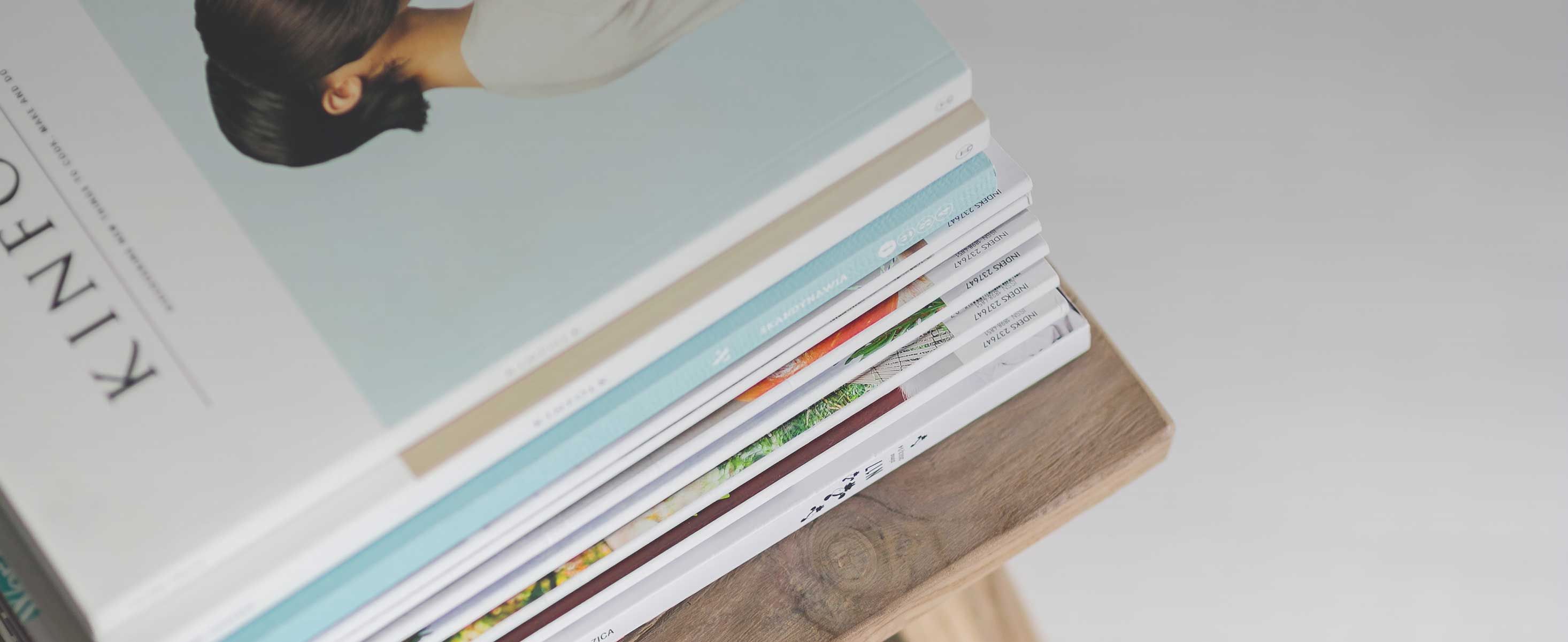
3 minute read
Predict and prevent impending equipment failures
DINGO PROVIDES PREDICTIVE MAINTENANCE SOFTWARE SOLUTIONS FOR ASSET-INTENSIVE INDUSTRIES, HELPING TO REDUCE MAJOR COMPONENT FAILURES, AND IMPROVE ASSET RELIABILITY AND SAFETY.
The profitability of mining operations is significantly affected by the availability and health of essential physical assets.
Dingo is a specialist in predictive maintenance, and its Trakka software provides actionable intelligence to asset-intensive industries such as mining and defence.
“Over many decades, Dingo has been servicing clients in the heavy mobile equipment space, across industries, providing unique and tailored advice to assist with the transition from preventive or older maintenance regimes to predictive maintenance strategies,” Dingo’s senior product manager Tom Mulherin told Safe to Work.
“Our core software product, Trakka, is a desktop application which monitors condition intelligence, essentially reviewing and analysing condition data from assets.”
The software captures health information from mining machinery and uses a proprietary analytics platform to assess equipment condition.
Most recently, Dingo has released intelligence, an automatic reporting app that provides high-level and quick insights into Trakka data. The app can also reveal data hygiene issues and cross-examine asset health program results.
“We also provide sophisticated mobile solutions to assist with the collection of inspection data for the provision of insights and analysis,” Mulherin said.
Dingo’s Trakka Asset Health Manager (TAHM) mobile app enables asset-intensive operations to access, understand and act on the condition of its equipment – anywhere and at any time. This app is part of a comprehensive suite of tools designed to help a team manage and maintain equipment health.
TAHM consists of two distinct but equally important functions: insights and inspect.
Insights enables users to see equipment health, recommend actions and track progress through to resolution.
Inspect allows technicians to easily perform equipment inspections and condition-reporting from the field using a mobile device. If problems are found, the system, which seamlessly integrates with a mining operation’s existing workflow, alerts maintenance teams and recommends corrective actions.
“Our software remains both OEM (original equipment manufacturer) and hardware-agnostic, so we’re happy for miners to have mixed fleets and choose any data provider and we’ll ingest that diagnostic information,” Mulherin said.
“Likewise, on the backend we seamlessly integrate with ERPs (enterprise resource planning) where maintenance work order management is completed.
“The software generates actions based on equipment reviews or analysis of the data. These actions transfer into the work order system, the maintenance work is completed, and unique to Trakka actions are tracked through to completion.
“Rather than assume the work order has been completed, and therefore the machine is now healthy, our software verifies whether the completed actions were in fact the right actions, returning the asset to a normal condition. And if not, the work order loop is restarted, ultimately leading to increased availability and fewer unplanned failures.”
Predictive maintenance is based on the actual operating condition of equipment, rather than predetermined factors.
Recent studies have suggested this form of maintenance can generate significant reductions in costs and downtime due to equipment breakdown.
“We provide analytic tools that capture a wide range of equipment condition data, including oil or fluid samples, vibration, thermography and ultrasonics,” Mulherin said.
“Additionally, we undertake simple tasks such as digitising the maintenance paper trail, allowing maintenance teams to use a digital inspection checklist and collate all that important data into one easily accessible platform.”
It’s not uncommon for mines to have data silos, where their condition-monitoring data is generated by different systems and reviewed by different people. But these types of fragmented systems and data storage make it easy to miss critical pieces of the puzzle, which can result in issues snowballing into larger and more expensive problems.
“Our experience tells us that the more mature mines believe they have to collect all of the data they can, while smaller mines believe they don’t have the ability to collect data due to the perceived expense,” Mulherin said.
“However, it’s really about collecting the right type of data that can have an immediate impact upon equipment health.”
The solution is to bring all data into a centralised predictive maintenance system like Trakka, which fits seamlessly within operations. Dingo’s early-warning software gives maintenance teams the actionable knowledge required to promptly rectify impending issues, resulting in increased availability and fewer unplanned failures.
Many mines assume they need to throw out their existing processes to implement predictive maintenance, but that’s not the case with Dingo. Trakka will support existing maintenance processes, thus avoiding the need to make significant changes to the way work is done.
If a mine is utilising an ERP system, for example, Trakka can be a powerful complement by directly integrating with it or by operating in parallel.
In addition, Trakka provides quantifiable data on breakdown avoidance savings, including parts and downtime, along with savings associated with component life extension. Users can immediately understand how equipment health has improved over time and the financial significance of each save.
“The power of Trakka is that our clients can transfer all their condition data into one place,” Mulherin said.
“When you have the complete picture of an asset’s condition, it’s much easier to make an informed decision in relation to its status”
The transition to a predictive maintenance regime can be facilitated by Dingo experts, offering implementation and training sessions remotely or on-site to guide employees through the process.
Dingo is a proud member of Austmine and fully embraces the collaborative and supportive environment fostered by the organisation across the mining, equipment, technology, and services (METS) sector.
Dingo specialises in providing optimised planning, minimising downtime and repair costs, creating safer workplaces, maximising asset health, and delivering superior financial results.
“With predictive maintenance, Dingo’s typical mining customers routinely achieve payback in six months or less, and a threeto-one return on investment,” Mulherin said.
