Both milestones represent high-end feats of engineering, with the mezzanine level made up of 183 pre-cast concrete beams, each up to 19 metres wide and weighing up to 70 tonnes.
The 220-metre-long platform is made up of 368 precast culverts, each weighing 6.5 tonnes.
Every piece of the station had to be lowered into the cavern down a 31-metre-deep access shaft.
Escalators are due to arrive on site and preparation works are underway for tracks to be laid in the station cavern over the coming months.
While tracks are being laid, crews will also
start installing platform screen doors in the station.
Albert Street cavern is 290-metres long, up to 34-metres underground, and generated about 83,000 cubic metres of spoil to excavate.
The cavern’s permanent lining is made up of around 17,738 cubic metres of concrete, about 2,977 tonnes of steel and 12,816 square metres of waterproofing membrane.
The mezzanine level – about 25 metres below street level.
The 220-metre-long platform is about 31 metres below ground and made up of 368 6.5 tonne culverts.
While the platforms will be within the station cavern, crews are also constructing a 50-metre deep station entrance and a second 28-metre deep northern entrance.
Railway crossings in South Australia are on track to receive safety upgrades due to the Australian Government’s Regional Level Crossing Upgrade Fund (RLCUF).
The RLCUF aims to improve railway crossing safety in regional areas and reduce
serious injury and fatal crashes, which have a devastating impact on communities.
The Australian Government has committed $160 million over four years to state and territory governments to fund up to 50 per cent of the cost of delivering railway level
crossing upgrades.
The South Australian Government will receive $6.2 million in the first round of funding, which will go towards a program of works to be delivered in partnership with rail infrastructure managers.
The proposed list includes six projects totalling $12.4 million, delivering priority upgrades to 18 locations in regional areas of the state’s road network – with one of the projects covering 13 locations to form a multi-site project.
Funded upgrades include road sealing and markings, along with the installation of boom gates, audible warning devices, updated signage and LED flashing lights to increase the visibility of crossings on both sides of the roadway in response to approaching trains.
All six projects are expected to be completed by early 2027.
More information on the RLCUF and its guidelines is available on the Department of Infrastructure, Transport, Regional Development, Communications and the Arts website.
Martinus is looking to shake up the rail design and construction sector and is doing so with a strong consortium of businesses and in-house engineering.
In Australia’s rail infrastructure landscape, a transformative force is emerging. Martinus, once a burgeoning entity focused on product delivery, is now distinguishing itself as a expert in the design and construct (D and C) realm. This strategic pivot is not merely an evolution but a revolution in an arena historically dominated by tier one giants. This venture into the space is intended to shake up the norm and o er an alternative for those in the construction space.
Martinus’s entry into the D and C sector is marked by a shift towards collaborative
engagement and innovation. Toby Briggs is the general manager for growth and articulated the approach.
“Our philosophy centres on fostering genuine partnerships through direct dialogue. This paradigm shift from transactional to relational engagements with clients and partners has propelled us into the spotlight, challenging the status quo and introducing a fresh perspective in project execution,” he said.
This strategy, underscored by a commitment to excellence and innovation, has catapulted Martinus from a new player to a critical disruptor in the D and C landscape, reshaping how projects are conceptualised and delivered.
Under design manager Zoë Cruice’s leadership, Martinus’s in-house design team has achieved progress, especially in executing major project.
A distinguished figure in the infrastructure sector, Zoë brings to Martinus a wealth of experience from her tenure at Fulton Hogan, where she managed a diverse portfolio of road and bridge tenders, and from her strategic role in coordinating contracts for Sydney Trains.
Her expertise has been pivotal in Martinus’s approach to complex rail and urban infrastructure challenges, exemplified by the team’s innovative work on the Albury
to Parkes project for Inland Rail.
The Albury to Parkes project involves enhancements to specific sites across the 355 kilometres of existing track running from Albury to Illabo and Stockinbingal to Parkes.
The enhancements provide the necessary vertical and horizontal clearance along the existing ‘Main South Line’ corridor to support the safe running of double-stacked freight trains up to 1,800 metres long and 6.5 metres high.
The Albury to Parkes section is divided into two separate projects.
The 185 kilometres of existing rail corridor from the Victoria and New South Wales border at Albury to Illabo includes adjustments to approximately 44 kilometres of existing tracks. The project comprises
works at specific sites to achieve horizontal and vertical clearance requirements for double-stacked trains.
The works include track slews and reconfigurations, bridge removals, bridge modifications, bridge replacements, track lowering, signalling gantry replacements, level crossing modifications and other associated works.
This 170.3-kilometre stretch of Inland Rail involves enhancing specific sites along the existing rail corridor between Stockinbingal and Parkes to achieve horizontal and vertical clearance requirements for double-stacked trains. The Stockinbingal to Parkes Project will also enhance capacity by constructing a new crossing loop north of the Daroobalgie Road level crossing (Daroobalgie Crossing Loop).
The works include track slews, bridge modifications, track lowering, other structure modifications, upgrading a level crossing at Daroobalgie Road, a new crossing loop and other associated works.
Cruice’s’s foresight led to the development of an alternative to traditional ‘proof rolling’ methods, a testament to her and her team’s forward-thinking approach.
Cruice expalined that the development signifies Martinus’s commitment to sustainability and efficiency, establishing new benchmarks within the industry.
This achievement not only underscores Martinus’s engineering strength but also cements its reputation as a trailblazer in the design space, ready to challenge conventional limits.
The strategic alliances Martinus has forged,
A consortium of businesses is ensuring Martinus brings the required skills to any project.
particularly with BG&E and Aurecon, are pivotal to its rising influence in the rail infrastructure sector.
These partnerships, built on a foundation of shared values and complementary expertise, have been instrumental in Martinus’s ability to deliver innovative and sustainable solutions.
Ben Keith, Associate Director from BG&E, sheds light on the essence of this collaboration.
“Our partnership thrives on mutual respect and a shared approach to innovation,” he said.
“Being privately owned companies with flat management structures, both Martinus and BG&E can make swift decisions, allowing for greater flexibility and responsiveness to project needs.”
BG&E has a team of more than 850 in 15 o ces across Australia, New Zealand, Singapore, United Kingdom and the Middle East.
These teams design and deliver engineering solutions for clients in the property, transport, ports and marine, water, defence, renewables, and resources sectors.
While BG&E has been a cornerstone in this collaborative e ort, the role of Aurecon cannot be understated. As another key partner, Aurecon brings to the table a wealth of expertise in engineering and design, further enriching the
consortium’s capability to tackle complex infrastructure challenges.
Aurecon is a design, engineering and advisory company. With more than 6500 employees across 11 locations and over 25 years’ experience, the company brings a wealth of knowledge to the consortium.
This collaborative ecosystem, underscored by the agility of Martinus and BG&E’s organisational structures, shows how strategic partnerships can drive the industry forward, breaking traditional barriers and setting new benchmarks for excellence in rail infrastructure development.
Martinus’s journey is emblematic of its broader strategy to redefine the parameters of success in the rail infrastructure sector. By embracing a holistic approach that integrates cutting-edge design with sustainable construction practices, Martinus is not only delivering projects but is also driving the conversation on how infrastructure development can be more innovative, inclusive, and sustainable.
The company’s proactive stance on environmental stewardship and community engagement further accentuates its role as a trailblazer, paving the way for a new era of infrastructure development that is as conscientious as it is ground-breaking.
Looking forward, Martinus is poised to continue its trajectory of innovation and growth. The company’s commitment to leveraging the latest technologies and sustainable practices ensures its projects not only meet current needs but are also adaptable to future demands.
This vision for the future, where rail infrastructure serves as a backbone for sustainable development, is at the heart of Martinus’s mission. As the company embarks on new projects and explores emerging technologies, its focus remains on shaping an infrastructure legacy that future generations will look back on with pride.
Martinus’s ascent in the rail infrastructure sector is a compelling narrative of innovation, strategic growth, and the breaking of traditional barriers.
The company’s journey from an emerging entity to a leading force in the D and C domain o ers a blueprint for how ambition, coupled with a commitment to partnership and innovation, can redefine industry landscapes.
As Martinus continues to chart its course in the development of Australia’s rail infrastructure, its impact extends beyond the tracks laid or projects completed. Martinus is not just building infrastructure; it is crafting the future of Australian rail, one innovative project at a time.
Martinus has a range of in house engineering skills, set up to support any challenge.
Rail Express speaks with the National Transport Research Organisation to better understand what can be done to reduce impacts to the Montague Street Bridge.
The National Transport Research Organisation (NTRO) has broadened its focus to include the rail sector. A critical component of this expansion is having roads teams from the NTRO touring some of Melbourne’s rail landmarks, including the Montague Street Bridge, to give them an understanding of issues the rail sector face.
The NTRO provides innovative research and practical solutions to challenges across road, rail, ports and airports, developing new knowledge, innovation, standards and specifications to shape the country’s transport future.
With more than 240 people and eight o ces in Adelaide, Brisbane, Canberra, Launceston,
Perth, Sydney, and Wellington and a sustainable materials research laboratory and o ce in Melbourne, NTRO is set to transform the way transport infrastructure is designed, built, used and maintained.
Naomi Dickinson is the chief technology leader – rail, safer smarter infrastructure at the NTRO, and explained why the organisation believes it is ideally set up to support the rail network in Australia.
“You can use the example of pavements. The NTRO has done research around new pavements and bitumen, and we can bring that to rail and light rail, for flood proofing and to create an even stronger system less susceptible to wear and tear,” she said.
“These tours have been fantastic because as we take people around the tram network we can begin to see the wheels turn in their heads and ideas begin to formulate.”
Dickinson is an electrical engineer born and raised in Melbourne, who has spent much of her working life in and around light rail. She delivered the first low floor trams from Germany to Melbourne in the early 2000s.
Recently completing a Masters of Energy Systems, Dickinson has been looking at the legal and regulatory frameworks around the electrification of residential buildings and public transport. She believes the tension between road and rail is coming to an end and the two systems are ready to work more closely.
Dickinson explained that the Melbourne tram network faces unique challenges but can take suggestions from other systems to try and solve some of these issues.
Melbourne’s rail network is one of the most integrated with road tra c in the world, posing a number of challenges, not to mention di culties surrounding that it was constructed more than 100 years ago.
“When you compare Melbourne to a network like Canberra or Sydney, they are operating on a dedicated line. Melbourne has to contend with vehicles far more than other networks,” Dickinson said.
Common incidents that occur in the shared tra c system include:
• Cars and trucks moving into the rail space and graze trams or crash into them.
• Road users make sudden u-turns in front of trams.
• Road user passing stopped trams while passengers are alighting.
• Pedestrians jaywalk in front of trams.
• Pedestrians may be distracted by mobile phones, other technology or other interactions and walk into trams or tram pathways.
• Tram-on-tram rear-ending or striking each other where rail lines diverge.
“We are looking at a legacy system when examining Melbourne. This is where bridges like the Montague Street Bridge come in,” she said.
“Our safety team would say it is important to evolve transport infrastructure and technology with how people are actually moving. You would never see a bridge like the Montague Street Bridge constructed now.”
To understand one of the nation’s most infamous bridges, it is important to look back at its history.
Although there are no open waterways or channels running through South Melbourne, it is an area that is prone to flooding. There are several drains including the Hanna Street main drain running along Kings Way, which is the most extensive.
Due to South Melbourne being an urban area, there isn’t a lot of green space to absorb rainfall. This results in water tending to run o towards lower lying areas.
Flooding on Montague Street was a continuous problem. For example, in 1916, there was a time when the area around the bridge was under a foot of water and pedestrians could not approach it. In 1934, South Melbourne council raised the
underlying street level by about two feet, thus reducing the clearance height of the bridge.
Construction firm Johns & Waygood was contracted to build the bridge in 1914 as part of the infrastructure of the Port Melbourne railway line. Montague Railway Station was located just south of the bridge and mainly served workers at nearby factories.
The last passenger train ran to Montague Station on 10 October 1987 after it was announced that the line would be converted to light rail. The light rail line was opened on 18 December 1987. Currently the bridge carries trams along route 109 between Box Hill and Port Melbourne.
The bridge currently has three metres
clearance, making it susceptible to strikes from any over height vehicle. The bridge strikes can cause serious headaches for the tram network of the city.
“When an incident like that happens, it does not just impact the 109 line, but in fact there can be delays to the whole tram network,” Dickinson explained.
“You are looking at economic loss. You also stop tra c on what is a critical road in and out of Melbourne’s inner suburbs, causing major tra c congestion.”
Dickinson stated that there are 26 warnings as a driver approaches the bridge. This includes signage, lights, as well as an overhead gantry with paddles on it to hit the top of a vehicle to notify the driver they are over height.
“The challenge when protecting the bridge from strikes is that we simply do not know what was going on in the cab when these strikes occur,” she said.
“When I come along that road, I always think that the area is very confusing. It has signs everywhere and it is a very grey area. It is easy to get confused I think.
“We are well aware of the warnings as we know the bridge, but it is easy to see how someone new can be overwhelmed and confused by all of the warnings.”
Dickinson believes the government has done all it can to rectify the problems, but it is the drivers’ responsibility to not hit the bridge. She contends that modern technology might be impacting a driver’s ability to critically think their way through a situation such as the Montague Street Bridge.
“Some people can simply listen to the
voice coming out of their GPS and blindly follow it, which can result in accidents like these,” she explained.
“This isn’t just true of the Montague Street Bridge but might influence other rail hazards such as level crossings around the country.”
Dickinson believes now is an opportune time for a human factors review on the warning systems around the bridge, the learnings of which may be applicable to other low bridges.
“Are people being hit by information overload due to too much signage?” she questioned.
Dickinson queried a human factors review within the heavy vehicle driver’s cabin, to establish if drivers were distracted in the lead up to accidents.
As far back as 2006 an article from Deutsche Welle reported that German and Dutch towns were removing road signs in the hopes of decongesting visual clutter along roads and making travel a less confusing experience.
“Is it worth us following the European path and finding better ways to impact drivers with warnings to ensure these impacts do not cripple public transport networks?” she said.
“I look at what we have here at the NTRO
and believe we have the exact capabilities to do a thorough review on something like this and provide advice around improving not only the safety around this bridge, but all bridges.”
Dickinson hypothesised the option of working closely with digital map developers on a system that can recognise the height of the vehicle and provide in car notifications they are approaching a potential hazard and potentially redirect over height vehicles along a more suitable route.
Similarly, around the world, in-cabin monitoring systems that allow for driver and occupant monitoring are being introduced to improve heavy vehicle safety.
“Government has done well to protect this bridge specifically, with an overhead gantry called the ‘can opener’ just before the bridge,” Dickinson said.
“You see similar things on the bridges between Flinders Street and Spencer Street where the bridge is protected from impacts by an overhead gantry.”
Whereas at level crossings in regional Australia, depending on the nature of the incident and size of the heavy vehicle involved, significant damage to the rail infrastructure might occur the result of an impact causes a significant derailment, and
that might see networks shut down for days or weeks.
“It is easy now. New bridges are constructed with these height constraints in mind, and we are doing a fantastic job of separating trams and vehicles on newer networks,” Dickinson said.
Much of Australia’s rail network was constructed more than 100 years ago where bridges were built without the knowledge we have now around vehicle height. Solutions are necessary for these bridges that will remain a part of the network for years to come.
“I think it is critical that we keep road users minds focused as they are driving,” Dickinson stated.
“Public transport operators have a higher obligation for safety, and they do all that they can in this situation. We need to begin considering what we can do with the heavy vehicle drivers.”
Melbourne’s Metro Trains has begun rolling out digital solutions to help get networks back on line quicker after a bridge strike.
New CCTV cameras and sensors installed at three hot-spot locations have captured the moment when over height trucks have hit rail bridges.
CCTV and impact sensors can reveal the full details of an incident, providing immediate notification and remote assessment of any damage caused.
Metro’s bridge inspector can now immediately evaluate the incident and decide if further investigation is required, meaning less delays for passengers.
Since being installed in May, the cameras have captured several incidents including a B-Double that failed to slow down on approach to the Warrigal Road Rail Bridge in Holmesglen, sending shrapnel into the air, halting both tra c and train services.
Previously the notification of bridge strikes was solely reliant on an incident report being filed by the person who caused the incident, a member of the public or a Metro team member.
Now, an alert notification is sent directly to Metro’s Security Operations Centre, including the time of the impact and images from the scene. Metro’s 178 rail bridges are struck on average once every week.
Jasper Milligan, Metro’s General Manager Infrastructure said Metro, will look to install more sensors to other rail bridges across the metropolitan network.
“Bridge strikes are hugely disruptive for our passengers, as we often need to stop trains while we assess if there’s any damage
to the bridge,” he said.
Bridge inspector Liam Featherstone said incidents like these are easily prevented.
“A simple check of the height of your vehicle could help to avoid thousands of dollars in damages and disruption on the road and rail.”
Siemens Mobility delivered AI-powered data analytics for Singapore’s Downtown Line, to optimise asset lifecycle management and drive sustainability.
How do railway operators achieve high reliability and e ciency at optimal cost while ensuring sustainability? The answer lies in harnessing deep railway domain knowledge and the power of Artificial Intelligence (AI). This helps analyse critical data that enables the most cost-e ective maintenance regimes and provides accurate prediction of potential events for necessary interventive measures to be taken.
Introducing Digital Asset Management for Rail Systems (DAMfRS), an innovative AI-driven product crafted by Siemens Mobility to meet these needs. DAMfRS serves as its digital services solution, tailored to empower railway asset owners, maintainers, and operators in making informed decisions that drive the maximum value from their asset portfolio.
Rooted in robust asset management principles aligned with ISO 55001 standards, this product draws upon asset and system data, and utilises Siemens’ domain expertise to fulfill its overarching mission: optimising whole life cost by enhancing reliability, availability, maintenance e ciency, inventory optimisation and renewal forecasting.
The Rail Enterprise Asset Management (REAMS) project in Singapore marked a milestone as the inaugural implementation of DAMfRS by Siemens Mobility.
Tailored to meet the unique requirements of the customer, this bespoke DAMfRS solution is recognised as a pivotal facilitator in realising the nation’s ambitious long-term transport and sustainability objectives. Aligned with Singapore’s Green Plan for 2030 and Land Transport Master Plan 2040, the overarching aim is to achieve a 75 per cent mass public transportation peak-period modal share, which also includes expanding Singapore’s rail network by 130 kilometres and deliver a convenient, well-connected, inclusive, and fast land transportation system.
To deliver the project, a dedicated team from Siemens Mobility worked closely with the customer, the Land Transport Authority (LTA) of Singapore to implement REAMS for the Downtown Line (DTL) – a driverless metro line comprising 34 stations, 42 kilometres of track and 92 metro trains.
The Siemens Mobility team covered the data value chain by extracting, processing, developing analytics algorithms and crafting telling visualisations from a range of customer data sources including:
• rail assets trains, signaling system, and platform screen doors, providing system specific event and diagnostic data;
• the Centralised Maintenance Management System (CMMS) that contains work planning, scheduling, assignment, and execution records of day-to-day maintenance
operations; and
• the Enterprise Resource Planning (ERP) system that contains the financial, costing and purchasing details of the assets within scope
Capitalising on the high volumes of system, diagnostics, operational and financial data from multiple assets, the REAMS solution o ered the customer timely alerts on the health statuses of its assets and insights on the long-term performance and costs aspects. This contributed to higher daily system availability, and greater appreciation of the anticipated total cost of ownership. The customer was able to utilise the solution output to execute immediate improvements to maintenance regimes and prepare adequately for capital intensive asset renewal activities in the coming years.
The head of digital services Asia Pacific for Siemens Mobility, Lester Lim, shared some details on the project and explained how Siemens worked closely with the LTA for a tailor-made solution.
“This project saw Siemens Mobility work in close collaboration with the customer, LTA, and our valuable local partner, ST Engineering Urban Solutions (previously known as ST Engineering Electronics, STE), to co-develop and implement REAMS for selected Downtown Line assets. It was important that we worked closely with the customer and the operator of DTL, SBS Transit (SBST), to obtain the required data to deliver lifecycle intelligence and decision support to achieve a balance between short- and long-term sustainability.
“We led workshops with key stakeholders to progressively identify software requirements that would allow the customer to achieve their operational and asset management objectives. We conducted thorough data assessment exercises and also led the implementation of pilot run trials to validate the maintenance regime recommendations put forth by the REAMS algorithms. We are happy to report that the customer is confidently pursuing fleet-wide regime changes”.
Ultimately, Siemens and the customer have achieved:
• integration and management of the performance and cost characteristics of the DTL line in a centralised digital rail asset management platform;
• managed limitation of system downtime for the maintenance of rolling stock and signaling systems; and • improvements to system and asset performance over the lifecycle
Following the successful completion and system acceptance of the REAMS project, the system is currently used by SBST and maintained by Siemens Mobility’s consortium partner STE.
Growth in the Australian and New Zealand rail industry is forecast to continue in the coming years, to enhance connectivity and support sustainable transportation to help reach net zero.
With the recent record level of investment in the rail networks across Australia and New Zealand, the need for robust digital asset management solutions is paramount. The scale and complexity of these railway projects necessitate advanced technological solutions to ensure optimal reliability, safety, and e ciency.
Much like its success in Singapore, DAMfRS holds immense potential to deliver substantial benefits in Australia and New Zealand. Through real-time asset status monitoring, maintenance optimisation analysis, inventory holding right-sizing recommendations, and data-driven asset renewal decision-making, rail owners, maintainers, and operators can maximise returns on investment, minimise downtime, and safeguard the longevity of expanded rail infrastructure.
The question then arises: How do we
embark on this journey?
“You start by embracing the Siemens Mobility Railigent X platform,” suggests Lim.
The Railigent X platform serves as a central hub for all railway community stakeholders seeking digital solutions to enhance their services and products. Siemens’ experience and expertise in railway design, construction, operations, maintenance and AI-led data analytics o ers an opportunity to develop digital solutions to address operational, maintenance, and strategic asset management needs. Siemens’ suite of in-house and partner-developed applications available on the Railigent X platform provides flexibility, enabling the activation of additional applications as needed in the future. By consolidating data and user needs e ciently, the need for costly overheads associated with purchasing discrete software programs is eliminated. In essence, Siemens serves as the singular supplier for all current and future railway data and
analytics requirements.
“The Railigent X data platform and analytics engines are not limited to Siemens products but can seamlessly integrate with other products as well,” Lim said. This openness, facilitated through APIs (Application Programming Interfaces), allows customers and partners to share and utilise generated data for various use cases while upholding rail safety and cybersecurity standards. Customers can e ortlessly adopt Siemens’ digital o erings uniformly across all their lines, irrespective of the manufacturer, enabling them to extract value and synergies from the entire network.
This ecosystem approach to harnessing value from AI-driven data analytics, combined with deep domain expertise, has the potential to optimise operational capabilities, maintenance strategies, and the total cost of ownership, ultimately benefiting railway organisations and passengers alike in the Australian and New Zealand markets.
Aptella is helping to improve safety on site with the Blindsight AI system, already improving safety on Sydney Trains work sites.
Aptella has rebranded itself from Position Partners to better reflect the variety of solutions it has available, one of which being the Blindsight AI system developed by Presien and currently being used by Sydney Trains.
Blindsight AI is an artificial intelligence safety system for mobile plant and fixed infrastructure. It stops accidents by alerting vehicle operators and people around to objects in blind spots, and automates health and safety reporting, including video, lead safety metrics, and risk analysis.
Cloud reporting automatically captures the near misses that are rarely reported with manual processes, so workers can understand their real site risk for the first time.
Unlike legacy approaches, Blindsight can detect objects without a physical tag or marker, prevent alert fatigue by detecting specified objects, and proactively alert operators and people around so they don’t miss the risk.
Damien Drew is the works management
lead, major works division at Sydney Trains. He has been instrumental in the rollout of this technology on plant and equipment on site. Beginning his career in the early 90s, Drew has spent much of his working life in and around equipment as an engineer.
“When working in track possessions, the major risk is not from trains but being struck by mobile plant and equipment moving around on site,” Drew explained.
“For multiple years we were looking for a solution. We came across the Blindsight AI system developed by Presien and took the opportunity to trial it.”
Blindsight is powered by Presien’s AI technology and therefore backed by a team of Australia-based, in-house engineers and data scientists with decades of experience. It has deployed thousands of devices with more than 300,000 hours of real-world operating
hours on heavy industry work sites, and regular automated over-the-air updates powered by the AI Engine.
Blindsight is an end-to-end solution, from on-vehicle alerts to cloud reporting. It is designed from the ground up for heavy industry applications and can be installed on any vehicle type, from forklifts to ultra-class mining trucks.
Blindsight then moves past operator alerts by automatically uploading and analysing detection videos in the cloud, so workers get real safety insights delivered to a single simple platform.
Blindsight does not require constant wi-fi or 4G for alerts, physical tags or special identifiers to be placed on objects to detect them, or special machine inputs or integration.
Sydney Trains ran a two-year project with the technology installed on a selection of plant and equipment used on its construction worksites.
“We worked closely with Presien when we first installed the technology as we got a few false positives. As with any new technology, it can take time to improve and we worked with them to do that,” Drew said.
“Presien refined the AI system, and it has made a di erence.”
Drew went on to explain that while some operators were reluctant at first, the overall response from users has been positive.
“It is about overcoming a cultural challenge. We are not trying to replace operators with technology but instead use it as a tool to make sites safer,” he said.
“Blindsight AI allows the driver to remain focussed. It is not drawing their eyes away from what is going on outside the cab and allows the operator to gain awareness of what is happening in their blind spots.”
Sydney Trains discovered that the best way to utilise the system was not alerting the operator in the cab but notifying those outside on the ground.
“When we reviewed the footage, you can see people approach the dangerous area and they will jump back when they hear the
warning,” Drew said.
“If we were just relying on the light or the buzzer in the cab, the operator might become numb to the noise. Whereas someone may only walk behind the plant once and the alarm will be more impactful to them.”
Coming out the other side of the trial, Drew and the team were impressed by the results and is planning out the next steps of Blindsight AI and Sydney Trains. Drew has also been pleased by the fact that the system has started new conversations around safety on site.
“We have developed a two-minute induction video that showcases the required change in worker behaviour,” Drew said.
“We use this to explain to those coming on site that we do not want them to trigger the system and this is what they can do to ensure they are being safe.
“It allows us to have robust conversations around safety.”
During the second 12 months of the project, Sydney Trains sampled 1000 random
detections each month. A project o cer reviewed them and they were categorised into safe or unsafe detections.
Safe detections represented those where the person was clearly aware of the equipment approaching and had positioned themselves in a safe place and stopped moving.
Unsafe detections were the instances of people unknowingly or casually stepping into the path of moving plant and equipment.
“At the beginning of the trial we saw 40 to 50 per cent of all interactions as unsafe but over the 12 months that dropped dramatically to around three per cent,” Drew said.
“I think it is a combination of the system improving the safety, but also facilitating conversations that gets all of our workers thinking about moving plant on site.”
Drew explained that rail poses unique construction and safety challenges. Narrow corridors, shared workspaces and very tight timeframes mean people inevitably are working close to mobile plant so technology like Blindsight AI is an asset.
“For us, the risk is always just sitting there. We are constantly seeking to improve our controls,” he said.
“This type of system just gives us one more layer of defence to make sure everyone gets home safely at the end of the day.”
Aptella’s market manager of Safety Solutions, Nick Corr, explained the importance of Blindsight AI in improving safety around trains.
“The work Sydney Trains has been doing with Blindsight has really put them with safety technology leaders in Australia. They are using the technology specifically to suit their operations and to great success.”
At Alstom, more than 350 rail cybersecurity specialists and their peer railway engineers cooperate with customers, regulators and technology partners to protect rail networks from the disruption of cyberattacks.
Cybersecurity is a top priority in preserving not only the safety and security of rail networks but also in ensuring that travellers’ peace of mind is maintained.
Through the concerted e orts of more than 350 rail cybersecurity specialists and their peer railway engineers, Alstom works hand-in-hand with customers, regulators and technology partners to keep rail networks safe from the disruption of cyberattacks.
Eddy Thésée, Alstom’s vice president of cybersecurity products and solutions, leads this global team who work behind the scenes, collaborating and developing tailored solutions to mitigate the evolving threats that could potentially impact operations.
With this progress comes a heightened need for cybersecurity measures to safeguard the intricate web of Information Technology (IT) and Operational Technology (OT) environments that power rail networks worldwide.
These rail technologies not only facilitate smooth operations but also ensure the safety and security of passengers and cargo. The imperative to secure a rail environment made of IT and OT components in railways cannot be overstated.
The integration of more software and connectivity in rail operations has enabled several transformative benefits, from predictive maintenance to real-time monitoring of train movements.
However, it has also introduced vulnerabilities that malicious actors may exploit. The railway industry is increasingly viewed as a viable target for cybercriminals.
Without robust cybersecurity measures, critical functions such as signalling, track switching, braking, distance management and communication systems are at risk of being
compromised, leading to potential disasters. Cybercriminals may also decide to attack ticket machines, passenger information displays and wi-fi systems. Proactively securing these environments is paramount to safeguarding against cyber threats and ensuring uninterrupted and safe rail services.
Behind the scenes, a multitude of teams diligently work to secure digital infrastructure and communications networks in rail.
From cybersecurity experts conducting risk assessments to IT professionals implementing robust firewalls and intrusion detection systems, each plays a crucial role in mitigating potential cyber threats. Operational teams continually monitor network tra c and promptly respond to any suspicious activities to prevent breaches before they escalate. Their concerted e orts are geared towards making every journey safe and secure for passengers and freight alike.
Alstom Australia and New Zealand signalling and infrastructure director, Dominic Clark, shares insight into the challenges and strategies securing rail networks.
“Railway systems are complex ecosystems. Our focus is on implementing a multi-layered defence strategy, combining advanced threat detection technologies with rigorous employee training to mitigate cyber risks e ectively,” Clark said.
Clark’s sentiments resonate with cybersecurity professionals across the industry. The dynamic nature of cyber threats demands a proactive approach to cybersecurity, where continuous monitoring and threat intelligence sharing are essential.
“Cybersecurity is not a one-time e ort but an ongoing journey,” emphasises Clark. “By staying vigilant and adapting to evolving threats, we can stay one step ahead of potential cyber adversaries,” he said.
Over the past 10 years, Alstom has developed a team of more than 350 internal experts with a dual cyber and rail culture, or a broad understanding of both cyber and physical security. This means they can identify the IT risks while speaking the same language as rail operators, in terms of reliability, operational e ciency and long-term commitment to performance.
Beyond Alstom’s e orts, collaboration among various stakeholders is crucial in fortifying rail cybersecurity. Government agencies, industry associations, and cybersecurity firms must work hand in hand to establish standards, share threat intelligence, and develop best practices tailored to the unique challenges
faced by the rail sector. This collective e ort ensures a unified approach to addressing cyber threats and reinforces the resilience of rail networks worldwide.
Alstom emerges as a leader in prioritising cybersecurity within its current and future plans. Recognising the evolving threat landscape, Alstom has integrated cybersecurity principles into every stage of product development, from design to deployment. By adhering to international standards and collaborating with industry experts, Alstom ensures that its rail solutions are protected against cyber threats. Additionally, the company invests in employee training and awareness programs to foster a cybersecurity-centric culture across its workforce.
“When Alstom started building its cybersecurity team in 2013, partnerships with cyber experts were focused on gaining knowledge on cybersecurity processes and learning from best practices in other industries. After a few years, the internal assets had been acquired, the processes set up and the impact on engineering identified. That’s when the company started looking for new partnerships, aiming to bring cyber solutions that would bridge the gap between the two worlds,” said Clark.
Alstom’s commitment to cybersecurity extends beyond product development to encompass proactive measures in securing rail infrastructure. Through partnerships with cybersecurity firms and government agencies, Alstom conducts regular vulnerability assessments and threat intelligence gathering to stay ahead of emerging risks. Alstom also
advocates for industry-wide collaboration to address cybersecurity challenges collectively, emphasising the importance of shared responsibility in safeguarding rail networks.
With a comprehensive portfolio spanning signalling systems, rolling stock, and rail infrastructure solutions, Alstom integrates cutting-edge cybersecurity features into each product. From advanced encryption protocols to intrusion detection systems, Alstom’s solutions are engineered to withstand cyber threats while maintaining seamless operations. The company also provides tailored cybersecurity consulting services, assisting rail operators in assessing vulnerabilities, implementing preventive measures, and building resilient cybersecurity frameworks.
Through dedicated research and development e orts, Alstom continuously enhances its cybersecurity capabilities, staying ahead of emerging threats and evolving regulatory requirements. This notion of regular reviews and updates to anticipate and adjust to new threats is new to the rail culture, but the challenge has been accepted by Alstom and is now part of the company’s DNA.
Rail operators can navigate the complex cybersecurity landscape with confidence in partnership with Alstom, knowing that they have a trusted ally committed to their safety and security. Together, it upholds the integrity of rail networks, preserving the trust of passengers and stakeholders alike. With Alstom’s expertise and unwavering dedication to cybersecurity, the future of rail travel is not only e cient and sustainable, but also resilient to emerging cyber threats.
MEGATRANS 2024 has taken a focus on sustainability for this year’s event. The aim of this is to better reflect the logistics sector.
The year 2024 will see the logistics industry make a shift towards sustainability, with investments in this space set to skyrocket, according to MEGATRANS Show Director Lauren Chartres.
“The sustainable supply chain is going to be the top focus in the new year,” Chartres said.
“The past few years have been about securing supply chains at any cost, after they were disrupted by the pandemic. Now that supply chains have settled, and stock levels risen, major logistics companies are telling us that they are looking to invest in sustainability.”
It’s an investment, Chartres said, that is being supported by the Federal Government’s most recent budget that provided more than $4.5 billion in climate-related spending. This includes $20.9 million over five years to decarbonise transport and infrastructure.
The freight transport sector currently contributes to 46 per cent of emissions nationally, and transporting people and goods around Australia is predicted to be
country’s largest source of emissions by 2030.
MEGATRANS2024 will also examine cold chain solutions and how they can impact the whole chain function.
To increase the focus on making the cold chain more sustainable, including reducing carbon emissions, minimising waste, and adopting eco-friendly technologies, MEGATRANS2024 will feature exhibitors working in this space as well as conference sessions covering the latest technologies, innovations and regulations.
“The challenge for MEGATRANS2024 is to unite the logistics industry in building a sustainable future,” Chartres said.
“By providing a forum for like-minded suppliers and industry leaders to connect to connect, across the exhibition, conference and jobs pavilion, we hope to play pivotal role in that process.
“It will take the most advanced technology, groundbreaking initiatives, forward thinking companies, and exceptional talent to create a truly sustainable supply chain that we can be proud to pass onto the next generation.”
Chartres notes that the logistics industry is still struggling to secure and diversify its workforce. For this reason, the show will feature a jobs fair component, with a $1 million marketing campaign to help attract new talent into the industry.
“We need to start building up the next generation of the logistics industry now,” Chartres said. “And it needs to be reflective of this generation so the industry can mirror its values and set itself up for the future.”
The show will similarly o er solutions for companies investing in traceability, as well as cold chain solutions, areas that are so vital for a sustainable supply chain at every level.
Charters and the team at MEGATRANS are supporting the industry’s sustainable priorities by focusing the entire conference and expo on the long-term sustainable supply chain.
MEGATRANS, Australia’s largest logistics event taking place in Melbourne in September 2024, tickets will be available on the MegaTRANS website.
WOMEN IN INDUSTRY NOMINATIONS ARE NOW OPEN.
Now is your chance to nominate an industry leader who you believe is advocating for positive change and deserves to be recognised.
PROUDLY PRESENTED BY
Thurs 20 June, 2024
The Women in Industry Awards recognise outstanding women leaders from across Australia’s industrials sector.
SICK Sensor Intelligence is finding ways to support train operators in France with its Ranger3 sensors.
SICK Sensor Intelligence has worked closely with RATP in Paris to investigate the rolling characteristics of its regional trains.
The process allows RATP to identify potential faults and areas on its lines causing wear, to quickly rectify issues on a network and minimise down time.
The use of eight SICK Ranger3 3D vision sensors enabled the project to be completed in record time.
Measurements were taken with 3D vision sensors, which by capturing the x, y, and z data, can shed light on how the wheels move on the rails.
RANGER3
The next generation Ranger3 streaming camera is highly accurate with good measurement speed, and can be configured for a range of needs.
Powered by the unique 3D sensor tailored for demanding vision applications, Ranger3 will serve as a key component in inspection systems. The camera extracts the true 3D shape of an object, regardless of its contrast or colour and as a result, improves quality for a multitude of products.
The Ranger 3 strives for cost-e ective integration through its GigE Vision and GenICam compliance.
The unit’s CMOS sensor enables
fast 3D measurement speed for increased throughput and reliable and accurate measurements on dark and bright surfaces.
It also has easy mechanical integration thanks to a compact housing, the ProFlex-Front, industrial connectors and 4Dpro accessories.
However, integrating the sensors to the trains was not without its challenges. To achieve the best results and remain within the clearance gauge, the space occupied by the sensor and its positioning on the car had to be adapted accordingly without impairing measurement quality.
The sensor also has to return a reliable result when exposed to impact, shock, vibration, and jittering while the train is traveling at a top speed of 130 km/h and an average speed of 80 km/h.
For the project, an RER-A regional train was fitted with Ranger 3D vision sensors during operation at night for a test period of six weeks.
IMAGES: SICK
and its suburbs.
The 108.5-kilometre (67.4 mi) line crosses the region from east to west, with all trains serving a group of stations in central Paris, before branching out towards the ends of the line.
The line gets around 300 million journeys a year making it one of the busiest rail lines globally.
System integrator, New Vision Technologies, installed the 3D cameras in a compact housing meeting the restricted volume requirements.
For 10 years New Vision has provided railway applications such as catenary measurement, rail position measurement and survey of a catenary area.
Cameras were mounted in front of the wheel, at the point of contact between rail and wheel, and behind the wheel on both sides of the train.
The measurement was taken by adapting the laser beam to the shape of the rail, which was reflected back to the 3D camera through a mirror.
The camera read and collated the measurement data, which was then processed to produce a rail profile characteristic curve.
With 2,000 measurements being taken per second, approximately 8 terabytes of data were captured and, which was then evaluated every 24 hours.
All of the information was collated and returned to RATP, to give the organisation the opportunity to rectify any faults or issues.
Brimble is bringing digitalisation to the fore as it upgrades and expands its fleet to meet the needs of the Australian rail industry.
Seven years ago, the Brimble siblings pooled their money to buy their very first rail resurfacing machine that would get the company o the ground in the Hunter Valley region of New South Wales.
Today, the organisation is unrecognisable from those early days and has expanded to cover the whole of Australia.
While the small beginnings were critical to the company’s success – they attribute their growth to strong values, relationships and a people-first focus – Brimble has grown to the largest fleet of rail maintenance equipment in the industry across every gauge.
Brimble has more than 65 machines including tampers, regulators, stabilisers, ballast cleaners, MFS wagons and recording vehicles. The company is also in the process of upgrading and refurbishing 40 more machines to add to the fleet over the coming years.
Brimble organises its fleet into three core o erings for the rail sector: the Ultimate Series, the Pro Series, and the Utility Series.
Managing Director, David Brimble, tells Rail Express about how a machine’s series designation is often defined by the level of capability of the machine.
“The more custom the machine, the more it can perform to our exact specifications,” Brimble said. “Our Ultimate Series sets a new standard in rail resurfacing capabilities, o ering exceptional power, versatility, and speed.
“Our customisations mean these machines are truly the best in the market when it comes to their ability to resurface tracks swiftly and e ectively.”
He said the Ultimate Series is well-suited to various settings, including metro, heavy haul, light country rail networks, or complex junctions.
“The Pro Series represents unbeatable value with outstanding performance. From production and turnout tampers to all-rounder tampers, regulators, and stabilisers, these powerful and versatile machines meet a wide range of railway maintenance needs,” he said.
“Our Utility Series represents an economical solution, coupled with quality results.
“Designed for restricted access and strategic usage, these highly capable machines excel in both turnouts and straight tracks. The Utility Series o ers a reliable and a ordable option to get the job done.”
To meet the needs of projects across the country, Brimble has continued to upgrade machines across its fleet with new technology.
The cornerstone of Brimble’s digitalisation is the Human Machine Interface (HMI) system. This technology moves away from
the historically complex and inconsistent technology used in track resurfacing, in many cases leaving behind antiquated control panels made up of countless dials, switches, lights, and alarms. Brimble HMI utilises userfriendly touch-screen monitors and a network of high-definition video cameras, making it simpler for operators to oversee, operate, and optimise rail resurfacing machinery.
Steven Johnson is the General Manager of Operations East at Brimble and knew this technology was setting Brimble apart when he joined the team in 2023.
“By replacing historic technology with our HMI system, we are improving efficiencies, reducing errors and keeping workers out of dangerous situations. We are also upskilling them on technologies such as remote control of the machines and using drones for visuals
in hard-to-access places,” he said.
“The HMI technology we have integrated into the machines removes all the failing switch components and gives the operator a better visual over what’s going on in the machines’ brains and more options for changes on the run.”
By removing physical components, Brimble ensures it is minimising downtime as Johnson explained.
“Digitalising these components minimises issues that can slow and even halt operations,” he said.
“If we are working in remote areas of South Australia or Western Australia for example, we no longer need to wait for technicians to attend on-site. We can rectify it remotely.”
Brimble is in the process of upgrading its full fleet of machines to the HMI systems.
Johnson said the organisation has upgraded the original control units.
“The HMI upgrading limits the amount of time our staff spends in dangerous situations. It also allows operators to easily adjust things in the field,” he said.
“We also have a lot more visibility to ensure the machine does not do any damage to the client’s assets when in travel and work mode.”
This technology was developed by the team working out on-site as Johnson explained.
“The HMI system was not designed by an engineer working behind a desk. It was developed by actual operators in conjunction with the broader team,” he said.
Brimble’s ballast wagons are a great example of how their technology is improving the delivery of ballast materials for the maintenance and construction of the track asset.
The wagons are controlled remotely, which limits interactions between workers and the drop zones, keeping sites safer for the team.
The wagons are digitally linked and in constant communication. They have wireless HMI operation of the hydraulic-actuated hopper doors, allowing the ballast to be dropped in precise locations.
“We’re proud to be making things more intuitive and safer for our workers through this technology, and it’s creating better results for our clients across Australia,” Johnson said.
Brimble’s team is expanding and the organisation will be aiming to add project managers and technical operations workers across the country in 2024.
RATP has been utilising digitalisation solutions across the globe to improve reliability of networks and is keen to test its solutions during the 2024 Olympics in Paris.
For the past century, RATP’s history has been marked by major breakthroughs and ambitious development e orts to improve service quality for passengers and create sustainable and safer mobility solutions, such as automated metros, on which it started trials as early as 1952.
This spirit of innovation has been passed along to its international branch, RATP Dev, actively involved in transforming transportation infrastructures worldwide, including in Australia, Hong-Kong, Qatar, Saudi Arabia, South Africa, France and the United States, and in exploring the key topic of digitalisation.
With more than 837 million trips operated annually worldwide, RATP Dev considers digitalisation as a key strategic lever to support public transport authorities in achieving their goals and accelerate the deployment of new innovations for an enhanced travel experience for passengers.
With the rise of connected objects, sensors and information systems, the volume of data created or replicated worldwide has increased
by more than 30 per cent in the past decade, and is expected to grow by an average of almost 40 per cent a year by 2025.
RATP Dev aims to support public authorities in their understanding and exploitation of their various data sources, which can be a powerful lever to improve service quality and customer satisfaction. Beyond public transport data, RATP Dev relies on open data to ethically combine multiple sources, including operations, maintenance, and passengers’ data along with local information related to urban planning, air quality or even the cultural agenda.
The company has developed data management solutions to optimise operational performance, o ering improved reliability and services to passengers at lower exploitation costs, such as Maint’Up, an IoT-powered maintenance solution.
This SaaS solution collects, centralises and analyses the data available from all equipment (rolling stocks, infrastructure and stations) in order to optimise operations and maintenance and facilitate the work of teams on a daily basis. Operators and maintenance teams can remotely analyse the state of equipment,
instantly identify incidents on the network for a coordinated response and track data such as energy consumption much more e ciently.
Since its deployment, Maint’Up has already strongly improved the operational e ciency of the trams network in Angers (France) and is currently experimented on Paris regional trains network. In Angers, a reduction of 8 per cent in the energy consumed by the tram rolling stock has been achieved since the end of 2022 due to precise monitoring of the energy consumed by the rolling stock in Maint’Up.
Another solution addressing the imperative for secure and centralised operational information management is SafeTracker. The platform provides access to detailed, up-todate, and reliable data, including information on incidents and team management. It also serves as an operational assistant, enhancing communications between departments, streamlining sta reports, and centralising the work permits process. It has been successfully implemented across various networks operated by RATP Dev, including the Gautrain’s commuter rail in South Africa, Cairo’s railway in Egypt, or sightseeing buses in Europe.
CITiO, an innovative company under RATP Dev has been involved in leveraging data to optimise public transportation. With CITiO Fraud Tracker, the pilot city of Creil near Paris has been able to fight e ectively against fare evasion, recording a +20 per cent increase in penalty tickets. Simultaneously, CITiO Rail Analytics focuses on optimising rolling stock and journey management. The subsidiary also explores the exploitation of data-driven insights to support real-time adaptation of transport networks, through passengers’ flow management in stations and associated optimised sta and equipment’s allocation.
These solutions showcase RATP Dev’s ability to transform public transportation through digitalisation, which the company aims to keep doing in Australia, through the Western Sydney Airport project first, and aims to bring to the Surburban Rail Loop and Sydney Metro West.
Digitalisation also o ers new opportunities to improve performance and optimise maintenance. RATP Dev is particularly focused on leveraging predictive maintenance to enhance the service quality and reliability of rolling stock, station equipment, fixed installations and infrastructure. Data gathered from sensors built into trains and tracks now make it possible to find out the health status of assets in real time, and throughout their life cycles. Predictive maintenance can detect rail
defects or anticipate breakdowns on sliding doors on automated metro lines, it can also use data to accurately predict temperature peaks likely to distort rails three days in advance, thus representing a true industrial revolution for enhanced service quality and safety of passengers, personnel and contractors.
Predictive maintenance also opens promising fields of exploration for cost optimisation of asset life and sustainability of the industry, as it will be instrumental to extend the life of equipment. In Paris, where the RATP Group has internalised almost all maintenance services, it intends to equip 30 per cent of its metro lines with predictive maintenance solutions by 2026. The implementation of predictive maintenance on the doors of RER A commuter train line has already led to a 50 per cent reduction in faulty doors, while the experimentation of a system that detects rail fissures via ultrasound waves has given positive results.
RATP also explores the development of digital twins for infrastructures, rolling stocks and maintenance workshops. The large amount of data available can be processed to create 3D virtual clones of structures. Through 3D simulation, procedures and decision-making can be optimised over the entire project life cycle: validation of feasibility, prototyping, adaptation, upgrades, predictive maintenance, and so forth. For example, virtual simulation applied to real estate, maintenance sites and mobility can make it possible to test automated driving technologies on a large scale over billions of virtual kilometres. These innovations allow the company to pursue continuous improvement of assets and services while minimising the impact on daily operations and passengers.
As Paris awaits 15 million visitors for the Olympic and Paralympic Games, data-driven insights will be a key tool to enable e cient
sta resource allocation and o er a seamless journey to passengers. One solution currently implemented in Paris is DetectAI, which detects passengers remaining on trains at the terminus of automated metros while responding to personal data protection requirements, improving metros availability. Moreover, international travelers can benefit with TradivIA from instant translation solutions, for audio as well as screen updates. A uence also leverages AI to track and smooth tra c flow, through the counting of passengers in real time on platforms and the suggestion of alternative routes, as well as accurate information on onboard occupation of arriving trains. RATP Dev’s goal is to create an inclusive travel experience for everyone, especially visitors unfamiliar with the network, by o ering the latest customer innovations. The company aims at implementing these solutions on other international networks as well, especially metro lines servicing largescale events such as Sydney Metro West.
As RATP Dev’s core objective is the continuous improvement of the services and functionalities o ered to passengers. Technologies are constantly being explored, tested, deployed. RATP Dev’s innovation lab in Casablanca developed the Walk in Peace app to enhance safety in public transport, which will be deployed on the Western Sydney Airport project.
Other innovations under investigation are the implementation of a Chatbot for enhanced e ciency in passengers inquiries, or a new digital solution for stop requesting onboard buses for passenger with disabilities.
RATP Dev remains committed to advancing digitalisation, incorporating predictive maintenance, advanced technologies, and AI applications. RATP Dev’s ambition is to showcase its ability to leverage digitalisation to deliver operational excellence, asset optimisation and increase customer satisfaction.
Step Global is making a foray into the rail sector due to its technology being a perfect fit for the industry.
Step Global provides digital solutions to Australian transport organisations including emergency services in Australia and has identified an opportunity to transition into the rail sector.
David Lloyd is the Managing Director at Step Global. Rail Express spoke with him to better understand how the organisation’s technology can work with the rail industry.
“For us, the rail sector made a lot of sense,” Lloyd said.
“It is simply a matter of using our experience in the areas we have worked in and bringing it to the rail industry.”
Level crossings remain front of mind for the rail industry, whether it be the level crossing removal projects or the Regional Level Crossing Upgrade Fund (RLCUF). Up to $40 million is available each year from 2023 to 2027 to make railway crossings safer in regional areas. This is where Lloyd believes Step Global’s technology can shine.
“When you are driving in regional areas, often when you approach a level crossing, the only indication the crossing is in use is some flashing lights and a bell ringing, which you cannot hear if you have the radio on,” Lloyd said.
“It comes down to getting the attention of the drivers in the vehicles and doing so in a low-cost way.
“We have a system that can be installed inside the vehicle, which will automatically connect to the device located near the level crossing and make an audible warning noise inside the cab.
This type of technology is something regularly installed by the Step Global team, with Lloyd believing that it could help lower the instances of fatalities on the rail network.
It is no secret that for Australia’s rail network, the sheer size of the country poses numerous challenges when it comes to connectivity.
“The idea of sending data digitally was always perceived as expensive,” Lloyd said.
“This was due to them trying to transmit too much data over that link. This was why much of the rail sector turned to copper wire to transmit data back to a central control centre.”
Lloyd said the solution lies in enhancing
trackside computing. Using a smart cellular router to compress the data would reduce the transfer required.
A small antenna would be capable of achieving this transfer while being better protected against vandalism and the elements compared to long runs of copper wire.
The Digi IX30 router o ered by Step Global meets the requirements of such a solution. The IX30 is an intelligent 4G LTE router designed for optimal performance and reliability across a range of infrastructure and industrial applications.
This solution is integrated with software and security, providing a secure, reliable connection to industrial controllers, process automation equipment and smart grid assets on third-party sites or remote locations.
Rail applications, such as railway network timing, railway signalling systems, track-totrack radio systems, station clocks, passenger information systems, ticketing systems, and CCTV, all require synchronised precise and accurate time. Step Global provides a range of time servers, smart GNSS antennas, and GNSS disciplined clocks.
Many advanced rail networks now use time as the safety separator between passenger trains travelling on the same track. This enables more trains per track and provides
precise speed control when there are delays. Obtaining precise location, speed, and time stamps, provides a chronological audit trail that may be vital for safety information records and incident identification.
Track-to-train communications also benefit from precise time, message transmission and reception, which must be precisely synchronised or there can be loss of, or scrambled, messages.
Station clocks and passenger information systems need to be synchronised across the network, giving travellers correct times for departure and arrival. Station management systems also require accurate time, CCTV, computer networks, automated announcements, automated ticketing systems, and security systems.
“The old techniques of running train systems just simply do not work anymore. We need
technology to better support rail infrastructure like ticketing, messaging and navigation,” Lloyd said.
The challenge that faces rolling out this technology is the use of multiple levels of Wi-Fi, 2.4, 5.8 and now six.
“The technology provided by Digi is designed to meet the needs of all users,” Lloyd said.
Ideal for challenging rail transportation environments, the Digi TX64 5G router o ers 5G/4G/3G cellular connectivity with true enterprise-class routing, security, firewall and integrated VPN. It o ers a flexible interface design with an integrated Wi-Fi 6 access points, USB, serial, inertial-guided GNSS, Bluetooth and 4-port Gigabit Ethernet switch, available in a variety of configuration options.
“It can work with handheld devices operating at 2.4 and work up to higher level systems required on train systems.”
Lloyd believes 5G is a game-changer for the rail industry. Until now, the speeds needed to securely move massive amounts of data quickly were reserved for wired networks. Today, with the rapid expansion of 5G (with LTE fallback), the rail-certified TX64 delivers 5G performance, either as a primary or failover connection.
A subterranean GNSS (global navigation satellite system) that regenerates satellite signals in real time, and is used to locate and track vehicles in road tunnels in Australia, is another solution provided by Step Global.
One advantage of such a system is that any standard consumer GPS receiver, a smartphone using Google Maps, or a dedicated tracking device, will be able to function as normal even though the receiver is underground.
Developed by Step Global, NoSky SatNav provides a regenerated signal that a receiver in a vehicle recognises as an actual satellite signal as if it had an open sky view.
The re-generated signals take into account the locations within the tunnel, achieved by using a series of radiating antennas in the tunnel ceiling. The signal from each of these antennas is relative to the precise position of each antenna.
The vehicle GNSS receiver will then calculate its position within the tunnel to the position of the radiating antenna. This system is a promising technique to keep the rail network connected, particularly as tunnel projects continue to be rolled out.
After the Optus outage shut down much of Melbourne’s trains last year, there was a fear that over digitalisation might leave the network susceptible to outages. Lloyd said Step Global ensures outages are not possible on its systems.
“When the outage happened, trains using the Optus network became unable to communicate, causing stoppages and massive delays.”
“Had a failover system, using dual carriers, been in place, they could have quickly transitioned to a backup network with a di erent carrier, preventing stoppages all together.”
Implemented correctly, digitalisation is a tool that can minimise risk and eliminate single points of failure. The Optus outage simply demonstrated the dangers of not having redundancy systems such as failover in place.
Traumatic incidents on the rail network can have a profound impact on the mental health and well-being of drivers and the wider sta .
Metro’s Trauma Recovery Guidebook: Volume Two provides layers of support, preparing and supporting drivers in responding to traumatic incidents that occur on networks, such as encountering trespassers.
Metro CEO Raymond O’Flaherty said ensuring the mental and emotional health of the team is just as critical as their physical safety.
“Our train drivers play a pivotal role in ensuring the seamless operation of our network. And in an ideal world, there would be no need for this guidebook,” O’Flaherty said.
“The reality is that our train drivers often face traumatic events such as encountering trespassers on the network, which can have
a profound impact on the mental health and well-being of our team members.”
The Drivers and Train Services team initiated the development of the guidebook to provide support and resources for Metro’s train drivers.
The first edition was developed in 2022 and aimed to be a guide to support drivers before and during a traumatic event. This second edition adds to that with new experiences direct from Metro’s drivers and more support for their families.
Metro has 1434 train drivers who are responsible for transporting around 500,000 passengers daily.
A peer support program has been running for several years where drivers receive trauma support training to be able to help their colleagues through traumatic situations. There are currently 57 peer supporters.
Metro Trains Depot Driver Manager, Brittany Fisher, explained the peer support program.
“Our peer support program has been running for several years where drivers receive trauma support training to be able to help their colleagues through traumatic situations,” she said.
“Tools like the guidebook and our peer supporters are really important, because it ensures our drivers and their families get the support they need after a traumatic incident on the network.
“It’s important for our people to know that they are not alone and that we back them all the way.”
The guidebook details the process that occurs in the event of a railway incident and the support mechanisms that will be given to drivers.
This support includes Workcover arrangements, allowing them the time o they need, as well as the support to ensure that when they choose to return to work, they are ready to do so.
Metro has an Employee Assistance Program available to all sta members and their families to ensure they have the tools and support to handle traumatic incidents, as well as the challenges that come from daily life.
Ian Webb has been a train driver for 10 years and is now involved in training new drivers.
He has had four previous near misses and one fatality, which occurred in April 2023.
“I absolutely love driving trains,” he said. “Following this incident, I took several weeks o work and was supported all the way through to my return.
“It’s important for people to take care and be safe around trains. Trains can take hundreds of metres to stop, and that’s if we see you. It’s just not worth the risk.”
He now spends his working life training new drivers and takes his experiences into the classroom to ensure they are ready for the
For two decades Step Global has supported numerous industries through the supply of asset tracking and monitoring technology. Over this time, we have grown both our product offerings as well as our product development capability to provide full system solutions.
Step Global supplies a wide range of rail products and accessories, we work with globally recognised manufacturers, to ensure our customers always have access to the latest and very best technology products.
Whether it be application knowledge, off-the-shelf products or a full turnkey design of bespoke systems, Step Global’s focus is to either build, create or integrate to meet your needs.
The National Rail Skills hub is working with industry and educators to grow a diverse rail workforce by showcasing the diverse jobs available in the industry.
In profile: Paloma Zafra Tunon Systems Engineer, Systra Paloma Zafra Tunon’s expertise is in Communication-based Train Control (CBTC). It’s the signalling system in which trains communicate to the tracks via radio. The system knows at all times where the trains are, with very little error.
“I’m quite a weird engineer. I’m very technical, but I’m also a very social person. I SCUBA dive, I like crafts, and I love sports,” she said.
“I also work on European Train Control Systems (ETCS). If a train is going too fast, the ETCS applies brakes. It’s a safetyrelated system.
“I grew up in Cadiz in the south of Spain, and moved to Madrid to go to university where I specialised in electronics which is similar to electronics engineering. I was focused on robotics and was considering doing a PhD when I attended a recruitment fair . I hadn’t thought about changing career paths, but a transportation company o ered
me good money and a career path.
“At first, I thought, ‘I have no idea about trains.’ Then I thought I’d give the private sector a go.
“Fifteen years later I’m still working in rail and I absolutely love it.”
In 2015, Tunon returned to Spain after working in the United States for three years. She was contacted through LinkedIn where she was o ered a job in Brisbane.
“I thought, there’s no way I’m going to move again,” she said.
“Then a couple of years later, someone else in Australia contacted me through LinkedIn and o ered me a job, also in signalling. In 2019, a third company from Australia approached me. I thought, ‘OK, life is giving me this. I should explore it.
“So, I packed everything and came out here.”
When Tunon first arrived in Australia, she was working from Brisbane but going to Melbourne to work on CBTC for the Metro Tunnel. In Brisbane, she was doing ETCS on its New Generation Rolling Stock.
Australia is installing signalling systems everywhere.
Tunon now works for Systra, a consultant company and her role is on the technical side.
“At the moment, we’re designing a smokealarm system. It needs to interface with the train and the tracks. I need to check the overall system part of it, but also the details, such as data sent between di erent systems,” she said.
“I also do a lot of work with Queensland’s Transport and Main Roads (TMR). Right now, I’m reviewing technical details from the suppliers of one of TMR’s rail projects: Alstom, who makes the trains; and Hitachi,
who is developing the ETCS.
“My job title is systems engineer. There’s not a lot of us considering how much work is out there. I always tell the young engineers, ‘if you like engineering, the rail industry gives you possibilities for almost everything’.”
In profile: Rhys Wilkinson Signalling Technician, ARTC Rhys Wilkinson began his electrician’s apprenticeship through PEER recruitment doing domestic, residential, and commercial work.
“The usual jobs for an electrician. Then in my fourth year, a position came up to be a signalling technician and I went for it,” he said.
“I live just south of Adelaide and work at the depot in Mile End for Australian Rail Track Corporation (ARTC).
“I like the railways because they o er
variety. Every problem is slightly di erent, and that makes you think outside the box. If you’re doing domestic or commercial work, you’re working on the same three wires.”
Wilkinson explained that the work he does is “reverse-engineering”.
“I find the location and extent of the fault, then think logically about how it came to be. Then, ‘Wow!’ I’ve fixed it,” he said.
“It’s the fault-finding aspect that appeals to me.
“It took a while for our team to unravel a problem that occurred near Mallala, north of Adelaide. The electrical system there was “old school”. We combed through 36 kilometres of track before working out the source of the problem. The wiring design was di erent to the wiring found on other parts of the network. After all that work to find the problem, I had to repair an activation circuit for the timing of signals.
Wilkinson said he had a technical mind as a child. Sometimes pulling apart old telephones to see what was inside, and how it worked.
“After my apprenticeship, I gained a Certificate III in electro-technology. Then ARTC put me through the Certificate IV course in rail signalling, giving me dual qualifications,” he said.
“I’ve been in the role of acting work group leader for eight months. I lead the other signalling maintenance technicians and manage ARTC’s signalling assets.
“The railways isn’t for everyone. It’s a very niche area of electrical work that is more mentally draining than physically draining. Many young blokes go o to work on the mines or start travelling. I’m happy to stay here with the railways in Adelaide.”
The push to extend the electrification of the Stony Point line in Melbourne to allow Metro trains to run further has became a hot topic of discussion with federal opposition leader Peter Dutton announcing a proposal to extend the Frankston Line.
The Stony Point line acts as an extension of the Frankston line with services running from Frankston station to the small town of Stony Point in south-east Melbourne. It serves 10 stations including Leawarra, Baxter, Hastings, and Bittern. The Stony Point line is operated by Metro Trains Melbourne and is the city’s only diesel service on the metropolitan network and the tenth longest line at 31 kilometres.
The line operates for 13 hours a day from 5:30 in the morning to 10:30 at night, unlike other lines on the network, which provide 24hour service on Friday and Saturday nights.
Headways of 90 to 120 minutes are operated throughout the day due to limited patronage and infrastructure constraints. Trains on the Stony Point line run as two one-car formations of V/Line Sprinters.
In May 2018, the Australian Government committed $225 million to deliver the Frankston line extension. Subsequently, a
preliminary business case investigating the project was undertaken by the Victorian Government and released in November 2020.
The business case centred around the need for electrification of the Frankston line as the areas around Frankston and the Mornington Peninsula have poor access to public transport.
According to the report, less than three per cent of residents use public transport in the Mornington Peninsula and less than six per cent in Frankston, which the study contends is far lower than other municipalities that are similar.
This low patronage of the line is indicative of several issues in the area, including accessibility, reliability and poor travel times. For residents in the area, less than 10 per cent of all jobs are accessible by public transport within an hour.
All investment options will provide public transport benefits for Frankston and the Mornington Peninsula. However, the economic costs of all options will exceed the benefits,
in particular for electrification of the line, which requires a large capital investment of stabling, stations, level crossing removals, and signalling works.
It is believed that the cost to electrify and duplicate the line all the way to Stony Point would be up to $1.5 billion, which included new stations at Frankston East, Baxter and Langwarrin.
Of the assessed investment options, the Stony Point Uplift is the likely preferred plan. This option requires less capital investment and has less impacts than the electrification options. It also provides additional rail services for population centres at Somerville and Hastings, which would not be provided under the electrification options.
The Stony Point uplift would see passing loops added along the Stony Point line at Tyabb and Bittern – to allow trains travelling in opposite directions to pass each other. The track would not be electrified, and the project would not include level crossing removals.
Joshua Sinclair from the committee for Frankston and Mornington Peninsula explained that the committee hoped a full business case as opposed to a preliminary business case would establish if the project was feasible.
“What is clear is that communities in Langwarrin and Frankston East – along with Frankston’s Education and Health precinct, which house Monash University and Frankston Hospital – do not have adequate public transport service,” he said.
“There is clearly a need to address that – and the electrification and duplication of the Frankston line to Langwarrin or Baxter overwhelmingly addresses those issues.”
While the committee is a firm believes in the duplication and electrification project, it is open to the prospect of the Uplift.
“In our view this is an option the Government should actively be considering,” Sinclair said.
“It’s significantly cheaper, does not require multiple level crossings and freeway connections, and could – according to the preliminary business case – provide services on the Stony Point line in both directions every 20 to 30 minutes. This would be more than enough to satisfy Mornington Peninsula residents in Western Port.”
Federal opposition leader Peter Dutton appeared in the region back in February where he made the pledge that if his party won the next federal election, he would commit to a 50-50 partnership with “a future Victorian state government that is willing to deliver this project”.
Dutton pledged a capped commitment of $900 million to support the delivery of a full business case and contribute to early works and construction of the project.
“This is a substantial commitment, which reflects the importance of delivering this critical project to give residents in Frankston South, Langwarrin, and Baxter faster and more reliable transport services and improved community infrastructure,” Dutton said.
“Tra c congestion and the availability of public transport is a major problem for this growing region. We have listened to local community concern, and we are delivering.
“The electrification of the Frankston to Baxter line will improve the e ciency of train services and reduce commuting times.”
In 2022, ahead of the state election, the Victorian opposition committed to the project if they won.
In 2023, the Victorian government made the commitment to no longer provide funding to the project.
This along with other projects were declined if the government believed they were not realistically going to be delivered with the funding available, have made little to no progress over a significant amount of time, and they do not align with Commonwealth or state
and territory priorities.
A Victorian Government spokesperson explained what the current government has done to support the region.
“We’re already investing $4 billion to make the Frankston line level crossing free and providing more train stabling so that it can return to the City Loop when the Metro Tunnel opens, allowing more trains to run more often. We’ve also upgraded Lathams Road, the Westernport Highway, Golf Links Road and have almost finished work to upgrade Hall Road,” the spokesperson said.
Sinclair explained that the Stony Point train line is the worst performing in Melbourne according to Metro trains.
“It’s the only train line in Melbourne that runs on a diesel service, and it is constantly plagued by faults, level crossing issues, and safety issues. It’s also incredibly unreliable, infrequent, and does not encourage Mornington Peninsula residents to use it,” he said.
“Improving the line via electrification and duplication is the gold-plated approach and will need to pass a full business case. However, many other projects across Victoria deliver worse returns and quite often receive upgrades.
“If Langwarrin or Baxter was the ultimate destination for the Frankston line extension, it would significantly improve the ability of Mornington Peninsula Shire residents to catch the train. Many would use Peninsula Link (the M11) exit to a train station with park and ride facilities. Currently, their only option is to drive into Frankston CBD and battle for a car park,”
Sinclair said.
He said the project would free up Frankston Station car park, connect growing communities like Langwarrin, would better connect residents from the Mornington Peninsula to the greater Melbourne area, and improve connectivity between the region’s only University and major hospital.
“Somerville, Bittern and Hastings are communities with growing populations, and getting them into Frankston CBD with frequent and e ective train services would encourage more people to use the line. This can all be done with a handful of passing loops and improvements to infrastructure that don’t include duplication and electrification,” he said.
“If cost is an issue for the Victorian Government, this is something they should be actively considering. The total cost for a Stony Point uplift option is a quarter of what the electrification and duplication would cost.”
While the Suburban Rail Loop (SRL) will not solve the Stony Point connection challenge, it will better connect the region to the East.
The SRL East will run between Cheltenham and Box Hill with stations at Burwood, Glen Waverley, Monash and Clayton.
Cheltenham is currently 11 stations before the end of the Frankston line so this connection to Melbourne’s east will better support those in Frankston and the Mornington Peninsula.
SRL East is expected to be completed in 2035, with construction beginning back in 2022.
It has been a busy period for PWI with the highlight to start the year being the PWI NSW awards night. This event was a chance to celebrate the year it was and turn the organisations attention to 2024 and what lies ahead.
The PWI NSW Awards evening was a celebration of the works and projects achieved within New South Wales’s rail industry. This event recognised the passion, dedication, and excellence exhibited by individuals and organisations.
The 2023 PWI Ken Erickson Innovation Award was bestowed upon Future Maintenance Technologies ARIIS, acknowledging its ground- breaking contributions and innovative solutions shaping the future of rail maintenance and operations.
Sione Tuitakau from Quickway was honoured with the 2023 PWI Welders Award in the welding category, celebrating his exceptional craftsmanship and commitment to quality in the welding discipline.
The Central Coast Civil Team’s maintenance practices were recognised with the 2023 PWI Alan Barham Maintenance Award, highlighting their crucial role in ensuring the safe and e cient operation of rail assets.
The 2023 PWI Steve Maxwell Award
winners exemplified outstanding project delivery across various scales and scopes. Next Rail Sydney Terminal Hurstville Crossover (Major Under $3M), Abergeldie – Southern Highlands Overtaking Early Works Werai (Minor), and Sydney Trains Linden To Lawson Derailment (Platelaying) were all celebrated for their achievements in project management, teamwork, and execution.
In the design category, GHD’s Penrith Resignalling + Remodelling project was honoured with the 2023 PWI Design Award below $ 1 million, while AGJV Sydney Metro Bankstown Corridor took home the award for projects over $ 1 million, showcasing innovative and cost-e ective design solutions.
Finally, the 2023 Electrical Safety & Quality Award was presented to Sydney Trains South Territory Network Maintenance, acknowledging its commitment to upholding and advancing the industry’s electrical safety and quality standards.
The PWI NSW Awards evening was a testament to the continued passion and dedication of rail industry professionals in New South Wales. Their relentless pursuit of excellence, innovation, and collaboration drives the delivery of world-class rail projects and services across the state.
The Awards evening not only served as a platform to honour the achievements within New South Wales’s rail industry but also underscored the collaborative spirit
and technological advancements propelling the sector to new heights. It was a night when the rail community came together in a spirit of camaraderie and mutual respect to celebrate the strides made in enhancing rail transport’s e ciency, safety, and reliability. Each award, chosen by a panel of industry experts, reflected a commitment to excellence beyond project completion. It highlighted innovative approaches, sustainable practices, and a forward-thinking mindset essential in addressing the complex challenges of modern rail systems. The event also allowed professionals to network, exchange ideas, and inspire one another, further fostering a culture of continuous improvement and innovation within the industry.
9TH MAY 2024
The upcoming PWI Breakfast, scheduled for May 9th at the Fullerton Hotel, promises to be enlightening for rail industry professionals. With Josh Murray, Secretary of Transport for NSW, as the keynote speaker, attendees can anticipate an event filled with discussions on the future of transportation in New South Wales. Murray’s expertise and leadership in transport are expected to shed light on new initiatives, technological advancements, and strategic plans to enhance the state’s rail infrastructure. This event o ers an opportunity for professionals to gain insights, engage in meaningful conversations, and connect with peers over shared interests and challenges. The breakfast is a forum for discussion and an occasion to foster collaboration and innovation within the industry.
50TH ANNIVERSARY OF PWI NSW
The event will feature distinguished speakers, workshops, and interactive sessions to explore the latest trends, challenges, and opportunities facing the rail sector. This event is a celebration of the past 50 years and a forward-looking platform that aims to shape the future of rail transport in New South Wales and beyond. It’s an occasion to honour the industry’s achievements while setting the stage for the next era of innovation and growth.
The RISSB Rail Safety Conference is set to be held in Melbourne in late April and is an opportunity for collaboration in the rail sector.
The Rail Industry Safety Standards Board (RISSB) and Informa Connect are hosting the 2024 RISSB Rail Safety Conference that will be held in Melbourne at the Grand Hyatt from April 30 to May 1, 2024.
The conference brings together hundreds of rail transport operators, engineers, project managers, investigators, safety professionals and senior industry executives, each year. All with participants have an interest in maintaining Australia’s reputation as one of the safest rail networks in the world.
With $155 billion in rail infrastructure investment planned over the next 15 years, prioritising safety is vital for productivity, sustainability, and importantly the impacts on our people. Our co-regulatory environment paves the way for improving e ciency and advancing optimisation.
This unprecedented pace of investment and how our industry responds, is the vision for this year’s conference theme – Australia’s CoRegulatory Model: Don’t Throw out the Baby with the Bathwater
The Australian rail industry’s co-regulatory model has been in place for a decade or more and has proven to be e ective. Governments are now intervening on a small number of big, important, and costly reform issues, but this intervention should not be seen as a signal that our co-regulatory model is broken.
RISSB believes that ongoing refinements to our industry’s co-regulatory model will add further value, and the 2024 RISSB Rail Safety Conference will explore the improvement opportunities available and how industry can get involved.
The conference will delve into the latest advances in technology and innovation, sharing case studies and project updates from successful rail safety projects in Australasia and around the world. Over the two-day program, attendees can expect presentations from international and Australian speakers, topics tackling emerging and important issues, engaging panel discussions with safety leaders and leading engineers in the industry, and an interactive shared learning session with a mock incident.
Key themes to be addressed during the conference include:
Australia’s rail safety regulatory environment:
• What role does regulation play in your planning and operations? Does coregulation help or hinder interoperability and harmonisation?
• Experiences and learnings from the current regulatory environment.
Lessons learnt from best practices in safety leadership:
• Share how you are driving continuous
improvements for a safe, e cient and digitally enabled future.
• Collaboration in project management and contractor safety.
Practical solutions from the latest innovation and technology
• Discuss your research, advances, trials and learnings for a safer, smarter rail future.
• Evidence of co-regulation in facilitating innovation.
Once again, this year’s conference will also feature the 2024 RISSB Rail Safety Awards Dinner. Established in 2022, the RISSB Rail Safety Awards are designed to recognise and celebrate individual and company safety achievements in the rail industry and promote diversity, excellence and innovation.
The RISSB Rail Safety Awards are open to any individual working in the rail industry and organisation operating in or a liated with rail in Australia and New Zealand. Entering the RISSB Rail Safety Awards provides the chance to recognise the contribution of you and your team to the rail industry.
The award’s categories for this year aim to identify individuals and organisations with a strong commitment to safety and have demonstrated diversity, inclusion, excellence and innovation all for the betterment of rail. We look forward to the di cult task of deciding on the category winners.
Category winners will also automatically be finalists in the ARI Awards 2024 in the RISSB Safety Excellence category.
More information can be found on the RISSB website.
RISSB encourages industry to join them at the only rail safety conference in Australia, where you can leverage the collective insights of some of Australia’s most esteemed industry experts. It is also an opportunity to connect and expand your network and catch conversations with others in the industry.
In line with our strategic priorities of industry harmonisation, sustainability and supporting a safe, productive, and e cient industry, the ARA is increasing its focus on the critical initiative Project i-TRACE, which it established in partnership with GS1 Australia and has the potential to significantly transform the rail industry.
As an industry we must move forward with this project as quickly as possible so its benefits can be fully realised – a productive, sustainable, and competitive industry with minimal waste and duplication.
Project i-TRACE, a whole-of-industry approach to identify, track, and maintain assets, parts, and components in the supply chain, will play a role in shaping the future of rail, driving progress and e ciencies across the industry.
The project slowed during the pandemic but is now gaining momentum as knowledge and understanding of its benefits grows across industry and government.
It is a huge issue that the Australian rail sector does not have a standard language to identify and mark material parts and components.
Eighty per cent of rail operators, manufacturers and maintainers are not confident in their master data and 70 per cent of the data reaching the warehouse is not fit for use in current and future software systems.
Ordering the wrong part costs money and considerable time is lost correcting errors, organising returns and duplicate or misidentified material and serial numbers or data attributes.
Generally, dealing with inaccurate or incomplete material or product attributes
costs organisations’ supply chain an average of 25 per cent more in labour costs.
Project I-TRACE o ers numerous benefits in the rail supply chain. It helps all stakeholders e ectively identify rail components and assets, electronically capture information about them and share that information with relevant parties – operators, suppliers, and maintainers.
It allows national and international product identification and traceability and enables automation and digitisation.
The objective of this project is to set an industry standard for automatic data capture (barcoding and/or tagging) and support e cient management of material master data to assist the procurement process of rail components and assets.
Project I-TRACE is even more relevant in the context of the Federal Government’s National Rail Procurement and Manufacturing Plan, which was released at the ARA’s AusRAIL PLUS conference in November 2023.
One of the key aspects of the plan is having a standardised and harmonised approach and the unique identification of parts, components and assets is an important starting point. Such an approach allows the rail industry to lay the foundations to enable digitisation of a range of operational processes.
In 2016 the rail industry, through the ARA Board, agreed a standardised and harmonised approach would be adopted with the application of GS1 standards for the marking of parts, components, and assets in the rail industry. This is often simplified as “barcoding” and forms the basis for further digital capture and sharing of material master data.
GS1 standards are the most widely used global data standards in the world– (globally over more than two million companies use GS1 standards in their supply chain activities – GS1 Australia currently serves over 22,000 companies).
GS1 is used in other sectors across 150 countries (e.g. grocery, fresh food and beverage, consumer goods, transport and logistics, construction, healthcare, humanitarian aid, defence), which allows suppliers who service customers in multiple sectors and global jurisdictions to adopt a single supply chain methodology. GS1 standards are used almost exclusively in Asia and Europe, which provide vital links to export opportunities for Australian manufacturers as well as identification compatibility with imported parts and components.
GS1 standards are also open and royalty free, scalable for even the smallest local
company, and are recognised by ISO and Standards Australia. It is also “technology agnostic” and able to work with a range of hardware or software solutions.
Project i-TRACE translates to incredible e ciencies – it is 2.5 times faster to identify and register part numbers and serial numbers and cuts the cost of physical data collection in half.
It contributes to risk reduction, improving data and material quality, workmanship and safety reliability. It also ensures regulatory compliance requirements are met and, with the ability of real-time tracking, allows the rail sector to develop a sustainable business model and speed up transition to a circular economy through the digitisation of data sharing.
The Australian rail industry has a massive task to ensure the optimum quality of maintenance repair and overhaul processes. E ciency is heavily reliant on e ective supply chain management practices, having the right parts and components at the right location.
Our industry has a way to go to achieve e cient inventory management and stock control. Manufacturers, operators, and contractors all agree that a collaborative industry approach to improving the inbound materials supply chain to the rail industry will have a positive e ect on costs overall.
Standardising the way parts and components in the rail industry supply chain are identified will bring industry-wide e ciencies including:
• Reduced inventory write-o s and waste; optimal inventory management.
• Improved maintenance and repair operations.
• Improved traceability and warranty management fundamental for lifecycle tracking.
• Reduced costs through fewer transaction errors and better quality data.
• Elimination of non value-added manual task.
As with other national industry sectors, adoption of a common language o ers
consistency, cost savings and lays a solid foundation for the harmonisation of the rail industry supply chain.
Critical information such as asset identification, serial numbers, batch and lot numbers, production dates, expiry dates and other relevant information can be captured within a consistent framework. This means that information can be more easily exchanged regardless of manual processes and di erent stakeholder computer systems.
The ability to digitally capture maintenance schedules and share that information through the life cycle of an asset provides a greater safeguard than would exist otherwise, improving safety due to the full traceability and timely access to critical information. Being able to record and exchange maintenance data will also build the intelligence required to achieve predictive maintenance.
Another example is being able to digitally access electronic documentation such as installation, service and maintenance
manuals or type approval documentation and engineering diagrams by scanning a barcode and doing away with the risks inherent in a paper-based system. That would also enable the installer to lodge a record of the time and place of the installation of that infrastructure asset and share that data to an asset management system.
Other sectors have benefited from the use of barcodes, some for more than 50 years, and we take for granted the information they provide, giving supply chains data accuracy and traceability and therefore a faster response to enquiries.
Rail organisations in Australia well on their digital journey include Queensland Rail, Sydney Trains, V/Line, Siemens, Alstom, Pandrol, Cold Forge, Knorr Bremse, Vossloh, PowerRail and Unipart. Dozens more are in the process of implementation, but industry needs everyone on board.
Project i-TRACE creates a common language and a single source of truth, provides a centralised platform via the national product catalogue, removing data errors and duplication between organisations.
Operators, maintainers and constructors/ manufacturers have similar supply chain needs and face similar challenges maintaining complicated infrastructure and assets. Ultimately, the standards that support Project i-TRACE will benefit all aspects of the rail industry in passenger, freight and light rail.
RAIL EXPRESS is compulsory reading and a vital tool for all people working in and around the rail sector.
Rail Express is Australia’s authoritative business to business rail publication.
Combining the resources of our respected journalism team and our unparalleled industry contacts and affiliations, Rail Express provides extensive, comprehensive and balanced coverage of breaking news and trends in key areas like infrastructure, investment, government policy, regulatory issues and technical innovation.
Published both in print and digitally every month, Rail Express is the only publication to have both the official endorsement and active participation of the main railway associations in Australia and the broad support of the rail industry.
The only way to ensure you get every copy of Rail Express is to subscribe today. Visit railexpress.com.au/subscribe.
At MTR, our vision is to “Keep Cities Moving”. We believe that world class metros enable thriving sustainable cities. We are proud and remain committed to our mission of connecting communities across Australia through close partnerships with Governments, the rail industry and the customers we have been serving over the last 15 years.