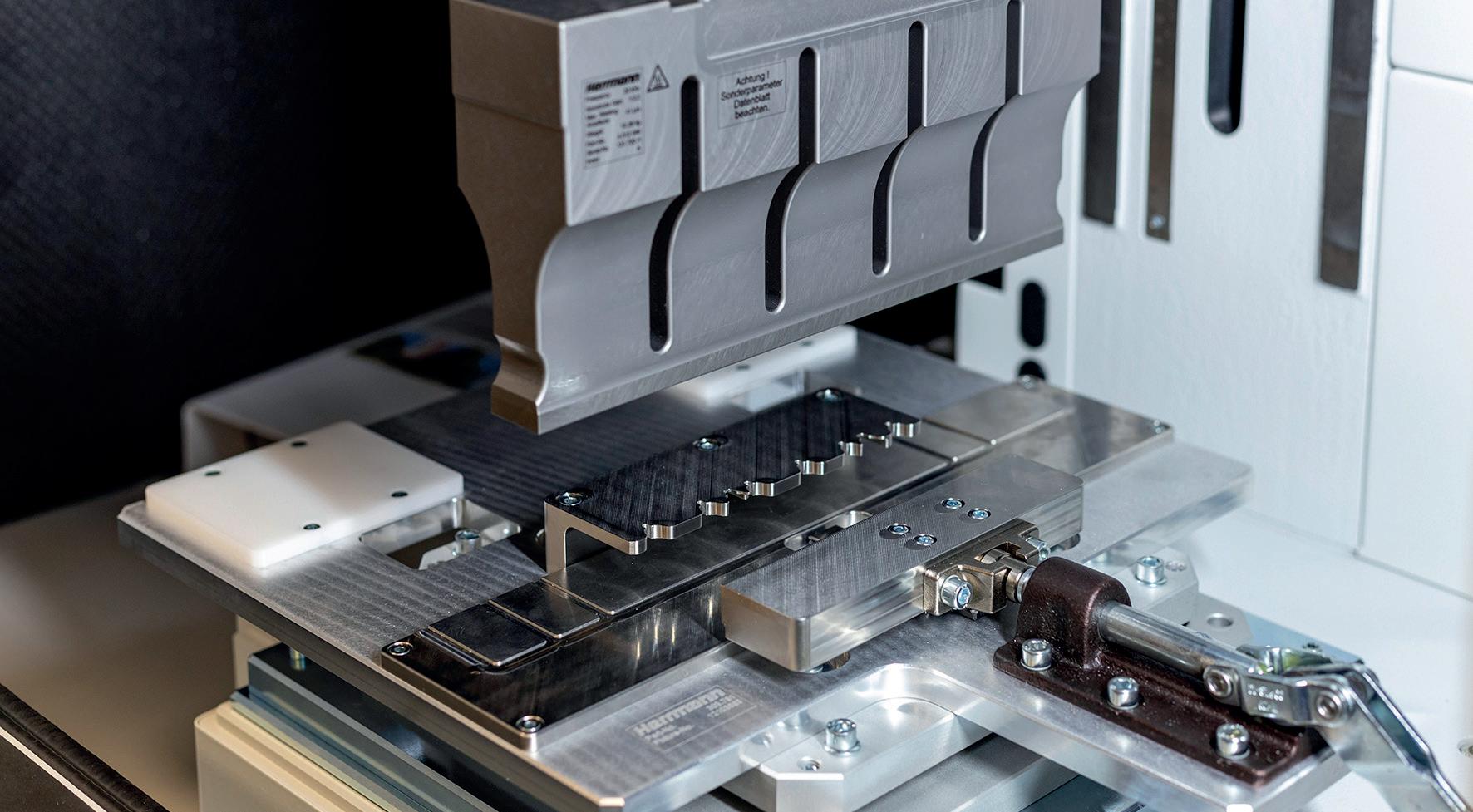
7 minute read
Saldaturaeconomicadipiccolilottigrazieagli ultrasuoni
Serie limitate ma efficienti Saldatura economica di piccoli lotti grazie agli ultrasuoni
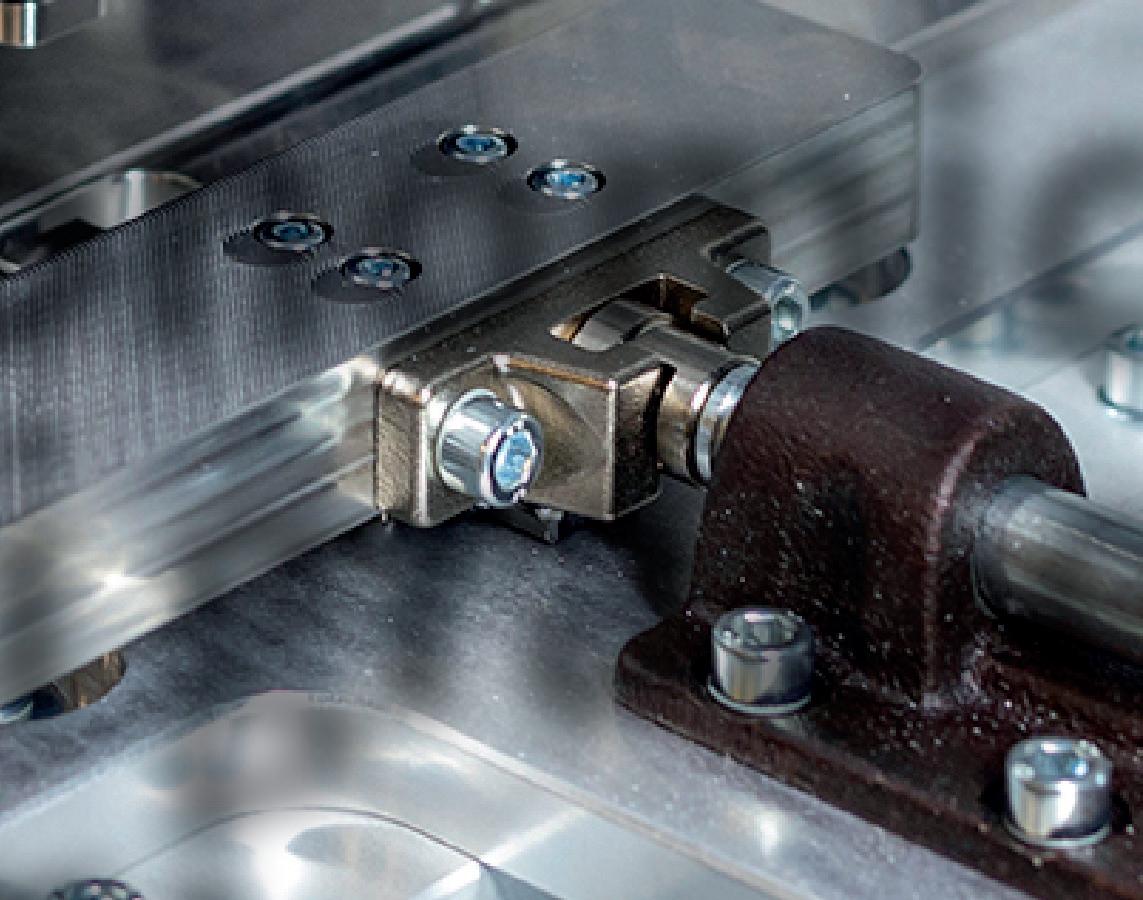
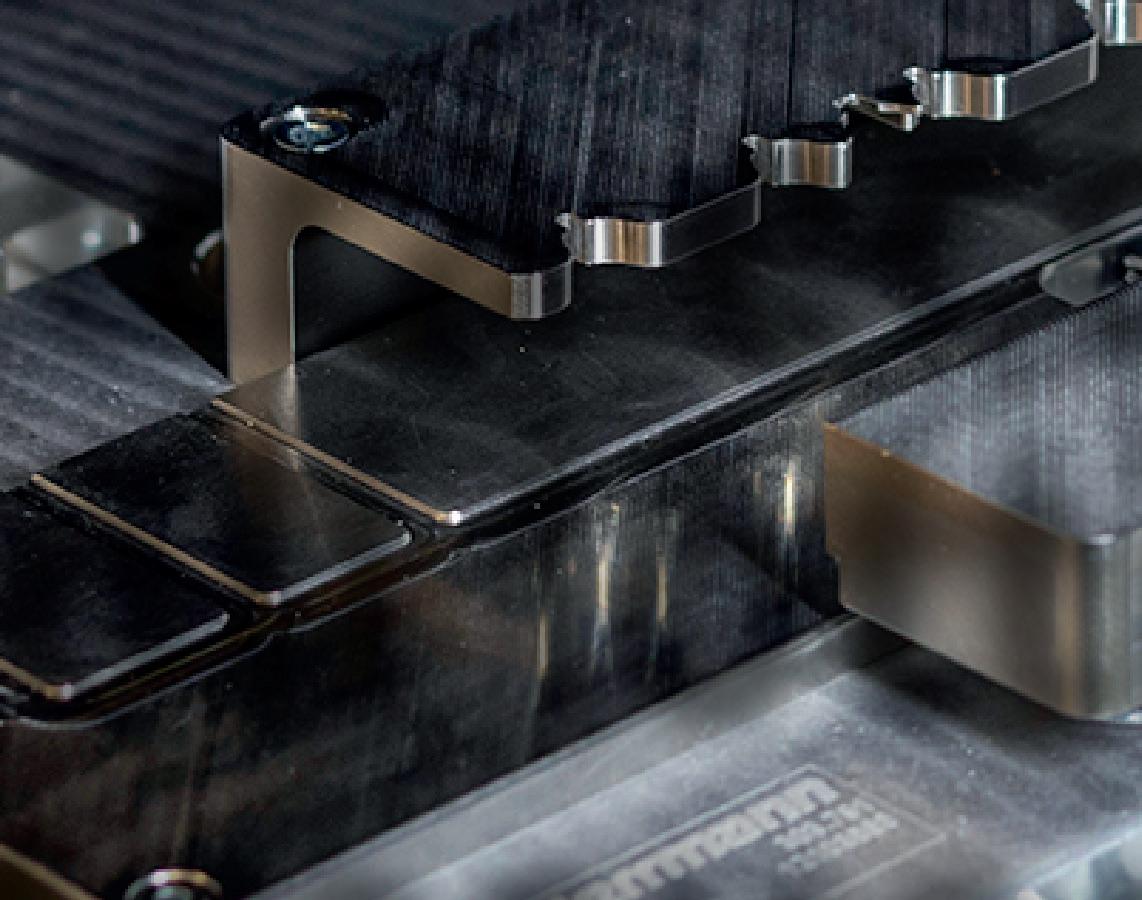
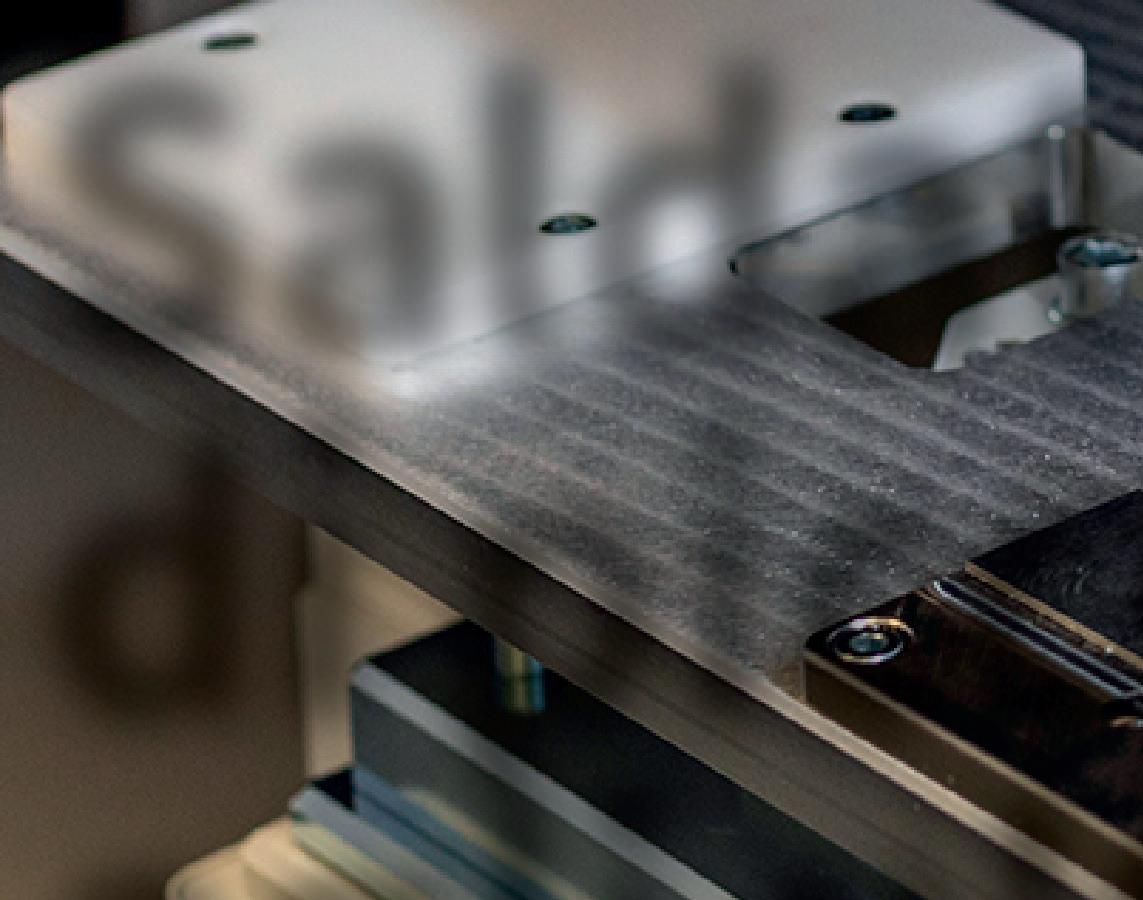
L’inserimento manuale di 18 connettori all’interno di un alloggiamento in plastica, su una centralina di controllo, rappresentava una procedura laboriosa e costosa per il produttore. La saldatura a ultrasuoni ha offerto un’alternativa efficiente, riducendo considerevolmente i tempi di ciclo, oltre a essere anche economica a dispetto del limitato numero di pezzi. Da questo punto di vista, svolgono un ruolo importante la versatilità del sonotrodo e i servizi di Herrmann Engineering
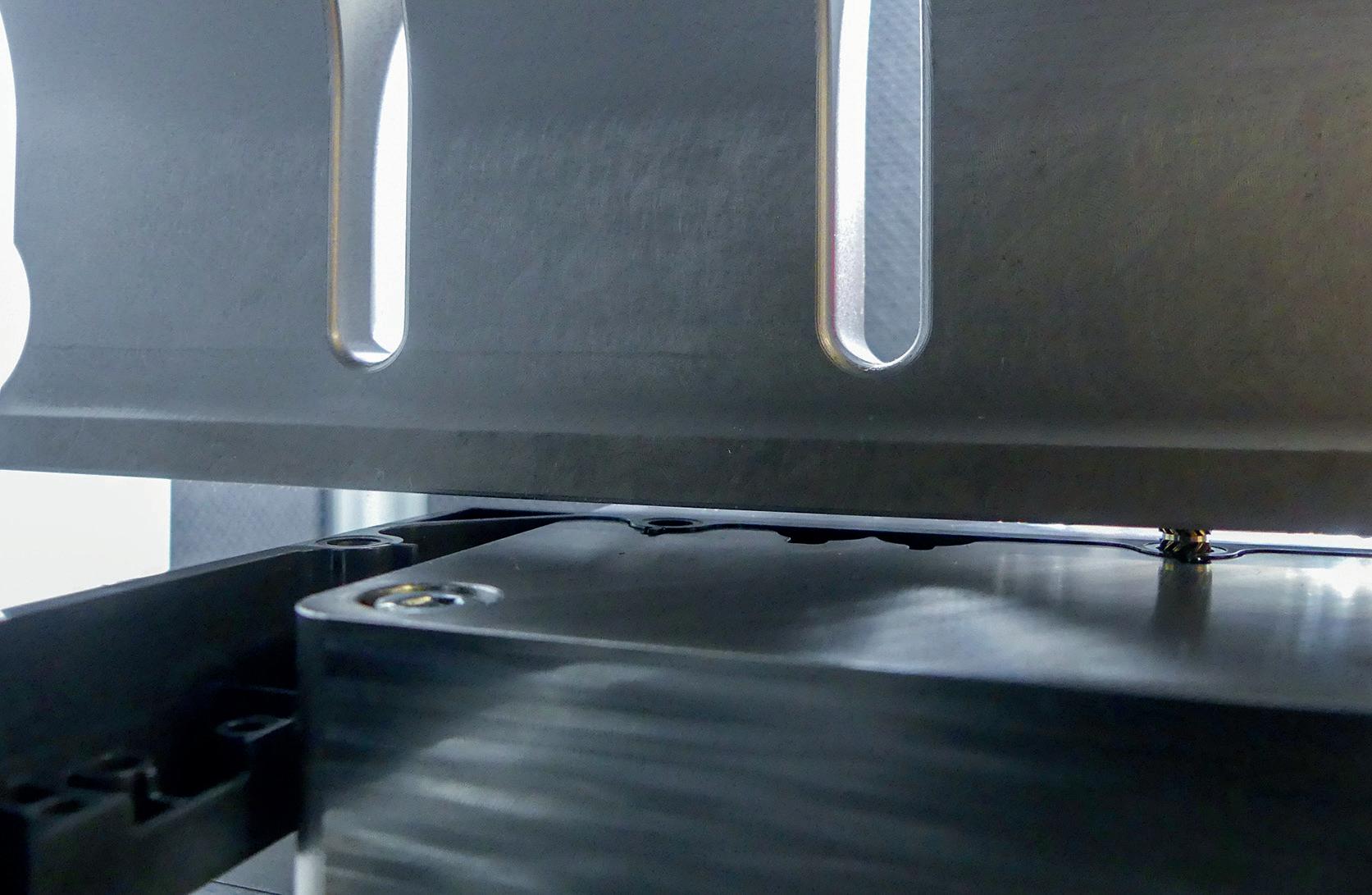
Con tempi di produzione superiori ai tre minuti, l’assemblaggio di un alloggiamento in plastica rappresentava un’operazione dispendiosa per apra-plast Kunststoffgehäuse-Systeme. Tali lunghi tempi di ciclo erano dovuti principalmente all’inserimento individuale, a caldo, di 18 connettori femmina in ottone. Inoltre, il limitato numero di pezzi da produrre sconsigliava il ricorso a un processo automatizzato e, a causa dei suoi costi elevati, è stata esclusa anche l’alternativa dello stampaggio dei connettori. In uno dei suoi periodici colloqui con apra-plast, la società tedesca Herrmann Ultraschall è venuta a conoscenza di questa sfida e ha presentato un processo più efficiente. Dalla collaborazione tra le due aziende è scaturita una soluzione specifica, basata sulla saldatura a ultrasuoni. Risultato: tempi di produzione dell’alloggiamento drasticamente ridotti ed efficienza del processo aumentata.
Cinque volte più veloce grazie allo speciale sonotrodo a lama
L’operazione consisteva nell’inserire contemporaneamente i connettori in ottone nell’alloggiamento in policarbonato mediante saldatura a ultrasuoni. Per questo scopo, innanzitutto, è stato sviluppato uno speciale sonotrodo in grado di saldare tutti i 18 connettori contemporaneamente, in maniera precisa e su ciascun lato dell’alloggiamento. È stato così possibile ridurre da 18 a quattro i passaggi necessari, riducendo il tempo di ciclo a poco meno di 40 secondi, ovverosia un quinto della durata originale. Durante il processo di saldatura, il sonotrodo a forma di lama viene applicato contemporaneamente a tutti i connettori in ottone presenti sul medesimo lato, per l’intera lunghezza dell’alloggiamento. I connettori vengono fatti vibrare dagli ultrasuoni e la vibrazione viene trasferita all’alloggiamento in plastica, avviando il processo di fusione. Il materiale fuso scorre nelle rientranze dei connettori creando in tal modo una giunzione ben salda. Questo processo consente ai connettori in ottone di essere incorporati nell’alloggiamento, proteggendo il materiale da eventuali danni e contribuendo, anche visivamente, a un risultato impeccabile. Dal momento che l’alloggiamento viene assemblato mediante viti su una centralina di controllo, è essenziale che durante il processo di saldatura i connettori siano inseriti perfettamente e uniformemente. Irregolarità sulla superficie, come quelle causate da connettori sporgenti, possono compromettere il successivo assemblaggio ermetico dell’alloggiamento. Per garantire l’innesto agevole dei connettori, durante il processo di saldatura il componente deve essere posizionato perfettamente in piano e fissato in modo tale da impedire ogni movimento. Per questo è stato sviluppato uno speciale staffaggio con scanalature, che consente d’inserire saldamente il componente al suo interno bloccandolo in posizione, di saldare il primo lato dell’alloggiamento
Durante il processo di saldatura, il sonotrodo viene applicato solo ai connettori in ottone, in modo tale da garantire un’azione delicata sull’alloggiamento in plastica
Un connettore prima (a sinistra) e dopo (a destra) la saldatura a ultrasuoni: l’inserimento corretto dei connettori è essenziale per garantire un prodotto finale di qualità ottimale
e di girare e bloccare il pezzo prima di saldare il secondo lato dell’alloggiamento. Tutti i 18 connettori vengono inglobati in soli quattro passaggi. La combinazione di sonotrodo e staffaggio, già in fase di sviluppo del progetto, ha consentito d’eseguire in maniera affidabile il processo di saldatura a ultrasuoni sui bordi dell’alloggiamento lunghi 310 mm.
Una singola macchina per diverse applicazioni
Per ridurre i tempi d’ammortamento della saldatrice a ultrasuoni, Herrmann Engineering ha sondato le ulteriori possibilità d’utilizzo in progetti attualmente in corso presso apra-plast, anche perché il sistema di cambio rapido degli utensili di saldatura consente di riattrezzare la saldatrice per un’applicazione diversa nel giro di pochi minuti. Un ulteriore progetto, anch’esso in lotti di dimensioni ridotte, è stato così realizzato in concomitanza con l’alloggiamento dei connettori. Si tratta del corpo in plastica di uno strumento di misura, in cui è inserita una finestrella d’ispezione in PMMA. In precedenza, tale finestrella veniva assemblata manualmente, ma ciò comportava diversi svantaggi. Per esempio, al fine di garantire il funzionamento impeccabile dello strumento, l’assemblaggio dei vari componenti deve essere a tenuta ermetica, ma con il montaggio manuale con adesivo si formavano spesso bolle d’aria che potevano comprometterne la tenuta. Oltre a questo, a volte i componenti scivolavano fuori posto, influendo non solo sulla tenuta, ma anche sull’aspetto del prodotto finale. I test iniziali hanno dimostrato che, in applicazioni come queste, l’uso degli ultrasuoni può contribuire a migliorare la qualità del prodotto. Tramite la saldatura a ultrasuoni, infatti, la finestrella d’ispezione viene unita al corpo in plastica dello strumento garantendo in tal modo una tenuta assolutamente ermetica. A sua volta, l’eliminazione dell’adesivo assicura anche un risultato visivamente impeccabile e crea una giunzione ecocompatibile senza l’impiego di additivi. Un ulteriore criterio di scelta a favore della tecnologia a ultrasuoni riguarda la possibilità di controllo del processo: monitorando e convalidando ogni singola fase del processo di saldatura, la macchina garantisce un livello di affidabilità mai raggiunto prima.
Fattori di successo e conclusioni
Le due soluzioni illustrate rappresentano per apra-plast l’ingresso nel mondo della saldatura a ultrasuoni. L’offerta di una formazione di base approfondita su questa tecnologia e di un servizio di consulenza sulla fattibilità finanziaria e tecnica del progetto sono stati ulteriori fattori cruciali per la decisione dell’azienda. Noleggiando una saldatrice, apra-plast è stata in grado di eseguire internamente i test in condizioni di produzione reali e di iniziare a familiarizzare con l’uso della tecnologia. Le soluzioni di saldatura sviluppate chiariscono che l’uso degli ultrasuoni si rivela utile anche nel caso di lotti di ridotte dimensioni. Da questo punto di vista, è fondamentale poter contare su un supporto puntuale per tutta la durata del progetto, in modo tale da mettere a punto una soluzione versatile. Soprattutto a confronto con i processi d’assemblaggio manuali, la saldatura a ultrasuoni offre il grande vantaggio di assicurare tempi di produzione più rapidi e una maggiore qualità del prodotto finale, il che significa che le aziende possono progettare processi produttivi mirati a economicità, sostenibilità ed efficienza.

Collaborazione Comerio Ercole - Herrmann Ultraschall Saldatura a ultrasuoni nella calandratura della gomma
Il costruttore italiano di impianti e calandre per materie plastiche e gomma, Comerio Ercole, e il costruttore tedesco di linee per la saldatura a ultrasuoni, Herrmann Ultraschall, hanno sottoscritto un accordo di cooperazione in merito a una nuova tecnologia per produrre carcasse in cui le estremità di cordoni tessili (“cord”) sono utilizzate per la laminazione. Il nuovo sistema di giunzione è denominato Ultrasplice e lo sviluppo riguardava la saldatura a ultrasuoni di fibre tessili con funzione d’inserto nelle carcasse. Comerio Ercole e Herrmann Ultraschall hanno realizzato una soluzione che rende il processo di giunzione dei “cord” ancora più veloce ed efficiente grazie a un ciclo più rapido, da cui risulta un legame più saldo, più stabile e più sicuro. La tecnologia tradizionale è legata al tempo minimo necessario per vulcanizzare la giunzione della gomma con presse riscaldate, in modo da unire la coda con la testa di una nuova bobina di tessuto; questo processo richiede circa 3040 secondi. Con Ultrasplice, invece, il processo di saldatura tra coda e testa si ottiene in 2-2,5 secondi e la saldatura a ultrasuoni viene eseguita in meno di un secondo. Nel processo di saldatura deve essere considerato anche il tempo di abbassamento e sollevamento degli attuatori, che richiede circa 1,5 secondi. Inoltre, la giunzione della gomma non è più presente sul prodotto, evitando ogni possibile problema che potrebbe insorgere durante il processo di calandratura, compreso l’impatto critico sul misuratore di spessore. Con la tecnologia a ultrasuoni, quindi, il tempo di giunzione è stato drasticamente ridotto, così da ridurre la capacità dell’accumulatore pre-calandra. Infine, la collaborazione tra le due società nel campo della calandratura della gomma ha permesso di sviluppare soluzioni personalizzate, dalla progettazione fino all’assistenza al cliente.
L’innovativa pressa di giunzione è prodotta da Comerio Ercole, mentre gli attuatori a ultrasuoni su misura sono forniti da Herrmann Ultraschall
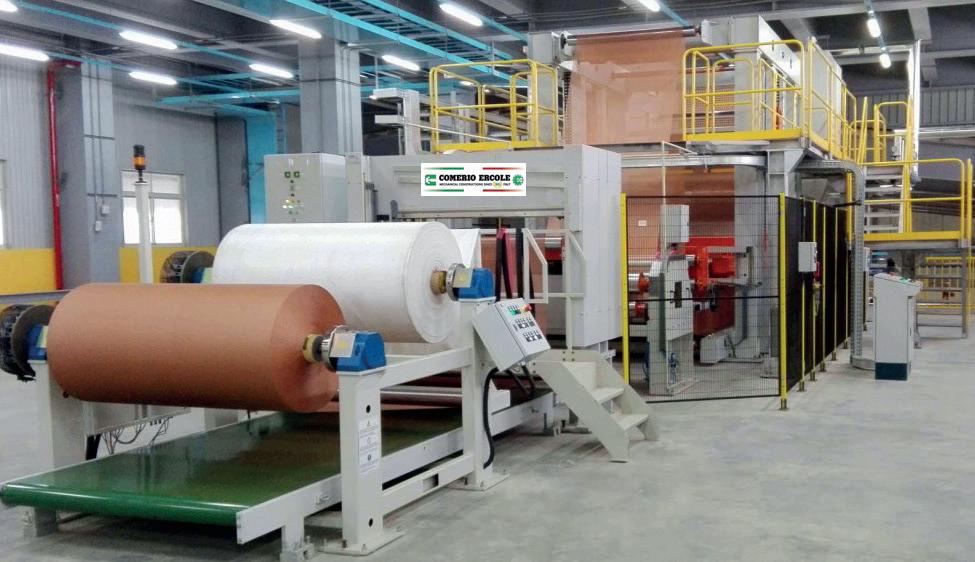