
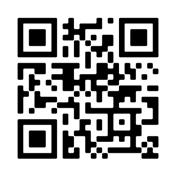
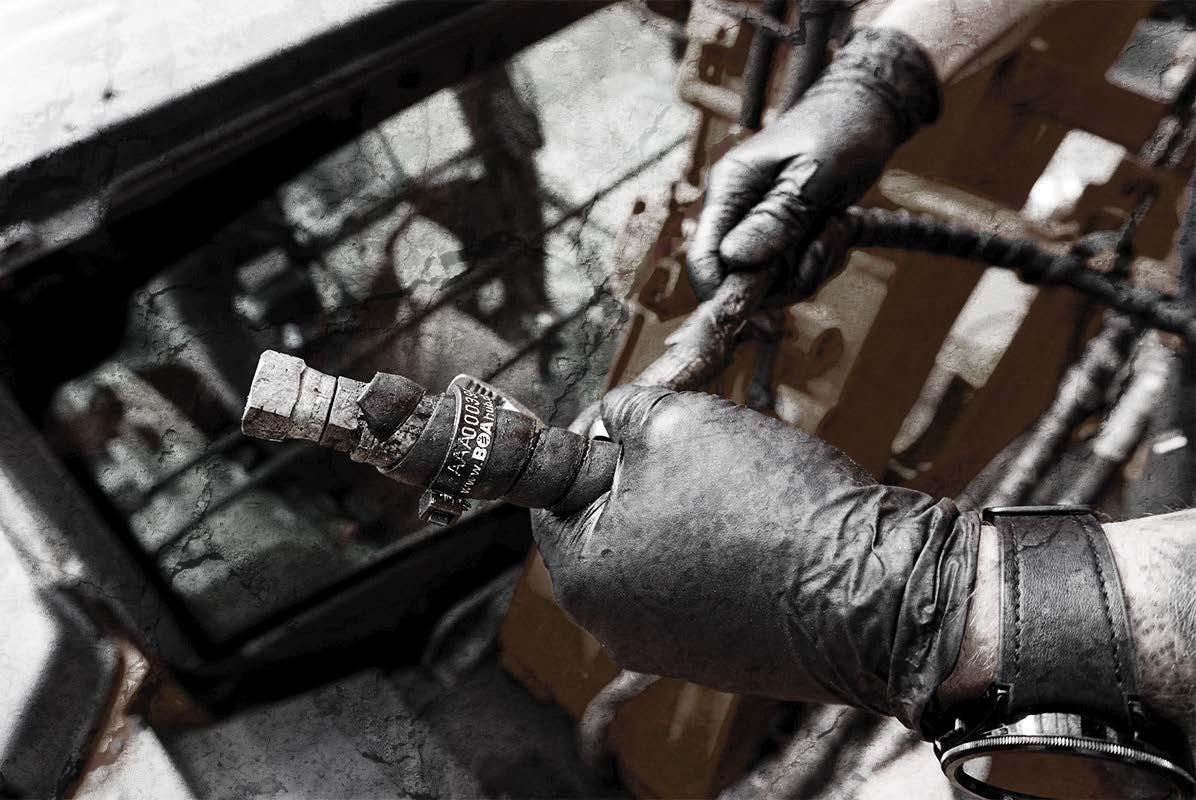


VicForests will cease operations on June 30.
The June 30 end date was revealed during a court hearing involving VicForests and environmental group Wombat Forestcare.
Nationals leader Peter Walsh said VicForests was being treated deplorably.
He said the State Government has not offered a single positive word, effectively ignoring its existence.
“This June 30 end date is painful enough, but VicForests are being kicked on the way out the door without an ounce of respect,” Mr Walsh said.
“The organisation has no way of defending itself. The Allan Labor Government remains silent, refusing to publicly defend its own logging company.
“This is a cruel, unfair ending for an organisation that has done so much for regional communities and made a huge contribution to Victoria.”
The winding-up of the body is part of the Victorian government’s decision to end native forest logging, which took effect on January 1.
Stand-down payments to VicForests contractors are
due to end on June 30.
Last September, the government paved the way for the organisation’s closure, altering its status as a state business corporation and making it a “reorganising body”, which allows its functions and staff to be moved around.
VicForests employs 140 staff. Of these, it is understood 60 will be made redundant while the remaining 80 will get new roles in the state Department of Energy, Environment and Climate Action.
”It has always done its best despite severe harassment from illegal protesters,” Mr Walsh said.
He said the contribution of VicForests should be applauded given so much of its work supporting the industry was amid continual litigation by extremists.
“VicForests had to use taxpayers’ money to defend itself from carrying out government policy,” Mr Walsh said.
He said the end of VicForests would also leave a gaping hole in fire management.
“The risk of mega-fires will increase. There won’t be tracks maintained by the timber industry and there won’t be control lines to
burn back from,” Mr Walsh said.
“There won’t be the heavy equipment and timber industry workers to go in and help fight fires.
“The Greens, so critical of the industry, will be hiding in inner Melbourne and nowhere to be seen as regional communities face the inevitable bushfires without the support of the timber industry to help fight them.”
Community and Public Sector Union industrial organiser Kassey Dickie said VicForests’ 100 employees were aware the company would close on June 30.
She said workers were able to apply for about 80 other government jobs, including five-year contracts with Forest Fire Management Victoria.
“Everyone’s going to lose their job at VicForests, whether or not a large portion find other work, that remains to be seen,” Ms Dickie told AAP.
The government initially planned to phase out native logging in 2030 but brought that forward over claims the sector had become unviable because of ongoing legal action.
Ms Dickie said many workers were stressed and find-
ing new roles had been a “very fast process” for them.
“They’re sad I think, to sum it up, many of them have worked together for a very long time,” she said.
“They have been rushed through a process made by government in a hurry that has been pretty stressful.”
VicForests recorded a net loss of $60.1 million in the 2022/23 financial year, blam-
ing court action brought on by environmental groups. During that time it harvested $17.9 million in timber, paid $110 million in compensation for undersupply to customers and $41 million to contractors who were not able to work. It received $149 million from the state to fund the compensation.
Forestry Australia has appointed South Australia’s Monique Blason and Victoria’s Ruth Ryan as new board members.
Forestry Australia CEO Jacquie Martin said Ms Blason and Ms Ryan would bring exceptional experience in filling the casual vacancy positions.
“Monique and Ruth’s experience in softwood plantations, fire management, stakeholder engagement, policy and regulation will make a valuable addition to the board’s skillset,” Ms Martin said.
“Monique has a 30-year career covering policy and regulation development, focused on public land, fire and biodiversity management, community and stakeholder engagement as well as developing and coordi-
nating whole of government emergency management, crisis resilience, public safety regulation in South Australia.
“Ruth is a Forestry Australia Fellow and has more than 40 years’ experience in forestry and fire in Australia, with a focus on commercial softwood plantation management in Victoria, and was
appointed to the European Union funded FIRE-RES research project and The Commonwealth’s Wildfire Resilient Landscapes Network.”
Ms Blason said she was honoured to have been asked to join the Forestry Australia Board.
“I look forward to contributing to the collective knowledge and leadership of the
Board to advocate for sustainable forest management and to support and develop our members,” she said.
Ms Ryan said she had a long-time member of Forestry Australia and was proud to be amongst the early cohort of Registered Forestry Professionals.
“I have always believed in the sense and purpose of the organisation to promote professionalism and dialogue to ensure wise management of our forests,” she said.
“I am excited by the recent revitalisation of the organisation and look forward to growing Forestry Australia’s future.”
Forestry Australia has also announced the appointment of Emily Post as an additional Board Observer.
Ms Martin said the Board Observer position provides a broader point of view and di-
versity at Board meetings, as well as facilitating pathways for younger members with an interest gaining executive level experience and developing their leadership and governance skills.
“We look forward to incorporating and capitalising on Monique, Ruth and Emily’s contribution as we work to increase recognition of the value of sustainable forestry in modern Australian society,” Ms Martin said.
Ms Post said that Forestry Australia and the broader forestry community had shown her unwavering support throughout the formative years of her career.
“I am humbled and delighted to have been offered an opportunity to contribute to the continued success of Forestry Australia and the professionals it represents,” she said.
Issue 2 – Volume 35
Established 1991
News 3 - 14
My View 5
Profile 8
Milestones 12
Silviculture 18
Training 19
Harvesters 20 - 21
Excavators 22 - 23
Front Cover: The HG6800TX Horizontal Grinder is Vermeer’s biggest, most powerful grinder. Page 15.
Publisher and Chief Executive: Hartley Higgins
General Manager: Robyn Haworth
Editor: Bruce Mitchell
b.mitchell@ryanmediapl.com.au
Adelaide Office: (08) 8369 9521
Advertising: Jon Andryciw
j.andryciw@ryanmediapl.com.au
Adelaide Office: (08) 8369 9517
Creative Services: Sudapa Rattanonda
Publication Design: Sudapa Rattanonda
Trader classifieds: Jon Andryciw
Adelaide Office: (08) 8369 9517
Subscriptions: subs@forestsandtimber.com.au
Adelaide Office: (08) 8369 9522
Subcription rates
One-year (6 editions) $44.65
Two-years (12 editions) $77.65
Accounts: ar@winetitles.com.au
Phone: (08) 8369 9500
Postal Address: 630 Regency Road, Broadview South Australia 5083
Phone: (08) 8369 9555
Fax: (08) 8369 9501
Melbourne Office: Suite 2262, 442 Auburn Rd, Hawthorn VIC 3122 Phone: (03) 9810 3262
Website www.timberbiz.com.au
Printed by Lane Print, Adelaide, SA Conditions
The Australian Forest Products Association has appointed experienced government relations professional Ms Diana Hallam as its new Chief Executive Officer.
Ms Hallam has a long and distinguished career working at senior levels of the Australian Public Service, as Chief of Staff to a former Deputy Prime Minister and in other senior political advisory and corporate roles with a focus on infrastructure, transport and agriculture.
“Diana’s breadth of experience across senior levels of government, politics and the corporate sector will stand her in excellent stead to manage the challenges and opportunities facing our sector,” AFPA Chair Stephen Dadd said.
“On behalf of the Board, staff and membership, I congratulate Diana and welcome her to the team.”
Ms Hallam was First Assistant Secretary in the Australian Government Department of Agriculture, Fisheries and Forestry. She began as AFPA CEO on 12 March 2024.
Ms Hallam served as Chief of Staff to Deputy Prime Minister and Minister for Agriculture Barnaby Joyce from 2014 to 2017 and pri-
or to that occupied senior roles at both Toll Group and Singapore Airlines.
She holds a Bachelor of Arts (Hons) and a Master of Science and Technology (Aviation) from the University of NSW, a Master of International Law from the Australian National University, a Graduate Diploma of Professional Communications from the University of Southern Queensland and is a graduate of the Australian Institute of Company Directors.
Ms Hallam said she was
VicForests will be gone by June 30. It really doesn’t come as any surprise.
It was the death by a thousand cuts.
The writing was on the wall, and writ large the moment the Victorian Government announced it would be shutting down the native timber industry by 2030.
It brought that death forward when it announced that the industry would be shut down at the end of last over claims the sector had become unviable because of ongoing legal action.
What is so disappointing is that the Victorian Government could have stepped in to prevent the “lawfare” campaign again VicForests. But it didn’t.
The number of injunctions issued by conservation groups over logging – coupe by coupe – has had an enormous impact on VicForests. Even when VicForests won cases it struggled to recover court-awarded costs against environment groups.
thrilled to be offered the opportunity to become AFPA’s CEO.
“I look forward to meeting AFPA’s membership and working with everyone across the forest products supply chain,” she said.
“The industry is at the forefront of key policy challenges from climate change to economic development and sovereign capability. I look forward to getting out on the ground and talking to stakeholders about the industry’s issues and opportunities.”
In 2021 the former Member for Narracan Gary Blackwood called on the State Government to introduce legislation stopping thirdparty litigation.
Of course nothing happened, leading Mr Blackwood to pose the question at the time as to why the then-Victoria’s Dan Andrews continued to leave his government’s commercial arm of forestry exposed to vexatious third-party litigation designed to cripple the industry?
The answer at the time seemed that by taking this approach Mr Andrews could
say his hands were clean. Sadly, it looks like it worked. Meanwhile, starting this month, we’re transitioning Australian Forest & Timber News to a bi-monthly publication schedule. This change allows us to dive deeper into each issue’s content, delivering richer, more comprehensive stories and features. This shift empowers us to cultivate a stronger connection with our audience, providing them with a thoughtfully curated magazine experience every other month.
Irecently completed an 18-month-long stint with the Australian Forest Products Association (AFPA).
I served first as an independent member of the board, then as CEO and finally, as chair.
I was attracted to the organisation by two things. First, my long-standing interest in, support for, and affection for the industry. An affection I developed over the 10 years I represented it in the Parliament, first as minister and for much longer, the shadow minister.
Second, I knew the AFPA team well, and was aware of the expertise, passion, energy, loyalty, and dedication each of them brought to their roles. Just the sort of team you want to be part of. Senior people in the or
I was also impressed with former CEO Ross Hampton’s decision to align the industry with community and political expectations by appointing a climate change policy manager, a job Natasa Sikman discharged with distinction.
Highlighting the greater role the forest and forest products sector can play in addressing climate change
AFPA’s focus on climate change is an important part of the sector’s determination to build its social licence. Forestry is now a sophisticated sector, embracing innovation and populated by big investment funds deploying patient capital to put more trees in the ground for eventual harvest while also offering nature-based solutions for many of our environmental challenges, and opportunities for those seeking to offset their carbon emissions.
One of AFPA’s great initiatives has been its participation in the annual Conference of the Parties (COP). Its participation has been a significant contributor to efforts to persuade decision makers to look more to the sector as they struggle to
for improved environmental outcomes. In pursuit of their extreme and uninformed ideological views, activists continue to peddle misleading information in their attempts to demonise the industry.
What they either don’t or do not want to understand is there can be no success on either the climate change front or attempts to reduce deforestation in developing countries without native forestry in countries with high environmental standards. The alternative to a sustainable forestry sector here is a reliance on imports from countries with no or corrupted regulatory frameworks.
Nor do they understand that our highly regulated, selective, and sustainable native sector is a critical part of the
native estate. This of course, is rubbish both in product and volume terms. What a tragedy it is that Australia no longer produces any white paper! I wonder where our green friends – many of whom live in homes replete with beautiful hardwood trimmings - think their product is coming from when they are printing-off their anti-forestry propaganda?
Thankfully the parties of government in Canberra –unlike their counterparts in some states – appreciate the contribution the sector makes to our economy, jobs, and the Australian way of life. They are also alert to what it would mean not to have a strong domestic forestry sector.
So there is hope that a united and strategically smart
PRIMEX, the family-owned brand that has been a part of the Australasian agricultural field days calendar since 1985 will this year feature a greatly expanded Forestry and Timber Hub.
Always at Casino, in coastal northern NSW, Primex has evolved from a localised event, with around 40 companies and a few thousand visitors, to one of the country’s leading primary industries expos.
It now boasts in excess of 300 exhibitors, 1000 different companies and more than 25,000 visitors across the three days.
In partnership with state and national forestry organisations, organisers say the Primex Forestry and Timber Hub is set to become the largest event on the forestry industry’s calendar.
“It brings together the entire supply chain of the forestry and timber industry. The hub will showcase the North-East NSW Region’s significant hardwood production, covering every aspect of the industry, from machinery to technology,” said Norco Primex Director Bruce Wright
This feature is coordinated in conjunction with Timber NSW, Timber
QLD, NE NSW Forestry Hub, South + Central Queensland Regional Forestry Hub, Aust Forest Contractors Association, Forest & Wood Communities Australia, NSW LLS (Forestry), NSW DPI (Forestry) and key
industry stakeholders.
The hub concept started last year and gained momentum from there.
“It’s carried on to now it is a lot bigger,” Mr Wright said.
“It was about 50 meters of displays last year, and it’s probably close to about 250 for this year,” he said.
If you have timber on your property and want to know more about maximising the income opportunity from it then give Koppers a call today.
Mark Hitchins (NSW) – 0439 291 163
Rhys Riddell (NSW) – 0409 674 372
Shane Griffin (NSW) – 0429 447 223
Tim McDonnell (QLD) – 0447 615 017
Come and see us at the Primex timber industry hub
While Primex is fundamentally an agricultural-focused field day Mr Wright said forestry did cross over a lot of different agricultural seg-
“I’m excited by the fact that we had some of the strongest areas of plantation forestry kicking off 20 years ago,” he said.
“So the fact that people are coming back and wanting to find out more about it, it makes sense. And if there’s actual proven applications that you know, you can run your livestock and also build a base or forestry on your farm, then that’s got to be a good thing, because it means planting more trees and having more sustainable products that
“I don’t think anyone would argue about growing increased forestry opportunities on farm, because
there’s a lot of areas where there’s no value for livestock that forestry can add to it
“And obviously farmers have got to look at this further.”
The immediate NE NSW Forestry Hub region has forest production of around 1 million cubic metres of hardwood and 400,000 cubic metres of softwood per year. The Forestry Corporation of NSW produces around three quarters of the region’s timber with the balance coming from private property.
There are over 3,700 properties within the region that contribute to the supply of timber from private land.
Most of the wood grown in the region is processed in the region with over fifty mills spread along the coast and many more portable mills.
While the Hub is still very much as NSW event at present he can see it becoming a national event.
“I think that that’s the thing that we’re looking at,” he said.
“I think it’s something that we are definitely going to be sort of investigating further on going forward.”
Big, really big or bloody massive?
Since the mid 60s, Ensign has been designing and building some of the world’s toughest log forks and supplying them to customers all over Australasia. Clamps, kickers, pivots, locks, high lifters… you name it, if it’s a feature that’ll help you pick up and put down stuff easier, faster or safer you can guarantee we’ve already built it.
So whether you're in the market for the biggest and baddest or something a bit more modest give us a call and we’ll build your perfect log fork.
The forestry industry has seen some profound changes over the last two decades. It’s altered the way companies are managed, as well as the people that are employed.
SFM is a leading natural asset manager with locations across Tasmania, South Australia, Victoria and Western Australia who celebrate the diverse workforce they have built. Almost half of the team at SFM is women, a significant figure above the industry average of 28%.
Leanne Chappell leads sustainability and compliance at SFM, after studying soil science at university, she didn’t expect forestry to be her career pathway. Leanne knew she wanted to find a role in environmental science and land management, and assumed she would end up in agriculture, but when an opportunity came up in forestry she took a chance. And now, more than 25 years later, she’s never looked back.
Despite having little experience with the world of forestry at the time, Leanne dived in, and was pleasantly surprised by the support and opportunities she found.
“SFM is probably the best workplace I’ve ever worked in. This comes down to the company being very family orientated and inclusive. Along with, the level of autonomy that’s afforded to staff. You can take on a role and run with it, and actually build your confidence in making decisions. You’re given opportunities to increase or develop your skills in all sorts of areas.” Leanne says.
Leanne was quick to follow new opportunities as they arose, and she appreciated the positive energy that rewarded hard work, no matter who you were.
“From what I’ve witnessed across the industry, if you want to work, and you have the right attitude, you could go anywhere. I don’t believe that there were any real barriers to women finding a place, whether it was supervising harvesting crews, or undertaking roading man-
agement, or in the silviculture area.”
“I always found those environments to be really quite inclusive. You are employed to do a job, and engaged based on your ability to do that work, rather than by male to female ratios. That’s what I saw, I actually have had a really good run.”
Leanne says.
“SFM is an easy place to work. As a female in the industry, I never felt that there were any walls that you had to try and get over. It was always very respectful. If you just throw yourself into any opportunity that comes along, then you’re going to have a very rewarding career. The opportunities are there if you want to take them.”
Leanne thrived in an environment that rewarded initiative and a drive to work hard, but she didn’t want that to come at the expense of having a family. In her experience, it’s the businesses that recognise the value of balancing work life with family life that have a happier, more engaged staff, and most importantly, become an employer of choice.
“From the top, the senior management group of SFM has a culture that doesn’t exclude people for where
they’re at in their life, in terms of raising a family. If you’re a mum, and you’re choosing to work part time to then raise your children, that is not a barrier here.”
Leanne says.
“I think that’s probably why we’re seeing those numbers increasing here, because there are people out there that have exceptional skills, experience that will work really well in the culture and overall context of what SFM is about.”
As demand for forestry products grows, and as we rely more on new forms of technology, the range of roles in the industry is expanding. Leanne has seen major shifts in the nature of work, and the different types of people it attracts.
“The interesting thing is that universities aren’t offering dedicated forestry degrees anymore. But we are still seeing women coming through, I think it’s a shift in knowledge that forestry isn’t just about cutting down trees, there is a whole whole swag of different roles.”
Leanne says.
“There are so many opportunities, whether that’s taking on a role in GIS or other more technical aspects such as carbon analytics, you
don’t have to be limited to say, working with a local government, or in a mining industry, it’s transferable. You’re not limited to what you studied at university. The message is getting out there that forestry is open to anyone.”
Leanne has gone from being a forestry skeptic, to being a committed forester, excited about the evolution of the space, and the opportunities that are emerging. She hopes that people will look deeper and realise it’s about more than just trees.
“I’m a classic example, I didn’t study forestry, but here I am. It’s life’s journey, it’s seeking out those opportunities, because you just don’t know what’s past that door that has forestry written on it.” Leanne says.
“Once you peek inside, you realise you can see more than trees. There’s a whole world in there that can open so many different avenues for anyone that wants to come in.”
It’s not just technology that’s driving changes in the industry. As the impacts of climate change grow, forests are being recognised for their huge carbon sequestration potential, which has given rise to a further specialisation around carbon accounting, which is soon to be followed by biodiversity and natural capital accounting.
It’s a complementary business to forestry, but it requires specialist skills and an appreciation for how to operate in a new market.
“I think we’ll see that you certainly need to maintain your production levels, that’s still very important, but we’ll also look at it from a carbon perspective. It’s about your conservation values along with your production values, and it brings together both economic and social issues.” Leanne says.
“Plus, we’ll also see a shift into natural capital accounting and measuring biodiversity values, they’ll be recognised as offsets as well. There’s going to be a really big push into that area.”
The Australian Forest Contractors Association has appointed two new directors.
Mark Blackberry is the Managing Director of Sunchip Group, a familyowned soft wood harvesting and haulage company based in Queensland. He was inducted into the AFCA Hall Of Fame in 2015.
Mark Brown is Professor of Forestry Operations, UniSC, Director – Forestry Research Institute – UniSC, Director – Forest Industries Research Centre - UniSC, Executive vice-chair & Communication chair - IEA Bioenergy TCP, and Task Leader, Biomass Supply –IEA Bioenergy.
He grew up in the forest industry and from the family sawmill and contracting business went on to get his career in applied forestry research and innovation having worked in research leadership roles both in Canada and Australia.
HVP Plantations has appointed Melanie Cook as its new CEO, after an extensive search following the retirement of Stephen Ryan in October last year.
Ms Cook will begin in the role in April, bringing with her a wealth of experience from a 25-year career with ExxonMobil where she held the roles of Chief Operating Officer in Malaysia and President and CEO in Indonesia, before returning to Australia in 2021 where she led her own consultancy business specialising in Leadership and Energy.
She holds a Bachelor of Engineering, Chemical Engineering, Chemistry and Mathematics from the University of Melbourne.
New
New Forests has appointed Michelle Elliot as Global Head of Funds, and Sanjiv Louis as Director, Investments Asia.
Michelle will be responsible for overseeing New Forests’ global funds management platform to support future growth and opportunities while Sanjiv will lead New Forests’ Asian investments team.
Effective collaboration across the timber industry and learning the lessons from past fire salvage efforts have been highlighted as key factors underpinning the success of the record salvage program in the Tumut and Tumbarumba regions following the Black Summer fires in a report commissioned by Forestry Corporation of NSW.
Forestry Corporation’s Sales and Procurement Manager
Peter Stiles said the report summarised the challenges, successes and lessons from the timber salvage program and was being shared with the industry to inform future fire recovery.
“The Black Summer fires were devastating for the local community and the region’s softwood timber industry was severely impacted, with about 50 per cent of the pine plantations in the south west slopes burnt,” Mr Stiles said.
“Unlike many native species, pine trees die when they are burnt, but the industry was able to mobilise quickly
and in numbers against the backdrop of the emerging COVID-19 pandemic to salvage a remarkable 2.7 million tonnes of timber in the
of this salvage program, so while we hope fires like this will never be experienced again, it is important for us to share the lessons from the
“ The lessons from past fires underpinned the success of this salvage program
two years following the fire.
“This was the biggest ever salvage effort in this country’s history and there is a lot to be proud of in what the industry achieved. The salvage program kept the lights on for our local processors immediately following the fires and created a boom in harvest and haulage work across the region, but importantly, it also maintained a quality supply of essential structural lumber and packaging products to the broader industry at a time of high demand.
“The lessons from past fires underpinned the success
Black Summer salvage with the industry for the future.”
Report author Damien O’Reilly from Mayday Hill Consulting said the review made it clear that collaboration across the timber supply chain was a key to the salvage program’s success.
“Forestry Corporation of NSW is a plantation manager that engages contractors to harvest timber and supply it to third party processors and close collaboration across the supply chain and with local and interstate forest growers was an essential ingredient in the salvage program’s suc-
cess,” Mr O’Reilly said.
“The timber industry as a whole shares the objective of maintaining a sustainable supply of timber not just for today but also for the future, so the industry worked to balance immediate and longterm timber needs in the decisions that were made following the fires.
“The salvage program benefited from experiences in assessing damage and managing the processing of burnt timber that were learnt following past fires in NSW such as the Billo Road fire in 2006 and Jananee fire in 2014, as well as invaluable advice and support from the industry across Victoria and South Australia, and through Forest and Wood Products Australia (FWPA).
“This salvage program demonstrated the effectiveness of remote sensing technology and estate modelling in prioritising salvage operations, and informing processors, contractors and the community about the medium and long-term impacts
on the resource.”
There was also significant investigation into log storage options under water or sprinklers, including a trial that provided useful lessons should long-term storage of burnt timber be required following fires in future.
Overwhelmingly, the report found collaboration with customers and contractors was a fundamental reason underpinning the success of the program. Flexibility from customers, coordination of contractor capacity and engaging with other growers enabled the industry to both maximise the salvage of burnt timber and minimise the harvesting of unburnt timber to allow it to grow on to deliver timber in future years.
The report is specifically focused on the salvage of softwood timber from the Tumut and Tumbarumba regions and has been published on the Forestry Corporation website to assist the timber industry.
Dwellingup sawmiller Jay Branson was virtually absorbed in the sawmill business at a young age.
After his mother took a job at the Mandurah sawmill in the 1980s, Mr Branson was taught as a child the intricacies of cutting hardwood logs by a retired Italian miller.
He opted to make a career out of hardwood and now runs the Dwellingup Sawmill 90 minutes southwest of Perth.
A family-owned business run by Jay Branson for the past 17 years, Dwellingup Sawmill originally specialising in Jarrah, has diversified over these years, adding mixed species to their range, such as Marri, Sheoak, blackbutt and Karri.
The mill, which employs around 14 staff, caters for Industrial infrastructure, structural, furniture, flooring, general public needs and firewood, with the team passionate about timber and always endeavouring to get the highest quality product for their client’s needs.
“When I was finishing school I was going to go to university, and I got a summer job at the mill,” Jay said.
“I did leave to do a trade but I’ve been there ever since.”
When the owner retired from the sawmill Jay purchased some of the machinery and started up on his own.
He had a saw bench from Grey Engineering, Gibson equipment and a large twin saw.
“It was a really big operation that was very rundown,” Jay said. “We actually had to pull the whole thing apart.”
He is now upgrading all his equipment through Grey Engineering to a fully automated process.
Jay said he was currently sourcing his timber from throughout Western Australia including plantation timber from the south west, and a lot of different species as they become available.
“When we started we only had a third-grade contract. It was very poor quality. But then over time, we actually got a better quality product available to us,” Jay said.
“We produce everything from the lowest of low grade and also the firewood market right through to the highest and higher grade kilndried product.
“We also do a lot of structural work, so we do a lot of repairs for heritage listed jobs and places around Perth that still have Jarrah fences or pergolas in need of repair.
“So we work with a smaller market as well as larger markets as well.” Jay said he had gone from 25 to 30 clients to 60 to 100 in the past year.
“So the problem with that is, I know, I can’t get enough product to sustain all of the markets that probably we’ve got,” he said.
“So that’s why we’re trying things like plantation timber.”
Jay said he couldn’t map the future following the State Government’s closure of the native timber industry in WA from the start of this year.
“We don’t know. We don’t know day to day, week to week, month to month,” he said.
“I’m navigating our way through it and I think a lot of people are doing the same and it’s really becoming a bit of an aggressive market.
“In the meantime, of course, we’re going to lose mills.
“There are boutique mills buying feature-grade or auction logs, then you’ve got a couple of players that are of our medium size that are planning on continuing,” he said.
“But I don’t believe that we are going to have many more exits.”
Western Victoria’s new plantation hardwood strategic alliance, GT Hardwood, is actively educating the community on its plans to invest in new plantation trees to meet the world’s growing consumption for fibre-based products and mitigate the continued decline in resource.
The collective, formed by the region’s main plantation hardwood (Eucalyptus globulus or Bluegum) growers, including ABP (Australian Bluegum Plantations), Midway Limited, and New Forests, recognised the need to collectively work on educating the community and government on the increasing market demand for its sustainable woodchip resource and plans for more local investment, including a focus on domestic value-add.
Founding Green Triangle Forest Industries Hub, CEO,
Liz McKinnon was recently appointed as the GT Hardwood external affairs manager to support stakeholder engagement, strengthening relationships and understanding of the contribution of the collective, which exports more than 3 million tonnes of sustainably grown plantation hardwood chip annually from the ports of Portland and Geelong.
This focus includes working with Midway promoting its commitment to invest up to $200 million in new plantations with associated carbon projects through new green field sites within the south west region.
The investment supports the Federal Government’s National Forest Industries Plan which has earmarked the planting of one billion plantation trees nationally by 2030, as well as the national ambition towards net zero.
Midway is also working with local farmers to facilitate forestry based carbon projects on their land which produce carbon credits that can be sold to large emitters, diversifying on farm income.
Ms McKinnon and Midway leaders have been in the region this week, undertaking consultation with the Corangamite Shire Council demonstrating how hardwood plantations complement existing agriculture investments, highlighting that their management activities rely heavily on local employment.
“Australia’s plantation estate is in decline, losing a further 28,000 hectares in recent years, equating to a 250,000 decline over the past decade. This includes a 10 per cent contraction in the nation’s blue gum estate over the past decade, with significant parcels of blue
gum land lost across the Green Triangle. This loss, largely due to conversion back to agricultural use, comes at a time when global demand for fibre continues to soar, with estimates the global market will quadruple by 2050,” Ms McKinnon said.
“Planting more trees to store carbon is a key lever to meet the international focus on decarbonisation. Our locally grown sustainable plantation hardwood chip also plays a valuable role producing recyclable paper and packaging to replace plastic products as well as replacing coal for energy generation.
“New trees will also play an instrumental role in reaching Net Zero Emission Targets for the agricultural sector. Our trees, which are often planted as woodlots and shelter belts, are a reliable tool in capturing and
storing carbon whilst supporting farmers to diversify their farm income by earning carbon credits through the government backed Australian Carbon Credit Unit (ACCU) Scheme.”
Ms McKinnon said GT Hardwood was focused on optimising the use of its fibre and diversifying its market base, investing in domestic value-add research to understand how to use globulus in new structural timber products.
MechLog started its operations in Northeast Tasmania in 1994. Since then, it has expanded its operational capacity throughout Tasmania, South Australia and Victoria.
It has an extensive fleet of machines, including five Tigercat HL855E Harvesters, three equipped with a Waratah harvester head, one with a 26-inch hot saw, and one with a Waratah FL100 directional felling head.
Additionally, their fleet features a Tigercat LH822E Harvester with a 23-inch hot saw and three Forestry Hidromek excavators.
The partnership between MechLog and Onetrak originated from the initial purchase of a Tigercat LH855E Harvester. The combination of industry experience and a focus on communication has meant the relationship has flourished.
MechLog still has this original machine, which continues to be operational 10 years later, having worked 18,000 hours.
In January of this year, the company received its latest Tigercat machine, another LH855E model. MechLog emphasizes that the standout feature of these machines is their exceptional uptime.
MechLog, in contrast to other brands, considers Tigercat’s machinery to be on par with other purpose-built brands in terms of performance but excels in stability on steep slopes.
The operators at MechLog admire this feature and commend the minimal machine movement during operation.
The exceptional support from the Tigercat factory provided by Steve Green sets a high standard for customer service. This along with Onetrak’s quality of service is appreciated my MechLog. Onetrak’s Territory Manager for Tasmania Rodney Onion was also recognised by Mechlog for his dedication and ability to get things done.
Onetrak is the official dealer for Tigercat equipment in Australia.
Visit www.onetrak.com.au or call 1300727 520to get in touch with Onetrak.
Mechanised Logging Pty Ltd
(MechLog) is celebrating three decades of service to sustainable timber harvesting practices in Tasmania, South Australia and Victoria.
Since its establishment in 1994, MechLog has been at the forefront of innovation, delivering unparalleled forestry solutions to the softwood and hardwood plantation timber industries across Australia.
MechLog CEO Jillian Aylett Brown said that MechLog’s 30th anniversary celebrated a significant milestone in the company’s commitment to excellence and sustainability.
“From our humble beginnings in 1994 – and with a commitment to taking a new approach to how the forestry sector had operated previously – MechLog has thrived,” she said.
“We are proud to be recognised as a progressive and innovative company, dedicated to championing the Australian forestry industry. MechLog has remained steadfast in our mission to provide quality services while continuing to promote sustainable and responsible forestry practices,” Ms Aylett Brown said.
“MechLog’s success is built on a systematic approach to harvesting operations that maximises efficiency while minimising environmental impact.
“In some respects, MechLog is leading the way in our approach to forestry practices, and we have our dedicated team of 40 employees to thank for that,” she said.
“We recognise the importance of investing in our workforce to ensure the continued success of our clients, the company, and every employee.”
MechLog provides ongoing training and development opportunities for the team to empower them to grow both personally and professionally. By nurturing talent and fostering a culture of innovation,
MechLog has maintained a competitive edge in the forestry industry and is recognised as an employer of choice.
“Our clients certainly appreciate our commitment to training and development, which directly benefits them through efficiencies and dedication to excellence,” Ms Aylett Brown said.
“At MechLog, we recognise that it is important to balance economic prosperity with environmental preservation. This is drilled into every member of the MechLog team from day one. As a result, they work tirelessly to ensure sustainable forest management practices, which safeguard Australia’s valuable timber resources for future generations, is the foundation of our operational philosophy.
For 30 years, in addition to its core services, MechLog has been a leader in adopting the latest technology to enhance productivity and sustainability in the forestry industry. By embracing cutting-edge equipment and practices, MechLog has been able to maximise yields for clients while minimising waste and its environmental impact.
MechLog’s ethical and sustainable approach to forest-
ry has earned the company a reputation as a preferred provider of harvesting services in Australia. The company prioritises developing strong relationships with clients and end-users, understanding their unique needs, and delivering tailored solutions that exceed expectations. The company also values a strong emphasis on community engagement and corporate social responsibility. The company actively participates in local and industry initiatives and supports environmental sustainability efforts, demonstrating its commitment to making a positive impact beyond
its business operations. As a multi-award-winning company in numerous categories, MechLog is widely respected by its industry peers for the company’s positive impact on the forestry industry, within government, and across the wider community.
“It’s all about sustainable innovation, ethical and efficient business practices, and advanced training methods. Our commitment to innovation and training drives our success and sets us apart in the industry. We are constantly exploring new technologies and methodologies to improve our operations and deliver exceptional results for our clients,” Ms Aylett Brown said.
“We value the trust our clients place in us, and we are committed to delivering exceptional service every step of the way. We are so proud of the MechLog team, who are all dedicated to providing innovative, sustainable, and cost-effective solutions that add value to our clients’ operations.
“MechLog is proud to have served the Australian forestry industry for 30 years, and we are looking forward to continuing our journey of growth and innovation in the years ahead,” she said.
Arecently completed research project has showcased great potential for the development of sustainable native forestry activities in the Northern Territory, led by Traditional Owner communities.
FWPA facilitated this important work by providing funding to match the investment made by project partners including the University of the Sunshine Coast (UniSC), Gumatj Corporation, Northern Territory and Queensland governments, and other regional organisations.
Together, the partners worked to boost the forestry capacity of Traditional Owner (Yolngu) communities in the East Arnhem region.
FWPA Research and Development Manager Dr Chris Lafferty said there is a growing interest in the commercial potential of northern Australia’s vast Indigenous owned and managed forest estate, and strong aspirations among Indigenous communities for self-determination and economic independence.
“Industries such as sustainably managed native forestry are critical to fulfilling these aspirations because they align with Indigenous notions of value and continue to care for Country,” Lafferty said.
“This FWPA-supported project saw professionally trained foresters engage with Indigenous communities to enhance Traditional Owner knowledge of modern best practice sustainable forest management principles.”
“The foresters also committed to learning about Traditional Owner forest management knowledge and practices, and investigating how the differing concepts and approaches could be integrated to achieve an optimal balance of production, environmental and cultural conservation outcomes.”
Another key project focus was creating business development opportunities for timber products manufactured in the region and driving stakeholder engagement around the potential of sustainable native forestry to support Indigenous livelihoods and regional economic development.
Northern Territory (NT) Government Project Manager Dallas Anson said the Traditional Owner training was delivered to enhance commercial forestry skills, and knowledge of western science forest management principles.
“The training was undertaken by 35 Traditional Owners and covered everything from forest resource assessment to harvesting operations, sawmilling, and valueadding processes for forestry products,” Anson said.
“In total, 1,647 hours of paid training was conducted through the project, injecting almost $48,000 into the Homelands of East Arnhem Land.”
The researchers used learnings from this element of the project and engagement with Traditional Owners on their own forest management knowledge and practices to develop a proposal for a forestry training program designed to drive the future development of the regional forestry workforce.
In addition to the training, inventory activities were conducted by the team to provide a clearer picture of the productivity and product mix of the East Arnhem native forest resource, and a harvesting and marketing pilot program was developed to identify, manufacture, and market-test value-added timber products.
The pilot program included the establishment of a demonstration site in the remote community of Birany Birany. This included, at the request of the community, the construction of several wooden shelters using the locally harvested Darwin stringybark (Eucalyptus tetrodonta) timber.
Naturally durable, solid roundwood products – prototype stringybark bollards – were also manufactured from small-diameter logs harvested at the site. A market assessment identified strong interest in the bollards, and Traditional Owners were linked with prospective purchasers, collaborative business partners and investors.
The development of a bestpractice Free, Prior, and Informed Consent (FPIC) process to help determine
● Northern Territory Government Project Manager Dallas Anson welcoming workshop attendees July 2023 on Birany Birany Homelands in East Arnhem Land. Pictures: FWPA
the commercial forestry interests, needs and desires of other Indigenous communities in the future was another key outcome of the project.
UniSC Associate Professor (Adjunct) Mark Annandale said the work provides a pathway to further develop financially and environmentally sustainable Indigenousled commercial forestry in East Arnhem.
“The project generated interest in forestry from Traditional Owners and other stakeholders by creating an understanding of its potential to support ongoing Indigenous livelihoods and regional development,” Annandale said.
The next-step project will also provide a model that could be refined for application in other areas of northern Australia.
A series of information initiatives aimed at advising potential farmers and landowners interested in the onfarm forest plantation sector is now available in South Australia as part of Trees on Farm initiative.
This includes a toolkit, developed by the South Australian Government, in tandem with the Green Triangle Forest Industries Hub featuring expert information and printable fact sheets to support and guide landholders in their commercial plantation investment.
Other information for perspective growers is also available from five research reports and associated seminar videos conducted under the Trees on Farm initiative from both the PIRSA and GTFIH websites.
The second round of grants for the $74 million Support Plantation Establishment Program is open for applications.
Farm foresters, First Nations businesses and the forestry industry are among those who will benefit from funding to support more new plantation forests in Australia. For more information or to apply for a grant, visit: Current Grant Opportunity View – GO6728: GrantConnect www.grants.gov.au Standards revision
This important project was a collaboration between FWPA and researchers at UniSC, the NT Government Department of Industry, Tourism and Trade (DITT), and the Queensland Government Department of Agriculture and Fisheries (QDAF) along with regional partners Gumatj Corporation, the Northern Land Council, National Indigenous Australians Agency, Arnhem Land Progress Association and Developing East Arnhem Limited. Learn more: https://fwpa. com.au/report/indigenouscommercial-forestry-opportunities-east-arnhem-northern-australia/ View the detailed report at https://fwpa.com.au/report/ indigenous-commercialforestry-opportunities-eastarnhem-northern-australia/
The Forest Stewardship Council ANZ has begun a revision of the FSC National Forest Stewardship Standard of Australia.
FSC International has also approved the composition of the Standards Development Group appointed by the FSC ANZ Board to draft the revised Standard.
The first round of public consultation is planned to occur in mid-2024 and will be announced through all available channels.
Ponsse review
Ponsse plans to renew its operating model globally.
It would create organisation that focuses on sales and service, including both our Ponsse’s operations and dealers in planned five market areas: the Nordics, Europe, South America, North America and Asia, Australia, and Africa.
Large grinding projects can carry an increased risk of metal entering the machinery hammermill, which can cause major issues for the equipment. Powerful machinery that offers protection against this kind of damage is the key to a successful project. Enter Vermeer’s Damage Defense system.
In large projects such as land clearing or mulch production, grinders are handling large materials like whole trees and large stumps, and metal contaminants can easily mix in with incoming materials. This can cause serious damage to machinery, which can be costly to repair and result in significant delays to the project.
Contractors seeking protection from such damage would benefit from partnering with a supplier that not only offers powerful equipment, but goes above and beyond in protecting machinery and ensuring success.
Powerful machinery handling tough material
With 950 hp and in a 41,730kg weight class, the HG6800TX Horizontal Grinder is Vermeer’s biggest, most powerful grinder. The engine is C-rated for increased engine life while providing the ability to power through materials with minimal operator interaction.
This kind of powerful machinery necessary for larger projects also rises to the challenge of an increased risk of metal entering the hammermill.
Equipment protection systems –such as Vermeer’s Damage Defense system – reduces the likelihood of metal being ground, offering contractors added security and safety.
Mitigating major machine damage
The Damage Defense system is a Vermeer-exclusive product and an optional add-on, offering additional protection for grinders by using exclusive technology to sense metal vibration in the infeed and the mill – reducing the likelihood of damage caused by metal contaminants.
Fully compatible with the HG6800TX, the Damage Defense system is perfect for any Vermeer tub or horizontal grinder operation that may encounter metal contaminants mixed in with its incoming materials.
If metal makes it into the mill whilst the machine is grinding, the grinder control will be alerted and the Damage Defense system will automatically initiate the shutdown process, slashing reaction time and boosting onsite responsiveness.
preventing significant damage to the grinder.
The Damage Defense system can be integrated into a grinder’s control system for maximised effectiveness – mitigating the need for tools or a manual reset. Further enhancing its flexibility and efficiency, the system’s sensitivity settings can be easily adjusted, enabling contractors to quickly adapt to specific jobsite con-
ditions and helping reduce nuisance shutdowns.
Built and supported by Vermeer, the Damage Defense system comes with robust components and is protected by a weather resistant box.
Backed by local support
When using Vermeer’s HG6800TX coupled with the Damage Defense system, contractors can have the confidence to tackle bigger projects
without worrying about contaminants causing project delays or costly equipment damage. The system gives contractors peace of mind and is backed by Vermeer Australia’s experienced and knowledgeable environmental equipment specialists. For more information on Vermeer products and services, call 1300 VERMEER or visit www.vermeeraustralia.com.au
If a contaminant is detected, the system automatically reverses the infeed system and immediately disengages the clutch to protect the machine, reducing the likelihood of metal being pulled into the
and
Innovation and safety are the key drivers behind OneFortyOne’s $8million nursery redevelopment, with a new state-ofthe-art undercover handling system leading a number of major upgrades for the Glencoe facility.
The two automated handling lines, designed in Europe and installed on-site, will see millions of radiata pines trees sown, lifted and dispatched under controlled conditions annually, significantly increasing workforce conditions and safety.
In March, as the industry marked International Day of Forests on March 21, flags a milestone for the 3-year redevelopment project, as the
new systems become operational.
Nursery Manager Craig Torney said the new infrastructure investment will substantially increase efficiency and signals a major shift away from traditional intensive in-field growing.
“The line has the ability to sow about 1-million trees per week, so it’s a lot cleaner and a lot more efficient,” Craig said.
“This work would normally be done on the back of a tractor in the elements. Now, from the time the container is introduced to the machine to the time that the finished product is pushed through the wall automatically out into the nursery, there is no
human intervention, apart from overseers.”
A new irrigation system is also part of the upgrades, improving efficiency at the establishment stage by decreasing water and chemical usage.
In operation since 1983, the Glencoe nursery is central to OneFortyOne’s Australian operations, growing around 7.5million trees annually for the company and other Green Triangle forest growers.
Employee safety and wellbeing is at the heart of the changes, Craig said, with infrastructure upgrades set to protect the predominantly outdoor workforce from the elements.
to 20,000
“It’s important to provide our team of people with a better work environment. The new infrastructure is entirely undercover and set to bench-top height, so workers will now enjoy a safer, more ergonomic workplace,” he said.
“We’ve had team members out here for 25-years plus, so the safety and long-time sustainability of the nursery’s workforce was a major factor in the decision to upgrade the facility.”
OneFortyOne Chief Executive Officer Wendy Norris said the key components of the upgrade share a strong alignment with this year’s theme for International Day of Forests – ‘Forests and In-
novation’.
“Innovation is at the centre of the upgrades, as the work will ultimately result in a better and more efficient end product for forest growers and OneFortyOne’s customer base,” Wendy said.
“By investing in long-term safety and efficiency measures at the nursery site, which is an essential supplier of trees across the Green Triangle forestry sector,
OneFortyOne demonstrates our commitment to the future of the industry, our people who have been with us for a long time, and also, our local communities.”
Tasmania has taken substantial steps to identify industry and community-supported priorities for addressing the urgent need for additional wood.
Private Forest Tasmania has collaborated with Forico to investigate costs and silvicultural practices, focusing on efficiently transitioning from short (pulpwood-focused) to longer (solid wood/sawlog or engineered wood-focused) rotations.
The goal is to promote stand improvement strategies within Tasmania’s existing plantation resources,
ultimately enhancing domestic sawlog supply outcomes in the short to medium term.
The transition from pulp to solid wood plantation regimes in Tasmania requires a comprehensive understanding of the costs associated with thinning operations and the factors influencing the productivity and costs of mechanised equipment in these conditions. This project utilises machine productivity data to assess mechanised thinning operations in Eucalyptus nitens stands, pinpointing the key factors affecting productivity and
costs. Additionally, sensing technology, including mobile LiDAR systems, has been employed to evaluate the quality features of the remaining trees, such as Diameter at Breast Height (DBH), height, branchiness, tree form, and stem damage. In addition to providing insights about machine productivity, the study implemented and validated a methodology for scanning trees before and after thinning to optimise data capture in terms of time and accuracy. This approach facilitated a detailed capture of tree features, including
diameter and height, for subsequent processing with automated algorithms and tools.
This study reaffirms the invaluable role of LiDAR technology in informed decision-making during thinning operations. Lidar point cloud data collected before thinning empower harvest planners to make well-informed decisions regarding the optimal location of thinning roads, tree selection during thinning, and alternative thinning strategies before field implementation. Real-time or pre-thinning Lidar data also aids harvester operators in
making optimal tree selection decisions, incorporating variables like tree density for removal decisions and other factors such as basal area, tree form, and branchiness. These considerations would be challenging to capture without the assistance of LiDAR technology.
The insights gained from this project are expected to provide valuable information for enhancing the costeffectiveness of mechanised thinning operations in Tasmania and the broader context of Australia.
Manuel Hall jokes that he was “born into the forest sector”.
The Triple H Contracting Director began working for his dad’s harvesting business in his mid-teens as a way to make money in the school holidays, only committing to the business fulltime in 1997. Manuel admits that it’s not as simple to attract young people to the industry these days.
“Recruitment seems to be a difficult area across the industry. Many have left the industry, so trying to attract new people to the sector needs to be a big focus,” he said.
Triple H Contracting—Hall Harvesting & Haulage— is a family owned and operated business that works across Tasmania.
“We started with a two-man crew and have significantly expanded with operations in both pine and hardwood clear fall and thinnings in the south, east and northeast of Tasmania,” Manuel said.
The business currently employs 22 people and six subcontractors. Of this group, a third of Triple H’s workers are currently enrolled in the new Forestry Leadership Skillset developed by the TFFPN alongside industry and administered by TasTAFE.
Manuel said the business prioritises professional and personal development and recognises it is key to good workplace culture.
“In order for the growing business to continue and be successful, our people need to feel empowered to strengthen their abilities, to develop new skills and become more effective in their roles,” Manuel said.
“This leads to a more positive culture which in turn flows through the whole business,” he said.
“This course was a perfect first step for our leaders in this business to help their growth. It has been tailored to the forestry industry which means it is relevant to our people and helps keep them more engaged with work.”
Manuel believes encouraging employees to expand on their knowledge and skills in the workplace positively
affects their confidence, motivation and overall morale.
“We want our people to gain additional valuable knowledge that can help them grow and open up different channels for them both personally and professionally,” he said.
People are at the centre of Triple H’s business and Manuel said the business doesn’t just talk the talk but also walks the walk.
In 2023 the business won the Tasmanian Timber Award for Excellence in Workplace Health and Safety, with judges commenting on the organisation’s proactive approach to supporting the wellbeing of its workers.
“We pride ourselves on keeping up to date with best practices, codes and standards – ensuring all personnel involved in our business understands their roles, responsibilities and duties, creating a culture where safety is paramount and always forefront of every decision we make,” Manuel said.
At the beginning of each year the team gathers in a central location to reflect on the previous year, plan approaches for the year ahead, and to re-induct staff. This annual meeting always strongly focuses on health and safety.
“These gatherings are a great opportunity to realign our mindsets and focus on educating the importance of safety in the workplace, embedding it into every aspect of our business and making sure that all workers and contractors understand the benefits of keeping everyone
safe,” Manuel said.
“All our employees participate in mental health training, first aid training, applicable certificate training based on job roles which includes Certificate 3 in Harvest and Haulage, Certificate 3 in Mobile Plant Technology and Certificate 4 in Work Health & Safety.”
The business proactively promotes mental health and shares its Employee Assistance Program (EAP), regularly discussing these topics in Triple H’s monthly toolbox meetings.
“We encourage open conversations and a safe environment where people feel secure to talk or listen to others. Having the EAP allows our team to utilise a service free of charge and anonymously if needed. Openly discussing the subject allows for obstacles to be removed that may be contributing adversely, in turn creating an improved and more beneficial workspace,” he said.
Manuel knows it is important to lead by example. He balances his mental health
The Forest Stewardship Council Australia and New Zealand is on the hunt for a new member for its Social Chamber on the Standards Development Group following the resignation of Lorraine Cassin.
The FSC ANZ Board has approved the process for appointing Ms Cassin’s replacement so that the SDG can continue its important work.
The process will be identical to that undertaken when the SDG was originally constituted. Upon publication of this call for Expression of Interest, applications will be closing on April 21.
Standards Development Group members are chosen for their experience and ability to represent key interest areas that are important for the revision and FSC’s values and policies. Eligibility for the Standards Development Group requires that applications include and demonstrate:
• Membership of FSC ANZ. Or submission and approval of an FSC ANZ membership application as part of the expression of interest process.
with regular exercise and spending time with those who support him.
“I still play a bit of football as well as volunteer at my local club helping with training and the kid’s games. I love skiing, camping and have a small farm I enjoy working on. At the end of the day, everything I do revolves around my family.”
Manuel encourages young people or those looking for a new career to consider forestry.
“My advice is, go for it! It is such a diverse industry that offers so many different great opportunities and different roles. There’s much more to forestry than operating a machine, cutting trees. In our business alone we have two apprentices –one is completing their Cert 3 in Mobile Plant Technology and the other enrolled in a Cert 3 in Engineering Mechanical Trade. Another employee has recently completed a Cert 4 in Work Health and Safety.
“The opportunities are endless.”
• Up-to-date knowledge of FSC’s systems and procedures.
• Representation of points of view from the social chamber, ideally based on experience from a workers’ rights organisation or equivalent experience from the cross-section of forest management and workers’ rights and employment conditions.
• An understanding of the impact of the standard on affected stakeholders.
• An ability to actively participate in the process until final approval of the revised standard.
• Support from two members of the corresponding chamber in the form of letters of support.
• Expert knowledge of and/ or experience in the development, implementation and/or analysis of standards will be highly regarded. More information on becoming an FSC ANZ member can be found at https:// anz.fsc.org/governance/ members
Eco Log´s new G series has been launched with an entirely new harvester cabin.
The development behind the cabin is one of Eco Log´s longest projects so far and the road has been lined with quite a few challenges. Also, it has been a learning process to many parts of the company. The new harvesters in the G series are now waiting for production to start in 2024.
Behind the decision to develop a new harvester cabin are several factors. Future regulations, new design possibilities and, not the least, the demands and requests from the customers was finally decisive and a first pilot study was started in summer 2017.
“A new cabin has been requested from our customers for a long time and, initially, production start was set during the winter 2020/2021. So, already in 2017 the first pilot study was initiated as well as tests of a cabin suited for the harvesters in the E series,” says Emil Forsblom, Head of Development at Eco Log.
What would happen next was something that no one could have predicted. Both the pandemic and the war in Ukraine caused major disturbances in the supply chain which made it impossible to keep the time schedule for the on-going cabin project.
“When a project gets delayed like this, it is more than just the time schedule that is affected,” he said.
“Several, large updates were going to be introduced on the harvesters at the same time as the new cabin and the G series – for example our new control system NexSci, new improved frames and updates in the hydraulic system. To phase different components in and out is complex and takes a lot of planning. So, when the cabin project was delayed several times, we couldn´t postpone the other updates any longer. Therefore, they were first implemented on the F series harvesters during 2022 and became what people call the F series – Phase 2.”
To develop an entirely new cabin is, to say the least, an extensive task and the factors to consider are many. In a pilot study, all input from the market is gathered with a variety of different parameters,
such as manufacturing costs, legal requirements, technical limitations, choice of suppliers and the conditions to manufacture and produce the product in an efficient way.
“Of course, the operator comes first regarding visibility, ergonomics, comfort and functionality. But there are a lot of things to consider and a huge job involving many people lies behind the development. Therefore, it feels great to be able to present this top-modern premium cabin that we are very proud of. It has really been a team effort from start to finish with many people involved who has performed an amazing job<’ Mr Forsblom said.
When the development work really starts there are a variety of thorough tests and simulations that must be conducted to ensure that everything from climate, materials and electronics to visibility and, above all, safety is well functioning and meets various requirements and standards. Magnus Pettersson is one of everyone involved and he is also the one who has headed the project.
Magnus tells us more about the development work and about different requests from the customers.
“A slightly different request is the turnable seat where the main reason was to create a space for having lunch without sitting with the food in your lap,” Mr Pettersson said.
“This solution has then resulted in several advantages. As an example, there are plenty of space behind the
seat to store your cooler bag or lunch bag and you can also spin the seat to get out of the cabin more easily. Another advantage is an easier service. Now, you can turn your seat around and easily access fuses, relays, diagnostic sockets and many other things that are placed under the panels behind the operator.”
Storage possibilities is a recurring request from the customers and Eco Log´s development department has put a lot of effort to find smart storage solutions – a task that comes with a lot of challenges. The cabin must also accommodate large amounts of electronics, a ventilation system suited both for summer and winter, noise isolation and now, the turnable seat.
“There are a lot of things that must be fitted into the cabin and so, finding various storage options is definitely challenging and the engineers have really used every space available,” Mr Pettersson said.
“Also, the operator needs an optimal visibility and the fact that we have the crane at the side of the cabin is another thing that affects that complexity. So yes, there has definitely been quite a lot of things to work out, but we are very pleased with the result.”
The tests and samples that needs to be conducted are many. To explain the extensive work, we describe a few of all of the tests that has been carried out during the project. Space studies and collisions can many times be performed trough 3D technique, but some of the tests needs a real model. The first one was made in wood interior to give a realistic feeling of the final result.
To Eco Log, driver safety is crucial. . We perform a lot of calculations on solidity and the possibilities to get out of the cabin in case of an accident. To verify all the calculations a couple of cabins are being tested. We simulate that a machine turns over (ROPS), release steel balls on the cabin to simulate a falling tree (FOPS) and ensures that the front windshield is resistant to chain shots. Also, OPS tests are carried out to make sure that the operator can´t be injured by example logs or other objects.
The cabin has a new HVAC system. The preparations of the climate tests are made in a simulation program, both regarding air flow and capacity for heating and cooling. The optimized result could then be 3D printed and tested in the first prototype cabin. Repeated tests have then been carried out to ensure a system that fulfills our highest standards. There are also requirements deciding how a cabin should be cooled without causing air drafts around your neck. This also applies to heating and the possibility to have windows free from condensation.
To have as even airflow as possible doesn’t only provide a good defrosting, but it is also vital to the comfort for the operator. The requirements today states that it can only differ a maximum of five degrees between head and foot for the operator.
Our measurements have shown a result of three-four degrees regarding heat as well as cold.
Nordic and US-based steel company SSAB and Ponsse Plc, one of the world’s largest manufacturers of cut-to-length forest machines, have joined forces in a partnership in which SSAB is to deliver fossil-free steel to Ponsse gradually beginning in 2026.
This partnership will further solidify Ponsse’s position as a provider of sustainable forest machines and bring SSAB closer to its goal of establishing a fossil-free value chain.
“It’s great to have a reliable partner like Ponsse now joining our fossil-free journey. Joint efforts are needed to meet the challenging CO2 reduction targets in forest machines. Both companies prioritize sustainable solutions and will strive to make a positive impact on forest machines using SSAB Fossilfree™ steel, fostering innovation while respecting nature,” says Lotta Ruottinen, Sales Director at SSAB Europe.
“Our products and services will play a crucial role in assisting our customers in achieving their climate objectives during the transition to a low-carbon economy. Our PONSSE EV1 forwarder concept with completely electric drive and our partnership with SSAB regarding fossil-free steels will lead our development towards carbon neutral forestry,” says Juha Inberg, Chief R&D and Technology Officer, Ponsse Plc.
SSAB plans to revolutionize the entire steelmaking process. SSAB aims to deliver fossil-free steel to the market at a commercial scale during 2026 and to largely eliminate carbon dioxide emissions from our operations in around 2030. SSAB works with iron ore producer LKAB and energy company Vattenfall as part of the HYBRIT initiative to develop a value chain for fossil-free iron- and steelmaking, replacing the coking coal traditionally used for iron ore-based steelmaking with fossil-free electricity and hydrogen. This process virtually eliminates carbon dioxide-emissions in steel production.
Weiler Forestry is launching a full line of track harvesters for worldwide market.
Since acquiring the forestry product line from Caterpillar in 2019, Weiler Forestry has been busy introducing new models suited for forestry applications across the globe.
Currently, Weiler Forestry has three track harvester models available and will be soon introducing a fourth.
Starting as the smallest harvester in the line-up, the H157 is a nimble, low impact harvester that can be set up with a fixed Weiler FH190 harvesting head, an aftermarket shear head at 23’ reach or an after-market dangle head on the 26’ telescopic stick. This machine is powered by a Caterpillar C4.4 engine running at 184 hp. The machine layout is geared towards serviceability and ease of access to all
major components and service items. The gull wing hoods open and provide a stable work platform to get around the machine. This H157 is one of the lightest track harvesters on the market and comes in at just under 47,000 lbs. (21,319 kg).
The H457/H458 are equipped with a T3 engine set at 300 hp. The H457A / H458A is set at 330 hp. These machines can come equipped with fixed or dangle harvesting heads for various applications. The H457 has industry leading lift capacity, swing torque and tractive effort to get around the block with ease. Three different boom and stick configurations are available, including 23’ fixed linkage and two dangle head fronts at 29’ and 32’ of reach. The machine can handle various applications and aftermarket heads.
H767/H768
The new full tail swing flat
bottom H767 and tilting version H768 are top performing machines with industry leading stability, swing torque, lift capacity and tractive effort. These models are outfitted with Cat C9.3B engines at 330 hp and weigh in at around 82,000 lbs. (37,194 kg) for the flat bottom H767. This machine has closed loop swing and travel circuits. These machines have the power and multifunctioning capability to work through severe applications. The 34-foot harvester linkage gives it long reach and excellent working range.
Coming soon – H357
Rounding out the smaller size class, Weiler will be launching the H357 in 2024. Using a Caterpillar C7 engine, this machine will be 250 hp to provide a smaller, nimble machine that comes in at just under 55,000 lbs. (24,948 kg). While lighter weight, this machine is built heavy duty with upsized fi-
nal drives, heavy duty undercarriage and the same Cat 325 sized swing bearing and swing motor used on the larger H457 model.
The demonstrated growth of the harvester product line is critical to Weiler’s ability to deliver machines that not only meet general industry needs, but the specific needs of individual customers.
Waratah Forestry recognizes the paramount importance of safety and efficiency in the forestry industry.
In line with this commitment, Waratah Forestry has developed a comprehensive training program known as “Working Around Attachments Training” to equip forestry professionals with the necessary skills and knowledge to safely and effectively operate machinery equipped with attachments.
The training program encompasses a range of topics essential for working safely around attachments, including understanding the functionality and limitations of various attachments, identifying potential hazards, and implementing best practices for safe operation. Participants undergo rigorous theoretical and practical training sessions conducted by experienced
instructors who emphasize the importance of adherence to safety protocols and procedures.
One of the key aspects of the training is familiarizing participants with different types of attachments commonly used in forestry operations, such as grapples,
saws, and mulchers. Trainees learn about the specific functions of each attachment, as well as the proper techniques for attachment installation, operation, and maintenance. Emphasis is placed on understanding attachment compatibility with different machinery
and ensuring proper setup to minimize the risk of accidents or equipment malfunction.
Safety is paramount in forestry operations, and the Working Around Attachments Training program places a strong emphasis on hazard identification and risk mitigation strategies. Trainees are taught to recognize potential hazards associated with working around attachments, such as entanglement, crushing, and impact injuries, and are trained to implement preventative measures to mitigate these risks. Through interactive exercises and scenario-based simulations, participants develop the critical thinking skills necessary to assess risks and make informed decisions in real-world situations.
Practical training plays a crucial role in the program, allowing participants to apply theoretical knowledge
“We really try to build what the customer wants, and if you make it too much more complicated than that, it’s just too complicated,” says owner and CEO Pat Weiler. “Loggers are great to work with and they’re open to telling us what they want, and as long as they continue to do that, we’ll try to get it built for them, it’s pretty simple.”
in a controlled environment under the guidance of experienced instructors. Trainees have the opportunity to operate machinery equipped with attachments, practice attachment installation and removal procedures, and simulate various forestry scenarios to reinforce learning outcomes. This hands-on approach not only enhances skill proficiency but also instills confidence in trainees to safely and effectively perform their duties in the field. Upon successful completion of the Working Around Attachments Training program, participants receive certification recognizing their proficiency in working safely around attachments in forestry operations. This certification not only validates their skills but also demonstrates their commitment to safety and professionalism in the industry.
2021
The threat of climate change means that forest management must become more clever in determining when to carry out fuel reduction burning, according to a senior East Gippsland fire expert.
Garry Squires, a former Gippsland forest manager who is now a consultant, said there was a lot of talk about climate change and the reduced window of opportunity for burning.
2018
Queensland’s high-value state forests will receive greater protection following the Government’s $455,000 investment in cameras to detect wildfires in the south-west of the State.
The initiative is jointly funded by Queensland Parks and Wildlife Service (QPWS) and the Department of Agriculture and Fisheries (DAF).
Environment Minister Leeanne Enoch, who is responsible for national parks in Queensland, said seven remotely-operated cameras had been installed in the wildfire-prone forests west of Toowoomba to improve fire detection and response times.
The cameras are being set up on poles 20-to-40 metres above the ground and send live vision to QPWS rangers and DAF staff in Toowoomba and Dalby who will monitor the areas during high fire-danger periods.
2013
THE VICTORIAN Association of Forest Industries (VAFI) and the Victorian Forest Contractors Association (VFCA) have welcomed the Victorian Government’s amendments to the declaration for public safety zones for timber harvesting, which will help protect the safety of forestry workers and protestors and streamline the areas covered by public safety zones to minimise the impact on the wider public.
Agriculture and Food Security Minister Peter Walsh said trespassers put everyone on the harvesting site in danger, including themselves and the officers who must attend to ensure their safe removal.
In the rugged New Zealand terrain where logging operations face challenges like steep terrain, diverse soil types, and budget constraints.
Komatsu Forest (KF) recognized the untapped potential of the standard hydraulic excavators from Komatsu’s Osaka factory. Specifically, the PC 270LC/300LC/400LC models with their unique compensated load sense hydraulic systems seemed promising for forestry applications. However, adapting these excavators to meet local requirements involved collaboration with aftermarket specialists, leading to a relationship with EMS, Active Engineering and Ensign Services in New Zealand.
The initial modifications, including forestry cabs, guarding packages, high/ wide undercarriages, and boom modifications, aimed to address the specific needs of the forestry industry in New Zealand. This collaboration laid the foundation for a close association between KF and EMS, with the latter’s Tractionline and Harvestline products seamlessly complementing Komatsu’s PC300LC/400LC models. Active Engineering also played a pivotal role, providing forestry cabins, guarding packages and establishing itself as a key supplier to KF.
Despite the success of these modifications, the escalating costs of aftermarket enhancements began eroding their cost advantage over purpose-built track carriers. Faced with this challenge, Komatsu Forest approached Komatsu Ltd (Japan) to embark on a journey of factorybased solutions for forestry applications. Brett Jones, Managing Director of Komatsu Forest, emphasized the necessity of a factory approach due to increased local costs and long lead times.
The first major decision in this collaborative effort was the design and manufacturing of a high wide track frame, replacing the existing standard track frame of PC270LC-8 and PC300LC-8 models. This factory costeffective initiative paved the way for a more harmonious product tailored for forestry applications. Subsequently, factory forest boom options for PC270LC-8HW and PC300LC-8HW were developed, proving to be a gamechanger in terms of efficiency and reduced workshop time.
The success of these factory solutions has been affirmed by positive customer responses and exceptional acceptance since their implementation in late 2020. The collaboration between
KF and Komatsu Ltd didn’t stop there. Additional developments, such as a new design main hydraulic pump from the factory for the PC400LC-8. The local development of the IQAN crane control system developed by Reentech, and the heavyduty high-performance forestry cooling packages further highlighting the serious level of commitment to continuous improvement for forestry applications.
The array of factory-developed and local options addresses various forestry requirements:
1. High-Wide Undercarriage: The 850mm high wide track frame features a reinforced design, heavy-duty slew guard, and robust track skies and motor covers.
2. Forest Boom Sets: The Working Gear (WG) boom set, developed in Japan and refined in Australia, accommodates a wide range of grapple harvesters, directional felling heads, and log grapples available in the market.
3. Forestry Cabin: The Komatsu forestry cabin, engineered in Japan with rubber isolators, offers flexibility with the option to install EMS or Active cabins, ensuring quality and adaptability.
4. Cooling Package: Two options include the standard cooling system with an aux-
iliary hydraulic cooler and a purpose-built forestry package with a side-by-side AKG cooling package, equipped with a hydraulic reversing fan.
5. Bump Rails: Multiple bump rail options, including KF’s own solution, cater to different guarding needs, ensuring safety and compatibility with Komatsu Xtreme machines in various applications.
6. Heavy Duty Panels: Various HD side door options, including a new gullwing design, enhance flexibility and adaptability for different forestry applications.
7. IQAN Controls: Two levels of IQAN control systems provide flexibility, allowing contractors to choose based on their specific needs, whether for crane circuits and auxiliary requirements or a total machine control system.
Today, the culmination of these developments has resulted in a range of nine Forest Xtreme models, offering logging contractors in both Australia and New Zealand a cost-effective and purposebuilt solution for their specific forestry requirements. Brett Jones expressed his enthusiasm, emphasizing that these machines and options now provide a highly economical and productive logging solution.
In New Zealand, Komatsu hydraulic excavators have steadily gained a moderate market share over the past 12 years. The introduction of the “Xtreme” models has further strengthened their position, proving successful in the face of robust competition. Notably, interest in Australia has increased with 15 Xtreme units delivered in the last couple of years, and KF holding orders for 6 units set for delivery in the coming months.
In the past month another three new Komatsu PC300HW’s were delivered in Australia. The initial unit, a PC300High/Wide featured a Komatsu Forest Cab, Forestry Booms (WG) from Osaka Japan and HD Panels & Guarding Package by Komatsu Forest in Wodonga. The first of these deliveries went to Orana Enterprises Pty Ltd Tasmania. This Komatsu PC300HW equipped with Komatsu Forestry Cab,
Booms and Komatsu Forest HD panels and guarding, was tailored for a debarking operation in native regrowth. Initially it was fitted with a Waratah 623C, it was quickly replaced by a Waratah 624C which was far more an appropriate size for the base.
“The new PC 300HW was handling the 623 too easily, so we switched it for a 624, making it more versatile for larger trees,” commented Dwayne Kerrison, General Manager of Orana Enterprises.
According to Dwayne, the new machine has been well received by the operator who appreciates the spacious cab’s excellent visibility, much superior to the old modified cabs from previous machines. In addition, the new factory forestry features, such as booms and high/wide undercarriage contribute to a great specification for their appli-
cations, offering a real cost advantage over purposebuilt machines.
Orana has two more PC300HW’s on the way, with one in their workshop and another sitting at a New Zealand port ready to be shipped. Both units share a similar specification and will be equipped with a Talon Grapple Saw and a Waratah FL100 directional felling Head respectively.
The latest deliveries are two units recently delivered to a customer in Victoria, they are working in
The Woodsman Pro range offers the ultimate blend of productivity-enhancing tech and brute strength. Designed and built in NZ with over two decades of development in the harshest forestry conditions, Woodsman Pro is now available in Australia factory-direct with total support.
tandem for a tethering and shovel logging operation in a pine plantation. The first unit, Komatsu PC300FX, equipped with factory high wide, standard booms, EMS Forestry Cab, Grapple & Guarding, while the second Komatsu PC300TL is equipped with factory high wide, EMS Traction Line, Forestry Cab & Guarding. These latest additions showcase Komatsu Forest’s commitment to meeting diverse forestry requirements with cutting edge equipment. In conclusion, the col-
laborative efforts between Komatsu Forest and Komatsu Ltd, coupled with the support of key suppliers like EMS and Active Engineering, have propelled the Komatsu hydraulic excavators into a new era of forestry relevance. The journey from aftermarket modifications to factory-developed solutions reflects a commitment to innovation, costeffectiveness, and meeting the diverse needs of the forestry industry in Australia and New Zealand.
There are many types of forestry tires and many traction aid styles and brands. The traction aid must be properly matched to the tire. It must be installed correctly and maintained. And the tire itself must be properly maintained. Let’s break this all down.
First off, to keep machine and tire warranty coverages intact, all traction aids must be Tigercat factory approved before installation. There are many configurations that most certainly will damage the drivetrain or tires. Work with your Tigercat dealer to ensure the proper documentation is submitted and approvals are received.
There are three main types of traction aid hardware and some important considerations surrounding each. In addition, it is important to remember that dual tire installations are considered traction aids and must also be approved.
Wheel chains are installed over individual tires and are commonly used to provide additional traction in ice and snow. There are many chain and cleat patterns available, each is designed to provide optimal performance in specific conditions.
Wheel chains add significant weight to the machine and do not increase the footprint of the machine. In addition to increasing fuel consumption, the added weight
results in higher ground pressure, and may cause increased ground disturbance. It is important that the chains are correctly sized and installed to avoid tire damage. Chains should be regularly inspected and tightened according to manufacturer instructions.
Wheel tracks, like chains, are installed tightly over individual tires, providing significantly increased traction, while offering protection for the tire.
Wheel tracks meaningfully alter the rolling circumference of the wheel. The increased circumference, along with the additional weight of a wheel track, reduces maximum tractive effort and increases fuel consumption.
Wheel tracks must install tightly on the tire. Deflating the tire slightly before installing the track can help tighten the track to the outside surface of the tire when the air pressure is then increased to the correct operating pressure. It is very important to maintain the tire manufacturer’s maximum recommended operating pressure. This provides additional support for both the track bars and sidewalls of the tires.
Differential locks should be used sparingly when running wheel tracks. Operating differential locks in good traction conditions
will cause the differential locks to slip while travelling through a turn. This will increase wear on the differential lock clutches.
Band tracks are designed to install on bogie-style axles. They add significant weight to the machine, increasing fuel consumption, but also increase the footprint. This can potentially reduce both ground pressure and soil disturbance.
Band tracks are designed to fit specific tire sizes and brands. Care must be taken to ensure compatibility. For example, imperial sized tires designed to run on fourwheel drive skidders have surface curvature across the width of the tire that makes running band tracks very difficult. They will consume significant engine power and walk off the tires relatively easily.
A properly sized track shoe for a given tire will have sufficient clearance between the sidewall and the track guides. There should be approximately 10 mm (⅜ in) gap on each side of the tire, between the sidewall of the tire and the track guide. Too little clearance will cause excessive wear on the sidewall of the tire.
Correctly tensioned tracks should have 40-70 mm (1½2¾ in) of sag between the tires. If the track tension is too low, the track could walk off the tires. If track tension is too high, running over obstacles could cause damage to the bogie structure, planetary bearing, and gears.
A properly sized track shoe for a given tire will have sufficient clearance on each side of the tire, between the sidewall and the track guides, approximately 10 mm (⅜ in) gap on each side of the tire, between the sidewall of the tire and the track guide. Too little clearance will cause excessive wear on the sidewall of the tire.
Band track shoes, or tread bars, are available with very tall grousers to provide additional traction in deep snow. This design requires substantially more power to move the machine than less aggressive grousers. Using tall grousers in applications with good traction will result in reduced tractive effort available to move the machine.
Like wheel tracks, differ-
ential locks should be used sparingly when using band tracks. In favourable terrain conditions, the differential locks will slip while travelling through a turn. This will increase wear on the differential lock clutches.
Forestry machines operate in extreme conditions, so tires must be properly maintained to avoid premature wear, as well as catastrophic and costly failures.
The most important factor in tire maintenance is correct inflation pressure. Tigercat’s tire pressure monitoring system or TPMS is an effective tool in monitoring inflation pressure. TPMS displays a detailed warning message for the operator via the machine control system touchscreen interface.
In addition, the TPMS system for Tigercat skidders, forwarders and harvesters now integrates with RemoteLog telematics. If TPMS detects that the pressure of any tire is out of range, a warning message is sent to the machine owner through the RemoteLog interface.
RemoteLog maintains tire pressure warning history, logging all out-of-spec occurrences. For machines without TPMS, it is important to check tire pressures daily.
The torque capacity of the tire bead is a result of the tire pressure and fitment. The load capacity of the tire is directly proportional to the air pressure in the tire. Operating an underinflated tire reduces the torque capacity and load carrying capacity and may result in damage or slippage between the tire and rim. Tire slippage on the rim will tear the valve stem on the tube and permanently damage the tire bead. It may also damage the rim knurling. Under inflation can also cause excessive
heat buildup. This could lead to sidewall, bead or lining damage when driving over obstacles.
Again, it is essential to maintain the correct inflation pressures. Failure to do so could void your tire warranty and lead to expensive repairs or replacement. Refer to the tire pressure chart in the Operator’s Manual. Required inflation pressures are also usually printed on the tire sidewall.
Here are some general traction aid guidelines. Again, due to the wide variety of tires and traction aids, as well as other important factors such as application, it is essential to work with your dealer to obtain factory approval for your specific configuration prior to the installation of any traction aids.
For four-wheel skidders and feller bunchers, the best configurations are identical chains on all four tires, or identical wheel tracks on all four tires. Assuming all tires have equal wear, this eliminates potential issues related to differences in rolling circumference and ensures equal gripping characteristics on all four tires.
For six-wheel skidders and harvesters, there are several possible configurations including:
• Chains on the axle and band tracks on the bogie axle
• No traction aid on the axle and band tracks on the bogie axle
• Chains on axle and wheel tracks on the bogie axle
• No traction aid on the axle and wheel tracks on the bogie axle
However, wheel tracks are never permitted on the axle when band tracks or wheel tracks are applied to the bogie axle.
Drones, also known as Unmanned Aerial Vehicles (UAVs), have surged in popularity for various applications, from recreational flying to commercial use.
They have emerged as valuable tools for monitoring and managing forests efficiently and sustainably. This article explores the applications of drones in forestry management in Australia, highlighting their benefits, challenges, and future prospects.
Drones equipped with high-resolution cameras and sensors enable forest managers to conduct comprehensive aerial surveys with unprecedented accuracy and efficiency. These surveys can provide valuable insights into forest health, species distribution, and environmental changes over time. In Australia, where wildfires pose a significant threat to forest ecosystems, drones play a crucial role in early detection and rapid response. By conducting regular aerial patrols, drones can identify potential fire hazards, monitor fire behavior, and assess post-fire damage more effectively than traditional methods.
One of the key advantages of drones in forestry management is their ability to collect precise spatial data. Using advanced mapping
technologies such as LiDAR (Light Detection and Ranging), drones can generate detailed 3D models of forested areas, including tree heights, canopy density, and terrain elevation. This information is invaluable for planning timber harvesting operations, identifying optimal planting locations for reforestation projects, and monitoring changes in forest structure over time. By optimizing resource allocation and minimizing environmental impact, drones contribute to the sustainable management of Australia’s forests.
Despite their numerous benefits, drones also face several challenges and limitations in the context of forestry management. Technical issues such as limited battery life, restricted flight range, and inclement weather conditions can hinder their operational effectiveness, especially in remote or rugged terrain. Moreover, the proliferation of drones raises concerns about airspace regulation, privacy rights, and data security, which must be addressed through appropriate regulatory frameworks and industry standards.
The Civil Aviation Safety Authority (CASA) regulates the operation of drones to ensure safety and compliance with aviation stand-
ards. Understanding the license requirements for drone pilots is essential for responsible and legal flying.
Commercial Drone Operations:
For those seeking to use drones for commercial purposes obtaining a Remote Pilot License (RePL) is mandatory. The RePL certifies individuals to operate drones for commercial gain and involves undergoing training from a CASA-approved training organization. The training typically covers topics such as aviation regulations, flight planning, emergency procedures, and drone maintenance. Upon successful completion of the training and assessment, applicants are issued with a RePL, enabling them to legally conduct commercial drone operations.
Operator’s Certificate (OC) for Advanced Operations:
In addition to the RePL, commercial drone operators may require an Operator’s Certificate (OC) for conducting more complex or risky operations. The OC is granted by CASA following a thorough assessment of the operator’s safety management systems, operational procedures, and risk mitigation strategies. Examples of advanced operations that may necessitate an OC include flying drones beyond visual line of sight (BVLOS), operat-
● Navigating the skies with drones in Australia requires a thorough understanding of license requirements and regulatory obligations.
ing in controlled airspace, or conducting aerial spraying or lifting operations. Obtaining an OC demonstrates a higher level of competency and compliance with regulatory requirements, ensuring the safety of both the operator and the general public. Compliance and Enforcement: CASA actively monitors and enforces compliance with drone regulations through a combination of education, surveillance, and enforcement actions. Penalties for non-compliance with aviation regulations can range from fines and warnings to prosecution and suspension or revocation of licenses. By promoting awareness of the rules and regulations governing drone operations, CASA aims to foster a cul-
ture of responsible and safe flying among drone pilots in Australia.
Navigating the skies with drones in Australia requires a thorough understanding of license requirements and regulatory obligations. Whether flying for recreational enjoyment or commercial gain, drone pilots must adhere to CASA’s guidelines to ensure safety and compliance with aviation standards. By obtaining the necessary licenses, undergoing training, and following best practices, drone operators can contribute to the responsible and sustainable integration of drones into Australia’s airspace, unlocking new possibilities for innovation and economic growth.
•
•
•
m
Free online safety training for Waratah equipment users.
As part of Waratah’s commitment to safety, we are excited to offer a free, online Working Around Attachments Training.
This training is designed to educate your team on the key safety measures to follow while working with Waratah attachments. Access to the training is quick and easy – simply scan the QR code with a mobile device or go to URL https://freeonlinesurveys.com/s/WorkAroundAttachments
An uncontrollable blaze ravaged hundreds of hectares of timber plantation at Mount Lonarch, west of Ballarat, marking a significant loss for Hancock Victorian Plantation Holdings. The fire, which ignited on 22 February, destroyed 1000 hectares of pine trees, heavily impacting the supply chain for mills in Victoria and beyond.
New Zealand’s WorkSafe is pulling out of funding safety programs to the tune of up to NZ$15 million a year, skittling a “really valuable” one in the high-risk forestry industry. ACC, which gives WorkSafe the money, says it stopping the funding will make no difference to the overall spend.
This decision does not reduce the overall amount of funds that ACC allocates to injury prevention initiatives but for the Forestry Industry Safety Council (FISC), the impact has been harsh with 35% to 40% of its NZ$1.1-2m annual funding will be hit.
A fatal and fast-spreading tree disease, Dutch elm disease, has been discovered in New Zealand. Tests confirmed a tree in Te Awamutu, on private property, has the fungal disease which is almost always deadly.
Elm bark beetles spread the disease by carrying the fungus from an infected tree and boring into new trees nearby. It does not affect trees unrelated to the elm species.
Fecon, a leading global manufacturer of heavy-duty site preparation attachments and forestry accessories, recently acquired Stumper Industries, a manufacturer of stump grinder attachments for mini and standard skid steers and compact track loaders, excavators and tractor applications.
The acquisition expands the landscaping and land maintenance solutions Fecon offers in the forestry mulching and vegetation management industries.
Södra’s venture in a new advanced technique for better seedling survival was recently field tested with promising results.
Södra’s ambition with the in-house developed BraSatt 01 planting machine is to accelerate technical advances in forest regeneration, which could potentially lead to considerable improvements for forestry.
Södra’s mission is to help refine and renew the value of family forestry. Improved seedling survival will create conditions for higher profitability for family forestry, while also contributing to more sustainable forestry.
“There haven’t been any major technical breakthroughs in forest regeneration since the planting tube. With Södra’s venture, we are giving the forest regeneration method a real boost and using a technique that is unusual in forestry. I hope this will have a ripple effect, so that forest owners can continue to benefit from more new techniques as we move forward,” said Anna Wallner, project manager.
Södra has been running a project called BraSatt since 2020, which is based on the development of a new method for scarification and planting seedlings to ensure the survival of the seedlings.
Seedling survival is a problem for all forest companies today.
Södra’s current rate of seedling survival is 70–75 percent, which means that only three of four seedlings survive longer than three years.
“In the project, we have created a concept and fieldtested a new scarification method and a self-propelled planting machine. BraSatt has covered the whole chain – from planning to planting the seedling in the soil,” said Anna Wallner. The autonomous planting was developed from the BraSatt 01 prototype. The aim is that the proposed machine will follow an overall route, find an accessible path through the terrain, select good planting spots, feed the seedlings through the system, scarify the soil and then plant successfully.
Södra has collaborated with companies with experience from various industries to find new solutions.
The participating companies are Axelent Engineering, Bit Addict, Boid, Chalmers, CIT, DB MakerLab, Ebeaver, LUE Engineering and the Forestry Research Institute of Sweden.
“In the project, we used a proven technique as far as possible and adapted it step by step in order to get closer to tomorrow’s planting machine. We’ve used a lot of techniques that are unusual for forestry, such as industrial robots, which are more likely to be found indoors on a concrete floor.
In the BraSatt 01 machine, the seedlings are handled automatically by a robot. We are therefore making a new technique available to forestry, and to forest regeneration specifically,” said Anna Wallner.
The project also developed a new method of scarification that is optimal for the seedling and energy-efficient, while also leaving a relatively even clearing behind.
This method affects a considerably smaller part of the surface compared with the current method. Another important part of the development process was
to account for the humanmachine interaction and factor in the operator’s role in creating a positive work environment.
The operator’s new role will be to work together with the machine, to provide support when it asks for help, plan the work on the clearing and to work with plant care. Now that field testing has ended, documentation and analysis will follow to find a possible way forward.
“Even though the test results are promising, the machine is not ready for use. What we want to show with this development is that this is possible to achieve. In the next step, we need to decide what parts of the development that we need to prioritise and run ourselves here at Södra, where we can find partners and where there are technical advances happening that we don’t need to push,” said Anna Wallner.
JohnDeere has entered into an agreement with SpaceX to provide cutting-edge satellite communications (SATCOM) service.
Utilising the industry-leading Starlink network, this solution will allow machine owners facing rural connectivity challenges to fully leverage precision technologies. This partnership, an industry first, will enable John Deere customers to be more productive, profitable, and sustainable in their operations.
The SATCOM solution will connect both new and existing machines through satellite internet service and ruggedised satellite terminals. This will fully enable technologies such as autonomy, real-time data sharing, remote diagnostics, enhanced self-repair solutions, and machine-to-machine communication, all of which help machine owners work more efficiently while minimizing downtime.
John Deere is bringing satellite communications service to rural areas at scale so those with cellular coverage challenges can maximize the value of connectivity to their operations. The SATCOM solution unlocks the John Deere tech stack so every machine owner can fully utilize their current precision agriculture technology in addition to the new innovative solutions Deere will deploy in the future.
John Deere’s SATCOM solution will leverage SpaceX’s Starlink satellite internet constellation. To activate this solution, John Deere dealers will install a ruggedized Starlink terminal on compatible machines, along with a 4G LTE JDLink modem to connect the machine to the John Deere Operations Centre. The SATCOM solution will initially be available through a limited release in the United States and Brazil starting in the second half of 2024.
Keith Smiley
Good fortune knocked at the door of Bakes Sawmill in Tasmania when the State Government effected a grant worth about $148,000 — creating a watershed moment for Glen and wife Cathy and their son Josh — completing a longheld belief that value adding can be achieved with a little ingenuity.
Seeking to increase local manufacture, the Tasmanian government offered this special grant under a $10 million program, so that companies like Bakes could value-add as part of an onisland processing commitment, adding employment growth and working smarter.
This new treatment plant will re-direct 420 cubic metres of timber per annum for a range of Bakes’ products, adding value to what was previously chipped as residue wood.
“Logs were being exported as a whole log but if we had a treatment plant up and running we could use a percentage of those logs, cut them up and treat them ourselves, and then put them into the local market. During Covid there was a timber shortage, so a little place like Tasmania was getting treated imported wood from Europe. I thought this was just madness. We can actually process and treat, so why the hell do we need to import logs when we could treat here,” said owner Glen Bakes.
“We filled out an application, did a cost estimate for 45% of the project, but with
all the shortages, the budget blew out, yet it was not the end of the world. So, our own investment was about two thirds of the total project.
“We received the grant money last June – two years start to finish, as we waited on contractors. The Minister for Resources Barnett rang me personally about winning the grant – then we had a series of approvals to go through: We had the idea, we had done our homework.
“Everything is totally enclosed in the shed including the treatment plant itself, a chemical storage and drip area. We’re the first business in Tasmania to use a chemical called MicroPro , which is like an organic material or closest to it, treating timber and living in the same building, backed by a 50-year guarantee.
Besides one-offs, Bakes
produces cladding, framing timbers; landscaping and garden products, and treated natural logs for cabins. Bakes manages a state hardwood quota, processing 3,500 cubic metres a year. ‘At the end of the day, timber treatment in hardwood is where you treat the sap, so we can leave the sapwood on the timber and treat it, while it becomes part of a sellable product’. “We’ve been in business for about 40 years, some have been bad days but the next morning you get excited about going back to work. My wife Cathy does the books and is quite active in the mill, driving the forklift, doing some of the docking and stacking — she is not frightened of work. Josh is a fitter by trade and is heavily involved in wood chopping, goes to royal shows, and is one of the best five in Australia. He is engaged to be
married, and is a great asset around the mill.”
Glen has been to Canada twice training in the design and construction of log cabins, built out of pine. He enjoys something with a challenge and is keen to grow the cabins’ side of the business. Few familyrun sawmills exist but Bakes has a solid operation, equipped with kilns, planing machines, a treatment plant, sawmill, and seeking new ways of adding value to their product range.
“The future is tomorrow, one day at a time, and it’s also about survival. We do something that doesn’t flood the market, and do what we enjoy doing, while other mills can’t or don’t want to do. We’ll take orders others won’t touch, one-offs included,” said Glen.
Bakes sell to state-wide Tasmania, acknowledging the difficulty in finding labour. They also cut Douglas fir or Oregon for structures requiring large beams, lintels, posts, and for log cabins. Glen is concerned about the future, in particular, what a change of government might bring, especially a Green-Labor government that ‘might shut the forest down’. Log supply contracts will run out in 2027 so Glen is hoping for a glimmer of light through renegotiation of a longer logging period.
“I believe if our forest was managed properly for the future, we could have sustainability, and go on forever. The Liberal Government has been very supportive of the timber industry and its workers.”
There have been a number of changes within the Forest Practices Association team with one long-term team member departing as well as a number of key recruitments in the areas of compliance, operations and biodiversity.
Luke Bond has been appointed the FPA’s Compliance Manager replacing Aidan Flanagan. Luke has extensive experience in compliance, having been in various enforcement roles including police, the Department of Natural Resources and Environment Tasmania as well as the Commonwealth and worked overseas in natural resource investigations and anti-poaching. Most recently Luke has been in charge of animal welfare investigations with Biosecurity Tasmania.
Willem Mulder joined the FPA team as FPA Operations Manager in March, bringing with him a wealth of forestry and operations management experience. Most recently, Willem was the Chief Operating Officer for the Baker Group.
Hafwen Pearce has joined the FPA s Ecologist/Adviser. Hafwen is a Forest Practices Officer with over 16 years’ experience in the forest industry including professional/technical roles in harvesting, planning and fire management with Sustainable Timber Tasmania. She also has expertise in natural values management. In 2022, she won the new FPO Excellence Award at the Forest Practices Awards.
After spending the past 12 months overseas, Finn Adams is moving to Hobart as an ecologist and adviser. He will work across programs at the FPA within the Biodiversity, Earth sciences and Compliance Programs. Prior to his overseas adventures, Finn worked as harvest manager with Timberlands Pacific, and completed the FPO course in 2021. Finn also has qualifications in natural resources management.