Towards greener, smarter mobility

Building better networks to change people’s lives
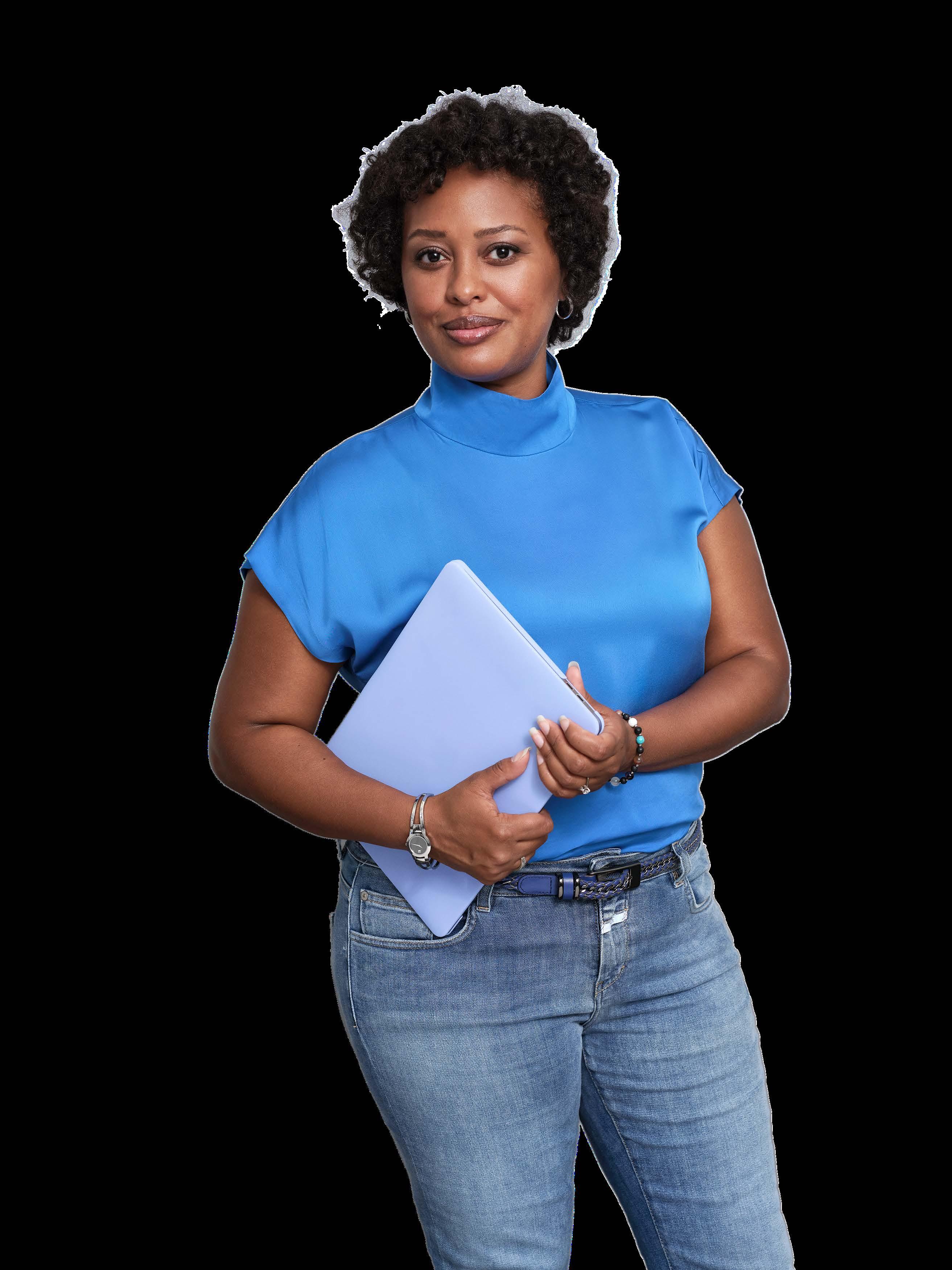
New campaign to boost careers in rail industry
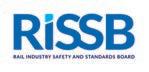
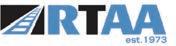
PAGE 52

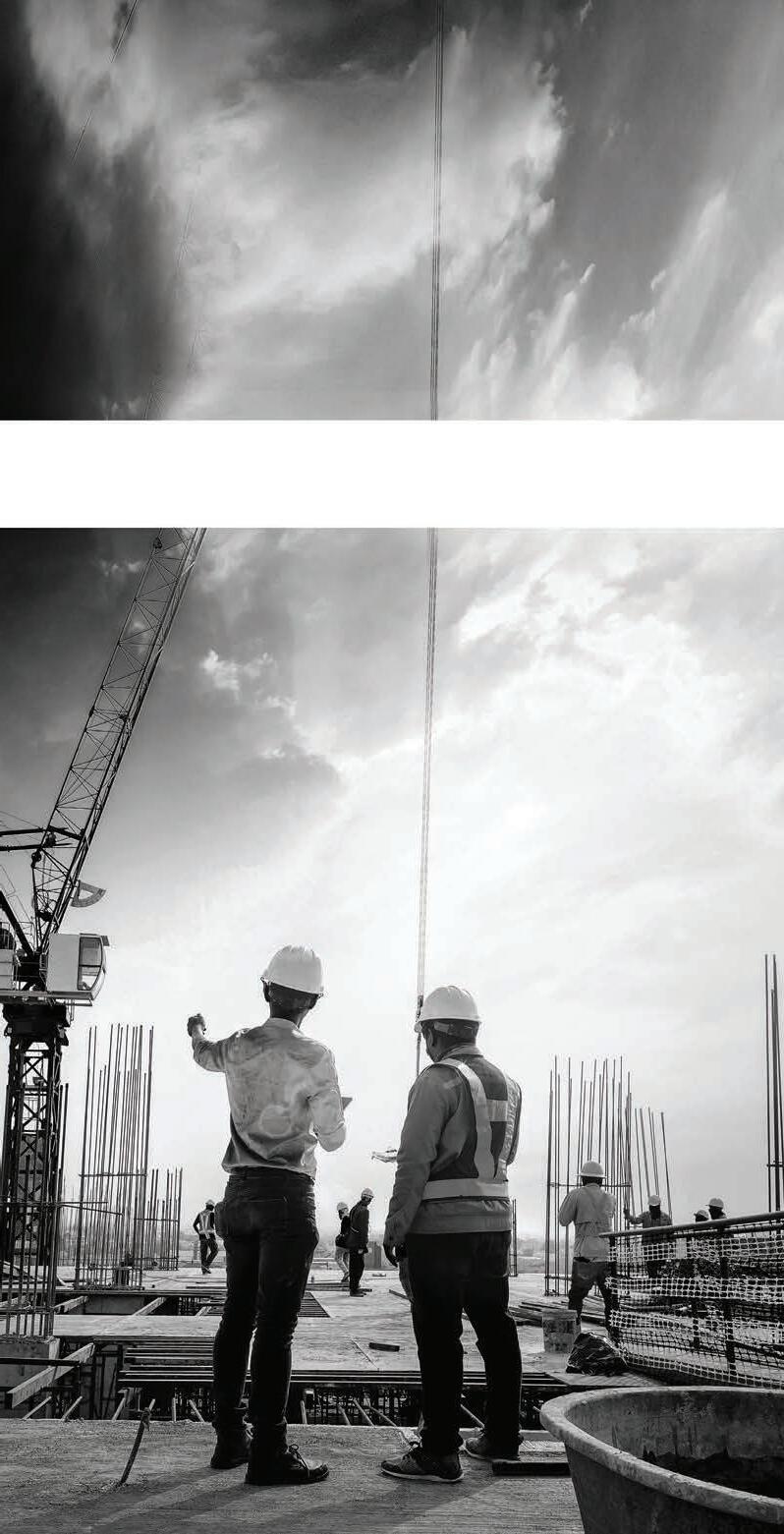


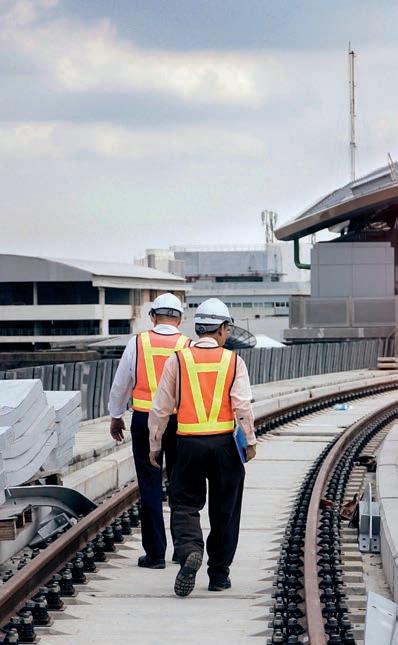





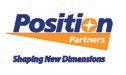



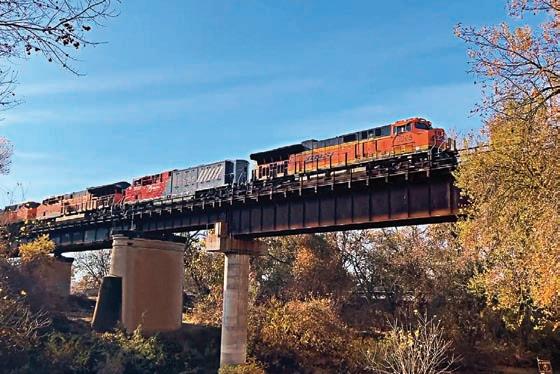

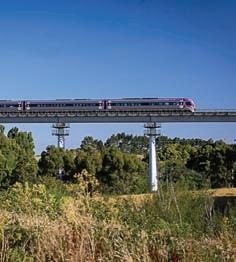
Building better networks to change people’s lives
New campaign to boost careers in rail industry
PAGE 52
ISSUE 5 - JUNE 2023
Published by:
379 Docklands Drive
Dockalnds, VIC 3008
T: 03 9690 8766
www.primecreativemedia.com.au
Publisher Christine Clancy
E: christine.clancy@primecreative.com.au
Chief Operating Officer
Christine Clancy
E: christine.clancy@primecreative.com.au
Managing Editor
Myles Hume
E: myles.hume@primecreative.com.au
Editor Ray Chan
E: ray.chan@primecreative.com.au
Business Development Manager
Alex Cowdery
M: 0422 657 148
E: alex.cowdery@primecreative.com.au
Client Success Manager
Salma Kenndey
E: salma.kennedy@primecreative.com.au
Design Production Manager
Michelle Weston
E: michelle.weston@primecreative.com.au
Art Director
Blake Storey
E: blake.storey@primecreative.com.au
Design Kerry Pert, Tom Anderson, Louis Romero
Subscriptions subscriptions@primecreative.com.au
www.RailExpress.com.au
The
Sustainability continues to be a major focus of the transportation industry, and rightly so.
In our annual feature on the subject, it is heartening to note that the rail sector has been making significant strides towards achieving a more renewable future.
It’s more than a buzzword. Sustainability refers to the ability of a system or process to be maintained over time without causing harm to the environment, society, or economy. It is a concept that recognises the interdependence of these pillars, and aims to create a balance between them.
Rail is one of the most energy-efficient modes of transportation, with trains capable of moving large amounts of cargo and passengers using a fraction of the energy needed by other modes of transportation.
One of the biggest challenges, of course, involves lessening the carbon footprint. Rail companies have been implementing various measures to reduce their emissions, such as switching to electric or hybrid locomotives, using biofuels, and optimising their operations to reduce energy consumption.
They are investing in new technologies such as regenerative braking, which recovers energy that is normally lost during braking and reuses it to power the train.
The industry is also improving the aerodynamics of trains and using lighter materials to lessen energy consumption. These efforts not only cut down carbon, but also the operating costs for rail companies.
As well, it’s important to participate in a circular economy. This includes recycling materials such as steel, aluminium, and copper from decommissioned trains, along with using sustainable materials in new train construction. By cutting back on waste, the rail industry is helping to conserve natural resources and curtailing the environmental impact of its operations.
In this edition, read about how Alstom’s advanced global innovations are providing greener mobility solutions to its customers; find out more about the battery-operated breakthroughs from Wabtec; and discover
how KLP hybrid polymer sleepers are diminishing pollution while giving a new lease of life to plastics.
There are informative articles on Driving Advice Solution (DAS) systems, which allow drivers to gain a complete picture of the current state of the rails along the route, and are recognised as a solution to optimising the performance of trains in the goal to pare down energy consumption.
We also take a look at the growing focus on railway station precincts as part of urban planning, which play their own part in boosting sustainability.
These areas often serve as gateways to cities and provide access to various modes of transportation, and are important centres of economic activity.
By providing access to public transportation and slashing the reliance on private cars, the localities help reduce traffic congestion, air pollution, and greenhouse gas emissions.
In addition, railway station zones encourage walking activities and more use of bicycles, reducing reliance on fossil fuels.
Our report reveals that more than a third of new dwellings built across Australia’s four largest capital cities over the last 15 years were built within a kilometre of a train station, in what is a trend that has been steadily increasing over the same period.
A recent analysis by KPMG Australia shows that of the 1.5 million new homes built in Sydney, Melbourne, Brisbane, and Perth between 2006 and 2021, 35 percent were within that distance of a train station.
There’s no doubt train stations have had a significant impact on housing supply, with the study highlighting that long term precinct planning policies can have a positive impact by clustering jobs and services near a major train station.
Along with our usual roundup of major news stories, major contract developments, and industry partner contributions, we are sure you will enjoy the read.
permission of the Publisher.
Dr Kerry Schott has been appointed acting chair of the Australian Rail Track Corporation (ARTC) for a period of three months.
Schott fills in for Peter Duncan, who was recently appointed as the new ARTC chair. He will be taking a three-month leave of absence to serve as acting Secretary of the Department of the Premier and Cabinet in New South Wales.
Federal transport minister Catherine King said it was a sign of how much Duncan’s expertise was valued that he had been asked to take on this role.
“We are sure his advice will be appreciated by Premier Chris Minns,” King said.
Dr Schott recently concluded a major review of Inland Rail, which found significant faults with the project.
“She is perfectly placed to oversee the initial implementation of the recommendations she made, and which the Government accepted,” King said.
During her three-month tenure, Schott will focus on recruiting a permanent chief executive officer of Inland Rail and addressing the governance and board capability shortcomings her report outlined.
While it confirmed that Inland Rail was an important project to meet Australia’s growing freight task, improve road safety and to help decarbonise the economy, the review also
found that it was running significantly over budget and significantly behind schedule, with just over 16 per cent of the 1700 kilometres of track completed so far.
Schott reported the estimated cost of Inland Rail blew out to approximately $31 billion under the previous government.
The revised estimate is almost double what the Coalition said it would cost as recently as 2020, a blowout described by Schott in her report as “astonishing”.
The Australasian Railway Association’s (ARA) flagship event, AusRAIL PLUS 2023, is shaping up to be the biggest yet, with expectations more than 5000 rail industry professionals will attend and more than 300 exhibitors will display their latest products and innovations, including from NZ, the UK and Europe.
ARA chief executive officer Caroline Wilkie said organisations wanting to showcase their offering at the industry’s premier event –whether as a sponsor or exhibitor – should book soon, with nearly three-quarters of exhibition floor space already secured.
“There are still some prime spaces remaining so I urge all organisations in the rail industry to ensure they secure their position so they do not miss out on this fantastic opportunity to network with colleagues, showcase their products or
services and learn more about innovations in the sector,” she said.
“AusRAIL PLUS 2023 provides a range of opportunities to meet new customers and suppliers, promote your organisation as a destination employer, showcase innovations and learn about the latest trends in the rail industry.
“We already have a wide range of organisations confirmed as partners and exhibitors for the three days of expert presentations, activations, workshops and our hugely popular social events.”
Due to the high demand for tickets to the social functions, AusRAIL PLUS 2023 delegates, sponsors and exhibitors will receive priority access to book tickets to the Yellow Dinner and Gala Dinner as well as the Women in Rail Breakfast and Young Rail Professionals Lunch.
In a program change for this year, the
“Somewhat surprisingly, the project has commenced delivery without knowing where it will start or finish”, she said, adding that the final date and cost remain uncertain, because of a lack of confidence in the current estimates.
King said the Government was grateful to Dr Schott for agreeing to undertake this important task and looked forward to welcoming Duncan back to the role later in the year.
Rebecca Pickering has been acting CEO for Inland Rail since July, 2021.
Yellow Dinner will be on the first evening, the networking exhibition drinks will be held on the second and the Gala Dinner on the final night.
Held at Sydney’s International Convention Centre (ICC) from November 13-16, AusRAIL PLUS 2023 will host six networking events, new and exciting activations, industry sessions, expert presentations and technical workshops.
“AusRAIL PLUS 2023 is a highlight on the ARA calendar, bringing together rail leaders from around the world to discuss the achievements, opportunities and innovations in our industry,” Wilkie said.
Some of the issues covered in the comprehensive program include addressing the skills gap, improving sustainability and promoting greater use of rail.
For more information, go to https://ausrail.com
The Office of the National Rail Safety Regulator (ONRSR) has charged Queensland Rail with three offences relating to management of safe systems of work following a fatality in Westwood in 2021.
On June 18 that year, a Queensland Rail locomotive collided with the rear of a stationary Aurizon coal train about 45 kilometres west of Rockhampton.
One Queensland Rail driver was killed in the accident, and a second driver and a tutor driver were both injured.
ONRSR will allege that Queensland Rail failed to comply with its safety duties as an accredited rail transport operator under Rail Safety National Law (RSNL).
The matter is being pursued in the interests of rail safety as part of the regulator’s role to
enforce compliance with the RSNL, and in the public interest to provide for the safe carrying out of railway operations and promoting public confidence in rail operations.
Under RSNL, the maximum penalty applicable to a rail transport operator for breaches of this kind is $1.5 million per offence.
In a statement, Queensland Rail said it remained deeply saddened by the incident and the loss of a colleague.
“We continue to support the family of the deceased as well as the other two drivers and their families,” it said.
“At Queensland Rail safety is paramount. We remain committed to operate a safe railway and to learn from this incident and do all that we can to prevent it from happening again — we want to ensure that when our
people come to work, they work safe and go home safe.”
Since the incident, Queensland Rail has implemented a comprehensive program to improve safety on the network, including permanently codifying long-end leading restrictions into its Safety and Environment Management System for all operators on the QR network, and Signals Passed at Danger (SPAD) prevention activities.
The operator has worked cooperatively with the National Rail Safety Regulator (and other authorities) to improve rail safety and said it would continue to do so.
Queensland Rail said it would not contest the prosecution and would work proactively with the ONRSR in relation to the charges to resolve the matter promptly.
The City of Logan in Brisbane has welcomed news that double-stacked trains will not travel through the local government area.
The recently released review of the Inland Rail project, by Dr Kerry Schott, has recommended the construction of an intermodal terminal at Ebenezer, near Ipswich, to effectively end the Inland Rail
to Kagaru, Acacia Ridge and Bromelton, including through Logan, to allow connectivity to ports and other rail networks.
Mayor Darren Power said the city had spent years of standing firm on the opposition to the proposed Inland Rail route.
“This really was a ‘David and Goliath’ clash but it shows you should never give up on something that is worth fighting for,” he said.
Power said it was a small and long overdue win when the newly-elected Federal Government committed to the independent review of the project last year.
“When I met last year with infrastructure minister Catherine King, I made her aware of our community’s long-held concerns about the project,” he said.
“We know the route was selected without consultation and impacted residents did not get an opportunity to have their say on the route or offer alternatives.”
After years of being ignored by the Australian Rail Track Corporation and the former government, Power said it was a relief that concerns raised by Logan residents had finally been heard and addressed.
It was projected that more than 40,000 people in Logan would live within a kilometre of the proposed Inland Rail corridor in the next 20 years.
As many as 45 trains each day, some up to 1800 metres, were expected to use the tracks, creating noise, vibration and air quality issues for nearby residents.
Logan City Council’s Infrastructure Chair Teresa Lane praised the decision to seek a new direction for Inland Rail.
“This just makes common-sense to explore a new route that has less impact on our growing city and booming residential areas,” she said.
Designs have been released for the new tram maintenance and stabling facility in the Melbourne suburb of Maidstone – giving locals a glimpse of what it will look like once it is complete.
The facility will be home to the new fleet of Next Generation Trams, located on the corner of Williamson and Hampstead roads.
It will be used to maintain, clean and store the accessible, low-floor trams, as well as house tram operations and administration staff.
The designs have been informed by community feedback and include modern and sustainable infrastructure, with energy efficient LED lights, recycled plastic materials and rainwater tanks which will harvest 80 megalitres annually to wash the trams.
The trams – which have space for up to 150 passengers – use around 30-40 per cent less energy per passenger, compared to an E Class tram.
The designs also celebrate Maidstone’s history, with the administration and maintenance building to include a saw-tooth roof design which is an acknowledgement of the industrial past of Melbourne’s west.
The State Government invested in the
building the new facility to deliver more comfortable, accessible, and energy-efficient journeys for passengers.
Early works are now underway, with crews to spend the next few months preparing the site for major construction to begin later this year. The facility is scheduled to open in 2026.
The site is on the Victorian Heritage Register,
permit by visiting heritage.vic.gov.au.
The project will create around 280 local jobs in construction, ongoing maintenance and the supply of materials and services.
It forms part of the Government’s $90 billion investment in transport infrastructure projects, which will provide better, more connected and more accessible services for Victorians.
The former Glen Huntly station in Melbourne is no more, closing ahead of the removal of two dangerous and congested level crossing removals at Neerim and Glen Huntly roads.
The original station opened in 1881 and has been a cornerstone of the community through
The current station building was opened, and the manual gates replaced with automatic
The new station was designed after listening to community feedback, and is also inspired by local architecture along Glen Huntly Road.
It will use familiar materials including brick, bluestone, and light-coloured granite in and
The area will be transformed to include a new vibrant forecourt, with seating and landscaping to create more open space for the
A new 700 square metre pocket park will planted by the Neerim Road level crossing which will pack in greenery and much-needed space for locals to connect and recharge.
The Big Dig will involve a one kilometre trench excavated with the rail lowered beneath the road and tram line.
Piling works continue on the site, with more than 2100 of the 3000 piles in place before excavation of the trench can start.
Frankston Line trains will run express through the station with shuttles between Caulfield and Ormond stations connecting passengers to train services.
Removing the dangerous and congested level crossings at Neerim and Glen Huntly roads will reduce congestion for the more than 20,000 vehicles that use the roads every day where the boom gates can be down for almost an hour of the morning peak.
Two sets of boom gates will be gone for good when the trains resume, and new station opens in early August.
The Frankston Line will be level crossingfree by 2029 with all 27 dangerous and congested crossings gone for good, and 17 new stations built, changing the way locals live, work and travel.
Since our first major rail commission in 1977, TBH has undertaken over 250 separate commissions on rail projects, including:
– Trackworks
– OHW
– Signalling
– Stations
– Rolling Stock
– Maintenance
With experience and deep industry knowledge across the entire project lifecycle, TBH brings practical project controls and portfolio management skills to every engagement.
We provide the insights that enable informed decision making that de-risk projects.
tbhconsultancy.com
Western Australians now have another reason to catch public transport, with access to free all-day travel on the first Sunday of each month as part of a plan to attract more people to public transport and help ease cost of living pressures.
The State Government’s ‘Fare Free Sunday Sessions’ initiative, which began on June 4 to coincide with the WA Day long weekend, aims to encourage more people to use public transport on weekends, supporting local hospitality and entertainment businesses.
Based on public transport patronage figures over the past year, this equates to about 400,000 free trips across the network each year, with the hope of boosting that figure over the duration of the trial and beyond.
The free travel will apply to people using SmartRider cards, so the number of rides can be tracked and the two-year policy assessed.
SmartRiders are available at Transperth InfoCentres and selected retail outlets, and the Public Transport Authority will run a campaign in coming months to rollout more SmartRiders.
The initiative will complement the Government’s existing two-zone cap scheme, which has saved regular public transport users in the outer suburbs thousands of dollars in the past year.
Premier Mark McGowan said free public transport on Sundays would help to encourage
on the weekend, supporting local businesses while boosting use of trains and buses.
“The free offer will allow more families to experience more parts of Perth, without the hassle or costs of parking,” he said.
“As more of METRONET is built, delivering a once-in-a-generation expansion to Perth’s public transport network, this new free travel offer will entice more people to experience our world-class network.”
Transport minister Rita Saffioti said that in recent months, there had been a really strong bounceback in patronage after the impacts of COVID.
Marking the end of an era, the iconic Bayswater Bridge in Perth has been dismantled to make way for the new METRONET Bayswater Station.
The works to demolish the bridge took place over two days during a 26-day shutdown of the Midland and Airport lines, essential to carry out critical construction on the new station and Morley-Ellenbrook Line projects.
Works undertaken during the period included the demolition of the old train station and old bridge, as well as the relocation of 1.8 kilometres of track and rail systems onto the new, higher rail bridge.
The removal of the old station will allow for piling works for the final two rail bridges and connection for the Morley-Ellenbrook Line to start along Railway Parade. All concrete removed from the old bridge, along with steel supporting beams and steel reinforcement from the supporting walls, were recycled.
Old signage from the bridge was donated to the City of Bayswater and retained for historic value or repurposed for use by local businesses and community groups.
In addition to segments of the old bridge being incorporated in landscaping around the new station, a public art piece has been commissioned that will repurpose the existing LED low-clearance signage, to create an interactive audio-visual piece for the new station forecourt.
The new station precinct will also activate the area with a number of tenancy opportunities available at the eastern station entry for mixed uses, supporting a lively plaza for the local community to enjoy.
Transport minister Rita Saffioti said while it would come with a tinge of sadness for some, the removal of the bridge would be welcomed by many, especially truck drivers.
people to use public transport on weekends, whether it be to watch sport, catch a movie or dine out with family and friends,” she said.
“This in turn will help support the local entertainment and hospitality industry to rebuild after what has been a difficult three years.
“The aim is to get people used to the idea of catching public transport on weekends, taking the hassle out of driving and allowing them to relax and enjoy themselves while out socialising.
“I am confident that by getting more people to use public transport on weekends, it will also encourage more regular public transport usage during the week.”
“The old bridge will make way for the new 4.8m high bridge that will form part of the new METRONET Bayswater Station, which will be a focal point for our significantly expanded rail network,” she said.
“The new Bayswater Station will be the biggest outside of Perth City, servicing three rail lines including the Midland, Airport and future Morley-Ellenbrook Line.
“At project completion, the new Bayswater Station will become a key transport hub with three rail lines connecting our communities, new public spaces and extensive public art in place for the community to enjoy.”
The 100-year-old bridge, only 3.8m above the road, caught many inattentive truck drivers off guard over the years, with hundreds of tall vehicles crashing into it or getting stuck under it. It even had a dedicated website devoted to its accidents.
• High Bending Stiffness & Strength
• Low Thermal Expansion
• 100% Recycled & 100% Recyclable
• No Glass Fibres
• Design Life of 50 Years
• Impact & Sound Dampening
• Good Slip Resistance when wet
removed, and an existing overpass upgraded, in new designs released for the Marion Road–Anzac Highway to Cross Road project in Adelaide’s southwest.
The removal of the crossings is part of ongoing efforts to reduce congestion and will make travel in the area safer, faster and easier for people who use public transport, walk, cycle or drive.
The Australian and South Australian governments have each contributed $200 million towards removing the Glenelg crossings at Marion Road and Cross Road, Plympton, by constructing a tram overpass across both roads.
Currently, boom gates impact traffic flow for up to 20 minutes each hour, with around 30 trams travelling through the crossings during morning and afternoon peaks – affecting approximately 50,000 vehicles each day.
This causes significant traffic delays, resulting in traffic diverting through local streets and consequently increasing the risk of accidents and slowing the movement of public transport in this area.
As part of the work, a new tram stop will be built between Marion and Cross roads, which will include lifts and stairs on both sides.
The Mike Turtur Bikeway and shared use path will also be elevated, while the area underneath will be revitalised with new open space for public use.
It is anticipated the tram line will be closed for between six to nine months to allow for construction, with substitute buses running in its place.
Closing the line will mean the projects
and will allow these overpasses as well as the rebuild of the South Road overpass to be constructed at the same time, within the existing corridor.
This will significantly reduce the overall construction time and impacts that would otherwise be required if these projects were constructed separately.
As part of the project, the capacity of turning lanes will also be increased at the intersections of Marion Road and Anzac Highway, and Marion Road and Cross Road.
These upgrades will further ease congestion and improve travel times and safety.
Concept plans are currently being developed for the intersection upgrades and will be released shortly.
Federal infrastructure and transport minister Catherine King said the Australian Government investment in this project would ensure commuters can benefit from safer, faster and easier trips along these crucial traffic links for years to come.
“This project demonstrates our government’s commitment to supporting more efficient, resilient and integrated traffic and transport solutions for South Australians,” she said.
SA infrastructure and transport minister Tom Koutsantonis said it was well-known that removal of level crossings works.
He said the removal of level crossings reduced congestion and improved safety for everyone who drives, walks, cycles or catches public transport through the area.
“The Marion Road and Cross Road crossings are unique in that there are two crossings, and an intersection, all in close proximity.
flow easier and faster,” he said.
“An overpass will cut travel times and make public transport services a more attractive option for commuters. Trams will be able to go up and over the roads, and buses won’t need to stop at the boom gates.”
State Member for Badcoe Jayne Stinson said with her own office metres from the intersection, she had experienced the frustrating traffic snarl every day.
“A tram overpass is the best solution for us locals because it drastically reduces the need to acquire homes, provides greater cyclist safety and delivers open space to our community,” she said.
“I’ll also be supporting those affected by the construction, including the very small number of people requiring help to find new homes and business locations.”
Transport Department chief executive John Whelan said the exact timing of the project and other details, including where the trams would be kept when the Glengowrie depot becomes inaccessible, were being determined.
He said trams travelling through the CBD, to the Royal Adelaide Hospital and Adelaide Entertainment Centre, were not likely to be impacted — but several properties would be compulsorily acquired.
“There are only about three properties being acquired for the actual construction of the tram overpass. Being able to close that tramline temporarily has enabled us to minimise land acquisition,” he said. “We are very confident we will be able to run trams from around the parklands, through the city through to the Entertainment Centre.”
The New South Wales Government will carry out a comprehensive independent review into the whole Sydney Metro program, to determine how to salvage the current projects.
This goes beyond the scope of a review of Sydney Trains’ rail infrastructure and systems, to be overseen by National Transport Commission chair Carolyn Walsh.
Premier Chris Minns said that upon taking office only a few months ago, it had become clear that the challenges facing the Sydney Metros “are major”.
“The Sydney Metro Program has been plagued by significant cost overruns and significant time delays,” he said.
The review will be led by Mike Mrdak, an experienced public servant in the infrastructure, transport, regional development, communications and digital economy sectors.
He was a federal departmental secretary for more than a decade, including as head of the Infrastructure Department.
He will be joined by deputy chair Amanda Yeates, who was previously the Deputy Director General, Department of Transport and Main Roads in Queensland, where she was responsible for the state’s infrastructure program.
Initial early briefings sought by the Government have revealed:
• Sydney Metro West is estimated to cost $25.32 billion – a cost overrun of at least $12b
• Sydney Metro West is estimated to open in 2030 at the earliest – compared to initial Coalition estimates of mid-late 2020s
• The estimated full cost of building Sydney Metro City and Southwest is at least $20.5b
- This is up to around $9b more than the initial estimated full cost
- This is at least $2b more than the price tag most recently touted by the former government.
The Sydney Metro Review will examine delivery models, project governance and passenger impacts and the best way to resuscitate Sydney’s major transport infrastructure pipeline.
The review will also thoroughly evaluate the delivery of Sydney Metro to date, the current state of progress against delivery targets and make recommendations for getting the maximum value out of the project, including looking at better land use, urban renewal and better integration with the wider transport network.
It will be undertaken with a view to determining how to deliver a fully integrated, safe, accessible and reliable public transport system, not just Sydney Metro.
The review team has been asked to deliver a preliminary report to help inform the 2023 Budget process, with a final report to be delivered by the end of 2023.
The Terms of Reference will be available on the Transport for NSW website.
“We said would be honest and upfront with the people of NSW about the true state of projects we inherited,” Minns said.
“We know we have significant challenges. This review is about assembling the right
rescue team to come up with solutions to get literally get the metro projects back on track.
“We’re not interested in casting blame –we’re interested in finding solutions.”
Transport minister Jo Haylen said the government had inherited significant challenges on the Metro program and in transport.
“Given the significant investment in the Sydney Metro to date, and the importance of delivering improvements to the broader public transport system, an urgent independent review into the whole Sydney Metro project is appropriate and warranted,” she said.
Infrastructure Partnerships Australia chief executive Adrian Dwyer said it was sensible and prudent to take stock of a program of this scale, particularly with its importance within the broader network context.
“The Sydney Metro program is Australia’s biggest public transport build and will have a profound impact on the way Sydney’s whole transport system works for decades to come,” he said. “It’s important this infrastructure is delivered properly, with the right governance and laser-like discipline.
“NSW has the unique status as the lone state with two AAA credit ratings, and it’s important the Government is open to all solutions to maintain this status alongside an ambitious infrastructure pipeline.
“It is entirely possible to have fiscal discipline and a world class infrastructure program but it requires careful planning and absolute precision in delivery.”
We’re the leading provider of end-to-end rail and transport solutions in Australia and New Zealand. From designing and constructing transport networks to operating them, we’re transforming the way people travel and providing better connections across the country.
Every year, more than one million passengers travel on our networks. Our long-standing experience in mass transport means we know how to put together the right solution - from start to finish. Focused on the future of transport, we innovate today for the best outcomes tomorrow. From digital engineering to digital asset management, to targeting zeroemission transport modes; we’re in it for the long haul.
johnholland.com.au
For the first time in New South Wales transport history, trains have been running deep below Sydney Harbour as the Sydney Metro City & Southwest project enters its next exciting stage.
Transport Minister Jo Haylen said new metro trains are now travelling in the 15.5-kilometre twin metro railway tunnels, which extends the Metro North West Line from Chatswood Station to Sydenham Station, as part of a rigorous testing and commissioning program.
“This is an important milestone. We have always said we’d back good projects no matter whose idea it was – this is one of them and it’s what the Sydney Metro project looks like at its best,” she said.
“Having a train travel under our harbour is an exciting and historic first step but more importantly, it means that more people can catch a train through the city and it will improve the broader rail network once the City Metro is ready to take passengers next year.
“I want to make sure that the Sydney Metro project delivers genuine improvements to transport services like this for passengers and for taxpayers.”
This is the first railway crossing below Sydney Harbour and delivers a critical connection into the city from Sydney’s north. Next year, metro trains will move more people across the Harbour in peak hour than the Sydney Harbour Bridge and Sydney Harbour Tunnel combined, taking significant pressure off Sydney’s roads and existing rail network.
Sydney Metro chief executive Peter Regan said on-track train testing and commissioning would continue throughout 2023, ahead of passenger services starting through the Sydney CBD in 2024.
“The first stage of testing is completed at low speed, with trains manually driven at a maximum speed of 25km/ph,” he said.
“Gradually, we see the trains move into high-speed testing, where the trains reach a maximum speed of 110km/ph.
“Each train will also undergo acceleration and braking testing on the newly built track
People with hidden disabilities such as autism, dementia, chronic pain or anxiety can now have more confidence navigating the New South Wales rail network.
Transport for NSW’s Sunflower Program lead, Clare Appleby, said train travel can be challenging for many customers, including the estimated 138,000 people with a hidden disability who use the state’s rail network each day.
“As part of the Hidden Disabilities Sunflower Program, customers can get a free lanyard to wear while travelling, discreetly indicating they have a hidden disability and may require assistance,” she said.
“These Sunflower lanyards are now available at 20 stations on the intercity and regional
train network. They are already available at 14 Sydney stations.
“This is a simple way of helping station staff, train crew and other customers understand that someone wearing the green and yellow sunflower symbol might need a bit of additional care or patience, or even just a little extra time.”
Transport for NSW worked with Autism Spectrum Australia to develop training for staff to support them to help people with hidden disabilities use trains with greater comfort.
Around 90 per cent of Sydney Trains and NSW TrainLink customer service staff have undertaken the training. Once completed, staff can wear a Sunflower pin.
NSW TrainLink customer service attendant,
the program.
“I have autism and sensory issues, and it is awesome that through this program people like me are being heard and better understood,” he said.
“I love my Sunflower lanyard and wear my whistle on it. It is important for customers to see some staff wearing a lanyard too, as it demonstrates we are an inclusive workplace.”
The Hidden Disabilities Sunflower program is a global initiative across 39 countries, where staff are being trained in workplaces such as airports, supermarkets and emergency services.
In Australia, it is estimated one in five people have a disability and of those, 80 per cent have a hidden disability.
mini soundprotection wall with high absorbing surface
The new version of the STRAILastic_mSW adds a higher wall to the product range. This version is used for train speeds of up to 120 km/h.
¬ No foundation required for installation
¬ easy and quick installation
¬ Short delivery times > noise hot spots can be supplied with products quickly
¬ Closer to the noise source than any other sound protection
¬ Break-proof due to bre-reinforced rubber compound with a cover layer of virgin rubber > UV and ozone resistant
¬ No material fatigue caused by vibrations or pressure and suction forces
¬ No problems with oversized loads
Due to the higher design, it gains even more e ect in the area of the wheel.
STRAILastic_mSW 730 is fastened to both rails with an insulated, decoupled substructure or directly in the subsoil using ground screws.
STRAILastic_mSW 730 > mini goes maxi.
1. STRAILastic_mSW 730 new version of the mini sound protection wall
2. STRAILastic_IP the infill panel
3. STRAILastic_mSW the established mini sound protection wall
4. STRAILastic_A inox 2.0 rail dampers
For decades, railway stations have simply been places where passengers could get on and off trains, and/or goods loaded or unloaded.
But they are so much more than that, as cities across Australia start to expand upon the potential of linking upgraded interchanges
with innovative and diverse businesses and high-quality public spaces.
The precincts are geared towards embracing design, sustainability and connectivity, ultimately transforming them into centres for the jobs of the future and economic growth.
One such state championing the concept is Western Australia, where its largest integrated transport and land use program, METRONET, is currently being delivered across Perth.
The Government initiative, led by Transport Minister Rita Saffioti, firmly believes that investment in rail will act as a catalyst for land use change in more than 8000 hectares of land within walkable catchments around METRONET stations.
“To contribute to the sustainable growth of metropolitan Perth, METRONET station precincts need to be designed and developed as inviting, active, safe and inclusive places for their local communities,” she said.
“They also need to offer housing, services, employment and recreation opportunities that benefit from access to high quality public transport.
“METRONET is the catalyst to turn over land around new stations to desirable places for investment in housing, jobs and services.”
Under the plan, areas around stations are called ‘station precincts’, which are generally the area within one kilometre of each station (around a 10 to 15 minute walk).
Each precinct will take a different approach to how it grows and changes over the next 30 years. While the long-term vision is outlined by the precinct planning, implementing the plans will involve private and public sector stakeholders.
“Station precincts are great locations for future developments of housing, jobs and community services as they make the best use of the State Government’s investment in transport infrastructure,” Saffioti said.
“Over time, these areas will become higherdensity active urban places, offering a range of living, employment, entertainment and recreation opportunities while the surrounding suburbs will remain largely ‘low-density residential’ in character.
“Not all station precincts will be the same. Some are in new growth areas and will be planned and developed from scratch, while others are in existing urban areas with established local communities and infrastructure in place.”
To help guide the type of place each
Train station precincts have the potential to enhance the liveability of urban areas and provide a range of benefits to residents and visitors.Investment in rail and stations across all METRONET projects in WA will be the catalyst to turn land around new stations into desirable places for people to live, work and play.
identified the following station precinct types:
• The City Centre Perth central business district (CBD): This has the highest concentration of jobs and services in the metropolitan region, and is served by three major railway stations to cater for the high volume of commuter traffic
• Neighbourhood Centre Neighbourhood centre precincts: These are predominantly medium to higher density residential in character with retail and services that meet the daily needs of the local community
• Strategic Centres: The metropolitan region has a number of existing and planned strategic centres which are key locations for jobs, services and higher density housing outside of the Perth CBD
• Specialised Centres: These precincts have a predominant focus on a specific activity, such as education, health, sport, science and innovation, or regional transport
• Town Centres: These precincts have increased density and a diversity of housing types, along with a retail and service centre that supports its district catchment and local employment
• Transit Nodes: These perform a primary transport interchange function, and generally include bus to rail transfer, station parking and drop off facilities
By adding more than 70km of rail and up to 18 new stations to Perth’s passenger rail network, the Government says people will have more opportunity to leave their car at home and catch the train to work, to go shopping, to watch their favourite team play on the weekend, to catch a flight from the airport, or to meet up with friends.
The current phase of METRONET involves
and construction of METRONET transport infrastructure, with progress already proceeding at pace.
METRONET is working with local governments, local communities, state government agencies and the private sector to establish the planning and development frameworks to enable the development of METRONET station precincts.
0-5 years: After the new stations are operational, the focus will transfer to building local infrastructure needed to support the station precinct’s development.
During this phase, METRONET will work with affected local governments, state government agencies along with the private sector to identify early development and activation opportunities.
This phase will also see the early stages of investment in public spaces to improve the comfort, amenity and attractiveness of METRONET’s station precincts.
0-15 years: Growing private sector interest will drive increasing development investment in METRONET station precincts.
This phase will see the start of greater housing product diversity catering for different family and lifecycle needs.
With the local community growing, an increase in population-driven employment and community services will occur.
Continued investment in public spaces will give the precinct an identifiable character and sense of place, making it more attractive for investment in strategic employment.
15-30 years+: The property market in METRONET station precincts has matured to
residential and commercial development.
This phase will see a continued consolidation of housing, jobs and services in close proximity to high quality public transport infrastructure. METRONET station precincts will be the focus for sustainable growth of the metropolitan region.
The METRONET Office will plan transport infrastructure to the point of funding decision by Government.
Once the project has funding approval, the Public Transport Authority (PTA) is responsible for building the transport infrastructure.
Saffioti said the transition from transport infrastructure planning to delivery is clearly defined, with the entire process typically taking up to five years.
The process for planning and delivery of the wider station precincts is less straightforward, with limited development typically occurring in the short term and full build out only achieved in the long term (30+ years).
Development responsibility will be shared across multiple State Government agencies, local governments and the private sector, which will require a high level of coordination to achieve successful outcomes
To help provide a boost for the projects, the Government is currently calling for applications for its inaugural $80 million Infrastructure Development Fund to remove barriers for new housing developments across WA.
The Fund was established to unlock land and facilitate development and has three streams – a targeted apartment rebate, funding to unlock priority infill precincts and funding to support the delivery of regional
worker accommodation. Saffioti said feedback from the development industry indicated that the cost of providing water, sewerage and electricity services was a considerable constraint to developing land for new housing.
“Up to $10,000 per multiple dwelling is available to support METRONET Station precincts, new apartment developments in selected local government areas, and Housing Diversity Pipeline (HDP) sites,” she said.
Under the HDP, a number of proposals received for nine State Government-owned landholdings are currently under assessment including a combination of long-term ground lease, partnerships and build-to-rent models.
The Fund can support the cost of servicing these large parcels of land that have potential to deliver medium to high density housing close to existing and new train stations.
Funding has been allocated equally with $40 million available for metropolitan and regional WA projects.
Apartment developments receiving funding under the program will be required to commence within two years of approval and complete construction within four years.
A second funding stream is available to tackle more complex infrastructure
local governments can also apply for funding through a third stream for proposed key worker accommodation projects within (or in the vicinity of) an existing regional centre, townsite or community.
Applications are open for 18 months, until September 6, 2024. For eligibility guidelines and to apply, visit https://www.wa.gov.au/ infrastructure-development-fund.
“Our Government is committed to ensuring that we provide more housing choice in close proximity to good public transport links, employment opportunities and key community services,” Saffioti said.
“This includes maximising the potential of new housing in priority infill locations, METRONET station precincts and key regional centres and we want to support development proposals that may otherwise be constrained.
“This Infrastructure Development Fund will reduce costs for the provision of water, sewerage and electricity services, unlock development potential and most importantly help grow the availability of affordable housing in WA.
“It will create a pipeline of medium to high density housing over the next two to five years, help secure regional workforces and
screen production facility, within the precinct of the new Malaga train station, to be built as part of the Morley–Ellenbrook railway line and due to open in 2024.
The site would provide purpose-built sound stages and other onsite screen production facilities to enable the production of film, TV and screen projects.
The development application includes architectural designs and technical reports for traffic, waste and bushfire management, and landscaping.
“The new proposed site, in the vicinity of the Malaga METRONET station precinct, has enabled the developers to undertake the necessary plans and assessments to complete the application,” Saffioti said.
“The site is part of the recently approved Planning Control Area (PCA) which is in the vicinity of future strategic community and employment hubs in Perth’s growing northeast with two high-frequency train stations, homes and businesses, and now the potential for a one-of-a-kind screen production facility.
“The PCA will enable coordination of all upcoming development within this location to ensure that the corridor benefits from the State Government’s significant
Transport Minister Rita Saffioti (second from right) helps open the Nicholson Road IGA, the first new supermarket to be built in a METRONET precinct.stations and new stations at Nicholson Road and Ranford Road.
The project is the catalyst for medium to long-term redevelopment in the area, with businesses already starting up.
For example, a new Tucker Fresh IGA has opened within the Nicholson Road station precinct, a short walk from the future station.
About 26 minutes from Perth by train, the station’s forward-looking design will meet passenger needs from day one of operations and support future long-term development in and around the suburb of Canning Vale.
The Property Council of Australia has been quick to welcome the initiatives to embrace more mixed used developments to create activated precincts at the train stations, and also plans to introduce light rail connecting Curtin University and UWA.
Council WA executive director Lino Iacomella said rethinking land use in the areas had the potential to significantly improve the quality of life for those living in the locality and those using the stations.
“Not only will stations be better connected to both the airport and the CBD, but on a practical level, the ability for a working parent to drop the kids at the adjacent day cares will save precious time and encourage people back to work, while having shops just metres from
and draw people to the area,” he said. “Similarly, plans to connect two of WA’s largest universities, Curtin and UWA with a light rail line will improve east-west connectivity and access to the amenities associated with each of the institutions as well as bring students into the CBD.
“Ultimately, strong communities are built through the integration of practicality, connectivity and vibrancy. These mixed-use developments will significantly add to the local area, making them places people want to live.
“Creating precincts around travel nodes such as train stations will ensure local area thrives, attracting residents and creating long term employment opportunities.”
Over in Melbourne, the Victorian Government’s Suburban Rail Loop (SRL) East project is helping deliver Melbourne’s vision of a city of centres, with investment, new local projects and urban planning in the broader precincts around new SRL stations helping to reshape how Melbourne grows in the decades ahead.
As the city expands to a host nine million people by 2056, the SRL will be crucial to ensuring the public transport network can deliver an extra 11.8 million daily trips and manage an 80 per cent increase in private
Work is continuing rapidly, with sites being established this year in Burwood, Glen Waverley, Monash, Clayton, Box Hill and the stabling facility at Heatherton, as crews pave the way for tunnel boring machines and prepare for construction of the six new underground train stations.
One of the most exciting projects is the Monash Precinct Network, whose founding members include Monash University, CSIRO, the Australian Synchrotron and the City of Monash.
Monash is already the largest hub for employment and innovation outside Melbourne’s CBD, and the SRL station at Monash will deliver a direct train connection to the area for the first time - turbo-charging jobs growth.
The broad area around the Monash SRL station will boom, with an additional 19,000 jobs when SRL East opens. By 2056, jobs are expected to increase by almost 350 per cent.
The station will improve access to worldclass education, health and research facilities, delivering important transport connections – spurring even more economic growth, employment and housing and helping to attract and retain leading global firms.
SRL is also funding a series of free local events for the Monash Precinct Network as part of the SRL Community Projects Fund.
conversation on three key topics to inspire and connect local researchers and organisationsJobs of the Future, Mobility of the Future and Innovation and Materials of the Future.
Construction of SRL East is underway, with works starting soon in Monash. Trains will be running by 2035.
More than 800 jobs will be created through the initial early works package for SRL East, and a recruitment drive has been launched to attract the best people for the job across a diverse range of fields including engineering and technical specialists, trades, and roles in sustainability, health and safety and importantly, urban planning.
The project will expand Victoria’s skilled workforce over the long-term, with about 14 per cent of hours to be completed by apprentices, trainees, and cadets during the first phase of construction.
In a Victorian first, girls studying science, technology, engineering, and math (STEM) subjects will be able to strengthen their career prospects with an innovative school-based SRL East traineeship program, to be delivered in partnership with Laing O’Rourke, Head Start and Holmesglen TAFE.
The group of Year 11 and 12 students will gain hands on experience on the SRL East project two days a week over the two-year program - supporting more women to pursue careers in the construction industry.
A study has found that more than a third of new dwellings built across Australia’s four largest capital cities over the last 15 years were built within a kilometre of a train station, in what is a trend that has been steadily increasing over the same period.
Of the 1.5 million new homes built in Sydney, Melbourne, Brisbane, and Perth between 2006 and 2021, 35 percent were within that distance of a train station, a recent analysis by KPMG Australia discovered.
According to KPMG urban economist Terry Rawnsley, train stations have had a significant impact on housing supply.
“Our analysis highlights that long term precinct planning policies can have a positive impact by clustering jobs and services near a major train station,” he said.
Between 2006 and 2021:
• Greater Sydney produced 430,000 additional dwellings, with 49 percent located within one kilometre of a train station
• Greater Melbourne produced 565,000 additional dwellings, with 35 percent located within one kilometre of a train station
• Greater Brisbane produced 273,000 additional dwellings, with 28 percent located within one kilometre of a train station
• Greater Perth produced 239,000 additional dwellings, with 16 percent located within one kilometre of a train station
• Housing development within one kilometre of a train station in Greater Sydney grew particularly strongly between 2016 and 2021, with almost 110,000 new dwellings compared with less than 60,000 in the previous five-year period
• In Greater Melbourne, 83,000 new dwellings within a kilometre of a train station were developed between 2016 and 2021, up from 70,000 in the previous five-year period
• In Greater Brisbane, 39,000 new dwellings were built within a kilometre of a train station, compared to 21,000 in the prior period
• Greater Perth saw 11,000 new dwellings within a kilometre of a station built
between 2016 and 2021, down from 14,000 in the prior five years.
“New rail line developments were not just new apartments but also detached homes and townhouses, with rail networks covering the CBD, middle ring and greenfield growth areas,” Rawnsley said.
“Across the four cities, within one kilometre of a train station of the new dwellings, 65 percent were apartments, 24 percent semidetached and 12 percent detached. This is compared to the overall mix of dwellings of 31 percent were apartments, 46 percent detached and 23 percent semi-detached.
“Rail lines constructed over the past two decades have opened up new development fronts.
“Examples of these new rail lines include the Mandurah Line in Western Australia; rail extensions on the Gold Coast; the Regional Rail Link in Victoria; and the Northwest Rail Link in Sydney.”
Greater Sydney’s long-term focus on centres such as Parramatta, Penrith, Campbelltown and Liverpool, have created a ‘polycentric’ pattern of housing development around the city’s train stations, Rawnsley said.
In contrast, Greater Melbourne has experienced much more of a monocentric development pattern with the inner suburbs.
Greater Brisbane and Greater Perth shared a similar pattern with train station development concentrated in the inner suburbs and in some coastal locations.
“The analysis shows that the housing markets vary within each city and that in the area surrounding each train station there is a need for appropriate land use planning and place-making initiatives to ensure that housing, local services and infrastructure is provided to help attract new housing developments,” Rawnsley said.
Because of the increased importance technology plays in various projects, some of the traditional project management and project controls are less effective; and as a result, it’s highlighting weaknesses in how the rail industry approaches projects.
Breschkin tells Rail Express that the management of technology development has now become a critical consideration.
“In my state of Victoria, rail projects are transitioning to new signalling and communication systems, and the successful management of these aspects rely less on traditional planning controls and more on controlling the technology development and integration,” he said.
“For example, in Melbourne, a new ticketing system – likely to be developed and rolled out – will be a heavily ICT (information and control technology) focused project.
“Then there’s the new train control systems, which will allow trains to operate in the new Melbourne Metro tunnels.
“In addition, there are several back-of-house legacy systems that are approaching end-oflife that are yet to be upgraded.
“The success of these projects will rely on the scoping, planning, monitoring and management of risk for the systems and software aspects needed for these projects.”
The combination of the time, cost and risk aspects is what leading project delivery specialist TBH defines as Integrated Project Controls.
“Traditionally, given our depth of experience working across a range of sectors and services
from planning and project controls in the construction industry and applied that to the ICT industry,” Breschkin said.
The result has been improved rigour, a standardised process and approach to early warnings, and the mitigation of delays for ICT projects.
Now, with ICT adopting new delivery methodologies such as agile or hybrid, there are some lessons that can be learnt in terms of ways to approach projects and dealing with risk – that could now benefit the construction industry.
“In rail, there’s a high priority placed on safety and reliability. With both being such a high priority, the consequence is that a traditional linear design, development and construction process is typically followed, accompanied by a long lead time before testing at the end of the project,” Breschkin said.
“That is, once you clear all the quality assurance hurdles – you finally give it a go – only to find that it doesn’t meet the end users’ needs.
“This is the opposite to recent approaches in ICT, which relies on rapidly developing systems to gather the end users’ feedback as early as possible.
“It’s only when the users get involved, that you find out how well the system will operate.
“In my experience, what you tend to find is the earlier you can get things in front of the user, the less rework and the quicker you can pivot towards a system that is functional and delivered in a timely manner.”
In this regard, the biggest challenge rail
software platforms online fast enough in a test environment (or some sort of parallel operation), to gather and incorporate that early feedback. The reduction in rework and lost time alone should make this an attractive consideration for rail.
Another challenge are the new tools and processes required to manage both the construction and ICT aspects of the projects.
In construction, there are the traditional time and cost management tools such as Primavera P6 and SAP.
“Traditionally, the project controls team will manage and maintain the project controls information using these tools, but may also rely on information provided in various formats, by the site personnel or subcontractors, who provide progress updates or further detail to coordinate works,” Breschkin said.
“When managing the ICT aspects of rail projects, the projects controls teams will have to become proficient in managing the scope, productivity rates and risk allowances within the ICT control tools.
“The essential aspect will be knowing the limitations of those tools and therefore, being able to integrate that information back into the traditional control tools to manage dependencies and forecast the project completion.
“With degrees in both Engineering and Computer Science, I’ve been fortunate enough to leverage both – as I have spent half my career in ICT projects and half in major infrastructure projects.
“I have benefitted from this experience with exposure to a variety of project controls tools and processes.
“This has helped me to plan and control both types of projects and also be able to successfully manage the respective risks when dealing with both in the same project.”
TBH is in a unique position to be able to help integrate both approaches to get the best out of the new challenges in the more integrated ICT and physical construction projects in the future.
Rail projects have transitioned from a focus on the physical construction to becoming an integration between construction and technology. Director of business management consultants TBH, Robbie Breschkin, reflects on what this means for the success of projects.TBH director Robbie Breschkin. New train control systems will be needed for trains to operate in the Melbourne Metro tunnels.
Freight transport, in particular rail, offers a unique opportunity to play a major role in that emissions target. Rail has been the cornerstone of the global transportation system and economy for more than a century – moving billions of tons of freight and billions of people every year.
The Australian Government has fully adopted the ‘55 by 35 target, as a key milestone on the way to net zero. This is a target set by the Australian Energy Council’s economy-wide interim target of a 55 per cent reduction in emissions, by 2035. It is an ambitious target, which requires identifying and investing in industries that can make a substantial reduction in emissions.
Wabtec Senior Regional Vice President, South East Asia, Australia and New Zealand, Wendy McMillan, affirms that rail represents the most cost-effective, energy-efficient, and safest mode of moving people and freight on land.
“Moving freight by rail instead of trucks lowers greenhouse gas emissions (GHG) on average by 75 per cent per year, which will be imperative to achieving a sustainable transportation network,” she said.
The combination of Wabtec’s product portfolio and digital intelligence solutions complement each other to help achieve the sustainability goals of the Government, community and industry.
“It is an exciting time to be in rail,” McMillan said. “The industry is on the verge of new technological breakthroughs that will advance the journey to clean, sustainable rail operations with locomotive fleets powered by batteries, biofuels, or hydrogen. These alternative power sources hold great promise for the railways decarbonisation strategies and ambitions.”
There are significant incentives for decarbonisation with fuel being the second largest operating cost for freight users.
The emissions reduction and benefits also are substantial. For each diesel-powered locomotive converted to alternative energy sources up to 3000 tons of CO2 per year can be eliminated.
Wabtec is already leading the industry in battery-powered solutions. The company’s FLXdrive is the world’s first 100 per cent, batterypowered heavy-haul locomotive.
with BNSF Railway in California. Wabtec has commenced commercial production of the FLXdrive and three Australian mining operators –Roy Hill, Rio Tinto and BHP – will be among the first customers to operate the battery locomotive.
To advance the development of this technology, Wabtec and General Motors announced in 2021 that it would collaborate to develop and commercialise GM’s Ultium battery technology for Wabtec locomotives.
The two companies also are looking at eventually applying HYDROTEC hydrogen fuel cell systems on locomotives.
“This collaboration advances the two companies’ shared vision of a zero emissions future in transportation,” McMillan said.
“Wabtec will bring its expertise in energy management and systems optimisation to develop a solution for heavy-haul locomotives that takes full advantage of GM’s advanced technologies. We can accelerate the industry’s path to zero-emission locomotives by leveraging these two important propulsion technologies.”
Biodiesel and renewable diesel are also important to reduce transport emissions. Liquid fuels like biodiesel and renewable diesel hold a similar amount of energy in the 19,000-litre tank as petroleum diesel, while reducing the GHG emissions significantly.
Biofuels are the quickest and easiest way to reduce the carbon impact of diesel locomotives with minimal updates to the locomotives. This means that railways can use their existing locomotives and existing infrastructure, while still reducing GHG emission significantly.
Wabtec is working to provide an engine compatibility statement that gives its customers as much fuel flexibility as possible.
Customers in Australia have access to different
GHG emissions as much as possible.
Wabtec is working with fuel manufacturers and is looking at the market to project what likely blends will be commercially.
THE HYDROGEN SOLUTION
Wabtec also is focused on hydrogen. The company is working on a dual technology strategy with fuel cells being one path and enhancing the existing internal combustion engines in locomotive to burn hydrogen being the other.
“We envision both paths will likely to be used in the future,” McMillan said. “We are working with GM on fuel cells given their experience and expertise with the technology. In parallel, Wabtec is working with Argonne and Oak Ridge National Labs in the US on burning hydrogen in locomotive engines.”
Wabtec projects that the economics on hydrogen will be viable later in the decade and will be commercialised as both a retrofit and a new unit option. The company anticipates the cost and performance of fuel cells will dramatically improve over the decade, while the cost of green hydrogen will reduce and become more available over the same period.
“Wabtec has a clear path to power new locomotives – and repower existing locomotives – with batteries, biofuels, hydrogen internal combustion engines, and hydrogen fuel cells,” McMillan said. “It’s part of Wabtec’s vision for the rail industry to play a key role in building a clean energy economy and will enable the reduction of up to 300 million tons of global carbon emissions per year.”
Being a market leader in technology solutions for the decarbonisation of the rail sector around the world is, and will continue to be, one of Wabtec’s highest priorities.
As the world’s foremost rail technology company, Wabtec is developing solutions that provide increased efficiency and emission reductions.Wabtec is leading the industry in battery-powered solutions.
Alstom RS has three key manufacturing sites in Australia and multiple depots. These sites play a critical role in Alstom’s operations, providing engineering, manufacturing, and maintenance services for a range of projects
One of Alstom’s significant projects in Australia is the supply of rolling stock and maintenance for Sydney’s Metro North West Line. The new metro system, which opened in 2019, has 36 kilometres of dedicated track, and is equipped with Alstom’s SIX-car
Working in collaboration with Metro Trains Sydney, the Metropolis trains operate using CBTC and offer a comfortable, safe and reliable travel experience for passengers.
“This was the first CBTC project of its kind providing one of the most efficient and reliable services Australia has ever seen. The trains run
In addition to the Metro North West Line, Alstom is also underway in producing the Victorian X’Trapolis 2.0 trains which will be manufactured in Dandenong and Ballarat, while the Victorian Next generation Trams are to be produced out of Dandenong.
Other rolling stock contributions include the NGR suburban trains in Queensland, VLocity DMU Suburban trains in Victoria, Metro ASuburban trains in South Australia and B and C series train sets in Western Australia.
“Our contribution to passenger rail is marked widely across the country and we have established ourselves as a trusted partner in the development of sustainable, innovative mobility solutions for local communities,” Godin said.
“We are proud of our current progression and influence across the industry and as one team, are strongly committed to working with our partners
As a national leader in sustainable mobility, Alstom holds a great responsibility towards its customers, partners, employees, passengers and ultimately society as a whole, to help the world transition towards a future driven by energy-efficient transport solutions.
At the forefront, Alstom incorporates advanced global innovations into its local solutions. This includes ongoing vigour to provide greener mobility solutions to its customers.
Alstom’s eco-design priorities focus on energy efficiency, recyclability, noise reduction, CO2emissions reduction and end-of-life management. While improving environmental performance, the company’s solutions give high-quality operating performance while lowering maintenance costs.
This is evident at Alstom’s Dandenong manufacturing facility in Victoria where Godin spends a lot of his time.
As Alstom’s hub of rolling stock manufacturing, the site is bustling with activity.
The manufacturing area utilises state-ofthe-art equipment and processes.
Currently Alstom is assembling trains and trams on site, including the Adelaide EMUs, VLocity trains and setting up to manufacture the Next Generation Trams and X’Trapolis 2.0 car body shell.
There is also a dedicated testing and commissioning area along with maintenance and servicing bays for rolling stock overhauls and existing fleet upgrades.
The company is committed to implementing strict measures in production to ensure the performance and safety of their people and vehicles, as well as exceptional compliance with industry standards.
The site is one of Australia’s only end-toend rail manufacturing facilities, playing a vital role in the development and production of rolling stock for the Australian and global markets, alongside innovative and sustainable transport solutions to meet the ongoing needs of modern commuters.
“Dandenong has been home to manufacturing in Alstom for many years and our team are continually seeking out ways to be more efficient and sustainable, not just in our rolling stock production but also how we operate day-to-day on site,” Godin said.
A key example of this is the exploration into using water-based paint solutions. Unlike traditional solvent-based paints, waterbased paints use water as a carrier for colour particles, significantly reducing harmful emissions that damage the environment.
“This approach presents current technical challenges, such as a short shelf life and strict requirements for application control, including humidity and temperature.,” Godin said.
“However, our team are committed to overcoming these challenges and ultimately delivering an innovative and sustainable product that has minimal environmental impact.”
The site is also committed to finding sustainable solutions in its production processes, and reducing its reliance on fossil fuels.
The company is currently exploring the installation of solar panels in Dandenong as a way to generate cleaner energy.
“We are currently seeking consultation from other companies on innovative solutions to further reduce our energy consumption and have just replaced our standard lighting across our Dandenong facility with more energyefficient systems.,” Godin said.
“By taking steps towards renewable energy and energy-efficient practices, we are demonstrating our dedication to sustainability and reducing our overall environmental impact.”
The VLocity fleet, built by Alstom, is a continually reliable and innovative rolling stock solution that has revolutionised regional passenger rail in Australia since 2005.
It features cutting-edge technology, including lightweight materials, regenerative braking systems, and advanced propulsion systems, which allow for faster, more efficient and sustainable travel.
“The success of the VLocity fleet has been remarkable, delivering significant improvements in reliability, comfort, accessibility and overall safety for regional commuters across Australia,” Godin said.
The fleet design has evolved overtime with the company looking at ways to make the design more cost-efficient and sustainable.
Recently, Alstom worked with its local supplier, Cummins, to develop a powersaving initiative referred to as Paralleled Gensets. This new engine technology provides significant benefits in terms of fuel consumption and maintenance requirements.
“Paralleled Gensets involve the use of multiple engines (three-phase power with one set on every carriage) that work together to provide power to the train, rather than relying on a single engine,” Godin said.
means that the workload can be distributed more evenly, reducing wear and tear on individual components and extending the lifespan of the fleet.
The Parallel Genset solution is designed to be modular, which makes it easier and more cost-effective to replace individual components as needed.
This innovation was delivered in 2021 and has seen drastic benefits creating the new standard for all vehicles.
As well as this, the VLocity fleet has undertaken multiple weight reduction initiatives to be more sustainable in its production and overall fuel consumption.
The VLocity fleet is a prime example of Alstom’s commitment to providing pioneering and sustainable transport solutions that meet the needs of modern commuters, while also helping to drive economic growth and development in regional areas.
Over in WA, Alstom’s Bellevue manufacturing facility is producing the new C-series railcars which has brought local
components that are delivered out to the production line.
These units have numerous benefits, including improved safety for workers, removal of cardboard packaging, reduced packaging waste, and high customisability depending on the requirements of each station.
“The trolley comes pre-kitted by the vendor with change configuration options depending on the needs of the station. This pre-kitted way of working will save more than 1500 cardboard boxes per train,” Godin said.
By using line side returnable stillages, Alstom is able to reduce waste and improve efficiency in its production processes.
The stillages are designed to be durable and long-lasting, making them a sustainable and cost-effective solution for the company’s manufacturing operations.
This is just one example that by investing in sustainable solutions like these, Alstom is not only improving its own operations, but also contributing to a more sustainable future for the rail industry as a whole.
Paralleled Gensets involve the use of multiple engines that work together to provide power to the train.by Link Asia Pacific (LAP), specialists in selling technical products that provide a competitive and compelling advantage to various Australian and New Zealand industry sectors.
As LAP business development director Gerhard Klooster explains, global warming has forced nations to rethink and change their operations.
“For example, the Australian Government introduced the Climate Change Bill in June 2022, legislating the nation’s commitment to reduce carbon dioxide emissions by 43 per cent below 2005 levels by 2030, and net zero by 2050,” he said.
“Responsible companies are implementing new strategies now to reach these targets.
“Plastic pollution has also become one of the most pressing environmental issues, as increased production of disposable plastic products exceeds the world’s ability to deal with it.
“Plastic waste can be dumped into landfill, incinerated, or recycled. The best solution is to recycle plastic waste into durable, lasting products, which can be recycled into new products in the future, such as the sleepers.”
Klooster said deforestation was another problem. “It makes no logical sense to cut down trees, convert them into timber sleepers which slowly rot away, only to replace them after eight to 15 years with new timber sleepers,” he said.
“In addition, recent bushfires and the ban on chemical treatments result in higher prices, longer lead times and lower life expectancy of timber sleepers.
“In a circular economy, things are made and consumed in a way that minimises the use of the world’s resources, cuts waste and reduces
carbon emissions. Products are kept in use for as long as possible, through repairing, recycling, and redesign – so resources can be kept in the economy and reused.”
The KLP hybrid polymer sleepers are a perfect representation of the circular process. At their end of life, the polymer and steel can easily be separated and recycled into new KLP sleepers.
Results have shown that here is also a 67 per cent reduction in the CO2 footprint by using recycled polymer, instead of virgin materials.
“An added benefit is that big railway sleepers made from recycled plastic will not break down into microplastics as easily as small consumer items like cups, bottles, cutlery and bags,” Klooster said.
“Laboratory tests confirm that the ductile KLP polymer formulation provides an extraordinary ability to withstand abrasion when bedding into the ballast.
“The encapsulation of steel rebar in this UV-stabilised ductile polymer prevents cracking under high axle loads or becoming brittle due to the harsh Australian sun. This ensures that the encapsulated steel does not rust.”
KLP sleepers incorporate solid steel rebars (encapsulated in ductile polymer) across the length of the sleeper (see page 13).
The steel rebar provides high bending stiffness and low coefficients of thermal expansion.
Polymer without the required level of reinforcement is strong by itself but will bend and plastically deform under operational loads.
“Steel’s low coefficient of expansion
achieves many benefits. It maintains the required gauge across high ambient temperature variations, and this dimensional stability also supports reliable signalling mechanisms, minimising bulging of sleepers in the sun which reduces abrasion,” Klooster said.
“The dampening properties of polymer allow for low ballast beds with minimal abrasion, offering solutions where track height must be kept low, such as overhead electrification and tunnels.
“Since KLP does not contain glass fibres, there is no need for special respiratory PPE. It can be easily milled, drilled, cut to length, and installed, just like timber.”
KLP’s ductile “High-Strength” polymer (specified for Australian applications) is made from specifically selected industrial and postconsumer waste.
Effective quality control on raw materials ensure that the specified properties are consistently obtained.
“Using recycled materials prevent these used plastics from being incinerated or going into landfill,” Klooster said.
“KLP products are primarily aimed at replacing timber sleepers, thereby preventing the deforestation by cutting down of trees.
“The trees can thus continue their valuable function of converting carbon dioxide into oxygen and storing the carbon.”
Internationally, 18 countries area benefitting from KLP products, with first installations in operation since 2006.
Local registered training operators like KiwiRail and TasRail have confirmed their satisfaction with KLP since 2018.
Transport is the source of a quarter of global carbon emissions, and in Australia, the transport sector contributed to 18.3 per cent of the country’s emissions in 2020.
As governments around the world prioritise achieving net zero emissions targets, the rail industry can play a critical role in supporting the transition to sustainable transport solutions.
Siemens Mobility is playing a vital role in the transformation of the transport industry in Australia by providing end-to-end solutions to help create a better tomorrow.
The freight industry is a major contributor to carbon emissions globally, and it is crucial that the sector works together towards a carbon zero future. This is particularly so in Australia, where approximately 10 per cent of Australian rail networks currently operate on electric power, while the other 90pc are still relying on diesel fuel.
Decarbonising the freight industry is not only crucial for reducing carbon emissions, but it also has economic benefits. With the increasing demand for sustainable transportation, there is an opportunity for freight and heavy haul companies to gain a competitive advantage by adopting cleaner and more efficient transportation methods.
According to Siemens Mobility Chief Executive Officer for Australia and New
Zealand, Raphaelle Guerineau, decarbonising transport lies at the heart of achieving net zero carbon emissions.
“In comparison to the estimated 50 per cent of European rail lines that are fully electric, Australia still has a long way to go in order to achieve net zero carbon emissions by 2030,” Guerineau said.
“But for many rail operators, the scope and the scale of carbon neutral rail projects are often exceeded only by the magnitude of the investment decarbonisation requires.
“In addition to time, resources and financial capital, retrofitting entire rail networks requires highly specialised knowledge, tools, and technology for effectively making rail systems more sustainable and more efficient.”
Siemens has long been regarded as a leader when it comes to sustainability. The company has consistently been ranked in the Dow Jones Sustainability Index as one of the most sustainable companies in the world.
Siemens was the first major industrial company committing to neo-zero in its own
Siemens Mobility is playing a crucial part in helping decarbonise the transport industry.Siemens Mobility has developed the next generation of hydrogen trains. How the Mireo uses electrification to decarbonise.
operations by 2030. In 2021, Siemens introduced the DEGREE framework based on six fields of actions around the topics of environment, social responsibility and governance.
“With rail technology advancing so rapidly, Siemens has had its hand in nearly every niche, currently trending, up and coming, or ‘still under review’ sustainability solution,” Guerineau said.
“From renewable energy solutions like solar and wind power, to hydrogen fuel cell technology and hydrogen storage to digitalisation, to electrification, artificial intelligence, and fully autonomous machinery.”
Guerineau said that as a world-leading technology provider and an active presence in the rail industry, Siemens Mobility owns a sense of responsibility for assisting with global decarbonisation efforts.
“I believe that we have an important role to play in supporting the government and the rail industry in achieving decarbonisation targets,” she said.
“The Siemens Mobility portfolio of digital and industry 4.0 technologies offers smart rail capabilities that essentially provide rail operators with a blueprint for achieving net zero carbon emissions in the future.”
In particular, Guerineau notes that digitalisation has shown great potential for scaling decarbonisation.
“The acceleration of digitalisation within the rail industry has continued to drive decarbonisation forward and transform the way operators can manage rail assets and envision future networks,” she said.
“It leads to a future where rail networks are designed, built, and maintained using smart technology and automated systems that monitor and track carbon emissions and energy efficiency, and identify opportunities for further reducing environmental impact.”
Siemens Mobility’s Railigent rail asset management tool is one example of how the company is supporting rail operations, by providing a digital solution for centralising all rail data connected to system sensors and remote condition monitoring software.
“Our Railigent platform is shifting the maintenance paradigm away from scheduled intervals that require a person to make trips out to site regularly, towards a system centred around predictive maintenance strategies,” Guerineau said.
“This ensures that rail maintenance is performed as needed, rather than wasting resources, and it allows operators to use predictive maintenance functions, anticipate
potential equipment failures before they happen, and in some cases, provide remote solutions.”
rail electrification.
The recently awarded Sydney Metro Western Sydney Airport project is the first rail infrastructure project in Australian history to commit to being certified carbon-neutral from the start of construction, all the way through to operations.
“There are two aspects to this project. Firstly, minimising the project’s carbon footprint by ensuring all the buildings and all the stations have five-star ratings for energy efficiency and emissions,” Guerineau said.
“Secondly, the trains will use optimised energy efficiency. Our trains use regenerative energy. So, when they are running, they generate energy and reuse this energy without using external electricity.
“The Western Sydney Airport project serves as a good example for Australia and New Zealand to demonstrate that we have the technology to transition to fully electric rail networks and become carbon neutral right now.
“We want the industry and government here to see it in action and recognise that this transition is something we have to work towards together, so that we can start accelerating the decarbonisation process in this part of the world.”
In Germany, pilots are underway with rolling
rail networks in places around the world right now,” Guerineau said.
Across Denmark and Norway, Siemens Mobility are providing sustainable solutions that eliminate diesel.
In Denmark, Siemens Mobility is electrifying 1300km of rail and supplying seven of the first Mireo Plus Battery trains.
Whilst in Norway, Siemens Mobility is electrifying the entire Norwegian network, covering approximately 4,200 track kilometers and 375 stations, with a scheduled completion date of 2034.
By investing in and deploying sustainable technologies such as electrification, battery and hydrogen trains, and incorporating digitalization through platforms such as Railigent to empower operators and allow the network to become more efficient and reliable, the industry can move towards a net-zero carbon future.
This will require collaboration between governments, businesses, and transport users to make the transition and achieve a truly sustainable and low-carbon transport system.
The rail industry has the potential to play a vital role in reducing global carbon emissions, and Siemens Mobility’s solutions are paving the way towards a more sustainable future.
KeTech’s C-DAS was developed with drivers to allow them to gain a complete picture of the current state of the rails along the train route.
The rail industry is feeling the pressure to do more on its journey to net-zero; not only because the time is right, but to mitigate the direct affects climate change has on the rails.
In Australia, the direct effects of climate change are already being seen, from extreme heat to bush fires and floods. These stresses on Australian infrastructure range from disruption, to supply distribution issues, to downtime of infrastructure assets due to these weather events.
The industry is welcoming innovation to meet its targets, but with some at such an early stage it creates uncertainty for decision makers in terms of choosing the right option.
A lot of work is ahead if the industry is going to deliver real progress. One key weapon in its fight to deliver decarbonisation will be technology, both in improving the efficiency of IT functions and in harnessing it to unlock new ways of transforming operations and ways of working.
As KeTech technical consultant Graham Cooke explains, when it comes to prime movers, heavy haulage rail and long-distance logistics, Australia’s current stock is predominantly diesel with no other real options available.
“The difference in regulations between states impacts the speed of the transition from diesel to cleaner options, most notably in freight, due to the required reviews and approvals from all jurisdictions to ensure they meet the regulations of each state,” he said.
“The replacement of diesel engines for rail freight traversing this large continent at this very moment would continue to be limited as the infrastructure to support cleaner options doesn’t exist.
“Range anxiety is real and problematic for this green transition and will only be addressed when underlying infrastructure is constructed for EVs, Fuel Cell Electric Vehicles (FCEVs), renewable biofuels and hydrogen powered vehicles which will take a considerable amount of time to implement.
“As the Australian rail industry works towards implementing a wider infrastructure strategy, there are technologies that can be applied now to current assets, not only to significantly improve efficiency, but to minimise waste and limit resource use.”
KeTech’s C-DAS is more intelligent and better connected with data exchange between the wayside and the train.
Driver Advisory Systems (DAS) are rapidly being recognised as the route to optimising the performance of trains in helping to reduce energy consumption.
There are many DAS products on the market, but the degree of sophistication the system possesses, will of course, affect the level of optimisation.
DAS has evolved significantly over the years, but it’s important to recognise the distinction that has been made between connected (C-DAS) systems and stand-alone (S-DAS/DAS).
“The latter is your less sophisticated advisory system, working only on the pre-planned timetable; meaning the advice it gives may not be useful if for any reason the trains planned paths is unavailable,” Cooke said.
“Train drivers’ situational awareness is limited to the process of driving their own train. They are able to perceive the state of the train they are driving via indicators such as, ATP, feedback from the engine and wheels, and the track ahead within their vision.
“Train drivers know how this information affects the train and so they can decide how to apply engine power and brakes to reach a certain speed, acceleration, and retardation, combined with a smooth and comfortable ride.
“However, train drivers completely lack any situational awareness concerning the traffic
alone DAS fitted, due to the fact that S-DAS run off static data, meaning train drivers’ only source of information is predefined timetables.
“Based on this, they can only assume everything is according to the original plan. As soon as the situation deviates, which is a regular occurrence in the complex and dynamic train traffic process, the DAS is ultimately rendered useless.
“The technology that we implement on our infrastructure assets now needs to be able to meet future needs in a net-zero environment, be flexible and able to adapt in the face of a changing climate.”
Cooke said KeTech’s C-DAS was developed with drivers to allow them to gain a complete picture of the current state of the rails, including changes in the traffic situation and operational plans due to the systems real-time data feeds and constant recalculation of the driving profile, taking into consideration the external elements affecting the trains route.
It’s important to note that all C-DAS on the market (and currently in service) are not built the same.
“KeTech’s C-DAS is more intelligent and better connected with data exchange between the wayside and the train happening constantly in
order to provide truly real-time information, this means the system has high availability and high performance,” Cooke said.
“KeTech’s system analyses all of the data on the wayside and transmits this to the train in real-time, avoiding many of the interoperability issues that have arisen with other systems on the market.”
KeTech’s C-DAS is fully signalling-connected, unlike other systems that are only connected to GPS, which allows the system to understand the current traffic situation supporting drivers to develop a much more comprehensive situational awareness, enabling them to adapt an optimal driving profile addressing a number of existing and emerging challenges:
• Increased rail network capacity
• Improvement in punctuality and adherence to timetable
• Significant reduction in fuel usage and industry carbon emissions, reducing operational costs in turn
• Improvement in recovery from disruption
• Reduction in operational incidents
The award-winning C-DAS that KeTech created
was developed with drivers and train builders. “As many companies who have tried to create a true C-DAS will know, it’s not an easy job unless you have extensive experience and knowledge in rail infrastructure and rolling stock,” Cooke said.
“Fortunately, KeTech does – over 20 years actually! That’s why KeTech has been able to create a truly situationally aware system that is as dynamic as the railways.
“Unlike other systems, KeTech’s C-DAS provides concrete driving advice to drivers, indicating recommended speed and other essential information regarding the route.
“Ensuring the right balance of detail in the advice is crucial to avoid additional mental workload for drivers.
“Traditionally C-DAS require a Traffic Management System, however KeTech’s C-DAS doesn’t. To provide all the benefits, it is connected to the signalling system and multiple other data sources to fill the absence of a TMS.
“KeTech built C-DAS with TMS in mind, providing all the benefits now, but having the capability to sit underneath one when it is rolled out.”
From product functionality to installation, KeTech’s C-DAS is a versatile system providing the route towards reduced carbon emissions in more ways than one. The system can be especially environmentally beneficial for trains relying on friction brakes, such as freight due to the energy saving speed profiles that seek to minimise energy loss through braking; in turn, maintenance savings will be made as a result of reduced brake wear and tear.
Spending money on retrofitting means less money spent on energy – investment rather than consumption spending. The modularity and scalability of KeTech’s C-DAS allows flexible deployment. It can be delivered as an integrated system, displayed on an iPad style device in the cab, or on existing hardware in the cab.
“KeTech recognises each operator may have different needs and requirements, so we developed it with endless possibilities of personalisation. Just ask the question,” Cooke said.
In a sector where decarbonisation and energy conservation are vital goals, suggesting that technology can provide immediate, measurable, and ongoing sustainability benefits to rail operations might sound too good to be true.
However, an established body of evidence, gathered from around the world, demonstrates that the Driving Advice Solution (DAS) system offered by public transport specialist The Trapeze Group is doing exactly that.
The Trapeze DAS has already been installed on more than 163,999 train and driver applications across 80,000 kilometres of track for 20 rail operators on four continents.
This includes France, where state rail operator Société Nationale des Chemins de Fer Français (SNCF) uses the software on its signature national high-speed service, the TGV.
Recent comments by the French Minister for Transport, Clément Beaune, highlighted the importance of the energy savings that DAS has delivered on that rail network.
‘’I will be going to Montparnasse to see the highly innovative system that SNCF and RATP have put in place for what we call eco-driving,” Beaune said. “With peaks and troughs of speed, you can still reduce energy consumption.
“Eco-driving is the solution, saving energy at the same average speed. I am not asking SNCF and RATP to run trains more slowly because, as I said, we cannot make the ecological transition without rail.”
Beaune was speaking about the French government’s ‘Turn it down, turn it off,
postpone it’ campaign, which aims to reduce national energy consumption. He explained the vital role that train services, including the DAS-enabled TGV, play in achieving more sustainable public transport.
“The restraint plan… does not include cancelling trains, reducing the public transport offer, slowing down our metros, trains or buses,” he said.
“The ecological transition means more trains, more public transport, more green transport, and they are part of this strategy.’’
As Beaune noted in his comments to the French media, DAS does not save energy by slowing trains down.
Rather, the technology generates and continually adjusts an optimal journey profile throughout each trip and provides the driver with real-time operating advice to achieve this goal.
An onboard computer suggests when the driver should apply one of four driving modes – power, hold speed, coast, and brake - values which have been calculated according to data relating to track geometry, speed profile, timetable, train characteristics, and train position.
By holding speed and then applying power at the correct time, such as when climbing an incline, the overall energy requirements of the locomotive are reduced to a minimum and fuel is not wasted. The instruction to coast at the optimal moment saves energy in turn
by reducing the need to apply the brakes on downhill sections.
When it is necessary to advise the driver to brake, this is done as efficiently as possible. Calculating the optimal braking requirements reduces wear on trains and tracks, improving the longevity of these assets and lowering maintenance costs.
Without DAS, operational efficiency levels between drivers can vary by as much as 50 per cent with identical train configurations running on the same route.
This significant difference reflects the train driver’s challenging role and can’t be explained away by newer drivers taking time to learn their route or equipment.
Even the most experienced drivers can exhibit bad habits, with some having originally been trained to always travel at the maximum permitted track speed.
The good news for rail operators and authorities is that these inefficiencies are overcome by supporting drivers with realtime advice.
This applies to any type of train, including diesel, electric, high-speed, freight, and heavy haul locomotives.
Sharing optimised advice equips drivers with the situational awareness to challenge their preconceived instincts. By enabling drivers to optimise their braking and acceleration, DAS reduces the amount of energy used during each journey. This cuts rail operators’ fuel costs and significantly reduces carbon emissions.
A data-led partnership between operators, authorities, and technology can help to decrease rail’s global carbon footprint without large-scale capital investment.The Trapeze DAS has already been installed across four continents.
travel more sustainable, is supported by measurable outcomes.
SNCF requires approximately 9TWh (terawatt hours) of electricity every year, equating to 3 per cent of France’s entire national energy consumption.
By installing DAS on all its TGV trains, SNCF achieved annual energy consumption efficiencies of up to 10 per cent, with approximate energy expenditure directly related to TGV trains dropping annually from €220 million to €200 million.
As well as saving millions of euros in electricity costs, this made a significant contribution to achieving SNCF’s decarbonisation targets.
While the TGV is a high-speed passenger service, impressive results have also been delivered in the freight sector by New Zealand’s largest rail transport operator, KiwiRail, which services approximately 4500 kilometres of track.
Since the Trapeze team installed onboard DAS systems in KiwiRail’s 180 locomotives and trained 350 drivers to use the system, ongoing fuel costs have been reduced by around 13 per cent. Between 2015 and 2020, the business saved approximately 17 million litres of diesel, worth tens of millions of dollars, and reduced its annual energy usage by 39 GWh.
KiwiRail’s annual carbon emissions also fell 15 per cent from 272,345 CO2-e tonnes in 2015/16, to 230,036 CO2-e tonnes in 2019/20. Experienced locomotive engineer, Robin
of DAS technology in 2014, despite his initial scepticism of the predicted fuel consumption saving of around five per cent.
“I eventually agreed to help, provided I was permitted to evaluate the product without anyone trying to influence me or push me in any particular direction,” he said. “Initial testing… led to about 10 per cent savings on energy year on year.”
In 2016, following the implementation of DAS, KiwiRail won the prestigious Deloitte Energy Excellence award, based on the greenhouse gas reductions and fuel savings achieved.
Another European passenger rail business that can demonstrate the technology’s significant decarbonisation impact is First Great Western.
The UK-based operator commenced a series of DAS trials in 2009 and completed its fleet fitment of 180s and HSTs in 2011.
In the first two years of using DAS, First Great Western HSTs reduced CO2 emissions by 70,500 tonnes and NOx emissions by 2600t.
Looking beyond the fuel efficiency outcomes, DAS delivers a range of additional benefits for authorities and operators, particularly those challenged by a crowded rail network such as First Great Western experiences in the United Kingdom.
Creating greater opportunities for on-time running is central to the technology’s functionality.
The entire network can be managed to ensure conditions, conflicts or adjustments are applied
Gates, said this minimises the costs that operators can incur through financial penalties imposed by transport authorities for late running services.
“The Trapeze DAS solution considers schedules, temporary speed restrictions, and on-the-day changes to provide driver advice on how to run on time,” he said.
“It can significantly raise driving standards and median performance levels by training drivers to be more efficient.
“It is of paramount importance that train services operate safely. DAS plays a key role in minimising both the potential for incidents and also the frequency of signals passed at danger, reducing the anxiety levels of drivers and operators alike.
“The algorithms underpinning this innovative technology have been developed over 30 years through the work of academics and our research and development teams.
“This work has led to energy and fuel savings that are consistently between five and fifteen per cent, saving millions of dollars for our customers every year.
“The beauty of this solution is that it goes beyond the well-documented fuel-efficiency and sustainability benefits by contributing to a range of key operational outcomes that are significant to any rail business.
“Our DAS is a globally proven, awardwinning system that supports global decarbonisation and optimises performance for any train, anywhere, any time.”
Rail projects are booming all round the country.
Whether it’s new lines like Inland Rail, extensions to existing tracks, or even possibly laying down infrastructure for faster speed rail, the fact remains that residents adjacent to existing or new corridors – suburban and regional – will be affected by the sounds and vibratons emanating from not just construction but train operations.
In fact, concern over such aural disturbances, which could last for years, has already led to resistance from various councils and residential areas towards the development of such projects, arresting planning approval progress.
For decades now, German-based company STRAILastic has been promoting a its noise attenuation tool kit which provides a solution to these problems.
STRAILastic is part of a business owned by German business KRAIBURG STRAIL (a composite word meaning ‘street meets rail’), which also includes STRAIL level crossings, STRAILway composite sleepers and TOR light rail track systems.
Its noise control tool kit employs an acoustically optimised absorbent facing plate mounted in a steel frame that can be fitted directly onto existing rails or adjacent rail structures. They are held by moulded recycled rubber panels which are protected against UV, fire and graffiti.
The panels are compressed with a force of about 1200 tonnes and then cooled in a special chamber. The noise wall panels can be shaped into various low height (360 to 1250mm high) small barriers to be fixed near the tracks, nullifying the worst noise effects.
Already used widely across Europe, the panels are placed as close as possible to the noise source, absorbing the sound before it leaves the rail corridor.
The products have a long life expectancy and can be then be recycled again.
In the Ammer valley in Germany, the Tübingen-Herrenberg railway line was reactivated in 1999.
Since this line runs through residential areas with houses immediately adjacent, the railway operator was seeking a sound protection solution that would be as effective
STRAILastic International director Andreas Goeschl said the company offered the mSW 360 product due to its low height and performance, which proved to be the optimal solution.
This mini-sound wall, placed 360mm above the top of rail, was installed against the kinematic envelope clearance area trapping to absorb the noise under the train. A higher wall can be installed at the structure gauge if needed.
“On the railway line in the Ammer valley, there were different types of sleepers, such as wooden and short concrete ones, with large tolerance deviations in sleeper spacing,” Goeschl said.
“However, these challengers were resolved by attaching the mSW 360 to the metal substructure with just a few screws, which in turn is fixed directly to the rail.
“To compensate for the large tolerance deviations in sleeper spacing, special rubber bellows were developed by STRAIL and installed successfully.
“Furthermore, there was the option of integrating small animal passages.”
Even with these modifications, the
railway operator and the residents were very satisfied with the STRAILastic noise reduction solution, as the residential area is now quiet with passing trains without impacting the local landscape.
The STRAILastic Version 2 wall panel was also significantly improved in 2022.
“Instead of using a material designed to reflect sound, the new wall panel actually absorbs sound,” Goeschl said.
“The result is significant acoustic performance rated A3 by German railways, from 8 to 11 dBA.
“We call it Surface 2.0: the next generation. The highly absorbent surface is made from several layers and materials, combining all the advantages of the individual components and moulded with the durable and stable rubber compound.
“The insulating effect of the elements and properties of rubber are now complemented by the absorbent surface, so we have three components in one highly effective product.”
There’s a perfect solution for reducing noise around rail tracks: and the best part is it’s environmentally-friendly.STRAILastic employs an acoustically optimised absorbent facing plate mounted in a steel frame that can be fitted directly onto existing rail structures.
John Holland is a leader in end-to-end rail and transport solutions, from design and construction, testing and commissioning, and right through to operating and maintaining completed transport systems.
Examples of its rail heritage date back to Melbourne’s City Loop in 1978, to the construction and delivery of the ninekilometre twin tunnels and five underground stations for the current Melbourne Metro Tunnel Project.
Today the rail and transport business is focused on transforming the way people travel and providing better connections across Australia and New Zealand. Expertise in all parts of the rail life cycle ensures the focus is on delivering the best solutions for its customers and communities at every stage.
John Holland Rail and Transport Executive General Manager, Steve Butcher, talks to Rail Express about the company’s success and its deep roots in the rail and transport sectors.
“At John Holland, I’m proud to see that the rail and transport networks that we build and operate can transform people’s lives. That’s the impact that safe, reliable, customer-focused transport can have,” he said.
“We have 1200 people working in rail and
transport across Australia and New Zealand, out of a total of 5500 direct employees all up within John Holland.
“There’s a further 8000 people working in our operations and maintenance businesses, which we operate with joint venture partners.
“Our design and construction capabilities are focused on using the best technology solutions and innovation to safely deliver value-for-money projects that minimise impact to the travelling public, promote economic growth, and connect communities.
“Our expertise spans concept design, including engineering; procurement; construction; and asset management.
“Our whole-of-life mindset means we’re not just designing and delivering for today: we’re thinking about the future.”
Butcher said John Holland’s in-house skills, knowledge, and resources, including the specialist machinery and equipment, allowed it to successfully deliver key rail, operations and maintenance services, and provide certainty and consistency of delivery across a range of disciplines, such as:
• Track work
• Overhead wiring
• Power and electrical
• Signalling and communications
• Signalling design, and testing and commissioning
• Rail safety
Butcher said John Holland specialised in the complex systems and processes that lead to the safe and successful design, construction and operation of heavy rail, light rail, bus, and other transport solutions.
This includes design management, design standards and waivers, and reliability, availability, and maintainability engineering.
“We carry out systems engineering, validation, verification, and safety assurance, commissioning and final safety accreditation,” Butcher said.
The group operates and maintains some of Australia’s largest public transport networks, providing reliable, safe, and customer-focused public transport services.
“Our train, tram and bus operations span the country, connecting hundreds of thousands of people to their destinations every day,” Butcher said.
“As an accredited operator, our transport services include the design, development, and implementation of customer experience strategies, network control and timetabling,
rail safety accreditation with regulatory agencies, along with asset management, maintenance, fleet, and depot strategies.”
• Canberra Light Rail
“John Holland was proud to be part of the consortium that designed and constructed the Canberra Metro light rail network that opened in 2019,” Butcher said. “This included the systems engineering delivery and integration to bring the network online.
“We now proudly operate and maintain the network as part of Canberra Metro Operations (CMET) for a period of 20 years.
“As the largest public transport project in the ACT’s history, Canberra Metro carries more than 15,000 customers each day.
“Our team is contracted to operate and maintain the Light Rail network - a 12km line with 14 light rail stops that connects Gungahlin with the city.
“Last year we were awarded the contract to deliver the Light Rail Vehicle Procurement, Retrofit and Depot Expansion (LPRDE) Modification to the CMET Operations and Maintenance Contract.”
This project which will prepare the CMET
network for the Stage 2A extension of light rail to Commonwealth Park includes:
• Procurement of five new light rail vehicles
• Retrofitting of existing 14 light rail vehicles with onboard batteries
• Maintenance of new Light rail vehicles and battery systems
• Expansion if the existing Mitchell Depot to allow for the increased fleet size.
• Sydney Metro
After leading the design and construction for Operations, Trains and Systems for Sydney Metro Northwest – the first stage of Australia’s biggest public transport project, Sydney Metro – John Holland now operates the nation’s first driverless metro as part of the Metro Trains Sydney consortium.
The new-generation metro trains are designed to make customer journeys easy –from level access and platforms, to multipurpose areas for prams, luggage and bicycles, and real-time travel information.
“John Holland is now part of the joint venture that manages the operations and maintenance for Metro Trains Sydney, across 13 stations from Tallawong to Chatswood in Sydney’s north and northwest,” Butcher said.
“Services operate every four minutes in the
peak in each direction. We have continued to be involved on the city extension including building the new tunnel under Sydney Harbour and excavating the station boxes, then where the tunnel emerges, we delivered all of the complex junction remodelling at Sydenham Station with the conversion from the existing Sydney Trains network.
“Along the route we are building the integrated station development at Waterloo. And as part of the Joint Venture operator, Metro Trains Sydney, we have been integral to the overall operational readiness and working with all of the teams getting the infrastructure ready to expand the operational railway.”
• Metro Trains Melbourne and Melbourne Metro Tunnel
“In Melbourne, we’ve been part of the Metro Trains Melbourne consortium since 2009 and we have recently agreed an extension until 2026, which will mean we are operating the network when the Melbourne Metro Tunnel opens with the new fleet of High Capacity Metro Trains,” Butcher said.
“For the Metro Tunnel, we are part of Cross Yarra Partnership that is delivering the tunnels and stations.
“While our people are leading the Rail
Network Alliance which includes the integration of track, power and signalling equipment, as well as testing the rail systems with the new trains to run in the Metro Tunnel. And that project team interfaces with our operations and maintenance projects integration team within Metro Trains Melbourne.”
“When I look at everything that happens on a railway there isn’t much we don’t do,” Butcher said.
Butcher said John Holland understands how to balance the competing demands from delivery and operations.
“We understand the importance of getting delivery right to ensure the railway works, so we are very focused on systems assurance and systems engineering in all aspects of delivery,” he said.
“We have a specialist rail engineering and integration team, and they are involved from the very beginning of every project to get the requirements right and focus on design management, then verification
and validation throughout the delivery. Our operations businesses are focused on customers, making sure that their journeys are safe, comfortable and reliable, and that they have the right information available to them in multiple formats.
“So, when we are delivering infrastructure like the Gold Coast Light Rail extension to Burleigh Heads, we’re ensuring that the customers are going to have excellent journeys when that opens, and we of course would love to help with the further extension to Coolangatta Airport to support the critical tourism connection.”
Butcher said that across all of the teams in both delivery and operations, the focus is always on how to improve safety and customer service.
“That takes a lot of my time because we are passionate about ensuring everyone goes home safely each day – all of our staff, contractors who work for us and our passengers,” he said.
“In Queensland we have a team working
on the early works for the Beerburrum to Nambour rail duplication project.
“In Western Australia, our team has been maintaining the metropolitan network for more than 25 years and we have an amazing team in the Pilbara working on the heavy haul networks, who are ensuring the reliability of the iron ore export sector.
“We are also looking forward to new opportunities to leverage our strengths, capabilities and combined end-to-end experience so we can provide the best possible passenger experience.
“In short, our capabilities mean we can connect all parts of the rail and transport lifecycle - from drawing a line on the paper, in the design and construct phase; to building the infrastructure; bringing the system online; and right through to successful operations, fleet maintenance and passenger journey outcomes.
“Experience in all of these areas means that we’re thinking of the whole project life cycle – to create better outcomes for our people, our customers and project partners, and the community.”
Rail Maintenance Services Pty Ltd (RMS Rail), has been servicing the rail industry since 1971 and has established a reliable reputation for the hiring of wet and dry plant, equipment and professional services. RMS Rail takes pride in its commitment to health and safety, environment and quality. Underpinning the quality of all our works is our ISO 9001, ISO 14001, ISO 45001 certified Integrated Management System.
RMS is providing services in project site maintenance, operational management with approximately 100 dedicated staff and trained operators. RMS has a strong commitment to provide competent operators and is continuously investing in the development of our people. Mindful of the needs of our clients, our technical team scoured Australia and the world for the latest innovations in plant and equipment to provide our clients more efficient, cost and time saving solutions.
We aim to have the highest skilled team with greatest specialised Road – Rail fleet in Australia.
– Head Office 165
leading railway operators for safety, reliability, customer service and cost efficiency, operating rail networks in nine cities across Asia, Australia and Europe.
The Australian subsidiary, MTR Australia, is currently delivering the Trains, Signalling, Maintenance and Operations package for Sydney Metro City and Southwest. It is also the major shareholder of the operating companies for the Melbourne Metro rail network and Sydney Metro Northwest.
Given that background, it is no surprise to learn that MTR is also regarded as a specialist in setting up metro operations successfully from the first day, often called on to offer advice on various rail projects.
MTR Australia’s senior manager for, business development and operations and maintenance, Dale Mitchell, talks to Rail Express about the lessons learned from transitioning a project to an operational railway, and the pitfalls to avoid.
“There are three key areas metro operators must consider: trial operations, the readiness of assets for handover, and the readiness of the organisation for handover,” he said.
“MTR has valuable real world experience to share,” Mitchell said.
“We are vertically integrated, meaning we
residential and commercial buildings.
“When it comes to trial operations and new rail line openings, MTR has opened eight railway lines in the last four years globally, including in Hong Kong, Beijing, London and Sydney. We are also currently planning three more in both Australia and mainland China.”
Of course, there is currently a large pipeline of automated metro projects throughout Sydney and Melbourne alone.
“Sydney’s plan is based around placemaking and improving access to Greater Wester Sydney, with Sydney Metro the government authority delivering the four projects that are transforming the city,” Mitchell said.
Sydney Metro Northwest, which is operated by Metro Trains Sydney (MTS) – an MTR-led consortium including John Holland and UGL – opened in 2019 and was the first GoA4 (automatic) railway in Australia.
Work is well underway for the city and southwest sections, extending the metro across the harbor and underneath the city.
“We have recently commenced testing and commissioning of the city section. In April, Sydney Metro Northwest won the Infrastructure Partnership Australia award for Operator and Service Provider Excellence, demonstrating the ongoing excellence that is being delivered at MTS,” Mitchell said.
The separate Western Sydney Airport Line is
the same time as the Western Sydney Airport in
Meanwhile, in Melbourne, the detailed planning and some early works for the Suburban Rail Loop project is currently underway and will eventually deliver a GoA4 loop around the city connecting the Melbourne passenger rail network. The procurement for the East section is commencing this year.
“The existing Melbourne passenger network, also operated by an MTR-led consortium, Metro Trains Melbourne, will undertake trial operations later this year for its Metro Tunnel Project, which is a new tunnel under the city, and will operate the new HCMT rolling stock in a combination of automated CBTC signalling under the tunnel with existing adjoining sections running under traditional signalling,” Mitchell said.
He said in order to achieve successful day one operations, which include the delivery of a reliable operations managed by competent staff, experience has demonstrated that there are a number of things to get right during trial operations.
These are:
• Sufficient train-running periods free of major incidents to stress the system and uncover defects. In MTR’s experience, about 70 days depending on the network is required.
• The validation of procedures and
processes, particularly emergency or operational disruption responses. This requires time, resources and appropriate stakeholder engagement.
• A robust defect rectification process. It is vital to a successful day one reliability that the majority of defects have not only been uncovered, but also either rectified, or managed in a way that imposes no residual risk to operations or safety.
“If a trial operations plan is well designed and executed, the result for day one of operations will be a reliably performing asset, with employees who are competent and ready to manage the railway,” he said.
“Although it is important to note that even following a successful trial operation, there is still an expected reliability growth period in which difficult to identify defects will present themselves.
“The approximate 70 days of major incident-free train-running should be achieved at or near the operator’s ultimate timetable. Based on factors such as the frequency of line openings for the organisation, or the complexity of the project being delivered, this number can move up or down.
“Experience also tells us that we should expect about 30 per cent of planned days to be lost due to faults and major defects, changes in priorities, staffing availability and errors or other unforeseen circumstances.
“At Sydney Metro Northwest, we opened the railway on time, although we had to shorten the trial operations period to a total of seven weeks, with 40 days of trial running.
“Through the shortened trial operations period on the Northwest, we decided to operate at an initially higher headway of 12 trains per hour (TPH) while the reliability of the system grew.
“As the reliability built over the first few months, so did the service, building to the 15 TPH in the third month of operations.
“Following the opening of the line, reliability grew over the initial six months up to the leading levels that are now being experienced by passengers.”
Mitchell said that major reliability issues in these first few months where things that would traditionally be rectified during a longer trial operation, such as first responders not familiar with protocols, the operations centre experienced a high volume of nuisance or unnecessary alarms, and dust impacting fire alarms.
“Following these initial reliability figures, the Sydney Metro Northwest quickly and consistently began to operate as not only the best performing railway in Australia, it also
consistently has the best customer satisfaction rates in Australia,” Mitchell said.
Mitchell said the most critical assets that provided the most operationally impacting defects in a new metro were likely to be either software or interface-related.
“Software issues relating to the communications and signalling systems are likely to cause a variety of defects, from false alarms through to complete shutdown or failure of systems,” he said.
“While there can be patches places on software to mitigate defects or provide workarounds, a software update or re-baseline is generally required to completely address the defect.
“In our experience, it will likely take two software re-baselines to rectify the most disruptive of the defects that will be discovered during and before trial operations.
“Given the resources and testing required to undertake a complete software realignment, it will likely take about three months to implement.”
Another key defect area is the interface between assets which are often delivered by separate contractors but require significant integration through joint dynamic modelling and design optimisation.
“These defects are typically more challenging to correct given that it may not be immediately apparent what the solution is, given that both of the systems will likely be
be completed in their entirety prior to trial operations commencing, with temporary procedures for managing outstanding works minimised.”
Mitchell said, from experience, there were some defects that have been evident multiple times, such as:
• Communications-based train control (CBTC) systems often exhibited a significant amount of bugs early on in operations. While workarounds are possible, usually the rectification requires a readjustment of the software.
•Some other techniques for minimising defects on the CBTC (and other systems) was demonstrated on the East Rail Line in Hong Kong where robust factory acceptance testing and early involvement with the traffic controller and train crews was prioritised.
Communications-based train control (CBTC) systems often exhibited a significant amount of bugs early on in operations. While workarounds are possible, usually the rectification requires a readjustment of the software.
Some other techniques for minimising defects on the CBTC (and other systems) was demonstrated on the East Rail Line in Hong Kong where robust factory acceptance testing and early involvement with the traffic controller and train crews was prioritised.
“Further to performing good factory acceptance testing, ongoing expert support will be required post trial operations, and we have found that posting the suppliers’ experts into the control centre during traffic hours is critical to identifying and responding
Adopting a pragmatic solution to this issue was achieved on the South Island line (Hong Kong) where the stopping accuracy was relaxed from 300mm to 450mm, which still provided sufficient room for departing and alighting passengers.
“Workmanship also resulted in defects with PSDs, with regards to cables being laid incorrectly or micro-switch adjustment being wrong, resulting in platform-wide PSD failure, Mitchell said.
“As PSDs are not a commonly installed device, it is difficult to source construction teams with experience in installing these sensitive units. We have had success where we have required there to be an engineer on site who is familiar with the PSD construction who can lead the installation team.
“Due to the movement of trains, a resulting pressure differential between tunnel and station area can cause the PSDs to not be able to open. During trial operations, it is important to run a full service, including degraded running conditions, or this issue (among others) may not present itself until you are running full operations. Door operating mechanism and ventilation systems all need to be designed to account for these conditions.”
Mitchell said passengers who are not familiar with PSD operation could also inadvertently cause system delays by not standing adequately clear, forcing doors open or not allowing them to close or getting caught by rushing through closing doors. Staff presence and clear messaging, particularly during early operational periods, is vital to passenger education around new assets.
Excessive arcing has been known to arise from a mismatch between dynamic performance of the overhead and the pantograph. This was evident in MTR Hong Kong where the transition bar stiffness was causing a poor transition.
“The stiffness profile was reviewed and optimised which reduced the arcing in these locations,” Mitchell said.
“All of these problems should be identified before or during trial operations and technical solutions deployed for permanent fix.
“In order to ensure there is appropriate time to fix all of these defects, you need to plan to have time in your trial operations program. If there is insufficient time for defect rectification, there will be defects that are carried into day one of operations.”
Trial operations are not only about getting assets performing, but they are also about
getting people and processes ready for the first passenger service and beyond, and all the unexpected issues that will come in the initial period.
Focusing on having the right people in place early is important. Different groups need to be engaged at different times, for example:
• CBTC and PSD maintainers should be in place during testing and commissioning to learn about the interfaces and defect identification and troubleshooting
• Other maintainers should be in in place during trial operations
• Operational Control Centre staff in position during trial operations
• Customer service staff need to be in place during procedure validation and drills, and be familiarised with the stations and the operations prior to first passenger service.
“To achieve this, it will be necessary to perform early and targeted recruitment of staff, as well as ensuring contracts are in place with outsourced maintainers and service providers to allow time for training prior to trail operations,” Mitchell said.
“During this time staff should be gaining experience and optimising their response plans rather than learning them.
“Outside of people, supporting systems need to be ready for day one of operations also.
“Getting asset information from the constructors presents a number of challenges. Without defining a clear structure of how you want to receive asset information, it is likely that it will be presented in a number of inconsistent ways, which will then take a lot of time and effort to input into the asset information systems.”
Mitchell said a robust change management program would also be required to ensure that the inevitable changes throughout the project are managed in accordance with the operational requirements.
“With materials and components, ensure sufficient spare parts are in place in time
for commencement of trial operations,” he said. “For all major changes, MTR implements a regime of babysitting or hypercare for new lines or operations until the reliability reaches a steady-state, which brings in additional staff, both customer service staff and maintainers.
“When the delivery contractor is also responsible for maintenance, understand that it will likely be a different team that performs the construction and maintenance, so ensure that the arrangement involves having the maintenance teams on hand during trial operations so the knowledge doesn’t leave, which has occurred for various systems including CBTC and PSDs at a number of our operations.”
Another lesson learnt was around asset handover. “We aim to invest in data scientists to take the large manuals and put the important key information into a maintenance system that supports the maintainers,” Mitchell said.
“Providing to the contractors operator-led taxonomy for assets, as well as specifying how the detail is provided, will allow us to populate the asset information system early and accurately.”
“Setting up for a successful first day of operations is a challenge for every railway, and there are many unique factors influencing each of openings,” Mitchell said.
“Experience has shown us that you need to have an experienced team managing the operational readiness strategy and there are always more lessons to be learnt.
“Each line opening has its own unique set of influencing factors, and there are a variety of approaches that would deliver a successful day one and beyond.
“With the amount of investment that the rail industry is receiving globally, and the amount of new metro systems in the pipeline, this is going to be an area that we will continue to learn lessons from experience.”
Commencing trading in 1970, MFB Products is a privately-owned Australian manufacturing company aiming to be the country’s market leader in design and manufacture of enclosures and metalwork for the communications, IT, security and defence industries.
Among its products which have led the industry are its sturdy and advanced stainless steel enclosures, such as its S280 industrial 19-inch units.
MFB sales executive Jack Grech explains that the fully-welded metal fabricated enclosures are manufactured in Australia from either mild steel or 316 stainless steel.
Stainless steel enclosures are preferred in highly aggressive environments such as food preparation, coastal or water treatment plants, and in mining (hazardous).
Fully welded enclosures provide greater ingress protection (IP) attributes.
MFB’S S280 range conforms to AS 60529:2004 Degrees of Protection standards for an enclosure.
As a minimum they meet IP54, where 5 = “dust-protected, limited ingress”, and 4 = “protected against water splashed from all directions, limited ingress”.
MFB S280 enclosures are third party accredited to IP66, where 6 = “dust-tight”, and the second 6 = “water from heavy seas or water projected shall not enter the enclosure”.
Grech said the S280 enclosures are built around the IEC 60297 19-inch racking format for data and electrical equipment.
“The MFB range of standard S280 outdoor enclosures offer a variety of heights measured in rack units (RU) widths, typically 600mm wide or 800mm wide, and in a variety of depths,” he said.
“We offer a zinc powder coat anti-corrosion pre-treatment, then full powder coating to a customer choice of colours.
“On request we can powder coat stainless
steel, though they are generally left with an industry standard linished finish.”
Grech said MFB appreciated that customer demands continually evolve, and as a result the company encouraged discussion.
“This allows us to work on finding the best solution to meet specific requirements,” he said.
“Importantly our design team are conversant with sheet metal fabricating and machinery. Utilising Autodesk inventor full modelling software, we can quickly establish possibilities of design to manufacture and acknowledge limitations.
“For example, the S280 split rack is a fully welded enclosure allowing users to separate key pieces of equipment, and in doing so allows freedom to separate potentially hazardous batteries and electrical components.
“Operating a predominantly DC power supply format, the lower compartment of the enclosure is set aside for housing battery systems which in turn drive the electronics in the upper compartment.
“Certain batteries give off gasses, so to ensure the electronics are not harmed, the batteries are separated. We can provide gland plates with suitable cable connectors, linking batteries to electronics.
“S280 enclosures house equipment safely and securely, ensuring peace of mind from vandals, vermin and the Australian climate.
“MFB offers a wide range of accessories to suit your applications, including shelving, power distribution, air management (both passive and active cooling) and cable management.
“If you need these accessories or your own personal accessories fitted, MFB can accommodate your request. Our goal is providing assurance your rack will serve you well and for many years to come.”
Grech said MFB’s accreditations have acted as cornerstones for the company throughout its history and would continue to drive the business forward.
“The core values of the business are built around the quality (ISO9001) and environment (14001) accreditations we proudly hold.,” he said.
“ We are also well underway in working towards the occupational health and safety accreditation (ISO 45001),” he said.
“We are constantly looking at ways to build our policies in a manner that aligns with evolving Industry standards.
“We boast experienced staff with many of them serving many years at the company.
“The company remains committed to securing mechanical engineer graduates and the knowledge they can bring to the business to help drive its business goals and objectives.
“MFB continues to provide customisable enclosures and services for the rail industry and wants the industry to know we are always looking at ways to optimise and increase our capabilities.
“For more information regarding our extended range, contact one of our dedicated and experienced sales members.”
Stainless steel enclosures are used often in highly aggressive environments, and that’s where MFB’s S280 industrial range comes to the fore.An MFB S280 industrial 19-inch unit.
Ensuring the safety, quality, and longevity of Australian rail lines requires highly specialised knowledge of the tools and technology used to measure, test, and maintain rails within an Australian context.
This is why Speno’s homegrown Aussie mindset, coupled with more than 50 years of accumulated knowledge and experience working in Australian rail, give the company a massive competitive advantage over other rail maintenance providers and newcomers.
Speno managing director Mark Green speaks to Rail Express about the company’s uniquely Australian journey, its evolving strategies for success centred on delivering quality and professionalism to clients, and new rail technologies on the horizon.
“First and foremost, our primary focus is on rail health and safety,” he said.
“There’s a lot at stake in our industry and we take our responsibilities very seriously. We try to maintain a constant state of growth as a business which has allowed us to stay on top of what’s going on in the industry while we continue to evolve our service offering.
“Another central focus for us is ensuring the provision of an accredited operator on all types of rail networks. Speno deliver products that are tailored to the specific environmental conditions and requirements of a rail network and above all else, we do what we say we’re going to do.
“This means providing our clients with the highest level of quality assurance and safety standards for the environment they operate in to ensure that passenger services, product delivery and rail networks continue to run smoothly and uninterrupted.”
Speno’s core services are twofold: providing rail grinding services for mainline
rail, switches, and turnouts to ensure rail profile and surface condition is sustained, as well as ultrasonic rail flaw testing and laserbased measurement systems that ensure the quality and integrity of tracks.
“Ultrasonic rail testing, combined with rail grinding is critical for the rail health and optimising wheel-rail interfaces,” Green said.
“Our ultrasonic technology interrogates the integrity of the rail and detects any degenerative defects buried inside the rail or the presence of surface condition safety hazards that could result in a rail breakage or failure.”
Particularly for Australian rail operators, ensuring that rail networks continue to operate at peak performance can present some unique challenges.
“The Australian rail industry must contend with harsh climate conditions, extreme temperatures, and the tyranny of distance in remote areas of the country, which can make the ongoing management of maintenance and repairs extremely challenging for even the most seasoned professional,” Green said.
When it comes to keeping Australian rail on track, there is no one-size-fits-all approach, he said. And yet, very few have measured up quite like Speno has over the years.
From the launch of its inaugural grinding
With more than half a century of industry-leading rail experience, Speno Rail Maintenance Australia continues to break new ground.Speno Rail Maintenance Australia continues to lead advancements in rail grinding technology.
train out of the Pilbara region in 1969, to the subsequent development of industry leading advancements in rail grinding technology, Speno has successfully established a significant presence in the Australian rail industry over the decades and continued to go from strength to strength.
“Our parent company Speno International had strong vision back in the late 1960’s to enter the Australian market and introduce the first grinding train in the Pilbara region,” Green said.
“Our Australian company is modelled off an international engineering model that focusses on precision tolerances, robustness, and high efficiency, and we’ve managed to maintain those high standards as we have grown into our Australian identity.”
Over time, Speno has translated this sophisticated engineering technology into a uniquely Australian product offering that is sustainable in an Australian context.
Currently, the company maintains operations spanning across Western Australia, Northern Territory, New South Wales, South Australia, Victoria, Queensland and an overseas arm based in New Zealand.
“We have been operating in Australia for more than half a century which has given us intimate knowledge of the Australian countryside including all networks located around the country,” Green said.
“What we have learned is that methods that may work in one country, likely won’t work in another because of the type of environment.”
For example, one of the key differences between a European rail line and an Australian rail line, is that typically European nations have
challenges with snowy environments and cold temperatures, whereas Australian rail operations typically must deal with the relentless heat and the tyranny of great distances.
Whether it’s a suburban rail network with high volumes of traffic, such as Sydney’s rail line that takes more than a million passengers a day, or a desert-like stretch in the outback of Northern Territory or Western Australia, Green emphasises the criticality that the flexibility of the Speno service matches the rail network they are used on.
“Every rail network has its own set of natural behaviours in how it operates,” he said.
“Being uniquely Australian, we understand the nature of the rail lines in different locations, the geographic conditions, the characteristics of the terrain and we understand how a particular network will behave under various traffic conditions, in extreme heat, or cold weather.”
Having this deep understanding of the country has been invaluable for building and maintaining strong relationships with clients.
Another aspect of this, Green said, had been employing the best local people who are not only highly skilled, but are also genuinely invested and dedicated to their work.
“How we manage the quality of the service we provide to our clients is of the utmost importance to us, and our people are our strongest asset when it comes to approaching every job,” he said.
“Our team is the front face of our business, operating the machines and engaging with the client on the site,” he said.
“At every level of the business, our team
is engaged, because we are invested in the products and services we deliver, invested in the business, and invested in the outcomes.
“I believe clients really feel that when they get that personal level service from us that is unique to every job we do. We understand that every client has different needs, different conditions, and different reporting structures, and we need to be flexible and adaptable to meet them.”
With the needs of customers continuously shifting and evolving with new rail technology, maintaining this flexibility and dynamism has been instrumental in Speno’s ability to adapt to a changing market and continue to innovate its products and services.
More recently, it has been working on a fully integrated, customisable, datamanagement system.
“It’s still early days for this data management system and we are in the testing stage with our first system in the Pilbara, but we have some highly talented people who have been working on developing this inhouse,” Green said.
“The system has been designed to aggregate rail maintenance data, generated by our machines and provide clients with more flexible options for how their data can be used, such as remote condition monitoring and predictive maintenance.”
The official launch date for the new system is yet to be determined, but Green confirms that it will transform the way Speno provides data to clients in the future.
“Right now, all I can say is watch this space,” he said.
The Australian Logistics Council (ALC) acknowledges the findings of the Inland Rail Independent Review led by Dr Kerry Schott, and supports the Australian Government’s response in implementing the recommendations in full.
As the report says, it is expected Inland Rail will accommodate and drive a modal shift of 200,000 trucks a year, so bringing significant benefits in terms of supply chain efficiencies,
The ALC endorses the review’s suggested staged approach for the Inland Rail project, which prioritises the section from Beveridge to Parkes.
This approach will increase the resilience and productivity of the supply chain and allows for enhanced connectivity between the future Inland Rail route and the existing NSW state network.
ALC is also pleased that the review
This terminal can provide an efficient double-stacked rail freight route between Beveridge, Parkes, and Perth, and can be instrumental in improving the efficiency and
This decision aligns with the government’s shift more freight from road to rail for a more
option for freight across Australia, particularly proposed to be complemented by significant
In summary, the ALC supports the Australian
The ALC has backed the recent independent review into Inland Rail, and its recommendations.Sheena Fardell, chief of policy, ALC. The report recommendations support the underlying objectives of Inland Rail, enhancing the competitiveness of rail freight.
The RISSB has announced the winners of the second annual Rail Safety Awards.
This year’s awards were presented at the Rail Safety Conference dinner in Sydney on May 2.
The awards were established in 2022 to recognise and celebrate individual and company safety achievements in the rail industry, and to showcase the work of rail safety champions who may not be otherwise publicly acknowledged.
The 2023 winners are:
• R
This award recognises programs within organisations that promote and improve the overall safety capability of the wider organisational leadership team (directors, managers and frontline supervisors)
Winner: Metro Trains Melbourne Infrastructure New Ways of Working Project Team
Metro Trains Melbourne’s Infrastructure Team is responsible for maintaining more than 1000 kilometres of track across the metropolitan network. The team works around the clock to maintain track, electrical networks, signals, structures, facilities, and operational control systems. Since 2021, the Infrastructure Safety Team has been rolling out the New Ways of Working Program comprising new processes, procedures, an application and training program, to keep its rail workers safe.
• FR
This award recognises programs within organisations that promote and improve the overall safety capability of the wider organisational leadership team (directors, managers and frontline supervisors).
Winner: Chris Polias, Sydney Trains Polias is a rail safety coach with the SEQR Service Delivery team recognised for his work as an advocate for the Rail Safety Coach Team in Sydney Trains, and contributions to the development of RISSB’s Harmonised Network Rule: Planning Works in the Rail Corridor, the ICON Corridor Safety Team, and championing of the PO Infield Rectification Program.
The community safety award acknowledges initiatives that deliver an improvement in
crossings, trespass or other community safety engagement initiatives).
Winner: Vikki Ducrow, Puffing Billy
In 2018, Ducrow was tasked with the cultural, safety and operational review of the Puffing Billy Railway. Through her leadership, she maintained strong relationships with the national rail regulator, the Puffing Billy board and drove the cultural and operational review across all areas of Puffing Billy Railway operations successfully.
This award is for excellence and innovation and will be granted to a new (less than five years) rail worker in the rail industry to recognise and encourage their contribution to the improvement of safety.
Winner: Julian Popowicz, Downer Popowicz was recognised for his safety contributions to the Warrnambool Line Upgrade Project where he was working as a site engineer during COVID.
This award acknowledges the overall achievements of a safety professional in improving the health, safety and wellbeing outcomes within a team or organisation. This year, we recognised two winners.
Carvolth commenced with Downer 19 years ago and is currently its Zero Harm Manager –Queensland. He has been widely recognised as an excellent role model and impressive safety professional who is committed to zero harm. In 2022, the Maryborough operations team achieved 1500 LTI-free days. He has worked tirelessly to better his team’s understanding and commitment to zero harm and safety including developing educational materials that inspire and motivate.
Joint winner: Tristan Lynn, Rio Tinto Lynn is the Superintendent, Health Safety and Emergency Services of Rio Tinto and has worked there for 15 years, 13 of these supporting the rail operations, rail maintenance, rail engineering and strategy divisions in various health and safety leadership roles. He was nominated for his significant contributions to on-site safety by implementing the updated Rio Tinto Safety Maturity criteria and process; helping run fatigue awareness training following postCOVID roster changes; providing leadership in the safety of rail maintenance contract partners; and ensuring there was compliance with directives from the Department of Fire and Emergency Services WA.
All winners automatically become finalists in the Safety Excellence category of the 2023 Australasian Rail Industry Awards.
The ARA has launched its Work in Rail campaign, part of a major push to boost employment in the industry.
Despite this, rail continues to offer longterm career opportunities: 2022 research commissioned by the ARA found rail construction and maintenance activity would rise to an average $14.4 billion per year over the next five years, after a record $12.9b in activity in 2021-22.
With the strong investment in rail set to continue for years to come, there has never been a better time to work in rail.
higher education students about opportunities in the rail industry, as well as relevant education pathways, while also helping those already working in other industries to identify roles that would suit their existing skills.
Creating a more sustainable, resilient rail industry has never been more important.
Australia has the seventh largest rail network in the world, with more than 40,000 kilometres of track crisscrossing the country. The industry supports 165,000 direct and indirect jobs, making it a major Australian employer.
But as the sector experiences an unprecedented infrastructure boom and demand for workers, the growing workforce gap must be addressed.
With $154 billion in rail construction activity planned over the next 15 years, the current 70,000-person skills gap across the industry, and an ageing workforce, action is needed to support the long-term needs of the industry.
Rail competes with other industries such as construction, energy and technology for skilled workers and has not traditionally been a top-ofmind employer.
People typically do not realise how large the industry is – there are more than 450 career opportunities with nearly 1000 companies in Australia alone, whether that be in heavy haul, freight, passenger, construction or the supply chain.
Despite this, rail offers many of the benefits skilled workers are seeking: a modern, innovative and sustainable industry that delivers essential services to support the economy and community.
The Australasian Railway Association’s (ARA) 2018 Rail Skills Capability Study drew attention to the looming skills crisis in the industry, identifying that partnerships and developing more formal training are critical to addressing the shortage.
In response to the skills gap, the ARA recently announced its Work in Rail campaign, backed by the Federal Minister for Skills and Training, Brendan O’Connor, who launched the program in Melbourne in April.
The campaign is timely, given the huge infrastructure investment being undertaken across the country on projects such as Inland Rail, the Sydney Metro, Melbourne Metro Tunnel and the Cross River Rail in Brisbane.
The Work in Rail website includes summaries of 80 different roles within the rail industry, outlining information about the work involved in the role, training and education pathways, salary data and links to current job vacancies.
Jobs are many and varied, including disciplines such as sustainability advisor, engineers, communications, project designer, boiler maker, protection officer, plumber, plant maintainer, procurement, heritage advisor, HR, mechatronics engineer, investor relations, IT, project management and customer relations.
Website users can use a self-assessment tool to find roles that best suit their interests and access information on rail industry employers.
The ARA has also been hosting a Work in Rail stand at careers expos in Melbourne, Perth, Brisbane and Sydney in May and June, in partnership with its members, to engage directly with school leavers on the significant career opportunities available in rail.
The ARA has been actively working with industry, the vocational education and training sector and Engineers Australia to
are in accessing courses. It is supporting the development of rail industry-specific courses, including within the engineering faculties of universities, to encourage more graduates into the industry.
TAFE in Western Australia is now offering specific rail courses in areas such as infrastructure and rail signalling to people who are not yet employees in a rail organisation.
This is an industry-first and will give the rail industry access to a talent pool with recognised competencies and qualifications, making training on the job a lot more efficient.
Currently, TAFE is generally not supported by government or industry to deliver courses for rail beyond apprenticeships, resulting in no clear entry pathways into rail afterwards.
The ARA is advocating for universities to include electives or units of study that are focused on rail learning in both civil and electrical engineering disciplines.
It is also establishing partnerships with the education sector to build a range of learning solutions that support careers in rail, as well as supporting the existing rail workforce to transition to new technologies. This will be critical as signalling systems and rolling stock become more technologically complex.
There is currently only one rail-focused engineering university course in the whole country – which came about due to a partnership between Transport for NSW, Engineers Education Australia and the University of Tasmania.
The Diploma in Rail Track Engineering is offered as an online course and does not require those undertaking the course to have a university degree, although many of its students already have a civil engineering degree.
Supporting a wider range of pathways that encourage students to consider a career in rail from the beginning of their career remains a strong focus for the ARA.
The ARA will soon publish a report dedicated to better understanding the available skills mix in the country and what is needed for the future.
The report will provide data on the investment and operation of rail and our future skills needs to help industry plan for capacity and capability requirements.
The ARA has partnered with the National Rail Skills Academy in the UK to use its Skills Intelligence Model (SIM) to determine what skills will be needed and where.
This research showed that the data collection process in Australia, typically using ANZSCO codes, does not provide a clear view of the rail industry’s current and future needs.
The ARA will be advocating strongly for additional codes and for the train driver code to be split between freight train driver and
passenger train driver to address this issue. The upcoming report brings together a range of data sources available within the Australian rail industry to provide an understanding of where specific skills are needed and what is on the horizon.
It will also provide insight into where rail investment is occurring and where skills needs are located across Australia, both now and in the future.
This level of information will also allow the ARA and education industry to collaborate to build courses and learning strategies to meet future needs in advance, supporting a more sustainable and robust workforce.
Industry and TAFE educators recently participated in an ARA workshop for the heavy haul industry which was focused on identifying critical skills needed to support the decarbonisation of the industry.
There have already been some positive steps taken to support this goal.
Earlier this year, the Western Australian transport, planning and ports minister Rita Saffioti and her colleague, training minister Simone McGurk, formally opened the new METRONET training facility in the state.
Rio Tinto and John Holland have been great supporters of the construction of the facility and Rio Tinto now have several staff undertaking the Certificate IV in Rail Signalling.
North Metro TAFE will also be delivering a Certificate II in Rail Infrastructure to graduating school students as well as running courses for people keen to enter the rail industry who are not yet employed.
The ARA’s Introduction to Rail Signalling course is a great example of a course that is accessible and gives participants an engaging and collaborative learning experience.
The course covers mechanical, electrical and digital signalling assets and discusses the challenges of systems integration. The first cohort for the five-week online course commenced in May, with the ARA receiving strong interest in this new offering developed in response to industry demand.
The course has built on the success of the Understanding Rail online course, an introduction to the rail industry.
The course has continued to receive a high level of interest since moving online, providing a broad overview of the industry for people new to rail, or those changing roles or seeking to improve their industry knowledge.
The ARA is also planning to develop an operations course that will leverage its capability in online learning, providing an overview of rail operations for those new to the industry or working closely with operations teams.
The ARA will also continue to work with the education industry to build learning solutions that meet industry need in under-served disciplines such as track engineering, rolling stock, rail systems engineering and rail asset management.
Ultimately, no one solution will address the skills shortage on its own.
These initiatives, and many more, will work together to support the short-term and longterm needs to ensure rail can continue to meet the needs of the economy and community long into the future.
The ARA has been encouraged by the strong focus on collaboration between government, industry and the education sector to create solutions and support the attraction of more people to the rail industry.
Together, these efforts will help us address current skills gaps and support a sustainable workforce over the long term.
Melbourne Tram Refranchising
Interested parties are invited to apply for pre-qualification in the 2024 operations and maintenance contract for Melbourne’s tram network.
Those pre-qualified will be invited to participate in a Request for Proposal phase commencing July 2023.
Notification of the tender is available on Buying for Victoria - Display Tender DOT2516-1 (tenders.vic.gov.au)
Melbourne’s iconic tram network is the largest in the world, with 250 kilometres of double track, over 1600 tram stops and 24 routes.
Operating for more than 100 years, its fleet has more than 510 trams, with eight depots, forming part of an integrated transport system with the road and rail network, servicing the city and linking to regional services.
The tram operations and maintenance will be under a newly designed contract, one that continues to modernise the experience for passengers and delivers improvements at every stage of the journey.
The Government has invested significantly in new trams and supporting infrastructure, and this next contract will ensure that these are delivered to benefit passengers.
crews started installing 4000 highperformance concrete panels to create an even base for the rail and ensure it was properly aligned.
The panels were cast in 300 different shapes to match the curvature and elevation of the tunnels as they wind from Kensington to South Yarra, up to nearly 40 metres underground. The 236 lengths of steel rail are extremely strong, but flexible enough to curve along the tunnels where needed.
With the track in place, the team is now preparing for the first test trains to run through the tunnel in the second half of this year, kicking off a period of meticulous testing to ensure the Metro Tunnel is safe and ready for passengers in 2025 – a year ahead of schedule.
A vital part of the Australian Rail Track Corporation (ARTC) Inland Rail Stockinbingal to Parkes project has been delivered, with more than 277 tonnes of rail arriving for the new Daroobalgie crossing loop in NSW.
Major construction on the Stockinbingal to Parkes section is expected to begin in late 2023 and involves enhancements or modifications to specific sites along the existing rail corridor to accommodate doublestacked freight trains.
ARTC is undergoing a competitive tender process to appoint a contractor to manage the detailed design and construction of the Albury to Parkes enhancement projects (Albury to Illabo and Stockinbingal to Parkes).
The Daroobalgie crossing loop and Wyndham Avenue road bridge works will be a construct only component, as detailed designs have been approved.
During this time, we are conducting various follow up environmental and technical investigations, engineering and design, hydrology studies and consulting with key stakeholders, communities, and landowners to finalise plans for this project,” he said.
“Early works in and around Forbes will be ongoing, including the relocation of gas and water infrastructure. These works are required because they will enable major construction works to proceed more efficiently once a contractor is appointed.”
ARTC announced the shortlisting of three construction firms to deliver the design and construct contract for the Illabo to Stockinbingal section in February:
• John Holland
• MBJV (Martinus Rail and BMD Constructions)
• Regional Trac JV (Seymour Whyte Constructions and Rhomberg Rail Australia)
Australian rail freight operator Southern Shorthaul Railroad (SSR) has secured a long term agreement with Manildra Group to carry out its rail haulage task from November 1, 2024.
SSR expects there will be significant investment in new rolling stock over the next 18 months, with train crew and service requirements now entering the planning phase.
The company said the new agreement would see the rail side of the business grow by about 75 people.
The new METRONET Lakelands Station in Mandurah, south of Perth, will open on Sunday, June 11.
Victoria’s Metro Tunnel, paving the way for test trains to begin running deep beneath Melbourne’s CBD in the second half of the year.
The tunnelling project was delivered by the Cross Yarra Partnership consortium (Lendlease Melbourne Metro, John Holland, Bouygues Construction, John Laing and Capella Capital).
The package of works involved main tunnelling, five underground stations, station fit-out, mechanical and electrical systems and specific maintenance services for the infrastructure, and commercial opportunities at the new stations.
When workers laid the final lengths of Australian-made steel rail on the tracks, it marked the culmination of nine months of work along the twin nine-kilometre tunnels and stations.
The process began in mid-2022, when
The successful contractor (tender expected to be awarded in mid-2023) will be required to deliver initiatives and meet targets related to industry participation, employment and workforce development.
Other works planned for Stockinbingal to Parkes include increasing vertical clearance on the Lachlan River rail bridge and Wyndham Avenue Road bridge in Forbes, modifying Forbes Railway Station, and enhancing several existing crossing loops, structures, and utilities.
Inland Rail director for the Albury to Parkes program delivery, Melvyn Maylin, said the crossing loop at Daroobalgie features 2.21km of new track built to the eastern side of the existing track, and will include the replacement and extension of culverts to mitigate flooding on neighbouring land.
“The Stockinbingal to Parkes project is now in the procurement and detailed design stage.
ADCO was selected as the head contractor to design and build the facility as part of the WA Government’s METRONET program of projects.
The facility will take pressure off nearby Mandurah and Warnbro stations and provide a journey time of 50 minutes to the CBD.
Lakelands includes an entry building complete with Aboriginal artwork, a pedestrian overpass, two platforms, park/ kiss-and-ride facilities, a bus interchange, a 400-bay car park, and cycling facilities.
The station has also been future-proofed with provision for additional facilities such as more escalators, more lifts and fare gates as needed.
The $72 million project has supported around 200 jobs since construction began in November 2021. The project was originally budgeted at $80m and was jointly funded by the Commonwealth ($64m) and the Western Australian Government ($16m).
It is a symbol of trust.
The trust can only be built with the specialised knowledge, and a deep understanding of the transport and industrial sectors.
Whether it is identifying a strategic marketing approach, or crafting a creative execution, we have the global perspective with a unique solution.
Create a better
#TomorrowWithUs
Discover impactful careers in rail at Siemens Mobility