
9 minute read
SCALABLE PARTNERSHIP
George Hatzimanolis and Dante Cremasco celebrate the launch of Repurpose It’s C&D washing plant.
REPURPOSE IT HAS PARTNERED WITH INTEGRATED SERVICES COMPANY DOWNER TO SUPPORT ITS RECENTLY UNVEILED CONSTRUCTION AND DEMOLITION WASHING PLANT.
Almost two years ago, the four founders of Repurpose It came together with a unique set of skills.
Each partner brought an array of knowledge and abilities from varying sectors, from logistics, to road sweeping and construction, organic waste processing and infrastructure maintenance.
They also shared a common pursuit of treating waste as a resource. When the opportunity presented itself, they acquired a unique 150-acre site in early 2017 in the Melbourne suburb of Epping. The site had been recognised by the state government as a significant hub for resource recovery and solidified the business case.
Since that time, the operators have made significant achievements in cementing their reputation in the Victorian market as a leader of repurposing construction and demolition (C&D) waste. From their work with the North Eastern Program Alliance on Victorian level crossing removal resource recovery, to being recognised by Westpac in the top 20 businesses of tomorrow, the founders sowed the seeds of growth.
The end of March marked the launch of Repurpose It’s Australianfirst construction and demolition plant – a facility that will divert more than 500,000 tonnes of C&D waste from landfill per annum.
Using its unique wet processing technology, the plant will be able to accept a variety of waste streams, from traditional excavation waste such as rock, sand and silt, to waste mixed with other manmade inert materials, including concrete, grit and rail ballast. It will also be configured to handle nondestructive drilling and drainage waste, and additionally dirty glass, which it will scrub clean.
Reflecting on the company’s achievements over the past 22 months, Repurpose It Founder
George Hatzimanolis revealed that integrated services leaders Downer had secured a 50 per cent partnership with Repurpose It. The new partnership will see the establishment of common board members with governance and oversight into new projects and opportunities for expansion in Victoria.
He tells Waste Management Review that Downer’s vision for a circular economy made sense for Repurpose It to enter into a partnership with the sustainability-focused company.
“We knew that Downer had potential to be a very important client and they had an intention to get into this space. With longstanding relationships, it made sense to leverage the best abilities of the two businesses,” George says.
Dante Cremasco, Executive Manager Road Services at Downer, says Downer’s ownership structure ensures it can continue to drive costs down while achieving its sustainability goals.
“We don’t own any virgin quarries anywhere in Australia and as a result of that, we’re always driven to ensure we can keep our costs down and that products have gone through the cycle can be repurposed into something even better the second time around,” Dante says.
Dante says that Downer is able to sell repurposed products into the marketplace, but mostly it intends on utilising these products in its own contracted infrastructure projects and existing manufacturing operations.
He says that Downer has a large products and services division that can use the repurposed materials to manufacture road construction materials to raw material inputs required in asphalt, microsurfacing and rejuvinators. Dante says the company also has its asset management services through DM Roads that maintains networks on behalf of agencies such as VicRoads and other
Repurpose It’s new facility will divert more than 500,000 tonnes of C&D waste per annum.

George Hatzimanolis Repurpose It Founder
local government authorities.
“We’ve also got the research and development capability of 18 scientists. These are PhD scientists up the road in Somerton that will take these materials and ensure they’ve been used in the best way possible.”
George says that Downer procures extensive amounts of sand and aggregates, and anything they can do to reduce their reliance on extractive resources is a step towards progress.
“There’s some natural synergies in the offtake and the business procures a lot of materials themselves locally,” George says.
“There’s a substantial balance sheet that sits behind the Downer business as one of the largest employers in Australia and a market leader in infrastructure and maintenance. That gives us the ability to grow and help Repurpose It reach its full potential in many ways beyond the capacity of the founders.”
Dante says that one of the advantages of the washing plant technology is that increasingly scarce virgin materials can be preserved for longer on bespoke projects.
“Ultimately we’re producing products that are as good and, in many cases, better than virgin material simply because any unsound portions from these materials have already been obliterated by time, weather and the impact of traffic.”
Adding to the organisational synergies is Repurpose It’s research grant in partnership with RMIT University to investigate the use of recycled glass for its washing process. George says that Repurpose It is fortunate to now be able to leverage Downer’s research and development capabilities, with the company’s facility just a few kilometres away from the Epping site.
As for the future, the pair hopes to use their unique capabilities to scale up, while continuing to push for updated specifications of recycled materials.
“We find VicRoads has been more than willing in recent times to embrace new specifications.
“Of course, there’s still some other work to be done across water infrastructure-related specifications, but there’s support at the highest levels of government, and this is just the beginning of making a circular economy a reality,” George says.
10 million bricks
PGH BRICKS & PAVERS IS TAKING A SUSTAINABLE APPROACH TO BRICK MANUFACTURING, REUSING CLAY SOURCED FROM METRO TUNNEL’S PARKVILLE STATION.
Clay material from Melbourne’s Metro Tunnel Parkville Station is estimated to weigh around 1.2 million tonnes.
With the new Metro Tunnel expected to be ready by 2025, Parkville Station forms one piece of a significant puzzle that includes new stations and tunnel entrances at Kensington, North Melbourne, Parkville, Melbourne CBD, Domain Precinct, South Yarra and West Footscray.
Historical industry practice would see that material sent to landfill, but in the case of Parkville however, a sustainable alternative has been developed that will see PGH Bricks & Pavers use the clay to create more than 10 million bricks.
Formed in 1958, after a merger between Hanson Consolidated Industries and Maxwell Porter &
PGH’s solution will help preserve the longevity of its Thomastown quarry.
David Galbraith, PGH has grown to become one of Australia’s lar gest clay brick manufacturers.
The company, now wholly owned by CSR, which employs more than 3000 throughout Australia and New Zealand.
Work began at the Parkville site on 14 January below Grattan Street, between Leicester Street and Royal Parade.
Reusing clay material has obvious environmental benefits, but it will also take pressure off PGH’s main quarry in Thomastown.
As with all natural resources, at some point the clay runs dry, forcing PGH to move to a new site, uprooting an established workforce, hindering businesses that work around the facility, and creating rebuild costs.
Andrew Peachey, PGH’s General Manager, says projects like this help
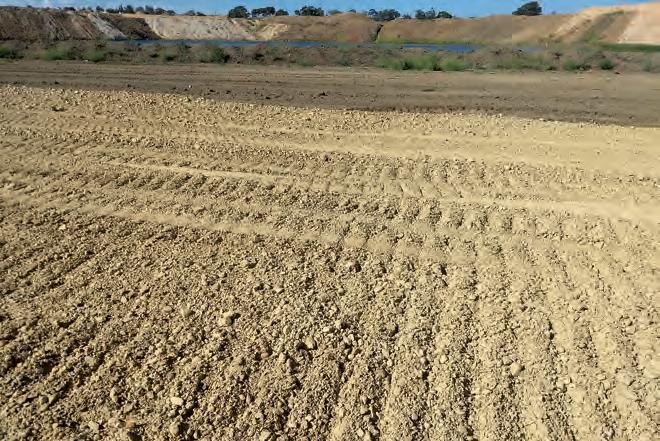
to secure Australia’s manufacturing capability into the long term.
“Normally we would extract this clay from our own quarry, so recycling material from construction sites also serves to provide longevity at our facility and continuity of work for everyone employed there,” Andrew says.
Ten million bricks from Metro saves 10 million bricks from the quarry and this safeguards the site.
“The longer we can stay at our existing facility is obviously good for builders because it keeps costs down for them. It also means we don’t have to go further out of Melbourne,” Andrew says.
“If we ran out of resources and couldn’t get anything at Thomastown, eventually we would be moving 10, 20, 30 or 50 kilometres out of Melbourne.”
With the majority of construction in Melbourne happening in growth corridors in the north and the west, close to the Thomastown manufacturing facility, it’s in PGH’s best interests to keep the quarry maintainable for as long as possible.
Andrew says that it’s fundamental to the sustainability of Australian manufacturing.
Parkville is not the company’s first foray into material recycling, PGH took clay from Blackburn Railway Station during the underpass redevelopment, and has used sandstone from various NSW infrastructure projects. They also have a history of using crushed bricks in their mixes.
Andrew highlights the importance of the project by citing concerns that Greenfield sites are being built on potentially clay rich areas, thereby sterilising resources.
“The ability to get quality material from a large infrastructure project is quite important to the company.”
The mining process can be broken down in three stages.
Stage one is a traditional mine, straight down, with the use of station boxes.
Joe Gauci, PGH’s National Raw Materials Manager, cites this as his preferred method, as material can be monitored more effectively, ensuring the best quality possible.
Stages two and three, which are yet to be tendered, will use a tunnel boring machine.
Joe says PGH will have to wait and see who wins those jobs before assessing the suitability of the material.
PGH, working through a contractor, has been in the planning process for roughly 18 months and has just started moving material to its main facility.
After geo-testing, the clay will be moved to the company’s largest mixer, where it will be combined with other materials to create an environmentally sustainable batch of bricks.
These will be sold to builders ranging from volume groups like Dennis Family, AHB Sheridon and Burbank Homes, to medium and small builders, who will use them to build predominantly residential properties.
The wider Metro Tunnel project will include two nine-kilometre tunnels running from South Kensington to South Yarra, and see the creation of five new underground stations, Arden,
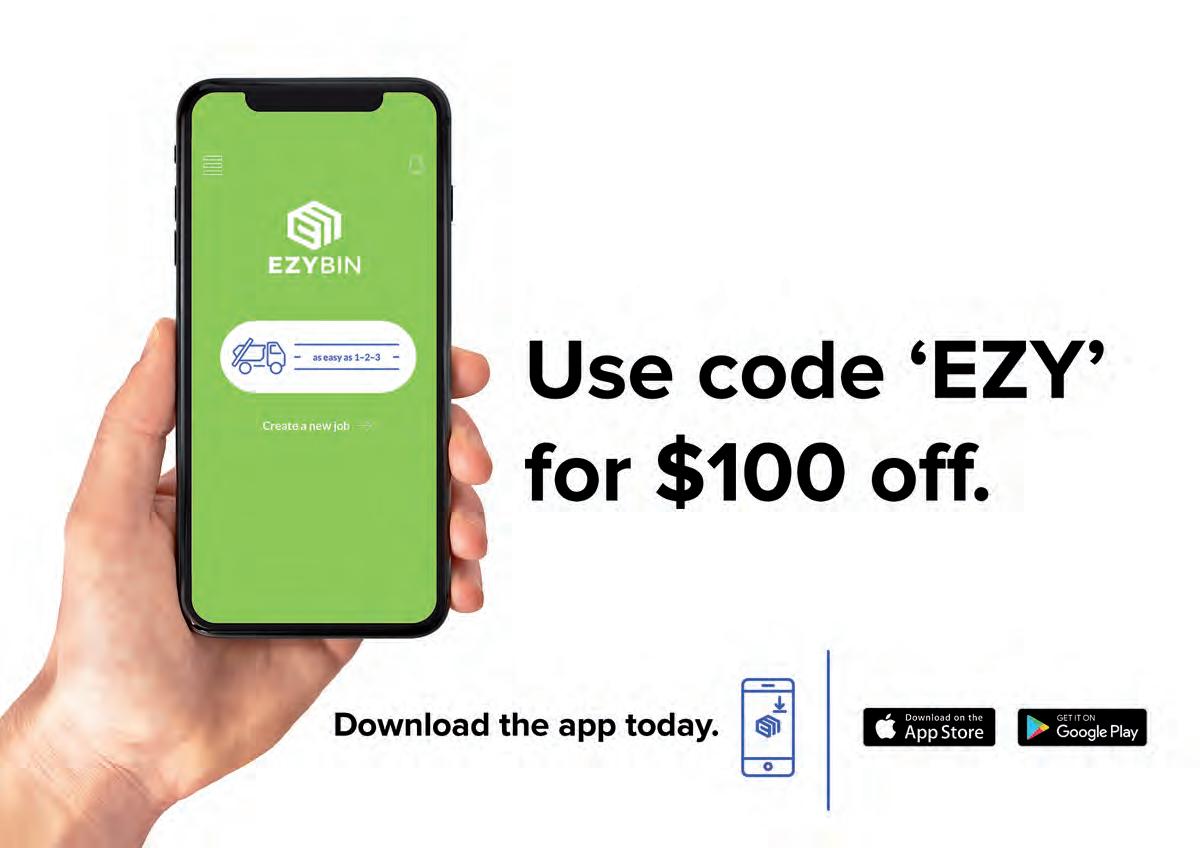
Parkville, CBD North, CBD South and Domain.
The sheer volume of clay material being moved by the project highlights the significance of material recycle initiatives like PGH’s.
The project has also opened vast opportunities for the company.
“I’ve had that many calls coming in from different people.
“All of a sudden we’re getting a lot more interest, people coming to us saying, we never knew you guys used this sort of material,” Joe says.
Andrew says the experience would make the company more proactive about finding infrastructure projects to partner with in the future.
“Everything gets evaluated on a case by case basis. It’s got to go through the stringent controls of our laboratory first, but it’s opened a lot of doors.”