Increased safety and productivity with smart operations
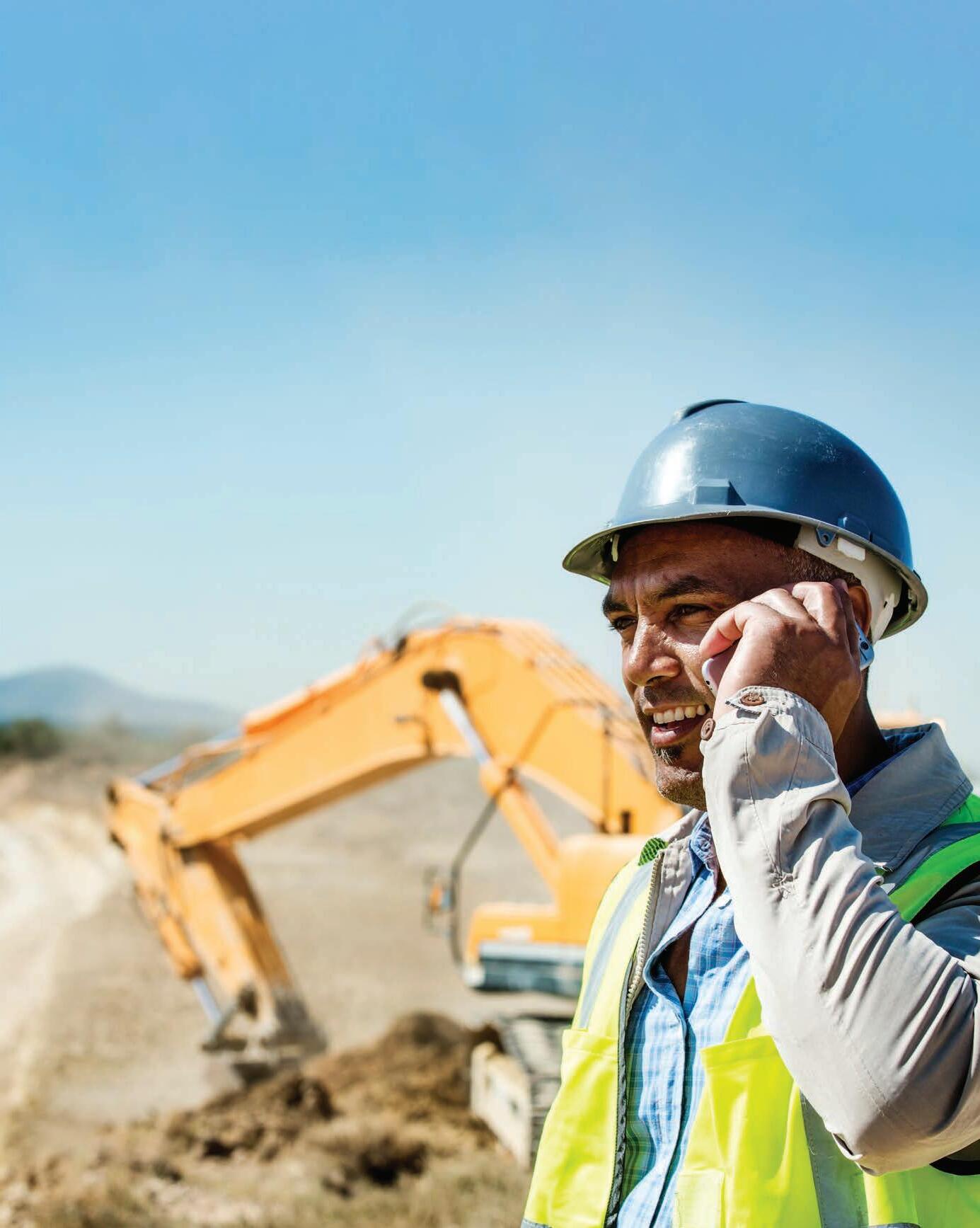
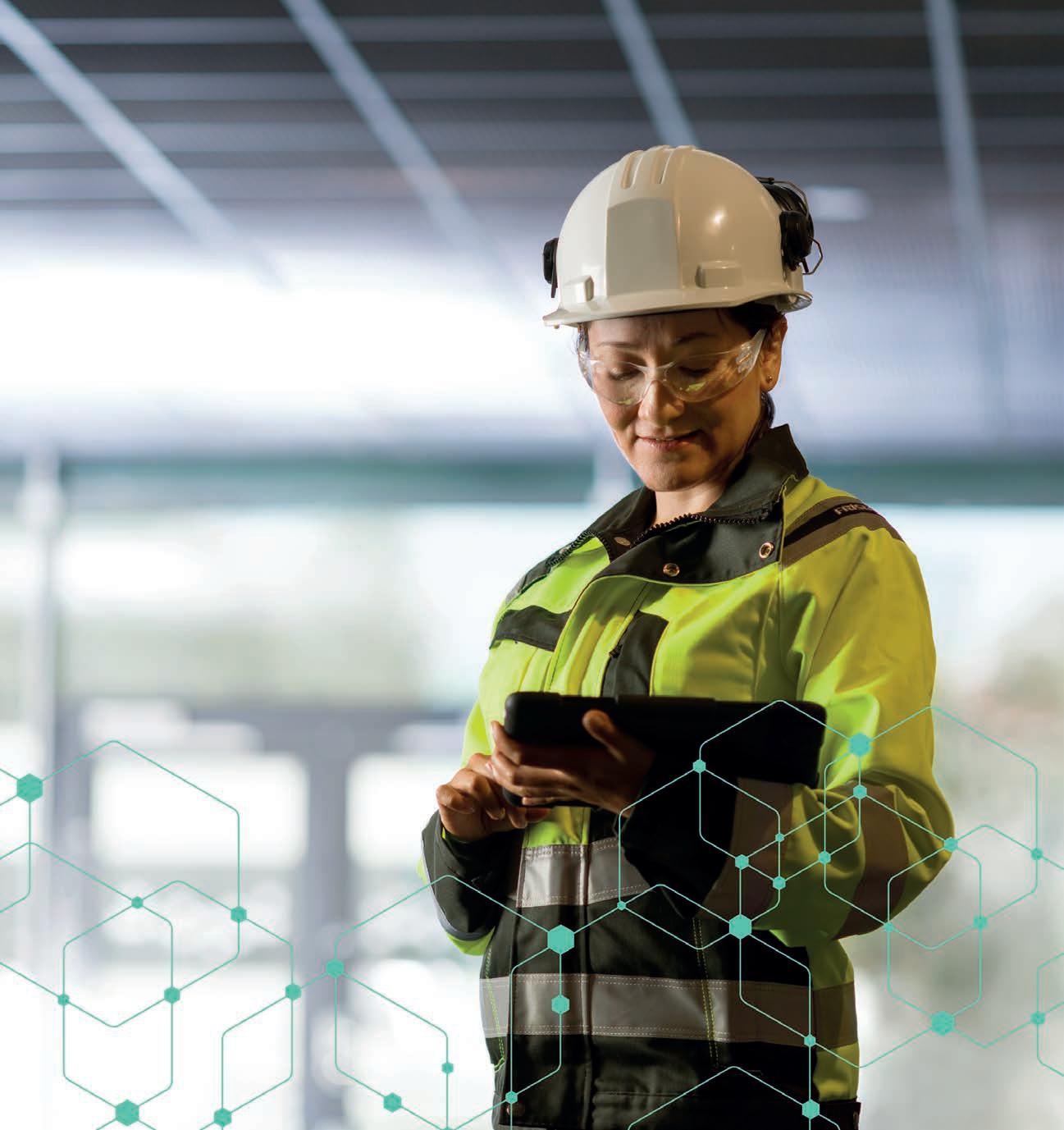
It’s about knowing, not guessing
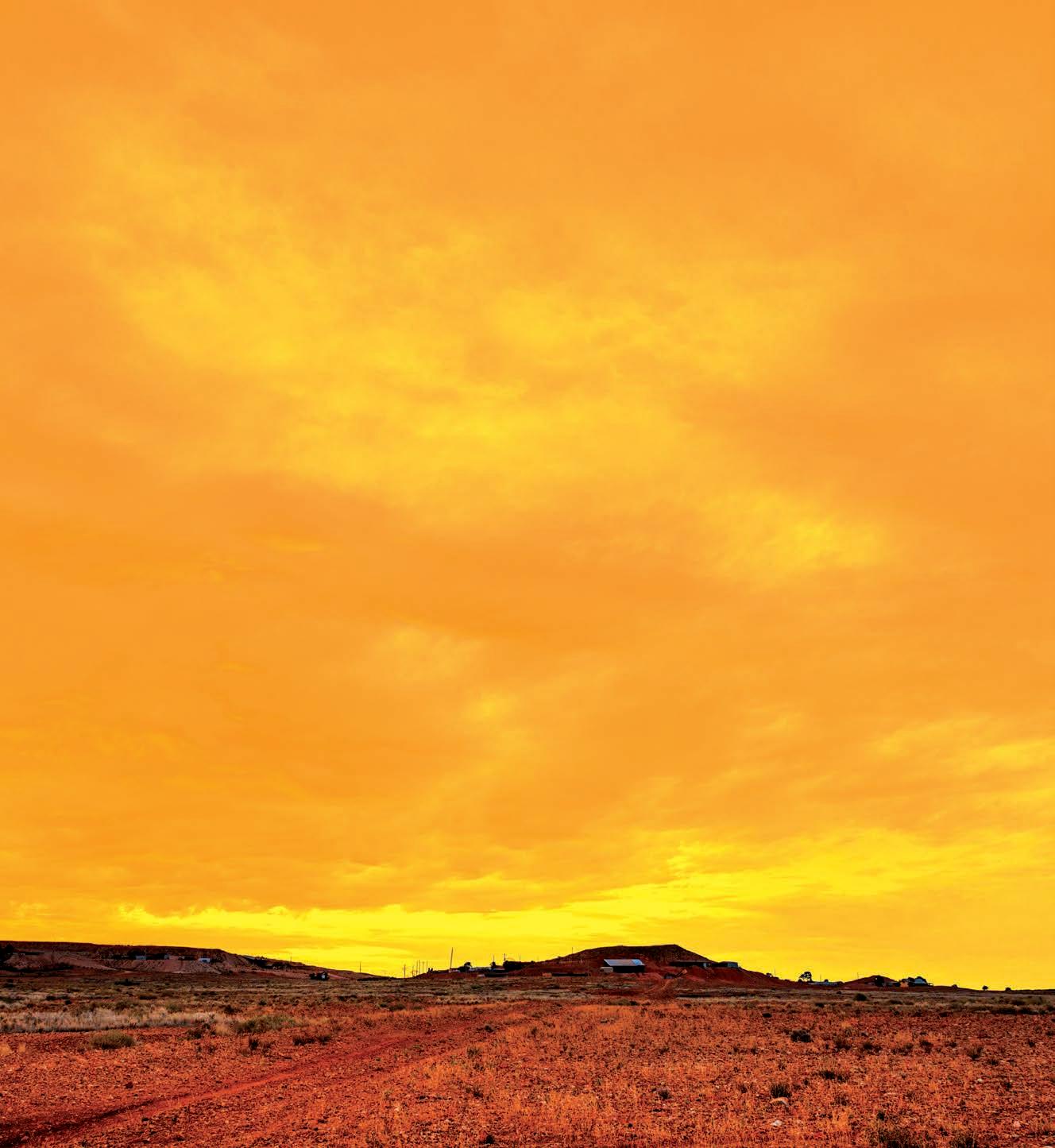
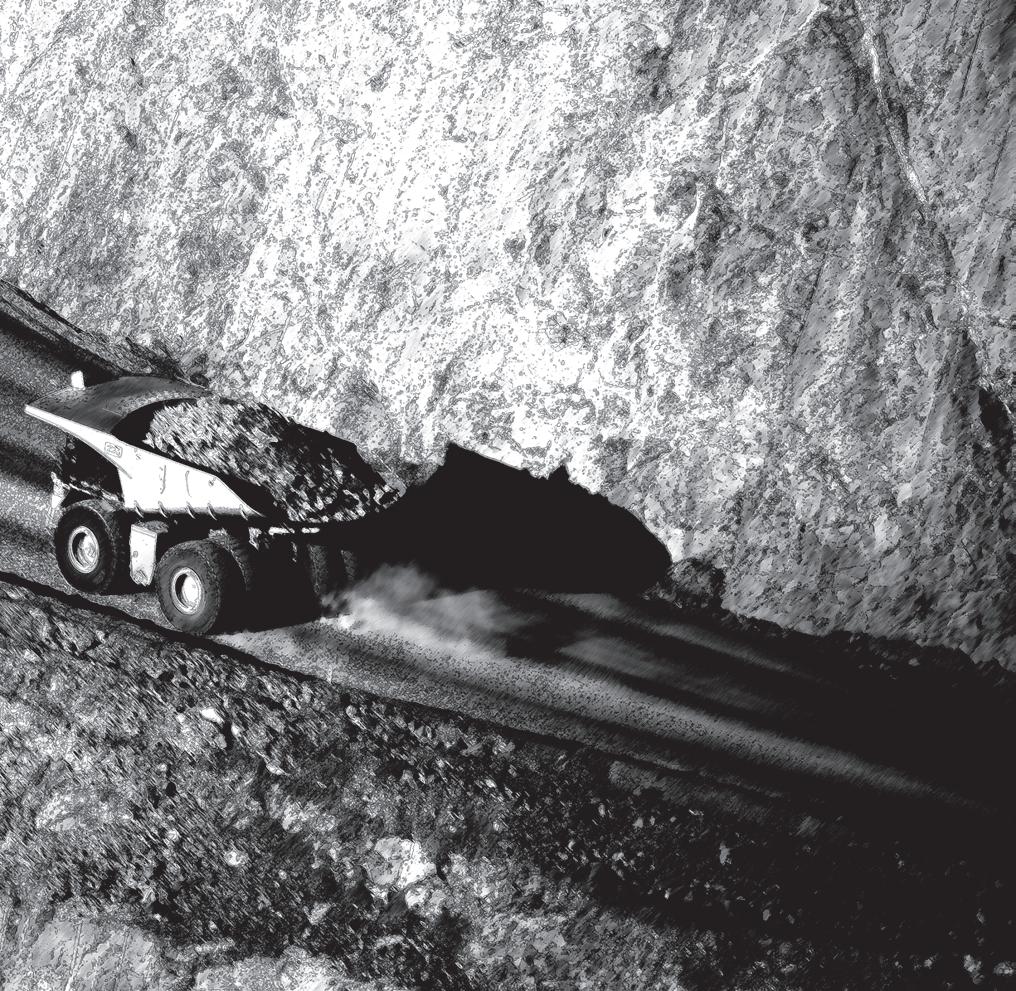
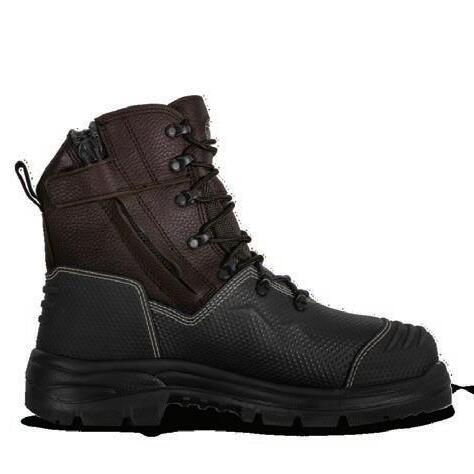
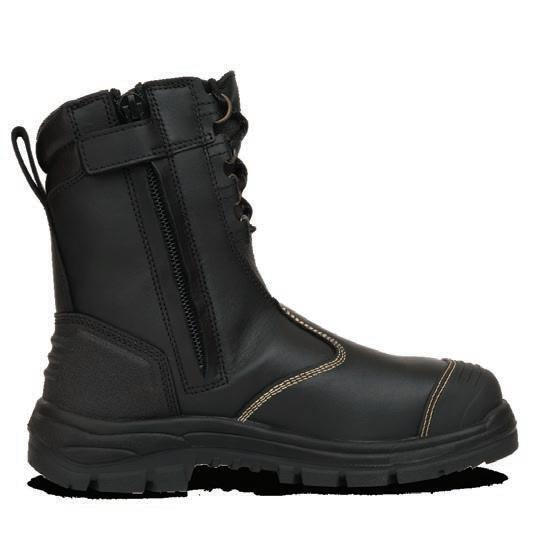

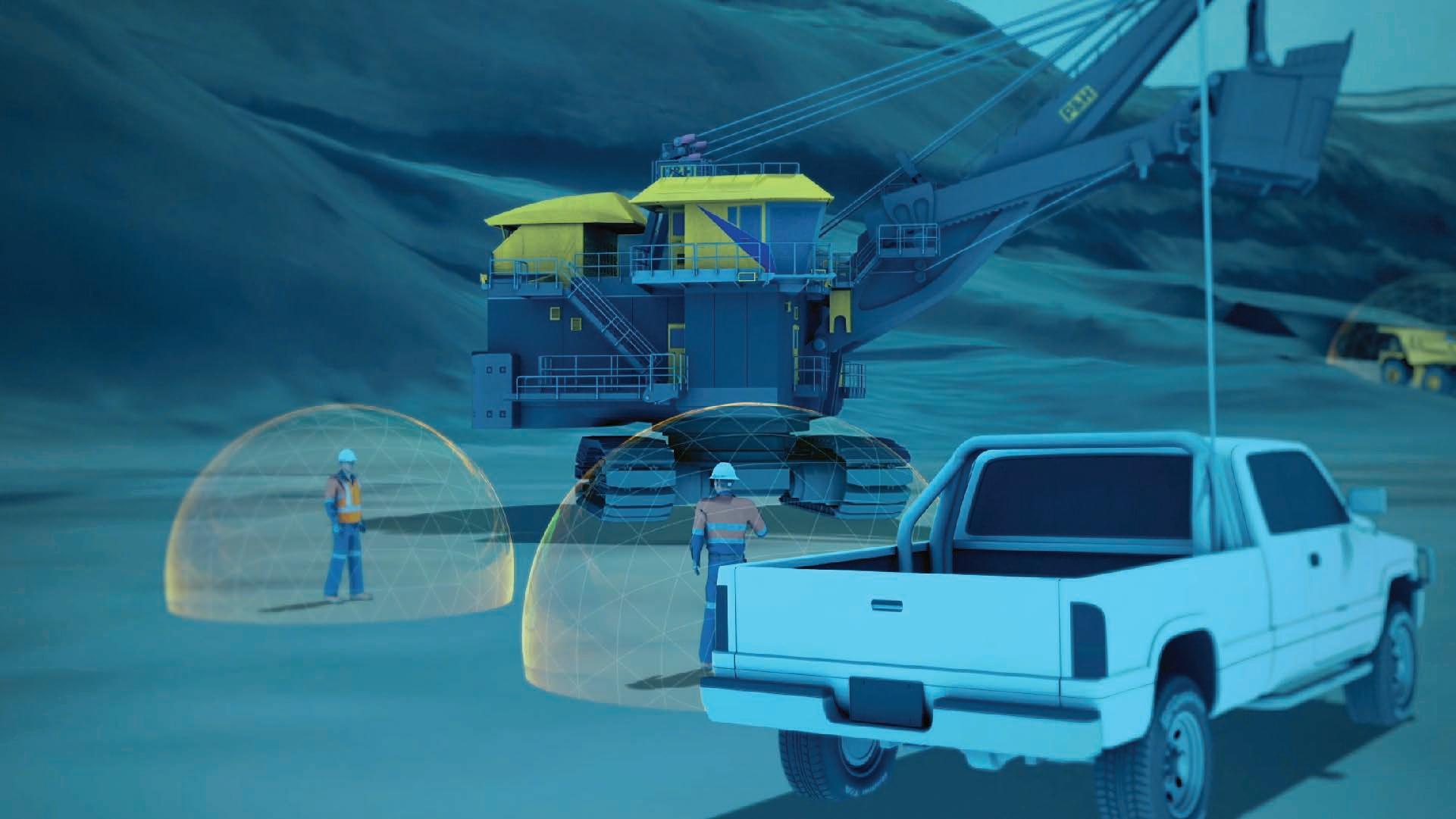
Increased safety and productivity with smart operations
It’s about knowing, not guessing
At the risk of sounding overly negative, the list of things that can go wrong on a mine site is just about endless.
With so much machinery working around the clock above and below the ground, as well as all of the people required to keep those wheels turning, it’s little wonder the resources sector takes safety so seriously. Fortunately, that seriousness pays off and the Australian mining industry has an excellent track record of keeping serious injuries and fatalities to a minimum.
One area, however, might not always get as much of the safety spotlight it should.
Fatigue is an insidious threat, one that can creep into a workplace unnoticed over time.
As most would know, fatigue is a state of cognitive and/or physical exhaustion that reduces a person’s ability to perform their work safely and
JOURNALIST
effectively. It can have some major consequences in cases where a worker is required to manage a high-risk situation.
Kind of like lots of the jobs performed on a mine site.
In this issue of Safe to Work we take a look at a few different areas of fatigue, including its effects on fly-in, fly-out (FIFO) workers and, importantly, employers’ liability of a fatigue-induced accident happens on their watch.
You might be surprised how far a company’s duty of care extends beyond the site itself.
Staying with slightly different areas of mine safety, we examine some issues associated with off-site risk and psychosocial hazards. After all, not all jobs in the mining industry involve hard hats and hi-vis gear and the risks people working off-site face are just as real as anywhere else.
This month’s cover story looks at how Epiroc is deploying sophisticated automated,
teleremote and data-driven solutions to safely remove operators from hazards underground.
Keeping people away from the face is one of the most significant benefits of autonomous mining systems, and Epiroc’s new rig control system (RCS 5) is designed to make that process easier than ever.
Paul Hayes Managing EditorEmail: paul.hayes@primecreative.com.a
ASSISTANT EDITOR
Email: ashley.perry@primecreative.com.au
RESOURCES
THE SAFETY THREAT OF WORKPLACE FATIGUE IS VERY REAL AND MINING COMPANIES CAN BENEFIT FROM BEING AWARE OF THE POTENTIAL RISKS, AS WELL AS THEIR OWN RESPONSIBILITIES.PAUL HAYES FRONT COVER Image: Epiroc
Epiroc is deploying sophisticated automated, teleremote and data-driven solutions to safely remove operators from hazards underground.
The fly-in, fly-out workforce is uniquely susceptible to the effects of tiredness. But workers, in conjunction with employers, can develop control measures to address the potential risks.
compliance with the ongoing rollout of long-haul fibre across the Pilbara and the recent arrival of satellite-powered internet with Starlink.
Bend-tech has long been at the forefront of providing specialist parts, repairs and maintenance solutions to miners operating below the surface.
It can be hard to see past the dozers and draglines, but it’s important to consider the health and wellbeing of the mining industry’s office-based players.
Kal Tire understands that more effective maintenance means less chance of injury.
Workplace fatigue is an insidious threat, and the scope of an employer’s liability in related injuries is broad. But steps can be taken to mitigate risks.
Pitcrew.ai has developed an automated tyre inspection incorporating AI vision processing with Teledyne FLIR thermal imaging technology.
Vocus continues to support ESG
Harnessing the power of integrated data, IMDEX’s BLAST DOG provides miners with the capacity to make the most informed extraction and blasting decisions. 16
• Brand new 793F, 785D, 777F and D10T tanks stocked and ready for delivery!
• Tank refurbishment available for a wider range – includes tank strip and assess, repair and pressure tested, blasted and high performance coating and a full report provided.
• Bend-tech’s Fuel Tank Rotable Program is fully operational with many sites around Australia on-board. The way it works, we send a new fuel tank out to be swapped with your damaged tank, we make the necessary repairs, then send the refurbished tank back to your site ready to be changed in when required.
Recent years have seen a steady increase in the number of fires associated with portable tools powered by lithium-ion and lithium polymer batteries in use across the Australian mining industry. The NSW Resources Regulator has made a series of key safety recommendations in relation to the use, charging and storage of these types of battery-powered tools. As the preferred source of power for portable tools lithium-ion and lithium polymer, batteries are the industry standard. But the high levels of energy the batteries produce significantly increases the risk of a fire or explosion when they are not used according to safety directions. Essentially, the batteries can enter
a state of ‘thermal runaway’ when subjected to over-charging, damage or abuse.
Depending on the state of charge, thermal runaway may lead to a rupture of the battery cells, with the subsequent fire, resulting in the complete destruction of the battery, or the production of a vapour cloud presenting significant risk of either of explosion or of exposure to toxic gases.
Any subsequent fire or explosion may place workers at serious risk of injury and result in potential damage to nearby plant and other materials. The regulator highlights several safety recommendations: only use charging equipment recommended by the manufacturer for that battery;
An uncontrolled bushfire late last year destroyed multiple buildings at the asbestos-littered Wittenoom, the abandoned town in WA’s Pilbara region.
Scheduled for demolishing soon after, the bushfire ripped through the site before crews could start dismantling properties.
The WA Department of Fire and Emergency Services (DFES) said the fire was reported by a nearby mining company on Boxing Day, but a firefighting crew was not sent due to asbestos contamination and because the town was empty.
Wittenoom was built to house workers for the nearby asbestos mines and their families. It is estimated 1200 workers and residents died from exposure to asbestos and the asbestos
tailings remain scattered throughout the region to this day.
The WA Government finalised a drawnout process to acquire the town’s remaining properties and remove the final residents. This process has paved the way for demolition of Wittenoom.
ensure that transporting of spare batteries does not expose them to risk of physical damage or short circuit of the connecting pins; do not expose batteries to water or temperatures greater than 50°C; always follow manufacturers’ safety instructions; have systems in place for managing the use of lithium-ion batteries.
The DFES spokesperson said the asbestos contamination meant an official survey of the damage had not been conducted.
Visitors to the region have been strongly discouraged due to asbestos contamination.
6th Sense is how we utilise collected insights to optimise your technology, value chain and employees -using automation, process and system integration. Give your connected operation an extra sense by enabling it to instantly share critical information, synchronising resources and coordinating a response in real-time. Improved planning capabilities mean less time spent in hazardous environments while improved performance means reduced frequency of changing tools. 6th Sense – Smart. Safe. Seamless.
epiroc.com/en-au
Bulldozer rollovers are a high-risk incident that can lead to catastrophic outcomes. The Queensland Coal Inspectorate has a series of key safety recommendations to avoid these deadly mine site hazards. There have been 10 rollover incidents on Queensland mine sites since December 2021, with another three occurring at surface mines in July, October and November 2022. A further six incidents, similar in nurture, have occurred across nine different surface mines between December 2021 and June 2022. Incidents have included dozers working on rehabilitation tasks, in bulk push operations, during floor clean-up and bench preparation.
Stephen Smith, regional inspector of mines, recommends that site senior executives (SSEs) include regular audits with examination of the effectiveness of supervisors’ hazard identification and risk control skills, the system for recording and correcting equipment defects and the allocation of shift tasks in relation to proficiency. Additionally, shift supervisors should confirm operators have identified all hazards in their workplace, confirm that the proposed risk controls to manage the hazards will indeed control the risk, monitor the effectiveness of the controls during the shift (and take corrective action when deficiencies
A 33-year-old drowned at a manmade lake 53km east of Bunbury, WA.
Formerly Amalgamated Collieries’ defunct Black Diamond Mine, the lake is a popular site for tourists.
The Western Australian Police Force confirmed to the ABC that a Taiwanese national tried to swim from one side of the lake to the other but failed to return safely.
It is reported that the man was at the lake with his partner and friends, entering the water at about 1.30pm for a swim before being noticed missing an hour later.
Police were alerted after the group searched and failed to find him. It took specialist divers 2.5 hours to locate the body after an extensive air, land and water search.
“They were swimming and, unfortunately the gentleman got into some trouble while he was swimming
and never made it [back] to shore,” acting senior sergeant Alan Dean told the ABC.
“It is tragic … it is a terrible time for this type of thing, there is never a good time for it.”
Dean thanked the members of the public who had assisted in the search.
are detected), require that ground implements (blades and rippers) are kept as low as possible during operation, and review stockpiles to confirm that valve locations are easily and readily identifiable for operators.
Black Diamond Lake is located in the vicinity of Allanson, a town on the banks of the Collie River, approximately 8km west of Collie.
It has become a tourist hotspot popular with Instagram users.
‘preventable’WA police were appreciative to those members of the public who offered their help and assistance. Shift supervisors should confirm operators have identified all the hazards in their workplace.
A bus driver suffered fatal injuries after being struck by his own vehicle at a mining camp in Queensland’s Bowen Basin.
A Queensland police spokeswoman told the ABC that early investigations suggested the bus struck the driver about 7.00pm on Friday December 31 at the Bacon Street mining camp in Moranbah, south-west of Mackay. The spokeswoman said no passengers were on board at the time of the incident.
The ABC reported that paramedics were called to the site of the incident at approximately 8.00pm and located the driver in a critical condition. The 62-year-old Brisbane man died at the scene.
WorkSafe WA recently released an information sheet with detailed advice for people with management or control of a workplace where soil is contaminated with asbestos containing material (ACM), as well as those involved in inspecting, removing, managing or disposing of asbestos contaminated soils at workplaces.
For the purposes of the safety advice, a workplace is defined as any location where a business or undertaking carries out work, including any place where a worker goes, or is likely to be. It also includes residential premises when paid work is occurring at that site. The information sheet deals specifically with soils that are contaminated with ACM and does not cover naturally occurring asbestos at a workplace. Asbestos-contaminated soils must
Police, along with Workplace Health and Safety Queensland, are investigating the death, which has been deemed non-suspicious.
The spokeswoman said the forensic crash unit would submit its report to
the coroner when complete. The Courier Mail notes the fatality in the Bowen Basin has “completely devastated and distressed” coworkers, who are reeling from the tragedy.
be inspected by a competent person, such as a consultant, who has acquired through training, qualification or experience, the relevant knowledge to carry out the task. The level of detail required for an
inspection depends on a number of factors, including background knowledge of the site, the likely amount and type of asbestos contamination, and the likely source of the asbestos contamination.
Disaster recovery assistance was made been made available to floodaffected communities in the Kimberley region after ex-tropical Cyclone Ellie crossed into WA on December 28 2022.
The heavy rainfall associated with Ellie caused significant inundation and damage to the region.
The shires of Derby West Kimberley, Broome, Wyndham East Kimberley and Halls Creek became eligible for assistance measures through the jointly funded Commonwealth–State Disaster Recovery Funding Arrangements (DRFA). Assistance measures were made available for individuals and families,
businesses, primary producers, nonprofit organisations and local and state governments.
The funding was allocated to emergency assistance, temporary living expenses, replacement of essential household goods, housing repairs, personal and financial counselling assistance.
Over the new year period significant and widespread rainfall totals of 200–500mm were recorded across the Kimberley.
Major flooding occurred along the Fitzroy River to Fitzroy Crossing, reaching record levels of 15.81m. Major roads and associated infrastructure were significantly
An SA steel fabrication business and two directors were hit with a $200,000 fine following serious injuries to a young worker.
The sentence was handed down in the South Australian Employment Tribunal on December 23. It followed a SafeWork SA investigation that found Port Augusta Steel Centre and the two business owners breached their work health and safety (WHS) duties by failing to provide a safe work environment for their workers.
In September 2020, a 16-year-old apprentice was crushed at work by heavy sheets of steel that fell suddenly from a failed storage rack. Working alongside his supervisor, the young worker was placing a delivery of steel sheets into storage racks when the steel materials in the storage slot moved unexpectedly.
The pressure of this movement caused two retaining posts to snap, with the
steel sheets falling onto him in an uncontrolled manner.
The worker was pinned between the wall of the workshop shed and 30 sheets of steel weighing an estimated 1200kg. The young worker experienced a broken leg and soft tissue injuries.
No risk assessment or hazard identification method was undertaken. There were also no procedures for
damaged and floodwaters isolated towns including Fitzroy Crossing and many other remote indigenous communities along the Fitzroy River. Some local communities chose to relocate to safer areas until the threat passed and a significant amount of community infrastructure, including homes, was impacted by the rain event.
During the event the WA Government worked closely with the Federal Government to fast-track the activation of the DRFAs, providing much needed support for the community.
“First of all, can I say thank you to the community that’s been impacted for their resilience,” Dawson said.
the unloading of steel delivered to the workplace into storage racks. There was no evidence of inspection or maintenance for the rack, and the safe working load of the storage rack was unknown.
In sentencing, Deputy President Judge Lieschke noted that while the worker’s supervisor instructed him on storing the steel sheets, this was not by reference to any set procedure.
The NSW Resources Regulator launched an investigation after a loader working underground fell about 15m through a void.
The loader’s operator was extracting material from a development heading on the 16th level in an underground section of the Potosi mine on November 27 2022, when the machine’s righthand side dropped into a void on the floor of the drive.
The uninjured worker exited the loader and notified their shift supervisor. The area was isolated immediately after the incident so an assessment of the situation could be conducted on the following day shift. However, the void enlarged overnight and the loader fell further
into a previously mined stope underneath.
The regulator is investigating the cause and circumstances of the incident and will explore the mine’s design and approval processes.
Queensland (RSHQ) is investigating a fatal accident resulting from a mine worker falling from the roof of a workshop.
In November 2022, opal miner Ronald Selig, a 66-year-old opal miner and reality television personality suffered fatal injuries when he fell from the roof of a workshop.
Selig appeared in Outback Opal Hunters and was well-known in the community of Opalton, near Winton.
Queensland’s Mineral Mines and Quarries Inspectorate believes the worker accessed the roof of the workshop to make repairs following damage caused by a severe weather event when a structural member failed, causing him to fall approximately 5.8m to the ground.
The inspectorate said several key safety issues were a factor in the incident –working at heights without appropriate fall restraint/arrest personal protective equipment (PPE), and damage to the structural integrity of the workshop. Inspector of mines Brett Holley indicated that senior site executives (SSE) should closely adhere to the following key safety recommendations, including: ensuring persons required to work at heights have adequate knowledge and are appropriately trained and assessed as competent to perform the task safely; ensuring appropriate facilities are provided to minimise the risk of persons falling from heights (ie scaffold, elevated work platforms, fall restraint/arrest PPE); ensuring repairs or modifications to fixed plant structures are performed in accordance with the
It was determined mine operators should ensure all known voids are documented and the process for any designs, including changes, are thoroughly reviewed before plans are approved.
original equipment manufacturers (OEM) design and instructions; and that emergency services are provided with detailed instructions on the location and travel routes to enable the most efficient access to remote mining operations. In addition, all operators should ensure plant and equipment is maintained in a safe state in accordance with the OEM’s instructions.
For WesTrac, Rio Tinto and Caterpillar, this tele-remote dozing system (TDS) at Rio’s iron ore operations in Western Australia is wholly focused on operator safety.
The solution utilises the Cat MineStar Command for Dozing technology and a dedicated operator control centre, allowing for non-line-of-site operation of dozers working in high-risk areas. There is also an over-the-shoulder console that allows operators to work within visual range, typically used for temporary or one-off movements of machines.
The remote operator control centre is similar to a simulator, with all of the in-cab controls replicated. Rio Tinto’s also incorporates a vision kit, making use of four cameras on board each dozer and relaying machine information and visuals in real-time via a Wi-Fi network.
• guardianangelsafety.co
The Atlas Copco HiLight B5+ light tower is suitable for a wide range of applications, including events, residential and road construction, temporary public lighting, and oil and gas requirements.
Designed to offer the widest choice when it comes to finding the light tower that’s right for your application, the HiLight range provides a flexible and dynamic set of lighting options, while addressing all aspects of efficiency. Safety operators can be assured of the robust build quality and compact size for which Atlas Copco is globally recognised.
Atlas Copco has put its innovation stamp on LED technology. The lenses in the LED light towers have a very special optic designed specifically for construction and mining applications.
This innovative, fully directional, LED lens design ensures the light coverage is maximised while a single HiLight tower can cover an area of up to 5.000m2 with a 20 lux (brightness) average – ensuring a brighter, safer, and more productive site.
To find out more, contact an Atlas CEA branch.
• atlascea.com.au
A&I Coatings, an Australian-owned industrial coatings manufacturing company, has developed a complete system that helps to reduce workplace exposure to harmful chemicals and increase efficiency in the spray booth.
A&I Coatings Vitrephos 560 Primer and Vitrethane 650 topcoat is designed to speed up throughput times during application. The V560 Primer and V650 topcoat system has strong wet-on-wet properties, with easy sanding and exceptional drying properties, especially in cold weather, and good film build which has seen a reduction of workhours required to complete works. The V650 topcoat can also help reduce labour hours due to its high coverage, and presents excellent gloss retention to finish, also a cost-effective option. Added to this are the safety features this system offers, with zero exposure to harmful isocyanate chemicals.
Exposure to isocyanates is known to cause both respiratory illness and skin irritation, such as allergic contact dermatitis.
• aicoatings.com.au
Crusader Hose has developed an innovative hose reeling system to manage largediameter flexible layflat hose.
The Bayswater Mobile Hose Crate 1600 reeling system is ready to assist in handling temporary, flexible pipelines, making it ideal for progressive mining companies eager to embrace the many benefits of layflat hose technology. Fabricated for the rapid deployment and retrieval of layflat hose, this reeling system has two off 1600mm diameter reels mounted within a crate, with each independent reel able to handle up to 100m of 8-inch hose and accommodates 200m capacity per crate.
The power pack-equipped trailer-mounted designed Bayswater 1600 has quickconnect couplers and free-spool capability.
Crusader Hose has been manufacturing layflat hose for over 36 years and, in consultation with industry, knows reliable reeling systems reduce the required workforce and assist in supporting occupational health and safety obligations. • crusaderhose.com.au
Epiroc is leading the charge towards sustainable mining with the Boltec M, a fully mechanised bolting rig with battery driveline.
Capable of handling most bolt types between 1.5–3.5m, including friction, inflatable, mechanically anchored and rebar bolts, the Boltec M is among the most advanced and productive fully mechanised rock bolting machine in its size class.
The optimised bolting unit with reduced feed length enables reduced drive sizes while retaining the same bolt lengths used previously.
The Boltec M series machines share a common four-wheel drive articulated carrier design with their Simba mining and exploration (M&E) and Boomer M&E stablemates, which ensures easy maintenance due to an open service architecture.
The standard and optional features of the Boltec M ensures operator safety, comfort and guarantees a job well done, while the battery driveline reduces the environmental footprint and creates a healthier work environment.
• epiroc.com/en-au
Bollé Tryon glasses are available in three versions: safety spectacles; OTG; and prescription. The glasses are ultra-wrap-around with a sporty design and are non-slip, providing a safer experience.
Like many Bollé products, the Tryon range is available in clear, smoke, copper, cobalt flash and polarised lenses, making them suited to use throughout a range of industries.
The cobalt flash lenses are suitable to use outdoors and indoors, as they protect the wearer from heat, while the copper lenses are ideal for activities that require exposure to alternating high and low light. Like all of Bollé’s products, the Tryon range combines style, innovation and protection to provide the wearer with the maximum comfort and safety.
• bolle-safety.com/au/industrial/glasses/safetyglasses/tryon-TRYON_INDUSTRIAL.html
One of the most significant benefits of autonomous mining systems is the ability to remove underground mine workers from hazardous areas, especially at the face.
Connectivity and mining automation also increases productivity and profitability
Epiroc, among the global leaders in automation, digitalisation and electrification in the mining and construction industries, provides solutions that enable the integration of smart connected machines, programmed to complete tasks such as precise drilling sequencing.
Machine sensors will alert the control room if there is an obstacle or the intervention of an operator is required. Without the normal constraints of staff schedules, this allows for extended machine uptime, reducing the wear and tear associated
with a manual operation.
Epiroc’s Rig Control System (RCS 5) makes full automation easier, ensuring increased machine uptime.
“RCS is our proprietary product and is the basis for automation across our drill rig equipment, our trucks and our scoops,” Epiroc global portfolio manager – face drilling Niklas Berggren told Safe to Work
“It’s very difficult to automate a hydraulic system but we’ve managed to achieve it through our development of a smart software solution.
“Our RCS is unlocking a whole new approach to eliminating the inherent hazards associated with live work in underground mining operations.
“By removing the many manual steps associated with working at the face, by employing our automation solutions, we can create new operational processes that are done in a safer manner. For instance, by enabling
greater drilling precision with enhanced navigation options, we can eliminate worker exposure to drilling at the face.”
RCS 5 provides several safety and interlock features, as well as a foundation to add new automation features or options without a major rebuild of the machine.
Safe productivity is ensured thanks to outstanding operator assistance features. With features like teleremote drilling, auto-level and set-up assist, RCS 5 unlocks and strengthens productivity and safety for operators.
“Thanks to teleremote drilling, the operator can drill a full face from a control room,” Berggren said. “Naturally, this is a safer workplace.
“In addition, when combined with Epiroc’s highperformance development
EPIROC IS DEPLOYING SOPHISTICATED AUTOMATED, TELEREMOTE AND DATA-DRIVEN SOLUTIONS TO SAFELY REMOVE OPERATORS FROM HAZARDS UNDERGROUND.
method and digital drill plans, customers can reach up to 25 per cent increased productivity.”
RCS 5 enables machines such as Epiroc’s Boomer M20, a highperforming, robust and reliable jumbo drill rig built for blasthole drilling in underground mining and tunnelling, to be remotely operated with a control panel that monitors local sensors and cameras.
The automation-ready carrier of the Boomer M20 is an ideal platform to enable mining operations to reach future automation goals.
To increase productivity, efficiency, reliability and precision even further, the Boomer M20 drill rig has smart automation options available, such as the ability to enable automated drilling according to digital plans.
“Significant efficiency gains can occur with the use of RCS, including time depth monitoring, which allows the operator to monitor what’s happening in the hole,” Berggren said.
“The jumbo’s operator can be located away from hazardous areas, situated in the safety and comfort of a control room. The operator can
also create and edit drill plans either on-board the jumbo or from a remote location, and accurate shift reporting can be completed as all the key parameters are closely tracked.”
Additional add-on features to the RCS 5 include machine-to-machine communication with machines operating on the same pattern able to share real-time updates of the progress each drill is making.
Epiroc continues the charge towards electrification in underground mining and the Boomer M20 comes with a battery-electric driveline option.
A battery-powered Boomer M20 brings additional savings on health, maintenance, ventilation and cooling. This level of safety is emblematic
of the great benefits gained from autonomous mining systems managing advanced drill rig technology.
Digitalisation calls for a new way of working and the role of data sits at the heart of an efficient mining operation.
Epiroc’s customers need people, processes and technology to synchronise, and the company calls this 6th Sense.
6th Sense is Epiroc’s way to optimise its customers’ value chain through automation, system integration and information management – enabling a smart, safe and seamless operation. This powerful platform is designed to collect, transfer, store, visualise and analyse the data, transforming it into useful
“Epiroc enables significant productivity and efficiency gains by providing a high-performance and integrated solution.”Operational data can be fed back to a central control room.
information for data-based decisionmaking.
Epiroc offers a variety of mining management software options to collect and analyse operational data within the 6th Sense product family, including My Epiroc, telematics, analytics, rig remote access and Underground Manager 2.0.
For example, the company offers a telematics solution that gathers, compares and shares equipment data to help you target improvement areas.
Epiroc’s real-time situational awareness software tracks everything from equipment to employees, whether users are locating the nearest pump to refuel a machine or verifying that all personnel have reached a designated safety area in an emergency.
Automated and teleremotely controlled operations can significantly increase productivity
and improve safety at the same time. They can also increase consistency of daily operations yet provide predictive results.
The 6th Sense Control product family combines different features, functions and packages that allow for improved processes and machine control in safe, consistent and reliable manner.
This product family includes Scooptram radio remote control, Scooptram automation single and multi-machine, a collision-avoidance interface, advanced boom control, boomer remote observation and a navigation and drill tracker.
The Scooptram ST14 is a 14-tonne underground loader designed for rugged performance in mid-sized operations, with the new lower-profile boom system offering what is said to be the best operator visibility in its class.
The Scooptram ST14 rig’s intelligent control system features numerous smart functions that increase safety and productivity, while operators can enjoy the new spacious cabin featuring Epiroc’s signature footbox feature.
Epiroc is ideally placed to maximise machine uptime with a scalable implementation plan.
Working together with customers, Epiroc can create a step-by-step plan, tailored for an automated mining solution and information management system that is based on specific situations and optimisation targets.
“Epiroc enables significant productivity and efficiency gains by providing a high performance and integrated solution, deploying smart, safe and connected products, underpinned by deep product and operational knowledge,” Berggren said.
The underground parts team at Bend-tech is made up of equipment experts who remain solely focused on ensuring a site’s machine downtime is kept to an absolute minimum.
It can be argued that underground mine safety does not attract the attention it should, particularly when it comes to maintenance on heavy mobile equipment.
Bend-tech is a leading end-to-end provider when it comes to certified safe solutions for the mining industry.
“We are specialists in designing, engineering and manufacturing access platforms, either made out of steel or aluminium, as well as producing storage benches and
containers, trestles, workbenches, work stands, equipment racking and workshop solutions,” Bend-tech marketing manager Rhys Werndly told Safe to Work
“We also have an extensive range of machine parts, including original equipment manufacturer (OEM) replacement parts for both surface and underground mining equipment, along with the capacity to undertake heavy structural engineering projects.”
Many machines operating underground require routine inspection, repair and maintenance at a height of around 3m, significantly lower than surface mining equipment, which can lead to a different tolerance for risk.
For example, the likelihood of catastrophic injury from a 3m fall may be relatively small, but it remains a height that could result in a worker receiving significant injuries and being forced to take time away from work.
It therefore remains critical that underground mobile equipment is fitted with robust and reliable safety handrails.
“We have the capacity to manufacture specialist access platforms and handrail solutions on various types of underground mobile equipment,” Werndly said.
“We are a leading supplier of handrails that suit a wide range of loaders and haul trucks, and they are designed to ensure fall protection as
well as enhanced safety for technicians completing routine maintenance or unplanned repairs.
“For instance, we have designed a handrail solution for the Epiroc, Sandvik and Caterpillar mobile equipment range.
“Our handrail solutions are robust and reliable and can withstand the harshest underground mining environments, and the OEM replacement handrails can be folded-up during scheduled downtime, ensuring handrail integrity and avoiding accidental damage and corrosion.”
Other OEM replacement parts include fenders, guards, travel motor covers, and much more.
The rigorous nature of underground mining means machine components are exposed to the risk of extensive damage. And when that occurs, it inevitably leads to costly repairs and maintenance.
There are also the flow-on costs associated with machine downtime and lost production, potentially resulting in significant loss in revenue.
“We are incredibly focused on making repairs and maintenance more efficient,” Werndly said. “And in order to achieve this outcome for our customers, we strive to eliminate machine downtime.”
All of Bend-tech’s products are fully certified and the Perth-based business prides itself on working closely with its mining customers.
“Often a tailored solution for a customer becomes a standard product,” Werndly said. “We have a dedicated research and development department with a team of mechanical engineers dedicated to innovation in terms of designing and manufacturing new equipment solutions for our customers and critically thinking about the way we innovate.
“We are always endeavouring to streamline our processes, including our design and manufacturing, so as to drive shorter lead times, lower costs and pass these benefits on to our customers.”
Bend-tech’s approach also accounts for the critical importance of safety.
“If the underground mining workforce feels safe and if, for example, we can where possible eliminate manual handling, then they’re going to be able to operate more efficiently. It’s that simple,” Werndly said.
Bend-tech’s underground parts team is constantly on-site and discussing equipment requirements with customers.
“Everything that we engineer at Bend-tech is fully certified to Australian standards, in some instances exceeding the Australian standard, containing certification plate and certification number,” Werndly said.
In essence, what sets Bend-tech apart within the market is that the company does it all.
“It’s all handled by us, and the customer can say, ‘Here, sort this problem out for us’, which is something we love doing. And that’s the reason we’ve got such loyal customers.
“Importantly, this approach also means we have a range of IP (intellectual property) that we can sell again and again.
“So the thing that sets us apart is that end-to-end solution. That’s the key advantage against our competitors that offer similar solutions.”
Through constant innovation, collaboration and a deep understanding of its customers, Bendtech can deliver a quality experience.
“We want to make sure our customers and potential customers are using equipment that is going to make sure they get home at the end of the day, especially when you’re talking about lifting and handling large equipment,” Werndly said.
“Inadvertent things can happen to underground mining equipment, but with control measures in place, safety and reduced downtime can be achieved to prevent serious injury and lost time.”
“Our handrail solutions are robust and reliable and can withstand the harshest underground mining environments.”Bend-tech is a specialist in designing, engineering and manufacturing access platforms.
There is an ongoing commitment to improve safety across the mining industry, especially when it comes to protecting workers maintaining heavy equipment.
Personal protective equipment (PPE) gives the worker a degree of safety, while administrative controls such as legislative requirements are implemented by companies in order to change the way people work. But the potential for injury remains.
The most effective way to improve safety in the workplace is to physically remove the hazard or, alternatively, undertake regular and effective maintenance.
Kal Tire Australia managing director Miles Rigney said his company uses a guideline called the “hierarchy of controls” as a means to identify the best way to keep its team members and customers safe.
“Controlling exposures to occupational hazards is a fundamental method of protecting workers,” Rigney said.
“Traditionally, hierarchy of controls has been used as a means of determining how to implement feasible and effective solutions to control hazards and their associated risks in the workplace.”
Eliminating the hazard and risk is the highest level of control in the hierarchy, followed by reducing the risk through substitution, isolation and engineering controls, before finally reducing the risk through the use of PPE, which represents the lowest level of control.
According to Rigney, Kal Tire uses the hierarchy of controls to ensure a continuous improvement in safety for its team members, especially when removing wheel assemblies from heavy mobile equipment, either during planned or unplanned maintenance.
Clear safe work procedures are followed throughout this high-risk maintenance process.
For example, installing and removing a tyre and wheel assembly begins with placing the tyre handler into the correct position, followed by the
operator shutting down the handler and exiting the machine. Only then can the technician enter the risk zone between the tyre handler and the actual tyre and wheel assembly to complete the removal.
Inspections are also an important and common task that can help improve safety on a mine site.
Current industry methods for detecting off-the-road (OTR) tyre damage involve routine manual inspection. This remains inherently hazardous, often revolving around a weekly schedule, and can involve machine downtime that results in production losses.
Manual inspection has significant limitations, including the potential for tyre damage to be missed. This has led mine operators to embrace autonomous inspection and monitoring technologies.
To help reduce the risk to technicians during manual inspections and improve productivity, Kal Tire joined forces with technology specialists Pitcrew.ai in 2021 to create a new automated solution for the detection of hot tyres, tyre separations and other tyre and mechanical damage on mine site machinery.
This smart technology has been deployed at Antofagasta Minerals’ Centinela mine operation in Chile, where an average of 200 hundred tyres are checked per week by a thermal imaging camera that, installed in one of the pit circuits, monitors the condition of these vital components.
As autonomous tyre inspection stations monitor front and rear tyres of passing mining trucks, the artificial
intelligence (AI) software scans the thermal imagery for anomalies or defects such as hot spots, and belt edge and tread separations.
The findings are then reported to Kal Tire’s proprietary TOMS (Tire and Operations Management System) before it automates inspection work orders, scheduling any necessary tyre change work based on the severity of the damage.
TOMS helps customers achieve efficiency targets for fleet use, tyre life and safety.
This information provides fleet planning teams with a 360° view of tyre maintenance activity with near-realtime 24–7 reporting and improves the mean time between service (MTBS) with automated, priority-based orders.
Thermographic inspection at the mine has produced strong results, not only because working remotely means it eliminates risk when people are directly monitoring the tyre, but also because it has managed to reduce downtime and had a positive impact on production.
“Tyres have a lot of contained pneumatic energy, and with this we are removing the operator from that
source of damage and danger, which is already a giant opportunity,” Centinela mine services superintendent Rodrigo Jorquera said.
“In addition, with this thermal imaging technology we have the capacity to monitor over 200 tyres per week. If we did not have it, each tyre would need a stoppage of more than 30 minutes for inspection, but now that it is monitored remotely, the truck does not stop and we save significant time.”
The thermographic camera relies on AI to categorise the damage that the tyre may have at different levels, depending on the temperature, automating and optimising work orders.
“Of the 200 weekly pieces of equipment that are inspected, an average of 10 per cent present different degrees of damage, according to what is monitored with this camera,” Centinela business administrator José López said.
“But of that 10 per cent, only five per cent show significant damage and must go to the checkpoint, which is the place where we physically inspect this equipment.
“With this we eliminate the stoppage time, therefore this monitoring station and this technology have allowed us to improve operational continuity and, in addition, our availability KPIs.”
Kal Tire’s Mining Tire Group senior vice president Dan Allan believes this technology allow miners to work smarter.
“Tire pressure monitoring systems (TPMS) can give a strong picture of what’s happening inside the tyre, but so much of what can indicate the potential for tyre failure happens outside the tyre,” Allan said.
“Pitcrew.ai’s artificial intelligence, and their vision for the technology, supports our goal of solving customer challenges in practical, impactful ways.”
Kal Tire’s ongoing use of Pitcrew.ai’s OTR tyre-detection system leads directly to carbon emission savings, which helps to meet environmental, social and governance (ESG) goals.
“Kal Tire is operating in a way that puts ESG at the forefront, which is very much a priority for our customers in Australia,” Allan said.
“So we’re proud to offer solutions that enhance safety, sustainability and productivity.”
WORKPLACE FATIGUE IS AN INSIDIOUS THREAT, AND THE SCOPE OF AN EMPLOYER’S LIABILITY IN RELATED INJURIES IS BROAD. BUT STEPS CAN BE TAKEN TO MITIGATE RISKS.
Fatigue is no doubt a potential issue in the resources sector, as it is in so many other industries. But the news is not all bad.
There are options available to employers to manage the risks of fatigue in the workplace to satisfy their duty of care and, most importantly, keep people safe at work.
Simply put, fatigue is a state of cognitive and/or physical
exhaustion that reduces a person’s ability to perform their work safely and effectively.
This can have serious consequences for employer and employee alike, particularly in cases where a worker is required to manage a high-risk situation.
Indeed, a 2007 study published by Caterpillar Global Mining showed that roughly 65 per cent of truck haulage accidents in mining operations are directly related to operator fatigue.
The national policy body Safe Work has identified shift workers and
people who undertake fly-in, fly-out (FIFO) and drive-in, drive-out (DIDO) work – all of which is very common in mining – as among the most at risk of workplace fatigue.
Some common contributing factors to fatigue include poor quantity or quality of sleep, shift work, long working hours, extended exposure to hazards (such as noise, vibrations, contaminants and loud noises), physically or mentally demanding work tasks, and lack of proper fatiguemanagement training.
Beyond the mental and physical toll fatigue can take on an employee, the consequences can also have tangible effects on an employer.
This was exactly what happened in a 2016 case against BM Alliance Coal Operations. The Supreme Court of Queensland ruled that the employer, host employer, and mine operator were jointly liable for $1.2 million after a worker was seriously injured in an incident brought on by fatigue.
As it happens, the accident did not occur at the work site but rather on the employee’s drive home after completing the last of four consecutive night shifts, each for 12 hours.
The decision to award damages to the plaintiff was made despite the fact there was no contractual provision connecting the plaintiff’s employment with travel to and from work.
The court nevertheless maintained that the employer’s duty of care extended to the accident on several grounds, most notably that
the employers created the risk by requiring the employee to work consecutive 12-hour night shifts, causing inevitable fatigue.
More recently, a 2022 NSW case against Coalroc similarly dealt with a DIDO mining employee who was injured in a car crash on his commute from work. The plaintiff had just completed the last of three 12-hour shifts.
Like the previous case, the court found that the “work-induced fatigue occasioned by the nature and conditions of the plaintiff’s employment with the company” significantly contributed to his accident. The employer was ordered to pay over $1.1 million in damages.
There are two notable takeaways from these cases.
Firstly, in the Coalroc case the employer had a fatigue-management procedure in place, which the court noted was a “crucial document” as it demonstrated recognition of the
risk of severe fatigue-related injury. Critically, it was the company’s failure to ensure employee compliance with this procedure that contributed to it being found liable.
To be specific, the court found that although the employee failed to submit a personal travel-management plan – as required by the company’s fatigue-management procedure – it was ultimately the employer’s failure to enforce the completion of the document that partly led to it being found liable. Had the travelmanagement plan been submitted, the risk of fatigue should have been identified and the accident avoided, according to the court.
Secondly, in both cases an employer’s duty of care was determined to extend beyond the time and place of the work site.
This means the scope of liability in relation to fatigue is considerably broad, calling for a significantly thorough fatigue-management plan.
Safe Work suggests that the process begins with education and awareness.
It is important for managers, supervisors and employees to know the signs and symptoms of fatigue which, according to Safe Work, includes excessive yawning, short-term memory problems, inability to concentrate, impaired decision-making, reduced hand–eye coordination, and increased rates of unplanned absences.
Safe Work and the Commission for Occupation Safety and Health provide checklists for fatigue risk assessment.
Safe Work recommends that mining employers should initiate a review of their fatigue-management strategies to ensure they comply with relevant legislation as well as developments to common law.
An effective fatigue management policy may implement measures such as consulting with workers, examining
work practices (ie employees having choice over hours, discouraging a culture of extended hours), examining sign-out sheets to identify excessive hours, consulting with experts, and reviewing incident data.
An effective policy may cover the roles and responsibilities of managers, supervisors, and employees in regard to identifying and managing fatigue, maximum shift-length – including consideration of a healthy sleep schedule – work-related travel, control measures for high-risk tasks, selfassessment checklists for employees, and procedures for reporting fatigue, as well as practices in place for managing employees too fatigued to continue working safely.
As far as the courts are concerned regarding discharging the duty of care of an employer, measures should be taken to adequately educate workers of the risks and injuries associated with their work, as well as those faced by long-distance commuters.
In the 2016 BM Alliance case, the court further suggested providing rest areas as well as transport facilities to and from the site, an
There are several organisations throughout Australia that provide information on fatigue risk assessment and management:
• SafeWork SA (under ‘health and wellbeing’)
• National Heavy Vehicle Regulator (under ‘safety, accreditation and compliance’
• Safe Work Australia (under ‘hazards’)
• Government of WA Department of Mines, Industry Regulation and Safety (under ‘health and safety topics’)
• Better Health Channel Victoria (under ‘sleep’)
implementation that it ultimately ruled would not have been unreasonable for the employer to have introduced.
Examples of effective fatiguemanagement strategies already in place within the mining industry, such as BHP’s fatigue management tip sheet, can be found throughout the sector.
The BHP policy suggests a review of any workplace practices that may increase the risk of fatigue, the review of roster design and operational requirements, the review and minimisation of practices that lead to extended hours or encroach upon sleep time, and even the implementation of biomathematical modelling of fatigue likelihood.
Looking somewhat more left of field, but still relevant to the greater goal of eliminating workplace incidents brought on by fatigue, Rio Tinto uses robots and automation to shoulder some of the most highrisk work.
The scope of liability for an employer’s duty of care regarding fatigue-related incidents is relatively broad. Precedent shows that the existence of a fatigue-management policy alone is not sufficient to discharge liability.
But digging through the rubble of past mistakes, there is a way forward.
Recommendations handed down by Safe Work, as well as the rulings of the courts, highlight three main aspects of a holistic fatiguemanagement strategy:
• A comprehensive policy for fatigue-related risk-assessment and management, such as those proposed by Safe Work and the courts
• Such a policy must be properly explained to employees through adequate training, with appropriate channels available for reporting potential risks before they occur
• It is up to the employer to ensure an employee complies with the policy by following up on essential documentation such as travelmanagement plans With a certain level of foresight and effort, the mining industry can continue to evolve the way it deals with workplace fatigue to help ensure everyone can get home happy and healthy.
Tiredness and fatigue can be caused by many factors, and the those hazards are frequently inter-related and, in some cases, cumulative.
Several factors combine often to increase fatigue to the point where a person may put their own – or another person’s – safety at risk.
This applies to people throughout the workforce, and employers and employees alike have a role to play in making sure any associated risks are minimised.
Perhaps unsurprisingly, evidence suggests sleep deprivation, sleep disturbance and fatigue are health risks commonly associated with working long hours.
Fatigue has been identified as a potential health risk with jobs that involve shifts or regular or periodic night work. It can lead to impaired physical and mental performance, thus increasing the risk of injury.
Fly-in, fly-out (FIFO) shift workers are a significant group of mining employees who have been identified by researchers at Western Australia’s Edith Cowan University (ECU) as missing out on valuable sleep due to a combination of factors, including roster design, individual lifestyle behaviours and even sleep disorders.
The ECU researchers conducted a study by monitoring the sleeping habits of 75 FIFO shift workers in Australia.
Over a three-week-period, study participants wore a validated sleep and activity tracking device across a “two and one” work rotation, comprising of seven-day shifts, followed by seven-night shifts and then a week off.
Participants were asked additional questions relating to their sleep and lifestyle behaviours.
The research found day shifts starting before 6.00am and requiring a wake-up time of 4.00am were reducing the opportunity to sleep and resulted in significant sleep loss prior to the shift.
Sleep duration was 77 minutes shorter following each night shift and 30 minutes shorter after day shifts, which resulted in a significant accumulated sleep debt before returning home for a sevenday rest period.
Research supervisor Dr Ian Dunican suggested such sleep loss may result in poor alertness and fatigue during a shift, or as the number of shifts accumulates over the roster cycle of 14 consecutive shifts.
“The nature of the roster means people are typically working shifts in excess of 12 hours, plus travel, time for eating, exercise and downtime,” Dunican said.
“When all these activities are combined it leaves little opportunity to get eight hours of sleep.
“The reality is many workers are getting less than seven hours of sleep per night.”
Other key aspects of the research indicated that 60 per cent of the participants were at risk of developing sleep disorders such as obstructive sleep apnoea and shift work disorder. These are disorders that may lead to further sleep loss if not treated and represent a significant hazard to the indicial workers exhibiting these health issues.
Significantly, Dunican’s research is the first of its kind to determine the risk of the potential prevalence of sleep disorders in Australian miners. The research also points towards other unhealthy lifestyle factors of
THE FLY-IN, FLY-OUT WORKFORCE IS UNIQUELY SUSCEPTIBLE TO THE EFFECTS OF TIREDNESS. BUT WORKERS, IN CONJUNCTION WITH EMPLOYERS, CAN DEVELOP CONTROL MEASURES TO ADDRESS THE POTENTIAL RISKS.
concern, including high levels of obesity (23 per cent) and hazardous alcohol consumption (36 per cent) in the study’s sample group.
A problematic combination of poor roster design combined with undiagnosed sleep disorders, hazardous alcohol consumption and obesity may be contributing to poor sleep patterns.
“Limited downtime and struggles with falling asleep may also be influencing alcohol consumption,” Dunican said.
“People may be turning to alcohol to help them get to sleep, but it’s actually having a damaging effect on the quality of their sleep and their overall health.”
The nature of the mining industry makes shift work especially common. Resources companies need to run their operations continuously, 24 hours a day, 365 days a year.
However, Dunican said it was concerning to find such high proportions of FIFO workers experiencing acute sleep loss and reduced alertness during a shift, particularly given the oftenhazardous nature of their work.
“This creates a largely preventable health and safety risk,” Dunican said, “Even small changes to shift start and finish times can significantly decrease risk, improve sleep
opportunities whilst not affecting production.”
The potential to consider travel times for the FIFO workforce, as well as the downtime transition periods in rostering, may lead to better sleep patterns and more restful sleep.
For Dunican, a combination of good sleep practices and healthy lifestyles, along with screening for sleep disorders and appropriate treatment programs, is required to underpin the sleep health of shift workers within the mining industry.
“It’s imperative we look for ways to improve the design of shifts and rosters and ensure workers are supported to have enough quality sleep and have access to help if they need it,” Dunican said.
The ECU research also recommended providing workers with risk-activity monitors to help measure their own sleep, as well as providing education around fatigue management.
In an era when resources companies are going to great lengths to create smarter and more sustainable mining practices, these types of technological interventions may greatly assist in reducing the health issues surrounding fatigue, poor sleep and sleep disorders experienced by members of the FIFO workforce.
It’s safe to say that when most people think of a mining operation, they see towering machinery and plummeting pits, where men and women toil beneath the ground on work sites far from the comforts of home.
And they’d be right to think as much – mostly.
There are so many more people at work beyond the mine sites themselves, operating behind the scenes to keep the gargantuan ship of industry afloat.
These people are the administrative and clerical workers of the mining industry.
In a report written by Stenning & Associates on the Tasmanian mining industry workforce in 2016, it was shown that nearly five per cent of people employed in the state’s
resources sector were administrative and clerical workers.
Quantifying this figure nationwide, that equates to thousands of people hard at work away from the front lines of the mining industry.
The Australian Government, in its labour market insights, lists several such jobs. These include occupational health and safety adviser, human research manager, human resource adviser, conservation officer, environmental research scientist, company secretary, and contract administrator, to name just a few.
While it can be hard to see past the dozers and draglines, it’s important to consider the health and wellbeing of the industry’s hidden players. They don’t wear hard hats or hi-vis gear, and they likely spend
most of their day behind a desk, but the risks they face are real.
While on-site miners undergo rigorous safety and operational training to help minimise the risks they might face at work, the dangers for administrative and clerical workers are much easier to miss.
To this end, SafeWork SA recently published information on hidden office hazards and how to manage them, detailing a few physical and psychological threats that workers may face in the office.
SafeWork SA makes the point that full-time office workers spend a lot of time sitting down.
Sitting for long periods of time is bad for the body and can lead to physical pain and discomfort.
IT CAN BE HARD TO SEE PAST THE DOZERS AND DRAGLINES, BUT IT’S IMPORTANT TO CONSIDER THE HEALTH AND WELLBEING OF THE MINING INDUSTRY’S OFFICE-BASED PLAYERS.A near-constant stream of information can lead to overload.
Long periods of inactivity such as sitting behind a desk can also contribute to cardiovascular disease, musculoskeletal disorders and weight gain – which may in turn affect an individual’s mental health.
The issue is further compounded by slouching. It may sound somewhat innocuous, but slouching can cause injury and lead to a decline in physical capability, and often has long-term effects on the body.
In order to combat the risks associated with sitting down, SafeWork SA recommends a variety of solutions.
Firstly, a sit–stand–walk routine every half an hour. The routine consists of sitting for 20 minutes, standing for eight, and walking for two.
Secondly, regular stretching at the desk in order to circulate blood flow, which prevents stiffness and reduces the risk of injury.
Thirdly, incorporating an ergonomically designed workstation to reduce the risks of injury from strains and sedentary work.
According to SafeWork SA, modern humans receive five times as much information per day than their counterparts from 30 years ago.
As a consequence, it is easy for office workers – who sometimes sit in front of multiple monitors – to
experience information overload.
Information overload is the feeling of being overwhelmed by the amount of data for the brain to process.
The seemingly never-ending emails,- updates, reminders and requests form a constant stream of information, which can lead to anxiety, mental fatigue and even panic.
In order to combat the feeling of being overwhelmed at work, SafeWork SA recommends workers:
• step away from the screen for a short period of time
• clear their head with a walk or
some physical activity
• turn notifications off
• be selective and prioritise workload.
Extended periods of sitting, coupled with complex mental work, can often lead to high levels of stress. The issue is often compounded by a lack of physical exercise because there is no release for built-up stress.
Prolonged stress can lead to burnout, which not only affects work performance but can also have serious consequences on a person’s health. Some of the adverse effects might include headaches, insomnia, anxiety and depression.
SafeWork SA provides a list of tips to manage work-related stress, including:
• taking a 10-minute break from the desk when stress builds up
• practicing meditation or breathing exercise for a few minutes
“There are so many people at work beyond the mine sites themselves, operating ... to keep the gargantuan ship of industry afloat.”Regular stretching at the desk helps circulate blood flow, which reduces the risk of injury.
• contemplating the source of the stress and trying to identify whether that stress is necessary or just perceived
• weighing up the salary and responsibilities of the job against the stress the job is causing.
Employers should consider implementing processes for identifying and reducing workplace stress. Such practices might include one-on-one conversations and reviewing past incidents of work-related stress to identify troublesome patterns.
Nutrition is primarily an individual responsibility, but there are certain workplace practices and norms that can enable unhealthy habits.
Many offices have kitchens in some form of another, leading to regular snacking throughout the
day. This is potentially problematic where the available food is unhealthy. Caffeine is also a staple of office culture, but consumption can cause restlessness, headaches, and heart palpitations.
Better Health Victoria points out that, similar to any drug, it is possible to develop a tolerance to caffeine, meaning bigger doses are needed to achieve the same effect. Long-term caffeine effects include nervousness, insomnia, dehydration, stomach irritation and fatigue.
As SafeWork SA notes, poor nutrition, and unhealthy food and drinking habits can affect a person’s ability to perform their job. Furthermore, when coupled with sedentary work, such habits can lead to long-term chronic disease.
SafeWork SA makes a number of recommendations to minimise such habits in the office, including:
• eating a healthy breakfast to reduce hunger throughout the day
• swapping out high-sugar or highcalorie items for healthy foods, such as fruit, unsalted nuts, Greek yoghurt, etc
• planning meals ahead of time rather than buying fast food throughout the day
• limiting caffeine intake to a healthy level, and abstaining after lunch
• talking to colleagues and management about implementing a healthy eating nutrition program. Clearly, the risks faced by clerical and administrative workers in the mining industry are many. By identifying those risks and incorporating healthy workplace practices, employers can reduce the risks of physical and psychological hazards to their behind the-scenes workers.
PITCREW.AI HAS DEVELOPED AN AUTOMATED TYRE INSPECTION SOLUTION INCORPORATING ARTIFICIAL INTELLIGENCE VISION PROCESSING WITH TELEDYNE FLIR THERMAL IMAGING TECHNOLOGY.
The rapid expansion of autonomous haulage system (AHS) fleets by Tier 1 mining companies in recent years has produced significant implications for the management of critical machine components, including off-theroad (OTR) tyres.
Given autonomous ultra-class haul trucks are the workhorses of modern mine sites, monitoring OTR tyre damage has become a vitally important operational requirement.
With immense payload capacities, ultra-class haul trucks are fitted with very large – and very expensive – tyres required to move at faster speeds and for longer periods than ever before. Continuous mining operations increase the stress on OTR tyres, leading to unplanned repairs and maintenance as a result of events such as heat and beltedge separation.
Detecting tyre damage has traditionally included visual inspections conducted at regular intervals, such as shift changes, or when operators smell burning rubber.
These types of manual inspections often require additional controls be placed on haul truck operators or technicians, leading to extended machine downtime and resulting in the potential for inspection frequency to be dramatically reduced.
The ever-expanding deployment of AHS fleets reduces the likelihood of early detection of tyre damage detection due to less frequent inspections occurring, resulting in several recent instances of major tyre fires and substantial damage occurring to autonomous haul trucks.
“Manual tyre inspections are labour intensive and require machine downtime, with operators often performing a simple tap test that is unlikely to detect rock-cut separations and other types of tyre damage,” Pitcrew.ai’s managing director Tim Snell told Safe to Work
“When a small degree of tyre damage expands over time it can develop into significant heat separation.
“If a hot tyre event is triggered it can remove a vehicle from operation,
sometimes for longer than 24 hours, as it must be repositioned to an isolation pad, resulting in significant disruption to site operations.”
The requirement for exclusion zones around AHS fleet operations ensures routine inspections are more difficult and time-consuming to carry out.
In responding to these operational challenges, Pitcrew.ai has designed, engineered and manufactured a sophisticated OTR tyre damage detection system.
The smart solution leverages
Teledyne FLIR thermal imaging and artificial intelligence (AI) technology, enhancing the management of AHS fleets by remotely detecting tyre damage without the need to modify or suspend mine site operations.
Even setting aside the safety and operational issues, tyres are a significant cost centre for mining operations, and the ability to extend their life results in significant savings operating expenses (OPEX).
“Tier 1 mining companies utilising the Pitcrew.ai OTR tyre damage detection
system extract the highest value proposition from the solution because every minute of machine downtime on a large mining site significantly increases operational costs,” Snell said.
The Pitcrew.ai inspection system is fully automated and enables insight into active tyre damage on-site, which enables unplanned repair and scheduled maintenance to occur safely and efficiently.
“Pitcrew.ai seamlessly integrates with a range of tyre pressure monitoring system, transportation management system and fleet management software packages,” Snell said. “And, if required, we can supply tailored integration services to ensure integration with existing on-site workflows.”
Every haul truck that passes the system is checked without any human intervention nor any requirement to cease operating.
Using a powerful AI algorithm trained on a library of thermal images, the Pitcrew.ai OTR tyre detection system can spot problems in their early stages prior to any type failure. This approach is critical to maintaining uptime for haul trucks, as even minor damage to a large mine tyre, such as a simple rock-cut, can result in complete failure if not detected.
The Pitcrew.ai system is typically supplied as a rapid-deployment, selfcontained, solar-powered kit that can be installed beside a haul road within a few hours.
“Our solution utilises low earth orbiting (LEO) technology, such as the Vocus Satellite – Starlink network, to seamlessly upload tyre monitoring and diagnostic data into the cloud,” Snell said.
The system utilises up to two FLIR A615 thermal machine vision cameras which produce high-quality infrared images, including the capacity to detect temperature differences as small as 50 milliKelvins (mK), while providing a 16-bit temperature linear output and high-frequency streaming.
“FLIR machine vision cameras combine powerful sensor technology with many features that enhance automatic control over image capture and on-camera pre-processing,” Teledyne FLIR sales manager –solutions division Sean Towner told Safe to Work. ¬
“Thermal issues on OTR tyres can be accurately detected and identified in real-time through integration between A615 machine vision cameras and Pitcrew.ai’s intelligent custom software.”
The Pitcrew.ai system uses a machine-learning algorithm that can project the growth of damage and predict when a change is necessary.
“Teledyne FLIR are the benchmark in thermography cameras, producing highly accurate and calibrated equipment that produces an array of diagnostic information and insights required to ensure our solution keeps updating and learning,” Snell said.
The system ensures vehicle downtime can be accurately planned well in advance, minimising the need to conduct unscheduled tyre changes and maximising tyre stock management.
In addition, tyre repair is much kinder to the environment and can play a major role in helping mines achieve sustainability targets within environment, social and governance (ESG) compliance regimens.
Similarly, the ability to predict the trajectory of damage means many of the risks associated with hot tyre events and fires can be eliminated.
That said, such events can still occur and the Pitcrew.ai system is able to detect hot tyres and immediately alert personnel via email, SMS or other communication options.
This ability to communicate incidents quickly and accurately allows for haul truck isolation to be carried out as quickly as possible, underpinning positive safety outcomes.
The system also offers the additional benefit of a remotely controlled thermographic inspection system that mine management can use to assess a vehicle remotely, improving visibility and intelligence during a mine safety event.
“Pitcrew.ai’s OTR tyre detection system offers a sophisticated autonomous inspection and monitoring solution, which is a critical tool for mining companies if they are to extract the greatest benefit out of the use of ultra-haul truck fleets.” Snell said.
PEGASUS HAS BEEN HELPING KEEP MINING WORKERS SAFE AND COMPETENT FOR DECADES. AS PART OF AVETTA, THE PEGASUS WORKFORCE PLATFORM CONTINUES TO UNDERPIN ON-SITE SAFETY.
Mining is a complex undertaking and, with significant labour and skills shortages and increased regulatory demands, the need to maintain a safe, inclusive, diverse and compliant workforce is more important the ever before.
“One of the key challenges we have as an industry right now is responding to a tightening of labour conditions,” Avetta technical lead –
mining and resources, John Furner told Safe to Work
“At the heart of this issue is the need for mining companies to be forward-looking and willingly encourage, develop and retain a skilled and more diverse workforce.
“The benefits that can be gained in terms of attracting and retaining a workforce underpinned by effective diversity, equity and inclusion policies is tangible and would
ensure mining companies meet their environment, social and governance (ESG) goals.”
A key solution for ensuring mining companies understand and manage their workforce is Pegasus Workforce. This product is part of the holistic Avetta One solution designed to manage workforce health and safety, alongside supplychain risk and liability, sustainability and ESG outcomes.
“The cloud-based platform controls the compliance of contract workers and mine company employees, essentially all workers,” Furner said.
“And it maintains a full induction and training record, providing companies with an operating learning management system for workers to complete online training. It also controls site access.”
The process begins with connecting qualified suppliers to a mine operation. Mining companies can collect, compare, and verify key information relating to prospective suppliers, including all relevant documentation, to ensure they meet specific standards.
This is followed by a health and safety audit and benchmarking, where Avetta determines compliance or corrective actions to be sent to the contractor to then address and update.
“With subtle differences between safety regulations across Australia’s multiple jurisdictions, Avetta can cater for variations in supplied documentation,” Furner said.
“We utilise our internal experts to verify that the documents satisfy requirements of the client in different jurisdictions.”
Flowing from the process of company pre-qualification is the clear requirement to ensure worker competency. Managing competency begins with creating a worker profile in the online system. Site and project roles are then assigned for each worker, with the ability to determine required training and safety inductions that must be completed for workers to effectively carry out their role.
Avetta implements a detailed roles matrix in which work roles are matched to the level of competency and training that is needed to do the job. Supporting documentation is uploaded as evidence of qualifications for verification.
“We ensure physical verification of documents in an accurate and timely manner, so it’s a set of expert eyes evaluating the documents,” Furner said. “This is a major point of difference, as other software providers do not provide this service.”
Mining companies can identify and report on exactly what roles fully inducted workers are qualified to undertake, before deploying them to site with the knowledge that they are competent.
Training can be planned and set for the workforce, either online or in the classroom, with Avetta induction and learning management. Importantly, Avetta tracks and reports on the results for meaningful analytics, and in order to meet safety and legislative requirements.
The dedicated Avetta eLearning team assists with the delivery of tailored course material via a practical online format, paired with assessments, to test worker comprehension and competency.
“The Avetta induction and learning management tool enables tailored online training, while capturing and maintaining the entire training record of an employee, or a contractor, specifically related to that particular mine site,” Furner said.
A key dimension of the platform relates to site access. This involves the linking of supplier and worker data to access control hardware, allowing the
mining company to fully control entry to its work sites.
Workers are issued ID cards that are scanned by the Avetta mobile app or site access points. It is only as they meet a company’s requirements that workers and assets are permitted on site. Log points, kiosks, mobile apps, and boom gates allow an accurate record of who is on site.
This level of monitoring ensures real-time insights, along with the ability to track and report on time, attendance and fatigue. It can also set and display emergency information and check who is safe during an evacuation.
“In essence, we validate contractors on behalf of mining companies, and once approved by them we start to undertake a validation process on the workforce,” Furner said. “It’s then a process of examining each worker individually and the information they have uploaded to ensure they meet the requirements for site.”
With its products helping Avetta gain a strong foothold in the mining industry, the company is continuing to grow its presence in the sector.
“We have diversified from our grassroots in coal mining to include partnerships with a number of large hard-rock mining clients over the last couple of years and will continue to provide mining industry customers with our sophisticated and reliable workforce management solution,” Furner said.
Vocus is a key player when it comes to the provision of fibre optic cable and low earth orbit (LEO) satellite communications to some of the most remote regions of Australia. And given so many Australian mining operations are located in far flung corners of the country, this is especially valuable in the resources industry.
“Many organisations across the resources sector are perceiving the benefits from our network connectivity solutions,” Vocus national industry lead –resources and utilities Simon Head said.
This ubiquitous and integrated internet connectivity underpins smart mine technologies, a data-hungry ‘fly in, fly out’ (FIFO) workforce and the many mining communities that remain dependent on fast, reliable and costeffective internet connectivity.
An ongoing infrastructure investment by Vocus across the Pilbara has resulted in the near-complete Darwin-JakartaSingapore Cable (DJSC) project.
Highclere is a 1000km highcapacity optic spur from the Australian Singapore Cable (ASC) to a pre-existing cable at Port Hedland forming the important DJSC.
“Construction is well underway and progressing to schedule, consistent with our strong track record of on-time, onbudget delivery,” Head said.
The DJSC is designed to provide a geographically diverse and protected submarine cable from the Pilbara to Perth, as well as a direct low-latency network to Singapore, providing connectivity to many major cloud computing hyperscalers located there.
The increases in data capacity derived from the DJCS will encourage the extension of cloud computing platforms and services into the Pilbara and are already attracting edge computing data centre providers for regional and remote mining operations and communities across Western Australia – and beyond.
“The ability to access both Perth and south-east Asia is extremely attractive, especially from the perspective of cloud computing services,” Head said.
This type of seamless network connectivity enables Vocus customers in the mining and broader resources industry to meet their environmental, social and governance (ESG) compliance requirements.
From supply-chain monitoring and data collection to reporting to the provision of multifaceted work health and safety (WHS) measures, the Vocus network is a reliable presence.
On target for completion in the second quarter of 2024 is the 1600km Project Horizon, designed to complete a ‘western loop’ of terrestrial network assets by connecting Geraldton to Port Hedland via Newman, providing further connectivity options to the Pilbara’s mining operations.
Vocus’ communications infrastructure has been described as a game-changer
VOCUS CONTINUES TO SUPPORT ESG COMPLIANCE WITH THE ONGOING ROLLOUT OF LONG-HAUL FIBRE ACROSS THE PILBARA AND THE RECENT ARRIVAL OF SATELLITE-POWERED INTERNET WITH STARLINK.Integrated internet connectivity helps to underpin smart mine technologies.
for the connectivity dynamic across the Pilbara.
“Significantly, when built the Horizon cable system will complete our western rings, providing a figure-of-eight cable system that has multiple terrestrial and sub-sea paths out of Western Australia’s most expansive resources provinces,” Vocus key account director – natural resources Benedict Boylson said.
“Having sub-sea routes provides significant protection from adverse weather events that can impact long-haul terrestrial based systems. Unfortunately, we are seeing more ‘once in a century’ type events, with our state’s worst floods on record in the Kimberley in 2022 and Tropical Cyclone Seroja across the central west coast in 2021.”
Last November, Vocus entered into an agreement with SpaceX to offer Starlink Business, powered by satellites in LEO, to Australian enterprise and government customers.
Sold as Vocus Satellite – Starlink, the solution provides premium installation or the option of selfinstallation, 100 per cent Australianbased support, and integration with existing network solutions.
Vocus Satellite – Starlink provides a high-gain antenna, additional throughput allocation and extreme weather performance, helping ensure high bandwidth and low latency for critical operations 24–7.
Vocus chief executive – enterprise and government Andrew Wildblood said it was exciting to be working with a global technology leader to bring game-changing satellite connectivity to customers.
“Starlink is innovation at its best, with some of the smartest minds in the industry and a phenomenal satellite broadband product,” he said. “Vocus is excited to be one of the first telcos in the world to work with Starlink to bring this to customers.
“Enterprise and government customers need a technical and service experience that is above and beyond – people who know how to work with large companies, can projectmanage installations, provide tailored services and consistently deliver brilliantly responsive assurance. And that’s Vocus’ specialty.
“Enterprise and government customers will experience satellite service delivery like never before with Vocus.”
New technologies that challenge the status quo – like LEO satellite –“need like-minded organisations to deliver full value”, according to Vocus development manager for space and satellite Ashley Neale.
“Customers on Vocus’ fibre network running mission-critical operations at their sites will now have another highperformance, attractively priced option for reach and redundancy, providing extra assurance for business continuity, with personalised service built on industry best practice,” he said.
In a rapidly evolving digital world, mining is no different from so many other industries in that high-speed, low-latency internet is critical for businesses.
“Starlink allows enterprises to manage their remote operations more efficiently,” SpaceX vice president of Starlink sales Jonathan Hofeller said.
“We look forward to providing Vocus’ customers with Starlink’s powerful and reliable connectivity solution.”
Vocus is making a significant competitive and structural impact on regional pricing across the Pilbara and more broadly across Australia. There is a strong historic correlation between the company’s significant geographic coverage and a shift in incumbent pricing to metropolitan equivalent rate cards.
“Our agreement with Starlink is a key pillar for providing an integrated network solution for Vocus customers, now and into the future,” Head said.
Vocus has recently announced its long-time partner Challenge Networks – a market leader in designing and deploying private mobile networks – will become part of the company.
Vocus has signed a contract to acquire Challenge Networks, which builds on Vocus’ strategy to provide secure, high-capacity connectivity to Australian enterprise and government customers – wherever they are –through its national fibre, satellite, and now wireless network infrastructure.
“Challenge Networks’ expertise in deploying private LTE (long-term evolution) is a perfect match for Vocus’ extensive experience supporting Australia’s government, defence, utilities, and resources sector customers with our fibre network and low earth orbit satellite capability,” Wildblood said.
Private mobile networks provide many of the technology advantages of public mobile networks, without the potential downsides. These networks are designed to provide perfect coverage for their target site and superior security and performance, and be dimensioned according to a known number of devices connected at the location. They can also prioritise traffic based on defined criteria.
This type of solution is incredibly useful in providing the forms of support demanded by ESG strategies, including the types of digital entertainment and online support services upon which the FIFO workforce depends.
“Through this acquisition, Vocus will be able to provide fibre or LEO satellite connectivity to the perimeter of a site,” Wildblood said.
“And then through a private LTE network provide campus-wide wireless connectivity for applications such as autonomous vehicles, IoT (Internet of Things) sensors, building management systems, voice calls, push-to-talk devices, smart phones, tablets, and computers anywhere on the site.”
IMDEX sits comfortably among top industry players in developing technologies that deliver better orebody knowledge.
As a leading global mining technology company, IMDEX enables drilling contractors and resource companies to safely find, define, and mine orebodies with precision, efficiency and speed.
The company provides unique endto-end solutions for the mining value chain, spanning four key portfolios: drilling fluids; drilling optimisation technology; rock knowledge sensors, and software.
IMDEX’s product offering includes an integrated range of drilling-optimisation products, cloud-connected rock
knowledge sensors, and precision data and analytics tools to improve the process of identifying and extracting mineral resources for mining, drilling and blasting contractors along with resource companies, both locally and globally.
These integrated technologies play an important role in making the mining and resource industry more sustainable, helping to ensure smarter and safer decisions are being made.
During mining operations, IMDEX produces significant amounts of live data that enables companies to make faster near-real-time decisions with greater precision and in a safe manner.
In recent years, IMDEX has developed BLAST DOG, a commodityagnostic and fully integrated sensing
and physical measurement technology that provides immediate blasthole physicals and orebody knowledge.
The value of the BLAST DOG lies in the power of integrated data, enabling experts to make informed decisions that affect each stage of the value chain.
The BLAST DOG probe is deployed using a track-mounted robotic platform with semi-autonomous hole positioning and alignment capability that can work over variable terrains and bench conditions.
With the delivery platform coming from Universal Field Robots, fast logging downhole multi-sensors designed and manufactured by IMDEX, advanced analytics, and the addition of the recently updated MinePortal 3D visualisation software integrated with cloud-based data storage, IMDEX has accelerated BLAST DOG capabilities for application in mining production and workflow.
“BLAST DOG is a technologically sophisticated solution that can undertake significant amounts of geophysical measurement and data” IMDEX general manager mining technology Stephen Jeric told Safe to Work
“We are also able to integrate existing data, such as MeasurementWhile Drilling data from the drills, in order to determine precise insights into geological characterisation.”
Directly and rapidly measuring the orebody via blastholes reveals what the
MINERS WITH THE CAPACITY TO MAKE THE MOST INFORMED EXTRACTION AND BLASTING DECISIONS.BLAST DOG is a commodity-agnostic and fully integrated sensing and physical measurement technology.
reserve looks like in the ground – at a high resolution and immediately before its extraction. BLAST DOG effectively creates a 3D sub-surface map to see what is being mined prior to blasting to enable precision mining.
“The BLAST DOG platform can work across multiple types of terrain, and the rapid deployment of its sensor technology means that it can produce and store large amounts of data very quickly,” Jeric said.
“BLAST DOG provides a high density of data, so a mining operation can get a very good view, and rapidly, of what the orebody looks like and its key geological characteristics.
“Due to its high productivity on the bench and in data processing, it provides one of the lowest cost solutions on the market today.”
Not only does the data have the potential to be used to provide insights that could improve safety, it can also offer environmental, social and governance (ESG) improvements. These include mine and process-plant planning, heap leach optimisation, waste characterisation, blast design, fragmentation, fume reduction, flyrock, vibration, control air-blast and dust, as well as improving material assignment following a blast.
“With the data BLAST DOG extracts, a mining operation can make many multidisciplinary decisions and construct sophisticated 3D visualisation of the orebody and blasthole physicals,” Jeric said.
“Additionally, with the significant increase in the cost of explosives in recent years, mining operations need the most precise data relating to rock properties, water levels and blasthole physicals measurement to ensure efficiencies with blasting.”
“For example, as Australian coal mines are becoming harder and harder to mine, BLAST DOG can support resource stewardship by accurately
determining where the coal is and how to efficiently extract the coal seams with minimal coal loss, while also minimising the associated stripping requirements, essentially mitigating some of the negative dimensions of these depleting resources.”
The reduction or management of variation creates value, with the characterisation of waste as important as the identification of the target metals or minerals. It creates the opportunity for better segregation of ore from waste during mining, managing the waste in a more sustainable way.
IMDEX achieved the first commercial contract with BLAST DOG in August 2022 at Fortescue Metal Group’s Iron Bridge in the Pilbara. The agreement provides for the staged utilisation of up to three BLAST DOG units together with associated field logging services, answer products,
software, data analysis, reporting and support.
Six commercial prototype trials are planned for the 2022–23 financial year under the first phase of delivering BLAST DOG to customers.
The technology will continue to evolve, with new answer products, novel and democratised modelling, and visual outputs being developed along with expansion to other commodities and geographies.
IMDEX, a proud member of Austmine, fundamentally believes in the value of sharing its technological achievements with the broader mining equipment, technology and services (METS) sector.
“BLAST DOG is a significant and important example of the data-led solutions driving the next wave of ore extraction in the mining sector,” Jeric said.
Since the first gold rush in the early 1850s, this industry has shaped Australia in many significant ways – and continues to do so today.
The country’s gold exports generated $25.8 billion in revenue in the 2021–22 financial year..
Strong gold exploration and production today and into the future means a greater range of career opportunities are available within the industry. And it’s important to note that many of these employment opportunities exist beyond the mines themselves, covering an interesting and diverse collection of fields such as communications, technology development, data science, environmental areas, and community relations.
“Not all roles will require previous qualifications or specific skillsets, so there really are opportunities for everyone,” Gold Industry Group chief executive officer Kristy Reilly said.
Gold companies across the country are developing workplace initiatives to promote the acceptance and inclusion of workers from all backgrounds.
The industry is making great progress towards ensuring genuine and equal opportunities for prospective employees, and that within gold mining people are encouraged to live their values and be their authentic selves in the workplace.
“It’s amazing to see people entering the industry from all different backgrounds,” Reilly said.
“With a wide range of roles available, the industry truly is open to everyone
and embraces diversity in all its forms.”
Reilly believes gold mining companies value a range of skills, not just those in the usual areas like geology, engineering and maintenance.
“Sometimes people can feel that because they don’t meet all the requirements of a particular role, and haven’t worked in gold or resources previously, that they aren’t confident in applying for a position,” Reilly said.
“What we are finding is that many of our members are now seeking out candidates with complementary attributes and values, and that skills and experience from other industries and sectors are highly sought-after by hiring managers.”
For Australian gold mining companies, recruitment remains an ongoing issue.
“The nationwide skills shortage and competition for workers is a constant challenge for our members,” Reilly said.
“Job-seekers with specialised skills in fields such as geology, mining engineering, metallurgy, and environmental management are highly sought-after and are often choosing between multiple job offers.”
A key feature and desirable characteristic of the gold industry, beyond a commitment to diversity and mental health, is its ability to harness technology and adapt to smart ways of work. Modern science is finding new applications for the rare metal, from components in smart phones to circuits in electric vehicles, and increasingly in medicine and other related disciplines.
For example, gold’s low reactivity makes it safe for use in the human body and it is used to coat medical components such pacemakers and stents. And gold nanoparticle technology is being used to treat cancer patients who undergo chemotherapy and radiotherapy.
“The acceleration of automation and AI (artificial intelligence) by the industry brings demand for new technological skills, as well as social and emotional intelligence in the workplace,” Reilly said.
The ability to streamline operations, reduce downtime and keep workers safe, while providing highly sought-after flexible work arrangements, makes it an exciting industry of which to be a part.
“These changes will require workers everywhere to deepen their existing skill sets or acquire new ones, and we’re seeing many members invest in their people to ensure they are fully equipped for the job at hand,” Reilly said.
“There are extensive opportunities for on-the-job training and career advancement because gold companies will always support workers who want to advance their skills and knowledge within their role.
“Continued improvements across the industry into flexible working policies are supporting those returning to work following parental leave, or the Gen Z cohort wanting to continue studying while managing a full work load.”
Many members of the Gold Industry Group offer a variety of apprenticeships, traineeships, and graduate programs designed to provide opportunities to explore the sector while developing skills to help launch their careers.
These programs help give the emerging workforce exposure to the industry as they learn. Apprenticeships,
traineeships and graduate programs often lead to full-time work.
“We want to see the best outcomes for those entering into gold and our members ensure workers are given the tools they need to contribute to the everevolving industry,” Reilly said.
In an effort to change perceptions and encourage future generations to consider careers in the resources sector, the Gold Industry Group proudly promotes the National Gold Education Program within primary and secondary schools.
“It’s incredibly rewarding to see the excitement on students’ faces when they realise there is a role for them in gold, no matter their skills or interests,” Reilly said.
The Gold Industry Group suggests prospective employees adopt a flexible attitude and consider embarking on advanced education or certification, or look towards gaining experience through internships or entry-level positions.
“Stay informed and don’t be afraid to continuously learn and grow your skillset,” Reilly said.
And like most areas of work, when starting out it is helpful out to build a network within the gold sector. Gold Industry Group events are a great way to connect with other professionals and learn more about companies and their operations.
As the country with the largest known gold resources in the world, Australia and its people have a unique opportunity to supply the globe’s evergrowing demand for the precious metal.
“Workers who do choose to build their careers in gold can make a real impact and contribute to shaping the future of the industry and beyond,” Reilly said. “Whether it’s developing new technologies, improving processes, or finding new ways to solve problems, the work done by people in the gold industry can have a lasting and meaningful impact.”
Stress itself may not be an injury, but if workers are stressed often and over a long period of time, or their stress level is high, it can cause significant harm.
Putting it simply, psychosocial hazards can create stress, which can in turn cause psychological or physical issues.
Psychological harm may include anxiety, depression, post-traumatic stress disorder, sleep disorders, and similar issues.
Specific examples of psychosocial issues in the workplace include bullying, sexual or racial harassment, aggression or violence, exposure to traumatic events or content, remote or isolated work, poor organisational change management, minimal recognition and reward, and poor workplace relationships.
These types of hazards may interact or combine to create new, changed or higher risks. It is therefore important to consider all potential psychosocial issues workers may be exposed to when managing mental health risks.
Some hazards may not create these types of risks on their own, but can rather do so if combined with other problems.
For example, when workloads are high the risk may increase if workers cannot take breaks or there is no one else available to help.
Some hazards, on the other hand, may only create risks on their own when severe.
Workplaces have a duty to protect the psychological health of workers in the same way they protect their physical safety.
Western Australia created three new
sets of work health and safety (WHS) regulations when the Work Health and Safety Act 2020 (WHS Act) took effect in early 2022, specifically identifying psychosocial risks and outlining control measures.
Many codes of practice were amended as a part of WA’s simplified and cohesive regulatory approach. New codes were written to cover psychosocial hazards, workplace behaviour, and violence and aggression, with an emphasis placed on the mental health of fly-in, fly-out (FIFO) workers.
“The Commission for Occupational Health and Safety has released various codes of practice to provide guidance on the laws, including the Code of Practice – Psychosocial hazards in the workplace, which should be present in every WA workplace,” WA Mines and Petroleum and Industrial Relations Minister Bill Johnston said.
By specifically dealing with psychosocial dangers in the workplace, the code captures situations and conditions that pose mental and social risks to workers, as opposed to only physical risks.
While these cover the more obvious factors of bullying, harassment, violence, and aggression, they also include the less apparent issues of fatigue, stress and burnout that can compromise a worker’s psychological wellbeing.
WA’s new regulations include the concept of a “person conducting a
PSYCHOSOCIAL HAZARDS ARE NOW CONSIDERED NO DIFFERENT TO PHYSICAL ISSUES, WITH RESOURCES COMPANIES REQUIRED TO IDENTIFY AND MANAGE THIS NEW WORKPLACE HEALTH AND SAFETY RISK.Sharing experiences with colleagues can go a long way in mitigating the effects of psychosocial issues.
business or undertaking” (PCBU) replacing the “employer” as the person with primary health and safety duties.
Under the code, it is the responsibility of PCBUs to facilitate a systematic approach to managing psychological dangers in order to meet their responsibilities under the WHS Act and create a safe and healthy work environment for employees.
Under the Act, the PCBU is responsible for either eliminating psychosocial risks or minimising them as much as is reasonably practical by ensuring these risks are placed on the same footing as other significant hazards such as falls or operating machinery.
WA businesses already have a duty to manage psychosocial risks under their primary duty of care responsibilities as outlined within the WHS Act. These new regulations serve to clarify existing duties rather than prescribing any further requirements.
“Psychosocial hazards are just as important as physical hazards and must be dealt with in the workplace, so it’s
an important step to have regulations specifically covering mental health issues,” Johnston said.
“The regulations will help industry to better understand the requirements for managing psychosocial hazards and will also ensure that the regulator – in the form of WorkSafe inspectors – can enforce those requirements.”
Other jurisdictions across Australia are at various stages of developing or amending their own regulations, often occurring off the back of workplace reviews recommending the strengthening of regulation to better address the risks associated with psychological health.
These regulations seek to make it clear that everyone has a role to play in creating a mentally healthy workplace and that now, more than ever, people must be aware of mental health and look for signs of distress among colleagues.
PCBUs are in a position to send a clear message to workers that they value mental health and wellbeing, which authorities believe can lead to benefits such as reduced
workers’ compensation claims and improved productivity, satisfaction and engagement.
For employees experiencing workrelated mental harm, key steps can be taken to help mitigate their effects, including as telling a manager and requesting to work together to address these issues.
Employees can also talk to others in their workplace for support, such as a health and safety representative or union representative, or they can talk to others outside work for support such as family and friends, a doctor, or a professional counsellor.
People can also maintain personal health by exercising regularly, eating healthily, getting good sleep, and trying not to rely on caffeine, drugs or alcohol to cope.
It’s important that employees, regardless of their profession or level of seniority, remember to do the things that they enjoy. It may sound obvious or flippant, but these recommendations can make a significant impact on positive mental health.
EVENT SUBMISSIONS CAN BE EMAILED TO EDITOR@SAFETOWORK.COM.AU
The Austmine International Conference and Exhibition will feature workshops, plenary sessions, tech talks, ‘Meet the Miners’ and interactive breakout discussions. There will be plenty of networking throughout, as well as the much-anticipated Industry Leaders’ and Awards Dinner where the achievement of leading innovators in the Australian METS sector is celebrated and recognised. With an expected 100-plus exhibitors, Austmine 2023 will showcase the leading technologies, innovations and transformative solutions for the global mining sector. In partnership with the SA Government, the Copper to the World Conference will be held in conjunction with Austmine 2023, bringing a spotlight on this key strategic mineral. • austmineconference.com.au
The Mineral Resource Estimation Conference 2023 will attract resource geologists to demonstrate Australasian excellence on resource estimation. The conference aims to showcase best practice, case studies and research on resource estimation and required software applications. Facilitating open exchange of information, the conference will feature interactive sessions, panel discussions and keynote presentations alongside case studies and peer-reviewed papers. Sessions will showcase advancements and examples in QA/QC and sampling, 3D geological and estimation domain modelling, geostatistical analysis, estimation, validation and risk analysis and reporting.
• ausimm.com/conferences-and-events/ mineral-resource-estimation
Inaugurated in 1958, the World Mining Congress is the leading international forum for the global mining and resources sectors. The World Mining Congress 2023 (WMC) is a unique opportunity for international representatives of the world’s leading resource economies to meet, find new partners, discuss current challenges, and share the latest research, technology, and best practice. WMC events have set the scene for international agreements and high-level discussions that have influenced mining practices and the resource industry for decades.
Join senior mining industry owners, investors, national and international government representatives, researchers, educators, regulators, suppliers and operators from around the world in Brisbane for this genuine opportunity to demonstrate real leadership and presence on a world stage.
• wmc2023.org
The 2023 Mine Waste and Tailings Conference welcomes delegates from across to globe to explore all aspects of lifecycle waste rock and tailings management, from site selection and design to post-closure care, and addresses current and future challenges affecting mining systems re-engineering.
Co-hosted by AusIMM and the University of Queensland, the conference will feature industry-leading keynote presentations, thought-provoking panel discussions, interactive Q&As, a suite of insightful technical presentations, and exhibitors showcasing the latest innovations.
• ausimm.com/conferences-and-events/minewaste-and-tailings
AusIMM and the University of Queensland’s Sustainable Minerals’ Centre for Mined Land Rehabilitation (CMLR) are welcoming attendees back to the highly successful Life of Mine Conference 2023.
The conference welcomed a record number of attendees from over 15 countries in 2021 and is set to bring a wider global audience in 2023. Join professionals, researchers, government, and academia from a diverse range of sectors as the program explores the full lifecycle of a mine, from exploration to rehabilitation. Delivered in-person and online, this technical conference addresses current and future challenges affecting the mining value chain and will present leading examples of sustainability in mining.
• ausimm.com/conferences-and-events/minewaste-and-tailings
Taking place in Brisbane in 2023, the Australian Mining Prospect Awards are a great opportunity to recognise and acknowledge the people and companies in the mining sector for their outstanding work.
Having recently celebrated the 2022 Prospect Awards winners, nominations are now open for 2023, with awards in categories such as Indigenous and Community Engagement, Mine Project Success of the Year, Outstanding Mine Performance, Sustainability Project of the Year, Discovery of the Year, and more.
Some 2022 award winners included Kestrel Coal for Australian Mine of the Year, Roy Hill for Mine Project Success of the Year, and Flexco Australia for Excellence in IIoT Application. The awards return to Brisbane in appreciation of the vibrancy of the state’s mining industry.
• prospectawards.com.au
The HxGN MineProtect Collision Avoidance System (CAS) is trusted in more than 40,000 vehicles worldwide. Learn more about our 360-degree operator awareness delivered via an unobtrusive cabin display unit for vehicles, assets and operators.
One platform. One partner. For the life of your mine. | Visit hexagon.com/mining