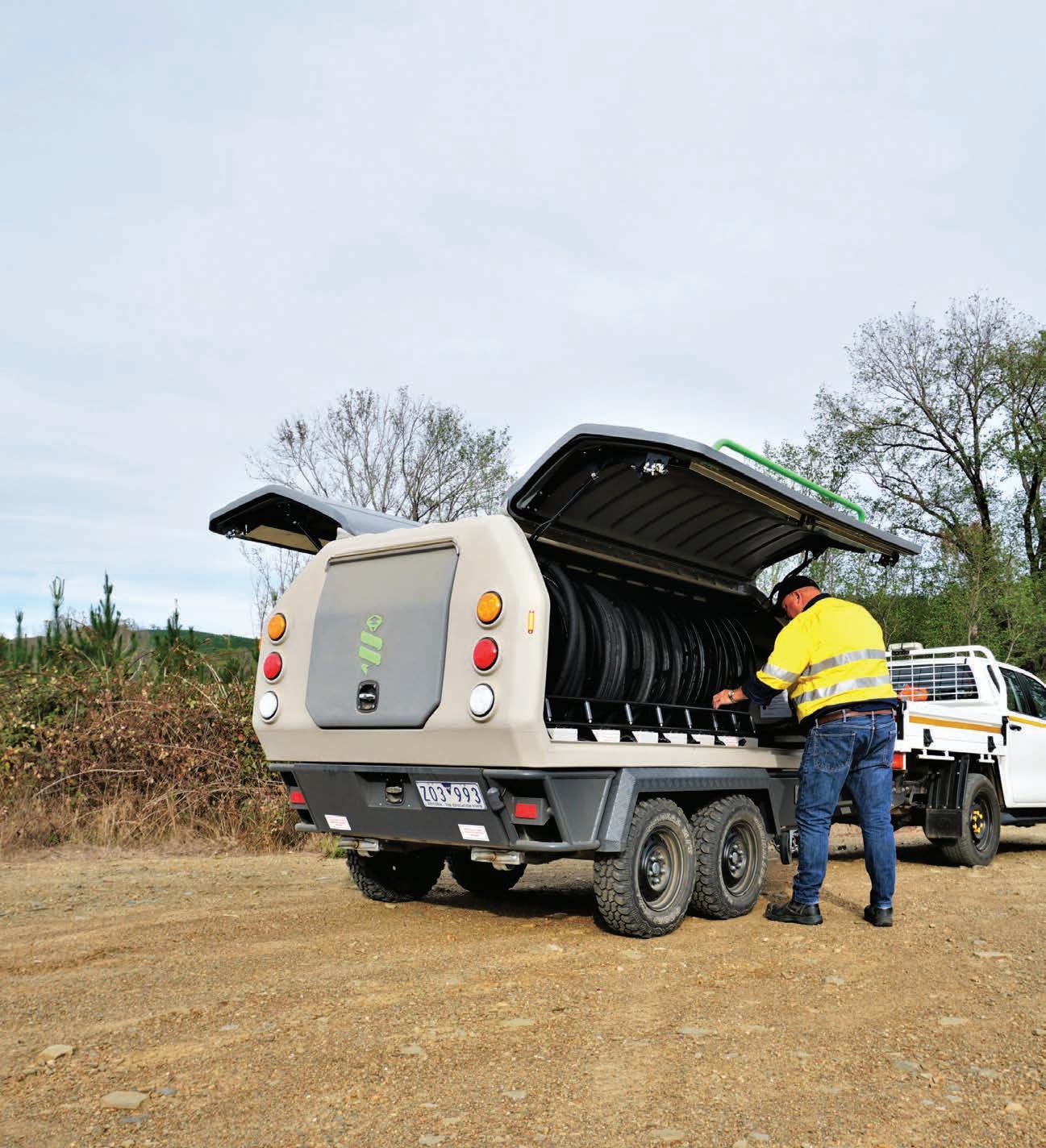
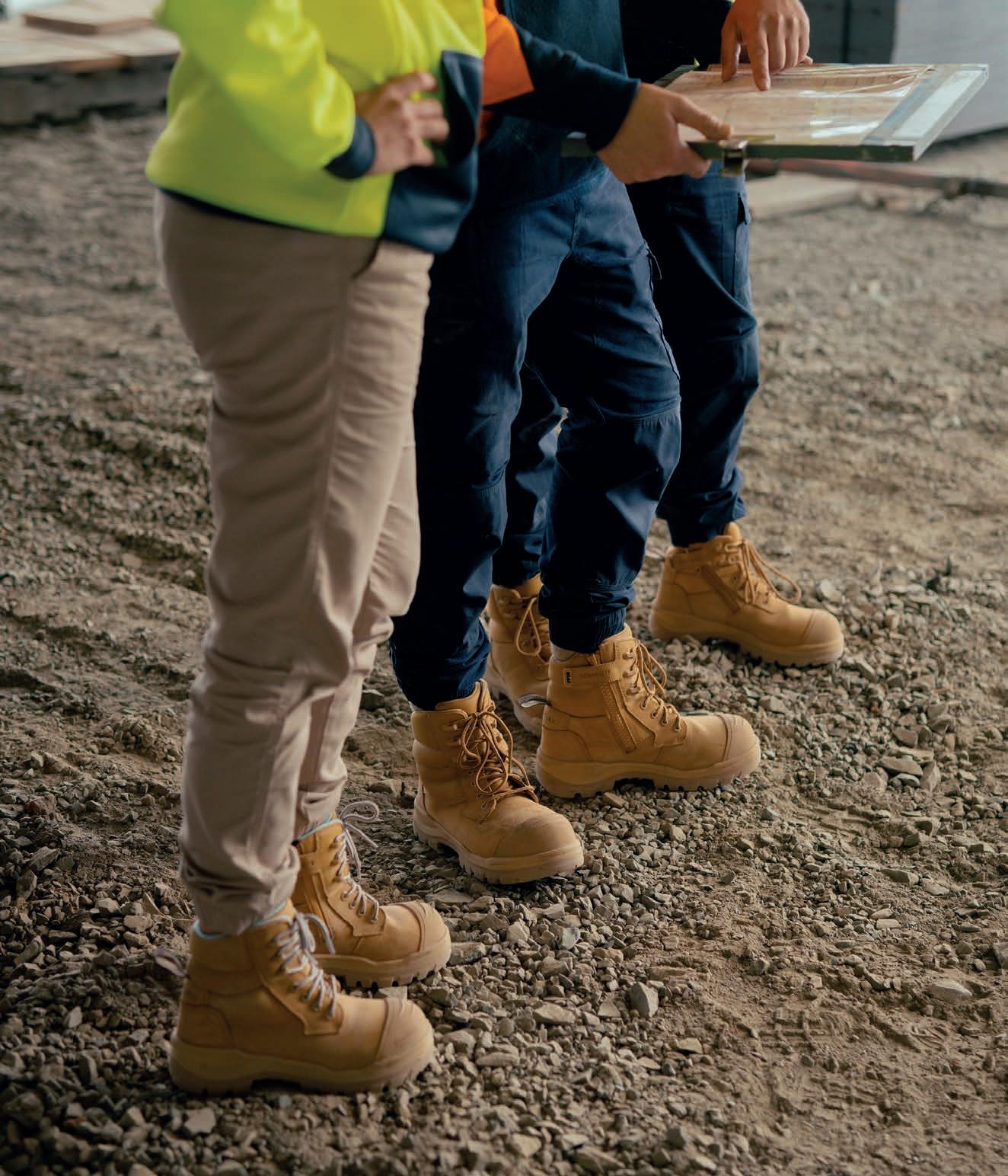
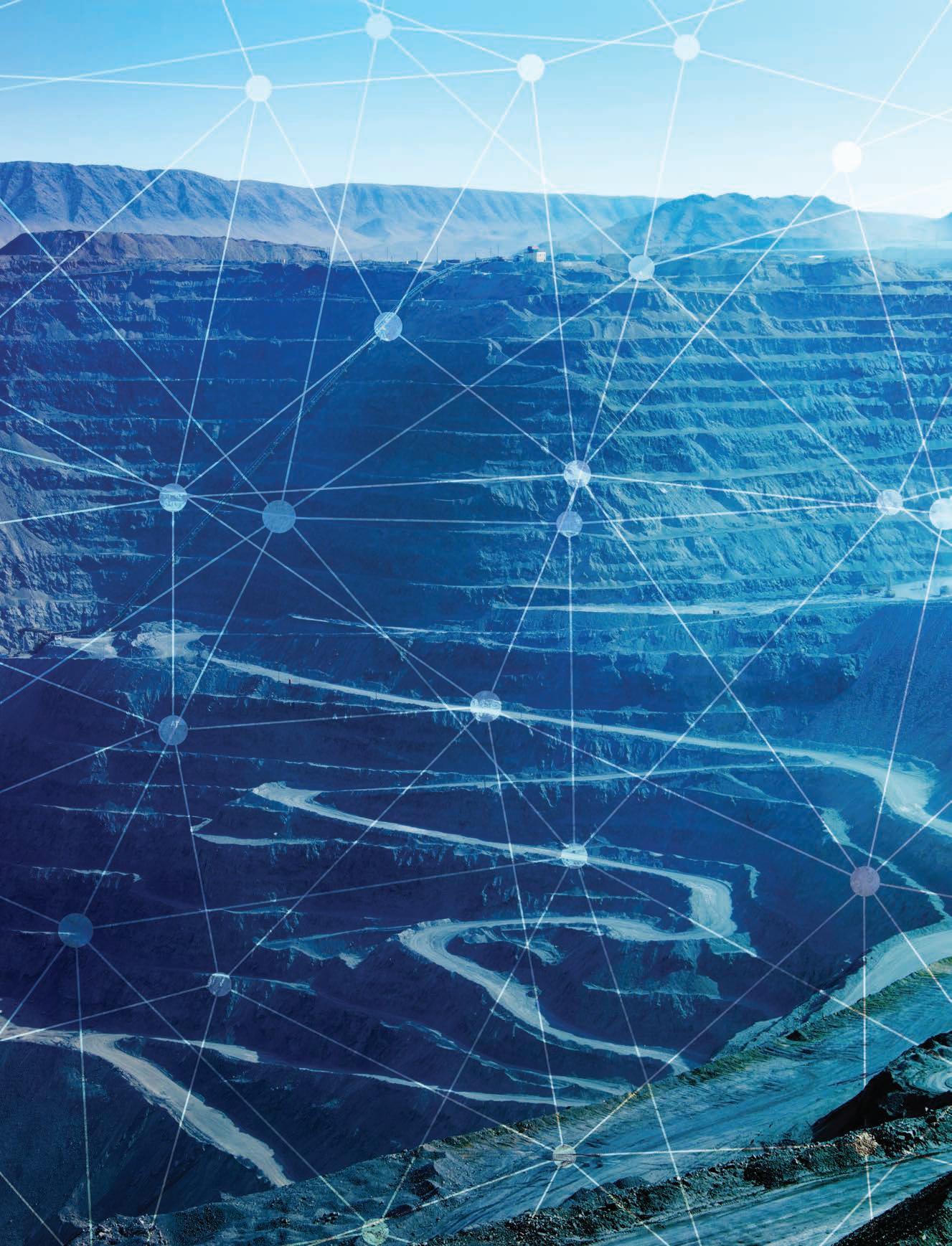

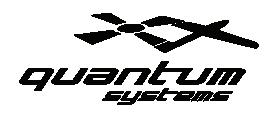
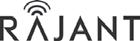
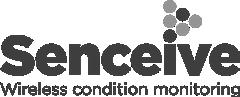
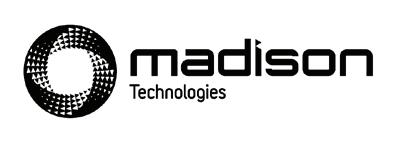
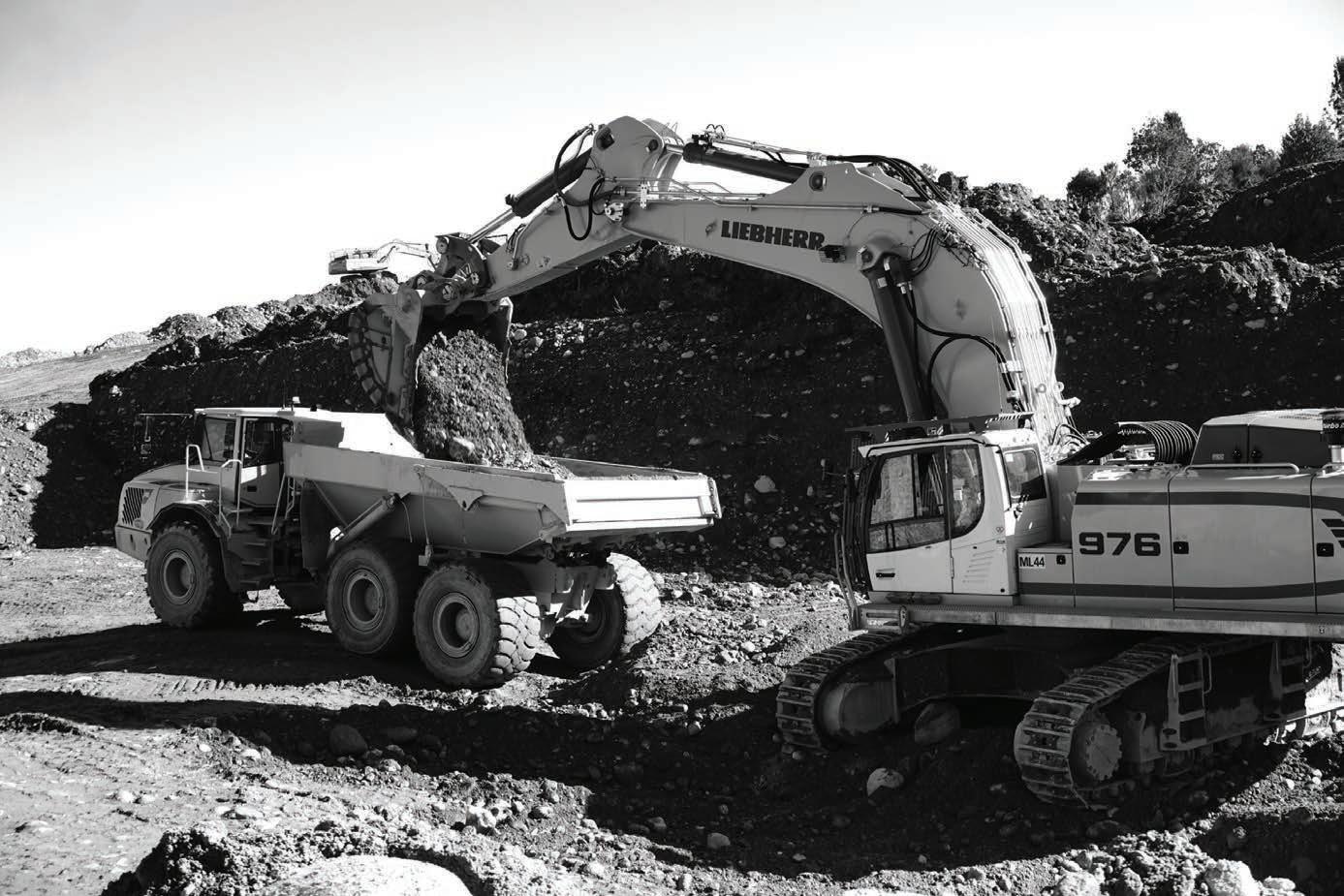
WHILE RECENT INCIDENTS SUGGEST THERE IS STILL ROOM
Amining operation is a busy place, with seemingly innumerable pieces of machinery running 24 hours a day, and all of those moving parts represent potential hazards for the people working on-site.
The Australian mining industry was rocked by two fatalities in October, at Gold Fields’ St Ives gold mine and Capricorn Metals’ Karlawinda gold mine in WA. At Karlawinda, a man died after the light vehicle he was travelling in was run over by a large dump truck, reaffirming the importance of hazard avoidance on mine sites.
While such tragedies suggest there is always room for improvement in health and safety, the Australian mining sector has made significant strides, reducing the incidence of fatalities and serious injuries.
In this issue we shine a light on the innovations, products and services that are helping keep miners out of harm’s way.
Proponents of hazard avoidance include A&I Coatings, which has developed an isocyanates-free coating solution for mining equipment.
Isocyanates have been used as a catalyst for polyurethane paints since the early 1950s but come with significant health risks, including long-term respiratory illness, allergenic contact dermatitis and skin and respiratory sensitisation.
We also look at Blundstone’s RotoFlex safety boots, which are the culmination of extensive research and performance testing. Reliable boots are at the core of the PPE for mining and industrial workers, and Blundstone remains at the forefront of innovative and sustainable safety footwear. Elsewhere, we catch up with MineGlow GM Carinne Pater to chat about emControl, a new interoperable emergency lighting system designed to improve safety in underground mines.
Hazard avoidance can also take on the guise of operational connectivity and ensuring networks are suited to remote locations. Vocus is a key driver through its Connectivity 4.0 solution, a holistic, flexible, and scalable approach to connecting the many apps, systems and equipment platforms on which mining companies depend in the digital age.
FOR IMPROVEMENT REGARDING HEALTH AND SAFETY IN THE AUSTRALIAN MINING INDUSTRY, THE SECTOR HAS COME A LONG WAY OVER THE LAST DECADE.
mine workers and their communities.
Eliminating potential health risks, preventing undue wear and tear on mining machinery and reducing equipment downtime are at the heart of A&I Coatings’ new polyurethane solution.
Vocus is playing a major role in the digital transformation occurring across the Australian resources sector.
KITO PWB has been a partner to Australian industry for almost 100 years, developing its hoist and chain technology
Being data-led – collecting and utilising the most relevant and valuable information –leads to insights-driven decision-making.
It may seem straightforward, but mine rescue training involves a lot more than just keeping a site safe.
Scan the QR code to find out more and book a demo.
Sonder, a leading wellbeing and safety company, urged employers to make psycho-social safety a top priority during National Safe Work Month. Observed every October, National Safe Work Month is an annual Safe Work Australia campaign that encourages businesses, employers and workers to commit to building a safe and healthy workplace. According to the World Health Organization (WHO), depression and anxiety are estimated to cost the global economy $US1 trillion each year, driven predominantly by lost productivity. Safe Work Australia figures show that each year around 7820 Australians are compensated for a work-related mental condition. Safe Work Australia defines psychosocial hazards as anything at work that could harm someone’s mental health,
including job demands, low job control, poor support, lack of role clarity, violence and aggression, and bullying.
Under model workplace health and safety laws, employers have a responsibility to do everything they reasonably can to prevent exposure to psycho-social hazards and risks.
A Sonder-commissioned survey revealed that 62 per cent of employees have experienced aggression from customers, 44 per cent from colleagues, and 35 per cent from managers.
The survey also 92 per cent of respondents considering it important for their next employer to offer mental wellbeing support.
Sonder chief executive officer Craig Cowdrey said that taking a systemic and evidence-based approach toward preventing and managing
psycho-social risks at work was good for business.
“Managing and preventing psychosocial risks is not only a responsibility for employers, but also makes sound business sense. Forward-thinking employers recognise that their employees expect and deserve greater control of their working environment and conditions. They are actively working with their team members to co-create and promote a mentally healthy workplace culture,” Cowdrey said.
Brandon Craig, the asset president for BHP’s Western Australian Iron Ore (WAIO), recently gave a speech outlining the company’s ongoing commitment to safety and the accelerating role of automation across its Pilbara mining operations.
Specifically, Craig highlighted the acceleration of autonomous haulage deployments at BHP’s Newman and South Flank operations and their critical role in creating a safer working environment.
For BHP, , Craig said, nothing is more important than safety and this ethos extends across the company’s WAIO operations.
“The continued rollout of technology and automation across our business is also having a positive impact on
our safety, including the Surface Mobile Equipment anti-collision program,” Craig said.
“We know from the safety performance at Jimblebar, autonomous trucks have resulted in 75 per cent fewer collision incidents than at our non-autonomous mines.
“We are accelerating autonomy deployment across our operations. All our production drills across our four hubs are already fully autonomous, and in line with our fleet replacement strategy, ore haulage will be approximately 85 per cent autonomous within the next four years.
“These exciting next steps in our autonomous journey are expected to deliver further and significant safety, production and cost improvements
as well as new job and development opportunities for people.”
BHP’s WAIO has a strong safety culture and track record with a largescale workforce of around 8000 full-time employees and more than 1000 contractors.
“The culture and capability within our teams is our strength, and together with our structured operating system, reliable assets and extensive infrastructure, we are able to deliver outstanding results,” Craig said.
BHP has an integrated system of four processing hubs and five mines In the Pilbara region of Western Australia.
Across the mines, BHP operates approximately 220 trucks, of which more than 30 per cent are fully autonomous.
BHP is accelerating automation for safer operations
Psycho-social safety should be front of mind
With the ABR (Auto Bolt Reload) function there is no need for the operator to exit the cabin and manually reload the feed carousel. The feed carousel is automatically reloaded from the bolt magazine located on the side of the machine, all while the operator stays safe inside the ROPS and FOPS certified cabin. The Boltec ABR is a solution that promises to become a game changer for safety in the mining industry.
United. Inspired.A Queensland truck driver received serious injuries that required hospitalisation after being crushed between the rear of a front-end wheel loader and the rear of a stationary fuel truck.
The incident remains under investigation; however, there are some preliminary findings from the Mineral, Mines and Quarries Inspectorate including:
• the driver parked the fuel truck close to the crushing plant and was fuelling plant in that area
• the fuelling task required the worker to be at the rear of the fuel truck
• the worker was crushed between the rear of the front-end loader and the rear of the fuel truck
• diesel powered crushing and
screening plant was operating in the quarry pit nearby, and when in operation is very noisy.
Several key safety recommendations have been highlighted by Trevor Brown, deputy chief inspector of Mineral, Mines and Quarries.
There have been numerous accidents at mines and quarries where pedestrian interaction with operating vehicles has resulted in serious injury or death to the pedestrian. In many of these accidents, critical controls necessary to prevent a vehicle from striking a pedestrian were absent or ineffective.
In the case of this accident:
• an exclusion zone had not been defined to account for other plant operating in close proximity to the fuel truck
• the noise of the operating crushing plant may have disguised the noise of vehicles operating in the near vicinity
• vehicles that could have been fuelled at a purpose-built facility were being fuelled in the operational area.
• site senior executives should review their on-site activities to identify situations where interactions between pedestrians and operating vehicles take place and determine what controls –including critical controls – are, or should be, in place to prevent pedestrian incidents.
Once identified, these controls must be implemented and monitored to ensure they are operational and effective.
Rio Tinto has published its second progress report on communities and social performance (CSP) practices. This includes direct feedback from Traditional Owners and details the actions the company has taken to rebuild relationships with Indigenous peoples and external stakeholders.
As part of efforts to increase transparency in its approach to cultural heritage protection, Rio Tinto established the ‘Communities and Social Performance’ report in 2021, engaging employees, Traditional Owners and others to improve CSP practices and outcomes.
The report details progress made in areas such as Traditional Owner partnerships and agreement modernisation in Western Australia.
It also outlines the implementation of new CSP organisational structures, standards and practices across the company; improved governance; and
increased social expertise within the business, with 500 CSP professionals working on 60 operations in 41 countries (compared to 250 professionals in 2020).
“We thank those Traditional Owners who generously shared their constructive feedback and perspectives for this report,” Rio Tinto chief executive Jakob Stausholm said “Listening to and responding to feedback is invaluable as we work to improve our practices. In the two years since the tragic destruction of the rock shelters at Juukan Gorge, we have been changing the way we work in every part of our business.
“While we have made progress, we know it will take time to rebuild relationships and regain the trust of Traditional Owners and the wider community.
“We remain focused on improving our engagement, and together with the
Indigenous peoples of the lands on which we operate, we are committed to ensuring cultural heritage is respected, valued and conserved.”
This report provides an update on:
• Rio Tinto’s progress against its commitments and internal workplans, external obligations and recommendations, including rebuilding relationships with Traditional Owners
• the views of Traditional Owners who work with Rio Tinto in the Pilbara on how successfully these commitments are being met
• governance arrangements to oversee progress against these actions
• how Rio Tinto is working to advocate for enhanced sector-wide cultural heritage management
• increasing Indigenous leadership, employment and cultural connection within Rio Tinto.
High-speed and reliable connectivity is a key part of any plan to attract skilled employees.
To learn more about what our high-performance fibre network can deliver for your business, visit vocus.com.au or call 1300 88 99 88.
vocus.com.au
Fortescue Future Industries (FFI) recently announced it will partner with the US Department of Energy’s National Renewable Energy Laboratory (NREL) to create green jobs in the US and advance green hydrogen production and technologies.
The relationship is expected to catalyse hundreds of millions of dollars of value and investment in the North American energy transition and economy.
FFI expects to invest $80 million over 10 years in research projects with NREL.
The collaboration has the potential to create more than 350 highquality research, engineering, and management jobs.
Combined with the impact of the Inflation Reduction Act (IRA), this
investment is expected to catalyse a strong increase in manufacturing in the green industrial ecosystem, which much be established if the world is to change to a zeropollution future.
NREL has a 45-year track record of leading science and research and development.
Beyond the direct 350 science and technology careers, this initiative is expected to, upon the commercialisation of technology, lower emissions and indirectly create thousands of new jobs in science, technology, manufacturing and green energy.
Fortescue’s executive chair Andrew Forrest attended a signing ceremony in Pittsburgh at the Global Clean Energy Action Forum with NREL Director Martin Keller.
The announcement builds on FFI’s new US technology hub, based in the burgeoning green energy research and development community of Colorado.
FFI’s technology investments in the Commonwealth, European Union, Australasia and now in North America helps to ensure Fortescue will stay ahead in a green science, technology and manufacturing ecosystem.
“NREL’s dream is to have its green technology commercialised. Our dream is to commercialise their green technology,” Forrest said.
“We are planning this investment because of NREL’s exemplary scientific and research competence in this technology and because of the world-leading green investment environment in America due to the IRA.”
The findings of an investigation into a 45-year-old coal mine worker who suffered serious injuries when he became pinned between a conveyor boom and a rib in early 2021 have recently been released by the NSW Resources Regulator.
The incident occurred at the Myuna Colliery in NSW, where the worker was helping a continuous miner operator and another worker to install roof bolts using the continuous miner. The regulator determined there were multiple factors that contributed to the incident, including:
• a lack of situational awareness by the continuous miner operator and the worker
• a failure to follow the safe work location rules by the injured worker
• a failure by the continuous miner operator to maintain an effective lookout while tramming the continuous miner
• the conveyor boom of the continuous miner was angled to the right in circumstances where the worker believed it would be centred while the continuous miner was being moved.
NSW Ambulance also told investigators it did not believe the organisation received enough information on the condition of the injured worker, and if its staff members had been given more they would have assigned a higher level response.
Some of the key safety recommendations include :
• that mining operators have a duty to identify hazards and manage risks to health and safety in accordance with the provisions of the Work Health and Safety Act 2011 and related legislation
• the implementation of higher order engineering controls in combination with lower order administrative controls (including safe work location rules and training) to manage risk airing from continuous miners, where reasonably practicable
• that existing risk assessments are reviewed concerning interactions between continuous miners and workers having regard to the previously mentioned matters
• that safe work location rules and
Coal worker pinned between continuous miner and rib
Fortescue brings hundreds of green jobs to the US
exclusion zones are adequate
• that safe work location rules are presented in a logical and consistent manner and understood by the workforce
• the provision of adequate training to workers on effective communication techniques when working in noisy and dark environments
• reinforcement of the need for workers to use effective communication when working in and around mobile plant
• that workers have a duty of care for their own health and safety and of their co-workers
• that situational awareness is maintained at all times.
The NSW Resources Regulator
The findings of an investigation into a coal mine worker who suffered serious injuries has been released.
is responsible for work, health and safety, as well as mine
rehabilitation compliance, across the state’s mining industry.
Lightning conditions during storms create hazards that need to be managed by operators to ensure risk to workers remains at an acceptable level. The safest way to eliminate hazards related to lightning conditions is to cease activities when lightning is detected within close proximity to a work site.
Resources Safety and Health Queensland’s (RSHQ) safety acts require that risk from operations remains at an acceptable level at all times and that steps should be taken to eliminate hazards where it is reasonable to do so.
A series of recommendations have been authorised by the chief inspector of mines – coal, Shaun Dobson.
RSHQ recently commissioned an expert review to consider the hazards arising from conducting operation during lightning activity and their relative risk to the safety of resources workers.
The report identified 10 hazards relating to the use of vehicles during lightning conditions.
Each of the hazards should be considered by operators when conducting risk assessments for carrying out surface activities during lightning activity. They include:
• exposure to high voltage while in close quarters to, but outside of, vehicles, ie flashover injury, touch and step potential voltage – high/ substantial increase
• exposure to high voltage while in an open area, ie direct strike, step potential, side flash – high/substantial increase
• t yre rupture or explosion via pyrolysis, ie projectiles, shockwaves, loss of vehicle control – high/substantial increase
• exposure to high voltage via UHF
The Australian mining sector has invested $30 billion in research and development since 2005, becoming a critical driver of global industry innovation, according to a recent report from the Minerals Council of Australia (MCA).
The ‘Digital Mine’ report shows this innovation has improved safety, driven greater productivity, delivered sustainable development and made Australia a top-tier jurisdiction for mining patent filings, creating an industry with unrivalled success globally.
These technology-driven improvements are occurring throughout the mining lifecycle, from exploration, development and operations to closure and rehabilitation.
Some key examples include:
• regenerative and kinetic braking to reduce vehicle fleet emissions by up to 35 per cent and operational costs by 10–15 per cent
• embedding integrated automation to improve productivity across operations by up to 30 per cent
• the use of advanced artificial intelligence (AI), virtual reality and wearable technology to improve worker safety
• the use of site electrification via off-grid solar farms and switching to electric vehicles.
While the mining industry is embracing technology-led innovation at an unprecedented rate, this transformation cannot be taken for granted. It requires coordination and shared commitment from industry and government to ensure Australian mining’s position as a global minerals power.
wiring or other conducting surfaces whilst inside vehicle, ie touch voltage – moderate increase
• exposure to high-voltage while sitting in cabin, ie direct strike, touch voltage, side flash – moderate increase
• initiation of other fires while inside vehicle, ie wiring electronics, batteries, fuel, interior furnishings –low/slight increase
• driver exposed to projectiles, ie fallen trees and branches or projectile rocks and pavement – negligible/low increase
• hearing loss, shock and mental trauma – negligible/low increase
• loss of electrical systems and controls leading to collision – negligible/low increase
• driver distraction and human error leading to collision – negligible/ low increase.
The recommendations of the MCA’s report are consistent with the Federal Government’s election commitments and the outcomes it announced following the recent Jobs and Skills Summit, including:
• improving collaboration to boost women in STEM careers
• identifying and formalising new skills in digital transformation for the existing mining workforce
• maintaining and growing support for industry-orientated research and innovation
• prioritising the recognition of new occupations by the Australian Bureau of Statistics
• leveraging strength of the tertiary education sector to guarantee a pipeline of mining engineers
• establishing regulatory sandboxes for mining innovation.
scan code
Honeywell protective coveralls are designed with quality, innovation and comfort in mind, to protect workers from occupational hazards while also protecting the work environment. With a range of ergonomically designed single-use coveralls, you can depend on Honeywell to provide the best protection for a variety of applications.
Scan the QR code to learn more.
www.sps.honeywell.com
New aeromedical bases for the Royal Flying Doctor Service of Australia (RFDS) and RACQ LifeFlight Rescue will be among facilities coming to north-west Queensland resource communities.
The new funding for the flight facilities amounts to more than $22 million secured from the second round of the $100 million Resources Community Infrastructure Fund (RCIF).
Deputy Premier and Minister for State Development Steven Miles said Mt Isa would gain the colocated aeromedical hub plus a new children’s aqua play park, while Cloncurry and Julia Creek would gain major new childcare centres.
“Queensland communities should be the first to benefit when the resource sector they support succeeds,” Miles said.
“North-west Queensland is the big winner in this round of funding, with over half the funding being granted to Mt Isa, Julia Creek, and Cloncurry.
“Most importantly, thanks to RCIF, north-west Queensland will have a new, co-located health emergency flight service that can better serve the region, as well as three excellent new facilities focused on children’s recreation, care and early learning.”
The two RCIF grants will help deliver a co-located RFDS facility at Mt Isa Airport featuring hangars and other facilities for RFDS’s fixed-
A recent global safety report indicates a gradual but steady improvement in mine safety, and that a strong safety culture and clear protocols are critical for blasting operations.
The ‘Safety Performance Report’ from the International Council on Mining and Metals (ICMM) benchmarked the progress of its members in 2021. Blasting solutions specialist BME believes a growing safety culture is a major factor behind positive trends in mining.
According to Ramesh Dhoorgapersadh, general manager for safety, health, environment, risk and quality at Omnia, safety must be ingrained into every activity, in line with standards and procedures.
“The blasting philosophy of BME (a member of the Omnia Group) is expressed through our innovative products and leading initiation
technologies,” Dhoorgapersadh said. “This also means aligning our policies with customer’s own safety protocols and broader regulatory requirements.”
This includes careful adherence to the regulated distances between communities and blasting sites.
Tinus Brits, BME’s global product manager for AXXIS (digital initiation system), explained that electronic detonation systems play an important role in achieving safe blasting.
“We design our electronic detonators in such a way that key blast impacts are both measurable and predictable,” Brits said.
“With our integrated blast planning software, mines can simulate each blast before it is implemented – so that they can predict aspects like ground vibration to ensure it will be within the required parameters.”
wing flights and RACQ LifeFlight Rescue’s helicopter services.
RFDS will gain over $6.9 million to help establish the new facility that will better meet the needs in northwest Queensland communities for emergency and primary health care services.
The facility will provide improved response times and experiences for patients.
The new RFDS base will include four hangars, patient-transfer facilities, nurses’ stations, offices, rooms for operations, communications, meetings and training, as well as kitchen, staff accommodation and maintenance facilities.
Brits emphasised that mines apply world-class standards in this regard, including blast-induced ground vibration criteria formulated by government agencies in the US and elsewhere.
Where BME conducts blasts on behalf of customers, it applies a blasting radius of 1km from any persons or communities, and 500m from material that might be negatively affected.
“For every blast, seismographs are then used to measure the resulting ground vibration and air blast,” Brits said. “This confirms that the blast did indeed achieve the simulated design parameters, to fall within the regulated limits.”
These vibration reports can confirm that a blast was fully compliant with standards or regulations, should there be a need for an inspector to investigate a blast-related incident.
With wearable gas detection, area gas monitoring and powerful data analytics, Blackline Safety helps businesses become more efficient and protect their people. All in one cloud-connected solution.
blacklinesafety.com encoremonitoring.com.au
Introducing KITO RY Wire Rope Hoists, the high-performance hoist beyond expectations.
Designed for safety, reliability and performance, these low headroom wire rope hoists have an M5 duty rating for any heavy-duty lifting demand. The RY Series wire rope hoists are designed for use in any lifting application where any five-tonne or 10-tonne wire rope hoist will be used.
The RY hoists are loaded with revolutionary features for high-demand applications, including inverter control as a standard. The inverter is a dual-speed variable frequency drive (VFD) which incorporates an easily accessible condition-monitoring system enabling users to plan their preventive maintenance based on the exact operations the hoist has done.
They come jam-packed with safety features and motor brakes that are maintenance-free for up to one million starts. It also provides more value over time due to its high-performance features and improved service life.
• kitopwb.com.au/
With an increased awareness of workplace health and safety when using protective coatings, A&I Coatings is continually looking for ways to reduce the risk of exposure to harmful chemicals, such as isocyanates in paint. Exposure to isocyanates is known to cause respiratory illness and skin irritation, such as allergic contact dermatitis. Utilising leading technology has led to a breakthrough in polyurethane coatings, with A&I Coatings formulating the first true isocyanate-free polyurethane coating available in Australia called Vitrethane 650IF.
Vitrethane 650IF is a premium-quality two-pack isocyanate-free polyurethane topcoat. Utilising full polyurethane technology and curing without the use of isocyanates makes Vitrethane 650IF a safer and more durable coating than conventional isocyanate-free coatings.
Vitrethane 650IF is a high-gloss, versatile polyurethane topcoat with exceptional durability and weathering performance, improved impact resistance and abrasion resistance.
• aicoatings.com.au
The BOApod is a mobile hydraulic hose repair and maintenance facility. This all-weather, all-terrain mobile unit enables the user to assemble hydraulic hoses following the same principles used in original manufacturing facilities. Whether you’re a miner looking for ways to reduce downtime while waiting on hydraulic hose repairs or a hydraulic machinery technician or mechanic looking to expand your service offering, the BOApod is an innovative facility worth looking at.
The unit has a robust chassis to live off-road, and features lightweight high-density polypropylene and UV-resistant materials with aluminium shelving.
The BOApod is available in Australia, New Zealand, Papua New Guinea, and the Pacific Islands.
• boahydraulics.com/boa-pod
Epiroc has launched a new long-hole production drill rig for medium-tolarge-sized drifts: Simba E70 S.
While the Simba E70 S will provide customers with cutting-edge automation features and excellent drilling quality, it will also feature Epiroc’s optimisation method; a step-by-step program that continuously improves how the machine is utilised in the mining process.
“Our new Simba E70 S delivers greater value to our customers’ operations through improved productivity, with zero compromise on quality,” sales and marketing at underground division vice president Sarah Hoffman said. Simba E70 S is part of Epiroc’s smart series and can be delivered with the optional battery-electric driveline for reduced environmental impact and healthier underground conditions.
However, the real value is found while the machine is producing metres. That is why the ability to track the Simba E70 S’s effectiveness and utilisation and produce metres when active is one of its main advantages.
• epiroc.com/en-au
Meet the hero of Blundstone’s new RotoFlex range – the six-inch 8560 in wheat nubuck and available in sizes 5–14 (half sizes 7.5–10.5). The boots combine leading biomechanical design, an all-new comfort system and composite toe protection with well-known Blundstone durability.
The 8560 provides strong levels of comfort and safety for wearers:
• GripTek – lightweight TPU sole designed for optimum grip and comfort
• AirCell – footbed built to ventilate, control moisture and cushion when you move
• Fortalite – compression-resistant composite toe cap, tested to resist a 200-joule impact
• Softcell – overarching comfort system utilising a biomechanical foot-cradling design to increase stability, balance and manoeuvrability
• Infinergy – E-TPU super elastic energy foam from BASF which is soft but resilient, providing enhanced cushioning and reducing the impact of every step taken.
• blundstone.com.au/work-boots/rotoflex-series
According to a 2019 Queensland Department of Resources report, 25 per cent of mining fatalities are related to interaction with machinery, which makes testing equipment extremely critical in ensuring safety and productivity. In the past, testing heavy machines often required workers to be near the vehicle to manually take measurements, leaving them at risk of serious injuries. Now with the SafeGauge Dial Indicator (DI), technicians can perform these tasks at a safe distance by enabling workers to remotely measure clearances, tolerances and wear on machine components safely, efficiently and out of the line of fire.
The SafeGauge DI connects via Bluetooth from a distance of up to 50m and measures up to 10mm of movement with an accuracy of 0.01mm. The DI unit is mounted on one machine component, with the pin resting on another.
The reading is ‘zeroed’ and the machine is run through the appropriate motions with the technician remaining at a safe distance. The SafeGauge MultiTool then displays the live reading between the two components in real-time to the technician, who is safely out of harm’s way.
• safegauge.com.au
WHEN IT COMES TO IMPROVING ON-SITE SAFETY, POSITION PARTNERS RECOMMENDS THE USE OF TECHNOLOGY TO REMOVE THE INTERACTION BETWEEN PEOPLE AND PLANT AND UNLOCK INSIGHTS FOR MANAGERS THROUGH MEANINGFUL DATA.
“Operational technology can involve one or many solutions that either drastically limit or altogether eliminate the need for people to physically interact with working machinery.”
That is Andrew Granger, mining business manager at intelligent positioning solutions provider Position Partners, talking to Safe to Work about the benefits of operational technology.
OPERATIONAL TECHNOLOGY INSIGHTS
Solutions such as high-precision machine guidance used on drills, dozers, excavators and graders give
machine operators greater visibility over their work, with live information about the distance to grade via a simple in-cab display.
The technology saves time and increases productivity, but also reduces the need for surveyors to check grade by driving out to the area.
“From a safety perspective, the fewer light vehicles and people that have to enter the vicinity of a working heavy machine the better,” Granger said.
“High-precision machine guidance empowers the operators to work to the mine design efficiently and safely without as much reliance on surveyors to set out peg lines or
check as-builts.
Fleet management systems (FMS) such as the iVolve Mine4D platform supplied and supported in Australia by Position Partners, give managers valuable insights into on-site operations, making it easier to see the bigger picture to identify productivity and safety-improvement areas.
“With the ability to see the location of all machines on-site, communicate with operators, and optimise truck loads and circuits, FMS helps managers proactively manage risk,” Granger said. “Accurate reporting and recording of data, machine speeds, over and under loading, maintenance records and so on, helps with early intervention and ensures that if an
incident does occur, management has the information at hand to assist with investigations to identify the cause.”
From cameras to proximity-measuring sensors, location-based safety systems, tags and thermal systems, there are several methods available to assist heavy machine operators identify and avoid potential hazards.
On-board proximity-warning technology is designed to alert operators to other machines, fixed infrastructure and more, with the ability to program working and avoidance zones.
One of the latest developments in vision safety and proximity-warning solutions involves the use of artificial intelligence (AI) to detect, alert and report on hazards and near-misses, benefiting operators and managers through near real-time reporting.
“Proximity alert and camera solutions can be effective to warn operators if there is an obstacle or other vehicle nearby, but they don’t help management with near-miss reporting,” Granger said.
“New AI-based platforms can automate safety reporting and even include video recordings of near-miss incidents for analysis and investigation,” he added.
This ability to give management real-time insights into on-site behaviours and machine interaction can be very powerful to improve long-term safety, Granger explained.
“Users can see near-misses and unsafe behaviours as they happen, to baseline the real risk profile and understand when, where, how and why an incident occurred to implement interventions and measure the impact of any changes implemented,” he said.
Mine surveyors and engineers are another group whose safety can be significantly enhanced by the latest in surveying and mapping systems, which now go far beyond the pointto-point measurements delivered by traditional global navigation satellite system (GNSS) and total station instruments.
From 3D laser scanning to aerial mapping and wireless monitoring, there is a plethora of solutions that quickly and safely capture accurate data over large areas.
Monitoring of mine infrastructure such as tailings dams, open-pit
Wireless monitoring captures accurate data over large areas.
walls, underground mines, and other critical assets has traditionally been done with either periodic survey measurements to check for movement or total station-based monitoring set-ups that can be challenging to install and maintain in hazardous areas.
Position Partners has assisted several mine sites with Senceive wireless monitoring technology, which uses compact nodes that can be installed and scaled to monitor almost any structure at any scale.
“Senceive is a highly versatile platform that gives surveyors and managers constant, near realtime monitoring information via a
web-based portal and the ability to set up customised alerts to notify stakeholders if movement out of tolerance is detected,” Position Partners monitoring manager Andrew Jones told Safe to Work.
Unlike optical monitoring solutions, the Senceive wireless platform offers a small footprint and little to no hardware maintenance. The sensors have a low form factor and long battery life that will last for 10 years in continuous use.
For critical applications such as measuring pit wall stability or any fissures in the wall, Senceive can be set up to trigger measurements every few minutes and escalate alerts quickly if any motion is detected.
The introduction of survey-grade mapping drones around a decade ago is another example of a step change in technological advancement that has significantly improved safety for
surveyors in mining, Granger said.
“Manual stockpile volumes done by survey crews on foot are a thing of the past thanks to aerial mapping technology using survey drones,” he said.
“Surveyors can conduct these surveys at any time from a safe distance well away from working machinery, as well as map hazardous and previously inaccessible areas, including water bodies and poor geotechnical areas of a mine site.”
Removing operators from heavy machinery altogether offers the greatest safety potential for mines.
Position Partners, along with autonomous technology development partner SafeAI, has successfully retrofitted autonomous technology to a haul truck in the Pilbara, Western Australia, with an agreement to roll out
a further 100 trucks in coming years.
“The majority of incidents involve a combination of machinery and either human error and/or fatigue, so taking people away from machines and having them control those machines remotely is the next frontier for minesite safety,” Granger said.
The ability to retrofit a solution onto a mixed fleet of trucks gives mine operators and managers greater flexibility to implement autonomy throughout a site and not just to a certain make of equipment as old trucks are retired and replaced by new ones.
“Autonomy will increase safety dramatically by reducing the need for people to operate and interact with heavy machinery. Instead of performing repetitive, mundane tasks that can lead to fatigue and human skill can be reserved for more complex operations,” Granger said
Low
Australian mining continues to evolve at a rapid pace, and at the heart of an evolving operating environment are smart and interconnected webs of data-driven services providing communications, predictive analytics, and a range of decisionmaking capabilities.
The forces driving digital transformation were in place well before the COVID-19 pandemic redefined the world, and mining companies that were focused on steadily achieving growth and efficiencies have accelerated their digitalisation plans.
Daniel McCormack, head of thought leadership (research) at Macquarie Asset Management, part of Macquarie Group, has watched the perfect storm of disruptive forces take its toll as businesses scramble to deal with new economic, workforce, cybersecurity and supply-chain risks.
“The world has changed in some very fundamental ways,” McCormack said.
The need to improve safety, health, and worker wellbeing, enhance productivity, adopt environmental, social and governance (ESG) commitments, and embrace the world’s decarbonised future are driving the need for more connectivity and the rapid adoption of technology.
The information technology (IT) landscape for the resources sector has become increasingly rich and complex.
There is a significant dependence on extensive, fast, robust, and future-proof communications networks for mining operations, ensuring they are best placed to embrace advances in Industrial Internet of Things (IIoT), artificial intelligence (AI), machine learning and augmented and virtual reality. Each of these technologies makes it possible to improve decision making, drive autonomous trucks, track assets and
monitor safe operating conditions.
As a result of this heightened connectivity and digitalisation, mining is enjoying a decrease in injuries and fatalities, with the International Council on Mining (ICMM) indicating in its most recent safety report that fatalities across its member companies had fallen from 287 in 2019 to 43 in 2021 while employing just-in-time productivity, delivering tonnage on-demand, and significantly improving efficiency with advanced interconnected machines and equipment.
Central to this technology transformation is Connectivity 4.0, a new era in which network technologies, and the requirements of mining operations, have evolved and merged to make ubiquitous connectivity a reality.
Given the increasing importance of data integration and dependency on digital connectivity, robust connectivity infrastructure is vital to the
success of whole-of-mine technology transformations.
However, just as mining companies have radically changed their approaches to IT over the past few years, network architects are readjusting their thinking to meet the connectivity challenges of today and tomorrow. They are looking beyond bandwidth to embrace Connectivity 4.0 – a holistic, flexible, and scalable approach to reliably connecting the many apps, systems and equipment platforms on which mining companies depend in the digital age.
Once upon a time, mine systems were built around slow, fixed wide area network (WAN) connections, while contemporary connectivity models have migrated onto internet protocol (IP) WANs.
These networks can run across several technologies, including highspeed fibre-optic cables, point-topoint microwave connections, local wireless, and low earth orbiting (LEO) satellite services.
Underpinning Connectivity 4.0 are fast, ultra-resilient, future-proof networks and connected technologies. At its core
is fibre, which can provide extremely high-capacity and low-latency networks for linking mine sites, networks and hybrid cloud environments. Low latency is the ability of a computing system or network to provide responses with minimal delay.
Fibre services can link operations to provide highly reliable connectivity that is also scalable. Augmenting fibre are wireless technologies such as microwave, a high-speed, point-to-point service for extending fixed connectivity across an area.
Microwave solutions are incredibly valuable on remote mine projects such as Minjar Gold’s Marvel Loch operation in Western Australia, located approximately 400km east of Perth and nearly 40km from the township of Southern Cross.
Through weeks of planning and feasibility studies and getting an intimate knowledge of the site’s needs, an engineering team from Vocus delivered a private network to Minjar that boosted connectivity speed from about 40Mbps (megabits per second) to nearly 500Mbps.
Vocus’ solution for Minjar Gold included working with GoldNet to implement a microwave technology solution that connects the mine through line-of-sight fixed IP wireless to Vocus’ fibre point of presence north of the Southern Cross township.
Minjar Gold senior network and systems engineer Sean Kocis said the benefits of the project delivery were multi-faceted, providing improved connectivity to both Minjar Gold’s mine site and the wider Southern Cross community.
“It’s hard to put into words the positive impact that this project has had, not just for our own employees but also for the greater community of the town’s farmers and local businesses that are offered access to our private internet network,” Kocis said.
“Our staff tells us they look forward to coming back to the site as the internet speed here is now better than at their own homes. We’ve also seen improved productivity among the team as we remain better connected through videoconferencing.”
Many large-scale mines are hauling billions of tonnes of material with autonomous fleets.
From Marvel Loch, nearly 400km of Vocus fibre running underground to Perth provides the high-speed connectivity Minjar Gold required.
Another key Connectivity 4.0 technology is private LTE (long-term evolution), privately operated mobile networks installed in specific locations –such as a mine – to provide continuous connectivity and latency low enough to support real-time control of autonomous vehicles or industrial processes.
Communications technologies have progressed enough that they no longer impose the speed or reliability trade-offs of legacy technologies.
Satellite was previously constrained by limited bandwidth, but with the launch of high-speed LEO services are now capable of delivering fast speeds and much lower latency anywhere in Australia or around the world.
The availability of LEO satellite services has resolved the coverage dilemma, allowing satellites to work together with the other elements of Connectivity 4.0 to provide mining with reliable, resilient and future-proof connectivity regardless of site location.
All of these technologies are fast, providing local-area-network-like speeds for upload and download streams.
They also offer much better latency profiles than in the past and can ensure mines keep digital processes running as smoothly as possible.
Connectivity 4.0 technologies are also highly flexible, since they can be reconfigured and scaled on the fly to match changing operational requirements.
In a time of rapid operational change, the importance of ensuring the resilience of mission-critical services cannot be overstated.
Disruptors might include weather events, cybersecurity attacks or political instability, and today’s mining companies must find the right balance of enabling technologies to ensure they operate continuously and reliably, no matter what external events or forces threaten to compromise them. This means automating routine processes wherever possible, embracing geographically diverse infrastructure to avoid ‘single point of failure’ weaknesses, and adopting redundant
connectivity to ensure the connected digital ecosystems of tomorrow can continue functioning.
Increasingly, connectivity solutions are not only enabling IT solutions but also integrating operational technology, such as supervisory control and data acquisition (SCADA) and other industrial control system platforms that manage mining and other industrial processes.
Faster, richer and more robust connectivity has created new opportunities and for many mining operations this has meant embracing cloud-based technologies that deliver the scale and ease of access to support new ways of working and operating.
Removing operators from heavy machinery altogether offers the greatest safety potential for mines
The adoption of autonomous haulage systems, deployed on private LTE networks, is resulting in safer and more productive mining.
In the Pilbara region in WA, many large-scale mines are reaping the benefits of this connectivity, hauling billions of tonnes of material with autonomous fleets.
In late 2020, Elizabeth Gaines, former Fortescue Metals Group chief executive officer and current nonexecutive director, commented on the critical role of autonomy and safety across the major miner’s Pilbara operations, having undertaken a large fleet conversion to autonomous haulage systems.
“Mining is one of the most innovative industries in the world, and Fortescue continues to build on our leading autonomy capability,” Gaines said.
“Most importantly, the introduction of (autonomous haulage systems) technology has improved safety outcomes across our operations and we’re very pleased that the team achieved this important milestone in the truck conversion program to the highest safety standards.”
Later, in 2021, Gaines further characterised the vitally important role of its large fleet of autonomous vehicles.
“Our fleet represents one of the largest in the world, with 79 trucks currently in operation at Solomon, 74 at Christmas Creek and 40 at Cloudbreak,” she said.
“Moving over two billion tonnes of material without a driver at the wheel is a significant milestone.
“Most importantly, the introduction of (autonomous haulage systems) technology has led to significant safety improvements for our team members, with our fleet safely travelling over 70 million kilometres to date – the equivalent of 91 return trips to the moon.”
Brandon Craig, BHP’s asset president for Western Australian Iron Ore (WAIO), recently outlined the importance of automation in relation to positive safety outcomes.
“The continued roll-out of technology and automation across our business is also having a positive impact on our safety, including the Surface Mobile Equipment anti-collision program,” Craig said.
“We know from the safety performance at Jimblebar, autonomous trucks have resulted in 75 per cent fewer collision incidents than at our nonautonomous mines.
“We are accelerating autonomy deployment across our operations. All our production drills across our four hubs are already fully autonomous and, in line with our fleet replacement strategy, ore haulage will be approximately 85 per cent autonomous within the next four years, with Yandi the only exception as the site nears end of life.
“These exciting next steps in our autonomous journey are expected to deliver further and significant safety, production and cost improvements, as well as new job and development opportunities for people.”
Both major miners have demonstrated how private wireless is increasing the safety, productivity, and efficiency of their` truck fleets.
These autonomous haul trucks are centrally controlled through a wireless network that integrates on-board vehicle controllers, high-precision global positioning, and obstacle detection and avoidance systems.
The system has full supervisory logic that utilises complex data fusion to control the dump truck to safely operate through a load, haul and dump cycle and allow integration with other mine vehicles such as light vehicles, dozers, loaders, and graders.
Private mobile networks offer the industrial-grade robustness, high capacity and low latency required for such operations. They support pervasive coverage for the delivery of real-time, high-definition video feeds and sensor data allowing operators to remotely halt and begin work in an instant.
Heavy vehicles and machines are equipped with integrated industrial field routers that connect them reliably to 5G networks, ensuring constant readiness and availability for data transfer.
Data and digitalisation are extremely important for mine operators and the value of a connected mine lies in digging deep into the wealth of data available across the entire value chain to provide integrated, end-to-end situational awareness and intelligent asset management.
Connectivity is underpinning the industry’s efforts to walk a new path, where safety, sustainability and advanced technology are driving the narrative.
An Australian-owned industrial coatings manufacturing company, A&I Coatings is at the forefront of developing and manufacturing protective materials for the country’s resources sector.
Mining equipment operates in harsh environments, usually either outside or underground, and is constantly under threat of damage and deterioration from unforeseen impacts, abrasions and corrosion.
Ensuring the most hard-wearing and durable coat of paint is applied to mining machines is a critical consideration
when attempting to avoid unplanned downtown or significantly reduce scheduled maintenance.
“Polyurethane coating is typically used as the topcoat on OEM (original equipment manufacturer) mining machinery or equipment components,” A&I Coatings business development and customer satisfaction manager Bill Chesterfield told Safe to Work
“Essentially, any steel structure used on a mine site has a topcoat in which there exist polyurethane, catalysed acrylics, modified epoxies and polysiloxanes.”
By eliminating the need to continuously re-paint machinery, usually off-site and with time delays, mine operators can reduce costs. But this painting can come with its own risk to workers, as many coatings contain harmful chemicals like isocyanates.
Commonly used as a catalyst for polyurethane paints since the early 1950s, the significant health risks associated with exposure to isocyanates – long-term respiratory illness, allergenic contact dermatitis, skin and respiratory sensitisation – have only recently become apparent.
The most significant risk to workers’ safety comes from direct exposure, through either physical contact or inhalation.
The risk can be limited with proper training and supervision, as well as the use of appropriate personal protective equipment (PPE); however, prevention is the best approach, and the removal of the damaging chemical is a powerful safeguard.
Fortunately for Australian mining and other industries, A&I Coatings has developed a highly-effective solution.
“We identified a need in the market for both a high-performing and extremely durable coating able to withstand harsh and difficult operating environments without containing isocyanates,” Chesterfield said.
Utilising advanced technology has led A&I Coatings to a breakthrough in polyurethane coatings, with the company formulating the first true isocyanate-free polyurethane solution.
“Over the last 18 months, our research and development team have been working to produce isocyanate-free polyurethane coating, called Vitrethane 650IF,” Chesterfield said.
Vitrethane 650IF is a premiumquality two-pack isocyanate-free polyurethane topcoat.
“In a standard polyurethane system, there are two components – the polyol component and the isocyanate component – and that’s how you generally form a polyurethane with these two components reacting together,” A&I Coatings formulation chemist Stephen Bailey told Safe to Work. “However, the drawback is that the applicator is exposed to isocyanate.
“Our R&D (research and development) team has developed a polyurethane system that doesn’t expose the applicator to isocyanate.
“In essence, we have developed an isocyanate-free polyurethane that is far safer for workers while
providing a significantly more durable coating solution.
“Vitrethane 650IF is an isocyanatefree alternative which doesn’t compromise the integrity of a polyurethane system.”
Many companies are currently using coatings such as enamels, catalysed acrylics, or modified epoxies to reduce worker harm, but these materials can be brittle and often have poor impact resistance. These established coatings are also often less capable of withstanding atmospheric elements such as acid rain, salt sulphates, or ultraviolet (UV) exposure.
These factors often lead to the early breakdown of the coating, with machinery and equipment subsequently exposed to corrosion and decay.
A&I Coatings’ new topcoat has been engineered to resist adverse impacts on machinery and equipment. Mining haul trucks are a classic example of machinery that is subject to impact.
“Commonly used coatings such as modified epoxy and catalysed acrylics have poor reverse impact (resistance), often shattering and delaminating on the outsides of the machine bodies from the impact of rock or other hard material falling into the tray,” Chesterfield said.
“Vitrethane 650’s flexibility, resistance and high performance to adverse damages such as reverse impact is critical to achieving the best value from the haul truck and the truck body.”
Polyurethane coatings are incredibly popular in mining, and with Vitrethane 650IF A&I Coatings has ensured this can remain – but in a safer formulation.
“We have a complete in-house laboratory to conduct all of our product testing, access to other testing facilities both in Australia and overseas, along with the capacity to utilise three external laboratories approved to conduct thirdparty testing in order to verify our own results,” Chesterfield said.
For mining operators, Vitrethane 650IF will provide a high-performing and flexible polyurethane coating, offering significant weathering performance along with superior abrasion and chemical resistance, all without endangering workers’ health.
“A&I Coatings has its own powerful FTIR spectrometer, enabling the presence of isocyanates to be accurately detected, and that’s how we can confirm our formulation is completely free of the harmful compounds,” Bailey said.
Vitrethane 650IF can be applied in a gloss or matte finish in an unlimited range of colours.
Alot can happen to a mine worker’s feet, whether due to potential hazard or the rigours of having to be on your feet for hours on end.
That’s why it’s so important people working on mine sites have the right footwear.
Reliable boots are at the core of the personal protective equipment (PPE) for mining and industrial workers, and Blundstone remains at the forefront of innovative and sustainable safety footwear with its new RotoFlex range.
Prior to the onset of the COVID pandemic, Blundstone embarked on a significant research project aimed at identifying the essential footwear requirements for workers.
“We invested in sophisticated research that encompassed product performance testing, user experience and brand equity,” Blundstone’s global work and safety range manager Adrian Blandford told Safe to Work
“Through a series of in-depth interviews and surveys, on-site discussions and trials with users in the construction, trades, mining and light industry markets, Blundstone was able to leverage the best insights, empathy and brand-building in order to understand what our wearers want in safety footwear.”
The significant scope of the company’s research revealed a fundamental desire from customers for a higher performing work boot, with an emphasis on tougher durability and increased comfort, ventilation, traction and greater overall safety attributes.
BLUNDSTONE’S STABLE, FLEXIBLE AND RELIABLE ROTOFLEX SAFETY BOOTS ARE THE CULMINATION OF EXTENSIVE RESEARCH AND PERFORMANCE TESTING.The RotoFlex range combines stability with the freedom to move.
In collaboration with a biomechanics expert from the University of Tasmania’s School of Health Science, emphasis was placed on exploring footwear design principles in relation to movement, flexibility and injury-mitigation.
The research culminated in the development and manufacture of an innovative ‘whole-of-boot’ design.
The most common injuries occurring on work sites are musculoskeletal, as well as ankle and knee issues from falls and slips.
Built from the ground up, boots in the RotoFlex range combine stability with the freedom to move, allowing the wearer’s foot to rotate and the ankle to flex to help avoid injury.
“A significant amount of the design of the new boot was new, built upon years of research and design, as well as years of testing and trialling, arriving at a boot that offers great stability, flexibility, manoeuverability, comfort and, above all, safety,” Blandford said.
Blundstone’s approach to sustainability has been a key decision-driver in the development of the RotoFlex range, and aligns to the company’s Every Step Better (ESB) program.
“Underpinning the biomechanical research is a desire to utilise the best materials in the manufacture of the RotoFlex range, including the use of recyclable and sustainable raw materials along with materials possessing longterm durability,” Blandford said.
“Blundstone is a member of the Leather Working Group (LWG), the recognised peak body that drives and accredits sustainable business practices within the leather industry.
“Elements of our RotoFlex range, including the heel grip, insole and counter-stiffener, employ sustainable raw materials, and the laces and lining of the boots are made with 100 per cent recycled materials.”
The sustainability considerations of the range highlight Blundstone’s ongoing commitment to minimise its environmental impact. This extends to the packaging, which is made up of recycled material and is 100 per cent recyclable.
The launch of the RotoFlex range at the beginning of September has been
“The team at Blundstone really wanted to make sure the launch of the RotoFlex range was commensurate with the sophistication of the product,” Blundstone’s Australasian marketing and communications manager Kate Gracie told Safe to Work
“It was important for us as a company to be loud and proud and express clearly to our customers the many benefits of the innovative RotoFlex range.”
The range comprises six styles, including four unisex boots and two designed specifically for women, with all boots featuring the innovative Fortalite composite safety toe cap, which holds strong under immense pressure and is designed to keep its shape without restricting movement.
“Since our launch, sales have been exceptionally strong across the entire RotoFlex range,” Gracie said.
“We are already fulfilling replenishment orders, as well as new orders with major customers for the rest of this year, completely validating all the hard work that has gone into bring the product to market.”
MineGlow was founded in 2014 by industry pioneers Roy and Carinne Pater, the original co-developers of the x-Glo product line, a robust LED lighting solution suitable for mining, tunnelling, ports conveyors and industrial environments.
The company has since become a market leader in providing purposebuilt, safe, durable and sustainable LED strip lighting solutions. And with several systems already deployed across Australia, New Zealand, Mongolia, the UK and West Africa, its new em-Control solution is providing even greater levels of safety for underground mining.
The em-Control is an intelligent, network-based solution that warns and directs an underground workforce to safety with multidirectional light pulses and colours.
The complete system comprises em-Lighting, the LED light strip, em-View, a web interface, and emController, a network-based controller that integrates with third-party systems via an open API (application programming interface).
“The em-Controller has been designed to be totally network-ready. It’ll work with any kind of network in underground mining conditions, be it Ethernet, Wi-Fi or Bluetooth, and the unit can be connected into any thirdparty system so any operator can send a signal to control the lighting
based on the situation or event,” MineGlow general manager Carinne Pater told Safe to Work
Installed throughout a mine’s underground tunnel network, em-Control alerts workers instantaneously of an emergency and directs the best way to designated exits, rescue chambers or other safe areas.
According to MineGlow, it is the only emergency LED strip lighting system on the market that is fully configurable, giving mine sites greater flexibility for different applications and the appropriate safety warning.
“We use high illumination to visually communicate critical information to underground teams, helping to maximise safety, suppress panic and provide comfort in highstress, dangerous environments,” Pater said. “The system operates on high sight impact rather than sound, making it perfect for smoke-filled or low-light conditions.”
Designed and engineered by MineGlow for tough industrial conditions, the IP65-rated, shockproof em-Controller integrates with third-party systems used in hazardous and industrial applications such as traffic management, zone identification, ‘no-go’ zones, vehicle awareness and seismic activity.
“With built-in network capability and an open architecture, any system can communicate with em-Control to provide an additional layer of safety and protection,” Pater said.
“When a safety event or incident occurs, the em-Controller receives the information and triggers the em-Lighting LED strip to emit a preprogrammed colour, direction, and pulse sequence.
“The system communicates critical information such as the severity of ground movement or
type of emergency, while informing workers of the direction of travel for a seamless evacuation.
“For example, minimal seismic activity might activate an orange light pulse to notify workers, but a more significant seismic event will activate a different colour, immediately pulsing in the direction of evacuation.”
One em-Controller can drive up to 500m of LED lighting, significantly reducing set-up costs and minimising downtime for installation.
“The lights are powered from both ends, providing a significant level of redundancy and allowing a longer installation distance, so if there is a break in the lights they will continue to operate from the break back to the power source,” Pater said.
The em-Control system can be configured to work effectively with a mine’s existing network infrastructure, or activated manually where network connectivity is not available, via various push-button activation points throughout the mine.
“If there is a break in network connectivity, the em-Controller has a manual override, featuring an on–off push button as well as a directional button, ensuring workers can be evacuated safely,” Pater said.
“The flexibility of our em-Lighting LED strip lights enables miners to install them easily and onto any fixed or mobile surface and at any height.”
All MineGlow solutions are certified to the highest national
and international standards. They are designed to operate in harsh conditions and are built for zero harm.
MineGlow transforms high-risk underground mines and other industrial applications into brighter, safer, and more productive places to work, while reducing energy and operating costs.
The company continues to evolve and expand its range of lighting solutions through ongoing investment in research and development.
This commitment to safety innovation in the LED strip lighting sector has delivered several significant industry-firsts, the company said, including installation of Australasia’s first LED strip light form factor purpose-built for mining, the world’s longest continual hazardous LED lighting strip, the world’s first LED strip emergency lighting for mining and tunnelling, and the world’s first Exm IECEx and ATEX-certified explosive-proof LED strip light for a range of industrial environments.
MineGlow identified an industry need and has a range of LED strip lighting solutions that are easy to install, durable and built to perform under extremely harsh underground mining conditions.
“The installation of MineGlow’s LED strips in underground mines has had a profound effect on working conditions for miners, providing constant ‘daylight’ conditions underground,” Pater said.
Up-to-date data allows safety personnel to retain visibility of a situation when no worker is present.
Adigital worksite leverages data from connected Internet of Things (IoT) devices to derive insights and optimise critical processes across all operations, including evacuation management. These insights make it possible to make smart decisions based on near real-time information to improve safety and efficiency.
For evacuation management, a digital worksite solution leverages personal gas-monitoring devices like Blackline’s G7c, which workers are already wearing to protect themselves from hazardous gases. These GPSenabled connected safety devices, coupled with online monitoring
software, make it possible to visualise each individual’s location throughout an evacuation, helping to accelerate response times and streamline the process of accounting for the wellbeing of each person.
A connected safety solution gives team leaders visibility into the entire drill through a network of connected devices associated with each crew member. With these personal monitoring devices, emergency notifications can be targeted by individual and by team, or sent to the full site, providing the ability to precisely direct workers to specific muster points; for example, “muster B unsafe – go to back-up”.
Teams can also deploy a beacon at each muster point, so the device pings the beacon and confirms the location as soon as the worker arrives. No manual headcount is required.
If a person is missing, their precise location is tracked, reducing the need for unnecessary searches. Operators can check the area map in the online portal, Blackline Live, to gain full visibility of the individual’s near realtime location.
Not only does connected safety increase the efficiency of drills as they are happening, but the technology also provides valuable insights to improve future emergency preparedness. For example, team leaders can track and
DIGITAL INSIGHTS MAKE IT POSSIBLE TO IMPLEMENT SMART DECISIONS IN THE CASE OF AN EVACUATION.
visualise how long it takes each person to reach a muster point and conduct post-drill evaluations to find efficiency time-saving and opportunities.
Furthermore, analysis of the data from the connected safety devices makes it possible to discover roadblocks that occurred during a drill. This means corrective action can be taken before a real evacuation occurs.
Traditionally, if someone doesn’t make it to a muster point and their location isn’t known, search parties must be deployed to try to find and rescue the worker, putting additional people at risk. And while conducting a rescue, the first responders don’t know the situation: Did the worker fall? Were they exposed to high levels of toxic gas? If so, what gas and at what concentration?
The responders are entering the situation blind, not knowing if they need to use SCBA (self-contained breathing apparatus) or whether it’s better for emergency services to respond for a health event.
Connected safety devices provide full visibility into the incident, as well as a more precise way to identify and locate anyone who hasn’t successfully evacuated so appropriate measures can be taken to ensure their safety.
As an example, personal gasmonitoring devices with cellular connectivity make it possible to
contact workers directly via twoway text messaging or push-totalk functionality to check on their wellbeing, even if they’re in a location prone to two-way radio issues. And if someone doesn’t evacuate, it’s possible to see their gas readings, fall detection or no-motion status to have full situational awareness and optimise the emergency response.
Unlike RFID (radio frequency identification) swipes, GPS location tracking enables emergency response teams to identify exactly where a missing person is located at that exact moment, saving time and lives with a faster response – without the need of exposing response teams to additional danger.
In an evacuation, after workers have left the hazardous area and made it safely to their designated muster points, real-time gas readings can still be possible thanks to area monitors deployed strategically around a worksite. Readings from these monitors allow safety personnel
to retain visibility of the situation even when there is no worker present in an affected area, and stream up-todate data to Blackline Live to inform stakeholders whether the danger has subsided or additional measures need to be taken. They can also act as the first source of alarm on the presence of a gas hazard before a worker enters an at-risk area in the first place.
Putting it all together, full visibility into the safety of a facility is enhanced when digital and supported by: connected area monitors and personal gas detectors to track worker safety and collect real-time data; online software and reporting to view and analyse that data; and 24–7 safety monitoring personnel to respond should an evacuation, rescue or emergency response be needed.
A digital worksite and connected safety technology streamlines evacuations and enables emergency responses that leave no one behind.
Visit encoremonitoring.com.au to learn more.
The development of technologically sophisticated, secure and robust communications networks is central to the safety, health and wellbeing of mine site workers, their families and those supporting mining industry operations in remote communities.
Vocus is playing a major role in the ongoing digital transformation of the resources sector.
And by offering Connectivity 4.0 solutions, the company’s network technologies are merging with the needs of mines and the their surrounding areas, making ubiquitous secure connectivity a reality.
“Our core business, and what we are in the business of doing through our advanced network connectivity solutions, is enabling the secure movement of data for organisations,” Vocus national industry lead –resources and utilities Simon Head told Safe to Work
“And we do it in a scalable way that gives our clients the very best ability to access the insights that data can provide them in order to make faster, better and safer decisions.”
Just as the fourth industrial revolution, or the transition to Industry 4.0, is having a deep impact on business via the integration of digital services, process, and practices into every aspect of operations, Connectivity 4.0 has the potential to significantly affect the way those services securely connect with each other and the world around them.
Connectivity 4.0 suggests a new era in which advanced communications networks, the very types of technologies being developed by Vocus, provide ubiquitous connectivity across terrestrial and sub-sea fibre, regional 4G and 5G mobile services, satellite coverage and private long-term evolution (LTE) networks.
In essence, Connectivity 4.0 is paving the way towards high-speed, low-latency applications such as autonomous vehicles and widespread sensor networks. This is transforming many dimensions of mine safety at organisational, operational and personal levels.
The networks powering these applications can operate over several advanced technologies, including high-speed fibre optic cables, pointto-point microwave connections, local
wireless and low-earth orbiting (LEO) satellite services.
This transformation is also driven by the requirement for universal digital connectivity for core operational needs right now, including building missioncritical services, enhancing the employee experience, and achieving environment, social and governance (ESG) objectives.
“At Vocus we provide the secure network foundations and the ability for organisations such as mining companies with the capability to accelerate their ESG initiatives whether it be decarbonisation programs, zero-harm processes and practices or supply-chain monitoring,” Head said.
In terms of mine safety – and the health and wellbeing of workers, their families and the many people who live in remote mining communities – network technologies are unlocking a new level of pervasive connectivity. This gives mining companies the ability to provide employees with a suite of digital services that are flexible, reliable and increasingly free of disruption.
The investment roadmap that Vocus is undertaking across the Pilbara region of Western Australia is substantial, with a 1000km high-capacity fibre optic spur
from the Australian Singapore Cable (ASC) to a pre-existing cable located at Port Hedland that is scheduled for completion in March 2023 and will form the Darwin–Jakarta–Singapore Cable (DJSC).
The DJSC will provide a unique, geographically diverse and protected wet route from the Pilbara to Perth, and a direct low-latency route to Singapore and many key cloud computing hyperscalers.
Additionally, the 2000km Project Horizon is under construction and scheduled to be completed by December 2023. The project will complete a ‘western loop’ of assets by connecting Geraldton to Port Hedland, via Meekatharra and Newman, linking natural resources hubs in the Pilbara.
Given the increasing importance of data integration and dependency on digital connectivity, robust connectivity infrastructure is vital to the success of whole-of-business technology transformations such as those required in the mining industry, as significant digitalisation programs are currently underway in the Pilbara and elsewhere.
The benefits of the DJSC include its capacity to support edge computing, LEO systems and private LTE/5G networks, while ensuring secure, reliable
Mine workers and their families, along with the communities in which they reside, desire scalable connectivity technologies that make their workplaces and homes safer and more attractive to live in, ensuring they are a part of a digitally transformed future.
“Living in metropolitan areas, we take for granted seamless access to digital services,” Head said.
“The resources companies Vocus provides network services and solutions for often look at connectivity in a holistic way – not simply what
do we require to support our mining operations, but how can we drive value back into the communities that we operate alongside.
“At Vocus we feel we have an incredibly important role to play in delivering Connectivity 4.0 to our industry partners, the exploration teams, mine sites and communities that rely on stable, fast and secure networks to complete their roles safely and efficiently, as well as enjoy the access and benefits to an array of digital platforms providing online health, education and entertainment services.”
high-performance internet connectivity.The KITO RY wire rope hoists are loaded with an array of safety and performance features.
KITO PWB understands that the most effective lifting solutions are those engineered for individual project specifications and requirements.
The company’s robust, reliable and custom-made hoisting solutions cover a breadth of industries, including mining, construction, infrastructure, manufacturing and transport to name just a few.
The KITO RY wire rope hoists are a new addition to the company’s existing product line and are loaded with an array of safety and performance features. These units are designed for use across multiple applications and
in any industry where a five-tonne or 10-tonne wire rope hoist is required.
The RY Series hoists are loaded with features for high-demand applications, including invertor control.
“The invertor control, a standard feature on all of our RY Series hoists, is a significant safety feature which allows for smooth start–stop capability, and the transition from slow to fast operation protects the load and supporting structure reducing load swing and bounce,” KITO PWB’s national hoist specialist Glenn Morgan told Safe to Work
The inverter is a dual-speed variable frequency drive (VFD). It
controls both hoist and trolley for optimum speed adjustability, as well as lifting and lowering accuracy. A low-load high-speed function allows for hoist operation at 1.5 times the standard high-speed, with a load less than 25 per cent of rated capacity to increase productivity.
The smooth start–stop and transition from slow to fast protects the load and supporting structure, reducing load swing and bounce, with the ability to adjust the lifting or travelling speeds to suit the user’s application. The VFD incorporates an easily accessible condition-monitoring system that allows for more specific forward planning.
“The condition-monitoring is a significant feature in all RY Series hoists in that operators receive precise information about the progress of the hoist’s design life via an hour meter and operation counter, so preventive maintenance is based around the exact hours of operation and the exact operations the hoist has done,” Morgan said.
Recognising the often-remote nature of work sites, this situation is ideal for companies that cannot afford lengthy unplanned downtime that may result in having to wait for an external operator to be driven or flown out to the site for repairs.
“At KITO PWB we sell the RY Series hoists, and although we stock a comprehensive range of spare parts and have fully trained and experienced staff that are willing to offer assistance and advice, we’re not trying to sell servicing and maintenance of the hoists, we empower our customers to do that,” Morgan said.
“The critical hoist information is not locked up, it’s available for our customers to access instantly.
“Major inspections on the hoist are usually scheduled for every 10 years but can be prolonged because users can base it on actual usage rather than time. Customers can plan oil replacements on gearings based on usage – most people don’t use the equipment as much as it’s designed for.”
The RY Series has many other innovative features.
“In combination with the inverter controls and VFD technology, KITO RY rope hoist also includes an electronic overload which can detect when the load is above the working load of the hoist,” Morgan said.
“When it detects that the load is 25 per cent over the rated capacity, the hoist will automatically stop and prevent that load from being raised. Additionally, it will log the overrated load as a fault
The smooth start–stop and transition from slow to fast protects the load and supporting structure.
and this information provides operators with valuable information.
“It’s a feature designed to keep people safe and to keep the lifespan of our hoists accurate.”
Overloading is detrimental to all equipment and reduces the number of hours that equipment can function at its intended capacity.
The components of the RY wire rope hoist are manufactured to be more durable, increasing times between replacements and ensuring they are less likely to fail while in operation. The deep grooves on the wire rope drum help to ensure the wire is seated and unlikely to come loose during operation to prevent the load from shifting, while the wire rope itself is resistant to wear.
“The hoist also has limit switches that are easily set on-site,” Morgan said. “When the hoists are installed, the limit switches can easily be set so that the hook doesn’t stop too short and also doesn’t go too far and hit the ground, which would cause slack rope.
“Not only is it dangerous to have the hook go past the site’s pre-determined stopping point, which is different for most places, but it also damages the wire rope and the hook if it’s allowed to hit the ground each time.
“And if for whatever reason the hoist goes past its upper limit, we also have
a final limit control set into the hoist, which will stop the hook from going past a certain point and disable the hoist to prevent any possible failures from occurring.”
Of particular importance on the RY Series hoists is the fact the trolley operation occurs with flangeless wheels and with side guides.
“You don’t get any wearing on the flange of the beam or operators are not required to replace wheels because of worn out flanges,” Morgan said.
“In essence, with flangeless wheels and side guides the trolley runs smoothly and there is no occurrence of wearing.”
KITO PWB is especially proud of its long history and today is a leading supplier of electric and airpowered chain hoists, electric wire rope hoists, lever hoists, manual hand chain hoists, push and geared trolleys, below-the-hook devices, material handling equipment, lifting chains, technical chains, and associated fittings.
“We are a completely independent company,” Morgan said. “We don’t compete against our customers and our customers know the quality of a KITO hoist.
“We have a very loyal customer base.”
West Coast Fever Head
Coach Dan Ryan was one of the panellists at the Gold Industry Group’s Leadership Breakfast, held at the recent Diggers & Dealers conference in Kalgoorlie and facilitated by Cannings Purple director Peter Klinger
Fresh off leading the team to its maiden Super Netball League Premiership, Ryan was able to bring a mining industry outsider’s perspective to the discussion and drew parallels between managing the culture in a high-performing sporting team to seeking similar outcomes highperformance workplace.
Safe to Work sought to expand on Ryan’s insights, exploring his belief that resources industry needs to look forward and work towards solutions that ensure psychologically safe workplaces, free of prejudice, are the minimum standard.
What is the importance of embracing vulnerability as a virtue in the workplace?
I believe vulnerability is a powerful catalyst for building deep and trusting connections and relationships within a team environment.
When you’re willing to be seen on a human level and can own and share your strengths and growth
areas without judgement or fear of retribution, people will see the real you.
And that’s where I believe the best version of ourselves are born and how the best teams are made.
What does authenticity, or being authentic, help to establish?
Thriving teams and workplaces will demonstrate a culture that embraces every individual for who they are and what they bring to the environment.
The best teams will empower everyone to be their authentic self and feel valued for the role they play and the contribution they make to the team.
When you feel the connection to a greater purpose and can appreciate the impact you’re having and feel truly part of the team, that’s when the magic happens.
What are some of the similarities between managing culture in a highperforming sports team and in a workplace?
To achieve anything as a collective, you must all be on the same page, heading in the same direction, wanting the same result or outcome.
That alignment is critical, as is the accountability that comes with executing your role and responsibilities for the team.
It’s about reinforcing that every role in the team or organisation is equally important and that we all must do our bit to get where we want to go.
On the panel you said, “If you see something and don’t say something, you are a part of the problem.” Would you expand on this point?
It’s the importance of accepting that we all have a role to play, and we are all responsible for the contributions we make to our team, workplace, or environment every single day.
If we hold ourselves to high standards, we will often get good
results; if we celebrate mediocrity, we will most likely underperform.
So when we are trying to shift and change culture and behaviour, we all must be part of the solution. If we let important moments slip by and we don’t address the real issues unfolding in front of
our eyes, we essentially become the enablers of these problems.
It takes great courage to stand up for what’s right and to make change, but if we really want to shift culture and behaviour we all must be prepared to do the work and play our part, even if it’s confronting and uncomfortable.
Will psychologically safe environments lead to real change within workplaces?
Absolutely, because if people feel safe they will feel much freer and supported. Free to be themselves and more confident to then stand up and speak up if required.
It’s not easy, but if an environment can create a safe space where openness and vulnerability is encouraged, where listening to understand is front and centre, real change can take place.
From an outside perspective, what might be some of the risks to the
mining industry if progress is too slow in this space?
Society is moving forward at a rapid rate so workplaces and industries need to move with it, or they will be left behind.
In some circumstances, progress can be slow, especially if some of the changes required are deeply entrenched in the culture. However, you must start somewhere and if the challenges have been acknowledged and identified, that’s the first step in making real progress.
Sometimes things will take time, as there’s not always a quick fix, but if there’s a shared vision in place with a clear plan detailing what it’s going to take to get to where you want to go, that’s progress.
To bring it to life, it becomes the responsibility of all those involved in the industry. Everyone has a role to play and is required to contribute for the greater good.
Small steps forward every day and real change is possible.
Accenture is working with mining clients to evolve their systems and processes.
Data is at the heart of digital evolution, but how do you become truly data-led?
Leveraging the power of data to transform operations and value chains gives you increased safety and worker connectedness, effective centralised functions and cost efficiency, and sustainable and responsible practises that support environmental, social and governance (ESG) strategies.
“At Accenture, we’re working with our mining clients to evolve their systems and processes through an array of business solutions, including large-scale and complex technology implementation, to build the necessary agility for future success,” Accenture’s ANZ mining lead Eric Croeser told Safe to Work
Accenture believes data and digitalisation are extremely important for mine operators. The company understands that the value of a connected mine lies in digging deep into the wealth of data available
across the entire value chain in order to provide integrated, end-to-end situational awareness and intelligent asset management.
For more than a decade, Accenture has been building a broad suite of engineering and manufacturing services called Industry X.
This initiative that has led to the development of a connected mine solution that helps enable companies to more effectively manage their operational environments through the use of embedded intelligence systems.
“We refer to Industry X as the application of advanced technology solutions specifically focused on the core operations of our mining clients,” Croeser said.
“We bring our global technology experience to drive large-scale transformation.
“In essence, we are a mining valuegenerator with the capacity to supply our clients with a solution for any operational requirement.”
Digital transformation is delivering significant rewards for mining companies, and Accenture looks for improvement opportunities across any mine situation.
The company can deploy many solution layers ,from strategy consulting, enterprise resource planning (ERP), instrumentation and cloud computing. It leverages its experience and size, with thousands of trained people in each technology area, to assist the process.
Accenture is platform- and partner-agnostic, which means it can deploy any technology, product or application according to a mining client’s needs. It also has alliances with most technology providers and is trained in their solution suites.
Connecting people, equipment, data and insights across a mine by utilising advanced digital technologies helps operators gain important intelligence and predictive insights. This in turn enables faster and more
accurate decision-making, leading to safer outcomes.
The ability to monitor everything from road conditions and truck performance to specific equipment productivity and worker fatigue is supported by Accenture’s connected mine solution, which provides accurate operational insights in real-time.
“Within our Industry X business we are making a massive play into robotics and automation technologies with the recent acquisition of Pollux, a provider of industrial robotics and automation solutions in Brazil,” Croeser said.
“Recent forecasts suggest that robotics and automation in mining will remove thousands of injuries from mining operations, and the industry has always strived to be at the forefront of safety and adopting safe practices.”
This ability to harness information through advanced digital technologies such as data science, machine learning, data engineering, artificial intelligence (AI), and augmented and virtual reality, linked to 5G connectivity, creates the
capability to make data-driven, valueand risk-based decisions.
“We’re starting to see a trend towards autonomous decisionmaking and our role at Accenture is to harness the vast amounts of data now being generated and convert it into insights as a way for our clients to augment their workforce decisions,” Croeser said. “Advanced analytics and intelligent decision-making for mining operations is providing critical insights across the entire value chain, driving better safety, sustainability and ESG outcomes, as well as greater efficiencies.”
Decarbonisation is critical. A key for resources companies is accurate, auditable carbon tracking that starts at the mine and extends downstream.
Accenture’s analysis points towards miners leveraging technologies like data analytics and AI in the near term to improve efficiencies such as automating operations. This can help companies reduce energy consumption by regulating and optimising machinery speeds and movement.
In the long term, Accenture believes mining companies can move on to
bigger and longer-horizon projects; for example, electrifying the mining infrastructure from renewable sources such as solar and wind.
The question is no longer about whether or not mining companies should pursue decarbonisation. It’s how to make decarbonisation environmentally and financially rewarding. Miners that formulate an approach to this combination will not only be better positioned to meet increasingly stringent carbon targets, but also stand to realise higher valuations and open more doors to capital investment.
The challenges associated with safety, ESG and sustainably, especially the process of decarbonisation, require a whole-of-industry approach and, for Accenture, the role of Austmine as a leading industry organisation is crucial.
“Austmine has kept the industry connected through a difficult period over the last 24 months,” Croeser said.
“As an industry, we face challenges but we also have opportunities, and Austmine has been very much the golden thread that has helped to facilitate our response.”
The challenges associated with decarbonisation require a whole-of-industry approach.
When Queensland Mines Rescue Services (QMRS) opened the doors of its new rescue station in April 2022, it ushered in a new era of mine safety.
The training facility has been described as the best such operation in the world. And with its state-of-the-art resources, it’s not hard to see why.
The site, located on the Capricorn Highway, includes a vertical rope rescue training tower, simulated mine and fourstorey confined space for training.
“The most important thing to come off any Queensland resource site isn’t the coal or minerals, it’s the workers,” Queensland Resources Minister Scott Stewart said.
“QMRS’ work in risk management and as first responders is second to none, which why opening this new training facility is so important.”
Rescue personnel have been trained by QMRS since 1909, and the new facility – the first to be built in the state in the last 40 years – represents a shift to 21st-century solutions for new rescue challenges.
“Mines rescue teams train hard for actions that they hope never to use but for which they must be ready for every day of their working lives,” QMRS chief executive officer David Carey said.
In March, Glencore also upgraded its mine rescue facility at its Mount Isa mine in Queensland, enlarging the space from 160 to 225 square metres.
Mine rescue is a specialised profession and involves training to rescue trapped and injured miners, combat fires and respond to an extensive range of emergencies.
And because mine rescue is not solely an Australian profession, the International Mines Rescue Competition (IMRC) runs each year at the MSHA Mine Health and Safety Academy in Beaver, West Virginia, in the US.
This year’s IMRC ran from September 11–16 and involved 22 teams from eight countries.
Teams engaged in a series of competitive events across the three days, including mine rescue, first aid, high-angle rope rescue, firefighting, and theory assessment.
IT MAY SEEM STRAIGHTFORWARD, BUT MINE RESCUE TRAINING INVOLVES A LOT MORE THAN JUST KEEPING A SITE SAFE.Rescue services are integral to the safety of a mine site.
Mine rescue training can involve collaborations, competitions, and specialty facilities.
The firefighting scenario was mandatory for all teams participating.
IMRC said the concept of training through competition has been a mainstay of global mine rescue organisations for decades, and the practice of nations learning from one another has been the foundation of the event since it was first held in 1999.
Back in Australia, Tasmania has also taken up the training-throughcompetition mindset, with the 33rd Tasmanian Minerals Emergency Response Competition taking place in 2021.
Up north, the 2022 Northern Australian Emergency Response Competition was held from May 12–15 and involved challenges such as firefighting, first-aid, heights rescue, breathing apparatus skills, underground search and rescue, hazardous materials, and road accident rescue.
Victoria also has its own mine rescue competition run by the Minerals Council of Australia (MCA). The Victorian Mine Rescue Competition (VMRC) has run since 1993 and sees mine rescue and emergency response teams compete against each other in simulated emergency situations.
“The scenarios are actually quite confronting, which is the aim of it, so it provides real life training,” MCA Victorian executive director James Sorahan said in a 2020 interview with Safe to Work
“It’s great exposure to learn about all the sorts of emergency situations that can arise at the different mine types.
“If you’re a coal miner, fire is much more of a risk than it would be for an underground gold mining team. And for open-cut mines it’s great experience to learn about underground emergency situations like the breathing apparatus scenario.”
Mine rescue training has even bled into other areas, including road safety, with eight members of Aurelia Metals’ Hera Mine emergency response team being qualified to attend road crashes.
The merger came about due to the close proximity of the mine site to one of 12 blackspots in New South Wales where roadside assistance response time is greater than 60 minutes.
Due to the high levels of training that the mine rescue team already possessed, the merger was a nobrainer for emergency response team (ERT) members, NSW Rural Fire
Service (RFS) volunteers and the NSW ambulance service.
Over six months, the team responded to four callouts between the mine site and the local community.
“We have the members and resources from Aurelia to respond to a scenario on-site and in the community at the same time,” Aurelia Metals’ Hera safety and training advisor Darren Mills said.
“We can respond within an 80km radius of our mine site while working closely with NSW ambulance and police.”
The nature of mining and mine sites means the vocation will always come with its risks. However, having well-trained and dedicated rescue teams will go a long way in mitigating these dangers.
“You hope that they don’t ever need to use the skills they learn in competitions, but at least they are ready if something does happen,” Sorahan said in a 2021 interview with Safe to Work.
“Every worker deserves to go home safely, and mine rescue teams take any training they can do extraordinarily seriously.”
When people think disability, their mind often jumps to a person with more obvious physical disability.
Yet a disability is any condition that restricts a person’s mental, sensory or mobility functions. It may be caused by accident, trauma, genetics or disease, and be temporary or permanent, total or partial, lifelong or acquired.
Disability can visible or invisible, as can people with disability in the workforce.
A disability should not stop anyone from finding employment; however, the realities of people with disability participating in the workplace can be challenging.
In an effort to make the process of working easier, Australia Post has created the Workplace Adjustment Passport, a new tool allowing team members with disability to capture and share their details and adjustment requirements in their own words.
The passport is designed to remove the need for people with disability to explain their circumstances every time they change roles or managers within the organisation.
“This passport allows us to manage workplace adjustments with dignity and respect, ensuring people with disability feel seen, heard, and valued wherever they work in our business,” Australia Post executive general manager, people and culture Susan Davies said.
A MAJOR AUSTRALIAN ORGANISATION HAS DEVELOPED A WORKPLACE ADJUSTMENT PASSPORT THAT ALLOWS TEAM MEMBERS WITH DISABILITY TO CAPTURE AND SHARE THEIR DETAILS AND REQUIREMENTS IN THEIR OWN WORDS. COULD SUCH A TOOL WORK FOR THE RESOURCES SECTOR?
Australian Resources & Investment is the country’s premier journal dedicated to providing cutting-edge insights into resource developments in Australia and around the world. Special feature articles include the best minds in the industry and examine investment, exploration and extraction, recruitment, engineering and mine management.
Subscribe to Australian Resources & Investment to stay up to date with the latest news on ASX-listed mining stocks and commodity prices.
australianresourcesandinvestment.com.au
EVENT SUBMISSIONS CAN BE EMAILED TO EDITOR@SAFETOWORK.COM.AU
AUSTRALIAN MINING PROSPECT AWARDS 2022 PERTH | NOVEMBER 17
Taking place in Perth in 2022, the Australian Mining Prospect Awards are a great opportunity to recognise and acknowledge the people and companies in the mining sector for their outstanding work.
Having recently celebrated the 2021 Prospect Awards winners, the 2022 awards will honour categories such as Indigenous and Community Engagement, Mine Project Success of the Year, Outstanding Mine Performance, Sustainability Project of the Year, Discovery of the Year and more. Some of the 2021 award winners included Roy Hill for Australian Mine of the Year and Hard Rock Mine of the Year, Mader Group for Contract Miner of the Year, and Metso Outotec for Minerals Processing of the Year.
This year will be the first time the awards will be held in Western Australia, in appreciation of the vibrancy and importance of the state’s thriving mining industry.
• prospectawards.com.au
AUSROCK CONFERENCE 2022 MELBOURNE | NOVEMBER 29 –DECEMBER 1
Hosted in partnership with AusIMM and UNSW Sydney, AusRock 2022 will be held in conjunction with the International Society of Rock Mechanics Regional Symposium from the end of November to the beginning of December.
Offering a hybrid format so delegates can attend the conference either in-person in Melbourne or online from anywhere in the world, AusRock 2022 follows on from earlier conferences that have successfully covered the various aspects of geotechnical engineering servicing the mining industry and shared best practices.
BHP, Jennmar, DSI Underground and GSS have confirmed their support, with exhibitions set to be held by Rocscience, Minova, MineGeoTech and DSI Underground. AusRock2022 will focus on new technologies and developments, industry needs, operational problem-solving, and case studies.
• ausimm.com/conferences-and-events/ ausrock
CONFERENCE 2023
BRISBANE | MARCH 27–29
The Underground Operators Conference is a flagship event in the AusIMM calendar and will return in 2023. Bringing together mining engineers, mine operators, technical service managers and consultants, this conference sets the benchmark for sharing underground operational experiences and industry best practice.
With deposits getting deeper or lower in grade, there is increased pressure to find smarter and more cost-effective ways to extract orebodies. To address this demand, key discussion topics for 2023 centre around the evolution of digital technologies, automation, and artificial intelligence and how these innovations are making it possible to mine at greater depths and lower grades. Major conference sponsor BHP will be in attendance, as well as a host of keynote speakers and exhibitors who will be announced closer to the event.
• ausimm.com/conferences-and-events/ underground-operators
BRISBANE | JUNE 26–29 2023
Inaugurated in 1958, the World Mining Congress (WMC) is the leading international forum for the global mining and resources sectors.
The World Mining Congress 2023 (WMC) is a unique opportunity for international representatives of the world’s leading resource economies to meet, find new partners, discuss current challenges, and share the latest research, technology, and best practice.
WMC events have set the scene for international agreements and high-level discussions that have influenced mining practices and the resource industry for decades.
Join senior mining industry owners, investors, national and international government representatives, researchers, educators, regulators, suppliers and operators from around the world in Brisbane for this genuine opportunity to demonstrate real leadership and presence on a world stage.
• wmc2023.org
LIFE OF MINE CONFERENCE 2023
BRISBANE | AUGUST 2–4
AusIMM and the University of Queensland’s Sustainable Minerals’ Centre for Mined Land Rehabilitation (CMLR) are welcoming attendees back to the highly successful Life of Mine Conference 2023.
In 2021, the conference welcomed a record number of attendees from over 15 countries and is set to bring a wider, global audience in 2023.
Join professionals, researchers, government, and academia from a diverse range of sectors as the program explores the full life cycle of a mine, from exploration to rehabilitation.
Delivered in-person and online, this technical conference addresses current and future challenges affecting the mining value chain and will present leading examples of sustainability in mining.
• ausimm.com/conferences-and-events/ life-of-mine