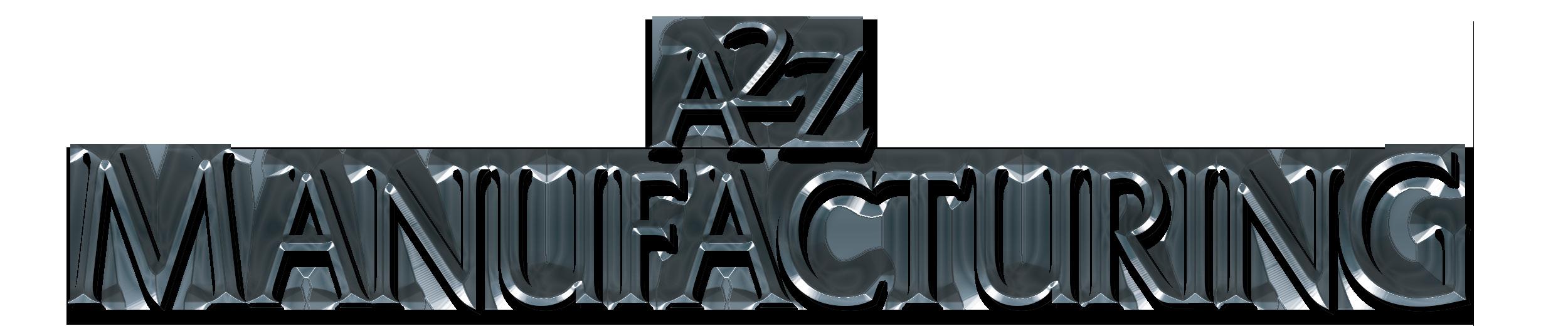
West Coast Edition (WA, OR, and CA)
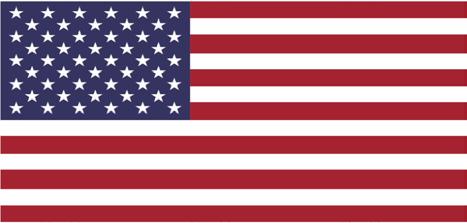

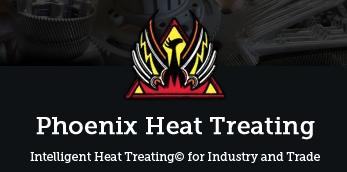
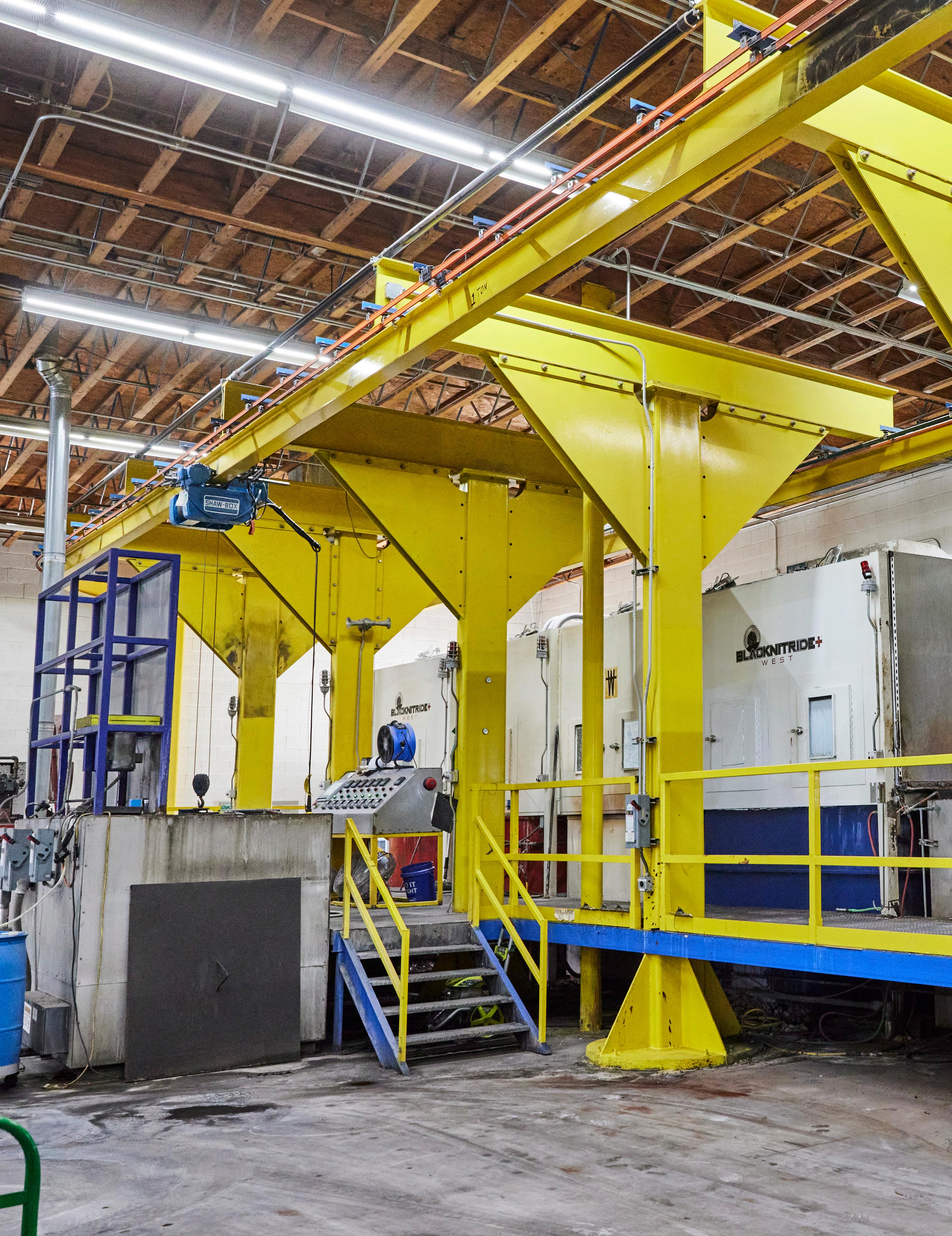

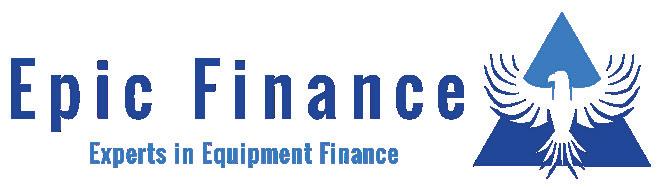
West Coast Edition (WA, OR, and CA)
We offer fast and simple financing solutions for businesses with an opportunity for growth and a need for capital.
is the perfect product when your business has a project or additional expenses. Simple application process and funds up to $250,000. Capital intended to grow your business.
up to $750,000 (without financial review) for your new or used equipment acquisitions. With 100% financing and terms up to 84 months, it allows you to reserve cash in your bank account.
Balancing the budget is a little like protecting your virtue:You just have to learn to say “no.”
Government’s view of the economy could be summed up in a few short phrases: If it moves, tax it. If it keeps moving, regulate it. And if it stops moving, subsidize it.
Ronald Reagan
When Ronald Reagan took the oath of office as America’s 40th President on January 20, 1981, the country was experiencing some of the bleakest economic times since the Depression. Taxes were high, unemployment was high, interest rates were high, and the national spirit was low.
To reverse the economic climate of the time, President Reagan put forth an economic policy that aimed to reduce government regulation, lower taxes, and promote free-market capitalism as a means to stimulate economic growth and increase individual wealth.
President Reagan earned a degree in Economics at Eureka College, and even though he would sometimes joke about “two economists having three opinions,” he knew what needed to be done and how to do it.
He consistently advocated for a straightforward and simple, yet detailed plan during his campaign: cut taxes, get control of government spending, and get the government out of the way so that the entrepreneurial spirit of the American people could be unleashed.
Given actual rates of inflation, through 1987, the Reagan tax cuts saved the median-income two-earner American family of four close to $9,000 in taxes from what it would have owed in 1980.
Tax cuts were only one “leg of the stool.” The second, jobs, was equally strong. Not only were there millions of new jobs, but the benefits of job creation were not limited to one segment of society. Employment of African-Americans rose by more than 25% between 1982 and 1988, and more than half of the new jobs created went to women.
Taming the lion called government spending was another key component of the plan – the “third leg of the stool.” Here, too, President Reagan did what he said he would do. During his Administration, growth in government spending plummeted from 10% in 1982, to just over 1% in 1987. With inflation factored in, Federal spending actually went down in 1987 – the first time that had happened in well over a decade.
So impressive was the Reagan Recovery that at the G7 Economic Summit in 1983, when it was obvious the President’s plan was working, the West German Chancellor asked him to “tell us about the American miracle.” That was quite a turnaround from two years earlier, when President Reagan outlined his economic recovery plan to an unconvinced group of world leaders.
Now, however, they all wanted to know how he did it, so he told them: reducing tax rates restored the incentive to produce and create jobs, and getting government out of the way allowed people to be entrepreneurs. From there, the free marketplace operated as it was supposed to.
History can ge a great teacher as long as we have a good memory. We’ve turned our country around before, we sure need the wisdom and fortitude to do it again. If there is anything we can do to help you promote your business and gain new sales, please contact us.
Kim Carpenter
Kim Carpenter & Linda Daly Kim@A2ZManufacturing.com
Mail Address: PO Box 459 Higley AZ 85296
Telephone: (480) 773-3239
Website: www.A2ZManufacturing.com E-mail:Kim@A2ZManufacturing.com
Linda Daly, Stephen Hannemann, Eugene Wirth
Published bi-monthly to keep precision manufacturers abreast of news, contracts, trends, and to supply a viable supplier source for the industry.
Circulation: A2Z Manufacturing West Coast maintains a master list of over 14,000 decision makers consisting of fortune 1000 companies, small manufacturing companies, engineering firms, DOD & Scientific Lab facilities, machine shops, fab-shops, and secondary source businesses. It has an estimated pass on readership of more than 25,000 people. The majority of our readers are based in CA, OR, WA area!
Advertising Rates have remained the same since 1999, deadlines and mechanical requirements furnished on our website at: www.a2zManufacturing.com.
All photos and copy become the property of A2Z Manufacturing.
The Publisher assumes no responsibility for the contents of any advertisement, and all representations are those of the advertiser and not that of the publisher.
The Publisher is not liable to any advertiser for any misprints or errors not the fault of the publisher, and in such event, the limit of the publisher's liability shall only be the amount of the publishers charge for such advertising.
Germantown, WI, - Hainbuch America, a leading name in machining technology, is proud to unveil its latest innovation at IMTS 2024: the revolutionary AC (Automated Change) Line. This groundbreaking solution marks a significant milestone as the first fully automated system for workholding device changeover, setting new standards in manufacturing efficiency and precision.
The AC Line represents a paradigm shift in workholding technology, offering manufacturers a seamless and error-free alternative to manual changeovers. By harnessing cutting-edge automation, the AC Line streamlines transitions between workholding devices with unmatched speed and accuracy. This innovation not only reduces downtime but also enhances overall productivity, empowering manufacturers to maximize their machining capabilities.
Key features of the AC Line include:
1. Precision Automation:
The AC Line’s precision-engineered automation ensures consistent and reliable changeovers, eliminating human error and optimizing machining processes.
2. Automated Clamping Heads (Collets) and End-Stops: In addition to workholding device changeover, the AC Line automates clamping heads (collets) and end-stops, further enhancing operational efficiency and accuracy.
3. User-Friendly Interface: Designed with ease of use in mind, the AC Line features an intuitive interface that allows operators to program and adapt quickly, enhancing operational efficiency.
4. Versatile Adaptability: From varying part geometries to diverse materials and machining techniques, the AC Line adapts seamlessly to meet a wide range of production requirements, ensuring versatility without
compromise.
5. Industry-Leading Support: Hainbuch America’s commitment to customer success extends beyond innovative technology. Our team of experts provides comprehensive support, from personalized solutions to hands-on guidance, ensuring a seamless integration of the AC Line into existing manufacturing workflows.
“We are thrilled to introduce the AC Line at IMTS 2024, marking a significant advancement in workholding technology,” said Tim Wachs, President at Hainbuch America. “This groundbreaking solution reflects our dedication to pushing the boundaries of innovation and empowering manufacturers with tools that optimize efficiency, precision, and productivity.”
Visit Hainbuch America at booth W-431636 at IMTS 2024 to experience the AC Line firsthand and discover how it is reshaping the future of manufacturing.
For media inquiries, please contact:
Michael Larson - Marketing Director • mlarson@hainbuchamerica.com
About Hainbuch America: Hainbuch America is a leading provider of innovative workholding solutions for the machining industry. With a commitment to excellence and customer success, Hainbuch America continues to push the boundaries of technology to drive efficiency and precision in manufacturing processes.
Anca’s Epx-Sf Processes Up To 1,900 Tools In 24 Hours While Achieving
Industry 4.0 connectivity and AI-assisted guidance on ANCA’s new edge preparation machine revolutionizes edge preparation for cutting tool performance
Renowned for launching industry-first tool and cutter grinding technologies, ANCA continues its legacy of innovation with the EPX-SF, guaranteeing productivity, quality, and profitability in edge preparation. The new EPX-SF stream finishing machine was debuted at GrindingHub in Stuttgart, coinciding with the company’s 50-year anniversary.
Armando Manzano, EPX-SF Product Manager said, “More than just an edge preparation machine, the EPX-SF is a strategic business asset. Its high level of precision will help manufacturers to secure more contracts by meeting the rigorous standards of industries that demand clean and consistent cuts. Its ability to deliver flawless quality in a single pass enhances operational efficiency, eliminating the need for extensive post-processing and ultimately saving costs for businesses.”
Key highlights of the EPX-SF:
• Unmatched automation: Process up to 1,900 tools in 24 hours with lights-out operation at the push of a button.
• Resource optimization: Standardization minimizes setup and learning curves, making the process accessible to all operators.
• Machine learning capabilities: Tailored recipes enhance tool IP value, providing a significant selling point for edge preparation.
• Traceability: Every product meets quality expectations with results saved, tracked, and retrievable directly from the machine.
• Predictable precision: Achieve nano-smooth surfaces (roughness < 100 nm) and micron-honed edges with a controllable K-factor.
The EPX-SF is a future-ready solution, designed with advanced functionalities to meet the evolving needs of manufacturing. Its performance-driven design with 11 axes, delivers predictable nanosmooth surfaces and micron-honed edges within a minute per tool. The Advanced Cyclic Mode allows users to adjust angles, optimizing chip flow and effectively combatting surface burrs. It utilizes AI-assisted guidance to provide tailored recommendations, enhancing tool geometries and streamlining process efficiency. With Industry 4.0 connectivity, advanced safety features, and remote technical assistance, the EPX-SF seamlessly integrates into production lines.
Contact your local ANCA representation for more information on how the EPX-SF is redefining edge preparation, or visit https://machines.anca. com/Products/Machines/Edge-Preparation/EPX-SF
For further information, please contact: Amanda Bakun
Marketing & Communications Manager - Americas 248-497-1168 amanda.bakun@anca.com
About ANCA CNC Machines
ANCA CNC Machines is a global leader in the design, manufacture, and service of advanced CNC grinding machines. With an illustrious history spanning over 50 years, ANCA is renowned for its cutting-edge technology, innovative solutions, and exceptional customer support. ANCA’s comprehensive range of products includes tool grinders, CNC grinding machines, software, and automation solutions, catering to diverse industries such as aerospace, automotive, medical, and general manufacturing.
Landmark Solutions has steadily grown its team of experts over the past decade and now serves businesses in seven states, making it the largest fabrication equipment dealer in the Western US. Backed by over 100 years of collective experience, Landmark offers industry-leading machines and support to ensure their customers’ long-term success. Get the Landmark Advantage and contact the team today to find ways to take your operation to the next level.
Contact: Chad Mooneyham, VP | (714) 393-3783 info@landmarksolutionscorp.com
Best Choice Parts: Convenient Source For Omax Oem, Accustream, And Hypertherm Waterjet Parts
Best Choice Parts offers immediate will-call or guaranteed same-day shipment on over 5000 American-made waterjet parts. The region’s proud exclusive dealer for OMAX OEM parts, Best Choice also stocks Accustream and Hypertherm parts for Flow, KMT, and other systems, and has quickly become the preferred parts source for shops throughout the region.
Contact: +1 (855) WATRJET | info@bestchoiceparts.com www. bestchoiceparts.com
Phoenix Heat Treating Is Proud To Announce That We Are FAA Drug And Alcohol Program Compliance.
Phoenix Heat Treating is especially known for its ability to resolve difficult heat-treating problems that are beyond the capability of a typical application. We offer a wide array of processing and consulting services. We take great pride in finding unique solutions to meet each individual customer’s requirements.
To learn more about how Phoenix Heat Treating can support all your heat treat needs, as well as specialized services, contact Tim Johnston, Director of Business Development.
Tim Johnston Director of Business Development is available to assist you at Phoenix Heat Treating and can be reached at 623-512-3233 or by email at tjohnston@phxht.com
FAA Drug and Alcohol Program
GrovTec Machining, a leading production machining facility, is thrilled to announce a significant expansion in both capacity and expertise. We have recently acquired over a dozen pieces of equipment and welcomed ten highly skilled workers from a prominent local machine shop that recently closed.This strategic move underscores our commitment to delivering exceptional service and highquality products to our customers.
multiple Tornos screw machines, Hydromats and an ABC Index, allowing for greater automation, higher precision, and increased production speeds. These enhancements will enable us to meet the growing demands of our customers and offer more versatile machining solutions.
The ten skilled workers joining our team bring with them years of experience and a wealth of knowledge. Their expertise spans various aspects of production machining, from programming and operating advanced machinery to implementing quality control measures and optimizing production workflows. We are confident that their skills will integrate seamlessly with our current team, fostering an environment of innovation and excellence.
“We are excited and blessed to have this opportunity to expand our operations,” said Bob Grover, Owner of GrovTec US, Inc. “The acquisition of these machines and the addition of such skilled workers will significantly enhance our production capabilities. This growth not only allows us to support our existing customers with greater efficiency and quality but also gives us the ability to take on new projects requiring even higher production volumes. We are committed to providing precision parts and reliable machining solutions, and this expansion is a testament to that.”
GrovTec Machining would like to extend heartfelt thanks to our loyal customers, dedicated employees, and supportive community. Without your continued trust and support, this exciting growth would not have been possible. We look forward to serving you with these expanded capabilities and continuing to exceed your expectations. For more information about our services and how we can assist with your production machining needs, please visit our website at www. grovtecmachining.com or contact us at info@ grovtecmachining.com.
About: GrovTec Machining is a premier production machining facility specializing in high-volume, precision machining services. With a commitment to quality, innovation, and customer satisfaction, we provide comprehensive machining solutions to a diverse range of industries. Our state-of-theart equipment and skilled workforce ensure that we deliver exceptional products and services every time.
In an industry where precision, efficiency, and expertise are paramount, the addition of these machines and additional team members represents a substantial enhancement of our capabilities.The new equipment includes
By Stephen Hannemann
3D Plastics in Newberg, Oregon has created something unique in the injection molding industry – a company with HEART! From their inception, 3D management has focused on taking care of the business of “The Customer is King,” and that has been communicated across the line to the people on the production floor who produce the parts.
The success of any manufacturing endeavor must be attributed to the folks who get it done. It boils down to the culture.True, ownership and management set the framework, areas of responsibility, and tone that creates the atmosphere, the working conditions. But the workforce produces the products that land on your shipping dock. The prep people, the setup tech, the molding machine operators, the second ops and assembly people, and the packaging and shipping personnel – all take pride in getting the work done right!
For 25 years dedicated 3D employes have been molding, assembling and shipping peerless injection molded components and assemblies throughout the United States and countries around the world. This is a tribute to the committed production employees at 3D Plastics in Newberg, Oregon.
To learn more about 3D Plastics visit 3d-plastics.com or call 503.537.0979.
Be sure to check out the full 3D story on Page 32.
By Stephen MacLeod
The plan comes as the national EV market is slowing, and the company acknowledges that customers are more cost conscious than early adopters were. Despite the headwinds, work continues at BlueOval City which is still in line to launch an all-new electric truck, codenamed Project T3.
“Construction continues at BlueOval City, where we are excited to launch our next-generation electric truck, which will build on Ford’s centurylong heritage of truck leadership,” said Lisa Drake, Ford VP, EV Programs and Energy Supply Chain. “While we incorporate new lower-cost battery technology, we will use the extra time to make the truck even more competitive — for the long-term benefit of BlueOval City and beyond.”
When first announced, BlueOval City was expected to begin delivery of its vehicles in 2025. In May 2024, Ford updated that timetable to say it was hoping to deliver the truck to customers starting in 2026. While construction continues, it is past the peak it was last year as work enters the later stages. The company said the move was to take advantage of lower-cost battery technology.
“West Tennessee is a linchpin in our plan to create a strong and growing Ford in America,” said Ford president and CEO Jim Farley. “BlueOval City will be one of the most advanced manufacturing complexes anywhere
in the world, and we are counting on the workforce in West Tennessee to produce advanced batteries starting next year, and then our most innovative pickup ever starting in 2027.”
One thing that is still going forward on schedule is BlueOval SK’s battery facilities. The joint venture between Ford and Korea-based SK Innovation is expected to start producing at its Kentucky site in mid-2025 and at BlueOval City in late 2025. The company is also realigning its battery sourcing to lower costs and be more efficient, ultimately keeping EV costs down.
The Kentucky operation is anticipated to provide batteries for Ford’s E-transit commercial van and the F-150 Lightning. In addition to Project T3, Tennessee is slated to produce batteries for Ford’s new electric commercial van to be built at Ford’s Ohio Assembly Plant in 2026 and “future emerging technology electrified vehicles.”
The company is also planning on stepping up its local presence. The company’s own donations and that of its philanthropic wing, Ford Philanthropy, have eclipsed $21 million so far in West Tennessee.
“Ford and Ford Philanthropy are stepping up our community initiatives because we want residents in every community neighboring BlueOval City to benefit as the campus comes to life. I look forward to introducing our Good Neighbor Plan, developed with the help of resident input and the community leaders who make up our Equitable Growth Advisory Council,” said Gabby Bruno, Ford’s community relations director.
Viasat Inc., Carlsbad, California, was awarded a $7,668,960 firmfixed-price contract modification (P00021) to exercise a fourth option year for Naval Senior Leadership Communication – Aircraft satellite communications services. The total cumulative face value of the contract is $38,213,204. The face value of this action is funded by fiscal 2024 operation and maintenance funds. Performance will be at contractor’s facility in Carlsbad, California, with satellite communication services provided to aircraft traveling worldwide. The period of performance for Option Period Four is Sept. 10, 2024, through Sept. 9, 2025.The Defense Information Technology Contracting Organization, Scott Air Force Base, Illinois, is the contracting activity (HC101320C0005).
SRI International, Menlo Park, California, has been awarded a maximum $125,641,325 long term, indefinite-delivery, hybrid cost-plus-fixedfee and firm-fixed-price, requirements type contract for generalized emulation of microcircuits production program. This was a sole-source acquisition using justification 10 U.S. Code 3204 (a)(1), as stated in Federal Acquisition Regulation 6.302-1. This is a five-year base contract with one six-month option period. Location of performance is New Jersey, with a July 31, 2029, performance completion date. Using military services are Army, Navy, Air Force, and Marine Corps. Type of appropriation is fiscal 2024 through 2029 operation and maintenance and defense working capital funds. The contracting activity is the Defense Logistics Agency Land and Maritime, Columbus, Ohio (SPE7MX-24-D-0030).
NewVac LLC,* Chatsworth, California, is awarded a $13,669,843 firm-fixed-price modification to a previously awarded contract (N6339422C0009) for the procurement, manufacture, assemble, test, and delivery of cables in support of the MK 41 Vertical Launching System. This modification combines purchases for the U.S. government (78%); and the governments of Netherlands (12%); and Germany (10%), under the Foreign Military Sales (FMS) program. Work will be performed in Chatsworth, California, and is expected to be completed by September 2025. Fiscal 2024 shipbuilding and conversion (Navy) $6,955,716 (51%); presidential drawdown authority funds in the amount of $2,676,906 (19%); FMS Netherlands (12%); FMS Germany (10%); and other procurement (Navy) funds in the amount of $1,052,150 (8%), will be obligated at time of award and will not expire at the end of the current fiscal year. The Naval Surface Warfare Center, Port Hueneme Division, Port Hueneme, California, is the contracting activity.
ace Exploration Technologies Corp., Hawthorne, California, has been awarded a $661,025,403 modification (P00018) to a previously awarded contract (FA8811-20-D-0002) for National Security Space (NSS) Launch Phase Two launch service procurements for NSS launch services from fiscal 2020 through fiscal 2024, for launches planned between fiscal 2022 through fiscal 2027.The modification brings the total estimated face value of the contract to $4,000,000,000 from $3,338,974,597. Work will be performed Hawthorne, California; Cape Canaveral Space Force Station, Florida; and Vandenberg Space Force Base, California, and is expected to be completed by March 31, 2028. The Contracting Division, Assured
Access to Space, Space Systems Command, Los Angeles Air Force Base, El Segundo, California, is the contracting activity.
Armtec Countermeasures Co., Coachella, California; and Lillington, North Carolina, was awarded an $11,700,000 firm-fixedprice contract for RR-196 countermeasure chaff for the F-22. This contract provides for the impulse cartridge program and is used by F-22 aircraft for combat and training purposes. Work will be performed in Lillington, North Carolina, and is expected to be completed by Sept. 30, 2027. This contract was a sole source acquisition. Fiscal 2024 ammunition funds in the amount of $11,700,000 are being obligated at the time of award. The Air Force Life Cycle Management Center, Hill Air Force Base, Utah, is the contracting activity (FA8213-24-D-B009).
General Atomics Aeronautical Systems Inc., Poway, California, is being awarded a $500,000,000 indefinite-delivery/indefinitequantity contract (H9240824D0002) with a $436,900 initial task order for program management support related to Medium Altitude Long Endurance Tactical MQ-9 and MQ-1C Special Operations Forces-peculiar modifications in support of U.S. Special Operations Command (USSOCOM). This contract will be funded with operations and maintenance; procurement; and/or research, development, and testing evaluation funds under the applicable fiscal year, and is not multiyear. The work will be performed in Poway, California, and is expected to be completed by Aug. 16, 2029. USSOCOM, MacDill Air Force Base, Florida, is the contracting activity.
Servicing our industry and trade customers in intelligence heat treating for over 60 years.
Established in 1963
Real Time Live Job Tracking
10+ Processes Performed
50+ Furnaces
AOG and Line Down Services
Over 10+ Prime Approvals
24/7 Processing
602-258-7751
cs@phxht com
www phoenix-heat-treating com
Northrup Grumman, Northridge, California, has been awarded a $26,800,000 cost-plus-fixed-fee ceiling increase modification (P00001) to previously awarded contract FA8651-24-D-B002 for on-going work within the scope of the statement of work and is needed to continue counter air science and technology efforts.The modification brings the total cumulative face value of the contract to $36,000,000.Work will be performed at Northridge, California, and is expected to be completed by Jan. 15, 2029. The Air Force Research Laboratory, Eglin Air Force Base, Florida, is the contracting activity.
Oshkosh Defense LLC, Oshkosh, Wisconsin, was awarded a $46,092,136 modification (P00002) to contract W912CH-24-F-0082 for the Family of Medium Trucks and related services. Bids were
solicited via the internet with three received.Work locations and funding will be determined with each order, with an estimated completion date of Nov. 30, 2026. Army Contracting Command, Detroit Arsenal, Michigan, is the contracting activity.
B.E. Meyers & Co.,* Redmond,Washington, is being awarded a contract (H9240324D0009) for the acquisition of the Miniature Aiming Systems –Laser (MAS-L) Squad Aiming Laser – Ultra High Power (SAL-UHP) and associated repairs. This indefinite-delivery/indefinite-quantity contract is being awarded with a maximum total ceiling of $49,900,000 and a $500,000 minimum ordering guarantee in support of U.S. Special Operations Command (USSOCOM).This contract will have an ordering period of five years. Fiscal 24 procurement funds in the amount of $11,000,110 are being obligated at time of award on the first delivery order. USSOCOM, MacDill Air Force Base, Florida, is the contracting activity.
Fluor Marine Propulsion LLC, Arlington, Virginia, is awarded a $1,396,995,054 cost-plus-fixed-fee modification to previously awarded contract (N00024-18-C-2130) to exercise fiscal 2025 options for naval nuclear propulsion work at the Naval Nuclear Laboratory. Work will be performed in Pittsburgh, Pennsylvania (52%); Schenectady, New York (39%); and Idaho Falls, Idaho (9%). Fiscal 2024 other procurement (Navy) funding in the amount of $14,979,962 (79%); fiscal 2024 research, development, test and evaluation in the amount of $3,551,000 (19%); and fiscal 2022 other procurement (Navy) funding in the amount of $495,000 (2%), will be obligated at time of award and funds in the amount of $495,000 will expire at the end of the current fiscal year. Naval Sea Systems Command, Washington, D.C., is the contracting activity.
Lockheed Martin Rotary and Mission Systems, Moorestown, New Jersey, is awarded a $61,000,000 cost-plus-fixed-fee and cost-only modification to a previously awarded contract (N00024-20-C-5392) for engineering integration, technical support, and depot operations in support of the MK 41 vertical launching system electronic systems and computer programs. Work will be performed in Moorestown, New Jersey (60%);Ventura, California (16%), San Diego, California (10%); Seattle, Washington (4%); Mayport, Florida (4%); Norfolk, Virginia (4%); and Virginia Beach, Virginia (2%), and is expected to be completed by July 2025. Fiscal 2024 shipbuilding and conversion (Navy) funds in the amount of $5,635,000 (43%); fiscal 2024 research, development, test and evaluation (Navy) funds in
the amount of $5,441,483 (41%); fiscal 2024 other procurement (Navy) funds in the amount of $1,254,750 (9%); and fiscal 2024 Defense-wide research, development, test and evaluation funds in the amount of $927,322 (7%), will be obligated at time of award and will not expire at the end of the current fiscal year. Naval Sea Systems Command,Washington NavyYard,Washington, D.C., is the contracting activity.
The Boeing Co., Seattle, Washington, is awarded a $27,658,912 modification (P00023) to a cost-plus-fixed-fee-order (N0001920F0647) against a previously issued basic ordering agreement (N0001916G0001). This modification exercises an option to procure three retrofit A-Kits for Royal Australian Air Force (RAAF) P-8A aircraft with Increment Three Engineering Change Proposal Six Capabilities. Work will be performed in Jacksonville, Florida (79.6%); San Antonio, Texas (10.9%); and Mesa, Arizona (9.5%), and is expected to be completed October 2026. RAAF Cooperative Funds in the amount of $27,658,912 will be obligated at the time of award, none of which will expire at the end of the current fiscal year. Naval Air Systems Command, Patuxent River, Maryland, is the contracting activity.
General Atomics Aeronautical Systems Inc., San Diego, California, is awarded a $9,672,322 modification (P00005) to a firm-fixed-price order (N0001921F0060) against a previously issued basic ordering agreement (N0001916G0006). This modification provides for the procurement and installation of upgraded dual gate drivers for the Electromagnetic Aircraft Launch System Power Conditioning
Subsystem Half Bridges to address reliability and obsolescence concerns. This includes a total of 686 kits that will be installed on Navy aircraft carriers (CVN 78, CVN 79) and the Lakehurst System Functional Demonstration test site, including on-board and site spares for each location. Additionally, this modification includes associated labor for engineering, program management, and logistics products. Work will be performed in Tupelo, Mississippi (56.1%); San Diego, California (40.7%); Newport News, Virginia (1.7%); and Lakehurst, New Jersey (1.5%), and is expected to be completed January 2027. Fiscal 2024 shipbuilding and conversion (Navy) funds in the amount $3,442,009; fiscal 2024 other procurement (Navy) funds in the amount $2,277,737; fiscal 2023 other procurement (Navy) funds in the amount of $2,676,182; and fiscal 2022 other procurement (Navy) funds in the amount of $1,276,392 will be obligated at the time of award, $1,276,392 of which will expire at the end of the fiscal year. Naval Air Systems Command, Patuxent River, Maryland, is the contracting activity.
Science Applications International Corp., Reston, Virginia, has been awarded a maximum $262,430,360 contract bridge modification (P00013) to previously awarded Government Wide Acquisition Contract Alliant 2 vehicle for continued Air Force cloud computing capability. The contract modification is for continued support of commercial cloud services, common architectural and foundational services, and software engineering services to assist with migration and modernization. The modification brings the total cumulative face value of the contract to $1,246,163,495. Work will be performed at the contractor’s designated facilities and is expected to be completed by Sept. 8, 2025. Fiscal 2024 operations and maintenance funds in the
amount of $13,804,881 are being obligated at the time of award. The Air Force Life Cycle Management Center, Hanscom Air Force Base, Massachusetts, is the contracting activity (FA8726-24-F-0001). Oshkosh Defense LLC, Oshkosh, Wisconsin, was awarded a $1,541,861,429 fixed-price with economic-price-adjustment contract for the Family of Heavy Tactical Vehicles. Bids were solicited via the internet with one received. Work locations and funding will be determined with each order, with an estimated completion date of Aug. 19, 2029. Army Contracting Command, Detroit Arsenal, Michigan, is the contracting activity (W912CH-24-D-0008).
Modern Technology Solutions Inc., Alexandria, Virginia, is being awarded a competitive, cost-plus-fixed-fee, indefinite-delivery/ indefinite-quantity contract with a maximum amount of $73,568,329. Under this new contract, the contractor will build advance the state-ofthe-art in collaborative, constructive experimentation and evaluation of missile defeat kill webs (MDKW). The contractor will create a digital engineering ecosystem that enables experiments and evaluations of MDKW including left-through-right of launch. A task order in the amount of $11,919,845 is being issued. The work will be performed in Huntsville, Alabama. The ordering period is from Aug. 19, 2024, through Aug. 18, 2029. This contract was competitively procured via publication on the government-wide Point-of-Entry website under the Missile Defense Agency’s (MDA) Broad Agency Announcement HQ0860-23-S-0001. Fiscal 2023 research, development, test and evaluation Congressional-Plus-Up funds in the amount of $1,804,347 are being obligated on the first task order. MDA, Redstone Arsenal, Alabama, is the contracting activity (HQ0860-24-D-0001).
The U.S. Navy is taking the first steps toward building the most advanced version of the Virginia-class fast attack submarine (SSN 774) -- an undersea warfare weapon expected to bring its reconnaissance and lethality from the ocean’s surface to the seabed.
Officials of the Naval Sea Systems Command in Washington announced a $181 million order in July to General Dynamics Corp. Electric Boat segment in Groton, Conn., for long-lead items for the Virginia Class Block VI submarines.
The Virginia Block VI submarines are to feature technology improvements in stealth, propulsion, and weapons, and should be one of the best submarines in the world for interacting with the water column from the surface to the seabed.
Long-lead items either are difficult and timeconsuming to obtain, and are funded early in the aircraft design process to keep overall production on schedule.
Related: Navy starts ramping-up production of large unmanned submarines for reconnaissance and special ops
The Virginia Block VI boats will be the second block of Virginia-class attack submarines with the Virginia Payload Module for large-scale land strike missiles.
The Virginia Payload Module places four multiple all-up-round canisters in the middle of the submarine in addition to two in the bow. Each tube can contain seven Tomahawk land-attack missiles.
Not only does the Virginia Block VI add land-attack firepower to the fleet, but it also offers the opportunity for the Navy to design mission-specific submarines.
The Navy is expected to order at least one Virginia Block VI specially designed for seabed warfare for undersea espionage and other special
The overall target of seabed warfare is infrastructure in place on the seabed
On this order, General Dynamics will do the work in Sunnyvale, Calif.; Minneapolis;York and Pittsburgh, Pa.; Spring Grove and Peoria, Ill.; Windsor Locks, Conn.; Tucson, Ariz.; Monroe, N.C.; and other locations, and should be finished by September 2035.
by Alex Hollings
The race to field reusable hypersonic aircraft got a whole lot hotter with GE Aerospace announcing a breakthrough in high-speed jet engine design that could potentially allow conventional aircraft to fly at speeds that exceed Mach 10.
According to GE’s press release, the company recently demonstrated “what is believed to be a world-first hypersonic dual-mode ramjet (DMRJ) rig test with rotating detonation combustion (RDC) in a supersonic flow stream.” This means leveraging rotating detonation combustion – a far more efficient means of power production – within a dualmode ramjet (also sometimes called a dual-mode scramjet).
Ramjets and scramjets are airbreathing jet engines that don’t function well at low speeds, but can power an aircraft or weapon from around Mach 3 up to Mach 5 and well beyond.
This would be a significant development toward producing dual-mode ramjet/scramjets with far greater range, but could represent an even bigger breakthrough if combined with a similarly Rotating Detonation Combustion-equipped turbofan engine in what’s commonly called a turbinebased combined cycle (TBCC) propulsion system. And those wheels are already turning. GE first acknowledged that it was working with the Defense Advanced Research Projects Agency (DARPA) and the Air Force Research Lab (AFRL) on an RDC-equipped TBCC engine in June of this year.
This TBCC engine would combine four different types of air-breathing jet engine technologies into a single combined system that would allow an aircraft to take off and land under conventional turbofan power, while also achieving hypersonic speeds under scramjet power during sustained flight – a concept that has been proposed by at least three other firms before. But GE’s design is the first to incorporate Rotating
which could make such an engine far more compact and efficient than previous efforts, potentially resulting in a much more practical approach to hypersonic flight.
A working TBCC engine has long been seen as the Holy Grail for reusable hypersonic aircraft, as the exotic propulsion systems powering today’s hypersonic weapons can’t function at low enough speeds needed to land aircraft, making them single-use.
Last November, Atlanta-based aviation firm Hermeus demonstrated their turbine-based combined cycle Chimera engine could successfully transition from turbojet to ramjet power in a high-speed wind tunnel. About a month later,Virginia-based Leidos secured a $334 million contract from the Air Force Research Lab to continue development on an even more capable turbofan-to-scramjet design that would function similarly but could potentially achieve much higher speeds. And most secretive of all, Lockheed Martin announced success in ground-testing a similar turbofan-to-dual-mode-scramjet design with Aerojet Rocketdyne back in 2017 as part of the now highly secretive SR-72 program.
But while each of these designs is quite promising, this new announcement out of GE Aerospace may represent the most promising combined cycle hypersonic propulsion system revealed to date, as it incorporates a similar turbofan-to-dual mode scramjet as the SR-72 and Mayhem efforts, but adds yet another exotic propulsion system into the mix in the form of a rotating detonation engine.
This addition could help to overcome the biggest technical hurdle Lockheed Martin’s SR-72 program was known to face: bridging the gap between speeds attainable under turbofan power (which begins to drop in efficiency above Mach 2) and scramjet power (which functions less efficiently at speeds below Mach 4).
to manage the placement of shockwaves in the airstream at different flight speeds.
Based on GE’s claims, their Hypersonic Dual-Mode Ramjet with Rotating Detonation Combustion engine could not only achieve similar or even greater speeds as other hypersonic engine designs, but could offer a significant boost in fuel economy — and as a result, range — in what may prove to be an overall smaller and lighter package.
This program has been underway for only about a year, according to the GE press release, but has matured rapidly thanks, in part, to GE’s acquisition of hypersonic-focused Innoveering LLC, last year. Inoveering brought a great deal of experience developing high-speed inlet designs, which play a vital role in the function of any jet engine. In a dual-mode scramjet, the inlet geometry must not only be precise but often also needs to be adjustable
In its simplest form, a rotating detonation engine (RDE) is a propulsion system that offers greater efficiency than traditional air-breathing jet engines thanks to a more effective means of ignition.
In some ways, a Rotating Detonation Engine is an extension of Pulse Detonation Engines (PDEs), which are, in themselves, an extension of Pulsejets. While this lineage may seem confusing, walking through each of them as developmental steps may make it easier to wrap our heads around how RDEs work.
Pulsejet engines work by mixing air and fuel within a combustion chamber and then igniting the mixture to fire out of a nozzle in rapid pulses, rather than under consistent combustion as you might find in other jet engines. In pulsejet engines, as in nearly all combustion engines, the way in which the air/fuel mixture burns is known as deflagration. In simple terms, deflagation means heating a substance until it burns away rapidly, but at subsonic speeds.
A pulse detonation engine works similarly, but instead of leveraging deflagration, it uses detonation. At a fundamental level, detonation is a
lot like it sounds: an explosion. In contrast to deflagration, in detonation, the mixture burns at supersonic speeds.
“You can get more efficiency by cramming all that reaction during a really short time in space. There’s, at least from a thermodynamic standpoint, potential for much higher efficiencies in engines that burn through detonation rather than deflagration,” Dr. Chris Combs, a Dee Howard endowed professor of hypersonic and aerospace engineering for the University of Texas San Antonio, told Sandboxx News.
When the air and fuel are mixed in a Pulse Detonation Engine, they’re ignited, creating deflagration like in any other combustion engine, but within the longer exhaust tube leading out of the engine, a powerful pressure wave compresses any unburnt fuel ahead of the ignition, heating it above ignition temperature in what is known as the deflagration-to-detonation transition (DDT). In other words, rather than burning through the fuel rapidly, the engine explodes it, producing more thrust from the same amount of fuel.
A rotating detonation engine takes that PDE concept to the next level. Rather than having the detonation wave travel out the back of the aircraft as propulsion, it travels around a circular channel within the engine itself. Fuel and oxidizers are added to the channel through small holes, which are then struck and ignited by the rapidly circling detonation waves. According to Dr. Combs, it’s not uncommon for a rotating detonation engine to have three to five of these detonation waves circling the chamber at once.
The result is an engine that produces continuous thrust, rather than thrust in pulses like a PDE, while also offering the improved efficiency of detonation combustion, rather than deflagration, as you’d find in a conventional jet engine.
But GE Aerospace has found a way to incorporate this Rotation Detonation Combustion (RDC) process into its dual-mode ramjet propulsion system, and it claims to be working toward incorporating it into its turbofan technology as well.This may just solve two of the most pressing challenges facing hypersonic aircraft propulsion today: first, managing the transition from turbofan to scramjet power; and second, reducing the weight associated with such a turbine-based combined-cycle (TBCC) engine.
Firms like Hermeus and Leidos are working to field a hypersonic aircraft that incorporates two different kinds of air-breathing jet engines into one: low-speed engines like turbojets and turbofans, and high-speed engines like ramjets and scramjets.This combination speaks to the innate challenges of managing airflow at speeds ranging from a dead stop, all the way up into the high-supersonic regime.
Turbojets and turbofans, the types of air-breathing jet engines that power many of today’s tactical aircraft, use a compressor fan near the inlet to suck air into the engine and compress it, before mixing that compressed air with fuel and igniting it for propulsion. As a result, these kinds of engines can work from a dead stop to accelerate an aircraft down a runway for takeoff and can continue to accelerate it up to around Mach 2 very effectively.Yet, they begin to see a drop-off in efficiency as they approach Mach 3. At that speed, the compressor at the front of the engine that’s meant to suck in and compress air instead becomes a hindrance to the air flowing in at the speed of the aircraft’s forward travel, limiting the engine’s efficiency. A2Z-Rosco-Hurco_DCX3226HT5Si_March_2024.indd
Phoenix Heat Treating is thrilled to announce the addition of Salt Bath Nitriding to its lineup of services. For over 60 years, Phoenix Heat Treating has been dedicated to servicing their customers’ unique heat treatment needs. This new addition supports the growing demand for advanced surface treatment solutions and complements our existing service offerings providing a one stop shop for all thermal process needs.
Salt Bath Nitriding, also known as Ferritic Nitrocarburizing, is a thermochemical process that diffuses nitrogen and carbon simultaneously into the surface of ferrous metals. During this process, a two-part surface layer is formed: an outer iron nitride layer and a nitrogen diffusion layer beneath it. Nitrogen and carbon are absorbed and diffused uniformly into the metal surface, creating reproducible and uniform layers with a predetermined thickness. This results in significantly improved surface properties for ferrous metal parts, all while maintaining dimensional and shape stability. Salt Bath Nitriding is a popular case hardening technique, alongside carburizing and carbonitriding, both of which Phoenix Heat Treating performs.
It was originally created as an alternative to gas nitriding that would produce a more uniform case through surface contact between the substrate and liquid salt.This method of directly heating the part via salt allows for faster process times compared to gas nitriding. Additionally, when steel parts are placed into a preheated liquid salt, there is sufficient energy localized near the surface due to differences in chemical potential that then allows
nitrogen and carbon species to diffuse from the salt into the steel substrate.The surface hardness a salt bath nitride part can range from 800 HV to 1500 HV. Not only is the surface hardness high the finish once polished is a beautiful jet black.
Salt Bath Nitriding/ Nitrocarburizing is well known under various trade names, including MELONITE® and QPQ®.
The benefits of Salt Bath Nitriding include:
• Increased Wear Resistance: Enhanced durability of metal surfaces, leading to longer part life.
• Improved Fatigue Strength: Greater resistance to cracking under cyclic loading.
• Corrosion Resistance: Better protection against rust and oxidation.
• Improved Lubricity: Reduced friction and wear during operation.
• Cosmetic Black Finish: Aesthetic enhancement with a sleek black appearance.
• Quick processing time
• Reduced shape distortion during the hardening process: The low processing temperature reduces thermal shocks and avoids phase transitions in steel.
Processing can be tailored to meet customer specifications or adhere to AMS 2753 standards, ensuring flexibility and compliance with industry requirements. With the introduction of Salt Bath Nitriding, Phoenix Heat Treating will now serve as a single source for both core hardening and the salt bath nitride finish, streamlining the
supply chain and enhancing convenience for our customers. Not only can Phoenix Heat Treating adhere to AMS 2753, but they are pleased to share that Honeywell has approved them for this process.
Their process tank size accommodates parts up to 32” DIA X 48”. For smaller parts, drum processing is also available. Yet smaller parts such as detent buttons, rolls pins, internal firearm related parts and dental picks are all processed in handmade pouches, providing versatility in handling various component sizes.
Nitriding is used for a range of applications, including:
• Medical equipment.
• Firearms and small weapons systems.
• Pump and gear components.
• High performance automotive parts.
• Oil & Gas.
• Mining & Marine equipment.
• Farming and Food processing equipment.
When asked for comment General Manager Charlie Hushek noted, “We are thrilled to add this business unit as it continues our efforts to be the most customer centric heat treater in the country. Salt bath nitriding is the first of a few big projects we are working on. It is nice to see it to fruition.”
Tim Johnston, Director of Business development added, “There is a huge need for quality salt bath nitriding not only in Phoenix but the entire west coast, we are pleased to offer support to those who need it.”
Phoenix Heat Treating continues to focus on its customers not only with the addition of new processes but by leveraging technology. Their entire quality system is paperless, and employees use iPads to track in and out of operations. Their latest 5 day Nadcap audit resulted in zero findings. This focus on technology has supply chain benefits for customers too. All Phoenix Heat Treating customers can log in and view live job tracking as well as download certifications and shipping tickets on demand. “I always like to say, we take the headache out of heat treat! Using digital tools to make communication effortless is what being a true partner looks like”, added Charlie.
For those not familiar with Phoenix Heat Treating, they offer an extensive array of services to their customers.Their heat treating processes include:
1. Ceramic Diffusion
2. Vacuum Processing
3. Aluminum Processing
4. Salt Processing
5. Atmosphere Processing
6. Metal Finishing
7. Specialized Services, Including: Aluminum Spray Quench; Cryogenic Services; Straightening; Fixture Tempering; Titanium; Argon Oil Quench; and blast cleaning.
Phoenix Heat Treating is especially known for its ability to resolve difficult heattreating problems that are beyond the capability of a typical application. In fact, we fix many problems caused by other heat-treating shops who aren’t customer focused and unable to gauge microstructure and hardness chemistry. With state-of-theart automation, computerized monitoring and control systems, inhouse metallurgical engineering and inspection labs, our company can handle the most difficult heat treating and processing jobs. Guaranteed repeatable, documented procedures will ensure compliance to your required standards and certifications.
It is clear that Phoenix Heat Treating spends time thinking about its customers. The addition of Salt Bath Nitriding underscores their commitment to delivering high-quality, advanced heat treatment solutions.
Ellison Technologies is a provider of advanced machining solutions to North American metal-cutting manufacturers and their global affiliates.
As a family of companies we are committed to the survival and growth of the American manufacturing industry. Independent offices provide us a local market focus and the flexibility to advocate the needs of each of our valued customers.
Our priority is to introduce technologies that strengthen our customers’ ability to compete in the markets they serve. Whether the solution involves a stand alone machine, multi-process equipment, or an integrated manufacturing system with robotic automation, our goal remains the same; to optimize throughput and quality at the lowest per-part manufacturing cost.
Our team of engineers, equipment and automation specialists, and project management professionals, are dedicated to helping manufacturers get the most from their technology investments. Service and parts engineers provide post-installation support aimed at optimizing machine availability, productivity, and cost of ownership.
We strive to make every customer worldcompetitive. Whether our customer competes globally or not, Ellison Technologies brings its full mastery of advanced manufacturing technology to provide the most comprehensive and productive solutions the industry has to offer.
Whenever you add a new technology, there’s bound to be a learning curve. At Ellison Technologies, we act as an extension of your operation as you get up to speed. If you have any questions – whether before, during or after the machine install – we’re here to help you identify the best way to do things.
There are Ellison branches all over the United States, and all of our employees bring experience (and a willingness to share it) that’s simply unmatched. No matter how new your machining adventure is to you, we’ve seen it, and we’ve solved for it already. It’s a welcome dose of peace of mind as your journey begins.
Our mission is clear: at Ellison, we equip American manufacturers to compete and win, both locally and globally. If you can’t shake the feeling that there’s a better way to do things, we are ready to help you increase quality and efficiency, win more work and increase your profits.
For more information on Ellison Technologies contact them at: 866-567-2580, www.ellisontechnologies.com
“Our overall confidence in the near-term future of the industry is high. We’re expecting economic conditions for businesses to improve over the next six months as interest rates decline and investment in U.S. manufacturing continues to grow,” says survey respondent Jeff Elliott, president of Huntington Equipment Finance.
Newly released survey results show improved confidence in the equipment finance sector. The August 2024 Monthly Confidence Index for the Equipment Finance Industry (MCI-EFI) reached 58.4, the highest level since February 2022, the Equipment Leasing & Finance Foundation reported Wednesday. The index shows an increase from the July figure of 50.7.
When asked to assess their business conditions over the next four months, 37.5% of the executives responding said they believe business conditions will improve over the next four months, an increase from 3.9% in July. 45.8% believe business conditions will remain the same over the next four months, down from 76.9% the previous month. 16.7% believe business conditions will worsen, down from 19.2% in July.
41.7% of the survey respondents believe demand for leases and loans to fund capital expenditures (capex) will increase over the next four months, up from 11.7% in July. 37.5% believe demand will “remain the same” during the same four-month time period, down from 73.1% the previous month. 20.8% believe demand will decline, an increase from 15.4% in July.
20.8% of the respondents expect more access to capital to fund equipment acquisitions over the next four months, up from 19.2% in July. 75% of executives indicate they expect the “same” access to capital to fund business, down from 76.9% last month. 4.2% expect “less” access to capital, relatively unchanged from 3.9% the previous month. When asked, 20.8% of the executives report they expect to hire more employees over the next four months, a decrease from 23.1% in July. 70.8% expect no change in headcount over the next four months, up from 69.2% last month. 8.3% expect to hire fewer employees, up from 7.7% in July.
None of the leadership evaluate the current U.S. economy as “excellent,” unchanged from the previous month. 91.7% of the leadership evaluate the current U.S. economy as “fair,” up from 84.6% in July. 8.3% evaluate it as “poor,” down from 15.4% last month.
37.5% of the survey respondents believe that U.S. economic conditions will get “better” over the next six months, up from 19.2% in July. 41.7% indicate they believe the U.S. economy will “stay the same” over the next six months, a decrease from 57.7% last month. 20.8% believe economic conditions in the U.S. will worsen over the next six months, a decrease from 23.1% the previous month.
In August, 33.3% of respondents indicate they believe their company will increase spending on business development activities during the next six months, an increase from 19.2% the previous month. 62.5% believe there will be “no change” in business development spending, down from 73.1% in July. 4.2% believe there will be a decrease in spending, down from 7.7% last month.
BARTON’s Transfer Hopper holds up to 4,400 lbs. of garnet eliminating the need to handle individual bags of abrasive.
• Saves time and labor
• Increases worker safety
• Minimizes clogs
• Reduces waste Interested in learning more?
Call 800-741-7756 or email info@barton.com
BARTON INTERNATIONAL USA/Canada 800-741-7756 • 518-798-5462 info@barton.com • barton.com • store.barton.com BARTON is a trademark of BARTON Mines Corporation.
“This flagship manufacturing facility will dramatically accelerate our efforts to deliver sodium-ion batteries to customers who are hungry for safe, reliable and environmentally responsible energy storage solutions,” said Natron Energy Founder and co-CEO Colin Wessells.
Anna
Smith
Battery manufacturer
Natron Energy has announced a $1.4 billion investment to establish a 1.2 million squarefoot sodiumion battery gigafactory in Edgecombe County, North Carolina. Once fully operational, the facility is expected to create 1,062 jobs and produce 24GW of sodium-ion batteries annually.
Subject to final approval from the Economic Development Partnership of North Carolina’s Board of Directors, Natron will receive around $30 million from the North Carolina Megasite Readiness Program. In addition, the factory at the Kingsboro megasite will be facilitated in part by a Job
Development Investment Grant.
The giga-scale facility will represent a 40x scale-up of the company’s current production capacity.The sodium-ion batteries are UL listed and will be delivered to industrial power space end markets.
The factory will join many other battery manufacturing facilities recently announced in the Southeastern U.S. as part of the ‘Battery Belt.’
Like traditional lithium-ion and lead acid batteries, Natron battery cells have a positive electrode (cathode), a negative electrode (anode), a porous separator between the two electrodes, along with a paste-like, non-aqueous electrolyte that enables charge (ions) to pass back and forth between the electrodes. The atoms in Prussian blue particles are arranged in large, cubic cages with empty spaces (pores) between them. Since the pores in Prussian blue are larger than sodium ions, they are able to rapidly absorb and release those ions in a process called intercalation. This rapid intercalation is the key benefit of Natron’s sodium-ion battery technology and sets it apart from other conventional storage materials found in lithium-ion and lead acid cells.
The Prussian blue structure also does not expand and contract as it charges and discharges sodium ions. This “zero strain” mechanism means greater chemical stability and less particle degradation that limits cycle life in other batteries.
Chucks and adaptations are available in round or hexagonal configurations
n Change from O.D. to I.D. to jaw clamping in < 2 minutes
n Use the same adaptations on your HAINBUCH turning or stationary chucks
n Keep the basic clamping device mounted on the machine
1.800.281.5734
Germantown, WI USA www.hainbuchamerica.com
Stefan Menin
Dimensional tolerances are critical for making parts that will fit together in an assembly and meet the design and performance goals. Getting the tolerances wrong could easily mean parts will be too expensive to make or will not fit properly with other components.
For example, if an engineering team designed a 0.875-in. diameter shaft that was supposed to mate with a precision bearing, but it sent out the drawings to a reputable manufacturer without specifying tolerances, the bearing may or may not fit on the finished shaft.
Machine shops that see an untoleranced diameter on a part and do not
know the design intent may typically apply a standard tolerance for threedecimal-place untoleranced dimensions, ±0.005 in. Unfortunately, this means the shaft may be too large for the hole it is designed to slide through. The machine shop will gladly rework the pieces to fit—for an additional charge—which will extend delivery times and possibly lead to missed deadlines and budgets.
Make no mistake, this happens all the time. Many machine shops take the extra step of verifying untoleranced dimensions, but many others don’t. Engineers who know the importance of tolerances, and how to use them, can easily avoid this problem.
ASME Y14.5M defines “tolerance” as “the total amount a specific dimension is permitted to vary. The tolerance is the difference between the maximum and minimum limits. This can be shown as upper and lower limits (0.2500/0.2498) or an allowable amount above and below a nominal dimension (0.2499 ±0.0001). Both methods define the same range—the tolerable band—of allowable dimensions rejected. The larger the difference between the upper and lower limits, the larger the tolerance band and the “looser” the tolerance. Conversely, a smaller tolerance band is considered a “tighter” tolerance.
Engineers should always use tolerances. Ambiguity is not a friend to mechanical designers. If dimension has no defined tolerance, no one will know the importance, or unimportance, of the dimension except the designer.
Tolerances ensure parts will fit properly and work as designed within an assembly whether it is uses a sliding or press fit. They also reduce costs. Unnecessarily tight tolerances make parts more expensive. And there is no reason to apply a ±0.0002 tolerance when ±0.002 will do. Also, although some manufacturers apply their own standard tolerances to untoleranced dimensions, many will not even begin making parts until all features are defined.
Expecting parts to be made to the machinist’s best effort is not realistic. The machinist does not know how parts interact, nor is that their responsibility. Furthermore, one machinist’s “best effort” may be maintaining features to within a few ten-thousandths of the dimension
indicated, while another may make the feature 0.015 in. larger or smaller than indicated.
Another significant benefit is that by using suitable tolerances, engineers pass the responsibility of making the part correctly to the manufacturer. By the same token, if the part is within tolerance but doesn’t fit or function properly, the manufacturer cannot be held accountable. Dimensions without tolerances leave the acceptable limits open, and it’s not the manufacturer’s responsibility to determine what is acceptable.
One of the most critical considerations when applying tolerances is to take into account fits.This refers to how shafts fit into bearings or bushings, how motors fit into pilot holes and so on. There are three basic types of fits: Clearance fits can compensate for thermal expansion, sliding fits provide better positioning; and interference (press)s have higher for holding capability. (For more information, check out Machinery’s Handbook.)
Another consideration is how “tolerance accumulation” (also called “tolerance stack”) affects a part. Consider a piece of equipment assembled from several different components, each with its own tolerances. If every part is at the low (small) end of its tolerance window or, conversely, very one is at its high (large end), will the machine still go together? Engineers must keep the final product in mind when they are setting tolerances.
Be careful when applying tolerances to a radius or
diameter.Tolerances on a radius will double when measured as a diameter. The tolerances on a radius might be looser than intended, while the one on a diameter might be tighter than intended.
Also, one need not assume measurements will be rounded when determining if a part conforms to its specified tolerance. If a part measured with a micrometer registers 0.2502, and the part’s dimension is supposed to be 0.250 +0.000/−0.002 the dimension is not rounded down to three decimal places; it is considered nonconforming. ASME Y14.5M states dimensions “are used as if they were continued with zeros,” even if not shown.
Both the location and size of alignment holes (such as for dowel pins) should not carry the same tolerances as clearance holes (such as for screws to pass through). If the dowel pin hole is too far from the desired spot (outside proper tolerances), it might make the parts impossible to assemble.The same level of an out-of-bound tolerance on clearance hole, however, will likely have effect to the assembly, except possibly a near-imperceptible aesthetic oddity.
Thoroughly dimensioning parts is important, but avoid redundancies. They can cause conflicts in inspection because certain features are defined more than once and in different ways. If a designer wants an over-defined dimension, they should use a reference dimension between parentheses and usually without tolerances.
Gartner survey says everyday AI is acting as more of a collaborator than a tool.
In less than two years, what Gartner calls everyday AI and digital employee experience (DEX) will be reach mainstream adoption, according to the firm’s new report, Hype Cycle for Digital Workplace Applications, 2024.
“Everyday AI promises to remove digital friction, by helping employees write, research, collaborate and ideate,” said Matt Cain, distinguished VP Analyst at Gartner, in a statement. “It is a core part of DEX, which is a concentrated effort to remove digital friction and improve workforce digital dexterity, which itself is one of the key factors that will drive organizational prosperity through 2030.”
Part of the reason for its increase in usage this year is the decrease in the focus on hybrid and remote work dwindles and the need for strategic concentration increases. The firm places AI on its Peak of Inflated Expectations on the Gartner Hype Cycle for Digital Workplace Applications, 2024.
“Everyday AI technology aims to help employees
deliver work with speed, comprehensiveness and confidence,” said Adam Preset, VP Analyst at Gartner, in a statement. “It supports a new way of working, where intelligent software is acting as more of a collaborator than a tool.The digital workplace is now entering the era of everyday AI. In many ways, everyday AI is the future of workforce productivity.”
Nearly all employees are becoming digital employees as they spend more time working with technology than ever before. Because of this, organizations must have a strategy to measure and improve DEX to attract and retain talent to improve employee engagement and maximize discretionary effort and intent-to-stay.
Business leaders are looking for guidance on how technology can help boost productivity and organizational alignment. DEX emphasizes best practices that boost digital dexterity, attract and retain talent, and help employees deliver against business outcomes.
DEX is in the Trough of Disillusionment on the Hype Cycle, meaning that interest is waning as experiments and implementations fail to deliver. To increase the appeal and relevance around DEX, business leaders should take a holistic approach across IT and non-IT partners to build a meaningful environment that empowers employees to adopt new ways of working.
Gartner says GenAI requires a higher tolerance for indirect, future financial investment criteria versus immediate ROI.
Poor data quality, inadequate risk controls, escalating costs or unclear business value are reasons that at least 30% of generative AI (GenAI) projects will be abandoned after proof of concept by the end of 2025, according to Gartner, Inc.
“After last year’s hype, executives are impatient to see returns on GenAI Investments, yet organizations are struggling to prove and realize value,” said Rita Sallam, VP Analyst at Gartner, in a statement. “As the scope of initiatives widen, the financial burden of developing and deploying GenAI models is increasingly felt.”
One the issues is the ability to justify the substantial investment in GenAI for productivity enhancement, which can be difficult to directly translate into financial benefit, according to Gartner. The research show that many organizations are leveraging GENAI to transform their business models and create new business opportunities. However the costs of this is high, , ranging from $5 million to $20 million.
“Unfortunately, there is no one size fits all with GenAI, and costs aren’t as predictable as other technologies,” said Sallam. “What you spend, the use cases you invest in and the deployment approaches you take, all determine the costs. Whether you’re a market disruptor and want to infuse AI everywhere, or you have a more conservative focus on productivity gains or extending existing processes, each has different levels of cost, risk, variability and strategic impact.”
Gartner research indicates GenAI requires a higher tolerance for indirect, future financial investment criteria versus immediate return on investment (ROI). Historically, many CFOs have not been comfortable with investing today for indirect value in the future.This reluctance can skew investment allocation to tactical versus strategic outcomes.
Earlier adopters across industries and business
Gold Plating
Silver Plating
Nickel Plating
Electroless Nickel Plating
Tin Plating
Heat Treat With Plate
Nadcap Approved Processes
Boeing Approved Processes + Expedited Turnaround + X-ray Fluorescence Thickness Verification + In-House Laboratory With Atomic Absorption (AA) + Expanded Capacity In Vibratory Plating
processes are reporting a range of business improvements that vary by use case, job type and skill level of the worker. According to a recent Gartner survey, respondents reported 15.8% revenue increase, 15.2% cost savings and 22.6% productivity improvement on average. The survey of 822 business leaders was conducted between September and November 2023.
“This data serves as a valuable reference point for assessing the business value derived from GenAI business model innovation,” said Sallam. “But it’s important to acknowledge the challenges in estimating that value, as benefits are very company, use case, role and workforce specific. Often, the impact may not be immediately evident and may materialize over time. However, this delay doesn’t diminish the potential benefits.”
by Brian Boyle
Artificial intelligence hype crashing headfirst into reality. The unwinding of the yen carry trade. The softening US consumer.
There were a lot of targets for finger-pointing amid the early-August meltdown-that-wasn’t. But Monday saw the eighth straight day of gains on the S&P 500, marking its longest winning streak of the year so far. Now the index, having recovered all its losses from earlier this month, sits just less than 2% away from the all-time peak it reached in July. As the dust settles, it’s becoming clear that the finger-pointing may have been a smidge aggressive.
The Vix Is In Doom-and-gloom headlines aside, it appears traders ultimately saw the AI sorta-crash simply as an opportunity to buy the
dip; Nvidia has now rallied some 30% since an early-August low, leading the charge for a megacap tech rebound. Meanwhile, Toby Gresham, investment counselor team lead at Citi Private Bank, said on CNBC this weekend that the unwinding of the yen carry trade has mostly “washed through,” and Nomura Holdings, Japan’s biggest brokerage, told Bloomberg that hedge funds and other investors are already pouring back into the carry trade game.
Last week, the Commerce Department also released new US retail spending data that pummeled expectations and suggested the American consumer isn’t slowing down just yet (a fear also allayed by a strong earnings beat from Walmart on Thursday). “Even the perma-bears would have struggled to find much in the slew of data released over the past week that would justify recent recession fears,” Neil Shearing, chief economist at Capital Economics, told the Financial Times on Monday.
You would be forgiven for feeling a fair amount of macroeconomic whiplash. Whether or not you should expect future volatility remains an open question:
The Cboe Volatility Index — a.k.a. the Vix, or Wall Street’s fear gauge — has fallen nearly 24 points since spiking on Aug. 5, which marks its longest decline since November 2008. Some experts are already saying that the spike was more likely a reflection of a quirk in how the gauge is calculated rather than a true reflection of trader panic.
But go a little deeper and there remains some doubt. The “Vvix” index, which is calculated on derivatives tied to the actual Vix, has similarly fallen since an Aug. 5 peak, but remains trading above its long-term average, per a recent FT analysis.
“We do think that volatility should normalise, it is mean reverting. But the speed at which [the Vix] came down was a bit too far too fast,” Maxwell Grinacoff, US equity derivatives strategist at UBS, told the FT. “We’re still not out of the woods yet.”
Hole in One: One thing that may or may not shoot some volatility back into the markets is Jerome Powell’s Friday speech in Jackson Hole,Wyoming, which he will give after spending the week conferencing with business leaders, economists, government officials, and fellow Federal Reserve bankers. The Fed is all but guaranteed to finally cut rates next month, though the question remains by how much
— and Wall Street is sure to hang on to every word that Powell says in search of clues.
Fiber Lasers
Press Brakes
Tube Lasers
Laser / Bending Automation
Waterjets
Deburring / Finishing
Plate & Angle Rolling
CNC Machining
Tapping Arms
Saws
Plasma & Oxy Cutting
Nitrogen Generation
Robotic Welding
Material Storage
Waterjet Parts
Industry Marketing
Technical Service
Tel: 1-631-273-1010
1-800-645-4174
Fax: 1-631-273-1066
1-800-424-2082
orders@royalprod.com
Abrasive Systems
KBC TOOLS & Machinery___714-278-0500
Air Cleaning Guns
Royal Products 631-273-1010
Auto-Bar Feed Systems
Western Machine Center____408-955-1000
Automation
Hainbuch Workholding____818-970-7874
Ballscrews
C & M Precision Spindle, Inc._ 503-691-0955
Band Saws/Saw Blades
Bandsaw Tech _________ 562--419-7675
Cycle Time Solutions_____510-708-8665
Saw Service
877-738-6437
Sterling Saw Blades 800-828-11800
Band Saw Replacement Parts
Saw Service 877-738-6437
Sterling Saw Blades ______ 800-828-1180
Band Saw Repair
Saw Service
Bar Feeders
Spinetti Machinery 775-996-3770
Boring
THINBIT
888-844-6248
Caabinet Spray Washers
ALMCO 507-380-1009
Cams
Dayton Lamina. 708-203-6684
Carbide Tools, Indexable
ARNO USA____________815-236-8118
Cycle Time Solutions 510-708-8665
Horizon Carbide 602-524-38028
Ceramic Cutting Tools
NTK Cutting Tools 425-365-3613
Chemicals: Ultrasonic
Star Metal Fluids 800-367-9966
ChuckJaws & Adapters
Hainbuch
www.coastaluminum.com jpalmer@coastaluminum.com
Palmer Jr. Vice President: Northwest Region
877-738-6437
Sterling Saw Blades 800-828-1180
KBC TOOLS & Machinery____714-278-0500
THINBIT 888-844-6248
Deburring Tools
Royal Products 631-273-1010
Die Tooling Springs
Dayton Lamina. 708-203-6684
Dot Peen Markers
MarkinBox 310-214-3367
Draw Tubes
Lucy’s Machine Co._______323-587-6162
Drills/Cutters-Magnetic
ARNO USA____________815-236-8118
Sulli Tool & Supply 714-863-6019
Drills/Reamers/Taps
ARNO USA____________815-236-8118
Sulli Tool & Supply ______ 714-863-6019
EDM Materials & Supplies
Desert EDM 480-816-6300
EDM Network_________480-836-1782
EDM Performance 800-336-2946
End Mills
ARNO USA____________815-236-8118
Horizon Carbide_______602-524-3802
Sulli Tool & Supply 714-863-6019
Filiter Mist Collectors
Royal Products_______631-273-1010
Fixturing
Hainbuch America______253-293-2062
KBC TOOLS & Machinery____714-278-0500
Form Tooling
THINBIT 888-844-6248
Grooving Head, Grooving Tools
CASEY JOHNSON
Head of Marketing (855) 222-7084
casey@sterlingfabtech.com sterlingfabtech.com
Cycle Time Solutions
510-708-8665
THINBIT ____________ 888-844-6248
Indexible Tools
SCT-USA.___________805-584-9495
Inserts
ARNO USA____________815-236-8118
Horizon Carbide_______602-524-3802
Sulli Tool & Supply______714-863-6019
Jaws
EDM Network________480-836-1782
US Shop Tools________800-243-7701
Keyseat Cutters
Sulli Tool & Supply 714-863-6019
Lifting & Material Handling
Ingersoll Rand 206-472-0826
Live Centers
Royal Products 631-273-1010
Load Unload Systems
Midaco Corporation _____ 847-593-8420
Lubricants / Systems
Star Metal Fluids 800-367-9966
Machine Tool Acccessories
US Shop Tools 800-243-7701
Mandrels
Hainbuch America 253-293-2062
Mounting Brackets
Lucy’s Machine Company 323-587-6162
Packaging/Shipping Supplies
Alliance Packaging 206-445-5898-
Parts Washing Equipment
Ebbco Inc 800-809-3901
Port Tools
“Equipping Your Success”
SCT-USA.
805-584-9495
Power Tools
KBC TOOLS & Machinery____714-278-0500
Precision Bearings
C & M Precision Spindle, Inc._ 503-691-0955
Probing Systems
Sherpa Design_ 503-771-3570
Profiling
THINBIT
888-844-6248
Punch Die Tooling
Dayton Lamina. 708-203-6684
Quick Change Systems
Hainbuch Workholding____818-970-7874
stRetention Knobs
Safety Products
US Shop Tools _________ 800-243-7701
Sindle Point Tools
SCT-USA. ____________ 805-584-9495
Solvents: Vapor degreasing
Star Metal Fluids 800-367-9966
Solvents:Hand Wipe
Star Metal Fluids 800-367-9966
Solvents: Mil PRF 680
Star Metal Fluids 800-367-9966
SpecialtyTooling
SCT-USA. 805-584-9495
THINBIT
888-844-6248
Spindle Deburring Machines
ALMCO 507-380-1009
Spindle Liners
Lucy’s Machine Company 323-587-6162
Stamping Tooling
Dayton Lamina. 708-203-6684
Stationary Clamping Devices
Hainbuch Workholding____818-970-7874
Support Stands
Lucy’s Machine Company 323-587-6162
Testing Measuring Technology
Hainbuch Workholding____818-970-7874
Threading Thread Mills
SCT-USA. 805-584-9495
THINBIT ____________ 888-844-6248
Tooling Pins & Bushings Dayton Lamina. 708-203-6684
Tool Sharpening (Grinding) Applications Specialities ___ 253-872-0305
Swift Tool Co, Inc. 800-562-0900
Tooling Systems
Vises & Vise Jaws Rick Smith C 408.396.1238 Rick@peopletechMT.com N.Calif-Santa Clara Office T 408.598.2200 S.Calif-Irvine Office T 949.398.0400 www.peopletechMT.com
Applications Specialities 253-872-0305
Bilz USA 224-563-7233
Cycle Time Solutions _____ 510-708-8665
Horizon Carbide 602-524-3802
Rosco Precision Machinery 253-333-2439
RyansDovetails.com 253-876-9981
Sulli Tool & Supply 714-863-6019
Spinetti Machinery 775-996-3770
THINBIT 888-844-6248
Von Ruden Manufacturing, Inc.763-682--3122
Western Sintering 509-375-3096
Tumbling Meda and Compounds
ALMCO 507-380-1009
Vibratory Deburrung Bowls
ALMCO 507-380-1009
Vibratory Deburrung Tubs
ALMCO 507-380-1009
RyansDovetails.com
Workholding
Cycle Time Solutions
253-876-9981
DISIGN FOR MANUFACTURABILITY 3-D Plastics, Inc. 503-720-0572
510-708-8665
KBC TOOLS & Machinery____714-278-0500
APPRENTICESHIPS & TRAINING
Aerospace & Advanced Manufacturing Apprenticeships
AJAC
AJAC
206-737-8342
Machining Apprenticeships
206-737-8342
Precision Metal Fabrication Apprenticeships
AJAC 206-737-8342
Training & Education
AJAC 206-737-8342
ADDITIVE MFG/3D PRINTING
Bramac Machinery, Inc. 951-383-4195
MLC-CAD
858-358-0067
APPRAISALS
Machinery Resources
480-694-9919
Perfection Global 847-545-6906
AUCTIONS/LIQUIDATIONS
Machinery Resources 480-694-9919
Perfection Global 847-545-6906
BANKING
Quick Turn Financial 415-608-5692
Tech Financial Services 414-224-0209
Valley Financial Services ___ 818-968-4861
BUSINESS ADVISORS
Muerller Prost 314-862-2070
CARRIERS & RIGGING
IRH Carriers & Rigging 435-230-1779
CNC PROGRAMING TRAINING
MLC-CAD 858-358-0067
DISIGN CAD CAM
THOMPSON MACHINE. 505-823-1453
DOOR SYSTEMS
Automatic Door opening Systems
Midaco Corporation 847-593-8420
ENGINEERING/DESIGN
Mechanical Design
THOMPSON MACHINE. 505-823-1453
Reverse Engineering
THOMPSON MACHINE. 505-823-1453
FINANCING EQUIPMENT
Tech Financial Services 414-224-0209
Valley Financial Services___818-968-4861
GARNET
BARTON 800-741-7756
GRINDING
Flywheel & Rotor Grinders, DCM Tech 800-533-5339
Grinding Filtration
Grinding Machines
Bramac Machinery, Inc. 951-383-4195
DCM Tech 800-533-5339
Ellison Technologies 206-669-3578
HS&S Machine Tool 408-472-2436
North-South Machinery 562-690-7616
Performance Machine Tools 510-249-1000
Guard & Vacuum Pedestals For Grinders
Midaco Corporation 847-593-8420
Grinders, Rotary
Bramac Machinery, Inc. 951-383-4195
DCM Tech -----------------------------------800-533-5339
Industrial Surface Grinders
Bramac Machinery, Inc. 951-383-4195
DCM Tech ____________800-533-5339
Silicon & Quartz
DCM Tech __________800-533-5339
Punch & Die Grinders
DCM Tech___________800-533-5339
INSPECTION EQUIP
HS&S Machine Tool 408-472-2436
Hexagon 206-304-3847
King Machine Inc. 509-435-6741
Rosco Precision Machinery 206-818-6813
Zeiss Industrial Metrology 800-327-9735
3D CAD for CMM
Hexagon 206-304-3847
CMM Probes
Hexagon____________ 206-304-3847
OGP 480-889-9056
Zeiss Industrial Metrology 800-327-9735
Coordinate Measuring Mach.
HS&S Machine Tool 408-472-2436
Hexagon 206-304-3847
OGP 480-889-9056
Zeiss Industrial Metrology __ 800-327-9735
Laser Trackers
Metrology Instruments
HS&S Machine Tool _______ 408-472-2436
Hexagon 206-304-3847
OGP _____________ 480-889-9056
Zeiss Industrial Metrology 800-327-9735
Optical Comparators
Hexagon 206-304-3847
Zeiss Industrial Metrology_800-327-9735
Particle Inspection Mach
DCM Tech 800-533-5339
INSURANCE
Business Insurance Solutions
Sentry Insurance 877-373-6879
LASER & FIBER LASER
MarkinBox
MACHINES
310-214-3367
MACHINERY/MACHINE TOOLS
Additive Manufacturing 3D Machines
Production Machine Tools, Inc. 425-881-1200
Boring Mills
Rosco Precision Machine ry 253-333-2439
Bridgeport Parts
Desert EDM 480-816-6300
CNC Controls & Retro Fits
Rosco Precision Machinery 253-333-2439
CNC Lathes
Desert EDM 480-816-6300
Ellison Technologies ______ 206-669-3578
Expand Machinery 818-349-9166
HS&S Machine Tool 408-472-2436
Machinery Resources 480-694-9919
Romi Machine Tools, Ltd 480-510-4146
Rosco Precision Machinery 253-333-2439 3 , 4, & 5 Axis CNC Mills
Desert EDM 480-816-6300
Ellison Technologies____206-669-3578
Expand Machinery_____818-349-9166
HS&S Machine Tool 408-472-2436
Machinery Resources 480-694-9919
Production Machine Tools, Inc. 425-881-1200
Rosco Precision Machinery 253-333-2439
CNC 3 & 5 Axis Routing Machines
Ellison Technologies 206-669-3578
CNC Slant Bed Turning Centers
Expand Machinery 818-349-9166
CNC Swiss Turn Machines
Ellison Technologies 206-669-3578
Machinery Resources 480-694-9919
Machinery Resources 480-694-9919
Methods Machine Tools Inc.
714-292-9384
Dot Peen Markers
Kwik Mark Inc
King Machine Inc.
815-363-8268
EDM Automation
EDM Die Sinking Machines
EDM Network_________480-836-1782
EDM Filtration
EDM Network 480-836-1782
EDM Machines
EDM Network _________ 480-836-1782
HS&S Machine Tool 408-472-2436
EDM Drilling & Micro Hole Machines
Current EDM, Inc.
612-840-0037
EDM Network_________480-836-1782
HS&S Machine Tool 408-472-2436
EDM Service
EDM Network
480-836-1782
EDM Tooling Systems
EDM Network 480-836-1782
Equipment Financing
Pacific Continental Bank 503-310-3604
Scottrade Bank Equip. Finance_ 206-948-0022
U.S. Bank Equipment 800-810-0038
Gantry & Bridge Systems
Ellison Technologies 206-669-3578
HS&S Machine Tool 408-472-2436
Horizontal Boring & Milling Machines (CNC )
HS&S Machine Tool 408-472-2436
Rosco Precision Machinery __ 253-333-2439
Jig Boring
Methods Machine Tools Inc. 714-292-9384
Lathes
CNC Machine Services 206-999-3232
HS&S Machine Tool 408-472-2436
Swiss Screw Machines
Spinetti Machinery______775-996-3770
Turning Centers
Spinetti Machinery______775-996-3770
509-435-6741
Rosco Precision Machinery 253-333-2439
Spinetti Machinery ______ 775-996-3770
Summit Machine Tool 800-654-3262
Laser Marking Machines
Spinetti Machinery 775-996-3770
Manual Mills And Lathes
Ganesh Machinery_______818-349-9166
HS&S Machine Tool 408-472-2436
KNUTH Machine Tools 847-415-3333
Machine Toolworks 800-426-2052
North Western Machinery ___ 206-583-2333
Sharp Machine Tool ______ 310-944-8016
Summit Machine Tool 800-654-3262
Swift Tool Co, Inc. 800-562-0900
Parts Washing
Gosiger 937-586-5067
Prototype Machines
DATRON 480-826-3689
Robotics & Automatics
Ganesh Machinery______818-349-9166
Saw Lubricants
Saw Service Of WA 360-738-6437
Sawing Machines
Fahey Machinery Co., Inc. 503-620-9031
KNUTH Machine Tools 847-415-3333
North-South Machinery 562-690-7616
North Western Machinery 206-583-2333
Performance Machine Tools 510-249-1000
Rocky Mountain Saw Blades 303-761-3000
Rosco Precision Machinery 206-818-6813
Saw Replacement Parts
Rocky Mountain Saw Blades 303-761-3000
Saw Service Of WA 360-738-6437
Sub-Spindle Lathe
Rosco Precision Machinery 253-333-2439
Used Wire EDM Machines
Current EDM, Inc. ________ 612-840-0037
Desert EDM
480-816-6300
EDM Network 480-836-1782
MASTERCAM TRAINING/SALES
MLC-CAD 858-358-0067
MATERIAL
Aluminum
Bralco 602-722-3324
Coast Aluminum 877-398-6061
DIX Metals
714-677-0788
Fry Steel 800-423-6651
Gorilla Metals Inc. 855-516-3825
Industrial Metal Supply Co. 818-729-3333
Ryerson Corporation 425-204-2601
Sunshine Metals 760-579-8327
Aluminum Extrusions
Aluminum Precision 805-889-7569
Bralco ______________ 602-722-3324
Armor:Commercial
Kloeckner Metals 480-389-2883
Service Steel 503-224-9500
Armor: Military Grade
Kloeckner Metals 480-389-2883
Service Steel 503-224-9500
Brass
Bralco 602-722-3324
Coast Aluminum 877-398-6061
Coastal Metals 800-811-7466
Fry Steel 800-423-6651
Gorilla Metals Inc. 855-516-3825
Industrial Metal Supply Co. 818-729-3333
Ryerson Corporation ______ 425-204-2601
Sequoia Brass & Copper 800-362-5255
Bronze
Carbon Steel
Bralco
Coastal Metals
Fry Steel
602-722-3324
800-811-7466
800-423-6651
Laser Cutting Services, Inc 503-612-8311
Ryerson Corporation 425-204-2601
Cobalt Alloys
United Performance Metals _888-282-3292
Copper
Bralco _____________ 602-722-3324
Coast Aluminum 877-398-6061
Gorilla Metals Inc. 855-516-3825
Industrial Metal Supply Co. 818-729-3333
Ryerson Corporation 425-204-2601
Sequoia Brass & Copper 800-362-5255
Electrical Steels
Fry Steel
800-423-6651
High Temperature Alloys
Altemp Alloys 800-227-8103
United Performance Metals _888-282-3292
Laser Cut Material
Laser Cutting Services, Inc 503-612-8311
Lead
Industrial Metal Supply Co. 818-729-3333
Material Sales
Altemp Alloys 800-227-8103
Coast Aluminum 877-398-6061
Coastal Metals 800-811-7466
Fry Steel ____________ 800-423-6651
Kloeckner Metals 480-389-2883
United Performance Metals _888-282-3292
Metals: Bar & Plate
Altemp Alloys 800-227-8103
Fry Steel 800-423-665
Ryerson Corporation 425-204-2601
Sequoia Brass & Copper 800-362-5255
Sunshine Metals 760-579-8327
United Performance Metals _888-282-3292
Nickel Alloys
Coastal Metals
800-811-7466
Sequoia Brass & Copper 800-362-5255
Altemp Alloys 800-227-8103
Fry Steel 800-423-6651
United Performance Metals _888-282-3292
Plate: Wear and Structural
Kloeckner Metals
480-389-2883
Ryerson Corporation 425-204-2601
United Performance Metals _888-282-3292
Sheet & Coil
Ryerson Corporation 425-204-2601
Stainless Steel & Steel
Bralco
Fry Steel
Gorilla Metals Inc.
Industrial Metal Supply Co.
Kloeckner Metals
Richard Amy Regional Sales Manager
B AR T ON INTER N ATIO N A L cell 951.551.2685 sales 800.741.7756 ramy@barton.com www.barton.com
Hexagon
206-304-3847
Metrology Software
Hexagon 206-304-3847
Portable Metrology
Hexagon 206-304-3847
Metrology Scanners
Hexagon 206-304-3847
Metrology Maintenence
Hexagon 206-304-3847
NEW & USED MACHINERY FABRICATION
Automation-Laser
Bystronic 702-340-6964
602-722-3324
800-423-665
855-516-3825
818-729-3333
480-389-2883
Laser Cutting Services, Inc 503-612-8311
Ryerson Corporation 425-204-2601
United Performance Metals _888-282-3292
Titanium Plate, Rod, Bar, & Wire
Bralco 602-722-3324
United Performance Metals _888-282-3292
Tool Steel
Industrial Metal Supply Co.
818-729-3333
CNC MASTERCAM TRAINING
Streamingteacher.com
METAL MARKING SYSTEMS
MarkinBox 310-214-3367
METROLOGY PRODUCTS
Hexagon 206-304-3847
Rosco Precision Machinery 253-333-2439
Metrology Hardware
North-South Machinery 562-690-7616
Perfection Global 847-545-6906
Sterling Fab Tech 855-222-708
Automation-Bending
Bystronic 702-340-6964
Band & Cut Off Saws
North-South Machinery 562-690-7616
Rosco Precision Machinery 253-333-2439
Sterling Fab Tech 855-222-708
CNC Turret Punches
Sterling Fab Tech ________ 855-222-708
Cold Saws/Saws
Hydmech Sawing Solutions 714-620-5560
KNUTH Machine Tools 847-415-3333
Laser & Fiber Laser Machines
Bystronic 702-340-6964
North-South Machinery ____ 562-690-7616
Sterling Fab Tech 855-222-708
Magnetic Drills/Cutters
Innovative Tool Sales 714-780-0730
Material Handling Systems
Hydmech Sawing Solutions __ 714-620-5560
Metal Marking Systems
Kwik Mark Inc 815-363-8268
MarkinBox 310-214-3367
Plasma/Gas Cutting Tools/Systems
Rosco Precision Machinery 253-333-2439
Plate Bending & Rolls
Bystronic 702-340-6964
Sterling Fab Tech 855-222-708
Plasma/Gas Cutting Systems
Sterling Fab Tech 855-222-708
Presses
Sterling Fab Tech 855-222-708
Press Brakes
Bystronic 702-340-6964
North-South Machinery 562-690-7616
Sterling Fab Tech 855-222-708
Shearing Machines
North-South Machinery 562-690-7616
Sterling Fab Tech 855-222-708
Welding Equipment
Sterling Fab Tech 855-222-708
Shipping Solutions
Perry Pallet Co. 360-366-5239
Tube Processing
Bystronic 702-340-6964
PRECISION TOOLHOLDING PRODUCTS
Tooling
Von Ruden Manufacturing, Inc. 763-682--3122
Tooling Systems
Von Ruden Manufacturing, Inc. 763-682--3122
PRODUCTIVITY
Productivity Tools and Systems
Sterling Fab Tech 855-222-708
PROG. SYSTEMS
Factory Automation/Logistics
North-South Machinery 562-690-7616
CAD/CAM Software, CAD Applied CAx ___________ 503-962-0287
Automatics & Machinery Co.__303-990-6190 MRP Software SigmaTEK 513-595-2022 Nesting Software SigmaNEST 513-595-2022
Software, Solid Modeling
Delcam Software 877-DELCAM1
PROTOTYPE MACHINERY
Santa Cruz Electronics
ROBOTIC AUTOMATION/
ROBOTIC INTEGRATION
Acieta ___________ 402-650-8132
Midaco Corporation 847-593-8420
ROBOTIC PRODUCTS
Cobots
Acieta 402-650-8132
Fanuc Robots
Acieta 402-650-8132
Gripper Systems
Acieta ___________ 402-650-8132
Robotic Welding Cells
Acieta 402-650-8132
ROBOT MAINTENANCE
Acieta 402-650-8132
ROBOT TRAINING
Acieta 402-650-8132
ROUTERS
Rosco Precision Machinery 253-333-2439
SHOT PEEN MARKING
Shot Peen
MarkinBox
310-214-3367
MLC-CAD
SAWS
Band & Cut-Off Saws
Swift Tool Co, Inc. 800-562-0900
SERVICES
AS9100 Registration
Great Western Registrar 623-580-1881
Custom Packaging/Shipping
Supplies
Alliance Packaging 206-445-5898Engineering/Mechanical Design
Sherpa Design_ 503-771-3570
Financial Services
Intech Funding 800-553-9208
Quick Turn Financial 415-608-5692
Machine Tool Rebuilding EDM Network 480-836-1782
Management Systems Training
BMSC______________ 602-445-9400
SOFTWARE CAD CAM
SOLIDWORKS/MASTERCAM
858-358-0067
Spinetti Machinery 775-996-3770
Mechanical Design
Cimatron 248-596-9700 ext. 237
Delcam 877-335-2261
MLC-CAD 858-358-0067
SPINDLES & SLIDES
Spindle Rebuilding/Repair
C & M Precision Spindle, Inc._ 503-691-0955
SURPLUS ASSET MANAGEMENT
Perfection Global 847-545-6906
TRAINING
ISO Consulting/Registration
BMSC______________ 602-445-9400
Lean and NADCAP Consulting Training
BMSC______________ 602-445-9400
ISO / AS9100 Certification
BMSC______________ 602-445-9400
Productivity Training
BMSC______________ 602-445-9400
USED MACHINERY
EDM Network __________480-836-1782
Jorgensen Machine Tools
800-952-0151
K.D. Capital Equipt 480-922-1674
North Western Machinery 206-583-2333
Performance Machine Tools 510-760-9518
WATERJET CUTTING
Flow Internatil 909-620-5707
Machine Toolworks 800-426-2052
Waterjet & Blast Abrasives, Garnet
Barton International _____ 800-741-7756
GMA Garnet Group 832-243-9300
Waterjet Bricks
Barton International
800-741-7756
GMA Garnet Group 832-243-9300
Waterjet Hoppers
GMA Garnet Group 832-243-9300
Waterjet Replacement Parts
Barton International
800-741-7756
EDM Performance 800-336-2946
BROACHING
Evans Precision 623-582-4776
FLATLINE FAB 503-707-9272
DIE CASTING
Ponderosa Ind _______303-298-1801
SMH Inc LLC 360-341-2226
SMH Inc LLC
ASSEMBLIES
___________
BENDING
Mandrel
Albina Co., Inc.
360-341-2226
Specialty Steel Services 801-539-8252
CASTING
Precision Enterprises Inc. 851-797-1000
Investment Casting-Precision
Dolphin Investment Castings 602-272-6747
Precision Enterprises Inc. ____ 851-797-1000
TVT Die Casting 800-280-2278
DIES
Tool & Dies
Micropulse West Inc. 480-966-2300
DEBURRING
Industrial Precision Grinding 310-352-4700
Precision Aerospace, LLC
602-352-8658
Stevens Tool & Die 503-682-3185
EDM Solutions
EDM: Wire
866-252-4628
Aeroform, Inc. 360-403-1919
Speciality Bending
Albina Co., Inc.
866-252-4628
Bending Solutions, Inc. 360-651-2443
Structrual Bending
Albina Co., Inc.
866-252-4628
Tube and Pipe Bending
Albina Co., Inc.
Cogitic
866-252-4628
BRAZING-JOINING
719-473-8844
Evans Precision 623-582-4776
PAS Technologies
Precision Casting Repair
Brazing:
602-744-2600
801-972-2345
Bolts Metalizing-CWST______602-244-2432
CHEMICAL ETCHING
CMR Manufacturing _______ 602-273-0943
PAS Technologies 602-744-2600
COATING
Bolts Metalizing-CWST______602-244-2432
COLD FORMING
ATF Aerospace, LLC.. 480-218-0918
CONTRACT MANUFACTURING
UNITED PACIFIC ELECTRONICS 760-438-2375
CUTTING
Bar & Plate & Die Cutting
AZ Tool Steel 877-795-1600
FLATLINE FAB 503-707-9272
Industrial Precision Grinding 310-352-4700
LASER CUTTING
DESIGN
FLATLINE FAB 503-707-9272
EDGING
United Performance Metals _888-282-3292
EDM
EDM: Dialectric Systems /Filtration
Ebbco Inc _____________ 586-716-5151
EDM: Drilling Small Hole Layke Inc. 602-272-2654
Milco Waterjet 714-373-0098
Precision Aerospace, LLC 602-352-8658
SOUTHWEST EDM 623-826-1025
EDM: Ram-Type (Sinking)
SOUTHWEST EDM 623-826-1025
Milco Wire EDM,, Inc. 714-373-0098
Clings Aerospace
480-968-1778
Evans Precision 623-582-4776
Micropulse West, Inc. 480-966-2300
Milco Wire EDM,, Inc. 714-373-0098
Micropulse West, Inc. 480-966-2300
Plastic Injection Molding 509-531-2634
Precision Aerospace, LLC 602-352-8658
SOUTHWEST EDM 623-826-1025
ELECTRO MECHANICAL
Sub-Assembly Builds
Cascade Systems Technology 503-640-5733
ENGINEERING/DESIGN
ATF Aerospace, LLC.. 480-218-0918
Cascade Systems Technology 503-640-5733
FLATLINE FAB 503-707-9272
Extrusions
Plastic Extrusion Services
Inline Plastics Inc.
909-923-1033 FABRICATION
Architectural Forming & Fabrication
AERO TECH MFG, Inc.
801-335-3283
FLATLINE FAB__________503-707-9272
Fabrication: Sheet Metal
Aeroform, Inc.
AERO TECH MFG, Inc.
FLATLINE FAB
503-707-9272
Industrial Thermoplastics
Cleveland Electric Labs. 330-697-4125
Precision Sheet Metal Fabrication: Medium & Large
Aeroform, Inc. __________ 360-403-1919
AERO TECH MFG, Inc. 801-335-3283
American Precision Ind.. 503-784-5211
360-403-1919
801-335-3283
American Precision Ind.. 503-784-5211
FLATLINE FAB
503-707-9272
NW Metalcraft Industries 888-280-7080
Mountain View Machine 435-755-0500
Precision Aerospace, LLC
602-352-8658
QUAL-FAB, Inc. 206-762-2117
SMH Inc LLC 360-341-2226
Weiser Engineering 303-280-2778
Fabrication: Custom Metal
AERO TECH MFG, Inc.
801-335-3283
American Precision Ind.. 503-784-5211
FLATLINE FAB
503-707-9272
Group Mfg Serv 480-966-3952
Industrial Machine Svcs 503-240-0878
Precision Aerospace, LLC ____ 602-352-8658
SMH Inc LLC 360-341-2226
Weiser Engineering 303-280-2778
Wrico 480-892-7800
Forming & Fabrication
AERO TECH MFG, Inc. 801-335-3283
Bending Solutions, Inc. 360-651-2443
FLATLINE FAB 503-707-9272
Precision Aerospace, LLC 602-352-8658
QUAL-FAB, Inc. 206-762-2117
SMH Inc LLC 360-341-2226
Solid Form Fabrication 503-435-1400
Weiser Engineering 303-280-2778
Tube & Pipe Bending Fabrication
Albina Co., Inc. 866-252-4628
Bending Solutions, Inc. 360-651-2443
FIBER OPTICS TESTING
Cleveland Electric Labs. 330-697-4125
AB Finishing Tech
Passivation
Coating Technologies _623-581-2648
Perfection Industrial Finishing 520-434-9090
Polishing
Arizona Hard Chrome 602-278-8671
Powder Coating
AERO TECH MFG, Inc. 801-335-3283
Perfection Industrial Finishing 520-434-9090
Sandblasting
Byington Steel Treating, Inc. 408-727-6630
503-803-3322
Advanced Precision Anodizing 503-661-6700
American Precision Ind.. 503-784-5211
Coating Technologies 623-581-2648
FLATLINE FAB 503-707-9272
Leadtek Plating 503-682-4410
Real Axis Machining 360-723-5386
DRY FILM LUBRICATION
Bolts Metalizing-CWST______602-244-2432
Leadtek Plating 503-682-4410
Perfection Industrial Finishing 520-434-9090 Shot Peen
AB Finishing Tech 503-803-3322
PAS Technologies 602-744-2600
Silk Screening
Arizona Finishing 602-438-4443
FIXTURING
K-Mol Engineering 530-906-1705
Real Axis Machining 360-723-5386
Nexus Grinding _________
480-230-9525
Superior Grinding 801-487-9700
Grinding, Blanchard Evans Precision _________ 623-582-4776
Industrial Precision Grinding 310-352-4700
Superior Grinding 801-487-9700
Grinding, Centerless LV Swiss 435-635-1482
Nexus Grinding 480-230-9525
Ron Grob Co ___________ 970-667-5320
Grinding, Double Disc
Industrial Precision Grinding 310-352-4700
TCI Precision Metals 800-234-5613
Grinding: OD
Nexus Grinding
480-230-9525 1 Ron Grob Co 970-667-5320
Superior Grinding 801-487-9700
Grinding: Surface
Industrial Precision Grinding 310-352-4700
StandardAero 602-744-2600
Superior Grinding
801-487-9700
Grinding: Tool & Cutter
Superior Grinding_________888-487-9701
Swift Tool Co, Inc. ________ 800-562-0900
GUN DRILLING
Evans Precision
623-582-4776
HEAT TREATING
ABS Heat Treating_________602-437-3008
Byington Steel Treating_____408-727-6630
Controlled Thermal Tech_____602-272-3714
Evans Precision 623-582-4776
MET-TEK Heat Treating______503-519-9864
PAS Technologies 602-744-2600
Phoenix Heat Treating______602-258-7751
Cryogenics
Phoenix Heat Treating 602-258-7751
Heat Treating/ISO/AS9100
ABS Heat Treating_________602-437-3008
Byington Steel Treating______408-727-6630
Phoenix Heat Treating_______602-258-7751
Heat Treating/NADCAP
ABS Heat Treating_________602-437-3008
Phoenix Heat Treating_______602-258-7751
Large Capacity Drop Bottom Oven/Aluminum
Byington Steel Treating______408-727-6630
MET-TEK Heat Treating______503-519-9864
HONING/LAPPING
PAS Technologies
Precision Aerospace, LLC
602-352-8658
Real Axis Machining 360-723-5386
Ron Grob Co 970-667-5320
SMH Inc LLC 360-341-2226
Sunshine Metals 714-225-4972
Treske Precision Machining 503-625-2821
TVT Die Casting 800-280-2278
VWeiser Engineering 303-280-2778
Industrial Thermocouples
Cleveland Electric Labs. 330-697-4125 JIGS & TOOLING
K-Mol Engineering 530-906-1705
Machining: 5-Axis
Accutech Machine Inc 801-975-1117
American Precision Ind.. 503-784-5211
Cascade Engineering Tech 503-266-1300
Strom Manufacturing 503-447-1021
Machining: Aerospace/Space
American Precision Ind.. 503-784-5211
ATF Aerospace, LLC.. 480-218-0918
Cleveland Electric Labs. 330-697-4125
Layke Inc. 602-272-2654
LV Swiss 435-635-1482
Precision Aerospace, LLC 602-352-8658
Strom Manufacturing 503-447-1021
SMH Inc LLC 360-341-2226
Teton Machine 208-642-9344
Treske Precision Machining ___ 503-625-2821
Machining: Ceramics Advanced
O’Keefe Ceramics 719-687-0888
Machining: Proto-R & D
American Precision Ind.. 503-784-5211
ATF Aerospace, LLC.. 480-218-0918
LUX Precision MFG 928-380-0317
Newport Tool. 801-295-7411
Real Axis Machining _______ 360-723-5386
Ron Grob Co 970-667-5320
SMH Inc LLC 360-341-2226
Strom Manufacturing 503-447-1021
Treske Precision Machining 503-625-2821
TVT Die Casting 800-280-2278
Machining: CNC Milling
Accutech Machine Inc 801-975-1117
American Precision Ind.. 503-784-5211
ATF Aerospace, LLC.. 480-218-0918
Cascade Engineering Tech ___ 503-266-1300
Die-Tech Precision Machining 669-888-3500
Faustson 303-420-7422
Grovtec US, Inc. 503-557-4689
Layke Inc. 602-272-2654
LUX Precision MFG 928-380-0317
LV Swiss 435-635-1482
Micropulse West, Inc. 480-966-2300
Precision Aerospace, LLC 602-352-8658
Real Axis Machining 360-723-5386
Ron Grob Co 970-667-5320
SMH Inc LLC 360-341-2226
Strictly Business 541-270-4878
Strom Manufacturing 503-447-1021
Teton Machine 208-642-9344
Machining: Large
Accutech Machine Inc 801-975-1117
American Precision Ind..
503-784-5211
Cascade Engineering Tech 503-266-1300
Machining: Medical
American Precision Ind.. ______ 503-784-5211
LUX Precision MFG 928-380-0317
Production
602-744-2600
Cascade Engineering Tech 503-266-1300
Alpha Precision Machining, Inc. _ 253-395-7381
+1.847.427.3333
+1.847.545.6906 direct +1.630.853.5408 mobile eric@perfectionglobal.com www.perfectionglobal.com
Industrial Manufacturing
866-252-4628
360-202-7342
Turnkey Product Services
Machining: Turning With Live Tooling
ATF Aerospace, LLC..
LV Swiss
Weiser Engineering
480-218-0918
435-635-1482
303-280-2778
MANUFACTURING VALUE ADDED
Contract Manufacturing
AATC
602-268-1467
Aeroform, Inc. 360-403-1919
Albina Co., Inc.
866-252-4628
Alpha Precision Machining, Inc. _ 253-395-7381
American Precision Ind.. 503-784-5211
ATF Aerospace, LLC..
480-218-0918
Bending Solutions, Inc. 360-651-2443
Cleveland Electric Labs. 330-697-4125
FLATLINE FAB
503-707-9272
LUX Precision MFG 928-380-0317
LV Swiss 435-635-1482
Teton Machine 208-642-9344
TVT Die Casting 800-280-2278
PAINTING
FLATLINE FAB
801-891-2740
Custom Airplane to Marine Polishing
503-253-5294
Personal Collectables Polishing
503-253-5294
503-253-5294
602-272-3714
503-707-9272
Perfection Industrial Finishing 520-434-9090
PLASTIC EXTRUSION
Custom Plastic Profiles
Inline Plastics Inc. 909-923-1033
Custom Plastic Tubing
Inline Plastics Inc. 909-923-1033
Custom Thermoplastics
Inline Plastics Inc. 909-923-1033
Extrusion Die Development
Inline Plastics Inc. 909-923-1033
Custom Plastic Spiraling
Inline Plastics Inc. ________ 909-923-1033
Anodizing
Advanced Precision Anodizing 503-661-6700
Collins Metal Finishing 602-275-3117
Frontier Group __________ 602-437-2426
Leadtek Plating 503-682-4410
Finishing 480-772-0387 Leadtek Plating 503-682-4410
Precious
Plastic Injection Molding
SMH Inc LLC
Aero Tech MFG
MOLDS
509-531-2634
360-341-2226
801-891-2740
Advanced Mold Technology 714-990-0144
Arizona Finishing 602-438-4443
Milco Wire EDM,, Inc. 714-373-0098
K-Mol Engineering 530-906-1705
Molds: High Volume Class 100
Advanced Mold Technology ____ 714-990-0144
Molds: Fast Turn Prototype and Bridge Molds
Advanced Mold Technology 714-990-0144
Molds: Expertise in Overmold and Insert Molding
Advanced Mold Technology 714-990-0144
PC BOARDS
Surface Mount & Thru Hole
Cascade Systems Technology 971-330-8054
Custom Plastic Finishing
Inline Plastics Inc. 909-923-1033
PLASTIC MACHINING
PLASTIC MOLDING
3-D Plastics, Inc. 503-720-0572
K-Mol Engineering ________ 530-906-1705
SMH Inc LLC 360-341-2226
Mold Making
3-D Plastics, Inc. 503-720-0572
K-Mol Engineering 530-906-1705
PLATING
Advanced Precision Anodizing 503-661-6700
ASKO Group 206-947-4052
Collins Metal Finishing 602-275-3117
EPSI 714-519-9423
Frontier Group 602-437-2426
Foresight Finishing 480-772-0387
Leadtek Plating 503-682-4410
Perfection Industrial Finishing 520-434-9090
Coating: Dry Film Lube
Coating Technologies______623-581-2648
Frontier Group
602-437-2426
Leadtek Plating 503-682-4410
Coating: Nickel/ Teflon/Chrome
Coating Technologies
Leadtek Plating
Arizona Hard Chrome
602-278-8671
ASKO Group 206-947-4052
NAD CAP & Boeing Approved Processes
623-581-2648
503-682-4410
Coating:Zinc & Mag.Phos.
Coating Technologies
Savon Plating, Inc
Copper
Foresight Finishing
Drylube
Frontier Group
ASKO Group
623-581-2648
602-252-4311
480-772-0387
602-437-2426
Electro-Polishing
206-947-4052
Collins Metal Finishing
602-275-3117
Embrittlement Relief
EPSI _______________
714-519-9423
Precious Metal Plating Co. 800-481-6271
Nickel-Bright & Electroless
Foresight Finishing 480-772-0387
Frontier Group __________ 602-437-2426
Leadtek Plating 503-682-4410
Precious Metal Plating Co. 800-481-6271 Passivation
Collins Metal Finishing 602-275-3117
Frontier Group 602-437-2426
Leadtek Plating 503-682-4410
Perfection Industrial Finishing 520-434-9090 Phosphate
Frontier Group 602-437-2426
Perfection Industrial Finishing 520-434-9090
Savon Plating, Inc 602-252-4311
Tin Plating
Precious Metal Plating Co. 800-481-6271
Leadtek Plating 503-682-4410
Zinc Nickel
PAS Technologies 602-744-2600
PLASMA CUTTING
G & G Custom Metal Fab ____ 503-931-7069
PRECISION FORMING
Aeroform, Inc. __________360-403-1919
QUAL-FAB, Inc. 206-762-2117
SpringWorks Utah 801-298-0113
Strictly Business 541-270-4878
Wrico 480-892-7800
Laser Cutting
Strictly Business 541-270-4878
PROTOTYPES
Cascade Systems Technology 503-640-5733
NW Rapid Mfg. 503-434-8557
RECYCLING MATERIALS
Wood Products
Perry Pallet Co.
CNC-PROS
REPAIR
360-366-5239
602-344-9753
Savon Plating, Inc
ASKO Group
602-252-4311
Electroless Nickel
206-947-4052
Collins Metal Finishing
602-275-3117
Foresight Finishing _______ 480-772-0387
Frontier Group
Leadtek Plating
Precious Metal Plating Co.
Gold
ASKO Group
602-437-2426
503-682-4410
800-481-6271
206-947-4052
EPSI 714-519-9423
Foresight Finishing_______480-772-0387
Leadtek Plating 503-682-4410
Precious Metal Plating Co.
800-481-6271
PAS Technologies 602-744-2600
Hard Chrome
Powder Coating
Perfection Industrial Finishing 520-434-9090
Shot Peen
AB Finishing Tech 503-803-3322
PAS Technologies 602-744-2600
Tin / Zinc Plate
ASKO Group 206-947-4052
EPSI 714-519-9423
Leadtek Plating 503-682-4410
Savon Plating, Inc 602-252-4311
Silver Plating
ASKO Group 206-947-4052
EPSI 714-519-9423
Leadtek Plating _________ 503-682-4410
PAS Technologies 602-744-2600
Precious Metal Plating Co. 800-481-6271
Aluminum, Brass, Plastics, Stainless Steel, Steel, Tin, Stainless Steels, Copper Alloys, Nickel and Nickel base alloys, Hastelloys, Monel, Cupro-Nickel, Nickel-Chromes, Cobalt base alloys, Stellites, Heat-Treat alloys, Complex-Nickels, Corrosion Resistant metals, Titanium, Tungsten, and Superalloys
Metro Metals Northwest 503-819-1284
Spectrum Alloys LLC 323-587-2284
Bin Service
Metro Metals Northwest 503-819-1284
Spectrum Alloys LLC 323-587-2284
Excess Material Handling
Metro Metals Northwest 503-819-1284
Spectrum Alloys LLC 323-587-2284
Full Service Scrap Management
Metro Metals Northwest 503-819-1284
Spectrum Alloys LLC 323-587-2284
THOMPSON MACHINE. 505-823-1453
Stamping:Flat Forming
ATF Aerospace, LLC..
480-218-0918
NW Metalcraft Industries 888-280-7080
SpringWorks Utah 801-298-0113
Stamping: Light
ATF Aerospace, LLC.. 480-218-0918
SpringWorks Utah 801-298-0113
THOMPSON MACHINE. _____ 505-823-1453
Stamping: Production/
Precision
ATF Aerospace, LLC.. 480-218-0918
Precision Die & Stamping 480-967-2038
THOMPSON MACHINE. 505-823-1453
SUPPLY CHAIN MANAGEMENT
Cascade Systems Technology 503-640-5733
TESTING
Non-Destructive Testing
Frontier Group 602-437-2426
Turbine Instrument Testing
Cleveland Electric Labs. 330-697-4125
THERMAL SPRAY
Bolts Metalizing-CWST______602-244-2432
Controlled Thermal Tech 602-272-3714
THREAD ROLLING
Ron Grob Co 970-667-5320
TOOL & DIE DESIGN
ATF Aerospace, LLC.. 480-218-0918
Newport Tool. 801-295-7411
Wrico 480-892-7800
TOOLING
Industrial Machine Svcs 503-240-0878
Mountain View Machine 435-755-0500
Newport Tool. 801-295-7411
Real Axis Machining 360-723-5386
TUBE BENDING & CUTTING FAB
Albina Co., Inc. 866-252-4628
Bending Solutions, Inc. _____ 360-651-2443
Clings Aerospace 480-968-1778 EZ-ACCESS 800-258-8503
TURBINE ENGINE TESTING Cleveland Electric Labs. 330-697-4125
WATERJET CUTTING
Accutech Machine Inc 801-975-1117
Aeroform, Inc. 360-403-1919
Milco Waterjet 714-373-0098
Precision Aerospace, LLC 602-352-8658
Rickard Engineering 866-845-8838
SW Waterjet & Laser 480-306-7748
United Performance Metals _888-282-3292 5-Axis Waterjet Cutting
Rickard Engineering _______ 866-845-8838
Micro-Machining Rickard Engineering 866-845-8838 WELDING Evans
3D-Plastics...16,40
ABS Metallurgical...40,47
Acieta...42`
Advanced Precision Anodizing...42
Aeroform, Inc...43
Aero Tech Manufacturing...41
Allied Tool and Die...45
ALMCO...36
American Precision Industries...42
ARNO...35
ATF Aerospace, LLC...35
Barton...24,38
Big O Metals...36
BMSC...18,34
Bramac Machinery Inc...35
Bystronic...11,35
Cleveland Electric Laboritories...40
Coast Aluminum...34.39
Coastal Metals...27,34
Coating Technologies...41
Collins Metal Finishing...43
Continenttal Machining Co...41
CRC Surface Technologies...23
Cutting Tool Control...37
Cycle Time Solutions...36
DCM Tech...37
Design 2 Part Long Beach..25
Die-Tech Precision Machine...41
DN Solutions... 1,20-22
Editors Corner...4
EDM Performance..34,35
Ellison Technologies...22,34
EPIC Finance...3,29
Evans Precision...43
Expand Machinery...37
Focused on Machining...17
Foresight Finishing...45
Frontier Group...
Gentech...41
Grovtec...40,48
HS&S Machine Tool...38
Haimer...36
Hainbuch...26,35
Hexagon...36
Horizon Carbide...38
Hurco...19
Industrial Metal Supply Co....9,38
K-Mol Engineering...41
KD Capital...38
Kloeckner Metals-Temtco...10,34
Landmark Solutions...31,36
Layke Inc...43
Leadtek...45
Lucy’s Machine...34,43
LUX Precision Machining...40
LV Swiss...41
Marzee...12
MC Sales & Marketing...35
MET-TEK Inc...41
Metal Rollforming Systems...1,20-21
Metro Metals Northwest, Inc...44
MetzFab...41
Micropulse West...42
Micro-Tronics...45
Midaco Corporation...10,36
Milco...45
MLC-CAD...35
Mountain View Machining...42
MRI , Machinery Resources...36
Nexus Grinding...28,41
North-South Machinery...34
Pacific Swiss...40
People Tech...35
Perfection Global...43
Perfection Industrial Finishing...33
Performance Machine Tools...8,38
Phoenix Heat Treat...1, 13,21-22,42
PMA Industries...10
Precious Metals Plating...29,40
Precision Aerospace, LLC...42
Precision Die & Stamping...14,40
RRBG, Inc. Quality MGMT...30
Ron Grob...30,42,44
Rosco Precision Machinery...19,34
Royal products...24,34
SCHUNK...35
SigmaNest...34
SMBHUB...39
SMH Inc LLC...32,40
Spectrum Alloys LLC...44
Spring Works Utah...41
StandardAero...42,45
Star Metal Fluids...35
Sterling Fab Tech...28-29,35,40
Strictly Business...38
Sulli Tool...34
Superior Grinding...17,41
TCI Precision Metals...34
ThinBit...2,34
TJ Davies...8,36
TJ Snow...5
Thompson Machine...36
TVT Die Casting...40
United Pacific Electrictronics...40
US Shop Tools...15,35,38
Valley Financial Services...37
Weiser Engineering...42
Western Sintering...40
Wrico Stamping...45