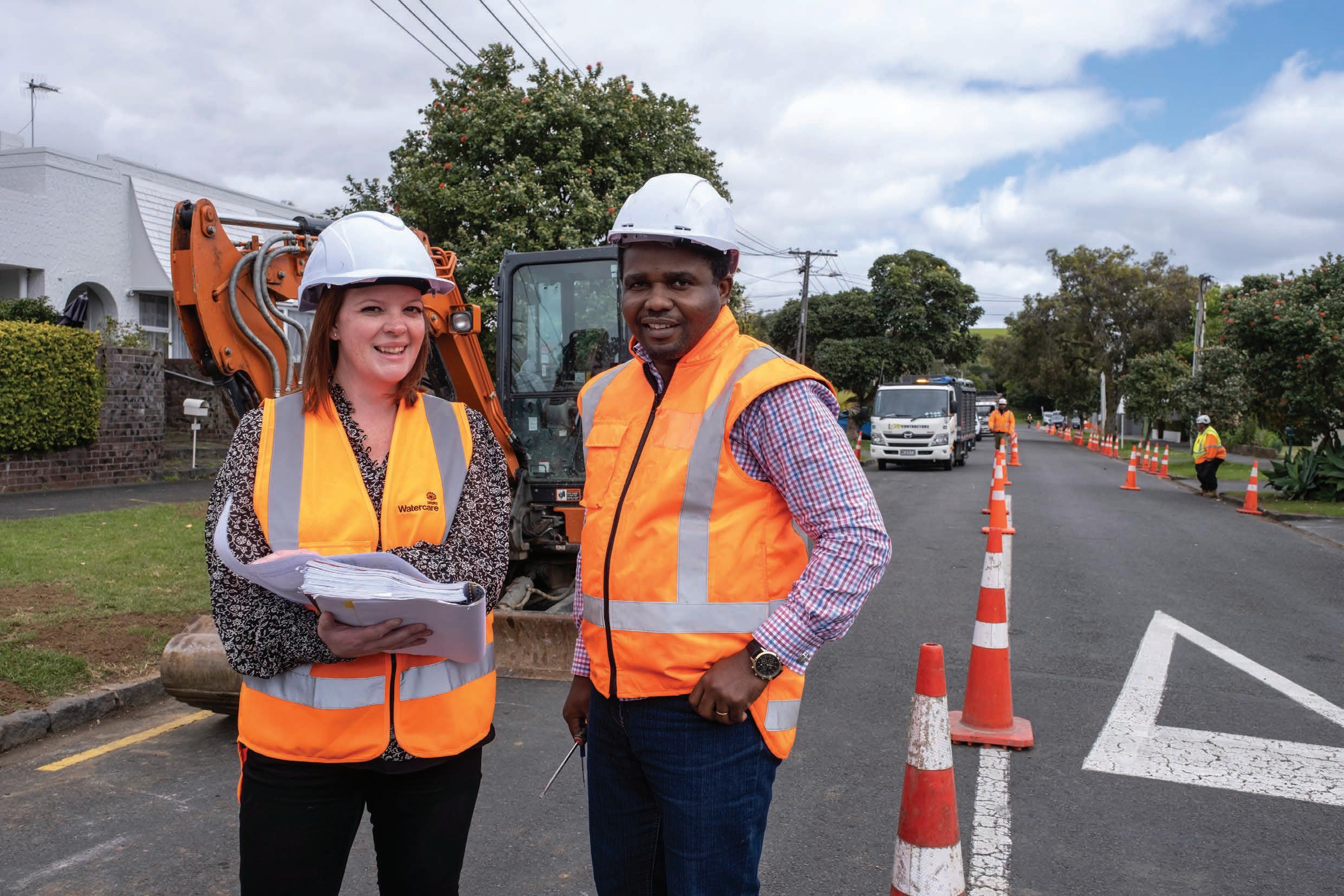
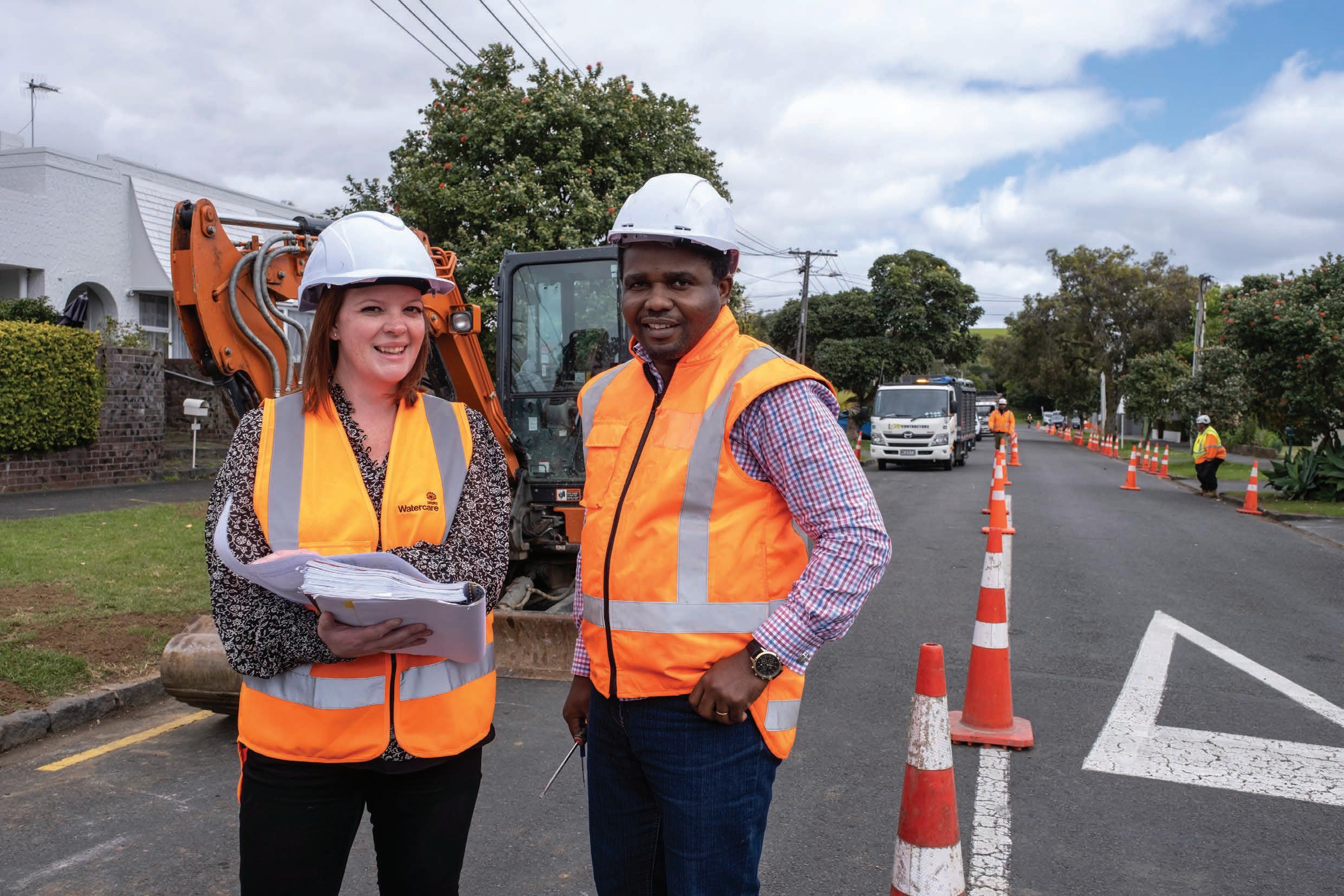
We’re Creating the Future of Water for New Zealand communities
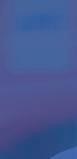
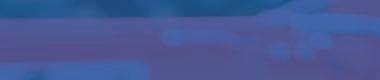
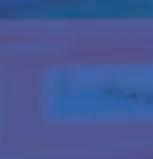

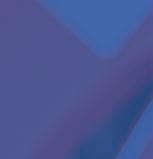
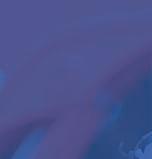
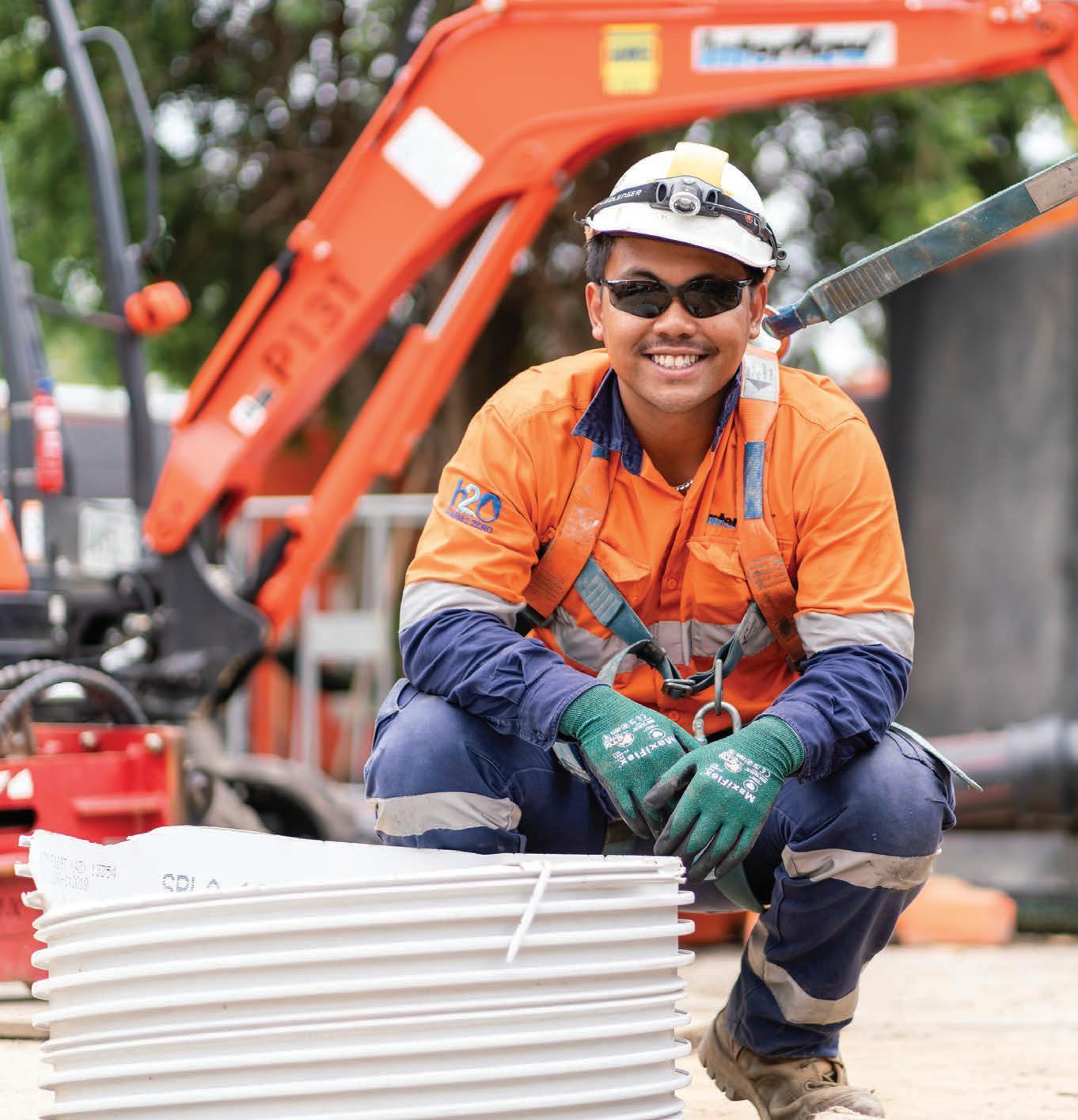
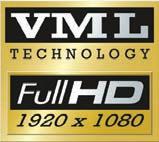
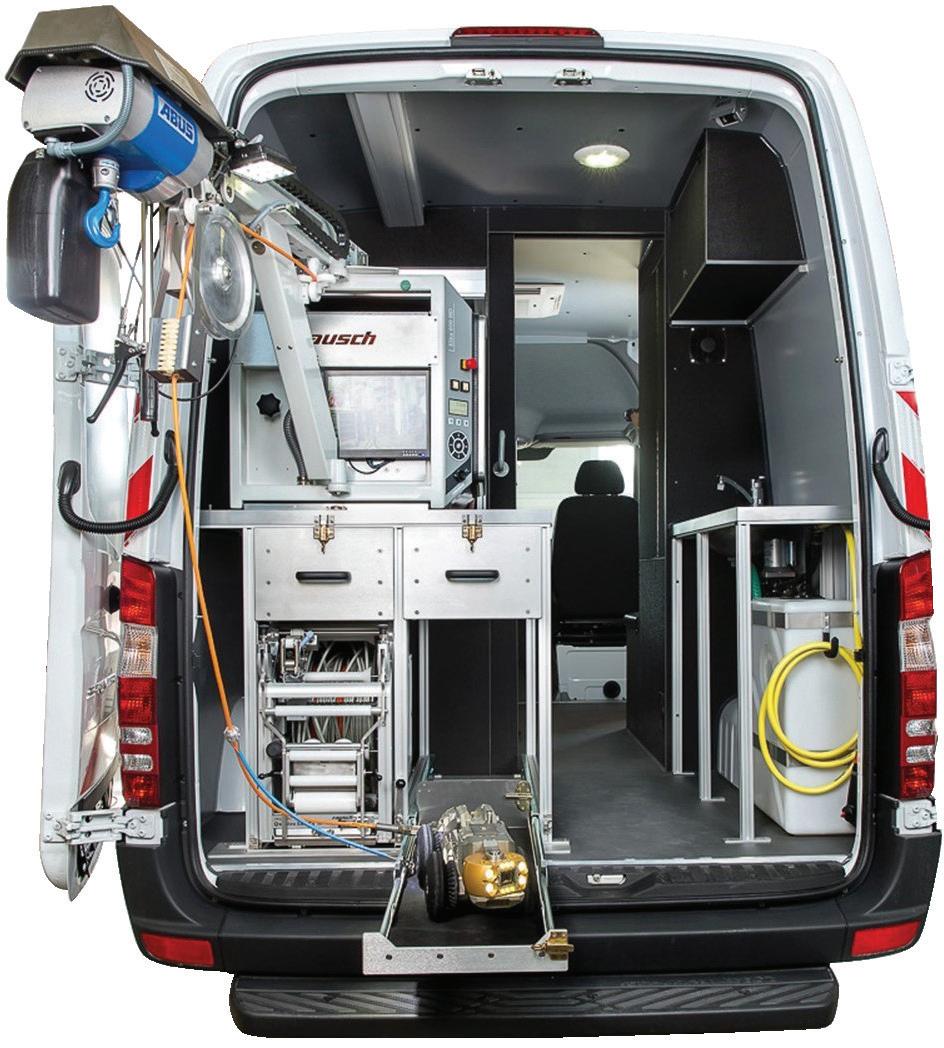
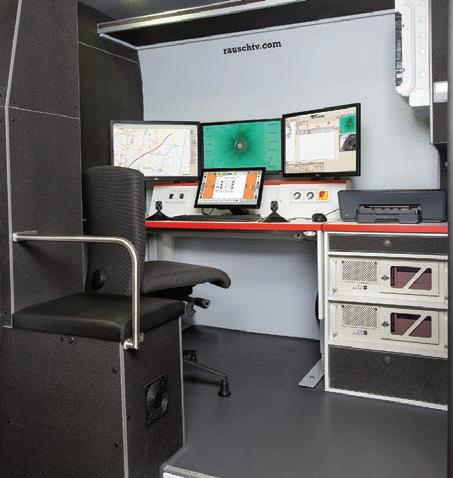
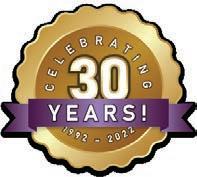
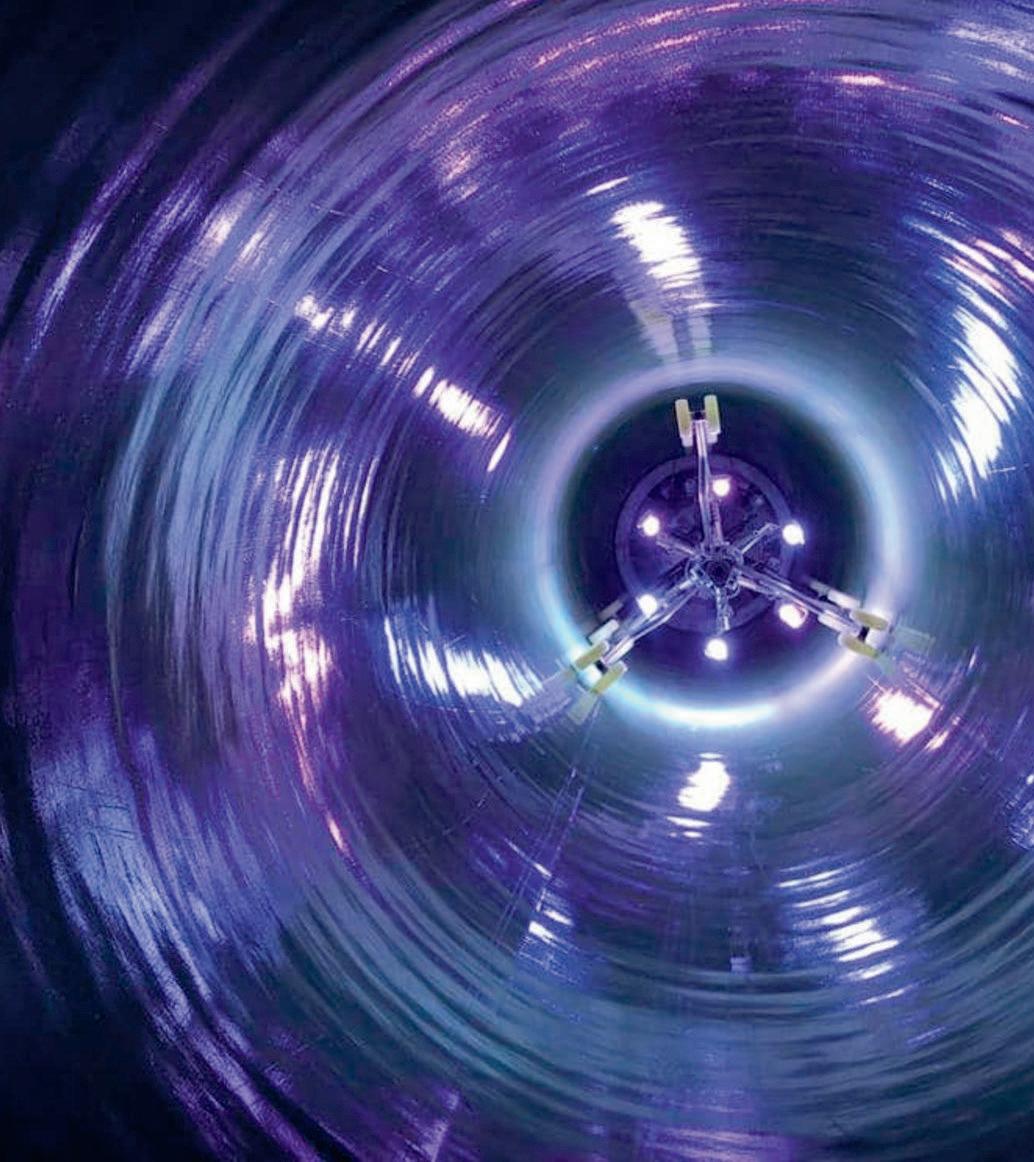
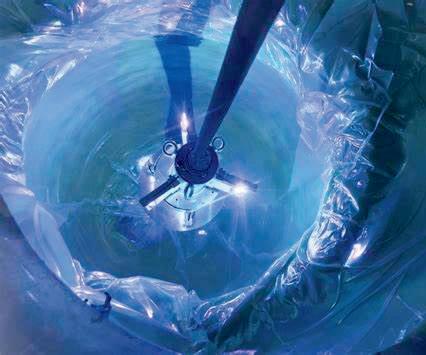
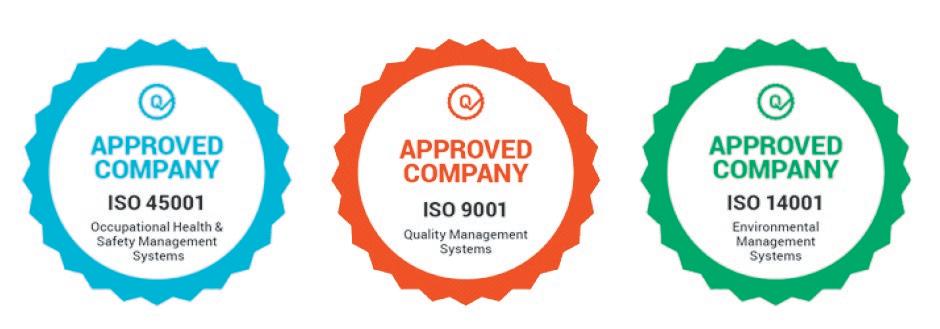

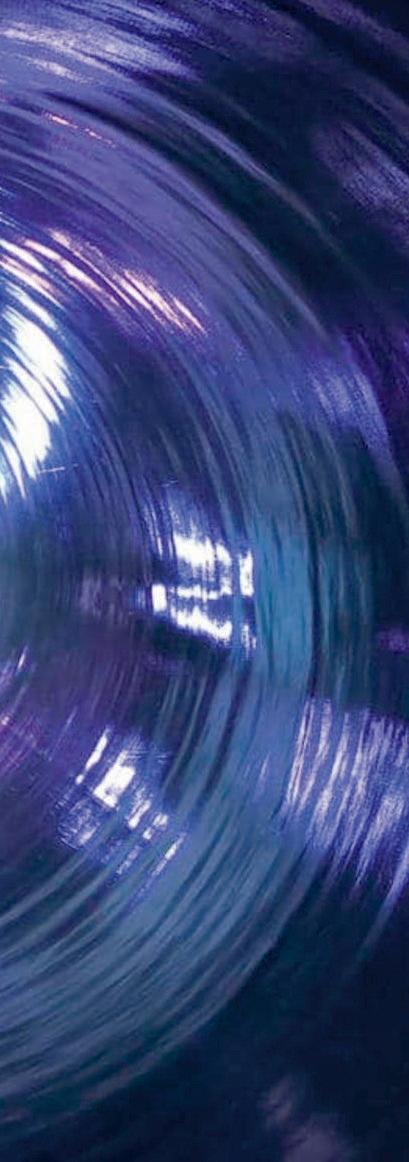
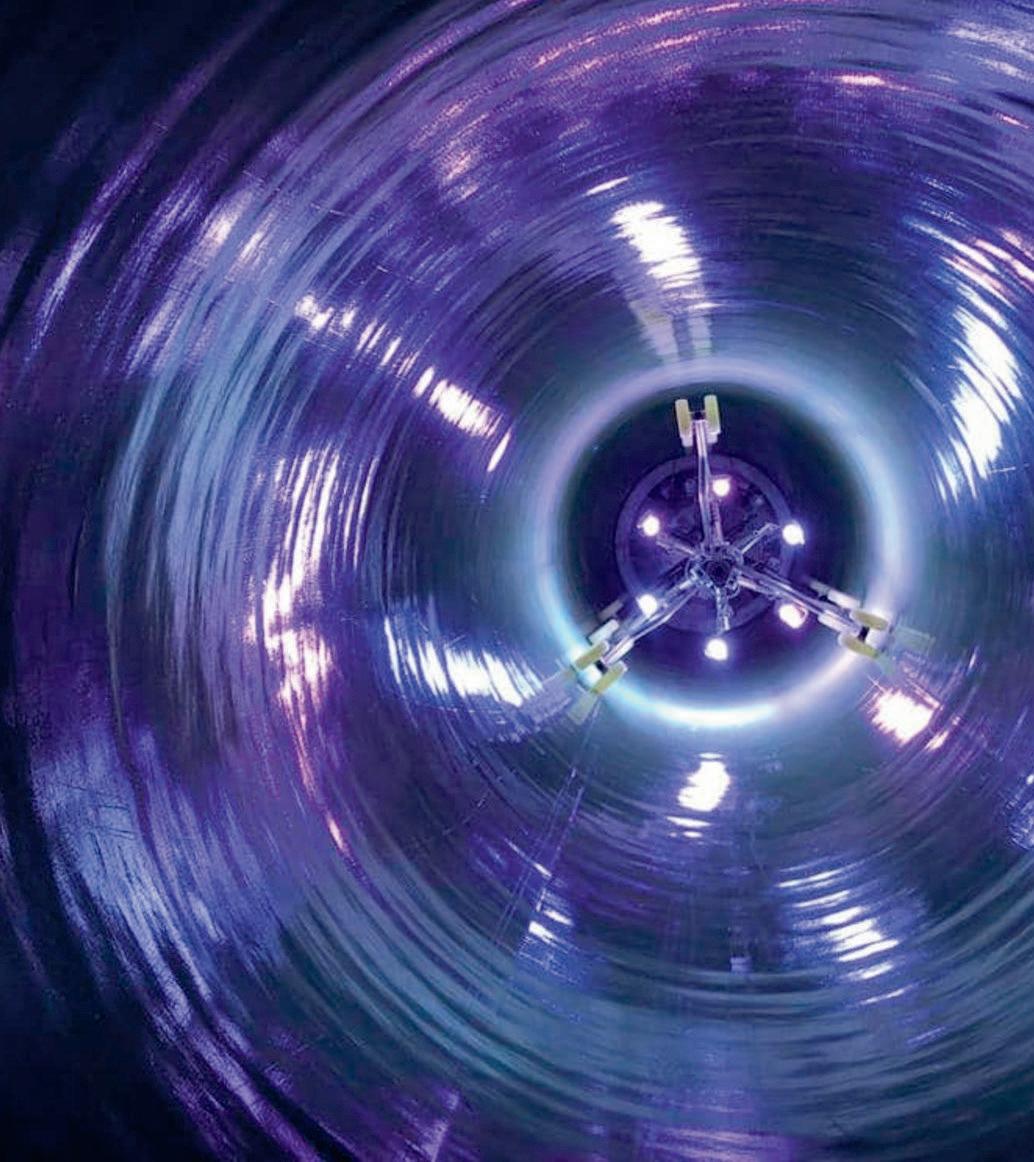
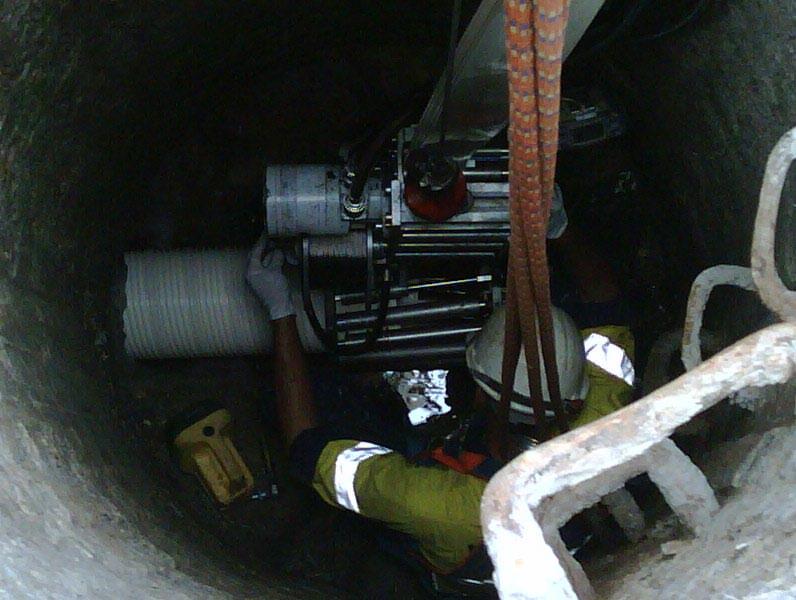
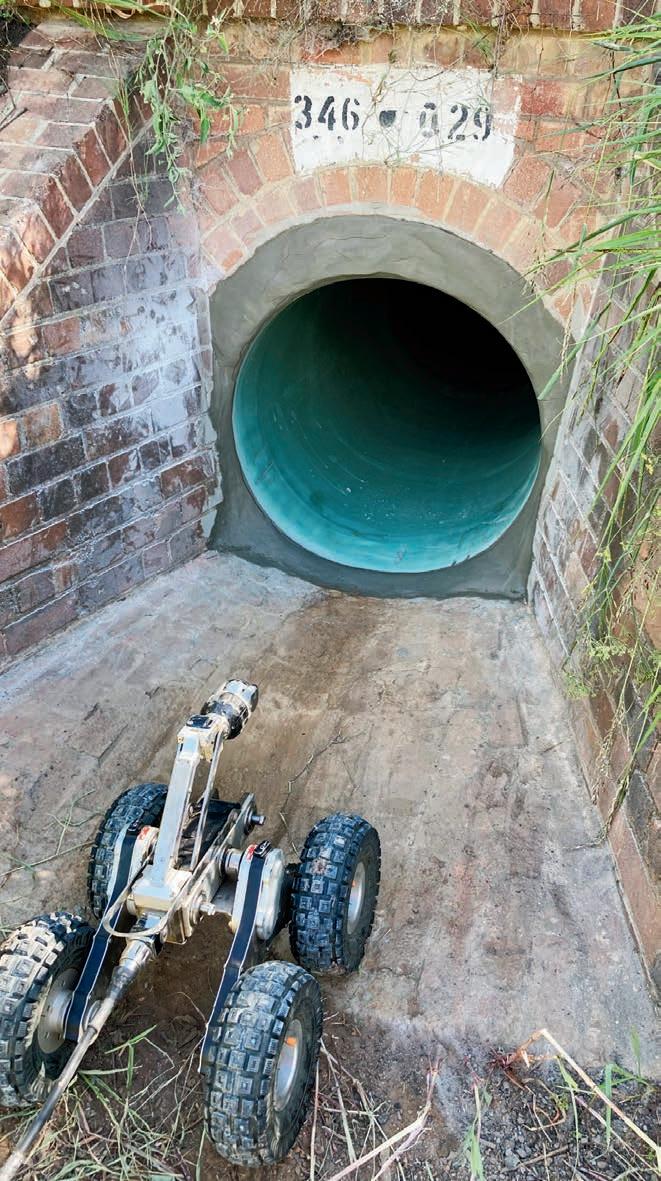
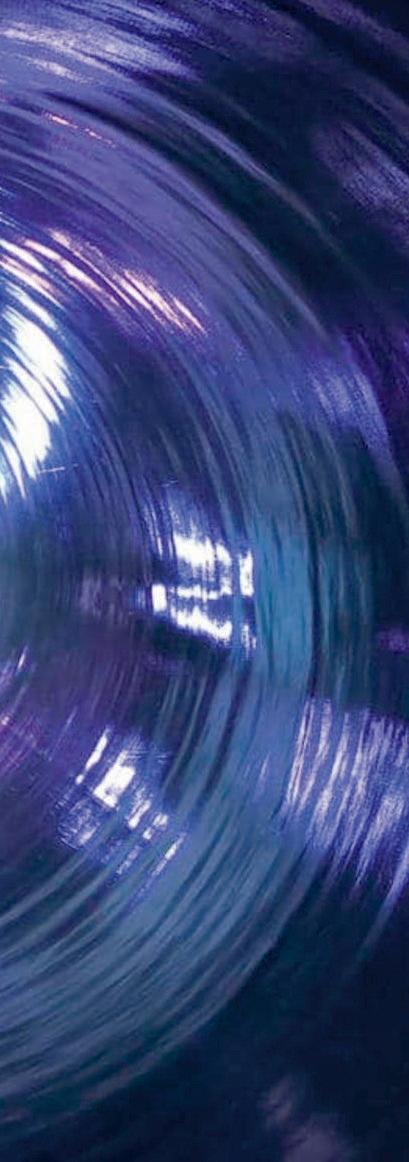
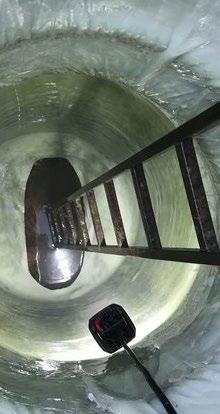
Contents
UNDER NEW ZEALAND
ASTT NZ Councillor: Industry Update New Zealand exemplifying long-distance microtunnelling projects
City Rail Link is bringing Auckland’s public transport to the future
Watercare proactively tackles massive pipe renewal program
The Barber Grove to Seaview Wastewater Treatment Plant pipe duplication project
Auckland wastewater pipes get 50 more years thanks to trenchless relining work
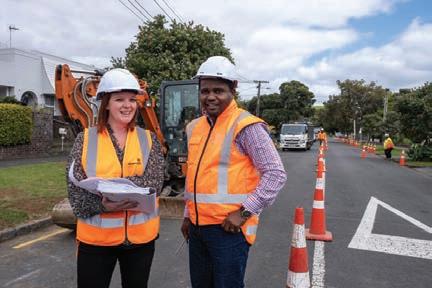
IMS Robotics Group to establish IMS Robotics Australia
PipeTech NZ aims to provide its clients with environmentally conscious solutions
Pipe Core supporting New Zealand’s trenchless industry with Europe’s leading solutions
Going above and beyond Trans-Tasman collaboration breeds success for trenchless JV
Keeping busy: Empire Infrastructure is involved in a range of remarkable projects across Australia and New Zealand Marley’s new CALIBRE™ range is leading the charge in NZ NordiTube presents the new NORDILONG: An independent longdistance pressure liner system Supporting the infrastructure upgrade boom in New Zealand Creating the Future of Water for New Zealand communities
From Australia to New Zealand and around the world, kwik-ZIP are the spacers of choice
Innovative drilling contractor provides pathways into trenchless education
Civtec has New Zealand’s fibre, power and water covered with support from Ditch Witch CEA
RELINING
It’s official: Veolia is the exclusive Australian partner of Thermoform Aussie Trenchless has the future of pipe rehabilitation solutions sorted It’s summertime – perfect conditions for pipe rehabilitation M. Tucker & Sons secures installation rights for additional maintenance rehabilitation product
16 18 20 24 26 30 32 34 36 38 40 42 44 46 48 50 52 54 56 58 60 62 64
HDD
Service your machine with the experts from Vermeer Australia Managing HSEQ on HDD Projects OptionX Group has trenchless technology sorted VACUUM & HYDRO EXCAVATION
A powerful, versatile and compliant vacuum excavation truck solution One of Australasia’s largest waste contractors takes delivery of its first KAISER unit
SOFTWARE & TECHNOLOGY
Drainchem plug supply deficit SECA elevates customer’s data efficiency with WinCan VX Smart Lock Group committed to the contractor and asset manager in first-rate trenchless sectional drain rehabilitation
MICROTUNNELLING
DJ Mac Cormick Contractors complete 234 m drive for 800 mm reinforced concrete jacking pipe Microtunnelling through basalt and very hard rock EVENTS
Get ready for No-Dig Down Under 2023 REGULARS
Editor’s Letter
From the President
image: Watercare extends life of wastewater pipeline by 50 years.
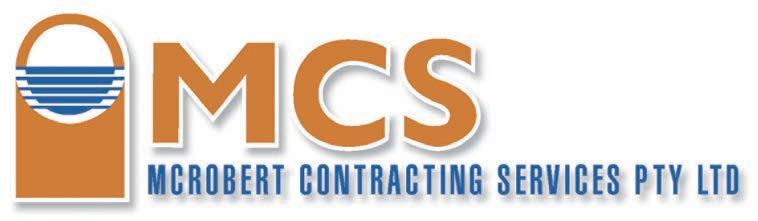
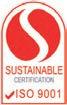
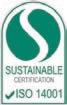
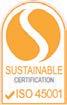


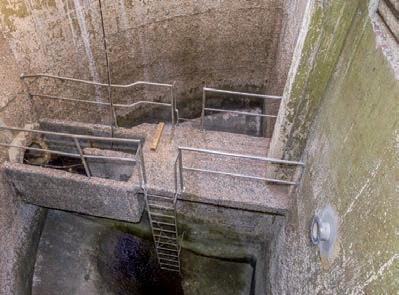
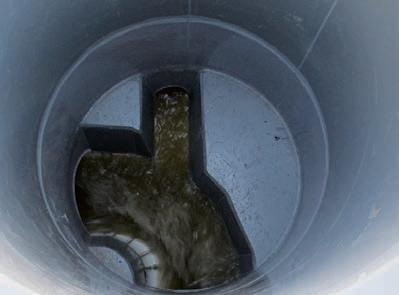
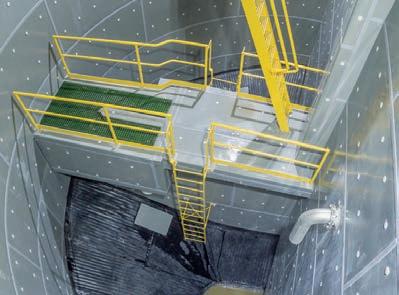
CEO John Murphy COO
Christine Clancy
christine.clancy@primecreative.com.au
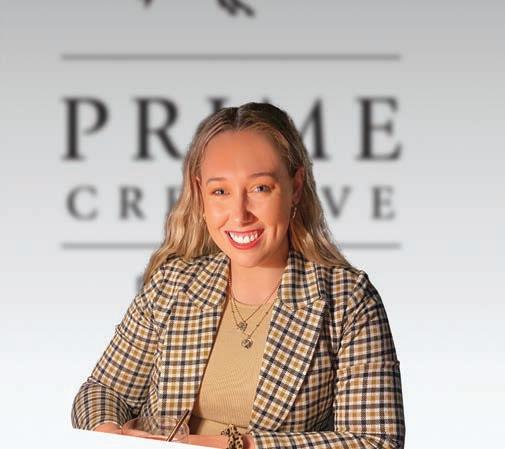
MANAGING EDITOR
Molly Hancock
molly.hancock@primecreative.com.au
EDITORIAL
Christian Alphonso, Jenna May
BUSINESS DEVELOPMENT
Nick Lovering
nick.lovering@primecreative.com.au
DESIGN PRODUCTION MANAGER
Michelle Weston
michelle.weston@primecreative.com.au
ART DIRECTOR
Blake Storey
blake.storey@primecreative.com.au
DESIGNERS
Kerry Pert, Tom Anderson, Louis Romero
COPYRIGHT
Trenchless Australasia is owned by Prime Creative Media and published by John Murphy. All material in Trenchless Australasia is copyright and no part may be reproduced or copied in any form or by any means (graphic, electronic or mechanical including information and retrieval systems) without written permission of the publisher. The Editor welcomes contributions but reserves the right to accept or reject any material. While every effort has been made to ensure the accuracy of information, Prime Creative Media will not accept responsibility for errors or omissions or for any consequences arising from reliance on information published. The opinions expressed in Trenchless Australasia are not necessarily the opinions of, or endorsed by the publisher unless otherwise stated.
© Copyright Prime Creative Media, 2021
ARTICLES
All articles submitted for publication become the property of the publisher. The Editor reserves the right to adjust any article to conform with the magazine format.
Head Office 379 Docklands Drive, Docklands VIC 3008 Ph: +61 3 9690 8766 enquiries@primecreative.com.au http://www.primecreative.com.au
Sydney Office Suite 303, 1-9 Chandos Street Saint Leonards NSW 2065, Australia Ph: (02) 9439 7227
Editor’s letter
Molly Hancock
It is hard to believe we are almost at the end of 2022. It is also now 12 months since I joined the Trenchless Australasia team as Editor.
Since taking over as Editor there has been multiple changes. The magazine itself has shifted from four editions to six and we have also welcomed two new team members – Jenna May and Christian Alphonso –both working on the editorial team.
In the past 12 months I have come to learn a lot about an industry I was not familiar with, and been extremely welcomed. From learning what microtunnelling and horizontal directional drilling (HDD) is to writing the ASTT 30th Anniversary book and attending my first No-Dig Down Under conference and exhibition, this year has been nothing short of eventful.
Looking back at my first Editor’s Letter in the December edition of Trenchless Australasia, I noted that it was inspiring to see so many new and old companies continue to work through the challenging times of COVID-19, and build towards a successful future.
Today, I have come to work alongside many companies, learning about their capabilities and sharing the stories of their successes, evolving technologies and projects they have been instrumental in.
Since moving the magazine to six
editions a year, we have been able to draw on different themes throughout, inspiring the industry to share their experiences and expertise alike. In this edition of Trenchless Australasia, we have a 30-page feature on New Zealand. Here we celebrate New Zealand’s trenchless industry with profiles of major utility projects in Wellington and Auckland, as well as an update on the last 12 months of the industry.
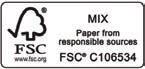
This edition also includes features on relining, HDD, vacuum and hydro excavating, software and technology, and microtunnelling.
With only one more edition of Trenchless Australasia left for 2022, it has been a pleasure to learn, grow and emerge myself in this forever evolving industry. I look forward to joining you again in December where we will reflect on the successes of Victoria’s trenchless industry and highlight how the sector is continuing to improve its safety.
Happy reading!
Molly Hancock Editor
molly.hancock@primecreative.com.au
Printed by: Manark Printing 28 Dingley Ave Dandenong VIC 3175 Ph: (03) 9794 8337
Empire Infrastructure is an Infrastructure solution provider with decades of experience supplying product solutions for complex infrastructure projects across Australia and New Zealand.
products, on time, in full. Empire is your one stop solution for Jacking Pipe and Shaft Solutions in Australasia.

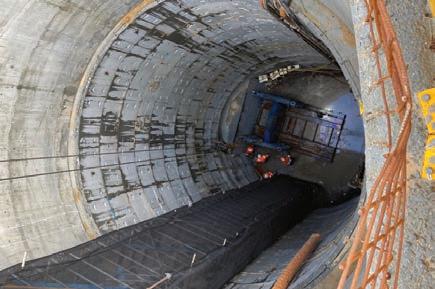
REINFORCED CONCRETE JACKING PIPE
Diameters from DN600 to DN3000
Available with HDPE, PVC or GRP internal linings
Suitable for very long drives, curved drives with a 100+ year design life
Lead times as low as 8 weeks from order date
Intermediate Jacking Station Sets are also available with options in mild or stainless steel.
CENTRIFUGALLYCAST GRP JACKING PIPE
Diameters from DN300 to DN2400. Pressure range from PN1 to PN32 and Stiffness range from SN20,000 up to SN1,000,000
WSAA Appraised and approved by asset owners across Australasia
High Abrasion resistance, suitable for long curved drives and highly ■ corrosive environments.
100+ year design life with lead times as low as 8 weeks from order date
FIBERSTRONG™ FILAMENT WOUND GRP JACKING PIPE
From the largest GRP pipe manufacturer in the world, this is Fiberstrong™ Jacking Pipe
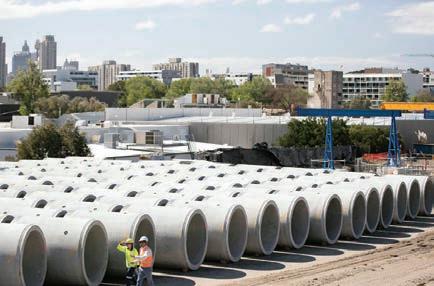
Diameters range from DN300 – DN3000
Suitable for use in corrosive environments, waste water, potable water, seawater and industrial applications

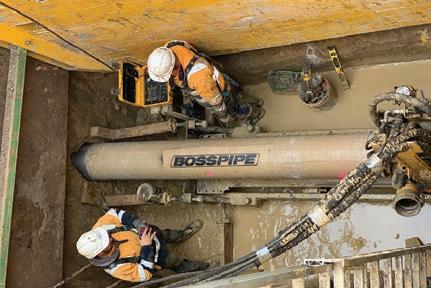
WSAA appraised, approved with water authorities and available within 8 weeks from order date
PRECAST CONCRETE UNIVERSAL SMOOTHBORE SEGMENTAL SHAFT SYSTEMS
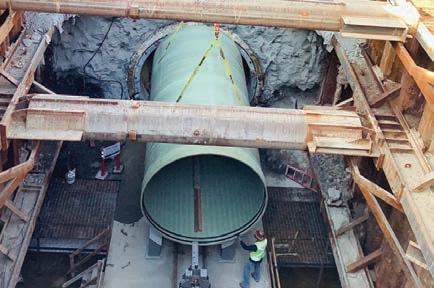
Diameter range from 2.44m to 27m diameter
Manufactured to the highest standards at their world class facility in the UK
Successful installations on numerous projects across Australia and NZ.
THE AUSTRALASIAN SOCIETY FOR TRENCHLESS TECHNOLOGY
ABN 43 893 870 966 18 Frinton Place Greenwood, WA 6024 www.astt.com.au jeffpace@astt.com.au
President: Ben Crosby
Secretary: Jeff Pace
Vice President: Blair Telfer
COUNCILLORS
Western Australia: Trevor Gosatti
Queensland: Ben Crosby
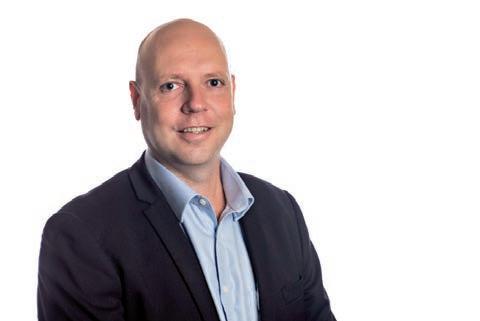
New South Wales: Matthew Boyle
Victoria: Justin Shepherd
South Australia: Shaun Melville
New Zealand: Blair Telfer
Northern Territory: Vacant
Tasmania: Vacant
INTERIM REPRESENTATIVES
Sudipta Basu
President’s Message
It is my pleasure to join you for the October edition of Trenchless Australasia. What a year it has been so far.
Over the course of the year the ASTT has been involved in a number of events aimed at further supporting the trenchless industry’s growth and evolution.
Earlier this year Queensland hosted a networking and presentation night which was an introduction to RestrainTMPVC-U sewer pipe.
RestrainTM - PVC-U sewer pipe is specifically designed for gravity sewer applications utilising trenchless techniques and the NEW PocketENGINEER Structural Design Tool.
Hosted by Iplex’s Andre Nunn, it was a great opportunity for the industry to learn more about RestrainTM and how it can be utilised in a number of trenchless projects.
Jerry Daly from Killard Infrastructure also gave attendees the latest updates from Insituform and Killard Infrastructure.
One of the biggest highlights from 2022 so far has to be the return of the 2022 No-Dig Down Under conference and exhibition.
I am pleased the ASTT persevered, and we didn’t give up and I’m sure you’ll agree No-Dig was a success and a great chance to reconnect with our industry and communicate our achievements and challenges.
As Australia’s only dedicated exhibition and conference for trenchless technology, No-Dig is incredibly important for our industry.
Thank you to our sponsors and exhibitors for continuing to believe in the vision of No-Dig Down Under, and supporting the event through a postponement. Given the standard of the conference program and the exhibition hall it was worth the wait.
The event saw an impressive 1861 delegates participating over the four days in the event.
With the last event in 2019, you could feel the buzz at the Sydney ICC, with attendees celebrating at the opening of the convention, the boat cruise and the gala
and awards dinner.
The ASTT Gala Dinner and Awards was a sell-out with 410 attendees celebrating the success of the industry. The gala dinner and awards ceremony was proudly sponsored by Bothar Boring and Tunnelling.
A chance to continue recognising the success of the industry and the challenges it has overcome in the last three years were the ASST Awards.
It was inspiring to hear the stories and emerging technologies of the industry, from the best rehabilitation project to the new installation project of the year, and new technology, there was lots learn and celebrate this year.
I hope you all give yourselves a pat on the back for a job well done over the course of the past few years. It has been tough, but I am grateful that we were able to finally host and attend a conference such as No-Dig.
A proposal has been made to Standard Australia to develop a design standard for lining of non-pressure circular pipes in order to bring more uniformity in liner design practices in Australasia. The proposed standard will capture the essence of the industry’s existing practices and will be aligned to the AS/NZS 2566.1 as well as the recently developed ASTT design specification reflecting existing Australasian practices.
The momentum doesn’t stop there with the Water New Zealand conference in Christchurch in October. The event features the largest water and wastewater exhibition in the country and a variety of industry-leading presentations through its technical program.
This year’s technical program will include a dedicated trenchless technology stream, supported by the ASTT.
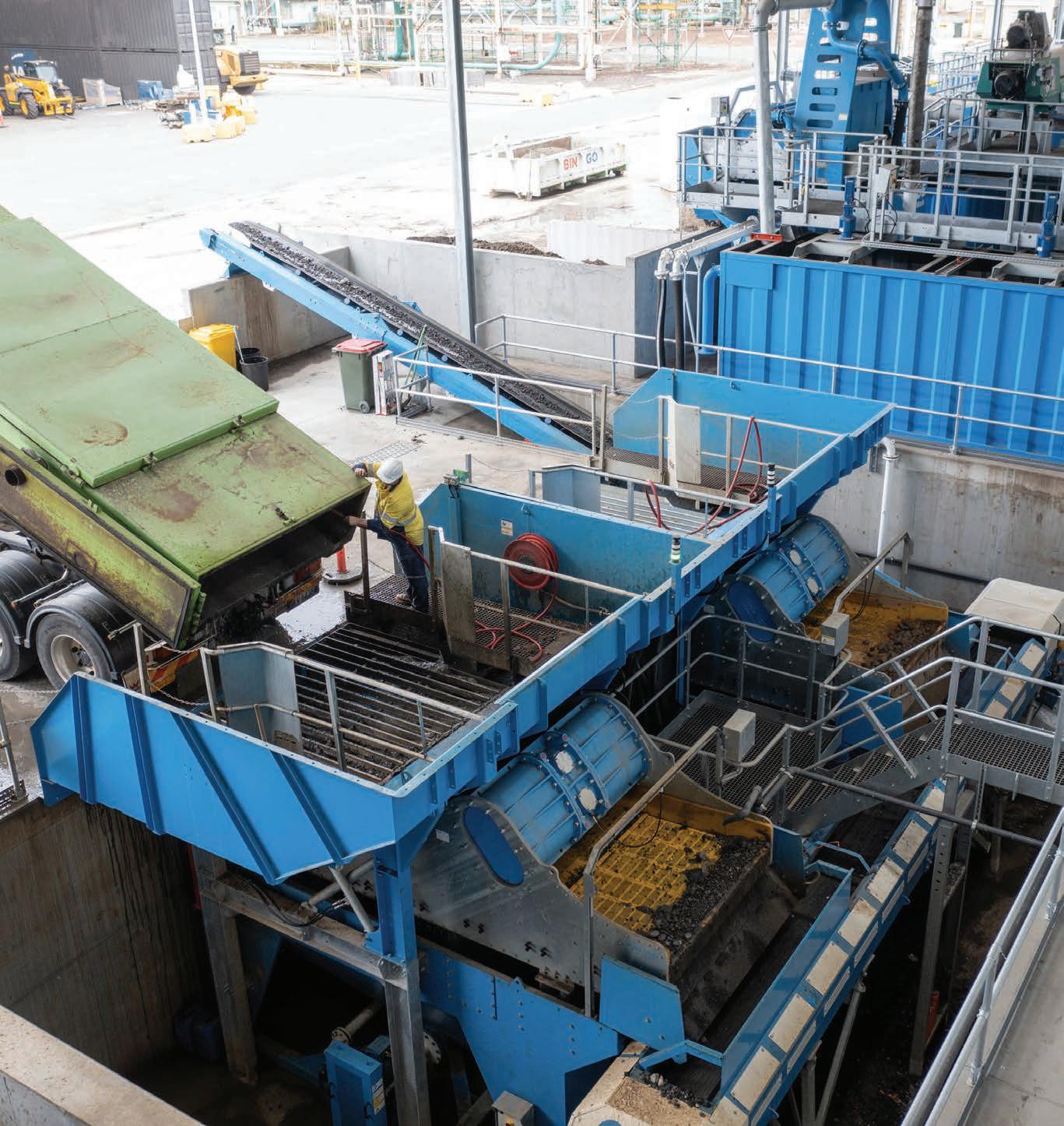
This also ties into the current theme for this edition – New Zealand. It is great to see so many trenchless pioneers creating technologies, pursuing projects, and further enhancing the trenchless industry there.
Ben Crosby ASTT PresidentENGINEERED FOR RECYCLING HYDROVAC WASTE
Our patented HYDRO:TIP™ technology dewaters slurry caused by hydro-excavation, easily and efficiently.
Our HYDRO:TIP™ solution not only facilitates cost-handling of waste mud but, when combined with our washing technology, enables operators to recover recyclable materials that can be re-sold as an additional revenue stream.
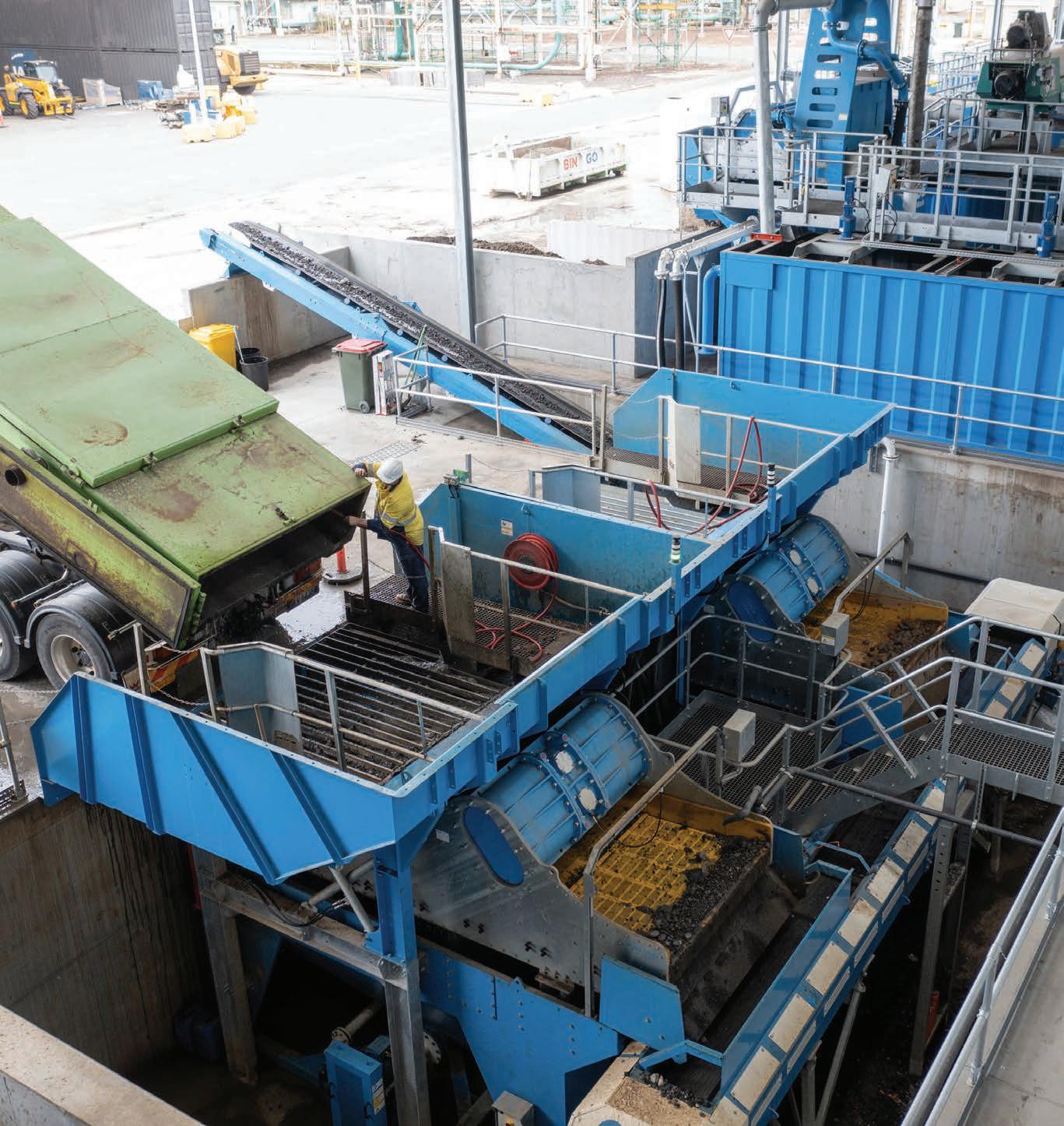
Find out more about our HYDRO:TIP™ by scanning the QR code.
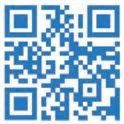
Secretary’s Corner September 2022
New Members
On behalf of the ASTT, I extend a warm welcome to the following new members.
Gold Corporate Members – Australia
Florian Jaehne from Orion Consulting.
Silver Corporate Members – Australia Peter Smith from BRP Corporation Pty Ltd.
Silver Corporate Members – New Zealand Nigel Lee from Marley.
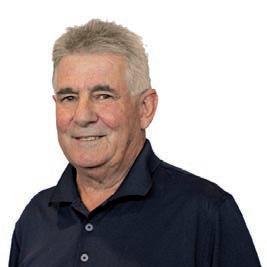
Asset Owners – Australia Zander Beard from Knox City Council.
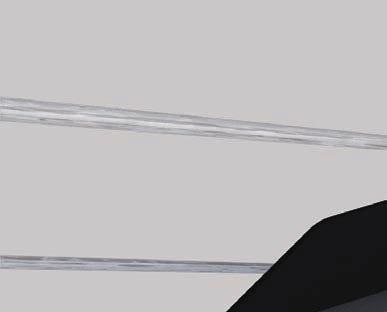

Asset Owners – New Zealand Deb Westlake from Auckland Council changed from Silver Corporate to Asset Owner.
Individual Members – Australia
Jason Marshall from Voeu Pty Ltd. John Lee from FJA Consulting Engineers. Shafin Rashid from Infraworks Projects Pty Ltd. Kenny Bowie from WSP.
2023 National Conference and Exhibition – Brisbane
The ASTT recently held its COVID-19 delayed 2021 National Conference and Exhibition at the new Sydney Convention and Exhibition Centre over June 14 to 17, 2022. From all accounts, this delayed event was extremely well attended and nothing, but positive feedback has been received from the surveys.
Well, now it’s back to the normal biannual programming of our events and to that end I am pleased to advise that the ASTT is now planning its 2023 National Conference and Exhibition that will be held in Brisbane at the Brisbane Convention and Exhibition Centre from Tuesday, 12 September to Friday, 15 September, 2023.
Exhibition sales are now available so if you are interested in exhibiting, then please contact Nick Lovering at nick.lovering@primecreative.com.au. More information is also available on the event website, refer: https://nodigdownunder.com/
Benefits of Gold Corporate Membership
I am often asked the question that all trenchless societies worldwide face, what are the benefits of becoming a member? To assist with this issue, the ASTT has created several new membership categories in order to provide more choice and therefore make it more attractive to new members to join.
Gold Corporate fees are:
$945.00 + GST for 12 months or $1512.00 + GST for 24 months. The 24 months option generates a saving of $378.00 + GST to your organisation.
Listed under is a summary of the top category, namely Gold Corporate Membership benefits:
• You can have a maximum of any 10 people from your organisation enjoy these benefits.
• The option for membership fee rate reduction where fees can be paid every 24 months instead of an-nually.
• Trenchless Australasia magazine – six issues per year.
• Acknowledgement in the ASTT’s Trenchless Australasia magazine.
• Trenchless Directory – one issue per year.
• ASTT’s annual Trenchless Directory acknowledgement.
• Logo recognition on Members of the ASTT web page.
• ISTT’s Trenchless Works magazine – six issues per year.
• Access to the last two ASTT Conference proceedings.
• Access a vast collection of past ISTT Conference proceedings.
• Opportunity to become involved in our Special Interest Groups (SIG’s) which are technical divi-sions of the ASTT representing specific trenchless sectors.
• Ability to maintain your company information through the ASTT database.
• Discount rates at ISTT International NO-DIG’s.
• Discount rates at the ASTT National Conference and Exhibition.
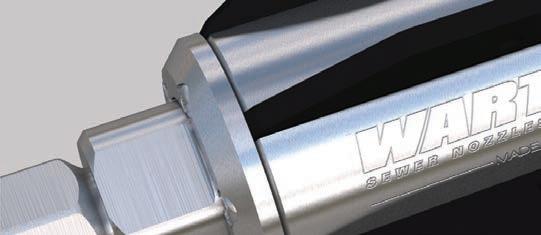
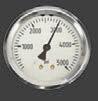
• Discounted rates at our Technical Forums.
• Discounted rates at our NASTT/ASTT Training presentations.
• A communication network to keep abreast of the advancement of the science and practices of trench-less technology throughout the world.
Companies interested in joining the ASTT are requested to complete the online form which can be found at the following: https://www.astt. com.au/how-to-become-a-member/.
When you have completed filling in the form simply click submit and your membership request will be e-mailed direct to me for processing. Acceptance to the ASTT is dependent upon receipt of payment.
Payments can be arranged through either PayPal, posting a cheque or by direct debit into the nominated ASTT account. Once processed, the ISTT is immediately notified, and you are sent your ISTT login and password that enables access to the thousands of past conference proceedings.
Should you wish to discuss memberships at any time, then simply e-mail jeffpace@astt.com.au with your questions and I will only be too pleased to respond.
Members Directory
A reminder to all members to review the information listed about you and your company on the ASTT website. To view, go to the Members Directory area of the ASTT website, refer: https://astt.wildapricot.org/directory
If any changes are required, you can either do the changes yourself or you can send the changes to me and I will amend for you.
Jeff Pace ASTT Secretarysecretary@astt.com.au
Packers: Drainchem now offer high quality pipe packers with or without bypass that are flexible for ease of installation. These high quality packers are available to suit pipe sizes 25mm up to 2000mm in diameter.




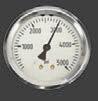
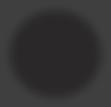
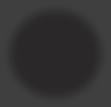
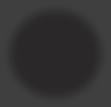
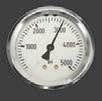


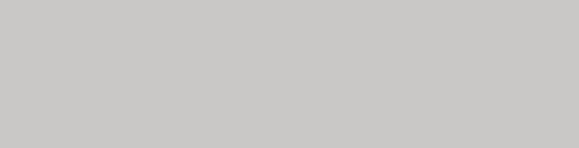


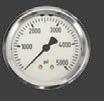



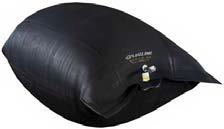
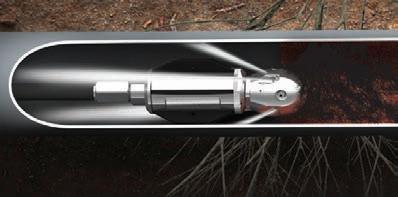


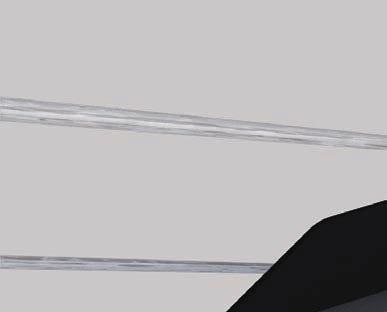
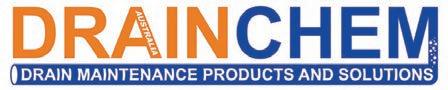


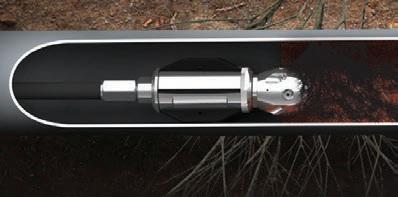
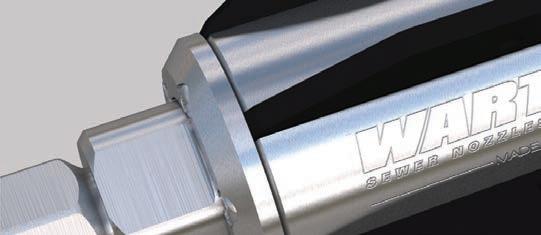

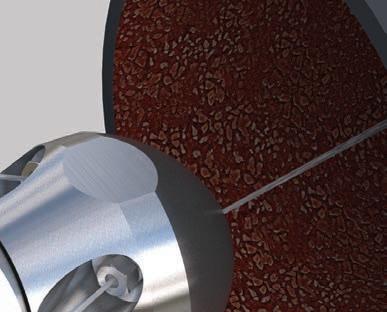

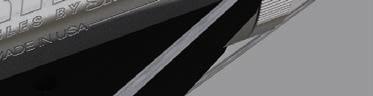
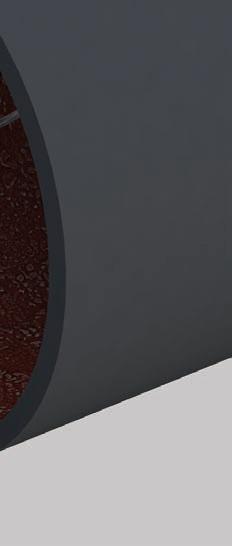
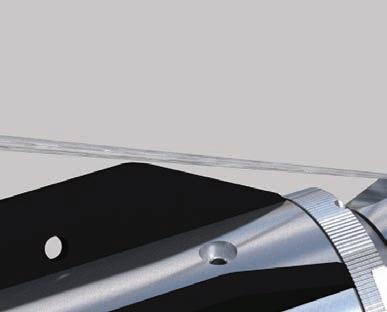
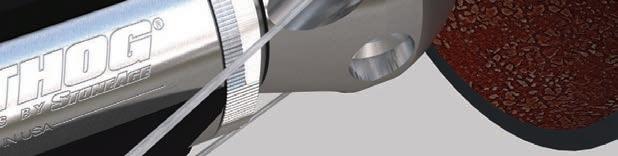
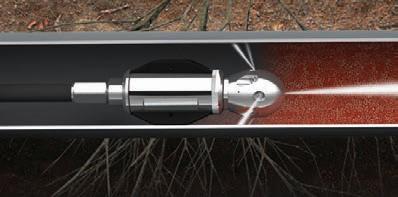
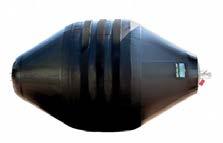
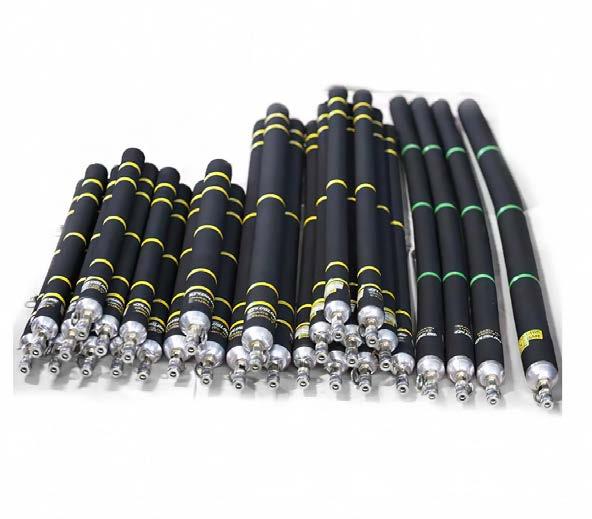
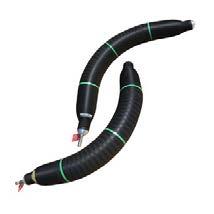
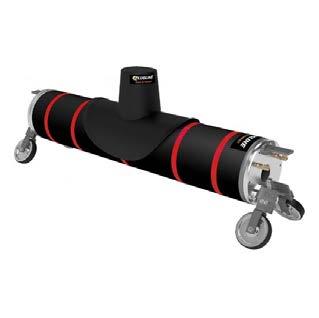
TopHat Packers: Drainchem have also introduced packers that allow the installation of top hats to laterals from mains and are available in 100x100mm, 150x100mm and 150x150mm.
Cone plugs: Also new to the Drainchem range are inflatable Cone plugs to suit multiple pipe diameters chloroprene and Aramid fabric reinforced with vulcanized rubber. The Cone plugs fold down much smaller than a traditional rubber plug and this enables ease of access into pipes and manholes. Pillow plugs: Another exciting product is the Inflatable pillow plugs. Ideal for larger pipes. These are flat like a matt and can be rolled up to help installation into the pipe. Available in sizes 600-100mm up to 1800-2800mm
50 m long mural dazzles Mannum to Adelaide pipeline
Dora the Bora completes first tunnel
The mini-tunnel boring machine, Dora the Bora, has completed its first tunnel as part of Victoria’s Level Crossing Removal Project.
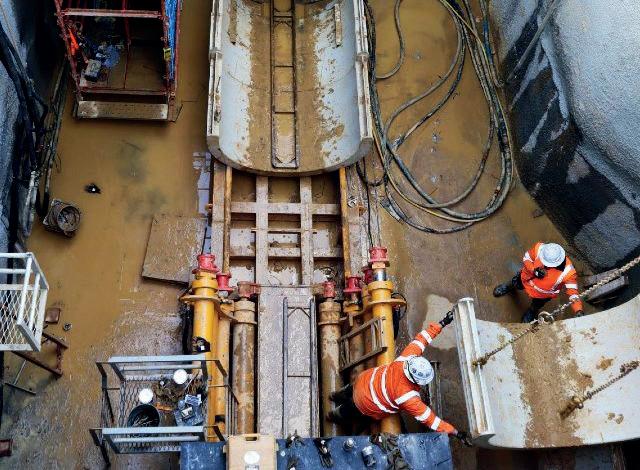
The first tunnel was drilled 10 m beneath the existing rail line and will be used to house a new route for a large watermain.
It is the first of three, with the second and third tunnels to be drilled to make way for massive stormwater pipes.
The drilling is part of a construction blitz that will see lane and road closures on Mont Albert Road and Union Road. The rail line itself will also be closed for a two-week period.
The River Murray area already has a diverse and popular range of silo artworks in Karoonda and Coonalpyn, and this piece provides yet another addition to this art trail.
One of South Australia’s largest water pipelines near Mannum has been given an incredible mural makeover as part of a community art project celebrating the region as Australia’s first dark sky reserve.
In collaboration with the Murray River, Lakes and Coorong Tourism Alliance, the Mid-Murray Council and Palmer’s Collier Park Community Association, South Australian artist Jack Fran has painted a mural on a 50 m section of the Mannum to Adelaide pipeline.
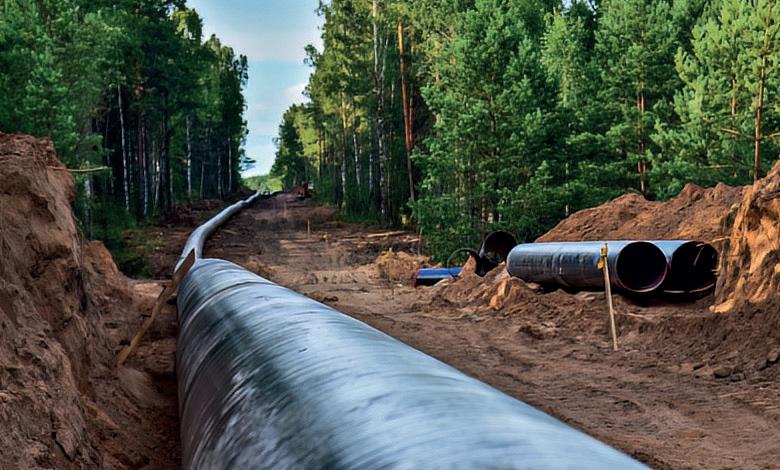
The 87 km long pipeline delivers raw River Murray water to SA Water’s drinking water treatment plant in Anstey Hill, before being distributed to thousands of customers across metropolitan Adelaide.
SA Water’s general manager of strategy, engagement and innovation Sandra Ricci said SA Water will continue to investigate ways to visually improve infrastructure for the benefit of the community.
The construction project includes the removal of boom gates at level crossings in the area – two years earlier than planned. To do so, the rail line is being lowered into a trench, over 1 km long, that will run beneath the two major roads, plans are also underway to build a new Union
TRACTO secures NZ service partnership
TRACTO has partnered with New Zealand-based Pro Mechanical, making it the company’s mechanical service partner in the country. For nearly a decade, Pro Mechanical has been servicing clients all over Waikato and Auckland on the country’s North Island. As a result of the agreement, TRACTO and Pro Mechanical will now be able to maximise operational availability and minimise unplanned downtime for horizontal directional drilling (HDD) clients.
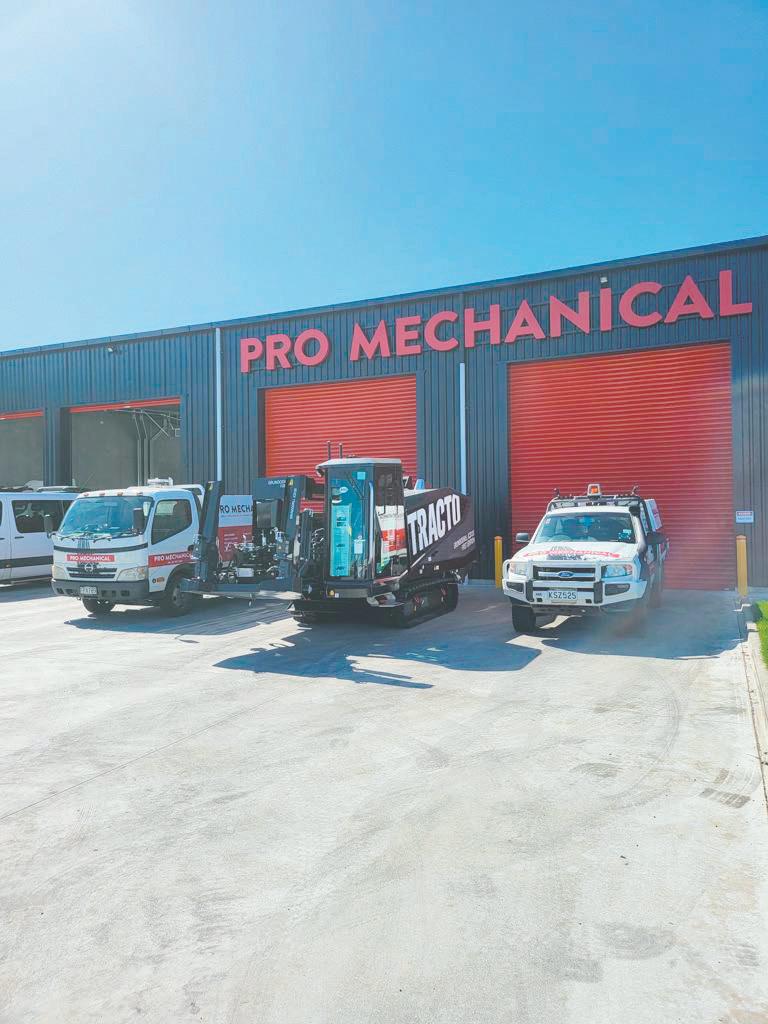
As a member of TRACTO’s global service support network, Pro Mechanical will provide on-demand and emergency maintenance and repair services, ensuring customers can be confident in their equipment. TRACTO Managing Director Jeff Rose said the partnership was an important piece of the puzzle for supporting the company’s growing client list over the ditch.
“We recognise the importance of being easy to contact and fast to
respond to our expanding HDD customer base in New Zealand,” he said. “TRACTO is proud to provide exceptional customer service and support, regardless of where you’re located in our region.”
TRACTO has partnered with New Zealand-based Pro Mechanical.
Rob Carr passes midpoint on Quinns Main Sewer
Central Coast Council sets precedent with ROV
The diversion tunnel, which is over 30 years old, is 415 m long with a diameter of 2.3 m. The last person-entry occurred during commissioning in 1989. While the Central Coast Council’s current team are well experienced in isolation maintenance, given the timeframe since last entry of this diversion tunnel, they were presented with some challenges to deal with.
Planning for the inspection was carefully done over a number of months to ensure the safety and success of the team, as well as ensuring that the four-week isolation would not adversely affect water treatment and systems operation.
Complications arose when, between the early stages of the project and the beginning of tunnel isolation activities, the dam level rose from 53 per cent to a record 91 per cent due to unprecedented weather. The team was forced to adapt.
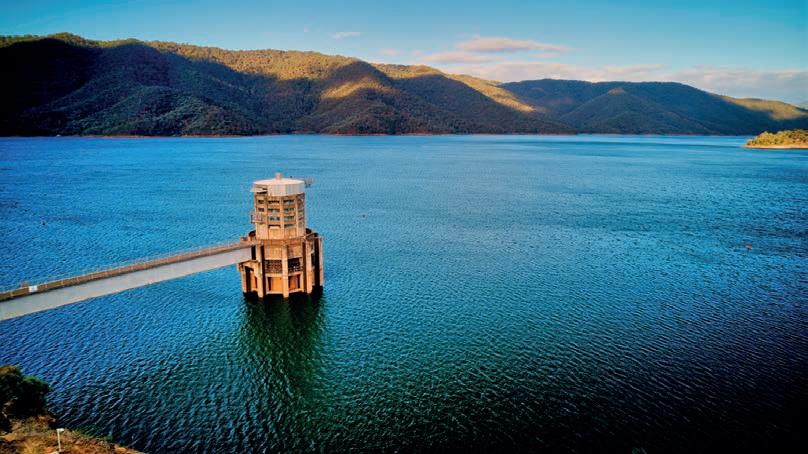

Rob Carr continues to kick goals on the construction of the Quinns Main Sewer project for Water Corporation with approximately half of the project now complete. The project commenced construction activity in February 2022, and has swiftly seen the completion of two of the four major micro tunnelled drives.
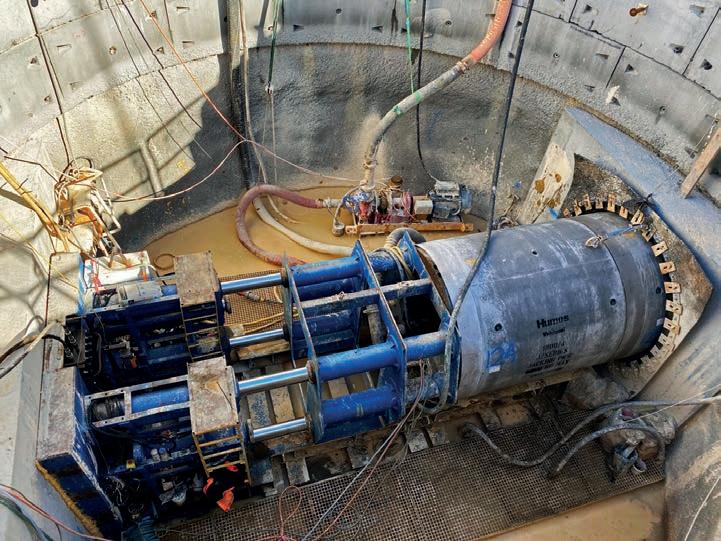
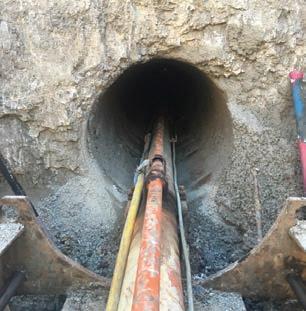
Work has since commenced on our 3rd drive, some 630 m long with our tunnel boring machine, Bakton, launched from this same 24 m deep shaft. Following completion of the tunnelling, construction will commence on the 27 m deep vortex manhole.
The entire project is due to for completion in early 2023.
• Specialists in free boring, sleeve boring and pipe jacking • Sizes ranging from 350mm > 600mm in most ground conditions
• Drill up to 120 meters with a +/- 10mm tolerance • 20 years experience in the drainage industry
At L&D Micro Tunnelling we specialize in laser guided boring. Our Tunnel bore machines use a vacuum extraction system where all spoil is sucked into interceptor tanks for easy disposal with no mess. All our heads are hydraulically driven and guided by a high accuracy laser to achieve precision over long distances. 47a Brunel Road, Seaford, VIC 3198 | luke@ldmt.com.au
Unrivalled reliability – Accuracy Guaranteed
Trenchless industry in NZ

Internationally, New Zealand punches well above its weight, whether it be in academia, entertainment or sports. The same is true in trenchless technology.
New Zealand has always been a strong supporter of trenchless technology and with our culture to strive, we have set a number of world achievements, most recently and notably in direct pipe installations.
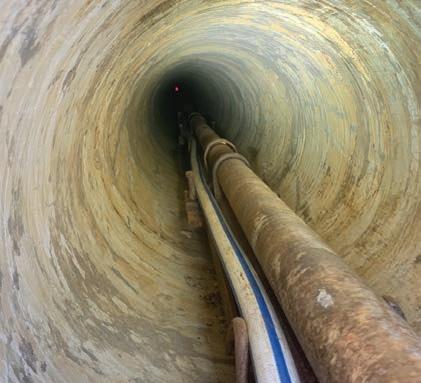
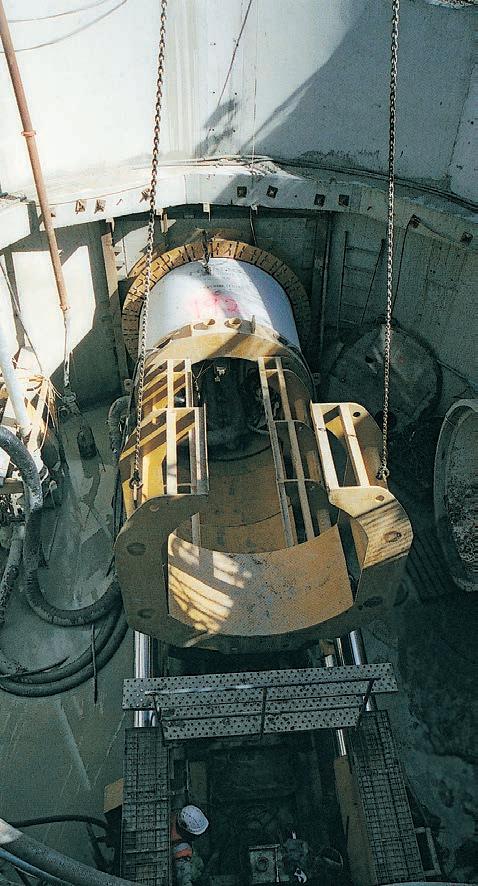
Trenchless technology in NZ covers the full range of techniques and technologies from new installation horizontal directional drilling (HDD), micro tunnelling and its direct pipe hybrid to renewal techniques of pipe bursting and lining. We also have pipe ramming and auger boring capabilities in the country, albeit not as well promoted.
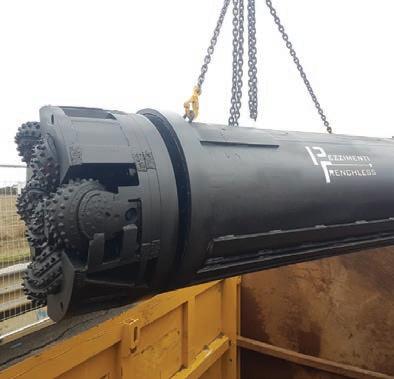
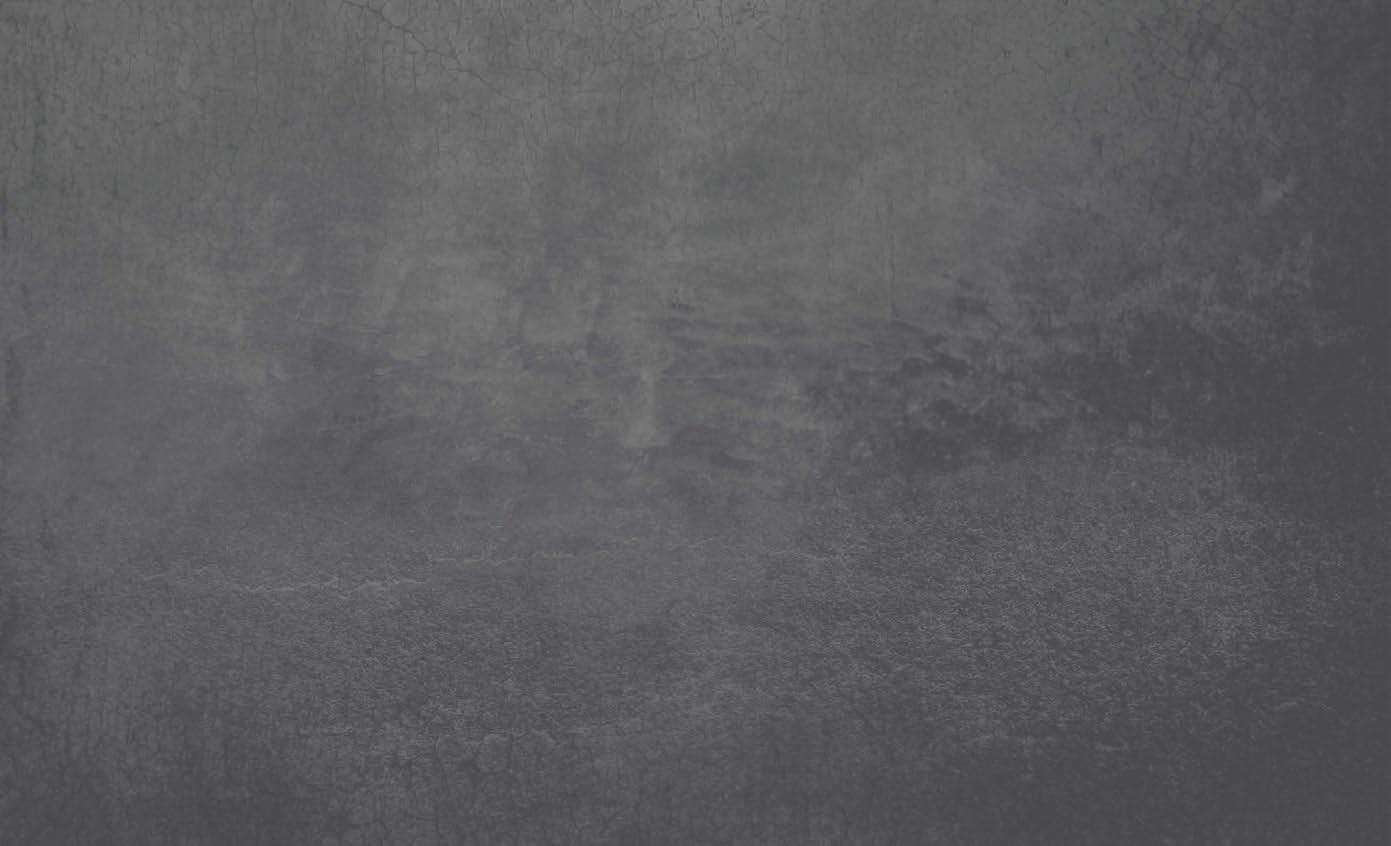
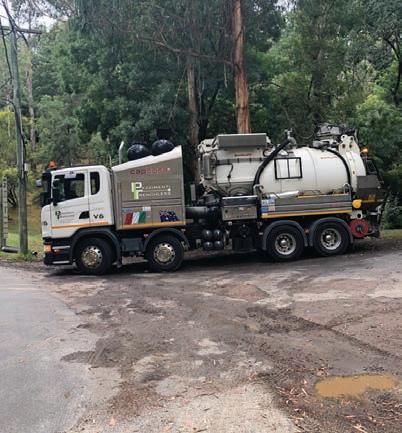
Large diameter TBM tunnelling projects for both transport and water have now also been undertaken.
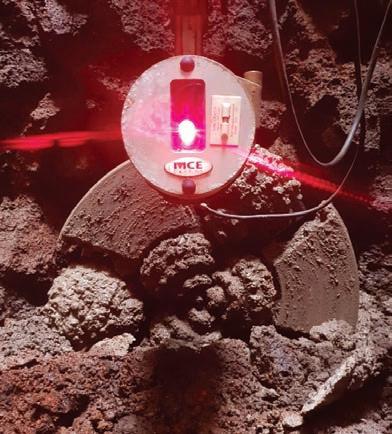
Trenchless technology is strong and growing in NZ. We enjoy, recognise, and appreciate the support we receive from the likes of such national institutions as WaterNZ as well as tertiary training institutions and the supply chain as a whole.
That being said, and as much as, in some areas, trenchless technology is now mainstream, in other
as a ‘first considered’. A lack of understanding knowledge, misinformation, inappropriate risk allocation and historical bias are reasons for this. This remains one of mine, and the industry as a whole, challenges.
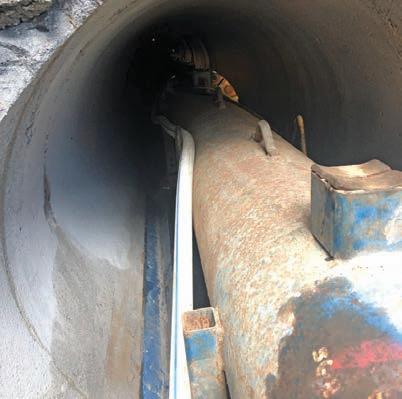
The NZ government requirements to meet carbon emissions and general climate change requirements should make the consideration of trenchless technology and techniques a bigger driver. Whilst again disappointing, that this focus requires central govt. legislation, this is neither unusual nor specific to trenchless technology – this seems to be NZ’s way. Health and safety management was and still is, a similar central government legislative enabler to create change. Higher levels of expectations from the public and minimizing disruption are other drivers toward more trenchless uptake by asset owners.
So, what, as both an industry and individually, as well as myself as NZ ASTT Councillor, do we need to do to increase the uptake and successful use of trenchless technology? As this article goes to press, the ASTT has undertaken a survey of
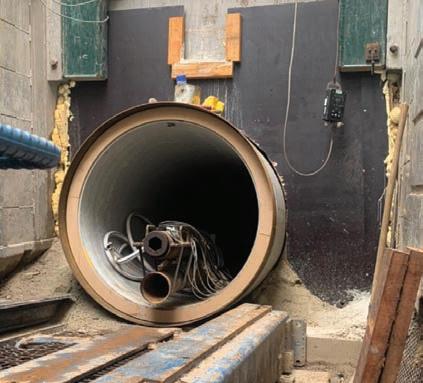
am keen to understand where our NZ industry see we can add value and where more efforts and support is required.
In the past two years, COVID-19 has been an international disruptor and as much as it has caused significant challenges it has also shown us and stimulated other benefits. One of those has been how we interact with our marketplace. Historically in NZ we have held face-to-face forums and bi-annual WaterNZ convention streams. COVID-19 has promoted the value of webinars and other such remote learning opportunities. I am keen to support and pursue any and all opportunities and initiatives to promote the trenchless value and message.
I am very proud and honoured to have been the NZ Councillor for the past five plus years, since 2017, to continue to promote the value and successes of our industry. I look forward to catching up with as many of you as I can during NZ Water conference in Christchurch in October.
Kia ora me te pai, keep safe and well.
Blair Telfer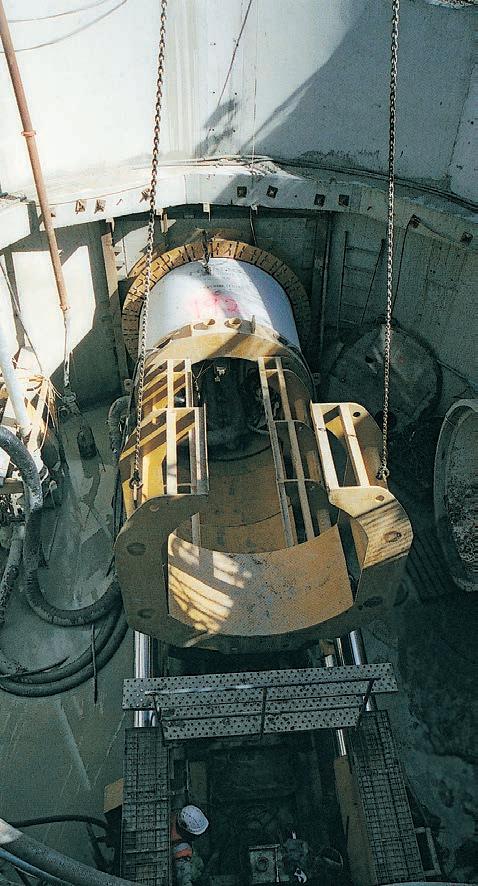
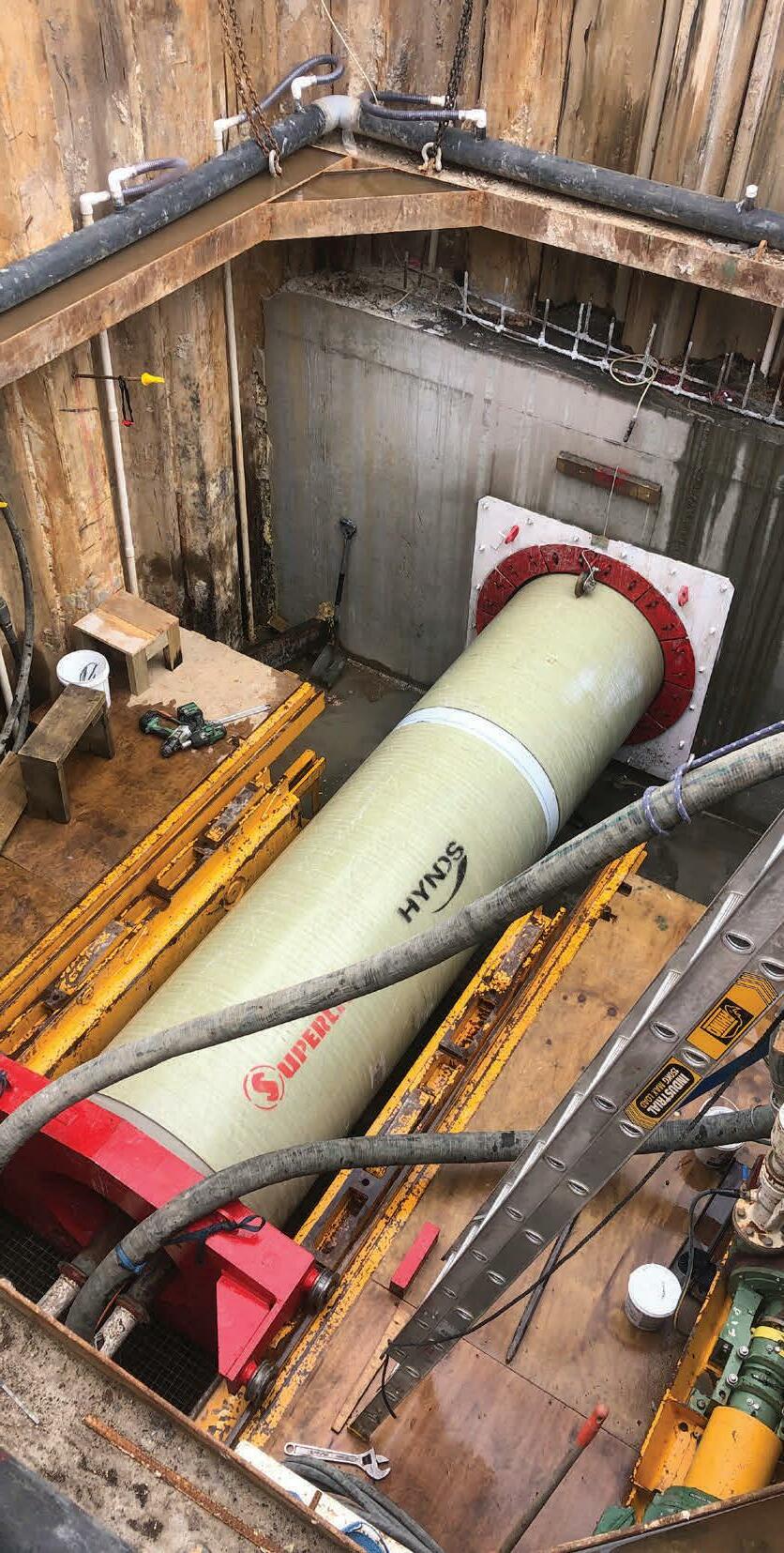
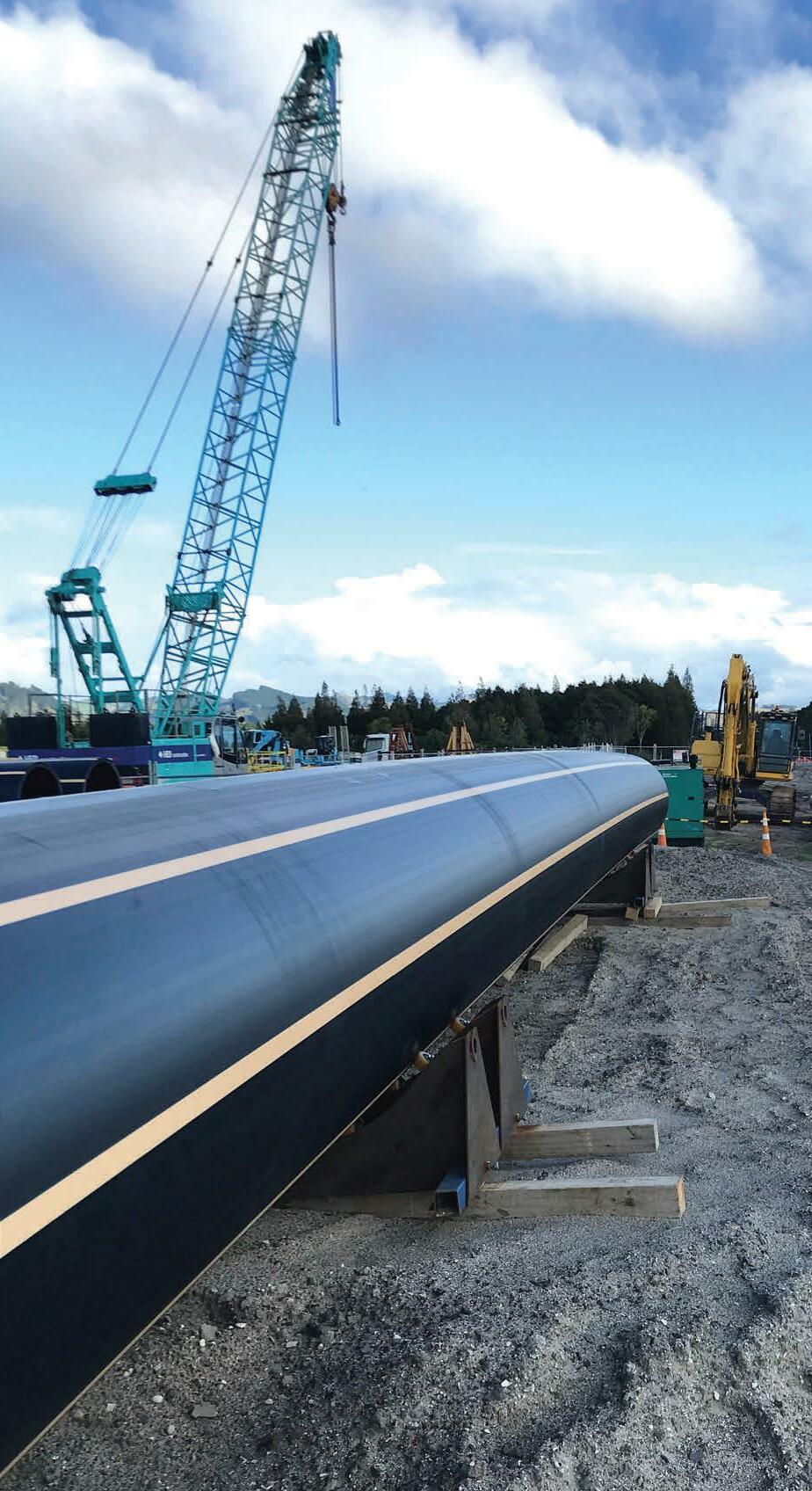
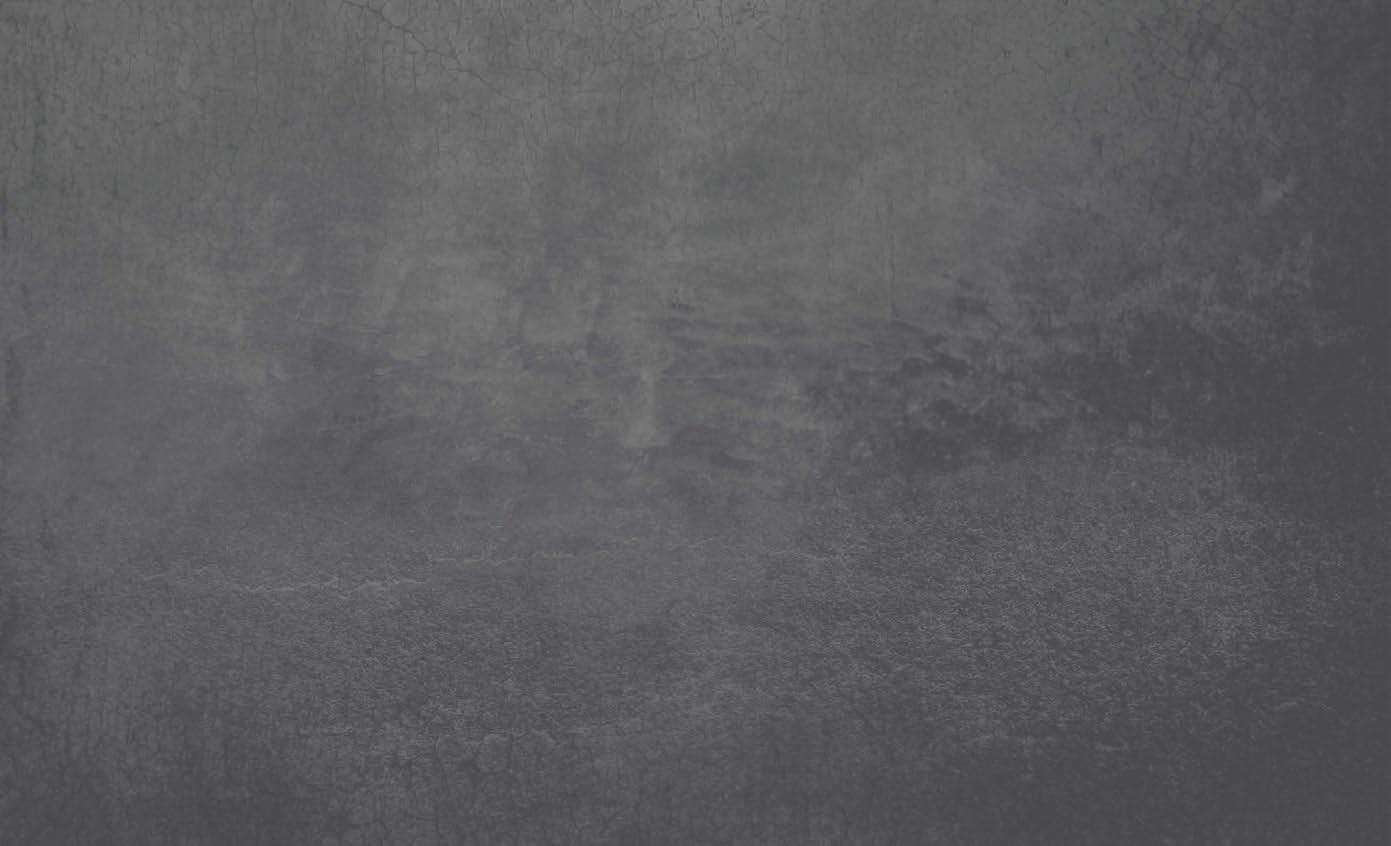
New Zealand exemplifying longdistance microtunnelling projects
New Zealand is responding to projected population growth and upgrading ageing wastewater pipes in the country’s major trenchless works for the last year.
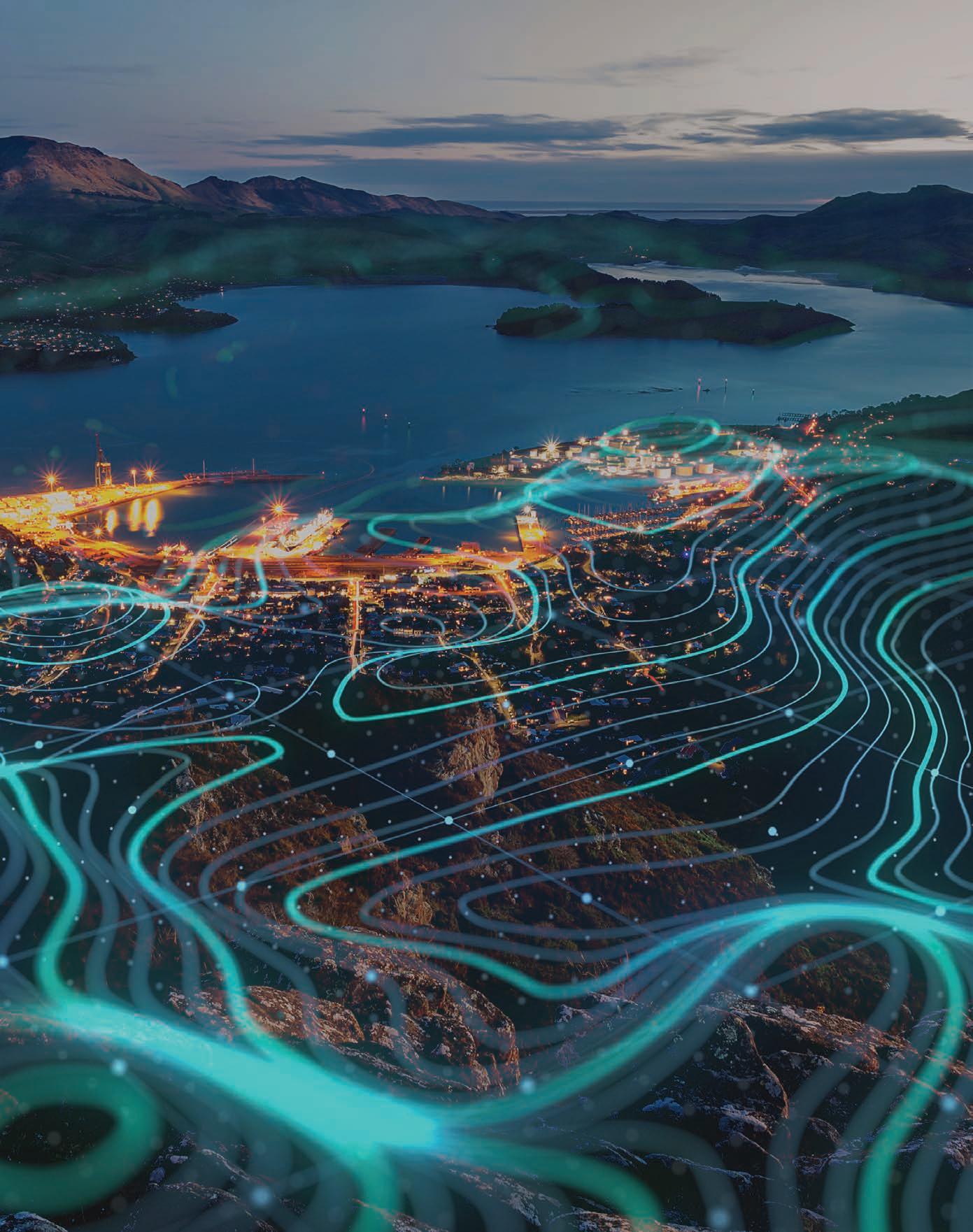
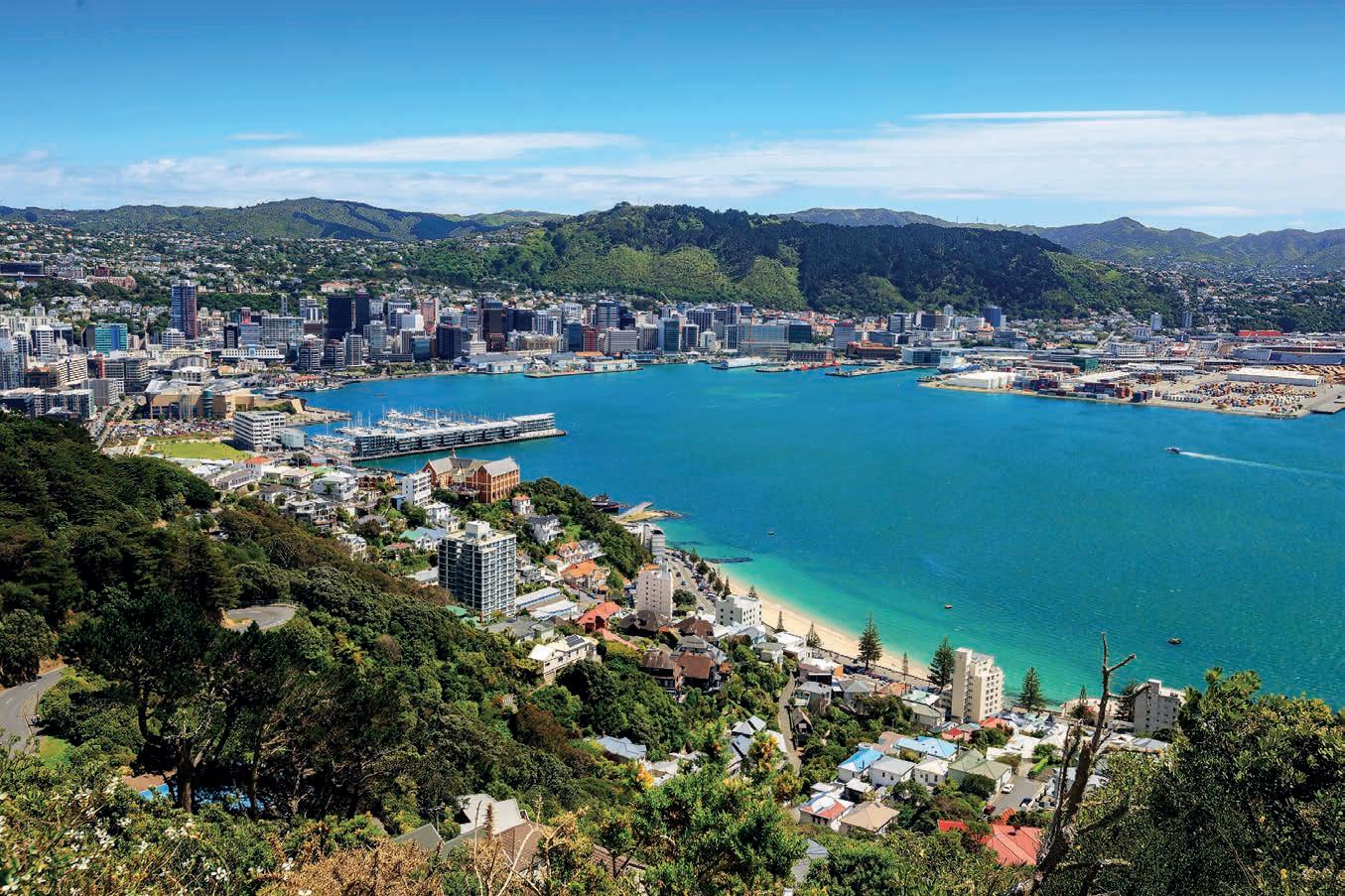
Central interceptor project marches on
In November 2021 Watercare okayed a design change that removed the need for one of the projected construction shafts on the Central Interceptor project, significantly decreasing the project’s impact on the local community.
The adapted plan involved a longer, slightly curved tunnel. Executive program director Shayne Cunis said that, at 1193 m, the new tunnel would be the longest micro tunnel boring machine (mTBM) drive in New Zealand.
The Central Interceptor project aims to drastically reduce wet-weather overflows, and keep up with the rapidly growing population of Auckland.
The primary tunnel boring maching (TBM), Hiwa-i-te-Rangi has been responsible for digging a 14.7 km long tunnel from the Māngere Wastewater Treatment Plant to Grey Lynn. It was delayed by the COVID Omicron variant for nine days – 26 February until 6 March – after which only limited tunnelling was allowed due to restrictions.
The mTBM Domenica reached a massive milestone in December last year when it broke through at the Haycock Avenue shaft in Mt Roskill, despite COVID lockdowns causing delays that risked Domenica becoming stuck if it remained stationary for too long.
The mTBM completed its second, shorter drive at the end of June 2022, connecting a 2.1 m sewer pipe to the main Central Interceptor
wastewater tunnel.
The Central Interceptor project is expected to be completed in 2026 and will store and transport stormwater and wastewater to the Māngere Wasterwater Treatment Plant.
Takapuna benefits $5.4 million wastewater pipe upgrade
In May 2022 work started with on relining the wastewater pipe that runs the full length of Takapuna Beach.
The pipe is over 60 years old and was identified as being in desperate need of an upgrade in order to reduce overflows and improve the quality of water at the beach.
Trenchless technology was used to line the pipes with PVC, making the project faster and reducing the impact on the community. The work included the assessment of 36 manholes and the necessary repair work.
Barber Grove to Seaview Wastewater Treatment Plant Pipe Duplication
The end of 2021 saw the microtunnelling contract awarded for the Barber Grove to Seaview Wastewater Treatment Plant Pipe Duplication project in the Lower Hutt region in Wellington.
Wellington Water, on behalf of the Hutt and Upper Hutt City Councils, worked on duplicating the existing water main by installing a new 1.2 km long, 1 m diameter rising main from the Barber Grove Pump Station to the Seaview plant.
At more than 50 years old the existing
pipe represented a higher risk of wastewater entering the Te Awa Kairangi and Waiwhetu stream in the case of an earthquake and conveyed 90 per cent of the wastewater from the Hutt Valley’s residents.
Wellington Water worked with partner Stantec and awarded the tunnelling contract to McConnell Dowell. 55 per cent of the project involved trenchless technologies.
On 5 August Wellington Water announced that the project’s mTBM, named Te Rū Tiokaoka, was in the ground for the journey along Randwick Road to the Seaview Roundabout. The project aims to be completed in early 2023.
Warkworth-Snells wastewater pipeline
In July of this year, Watercare announced that it had received the green light for the construction of a new wastewater pipeline from the Lucy Moore Memorial Park Pump Station in Warkworth to the new Snells-Algies Wastewater Treatment Plant.
The 5 km pipe is a critical element that makes up part of a more than $300 million investment program for the north-east region.
The pump station was in the process of being built, and the new treatment plant at Snells Beach under construction. As well as supporting the growing population in the area, connecting the pump station with the treatment plant will help to clean up the Mahurangi River, which currently receives discharge from the existing Warkworth Treatment Plant.
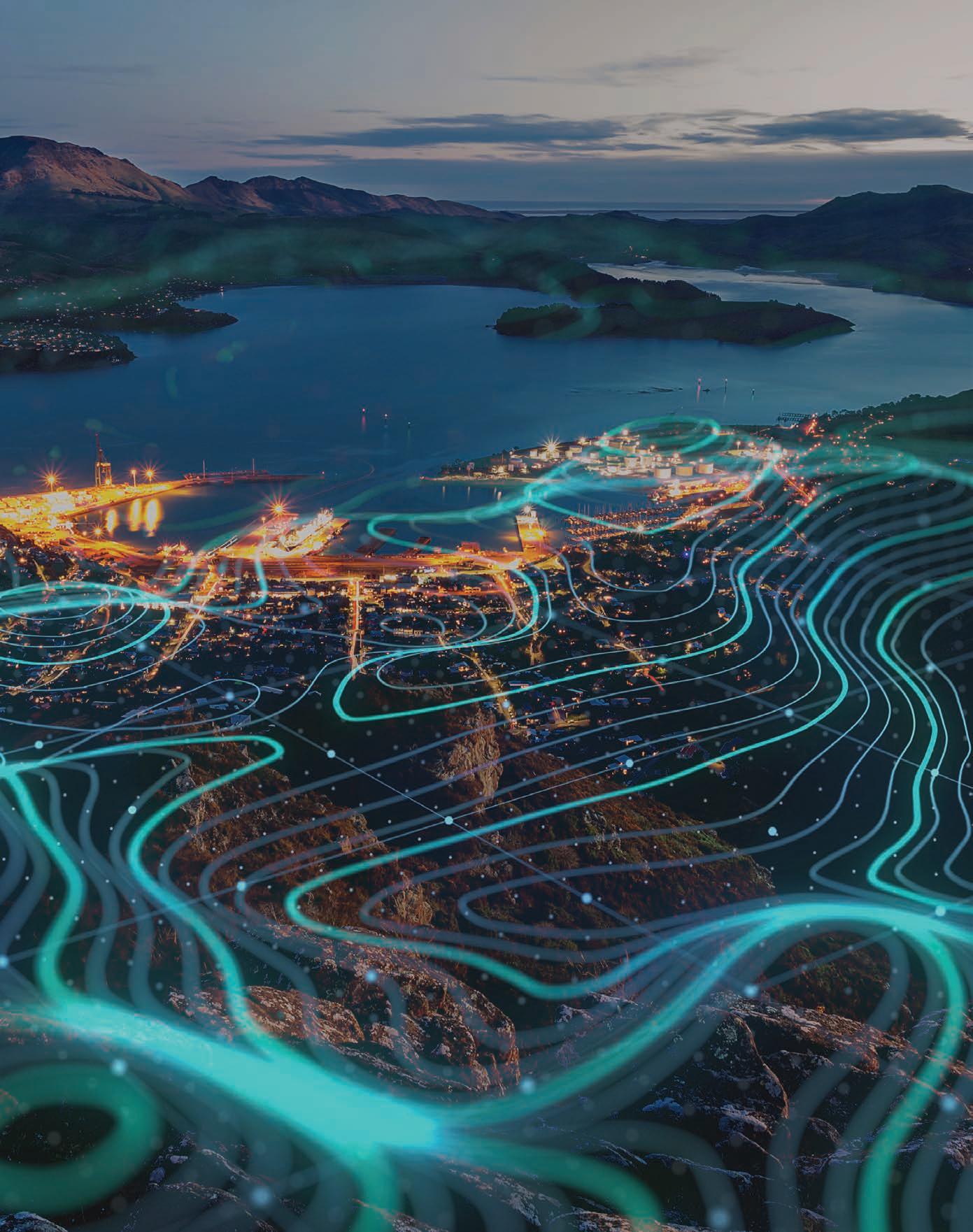
City Rail Link is bringing Auckland’s public transport to the future
What is the City Rail Link?
The City Rail Link (CRL) project is a huge project with an equally huge impact on the growth of the city of Auckland and its future prosperity. The CRL is a 3.45 km twin-tunnel underground rail link up to 42 m below the Auckland city centre. The goal of the project is to transform the downtown Waitematā Station (Britomart) into a two-way through-station that better connects the city’s rail network.
The tunnels will connect Britomart with a re-developed Mt Eden station on the western line. Additionally, two new underground stations, Karanga a Hape and Aotea, will open central city access.
The project allows the rail network to have at least double rail capacity.
An ambitious $4.4 billion project, the CRL will double the number of people within 30 minutes of central Auckland which is the country’s largest employment hub. When fully operational 54,000 passengers an hour will use CRL stations at peak hours. This is the rail equivalent of an additional 16 lanes of road or three Auckland Harbour Bridges.
A brief history of the CRL Moves to create an underground rail system in Auckland go back almost a hundred years –beginning in the 1920’s.
In 1923 the then Railways Minister, Gordon Coates, granted his support for a city-toMorningside underground rail line. ‘The
Morningside Deviation’, as it was then known, was to be an underground tunnel from the CBD to Morningside.
Envisaged was a rail link between the main trunk line station on Beach Road, underneath the central business district with a station near the Auckland Town Hall.
The cost of the project was estimated to be around £400,000. An equivalent today of approximately $45,934,199 New Zealand dollars.
Several years later, in 1930 the proposal was rejected, and the main terminal relocated to Beach Road. Nevertheless, references to a Morningside deviation continued to arise – in 1937 there was further discussion regarding the plan to reduce unemployment.
In the 1940s, the Ministry of Works released an expansive rail plan for Auckland, refining the Morningside proposal. The report discussed electrification, proposed an underground inner-city loop and an overground suburban western loop.
In the end, Wellington’s rail was electrified not Auckland’s.
In 1955-1956, Auckland City Council moved to embrace the advancement of motorways and ordered a Master Transportation Plan to decide the rail versus motorway issue.
The plan considered the Auckland Morningside deviation, which was to take a similar yet not wholly identical, route to the 1928/29 plan. An investigation of buildings along the proposed route was undertaken, looking at their condition,
type of foundation and value.
The plan recommended a massive increase in motorway construction at the expense of rail. It was argued, at the time, that buses could use motorways making rail unnecessary.
Near the beginning of the new millennium, the Auckland Regional Authority once more revived the push for the electrification and expansion of a passenger rail network. The push was spearheaded and championed by the authority’s chair and long-time public transport advocate, Mike Lee.
In 1993, 19 second-hand railcars were delivered from Perth as an interim measure.
Several years later, in 2009, KiwiRail and Auckland’s Regional Transport Agency (ARTA) announced it would begin a detailed study into the possibility of an underground route that would link the Britomart rail terminal with the Mount Eden railway station.
The cost of a twin-track tunnel was estimated to be more than $1 billion.
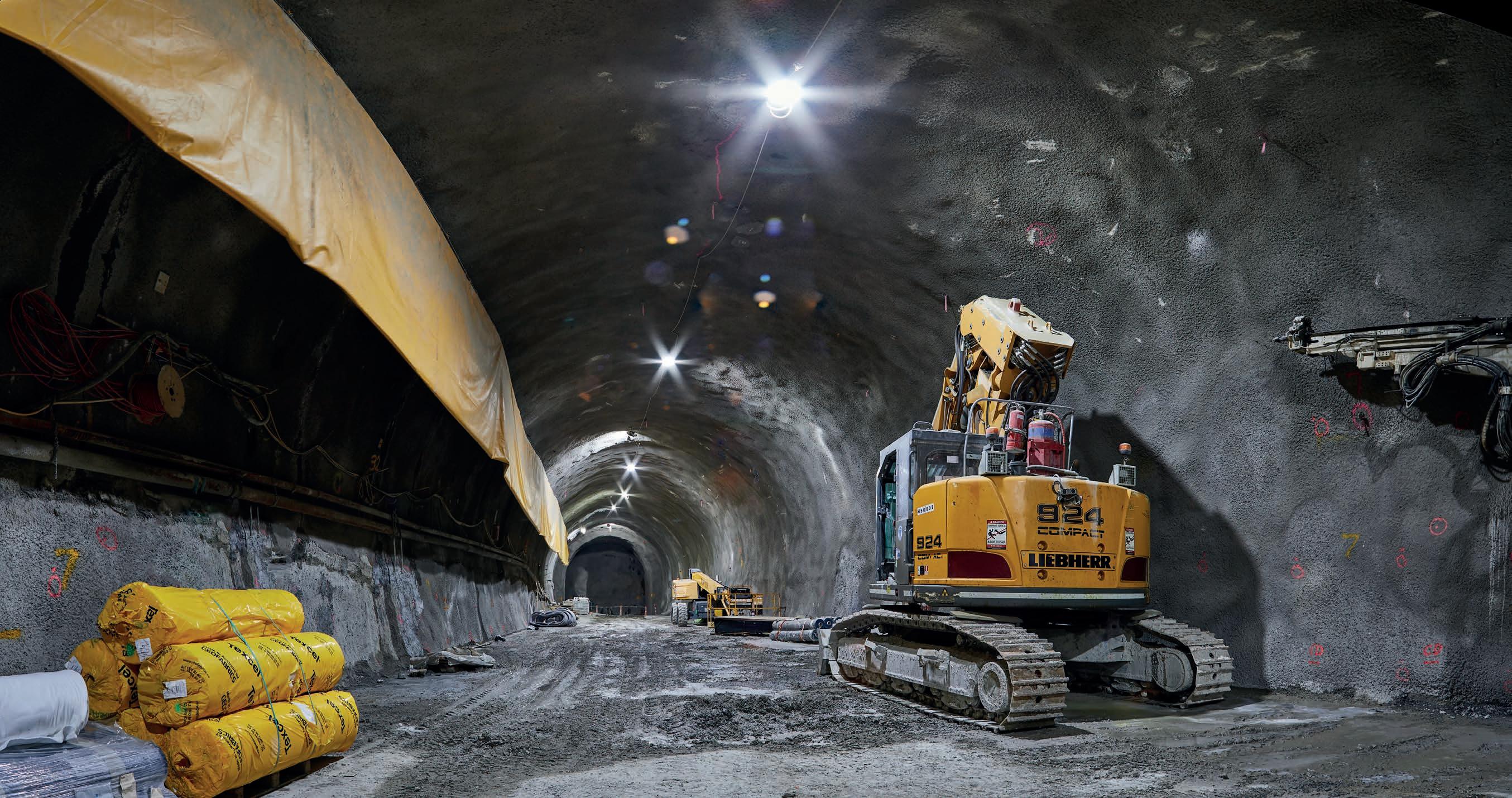
Electrification was announced as a major plan by the Labour government in May 2007 and confirmed two years later by a National government in 2009.
Following the 10-year anniversary of the opening of the Britomart Transportation Centre, Auckland Council announced that it was in discussions to build a section of tunnel under the Downtown Shopping Centre during a redevelopment planned for 2016-2017.
On 1 August 2014, Auckland Transport announced a significant design change to the
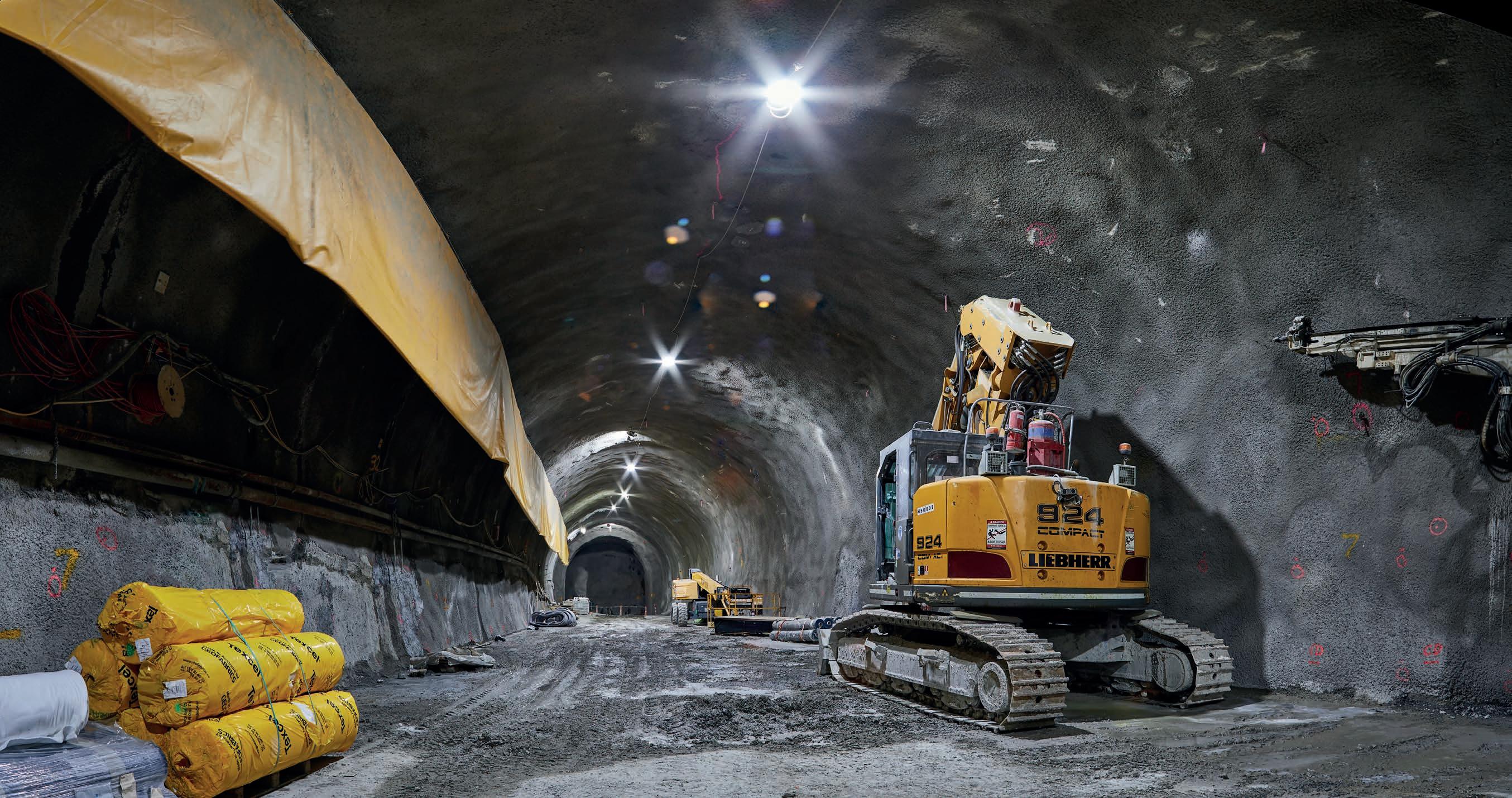
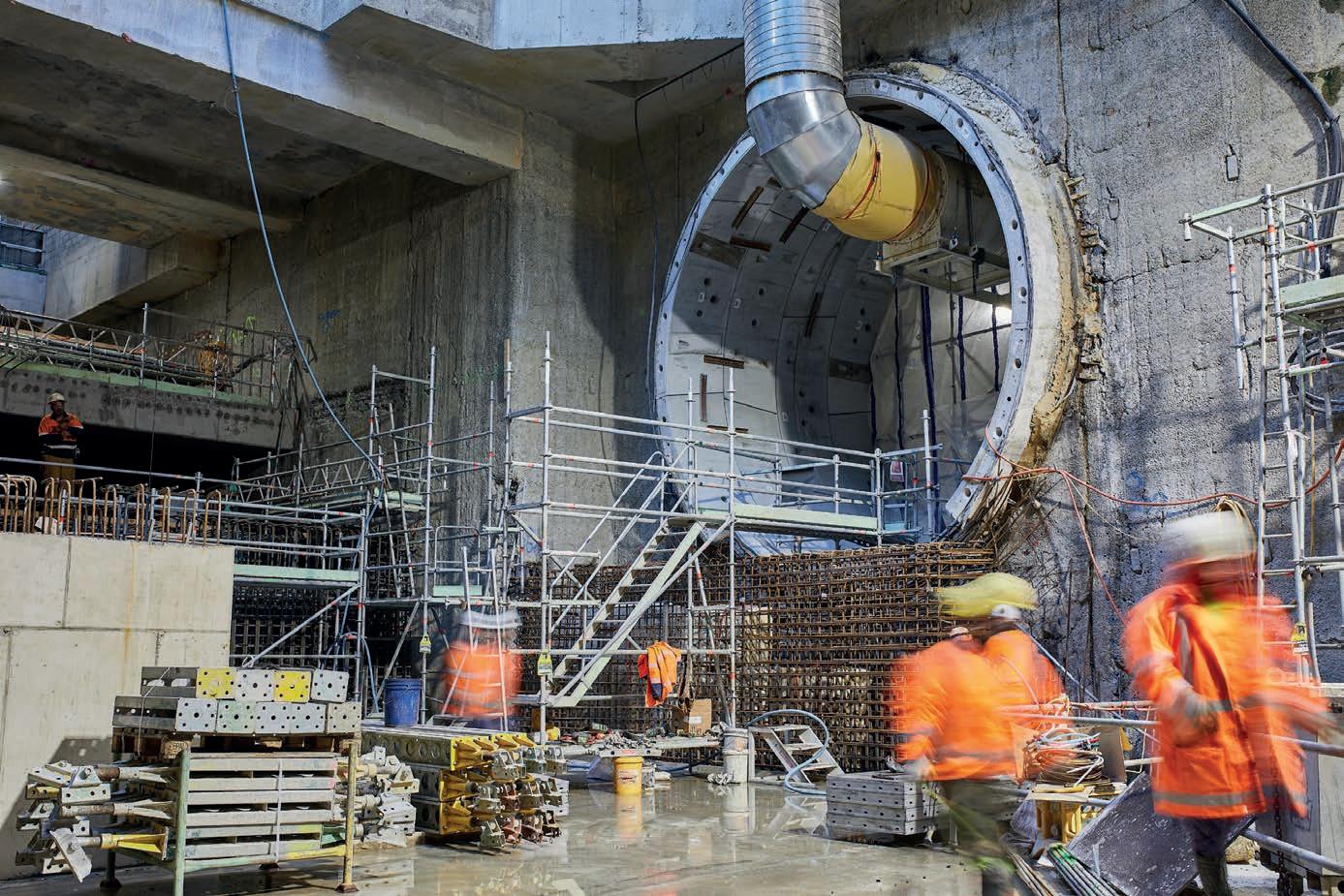
Auckland’s biggest infrastructure project begins construction
The City Rail Link tunnels have been constructed using both cut-and-cover and tunnel boring machine (TBM) methods depending on the location and requirements of construction. The ground through which the tunnels are built vary between firm rock and soft soil and, likewise differs in depth to natural ground level between 40 m and 0 m.
The project officially began its early works package in October of 2015 between Britomart and Wyndham Street.
Working since December 2015, the Connectus – a joint venture consisting of McConnell Dowell and Downer – installed 362 reinforced concrete piles around the future CRL twin tunnels.
CRL Chief Executive Dr Sean Sweeney noted that construction undertaken in the middle of a thriving city such as Auckland is never easy, but that the CRL took a big step toward establishing itself as a project that will change the way people can travel throughout the city.
Flashing forward, the CRL’s Dame Whina Cooper TBM – named after the inspirational Māori rights activist Dame Whina Cooper – reached the milestone of 500 m bored in
late 2021.
Dame Whina Cooper began tunnelling CRL’s southbound tunnel in late May earlier that year. With works having been restricted by COVID-19, the TBM continued to operate at low capacity during the five-week lockdown to reduce the risk of becoming stuck. Nevertheless, Dame Whina managed to complete its first 860 m leg from the Mt Eden site to Karangahape in October 2021 despite the restrictions and difficulties.
On 10 November 2021, the Dame Whina Cooper TBM began the second leg of its fourstage journey below the Auckland streets.
The TBM’s 785 m venture from Aotea Station concluded early in the new year and saw Dame Whina dismantled underground before being returned to Mt Eden in sections, reassembled and then ready to excavate the second rail tunnel in 2022.
Throughout 2022, works continued to ramp up on the CRL.
The TBM continued to power away beneath NZ’s surface, excavating the second 3.45 km underground rail tunnel and removing dirt and rocks to the surface. However, the TBM was doing more than just excavation.
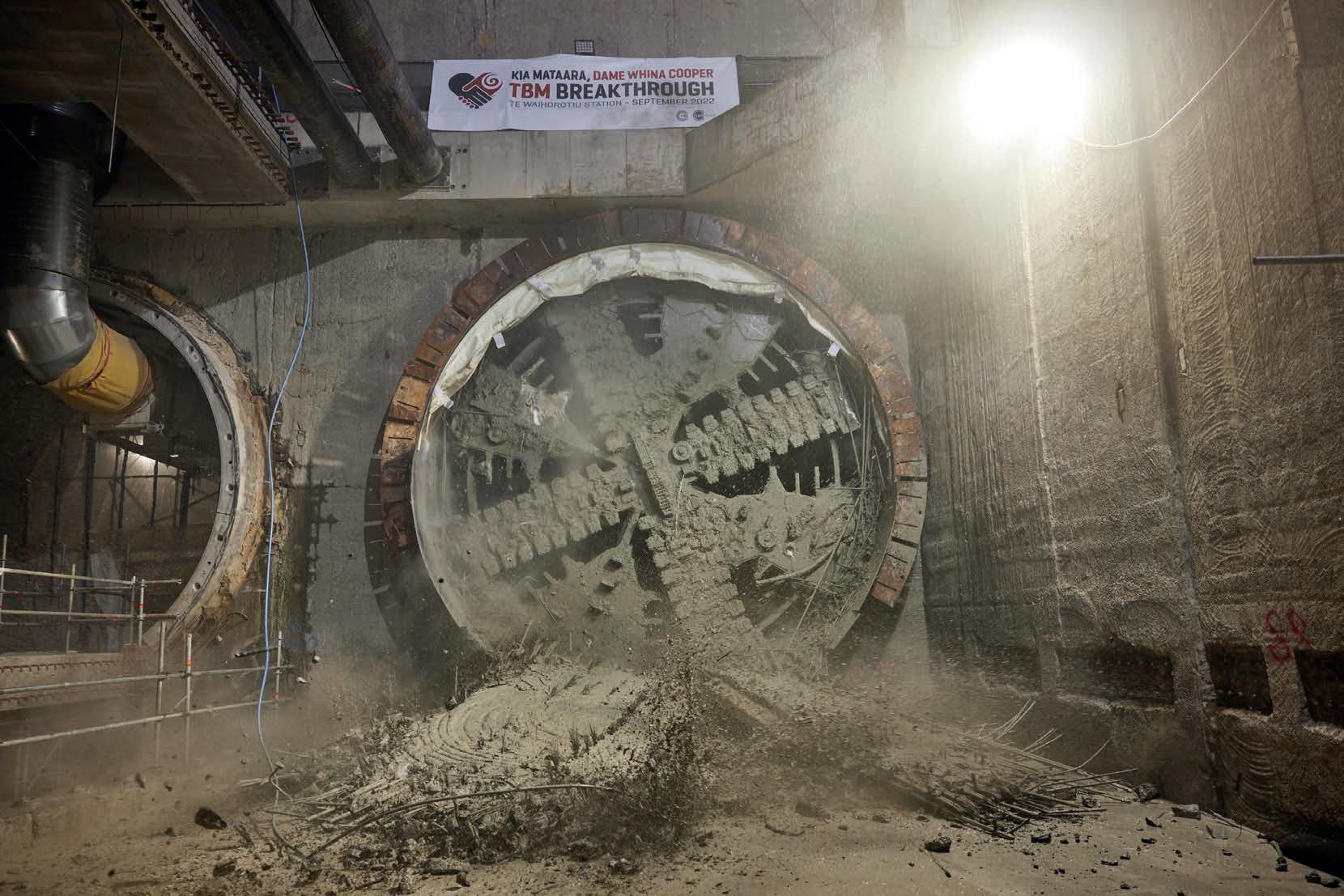
The machine had also been busy installing precast concrete panels to line the tunnel walls.
Upon reaching its destination in September, the TBM had travelled 840 m from the Link Alliance Maungawhau (Mt Eden) Station construction site, placed 519 segment rings and removed 74,000 tonnes of soil.
A future just unfolding – what comes next for the CRL?
Since the beginning of the CRL project, more than 2000 jobs have been created, the complexity and innovation of which has upskilled the workforce and will continue to benefit future generations long after the project is completed.
Now that the twin 3.45 km tunnels have been built, the next stage of the project is primed to commence: installing the tunnels with tracks and necessary rail systems required to convert them to rail use.
Building an underground rail network has never been attempted in New Zealand before and to have achieved what the CRL project team has in the face of a global pandemic, multiple lockdowns, restricted working conditions and a myriad of other challenges is a remarkable feat.
Though the project is far from completion, the final breakthrough of the TBM and the
completion of digging the final tunnel is an achievement not to be taken lightly. The project has seen the Dame Whina Cooper TBM travel more than 3.5 km, place 1067 segment rings and remove 130,000 tonnes of soil during the boring of the twin tunnels. The project likewise saw more than 64,200 cubic m of concrete was used to build the CRL tunnels which is equivalent to 25 Olympic sized swimming pools.
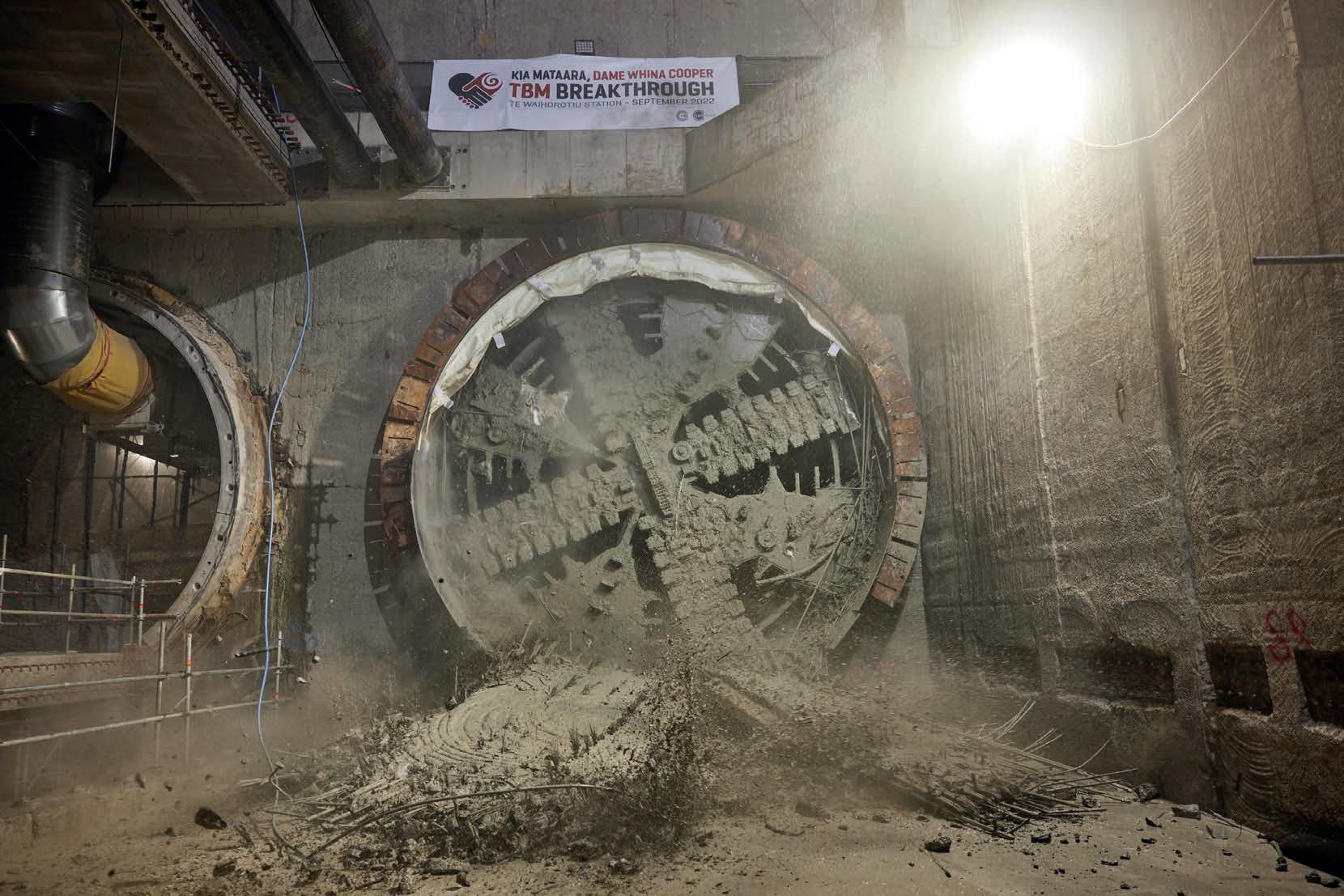

“There is so much more to do on the CRL project, but the final breakthrough is an appropriate moment to pause and reflect on the extraordinary job our people have done in building these twin underground tunnels,” Dr Sweeney says, reflecting on the reaching the major milestone.
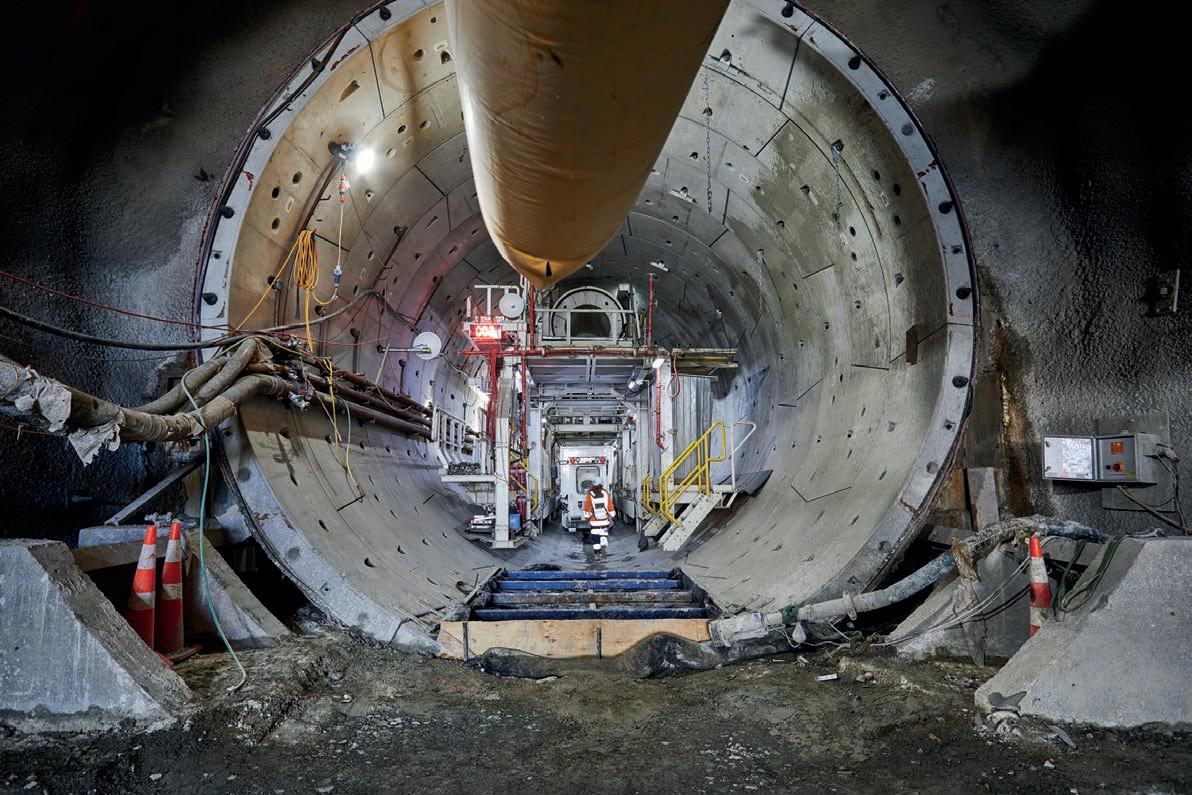
“These tunnels are the cornerstone of the country’s first rapid transit rail network and will enable a transformational change in our biggest city.”
Upon completion of the project, Auckland’s rail network will be granted at least double the rail capacity and will be primed to provide efficient public transportation across the city of Auckland. A landmark achievement, the project has proved New Zealand’s infrastructure capacity to take on such a large and innovative project.
Watercare proactively tackles massive pipe renewal program
Auckland’s water and wastewater company, Watercare, has turned to trenchless technologies to overcome many of the challenges of its pipe renewal programs.
The company’s asset upgrades and renewals department was assembled to roll out a series of programs focussed on upgrading Auckland’s ageing water and wastewater pipe infrastructure.

A new plan to get ahead Suzanne Lucas joined Watercare as General Manager of its newly formed Assets Upgrades
and Renewals team in January 2022. She spoke to Trenchless Australasia about the reason the team was formed and how the company has adjusted its approach to network renewals.
“Traditionally our pipe renewal work has been carried out on a reactive basis when the assets fail – our operations and maintenance staff do a huge amount of work in this
space. But now, we’re focusing on proactive planned renewals as well as the reactive work. With more investment upfront in proactive targeted renewals, we’ll be able to provide more reliable service to our customers, and in time we should be spending less on reactive replacements.
“We’re just coming to the end of our first proactive watermain renewal program – a
$20m targeted investment in parts of west and central Auckland – and are now looking to the next program of work,” Lucas says.
Lucas also indicates that the programs are increasing year on year as Watercare embraces a proactive approach to extending the life of its assets without having to do full replacements.
Balancing priorities
As part of the construction delivery team, project manager Mark Chijindu’s role is to make sure these numerous projects that make up the renewal programs are delivered to standard, to cost and to schedule.
In 2020, he says, Watercare started to emphasise the proactive renewal in order to get ahead of potential failures of the system. The city has over 9000 km of water pipes,
some of which are nearing the end of their design lives.
“We don’t wait for failure to happen on the network before we renew. We’ll have a program plan to make sure we renew proactively,” says Chijindu.
The company still has an efficient team who has responded to leaks and outages when and where they occur, and who have done so for years. “There will always be a need for reactive replacement,” Lucas says.
Upgrading the pipes beneath the streets of Auckland is not without its own unique challenges. A good portion of the projects required for the program involve accessing pipes that run beneath suburban footpaths.

“Most of our challenges have to do with impact on our customers, and also hitting other utility services,” says Chijindu. “Accuracy and efficiency, then, are of vital importance to the success of the projects,” he says.
The various projects have been designed and executed to minimise the impact on customers and communities. Trenchless technology –specifically horizontal directional drilling (HDD) – is perfect for the fast, accurate, lowimpact execution of the works.
“Trenchless technology is really helping us in terms of saving us from carrying out excavation operations, and closing footpaths. With these technologies we can just open two or three holes and reduce the impact on customers and pedestrians,” Chijindu says. “It’s also safer for the crews doing the work –and for the communities we’re working in,” he says.
Futureproofing
Longevity and innovation are also a major focus of the program. Getting ahead of leaks and water pipe breakages is even more vital as Auckland remembers the record-breaking drought that occurred only two years ago. In 2020, Aucklanders experienced water restrictions for the first time in 25 years as dam levels dwindled.
Water preservation is important, but so is minimising community disruption and environmental impact. For this reason, Watercare is adopting a ‘dig once’ approach which involves actively seeking opportunities to coordinate with other projects in the area.
“We do look at technology as often as we can to make sure that we are using the most efficient means to deliver the projects. It’s exciting to challenge the traditional methods of how we used to replace assets,” says Lucas.
“On the water side of things, the whole benefit is to reduce leaks, to improve our
resilience to our critical customers, and to reduce community and customer supply disruption,” says Chijindu. “While on the wastewater side, it has to do with our reducing risk of pipe failures, reducing groundwater infiltration, and improving the network benefit.”
Watercare has developed a number of criteria, prioritising certain sections of water and wastewater infrastructure by looking at age, recent failures and material type to determine what sections to renew for the greatest net benefit.
Investing in pipes and people
The most recent program is on track to be finished in October, but that will not be the end of Watercare’s upgrade efforts. The company is secure in the investments required to roll out multiple upgrade programs over the next decade – resulting in further value from the efficient use of HDD to get individual projects completed.
The benefits of Watercare’s approach to water asset renewal and repair are many. Not only does it reduce the risk of failures throughout the system in the future, but it also creates a stable, reliable, ongoing work program.
“It reduces downtime for our contractors and our customers,” says Lucas. “I’m not sure we’ve done a lot of that proactive planning of renewals in the past, so to have that call out role now is exciting and it’s a great outcome, I think, for the community. If we get year on year programs, we can invest in the right people to deliver those. We get consistency, and they can invest in the right technology, they can make the investments they need to deliver well. So absolutely the plan is to have year on year programs, which just continue to roll,” Lucas says.
The renewal program is part of Watercare’s long-term asset management plan which is projected over the next 20 years. Lucas and her team oversee programs over a 10-year period at a time within that projection.
With the proactive renewals strategy set to continue, multi-year renewal programs will allow contractors to develop specialist teams.
“That’s where you get value, right? With being able to provide security to those contractors and the technologies they need to deliver,” Lucas says.
In the long run, the programs will result in better health and safety outcomes, more efficient projects, and higher quality work.
For more information visit www.watercare.co.nz
The Barber Grove to Seaview Wastewater Treatment Plant pipe duplication project
Wellington Water and McConnell Dowell Constructors Ltd have partnered together in a key infrastructure project to strengthen the Hutt Valley’s wastewater network in preparation for future growth and to reduce the risk of wastewater entering the environment in the event of a major earthquake.
acknowledged the difficult site conditions, high traffic volumes and likely impacts on the environment, community, and businesses,” Fairbrother says.
To minimise traffic congestion and to avoid reducing the busy suburban Randwick Road to one lane, micro tunnelling was the obvious choice. It meant approximately 55 per cent (600 m) of the new duplication pipe would be drilled up to 9 m below ground level to the Seaview roundabout.
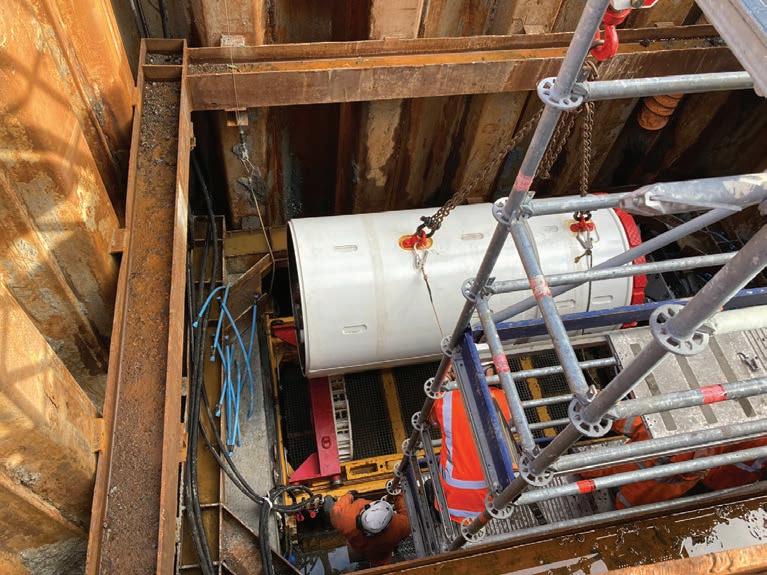
The route is not direct. It involves intermittent excavations along Randwick Road about 200 m apart with the final retrieval pit at the roundabout. From there, the new pipe will be fed through existing concrete pipes (sleeves) to safely cross the local Awamutu and Waiwhetū streams to the final phase and open trenching to the Seaview Wastewater Treatment Plant.
Community engagement
Ageing infrastructure and historic under investment in critical assets such as wastewater networks are an all too familiar tale in New Zealand’s capital city Wellington.
Just across from Wellington Harbour in the Hutt Valley there is a tale of another city where multiple water infrastructure projects are active throughout the community.
One of the more ambitious projects is being undertaken by Wellington Water and McConnell Dowell. It involves duplication of an old wastewater pipe that transfers about 90 percent of the Hutt Valley’s wastewater servicing over 150,000 people.
The installation of a new 1.2 km long by 1 m wide pressurised wastewater pipe from the Barber Grove Pumpstation to the Seaview Wastewater Treatment Plant is a fascinating challenge says Wellington Water project lead Linda Fairbrother.
“Since taking over the project, I’ve
learned the value in having early contractor involvement (ECI) in place. It allows time to foster a customised approach and for greater innovation, which in this case led to innovation, utilising trenchless technology,” says Fairbrother.
In an area susceptible to earthquakes, going trenchless is advantageous, enabling the new duplication pipe to be positioned deeper into more solid layers of earth. In the event of a large earthquake, the new pipe is less likely to be compromised by ground liquefaction.
This approach is also favourable towards protecting the existing environment. A key attribute of micro tunnelling is the accuracy to excavate only the required earth to install the pipe while bypassing other underground network pipes and cables, without the need to cut or move them.
“McConnell Dowell and our design consultant Stantec, clearly had the expertise and made the most compelling tender. They
Excavating near waterways to access existing pipe sleeves, presents challenges from a cultural and environmental perspective with the project route having to negotiate the protected Waiwhetū Artesian Aquifer.
Wellington Water engaged early with mana whenua after commissioning a cultural impact assessment to identify cultural values or interests in the area. Maoridom places great importance and emphasis on guardianship (Kaitiakitanga) of the land and environment.
“I took local iwi through the site, and they provided a statement of position in support of the project. They had legitimate concerns about the mana and spiritual wellbeing of the waterways during construction and that Wellington Water would manage contamination risks and respect mana whenua protocols around a urupā [burial ground]. For me, personally, it’s vital to have a meaningful and authentic relationship with a key stakeholder to establish goodwill and
trust,” recalls Fairbrother.
name for the micro tunnel borer machine and chose Te Rū Tiokaoka as this relates to Rūamoko the Maori ‘God of earthquakes’ and the journey, it will make moving through Papatūānuku [land], tunnelling residue and soil aside.
“We are honoured to receive the iwi’s blessing and thrilled about using Te Rū Tiokaoka. It’s the first time Wellington Water has used this technology, and it recently set a world record in Auckland for its tunnelling prowess, so we’re excited to have it in Wellington,” says Fairbrother.
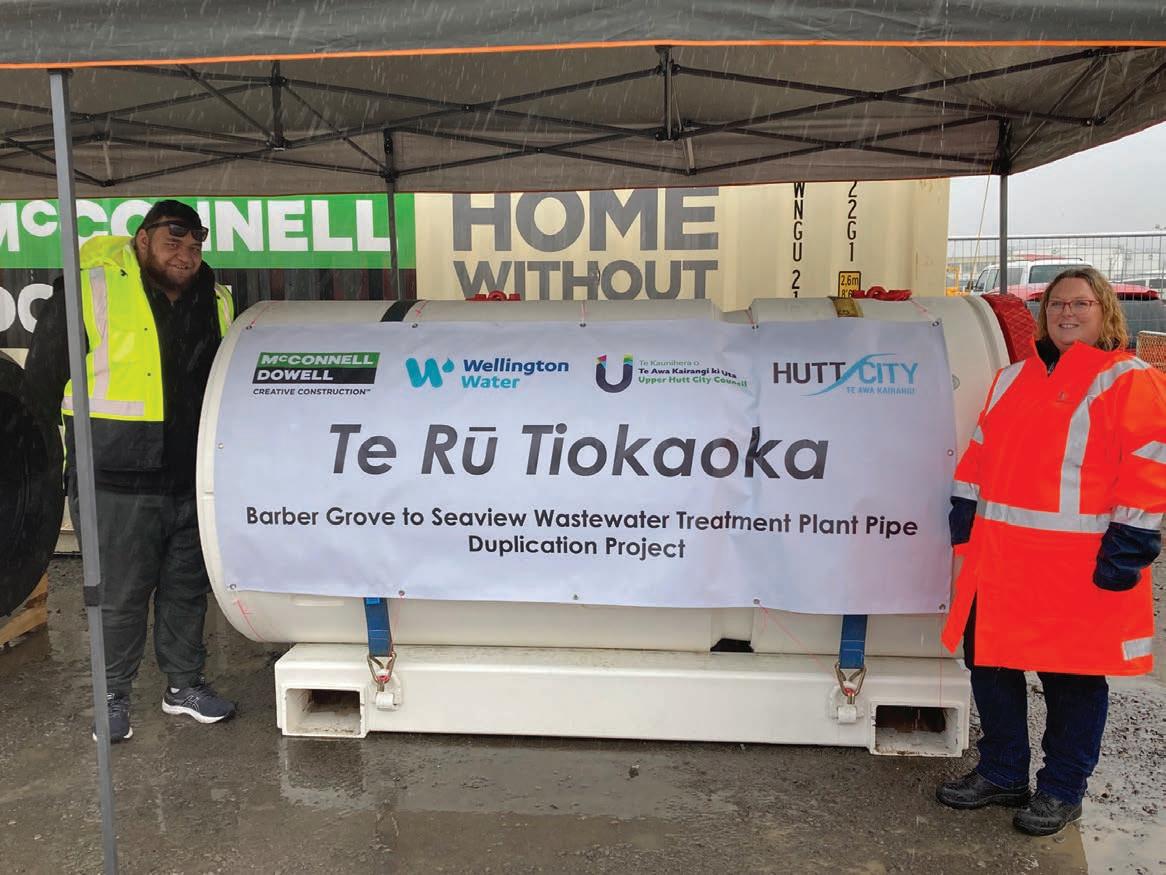
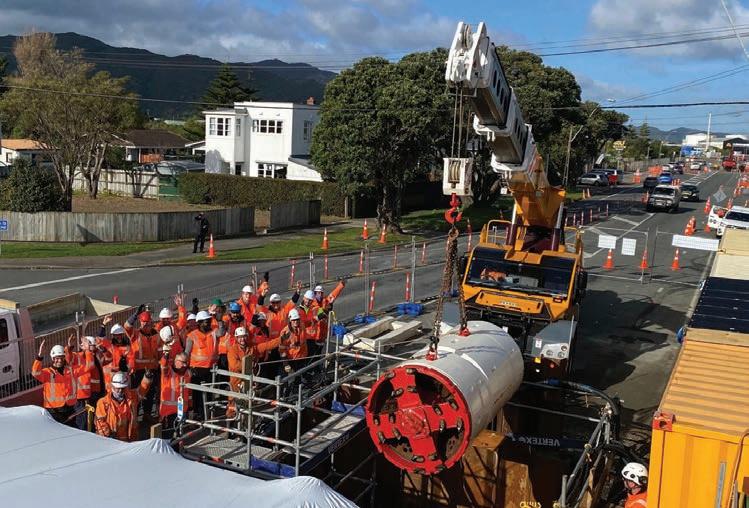
Tunnelling approach
Randwick Road is a confined site, with alluvial soils and a high-water table. These challenging geological conditions can be alleviated through micro tunnelling, which offers greater precision, reliability, reducing risks to crews and machinery in comparison to open cut trenching.
For this project, a launch pit is established with hydraulic jacks propelling the German manufactured Herrenknect AVN 1000 forward at 2.6 m intervals. The pipe sections are pushed behind the machine using a jacking frame. Excavation depths across the
Te Rū Tiokaoka is controlled remotely by a surface operator with laser-guided steering. This enables real-time data on location and orientation of the micro tunnel borer. It allows for the operator to adjust alignment and maintain line and grade. The friction and weight of the concrete pipes (1.2 tonnes) is mitigated through interjacking stations
of the new pipe.
Swedish Grindex Minette single phase drainage pumps, are employed to stabilise water levels in a restricted space. They are aluminium and relatively small, weighing 29 kgs with a 240 mm diameter.
Tunnel Superintendent Peter Farr says, “Water is the biggest nemesis for micro
tunnelling, you have to control water, or it controls you.”
To manage the high-water table, the flows and pressure, Te Rū Tiokaoka operates in earth pressure balance (EPB) mode, providing a shield to maintain the stability of the tunnel face, adjusting the pressure inside the cutterhead chamber to achieve a balance with the water and ground pressure in front of the cutterhead. Rubber seals are installed at the entry and exit points to restrict waterflows into the shafts.
The operation site is bunded and contained, so any spillage is recovered and recycled through the slurry separation plant, minimising the risk of contamination
This plant transports waste, sediment, and solids back to the surface for screening and recirculation. Any loss of slurry in the mining operation into the gravels is absorbed, as the Bentonite is a natural clay.
One hazard to the tunnelling route is the presence of timber or fibrous materials. Given the project site is on alluvial plains there is the likelihood of unwelcome deposits such as timber, which cannot be transported through the slurry plant.
“We have modified Te Rū Tiokaoka so it can adapt accordingly to the environment. The wheels were changed and the cutting head profile from a mixed face to a soft head, this way, it can tackle the likes of timber. It’s not uncommon to hit chunks of Pohutukawa which have been washed down from the riverbed,” says Farr.
“Te Rū Tiokaoka’s journey will vary with the unpredictable ground conditions. The drive lengths are essentially short. We expect it will achieve speeds of up to 50 mm a minute and we’re hopeful it will complete around three to four pipes a day, equating to 7.8 m.”
Project risks
The lingering shadow of COVID and related impacts is an ongoing challenge for this 13-month project which is due to be completed in mid-March 2023.
While final project preparations coincided with peak COVID restrictions, Wellington Water undertook early procurement to minimise the impact of cost inflations and disruptive supply chains. The delivery of the micro tunnel borer from Germany and the slurry separation plant from Australia were welcome milestones given the uncertainties of global shipping.
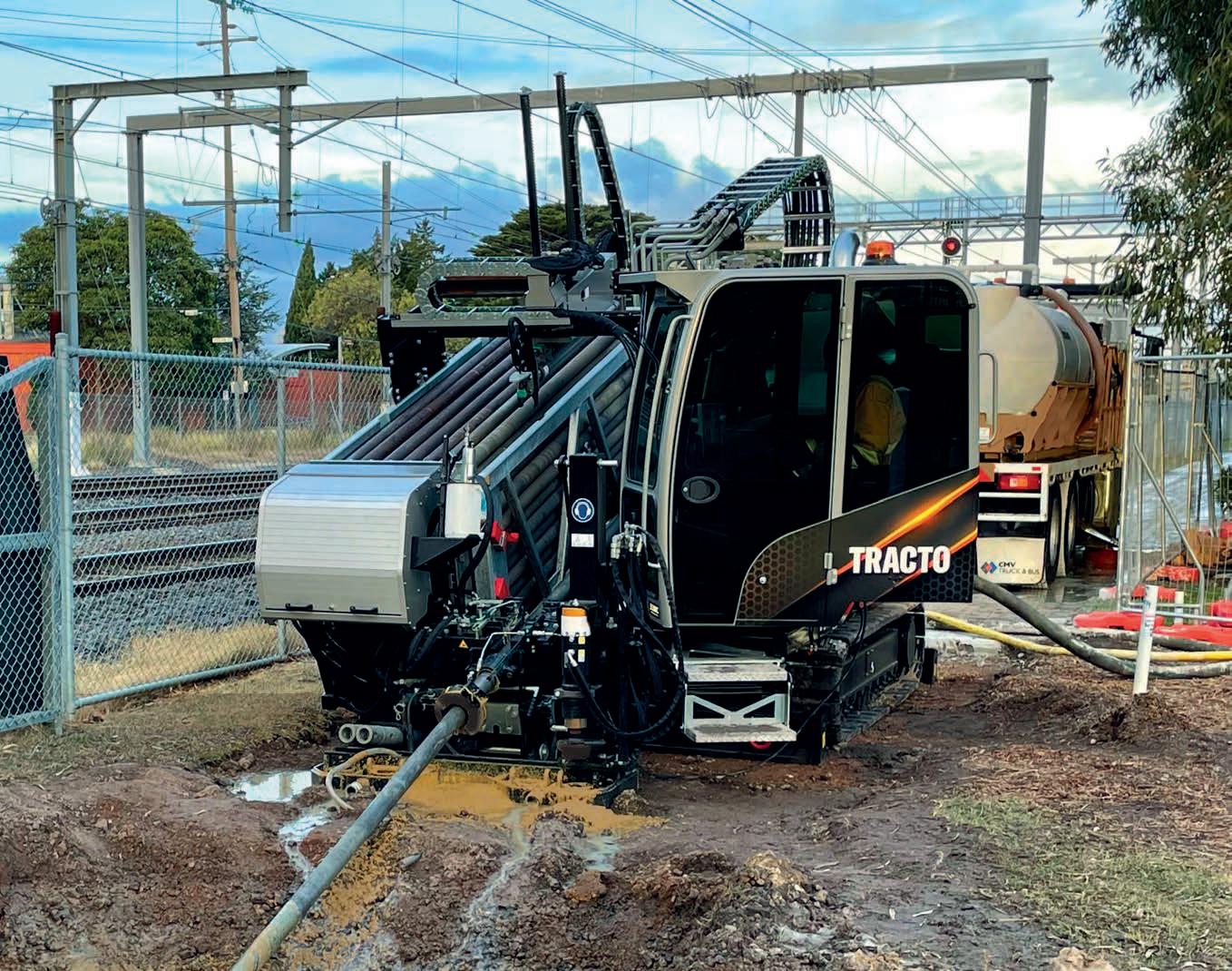
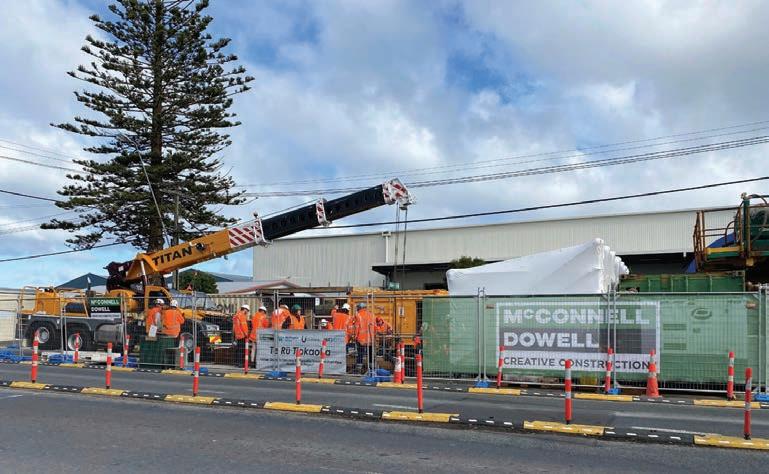
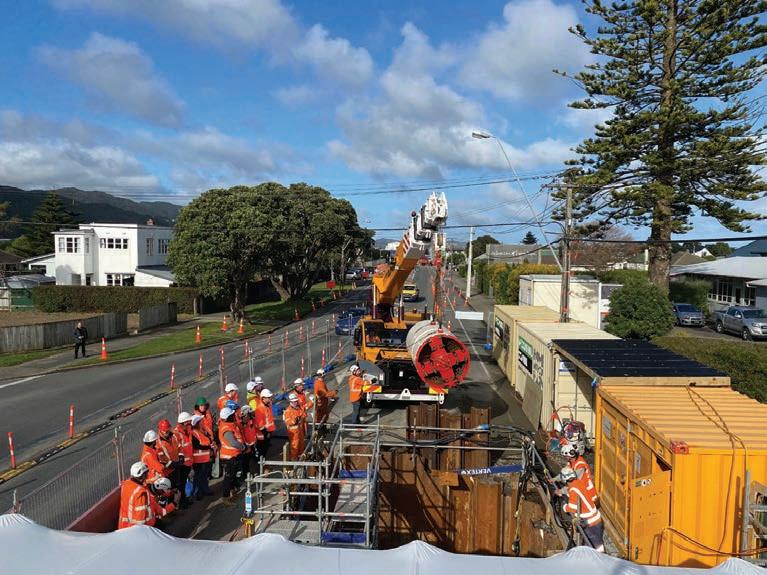
“The project team has learned to become more agile, there was never the danger of placing an order and forgetting about it,” says Fairbrother.
Leading a key infrastructure project
A much-discussed initiative for a generation, before Wellington Water was conceived in 2014, this $27 million dollar Hutt City Council and Upper Hutt City Council investment, will strengthen community resilience towards natural hazards and protect the wider environment.
Fairbrother describes the project as a career highlight since joining the water entity six years ago. An advocate for social responsibility and late starter to infrastructure project management, she has a passion for delivering communityoriented outcomes.
“My background is local government so there were connections and that element of shared values, and vision of leaving things better than you found them.”
Fairbrother is particularly comfortable working in a male-dominated sector where there is no ceiling to ambition and the pursuit of bigger and more complex projects.
“I’m fulfilling a personal aspiration and feel privileged to get this finally off the ground and be involved in a leadership capacity. The wider Wellington Water whanau are supportive, and we have great women role models in senior positions who nurture and encourage personal development.
“The company is growing in size and expertise, we’re not just about pipes, we’re leaning into bridges and large reservoirs as well and that’s certainly an interesting field I would welcome and embrace in the future,” says Fairbrother.
For more information visit www.wellingtonwater.co.nz
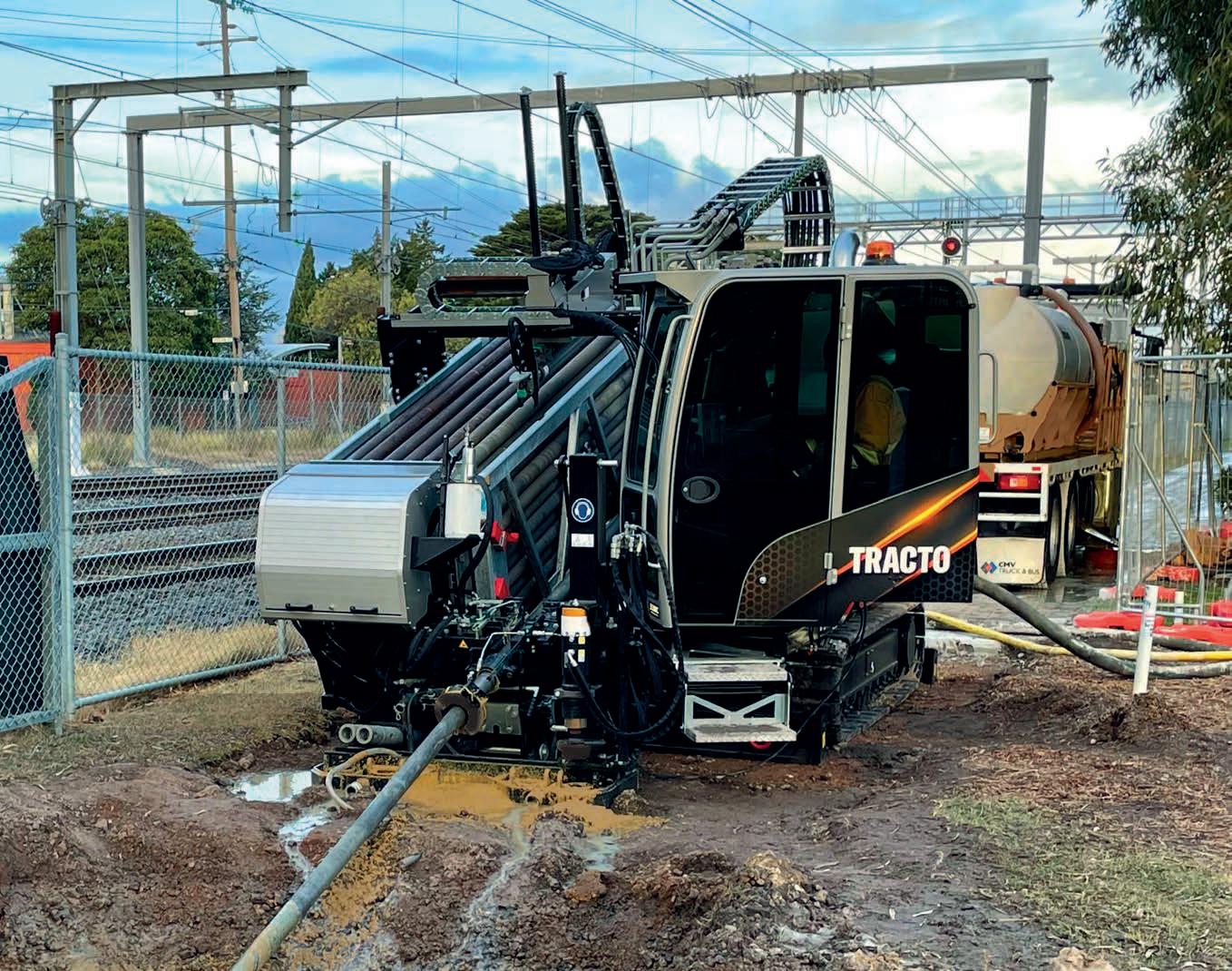
Auckland wastewater pipes get 50 more years thanks to trenchless relining work
Auckland’s water and wastewater service provider Watercare is nearing the end of a $4.5m project to upgrade the wastewater network in the seaside suburb of Takapuna.
Watercare project manager Johan Gerritsen says relining the 1.6 km pipe that runs the full length of Takapuna Beach will significantly reduce wastewater overflows and improve beach water quality.
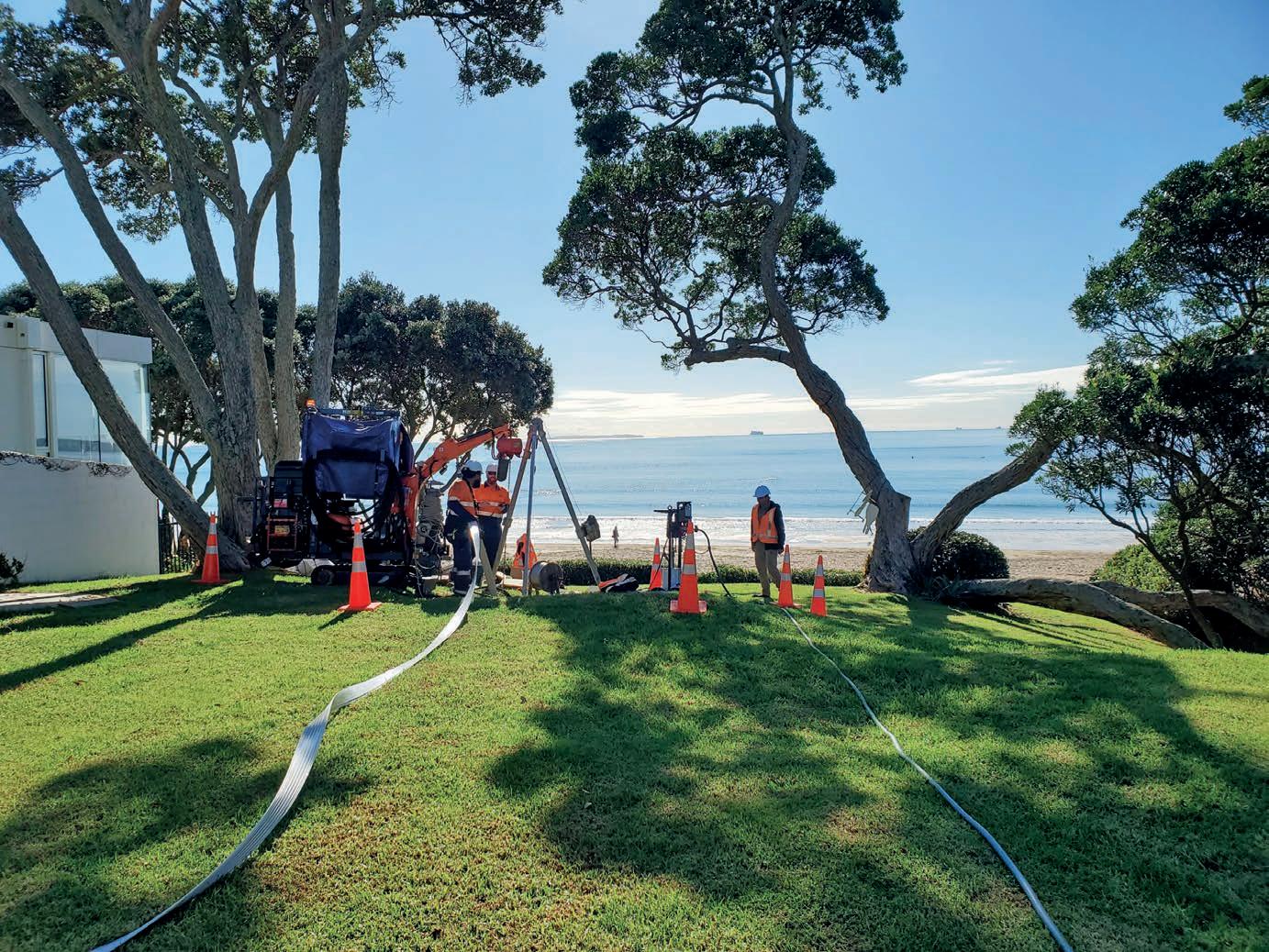
“The original pipe was built in the 1940s and was a mixture of concrete and cast iron. Earlier this year we discovered it was in urgent need of an upgrade to prevent exfiltration, so, with the help of our construction partners March Cato, we moved quickly to design and deliver a solution,” says Gerritsen.
“By relining this section of pipe with PVC, we’re giving an 80-year-old asset another 50 years of life – and we’ll significantly reduce wastewater overflows in the area.”
In addition, a team from Interflow came over from Australia to carry out the relining work.
A mechanical self-propelling device lines PVC through the pipe by spinning around and lining the inner circumference.
“The PVC is spun into the pipe and
extended from one manhole to the next. When it’s all in place, a locking system is released and the lining slowly expands to create a seal against the existing pipe,” Gerritsen says.
“The beauty of this trenchless method is that the wastewater pipe can be kept in service while the relining work is carried out.
“We monitor flows and can continue working with flows up to 30 per cent – if it looks to be getting higher than this, we stop work.”
Downpours over winter have brought the project to a halt a number of times, but most of the work is now complete. More than 30 manholes have also been assessed and repaired where necessary.
“We check for leaks, cracks, tree roots or damage to make sure the manhole is going to last another 50 years, in line with the pipe,” Gerritsen says.
With most of the relining and manhole assessments now complete, the next focus is carrying out the lateral joint repairs, where other pipes connect to the recently relined trunk sewer.
“We found an alternative solution to fixing the internal connections to our trunk main. It’s
a great win for us – it means we don’t have to dig up people’s properties to seal the joints at each connection to the main trunk sewer,” says Gerritsen.
“The particular machine we’re using for the lateral joint repairs has a camera inside so you can see the work as it’s happening, and the operator can carry out the quality assurance checks as it’s being installed, which is a big advantage.”
Work ploughing on in central suburbs too
A similar wastewater pipe relining project is underway on the other side of Auckland, in the city fringe suburbs of Parnell and Newmarket.
Under Gerritsen’s direction, about 3.8 km of ageing wastewater pipes will be relined using the same technology. The project is at its halfway point.
“One of the biggest challenges we face is finding specialist contractors available to do the work,” Gerritsen says. “There simply aren’t enough for the amount of work we want to do here in Auckland.”
For more information visit www.watercare.co.nz
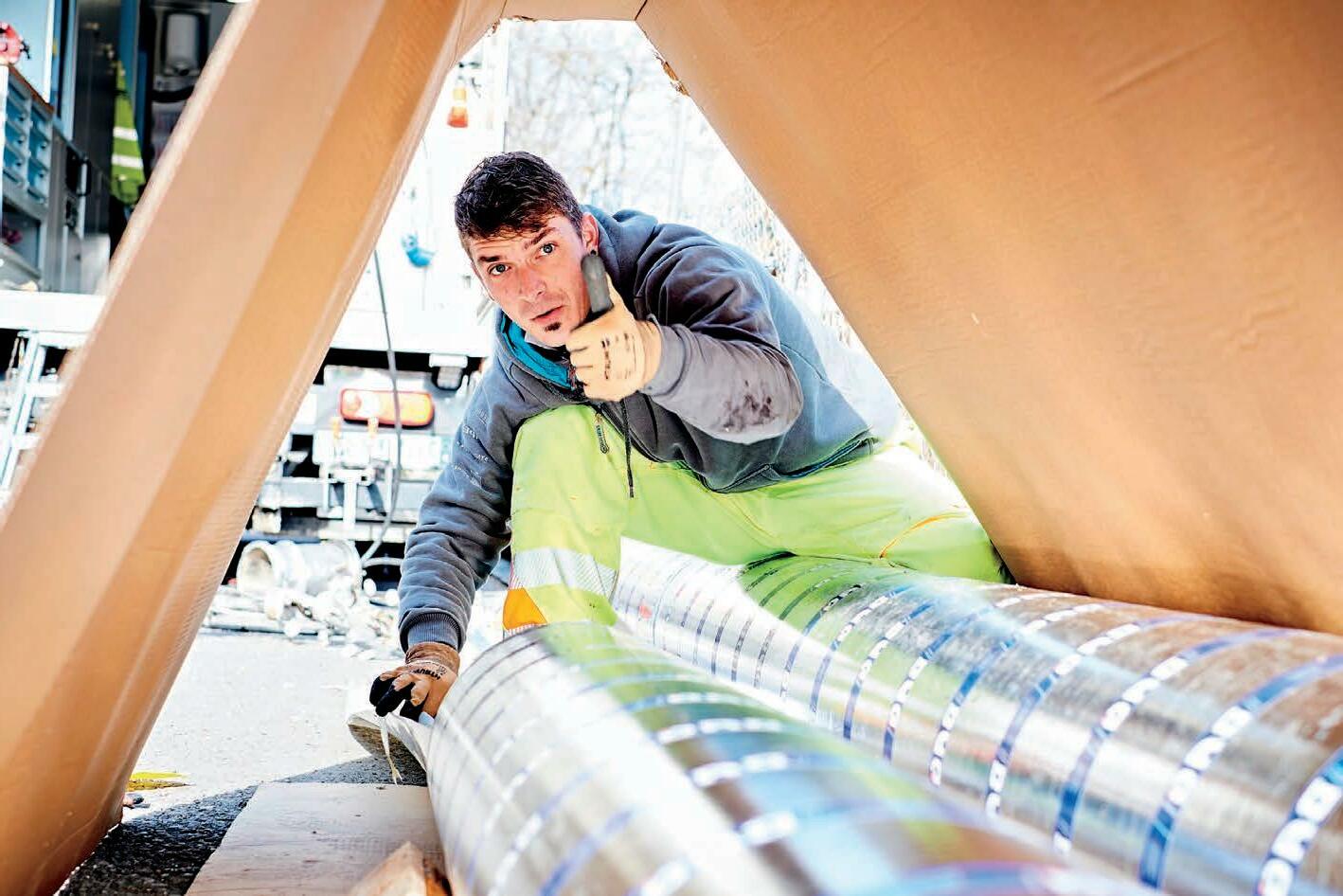
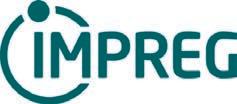
IMS Robotics Group to establish IMS Robotics Australia
The IMS Robotics Group, the German industry-leading developer, manufacturer, and supplier of investment goods, as well as materials for the trenchless sewer rehabilitation, has announced the establishment of yet another affiliated company: IMS Robotics Australia Pty Ltd with headquarters in Miranda, Sydney, Australia.
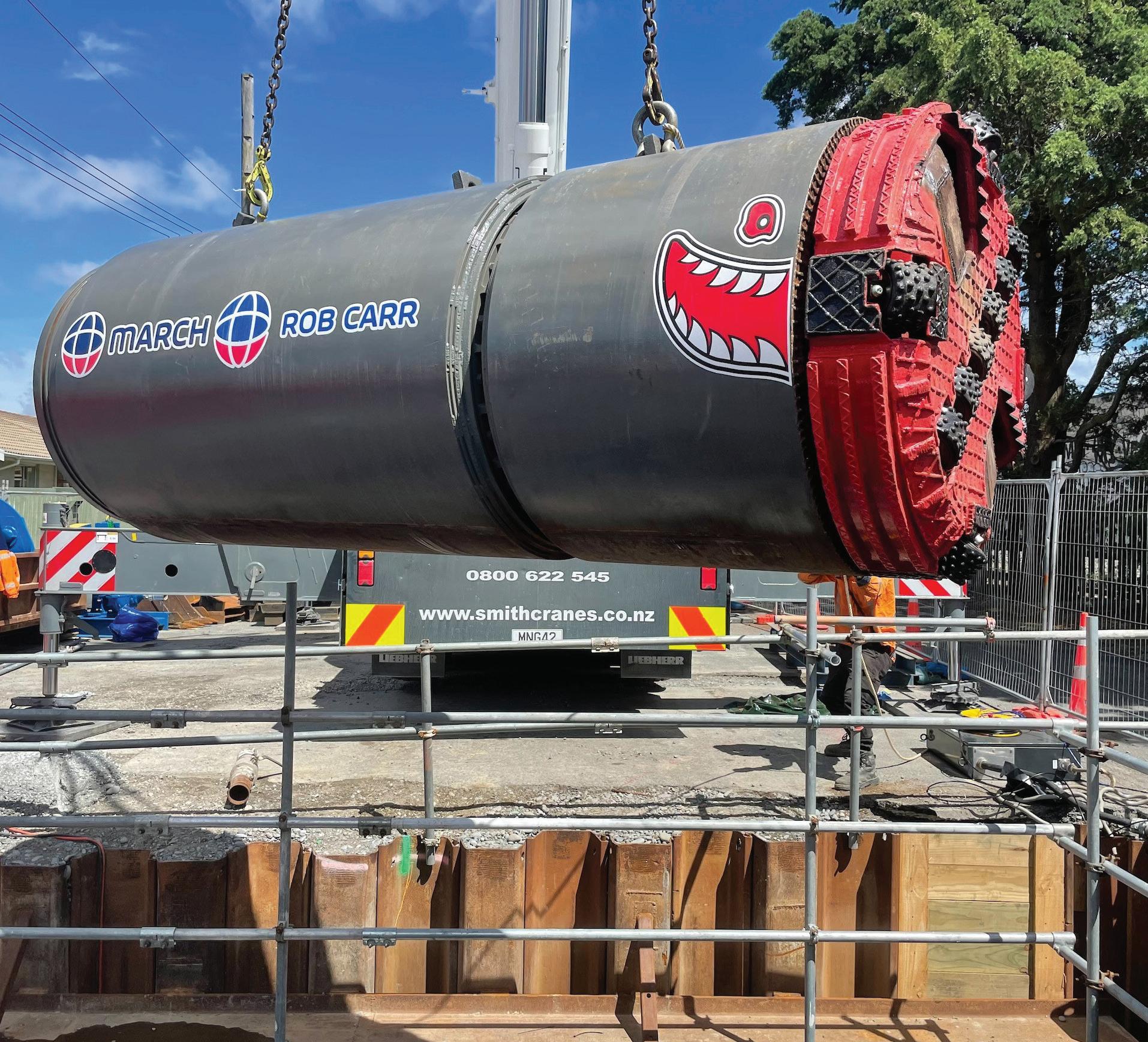
With the establishment of the newest member of the IMS Robotics Group, the further development of the Australasian market in the areas of main line cutting robots, and main line UV curing technology will be accelerated.
To that end, the IMS Robotics Group is happy to announce its partnership in the new company with two well-established, and renowned local companies in Australia: KRE Engineering Services, and UVR Hire Pty Ltd.
KRE specialises in developing and distributing main line cutting robots for the Australian and Asian market and has established itself since 1991 with a remarkable footprint in these regions. UVR Hire will be the third shareholder in the joint company and is in the business of renting out UV curing technology in the Australasian trenchless market.
“With this new partnership we strive to promote the IMS Robotics brand in Australasia beyond our well-established house connection cutting technology,” says Konstantin Wolf, Head of Sales, and member of the executive board at the IMS Robotics Group.
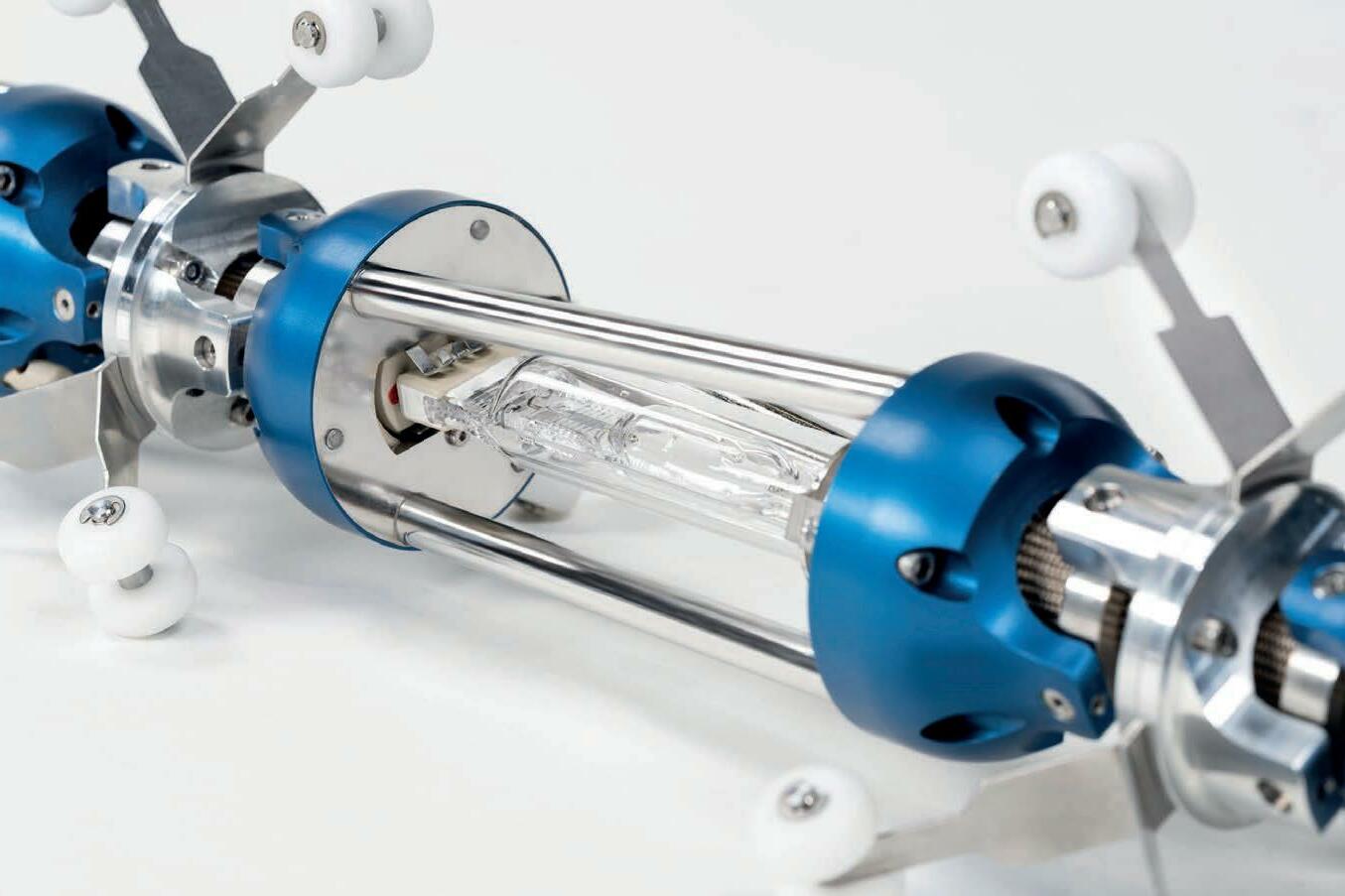
“We think that our comprehensive portfolio of small to huge main line cutting robots, and our broad offer in terms of UV curing technology will be in high demand in the market. We appreciate our distribution partnerships in the house connection cutting
sector but would now like to add the two missing product areas as well.”
Besides sales services to the market, the new company will, also provide repair and maintenance services for the main line product portfolio of IMS Robotics, as well as offer rental options to clients.
“We are very excited about the opportunity to represent the product portfolio of IMS Robotics and look forward to rendering the same level of services to the market, as we used to do for other brands, and of course, our own robotic cutting equipment,” says Keith Edmunds, Director of KRE.
Ned Robinson, Director of UVR Hire says the company strongly believes in the rental business model.
“It is not only a profit centre itself, but also prepares for capex investment deals, and helps to keep clients operational in case of the need
for their unit being to be at service station for repair or maintenance,” Robinson says.
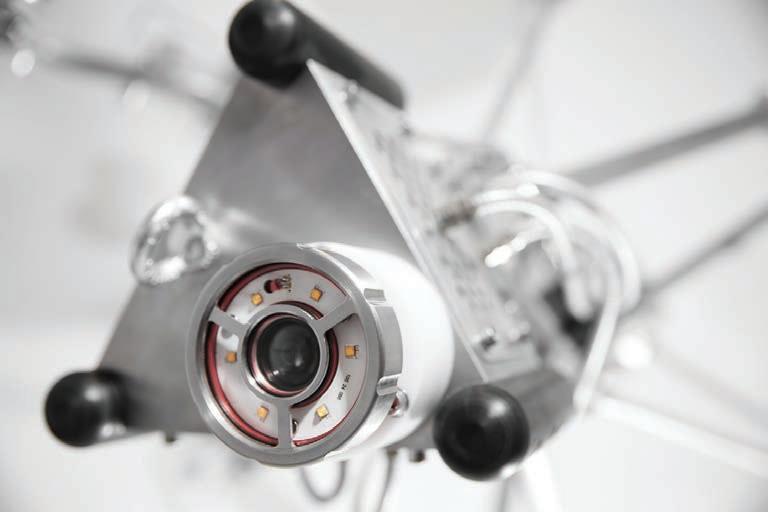
“IMS Robotics Australia Pty Ltd will mark another step in establishing the group in yet another market and to further promote our full product portfolio, whilst we appreciate the business as generated by our existing distributors in Australia,” Wolf says.
“The new company will, besides the main line cutting and UV curing technology, also promote the brands and products of other IMS Robotics Group companies, such as Kardiam Diamond Tools, and Hurricane Trenchless Technologie. We are certain, that we can add more value to the trenchless industry down under and look forward to the next steps.”
For more information contact: Keith Edmunds: +61 415 899 021 or keith@kre.com.au
Excellence in tunneling for water, wastewater and energy infrastructure.

With a focus on safety, innovation and collaborative delivery, Rob Carr and March Construction have achieved outstanding outcomes in water, wastewater and energy infrastructure projects respectively in Australia and New Zealand and together as a joint venture in New Zealand. Both Rob Carr and March, are a part of Soletanche Bachy a world leader in foundation and soil technologies and subsidiary of VINCI, a global player in construction across more than 100 countries. With outstanding capabilities to manage the complexities of any project, Rob Carr and March have the people, knowledge and experience to deliver success. marchcon.co.nz
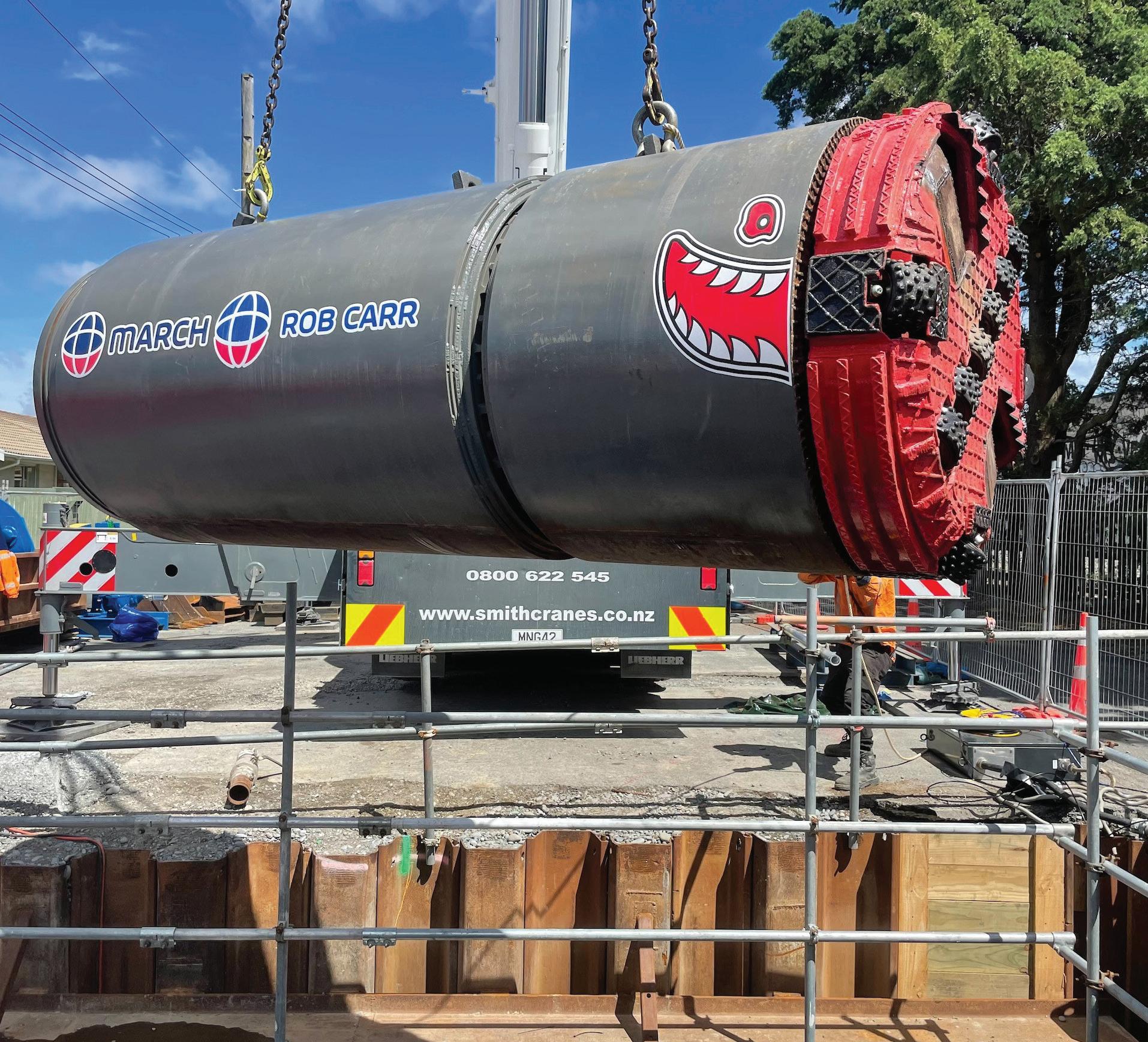
PipeTech NZ aims to provide its clients with environmentally conscious solutions
From initially being a CIPP patch
installing only company, PipeTech has strived to bring in sustainable products and services. Thanks to its good relationships with both colleagues and suppliers in NZ, Australia and the United States and through the sharing of knowledge and experiences, the company has been able to continually grow itself to be better.
Managing Director Rowan Burgess comes from a background within the civil engineering and construction industry. When the opportunity arose to move into his current role at PipeTech, Burgess was interested in the challenge posed by the increased responsibility and the opportunity to make his mark within the business.
According to Burgess, PipeTech prides itself on its integrity and reliability. Through these attributes, the company has been able to do best by its clients and forge longstanding relationships which continue to drive the company further towards success.
“Within PipeTech we push humility, perseverance, and determination. Something we not only focus on for our clients, but as a company as a whole including all our staff,” says Burgess.
“The phrase ‘no, it can’t be done’ doesn’t fit in our vocabulary or mindset. There is always a way or another solution and finding the right one is the most satisfying aspect of the job.”
PipeTech deeply values its ongoing relationships that are forged through these philosophies over any profit margin, explains Burgess. The company is constantly striving to provide consistent high-end quality service to its customers and have continued to push themselves in a bid to enhance its technology and materials for all its products and services.
“It’s a very niche market in New Zealand. I believe our smaller size —for now— compared to some of the bigger players helps us keep
costs down while continually investing in better technology and sustainability,” says Burgess.
Recently, PipeTech has been working on a large-scale project in Masterton in which they were awarded the opportunity to install over 1100 m of 300 mm diameter liner, including 120 lateral cut-outs. This project was completed using PipeTech’s New Zealand licenced uPVC fold and form product, AM Liner.
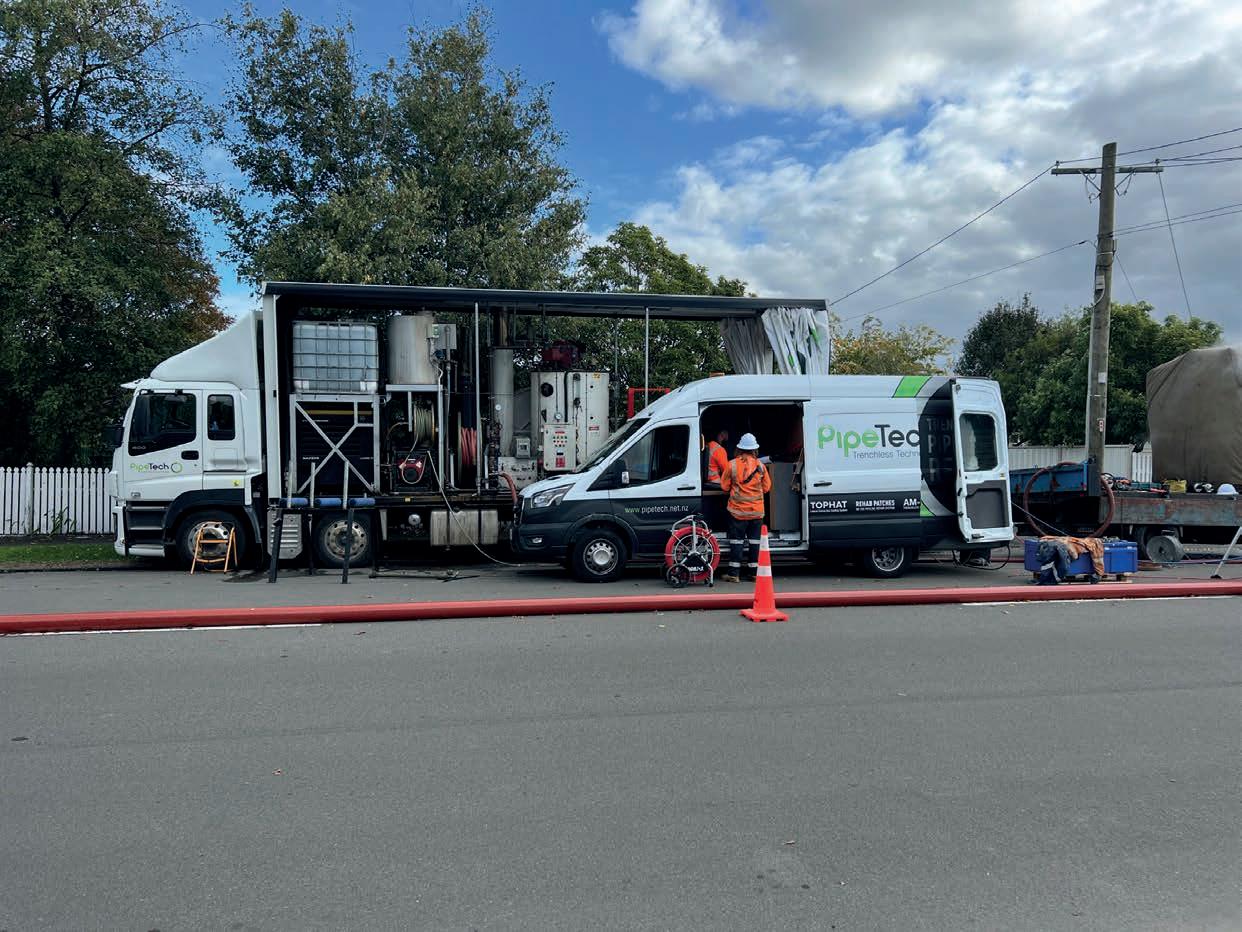
This project had come following a successful 150-225 mm lining programme the company had completed on behalf of the Masterton for the district council.
The Masterton job involved a major overland pumping set up which local contractor City Care managed alongside us to complete the job.
“Some of the distances of liner we pulled in were stretching our capabilities as our manufactures had never had this length of uPVC on a reel either,” says Burgess.
There were several logistical factors that the PipeTech team had to consider when attempting to fit the oversize reels into containers for shipping from American to New Zealand.
Ultimately, the team was able to achieve what they had planned with the council working alongside City Care and removed the need for extra manholes to be installed to achieve the lining which, in turn, saved the client substantial costs and assured they maintained their budget. It was a long project for the PipeTech crew due to a peppering of unavoidable complications that pushed out operations, including the tail end of the project being located close to and under a state highway meaning the project had to be completed on a night shift.
“We weren’t surprised as we knew PipeTech could achieve the programme but it’s still a good feeling when you deliver a project that meets the client’s needs and expectations,” says Burgess.
“I’m super proud of the relationship we have with Masterton District Council —along
with our other long-standing clients—and I believe our core values of integrity, honesty and humility are a catalyst for this.”
Since the company was established, PipeTech has been dedicated to further developing and maintaining the relationships it has built with its customers and suppliers to achieve more in the trenchless industry.
“Whether this be by reducing costs, speed of delivery, environmental impact minimisation — we are continually working towards improving these aging and deteriorating underground assets for future communities and our tamariki,” says Burgess.
The upcoming Three Waters Reform Program in New Zealand will see the overhauling and rehabilitation of drinking water, wastewater and stormwater infrastructure country wide.
“The three waters reform is going to have huge implications towards change in New Zealand and we are working to ensure we’re positioned in the right way to make the transition towards these changes manageable and as efficient as possible,” says Burgess.
Reflecting on the past year, Burgess noted that while the year has been busy so far, the workflow has no signs of dropping off anytime soon – which is absolutely a positive.
“We have just purchased a new Cosmic TopHat system so this will be fit-out in a new IVECO van arriving soon so it will be nice having that unit operational and on the road.”
“Over the next few years and beyond we are already poised for increasingly more development and investment into NZ’s underground pipework assets, with I believe a huge increase in use of trenchless renewals. It’s becoming a more widely known and viable option in the technological advancements.”
To find out more about PipeTech’s services, visit the website www.pipetech.net.nz
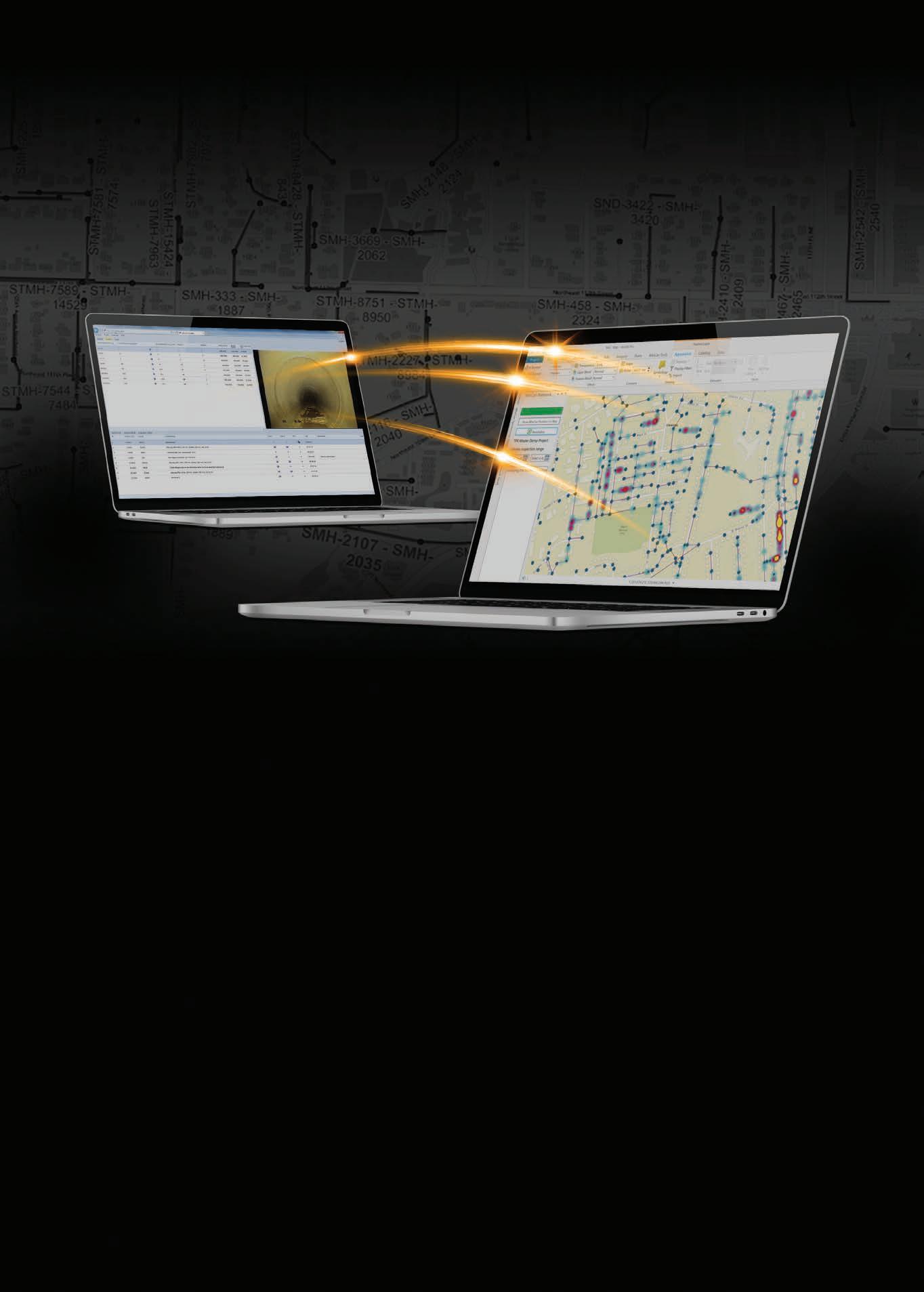
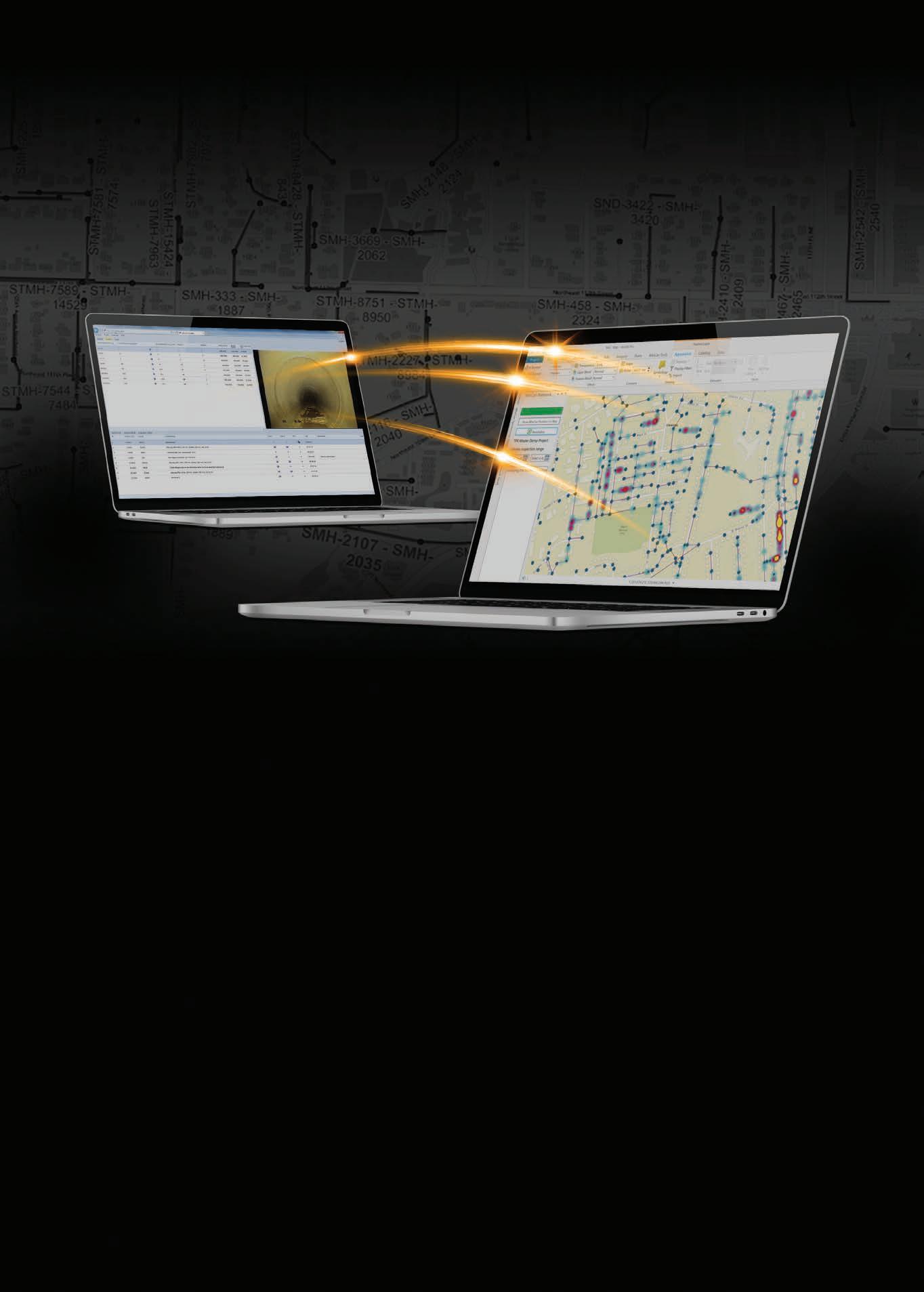
Pipe Core supporting New Zealand’s trenchless industry
with Europe’s leading solutions
For almost 15 years, Pipe Core has used its expertise in trenchless technology to support Australia and New Zealand’s trenchless industry with quality products and equipment from some of the world’s leading European suppliers. This now includes the SAERTEX-LINER® H2O, an award-winning pressure pipe relining product which is now accredited for use in potable water lines in Australasia.
Pipe Core was founded in 2008 with the intention of supplying the latest curedin-place pipe (CIPP) technologies to the Australia and New Zealand market. By working alongside global suppliers and maintaining long term relationships, the company keeps its knowledge of traditional CIPP systems sharp, while simultaneously taking on new innovations and staying ahead of industry challenges.
With this dedication to growth, Pipe Core is now a distributor of a range of premium CIPP pipe relining equipment and materials in Australia and New Zealand, with products, equipment and technologies supplied from leading manufacturers around the world.
Pressure-resistant, hygienic and awardwinning
This includes German-based SAERTEX multiCom® GmbH, which offers a visionary portfolio of UV-cured fiberglass-reinforced liners
for wastewater and supply lines. SAERTEXLINER® MULTI has proven itself in over 99,000 installations world-wide, saving time as well as being a flexible and sustainable choice for the trenchless rehabilitation of municipal wastewater pipes and pressure lines.
SAERTEX multiCom GmbH has now brought the final piece of the puzzle to life in Australia and New Zealand with the introduction of the SAERTEX-LINER®
H2O, a fiberglass-reinforced lining tube for the trenchless rehabilitation of ageing potable water pipes. The product has been successfully tested for use in contact with drinking water according to AS/NZS 4020:2018 by AWQS –Australia’s leading NATA accredited product test laboratory.
“We are proud to announce that SAERTEXLINER H2O has been successfully tested for use in contact with drinking water according to AS/NZS 4020:2018,” says Katharina Helming,
Business Development Pressure at SAERTEX multiCom.
“For the approval, SAERTEX worked closely with Pipe Core and are now looking forward to exciting projects in Australia and New Zealand.”
This hygienic and pressure-resistant liner has been used worldwide on more than 350 UV-CIPP installations on over 100 projects to date. It is the first liner made from sheer glass fibres to be ‘Class A’ classified, meaning it is fully structural and results in an independent pipe after installation, in accordance with DIN EN ISO 11295.
Notably, this liner was awarded the No-Dig Innovation Award by the International Society of Trenchless Technology in 2019.
Innovative trenchless maintenance hole rehabilitation
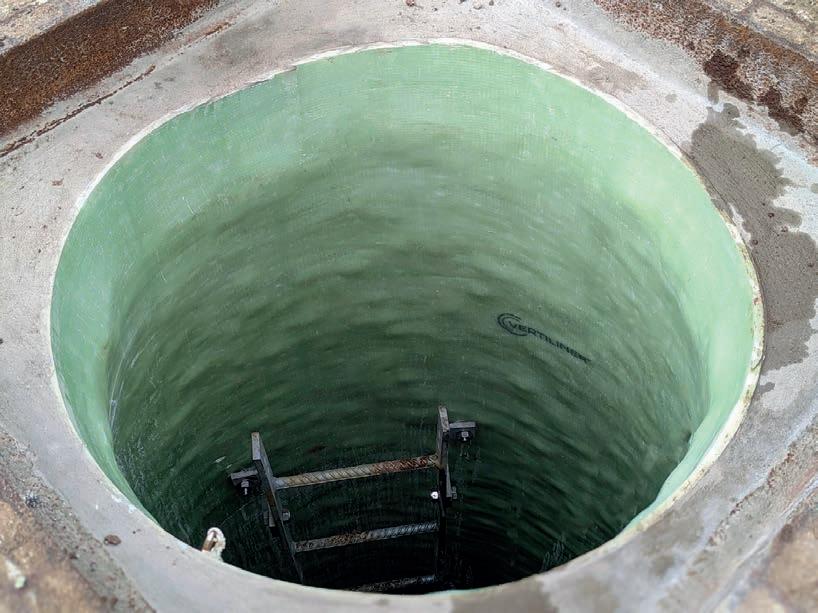
Another solution offered by Pipe Core is the German-manufactured relining solutions from Vertiliner®, innovative trenchless methods for rehabilitating deteriorated wastewater maintenance holes and vertical shafts. Made of high-quality GRP liner, Vertiliner is a seamless tube, impregnated with a light-cured synthetic resin that is inserted into a shaft and then cured using advanced UV-light technology to form a new inner relined surface of the structure.
The unique system is custom made offsite using the measurements of the shaft and accommodates the various changes in crosssections present within the asset. Unlike other vertical rehabilitation systems, Vertiliner is not a coating but a fully structural tailored lining system that does not rely on the integrity of the existing shaft to be installed successfully.
“Angular, oval and walled maintenance holes, with major changes in cross-section are no problem thanks to this patented technique,” says Pipe Core Manager Sergej Fast.
“The Vertiliner system is an economical alternative to excavation and maintenance renovation, providing structural stability and surface protection for many years.”
Complete pipe and sewer rehab solutions
Since it was established almost 15 years ago, Pipe Core has been supplying Innovative Sewer Technologies (I.S.T.) products to the Australian and New Zealand markets. The internationally renowned brand offers a comprehensive offering in the pipe and sewer rehabilitation space.
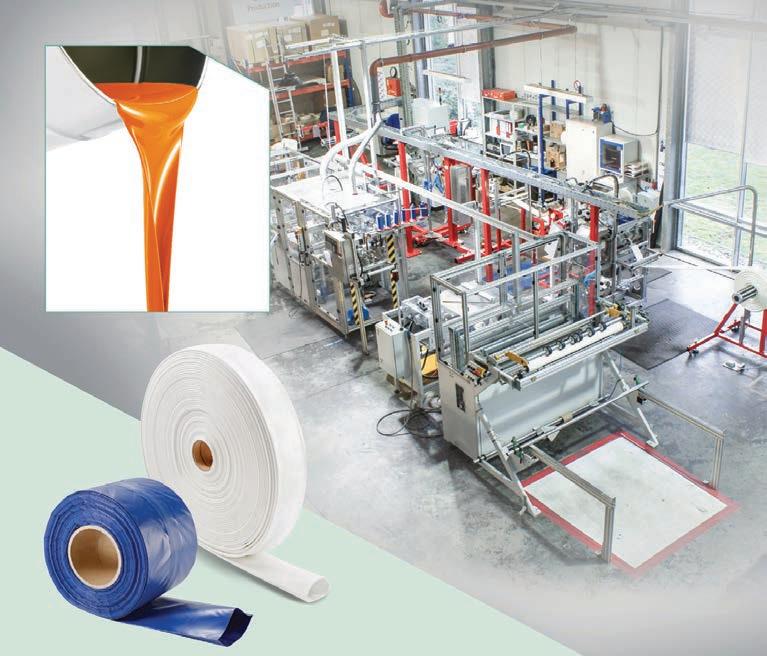
Fast says I.S.T.’s WaterMark certified
“The core WaterMark certified liners alongside resin systems from I.S.T. continue to be our leading CIPP products,” he says.
“Pipe Core’s own evolution and growth has allowed for various curing optimisations to be made available.”
I.S.T.’s own silicate resin spot repair system has been approved by the German
years of service life and has been used globally for over 20 years.
It has been specifically designed for short liner applications on damp pipe surfaces and is ideal for partial repair work in sewer rehabilitation. The different product variants enable a high degree of versatility and variability in terms of processing and curing times.
Pipe Core’s longstanding relationship with I.S.T. means the company is now also supplying Australia and New Zealand with the latest UV and LED curing equipment.
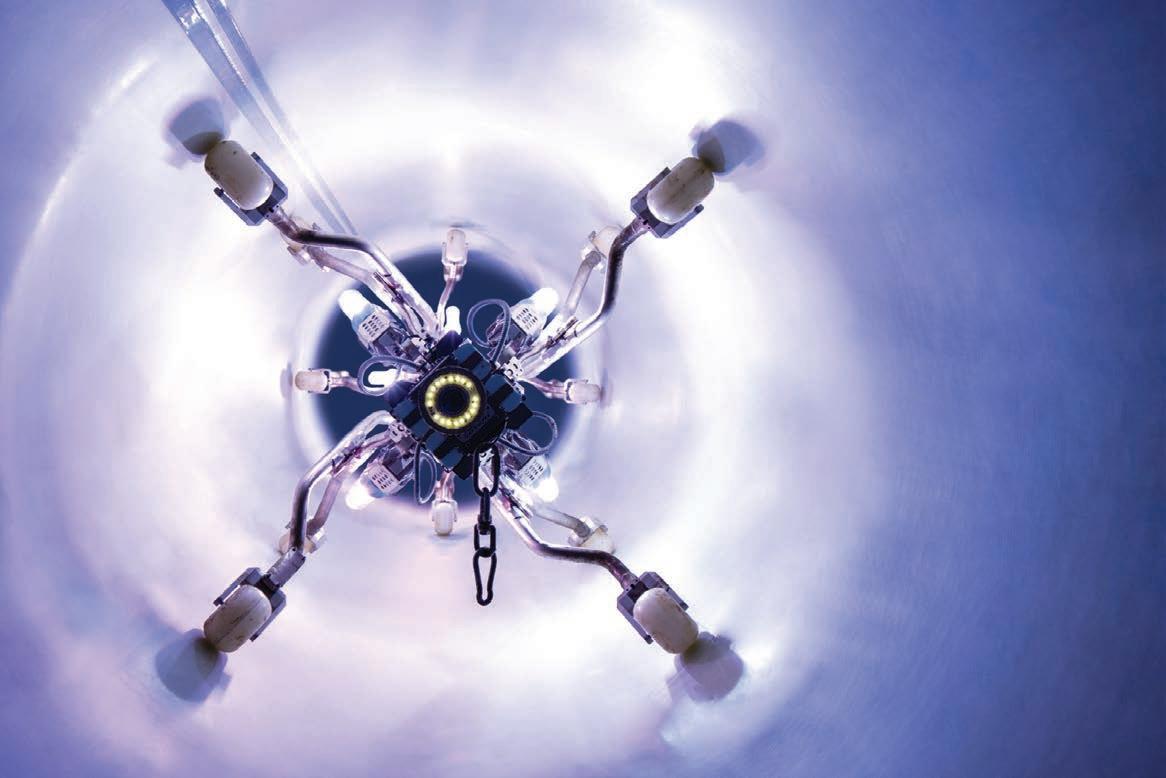
Fast says by offering the latest in UV LED curing technologies from I.S.T., Pipe Core’s customers can be assured the technologies are tried and tested, and supported globally by one of the largest CIPP manufacturers. Pipe Core also assists its customers in the supply and service of specialised equipment required by installers of traditional CIPP liners and resins including milling, drain cleaning, CCTV inspection, wet out and inversion equipment, as well as the latest equipment to support the installation of UV liners. “We’re always ready to embrace new technologies and with an appetite for innovation Pipe Core will continue to strive to bring the world’s leading trenchless solutions to the Australian and New Zealand industry,” says Fast.
For more information visit www.pipecore.com.au
Going above and beyond
Building off the company’s 60-year experience in remote resources and energy projects to city-shaping infrastructure, McConnell Dowell has built thousands of quality assets and facilities for customers and communities.
Its expertise has grown steadily to span building, civil, electrical, fabrication, marine, mechanical, pipelines, rail, tunnel and underground construction.
With over 3000 employees and professional engineering and construction teams in Australia, New Zealand, the Pacific, and Asia, its customers benefit from its combined local knowledge and international experience.
Over the past 20 years, outfall pipeline construction in particular has evolved with the development of trenchless technology as a result of McConnell Dowell’s experience in New Zealand.
Engineering Manager NZ & Pacific Daniel Patten says this evolution has eliminated and greatly reduced a number of adverse effects, including: disturbance of the natural environment during the shore crossing construction, visual, emissions and noise impact during construction, and exposure to inclement weather and sea state.
“Elimination or reduction in disturbance of the natural environment then has the potential to ease the planning process, particularly assessment of effects, stakeholder engagement and ultimately obtaining resource consents – typically the most significant of client risks in the development of a treated wastewater discharge solution,” Patten says.
During these 20 years of evolution, McConnell Dowell has used a range of trenchless methods at numerous New Zealand projects to get where it is today.
Traditional methods
As recent as the early to mid-2000s outfall pipeline construction for McConnell Dowell has typically involved trenching or jetting techniques to bury large pipelines, particularly in foreshore area.
Examples include the Waimakariri District Council and Clandeboye Ocean Outfalls, both
of which used staged temporary sheet piles cofferdams to complete shore crossings in tidal and active wave zones.
“The resulting methodologies were complex, requiring underwater flanged connections completed by divers to join the outfall pipeline sections with each stage of trenching and significant temporary works to enable crane and personnel access over water,” says Patten.
Adopting trenchless technology to reduce impact
Later in the decade the Christchurch City Council Ocean Outfall, through the adoption of pipe-jacking, eliminated the need for trenched pipeline construction through the foreshore area.
“While this was an improvement on previous approaches, tunnelling distance limitations and site constraints meant disturbance of the coastal dunes in Bromley could not be avoided,” Patten says.
In 2010, McConnell Dowell used its expertise in creative construction when it was contracted for the Rosedale WWTP Ocean Outfall project by the North Shore City Council in Mairangi Bay, Auckland.
The original scope of works included a section of open trench, a tunnel, and a marine outfall. Through an interactive tender process, the team developed an alternative for a single bored segment lined tunnel by Earth Pressure Balance machine and marine outfall connected by an innovative offshore riser. The alignment was also straightened resulting in a $7m cost saving to the client.
This collaborative approach led to robust, innovative design solutions, further exemplified by the 45 m deep, 6 m internal diameter cascade drop structure connecting the inlet work from the ponds and UV plant to the outfall pipeline. The cascade drop structure was the first of its kind in New Zealand and was developed in
partnership with the University of Auckland.
“The project was successful for all parties with local residents and other key stakeholders very satisfied with the project execution – a key objective of the client,” says Patten.
Providing a step change
Fast forward to 2017, McConnell Dowell has found that Direct Pipe® provides a step change allowing shallow ground entry and potential for significant drive lengths further reducing impact.
Watercare engaged McConnell Dowell and its design partner, McMillen Jacobs in March 2017 to install a new wastewater outfall, upgrade the existing pump station and build a new ultraviolet disinfection facility to increase the outfall capacity for its Army Bay Wastewater Treatment Plant at Shakespear Regional Park on the Whangaparaoa Peninsula.
Direct Pipe®, a methodology new to New Zealand, was ideal for this project as it enabled pipelines to be installed over larger distances and more accurately than some traditional trenchless tunnelling techniques. In delivering the project, McConnell Dowell achieved a world-record for the longest Direct Pipe drive at 1929 m.
McConnell Dowell selected Herrenknecht’s Direct Pipe® as the most appropriate tunnelling methodology for this project because it was the most efficient and safest way to install the pipeline at Army Bay.
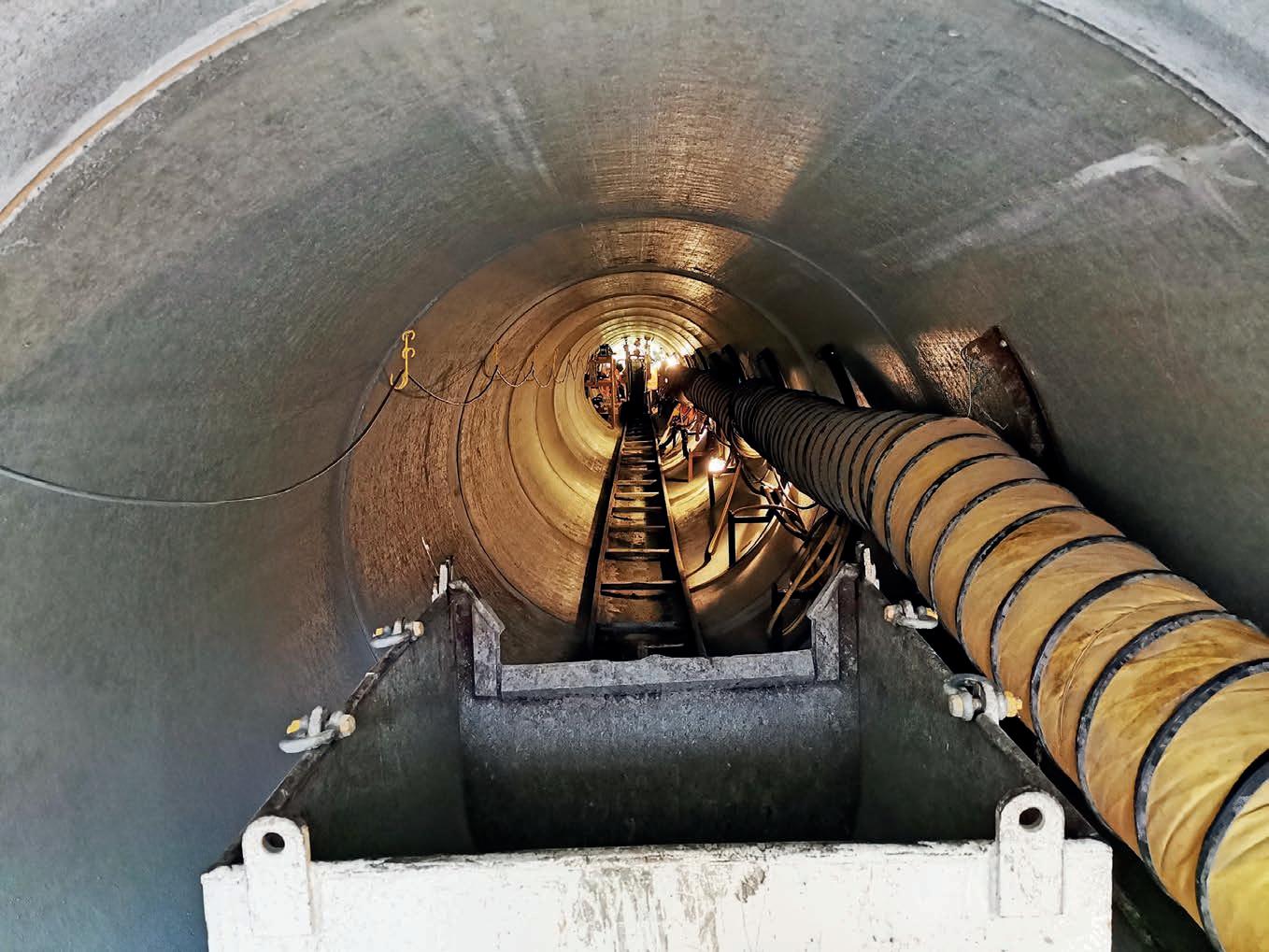
For this project, only an entrance and two inspection shafts (one temporary), (excluding the shallow dredged offshore retrieval pit) were required in the park to install the pipesignificantly reducing the overall site footprint.
“The ability to install long pipe strings in a single drive reduced the amount of time required for construction and the Direct Pipe method also significantly reduced the risk of frac-out (drill fluid loss) into the sensitive environment,” Patten says.
A state-of-the-art new Herrenknecht TBM Direct Pipe system was used for the tunnelling works. The TBM was an impressive 34 tonne 13 m long Herrenknecht AVN1000DP TBM, with a cutter head diameter of 1325 mm and dual pipe thrusters with a combined available thrust force of 1,250 t.
The Direct Pipe method was used to pipejack a 2 km long 1200 mm OD steel carrier pipe, with a 1100 mm diameter HDPE liner, 45 m deep from the new pump house to a transition point in the Hauraki Gulf.
Patten noted that, “this same technique has been repeated to similarly benefit the Snells Algies Ocean Outfall, which reset the Direct Pipe® distance record at 2,021 m and the Westland Milk Products Ocean Outfall in a high energy wave climate off the West Coast of New Zealand’s South Island”.
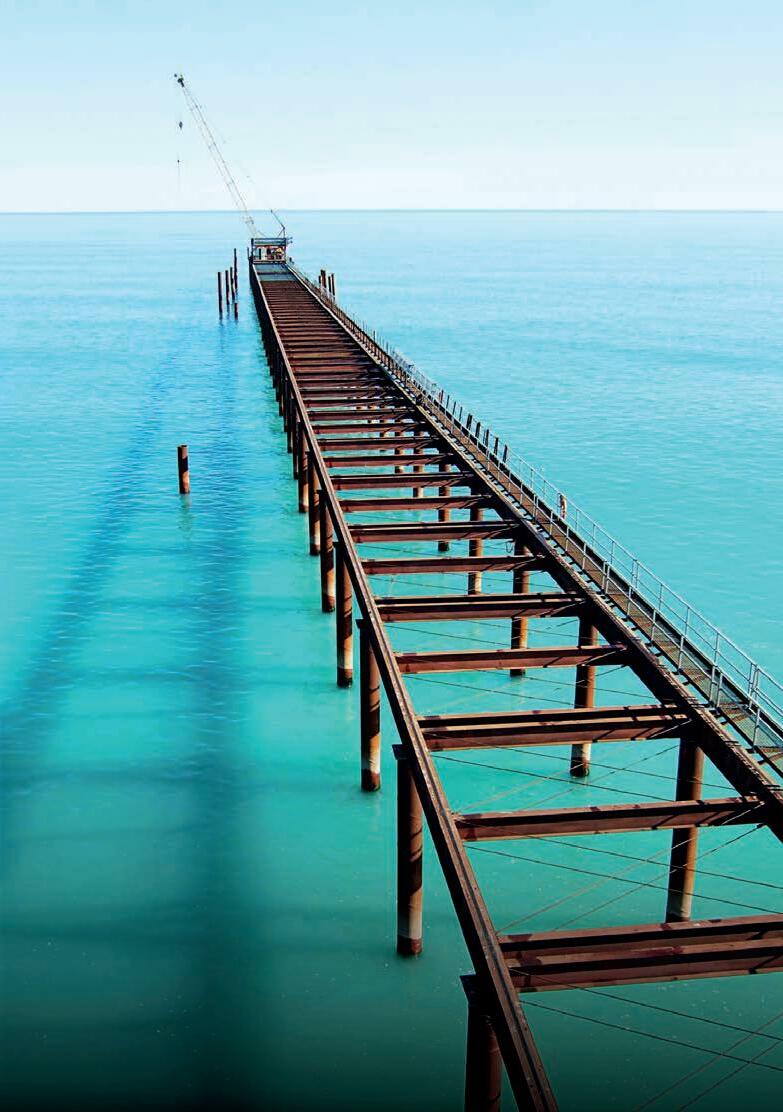
Building from the past for the future
With a strong footprint in New Zealand, McConnell Dowell was contracted as a specialist tunnelling subcontractor to deliver the Culvert E530 microtunnell pipejack for the Puhoi to Warkworth Motorway under State Highway 1.
Project Manager - Corban Reserve Stormwater Upgrade – Richard Atkin says the tunnelling operation was under the direct control of McConnell Dowell as the mine operator.
“The tunnel drive involved a 40 m long, 3 m diameter excavation, installing a total of 17 no. precast concrete pipes, weighing 13 tonne each,” he says.
“Tunnelling commenced by way of an openface excavation utilising a semi-mechanised shield developed specifically for the project.”
McConnell Dowell undertook strong in-house temporary work designs, detailed construction planning and risk assessments, with the tunnel equipment developed and fabricated in house to provide a bespoke solution to a low cover pipejack.
Atkin says the scope of the project works included installing a 2.4 m diameter, reinforced concrete pipe, installed 40 m by pipe jacking and 70 m by open cut method.
“We also had to consider temporary launch and receiving pit for the pipejack, slope stability and settlement analysis, and permanent headwall and wingwall structures with associated aprons at the inlet and outlet,” Atkin says.
As part of McConnell Dowell’s construction method for the project, it equipped the lead pipe with a steerable shield to the required profile that controlled the amount of overcut to guide it back to the correct line and level from a fixed reference point.
In hard stable ground, the face was excavated
then pipeline and shield were jacked forward.
“This sequence was repeated until the advance was complete, taking several cycles to complete a stroke and allow the next pipe to be installed,” Atkin says.
“The tunnel face was mostly self-standing and could be trimmed to the shield profile without significant overbreak or collapse.”
However, the project didn’t come without its challenges. Atkins says several obstructions were encountered including an unknown steel pipeline, redundant cables and service ducts containing data/communication cables, all of which could be exposed and tested by service specialists before being cut and removed by hand from within the front shield.
The open-face nature of excavation required there to be provision for face support within the shield.
Atkin says the face support system has been developed with due consideration to safety, effectiveness, and time taken to install.
“Most importantly, the system was to provide certainty that the working crew can quickly respond to support the face effectively in the event of ground disturbance or instability, poor or rapidly deteriorating ground conditions, surface settlement, or any other need to stop for a prolonged period,” he says.
From this collection point the spoil was discharged onto a series of conveyors positioned under the sliding frame of the backhoe unit to remove the excavated spoil away from the face, and further transported in the tunnel via rail-mounted muck skips.
“The skips were initially manoeuvred by hand and then later by a pulling tug equipped with a secondary drop-pin braking system. They were also fitted with a drop-pin brakes at each end to prevent inadvertent runaway when parked,” Atkin says.
“When the skips were full, they were transported back to the jacking area for lifting of the shaft by crane. Spoil was tipped into a bunded stockpile via the quick-release doors while remaining rigged to the crane.”
McConnell Dowell used its expertise and experience to deliver not only the tunnel but the full scope of the project on time, within budget, and incident free.
Atkin says the culvert was constructed in accordance with the drawings and specification, achieving the alignment between points 110 m apart.
“This enabled the main contractor to construct the required connections from existing manholes within the area to tie into the main pipeline at the correct position, level
For more information visit www.mcconnelldowell.com
Temporary crane access trestle for the Clandeboye Ocean Outfall.
Trans-Tasman collaboration breeds success for trenchless JV
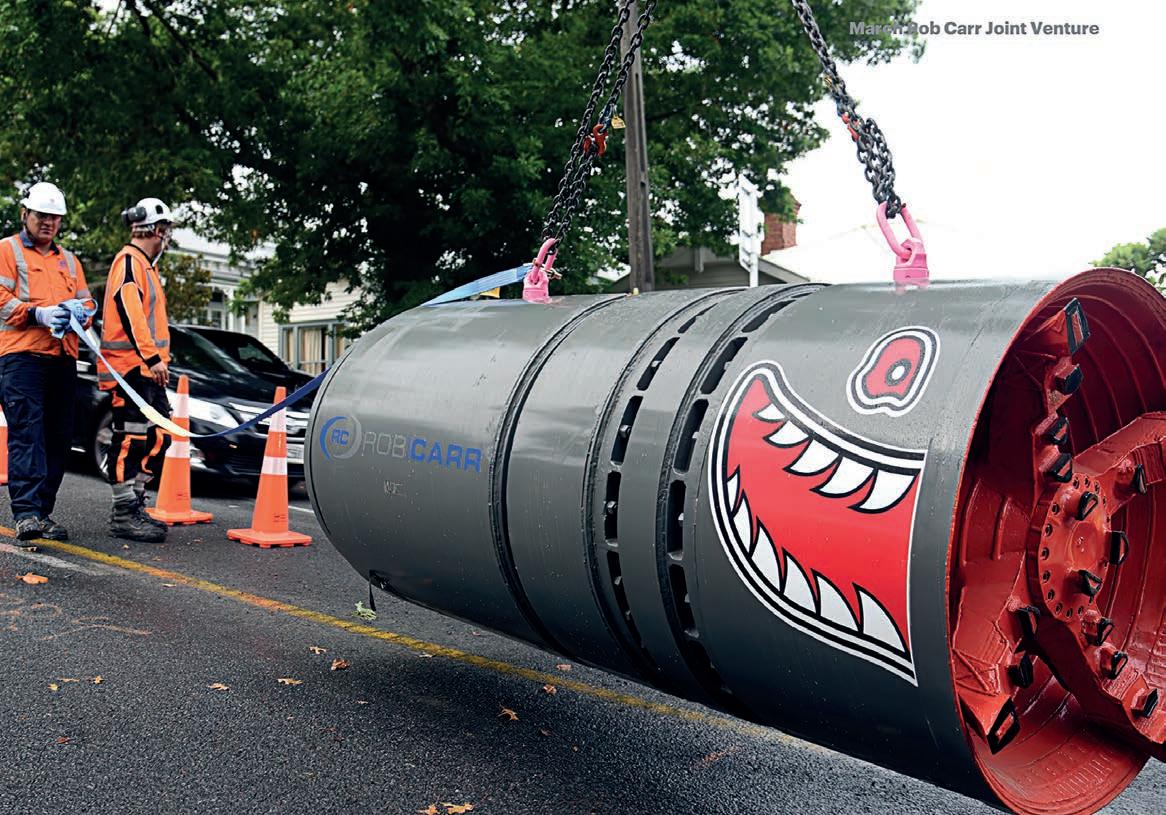

The partnership of two Soletanche Bachy Group companies, Rob Carr and March Construction, is providing unmatched experience and capability in civil and trenchless construction in New Zealand. From upgrading stormwater networks in Auckland, to tunnelling under live rails in Christchurch, the joint venture (JV) proves the power of collaboration.
Tunderpinned by 50 years of local expertise. The JV has tackled trenchless construction projects to install pipelines beneath major transport
tunnelling and microtunnelling machines, has allowed the JV to develop a proven track record for tackling difficult projects across New Zealand.
The partners behind the JV Rob Carr has been developing its capabilities across Australia’s utilities sectors since 1989. The company has a reputation for excellence in the delivery of energy, water and wastewater infrastructure, working as either head contractor or subcontractor on diverse projects in varying conditions, valued up to $35 million.
The company’s team of Australian-based tunnelling experts provide support and knowledge to their counterpartsW in New Zealand. From operational support through to mechanical maintenance and knowledge of the differing tunnelling machines, Rob Carr management and off-site staff are heavily involved in all New Zealand trenchless projects, ensuring collaborations between March and Rob Carr are seamless.
March is one of New Zealand’s leading geotechnical and civil engineering contractors. Since it was founded in 1971, March has delivered projects with high quality workmanship and an exceptional level of
commitment to helping clients achieve their goals. The company thrives on technically challenging projects, many involving significant temporary works including sheet piling and dewatering.
Preparing for Auckland’s CRL Auckland’s City Rail Link (CRL) is the largest transport infrastructure project in New Zealand’s history. The project comprises a railway tunnel crossing Mt Eden Road, close to the existing Mt Eden Station.
The tunnel clashed with an existing stormwater drain, which had to be replaced before the main railway tunnel could be built. The contract for the CRL C6 Project was awarded to a JV between March and Bessac, which was tasked with installing 423 m of new 2.32 m OD stormwater pipe, diverting the existing asset. Bessac, like Rob Carr, are also a Soletanche Bachy group company further showcasing the wider group capability.
Using its expertise and experience, the JV proposed an alternate alignment and design optimization to launch at the Water Street shaft and implementing an S-Curve to avoid the need for a third shaft to be constructed. By adopting an S-curved alignment the team were able to avoid the worst of the impeding basalt lava flow and still construct the tunnel in one single continuous drive.
However, this S-curve required the tunnel be constructed with a radius of 150 m in one direction – something which had not previously been attempted in New Zealand. The alignment also turned back in the opposite direction on a radius of 450 m to avoid the lava flow.
The original two drives were combined into one, which required the use of a hydraulic joint, designed by Jackcontrol, and ongoing surveying of the installation provided by VMT. The JV also installed the main drive shaft, a 15 m deep secant piled structure, through difficult ground conditions, including the construction of the permanent works inside the main drive shaft.
Dual MTBMs upgrading century old
pipelines
Freemans Bay Stormwater Network Upgrade required the renovation of separate, centuryold, combined stormwater and wastewater pipes in the Freemans Bay area of Auckland. The Rob Carr-March JV was engaged by the client to deliver the project, including the construction of 1,200 m of new stormwater pipeline which consisted of 895 m of DN600, DN900, DN1200 and DN1400 glass reinforced plastic (GRP) pipe.
To install the pipeline, the JV used four
each suited to particular size and ground condition combinations. The pipelines were installed depths up to 9 m below ground level. To facilitate the launch of MTBMs, the project team constructed several launch shafts by various methods but predominantly steel shoring boxes and sheet-piled shafts.
A further 485 m of DN300 and DN375 concrete pipe was also installed using traditional open cut pipelaying methods along with the associated connections, catch pits and manholes.
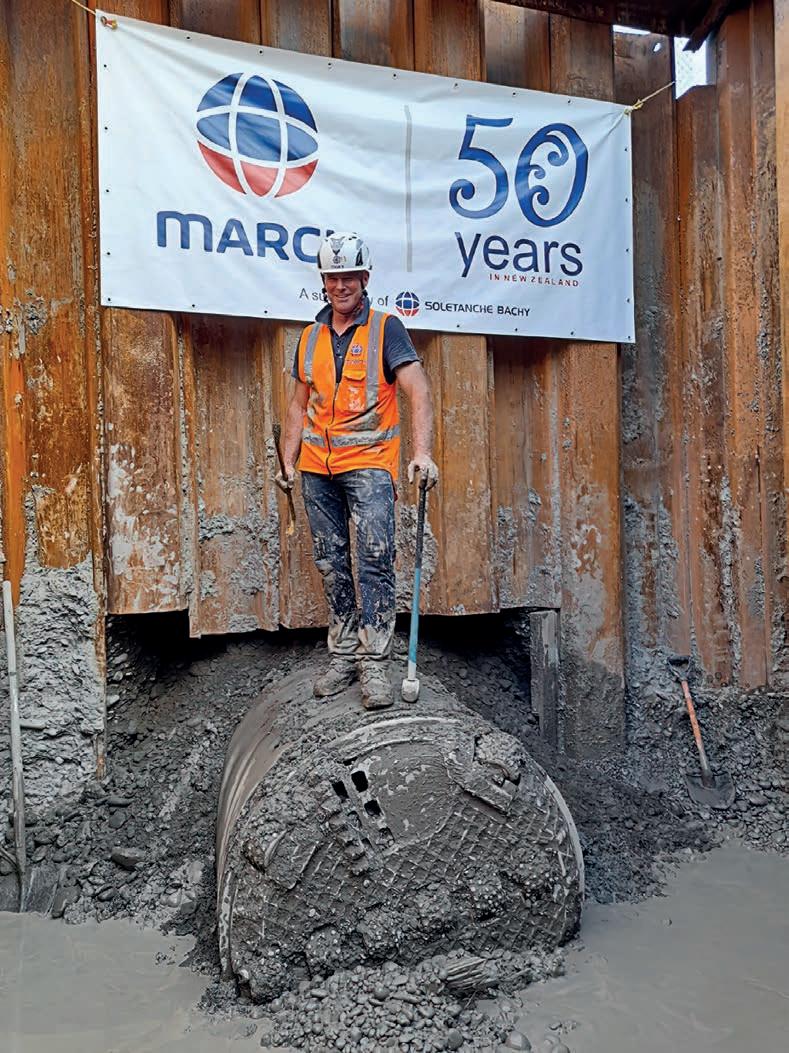
Tunnelling under live rail Hayton Road Wastewater Mains Upgrade required 430 m of existing DN525 wastewater main to be upsized to DN900 and DN1000 from Hayton Road to Alloy Street in Christchurch. The Rob Carr-March JV successfully completed tunnelling under a live rail corridor to replace a section of wastewater main under Hayton Road. The project team
experienced by the KiwiRail assets. The construction team were able to overcome some challenging ground conditions through complex geotechnical engineering.
A masterclass in collaborative success
The JV sees both companies’ strengths foregrounded, carving the way for success on technically complex projects. It brings with it the full force of Rob Carr’s hard-earned 30 years of experience in trenchless civil construction, combined with March’s trust and knowledge that comes from 50 years of local presence in the communities where the JV works. With further support from sister company Bessac, the combined offering is simply unmatched.
For more information visit www.robcarr.com.au and www.marchconstruction.co.nz
Keeping busy: Empire
Infrastructure is involved in a range of remarkable projects across Australia and New Zealand
Empire is an infrastructure solution supplier with decades of experience providing solutions for major infrastructure projects across Australia and New Zealand.
Empire Infrastructure prides itself on supplying quality products, on time and in full, making them a one stop solution for jacking pipes, shafts and manholes. The company works with some of the highest quality suppliers across the globe -- all of whom are industry leaders across their own specialised fields.
Their expert sourcing team travels the world regularly in order to seek trusted manufacturers, Empire Infrastructure is equipped to deliver the kind of high caliber products required for large-scale civil infrastructure projects.
Empire Infrastructure has an expansive range of trenchless products including Centrifugally Cast GRP jacking pipe, Filament Wound GRP jacking pipe, Reinforced Concrete jacking pipe which can also be lined with HDPE, PVC, GRP and Steel. The company also supply’s precast concrete segments for shaft and sewer pump station applications as well as Centrifugally Cast or Filament Wound GRP manholes.
Keeping busy on Picton Involving the separation of century-old stormwater and wastewater pipes, the $24 million Picton Street Network Separation project in Auckland NZ is an impressive addition to Empire Infrastructure’s resume.
The project, taking place in Freemans Bay, will help expand the network’s capacity to manage the increasing demands of Auckland’s growing population. The Freemans Bay area continually experiences around 40 overflows each year and has suffered from decades-long flooding issues.
The scheme saw 1 km of DN600 –DN1400GRP jacking pipe supplied by BOSSPIPE. In the lead up to the award of the project, in depth discussions took place between BOSSPIPE, the principal contractor for the project, March Constructions, and
tunnelling contractor Rob Carr. It was decided that the option to use GRP jacking pipe in place of the previously specified concrete jacking pipe would be not only more cost effective but also timelier and would present a lower risk for the contractors during the installation process.
Once March Constructions were successfully and officially awarded the contract, they engaged BOSSPIPE to supply the pipe to this high profile and sensitive project.
Empire Infrastructure contributed to the progress and success of the project greatly by supplying 360 metres of OD616 BOSSPIPE GRP jacking pipe, 365 metres of OD1127
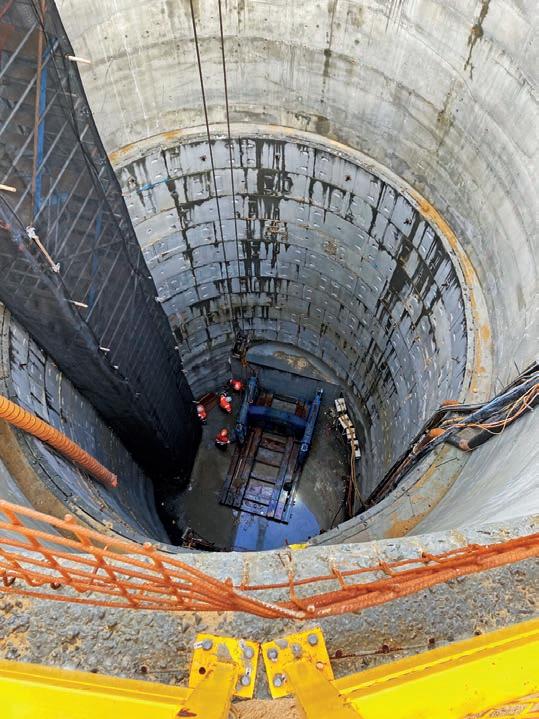
BOSSPIPE GRP jacking pipe and 210m of OD1499 BOSSPIPE GRP jacking pipe.
Brooklyn and Ettamogah mean more than just sewers
UNDER NEW ZEALAND
The renowned and famous border town of Albury, NSW, is home to a collection of major sewer upgrades.
Local Albury company Longford Civil constructed sewer augmentation works alongside the Nexus Industrial hub at Ettamogah, just outside of Albury in NSW. An important step in preparing the 450-hectare site to become a major manufacturing, transport and logistics hub for the region.
The NSW Government is contributing $9.9 million to the critical infrastructure works as part of the Regional Growth Fund’s Growing Local Economies, funded from the Restart NSW Fund. This is in addition to funding from Albury City and the Australian Government and complements previous NSW Government funding for associated road and rail upgrades.
Much like with the Picton Street Network Separation project, Empire Infrastructure supplied 1650 m of OD478 BOSSPIPE GRP jacking pipe, 90 m of OD427 BOSSPIPE GRP jacking pipe. Just a bit up the road and currently under construction is the Brooklyn Fields Sewer which incorporates 1100m of DN450 jacking pipe. The trenchless aspects of both of these Albury City were handled by the Adept Civil group.
Gippsland wastewater services to get helping hand thanks to Empire Gippsland Water supplies wastewater services to approximately 70,000 customers in a 5000 km2 region, southwest of Melbourne. In recent times, CRE Excavations have been a huge contributor to the upgrades in the region.
CRE managed to have installed almost 2800 m of DN300 - DN525 BOSSPIPE across five separate projects. As part of each project, CRE engaged the services of L&D Micro Tunnelling, and they successfully installed the jacking pipe using trenchless methods.
It made sense for CRE to go for the trenchless option, given the design depths and existing infrastructure. The size of the open trenches, the requirements of shields, the amount of backfill required and the safety risk were all eliminated by choosing the micro tunnelling with the BOSSPIPE CCGRP Jacking Pipe.
All part of Victoria’s big build: Empire on Glenroy level crossing
As part of the Victorian’ governments monumental level crossing removal project, the John Holland Group completed the removal of the Glenroy level crossing.

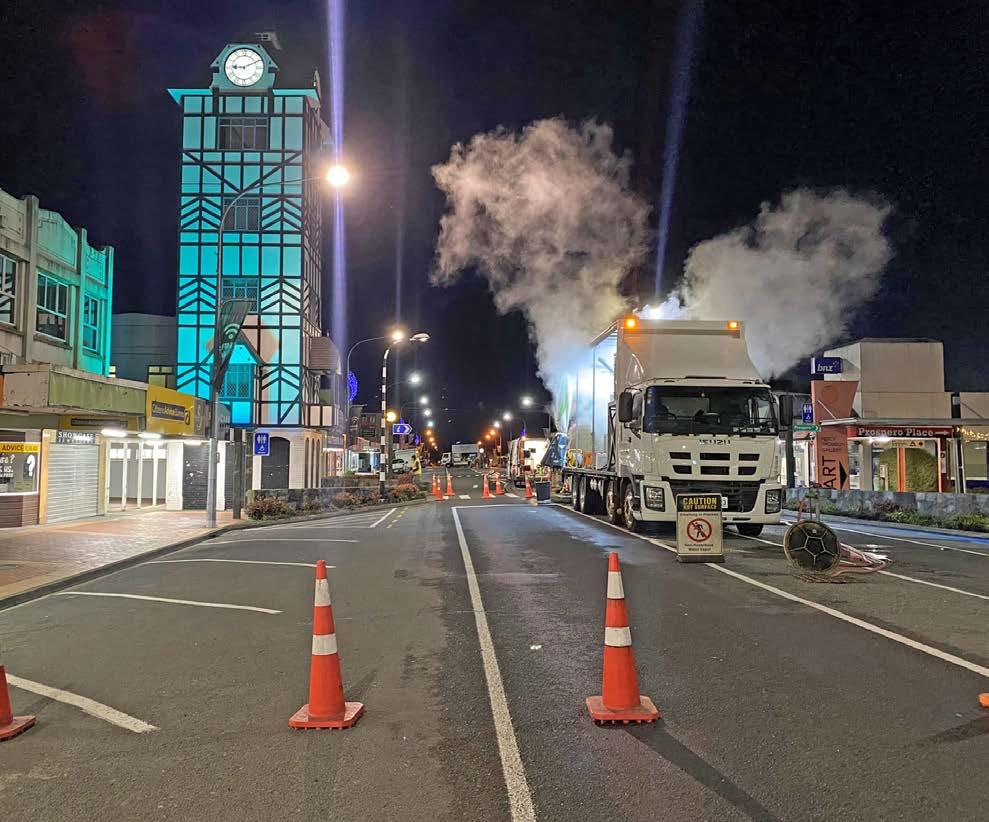
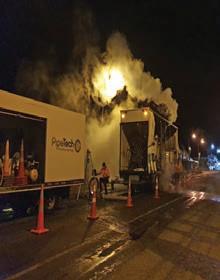
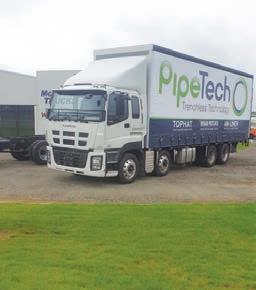
The removal of the level crossing is set to improve congestion for the 19,000 vehicles that pass through the crossing each day as well as significantly improve safety for pedestrians, cyclists and drivers.
As part of the upgrade, the major stormwater pipeline needed to relocate as well. CP&P Australia was able to supply JHG with
370 m of reinforced concrete jacking pipe in order to allow the installation to be completed successfully and on time.
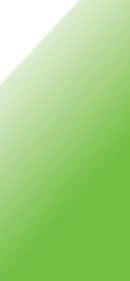
Creating new communities with the Parramatta Light Rail
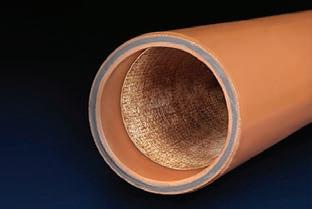
A similarly major project which is set to create new communities, connect locations across NSW and help both locals as well as visitors navigate and explore all that the region has to offer, is the Parramatta Light Rail. Delivered to serve the ever-growing population of Sydney, the project is one of the NSW government’s latest major infrastructure projects.
Rob Carr were tapped by CPB/Downer to install 510 m of DN1500 and 72 m of DN1200 reinforced concrete pipe supplied by CP&P Australia in order to upgrade the stormwater infrastructure in the Parramatta region.
Extending Quinn’s Main Sewer
Continuing Empire Infrastructure’s tradition of an involvement with noteworthy infrastructure projects is their supplying of Macrete precast concrete segments to the Quinn’s Main Sewer Extension in Perth.
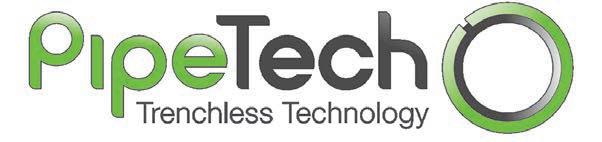
The Quinn’s Main Sewer, will allow conveyance of wastewater flows from Ellenbrook, Jandabup and Neerabup main
pump stations into the Alkimos WWTP as the existing wastewater conveyance infrastructure, does not have sufficient capacity in the long term.
As of this writing, Rob Carr is currently undertaking the final leg of construction for the project. The project includes a large sewer pipeline and a number of deep shafts up to 9 m in diameter and up to 27 m deep. The concrete shaft segments are engineered and produced to the highest standard and suitable for various shaft diameters and depths.
Empire Infrastructure works with companies that have an extensive track record of successful project supply, delivering on time and in full, the company typically chooses to work with suppliers who have a strong focus on quality assurance. This also means Empire’s supply partners offer extensive experience in their respective field of expertise.
Thanks to the company’s position as a one-stop-shop for a variety of trenchless projects, Empire Infrastructure has been the infrastructure solution supplier across a wide range of recent projects in both Australia and New Zealand.
For more information visit www.empireinfrastructure.com.au
The CALIBRE range is set to redefine how underground cable ducting and fittings perform.
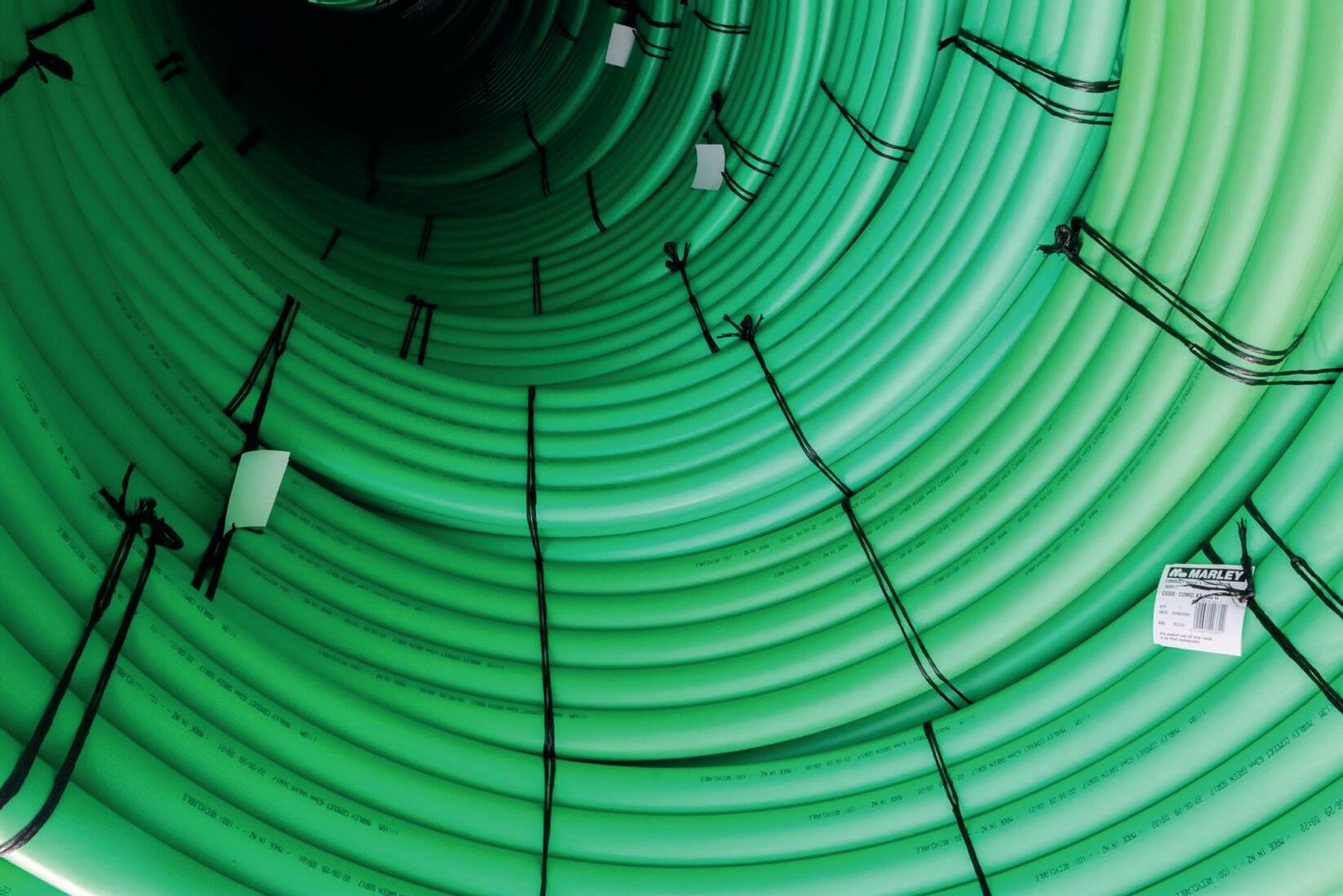
Marley’s new CALIBRE™ range is leading the charge in NZ
An iconic Kiwi brand, Marley has become one of New Zealand’s largest manufacturers in the plastics industry. Involved with extruded and injection moulded products, Marley manufactures using PVC, polyethylene and polybutylene.
Belonging to the Aliaxis Group, it has also provided Marley with access to thousands of new products around the world. The Aliaxis Group is passionate about creating sustainable innovative solutions for water and energy. Providing people around the world with advanced plastic piping systems, it leads the industry in a way that anticipates the rapidly evolving needs of its customers.
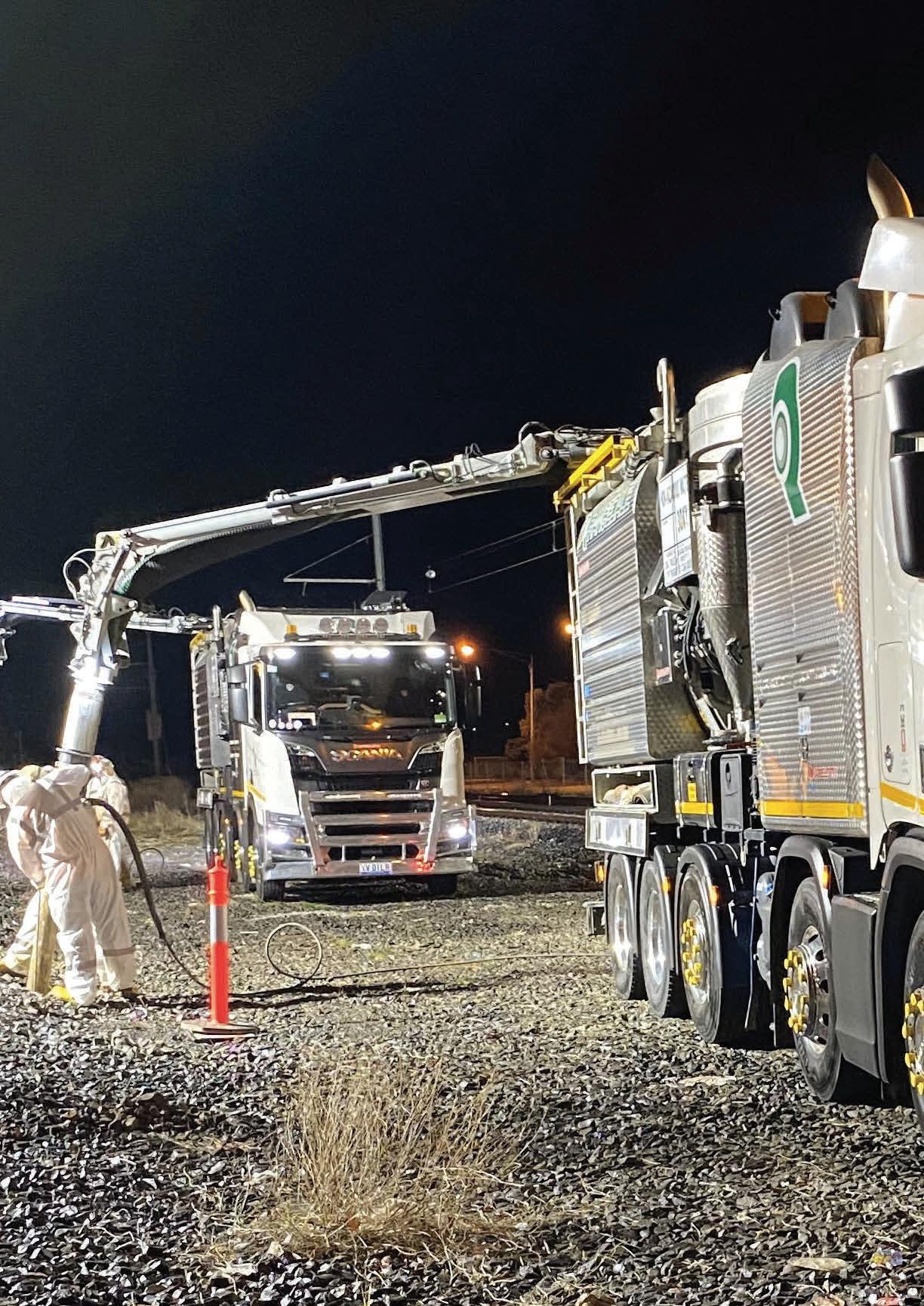
A simplified performance-based range Marley New Zealand’s most recent innovation – the new CALIBRE™ product range – is only going to further cement the company’s place as a staple infrastructure choice within the New Zealand market.
Having been with the company for several years, Senior Project Manager for Marley New Zealand, Nigel Lee has watched the CALIBRE product range evolve across all stages of its development.
The new range is an amalgamation of the Marley PVC Cable Duct segment (particularly the 700 Power & TC Comms series) and the Marley PE Cable Duct segment from the COMD series. However, the CALIBRE range redefines how underground cable ducting and fittings perform.
As a fully featured PE and PVC cable duct range, CALIBRE cable duct systems are manufactured to the electrical purposed AS/NZS 61386 standard with product classification according to a performance-based mechanical duty rating. In particular where PE cable ducting conformance has been to the pressure based AS/NZS 4130 standard, conformance to pressure, SDR and resin requirements is no longer the case.
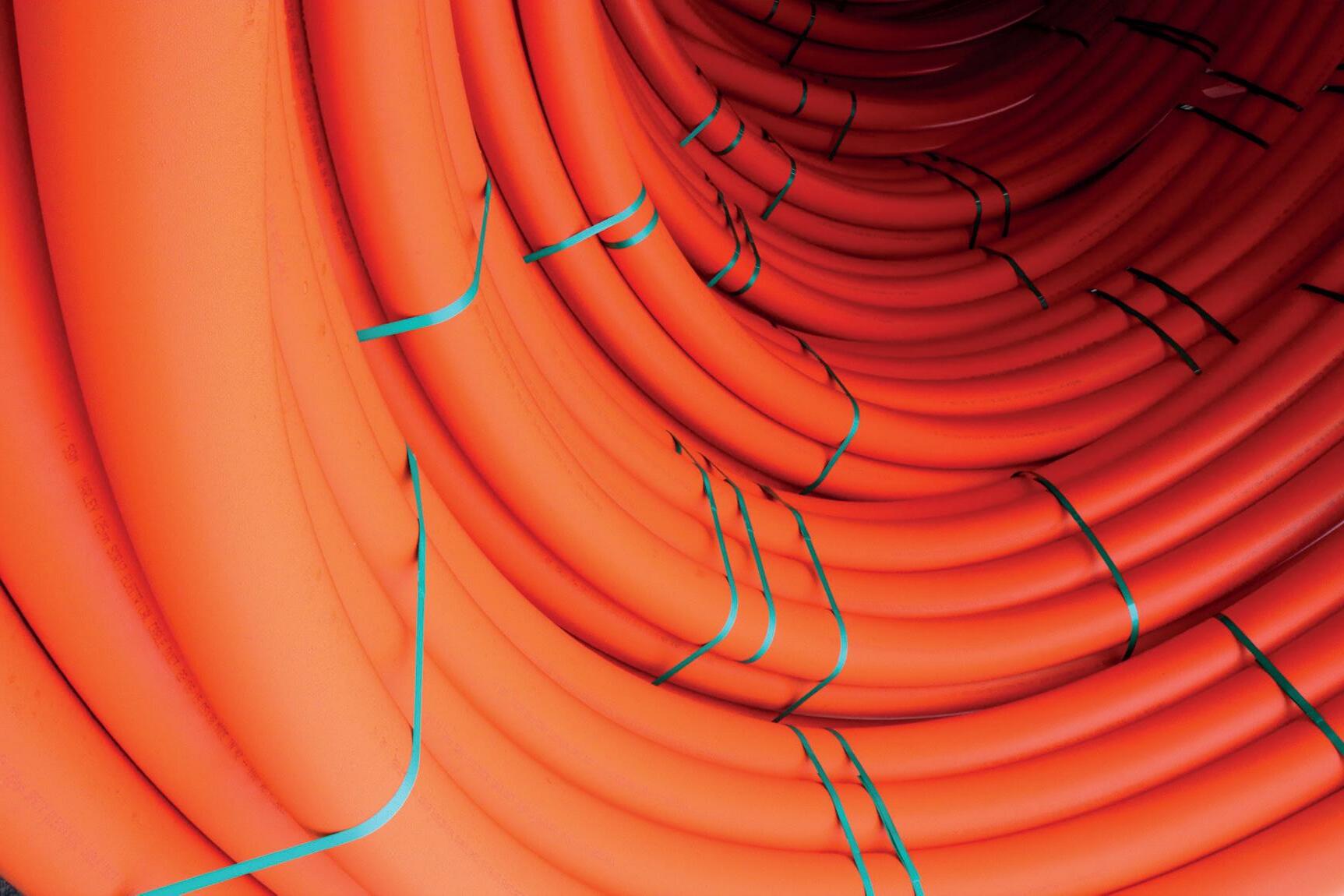
Trench or trenchless: CALIBRE has got it covered
There are a range of notable factors that need to be considered when selecting between a trench or trenchless cable duct for electrical utility projects. Dependent on the replacement, renewal or future proofing requirements of an asset, several project parameters and sustainability factors may influence the outcome.
Some of the project parameters which could influence the outcome, includes the design of the cable and ducting as well as the speed of installation. Likewise, the engineering design and reliability, site conditions, preferences of the contractor working on the project in addition to environmental and social complications may also contribute.
“There are really two types of installation methods: trench and trenchless,” says Lee.
“Using a trenchless drilling and installation method, ensures that there is minimal disruption to the surface. This unlocks the potential for works to be undertaken beneath roading, under bodies of water or buildings without disrupting the everyday lives of people – particularly if works are near major roading.”
Similarly, the trenchless method also comes with the added benefit of having a faster installation rate for larger scale project and has the capacity for longer and deeper installations, with fewer joins required than compared to open cut trench.
Alternatively, utilising a trench is ideal for working around unidentifiable services and geotechnical features. The trench method also grants the opportunity for shorter runs, a lower depth of excavation and doesn’t require specialist equipment or personnel when compared to the expertise to operate and facilitate horizontal directional drilling (HDD) works.
“Having the choice between a trench and trenchless option guarantees that there’s a way for projects to reap the full benefits of using the CALIBRE range,” says Lee.
Fully featured and fully formed
“CALIBRE is fully featured,” says Lee. “Which means each product comes with a whole lot a benefits which we at Marley have grouped into three major segments: durability, productivity and compliance.”
When it comes to durability, the CALIBRE product range is certainly built to last: having been designed for over 100 years of in-ground and in-service performance and very heavy duty, heavy duty and medium duty capabilities.
The range also takes into consideration the need for installers’ swift, effective and safe installation and burial by ensuring ease of handling capabilities, with customised lengths, metre marking and colour coded power and/or comms identification. Likewise, the trenchless CALIBRE option offers PE Electrofusion joining and PE Compression fittings with the trench CALIBRE option offering both the aforementioned options in addition to PVC Solvent joining.
When it comes to quality assurance and compliance, Lee reflects, Marley has undertaken extensive efforts to ensure that designers and contractors can be confident that they’re in the right hands selecting the CALIBRE range. Both the trench and trenchless CALIBRE range are 100 per cent recyclable and have undergone rigorous thirdparty verification and testing to assure that they are up to the task.
“It’s been important to us since the beginning of the development of this range to ensure that it’s up to – or even exceeds –industry standards. By working with a independent third-party organisation to verify the quality of the range, we’re doing our due diligence on behalf of designers to ensure what we’re installing into our infrastructure can last for years or decades to come,” says Lee.
The CALIBRE range launched on 30 September in New Zealand, to find more visit www.marley.co.nz
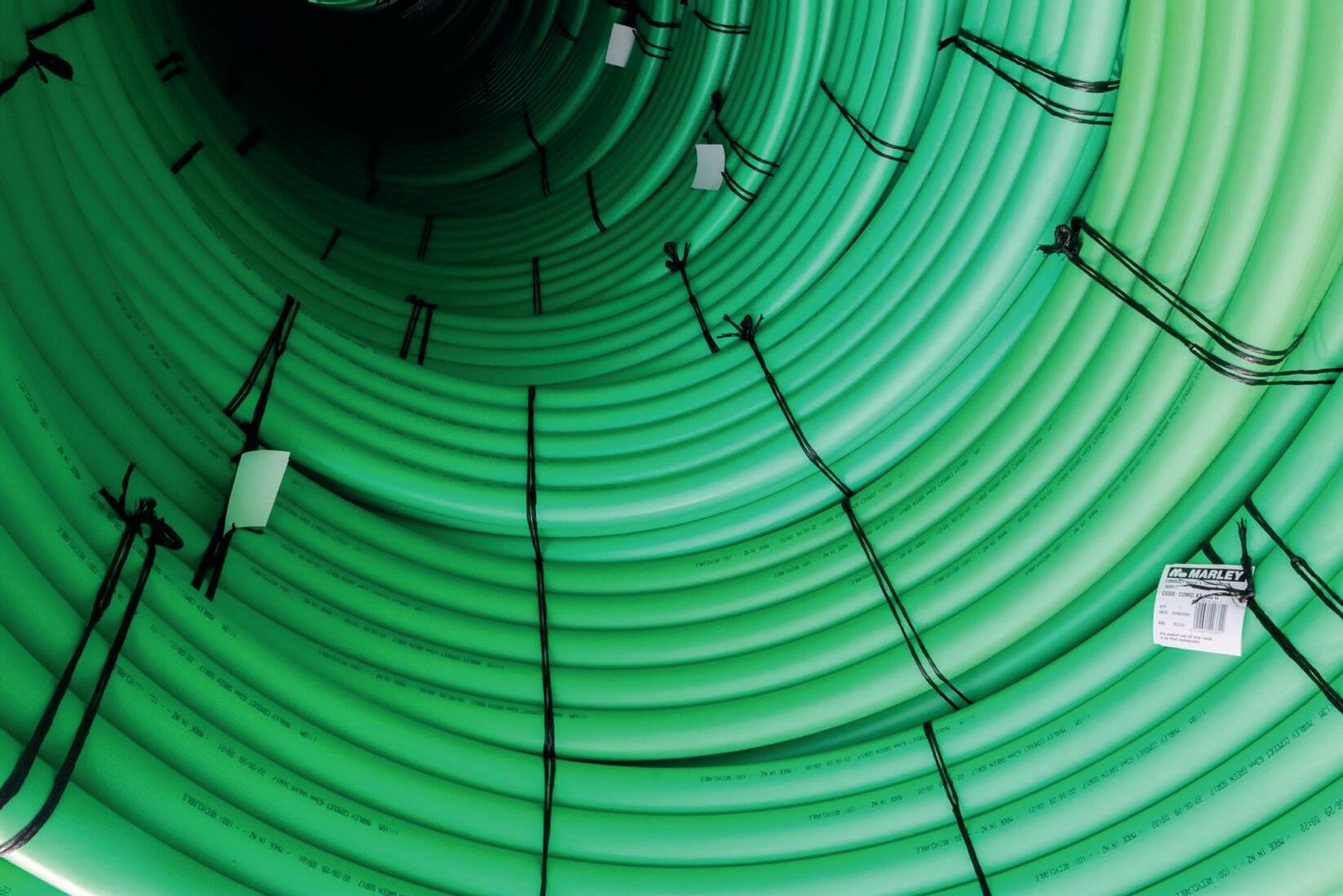
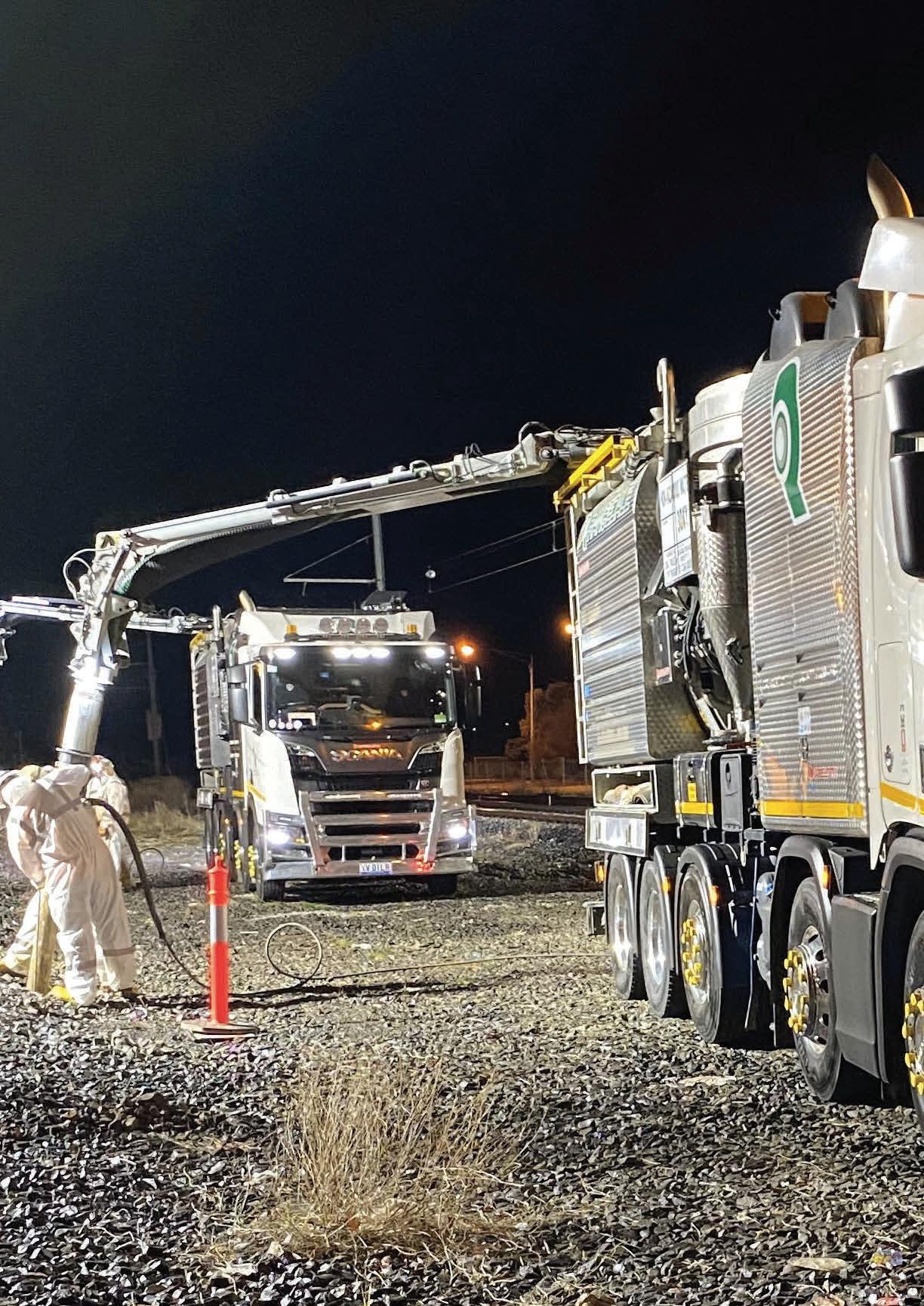
NordiTube presents the new NORDILONG: An independent long-distance pressure liner system
NordiTube Technologies has established a global position as a technology provider for trenchless pipe rehabilitation.
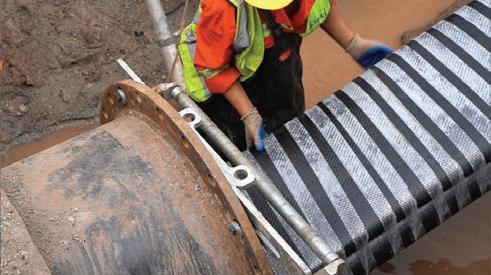
NordiTube has provided rehabilitation products for pressure pipe applications, like portable water and gas, for more than 35 years.
A rehabilitation solution for all kinds of pipes
In the 1980s, the first pressure pipe rehabilitation technology, the Phoenix System, was developed in Japan. The system was designed to reduce damage to pipes during earthquakes. Shortly after, NordiTube developed the Phoenix system further to match with TUBETEX liner – the European water and gas pipe network’s standard. New products followed, like the fully structural NORDIFLOW pressure system, the NORDIWALL gravity system, the r-tec CloseFit PE Pipe system and recently the
NORDILONG, a long-distance, resin-free liner system from DN 50 up to DN 1200.
NORDILONG system
The NORDILONG liner is an insertedhose according to ISO 11295, and is rated as an independent pressure liner. The inner layer of the liner is selected depending on
the transported medium; gas, oil, steam or water. The liner has the US NSF drinking water certificate. The middle layer is designed to provide high flexibility and high-pressure resistance. The outer cover protects the fiberreinforced middle layer and prevents the liner from elongation or shrinkage. The diameter ranges from DN 50 up to DN 1200, and the long potential insertion length of up to 3 km in one pull, in combination with special linerconnectors provide economical rehabilitation solutions for most existing transmission pipelines.
World record project
In 2019 the Tangshan Portable Water Pipeline company had to repair a DN 800 steel water pipe. The pipe was leaking and, after a major burst, the decision was made to upgrade the
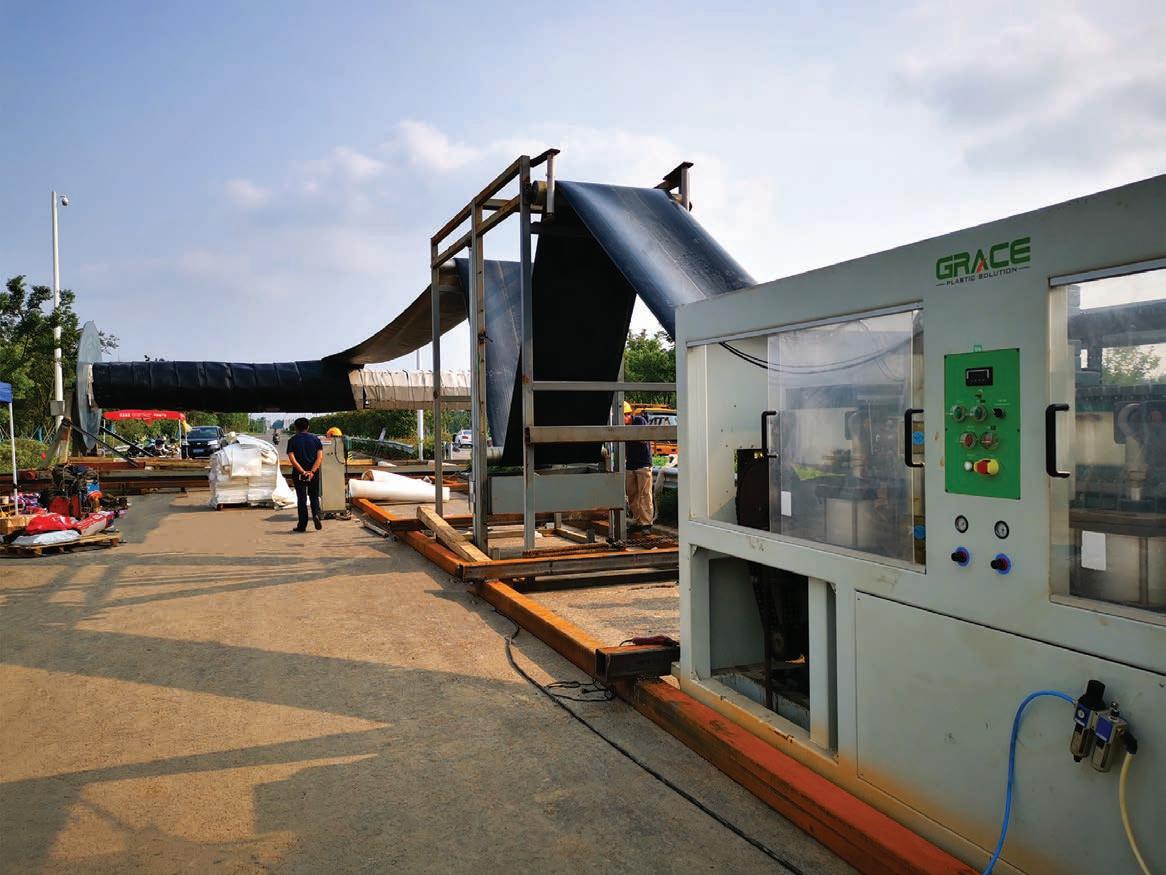
line. During the design process it appeared that 1200 m of the pipe crossed a sensitive agriculture area. A replacement of the pipe at the same route was not possible and a relocation of the pipe was too costly. A further challenge was the available construction time window – the 1200 m had to be renovated in less than two weeks. In addition, Tangshan Water requested to keep the flow capacity of the original DN 800 pipe and an operational pressure of 1.0 Mpa.
The only Technology available to meet all the criteria was the NORDILONG IH Liner system. The inserted liner can be produced in long lengths and in diameters up to 1200 mm. The end-connector system covers the range from DN 50 to DN 1200 and the PE coating provides excellent hydraulic characteristics.
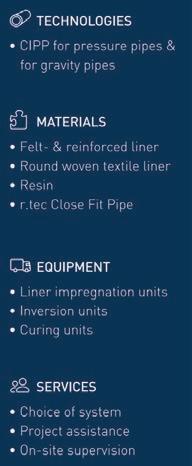
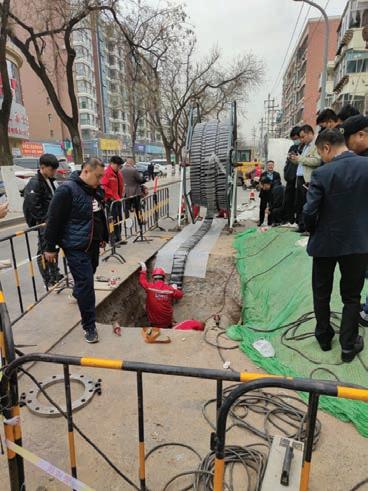



The installation of a DN 800 3-layer inserted liner over the length of 1.2 km was a world record. The construction team completed the pipeline repair project of the total length of 1.2 km in only 5 days. After the completion of the project, the safety and stability of the pipeline water supply were greatly enhanced, the flow capacity of the pipeline was improved, and the risk of burst was eliminated.

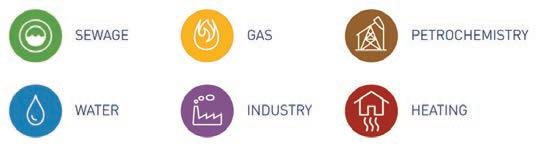
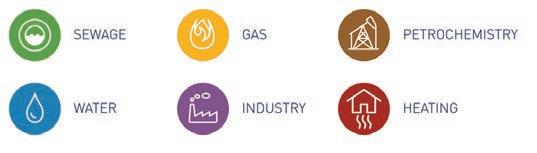
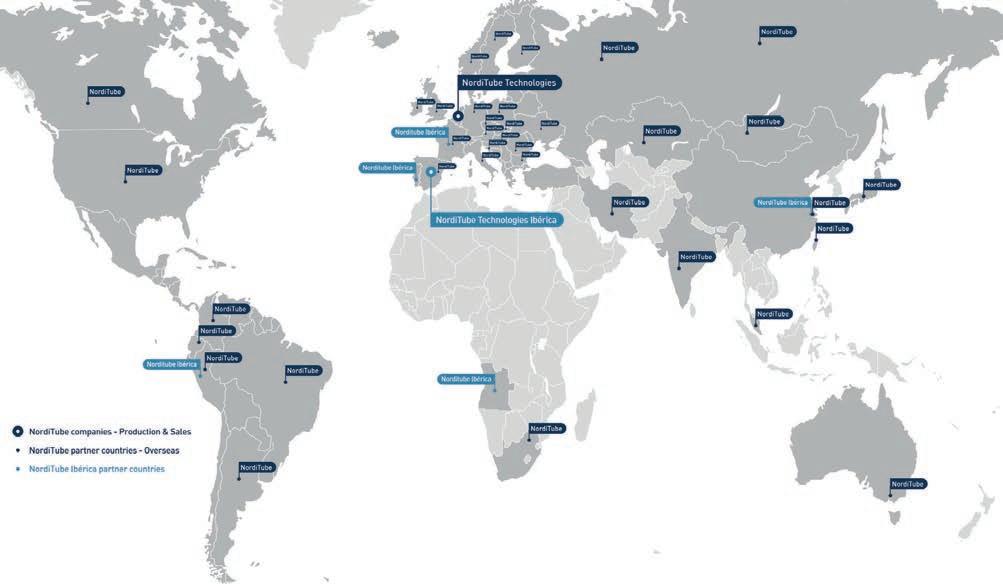
Cooperation TDM pipeline solutions & NORDITUBE
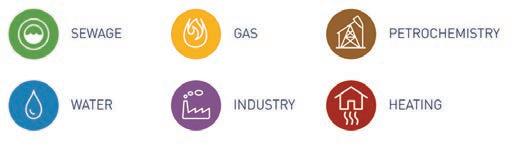
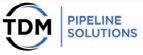
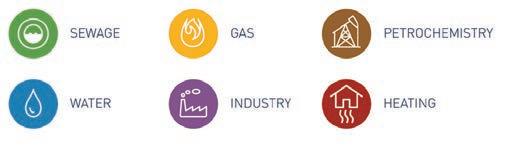

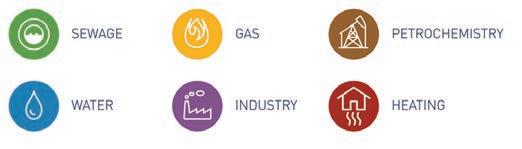
In the lead-up to the No-Dig 2022, The Drain Man (TDM) Pipeline Solutions, AUS, and NordiTube entered in a partnership to expand the product portfolio for NORDITUBE’s
technologies in Australasia. The local TDM representations and services will be a perfect complement to the global NORDITUBE partner network. As a first step, TDM and NordiTube will concentrate on entering the AUS/NZ market with liner products for gravity pipes and drinking water. For the future, TDM and NordiTube are ready to support gas pipe upgrade projects and the mining industry as well. TDM Pipeline Solutions is a division of Group Australia along with other entities and divisions including TSE, with operations in Melbourne, Sydney and Perth. TDM Pipeline Solutions specializes in commercial, industrial and network services working most prominently with civil infrastructure, water utilities and local government markets. Triple certified to ISO 45001 (Safety), ISO 9001 (Quality) and ISO 14001 (Environmental), TDM Pipeline Solutions provides services that include CCTV pit and pipeline inspections, drain cleaning, CIPP relining, sectional pipe repairs/patches, top hat & junction relining and robotic cutting.
For more information visit www.norditube.com
Now in AUS and NZ in Partnership with TDM GroupNORDILONG IH Liner installation diameter DN 50 to DN 1200 range.
Supporting the infrastructure upgrade boom in New Zealand
Hynds manufacturing has empowered customers across New Zealand to succeed by delivering highquality products and innovative solutions, designed with the specific challenges of each new project in mind.
Over 49 years of partnership with New Zealand’s infrastructure industries has equipped Hynds with the local knowledge and expertise to deliver on many projects in New Zealand.
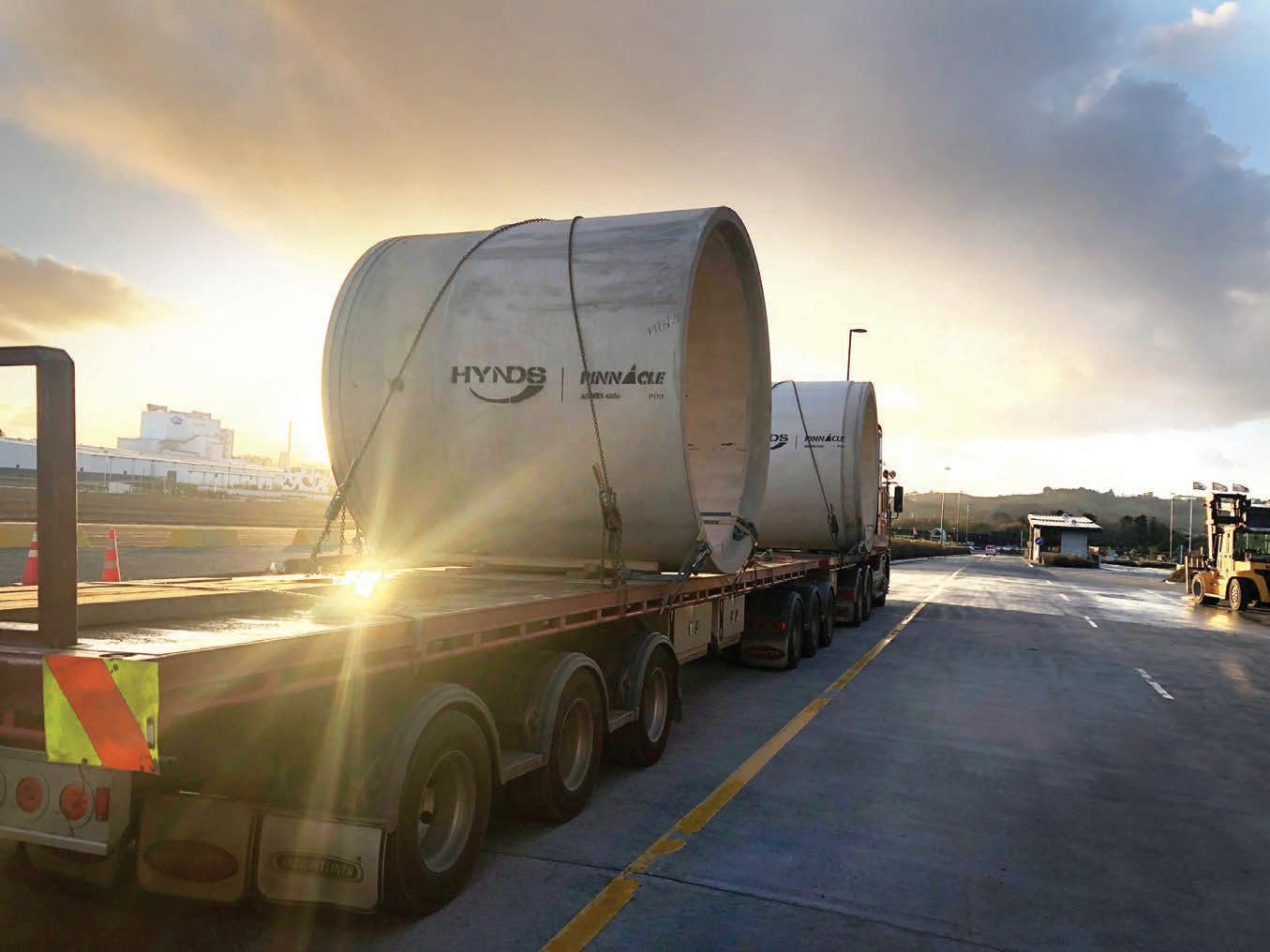
Sections of water infrastructure across the country are nearing the end of their service life, prompting a series of upgrade projects to ensure the safety of their water and wastewater networks for years to come.
conditions beneath the ground has pushed Hynds to innovate and adapt, enabling clients to succeed.
Success under pressure Hūnua 4 is Auckland’s biggest water project. Completed in 2022, it includes a new 31 km watermain that connects Watercare’s reservoirs to water storage in the city centre.
Section 11 of the project consisted of three
ID, 3000 mm OD Jacking pipe, with a total length of 2.8 km under major arterial roads, well-established residential and commercial suburbs. This section provided a temporary works tunnel that allowed teams to install the 1600 mm OD CLS watermain.
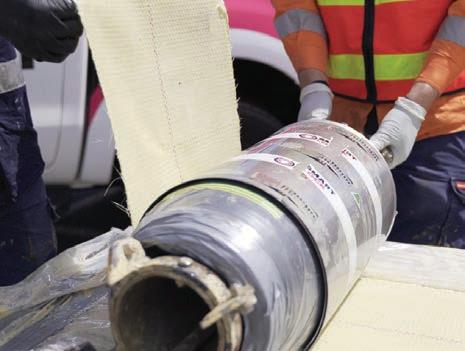
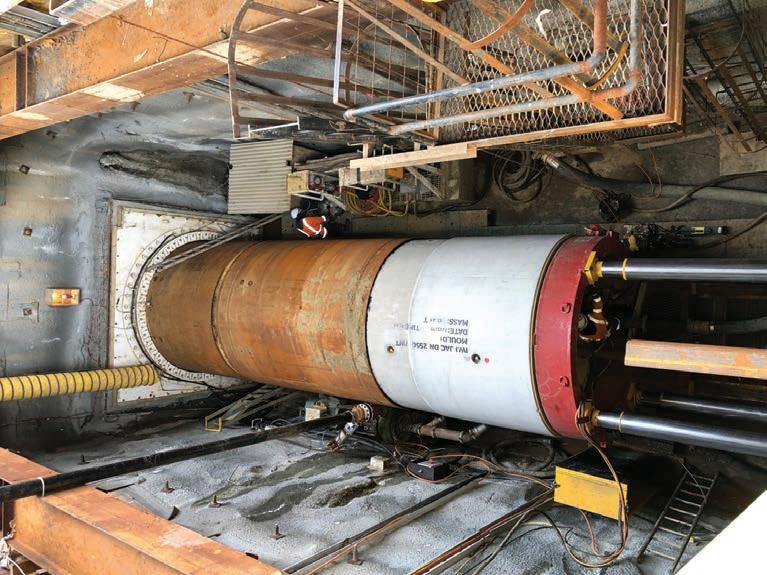
The second drive for the Hūnua Section 11 set the record for the longest single pipejacking drive in the southern hemisphere by a tunnel boring machine (TBM). The drive was 1216 m, and the record was broken straight after, with the third drive hitting 1263 m.
The drives included multiple compound curves, highly fractured and variable basalt and lava caves presenting the contractor McConnell Dowell with many challenges.
In addition to the jacking pipe the length of the drives meant that McConnell Dowell required five to six intermediate jacking (interjack) stations for each drive.
Throughout the project, Hynds supported McConnell Dowell to deliver the project and set the bar for future works. The success of the project created a resilient water supply, safeguarding the future of the city’s water supply from the Auckland’s southern reservoirs.
Adapting and delivering
More recently, Hynds has been supporting McConnell Dowell in Wellington who have
partnered with Wellington Water on the Barber Grove to Seaview Wastewater Pipe Duplication project.
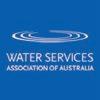
The project requires a new 1200 m long, 1000 OD PE pipeline. It will connect the Barber Grove wastewater pump station to the Seaview treatment plant. The existing 50-yearold concrete pipe is vulnerable to earthquakes and will be supported by the new pipe. The pipes carry 90 per cent of the Hutt Valley’s wastewater.
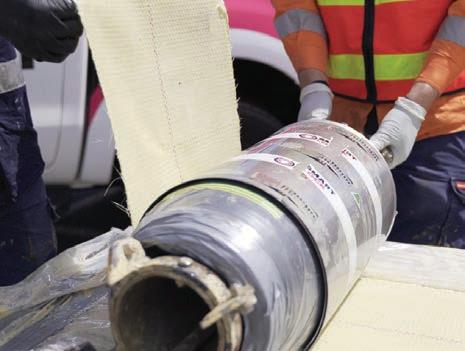
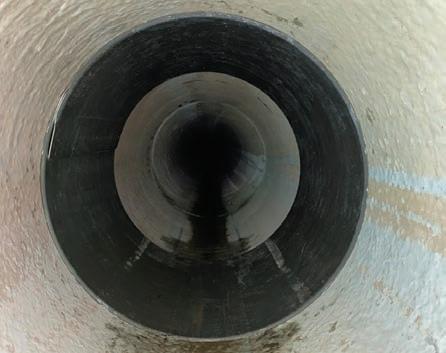
Over half of the total length being installed for the project (55 per cent) runs down the centre of Randwick Road, a main arterial route. With housing on either side of the road, as well as a school and a golf course, the decision has been made to use micro tunnelling to install a concrete conduit jacking pipe which will carry a slip lined DN1000 PE100 wastewater pressure pipe along this stretch of the project.
Hynds supplied the contractors with its 1200JACZ marine grade pipes manufactured in the Hynds Christchurch Factory. The pipes were fabricated to a class 4 loading with increased concrete cover as required for marine environments. The 1080 mm ID and 1310 mm OD – perfectly matched McConnell Dowell’s tunnel boring machine. The 1000 OD PE pipe fits snuggly into the concrete conduit pipe with
minimal packing required.
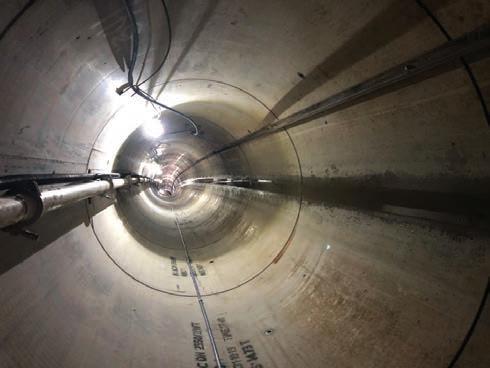
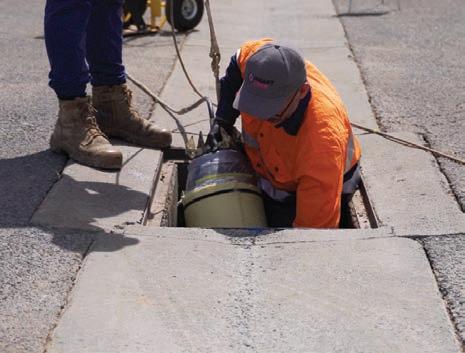
Installation of the concrete pipe along the road has been split into three portions, or drives, at 160 m, 200 m, and 230 m. To further minimise disruption, there are two launch shafts and two retrieval shafts – limiting the disruption caused by moving equipment as work progresses.
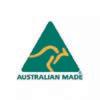
Three grout ports have been included on every third pipe length – so that bentonite can be pumped in during jacking and allow for grout to be installed, fully sealing the void between the outer wall and the surrounding earth.
Two inter-jack pipe sets have also been supplied, with the goal of recovering and reusing the first set after drive 1 is complete. The inter-jacks provided a unique challenge, as each pipe has a 32 mm thrust plate cast-into-eachend with threaded holes to allow the inter-jack station to be secured to the leading pipe.
The mould had to be modified to hold the plate in place while it was centrifugally spun. Hynds Pipe Systems completed the design of the steel CAN pipe required by the interjacks thus supplying the customer with a full concrete jacking pipe package including MDF timber packers used as cushion between the pipe faces to transfer jacking forces evenly.
Family-owned
The Hynds group includes nine business units that include the manufacturing of concrete, metal and plastics, production import and distribution, and trade supply. Though it has expanded to include over 900 employees, the company remains proudly family-owned, and has earned its reputation as an innovative, customer-focused company.
For more information visit www.hynds.co.nz
Creating the Future of Water for New Zealand communities

Leading pipeline infrastructure company, Interflow, has an ambitious goal: to improve the lives of the communities they serve and the environment they work in for generations to come.
With an estimated spend of up to $185 billion on infrastructure over the next 30 years, companies like Interflow are helping local councils and authorities to create, renew and maintain the nation’s pipeline infrastructure in sustainable and cost-effective ways.
An all-in-one delivery partner Servicing the needs of pipeline infrastructure asset owners for over 85 years, Interflow has earned its position as a leader in the water industry by continually challenging the status quo.
Innovation lies at the core of its service offering. The company is dedicated to developing bespoke solutions that drill to the heart of its customers’ problems; robust, sustainable solutions that will service the growing needs of the community for generations to come.

its self-performed capabilities and network of trusted subcontractors. With extensive inhouse expertise, Interflow is delivering for New Zealanders, by New Zealanders.
Delivering trenchless solutions across the
wastewater and stormwater sectors.
By saving the time, costs and social impact associated with excavation, trenchless technologies have quickly become the preferred construction methods of choice for local councils and water authorities across the country.
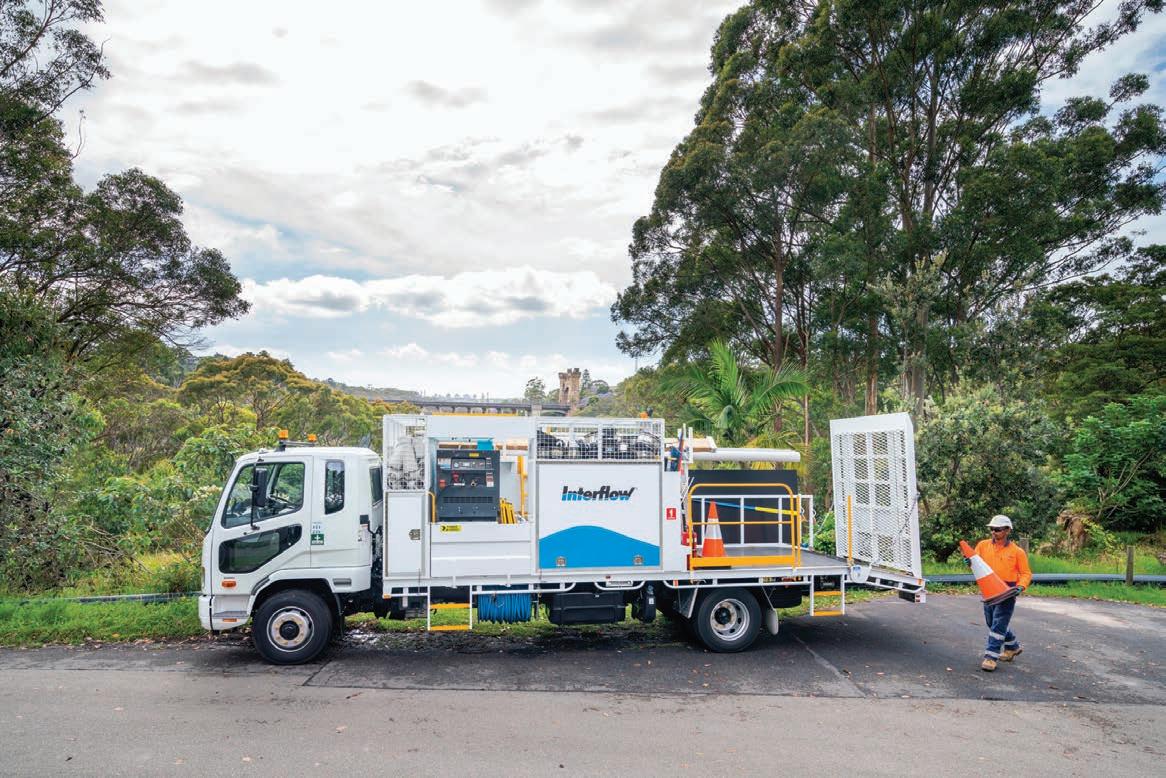
Dig and replace methods, particularly in urban areas, can be disruptive, impacting residents, commuters and the environment with dust, noise, and a hefty site footprint. Outside of urban hubs, challenging natural landscapes and the need to minimise the impact on local ecosystems often rules out extensive excavation altogether.
Trenchless technology can minimise these impacts by reducing environmental disruption to a single point of entry – or eliminating it altogether – as well as minimising project time. This also presents valuable cost savings to asset owners, who often look for the most efficient
work for the community and the environment.
A recent example comes from the bayside city of Nelson in New Zealand’s South Island. Urgent action was needed to improve the reliability of the Nelson community’s wastewater service and to protect the Waimea Inlet, a haven for bird and aquatic life.
Interflow’s customer, the Nelson Regional Sewerage Business Unit, considered a wide range of options, focussing on those that reused existing but decommissioned pipelines within the network, and that eliminated work in the Inlet.
The solution was to recommission a section of sewer that ran directly under the Inlet and had been out of service since 2007 using Primus Line, a strong and flexible liner designed specifically for pressure pipelines. The liner was installed in an ambitious single pull of 1.1km, which at the time was the longest ever attempted by Interflow.
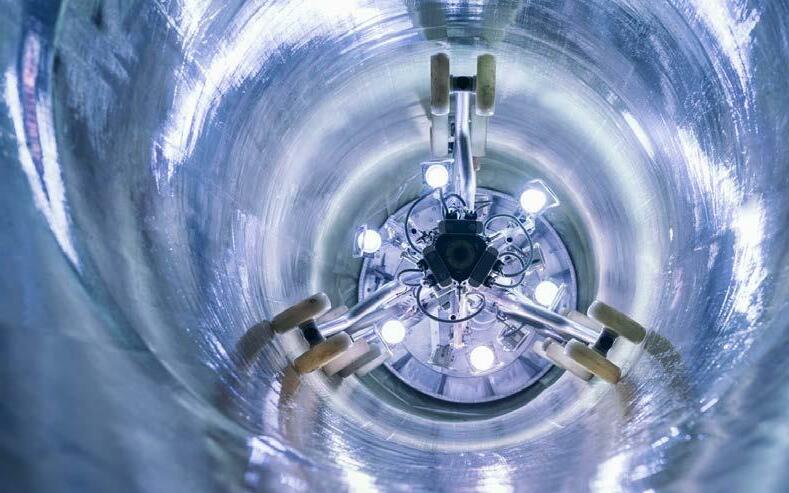
“As the pipeline we rehabilitated ran underwater, our crews operated with specialised equipment and great caution to ensure no discharges into the surrounding bay peninsula in order to protect Nelson’s pristine coastline,” says Interflow’s National Product Manager, Will Zillmann.
“We were able to quickly and effectively rehabilitate the pipe, therefore providing a cost-

effective, sustainable solution for our customer.”
Unlocking potential across the country
Over the next 30 years, it is estimated that New Zealand will need to spend between $120 and $185 billion to upgrade its water infrastructure. Adopting trenchless methods and embracing innovation is key to unlocking value and costsavings for asset owners and their customer base.
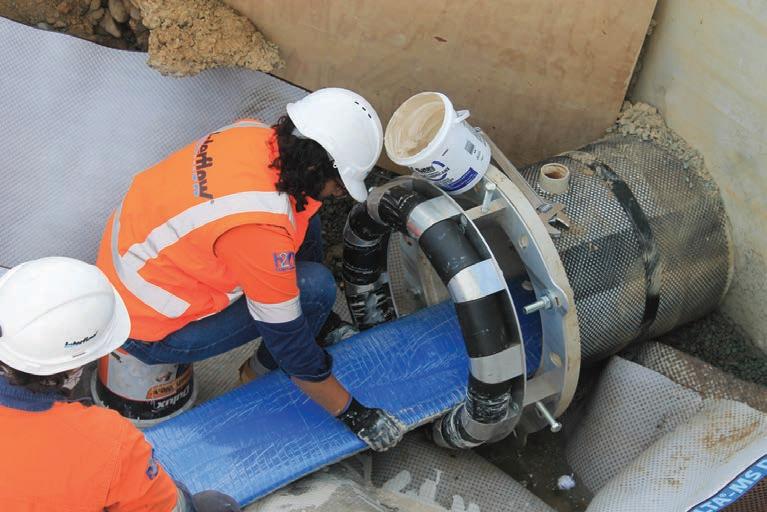
Early engagement with local delivery partners, like Interflow, can help asset owners leverage leading technologies to get the most out of their rehabilitation programs and ensure all New Zealanders have access to safe, affordable and sustainable water services.
For more information visit www.interflow.com.au
From Australia to New Zealand and around the world, kwik-ZIP are the spacers of choice
Used and recommended by pipeline and civil contractors around the world, kwik-ZIP centraliser and spacer systems are solving production casing centralisation challenges across New Zealand.
kkwik-ZIP has an established stockist in Australia, US, UK and New Zealand.
kwik-ZIP Spacers and Centralisers have been developed to solve support, grading and centralisation challenges in the trenchless and pipeline, vertical production drilling, and ground engineering industries.
Manufactured from kwik-ZIP’s engineered thermoplastic blend, the HDXT Series is suitable for heavy-weight pipe materials including: steel, ductile, mild steel cement lined (MSCL), glass reinforced epoxy (GRE), polyvinyl chloride (PVC) and high-density polyethylene (HDPE).
They can be used on all diameters from 300 mm and beyond through the simple addition of multiple segments. The casing spacers utilise a segmented design that enables the system to be used on a variation of carrier pipe sizes.
The spacers incorporate low friction high abrasion resistant wear pads, attached to load sharing runners. The number of segments required for each spacer is determined by the outside diameter of the carrier pipe.
kwik-ZIP’s spacers were installed in June 2020 as part of the Wairi trunk watermain project, located in Te Puke, the Bay of Plenty, New Zealand.
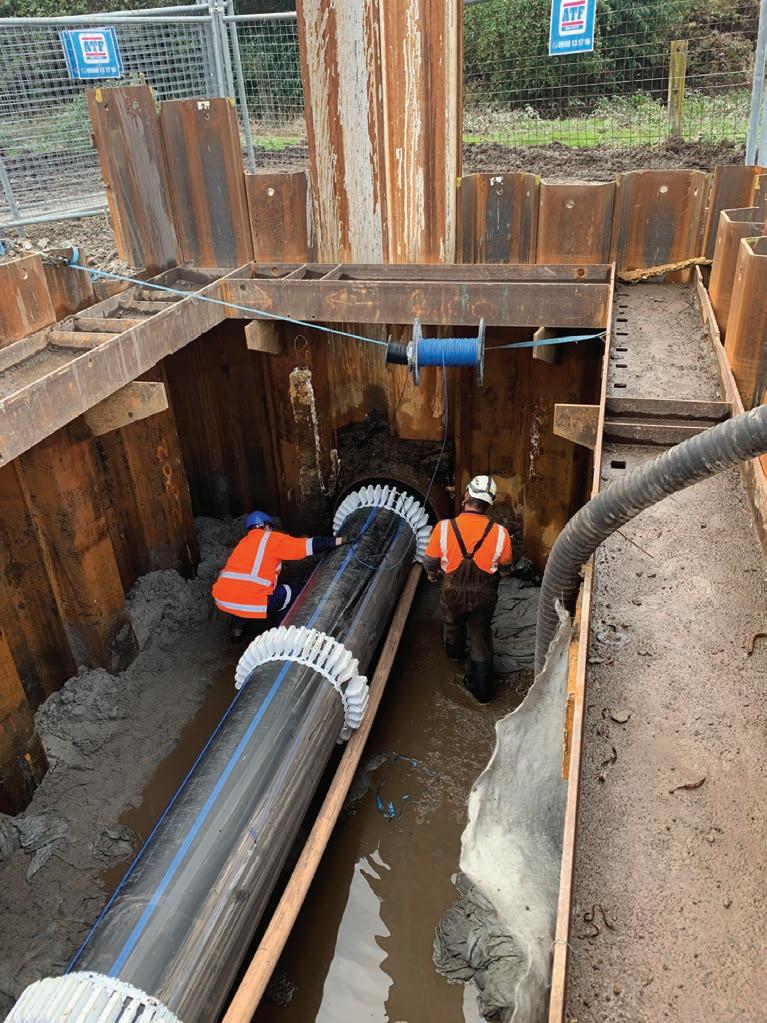
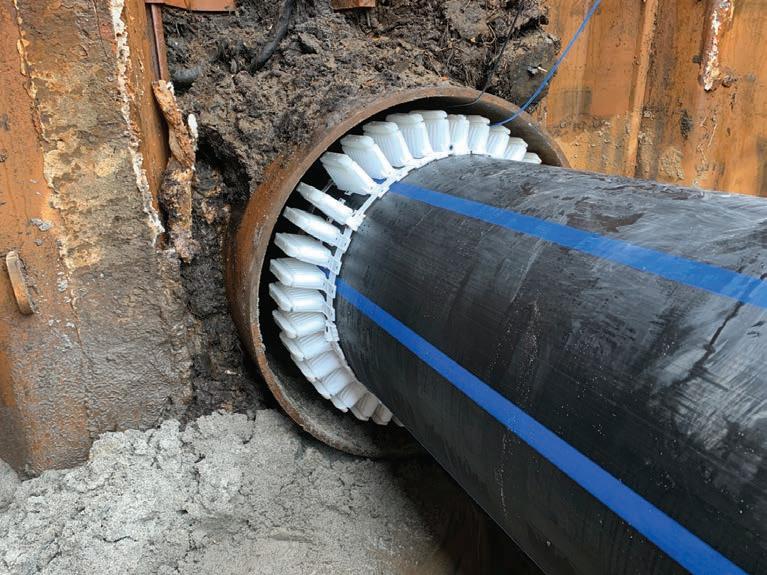
The spacers were installed around the circumference of a 710 mm PE pipeline to ensure the newly installed PE pipeline will sit centre, while pulling the pipeline through a 1040 mm steel jacking pipe.
By using the kwik-Zip HDXT 103 model spacers, the construction company have avoided any potential damage to the PE pipe on installation and protected against any future damage caused by the steel jacking pipe coming in to contact with the newly installed PE pipeline.
The construction company used the kwik-Zip brand due to the easy and quick installation with the screw lock system. This was key, due to the complexity of working below ground level. If the installation was to take longer or was more complex it could have created delays for the drillers pulling the pipeline through the jacking pipe, and therefore caused knock on delays for
the project.
Spacers were placed at either end of the jacking pipe, from there the spacers were installed at 2m intervals between each end, to avoid any sagging in the pipeline.
On site personnel were inducted into the
kwik-ZIP’s installation guide, which ensured the product was used correctly and efficiently. The product worked exactly as it should and no issues were encountered. They were very quick and easy to install and HEB Construction would not
hesitate in using them again should the situation arise.
More recently, in October of 2021, kwik-ZIP’s HDXT 103 model spacers were installed as part of the Te Maunga Outfall project located in Tauranga, also located in the Bay of Plenty. The spacers were installed around the circumference of a 1200 mm PE pipeline to ensure the newly installed pipeline would sit centre, while still pulling the pipeline through 100 m of 1500 mm existing concrete duct under the TEL.
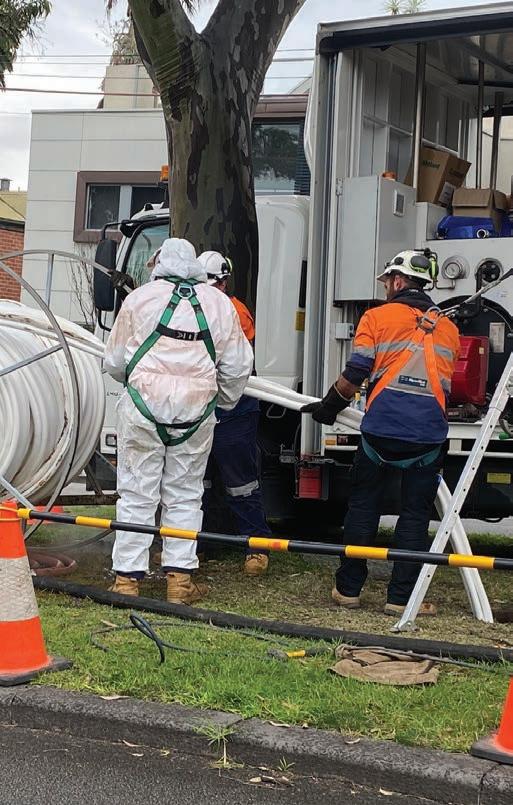
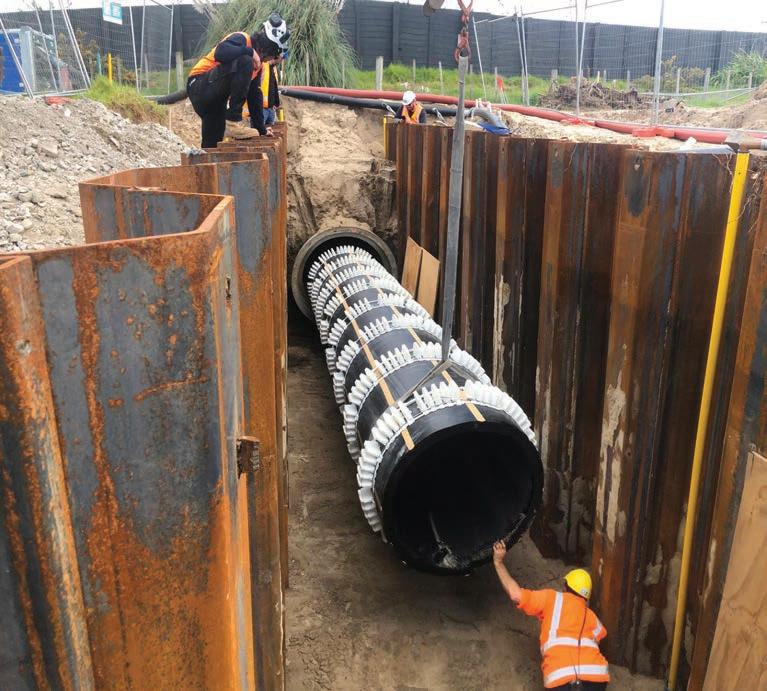
By using the kwik-ZIP spacers, the construction company have been able to avoid any potential damage to the PE pipe during installation.
Spacers were placed at either end of the jacking pipe, from there the spacers were installed at 1 m intervals between each end. The personnel at the site were fortunate to have experience with using kwik-ZIP’s products and were familiar with the easy to understand installation guide, ensuring the product was used correctly and efficiently.
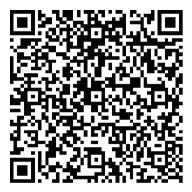
With the successful completion of these projects in New Zealand, it’s clear kwik-ZIP is continuing to build a strong reputation for hard work and innovation not just in Australia but worldwide.
For more information visit: www.kwikzip.com
Innovative drilling contractor provides pathways into trenchless education
Te Aratika Infrastructure is a unique trenchless contractor, with education and a desire to improve the lives of its community a driving factor behind the company’s operation. Always on the search for the latest technological advancements, the company has partnered with TRACTO and acquired a GRUNDODRILL 28N, and subsequent training, and is already educating the next generation of drillers on New Zealand’s North Island.
Located in Silverdale, New Zealand, about 30 km north of Auckland, Te Aratika Infrastructure is more than your stock standard civil construction and horizontal directional drilling (HDD) contractor. The innovative family business was established in 1998 to service the underground utility service industry with a passion for bringing positive change to the company’s community.
“Te Aratika” means “The Right Path” and reflects Te Aratika’s core intention of investing extensively in its people through education and employment outcomes to promote healthy, thriving families.
He aha te mea nui o te ao? What is the most important thing in the world? He tangata, he tangata, he tangata! It’s the people, the people, the people!
A grassroots beginning paved the way for the company to grow organically across industry sectors, and Te Aratika now has offices in six regions across New Zealand. Alongside the infrastructure arm of the group is Te Aratika Academy, a special character high school for students from years 9 to 13; Te Aratika Creative which teaches transferable skills
through creative arts; and Te Aratika Industry Training, a registered private training enterprise that develops and delivers qualifications in vocational pathways.
The right intentions
Te Aratika Group collaboratively encompasses its cradle-to-career model that focusses particularly on what Te Aratika’s Director Ronnie Rochel calls “young, A-typical stars”, allowing them to build their own pathways to success. Typically, more than 70 per cent of the group’s employees are aged between 17 and 26 years, often starting out with limited knowledge of the industries it works in and many from challenging upbringings.
The business owners’ indigenous roots as Māori, and in excess of 25 years of expertise in the industry, means Te Aratika understands the importance of utilising the right tools, leading the company to recently partner with TRACTO and take delivery of GRUNDODRILL 28N.
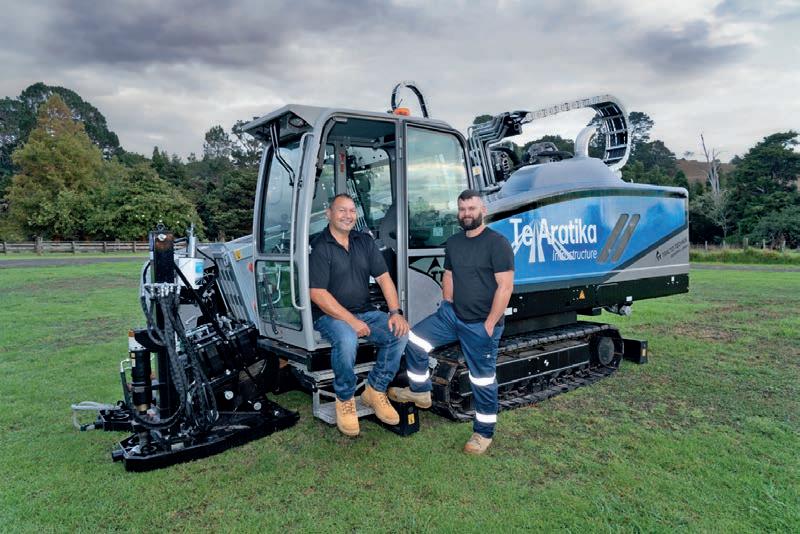
The right equipment
used on important trenchless utility projects and came with a range of extensive product training from the manufacturer which has contributed to developing the skills of Te Aratika Infrastructure’s employees.
The 28N is one of the most powerful drills on the market, with 100 per cent of the machine’s 224 kW of power directed towards drilling operations, making the rig unique in the up to 300 kN pulling force power class. The extra power also supports an advanced mud system, supplying up to 650 l per minute of bentonite, facilitating increased productivity and faster drilling, as well as opening up the possibility for contractors to undertake larger and longer bores. In addition to this power and the effect it has on the functions of the GRUNDODRILL 28N, the drill also features automated and comfort benefitting the end user. Two multi-function joysticks are used for all functions in bore and drive mode and can be switched between manual, semi-automatic and fully-automatic modes.
In the airconditioned cabin is a panel PC with touchscreen and internet connection, making operations straight forward for the end user. Custom ergonomics have also been considered, with an extra-large and comfortable seat, equipped with air suspension and automatic weight adjustment.
The right direction
Te Aratika’s new machine arrived in Auckland, New Zealand on January 2022 and the company is proud of its achievements with the machine since. Significantly, the contractor recently completed a complex circuit of installations, totalling 5000 m, for power utility Vector, the country’s largest distributor of electricity and gas.
For more information visit www.tearatika.school.nz
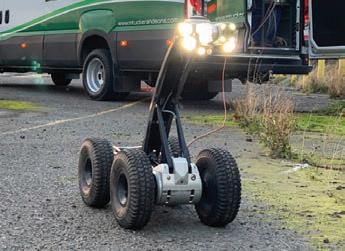
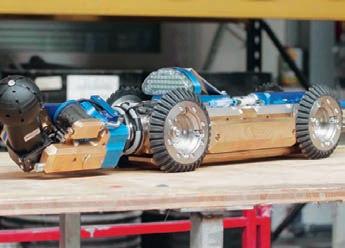

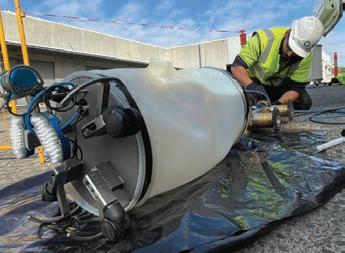
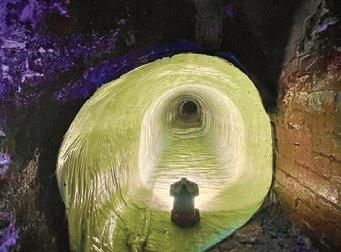
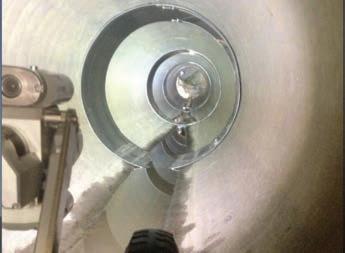
Civtec has New Zealand’s fibre, power and water covered with support from Ditch Witch CEA
Ditch Witch CEA is helping infrastructure specialists deliver on telecommunications networks, civil and utilities infrastructure.
Since the company’s inception in 2014, Civtec’s mantra has always been to ensure its clients and customers receive the most effective and swift service possible. This, coupled with a strong foundation of modern equipment and hardworking staff has helped Civtec become a renowned and awardwinning company that time, and time again proves its dedication to delivering on behalf of its clients.
With a modern fleet of specialised equipment, Civtec has the experience, expertise and the gear to get the job done.
Sitting down to speak with Trenchless Australasia, founder Shane Smart reflects on Civtec’s early 2010’s beginning and its remarkably swift success within the trenchless industry.
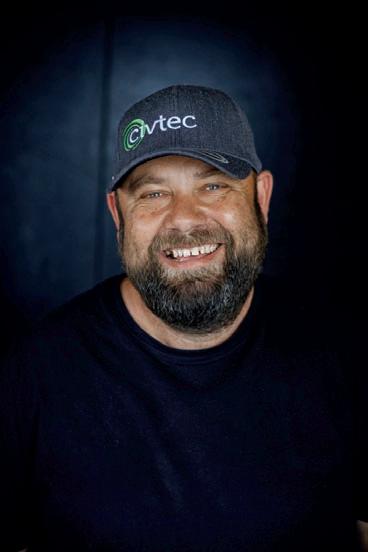
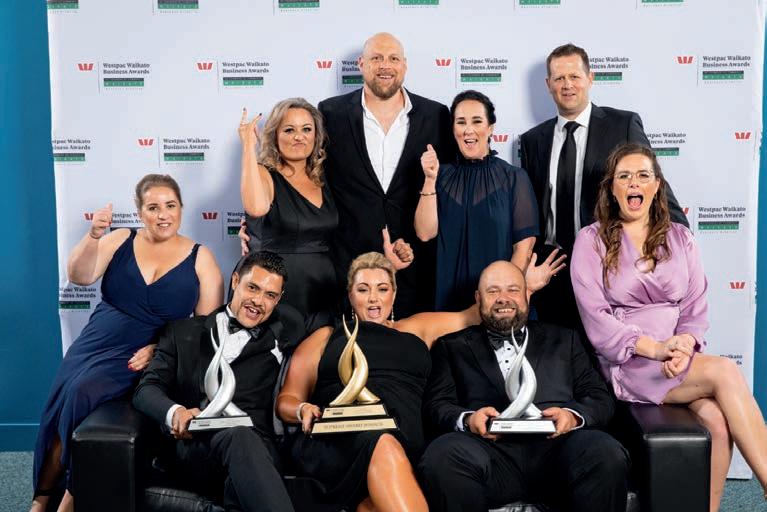
“I began my telco career off the back of the fibre rollout for New Zealand in 2013, my role was managing a bunch of contractors and I was a project manager for a handful of projects,” says Smart.
As time went on, and after making some connections with previous clients who had come to know Smart for his hard work and dedication, he decided to strike out on his own. Within a year, the business grew from being just a hardworking man and his van to a company with over 20 staff.
When the time came, Civtec purchased its first drill.
The drill was a JT5 model from Ditch Witch CEA, known as the ideal compact rig with just the right amount of thrust and pullback for shallow installations of cable, fibre and water systems. The JT5 rig can reach up to 46 m in length beneath roads, driveways, sidewalks, sensitive landscaping and other surface obstacles ensuring little to no surface disruption.
Ditch Witch CEA is dedicated to delivering the highest level of product support to its customers. Employing factory-trained sales and service specialists who are dedicated to supporting clients and all machinery requirements, CEA is equipped with the
like Civtec develop a strong reputation in the industry.
“Looking back, when comparing buying that drill to all that has come since it pales in comparison to everything else, we’ve been able to achieve,” says Smart. “But really that was such a big step for me and for the company, it really helped set us up and continue growing
into what we are today.”
Since then, Civtec has grown to employ over 380 staff with locations across New Zealand and is fully equipped to take on larger-scale projects from beginning to end.
“We like to say that we can offer the whole package, especially when it comes to fibre, water and power,” says Smart.
“We take on a wide range of projects and commit to each and every stage fully – we’re not just a directional drilling service, we’re actually able to take on a lot more than just that and constantly deliver a full-service solution.”
What makes Civtec stand apart from its competitors is just that – its flexibility. Thanks to its independence from a larger internationally based infrastructure cooperation, Civtec is able to maintain its flexibility and agility which its clients benefit from greatly.
“It’s important for us to be able to prioritise the needs of our clients and be able to adapt to their requirements at the drop of the hat, so to speak, because at the end of the day we really do care about delivering the outcomes they need.”
“New Zealand is a small place, the industry is fairly tight-knit and you get to know quite a few people,” says Smart.
“While I might not remember the name of each and every person we have worked with, there’s always someone who cares and supports your needs both in the business and in the wider industry.”
“Building relationships with businesses like Ditch Witch CEA, you get to know them over the years and are able to help grow alongside them.”
Recently, Civtec and Ditch Witch CEA have continued to build on this relationship with Civtec having added the AT30 directional drill to their fleet of 10 Ditch Witch machines. Designed to tackle the toughest conditions from solid rock to cobble, the AT30 was the perfect choice for the job which involved working on 7 km of waterpipe.
With a greater horsepower, a higher capacity pump and easy to operate the AT30 is not only the most powerful Ditch Witch machine in its class; but also, the quietest. This ensures significantly lessened impacts to the environment as well as less disruption in urban areas and greater operator comfort.
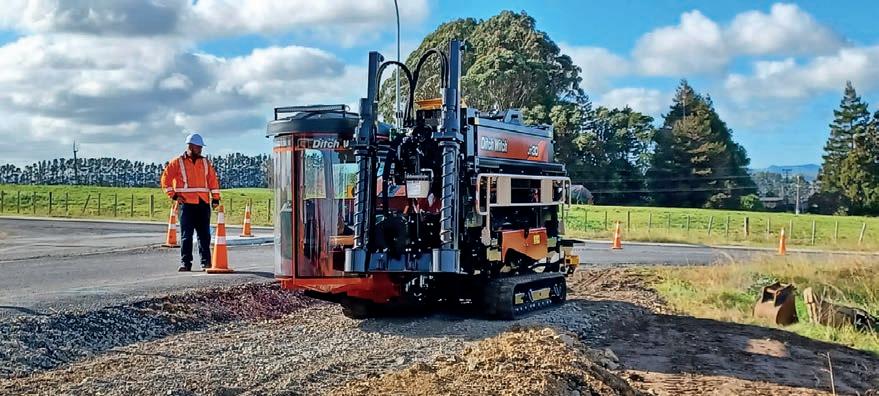
“I was confident I had the backing from Ditch Witch that they’d be able to have AT30 to me once we had the go-ahead for the project
we’d been tapped for,” explains Smart. “We wanted to start work straight away once we had that green light and having the assurance from Ditch Witch that this would be possible was amazing.”
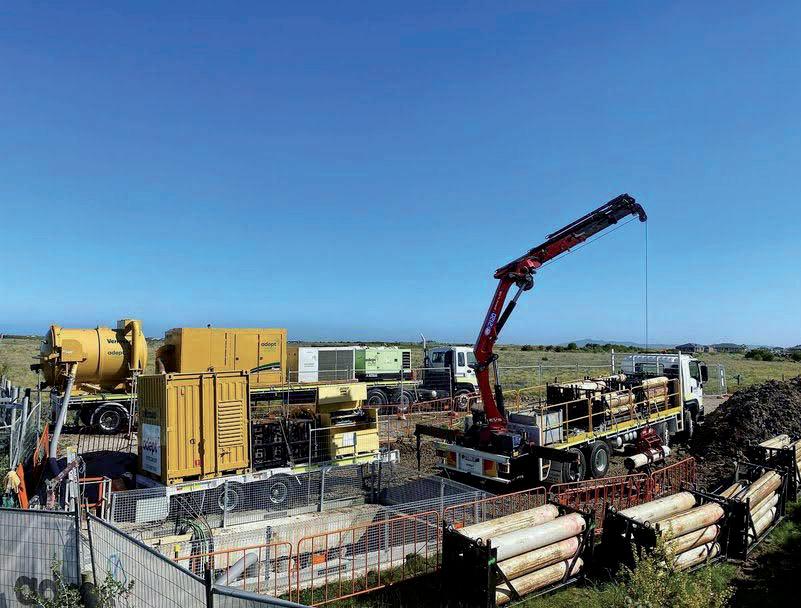
Looking to the future, it seems the only way to go is up, Civtec is preparing to tackle a range of ambitious projects thanks to New Zealand’s Three Waters Reform Programme, which will see the overhauling and rehabilitation of drinking water, wastewater and stormwater infrastructure across the country.
“There is a lot happening with Infrastructure at the moment, Three Waters is a hot topic and when this kicks into gear, there’s going to
be a lot of renewals and rehabilitation projects which we’re definitely excited to get stuck into,” says Smart. “It’ll be a great opportunity for Civtec to become more involved in the water infrastructure side of the trenchless industry and to really flex our muscles in that respect.”
Supporting them during this exciting time, Ditch Witch CEA is committed to continuing to provide the company with expert advice on what equipment best suits the company’s needs and ensuring each piece of machinery is of the highest quality.
It’s official: Veolia is the exclusive Australian partner of Thermoform
Veolia is teaming up with North American-based company Warrior LLC to provide an even better relining service to its customers.
Veolia is a leading environmental services provider across water, waste management, resource recovery and energy throughout Australia and New Zealand. As a globally recognised company it provides game-changing solutions for clients which are both useful and practical for the water, waste and energy sectors.
Recently, Veolia expanded its offering to the water sector in the area of trenchless pipe relining through a new and exclusive partnership with Thermoform.
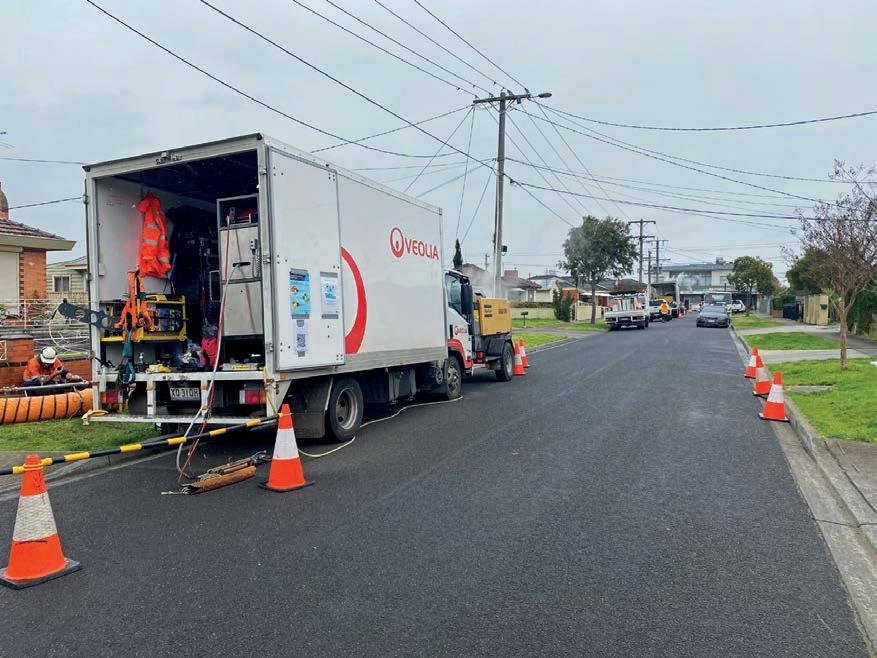
Daniel Spiller, Veolia’s Chief Operating Officer for Water, leads the team of professionals working across Australia and New Zealand. He says this latest offering will continue to support many of its network customers, helping them achieve more effective relining outcomes in less time and with less disruption. The combination of Veolia’s deep expertise in water networks, coupled with a gold standard technology in relining, will add additional value to the market.
“Our business is water,” Spiller says. “We’re committed to working with our customers to understand their needs, because we know how integral that is to delivering ecological transformation. Right now, the market is
telling us it is struggling with ageing water infrastructure and it needs fast and cost effective solutions to help address it.”
According to Spiller, the signing of an exclusive supplier deal for the Thermoform product exemplifies Veolia’s commitment to trialling and providing innovative yet proven solutions to suit its broad client base.
“Thermoform is a PVC pipe lining solution made from alloy materials which are designed to extend asset life by at least 50 years,” Spiller says.
“It is ideal for providing structural support to pipelines that prevent sewer collapse and subsequent spillage that would otherwise adversely impact the community and the environment.
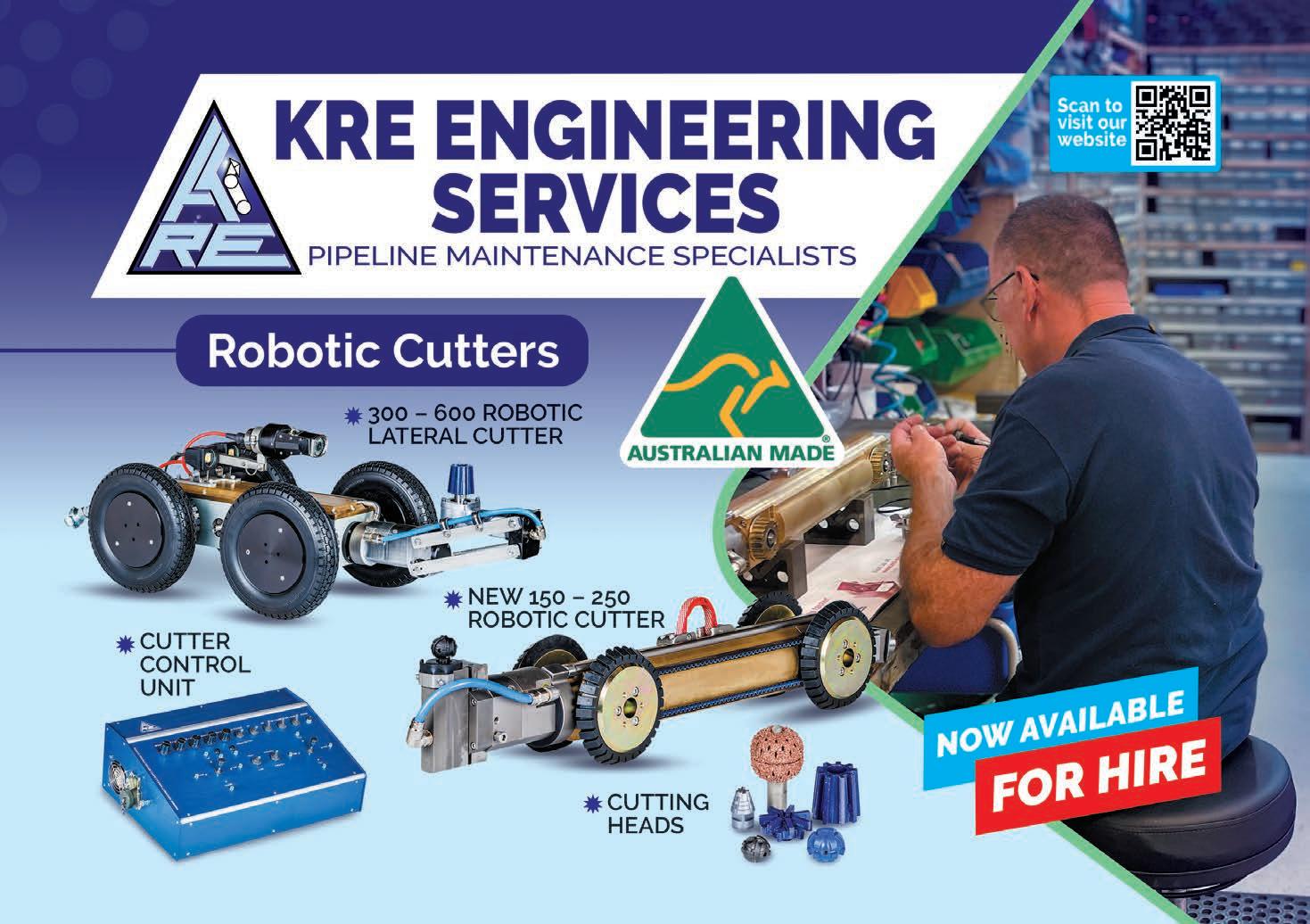
“We are seeing additional benefits for our customers who are seeking to improve pipeline serviceability by preventing blockage resulting from tree root intrusion.
“Perhaps best of all, the product is installed without the need to dig trenches, resulting in a low impact on the community and the environment.”
The liner is structurally sound and provides a tight fit into the host pipe that prevents infiltration and ingress of tree roots, presenting a money saving opportunity from not having to install tophats (junction seals).
Thermoform liners conform to the shape of the hosting pipeline. Despite these forming mechanisms, the liners are able to remain tight and protect against tree roots, infiltration and other common causes of structural damage.
The final product is a seamless ‘joint-free’ pipe with minimal reduction of the host pipe increasing and any consequent adverse operational impact. This increases the pipe hydraulic capacity and extends the underground wastewater asset by at least 50 years.
Spiller says the product’s all-round flexibility and suitability for a host of applications means it aligns well with Veolia’s existing suite of products.
“We are not only adding the pre-eminent product of its kind to Australia and into our toolkit, but also stability at a time when it’s really needed,” he says. “For us, this is about continuing to put our clients’ needs first and being on the front foot when hiccups arise.”
Spiller says one only needs to look back on the first half of 2022 in Australia to know just how important it is for critical service providers to be prepared.
“As the sole provider of Thermoform in Australia, we’re now more prepared than ever for any situation our clients may throw at us and we know that’s something they appreciate, particularly as managing aging assets is an increasing challenge,” he says.
Due to its proprietary ingredients, the product itself can be manufactured with a variety of sizes and wall thicknesses that can be tailored to meet each client’s exact requirements. For example, the SDR32.5 liner is best if the purpose of the pipe relining is to provide structural support and extend the asset life. Meanwhile, a cost saving with a thinner liner – such as the SDR40 – can be achieved if the client’s objective is only to resolve an infiltration and inflow problem in the wastewater network. This approach subsequently reduces the significant load on the wastewater treatment plants.
Thermoform is a product that has been in use over the past decade throughout North and South America, Europe and the far east, installing over 600,000 m on average every year. Tony O’Brien of Warrior LLC, the company behind Thermoform, says his team
continuously works to improve the product to ensure adaptability to meet customers’ requirements and specific needs.
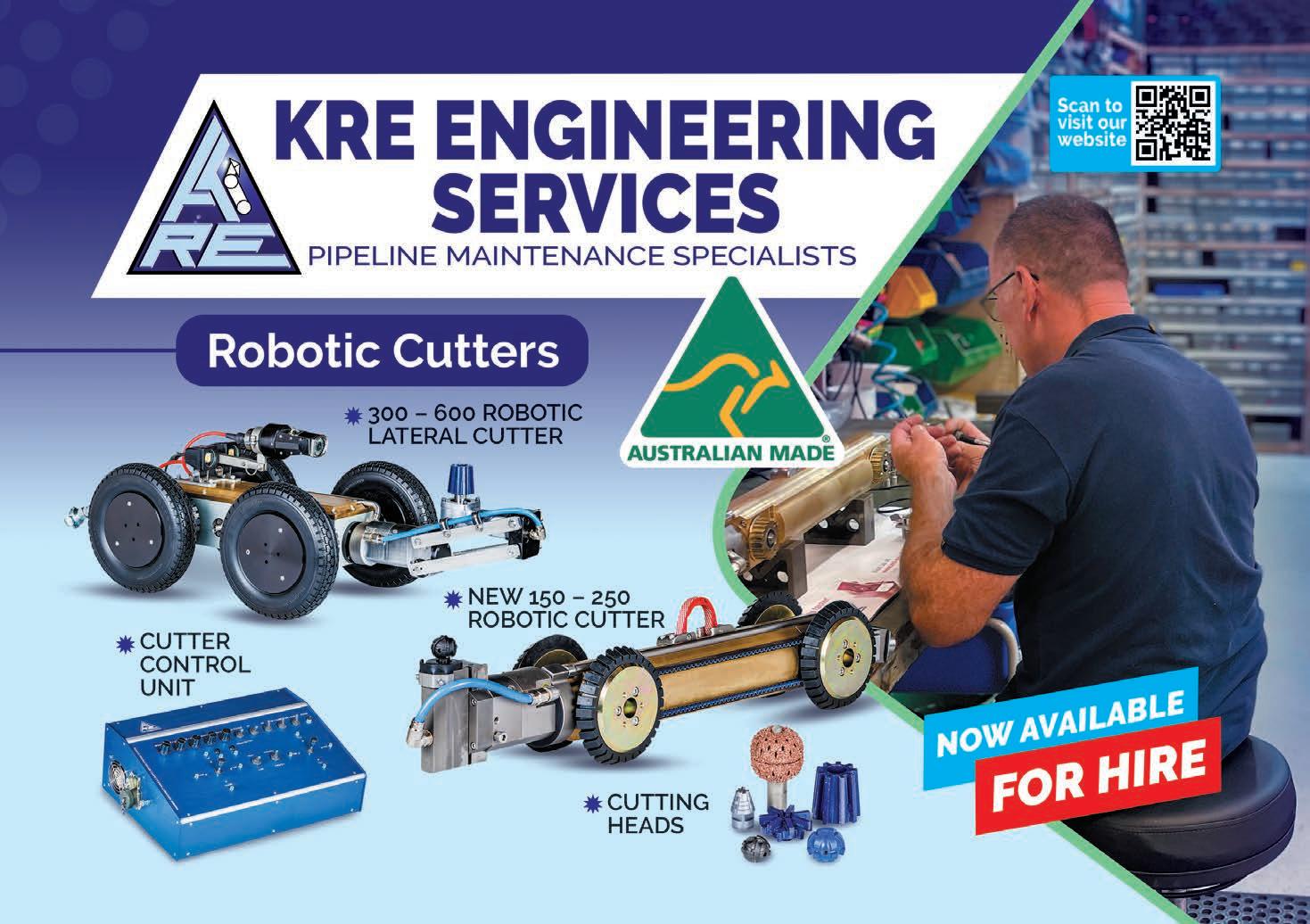
“Warrior is always looking at ways in which Thermoform can be developed beyond where it is now,” he says. “We have recently designed and built a new die that will provide diameters up to 1200 mm making Warrior the only company in the world to produce such sizes.”
Veolia has already rolled out Thermoform on several contracts across Victoria, New South Wales and Queensland. Rehabilitation of deteriorated pipes has been the key objective of these contracts and where Veolia’s existing depth of experience in relining has combined with the flexibility of Thermoform to deliver outstanding results for clients.
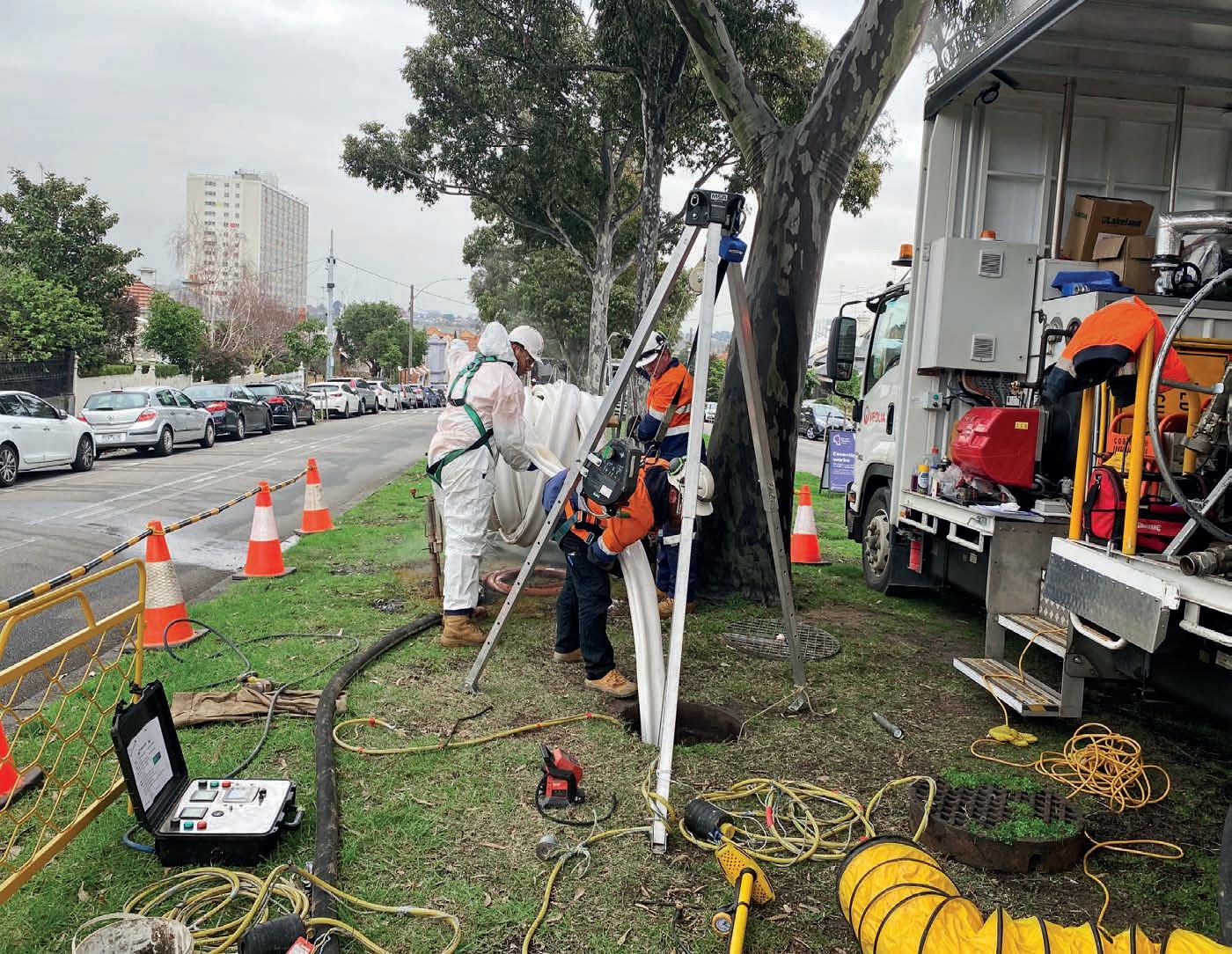
In keeping with Veolia’s aim of becoming the global benchmark for ecological transformation, the Thermoform product contains no harmful or toxic chemicals that could negatively impact the environment or the community.
“No additional chemicals are used during installation of the product, ensuring the safety of installers while also guaranteeing accurate installation,” Spiller says. “That’s something that’s very important to Veolia because we see it as part For more information
visit Installing 70 metres of DN225.Aussie Trenchless has the future of pipe rehabilitation solutions sorted

Aussie Trenchless Director Chris Meredith and the team are committed to pioneering state-of-the-art solutions and furthering business in the trenchless industry. As part of that innovation, the company offers a wide range of unique products both in Australia and internationally.
Aussie Trenchless’s SRP-EXP Spiral Lining System is designed to rehabilitate pipes from DN150 to DN1200 using a selection of six different sized profiles. The SRP-EXP system is a close fitting structural spiral ribbed PVC trenchless pipelining system.
The SRP EXP sizes range from a profile type E7-050-5 for DN150 to DN250 pipes, E9085-6 for DN300 to DN450 pipes, E14-085-6 for DN375 to DN600 pipes, E20-085-6 for DN600 to DN900 pipes.
Wastewater and sewer pipeline networks are under stress, and as time goes by, underground pipeline networks continue to age and breakdown. Aussie Trenchless believes repairs using traditional civil open cut methods are far too costly and disruptive on communities.

Meredith says trenchless rehabilitation techniques continue to grow in volume as they are a cost-effective repair solution.
“The SRP EXP Spiral Lining System can be installed under flow conditions, with no bypass pumping needed it is quick and efficient using a third-generation high quality profile to ensure ease of installation, providing a valueadded outcome for the network owners,” he says.
The SRP EXP Winding Unit and Cages are a standard design. Each winding unit supplied is the same, the cages vary in diameter to suit the underground pipe size and all parts that make up the cages are standard and interchangeable on some cage sizes.
The special winding machine is positioned into an access chamber or pit, then helically winds the SRP-EXP ribbed strip in order to produce a pipe within the existing pipeline. Aussie Trenchless’ SRP-EXP is first installed at a smaller diameter, then expanded in order to closely fit against the internal surface of an existing pipe.
During this initial wind-in process the spiral pipe lock holds the spiral wound pipe tight to
the initial and smaller diameter.
Once the far end of the installation length is reached, the SRP-EXP Liner end is then restrained, with the lock area sequentially released such that the SRP-EXP pipe expands in a controlled manner until it has been pressed hard against the inside wall of the pipe its being installed to.
The installation process is entirely mechanical, meaning that no chemical curing
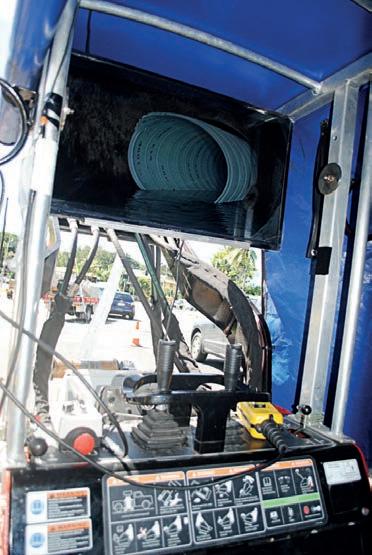
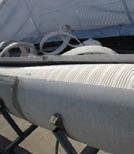
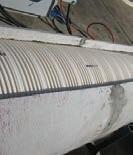
nor steam heating is utilised during the process. Not only is the system easy to install, but it’s likewise easy to remove if necessary.
The SRP-EXP system is capable of negotiating displacement and slight bends while also maintaining a relatively small site footprint. Furthermore, the system is smooth to both work with and install, with minimal and recyclable wastage.
If a client requires a special diameter cage
outside of the SRP EXP product range, Meredith says the company can design and supply it.
Spiral lining and pipe segment technology is now available to all trenchless rehabilitation contractors in Australia and overseas through Aussie Trenchless.
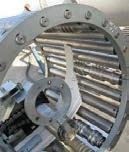
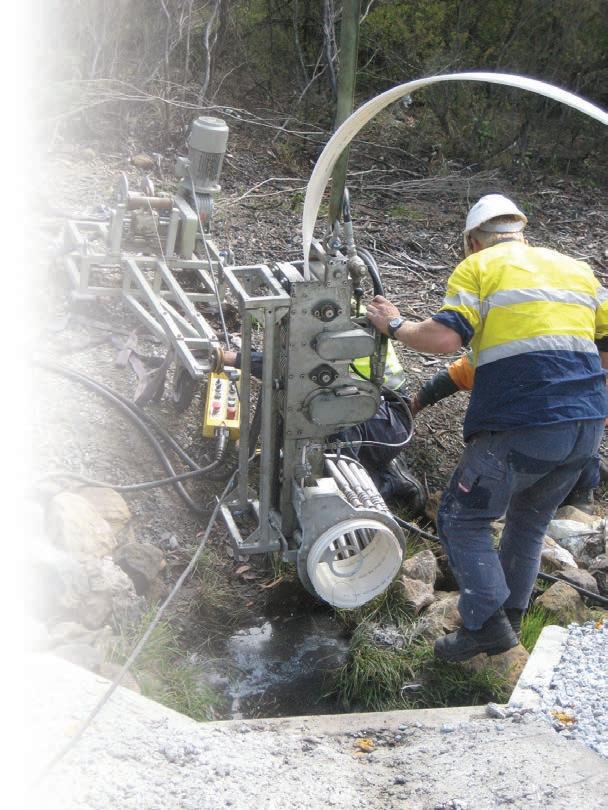
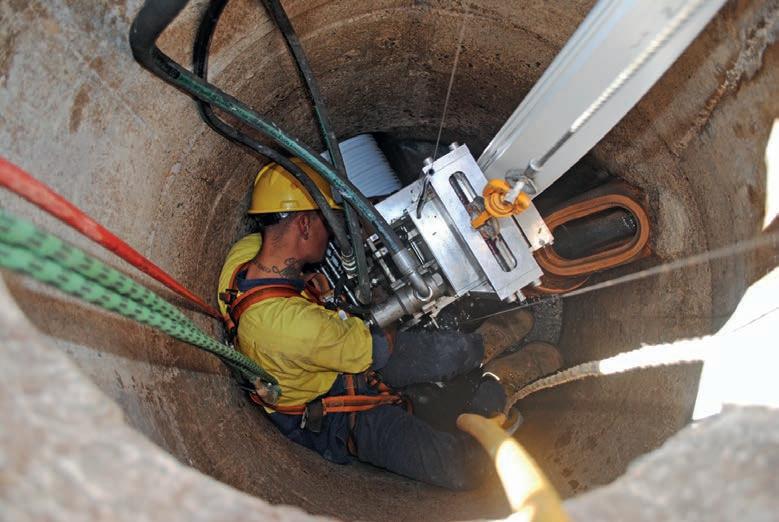
It’s summertime – perfect conditions for pipe rehabilitation
Spring and summer are the perfect seasons to get your water pipe project underway. The weather conditions generally allow easy access to wastewater pipes and the quick IMPREG installation process allows for an uninterrupted life overground.
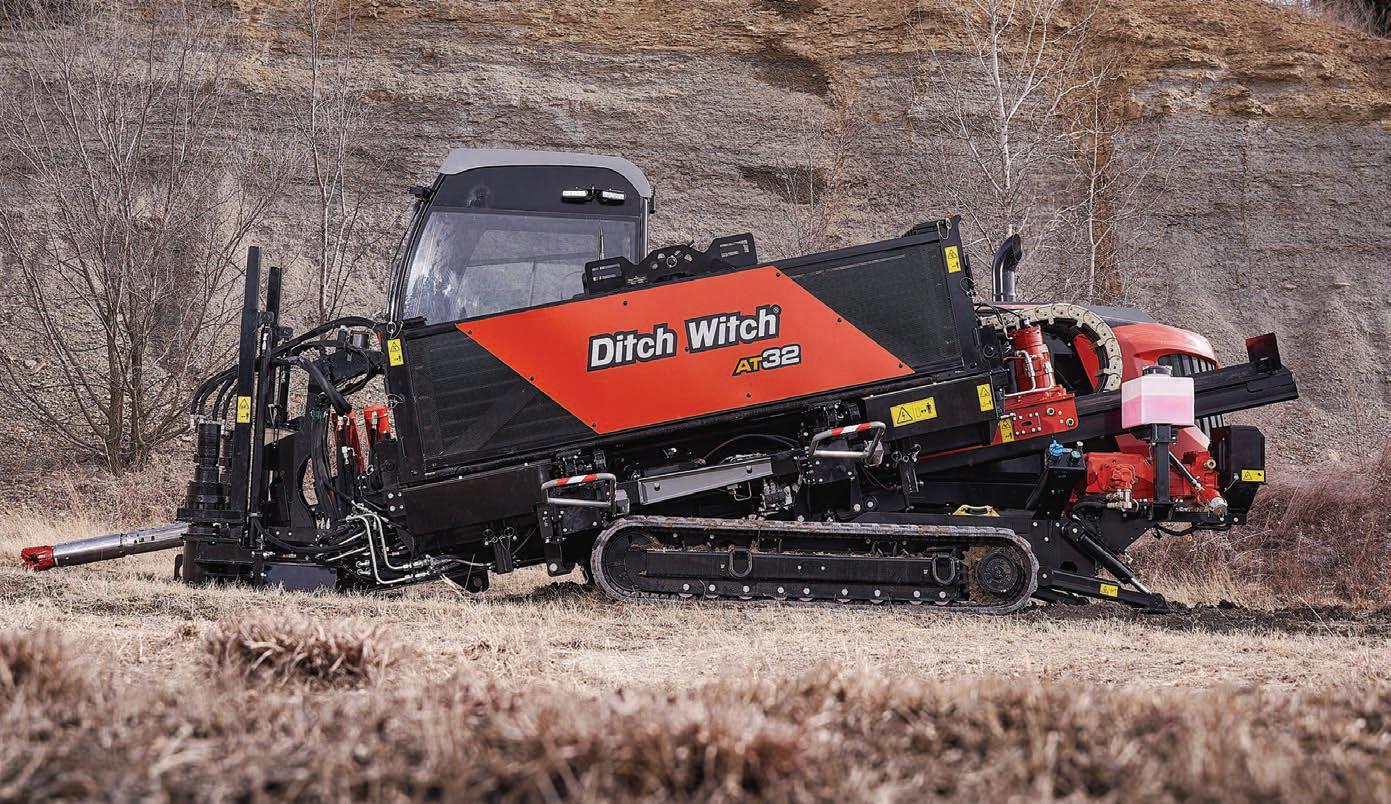
Traffic, public transport, or pedestrians will continue to flow with zero or only very limited restrictions during the IMPREG Cured-In-Place-Pipe (CIPP) liner installation. It doesn’t matter where in Australia, whether it is a big metropolitan area or out in small regional towns, IMPREG’s CIPP solution can be installed anywhere.
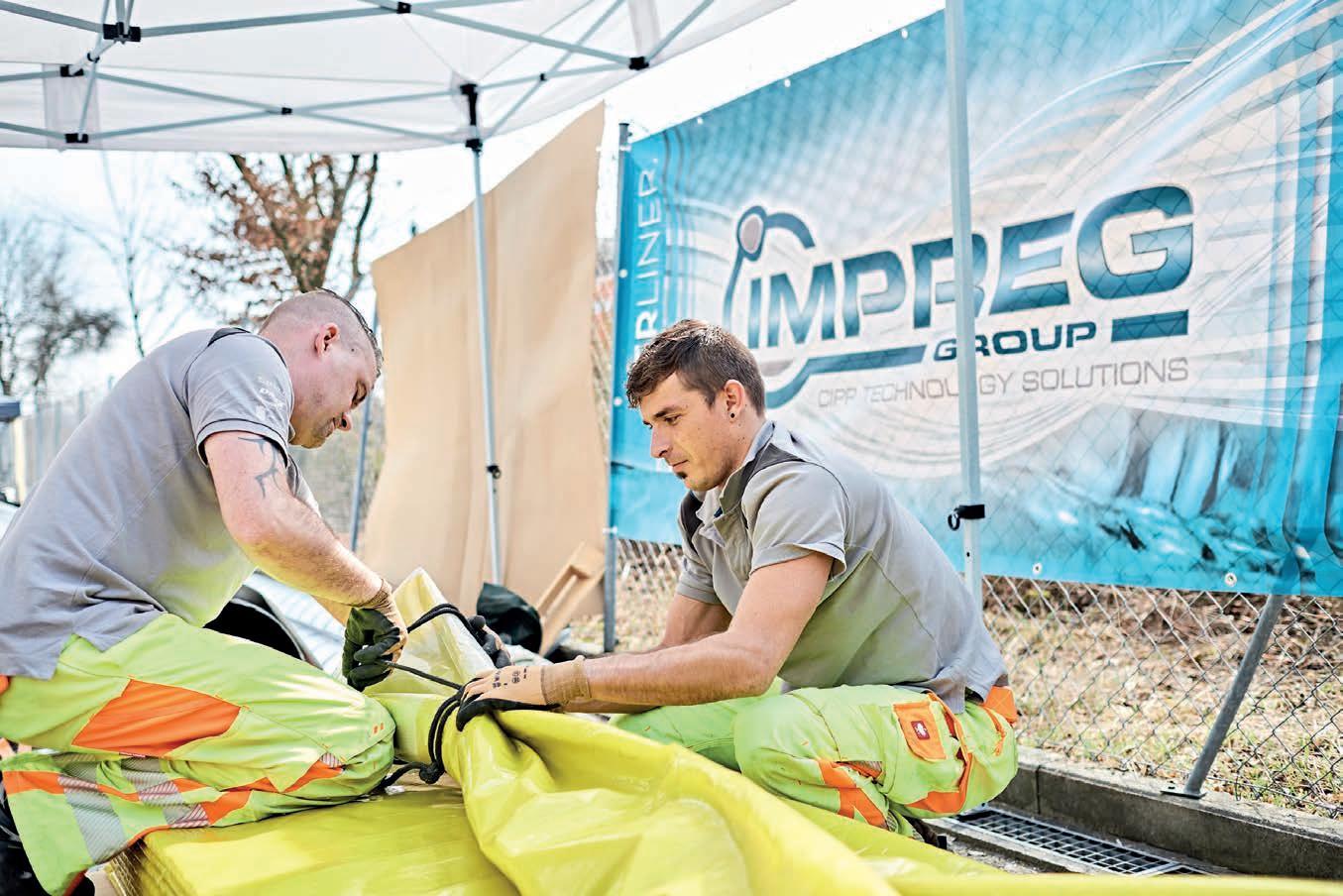
No dig – No interruption to life above the surface
The IMPREG Liner replaces old crumbling and often toxic lines with new UV-cured fibreglass lining. This superior piece of technology is environmentally safe and four to several times stronger E-modules than old traditional felt liners. The GL16 liner by IMPREG is the most versatile and costeffective rehabilitation technology on the market today.
The inflatable fibreglass tubes designed to 50 years’ service lifetime and can be installed at up to 1000 feet at a time – no digging needed. This installation is done through an automated system which makes it not only cost-effective but also precise and safe. The job is completed
in a single day. IMPREG’s solution is more CO2 friendly than traditional felt liner method on the market.
No matter whether its a busy road crossings or city centres to work beneath, with the trenchless pipe rehabilitation solution, users won’t interrupt any flow happening above the surface. Life goes on while preparing wastewater pipes below the surface for the generation ahead. IMPREG guarantees the least amount of intrusion to surroundings.
Preparing wastewater pipes for the future has never been easier
IMPREG guides clients through the whole installation process and assists from start to finish. The project-based production guarantees the maximum amount of flexibility and a perfect liner. Its factories have state of the art technology to deliver the highest standard of quality and a fast turn-around – from ordering to delivering from Brisbane warehouse in only a few days. Once IMPREG are on site with its customer, installation is a quick and easy process. At first, the old pipe will get a high pressurised cleaning after which the pipe
is ready for the new IMPREG CIPP lining. The deflated liner is pulled into the faulty pipeline and sealed on both ends afterwards. High pressurised air follows to inflate the liner and lastly, a chain of UV lights is pulled through the pipe to cure and harden the liner. All this process is happening with the help of technology which will make the installation a unique, fast and safe experience.
Globally trusted – Now available in Australia
IMPREG has completed projects all across the world, from its origin in Germany, then moving to broader Europe, North America, Asia and now Australia. Customers benefit from a team that has a wealth of experience and a manufacturer that produced over 100,000 liners to date.
Cornelia Camacho is your person of contact here in Australia and can easily be reached via ccamacho@impreg.com. IMPREG is looking forward to turning your project into full success with a globally trusted pipe rehabilitation solution.
AT32 ALL TERRAIN DIRECTIONAL DRILL
An integrated wireless remote control gives operators the ability to set up the rig outside of the cab, allowing more precise positioning of the unit on the job.
Unique
Patented
Bursting at the seams with power, the AT32 is the next generation of all-terrain drilling, packing performance and strength into a sleek package.
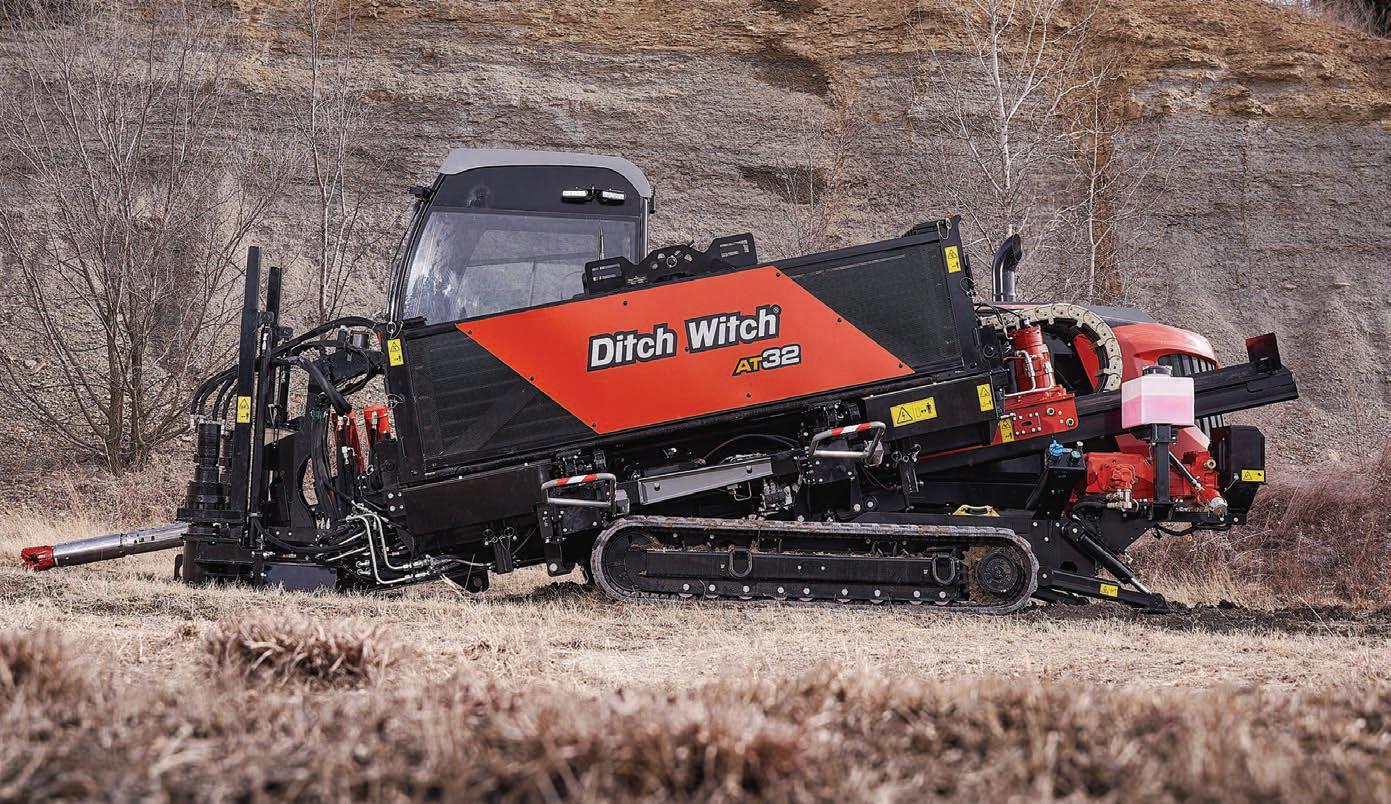
Featuring a 155hp Cummins diesel engine the AT32 provides plenty of thrust and pullback when the task demands, and with 5694Nm of rotational torque there really is no question, drill beats rock every time.
With a focus on ergonomics the operators station has been built specifically for HDD operators. Offering industry- leading visibility with the best view to all critical vision points including ground entrance, wrenches, shuttle-retract location and rear connection. The AT32 also features a climate-controlled cab with tinted glass for the ultimate in operator comfort.
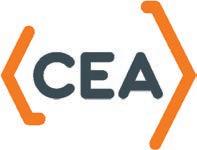
Like to know more?

M. Tucker & Sons secures installation rights for additional maintenance rehabilitation product
M. Tucker & Sons has continued its commitment to diversification of its trenchless capabilities, becoming the exclusive installer of Brandenburger’s BBS.8 maintenance hole liner in Victoria, South Australia and Tasmania. The contractor has already successfully applied the rehabilitation solution to badly deteriorated assets in Regional Victoria, in July.
Located in Melbourne, Victoria, M. Tucker & Sons is a family-owned civil and trenchless drainage specialist with strong focus on its customers and quality assurance. With more than 30 years experience in civil and trenchless rehabilitation, the company has a track record for delivering high quality pipe rehabilitation, asset management, relining and drain cleaning projects and is repeatedly called on in situations of high technical difficulty.
M. Tucker & Sons has a suite of trenchless products at its disposal, including options for trenchless maintenance hole rehabilitation; however, with a view to diversifying its capabilities, the contractor has secured the exclusive installation rights to Brandenburger’s BBS.8 in its home state of Victoria, as well as South Australia and Tasmania.
Powered by UVthe asset, using only air pressure, without the need to pre-measure or laser scan the asset prior. This eliminates the time required to measure the dimensions inside the structure, ultimately reducing the cost of the rehabilitation project and lead time involved in planning.
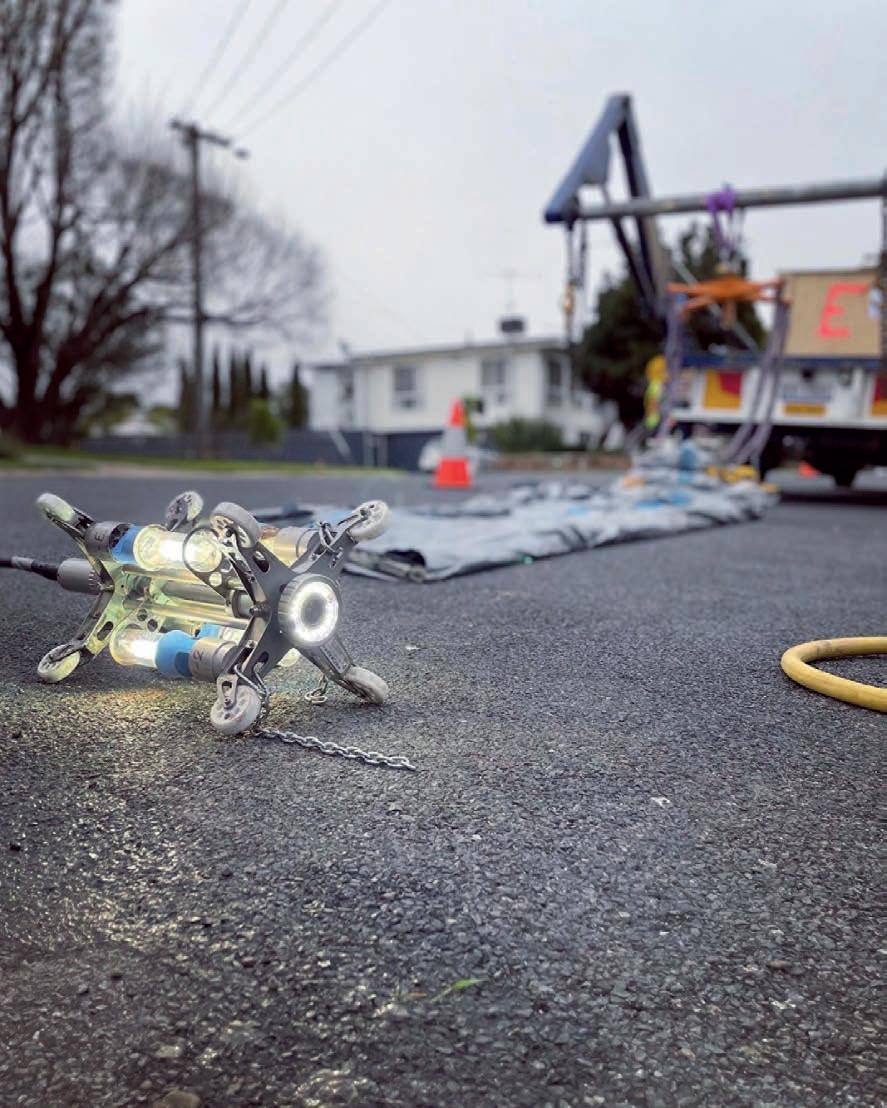
With specific installations procedures, BBS.8 is able to rehabilitate the chosen asset entirely including the bench, chamber, taper and neck in one homogenous liner, free of joints or stitching.
Brandenburger liners have been used to successfully rehabilitate assets around the world in Germany, France, Switzerland and Finland. In June, BBS.8 liner was successfully demonstrated at the International Conference of Trenchless Engineers near Krakow, Poland.
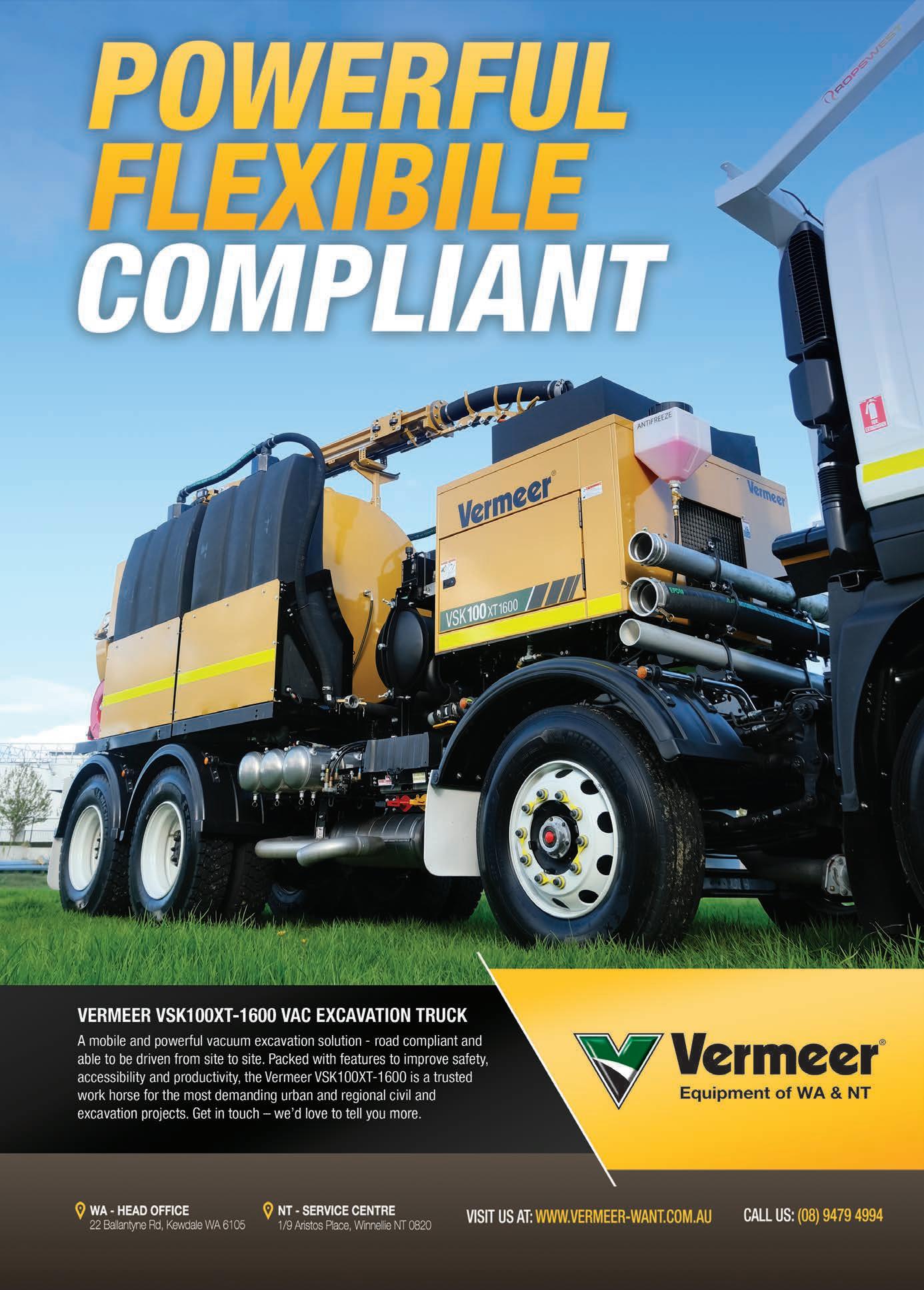
Rehabilitating Regional assets
M. Tucker & Sons has already used BBS.8 on a project in Wangaratta where 2 maintenance holes on a rising main were in desperate need of rehabilitation. The structure had suffered an extensive hydrogen sulphide (H2S) attack, a form of corrosion which can occur in wet environments and results in the presence of a dangerous gas and bad odours.
After inspecting the state of the maintenance hole, the contractor ascertained that the structure was suitable for the application of the BBS.8 liner. The resulting rehabilitation delivered a costeffective, structural solution for the client and extended the service life of the maintenance hole for another 50 years minimum.
Excitingly, the addition of the Brandenburger liner to its existing toolbox of trenchless solutions means that, in conjunction with UV GRP mainline liners, M. Tucker & Sons can supply a structural rehabilitation solution for an entire sewer system.
For more information visit www.mtuckerandsons.com
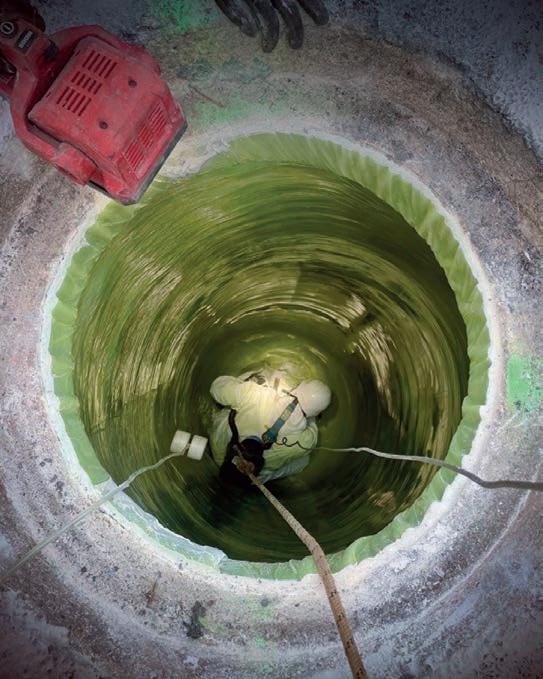
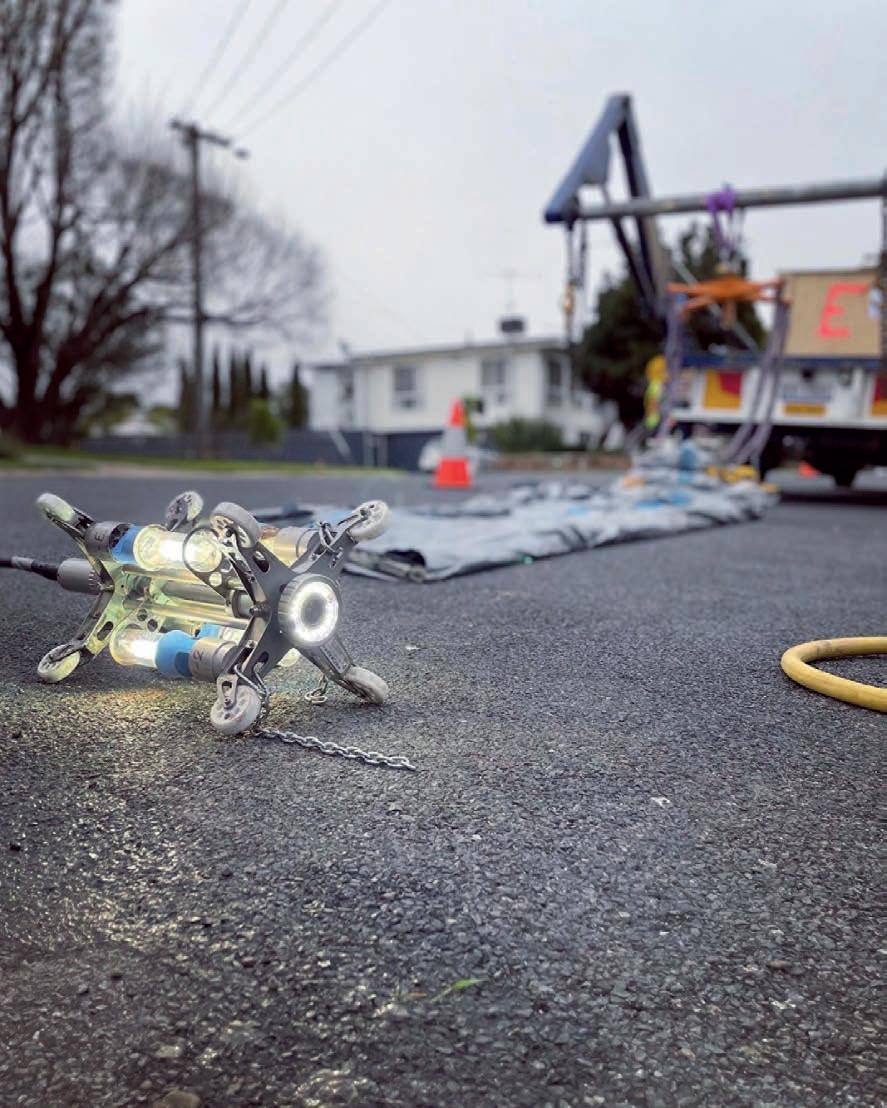
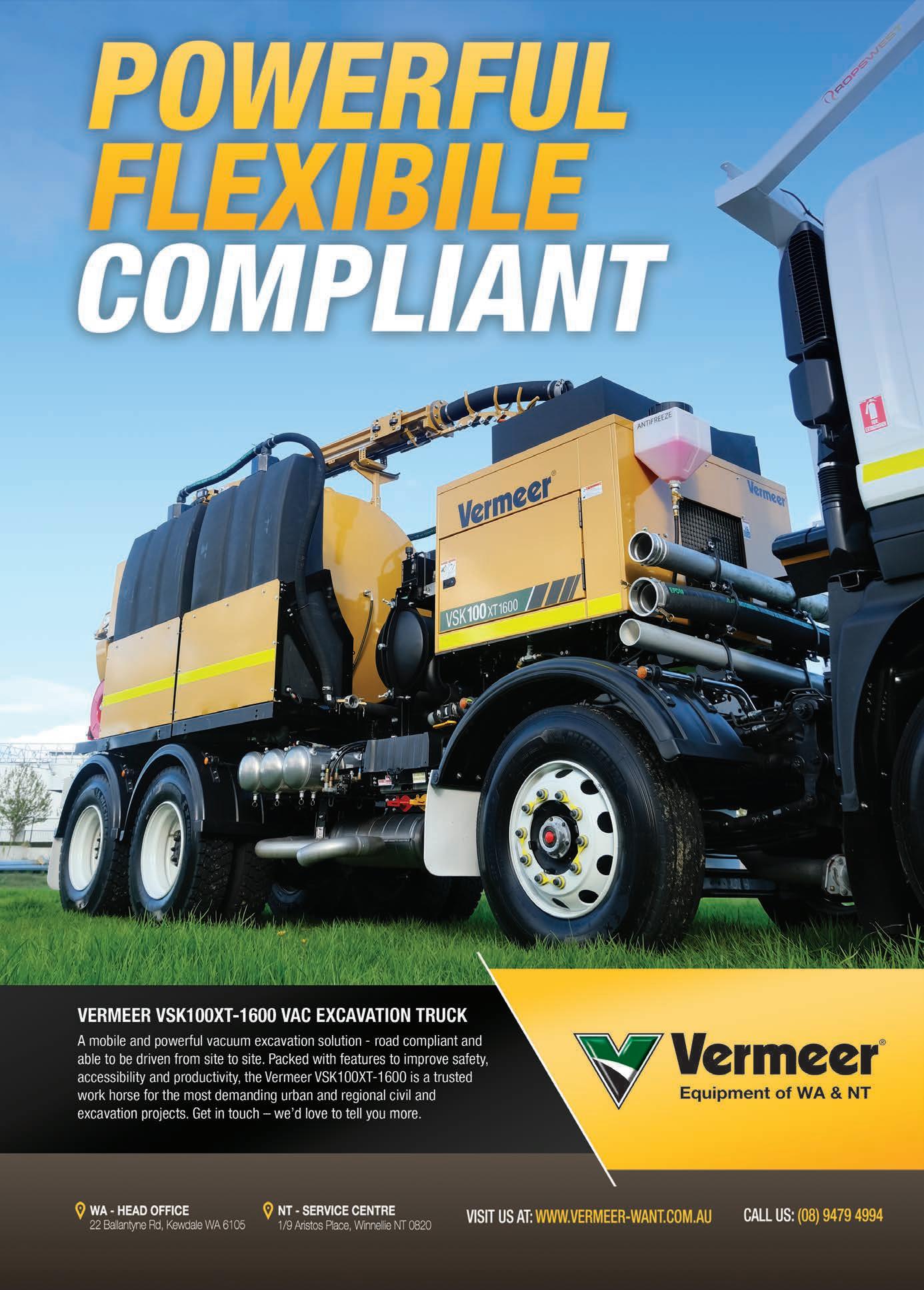
Service your machine with the experts from Vermeer Australia
Servicing can be hard to fit into the busy schedule of an owner/
COMPACT FOOTPRINT. LOW NOISE. COMMON CONTROLS.
From small but mighty clay and dirt drills, to large bore rock drills, Vermeer drill rigs are famous Australia wide. And now, with common controls, it’s easy for operators to transition from dirt to dual-rod rock drilling. Every Vermeer HDD Drill is about capability, productivity and profit. Get on board.
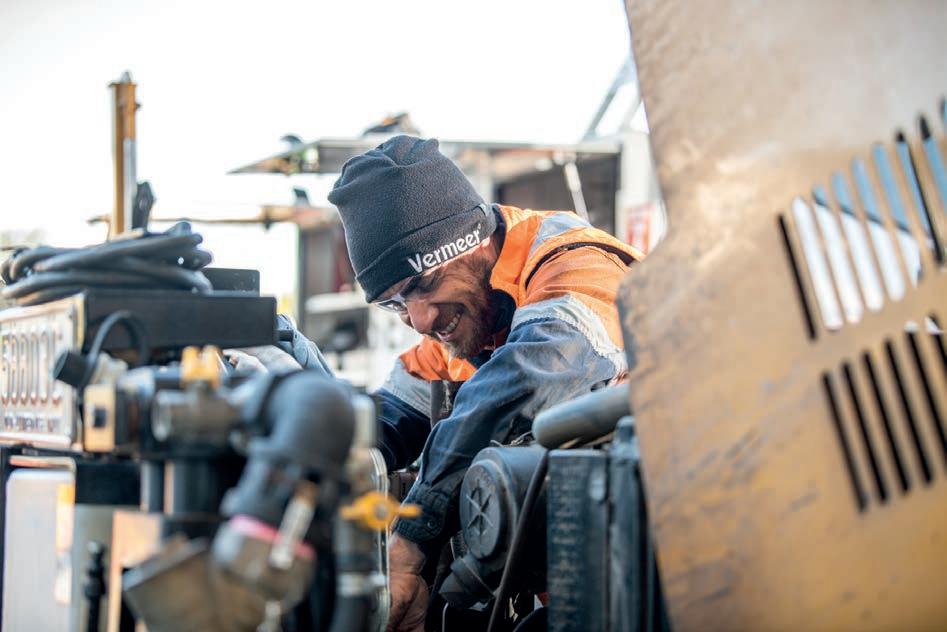
Talk to the leader in HDD today and visit your local Vermeer Australia branch.
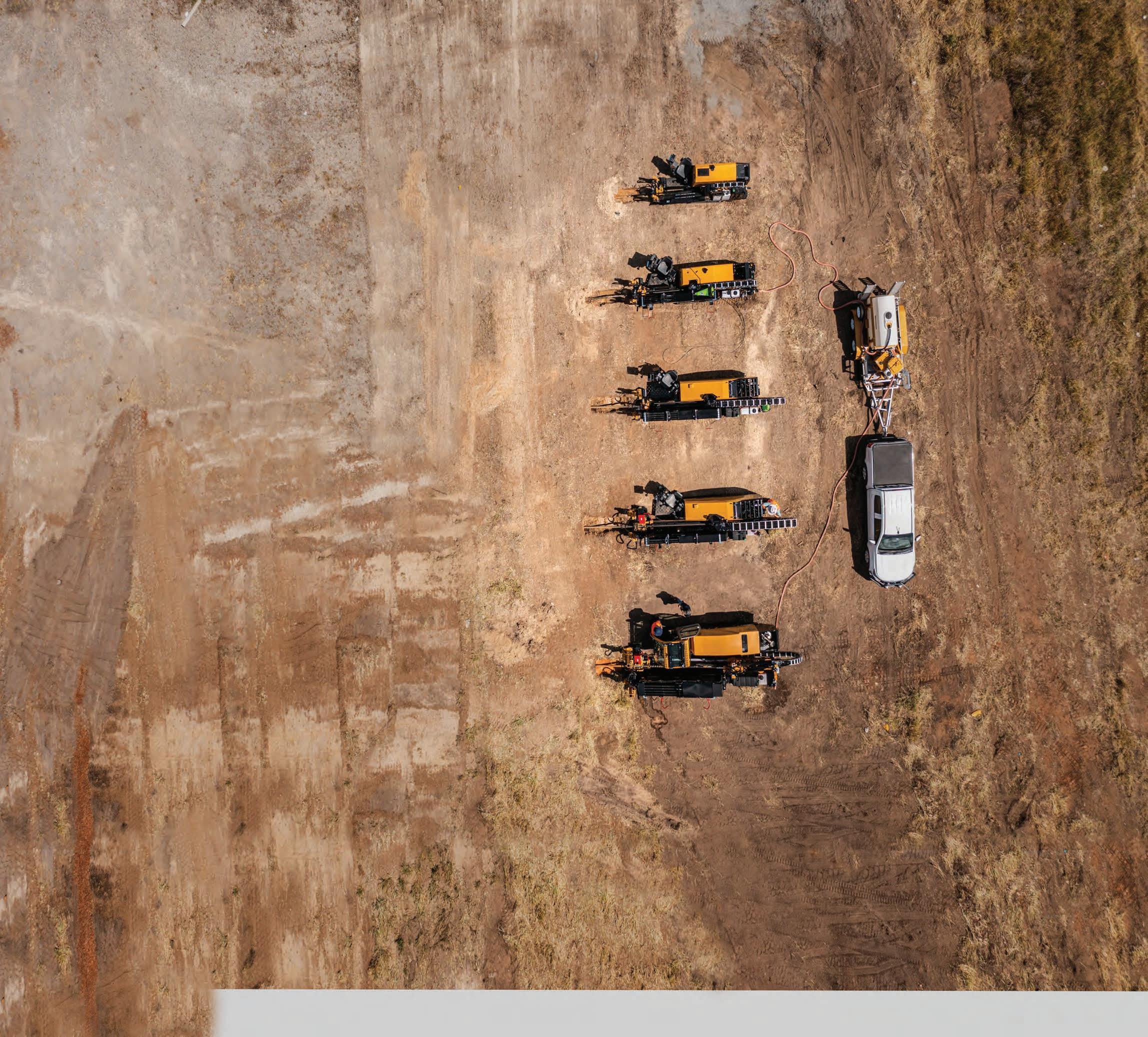
HDD
Scheduled maintenance – anywhere, any time and machine use and hours. Some things Vermeer Australia’s expert technicians might
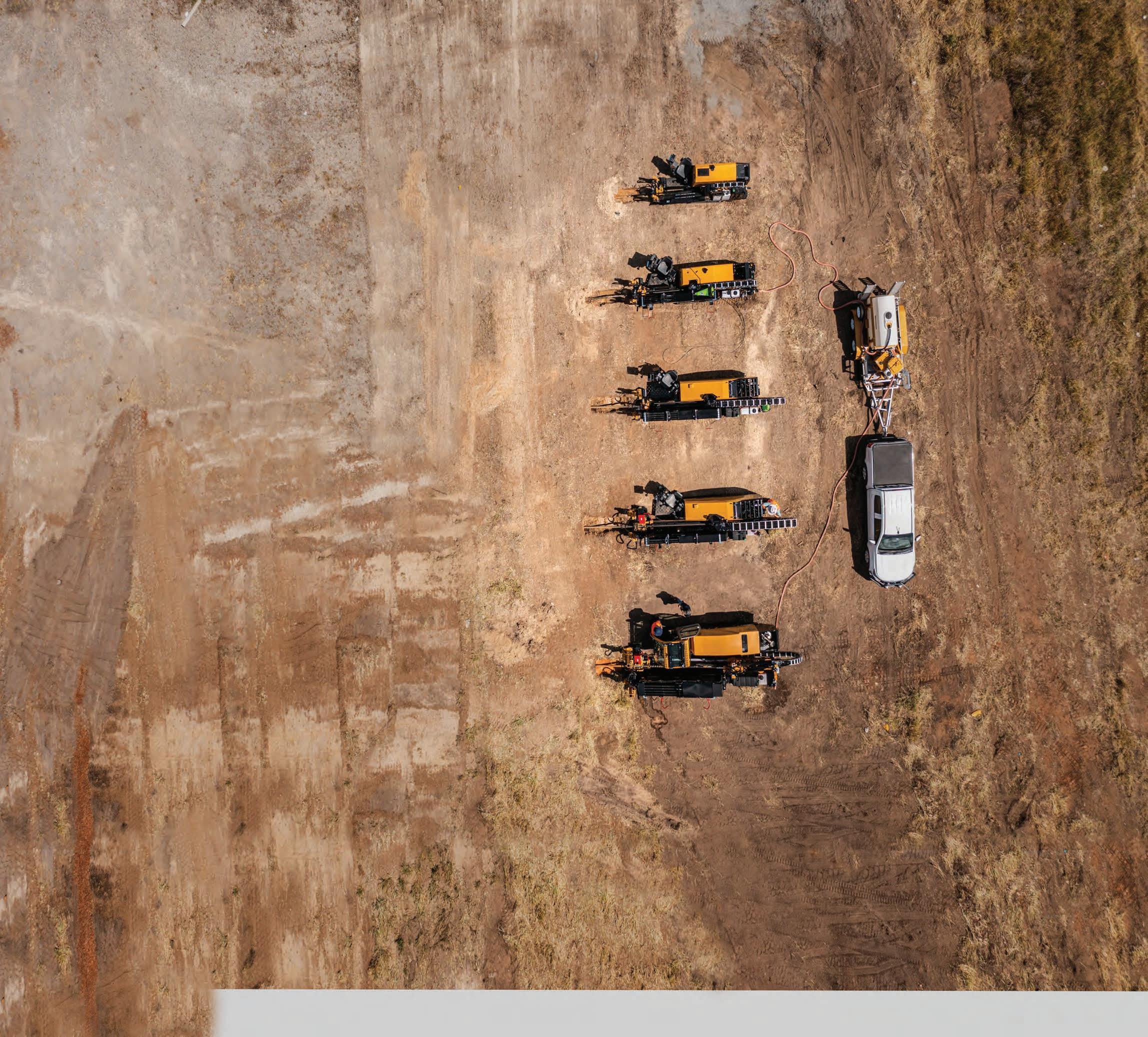
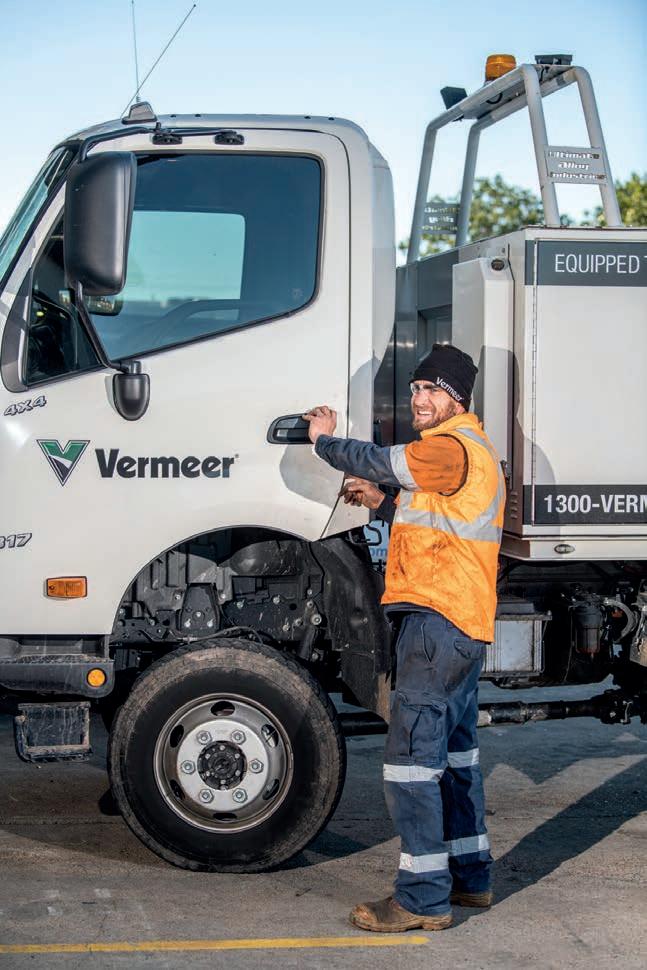
Managing HSEQ on HDD Projects
All industry operators want to deliver quality work for their clients. Maxibor’s Health, Safety, Environment and Quality (HSEQ) Manager Rebecca O’Meley understands the connection between holistic safety practices and quality assurance in HDD.
Health & safety and the link to quality assurance
Like all specialised fields, horizontal directional drilling (HDD) has its moments when it comes to managing Health and Safety.

“Rotating rods, breakout gear, plant movements, entry and exit holes, utility services, slips, trips and falls, mobilization – the list of things that could harm our crews whilst drilling the bore hole and installing the pipeline goes on and on. If that wasn’t enough throw in a pandemic, a bushfire-prone country and a few floods to keep us all on our toes,” says O’Meley.
“The work health and safety (WHS) risks that we can clearly point out to crews are fairly straightforward. For the most part, crews are willing to discuss visible risks – it’s the unseen risks that can be problematic and are sometimes not addressed.”
Psychosocial risks and company culture
Psychosocial risks arise from the influence of psychological factors and the surrounding social environment on individuals, their physical and mental wellness, and their ability to function.
HDD workers are not exempt from psychosocial risks. “Our workers are away from home more often than not, working long days in the wonderous but harsh environments Australia has to offer,” says O’Meley. Part of the job is making sure that crews are not suffering under the mental load.

“Currently there is a strong focus on mental health across all industries, and rightfully so,” says O’Meley. Not only does a proactive approach lead to better health and wellbeing, the benefits have a direct flow-on effect to the overall outcomes that businesses are striving for.
O’Meley says if HSEQ is treated holistically, and the relationships between each individual system and overall corporate performance is understood, the company will be better equipped to assess and improve all areas of the business, most importantly the health and wellbeing of the workforce.
“At Maxibor we have found that, if the health and wellbeing of the workers is treated as paramount in day-to-day operations, a culture of continual improvement is forged with the workers as the driving force,” she says.
Workers need to make choices without fear of
repercussion as raising questions, reporting and taking action are essential elements of a good workplace culture. One thing for sure is that a “no blame” safety culture helps to avert and capture data on seen and unforeseen risk and errors. It is a human condition to make errors and the role of safety systems is to mitigate, minimise and, most importantly, capture and learn from events.
Diversity and the link to wellbeing
Part of the HDD wellbeing strategy should include diversity. While HDD may be a specialised field, there are many roles within that can benefit from a diverse group. Expertise and knowledge coming from a range of sources allows one to assess all functions of the business model and not get stuck in a rut, doing the same processes without looking for improvements across the business. “Studies have shown a link between diversity and wellbeing, as inclusiveness not only creates a culture of support in the workplace but opens workers up for change management,” says O’Meley. This, in turn, gives workers a sense of ownership and value in the work they do as well as embracing the cycle of continuous improvement. Maxibor has found that diversity in gender, age and race creates a much more accepting and welcoming workforce, with benefits reflected in individual wellbeing and overall productivity of the business.
Risk appetite in HDD
HDD, by its nature, is a risky business. Drilling into often-unknown conditions requires switched-on people for the design, engineering and installation processes. “As a safety professional my brain automatically goes
to health and safety when dealing with risks but as mentioned earlier, this is the easy part. What about the business risks: governance, operational and project specific risks?” asks O’Meley. “I stand my ground that the physical safety wellbeing of the workforce must be at the forefront. However, by managing the broader business risks we are also assisting the wellbeing of the workers.” Managing all risks within the business holistically allows the workers to engage in meaningful work, gives a sense of purpose, ownership and job security. These factors lead to workers feeling valued and empowered by their efforts thereby ensuring that their work does not have a negative impact on their health and wellbeing. Compliance with the related HSEQ ISOs is a positive process that should be given the time it deserves and utilised to address all facets of business risks. By engaging with the relevant (and diverse) stakeholders, both internal and external, companies can ensure that no stone of significance is left unturned. Undertaking a comprehensive risk analysis and developing and implementing action plans to mitigate key risks will allow an HDD business to flourish and grow. With risks to business ever changing these processes need to be reviewed regularly and not ignored. Maxibor’s integrated HDD risk management system provides a disciplined means of understanding the specific and broader risks associated with each project.
The flow on effect to quality assurance
So how does this all tie into Quality Assurance to Maxibor’s clients? In its simplest form, a worker who is valued and considered an integral part of the business as a whole will be more empowered in the workplace. O’Meley says that by allowing workers to take ownership of their work, the company finds that the quality of the work improves. Good site management practices, well maintained plant and equipment and compliance all come from a worker that is happy, well and included in the business processes.
“In addition, addressing worker health and wellbeing will also improve staff retention which we all understand can be a major stressor both on and offsite,” says O’Meley.
For more information visit www.maxibor.com.au

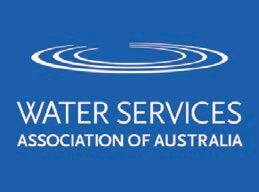
OptionX Group has trenchless technology sorted
OptionX Group has formed and is ready to service all areas of the drilling and tunnelling industry.
Trenchless industry veteran and founder of microtunnelling powerhouse Edge Underground, Stuart Harrison, has established OptionX Group – connecting a selection of drilling and tunnelling businesses, including Edge Underground and Bournedrill. The new group will be equipped to service all areas of the tunnelling, drilling and boring industries.
A company with the edge, underground
As the Managing Director and founder of Edge Underground, Harrison has an in-depth and expansive knowledge of the industry and the necessary requirements to succeed in horizontal and vertical drilling.
Over the course of his impressive career, Harrison has established himself as an innovator within the industry and is the inventor of the Vermeer AXIS guided boring system.
The Vermeer AXIS guided boring system is a pit-launched trenchless installation method designed to achieve pinpoint, ongrade accuracy while eliminating some of the difficult steps associated with other installation techniques. A wide range of product pipe,
requirements can be met with the versatile capabilities of the AXIS system.
Since creating this system, Harrison has continued to work extensively with Vermeer in the USA and drive innovation within the industry.
Across Australia, Edge Underground has become a contractor of choice for many sewer and water pipeline installation projects. The company specialises in installing gravity sewer mains utilising installation techniques including microtunnelling, laser boring, auger boring and thrust boring.
Bournedrill, building on potential across Australia
Yet another long-standing fixture within the Australian drilling and boring scene is Bournedrill.
Helmed by brothers Graham and George Bourne since 1965, Bournedrill is known for its extensive innovative equipment and dedication to finding solutions for its clients.
From its humble beginnings those years ago, Bournedrill has expanded to house a major design and manufacturing operation; utilising
exacting standards.
Bournedrill has continued to take pride in its capabilities – and in its reputation which now extends world-wide, offering services over a wide area encompassing all of Australia, the Pacific region, Southeast Asia and Africa.
A meeting of the minds
Harrison, through his work leading Edge Underground, teamed up with Bournedrill while working on the challenging Donnybrook Link Sewer Stage 2 project.
Ground conditions in Donnybrook are notoriously difficult to manage. Others believed the project’s only option was to upsize from DN700 to DN1200 and install a concrete casing pipe. Edge Underground and Bournedrill came together to combine ideas and successfully used high-pressure air hammers to complete the job.
The two team’s pursuit of excellence and innovation not only saw the successful completion of the job, but also won Edge Underground the ASTT award for New Installation Project of the Year in 2021.
When searching for an Australian manufacturer to produce a new adaptable modular drilling and tunnelling machine, it was only a matter of time before Harrison realised that Bournedrill not only had the engineering expertise required, but the workshop capabilities to get the job well done.
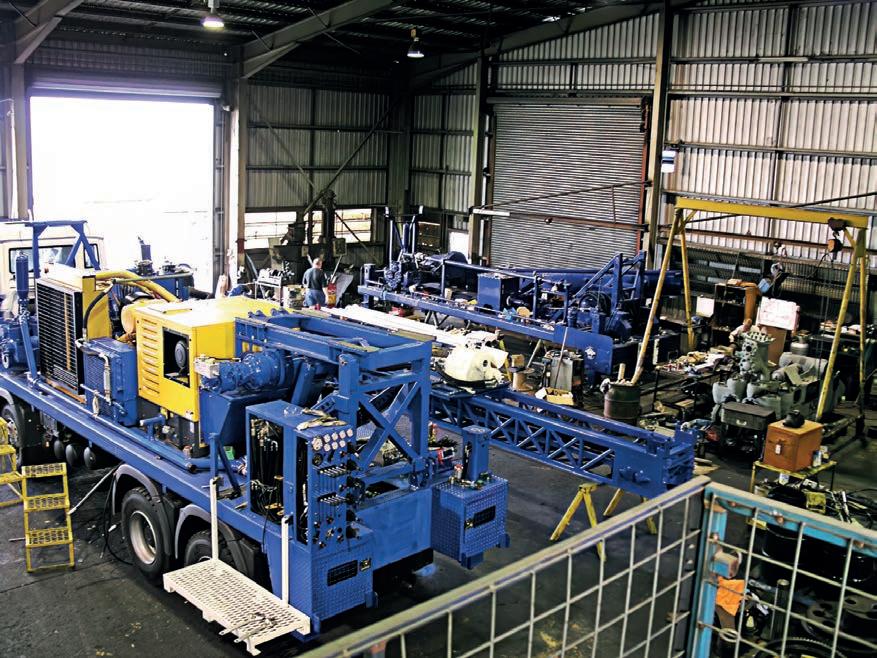
While Bournedrill wasn’t on the market when Harrison approached them to work on this new machine, as he briefed them on the concept, Graham and George Bourne recognised the same passion in Harrison for manufacturing drilling machinery that had driven them to jumpstart their business all those years ago.
Strength and innovation in numbers
Promising to continue Bournedrill with extreme passion and further its reputation both at home in Australia and internationally, Harrison purchased the company and began to form the basis of OptionX Group.
“The Bourne brothers have done a great job for many years, and everyone knows them as guys who seriously know what they are talking about. They weren’t willing to sell Bournedrill
to just anyone, and I’m determined to grow Bournedrill with similarly passionate people from the industry,” says Harrison.
“Bournedrill has always been known in the industry for having expert knowledge, amazing service and creating high-quality equipment that lasts. We’re now building on that with cutting-edge technology to give the workshop the most extreme capabilities in the industry.”
OptionX Group has already begun to invest heavily into the progression and success of Bournedrill; by investing in the company’s Queensland workshop and building upon the already existing technologies of automated and manual CNC equipment, with robotic welding, friction welding and other new equipment to be added shortly.
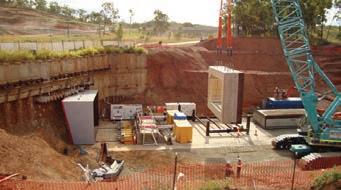

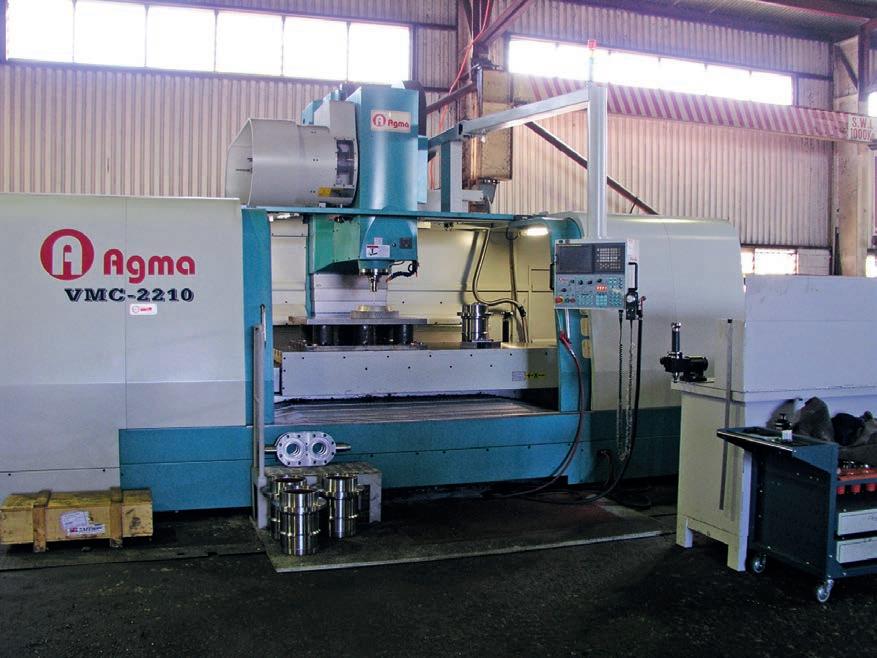

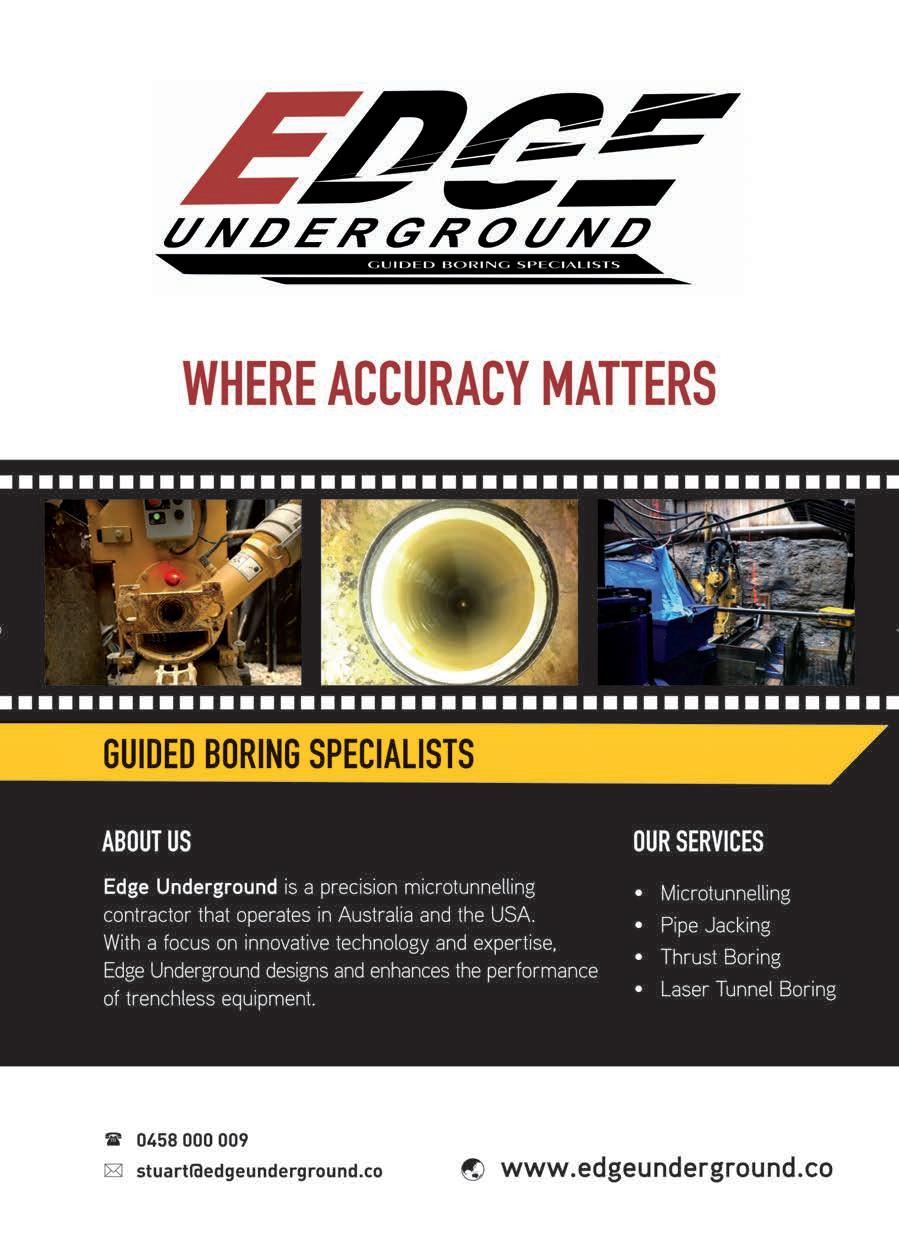
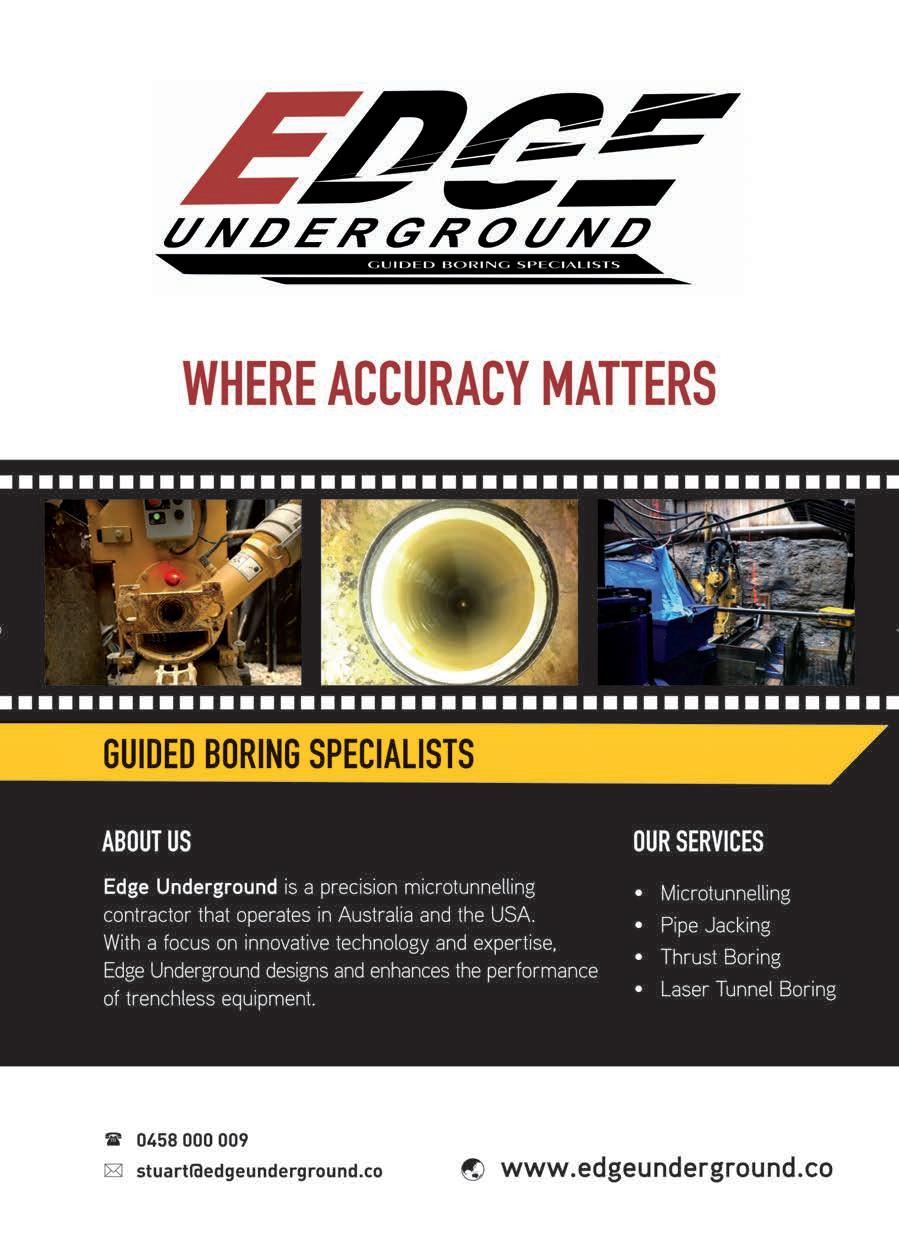
“I’ve worked in the industry and will continue to listen to what it needs. We’ll adapt and are already looking at things like adding rod loading to all the Bournedrill machines,” says Harrison.
industry, the products and services offered by this group of companies are exactly what I’ve needed. I’m excited to take on the group’s CEO role and see these businesses continue to grow,” says Harrison.
Visit the Option X Group website, www.optionxgroup.com.au.
A powerful, versatile and compliant vacuum excavation truck solution
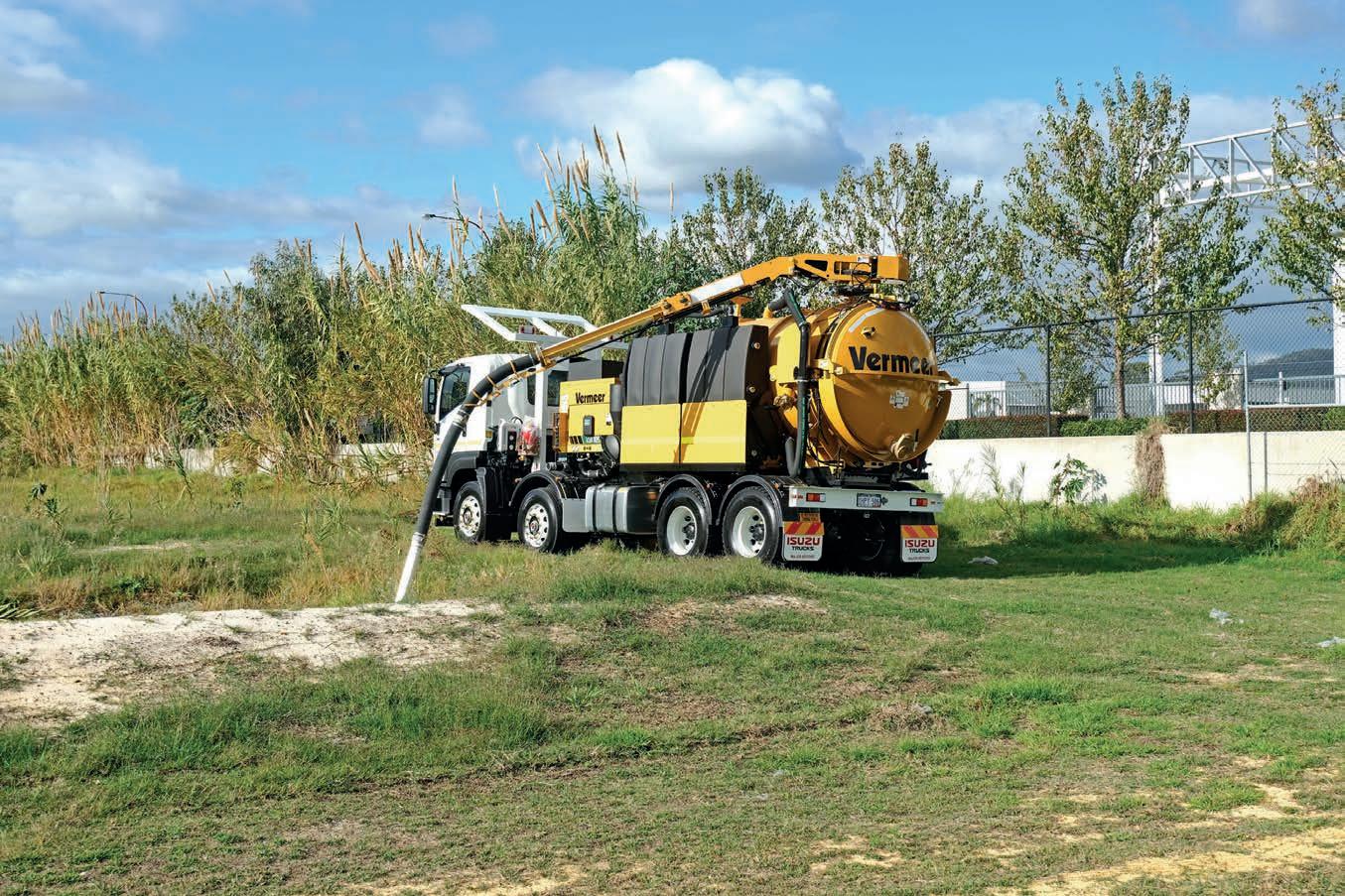
Finding a versatile and powerful vacuum excavation solution has always been a challenge for both civil and mining contractors. Due to high demand, overland transport options have become limited, and expensive, with delays affecting project schedules. Transport regulations have also limited driving trucks on public roads. Working closely with its customers and suppliers, Vermeer Equipment of WA & NT has developed a practical solution that ticks all the boxes.
The Vermeer VSK100XT-1600 vacuum excavation truck is one of the biggest road compliant vac trucks in Western Australia. The truck features the Vermeer VSK100XT-1600 power horse, which is installed onto a 4-axle heavy rigid (8x4 HR) truck. Particular attention was placed in the design of the vac truck to allow for operator accessibility, safety, balance and manoeuvrability. Additional features were also included to meet mine site operational and safety specifications.
Built to perform With a compact one-piece skid design, the Vermeer VSK100XT-1600 vacuum excavation unit offers a number of key features to assist contractors to maximise their productivity.
It is the first of its kind to be released with a 5-inch hose - providing higher air flow velocity and increasing suction speed by as much as 20 per cent. A dual oil bath RootsTM blower provides machine longevity and the ability to quickly offload blockages and spoil.
The vacuum excavator also incorporates compact baffle tanks that maximise water storage without compromising on space and side profile.
An integrated silencing system provides quieter operation on noise-sensitive sites. Job accessibility is enhanced with a hydraulic boom that maintains hose length during extension, and incorporates a remote-
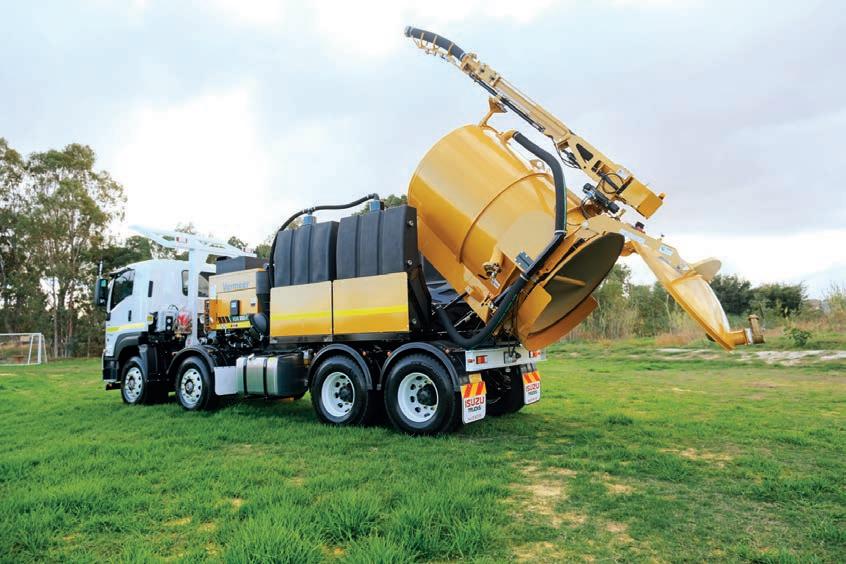
The Vermeer VSK100XT-1600 vacuum excavation truck is one of the biggest road compliant vac trucks in Western Australia.
controlled hydraulic valve for vacuum shut off.
Cleaning is made easy with an in-tank washdown system and cam-over hydraulic rear door, which provides a positive door seal even under reverse pressure.
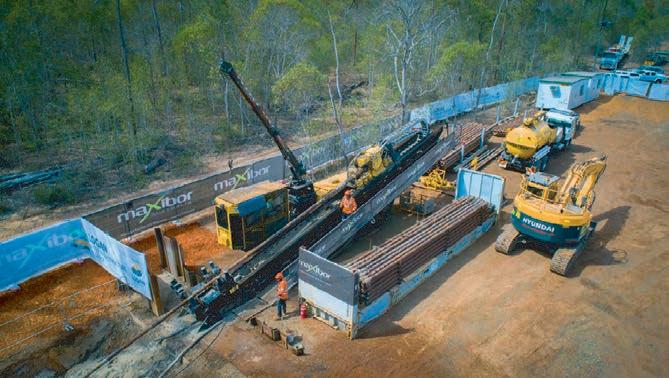
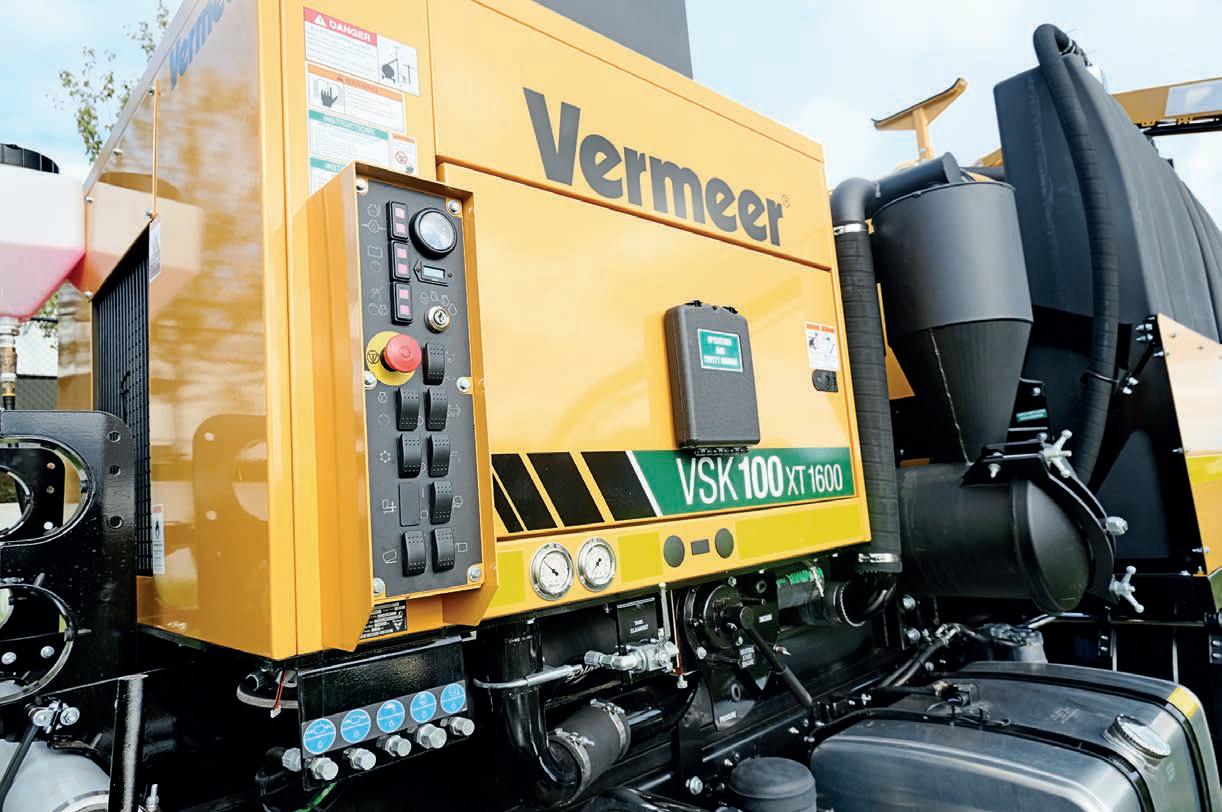
One of Australasia’s largest waste contractors takes delivery of its first KAISER unit
One of Australia and New Zealand’s largest trenchless and waste contractors has taken delivery of its first KAISER machine. The Elegance 2.0 HydroVac Superior 8x4 features class leading payload, performance and value, and illustrates KAISER’s continued growth in the region, with more plans for expansion in the pipeline.
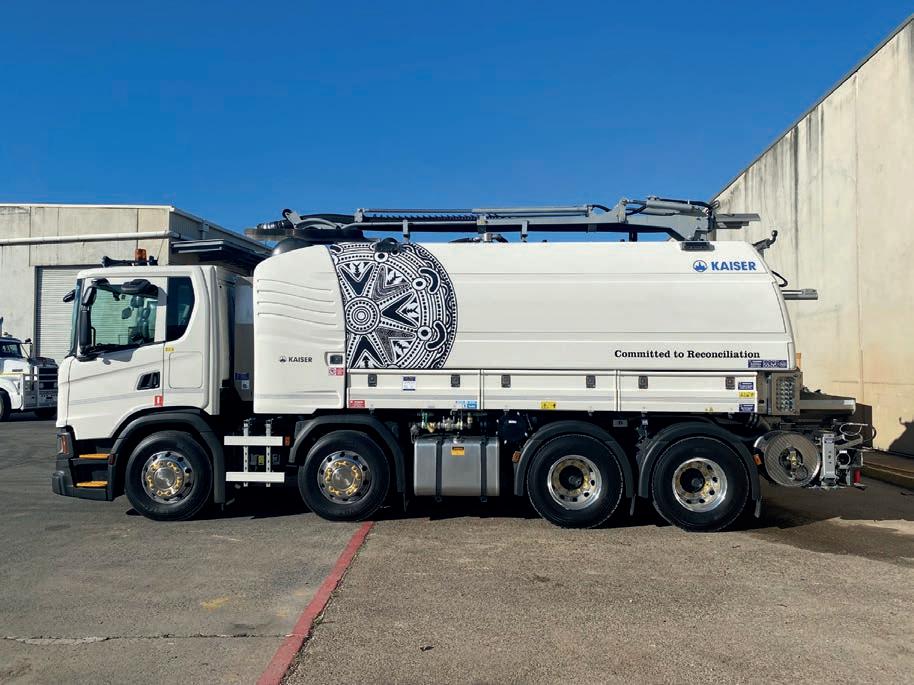
KAISER specialises in the design, engineering and manufacture of world class vacuum and jetting vehicles for water recycling, sewer, stormwater, hydraulic excavation, industrial and dry suction applications. The company is constantly advancing its product portfolio to keep ahead of the competition and maintain its standing as the supplier of the worlds most advanced vacuum loading and high-pressure water jetting vehicles.
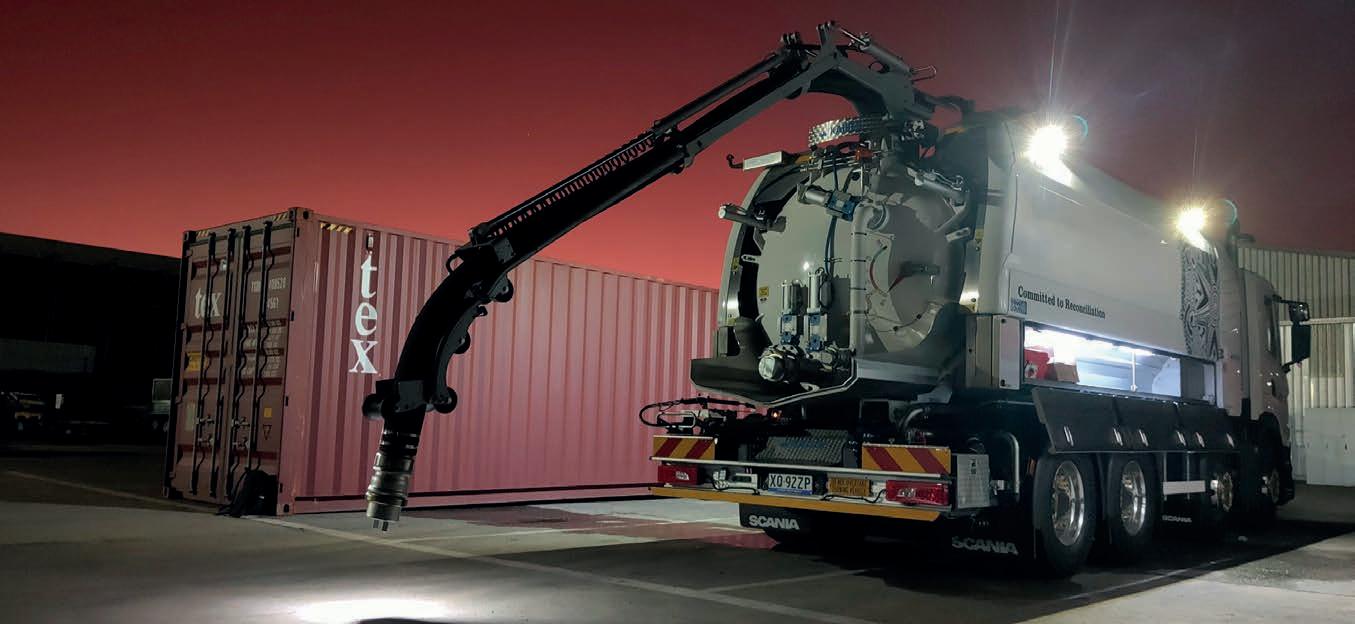
Highly engineered with a focus on maximising the available payload through intelligent design ensuring optimum axle balance, the Elegance 2.0 HydroVac Superior was delivered to Southeast Queensland in August to diversify the contractor’s fleet of vehicles and extend the company’s capabilities.
The machine is the first KAISER unit which will be delivered to the contractor in 2022, with an AquaStar recycler to be handed over before the end of the year, also in Southeast Queensland. KAISER is looking forward to a longterm partnership with the contractor in the future. The AquaStar perfectly balances performance, versatility and payload, with this
maximised efficiency resulting in industry leading water preservation and sustainability. It features KAISER’s unique single-stage recycling system which uses in-house designed and purpose-built pumps and patented RotoMax filter.
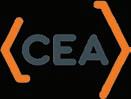
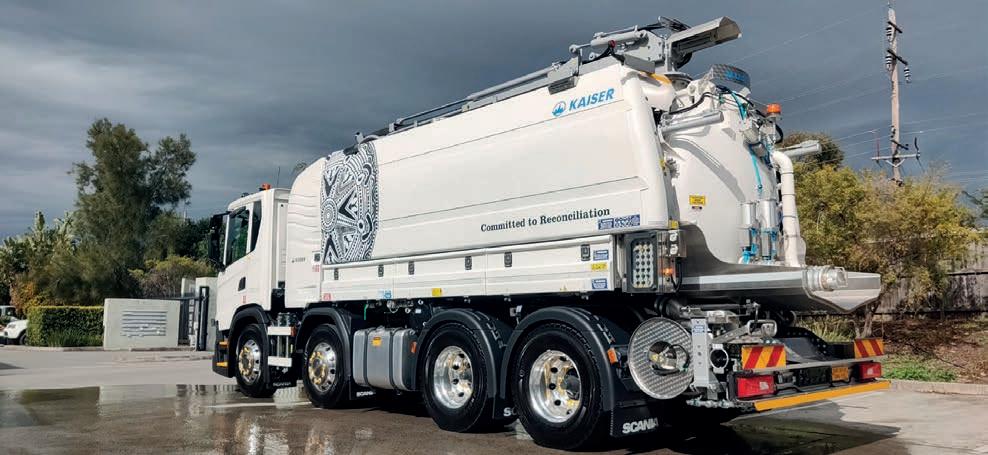
Compared with similar technology available on the market, AquaStar requires less cleaning and maintenance, resulting in reduced downtime and superior payloads, meaning a greater return on investment for operators.
Continuing Australasian support KAISER is currently investigating a number of ways to continue to develop and support its local clients and partners. This includes the further development of a larger range of spare parts, which could be quickly supplied to clients around Australia, as well as stocking and displaying a range of machines, leading to increased access and reduced lead times for the local market.
Despite recent challenges affecting the market globally, as a result of the COVID-19 pandemic and supply chain issues, KAISER has been able to maintain a consistent supply of machines for local operators. In the meantime, increased inventories, in some cases a change in production methods and, above all, a

substantial anticipation in truck procurement continue to guarantee short delivery times. These measurements led to consistent deliveries of vehicles to the Australian market and the securing of subsequent supply for 2023 and beyond. KAISER entered the local market by setting up an Australian subsidiary in 2020. The dedicated facility would complement local partnerships with NATEE and SECA to provide servicing and spare parts
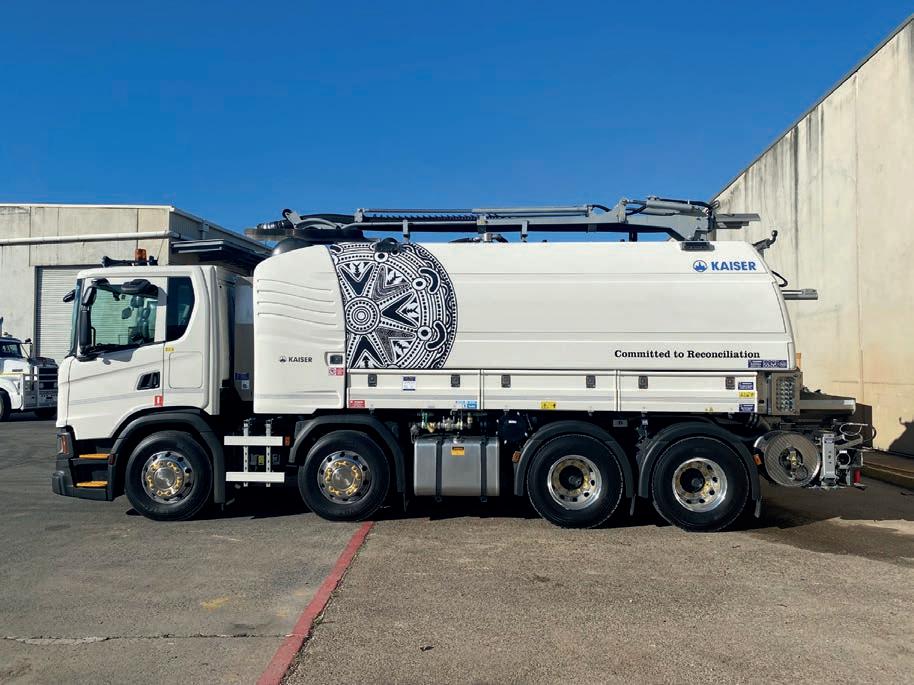
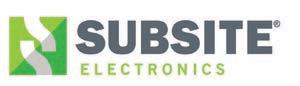
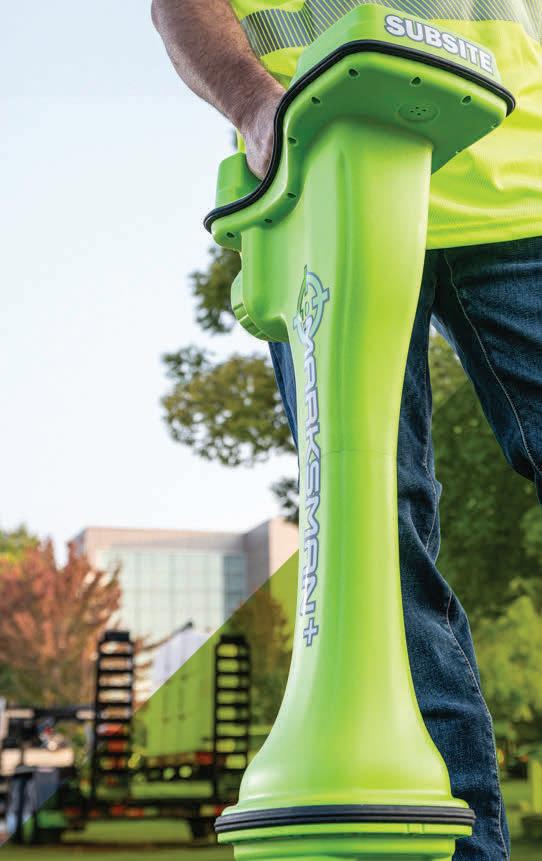
MARKSMAN HDD GUIDANCE SYSTEM. CUT THRU THE NOISE.
The Subsite® Marksman HDD Guidance System provides superior performance in high-interference environments with the industry’s widest range of frequencies in a single beacon.
Scanning the most usable frequencies, the Subsite® Marksman selects the best choice to avoid interference while its increased beacon power signal improves performance at extended depths.
Easy to use with your choice of user interface, the new Marksman View features intuitive graphics and clear data, and with a simple single toggle control you’re more productive from day one.
for the company’s machines. In addition to these partnerships, KAISER is also exploring the potential of establishing a truly national support network for the company’s machines, providing access to multiple service and repair facilities in capital cities and regional areas around Australia.
For more information visit www.kaisertechnology.com.au
Drainchem plug supply deficit
Drainchem has teamed up with Plugline, one of Europe’s leading plug manufacturer, to introduce an exciting range of Packers, Pillow Plugs, Cone Plugs and lifting bags are – now available in Australia.
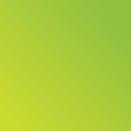
Drainchem has been as a reliable supplier of high-quality pipe plugs and joint testers for many years now. Drainchem also build plugs for custom applications including high and very high pressure inflatable plugs. Drainchem also carry a huge range of lowand high-pressure mechanical plugs up to 900 mm in stock.
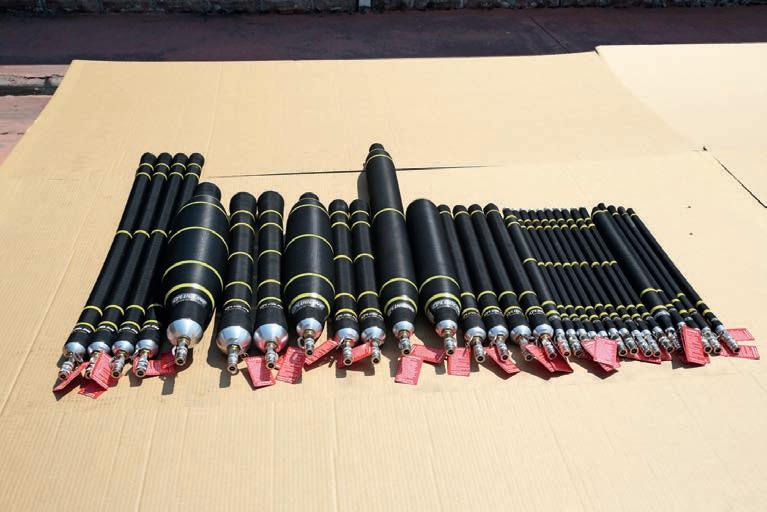
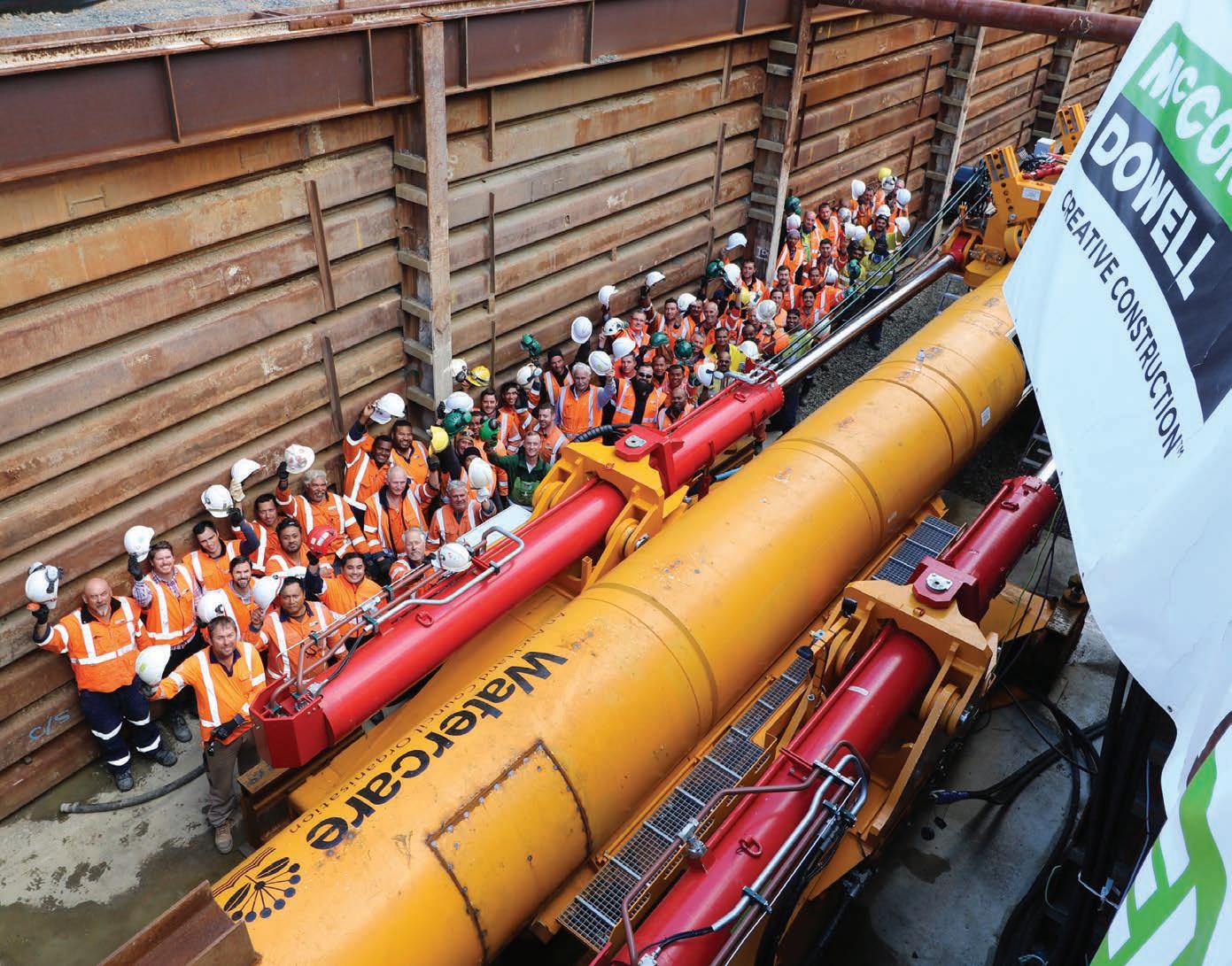

A recent project completed for Fortescue Metals Group involved 3 joint testers for 900 mm, 1000 mm and 1100 mm pipe with a test pressure rating of 50 Bar.
Packers: Drainchem now offer high quality pipe packers with or without bypass that are flexible for ease of installation. These high-quality

packers are available to suit pipe sizes 25 mm up to 2000 mm in diameter and a patch length range from 400 mm to 5000 mm. Packers can be supplied with your required air fittings. The most common sizes of lateral packers and main line packers are in stock and available for shipping. Feedback from customers has been very positive for both quality and price.
TopHat packers: Drainchem have also introduced packers that allow the installation of top hats to laterals from mains and are available in 100x100 mm, 150x100 mm and 150x150 mm. The host packer can be used as a standard packer and has an additional inflation port to enable the inflation of a top hat packer when fitted.
Cone plugs: Also new to the Drainchem range are inflatable cone plugs to suit multiple pipe diameters chloroprene and aramid fabric reinforced with vulcanized rubber. The cone plugs fold down much smaller than a traditional rubber plug and this enables ease of access into pipes and manholes
Pillow plugs: Another exciting product is the Inflatable pillow plugs. Ideal for larger pipes, these are flat like a matt and can be rolled up to help installation into the pipe. Available in sizes 600-100 mm up to 1800-2800 mm.
Lifting bags: A range of Inflatable lifting bags from 1000 kg to 77,000 kg lifting capacity with lifting height up to 600 mm. Ideal for positioning pipe in trenches or pumps onto pipes.
For more information visit www.drainchem.com.au
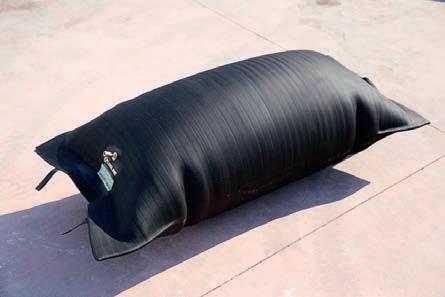
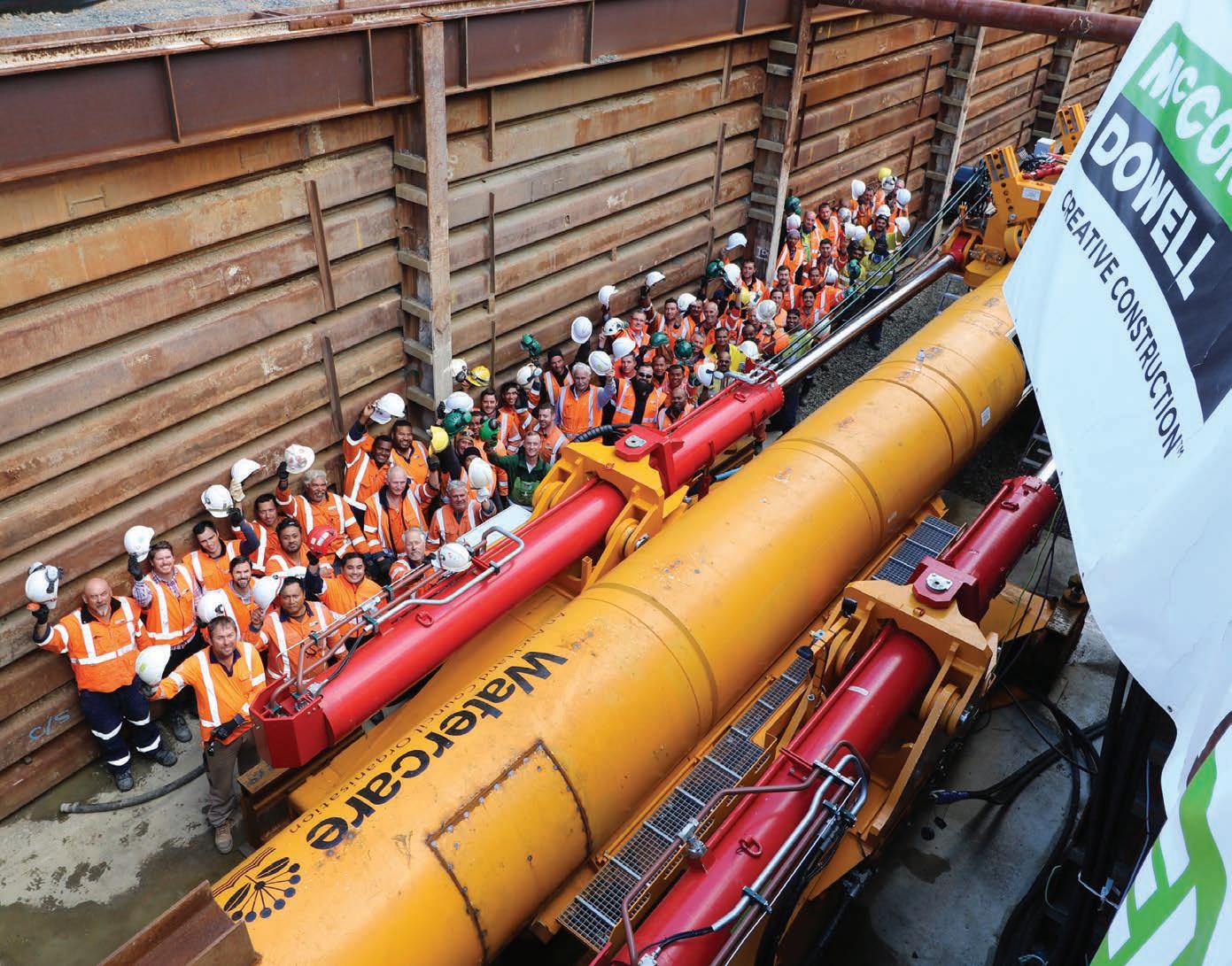
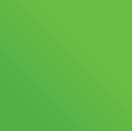
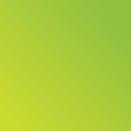
SECA elevates customer’s data efficiency with WinCan VX
Sewer Equipment Company (Aust), better known as SECA, is one of the country’s leading suppliers for pipeline, sewer and plumbing equipment.
The company was founded in 1967 and has been providing innovative technologies for sewer asset management for decades. SECA’s customers range from residential plumbers to councils, water authorities and contractors.
The leading edge of asset management software
Part of SECA’s arsenal for asset management is
WinCan VX – a powerful software that can be used to collect pipe inspection data, organise it into a database and generate inspection reports.
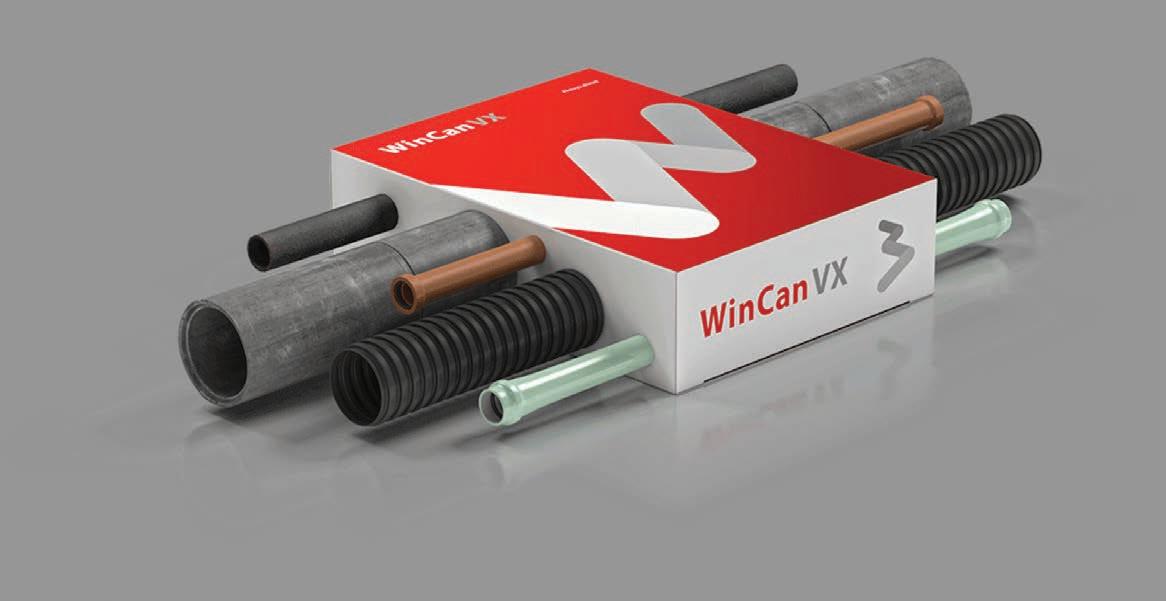
WinCan VX can be used interchangeably with any of their major brands of pipe inspection cameras, can be adapted for pipe inspection projects ranging from small municipalities to major metropolises, and supports all current major GIS systems.
The software’s full-featured geographic information system (GIS) and mapping implementation make data utilisation easy – enabling users to create entire WinCan projects by simply clicking and dragging on a digital map to generate pre-populated section data, helping to increase data efficiency and eliminating human error.
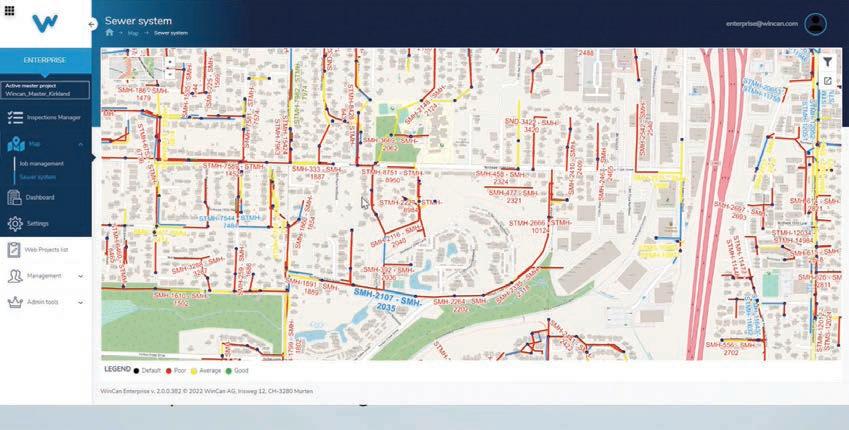
This mapping capability allows users to create graphic layers with specific data and information. Base layers – also called “tiles” – are able to provide geographical data, including:
erial Imagery – A high-definition “bird’s eye view” of the mapped area that can grant operators information about asset locations, potential hazards and influences on infrastructure.
Terrain Maps – A geographical layout of the topography in the mapped area that assists in understanding the flow and risks associated with pipe systems.
treet Maps – An overview of roadways and other features in the area that makes site navigation and locating manholes and other important features.
Tiles are further augmented by more detailed, specific layers that provide deeper information on the pipe infrastructure in the project area.
These layer options are:
1. Heat Maps – Colour-coded information that can be used to highlight critical areas in the project area. Heat maps are a powerful tool for the identification and prioritisation of pipes that are in critical condition. The heat map is a graphic display of any numeric variable put in by operators – number of observations, grade, total inspections, etc.
2. Rehab Layer – Excellent for determining work order. The Rehab layer is colourcoded to indicate section that have received rehabilitation, or still require it.
3. Observation Layer – Overlaid iconography allows operators to view what observations have been made in what areas. This layer helps rehab teams isolated locations for repair projects.
4. Ratings Layer – An overlay of map sections that applies ratings to indicate pipe condition and also helps identify critical areas in the infrastructure.
Perhaps most importantly for an industry that is constantly evolving and innovating, WinCan software is designed with modularity in mind –allowing users to add whatever functionality is required.
For use by anyone
For such powerful and versatile asset
management software, WinCan VX is still user friendly.
The software can be adapted to the skill level of the user, meaning it can increase the effectiveness of operators at all levels, empowering project leaders with data sets that can be quickly updated by workers in the field, and increasing the efficiency and autonomy of working groups at the ground level of infrastructure projects.
The user interface can be customised to the operator’s preference, and can be adjusted for use on any screen size – perfect for use during projects in the field and teams that need to run work from the van.
WinCan VX software is so useful that there are a number of councils that are actively requesting their reports in WinCan format.
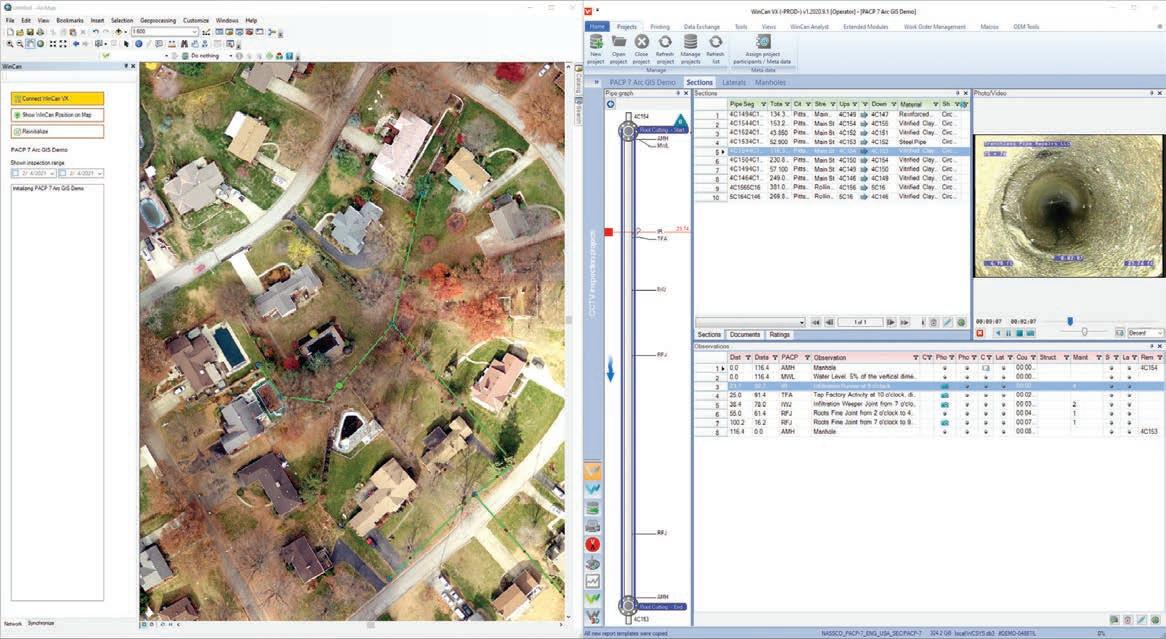
Support and training
SECA’s experience and expertise in asset management technologies for the trenchless industry uniquely positions the company to empower customers with WinCan VX software.
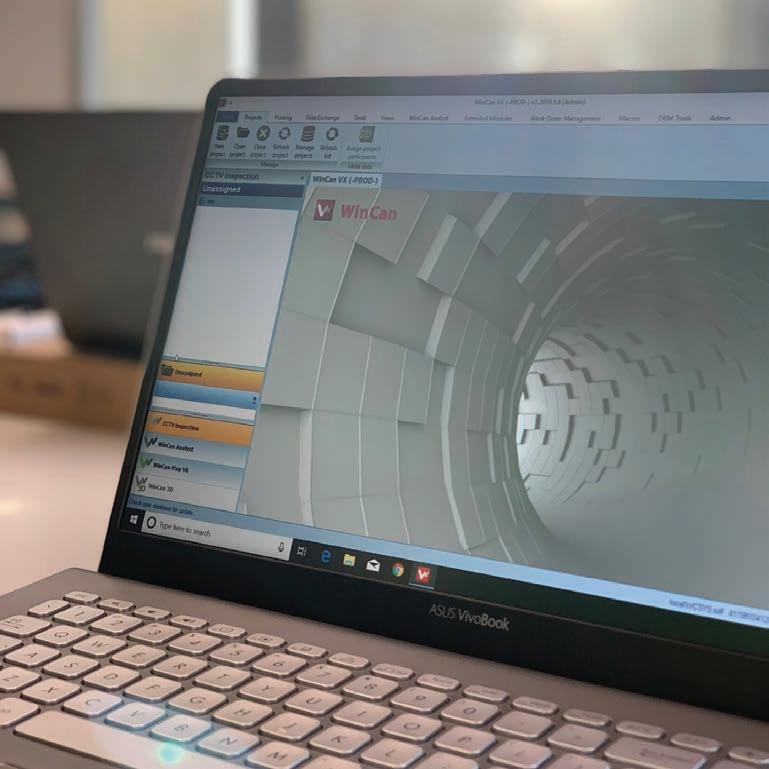
Based out of its Sydney warehouse, SECA is able to provide conduit training in the use of the software so that customers are able to get the most out their equipment.
In doing so, SECA provides the highest possible standards of service to their clients across the country.
For more information visit www.seca.com.au
Smart Lock Group committed to the contractor and asset manager in first-rate trenchless sectional drain rehabilitation
What to do with Australia’s vast ageing drainage network? Trenchless pipe rehabilitation is a fraction of the cost compared to the excavation and the construction of a replacement drain in built up areas. Reinstatement of paved surfaces and returning the street scape can be significantly more than the drain’s
Once there, it is left on an ongoing basis. When cleaning cycles over many years have passed it progresses, heading away from maintenance as it arrives usually onto the reline or replace pipe register.
Clean & camera of known drainage chokes

Solutions for 100 to 900 mm pipes.
years plus design life, but it is expensive. Pit to pit trenchless drain rehabilitation lessens the impact of a civil open trench upgrade. Advanced cleaning and robotic cutting equipment, coupled with high end CCTV pipe cameras, are readily available Australia wide. High quality technology opens up the ability to provide comparable longevity in drain rehabilitation at a reduced cost. Sectional and full relining use materials that provide the asset owner with a higher coefficient in the pipes surface, increasing flows. As a bonus, modern rehabilitation technology and installation techniques exploit what once was regarded as near impossible, or “extreme measures”, to a viable solution. Today pit to pit relining and sectional pipe repairs are all rated well beyond a 50 year service life, assisting in the accountability to maintain the life cycle of an asset. If we think of the oldest successful drain specification – that being a fired or even a nonfired clay pipe – we know that it enjoyed a long service life but was heavily reliant on strong pipe joints. A major issue today is root intrusions at the pipe joint and unwelcome drain movement.
When this movement continues over the assets lifespan it generally results in cracks and increasing displacements. Further to this issue is the physical abrasive wear factors and, in sewer systems, H2S gas attack of the concrete itself.
Drainage network maintenance program
In most cases where the pipe surface remains serviceable but for only a few defective joints, the pipe section is often left to become a maintenance liability. This section may be marked up after a few years of random response cleaning to qualify for the routine cleaning list.
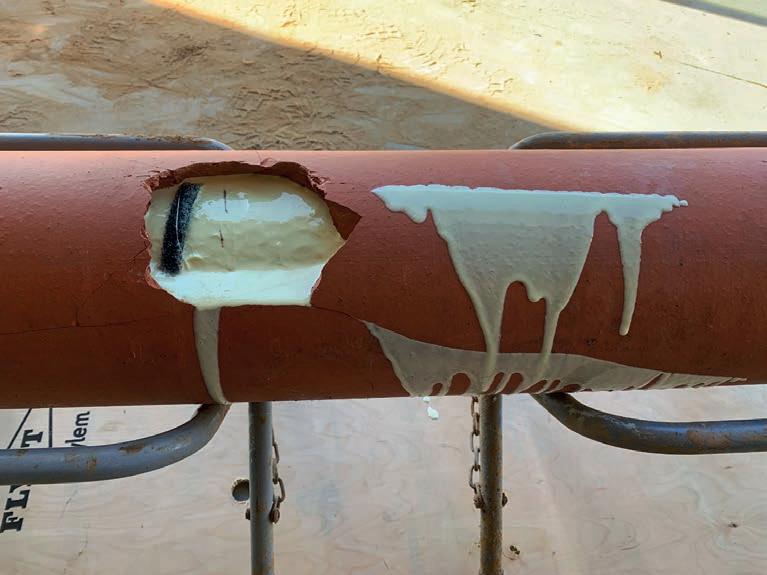
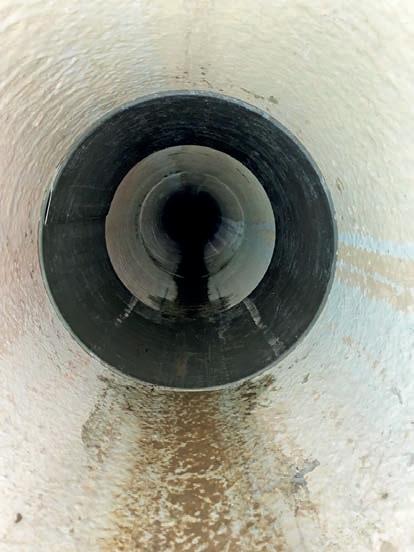
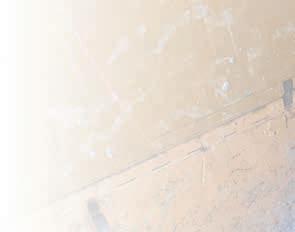
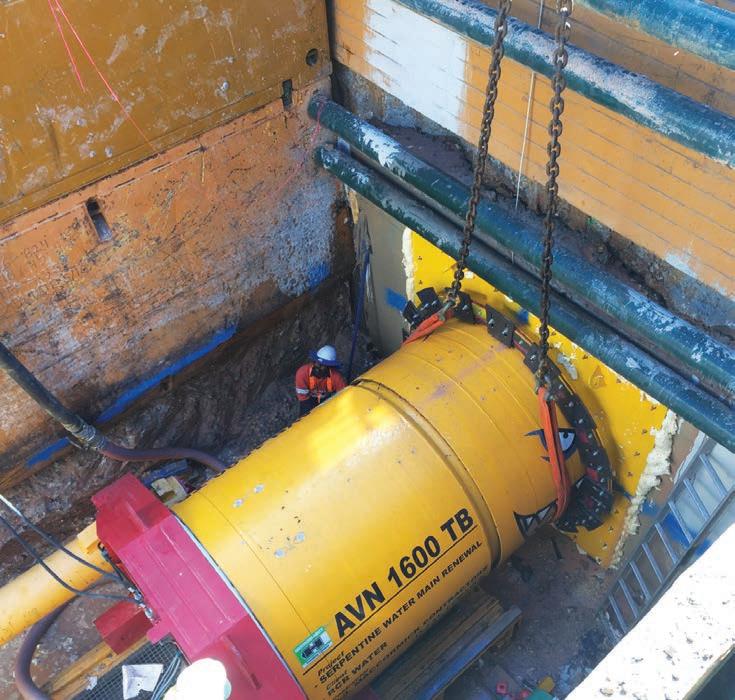
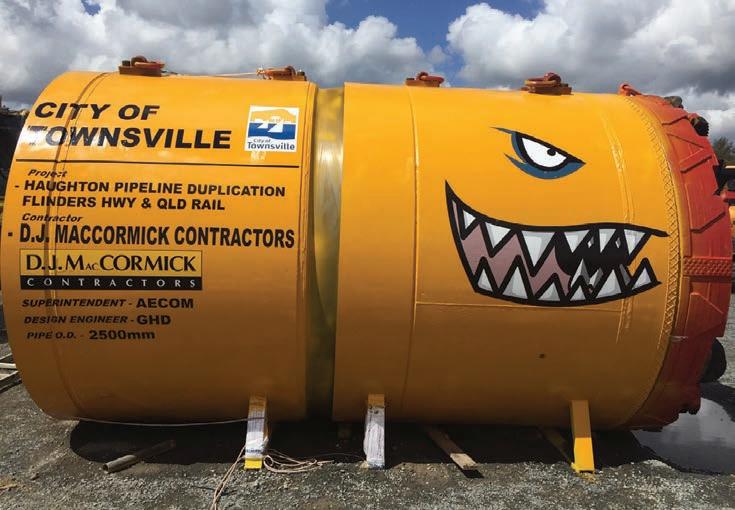
High-pressure water jet clearing of reoccurring blockages in drainage assets can, in some cases, increase root intrusion growth and further destabilise pipe bedding, which impacts a defect further. The most effective solution is to reopen a drain, but without a CCTV vision review an opportunity window to rehabilitate may pass by. A pipe section may simply require a morning’s effort of cleaning and some simple point or sectional pipe repairs. If the CCTV assessment finds multiple issues resulting in many pipe defects the drain may be ideally suited to a full length reline. Typically speaking, drainage officers prefer a full reline when the rehabilitation of sectional repairs range between 50-70 per cent of the reline cost. The high impact raise and lay replaces cost that are reserved only for those drainage sections that warrant the upgrade.
Providing valuable trenchless solutions
The Smart Lock Group is a product supplier to drainage rehabilitation contractors and local government pipe maintenance crews alike. With industry knowledge and experience in pipe rehabilitation, its drain defect solutions begin with 100 mm to 900 mm pipes, engaging the use of various installation packer-style trolleys. In larger pipes it provides confined space entry pipe rehab solutions. All products are approved and are true structural trenchless repairs.
For more information visit www.smartlockgroup.com
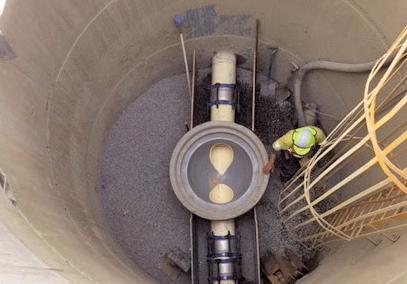
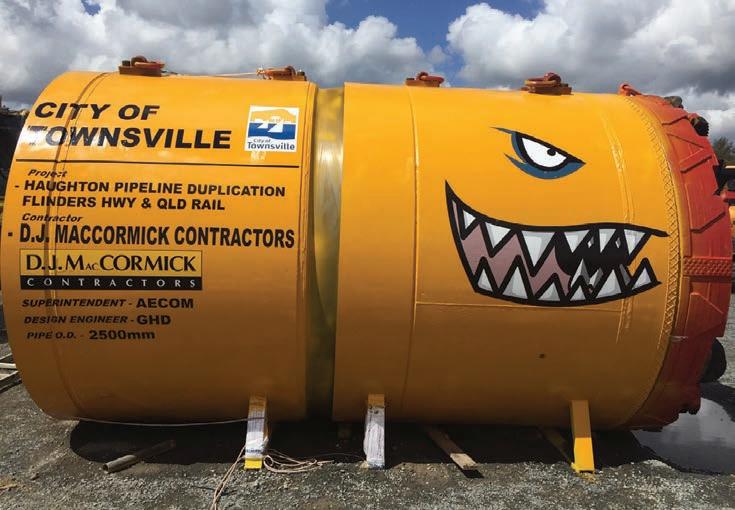
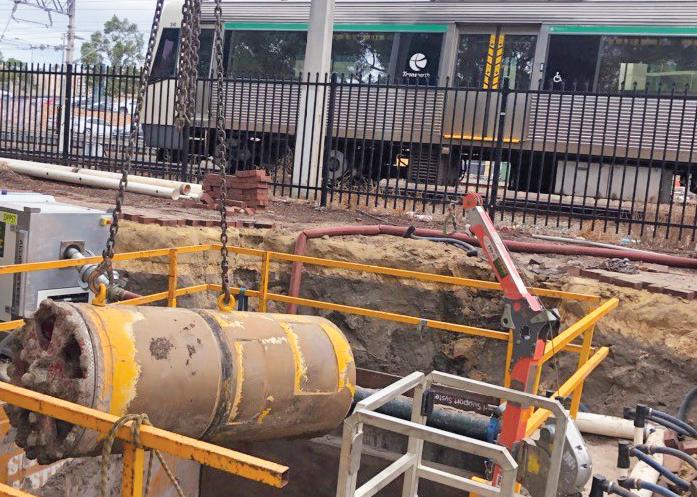
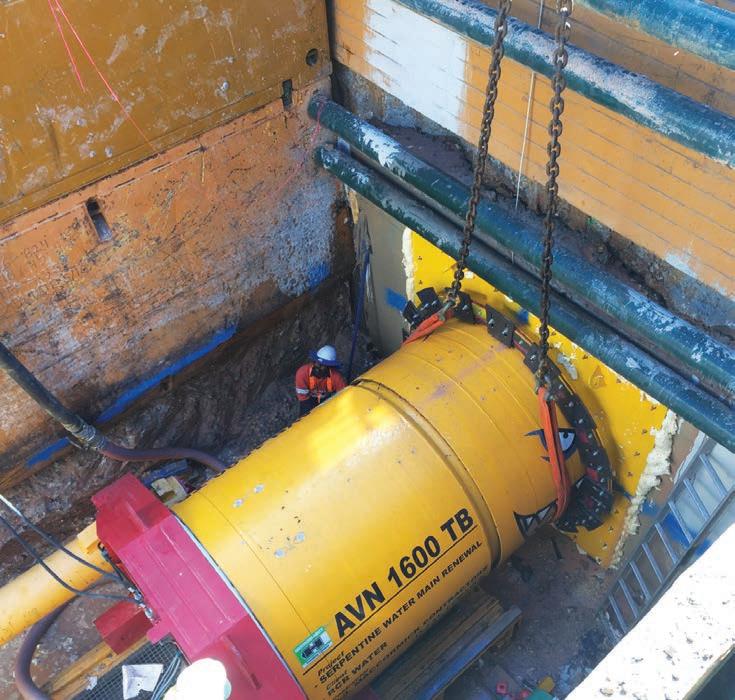

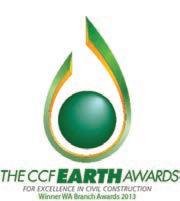
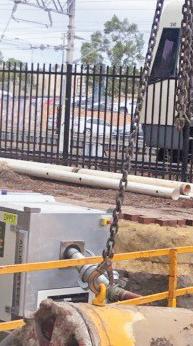
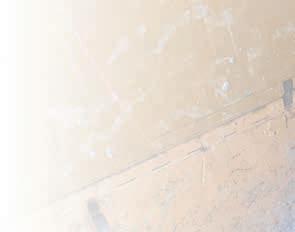
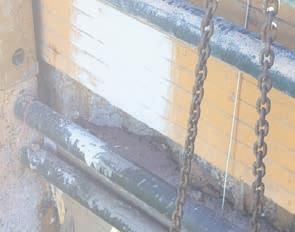
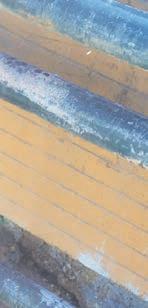

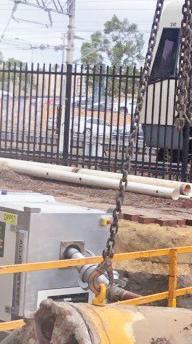
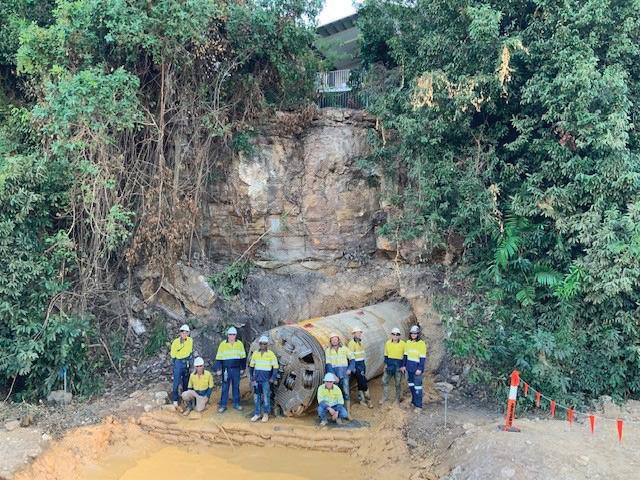
DJ

reinforced concrete jacking pipe
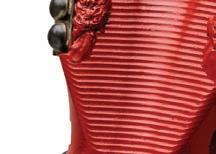
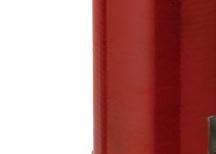
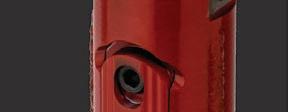
DJ Mac Cormick Contractors have undertaken one of longest single drives for an 800 mm diameter closed face slurry shield micro tunnelling project, with no man entry available for installing intermediate jacking stations or slurry pumps.
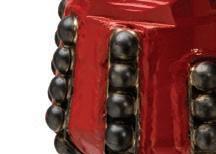
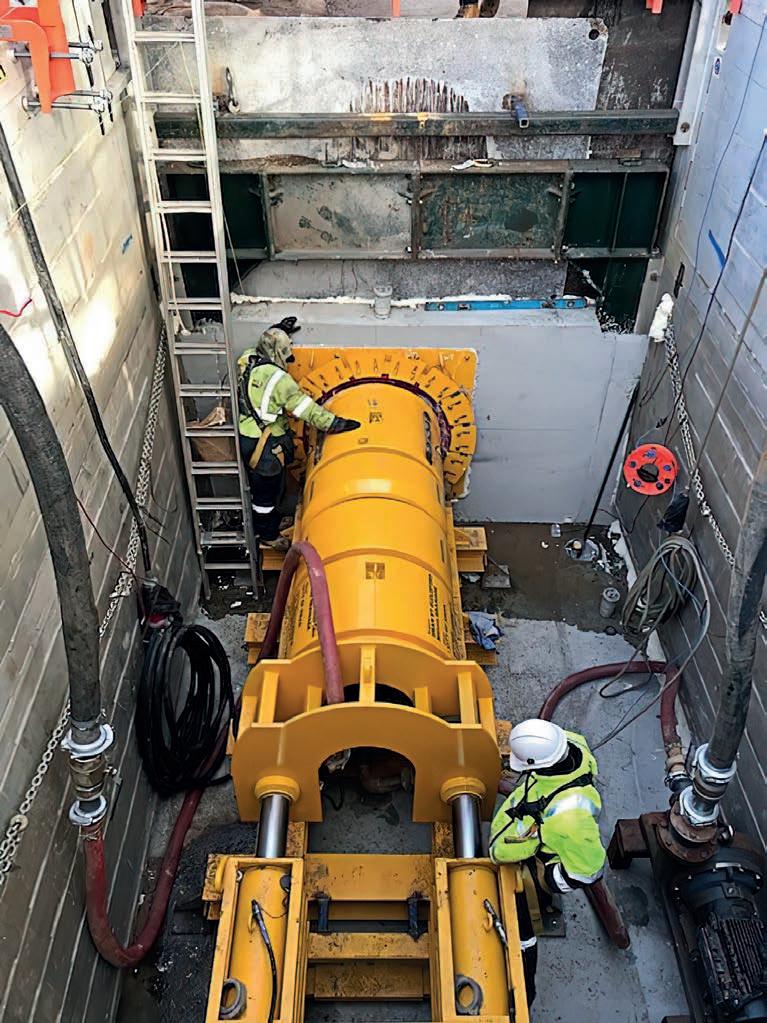

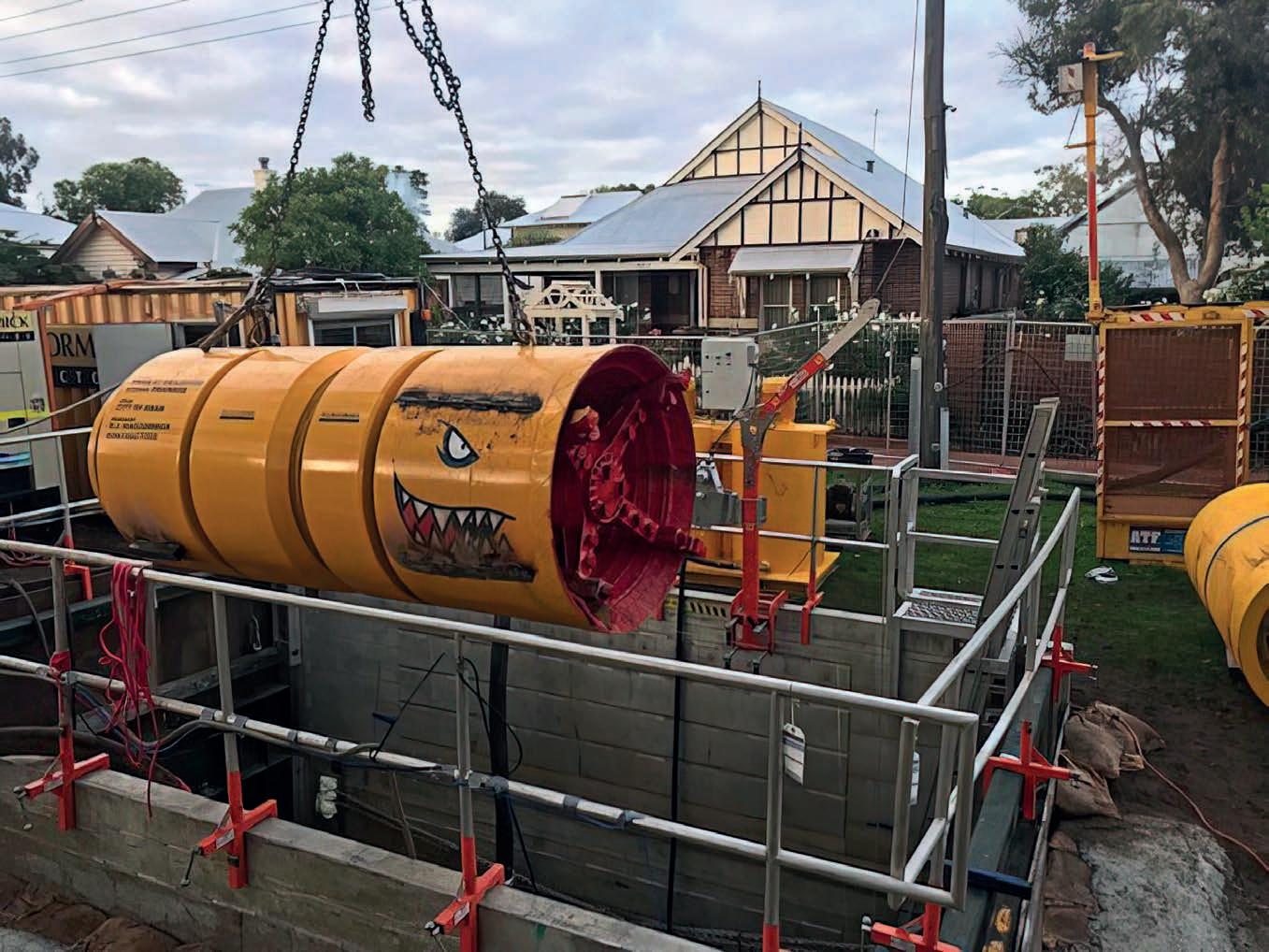
The project was completed on behalf of the city of Swan, located in the eastern metropolitan region of Perth in Western Australia.
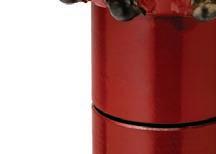
The drive length for a main drain was 234 m and due to the high level of traffic, community use and business trading work was only able to be undertaken over the Monday to Friday traditional work week.
Launch and receival shafts were constructed utilising Ground Support Systems (Aust) shoring and associated safety equipment, which included certified structural KPA ratings for all the shoring.
Temp designs were certified by structural engineer & undertaken for thrust block, entrance wall and concrete pad.
DJ Mac Cormick Contractors had previously undertaken the previous stage back in 2019.
The works in this stage involved several high complexity traffic MGE plans staged to ensure continual flow traffic through locality in order to minimise disruption to businesses as well as the broader community and residents.
Ground conditions ranged from stiff clay to running sand. Underground streams encountered throughout the project also meant working on river sands and river stone cobbles during the drive length. All works were undertaken within 20 mm tolerance over drive.
Upon completion of the drive, various
2500 mm diameter with its a fleet of Iseki & Herrenknecht closed face tunnel boring machines (TBM). The company boasts a variety of TBM cutting wheels to suit soft, mixed and rock ground conditions in varying ground conditions, both wet and dry, to fit the needs of the Australian people and its landscape country wide.
The company has the capacity to complete drives up to 1 km utilising intermediate jacking stations and intermediate jacking units to run another four stations from within pipelines or intermediate slurry pumps in which pipe diameter is 1500 mm or greater. For these sizes and more, the company has TBM’s with the ability to change cutters from within where required along the drive length.
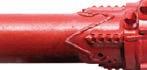


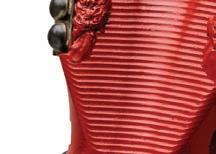
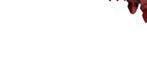
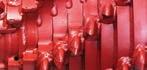
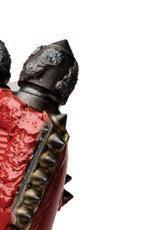




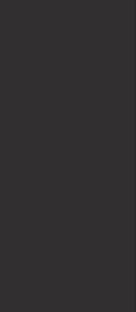
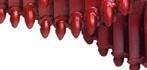

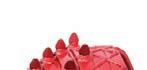

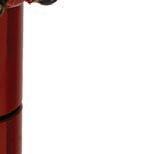

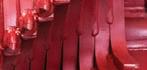



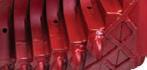
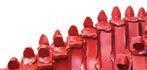
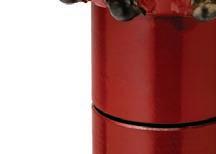


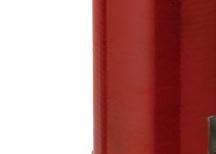

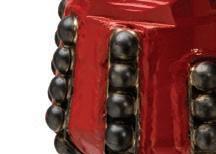
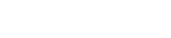



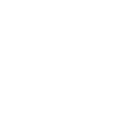
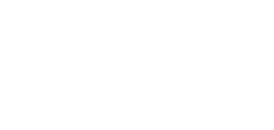
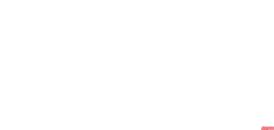
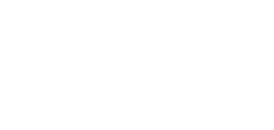
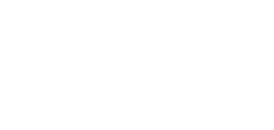
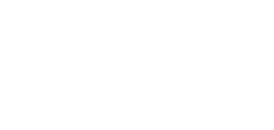
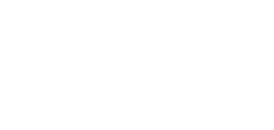
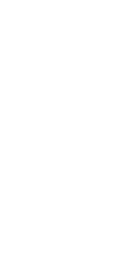
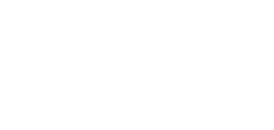
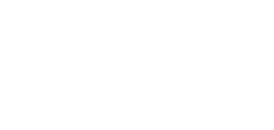
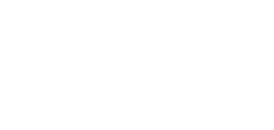
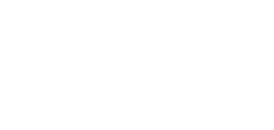



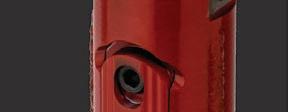

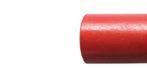


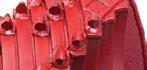

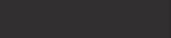

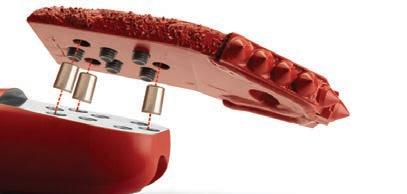

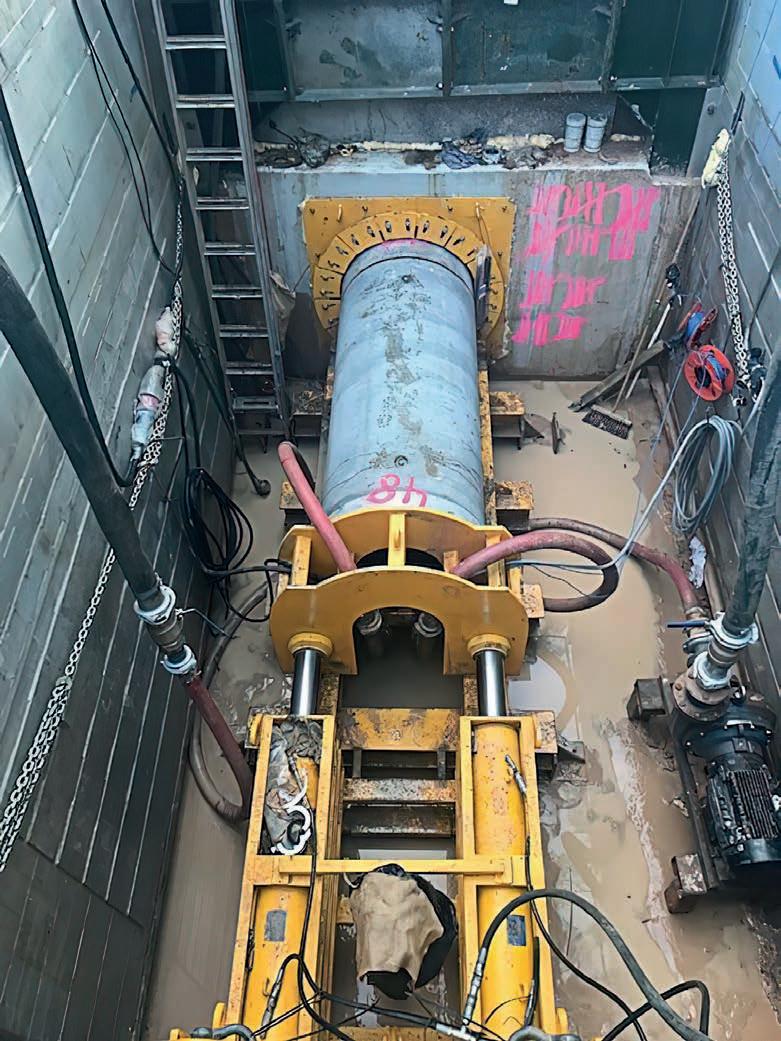


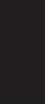
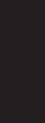
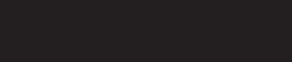
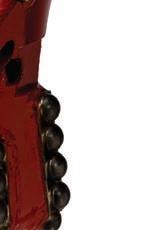
Not only that, but also DJ Mac Cormick Contractors has rock cutting wheels suitable for 200 MPA rock.
With offices in Perth, Adelaide, Sydney, Melbourne, Brisbane and Townsville DJ Mac Cormick Contractors is able to provide their expertise to its clients throughout Australia.
Further information or enquiries to info@djmaccormickcontractors.com.au
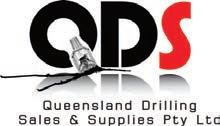
Microtunnelling through basalt and very hard rock
Installing pipelines via trenchless methods such as microtunnelling in areas where there has been volcanic activity presents a number of challenges.
difficult ground conditions, consisting of clays and boulders from the underlying Quaternary Age Newer Volcanics basalt and multiple basalt flow boundaries.
Heading into a project in Donnybrook that comprised 2.4 km of DN700 GPR pipe – 1 km to be completed by trenchless with depths from 10-14 m over ten bore lengths – Edge Underground knew the job would not be easy.
But when ground conditions presented as more challenging than expected, it provided an ideal opportunity to prove the capabilities of its innovative pneumatic rock hammer.
“We knew the area was made up of intersected lava flows from different volcanoes that were located in different directions, and we were prepared to adapt based on how the drill performed,” Harrison says.
“The thing to keep in mind is that if you drill at the intersection of these flows, you will find abnormalities; you may find the drill will go well in some directions but not others.
“In Donnybrook, when we hit those intersections, we found there were elements of water quenching in the rock – a condition that is rarely seen and wasn’t in the geotech we were provided with.
“We found the ground in these sections was .5 Mohs and was formed from two layers of lava flow meeting with a gaseous layer which created a lava tunnel, so when we tried to drill there was no support, which put the drill head at risk of snapping.
Dpipeline route and specifications, there could be few options available and may result in higher costs for the client. However, a new, innovative advancement by Edge Underground is allowing for easier drilling in difficult hard rock conditions.
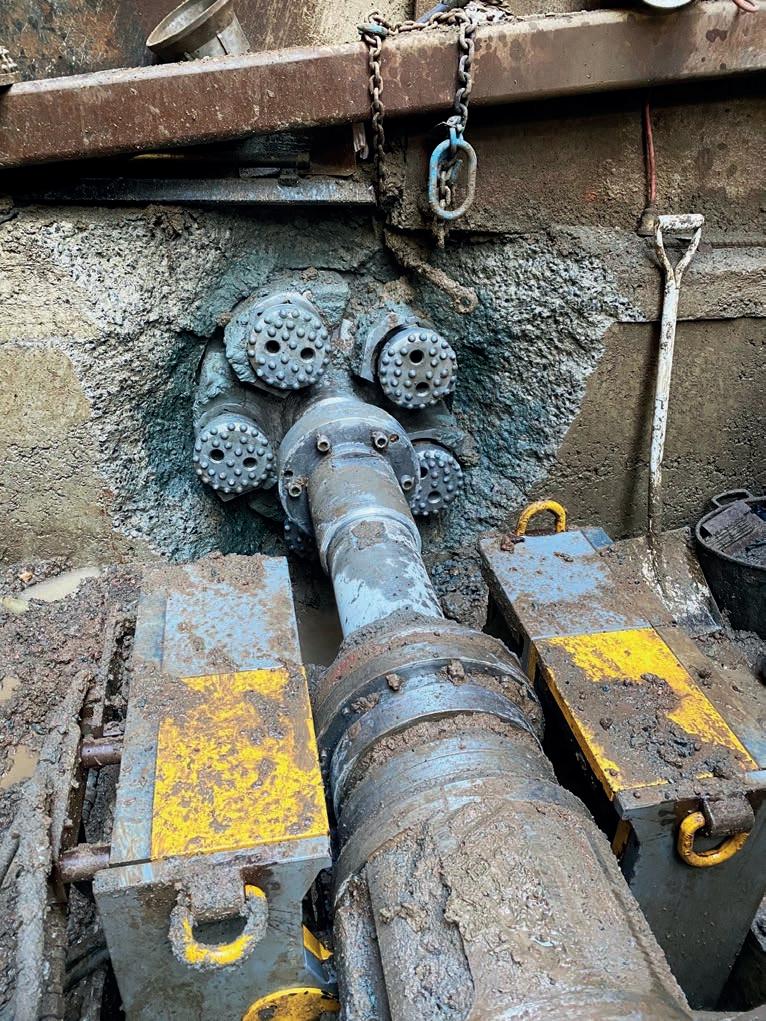
Stuart Harrison, Managing Director at Edge Underground, says that there are a number of conditions that can be found in areas where volcanic activity has taken place, including intersecting lava flows, quenching, lava tunnels and extreme rock hardness.
“Due to the nature of lava flows, drilling in areas of volcanic activity can be particularly challenging as ground conditions can vary a lot
information will be provided prior to drilling, it’s not uncommon for it to be inaccurate in such areas,” Harrison says.
“This is because it doesn’t provide the details of the ground along the entire length of the pipeline route; all it shows are the conditions at the location of the core sample, which could be vastly different to the conditions a short distance away.
“However, where areas are notorious for having difficult ground conditions, and if you’re accepting a project in those areas, you know there is a high chance of challenges arising.”
Donnybrook in Victoria is notorious for its
“On top of that, we also found high water flows where water quenching had occurred, adding the extra challenge of the drill head changing structure where hot steel met the water. This caused further issues as the water flows had caused a crust to form and there were areas of rock over 250 MPa, which hadn’t been identified in the geotechnical information.
“So we had extreme hard rock, what we thought at the time to be basalt up to 800 MPa, intersecting lava flows, voids, and lava tunnels filled with water.”
Harrison says that, in this situation, usually the only option would be to upsize from DN700 to DN1200 and install concrete
casing pipe, which would incur a greater cost to the client.
However, Edge Underground proposed using a new innovative and pioneering advancement based on its new pneumatic rock hammer that its team had just developed.
The technology uses air-driven hammers (similar to vertical DTH heads) on Edge Underground’s AXIS laser guided system. This system was previously untried and is a new technology to the microtunnelling market, enabling drilling in very high strength rock, a ground condition that has traditionally been a challenge for the industry to work with.

“It can be operated via the next generation AXIS drill rods with a power enhancing driver. The system uses high pressure air hammers in sequence – exhausting cuttings through a custom removal system – and is ideal for very high strength rock,” Harrison says.

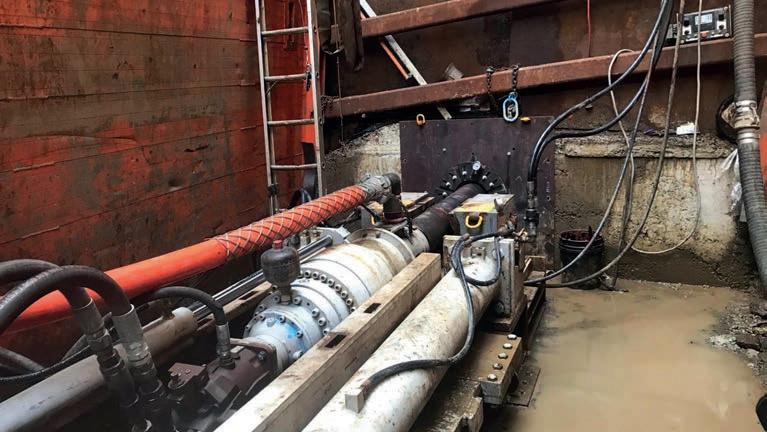

“The new system also has environmental and workplace health and safety benefits, enabling small to medium-size pipe diameters to be installed in hard rock faster, with a significant reduction in spoil removal and truck movements compared to open cut methods.”
For more information visit www.edgeunderground.co
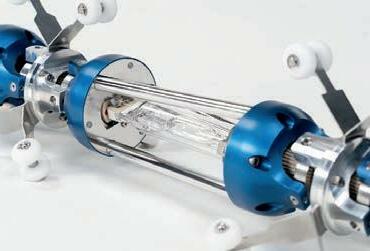
IMS Robotics Australia Pty Ltd. now established to
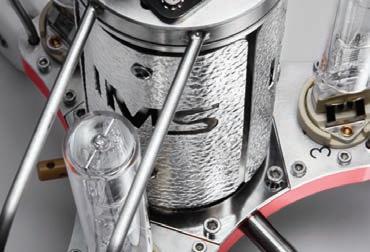
• Service main line robotic and UV curing equipment
• Stock spare parts and consumables locally to reduce shipping costs and lead times
• Represent all main line products of the IMS Robotics Group in Australia and New Zealand
• Support clients with rental UV units
Unit 32, 205 Port Hacking Road Miranda,NSW 2228, Australia keith@kre.com.au +61 2 9522 4922
Get ready for No-Dig Down Under 2023
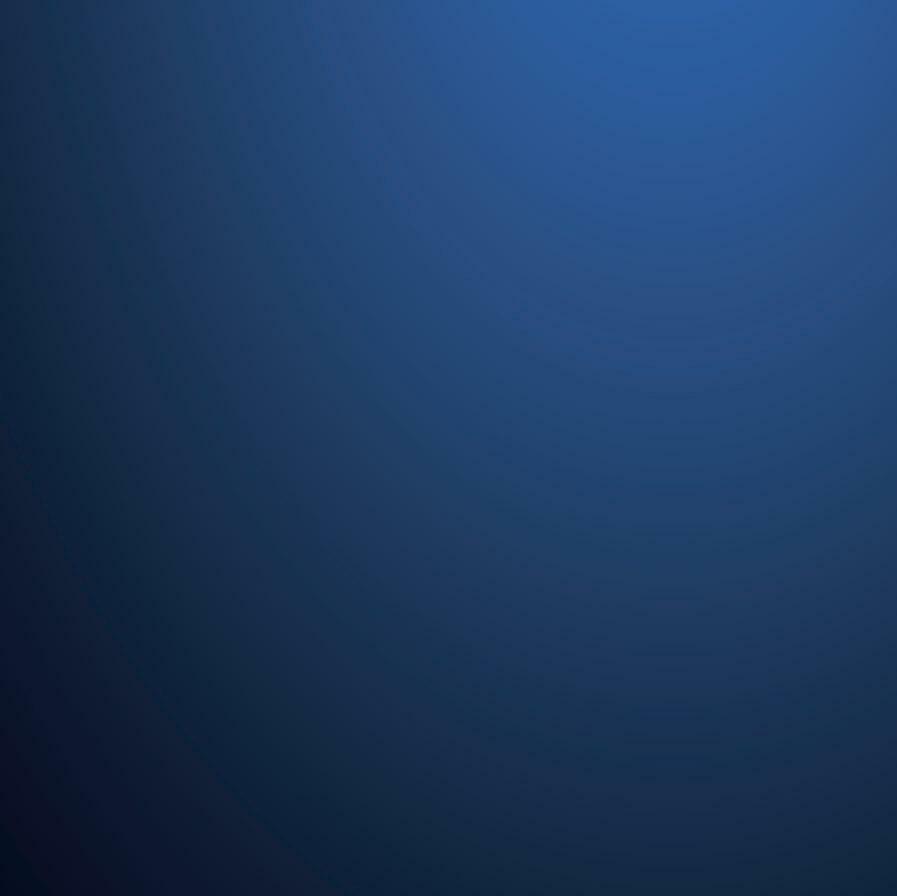
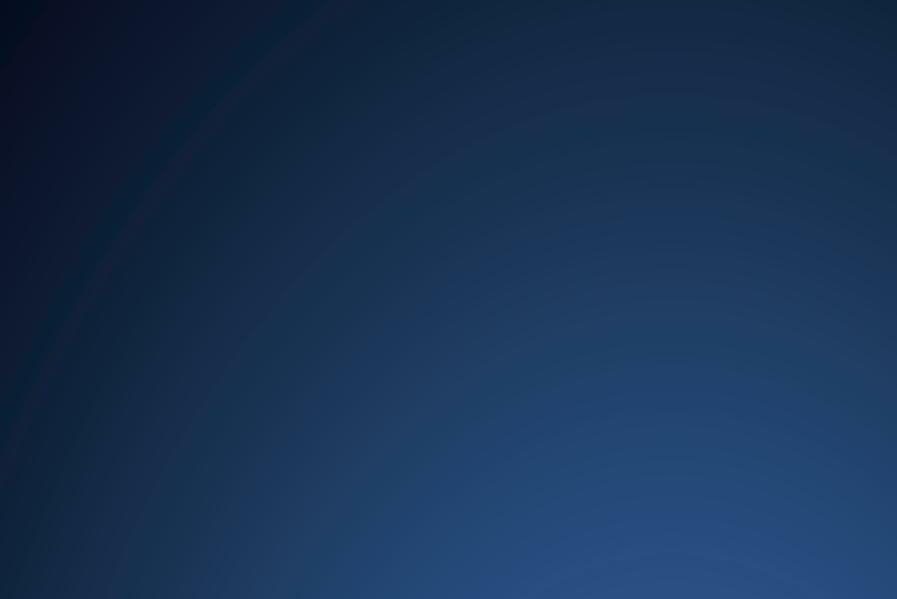
No-Dig Down Under is the southern hemisphere’s only large-scale conference and exhibition dedicated to trenchless technology, and it is back in 2023.
Supported by the Australasian Society for Trenchless Technologies (ASTT), NoDig Down Under 2023 is continuing its reputation as the essential industry event, but places are filling fast. With 55 per cent of the available exhibition space already booked, No-Dig Down Under 2023 is looking to be better than ever.

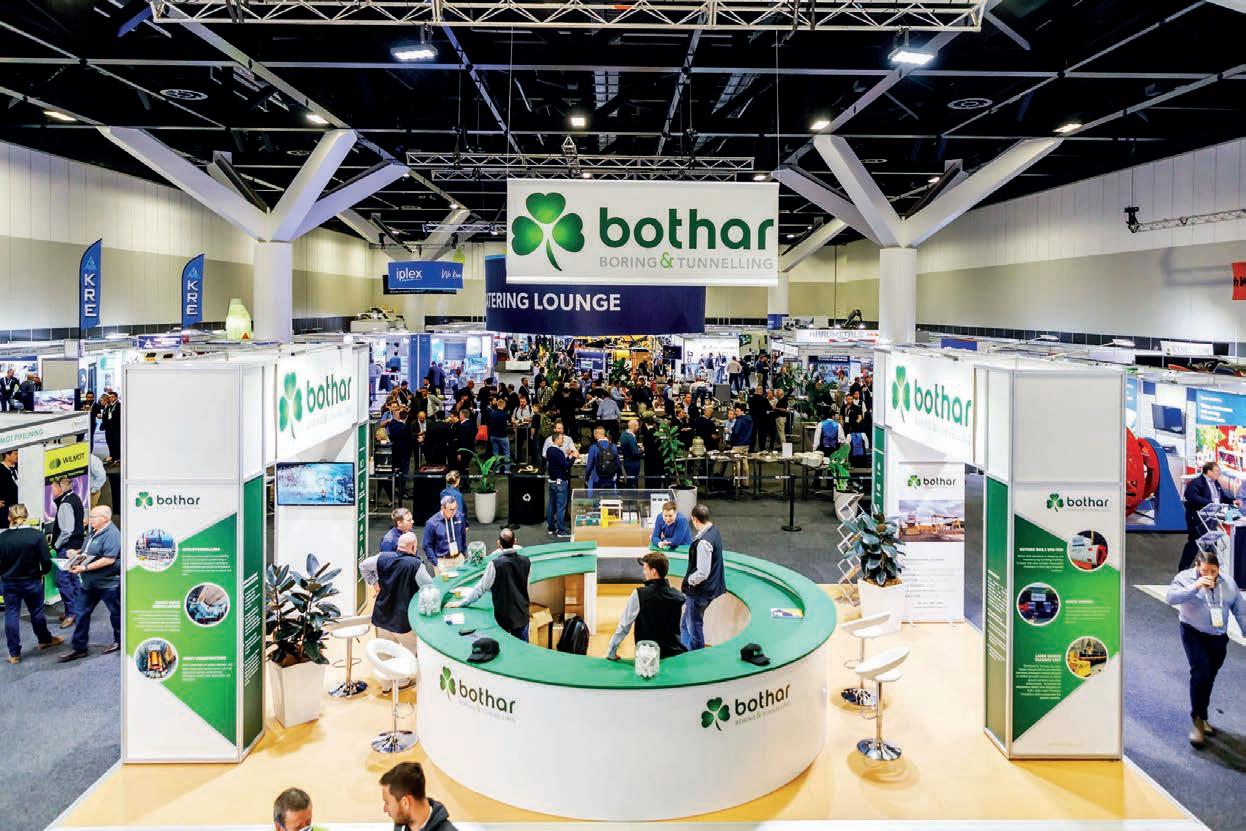
After the undeniable, sold-out success of No-Dig 2022, those who want to exhibit at the event are encouraged to book early to ensure they will have a space on the floor.
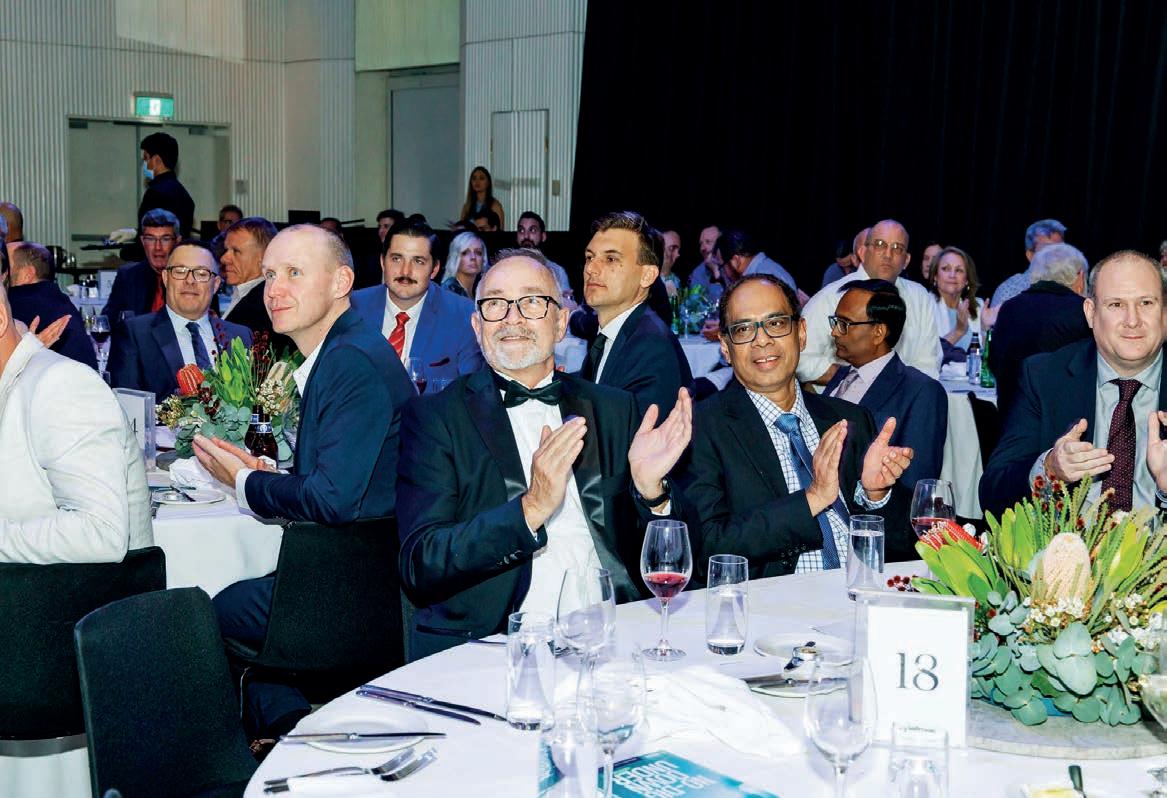
No-Dig Down Under will include networking and sponsorship opportunities, training courses, the ASTT Gala Dinner and Awards evening, and exhibitions of the latest and greatest in no-dig innovations.
The second-largest no-dig technology event in the world has become the must-attend calendar event of the year for all professionals in the trenchless technology industry.
A range of training courses on trenchless methods will be presented prior to the conference. These will be presented by industry leaders from Australia and overseas and will be of value to anyone who encounters trenchless technologies as part of their employment.
The event will be held at Brisbane Convention and Exhibition Centre on September 13 and 14, 2023.
Want-to-be exhibitors can register their interest here: www.cognitoforms.com/PrimeCreativeMedia/ NoDigDownUnder2023ExhibitorRegistration
For more information about No-Dig Down Under 2023 visit: www.nodigdownunder.com/
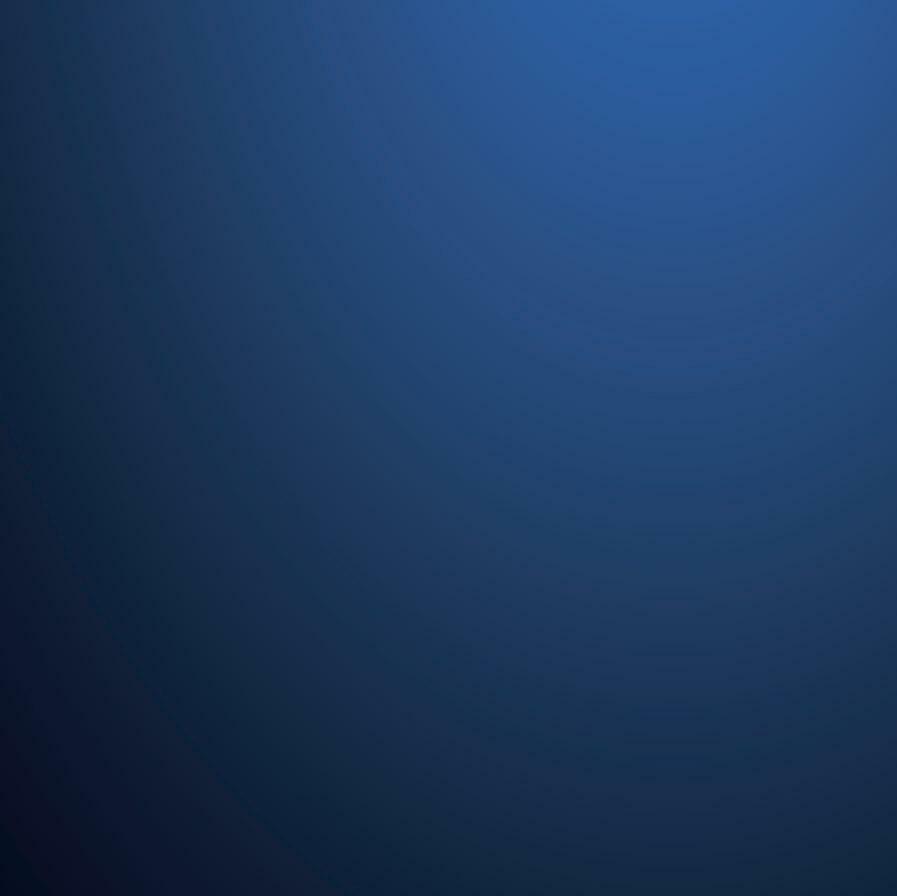
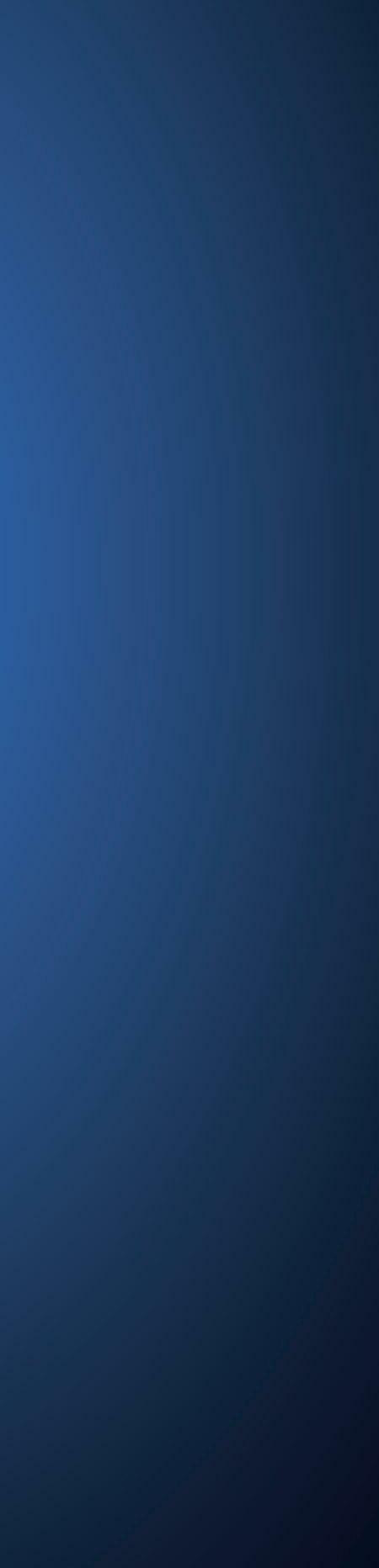

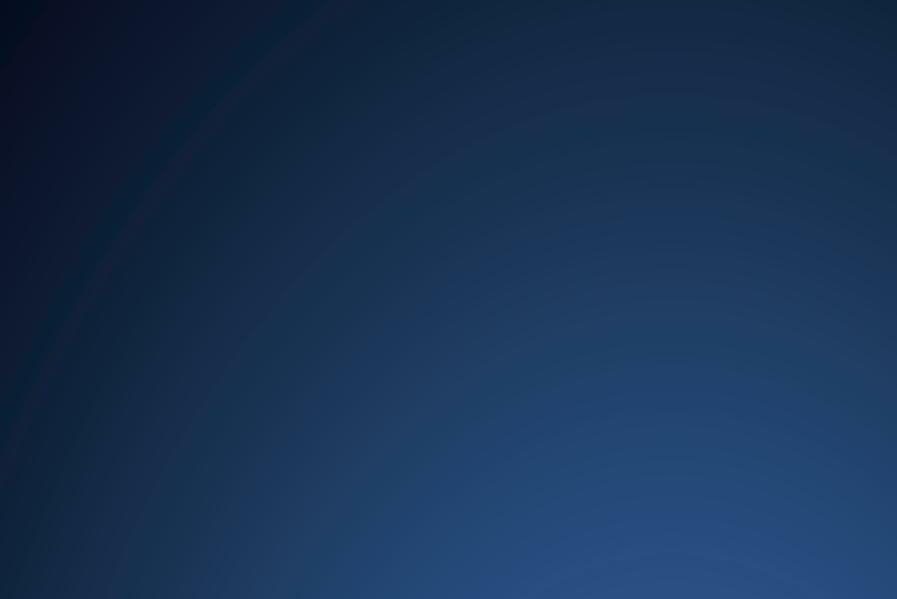
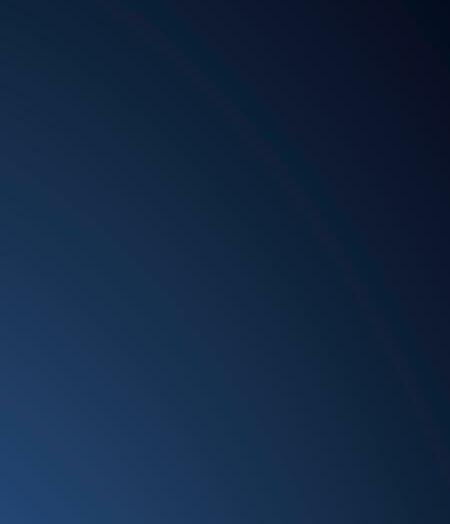
Corporate Members
Gold Corporate Members
Bamser Holdings Pty Ltd
Michels Asia Pacific Pty., Ltd.
Arcadis Australia Pacific Pty Ltd
Veolia
J&R Contracting Limited
Orion Consulting
Silver Corporate Members
Aaro Group
Abergeldie
Abergeldie Rehabilitation Pty Ltd
Adept Drainage Pty Ltd
AECOM New Zealand Ltd
Applied Felts
Aqua Assets
Aqua Metro Pty Ltd
Atteris Pty Ltd
Aurecon
Aussie Trenchless Supplies Pty Ltd
Austunnel Pty Ltd
Ballarat Underroad Boring and Excavations Pty Ltd
BG Risk Solutions
Blick Group
Bortec Laser Bore Pty Ltd
Bothar Boring
BRP Corporation Pty Ltd
Bullseye Boring
CEA
Connect 8
D.J. Mac Cormick Contractors
Denso (Australia) Pty Ltd.
Digital Control - Australia
Directhitt Pty Ltd
Directhitt Trenchless Pty Ltd
Diversified Services Australia
DKM Utility Services Pty Ltd
DM Civil
Dormway Pty Ltd
Drillers World Australia
E&CC
Eco Relining Supplies
Edge Underground
ELB Equipment Pty Ltd
Empire Infrastructure Eptec Pty Ltd
Finlease
Fulton Hogan Construction Pty Ltd
Asset Owners
Knox City Council
Watercare Services Limited
Greater Western Water
Future-Proof Solutions
GM Microtunnelling
GN Solids Control
Golder
Hard Metals Australia Pty Limited
HDI Lucas
HEB Construction
Holcim (Australia) Pty Ltd
Hynds Pipe Systems Ltd
Independent Sewer Consulting Services Pty Ltd
Insituform
Insituform Pacific Pty Ltd Interflow Pty Ltd
Iplex Pipelines Australia
JB Trenchless Pty Ltd
JJ Ryan Consulting Pty Ltd
KAISER Technology Pty Ltd kwik-ZIP Spacers
L P Pipe Civil
LKL International Pty Ltd M. Tucker & Sons Pty Ltd
March Cato Ltd
Marley
Maskell Productions Ltd
Maxibor Australia Pty Limited McBerns Innovative Solutions
McConnell Dowell Constructors (Aust) Pty Ltd
McElroy Manufacturing Inc.
McMillen Jacobs Associates (NZ)
Melbourne Water
Metrocorp Technologies
Mudex
Mullane Trenchless Pipeline Solutions Pty Ltd
Nu Flow Technologies 2000 Pty Ltd
Openshore Pty Ltd
Pezzimenti Laserbore Pty Ltd
Pezzimenti Trenchless Pty Ltd
Pezzimenti Tunnelbore Pty Ltd.
Pipe Core Pty ltd
Pipe Doctor Australia Pty Ltd
Pipe Insight Ltd
Pipe Tek
Pipeline Drillers Group
PipeWorks
Prime Creative Media
Prime Horizontal Pty Ltd
Qalchek Pty Ltd
Qenos Pty Ltd
R & R McClure Excavations
Raedlinger Primus Line Pty Ltd
Ravago NZ Ltd
RBM Plumbing and Drainage Pty Ltd
Reline NZ Ltd
Rob Carr Pty Ltd
Rose Atkins Rimmer (Infrastructure) Pty Ltd
RPC Pipe Systems SA Water
SASTTI Joint Venture Schauenburg MAB
SEKISUI Rib Loc Australia Pty Ltd
SEQ Trenchless
Sewer Equipment Company (Aust)
Sika Australia
Stiles Electrical STRABAG
Sydney Water
The Drain Man
TRACTO-TECHNIK Australia Pty Ltd Trenchless Advisor Pty Ltd
UEA Pty Ltd
Universal Underground Limited
Vermeer Australia
Vertical Horizonz Australia
Vinidex Pty Limited
Warren Smith & Partners
Wilmot Pipelining
Wilsons Pipeline Solutions
Yarra Valley Water
About the ASTT
The Australasian Society of Trenchless Technology (ASTT) is a non-profit organisation comprising of members throughout Australia and New Zealand.
The successful establishment of the trenchless industry in Australasia has been supported and promoted by the peak industry organisation, the ASTT, since it was established in 1991.
The society works tirelessly to promote the use of trenchless technology in Australasia, lobbying government and client organisations to highlight the advantages of using trenchless technology and the benefits of training for industry.
Membership is open to all who are concerned with the provision of gas, water, sewerage, drainage, roads, telecommunications and electrical services.
ASTT membership provides trenchless professionals the tools and services they need to be better informed and better connected in this industry.
The ASTT is part of the International Society for Trenchless Technology (ISTT), an affiliation of societies in more than 30 countries worldwide.
Membership applications
The ASTT currently offers seven levels of membership available to all residents of
Australia and New Zealand or anyone who is also a financial member of an existing ISTT Affiliated Society.
The benefits of Membership
depending upon category can include: Up to 10 people from your organisation may be included in your membership and are entitled to receive the below benefits:
• Acknowledgment of your company in every edition of the Trenchless Australasia magazine
• An annual subscription to Trenchless Australasia magazine (four issues per year)
• An annual subscription to ISTT’s Trenchless Works
• A company listing Australasian Trenchless Directory (print and digital)
• Opportunity to promote your membership of the association by including the ASTT logo on your business communications and website
• Access to Guidelines and Standards
• Discount rates (normally 10%) at National Conferences and Exhibition.
• Discount rates (normally 10%) at International Conferences and Exhibition.
• Discount rates (normally 10%) at Trenchless Forums.
• Opportunity to become involved in our Special Interest Groups (SIG’s) which
are technical divisions of the ASTT representing specific trenchless sectors.
• Special offers and links with international organisations including the ISTT
• Opportunity to nominate for ASTT and ISTT awards
• Free access to ISTT past conference proceedings
• A communication network to keep abreast of the advancement of the science and practices of trenchless technology throughout the world
• Discounted rates at International No-Digs and national events including No-Dig Down Under.
How to apply
Visit the ASTT website: https://www.astt. com.au and refer to MEMBERSHIP and check out the membership benefits that apply for each category.
Your membership request will be emailed directly to the ASTT for processing. You will receive an invoice based on the information you supply. Acceptance does not take effect until payment is received in full.
For more information visit www.astt.com.au or email secretary@astt.com.au
Advertisers
Adept Civil 57 Austeck 3
Aussie Trenchless 61
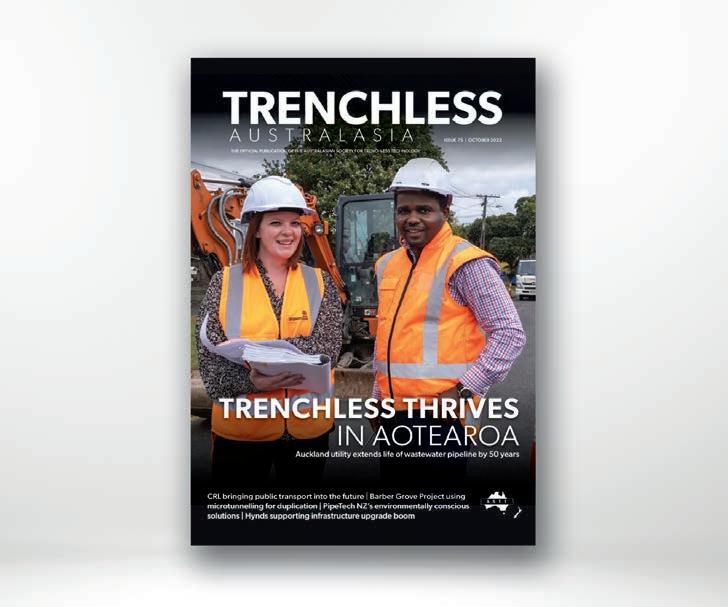
CEA 63, 75
CDE 11 DJ Mac Cormick 81
Drainchem 13
Empire Infrastructure 9 Edge Underground 71 Hynds 17 iMPREG 31 Interflow IFC
KAISER OBC
KRE 59,85
Kwik-ZIP 69
L&D Microtunnelling 15 Maxibor 73
McConnell Dowell 77 McRobert Group 7 M. Tucker & Sons 55
No-Dig Down Under 87 OptionX Group 23 Pezzimenti Trenchless 16
Pipe Core 51
PipeTech NZ 43 Queensland Drilling Sales & Supplies 83
Rangedale 45 Rob Carr 33
RTi 47 SECA 35 Smart Lock 49 M arley 19 TRACTO 29 Veolia 53
Vermeer Australia 66-67
Vermeer WA & NT 65 Wilmot Pipelining 2-3
Here's what's coming up in the next edition:
Safety HDD Pressure pipe relining Inspection & condition assessment Rehabilitation & repair Training
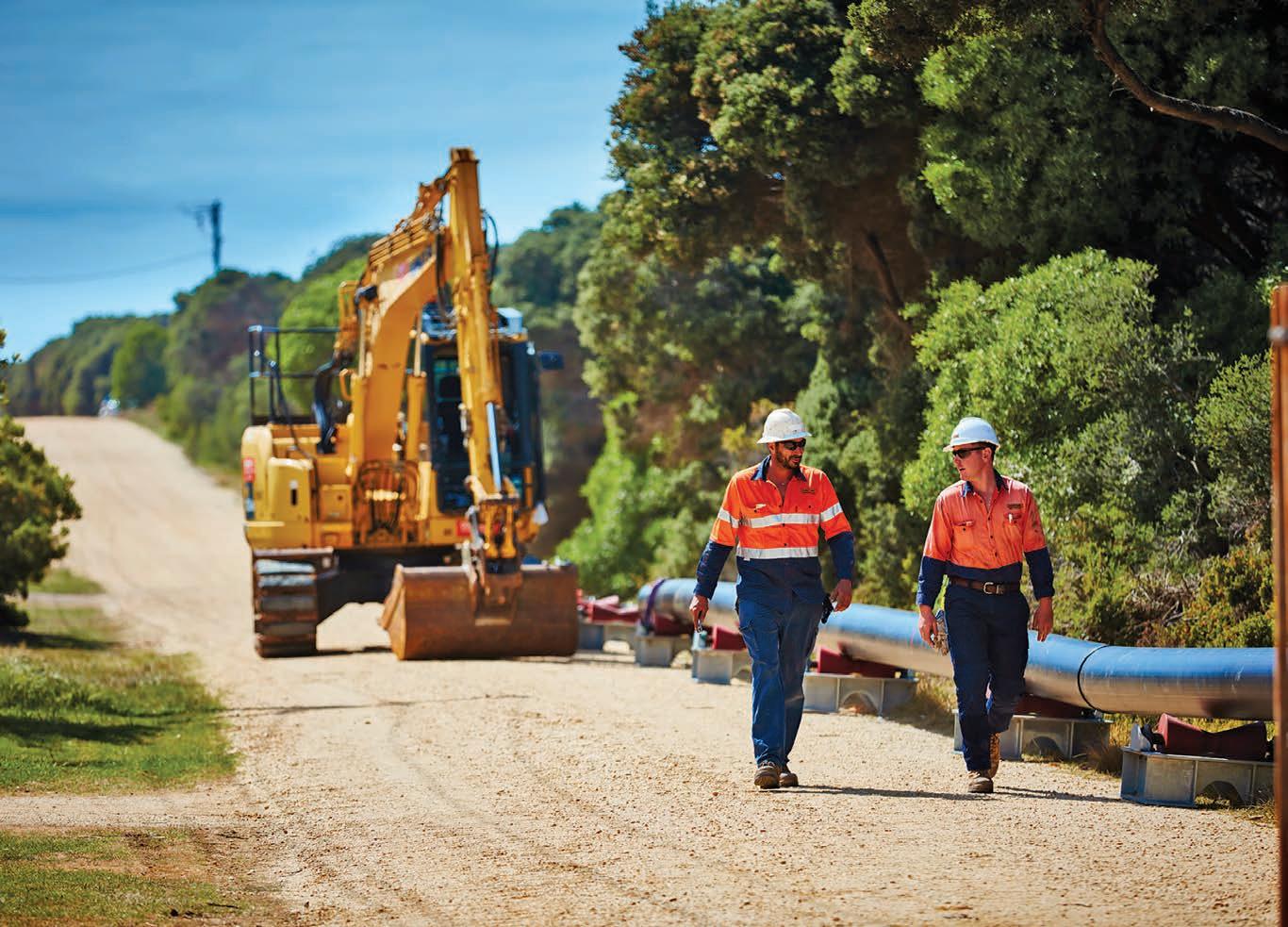
Kaiser. Performance counts.
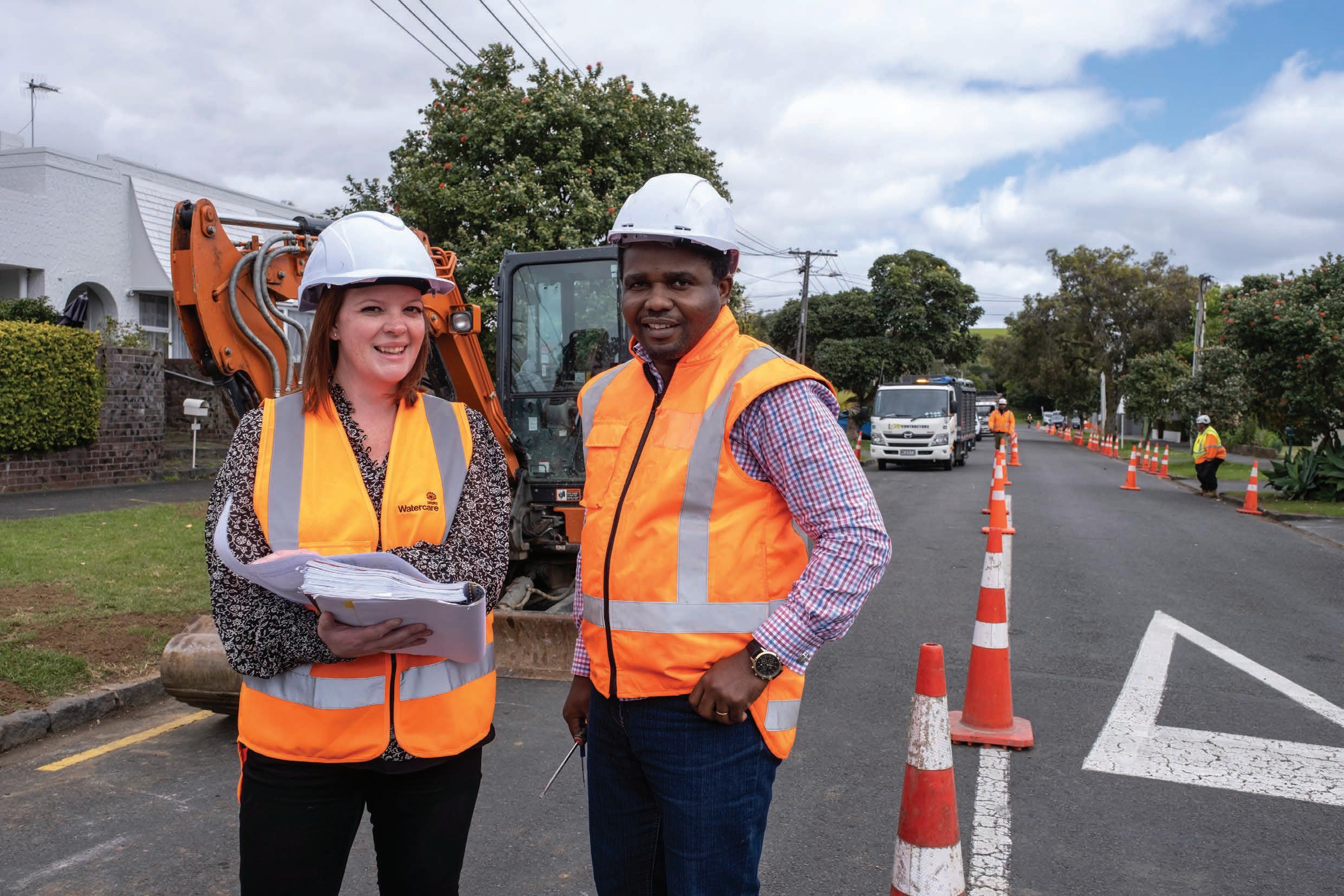
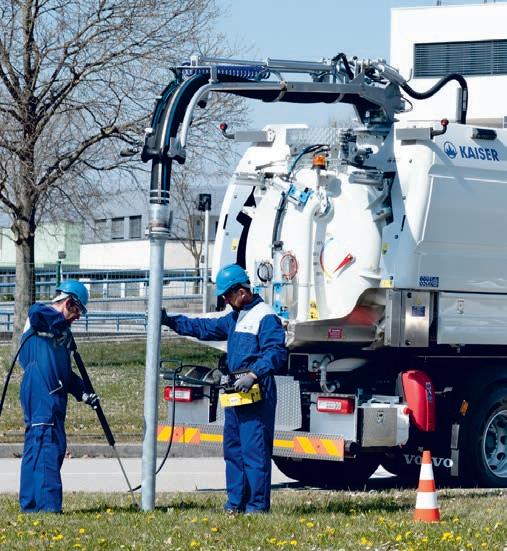
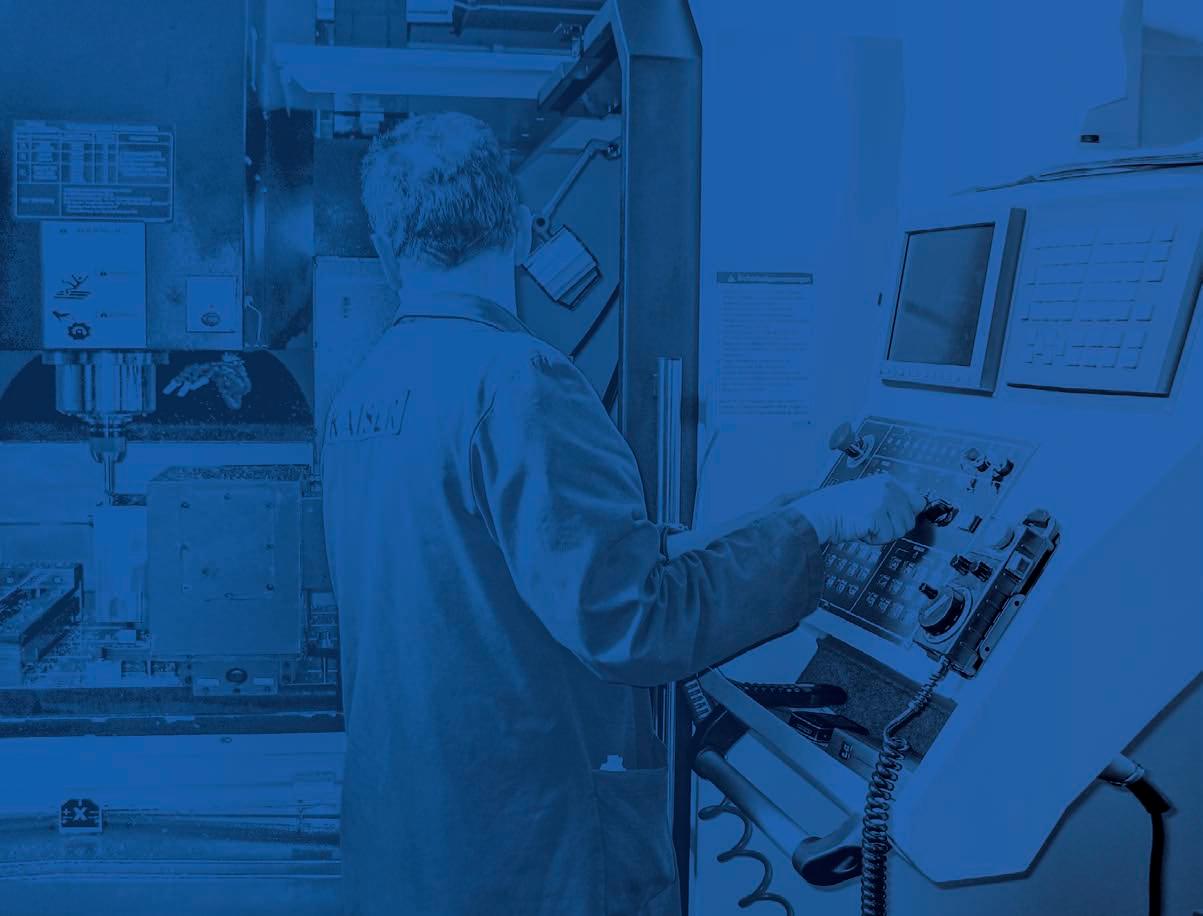
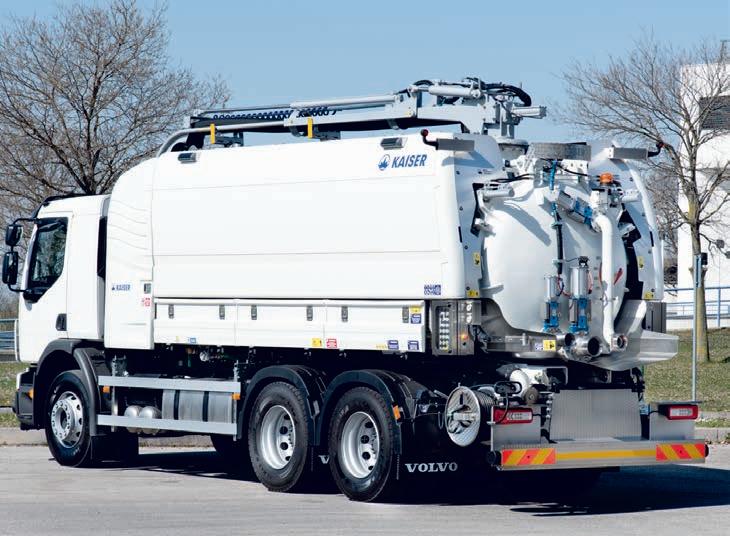