
6 minute read
Sustainable bitumen supply: Lessons from SAMI
SAMI has been implementing measures to minimise emissions from its import, storage and manufacturing processes.
SAMI BITUMEN, A LONG-TERM SUPPLIER OF BITUMEN PRODUCTS IN AUSTRALIA, IS KEEN TO PLAY ITS PART IN MORE SUSTAINABLE BITUMEN DELIVERY FOR ROAD CONSTRUCTION. HERE’S A LOOK AT THE COMPANY’S BITUMEN SUPPLY CHAIN FOR MORE INSIGHTS.
Every year, Australia uses more than 800,000 tonnes of bitumen for asphalt and sprayed sealing applications. With all this bitumen imported from overseas, bitumen importation and storage processes have an impact on the overall sustainability of road infrastructure.
SAMI Bitumen Technologies, as the first independent bulk bitumen supplier in Australia, has been involved in importation of bitumen to Australia since 2005. The company’s facilities in Brisbane, Kwinana, Fremantle, Sydney and Geelong have a combined capacity of over 50,000 tons for bulk bitumen storage.
Apart from supplying all bitumen grades as specified in the Australian Standard AS2008 – including multigrade and EME(Enrobés à Module Elevé) grade bitumen – SAMI’s facilities also manufacture a range of speciality bituminous products, such as polymer modified binders, emulsions and polymer modified emulsions.
As part of a broader company mission to cut greenhouse gas emissions by 30 per cent by 2030, SAMI has been implementing a series of measures to minimise emissions from its import, storage and manufacturing processes. The goal, as Scott Olsen, SAMI’s State Manager for Western Australia explains, is to achieve emission reductions across the entire SAMI supply chain.
“SAMI’s is a cradle-to-grave solution across the entire network,” he says. “From having due consideration in picking our source refineries and transport options, to installing solar panels on our storage sheds and helping with reduction or removal of kerosene use in sprayed sealing applications with our products, SAMI has been progressing on all fronts towards greater sustainability,” he tells Roads & Infrastructure.
As a supplier of crumbed rubber modified binders, Olsen says recycled tyres account for about 30 per cent of SAMI’s annual production by tonnage. SAMI has also developed sprayed sealing binders that eliminate the use of petroleum-based solvents for sprayed sealing operations, thus preventing the emission of solvent into the atmosphere.
“SAMI has been pioneering in the introduction of speciality hard-grade binders, which enable high modulus asphalt to be used in heavy-duty pavements. This helps reduce the pavement thickness by up to 25 per cent, thus helping minimise use of non-renewable products. Other examples of sustainable SAMI solutions include developing micro surfacing binders to enhance skid resistance and extend the service life of the road surfac, as well as developong the environemntally friendly BioPrime solution to replace kerosene-based bitumen cutters for priming purposes,” says Olsen.
THE SAMI PROCESS Olsen, who also oversees SAMI’s bitumen shipments and storage via Kwinana and Fremantle Port in Western Australia, says all of SAMI’s bulk bitumen is imported from carefully selected refineries, predominantly in Asia.
“Having the majority of our sources located locally within Asia helps reduce our carbon footprint from transport,” he says. “Additionally, we have been studying bitumen fume emissions over the past few years to develop predictive models that are used for the selection of bitumen sources.”
In pursuing its goal, SAMI also enjoys the global support of its parent company, the Colas Group. Colas’ subsidiaries own and operate a fleet of bulk hot bitumen shipping vessels. Having recently added LNG-fuelled bitumen cargo vessels to its fleet, Colas is expecting the initiative to help cut carbon dioxide emissions by 30 per cent compared to using oil fuelled cargo ships.
Tiffany Pham, Bitumen Procurement Manager for SAMI, says apart from enjoying a greater control over the shipping process, the partnership between Colas and SAMI also ensures access to reliable sources.
“When it comes to imports, SAMI is focused on delivering quality products compliant to the Australian specifications. We carefully select our source refineries, where we procure bitumen under medium- to long-term arrangements, to ensure that the material provides the best performance and value for our clients. Our bitumen is usually shipped by a fleet of cargo carriers owned by our parent company. This provides us the advantage of not compromising quality due to constraints on procurement and transport,” she points out. “In addition, our parent company owns and operates a dedicated bitumen refinery in Asia, which guarantees an ongoing supply of bitumen into Australia. This is critical with uncertainty surrounding the future bitumen supply from fuel and lubes refineries,” she adds. This process, she says, ensures SAMI can maintain a reliable supply to its clients. It also helps minimise risk or shortages.

RIGOROUS TESTING Product testing is another important step in the supply process when it comes to quality assurance, Pham says.
“SAMI works with globally recognised refineries in Southeast Asia. We have longterm contracts with these refineries and in some cases partnership arrangements have been established to ensure continued long-term supply. If we want to sign up a new refinery, we first go through a process of rigorous product testing to ensure the bitumen quality is consistent with the AS2008 standard,” she explains.
“We import single refinery source in each of our cargo, making sure the composition of bitumen is consistent and that the bitumen is suitable for modification with polymers and emulsifiers. Further, each cargo vessel’s load is tested for compliance to specification prior to loading. The cargo is monitored constantly while in transport to make sure the bitumen temperature remains within the recommended temperature throughout the journey. Samples are taken and tested when
SAMI recently invested heavily on its new and existing bitumen storage and manufacturing facilities.
SAMI’s parent company, the Colas Group, now has LNG-fuelled bitumen cargo vessels in its fleet.
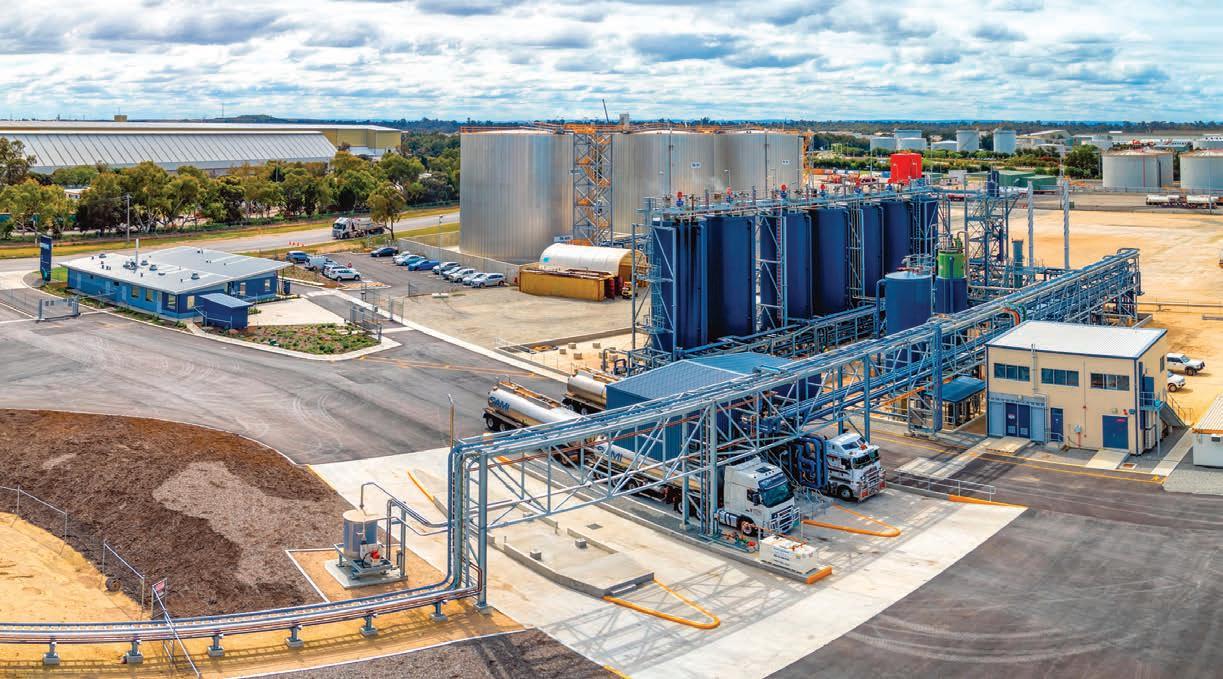
the cargo arrives at our storage facilities and also before leaving SAMI’s facilities to reach the client.”
SAMI also regularly tests the quality of bitumen in its manufactured products, such as emulsion and polymer modified bitumen (PMB), Pham adds.
“We are fully invested in the supply chain of products derived from bitumen, so our customers have the certainty that our bitumen will give them satisfaction.”
SAMI’s independent research and development (R&D) facilities, including the main SAMI laboratory in Camellia, New South Wales, provide support with binder and asphalt testing for SAMI’s clients.
“SAMI’s in-house testing and product development expertise is further supported by the global network of Colas Group’s bitumen experts. Colas’ Centre of Excellence in Paris is a fully dedicated bitumen R&D centre that can support us for specialty tests,” Pham says.
SAMI recently invested in its new and existing bitumen storage and manufacturing facilities. The company has also invested in a large fleet of road tankers and bitutainers to be able to supply binders to all locations across Australia and neighbouring islands.
Olsen says through these investments, SAMI is prepared to play an even bigger role in improving the sustainability of Australian roads.
“With the financial stimulus flowing through the Australia infrastructure industry, the market for bitumen and bituminous products is likely to grow in the coming years. With SAMI’s strong supply chain, we are ready to keep supporting the industry, like we have done since 1978.”