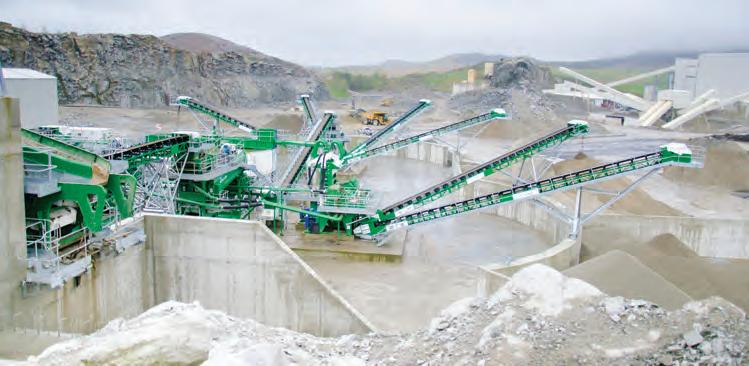
4 minute read
SUSTAINABLE RESOURCES
CDE’S DANIEL WEBBER HIGHLIGHTS THE CORE INGREDIENTS OF A SUCCESSFUL BUSINESS CASE TO TURN CONSTRUCTION AND DEMOLITION WASTE STREAMS INTO A RESOURCE.
Extractive resources are high volume, heavy, low value materials that are ideally extracted as close to their end destination as possible.
About 535 quarries produce 50 million tonnes of stone, limestone, gypsum, sand and gravel each year, according to the Victorian Government’s Extractive Resources strategy.
The report shows demand for extractive resources is at an all-time high and at the current rate predicted, will need to increase to more than 100 million tonnes by 2050.
With the spread of quarries further out in metropolitan cities and increased cartage costs, infrastructure projects and recyclers are looking to novel ways of treating unsustainable natural resources.
CDE is one organisation orchestrating a global solution with its bespoke materials wet processing plants. These plants utilise the company’s patented scrubbing, washing and screening technologies to separate organics, plastics and metals to then fractionate the resulting sand and aggregates for reuse in new projects.
CDE’s waste recycling plants around the world now divert over 15 million tonnes of waste from landfill each year. With a variety of projects successfully completed across the country over the past 10 years and counting, CDE has become well known throughout the
CDE Global has completed first-of-its-kind projects in India, North and South America and Australia.
Australian quarry and mine sector.
Having a mineral processing background, Daniel Webber, Regional Manager – Australasia CDE, is passionate about developing solutions for problematic material streams.
“About 15 years ago we installed the first construction and demolition (C&D) waste plant in the UK, and since then we have been steadily growing this area to form a key part of our business,” Daniel says.
CDE built a range of modular wet processing plants in Northern Ireland with three initially developed that could be dry fitted to existing facilities.
The company designed a modular small-sized plant that could be up and running in as little as three weeks.
UK recycler Gaskell Bros was the first business to make the investment. Daniel says that given there was no landfill levy in place at the time, the decision was a forward thinking move.
Through research and development supported by CDE, Gaskell Bros was able to recover up to 90 per cent of the waste into recycled sand and aggregates which was used directly back into the construction trade. Off the back of success in this area, the company has completed first-of-its-kind projects in India, North and South America and now Australia.
To ensure that CDE could service a significant proportion of the market effectively, the company differentiated its washing plants into four different subsectors, including quarrying, specialty sands, mining and C&D waste recycling.
In the C&D space, its Reco plants are designed and built according to the specific requirements of each site. Often
this is dependent on differing levels of contamination, fines content and the variability of input materials.
“There are very different pressures for a C&D waste plant. You’re generally located in a metropolitan area and can’t have large tailings ponds, make excessive noise or have contaminated by-products. You need an end-to-end solution and that’s where I think we’ve excelled with a plant that has a small footprint,” Daniel says.
He says that historically, the issue with finding a home for the C&D waste has been gaining certification on the materials for use in areas such as structural concrete, but this is now changing.
He says the business case is also well and truly established, with businesses saving on cartage costs and providing a circular economy solution.
“Even with slightly higher input costs, our solution is more viable due to a large reduction in cartage.”
He adds that businesses are also starting to set targets on material reuse, along with an increase in market signals, with landfill levies in states such as Queensland playing catch-up.
His one word of advice: material sizes can fluctuate, so operators need to ensure they oversize all pieces of equipment to handle everything going through the gate. “We can perform extensive testing beforehand, but every day of the week the materials coming through the gate are different, so the flow sheet has to be very robust.”
He says that all the water is processed in the plant with a dry tailings material emerging, ensuring no large ponds need to be bored with their associated environmental and safety risks.
Australia’s first foray into a CDE plant begun with the launch of Repurpose It’s C&D washing plant in Melbourne.
This year, CDE also increased its plants capabilities with a purpose-built R4500 apron feeder and screening module, growing its capacity to process dirty feeds of up to 300 tonnes an hour.
The company has also developed additional remote monitoring technology to safely operate the plants with minimal workforce. Sensors can be installed throughout the plant so that if materials appear to be out of balance, a text message or email alert can be sent to the operator.
As for the future, Daniel predicts CDE will continue to look to new and innovative solutions – reducing resources and water consumption and maximising product yield.
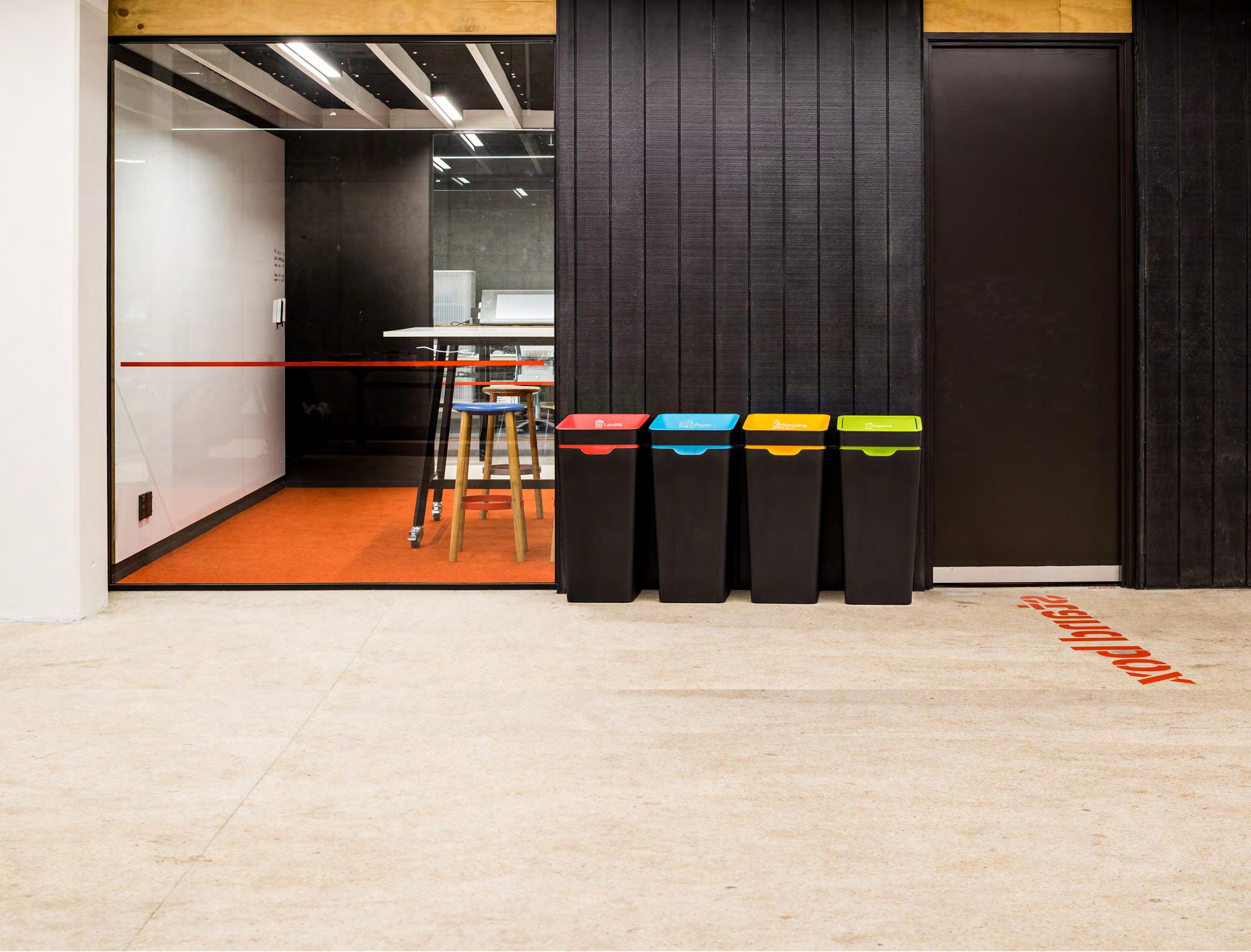