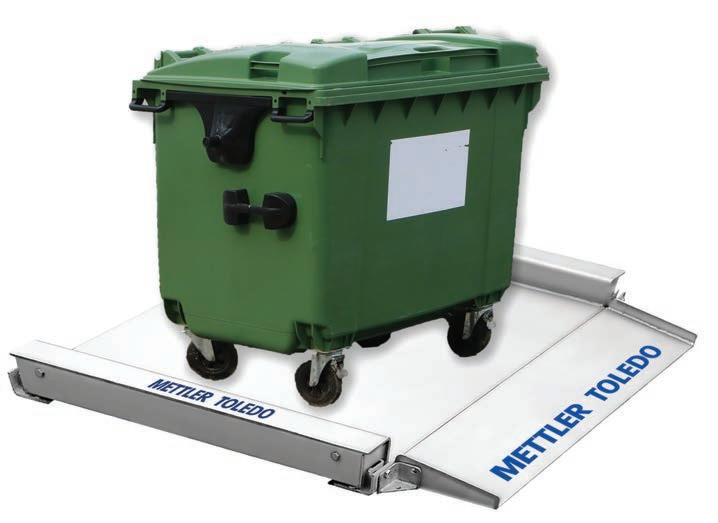
15 minute read
ACCURATE POWER
The power of accuracy
AFTER UPGRADING ITS WEIGHBRIDGES WITH POWERCELL TECHNOLOGY, A MAJOR AUSTRALIAN RECYCLING OPERATION SAW RETURN ON INVESTMENT IN LESS THAN TWO MONTHS.
As landfill levy rates surge across the country, waste operators are becoming increasingly conscious of ensuring they have accurate weighing systems in place.
According to John Beard, METTLER TOLEDO Weighbridge Business Area Manager, vehicle weighing is key to managing operational profitability at waste and recycling facilities.
He notes a recent METTLER TOLDEDO project, where the company helped a major Australian recycling operation upgrade several of their weighbridges with POWERCELL PDX load cells, driver control stations and security measures such as cameras and boom gates.
“The operation had purchased weighbridges from a non-METTLER TOLEDO supplier a few years back and through an audit, identified problems around the weighbridge operations,” Beard says.
“This was later identified as a combination of lack of accuracy around the weighbridge technology and cheating drivers using the weighbridge.”
This yielded significant profit loss, Beard says, as well as traceability issues. He adds that drivers taking advantage of the old system were being paid for more than they
POWERCELL technology offers an additional level of filtering on top of a digital core.
delivered.
“The solution to upgrade their existing weighbridges with new load cell technology, driver control stations and other accessories helped to provided alerts and safeguarding measures to improve daily operations,” Beard says.
“By incorporating boom gates, cameras and traffic lights, the company reduced the risk of improper truck positioning, altering data, stealing at the weighbridge and load cell tampering. They now receive real-time alert notifications of any misconduct.”
After adopting these technologies, the recycling operation received return on investment in less than two months.
“The company has been extremely satisfied with the upgrades and are continuing to implement more security measures to prevent cheating at their weighbridges,” Beard says.
METTLER TOLEDO is a global manufacturer and supplier of complete weighing systems and precision instruments, offering reliable solutions and services for the waste and recycling industry.
Kevin Diep, Systems and
Innovations Business Area Manager, says METTLER TOLEDO industrial weighing solutions work in two ways to help ensure accurate and efficient billing in the waste industry.
“First, our solutions offer smart load cell technology to achieve the highest levels of accuracy at the scale. Starting with accurate weighments is the first step in ensuring accurate billof-sales,” he says.
“Second, we offer user-friendly weight transaction systems that work to capture data automatically, eliminating the risk of human error. When combined, the result is a system with foolproof billing.”
METTLER TOLEDO weighbridge designs are meticulously tested for durability before new designs are released into the market, Diep says. He adds that customers can be confident that their weighbridge will stand up to the harshest environmental conditions.
Furthermore, Diep highlights a distinction between METTLER TOLEDO’s technology and traditional digital load cells.
Proven POWERCELL technology offers an additional level of filtering on top of a digital core, he explains, which works to filter out environmental noise that affects the accuracy of a weight reading.
“Additionally, POWERCELL load cells offer advanced diagnostics down to the specific load cell in a system, enabling an operation to catch any problems before it would cause a scale shutdown,” Diep says.
“This helps to minimise unexpected downtime and provides customers peace of mind where they are always informed.”
In addition to its trusted weighbridge systems, METTLER TOLEDO offers a range of floor scales and industrial weighing software solutions ideal for the waste
METTLER TOLDEDO systems send operators real-time alert notifications of any misconduct.
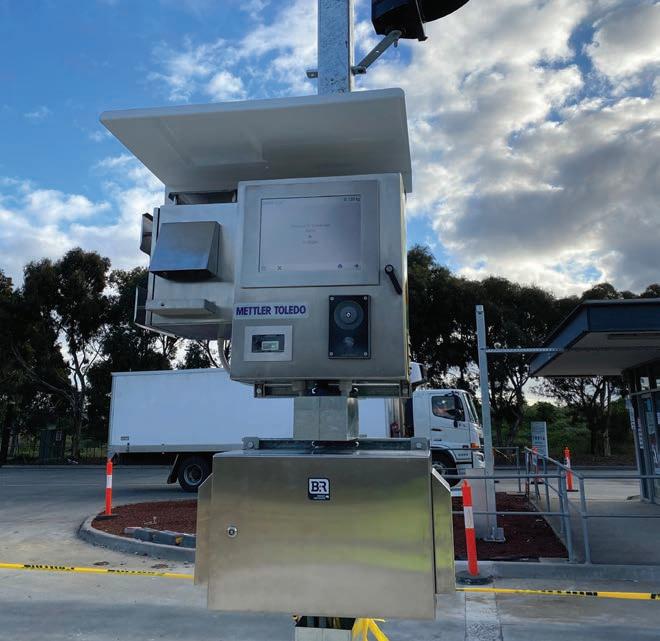
industry. For higher-cost waste and recyclables, Jim Lambros, Standard Industrial Product Manager, says a floor scale is necessary to get an accurate weighment.
“POWERCELL technology is available in our PowerDeck floor scales, bringing accuracy, operator guidance and advanced diagnostics into your bulk-handling operation,” he says.
“Our transaction software is available in standard versions for plug-and-operate simplicity, and customisable versions which can be designed to fit exact workflows.”
METTLER TOLEDO sales and service personnel are available to help operators throughout their entire project, offering a consultative approach.
“We can help from solution selection, to optimising site layout for maximised efficiency, through the installation process,” he says.
Lambros explains that professional weighbridge installation ensures equipment is ready for vehicle traffic, right from the start.
“Our factory trained service technicians work to ensure a smooth installation, with onsite support including confirmation of weighbridge foundation quality, safe weighbridge installation consistent with site requirements and traffic control and peripheral devices that are ready for operation,” he says.
“Our expert sales and service teams across Australia and New Zealand can help operations select from a variety of durable floor scales, indicators, weighbridges and software solutions.
“These smart solutions are designed to maximise uptime and efficiency.”
Contact – METTLER TOLDEDO
P 1300 659 761 W www.mt.com/au/en/home.html
The weight of expectations
AS THE WASTE INDUSTRY MOVES INTO AN AUTOMATED FUTURE, EFFECTIVE TECHNOLOGY ADOPTION CAN TIP THE SCALES. TRIMBLE’S PAUL CORDER EXPLAINS.
From smart bins to artificially intelligent waste sorters, waste management is undergoing a digital transformation.
As waste haulers begin to make this shift with the adoption of more automated data systems, it’s a good time to learn from other heavy industries that benefited from the move to digital.
According to Paul Corder, Trimble Head of Payload Technology,
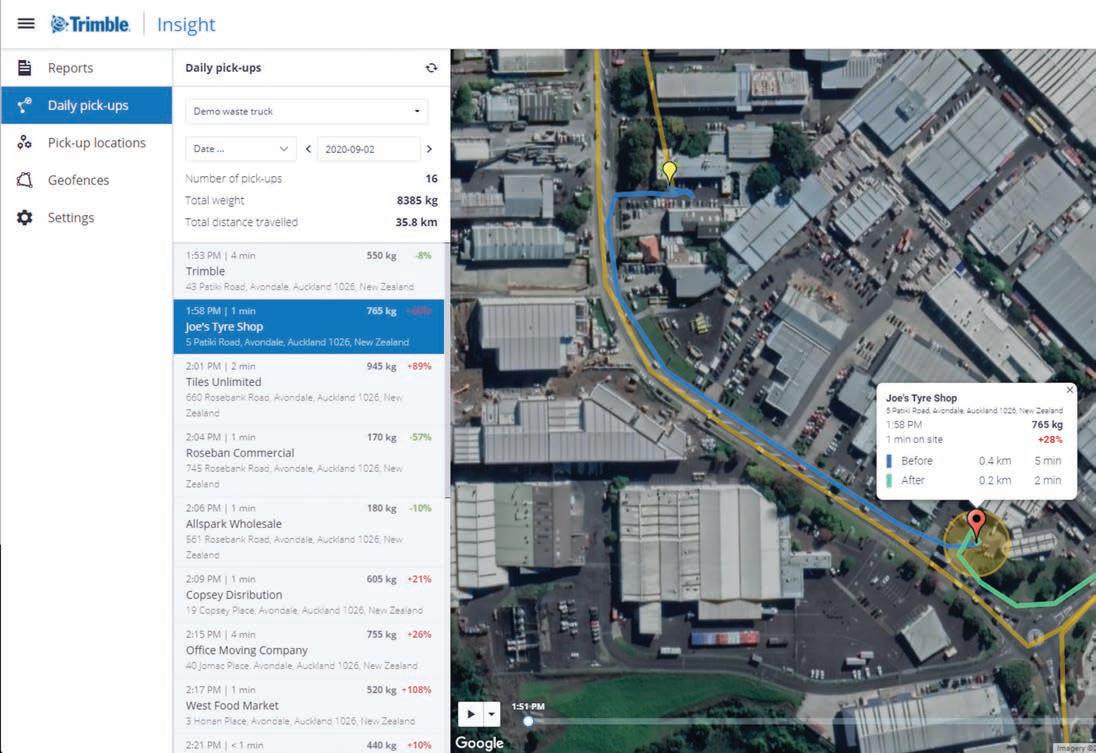
experience shows that it’s not enough to simply automate a task – there must be certainty as to how data is gathered.
Then, he says, operators can make the right decision at the bin pick up,
and sales or fleet managers have the confidence to make improvements using actionable intelligence at the office.
“Analytics and business intelligence can be a competitive advantage to make the most out of fleet investments,” Corder says.
“It enables answers to questions like: which bins are overloaded and costing you money? Where are the most profitable pickups? Is a pickup a safety hazard? How much profit does this customer generate? And what other prospects are in the same area?”
To understand the potential of emerging systems, more advanced data systems look beyond the weight of a bin to deliver intelligence and drive operational profitability.
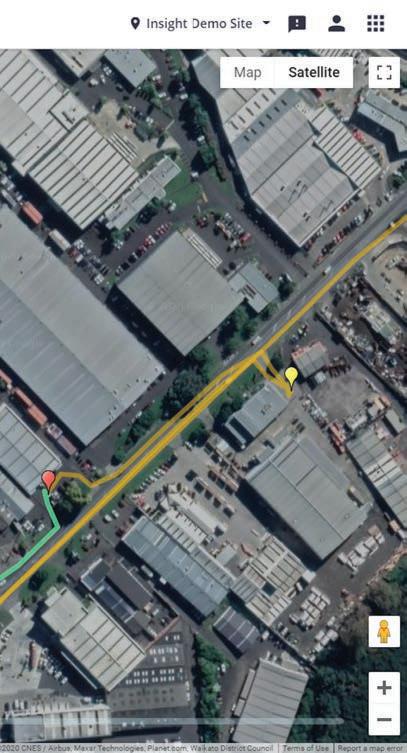
With a connected tool, fleet managers can evaluate and educate about incidents with clear visualisations and hard data.
“At present, waste haulers use traditional onboard scales to ensure safe lifts and measure bin weight,” Corder says.
“They may integrate with route management systems that optimise drive routes, thus improving efficiency and reducing wear-and-tear on equipment.”
Route management systems are feature rich, and a good first step to automation of waste management activities, Corder says.
He adds, however, that many of these systems are focused on the pickup, not the profitability of processes.
“For instance, route management systems may not convert bin weight data and locations into useful information to manage enterprise profitability,” Corder says.
“In fact, in many cases, there is no real way to look at the individual profitability of each customer, or even overall profitability of a route.
“Answering these questions using waste management system automation transforms waste haul and unleashes opportunity.”
Furthermore, Corder explains that pick up locations, bin weights and truck totals do more than help operators complete their job – they drive business profitability, productivity and efficiency.
“The ability to drill deeper into your waste collection operations and track profitability is a critical step in the technological transformation of any waste management organisation,” he says.
With accessibility to data, an operation’s manager can see operational metrics and summarise key performance indicators to identify lost productivity and compare customer data in a visual environment.
Access to customer data makes it easy for sales teams to identify customers with heavier than expected bins, review customer activity and negotiate pricing with the confidence of accurate data.
“They’re also able to identify profitable and unprofitable customers. And weight is just part of the makeup of cost,” Corder says.
“Delays at the pick-up such as locked gates, awkward bin locations and time to forklift the bin out are all costs that are often invisible.
“As performance managers have seen, a dashboard that compiles data into actionable intelligence provides value.”
Waste stream monitor visualisation includes reporting tools to review the route, monitor pickups for overloaded dumpsters and plan route capacity.
Safety is another invaluable benefit of waste stream monitoring. With waste data intelligence, it’s easy to prevent truck overloading and replay historical fleet activity to highlight issues, improve driver training, perform efficiency analysis and route reviews.
With a connected tool, Corder says fleet managers can evaluate and educate about incidents with clear visualisations and hard data.
They can optimise routes by expected payload weights to maximise tonnes per cycle. Operators can also make informed, ‘one-more pick-up’ decisions with confidence.
“As the waste industry moves into the future with an increased focus on automation and data-driven decision making, tools can empower their teams to capture waste collection business opportunities, increase route profitability, improve safe loading and improve customer satisfaction – and most importantly gain competitive advantage,” Corder says.
Contact – Trimble
P (02) 9531 6732 W www.trimble.com/waste
AMCS’s Front End Loading system is intelligent and able to distinguish between a true lift and false lifts caused by partial arm movements.
Intelligent weighing
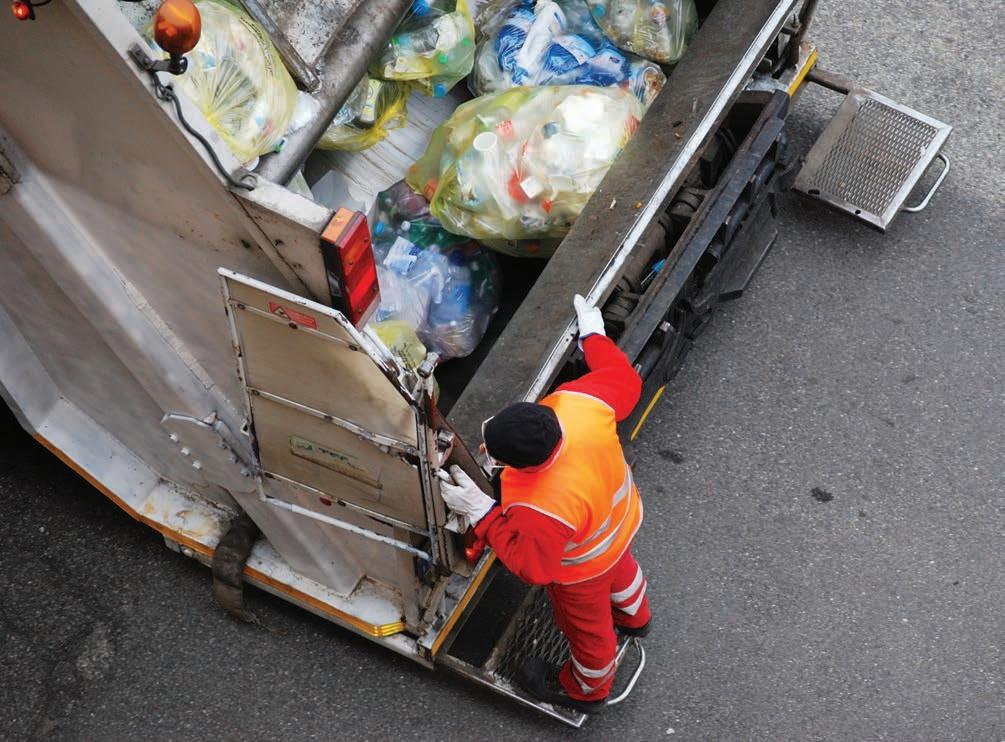
AMCS INNOVATION IS REMOVING THE COST BARRIERS ASSOCIATED WITH FRONT END LOADING WEIGHING SYSTEM ADOPTION.
The new Front End Loading (FEL) system by AMCS Group is the next generation in weighing system technology, while eliminating the need for load cells and additional installation costs.
Typical FEL systems rely on load cells that generate readings of the waste collected, but not without significant cost factors involving equipment, installation, calibration and the load cell technology itself.
This, along with the long-term maintenance required, often makes FEL systems cost prohibitive.
Currently, over 160 certified FEL systems are deployed worldwide.
AMCS’s solution is expected to raise the numbers in Europe and Australia, with New Zealand next on the horizon.
According to Michael Bates, AMCS Head of ANZ Region, the new system’s development was driven by the company’s experience using load cells on FEL and the cost of fabrication on the forks. Another consideration, he adds, were issues related to load cells being damaged by containers being shunted.
“The industry challenge was to develop a system that could be easily retrofitted to FEL with no modification to the forks, that was robust and also provided accurate weighing. The AMCS FEL extensometer solution delivers on all these challenges,” Bates says.
AMCS’s FEL technology sheds load cells and uses extensometer technology. This in-motion, dynamic scale doesn’t require action from the driver.
“It measures the extension in the FEL arms during lifting using tilt sensors, which enables a lift cycle customised for the customer’s needs,” Bates says.
“This eliminates fixed-mount proximity sensors that communicate where the container is in the lift cycle.”
AMCS’s FEL system is intelligent and able to distinguish between a true lift and false lifts caused by partial arm movements.
“Using our weighing algorithms, along with the tilt sensor to provide constant position of the lifter, allows AMCS to determine both the best position to weight and also to be able to identify what is a true lift verses a driver just moving a container position,” Bates explains.
The system is also more accurate at recording weights than traditional FEL systems, he says. Bates adds that it can deliver +/- 20 kilograms on average per lift or better, compared to traditional systems that have weight accuracies of +/- 50 kilograms. As such, waste management companies will know the actual weight of each container.
“They’ll no longer have to absorb the costs they don’t charge for,” Bates says.
By generating real-time collection data with AMCS’s FEL system, companies can analyse their activity and container weights. This in turn enables actionable insight.
“They can determine which customers are profitable and develop new strategies to increase revenue and customer satisfaction,” Bates says.
“They’ll know if they’re selling the right container based on a customer’s actual composition data, weight data and disposal habits. They can also increase revenue by shedding unprofitable customers.”
Additionally, companies can track lifts and verify collection on each route.
“This ensures that collections are completed, which eliminates additional callouts. Higher fleet efficiency is another way to prevent revenue leakage,” Bates says.
Where traditional load-cell FEL systems need intensive modification to vehicle forks, AMCS fits extensometers to the FEL arms, which represents a significantly lower hardware cost.
Traditional systems require time investment for installation, set up and testing, particularly where calibration and frequent adjustments are concerned. The AMCS system requires little calibration or maintenance.
“Our solution can work in standalone mode or integrate with AMCS On-Board technology options, including mobile tablets or 3rd party in-cab devices,” Bates says.
“Our goal is to make technologies for the waste industry cost effective and easy to use. Our new system is one more way we’re doing that.”
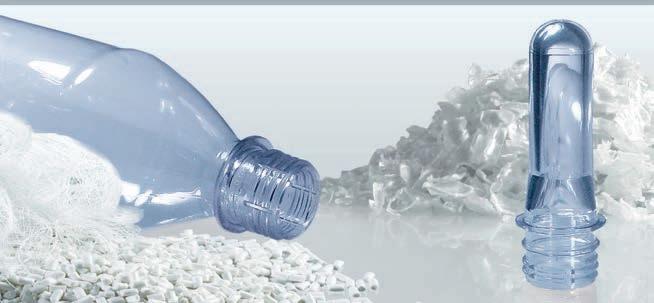
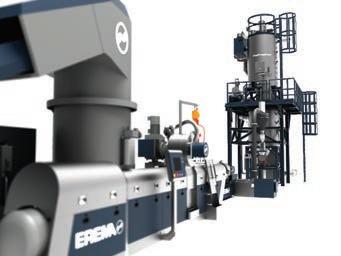
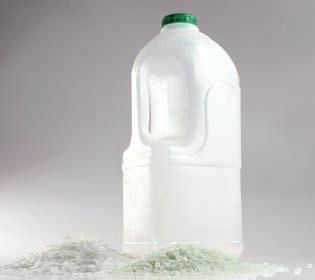
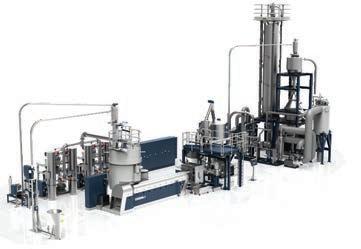
Contact – AMCS Group
P 02 9499 6222 W www.amcsgroup.com.au
Matt and Chris Calleija have been working with Bincorp’s Tony Nott since Dump It Bins’ 2006 inception.
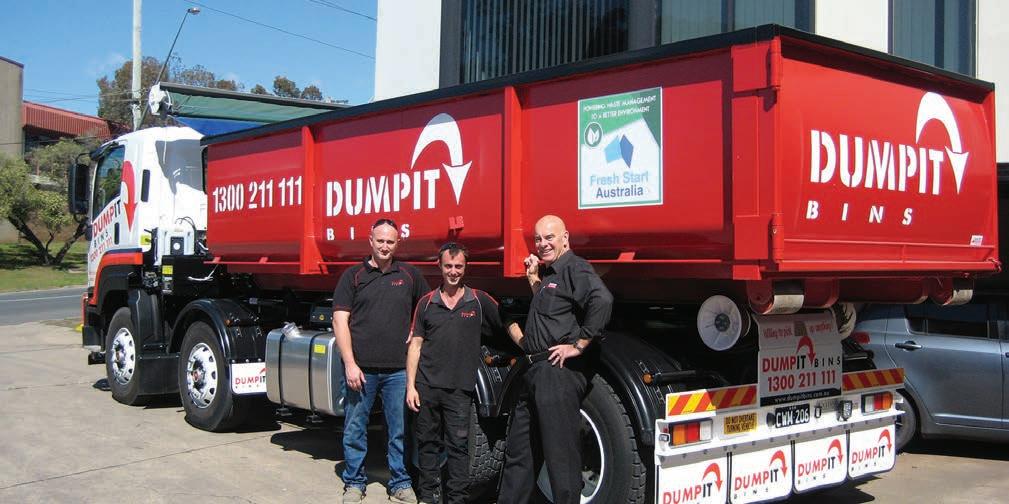
Bins to last a lifetime
DUMP IT BINS DIRECTOR MATT CALLEIJA SPEAKS WITH WASTE MANAGEMENT REVIEW ABOUT HIS DECADES LONG PARTNERSHIP WITH BINCORP.
In June, the NSW Government committed $3 billion to its infrastructure and jobs acceleration fund. The new funding will be used for smaller, ready to go projects across the state, and is anticipated to provide an extra 20,000 jobs for the NSW workforce. As the infrastructure pipeline expands, however, so too does the generation of construction and demolition waste.
Regardless of the size of a construction site, sharp and dangerous materials such as glass, concrete, steel, plastic and wood quickly accumulate.
This is a fact well understood by Dump It Bins Director Matt Calleija, who has been working in the waste management industry for over two decades. Dump It Bins operates extensively throughout the Sydney region, supplying skip bins to residential customers, tier one builders and major infrastructure projects.
The company also run a recycling centre and skip bin manufacturing plant, and are a proud member of the Green Building Council of Australia.
Calleija and his brother Chris started Dump It Bins in 2006 with just one truck. The company has since grown to over 30 trucks and 2500 bins, with the ability to serve the entire Sydney region.
“All our waste is tipped and sorted at our EPA licensed facility. Nothing is sent directly from our site to landfill, and anything we can’t process on site is sent to one of our recycling partners,” Calleija says.
Calleija’s family has been working in the waste management industry for generations.
His father owns and operates his own skip bin company, as do his uncles and cousins.
Together, the Calleija family has decades worth of knowledge in the waste management industry.
This industry stalwart status is mirrored by their friend and equipment supplier Tony Nott, Bincorp Managing Director, who has been working in the waste management sector for 38 years.
Calleija explains that Nott and Bincorp have been supplying Dump It Bins with hook lift frames and bins since the company’s inception.
“In my opinion, Bincorp manufacture the best quality bins in the market. You pay more upfront, but we’ve got Bincorp bins in circulation that have been going for over 15 years,” he says.
“You won’t get that sort of lifespan anywhere else.”
Durability is particularly important when dealing with construction and demolition waste, Calleija explains, due the often abrasive and heavy nature of the material. Add to that the common presence of hazardous waste, and one can see that high-strength, heavy duty bins are critical.
Bincorp manufactures hook lift bins in various sizes up to 60 cubic metres.
The containers are designed to
suit individual customer transport requirements, with customisable hook height and rail spacing.
Containers are manufactured to variable thickness and design, with different heavy-duty and door options with rope rails, ladders and tarps available.
Similarly, Bincorp’s hook lift frames can be fitted to suit various hook heights and rail spacings, with a variety of controls and accessories available.
With sliding and articulating jibs, Bincorp’s frames can facilitate loads from six to 35 tonnes. The frames come equip with an automatic centre framelock to secure containers stay in place, ensuring operates meet and exceed their safety requirements.
“Over the years we’ve acquired two other styles of hook lift frames from other manufactures, and they didn’t measure up. Nott’s products are a real industry standout,” Calleija says.
In addition to hook lift frames and bins, Bincorp design and manufacture a range of containers to suit all environmental and waste requirements.
The company’s factory is fitted to suit the manufacture of all container sizes, up to some of the largest built in the industry.
Bincorp also offer customisable hooklift trays made to different lengths with chequer plate floors, rope rails, front load boards and hook lift pick-up depending on customer’s needs.
Calleija says he looks forward to continuing his relationship with Nott and Bincorp.
He adds that it’s not just the quality of the product that drives the partnership, but also Nott and his team’s commitment to customer service.
Bincorp’s hook lift frames can facilitate loads from six to 35 tonnes.

“We’ve had such a long relationship because Nott understands the industry and all the requirements it entails. You can’t go wrong with Bincorp.”
Contact – Bincorp
P (02) 9756 3616 E bincorpequip@bigpond.com W www.bincorpequip.com.au/
How much profit are you making on each lift? THE DIFFERENCE BETWEEN GUESSING AND KNOWING
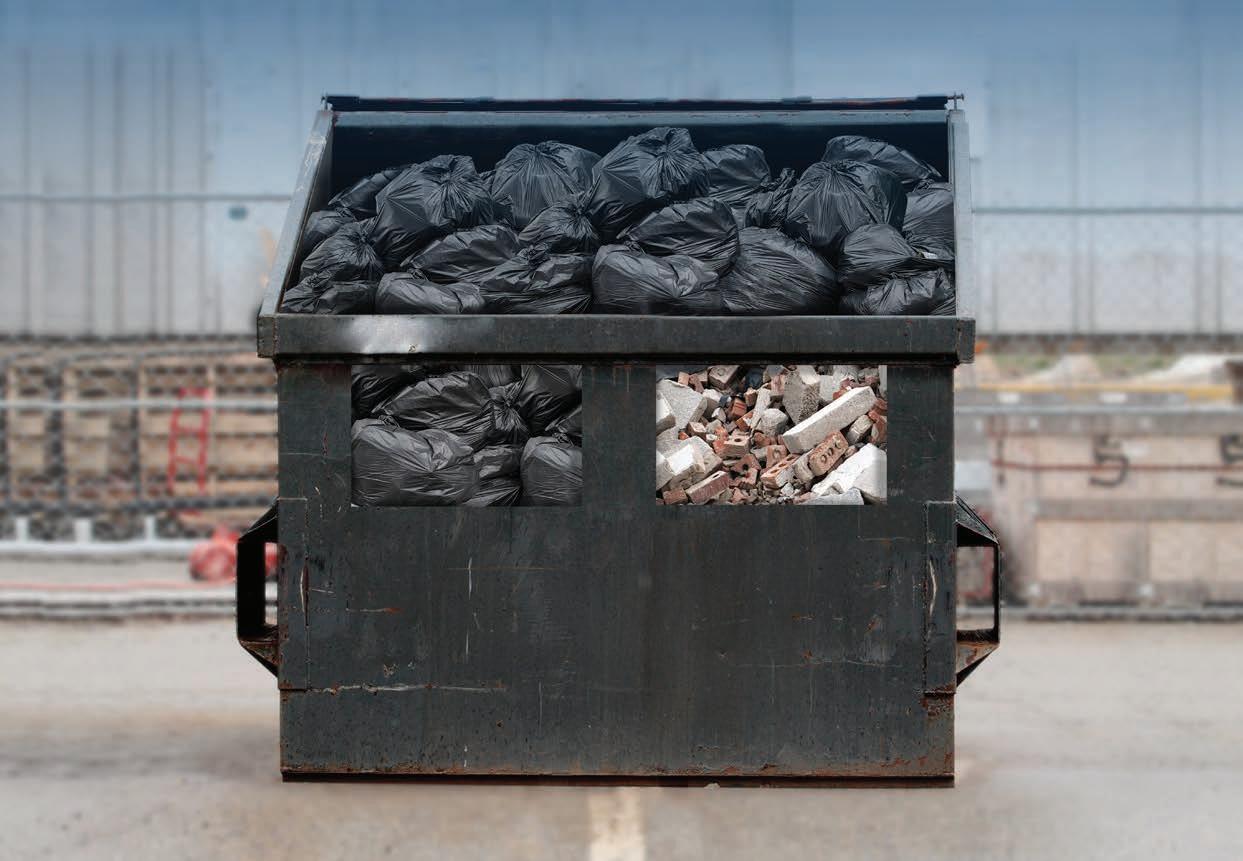
Choose Trimble LOADRITE Onboard Scales and information systems, learn more at trimble.com/waste