
26 minute read
ITALIAN MADE
TUTT BRYANT’S NEWEST DISTRIBUTION PARTNERSHIP WILL SEE VENIERI WHEEL LOADERS ON AUSTRALIAN SHORES FOR THE FIRST TIME. BUSINESS DEVELOPMENT MANAGER MARK EWAN EXPLAINS.
The special design of the Venieri loaders counterweight guarantees manoeuvrability and maximum drive angle.
Despite manufacturing in Italy since 1948, Venieri Earthmoving Machines might be a name unfamiliar to much of Australia’s waste and recycling sector. That is set to change, however, with the first Venieri wheel loader arriving on Australian shores in late September.
After expanding its footprint in the United States and Canada, Venieri recently began eyeing the Australian market.
At the same time, machinery and equipment supplier Tutt Bryant was looking overseas for a wheel loader range to complement its existing portfolio. From there, the partnership was born.
According to Mark Ewan, Tutt Bryant Business Development Manager, the initial enquiry came through Tutt Bryant’s existing equipment partner Yanmar.
He explains that Venieri and Yanmar had a joint venture agreement, whereby Yanmar would rebadge Venieri loaders for sale on the European market.
Due to Tutt Bryant’s long-standing partnership with Yanmar equipment and their quality requirements, Ewan says the company felt confident about the Venieri product and its ability to meet the needs of the Australian Market.
“Following the initial enquiry, we travelled to Italy for a week to demo the machines and assess how they spec’d up against major competitors in the Australian market,” he says.
“We also spoke with a number of customers in Europe who were or had run with major brands in their fleet to get feedback on their experiences with the loaders, which was all positive.”
Ewan explains that the customers he spoke with all noted the durability, reliability and performance of the Venieri loaders and all believed they were as good, if not better, than any other brand they had used.
“After further testing, we came to the conclusion that Venieri loaders were a good fit for our market,” he says.
Venieri wheel loaders offer hydrostatic transmissions, Z and parallel front bar linkage, inching brake pedals, precisely balanced weight distribution and oscillating axles on the rear chassis section.
Built for power, the new Deutz fouror-six-cylinder turbo charged diesel engines ensure high-level performance and reduced fuel consumption.
Venieri’s next generation range brings
Mark Ewan Tutt Bryant Business Development Manager
significant stylistic innovations to its cabin design, Ewan says.
He adds that the loaders offer great visibility, reversing cameras, adjustable suspension seats and steering columns, and a single joy stick lever with a forward reverse switch. The loaders also have significant storage space and a good ventilation system with climate control.
“As anyone familiar with waste environments such as transfer stations understands, ventilation is critical due to the often hot and dusty conditions. This is also backed up by an automatic and inbuilt reverse fan and self-cleaning unit,” Ewan says.
The air cleaner system offers two-stage filtration through high efficiency primary and safety filters, which can be integrated with a high efficiency precleaner removing dust from the filter automatically, via a scavenge linked to the exhaust line for maximum engine protection.
Made with sound absorbent materials and special anti-vibration rubber shock absorbers, Venieri cabins facilitate significant noise reduction, thereby providing a comfortable working environment for operators.
While suited to a range of industries, Ewan notes the loader’s hydrostatic transmission as a key benefit for waste and recycling applications.
“Because the loaders are hydrostatic, they can operate in small spaces efficiently, which are common in the waste industry especially transfer stations and small yards,” he says.
“It also drives power to the ground, making back and forward motion in tight areas more efficient compared to traditional drive loaders.”
Tutt Bryant offers an optional waste package with the loaders, which Ewan says includes waste guards for the front and rear which can be tailored to suit various applications.
The additional counter weights are useful for loading large buckets, Ewan adds, with an additional option of high lift booms available for hopper loading.
The Venieri range is available through Tutt Bryant in four models, all of which Ewan says meet and exceed waste industry needs.
For larger transfer stations or when dealing with glass and paper, Ewan recommends the VF 12.63 loader, which is fitted with a parallel linkage for powerful lifting performance. For smaller local government run transfer stations, he recommends the VF 7.63.
“The special design of the counterweight guarantees manoeuvrability, maximum drive angle and protects the rear light system,” Ewan says.
As with all Tutt Bryant equipment offerings, the Venieri range is backed up by 24/7 servicing and parts support.
“The machines themselves are also fitted with Venieri global GPS, so we can diagnose any problem remotely and troubleshoot with the customer.”
Wastech Sorting and Screening Equipment
Australian designed, world-class innovation
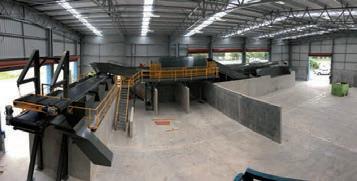
As Australia’s leading design and manufacturing company servicing the waste management and resource recovery sectors across Australia and New Zealand we know that now more than ever reliability and efficiency are top of mind.
We have a range of fully customisable and scalable solutions to meet and exceed your every need including sorting and screening equipment.
From manual picking lines to fully automated systems, our highly skilled engineers and technicians can provide an end-to-end service to deliver a solution you can have confidence in, plus receive long-term value from.
Contact the team to discuss your needs and see our full range of customisable solutions online.
OCC Screen Optical Sorter
Trommel Over-Belt Magnet
Material Steams catered for
Comingled Recycling Commercial and Industrial Construction and Demolition Organic Food De-packaging Product Destruction Other Equipment Offered
Complete Systems Optical Sorters OCC and Fibre Screens Glass breaker Screens Vibrating Screens Trommels Turbo Separator Robotics Other
Our core mission is to solve our customer’s problems
Maturing the market
ELMORE COMPOST’S FRANK HARNEY SPEAKS WITH WASTE MANAGEMENT REVIEW ABOUT THE IMPORTANCE OF PASSIONATE PLAYERS AND GOOD QUALITY COMPOST.
With government’s across Australia accelerating their efforts to divert organics from landfill, it’s an exciting time for the sector. In Victoria, the state government is targeting a 50 per cent reduction in organics sent to landfill by 2030. While this is a noteworthy target, Frank Harney, Elmore Compost & Organics Manager and AORA Victoria Chair, says for the organics industry to really expand, a number of key market issues need to be addressed.
Despite seeing organics as the recycling industry’s success story, Harney notes concerns around contamination and large corporate players dominating the market.
“A lot of the big players are waste processors not composters, so they get paid the gate fee and ship the material off without much care for the product. If new legislation is structured around just those big corporate players, I can see the circular economy going square,” he says.
Elmore Compost & Organics is a family-run business of fourth generation farmers.
Harney explains that the enterprise evolved out of a happy coincidence, with a wet hay season resulting in spoiled hay and straw.
A rich soil fertiliser emerged from mixing the hay and straw with manure from Elmore’s piggery.
“Our composting process involves recycling green waste from Melbourne and returning it to consumers as a carbon source for paddocks, gardens
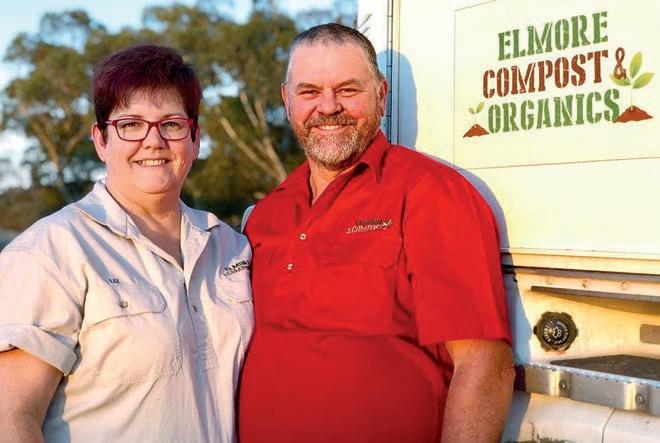
Elmore Compost & Organics are proud holders of Australian Organic Certification. and pot plants,” he says.
Harney got involved with AORA due to a belief that when you’re working in an industry you need to participate.
As such, he is a passionate advocate for maturation and supporting the entry of small players into the market.
“The market needs to push back, with operators getting paid to get product out of the gate as well as in the gate. When that happens, we’ll see a betterquality product downstream.”
Harney draws parallels to the plastic problem and China’s National Sword.
“China still wants our plastic, but they don’t want to be our waste tip.
“When you make a good quality product there’s no issue selling it, and that’s where recycling lost its way. But there’s an exciting future on the horizon, we just need people that are passionate about good quality compost.”
Looking forward, Harney says the organics industry needs to have a concrete plan in place whereby operators are rewarded for facilitating carbon improvement in soils.
Once this is achieved, soil becomes more drought resistant and the true benefits of composting and organics recovery are realised.
“When we’re providing gain for the agricultural industry through good quality products, the organics sector is poised to be in a really strong position,” he says.
How one company handled the COVID-19 crisis
UNWANTED DISRUPTION CAN BE A BLIGHT ON A COMPANY, BUT IT’S HOW YOU HANDLE THE INTERRUPTION THAT SHOWS WHAT THE COMPANY IS MADE OF.
Contracts are signed, tradies are ready to start, the building site is now open and there are deadlines to meet. Then a once in a century event happens – the COVID-19 pandemic. What happens now? Does the site close down? How long will government restrictions last? How are staff looked after? What about penalty clauses in the contract if deadlines are missed? These and a dozen other questions go through the collective heads of many executive committee members at construction companies.
For engineering construction specialist Total Construction, it was a matter of building on health and safety procedures it already had in place before COVID-19 struck and restrictions were enforced. Total Construction has been operating since 1994, and after noticing opportunities in the waste-to-energy space, entered the waste market in early 2018. In regard to COVID-19, Jeff Jones, Total Construction CEO, says they were being proactive from the get-go.
“We adopted temperature testing before it was put out there by the government,” he says.
“We were testing every single person who came onsite. We asked people to sign declarations about whether they had travelled overseas. We did all the virtualisation of the office space – less people on site where possible. We had project managers dialling in – all that sort of stuff.”
Jeff Jones says COVID-19 is likely to change the way companies conduct business in the future.
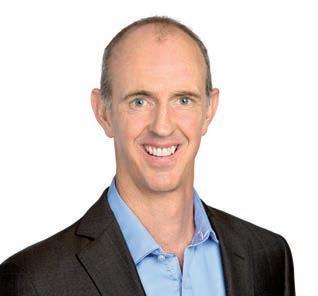
Throughout the first few of weeks, Total Construction did have a couple of scares, resulting in a site being shut down, and a hygienic clean of the whole area. However, there have been no reported cases on any of Total Construction’s worksites.
Procedures put in place included the company’s Cod Red process, which is part of its administration online tool.
It elevates that Total Construction has a notification of an incident onsite and controls who communicates to the client and contractors. Because if it not controlled properly, issues will arise, according to Jones.
“We decided early on there would be one source of information and that would be me for the vast majority of it,” he says.
“There are updates for the staff throughout the process about an infected site or possible infected cases. They come to me and I was responsible for communicating to clients and subcontractors.”
One of the key ingredients to making sure operations ran smoothly was how staff reacted to the changes. Without their cooperation and buying into the
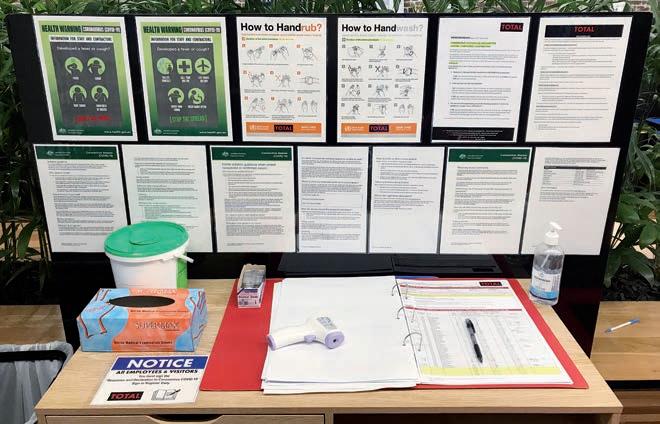
Total Construction built on health and safety procedures it already had in place before COVID-19 struck and restrictions were enforced.
new “normal”, Jones says it would have been harder to implement the new processes. As for the business itself, there was the expected downturn in terms of projects going ahead.
Total Construction had almost 40 projects ready to go at the beginning of the year, but when COVID came around, only eight went ahead. The good news is that another 10 have started since the beginning of May. However, some of the issues were not so much if the client was ready to green light the project, but whether supplies – especially those sourced from overseas – were available.
“We did have some early concerns about some supply items. We were caught short sometimes due to deliveries not arriving,” Jones says.
“We were lucky. We didn’t suffer too much delay from that. We did see a little drop in productivity due to the social distancing. In its early stages, certain trades were finding it hard to get people to turn up to site if there was a concern about health. But by making our sites as healthy as we possibly could, we saw a swing around the other way, where we had contractors wanting to turn up to our site because they knew we protected their workforce better than some other contractors. It became an opportunity to have more resources on site.”
With the construction industry, some builds have got underway while others have had to be put on hold, but not for reasons related to the COVID-19 pandemic itself, but peripheral issues, too.
“It’s been a mixed bag with engineering project builds,” Rob Blythman, Engineering Construction Group General Manager says.
“When they are crucial projects, and when they are vital to their operation, time wise and production wise, they have all gone ahead. Whereas there have been others that have stalled because even though they’re sort of necessary works, they can wait. Some are sitting back and waiting for things to change in the general environment, particularly with regard to government stimulus and things of that nature, before they push the go button.”
Looking forward, Jones says he believes COVID-19 might tweak the way some companies now do business.
“It might even change the long-term employment relationship,” he says.
“This is because we’ve talked in the past about how people used to work in one job for their whole life and how there was loyalty both ways. That has probably changed now with the flexible workforce. I think this pandemic has re-established the need to retain the muscle within the business.” METTLER TOLEDO provides accurate and reliable weighing solutions and servicing to meet EPA compliance and the needs of landfills, transfer stations, and other facilities that handle waste.
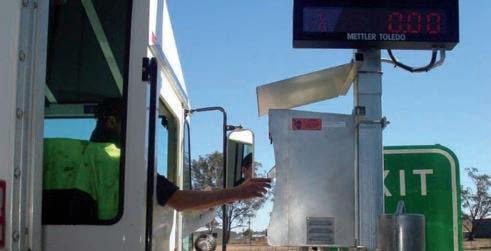
Weighbridges and Driver Control Stations Trade approved, world class and cost-effective weighbridges and axle weighing for high volumes

Data Management Software Automate data entry, save time and money and take control of your weighing operations
Floor Scales and Terminals Withstands the heavy loads typical of waste facilities for accurate and reliable weighing
Factory Trained Service Technicians Supporting measurement equipment installation, calibration, preventative maintenance and repairs
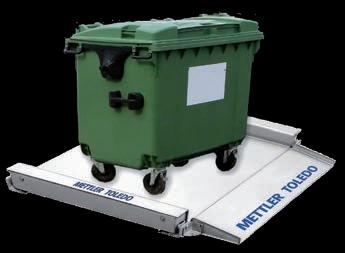
Call 1300 659 761 Australia Wide www.mt.com/industrial
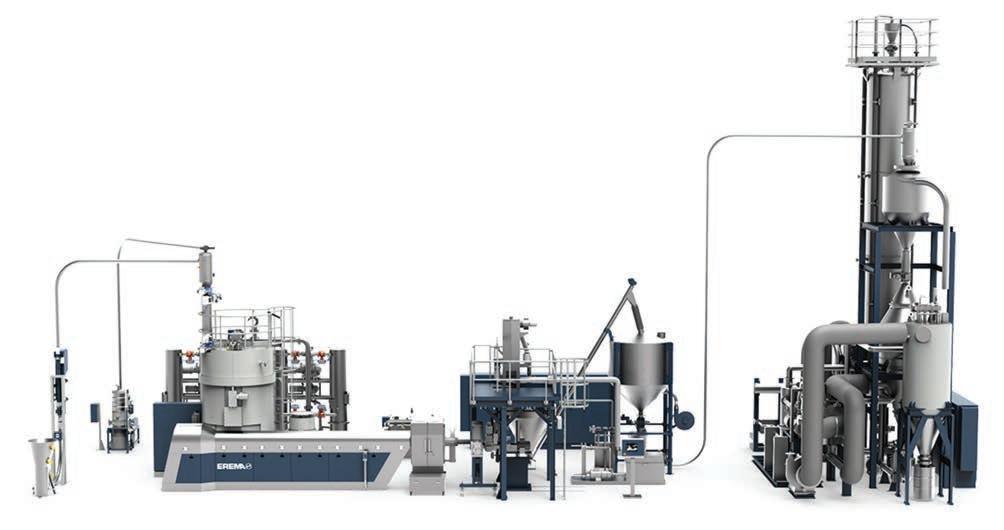
Closing the onshore gap
MARTOGG GROUP OF COMPANIES IS LEADING THE WAY IN BUILDING LOCAL RECYCLING CAPACITY WITH EREMA VACUREMA PET TECHNOLOGY.
Martogg Group of Companies is Australia’s largest privatelyowned polymer distribution, resin compounding and plastics recycling company. Manufacturing polymer compounds for the Australian plastics industry since 1975, Martogg LCM invested as early as 2006 in local plastics reprocessing and since 2015 specifically in PET materials.
Martogg Group’s recycled polymer division Martogg LCM® takes a cradleto-cradle approach to the life cycle management of plastic products and is leading the way in investing in onshore re-processing.
Using Martogg’s extensive knowledge of the plastics industry and polymer technology, along with the company’s compounding expertise, Martogg LCM® formulates and recycles endproduct plastic waste into value added, quality polymers to be used in the manufacture of new plastic products.
Martogg LCM’s RECYCLENE® range of commodity recycled polymers includes PP, LDPE, HDPE, LLDPE, ABS, HIPS, and GPPS products that are suitable for a wide variety of industrial and durable end use applications.
In 2015, Martogg commissioned their first VACUREMA® ADVANCED decontamination and recycling line, and after successful implementation and market development of the PET resin branded marPET®, invested in the second line in 2019.
It is now commissioning the third and largest VACUREMA® ADVANCED, which will be operational in late 2020 with a collective production capacity of 23,000 tonnes of food grade rPET.
The VACUREMA® bottle-to-bottle technology from the Austrian recycling machine manufacturer EREMA®, combines several advantages and functions in one.
“The unique SafeFlake technology in the vacuum reactor, in particular the flake decontamination, drying and IV treatment prior to extrusion, enables immediate drying, fast migration of contaminants out of the polymer and flexible IV management at lowest energy costs,” Ben McCulloch, Martogg marPET® Product Manager says.
By pre-treating the PET flakes in a vacuum at the correct temperature, moisture and migratory substances are removed effectively as part of the process before extrusion.
McCulloch explains that this prevents any hydrolytic and oxidative decomposition of the melt in the extruder.
“This is a clear advantage in terms of melt quality, and therefore the basis for a stable, highly clean and foodcompliant end-product with the best colour results,” he adds.
The simple operation and effective blending in the reactor, as well as the high degree of automation, allows production of consistent quality PET resin for direct food contact and IV values on par with virgin materials, even if the input material parameters change.
“Therefore, the technology is ideal for processing in Australia and being able to deal with local challenges,” McCulloch says.
Electricity accounts for around one third of the costs of bottle-to-bottle recycling. Technologies that use
energy economically therefore have a clear advantage.
The VACUREMA® sets the standard with the VACUREMA® Prime’s energy demand as low as 0.30 kilowatt-hours per kilogram specific total energy consumption. For the VACUNITE®, demand is only 0.35 kilowatt-hours per kilogram consumption for the complete process – from flake to finished rPET pellets, including solid state processing.
The VACUREMA® range covers all applications of PET processing, from inline extrusion to thermoforming sheet, to high end bottle-to-bottle applications and capacities over 3000 kilograms per hour. With the latest addition of the VACUNITE® to the VACUREMA® range, EREMA now offers the unique combination of two technologies: the well proven and tested VACUREMA® technology, together with newly patented vacuum-assisted V-LeaN Solid State Polycondensation (SSP), which Polymetrix developed for EREMA especially for this demanding application.
VACUNITE® offers further enhancement of IV and colour management at lowest energy demand, where all thermal process steps take place in a nitrogen and/or vacuum atmosphere.
After testing the first VACUREMA® line and finding it to suit their requirements, Martogg showed industry leadership and committed further investment in local re-processing, closing the gap for onshore processing.
Now coinciding with the renewed recycling content targets released by APCO, Martogg’s PET resin marPET® has an annual capacity of 23,000 tonnes, which is being offered to Australian based packaging companies seeking a range of high-quality rPET resins to meet the local recycling content targets.
“The Erema technology has been instrumental in allowing the Martogg Group to produce and offer business and brands with the highest quality rPET for use into a diverse range of packaging applications,” McCulloch says.
EREMA is represented in Australia by CEMAC technologies.
“We are proud to be able to offer these advanced technologies to the Australian markets and to be able to assist in building local infrastructure in materials re-processing towards a circular economy,” CEMAC Managing Director Eric Paulsen says.
“We applaud the initiative and dedication that Martogg is showing in this emerging market and are very grateful for being able to assist in the process.”
AMCS FEL Weighing enables you to reduce costs and helps eliminate revenue leakage in your collection operations
• Certified for trade weighing (NMI 6/20A/14) • Very cost effective solution • No dependency on driver behaviour • Reduce revenue leakage & ensure accurate pricing
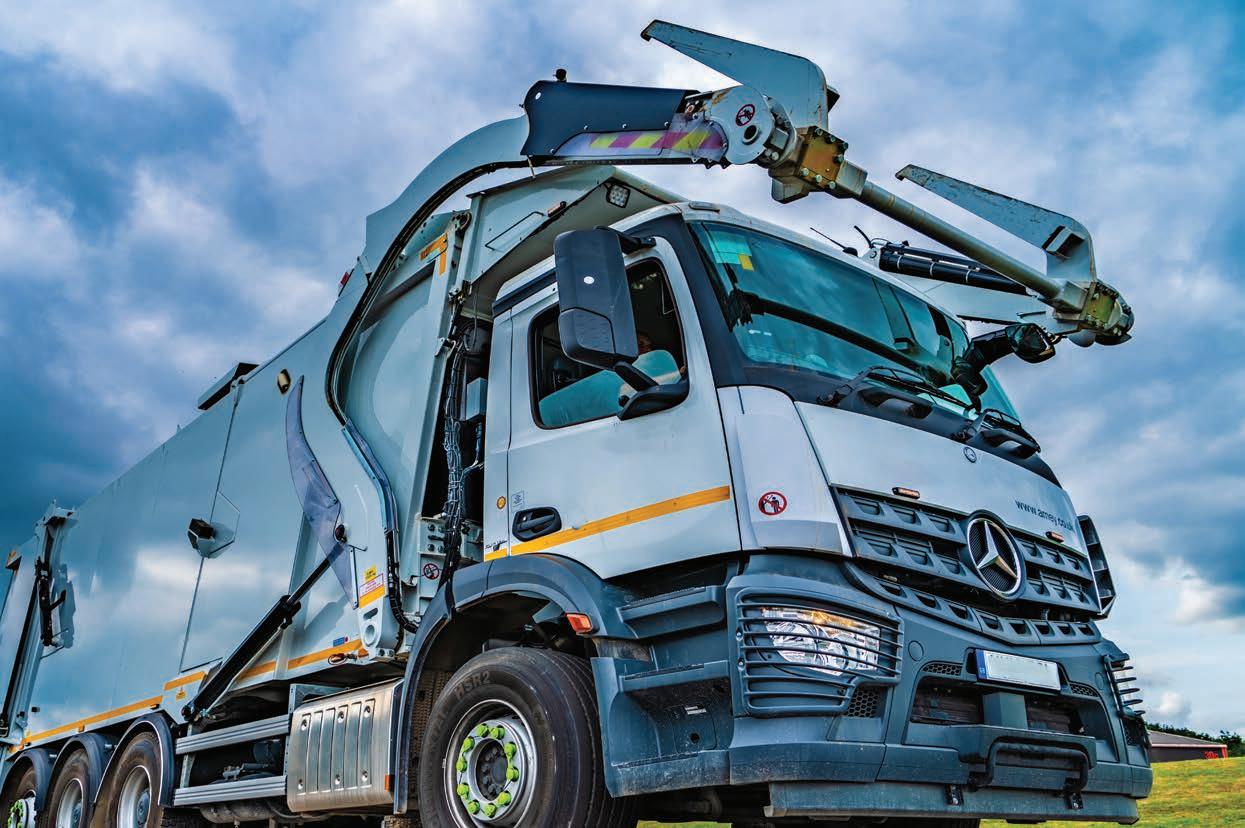
amcsgroup.com
Hobsons Bay goes digital
WITH THE LAUNCH OF RECYCLING 2.0, HOBSONS BAY CITY COUNCIL OUTLINES AN INNOVATIVE APPROACH TO WASTE MANAGEMENT AND RECYCLING ENGAGEMENT.
Q: What are some of the challenges surrounding collection and recycling in Hobsons Bay?
A: As with any change, some residents are still adjusting to the new recycling requirements, but overall, our community has done a great job so far in familiarising themselves with the new service. As you could imagine, contamination rates have been a big challenge. Our community is doing very well in using the new glass and FOGO bins, but we are doing poorly with the comingled recycling system. We need to see a big improvement in sorting our waste from our recycling to reduce the high rates of contamination we are still seeing within our fourbin kerbside service. As with most municipalities, the Coronavirus pandemic has led to increased waste volumes for most households. In response, council has established a free interim weekly excess rubbish drop-off service.
Q: What has been working well over recent years in terms of waste management services?
A: In 2018 and 2019, we carried out significant community engagement on our Waste and Litter Strategy. This meant when recycling was hit hard with industry wide changes, we had a clear direction to follow. As a result, in October 2019 we were able to launch the Recycling 2.0 service and embarked on a community education program that had hundreds of local volunteers, known as Recycling Champions, at the heart of it. Through the months that Recycling 2.0 has been up and running, we have advanced our digital offering for a range of aspects of the service to deliver outcomes faster and more efficiently.
This includes a digital tool to track contamination checks, a simple online ordering system to order bins, and our Recycling 2.0 App. The digitisation of bin orders, contamination inspections and bin management has enabled us to quickly analyse data and make changes to deliver positive recycling outcomes.
Q: Why Council choose to develop the Recycling 2.0 App?
A: While not everyone uses a smartphone, more residents than not have one these days. The app complements other communication channels as a way to quickly get helpful information about their recycling service – whether it’s checking the bin schedule or using the Which Bin Does This Go In? feature.
The vision for the app is also to make recycling fun, with further releases planned that will be quite interactive with both data on system performance, and games and targets that households and individuals can play to improve recycling. A collaboration with Code for Australia, the app was released with a Minimum Viable Product, with new features being added regularly.
It has been built with an open source approach, and the architecture has been designed so other councils could easily pick the app up and tailor content for local reuse. Hobsons Bay is happy to share with other municipalities as the new four bin model begins to roll out state-wide.
Q: How has the Hobsons Bay community reacted to the new app?
A: Since the launch of the Minimum Viable Product in mid-April, there have been 1160 downloads of the Recycling 2.0 App. Downloads are increasing each week, with residents frequently searching their addresses for bin schedules and using the interactive feature Which Bin Does This Go In? to search their household waste items. The community is keen for further releases and updates to come, including bin reminder notifications which should go live within weeks. As each new feature is released, we expect to see downloads grow.

A German approach
WITH THE EXCLUSIVE RELEASE OF GREMAC’S E2 TROMMEL SCREEN, GCM ENVIRO IS BRINGING GERMAN INGENUITY TO AUSTRALIAN SHORES.
According to 2017 data from the European Environmental Bureau, Germany is the world’s leading recycler, achieving a selfreported recovery rate of 66 per cent.
Alternatively, Blue Environment Group figures from 2018 estimate Australia’s national recycling rate at 55 per cent, suggesting Australia could take cues from its northern European counterpart.
While much of Germany’s recycling success is attributed to engaged citizens and strong policy settings, Australian equipment distributor GCM Enviro is capitalising on the German approach at the ground floor – via an exclusive distribution deal with machinery manufacturer Gremac.
Gremac launched its E2 Trommel Screen to market in March, with the trommel arriving on Australian shores through GCM in September.
According to GCM’s Adam Krajewski, the advanced screening system is set to be a game changer for landscape companies, recycling businesses, contractors and farmers.
Suitable for soil, sand, gravel, stones, green waste, wood chips, compost, recycled materials, glass and alternative fuel, the Gremac E2 has a maximum weight of 3.5 tonnes, making it small enough to be towed by car.
Krajewski explains that the trommel can process up to 50 metres cubed an hour, featuring strong electric geared motors and a hopper with a capacity of up to 1.6 metres cubed. Screen segments can be changed with ease, he adds, with a large door providing ease of maintenance to the lower belt and cross belt.
The trommel is electrically driven, with load sensing control for continuous workflow.
“No material is lost during processing due to a one-piece fines discharge

The trommel has state-of-the-art control and set up, with the frame and all material guiding parts manufactured with galvanised steel. conveyor, with four crank support winches for secure positioning,” Krajewski says.
“The trommel has state-of-the-art control and set up, with the frame and all material guiding parts manufactured with galvanised steel for long machine life.”
The drive is available as either a petrol or diesel generator or can be plugged into mains to power the internal electric motor.
Since its founding in 2004, GCM has committed to providing its customers with cutting edge waste management technology, combined with state-ofthe-art control and monitoring systems. GCM’s ultimate objective is enabling its customers to increase revenue through the extraction of value from waste.
As such, when GCM became aware of the Gremac E2 trommel, Krajewski says it made sense to update the company’s existing equipment portfolio and provide a new advanced solution for Australia’s waste and recycling sector.
When operators invest in GCM equipment, Krajewski says they are guaranteed high-quality machinery that exceeds Australian standards, combined with efficient service back up and approachable personnel.
“A constant dialogue between manufacturers and clients is maintained to ensure that design is governed by market requirements, particularly in the harsh climatic conditions we experience,” he says.
Contact – GCM Enviro
P 02 9457 9399 E sales@gcmenviro.com.au W www.gcmenviro.com
TEREX ECOTEC’S VERSATILE PH1600T TROMMEL SCREEN
The Terex Ecotec Phoenix 1600T trommel screen is versatile by design, easily screening a variety of material including topsoil, compost, sand and gravel, wood chip and construction and demolition waste.
The trommel has been innovatively designed to provide excellent fuel efficiency and low operating costs, while also reducing emissions and noise levels due to the machine running at a low engine RPM.
The trommel is available through Finlay Waste and Recycling either tracked or wheeled, with a 4.9 by 1.54 metre drum guaranteeing high throughput due to the large screening area.
Woven mesh or heavy-duty punch plate panels can be fitted to the drum, ensuring all application requirements are met.
A 180-degree swivel fines conveyor facilitates the creation of impressive stockpiles, with a discharge height of 5.9 metres. The swivel feature can be controlled via a remote while the machine is in operation to minimise downtime.
A powerful four-wheel drive system with high performance friction wheels is used to turn the trommel drum, giving operators the ability to run bi-directionally.
A powerful four-wheel drive system with high performance friction wheels is used to turn the 1600T’s trommel drum.
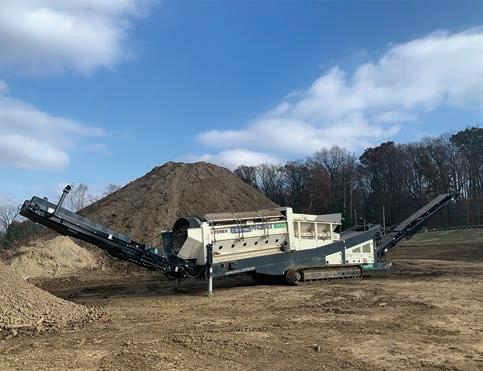
Powered by a Caterpillar C4.4 – 130HP Tier 3 engine, the powerful hydraulics and intelligent feed control system ensure the Phoenix 1600 is always working at optimum levels.
Contact - Finlay Waste and Recycling
P 1800 777 300 E info@finlay.com.au W www.finlay.com.au
THE KOMPTECH MULTISTAR L3
Screening is a fundamental treatment stage in the processing of waste, recyclables and biomass.
Star screen technology is increasingly used for separation work, and in most cases the screener is a Multistar.
Komptech’s Multistar L3 – available in Australia exclusively through Kompech CEA – facilitates high throughput across a wide range of applications. One machine and one pass are sufficient to divide material into two or three fractions.
The hopper, feed system and design and dimensions of the screen decks combine to form a compact unit with unbeatable throughput. Effective wear protection of all parts in contact with material and an efficient diesel-electric drive system ensure low operating costs.
Very low dust emissions, largely screening internally also make this a strong competitor.
The power for the drives can come either from grid electric power or the optional built-in diesel generator. The use of grid power reduces energy consumption by up to 75 per cent compared with diesel-hydraulic power.
The cassette configuration of the screen decks facilitates rapid changes and flexibility, while particle size can be controlled by varying the rotation speed of the star shafts.
In just seconds, particle size can be changed within the range provided by the star size using a touchscreen graphic
The cassette configuration of the Multistar’s screen decks facilitates rapid changes and flexibility.

control panel. Different star dimensions and arrangements cover screening sections from eight to 150 millimetres.
Contact - Komptech CEA
P 1300 352 378 W www.komptechcea.com.au
APPLIED MACHINERY’S GENOX TYRE RECYCLING SYSTEM
Applied Machinery’s GENOX Tyre Recycling System is a fully integrated recycling line designed to simplify the heavy-duty process of rubber extraction.
The system uses M and X-Series Pre-Shredders as powerful first stage size reducers, that are capable of processing whole car, truck and off-the-road tyres down into approximately 50-30 millimetres shreds.
Next, material passes through a recirculation system that combines conveyors and disc screening units, before being transported to the Heavy Duty Rasper for secondary size reduction. S-Series Heavy Duty Raspers with serrated edge biades work to aggressively process the material.
Overband magnets mounted above conveyor belts or vibratory feeders efficiently remove liberated steel wire from the rubber crumb, with high strength, rare earth magnetic elements ensuring effective separation.
The system’s GXE-Series Granulators are ideal for the third stage reduction of rubber crumbs into high quality granules. Rubber granules from the fine granulation stage can be classified by size into different product streams, with oversized material then recirculated back to the granulators for further size reduction. The fine granulation system is equipped with a special rotor designed for tyre rubber size

The fine granulation system is equipped with a special rotor designed for tyre rubber size reduction.

reduction. It provides maximum throughput, while minimising the amount of fines created. The machine is also optimised for low operational and wear costs.
Finally, a Zig-Zag separation system removes remaining textiles from the rubber granulate, with a motorised magnetic drum available to remove tramp metal fines and ensure a high-quality product. A control panel is supplied to provide full automation of the recycling system, with the option of touch screen displays to provide ease of access for system programming, maintenance and inspection.
Contact - Applied Machinery
P 03 9706 8066 E sales@appliedmachinery.com.au W www.appliedmachinery.com.au
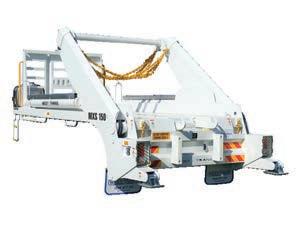