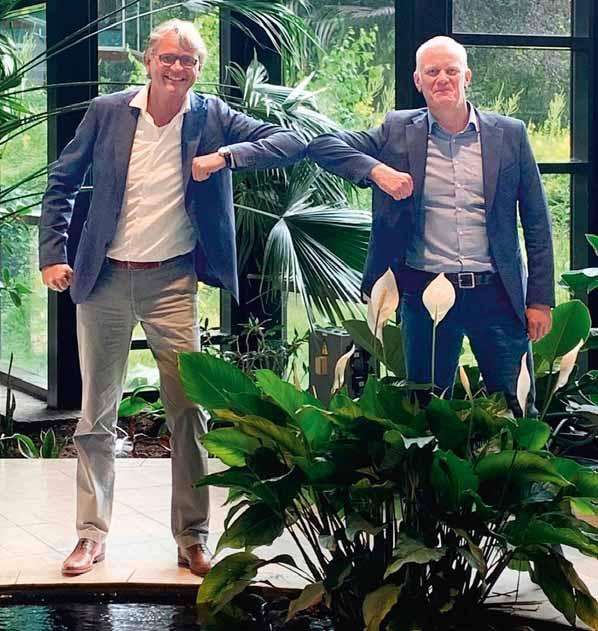
32 minute read
Column
SAMENWERKING FOSFAATTERUGWINNING
Aquacare en Royal HaskoningDHV gaan een baanbrekende oplossing voor fosfaatverwijdering en fosfaatterugwinning naar de markt te brengen, genaamd BiOPhree. De samenwerking richt zich op de huishoudelijke afvalwatermarkt in Nederland en het VK. Door het fosfaat vergaand uit afvalwater te verwijderen treedt er minder algengroei op, wat goed is voor het watermilieu, terwijl er tevens grondstoffen worden teruggewonnen.
Tako van Croonenborgh (links), managing director Aquacare, en Paul Roeleveld, director business development & innovations Royal HaskoningDHV, geven elkaar ‘de elleboog’ in het kader van de samenwerking. (Foto: Royal Haskoning DHV)
Het rapport ‘Waterstofversnelling: mogelijkheden in het Noordzeekanaalgebied’ van Roland Berger laat zien dat het potentiële gebruik van waterstof in het Noordzeekanaalgebied (NZKG) zo groot is dat de regio als vliegwiel kan fungeren voor de Nederlandse waterstofeconomie. De industrie, zee- en luchthavens in het NZKG willen in 2050 CO₂-neutraal te zijn. Dit vereist snelle opschaling van de waterstofeconomie, want uit het rapport blijkt dat het gebied al in 2030 ongeveer acht keer zoveel waterstof nodig heeft als het kan produceren. De grootste toekomstige afnemer van waterstof is Tata Steel die waterstof gebruikt om groen staal mee te produceren. Daar bovenop is er veel waterstof nodig voor de productie van duurzame brandstoffen voor de scheep- en luchtvaart. De totale vraag naar waterstof van deze ontwikkelingen samen bedraagt 220 kton in 2030 en zelfs 555 kton in 2035. Deze schaalgrootte is ongekend in Europa en maakt NZKG mogelijk tot internationaal vliegwiel van de waterstofeconomie. Het is dan wel nodig de benodigde infrastructuur versneld aan te leggen. Met name het aansluiten van de regio op de een nationale waterstofruggen graat (hoofdleiding) is essentieel. Bottleneck is de financiering vanuit de overheid die onvoldoende is om de opschaling van de waterstofeconomie te realiseren.
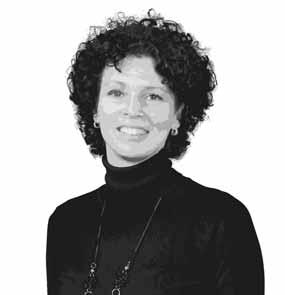
Noordzeekanaalgebied kan vliegwiel worden voor de waterstofeconomie. (Foto: info@noordzeekanaalgebied.nl)
COLUMN FIT FOR 55 : 55% REDUCTIE IN 2030!
De titel doet misschien vermoeden dat ik tips ga geven over hoe je fit de leeftijd van 55 jaar kunt aantikken. Maar nee, ik bedoel het Fit for 55-pakket waarmee de Europese Commissie wil voorzien in een eerlijke, concurrerende en groene transitie naar een klimaatneutraal Europa. Een pakket waar ik benieuwd naar ben. Want met de klimaattop nog vers in het geheugen, lijkt het erop dat we veel praten, maar nog weinig in ‘action, action, action’ komen.
De uitstoot van broeikasgassen moet in 2030 met 55% omlaag ten opzichte van het niveau van 1990. Vandaar het ‘Fit for 55-pakket’. Commissievoorzitter Ursula von der Leyen noemt het een van de meest ambitieuze hervormingen van het EU-beleid ooit. Een tiental wetsvoorstellen moet zorgen voor realisatie van de doelstellingen van de Green Deal. Uiteindelijk is Europa dan in 2050 klimaatneutraal.
Ondernemersorganisatie voor de technologische industrie FME is blij met het Fit For 55-pakket. Er wordt niet langer gestuurd op nationale CO₂-reductie, maar op een gezamenlijke CO₂-reductieopgave voor alle EU-lidstaten. “Zo beschermt Fit For 55 enerzijds de concurrentiepositie van onze industrie en vergroot het anderzijds de kansen van Nederlandse energie-innovaties op de Europese markt”, aldus FME.
De technologische industrie wil de vernieuwde Europese ambitie onder andere behalen met Plan 6-25. De focus ligt op innovaties die de procesefficiency verbeteren en kosten verlagen. Zo moet tot en met 2025 een reductie van 6 Mton CO₂ per jaar worden gerealiseerd.
Mooie plannen, maar zijn we niet aan de late kant? Gelukkig zijn er bedrijven die het roer al lang hebben omgegooid. Neem het bedrijf Interface (producent van tapijttegels) waar duurzaamheid en circulariteit inmiddels de leidraad vormen voor hun businessmodel. Interessant hoe zij dit samen met hun ketenpartners succesvol in de praktijk brengen en wat de visie en drivers hierachter zijn. Wil je hier meer over weten, kijk dan de film ‘Beyond Zero’.
Met dit soort praktijkvoorbeelden kunnen we wat! En er is er geen tijd te verliezen. De roep om duurzame productie en consumptie en een circulaire economie wordt groter. Daar kunnen we eindeloos over blijven brainstormen, maar laten we vooral samen met onze ketenpartners de mouwen opstropen en beginnen!
Astrid van Ballegoy Marketingmanager Hitma
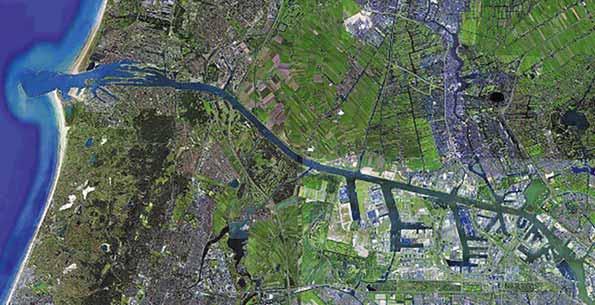
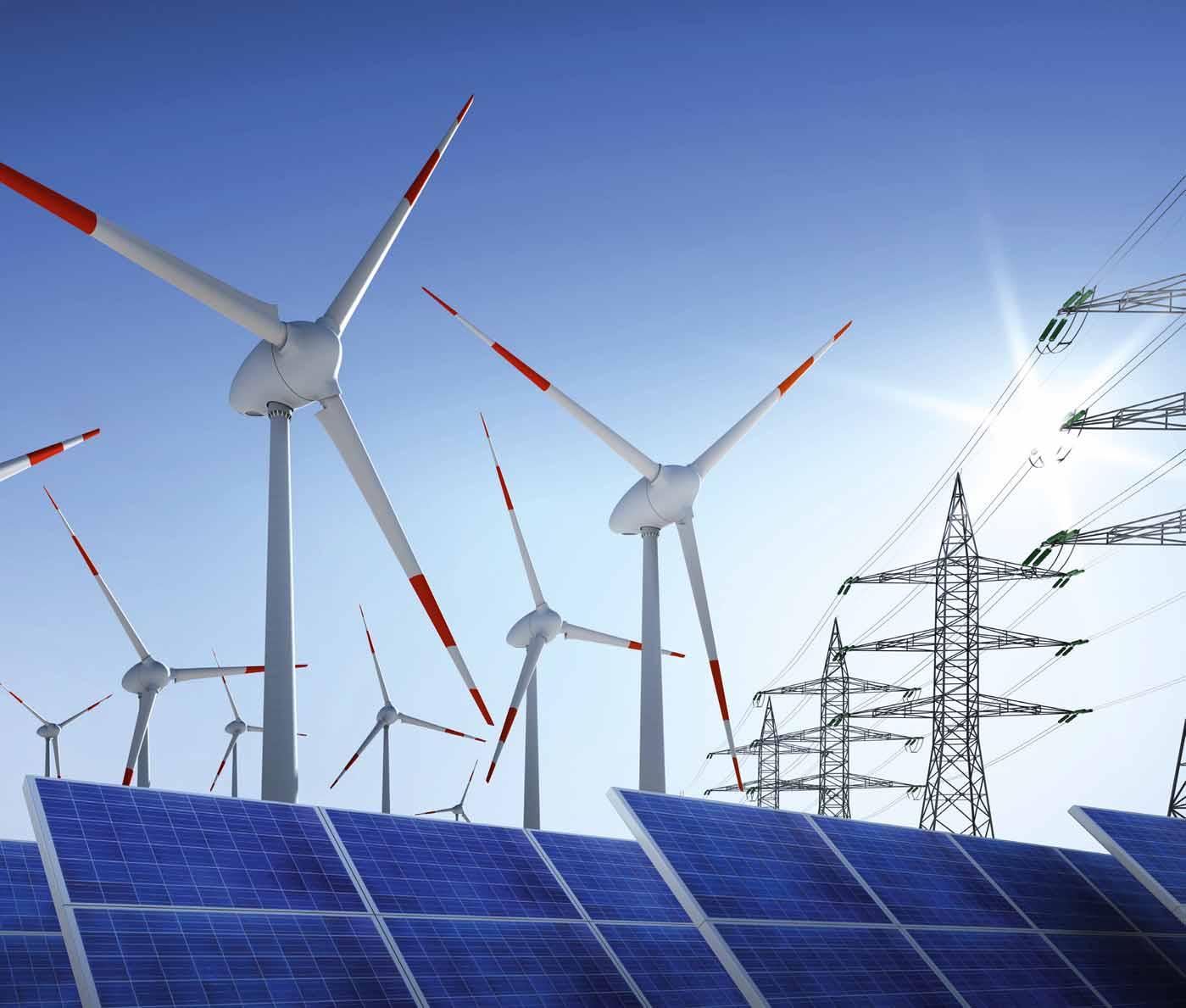
ENERGIETRANSITIE: ‘GENOEG LAAGHANGEND FRUIT’
De belangstelling voor de ‘energietransitie’ resulteerde in een goede opkomst tijdens de ‘Ronde Tafel Duurzaamheid’ die tijdens de combibeurs Solids en Pumps & Valves Rotterdam werd georganiseerd. Deelnemende leveranciers hebben de technologieën klaar staan om fors op het energieverbruik te besparen en zo de CO2-uitstoot te reduceren.
Alternatieve energiebronnen. (Foto: Adobe Stock) Afgevaardigden van de droge en natte procesindustrie lanceerden tijdens het rondetafelgesprek hun praktische oplossingen waarmee de industrie de emissies de komende jaren fors omlaag kan brengen. Op het podium stonden Dinnissen Process Technology, Gorman-Rupp Europe, Hosokawa Micron en Van Beek Schroeftransport. Ze kwamen niet met vergezichten over de techniek van de toekomst, maar leverden boter bij de vis. Tientallen procenten terug in uitstoot is nu al mogelijk. De technologie is er klaar voor, nu is de industrie aan zet. Die lijkt nog wat te aarzelen. Aan de reacties uit de zaal af te lezen is ‘energietransitie’ voor menigeen nog een ver-van-mijn-bedshow.
ZONNEDAKEN Op het podium stonden salesmanager Rieks Reyers namens Dinnissen, algemeen directeur Chris van der Gaag van Gorman-Rupp Europe, Perry Verberne, Machevo-voorzitter en directeur van Van Beek, en manager sales & marketing Berthram Mak namens Hosokawa Micron. Alle vier hebben ‘energietransitie’ in chocoladeletters in hun strategische visie geschreven. De eerste stappen zijn ook al gezet, te beginnen bij de productie van machines. Dinnissen zet volgens Rieks Reyers binnen de eigen processen op diverse fronten in op duurzaamheid. “We hebben zonnecellen laten installeren op het dak van de oude en nieuwe fabriekshallen. Daarmee wekken we genoeg energie op om klimaatneutraal te kunnen produceren, mede door energiebesparingen in ons proces. De nieuwe fabriekshal is ingedeeld op minimaal intern transport.”
STARTUPS Zonnepanelen liggen trouwens ook op de daken van Gorman-Rupp, Van Beek en wereldwijd bij Hosokawa Micron. Van der Gaag: “Ons zonnedak maakt ons eigen proces energieneutraal. Intern kun je, zoals Rieks aangeeft, ook nog van alles doen. Ook al eens gedacht aan het vervangen van traditionele schoonmaakmiddelen door alternatieven op basis van natuurlijk ingrediënten? Een hele
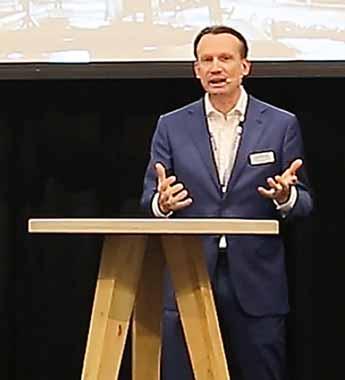

mooie startup is Peel pioneers die grondstoffen voor reinigers uit sinaasappelschillen wint. Wij hebben nu reinigingsmiddelen in de productie en werkplaats vervangen door een biologisch afbreekbare variant. Daarmee kun je gelijk dit soort startups steunen!”
MINDER LOGISTIEK Mak: “Naast dat we voor onze gebouwen, bedrijfsvoering en fabricage in diverse Hosokawalocaties zonne-energie opwekken, kiezen we voor ledverlichting en een centraal persluchtsysteem. Met computergestuurde regeling van werktuigmachines – ons hele CNC-machinepark is gemoderniseerd – verlagen we de carbon footprint van het primaire fabricageproces van de apparatuur. Binnen onze logistieke processen realiseren we minder logistieke bewegingen door nieuwe en slimmere inrichting en routing tussen bewerkingscentra binnen het eigen fabricageproces en van assemblage en eindmontage. Onze nieuwe centrale locatie voor verzending, ontvangst en opslag van onderdelen en machines is in dit kader het noemen waard. “
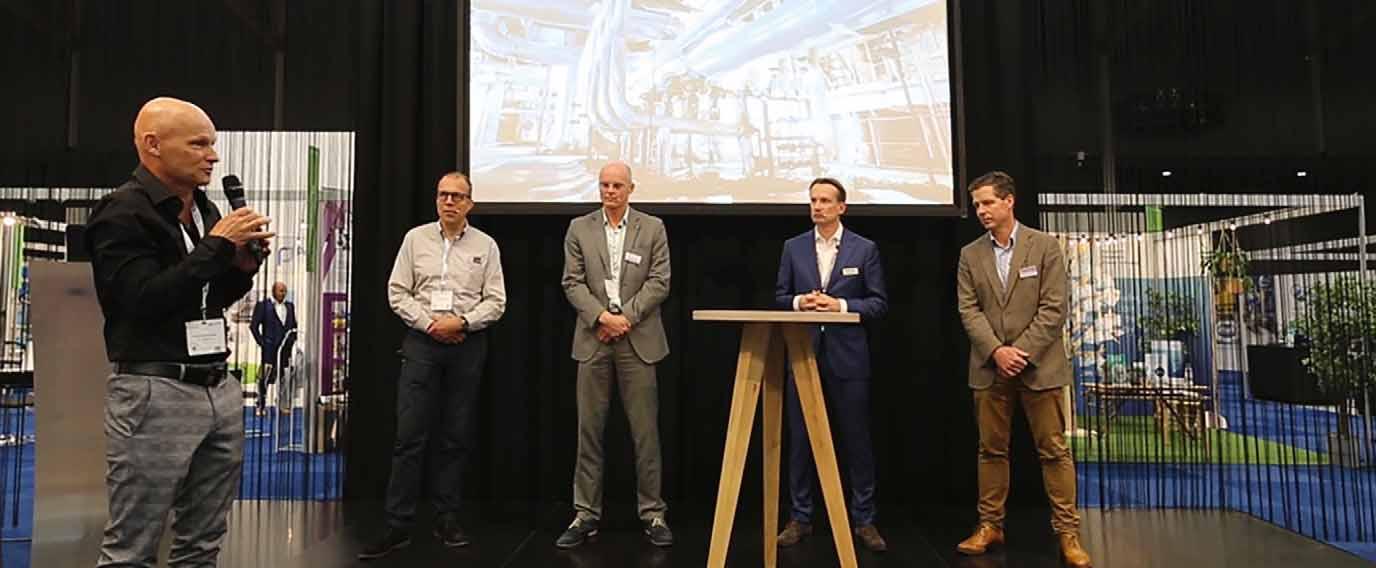
Ronde Tafel Duurzaamheid tijdens de combibeurs Solids en Pumps & Valves Rotterdam, oktober 2021. (Foto: Foodnote)
REDUCE, RE-USE, RECYCLE Bij Van Beek is circulariteit van installaties al jaren belangrijk in het ontwerp. Machines worden zo gemaakt dat ze gereviseerd kunnen worden, en er wordt nagedacht over hergebruik van componenten in het eindstadium. Verberne. “Wat betreft circulariteit baseer ik me met name op onze terugkoopgarantie en refurbished programma. Bij duurzaamheid worden vaak de 3 R’s van Reduce, Re-use en Recycle gehanteerd. Wat mij betreft is hergebruik van machines dus een prima invulling van dit principe, aangezien daardoor ook minder nieuwe machines gemaakt hoeven worden. Door goed onderhoud kunnen machines langer meegaan. Dit bevordert dan ook het minder snel hoeven te kopen van nieuwe machines. Goed onderhoud kan veel energie besparen en minder nieuwe machines bouwen scheelt in de grondstofketen. Kortom, allemaal winst.”
EFFICIËNTERE ELEKTROMOTOREN Het inbouwen van moderne elektromotoren kan een fors verschil maken in energieverbruik. Alle deelnemers gaven aan hun apparatuur zo veel mogelijk met deze motoren uit te rusten. IE4motoren staan voor superpremium efficiëntie volgens de standaarden van de International Electrotechnical Commission. De IEC ontwikkelt en publiceert de algemene internationale normen voor elektrische componenten en apparatuur. Nu IE4 is uitgerold, is IE5 de volgende stap in zuinigere motoren. De parameters van deze efficiëntieklasse zijn nog in ontwikkeling. Naar verwachting van de IEC zullen motoren in
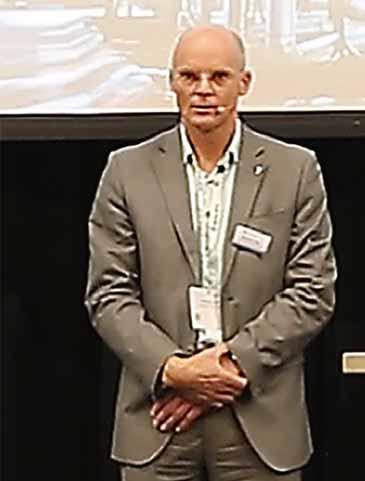
Berthram Mak, manager sales & marketing Hosokawa Micron
“Met technische optimalisatie bij het ontwerp van installaties valt veel winst te behalen. Denk ook aan het optimaal op elkaar afstemmen van bestaande en nieuwe productieprocessen voor een hogere productiviteit. En het uitrusten van installaties met Internet of Things. Dat verhoogt de uptime, en dus het rendement en de productie, en kan 10% of meer besparen in de uitstoot.”
deze nieuwe klasse het energieverlies met ongeveer 20% verminderen ten opzichte van de IE4motoren. Rieks Reyers. ‘Ja, we bouwen dat type energiezuinige motoren in.” Mak ziet op het vlak van elektromotoren nog veel laaghangend fruit hangen. Want IE4 is absoluut nog geen standaard in de industrie. “Bedenk dat het toepassen van elektromotoren met de IE3 efficiëntieklasse pas sinds 1 juli 2021 van kracht is voor praktisch alle motoren! Maar het kan nog veel zuiniger, want het rendement neemt, afhankelijk van het vermogen en gebruik, tussen de 2 en 10% per stap in de klasse toe. De vervanging van bestaande oude elektromotoren door efficiëntere motoren levert direct en veel energiewinst op.”
BESPAREN OP PERSLUCHT Een stille energievreter in de (droge)procesindustrie is perslucht. Het kost veel energie die op te wekken, en persluchtsystemen willen nog wel eens lekken. Hier wordt veel te weinig bij stil gestaan, stelt Perry Verberne. “En dat is zonde. Over nut en noodzaak van het controleren van luchtafdichtingen hebben wij een whitepaper geschreven. Als vuistregel gebruik ik dat 1 kuub perslucht ongeveer 2,5 eurocent kost – uitgaande van een elektriciteitstarief van +/- 0,20 euro per kWh. De jaarlijkse kosten voor perslucht lopen daardoor gauw op. Stel je produceert 100 kuub perslucht per uur met een compressor van 11 kW. Dan zit je in een uurtje al op 2,5 euro! Dat gaat dus heel hard. Wat dat voor individuele gevallen aan kosten is, valt lastig te becijferen. Dat hangt af van het soort afdichting, het aantal afdichtingen, en de exacte staat van de afdichtingen, etc. Maar ik wil er maar mee zeggen dat er meer bewustzijn rond dit onderwerp mag komen. We hameren erop bij onze klanten dat ze hun persluchtsystemen op orde hebben. Alles wat je daar bespaart, is winst voor het milieu en je portemonnee!”
HERNIEUWBARE BRANDSTOF Chris van der Gaag stelt dat het gebruik van duurzame brandstoffen tot een enorme uitstootreductie kan leiden. Maar dat is gemakkelijker gezegd dan gedaan, omdat de motoren van de pompen hiervoor aangepast moeten worden. Gormann-Rupp heeft dit traject nu succesvol doorlopen en biedt daarmee pompgebruikers een veel duurzamer alternatief. “Onze dieselaangedreven pompsets zijn vrijgegeven voor het gebruik van 100% HVO niet-fossiele brandstof. Dat is diesel geproduceerd op basis van met waterstof behandelde plantaardige oliën en restafval, zoals dierlijke vetten. Daarmee bereik je een ISCC- gecertificeerde CO2-reductie van 89%.” Helaas is die indrukwekkende milieuwinst onvoldoende om de markt massaal over de streep te trekken, ziet ook Van der Gaag. Als kosten voor de baat uitgaan hebben gebruikers een duwtje in de rug nodig. “Overheden als gemeenten en waterschappen moeten hierin het voortouw nemen. Zij kunnen heel eenvoudig voorschrijven dat het gebruik van dergelijke brandstoffen bij bouwprojecten binnen hun verantwoordelijkheid op zijn minst de voorkeur geniet, zo niet verplicht gesteld moet worden. Zonder de dwingende vraag vanuit de eindklant zal de markt hier niet zomaar op overstappen. Technisch zie ik geen obstakel. De aanpassingen aan de motor en brandstofsysteem zijn voor een professionele OEM-fabrikant prima te doen.” Overstappen op elektrische apparatuur zet eveneens zoden aan de dijk, voegt hij toe. Zijn bedrijf ontwikkelt daar complete oplossingen voor. “Voor elektrificatie van de mobiele vloot, waarbij we zelfs een concept hebben ontwikkeld om elektrische pompsets aan te kunnen sluiten op een auto-oplaadpunt.”
LIJNOPTIMALISATIE Processen als mengen en drogen kosten nu eenmaal veel energie. Juist hier valt met technische optimalisatie bij het ontwerp van installaties nog veel winst te behalen. Cruciaal daarvoor is een goede samenwerking tussen de verschillende partijen die betrokken zijn bij het ontwerp en de installatiebouw, stelt Mak. Door technische onderdelen goed op elkaar af te stemmen kan een installatie als totaal zuiniger draaien en kan er bijvoorbeeld door warmteterugwinning veel energie worden bespaard. “Denk bij lijnoptimalisatie ook aan het optimaal op elkaar afstemmen van bestaande en nieuwe productieprocessen voor een hogere productiviteit. En denk aan het uitrusten van installaties met Internet of Things. Dat verhoogt de uptime, en dus het rendement en de productie, en kan een besparing van 10% of meer opleveren in de uitstoot.”
HETER = ZUINIGER Het investeren in zuiniger installaties zet eveneens zoden aan de dijk. Mak: “Wij hebben geïnvesteerd in de ontwikkeling van efficiëntere maal- en classificeerinstallaties die tot wel 25% of soms zelfs nog meer minder stroom gebruiken. We hebben onze convectieve droogtechnologieën doorontwikkeld en weten met hogere luchttemperaturen een energiebesparing te bereiken tot 25%.” Dat zit zo: “Een luchttemperatuur van 600-650 °C maakt het mogelijk je apparatuur kleiner uit te voeren, wat per saldo deze lagere carbon footprint oplevert. Bij onze conductieve droogtechnologieën is de besparing ook altijd nog 10% of meer.” Andere optimalisaties leveren juist verderop in het proces winst op. “We weten uit studies naar productbeweging in mengers en mengwerking dat verbetering van efficiëntie daar relatief weinig elektrische energiebesparing oplevert, maar wel een merkbaar hogere lijnproductiviteit oplevert.” Opstartverliezen kosten geld én energie. Dinnissen heeft zijn mengapparatuur daarom ontworpen om dit tot een minimum terug te dringen. “Optimalisatie van mixprocessen is bij onze apparatuur niet nodig”, stelt Reyers. “De Pegasus menger is binnen 30 tot 45 seconden klaar.”
FAT/SAT OP AFSTAND Dinnissen heeft gedwongen door de coronapandemie vaart gezet achter commissioning van installaties op afstand. Voor de zogenoemde Site Acceptance Tests moest altijd personeel ingevlogen worden. Voor Factory Acceptance Tests moest de klant naar de fabriek komen. Beide gingen gepaard met veel vliegbewegingen. Toen dit ineens niet meer mogelijk was, werd het op afstand testen een serieus alternatief. “We kunnen wel stellen dat ingebruikname van nieuwe proceslijnen via remote controls de nieuw standaard is geworden bij ons. En niet onbelangrijk: tot zeer grote tevredenheid van de klant. Danone Argentinië heeft zelf een bericht geplaatst op LinkedIn, waarin ze hun waardering laten blijken over onze aanpak. We hebben de FAT bij Dinnissen met camera’s gedaan: een succesvolle remote FAT, zonder dat Danone personeel ter plekke was. De commissioning bij Danone Argentinië is ook met camera’s gedaan: een succesvolle SAT zonder aanwezigheid van ons personeel.” Of ‘remote’ de standaard wordt na COVID-19, is afwachten. “Remote is niet ideaal, maar wel werkbaar gebleken in periode met COVID-19. Klanten accepteren de randcondities en willen zelf ook verder. Opvallend is wel dat Danone dit protocol internationaal wil uitrollen, dus ‘remote’ blijft denk ik in de toekomst een belangrijke rol spelen. Dat het tijd en kosten spaart maakt het extra interessant. Onze omzet stijgt, terwijl de reisbewegingen dalen.”
DUURZAME STRATEGIE Op de vraag ‘wie er actief met duurzaamheid bezig is’ bleef het opvallend stil in de zaal. Bedrijven zijn vooral bezig met procesoptimalisatie of hun park draaiende te houden. Het thema energietransitie staat nog niet bij iedereen even scherp op het netvlies. De leveranciers aan de ronde tafel zien dat ook. Waar de één voor de troepen uitloopt, wacht de ander rustig af. Reyers: “Het invulling geven aan duurzaamheid is bij klanten sterk verschillend. De ene klant is hier veel meer mee bezig dan de andere. Wij hadden bijvoorbeeld een klant die wilde weten met hoeveel vrachtwagens wij zouden komen vanwege de CO2-uitstoot, die rekent alle milieubelasting door, terwijl een ander daar niet eens bij stilstaat.” Van der Gaag: “Zeker is dat duurzaamheid steeds meer begint te leven, al is dat nog lastig te kwantificeren. Maar er duidelijk een trend zichtbaar, wij noemen dit markt en mentaliteit. Wij kiezen duidelijk vanuit ons als leverancier voor een duurzame strategie omdat we ervan overtuigd zijn dat bedrijven die dat niet doen, over vijf jaar niet meer relevant zullen zijn.” ●
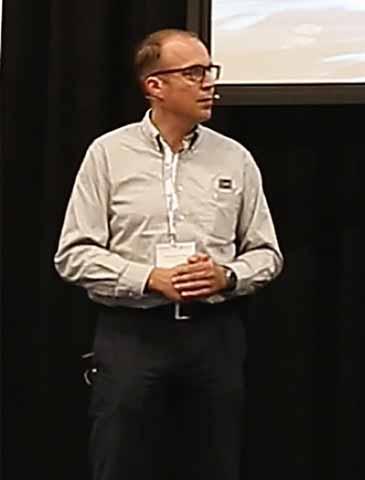
“Overheden als gemeenten en waterschappen moeten het voortouw nemen en voorschrijven dat het gebruik van niet-fossiele brandstoffen de voorkeur geniet, of zelfs verplicht gesteld wordt voor bouwprojecten binnen hun verantwoordelijkheid; zonder de dwingende vraag vanuit de eindklant zal de markt niet zomaar overstappen.”
RS Contracting levert al bijna 20 jaar mengsystemen voor de food-, chemie en farmaceutische industrie. Tot voor kort betrof dit standaard mengmachines van Duitse makelij. “In de afgelopen periode hebben we hard gewerkt aan een eigen alternatief. Nu is het dan eindelijk zover en lanceren we onze eigen Rmixx-productenlijn!”, zegt directeur Richard Scherpen van het bedrijf uit Coevorden.
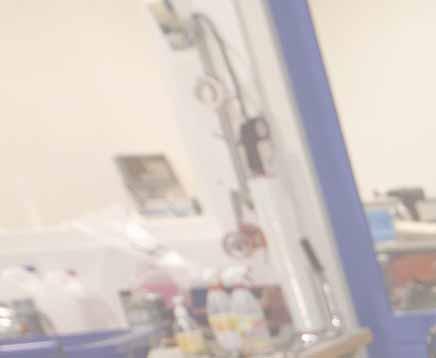
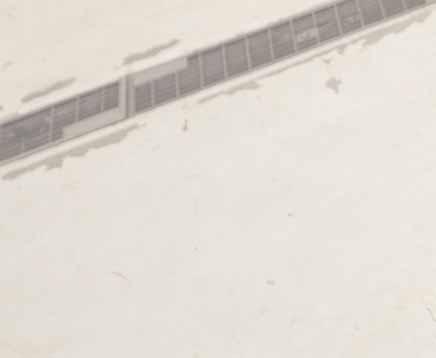
In de afgelopen twintig jaar heeft het bedrijf van Richard Scherpen veel expertise opgebouwd in het mengen, dispergeren en het oplossen van poeders in vloeistoffen. “We bouwen complete installaties en zorgen voor het onderhoud daarvan”, aldus de directeur-eigenaar. “Aanvankelijk deden we dat met standaardmachines en -componenten van Duits fabricaat. Onze klanten hebben steeds meer behoefte aan flexibiliteit. Dat is toch lastiger als je de productie niet in eigen hand hebt. We hebben nu onze ervaringen en ideeën gebruikt voor eigen ontwikkelingen en innovaties, wat heeft geleid tot onze nieuwe Rmixx-lijn. De lijn biedt legio nieuwe kansen en past in de verdere professionalisering van ons bedrijf. De kwaliteit is hoog én betaalbaar. Onze focus ligt primair op de Benelux, maar we realiseren daarnaast projecten in heel Europa en daarbuiten.”
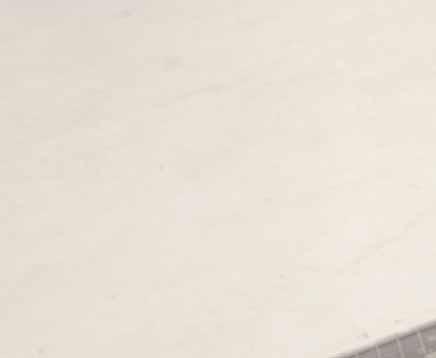
SERVICEDIENST Revisie, service en onderhoud aan installaties, mengers en poederoplosmachines is dagelijkse kost voor RS Contracting. “Klanten waarderen de korte lijnen en onze flexibiliteit. We staan paraat wanneer dat nodig is en kennen hun installaties van haver tot gort. Daarbij leveren we alle componenten die vervangen moeten worden. Dat zijn zorgvuldig geselecteerde en geproduceerde ‘after market’-componenten, zodat onze klanten te allen tijde bedrijfszeker blijven.” Hij pauzeert.: “Ze weten wat ze aan ons hebben. Ze kennen onze service, weten dat we snel beschikbaar zijn en dat ze een Nederlandstalige gesprekspartner met kennis aan de lijn krijgen. We leveren de juiste componenten en service, en doen dat voor een goede prijs.”
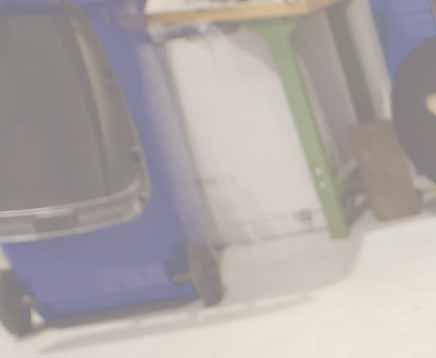
RMIXX-PROGRAMMA Technici leggen momenteel de laatste hand aan het eigen productgamma. De Rmixx-lijn bestaat uit machines voor het mengen, dispergeren en oplossen van poeders in vloeistoffen. De eerste machines komen binnenkort op de markt. De bouwgroottes lopen uiteen van kleine Technicum machines tot productiemachines met zeer hoog vermogen.. “Onze poederoplosmachine, de Rmixx-RMC, neemt een centrale plaats in het programma in”, vertelt Scherpen. “We zijn goed in het bevochtigen en dispergeren van grondstoffen, zodat die optimaal verwerkt kunnen worden. Bij het aanzuigen van hydrocolloïden bijvoorbeeld ontstaan snel klonten. De buitenkant neemt vocht op, de binnenkant blijft droog. Als dat gebeurt, benut je de eigenschappen van de grondstoffen onvoldoende en krijg je geen optimaal eindproduct. Wat wij doen is de poeders stuk slaan tot op partikelniveau, met vacuüm de lucht eruit trekken en dan de vloeistof injecteren. Die trekt in de kern van de partikels, waardoor de eigenschappen van de soms dure grondstoffen maximaal benut worden en recepturen geoptimaliseerd kunnen worden.” Naast deze machines levert Scherpens bedrijf alle overige onderdelen die nodig zijn voor een installatie. Van tanks en mengers tot trechters en bigbag losstations en besturingen, waardoor een klant compleet ontzorgd wordt.
GROEIENDE MARKT Het is nichemarkt, maar wel een belangrijke, zegt Scherpen. “Steeds meer marktsegmenten ontdekken deze wijze van dispergeren van poeders in vloeistoffen. Deze techniek werkt niet alleen vaak beter en efficiënter, maar er ontstaan ook nieuwe mogelijkheden voor bedrijven. Soms kan door toepassing van deze technieken de bestaande productie relatief eenvoudig worden uitgebreid. In het geval van nieuwbouw kan er effectiever ontworpen worden, waardoor er bijvoorbeeld ook op de utiliteitsbouw bespaard kan worden.”
Klanten kunnen hun producten in de praktijk in de fabriek in Coevorden testen. “Zo weet de klant precies hoe zijn product reageert en welke mogelijkheden dat schept. Samengevat is dat vaak een stabieler en hoogwaardiger eindproduct met een kortere procestijd.”
Geïnteresseerde partijen bevinden zich in de food, de chemie, de farma en de cosmeticabranche. De machines worden in Coevorden gebouwd. Dat gebeurt altijd op specificatie van de klant. “We zijn inmiddels gestart met het produceren van halffabricaten in kleine series. Machines worden altijd klant- en toepassingsspecifiek afgebouwd”, zegt Scherpen. “We streven naar een gezonde voorraad. Met ons eigen team van engineers bouwen we ze samen en zorgen we voor de installatie en inbedrijfstelling. ●
GMACHINES’
Richard Scherpen, directeur-eigenaar van RS Contracting.
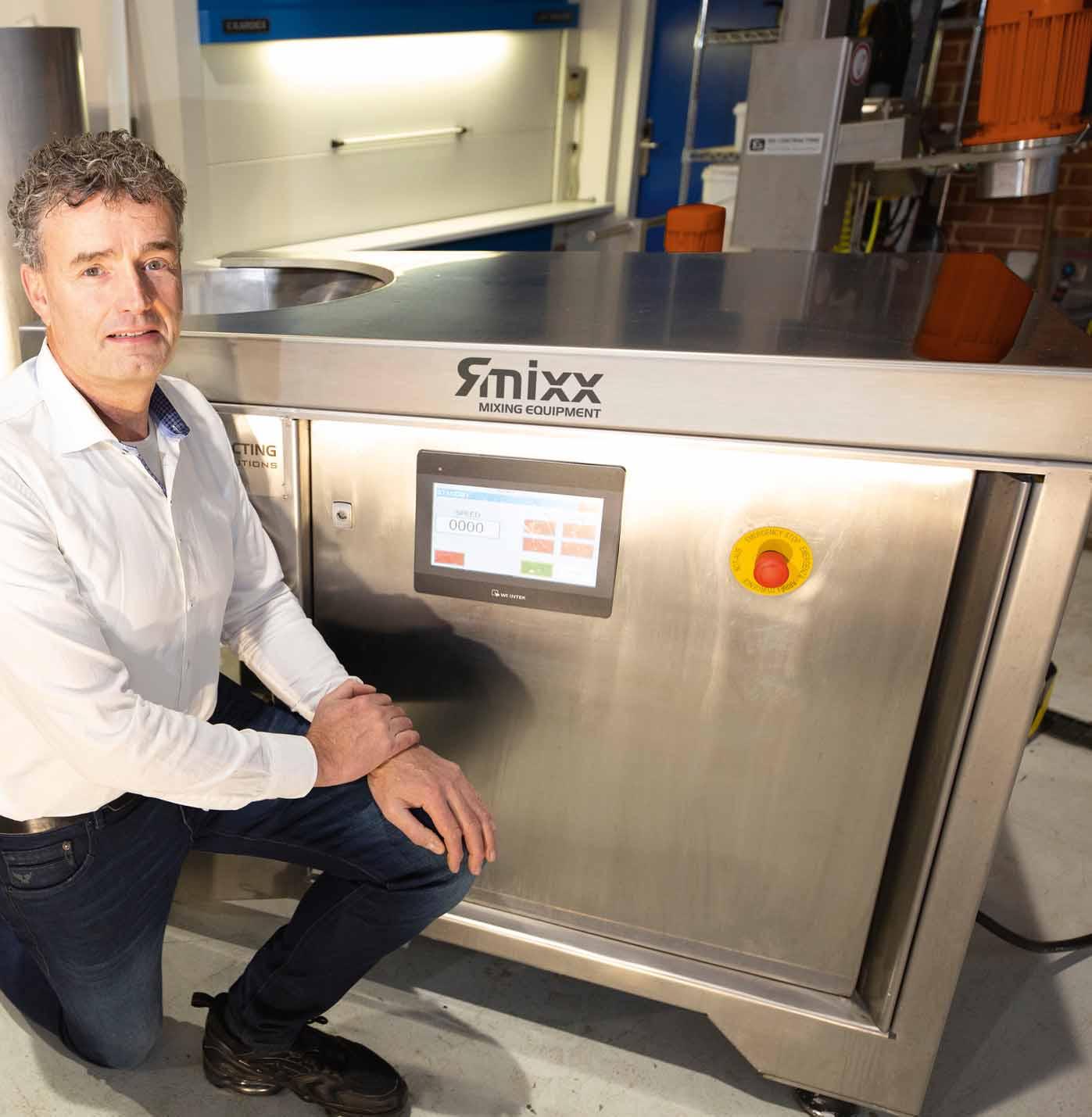
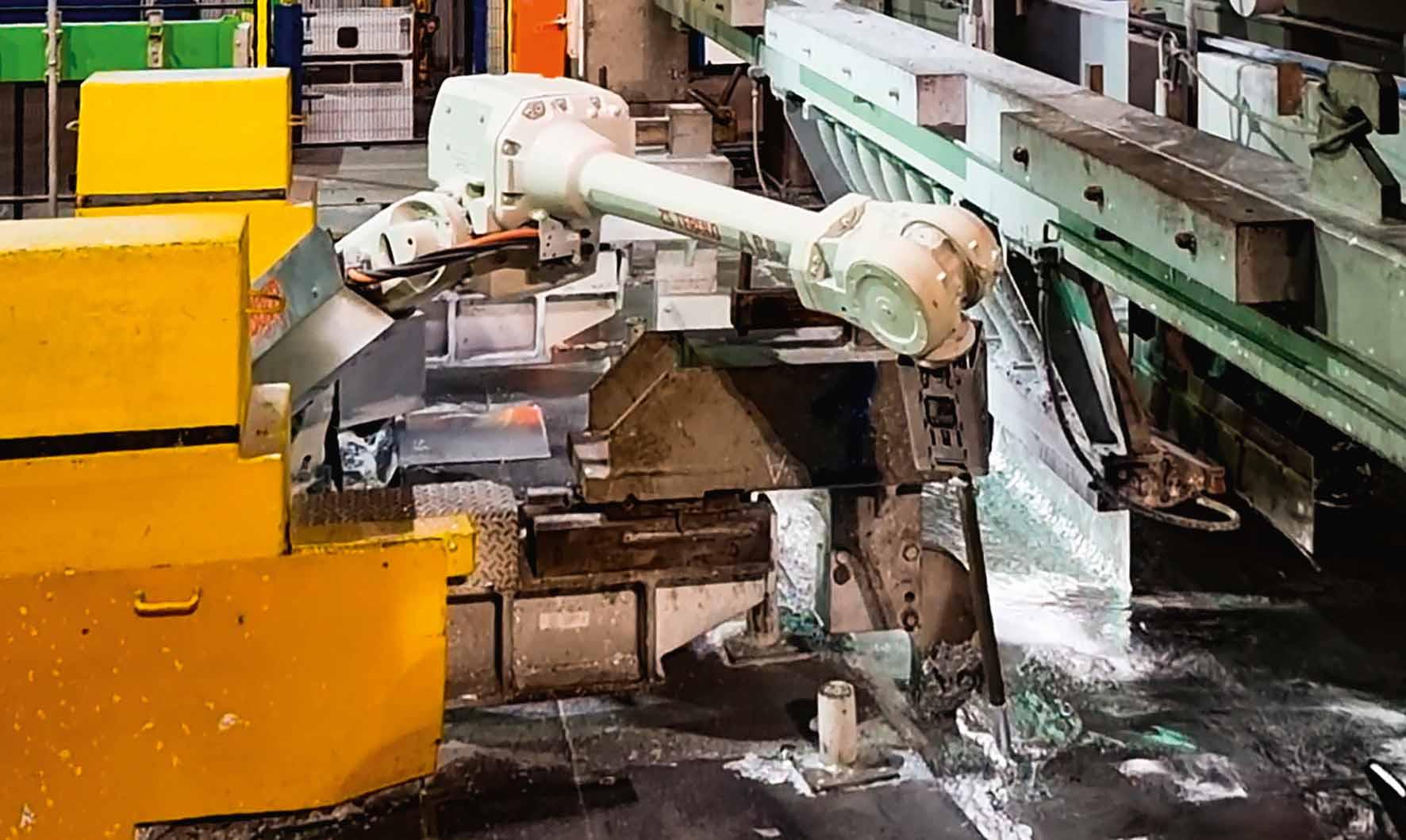
De frontrobot die het dross van het zinkbad schept om de staalplaatproductie schoon te houden.
GEROBOTISEERD DROSSEN MAAKT VERZINKEN VEILIGER
Gerobotiseerd drossen is veiliger dan handmatig verwijderen van dross in verzinkbaden. Een eenvoudig te bedienen dross-robotinstallatie met slimme gereedschapswisselaar zorgt voor veiligheid, bedieningsgemak en een constantere productkwaliteit. De robotinstallatie is in te passen in bestaande zinkprocessen, zelfs als de ruimte beperkt is.
Het verzinken van staal gaat nog vaak gepaard met – onveilige – handarbeid. Een voorverwarmde staalplaat wordt door een zinkbad van 400-500 °C getrokken, terwijl operators in oncomfortabele, beschermende kleding in een extreem hete omgeving handmatig het dross van het zinkbad afscheppen, zodat er geen vervuiling op de staalplaat kan komen. Maar het kan ook anders. Tebulo Industrial Robotics ontwikkelde een dross-robotinstallatie die het dross doorlopend aan beide kanten van de staalplaat weghaalt en de veiligheid en het bedieningsgemak voor de operators verhoogt. Onderscheidend aan de nieuwe oplossing is dat deze kan worden ingepast in elk bestaand productieproces, ook als er sprake is van een beperkte ruimte. Gekozen is voor een oplossing met een frontrobot, een V-zijde robot, slimme, gebruiksvriendelijke besturingssoftware en een gepatenteerde gereedschapswisselaar.
CORROSIEBESTENDIGHEID Bij het verzinken gaat een staalplaat vanuit een oven met een geconditioneerde, inerte stikstofomgeving direct het zinkbad in, zodat de plaat zo min mogelijk in aanraking komt met zuurstof. Via een keerrol (lees: zinkrol) komt de plaat aan de andere zijde weer uit het zinkbad omhoog, met aan twee kanten een dun laagje zink. Met behulp van luchtmessen wordt het overtollige zink eraf geblazen, zodat een flinterdunne constante zinkfilm overblijft. Tijdens het aanbrengen van het zink wordt de plaat zo stabiel mogelijk gehouden met behulp van stabilisatoren, correctierollen en/of stabiliseermagneten. Om de vervuiling die ontstaat als gevolg van de chemische reactie in het zinkbad (het dross) te verwijderen, moeten operators onder extreme omstandigheden dit dross handmatig wegscheppen. “Dit gebeurt vaak als het nèt te laat is, waardoor het dross zich ophoopt en op de staalplaat terecht komt”, zegt Hans Spaans, technisch directeur bij Tebulo Industrial Robotics. “Die vervuiling gaat ten koste van de corrosiebestendigheid en heeft ook cosmetisch een negatief effect op het eindproduct. Maar minstens zo belangrijk zijn de onveilige werkomstandigheden waaronder de medewerkers dit werk moeten uitvoeren.”
AANTAL ROBOTS Drossen kan naar keuze met één, twee of zelfs meerdere robots worden uitgevoerd, afhankelijk van allerlei factoren, zoals de beschikbare ruimte bij de staalplaat, het gewenste eindresultaat, het proces in het zinkbad en het beschikbare investeringsbudget. Zeker bij bestaande zinkbaden is het plaatsen van twee robots al een hele uitdaging, omdat alles vaak krap bemeten is. Spaans: “Voor zo’n situatie moesten we dus zoeken naar een creatieve en veilige oplossing, zodat de bestaande installatie volledig intact blijft. Dit hebben we opgelost door een V-zijde robot aan een track boven het zinkbad te hangen met diverse gereedschappen en die te laten samenwerken met de frontrobot aan de voorzijde.”
‘HANGENDE V-ZIJDE ROBOT’ De track (een soort railsysteem) waar de V-zijde robot aanhangt, is gemonteerd aan de bestaande staalconstructie van de oven, waarover de robot van links naar rechts en weer terug kan bewegen. Om de gewenste stijfheid bij deze constructie te kunnen garanderen, is een extra portaal bijgeplaatst om de ‘track’ te ondersteunen. De V-zijde robot werkt met twee soorten harken aan de achterzijde (V-zijde) van de staalplaat en zorgt
Hans Spaans, Tebulo
dat het dross gecontroleerd wordt aangeboden in het werkgebied van de frontzijde robot, die het dross-proces vervolgens overneemt. Beide robots werken met een in eigen beheer ontwikkelde gereedschapswisselaar. Die van de V-zijde robot bevat twee soorten harken en die van de frontrobot heeft harken en scheppen in diverse uitvoeringen. Per project worden deze gereedschappen op maat gemaakt voor een optimaal dross-proces. Voor de kwaliteit van het eindproduct is het van belang dat het zinkbad zo min mogelijk wordt verstoord. Alle noodzakelijke bewegingen, zoals het harken en het wegscheppen van het dross, moeten dus zo rustig en efficiënt mogelijk worden uitgevoerd. Maatwerk gereedschap draagt daar aan bij. GEREEDSCHAPSWISSELAAR Het gepatenteerde, volledig mechanisch werkende gereedschapswisselsysteem kan probleemloos bij een zinkbad van zo’n 500 °C worden toegepast. Het bestaat uit een gereedschapsstation met losse harken en/of scheppen en een gereedschapswisselaar (robot-actuated toolchanger) die met een ingenieus koppelsysteem is gemonteerd op de pols van de robot (EOAT, End of Arm Tooling). Spaans licht toe: “De meeste gereedschapswisselaars op de markt zijn pneumatisch of elektrisch aangedreven en daarom minder geschikt voor deze heavy duty, met zinkstof vervuilde omgeving. Zo ontstond het idee om zelf een geschikt gereedschapswisselsysteem te ontwikkelen, waarmee de robot met een robuuste gripper zelf de gereedschappen kan halen, terugbrengen en borgen. Door gebruik te maken van de robotbewegingen, zijn extra cilinders en/of elektrische actuators overbodig. Deze ‘robot-actuated toolchanger’ hebben we gepatenteerd.”
GEREEDSCHAPSTATION Het gereedschapstation wordt in het bereik van de robot opgesteld. Zodra de robot er een gereedschap uithaalt, wordt dit mechanisch vergrendeld met het koppelmechanisme, gemeten en gekali-
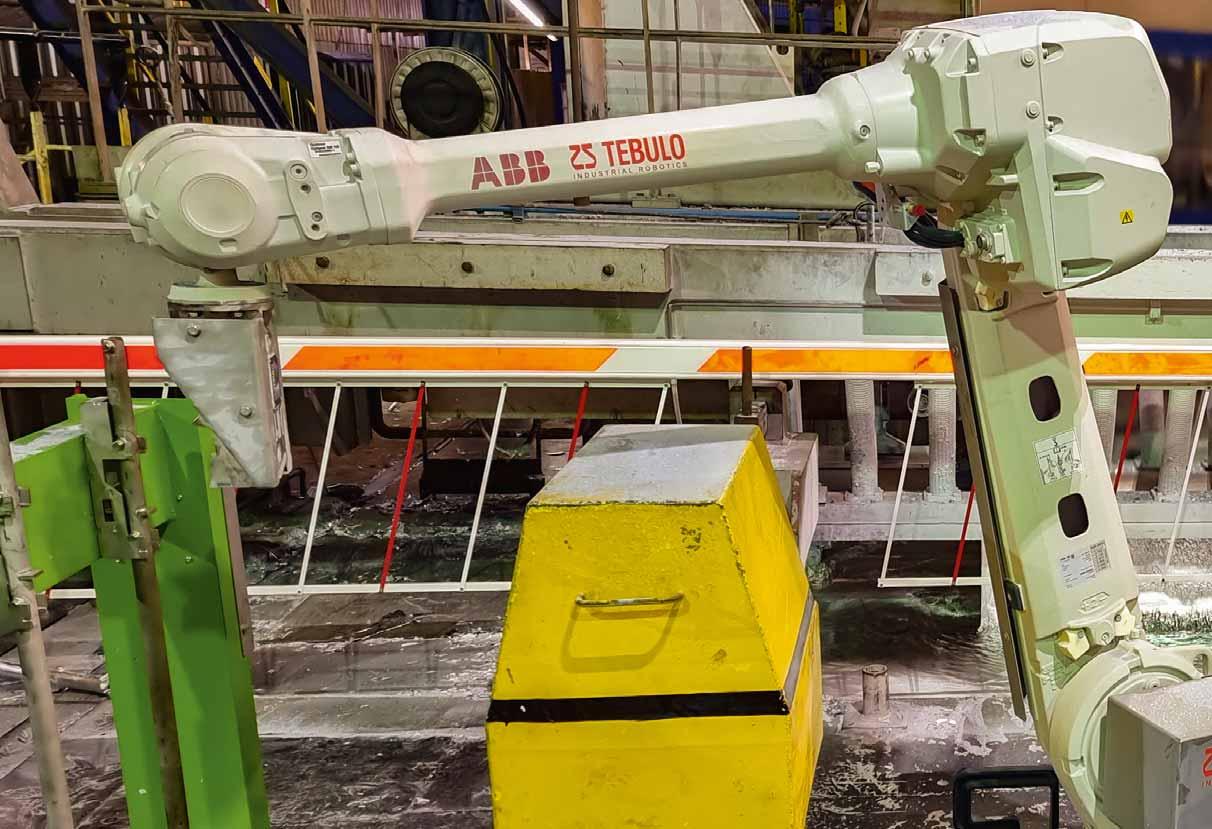
breerd. Na gebruik wordt het gereedschap teruggeplaatst en ontgrendeld. Rob Beentjes, algemeen directeur van Tebulo Industrial Robotics legt uit hoe dit werkt: “We werken met een unieke oppak- en parkeerplek ofwel een soort sleutelsysteem, gebaseerd op het Japanse poka-yoke systeem. Het sleutelsysteem is geborgd doordat elk gereedschap een opnamepunt met een eigen vormgeving heeft. Bij het wisselen van een gereedschap kan het dus niet op een verkeerde plek teruggezet worden. Door middel van schakelaars wordt de gereedschapsbezetting voortdurend bewaakt.” Tebulo heeft intussen al verschillende meervoudige gereedschapstations voor diverse applicaties in de wereld gemaakt en geleverd.
Rob Beentjes, Tebulo
GEBRUIKSVRIENDELIJK Voor elk type zinkpot programmeert Tebulo op voorhand vijf verschillende programma’s in, zodat aan de hand van de verschillende procesvariabelen snel de meest ideale bewegingsafsloop kan worden gekozen. Bij elk programma worden de robotbewegingen zo ingeprogrammeerd dat naar keuze alle hoeken en wanden van de zinkpot bereikbaar zijn met de speciaal hiervoor gemaakte gereedschappen. Per zinkpot-programma kan de aansturing naderhand eenvoudig worden geoptimaliseerd via de geavanceerde, gebruiksvriendelijke HMI. “Naast de vijf automatische cycli is het ook mogelijk om een eigen cyclus handmatig in te stellen”, zegt Spaans. “Bij alle ingeprogrammeerde programma’s kan de operator eerst een soort filmpje afspelen waarin te zien is welke bewegingen de robot gaat maken. Als het geselecteerde programma correct is, kan de definitieve keuze worden geactiveerd.”
DROSSBAK Voor de zinkbak zet de operator een drossbak neer, waar de robot alle dross die van het zink wordt geschept deponeert. Zodra de drossbak staat, kan de robot de positie en de vullingsgraad van de bak detecteren met sensoren die in de robotarm zijn geïntegreerd. Als de drossbak bijna
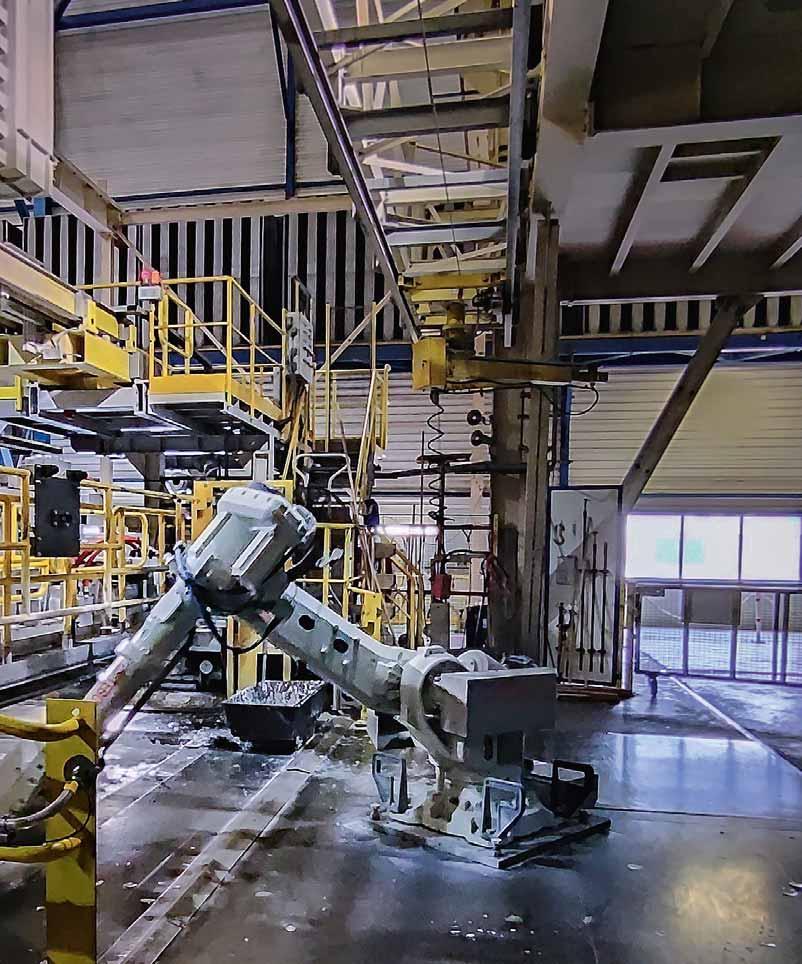
Wegneembare frontrobot met heftruck-steunen.
vol is, geeft de sensor een signaal aan de HMI, zodat de operator de bak tijdig kan vervangen. De vullingsgraad van de drossbak is ook visueel af te lezen op de HMI.
MULTIFUNCTIONEEL Behalve voor het verwijderen van dross, is de robot ook inzetbaar voor het uitvoeren van andere soorten werkzaamheden, zoals het reinigen van de omgeving, het (ver-)plaatsen van het 5 meter brede veiligheidshek en het nemen van zinkmonsters. Andere attributen kunnen namelijk moeiteloos aan de robot worden gehangen. “De mogelijkheid om het veiligheidshek te plaatsen en verplaatsen was al in het initiële ontwerp van de robot meegenomen”, vertelt Spaans. “In totaal zijn er drie posities ingericht waar het hek kan worden geplaatst: op de rand van de zinkpot; een meter van de rand van de zinkpot; en in de parkeerpositie boven het zinkbad. Tijdens de productie staat het hek op de rand van de zinkpot, bij een wissel van de zinkpot of in geval van stilstand staat het hek op een meter van de rand, en als er geen mensen in het werkgebied van de robot zijn, parkeert de robot het hek boven het zinkbad.” Ook hier wordt gebruik gemaakt van de ‘robot actuated toolchanger’ met aanvullende dubbele haken en een adaptorplaat op het veiligheidshekwerk, om deze goed en stabiel te kunnen hanteren. De componenten zijn zo vormgegeven dat het hek bij het plaatsen en wegnemen automatisch centreert op van tevoren ingeprogrammeerde posities.
FRONTROBOT WEGNEEMBAAR Wanneer de staalplaat breekt of als er tijdens een stilstand ruimte nodig is, dan kan de frontrobot met een heftruck uit de ruimte worden weggehaald zodat er een volledig vlakke, struikelvrije vloer overblijft. In de zo vrijgekomen ruimte kan een lieraandrijving worden opgesteld om de staalplaat weer terug te brengen in positie, of de ruimte kan worden gebruikt om de nodige werkzaamheden veilig uit te voeren voor het zinkbad. Speciaal voor het verwijderen en terugplaatsen van de robot heeft Tebulo een ingenieuze robotbevestigingsconstructie ontwikkeld, met behoud van positienauwkeurigheid. ●
NIEUW PRAKTIJKLEERBEDRIJF VOOR JONGE TECHNEUTEN
Twee technische bedrijven uit Brabant gaan het gebrek aan jonge technici te lijf en starten een eigen opleidingsinitiatief. De opleidingen zitten in de opstartfase, een bijbehorende ‘gezonde’-drankjesfabriek met eigen werkcafé is in aanbouw.
Begin 2021 sloegen Flowfirm en Van Doren Engineers de handen ineen om het grote gat tussen technische opleidingen en de praktijk te dichten. Michiel Werner, directeur van Flowfirm, ziet het glashelder: “We kunnen gewoon niet wachten op de overheid, we zullen het vanuit de werkgever moeten opzetten.”
DRANKJESFABRIEK De twee bedrijven hakten de knoop door en besloten het structureel aan te pakken: ‘gewoon’ een echt fabriekje bouwen in Veghel en de bijbehorende opleidingen opzetten. Werner verduidelijkt: “Waar we altijd tegenaan liepen was het gegeven dat jongeren onder de 18 jaar niet in de fabriek mogen komen. Met onze drankjesfabriek bieden we de mogelijkheid om alvast experimenteel te kunnen leren en ontwikkelen in een echt bedrijf.” De Starcker Factory is een fysieke fabrieksomgeving. Het pand is 25 x 40 meter, heeft een echt werkcafé (nadrukkelijk geen kantine, want de locatie is Brabant) met uitzicht op de werkende installaties en is speciaal voor scholieren, tech- studenten en professionals.
VAKSCHOOL Met een eerder, door Flowfirm succesvol geïmplementeerd opleidingsproject – Bqaam – is aangetoond dat een vakschool voor technici in voedingsfabrieken door te vertalen is. Werner ziet het als pure investering, goed voor de procestechniek als geheel: “De vakschool Bqaam was al opgezet. We maakten daar toen al de combinatie tussen de jongeren en techniek. De techneuten maken een bewuste keuze als het om hun opleiding gaat, en wij houden de interesse op deze manier levend voor deze tak van sport. Vergeet niet dat Nederland een toppositie bekleedt als het gaat om de export van food en farma. Wij hebben als werkgevers dan de taak om ons steentje daarin bij te dragen en aankomende technici kennis te laten maken met de praktijk.”
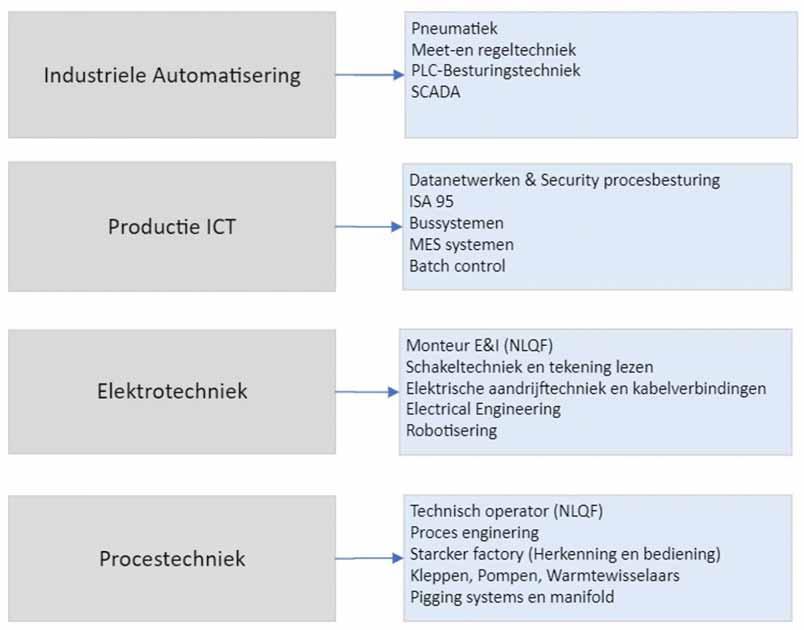
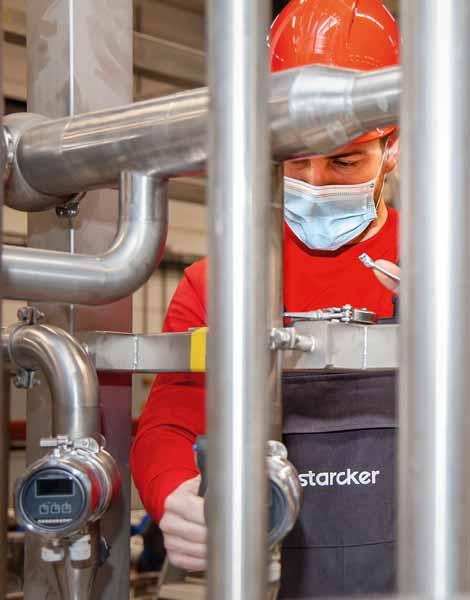
De Starcker Factory: een praktijkleerbedrijf voor jongeren, met bijbehorende vakschool.
Michiel Werner, Flowfirm
EIGEN INBRENG Momenteel wordt er ter plekke druk gesleuteld en gebouwd. HBO-studenten bedenken en werken zo veel mogelijk aan de realisatie en verdere invulling van het project. De producten – gezonde drankjes – hebben een zelf ontwikkelde receptuur en zijn uiteraard geschikt voor consumptie. “De engineering is geheel van de studenten, al krijgen ze back-up van de oude rotten in het vak,” licht Werner toe. “Zo is er ook een groep studenten bezig geweest met een opdracht in de vorm van een escape room, ze sparren als het ware op de werkvloer in spelvorm.” ●
Er is een nieuw type magneetaangedreven centrifugaalpomp leverbaar voor toepassingen op extreem hoge temperaturen tot 450 °C. Problemen als hoge uitstraling naar de kogellagers zijn verholpen, en het is niet meer nodig de magneetkoppeling apart te ontluchten.
De nieuwe oplossing komt van Dickow Pompen, een van de marktleiders in magneetaangedreven centrifugaalpompen. De pompen worden onder andere ingezet voor thermische olie-installaties waar gewerkt wordt met temperaturen tot boven de 400 °C. Binnen het pompenprogramma van Dickow bestonden hier verschillende oplossingen voor.
TWEE CONSTRUCTIES Voor hogere temperaturen ( > 280 °C) paste Dickow twee constructievormen toe: één met een normale interne circulatiestroom, die tot maximaal 350 °C werd ingezet, en één waarbij er een scheiding aangebracht werd tussen het pomphuis en de magneetkoppeling, voor temperaturen boven de 350 °C. Beide constructies hadden hun beperkingen. Bij constructie 1 was de uitstraling naar de kogellagers vrij hoog, wat de levensduur van de kogellagers negatief beïnvloedde. Bij constructie 2 moest de magneetkoppeling bij opstart separaat ontlucht worden.
NIEUWE CONSTRUCTIE Daarom heeft Dickow een geheel nieuwe pomp ontwikkeld – het type NMX – die in principe het hele temperatuurbereik dekt zonder nadelige gevolgen voor de levensduur van de kogellagers of de noodzaak tot apart ontluchten van de magneetkoppeling. De pomp is geschikt tot een temperatuur van 450 °C. De belangrijkste voordelen van de pomp zijn: • Verhoogde standtijd van de lagers • Geen externe ontluchting noodzakelijk, dus zeer gemakkelijk in bedrijf te nemen • Minder kans op fouten bij het in bedrijf nemen • Verbeterd rendement • Geen externe koeling noodzakelijk • Uitwisselbaar met de bestaande Dickow thermische oliepompen en de meeste andere fabricaten.
VERWARMD De pomp is ook verkrijgbaar met een verwarmd pomphuis en verwarmde magneetkoppeling. Hierdoor kunnen ook producten verpompt worden die op een lagere temperatuur stollen. Recent is een aantal van dit soort pompen geleverd voor een bedrijf dat aan plastic recycling doet. Daar worden de pompen ingezet op vloeibare (gesmolten) plastic op een temperatuur van 415 °C. ●
Voor meer informatie: Multipomp BV +31 (0)64 632 040 info@multipomp.nl Voor een video over de pomp, zie
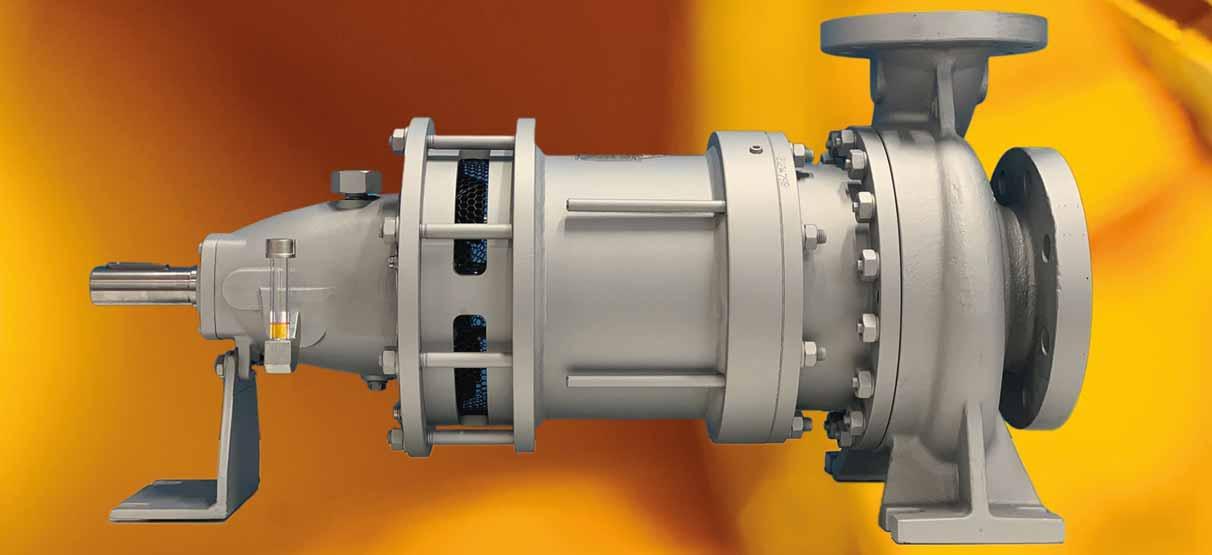

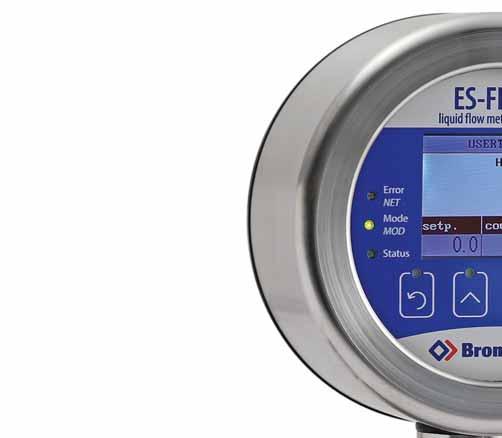
ULTRASONE FLOWMETING IDEAAL VOOR LAGE DEBIETEN
Ultrasone flowmeting is zeer geschikt voor het meten van laag-debiet vloeistofstromen in de food en farmaindustrie. Deze techniek is nauwkeurig, kent een hoge lineariteit en beïnvloedt de flow niet.
Om lage debieten te meten, bestaan diverse opties. Thermische flowmeting is vooral geschikt voor zeer lage debieten in de orde van een gram per uur. Coriolis-flowmeting is ook prima voor het meten van lage debieten, maar heeft als nadeel dat het trillingsgevoelig is, wat het voor sommige toepassingen minder geschikt maakt. Dit verklaart mede het succes van ultrasone flowmeting, een toepassing waarvoor Bronkhorst sinds 2017 de ES-FLOW op de markt heeft. Deze flowmeters zijn geschikt voor debieten van 2 tot 1.500 milliliter per minuut.
VLOEISTOFONAFHANKELIJK Ultrasone flowmeters werken als volgt: aan één kant van een rechte buis wordt een ultrasoon signaal verzonden, aan de andere kant van de buis wordt dit signaal weer opgevangen. De door de vloeistof veroorzaakte vertraging waarmee dit signaal wordt opgepikt, bepaalt de flow. Product manager liquid flow technologies Ferdinand Luimes: “Er zijn wel meer factoren in het spel: ons algoritme corrigeert voor de temperatuur van de vloeistof en de dichtheid en stroperigheid daarvan (actuele geluidssnelheid). Een klant kan dus temperatuur- en vloeistofonafhankelijk de flow meten.”
De ES-FLOW ES-113I met rvs behuizing en display.
IN-LIJN TOEVOEGING De delen van ES-FLOW flowmeters die in aanraking komen met de vloeistof zijn uitgevoerd in roestvast staal, terwijl de behuizing van aluminium (ES-113C) of rvs (ES-113I) is. Dat maakt de flowmeters goed reinigbaar en geschikt voor inzet in de voedingsmiddelen- en de farmaceutische industrie. Luimes: “Een toepassing die steeds belangrijker wordt, is de in-lijn toevoeging van additieven. Er is dus geen mengvat meer nodig;
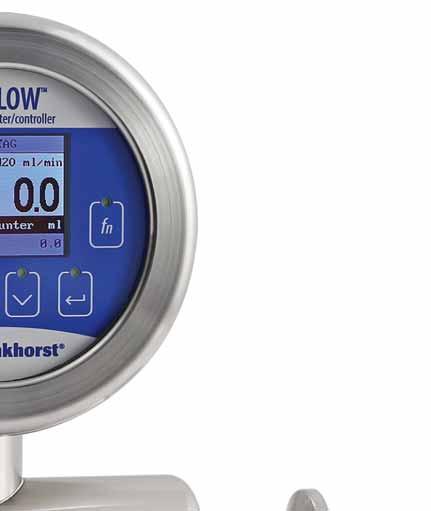
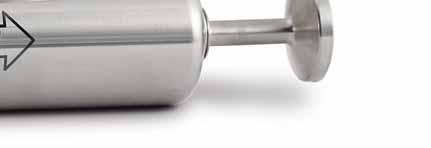
Ferdinand Luimes, Bronkhorst
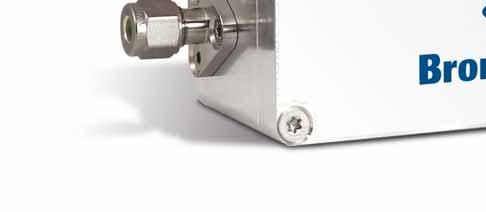

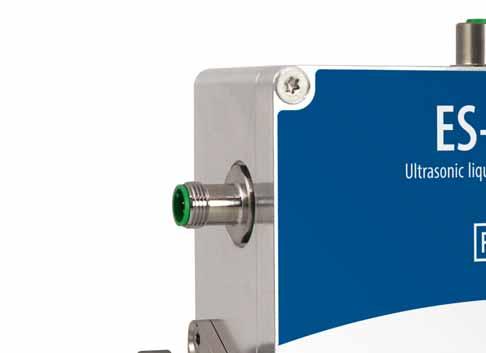
Compacte, ultrasone flowmeter ES-FLOW ES-113C zonder display. additieven kunnen via de leiding met de flowmeter zeer nauwkeurig en volledig traceerbaar aan de hoofdleiding worden toegevoegd.”
ZONDER DISPLAY Naast de ES-FLOW met een display heeft Bronkhorst recent de versie ES-113C zonder display gelanceerd. Die is niet alleen goedkoper, maar is vanwege zijn compactheid ook heel makkelijk in te bouwen. “Want daar is deze variant voor bedoeld: inbouw in de machines van derden. Ingebouwd in een machine is een display niet nodig, maar compactheid juist wel.” ●