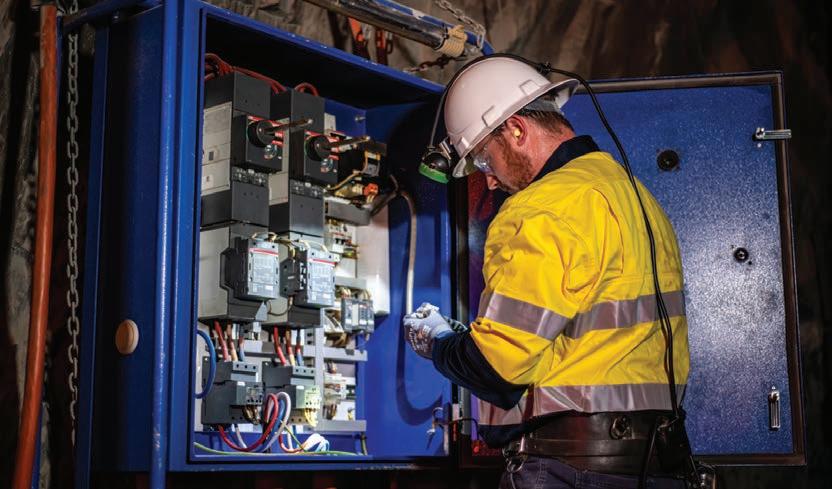
4 minute read
Gold mining is reinforced by critical maintenance
WESTGOLD’S SOPHISTICATED APPROACH TO MAINTENANCE IS BASED ON DETAILED PLANNING AND SCHEDULING, ADVANCED TECHNOLOGY AND HIGHLY SKILLED TEAMS OF PROFESSIONALS.
The need to undertake regular and effective machinery and equipment maintenance is vitally important for gold mining operations, specifically in relation to the health, safety and wellbeing of employees.
Gold miners operate complex equipment in often-harsh surface and underground environments, ensuring mine maintenance is no easy task.
Westgold’s regional operations maintenance manager Bryan West notes that protecting the safety of the machinery and equipment operators, and those working within an underground gold mining environment, is critical.
“Ensuring the safety of the operators and all the other personnel who work underground is the most essential part of what we do,” West told Safe to Work.
The requirement for properly maintained and reliable mining tools is key to achieving uninterrupted and sustainable safety outcomes.
“Well-maintained equipment allows us to operate our assets efficiently and predictably by limiting unplanned and costly downtime, and boosting productivity by keeping the wheels turning,” West said.
“It allows us to predict and control costs, and to reach the required operational targets required to remain profitable.”
West is responsible for the maintenance of Westgold’s mining fleet and auxiliary assets, ensuring compliance for classified plant and equipment. He acts as a link between corporate and site-based personnel, facilitating continuous improvement.
He also helps to ensure company processes and operating procedures are followed, while supporting and engaging the company’s personnel by working closely with recruitment and HR teams.
Westgold is a dynamic and responsible explorer and developer of gold mines, operating in the prolific goldfields of Western Australia.
The company typifies Australia’s world-leading mining technology, ingenuity and pioneering attitude. It has two main pillars: gold operations in Murchison and Bryah Basin in WA; and a specialised underground mining services arm, Westgold Mining Services.
With a workforce of more than 1000 people, Westgold is the dominant explorer, developer, operator and gold mining company in the Murchison region.
With over 1300 square kilometres of tenure across the Murchison and Bryah Basin, the company operates four underground mines and three processing plants with an installed processing capacity of around four million tonnes per annum.
Westgold is the owner–operator of all its underground and open-pit mines. This vertical integration provides greater cost control and operating flexibility across the company’s assets.
Westgold operates on a ‘hub and spoke’ model. Its Murchison mines are able to feed ore to the Meekatharra and Tuckabianna processing hubs, with the Bryah Basin mines sending ore to the Fortnum hub.
All of Westgold’s mining operations rely on specific types of machinery and equipment maintenance. The company undertakes its scheduled maintenance via utilisation or calendarbased maintenance.
“The majority of Westgold’s frontline equipment, haul trucks, loaders and drilling equipment is serviced under a utilisation regime based on intervals of 250 machine hours,” West said.
“Calendar-based service intervals require inspections to be conducted either on a weekly, fortnightly, monthly and three-monthly basis.”
Westgold has many equipment programs that support mining activity, including the rebuild and replacement of machines and components.
“Additionally, there is classified plant servicing, which is conducted on three-, six- and 12-month intervals dependent on the regulations that apply to the specific regime,” West said.
Westgold has many equipment programs that support mining activity, including the rebuild and replacement of machines and components.
The company monitors the life expectancy of machinery and equipment according to economical and productivity expectations.
It also engages in continuous improvement projects, including the acquisition of Caterpillar’s R2900 XE, a new diesel-electric underground loader that is currently in service at the miner’s mid-west operations.
The diesel-electric combination of the R2900 XE offers more than a 31 per cent improvement in fuel efficiency, alongside reduced maintenance costs and greater productivity compared to earlier models.
Westgold believes this type of machine innovation is a key driver for enhancing productivity and profitability.
The company also undertakes predictive and preventive maintenance using the maintenance management system, Pronto. This system allows for the capture and storage relevant data relating to individual machines and groups of assets.
Westgold utilises reporting tools, such as Qlik Sense, that provide information relating to machine availability, utilisation, downtime and repair trends, and cost analysis, using this information to make improvements to the overall reliability of its assets by targeting potential problem areas.
Westgold has been improving its workshop facilities and tooling over the last couple of years, which has given the company’s personnel the ability to perform the right level of maintenance. Additionally, Westgold is deeply engaged in providing the most appropriate types of training.
“For employees without a trade certificate, we have apprenticeship training programs in place for heavyduty fitters and auto electricians, while also providing opportunities for trade upgrade training,” West said.
“We are in the process of setting up a dedicated training facility at our Great Fingal operation in the Cue region, where our apprentices can spend time with trained and experienced tradespeople to help reinforce the knowledge they have learned through TAFE programs and on-the-job training
“They will get to work on components and systems that they might not get the opportunity to work on often at site in a non-productionbased environment, and on operational equipment and components.
“For those that have already completed an apprenticeship, we offer various tailored training with our OEM (original equipment manufacturer) partners and other outside sources to help upskill and engage our teams.”
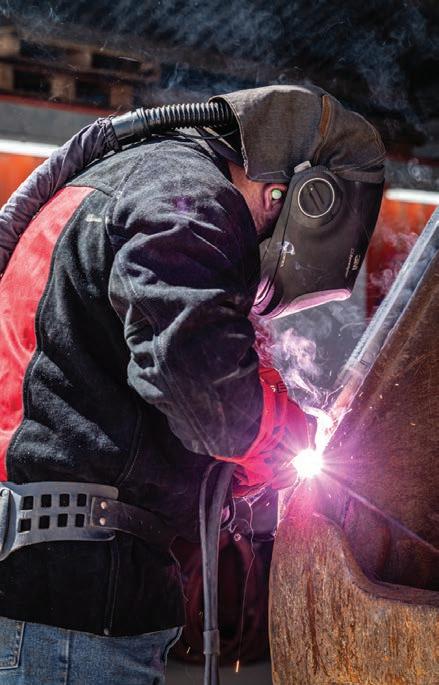
Westgold is also a proud member of the Gold Industry Group, a memberbased, not-for-profit association that represents gold producers, explorers, prospectors, fabricators and service providers. The organisations champions long-term initiatives that grow an understanding of the gold sector’s value to the economy and community.
The Gold Industry Group, along with members such as Westgold, is working to build a strong, sustainable, connected and safe gold industry, exemplified in its commitment to the role of maintenance.