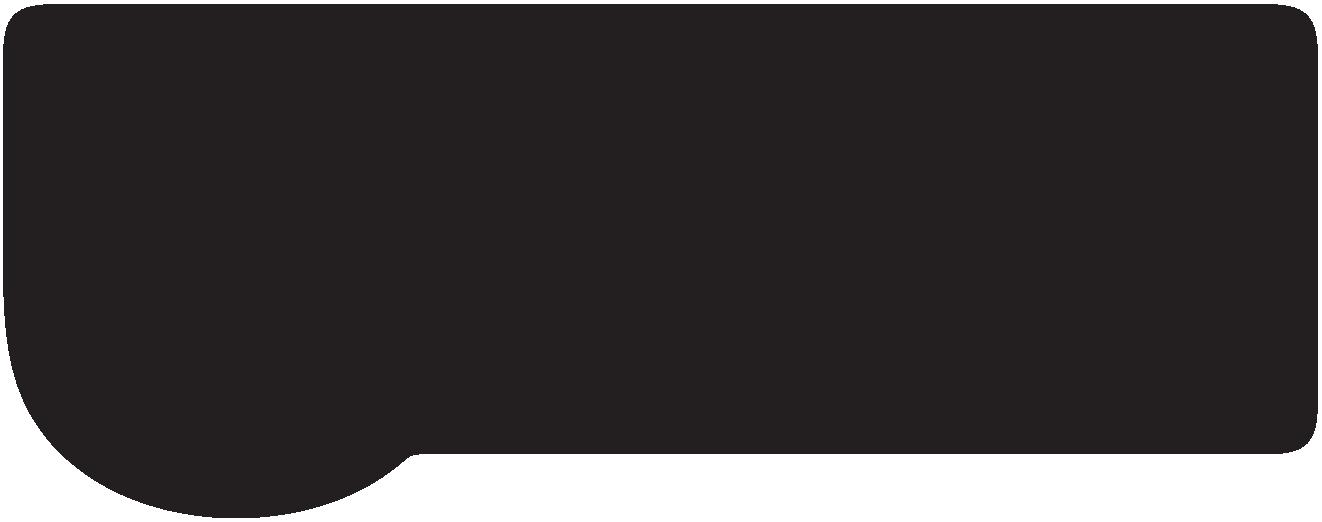
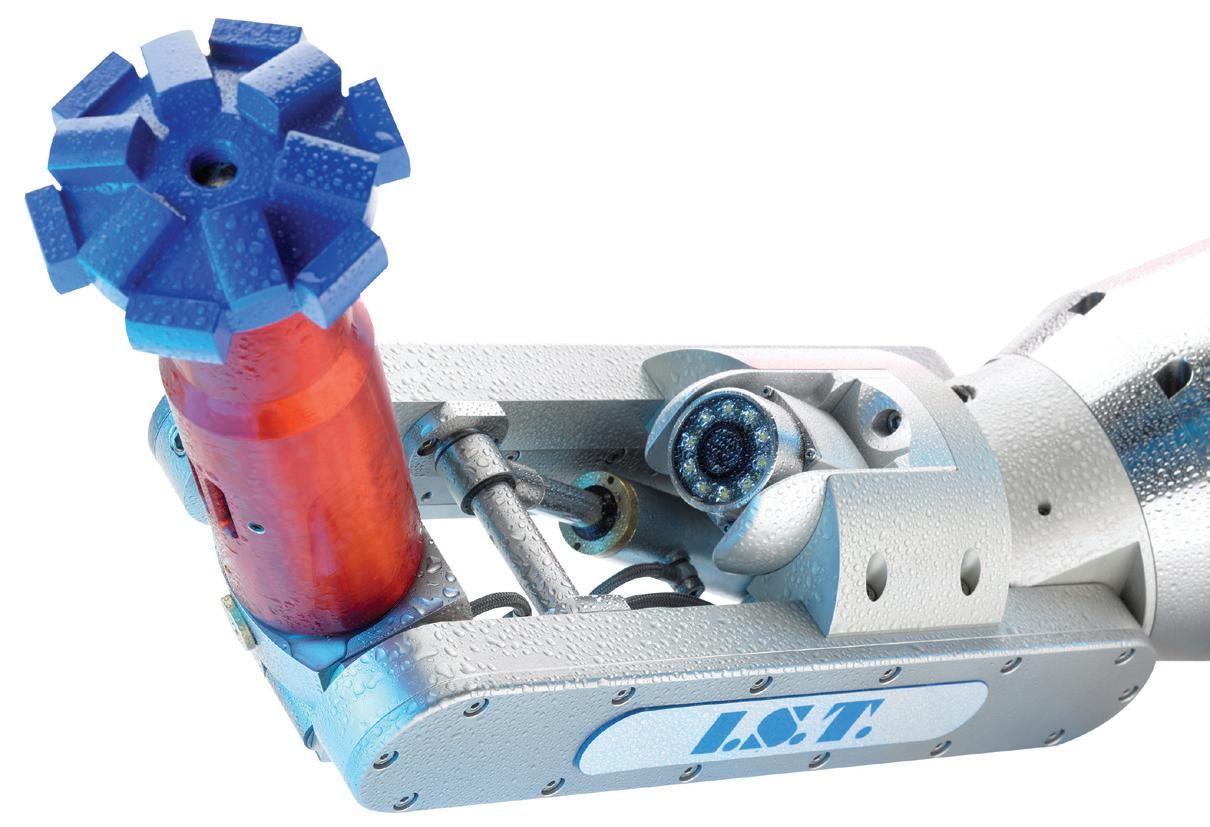

ASSET MANAGEMENT THE RISKS OF NOT INNOVATING IN WASTE TO ENERGY: A NEW ROLE FOR UTILITIES
HYDRO TAS: POWERING OUR NEXT 100 YEARS
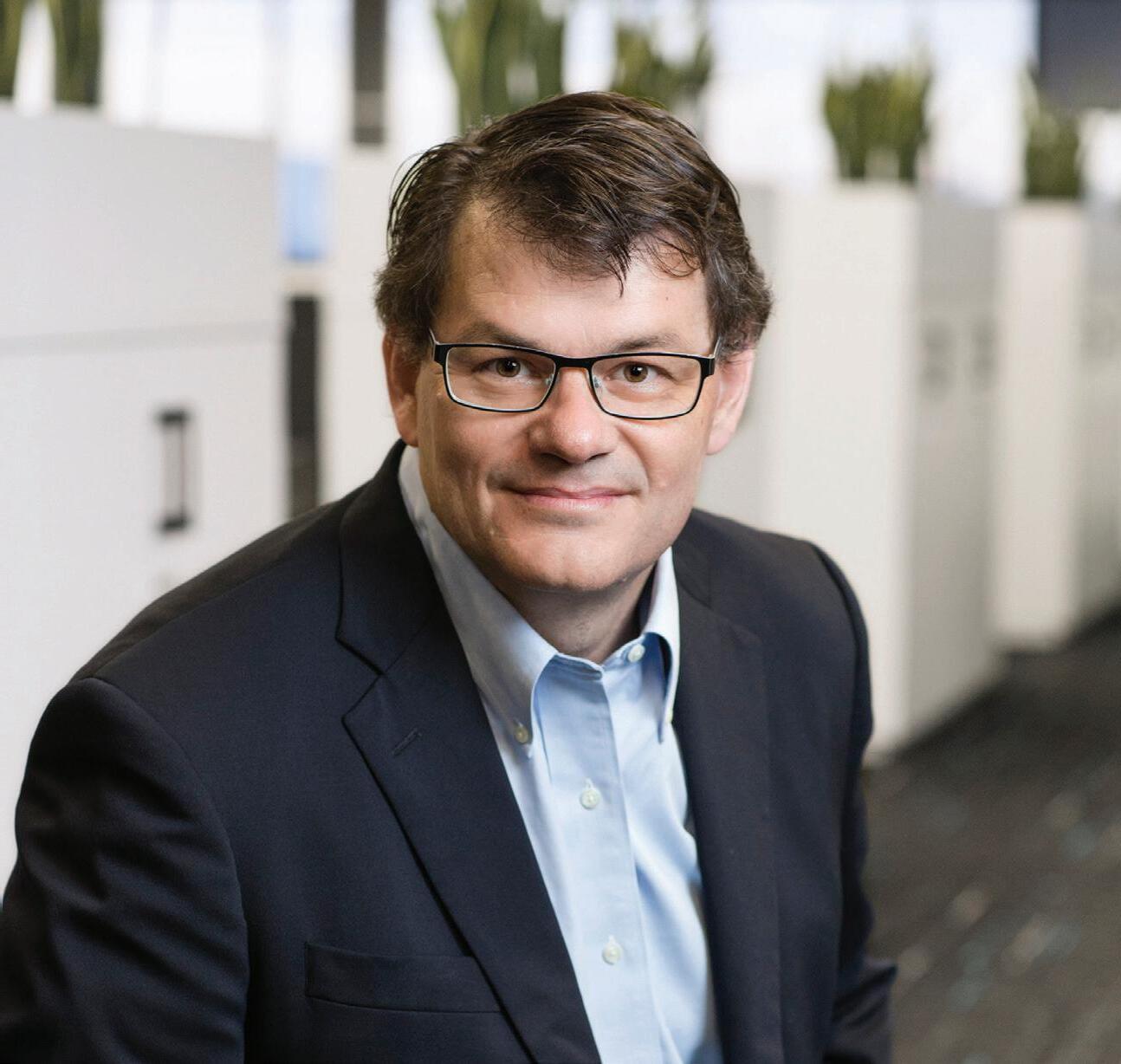
comdaininfrastructure.com.au
ASSET MANAGEMENT THE RISKS OF NOT INNOVATING IN WASTE TO ENERGY: A NEW ROLE FOR UTILITIES
HYDRO TAS: POWERING OUR NEXT 100 YEARS
comdaininfrastructure.com.au
Jim is an integral part of the senior executive team at Comdain. He has 25 years of experience in the planning, construction, operation and maintenance of infrastructure across Australia, Asia and the USA.
Jim offers experience and insight to our dedicated teams and encourages continual development. He leads by example, empowering Comdain employees to challenge convention and deliver innovative solutions for our clients.
ow that we’ve all had the chance to digest the Finkel Report, the question for the energy industry is “Where do we head from here?”
I’ve heard varying reactions to the report from the industry; but on the whole, the response has been mostly positive, and the fact that the report has noted the need for a price on carbon has been widely welcomed.
The other consistent message I keep hearing is that the energy industry needs to move forward with its own plans for the transition to cleaner energy sources. The measures outlined in the Finkel Report are important; and it would be fantastic if there could be bipartisan support for the measures that should be adopted.
However, the reality is, in the current political climate – which domestically and globally is volatile to say the least – we are unlikely to see such certainty.
It’s time for the energy industry to step up to the plate, and start making the changes we need to see for ourselves – rather than as a result of a policy mechanism that may or may not be put in place. The reality is, unless energy utilities take the lead on this issue, other companies will.
We’ve seen the uber-isation of a number of industries, and it is my belief that if we as an industry don’t step up and view the changes that will come with transitioning to clean, affordable and reliable forms of energy as an opportunity, rather than a threat, we will be left behind by innovative organisations who have the ideas, and aren’t afraid to put them into action.
I do genuinely believe this massively transformative time in the history of the energy industry is full of opportunities for the utility sector – the time is now to stand up and grab these opportunities with both hands. I’m looking forward to bringing this issue of the magazine to All-Energy Australia in October, and I’ll look forward to discussing these issues in more depth with you all then.
One of the opportunities I’m most excited about is the potential for waste to be transformed into energy. In this issue, we’ve taken a closer look at how Sydney Water and Melbourne Water are utilising waste to generate energy to power their treatment plants. It’s a great start, and both utilities believe that in the future, they will have the ability to be generating enough energy to be exported back into the grid.
Water operations, and the operators themselves, are two topics that are close to our hearts here at Utility. We regularly make a point to recognise the individuals that help to provide this most precious of resources to customers, and in this issue it’s no different, with a feature on four water industry operators who have recently received prestigious “Operator of the Year” awards from the Water Industry Operators Association. If you’re reading this magazine at the WIOA Bendigo event, where Utility is being distributed, I encourage you to seek these individuals out and congratulate them on their efforts.
Awards have an important role to play in industry, and in recognition of this fact, we’ve recently launched our own awards –the Digital Utility Awards, to be presented at Digital Utilities 2018, the event we will be hosting in May next year. Turn to page 16 to learn a little bit more about these awards, why we’re holding them, and how you can be involved.
Before we get too far ahead of ourselves, we have our second event to host, Asset Management for Critical Infrastructure, running August 16-17 in Sydney. If you have not yet registered for this event, there’s still time – and I encourage you to do so.
You’ll be able to find this issue of the magazine at this event, as well
Professor Alan Finkel identified two ambitions when he addressed the National Press Club in June. At first they might seem trifling, yet they speak volumes about the state of Australia’s energy market.
“We will know that we have been successful,” said the Chair of the Review of National Electricity Market Security, “if, in three years from now, electricity is no longer a topic of discussion in the general community.”
Energy is the hot topic of 2017. In fact, it’s been too hot for too long – a hothouse now overtaken by the choking jungle of climate wars, wedge politics and even internal divisions in political parties.
Taking power politics off the front page will be difficult, but Finkel’s second modest ambition for the energy sector will be just as challenging. In an era of breathtaking advances in generation, storage and consumer technologies, Finkel said: “Everything must change, so that everything can stay the same.”
Finkel’s blueprint is so vital because Australia’s energy system cannot afford to be caught on the back foot in this environment. Recent analysis for the Electricity Network Transformation Roadmap shows that within a decade, the penetration of variable renewable energy in Victoria and Western Australia would be over 40 per cent, equivalent to South Australia today. In the same timeframes, rooftop solar capacity in New South Wales would exceed its coal-fired generation capacity today.
One of the key recommendations in the Finkel Report is that Australia adopt a more proactive, strategic approach to transmission planning for Renewable Energy Zones (REZ), as applied in Texas (USA), the United Kingdom and Germany. REZs are being used internationally to align the timing of renewable generation development and transmission planning, which can
otherwise be trapped in “chicken and egg” investment deadlocks. Because it takes far longer for transmission infrastructure to be planned and delivered than new large-scale renewable generation, access to transmission can undermine the commercial certainty of renewable energy projects, yet the uncertain outlook for generation utilisation undermines the business case for the Transmission Network Service Providers (TNSPs).
Under this new approach, the Finkel Panel recognises the continuing need to ensure disciplined assessments of transmission spending through the regulatory investment test. If needed projects are not supported by market investments, the Finkel Review provides a framework for governments to assess direct investment for strategic purposes. The blueprint proposes that governments assess investment options using an economic framework developed by the Australian Energy Market Commission (AEMC). Significantly, the Finkel Review also calls for the AEMC, or a new Energy Security Board, to review the entire National Electricity Rules by 2020. This would be the first complete review of the 1000 pages of National Electricity Rules since their inception.
A lot has been said about the millions of customer-side distributed energy resources – solar and batteries – that are taking the market by storm. Distributed energy resources can enable a more efficient transition to a low emissions future if the system can unlock their full value, including to individual customers, energy markets, networks and ancillary services. For instance, the blueprint recognises Electricity Network Transformation Roadmap analysis showing $16 billion in future network spending could be avoided by orchestrating millions of distributed energy resources. The
Finkel Panel recommends the AEMC report to Ministers by mid-2019 on proposed draft rule changes to better incentivise and orchestrate distributed energy resource participation.
The blueprint has a lot to say about the new capabilities needed in a distributed energy future, including achieving visibility of distributed energy resources to networks and system operators and the management of data. It recommends the development of a data collection framework by the COAG Energy Council and a data strategy for the National Energy Market by the Energy Security Board, in collaboration with the Australian Energy Regulator. At the same time, preparing for and responding to cyber security threats and modernising the regulatory framework will be crucial as we move to more sophisticated and intelligent systems and markets. The blueprint recommends developing an annual report into cyber security preparedness of the National Electricity Market.
If, as Finkel says, “everything must change”, then workforce planning and skills strategies are fundamental to dealing with the new operational challenges. The blueprint highlights a report undertaken for the Electricity Network Transformation Roadmap by Energy Skills Queensland, titled Future Workforce Skilling Impacts. This provides a ten-year pathway for the workforce to gain the skills required to maintain network safety and reliability into the future, within an increasingly complex and decentralised energy system.
We can make disruptive technologies work to our advantage if we view them through the prism of fresh opportunity. As John F. Kennedy said at the dawn of another era of momentous change in 1960, “The New Frontier is here, whether we seek it or not.”
The world’s largest lithium ion battery will be installed in South Australia under a historic agreement between the South Australian Government and two leading energy companies.
Batteries from Tesla will be paired with renewable energy from French company Neoen’s Hornsdale Wind Farm.
South Australian Premier Jay Weatherill said, “South Australia has been leading the nation in renewable energy – now we are leading the world in battery storage.
“I’m thrilled with the selection of Neoen and Tesla, whose experience and world leadership in energy security and renewables will help South Australia take charge of its energy future.
“Battery storage is the future of our national energy market, and the eyes of the world will be following our leadership in this space.”
Tesla CEO Elon Musk has agreed
to deliver the battery within 100 days or it will be free, with the 100 days to begin once the grid interconnection agreement has been signed.
After leading the nation in renewable energy, the 100MW/129MWh battery places South Australia at the forefront of global energy storage technology.
The battery will operate at all times, providing stability services for renewable energy, and will be available to provide emergency backup power if a shortfall in energy is predicted.
Neoen Deputy CEO Romain Desrousseaux said, “Neoen is extremely proud to be working with the South Australian Government and Tesla
to expand the Hornsdale Wind Farm in Jamestown.
“At 100MW and 129MWh, the Hornsdale Power Reserve will become not only the largest renewable generator in the state, but it will also be home to the largest lithium ion battery in the world, with our company’s long-term, direct investment in South Australia growing to almost $1 billion since 2013.”
“Together, the South Australian Government, Neoen and Tesla will demonstrate that renewables can provide dependable, distributable power that will turn a new page in Australia’s energy future.”
The deal will also bring other investments by both Neoen and Tesla into South Australia’s economy, with details to be announced in the future.
The battery is expected to be installed before summer.
Wannon Water has proposed the construction of two intermittently decanted extended aeration (IDEA) tanks to increase the capacity of its Warrnambool Sewage Treatment Plant to cater for future investment and growth across the district.
The IDEA tanks are planned for construction on the northern side of the facility to supplement the four existing tanks.
The project, estimated to cost between $30 and $40 million, will be the largest ever single project undertaken by Wannon Water. It will ensure the plant has sufficient capacity for a projected increase in sewage volumes, while continuing to protect the environment.
A stakeholder reference group, consisting of residents, customers, and representatives of key interest groups and major customers, was established to help determine the preferred upgrade option for the community and the region as a whole.
The preferred option, based on balancing capital and operational costs, technical considerations, and environmental and social impacts, was endorsed by the Wannon Water board in May 2017.
The IDEA process has been in use at the plant for more than 20 years and is a robust and proven technology, both at the site and throughout the water industry.
Wannon Water Chair Jacinta Ermacora said the upgrade
will allow Wannon Water to support residential development and the economic growth of local industries.
“We will continue to maintain sustainable sewage and trade waste treatment practices, and ensure the environment continues to be protected,” Ms Ermacora said.
“The plant currently treats sewage from 13,900 properties in Warrnambool, 300 in Allansford and 700 in Koroit. Figures show demand is growing by 225 additional lots each year, with residential growth in Warrnambool alone anticipated to increase by 81 per cent to 25,000 properties in the next 50 years.
“It will also cater for a projected growth in the food processing industry across the region.”
Wannon Water Managing Director Andrew Jeffers said the capital cost of the upgrade will be included in Wannon Water’s Pricing Submission to the Essential Services Commission for the 2018-2023 regulatory period and will form part of a much larger capital works program over the next five years.
“The facility will be designed as a long-life asset, meaning the capital cost will be spread over an extended period and across a growing customer base,” Mr Jeffers said.
The design and approvals process will begin in late 2017 with construction expected to begin in 2019 and take two years to complete.
SPEED. SIMPLICITY.
SOUND. THE NEW VERMEER D40X55 NAVIGATOR® S3 TICKS ALL BOXES.
[Speed] The D40x55 S3 has torque and cycle times to suit a range of applications –from long fibre shots to light pipeline work.
[Simplicity] Familiar cockpit layout and the new DigiTrack® Aurora™ display offers ease of use and unmatched feedback.
[Sound] 104 dB(A) sound power level and in-cab operator ear rating of 75.7 dB(A) makes the 40x55 S3 incredibly jobsite and operator friendly.
See your local Vermeer product specialist to get equipped.
D40X55 NAVIGATOR ® S3. GET EQUIPPED.
WWW.VERMEER.COM.AU | 1300 VERMEER
The Federal Government’s announcement of measures to reform the Australian energy industry – in response to the Finkel Report – has been met with mixed reactions.
domestic market, putting downward pressure on gas prices which have risen because of supply shortfalls,” the statement said.
• Identify the existing and potential loss of continuous, dispatchable (baseload) generation
The measures announced by the Government include:
• Tough new regulations in the gas sector to give Australian customers priority access to gas supply before it is exported, which came into effect on 1 July
• Strengthening the Australian Energy Regulator by providing it with an additional $67.4 million to stop energy network companies gaming the system and overturning rulings in the courts
• Asking the Australian Energy Market Operator (AEMO) how to ensure that new continuous dispatchable power is provided, including what support is needed to promote new investment
A joint statement from Prime Minister Malcolm Turnbull, Minister for the Environment and Energy Josh Frydenberg and Minister for Resources and Northern Australia Matt Canavan said these measures put the needs of Australian families and businesses first, ensuring all Australians have access to reliable and affordable energy supplies.
“The finalisation of our tough gas regulations will increase supply to the
“We simply cannot allow Australians to pay more for Australian gas than competitors overseas do.
“Restrictions will be placed on gas exporters when there are shortages in the domestic market.”
The Australian Government will also take immediate action to address escalating electricity prices.
“We will stop big electricity companies from running to the courts to try to overturn the Australian Energy Regulator’s decisions. Companies have made 52 appeals and the courts have ruled against consumers 31 times. This will end,” the statement said.
“To back this, we will strengthen the Regulator by providing it with an additional $67.4 million to ensure it is fully equipped to address behaviour in the market that is pushing up electricity prices.
“Baseload power anchors our electricity system. Continuous generation underpins our household and economic security. With a significant amount of baseload generation being phased out over the next 15 years, we need to ensure we are prepared and have enough power to meet future needs.”
The joint statement also asks the AEMO to:
• Talk to suppliers and customers, particularly large-scale emissions intensive industrial users, about what they need to secure future investment
• Examine how much continuous power is needed in the short term to stabilise power prices
“On the back of the identified need, we will ask AEMO how best to ensure the new continuous dispatchable power is provided, optimising affordability and security for consumers, including what, if any, support, including support from governments if new investment is needed,” the statement said.
“At an emergency COAG Energy Council meeting last year, following South Australia’s state-wide blackout, the Chief Scientist was tasked with developing a long-term blueprint for the future security of the national electricity market.
“The Chief Scientist’s report was provided to COAG on 9 June. We are continuing to examine his report with the care it deserves.
“The Commonwealth will progress the recommendations of the Chief Scientist, through the COAG Energy Council, which focus on enhanced security, stability, transparency and governance of the energy system, and
will continue further to consider and analyse the Clean Energy Target.”
AEMO has welcomed the initiatives announced by the Federal Government.
AEMO Chief Executive Officer Audrey Zibelman said, “The Federal Government’s focus on securing Australia’s energy future is consistent with the recommendations made by Chief Scientist Dr Alan Finkel, together with findings from our recently released Energy Supply Outlook
“The energy system as a whole is undergoing unprecedented transformation. We look forward to working with customers, industry participants and the state governments to ensure consumer and investor confidence in the markets is maintained.”
Energy Networks Australia said it supports real reforms which lower energy bills but a Federal Government plan to abolish regulatory appeals would create cost and service risks for customers.
CEO John Bradley said the Federal Government’s announcement that it would unilaterally abolish regulatory appeals rides roughshod over the
Federal Court and the intergovernmental agreement underpinning the National Energy Market.
“Wholesale market and retail costs have been driving increases, while network costs have been falling,” Mr Bradley said.
“The decision sidelines COAG Energy Council decision-making, less than a week after the Finkel Blueprint tried to address dysfunctions in intergovernmental decision-making.
“This action would undermine basic foundations of the energy market –legislating away the powers of state governments, the role of the courts and the right to correct regulatory errors.
“The Finkel Review highlighted that political interventions by single governments have caused Australia’s energy crisis – they’re no solution for customers who want secure and affordable energy.”
Mr Bradley said energy networks and other stakeholders were blindsided by the Federal Government’s announcement which contradicted the COAG Energy Council decision in April 2017.
“Two months ago, the COAG Energy Council chaired by Minister Frydenberg
agreed to finalise reforms to the appeals regime in July 2017, yet now the Commonwealth proposes to abolish the regime without consulting other governments or impacted stakeholders,” Mr Bradley said.
“The new Western Australian Government has only just launched a consultation process with its energy stakeholders to inform a decision it thought was being made in July.
“Energy networks support reforms which genuinely lower energy costs to customers, but hiding regulatory errors from independent review just risks poor service and catch up spending later.”
Mr Bradley said a COAG Energy Council review of the Limited Merits Review framework in 2016 saw 80 per cent of stakeholders reject abolition of the appeals process (even excluding network businesses).
“The appeals process only exists because high-quality regulation produces better outcomes for customers, who end up paying more in a system where errors can on occasion go uncorrected,” Mr Bradley said.
In an Australian-first, the Water Corporation has conducted a trial in Northam, Western Australia, using two specially trained sniffer dogs to detect hidden leaks in below ground water mains.
The two dogs are being trained as part of a Water Corporation research and development program to smell water when there is a potential break along underground mains.
The utility is investigating whether the dogs can better detect hidden leaks in areas where other detection methods are deemed unsuitable or where human access is difficult.
Western Australian Minister for Water Dave Kelly said, “With nearly 34,000km of water mains across our vast state, it is important we continue to explore new and innovative methods of detecting hidden leaks.
“When pipes are buried underground it is much more challenging to detect a leak. Leaks in water mains can waste precious water, and have the potential to interrupt water supplies to homes and businesses.
“These field trials will not only test the dogs’ ability to sniff out hidden leaks, but they will see how close they need to be to the leak for it to be detected and how many kilometres a day they can travel.”
The dogs, a Springer Spaniel called Tommy and a Cocker Spaniel called Emma, are being trained by leading Australian
dog trainer Steve Austin. Steve has worked with a number of agencies in Australia to train dogs to detect different smells for situations, including feral animal control and narcotics detection.
Jemena’s $800 million Northern Gas Pipeline project has reached another key milestone with construction of the pipeline now underway.
Attending a sod-turning ceremony near Tennant Creek to mark the occasion, Jemena Managing Director, Paul Adams, said the Northern Gas Pipeline will play a crucial role in helping to resolve the east-coast gas supply crisis.
“This project is a boon for businesses that rely on gas as either a feedstock or fuel source by providing them with access to new gas at a cheaper price, particularly when compared to the costs associated with transporting gas over long distances from the Moomba Gas Hub to Queensland and New South Wales,” Mr Adams said.
“Jemena has already commenced investigative work on expanding the Northern Gas Pipeline and extending it south from Mt Isa to the Wallumbilla Gas Hub to further integrate Territory gas into the east-coast gas grid, provided additional gas supplies are made available in the Territory.
“Our modelling suggests that the pipeline can be relatively easily expanded and extended to transport up to, or beyond, 700 TJs of gas per day. This far exceeds gas used on an average day in the New South Wales and Queensland markets.
“The pipeline will also benefit Australian households and businesses in the southern states, as it will free up gas
currently flowing north to supply LNG plants in Queensland, making this gas available for use in New South Wales, Victoria, and South Australia.”
More than 80 people attended the sod-turning ceremony near Tennant Creek including Northern Territory Chief Minister, Michael Gunner, and former New South Wales Premier, and Chairman of Jemena’s Northern Gas Pipeline company, Nick Greiner.
Mr Greiner commended the Northern Territory and Queensland Governments for their ongoing support of the Northern Gas Pipeline project.
“Northern Territory and Queensland Governments both past and present have been fantastic advocates for the Northern Gas Pipeline, and are to be commended for their vision and ambition in supporting the development of this critical project,” Mr Greiner said.
The Northern Gas Pipeline will span 622km from near Tennant Creek, in the Northern Territory, to Mt Isa in Queensland. Approximately half of the Territory section of the pipeline and most of the Queensland section of the pipeline will be constructed in 2017 with the remaining pipeline to be constructed in 2018.
First gas on the Northern Gas Pipeline is expected to flow in late 2018.
COMING IN 2018, THE DIGITAL UTILITY AWARDS
Digital Utility of the Year
Utility Innovator of the Year
Best Use of New Technology
Best Customer Innovation
Digital Utilities MAY 2018 To be presented at
Nominations open soon, visit utilityawards.com.au for more information
Across Australia there is growing momentum towards finding solutions to traditional and emerging threats to water resources and infrastructure through innovative technology and programs. Water Corporation and South East Water have recently been recognised for their innovations in the water industry, and have been appointed members of the Leading Utilities of the World (LUOW) network.
At the 2017 Global Water Summit in Madrid, Spain, the Global Water Leaders Group launched LUOW to highlight the achievements of the top performing water utilities in the world, with ambitions to change the way the industry works through the promotion of performance and innovation.
Samantha Yates, Secretary General of the Global Water Leaders Group, said, “It is a space where utilities doing remarkable and innovative things can shine a light on their achievements, share their experiences, and get involved in an ongoing conversation about how to do things even better – because we always perform better when we work together.”
Twelve water and wastewater utilities were inducted into LUOW at the Summit. Six utilities joined as founder members of the group’s Advisory Board, with another six selected to join by acclamation after presenting their innovations and future plans for innovation to the board.
Water Corporation was appointed a founder member of the LUOW Advisory Board along with DC Water (US), Milwaukee Metropolitan Sewerage District (US), Waterworks Bureau of City of Kitakyusha (Japan), Waternet Amsterdam (Netherlands), and Public Utilities Board (Singapore).
REDUCING WATER USE, THROUGH INITIATIVES SUCH AS WATERWISE GARDENS, FORMS AN IMPORTANT PART OF WATER CORPORATION’S LONG-TERM PLANNING.
An innovative solution to reduced water supply
A Water Corporation spokesperson said its appointment to the board was recognition of its reputation for performance and innovation in the utilities sector.
“Water Corporation’s achievements to secure water supplies in response to climate change are well regarded by water utilities across the world. The south-west corner of Western Australia is known as one of the areas of the world most impacted by climate
We’re proud to introduce the new fifth-generation HYDROVAR variable speed pump drive. It’s more efficient than ever, plus it’s so much easier to install and operate. Learn just how easy at hydrovar.com
change. Since the 1970s rainfall in the south-west of WA has reduced by around 19 per cent, but inflows to dams have declined much more dramatically,” the spokesperson said.
“Before 1975, Perth’s dams received about 394 billion litres of streamflow each year – more than enough to supply the entire Integrated Water Supply Scheme even now. However in 2015, Perth’s dams received the lowest level of streamflows since records began in 1911 – only 11.4 billion litres of water.”
Securing Western Australia’s water supply
Water Corporation’s long-term plan to secure water supplies in response to climate change, titled Water Forever, is based on a three-pronged approach, which includes working with the community to reduce water use, increasing the amount of water recycled and developing new water sources.
“We are progressing well towards the targets set in Water Forever, including the development of climate-independent sources such as desalination and groundwater replenishment. Desalination is now the largest source of water for Perth, contributing 47 per cent of total supply in 2015-16,” the spokesperson said.
“An important part of Water Corporation’s Water Forever plan is our continued work with our customers –households, businesses and industry – to reduce water use.
“Water saving efforts in Perth helped save around 130 billion litres of water in 2015-16. To put that into perspective, that’s more water than WA’s largest desalination plant produces in a year.
“Investment in ongoing programs and education, to help the community reduce water use and ensure water is used sustainably, has deferred the need to invest in new water sources.”
Water Corporation also works closely
with business and industry to save water.
“Through various programs, water saving advice has been provided to 326 large businesses, industry customers, office buildings and housing developments. This has helped save more than 72 billion litres of drinking water since 2007,” the spokesperson said.
Innovating the water industry Showing innovation is key to LUOW, and Water Corporation believes it is vital for water utilities to keep up with the changing ways in which customers want to be engaged, as well as providing operational improvements.
Water Corporation’s innovation in helping its customers to save water won the utility an Australian Water Association award, taking out the 2016 Water Innovation Challenge for its online Water Use Calculator.
“The Water Use Calculator allows households to create a water saving plan, quickly and tailored for their home. The water use calculator uses a traffic light system to give a rating for each room of your home, including the bathroom, kitchen and living area, laundry and garden,” the spokesperson said.
“This provides an overall waterwise rating for a home, compared to others of a similar size. The calculator then creates a water saving plan, personalised to the household.
“By calculating the amount of water used in each area of the home, the action plan is able to hone in on areas which can achieve the most significant savings. Users are then able to print, email or even share their action plan on social media.”
On the operations side, the utility also won the national Water Industry Safety Award at the 2017 Australian Water Awards, held during the Ozwater conference in May.
“The innovation is known as a ‘crawler’ - a remote-controlled device that attaches to the external steel wall of a water tank and measures the thickness and condition of the steel using ultrasound technology. The device can roam up to 30m high, which allows Water Corporation to get a clear picture of the condition of the tank,” the spokesperson said.
“This technology means Water Corporation workers no longer need to use cherry pickers to physically inspect tanks, eliminating safety risks posed by working at heights.”
South East Water was inducted as an inaugural member of LUOW at the Summit, along with Budapest Waterworks (Hungary), Atlanta Department of Watershed Management (US), VCS Denmark (Denmark), Los Angeles Department of Water and Power (US), and K-Water (South Korea).
Innovating solutions to meet challenges
South East Water Chair, Lucia Cade, said the utility was given the
RAINWATER TO HOT WATER SYSTEMS ARE ONE OF THE INNOVATIONS SOUTH EAST WATER IS DEVELOPING TO BUILD MORE RESILIENT COMMUNITIES IN THE FACE OF CLIMATE CHANGE.
Promoting best practice in water management by building the knowledge, skills and networks of industry operators. WIOA annual conferences provide a medium for individuals involved in water operations to:
• Listen to the experience of others through the latest “operational” technical and research based information through platform and poster presentations.
• View and discuss the latest advances in technical equipment, products and services with suppliers and trade consultants.
• Update their knowledge and skills through interaction with fellow water industry employees.
All industry personnel involved in the operation and maintenance of urban, rural and industrial water related infrastructure for the management, conveyance, treatment, discharge and reuse of water and trade wastes should attend this conference.
The Water Industry Operators Association of Australia (WIOA) is a national association facilitating the collection, development and exchange of quality information between people undertaking operational roles in the water industry. Sponsored
opportunity to talk about the solutions it is developing to deal with challenges such as climate change, population growth and shifting customer expectations.
“We demonstrated how we’re leveraging emerging technologies to tackle these challenges. A good case study is Aquarevo, a collaboration with Villawood Properties, to build what’s on track to become Australia’s most water-efficient residential development,” Ms Cade said.
“Aquarevo is intended to show there’s a better way to use water in the home without losing liveability. Solutions include an app that will enable Aquarevo homeowners to track and monitor all energy and water use in near real time on a single interface, and a rain to hot water system for bathing and laundry. We have also designed an intelligent pressure sewer system that takes wastewater to a treatment plant on the estate, treats it to Class A standard, and returns it to homes for irrigation and toilets.
“These solutions are all underpinned by South East Water’s intelligent OneBox® monitor and control technology, which we developed to make our water and wastewater systems smarter and more flexible. The solutions have the potential to support liveability not just in our service region, but across Australia and beyond, and it’s fantastic to see them recognised.
“It’s rewarding to see our work recognised globally, and to share the stage with so many other innovative organisations. However, it’s also a reflection on the local water industry as a whole. In Victoria, we have a history of collaboration as a
sector to find new ways to deliver value for customers. Whether it’s integrated water management, IoT enabled meters, or innovative community support programs, our goal is to work together where we can for the benefit of our customers.”
Innovations that cross national borders
Ms Cade said that water utilities around the world are facing many of the same challenges; cities are growing, climate change is creating increased uncertainty about future water supplies, and millions of people in the world still don't have access to reliable safe drinking water and sanitation.
“Leading Utilities of the World has a role to play in sharing expertise to help rectify this, and achieve the UN Sustainable Development Goals,” Ms Cade said.
“An example is the application of South East Water’s OneBox® technology in the Wellcome Trust/Asian Development Bank funded research project in Indonesia and Fiji.
“Led by Monash University, the project will help to bring cost-effective and reliable sanitation to clean up the water in unplanned slum developments in large cities that haven’t been able to keep up with population growth.”
In the spring of 2016, VEGA launched the first radar level transmitter for liquids – VEGAPULS 64 – that operates with the very high frequency of 80GHz. The biggest advantage of this new instrument is the precise focusing of the radar beam. Much higher measurement reliability can now be achieved, even under difficult conditions like those found in tanks with heating coils or agitators.
In many areas of industry, radar level transmitters have largely replaced older measuring methods such as electromechanical devices or ultrasonics. Step by step, their range of application has been extended, with the result that users have increasingly come to rely on this technology.
Today, well over half a million radar sensors from VEGA have been installed worldwide. After VEGAPULS 69, the 80GHz radar sensor for bulk solids, was successfully introduced in 2014, it really wasn’t surprising that the question quickly came up: “When will a high-frequency radar level transmitter for liquids come on the market?”
Whether it’s agitators or other tank internals, buildup or deep shafts – there are still many challenges in measuring the levels of liquids. In applications with especially strong signal damping or interfering reflections, measurement until now was only possible by employing highly complex technical solutions or by simply accepting various performance limitations.
Thanks to the tightly focused radar beam, measurement with VEGAPULS 64 in tanks with heating coils, agitators or other installations is considerably easier. The sensor also has a larger
dynamic range, which ensures higher measurement certainty when build up, condensation, foam or a turbulent surface become a disturbing factor.
The strong signal focusing of the sensor opens up completely new areas of application, e.g. in liquefied petroleum gas storage. VEGAPULS 64 delivers reliable measuring results even when mounted on long mounting sockets, because due to the precise focusing, the radar beam does not touch the socket at all and no interfering signals are generated.
The smallest antenna of VEGAPULS 64 is no larger than a one dollar coin. This makes it ideal for use in vessels with small process fittings. Due to its design and hygienic materials, the sensor is ideally suited for use in the pharmaceutical and food sector.
Thanks to its encapsulated antenna system, VEGAPULS 64 operates reliably and maintenance-free even in rough seas, and is never bothered by turbulent surfaces, build up or condensation
I have been working in a workplace health and safety capacity for Shoalhaven Water Operations, heavily focusing on inspection, testing and monitoring schedules and plans.
Every day is varied especially when dealing with water and wastewater operational issues. My average day can involve site inspections, meetings with operators, contractors and management and computer work, creating spreadsheets for data recording involved with routine inspection programs. I am often called upon to do small projects for operational engineers.
One of the most exciting innovations I’ve seen in the industry came from Kaitlyn Bell, a trainee engineer for Shoalhaven Council. Kaitlyn designed a revolutionary mobile device for measuring the operational performance of sewer pumps. While attending the WIOA Conference in Canberra, I saw another exciting innovation from a company which displayed a simple but effective rubber flap designed for sewer pump station emergency overflow pipes. It was tough, robust, easy to install, and pressure-operated even if buried.
The biggest challenge we face on a daily basis is the instability of our coastal weather, with the damaging low pressure systems that can dump high volumes of rain in short periods. These events can overload the sewer treatment plants and infrastructure, so controlling this is a real challenge. Our management has been very proactive in this area, continually updating technology to assist operators in the monitoring of flow levels at sewer pump stations and treatment plants. Also I stay in touch with BOM forecasts and make early adjustments to the plant in readiness for the worst.
What I love about working in water operations is the variation of work, the cohesion between staff members from water and wastewater, and looking after the environment. Of course being privileged enough to achieve my WIOA award, and win the trip of a lifetime, was an incredible highlight too!
I am the senior operator at Whitsunday Regional Council. My role requires that I work with the operation manager (Peter Stapleton) to ensure all plants are operated at optimal performance and meet all licence conditions and requirements.
I also work with Kerry Pearson, from environmental management, and Rick Jennings, from the laboratory, to ensure all environmental and testing requirements are met.
In summary I:
• Manage the operational staff as required
• Operate treatment plants and provide advice to other operators in regards to their treatment plant issues
• Order all of the bulk chemicals for the treatment plants: all testing reagents, and plant equipment required to maintain treatment operation
• Schedule maintenance services to the plant equipment as required
• Am involved in the electrical and mechanical repair and maintenance
• Am involved in WRC capital works programs involving treatment plants
• Work with Peter on improvements to the treatment plants and reticulation network
• Follow up on the training needs of the operational staff
• Follow up on the safety requirements of the operators
• Check all results from external labs for issues
A typical day starts in the morning with a review of all treatment plant operations for any issues or problems. This allows for issues to be solved and work scheduled, and for any major issues to be passed on to the manager.
I follow up on all work to be performed at the treatment plants; then order chemicals, reagents, parts and equipment as required for all treatment plants. For plants being operated, I check the process and equipment trends; then take samples and test all process streams, collect other samples as required for testing or send them to external labs for testing.
I’ll check all treatment plant
Every year, the Water Industry Operators Association celebrates the best of the industry with its Operator of the Year awards. We spoke with four recent winners from around the country to learn a little bit more about the role they play in making the Australian water industry tick.
equipment, and review all parts of the process to ensure proper operation; and perform maintenance work as required, such as on-line instrument calibrations and preventive maintenance work.
I follow up on the sewage pump station odour dosing program, ensuring all equipment is operating and dosing correctly, then download odour logger information and check for any issues and make changes as required to dosing equipment.
The revolution in programmable logic control of treatment plants and the benefits of instrumentation (both online and in the lab) have had a huge impact on the operations side of the water business.
Changes in the operational process of treatment plants, to save chemicals and increase water quality, have also been big changes, as has the standardisation of treatment plant equipment and the use of higher quality equipment.
Solar power generation and integration with the treatment plant's power usage have also changed the way we operate. Recently, we’ve also completely reviewed all aspects of the water/sewage treatment and delivery process, as well as our disaster management and the resilience of the water treatment plants and supply to customers.
Whitsunday Regional Council is a cooperative and inclusive workplace, where all staff are included in projects. The water and waste team is very professional and works extremely well together – we’re all very happy to be a part of it.
We face a number of challenges as operators in the water industry. You must ensure you have a good understanding of all processes within treatment plants – the equipment may change, but processes are a constant. An understanding of chemistry is an aid, as treatment plants are essentially
big chemical reactors, and sewage treatment plants are biological reactors. Many of the processes we see are common to both.
The aging workforce is a challenge we need to overcome, and we’re working on doing this by choosing good trainees committed to the work and area. All of our staff need to keep up-todate with all the new innovations within the industry – continuous learning is standard and we must be open to all ideas and input from all people.
Disaster management is also important in our area – we try to over prepare where possible, and be able to stand alone for at least two weeks by ensuring the treatment plants have adequate chemical and spare parts on hand.
I love working in this industry – I enjoy working with the equipment and the process, ensuring it all runs to optimal performance to produce the best quality water at the best price. Most of the time the community never thinks about where their water comes from or where the wastewater goes, but it's good to know that the work you are doing is making a difference to the community every day.
I’m currently employed at the Bryn Estyn water treatment plant, which
supplies the majority (approximately 70 per cent) of treated water to the Greater Hobart Area.
My role is Maintenance Relief Operator, covering shift duties as required and performing mechanical maintenance duties on the plant while not relieving shifts. Bryn Estyn is the only WTP manned 24/7 due to its size and mostly manual nature.
Bryn Estyn consists of two treatment plants, one clarification and the other direct filtration. Maintenance consists of pump rebuilds, valve replacements, safety improvements and preventive maintenance.
The treatment plant operator’s daily duties include routine testing of raw and final water, chemical dosing, plant equipment checks, water consumption demands and SCADA observations and optimisation.
The most recent innovation I’ve seen in water operations is the implementation of carbon dosing; this is due to increasing taste and odour issues in the raw water supply.
A new powder activated carbon (PAC) plant has been built; dosing carbon to the clarification plant, while the direct filtration plant has had granulated activated carbon (GAC) added as filter media, the carbon removes Geosmin and MIB compounds from the water reducing taste and odour issues.
The business is going through constant changes since the formation of TasWater with new package plants continuing to be rolled out across the state. This plant, much of which has been operating for around 50 years is in line for planned upgrades to it facilities to ensure it keeps pace with water treatment technology and ongoing water demand.
The main challenge for the Bryn Estyn operator is the water source. The water characteristics and properties of the Derwent River can vary dramatically due to weather conditions and rainfall levels, making it challenging
to consistently produce quality water and, at times, keep up with increased demands. The catchment use is also changing with more impacts from human impact. A lot of work has already been done to improve and replace equipment. The operators work well as a team to achieve excellent water quality.
I love working in the operations area of the water industry, as we are continually learning new skills and applying them to the job. Bryn Estyn is a great place to work and with the challenges changing daily it is rewarding, interesting and enjoyable.
It is a great achievement and honour to represent South Australia as the WIOA Water Industry Operator of the year. Winning the award has given me an opportunity, which I otherwise wouldn’t have had, to learn from operators from all across Australia and
New Zealand.
SA Water has a safety culture program called Mate Watch, and as part of that program, I identified two hazards at the plant where I was working, which led to me winning the WIOA award.
Firstly, when a suction hose attached to our Kelly & Lewis three-inch pump was used to clean our contact tank, the grate had to be removed. I noticed that taking away this grate created a fall risk for employees into the three-metre deep tank. I was keen to make this
cleaning job safer, so I came up with the solution to adapt scaffolding to fit over the handrails around the tank. This eliminates the potential for an employee to fall into the tank when the grate is removed.
The second hazard concerned the process for changing over the mixers in the bottom of our reactors. Employees at our plant were required to disconnect a cable holder from the top of a winch, around 2.4 metres off the ground. Due the height of the winch, workers had to either use a ladder or step on the handrail to reach the cable holder, risking a fall. To fix this problem, I worked as part of a team and we decided to put in a piece of chain which lowered the cable clip. This made it easy to reach without a ladder or using the handrail, eliminating the fall risk for workers.
I wanted to improve efficiency at our plants too. The Heathfield Wastewater Treatment Plant experienced higher than average inflows during the wet winter of 2016. Aluminium sulphate is used to remove phosphorous from wastewater,
and at Heathfield we used flow-paced dosing of aluminium sulphate during highly variable flow periods. I identified an opportunity to improve efficiency within the aluminium sulphate dosing system, by changing from a flow-paced to a fixed-dose system. This reduced chemical use at the plant.
I also suggested using a larger frontend loader to transfer biosolids into our transport container – reducing the time taken for this task from one hour to just 15 minutes.
SA Water’s Mate Watch program prompted me to review the work I was doing and think about how I could make it safer. The Mate Watch program is a behavioural based safety program that encourages employees to look for hazards/potential risks and come up with solutions. It also includes modelling good behaviour.
If you work hard, keep your options open and stay positive, you never know what opportunities may come your way in life and where they may take you.
As part of the WIOA award, I had the opportunity to visit New Zealand to see other operators in action. Prior to this, I hadn’t previously seen a wastewater process which dries out dewatered sludge from a centrifuge in a 100 metrelong glasshouse. When compared with conventional systems, this is really efficient, taking the total solids yield from 20 per cent up to 85-95 per cent.
It was interesting to see that a variable speed drive (VSD) can be incorporated into the pump motor on certain pumps to monitor torque. When torque increases due to "ragging up" (a pump becoming clogged with non-flushable items) the VSD stops the pump, then reverses it to clear the blockage.
SA Water is keen to improve how we manage the turbidity wet rack lines at our plants. A wet rack is where water is pumped to be analysed for turbidity – a key test for water quality. Fortunately, as part of the tour we were able to visit a number of water and wastewater
treatment plants, which have wet racks, to get ideas. I have taken details of several pumps that supply water to wet racks with a view to trialling some these over the next few months.
I also learned that the water catchment environment is quite different on New Zealand’s South Island compared to South Australia. In my home state raw water from our catchment areas requires filtration barriers and treatment because it contains contaminants that enter the water from the environment. By contrast some water processed at the South Island’s water treatment plants is pure enough to be pumped straight from the bore to the customer without any treatment.
I think it’s important for operators to develop an in-depth and current knowledge of pump products on the market. It’s vital to get the right pump that is durable and can achieve the required flows rates and pressures for the job you need it do.
A remote telemetry unit that provides a high return for a low investment. Packed with functionality, Point Green’s key feature is its Serial Communications, allowing the RTU to integrate with any sensor with a Modbus or SDI-12 output, interrogate directly and gain wide-ranging information.
As part of our Point Colour range, Point Green is the base defining unit upon which all other Point Colour RTUs stand. A battery operated unit that offers great flexibility, programmability and versatility for use in remote locations.
Point Green shares most of the features of the highly successful Point Orange; 2 digital inputs, external power switching, automatic switchable internal/external antenna, IP68, 3G and in time 4G, with just one key differentiating factor, Point Green does not support analogue inputs.
All these features, all this functionality for much less than you’d imagine.
Suitable applications for Point Green include:
l Pressure and Flow Monitoring
l Rain Gauge Monitoring
l Water Quality Monitoring
l Asset Condition Monitoring
l Flood Warning & Monitoring
l Bi-directional Flow Monitoring
To find out more contact email info@metasphere.net.au or call 1300 785 681 www.metasphere.net.au
WaterAid is an international not-for-profit, determined to make clean water, decent toilets and good hygiene normal for everyone, everywhere, within a generation. We caught up with WaterAid Australia Chief Executive Rosie Wheen to learn a little bit more about the organisation, and hear how members of the Australian water industry can get involved with their work.
CAN YOU PROVIDE A BIT OF BACKGROUND TO WATERAID
– WHEN AND HOW WAS THE ORGANISATION ESTABLISHED, AND WHAT ARE YOUR KEY AIMS?
We are resolutely focused on tackling the three essentials – clean water, decent toilets and good hygiene – that transform people’s lives. Without all three, people can’t live dignified, healthy lives. With all three, they can unlock their potential, break free from poverty, and change their lives for good. Children grow up healthy and strong, women and men get to earn a living, whole communities start to thrive. It sounds normal and it should be.
By inspiring people and sparking chain reactions, we help deliver lasting change in what’s normal. By working closely with partners internationally and on the ground in some of the toughest places in the world, we help achieve widespread change. Millions of people have already taken control of their lives and built better futures.
Now we are working with our supporters and partners to get clean water, decent toilets and good hygiene to everyone, everywhere, by 2030. It’s about more than installing taps, toilets, boreholes and wells. To make lasting change happen on a massive scale, we:
• Convince governments to change laws
• Link policy-makers with people on the ground
• Change attitudes and behaviours
• Pool knowledge and resources
• Rally support from people and organisations around the world WaterAid was started in the United Kingdom in 1981 and WaterAid Australia was founded in 2004 in collaboration between the water industry and the international aid sector.
I have worked at WaterAid Australia since its inception in 2004, and was Director of International Programs prior to becoming Chief Executive in 2016. I have worked in development for 20 years including six years living and working in Indonesia, working at the Australian Council of International Development, and in a range of education and community development projects in Indonesia and Timor-Leste.
volunteer and it was the best thing I ever did. I had two years in Kupang, West Timor and then I moved to Rote, a village with no running water and no electricity in a household that fluctuated from 15 to 20 people, for two years. Those two years cemented my passion for community development and demonstrated to me the devastating impact of life without clean water, particularly for women and girls.
HOW CAN AUSTRALIAN UTILITIES BECOME INVOLVED WITH WATERAID? WHAT SERVICES AND/OR EXPERTISE COULD UTILITIES PROVIDE YOUR ORGANISATION AND ITS PARTNERS?
My interest in social justice and working across cultures came from my childhood and living in Hong Kong when my father worked for the Australian Department of Immigration. Every couple of years a new family was always enveloped into our family. We have welcomed families from Vietnam, Myanmar and more recently Rwanda into our family. Throughout my childhood we travelled a lot and when I finished my teaching course I realised I didn’t
WaterAid’s cause of transforming lives through access to clean water and toilets excites and engages people. A company’s support for WaterAid’s work can positively impact on the company’s internal culture, get people working together across departments and resonate with discerning customers who want to support a company that has a social heart.
WaterAid has committed corporate supporters whose employees
benefit from employee engagement programs, leadership challenges, water challenges, corporate in-country experiences, technical and human interest presentations and insights into different life challenges, alongside other initiatives to increase professional networks through their relationship with WaterAid.
Australian utilities can join a growing list of companies in Australia supporting WaterAid and our global vision to end extreme poverty by 2030 by becoming a WaterAid member. The membership structure has three levels, including a new opportunity for corporate supporters in Australia to participate in WaterAid’s annual employee engagement program, Water Innovators. Cross-functional departmental company teams work together to learn new skills, fund our work and solve real WaterAid challenges.
Currently over 650 million people in the world do not have access to clean water. This is roughly ten per cent of the world’s population. Some countries right on our doorstep, such as Papua New Guinea and Timor-Leste, suffer from some of the worst water and sanitation coverage rates in the world. In some parts of the Pacific, more than one in two people don’t have easy access to clean water.
Accessing clean water is an everyday battle; one that involves mostly women and young girls walking vast distances a day to collect enough water to drink, cook and wash with. When women and children spend hours collecting water every day they do not have time to earn a living or get an education, entrenching them in a cycle of poverty. Lack of clean water close to people's homes affects their time, livelihood, health and quality of life. People are often collecting and drinking unsafe water which causes illness. Without clean water, people can’t have healthy lives. Children regularly get diarrhoea and often die before the age of five. It’s estimated that 800 children die each
day from diarrhoea caused by unsafe water and poor sanitation.
Climate change is also impacting global water supply. The impacts of climate change are mostly felt through water – droughts, floods and contamination of water sources. Simply having access to clean water and a toilet increases people’s resilience and makes them better able to adapt to the negative impacts of a changing climate.
The United Nations’ Sustainable Development Goals are 17 goals which aim to transform our world by 2030. The goals to end poverty, protect the planet and ensure prosperity for all were adopted by countries in 2015, and each goal has specific targets to
be achieved by 2030. The goals outline a bold vision for a better world, and include a dedicated goal for water and sanitation. Goal 6 commits nations to delivering access to clean water, sanitation and hygiene to everyone, everywhere by 2030.
Addressing the global water crisis requires the collective energy and expenditure of governments, the private sector and individuals. We all have a role to play. Leading companies have gone from asking why global goal six matters to asking what their role is and playing their part. Corporates are critical in bringing water and sanitation to all.
We are always adapting and innovating the way we work. We
work to highlight the rights of people with disabilities to access water, sanitation and hygiene across the world. We also work to support women’s empowerment and gender equality. Through the power of sport we are finding new ways of enabling leadership of women and girls and talking about menstrual hygiene management and handwashing in Papua New Guinea.
In many parts of the world health care centres lack water, sanitation and good hygiene practices, increasing the likelihood of them becoming hotspots for untreatable infections. WaterAid is committed to improving hygiene, water, toilets and waste systems in health facilities to ensure everyone everywhere can enjoy dignified and quality healthcare services to improve their lives.
We work closely with local governments to support the development of strategic and operational plans that map out an approach to provide and maintain water, sanitation and hygiene services across a district. Establishing a clear districtwide plan encourages better sector coordination and sustainable services. We also work in the area of climate change to enhance communities’ water security and their resilience to climate change.
You can help communities in the world’s poorest countries to reach their full potential with access to clean water, decent toilets and good hygiene by getting involved in WaterAid’s work through activities such as participating in events, fundraising, donating, campaigning and corporate membership.
We’re keen to work with utilities that want to stand out from their competitors, inspire customers, make a difference and contribute to the achievement of the United Nations’ Sustainable Development Goals. To find out more, head to www.wateraid.org/ au or get in touch with our corporate team on 1300 858 022 or info@ wateraid.org.au.
On the rocky Antarctic plateau adjacent to the Larsemann Hills, at temperatures down to minus 40°C, India has been operating a science research station since 2012. To enable researchers to continue their vital work in extreme conditions during the Antarctic winter, the facility required especially robust drinking water and heating solutions.
The research station, named "Bharati", after the Hindu goddess of wisdom and knowledge, serves as headquarters for climate change and oceanographic research.
This high-tech station consists of one main building, fuel farm, fuel station, seawater pump house, a summer camp and a number of smaller containerised modules. The main building offers regulated power supply, automated heating and air conditioning with hot and cold running water, flush toilets, sauna, cold storage, PA system, living areas and laboratory space.
Drinking water hygiene is particularly vital at the remote location. Contamination by legionella or similar harmful microbes would be disastrous not only for the researchers – the future of the mission would be placed at risk.
This is why planners chose Viega’s Sanpress Inox system, with pipes made of premium quality EN1.4521 stainless steel, and Viega Easytop circulation regulating valves that ensure the hot water is kept at a constant 60°C. The facility’s thermal disinfection system provides further protection against legionella, while Easytop extraction valves allow easy regular monitoring of drinking water quality.
Kerosene is used to generate heat and power, because it remains liquid down to minus 54°C. To aerate the tank, engineers installed the Viega Sanpress Inox G piping system because of its permanent resistance to the media being pumped. Sanpress Inox G, usually used for gas and heating oil pipes, was launched in
Australia in 2013.
The Viega Prestabo galvanised steel system was used for Bharati’s heating installation. To prevent the heating water from freezing, a 57 per cent glycol-L additive is mixed into it. For the project, Viega tested the reaction of the EPDM sealing rings to such extremely high glycol content levels. The end result: the sealing rings of the press connectors are fully usable for the heating water/glycol mix. They are also suitable for operating temperatures from minus 40°C up to 80°C plus.
Some 25 people will be working under extreme conditions at the Bharati station all year round for at least 20 years – in part thanks to Viega press-fit technology.
For more information, visit www.viega.com.au or call 1800 4 VIEGA.
And a piping system that supplies all of the essentials right from the start.
With something as fundamental to the construction of an Arctic research station as the vital supply of warmth and clean drinking water, you don’t experiment, but trust uncompromising quality and absolute reliability. Viega met these high demands using Sanpress Inox for drinking water and Prestabo for heating installation, and also delivered the know how to go with them. Viega. Connected in quality.
viega.com.au/About-us
© Architects: IMS Ingenieurgesellschaft / bof architekten / m+p consulting; Photographer: Rakesh Rao/NCAOREffective management of assets can mean the difference between average and exceptional performance. At the Perth Seawater Desalination Plant in Western Australia, SUEZ has combined strategic asset management and deep innovation to realise significant gains.
Desalination – the process of removing the salt from seawater in order to make it drinkable – has become a key element of water management strategies here and abroad. The cost and impact of producing desalinated water is highly variable, contingent on a range of factors including plant efficiency and the type of systems in use.
The Perth Seawater Desalination Plant (PSDP) at Kwinana, 30 kilometres south of Perth’s CBD, is operated by SUEZ for the state-owned Water Corporation. The first large-scale desalination plant in the Southern Hemisphere, for more than a decade it has supplied two million Perth residents with more than 45 billion litres of fresh drinking water annually – around 18 per cent of Perth’s total water supply.
SUEZ and Multiplex were awarded the construction contract in 2005, completing it ahead of schedule to deliver PSDP’s first water order just 18 months after breaking ground. The plant continues to consistently produce above its 143.7ML/d design capacity.
Chris Young, SUEZ General Manager Operations West (WA, NT, SA) said
that PDSP’s innovative design features provide a solid foundation for efficient and effective operation.
“SUEZ’s reverse osmosis technology in use at PDSP features double-pass membranes that deliver salinity levels below 200 milligrams per litre and a bromide content below 0.1 milligrams per litre,” he explained. “The system also allows for full pressure and flow control for greatly reduced energy consumption, while our advanced brine dispersion technology protects Cockburn Sound’s sensitive marine ecosystem.”
PSDP’s comprehensive asset management strategy is critical in minimising risks without compromising assets. The systems in place support fast and effective decision-making processes at the plant – a key factor in delivering safe, reliable and costeffective output in the long term. In line with these principles, the team is currently working on achieving ISO 55000 Asset Management certification.
Mr Young said that SUEZ takes a continuous improvement approach to asset management, constantly monitoring performance and seeking innovative ways to boost efficiency in
areas such as energy consumption.
“Water pressurisation prior to reverse osmosis accounts for around 50 per cent of operational costs. At PSDP, we utilise pressure exchangers to recover residual pressure from the concentrated brine discharge, for energy savings of up to 20 per cent.”
SUEZ received the Operator & Service Provider Excellence Award at the 2017 National Infrastructure Awards for its work with Water Corporation on the plant. PSDP is widely recognised as one of the most efficient and cost-effective desalination operations in Australia; it also enjoys an enviable safety record and culture, recently surpassing 4100 Lost Time Injury Free days.
“The team are constantly seeking new and safer ways of working, and we have developed a multi-layered safety process to reduce manual handling requirements and enhance membrane removal and installation processes,” Mr Young said.
“PSDP is an important asset for Water Corporation, and we are proud of what we’ve achieved here in ensuring it consistently performs at the highest possible level,” he added.
Melbourne Water treats in excess of 800 million litres of wastewater per day at its two metropolitan wastewater treatment facilities, which treat more than 90 per cent of Melbourne’s domestic, commercial and industrial wastewater.
Located in Werribee, the 10,500 hectare Western Treatment Plant (WTP) is a world leader in technical and environmental innovation. It processes around half of Melbourne's sewage and produces almost 40 billion litres of recycled water a year.
The options for disposal of high-strength organic wastes (that cannot be accepted into the centralised sewer system) have been declining over recent years, and so there is a need to support industry through providing an alternative, costeffective outlet for high-strength organic wastes.
Melbourne Water has been collaborating with both City West Water and South East Water and their customers to identify opportunities to use existing infrastructure and resources to help deliver more sustainable practices around waste treatment, reuse and disposal.
A co-digestion trial at WTP was commissioned to provide more qualitative and quantitative data on the organics waste market, leading to more informed decisions on Melbourne Water’s future role in these markets.
Melbourne Water undertook an extensive expression of interest process to canvas the organic waste transport industry and major businesses for the supply of highstrength organic wastes. Safety and risk were a high priority. Shortlisted transport companies and businesses then responded to a more detailed Request for Proposal.
Ultimately contracts were signed with Veolia and Stows Waste Management, recently followed by J&M Zammitt. There are other interested parties, with whom Melbourne Water is currently in negotiation with.
As part of the trial, high-strength organic liquid materials which are unable to be sent down the sewer – due to their potential to corrode and increase odour from the network – are transported to the WTP trial site and pumped into the main inlet.
The material mixes with the incoming wastewater from the sewer, then travels directly into the covered anaerobic lagoon where the biogas is collected to generate electricity for operating the wastewater treatment plant.
This trial was implemented to determine the market need for, and interest in, this new treatment service, and is the first step to help Melbourne Water build the business case for augmenting existing infrastructure or to construct a separate anaerobic digestion facility.
Through the trial Melbourne Water is seeking to build meaningful customer relationships and to gather information related to:
• Market volumes of high strength organic wastes
• Value of service to industry
• Market interest in long term contracts and stability
• Controlling and managing potential contamination of wastes received
• Tracking and billing systems for waste deliveries
The trial is the stepping stone to a service that provides a competitive choice to the manufacturing sector for high strength organic waste outlets.
Depending on the waste delivered, it is likely that there will also be improved environmental outcomes including:
• Avoiding landfill and methane emission to atmosphere
• Capture and use of biogas to produce electricity
• Avoiding 100km+ of transporting
• Use of recycled water for truck washing
• Transparency of the sustainability of waste treatment at a publicly scrutinised, EPA-licensed facility
Melbourne Water charges a gate fee for the acceptance and management of the high-strength organic wastes. This gate fee will cover the costs associated with the service and generate non-regulated revenue. Melbourne Water needs to
comply with commercial neutrality requirements and does this by creating a commercially priced service. Any profit generated through the waste-to-energy process will provide greater community value through offsetting wastewater treatment costs and/or enhancing outcomes including liveability.
Through the co-digestion process, Melbourne Water’s WTP has the chance to not only treat the wastewater that is sent
Melbourne Water is currently investigating the feasibility of adding organic waste into the anaerobic section of the sewage treatment process at its Western Treatment Plant.
to it, but to also generate clean energy for use at the plant –and to potentially be exported to the grid.
Energy generation isn’t new to Melbourne Water – the utility has been generating electricity from sewage since the 1970s and has been a leader in resource recovery in the water industry. Melbourne Water has kept a watching brief in the waste-to-energy space for a long time, periodically assessing new technologies, products and markets.
Anaerobic digestion of high-strength organic wastes from the commercial food industry is a new service that seamlessly
fits with existing capabilities and service levels, and has the potential to provide additional benefits in the following areas:
• Through avoidance of waste to landfill, such facilities can be registered as carbon offset schemes
• Further generation of renewable energy, from a source not dependent on the sun shining or the wind blowing
• The ability to blend the organic digestate with other Melbourne
The organic waste currently being supplied to the WTP is not suitable for disposal via sewage, and hence it often ends up in landfill after processing, potentially releasing methane gas into the atmosphere. Co-digestion into the sewage offers an alternative treatment option for this waste.
Co-digestion has successfully been demonstrated to deliver multiple benefits at international sewage treatment plants.
If the co-digestion trial proves to be a success, the benefits of providing this service at a larger scale include:
• An increase in renewable energy from biogas that can be used on site for treatment plant operations or supplied to the grid
• An alternative revenue source, the benefits of which will be passed on to customers
• Reduced waste to landfill
• Reduced travelling distance for waste transporters.
If there’s one thing you don’t want to take a chance on, it’s the ability of your DC power system to protect your critical assets. Our DC power systems are designed to meet Australian standards and to deliver maximum longevity. By custom designing every system, we provide engineered solutions that meet the unique technical requirements of your site. This innovative approach combined with our maintenance support means we leave nothing to chance when it comes to protecting your critical assets.
To learn more about our DC power systems and maintenance services, visit our website.
For enquiries call 1300 364 877 www.intelepower.com.au/ value-dc
Hydrogen sulphide (H2S) gas in sewer systems can cause significant corrosion and odour issues, but dosing chemicals into sewer networks is an effective means of controlling gas levels. Sydney Water Corporation recently undertook a project to optimise the chemical dosing in the Malabar Wastewater Network through the development of online monitoring equipment.
To reduce concrete corrosion rates to less than 1mm per year, Sydney Water’s Corrosion and Odour Strategy specifies an average gas-phase H2S level of less than 5ppm, and average dissolved sulphide levels less than 0.5mg/L. Sydney Water operates 60 chemical dosing units (CDUs) across the wastewater networks as a means of minimising H2S gas production to manageable levels.
Proper and efficient management of H2S gas in wastewater networks requires reliable data capture and modelling of key parameters at strategic locations. A project was undertaken to optimise chemical dosing in the Malabar Wastewater Network, Sydney Water’s largest wastewater system, which covers an area of 50,000 hectares and services 1.6 million customers in Southern and South Western Sydney.
The Malabar Wastewater Network was chosen as the focus of this optimisation project due to the large number of ferrous chloride-dosing CDUs within the network (eight), and therefore, the high potential for improvement and cost savings.
A review of the Malabar Wastewater Network was completed in two parts: analysing long-term H2S gas levels at various monitoring sites in the network, and modelling a number of scenarios using the Integrated Sewer Network (ISN) model, to determine the optimal chemical dose rate at each CDU site.
Historical H2S data from monitoring sites at strategic locations within the network were inputted into the ISN tool to validate that it was properly calibrated prior to performing a desktop study of the optimisation.
During the monitoring process, the Thermo Fisher Odalog ™ H2S logger provided continuous monitoring of gas
phase H2S levels. This data was sent via fibre optic cable to the Odatrack ™ adaptor, which then outputs the corresponding signal on a 4-20mA loop. This equipment was selected due to proven reliability and availability within the Sydney Water business.
Following ISN modelling and the development and installation of reliable online monitoring equipment at strategic locations, dosing at selected CDUs was progressively optimised, with modelled dosing flow rates used as an initial starting point. In order to avoid a system-wide, uncontrolled change in dosing, which could have resulted in enormously negative impacts on H2S gas levels, the optimisation followed the same division of sub-systems as was used during modelling.
Beginning with the Upper Northern Georges River Submain (the sub-system furthest from the Malabar Wastewater Treatment Plant) chemical dosing was reduced incrementally, with changes in H2S gas levels monitored continuously via the portable online monitoring equipment and on-site liquid sampling at selected sites. This process was repeated until the frequency and magnitude of H2S gas spikes downstream of that point increased, or, the average daily H2S gas concentration exceeded 5ppm. At this point, dosing at the CDU would be returned to the previous increment.
Modelling suggested that average H2S gas levels in the system could be maintained below 5ppm if total dosing was reduced by approximately 33 per cent. Incremental dosing reductions resulted in the dosing at two CDUs within the Upper Northern
Georges River Submain being reduced by up to 50 per cent, and one CDU decommissioned. Mascot, the largest CDU in the Malabar Wastewater Network, was the final CDU to be optimised.
Review of the H2S gas levels revealed consistency in diurnal pattern of average dry weather flows and H2S gas levels. This indicated that implementation of profiled dosing at CDUs in the network would be beneficial in reducing variability and peaks in downstream H2S gas levels. Diurnal chemical dosing profiles were developed and implemented at CDUs.
Sydney Water has successfully optimised chemical dosing within the Malabar Wastewater Network through:
• The review of historical H2S gas levels at various monitoring sites in the network
• Use of the ISN model to simulate a number of scenarios to determine optimal chemical dose rates at each CDUs site
• The development and installation of an innovative system of online liquid-phase and gas-phase monitoring equipment
The ISN model enabled prediction of H2S gas levels in the Malabar Wastewater Network and the development of chemical dosing scenarios which formed the starting point for the optimisation.
Sydney Water has now installed an additional 19 permanent online H2S gas monitoring units at strategic locations in two of its largest wastewater systems. In addition, eight relocatable online H2S gas monitoring units have been deployed downstream of high-risk trade waste customers.
Installation in, and optimisation of, chemical dosing in the remaining wastewater systems will follow in the future.
Water treatment systems need continuous improvement for reliability and quality. Chemitec online monitoring sensors and controllers achieve higher degree of precision and are available to monitor water conductivity, pH, corrosion rate, turbidity, dissolved oxygen, sodium, fouling, biological activity, and halogens.
In April, Prime Minister Malcolm Turnbull unveiled plans for a massive expansion of Tasmania’s hydropower system, establishing the state as Australia’s hub for utility-scale battery storage and renewable energy.
Thursday 20 April was a proud and historic day for Tasmania. It was the day Tasmania’s role as the clean energy leader of Australia was established beyond doubt.
More importantly, it was the day that we, as Tasmanians, were called upon to play a much bigger and more crucial role in Australia’s energy future.
Tasmania is uniquely placed to help lead Australia through its energy challenges. That conclusion is now vocally supported at the highest level, and has widespread backing. Through Hydro Tasmania, and our consulting business Entura, our island offers the necessary experience, skill, and renewable energy platform to take a leadership role.
The “battery of the nation” concept is particularly timely, because large storage devices like batteries and pumped storage hydro will become much more important as Australia seeks to replace coal-fired power and get more energy from other sources, including solar and wind.
Sources like wind and solar only supply electricity when the wind blows or the sun shines – and are therefore known as intermittent. That’s fine when we have coal and gas to supply power at other times. But as older sources close, the market needs ways to supply customers and industry.
During windy and sunny times, wind and solar may generate more electricity than is immediately needed, but that surplus power could be stored for later use. That’s why energy storage through batteries is becoming crucial.
A battery in the electricity network is like a rechargeable battery at home. It’s good at supplying a lot of power quickly for a few hours. But storing enough energy to meet demand for several days or weeks would require an enormous number of batteries.
So when it comes to clean energy storage on a very big scale, the biggest excitement at the moment is understandably about pumped hydro storage.
Here’s how it works:
Conventional hydropower systems
collect water in a lake or reservoir on higher ground. That water is run downhill through a pipe or tunnel to spin a turbine in the station below, generating electricity.
Pumped storage hydro is effectively a battery for storing energy (by storing water), by pushing the water back up the hill to be re-used. It uses electricity to pump water upwards from a storage pond to the reservoir, often simply by running a specially-designed generator backwards.
Pumped storage can keep storing water, and therefore energy, until the top reservoir is full. And depending on the size of the uphill and downhill bodies of water, the energy stored could run the generators for days, weeks or months.
Since connecting to the National Energy Market via Basslink in 2006, Tasmania's flexible hydropower system has already acted as a giant 500 megawatt battery for Australia, because of our water in storage. So while pumped storage hydro may form part of an exciting future, the foundations of Tasmania’s energy storage evolution are already in place.
Our state is already living proof that hydropower can provide the reliable and affordable baseload power Australia badly needs into the future.
We also have nation-leading expertise when it comes to integrating renewable energy into the grid in a stable and affordable way. We’ve done that innovatively and successfully in Tasmania, and it’s the very challenge mainland Australia is starting to grapple with.
Let me briefly recap the announcement of 20 April by the Prime Minister and Tasmanian Premier about boosting Tasmania’s clean energy capacity and making a greater contribution to the National Energy Market:
1. The Australian Renewable Energy Agency (ARENA) will work with Hydro Tasmania to explore up to 13 new pumped storage hydro schemes (four major projects and nine smaller ones) that could deliver up to 2,500MW of pumped storage generation capacity – nearly doubling Hydro Tasmania’s current capacity. If they prove to be feasible, those projects would position Tasmania as the “battery of the nation”.
The four major projects are earmarked for MerseyForth (two projects), Great Lake and Lake Burbury. They’d have a combined capacity of about 2,000MW (the largest being changes to the Great Lake/Poatina scheme with an increased capacity of 570MW). If committed to, each project would take a few years to establish.
2. The nine smaller projects are earmarked as additions to existing hydropower schemes at various locations around Tasmania, and would have a combined capacity of about 500MW.
3. ARENA will consider a study which includes replacing one of Hydro Tasmania’s oldest power stations at Tarraleah with a modern design – boosting production by more than 200 gigawatt hours each year, and extending the station’s operating life by 80 years. The Gordon Power Station (our largest) would also have an extra turbine installed to boost efficiency.
As well as those proposals, Tasmania has many prospective wind farm sites, and we’re already considering more interconnection with Victoria. Tasmania currently has on-island wind power capacity of 308MW, and the introduction of pumped storage hydro could significantly boost wind farm development.
Hydro Tasmania has powered this state for more than a century. These projects are part of powering generations for the next 100 years through innovative renewable energy development.
At the moment, about 80 per cent of the national market is supplied by coal plants that will eventually close. Australia badly needs reliable and affordable replacement energy, and renewable energy, firmed by pumped hydro or other firming capacity, can supply that energy.
Tasmania currently provides about five per cent of the national market’s energy, and more than 40 per cent of its renewable energy (easily the largest single renewable producer). By increasing our interconnection, boosting our hydropower system, including with pumped storage hydro, and further developing our world-class wind power, we could increase that contribution significantly.
Tasmania would become a large, flexible renewable energy supplier for the nation, providing clean power when customers need it.
It’s the right time to see if that vision for Tasmania stacks up – either fully or partly.
If we’re right, and it’s a good answer for Australia, then Tasmanians will also reap the benefit of extra development and jobs, as well as having the most reliable and best-priced energy supply in Australia.
We have a successful history of providing transformer solutions for the renewable sector, particularly in the wind, solar and hydro energy projects.
Our product range includes:
Power Transformers (≤550MVA)
Distribution Transformers (≤5,000kVA)
Compact MV Substations
Open Skid Solar Substations
Padmount Substations for Data Centers
Special Transformers
Fault Current Limiters
Special Applications
Monitoring & Control Solutions
ARENA’s new investment plan, which will guide almost $800 million of renewables funding over the coming years, expands the agency’s focus to better facilitate Australia’s transition from fossil fuel-dependence to low emissions energy. The agency’s new investment priorities aim to accelerate grid adaptations to increase productivity and flexibility, and integrate higher levels of renewable generation without compromising on energy security, reliability or affordability.
The Australian Renewable Energy Agency (ARENA) recently launched its new investment plan, titled Innovating Energy. The plan sets out the agency’s four new priorities:
• Delivering a secure and reliable electricity system
• Accelerating solar PV innovation
• Improving energy productivity
• Exporting renewable energy ARENA will now assess funding proposals according to these key priorities, as well as the agency’s larger objective – to accelerate Australia’s shift to an affordable and reliable renewable energy future by enabling more affordable, higher value renewables; increasing options for secure and reliable energy supply; improving energy productivity through innovation; increasing industry skills and knowledge; and collecting data to inform new business models and regulation.
ARENA intends to help provide affordable, secure, and reliable electricity into the future for all Australians by investing in innovative projects relating to renewable energy use, storage, and sharing.
Innovation in enabling technologies and new ways of managing electricity networks will smooth Australia’s path to having a higher percentage of energy generated by renewable sources. These innovations will protect the security, stability, and reliability of electricity systems, and also help manage costs and make further investment in renewable energy (such as rooftop solar and storage) more attractive to Australian households and businesses.
Through this investment priority, ARENA aims to demonstrate how the costs of renewable integration can be reduced and where it can add value to electricity systems.
In assessing proposals according to this goal, ARENA will be particularly looking for:
• New flexible capacity and
grid stability technologies, or commercial pathways to balance the electricity system with higher shares of renewable energy, ensuring electricity is there when needed
• New ways to evolve electricity grids to integrate more distributed energy resources, including solar PV, energy storage and demand management
• Projects to extend knowledge relevant to decision-making in energy policy, market rules, regulation, or network practices and procedures
ARENA’s new plan includes a specific focus on solar PV research and development.
The agency aims to help make solar PV more affordable and competitive, to drive continuing innovation in this area and fulfil the Australian Government’s commitment to double renewable R&D spending by 2020. Reducing the costs
associated with solar PV also has the potential to make it more economically viable to build excess PV capacity to charge storage and counter intermittent renewable generation to improve grid stability.
In particular ARENA will be looking to invest in:
• New technologies and tools to reduce installed cost of PV systems, improve system reliability and longevity, and develop materials for new markets or applications
• Opportunities to help Australian businesses translate these ideas into PV manufacturing supply chains
ARENA’s new investment plan broadens the scope of the projects it can fund to include those aiming to improve energy use productivity.
The agency intends to accelerate improvements in energy productivity to meet or exceed the National Energy Productivity Plan (NEPP) to improve Australia’s energy productivity by 40 per cent from 2015-2030.
To achieve this, ARENA will provide support or projects to increase the adoption of renewable energy and replicable, innovative and efficient energy use across the building, transport, and industrial sectors. This will be undertaken towards the larger goal of demonstrating how various technologies and approaches (including energy efficiency, electrification, and fuel-switching) can reduce energy use and emissions while increasing productivity and growing the economy.
In assessing related funding proposals, ARENA will be looking for:
• Accelerated improvements in energy productivity and adoption of renewable energy by industry, particularly in applications that contribute significantly to emissions
• Innovative building technology and design to increase energy productivity
• Improvements to energy productivity in the transport
sector, including electrification and fuel switching
• Opportunities to improve energy productivity and integrate renewable energy by optimising value chains across sectors
By accelerating innovation in the renewable export industry, ARENA aims to position Australia as a key long-term renewable energy exporter.
As the global economy transitions to low emissions energy, with the right investment and innovation, Australia will be able to take advantage of its vast renewable energy resources, good export capabilities, and strong international market relationships to export renewable energy as
primary energy (such as hydrogen or ammonia) or embodied in processed raw materials. This will contribute to Australia’s economy and create new jobs, while helping satisfy demand for low emissions energy in countries with limited renewable resources of their own.
ARENA will be looking to invest in:
• Australian innovation in future renewable energy export industries
• Innovation in technologies to improve cost and efficiency of using renewable energy to supply export value chains
• Feasibility of first-of-a-kind projects using renewable energy to supply export value chains
Innovating Energy is intended to achieve maximum impact and value from ARENA’s funding across the innovation chain, from research to pre-commercial development.
“We are looking for new ways to adapt our electricity grid to increase productivity, make the grid more flexible and better integrate renewable energy so it can be stored and shared when and where it is needed,” said ARENA CEO Ivor Frischknecht.
The new investment plan is set to build upon the agency’s previous successes, which have included driving down the cost of large-scale solar and contributing to 14 world solar efficiency records being broken, and to accelerate Australia towards a reliable, efficient clean energy future.
RFI is a global technology solutions company, specialising in wireless coverage and solar power. RFI offers a unique portfolio of products & solutions from remote site communications, utility metering, data monitoring, SCADA, right through to industrial solar & energy storage systems.
The industries we serve include Electricity, Gas, Water, Mining, Telecommunications, Transport and Government.
Silicon Valley was recently abuzz with the completion of the first of three modules in the Free Electrons Accelerator Program. The program saw 12 innovative energy start-ups joined by eight leading global utilities and the program accelerators to commence a journey to jump-start their company’s clean energy future.
Hosted from April 30 to May 6, module one immersed the eight leading global utilities and start-ups in the world’s leading clean tech innovation ecosystem, connecting the new businesses to the epicentre of technology innovation and investors.
AusNet Services was among the eight global utilities represented in the program, with Mark Judd, Manager Community Energy, and Dominic Toffolon, Energy Solutions Engineer representing the utility in San Francisco.
Mr Judd said the first module at Free Electrons offered an invaluable opportunity to collaborate and exchange knowledge between the start-ups and global utilities. He added that the insights garnered will help shape and inform AusNet Services’ future role in the renewable energy future.
“These forums are vital to the advancement of energy across the globe. Our involvement in this open innovation environment will assist the AusNet Services Commercial Energy Services team to better navigate the rapid change facing our industry from a network operations and commercial product and services perspective.”
The module concluded with the 12 start-ups pitching impressive presentations that offered high-calibre innovations and pilot programs, such as:
• DepSys (Switzerland) unveiled a real-time control platform for the management of low-voltage networks to effectively master the impact of distributed
generation and to limit its disruptive effects
• Driivz (Israel) has developed a world-class intelligent software engine to support EV charging
• OhmConnect (USA) has developed a residential demand-management solution with a very clever customer engagement model involving gamification
A panel discussion featuring the eight partner utilities with a focus on the future of global renewable energy was a clear highlight of module one. The panel session featured areas of intense discussion centred on blockchain technology, the monetisation of data, future business models for grid-less utilities, and methods of introducing new products and services.
A group visit to the Stanford University Linear Accelerator Facility (SLAC) was another highlight. SLAC is celebrated for its fundamental particle research, and interestingly, its leading energy research program. The visit provided insight into the future of network data acquisition and integrated LV network modelling in the greater context of Distributed Service Operations (DSO).
AusNet Services’ global energy renewable journey will continue as the team attend the second Free Electrons module in Lisbon, Portugal, which will conclude with a pitch event in Dublin, exposing the start-ups to Europe’s growing utility market.
WATER CORPORATION’S PIPES FOR PERTH PROGRAM WILL REPLACE 150KM OF WATER MAINS.
Many of Perth’s water mains were installed from the 1890s onwards, with some sections now over 100 years old. Like anything that age, they’re starting to show wear and tear. Water Corporation’s $100 million Pipes for Perth program is replacing these pipes to avoid future bursts and leaks.
Following a water main on Wellington Street breaking three times in the space of a few weeks in 2013, Water Corporation undertook a review of its cast iron water mains throughout the Perth metropolitan area. This review led to the decision to increase investment in water main renewals and the implementation of the Pipes for Perth program which is currently in the process of replacing 150km of water mains across the Perth metropolitan area. The program is expected to be completed in 2018.
“About 46km of water main has already been replaced or renewed as part of the project during 2017,” a Water Corporation spokesperson said.
“Work is under way in the following eleven local government authorities – Bayswater, Cambridge, Cottesloe,
Fremantle, Perth, South Perth, Stirling, Subiaco, Swan, Victoria Park and Vincent.”
The spokesperson said that Water Corporation’s planning team identifies which mains are prioritised for renewal based on the pipe’s age, material, history of faults, and the potential for disruption to the local community should the pipe fail.
“There is also a lot of preparation work contractors need to do before they can actually start digging. We need to locate all underground services, such as gas, power, telecommunication cables and existing water connections. Then confirm the planned alignment of the new water main is suitable – then we can start the physical replacement of the water main,” the spokesperson said.
In the past, Water Corporation generally used open trench excavation to install water mains. Now, the majority of water mains are installed using trenchless technologies such as directional drilling, which has been made possible due to the more flexible nature of polyethylene (PE) pipe. This reduces the amount of excavation required, minimising impacts on local households and road users.
“We have also started using other trenchless technologies, such as relining. Relining can be used to renew larger distribution mains that transport large quantities of water around Perth but don’t directly supply water to customers,” the spokesperson said.
“We excavate pits above the distribution main every few hundred metres, and then pull a new liner from one pit to the next. This process is
repeated at several locations along the route until the entire distribution main is relined.
“Relining work is underway along Oxford Street in Leederville and Mount Hawthorn, Walcott Street in Mount Lawley and North Perth, and Swan Street in Guildford.
“A number of local contractors have been engaged to carry out the work across the Perth metropolitan area. It is estimated that in the order of more than 400 jobs have been created as a result of this program of work.”
Water Corporation has a dedicated Community Engagement Team that visit impacted businesses, and provide regular updates to the community throughout the works. The overriding objective is to complete the project as quickly as possible while ensuring the safety of the community and contractors at all times. This has meant contractors working seven days a week
in the Perth CBD, including regular overnight work and engaging extra crews. In other areas, contractors are regularly working six days a week.
“These projects are happening in busy inner suburbs and there will be impacts on traffic, however we do all we can to minimise impacts by working closely with Main Roads WA and local governments,” the spokesperson said.
“We coordinate work with other utilities and local governments where possible to minimise disruption to the community. For example, we coordinated our water main renewal along Hay Street, West Perth to coincide with a gas main renewal being carried out with ATCO Gas. A similar coordination of work is also taking place at Kings Square in Fremantle.”
The spokesperson said Water Corporation’s investment in asset renewals, including water mains, are reviewed each year, with work
prioritised based on a risk-based approach to pipe replacement.
Through this approach, Water Corporation uses information on the condition and performance of water mains to determine when pipes need to be replaced, usually when they have reached the end of their useful life.
This proactive approach has resulted in Perth recording the lowest number of water main breaks in six years in 2015-16, with 12 leaks and breaks recorded per 100km of water main. This was a 20 per cent decrease from the previous year, and is the fourth lowest out of 14 similar sized utilities across Australia. The average number of leaks and breaks for similar sized utilities was 22 breaks per 100km of water main.
Water Corporation continues to invest in the water supply scheme to minimise leaks and breaks, with $75 million invested in 2016-17 to renew water mains across the Perth metropolitan area.
Increased competition, shareholder expectations, and new technologies making traditional methods obsolete – all of these factors mean that the need for companies to focus on innovation in their asset management has never been higher. Here, Steve Doran, Director of Infrastream, and Chair of the Asset Management Council’s Sydney Chapter, discusses balancing innovation with adherence to standards, how new technologies are helping move things along, and the risks companies face if they aren’t willing to think outside the box.
The need to innovate in asset management has become a necessity in order for asset managers to meet shareholder expectations for critical assets amid tightening costs and risk constraints. Ahead of his keynote presentation Leading innovation in asset management at the Asset Management for Critical Infrastructure conference, running 16-17 August in Sydney, Mr Doran says companies responsible for managing assets need to address several risks when considering if they are willing to invest in innovation.
He says companies in a competitive commercial context need to identify
and address the following types of risks when considering their focus on and investment in innovation:
• Their traditional technologies becoming obsolete within broader engineering systems
• More agile start-ups or offshore firms providing more costeffective offerings for the same or better outcomes
• Shareholder perception that they are not future-proofing themselves and therefore are not a sound investment
• Sinking staff morale as their people are expected to deliver greater productivity without the tools to do so
Mr Doran has seen these risks firsthand from his 20 years of experience in asset management, including his current roles as director of an asset management consultancy, Infrastream, and Chair of the Asset Management Council’s Sydney Chapter. He has also helped implement innovative practices at Sydney Water, and through his certification as an ISO 55001 Asset Management Assessor.
Mr Doran says companies who want to innovate can look to new technologies that are changing the way assets are managed in Australia. He says new technology on its own is
simply a capability or an enabler until it is used in a new way to generate outcomes beyond expectations and therefore becomes innovation.
Mr Doran believes the Internet of Things, combined with Big Data and artificial intelligence, are currently the most prominent technological shifts opening doors for innovation in asset management.
“Essentially, the innovative application of this in critical infrastructure is about assets talking to each other for the benefit or protection of people, in real time,” he says.
“Imagine water mains isolating themselves via stop valves at the moment a pipe failure occurs, self driving vehicles being remotely prevented from crossing a bridge showing sudden excessive flexion, or customers being informed on their devices of alternate commuting options as a rail line section warps due to extremely hot weather.”
Mr Doran also says the rise of nano-materials with incredible strength, non-corrosive capabilities, and low production cost are also changing the face of asset management.
“It is paramount that we incorporate this reality into planning and design now as we invest billions into infrastructure in Australia with a long horizon.”
While investing in innovation can be rewarding for companies, innovation also typically requires some form of risk taking, or circumventing norms. This can be seen as direct opposition to industry standards which tend to minimise risk, and drive toward conformity.
Mr Doran says with the need to innovate, asset managers and owners "must take a position that standards can be challenged to varying degrees on a case-by-case basis."
“While at one extreme there may be standards that are compulsory via legislation that should not be bypassed due to commercial risk exposure, there will also be many that are effectively only optional guidance or allow significant leeway,” Mr Doran says. “Perhaps the most relevant example to us all as asset managers are the ISO 5500X suite of asset management standards. Earlier this year, due to my passion for innovation and role in the field of asset management, I performed an analysis of clauses throughout these three standards to determine whether innovation and ISO 5500X were ‘friends or foes’.
“Refreshingly the outcome of this analysis was that these standards do not restrain us from innovating. The ‘how’ we implement management of assets is up to us and the only real innovation limits in this case are preconceptions and misconceptions and the nature of our interaction with the key stakeholders around us.”
If the risks of not innovating are clear, and new technologies and practices are helping to facilitate companies to think differently about their asset
management plans, one would think the path to innovation would be clear. However, Mr Doran says there are a number of factors that keep the industry doing things the same way, which can be categorised as historic, cultural, and psychological at the personal level.
“Historic approaches in engineering: hierarchical organisational structures, and education that has followed long held theories with one right answer and success from repetition (for example in the way we build roads), all have the heavy effect of keeping us in familiar and stable paradigms.
“Culturally, as asset managers we take the minimisation or elimination of risk as being a bestowed responsibility and typically respect logic, rationale and critique rather than ‘out of the box’ questioning as being our dominant guides.
“Psychologically, we not only tend to follow familiar thought and action patterns and are blind to unconscious assumptions, but we have an underlying awareness that pushing a different line may be a ‘bad career move’ and that the outcome with innovative efforts holds no guarantees, or worse, leads to a self-defining personal failure.”
While these all need to be taken into consideration, Mr Doran says that companies do have the ability to overcome these factors and be more innovative in their asset management plans.
“The good news is that the strengths that are common among asset managers, such as systematic thinking, turning principles into working realities, and measuring success actually, enable us to be among the most effective innovators of all, if we are given an appropriate policy environment and adopt the right tools and frameworks.”
With a rapidly evolving technological landscape, changing regulations, and a high level of public scrutiny, professionals working in the management of critical assets in Australia have a lot to keep up with.
With this in mind, Utility and Infrastructure magazines have partnered to bring you Asset Management for Critical Infrastructure, a two-day conference in Sydney giving asset owners and managers an opportunity to become informed about the latest trends, technologies, projects, standards and best practices in the sector.
The conference will bring experts from Australian utilities, infrastructure companies, consultancies, and government organisations together in one room to discuss what you should know if you’re working in the asset management space in 2017.
Keynote speaker Steve Doran, the Chair of the Sydney Chapter of the Asset Management Council and Director of Infrastream, will talk about how companies can become
more innovative in their operations, leading to cost savings and increased shareholder satisfaction.
Another keynote will be delivered by Antony Sprigg, CEO of the Infrastructure Sustainability Council of Australia, who will explore the role of sustainability in asset management, not only focusing on environmental sustainability, but also economic, social and governance.
The conference also includes engaging presentations from Sydney Water, Standards Australia, Jemena, NSW TrainLink, KPMG, TransGrid, the Australian Association for Unmanned Systems (AAUS), GS1 Australia, Jacobs and Arup. All speakers are senior experts in their field, with the majority working as general managers of asset management in their organisation.
At Asset Management for Critical Infrastructure, delegates won’t just sit and listen to speakers list technologies or standards they already know, but rather, the conference will focus on how delegates can actually implement these concepts into their everyday practices to make their jobs safer, easier, cheaper and more reliable.
Delegates are provided ample opportunity to network with each other and the speakers, through both structured and informal networking sessions, and everyone in attendance is encouraged to become a part of the asset management conversation.
These critical conversations will explore topics that include, but are not limited to:
• Updates to ISO 55000: What the industry should know
• The role of an ISO 55000 Asset Management system at Jemena
• How Sydney Water is implementing customer centric asset management
• How to balance cost, risk and performance
• The challenges of asset management in the electricity transmission industry
• Investing in new infrastructure in spite of disruption
• The identification and marking of assets in the rail industry
• Practical uses of drones in critical infrastructure
• Demystifying the Internet of Things to explain how exactly it can benefit your business
A room full of the industry leaders providing practical information will be highly beneficial to anyone working at a utility or infrastructure company that deals with critical assets – make sure you don't miss out on this opportunity by booking your tickets today.
There are also a few tickets left for the event. For more information or to register, visit www.assetmanagementforcriticalinfrastructure.com.au.
Tunnelcorp provides trenchless services to the Infrastructure and Mining sectors throughout Australia and New Zealand.
• Laser Guided Vacuum and Slurry Microtunnelling
• Laser Guided Pipe Jacking
• Box Culvert jacking
- For Pedestrian Cycle Ways,
- For Road and Rail Underpasses,
- Conveyor Underpasses for Mining Applications
Auger Boring
Shaft Sinking
• Tunnel Support Canopies
• Trenchless and Civil Contracting.
• Project Management.
Looking for a new TV? If so, you won’t have missed the latest models advertising a massive 4K resolution that offer immersive viewing, naturallooking images, a richer, wider colour range, high-quality sound and more. We’ve come a long way from the old black and white models with their 576i resolution. But what about our water utilities? Are they getting the benefit of higher resolution data made available through new technologies?
Most water utilities have a SCADA system which monitors and controls many aspects of their water capture, transmission and treatment but, when it comes to distribution, many utilities have little or no monitoring at all. What may come as a surprise to many is that the assets not being monitored in a meaningful way often account for up to 60 per cent of the utility’s overall asset value. So, why don’t most water utilities have detailed monitoring on a significant part of their assets? Well, like a lot of things, it comes down to cost.
Until recently, communications options for the monitoring of water meters, flow meters, sewer overflow sensors, pressure sensors, rain gauges, weather stations and the like were limited to point-to-point data radios, the mobile telephone network and meshed radio networks. While each of these was capable from a technical standpoint, the economics of collecting data from hundreds or thousands of low-value endpoints using these methods was impossible to justify.
Times have changed. The advent of Low Power Wide Area Networks (LPWANs) is making the collection of data from low-value field devices much more affordable, and the insights being revealed through finally having a better view of what’s happening in reticulation networks are transforming the way utilities run their businesses.
Imagine being able to put a sewer overflow sensor in every chamber, and having rain gauges throughout your region. Imagine what you could learn through being able to correlate high
density rainfall data with sewer behaviour. The impact on your management of inflow and infiltration would be enormous.
Do you have water bores in your area? Would it help to have high-resolution aquifer level data to compare to high-resolution rainfall data? Groundwater managers are already using LPWAN to collect such data, leading to a better understanding of aquifer drawdown and recharge rates.
With demand management being such a hot topic in water supply circles, particularly where water security is uncertain, hourly data from all of your customers’ meters, district flow meters and other outlets can expose a variety of water use reduction possibilities: customer-side leaks, network leaks, forgotten meters, unauthorised connections and incorrectly sized meters and pipes.
More pressure readings from around your water supply network will give you greater ability and confidence in managing network pressure, extending the life of your pipes, reducing losses through existing leaks and, maybe, giving you a head start on avoiding costly catastrophic pipe bursts.
Business managers are familiar with the idea that if you don’t measure it, you can’t improve it. While the origin of this notion is somewhat cloudy, there is no doubt that having data which gives you better information on what’s happening in your water or sewerage network is a good thing.
So, just like the 4K TV, having LPWAN communications in place unlocks a rich source of data which will give you a much clearer picture of your assets.
Beware, however, of getting too immersive – particularly if you look after the sewage.
It’s a message utilities have been hearing with increasing urgency in recent years – we must innovate, and digitise, in order to stay relevant in a rapidly changing world. But while most utilities know they need to digitise their operations, the question of how to do this across multiple elements of a large scale business – many of which have spent decades utilising analogue operating systems – can present a significant challenge.
The reality is, for today’s utility, the emergence of new business models, and the escalating market penetration of digital opportunities, have made most traditional product and service delivery processes obsolete.
A particular challenge in this space is the need to automate existing, paper-based processes, such as incident reporting, for reporting and/or legislative requirements.
It seems like it should be a straightforward process – find an appropriate solution, educate your staff and implement the solution – but for many, the process is far from simple.
While the digital economy is an opportunity to transform businesses and drive an organisation’s performance through digitisation, for many the process is so daunting that rather than being viewed as an opportunity, it is seen as a threat.
The problem many utilities have when it comes to automation and digitisation is working with partners who offer an off-the-shelf system. While the solution may initially seem viable, often, utilities will find that a standard off-theshelf solution does not meet all of their requirements.
For example, with incident reporting, the process will be similar from one utility to another – but inevitably, individual organisations will want to follow their own processes and procedures.
This is where a customisable off-the-shelf solution can offer major benefits. It allows utilities to take a program which is largely uniform, but then add their own customisations to make the basic program suit their own particular needs.
FiNAO is a solutions provider that works directly with utilities, assisting them in the successful transition from manual, paper based forms and processes to fully automated, smart online systems.
FiNAO enters into a partnership with its clients, conducting a detailed analysis of the business, its goals and the potential structure of digitisation in the organisation. The team can then determine realistic goals and create a roadmap that will get the organisation to its digital destination.
Returning to our incident reporting example – FiNAO offers
multiple incident reporting systems, but not one of them is the same.
“We find clients want their own incident reporting system, they don’t want to change their process and procedure to fit an off-the-shelf system,” said a Terry Down. “This is where we come into our own.
“This is the major difference between FiNAO and our competitors; we don’t start off with a predetermined process or system, we start off with our basic system, and build the forms and processes onto this platform.”
“Therefore our customers get 100 per cent of what they need, and nothing they don’t need.”
FiNAO’s customised solutions are built on the powerful PRIME platform. Key functionality is incorporated through a modular system, with features and functions based on specific business requirements. Modules include forms (the data collection component), custom workflow and notifications (through email and SMS). Each component generates actions, ensures accountability and communicates relevant and timely information.
The benefits of moving to digital recording systems are enormous. For example, looking at efficiency gains alone –if a company completes 20,000 forms per year comprising of 1-5 pages per form, and assuming it takes approximately 60 minutes to complete each form, that company will be spending 1.2 million minutes (20,000 hours) per year on completing forms. Allowing an average staff cost to the business of $50 per hour, the cost to the business of processing these forms could be around $1 million per annum.
A FiNAO Management system would cost a fraction of this cost to build, support and maintain, therefore providing cost savings in the first few months. The systems also prevent double handling of data, as the information is keyed in once. This makes all users more efficient in their day-today tasks.
The fact that a number of manual processes become automated with a FiNAO system also offers significant benefits in terms of increases in employee efficiency and
productivity. Automated emails, SMS and online notifications keeps users informed of expectations in terms of forms to be completed and data to be collected, all within specific time frames in real-time.
FiNAO has 2 major systems currently in place at Sydney Water: the Delivery Management Data Portal and the SWConnect system
The Delivery Management Data Portal was originally designed to enable contractors to be on-boarded, to be assigned to projects and to complete real time forms (such as site diaries) to allow delivery management to review project progress, measure contractor effectiveness and be made aware of any issues (through Request For Information or incident reporting forms).
Since it was first introduced four years ago, the data portal has continued to develop to serve and meet the ever-changing needs of delivery management, from both an operational and reporting perspective.
Sydney Water’s Delivery Management team is responsible for delivering much of Sydney Water’s capital investment program – this means ensuring projects are delivered safely, on time and within budget, and with minimal impact on the community and environment. To do this, the team needs to manage hundreds of project
sites. The Delivery Management Data Portal custom system allows Sydney Water to on-board hundreds of staff and projects. Through the system, work is allocated and managed as part of a collaborative contracting model.
The online system tracks and manages the progress of multiple construction projects (of various values) in line with GC21 contract conditions utilising accredited management systems compliant with ISO 900114001/AS4801 and Australian Federal Government Safety Commission accreditation scheme.
Sydney Water’s SWConnect system provides several in-field services to the broader networks and customer delivery business, ensuring:
• Compliance of new assets connecting to the network
• The integrity and maintenance of existing assets
• The safety of staff during network operational work (FIFM, chlorination and flush and sample, among others)
The old process was manually managed by 40 office and field-based staff. Customers initiated work via a variety of forms emailed to centralised mailboxes. Field implementation was via hardcopy, with variable quality and availability of data. The old process was highly transactional and manual with minimal automation, and was supported by five administration staff.
For more information about how FiNAO can make the process of digitisation more simple, straightforward and beneficial for your business, head to www.finao.com.au or contact the team on 02 9906 7890.
The SWConnect system takes paper-based transactions, systems and processes and converts them to an automated digital process. This increases productivity and efficiency, reduces paper-based administration, ensures accountability (at all levels) and improves communication.
The aim of this system is to increase the efficiency of the office and fieldbased staff and reduce reliance on manual business support.
FiNAO offers a range of digital management systems to the utilities industry, covering safety systems and business systems - both critical elements to any utility's operations, and both areas where significant productivity gains can be made by making the move to digitised processes and systems.
Gaining a competitive advantage relies on the ability to provide real value to customers in a marketplace that offers increasing choice. The best way for utilities to stay ahead of their competition is by providing customers with access to readily available data anywhere, any time.
Having the equipment that provides real-time and readily available data is the key to doing this, and thanks to the range of NHP industrial remote access devices, this is now easier than ever before.
Secure remote access solutions enable superior visibility and control for better preventive and predictive maintenance. These remote access devices provide superior customer service, and with the capability to identify and troubleshoot performance issues as, and in many cases before, they occur, they increase the uptime and efficiency of your installations.
These remote access devices can be the difference between success and failure for your customers, as the remote diagnostic capability eliminates the need for major travel to fix minor issues.
NHP brings to market high-quality, industrially rugged remote access devices that provide wireless
communications solutions for a range of applications.
The extensive range is designed to offer easy remote access, across the internet, to machines and installations on customer sites or in the field.
These devices allow the users to troubleshoot machines, debug their PLC program, upload projects and gain remote access of an HMI or a drive – all without the need to go on site, drastically reducing support costs.
This industrial modular M2M (machine to machine) router and data gateway is designed for data monitoring, alarming (SMS and email) and data collection to provide a lowcost solution for large deployments.
This range provides the capability to communicate with the most varied field equipment. This is increasingly
important in an environment where communication technologies are constantly changing.
NHP’s remote access offering allows utilities to upgrade easily to new technology and connect to a wide range of industrial devices for seamless communication.
When it comes to the water and wastewater industry, companies can stay ahead of the competition with readily available data, accessible anywhere and anytime. By implementing an enhanced automation system with advanced networking, companies can now tackle challenges impacting the utilities sector.
For more information on how NHP can help provide efficiency and superior performance for your next project, contact your local sales representative or call 1300 NHP NHP.
Ensure
Re ecting the need for sustainability in Water and Wastewater, NHP delivers innovative automation and networking engineered products and solutions.
When it comes to the utility sector, NHP o ers increased e ciency and lower costs of ownership to transform data into actionable and real-time information. Employing standardised and secure networks, NHP provides a wide range of devices insuring connectivity and equipment safety.
Providing the optimal balance of knowledge and experience,
a partnership with NHP promises to last the life of your project, providing quality, assurance and peace of mind.
To achieve a reliable and e cient solution, trust NHP to engineer a customised solution to help you gain a competitive edge.
For your next utility project visit nhp.com.au/more/watercomm
With more than 50 years of experience in the Australian market, Denso Australia has the solutions to help modern utilities mitigate the potentially crippling effects of corrosion.
Denso (Australia), a subsidiary of Winn & Coales (Denso) Ltd, commenced operations in Victoria in 1961. Today, the company manufactures and supplies Australian utilities with anti-corrosion coatings, including liquid epoxies, mastics, primers, petrolatum, bitumen and butyl tapes, heat shrink sleeves, HDD wraps and tanking systems.
Denso’s range of products has been developed to treat and prevent corrosion for above or below ground substrates in all environmental and climatic conditions. Common applications include pipelines, valves and fittings, tanks, structural steel work and marine structures.
Denso Australia has a dedicated team who are constantly refining and improving their existing products and developing new ones to address corrosion across a wide range of industry sectors.
A recent innovation is Premier's new heat shrink sleeve (HSS), which has an advanced butyl-based mastic adhesive. This new addition to the range has an imprinted indicator to confirm that the correct amount of temperature is being applied during installation.
The sleeves are designed to be used on butt welds, seams, or slips in collar-type joints. The new HSS is compatible with factory coatings such as polyethylene, polypropylene, epoxy resin, polyurethane and bitumen.
Due to their high mechanical stability, low water vapour and oxygen permeability, the Premier HSS with indicator is a reliable corrosion protective system.
With 65 per cent of their products being locally manufactured, Denso is proud to be endorsed by the Australian Made campaign.
Denso Australia looks forward to continuing to meet the needs of the utility industry, delivering high quality products from globally-recognised brands including Denso, Protal, Archco Rigidon, PCS, Premier and Sylglas.
There's a proliferation of spatial data available at our fingertips - why aren't utilities using this technology to remotely access a real-world view of their own assets?
Look around right now. There are probably several devices you could use to access detailed satellite imagery, turn-by-turn directions from here to anywhere, or even a streetview of a shopfront in New York City.
A few short years ago, accessing this level of spatial information would have been considered science fiction, but now we use it daily in our personal lives. However, when it comes to assessing the condition of railways, electricity assets or other critical infrastructure, often people are still sent out into the field to physically view the situation. Not only does this take time and cost money, it exposes people to safety risks, is subjective, and results in fatigue leading to increased inaccuracies and human error.
Through a fusion of high definition 3D and 2D imagery, LiDAR and advanced mapping capabilities, Geomatic Technologies’ new AIMS3D product provides a highly accurate digital-twin of your real-world assets and infrastructure.
AIMS3D delivers this combination of high-value geospatial data in a powerful, yet intuitive cloud solution, accessible across the business via a standard web browser. Geomatic Technologies’ capture equipment can operate on road, rail or aircraft, and even be carried into difficult to access locations. The capture is completed
quickly, in a single pass, providing access to data insights fast.
AIMS3D gives you the power to provide:
• Millimetre-accurate rail clearance at a remote bridge or overpass
• Location and condition assessments of assets
• Precise clearances to critical infrastructure including electrical conductors
• Access to your virtual data for accurate network design and works planning
The speed and convenience of AIMS3D capture, combined with the powerful interface, means users can acquire and explore asset information at multiple points in time. This empowers users to see and predict degradation, clearance encroachments (such as vegetation) or to audit completed works. All of this is possible from a web browser, reducing the need for physical field inspections.
AIMS3D is the secured digital version of your network, accessible at any time, which can be used for countless purposes and even future requirements you’re not yet aware of.
To maintain its position at the forefront of asset intelligence, Geomatic Technologies is experimenting with how AIMS3D integrates with developing technologies such as machine learning and self-driving cars.
Imagine being automatically notified of impending asset failure or safety issues in the most remote corners of a network. Machine learning is making it feasible to automatically detect tiny changes in asset condition before they are visible to the human eye.
Self-driving cars and automated drones are no longer a fantasy. When coupled effectively with sophisticated capture equipment, we will see fleets of robotic vehicles able to constantly, repeatedly and affordably scan your infrastructure.
Advanced asset intelligence systems like AIMS3D are fast becoming more affordable, more accessible and more sophisticated – the present is exciting and the future is bright.
Geomatic Technologies is part of the Commercial Division of AusNet Services.
The largest ongoing study of corporate social responsibility (CSR) capabilities in Australia and New Zealand has named the ten highest performing organisations for 2017, with one Australian utility making the list. It has also highlighted some key areas that Australian utilities can focus their own sustainable development goals on for optimum customer and organisational benefits.
In its 9th annual review of the state of corporate social responsibility in Australia and New Zealand, the Australian Centre for Corporate Social Responsibility (ACCSR) analysed key trends in CSR across several industries and determined the organisations that had the highest rate of these capabilities embedded in their culture.
The 2017 report Re-imagining sustainable value: the Sustainable Development Goals gather pace focused on
online survey that was completed by 1,215 professionals from 30 organisations. Employees from the 30 participating organisations assessed the extent that CSR processes and values are present in their company.
Dr Leeora Black, Managing Director of the ACCSR, congratulated the organisations that made the CSR top ten and top three lists.
“The assessment reflects the perceptions of employees
From potable and wastewater treatment, reservoirs, pipelines, drainage, telecoms or power substations, be it new design and construction or upgrades and refurbishment, Abergeldie is committed to sustainable and socially responsible delivery of the complex infrastructure that builds better communities.
Rated in the ACCSR’s top 10 companies in Australia for Corporate Social Responsibility in 2016 and 2017, Abergeldie is serious about sustainability.
www.abergeldie.com
Development the sustainable way
creation of a like-minded workforce.
“We have always had a belief at Abergeldie that the reason for business is to build better communities. We applied for the award to benchmark our CSR philosophy and actions against other businesses and to encourage others to strive to improve in this area,” Ms Craig said.
“We monitor our activities against all of the goals, but our key focus in the next year will be gender equality –looking at ways of getting more female representation in the construction industry; as well as affordable clean energy – researching ways we can use our world-leading shaft drilling equipment for renewable energy storage.”
Key findings from the survey highlighted the extent that organisations in Australia and New Zealand use SDGs in their business strategies.
SDGs can include no poverty; good health and wellbeing; quality education; gender equality; clean water and sanitation; affordable and clean energy; decent work and economic growth; industry, innovation and infrastructure; reduced inequalities; and sustainable cities and communities, among others.
More than half of the survey respondents said that SDGs have been mapped against business strategy as much as they have been against CSR strategies or reporting. They also reported that their organisations have been “assessing their impacts through the lens of the SDGs, setting targets, developing partnerships, and reporting performance”.
The report found that the top corporate social responsibility priority for Australian organisations is a focus on building stronger relationships with stakeholders. Across the board, the top three SDGs that are being addressed by the respondents' organisations are gender equality, good health and
wellbeing, and industry, innovation and infrastructure.
For utilities such as electricity, gas and water companies, the five sustainability goals that should be top-of-mind are:
1. Sustainable cities and communities
2. Clean water and sanitation
3. Good health and wellbeing
4. Gender equality
5. Industry, innovation and infrastructure
Given that 43 per cent of respondents reported a behaviour change in their organisation as a result of mapping the SDGs to reporting or strategy, and more than half believe that sustainability reporting should be mandatory, the ACCSR report highlights the growing importance that corporate social responsibility has in Australian and New Zealand organisations.
IIn the past, the use of trenchless technologies for installing and rehabilitating water and sewer pipelines were considered after other methods such as open-cut. However, water authorities have started to take notice of trenchless, and for those that have embraced these technologies, the benefits have been rewarding. Unitywater, the water and sewerage service provider for Moreton Bay, the Sunshine Coast and Noosa, has made trenchless methods its first preference for pipeline projects.
n November 2016, Unitywater put out a tender for trenchless construction services throughout its operational area.
Simon Taylor, Executive Manager Infrastructure Planning and Capital Delivery at Unitywater, said the tenders were released with some specific pipeline installations in mind.
“We knew that these would be through areas of important environmental considerations, along some major traffic routes, and would also be going past areas of commercial business. If we’d chosen more conventional open-trench type construction, we’d have caused disruption in all three of those areas,” Mr Taylor said.
“So the idea of using trenchless technologies was to limit, or have as little impact as possible in those sorts of areas.
“We released the tenders last November, looking for those services across the network. We put services out which included things like horizontal drilling, pneumatic ramming, some rock breaking, vacuum excavation, and also pipe jacking.”
Mr Taylor said overall, Unitywater received 17 offers, and three contractors were offered a contract for a five-year period.
“Horizontal drilling has gotten underway, as well as some pipe jacking, but the major technology we’re using is horizontal directional drilling. We’ve got three major jobs underway using that technology.”
Mr Taylor said one of the most important benefits Unitywater has realised from the use of trenchless technologies is the reduction of environmental impact.
“The environmental benefits have been very important to us. That’s been a very good outcome, as we’ve been working in areas of great sensitivity, and we haven’t had to excavate in places like reserves, or fragile environments. That’s made a big difference,” Mr Taylor said.
“A great benefit has been the lack of impact on customers and disruptions to road traffic.
“The work is going on in the background without disrupting people.
“That’s really important to us because we’re working alongside main roads and areas of important commercial activity, and to disrupt that would cause some form of cost to people who are our customers. We’re pleased that we’ve been able to significantly minimise disruptions in our communities.”
Mr Taylor said that trenchless technologies are being used for both new pipeline installations and the rehabilitation of existing assets.
“The split in expenditure between those two is round about 50/50 as we go forward over the next few years for Unitywater,” Mr Taylor said.
“It’s fair to say that trenchless technology is probably the first adopted technology that we would go to, which wouldn’t have been the case a few years ago.
“Our experience in the last 12 to 18 months or so has really changed our thinking. We now consider how we can use trenchless technology as a first port of call, rather than as an afterthought.
“We can now ask ‘why would we not use trenchless technology?’ whereas a few years ago it would have been, ‘well, that’s a bit novel, do you think it will work in that situation?’”
Mr Taylor said that while the tender process didn’t come up with any new technologies or methodologies, the five-year contract encourages the contractors to look at opportunities to innovate while retaining the certainty of the contract.
“It’s as much about creating the opportunity. There was nothing new at the start, but now we’re exploring the opportunities, with the knowledge of a long-term relationship, so they can trial new things without having to worry. Having that certainty of working with us gives them the chance to develop.”
Filtec is pleased to have recently established itself in the Australian water market. Filtec has an outstanding reputation in New Zealand for the design and construction of small to medium-sized water and wastewater treatment systems for the municipal and industrial market. Filtec also sells an extensive range of specialised water and wastewater treatment equipment backed by excellent after-sales service.
We recently completed Wannon Water’s Casterton water treatment plant (WTP) upgrade using Parkson Lamella® technology to significantly reduce the turbidity load on the existing filters. This has resulted in significantly improved filter run times and treated water quality.
While open-cut technology may still be acceptable in areas with less existing infrastructure, and less environmental and community impact, in high-density urban areas water authorities need to be seeking alternative technologies.
Due to the corrosive nature of the raw bore water, the plant is designed with external paint specifications for a 50-year life. All internal wetted parts of the Lamella® are of 316SS construction, and built in Filtec’s own Auckland
specialist fabrication facility under license from Parkson, United States.
“There are real benefits in using the technology, especially minimising disruptions to other users of utilities or spaces that you might be working in.
Filtec is currently commissioning a fourmillion-litres-per-day GE ultrafiltration plant for the new Fonterra cheese factory at Stanhope in Victoria. The turnkey WTP incorporates
“I think utilities need to throw away all the old preconceptions about trenchless technologies. Come and talk to those who have used it, and to those who’ve been converted,” Mr Taylor said.
Fchemical coagulation, UF and TrojanUV disinfection technology.
“Our construction needs are no longer impacting on locations such as important road junctions, or important environmental sites, because now we simply don’t need to be working in those spaces. Talk to those who have got some real experience. It’s really good technology.”
For further information on Filtec’s skills and capabilities for your project or equipment needs, please contact Colin Nash on 0419 347 054 or colin.nash@filtec.co.nz or visit www.filtec.co.nz.
Pipeline Drillers has achieved one of its longest and largest horizontal directional drills, crossing under a waterway for Unitywater. Located on the Sunshine Coast, the drill extended 908m from the Kawana Sewage Treatment Plant to cross under the Wyuna Canal and onto Kawana Way to install the 900mm diameter, high-density polyethylene pipe.
After being awarded the principal contract for the 5.6km Mountain Creek to Kawana and Caloundra sewage pipelines last October, delivery of this first HDD puts Pipeline Drillers on track for completion in early 2018.
Pipeline Drillers Managing Director John Whitbread said it’s a credit to the experience of Pipeline Drillers’ maxi HDD rig crew, together with drill rig heavyweights, Herrenknecht HDD250 and Gallagher HDD660, that this significant HDD was successfully executed.
“I have no doubt a key ingredient to the efficient delivery of the 908m pilot within seven days and 500mm of the exit peg, was the experience of our team, who in the past year have completed more than ten waterway crossings in various locations throughout Queensland and Victoria,” Mr Whitbread said.
Situated beside the stunning Mooloolah River National Park on one side, and built up Kawana Island on the other, the Wyuna Canal crossing required substantial planning and consideration to lessen the impacts of construction.
Therefore, prior to the commencement of the Kawana to Mountain Creek Sewage Pipeline, numerous redesigns increased the trenchless methods used to 70 per cent, to include three HDD and one thrust bore section. This outcome safeguarded the lowland habitat and significantly minimised disruption to the surrounding community.
Pipeline Drillers commenced drilling in late February, and confronted below and above ground environmental conditions of drilling in clay, working in wet weather, and utilising electromagnetic wire line tracking, due to the heavy vegetation within the national park, to complete the pilot within a week.
Further challenges of this large canal crossing related to the 900mm PN20 HDPE product pipe, namely the significant pipe stringing space required, the anchor block to support the high pull-back capacity, and pipe buoyancy control during installation.
While the Gallagher and HK250 reamed the bore to a final diameter of 1200mm, the welding team fabricated the 924m pipe string using fusion welding. The pipe string, once completed, extended from north to south along the western side of Kawana Way, and became an unmissable site for local road users until installation took place.
Pull-back was achieved within approximately eight hours, thanks to the Gallagher, which from the Kawana STP pulled up to 220 tonnes of its impressive 330 tonne capacity, the assistance of three 22 tonne excavators to hoist and guide the pipe, as well as a dozen crew members, the Unitywater, Bamser and Pipeline Drillers project team.
The Wyuna Canal crossing has undergone successful testing and will soon connect to the Kawana Way HDD which will extend 1.2km north towards the Mooloolah River.
COMMENCEMENT
Learn more about this project or Pipeline Drillers’ project capability and how they can assist you with a trenchless solution for your next pipeline installation by visiting www.pdgroup.com.au
TRACKING THE DRILL HEAD THROUGH A NEWLY BUILT ROUNDABOUT, WHICH WOULD HAVE TO HAVE BEEN EXCAVATED USING A TRENCHING CONSTRUCTION METHOD.
Townsville Council is employing innovative technology to undertake a major upgrade on underground sewer pipes in the suburbs of North Ward and Belgian Gardens.
The sewer infrastructure in Townsville is being upgraded to support existing and future population growth in North Ward and Belgian Gardens.
The installation of approximately two kilometres of sewer pipeline from the pump station at Howitt Street will provide an additional link that will connect the Belgian Gardens and North Ward sewer network with upgraded facilities in Leichhardt Street (part of the CBD Utilities Upgrade Project).
The $1.5 million project is using trenchless construction technologies to lay lengths of pipe to minimise the impact on residents and motorists in the busy suburb.
The pipe will be laid along Isley and Mitchell Streets, connecting the Belgian Gardens and North Ward sewer network with upgraded facilities in Leichhardt Street.
Townsville Water and Waste Committee Chairman Cr Paul Jacob said the use of trenchless technology would ensure minimal disruption to the road network, which was especially
important given the area’s popularity as a thoroughfare for The Strand.
“By using an advanced drilling process to tunnel an underground passage for the pipe, we won’t need to excavate large sections of the road, verge or footpath,” Cr Jacob said.
“Instead, the pipe is fed through entry and exit pits spaced 100-300 metres apart, meaning the surface stays intact. It also means we can install the pipe below other existing services without any disruption to those services.”
Currently, approximately 50 per cent of the 2km pipeline installation has been completed. Drilling through variable ground conditions (sand, mixed ground and sandstone) in a single bore length has proved to be challenging, and has slowed down the speed of the pipe installation somewhat.
According to a Townsville Council spokesperson, drilling in the tight space between service crossings worked well, highlighting the benefits of
utilising a trenchless technology.
By using trenchless technology, the council has also been able to install some sections of the pipeline approximately five metres below the surface, avoiding existing buried assets.
There were a number of reasons why trenchless appealed to Townsville Council. Given that the installation needed to take place in a built-up suburb with a number of busy road intersections and roundabouts, and with a number of underground services crossings, a trenchless methodology quickly emerged as the only feasible solution.
When these factors were combined with the high impact on traffic and the environment, and the restoration costs associated with a conventional trenching method, the case for a trenchless solution was further enhanced. The potentially shorter construction duration that comes with trenchless technology was another factor that appealed to council.
Divisional Councillor Ann-Maree Greaney said the new 315mm diameter pipe would substantially increase the capacity of the sewerage system to meet the demands of a growing population.
“The duplication of the sewer network in Belgian Gardens and North Ward will increase its capacity, which is important in suburbs with medium density buildings,” Cr Greaney said.
“The new sewer pipeline will also reduce the risk of failures and environmental issues that can be associated with older infrastructure.”
Construction started in early March this year, and is anticipated to take six months. Works will be staged with installation of the pipeline currently underway in Mitchell Street, between Howitt and Landsborough Street.
Safety fencing, signage and traffic control will be in place during construction to keep residents and motorists safe.
Several temporary laydown areas for storing pipe will be created in the work area.
With the project expected to be completed by early September, council is now considering other projects on which they can utilise trenchless technologies.
According to a council spokesperson, on projects in heavily built-up areas, and which feature a number of road, rail or waterway crossings, trenchless technologies will be the obvious choice moving forward.
Veolia’s Network Services division provides infrastructure solutions to Australian utilities to help build sustainable communities.
We are specialists in the design, construction, rehabilitation and maintenance of water, wastewater and stormwater networks.
www.veoliawatertechnologies.com.au
Sydney Water Corporation (SWC) is arguably the largest water utility in the Southern Hemisphere and is highly regarded in Australia and around the world for innovative approaches to water management. In January 2017, Sydney Water approached Primus Line in regards to the rehabilitation of two critical trunk mains.
At Pymble in Sydney, a DN225 CICL main 47m in length under the Pacific Highway with 2x45 degree bends had to be renewed. This main developed a leak in the 1980s and, as no technical and commercially acceptable method of rehabilitation was known, the main was isolated, as traditional dig and lay was not possible given the critical nature of the Pacific Highway as a main carriageway.
In 2016, Sydney Water was informed that one of Australia’s largest retailers wanted to build a new outlet at this location and required a certain volume of water that would place a strain on the existing network. Sydney Water engineers noted the isolated DN225 and sought out trenchless solutions.
The solution was a DN200 PN40 medium pressure Primus Line®system.
Given the congested nature of the Pacific Highway, all work had to take place between 9pm-4am. Once cleaning and CCTV were performed, the Primus Liner was pulled through the host pipe in one night.
Over in Penshurst, a DN300 CICL main 77m in length under a twin-track railway with 4x45 degree bends also had to be renewed. This main was damaged by a rail authority contractor over two years ago, and as a result was leaking. As no technical and commercially acceptable method of rehabilitation was known, the main was isolated. Traditional dig and lay was not possible given the critical nature of the railway.
Sydney Water estimated that HDD was in the vicinity of over $600,000. The solution was a DN300 PN25 medium pressure Primus
Line®system. This main was servicing a small retail area and a public amenities block, so all work had to be completed during the night as the main had to be isolated. After the cleaning and CCTV were performed the Primus Liner was successfully pulled through in one night.
The service life of these critical water mains was extended by at least 50 years. Sydney Water was able to renew both pipes in one week, including CCTV inspection, pipe cleaning, and liner installation. Cost savings in excess of 80 per cent could be realised compared to conventional methods.
The client opted to renew the leaking water main with the Primus Line® system, a proven solution for the trenchless rehabilitation of pressure pipes. The AS/NZS 4020:2005 certified three-layer composite liner consists of a PE inner coating, a Kevlar® core to accommodate the operating pressure independently from the host pipe, and an abrasion-resistant PE outer layer to protect the Kevlar® core during the installation process.
The semi-structural solution is not bonded to the host pipe, can traverse bends of up to 45 degrees, and can be inserted in lengths of 1,000m and more in one single pull. Furthermore, due to the low wall thickness of only 6mm compared to corresponding HDPE pipes, the hydraulic capacity is only reduced minimally.
For more information please contact Mark Trembath at +61 435 924 252 or mark.trembath@primusline.com.
With 2245km of water mains, 1904km of sewer mains, and 48km of recycled water infrastructure to manage across 16,550 square kilometres in NorthCentral Victoria, Coliban Water is one of the state’s largest regional urban water corporations. To ensure the continued delivery of safe drinking water and efficient services to its customers, Coliban Water has an ongoing mains cleaning program to help manage its assets.
Manager Assets and Operations at Coliban Water, Steve Dunlop, said cleaning water mains is an integral part of the water corporation's maintenance program to ensure it is able to continue to meet the Australian Drinking Water Guidelines, as well as assisting to protect the integrity of its water main network and help prevent service issues.
“The cleaning of our sewer network is important to help prevent blockages and improve the efficiency and reliability of our service. Sewer overflows are costly to clean up if they occur inside a home, and pose a significant risk to the environment and waterways. We have increased preventative maintenance works to reduce the number of blockages in our network.
“During 2015/16, we spent approximately $200,000 on our water mains cleaning program. Cleaning works were carried out in Bealiba, Boort, Cohuna, Dunolly, Elmore, Junortoun, Laanecoorie, Lockington, Pyramid Hill, Rochester and Tarnagulla.”
Most recently, water mains cleaning was completed in Heathcote in May, and a program of water mains cleaning works for 2017/18 is being planned. The 2017/18 program of works for the inspection and cleaning of sewer mains in Bendigo is underway.
There are a number of different techniques that water corporations are able to use to clean water mains. The technique to be used is selected based on site-specific conditions and the identified cleaning objective.
All mains cleaning techniques help improve water quality by removing any deposits, such as grit and debris, that build up over time and can cause the water to become discoloured.
Coliban Water hires contractors to carry out mains cleaning using four techniques, including:
Flushing
Water mains are flushed if there is a build-up of natural sediments. This can occur after changes in pressure or flow rate after a burst water main. Flushing the main involves opening hydrants to flush the water and any sediment through the mains at high speed.
Air scouring
Air scouring involves forcing a mixture of compressed air and water into the mains. This process also removes any sediment and helps maintains chlorine levels within the water supply network.
Ice pigging
Ice pigging involves pushing a thick
ice slurry, a mixture of semi-solid ice and water, through the main. The slurry is then removed from a hydrant and collected in a tanker. This method uses minimal water and is environmentally friendly. It reduces risks to the network and there is no need for excavation.
Swabbing involves forcing a large ‘sponge’ through a water main to remove sediment. The sponge is propelled by water pressure, and is removed along with any sediment and debris it collects.
“For sewer main cleaning we utilise a variety of techniques tailored to the condition of the main. The condition of the sewer mains is assessed using CCTV and acoustic sensing technology,” Mr Dunlop said.
The jetting of sewer mains is the most common form of cleaning. Jetting takes place in a section of sewer main between two manholes. It involves pushing a high-pressure hose with a cleaning nozzle through the main against the flow and then pulling it back through. Jetting is often used prior to inspection or renewals.
Chemical tree root treatment
“Tree roots cause more than 70 per cent of sewer main blockages in our region. Roots searching for nutrients intrude into pipes and catch fats, oils and foreign materials which can reduce the flow and cause blockages,” Mr Dunlop said.
Chemical tree root treatment is a foam herbicide that eliminate roots and prevents further structural damage of the main. Only roots within main pipe and a very short distance outside are affected. Trees and shrubs immediately above ground are not harmed.
Mr Dunlop said Coliban Water has had good results from its water and sewer mains cleaning program, with further mains cleaning works planned across its service region for 2017/18.
Water main cleaning works take place in autumn and winter out of our spring-summer peak-demand times, while sewer mains cleaning takes place all year round.
Edge Underground is a precision microtunnelling contractor that operates in Australia and the USA. With a focus on innovative technology and expertise, Edge Underground designs and enhances the performance of trenchless equipment.
With a proud history of innovation and equipment development, SECA - who are celebrating their 50th year of operation in 2017 - offers a wide range of sewer and drain cleaning options to utilities and councils across Australia.
It all began when company founder George Rose was on an overseas working holiday in the 1960s, with his observations of equipment and practices whilst working in his trade as a plumber on several sites throughout Europe.
On returning home he established GH Rose & Co., and shortly after formed Rose & Milne in Double Bay in the eastern suburbs of Sydney.
There were several different methods of drain cleaning in Europe and the USA, and he was impressed with the strong construction of the cable and driving power of the Electric Eel machine manufactured in Ohio, US. He established a great relationship with the Hale Family and SECA has represented that company since 1967.
With minimal capital, it took some time to convince plumbers that cable drain cleaning was the way of the future, so Mr Rose established a separate business called Sewer Services to advertise and expand the awareness of the machines in the industry. The first customer was SG McElroy & Son, who are today in their third generation of business and still have the original drive unit.
Once established, Mr Rose then returned overseas to several trade shows and conventions from which he added the CHERNE Plug range, Burton small drain cleaning equipment and Flexible Pipetools and Sewer Equipment Company of America (O’Brien) solid rodding equipment.
This success caught the eye of a large electrical contracting and servicing company, Hodgson & Lee, who wished to introduce a plumbing division to their already expanding business.
Their injection of capital soon saw Sewer Services as an exclusive drain sewer cleaning business with branches Sydney-wide and operating 30 service vehicles.
Again, on an overseas trip, Mr Rose secured the agencies for high-pressure water jet cleaners which led to various agencies for high-pressure hoses, nozzles and accessories.
With the introduction of water pressure jet cleaning, he realised the need for wholesale agencies to be better promoted, thus forming Sewer Equipment Company Australia (SECA) as a truly wholesale business.
SECA then began manufacturing many products themselves, including rods, tools and hybrid drive units for both flexible and solid rodding known as the “Rose Rodder”.
In 1993 SECA started the local manufacture of water jetting units. Large success was achieved with the Projet Muni, aimed at the local government. The company sold close to 330 of these units Australia-wide. SECA also started selling small jetting units into the plumbing market, which at the time was a new form of drain cleaning for plumbers to accept – as was the Electric Eel 30 years earlier – but today it is a common tool for most plumbers involved in drain cleaning.
In 1989 SECA moved into supplying pipeline inspection equipment. As this was fairly new and costly technology to sell, for a short time, SECA moved into contracting and started up a separate CCTV inspection company called Drainscan, which at one stage had a dozen employees.
With increased sales of CCTV equipment, the company backed out of contracting in 1994 and returned to their core business of sales.
In 1994, the company expanded their Marrickville warehouse with the purchase of the adjoining property. They continued to build water jetters until the late 2000s, but with the parity of the US dollar, manufacturing became uneconomical and SECA moved on to importing jetting equipment from both the US and Europe.
In 1998, SECA began a long-standing relationship with iPEK Spezial TV. Their success with iPEK in Australia saw them become the second biggest iPEK dealer in the world. In 2000, they began to the sell the WinCan program into Australia, with 14 employees.
Over the next few years, the CCTV range expanded to MiniCam and Quickview and in 2005 SECA became the agent for jet/vac truck manufacturer JHL from Denmark.
By 2009, continued growth saw SECA move to their current 1700m² warehouse in Chipping Norton.
Today, SECA proudly represents 18 leading overseas suppliers and has warehouses in Sydney, Melbourne and Brisbane. With 27 staff, including three second-generation team members, seven CCTV service technicians and a dedicated jet/vac service mechanic, the company continues to source and support the best equipment in the world for sewer and drain cleaning, inspection, testing and rehabilitation equipment.
SECA’s vast range of pipeline inspection cameras deliver superior data, expandability, productivity and support
Intelligent, Flexible, Rugged With Total Inspection Productivity
SOLOPro Plus has all you need to inspect pipes, document your findings, and create detailed reports for on-site delivery. Its interface offers robust tools – including observation entry and reporting options – and accepts USB and SD media for easy offload of data, video, images and reports. SOLOPro Plus is WiFi enabled to allow remote access to stored images and data.
Steerable Lateral Inspection
Camera & Cleaning
JetCam™ 40 uses high-pressure water for propulsion, steering and cleaning as it captures live inspection video from inside lateral lines.
Quick, Easy Way To See What You’re Jetting
Traverse lines 150 to 600mm* dia.
Capture HD video with self-leveling, illuminated camera, that can be viewed moments later on a PC or tablet.
ROVION. One System - All Options
The user-friendly ROVION®-pipeline inspection system is the one system that lets you do everything: control inspections, view and record digital video, log observations, generate reports, and link directly to asset-management software. Depending on the combination of the high-quality components pipe diameters ranging from 100 to 2000mm* can be performed.
Wireless HD Pipeline Zoom Assessment
A quantum leap in zoom assessment technology, the new cable-free QuickView airHD camera captures high-definition (HD) video from pipelines, and transmits it wirelessly to a touchscreen tablet for live viewing.
Rapid, Automated Manhole Inspection
Using five HD cameras and laser measurement, Cleverscan delivers: A flat scan that captures image detail from every inch of the manhole wall. A dense point cloud for 3D visualization and CAD.
A virtual environment for offline pan/tilt navigation.
Full intergration with Wincan VX
Vacuum excavators have become one of the most common tools used to identify existing utility assets during underground construction projects. With new advances in technology, they are quickly becoming a must-have machine to support HDD rigs in trenchless projects, as well as projects that require the removal of spoil while minimising ground disruption and removing the risk of damaging assets.
There’s no one-size-fits-all solution for every excavation job, but there are a number of key differences between vacuum excavators that should be considered when selecting the best one for your project. Here, Jeff Lawson, National Construction Equipment Sales Manager at Vermeer, discusses the key factors that should be considered when choosing the correct vacuum excavator for your specific job.
Vacuum excavators use pressurised water or air to displace the soil. Water digs through most types of material faster than air and is more effective on a wide variety of materials. As the materials will be wet, more spoil can also be held in spoil tanks. However, there is also a risk of spoil becoming contaminated and needing to be removed from the site.
“Air is not as fast as water, but it allows for a neater process as the materials are dry so they can be replaced to the site immediately. Using water, the material can’t be returned to the site unless it has dried out,” Mr Lawson said.
“Operators can also select the level of air or water pressure to use depending on the utility asset they are identifying. Low pressure should be used for gas and fibre lines, and high pressure for water pipes.”
There are three distinct types of vacuum blower used in the industry that you should be aware of: liquid ring pumps, centrifugal fans, and positive displacement blowers. Mr Lawson said selecting the right blower for your application is an important step.
“Vermeer’s vacuum excavators use positive displacement blowers as they maintain constant volume and speed, and reduce loss of airflow,” Mr Lawson said.
“They also come in a range of power levels and hose diameters to suit each job site. The VX200 is particularly
suited for big jobs. It has a large 6” (15.2cm) hose diameter with a 3200cfm (90.6 m3/min) blower at 457.2mm of mercury. At the other end of the scale, for smaller jobs the VSK100 has a 3” (7.6cm) hose diameter with a 573cfm (16.3 m3/min) blower at 254mm of mercury.”
Spoil tanks come in a variety of sizes, which will determine how much spoil you can remove during the day. Mr Lawson recommends that operators select a tank size that can hold a minimum of half a day's worth of spoil, although a full day’s is ideal.
“The bigger the tank, the more material you can vacuum up and store. Another thing to keep in mind is that the size of the tank will also affect which tow vehicle or truck is required,” Mr Lawson said.
Vermeer has units with spoil tank capacity ranging from 500L to 11,000L. For larger projects, the VX200 has a spoil tank capacity ranging from 4000L to 11,000L, with a standard option of 3000L of fresh water shared between two self-equalising saddle tanks. Small projects with restricted space are also catered to, with the smallest unit, the 100 gallon VSK100, fitting into the bed of a full size half-ton truck.
Selecting a unit that has a hydraulic door with a strong seal and manual locking mechanism is a feature that contractors should consider. This will not only prevent material from escaping the tank, but it reduces manual handling risk, making the process safer and boosting productivity.
For example, Vermeer’s VX200 has a cam-over autolocking hydraulic rear door that provides a 360-degree positive seal without additional clamping requirements. The cam-over design also has no moving parts, so all maintenance is external.
“Having the hydraulic mechanism located on the outside of the tank is important, as if it is inside, it could potentially leak hydraulic fluid, causing the spoil to become contaminated,” Mr Lawson said.
“Contaminated spoil is a hazardous material which, if put back in the ground, could cause a variety of environmental issues to the area. It’s critical to prevent this contamination from occurring.”
While the vacuum blower and spoil tank are the things that are front-of-mind for most people, Mr Lawson said it’s also important to select a filtration system that is able to filter the spoil and avoid clogging.
“Vermeer’s VX200 has a three-stage cyclone filtration system which has been designed specifically for 3200cfm blower systems. Three-stage cyclone filtration systems are one of the most effective filtration methods as they allow for both wet and dry vacuum excavation, while also prolonging filter life and keeping maintenance costs low.”
All job sites are different so choosing an excavator that is best suited to your work site will provide the most benefit.
Smaller sites demand less power, and therefore less equipment and labour. Larger sites, on the other hand, demand heavy-duty equipment, and harder-to-reach sites where there is uneven or rough terrain require heavy-duty trailer options.
To accommodate various site requirements, Vermeer’s VX200 can be mounted on either a new or repurposed truck chassis. The tank, power pack and water system all have a modular design, offering the versatility of mounting the unit in the configuration that best suits vehicle and operational needs.
As vacuum excavators can also be used with a wide range of attachments and tools, they are used for a variety of other projects, including cleaning catch basins, digging post holes, sewer jetting, and exercising water valves.
Vacuum excavators continue to gain popularity for projects that require minimal landscape disruption and a reduced risk of utility asset damage, and are saving contractors time and money on trenchless jobs.
Over the past decade, Australia’s water utilities have become increasingly reliant on trenchless methods of pipeline installation and rehabilitation. There are many benefits to be gained through the use of trenchless technologies, including substantial cost savings, reduced environmental impacts and minimised disturbance to communities when compared to the traditional open trench methods of installation.
Iplex Pipelines, recognising the growth opportunities and the market’s demand, have focused on their trenchless portfolio to become a leading Australian manufacturer and distributor of pipeline rehabilitation and installation products, including microtunnelling, horizontal directional drilling, bursting, slip-lining, cracking and reaming technologies.
Trenchless pipeline construction technologies have favoured polyethylene (PE) pipe, due to its ability to be fusion-welded on site into long strings. This trend has in turn resulted in demand for a higher performance, long-life PE that will provide reliable service. This motivated Iplex to look toward the evolution of PE100 pipe materials that can withstand the inevitable damage that will occur in trenchless applications, where undetected surface damage and rock impingement may occur during construction. This has ultimately resulted in the development of Iplex Millennium®
Iplex Millennium® is a high stress crack resistance (HSCR) grade of PE100 pipe that provides up to ten times greater resistance to slow crack growth than conventional PE100 pipe. It has the same pressure burst strength of conventional PE100 pipe, but is specifically designed for use in critical or high-value pipeline assets where the risk of premature failure from slow crack growth is possible.
In trenchless applications requiring
a jacked pipe solution, Iplex Pipelines was an Australian pioneer. Back in the 1980s, Iplex first introduced Hobas GRP pipes into the market and drove the growth and market acceptance of GRP pipes in the Australian water industry. Over the past decade Iplex’s Flowtite® continuous spirally wound range has expanded into jacking pipes. To date many hundreds of projects have been supplied in Flowtite® GRP pipe, including the recently completed Amaroo project undertaken by John Holland for Yarra Valley Water. At 7.5km in length, this installation is the largest jacking pipe project undertaken in the Southern Hemisphere.
To remain at the forefront, Iplex keeps up to date with technological developments from around the world. The properties of PVC pipe are well known and appreciated by water industry asset owners to an extent where the material has been significantly adopted as the default material of choice for the construction of Australian urban pipelines. In the US, research into the formulation of a weldable PVC compound in concert with the development of specialised equipment and process conditions has enabled PVC to make significant inroads in trenchless applications. Iplex recognised the opportunity for this product in Australia and has entered into a licence agreement with the owners of the patented weldable PVC pressure pipe technology, Underground Solutions Inc., to manufacture and fuse
PVC pipe within the Australian territory where it is trademarked, Novafuse™.
Whilst Fusible PVC™ could be successfully used in place of polyethylene pipe in most installations, it is Iplex’s intention to focus on projects that will benefit most from the pipe’s higher tensile strength and lower weight, to permit longer shots and smaller bore holes. As the welding process demands specialist skills and equipment, Iplex provides a fully welded string of pipe to site and monitors the installation process, reducing project risk. The innovation of Fusible PVC™ represents an opportunity for engineers to design trenchless pipelines in diameters and lengths at a cost that was not previously possible.
Adding further to their trenchless PVC pipe range, Iplex has developed Restrain™ PVC-U Sewer Pipe, specifically for gravity sewer applications utilising trenchless techniques for the installation, repair or replacement of underground drainage infrastructure. Restrain is a rubber ring jointed PVC-U pipe, with a threaded spigot and socket, which provides immediate axial capability during installation and is compatible with both solvent-welded and rubber ring jointed DWV PVC-U sewer pipe and fittings.
As the Iplex Pipelines portfolio of trenchless products is so diverse, their application specialists are available to provide honest and professional advice on the best product fit for every trenchless pipeline project.
As a leader in the pipe industry, Iplex can provide trenchless solutions for Micro-tunnelling, Horizontal Directional Drilling (HDD), Static pipe bursting, Slip lining, Pipe cracking and Pipe reaming.
MPC Group’s focus on in-house innovation has reinvented the way the industry installs high voltage and fibre optic cabling, resulting in increased crew safety and significant production efficiencies.
providing crews with full visibility for accurate cable installation into trenches, but also with all round safety oversight during operation.
MPC Group has just rolled-out its fully track-mounted cable crawler – a hybrid, modular unit that is designed to fit upon its fleet of winches.
The list of the machine’s innovative modifications is long, but sure to gain interest is the fact that it is trackmounted, providing increased stability on any terrain, and its innovative swing arm assembly, ensuring accurate cable guidance into trenches at all times.
It’s also a more cost-effective means of installing cabling, with only two crew members and one machine required to install cable, compared to three crew and three machines using conventional methods.
A unique re-spooling mechanism also enables road and rail crossings to be performed without the need for cable joints or excavation of bell holes.
The machine’s safety credentials are also outstanding, with its purposebuilt, remote-controlled hydraulic arm system lifting cable drums safely into place, without the manual handling risks often associated with conventional cable install methods.
The remote control capability also extends to the swing arm operation,
The safety and accuracy advances are sure to rate highly within a marketplace constantly seeking safer operations and increased cost efficiencies. However, the machine’s operational speed is sure to be the biggest drawcard, and likely to see it dramatically change the cable install industry landscape that we know today.
With installation speeds of 5km per hour for cable diameters right up to 110mm, it’s simply the fastest cable install machine on the market.
Already delivering massive production increases on project sites across Queensland’s Surat Basin, MPC Group believes it won’t take long before this innovative machine becomes common place within the industry.
MPC Group Electrical Superintendent Garry Muldowney describes the innovative machine as 21st century thinking.
“Our R&D team put in extensive effort in the machine’s design phase, collaborating closely with our cable install crews to ensure this purpose-built machine provided them with a much safer and far more effective machine to work with,” Mr Muldowney said.
“It has undergone extensive field testing over the past 12 months to allow our fabrication team the opportunity to ‘engineer out’ any operational risks and ‘engineer in’ unique safety features and efficiency gains.
“This is next-generation thinking and I’m confident we’ve got the design right. The proof of that is in the fact that the machine is already delivering `best-for-project’ outcomes for our clients right across the Surat Basin,” he said.
Cable Crawler features and benefits
• Bi-directional spooling capability for crossings
• Ground pressure (loaded): 6.7Psi
• Max drum diameter: 3.1m
• Min drum diameter: 1.90m
• Max drum width: 2.09m
• Max drum weight: 7 tonne
• Cable diameters: up to 110mm
• Drum lift @ 1.9m from rear of machine: 7 tonne
• Drum lift @ 2.94m from rear of machine: 4.5 tonne
• Travel speed: 5 km/h
• Trench edge distance: up to 3.2m
Safety features
• Pressure transducers to limit drum lifts to machine capacities
• Hydraulic stabiliser legs
• Full variable drum speed for safe cable reel out
• Hydraulic spindle locks with electric lockouts to other controls
• Full roller bearing lift points on spindles so lift chains are left in place until drum removed
• Safe all over maintenance access
• Cab cameras so operator can see rear of machine, cable drum and down arms into the trench
When it comes to vehicles to help service the utility industry, clients are after a product that can be fully customisable to the job it needs to perform. MFI Service Bodies understand the requirements of commercial vehicles, and they offer a range of solutions that can meet the needs of almost any application.
MFI Service Bodies know commercial vehicles and commercial bodies. When it comes to commercial vehicles and bodies, they need to be more than good looking – they have to be tough, lightweight and exceed any safety or legal requirements. Most important of all, they have to work well for your business, and yet still be flexible enough for changing demands.
MFI has the skill and technology to customise every service body for optimum vehicle and personnel safety, load and cargo management, operational ease and productivity, dust and water exclusion, and corrosion protection. All MFI commercial bodies have quality build features that minimise downtime and underpin the return on investment.
MFI builds bodies for every type of trade and business. There’s an extensive range of options and accessories that can make your crew’s job easier and safer. And MFI options are only the beginning. We have the expertise to customise every service body to your exact requirements.
Expertise in space management and storage design makes MFI the most effective solution for even the most challenging applications. The range of options is extensive, including racking, single or two draw configurations, as well as slide out benches and workspaces.
Sometimes the solution is a mix of secure storage and open load space for bulky items or equipment. That’s when an MFI canopy combo can provide the ideal solution. The way the available space is divided and configured is completely customisable, always coming back to the client’s particular requirements.
MFI can provide quality custom truck bodies for industrial service, removal, haulage, and any other truck body application. Their experience with accommodating complex equipment, and load control and management, makes MFI the preferred supplier to industrial customers Australia wide.
No matter what the load, no matter what the application, an MFI tray will do the job and go the distance. All trays are custom made from the best materials and with the best techniques available and finished with a colour matched two pack finish.
Mr Chalkley came to Western Power with a varied career history. Having trained as an accountant in the 1980s, he worked in a range of industries in countries such as Nigeria, Poland, Russia, Hong Kong, Brazil, Mexico and Nicaragua; had brokerage stints in New York and a sugar refinery in Queensland; and worked in the airport sector in Shanghai, Mauritius and Naples.
It was after this experience that he made the move to utilities, joining Veolia Water. Mr Chalkley finished his stint there in the role of Finance and Regulation Director, during a period in which the business changed hands four times in ten years. Five years ago, Mr Chalkley made the move out west, and transitioned from a finance role at Western Power into the CEO role last year.
Coincidentally, Mr Chalkley’s first 12 months as CEO have come at the same time as some major transition points for both Western Power, and the energy industry more broadly.
For Western Power, in June last year it looked as if the organisation would shift from being regulated by the state Economic Regulation Authority, to the national regulator, the Australian Energy Regulator.
Against the backdrop of this change, in Mr Chalkley’s first weeks in the role of CEO, the organisation announced a major transformation program, designed to help Western Power provide its customers with safe and reliable power in a more efficient manner.
“This transformation program had a strong focus on positioning the business to respond to an economic downturn, understanding that it would have a major impact on our people,” said Mr Chalkley.
“We announced the potential people impact in my first week in the role, as it was important to be open, honest and transparent through the journey. We knew we would only be successful with everybody on board.
“While we made mistakes, I believe the openness and honesty of our approach to change allowed us to move forward together at a very fast pace.”
The amount of change we’re currently seeing in the energy industry more broadly has also had its implications for Western Power. New technologies – including renewable energy sources and battery storage – are naturally having an impact on the way Western Power approaches is long-term planning activities.
“Long-term strategic planning is an interesting concept nowadays. Traditionally we had 50-year plans – these have now become 50-year outlooks,” said Mr Chalkley. “A 50-year plan was fine in an era where the investment solution was the same, but this cannot be said now.
“The challenge for all of us is to move away from the belief that the wood pole we put in the ground today will still be the only solution in 50 years’ time. The rapid march of technology in the energy industry will constantly refine the 50-year outlook, especially in the shorter term. It will be vital to have information and be flexible to meet the challenges
Guy Chalkley was appointed Chief Executive Officer of Western Power in August 2016, after acting in the role from March in that same year. As Guy marks his official 12-month anniversary in the top job, we sat down to talk with him about the changing energy industry, integrating renewables into the network and embracing change as an opportunity – not a threat.
of the next ten years, while not overlooking the immediate needs of the next two to five years.”
According to Mr Chalkley, Western Power’s new business intelligence and data analytics team will play an important role in meeting these future challenges. Western Power has also created a change and innovation business unit, with the Executive Manager forming part of the leadership team. Bedding down the way these teams interact with the entire business – especially the emerging technology unit within asset management – will be of critical importance.
“The combination of these functions will allow us to pilot and test new ideas and customer-focused asset solutions based on emerging trends and patterns now, rather than in five or ten years’ time.”
For Western Power, as a traditional network with both transmission and distribution functions, and with high solar PV penetration on one side and substantial renewables projects on the other, the broader shift in the traditional energy chain of generation, distribution and retail is being keenly felt.
“We are experiencing a greying of the lines between generation and distribution and distribution and retail,” noted Mr Chalkley.
“The advent of battery storage on one side, as well as smart meters and Big Data on the other, is also providing
a challenging environment for distributors. Add to this grid defection from solar PVs and large-scale renewables, and you have a real melting pot.”
For Mr Chalkley, it’s been important that Western Power recognises this evolution as an opportunity, rather than a threat.
“The challenges we’re facing can be overcome with changes to current legislation and regulation, which haven’t kept pace with industry changes,” said Mr Chalkley. “We are also in a strong position as a trusted provider to test and pilot the new technologies that have emerged.
“This will counter the revenue decline as solar PV continues to grow.”
Mr Chalkley also believes that the disruption being seen in the industry, in the form of new technologies, will significantly challenge the business to consider the best investments when it comes to new asset planning.
“I believe that the disruption has added another step, very early in the planning stage, that challenges whether the traditional form of investment will be the best solution.
“Our traditional network assets and solutions have long lifecycles and long payback periods – but new, emerging technologies could make these assets obsolete over a short period of time.
“We do not have all the answers yet, but we remain committed to safety and reliability, whilst we wait for a fuller view of impact of disruption or alternative investment solutions.”
For Western Power to sufficiently take advantage of the opportunities renewables provide – rather than be threatened by them – Mr Chalkley firmly believes the utility needs to take the right approach to integrating renewables into their network.
“Renewables need to be connected in the right places and with the right level of investment in the network to enable their efficient use,” said Mr Chalkley.
“The current network wasn’t designed for renewables, or the two-way flow of electricity for that matter. We do need a good forward picture and plan of what and where future renewables are likely to be located, so we can prepare the network for the changes that will take place.
“This needs to be done at a high level so that we are not simply adding piecemeal, point solutions. A longer-term view has to be taken that secures the network for future generations utilising a mixture of renewables and traditional generation.”
One of the key points to consider is the fact that there is a wide variety of emerging technologies out there, that can be considered for implementation into the network. As Mr Chalkley says, there is no one “silver bullet” solution to meet the brief of providing energy that is reliable, affordable and clean.
“All of the new solutions provide customers with alternative options that can be better than existing options,” noted Mr Chalkley. “And ultimately, this can only be good for the customer. From a network position, the customer’s particular set of circumstances has to be considered to deliver the most efficient solution possible, to meet their needs for safe and reliable energy.”
To that end, Western Power is moving forward with a number of projects that incorporate innovative technologies that answer customer needs.
“We are piloting a large-scale microgrid in an edge-of-grid eco-tourist town, a battery storage system in a remote town that suffers above average outages, and a stand-alone power system in a farming community with below average reliability,” said Mr Chalkley.
“Along with these physical projects, demand management tools are helping shape customer behaviours, which is proving to be a smarter investment than the traditional sub-station build in urbanised areas.
“These are four of many options that we will continue to pursue in the future. As an organisation, we need to work now to be more prepared for higher levels of PV and batteries on customer premises, as well as technologies such as ‘peer-to-peer’ trading.
“Western Australia has very good sun, wind and wave resources, with global technological partners queuing up to partner and test their projects in an environment that can provide an available site. The fact that land is available and the population is sparse has become an advantage.
“Add to this our committed people who have always got things done and delivered, often in adversity, and you have an excellent mix for the future.”
The focus on integrating solutions into the network that offer the best benefits to customers is a sentiment echoed in other areas of the business, particularly when it comes to affordability.
The transformation program that Western Power embarked on at the beginning of Mr Chalkley’s tenure is already delivering significant savings in terms of efficiency gains, and importantly, safety and reliability has not diminished.
“We also want to improve the process for access and with new technologies, better communication and by taking the time to listen, we believe the customer experience has improved and will continue to improve.
“One of the things that you realise quickly, as a monopoly, is that we have responsibilities. We are embedded in the community, our employees are also customers and we all reside in the community. Fundamentally the customer has little choice but to use us in some form.
“It is important that we treat people with respect and act with integrity, this involves actively listening to and engaging with our customers and the community to identify and implement innovative solutions that take their input into consideration.
“We aim to engage with the community early and proactively to address social impacts. We engage across a broad platform of stakeholders and community members, from people who are potentially impacted by new or existing infrastructure – through to our regionally based community investment program that aims to make a meaningful contribution to our communities.”
A new addition to the CMC product family from OMICRON, the CMC 430 is the lightest and most precise protection test set in the world.
Weighing in at a mere 8.7kg, and with a robust design –including edge protection – the CMC 430 is ideally suited to portable applications, even when subjected to harsh ambient conditions and extreme temperature fluctuations.
The CMC 430's technical merits really come to the fore when testing numerical and communication-based relay systems and measuring systems, especially during tests with up to three currents of 12.5A at the same time. Here, its outstanding performance as a relay test set is combined with functions for hybrid measurements and recordings (analog, binary, GOOSE, and Sampled Values in accordance with IEC 61850). The EnerLyzer Live software option enables hybrid measurements and recordings to be taken simultaneously with active output channels.
The six voltage outputs allow the synchro-check function to be tested, as well as bay control systems with six voltage inputs – without an additional voltage amplifier. Red LEDs indicate the status of the voltage and current amplifier (continuous light for active output and flashing light for output overload). They are accompanied by an acoustic signal that can be switched off.
The three powerful 100W current amplifiers enable burden measurements to be taken and older protective device models to be tested. Thanks to its extremely high amplitude and phase accuracy (current and voltage), the CMC 430 is an ideal source for calibrating measuring instruments, such as energy meters, measuring transducers, PQ measuring instruments, and PMUs.
The device can be controlled using either a Windows laptop or an Android tablet PC, on which the high-performance software testing tools from OMICRON come into play: Test Universe, CMContol App or RelaySimTest.
OMICRON offers two options for transporting the CMC 430. The trolley with rucksack function is the highly portable choice. There is also a
multi-functional transport case which can be used as storage for the test set and also as a work table.
The device is certified by TÜV SÜD AMERICA Inc. and meets European, North American, and international health and safety requirements.
Our 3-phase test set CMC 430 is the newest member of the CMC family and combines its outstanding performance as a relay tester and calibrator with hybrid measurement and recording facilities. Its lightweight and rugged design ensures excellent portability. Appropriate software tools also allow numerous applications from quick manual testing to distributed scheme tests which makes the CMC 430 a highly flexible solution.
Discover our new CMC family member.
www.omicronenergy.com/newCMC430 info.australia@omicronenergy.com
Australia: 03 9473 8400
New Zealand: 0800 6642 766
After twelve months of design and meticulous planning, Zinfra gas pipelines and facilities crews worked at full tilt to construct the new regulators and pipework at AusNet Services' Corio City Gate in Victoria.
This project was significant for AusNet Services as the Corio City Gate is their most critical gas asset, in terms of the number of customers it supplies and as a major supplier of natural gas to the region.
The gas infrastructure was originally constructed in 1971 and is the sole supply of gas to Geelong, Torquay and the Bellarine Peninsula – over 200,000 customers. The City Gate reduces gas pressure from 7200kPA to 1700kPA as it arrives from the APA-owned 350mm Brooklyn to Corio transmission pipeline, and then injects this gas into the Corio to Point Henry pipeline.
The age of the asset, as well as increasing demand, dictated the need to upgrade the regulators to ensure consistent and reliable pressure control. Zinfra was engaged to design, procure and construct the pipework.
To facilitate construction, the existing meter had to be bypassed by a temporary piping arrangement. This temporary bypass, however, could only sustain off-peak demands
in the summer months, which meant all works had to be completed in the short month of February to avoid the risk of downstream loss of supply to customers.
To plan for this tight timeframe, Zinfra’s work started nearly a year earlier when their in-house design teams put pen to paper to design the pipework. Designs were planned to meet AusNet Services’ piping specifications and requirements, and pipe stressing was then completed to ensure the new design was compliant and fit for purpose to all the relevant codes and standards around fabrication and constructability.
Approval of the final design was required from both AusNet Services and APA Group before fabrication could commence. These approvals, along with a detailed project plan, all procurement and all off-site fabrication works and commissioning plans had to be in place well before construction commenced.
The scope of the project included the removal and replacement of the existing Welker jet and jet stream regulators, their respective legs with Gorter R100 regulators, as well as the replacement and relocation of the outlet header to above ground.
Other works required included the installation of mechanical protection bollards to protect the new above ground outlet header and other assets on site, and the inspection of above and below ground piping transitions to inspect their condition and to repair and recoat as necessary.
Zinfra’s Delivery Manager for Gas and Water, Ben Gliwa, was delighted with the overall outcome on the project. “This is a prime example of the high-quality facility and SMP construction work Zinfra is delivering in the gas sector. Not only was the project well managed from the outset, it met the client’s tight timeframe and was delivered without incident. We are very proud of what we have achieved here.”
“We chose Zinfra to install a new connection point on TasNetwork’s distribution network, based on their expertise and proven track record in complex design and construct electrical infrastructure projects.
The Zinfra team delivered the technical requirements of the project on time and without a significant safety or environmental incident, despite the complexities of the logistics, geography, location and stakeholder management associated with this job. And that’s no easy feat.”
www.zinfragroup.com.au
Much has been written about new energy sources and the customer as drivers of energy reform. But another factor is gathering pace and looks certain to deliver a greater impact on all aspects of a utility’s operation, and its relationship with stakeholders. Automation is coming – and how energy companies define and control its impact may be their biggest test to date.
Reform without purpose is futile. Understanding the drivers of each energy reform process and holding a clear view of where the market is now and where it needs to be, the specific circumstances of each country, its history and culture and particular barriers, is critical if reform is to meet objectives without delays and cost blowouts.
As many of the world’s energy markets wrestle with the challenges of reform, another change looms large.
Automation – when technology takes over a task previously performed by people – is forecast to impact almost every aspect of utility company operations over the next 30 years. Of course, automation has already displaced many energy sector workers:
• Meter readers have been replaced by smart meters
• Call centre staff have been replaced by smartphone apps that allow customers to log outages and track
• Line inspectors have been replaced by drones
But as the reach of digitisation and new technologies expand exponentially, more and more processes will be performed by robots or artificial intelligence. Automation is the ultimate fulfilment of the quest to ever perfect technique and remove cost. Yes, digitisation creates jobs too – but not nearly as quickly as it culls them. By removing human capital, automation may represent the greatest energy reform ever to strike global energy markets.
Everyday energy companies make decisions to adopt new technologies to automate processes. When a task is automated, it’s through the application of technique. That is, the expenditures of the company, both with and without
1
2
It’s tough in the Energy & Utilities sector. Regulators and customers expect your performance to be reliable and secure. We’re here to help. Built by telecommunications network engineers for an innovative communications experience for now and into the future1
IoT Leader2 designed “Network Heartbeat Function” in place for proactive communications experience that ensures read-rate maximisation
EnergyConnect, powered by a Vodafone Global Sim3, is a new device that protects mission-critical projects and communication ecosystems using a unique security profile
Management, monitoring and protection of your infrastructure made simpler and more cost effective by utilising a carrier built device and ecosystem.
Industry Recognition and Award Winning. “Best Digital Transformation Project”
Australian Utility Innovators Awards 2016
Now Narrowband-IoT Ready
the new technology, are determined, the technology is then purchased and implemented and corporate and culture changes are made to reap its benefits.
But for all these undoubted economic benefits, automation poses the genuine threat of increasing already high levels of societal inequality. Of course, most utilities are aware that more automation means less people, but few follow the logic further. Are utilities considering how automating their processes will impact their company’s internal culture, employee morale – and society? How do these implications fit with a utility’s defined notion of purpose, which is their window to the world?
The benefits of purpose to utilities, and the countries in which they operate, have long been recognised. Put simply, purpose defines why energy companies exist. It helps them sift “on-strategy” tasks from the irrelevant. It allows the development of KPIs that highlight exactly what achieving that purpose looks like. In this way, a defined purpose has challenged utilities to crystallise the reason they exist and what they are hoping to achieve. They have found, in almost all cases, that what they and their customers value goes beyond profit. Outstanding service, freedom of choice, creating communities, alleviating hardship and powering developing countries are just some of the purposes identified.
Most importantly, knowing and understanding its purpose defines a utility’s targets. It also helps choose the technique employed to achieve these and – critically – it constrains those techniques, or parts of technique, that would lead it astray. For example, requiring a technique of cost reduction may impact social obligations such as diversity. Each day, energy companies deal with these mild tensions through a clear view of what they stand for, which overrides the pure pursuit of profit through the unconstrained adoption of techniques.
Automation is set to scale up these tensions quickly. Large utilities with a high degree of linear processes and which would profit most from mass unconstrained adoption of efficiency measures may experience this most intensely.
Low margin businesses in highly competitive fields, such as energy retailers, may find that survival offers few options but to follow the path of automation.
Others will face a choice between their purposes and techniques. They will have to ask themselves what they stand for in terms of employment. They will have to consider their role in society and how to meet the expectations of their stakeholders, customers and employees.
The wrong decision that favors profit over purpose may prove perilous. Instead, utilities may have to consider how lessons learned from tackling other workforce challenges such as improving diversity of gender, age, background and orientation may be applied to the impacts of automation. Is it time to design programs to employ people at high risk of losing their jobs through automation, such as the young, the old or the newly graduated? How will the industry and the community as a whole judge those companies that prove their dedication to people within an environment where it is increasingly expedient not to use them?
When utilities design for themselves a space in the future energy value chain it implies holding a certain place in society. It means accepting a role that balances the interests of stakeholders, government and customers. Purpose must span the interests of all of these. As utilities transform, most are embracing changes through a strategic lens. They are investing in new energy technologies, seeking alliances and partnerships, and overhauling their business model. But few are asking themselves what they stand for and how they balance their values in a world where technology offers us increased ways to skew returns dramatically towards one interest at the expense of another. How will utilities balance the needs of their various stakeholders and weigh their responsibilities as an institution, an employer and a corporation?
As the world in which utilities operate changes, the need for companies to examine their purpose is more important than ever. Automation will create the greatest energy reform since 1881. Where will your company stand?
29-30 November 2017
Melbourne Convention & Exhibition Centre, Australia
www.australian-utility-week.com
Sydney Water is currently conducting an innovative research project where food waste is being added to sewage through a co-digestion process – generating clean energy to power its own treatment plants, with the potential to one day generate sufficient energy to power surrounding homes and businesses.
The first stage of the research project is utilising waste from beverage production and turning it into green energy at a facility in Shellharbour. The project is essentially turning beer, wine and soft drink waste into potential power for homes and businesses.
The process sees food waste being blended with sewage, and the mixture is then converted into methane gas through a process called anaerobic co-digestion. The obtained methane is then used as fuel to heat an anaerobic digester and to produce electricity to power the treatment plant. The entire process occurs in a contained system to eliminate any odours.
A typical Sydney Water customer is now saving nearly $100 a year on their water bill, and projects like this could make even more savings possible in the future.
Adding food waste like beverage waste to the wastewater treatment process provides a number of benefits:
• More power is able to be generated by the co-digestion process through additional biogas production
• Food waste is diverted away from landfill
• Greenhouse emissions are reduced
• Producing green energy at the treatment plant keeps the operation costs of the treatment plant lower, which in turn puts downward pressure on water bills for customers
According to Brendan Galway, Service Planning Analyst at Sydney Water, the utility began looking at co-digestion several years ago, with a lab-scale and then a pilot trial of glycerol at its Bondi treatment plant.
“This trial was successful in showing that Sydney Water could handle trucked organic waste and add it to our anaerobic digesters and then capture this increased biogas and turn it into electricity,” said Mr Galway.
Further lab testing identified other waste substrates that could also be used. These lab tests were built around Biomethane Potential (BMP) testing completed by the University of Wollongong.
“Although these tests could tell us that methane would be generated and the indicative
volumes, they did not give enough data for the organisation to proceed further for the more complex organic materials,” noted Mr Galway.
To be able to meet the business requirements, Sydney Water embarked on the research program that resulted in the construction of the research digesters that are now at Shellharbour.
Now, together with the University of Wollongong, the University of NSW and DC Water in the US, along with various waste companies and commercial and industrial producers of food waste, Sydney Water is utilising funding from the Australian Research Council (ARC) Linkage Projects scheme to extract the most energy possible from waste products that would have previously gone to landfill – a win for the environment, customers and all of the organisations involved.
Anaerobic digestion is a process where microorganisms break down organic materials, such as wastewater sludge or food waste, in the absence of oxygen, into biogas and biosolids. Biogas is a renewable fuel, while biosolids are valuable fertiliser and soil conditioners.
Co-digestion is an emerging opportunity for economic savings and significant reduction of greenhouse gas emissions through the production of biofuel. Organic wastes originating from both municipal (e.g. food waste) and industrial (e.g. beverage production and food processing) sources are rich in carbon, hence, energy.
“By adding these products to our wastewater, we can generate more biogas,” said Mr Galway. “The more biogas we capture, the more electricity we can generate.”
In addition to utilising existing wastewater treatment plants to produce energy, and divert organic waste away from landfills, co-digestion can deliver a range of benefits to the anaerobic digestion process itself.
“The addition of carbon-rich organic wastes to nitrogen-rich wastewater sludge can improve the elementary stoichiometric ratio of the feed, thus enhancing anaerobic digestion performance with respect to biogas production, volatile solids reduction, and process stability,” said Mr Galway.
“In addition, hydrolysis can be the rate-limiting step in the anaerobic digestion of wastewater sludge because of its protein-rich content. On
the other hand, de-ammonification of protein-rich wastes can stabilise pH, and prevent rapid pH decline, thus increasing stability.
“Thus, the synergistic effects of co-digestion can be realised by determining the balanced stoichiometric range.”
Co-digestion with readily degradable organic wastes can also enhance the growth and intensified yield of anaerobic microbes, leading to a higher hydrolytic rate than that when wastewater sludge is the only substrate.
Through this research project, Sydney Water will be considering two broad types of results.
Firstly, the team will be looking at the amount of biogas that a particular food type produces, and at what volume the food waste achieves this optimum. Various types of food waste are being trialled, and each one has a maximum loading rate associated with it. This trial will ascertain what that level is and how much biogas it produces. This helps Sydney Water determine the amount of electrical generation assets that will be required.
The second important type of results the team will be reviewing is the impact adding food waste will have on Sydney Water’s system, the biosolids and the centrate from the dewatered sludge.
“As we co-digest material there needs to be a balance between the potential increase in biosolid tonnages, the impact that certain wastes may have on how well the biosolids dewater, and what increased nutrients this centrate contains,” said Mr Galway.
“As this liquid is returned into the plant for treatment, we must be careful not to adversely impact how much energy will be required to remove these added nutrients.”
Customers, be it residential or commercial, will benefit from reduced pressures on their charges, noted Mr Galway. “By increasing the amount of self-generated energy we can generate, we can pass on these savings to our customers.”
Commercial customers utilising the service will receive the added benefits of a competitively priced service that diverts their waste product away from landfill with a strong environmentally sustainable story.
Sydney Water currently generates more than 20 per cent of its total energy needs across its network from wastewater treatment, along with hydro and solar power. That’s the equivalent energy to power over 11,000 homes each year, reducing greenhouse gas emissions by over 70,000 tonnes a year. It’s also the equivalent of keeping 17,500 cars off the road for a year.
In addition to producing 20 per cent of its power needs, Sydney Water also exports eight gigawatt hours to the electricity grid a year, enough energy to power about 1000 average NSW homes.
With the research that is currently taking place, the utility hopes to increase these figures.
The areas of Sydney Water’s business open to this type of waste-to-energy are its network of anaerobic treatment plants in the Sydney and Illawarra. Sydney Water currently has eight treatment plants that are anaerobic and have co-generational engines, with a further three plants that do not currently have an engine in place.
For other utilities considering establishing their own energy generating facilities at treatment plants, Mr Galway has several tips and tricks to take into account.
“The best advice I could give is, if you have available co-generation capacity as well as digester capacity then increasing biogas generation through the addition of food wastes is a process worth investigating,” said Mr Galway.
“The key to doing it well is being prepared to walk before you run and utilising both experimental and piloting projects. Individually, each type will not give you enough information.
“With piloting, so far, we have had a harder time identifying the impacts the product is having, especially how much gas or energy is directly attributed to the product. But research has provided a good understanding of how to handle products, how products vary between loads, even the best way to bill customers on truck deliveries. These are areas that Sydney Water has traditionally not been involved in, so these learnings are essential if co-digestion is going to work.
“It’s also worth noting that the return on investment requirements for co-digestion have changed over the program. Initially, the benefit split was around two-thirds from the gate fee and one-third energy. But with the large increases in energy prices these ratios have altered, and although not 50/50, the energy payback has become more favourable and shortened the overall payback period.”
For Sydney Water, waste-to-energy is an exciting new frontier that it's excited to be a part of, with the potential to benefit not just water utilities, but the broader energy industry as well.
The ability to recover energy from wastewater will see treatment plants become bio-generators of the future.
G OLD COAST CONVE NTION CE NTRE
Held in conjunction with “No-Dig Down Under”
Wednesday and Thursday Sessions to include:
• Insurance
• Lidar
• Permanent Markers
• CGA
• Data collection
• Locate Principles and Procedures
• GPR and Multi Array GPR
• AS5488
• DBYD Locator Certification
• Overhead utilities
• Identification of Damage Prevention Technologies
• USA 811 Process
• Trenchless Technique issues
• Plan Access
• Vacuum Excavation Wednesday night event sponsored by DitchWitch Thursday night event sponsored by Vermeer
Friday Sessions:
• Trial Simulation Who’s at Fault? (Sponsored by DBYD NSW)
• Open Plenary session (Panel including local and international guests)
• NULCA AGM (attendees receive a $100 discount on next year’s NULCA membership fee)
An accommodation package is being arranged at the Crowne Plaza. Details will be provided shortly.
Sponsorships are available for speaker sessions and meal breaks Prices start at $300 Contact president@nulca com au to learn more.
- One trip for two to the CGA to be held in Phoenix Arizona in March 2018 (sponsored by PelicanCorp)
- Two entry passes to the CGA conference (sponsored by CGA & NULCA)
Prizes will be drawn on Friday 15 September, conditio ns apply.
In the latest instalment in our regular Women in Utilities feature, we speak to three women working in different areas of the EnergyAustralia business.
I got my start in the utility industry when a former colleague, who was working at EnergyAustralia, told me a senior analyst role had became available; I applied and the rest is history!
I joined EnergyAustralia in 2013 as a senior analyst on a business improvement project. While my career has always been focused on improving business operations, problem solving and bettering the customer experience, this role was my first exposure to the energy industry, having spent most of my career in the banking sector.
I spent six months on the business improvement project, gaining significant knowledge of the business and industry before being offered the opportunity to work as the head of our hardship program – EnergyAssist.
In 2015 this role was expanded to include our complaints department, and now, I manage a team of around 80 people responsible for our hardship program and customer resolutions.
Our EnergyAssist program supports around 12,500 vulnerable customers in a number of ways, including through payment plans, matching payment opportunities, debt waivers and other initiatives.
We also find resolutions for customers who haven’t had a positive experience. A big part of our role is to identify the drivers that are making customers contact us, before working with the business to address these issues. Since managing the complaints team, our complaints have more than halved, which is testament to the dedication and hard work of my team.
I believe what we do is fundamentally good and important. But I especially enjoy being in a position where I can directly support customers in financial difficulty by ensuring gas and electricity is still accessible.
I enjoy working with the financial counselling industry, and the community sector, who share our passion for supporting those that need it the most.
In November 2016, EnergyAustralia
was one of 12 “trailblazers” – and the first energy company – to launch its Financial Inclusion Action Plan (FIAP). The EnergyAustralia FIAP sets out a program of activities and commitments aimed at helping people achieve financial security and independence. As a provider of an essential service, my team has seen firsthand how a lack of access to financial services can impact the community.
The plan is designed to:
• Improve EnergyAustralia’s understanding of why and how customers face financial exclusion, particularly groups overrepresented in hardship statistics
• Understand how EnergyAustralia can improve its products, services, policies and practices to better support vulnerable customers
• Help EnergyAustralia employees better understand financial inclusion, the issues that affect it, and how they can support customers
• Foster relationships between
EnergyAustralia and community groups, advocacy groups and partners in business to lead change and improve lives
I was part of the working group which built the plan and my team, along with other areas in the business, will deliver the 19 key actions.
The energy sector is incredibly complex. There are a lot of regulators and a heap of regulation we have to manage. Regulation can be good for consumers and the sector when it drives investment towards better, cleaner energy for all Australians. But inconsistent regulation across geographies can have significant and unintentional consequences that add cost for retailers and therefore customers.
The cost of energy is one of the main challenges facing energy companies at the moment. Electricity bills have increased across the country, with recent rises reflecting the impact of higher wholesale costs (the cost of buying electricity on behalf of customers) following the closure of large coal-fired power stations, increased demand for gas by LNG
projects in Queensland and reliability issues with some big generators.
We know that's bad news for customers and in June we announced we would commit an additional $10 million to financial and other support for some of our most vulnerable customers. The funding will be used to expand our existing hardship program; it will also go towards doing new research aimed at alleviating chronic, long-term financial hardship.
We’ve been consulting with social services groups on how to best apply the additional funds, with an emphasis on energy efficiency and measures that provide lasting, long-term relief.
The funding will also support initiatives arising from our Financial Inclusion Action Plan.
I’ve always aligned myself with mentors, usually female but not always, who are in roles that differ from what I do day-to-day. I look for people who have similar values to me, are confident and have high emotional intelligence.
Advice from one mentor I’ll never forget was around the importance of building trusted relationships, particularly with your direct reports. Managing a team of 80 people, you can’t do everything yourself, so having the right people, in the right roles to get the job done is fundamentally important.
Our Managing Director, Catherine Tanna, is a huge inspiration. Catherine has driven a customer-centric culture within EnergyAustralia, she is values driven and focused on doing the right thing by the customer and the community. She has a deep respect for cultural awareness which I admire, and she is a working mum which I relate to.
I haven’t found EnergyAustralia to be a male dominated organisation. Half of the EnergyAustralia Board are women and around 40 per cent of the organisation’s managers are women; these are across a diverse range of roles and areas. I actually found the banking sector less diverse.
I see myself continuing to work in the utility sector. It’s a great industry with lots of opportunity, especially for improving the customer experience.
Outside of work, my family keeps me busy. I have a seven-year-old daughter, Makayla, and spending time with my family is the most important thing to me. In general I have a busy lifestyle, love travel and am planning a trip to New Zealand this summer. I also love the cricket and barrack for the Bombers in the AFL.
Following completion of my science degree at university, I secured my first position at the Yallourn power station as a Scientific Technical Officer responsible for chemical routines. Since then I have held five diverse roles at EnergyAustralia, including Settlements Officer (working within our Energy Markets business), Contract Advisor (Procurement) and most recently as a Site Chemist. All up I've been with EnergyAustralia for 22 years.
The Chemical Team at Yallourn is responsible for monitoring and maintaining boiler water chemistry and producing high-quality water for use in the boilers. We also provide testing, monitoring and specialist services to other areas of the business. My key responsibilities relate to atmospheric monitoring and the on site management of hazardous materials.
I first came to Yallourn as a vacation student while studying science at university. This was a great way to see how what I was studying could be applied in the workplace. I am pleased to say that we have since had a number of vacation students in the Chemical Team and
EnergyAustralia continues to support this workplace learning.
We have online programs that help us to manage hazardous materials at the various EnergyAustralia sites and we are looking to consolidate these into one system. My role has been to initially draft the functional specification for the consolidated approach to be approved and to participate in a team involving a number of key stakeholders for this project. The team members come from various areas of the business, so communication has been key – not only to articulate Yallourn’s requirements but to listen to others so that the approach is agreeable to all parties.
I get satisfaction from knowing that the role that the Chemical Team plays contributes to providing an essential service to our customers. The utility sector contains a great variety of roles which enables people working within the sector to have a very fulfilling career. This has enabled me to have a number of varied and interesting roles without needing to leave the sector.
On the flip side, the utility sector is constantly changing so businesses and individuals working within the sector need to be adaptable to change.
There has been significant change during the last few years in our industry, particularly with the introduction of cleaner energy and the recent retirement of coal-fired power stations. I am pleased that EnergyAustralia is being proactive in leading change within the industry and looking at ways to diversify the business.
Early on in my working career, I had a number of leaders that instilled in their teams a good work culture that encouraged dedication, respect and pride in your work. That set the foundation for me and I hope that I have continued this throughout the various roles I have had at Yallourn.
We have had a number of women at Yallourn working in commercial, procurement and technical areas. I have been lucky enough to work closely with many capable women who go about their roles in a professional, no-fuss manner and have the interests of the business in the forefront of their minds. These women provide a different mindset and way of going about their roles and I have learnt a lot from working with them.
For the majority of my career, I have worked in maledominated teams. I have tried to be who I am in my roles and encouraged the teams that I have worked in to take advantage of the skills that each team member can contribute.
I see myself continuing to work in the utility sector – it has provided me with a variety of roles that I never envisaged that I would do and a great workplace and lifestyle.
Outside of work my family life keeps me busy (my husband and I have a son, ten, and a daughter eight). I do enjoy travelling but also like to be at home gardening and cooking for family and friends.
I started in utilities as a power plant operator on a technical traineeship in 1983; then worked as a Unit Attendant at the Loy Yang A power station for a couple of years before becoming an Assistant Unit Controller (AUC) at the Hazelwood power station.
I fulfilled many AUC roles at Hazelwood including AUC, before being appointed to the position of Shift Manager in 2014.
I was appointed Operations Team Leader (OTL) at EnergyAustralia’s Yallourn power station in April this year following the closure of the Hazelwood power station.
As an OTL I manage the day-to-day operations of the power station, which includes bidding in the electricity market, ensuring Yallourn’s units are running within their capabilities, and that we’re compliant with station health and environmental rules. I oversee the permit to work system, liaise with stakeholders, including our maintenance colleagues, so that tasks can be completed without interruption to generation, and other tasks such as coordinating rosters and providing guidance to my team.
As a new member at EnergyAustralia, my focus has been on becoming familiar with my new role as OTL and getting to know the business more broadly. That said, I look forward to taking on projects in the future.
One of the main challenges in the energy industry is how we provide customers with reliable, affordable and cleaner energy. EnergyAustralia has said publicly it recognises that owning big power plants comes with the responsibility of leading the development of cleaner forms of energy.
So as we make the transition to cleaner forms of energy, gas, coal and traditional hydroelectricity will provide security for the National Electricity Market. That’s why at Yallourn, we’re working to make the site as efficient as possible by investing so our operations are as carbon-efficient as possible.
In 2015, for example, we completed a five-year maintenance program at Yallourn that allows us to do the equivalent of powering an additional 100,000 homes without needing to burn any additional coal.
I haven’t really had any female mentors in my career, as I have had very few female peers. My brother Robin was, up until recently, an OTL at Yallourn and he has certainly been a positive influence. That said, EnergyAustralia’s Managing Director, Catherine Tanna, is an inspiration to me.
When I first qualified as an AUC in 1989, I was supervising men twice my age which presented some challenges, but I always remember by father’s advice: “Treat people as you would like to be treated.” This proved to be very helpful advice. I have also learned that you need to pick your battles!
I see myself continuing to work in the utility sector until I retire, I love it.
Outside of work I have four adult children, one of whom has a disability, so I don’t have much free time. I work twelve-hour days and night shifts and I love the amount of time off available to shift workers, it fits in well with my family. I do the Variety Bash every year and have been doing that for eleven years so a fair bit of time is spent fundraising for that.
With a key focus on awarded tenders, industry news and project summaries, as well as policies and regulations that are shaping the industry. This is an indispensable guide to what is really happening in the Australian water industry.
First month is free
Cancel anytime
Sent directly to your inbox
Market insight for effective planning TO
In the latest in our ongoing series of utility profiles, we take a look at City West Water, one of the three retail water businesses in Melbourne, providing drinking water, sewerage, trade waste and recycled water services to customers in Melbourne’s CBD, inner and western suburbs.
Our business exists because people, places and spaces need water and wastewater services. At the turn of a tap, or the press of a button, City West Water services are at work, safely delivering clean drinking water, and providing safe collection, treatment and disposal of wastewater. Each year we supply around 110 gigalitres of drinking water to over 430,000 properties and transfer approximately 96 per cent of the sewage and trade waste to Melbourne Water’s Western Treatment Plant in Werribee. The remaining four per cent is treated at our Altona Treatment Plant.
Our service area is home to the fastest growing population base across Victoria and we currently service both residential and non-residential customers within the municipalities of Brimbank, Hobsons Bay, Maribyrnong, Melbourne (north of the Yarra River), Moonee Valley, Wyndham, Yarra and parts of Melton and Hume. We purchase bulk water and sewerage services from our wholesaler, Melbourne Water, along with the other two metropolitan water retailers, South East Water and Yarra Valley Water.
Our 464 employees are a mirror to the wonderfully diverse community we serve. The differences among us provide opportunities to learn and grow and make our workplace vibrant and respectful. Our people are: agile – responsive to customer needs and a changing world; diverse – reflect the community we serve; and trusted – make evidence-driven judgements, exercised with integrity.
Our service area:
• Has the fastest population growth in metropolitan Melbourne – set to increase from 1 million to 2.3 million over the next 50 years, of which established areas will absorb 68 per cent of the growth, and greenfield development will absorb 32 per cent of the growth
• Includes the Melbourne CBD – a critically important and nationally significant economic hub that caters to multinational companies, major hospitals and universities
• Is home to internationally renowned sporting venues
• Has the greatest concentration of industrial customers in Victoria and some of the largest single water users
• Has less rainfall than other parts of Melbourne – 500mm to 650mm in Melbourne’s west compared to 650mm to 1100mm in eastern and southeastern areas.
The biggest change that we have faced in recent years is re-positioning ourselves to deliver the best possible service that takes account of the pressure on demand for services created by a growing population, and changes in the supply of water created by a changing climate. We also aim to be more customer-focused – how can we deliver the services that our customers want, when they want it and how they want it? Making sure that customers are at the centre of everything that we do. This means that we have begun implementing smarter, more efficient ways of delivering
infrastructure, connecting new customers and managing our customer and asset information.
Putting our Customers First
We are currently developing a web portal that will allow our customers to access information about current and proposed field work or report a fault from the same portal. Use of the portal will reduce customer waiting time in phone queues, reduce Operations Control Centre resource strain and improve accuracy of emergency fault diagnosis. Customers will also have advanced notification of planned and unplanned water supply interruptions and other key water and sewerage field works. Users of the service will be offered an opportunity to respond to an interactive survey to further improve our interactions with our customer base.
Early in FY 2017/18 we will be making our submission to the Essential Services Commission on proposed service outcomes and prices that will prevail from July 2018 to June 2023. This follows an extensive period of customer engagement via community meetings, deliberative forums, surveys and shopping centre pop ups, with the objective of gaining a full understanding of what it is that our customers expect from a water and wastewater services provider. We will be using those insights to provide services that customers value.
Investing in the West
Greening the West
Greening the West is a regional initiative that aims to deliver positive health and social outcomes in the
City West Water
western suburbs of Melbourne through urban greening. It is driven by a steering committee consisting of 21 partners including local councils, community groups and government departments. In the coming year, under the Greening the West banner, we will:
• Expand participation in a Trees for Schools initiative (in partnership with VicSuper and Environment Education Victoria) in an effort to increase canopy cover at schools in the west of Melbourne and broaden community understanding of the benefits of trees
• Work with major developers to pilot VicRoads’ proposed code of practice for street works that ensures landscape is a valued part of infrastructure decisions
• Identify additional projects to showcase Greening the West to the broader community
Our long term goal is to facilitate a doubling of the canopy cover in Melbourne’s inner-west by 2050.
Education
In the coming year we will be looking to formalise a program to develop community water literacy targeting community members with English as an alternative language and continue to grow the Schools Water Efficiency Program within the west.
Respecting our Cultural Heritage
In 2014, City West Water formalised our commitment to Aboriginal people
through the launch of our inaugural Reflect Reconciliation Action Plan (RAP). The Reflect RAP committed our business to eleven actions with the aim of building relationships with local Aboriginal people and their communities both internally and externally, and raising awareness to ensure there is shared understanding of the importance of Aboriginal engagement and inclusion.
Since its establishment, there have been some significant developments within our business. These include capturing baseline data on our employees’ current level of understanding around Aboriginal history, cultures and contributions; fostering a greater sense of awareness of Acknowledgement of Country and Welcome to Country protocols; and actively encouraging all staff across the business to participate in and celebrate National Reconciliation Week and NAIDOC Week. Given the growth of the Aboriginal population within the regions we serve, we believe that we can make a significantly greater contribution towards reconciliation by adopting more comprehensive actions and commitments across our business. Accordingly, we have developed an enhanced iteration of our RAP embedding a range of programs across the organisation that build stronger relationships, respect and opportunities with and for Aboriginal people and their communities. In order
to maximise the contributions we can make, our commitments are aligned with complementary developments in Victoria’s water industry, such as the launch of VicWater’s Water Industry Diversity Strategy which aims for 2.5 per cent of the water industry workforce to identify as Aboriginal by 2020.
City West Water creates an environment for people to make good safety choices – we ‘live and breathe’ safety and wellbeing for our people. We care about people, and don’t shy away from any difficult safety conversations – instead we approach them with sensitivity and respect. We work closely with our contractors on safety to ensure we are designing and delivering our services in a way that keeps them and our customers safe. Going forward we will be raising the bar, looking at how we can do safety differently, innovating our approach, technology, and how we collaborate, so we continually improve our safety outcomes through being proactive.
In December 2016, we launched our new business strategy, Customers First, benefiting communities. The strategy articulates what is important for our customers, and therefore City
West Water, with a view out to 2030. Providing focus and aligning the many components of our business ensures that we’re delivering a better service for our customers, in a way that puts them first.
Affordable, reliable, easy to deal with. At City West Water, we put our customers first, to benefit the community. Our services are affordable, and we align our activities to meet customer expectations. Our people are reliable and trustworthy, and we manage our resources in a way that recognises the need for long-term water security, particularly in the face of a changing climate and growing population. Lastly, we are easy to deal with. We recognise the diversity of our customers and understand that multiple lines of communication are required to suit their needs. We make ourselves available to ensure whatever the mode of communication, our customers can access the information they need and are supported by our friendly and courteous approach to customer interaction.
In this article, the first of a two-part series, our HDD expert Charles Stockton takes a closer look at the impact HDD technology has had on shore crossings in pipeline installations.
Working in the nearshore environment, especially on Australia’s exposed coastlines, can be very challenging and inhospitable for both land-based and water-based construction equipment. Neither construction method is ideally suited to construction in this shallow, tidal, high-energy zone; it is too shallow for marine vessels which risk grounding, and too deep and exposed for land-based work which risks flooding and equipment damage. This is the zone that neither the offshore contractor or the onshore contractor are ideally placed to manage, it is not their normal working environment and it is this challenge that makes shore crossings very interesting to design and construct.
Up to 15 years ago, these crossings would have required large-scale open battered excavations onshore which would connect to a piled cofferdam through the surf zone followed by a dredged channel offshore. A concretecoated pipe section would be floated into position using floatation devices and hydraulic winches. The process was very susceptible to adverse weather conditions and tidal variations, as well as presenting numerous challenges for managing worker safety and potential damage to the environment including oil spills and erosion.
WHAT ARE THE BENEFITS OF USING HDD FOR SHORE CROSSINGS?
By using HDD to construct the shore crossing, you are totally eliminating the requirement for works to be constructed in the nearshore environment. Using HDD allows for the crossing length and depth to be increased, which positions the rig back on level land and also allows for the exit to be beyond the surf zone. The rig will be placed well behind the dune system, which can then be preserved to prevent erosion and maintain existing flora and fauna within
the coastal corridor. The exit point will be selected to provide appropriate conditions for positioning subsea structures or providing a suitable transition to offshore pipeline. The exit location must provide sufficient water depth to allow safe vessel access and anchoring as well as diving operations.
The pipelines can be prefabricated onshore and thrust through the bore from entry to exit, or alternatively, the HDD rig can be used to pull back the pipeline from offshore if the pipe is fabricated by a lay barge or towed offshore from a spool base/launching area. This is particularly convenient if the product pipe is HDPE, which will float without the use of external buoyancy control measures.
One of the main challenges for designing an HDD shore crossing is selecting an appropriate exit location and then obtaining reliable, cost-effective geotechnical offshore information. For shorter crossings, it may be possible to interpolate
onshore and nearshore boreholes, but for longer crossings it is extremely important to develop an understanding at the exit topography and geology. This is critical for developing the HDD methodology; determining whether the hole will be forward reamed or back reamed and if the pipe will be thrust or pulled into the bore.
Another key factor that needs to be carefully considered is weather. Even though the majority of the works can be conducted onshore, marine vessels and divers will still need to be deployed during a number of critical stages of the operation. Having these windows well identified, and then having contingency planning for delays is essential. Clearly setting out what conditions the marine vessels can operate in and determining how this risk will be costed will be important to prevent cost escalation and potential disputes between parties.
In the next issue of Utility, Part 2 of this article will look at the differences in using HDD in water environments as opposed to standard environments; and some of the shore crossing projects Charles has been directly involved in.
UK-born Charles Stockton has been a part of the HDD sector in Australasia since 2003. He is the Managing Director of Stockton Drilling Services, a leading engineering consultancy specialising in HDD and other trenchless pipeline installation methods. For more information please visit www.stocktondrillingservices.com or contact Charles on 0400 623 441
charles@stocktondrillingservices.com to discuss your next trenchless project.
The utility industry is regularly required to call on an enormous and varied range of specialists; from mapping, to drilling, to wastewater treatment, to asset management, to pipe relining, to pipeline integrity, to land access, to risk management, and the list goes on. To make the process a little easier, Utility is bringing together experts from various fields to answer your questions.
In what circumstances is microtunnelling most appropriate for executing gravity slope sewer lines?
In the past, gravity slope sewer lines were installed via open cut or tunnelling methods. Today there are two main methods of trenchless sewer construction: horizontal directional drilling (HDD) and microtunnelling. The key is selecting the most appropriate and technically feasible method - the method chosen must be capable of doing the job in the prevailing environmental conditions and within project specifications.
Here are some environmental conditions and project specifications where microtunnelling is the most appropriate method for a gravity slope sewer installation.
Proper slope of gravity sewer pipes is important to ensure liquids flow smoothly and any solids don’t clog the pipe. If the pipe is too flat, waste won’t flow away and a pump station will need to be installed to help move the liquid, but a pipe that is too steep will cause liquids to flow too quickly and solids will not be carried away.
Therefore, the chosen method of installation will be dependent on the ultimate grade on that line and the accuracy required to complete the installation.
Microtunnelling is the most accurate pipeline installation method available for civil construction and can install sewer pipelines on-grade, so if the installation needs to be within +/-25mm
of accuracy it is the best method.
On-grade installation ensures a steady declining grade is maintained, allowing sewage to be transported down the pipeline by gravity alone.
On the other hand, sewer pipes installed by HDD can incorporate variations throughout the route, and will require pump stations to be installed to ensure the continuous transportation of liquids. These pumps incur additional cost, require ongoing maintenance, consume energy and produce emissions.
As gravity slope sewer lines are installed in urban areas, there is a risk of hitting existing critical underground infrastructure if it is not accurate.
Microtunnelling avoids this risk because the installation will typically go from a manhole to a manhole, or a manhole to an inspection shaft of some sort. Microtunnelling gives you a means of working out of both shafts to install a pipe at the best invert rate required, which in most instances will be completely below all existing infrastructure.
Microtunnelling is also the best choice for urban areas where the site footprint has to be kept to a minimum.
Microtunnelling allows a pipeline to be installed from an exact location to an exact location with only enough room for an entry and exit pit to be excavated. This means there is no need for access to any other land as the pits will be along the required pipe route.
As HDD is surface launched, the equipment needs to sit back from the starting point, and because it uses a continuous style of pipe there also needs to be enough room at the exit point to have the pipe laid out.
This can become a problem in urban areas as there is not much space to work in, and depending on the route of the pipe there is a chance that the necessary setback will mean the HDD rig would need to be on someone’s property. At the exit point there may also be limited room where the pipe can be laid out.
When it comes to choosing a method of installing gravity slope sewer lines it is important to take into account the environmental conditions at the site and the project specifications as there may be factors present that will make one technology better than another. Microtunnelling is only one method of installation but it’s ability to install pipelines on-grade, its limited site footprint and ability to avoid existing underground infrastructure makes it an ideal choice.
Global microtunnelling pioneer Stuart Harrison is the Managing Director of Edge Underground, where he specialises in on-grade microtunnelling installations with millimetre accuracy. Stuart is also the inventor of the Vermeer AXIS Guided Boring system, and he is constantly working to improve the effectiveness of this and other trenchless systems used in the installation of gravity sewers. To discuss your next microtunnelling installation, contact Stuart on 1300 JACKED or at stuart@edgeunderground.co.
The PC200 ticks all the boxes and is now available across Australasia for PURCHASE or HIRE *
*Conditions apply. Contact Austeck for details.
Unprecedented power input/output ratio
4 degrees of movement including continuous 360º rotation
Unique “single pass” methodology for simultaneous top hat & short liner installation
Patented software interface for pre-lining logging & post-lining relocation of connections
Hi res forward and reverse cameras with optional pan, tilt & 10:1 zoom camera also available.
Cameras equipped with vibration proof liquid lenses.
Compartmentalised stainless steel chassis with no exposed cables or wires
Multiple heat, moisture & pressure sensors that monitor and protect all internal electronics
CAN bus control enabling full systems diagnostics from anywhere in the world
24 hour support guarantee*