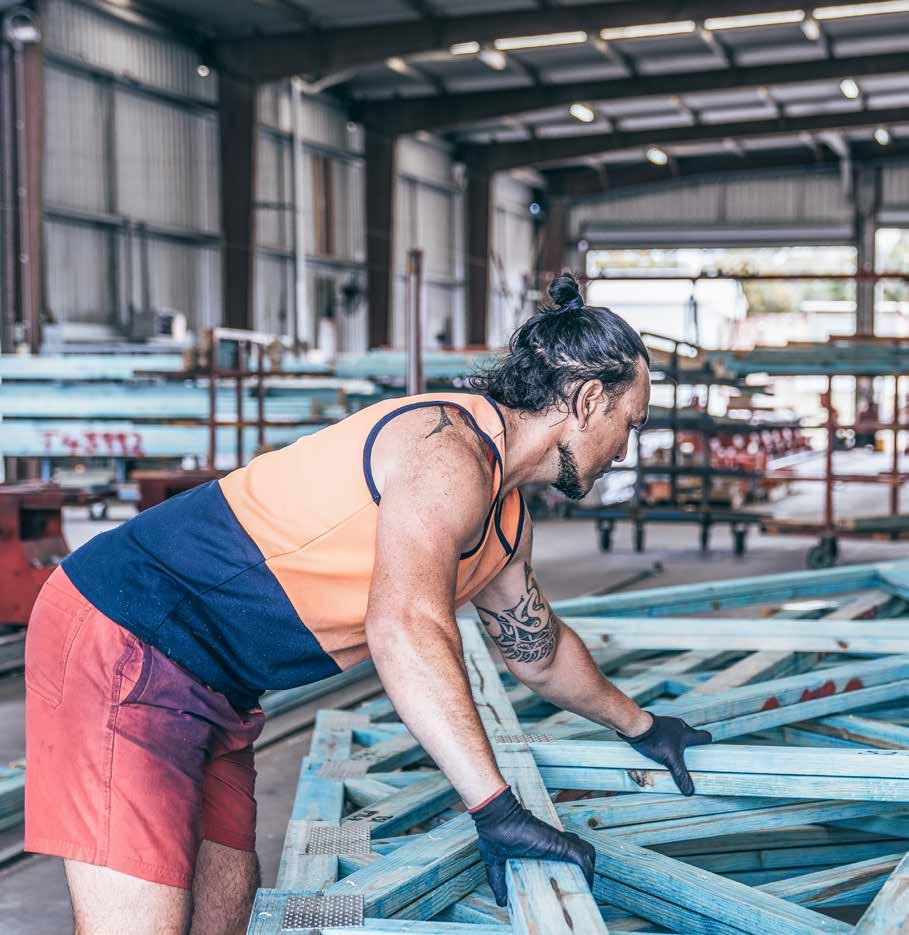

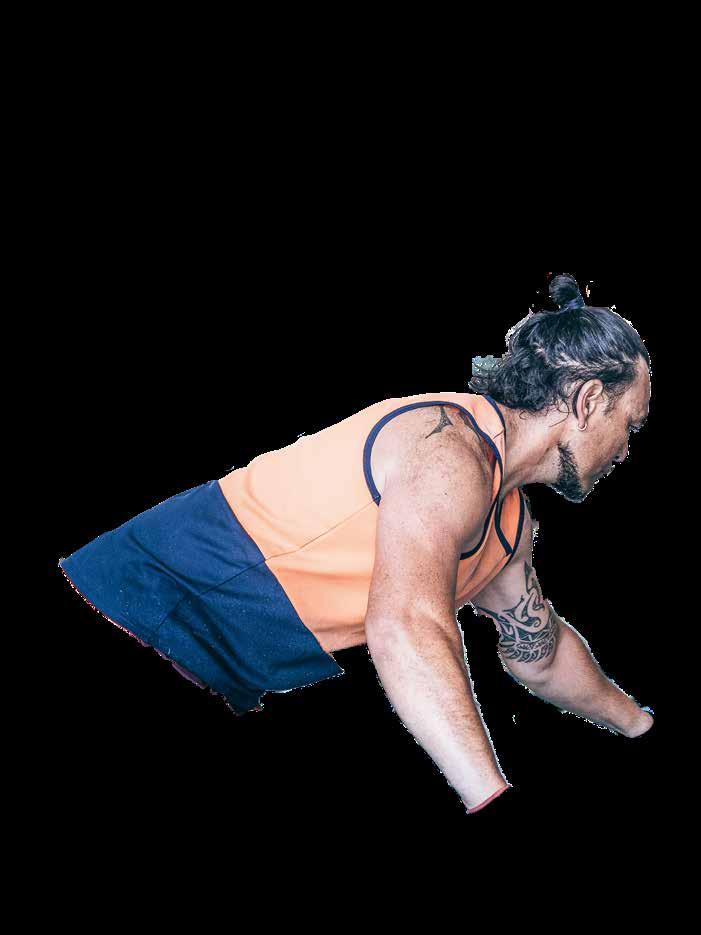
JUNE 2023
Issue 4 – Volume 33
Incorporating Australian and New Zealand Timberman. Established 1977. News 3-7
6 Tooling 10
Associations 16-19
FRONT Cover:
It’s time to take a closer look at the materials we use and to source those that we trust to meet the Australian Standards. Story page 3
PUBLISHER and Chief Executive:
Hartley Higgins
General Manager: Robyn Haworth
Editor:
Bruce Mitchell
b.mitchell@ryanmediapl.com.au
Adelaide Office (08) 8369 9512
Advertising: Jon Andryciw
j.andryciw@ryanmediapl.com.au
Adelaide Office (08) 8369 9517
Creative Services: Tim Coleman
Publication Design:
Tim Coleman
Timber classifieds:
j.andryciw@ryanmediapl.com.au
Adelaide Office (08) 8369 9517
Subscriptions: subs@forestsandtimber.com.au
Adelaide Office (08) 8369 9522
Subcription rates
One-year (8 editions) $55
Two-years (16 editions) $95
Accounts:
Adelaide Office (08) 8369 9514
Postal Address: 630 Regency Road, Broadview South Australia 5083
Phone: (08) 8369 9555
Fax: (08) 8369 9501
Melbourne Office: Suite 2262, 442 Auburn Rd, Hawthorn VIC 3122 Phone: (03) 9810 3262
Find us on Facebook @AustralasianTimber
Website www.timberbiz.com.au
BUILDING approvals in April remained at their lowest level in over a decade, with declines continuing for both houses and multi-units.
The Australian Bureau of Statistics’ monthly building approvals data for April for detached houses and multiunits covering all states and territories showed a 3.9 per cent decline in detached house approvals while multiunits approvals fell by 16.9 per cent.
HIA Senior Economist Tom Devitt said that on a quarterly basis, this left detached house approvals 15.4 per cent lower than the same time last year, and multi-units down by 38.9 per cent.
“This continues the longlagged response of Australian homebuyers to the RBA’s interest rate hiking cycle, with further declines expected in the coming months,” he said.
“The combination of construction cost blowouts, labour uncertainties, increased compliance costs and taxes on investors has seen approvals for multi-units fall.
“These disappointing approvals numbers are occurring as population growth surges with the return of overseas migrants, students and tourists.
“This imbalance will see the affordability and rental crisis deteriorate further,” Mr Devitt said.
Total building approvals were down across all the jurisdictions in the three months to April 2023 compared to the same period last year. In seasonally adjusted terms, decreases were led by Victoria (-35.3 per cent), followed by New South Wales (-28.7 per cent), Western Australia (-14.6 per cent), South Australia (-12.1 per cent), Queensland (-4.2 per cent), and Tasmania (-2.2 per cent). In original terms, the Aus-
tralian Capital Territory and the Northern Territory saw declines of 49.8 per cent and 27.3 per cent respectively.
Meanwhile concerns are mounting in the building community with building approvals hitting their lowest levels since April 2012, impacting Australia’s ability to meet its housing targets says Master Builders Australia Acting CEO Shaun Schmitke.
“According to the ABS, new home building approvals sank by 8.1 per cent over the month with a total of 11,594 dwellings approved in seasonally adjusted terms.
“The reverses in new home building approvals come in the aftermath of twelve months of rising interest rates and inflation at its highest in over 30 years.
“The data reflects the cautious approach being taken by developers and consumers in the face of economic uncertainty and high building costs.
“The biggest drops were in higher density home building approvals and home renovations falling 16.9 per cent and 26.6 per cent respectively.
“Although demand for medium and high-density housing is surging, the pipeline of new stock is rapidly diminishing.
“Builders recognise the importance of a healthy and vibrant building and construction sector in supporting economic growth and addressing the housing needs of a growing population.
MUCH has been said, much has been written and there is no doubt more to come on the Victorian Government’s native timber decision.
But comments from Australian Sustainable Hardwoods general manager Vince Hurley perhaps as much as anyone set the scene well. He certainly didn’t mince his words.
He wrote in the Weekly Times that the government’s campaign had been “driven with military precision by the environment minister, with every aspect aligned to the objective”.
“This includes picking and choosing the science and eco-
nomics that are used and promoted, the results of surveys and workshops, the media they align with and exploiting the complexity of forest management to broadcast simple, negative messages for media consumption,” he wrote.
“The result is the decimation of a recognised world-class industry that contributes significantly to Victoria’s economy and employment. Soon Victorians will be unable to have high-quality hardwood products available at an affordable price.”
He pointed out, as many have, that the growth of manufactured imports from countries with significantly less environmental and social requirements and the exposure to quality, availability and price fluctuations is inevitable.
Mr Hurley wrote that every Victorian is hurt by this decision.
He said people will lose their livelihoods in regional Victoria and in joineries, furniture manufacturers and other metropolitan businesses and the flow on-effects are enormous.
“The government’s objective is not environmental, economic, or social.
“The closing of native forestry is fulfilling a political objective and hurting Victorians for no good reason,” Mr Hurley wrote.
And hurt they will. And they will need help in so many ways.
The building industry in this country is in a lot of bother at present, and this won’t help. Tasmania and Queensland are the only State’s now harvesting native hardwood. And operators in those States will no doubt be holding their collective breaths.
RECENT research from the Timber Framing Collective shows that people continue to choose timber framing over steel due to its low cost, fast assembly, flexibility and ease of renovation.
But it’s the incredible environmental benefits that are really resonating in a world that is increasingly looking to reduce its impact.
The research was collected through anonymous surveys among consumers and builders from December 2022 to January 2023. Findings were compared with research conducted in 2021. The sample size included 220 consumers who have built their home in past 2 years or plan to build in next 18 months, as well as 182 carpenters/builders.
The research shows that steel is beginning to lose its shine among people building new homes, with an 11% decrease over the last two years in consumers who rate steel as superior.
More consumers are being inspired by timber framing’s environmental and emotive proof points, such as:
– Australia’s plantation forestry is 100% sustainable as they are replanted after harvest
– Each year Australian Forest Industries replant more than 70 million trees
– Plantation trees are necessary to fight climate change and move towards net-zero by 2050
– Choosing timber is helping build a better world.
The research also highlights that 48% of builders value green credentials as one of the most important factors in choice of materials. That’s an increase of 27% since 2021. And 72% feel positive about timber framing’s environmental impact, an increase of 21% since 2021. More
and more builders are aligning with timber framing’s key environmental messages — that it’s renewable, responsibly sourced and removes greenhouse gases from the atmosphere. This is a space where steel simply cannot compete.
Whilst the steel framing industry is working to reduce its impact (which is great news for our planet), there’s a long way to go and timber framing will continue to come out on top for the foreseeable future.
Right now green steel is simply a concept. The intent is that it will be produced using low-carbon energy sources, which will significantly reduce carbon emissions compared to traditional steel production. It can also be made from recycled scrap metal, further reducing waste and environmental impact. However, the production of green steel still requires significant amounts of energy and resources, which releases greenhouse gases into the air.
On the other hand, timber is a renewable resource that is grown and harvested sustainably with careful management. Trees grow for around 30 years before they are harvested, allowing them to capture large amounts of carbon dioxide from our atmosphere. This carbon is locked up and stored for the life of the timber. And the timber in framing is actually carbon positive, meaning the entire production process removes more carbon dioxide than it emits.
The research was collected through anonymous surveys among consumers and builders from December 2022 to January 2023. Findings were compared to research conducted in 2021.
The sample size included 220 consumers who have built their home in past 2 years or plan to build in next 18 months, as well as 182 carpenters/ builders.
THE National Timber & Hardware Association (NTHA) brought the timber and hardware industries together for a joint celebration for the national awards took place at the first conference since the merge of TABMA Australia and Hardware Australia in the Hunter Valley, New South Wales. The occasion recognised leading professionals and organisations in both the timber and hardware industries who are working above
and beyond to deliver quality products and services.
NTHA CEO, David Little said the national awards provided a significant opportunity for timber and hardware professionals to be acknowledged on a larger scale.
“This event was the first time since the merger earlier this year that our industries have come together and the atmosphere in the room was electric – with plenty of opportunities to network with a wider stakeholder group,” he said.
“Congratulations to all of our finalists and winners who have all shown dedication to their work and achieved above and beyond results for their businesses.
1. Timber Supplier of the Year – ITI Australia (Australia Wide)
2. Hardware Retail Supplier of the Year – Dulux (Australia Wide)
3. Best Hardware Retail Store under 2500sqm – Pink’s Mitre 10 (Clare, South Australia)
4. Best Hardware Retail Store over 2500sqm – Porters Mitre 10 (Mackay, Queensland)
5. Best Hardware Garden Department – Acheson’s Mitre 10 (Forbes, New South Wales)
6. Timber and Building Materials Store of the Year –Hardware & General (Sydney, New South Wales)
7. Best Frame and Truss – Big River Group’s MB Pre-Fab (Breakwater, Victoria)
8. Industry Icon – Ken Robertson, Fix-A-Tap Australia
Best Timber Manufacturer – Ultraflex Architectural Linings (Condell Park, New South Wales)
SCREENWOOD is a Responsible Wood certified company committed to securing a sustainable future through the use of renewable resources.
The company sources its products responsibly and is transparent about its supply chains. As a result, Screenwood has earned Responsible Wood chain of custody certification, demonstrating the company’s commitment to sustainability.
A commitment to sustainability and responsible sourcing also helps to secure a social license to operate and build brand credibility.
By demonstrating a commitment in these areas, Screenwood is not only able to attract and retain customers, but it is also able to differentiate itself from its competitors and establish itself as a leader in the industry.
By ensuring that its products are responsibly sourced and produced, Screenwood is able to demonstrate to its customers that it is a brand that they can trust and rely on for high-quality products that have been produced with care for the environment.
Screenwood General Manager Tim Russell says, “At Screenwood, we understand the importance of taking action towards sustainability. That’s why we are committed to using only high-quality, sustainable materials and
supplies in our production processes and business. Our Responsible Wood certified status is a testament to this commitment.”
Matt de Jongh, Responsible Wood’s Sustainability Manager, says, “Certification plays a crucial role in preventing deforestation and ensuring that our forests are managed sustainably. By choosing Responsible Wood certified products, Screenwood publicly demonstrates its commitment to sustainability and responsible resource management. This is commendable and serves as an inspiration for other companies to follow.”
Screenwood produces linear panels made from a selection of five timbers and are prefinished in a variety of colours. The modules are assembled and cut to specified lengths for ease of installation. The company is fair-rated, VOC tested, acoustically rated and environmentally certified, ensuring that sustainability concerns are integrated throughout the entire value chain.
For their chain of custody certification Screenwood uses a physical separation method as a means of managing and identifying certified timbers, sourcing only Responsible Wood/PEFC
timbers. The company is committed to continuous improvement and compliance with all applicable laws regarding environmental im-
pacts and workplace health and safety.
In addition to its commitment to sustainability, Screenwood is also dedicat-
ed to delivering high-quality products to its customers. The company’s responsible sourcing and sustainable practices ensure that its products meet the highest standards, both in terms of quality and environmental impact.
Screenwood’s Responsible Wood certification, provides customers and consumers with peace of mind that they are purchasing a product that has been responsibly sourced and produced sustainably with care for the environment and the workers harvesting the forest material.
AS leading forklift manufacturer Combilift continues its 25 years in business celebrations, this week saw the launch of another new model truck, this time at Ligna, the international timber and woodworking show in Hanover.
The new Combi-CB70E is a further addition to Combilift’s ever growing range of electric models which offers powerful performance, extensive battery life and unrivalled ergonomics. This model, in the vibrant Combigreen livery first seen on the recently launched Combi-CUBE product, boasts the distinction of being the shortest 7t capacity counterbalance truck on the market whilst also benefitting from multidirectional ability, enabling the versatile space saving handling of both long and bulky loads. Design features incorporated into the high-capacity Combi-CB70E such as its large super-elastic tyres and compact wheelbase make it ideally suited for the operational demands of the timber industry. With a 7,000kg/15,500lb lift capacity, this model benefits from an impressively small footprint as well as exceptional manoeuvrability meaning that it can easily move bulky loads of timber around in confined spaces.
Occupational health and safety requirements mean that the welfare of the workforce has become ever more important over the years. Drivers of industrial vehicles, who are often required to spend extensive periods in their work stations, quite rightly expect the highest levels of comfort and safety. Combilift’s designers have therefore gone to great lengths to ensure that the latest generation of models are kitted out with top quality components that ensure sophisticated ergonomics for a stress-free in-cab environment. Features in the spacious cab include generous glazing for
excellent all-round visibility, the tilting steering column, hydraulic steering and the Grammer MSG65 seat.
What sets the Combi-CB70E apart from other forklifts is its gas strut suspension cab, which uses components such as those found in large scale industrial machinery with cab suspension. Combined with the super-elastic tyres this guarantees the smoothest of rides over uneven or less than perfect ground conditions such as those typically experienced in lumber yards.
Combilift’s newly developed Auto Swivel Seat was also premiered at the Ligna show. This optional feature automatically engages and swivels the seat and armrest 15° to the right or left to accord with the direction of travel selected by the operator - reducing driver strain, particularly when travelling in reverse. (Patent Pending Application No. 2305983.5)
The truck also features Combilift’s internationally patented and Red Dot awarded independent electric traction which provides all front and rear drive wheels with 100% traction control. This negates the need for differential lock on slippery surfaces and significantly reduces long load momentum twisting when travelling sideways. Each electric drive incorporates parking and regenerative dynamic braking for power efficiency. Roll-out access for major electrical components also simplifies maintenance tasks.
This mix of next-gen performance, extensive battery life and exceptional ergonomics combined with all the advantages of the Combi-CB range, makes this the most powerful compact electric multidirectional forklift to date.
“The increased capacities that we are offering in our electric range will answer the demand for ever more powerful products which at the same
time help companies to achieve their aims for more sustainable operations,” Combilift CEO and Co-Founder Martin McVicar said.
“We chose Ligna as the platform for launching the Combi-CB70E due to its
innate suitability for customers in the timber sector, but we are confident that this model will be a popular addition to our portfolio for many other industry applications.”
JS-50 X6B NEW
JS-50 WX
EMBODYING South Australia’s appreciation of the arts and cultural landscape, the new Festival Plaza public realm is one of Adelaide’s largest public redevelopment projects to be undertaken in recent times.
The space, which now features a combination of dynamic entertainment and social areas, has been upgraded to regenerate the city centre and to revitalise and connect formerly disparate parts of Adelaide’s major events and entertainment precinct, including Adelaide Oval, the railway station, Sky City Casino and the Festival Centre.
The biggest stage of the public realm has now been completed and opened in March 2022, it incorporates 8,000sqm of reinvigorated public space and has been designed to attract and accommodate a larger number of guests, both locally and internationally. Further stages of the Festival Plaza public realm upgrade will provide an additional 7,900sqm of renewed open space, totalling 16,500sqm.
At approximately two hectares in size the stunning Plaza is the centrepiece of a wider regeneration. It includes a 20-metre-long interactive water feature, six 11-metre-wide arbours and, completing the space as a destination for recreation and relaxation, statement curved seating and shelters are set within raised landscaped surroundings alongside an intricate pattern of stone paving.
Supporting this significant stage of the upgrade, leading Australian timber and building supplier Big River Group has delivered a range of quality formwork materials, including its premium bendable formply, ArmourForm overlay 1 side. The 5mm and 9mm ArmourForm, which comes in 2400x1200mm sheets, is ideal for curved formwork applications and was instrumental in enabling the unique design character of the space.
“Our bendable formply was key in helping to deliver the contractor, Outside Ideas’, vision of the featured curved structures and seating in the Festival Plaza precinct,” says Brian Relph, National Formwork Manager, Big River Group. “Our 5mm ArmourForm has so much flexibility which helped to overcome some of the challenges that presented without too much labour.”
Well known for its customer service, smooth ordering and delivery solutions, industry innovator Big River Group worked closely with Outside Ideas to provide code compliant solutions with a focus on performance, that have improved efficiencies throughout the project.
“To be part of one of the best looking landscaped and multifunctional facilities in the Adelaide CBD is second to none, also the fact that we could
help with final outcomes of some of the more difficult structures was very rewarding,” says Brian.
Additionally Big River supplied Formwork LVL which is suited for heavy load construction and concrete structural applications. It is available in three sizes, edge sealed for protection with lengths colour coded for convenience. Big River Formwork LVL represents a substantial improvement over conventional timber and is an easier to use, more convenient alternative to other materials.
Part of the Big River formwork solution was the use of Deckply F17 which is a high-quality plywood panel developed and engineered predominantly from graded eucalyptus veneers to the Australian Formwork plywood standard AS6669 as well as to the Australian and New Zealand standard AS/ NZS2269-Structural Plywood.
The Festival Plaza public realm upgrade is a key component of the larger Festival Plaza redevelopment, undertaken by the State Government in partnership with SkyCity Adelaide and Walker Corporation. The project represents $1 billion in public and private investment, including $213 from the State Government. The Adelaide Festival Plaza redevelopment, which also includes a new 27-level office tower, Festival Tower and a five level, 1646 space underground car park which opened to the public in May 2022, began in 2016 and is due to be completed in full in 2025.
For more information visit: www.bigrivergroup.com.au
Enabling sustainability... with world-class, science-based standardsLearn more about third-party certification for forest products • Big River Group’s premium bendable formply has been instrumental in enabling the unique design character of the Festival Centre Plaza.
FTMA is recognised as the trusted representative body and unified voice for all timber frame and truss manufacturers in Australia, whilst strengthening the connection with the broad supply chain.
EVERYONE along the supply chain plays a critical role in ensuring that products or services are delivered to customers in a safe, ethical, and sustainable manner.
Each person or organization involved in the supply chain can impact the quality, safety, and environmental impact of the final product. Therefore, it is important for everyone to take responsibility for their actions and work together to achieve common goals.
Unfortunately, there are often unfortunately too many breaks in the supply chain, which can result in an entire industry being impacted.
One fall – affects us all and for this reason, we must ensure everyone within our supply chain is taking the necessary steps to guarantee we are only using fit for purpose timber.
We all know how hard it was over the past few years with the timber shortage. As timber supply tightened through our usual suppliers, we literally had new importers and suppliers coming out of the woodwork.
Fabricators, who were desperate for timber would call or email me, providing certificates which claimed to demonstrate the structural properties of the timber, but what who really knows how to read these certificates.
If the product doesn’t meet the claims, then it is not fitfor-purpose. Just because a fabricator claims they thought the timber was fit for purpose, or the supplier had shown them a fancy certificate to indicate it had all the relevant structural properties, means nothing. You, the fabricator is liable for any future damages resulting from a fall or non-compliance.
Every fabricator uses engineered software, supplied by Mitek, Multinail or Pryda. If you are using the software, then you have received training in how to use the software.
One of the lessons you would have learnt was the importance of ensuring the right timber was selected in the engineered software. You cannot simply choose a substitute timber, if what you are looking for is not included in the software.
KERSTEN GENTLE Executive Officer FTMA AustraliaBy doing this, you are not only using the engineered software incorrectly, but you are also ensuring your warranty is null and void and if there is a fall, you will be personally held responsible and could face criminal charges.
Our three nail plate companies test the timber to ensure it has the correct JD ratings, that it can handle the loads and is fit for purpose. Therefore, if it is not in the software, you cannot use it.
So what does non-conforming building products actually mean?
According to the ABCB Website, non-conforming building products (NCBPs) and materials are those that:
• claim to be something they are not;
• do not meet required standards for their intended use; or
• are marketed or supplied with the intent to deceive those who use them.
This is different to noncompliant products (NCPs) and materials which are products or materials used in situations where they do not comply with the requirements of the National Construction Code.
So, how am I responsible?
The ACBC is very clear on what different sectors of the supply chain are responsible for, which you can view at https://www.abcb.gov. au/ncbp/my-responsibility. However, a snap shot includes:
Manufacturer – ensure they know the requirements of compliance and conformance of their products and materials and the evidence required to demonstrate compliance. This involves being aware of a range of related requirements such as testing, assurance, and certification. It also requires manufacturers to understand how customers should and should not use their products.
Importers, wholesalers, distributors and retailers
Importers, wholesalers, distributors and retailers need to ensure that the products being supplied do not breach trade or consumer laws or industry-specific requirements for safety or performance. Some products or materials have specific requirements to demonstrate safety and suitability before they can be lawfully sold and may require independent testing and certification before being supplied.
If you know as a timber importer, wholesaler, distributor or retailer, that the timber has not been tested by the nail plate companies, you have a duty to ensure this information is passed on to fabricators buying the timber from you.
Developers, Builders and other specialist tradespersons
Developers, Builders and other specialist tradespersons do the work of installing and building with products and materials. They are not the only people responsible for ensuring that conforming and complying products and materials are used, but much of the risk and responsibility falls to them because they are the ones that ultimately do the building work.
Developers and builders are responsible for ensuring that cost management does not compromise the performance of the selected building materials. They should also ensure that certificates demonstrating the compliance of purchased and installed materials comply with the certification documents/ building approval. This documentation should be kept with the contract documentation and provided to the building owner on completion of the building work.
As you can see, everyone in the supply chain has a role to play to ensure our industry is meeting standards and providing fit for purpose products.
If you have any questions, please contact me on 0418 226 242 to discuss. I cannot stress the importance of only using timber which has been tested by the nail plate companies and is included in the software.
FTMA thanks our dedicated partners and encourages you to support those who support your industryPrincipal Partners Strategic Partners Supporting Partners
OF the many issues raised by timber employers on our TTIA National Employment Hotline, the most confusing is the ability to pay a loaded or ‘all up rate’. For an employer, paying a loaded hourly rate can seem a much simpler way of managing payroll as compared to a constantly fluctuating rate of pay.
I recall many years ago, in the early 1980’s, being told by my seniors, while working at a major industry association, that the IR inspectors responsible for compliance operated on what was referred to as an “unders and overs system”.
Put simply, as long as your over award payment or salary covered any additional penalties, loadings or allowances, there would be no prosecution by the relevant authority, you would be left alone and in effect be complying with your award obligations.
It probably doesn’t come as any surprise that in 2023 and 40 years on, it’s now a little more complicated. As always in business today, paperwork and record keeping are the key. So what steps should an employer take if they want to incorporate award entitlements like penalty rates, loadings and an allowance within a salary or rate of pay?
It is common practice to include award entitlements within a salary or rate of pay, which is usually fine so long as:
• an employee’s total remuneration is no less than their award/enterprise agreement requires;
• there is a written agreement acknowledging that certain award entitlements are included within an employee’s remuneration; and
• employers keep adequate records of hours worked and duties performed.
In the case of any employees who have a guarantee of earnings in place
and who are paid above the high-income threshold (‘HIT’), this becomes a moot point as modern awards do not apply to them because their income is deemed adequate compensation for all award entitlements.
The high-income threshold as of now (May 2023) is $162,000 per annum.
For employees below the HIT (or above the HIT without a guarantee of earnings), the employee’s specific award/enterprise agreement is very important as many have clauses that will describe exactly how certain entitlements can be included within the salary or rate of pay.
Some modern awards like the Clerks Private Sector and the Manufacturing and Associated Industries Award now incorporate an “Annualised Wage Arrangements” model clause which details the minimum requirements for such an arrangement:
1. The clause first lists those penalty rates, allowances and loadings that can be included within an annualised wage.
2. It requires that a written agreement be made specifying:
• which of the provisions of the award will be satisfied by payment of the annualised wage;
• the method by which the annualised wage has been calculated, including specification of each separate component of the annualised wage and any overtime or penalty assumptions used in the calculation; and
• the maximum limit on what the annualised wage will cover whereby any hours worked beyond that limit would earn additional pay in accordance with the award.
3. At least once every 12 months employers must calculate the total remuneration an employee would have earned if paid according to the award i.e. earning the award minimum rate plus all other applicable award entitlements (e.g. penalty rates, allowances, loadings etc) for the exact hours they worked. If their annualised wages fall short of the award, and the shortfall wasn’t made up in the relevant pay cycle when it occurred, then employers must backpay that shortfall in the annual review.
4. The employer must keep a record of the starting and finishing times of work, and any unpaid breaks taken, by each employee for the purpose of undertaking the 12 months comparison mentioned above. This record must be signed by the employee each pay period or roster cycle.
Many businesses question that fourth point as they hope to avoid such time and record-keeping requirements. The positive news here is that in practical terms employers only really need to keep records of hours worked and duties performed outside of those that the annualised wage has been calculated to cover. For example, let’s say an annualised wage was calculated to compensate for an average of 45 hours work per week (inclusive of applicable overtime and shift penalties under their award), and presumed no weekends or public holidays would be required. Then employers only need to record hours outside those parameters i.e. hours beyond 45 per week, and any weekend or public holiday hours, or when the employee was filling for another on higher duties. Then these extras would have to be paid for separately within each pay cycle, to comply with the annualised wage clause.
Whilst the Timber Industry Award does not provide for an annualised salary clause, another way to incorporate award entitlements into a higher salary or rate of pay is through a written Individual Flexibility Agreement (IFA). The benefit of IFAs is that they are sourced from the award, the source of the legal obligation to pay the entitlements and IFAs expressly permit the varying of employer obligations relating to payment of overtime/penalty rates, allowances and annual leave loading. However, the two drawbacks to an IFA are that firstly they cannot be made a condition of employment (i.e. they can only be made with an existing em-
ployee, not a new employee) and secondly, either party can unilaterally cancel the agreement with 13 weeks’ notice.
Finally, an approach that is also worth discussing with our Legal team for those employers wanting to incorporate award entitlements into an employee’s remuneration while ensuring that they are not underpaid, and minimising the record-keeping burden, is to use a compensation for legal entitlements clause or offset clause in an employee’s common law contract. Such a clause should make clear that both parties agree that the remuneration specified in the employment contract compensates the employee for any award entitlements (such as wages, overtime, allowances, penalties, and loadings) that may arise for any hours worked in the course of employment.
Of course, the remuneration provided must meet or exceed what the award requires for the same hours and duties performed. A well drafted set-off clause should make specific references to the award clauses being amended, they should not be generic. It is highly recommended that employers seek legal advice from TTIA on the drafting of such clauses and ensure the correct award that covers the employee (if any) is identified as well as the relevant classification.
The bottom line for Employers: Employers in our industry can incorporate award entitlements into a higher remuneration, so long as a written agreement is in place, specifying what entitlements are compensated for and employers ensure an employee’s remuneration does not fall below what the award requires. Employers must maintain adequate records of work performed because the onus of proof is always on employers in answering any underpayment claim.
It’s an opportune time to get this aspect of your house in order with the changes flowing through at present on a range of industrial relations issues. If you’re not a Member of the TTIA, now is the right time to join.
Any existing Members wanting assistance with drafting of employment contracts or a review of their existing employment contracts should contact the TTIA on (02) 9264 0011 or the Timber Industry’s dedicated Legal Officer on 0414 557 235.
TTIA will be running seminars in July/August of this year dealing with this and any other substantive industrial relations/award matters. Please contact TTIA on (02) 9264 0011 or by email ttia@ttia.asn.au for seminar dates and venues.
TIMBER veneers can be used to create many different effects.
When visiting the Aesop store in Burnside Village Fashion Mall the first thing that strikes you is the distinctive perforated panelling. The panelling is Big River’s ArmourPanel with a blackbutt face veneer.
Claimed to be Australia’s strongest decorative plywood, ArmourPanel is designed, tested and approved to tolerate extremes of heat and humidity and to resist shrinkage. Its tolerance of changes in ambient temperature, and its toughness, make it ideal as flooring, ceiling or wall linings in hard wearing areas.
Every panel is made from layers of Australian eucalypt hardwood veneers bonded together to form a strong, solid, stable panel. No two sheets are alike meaning no pattern repeats – every sheet is individual and natural.
Big River holds long term wood supply agreements with the State Government of NSW for sourcing the raw ma-
terial that goes into ArmourPanel. Forest NSW estates are certified by the international program for endorsement of forest certification (PEFC).
Certification to the Responsible Wood and PEFC certification schemes provides consumers with confidence that wood products have met strict requirements for timber harvesting and the sourcing of wood products.
Established in 1987, Aesop aims to formulate skin, hair and body care products using plant-based and laboratorymade ingredients. The warm environment created by the blackbutt panelling complements the amber coloured
containers on the store’s shelves.
According to Kerstin Thompson Architects, choosing timber as the dominant element fitted with the arti-
san vision for the Aesop store – one that in subtle ways represented the craft and care that goes into the making of Aesop products.
Images of other outstand-
ing veneer projects can be found on the Timber Veneer Association’s website at https://timberveneer.asn.au/ by clicking on the “Projects” tab in the TVAA address panel.