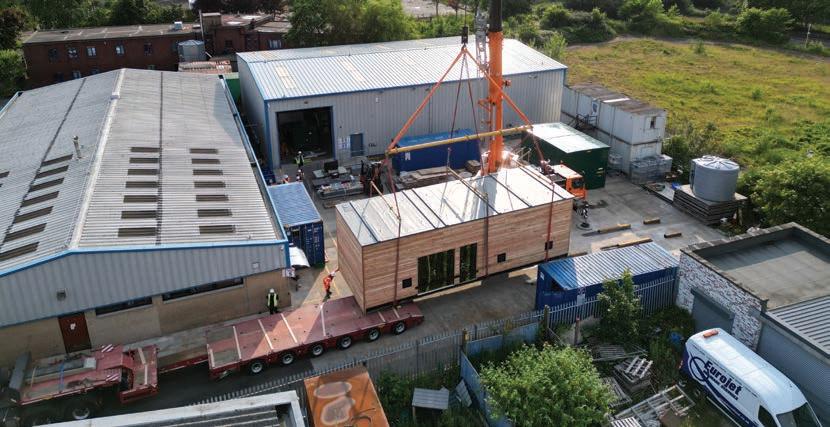
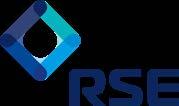
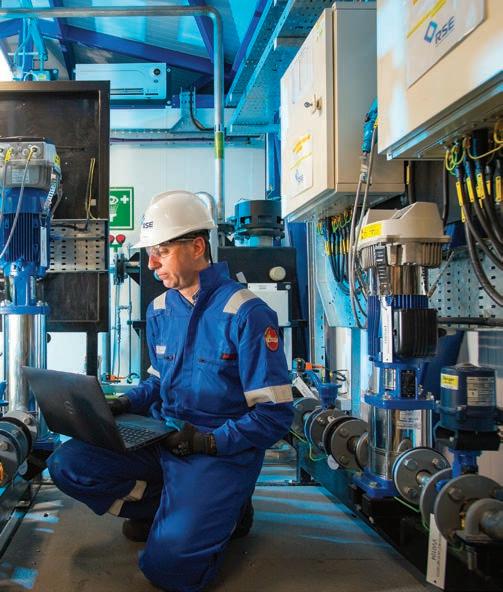

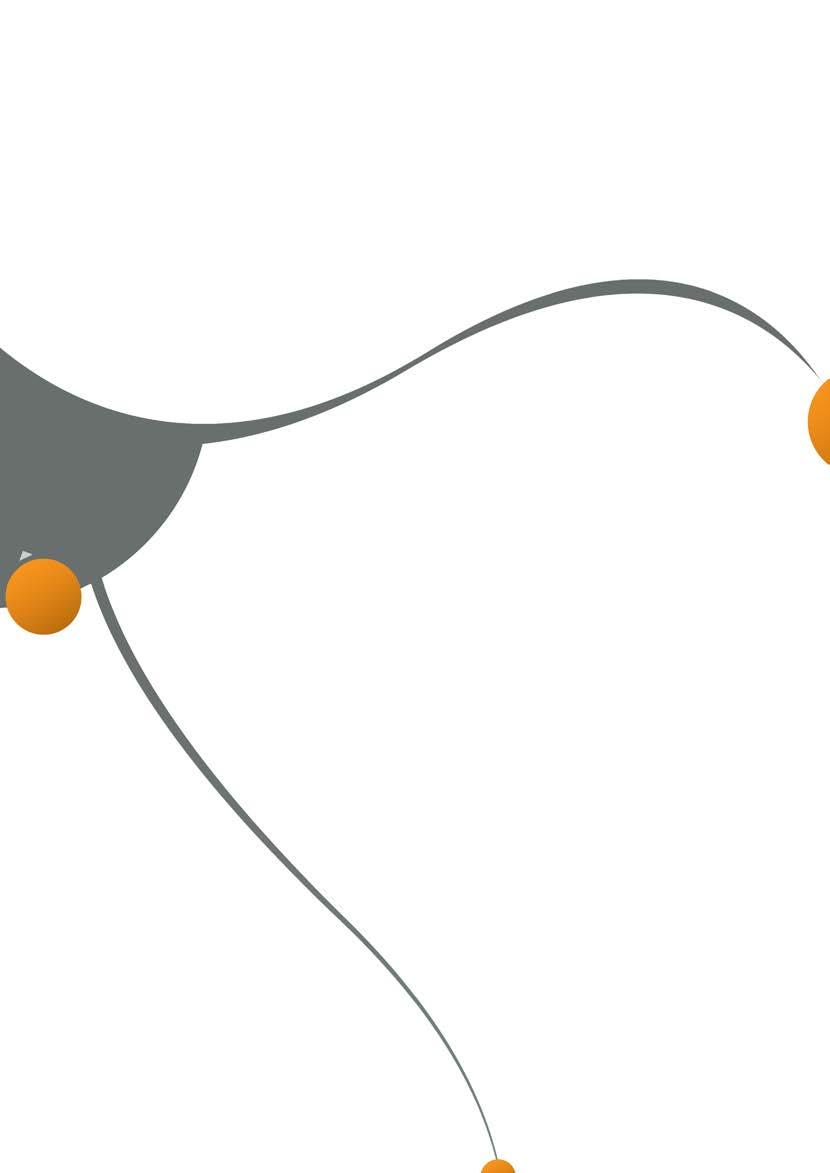
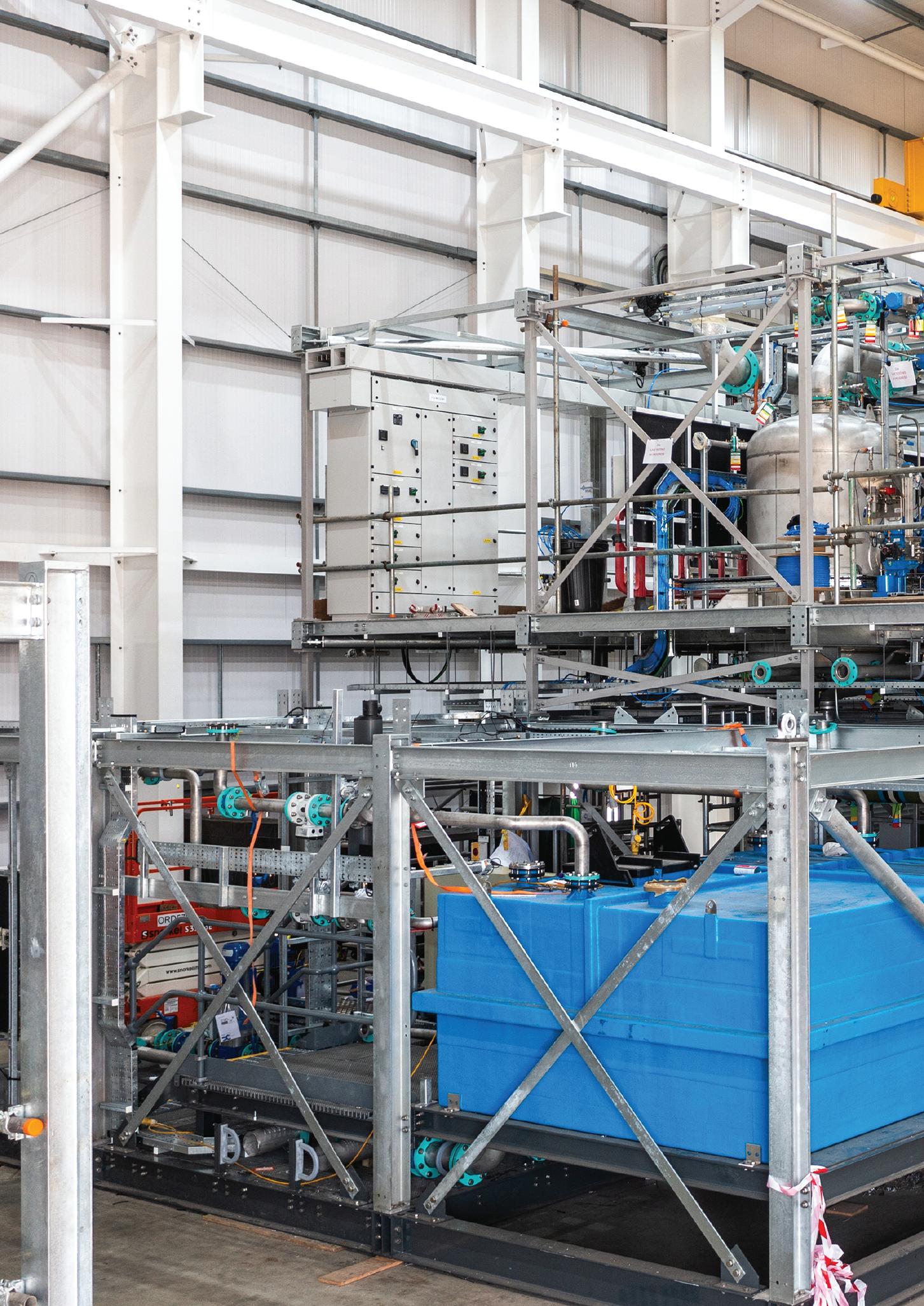
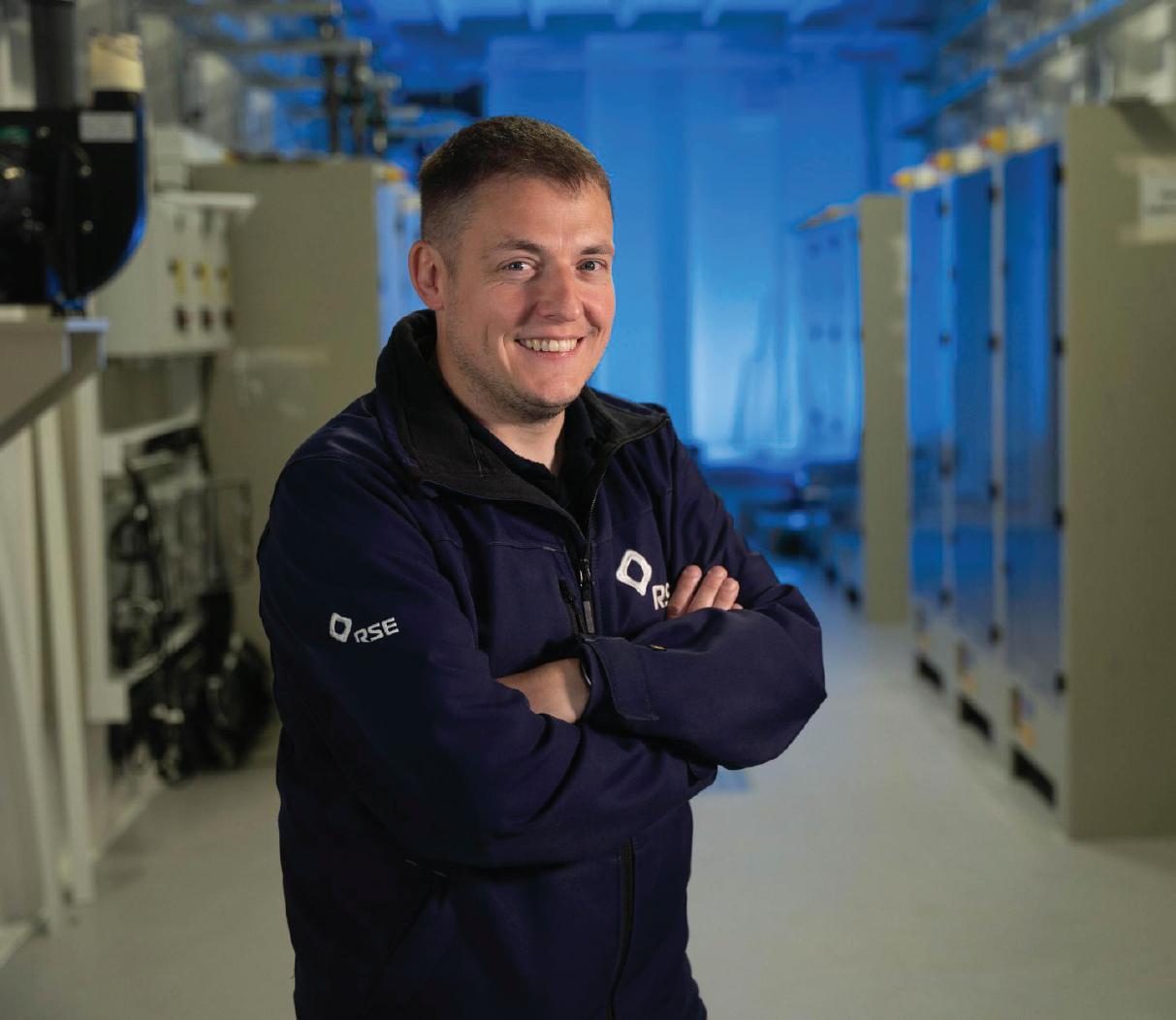
A trusted clean water technology company, RSE, develops market-leading products and solutions for purifying drinking water, recycling wastewater and cleaning water in industrial processes across the UK water industry. Business Development Lead Gary Callachan, Sustainability Coordinator Leia Pol and Sustainability Manager Stephen Webb discussed the company’s innovations. Report by Antonia Cole.
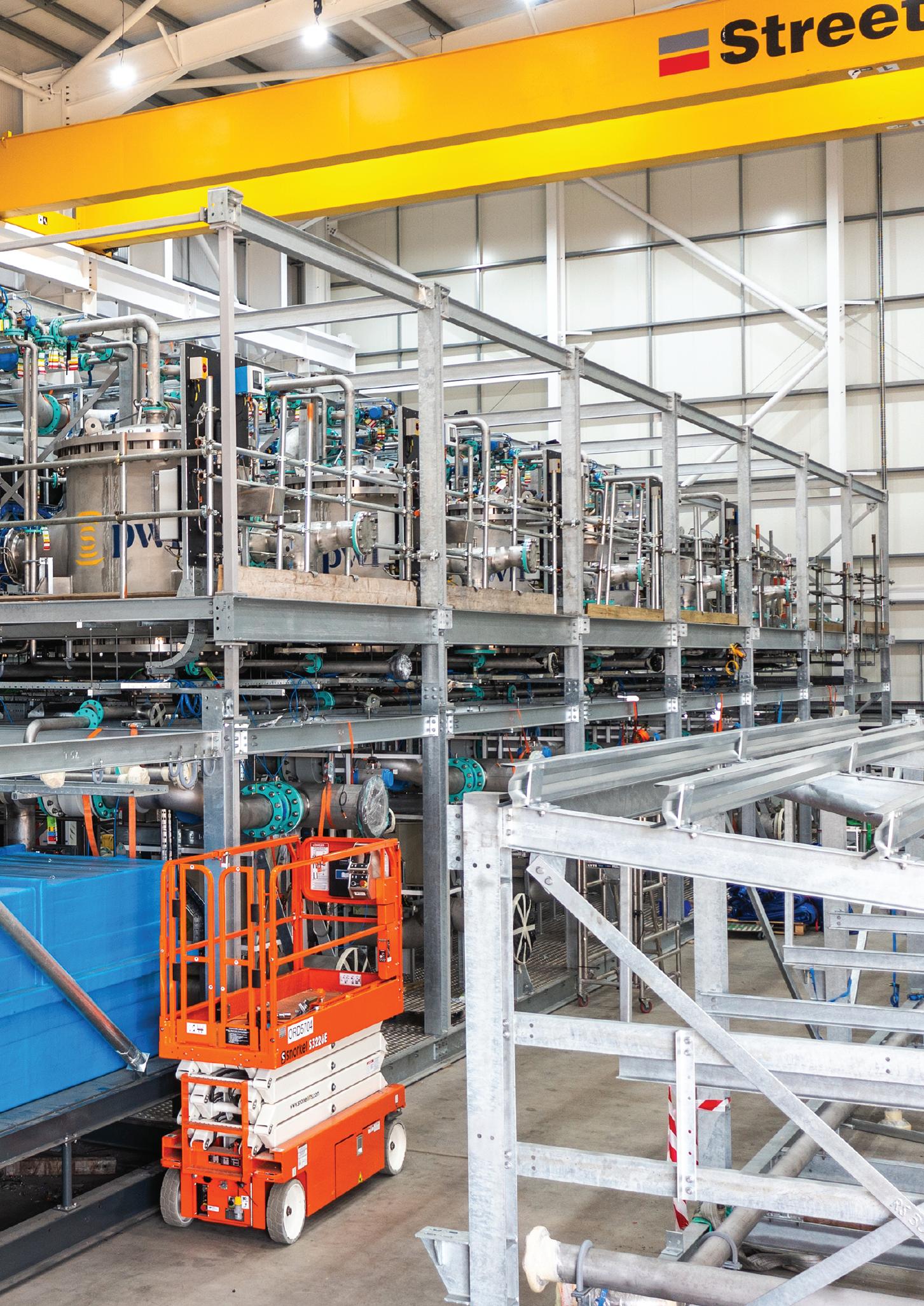
ASa company, RSE is committed to innovation and continuous improvement, Business Development Lead Gary Callachan said: “We are a really unique and dynamic company. RSE encourages the growth of all employees; it recognises talent and gives it the appropriate environment to grow. This is what has allowed us to deliver effective solutions to the sector.”Headquartered in Inverness, Scotland, RSE has facilities across the UK in Inverness, Aberdeen, Edinburgh, Glasgow, Darlington, Basingstoke, London and more. The company was established in 1982 and employs over 1,900 people, more than 350 of whom are professional design-based engineers. RSE’s in-house water technologies division designs, manufactures, tests and delivers
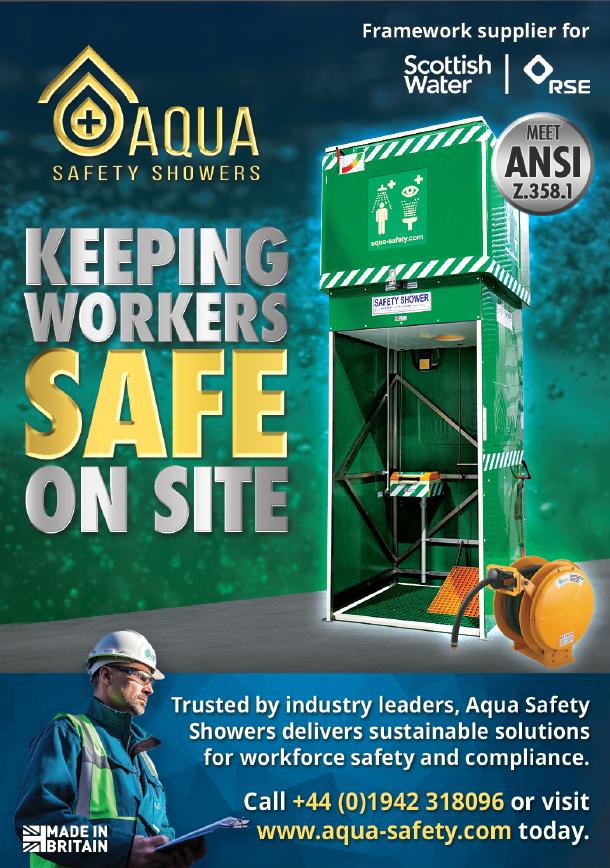
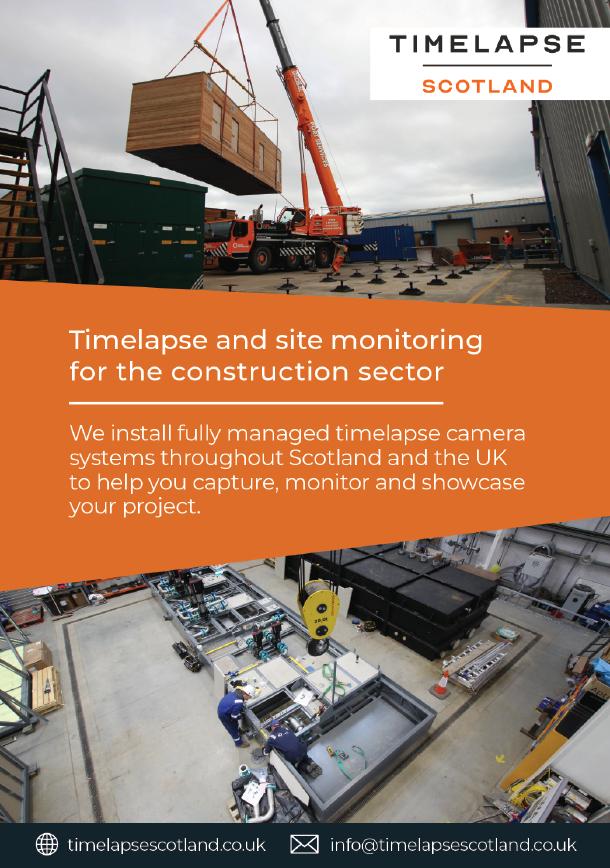

To ensure hygienically perfect drinking water for people in the Scottish Borders, Ross-shire Engineering (RSE) relied on ProMinent’s smart chemical dosing technology.
As a 15-year-long solutions partner, ProMinent’s products were used in systems designed by RSE for various water treatment applications, including disinfection, neutralisation and cleaning in place (CIP). 40 smart metering pumps, which met Scottish Water’s specifications, were supplied – including the peristaltic DULCOFLEX DFXa, motor-driven Sigma and solenoid gamma/ X and XL.
ProMinent is proud to have worked on another successful project with RSE, which will serve people in the local community.
editorial mention
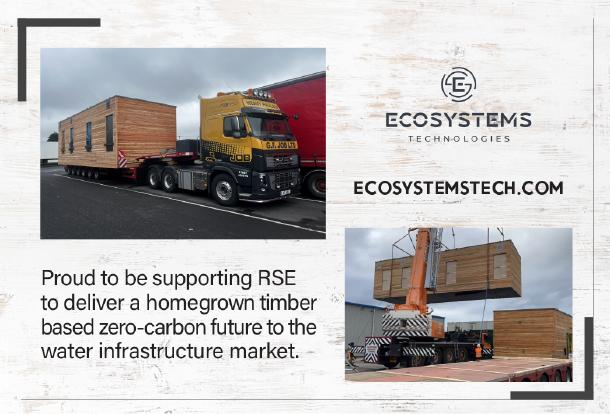
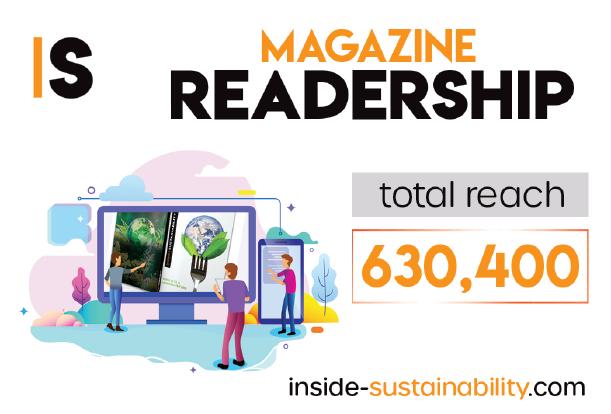
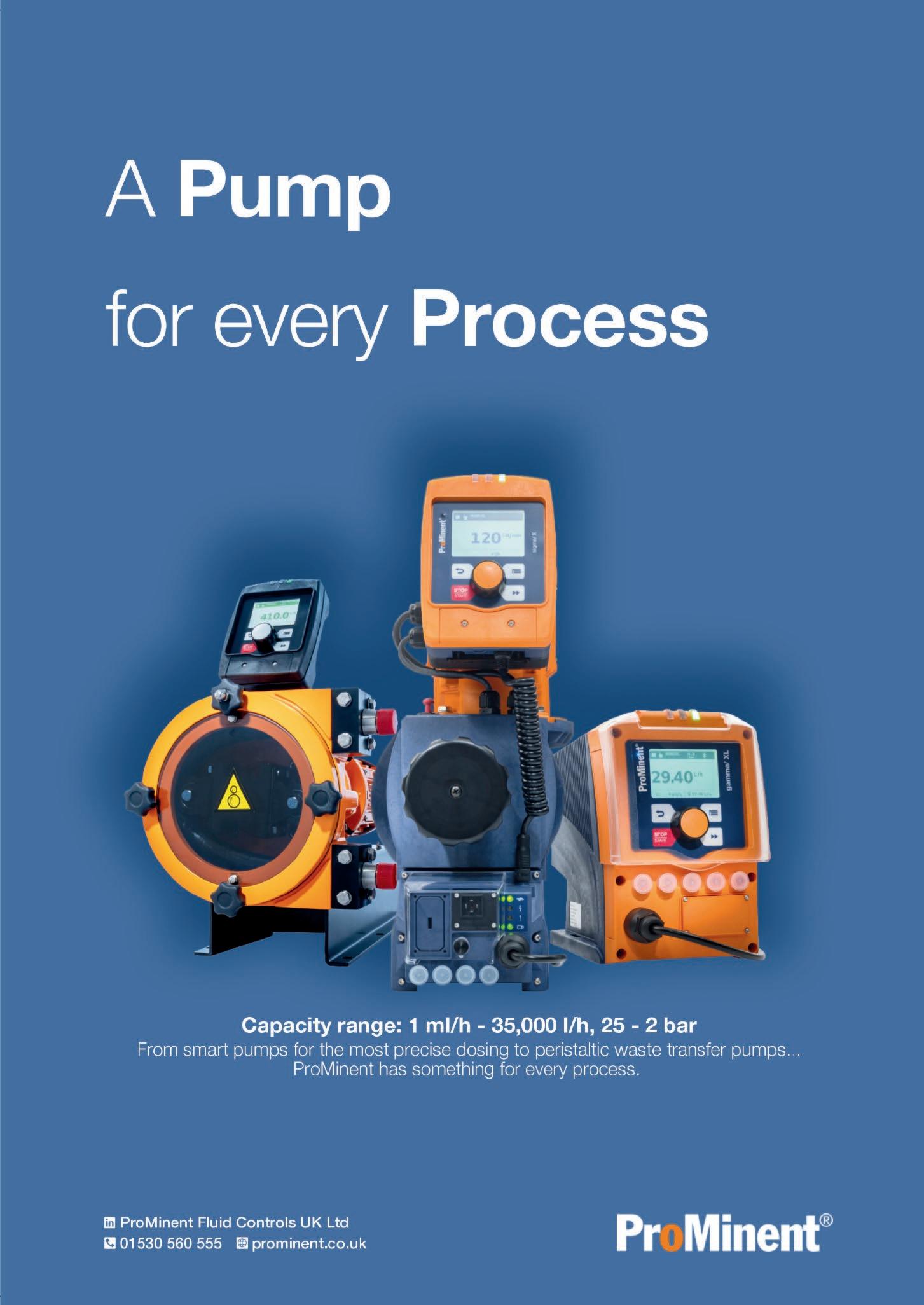
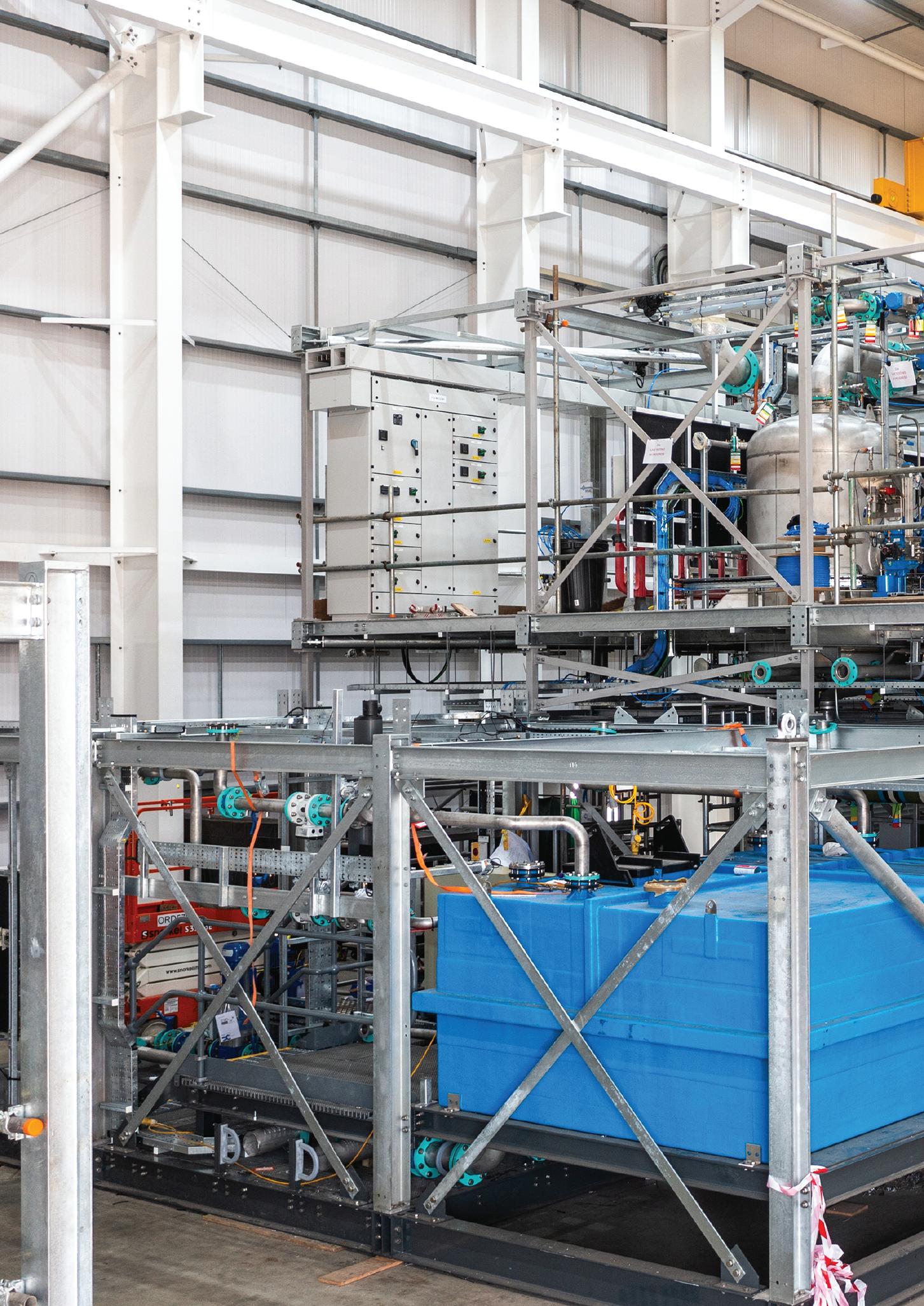


a range of mechanical filtration, chemical dosing and biological water treatment solutions. Multiple modular plants operating at up to 500 megalitres a day have been delivered, providing environmental and water quality improvements to end-users.
“Our engineers and field technicians manage inspection, repair and maintenance tasks for over 35,000 water sector assets a year,” added Mr Callachan. “We provide clients with flexibility, reliability and trusted expertise.
“Outside of the automotive and aerospace sectors, we have the largest manufacturing capability in the UK, with our sites measuring a combined total in excess of 350,000 square feet. This allows us to build our Transportable Treatment Units, which offer massive environmental benefits compared to traditional site construction methods.”
Developing processes
The company’s Transportable Treatment Units are constructed at its state-of-the-art fabrication facility, before they are transported
to the specified site and assembled to create a water treatment plant. This means that the unit can be built while the concrete it will be placed on is being set, almost halving the installation time. Each unit is contained within a steel frame and primarily uses ceramic filtration technology to transform water quality from poor to excellent.
“We’ve been working to decarbonise these units using sustainable materials,” explained Sustainability Manager Stephen Webb. “This includes sourcing from low-carbon and recycled steel suppliers, as well as introducing Timber Modular Build units as a sustainable alternative. Timber is a renewable and low-impact resource that massively improves the sustainability of the product, allowing us to offer environmentally conscious solutions to clients.”
Additionally, RSE is using ceramic membranes, an innovative technology for water treatment. Used for various water sources, including drinking water, wastewater and industrial process water, ceramic membrane filtration offers higher efficiency, a longer lifespan and lower operating costs. They are a sustainable solution as they reduce waste, require less energy to run and use fewer chemicals.
“A lot of these solutions will be important for the future, with climate-related challenges like water scarcity growing,” continued Sustainability Coordinator Leia Pol. “These solutions are being developed to minimise the impact of that. We are also taking a lot of steps to decarbonise our operations and have installed solar panels, as well as a biomass boiler that uses sustainable wood
Our engineers and field technicians manage inspection, repair and maintenance tasks for over 35,000 water sector assets a year.
RSE Sustainability Manager Stephen Webb

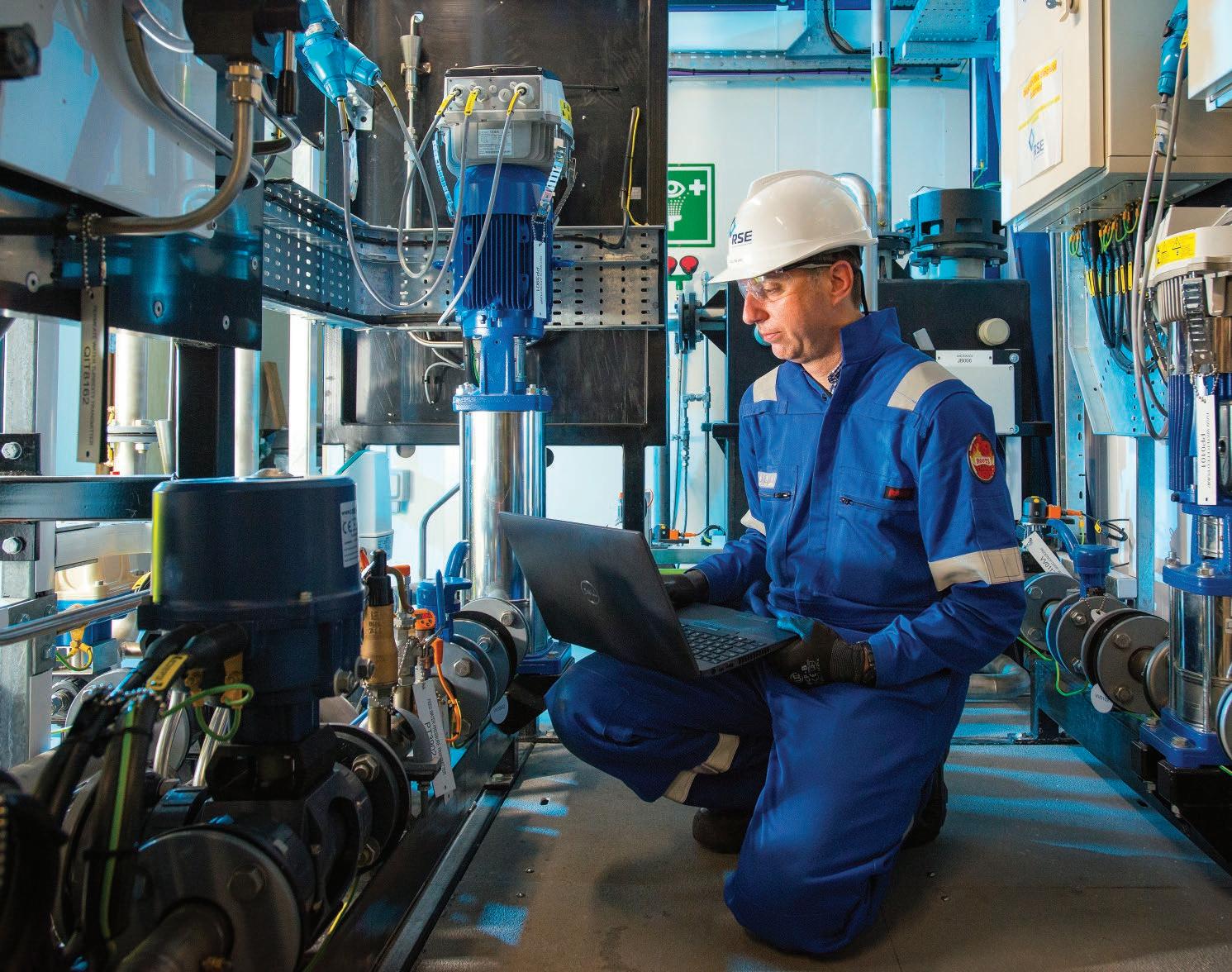
pellets to generate our power. One of our locations has a rainwater harvesting plant and we are introducing hydro-treated vegetable oil to replace diesel used by our fleet too.”
The Transportable Treatment units minimise the environmental impact of an installation as only a single delivery needs to be made to the site from just one location. The external structure of the unit is also reusable. This means that if a unit is no longer used for any reason, the frame can be taken back to site, upgraded and used in another project. Reusing the frame promotes a more circular economy and, in one project, saved up to 20 tonnes of carbon.
Engineering solutions
All over the UK, RSE’s Transportable Treatment Units have made a significant improvement to water resource use. For example, in Scotland there are many rural areas with very shallow lochs and water sensitive areas that are at risk of drought. The units help to combat this with efficient and resourceful treatment solutions.
By the end of March 2025, RSE plans to have completed the construction, installation and commissioning of the ceramic filtration stage of the world’s largest ceramic membrane plant. Located at Hampton Loade Water Treatment Works, Shropshire, this project is
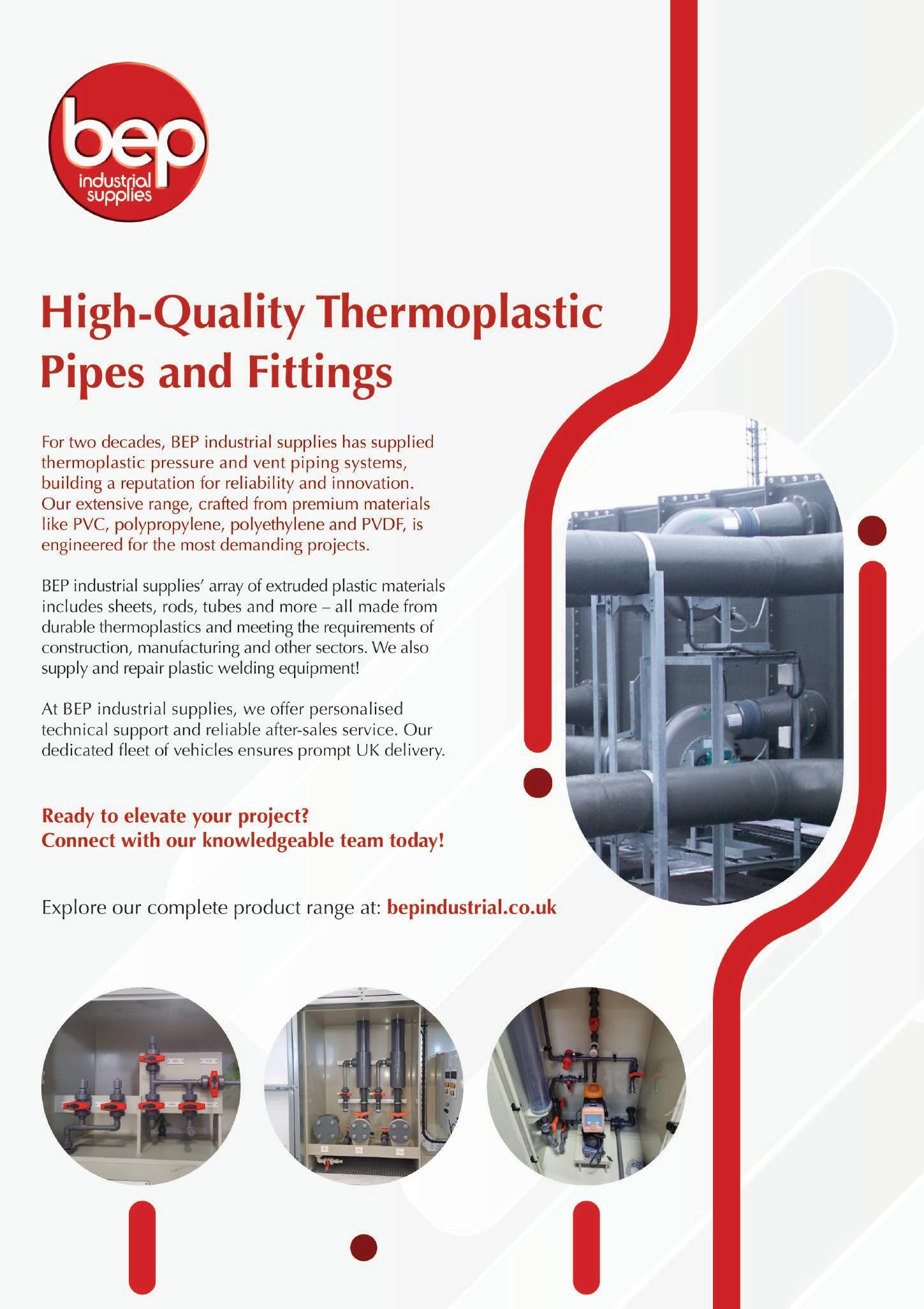
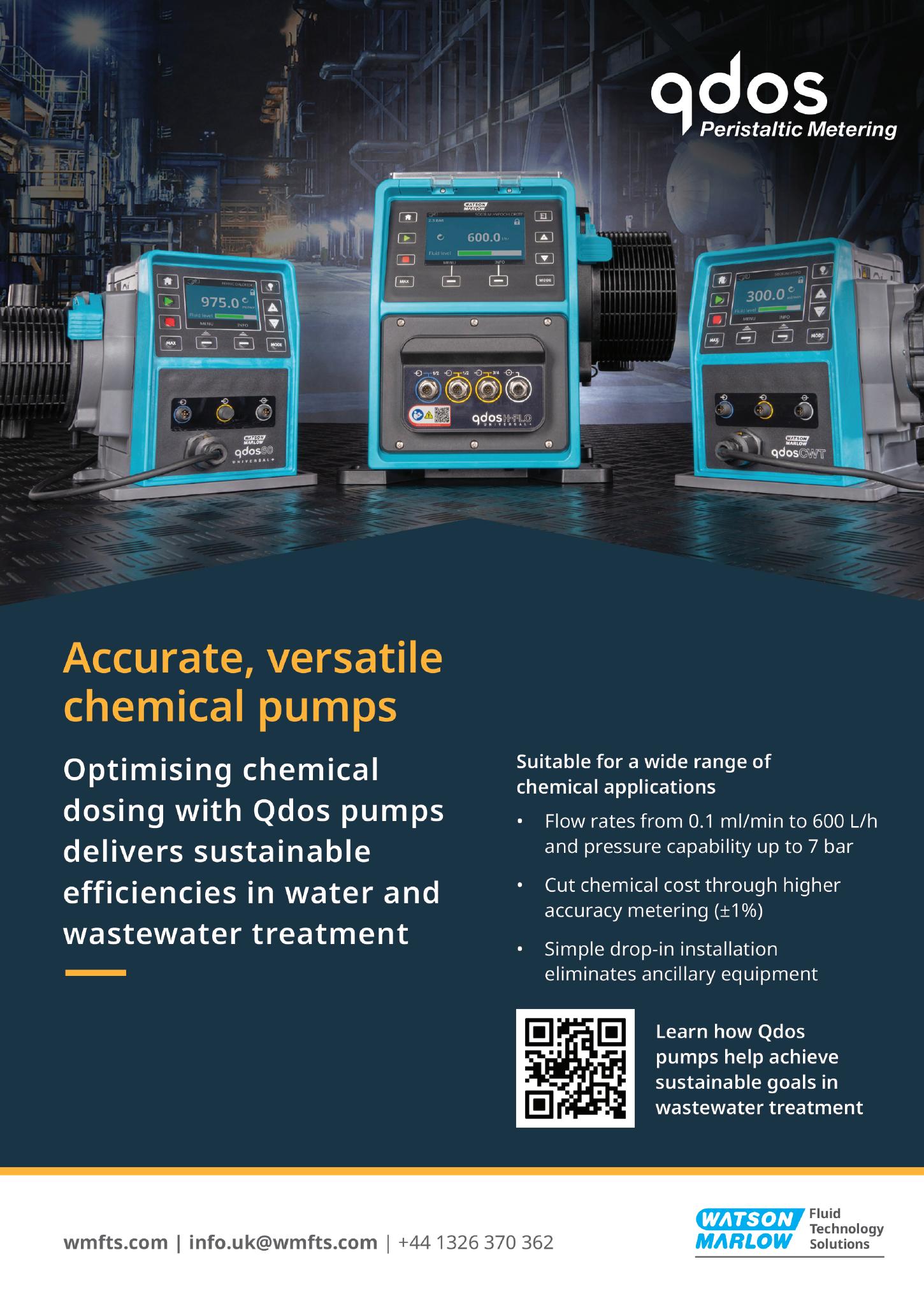
part of a £57 million refurbishment plan. The site has the capacity to produce 210 million litres of high-quality water every day, serving approximately 700,000 customers. RSE will increase the capacity of the facility with a ceramic membrane filtration solution.
“Another significant project of ours was at the Bonnycraig Water Treatment Works,” commented Mr Webb. “We designed and constructed a 4.5 megalitres per day ceramic membrane modular solution within Transportable Treatment Units, commissioned by
Scottish Water. With 17 modular units within a two-storey building, this has been our biggest project of this kind. It was also the first ceramic membrane plant built and installed in Scotland.”
Using an off-site manufacturing process saved RSE approximately 18 months of work compared to traditional methods, significantly reducing carbon impact. The roof also accommodates a system of solar panels, minimising reliance on unrenewable energy sources.
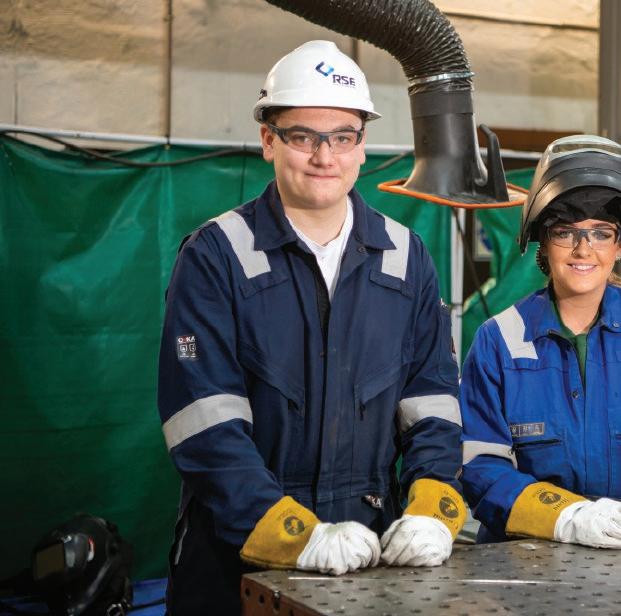
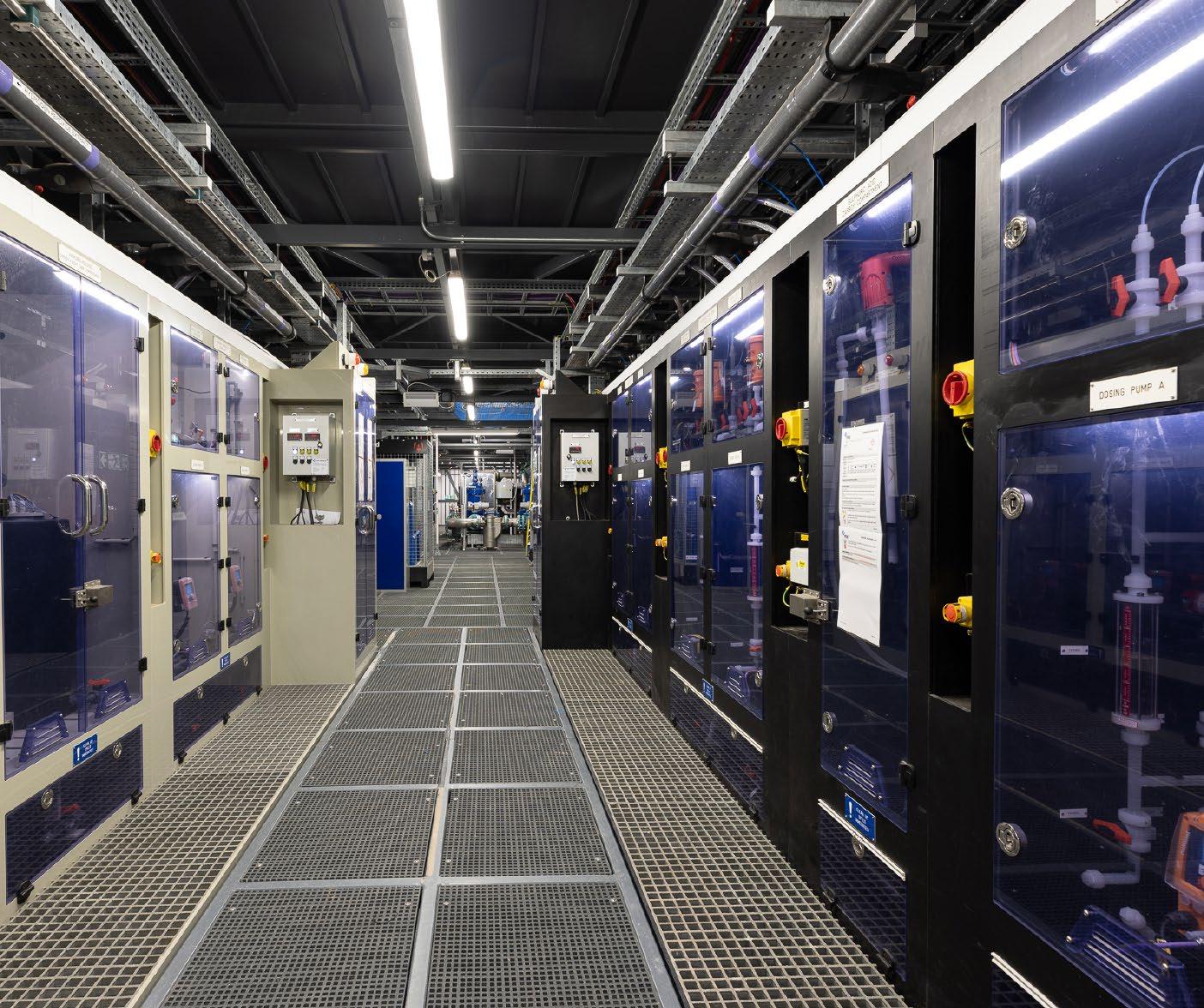
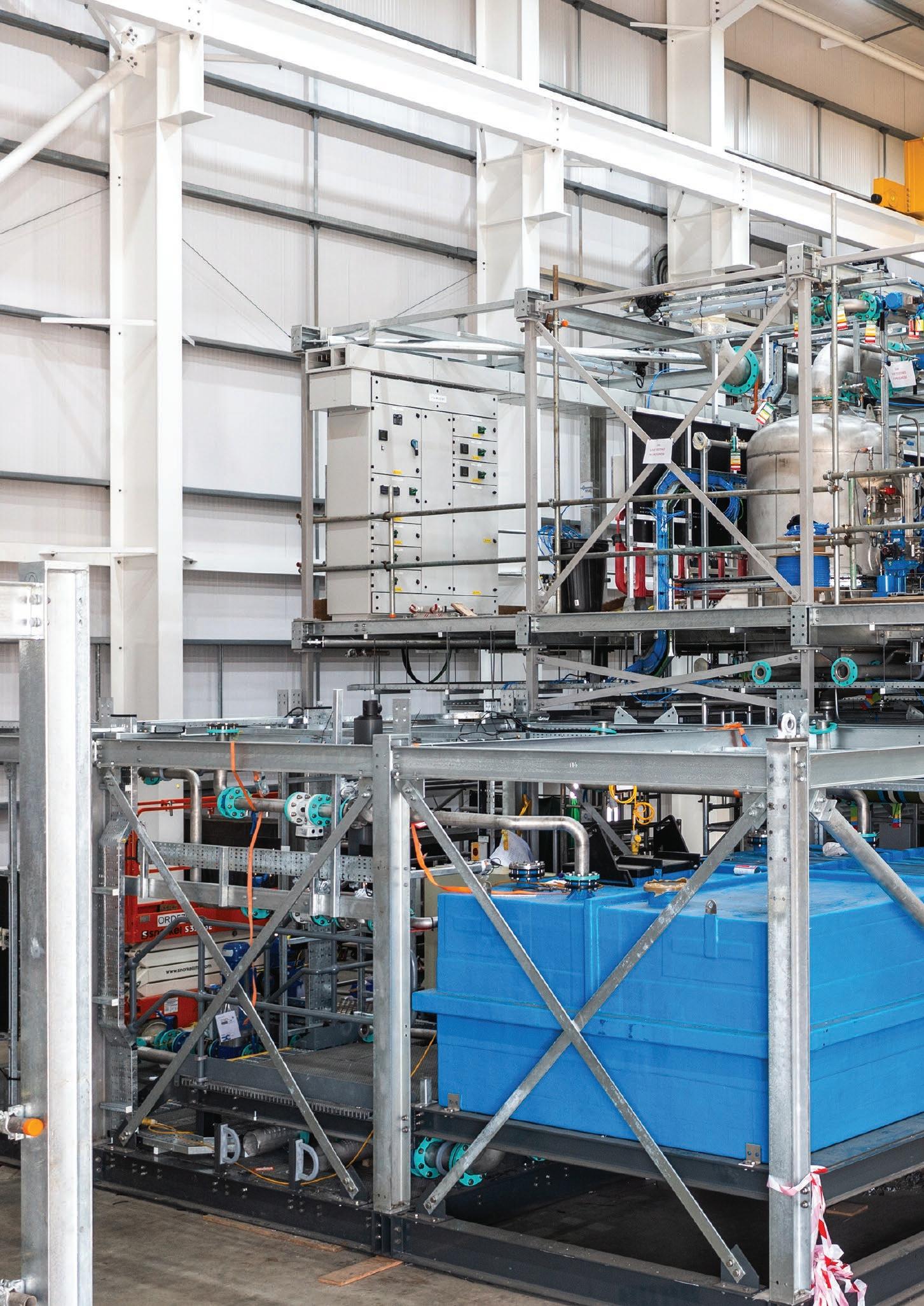
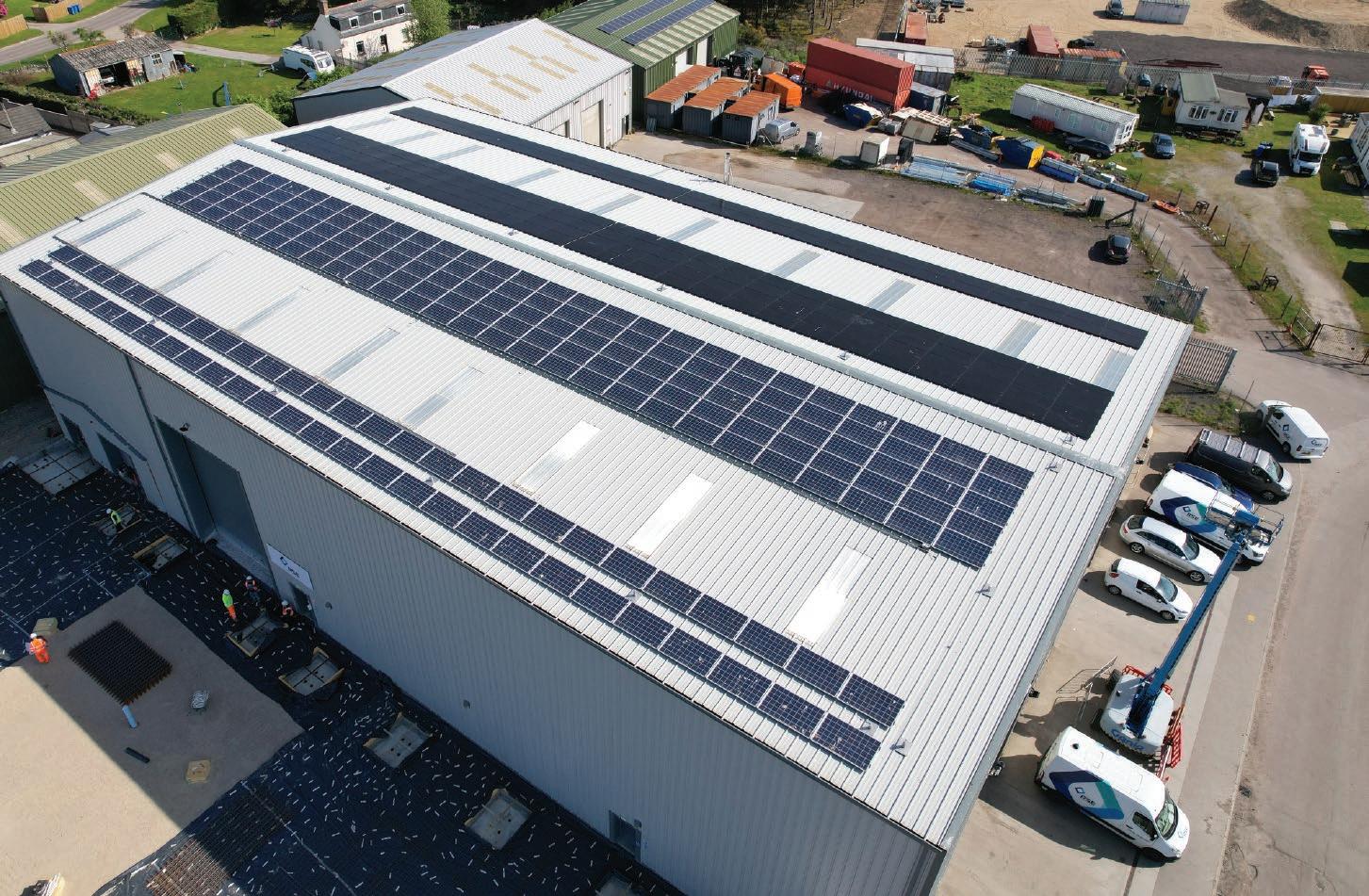

Innovative partnerships
For RSE, it is vital to engage with the supply chain to enable large projects to be carried out sustainably. Through collaboration and the exploration of innovative materials, the company is able to make the necessary progress to reach net zero targets.
“We have been working closely with our supply chain,” said Ms Pol. “RSE is focusing on strategic sourcing, as well as gathering environmental product declarations from suppliers. Right now, this can be difficult as not all suppliers have them, but we are showing that the demand is there so that we can work together and make sustainable advancements within the industry.”
One of RSE’s key suppliers is GF Piping Systems, a global expert in plastic piping systems. Through this partnership, the company has developed a number of innovative piping systems that use

infrared radiation instead of a chemical solvent to join partly bio-based PVCU pipe and fittings, offering a more sustainable solution to RSE’s customers.
“These sustainable innovations are what really drive the company forward,” continued Mr Callachan, in conclusion. “Since I started with the company in 2020, our turnover has grown from £70 million to £330 million, which has been great to see. We are working with water authorities all across the UK and are now looking at how we can expand both internationally and into new sectors, such as the hydrogen and lithium markets.
“To continue this growth, RSE has many initiatives in place to encourage future talent, including apprenticeships and graduate programmes. By harnessing the ideas and innovations of young people, we can really move the industry forward. It’s great to see people develop through the company, just as I have done over the years.” n
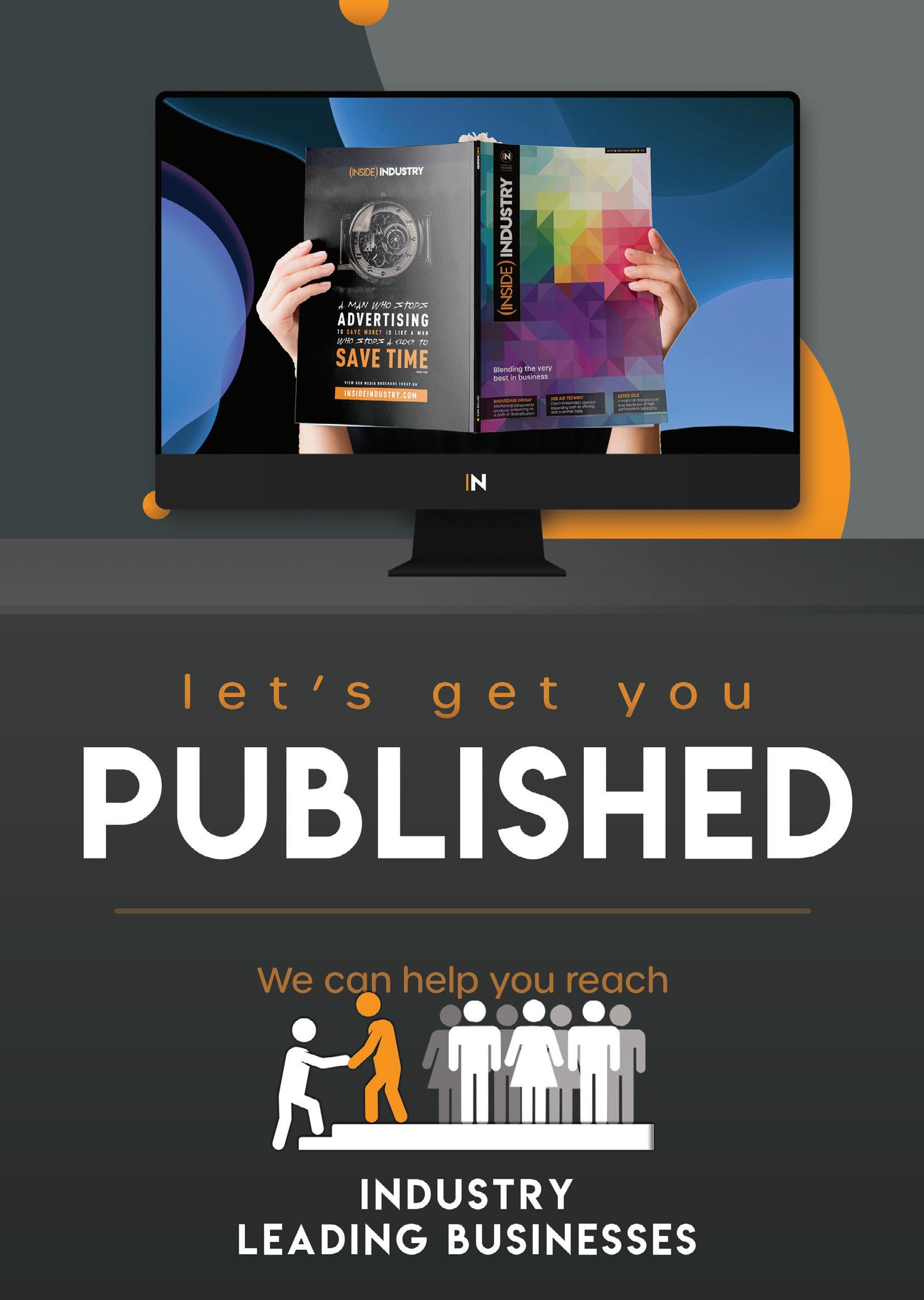
