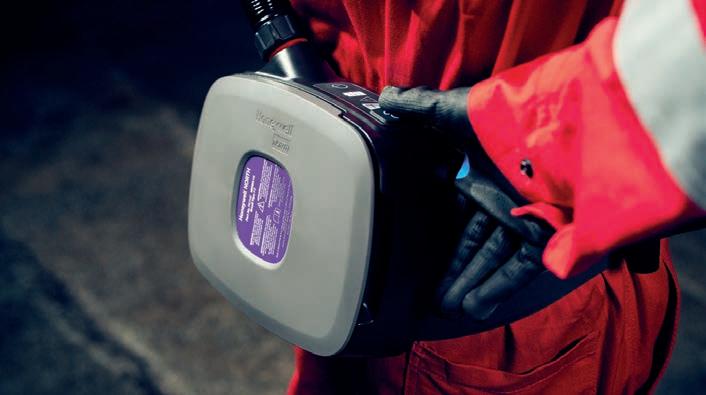
3 minute read
Work hard and breathe easy
Silicosis has been flagged as a problem in the Australian mining, manufacturing and construction industry for some time, yet the dust disease remains highly prevalent today.
It is estimated that hundreds of thousands Australian workers are exposed to silica dust and black lung disease each year, with many developing lifelong issues as a result.
Recent legislative changes are aimed at tightening occupational exposure limits (OELs) or workplace exposure standards (WES) for coal and silica dust in mining operations.
As the regulatory environment has changed and new safety requirements mandated, Honeywell has continued to innovate to ensure its solutions meet the changing needs of mines and constructions sites across Australia.
The legislative changes regarding silica, adopted from July 1 2020, include most states accepting Safe Work Australia’s recommendation to halve the WES for respirable crystalline silica from an eight-hour time-weighted average airborne concentration of 0.1 milligrams per cubic metre (mg/m³) to 0.05 mg/m³. Tasmania remains an outlier, observing standards set in 2018.
And for coal dust, since October 1 2022 all coal mines across the country are regulated by a new dust respirable exposure standard of 1.5mg/m³, a reduction from the previous standard of 2.5mg/m³. Queensland moved early and adopted these standards in 2021.
To achieve consistent site-wide dust control and to stay within mandated OELs most effectively, mines must address each dust-generation point separately with targeted solutions. This includes every stage of the mining process from pit to port.
Many mines focus most dust control efforts on haul road networks; however, it is critical for mines to tackle dust issues in relation to production and processing plants, as well as activities where workers are directly exposed to dust in more confined spaces, such as underground mining and drilling, or spaces within processing plants.
In general, work health and safety (WHS) regulations involve managing risks to everyone in the workplace.
Creating a safe work environment is a legal requirement, critical to the long-term success of mining and construction. It can help with staff retention and improve productivity, reduce injury and illness in the workplace and reduce the costs of injury and workers’ compensation.
Under Australian WHS laws, mines must ensure the health and safety of workers and not put the health and safety of other people at risk.
People working in the mining and construction industries have WHS obligations and they must take care of their own health and safety, take care not to do anything that could hurt others, follow WHS instructions, and follow the workplace’s WHS policies and procedures.
Across the mining, manufacturing and construction industries, personal protective equipment (PPE) is no less important than any other safety measure contained within WHS regulations. The biggest challenge with PPE is that it relies on worker behaviour to be effective 100 per cent of the time.
When respirators are required in a workplace, the need to develop a Respiratory Protection Program (RPP), as per the AS/NZS 1715 standard is critical; however, this can be challenging as workplaces aren’t often aware what an RPP entails.
The use of respirators means a systematic approach to provide a high level of confidence and ensure workers are going to be protected, especially from silica dust.
There are three main areas that must be addressed with RPP: the type of filter; the adoption of the respirator (as it needs to be worn 100 per cent of the time when protection is required); and that it must fit the wearer to create an adequate seal.
Workers also need to consider other factors that fall within these three main categories, such as whether the respirator is adequate and suitable for the work that is being completed. Selecting respiratory equipment goes well beyond the filter. Facial structure, facial hair, the time in which a task is performed, environmental conditions, physiological impacts and communication requirements are essential to the selection process of a respirator.
Honeywell offers a range of reusable respirator solutions, half-face and fullface masks, and 7700 Series P2/P3 asbestos silica kits.
Honeywell’s new product offering is the powered air-purifying respirator with a selection of hoods that supports most industry requirements. These are designed for superior comfort, safety and easy operation so users can work hard and breathe easy.
Silica dust can be found on almost all mine sites, particularly where workers are grinding, sawing, and cutting materials like concrete, stone, brick, mortar, and sand. Without the proper respiratory protection, workers may not see or feel the effects in the short term, but could end up with serious health issues later in life. That’s why WHS mandates that employers limit workers’ exposure to respirable crystalline silica and provide the appropriate filtering respirator.
It’s also why respirator solutions such as those provided by Honeywell are so important.
Comfort plays a large part in respiratory protection compliance and if respirators aren’t comfortable workers won’t wear them correctly – or even at all.
Honeywell’s respirators more than fit that bill. The company’s safety solutions help to effectively mitigate the effects of silica dust, lead to productivity and efficiency gains, and do not get in the way.
Above all, they don’t stop working until the last person safely clocks out and heads home.
Visit the Honeywell website for further information.