
10 minute read
EARLY WARNING RESPONSE
FLIR’S THERMAL IMAGING CAMERAS HAVE BEEN HELPING DYNAMIC WASTE FACILITIES IN AUSTRALIA AND AROUND THE GLOBE TO REDUCE THEIR FIRE RISKS.
Swedish energy company Jönköping Energi, based in Torsvik, has been transforming waste into district heating – a common practice in the Scandinavian country.
The critical issue for any waste operator is detecting fire risks as efficiently and quickly as possible to control fires and prevent them from spreading.
Its of particular importance for sites maximising uptime at high volumes, as Jönköping Energi transforms up to 145,150 tonnes of waste per year, or 18 tonnes per hour, into heat and electricity.
The district heating is enough to power 25,000 households and has been up and running since 2006. It provides about 90 per cent of district heating demand and 20 per cent of electricity used in the surrounding area.
According to Magnus Olsson, Plant Manager at Jönköping Energi Torsvik, preventing and controlling fires in the waste bunker is not only a matter of safety, but also of economics.
“We have trucks coming in bringing in waste from the surrounding area, but also from different places in Europe. This waste is then dumped in a waste bunker and is mixed by means of automatic cranes, waiting
Magnus Olsson Plant Manager at Jönköping Energi Torsvik
to be transported into the boiler,” Magnus says.
These waste piles can be a dangerous mix.
“Spontaneous combustion from biological products or other heat sources is a continuous threat and something that we need to keep an eye on 24/7,” he says.
Aside from the environmental consequences and obvious safety risks for people at the plant, a fire outbreak in a waste bunker can be a costly affair.
“If a fire should break out, we need to shut down the plant immediately. These shutdowns cost us quite a lot of money, up to half a million Swedish Crowns a day. That’s why it is important to have a reliable early warning system that detects fires as soon as they originate,” he says.
Jönköping Energi published a tender in 2016 for the implementation of an early warning fire detection system. The tender was awarded to the Linköping-based company Termisk Systemteknik, a distributor of FLIR thermal imaging cameras and provider of fire detection systems with FLIR cameras since 2010.
FLIR and equipment supplier Industrial Monitoring Control have worked with largest operators in the Australian waste and recycling industry to develop off-the-shelf early fire detection solutions for landfills, transfer stations, materials recovery facilities and recycling sites.
Thermal imaging cameras are now a widely accepted tool to detect fires and potential fire hazards at the critical early stages. Permanently installed cameras, operating in harmony with conventional detectors, offer a range of significant benefits over standard technologies. These include the ability
to see heat build up before a fire can start, as well as seeing through airborne dust and particulates that can impede or cause false alarms from other detector types. This is because thermal imaging cameras capture thermal radiation in the long wave infrared portion of the electromagnetic spectrum, far beyond what our eyes can see.
It gives operators the ability to stop a fire from occurring or be able to lessen its impact, making the site safer and reducing business costs.
As waste management sites can be dynamic with a number of moving vehicles and infrastructure, camera mounting locations must not be impeded by equipment or the camera will be ineffective.
On a landfill site, for example, FLIR Systems ThermoVision GasFindIR can be used to identify a range of volatile organic compound gases, including methane. Where gases are captured for energy, the cameras detect leaks in pipework. They can also identify vegetation health where vegetated soil covers are used to reduce the drainage of rain water into waste using water balance mechanisms rather than traditional barriers.
Claes Nelsson, Product Manager at Termisk Systemteknik AB, says the Torsvik plant was already working with an aspiration-based smoke detection system. The system pulls in air from the environment, which is then analysed for the presence of smoke.
He says that for fire detection, thermal imaging is superior, as operators sense the temperature of the material and are not dependant on smoke or temperature spreading in the room.
The fire detection system at Torsvik
The critical issue for any waste operator is detecting any fire risks as efficiently and quickly as possible.
consists of two FLIR A615 cameras in protective housings mounted on pan tilt systems, one at each end of the bunker. They are controlled via the dedicated TST Fire software from Termisk.
When a hot spot is detected by one of the two cameras, the other is directed at the hot spot. The TST Fire software then calculates the accurate coordinates of the hot spot, based on the combined thermal images, and an alarm is generated. Upon activation in the waste bunker control room, the water canon is directed at the detected hot spot and the fire is extinguished. Termisk’s TST Fire software uses thermal imaging cameras from FLIR to monitor and
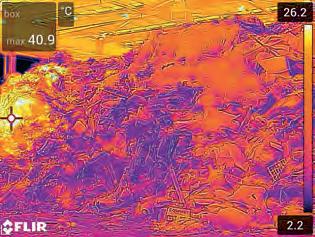
analyse assets for hot spots.
Claes says that thanks to the high resolution of the two FLIR A615 cameras – 640 by 480 pixels – the entire bunker can be monitored in high detail, enabling control room operators to detect really small hot spots.
“The FLIR A615 is one of our preferred FLIR cameras for this type of application,” Claes says.
Contact: Sean Towner
Phone: 0419 155 500
Email: sean.towner@flir.com.au
Know your risk
BIOGAS SYSTEMS MANAGING DIRECTOR DR BEN DEARMAN EXPLAINS THE COST SAVINGS ACHIEVABLE BY LEVERAGING CONTINUOUS LANDFILL GAS MONITORING.
Landfill gas monitoring is critical to preventing environmental pollutants from contaminating the groundwater, surrounding air or averting explosive risks and asphyxiating atmospheres.
The frequency at which operators are conducting these checks and balances could hold the key to lowering environmental and safety risks and their associated costs.
According to Dr Ben Dearman, Managing Director of Biogas Systems, spot monitoring of landfill gas (LFG) bores for compliance only provides a single snapshot in time. Ben says that as this is generally conducted monthly, it may not provide enough data to make informed decisions.
He says that this adds unnecessary costs linked to potential gas mitigation measures. These can be anywhere in the hundreds of thousands to millions, depending on surrounding infrastructure.
Ben says that effects such as barometric pressure, temperature, groundwater and a host of other environmental parameters can affect LFG risks.
“These risks are not easily identified from spot monitoring. Therefore continuous monitoring provides a greater level of confidence and more robust data,” Ben says.
He says that continuous monitoring is an excellent way to quickly build up an accurate representation of LFG and ground gas behaviour on contaminated land and landfill sites, coal and other oil and gas facilities, as well as for carbon sequestration projects.
Biogas Systems is the distributor for cloud platform monitoring organisation AmbiSense, offering its customers the Gasflux and Multiflux continuous monitors. Ben says the Gasflux continuous monitor is the world’s first flow monitoring device for LFG and ground gas applications.
He says that small and mediumsized operators are taking advantage of the technology, ranging from waste companies, councils and even property developers.
The Gasflux continuous monitor provides continuous monitoring of gas and air and reports the data via telemetry systems stored on a cloud network. The comprehensive data set can then be used in a variety of applications to provide key decision making insights on LFG and ground gas behaviour.
“It can continuously monitor bulk gases – from methane, carbon dioxide, oxygen, balance gases – as well as trace gases – carbon monoxide, hydrogen sulphide and total volatile organic compounds,” Ben says.
“It also measures flow, which is the critical difference. When you undertake a risk assessment you need to understand this. No other continuous monitor in the market can do that coupled with measuring the variety of gases.”
Ben says the Gasflux and Multiflux continuous monitors can be installed on a range of pipe diameters and in a range of applications and not limited to monitoring bores. He says this provides a diverse range of deployment options and greater choice for LFG
The Gasflux continuous monitor provides continuous monitoring of gas and air.
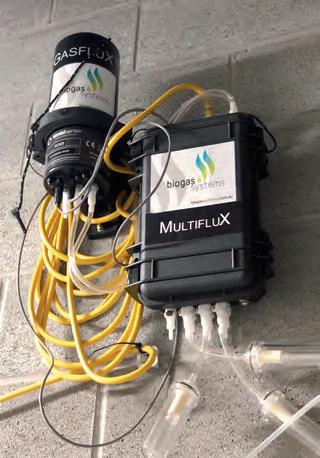
and ground gas monitoring.
The Gasflux continuous monitor can also be connected to real time water level loggers, dissolved gas (methane, carbon dioxide and total dissolved gas) probes and can have integrated total volatile organic compound sensors at both parts per million and parts per billion level.
Going forward, Ben hopes to increase awareness of the technology in the marketplace among regulators and operators and the financial savings possible for users. He adds that the usability and interface will also be improved over time.
Contact: Biogas Systems
Phone: 1300 651 412
Email: info@biogassystems.com.au
Position Partners offers a unique machine guidance technology and services package specifically designed to increase productivity in landfill applications. It stands apart in two important ways. First, the machine guidance technology has been specifically designed for the waste management sector, not the construction industry, and secondly, the company can assist with a complete support, reporting and data management package to optimise return on investment. Carlson LandfillGrade combines hardware for the compactor, namely a precision Global Positioning System unit for the roof of the machine, a control box for the operator in the cab and a range of sensors, along with software that delivers a wide range of reporting capabilities. To eliminate the need to upskill or hire additional staff, Position Partners now offers comprehensive data management, reporting and remote troubleshooting services. This managed service is designed to save time and maximise productivity by maintaining data integrity, generating and distributing reports and hosting the data on a client’s behalf. “Our landfill solutions aim to help operators manage their sites more efficiently by delivering relevant information on their site operations without any additional workload for them or their team,” said Andrew Granger, Position Partners Business Development Manager. “If operators experience any technical problems or the system needs new software, we can handle this remotely via our support hubs throughout Australia, without the customer having to wait for support to arrive on site.”
Position Partners offers comprehensive data management to eliminate the need for operators to hire additional staff.
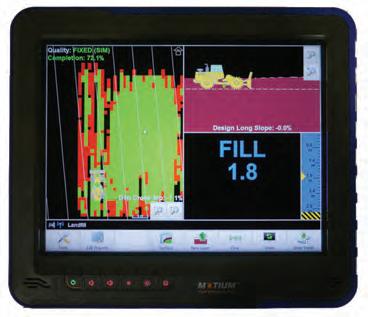
Contact Contact: Position Partners Phone: 1300 867 266 Email: www.positionpartners.com.au/online-enquiry Website: www.positionpartners.com.au
DRONE VOLUMETRIC SURVEYS FOR LANDFILL MANAGEMENT
AirBorn Insight utilises advanced drone scanning technologies to provide Australia-wide volumetric surveys that are highly accurate, cost-effective and fulfil QLD waste levy requirements. Increased efficiencies mean sites can be measured more frequently and in high detail. With powerful analytic tools at their fingertips, landfill managers can now be empowered to tightly monitor, measure and visualise their sites in 3D, without the use of CAD or GIS software. AirBorn Insight provides independent third-party volume calculations for compliance reporting. Alternatively, the company can supply photo-realistic 3D survey models to operators via its secure online data platform (propeller) with automated airspace calculations, stockpile volumes and measurement analytics to assist operations and reduce costs. The volumetric survey data automatically detects, highlights and tracks volume change across sites. AirBorn Insight engineers integrate existing cell design files into the survey model for automated airspace calculations and cell fill-up tracking against fill plans. For QLD leviable waste disposal sites and resource recovery areas, the company’s surveys are certified Increased efficiencies means sites can be measured more frequently and in high detail.
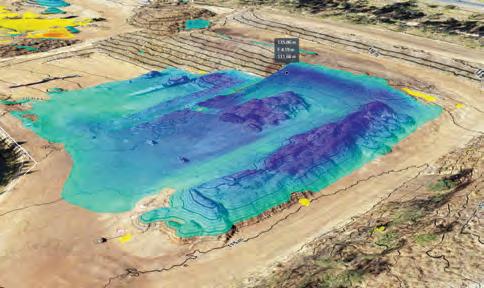
accurate by registered surveyors and fulfil the necessary legal requirements. According to the Waste Reduction and Recycling (Waste Levy) Amendment Act 2019, a baseline volumetric survey must be carried out between 1 June 2019 to 31 August 2019.
Contact Contact: Loren Otto Phone: 0490 307 608 Email: loren@airborninsight.com.au Website: www.airborninsight.com.au