
4 minute read
WASHING AWAY THE PLASTIC PROBLEM
AEROFLOAT’S MICHAEL ANDERSON OUTLINES A CLOSED-LOOP WASHWATER TREATMENT SOLUTION FOR THE WATER INTENSIVE PROCESS OF PLASTICS RECYCLING.
Unlike traditional systems, the AeroDAF does not require mechanical scrapers, resulting in a compact and mechanically simple solution.
Earlier this year, Pact Group, one of Australia’s largest rigid plastic product manufactures, announced a $500 million investment in plastics recovery.
The announcement was made at the first National Plastics Summit at Parliament House, with Non-Executive Chairman Raphael Geminder highlighting the company’s vision to include 30 per cent recycled content across its product portfolio by 2025.
While the commitment is noteworthy in terms of scale, it’s not the group’s first foray into plastics recycling, with Pact’s sustainability division Astron Plastics transforming millions of kilograms of plastic waste into new products each year.
To maintain its operations while achieving full process sustainability, Astron recently engaged wastewater treatment specialists Aerofloat to design a washwater treatment system at its Sydney recycling facility.
According to Michael Anderson, Aerofloat General Manager Engineering, Astron needed a solution that provided lower turbidity water for washing while reducing plant and product odour. Astron also needed a bag dewatering system to allow sludge to be disposed of in a skip rather than liquid waste in an intermediate bulk container.
Utilising its patented dissolved air flotation unit, Aerofloat custom designed a washwater treatment solution. The project was a success, Anderson says, with the plant meeting and exceeding specified performance criteria. He adds that prior to the plant’s commissioning, Astron transported its wastewater to another facility for processing.
“The installation of our washwater treatment plant eliminated that process, with all water now treated on site,” Anderson says.
Co-founded by Anderson, his father Ray and Business Operations General Manager Katie Moore, Aerofloat has been engineering, manufacturing and constructing wastewater solutions since 2009.
Offering a range of treatment systems for the food and beverage, industrial and utilities industries, Aerofloat expanded its market presence to the recycling sector in 2016, designing a wastewater treatment system for Australian Recycled Plastics.
Australian Recycled Plastics’ facility is located in Narrabri, NSW, which has an average mean rainfall of 640 millimetres per year. Limited water supply paired with operational downtime and the costs associated with replacing washwater inspired the company to engage Aerofloat.
Within a week of Aerofloat installing its fully automated system, odour problems at the facility where eliminated. To date, Australian Recycled Plastics has recycled one billion litres of water through the system.
While wastewater might not be ones first thought at mention of plastics recycling, Anderson explains that recirculating water is used at almost every stage of the process – from sorting, shredding and washing.
“Depending on the desired quality level of the plastic output, operators may continuously add fresh water into
the system to keep contaminants low, which is fine, but it means they’re using a lot of water, which has significant economic and environmental costs,” he says.
Operators producing a lower quality plastic may use the same water for a week, which by Sunday is understandably dark and contaminated.
“Operators then need to dump the water and refill, which for one of our clients meant one day of down time every week,” Anderson says.
“Since installing our system that client has been using the same water for nearly a year, meaning down time is eliminated and product output is increased. Pay back on the system was quick, as they can now run their factory for an extra day per week.”
Aerofloat offers custom designed solutions employing patented Aerofloat technology, as well as other leadingedge products to address a range of wastewater treatment requirements. While each facility is unique, Anderson says most plants follow a three-step process.
First is primary treatment, which screens the water to remove labels, pulp and small bits of fine plastic.
Next, the water goes through a dissolved air flotation process that separates solids from the water.
Aerofloat’s patented dissolved air flotation technology is called the AeroDAF, which uses a unique tank with a 60-degree conical bottom and top and hydraulic float removal system to funnel waste and float materials to the top of the tank.
Unlike traditional systems, the AeroDAF does not require mechanical scrapers, resulting in a compact, mechanically simple and affordable solution.
The final process is passing the water through a moving bed biofilm reactor, which removes soluble contaminants by aerating water in the presence of microorganisms. The microorganisms break down the contaminants and excrete a bio-solid, which is then removed.
Aerofloat’s expansion into plastics recycling has proved successful, with the company winning a Consensus GreenTech Award for its innovative designs in 2019. Previous winners included software giant Atlassian.
“Winning the Consensus GreenTech Award is a terrific honour. It is wonderful to be recognised for our achievements and dedication to the wastewater recycling industry and in particular our recent successes in the plastic recycling industry,” Anderson says.
“The ability to offer affordable and sustainable wastewater solutions at a time when water scarcity is a growing concern is critical to the future of Australian industries.”
vertical shredders. Built tough for the most demanding of shredding applications.
HEAVY DUTY VALUE FOR MONEY CIRCULAR ECONOMY
• Aggressive size reduction and densification of preshredded materials • Clean, high bulk density output for easy sorting and transportation • C&D waste, scrap metal and other heavy duty applications • Available with up to 440kW of power • Industry-proven and built tough for Australian conditions
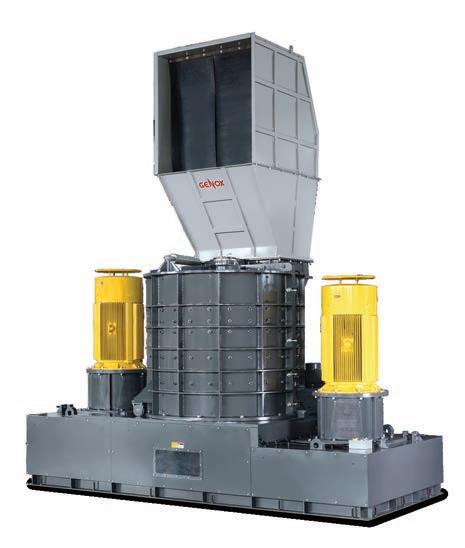