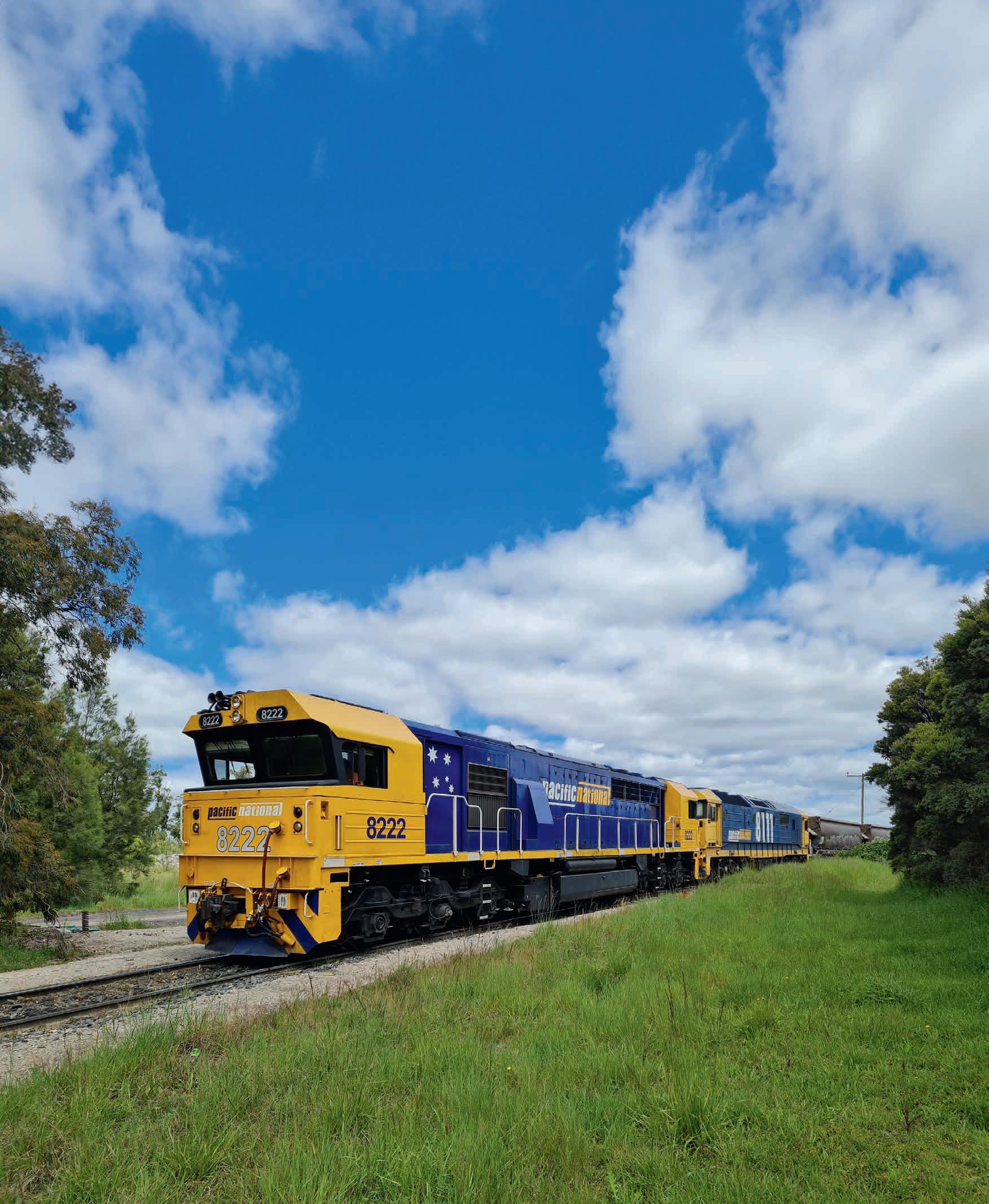
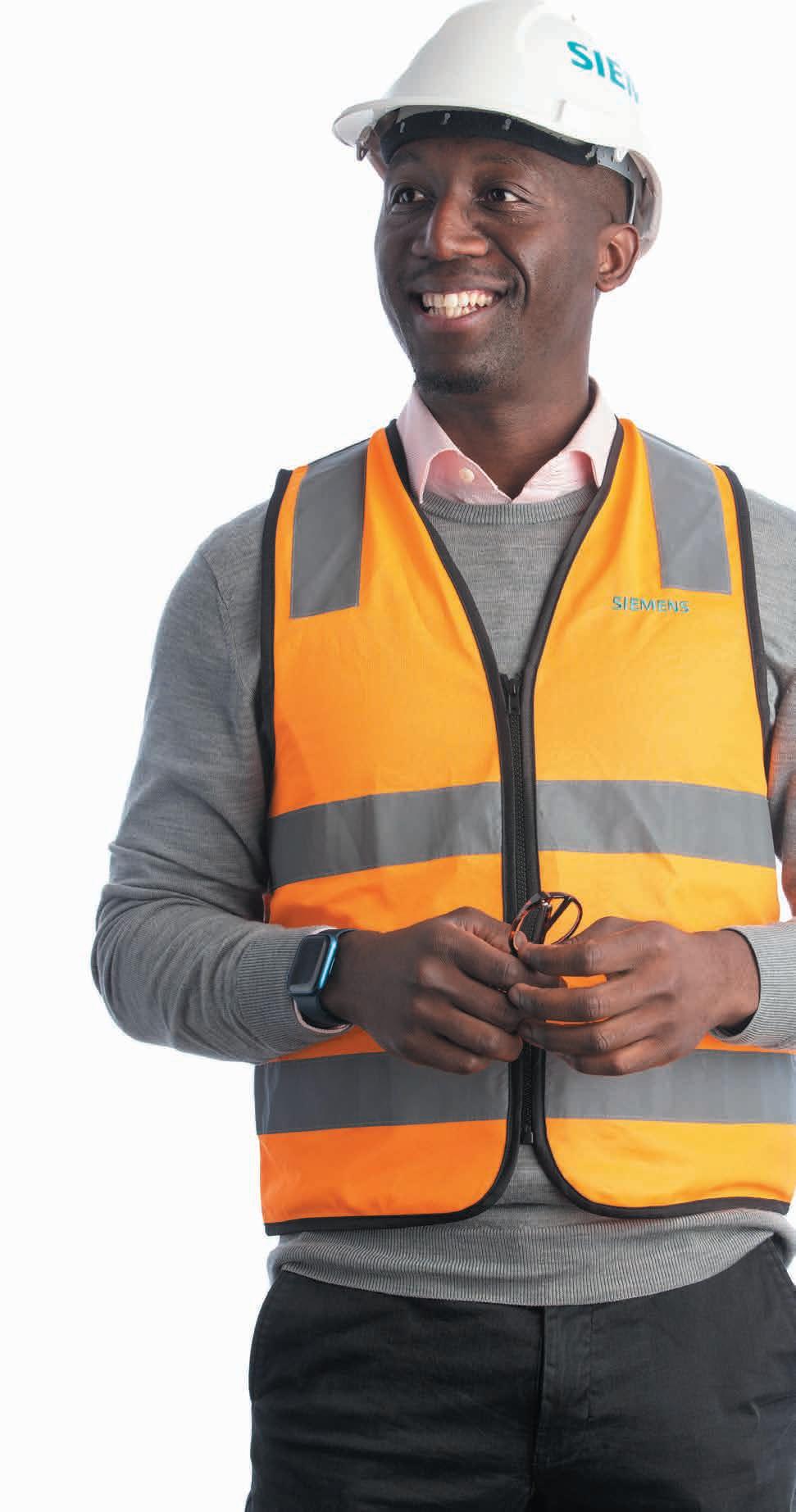
At MTR, our vision is to “Keep Cities Moving”. We believe that world class metros enable thriving sustainable cities. We are proud and remain committed to our mission of connecting communities across Australia through close partnerships with Governments, the rail industry and the customers we have been serving over the last 15 years.
4 - MAY 2024
Published by:
379 Docklands Drive
Dockalnds, VIC 3008
T: 03 9690 8766
www.primecreativemedia.com.au
Publisher John Murphy
E: john.murphy@primecreative.com.au
Chief Operating Officer
Christine Clancy
E: christine.clancy@primecreative.com.au
Managing Editor
Mike Wheeler
E: mike.wheeler@primecreative.com.au
Editor Joshua Farrell
E: joshua.farrell@primecreative.com.au
Business Development Manager
Alex Cowdery
M: 0422 657 148
E: alex.cowdery@primecreative.com.au
Client Success Manager
Salma Kennedy
E: salma.kennedy@primecreative.com.au
Design Production Manager
Michelle Weston
E: michelle.weston@primecreative.com.au
Art Director
Blake Storey
E: blake.storey@primecreative.com.au
Design Caterina Zappia
Subscriptions subscriptions@primecreative.com.au
www.RailExpress.com.au
The Publisher reserves the right to alter or omit any article or advertisement submitted and requires indemnity from the advertisers and contributors against damages or liabilities that may arise from material published.
© Copyright – No part of this publication may be reproduced, stored in a retrieval system or transmitted in any means electronic, mechanical, photocopying, recording or otherwise without the permission of the Publisher.
Editor - Rail Express
These events are so critical for the industry for the sharing of ideas and ensuring freight rail in Australia is moving as one towards sustainable goals. We always encourage those in our industry to attend these events for the betterment of rail.
Wendy McMillan is the Senior Regional Vice President at Wabtec. She spoke at HHR and said to go down the sustainability path, the OEM needs partners.
“There’s a pathway, by using partnerships from government, private enterprise and universities,” she said.
McMillan explained that railroads need to have the capability and the flexibility to still run on diesel, or hybrids when biofuels are unavailable, and that it is imperative that industry takes a clear pathway to decarbonisation.
The Australian rail industry should have a sense of pride as McMillan said many of her US colleagues are asking how we are so far along in our 2050 net zero targets, particularly when compared with our North American counterparts.
The industry is doing fantastic work when compared to the current global standard, but we must continue to push the envelope.
Back in early March the Australian Renewable Energy Agency (ARENA) announced $9.4 million in funding to a new project to electrify rail freight transport of commodities.
The grant to Aurizon will contribute to an $18.8 million ‘Battery Powered Tender for Heavy Haul Fleet Decarbonisation’ project and is a world-first proof-of-concept rail tender.
The project will develop, test and trial a battery electric tender, to power a dieselelectric locomotive in a hybrid diesel and battery configuration, working to cut
emissions from Australia’s resources industry.
This is a clear push from both end users and OEM’s to meet these sustainability targets and I encourage the industry to continue this great work.
I expect the coming years to be full of exciting developments that will see the industry at the forefront of Australia’s decarbonisation journey.
It has been a pleasure collating the May edition of Rail Express with a strong focus on freight and heavy haul.
The cover story explores Pacific Nationals’ push to improve level crossing safety with CEO Paul Scurrah attending a roundtable in March to push for collaboration and clarity around safety at level crossings. He called for a singular industry body to support a clear message to the general public around level crossing safety and greater responsibility from transport organisations.
It was also great to chat to the team from Downer as they make moves to re-enter the rail freight space to support the industry’s transition towards net zero by 2050. The company has brought the ZTR range to Australia for the here and now solution many companies are looking for but will be closely working with industry to improve their offerings.
Further on the team got the opportunity to speak to the team from DT Infrastructure to learn about its recent acquisition by Gamuda and how it sees infrastructure support working moving forward.
Finally, it was enjoyable sitting down with Ram Rajagopal from Siemens to learn more about the international company’s commitment to supporting the local Australian market. The organisation has its Port Melbourne facility exporting all over the world, but its commitment to local content is very impressive.
Happy reading!
joshua.farrell@primecreative.com.au
Building the #NextGenRailways of tomorrow
A $1.2 million trial of new digital technology to improve level crossing safety in rural and regional areas will soon get underway in New South Wales.
Transport for NSW will run the trial, in partnership with the Australian Government, the Australian Rail Track Corporation (ARTC) and technology company Rail Safety Systems.
The technology, called Rail Active Crossing System (RAXS), is a modular low-cost wireless solution specifically designed for rural and remote locations to turn passive level crossings into active sites.
This will be done using both flashing lights at the crossing as well as wireless train-activated advanced signage that warns motorists that there is a train approaching the level crossing.
In the rare event of a system disruption, it automatically enters ‘stop sign’ mode, and becomes like a passive crossing – with motorists having to obey the stop sign
rules. This compares to existing active level crossings, which activate warning bells and lights until maintenance crews arrive.
There are more than 2,700 level crossings in NSW, including 1,307 on public roads and of these, 858 are passively controlled by stop or give way signage.
Installation of the first level crossing with the new technology is due to occur this year and Transport for NSW is working with ARTC to determine a suitable location.
Metro services through the Sydney CBD are in sight, following a testing milestone ahead of services starting on the Sydney Metro City & Southwest line later this year.
All 45 metro trains in the current fleet have now completed at least one return journey between Tallawong and Sydenham at operational speed.
Preparations are now underway for the next major phase of testing – trial running, which is expected to begin soon.
Trial running is the last stage of testing before the launch, where network operator Metro Trains Sydney will run a series of timetable running and operational tests.
Transport Minister Jo Haylen said that world metro services into the city are within reach.
“Commuters from Tallawong in the Northwest to Sydenham in the inner west can look forward to easy and reliable turn-up-andgo metro services every four minutes in the peak,” she said.
“From the middle of this year, our city will be served by six brand new metro stations, giving
commuters more travel options.
“As we hit a critical stage of integrating the existing Metro North West line with the extension under the CBD, I want to thank the community for their patience.”
Each train stopped at every station during the 51-kilometre journey to confirm train and platform screen doors performed as designed. Passenger help points and information displays on the trains were also put through their paces.
The performance of each train is being monitored closely to ensure passengers can look forward to the new turn-up-and-go metro timetable of a train every four minutes during peak periods.
new features to be developed and tested.
As part of the trial, Transport for NSW will be seeking community and industry feedback on the use of advanced warnings and developing future features to improve level crossing safety. The NSW Government is providing $715,000 funding for the trial, along with $500,000 from the Australian Government’s Regional Australia Level Crossing Safety Program.
Extensive integration testing is continuing between the Metro North West Line and the new City section to ensure the trains, signalling and station systems are working together and functioning along the length of the line.
Since the rigorous testing and commissioning program started in April 2023, more than 8,700 hours of a total of 11,000 hours of required testing has been completed.
When metro services extend beyond Chatswood and into the city this year, passengers will benefit from direct, fast and reliable public transport services in the peak, including from:
• Mar tin Place to Crows Nest in seven minutes.
• Sydenham to Macquarie University in about 30 minutes.
• Central to Chatswood in 15 minutes.
• Nor th Sydney’s Victoria Cross in North Sydney under the harbour to Barangaroo in three minutes.
The Byford Rail Extension continues to make progress as part of the transformational METRONET program, with all rail infrastructure between Armadale and Byford and the rail bridges over Neerigen Brook and Wungong Brook now removed.
Earthworks have started along the rail corridor in preparation for laying ballast, sleepers, and rail.
“This investment will greatly enhance and streamline access commuting to and from Perth and provide better integrated links into the city’s public transport network,” said Federal Infrastructure, Transport, Regional Development, and Local Government Minister, Catherine King.
More than 25 per cent of the piers have been installed to support the elevated rail over Armadale Road, Forrest Road, and Church Avenue.
WA Premier Roger Cook said that METRONET is coming to life across the city.
“The Byford Rail Extension will be
The High Speed Rail Authority (HSRA) is seeking out businesses to help develop and plan Stage 1 of an east coast high-speed rail network between Sydney, the Central Coast and Newcastle.
The Government is seeking tenders for eight work packages that will support the HSRA deliver a business case for the Sydney to Newcastle section of the high-speed rail network by the end of 2024.
The eight packages include project controls (costs, schedule and risk), Rail Operations Planning, First Nations Participation and Engagement, Commercial, Delivery Strategy, and Industry Engagement.
This critical work will help inform important elements of the business case including proposed alignment, station locations, fleet, cost estimate and future construction timeframes.
High speed rail is a transformative transport project that will slash transport times, open up regions to new development,
transformative for Perth’s south-east, connecting these rapidly-growing communities to the city while creating hundreds of local jobs in construction,” he said.
Other works include:
• more than 50 per cent of earthworks for the Byford Station site completed, including the bus interchange and parking areas;
• more than half of the walls forming the Byford Station metropolitan platform installed;
• piling completed for the eastern side of the Eleventh Road bridge, and;
• foundations commenced for Larsen Road pedestrian bridge.
Sustainability is a key focus for the project with a new renewable diesel (HVO100) trial about to commence, a first in the Western Australian construction industry.
The project continues to create hundreds of direct employment opportunities project-
wide, as it makes strides towards connecting residents in Byford and the wider Serpentine-Jarrahdale area to the Perth CBD on a seamless 42-minute train journey.
The Byford Rail Extension will deliver a new Byford Station in the existing rail corridor 400 metres north of Abernethy Road, linking the old and new town centre with pedestrian-friendly eastwest connections.
It will also rebuild Armadale Station as a new elevated station passing through the town centre, remove level crossings at Armadale Road, Forrest Road, and Church Avenue, and provide around eight kilometres of continuous shared path for pedestrians and cyclists.
The project has been jointly funded by the State and Commonwealth Governments.
and improve access to services.
The Government has committed $500 million for the planning and corridor protection of the Sydney to Newcastle section, established the High Speed Rail
Authority, and is determined the business case will be done by the end of this year.
Businesses interested in working with the HSRA to deliver the business case can find further information on AusTender.
The dangerous and congested level crossing at Brunt Road, Beaconsfield will be gone for good one year ahead of schedule, with a final construction push started in April
When traffic flows over the new road bridge, the Pakenham Line will be one step closer to being level crossing-free by 2025 – improving journeys for the 8,400 drivers passing through each day and allowing for more trains after the Metro Tunnel opens in 2025.
Works occurred until late April to finish the new road bridge that will separate cars and trains for good.
There will be a new footpath and shared use path across the new road bridge, providing a direct link to local schools, shops and services on either side of the rail line.
The team has recently installed 160 panels to be painted in earthy, brick tones to form the retaining walls, with 100,000 tonnes of material placed between the
The project has finished in April, over a year ahead of schedule.
panels to form the new bridge.
Road users will have a safer, more reliable way to cross the rail line, allowing works to start to close the Station Street, Officer level crossing.
Early works will start in Officer shortly
after the Brunt Road bridge opens, with the level crossing to be closed for good by 2024. Closing the Station Street, Officer level crossing will improve safety, reduce congestion, and contribute to a level crossing-free Pakenham line by 2025.
The Parramatta Light Rail project has reached a milestone in the heart of Western Sydney, when the first tram rolled through Parramatta CBD as testing ramps up ahead of services beginning later in 2024.
The 45-metre-long light rail vehicle travelled slowly under police escort on its inaugural 6.6-kilometre journey from the stabling facility in Camellia, through Parramatta Square, along Church St, through the hospital precinct, to its final stop at Westmead.
Parramatta locals and visitors can look forward to seeing more tram trials through the city, during the day and night, with more than 2000 hours of testing to be completed before it’s given the green light to take passengers.
NSW Premier Chris Minns said he was delighted to mark this milestone of a tram running through Parramatta CBD for the first time in 80 years.
“The light rail will breathe new life into Western Sydney, boosting local businesses, connecting key precincts and servicing an estimated 28,000 passengers each day in
our west,” he said.
When the light rail is in service, more than 16,000 people are expected to use the Church Street stop each day to connect to more than 60 local eateries, shops and businesses.
Transport for NSW Infrastructure and Place Deputy Secretary, Camilla Drover, said the project is advancing well.
“Safety remains a key priority for the project, and I encourage everyone to stay safe around the light rail as testing continues,” she said.
“This is the first time vehicles, pedestrians and cyclists have had to interact with light rail in Parramatta, so we ask all road users to remain vigilant.
“Please take extra care to be safe when walking, riding or driving near the light rail and pay attention to the signs and traffic directions.”
The test also marks the first time a 63-tonne tram travelled over the new Bidgee Bidgee Bridge in Rosehill, which allows vehicles to cross James Ruse Drive without disrupting traffic. The bridge
completion.
– named after the famed leader of the Burramattagal clan of the Dharug People – is the largest of six new bridges built for the project.
Parramatta Light Rail Stage 1 connects Westmead to Carlingford via the Parramatta CBD and Camellia.
The Parramatta Square light rail stop will connect to the future Metro West station, due to open in 2032, and Parramatta Light Rail Stage 2, which has now been granted NSW planning approval.
As a company, Pacific National has many reasons why it is championing a greater focus and coordination on level crossing safety nationwide. Here’s why.
In the wake of the tragic death of two of its drivers following a collision with a truck on New Year’s Eve 2023, Pacific National has led calls for action and a national roundtable to improve safety around level crossings to save the lives of motorists and train crew.
With industry, regulators, unions and government coming together for a national roundtable back in March in Brisbane to consider life-saving actions, measures and reforms, Pacific National is hopeful Australia can realise its vision and achieve zero harm at level crossing.
Pacific National CEO Paul Scurrah said the business was profoundly reeling following the deaths of its experienced Port Augusta train crew Mick Warren and Kevin Baker and
had immediately committed to rolling out a public awareness campaign to educate communities on railway level-crossing safety.
In a statement released by Pacific National following the incident, he said it was such a cruel way to end the year.
“In times like these, words can never truly capture the magnitude of our grief. The loss of our colleagues has left an indelible mark on Pacific National, and we are all grappling with the profound sadness that comes from such an unexpected tragedy,” Scurrah said.
“Mick and Kevin were deeply respected and beloved members of our Port Augusta team, and their memories will be honoured by our organisation.
“Our commitment to safety above all else
has never been stronger. We all owe it to Mick and Kevin to learn from this event and do everything in our power to prevent such a tragedy in the future.”
MOVING LEVEL CROSSING SAFETY AWARENESS INTO HIGH GEAR
Scurrah said the business has developed the ‘Don’t take a chance, take a look’ campaign to ensure the spotlight was on safety around level crossings and honour Mick and Kevin’s legacy.
“As Australia’s largest private rail freight company, our drivers are acutely aware of the high frequency of near miss incidents at level crossings, which is why we want to ensure the safety message is heeded by drivers to avoid future tragedies,” he said.
Pacific National has been deeply impacted by the recent incident and is determined to make a difference.
“A train can’t swerve or stop quickly, so we want to remind motorists to not take a chance when they approach a crossing so everyone can all go home safely, every day.”
With more than 23,000 level crossings around Australia where road intersects with the country’s rail network, Pacific National’s campaign is designed to complement and build on existing industry and government campaigns that run annually.
Scurrah delivered a keynote address at the level crossing safety roundtable and highlighted Pacific National’s campaign and the importance on addressing behaviour around rail crossing.
“It’s easy to get bogged down in the statistics, but each collision and near miss is a human experience. And while some people escape unscathed and are only shaken, too many families are burdened with tragedy like Mick and Kevin’s families,” he said. “The collision in Bindarrah was a tragedy. But one that I believe was entirely preventable. Five of the last six major level crossing collisions occurred at sites that already have the highest level of protection and visibility.
“This means while we can’t afford to de-prioritise level crossing upgrades, right now we need to up the ante to target human behaviour.”
Scurrah said this was consistent with the National Level Crossing Safety Committee and Freight on Rail Group (FORG) positions and the
industry must prioritise behaviour change in a far more aggressive way than we have done to date.
Scurrah encouraged those attending the
“The solution is not exclusively at the level crossing,” he said.
“It also sits in the boardrooms and offices of transport companies, road and rail infrastructure owners, regulators, local council chambers, state and federal
“We know the majority of level crossings across the country will never be grade separated and those that are earmarked will take a longer time.
“Recent research from the Queensland University of Technology has shown that the majority of risky behaviour at level crossings relate to vehicle driver behaviour.
“The research showed that risky behaviour relates to violation of road rules including fatigue, not driving to the conditions, complacency, and distraction.”
With the release of the new National Level Crossing Strategy, Scurrah said industry has a blueprint to drive change and improve safety.
The Strategy represents a commitment to reducing the incidence of fatalities and injuries across Australia’s level crossings and is based on national rail safety data analysis.
It was developed following engagement with more than 30 organisations from the community, government, road and rail industry providing expertise and insights.
The objectives are:
• Education and Enforcement
Increase awareness of level crossings that trigger desirable behaviour change in users and reinforce compliance through improved enforcement.
• Assets, Technology and Innovation
Leverage a combination of asset and technology-based solutions that are costeffective, innovative and shown to reduce the risk of harm.
• Data Improvement and Knowledge Management
Capture level crossing data in a nationally consistent manner and share analysis that delivers insights to inform practical safety improvements and decisions.
• National Coordination
Develop a consistent and nationally coordinated approach to improve collaboration, share knowledge and drive actions that will be most effective if implemented nationally to reduce incidents at level crossings.
“We will continue to play our part in helping to achieve the objectives,” said.
“Pacific National also endorses and contributes to the committee’s position that calls for effective technology in preventing level crossing incidences.
“We want to see improved and consistent enforcement of breach of the law and a consistent national approach to improving awareness and education for drivers around level crossings.”
Scurrah touched on an example of when an increase of enforcement made a difference to vehicle safety around low bridges.
The NSW government introduced a sixmonth registration suspension penalty to the owners and operators of heavy vehicles who struck bridges, while truck drivers face a $4,097 fine and 12 demerit points for an incident.
“We want to see enforcement as a catalyst for behaviour change,” Scurrah said.
“After the government brought in these harsh penalties for bridge strikes, the instances have dropped dramatically.
“The difference in penalties in each state should be brought together under one consistent, strict model to create change.
“We also want to see improved and consistent enforcement of breach of the law and a consistent national approach to improving awareness and education for drivers around level crossings.”
Scurrah called for greater coordination between Federal, State Governments and agencies on level crossing priorities and a focus on the interface between road and rail infrastructure.
“We want to see a revision and effective training for road vehicle drivers about level crossing safety, with training to be required before a license is granted,” he said.
“Pacific National agrees with the strategy and we must prioritise behaviour change in a more aggressive way than we have done.”
Education is one of the key components of the strategy and Scurrah believes this section is critical.
“A properly coordinated singular industry voice with the goal of educating the public in a persistent way [is needed], not just a one-off or service campaign that we have traditionally done. We’re going to need government support to do this,” he said.
“We believe for behaviour change we want to see that being driven through real-time awareness through technology and innovation.”
Scurrah made a more personal call out to regulators at the end of his speech.
“There is no silver bullet, but if everyone works together and continues to focus on improving level crossing safety, we’ll have ensured that the passing of Mick and Kevin and the lives of every other person who has been impacted by a level crossing fatality in Australia has not been in vain.”
Downer Group has returned to the freight market with a focus on decarbonisation and working closely with customers and industry to deliver Australia and New Zealand’s specific needs.
Downer has made a return to the rail freight sector, identifying a need to support Australian and New Zealand rail freight companies to decarbonise and bringing a range of skills to the fore to support this transition.
The organisation is not looking to subtly re-enter the freight sector, but go on the decarbonisation journey, bringing the ZTR range of products for a here-and-now solution, while also looking to the future.
Rail Express spoke with Downer’s Troy Sparkman who is the executive general manager, Freight & Motive Systems to learn more about the company’s vision for the future of freight.
“While we have our manufacturing and overhaul divisions, our main focus on our return to the freight market is decarbonisation
technologies,” Sparkman said.
“We all have an obligation to contribute to a cleaner environment for future generations.”
“As an industry we made the transition from steam to diesel, now it is time for the industry to look at the next advancements in technology, and Downer see ourselves as enablers to drive this change.
“If a partner wants to trial a battery locomotive, we want to go on that journey and to be a part of the solution and develop products that meet the customer’s specific needs, be it in Australia or New Zealand.”
MEETING THE NEEDS OF THE FUTURE
Downer believes it has the capabilities to meet the needs of the freight industry but is prepared to expand to encapsulate the
diversity prevalent in Australia’s geographies.
“We have our manufacturing facility for narrow gauge in Maryborough, Queensland and for standard gauge in Cardiff, New South Wales,” he said.
Downer’s well-established footprint ensures it is prepared for any challenge that may come with supporting Australia’s freight network.
The challenge for Downer and the wider freight sector will be meeting the needs of the industry currently, while also keeping an eye on the future.
The mature and well-established rail industry will not be looking to simply abandon every diesel locomotive for a new one. The decarbonisation journey will need to be mapped out and thoroughly planned in a collaborative manner.
“The question is: how do you achieve net-zero before 2050 with the existing locomotives?” Sparkman said.
“You need to start with modernisation of the current fleet and then transition to a net zero engine from there.”
Sparkman explained that decarbonisation needs to be an industry focus with all stakeholders maintaining clear goals to ensure success.
“We would like to partner with our customers for research, development and innovation so we can ensure they receive exactly what is needed for successful business outcomes,” he said.
“We have several products which we have developed, but we need to break that down to the individual customer needs and requirements.”
Sparkman explained that it will be critical to carefully consider which freight routes can decarbonise ahead of others.
“There are significant opportunities in the bulk commodities from pit to port right now,” he said.
“These are all cyclical in nature. This is where the focus on reduced emissions should be and then we can begin to consider ways to decarbonise on longer journeys such as across the Nullarbor.”
In January 2024, Downer announced they are the exclusive partner for the ANZ region with Canadian company ZTR.
innovative solutions that extend the lifespan of aging locomotives while simultaneously improving the reliability and availability of locomotives and railcars.
Among ZTR’s notable products are the SmartStart Automatic Engine Stop-Start system, KickStart, NEXSYS locomotive control systems, Pivot advanced rail car remote monitoring, and BOA II adhesion control systems. ZTR has been actively involved in the development of hybrid locomotive technology, positioning itself as leaders in this area of market expansion.
“The ZTR products can provide an immediate here-and-now solution on fuel emissions and fuel use,” Sparkman said.
“This is a win for an older diesel engine that may have a lifespan of another 10 plus years.”
Sparkman emphasised the importance of incremental changes as an industry.
If the freight sector moves too slowly, it will reach a point that will create numerous challenges.
“A lot of companies are making the commitment of 33 per cent reduction emissions by 2035 and that is where the ZTR products tie in perfectly as they can give an immediate and sustainable saving,” he said.
“Once you bring that in, you can begin looking towards hybrid or battery locomotives and then even further ahead to what the next technological solution will be.”
A product from ZTR that excites Sparkman
helps reduce and manage locomotive idling, and also delivers fuel savings. It has been doing so for more than 30 years across the globe.
SmartStart AESS can be applied to just about any locomotive – from relay logic to microprocessor – regardless of manufacturer, model, age, or usage. SmartStart AESS is a compact system designed to mount easily.
The product:
• Reduces emissions and exhaust smoke.
• Provides consistent fuel management and verification of fuel savings.
• Meets EPA locomotive emission requirements.
• Reduces fuel and lube oil consumption. The challenge for operators was the battery would often be drained when the AESS system kicked in, so operators isolated the AESS and as such did not realise the benefits, so ZTR developed the KickStart solution to rectify this.
KickStart uses supercapacitor technology to supplement the locomotive batteries during engine start, reducing the strain on the batteries. The result is less energy drainage, longer battery life, faster cranking speed, less time to recharge, improved cold weather starts, and ultimately, increased locomotive availability.
“The challenge this technology faced in the past was that when they went to restart the locomotive some hours later, it would not start,” Sparkman said.
not want to shut down the engines for various operational reasons.
“By putting these two systems on locomotives, you can see immediate fuel savings and a reduction in emissions.”
Partnering with ZTR was a no-brainer for Downer. The organisation had the engineering capabilities locally to tailor the solution to any fleet and to ramp up the rollout.
“We have a technical advisor from ZTR
“We have our own in-house engineers trained in the ZTR products, meaning we have the local knowledge to support customers immediately, and can call upon further product expertise of ZTR’s engineers when needed.”
Australia and New Zealand have some unique challenges when it comes to sweeping
Sparkman explained.
“Whether you are in the Hunter Valley, Queensland or intermodal across the Nullarbor, there is not one size fits all in Australia.
“You could introduce battery electric locomotives into port shuttles tomorrow, but this is simply not an option for a lot of other areas of Australia’s rail freight sector.”
Sparkman detailed that this is why Downer is placing such an emphasis on collaboration with customers. A hybrid locomotive may be the solution for the next 15 years on specific routes and then battery electric after that, he explained.
“When we were considering returning to freight, we ensured we had the people in our business who had the expertise to help us succeed,” he said.
“We have 250 capable and experienced engineers and we have recruited globally for candidates with strong experience in the decarbonisation space to ensure we have the capability to ensure success.”
Sparkman believes that the Australian rail freight sector has a thirst for decarbonisation and Downer is primed to support this.
“Trucking has made great advances in this sector for short distances, but they are still to determine how to cover great distances in a sustainable way,” he said.
“Downer is in for the long haul, but we need to start now with incremental
Siemens Mobility is focussing on supporting the local Australian supply chain for its rail signalling products, building long-lasting relationships to ensure success for all.
As a global company, Siemens Mobility strives to be innovative and sustainable. One way that it achieves this is through partnerships with local suppliers.
By collaborating with these suppliers, Siemens can support both its customers, the growth of local businesses, and the rail industry in Australia. That said, Siemens Mobility has embraced its Australian base with more than 75 per cent of its suppliers being Australian-owned businesses, and more than 80 per cent of the components of its locally manufactured point machines, signalling and train stops are purchased from local vendors.
By collaborating with these suppliers, both Siemens Mobility and its partners can share valuable knowledge and experience that continues to improve the design, manufacture and implementation of products for its customers.
Rail Express had the opportunity to sit down with Ram Rajagopal, who is the Head of Procurement for Rail Infrastructure Products
at Siemens Mobility to learn more about how the company is supporting the local supply chain through their Port Melbourne facility.
“The businesses that we work with would probably say they have Siemens blood in their veins,” Rajagopal said.
“During COVID, as the international supply chain shut off, our local suppliers made sure that Siemens did not stop servicing its customers.”
Rajagopal explained that these businesses do more than supply components and parts to Siemens – they are true partners.
“We design the products, but our suppliers have been our manufacturing interface, and they have the knowledge and understanding to come back to us with samples made through rapid prototyping or 3D printing for suggested changes. Our suppliers provide their expert knowledge of new methods and support us in the innovation of our products,” he said.
“For Siemens we want to be a technology partner for our customers and support the
local rail industry to grow.
“By having this local support, we can ensure our products meet the high-quality standards that are defined by Siemens, the industry and our customers.”
One company Siemens Mobility works closely with is Filcon Precision Engineering. Factory Manager and Director, Jim Tsironis, has seen the value of a long-term positive working relationship with Siemens.
“Siemens Mobility is our largest customer by volume and value, and accordingly our growth and economic viability is inextricably linked to their continued growth and success,” he said.
“Profits earned from our relationship have enabled us to reinvest in modernising our manufacturing plant and equipment, which has enabled us to keep price increases to an absolute minimum in these inflationary times.
“The benefits to us are that the lines of direct communication are at a local level, which is very important.
“Whether that’s with Siemens’ procurement
section or engineering team, issues can be dealt with quickly and with a level of local understanding of the current environment.
“There have been many occasions when I have jumped in the car and visited Port Melbourne to give input on a design change or resolved a blocking point, which would be much more difficult if we were dealing with an offshore touch point. The other major advantage is keeping the product totally Australian made.”
Steelrod is another Australian manufacturer that Siemens Mobility partners with and Director Damian Veneris said that Siemens Mobility is one of the company’s most valued partners.
“Steelrod has been in partnership with Siemens Mobility for more than 10 years,” he said.
“Our business partnership has seen a wide range of specialised products utilised throughout the country, with the benefits to both companies growing each year. The mutual customers of Steelrod and Siemens have benefited by being able to access local support and expertise for their many specialised requirements.
manufactured in Australia promotes and supports our investment in the skills of local workers. We take pride in supporting the Australian economy and jobs growth for Australian workers. Steelrod values working alongside Siemens and appreciates the partnerships that we have established over the years.”
Rajagopal detailed the continuous product development that Siemens Mobility has with its local suppliers that supports the improvements needed to meet the changing landscape of the rail industry.
“There are continuous improvements in our products because the market is always evolving and materials we had 10 years ago may no longer be available now, or something better might be out there,” he said.
“The local manufacturers give us constant input. They know the other end, such as what materials are in short supply, or if a supplier has upgraded to an even better material that they could use.
“This improves the product, which means we are doing better than we were yesterday.”
that Siemens Mobility can continue to service customers whilst continually improving its products as technology and materials improve.
“When we talk to the manufacturers who made the product 25 years ago, we can rely on them to source a newer and improved version of it for us,” Rajagopal said.
“This knowledge is imperative. It means that even long after I have departed the business, that IP remains in the supply chain process.”
The pandemic put a strain on the skilled labour workforce and Siemens Mobility and its partners were affected by this issue; which meant that the company and some of its suppliers needed to find new ways to keep the supply chain moving.
“The product and components suppliers approached us and offered to provide us with the sub-assembly itself,” he said.
“These companies became an extended part of the Siemens Mobility assembly unit.
“This is the advantage of local suppliers. They knew the product and how it was
in and offset the labour shortage we were facing.”
Siemens Mobility then would test these components to ensure they met the strict industry quality standards.
The pandemic was not the only time this collaboration with Australian businesses allowed Siemens Mobility to deliver outside the norms.
Rajagopal told the story of a customer who wanted a product outside the standard lead time of 12 weeks and was enquiring whether it could be delivered in eight weeks instead.
“We went back to Steelrod to just ask the question expecting them to say it is not possible,” he said.
“They came back and agreed they could deliver this for our client. Steelrod kept their business open until 6 pm on a Saturday night to allow the customer to pick up the product and get it out on site at the end of the eight weeks.
“Without the relationship we have with Steelrod, this would have simply not been possible.”
Rajagopal said that Siemens Mobility aims to have long-term partners but sometimes it is necessary to change suppliers.
“We had a supplier recently retire and so we had to go out and source someone else to fill that gap in our supply chain,” he said.
“Our retiring supplier actually suggested a few potential companies he knew that did good work so they went to the top of our list, and we began auditing them.”
Rajagopal lauded the maturity of the Australian manufacturing landscape in ensuring the industry support each other.
“Going with the referral made the whole process seamless. Our new supplier purchased some of the other business’ equipment and ensured that the IP that had been gained was passed onto the new organisation,” he said.
It’s this maturity and passionate fostering of IP within the local supply chain that Siemens Mobility values, leading it to focus on supporting its local partners wherever possible.
More than 95 per cent of the products made in Siemens Mobility’s Port Melbourne facility are locally designed and exported to more than 10 countries including New Zealand, Thailand, Taiwan, Singapore, Malaysia, Mexico, and Brazil.
But while Siemens Mobility exports
collaborate with its local suppliers to ensure that the customer receives what they need.
“The components we needed to export to Mexico were all in grey. The client needed it in black to match the rest of the fleet,” Rajagopal said.
To repaint the machine was going to cost Siemens Mobility nearly as much as the new component.
The supplier was based out of New South Wales. He offered two things, he could take it back and do the repainting free of charge or he could do it brand new for the company, depending on the lead time.
“We had some really tight deadlines on this and by working closely with the local supplier, we made this achievable,” Rajagopal said.
The supplier agreed to manufacture a new
“Then we had a little operational issue there. We didn’t have a warehousing space to hold both stocks. He offered to take back the grey ones, hold it in his stock, and give us the black ones to export out of Port Melbourne,” he said.
This meant that Siemens could meet the requirement and deadline for the Mexico client while ensuring no products were wasted in the process.
“It is so great for us to have this level of trust and then in turn we can utilise that trust to better support our customers,” said Rajagopal.
“These relationships are so critical for our success and without them we would not be able to supply the high-quality components we do.”
Martinus is utilising its unique position in the infrastructure space to bring new technology to the forefront of what it does.
Martinus is continuing to bring fresh ideas into the rail maintenance and infrastructure space to shake up the broader industry.
General Manager of projects at Martinus Travis Rawling has been a major driver of this incorporation of technology into Martinus’ construction processes.
“We are constantly canvassing the industry to find and understand new technology that comes out to the market and engaging with those suppliers where we see alignment to our current way of working, or the opportunity to incorporate into our existing systems to improve project performance,” he said.
“Once we identify something we want to run with, we typically select a live project and look to run a pilot programme in parallel to current ways of working. This provides a kind of sandbox or test environment where we can better look to understand the new technology or software in a live project environment. It
“What we are finding with the successful implementations is that our project teams are gravitating to the newer process or way of working, as they see the benefits, improvements and efficiencies these new technologies are providing.”
Martinus has recently brought on board the Construction Industry Solutions (COINS ERP) software system to help improve its technological support.
COINS ERP is a leading construction management software and services company providing end-to-end business solutions to the construction, engineering, home building and service sectors.
The COINS ERP software was built by industry with the team having more than 40 years’ experience serving construction professionals.
The global team has unrivalled industry
add true business value throughout the construction lifecycle.
Martinus’ chief operating office Ryan Baden said COINS ERP will provide a fundamental business management system across its international organisation and will assist with consistency and reporting throughout the organisation.
“COINS ERP will allow the Martinus business to standardise operational processes and consolidate data across global business units – a key factor in the evolution for the company,” he said.
The COINS ERP software allows Martinus to simplify the communication between itself and subcontractors.
The organisation is also using the Aphex system to help deliver on time for customers.
The Aphex system creates a reduction of claims, planning efficiency, increased accountability and reduced “firefighting”.
Martinus is currently delivering one of the
complete a range of works and this use of technology has been revolutionary in helping to deliver the Inland Rail project.
“We have been delivering major infrastructure projects for a number of years now, utilising the skills and expertise of our people and the existing business systems,”
Martinus’ unique offering within the rail industry.”
Mar tinus have worked diligently to ensure the technology it brings on board truly
got better connectivity meaning they can connect and share virtually.
“You can have members of the team with fantastic experience but working in different sections,” Rawling said.
“We can now allow them to share their invaluable knowledge across multiple teams, something that we have not been able to do before.
“The implementation of technology has improved productivity and overall performance, by allowing our rail experts to focus on a large proportion of their time on their passion – delivering rail projects.”
Rawling explained the intense processes the organisation goes through to ensure the technology is right for its needs and will fit seamlessly.
“We will create a sandbox or test site, run a pilot in parallel, sequentially phase or integrate into an existing project,” he said.
“We also look to introduce new technologies during the pre-contract phase of the project so we get the benefit of the technology early and can engage with our customers on the benefits prior to delivery.
“We then utilise on the job training and live demonstrations as we believe our team learn best when they are doing.
A lot of companies often rely on outdated software, we have the advantage of integrating modern, fit-for-purpose software solutions. This allows us the opportunity to select the very best options available to suit the needs of a modern rail industry.”
flashbutt welding solutions.
“I suppose RWECA is the new kid on the block in Australia, but we are heavily supported by RW LLC and that is what has ensured our success,” said RW Equipment & Consulting Australasia (RWECA) technical advisor Matthew Reilly.
“We were never going to go out and big note ourselves – we let the work do the talking.”
RWECA is working with a range of mining companies in Western Australia, touching base with many critical customers at the Heavy Haul Rail event held in Perth in March.
“One of our larger clients we have taken on based in the Pilbara has seen an impressive improvement in uptime from 56 per cent to now over 85 per cent,” Reilly said.
“It has been about 12 months of hard work, but our overall goal will be getting as close to 100 per cent as possible.
“Our guys on the ground would have close to 40 years’ combined experience and we have the strong support network across our team coupled with our international team.”
Reilly explained that the years of
“We have had the opportunity to learn the ins and outs and uncover potential problems that others may not have even had come up yet,” he said.
Much of the equipment utilised on sites across Western Australia were delivered by the team in previous roles, giving them a unique insight to the needs of various companies.
“I think Vic and Chuck from head office have delivered 200 plus machines. This experience is invaluable,” Reilly said.
“We have begun working on our delivery processes here as well.
“We recently delivered some equipment, that, between arriving on the boat and being out and working on site, was about three weeks. It was seamless.”
Reilly said that RWECA can have a range of machines working across multiple companies at any one time, making it imperative that they tailor its offering to individual businesses.
“The data we provide is different for
develop,” he said.
“We know what works and what doesn’t When they deviate away from that, that is where you see failures.”
For RWECA it has the benefit of working in the field closely with its clients in order to collect data and send it back to the factory. Reilly explained the company can collect data around material, sizing, sensors, slip detection, control of the heads clamp and temperature, which are all imperative to improving the welds.
“That’s information that we think could be useful in analytics and making the machine better. We will go to the factory, they’ll implement it, we can then put out a suite of upgrades,” Reilly said.
“We can then implement those changes into the next purchase.”
RWECA have transitioned from manual data analysis to digital tracking for simplicity. Reilly said that a lot of people can have opinions around what will make the welding systems successful, but the organisation prefers to rely on facts.
“Anything that we want to see trended
across multiple welds, we can capture it and present it instantly,” he said.
“These systems make it much easier to get quality welds over time. We want repeatability and by utilising strong data tracking we can deliver that.”
Although RWECA is based out of Western Australia, it is supporting the entirety of
“Basically, wherever the machines are needed, we are there,” Reilly said.
“We have clients on the East Coast, South Australia and moving into the Northern Territory. Wherever there is flashbutt welding, we are there to support.”
RWECA has done work on almost every railway, working with major companies on diverse networks. Australia’s unique rail networks with varying gauges always poses
look forward helping solve any issues that arise because of those discrepancies.
“Our team is all over the country and we can react quickly to any issues,” he said.
“We have people working at major mining companies full time, and then we have floaters who can respond quickly to provide support.”
Reilly explained the company has established itself as a solo operation here in Australia, utilising learnings from RW LLC but being prepared for any challenge the local market may face.
“When we first started, we would be on the phone all the time, but we knew that was not sustainable,” he said.
“It was a little bit of trial by fire, but we were passionate and we built up our skillset and a core group to support Australia.
“People ask us why our machines are so reliable and simply it comes down to experience and understanding.”
The flashbutt process is gaining favour as a preferred technique by rail operators. It utilises regulated electric short circuits to provide accurate welds without filler metal, as well as a consistent hardening process.
The traditional method of welding has been aluminothermic welding, which requires the filler, resulting in a weaker weld, with a longer cooling and solidifying time. RWECA has a number of machines to support the diverse needs of the Australian rail network.
RW20 CONTAINER WELDER
The RW20 is a self-contained, ready-forservice rail welding system. It is suitable for mass production of rail string in shop (static) condition or in track welding.
RW30 AND RW50 CONTAINER WELDER
These containerised welders are also selfcontained, ready-for-service, rail welding systems that can be used for production welding of long welded rail in a static arrangement. Alternatively, they can be mounted to a track machine and used for intrack welding for either track maintenance, or full renewal including destress capability.
RW1000 STATIONARY FLASHBUTT WELDING PLANT
The RW1000 is designed for high-pace, mass production welding under stationary conditions, with flash removing immediately after welding. It is also available in a containerised option, which makes it easy for mobilisation and set up in remote areas.
MTR corporation is working in conjunction with Metro Trains to diligently improve the customer experience.
MTR corporation has been a critical cog in the success of Metro Trains Melbourne (MTM) network. The organisation is a part of the consortium of businesses that make up MTM.
Partnering with John Holland and UGL it brings a range of international experience to the fore.
MTR is a recognised world-class operator of sustainable rail transport services and takes safety, reliability, customer service and efficiency seriously.
MTR has end-to-end railway expertise with more than 40 years of railway projects experience from design to planning and construction, through to commissioning, maintenance, and operations.
A spokesperson from MTM said that since the start of MTM’s franchise in Melbourne in 2009, MTR is proud of the work MTM has done to put the passenger first.
During the covid pandemic, a number of passenger initiatives were introduced and they have become a mainstay of the MTM system. These include enhancements to Platform Information Displays at Metro’s busiest stations.
technology being introduced at 147 stations transparent communication.
A number of initiatives have continued to improve the passenger experience including the use of QR codes, providing passengers with a one-stop shop of disruption details, replacement services and up-to-date travel information.
When the City Loop was closed to trains and passengers for the first time in its 42-year history in January 2023 – affecting 222 stations and 16 train lines – a range of innovative communications measures, including specialist wayfinding assets, helped to address this disruption. The organisation also ensured customer service staff and wheelchair accessible taxis were available.
This approach resulted in an Australasian Rail Industry Awards (ARI) – Customer Service Excellence win.
The team is committed to ongoing improvement and will continue to look at ways to further enhance communication including the current trial of SMS notifications for residents and traders during maintenance and renewal works.
delivered effectively.
One component is the geotechnical services that diagnose and solve problems that affect the condition and performance of railway tracks by combining expertise in track roadbed materials, maintenance techniques and data analytics. This results in an advanced diagnostic profile of the health of the track and identifies trends over time for proactive future substructure maintenance program planning.
The core of this technology is the Ground Penetrating Radar (GPR), which provides substructure depth analysis delivering fouling, moisture, and substructure layer mapping at depths up to 10 feet.
Rail Express spoke with Loram sales managers Stephen Hill and Darren Riley to get an understanding of how the technology works with its overall offering.
“For us, this technology allows users to make informed decisions around their rail maintenance processes,” Riley said.
“It can show us where we can use our exciting new shoulder ballast cleaner product for example.”
The GPR can identify areas where water is
at the end of the ties, screening the ballast and discarding fines and fouling material and restoring the good ballast to the shoulder.
Hill used the example of the recent rains in Northern Australia, which caused a lot of flooding, which resulted in some sections of the rail to dip.
“Over time you will see the ballast rub against each other, and dirt and dust can enter and it can cause the ballast to deteriorate and lowers the effectiveness of the ballast to drain out the water,” he said.
“The GPR is able to look below and through the ballast at the drainage patterns to better plan maintenance schedules and minimise catastrophic failures with strong plans.”
The pair explained that the GPR can be utilised as a part of a medium term ballast management strategy.
“Sometimes the rail industry can get a bit bogged down in the here and now and not plan ahead,” Riley said.
“The GPR is a part of the broader Loram service with our rail inspections and grinding.
have this problem until they get heavy rain and
The GPR program will give an overview of the area scanned and put each area in either green, yellow or red depending on the quality of the surface.
“We are able to ascertain which areas of the tack need immediate fixes and which areas can wait,” Hill said.
“We can do another run 12 months later to confirm if there has been further deterioration and we can fix very specific areas of track that need it as opposed to fixing great lengths unnecessarily.”
The data that is collated in Australia is then passed on to a team of specialist engineers based in Finland who analyse the data and provide the simple, easy-to-follow results back to the team in Australia.
Australia has battled a number of severe weather events to start 2024, including cyclones across the north of the country and bush fires in Victoria. The cyclones closed the Mt Isa line for an extended period causing delays. Hill explained why Loram can support organisations through these challenges.
“You will often see up north where it is dry for a long time, everything goes hard,” he said.
“As soon as it rains you have massive amounts of mud moving around and the GPR system can be critical for understanding which areas might be susceptible to damage.”
result in speed restrictions on the network,
meaning maintenance is critical to making sure it runs efficiently.
“Often after a severe weather event, depending on the network, the first train may not be aware of faults which can lead to major safety issues,” Hill said.
“If you use the GPR you can accurately understand issues within the network, it will show yellow or red areas that need repairs.”
The pair explained that even though tracks may appear in good condition after a severe weather event, it may have faults or issues that are not apparent on inspections done by the naked eye. By using the GPR system it allows users to make accurate decisions around maintenance that can protect the network far better than systems used previously.
Alongside the GPR system, Loram utilises the LiDAR program to offer insights to predictive maintenance and better plan processes.
LiDAR data mapping provides a scan of the right-of-way to determine shoulder conditions, drainage ditch location and depth and cut/fill conditions. This track topography is used in conjunction with the GPR and track geometry
LiDAR information can also be used to identify the width and height of the shoulder to determine the volume of excess or needed ballast.
Integrating the topography from LiDAR with the GPR fouling index and moisture profile data provides documented clarity on the internal drainage capacity of the track, and the adequacy of the ditch to convey water from the right-of-way.
Riley explained that the LiDAR system can ensure it gives a better understanding of the integrity of the shoulder of the ballast.
“We use both systems hand in hand,” he said.
“The GPR gives you a great understanding of what is going on underneath the ballast and LiDAR can analyse the profile and uncover deficiencies.”
Similarly to the GPR system, the LiDAR can allow the accurate deploying of Loram’s systems. This includes its shoulder cleaner that ensures the ballast is working efficiently, or even adding ballast to sections to ensure efficiency.
“These systems all ensure the most efficient use of our maintenance services, giving real data and an ability to analyse
Molycop has a history supporting the Australian railway sector and traces its heavy haul support back to the 1980s. It began supporting the iron ore industry in the mining region of the Pilbara with an aim towards improving the payloads that can be carried.
Molycop’s Australian operations began in 1917 when the Commonwealth Steel Company established a facility at its Waratah site in Newcastle, NSW. Through the 1920s and 1930s Commonwealth Steel developed some of the first grinding balls and then the first heat-treated grinding balls to improve wear performance.
Molycop now comprises 15 major operational sites in Africa, Australia, Canada, Chile, Indonesia, Mexico, Peru, Spain and USA supported by local sales, service and distribution presence .
Rail Express spoke with sales manager Ian Forbes to better understand the history of the company and how that has delivered Molycop to where it is today and its support for the
heavy haul rail sector in Australia.
“When we first started with a focus on heavy haul, it was about pushing the nominal axle load from 25 tonnes through to 35 and now up to 42 tonnes,” Forbes said.
“Australia has the heaviest haulage in the world, and I think a lot of that was off the work we did developing these wheels in conjunction with the industry.”
Forbes said that the development occurred in two phases. It started with improving the plate design to maximise the efficiency and the strength of the wheel.
Once Molycop had improved this design they then released the design to the broader industry.
Forbes explained that as Molycop had worked closely with industry to develop these improved wheels, it wanted to give it back to the sector.
“The second phase of the development was improving the materials we were using,” he said.
“We began pushing what we were doing to make our wheels far exceed the specs that were required by the Association of American Railways.
“By doing this it improved interoperability and safety for users.”
Molycop wanted to ensure that the wheels could spend longer in the field working before needing to be repaired or replaced. This included its improved materials that were longer lasting.
Flash forward 30 years and Molycop is continuing this level of development and improvement of its wheels.
Forbes believes the axle weights have topped out now and to go higher will require infrastructure improvements. Molycop has now turned its attention to the wheels that will support the next generation of locomotives, passenger cars and freight rollingstock.
“We have been working closely with a lot of North American locomotive builders as
be far heavier than the locomotives we have currently, particularly the first couple of generations.
“We have done a lot of work around plate design once again to improve the actual capabilities of the wheel.”
The company is once again working to exceed the Association of American Railways standards for locomotive wheels. Forbes expects most of these locomotives to work in the iron ore space initially.
“We have done multiple streams of modelling for these customers to better understand how these locomotives will behave on these lines,” he said.
“We can develop different braking scenarios and extrapolate that to find
Molycop has been operating for more than 100 years and owes this to the collaboration it has maintained throughout its existence.
The organisation has always collaborated with university and institutes, but Forbes believe the success lies in its association with other collaborators.
“We have always been industry led,” he said. “We help them with challenges Instead of telling industry what it needs, we listen to what is required and design a product to meet these needs.
“We always seek to understand the problem first and then design the solution for that specific problem.”
For research and development (R&D)
Molycop will work closely with universities and then also there is an internal team of technical experts.
“We are working diligently on new technology, chemistry and the way in which we actually manufacture the wheels,” he said.
“We are improving how we are hot forging the wheels to ensure they last longer.
“We have also been improving our machining processes and we have passed European standards with flying colours.”
Forbes said that he believes Molycop is not just in the business of supplying wheels but is also about supplying its expertise.
“This is something that will never change for us as an organisation,” he said.
“A customer will always need someone who knows what they are doing and that is what we are.
“The future for us is about continuing to develop the correct technical capabilities to meet the ever-increasing needs of the industry.”
Molycop is continuing to develop standards for its manufacturing of wheels with a focus on sustainable practices.
The company is currently reporting and tracking its Greenhouse gas (GHG) Emissions annually for Scope 1,2 and 3.
Recently, Molycop formally lodged the Science Based Targets (SBTi) commitment letter and was accepted by the SBTi in February 2024, establishing its intent to set a science-based targets.
Molycop focus is currently on three streams:
-reduction of gas usage through efficiency and electrification where practical;
-procurement strategies aligned to the reduction in Scope 3 emissions; and
-leveraging supply chain excellence for freight efficiency and utilisation of assets across the Molycop value chain.
“With a focused and measured approach to a lower carbon operating model, we are well placed to support our customers on the journey to a more sustainable future,” Forbes said.
“With a history of more than 106 years, our products have been at the forefront of many transitions in the rail and manufacturing industries.
“Supporting our customers and leading our own transition across the century, the challenge has been accepted on this new evolution and we have the right team in place to make it happen.”
DT Infrastructure has been brought under the banner of Gamuda Berhad and is changing the way infrastructure is delivered in Australia.
DT Infrastructure is utilising its change of name as a catalyst to shake up the infrastructure sector and lead the industry’s cultural change, with a focus on people and its culture.
For almost 10 years the infrastructure projects division of Downer successfully delivered multi-disciplined solutions for customers. Acquired by Gamuda Berhad in June 2023, the new organisation is continuing this legacy. The leadership and 1,200 strong team transitioned from Downer to DT Infrastructure, retaining their experience and capability in the delivery of complex projects.
Specialised capabilities include the design and construction of light and heavy rail, signalling, track and station works, rail safety technology, roads and bridges, energy and defence.
DT Infrastructure’s transport and rail capability is further strengthened by Gamuda’s 65 new stations in Kuala Lumpur.
“My passion is for safety and elevating
individuals to achieve at their highest levels. This is how I believe we can create a high performing organisation,” Ross said.
“We take the quality we have developed amongst our team and deliver it to our clients”.
“We are more than just a contractor that focusses on revenue; we are a genuine company fostering genuine long-term relationships built on success.”
DT Infrastructure offers a collaborative approach to its delivery of infrastructure to the rail industry. It has a clear understanding of the unique challenges freight rail has compared to passenger.
“What we do is listen to the client to understand their need, and then work with them to achieve the best outcome” he said.
“We build a relationship over time, which then comes with the trust required to share the risk with the client where possible. We understand some risk cannot be managed entirely by the contractor in the operational space for freight and Heavy Haul railways.
“This approach through collaboration allows us to improve our internal processes and also how we work with external partners.”
Ross went on to explain how he believes DT Infrastructure can deliver projects to the highest quality.
“Something we pride ourselves on is that we are honest with clients and ourselves about what we offer,” he said.
“We work closely with clients and other industry partners to deliver the outcome that is required. DT Infrastructure are one of the few contractors who can deliver ’turnkey’ solutions in rail, however, if clients require an expanded scope, we also lead collaborative efforts between all delivery partners and the client. Bringing together the right people for the jobs means a positive outcome for all stakeholders,” he said.
“You have to have the confidence to challenge yourselves to try something new, that is how you grow.”
Ross had the opportunity to speak at the Heavy Haul Rail Conference.
The event brought together key decision makers and the agenda showcased the best in local and international project expertise and gave attendees an understanding of the strategic direction of major players together with critical industry and market updates to ensure efficient, safe and reliable operations in Perth.
Ross spoke around the importance of strong culture. This passion ensures team members make it home safely at the end of the day. He touched on an experience he had when he first entered a leadership position at a different organisation.
“There was an accident, and I sat down with my manager, and he asked me why it happened,” he said.
“I began explaining the reasons, the lessons learnt and the investigation conclusions. But he stopped me and again asked why it happened.
My manager asked me: “Why are people coming to work and taking risks.”
Following some training which enlightened Ross’ thinking about people, culture, and the connection between values and [safety] performance Ross said he “discovered we were paying too much attention to the wrong aspects of safety performance and not enough understanding our people, their backgrounds, their value systems and behaviours,” Ross said.
“People were taking shortcuts because they thought it was the best way to do something, instead of following carefully laid out plans and putting their own safety and the safety of their colleagues front of mind at each step.”
“The team were not engaged through their value system, and this is what I believe is a significant factor in risks being taken, which can result in accidents.”
Ross explained that everyone wants to come to work and contribute and feel like they are a part of something bigger than themselves. People want to leave a legacy, and this includes the team that they work in. This is what he and the team at DT Infrastructure do to ensure it delivers high quality projects.
“When I re-joined the industry in WA in 2021, I made the decision that we needed to make a paradigm shift,” Ross said.
“I use the phrase ‘paradigm shift’ as opposed to ‘step change’ because it represents a fundamental change; it addresses the underlying issues we are facing.
“A lot of what we do is deeply embedded over time because of attitudes, assumed
ways of thinking, penalties or incentives, and industry norms.”
Ross went on to detail the importance of setting expectations to mitigate risks. He also emphasised the importance of bringing the team along for the ride.
“It is important that we value the diversity that we have in our workplace,” he said.
“We do not need to just empower leaders –empowering the whole team ensures they are successful.”
Gamuda Berhad is a regional engineering, property and infrastructure company based in Malaysia.
Established in 1976, Gamuda have become Malaysia’s leading infrastructure and property developers, providing innovative solutions and delivering sustainable developments.
Gamuda operates in nine countriesMalaysia, Taiwan, Singapore, Australia, United Kingdom, India, Vietnam, Bahrain and Qatar.
“It has been a highly positive journey,” Ross said.
“The organisation is very open to our current knowledge and systems, and do not necessarily want to replace that with their own processes.
“They are willing to look at what we have and establish if it is the right fit, or if Gamuda have a better program that they can bring to the table.”
DT Infrastructure is updating its IT processes currently, an example of identifying processes that Gamuda has that would improve the work DT Infrastructure is doing.
“We can take the parts that have worked well for us and combine it with Gamuda’s to create a system tailored to our needs,” he said.
DT Infrastructure operates as a standalone company within the Gamuda Berhad group in the Australian market. The establishment of DT Infrastructure complements the growth and success of Gamuda’s continued expansion in Australia, which began in 2019 with three major project wins and revenue of more than $3.3 billion.
The West Australian government has provided an update for the states freight industry and what it is doing to support the Heavy Haul sector in the state.
Meredith Hammat, Parliamentary Secretary to the Minister for Transport explained that the heavy haul industry in Western Australia is going through a period of significant progress. Which includes decarbonisation, shifts in the labour market and leaps in innovation and automation.
“Our government is committed to supporting the industry and reducing freight costs for operators,” she said.
Hammat touched on the recent flooding that had closed the East West line as some parts of the region received half of their annual rainfall in 24 hours.
“We have seen significant water across the roads and railways,” she said.
“Ninety per cent of WA’s groceries come on the rail freight network and the WA supply
chains have been significantly affected over the last few years.
“The resilience of our supply chains is essential; we cannot always predict these weather events but we have to be prepared to manage them.
“This is why the Department of Transport is developing a regional freight strategy, which will address changing freight requirements, including decarbonisation and supply chain resilience.”
The regional freight strategy will identify essential supply chain corridors and prioritise projects and programs that will improve road, rail and intermodal resilience.
Hammat explained that this work is important, and the state government will not rush the roll out of infrastructure because
long-term resilience takes time.
Hammat said that the Fremantle container subsidy scheme is helping to remove more than 100,000 one-way truck movements in and around Perth and putting containers back onto rail.
Under this arrangement the state government pays a contribution of $50 per eligible 20-foot equivalent container moved through the north key rail terminal.
“Not only is this arrangement reducing costs to the industry, but it is reducing congestion in the community,” she said.
“It is a terrific win-win. The proportion of freight moved on rail into Fremantle has increased from 15 per cent in 2016-17 to consistently exceed the 20 per cent target in the years since.”
demand it will face.
“ASCI package 1 includes 11 rail siding upgrade projects valued at $68 million,” Hammat said.
The government will also be investigating the potential recommissioning of tier three lines to support the uptake of rail freight.
“The rail siding upgrades at Cranbrook will enable longer trains to load more efficiently at CBH sites,” Hammat said.
This will provide enhancements to WA’s grain export supply chain, according to Hammat.
Extending the rail sidings will allow 60 wagon trains to be loaded off the main line in four hours.
Konnongorring will have sidings upgraded to allow 52 wagon trains to be loaded in just four hours, quicker than the previous 14.
“This in turn increases the average price per ton from $25 to $27.”
Westport is a long-term planning program to move container trade from Fremantle to Kwinana.
Westport is investigating, planning and delivering a future port in Kwinana with integrated road and rail transport networks.
“While Fremantle’s inner harbour will continue to play a key role, the new port will provide an opportunity to establish a major freight network that can adapt to future growth and technologies over the decade to come,” Hammat said.
“Last November the government announced a preferred design for WA’s future container supply chain, which includes the new container
Hammat explained that a key focus for Westport is maximising the number of containers moved on rail.
Westport has completed modelling and worked closely with industry to understand current freight bottlenecks and preferred network designs.
The WA government believes the heavy haul industry has an important role to play in its decarbonisation journey.
“Rail haulage is up to four times more fuel efficient than roads freight,” Hammat said.
Hammat explained that while rail helps to reduce CO2 emissions from trucks, it needs to decarbonise itself.
“WA’s rail freight emissions are around 1.9 million metric tons of carbon dioxide equivalence,” she said.
“The industry has a bit of work to do in this space but we have a clear focus to reduce freight emissions.”
Hammat explained that the government is committed to supporting the industry through this time.
“We have a very clear focus to help reduce freight emissions, to reduce freight costs, reduce emissions from trucks on roads, improve rail and port infrastructure and improve the efficiency and productivity of rail freight,” she said.
“It will not happen overnight, but it will be important that the government supports the industry on this journey.”
The ARA has partnered with GS1 to implement rail standards that will allow the rail sector to better track and trace components in its supply chain
The Australian Rail Industry is driving the development of Project i-Trace which is set to transform the Rail supply chain
Project i-TRACE is an encompassing industry approach that uses GS1 standards to identify and track assets, parts,and components in the supply chain through the adoption of digitisation in rail operations.
GS1 is the standards body selected by the ARA for the project as it brought its global supply chain experience to the venture. It has a global network of member organisations, which ensures it can bring global experience to implement the project locally.
Dimi Pachiyannis is the senior advisor of freight, rail, and construction at GS1 Australia. She explained that i-TRACE is the umbrella term for describing a program of works to implement the standards used to track components and assets throughout their lifecycle in the supply chain.
“Project i-Trace will enable tracking and tracing parts and components through the use of unique identifiers, such as 2D barcodes, which can capture data that includes important information like serial numbers and batch numbers,” she said.
“These barcodes, and the data behind them, are all standardised, which allows all operators in the rail network to capture that data electronically, and all be speaking the same language.
“Whereas in the past, companies have had individual systems, using proprietary
exciting to the rail sector, but it can trace its roots back to retail and the introduction of barcodes across the supply chain.
“There are inherent benefits that are realised within organisations that are implementing GS1 standards themselves. Included in that are the efficiencies, accuracy and traceability that will help organisations to meet their own key initiatives.”
Pachiyannis explained that i-TRACE is implementing standards to an industry that already has excellent practices in safety and technical engineering. Project i-Trace is aiming to bring excellence to the supply chain practices as well.
“The Australian Rail network is one of the largest in the world and rapidly expanding with significant growth plans,” she said.
“The management of those components and assets will be critical and we have the opportunity to implement supply chain
standards and enable traceability across our rail network to support this growth.”
Pachiyannis explained that the i-TRACE journey is different for all organisations and is being rolled out in a number of rail companies already.
Queensland Rail recently completed its pilot with i-TRACE, which involved a subset of five suppliers using the system. It is now accelerating its implementation with suppliers.
Peter Burton is the operations director at Unipart Group Australia, which has been utilising the program. He is proud to support project i-TRACE.
“Continuous improvement is in our company DNA and the strategic fit with GS1 was immediately apparent,” he said.
“Traditionally in the rail industry, master data is bespoke to both the customer and the supplier with little cross referencing making for additional work and errors.
“The process we undertook to standardise our master data in an internationally recognised format helped us define and refine our system data, which has had follow on business benefits in terms of process efficiency and customer visibility of our business.
“The benefits we realised also flow through to our customers, who additionally, have increased traceability with less data mismatches to manage.
“I would encourage all rail industry leaders to get on board and start the process of standardisation for the benefit of everyone.”
Mick Cooper, who is the director at PowerRail Australia, echoed a similar sentiment when discussing the project.
“Our experience with GS1 has been far less intimidating and far more rewarding than expected,” he said.
“From the extensive onboarding to implementation, introducing GS1 was not daunting and easily became part of our processes.
“We have learnt so much as a business on process and part validation.
“Our processes have improved in accuracy and as a by-product, we have simplified our warehouse procedures, giving our customers greater information while not complicating normal operation.”
Pachiyannis explained that regardless the size and complexity of these companies, i-TRACE can have similar benefits.
“This complete traceability can increase supply chain throughput to 20 per cent increase in productivity,” she said.
“It can eliminate costly annual stocktakes
as possible.”
GS1 Australia is based out of Melbourne and Sydney but works with the industry nationally.
It works closely with all industry partners to develop the standards that are represented in Project i-Trace. Industry events, such as AusRail and industry user groups are vitally important to this collaboration.
Currently, GS1 is working with mostly passenger rail companies but Pachiyannis expects that the benefits will be applicable across the entire rail industry.
“The rollout of GS1 standards will be important and of benefit to the industry,” she said.
“We see this being the same as it was
utilising this.”
Pachiyannis said that this similar system has also been rolled out in health care settings.
“A hospital environment prioritises patient safety, and these standards were developed to support safety and traceability,” she said.
“The rail industry similarly, has great focus on safety and these standards enable proactive maintenance to support existing safety practices.”
The GS1 mantra is about productivity improvements. As Pachiyannis explained, she expects this rollout to be a success.
“Harmonisation, traceability and sustainability are all important parts of the industry, and i-TRACE provides a solution for this.”
4AI Systems is looking to bring a highly targeted AI system to the rail industry to support a safer sector.
4Tel is the parent company for 4AI Systems and began down the path of artificial intelligence (AI) in rail almost a decade ago. It soon became apparent that the AI division could support a separate business.
Chief technology officer Mark Wood spoke at the Heavy Haul Rail conference, providing an insight into AI and what it could mean for the rail industry.
“4Tel actually started down the AI path in 2016 and we formed 4AI Systems to focus in that area and allow 4Tel to remain in the rail space,” he said.
By focussing on the AI technology, the company has quickly developed an impressive system designed to support the rail industry.
4AI Systems deploys customised artificial intelligence and machine learning systems for transport operations.
The company was founded in 2021 as a subsidiary company of 4Tel, drawing on 24 years of experience in delivering industryleading solutions to the rail industry. The specialised team comprise of professional AI scientists, mathematicians and engineers.
Separating the focus on artificial intelligence from 4Tel ensured that 4AI Systems could invest and develop emerging AI technology at a much greater scale to support the rail industry.
“We see the business case now as helping both the onboard operations and the offboard maintenance and the information provided in that operational environment,” Wood said.
Using sensors from the driverless car industry, the 4AI Systems team has developed ‘HORUS’, an AI system to provide greater situational awareness to train drivers performing operations in the rail corridor.
”Rail corridors rarely change, making it ideal to explore and develop real-time visual detection software.
By capturing the corridor master sequence and then using an on-board supercomputer to perform real-time visual processing, the corridor information is cross checked with a detailed database enabling the system to detect if a trespasser or object is in a
potentially dangerous position in relation to the train’s path.
While the system won’t stop incidents from happening, it will minimise the impact by eliciting an earlier response.
Wood explained how the organisation has developed the system over the years.
“We have a good collaboration with University of Newcastle and we draw on their robotics and AI areas to supplement our own research and development,” he said.
“What is really interesting is that with our approach, we understand the weaknesses that some sensors may have, and then supplement that by other sensors.”
This development has been important for 4AI Systems to develop what it believes is a complete solution.
Each locomotive or railcar needs to be fitted with any combination of advanced sensors to gather information, including GPS, inertial navigation, cameras, and optionally, radar, lidar, and ultrasound sensors, with other incidental inputs such as odometers, speed and temperature sensors.
All of this data is then collated to support the AI system. Fusing multiple-sources of sensor data frame-by-frame and integrating it over time, the locomotive or train inference computer can use AI to support to support driver decision making and situational awareness.
Mark Wood explained the mission of 4AI Systems in greater detail.
“Our mission is to provide solutions that empower people and organisations to ultimately make better, data-driven decisions in their rail operations. We believe AI is the next step in creating more efficient rail networks,” he said.
“Onboard AI minimises investment into third-party infrastructure systems because it creates smart trains owned by the train operator. AI handles boredom better than humans. AI never gets tired or distracted, has better visibility, can monitor location, speed and route in real-time, and assess track infrastructure for risks.
“You can highlight a person as they walk around the corridor – they are highlighted red when in the rail corridor, yellow in the
safe distance.”
4AI Systems has been developing systems to deliver the right kind of information to the driver to not overwhelm them but also provide what is necessary.
“We need to ensure we do not distract the driver and there are a number of ways we can provide that information to them,” Wood said.
“A warning will appear in the same spot on the screens so the driver knows where to look when an alert is heard.
“A simple graph can show where an obstacle may be as opposed to live pictures.
“A driver may want additional information, or access to the cameras in high-risk scenarios, and they can gain access to that.”
The HORUS system can provide accurate location definitions to a specific track and location in multiple-track territory by fusing imagery and navigational data.
It can detect an unexpected object or hazard that may be on or around the rail track.
It also provides speed checking and authority enforcement. 4AI Systems can recognise signal posts and reading of displayed aspect. It can also monitor the condition of infrastructure to report back to maintenance teams and provide realtime feedback.
“This type of real-time data can minimise downtime for maintenance on tracks and
Wood said.
The system can also track events, processing all log files, cameras, accelerometers and speed data onto an event sequence file that can then be replayed.
Another scenario HORUS can assist with is adding situational awareness around level crossings improving level crossing safety.The HORUS system allows for warnings and alerts for approaching and around high-risk areas.
Algorithms can calculate probable hazards and provide a warning classification to ensure an appropriate response to potential hazards.
“When it comes to level crossing detection, a few seconds extra can make all the difference,” Wood said.
people that are travelling towards the danger zone and we can alert the driver ensuring that they get an early warning.
“A few seconds can make the difference between a fatality and a near miss.
“You can’t beat the laws of physics. If you can buy a few seconds, it might be the difference between someone going home safely at the end of the night or not.”
In 2022, 4AI Systems completed an AI vision system feasibility study for Rio Tinto Iron Ore’s AutoHaul in Western Australia’s Pilbara region.
Rio Tinto Iron Ore installed a 4AI Systems HORUS AI solution on a locomotive to learn and understand the system’s capability and potential as a complimentary technology solution.
Five cameras and other sensors were installed on the AutoHaul locomotive to great success.
The program demonstrated how AI software can detect hazards in different conditions and from different distances.
The study was able to identify people and objects beyond 1000 metres including around curves with line of sight. The system performed continuously well in all weather conditions.
The system has also been trialled on New York’s metro network. This trial gave the team a unique insight into the New York subway operating conditions.
“Our team was very excited to test the system again in New York’s colder weather conditions. The data provided was an interesting contrast to Pilbara’s dry heat,” Wood said.
It was exciting for us to see our system working across a range of environments
Lycopodium is providing support around maintenance requirements, bringing expertise to the fore to ensure success for operators.
Maintenance supporter Lycopodium Infrastructure is aiming to lead the rail industry’s maintenance and safety practices. Whether it be in the smallest yard moving low amounts of freight to the largest coal company – no challenge is too big or small.
The company has spent the past 14 years honing its skills and bringing science and ingenuity to process, engineering, construction management, maintenance and operational challenges.
Lycopodium can ensure companies are
collaborating with a range of stakeholders to deliver all components successfully.
Within the rail group, Lycopodium has 40 staff, including track inspectors and certifiers, maintenance managers, and condition analysts.
Rail Express spoke with senior maintenance engineer Robert Taylor to learn more about how the company works with rail organisations.
Taylor has more than 30 years’ experience working in engineering, and has an
engineering background thanks to his time in the Navy. This experience has been invaluable in his work with Lycopodium.
Lycopodium takes a unique approach to every organisation it partners with, which allows it to work with a company of any size and provide the support needed.
“We have a good system that is tailored to the needs of any organisation,” Taylor said.
“The system is geared up to give us flexibility by using our experience and knowhow along with best engineering practices to maximise success.”
Taylor explained that often for the team at Lycopodium, it is about building trust quickly to ensure mutual success.
“We have an open and transparent system,” he said.
“My main job is to communicate with clients around maintenance needs. This can be extending certain maintenance practices or bringing them forward.
“Once we have built that trust and they understand we are here to support, it all runs like clockwork.”
Taylor explained that if organisations blindly follow industry standards without accurately considering the needs of the network, it can cause a lot of ‘over maintenance’ that is not needed.
“Many of the tracks we are working on run
heavy trains but only at a maximum of 20 kilometres per hour,” he said.
“These networks do not need the same sort of maintenance as a freight network running through busy areas of Australia carrying heavy weights at great speed.”
Many of the companies Taylor works with may not be operating in the rail space more broadly but utilise it for a small subsection of its operations, which pose unique challenges. It has forced the team to simplify its processes.
“Often I am working with people that don’t understand our rail jargon,” he said.
“We are working with mechanical engineers and people like that. My experience in different fields throughout my career allows me to understand what they are thinking and provide the information they need.
“We don’t come in wearing high flying suits and tell them what to do. We work closely with them, so they understand why we are doing what we need to do.
“This is where programs like the LycoMMS are so helpful.”
The LycoMMS system manages rail maintenance by collating data and information onto one easy-to-follow platform. Lycopodium has built LycoMMS from the ground, and they have done so by
implementing a range of tools. These include rail infrastructure management inspections and asset management services, track defects, asset history and work orders.
Lycopodium was the recipient of the Permanent Way Institution (PWI) Ken Erickson Innovation Award in 2016 for the LycoMMS system and app.
“Clients have a great deal of transparency when it comes to using this system,”
Taylor said.
“The work order system is very clear as well. It explains in simple terms the work that needs to be done and why we are doing that work.
“This ensures that all people in the decision-making process have a clear understanding of why we are recommending this work.
“We don’t want to railroad clients and force them to do work. This system gives them the ability to make informed decisions about their track maintenance needs.”
The key for Lycopodium, as Taylor explains, is collaboration between a range of stakeholders. The organisation acts as a conduit between every person in the maintenance process.
“The key is we don’t want to overcook it or undercook it,” he said.
“The phrase I use with all our clients is it needs to be fit for purpose and with no surprises.
“If things are breaking it obviously costs a fortune, but we also don’t want to over maintain. It is about finding that balance.”
Taylor explained that being in the position that many of his clients are in when he has worked for similar companies in the past, ensures he understands what they are looking for from Lycopodium.
“We aren’t consultants sitting in a board room. We understand these companies intimately and provide a bespoke service for what they need,” he said.
“We do the thinking and the smarts around what is needed,” Taylor said.
“A lot of the muscle is hired and we cherrypick the right contractors for a company’s needs. We need to have the right contractor that requires little supervision, and we need to have a strong relationship with them.”
Taylor explained that Lycopodium is always aiming to stay on top of changes and practices in the maintenance sector to ensure it is always meeting the needs of clients.
“We learn as we go and it is not always constant,” he said.
“Every day we learn something, and we adjust our manuals to better assess the needs of the industry and that is what is important for us as maintenance supporters.”
Remote condition monitoring is fast becoming a critical component of rail and KeTech is bringing this technology to Australia.
KeTech has re-shaped the way train operators and builders can manage their assets through smart Remote Condition Monitoring (RCM).
KeTech has utilised its expert data understanding, and 25 years of experience in rail, to create an RCM system tailored to the rail industry; to prolong asset life, prevent failures and malfunctioning equipment, and present actionable insights for a seamless maintenance operation, centralised and in real-time.
KeTech have engineered an RCM system with intelligence at its core, through a blend of machine learning, and asset expertise.
The company finetune algorithms for each specific asset to align with its characteristics a holistic view and the complex interactions between assets.
is expected to increase each year over the forecast period for each state and territory.
floods, droughts, bushfires, and coastal erosion is driving investment in Australia’s rail transport
Some of the assets on the railways are more than 100 years old, as are the methods used to inspect them. The rise of digitalisation has led to the development of ‘game changing’ technology in the rail industry, RCM being a prime example.
RCM has the potential to empower the rail industry to pre-emptively oversee the status and well-being of essential assets, anticipate potential malfunctions, and refine maintenance approaches through the use of sensors, to make maintenance works more efficient.
However, it is important to recognise that RCM alone is not enough. Many RCM systems rely on historical data alone to predict equipment failures, whereas KeTech take it to the next level.
Sensors collect multiple pieces of data, sometimes duplicates, that are then stored in silos, which can quickly lead to Redundant, Outdated, Trivial (ROT) information, which
decisions are based on outdated information, particularly in the realms of maintenance.
Discussions around digitalisation often bring up the topic of big data and how it has potential to re-shape the industry. However, the big data revolution will not live up to its promises if it led by the premise of ‘the bigger, the better’. Therefore, collecting more data is not the answer. The first step towards it, is through collecting better quality data.
A problem appears when monitoring systems collect data based on its subject alone. It creates a data silo that has no understanding of how the data collected may or may not be influenced by another asset. This violates the fundamental rule of understanding data – no data has meaning without its context. Without context, this data is just noise. Without it, operations staff won’t know if the data collected reflects a positive or negative outcome and will have no idea what action to take, this can actually
lead to a longer resolution time as they navigate from one Graphical User Interface (GUI) to another.
The only way to find true context across all data is to combine RCM with engineering expertise and centralised intelligence to extract actionable insights in real-time.
KeTech has been collaborating with train operators and train builders for 25 years, providing real-time journey information systems tailored to specific requirements through the use of intelligent data and real-time processing and presentation of information.
KeTech’s RCM is no different. It helps train operators and builders to target specific realworld problems.
Its teams collaborate with asset experts to define a set of rules for the pieces of equipment that are being monitored, here it creates algorithms to separate normal variations and true threats allowing the data to be interpreted in a meaningful way so both the root cause can be identified, and a course of action taken.
Although relying on historical data alone isn’t the best way to predict potential failures, it does play an important role; but only in conjunction with AI and machine learning and context provided by the engineering expertise to identify the most accurate trends, perform real-time analysis and present meaningful information.
Using only historical data doesn’t account for unforeseen failure modes. This is why engineering expertise is necessary to take the system to the next level. KeTech ensures that the rules for each asset is specifically tailored and fine-tuned to align with the assets characteristics and the environment in which it sits. Unlike other systems, KeTech’s RCM doesn’t only provide information on singular assets, but offers a holistic view of all assets on one centralised dashboard. It is also able to understand complex interactions between different components and provide usable information in real-time.
Developed to the latest cyber security certification, KeTech’s system is created by data experts for the rail industry and truly unlocks the power of RCM.
KeTech combine years of expertise, intelligent data processing, real-time technology, AI and machine learning to provide a centralised end-to-end solution. Its system will move away from fix-on-fail, to predict and prevent, allowing the operations team to be proactive and optimise its maintenance strategy.
The Australasian Railway Association has a number of focusses for 2024 but is placing a particular emphasis on one that is intended to help meet the current skills shortage.
Improving gender diversity and inclusion in the Australian and New Zealand rail workforce is a key focus for the ARA and the rail industry.
We know that having more women in our workplaces plays a vital role in the long-term sustainability of the industry and also leads to innovation and better outcomes.
The ARA, on behalf of the rail industry, collates diversity data to benchmark the us against the national average and to measure the progress over time.
The information that we gather enables the industry to identify areas of success
Australian Government’s Workplace Gender Equality Agency (WGEA), and it shows some promising progress.
It is a particular passion project of mine because I feel strongly that we cannot move female participation forward in a meaningful way until we fully understand the representation across sectors, roles and responsibilities.
This is the ARA’s fourth WGEA survey and provides an important platform to guide future policies and programs. Organisations from the ARA’s diverse membership contributed to the data, including passenger operators, freight and heavy haul operators, suppliers and manufacturers, and consultants.
The report, based on 2022/2023 data, shows that there has been an overall increase in the participation of women in the rail industry to 28 per cent. This is a four percentage point increase from 20202021, which followed an improvement of two percentage points from the previous reporting period of 2018-2019.
Female representation is steadily increasing across management categories.
making in key management personnel roles. In regards to non-managerial roles, females hold 24 per cent of positions, with the highest representation in clerical and administrative positions (37 per cent).
The report also shows that resignations of females has dropped to 20 per cent of all resignations, from 29 per cent previously. This remains a significant outlier compared with the WGEA average of 54 per cent.
Governing bodies had 30 per cent female representation. However, we have seen a drop in the number of women who held positions as Chair, from 27 per cent to 14 per cent.
Across all the rail sectors, the most notable jump was for freight, with female participation increasing from 23 to 30 per cent. Consultants continue to have the highest proportion of women in their workforce at 39 per cent, and rail manufacturers and suppliers have the lowest at 13 per cent.
The ARA was pleased to see that the majority of our members have formal policies or strategies in place that specifically support gender diversity, at 80 per cent of
or strategies to improve gender equity overall
Caroline Wilkie, Chief Executive Officer, Australasian Railway Association The ARA wants to see more women in rail to support a growing skills shortage. IMAGES: ARAthose surveyed, 91 per cent of respondents had conducted a gender pay gap analysis within the last 24 months, up from 44 per cent since 2020-21.
However, while this survey data shows that the rail industry is headed in the right direction, we are still a long way from achieving gender parity which, at the current rate, will take until 2049.
For example, on average, the WGEA data shows that 86 per cent of respondents have formal policies surrounding performance management processes, whereas the average for the rail industry is only 47 per cent. A large policy gap remains in several areas including training and development, succession planning and talent identification.
The push for change is more critical than ever given the estimated 70,000 workforce shortage across Australia in the rail industry, which is exacerbated by a looming retirement cliff (the ARA’s 2023 Rail Workforce Report shows about 35 per cent of the Australian rail workforce will retire by 2035, with almost a third of train drivers currently aged over 55).
The ARA has a Women in Rail Committee, founded in 2016, with the goal of developing a national strategy and action plan to achieve gender diversity across the industry. The group is also focused on improving the representation of women across industry and addressing systematic barriers preventing the success of women in the industry.
In 2023, the ARA welcomed new Board member Rebecca Want, Market Leader –Transport, GHD, who is also the Chair of the Women in Rail Committee, as an ARA Board Appointed Director until the 2025 AGM to reflect the importance of the diversity and inclusion work of the ARA.
Last year, we also released an updated Women in Rail Strategy 2023-2026 aimed at breaking down barriers for women in rail and creating a more diverse and inclusive industry.
It outlines the ARA’s initiatives to support and promote female rail professionals and is guided by four strategic areas of focus:
• Industry Knowledge – measure successes and understand the issues.
• Organisational Impact – encourage inclusive and respectful workplaces.
• Professional Development – grow capacity and capability of women in rail.
• Promote Rail to Women – increase female participation in rail.
One of the key initiatives of our Strategy is the Women in Rail Mentoring Program. This is the sixth year of our program, which has grown to more than 90 mentee and mentor
pairs from our original group of 40 pairs when the program first began in 2019.
The Program was established to support, guide and retain women working in rail through a tailored professional and leadership development program.
This year’s mentors are drawn from a pool of rail professionals from various rail organisations, including Alstom, Rio Tinto, Sydney Trains, Laing O’Rourke Australia Construction, Arup, John Holland, Downer, Arc Infrastructure, and Aurecon.
Also as part of our strategy, we have partnered with National Women in Transport to engage Diversity Partners to conduct qualitative research into gender diversity in our industry, to understand the ‘why’ behind the numbers in the ARA’s WGEA Gender Diversity Report.
This research will help us better understand the barriers and challenges hindering greater gender diversity and identify best practice initiatives aimed at achieving gender parity.
The research sought the voice of rail employees via a survey, focus groups across the industry sectors, and written submissions, where industry shared their personal lived experiences. The ARA will share recommendations coming out of the research with industry in coming months, which will highlight responsibility for the sector as a whole, rail organisations, and individuals.
Participants also shared good practices across industry, as well as challenges, providing valuable insights as to the key priority areas we as an industry should focus on.
Improving gender diversity and inclusion will continue to be a focus for the ARA because it is essential for a sustainable rail industry for the future.
Having a diverse workplace fosters innovation and enriches the talent pool, driving economic growth. We are at a crossroads, faced with gaps accelerated by rapid technological advancements and a retiring workforce, and must do all we can to build a more resilient and adaptive industry. Increasing the representation of women in rail is not just a moral imperative but a necessary one for a successful future.
KEY FIGURES FROM THE ARA 2022-23 GENDER DIVERSITY REPORT:
• 28% of the rail workforce are women (24% in 2020-21)
• 33% of key management personnel are women (26% in 2020-21)
• 26% of CEOs are women (16% in 2020-21)
• 100% of organisations have paid parental leave for both men and women (93% in 2020-21)
• 30% female representation on governing bodies (26% in 2020-21)
• 36% of promotions were awarded to women (32% in 2020-21))
• 80% of organisations have formal policies in place to support gender diversity (79% in 2020-21)
• 34% of new appointments were women (32% in 2020-21)
• 77% of respondent organisations have a formal policy/strategy to support employees who are experiencing family or domestic violence (61% in 2020-21)
• 91% of organisations had conducted a gender pay gap analysis the past 24 months (44% in 2020-21)
The Permanent Way Institution of NSW is making a commitment to continue driving the success of the rail sector.
The Permanent Way Institution (PWI) of New South Wales is an Australian transport industry organisation commemorating its 50th anniversary this year. This milestone is a testament to PWI’s enduring dedication to fostering the transport sector’s growth, innovation, and resilience, an industry foundational to Australia’s economy and daily life. As we look ahead, the focus on the upcoming conference in October 2024 encapsulates the institution’s forward-thinking vision and commitment to community, inclusivity, and lifelong learning.
PWI NSW offers an professional development and networking platform. Through its diverse array of events and initiatives, the institution embodies the ethos of lifelong learning, ensuring that individuals within the transport industry remain at the forefront of technical advancements, best practices, and leadership skills. This commitment to education and growth is crucial in an era where technological innovation and sustainability practices are rapidly reshaping the landscape of the transport sector.
Among the myriad opportunities PWI NSW provides for engagement and professional development are Technical Meetings, Lunch & Learn sessions, Industry Site Inspections, Executive Breakfasts, Country Meetings, an Annual Golf Day, a Winter Dinner, and the Annual Conference. Each of these events is designed to cater to the membership’s varied interests and professional needs, fostering an environment of inclusiveness and shared knowledge.
Technical Meetings and Lunch & Learn sessions allow members to delve into the latest industry trends, technologies, and challenges. These gatherings facilitate knowledge exchange and encourage collaboration and idea-sharing among peers.
Industry Site Inspections offer a unique, hands-on experience, allowing members to gain insights into operational best practices and innovations in infrastructure and transport technologies.
The Executive Breakfasts and Country Meetings are tailored to foster strategic discussions and networking in a more intimate
setting, enabling members to connect with industry leaders and influencers. These events are instrumental in building a strong sense of community and camaraderie among members, encouraging a collaborative approach to addressing industry challenges and opportunities.
The Annual Golf Day and Winter Dinner are standout events in the PWI NSW calendar, offering members a chance to engage in informal, relaxed settings that further cement the bonds within the transport industry community. Such occasions underscore the institution’s belief in building personal connections and fostering a supportive network that transcends professional interactions.
The much-anticipated Annual Conference is central to PWI NSW’s annual activities, which is significant this year as we celebrate the institution’s 50th anniversary.
The conference in October 2024 promises to be a landmark event, encapsulating the spirit of innovation, community, and lifelong learning that PWI NSW champions. This gathering will reflect on the journey and achievements of the past five decades and set the direction for the future, highlighting cutting-edge research, sustainability practices, and the technological advancements shaping the future of transport.
The focus on community is paramount. PWI NSW exists within a vibrant ecosystem, acknowledging that the strength and vitality of the transport sector are intrinsically linked to the well-being and progress of the broader community it serves.
Through its events and initiatives, PWI NSW fosters a culture of inclusiveness, ensuring that diverse voices and perspectives are heard and valued. This approach enriches the industry’s
collective knowledge and drives innovation, making the transport sector resilient and adaptable to changing societal needs.
PWI NSW’s commitment to its members and the wider community remains unwavering as we move towards the conference and beyond. The institution provides varied networking opportunities based on lifelong learning and inclusiveness.
In celebrating this 50th anniversary, PWI NSW honours its rich history and renews its pledge to be a pivotal force for growth, education, and collaboration in the Australian transport industry.
This year’s conference will not only reflect where we’ve come from but also declare where we’re headed as a united, informed, and vibrant community.
We stand at the threshold of new beginnings, ready to tackle the challenges of tomorrow with the wisdom of the past and the innovative spirit that has always defined us.
Our golden anniversary will celebrate past achievements and a stepping stone towards a future where the transport sector thrives through education, inclusiveness, and a strong sense of community.
It is a testament to the institution’s enduring impact on its members and the Australian transport industry.
Joining PWI NSW is your gateway to being at the forefront of the transport industry, offering rich professional development and networking opportunities. As we mark our 50th anniversary, don’t miss out on our Annual Conference—a highlight event celebrating our journey and future. Watch for tickets releasing soon; this is an opportunity to connect, learn, and celebrate with the heart of Australia’s transport community.
Lycopodium is trusted by private and public transport operators across the nation. We provide routine safety critical independent track inspections and assessments of rail infrastructure and annual detailed inspections and asset condition reports, including:
Long term asset management plans and preventive maintenance plans
Fit for purpose inspections and maintenance to suit your specific operational requirements
Trusted to manage upgrades and maintenance, whilst remaining independent
We manage your safety and compliance leaving you to do what you do best
Lycopodium operates and maintains a purpose-built maintenance management system (MMS) which provides a high level of transparency to our clients with regard to the risk management required under safety legislation.
Asset owners can access real-time information about their assets, including a full list of assets with corresponding inspection and maintenance records, current and historical defects, as well as the maintenance schedule for each asset.
Contact us to arrange a live demonstration of the LycoMMS.
We operate with the simple goal that your assets be fit for purpose with no surprises at minimal cost