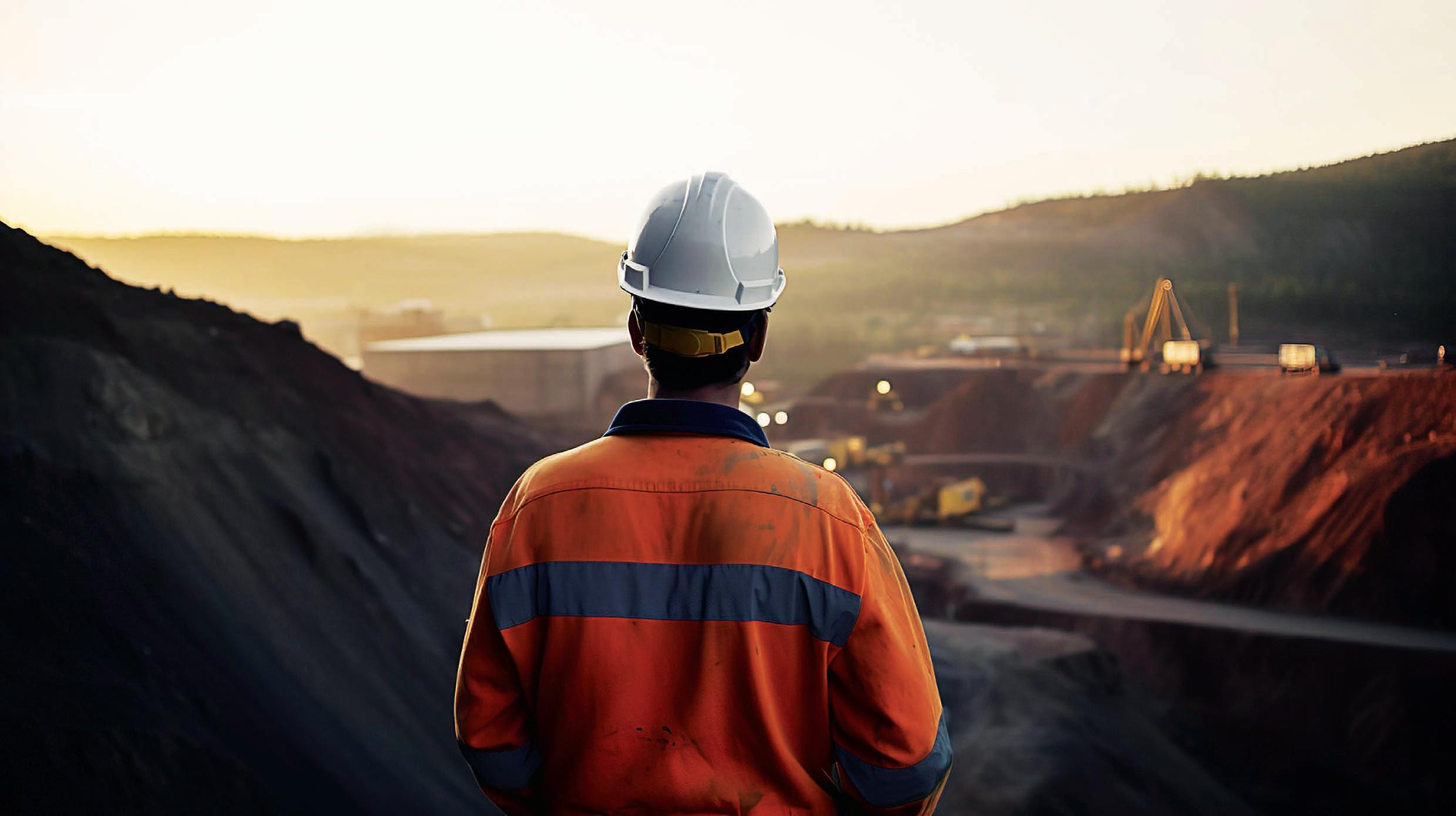
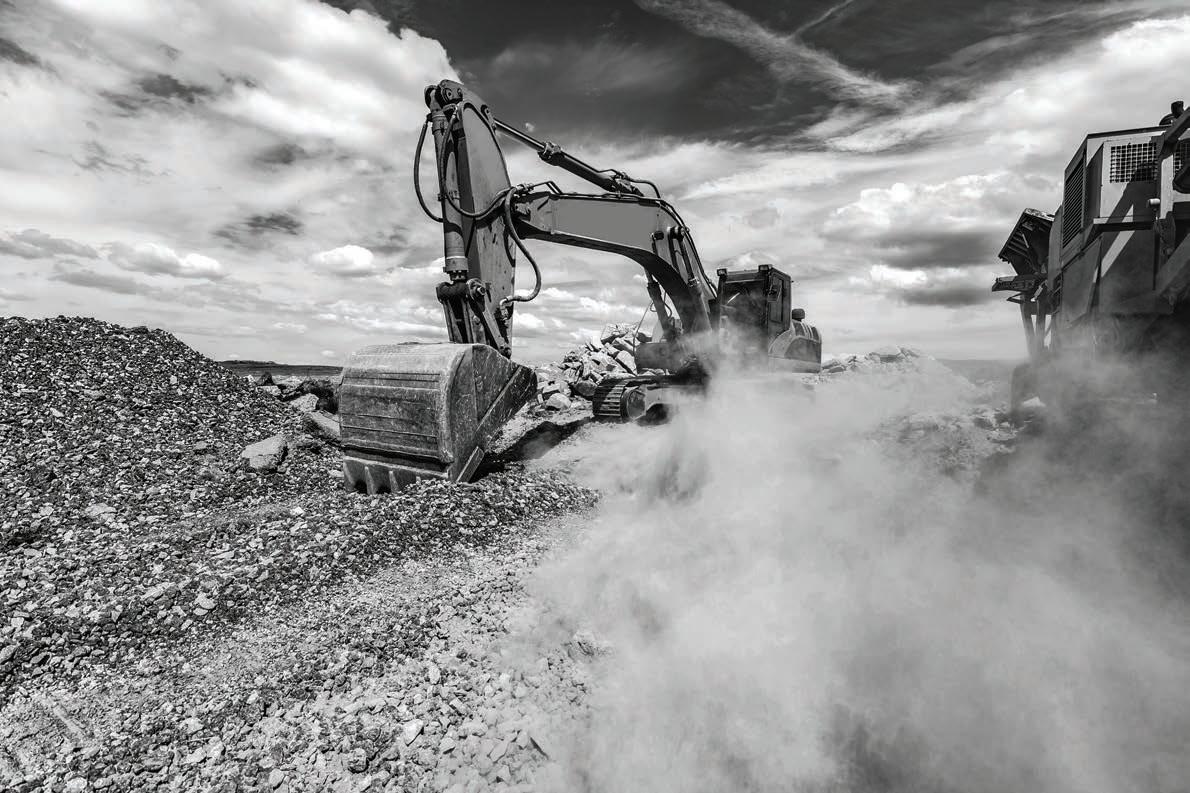
Packed with next-gen features, RotoFlex Steel are our toughest, most advanced boots yet. Every single component, from the steel toe cap through to the stitching, is extensively tested for stability, safety and comfort.
When you think of safety in the mining industry, you might automatically think of physical dangers.
But mental health is just as important as physical health and deserves as much recognition.
Safety is not limited to driverless equipment or the correct personal protective equipment (PPE) – though both are unquestionably important – but also sitting down with a mate and asking them that all important question: are you okay?
This edition of Safe to Work coincides with R U OK? Day on September 14 and takes a look at how miners can look after their mental health in the industry.
We take a look at Glencore’s successful partnership with MATES in Mining program to tackle workplace mental health.
JOURNALISTS ALEXANDRA EASTWOOD
Tel: (03) 9690 8766
Email: alexandra.eastwood@primecreative.com.au
“The beauty of this training is that it isn’t just applicable to the mining industry. It allows us to create a network of empathy and resilience, strengthening not only our mines but also our local communities,” Glenore director of health, safety and training Kylie Ah Wong said.
“This partnership is about training our workforce to identify behavioural changes in their mates so we can offer support when needed most.”
Elsewhere, we shine the spotlight on dust suppression and fire safety, two of the most important considerations for the mining industry.
This is highlighted by Newcrest springing into action to rectify air-quality issues discovered at its Cadia Valley mine in NSW. Safe to Work looks at the timeline of the NSW Environment Protection Authority investigation and Newcrest’s proactive response to rectify the issues.
JSG Industrial Systems tells us that “a fire is never just a fire”, showcasing how muster fire suppression systems can be fitted to mobile assets and fixed plant, automatically triggering in the event of a fire.
This edition also takes a deep dive into the winner of the second Queensland Mines Rescue Services State Cup, where Anglo American’s Grosvenor coal mine took out the top prize.
Anglo American is also paving the way for all-women mine rescue teams, forming the first ever all-female team at its Capcoal open-cut mine near Middlemount, Queensland, in March of this year.
Paul Hayes Managing EditorCOO CHRISTINE CLANCY
MANAGING EDITOR
PAUL HAYES
Tel: (03) 9690 8766
Email: paul.hayes@primecreative.com.a
ASSISTANT EDITOR
TIMOTHY BOND
Tel: (03) 9690 8766
Email: tim.bond@primecreative.com.au
OLIVIA THOMSON
Tel: (03) 9690 8766
Email: olivia.thomson@primecreative.com.au
CLIENT SUCCESS MANAGER
JANINE CLEMENTS
Tel: (02) 9439 7227
Email: janine.clements@primecreative.com.au
RESOURCES GROUP LEAD
JONATHAN DUCKETT
Mob: 0498 091 027
Email: jonathan.duckett@primecreative.com.au
BUSINESS DEVELOPMENT MANAGER
NATALIE HERBSTREIT
Mob: 0412 741 068
Email: natalie.herbstreit@primecreative.com.au
DESIGN PRODUCTION MANAGER
Michelle Weston
ART DIRECTOR Blake Storey
SUBSCRIPTION RATES
Australia (surface mail)
$140.00 (incl GST)
New Zealand A$148.00
Overseas A$156.00
For subscriptions enquiries please call 03 9690 8766
PRIME CREATIVE MEDIA
379 Docklands Drive Docklands, VIC 3008 Australia
www.primecreative.com.au
© Copyright Prime Creative Media, 2016
All rights reserved. No part of the publication may be reproduced or copied in any form or by any
The second Queensland Mines Rescue Services State Cup was held in July. Safe to Work takes a closer look at the proceedings.
Glencore discusses the success of its partnership with MATES in Mining in tackling workplace mental health.
Superchute is helping mining and industrial sites tackle dust at their stockpiling and loading applications.
This year’s International Mining and
Muster fire suppression systems come in a range of variations, each suited to different industrial environments.
Martin Engineering provides advice on avoiding a devastating conveyor fire.
Epiroc has set itself the ambitious goal of zero injuries by 2030, which it plans to achieve via a threefold approach to mine safety.
Blundstone has launched its R range of heavy-duty steel-capped
Two recent incidents have prompted a warning from the NSW Resources Regulator about the dangers of fatigue.
The first event involved a worker micro-sleeping behind the wheel on their 20th consecutive 12-hour shift, resulting in a crash. The worker fortunately escaped injury. After investigating, the safety watchdog determined that control measures such as fatigue risk assessments were not being undertaken for workers who had a combined work and travel time in exceedance of the mine’s fatigue management plan.
The second incident, the nature of which has not been disclosed, involved a mining electrician who was on their 10th consecutive 12.5hour shift when they had an accident involving a vehicle.
Regardless of how large and efficient mining operations become, the
Glencore was recently recognised by the NSW Minerals Council for its Operator Awareness System, which monitors vehicle drivers for signs of tiredness, triggering alarm and vibration systems when the operators’ eyes close. Wearable monitoring technologies also present a possible real-time defence against fatigue. To manage the risks, the NSW Resources Regulator recommends that mine operators:
• have assessed if fatigue is a risk for the mine
• ensure controls identified in their fatigue management plan are implemented monitored and regularly reviewed
• control measures are consistently applied across all areas of the mine site including contractors and project works
• provide training, information and instruction to workers
• where reasonably practicable, fatigue monitoring systems are installed on mobile plant
• have systems in place to monitor compliance with the management plan for all on-site workers
• complete risk assessments for all on-site workers that are working more than 14 hours (including travel time)
• where journey management plans are identified as a control measure, they are implemented for workers at risk (such as workers who have a combined total of 14 hours of work and travel time)
• ensure there is a process in place to trigger the review of journey management plans. Reviews should occur to ensure the workers nominated travel point during the work roster period is up to date; this should also include travel requirements before and
The drill bit has a major impact on safety, as every time it has to be changed, the operator is exposed to danger. Powerbit X, with a diamond protective layer, gives the drill bits substantially longer service life, which means fewer changes. This is just one example of how we accelerate the transformation in the mining and construction industry.
harmful workplace culture within parts of the company.
“We are creating an open and transparent environment which will make positive and lasting change and strengthen our workplace culture for the long term, as we continue to implement the 26 recommendations of the ‘Everyday Respect’ report,” the company said in its quarterly.
“We continue to promote respectful transparency … to highlight disrespectful, discriminatory and hurtful behaviours occurring in our organisation, in the same way we highlight safety concerns.
records, but how well did the miners stack up for safety?
BHP reported two fatalities for the financial year. Jody Byrne lost his life at a BHP rail yard at Port Hedland in February; and Nathan Scholz lost his life at BHP’s Olympic Dam copper mine in May. Both of these fatalities involved vehicles.
BHP chief executive officer (CEO)Mike Henry opened the financial year report by touching on these incidents.
“These tragic events underscore the absolute importance of safety and we are resolute in our commitment to eliminating fatalities and serious injuries at BHP,” Henry said. “Inflationary pressures impacted our business in the year, and we remain laser focused on safety and productivity to remain competitive.”
BHP also recently completed a $300 million safety renovation of its Pilbara worker villages. Over 10,000 rooms were upgraded across 13 Western Australia Iron Ore villages,
and 4.75m of fencing installed. Rio Tinto reported an all-injury frequency rate of 0.36 for the quarter, a small increase on the previous two quarters. The company also reported two significant process safety incidents.
“There were two incidents at our Rio Tinto iron and titanium SorelTracy complex which did not result in injuries,” the company said in its quarterly review.
“The Kennecott operation experienced an escape of furnace gas during the maintenance shut, where all treated people have been cleared.
“We are heightening our focus on managing these risks and continue to prioritise the safety, health and wellbeing of our workforce, and communities where we operate.”
Rio is continuing to implement recommendations laid down in the ‘Everyday Respect’ report. The independent report – published last year by Rio Tinto –spotlighted
“Village councils are being implemented across sites to provide a safe and constructive way for employees and contractors to raise concerns and give feedback. In addition, over 950 people responded to our Pilbara Iron Ore’s contractor survey, which was designed to better understand their experiences.”
In May, Rio Tinto and BHP came together to invite expressions of interest to innovate tailings technologies.
“Together, we aim to jointly identify a portfolio of tailings management partners with whom they can work to accelerate the development of technologies that could increase water recovery and reduce potential safety risks and environmental footprints associated with tailings storage facilities,” Rio said. It followed a partnership agreement in late 2022 to accelerate the development of tailings technologies and management, including tailings dewatering and transport technologies, chemical amendment, and dust mitigation.
The Universal Ret Ring is an innovation that simplifies socket retention for threequarter-inch and one-inch square drives. It replaces the need for 13 different Ret Ring sizes with just three – ESR #1, ESR #2, and ESR #3 – designed to fit multiple sockets. The Universal Ret Ring is made of polyurethane plastic and features a one-piece design with a hardened resin insert. It securely holds the socket in place while operating high-speed impact wrenches that can reach speeds exceeding 5000RPM. The original Ret Ring was introduced to enhance safety by preventing injuries caused by flying or slipping steel pins used in older socket retention systems. The new resin pin with a crush gauge in the Ret Ring is designed to index in the retention holes on the tool anvil and socket. This ensures proper alignment and maximises safe retention of power sockets during high-speed operations. The Universal Ret Ring offers a safer, streamlined solution for socket retention, reducing risk of accidents and enhancing convenience. • retring.com
Australian-owned safety solutions company SafeGauge is launching its latest in heavyvehicle maintenance technology. The MultiTool Pro can connect up to 12 SafeGauge wireless tools with added data-logging and reporting capabilities. Maintenance crews can safely and efficiently accurately log and report readings across a range of vehicles for routine and unplanned maintenance. They can also generate and export reports to enhance troubleshooting and data analysis using the interactive graph or digital view. There’s also the ability to customise a template for each machine and task, simplifying the set-up process. Reports can be downloaded and shared locally or via email straight from the device – facilitating collaboration across teams.
SafeGauge call the MultiTool Pro a “game-changer”, taking safety, and elimination of live work (ELW) into the digital age. Pre-order for October 2023 release. safegauge.com.au
For WesTrac, Rio Tinto and Caterpillar, this tele-remote dozing system (TDS) at Rio Tinto’s iron ore operations in Western Australia is wholly focused on operator safety. The solution utilises the Cat MineStar Command for Dozing technology and a dedicated operator control centre, allowing for non-line-of site-operation of dozers working in high-risk areas. There is also an over-the-shoulder console that allows operators to work within visual range, typically used for temporary or one-off movements of machines.
The remote operator control centre is similar to a simulator, with all of the in-cab controls replicated. Rio Tinto’s also incorporates a vision kit, making use of four cameras on board each dozer and relaying machine information and visuals in real time via a Wi-Fi network. westrac.com.au
The Atlas Copco HiLight B5+ Light Tower is suitable for a wide range of applications, including events, residential construction, road construction, temporary public lighting, and oil and gas requirements. Designed to offer the widest choice when it comes to finding the light tower that is right for your application, the HiLight range provides a flexible and dynamic set of lighting options, while addressing all aspects of efficiency and safety. Operators can be assured of the robust build quality and compact size for which Atlas Copco is globally recognised.
Atlas Copco has put its innovation stamp on LED technology. The lenses in the LED light towers have a very special optic designed specifically for construction and mining applications.
This innovative, fully directional LED lens design ensures the light coverage is maximised while a single HiLight tower can cover an area of up to 5.000m2 with a 20 lux (brightness) average – ensuring a brighter, safer, and more productive site. To find out more, contact your nearest Atlas CEA branch.
• atlascea.com.au
When a Queensland Fitzroy Mining Operation site went up in flames in July, there was no cause for alarm: it was simply the start of the Queensland Mines Rescue Services’ (QMRS) second State Cup.
Eight mines rescue teams from across Queensland took part in a series of exercises from search-andrescue scenarios to simulated vehicle collisions and firefighting.
And although all teams gave it their best, only one could be crowned winner.
That major honour went to the rescue team from Anglo American’s Grosvenor coal mine in Moranbah, who will go on to compete in the Australia-wide competition in October.
It wasn’t the first time that Anglo American’s mines rescue team had taken out a top prize. In 2019, the team was named national champions of that year’s competition.
Then-team captain Boyd Buschmann said the simulations in the competition represented an important opportunity for all teams to test their skills.
“These competitions help ensure we have absolute confidence in our skills if we’re ever called on to undertake a rescue,” he said at the time.
“I’m very proud of the team’s hard work, dedication and professionalism. We’re also the first mixed-gender team to ever win the competition, which is a fantastic achievement.”
Hot on Anglo American’s heels in 2019 and 2023 was Moranbah North, placing second on both occasions.
This year saw the team from Broadmeadow come in third, while Oaky North took out fourth place.
The mines rescue teams battled it out over several intense simulated emergencies.
QMRS operations manager Luke Ludlow emphasised the importance of industry events such as these types of competitions.
“These annual competitions provide a chance to acknowledge these teams for their contribution to mine safety and the opportunity to execute learnings for future training,” Ludlow said.
Fitzroy Mining Operation’s chief executive officer Brian MacDonald said he was pleased to show the broader industry Fitzroy’s operation and capabilities.
“We at Fitzroy are honoured to have hosted the State Cup for the first time at our Carborough Downs mine,” he said.
Mine rescue has been a necessity ever since the first tonnes of coal were exported in Australia in 1799. But it wasn’t until 1909 that the first mines rescue brigade was formed.
That first brigade found its home in the Ipswich coal fields in central Queensland, building the first permanent mines rescue station there in 1923. Stations were then built further afield in Collinsville, Blackwater, Moura and Dysart.
From the early days, mines rescue teams have been an integral part of the Australian resources landscape. And as the sector diversifies, so too do the teams.
Anglo American formed the first ever all-female mines rescue team at its Capcoal open-cut mine near Middlemount, Queensland, in March of this year. The team is made up of seven women, who have named the team ‘Women of Steel’.
Team captain and Capcoal emergency response team coordinator Kiri Blanch said she had wanted to put together an all-female team for some time.
“Our team is a dedicated group of women who really gel together,” she said. “Everyone has been very supportive, especially our male
counterparts. It’s a reflection of the culture at our site that continues to both support mines rescue and empower the women we work with.
“This has inspired our team to commit to the challenge, improve our health and fitness and achieve the best results possible whilst representing women in mining.
“We will train closely with the Capcoal open-cut men’s team and support each other during competitions.”
Anglo American CEO Dan van der Westhuizen said the company is proud of the Women of Steel.
“We’re so pleased to support this outstanding group of women as they get set to make a real mark on Queensland’s mines rescue circuit,” van der Westhuizen said.
“Our mines rescue teams play a critical role in any incident response or rescue, and these competitions help ensure their skills are well honed if called upon to undertake a rescue.”
Miners face a specific and taxing set of circumstances compared to most Australian workers.
Many in the mining industry are in remote areas on demanding rosters away from support networks and family. Combined with the unrelenting nature of the Australian heat and the mine site’s taxing terrain, the industry is not for the faint-hearted.
Leading mining company Glencore recognised the unique challenges workers face and needed tailored solutions to support their wellbeing. This recognition grew into a long-standing partnership with MATES in Mining.
The MATES program started nearly two decades ago to provide on-theground training programs to help miners recognise the signs of mental struggle in their colleagues.
The program was launched from the successful nationwide MATES in Construction initiative. Both programs were designed to tackle a key issue in the sectors.
Recent data shows suicide is the leading cause of death for Australian people aged 15–44, while men have been consistently shown to make up three-quarters of suicide death.
The University of Melbourne report, ‘Suicide in the Australian mining industry: A national study’, estimated that the suicide rate among mining workers is between 11 and 25 per 100,000.
Safe to Work sat down with Glencore director of health, safety and training Kylie Ah Wong and MATES chief executive Chris Lockwood to discuss the success of the partnership and its outcomes for workers.
Glencore was one of the early adopters of the MATES program, as it looked for an evidence-based approach to support its employees’ mental wellbeing.
The positive impact of the training does more than create a strong work culture for Glencore. It helps to empower employees who are social leaders to support their communities.
“The beauty of this training is that it isn’t just applicable to the mining industry. It allows us to create a network of empathy and resilience, strengthening not only our mines but also our local communities,” Ah Wong said.
“This partnership is about training our workforce to identify behavioural changes in their mates so we can offer support when needed most.”
The findings in the University of Melbourne report suggested that the suicide rate for male mining workers could be increasing while rates in other industries were comparatively decreasing.
“That is the clearest picture we can establish,’’ study author Associate Professor Tania King said.
“Research that might inform the development of industry-specific suicide-prevention programs has been hampered by a lack of historical data into rates of workplacespecific suicide.’’
The mining industry features men making up 80 per cent of its workforce, which spurred the decision to make a change to ensure miners had adequate access to mental health support and training.
techniques were major reasons behind this success.
“The main success of the program is that it’s built on trust. It’s built on the trust of those working in the industry, as well as those managing the operations that this program is real and it works,” he said.
“Mental health impacts the entire mining industry, so we all need to take the time to learn the signs and know what to do. And we know we can achieve this in the miner sector because we have an evidence-based approach from MATES in Construction that shows it works.
“The program has been tweaked based on workers’ feedback, and that ensures it is speaking the language of miners and is relevant to their needs.”
Mental health awareness has been one of the significant shifts within the mining industry in recent years. Companies, as well as the sector more broadly, have been proactive in looking for actionable solutions
The MATES program has regional officers who conduct on-site training, which allows workers to feel safe to have open and honest conversations
other about how they’re feeling and recognising it is nothing to be afraid of,” Lockwood said. “We’re flipping the script with the program to have more of those conversations, so blokes can recognise their mate is struggling and start a conversation to help him.
“On-site, you have those small teams working together. And these close, trusted relationships can be important in providing support.
tools in their toolkit so they feel
confident to provide support to a mate when needed.”
Ah Wong said Glencore value the wellbeing of its employees, who are the pillar of the company’s success.
“We know that when someone is struggling with mental health issues, they’re unlikely to seek help,” she said.
“Our employees look out for one another’s safety every shift, and that sense of camaraderie is deeply embedded in the mining industry.
“It makes sense to use that same approach when it comes to looking out for the mental health and wellbeing of our workmates.”
Lockwood said MATES had been impressed by the willingness of Glencore and its employees to embrace the program.
“It’s a problem that can only be solved by stepping forward and taking on the responsibility to look after each other, which Glencore has embraced,” he said.
“It’s not just one part of Glencore that is doing this; it’s a belief shared across their whole business, which buys into how important this issue is for their workers.”
Safe Work Australia has recommended a reduction in the silica threshold from 50 micrograms per cubic metre of air (ug/m3) to 25ug/m3.
The recommended reduction is expected to significantly improve air quality in operator cabins that comply.
ISO 23875 covers the lifecycle of the machine from design at the original equipment manufacturer (OEM) level or in the aftermarket, and throughout its service life. The standard requires the use of effective engineering controls, which are validated by performance tests of the cab.
ISO 23875 is the only standard that addresses the specific engineering control requirements necessary to achieve this low level of silica exposure in operator enclosures, addressing air quality throughout the lifecycle of a machine.
“ISO 23875 is unique in the world of standards, as it was the product of 20 years of research and global collaboration between the best and brightest in the cab air quality space that included occupational hygienists, machine manufactures, end users, regulators, researchers, and academics from
10 countries,” Sy-Klone International project lead ISO 23875 Jeff Moredock said. “It is the roadmap to the future of cab air quality and compliance with the lowered silica exposure limit.”
It ensures the regulated silica level proposed can be achieved in all cabs that are certified under the standard.
Implementing the standard reduces exposure to all dust-disease-causing respirable particulate, not just silica. This includes asbestos, beryllium, coal dust, and diesel particulate matter (DPM), to name a few.
It is recommended that people familiarise themselves with the international standard, Mining – Air quality control systems for operator enclosures – Performance
requirements and test methods, as there are important details specific to testing and certification that must be understood to achieve compliance with the standard.
Under ISO 23875, there are five engineering controls specified to protect operators.
The first is having defined carbon dioxide (CO2) levels with alarms when thresholds are exceeded.
CO2 buildup from the operator’s exhalation can happen quickly in small enclosures like operator cabins, especially with heating, ventilation and air-conditioning (HVAC) systems in the recirculation mode. CO2 build-up has been identified as a probable cause of operator fatigue events.
The second control is having defined pressurisation requirements. When the key is in the ‘on’ position, cab pressure
must be a minimum of 20 pascal (Pa) since stabilised maximum cab pressure should not exceed 200Pa.
The third control is having defined, real-time monitoring of pressure and CO2 in place. This way the operator is alerted to hazards by audible and visual alarms, which indicate low cab pressure or high CO2.
The fourth control is to have defined fresh and recirculation system efficiency with 120-second decay time.
The maximum respirable particulate concentration less than 25 ug/m3 at start and end of the decay test means the operator is protected regardless of dust type, whether silica, asbestos, DPM, or coal dust.
The fifth control is having increased filter efficiency requirements from previous mining standards.
Not all CO2 monitors meet the ISO 23875 standard.
The standard specifies nondispersive infrared sensors (NDIR), as they are the most accurate, such as the sensor used in Sy-Klone’s RESPA Advisor+ in-cabin air quality monitor.
While some believe that a highefficiency particulate air (HEPA) filter is required, HEPA is not needed and in many cases is too restrictive for the HVAC recirculation system.
Restriction of the airflow through the recirculation system will cause high head pressure in the HVAC compressor and lead to premature failure. Restrictive HEPA recirculation filtration causes more intake air to be brought through the HVAC system, resulting in the production of excessive amounts of condensate.
Modern mining machine HVAC systems are not designed to accommodate the restriction to recirculation airflow caused by HEPA filtration. Instead, the ISO 23875 standard requires a minimum level of air quality performance.
The performance requirements needed high-efficiency filtration, which is identified on the filter label as an efficiency based upon 0.3 microns. ISO 23875 recommends, but does not require, that the filter efficiency exceed 94 per cent at 0.3 microns.
The best filter is the one that allows the system to deliver compliant air quality.
The standard defines air quality in terms of dust concentration in the cabin – the dust concentration must remain below 25ug/m3 when the cab is operating under stabilised conditions.
Lyons Airconditioning Services WA business development manager Ryan Wheeler said that newer filter technology has emerged in the past few years, including Sy-Klone
International’s durable high-efficiency particulate air (EPA) filters.
“(These filters) offer near HEPA protection with far less restriction, resulting in longer filter life and better HVAC performance,” he said.
“Filtration that is too restrictive can cause the HVAC to fail, so our customers have been pleased with this ISO 23875-compliant alternative.”
Another common misconception is that the higher the pressure in the cabin, the better.
When pressure is too high, in addition to operator discomfort, the volume of air exiting the cab at leak points can enlarge the leak points and cause door and window seals to gap, thus degrading the HVAC performance.
Pressure should not exceed 200Pa with the HVAC fan on high.
The cabin does not need to be completely sealed to hold pressure. In fact, it must leak some air, or fresh air would not be able to enter, CO2 build-up would be unavoidable and the door would not be able to close properly.
When sealing a cab, care must be taken to achieve but not exceed pressure within the 20–200Pa range.
One misconception is that if the filtration meets the specified efficiency target and the cabin is pressurised, the system should also meet the target.
Efficiency is a measure of how quickly the system removes particulate from the air and can only be determined by testing, as specified in the ISO 23875 standard.
Pre-cleaned and pressurised fresh air makes up only 20–35 per cent of the cabin airflow. Most of the air comes from the recirculation system, so high-efficiency, lowrestriction recirculation filtration is essential.
introduced when the door is opened, or dust comes off the operator’s vestments or puffs out of the seat. Decay rate is the time it takes the system to reduce the particulate level below 25ug/m3 after a spike in particulate levels.
To meet ISO 23875 requirements, the cabin air quality system must be efficient enough to do this within 120 seconds.
Cabin air quality systems are not created equal. Systems that are ejective, that expel the dirt they remove from the fresh air, are far more effective at achieving extended PM intervals.
According to NB Industries national director of sales Rob Greco, Sy-Klone’s RESPA CF2 uses a proprietary ejective particle-separation technology to achieve filter life up to 750 hours.
“Systems that ingest the dust, holding the debris inside the system, are continuously putting dust on
causing unplanned downtime.
“With an ejective system like the RESPA CF2, the filter housing empties itself. Coupled with the selfcleaning properties of the RESPA RadialSHIELD filters, which shed dirt, these systems are the best of both worlds and provide the highest level of customer satisfaction.”
The ISO 23875 cabin air quality standard, Moredock said, is designed to protect machine operators from lower lung diseases that reduce quality of life and, in many cases, shorten lives.
“When the standard is understood and applied as intended, with technologies that are harmonious with the goals of the standard, Australian miners win,” Moredock said.
rom preventing silicosis to protecting neighbouring worksites to minimising valuable product loss, there are a lot of reasons to take dust suppression seriously.
And few take dust control more seriously than Mincore, a local provider of engineering, contracting and equipment-supply services to the resources industry.
With over 25 years in the industry, Mincore has an arsenal of solutions at its disposal. One of its most impressive is Superchute, a dust control system for bulk material handling.
At many mines and quarries, as well as other industrial facilities around the country, conveyed material freefalls from the end of conveyors to the stockpile below. This material stream can generate a considerable amount of dust, often exacerbated by local wind conditions.
That’s where Superchute comes in.
One end of the Superchute is fixed to a stockpiling conveyor, and the body of the chute extends to nestle onto the stockpile below. The telescopic interlocking design with a flexible bottom skirt creates a sealed path through which material can fall, dramatically reducing dust from the stockpiling operation.
Dust in this situation often contains silica, heavy metals or other potentially harmful minerals, which can add significant costs if carrying through the facility or operations, and can
negatively affect long-term health of people working there.
“With Superchute, even on a windy day all you’re getting is a minimal amount of dust at the stockpile itself,” Mincore general manager John Tusa told Safe to Work.
“By mitigating dust, the health of the workers is protected.”
Beyond significant benefits in guarding the physical health of workers, effective dust suppression also comes with a number of operational advantages.
“Dust can get into electrical equipment and machines and can block filters and cause premature bearing failures,” Tusa said.
“Ventilators for electrical rooms can become blocked, which causes all sorts of problems with the electricals.”
All of these issues add up and can ultimately sting operators in terms of maintenance downtime and clean-up.
“There are very real cost consequences to leaving dust uncontrolled,” Tusa said.
Aside from clogging machinery, dust can disperse widely across natural and built-up environments, causing significant issues with neighbours and regulators.
One of the Superchute’s key features is the automatic operation mode, which allows the chute length to adjust automatically, thereby maintaining close contact with the top of the stockpile.
In automatic mode, the Superchute will lower itself down from the gathered position until the skirt encapsulates the top of the stockpile. This discharge skirt at the bottom end of the Superchute creates a seal to prevent dust-laden air from escaping into the environment. The chute will them incrementally raise itself as the stockpile grows, allowing the skirt to remain in contact with the stockpile.
Mincore’s engineering expertise, coupled with Superchute’s flexibility as a manufacturer, allows the product to be expertly tailored to a range of different applications.
flexible designers with considerable experience across a broad range of installations,” Mincore business development manager Clive Higgins said. “They’re capable of adjusting the design to suit different needs.
Superchute system is typically constructed from ultra-high-molecular-
weight polyethylene, which offers a superior wear resistance, with very low surface friction, high impact strength and excellent corrosion resistance.”
The telescopic design means sections of the chute can be added or removed to suit the particular operation, making it ideal for almost any height of stockpiling operation, and for ship-loading operations. And a fast turnaround of 4–5 months for delivery of customised Superchutes means site operators can solve their dust issues quickly and with ease.
The Superchute is being used in mining and quarry operations all around the globe, including in Australia at a Boral cement plant in
Boral, one of the biggest names in the Australian building materials industry, was looking at ways to improve its recently built Geelong operations. In the design phase for this cement grinding and blending plant, the managers at Boral wanted
to be proactive about mitigating dust for its ship-unloading gypsum stockpile, so they contacted Mincore for a solution.
“Having a discharge height of approximately 30m above Boral’s gypsum bunker floor, this Superchute is designed to span the full height, containing the gypsum within the close-fitting telescopic chute sections, which otherwise would be releasing significant dust throughout the freefall down to the stockpile,” Higgins said.
“With the help of the Superchute manufacturing team, we worked with Boral in the design and installation of this gypsum stockpile Superchute, tailoring it specifically for the site.
“Boral took the initiative in assessing dust suppression options, anticipating that the gypsum stockpile feed would be prone to release significant dust even in light winds.
“Choosing Superchute for this operation was a key strategy.”
The next step for Boral in terms of the gypsum Superchute is to tackle the dust generated at the actual stockpile surface. This is being addressed over coming months by introducing a larger skirt and automating the operation of the Superchute
In addition, Mincore and Boral are currently evaluating the installation of an additional Superchute to handle a ship-unloading stockpile for fine granulated slag, a more abrasive material than gypsum, to similarly mitigate dust from its stockpiling operation.
Superchute is also set for a gold mine operation in WA, with Mincore currently working through the final stages of the design process with the customer.
“The client has a large stockpiling conveyor operating at 800 tonnes per hour, but the issue they were facing was that the conveyor couldn’t support the weight of the Superchute without some changes to its design,” Higgins said.
“We went through a long sequence of exploring other options. We considered high-pressure fogging sprays, wind walls, wind fences and adding water to the material being stockpiled – but each alternative can create problems of its own.
“The client has ultimately come back to the Superchute as the equipment of choice, noting that nothing will really suppress the dust like the Superchute will.
“When it comes to dust suppression, the Superchute’s design and its ability to contain the dust at its source is just superior to anything else.”
Mincore is in the process of firming upgrade design options for the conveyor structure to support the weight of the Superchute.
Outside of Australia, Superchute is supplying its highly regarded equipment solutions globally, with
Superchutes helping a wide range of operations to suppress dust in Singapore, Canada, Norway, the US, and beyond.
The Superchute system, under the local guidance of Mincore’s engineers,
is helping mine and quarry sites around Australia keep a leash on dust. The precision modular design is helping to keep workers safe and sites virtually free from stockpile-dustrelated issues.
Being surrounded by dust amid the unrelenting Australian heat on remote mine sites will be a tale familiar to many in the resources industry.
The sector has worked tirelessly in recent years to raise awareness about the long-term impacts dust can have on workers. Given its links to lung disease and silicosis, dust is always a pertinent concern in terms of workers’ health, but it can also impact safety in other ways.
Dust has been shown to reduce visibility on a mine site, and that limited visibility can in turn lead to increased risk of accidents. It also clogs equipment and presents an ever-present slip hazard.
This is a situation Australian miners confront daily, so more and more workers are looking for brands that can tailor a solution to ensure they can walk another mile in their boots the next day.
Family-built safety footwear business KAMU understands that these challenges require dedicated solutions.
“Good safety footwear protects the feet. But great safety footwear can be the first step to shield miners from bodily injuries and health issues,” KAMU founder and global head of sales Lusy Hartanu said.
KAMU looked at the safety hazards caused by dust from a unique lens, as the three Hartanu sisters combined their family’s three-generation long history in personal protective equipment with the latest innovations in performance footwear technologies.
“We recognise these challenges and provide a robust line of defence against this invisible threat,” Hartanu said.
KAMU changed how the soles, uppers, seams and closures could work together to produce a better shoe. The result is a lightweight boot with several features that combat dustrelated risks.
The boots have a snug-fit ankle design with a connected tongue and sealed protective closures to prevent dust from permeating through gaps, eyelets or zips.
KAMU constructs its products from Coolmax material and breathable leather, preventing dust adherence and ensuring foot airflow.
Combined with a sealed YYK zip that prevents dust from clogging its teeth, the boots deliver workers a
barrier against the irritating dust of Australian mine sites. Additionally, steel toe caps shield against impact and compression hazards. Coupled with the optional puncture-resistant midsoles and metatarsal guards, the boots safeguard workers’ feet against hidden hazards in dusty environments.
Muster brings unmatched fire protection to your world. With cutting-edge systems and vigilant technology, we stand as your steadfast defense against the unexpected. From engine bays to critical spaces, Muster ensures safety and security. Discover peace of mind with Muster Fire Suppression systems.
Our strength comes from high-quality distribution partners who manage installation, service, technical support & training nationwide.
The boots also feature antistatic protection, reducing the risk of electrocution in dusty mining sites.
Hartanu said that these features are critical to keeping workers safe from the long-term health risks associated with dust.
Dusty surfaces get more slippery, particularly when wet. The boots’ outsole features pronounced lugs to provide traction and stability on various terrains encountered in mining operations, thus reducing the risk of
Hartanu said mining boots require an extra level of durability and extreme breathability.
“We solve this issue by pairing highperformance materials like Coolmax and Sympatex with waterproof full-grain leathers of premium quality,” she said.
“The membrane functionality ensures potentially harmful dust particles stay out while air and sweat can circulate, providing a healthier skin climate and keeping the body temperature down to prevent heat
KAMU footwear keeps dust out and energy in. At the heart of the design is the additional Infinergy midsole, which returns part of the energy expended with every step.
“The Infinergy technology has come to world fame for use in top-performance running shoes, empowering movement with a 57 per cent return on the energy we put into every step,” Hartanu said.
The company’s Infinergy antifatigue sole helps workers move with an athlete’s efficiency.
The innovative closed-cell technology by BASF helps reduce the impact of moving on the workers while using less energy per stride. It combines the high elasticity and rebound of foam with the hardiness of rubber, making the boots lighter than other comparable models.
The Infinergy midsole, like the technology used in top sports shoes, provides enhanced rebound and cushioning, which fights fatigue and improves stabilisation.
KAMU designs its footwear from beginning to end, with the mouldmaking done in-house. This allows the company to purpose-build models that help mitigate issues faced by workers that are specific to the mining operations in Australia and New Zealand.
“Mining work often requires traversing uneven terrain,” Hartanu said.
“Our higher-cut models such as the Edison 170 and the Volta 270 highleg rigger are designed with leather reinforcement and a lacing system that provide better support in the ankle and lower-calf areas.
“We have also developed our rubber nitrile outsole specifically for mining boots. It’s heat resistant to 300°C, resistant to oil, acids and chemicals, as well as anti-static.
“Given that Infinergy is similarly chemical-resistant, we can ensure that the KAMU soles are highly durable in environments where fuels, cleaning agents and other chemicals are present.”
The footwear is certified Safety, Rehabilitation and Compensation Act 1988 ), exceeding standards by 10–38 per cent.
Hartanu said KAMU delivered on its ambition to keep workers safe with its high-level design and groundbreaking midsole technology.
“When you’re less tired and distracted from discomfort, you can keep your mind on safety in environments where hazards like dust require extra focus and alertness,” she said. “We are not just protecting the workers; we are empowering them.
“Our boots improve physical and mental wellbeing at the workplace. We want to help increase productivity and make work more enjoyable.”
From the company’s experience as the trusted supplier of safety boots to Rio Tinto, Newmont, Orica and Thiess in Asia, the Hartanu sisters know the little things in safety make a big difference on the mine site.
Thanks to KAMU’s innovations, Australian miners can walk a dusty mile safely, soundly and comfortably in their work boots.
The International Mining and Resources Conference (IMARC) is where the most influential people in the mining industry come together, delivering ideas, inspiration and serving as a meeting ground for the industry. From ground-breaking technology and world-class content to a vivid showcase of all the elements that make the mining industry great, IMARC is an opportunity to learn from more than 500 mining leaders and resource experts with a program covering the entire mining value chain.
The world-class conference program now features seven concurrent streams with more than 340 technical talks, panel discussions and strategic keynote presentations taking place throughout the three days. Gain strategic insights from c-suite executives on topics including reshaping the mining value chain, progressing ESG and environmental resilience, accelerating mining’s energy transition and so much more.
Attend one of the many networking events or simply catch up with industry colleagues on the 18,500m2 expo show floor featuring 470+ leading companies. There are thousands of opportunities to network, brainstorm, and knowledge share across the three days at the ICC Sydney from 31 October - 2 November 2023.
IMARC 2023 will also see us celebrate 10 years of IMARC and industry, reflecting on the progress the industry has made, and the new directions that mining companies, METS, Governments, and its value chain partners are embarking on to prepare for the future.
VISIT IMARCGLOBAL.COM
TO REGISTER FOR AUSTRALIA'S MOST INFLUENTIAL MINING EVENT AND RECEIVE 10% OFF WITH THE DISCOUNT CODE PRIME10
7 conference streams acrossIn the dynamic realm of mining, effective communication serves as the bedrock for safety, efficiency, and overall operational excellence.
The ever-looming spectre of dust and grime infiltrating communication devices presents a formidable threat that can halt operations, eroding profits and imperilling on-site personnel in an instant.
To help address this issue, Sepura’s cutting-edge TETRA radios have been meticulously engineered to excel within environments that are rugged, dusty, damp and dirty – all of which define mining operations.
A diverse range of accessories complements Sepura’s holistic solution to empower users across a spectrum of environments and requirements.
Sepura’s dust suppression and water porting features are designed to ensure crystal-clear audio continues even in the most demanding circumstances.
Deflecting the dual onslaught of dust and water is pivotal.
Countless mines rely on water to quell dust disturbances, reducing airborne particulates. Dust settling on electronic components can infiltrate minuscule crevices, ultimately eroding performance and durability.
Sepura’s devices repel dust from the audio components, bolstered
by a robust IP67 rating, rendering them impervious to submersion and facilitating effortless cleansing under running water. They are ready for immediate operation after they are cleaned, in turn eliminating downtime.
This resilience helps equipment endure torrential downpours. Vibrations expel water from the speakers, swiftly restoring pristine functionality. This dynamic capability allows for uninterrupted operations and fortified safety protocols.
In addition, a dust guard acts as a staunch sentinel against magnetic dust, which may gravitate toward the speaker cavity due to its magnetic properties. Safeguarding the speaker interface, this shield thwarts dust and moisture infiltration
without compromising audio quality, an instrumental layer of defence amplifying miner wellbeing.
Continuous refinement of the sRSM is an outcome of intensive consultation with mining practitioners during comprehensive field trials.
Its user-centric design features amplified push-to-talk buttons, strategically relocated emergency buttons atop the device for intuitive access during crises, and adaptable clips and cables tailored to individual proportions and usage preferences.
Enlarged lip enveloping device buttons enhance structural integrity by channelling impact forces toward the device’s rugged casing rather than its more delicate elements, all while thwarting dust infiltration.
Sepura’s commitment to excellence extends to the meticulous validation of its products in its labs located in the UK. The depth of its scrutiny even includes a specially crafted rain chamber simulating delugelike monsoons.
Collaborative dialogue with mining entities informs Sepura’s submersion testing, meticulously mirroring real-world usage and cleaning scenarios to help guarantee unwavering and consistent performance, a testament to the customer-first ethos of Sepura.
Do you have blanket specs for turbos, manifolds and engine pipes?
Do you protect your crew and heat-critical exhaust parts with blankets?
Protect your dozers, drills, diggers, graders, and trucks with our blanket kits
Entering its 10th year, the International Mining and Resources Conference (IMARC) has long been seen as a key international forum to facilitate continuous improvements and initiatives that are transforming the landscape of an industry that has historically been seen as high-risk.
and, according to IMARC event director Paul Phelan, that is driven by greater levels of scrutiny and the need to create workplaces that represent attractive long-term employment opportunities for the diverse range of workers the industry needs.
“One of the great features of IMARC is how it brings out the best in a global challenges that can only be addressed
at an industry level,” Phelan said. “It is therefore highly collaborative by nature and brings together a wide range of expertise and experience, sharing industry best practice and lessons learned.
“Unlike many conferences where it is about sitting and listening to speakers, IMARC facilitates meaningful discussions and leads to real partnerships and real solutions.
“Safety is very much at the top of the agenda.”
Phelan said a key theme at IMARC this year is the way data-driven decision-making, using analytics and insights, is addressing safety challenges; for example, predictive maintenance that not only enhances safety but also extends the life of plant and equipment.
This data-centric approach has enabled the industry to take a proactive stance in identifying potential risks and implementing targeted safety measures.
THIS YEAR’S INTERNATIONAL MINING AND RESOURCES CONFERENCE IS SET TO BE A SHOWCASE FOR THE PURSUIT OF SAFE AND SUSTAINABLE MINING PRACTICES.The expo will show there has never been a greater focus on safety in mining operations. Safety is “very much at the top of the agenda” at IMARC.
Fine particles of dust pose a serious health risk, especially when fine particles are inhaled. Other safety risks include the increased risk of slips, trips and falls in areas of poor visibility caused by dust.
Dust is a significant operating, environmental and occupational hazard unacceptable to the modern Bulk Materials Handling
“Due to mining’s inherently hazardous nature, the risks of accidents, injuries and fatalities are all too real, leading to a pressing need for enhanced safety measures,” Phelan said. “IMARC has for a number of years recognised this imperative and we have responded by providing greater scope in our program for industry to engage on these common challenges.”
The adoption of artificial intelligence (AI) within the mining industry has emerged as a game-changer in recent years, facilitating a new era of mining safety.
IMARC speaker Alex de Jager, managing director of Conundrum Australia, which creates advanced machinelearning software for the metals and mining industry, believes AI is revolutionising safety in the sector.
“The speed at which the new platforms can identify and assess potentially dangerous situations, swiftly triggering system shutdowns, is almost instantaneous,” de Jager said. “The potential savings, not only in terms of employee safety but also equipment preservation, would have been deemed unthinkable not long ago.”
Over the past decade, IMARC has played a key role in driving the transformation of the mining industry in response to heightened expectations of the communities in which it operates, its investors and its own people.
Through its emphasis on technological integration, safety training, data-driven solutions, and environmental stewardship, IMARC has championed a paradigm shift that prioritises the wellbeing of workers and the sustainability of mining operations.
“IMARC continues to support collaborations that lead to greater standards across all aspects of the mining and resources industry, from environmental performance to finding the minerals we need for the future,” Phelan said.
“But, importantly, we are proud to provide the global mining industry with a high-profile forum to demonstrate its commitment to protecting its most valuable resource – its people.”
The Quickfit nozzle is part of the ESS Dust Suppression System designed to dramatically reduce the dust emissions generated as part of materials handling processes.
ESS Dust Suppression systems are suitable for most applications where the process will allow for small amounts of added moisture.
ESS Dust Suppression System utilising Quickfit Nozzles are
• Easy to Install and maintain – with service occurring outside the structure
• Low Maintenance – by using filters to reduce blockages
• Low Water Consumption Units – using 2 litres of water a minute over a range of pressures. Making it suitable for drier environments
• Designed in Kit Forms – available in kits of 2, 4 or 6
• Tailored to suit your sites needs
The Australian mining industry is a goliath, with operations and people hard at work at all hours across the country. It’s a multibillion-dollar industry but, as the saying goes, you’ve got to spend money to make money – and miners spend big.
One of the biggest and most complicated costs is labour.
Advanced Time and Attendance software is helping miners take control of all aspects of their workforce, from juggling award rates to managing overtime.
The Advanced solution does away with dated time and attendance procedures, which are often still done manually, through automating the process with a real-time clock-in system that utilises biometrics to verify the identity of employees.
But it’s about much more than just
The system provides all sorts of insightful data that can optimise a company’s operations from top to bottom, as is the case with award rates.
“Our system has an in-built award interpretation tool which keeps award
of the operation,” Advanced Software Solutions head of sales Damien Durston told Safe to Work.
“We have a customer with over 4500 employees and 26 different entities under their corporate banner. In this instance, we work with up to 74 different awards at any given time
With over 100 award rates in Australia, applying them correctly is no small feat, and mistakes can cost a
“Unlike our competitors, we do implementations onshore, working closely with Fair Work Australia, the Australian Tax Office, and the Fair Work Ombudsman,” Durston said.
“That means we know the award rates and exactly how to apply them.”
By providing a real-time overview of attendance, employers are able to see exactly how many hours each employee works in real-time and take action to
address issues such as any potential overtime or roster discrepancies for which the business has not planned.
“I think employers would be surprised at the amount of unauthorised overtime they’re leaking out the back door,” Durston said.
“Our system is giving supervisors and managers the real-time data they need to validate these hours, reducing overtime whilst ensuring the authorisation process is being adhered to and significantly saving money if potentially required.
“Overtime isn’t necessarily a bad thing, but having control over it means you can optimise overtime when it’s really needed.”
This kind of time validation is essential payroll information, which saves companies hours of administrative, manual work. It creates
efficiencies and assists with validating pay rules and award interpretation
Greater oversight of time and attendance also helps solve another issue faced by all industries: time theft.
“The system creates one source of truth, meaning you can’t tamper with start and finish times,” Durston said. “However, tampering can be defined as time theft and correct pay details in preparation for payroll submission.
“Our facial recognition signin means workers need to be physically present. This needs to occur for each individual, which eliminates any buddy clocking.”
Beyond validation and guarding against time theft at a management level, Advanced Software Solutions provide a helpful, streamlined tool for the workforce that brings accuracy to business operations.
“The system is automated and has a real-time rostering solution. It allows workers to efficiently manage their schedules, enabling them to change duties, take breaks and request leave,” Durston said.
“If someone calls in sick, the system has an auto-resolve function where it suggests the most capable replacement based on skill and capability.”
From a safety point of view, site operators having access to live data that shows exactly who is on-site is an invaluable tool in an emergency.
From minimising value-leakage to optimising a workforce, there are many reasons for the mining sector to automate its time and attendance systems. But few system providers offer such a robust, comprehensive solution as Advanced.
Personal protective equipment (PPE) is an absolute must in the resources sector to ensure workers are kept physically safe from potential hazards.
But what about protecting their mental health?
This is something Safety Mate has considered in supplying the Black Dog safety gear for hand and eye protection.
The product range supports Black Dog Institute, a not-forprofit research institute that investigates mental health across a lifespan and aims to create better mental health for everyone.
For every pair of Black Dog Stream EVO safety glasses sold, Safety Mate will donate $0.50 towards the institute, and $1 for every pair of Black Dog Cut D gloves and Cut F impact gloves sold.
“Most of the work that our team does is out in the field with workers that use gloves. We help to identify any potential safety risks or hazards in
the workplace” Safety Mate managing director Clint Tee told Safe to Work.
“We then make recommendations from within our range and run complementary glove trials. Our goal is to supply safety products that provide better protection, comfort and improved durability.”
The Black Dog Cut D gloves are lightweight, touchscreen-compatible and designed to be comfortable and durable to wear.
The Black Dog Stream EVO safety glasses, which were designed with maximum comfort and protection firmly in mind, are Tecton 400 antiscratch and anti-fog. They are also soft, adjustable, and feature an antislip nose bridge.
As is evident with this range of safety gear, Safety Mate wants to be known as not only a supplier of superior eye and hand protection, but as a supporter of improving mental health across the mining, construction and manufacturing sectors that helps to facilitate safer, healthier, and more productive workplaces.
“Right now, the stories that are relevant to most people are stories to do with mental health,” Tee said. “We have these products that help raise money that supports mental health research conducted by the Black Dog Institute. We’re not just another supplier distributing a brand of safety products.”
The company is also available to help customers find the right glove for them.
“If a worker was using a particular glove and we thought there was a risk of a cut or impact injury, we would make some suggestions as to where they get a glove with a higher cutresistance, or we provide them with a glove that has impact or anti-vibration protection,” Tee said.
Safety Mate has had a strong association with Black Dog Institute for more than three years. The relationship began when Safety Mate was looking for ways to contribute to a social or charitable cause that aligned closely with its values and business.
“The collaboration is something that we as a company are very proud of,” Tee said.
“When people use the Black Dog products, they know that by using those safety products, physical protection is being provided for the workers.
“We proudly say we are also helping mental health research by contributing to Black Dog Institute to help them continue important work in this space.
“If we can contribute through a collaboration like this, we can help provide information and resources to those that need it.”
rom electrical fires to catastrophic bushfires, Australians know only too well the dangers even a single ember can spark. Though we have far from conquered the threat of fire, strides have been made in minimising its harm.
Muster, through its exclusive distributor JSG Industrial Systems, is helping to keep the resources industries safe with its automatic fire suppression systems.
“Wherever you have heat generation with a potential mechanical or electrical
Muster fire suppression systems can be fitted to mobile assets and fixed plant, automatically triggering in the event of a fire.
A frontline defence against fire like Muster keeps people safe, minimises environmental impacts, and can often save expensive machinery and infrastructure from catastrophic damage.
“The costs of asset replacement and lost production can be crippling but are insignificant compared to the potential loss of life,” Sharpe said.
Muster fire suppression systems come in a range of variations, each suited to different environments.
“A fire is never just a fire,” Sharpe. “That’s why we have multiple agents for multiple variations in risk.”
The foam-based suppression system is ideal for suppressing dieselengine fires, particularly in vehicles and fixed plant.
Water alone is ineffective at managing fires caused by diesel and other refined petroleum products and, in some cases, it can even be dangerous.
The foam element of this suppression system amplifies the effectiveness of water by breaking down the surface tension, making the droplets smaller and enhancing the cooling effect. The foam also creates a blanket, which seals vapours to prevent ignition.
The aerosol fire suppression system is suited to electric motors and server rooms. It contains a solid chemical which, when the system is activated instantaneously, transforms into an aerosol that interrupts the chemical chain reaction in the flame and, in turn, suppressing it. Due to the self-generating nature of the chemical reaction, the aerosol system is compact and does not require a pressurised cylinder. It is appropriate for enclosed spaces in order to achieve consistent dispersing of the aerosol, without leakage from airflow.
The aerosol is also environmentally safe and free of harmful chemicals.
The impulse power fire suppression system utilises a dry chemical powder that rapidly fluidises when triggered. The system dilutes the flame zone with a powder-gas cloud and creates a powder fire blanket over the flaming surface. The result is a rapid knockdown of the fire.
Impulse system canisters come in a range of sizes and can be mounted directly within the risk area. The system is resistant to vibration, corrosion and moisture.
It is also similarly environmentally safe, with an operational life of 7–10 years.
Each Muster systems can be configured as a standalone defence or in conjunction with another in a dualagent system to cover multiple risk types on the same asset.
Muster also offers a transferable unit for firefighting (TUFF) system and portable fire extinguishers and accessories.
The core of the technology is the Muster alarm panel, which monitors the integrity of the fire suppression system around the clock and automatically controls the activation of the systems.
“The alarm panel is the heart and brains of the system,” Sharpe said.
“It’s got data-logging features that keep track of everything happening with the system, even unauthorised tampering.
“It also has applications in the autonomous world. You can have a fleet operating in the Pilbara and a control room in Perth that can remotely monitor and even manually trigger the suppression systems.”
Depending on the requirements of the customer and the installation, the alarm panel is configured to support either linear heat detection or loss-ofpressure fire detection.
Its circular design means the panel is extremely flexible and can be mounted in any orientation, including on the supplied stainlesssteel mounting ring, or set flush into a dashboard or overhead panel.
It also has an in-built fire activation button in linear heat detection mode, removing the need for an additional actuator to be fitted in the cabin.
The Muster diagnostic module can be connected to the rear of the panel, allowing a technician to see and download a log of any faults that have occurred.
The panel records time- and date-stamped information such as the event type, details of the event, system status, system pressure at the time of the event, and the percentage of battery in the alarm panel.
Downloading incident data allows technicians and site operators to identify trends among incidents, potentially helping to avoid future fire hazards. Each diagnostic module can hold information from up to 120 alarm panels, and each alarm panel can hold the most recent 448 events before overwriting the oldest.
With so much at stake, choosing the right system is essential. Fortunately, Muster takes the stress out of this decision with Muster360.
“Muster360 is a cloud-based program where we do a full fire risk assessment for our customers,” Sharpe said.
Muster360 considers machine details, along with any requirements such as minimum required discharge time, before proposing a 2D overview template of the fire suppression system overlayed on the asset. Once a customer accepts this design, system installation can commence.
“Muster360 is what really sets the system apart,” Sharpe said.
Prevention is a vital component of fire safety, and this is where JSG Industrial Systems’ expertise comes into play.
“We look at all the risks and ask, what can we do to prevent that? Or what do we do in the event that it actually happens?” Sharpe said.
“We give our customers specialised fire safety advice about their equipment, which greatly reduces the risk of fire.”
The Muster fire suppression system is hard at work in the mining industry, stopping fire in its tracks.
Sharpe detailed a recent incident that occurred at a mine site in Angola.
“The mine had recently installed the Muster fire suppression system on its largest excavator fleet,” he said.
“On the very first night of operation, the system suppressed an accidental engine bay fire that could have been catastrophic.”
In another instance, Muster was installed on a wheel loader in WA.
“Just three weeks after the system was fitted, the wheel loader caught fire,” Sharpe said. “It was a pretty intense fire because it was a burst hydraulic line straight onto the turbo. The Muster system detected the fire, actuated and suppressed the fire.”
With its range of intelligent fire suppression systems, Muster, through its exclusive distributor JSG Industrial Systems, is curbing the threat of fire in the resources industries.
Bodytrak® keeps your team safe by preventing incidents caused by heat stress, fatigue and noise exposure through accurate real-time data analytics.
With enough friction and heat, many conveyor belt constructions are capable of self-sustained fire propagation. Once ignited, they tend to produce a thick, black smoke resembling a tyre fire, which is often a worse risk to personnel than the flames themselves.
Although heat caused by friction is the principal trigger of conveyor fires, there can be several underlying causes.
Af ire is one of the worst catastrophes that can happen in any mining facility. But operations involving large conveyor networks are at particular risk of large-scale fires and the hazards they pose.
Bulk material conveying generates dust that can serve as fire fuel and even an explosion hazard, and controlling fugitive material in these operations is an ongoing challenge.
Another issue is the fact conveyors are notoriously under-maintained. They are often huge, complex structures that are only serviced when a component fails. A seized idler or mis-tracking belt can create sufficient frictional heat to cause ignition.
The size and speed of conveyors also present the opportunity to spread even a modest fire outbreak over great distances in a very short time.
Conveyor fires are also typically difficult to fight. The belt is a long
structure, often easily ignited itself, and a fire can spread all along this extended route with frightening speed.
If it’s not spotted in time, burning material can even be transferred from one conveyor to another. The belt path will often run around or through a variety of enclosures and structures, all of which carry the risk of fire inside them.
Inclined conveyors can develop a flue-like effect that intensifies the air flow, feeding the blaze and magnifying the damage.
Seized components such as rollers, brakes or bearings are a common source, often exacerbated by fugitive material that acts as an abrasive. Carryback on pulleys can also cause belt slip, creating friction.
Static electricity can also trigger an event, particularly when significant amounts of airborne dust are present. It has been estimated that frictional and static ignitions may account for up to 40 per cent of all belt fires.
Other causes are less predictable, such as overheated motors, electrical fires, incidental ignition of surrounding spillage and foreign material entering
• Frictional heating of belts riding on non-rotating components
• Heat from brake friction
• Belt rubbing on structure
• Bearing seal failure leading to seized bearings
• Combustible dust
• Out-of-control hightemperature processes where bulk material temperature exceeds belt capability
• Spillage of combustible bulk materials
• Accumulations of bulk materials that can spontaneously ignite
• Slip of a belt on a pulley
• Cutting and welding
• Mis-tracking
The desired results:
• The belt should resist catching fire due to friction
• The belt should be difficult to ignite with an open flame
• An ignited belt should not propagate a fire
• Excessive temperature of the drive
• Hot surfaces
• Flammable liquids• Sparks and electrical causes
the cargo stream producing sparks. These sudden ignitions can be spontaneous and, in some cases, leave little trace as to the trigger for the fire.
To create a fire there must be three elements: oxygen, heat and fuel – “the fire triangle”.
One factor that makes conveyor fires so hazardous is that the belt itself can be the fuel. According to a study of belt fires conducted by National Institute for Occupational Safety and Health, any of the standard neoprene, PVC, chloroprene and BELT-approved SBR belts can ignite.
Although some belts in the study were hard to extinguish and burned completely while others ignited quickly and went out on their own (self-extinguishing), the conclusion is that there is no non-flammable belt, particularly when accompanied by a combustible material.
What leads to friction can often be sourced back to either the discharge zone or the loading zone, or both.
Inadequate belt cleaning in the discharge zone can lead to dust and carryback on the return side of the belt, causing a fouled tail pulley to run under a stalled belt, which creates tremendous heat.
A fouled tail pulley can also cause the belt to enter the loading zone unevenly. As a result, cargo dropped from the transfer chute can settle on one side of the belt, causing the belt to drift further and come in contact with the structure or fixed components, resulting in high temperatures caused by friction that can ignite a fire.
Dust emissions of any kind (combustible or non-combustible) originating from the loading or discharge zones have a tendency to foul rolling components, leading to failure of the seals and contamination in the bearings, eventually causing the roller to seize. A rolling component can also stall if impact or cargo weight causes the bearings to collapse.
Continuous frictional contact with a seized idler or the roller face can cause a loaded belt to exceed safe operational temperatures. It can also result in extreme wear on the belt, degrading the fire-retardant layer and exposing the heat-sensitive materials found in the belt’s inner construction.
The “drum friction test” uses a sample of conveyor belt suitably mounted around a drum that rotates at a specified speed and belt tension. This allows testers to simulate the conditions of a stalled belt in contact with a fast-rotating drive pulley, or a belt passing over a seized idler.
The test measures different specified tensions for a given period until the belt breaks. The presence, or absence, of flame or glow is noted and the temperature of the drive drum is measured.
Conducted in either still air and/or moving air depending on conditions, in most standards the belt or the belt debris emitted from the drum rotation must not catch fire during a specified test duration. Although the sample may break or remain intact depending on the test standard, testers must specify the maximum temperature the drum reaches during the testing.
Fugitive material control and regular cleaning of spillage are imperative. Without proper belt cleaning, chute sealing and belt tracking, spillage that collects around the loading or discharge areas and along the belt path can damage moving components, restrict access by fire crews and potentially act as fuel.
Dust control is extremely important when handling combustible substances, and it is recommended that operators, instead of just taking into account the fire triangle, consider the “dust explosion pentagon”.
Significant amounts of dust can collect on the walls of the loading zone chute. If a foreign metal object is accidentally introduced into the enclosed area, a spark can potentially create an explosion.
In addition, common maintenance within the chute, such as removal of the wear liner using a cutting torch,
spillage mitigates the collection of potential fuel around the conveyor and requires less labour for clean-up.
Modern belt trackers with troughed idlers or gripping return idlers are so sensitive that they detect mistracking the moment it happens and immediately correct the belt path, reducing the chance of a friction fire due to belt drift. This also reduces spillage along the belt path.
often requires entry into a confined space by workers. If the inside of the chute is not adequately cleaned, this task could pose a serious hazard.
Examining conveyors should be approached with the mindset of an inspector from a government agency or fire department.
Safety professionals recommend a holistic view of the system, taking into account the combustibility of the material being conveyed and how the areas around the conveyor could be affected. It’s important to assess spillage levels and cleaning schedules, the conveyor’s proximity to work stations, how conveyor design (enclosures, narrow walkways, etc) could create a hazard for employees, safe storage of flammable liquids, and compliant signage.
Conveyor designs are always evolving and often retrofitted with new equipment based on changes in production and volume.
The potential return on investment for prevention equipment often isn’t recognised until managers are inspecting burnt rubble and negotiating with insurance adjustors. However, safety-minded operators understand that the same
equipment they would implement for increased efficiency, such as belt cleaners and impact cradles, can also help prevent fires.
Impact cradles and support cradles help reduce fugitive material by providing a stable belt surface that facilitates effective sealing.
Transfer chute design is a critical element of fugitive material control, with sufficient settling zones and confinement. New raised chute designs also allow for external wear liners that eliminate the need for confined space entry or torch removal.
When paired with improved skirt seal designs, fugitive spillage and dust emissions are drastically reduced, which protects rolling equipment from
A heavy-duty belt cleaner system featuring modern primary and secondary cleaners with an effective tensioner increases the volume of discharge and limits the amount of carryback and fugitive dust. Along with limiting spillage, tail pulley health is improved and there is less fouling of rolling components.
Improving the fire retardance of its belting is just one of the ways an operation can reduce the risk of conveyor fires. The development of fire-retardant belting has made an important contribution to safety, but even fire-retardant belts can burn in the presence of another fuel.
These potential fire hazards can only be minimised through high standards of conveyor installation, maintenance and cleanliness.
Experience has shown that clean conveyor systems, good firefighting capabilities and ongoing maintenance
For most people, the term “fire safety” likely conjures images of emergency crews battling infernos while deckedout in uniform. But most fire safety, especially when done well, takes place before a blaze ever sparks.
Few in the industry know this as well as Aletek, experts in thermal lagging and exhaust-related solutions for mining equipment.
Aletek national sales manager Arnie Hill said one of the biggest fire risks facing the industry is inconsistent maintenance.
“The failure of turbo feed lines, oil and coolant hoses is, in my opinion, the biggest challenge that the industry is facing right now in terms of fire safety,” he told Safe to Work.
“This comes about because of labour and time constraints, which has led to inconsistent levels of maintenance for these critical hoses.”
Proactive maintenance is another vital consideration.
A burst fluid line significantly increases the risk of fire, which is where Aletek’s thermal lagging comes into play.
Thermal blankets create a layer of insulation between super-heated engine and exhaust components and potentially flammable material.
“Lagging reduces the surface temperature and creates a barrier between the flammable material and the super-heated engine and exhaust components, which can otherwise create an ignition point or instant flame thrower,” Hill said.
In its report, ‘Mobile and transportable plant for use on mines
and petroleum sites’, the NSW Resources Regulator recommends the use of thermal blankets to significantly reduce the risk of a fire.
When thermal lagging does its job, something has already failed in the machine, and that’s why Aletek marketing executive Josh Lawrence calls it the last line of defence.
“You don’t wear a seatbelt with the intention of crashing your car. You wear it as a last line of defence,” Lawrence said.
“So you want to make sure it’s good quality – it’s the same story with thermal lagging.”
Although few come close to matching the premium quality of Aletek’s thermal lagging, it’s the company’s expertise in the field that really sets it apart.
Aletek works hard to understand its customers’ issues, drawing on its suite of fire safety solutions such as thermal lagging, dual wall exhausts, and sleeve burst protectors.
But it’s not enough to simply install these solutions; proper maintenance is an essential part of preventing fires. Up to 20 per cent of fires occur after maintenance,
according to a mobile equipment fires bulletin from Resources Safety and Health Queensland.
“So poor-quality maintenance is a fire risk just like failing to maintain a machine at all,” Lawrence said.
Aletek’s lagging is designed to be engine-specific for a snug fit, with quick-fit springs for establishing ideal tension. Turbos, manifolds, junctions, engine pipes and mufflers are the key components for lagging consideration.
The company knows that maintaining and installing lagging is a dexterous task, so the company runs training sessions and provides helpful install guides and cheat sheets to simplify the process.
“The reality is that no one loves fitting lagging, but the understanding of its purpose for fire safety on-site makes it all very worthwhile,” Lawrence said.
“We say this is what the lagging is used for, this is what happens when it’s not fitted correctly, and here are a few tips and tricks to make your life easier.”
Aletek offers customers lagging and exhaust-related fleet condition audits as a benchmarking tool.
Mental health is becoming widely acknowledged as an important component in business stability, workforce and even productivity. 20% of Australians will experience symptoms of mental illness each year. The Black Dog Institute does important work in this space.
BLACK DOG CUT D GLOVE
• Lightweight cut level D
• Touchscreen compatible
• Comfortable and durable
• $ 1 per pair donated to Black Dog Institute
BLACK DOG STREAM EVO
• Maximum comfort and protection
• Tecton 400™ Anti-scratch and Anti-fog
• Soft, adjustable, anti-slip nose bridge
• 50c per pair donated to Black Dog Institute
Now available with QR code on vending wrapper that provides quick access to tools and resources to help boost better mental health.
BLACK DOG IMPACT CUT F
• Lightweight for market-leading dexterity
• Excellent fit, breathability and comfort
• Touchscreen compatible
• Soft and flexible TPR for impact protection
• Durable and breathable nitrile coating
• $ 1 per pair donated to Black Dog Institute
Contact us for trial samples or to find a local distributor.
prevent incidents through real-time alerts,” Marsh said.
“Our advanced algorithms have been developed by data scientists and physiologists to accurately reflect the health status of users and ensure that both the user and supervisor will receive alerts when configurable thresholds are exceeded.”
Bodytrak streamlines a workplace’s approach to personal protective equipment (PPE), providing a single, comprehensive and integrated safety solution covering a range of hazards.
When it comes to safety, response time is key. The advent of real-time data has made it easier than ever for employers to keep a finger on the pulse of the status of their people and assets.
The Bodytrak solution takes this ethos and pushes it to its limits.
“Bodytrak is a smart safety solution designed to monitor the physiological responses of workers in challenging and hazardous environments,”
Bodytrak founder and chief executive officer Leon Marsh told Safe to Work
The high-tech earpiece measures several physiological markers such as core body temperature, heart rate and physiological strain index to prevent heat stress, fatigue and noise-induced hearing loss.
The system also features geolocation, geofencing, a user-activated SOS alarm, and fall detection. All of this data is transmitted in real-time to an incident management platform, allowing a site manager to view the live status of their employees.
“Think of Bodytrak as an employee’s buddy system that provides them with a nudge when they need a break or to remove themselves from a situation to cool down before they become high-risk,” Marsh said.
“The great thing is this is completely based on real-time actionable data of each individual, removing any guess work and replacing one-size-fits-all approaches.”
Bodytrak is helping solve two of the mining industry’s most insidious threats: fatigue and heat stress.
“Traditional tools like ambient temperature measurements fail to consider differences across individuals, making them less effective for heat stress prevention,” Marsh said.
“Similarly, quantifying fatigue has been challenging, with unreliable methods like questionnaires and blinkmeasurement cameras.”
It is exactly this gap in safety that Bodytrak was developed to address.
“Through a wearable earpiece with advanced sensors, we have the ability to provide individualised monitoring where precise data is captured to
“Previously, organisations have had to resort to using different devices and PPE to address each individual hazard, which is inefficient, costly, and onerous for users and supervisors,” Marsh said. “The Bodytrak wearable solution not only prevents incidents related to heat stress, fatigue, and noise exposure, but also offers other important features such as noise metering, geolocation, geofencing and SOS alerts to add another level of protection.”
Bodytrak is providing workplaces with essential data, helping to enhance safety and productivity.
“The data captured isn’t just numbers. It offers organisations with a clear lens to obtain valuable insights into workplace trends and patterns,” Marsh said.
“The automated reports provide vital information to enhance safety protocols, optimise processes and boost overall productivity.”
Bodytrak is helping solve some of the biggest safety issues in mining with one comprehensive and integrated solution.
The word ‘sustainability’ gets a lot of mileage in the mining industry these days. Most often, it concerns environmentally conscious mining practices, carbon emissions, and circular economic practices.
But there is another integral aspect of sustainability: safety.
A business that can’t keep its employees safe at work is inherently unsustainable, and that’s why Epiroc has set itself the 2030 target of zero accidents at its mining operations.
The path to such an ambitious goal is threefold. It involves autonomous mining solutions, reducing the amount of drill bit changes for operators, and shortening site evacuation times.
Automated machinery helps keep workers away from the frontlines of mining operations, minimising human contact with potentially hazardous equipment.
Epiroc is a market leader in automated drilling, loading and hauling technologies, and one of the best examples is the company’s fully autonomous Pit Viper drill rigs series.
Capable of completing an entire drill pattern autonomously without an operator on board, the Pit Viper is 22 per cent more productive than conventional drilling.
Another example is Epiroc’s Boltec with auto bolt reload (ABR), the first ever underground rock reinforcement drill rig of its type.
The main design feature of the Boltec ABR is the fully mechanised bolt reloading system that automatically feeds bolts from a large carrier magazine to the feed magazine, all while the operator remains safe inside the cabin.
And when it comes to load and haul, Epiroc’s mine trucks have a full autonomous cycle. The company is able to fit its autonomous solution to vehicles designed by different manufacturers, allowing for a mixed fleet of vehicles all controlled via Epiroc’s traffic management system.
With this system, one operator can control loaders and trucks from the safety of the operating station.
And perhaps one of the company’s most notable accolades in the sphere of automation was securing a major contract at Roy Hill, under which Epiroc, together with its partner ASI Mining, will convert the site’s fleet of 96 haul trucks to driverless operation, making Roy Hill one of the world’s largest single autonomous mines.
In addition to keeping workers away from heavy machinery, site automation means mines can operate during shift changes and blasting, greatly improving safety and productivity.
Another angle of Epiroc’s 2030 zero-accidents goal is improving safety by reducing the number of drill bit changes.
One of the methods by which Epiroc achieves this goal is with the Powerbit X, a drill bit with a diamond
protective layer that gives the drill bits longer service life, meaning fewer changes and less exposure to hazards for operators.
The extremely hard surface of the Powerbit X lets it drill longer and more efficiently than standard drill bits, reducing emissions per drilled metre by up to 90 per cent.
And when it comes time to change drill bits, rigs such as the Pit Viper can perform this function automatically, allowing operators to quickly change bits from the safety of a control room.
When working underground, ensuring miners are able to be reliably co-ordinated, especially in the case of an emergency evacuation, is one of the most important factors to consider in ensuring safety.
Epiroc has revolutionised underground mine safety with Mobilaris Emergency Support, a real-time workforce safety toolbox that allows rescue leaders to better coordinate evacuations.
Mobilaris emergency is
a technology that visualises the live location of workers in a mine. The system can relay emergency messages through mine phones and related equipment such as the Mobilaris virtual tag and the Mobilaris cap lamp. Personnel can easily acknowledge emergency warnings with the click of a button, allowing rescue leaders to see who is aware of danger and who is not.
“Ensuring that evacuees are mobilising towards safety rather than the hazard and ensuring people are using the shortest possible routes to refuge chambers is heavily dependent on real-time information,” Epiroc product sales manager Andreas Prill told Safe to Work Mobilaris can highlight and prioritise individual personnel for rescue efforts where necessary, such as if they are unaware of the emergency, injured or trapped. The technology can even guide rescue personnel remotely in real-time.
With its Mobilaris Emergency Support, Epiroc is able to shorten evacuation times by 25–50 per cent.
This type of digitalisation technology is making mining operations safer and more efficient.
“You can’t improve what you can’t measure, and you can’t measure what you can’t see,” Prill said. “Realtime data is required to improve on productivity and safety.
“By comparing one shift to another or one cycle to another, we can start to understand why one performed better than the other and implement continuous change and improvements.
“Removing uncertainties and variables, operations can stabilise and then optimise operations, benefitting not just their ability to ensure safety, but also the productivity of the mines.
“Digitalisation is integral for this, as it’s how these variables are uncovered. Knowing what is working and what isn’t in real-time is how safety and productivity is improved.”
A leader in mine safety, Epiroc is leveraging a range of intelligent solutions as it strives for its 2030 goal of zero injuries.
Hoists are complicated pieces of machinery that support a range of industries. That’s why picking the right one is so important.
It’s also why Kito, a leader in the global hoisting sphere, has launched Mediahub, a new feature on the company’s website that allows users to see a 3D visualisation of all Kito products.
By breaking down hoists into their individual components in a 3D space, the visualiser gives users the opportunity to view and read about those individual components and compare products alongside one another.
“It can be challenging for customers to find a balance between budget limitations, safety regulations and the quality and features they require in a hoist,” Kito national hoist specialist Glenn Morgan told Safe to Work
“The 3D visualiser is Kito’s way of helping customers understand the quality of our products, as well as the attention to detail we pour into every aspect of our design process.”
Mediahub also includes videos of each product to explain some of the more technical functions.
Kito is continually advancing its technology and stocks a wide range of specialty hoist and chain products, such as the heavy-duty ER2 electric chain hoist, which are designed with performance at heart.
The compact aluminium diecast body is exceptionally rigid and provides effective protection against
dust and water. With capacities ranging from 250kg to five tonnes, the ER2 range is ideal for heavy industries such as mining.
The ER2 is specifically designed to operate quietly. It also features an ergonomically designed control pendant with light-press buttons, helping fight fatigue as well as workplace noise pollution.
“The ER2 hoist is known for its durability and reliability, ensuring
consistent performance even in tough working conditions,” Morgan said.
“Equipped with safety mechanisms like limit switches, thermal protection and magnetic brake, the ER2 hoist prioritises operator safety and prevents overloading.”
Another new offering from Kito is the efficient EQ electric chain hoist. With capacities ranging from 125kg to one tonne, the EQ is designed to be lightweight and faster than other comparable hoists on the market.
A low-load high-speed function allows for hoist operation at 1.3 times the standard highspeed, which helps to significantly increase productivity.
The EQ electric chain hoist also features fast and slow lifting speeds for precise positioning and reduced load swing, ensuring safety and easy handling.
The EQ and ER2 series share some common features not found as standard anywhere else in the market, including a dual-speed inverter for
Sepura's broadband products combine powerful mobile data with TETRA mission critical voice capability, supporting safe, efficient operations
For further information visit www.sepura.com
reduced load swing and precise positioning, a built-in count metre for maintenance scheduling and overload prevention, and a unique nickel-plated chain for maximum strength and corrosion resistance.
“Designed to endure the toughest conditions, Kito’s wide range of hoists boast unrivalled durability, ensuring continuous operation in challenging mining environments,” Morgan said.
“Kito hoists are built to require minimal maintenance, enabling mining companies to focus on their core activities without interruptions.”
Kito has a long history of manufacturing specialised lifting solutions with a focus on usability, safety and endurance.
Mediahub perfectly captures the company’s ethos of delivering a highquality and streamlined experience to its customers.
Ahouse won’t last if the base isn’t perfectly balanced – and the same is true of people and footwear.
From underground to surface operations, mine workers endure a range of different conditions that demand specialised and high-calibre personal protective equipment (PPE).
A one-size-fits-all approach to footwear just doesn’t fly when it comes to mining.
That’s why Blundstone has launched the RotoFlex steel line, adding 17 new styles of footwear to its already expansive suite of options.
This is the biggest safety footwear launch in Australia in a decade.
“The RotoFlex steel range is our toughest and most advanced range of footwear yet,” White said.
Steel caps are well-suited to work such as underground and surface mining operations, offering cut and crush resistance.
The footwear’s steel cap is impact-resistant to 200 joules, the equivalent of dropping a 20kg weight from waist height.
The RotoFlex steel range is unisex, with the exception of two new styles biomechanically designed to suit women. With so many new options, there is a boot to fit just about anyone – and any job.
“We have launched nine new
have six new RotoFlex HD boots with a TPU outsole. These are lighter and have better hot and cold transmission and better abrasion resistance.”
“Then we have two new styles in the RotoFlex MAX, which is our most premium boot. These have additional features like penetration resistance, Kevlar stitching, better waterproofing, and one with a BOA fit system.”
The boots combine the strength of steel with RotoFlex’s innovative design for a paragon in comfort, safety and style.
“The RotoFlex range of boots is where stability meets the freedom to move, allowing the wearer’s foot to rotate and the ankle to flex to avoid injury,” White said.
RotoFlex was designed in collaboration with the University of Tasmania, where Blundstone commissioned the School of Health Sciences to investigate the biomechanics of common foot injuries and fatigue in a research program that ran for two years.
“The research told us that a flexible boot that is able to rotate freely can
be safer than a stiff or bracing boot,” White said.
“Movement is important for safety, as it allows the maintenance of balance and control. So that’s exactly what we did with RotoFlex.”
RotoFlex boots utilise a range of premium materials.
The GripTek sole is designed to reduce ankle injury with a wide contact surface. The heel design provides cushioning and clearance over obstacles, while the tread geometry is designed to grip ladders and protect when using tools such as shovels.
The AirCell footbed has cushioning zones that pump air around the underside of the foot, reducing moisture. The SoftCell interior design of the boots has a form and fit, developed over 18 months of trials for maximum comfort.
RotoFlex was also designed to be environmentally conscious, incorporating 3D-printed reinforcing materials to minimise waste, recycled polyester for the internal lining, and laces made from recycled material.
As part of the design process, Blundstone sends out samples of its boots for real-world trials that last for months, incorporating that feedback into final designs.
“Every single component used in the construction of the RotoFlex range has been researched, tested and trialled to create truly innovative, better-performing safety footwear,” White said.
The result is heavy-duty boots that are lab-crafted, field tested and can handle just about anything the industry can throw at them.
Breadth of options is at the heart of the RotoFlex range.
Fly-in, fly-out (FIFO) workers – or those who wish to enjoy something a little lighter – might prefer the airport-friendly composite cap variation of RotoFlex boots. Suited to surface mining, the composite cap is compression resistant to 200 joules. Composite boots also perform better in particularly cold and hot climates, as they provide better insulation than steel.
They might be designed in a lab, but they certainly don’t look it. The RotoFlex line comes in a range of stylish designs.
RotoFlex combines Blundstone’s 150 years of expertise in footwear manufacturing with the best in modern footwear technology. With 17 new styles of footwear, the RotoFlex steel range has something for every worker in terms of technology, style and, of course, safety.
Legislation shapes systemic change, and for sexbased discrimination and harassment, the pivotal Respect at Work Act marks the beginning of this transformation. Now the clock is ticking for employers to ensure compliance.
The Respect at Work Act 2022 has been the most significant evolution in workplace law in recent years. The Act affects a number of different pieces of legislation, creating strict obligations for employers when it comes to sexual harassment and sexbased discrimination.
Helen Jamieson, head of customer success at online compliance training company Safetrac, said she has never seen such significant changes to the law in her 19 years in the legislative compliance sphere.
“The ‘Enough is Enough’ report that the WA Government put out last year highlighted some horrific stories of sexual harassment and abuse against women in the FIFO (fly-in, fly-out) industry,” Jamieson said.
“So it is very timely that the latest amendments to the Respect at Work Act explicitly prohibiting sex-based harassment and placing a positive duty on employers to eliminate sexual harassment in the workforce have been introduced.”
Amendments to the Sex Discrimination Act 1984 (SDA) now require employers to adopt proactive measures to prevent sexual harassment, sex-based discrimination and related victimisation. This covers not only the actions and behaviour of
the employer, but also their employees and others who work for them.
Under previous laws, employers could be held vicariously liable for sexual harassment and discrimination where they failed to make all reasonable steps to prevent the behaviour from occurring. This is still the case; however, this is the first time the law has enforced a positive duty on employers to take reasonable steps in eliminating sexrelated discriminatory behaviours in the workplace.
This means that employers need to proactively take action to prevent unacceptable behaviour relating to sexual harassment in their workplace, regardless of whether a complaint has been made.
These changes are bolstered by the fact that the SDA now makes it an offence to subject someone to a hostile work environment (based on sex).
Similarly, the threshold of what constitutes sexual harassment has been lowered from “seriously demeaning conduct” to “demeaning conduct”.
In another significant change, Respect at Work also vests the Australian Human Rights Commission (AHRC) with inquiry and enforcement powers relating to an employer’s new duty to prevent discrimination.
As part of its new functions, the AHRC may inquire into, and report on, issues of systemic unlawful discrimination or suspected systemic unlawful discrimination across all four federal discrimination acts.
“The AHRC can now provide non-compliant employees with recommendations. They might be issued with compliance notices or become subject to court orders,” Jamieson said. “The AHRC can also issue enforceable undertakings, which has never happened in this space before. It’s really quite significant.”
Owing to the gravity of the changes, employers have been given a one-year grace period to demonstrate this positive duty of care. That door will close on December 13 this year, at which time the AHRC will commence its new responsibilities.
These changes to the law can be complex, but Safetrac has employers covered with its thorough compliance training.
“Safetrac offers online training courses, helping employers stay compliant under their new obligations,” Jamieson said. “Through our legally
updated training, employers can rollout online learning programs, either on our platform or through their own learning management system, on key legislated areas such as sexual harassment, discrimination, anti-bullying, anti-harassment, psychosocial hazards, and work health and safety.
“Every employer must grasp these new legal changes, as they are now obligated to proactively implement measures that deter sexual harassment within their businesses, and the deadline to demonstrate this commitment is approaching swiftly.”
With over 2.3 million online training courses delivered and a customer retention rate of 97 per cent, Safetrac is a leader in the compliance space. The company offers an extensive range of legally up-to-date courses.
“Our training comes in a lot of different formats to suit different
learning audiences,” Jamieson said. “One option is the structured learning format, which is quite robust and engaging, suitable for employees who have little latent knowledge on the topic.
“Accelerated training is less interactive, but completely devicecompatible, meaning it can be easily accessed on mobile phones or tablets. ShortBurst training is short scenario-based training, and microlearning is shorter training broken into little video packages.
“We also offer our clients booster courses which are available as soon as there is significant legislative change which impacts an area of legislation. It gives our subscribers an understanding of the change without forcing them to redo their whole training.
“Additionally, we supply surveys and policy distribution and hosting,
aiding employers in ensuring organisations ensure their staff agree to comply with requisite policies and to demonstrate their understanding of the law. Complementing these offerings are our specialised online courses for managers, equipping them with the knowledge to appropriately address any instances of unacceptable behaviour that their staff may encounter.”
Jamieson says compliance training for a company is a lot like insurance.
“Good-quality training helps protect a company from staff doing the wrong thing,” she said.
“But if they do (the wrong thing), the reporting can demonstrate the company’s efforts to ensure they did everything possible to ensure staff understood the laws.
“In the event of regulatory intervention, this can help reduce liability.”
With the clock ticking for all statutory persons in the Western Australian mining industry to achieve their WHS (Work Health and Safety) Statutory Competency Certification by March 2025, Optimised Mining has developed an educational method designed to guide teams through the process.
“Western Australia has recently changed the legislation to a new WHS Act which requires statutory persons to pass a new examination,” Optimised Mining director Kiernan Smithson told Safe to Work. “We have an extensive background in this area from our work in Queensland, so we’re in a good place to help those in statutory roles in Western Australia.”
Optimised Mining co-founder Chris O’Donnell explained statutory roles in the mining industry.
“Statutory roles are required to ensure the health and safety of a site,” he said. “The site senior executive is the most senior of those roles; they’ll be in charge of running the entire site.”
Statutory roles are written in WA’s legislation to ensure the safety of mine sites is kept to a high standard. To achieve this goal, however, statutory persons must keep up to date with the education surrounding safety.
And that’s where Optimised Mining can help.
“Historically, most exam prep courses might be a two-to-three-day affair where employees are taken offsite for a couple of days,” Smithson said. “They go in, get taught some legislation, then they get told, ‘see you later, good luck on the exam’.
“But our approach is cohort-based; it’s an online, structured, four-week flexible course which involves a oneday workshop and then work through the content in our app for roughly an hour per day.”
Optimised Mining’s in-house built app means the team can coach participants through the whole course.
“We’re with them every step of the way,” O’Donnell said.
“At the end of the last financial year, the average industry pass rate was 39 per cent, but Optimised Mining has seen a 97 per cent pass rate. We also customise the coaching to meet different job titles. A manager will have different content than a senior executive, and so on.”
According to Smithson, the key to Optimised Mining’s technique lays in coaching, rather than training.
“Both myself and Chris have done the exams ourselves, so we know what people need in order to pass them,” Smithson said. “We make sure that the people who go through our program are 100 per cent ready to sit the exam at the end. We know what the challenges are but we also know how to overcome them.”
Optimised Mining also understands that balancing work, family, social commitments and study can be challenge, and the team tries to customise the course.
“Through the app, we can check on each person’s progress and we’ll give them a call or an email to offer some extra support,” O’Donnell said.
While 2025 might sound like a long way away, O’Donnell emphasised that the clock for certification is ticking.
“If employers don’t get people through the course by the 2025 deadline, they won’t be able to keep operating. It’s imperative that sites get onto this now,” he said. “With Optimised Mining’s app and course, we can get ... people over the line without making them feel like a number.”
Everything you need for autonomous fleet operations using your existing vehicles, even in the harshest environments.
Radio Network Repeater Station
Radio Network Base Station
Server & Control Room
Site Traffic Management System
Driver Connectivity System
Vehicle Automation System
Plan routes, assign tasks and manage multiple vehicles at once with Indigo Drive’s user-friendly software and modular ecosystem of hardware. Designed to meet functional safety and ISO standards. High availability architecture for risk prevention. A proven system built by safety experts with over 30 years of experience.
abdsolutions.com
When Kevin Cant escaped serious injury after the belly plate he was removing from a bulldozer slipped and fell, he knew things in the industry needed to change.
From this incident, Nivek Industries and, later, TED was born.
TED, which stands for Tracked Elevating Device, was first launched by the Nivek team in 2011. The design has since undergone updates and enhancements to make it the industry favourite it is today.
Now, Nivek has introduced Big TED, a larger and stronger version of its predecessor.
“Big TED has an increased lifting capacity of three tonnes,” Nivek general manager Derrick Cant told Safe to Work. “Our original TED has been on the market for over a decade now, and we have designed Big TED based on customer feedback”.
“With Big TED, you don’t need a bobcat, a crane, or a forklift. Big TED will carry the load, lift it, and hold it in place while equipment is installed or uninstalled.”
With its joystick-activated remote control, Big TED helps to take workers out of the line of fire by reducing manual-handling-related injuries.
It also features dual emergency stops on the machine and remote
control, meaning Big TED can come to a halt as soon as a worker pushes a button.
“Anything that is less physically demanding on an employee is going to translate to a safer workplace and minimal downtime,” Cant said.
A tilt sensor to reduce the risk of overbalancing and a deadman switch on the remote work to ensure that there are no unplanned movements putting workers are not put in harm’s way.
Nivek has sold three Big TEDs to date and has heard nothing but positive feedback.
“They’re saving so much time for the operators out there,” Cant said.
“We’ve heard already they’re seeing an increase in safety and efficiency.
“They’re just really happy with the quality and the benefits.”
Listening to customer feedback is a key focus for Nivek, as the company wants to ensure it is developing
equipment people in the mining industry need to stay safe.
“Not only does Big TED lift more weight than the original, but it’s got more functionality in relation to a built-
in side shift, powered turntable, and tilt sensors” Cant said. “You can also measure the weight that’s sitting on it, making it a lot more user-friendly.
“There’s a display on the remote control that provides operational feedback so that operators don’t have to go up to the machine.”
Nivek designs its equipment so its customers can attach and carry almost anything on them.
“We design our machines as a platform, customers can then contact us to design a cradle or an attachment to go on top, so it can really be configured to each customer’s needs,” Cant said.
Heavy industries like mining all come with inherent safety risks, but Nivek works every day to ensure sites can remain as safe as can be.
Whether the team is training fitters on-site, designing and building TED attachments or providing after-sales support and services, safety is the reason the team does what does.
Just about every mine operator is familiar with the term ‘skill shortage’. The industry is currently in the throes of a very tight labour market, battling not only availability, but also costs.
It is in this environment that the Australian’s Government’s ‘same job, same pay’ reforms have raised concerns among many miners.
The proposed law will require host employers to pay labour hire workers the same rate as direct employees performing the same job.
The concern is that this change will put additional pressure on a fragile labour market. The change encompasses all industries, but it is the resources industry – where labour hire makes up a significant portion of the workforce – that will really feel the sting.
The Minerals Council of Australia (MCA) believes the legislation will result in inexperienced workers earning the same as veteran workers and, more generally, potentially disincentivise hard work.
BHP Australia president Geraldine Slattery recently expressed concerns over the resulting competitiveness of the Australian resources sector in her address to the American Chamber of Commerce.
She said the major miner predicts that the reforms may harm its operations, including its Olympic Dam copper mine in South Australia.
“We believe ‘same job, same pay’ could increase the operating costs of our existing operations (in SA) by nearly $200 million per year and maybe up to $500 million in a worstcase scenario,” Slattery said.
“The hit to the value of any potential growth plans in SA could be anywhere up to $US2 billion ($2.98 billion) and this would make it much harder for any South Australian investment case that has to compete with alternative options in other parts of the world.”
Federal Workplace Relations Minister Tony Bourke said the law is only meant to lift labour hire workers to the same pay as those on enterprise agreements.
Bourke believes the reforms do not override individual enterprise agreements between employee and employer. It is therefore possible for the ‘same job, same pay’ laws to mandate a baseline entitlement for labour hire workers that is separate from a higher rate of pay enjoyed by
senior staff in accordance with their individual enterprise agreements.
Much of what is known of the proposed reform comes from the original 2021 ‘same job same pay bill’, which was rejected at the time.
In an effort to mop up some of the uncertainty, the MCA called for a clear and straightforward definition of a service contractor to be entrenched in the legislation, and to exclude those businesses from the law.
Bourke has said he does not expect the ‘same job, same pay’ laws would cover contractors performing genuinely specialist or short-term work.
“I’ve been crystal clear with all stakeholders that there are legitimate uses for labour hire that we don’t want to get in the way of,” he said. “They include for specialist workforce, for surge workforce and for temporary replacement.
“The problem that we’re trying to solve is where an enterprise agreement has been put been in place, where there are agreed rates of pay and then an employer uses a labour hire firm to undercut those rates of pay.”
Rather than an industry-wide exemption of service contractors, Bourke said the Government was
considering a multi-factor test to distinguish specialist services from supplemental labour firms.
In an article by Paul Burns, a partner at the law firm Corrs Chambers Westgarth, he noted that even if problematic practices do exist in the labour hire sector, there are already pathways to address such behaviours.
“Labour hire businesses are required to comply with modern awards and can be forced to engage in enterprise bargaining in just the same way as hosts,” Burns wrote.
“This suggests that perhaps the pay differential between labour hire employees and direct employees engaged by hosts is more a function of the operation of the labour market.
“At a time of historically low unemployment, these arrangements may simply be a reflection of the laws of supply and demand.”
According to the Australian Bureau of Statistics, 81 per cent of labour hire workers are full-time, with 84 per cent not entitled to leave or other entitlements enjoyed by contracted full-time employees.
In 2019 and 2020, the median annual earnings of people in labour supply services was $33,100, reflecting the short-term nature of the work.
While this type of data is clear, until the legislation is clearly defined, and its effects made more evident, the industry will be left to speculate.
OLIVER FOOTWEAR’S CUSTOMER-DRIVEN APPROACH DELIVERS A VERSATILE WORK BOOT FOR ANY AUSTRALIAN MINING SITE.
When considering versatility, many people would raise the ability to perform multiple roles or take on various tasks.
Footwear and personal protective equipment (PPE) are rarely thought about in this sense, but rarely is versatility more important than in a miner’s work boots.
Australian mines can be exacting and relentless places, often characterised by heat and uneven terrain. The people working in these conditions need footwear that can match the task on a daily basis.
Honeywell understands that safety boots for mining need to be tough
and rugged, able to handle water, and comfortable to take on long shifts.
And that’s why Oliver Footwear is designed with the modern-day miner in mind.
Oliver Footwear has expanded the range for its renowned AT 55 series, AT 45 series, and the PB 49 series women’s with a new stone colourway.
Safe To Work spoke to Honeywell senior sales executive John Watts about the key features that set Oliver Footwear apart.
“It is about how it handles being in the field and the all-day comfort that sets Oliver apart from the other brands,” he said. “We’re constantly updating the design to stay at the
forefront with our Australian design team, led by industry feedback, to make the changes.
“This approach has helped us develop a reputation for long-lasting and comfortable work boots, and that’s where we have an edge.”
The Oliver AT 55-352Z is designed for miners who need the all-terrain versatility delivered in the style and comfort of a nubuck leather steel-toe safety boot.
The new stone zip-sided boot features water-resistant leather and a lightweight 300°C heat-resistant rubber outsole, helping to ensure workers can tackle any mining site environment with peace of mind.
“It’s a hard-wearing sole and good for the mining industry’s type of work, because when you’re out in the dirt with harsh conditions, a hard-wearing sole becomes important,” Watts said.
“In mining sites you’re on your feet all day, so we’ve got up to four layers of cushioning in there because you’re on hard and rough surfaces all day and need that level of comfort.”
Oliver Footwear has paid attention to the small details to make sure workers can tackle every challenge on-site. This includes adding Kevlar threads to provide chemical and abrasion resistance on critical seams, and slip-resistant soles (SRC rated).
“The sole is rated as anti-static as well, which is great if you’re working with sensitive equipment in a volatile area,” Watts said.
“The Kevlar thread is the highest-grade material you can get, which stops the boot from wearing out on-site.”
The boots have also been designed with fly-in, fly-out (FIFO) workers firmly in mind.
Oliver Footwear understands that FIFO workers often carry their belongings in and out of camp. Considering the effort this task can demand, especially following
offers a lighter alternative to alleviate the burden.
One of the main features on this boot is the composite toe-cap made of fibreglass and plastic. While rated the same as the steel toe-cap, the composite is 40 per cent lighter, making it easier to transport and pack.
“It’s ideal for fly-in, fly-out workers because it is completely metal-free; you can get through airport security without alarms going off,” Watts said.
“We’ve made our boots lighter with the composite toe-cap but retained the hard-wearing sole, which is still suitable for those harsh environments.”
With more women taking up mining roles, Oliver Footwear is aware of an increasingly diverse customer base.
Data from the Australian Bureau of Statistics shows that the number of women who have become employed full-time in the mining industry has increased from 8700 in August 2002 to 45,000 in August 2022.
The data also showed that the number of female apprentices had significantly increased, from 434 female apprentices and trainees in 2019 to 831 in 2022.
With this increasing shift in the diversity of the mining site, PPE
manufacturing focus to better accommodate the female workforce. After all, as Watts said, every worker should be able to walk away in comfort at the end of the day.
Oliver Footwear’s PB 49 Series Women’s has channelled this focus with a specially designed range that meets the needs of women in the industry.
Among a range of other features, the PB 49 Series offers multiple styles of work boots, a 300°C heat-resistant rubber outsole, COOLstep lining to effectively absorb moisture and odour, and SOFTstride built into the insole, providing not only comfort but also contour support.
Designed with versatility in mind, this range of boots ensures suitability for extended, all-day wear.
“It is designed around the unique contours of a woman’s foot, setting it apart from the usual method of scaling down from a man’s boot. We wanted to design a boot specifically for women,” Watts said.
“More women are joining the mining workforce. We were very aware of that and wanted to take that on board to give women more flexibility in their options with what they can wear on site.”
Oliver Footwear takes a tailored, customer-driven approach to its safety boots, and the result is a modern, versatile shoe that can handle the rigours of the Australian mining industry.
“We’ve listened to what people have to say and requested different features and colourways,” Watts said. “We must understand what our customers need because they work in that harsh environment.
“The less time you spend replacing boots and the more time you spend being comfortable out in the field, the better for everyone, and that’s what we’re focused on.”
Leading vehicle automation provider ABD Solutions is aiming to transform safety in the mining industry by removing drivers from harm’s way.
According to research from the US, powered haulage accounts for the most fatalities in all mining.
Western Australia’s Department of Mines, Industry Regulation and Safety has also found there were 425 reported incidents involving vehicle rollovers between 2017 and 2022, citing traffic management, human and organisational factors as key contributors.
The automation of vehicles mitigates a lot of this risk.
In 2017, the World Economic Forum predicted that automation and digitalisation in mining will decrease deaths by 10 per cent and reduce injuries by 20 per cent over the next 10 years.
This is where ABD Solutions and its autonomy technology, Indigo Drive, is aiming to make a big impact on the sector.
ABD Solutions creates safer and smarter work environments by delivering vehicle autonomy solutions. With expertise in actuation, perception, localisation and safety systems, the company transforms existing machinery and vehicle fleets
to become autonomous, and partners with original equipment manufacturers (OEMs) to deliver novel solutions.
As part of the global AB Dynamics plc Group, ABD Solutions has a heritage of driving vehicle safety and has operations around the world, including in Australia.
Indigo Drive is a full-stack, selfdriving system that delivers safetyenhancing autonomy by significantly reducing the exposure of personnel to dangerous environments.
The system is vehicle-agnostic and enables a limitless number of mining vehicles to be automated. It includes user-friendly software for route-planning, the hardware to move the vehicles (such as drive-by-wire
and driving robots), communication (radio, V2X, GPS/GNSS), obstacle detection (LiDAR, camera, radar) and vehicle health and diagnostics (OBD2, telemetry, sensors).
Safety and reliability have been at the heart of the development of Indigo Drive, which is evident in its functionally safe and robust build.
Designed to meet the rigorous safety standards of IEC61508: 2010 and ISO17757: 2019, as well as cyber security engineering standard ISO21434, it operates on a highavailability redundant architecture and removes single points of failure for reliable and continuous operation, giving mining companies and workers peace of mind.
With a technology readiness level (TRL) of seven, ABD Solutions has demonstrated the viability of its technology in real mining environments and is working on tailored solutions for Australian customers.
Beyond safety, Indigo Drive also designed to enhance productivity in mining operations. It enables an entire fleet to be synchronised and managed on a single platform to maximise efficiency. Its task-planning software ensures that
vehicles take the most efficient routes, reducing fuel consumption and time to complete operations.
The system also digitises the vehicles, providing critical new data streams that are invaluable to fleet
operators to assist with strategic decisions, fleet maintenance scheduling and logistics planning.
describes Indigo Drive as a “game-changer” due to the fact it removes personnel from hazardous environments through functionally safe autonomous vehicle technology.
“The key benefit being that by integrating with existing vehicle fleets, it can keep workers safer, sooner,” the company said.
Austmine represents over 700 mining equipment, technology and services (METS) companies across the country.
It brings the industry together through events and innovation opportunities to drive developments in safety, decarbonisation, and almost any issue faced in mining.
We chatted with chief executive officer Christine Gibbs Stewart about Austmine’s role in bringing the industry together, particularly around the issue of safety.
Making a difference on a couple of different levels.
At an industry level, we have a lot of challenges upon us. We need to be more sustainable; we need to have a very good public perception.
People don’t necessarily want to work for the mining industry, but with the programs that we run, and with the exciting high-tech METS sector that we represent, we’re helping to change the conversation.
At a sector level, we’re getting out there and promoting what the METS sector does. We’re raising the reputation and creating opportunities for the METS sector on the global stage.
And for individual companies, I love it when we can help our members
industry stronger. That’s the most exciting part to me.
Bringing people together is the core of what we do.
When we get our member companies together, they realise they have synergies and they come up with ideas to work together. This could be anything from helping each other optimise manufacturing processes to coming together to solve an issue in the digital space.
The other thing we do is run innovation opportunities for mining companies.
Miners often need more than one solution to a problem, or they’ll need a solution that isn’t available yet from a single source.
So we can bring members together in that way to help them collaborate to provide solutions to those mining companies.
Decarbonisation is a big issue, and learning from each other in that space is a really important thing to do.
So the mining industry really coalesced around the idea of coming together through different committees and organisations to crack the safety problem. What we’re seeing today is far fewer fatalities and injuries.
Safety was one of those areas –akin to the decarbonisation effort today, though we’re not quite there yet – where the mining industry said “forget about competition”. Safety is one area where collaboration has really benefited the mining industry.
One of the things I’m proudest about with Austmine is that we’ve created a real community of people passionate about the sector, and getting together to collaborate on solving these bigger issues.
One of the biggest efforts that we facilitated was the Charge On Innovation Challenge. We partnered with Rio Tinto, BHP and Vale and challenged innovators to find a solution for charging large electric haul trucks on open-pit mine sites.
We had over 350 suppliers across 19 industries participate in an expression of interest, which were whittled down to eight finalists in the end.
Charge on Innovation is a great example of how Austmine brings opportunities to our members and the wider METS community.
Mineinnovate is a new tool that we have just put out to help drive collaboration. It’s a digital space where mining companies, OEMs (original equipment manufacturers), engineering firms, contract miners, and others can put up the challenges they’re facing –or innovation opportunities, as we call them – for our members, and the wider community, to respond to.
The platform will be able to link people together from a collaborative point of view to engage with one another and see what’s going on in
the industry, and ultimately improve the way things are done. The platform is also linked to some other programs and ecosystems like Austmine from all over the world.
It’s not just a space for Australia, it’s a space for the world. The first challenges that were put on mineinnovate were from India and Saudi Arabia. That just goes to show that the mining industry is a global industry.
With a digital space like mineinnovate, business can flow in a borderless way.
It recognises that the industry is mature enough to get out there
and want to work together on the challenges it faces.
Going back five years, people weren’t that open to discussing their biggest issues in a public format. But now we’ve moved on such that the industry recognises that because of the challenges it faces, everyone needs to be contributing.
Things are much more open these days, not just in what is being put out, but also in how others are responding.
One of the things I kept hearing at this year’s Austmine conference, and also at the World Mining Congress, is that we need more collaboration.
And it’s probably a deeper type of collaboration, one that involves more trust and more respect for all the players involved. A trust that really drives our industry forward.
Paramedic, trauma counsellor and international speaker, Paul Spinks shares his unique insight and solutions on reversing the spiral of mental health, maximising human performance, growth and self-worth.
When was your last normal? A life crisis can happen to anyone regardless of position or wealth. What is the point of success if we lose ourselves and the connection to the things and people we love?
Most inspirational presentations wash off quickly. This one will last a lifetime.
AFTER AIR-QUALITY ISSUES WERE DISCOVERED AT NEWCREST’S CADIA VALLEY MINE IN NSW, THE GOLD MINER MOVED TO ADDRESS THE PROBLEM.
The air we breathe affects many aspects of our health and environment, and highquality air control within mining operations is vital for people in and out of a mine.
Australian gold miner Newcrest has committed to strengthening its air quality control following investigations into its wholly owned Cadia Valley Operations in New South Wales, one of the largest gold mining operations in the world.
Safe to Work looks at the timeline of the New South Wales Environment Protection Authority (NSW EPA) investigation and Newcrest’s proactive response to rectify the issues.
The NSW EPA launched an investigation into the Cadia Valley Operations in late May by issuing a draft pollution prevention notice and a draft licence variation regarding the
management of emissions of dust and other pollutants. NSW EPA chief executive officer Tony Chappel said Australian industries have moral and legal obligations to limit impact on communities.
“Everyone in NSW has a right to clean air no matter where they live,” Chappel said. “Last week, the EPA received new evidence from the community to suggest actions by the mine to reduce dust pollution have not been effective.
“As part of the notices, we are requiring immediate re-testing of the mine’s main vent and an extension of the ambient air sampling network to deliver expanded air monitoring.”
Chappel said this was an important step in requiring Cadia to demonstrate compliance and would inform further actions that may be needed.
Cadia conducted testing in response to these notices, ultimately determining that the site’s main vent was releasing an “unacceptable level
of dust.” This prompted the site to adopt its own measures, as well as those directed by the EPA, to address the issue. The NSW EPA then told Cadia in late June that it must comply with relevant legislation.
“We require the mine to take all necessary steps to ensure dust emissions are significantly reduced and this may include a reduction in production,” Chappel said of the notice.
Newcrest, for its part, fully committed to following all necessary steps to ensure Cadia’s dust emissions were reduced.
Newcrest understood the issue and undertook a number of steps to ensure Cadia’s dust emissions were reduced.
These steps included regular vent emission monitoring and providing a monthly report on dust discharge from one of its main vents.
The gold miner also committed to providing:
• additional reports on lead dust fingerprinting research
• analysis of dust impacts and sources
• an independent health risk analysis
• an updated air quality impact assessment
• undertaking works to manage dust generation underground
• monthly reports on works undertaken in relation to the dust suppression plan for the tailings dam.
To achieve these goals, Newcrest implemented a collection of actions to lower dust production levels.
The company also committed to installing additional dust sprays and spray curtains, reconfiguring dust extraction systems, sampling of the vent rise emissions as required by the latest variation to its licence,
fitting additional dust sampling instrumentation, and accelerating additional dust filtration units that were on order at the time.
Newcrest elaborated further on these efforts in its June 2023 quarterly report.
“During the quarter, the NSW EPA issued Cadia with variations to its environment protection licence and a prevention notice regarding the management of dust emissions and other air pollutants,” Newcrest said.
“The licence variations largely formalised the actions Cadia had developed in consultation with the EPA and were already undertaking across a range of measures, following dust emission exceedances from a ventilation exhaust rise and concerns from some local community members of elevated levels of contaminants in their water tanks.
“Cadia received a letter from the EPA in June 2023 requiring it to immediately comply with specific statutory requirements and licence conditions. Adjustments were implemented underground, including a reduction in mining rates, modifications to the ventilation circuit and the installation of additional dust sprays and spray curtains.
“No material impacts to production are expected, with mill feed supplemented by surface stockpiles whilst the planned commissioning of additional dust filtration units is progressively completed in the December 2023 quarter.”
Newcrest also addressed a 12-month study undertaken by the Federal Government’s Australian Nuclear Science Technology Organisation (ANSTO).
“(The study) highlighted that all air quality standards at Cadia and the surrounding region have been met,” Newcrest said. “The study also highlighted that metals of concern
recently identified by the community, such as lead, nickel, selenium and chromium, were not in exceedance of any national standard and only occurred at very low levels in the measure for air quality standard.
“This study further supports the community water testing program undertaken at 144 residences surrounding the mine in March 2023, that showed water tested was safe to drink.
“Further to the ANSTO study, a lead fingerprinting analysis was commissioned through the University of South Australia to determine the extent to which Cadia could have contributed to community drinking
water concerns. This analysis was independently interpreted and found no evidence linking Cadia to the lead sampled in district rainwater tanks.”
In early July, the NSW EPA received results from the first round of dust emissions monitoring from Cadia’s vent rise 8 outlet, demonstrating that operational changes reduced the discharge of total solid particle from underground operations through. Cadia reported that the concentration of total solid particles on June 28 was below the requirements set in the clean air regulation.
The EPA requested that Cadia undertake further testing to confirm the impact of the operational changes.
“The NSW EPA has quite rightly pulled us into line on the lack of compliance because there’s too much dust coming from the vent rise,” Newcrest Cadia Valley Operations general manager Mick Dewar told the ABC in response to the results.
“What we’ve been doing, and the studies we’ve been doing, is trying to look at the concerns which have been raised in the community — which are quite reasonable — as to whether there’s a health impact.
“When the EPA required us to immediately comply, we did. We’ve adjusted our operations pretty heavily to do so and we’re currently operating in compliance.”
Despite the progress made, Dewar said there is more to be done.
“It doesn’t absolve us from being non-compliant,” he said. “What it seeks to do is provide some assurance to the people around Cadia that the dust is not impacting their health and the air they’re breathing is safe.”
Newcrest echoed similar sentiments in its June 2023 report.
“Cadia continues to work openly and transparently with the EPA and the local community to ensure all statutory obligations are met in a way that is aligned with Newcrest values,” the company said.
When the EPA announced on August 21 it had commenced proceedings in the NSW Land and Environment Court, a Cadia spokesperson said the site was now compliant with clean air regulations.
“Mining responsibly is what the community expects of us, and what we demand of ourselves,” the spokesperson said
“We remain firmly committed to rebuilding trust and confidence in our operations with the community and regulator, so we can continue to support jobs, regional investment, and the energy transition.”
“Cadia continues to work ... with the EPA and the local community to ensure all statutory obligations are met in a way that is aligned with Newcrest values.”
WOMEN IN INDUSTRY NOMINATIONS ARE NOW OPEN. Now is your chance to nominate an industry leader who you believe is advocating for positive change and deserves to be recognised.
PROUDLY PRESENTED BY
Thurs 20 June, 2024
The Women in Industry Awards recognise outstanding women leaders from across Australia’s industrials sector.
THE WOMEN IN INDUSTRY AWARDS RETURN FOR ANOTHER BUMPER YEAR IN 2024.
Asold-out gala dinner, 160 nominations and a 55 per cent increase in attendance on the previous year were some of the biggest moments of the 2023 Women in Industry Awards.
But the real highlights were the exceptional women whose success was showcased throughout the night.
Held in Melbourne on June 8, the 2023 awards celebrated the nominees and winners across industries such as mining, road transport, manufacturing, engineering, logistics, bulk handling, waste management, rail and infrastructure.
The awards are set to return in 2024 to recognise exceptional women who have achieved success through leadership and innovation.
There are 11 awards up for grabs in 2024, including the Safety Advocacy Award, Excellence in Mining, and the esteemed Woman of the Year award.
Giselle Phillips, HSEQ (health, safety environment and quality)
advisor at Fredon, was named both the Safety Advocate of the Year and the Woman of the Year at the 2023 awards.
“This is a celebration not only for me but for the team as well, because we are making change in our field,” Phillips said in her acceptance speech.
“Women are not in competition with each other. We need to advocate and help each other to get where we need to be.
“So this is not only for me, but also for every woman that is in the room.”
Past sponsors Atlas Copco, SEW Eurodrive, Fulton Hogan and PACCAR Australia have confirmed sponsorship for 2024, with more to be announced.
Atlas Copco, which sponsored the 2023 Rising Star of the Year award, said diversity is a key contributor to the long-term success of a business.
“The Women in Industry Awards is a special way in which we can show our commitment to advancing the gender balance in industry,” the company said.
these awards is just one way that we can show that Atlas Copco recognises the talent and achievement of females across our industry.”
With such a successful event behind it, there is no doubt that the 2024 iteration of the awards will be better than ever.
Nominations are now open and close April 19 2024. Winners will be announced at a gala dinner in Sydney on June 20 2024.
AGRICULTURE FARMING EDUCATION WASTE MANAGEMENT RESOURCE MANAGEMENT
CONSERVATION MANUFACTURING RESOURCES
ENERGY HEALTH & SAFETY INFRASTRUCTURE
ENGINEERING MINING CONSTRUCTION
QUARRYING AGRICULTURE FARMING EDUCATION
WASTE MANAGEMENT RESOURCE MANAGEMENT
CONSERVATION MANUFACTURING RESOURCES
ENERGY HEALTH & SAFETY INFRASTRUCTURE
ENGINEERING MINING CONSTRUCTION
QUARRYING AGRICULTURE FARMING EDUCATION
WASTE MANAGEMENT RESOURCE MANAGEMENT
CONSERVATION MANUFACTURING RESOURCES
ENERGY HEALTH & SAFETY INFRASTRUCTURE
ENGINEERING MINING CONSTRUCTION
QUARRYING AGRICULTURE FARMING EDUCATION
WASTE MANAGEMENT RESOURCE MANAGEMENT
SEARCH FOR TOP INDUSTRY TALENT THROUGH OUR JOBS BOARD.
CONNECT WITH ALIGNED CANDIDATES.
BOOST YOUR CHANCES OF FINDING SKILLED APPLICANTS.
SCAN TO CREATE AN ACCOUNT TODAY AND DISCOVER YOUR PERFECT MATCH!
POWERED BY CAREERONE
EVENT SUBMISSIONS CAN BE EMAILED TO EDITOR@SAFETOWORK.COM.AU
The International Mining and Resources Conference (IMARC) creates a global conversation, mobilises the industry for collaboration and attracts some of the greatest leaders in the mining, investment, and technology industries for three days of learning, deal-making and unparalleled networking. Learn from more than 500 mining leaders and resource experts with seven concurrent conferences covering the entire mining value chain. Gain strategic insights from C-suite executives on progressing ESG and environmental resilience, accelerating mining’s energy transition and the digitisation of mines. Discover inspiration and new ideas, find practical solutions, and see demonstrations of the latest products and innovations from start-ups through to some of the biggest names in the mining industry with more than 470 exhibitors throughout the 18,500m2 expo floor all under the one roof.
• imarcglobal.com
Taking place in Brisbane in 2023, the Australian Mining Prospect Awards are a great opportunity to recognise and acknowledge the people and companies in the mining sector for their outstanding work. Nominations are now open, with awards in categories such as Indigenous and Community Engagement, Mine Project Success of the Year, Outstanding Mine
Performance, Sustainability Project of the Year, Discovery of the Year, and more. The awards return to Brisbane in appreciation of the vibrancy of the state’s mining industry.
• prospectawards.com.au
Critical minerals are essential components in many of today’s rapidly growing clean energy technologies – from wind turbines and electricity networks to electric vehicles. The increasing appetite and rapid pace of the transition to cleaner energy sources continues to drive the growth in demand for these minerals, and the supporting industries are also growing at unprecedented rates.
AusIMM will launch its inaugural Critical Minerals Conference in 2023. The event will include a multi-stream format and seek to engage with a larger audience from multiple disciplines as well as a wide range of industries.
• ausimm.com/conferences-and-events/ critical-minerals/
These awards are an opportunity to celebrate the success of women in the mining industry. To be held in Sydney, the 2024 awards feature multiple categories that showcase exceptional examples of industry advocacy, mentorship and excellence.
The Women in Industry Awards recognise outstanding women from across a range of industrials sectors; for example, those who work in mining, transport, manufacturing, engineering, logistics, bulk handling, waste management, rail and construction and infrastructure – all sectors that are traditionally male-dominated.
This is an opportunity to recognise the women who are driving change in industry and, in doing so, break down barriers and creating new possibilities for the next generation.
• womeninindustry.com.au
The 2024 PNG Industrial & Mining Resources Exhibition will showcase over 100 local, national and international manufacturers and suppliers with the latest innovations in the supply of services and equipment for the industrial, mining, and oil and gas sectors. The two-day exhibition is the premier meeting place to connect and network with thousands of industry decisionmakers across a broad industry reach, including senior management, procurement, government personnel, engineers, contractors and trade technicians. With extensive support from key stakeholders in government, associations and industry, PNG2024 is a high-level industry trade event and a forum for establishing high-quality customer contacts and conducting business.
• pngexpo.com/