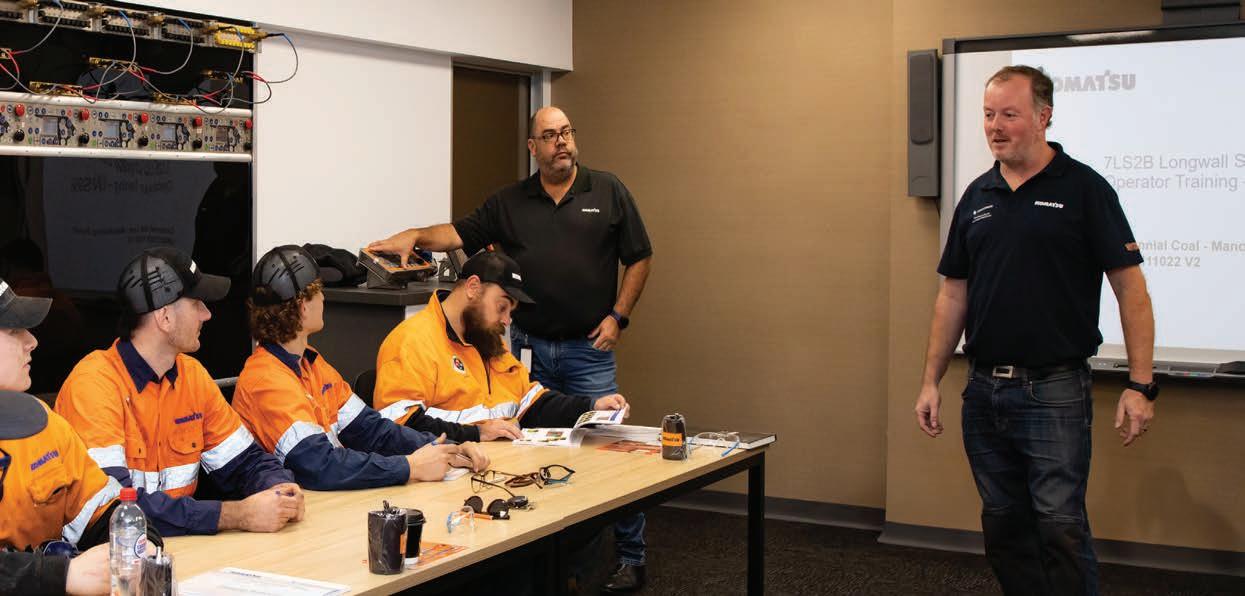
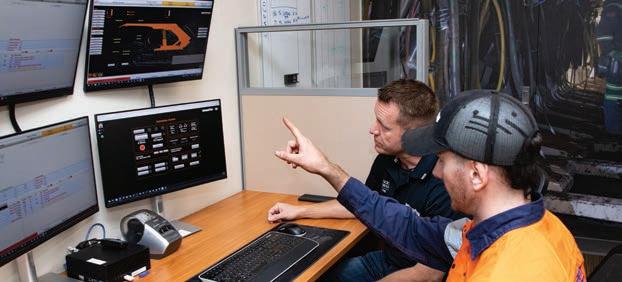
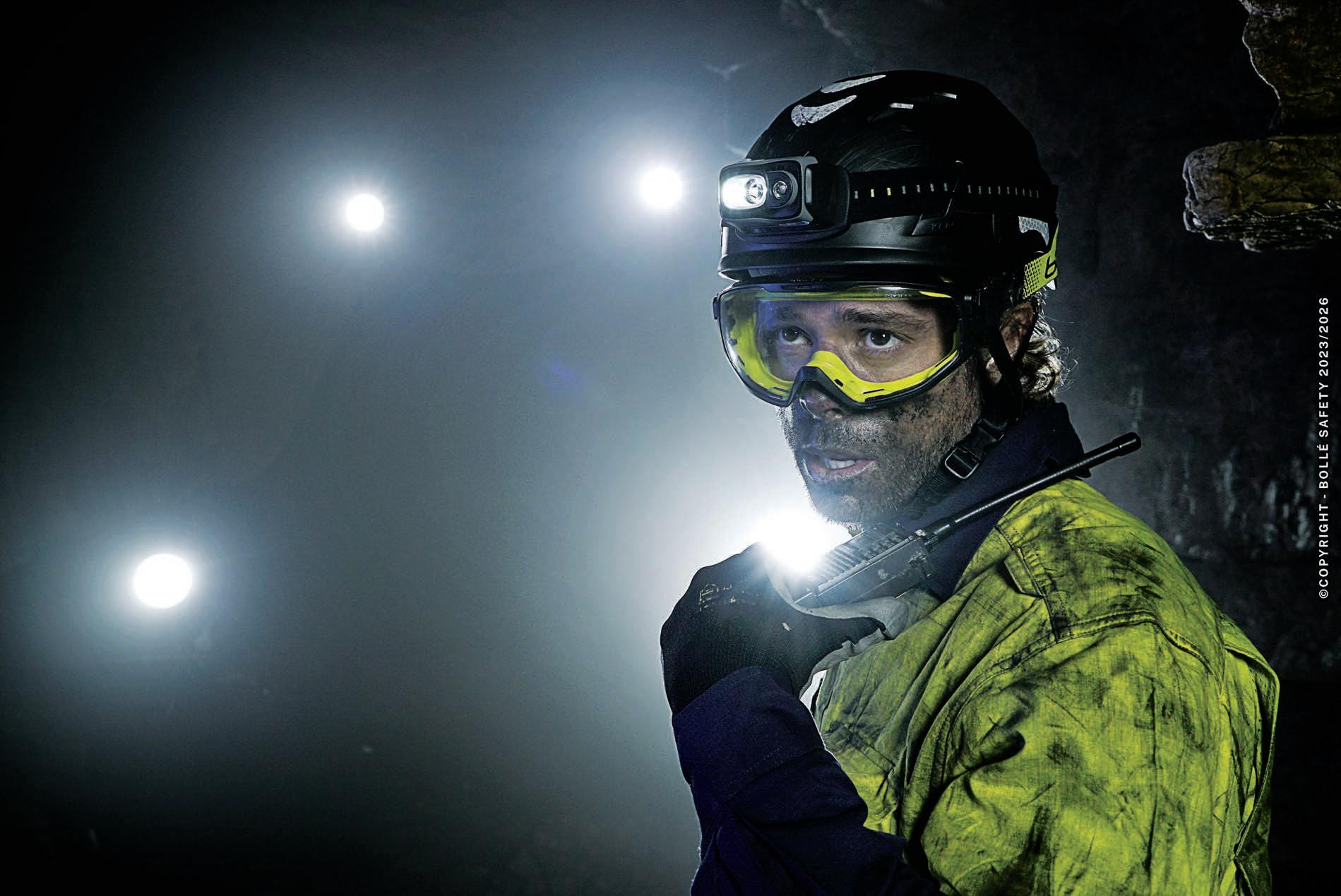
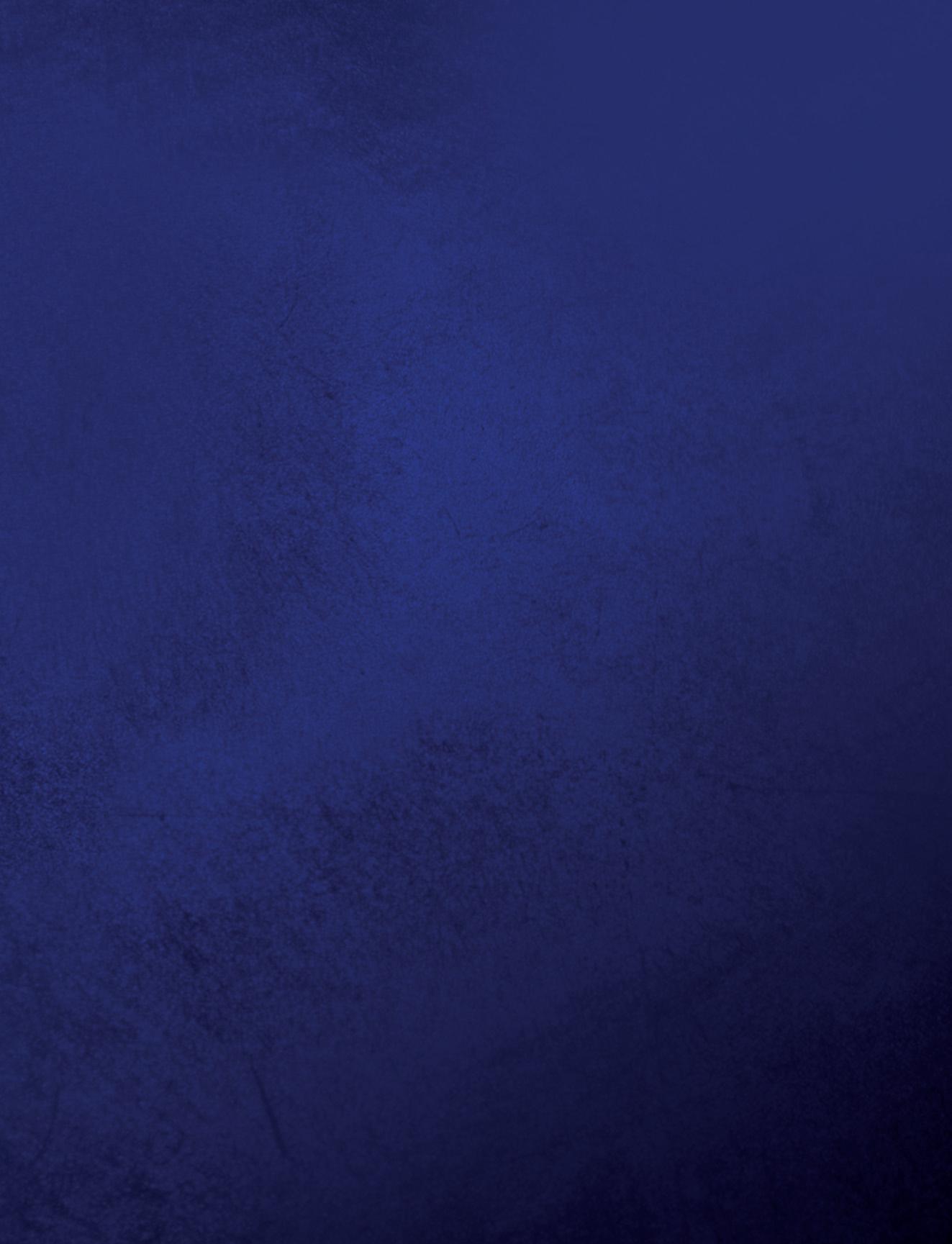
United. Inspired.
Awareness is crucial for safer and more productive operations. Mobilaris Situational Awareness provides real-time data and 3D visualisation to keep everyone informed, from the control room to the field. It allows personnel to locate people and assets, monitor production status, and access IoT sensor data, enhancing response times and operational control. Utilising diverse technologies like LTE, WiFi, and RFID ensures futureproof investments. Mobilaris tags enable effective tracking of personnel and equipment, while the History viewer helps analyse past shifts and incidents to improve safety procedures.
FLY-IN, FLY-OUT WORKERS ARE VITAL TO THE AUSTRALIAN RESOURCES INDUSTRY, AND MINING COMPANIES KNOW THEY NEED TO INVEST TO KEEP THEM SAFE AND COMFORTABLE.
While Australia was built on the sheep’s back, it’s safe to say the modern version of the country owes just as much to the boom of the mining industry.
But the fact so much of the precious ore extracted from the ground is located in some of the most remote corners of the country necessitates fly-in, flyout (FIFO) work.
In its most straightforward terms, FIFO work is a situation in which an employer will temporarily transport the employee to a location or site of work before transporting them back for a period of rest.
But it’s far from that simple.
FIFO workers often operate on a two-week
on, two-week off basis, so the task of transporting, housing, and feeding them can be a logistical headache for any organisation. But emerging technologies and conscientious operational expenditure are helping companies get the most out of their FIFO workforce.
That’s why mine operators go to great lengths to keep FIFO workers comfortable and safe while away from home.
Whether it’s more regular and comfortable flights to site, BHP spending $300 million to upgrade safety throughout is accommodation villages, Minerals Resources building resort-style accommodation at Ken’s Bore in Western Australia, or numerous
others employing different technologies to keep workers safe, mining companies are sparing no expense when it comes to their FIFO workforce. The industry has come a long way since the more roughand-ready approach to FIFO work in the 1990s, and with the rise of safety technology, a growing emphasis on highquality accommodation, better flights, and generous wages, one could argue that there has never been a better time to be a FIFO worker.
Paul Hayes Managing Editor
COO CHRISTINE CLANCY
MANAGING EDITOR
PAUL HAYES
Tel: (03) 9690 8766
Email: paul.hayes@primecreative.com.a
ASSISTANT EDITOR
TIMOTHY BOND
Tel: (03) 9690 8766
Email: tim.bond@primecreative.com.au
JOURNALISTS
ALEXANDRA EASTWOOD
Tel: (03) 9690 8766
Email: alexandra.eastwood@primecreative.com.au
OLIVIA THOMSON
Tel: (03) 9690 8766
Email: olivia.thomson@primecreative.com.au
KELSIE TIBBEN
Tel: (03) 9690 8766
Email: kelsie.tibben@primecreative.com.au
CLIENT SUCCESS MANAGER
JANINE CLEMENTS
Tel: (02) 9439 7227
Email: janine.clements@primecreative.com.au
RESOURCES GROUP LEAD
JONATHAN DUCKETT
Mob: 0498 091 027
Email: jonathan.duckett@primecreative.com.au
BUSINESS DEVELOPMENT MANAGER
JACOB NIEHUS
Mob:
10 Investing in the FIFO future
Looking at new and existing technologies that are making things more comfortable for the FIFO workforce.
14 Safe way every day
Safe to Work sat down with Yancoal Australia head of training Craig Hagan to discuss how mine operators can implement a culture of safety excellence.
18 Blasting to new heights
Epiroc is bringing a proven underground safety technology to
22 Enhancing operator experience
Komatsu’s automation solution is improving safety and operational efficiency at Centennial Coal’s Mandalong mine in NSW.
24 The science of blasting
BME is delivering safe and highquality blasting solutions to the Australian mining industry.
26 The multi-tool of mine safety
MST Global is improving safety and productivity in underground mines with its modular hardware
30 Simplifying hydraulic management
BOA Hydraulics is helping the mining industry gain control over its systems.
36 Safe shutdowns
Prepping for conveyor maintenance and improvements with Martin Engineering.
44 Form-fitting safety
The latest protective goggles from Bollé Safety use a “first-of-its-kind” technology designed to conform to a user’s face.
Celebrating 30 years of designing and developing high quality cable coupler solutions for domestic and international industries, AusProof remains committed to increasing safety, creating long-term savings, and reducing downtime. Much of what has been achieved over the past 30 years would not have been possible without the support of our customers.
ESS air cannons are innovative pneumatic systems designed to resolve bulk material blockages safely and efficiently. Utilising high-velocity compressed air, these systems break up compacted materials in storage structures like silos and hoppers, restoring flow and material capacity.
Safety is paramount with ESS air cannons. Unlike traditional systems, these cannons fill just before firing, minimising the time they are pressurised. According to ESS, this approach significantly reduces the risk of accidents, as the vessel remains uncharged for 90 per cent of the time. These robust 150L cast vessels are designed to endure pressure cycles indefinitely, with no need for frequent inspections.
Additionally, ESS air cannons feature a single moving part with no metal-on-metal contact, enhancing durability and reliability. Remote activation via a sequence controller ensures safe operation, keeping workers from the danger zone during pressurisation and firing.
• esseng.com.au
TAKRAF’s X-TREME class sizer is a new generation of sizing technology specifically tailored to hard rock applications. These sizers incorporate custom-selected crushing segments and drive components with pre-engineered shaft and housing modules, resulting in a cost-effective solution with high availability, high maintainability and high value. The main technical advantages of the TAKRAF X-TREME class sizer are the tooth configuration that is optimised for rock intake and the heavy-duty shaft assemblies designed to withstand increased bending and twisting. The TAKRAF sizer portfolio covers primary, secondary and tertiary sizing applications in all types of commodities. The standard class sizers offer a highly optimised and economical solution, while X-TREME class sizers offer maximum reliability in extreme conditions. With its own product and service centre, TAKRAF said its sizers have an advantage in the manufacturing process: a reliable supply chain, control of the schedule, and quality control. takraf.com
INTRODUCING KITO HOISTS: A SOLUTION TO UNNECESSARY REPLACEMENTS
Kito 415V chain and wire rope hoists come standard with state-of-the-art condition-monitoring features, including hour meters and operation counters. This technology allows for tracking of hoist usage, facilitating timely maintenance based on actual usage rather than arbitrary calendar schedules. “With Kito hoists, you can say goodbye to premature replacements and unexpected downtime, saving time and money,” the company said. “Our dedication to innovation ensures that your lifting operations run smoothly and efficiently, minimising disruptions, and maximising productivity.
“Upgrade to Kito hoists today and witness the difference in performance, reliability, and costeffectiveness.”
Kito’s innovative hoists and lifting technologies prioritise safety and efficiency. Since 1932, Kito precision-engineered solutions have been trusted globally for heavy lifting across various industries.
• kitopwb.com.au
Sepura, a UK-based company with over 20 years’ experience in mission-critical communications, has a suite of TETRA products tailored to the mining industry, including:
• VHF handheld and vehicle devices – offering superior range and lower base station density, reducing costs
• SC23 – a robust handset with a simplified user interface that utilises existing SC20 accessories
• Ultra CSM speaker microphone – utilising anti-magnetic technology for iron ore sites where metallic particle ingress can impact product life and performance.
Sepura’s design philosophy is to provide comprehensive solutions for its customers. Its focus in the mining sector is robustness, with the radio and speaker microphone being easy to maintain, rated to a minimum IP67 ingress protection and featuring Sepura’s unique waterporting technology. This means they undergo minimal degradation in audio clarity or loudness when exposed to driving moisture, such as during dust-suppression activities.
• sepura.com/industries/mining
The Avetta Customer Awards celebrate the companies and individuals who are setting the standard in workforce safety, risk management, and sustainability. This year’s finalists from the mining industry lead the way in fostering safer and more sustainable workplaces.
Client Award Finalists
Craig Hagan, Yancoal
Change Maker
Aurelia Metals
Rio Tinto
Health & Safety Leader
Supplier Award Finalists
Pilbara Traffic Management
Health & Safety Leader & Risk 360
Whitehaven Coal Risk 360
Yancoal
Digital Transformation Innovator & Premier Partner
Elastomers Australia
ESG Trailblazer & Risk 360
The Avetta 2024 Customer Awards will be presented at the Avetta Summit User Conference in Sydney on July 25.
A new fact sheet from the Cancer Council discusses how workers can stay safe around carcinogenic diesel engine exhaust. From trains to haul trucks to generators, diesel powers a lot of equipment in the Australian mining industry, and while mines continue to make the shift to electric assets, it will take time to phase out diesel-powered equipment.
But that exposure to diesel engine exhaust (DEE) can cause a range of health issues, including cancer.
“DEE is created by burning diesel fuels. It contains a mixture of airborne chemicals that can be harmful to people,” the Cancer Council said
“When breathed in, these chemicals increase your risk of developing long-term health problems. In Australia, DEE is the second most common carcinogen workers are exposed to, behind solar UV radiation exposure.”
Diesel engines will have a role in mining operations into the future, so it’s important operators and workers learn how to minimise the risks.
Workplace standards require sites to limit diesel particulate matter (DPM) exposure to 0.1 milligrams per cubic
The NSW Resources Regulator has intensifies efforts to combat psychosocial hazards in mining. But what exactly are these hazards?
Psychosocial hazards extend beyond bullying and harassment and may include sexual assault, physical assault or psychological abuse. They are defined as a threatening, violent, forced, coercive, or exploitative behaviour or act where the victim has not consented or was unable to do so.
Under relevant workplace health and safety legislation, any incident that results in a notifiable injury or illness must be reported to the Regulator.
metre of air. DPM must not exceed this threshold over a time-weighted average for an eight-hour period.
Safe Work Australia poses the following questions to help sites work out whether diesel exhaust emissions may pose a risk to workers:
• Is there visible smoke near the exhaust point? What is the type of smoke? For example, is it white, black or blue? How could it be avoided?
• Is there a visible haze in the workplace? Can it be avoided, and how?
• Are vehicles and plant left idling when indoors or in enclosed spaces?
• How many engines are running at any one time? Are they all necessary?
• Are there soot deposits in the workplace? How significant are they? What can be done to avoid them? What methods are in place for regularly cleaning the workplace?
• Have there been any ill-health complaints from potentially exposed groups? If yes, what has been done about it?
Safe Work Australia defines a psychosocial hazard as anything that could cause psychological harm, such as low job control, lack of role clarity, isolated work, and traumatic events or material. This includes physical assault and related harm.
“Psychosocial hazards can create stress,” Safe Work said. “This can cause psychological or physical harm.
“Stress itself is not an injury, but if workers are stressed often over a long time, or the level of stress is high, it can cause harm. [This] may include anxiety, depression, post-traumatic stress disorder, sleep disorders,
• Is the engine being operated at full speed or left idling?
• What is the state of the engine, and how many kilometres or hours have been completed? Can the engine efficiency be improved, and can operating times and distances be reduced?
• What happens to the exhaust emissions? Do they enter directly into the workplace, or are they piped away so they don’t enter the workplace where they are being produced or other any premises? Are they processed through a treatment system? Could they trigger your fire-detection system?
• Is it necessary to use diesel engines, or can alternative power sources be used?
DPM can be driven down via a hierarchy of controls: elimination of risk; substitution; engineer controls; administrative controls; and personal protective equipment. Higher order controls include replacing diesel with electric or gas, using ultra-low sulphur and low-emission diesel fuels, refurbishing engines to improve efficiency, installing devices to reduce DPM and emissions, etc.
“Physical harm may include musculoskeletal injuries, chronic disease or fatigue related injuries.”
NSW Resources Regulator chief inspector Anthony Margetts said the watchdog is steadfast in its commitment to eliminating issues that could impact workers’ mental or physical health.
“We aim to create safer, more respectful workplaces for everyone,” he said. “Psychosocial hazards ... may cause a response resulting in psychological or physical harm caused by workplace environments, workload, work tasks, equipment provided or working relationships.”
The Queensland Government has passed the Resources Safety and Health Legislation Amendment Bill 2024
The reforms are designed to modernise regulatory enforcement powers, ensuring the state’s resources safety and health legislation is contemporary and effective.
Mine and quarry sites will now be required to introduce critical controls in their safety and health management systems, with ‘enforceable undertakings’ being introduced for the first time in the Queensland resources industry.
Regulating critical controls will help to ensure more incidents are prevented before they occur.
An enforceable undertaking is an alternative to prosecution and allows the regulator to
accept a legally-binding promise to take action from individuals and companies where they have breached the safety and health legislation, but not in matters involving workplace deaths.
“The most important thing to come out of out of any workplace at the end of each shift is its workers, and that is why safety is my number-one priority,” Queensland Resources and Critical Minerals Minister Scott Stewart said.
“Our goal for these reforms was to improve the resource sector’s safety and health performance, and to reduce the number of fatalities and serious accidents.
“The resources industry is a key driver of the Queensland economy, but we can’t have a thriving
resources sector without robust safety measures in place.”
The changes will be implemented over the next five years.
The changes to the Resources Safety Acts were informed by recommendations from the Brady Review into fatal accidents at Queensland mines, the Queensland Coal Mining Board of Inquiry, the coronial inquest into the death of Gareth Dodunski, and industry consultation.
“This has been a monumental effort and I want to thank everyone who contributed to these reforms,” Stewart said.
“In particular, [I’d like to thank] the parents of Gareth Dodunski, Michelle and Phil, who bravely recounted the devastating loss of their son during the Committee hearings.”
The NSW Resources Regulator is calling for vigilance after two recent incidents involving unintended vehicle movement.
Both incidents occurred over a single week in April.
The first incident took place at an underground coal mine in NSW. Two operators were installing a section of steel pipe to a roof using a machine designed to carry and lift pipes for installation. The machine was connected to a vehicle.
Before commencing work, the miners positioned the vehicle to install the pipe, then installed wheel chocks.
The operators left the door of the vehicle open and the vehicle in first gear. During the lift, there was a mechanical declutch failure and the vehicle unexpectedly rolled away about one metre.
The Regulator said of the incident that mine operators must ensure equipment is maintained to appropriate standards and that a risk-management approach is
taken to designing preventive maintenance strategies.
The Regulator also recommended that mine workers should not rely on safety interlocks (such as wheel chocks) for general isolation of equipment unless the interlock is specifically designed for such a purpose.
The second incident occurred at an underground metals mine. A truck operator let the vehicle idle down
before shutting it off in neutral and engaging the park brake.
It sat for roughly 15 minutes on the production level of the mine before the driver heard a creaking noise and the truck moved backwards a short distance.
In each of these cases, no one was injured. However, both incidents had the potential to cause serious harm and demonstrate how crucial it is to properly maintain vehicles.
FLY-IN, FLY-OUT WORK IS A FUNDAMENTAL PILLAR OF THE RESOURCES SECTOR, BUT IT HASN’T ALWAYS BEEN AN EASY LIFE. SAFE TO WORK LOOKS AT NEW AND EXISTING TECHNOLOGIES THAT ARE MAKING THINGS MORE COMFORTABLE FOR THE FIFO WORKFORCE.
Much of Australia’s history is scrawled with iron and written in gold. From Ballarat to Mt Isa, mining has driven the development of many of the country’s major settlements, with prospectors moving to the mineral-rich areas with their families, establishing a community, and settling in for what often became generations.
But the nature of the mining industry has changed. The modern miner surfs on the east coast on Sunday and heads to work in the Pilbara on Monday.
Such is the nature of fly-in, fly-out (FIFO) work for more than 100,000 people in Australia.
Having access to this kind of mobile workforce allows mining companies to set up shop in some of the most remote parts of the country. Workers often operate on a two-week-on,
two-week-off basis, so the task of transporting, housing, and feeding them can be a logistical headache for any organisation.
But emerging technologies and conscientious operational expenditure are helping companies get the most out of their FIFO workers, while also keeping them safe and comfortable.
Rio Tinto managing director for iron ore port, rail and core services Richard Cohen recently described some of the difficulties faced by FIFO workers in the 1990s.
“Things were pretty tough. It was very remote. They were in locations where supply chains were challenging … options were limited for flights,” Cohen said in an interview with WA Times. “People spent a lot more time away from family.”
These days, flights are more plentiful and supply chains more robust, making for a much more pleasant experience for workers.
As recently as February this year, Mineral Resources (MinRes) struck a deal with Skytraders to operate weekly return flights between Brisbane and two of the company’s mine sites in the Pilbara.
Rio Tinto, which has 25 accommodation villages in the Pilbara alone, requires 170 flights from 15 different airports every week. On site, 160 buses move 11,000 workers around the mines every day. And villages receive weekly supplies from close to 150 semi-trailers, which drive thousands of kilometres from Perth.
FIFO work has so thoroughly cemented itself as the norm that equipment and service providers tailor their products to a mobile workforce.
FIFO work has long enabled the effective operation of remote mines.
Most modern work boots, for example, come with the option of an airport-friendly composite toe cap which, unlike typical steel caps, can easily pass through metal detectors. And mandatory drug and alcohol testing can now be done remotely, with results sent to the mine before a worker arrives.
As the industry grapples with a stretched labour market, mining companies are actively trying to
improve the quality of life for FIFO workers in order to attract more talent.
MinRes has been on a mission to boost the mental and physical wellbeing of its FIFO workers with the construction of 750 resort-style ‘pods’ at its Onslow Iron project in the Pilbara.
These apartment-like rooms will feature a queen-size bed, separate ensuite, laundry with washer and dryer, kitchenette, lounge, big screen television with video-call function, and a balcony.
Outside of the pods, on-site amenities include an Olympic-size swimming pool, bistro, café, lounge and indoor fitness centre, as well as a recreation building with a cinema, golf simulators, pool tables, and more. There will also be multi-purpose courts for a range of sports, including outdoor gym facilities, and places for quiet reflection.
“We want to redefine what it means to be a FIFO worker by creating a home away home and a genuine community environment for our people,” MinRes chief people and shared services officer Bronwyn Grieve said. “To do that, we must have high-quality, comfortable and secure accommodation. That’s exactly what these pods will deliver. They are a game-changer.”
BHP has taken an alternate path to the wellbeing of their FIFO workforce. In July 2023, the company completed a three-year and $300 million safety upgrade to its Pilbara accommodation.
The investment saw more than 10,000 rooms upgraded across BHP’s 13 Western Australian Iron Ore (WAIO) villages. The project included installation of over 10,000 new doors, 8000 lights, 1500 CCTV cameras and more than 4km of fencing.
“Safety continues to be our number-one priority and I’m happy to see this work complete to make our villages feel safer and more accessible for everyone who visits them,” WA Iron Ore non-process infrastructure general manager Kate Holling said.
The drive to make FIFO workers more comfortable arises because the nature of the work is inherently tough. Spending weeks away from home in remote parts of the country and working shifts as long as 12 hours can challenge even the hardiest miner.
The national policy body Safe Work identified FIFO workers as among the most at risk of workplace fatigue.
Contributing factors to fatigue include poor quantity or quality of sleep, shift work, long working hours, extended exposure to hazards (such as noise, vibrations, contaminants and loud noises), physically or mentally demanding work tasks, and lack of proper fatigue-management training.
Fortunately, mine sites are integrating technology to help make workers less susceptible to fatigue, and to drive down fatigue-related incidents.
This includes advancements as specific as eye-tracking technology for vehicles, which can trigger a warning if any tired signs are detected in the operator. More generally, collisionavoidance technology also helps to minimise the effects of fatigue, as the system is able to detect and, in some cases, prevent an accident on its own.
Personnel tracking is another way mines are combating fatigue. Electronic tagboards are being used keep track of personnel in underground mines, ensuring they don’t work longer than rostered.
A relatively new technology is wearable condition-monitoring devices, which allows mines to monitor things like heat stress and fatigue in their employees in real-time. This means fatigued workers can be removed from potentially hazardous areas before an incident can occur.
Automation is also playing a major role in driving down fatigue-related incidents by removing workers from hazardous areas.
A 2007 Caterpillar study showed that roughly 65 per cent of truck haulage accidents in mining operations are directly related to worker fatigue. Automating machinery and equipment eliminates such risks, allowing people to work remotely from the comfort and safety of an office.
Another benefit is that downtime due to shift changes is eliminated because the machines can stay up and running. This is paving the way for shorter shifts, which is a significant step towards achieving a healthier sleep schedule.
With the rise of safety technology, greater awareness of mental health, an increasing emphasis on highquality accommodation, more direct flights, and generous wages, one could say there has never been a better time to be a FIFO worker.
Looking for a way to streamline your mining operations with a single, unified platform?
3DConnect is your eyes and ears underground. This software package provides visual and tracking information in real-time and was built understanding the unique complexities of your environment.
> Provides a real-time overview of your operations underground
Automation allows you to configure, manage and monitor localised and distributed automation events such as ventilation on demand, turning on and off water pumps, automated opening and closing of ventilation doors and better traffic management
> Consolidated view from multiple mine sites
> Customised views, dashboards, and reporting designed to focus the information that is important to you
> Tracking viewing options to scale with increased granularity, or coverage
> Direct messaging from within the tracking map
> Inclusion of surface maps to gain a total view of your mine operations
> Reallocation of resources from manually undertaking these localised processes
> Integrate your third-party smart sensors and control technology into our digital ecosystem to monitor, control and report on
> Set up unique rules for your individual needs such as tracking information of people, vehicles and equipment entering an area or zone
MST Global +61 2 9491 6500
> Multiple control units can be used to ensure the entire localised process is automated
We specialise in mining and tunneling technology that empowers you to unearth safety and productivity improvements. Over the last 30 years we have consistently delivered innovative solutions that not only address the needs of our customers today, but also their future needs.
> Use the pre-written sensor templates provided
Sentinel digitally manages the location of your personnel underground. We monitor the tracking of your people from the moment they sign on, how long they have been in certain areas for and help with the management of their individual health and wellbeing, and in the event of a crisis.
> Helps to manage your personnel from how many people are in one area at a time
> Health & wellbeing management from an individual perspective
> Tracking of personnel with full profile information provided when selected
> Removes human error by digitalising this process
> Increases safety management of personnel underground in the event of a crisis
SAFE TO WORK SAT DOWN WITH YANCOAL AUSTRALIA HEAD OF TRAINING CRAIG HAGAN TO DISCUSS HOW MINE OPERATORS CAN IMPLEMENT A CULTURE OF SAFETY EXCELLENCE.
Yancoal Australia rolled out its ‘Safe way every day’
up-and-down nature of a game of snakes and ladders.
you land on a snake, you know how to keep climbing upwards.
If you ask Hagan, it starts with knowing the data.
“The most important thing is to understand why your incidents are happening and how they relate to human-factor elements,” he said.
“Having that kind of operational knowledge will allow you to build your framework around it.”
When Yancoal examined its own data, the company found that 85 per cent of incident root causes of safety incidents were related to an element of human behaviour, such as rushing, taking a short cut or a loss of concentration. Despite the implementation of comprehensive layers of risk assessment, governance and supervision, a persistent theme emerged: inconsistent individual behaviour often led to incidents.
“As humans, we’re often prone to trying a different approach – to taking a short cut and deviating from the norm – and if we do that enough times in a row and get away with it, we actually
create a new neurological pathway where that behaviour becomes a natural occurrence,” Hagan said.
While there is a role for rigorous, legally compliant, up-to-date safety procedures on a mine site, part of the journey towards a culture of safety involves empowering employees to recognise the significant impact of human behaviour, and the ability to normalise risk, on their decisionmaking processes.
‘Safe way every day’ tackles this situation with a coaching approach, where every individual is empowered to speak out if they feel unsafe, or see something unsafe, on-site.
This allows employees to keep themselves and others in check without fear of speaking out.
At an operational level, Yancoal has implemented ‘12 safe way behaviours’:
• I will always stop the job if I feel it is unsafe or I am unsure of the safe way to perform the work activity
• Extend coverage
• Reduce operational costs
• Full accessory portfolio
• I will always consider health, safety and wellbeing when planning work
• I will always attend fit and healthy for work, both physically and mentally
• I will only operate vehicles, plant and equipment for which I am trained and authorised
• I will always complete pre-start checks before operating any mobile plant, equipment or machinery
• I will always follow mine site traffic rules and vehicle operation requirements
• I will always use safety or protection devices, and never remove, bypass or interfere with them
• I will always establish effective isolation and verification when working on plant or equipment
• I will always remove my hands and body from the potential line of fire or risk exposure
• I will never lift a load over any person or enter under a suspended load
equipment or when in a designated operations area unless instructed “People can get into a false sense of confidence when it comes to risk-taking behaviour and, after long enough, not realise that they have created bad habits,” Hagan said. “Unless you’ve got that peer support,
and unless you’ve got that confidence in a no-fear leadership process where people can put their hand up and say, ‘hang on a minute, I might have lost my way’, then you’ll end up seeing a higher numbers of incidents.
“As humans, we’re all subject to making mistakes, and having that better peer support network allows someone else to be able to keep an eye on us when we’re conducting high-risk tasks.”
‘Safe way every day’ has taken safety at Yancoal to new heights. The company has not only experienced significantly fewer incidents, but has increased incident reporting by 32 per cent and achieved a 96 per cent positive safety feedback rating from its employees.
But a change like this doesn’t come about overnight – it’s the result of years of dedication and determination from the whole Yancoal team.
“The key thing is that when you start down this path, you have to be committed to implementing a long-term operating model change,” Hagan said.
“There will be ups and downs, but you have to commit to the cultural framework and maintain that energy as an integral part of the business model going forward.
“There is a fixed mindset that when people go to work, safety is the responsibility of the company.
“What we’re teaching people is that safety is a shared responsibility and, in actual fact, we’re all safety leaders, regardless of our role in the business.”
Systems and technologies designed to increase the safety of people working in and around heavy mobile machinery.
Centralised software platforms for monitoring, training and reporting
Proximity Detection & Collision Avoidance Systems
• HazardAVERT® Electromagnetic
• HazardAITM Artificial intelligence detection systems
• Full Level 9 EMESRT capability
When it comes to mining, drill and blast remains the most effective way to unlock orebodies and move earth.
But as effective as the results may be, the process can be a dangerous one, and that’s why mine sites go to great lengths to ensure people and assets are clear from the blast.
On a medium- or large-scale mine site with many employees, this preparatory work is time-consuming.
“It generally takes a long time to ensure that an area is cleared,” Epiroc business line manager digitalisation Andreas Prill told Safe to Work
“Sometimes hundreds of people need to be accounted for, and the blast area needs to be visually inspected often to ensure nobody is left behind.
“This results in inefficiencies, underutilisation of resources, reduction of production output, and reduced safety at the blast.”
But what if there was a faster and safer way of preparing an area for blasting?
That was the question pondered by the minds at Epiroc. Their answer? That the foundational technology already existed in the company’s own portfolio, and it just needed a little recalibrating for surface operations.
So it was that Epiroc coupled its proven underground safety technology, Mobilaris Situation Awareness, with new technological developments. The result was Blast Support, a new-generation safety solution for surface mining.
“Blast Support can tell in real-time whether an area is safe to blast or not,” Prill said.
“It works by assigning Wi-Fi or LTE [long-term evolution] tags to people in the mine and utilising open-space positioning and satellite imaging to create a 3D map of the blast area, including surface blast zones and tunnels.
“With these two tools, we are able to create different blasting and clearance areas and the system can account of everybody in real-time.”
Blast Support is a modular addition to Mobilaris Situation Awareness, which allows live tracking of people and 3D visualisation, as well as the ability to send zone-based messages. This not only includes 3D mapping of the blast area but also other hazardous areas such as where there is a risk of rockfall or land slide.
With Blast Support and ZoneBased Messaging, a site can map out danger zones, monitor the position of
workers in real-time, and send informed warnings or alarms to those workers to clear the area. The new system is also technology-agnostic, making it compatible with various LTE networks and tags, including Epiroc’s virtual tag, an application for Android smartphones.
Prill said it’s important for Blast Support to be interoperable with thirdparty communication infrastructure already in place at mine sites, allowing for simple integration and reduced capital expenditure.
“Blast Support reduces time for blasts by ensuring that all personnel and equipment are cleared from the area on time,” Prill said. “And, most important of all, it provides another layer of safety for workers.”
The foundational technology has been on the market for over a decade and deployed at more than 40 sites around the world.
“Although open-pit mining faces different challenges than underground operations, it also shares many similarities,” Prill said.
“We are now unleashing battleproven solutions from underground mines to create new values for surface mines.”
Epiroc has not stepped onto this path lightly. The ability to map people and assets on a surface mine in 3D is a significant achievement; it lets command centres track the precise position of workers, including at depth, which is particularly relevant when conducting blast work at a tiered pit.
“We believe that Blast Support is second to none,” Prill said.
“Blast Support avoids this limitation. It is not a trivial thing to define a 3D
Ensuring people and assets are cleared from the blast zone can be a time-consuming process.
space in a virtual map, which then reflects an exclusion zone for blasting.
“Epiroc has years of experience in underground blast safety, and with Blast Support we have brought this important technology to the surface.”
Epiroc’s Blast Support strikes an ideal balance between safety and speed in blasting operations. And with the technology’s proven history underground, Epiroc’s rise into surface mining is sure to kick off with a bang.
If there’s one word Strata Worldwide managing director Tony Napier uses to describe the company’s collision avoidance technology, it’s ‘dependable’.
Strata’s HazardAVERT system is designed to alert workers to imminent machine-to-machine or machineto-person collisions. The system works via communication between electromagnetic devices worn by workers and attached to machinery. That means no machine learning is required, just good old-fashioned physics.
“One of the biggest issues with other proximity systems is variations in performance,” Napier told Safe to Work. “A huge strength of the HazardAVERT system is its reliability and consistent performance across variations in worksites.”
With the continued rise of artificial intelligence (AI), mine sites have recently been graced with tagless systems that are able to identify people and assets using machine learning.
And while there are certainly places for those AI technologies, there’s no replacement for tried-andtrue collision avoidance technologies like HazardAVERT.
That was what global mining titan BHP felt when it selected Strata’s HazardAVERT technology at the Olympic Dam copper mine in South Australia.
After a two-year selection process, HazardAVERT is being deployed across 700 underground vehicles at the site – the largest single order of HazardAVERT to date. The system will also be implemented
with 120 underground refuge chambers, so drivers would easily be able to locate their nearest safety pod in an emergency.
While many proximity-detection systems provide coverage of up to 20m, HazardAVERT extends out to 50m, which was a requirement from BHP. Napier said this gives pedestrians and vehicle operators critical extra seconds to take corrective action. And as the mining industry has previously discovered, those additional seconds can be the difference between safety and fatality in a collision event.
HazardAVERT is dependable and simple to integrate, making it a great fit for a range of mine sites. The technology has been deployed at new and established mines, and at a range of intervention levels. This spans from intervention level seven (audible and visual alarms) through to level nine intervention controls, where HazardAVERT will physically stop a vehicle in a proximity event.
It has long been said that people learn from their mistakes, and while this remains true, HazardAVERT’s data capture allows mine sites to learn from the mistakes they don’t make.
Proximity-detection data is reported to management via the cloud, giving site leaders the ability to identify
and action potentially high-risk behaviours in the workforce. While not something that can be quantified, this can help avoid future proximity events altogether.
Strata also has an AI proximitydetection system called HazardAI, which has its own unique applications. Using a combination of stereoscopic 3D cameras and AI, the system is able to differentiate between people, machines and obstacles out to 30m, and analyse collision potential.
“HazardAI and HazardAVERT can work concurrently, because while they have the same purpose – collision avoidance – they operate in different manners and have different strengths,” Napier said.
HazardAI’s applications are relatively broad, including static and mobile applications like workshops to monitor the interactions between people and vehicles, or in high-risk areas thanks to its ability to establish exclusion zones.
In the case of mobile applications, the system can be mounted to mobile assets to monitor the interactions between people and vehicles.
HazardAI also has the benefit of not requiring tags, making it well suited in circumstances in which those tags cannot be guaranteed. In the resources industry, this might be a fabrication workshop, vehicle depot, or quarry, where members of the public might be located in the immediate vicinity.
In high-risk areas requiring an exclusion zone, HazardAI could be used to trigger an alarm if a person enters a zone in which heavy vehicles travel.
Similarly to HazardAVERT, HazardAI sends proximity data back to management via a series of reports and online portals, providing a more accurate picture of the day-to-day situation on the ground.
Mine safety technology has made significant strides in recent years,
making work safer and more efficient than ever. However, if disaster strikes, operators need to know their people will be safe.
For over 20 years, Strata has been supplying the mines all over Australia with its high-quality refuge chambers, which are designed to shelter workers in an emergency, providing oxygen and other essential supplies.
Napier describes Strata’s refuge chambers as premium quality at a fair price. The chambers come in 24- and 36-hour variants and can house 4–20 people depending on the model. Strata also offers optional extras such as communication support and collision avoidance capabilities.
Whether it’s the dependability of HazardAVERT, the flexibility of HazardAI, or the robustness of underground refuge chambers, from the surface to the underground, Strata Worldwide has the mining industry covered.
Wcoal mine’s longwall operations, workers welcomed the change with open arms.
This reception was due to the fact those workers knew what is not always clear to others: automation is here to enhance the operator experience, not take away jobs.
Centennial Coal’s Mandalong mine reached a crux with its longwall operations when the coal seam changed from a 4m height to just 2m. Work in such a confined space is hazardous, compressing the senses and straining the body. Add in all the bulky equipment necessary for a longwall operation, and miners needed to crouch just to go about their jobs.
So for the sake of its workers, Centennial turned to Komatsu for a solution.
autonomous systems with thirdparty equipment, the straightforward approach is sometimes the best.
“Mandalong adopted a full Komatsu approach,” Komatsu engineering manager, control and automation Shane Cooling told Safe to Work
“What they wanted was a turnkey solution; they didn’t want to risk delays associated with relying on multiple vendors.”
Taking the reins of the project, Komatsu delivered a top-to-bottom autonomous software package.
“We helped build a full control room which has access to equipment that you would normally find underground, such as roof supports and shearer control systems,” Cooling said.
“This allows operators to work from the safety and comfort of a remote office.”
designed to enhance an operator’s skillset, rather than replace the worker.
“We’re focused on moving industry away from the stigma that automation and remote work will take away jobs,” Louw said.
“Instead, we’re focusing on how we can take experienced operators and apply their skills in a safer environment, giving them access to additional data that they wouldn’t have underground.
“We find that they’re becoming better operators of the longwall.”
Any underground miner understands that sight is critical to safety. In the case of Mandalong, each roof support machine was mounted with a camera to provide remote operators with a fronton view of the seam.
Komatsu’s graphical user interface (GUI) for cameras took this to a whole new level.
“Operators can customise our camera GUI, allowing them to focus on any aspect of the longwall operation that they choose,” Cooling said.
“The intention is to recreate what an operator experiences underground, rather than providing a static screen.”
Komatsu takes this principle and elevates it by providing operators with camera coverage of parts of the process not ordinarily visible.
“Our camera GUI allows operators to have multiple camera layouts for a holistic view of the operation –you just don’t get that same level of awareness when down at the face,” Cooling said.
“In many cases, this means being able to see when things are going wrong. Some of our customers use our system to make sure longwall shields aren’t being left behind.
“Starting another advance cycle while a shield is left behind could damage the equipment, causing a significant disruption of operations. This is just one application of many.
“Having access to all of those different camera angles is very critical.”
The technology also includes critical safety functions such as personal proximity detection to halt the machine if a worker is spotted in the immediate vicinity.
Komatsu’s automation system not only gives operators a visual overview of operations but also an audible one.
“When operating longwall machinery, it’s important that a worker can hear what’s going on to know that everything is moving as it should,” Cooling said.
“We have system-generated prompts, which gives operators a visual and audible alert for a range of events in real-time.”
In addition to ensuring familiar working conditions, this also keeps employees safe from harmful levels of noise and vibration.
Put these pieces together and it’s clear that enhancement, not replacement, is the ethos behind Komatsu’s automation profile.
Since partnering with the OEM, Mandalong has reaped a range of safety and operational benefits.
Being able to receive audible instructions means workers do not
have to stay glued to the screen at all times. In certain circumstances, this time can be spent on administration work, with the operator keeping an ear out for any alerts.
Remote operation also eliminates downtime during shift changes, where machinery would ordinarily have to power down, due to transportation between the face and the surface.
“Automation presents an increased value because mines are able to continue operating during shift changes where they weren’t producing before,” Cooling said.
“And the other side of this is that it allows the business to roster better shifts for the operators on the surface.
“With reduced machine downtime, shifts for surface operators don’t need to be as long as traditional 12-hour underground shifts, which means operators are less tired and less prone to fatigue-related errors.”
Most importantly, automation is trading difficult working environments like Mandalong’s low seam for the safety of a remote management location.
Safety, quality and innovation are the pillars that underpin blasting specialist BME, and guide every aspect of its operations. A member of the Omnia Group, BME has been ramping up its presence in Australia for the past year.
The company’s safety-first approach to blasting has resonated strongly with the mining industry. This reception has been instrumental in BME’s decision to announce the establishment of a new manufacturing facility in Western Australia.
When asked what sets it apart from the rest, BME senior product manager Dr Rakhi Pathak said it was the company’s ability to deliver customers tailored blasting solutions suited to their specific requests.
“Whether underground or on the surface, BME can customise its emulsion, blasting design, delivery systems and software solutions to suit
the varied needs of our clientele,” she told Safe to Work. “BME Australia can offer customised solutions that deliver safe, reliable and high-quality blasting.”
BME’s manufacturing methodology is characterised by meticulous attention to detail. Each raw ingredient used in its emulsions goes through a series of quality tests, while automation assembly lines used in the manufacturing process feature built-in safety and quality assurances.
This type of precision is crucial in safeguarding against the introduction of unforeseen elements into the product, thereby preserving its quality and stability.
Emulsions are also manufactured at low temperatures using recycled oil, which helps to reduce power consumption and waste, while also lowering carbon emissions.
“Dual-salt emulsions have extended shelf life, can tolerate extreme operating conditions, and offer increased blast performance,” Pathak said. “They are also much safer to transport than traditional emulsions, which is very important in Australia, where operations are often in remote and hot environments.
“Dual-salt-based emulsions are highly robust systems that can be successfully pumped multiple times and are less susceptible to crystallisation, the cause of product breakdown and fumes.”
Speaking of fumes, the emission of harmful gases during blasting has long been a safety concern of the mining industry. But BME’s dual-salt emulsion significantly reduces these risks.
“The chemical composition of dualsalt emulsions can be easily optimised to minimise the generation of harmful gases,” Pathak said.
“A careful balance of the oxidiser – the ammonium nitrate and calcium nitrate – and the fuel in an emulsion is necessary to ensure only harmless gases are generated.”
These emulsions are also less susceptible than traditional explosives to nitrate leaching, which can cause environmental damage and threaten a mine’s compliance with relevant legislation.
BME’s blast detonation technology AXXIS is where the safety functions truly come to life.
AXXIS Titanium is the latest product introduction of the initiation system, which includes several safety gates against stray currents and lighting to prevent accidental initiation. Blasts can only be triggered by a robust, encrypted blast command from AXXIS Titanium, which ensures all electronic delay detonators receive their respective commands and fire as planned.
In other words, the detonator will only react if it receives the correct encrypted firing sequence from the blasting equipment.
AXXIS Titanium also incorporates dual capacitors and dual voltage, allowing users to conduct low-voltage testing and logging to avoid any chance of detonation.
“These detonators also bring significant additional safety benefits
in blast initiation due to their ability to be tested before being fired, facilitate two-way communications, reliability, programmability and precision,” BME general manager Australia Michael Wiseman said. “Mining operations can now be more confident that misfires can largely be eliminated due to these attributes.”
In an important strategic milestone for BME Australia, the company is advancing a manufacturing facility for its detonators in Kalgoorlie, WA. When operational, this facility will make BME the first local manufacturer of electronic detonators in the state. And, importantly, the facility will also provide the WA mining industry with significant supply chain security and logistical benefits.
“There has been a significant market shift away from shock tubes and towards electronic detonators in Australia’s mining sector,” Wiseman said. “BME’s explosive systems have a range of safety features, including a double-insulated copper core, giving
market-leading strength to in-hole stresses during loading and firing; two-way communication between detonator and firing system; full trackand-trace from plant to pit; and onemillisecond accuracy across the full range of firing times.
“BME’s technology contributes to industry’s risk-mitigation efforts, but also holds performance benefits in terms of facilitating large, accurate and reliable blasts.”
Pathak said BME adopts a comprehensive “end-to-end valuechain strategy” to its operations, addressing not only safety and supply chain considerations but also environmental factors.
In line with this ethos, the company is developing a sustainable blasting solution, which has so far yielded exciting results.
In partnership with Hypex Bio, BME is developing a nitrate-free emulsion, which will have significant environmental benefits. The new emulsion has so far demonstrated a 90 per cent reduction in nitrogen oxide gases.
“At BME, we’re always looking for the next thing – harnessing new technologies to make things safer not just for people but for the environment, too,” Pathak said.
For BME, everything from the design stage through to when the dust settles on a blast has been painstakingly engineered.
From the underground to surface mining, the company’s suite of blasting solutions is making mining operations safer across Australia.
As technology evolves at a rapid pace, it is becoming more of a challenge for mines to maintain interoperability between communications and safety systems.
While mine operators prefer to have the flexibility to buy from different vendors, this freedom can, somewhat ironically, become a restraint.
Having multiple systems onsite means operators must ensure those systems are able to talk to and interface with each other.
Multiple systems also means multiple vendors, which can cause logistical issues. Some vendors may be more responsive than others, while others may not be in the practice of regularly updating their product.
A break in this chain, the strength of which depends on so many parties, jeopardises a whole operation. That’s why mining companies are favouring a single port of call when it comes to communication and safety systems.
Not a link in a chain, but a suit of armour. Not a vendor, but a technology partner.
MST Global, which has been making underground mines safer and more productive for more than 30 years, is just such a partner. The company has a portfolio of safety and productivity solutions perfectly suited to the resources sector.
When it comes to communication technology, MST is a one-stop-shop for miners. This helps to remove the stress and time delays that can be associated with multiple vendors, giving operators more time to focus on what they do best – production.
“We create a partnership with our customers to help them achieve their goals, providing seamless integration between our modular solutions, which encompass everything from telemetry to safety to productivity,” MST general manager of product management and marketing Alexander Gawad told Safe to Work “Everything comes together in a very tightly integrated way.”
HELIX is MST’s modular software platform for underground mining. The foundation module allows realtime location tracking of personnel and assets using Wi-Fi tags. This is accomplished through MST’s wireless network infrastructure, eliminating the need for dedicated tracking infrastructure.
But where HELIX really distinguishes itself is in its modular design. Mine sites can adopt modular software features such as
equipment condition-monitoring, sensor-monitoring for strata and environmental conditions, fleetmanagement system, automation solutions, and many more.
These options help operators customise their approach to mine safety and productivity, allowing them to focus on a range of factors at once, or home in on niche issues affecting their site.
Modularity also means operators are not bound to an entire package but can instead purchase modules as needed, helping to manage capital expenditure, and providing scalability as operations grow or demand for complex solutions increases.
HELIX IoT (Internet of Things) is a software module that works in tandem with its hardware counterpart, AXON Gateway.
The AXON Gateway collects data from different sensors around a mine, and HELIX IoT displays that information via an easy-to-read dashboard.
While AXON Gateway and HELIX IoT are both MST products, the sensors are third-party products that MST sources for its customers when integrating the solution to a mine.
“These sensors can be used to measure a range of factors in the environment and on structures,” MST product manager for HELIX Ramodh Rangasamy said.
“These can be used to measure key data such as strata movement, diesel particulate matter, air quality, temperature humidity, equipment temperature, and so on.
“We provide the sensors based on what a mine is trying to achieve, and then AXON Gateway and HELIX act in tandem to communicate this information. This gives mine operators a clear view of what’s going on inside their mine.”
HELIX Sentinel is a digital tagboard that extends the safety capabilities of traditional personnel tag-in, tag-out systems at mines.
“Sentinel gives mines a visual representation of who is underground,” Rangasamy said.
“In addition, we can set some rules to, for example, track if people have been underground longer than they should be or if they are entering a restricted area.
“In such a case, Sentinel will show a notification in the digital tagboard and action can be taken.”
Sentinel can be accessed on any browser-enabled device, giving operators and supervisors the ability to keep an eye on their people while on the go.
If Sentinel is the eyes on a mine, then HELIX Automation is the brain. This system works in tandem with, AXON Control. This combo is best understood as a rule engine.
Rangasamy explains it best.
“With HELIX Automation, we can create rules based on different inputs, like sensor readings or asset and personnel positioning, and the system triggers a response,” he said.
“For example, if a sensor reads that the temperature or water level is too high in an area, then the system can activate automatically to turn on a ventilator or water pump.”
Moving into the production side of things, HELIX Dispatch is MST’s fleet-management solution that helps underground mines to maximise their material extraction by increasing productivity.
“We accomplish this through task management and equipment-status tracking, allowing command centres to monitor the activities and statuses of vehicles in real-time, meaning that any decisions or adjustments can also be made in real-time,” MST product manager of Dispatch Nick Rebeiro said.
“One of the other foundational pieces of Dispatch is automating production-tracking, which eliminates the need for operators to manually write down their load data, saving a lot of time”
While vehicles in a mining operation
“HELIX Dispatch was designed to work offline, meaning it can run all of the logistics on-board and then re-synchronise once the network connection is re-established.”
On the safety side of the equation, Dispatch has digitised and enhanced existing processes such as pre-start checks.
MST has another two modules currently in development: Telemetry, a machine health monitoring software; and Safety, a tool for teams to analyse collision events.
HELIX is constantly expanding to help optimise mine-sites safety and operational performance. This is not only achieved through the addition of new modules but also in the improvement of existing modules through software updates.
“HELIX is purchased via annual subscription basis, meaning customers benefit from receiving regular updates to maintain and add new features and capabilities,” Gawad said.
“HELIX is not a one-off sale and product; we partner with our customers, listen to what they need, and deliver those additional capabilities.
“What we offer is a multi-tool for mine safety, productivity, and automation. With HELIX, there is a solution to most problems in the underground.”
When asked why collisionavoidance systems are so critical to a mining operation, Hexagon will tell you it’s about sustainable mining, which cannot happen independent of safety.
“Good mines are safe, and safe mines are good,” Hexagon senior product manager – safety Christian Schorr told Safe to Work
“Safety is an investment that protects people and assets, which pays off very quickly.
“In addition to the obvious benefits for personnel, investing in safety technology also brings economic benefits by avoiding production outages associated with incidents, and helps keep insurance premiums to a minimum.
“Fortunately, Hexagon’s Collision Avoidance System [CAS] helps solve these issues.”
Hexagon CAS utilises a global navigation satellite system (GNSS) unit that calculates a vehicle’s speed and path of movement, improving vision and heightening situational awareness to prevent collisions.
“GNSS-equipped vehicles can warn each other against potential threats by broadcasting their position and direction of travel via a radio signal, which is received by other vehicles using the same technology,” Schorr said.
Hexagon CAS provides 360° operator awareness through cabin display units, which improves operator vision, eliminates blind spots, and heightens situational awareness within 500m.
The system is also able to detect people on the ground via a Hexagon Personal Alert tag, which is smaller
and lighter than a smartphone and can be easily worn by workers.
“Hexagon Personal Alert tags measure the distance between the person and the vehicle via ultrawideband technology contained with the Hexagon CAS smart antenna,” Schorr said. “This makes it possible to alert an operator to the presence of a pedestrian.
“Hexagon CAS protects people and equipment from collisions by combining location and positioning technologies in one smart antenna.”
While vehicle-to-vehicle and vehicle-to-person detection provides a significant degree of protection, object detection takes it to a whole new level.
“Collision with passive objects, such as a haul truck reversing into a structure, can cause severe damage,” Schorr said.
“Our CAS uses radar to protect against interactions with untagged objects, including people and mobile assets.
“Radar adds a significant layer of protection. It works day and night, and in challenging environmental conditions it continues to signal the
operator when a potential collision is detected.”
According to Hexagon, radar reliably works in areas where the GNSS satellite signal is not available, such as steep or deep pits, which rounds out the company’s CAS portfolio.
While preventing accidents is important, regular review and analysis of near-misses is essential to continually improve operations. That’s why Hexagon has introduced CAS Insights to turn unwanted vehicle interactions into actionable data.
“While our other products prevent accidents from happening, CAS Insights aims to alleviate future risks,” Schorr said.
“All the valuable information from the field is collected and provided through dashboards and interactive maps to form the basis of data-driven decisions.”
Hexagon CAS, in combination with CAS Insights, is providing mine sites with well-rounded, multi-dimensional protection. Enhancing safety with the use of radar, wearables and fatigue sensors can make all the difference in mining safely.
BOA HYDRAULICS IS HELPING THE MINING INDUSTRY TAKE COMPLETE CONTROL OF ITS SYSTEMS.
Hydraulics are an integral part of a mine’s mobile assets but, as with any other working part, they are subject to failure.
A burst hydraulic hose, for example, will put a machine out of action, having a significant flow-on effect that results in reduced productivity and profitability. High-pressure hydraulic hose lines also come with a safety risk.
BOA Hydraulics’ hose maintenance and management platform integrates hardware and software to help miners avoid injuries and machine downtime
associated with hydraulic hose failures on heavy machinery.
BOA’s integrated approach is built around the BOAhub app and BOApod mobile repair trailer. The platform is designed to deliver speedy, safe hose repairs, while simultaneously providing full document control and legislative compliance.
Working with hydraulic systems is a heavily regulated area.
Recognised Standard 23 (RS23) guidelines were rolled out in Queensland in 2021 to improve safety and prevent injury associated with fluid power systems. The standard
mirrors legislation in other jurisdictions such as New South Wales.
RS23’s inherent complexity makes maintaining site compliance a challenge. BOAhub offers the advantage of built-in RS23 management functionality across multiple devices.
BOAhub helps to free miners to manage hydraulic systems across quality control, maintenance history, asset-tracking, and automated inventory management.
This helps to ensure hydraulic systems are maintained to a high standard, backed by a secure digital record to ensure RS23 and other relevant regulatory compliance.
“BOAhub eliminates paperwork hassles and compliance concerns,”
The BOApod is an all-weather, allterrain mobile unit that enables users to assemble hydraulic hoses on the go, adhering to original equipment manufacturer specifications applied in manufacturing facilities.
The towable BOApod streamlines repair of hydraulic hoses by enabling vehicles to be serviced in the field.
Delivered to mine specifications, this mobile unit is made for the tough resources landscape. The unit houses precision crimping and cutting machinery, along with all the matched hoses and fittings and all the tools necessary to get the job done.
“The BOApod is known for its ease of use, built with the operator in mind,” BOA said.
“The state-of-the-art hose reel system, which uses a safe remote hose handling system, ensures easy hose management on-site. This also has the added benefit of reducing the risk of injuries associated with manual handling.”
“This smart trailer is fully integrated with the BOAhub software platform, allowing automatic inventory management. Every product within the trailer has a barcoded location, which allows operators to simply scan the barcode to reorder or to add to a job card.”
The mobile BOApod unit can be backed up by the BOA Workshop, a support container set-up with an extensive range of stock tailored to the hydraulic machinery that technicians service on-site.
This unit replenishes the BOApod’s on-board stock and contains a hosetesting facility to carry out on-site pressure testing for RS23 compliance.
BOA Hydraulics has gone to great lengths to source premium hose and fitting brands.
“We know how important products that are superior in performance and service life are when working in high-pressure environments,” BOA Hydraulics said.
“All our hose brands meet ISO standards and are compliant with mine specifications.”
The company sources its hoses from its partner Yokohama, which has its own rigorous approach to quality assurance.
“Yokohama has a proven long-life and high-durability hose,” BOA said.
“These hoses are tested using the rigorous Hitachi and Komatsu spiketesting method.
“This method uses a higherpressure cycle than standard testing – at 1.2 million impulses compared with standard testing of 400,000–500,000 impulses.”
The end result is a hydraulic hose that’s made for mining conditions.
BOA Hydraulics’ fittings are of a similar calibre, meeting all relevant Australian and international quality standards.
“Our products are tested by reputable third-party certifiers,” BOA said.
“And our warranty claim rate is less than 0.03 per cent, so mines can be sure our products are built to last.”
The company supplies its products from strategically located distribution centres, including in Brisbane, Perth, Adelaide and Melbourne.
Hydraulic systems help keep the wheels of industry turning, but tough mining conditions can wear these components down, potentially leading to issues such as equipment failure, injuries, and even fire.
BOA Hydraulics is simplifying hydraulic system management on all fronts, delivering highquality hose and fittings, a mobile maintenance solution, and stress-free RS23 management.
As an island nation, Australia’s ports are critical to its economic health.
Shipping raw materials like iron ore, coal and spodumene to international trade partners is the most efficient way for the resources industry to move its product, but it cannot be done effectively without proper infrastructure.
One key area of this infrastructure is railyard equipment like cranes, stacker-reclaimers and ship-loaders, all of which enable throughput on a massive scale.
But in an environment like Australia, which is rocked by the occasional extreme weather event, these assets have to be sturdy.
“Railyard equipment can have a substantial surface area,” Johnson Industries chief executive officer Lawrence Johnson told Safe to Work
“When subjected to high wind speeds, these surfaces can act like sails, catching wind and leading to uncontrolled movements.”
This movement can pose a risk to people, equipment and production, which is why Johnson Industries is helping to secure machinery with its range of industrial brake systems.
Rail clamps, otherwise known as storm brakes, firmly secure rail-mounted machinery such as a crane to its tracks, helping to ensure those assets remain stationery even in adverse weather conditions.
Johnson Industries’ storm brakes provide a robust grip by squeezing the rail from both sides, which offers greater stability.
These clamps come in a range of capacities from 450kg through to 68 tonnes – or 4.4–667 kilonewtons (kN) – of holding force. Their mountings,
bridge, gantry and container cranes,” Johnson said.
“Our standard assembly includes the floating yoke clamping mechanism, manual release bolt, stainless steel pins, spring actuator, enclosure support structure, limit switch, and flow-control valve.
“Each clamp is supplied as a complete assembled unit, ready for easy installation.”
These storm brakes also come with a failsafe feature: they are designed to remain engaged or immediately engage where there is a loss of power or system malfunction.
“This inherent safety feature is crucial in preventing potential disasters in industrial settings,” Johnson said.
mounted equipment such as stackerreclaimers, and any type of bridge, gantry and container crane.
Johnson Industries manufactures three sizes of wheel grippers, rated at 5.6 tonnes (55kN), 11.3 tonnes (110kN) and 15.8 tonnes (150kN) of holding force.
For an extra layer of safety, each mechanism hosts one or more limit switches, which indicate gripper release, set and wear. These may be interlocked with other equipment, which prevents rail car movement until the gripper is fully released.
Johnson Industries’ brake systems are helping to ensure Australia’s ports stay up and running. The company has been improving its expertise for over a century, keeping operations running and workers safe from harm.
WAVE
TECHNOLOGY
ADAPTABLE F I T
COLOUR CODE
SIMPLIFIED SELECTION
COATING
ANTI - FOG & ANTI-SCRATCH
UNIVERSAL was engineered to combine strength, flexibility, and ergonomics in a light yet panoramic eyewear. Through these innovative goggles, bold adventurers can explore the furthest reaches of time and space. As they venture outward, they can have peace of mind that their eyes are protected with confidence in their enhanced vision.
IT’S TIME TO RISE TO THE CHALLENGE.
JSG Industrial Systems has been a leading distributor of solutions that increase asset lifespan and reduce operational risks for more than five decades.
The backbone of JSG’s portfolio is the strong relationships it shares with its premium suppliers, and FloMAX International is among those partners.
Driven by quality, innovation and value, the US-based FloMAX manufactures industrial fluid transfer system components such as fuel nozzles and fuel receivers, both of which play a pivotal role in efficiently delivering and transferring fuel to industrial machinery.
Known as one of the smallest and lightest such diesel units at just 2.7kg, the FNBL nozzle holds a minimum flow rate of 151L per minute and maximum flow rate of 682L per minute.
“The design includes a sealing mechanism that closes immediately after fuelling, minimising the risk of drips when the nozzle is removed from a tank.”
Fuel nozzles control the flow, atomisation and mixture of fuel with air.
FloMAX’s nozzles provide users with a leak-free process to transfer large fuel volumes at high flow rates. They are available in multiple designs and configurations to accommodate different types of fuelling systems and equipment across a range of industries, including mining.
“The FloMAX fuel nozzles include a flow control mechanism, allowing operators to adjust the speed of fuel delivery,” JSG said.
“This control helps prevent splashing and overflowing, especially in smaller or irregularly shaped tanks.”
FloMAX’s FNBL nozzle offers durability and reliability within harsh environmental conditions due to its all-metal construction and stainlesssteel nose.
The FNBL’s pullback assembly can be removed without tools, ensuring ease of use and cleaning by allowing the nozzle to be maintained and repaired while on site.
“No-spill nozzles are easier to handle and operate,” JSG said. “FloMAX nozzles feature comfortable grips and user-friendly mechanisms that reduce the likelihood of accidental spills caused by operator fatigue or handling errors.”
The FloMAX FN600 nozzle holds the same flow rate and weight as the FNBL; however, the FN600 works best in maintenance facilities and less demanding environments, as it securely latches with a ‘snap’ sound when properly connected to a receiver.
“FloMAX fuel nozzles feature an automatic shut-off mechanism that activates once the fuel reaches the tip of the nozzle or when the tank is full, preventing overfilling and subsequent spills,” JSG said.
According to JSG, a Caterpillar 797B truck with a 6814L tank can be filled in just 13 minutes at 500L per minute by using FloMAX nozzles, saving 21 minutes per fill.
“This speed not only enhances operational time but addresses additional concerns such as safety, environmental protection and fueltheft prevention,” JSG said.
Every FloMAX fuel nozzle connects to all standard fuel receivers and undergoes a 11,360L test before its shipped to ensure functionality and leakage prevention.
“These nozzles are compatible with various sizes of fuel tanks, which translates to efficient fuelling and spill-prevention across diverse applications,” JSG said.
“With an ergonomic design and comfortable grip, the user-friendly nozzles reduce the likelihood of accidental spills caused by operator fatigue or handling errors. And, critically, the nozzles are built to
handle the harsh conditions of the mining industry, maintaining their effectiveness over time.”
Fuel receivers facilitate a secure connection and flow between fuel lines. Every FloMAX fuel receiver has been designed with a patented enclosed poppet stem spring that provides a smooth fuel flow path, extending the life of the receiver and nozzle.
The spring is enclosed inside the poppet so the spring is removed from the flow path, increasing fuel flow and reducing back pressure and vibration.
FloMAX has a range of standard diesel fuel receivers and removable sleeve diesel fuel receivers.
The FR-RS removable sleeve fuel receiver comprises an aircraft-grade anodised aluminium body with a removable stainless steel wear sleeve. Its patented design allows the fuel receiver wear surfaces to be replaced without removing the fuel receiver from the tank.
FloMAX also offers anti-theft fuel receivers for maximum flow with minimum back pressure.
Their removable sleeve disconnects separately from the entire receiver, providing maintenance cost savings and enhanced security.
Relatively new to the FloMAX range, top fill units are an all-in-one nonpressure fuelling system designed to eliminate the need to pressurise fuel tanks or use splash filling techniques.
Since the flow of the non-pressure fuelling system is gravity-driven and typically slower, operators will have more time to stop the flow before overfilling takes place. This is especially beneficial when filling smaller tanks, as precision is necessary.
“This typically results in a more controlled and slower flow rate, reducing the likelihood of splashing or overfilling that can occur with highpressure systems,” JSG said.
“The absence of pressurised pumps and complex mechanical parts
means there are fewer components that can fail or malfunction, which is a common cause of spills in pressurised systems.
“They can also be more costeffective to install and maintain, as they don’t require expensive pumps and control systems. This can make them a practical choice for smaller operations or in remote locations.”
Every FloMAX fuel receiver has been designed with a patented enclosed poppet stem spring.
Equipped with a minimum flow rate of 19L per minute and maximum flow rate of 265L per minute, the unit’s compact design allows filling and venting from a single tank opening.
FloMAX nozzles, receivers and non-pressure fuelling systems make JSG a go-to distributor of components designed to ensure fuel is delivered in the safest way possible.
Scheduled plant shutdowns help to ensure optimum productivity, but they are also necessary from a maintenance and safety standpoint.
There are a few unwritten truths about shutdowns that anyone familiar with the process will understand: there is never a “convenient” time; it is impossible to be totally prepared; and completing a shutdown with zero injuries equals success, regardless of how much was accomplished.
Shutdowns are busy times, with in-house and contractor personnel working on tight timetables to complete an array of projects before the scheduled restart date. Budgets, times and production quotas all complicate plant shutdowns.
Despite the best planning, pushing to stay under budget and ahead of time can put sub-optimal equipment back into service, resulting in early failure. The rush to get back into production can also quickly cascade into a workplace hazard that causes “turnaround injuries” or incidents
that result from working too quickly under stringent – sometimes unrealistic – timelines.
Planning for a shutdown should start directly following the previous one, as it can take months to complete all of the required steps.
Scheduled shutdowns have five general, often complicated, steps:
1. Scope
2. Plan
3. Schedule
4. E xecute
5. Evaluate
It is important to identify the main areas of concern and prioritise the list by adding task labels to checklist items according to need: test; repair; replace; defer; do nothing.
For safety and efficiency purposes, it is wise to choose trusted providers
involve them early in the process to gather bids, discuss details and obtain their expert input.
The terms “servicer” and “contractor” are sometimes used interchangeably, since servicers are contracted, but their roles can be very specific: servicers are technicians who perform specialised scheduled tasks like belt cleaner replacement or other conveyor maintenance; contractors are often generalists supplying outside labour or specialists used for major equipment installation and construction, such as crane operators or structural engineers.
However, it is important to note that during a shutdown these may be the same person or company.
In most cases, factory-trained technicians will have greater experience and expertise than in-house personnel or third-party workers.
The goal should always be a project completed safely within the allotted time and budget, but that’s often not the case. An unexpected obstacle that requires a pivot in the plan, a logistical issue with receiving the proper equipment or a serious workplace injury can derail a timeline, resulting in extended downtime and increased costs.
There are several benefits to using the right specialised servicers during a shutdown:
• Training and expertise – they can quickly get the job done, identify potential issues and troubleshoot if necessary
• Faster access to the supplier –they often have maintenance and installation documentation on hand, and quick access to support from the supplier
• Safety and certification –certifications are required for some specified tasks for safety purposes;
using an uncertified individual can increase the risk of injury and could be a liability issue
• Equipment considerations –specialised contractors generally have the proper tools on hand to overcome obstacles
• Engineering solutions – when unforeseen problems arise midproject, experienced contractors can devise a safe workaround either on-site or by communicating with the equipment manufacturer’s engineering staff
• Logistical considerations –servicers often work for or have a parts agreement with the equipment manufacturer, allowing quick access to replacement parts
• Insurance – specialty contractors typically carry specialised liability and workers’ compensation insurance, which provides better protection for the customer than general insurance coverage
Detailed proposals are a key reason contractors and servicers are so valuable. It is helpful to identify outside resources who can help complete items on the checklist and then solicit plans and bids, ie a request for quote (RFQ). These bids, delivered as a proposal or statement of work (SOW), will offer a detailed account for materials, purchased components, contract services and in-house labour.
Quotes for materials should consider lead time not only for delivery, but also for the secondary operations such as preparatory engineering, electrical installation or component fabrication. When the RFQ is issued, ensure all necessary specifications for purchased components are provided.
This is where the budget comes in.
Once the scope, specifications and timeline have been established, operators find that a large portion of planning has already been accomplished; however, sign-off is needed on the bids, which can take
time. Be aware that each SOW may have a purchase order (PO) and, once that’s signed, the plant has committed to the provisions on the SOW.
A PO generally contains a payment schedule with an upfront payment before the shutdown begins to complete material orders, confirm commitments to sub-contractors to secure their schedule, etc.
When planning, be aware of weather, holidays, pending labour contracts and compliance (permitting) issues during the closure period. Each of these can bring a project to a grinding halt.
This is also the phase during which key performance indicators (KPIs) are set for each project. These are metrics that indicate the performance and measures of success of each project involved in the shutdown.
When designs for components and sub-assemblies are finalised, the handover between design and manufacturing must take place.
The project manager should review the schedule, scope and specifications with all of those involved in the supply of the project components and subassemblies. When a project is underway is not the time to experiment with new vendors.
Materials, components and subassemblies need to be inventoried and inspected as they are delivered. To avoid project delays, vendors need to be informed immediately of any shortages or non-conforming items, as well as the intended resolution determined.
Material shrinkage – via damage or pilferage – is a concern on many sites and can affect cost and schedule.
The scheduling process is a good time to ensure all of the required safety protocols and equipment are clearly understood by everyone involved in the shutdown.
Ensure proper certifications are up to date and any specialised equipment is available, lockout or tagout procedures are explicit and followed religiously, and all contractors are certified with the appropriate health and safety authorities.
Underestimating project timelines can rush the work and drastically erode safety, as can several different projects overlapping in the same area.
The project manager is responsible for controlling all work produced within the project scope.
They must watch for and carefully control any changes in scope,
commonly called “scope creep”. Changes for any reason must be documented by a change order.
This phase of the project will utilise the pre-defined KPIs to measure the success of the solution.
Evaluation regarding the performance of the system should be ongoing to ensure that it meets or exceeds expectations measured against the initial requirements in the scope and specifications phase of the project.
An important part of the evaluation phase is also measuring the return on investment for each project. This will often inform budgets into the future and could serve to raise budgets in forthcoming shutdowns to deliver greater improvements.
By thoroughly following these steps, maintenance managers will have a good starting point from which to deliver a successful shutdown. Skipping steps, on the other hand, may result in more unanticipated complications that could extend downtime and reduce overall efficiency.
Allowing the time for projects to be completed in a safe, systematic and compliant manner helps result in fewer injuries and better performance of installed equipment over the long term.
Hexagon's integrated solutions help mines become safer, smarter and more sustainable as they pursue:
Zero harm
Zero equipment failures
Zero mine stoppages
Zero dirty emissions
Zero profit leakages
One platform. One partner. For the life of your mine.
Visit hexagon.com/mining
Nivek Industries is no stranger to making maintenance safer and easier, and the latest tool in the company’s kit, the Lift Assist 80 (LA80), is already easing the burden for fitters all around Australia.
“The LA80 is designed to lift components like heavy tooling, truck brake callipers, wheel cleats, pumps, and more into place,” Nivek general manager Derrick Cant told Safe to Work.
“It’s made for those annoying 40 or 50kg components that workers often have to lift and hold in awkward positions with chains and slings while a co-worker bolts the part into place.
“Since the LA80 is powered by linear actuators, there’s no bounce in the arm, which allows for stable and precise alignment of components even in confined spaces.”
The LA80, a lift-assist arm with a carry capacity of up to 80kg, can lift and hold heavy components in place while it is being mounted or support the weight if being removed.
One of Nivek’s customers is currently using the system to install super-nuts on the underside of a crusher.
“That particular LA80 is mounted onto a fixed structure and is used to hold and manoeuvre 40kg supernuts into position during install and removal,” Cant said.
“Ordinarily, a worker would have to lift and hold these 40kg nuts in place overhead while another person tightens them up. The LA80 makes this a one-man job, lifting and holding the nuts in place while the worker safely secures them.
“This not only makes the job easier and faster, but workers no longer have to risk an injury while lifting these heavy components.”
This example is just one possible application of many. Whether the workspace is open or confined, the LA80 can be used to lift and hold just about anything up to 80kg.
Linear actuation means the carried component won’t move around while being loaded or unloaded from the arm, an important safety feature when handling heavy items.
The LA80 can also be used to hold heavy tooling like rattle guns in place for safe and easy operation. Fitters would typically have to manually handle these tools over many hours, leading to fatigue and increasing the risk of injury, but those hazards can now be a thing of the past.
The LA80 is an invaluable tool to eliminate manual handling tasks and the many associated risks.
For lighter tooling, and where precision is critical, the Lift Assist 40
The LA40 has a lifting capacity of up to 40kg and utilises a springassisted lifting mechanism, giving the operator manoeuvrability when it comes to lining up tools.
“The arm can take the weight of rattle guns, impact drivers and torque tooling, reducing the risk of fatigue and musculoskeletal injuries for anyone working with heavy tools,” Cant said.
“Using the spring-assisted arm mechanism, the LA40 holds the tools’ weight while the operator guides it into place.”
“Not only does this allow for precise work but it reduces vibrations and manual handling for workers.”
The LA40 mounting plate has been engineered to allow operators to easily design a fixed attachment point, or it can be mounted to Nivek’s Tracked Elevation Device (TED). When mounted
LA40 and LA80 can be used almost anywhere thanks to the ability of TED and the larger-model Big TED to access confined and elevated spaces.
While the LA80 is new to market, the LA40 has been around for a number of years, during which time Nivek has furnished it with optional
attachments, such as the hydraulic torque wrench tool, to make the lives of fitters easier.
“The hydraulic torque wrench tool attachment allows operators to position the tool in place and stand back during operation, therefore eliminating the risk of finger crush or oil-injection injuries,” Cant said.
“It was created to stop people from holding these heavy hydraulic tools, particularly above their shoulders.”
And never one to settle for ‘good enough’, Nivek is currently developing a mobile stand for the LA40, which the company is hoping to have ready later in 2024.
Though technology in the mining industry evolves every day, Nivek Industries is keeping pace.
With a dynamic approach to safety technology and a suite of tightly engineered products under its belt, Nivek is helping to make maintenance work safer and more efficient.
BME is a global mining solutions provider. We are a leader in providing sustainable bulk emulsions for commercial mining applications. Our blast design software and AXXIS electronic delay detonators deliver precision and accuracy to improve blasting efficiencies. Our premium dual-salt emulsion systems further deliver effective blasting to reduce costs. This helps to boost our clients’ efficiency, safety and environmental performance.
The Queensland resources sector is set for a major shakeup, with critical controls soon to be mandatory in coal and mineral mines across the state.
Proposed amendments to the legislation address recommendations from the Brady Review of mining fatalities, the Coal Mining Board of Inquiry into the Grosvenor coal mine explosion, and feedback from the Queensland Government’s industrywide safety resets.
The changes proposed by the bill are considered significant, amending the Resources Safety and Health Queensland Act 2010, the Coal Mining Safety and Health Act 1999, the Mining and Quarrying Safety and Health Act 1999, and a number of others.
“The resources industry is a key driver of the Queensland economy, creating jobs and delivering a range of benefits for the state, including royalties,” State Minister for Resources Scott Stewart said.
“However, the most important thing to come out of any workplace at the end of each shift is its workers.
“Our resources industry can only thrive when it has safe and healthy workplaces. These changes are important to address recommendations concerning a number of serious incidents that should not happen again in the resources industry.”
The bill was created in consultation with industry, unions and the community, and focuses on implementing high-reliability organisation (HRO) behaviours in the mining and quarrying industries.
Such HRO behaviours focus on identifying incidents that are precursors to serious accidents, and using that information to identify and act on hazards to remove them.
In order to achieve this goal, the bill proposes a number of changes to the law. One of the most significant changes is the requirement for mines and quarries to develop a set of critical controls with performance criteria that must be incorporated into their respective principal hazard management plan.
These proposed critical controls require:
• senior site executives (SSE) to notify the regulator in the event of a failure of the critical control to meet its performance criteria
• SSEs to monitor the effectiveness of the critical controls, and report the results to the mine operator, on a monthly basis
• coal mine operators to audit critical controls.
Once implemented into a site’s safety and health management system, these critical controls will be overseen by Resources Safety and Health Queensland’s audit and inspection program.
The bill includes additional competency requirements under the Coal Mining Safety and Health Act for key safety critical roles for coal mines and for those left in charge during absences of these roles. This will include improved training and continual professional development requirements.
Safety data and incident reporting is also set for a boost, with the proposed removal of lost time injuries as a safety
indicator. It is believed this will provide a more accurate representation of a site’s safety levels.
The window for reporting has also been extended, with sites now having up to 12 months to report a safety incident. This comes in tandem with increased penalties for failure to report, and further legislative changes to support the transition to a new webbased incident reporting system.
The bill also seeks to modernise regulatory enforcement powers. Under new laws, the regulator will be able to enter into binding agreements where specific improvements to safety and health management are required. This power is comparable to enforceable undertaking provisions in the Work Health and Safety Act 2011 (WHS Act).
Enforceable undertakings are given in connection with a contravention or alleged contravention of the WHS Act. Such agreements can compel a
party to complete an action for the benefit of the workplace, including engaging an external safety provider, stopping behaviour that led to the breach, creating a safety management system, etc.
These agreements are entered into as an alternative to prosecution and will soon be available to the Queensland resources industry.
When it does come to prosecution, the court’s powers will be expanded to enable broader sentencing options that can be tailored to the situation. This is intended to achieve a better balance between increasing compliance, improving safety outcomes, and deterrence.
The broadened court orders proposed will align with those available under the WHS Act.
The changes also mean labour hire workers and agencies will be classed as contractors under the legislation,
Modular wear components
Heavy-duty bearing design
which removes any doubt that health and safety obligations apply to labour hire agencies, another recommendation from the Board of Inquiry.
Industrial manslaughter provisions will be refined to ensure they apply to whomever employs or engages or arranges for a worker to perform work and whose negligent conduct caused the death of a worker.
The new legislation also seeks to clarify that risk-management obligations extend to off-site remote operating centres for mines. This will be achieved by requiring the site’s safety and health management systems to address risks from remote operating centres and remote operation of plant and equipment and establish clear obligations applying to people at these centres who give information on which site-based operational decisions are made.
The bill is currently being reviewed by parliament and may be subject to change before becoming law.
THE LATEST PROTECTIVE GOGGLES FROM BOLLÉ SAFETY USE A “FIRST-OF-ITS-KIND” TECHNOLOGY DESIGNED TO CONFORM TO A USER’S FACE.
Safety glasses have long been a staple in industrial workplaces, but workers are increasingly turning to goggles as a more robust alternative.
“While safety goggles are certainly not a new concept, a host of new
shift to the additional protection that goggles provide,” Bollé Safety product
around the world, Bollé Safety is a premier expert in protective eyewear.
distribute sealing pressure,” Azibert said. “The result is a safe, reliable and comfortable fit for various face shapes.”
The goggles’ frame is constructed of thermos-propylen rubber and non-UV stabilised polycarbonate, making it flexible and impactresistant. It is also compatible with prescription glasses, with slots allowing most glasses to fit perfectly under the goggle without creating any pressure points.
The goggles are rounded out with Bollé Safety’s signature platinum antiscratch and anti-fog coating on both sides of the lens, allowing for greater durability and maximum optical clarity.
The UG range is also compatible with a shield designed to protect the lower part of the face. This shield clips easily and intuitively onto the UG, and is ideal for applications where there is a risk of flying debris.
The UG collection includes a variety of models suitable to different industrial applications.
“There are various situations where wearing goggles is important, but they do not all include exposure to the same risks,” Azibert said.
“Some workers may need protection against dust or even gas hazards, requiring a fully sealed and tight eyewear solution, while wellvented goggles would serve better in a humid environment. So the industry has been challenged with a need to develop a variety of use-specific protective eyewear.”
And that is exactly what Bollé Safety did with the UG range.
Each model is distinguished by a unique colour strap, marking differences in ventilation, lens colour, material, and the intended application.
The green UG model is ideal for the mining industry, as it is completely waterproof. It is also suitable for work involving inflammable products, dangerous gases, and fine particles.
The yellow UG offers indirect ventilation and is suitable for applications where impact is the primary hazard, such as many areas of surface mining operations.
The cool grey version is made with a neoprene strap, which is more chemical-resistant than nylon. This model is ideal for workers who are around solvents and acids.
Finally, the grey UG is designed with welding lenses and is suitable for welders handling class 2–5 gases.
The Bollé UG range is also designed with sustainability at heart to help sites meet their environmental, sustainability and governance commitments.
The goggles can be easily dismantled, allowing the materials to be recycled separately. The
packaging, a high-density polyethylene bag, is also completely recycled and recyclable.
Whether it’s guarding against gas, debris, or impacts, Bollé Safety’s UG range has a solution to almost any eye-related workplace hazard.
“Our role as personal protective equipment eyewear specialists is not to move people away from safety glasses towards goggles,” Azibert said.
“It is to make sure that people use the best-suited protection for their job, allowing them to work safely and effectively.”
The world’s transition to clean energy and net-zero technologies has so far been fast and hard. It has demanded the rapid development and implementation of new technologies that bring about new ways of doing business.
In the context of the mining industry, there is an increasing understanding that many of the sector’s sustainability challenges are insurmountable for a single company to tackle alone. This realisation has seen mine operators increasingly turn to the mining equipment, technology and services (METS) sector for help.
Austmine recently launched Accelerating Sustainable Mining, a
publication it hopes will elevate more Australian METS companies to the global stage.
“The publication is fundamentally a directory for mining companies to find METS companies with specific sustainability capabilities,” Austmine director of strategic development Marianne Cummings told Safe to Work
“The purpose is both to promote the cutting-edge sustainability technologies of Australian METS
companies to the global market and to provide mining companies with simple access to sustainability solutions.
“By making it easier for miners to identify and procure relevant technologies and solutions to meet their decarbonisation and broader
Mining companies are looking to decarbonise their operations.
environmental, social and governance [ESG] targets, we hope to contribute to accelerated implementation of sustainable mining practices.”
The publication, which was developed in collaboration with the Australian Trade and Investment Commission (Austrade), covers five key sustainability areas:
• ‘The waste free mine’ – showcases various METS companies’ capabilities in waste management, including waste-to-energy technologies, sustainable waste management practices, tailings management, circular economy models for mining, and more
• ‘The small footprint mine’ –examines METS companies that can help reduce the size and impacts of mining operations, including improving in-situ recovery techniques, low-impact processing, agile and modular mine design, and more
• ‘The smart water mine’ – covers METS companies with capabilities in mine water management, desalination, water treatment technologies, and more
• ‘The community mine’ – showcases METS companies with expertise in stakeholder engagement, cultural heritage preservation, mine closure planning, and more
• ‘The zero carbon mine’ – looks at METS companies involved with carbon capture and storage, clean energy solutions, electrification technologies, and more.
how the sector is contributing to sustainability efforts around the world.
“To meet these challenges in the short timeframe required will require rethinking technologies and implementing new solutions,” Cummings said.
“Most miners do not have the inhouse resources to develop these solutions in acceptable timeframes and need to look to the METS sector for expertise.”
These technologies are demonstrated in case studies throughout the publication, demonstrating how Australian METS companies are helping miners solve their biggest sustainability issues.
Cummings said the publication highlights the pioneering spirit, innovation and can-do attitude of Australian METS companies and
As 2030 climate targets loom and stakeholder pressure builds, mining companies will need sustainability solutions that can be implemented quickly without reinventing the wheel.
Accelerating Sustainable Mining offers the high-quality Australian METS sector the international recognition it has worked hard to deserve. And, perhaps most importantly, the publication is helping drive the global transition towards sustainable mining.
While proximity-detection systems play a vital role on modern mine sites, there is no replacement for communication between personnel.
As recently as April, the NSW Resources Regulator highlighted a high-potential incident that occurred at an open-cut industrial minerals mine.
A front-end loader and semi-tipper were loading crushed stone at the site when the semi-tipper parked behind the loader without communicating. The loader operator then reversed and the two vehicles collided. Fortunately, neither worker was injured.
The Regulator took the opportunity to make a series of safety recommendations and stress the importance of positive communication between workers.
But even the most rigorous communication procedures won’t amount to much if the hardware itself can’t keep up with tough mining conditions. That’s why communications expert Sepura is a leading choice among mine operators in Australia.
Sepura’s terrestrial trunked radio (TETRA) radios are built to handle the conditions found on mine sites, while reliably delivering mission-critical communications.
TETRA networks provide narrowband voice and data services, with a high standard of service and exacting requirements for availability, reliability and security.
Sepura’s devices, such as the SC23 handheld radio, are designed to be able to repel dust from their speakers. They are also IP67-rated, which means they can be submerged in water or held under a running tap for cleaning.
This not only means units will be available for work immediately after cleaning and do not need to be dried, but they can continue to work during heavy downpours that can be a feature of outdoor work.
While TETRA is a tried-andtrue means of communication, the technological requirements of modern mine sites are evolving beyond narrowband networks.
Mines have an increasing need for data services such as video, access to online tools or databases, and the ability to upload or download large data items. These tasks typically need a higher bandwidth than narrowband systems can deliver, and require broadband data services, such as LTE (long-term evolution). The challenge is to deliver the performance of TETRA while at the same time provide the additional services that LTE enables.
LTE is considered a strong technology, but it is still evolving and users need a solution that meets their present demands.
Sepura is helping to bridge this gap
Designed to support organisations in their migration strategy and for use in all situations, including vehicles, fixed locations and body-worn, both solutions support TETRA for missioncritical voice with data through LTE or Wi-Fi connectivity. The SCL3 and SCU3 also support existing TETRA audio accessories, providing users a full set of options.
These options allow sites to run hybrid fleets; for example, vehicles and control rooms using dual-mode SCU3 devices and frontline staff using the SCL3 TETRA hand-held portable device.
“Organisations are increasingly looking for flexible, rugged devices capable of providing the best of both worlds – mission-critical voice and high-speed data capability,” Sepura country manager for Australia Ronan Rafferty said.
“Our complete portfolio, including the new SCL3, offers this in a familiar, secure and rugged format, enabling organisations to extract full value from their critical communications solution whatever stage of the migration journey they are at.”
It’s this kind of dynamic approach to communications that has made Sepura a market leader for two decades.
Those who ignore the past are, as they say, doomed to repeat it. That’s why one of the most important activities in the Australian mining industry is reviewing safety incidents to determine what can be done differently in order to avoid the same issues in the future.
Accidents will always occur, and their valuable insights should never be ignored.
Resources Safety and Health Queensland (RSHQ) called for greater caution and improved training for personnel after a loader operator drove into a stope void. The incident occurred at an underground metalliferous mine, when the loader and its operator fell into a stope void from a tipping point.
It is understood the operator was attempting to place a fabricated steel stop log near the open edge of the stope in preparation for backfilling works. While the investigation was in its early stages at the time of writing, RSHQ has suggested the operator drove beyond a safe operating area
into the open stope, lost control and became stuck.
“Stope voids without adequate edge protection can lead to serious harm or death,” RSHQ said.
RSHQ released a list of factors that may contribute to incidents of this nature, including:
• the manoeuvrability of machinery and operator’s visibility
• inadequate training or hazard awareness for persons involved
• the appropriateness of machinery for the activity
• signage/mark-up.
The regulator suggested that risk assessments should consider the appropriateness of machinery being used, including whether its manoeuvrability is appropriate for the task and conditions and does not limit an operator’s visibility in the circumstances.
The loader operator in this incident was fortunately rescued without injury, though fatal incidents involving voids have occurred in the past.
In light of incidents past and present, RSHQ stressed the importance of training personnel
working around vertical edges, such as stopes, as well as ensuring the quality of this training.
A haul truck recently collided headon with the wall of a decline at an underground coal mine in NSW. The collision is understood to have occurred when the steering function of the vehicle failed.
Fortunately, the operator was uninjured in the incident.
Subsequent investigation identified fluid loss from a damaged hydraulic hose as the cause of the failure.
“Safety critical systems such as braking and steering systems should be inspected, maintained and tested in accordance with the manufacturer’s recommendations,” the NSW Resources Regulator said.
“Mine operators must develop and adhere to strict inspection and maintenance standards and practices to prevent loss of fluid due to loose fittings or damaged hoses.
“Operators should review their maintenance procedures to ensure commissioning checks are carried out by competent people before plant is returned to service as fit for purpose.”
Workers at a coal mine in NSW accidentally started a fire on an excavator during recent maintenance works.
When an excavator operator noticed excess oil building up on top of the stairs and engine compartment of the machine, they contacted the site’s clean-up crew. These workers identified the cause of the oil spill as a failed hose.
In order to remove the oil, the workers applied degreaser on the affected areas; however, the degreaser dripped through the floor to the engine room below. When the degreaser came into contact with a hot exhaust manifold, it ignited. Workers evacuated the vehicle and triggered the fire-suppression system. No injuries were reported.
The NSW Resources Regulator offered words of advice following the incident.
“Where products such as cleaners and degreasers are used near hot engine components, the ignition point should be assessed and compared with surface temperatures to manage the risk of fires,” the Regulator said.
“When selecting products, higher ignition point products should be used.”
The Regulator recommended reviewing fire-prevention standards for mobile and transportable equipment AS 5062:2022 and updating site systems and procedures accordingly.
Another string of maintenance incidents occurred in the Queensland coal industry.
RSHQ called for greater caution during the maintenance of continuous miners after three related highpotential incidents occurred in the state in 12 months.
Each incident involved the ejection of a cutter head stop pin from a continuous miner.
In one instance, a coal mine worker was struck directly in the chest. In the second, the worker was struck on the elbow. In the third incident, the ejected pin hit a rib pillar at the mine.
“In the incidents involving personal injury, the coal mine workers were transported to hospital,” RSHQ said. “Medical examination indicated severe bruising but no long-term injury.
“These incidents are concerning because while there were no longterm injuries, there was the potential for a fatality.”
In each of the three incidents, the continuous miner was stopped for maintenance. This required resting the cutter on the head stops before works could be conducted. In each case, the safety pin had not been inserted all the way and the weight of the cutter head was acting on the tapered area of the pin, causing the pin to eject.
The Regulator recommended developing a safety procedure in consultation with the original equipment manufacturer (OEM) for installing and using stop pins. This includes introducing procedures to ensure both head stop pins are fitted, exclusion zones are established, cutter booms are slowly lowered onto the stops, rather than forced down heavily, and using longer pins with OEM consultation.
While it is unfortunate that safety incidents occur, they provide important lessons to the industry. Learning from such incidents can help drive industry towards its ultimate goal of eliminating workplace injuries.
FloMAX Fuelling Systems offer high-efficiency diesel transfer, automatically adjusting to tank pressure changes. Our system tackles pressurisation issues in plastic tanks, vent malfunctions, and operational uncertainties. Ensure a seamless and spill-free fueling experience with FloMAX - your solution for safer, cleaner, and more reliable fuel management!
Our strength comes from high-quality distribution partners who manage installation, service, technical support & training nationwide.
DISCOVER THE WINNERS OF THIS YEAR’S WOMEN IN INDUSTRY AWARDS, WHICH RECOGNISE OUTSTANDING WOMEN FROM A RANGE OF TRADITIONALLY MALE-DOMINATED SECTORS.
The 2024 Women in Industry Awards, as they do every year, celebrated the achievements and success of exceptional women in the heavy industries.
This includes mining, energy, transport, manufacturing, engineering, logistics, bulk handling, waste management, rail, construction, and infrastructure.
The 2024 awards, held in Sydney on June 20, featured 12 categories, including the newly introduced Excellence in Energy category, sponsored by Safe to Work sister publications The Australian Pipeliner, Energy Today and ecogeneration. This category recognises an individual who has made a positive contribution to the renewables, pipeline or oil and gas industries.
In addition to this new category, safety played a central role at the events, with several excellent nominees in the running for a key award.
SAFETY ADVOCACY AWARD
The awards recognised women who are actively working to make industrial workplaces safer.
The nominees for the Safety Advocate Award:
• Ally Boys – Toll Group
• Ann Redfern – Fulton Hogan
• Colleen Ning – GroundProbe
• Gail Harvey – Guidera O’Connor
• Kahlia Foster – Harvey’s Towing
• Kathleen Kelly – McConnell Dowell
• Liana Walsh – Elgas
The award was ultimately taken out by Kathleen Kelly for her important work as health and safety advisor at McDonnell Dowel.
INDUSTRY ADVOCACY AWARD
Sponsored by Komatsu, this award celebrates an individual who has helped shape a positive view of their industry or helped create a policy change that benefits those working in the sector.
Winner: Steph Gee – CM & SM Gee Electrical
EXCELLENCE IN MINING
This award highlights an individual making significant impacts within Australia’s resources sector.
Winner: Sinead Booth – Fortescue
BUSINESS DEVELOPMENT
SUCCESS OF THE YEAR
This category celebrates an individual who has created new growth opportunities that have allowed their company to generate greater revenue.
Winner: Sandra Robinson –United Rentals
MENTOR OF THE YEAR
This category recognises an individual who has committed to developing female talent within their organisation or industry.
Winner: Kirstin Reblin – Opal
The Women in Industry Awards recognise the achievements of exceptional women in the industrial sector.
RISING STAR OF THE YEAR
The industry talent of today will inform the results of tomorrow, and this category recognises an individual who is making significant strides at the start of their career in the resources sector.
Winner: Kate Leone – UGL - M6 Stage 1 Project
EXCELLENCE IN TRANSPORT
Proudly sponsored by Kenter Logistics, this award celebrates an individual who has made a significant impact within the Australian transport industry.
Winner: Anne Modderno – Swietelsky
EXCELLENCE IN ENGINEERING
Proudly sponsored by SEWEURODRIVE, this category recognises a leader in engineering, technological excellence and innovation.
Winner: Allyson Woodford –APA Group
EXCELLENCE IN MANUFACTURING
Proudly sponsored by PACCAR Australia, this award celebrates an individual implementing innovation in their manufacturing business or the wider industry.
Winner: Derelle Mitchell – Health Focus Manufacturing
EXCELLENCE IN CONSTRUCTION
This category singles out an individual who has made a positive contribution to the construction industry.
Winner: Sinead Redmond – GeelongPort
EXCELLENCE IN ENERGY
Proudly sponsored by Energy Today, The Australian Pipeliner and ecogeneration, this new category celebrates an individual who is taking charge in the renewables, pipeline, or oil and gas industries.
Winner: Vesna Olles – BOC Limited
WOMAN OF THE YEAR
Proudly sponsored by Fulton Hogan, the prestigious Woman of the Year award recognises the incredible women leading change within their sectors. It is awarded to an individual who represents how these industries are changing for the better.
Winner: Derelle Mitchell – Health Focus Manufacturing
Moving parts and pinch points pose a serious danger to people who work around machinery. While most machinery guards eliminate incidents around moving parts, it is often heavy and cumbersome enough to become a manual handling hazard.
The patented ESS EZI-GUARD system comprises of a range of versatile, easy to install brackets, lightweight panels and standard structural tubing which forms an ‘off the shelf’ system that can be adapted to almost any application.
The EZI-GUARD System has been developed to exceed the guard design requirements of AS4024.3610:2015.
The patented ESS EZI-GUARD is;
• Quick and easy to retrofit
• Easy to remove for maintenance
• Modular ‘off the shelf’ design
• Corrosion Resistant
• Strong but lightweight panels
• Easily handled
• Available in a variety of materials
• Available in barricade form
• Coloured Safety Yellow or black as standard Proudly Manufactured in
The WA Mining Conference and Exhibition (WAME) aims to integrate the innovation and research ecosystem, while addressing the social and environmental standards driving a more sustainable industry.
The significantly expanded exhibition will showcase technical and digital innovation across the entire mining value chain, while the highly targeted conference will illustrate the economic importance of Western Australia and its contribution to the industry.
The conference will provide mining professionals with the technological insights that will shape the future of the mining industry in WA.
With digitalisation and automation pushing the industry into new frontiers, new technologies will be front and centre at WAME, with cyber security managers, technology heads and chief technology officers in attendance as they look to discover the technological step-change.
WAME show director Siobhan Rocks said the event is set to feature an impressive number of companies offering advanced technology focused on innovation and decarbonisation.
“The industry has a real appetite for these technologies that are supporting many of the leading mining companies’ goals on decarbonisation and offer cost-savings through the latest technological advances,” Rocks said.
Given industry and stakeholder engagement is paramount to the success of the mining industry, the conference will also look at the social license to operate and the most effective way to limit the environmental impacts of mining in WA.
Environmental managers, stakeholder and community engagement managers will hear from industry and government experts.
The conference will also be held in conjunction with the Australian Mining Prospect Awards, which recognises those in the industry who are excelling and going above and beyond.
Last year’s WAME was one of the most successful to date, with almost 5000 visits across the event. Rocks notes a strong representation of engineers at the last event, representing 20.4 per cent of visitors. Another 16.1 per cent of visitors identified as senior management.
Major mining companies were also well represented at the event,
including key personnel from BHP, Rio Tinto, Fortescue, South32, Newcrest, and more.
“This really is a great event for key industry decision-makers to see what innovative solutions are available on the market,” Rocks said.
“Engineers have also expressed a strong interest in the 2024 event, not only as visitors but also as exhibitors.
“Following popular demand, WAME launched ‘engineering companies offering advanced solutions to the market’ as a new product category for 2024 – and the uptake has been impressive.”
Other new industry categories being launched at this year’s event include Mining 4.0, renewables and circular economy.
WA has long been considered the mining capital of Australia, a veritable cornucopia for the resources industry, where juniors and giants alike come to play. WAME brings all of this exciting potential together in one event.
The WA Mining Conference and Exhibition will be held at the Perth Convention and Exhibition Centre from October 9–10. Visit waminingexpo.com.au
REGISTRATION IS NOW OPEN FOR THE QUEENSLAND MINING INDUSTRY HEALTH AND SAFETY CONFERENCE 2024.
The Queensland Mining Industry Health and Safety Conference (QMIHSC) stands apart as a dedicated hub of safety across the mining industry.
QMIHSC 2024 will mark the 35th iteration of the event, which has showcased the best in mining industry safety technology and workplace culture for decades.
This year’s theme is ‘Back to the future’, which will explore whether the relative simplicity of the past can work in harmony with advancements in the present to create a safer future.
One prominent safety figure set to share his expertise at QMIHSC 2024 is Professor Arnold Dix, an
A scientist and expert in all things underground, Dix was contacted by India’s Chief Engineer and the Secretary for the Prime Minister asking for his help.
After more than two weeks spent battling the challenging and evershifting conditions imposed by the
QMIHSC 2024 will mark the 35th iteration of the event, which has showcased the best in mining industry safety technology and workplace culture for decades.
“The Silkyara rescue demonstrates that almost anything is possible when we unite and be nice,” Dix said.
What separates QMIHSC from other safety conferences is its broad scope. Last year’s theme was ‘Inside looking out’, which brought together safety speakers and exhibitions from across the mining industry and beyond.
Experts from different walks of life, including air traffic control, military, psychology, and more gave mining delegates exposure to new practices and ideas to apply to their own operations. This was so popular that it has returned to this year’s event, which will similarly feature a broad scope of speakers and exhibitors.
Popovic aims to help people perform at their peak throughout their career, eliminate brain fog, and avoid Alzheimer’s and associated issues in retirement. She also seeks to provide a roadmap for living a longer, stronger, healthier and happier life.
“Discovering how to boost our brain is the single most important investment we can make to achieve our goals, solve complex problems and create a fulfilling life,” Popovic said.
The QMIHSC team has also taken in feedback from last year’s event and made several improvements to the delegate experience.
Dix believes many lessons can be learned from the adaptive and resilient solutions employed underground to help solve most of the challenges facing the world today.
06-07_STW_InsertV1.pdf 1 6/7/24 2:23 PM
One such 2024 speaker is Dr Helena Popovic, a medical doctor, author and high-performance coach who has spent more than 30 years researching the brain and teaching people how to reach their full potential.
This year’s conference places the guest experience front and centre, channelling the successes of 2023 and making improvements in several other areas.
QMIHSC 2024 will take place at The Star, Gold Coast, from August 18–21.
Whether due to retirement, relocation, or attrition of some other kind, legacy knowledge can easily walk off the job. And without continuing education, the inexperienced staff left behind can slow your production down.
For more than 80 years, Martin has delivered the cleanest, safest, most productive solutions to countless bulk material handling issues. That history has taught us the value ongoing training can contribute to employee wellness and company profits.
To that end, our Foundations™ Learning Center provides around-the-clock, online access to many and varied instruction options — all to keep your staff both safe and informed.
Click and log on. Classes now in session.
EVENT SUBMISSIONS CAN BE EMAILED TO EDITOR@SAFETOWORK.COM.AU
MACKAY | JULY 23–25
The Queensland Mining & Engineering Exhibition (QME) connects leading suppliers and technical experts with those seeking better efficiency and productivity, and increased optimisation for their business and site.
INTERNATIONAL FUTURE MINING CONFERENCE 2024
WA MINING CONFERENCE AND EXHIBITION
QME will feature over 250 suppliers, and beyond the exhibition floor and will host a free-to-attend seminar series that will give people the opportunity to hear from industry professionals who will address the current needs of the industry. With live demonstrations and topical presentations, QME will be the ultimate destination for the Queensland mining industry.
QME is a key place for the industry to come together to be inspired, innovate and connect over three days. In one of the world’s most dynamic industries, QME has maintained its relevance and importance within the mining sector.
It’s the event on the mining calendar that simply cannot be missed.
• queenslandminingexpo.com.au
MINE VENTILATION CONGRESS 2024
SYDNEY | AUGUST 12–16
The 12th International Mine Ventilation Congress (IMVC) is an opportunity for the mine ventilation community to come together and discuss new technologies and developments with a view to improving and refining ventilation, refrigeration, cooling, and health and safety in mines around the world. The IMVC series is the only global gathering of the mine ventilation engineering community and as such presents a unique chance to share knowledge and grow professionally. IMVC brings together mine ventilation professionals to promote improvements in engineering and related aspects of health and safety
• ausimm.com/conferences-andevents/international-mine-ventilationcongress-2024/
SYDNEY | SEPTEMBER 2–4
The 6th International Future Mining Conference will explore transformative technologies, champion innovation and push the boundaries of possibility.
The carefully curated 2024 conference program will review the digital leap, mining in extreme environments, future skills requirements, opportunity exploration, energy innovations and a green mining future.
Experience the world of digital transformation, the vast potential of space mining and explore decarbonisation strategies, circular economy models and waste management in Sydney from September 2–4.
• ausimm.com/conferences-and-events/ future-mining/
PERTH | OCTOBER 9
Mining has always been a part of Australia’s landscape, playing a major role in the development of this nation from its early days.
The sector remains vibrant and innovative, and for more than a decade, the Australian Mining Prospect Awards have been the only national awards program to stop, take a look at what the mining industry is doing, and reward those who are excelling and going above and beyond, recognising and rewarding innovation.
The Prospects are the most esteemed and prestigious awards program for the mining and minerals processing industry within Australia.
• prospectawards.com.au
PERTH | OCTOBER 9–10
The WA Mining Conference and Exhibition will integrate the innovation and research ecosystem while addressing the social and environmental standards driving a more sustainably conscious industry.
The largely expanded exhibition will showcase the technical and digital innovation across the entire mining value chain, while the highly targeted conference will illustrate the economic importance of Western Australia and its contribution the resource technology sector, its innovation capability, its job creation, and the attraction of capital to the state.
WA Mining is the ultimate event for mining and engineering professionals, showcasing the technical and digital evolution transforming the mining industry in Western Australia
• waminingexpo.com.au
SYDNEY | OCTOBER 29–31
The International Mining and Resources Conference (IMARC) is where people from across the entire industry come together to deliver ideas and inspiration.
Learn from in excess of 500 mining leaders and resource experts throughout seven concurrent conferences with a program covering the entire mining value chain.
Attend one of the many networking events or catch up with industry colleagues on the exhibition show floor featuring more than 470 leading companies.
There will be practically endless opportunities to network, brainstorm and share knowledge over the three days at the ICC Sydney.
• imarcglobal.com
18–21 AUGUST THE STAR, GOLD COAST
2024 KEYNOTES
Anders Sorman-Nilsson
Anthony Laye
Arnold Dix
Helena Popovic
Josh Jones
Mariette Bylsma
Matt Hall
Susan Johnston
Tim Baker
Trent Gri ths
On-site training, or you can visit us at a Komatsu facility
Gain real-world experience with hands-on support from experienced, qualified trainers and assessors
Contact us about a training program that’s right for your operation.
Maintaining a skilled, knowledgeable workforce is the key to driving performance and safety at any operation. Gain a better understanding of your Komatsu machines with our underground mining product training programs, designed to help operators and maintenance personnel understand how to use and care for your machines safely and optimize their performance.
Refine equipment skills with hands-on support from in a controlled environment without disrupting production
Accelerate development skills with an interactive learning approach
Identify and troubleshoot equipment issues with state-of-the-art training simulators