


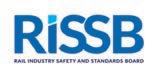
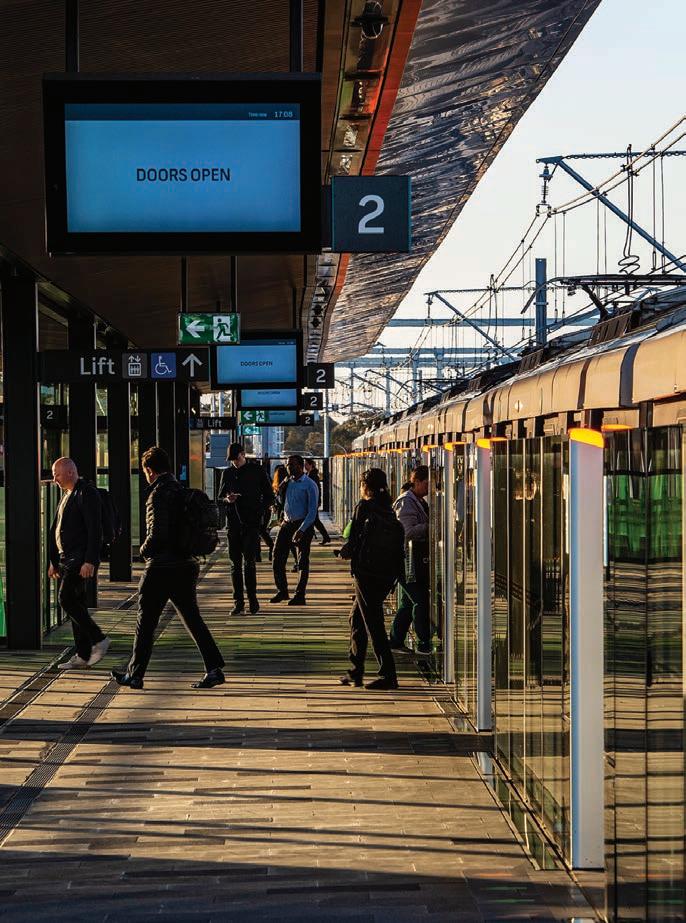

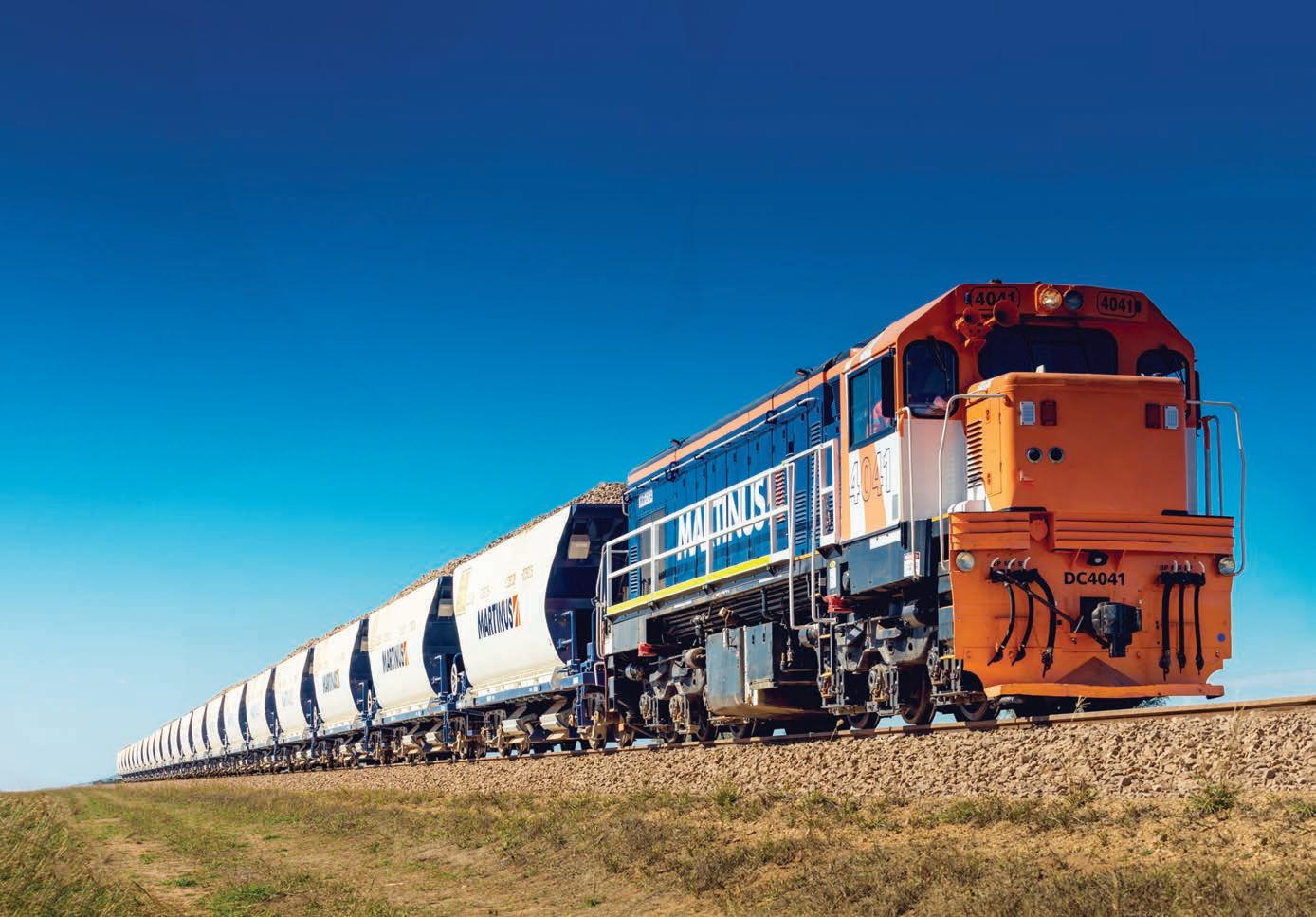
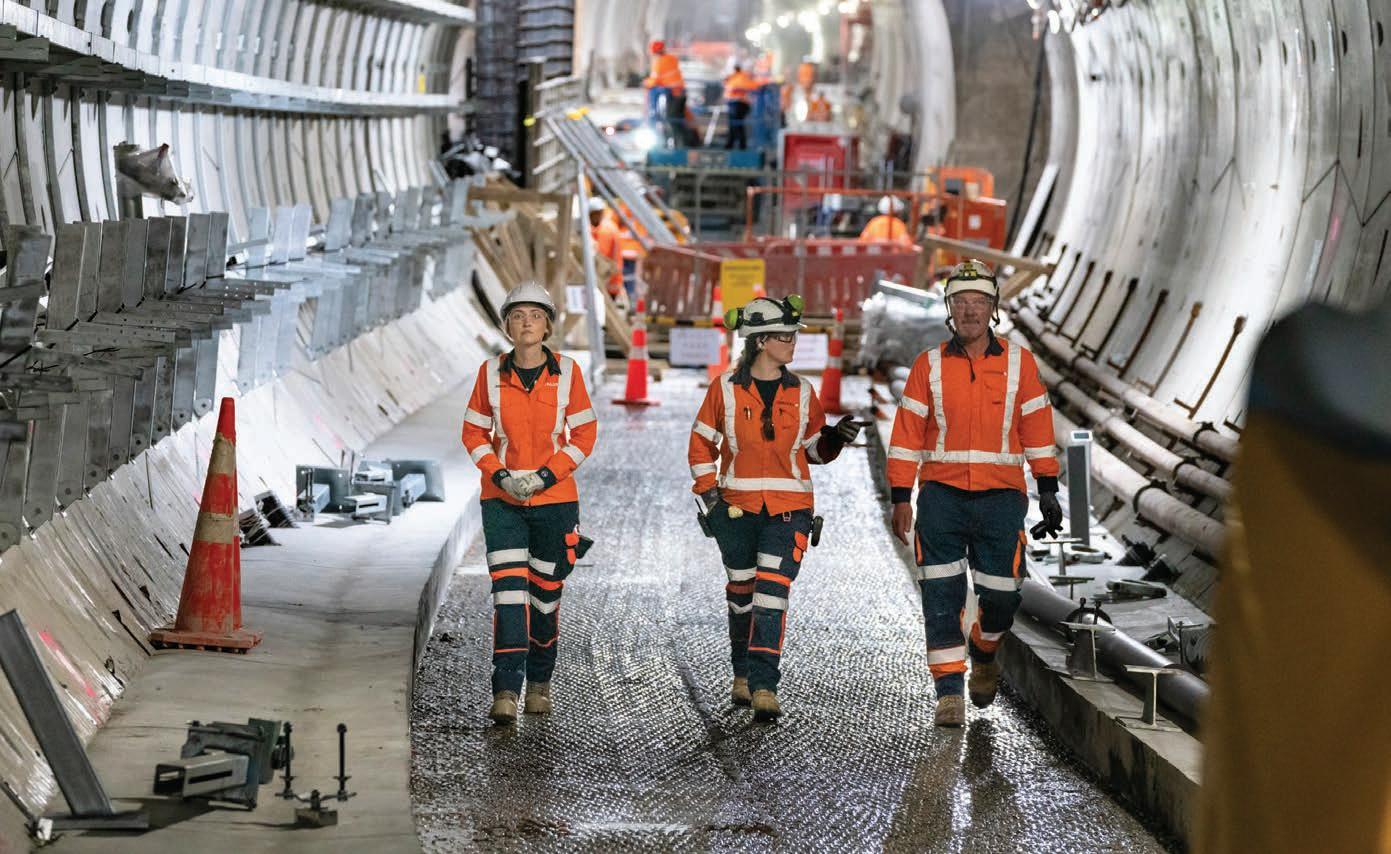
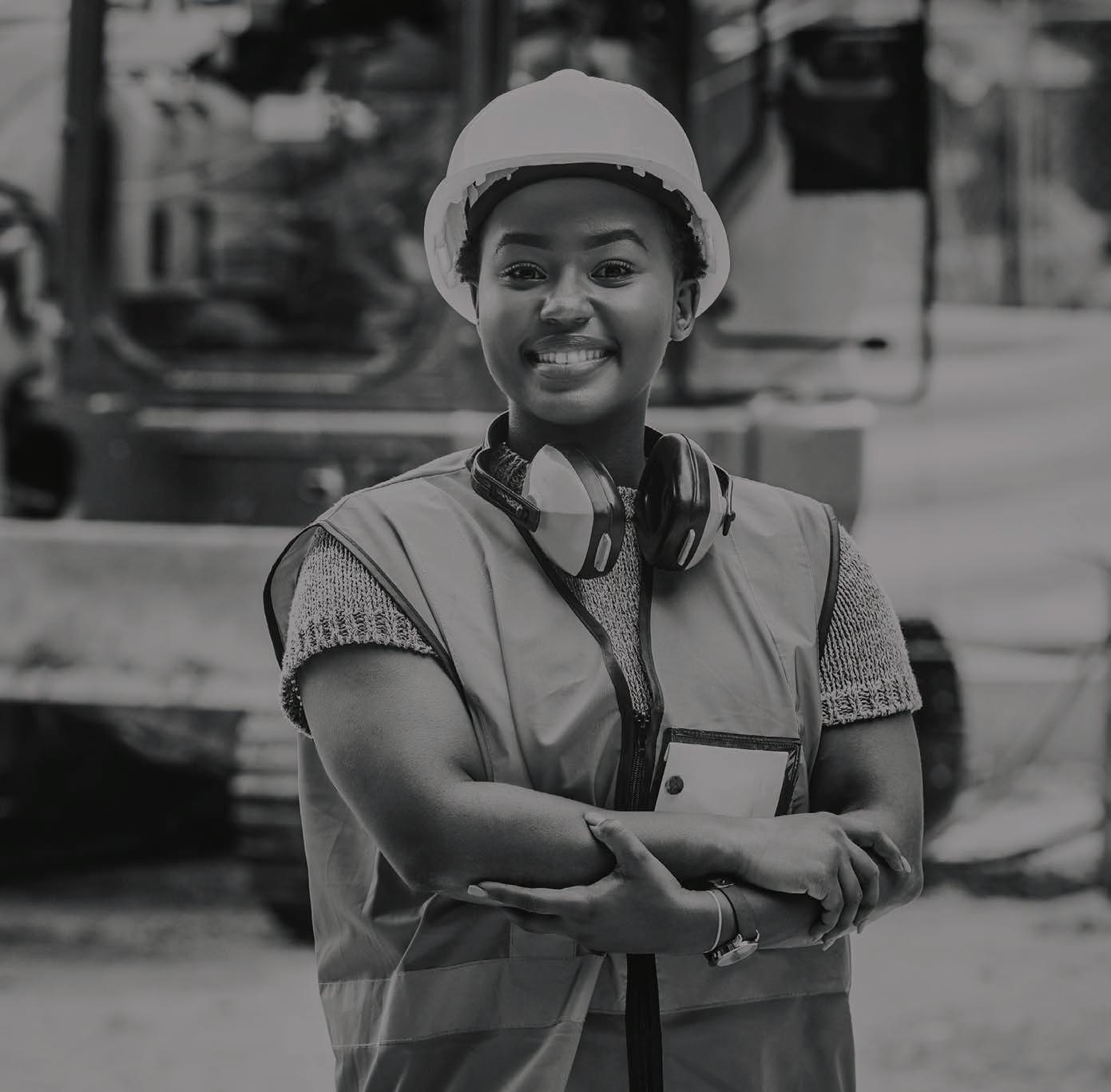
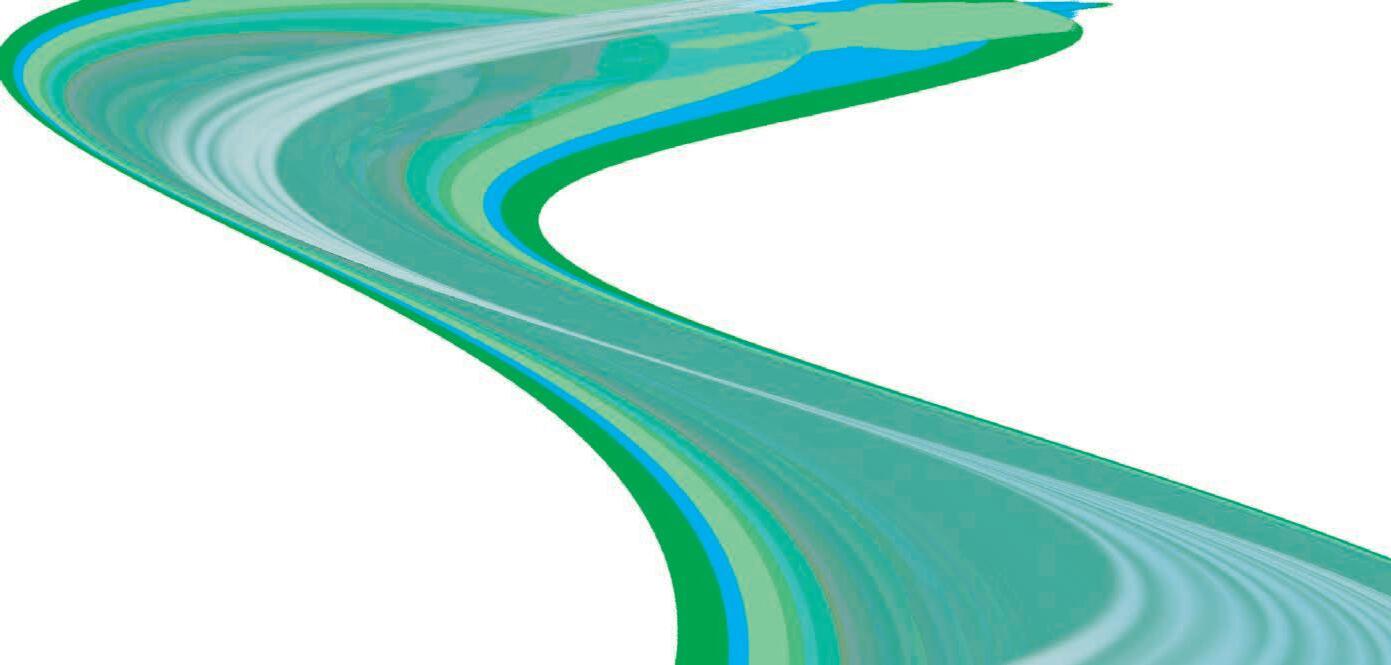
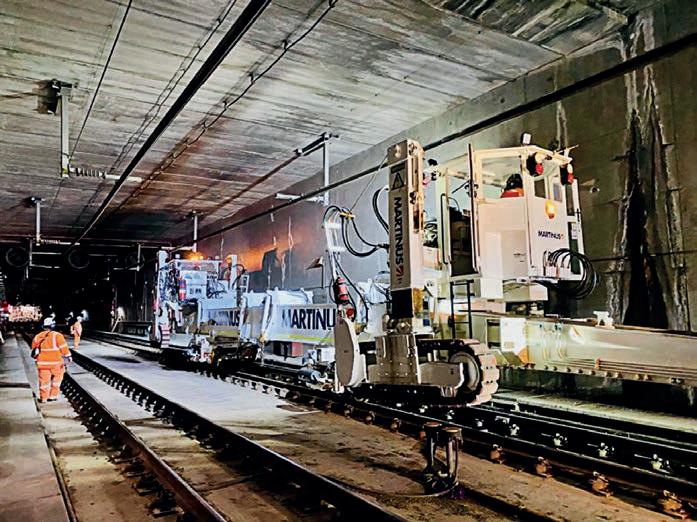


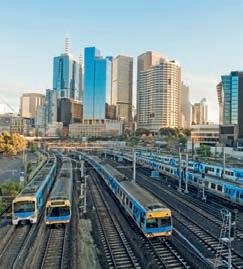
Published by:
Ray Chan Editor - Rail Express379 Docklands Drive
Dockalnds, VIC 3008
T: 03 9690 8766
www.primecreativemedia.com.au
Publisher John Murphy
E: john.murphy@primecreative.com.au
Chief Operating Officer Christine Clancy
E: christine.clancy@primecreative.com.au
Managing Editor
Myles Hume
E: myles.hume@primecreative.com.au
Editor
Ray Chan
E: ray.chan@primecreative.com.au
Business Development Manager
Alex Cowdery
M: 0422 657 148
E: alex.cowdery@primecreative.com.au
Client Success Manager
Salma Kennedy
E: salma.kennedy@primecreative.com.au
Design Production Manager Michelle Weston
E: michelle.weston@primecreative.com.au
Art Director Blake Storey
E: blake.storey@primecreative.com.au
Design Caterina Zappia
Subscriptions subscriptions@primecreative.com.au
www.RailExpress.com.au
The
photocopying, recording or otherwise without the permission of the Publisher.
This month we feature our annual focus on plant and equipment for the rail industry.
It goes without saying that to ensure the efficient operation of rail systems, the quality of assets used in this industry is of paramount importance.
It’s something we can’t afford to take for granted. The need to use quality plant and equipment is demonstrated none more so than in their role in maintaining the highest safety standards.
Heavy machinery, high speeds, and dense passenger traffic: any malfunction or failure in apparatus or machinery can lead to catastrophic rail accidents.
Regular maintenance, modernisation, and adherence to safety protocols are essential to minimise risks and ensure the safety of passengers, employees, and surrounding communities.
Using quality equipment also provides greater reliability to services, the key to building confidence with customers and stakeholders in the form of trustworthy journeys that adhere to schedules and minimise disruptions.
Good plant and equipment are more dependable, resulting in fewer breakdowns and service interruptions.
And in this day and age, it is imperative that trains and locomotives be geared up for maximum environmental sustainability.
Already touted as an eco-friendly mode of transportation due to its lower carbon emissions compared to road and air travel, the rail sector must prioritise investment in modern, environmentally-friendly plant and equipment, such as electric locomotives and energy-efficient infrastructure, to further reduce the industry’s carbon footprint.
In this edition, read about many of the technological advancements made by various rail equipment manufacturers, such
as the latest ballast cleaning units from Swietelsky, flashbutt finesse from RWECA, terrific tampers from Plasser, and track reconstruction packages from George’s Loader Hire.
Keep up to date with the latest releases from specialist innovators such as Manco Rail and Harrybilt Engineering, and find out more about Key Source Rail’s tracklaying products and Alltrack’s impressive pedigree in sourcing rail equipment from all over the globe.
We also talk to Natalie Loughborough, the newly-appointed Executive Director of Rail for the National Transport Research Organisation, about her role and the challenges facing the rail industry.
Known as the source of independent, reliable and robust guidance on the delivery of next generation infrastructure to serve the mobility needs of the community, the NTRO provides timely, accurate and impactful solutions to support governments to achieve their objectives.
In the face of the complexities facing rail, including the fragmentation of the networks across Australia, with its three gauges and 11 separate signaling system, Loughborough gives an interesting insight into how she plans to work on the interoperability challenge and focus on the possible economic benefits of a more cost-effective, efficient and sustainable rail system.
We also include the regular informative articles from our industry associations, and welcome a new partner in the form of the Permanent Way Institute of NSW, a diverse and inclusive rail infrastructure community that excels in delivering safe, efficient and sustainable railways.
We hope you enjoy the read.
The review of the National Freight and Supply Chain Strategy has commenced, following agreement with state and territory infrastructure and transport ministers.
The strategy is a holistic, coordinated and multi-modal approach to increase the safety, productivity and resilience of freight and supply chains, agreed by all jurisdictions. It sets an agenda for government and industry action across all freight modes to 2040 and beyond.
Federal infrastructure minister Catherine King said Australia’s supply chains were critical to the country’s future economic success and to strengthening the connections between its regions and urban centres.
“That is why infrastructure and transport ministers across Australia have responded to calls from industry to commence the first review of the strategy,” she said.
“The review will ensure it remains fit-forpurpose for the Australian freight and supply chains industry.
“We know this industry has experienced unprecedented and compounding disruptions over the past four years including a global pandemic, extreme weather events, geopolitical tensions, skills shortages and more.
“The review is a critical opportunity to take stock of what has changed and what has been
address Australia’s growing and changing freight task.”
The review will assess if there are gaps in the strategy’s goals and identify priorities for the next five-year National Action Plan. Stakeholder engagement will be an important part of identifying these gaps and priorities.
The review will undertake stakeholder consultation and consider public submissions.
“In late August, I am looking forward to hosting a round table to hear directly
The Board of the High Speed Rail Authority (HSRA) is moving quickly to formulate plans for the establishment of an east coast high-speed rail network in Australia.
The first such project is expected to link the cities of Sydney and Newcastle.
Board members have already had detailed briefings with New South Wales transport officials regarding the existing rail corridor between the two locations, and also visited Newcastle for a follow-up meeting.
The HSRA commenced operations on June 13 to lead, plan, develop, coordinate, oversee and monitor the construction and operation of fasterspeed operations in the country.
High-speed rail will revolutionise interstate travel on the east coast, providing a fast alternative for people to move between cities and regional centres, promoting sustainable settlement patterns, and generating and spreading economic benefits beyond the outskirts of major capitals.
The HSRA Board is committed to working transparently within a framework of high standards of governance and accountability.
It is enthusiastic about the important foundational and planning activities currently underway, and is working to build the HSRA with a strong leadership team, organisational capability, positive culture and transparent processes and decision making.
Infrastructure minister Catherine King said high-speed rail would be instrumental in improving the lives of Australians by supporting shifts in population settlement, better connecting skilled workers with major job centres and be a key enabler of achieving ambitious carbon reduction targets.
“It is essential the HSRA takes the time now to establish a robust foundation on which to build and this means the planning has to be done properly and in detail,” she said.
“Given the size and scale of building an east coast high-speed rail network, it must be based
The Department of Infrastructure, Transport, Regional Development, Communications and the Arts will lead the review in close collaboration with industry and state and territory governments.
Ministers will consider the recommendations of the review by the end of this year.
For more information, including to make a submission to the review, visit: www. freightaustralia.gov.au/2023-review.
on meticulous planning, good governance and highly effective project management.
“High-speed rail is still in its early days and we acknowledge this project will take time.
“We have a vision about how we want to see Australia develop, not just next year or next decade but decades from now.”
Federal Member for Newcastle Sharon Claydon said the HSRA Board meeting in Newcastle was a milestone achievement that recognised the lead role the city would play in shaping high-speed rail in Australia.
Queensland Rail has added additional 16 railway officers to its patrol squad.
Queensland Rail security and emergency preparedness senior manager Drew Brock said the new members were an expansion of its partnership with Queensland Police Service (QPS) and would take numbers up to 102 officers.
They will support Queensland Rail authorised officers, the security monitoring team and private security teams.
“Railway squad officers are QPS Officers with specialist training that operate in teams from dedicated outposts at key stations on the network,” Brock said.
“The squad, along with Queensland Rail’s security members, undertook 716 joint operations last financial year across the SEQ network to enhance customer security.
“Our teams work closely with QPS to create an active and visible presence and stop people doing the wrong thing.
“Anti-social behavior has no place on Queensland Rail trains and precincts, and we’ve made that clear with authorised officers issuing 869 penalty infringement notices and 579 warning notices for behavioural and safety incidents last financial year.
“Some of the top behaviours we issued
fines for were alcohol, smoking, nuisance and pedestrian incidents at level crossings/crossing the tracks.”
Queenslanders have been given a rare glimpse into a day in the life of security personnel in a range of social media videos shot for the ‘Your safety and security is our priority’ campaign.
The campaign also features new posters at stations and on trains, and Spotify ads.
“This campaign is about making sure our customers know we are here for them —that
their journeys are not only safe, but pleasant,” Brock said.
“We have 11 canine teams patrolling stations, and guardian trains at night with security officers onboard, rail squad officers on bikes in the rail corridor and more than 12,000 CCTV cameras around the network.
“If any behaviour is concerning to our customers we want them to know we’re here to help at any time.”
The additional officers will be added to the squad over the next four years.
“The trains were initially known as ‘Cairns Tilt Train’ before being renamed ‘Spirit of Queensland’ in 2013, “ he said.
“Since it began operations, the fleet, which is now made up of three trains, has travelled more than 11 million kilometres, equal to around 275 laps around the Earth or 14 return trips to the moon. The iconic service has conveyed more than 1,368,000 passengers along Queensland’s coastline.
“The ongoing success is a testament to our hardworking teams that keep it running including our onboard staff, station staff, maintenance crews and everyone behind
fleet completing 1.3 million passenger trips since entering service.
Tilt trains have a mechanism enabling increased speed on regular rail tracks to
said the Diesel Tilt Trains first ran on the North Coast line in mid-2003 and have continued to connect communities from Brisbane through to Cairns for two decades.
To support planned maintenance on Queensland Rail’s Electric Tilt Train fleet, there were additional Spirit of Queensland travel options added.
Services were increased from eight to 10 one-way services each week between Brisbane and Cairns.
Alltrack Rail is a leading Australian purveyor (seller and dealer) of railway locomotives, rolling stock and associated rail maintenance parts and plant. We also source new and used railway perway materials such as rails, sleepers, turnout components and fastenings.
Our business is based in the Hunter Valley NSW, where it is owned and managed by rail industry veteran, Bob Taylor. With over 45 years’ experience in the rail sector, we boast an impressive list of clients and contacts in each of the continents across the globe which include major maintenance
providers, rail track operators, major construction firms and contracting businesses.
With our network of contacts we can also find a home for quality used equipment when the times comes to move your equipment along.
Our background is underpinned by our reputation for spotting opportunities and ensuring the best possible outcomes for our customers. Whether it concerns the sale or sourcing of new or used plant and equipment, Alltrack Rail can assist.
A large section of Western Australia’s freight line will be relocated, to enable works to begin for the next stage of the METRONET ThornlieCockburn Link Project.
In the coming months, about 11km of new freight line track will be installed in both directions on the northern side of the rail corridor, between Kwinana Freeway, Jandakot and Spencer Road Bridge in Canning Vale.
Once the new tracks are built, the old section of freight line will be removed. This will make space on the south side of the rail corridor for the Thornlie-Cockburn Link passenger line, which will operate side by side in the existing rail corridor.
More than 5km of retaining walls have been built ahead of these works to allow ground levels to be adjusted to make way for the new rail.
Once works are complete, freight operations will improve with new tracks and nearby residents will benefit from noise walls and under-ballast matting, reducing overall rail noise and vibration.
Transport minister Rita Saffioti praised the co-operation between the Public Transport Authority and freight rail operator Arc
Connecting the Mandurah and ArmadaleThornlie lines will open new opportunities for longer-term developments around the new stations at Nicholson Road and Ranford Road.
The Link will support growth and
The Armadale Line Shutdown will begin on November 20, with preparations ramping up for the removal of 13 level crossings, building seven new stations and the addition of 5.5 kilometres of elevated rail across three METRONET projects.
Western Australia’s Armadale Line shutdown will commence on Monday, November 20, paving the way for a transformational upgrade of the 130-year-old train line over the next 18 months.
During the closure, 5.5 kilometres of elevated rail will be constructed, along with seven new stations, and the extension of the line to Byford.
The project will also remove 13 level crossings that cause significant disruption to the local community, and the creation of around six hectares of public open space that will be turned into new public amenities.
They will be immediately removed following the commencement of the shut.
The Government also announced seven new temporary bus routes and five enhanced existing bus routes will be put in place during the shutdown.
The replacement bus services will be a combination of limited stop and all stop bus routes, giving passengers options to get
to the CBD and other local destinations. More than 100 additional buses will be used to provide support, as well as around 1.2km of bus priority lanes, along with the installation of intelligent system technology to help to minimise disruptions to passengers and road users.
There will be some changes to Optus Stadium transport arrangements. Trains will continue to stop at Stadium Station on weekends, public holidays and during events. A new special event bus service (Route 651) will also help eventgoers in Perth’s southeast get to Stadium Bus Station.
The Government is currently assessing options for fare relief to regular Armadale Line passengers impacted by the shut. Timetables for the new and enhanced routes were released in September in line with the launch of a community awareness campaign.
Three temporary bus interchanges in Armadale, Cannington and Victoria Park are also being built to support the additional
services. The Cannington bus interchange is now complete, with Victoria Park and Armadale to be completed in October.
Safety has been a key consideration in getting ready for the shutdown, with an increase of up to 20 per cent more Transit Officer hours, as well as additional security vehicles being deployed to support the operation.
There will be increased surveillance at the new interchanges and the installation of new CCTV cameras, which are monitored 24/7.
A full line closure will be in place for three days from the start of the shutdown to allow for essential works to enable passenger services to operate between Victoria Park and Perth. After this, trains will run between Victoria Park and Perth.
The community will be able to access the latest information from the Armadale Line Shutdown Hub on the Public Transport Authority website: www.transperth.wa.gov.au/Track-Closures/ Armadale-and-Thornlie-Line-Shutdown
NARROW GAUGE HI-RAIL UNDERCUTTING & RAIL STRESS MANAGEMENT SPECIALISTS WITH TWO DEPOTS IN QUEENSLAND
for luggage, prams and bicycles, and modern heating and air conditioning.
They will also open up greater options for travel for people with disabilities and mobility issues with dedicated spaces for wheelchairs and accessible toilets.
A timeline for the introduction of the New Intercity Fleet will be finalised with operations expected to commence in 2024.
Transport minister Jo Haylen said the trains were supposed to be on the tracks five years ago.
complement of New Intercity Fleet trains on the tracks in the shortest possible time.
Transport for NSW and the Rail, Tram and Bus Union (RTBU) has signed a deed on a final operating model for the new electric Mariyung trains, which will run on the Newcastle and Central Coast, Blue Mountains and South Coast Lines.
This deed aligns the New Intercity Fleet operating model with that of the Waratah fleet, and subject to approval by the Office of National Rail Safety Regulator, will allow the new trains to enter passenger service in the most efficient way.
Following last year’s agreement between government and unions to modify the fleet, Transport for NSW has now confirmed the final scope and detailed design of the
Meanwhile, a process has begun to transition the operation of the Mariyung trains and the majority of intercity passenger services, crew and stations from NSW TrainLink to Sydney Trains.
This transition will take advantage of the scale within Sydney Trains to help improve access to resourcing, crew availability and training that supports getting the new trains into service as soon as possible.
The New Intercity Fleet will set a new standard of travel for commuters who make approximately 26 million journeys a year on the electrified intercity network.
The improvements include wider, more spacious two-by-two seating with arm rests, tray tables, and high seat backs, charging ports for mobile devices, dedicated spaces
“It’s been a priority of mine to ensure we get these trains out of sheds and on the tracks next year,” she said.
“I can announce that the New Intercity Fleet Trains will be on the tracks and carrying passengers by 2024.
“We have reached a vital agreement which will get the full complement of the trains on the tracks in the shortest possible time.
“Like the passengers who rely on our intercity network who have waited a long time, I look forward these new modern trains, with more room, more comfort and more features than any other fleet in Australia.
“Passengers deserve to have a first-class safe and reliable public transport system that helps them travel from our regions to the city to conduct business, to go to school and work and be with their families.”
Construction of the new Martin Place station precinct is nearing completion ahead of worldclass metro services starting on the Sydney Metro City & Southwest line next year.
The metro platforms located 25 metres below ground level are almost complete. The tiles and wall panels are in place, with the finishing touches now being made, as workers install signage and seats on the 170 metre-long platforms.
The 25 escalators that will take commuters to their train are undergoing testing and commissioning, while the 14 lift shafts are ready to be fitted with elevators in October.
The new metro precinct has a footprint of more than an entire city block and will include 3000 square metres of retail, dining and beverage outlets over three floors. Station shopfronts have been installed and
tenants will be handed the keys to start their fit-out in early 2024.
Changing trains at Martin Place will be seamless, with direct access from metro platforms to the T4 Eastern Suburbs & Illawarra Line. A new all-weather pedestrian walkway will link Martin Place station with Hunter Street.
Above the station, the 39-storey building at the northern entrance topped out at the end of June 2023, and the highest feature of the 28-storey office building above the southern entrance is due for completion in September.
In the coming months, Metro’s construction partner Lendlease will focus on building the station entrances. Sections of Martin Place Plaza used during construction will start reopening to the public early next year.
When Sydney Metro services start running
under the harbour and through the city, passengers will be able to travel from Martin Place to Central in four minutes, Victoria Cross in five minutes, or to Sydenham in just 11 minutes.
Transport minister Jo Haylen said it was full steam ahead to complete work at Martin Place as work continued towards the opening of the new line between Chatswood and Sydenham to passengers next year.
“50,000 people have worked on this project from start to finish, so the stateof-the-art station we’re take shape is a testament to their brilliant work,” she said.
“Metro will be a transformative project for Sydney, and this landmark station will offer passengers an incredible new transport hub, coupled with commercial, retail and dining options.”
Trains are now being tested at maximum speed inside the Metro Tunnel beneath Melbourne’s CBD.
The team has been gradually increasing train speed since the first test trains entered the tunnel in July.
Trains were first tested between five and 25km/h, but are now moving through the tunnels at up to 80km/h – the same speed they will travel when the Metro Tunnel opens in 2025.
By starting at low speed, the team was able to prove the reliability of the Metro Tunnel’s High Capacity Signalling (HCS), which will allow for more trains to run more often.
The majority of testing for the remainder of the year will continue at up to 80km/h.
Testing will continue progressively to ensure the Metro Tunnel’s complex systems are working well together with the project’s new High Capacity Metro Trains, and alongside the wider network’s existing signalling system – an incredibly complex process.
The next step is to run multiple trains in the same tunnel at the same time.
Second half of 2023 to 2024:
Testing in the Metro Tunnel
The first test trains entered the Metro Tunnel
in July 2023, kicking off rigorous testing of the signalling and other systems which will continue into the first half 2024. This includes:
in the tunnels
• more complex testing – from one train at low speed using minimal power, through to multiple services in the tunnel at greater speeds
• ensuring the train doors open and close automatically at the same time as the platform screen doors when stopping at the stations
• testing all electronic systems at the stations – such as passenger information
Trial HCMT train services will run from Clayton to West Footscray through the Metro Tunnel, using all the new systems. These trial runs are like a dress rehearsal – they will simulate timetabled services and a range of possible real-life scenarios with station staff, drivers and passengers.
These trials will confirm that everything is ready for a safe, reliable and efficient passenger service to begin when the Metro Tunnel and five new stations open in 2025.
Work on major rail projects in regional Victoria will step up this spring to cater for more frequent and reliable services.
Among these is the South Geelong to Waurn Ponds Duplication, where key infrastructure will start to take shape while coaches replace trains.
Local road users are encouraged to plan ahead while the new rail bridge at Surf Coast Highway is lifted into place during a road closure between Baanip Boulevard and the level crossing.
The project includes the removal of the Fyans Street and Surf Coast Highway level crossings which cater to more than 70 trains and around 46,000 vehicles each day.
Work will also continue on major upgrades to South Geelong and Marshall stations, preparing for the new second platforms, pedestrian overpasses and ramps.
Upgrades to train detection technology will continue at level crossings between Waurn
Ponds and Warrnambool, as part of the more than 50 public level crossings being upgraded as part of Stage 2 of the Warrnambool Line Upgrade to allow modern VLocity trains to run to Warrnambool for the first time.
Coaches will replace trains between Geelong and Warrnambool from Wednesday, November 8 until Thursday, November 23.
Major upgrades to the Shepparton Line will be delivered in October and November, as part of the third and final stage of the Shepparton Line Upgrade to enable nine weekday return services between Shepparton and Melbourne.
Sleepers and ballast will be replaced, and bridges and culverts upgraded on more than 25 kilometres of track between Mangalore and Murchison East to enable trains to travel faster and make journeys more reliable.
Coaches will replace trains between Southern Cross and Shepparton from Sunday, October 1, until Friday, November 24.
V/Line will carry out important maintenance and upgrade works progressively over the next few months on the Ballarat, Ararat and Maryborough Lines, the Seymour and Shepparton lines, and the Gippsland Line.
The work includes heritage restoration works at Ballarat station, a major upgrade to the Goulburn River rail bridge, and the installation of box culverts which allow water stop flow under the rail line without interrupting services.
Coaches will replace trains between Seymour and Southern Cross from Sunday, October 22 to Friday, November 10.
Similar arrangements will be carried out between Southern Cross, Traralgon and Bairnsdale from Thursday, November 23 to Saturday, December 9.
Work to prepare the Gippsland Line for a new signalling system will take place alongside V/Line maintenance.
The Victorian Government is testing the use of reservation-only seating for weekend services on the Albury Line, as part of ongoing moves to support their increasing popularity and give passengers more certainty on seat availability.
Public transport minister Ben Carroll said a recent survey of weekend passengers by V/Line found more than 70 per cent supported such a seating system on the busy Albury Line trains.
Since being introduced on March 31, the regional fare cap has proved extremely popular with locals and visitors, with about 150,000 Albury Line passengers benefitting from the cheaper travel.
Under the trial, if all seats are booked on a service, passengers would then have the option of purchasing an unreserved ticket, which alerts them that they may have to stand for some or all of their journey.
Alternatively, passengers may also have the option to travel on an overflow coach, on services where these are available.
The trial started from the weekend of September 2, and runs until late November.
V/Line will keep Albury Line passengers updated as details of the seating reservations trial are finalised ensuring
In the meantime, Albury line passengers are encouraged to plan ahead and reserve a seat for all long-distance services by booking online at a staffed V/Line or premium Metro station, by calling 1800 800 007 or by visiting a retail ticket agent.
Passengers with accessibility needs are also encouraged to call 1800 800 007 to book a reserved seat or accessible space with special
“We’ve improved the trains and services on the Albury Line and dramatically slashed the cost of travel. Now we’re ensuring passengers have more certainty about when seats will be available on the busiest services,” Carroll said.
“By asking V/Line to trial reservation-only seating on Saturday and Sunday services, we’re giving passengers peace of mind when they book their travel.”
hundreds of pigeons doing so in the many buildings that house trams and maintenance equipment.
The trial tackles serious problems caused by the build-up of nesting material, feathers and bird droppings in its depots.
The new technology has been recognised by the World Wildlife Fund and Birdlife Australia as animal and environmentally friendly, sustainable, ethical and safe and has been selected primarily because it is a non-harmful option for birds and other wildlife.
The laser units will be trialled for eight weeks and if successful, may be rolled out across all depots.
trialling the use of lasers to reduce damage caused by birds at a busy tram depot and slash cleaning and maintenance costs.
An automatic bird deterrent laser called Bird Beam has been installed at the Malvern Tram Depot.
The system uses low-power lasers to create
without harming birds and other wildlife.
Birds perceive laser beams as solid objects, with the lasers making the depot an unattractive place to roost from a bird’s perspective.
Tram depot buildings are an attractive option for roosting birds at night, with
Yarra Trams chief executive officer, Carla Purcell, said the company had been working to identify a solution to the problem of bird fouling for many years, and she would be excited to see the results of the trial.
“Keolis Downer is investing in a wide range of innovative trials that will deliver significant benefits to our passengers and employees,” she said.
South Australia’s Gawler line is now fully running with electric trains.
A 10th new Electric Multiple Unit (EMU) train was recently added to the Adelaide Metro fleet to service the line.
The remaining two of the 12 ordered will enter operations in coming months.
The benefits of the full electric service include:
• cleaner and greener high-performance trains
• an improved customer experience with quieter, faster and smoother journeys for passengers
• better reliability and safety
• decreased noise and no diesel emissions for residents along the rail corridor and passengers at stations
• better energy efficiency through regenerative braking
• encouraging people to take public transport and leave their cars at home.
Transport minister Tom Koutsantonis said it was another step forward in the transition to an efficient, zero-emissions public transport system to support the State Government’s target of net zero emissions by 2050.
“These EMUs have been custom-fitted for the Adelaide Metro fleet by Alstom to provide maintenance services to the metropolitan train operator, Keolis Downer Adelaide,” he said.
“Once the remaining two EMU trains enter service, Adelaide Metro will have a fleet of 34 EMU trains to maintain fully electric services on the Gawler, Seaford and Flinders lines.
“The addition of the 10th train to the Gawler line gives us the capacity to run a fully-electric service on the line.
“On occasions, it may still be necessary to run on a diesel train on the line due to maintenance and fleet improvements across the network. However, each additional EMU
builds greater capacity to continue all-electric services during these periods.”
The State Government committed to purchasing 12 new EMU trains as part of the Gawler Rail Electrification Project.
The first of these new EMU trains was introduced into service in April 2022.
“We’re flicking the switch on a new era for the Gawler line – with sufficient capacity for passengers to enjoy electric trains on every service,” Koutsantonis said.
“Electric services not only deliver a better experience for our passengers with efficient, quieter and more comfortable rides, but also supports the State Government to reduce emissions and deliver a greener future.
“By leaving your car behind and embracing public transport, you’re actively contributing to easing traffic congestion and supporting sustainability of cars off our roads.”
Rail Express speaks to Natalie Loughborough, the newly-appointed Executive Director of Rail for the National Transport Research Organisation, about her role and the challenges facing the rail industry.
Loughborough was appointed to the role in August this year, bringing with her an extensive background in public transport delivery.
Her focus will be on delivering an innovation pathway for the rail sector, linking the highly experienced transport professionals with their scientific and evidence-based approaches to asset performance, sustainability and materials performance, and infrastructure measurement to challenges that the industry is seeking to find solutions for.
Integrated mobility is at the heart of the National Transport Research Organisation (NTRO) – innovative, impactful mobility solutions that benefit all Australians and New Zealanders, Loughborough said.
“A for-purpose organisation and registered research provider, we collaborate with all levels of government, transport agencies, consultants, academia and private sector organisations on all aspects of transport and mobility,” she said.
“At NTRO, we provide transport projects with safer, more sustainable, value-for-money mobility solutions – and have done via the Australia Road Research Board (ARRB) for over 60 years for road and transport across Australia and New Zealand, with connections in the UK, Europe, USA, Asia and China.
“We have also brought the Australasian Centre for Rail Innovation (ACRI) inside the NTRO with its project stream, connections and history of work over the past nine years in rail.”
NTRO is known as the source of independent, reliable and robust guidance on the delivery of next generation infrastructure to serve the mobility needs of the community.
With a clear role of partnering with local, State and Federal governments, NTRO staff provide timely, accurate and impactful solutions to support governments to achieve their objectives.
“Joining the organisation, I believe it is the right time to step up and consider what the challenges are in rail and what is needed for future progress. We want to be able to help solve the challenges of tomorrow, today,” Loughborough said.
“With key agreements in place in Queensland (National Asset Centre of Excellence), Western Australia (WA Road Research and Innovation Program) and New Zealand, NTRO is partnering in initiatives that really do make a difference to the future of transport and importantly, a positive impact on value for money outcomes for the public purse with real, demonstrable benefits and returns.
“At NTRO, the team are excellent problem solvers who operate with real clarity and objectivity. The NTRO team is the trusted partner for government and industry, providing a single source of truth for the work that we undertake.
“With deep rail skills now embedded over the past five years of organisational transformation, there is the opportunity to use the excellent research skills across the broader infrastructure space that parallels from one mode to the other, but also focuses
on the challenges specifically facing the rail industry of today and the future.”
Loughborough said that with more than $150 billion in the pipeline for investment in rail infrastructure across Australia and New Zealand, and a large proportion of that funded by agencies and public sector organisations, there was a need to get it right first time, attract people to the industry and ensure the skill sets developed are cultivated across Australia and New Zealand – as well as having processes and systems that foster rather than hamper the much needed innovation in the sector.
“The starting point is ensuring that robust data is informing decision-making,” Loughborough said.
“At NTRO we have the ability to be that scientific source of truth. We can apply over
60 years of experience in mapping road data to gaining the same robustness in rail.
“Using systematic processes to continuously collect data enables a deep understanding of all information and drives effective outcomes that are supported by evidence-based decision making.
“In turn, this delivers a sustainable network with longevity, and ultimately more costeffective delivery of full life-cycle maintenance.
“With the advent of AI, digital twins and the like, a more advanced and real-time ability now exists to consider this data for the benefit of current and future operations.
“And of course, the key to driving these effective decisions into delivery is having consistent standards and approaches.
“The developments now coming to fruition from the Hansford Review that Network Rail (UK) commissioned in 2017, protect the integrity and ability to trace any changes but moves away from taking an approach that stagnates the industry, and encourages innovation – with the Standards Challenge encouraging broader industry involvement too.”
Loughborough said that in the much earlier stages, the rail industry in Australia has that opportunity with the work of the National Transport Commission’s National Rail Action Plan.
Acknowledging the complexity and fragmentation of the 29 networks across Australia, with its three gauges and 11 separate signaling system, she said that now is the time to work on the interoperability challenge and focus on the possible economic benefits of a more cost-effective, efficient and sustainable rail system.
“It is crucial to also support the National Rail Action Plan in addressing the skills shortage, looking at different ways of doing things to both ensure that there is effective training available for shortage areas, but also reduce the reliance on disappearing skill sets,” she said.
“NTRO is well-placed to step back to take an independent position to work with agencies to consider what is best for industry in an objective way.
“With the need for rail to move with the
times and consider its carbon footprint to remain a mode of choice – assets, energy use and new materials alike must undergo scientific testing to be proven and introduced.
“Our world-class laboratory in Port Melbourne has the capability to conduct a full range of engineering and performance testing services on surfaces and materials, and our accelerated loading facility has the ability to carry out true commercial scale research testing and modelling.
“NTRO has developed a robust model for the determination of sustainability overlays for materials used in the road and rail sectors.
RMS
“The NTRO model is presented in a cloudbased tool that ensures a common platform for industry to compare material profiles and greenhouse gas contributions, as well as calculating the benefit-cost ratio outcomes from choices made.”
Loughborough said freight also played a very important part of the complete rail jigsaw.
“When the National Freight and Supply Chain Strategy was produced in 2019, it was predicted that between 2018 and 2040, rail freight would increase by over 35 per cent, an increase of 270 billion tonnes to a total over one trillion tonnes,” she said.
“The 2023 review commissioned in June will provide a whole new landscape, particularly in the wake of the pandemic and significant severe weather impacts, for freight. The outcomes of this review will produce a revitalised position for the industry and one which NTRO will respond to.
“This is the perfect time for an independent organisation like NTRO to be taking on the mantle for putting rail at the forefront of getting it right first time, with truly evidence-based decisions.
“It is an opportune moment to be joining such a visionary organisation. Never has there been a more exciting time to be part of the future of a multi-modal approach to the strategic direction for transport, alongside the opportunity to take forward rail with the breadth already applied in the road, ports and airports space.”
Loughborough has high level experience within the transport sector, both overseas and in Australia, having worked for operators in the UK such as First Group, Serco and Abellio, in addition to local government bodies such as Transport for Greater Manchester.
In Australia, she was managing director of Transdev in Queensland, responsible for its bus and ferries businesses, and most recently has been general manager at Metro Trains Melbourne before joining the NTRO in 2019.
She brings more than 15 years of board director level experience to the new role, with a wealth of experience across all areas of organisational development, production of standards and operations across transport, criminal justice and the education sector.
To find out more about the National Transport Research Organisation, visit ntro.org.au
Vertical integration and precinct integration are key enablers of seamless and convenient metro services that drive the sustainable growth of cities. Yet integration is often overlooked as an ingredient to a successful metro.
Being recently ranked as the city with the best public transport (Ranking Royals), Hong Kong runs a metro system operated by MTR Corporation that delivers world-class service to more than one billion passengers annually.
And MTR is today regarded as one of the world’s leading railway operators for safety, reliability, customer service and cost efficiency, operating rail networks in nine cities across Asia, Australia and Europe.
The Australian subsidiary, MTR Australia, is currently delivering the Trains, Signalling, Maintenance and Operations package for Sydney Metro City and Southwest. It is also the major shareholder of the operating companies for the Melbourne Metro rail network and Sydney Metro Northwest.
MTR category manager Cynthia Ma said as an example of MTR’s longevity and success, MTR managed more than 16 types of rolling stock in its Hong Kong network which have been built by 12 different manufacturers, including ABB, Alstom, Bombardier, CAF, CRRC and subsidiaries, Itochu Kawasaki Kinki-Sharyo, Metro Cammell, ROTEM, and Stadler.
“MTR has continuously improved the reliability performance that it maintains, irrespective of whether the trains were specified and procured by MTR or by the client,” she said. “This make sures that MTR is always able to procure from the emerging suppliers ahead of the market.”
MTR integration manager Aritra Chakravarty said that this approach was not without its challenges.
“Compatibility and standardisation across the train types and interfaces with signalling and communication contracts, Human Machine Interface (HMI) of train control panels, human factors, and operating procedures, were the issues to overcome, even when they are from the same supplier,” he said.
“MTR’s project management, engineering, and system integration teams, along with our consultants, consistently verify that operational and interface requirements are integrated into
the design and are compatible across trains and its interfacing systems, even when they are from the same supplier.
“This thorough oversight extends beyond design phase and encompasses production, testing, and commissioning to ensure a safe, reliable and integrated rail system fit for operations.”
“Having managed the entire lifecycle of different systems, we have learnt that taking a technology agnostic approach for procurement allows us to tailor the system to delivering a cost-effective service for our clients and passengers; aligning with a specific technology provider prior to determining the service requirements is a suboptimal solution,” Ma said.
“The key advantages of this approach are inviting competition, mitigating the delivery risk, and obtaining the best technologies from between them.
“Instead of adopting a discrete, projectby-project engagement, MTR recognises the importance of regular engagement with the supply chain and recently developed a Category Strategy Plan that identifies key railway systems and includes regular reviews
of the available technology and products in the market against MTR’s project pipeline across the globe.
“The plan also identifies opportunity for joint procurement across different projects and business hubs where there is synergy.”
MTR typically adopts a “fast follower” approach to new technology in railways to ensure that innovations are implemented safely and predictably.
MTR’s agility shines through in its deployment of technology to address emerging needs.
For instance, as the industry transitions towards Fully Automatic Operation technologies, MTR proactively introduced an advanced real-time track image recording system to pre-empt potential issues arising from traditional broken rail detection methods.
MTR also recognises the increasingly market-leading role that Chinese suppliers are playing for the design and delivery of Communications-based Train Control (CBTC) and Vehicle-to-Vehicle Communication Based Train Control (VBTC) Systems.
With more than 40 years of experience, Hong Kong-based rail operator MTR has accumulated valuable experience from managing generations of assets.
“There are around 7500km of metro with CBTC coverage in Mainland China, which is by far the biggest market in the world,” Ma said.
In recognition of its innovative management model and technique, and the proven success of MTR in delivering the Beijing Rail Transit Expansion, Beijing MTR received the nationwide achievement of “First Grand Award” for the “Realization of Sustainable Development through Life Cycle Management of Operational Asset” from the China Association of Communication Enterprise Management.
MTR was the first railway company in the world to be certificated to PAS55 (2005) and then ISO55000 (2015).
MTR delivers levels of train punctuality exceeding the customer’s requirements in every city that it operates, namely Hong Kong, London, Melbourne, Stockholm, Beijing, Shenzhen, and Hangzhou.
With a mission to drastically reduce traffic congestion in the city, the MTR network in Hong Kong was designed to maximise its convenience for passengers.
“As population in Australia continues to grow and property prices continue to increase, successful integration of railway with precinct and adjacent developments will unlock substantial social, environment and economic benefits to local communities,” Ma said.
“For MTR projects, patronage forecasts and station catchment studies are done in early stages of projects to determine the optimum corridor alignment, location stations and entrances.
“This results in an effective and optimised operational solution where external factors such
as geography and environment are taken into consideration, as well as public facilities including hospitals, population, and design parameters.
“Once the project alignment is designed, the station is designed to seamlessly integrate with its community through carefully planned station accesses and pedestrian circulation.
“Through arranging and optimising station space, the station can improve pedestrian circulation in the precinct and unlock commercial values in the station that regenerates the substantial costs of operating and maintaining a high-quality metro service.”
Apart from station precincts, MTR adopts a “Rail + Property” model to integrate railway with adjacent development.
The economic value of adjacent development is unlocked through the convenience of railway and in return, the patronage of metro service is also increased.
This presents several complexities as the railway is brought adjacent to development:
• Engineering challenges (structurally, geotechnically and fire engineering)
• Balance of land use (railway facilities against residential, commercial and government facility)
• Impacts to metro operations, especially during construction phase
• Interactions of different and sometimes conflicting statutory requirements
• Ownership, management and maintenance responsibilities and adjacent assets
• Risk ownership, allocation and project management
MTR achieves highly complicated integration between the facilities with a multi-disciplinary team, enabling a seamless vertical and horizontal integration, and maximises the synergy from “Rail + Property”.
Kowloon Station, a prime example for mixed used development adjacent to a railway station development.As one of the only ballast cleaning specialists in the country, Swietelsky Rail Australia (SRA) has significant runs on the board to demonstrate that its proactive approach to ballast rehabilitation has stood its clients in good stead.
The company’s methodology is not only more cost-effective in the long run, it is less resource-intensive, extends the life of the asset, as well as harnessing sustainable practices and being environmentally friendly.
SRA Managing Director Anne Modderno is in no doubt that the business’ dynamic approach has formed the basis of its success.
“When we first established ourselves in Australia, we leveraged our decades long international experience to secure mechanised maintenance plant and equipment specifically
for the Australian rail industry,” she said. “From there we have quickly become known as ballast cleaning specialists, due to our performance, equipment and approach.”
SRA is the only rail maintenance company in Australia with ballast cleaning as its core activity.
Coupled with SRA’s innovative approach to mechanised maintenance, this makes it one of the few companies with ballast cleaning capabilities, a point of difference that drew Technical and Risk Director Gary Holden to join the team more than six years ago.
“I’ve worked in the rail industry for over 40 years, with a focus on the safety, compliance and risk management aspects,” he said.
“The SRA approach to ballast cleaning continues to meet and exceed in all aspects of safety and quality of finished work.
Hunter Valley Ballast Cleaning project manager Greg Buckley with undergraduate civil engineer Matt Young at Boggabri in NSW, where the Swietelsky Rail equipment was used.“Our RM80 ballast cleaning machine has set the bar here in NSW in the length of track cleaned to the highest standards. It is a workhorse of our fleet, and a reliable and efficient machine.”
In more recent years SRA has also invested in a fully refurbished RM95, a two-section highcapacity ballast cleaning machine, which can be used for plain track, as well as switches and crossings with an extendable cutting bar.
It also has the capability to install geofabric as it operates, providing improved rail asset performance benefits for clients.
It is fully compliant with the narrow non-electric rolling stock outline, allowing it to work and travel within more networks across Australia.
“The RM95 employs a swivelling main distribution conveyor belt so that the cleaned ballast is returned across the entire cross section of the track. This combined with a secondary lifting unit allows the rail to be ‘copied’ or improved, through three-dimensional measurement,” Holden said.
“This leaves the cleaned track in condition similar to having had a first tamping pass performed, leaving the track close to design super-elevation and line.
“Our commitment to great outcomes like this and our continuous improvement ethos is one of the reasons that ARTC has recently extended our well-established partnership, for another two years.”
ARTC and SRA first established their alliance in 2014 and since then have delivered more than 300 kilometres of ballast cleaning, with work locations on the Ulan and Main North lines and the rail corridor between Sandgate and Singleton.
This ongoing contract has benefited the local coal transport network by improving infrastructure reliability without putting in place track speed restrictions. This has enabled ARTC to maximise the operating efficiency within their network, securing increased value for their customers.
“We understand that being a reliable industry partner is central to our success. This is achieved through our dedicated team and state-of-the-art equipment, which form the cornerstone of delivering the results our clients and their customers can rely on,” Holden said.
SRA’s ballast cleaning machines are supported by two fleets of material handling wagons (an eight-MFC wagon consist and an eight-MFS consist).
Utilising spoil wagons during ballast cleaning allows SRA to mitigate any resulting environmental impacts. Spoil material is unloaded at designated safe locations and the
material is then used to upgrade access roads or stockpiled for alternative reuse options.
The Australian arm of the business has instilled Swietelsky’s long established culture of sustainable and recycling practices.
SRA’s MFC wagons were fabricated by employing stock wagons originally used by the
on delivering a result that provides better than expected outcomes,” Modderno said.
In line with its best practice approach to service delivery, SRA also has proven flashbutt welding capability, with three flashbutt welding units, two mobile units (Holland DX170RW) and one static unit
the rail industry, and have developed our fleet and team capabilities to ensure we continue to provide the equipment and expertise our clients need, no matter their complex requirements.”
SRA has had a presence in Australia for more than a decade and as a result has
All across the world, cities are expanding. People need better connections to access new places, MTR makes it happen in Hong Kong, Melbourne, Sydney, the United Kingdom, Sweden, as well as in the Mainland of China and Macao.
For traction industry specialist WIRED Overhead Solutions, only one company matters when it comes to quality hi-rail equipment: Manco Rail.
Over the past eight years, WIRED Overhead Solutions (WIRED) has established itself as a leader in the traction industry, not just in its home state of Queensland, but across the country as well.
And since inception, the company has partnered with one of the most reputable manufacturers of hi-rail machinery, Manco.
Rail Express speaks to WIRED general superintendent Matthew Eglinton and general manager Jason Priest about the work the company does and why it partnered with Manco from the start.
“WIRED is a provider of inspection, construction and maintenance services to the overhead wiring (OHW) railway industry in Australia,” Eglinton said.
“As leaders in our industry, we pride ourselves on our expert knowledge, experience and quality outcomes.
“By providing a complete overhead wiring solution, we have specialised in the field of traction power, allowing us to excel at what we do through innovation and expertise.
“The unique know-how and experience in our team enables us to adequately assess and determine maintenance and construction requirements, develop a comprehensive plan of action and implement this plan, while ensuring that compliance with industry standards and the safety of those working on the traction infrastructure is maintained.”
Priest said the company had the experience and know-how through delivering these services in Queensland, New South Wales, Western Australia and Victoria across the major network owners and private sidings operators.
He said WIRED’s unique capabilities include:
• Design: Maintaining a highly specialised and experienced in-house overhead wiring design team.
• Engineering: Providing experienced engineering and supervision support to deliver project works
• Project management: Coordinating the planning, construction, handover and commissioning of overhead wiring works
• Construction: Employing a skilled team of qualified, experienced and motivated overhead wiring professionals to enable successful construction of any size project
• Maintenance: Delivering required
The company has been involved with and continues to be a part of a range of high-profile rail projects, including Sydney Metro Central, Queensland Rail, Gold Coast light rail, Cross River Rail, the Caulfield to Dandenong line, Sydney light rail and Victoria’s Mernda line.
Part of the success of WIRED is based in its investment into state-of-the-art
The current Manco fleet used by WIRED includes an extensive range of purchased and hired hi rail and auxiliary units, from rail booms and elevated work platforms to various types of trucks specially built to purpose.
“Both Matt and I had more than 13 years of experience in the rail industry when we founded WIRED,” Priest said.
“Having dealt with many equipment suppliers, we knew we wanted to work with someone who aligned with our
values regarding customer service and our commitment to quality.
“Shortly after we started, we met with the management team of Manco in New Zealand and they were very accommodating in showing us their operations: their production processes, the support systems in place and innovations in progress. Knowing the high quality of their products, we felt it would be a great partnership.
“And we weren’t disappointed: from the very beginning, every machine we have received from Manco has been absolutely top-notch, we couldn’t be happier with their products.”
Eglinton said that one of our biggest attractions for Manco is that the business is an original equipment manufacturer, which means it has its own engineering and innovation processes in place and manufactures its own products, in contrast to third-party distributors.
“They know their products, they take pride in their products and it translates into their excellent customer service,” Eglinton said.
“They provide us with 24-hour on-call support, on-site support, operator training, mechanical training, and they manage and complete all the periodic servicing and maintenance of all of our machinery, whether we’ve purchased it or hired it.”
Priest said both WIRED and Manco ran along the same principles of being customer-focused and ensuring quality outcomes.
“This is yet another reason why WIRED’s values so strongly align with Manco,” he said.
“Any questions or issues we have with our machines are directly addressed by the managers themselves, Bryan or Ryan.
“Having direct communication lines with the people in charge at Manco that are problemsolvers means we save time and money.”
Eglinton said while “anyone can buy a machine from a supplier”, keeping these machines operating and compliant to Australian New Zealand standards was costly and time-consuming.
“Manco provides ongoing in-house maintenance and supports WIRED with all maintenance, servicing, compliance and certification, making it a no-brainer for us,” he said.
Manco’s ability to engineer and custom-fit its equipment has also been beneficial for WIRED.
“In the fast-paced rail industry, we make a conscious effort to continuously upgrade our machines as technology improves. Manco has shown that they are at the forefront of technology with innovations in their engineering and manufacturing, leading to a prolonged life of our machinery fleet”, Eglinton said.
for overhead wiring works in Australia, having strong and positive relationships with stakeholders is important in leading to successful project outcomes.
building long-term, positive relationships with our valued clients,” he said.
strengthened and developed through mutual trust, expertise and our proven success“We are proactive, solutions-focused and committed to delivering outstanding results on time and on budget, and we can only do that with the best plant and equipment at our disposal.”
As a subsidiary of Manco Engineering Pty Ltd, a company with a legacy since 1973, Manco Rail has established itself as a leading
AS7502 and AS1418:10, ensuring complete regulatory compliance.
Manco Rail Hire offers several compelling benefits, including five decades of experience and expertise; ability to design and manufacture top-quality products that meet the highest industry standards; a strong focus on innovation; a wide range of rail equipment, catering to various construction and maintenance needs; and a dedicated team always ready to support clients throughout the project life cycle.
The enclosure’s versatility in door options, with both glass and full metal alternatives, highlights its adaptability to diverse environmental conditions.
The choice between these door variants allows users to strike a balance between visibility and security, accommodating preferences without compromising safety.
Maintaining optimal internal temperatures is critical for electronic equipment’s longevity and performance.
To this end, the MFB S280 offers a dual approach: filter fans for passive ambient airflow and Seifert air conditioners for active cooling.
This intelligent cooling system ensures that equipment remains within specified temperature ranges, preventing overheating and associated downtime.
“This feature is of paramount importance, given the harsh conditions that the Australian rail industry frequently faces,” Grech said.
The MFB S280’s suitability for the Australian rail sector is underscored by its unique design.
our policies in a manner that aligns with evolving Industry standards.
“We boast an experienced staff with many of them serving many years at the company. The company remains committed to securing mechanical engineer graduates and the knowledge they can bring to the business to help drive business goals and objectives.”
Grech said the S280 Outdoor Data Enclosure served as an exemplar of technological prowess and adaptability for rail.
“MFB hopes the S280 is poised to play a pivotal role in shaping the industry’s technological landscape,” he said.
“MFB continues to provide customisable enclosures and services for the rail industry and wants the industry to know we are always looking at ways to optimise and increase our capabilities.
“For more information regarding our extended range, contact one of our dedicated and experienced sales members.”
In the evolving landscape of the Australian rail industry, the need for reliable and durable infrastructure is paramount.
And in this regard, MFB Products is proud of its S280 19-inch Industrial Outdoor Data Enclosure unit, which has been tailored to meet the rigorous demands of the industry.
As MFB sales executive Jack Grech explains, the cabinet combines state-of-the-art features with robust construction.
“It is a beacon of innovation that stands as a symbol of technological advancement, offering solutions for protection, cooling, and security,” he said.
“The heart of this enclosure lies in its construction. Crafted from 1.6mm galvaneal steel or 316-grade stainless steel, the unit’s fully-welded body ensures uncompromising strength and durability.
“This industrial-grade foundation forms a solid defence against external elements, safeguarding sensitive electronic equipment housed within.
“The structural integrity is further fortified by its IP54 ingress protection, with the capability to upgrade to the more stringent IP66 standard – a testament to its third-party accredited security against dust, water, and environmental contaminants.”
A variation of the S280 is a split configuration tailor-made for the industry’s specific requirements.
The incorporation of distinct compartments – battery compartment, data/electrical compartment – ensures a logical organisation of components, facilitating easier access, maintenance, and troubleshooting. This design ethos optimises operational efficiency.
“Weatherhoods and sunshields stand as additional layers of defense against the Australian climate’s unforgiving nature,” Grech said.
“These accessories shield the enclosure from direct sunlight, rain, and other elements, preventing damage and ensuring consistent operation.”
Grech said MFB’s accreditations have acted as cornerstones for the company throughout its history and will continue to drive the business forward.
“The core values of the business are built around the Quality (ISO9001) and Environment (14001) accreditations we proudly hold,” he said.
“We are also well underway in working towards occupational health and safety accreditation (ISO 45001).
“We are constantly looking at ways to build
MFB’senclosure units are standing up to the
harsh demands of the Australian rail industry.The robust S280 Industrial Outdoor Data Enclosure unit. The units use intelligent cooling systems that ensure that equipment remains within specified temperature ranges.
John Holland’s long history in rail has seen it become the go-to partner for complex rail construction and maintenance work.
A commitment to delivering all parts of the rail life cycle has seen John Holland’s Rail and Transport team establish one of the largest specialist plant and equipment fleets in Australia, supported by the in-house skills and knowledge to deliver rail services and maintenance, creating better outcomes for clients.
John Holland’s Executive General Manager – Rail and Transport, Steve Butcher, tells Rail Express about the benefits the National Plant team provide.
“Our plant team spans Australia, with operations managers based in Perth, Melbourne, Sydney and Brisbane, as well as a team in New Zealand, who are supported by a multidisciplinary national engineering team,” he said.
“Maintaining a large in-house fleet of plant
machinery and equipment with an ability to mobilise from any of our locations across the country means that we can increase delivery certainty and enhance project safety, logistics, program and cost outcomes for our clients.
“The plant team manages the full life cycle of the equipment, with more than 4100 assets nationally, including a large fleet of major and minor rail plant. This includes everything from track resurfacing and flash butt welding machines, to hi-rail elevated work platforms and trucks, PEM/LEMS, Trac Rail Transposers (TRTs), as well as specialised rail tools and equipment.
“They’re responsible for maintaining John Holland’s plant and equipment in accordance with technical maintenance plans and regulatory and network Rail Infrastructure Manager (RIM) requirements for the entire asset life cycle.
“Our national engineering team is
experienced in the certification and acceptance processes for rolling stock on networks across Australia. They’ve developed an Integrated Management Plan that ensures our plant and equipment is designed, built and maintained to appropriate standards by skilled people using accurate data and information.
“Changes, modifications and integration of new equipment are managed through a structured change management and peer review process as part of a continuous improvement approach to maintenance. This means our clients can be confident that the equipment we bring to site is safe, reliable and fit for purpose.
“The team’s commitment to self-performing maintenance activities and operational capability provides certainty to our customers that our fleet is well maintained and always available. Downtime is minimised through the rapid deployment of maintenance teams,
As a leader in end-to-end rail and transport solutions – from designing and constructing transport networks to operating and maintaining them – John Holland is involved in all parts of the rail life cycle.The John Holland Ballast Regulator after redesign and remanufacture at the company’s WA plant workshop.
stocking of critical spares and the ability to access replacement machinery and plant if required. This reliability is best demonstrated by our 95 per cent availability rate for track resurfacing equipment across Australia.
“Along with our workshop facilities our dedicated field service teams provide unparalleled technical expertise.
“They’re equipped with specialised field service vehicles carrying all tooling required to carry out critical repairs, preventive maintenance and shutdown support onsite with minimal disruption to productivity.
“We have a strong understanding of the links between plant and rolling stock and the impacts on maintenance activities on complex networks, thanks to our accreditation as a rolling stock operator and rail infrastructure manager.”
Butcher said the company’s end-to-end experience as a contractor and operator allowed it to seamlessly integrate track surfacing operational requirements into design, maintenance, and construction planning.
“Our whole-of-life cycle thinking, combined with our experience in rail across Australia for around 40 years, is what sets us apart,” he said.
“We are always looking to grow our plant capability to ensure we have the right equipment to deliver value for our clients.
“John Holland was the first rail contractor to operate PEMs and LEMs in Australia in 2009. With the delivery of another 14 PEM XLs this year, we continue to lead the industry, owning the largest fleet of PEMs nationally.
“With over 14 years of experience in the installation and replacement of turnouts using this methodology, our clients can be confident that we have the expertise to consistently and reliably deliver even the most complex turnout installation projects.”
The NSW plant department recently commissioned a new set of six PEM-XLs. The new units, which complement the six standard John Holland PEMs in NSW, were first deployed to the company’s Hunter Valley possession in August, followed by a five-day possession on the Botany Rail Duplication project.
“Our WA plant department is currently commissioning eight new PEM-XLs to add to the existing fleet of eight PEMs already working throughout WA,” Butcher said.
The PEM-XLs have increased lifting capacity and lift height, making them more efficient when delivering work on possessions. They also cater for all weight of track and can be used on all standard gauge networks in Australia.
“As part of John Holland’s journey to net
zero, we’re actively seeking out opportunities to reduce our carbon emissions within our plant fleet and across our projects to create more sustainable outcomes and minimise the impacts of climate change,” Butcher said.
Butcher said the WA plant Department managed more than 1200 plant and equipment assets from its main workshop in Welshpool and satellite workshops in Karratha and Port Hedland.
“We’re one of the only rail contractors in the country capable of manufacturing and
refurbishing our rolling stock equipment locally, supporting local jobs and sustainability.
“Incorporating local manufacturing in our WA plant facility has created positive connections within the local economy and communities through our commitment and support of the local workforce, engineering teams and suppliers – plus, the ongoing experience it creates in our plant services team.
“This in-house investment has allowed us to maintain a high-quality local skills base, while engaging and developing apprentices and graduate engineers through continuity of work and development opportunities. This is critical for a robust rail industry in the future.
“Our Welshpool facility in Perth is committed to developing innovative initiatives that support and benefit the local community.
“The team currently employs 24 people, including two apprentices, and provides valuable work experience to local high school students working towards their preapprenticeship qualifications.
“The WA plant services team’s focus on innovation and providing safe, compliant and cost-effective rolling stock solutions for use across our internal projects, saw them undertake the redesign and remanufacture of the John Holland Ballast Regulator (JBR).
“The original JBR was in service for more than 15 years. So, one of the key design objectives of the redesign and manufacture project was to ensure the new design met all modern safety standards, including supporting seated operation.
“With the existing units designed to be operated while in a standing position, there was an increased risk to the operator in the event of a collision or sudden stop. In
recognition of this increased safety risk, this configuration has become non-compliant on a number of networks in the region.
“The innovative new JBR redesign achieved a range of safety improvements, including a seated operating position, audible and visual alarms, lighting upgrades, fire suppression, improved access and egress via wider steps and doors; reduced ingress of dust via fitment of cab pressuriser system; improved visibility; electric over hydraulic control systems; upgraded warning devices, and a trainer seat in the cab.
“The redesign also provided a range of valuable operational improvements such as electric over hydraulic control systems, which improves the speed and precision of the wing, plough and broom movements to reduce delays while working and achieved a superior finish for our clients.”
Butcher said another benefit of manufacturing and operating the JBR in-house was the organic and effective process of continuous feedback and improvement.
“This means the redesigned JBR continues to evolve to meet safety and performance requirements, and deliver optimal outcomes,” he said.
“The other exciting part of the redesign is it allows gauge conversions to be completed within two days of requirement.
“This means our WA business can move JBRs between standard gauge networks of Arc Infrastructure and BHP, to narrow gauge networks of the Public Transport Authority with minimal delays or disruption – which is a great outcome for our customers. “
Butcher said he was passionate about the ability to connect all parts of the rail and transport life cycle at John Holland.
“Not only do we design and construct networks, but we have the in-house capability, supported by our large fleet of specialist plant and equipment, to deliver design, testing and commissioning, and maintenance,” he said.
“This truly creates value, certainty and consistency of delivery for our customers.”
In just a couple of years, RW Equipment & Consulting Australasia (RWECA) has gained a reputation as a high-level specialist in flashbutt welding equipment and services for the rail sector throughout the region.
As an original equipment manufacturer – whose parent company is based in the US – RWECA boasts products manufactured by engineers with more than 50 years of combined knowledge, and who have served some of the best international companies in the industry.
This experience is utilised to not only create quality products that surpass expectation – including container welders, excavator welders, fixed plant welders and more – but also to provide a wealth of expertise and advisorial capacity on flashbutt welding processes.
Rail Express speaks to RWECA flashbutt electrical engineer Jordan Tavo about the unrivalled range of services offered by the company.
“We’re designers and manufacturers entering the maintenance and consulting space,” he said.
“The focus is on quality welds. We do this though using quality, parts, people, and processes, informed by decades of experience.
“Well-maintained machines make better welds. We focus on improving our processes and products to outpace the industries’ ever-growing need for more tonnes and tighter tolerances.
“My focus is on making sure clients do not only make good welds, but prove they’re making good welds.”
The flashbutt process is gaining favour as a preferred technique by rail operators, using regulated electric short circuits to provide accurate welds without filler metal, as well as a consistent hardening process.
The traditional method of welding has been aluminothermic welding, which requires the filler, resulting in a weaker weld, with a longer cooling and solidifying time.
“Aluminothermic (AT) welding relies on a chemical reaction and the addition of external metals,” Tavo said.
“It’s sub-optimal and proven to be not as reliable, not as strong nor as long-wearing
as the flashbutt process, which has better properties and is faster.
“It’s definitely the preferred welding process in the industry, and the trend shows more companies are transitioning over to flashbutt welds.”
Tavo defined the range of flashbutt welding services offered by RWECA.
• Qualifications
Tavo said that mining companies, in particular, were already moving to reduce the amount of AT welds in their network.
“It’s getting to the point where companies need prior approval to put AT welds in. But Flashbutt welding standards are tight and can be complicated to execute,” he said.
This is where RWECA comes in, with its unparalleled expertise in flashbutt technology.
“We develop quality assurance and quality control procedures and guidelines that enable rail networks to meet the rigorous testing requirements imposed on them by the Australian standards and their own quality department and standards,” Tavo said.
“As original equipment manufacturers of flashbutt welding equipment, we are experts in the field.
“We can very quickly use our processes
should be.
“The flashbutt welding machine will have a program that it runs. And a lot of the tweaking happens to adjust the heat timing and force required. But once you get the program right you rarely have to change it.
“Our specialists are highly adept at tuning these programs, and finding the right balance to get it the equipment to pass whatever specification given at the time.
“That’s one of the more difficult things about welding: you need to meet the Australian standards, as well as the standards that the clients will adapt for their own application. Often the team imposing the standards are different from the teams that are required to adhere to them.
“Our job is to help them our client with this and then to eventually prove that they’ve done it correctly whenever they get audited.
“We can tune a new machine to weld any required rail type or combination, under increasingly strict industry requirements, including Australian standards and company procedures.
“We utilise trades, engineers, and operator expertise to make informed changes to machine settings that lead to weld optimisation.
“We also provide full qualification services
Flashbutt welding is gaining popularity among rail operators for its exceptional efficiency and structural integrity, but ensuring optimal performance and longevity necessitates meticulous and accurate servicing to address the requirements of this advanced welding technique.One of RWECA’s flashbutt specialists, Jack Rankcom, on-site for a job.
in-house or advise on possible improvements. We can do the same for machines already in service, enabling companies to expand their capabilities by adding new rail combinations to their machines, or optimising old ones.”
• Execution support
Tavo said support included preparing machines for use, maintaining machine cleanliness and OEM standards, along with pre-and post-execution checks.
“Our specialists are also nationally accredited welders and can support track production and maintenance,” he said.
“They are experienced in field fault finding and rectification, and can provide standardised reporting to allow data analysis and recommendations.”
• Engineering support
“Based on each customer’s needs, our engineers can create easy-to-follow procedures that ensure repeatable quality.
“Our on-site specialists will go and check everything, ensure that the machines operate correctly, and that the data tells a good story. And if it does, then we’re happy.
“And if not, then they will use their expertise to decide or to advise on the options for the customer.
“And if they need more support, they’ll escalate it to an engineer, or even go straight to the designers,.”
Tavo said the advantage of being an OEM was this fundamental design knowledge.
“We have the people who have the design principles to feed back into the field and solve any problem that we’ve got,” he said.
errors, because we know and we understand what they’re trying to do with that part: we know what it’s for, we know why it’s there.”
• Turnkey maintenance strategies
Rather than managing maintenance tasks separately, turnkey solutions provide a comprehensive all-in-one approach to plant maintenance.
“By entrusting maintenance requirements to a single provider, clients gain access to a wide range of specialised services that can significantly benefit welding operations,” Tavo said. “The flashbutt turnkey services include maintenance scheduling, service kits, service execution, and the maintenance of standards and specifications.”
RWECA’s biggest clients are currently the mining companies in WA’s Pilbara, notably BHP, which recognise the efficiency of flashbutt welding for their heavy haul rail networks.
“But we’re expanding rapidly, and looking interstate as well. For example, we’ve been to Queensland to provide on-site assistance,” Tavo said.
RWECA is committed to continuous improvement and proactively identify areas for enhancement in the flashbutt welding process. Through close collaboration with the engineering team, it will continue implementing innovative solutions that drive
The 2022/2023 period has seen rapid growth and diversification for George’s Loader Hire (GLH), the trusted supplier of equipment for both the rail and civil sectors in South East Queensland.
Its team of professionals has continued to perform the track reconstructions, repairs and maintenance it is renowned for, while adding a brand new rail stress management service to its portfolio.
GLH managing director Kelly Cooke tells Rail Express that the company now offers a complete package of rail maintenance or construction capabilities, inclusive of specialised hi-rail plant and equipment, specialist operators and rail stress management, labour hire and welding.
“From the dig-out to the re-stressoperating from the Gold Coast to Cairns and west to Isa and St George, GLH has got you covered,” she said.
“In addition to our regular valued clientele, with the likes of Queensland Rail, CPB, Martinus, the Logan council, Ipswich City council and Remondis to name a few, GLH has gained the trust and consequent business of
the Department of Transport and Main Roads, Rockhampton Council, and Aurizon.
“In a major expansion move, we opened a second depot based in Gracemere in Central Queensland.”
Cooke said the first rail stress management tasks with Queensland Rail and Aurizon were carried out with great success.
“GLH has three experienced weld crews available for small and large welding and restress jobs throughout Queensland,” she said.
“The re-stress teams are supported by modern, state-of-the-art rail specific excavators and clipping and de-clipping equipment with tool vehicles.”
Now with its two depots in Brisbane and Rockhampton, GLH has gained efficiencies in mobilising and demobilising equipment and crews.
Part of the investment in new equipment has included trucks and trailers, including B double and road train capabilities.
“Director Cameron Baird worked with FWR to design the new trailers specific to
includes five prime movers, seven trailers and two dollies, not to mention our modern fleet of utes, flat bed trucks, tip trucks, water truck and Hydrema dump trucks. GLH covers all corners of Queensland with ease.”
Other significant purchases for GLH in 2023 include a rubber-tyre 17 tonne and 14t hi-rail Hitachi excavators, which Cooke said were perfect for reconditioning work.
“We have two CAT RMT 15F hi-rail excavators which are specifically set up for undercutting capabilities and more, and two new 4.5m trolleys with 16t capacity each, making it a perfect combo when coupled with our excavators for transporting materials to and from the specific job site, especially if the rail is the only/quickest access,” she said.
“We also have two brand new Volvo L90H’s and one L110H, including quick coupler for use with various specialist attachments. Why work harder, when you can work smarter.”
Cooke said the first job for the CAT RMT excavator was in the Cross River Rail tunnels. “We pilot tested various methods of
capturing fresh mixed concrete with the hirail trolley on our custom-built in-house test track, before settling on a system that allowed 13 kilometres of footpaths to be poured for our customer, Rhomberg Rail,” Cooke said.
“We pride ourselves on being innovative and providing solutions. Having our own GLH engineer that understands the rail industry is a definite advantage.”
Other projects that GLH has been involved in over the last year include rail reconditioning projects in Mt Isa and Emerald, and undercutting in various locations throughout Queensland.
Rail services offered include re-sleepering, re-railing, hi-rail trolleys, hi-rail clippers and de-clippers, hi-rail mulchers, hi-rail ballast brooms, welding, re-stress management and labour hire.
“In order to support our existing and new customer base with all our machinery, we have doubled the staff levels this past year,” Cooke said.
“From track workers, spotters, operators, administration and management, team GLH have got you covered.
“As our allocator Mohammed Akber keeps saying: “Without great staff, we have no customers, and without customers, we have no business”.
“We also have our own workshops to undertake maintenance and repairs on our equipment, ensuring machinery and vehicles
capability for efficient allocations, compliance document ease, staff capabilities, invoicing and automatic compliance indicators for both assets and staff.”
As directors, both Cooke and Baird are looking things can have on your business,” Cooke said.
“Throw in a world pandemic, just to make life interesting. On top of this, businesses like ours face day-to-day challenges in maintaining consistency of work, increasing health and safety compliance, competition, increasing cost pressures together with difficulty in obtaining parts and materials.
“Cameron and I are very humbled to see that the small company that dad started over 20 years ago has developed to what it
“We are fortunate to have a great team of professional staff helping us to grow and expand this Queensland-owned
GLH has plans for next year to grow even more. The business will move its headquarters to a new Brisbane location with a state-ofthe-art modern facility. Architectural designs
“Since our inception and through our growth and expansion, GLH have and always will strive to offer superior outcomes and benefits for our clients together with an unrivalled level of service, support, solutions and exceptional experience that exceeds
“We are a trusted supplier to both rail and civil sectors of Queensland. Feel free to give our team a call on 07 3879 1936 or visit our
Key Source Rail is an end-to-end railway maintenance plant and equipment and parts supplier and railway solutions consultant, with offices and workshops in Midland, Western Australia, Brisbane, Queensland, and Newcastle, New South Wales.
Boasting extensive railway wagon and locomotive building experience, the business oversees the design, manufacture, quality control and commissioning of freight and ore wagons, ballast wagons, grain hoppers, crew cars and locomotives for the Australian and overseas markets.
And that means the company literally does it all, as its motto goes, from the largest infrastructure owner to the smallest maintenance provider. It’s backed by more than 120 years of combined in-house experience in rail operation, rail maintenance equipment, track laying, wagon building, rolling stock and wheel-set maintenance.
A significant development at Key Source Rail has been its focus on decarbonisation, sustainability and reduced carbon emissions products. The main product here has been the supply of Rosehill rubber crossings to the Australian and New Zealand rail industry.
Gallagher said Key Source Rail was also the exclusive distributor for the Geismar range of railway maintenance plant and equipment in Australia.
Geismar is a recognised world leader in the manufacture of equipment and services for track laying, rail maintenance and track measurement and recording.
“And we are supplier of BTI hard wearing tungsten carbide tamping tines, ballast wear plates and undercutter bars and chains,” Gallagher said.
As mentioned, another notch in the belt is Key Source’s ownership of sole distribution rights in Australia and New Zealand for Rosehill removable crossings.
“We have overseen the supply and installation of these from the harsh conditions of the Pilbara to inner city, suburban and regional county installations in Victoria, WA and New South Wales,” Gallagher said.
A feature he’s particularly proud of is Key Source Rail’s commitment to environmentallyfriendly operations and products.
“The railway industry has seen a recent committed focus towards environmentally responsible applications, particularly within the railway plant and equipment and maintenance arenas,” Gallagher said.
“The industry has undergone significant change over the last few years largely in the two environmental areas of reducing carbon footprint and industry sustainability.
“Key Source Rail has embraced these moves and, working with our suppliers, have focused on these two issues.”
Meanwhile, the sustainability aspect is exemplified by the Rosehill rubber crossings, which are made from recycled tyres, instead of traditional bitumen and concrete for the surface.
“Large railway owners are turning to this product and embracing this as a greener, more sustainable solution for pedestrian, vehicular and track access panels and crossings,” Gallagher said.
“Rosehill panels are made from recycled tyres through a cold mould pressing process that produces a solid rubber, non-laminated product that does not crack, chip or delaminate.
“The panels are produced to suit the profile of the sleeper design supplied by
the customer. Rosehill panels are designed for a variety of installations ranging from pedestrian crossings, Rail Road Access Pads (RRAPS), medium duty crossings through to the heavy duty and extreme heavy duty Titan crossing panel used in extreme load and weather conditions found in the iron ore and other heavy duty mining industries.”
Rosehill field panels can be produced in standard widths to fit between the outside web of the rail to the end of the sleeper, or in a wide configuration, extending past the end of the sleeper and supported by a solid rubber edge beam to allow for additional clearance for maintenance of way tamping operations.
Key Source Rail oversaw the installation of a heavy duty crossing on the technologicallyadvanced Rio Tinto Gudai-Darri project in the Pilbara, which endures extremely heavy traffic. Crossings have also been placed for Metro Trains Melbourne and the Sydney train network.
“Large rail owners and miners are starting to realise the value of installing these removable panels that enable easier track maintenance and jewellery inspection, and have the added green value of using recycled materials to replace concrete and bitumen,” Gallagher said.
“We are addressing the second issue, the
decarbonisation initiative, by promoting new environmentally responsible technology such as the Geismar Activion battery-powered range of equipment.
“This electric-powered rechargeable technology is proving itself overseas, particularly in tunnel work and built-up residential areas where we get the additional bonus of having zero greenhouse gas emissions as well as reduced noise issues. On top of this we have the occupational, health and safety bonus of not exposing the operator to exhaust fumes.”
Key Source Rail has assisted in the management of manufacture and the procurement of wagons and locomotives in Australia and overseas.
“We have a team of onsite inspectors based in China that carry out total production coverage. We are well versed in the needs of the country that the rolling stock is entering,” Gallagher said.
Some of the types of wagons include flat cars, well wagons, five pack wagons, grain hoppers, tanker wagons for fuel cartage, crew cars and gondola wagons for ore cartage.
“Evidence of the quality of our product can be seen in the 40 radio-controlled ballast wagons that we delivered to Martinus Rail last year,” Gallagher said.
“The pneumatics and hydraulics were all manufactured in Australia and fitted overseas and the wagons were delivered into Queensland in 2021, and are state-of-the-art pieces of ballast laying equipment.
“Key Source Rail also carries a large range of rolling stock consumable parts, including Chinese 150 brake system components and bogie springs, wear plates, adaptors, and the like. We also have a brake valve overhaul
The company runs its own wheelshop in Midvale, Perth, that has been established purely for railway wheelset maintenance, including re-wheel, reprofile, new assembly and bearing inspection.
It has successfully undergone and passed extensive audit by wheelset owners across the industry and has been accredited to ISO 9001:2015.
“We remove all package bearings from wheelsets ranging from 50t to 130t axle load and overhaul and refit.,” Gallagher said.
“This includes stripping and overhaul of axlebox wheelsets for all freight and track machine wheelsets.
“Part of our process is to inspect all axles
“Our wheelshop facility has the capacity to reprofile to any customer requested profile, eg ANZR-1, WPR2000, LW3, including all the various Pilbara requirements, including narrow gauge and standard gauge wheelsets.
“We are equipped to dis-assemble and assemble wheels on freight and track machine wheelsets to customers’ requirements, including the machining of wheelseats and boring of wheels.
“Being a relatively small yet versatile wheelshop, we can offer competitive rates and quick turnaround times to keep customers on the right track.”
For any enquiries about Key Source Rail products, contact David Gallagher on +61 413 608 652
Martinus has been winning railway industry contracts consistently for decades, testament indeed to its professionalism and quality of work that has made the company one of the most well-known names in the sector.
The leading full-service railway infrastructure business specialises in constructing and maintaining large scale railways and intermodals across Australia, New Zealand, Chile and North America.
Australian-owned and operated, Martinus applies its extensive civil and rail knowledge and project management skills to deliver infrastructure solutions for its clients across greenfield and brownfield projects.
Today it runs projects in four core countries, has 17 office locations, with more than $2.7 billion worth of works in hand.
Martinus head of plant and assets, Dave Van Hoos, tells Rail Express that the key to the company’s success and sustainable organic growth was its vertically integrated, selfdelivery model.
“Our organic growth can be attributed to a decision made to double down on becoming the railway infrastructure experts and to drive self-delivery of our projects,” he said.
“Martinus has the in-house capability for full turnkey project development of complex railway infrastructure, from feasibility and operational transformation, engineering management, through to project management, construction management, and seamless integration.
“We provide a cost-effective and low-risk solution to clients by streamlining engineering and construction processes.
“As a self-delivery contractor and project developer, we take full responsibility for the entire project, eliminating the need for multiple
contractors and suppliers. This simplifies communication and coordination throughout the project lifecycle.
“And a key aspect of this is the investment placed in our plant and equipment.”
Martinus currently has the largest privately owned portfolio of specialist narrow and standard gauge railway plant and equipment in Australia, and continues to invest in it every year.
“Our plant and equipment is vital to our ongoing growth strategy not only in Australia, but in our global core markets of NZ, Chile and North America as well,” Van Hoos said.
“The assets include high production sleeper layers, high production track layers, gantry cranes, combilift straddle carriers, locomotives, wagons, RRV shunters, track laying point systems, tampers, regulators, flashbutt welding units, excavators, rail cranes, PEM-LEMs and the list goes on.”
Van Hoos said there were clear benefits to keep investing heavily in machinery.
“Our experience in delivering large scale, complex railway infrastructure across both greenfield and brownfield environments has taught us that access to a readily available fleet provides several key advantages,” he said.
These include reliability, customisation, cost efficiency, adaptability, project control, and timely delivery.
“It allows us to mobilise quickly all over the country and adapt to the different environments across our regional and urban sites,” Van Hoos said.
“We can just as easily service downtown Brisbane as we can the Pilbara in WA.
“The control we have on our plant and equipment has allowed us to provide industry
leading productivity records along the rail corridor, including:
• Ballast placement: 8000 tonnes in 24 hours
• Skeleton track: 6000 metres per shift
• 65 flash butt welds per shift on formation
• 15 kilometres tamping per day
“Additionally, we are proud of our safety performance record. This is underpinned by a mature and robust rail safety and safety management system through our comprehensive rail accreditation as a Rail Transport Operator (RTO).
“Accredited with ONRSR as a Rolling Stock Operator (RSO) and Rail Infrastructure Manager (RIM) in Australia, Martinus operates rolling stock to maintain and construct railway infrastructure, prioritising rail transportation for the movement of construction materials - we build railways from the railway.”
Martinus is supported by a dedicated plant and equipment team and workshop in Rocklea, Queensland.
“Our in-house plant management team manages the asset lifecycle from procurement and logistics to operations and maintenance,” Van Hoos said.
“We are a diverse and multi-skilled team made up of mechanical, electrical and boilermaker/fabricator tradespeople, civil and rail plant and equipment operators, and supervisory, management, safety and engineering teams. We are also investing in the next generation of railway experts with an apprenticeship and trainee program.
“The plant department is committed to supporting Martinus and the rail industry in providing safe, fit-for-purpose, compliant and reliable plant and equipment to deliver our many complex rail projects.”
Prioritising plant and equipment has played a key part in the self-delivery model which Martinus has based its growth on.Martinus’ track-laying machine in action.
Renowned for its innovative designs and equipment, all built in the factory at Ballarat in Victoria, Harrybilt Engineering continues to build on its reputation of providing highly-specialised solutions to local and national rail customers, which it’s been doing for almost 40 years.
Harrybilt’s typical customers perform maintenance on rail tracks. The business has continued to expand and now services the rail and utilities sector, along with general engineering projects.
Harrybilt Engineering finance and marketing manager Beth Martino tells Rail Express that with rail projects booming around Australia, the outlook for business growth was positive.
“Lots of our customers are buying not just one machine from us with attachments, they are buying a few,” she said.
“Everyone seems to be getting ready to make sure they have enough product to get things done.”
In fact, the business had to double floor space a few years ago because business was expanding so rapidly.
“We also opened a new factory at the end of 2022, which allowed us to increase our labour force and be able to build up stock of rail maintenance attachments,” Martino said. “Sales are strong, with many new
opportunities for our products in the overseas markets.
“We are also growing in places like New Zealand where we supply customers with our attachments and look forward to continuing to grow our presence there.”
Boss Attachments is Harrybilt Engineering’s distributor for rail maintenance attachments in New Zealand.
“We have been working with Boss since the end of 2021 to supply a wide range of attachments to New Zealand customers and to have a permanent stock level of both attachments and spare parts in that country,”
“We have seen a positive response to this dealership in New Zealand and we look forward to continuing our partnership with them.”
It’s Harrybilt’s ability to design and customise equipment to client needs that has cemented
Martino said the company was often challenged with unique rail problems, and by listening to customer feedback, the team was able to come up with and manufacture
“This includes rail maintenance attachments such as the Mini Bullant and Mini Pole Grab that we have recently released into the rail
The Mini Bullant is a smaller version of the company’s popular general purpose grab called
the Bullant. Suitable for light rail excavator ranges, this grab can be used for moving or side insertion of all types of sleepers.
The Mini Pole Grab is an attachment that suits 7-12t excavators and backhoe loaders and has been designed to safely and efficiently pick up, lift and handle round loads or beams.
And of course the hi-rail solution Harrybilt developed that enables units to perform easily over different lines and track gauges – the Hi Brid Rail System –continues to be a best-seller.
“As well, we’ve seen a vast amount of enquiries for light rail machines over the last 12 months,” Martino said.
“Currently, we are in the middle of a large order of hi rail excavators and another project with multiple hi rails coming up.
“We also have an order of two rail guidance systems fitted to Cat M314s for a company in Singapore.
“And there are a couple of exciting new products that are currently in development and we hope to have released this year.”
Martino said the company had been busy hiring across its business and was looking to keep doing so into the future.
“Our typical staff are fitters and turners, diesel mechanics, fabricators, labourers,” she said.
“An engineering team is also employed, which enables an end-to-end solution for our clients.”
It says a lot about family-owned Harrybilt Engineering that its success continues to grow, despite challenges posed by the pandemic.The company’s Mini Pole Grab being put through its paces at the onsite test track. Harrybilt Engineering’s hi-rail system fitted to a light rail machine.
Alltrack Rail may be an Australian-based company, but its clientele stretches out across the ends of the Earth.
Based in the Hunter Valley of New South Wales and owned and managed by rail industry veteran Robert (Bob) Taylor, Alltrack is a leading purveyor of railway locomotives, rolling stock and associated rail maintenance parts and plant.
It also sources new and used railway perway materials such as rails, sleepers, turnout components and fastenings.
In fact, Bob prides himself and Alltrack Rail on being able to acquire any type of used locomotive or specialised rail plant from almost anywhere in the world, at an acceptable price.
The company boasts an impressive list of clients around the globe, including major maintenance providers, rail track operators, large construction firms, contracting businesses and key individuals in the railway industry.
“We have more than 45 years’ experience in the rail sector working both in Australia and overseas. Our wealth of knowledge and industry specific experience is almost unsurpassed,” Bob said.
“We have an exceptional list of contacts within the worldwide railway construction and maintenance industry, and we have a reputation for spotting the opportunity and closing the best possible deal for our customers.”
AllTrack Rail had been established more than 25 years ago to help clients secure new and used railway maintenance plant, used locomotives and pre-used railway materials.
“We saw a real need for rail company executives and plant managers in the rail sector to have a reliable, reputable, affordable option when it comes to sourcing goods, especially from Asia, Europe and North and South
America,” he said. “Simply put, we are a conduit for sourcing selected used locomotives, rolling stock and maintenance plant equipment.”
Not only does the company assist in the location and procurement of used locomotives from across a wide variety of locations, but it facilitates the sale of these items to large markets that are always seeking value-added delivery options (such as gauge conversions to suit buyers’ respective requirements).
“We also assist with land transport and shipping from the Australian end of the operation,” Bob said.
“We source and sell used railway maintenance plant from resurfacing equipment to basic railway plant used in the maintenance.”
Alltrack Rail also has access to a large group of manufacturers across the world and enjoys close relationships with all key suppliers.
As an example of how well the company is regarded across the continents, Bob was engaged by a Japanese corporation late last year to find a new home for a series of diesel multiple units (DMUs) from Hokkaido in Japan.
Bob met with his Japanese partners and team members from the country’s leading rail company, Japanese Railways (JR), to review the condition of the units that were to be released.
Considering the excellent condition of the trains, it was apparent that given certain conditions, they would be suitable for cape gauge operations – a track gauge of 3ft 6in (1067 mm) – used predominantly in Africa.
“It was a priority of the JR system team to see these units repurposed to a suitable new home,” Bob said.
“A plan was then devised to seek out
opportunities using my network of contacts and see who ultimately would have been interested in all or a specific number of the 26 units being made available.
“Several parties then started to show interest in what could assist in providing sustainable transport option in particular African countries.
“Eventually a prominent rail entity decided these could possibly work for them, and after an onsite inspection of the units in full operation, it was clear they would look to pursue a package of units for their initial needs.”
Alltrack Rail has assisted in the coordinating of the movements of the units to the port, where they now await shipment to their new home in Sierra Leone.
Bob assisted in the provision of maintenance manuals and a select group of spares, so the operators could be confident that the maintenance required could be undertaken and supported by a discreet package of extra units to keep the availability high while in service.
He also aligned with a group of specialists for these sorts of DMUs to help train and transfer maintenance knowledge to local ground crews in Sierra Leone.
THE ALLTRACK RAIL DIFFERENCE
• Knowledge of customers and vendors
• Knowledge of the products being offered – quality, reliability and compatible
• Knowledge of the procurement and disposal systems of agencies within Australia
• Understanding of customers’ requirements
• Willingness to see that the customer achieves the best economic outcome
Alltrack Rail continues to make global waves in the quality-used railway equipment procurement business.
Known for track maintenance and construction innovations, Plasser & Theurer has played a pivotal role in mechanising track work since the 1950s.
In the early 1950s, the company recognised that the mechanisation of track work would be decisive in the development of the railway system.
What was missing was a tamping technology that could withstand the enormous amount of loading on the track.
By inventing tamping machines with hydraulic squeezing, operating according to the principle of “non-synchronous constant pressure tamping”, that gap was filled.
Today, Plasser & Theurer holds 936 patents for tamping technology alone and a total of 2500 active patents.
Manual work processes, such as levelling, lifting, and aligning the track, were successively integrated into the machines.
Finally, 1967 saw the launch of compaction and profiling machines, which made it possible to offer the first fully mechanised maintenance train, enabling about 1300 working hours for maintaining one kilometre of track to be turned into just 130 hours: savings of nearly 90 per cent.
Plasser & Theurer Director for Global Marketing and Communications, Johann Dumser, tells Rail Express that the company’s commitment to innovation gradually expanded
technological features still influencing modern track renewal trains,” he said.
“The assembly-line method also played a crucial role in enhancing various other categories of machines.
“The transition to continuous working action significantly improved tamping machines.
“By decoupling the tamping unit frame from the machine frame, machines could work without stopping for every tamping process, resulting in higher working speeds.
“The vision of fully mechanised track construction became a reality, and Plasser & Theurer became a comprehensive supplier of machine technologies for various work processes in the railway sector.”
Plasser & Theurer is also addressing the topic of sustainability from a technological point of view.
emissions – of both pollutants and noise –to a minimum.
Dumser said that the company was also making full use of digitalisation, which has opened completely new opportunities for machines and infrastructure.
“The Plasser Tamping Assistant, a modular turnout tamping assistance system, makes it possible to automatically perform all the steps involved in turnout tamping from start to finish,” he said.
“The EM-VT track inspection vehicle series is equipped with measuring systems featuring 360° 3D laser scanners and high-resolution colour cameras.
“With these vehicles it is possible to measure a 50 km railway line within two days and provide all the data for generating a digital twin.
“Experts agree that this is ushering in a new era of railway infrastructure planning where planning processes speed up significantly and costs go down drastically.”
Dumser said Plasser & Theurer machines had been in operation for decades.
“Customers across the globe can count on a network with 22 partner companies,” he said.
“In addition, our highly dynamic customer services team is an organisation which supports customers over the entire service life of their machines.
“When it comes to customer services, one fact alone reflects how great the demand is: out of 17,400 machines that have been delivered, 50 per cent are still in operation.”
Plasser & Theurer has been a driving force in enhancing the rail industry’s appeal as a costefficient, safer, and more sustainable mode of transportation than its counterparts.The world premiere of the company’s 09-4X E3 Dynamic Tamping Express in 2015: the first track construction and maintenance machine works with hybrid drive. The first levelling, lining, and tamping machine working continuously in 1983.
A third tunnel boring machine (TBM) was recently launched for the Sydney MetroWestern Sydney Airport project, named after a prominent women’s rights advocate.
The machine will be used at Orchard Hills in a major milestone towards the delivery of world-class metro services.
This is the first Sydney Metro project to use earth pressure balance TBMs, which are designed to support the ground as they excavate through shale rock and clay along the northern section of the line.
TBM Catherine will carve out one of the 4.3-kilometre tunnels from Orchard Hills to the new metro station site at St Marys.
The TBM is named after Catherine White, who has worked tirelessly to advocate against violence towards women in the Blacktown area.
TBM Catherine joins TBMs Eileen and Peggy which are well into their journeys to build the 5.5-kilometre southern twin metro tunnels after launching at Airport Business Park towards the Aerotropolis station site this year. Each TBM will excavate about 120 metres a week.
A fourth and final TBM for the project will launch at Orchard Hills in the coming months to build the tunnel alongside TBM Catherine.
The new metro line is a city-shaping project that will provide communities with easier access to job hubs, commercial and education facilities, and connections to Sydney’s wider public transport network.
The Sydney Metro–Western Sydney Airport line will be operational when Western Sydney International Airport opens for passenger
services, with an expected travel time of 15 minutes from St Marys metro station to Airport Terminal Station and a further five minutes to Aerotropolis Station.
White has worked tirelessly to promote social justice and gender equality and is a relentless advocate against violence towards women, directly impacting the lives of countless women. She managed the Women’s Activities and Self Help House (WASH) House from 2003 to 2013.
She has worked in many roles in the Blacktown Local Government Area since 1995, including for the Blacktown Women’s and Girls’ Health Centre. White won the Blacktown Woman of the Year Award in 2012 for her ongoing advocacy work, and her contribution to helping many local women and children escape domestic violence.
It is women like her who are celebrated each year at the Women in Industry Awards, which recognise outstanding women from across a range of industrials sectors, for example those who work in mining, transport, manufacturing, engineering, logistics, bulk handling, waste management, rail and construction and infrastructure – all sectors that are traditionally male-dominated.
Prime Creative Media mastheads Rail Express, Australian Mining, PACE, Manufacturers’ Monthly, MHD Supply Chain Solutions, Prime Mover, Inside Construction, Waste Management Review, Inside Water, Roads & Infrastructure Australia, Energy Today, Quarry and Australian Bulk Handling Review have partnered to
have achieved success through their invaluable leadership, innovation and commitment to their sector.
Nominations are now open for the 2024 Women in Industry Awards. It’s an opportunity to recognise the women who are driving change in industry and – in doing so – breaking down barriers and creating new possibilities for the next generation.
These may be women colleagues, women whose achievements are inspiring from afar, or women who are providing invaluable guidance and support.
The categories are:
• Rising star of the year
• Business development success of the year
• Industry advocacy award
• Mentor of the year
• Safety advocacy award
• Excellence in manufacturing
• Excellence in transport
• Excellence in engineering
• Excellence in mining
• Excellence in construction
• Woman of the year
Nominations, to be made on-line, will close on Friday, April 19, 2024, and are unable to be withdrawn after this date.
Nominations must be completed in one sitting; a partially completed form cannot be saved and reopened at a later date. All nominees must reside and work in Australia.
Supporting documentation (i.e. references, photographs, resumes) should be ready to upload; file sizes shouldn’t exceed 5MB.
All nominations must be accompanied by a high resolution image (at least 1MB in size) suitable and approved for print publication.
All finalists are required to have a representative at the Gala Awards evening should they be successful. To assist with this, all finalists will be provided with one complimentary ticket to attend.
To nominate: womeninindustry.com.au/ nominations/
Nominations are now open for the 2024 Women in Industry Awards.A Sydney Metro TBM has been named after Catherine White. The Awards celebrate the dedication and exceptionalism of women in industry.
Breakfast, the Winter Dinner, the PWI Awards Night and the Annual Convention.
For more information, visit www.pwinsw.org. au/membership/
This year’s PWI NSW Annual Convention is titled “Back to Basics 2.0,” and will look at the importance of the core principles of rail engineering and infrastructure maintenance.
This theme harks back to the ‘Back to Basics’ Annual Convention of 1994, which also sought to revisit the fundamentals of rail infrastructure construction, maintenance and design.
The PWI NSW held its first country convention in 2019 at Bathurst, which was a huge success with a great turn out.
and logistical environments, not to mention the occasional flood or raging bushfire?
The convention’s theme underscores the importance of revisiting and reinforcing these fundamental skills, fostering resilience and leadership at all levels, planning for succession, transferring knowledge, and better project planning and management, as well as exploring how rail in regional NSW continues to perform well in the face of limited funds and challenging conditions.
The 2023 PWI Annual Convention will get underway in Orange on Thursday, October 12, with a dedicated train from Central to Orange, with the full day conference on Friday, October 13 and an optional PWI Wine Tour on Saturday, October 14. See the program below:
aptly named “Back to Basics 2.0,” is an event in the rail calendar not to miss, highlighting the need to return to the roots of railway engineering while celebrating the ingenuity of Regional NSW’s rail professionals.
The Permanent Way Institution NSW has been a cornerstone of railway knowledge and networking for almost 50 years.
It is a member-based association which advocates for and brings together the rail infrastructure community, representing all parts of the industry, including constructors, suppliers, designers, operators and maintainers. Its mission is to advance the knowledge and skills of rail industry professionals, providing a platform for collaboration and sharing of expertise.
The PWI NSW now also includes an OHW and electrical subcommittee to provide a greater opportunity to integrate broader rail disciplines and increase the industry’s capabilities.
Throughout its history, PWI NSW has played an instrumental role in developing railway professionals who have designed, built and maintained the NSW rail network, from the dense urban rail networks of Sydney to the vast and rugged terrain of regional NSW.
The PWI NSW hosts a full calendar of events throughout the year for its members including technical meetings, site visits, the Executive
This year the PWI returns to Regional NSW with the 2023 Annual Convention in Orange.
It could be argued that the focus on highcapacity rail networks in metropolitan areas has diluted the technical rail infrastructure skills necessary to operate and maintain an efficient rail network - that we are producing too many ‘generalists’ that don’t truly understand the fundamentals of railway engineering.
However, regional NSW has traditionally
The full day conference for PWI members only features innovative papers, a gourmet two-course seated lunch, and an exciting panel session.
THURSDAY, OCTOBER 12
• 11:40am: Special Train to Orange, $10pp (ticket proceeds will go to TrackSAFE)
• 4pm to 6pm: Pre-registration Event with UGL Regional Linx, Orange Ex Services’ Club (free)
FRIDAY, OCTOBER 13
As the rail industry landscape evolves with a growing emphasis on technology, automation and innovation, it is essential not to overlook the importance of core railway engineering skills to design, build, operate and maintain an efficient rail network.Mark Harris, president, PWI NSW. Last year’s packed PWI NSW Annual Convention.
While there have been many improvements introduced into the Australian rail industry through the development and adoption of RISSB’s standards and other products over a number of years, continued innovation is required in order for rail to improve its safety, productivity and sustainability outcomes.
Informed by extensive engagement with industry and government, the RISSB 2023/24 Work Plan include key changes such as:
• Identifying industry safety risks informed by the Australian Rail Industry Risk Model (the rail industry’s only quantified risk tool)
• Informed by engagement with industry leaders and governments
• Inclusion of national priorities relating to rail inter-operability and harmonisation
• ONRSR’s national priorities
• Major incident investigations
• A focus on adoption and benefit realisation. Another significant change, informed through engagement with industry leaders and governments, is an increased focus on product adoption and benefit realisation.
The work that RISSB undertakes is valuable, and they know that they can add further value by having a greater emphasis on helping industry realise the benefits of RISSB products.
Barriers to adoption are now being identified during the Work Plan development process, and benefit realisation opportunities are being identified for RISSB to assist members during the implementation process.
These opportunities can include undertaking a gap analysis of the old standard compared to the requirements of the new standard, the provision of targeted training, and the development of procedures and work instructions to assist members imbed RISSB products into their operations.
The 2023/24 Work Plan can be found at www.rissb.com.au/work-plan-2/ RISSB is inviting feedback on the plan (info@rissb.com.au), particularly ideas that can assist in improving product adoption and benefit realisation.
ReviewStandardAS 7531 Lighting and Visibility
ReviewStandardAS 7502 Road Rail Vehicles
ReviewStandard AS 7503 Train Identification
ReviewStandardAS 7505 Signalling detection and interface
The lighting and visibility requirements for new and existing locomotive, freight, passenger, and infrastructure maintenance rolling stock are set out in this standard.
This standard sets the core requirements for the safe design, construction, testing, maintenance, modifications and decommissioning of road rail vehicles.
The standard provides a framework to maintain consistency in the identification of rolling stock, including the location and programming of Automatic Equipment Identification (AEI) tags on Australian rail networks.
AS 7505 Signalling Detection Interface aims to ensure the continuing harmonisation of signalling systems across Australian networks. Under these requirements, the new and modified rolling stock should be compatible with signalling detection systems beyond those identified for the individual networks upon which it is intended to operate.
ReviewStandardAS 7510.2 Brking Systems-Part 2 Hauled Rollingstock
ReviewStandardAS 7640 Rail Management
The AS7510 standard provides safety benefits in that proper braking performance contributes to the prevention of collisions or derailments of railway rolling stock by providing controls for the hazards listed
This standard establishes general principles for managing rail throughout the asset lifecycle, excluding design and manufacture. This Standard does not cover: (a) non-running rail infrastructure such as check rails and guard rails; (b) turnouts and other special works; or (c) cane railway and monorail networks.manufacture.
New StandardAS 7739.2 Digital Engineering Data Model
New StandardAS 7661 Ballastless Track systems –Elevated railway, Long Tunnel and Bridges – Performance specification.
New StandardAS 7451 Rolling Stock Integrity
New Code of Practice Driver Only Operations
ReviewCode of Practice Rail Safety Investigations
This standard will define best practices for the Australian Rail Industry and will cover data management processes and technical requirements for digital project deliverables.
This standard defines a minimum set of requirements for ballastless track (BLT) systems. This standard will also provide requirements and guidance for the decision making of BLT system selection based on WoL cost, maintenance requirements, safety and RAM target.
This standard describes the train integrity requirements. This standard includes minimum requirements for train inspection and “carding” requirements for vehicles requiring repair.
This code will provide principles and practices for the safe implementation and maintenance of Driver Only Operations. The document will provide a consistent approach using a reserve SFAIRP methodology to identify key controls necessary for implementation.
This code provides procedures, tools and examples to assist accredited Rail Transport Operators (RTOs) in conducting rail safety investigations in order to prevent a similar occurrence.
The RISSB 2023/24 Work Plan has now been launched, which this year has been developed with a number of key changes being introduced into the development process.
Moves towards decarbonisation must be addressed as a shared responsibility, with industry and governments coming together with common goals to accelerate the highest-priority initiatives to drive lasting change and new innovation.
The transport sector, and therefore rail, plays a critical role in Australia’s journey to net zero.
Reducing emissions within the Australian transport sector is not only the right thing to do, but is also important to support the country’s long-term economic growth and resilience.
To support this effort, the ARA has joined with seven private sector peak bodies and three federal agencies to launch a new, significant initiative to accelerate decarbonisation in the infrastructure industry.
Infrastructure Net Zero is an Australian-first joint initiative to coordinate, collaborate and report on Australian infrastructure’s pathway to net zero.
Its primary objective is to decarbonise Australia’s infrastructure through collective action so that it meets or exceeds our national targets of 43 per cent by 2030 and Net Zero by 2050.
Infrastructure Net Zero will help the whole sector go further, more quickly.
We are pleased to be partnering with the Australian Constructors Association, Clean Energy Finance Corporation, Consult Australia, Department of Infrastructure, Transport, Regional Development, Communications and the Arts, Green Building Council Australia, Infrastructure Australia, Infrastructure Partnerships Australia, the Infrastructure Sustainability Council and Roads Australia as part of Infrastructure Net Zero.
The ARA’s commitment to this important initiative builds on its focus on sustainability leadership, confirmed in its 2021 Sustainability Strategy and the identification of sustainability as one of the organisation’s five strategic priorities in 2022.
It will provide a forum to act on the key findings of the landmark Journey to Net Zero report released in 2022 – a collaboration between the ARA, Roads Australia and the Infrastructure Sustainability Council – and support decarbonisation efforts that will
require an integrated, multi-modal approach to achieve significant change.
Infrastructure Net Zero will focus on four key workstreams to drive that change.
The first workstream will focus on defining net zero for infrastructure, outlining the guiding principles to decarbonise the sector.
This is a critical piece of work to ensure we can support a strong vision for the sector and establish a clear pathway to net zero.
The second area of focus will be on public/ private sector alignment.
There is significant work underway by both government and industry to deliver decarbonisation initiatives and strategies across the country.
Ensuring strong alignment and cross-sectoral engagement will not only maximise the effort and investment that is required to support this goal, but it will ensure we can work together to support practical policy and regulatory outcomes that enable positive change.
Third, we will focus on uplifting capacity in the supply chain. We know there will be new skills, new innovation and new industry capability required to achieve a decarbonised infrastructure sector.
This workstream will provide the opportunity to explore how we can support the private sector’s efforts to continually improve, innovate and prosper as we move towards net zero.
The final workstream will explore procurement for net zero. The way we plan, build and operate infrastructure will need to evolve to reduce emissions and support longterm sustainable outcomes.
This will require a new procurement approach that considers opportunities to reduce embodied emissions and ensure improved outcomes across the life of an asset.
Infrastructure Net Zero provides an opportunity for the ARA to engage with the broader sector on these common decarbonisation challenges and leverage our collective efforts to effect meaningful change.
Rail will be essential to our net-zero future, with greater use of public transport and rail freight set to drive emissions reductions as we evolve to new transport models.
The Journey to Net Zero confirmed the importance of placemaking to promote greater use of public transport in our daily lives and reduce our current reliance on private vehicles.
The benefits of doing so are immediate. The ARA’s 2020 Value of Rail report found that if an additional 20 per cent of people use train or trams to travel to work (compared to 2016), it could result in $1.2 billion per annum of social and environmental benefits for society by 2021.
On our regional networks, rail freight provides significant sustainability benefits, generating 16 times less carbon pollution than road freight.
A number of governments have set mode shift targets in recognition of this, with greater use of rail freight set to drive safer, more sustainable freight services to meet our future needs.
While these clear sustainability benefits demonstrate the essential place rail has in our journey to net zero, there is more to do, from decarbonising operations to improving how we plan, procure and build new projects to achieve more sustainable outcomes.
With jurisdictions overseas preparing to phase out diesel trains and ambitious net-zero targets in Australia now confirmed, a strong
national approach will be critical to support the rail industry’s transition to net zero in the years ahead.
The ARA is working closely with its members on these issues, providing opportunities for collaboration and information sharing among those implementing new technology trials and other sustainable solutions across the industry.
Further projects are planned to articulate the range of policy and other issues that will need to be considered to support the industry’s transition to net-zero, particularly when it comes to decarbonising rollingstock operated on the vast regional rail network across Australia.
KEY PRIORITIES
While rail offers significant opportunities to reduce transport emissions, the industry will need to continue to decarbonise its own operations to support the achievement of netzero targets.
Establishing new technologies and related infrastructure to achieve a decarbonised fleet – particularly on the regional passenger and freight networks – will be a key part of moving to net zero.
This will require a strong focus on research and innovation to drive new solutions.
While Australia has traditionally lagged the rest of the world when it comes to rail innovation, the development of the National Rail Manufacturing Plan provides a strong opportunity to tackle some of the challenges associated with decarbonisation locally.
A dedicated focus on innovation can lead to breakthroughs in propulsion systems, battery technologies, and energy storage, ultimately reducing the sector’s carbon footprint.
Collaborative research initiatives involving universities, research institutions, and industry experts will better support Australia’s rail industry in reaching sustainabilitys and complement technology trials already underway within the industry.
Public engagement is also essential in any successful transition – it is important that we continue to educate the community on the benefits of decarbonisation and the role of rail in reducing overall emissions.
Collaborative efforts to integrate rail networks with other modes of transportation, such as buses and bicycles, can create seamless, sustainable travel experiences that appeal to a broader segment of the population.
The importance of decarbonisation in the Australian rail industry cannot be overstated.
Beyond being an environmental necessity, it holds the potential to transform transportation, foster economic growth and enhance community wellbeing.
By learning from successful examples overseas and fostering collaboration between stakeholders, Australia can position itself as a global leader in sustainable rail systems.
A 16-kilometre section of twin tunnels between Cheltenham and Glen Waverley will be constructed by Suburban Connect, a consortium of global leaders in tunnelling including CPB Contractors, Ghella and Acciona Construction and with extensive experience in Victoria and Australia.
Up to 10 tunnel boring machines (TBMs) will be used in the 2026 project and thousands of jobs created on the cityshaping Suburban Rail Loop.
SRL East will create up to 8000 direct jobs and deliver six new underground stations between Cheltenham and Box Hill – slashing travel times and congestion and connecting people to key employment, health and education destinations in Melbourne’s east and south east.
The TBMs will be used to dig the total 26 kilometres of tunnels, launching from Monash, Burwood and Heatherton, with a second contract to be awarded next year for the tunnelling between Glen Waverley and Box Hill.
A SRL Precincts Discussion Paper has also been released, to kick-start a massive program of community consultation.
Feedback from the paper will inform the formal planning process for the areas around the SRL East stations. Later this year, detailed draft Precinct Visions for each of the siix station areas will be released –outlining potential new housing options and land use changes.
RAIL
Construction contractors CPB Contractors, John Holland and McConnell Dowell have been shortlisted to build the final eight Inland Rail projects in Victoria.
The three contractors will now develop their final design and construct tender submissions for the Inland Rail Beveridge to Albury section for Tranche 2 works at Benalla, Euroa, Broadford, Wandong, Seymour, and Tallarook.
The Request for Tender shortlisting follows a rigorous expression of interest process,
which drew a high standard of responses from local and interstate construction firms to deliver Inland Rail, a nation building project that will transform how goods are moved around Australia.
In Victoria, work will be undertaken at 12 sites to enable double-stacked freight trains to pass safely and ensure everyday products can be delivered faster and more reliably around Australia.
McConnell Dowell is currently delivering four Beveridge to Albury Tranche 1 sites at Glenrowan, Barnawartha North, Wangaratta, and Seymour.
The preferred contractor will be announced in mid-2024, with Tranche 2 construction starting from 2025.
Bruce Highway
A critical piece of the biggest road and rail infrastructure project in Far North Queensland has been officially commissioned, marking the final step towards the completion of the project.
The $535 million Bruce Highway-Cairns
Southern Access Corridor (Stage 3)-Edmonton to Gordonvale project is delivering long-term improvements to traffic flow and road safety through reducing congestion and highway travel times, and improving road access and active transport networks.
The opening of the Menmuny Overpass, which spans 141 metres, is a significant milestone for the project.
The project was delivered by joint venture contractors John Holland, Seymour Whyte and AECOM.
John Holland operations manager Natasha Roy said the collaboration between the teams and the local subcontractors made the achievement possible.
“We have received support from the local community, from farmers to local businesses and residents, all understanding the disruptions from the construction because they knew it would result in a significant improvement of their future travel to and from Cairns,” she said.
“The sustainable construction methodologies used during the works have been recognised across the industry. The team was also conscious of the significant heritage and sensitive areas surrounding us, and implemented high standards of controls to ensure the project would be delivered with no harm to the land or the environment.”
In addition to upgrading and duplicating the highway, the project also delivered:
• New road and rail bridges at Wrights Creek and Stoney Creek
• A rail track upgrade and realignment of 4.5 kilometres of the Queensland Rail North Coast Line
• One new intersection along with two upgraded intersections
• More than eight kilometres of upgraded local roads (8.9 kilometres)
• Cycleway bridge at Collinson Creek
• 10.4 kilometres of cycleway
• Twenty-seven kilometres of drainage
• Three new pedestrian crossing facilities, including a pedestrian overpass
The project is funded by the Australian and Queensland governments under the Bruce Highway Upgrade Program.
Martinus and FCC Construction Australia have signed a Memorandum of Understanding (MOU) to collaborate on railway infrastructure projects, both in Australia and internationally. Both parties have already joined forces on a number of railway infrastructure projects across New South Wales, Victoria and Queensland that showcase the types of projects companies can collectively embark upon in Australia and internationally.
Martinus and FCC Construction Australia boast complementary skillsets that provide a holistic approach to complex railway infrastructure from the design phase right through to project completion.
Martinus chief executive Treaven Martinus said although the collaborative relationship had first been demonstrated in Australia, Martinus and FCC Construction Australia’s relationship would extend beyond borders.
“Martinus will utilise its impressive expertise working across Australia, New Zealand, North America and Chile to expand the corporation internationally in conjunction with FCC Construcción’s established network of global rail projects,” he said.
“Supplemented by FCC Construcción’s global railway construction with a deep appreciation of complex integration, this partnership combines the best aspects of the two corporations, effortlessly blending local experts in each market with proven global expertise,” Martinus said.
FCC Construction Australia, as part of FCC Construcción, has a presence in over 20 countries, supported by 120 years of international experience delivering major infrastructure projects. Since its establishment, FCC Construcción has set the benchmark for construction excellence and have extensive experience in the design and execution of large civil infrastructure projects.
NOW AVAILABLE
Thurs 20 June, 2024
The Women in Industry Awards recognise outstanding women leaders from across Australia’s industrials sector.
We’re the leading provider of end-to-end rail and transport solutions in Australia and New Zealand. From designing and constructing transport networks to operating and maintaining them, it’s our long-term, trusted partnerships with our clients that helps provide better connections across the country.
Our long-standing experience in mass transport means we know how to put together the right solution - from start to finish. With our in-house experience - supported by our large fleet of plant machinery and equipment - we deliver value and certainty to our clients.
johnholland.com.au